Федеральное агентство по образованию
Государственное образовательное учреждение высшего профессионального образования
Пермский государственный технический университет
Строительный факультет
Кафедра строительных материалов и специальных технологий
Контрольная работа №1
по курсу «Материаловедение. Технология конструкционных материалов»
вариант №3
Работу выполнил студент
Группы ПГСз-08.02
Е.К. Волегова___________
Работу проверил и принял
Э.Б. Белозерова__________
ПЕРМЬ-2010
1.
Образец известняка-ракушечника имеет водопоглощение по массе 12%, а по объему 17%. Найти коэффициент теплопроводности данного материала.
- водопоглощение известняка-ракушечника по массе;
- водопоглощение известняка-ракушечника по объему;

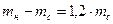



- объем известняка-ракушечника;
- плотность сухого известняка-ракушечника (по объемному весу, можно предположить, что это известняк-ракушечник молдавский );
- плотность воды;
Коэффициент теплопроводности материала
- величина, численно равная плотности теплового потока, проходящего в изотермических условиях через слой материала толщиной в 1 м при разности температур на его поверхностях один градус Цельсия (Вт/(м×°С)).

Ответ
: коэффициент теплопроводности известняка-ракушечника .
2. Определить плотность известкового теста, в котором содержится более 56% воды (по массе), если плотность извести-кипелки 2,08 г/см3
.
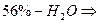 в данном объеме.
- плотность извести-кипелки;
- плотность воды
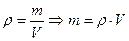
- масса 56% воды;
- масса 44% извести-кипелки;
Плотность известкового теста можно определить как отношение суммы плотностей извести-кипелки и воды, к объему известкового теста.
- плотность известкового теста.
Ответ:
плотность известкового теста .
1. Породообразующие минералы осадочных горных пород и их основные свойства.
Минерал – природное тело, однородное по химическому составу, строению и свойствами, образующиеся в результате физико-химических процессов на поверхности и в глубине земли. Минералы в подавляющем большинстве – твердые тела: кристаллические и аморфные.
Породообразующими минералами называют минералы образующие крупные скопления.
Осадочные горные породы – вторичные породы, образовавшиеся в результате выветривания магматических пород.
Осадочные породы в зависимости от происхождения делят на:
- механические осадки
, при образовании которых главную роль играли физико-механические процессы (воздействие воды, мороза, нагрева и охлаждения и т.п.); при этом не менялся минеральный и химический состав исходных пород;
- органогенные осадки,
которые образовались из остатков (скелетной части) живых организмов, как правило, морской фауны (ракушки, кораллы и т.п.);
- хемогенные осадки,
образовавшиеся в результате растворения первичных пород и последующей кристаллизации из водных растворов.
Механические осадочные породы
могут быть рыхлые
(гравий, песок, глина, щебень) и сцементированные
– те же рыхлые осадки, частицы которых склеены природным цементом (брекчии, конгломераты, песчаники).
Химические осадки
состоят из карбоната кальция CaCO3
, кремнезема SiO2
(гипс, ангидрид, магнезит, доломит, некоторые известняки (оолитовые), известняковые туфы).
Органогенные отложения
(мел, большинство известняков, ракушечник, диатомит, трепел).
При увлажнении осадочные горные породы теряют часть своей прочности.
Песок –
преобладающим минералом является кварц. При выветривании гранита кварц оказывается самым твердым и химически стойким минералом, не подвергающимся разрушению, а разрушающим более слабые соседствующие с ним минералы (полевой шпат, слюду и т. п.).
Глина –
рыхлая механическая осадочная горная порода. Источником образования служат самые распространенные минералы изверженных пород – полевые шпаты.
Песчаники -
сцементированные механические отложения. Состоят из зерен кварцевого песка, сцементированного природным цементом, например карбонатом кальция, водным кремнеземом, гипсом и т. п. цементация происходит путем постепенного осаждения на зернах песка цементирующего вещества из воды. В зависимости от цементирующего вещества песчаники называют известковыми, кремнистыми, глинистыми и т. д. Цвет их зависит от цвета цементирующего вещества. Известковые песчаники легче обрабатываются, кремнистые более прочные и стойкие.
Плотность песчаников – 2300…2500 кг/м3
, прочность – от 10 до 100 МПа. Песчаники в зависимости от содержания в них глины могут терять большую часть прочности (до 70%). Увлажнение изверженных пород практически не снижает их прочности.
Используют для фундаментов, подпорных стенок, тротуаров, а особо стойкие – для облицовок, делают щебень для бетонов и дорожных покрытий.
Конгломераты и брекчии –
породы, состоящие из сцементированных крупных зерен гравия или из остроугольных с шероховатой поверхностью зерен щебня. Используют в качестве заполнителей для бетонов, для изготовления штучного камня и облицовочных плит.
Известняки плотные –
органогенные осадочные горные породы. Плотность известняков – 2000…2600 кг/м3
, прочность при сжатии 10…100 МПа, коэффициент потери прочности при увлажнении плотных известняков 07…0,5. Твердость – 3…3,5, что позволяет легко добывать и обрабатывать известняки. Морозостойкость зависит от пористости, степени цементации, наличия примесей. Абсолютно не стойки к воздействию кислых сред. Использую для облицовочных плит, щебня для бетона, производства извести и портландцемента.
Мраморовидные известняки –
переходные породы от известняков к мраморным. Состоят из зерен кальцита, тесно связанных между собой небольшим количеством карбонатного цемента. Мраморовидные известняки более плотные, чем обычные, имеют большую объемную массу 2600-2800 кг/м3
и более высокий предел прочности при сжатии 60-180 МПа.
Известняк-ракушечник –
органогенная пористая порода, состоящая из раковин и панцирей моллюсков, корненожек и других остатков, слабосцементированных известковым цементом. Плотность ракушечника 900-2000 кг/м3
, прочность при сжатии – 0,5…15 МПа. Имеет малую теплопроводность и легко поддается распиловке. Использую как щебень для легкого бетона, в виде каменей и блоков как стеновой материал, а так же как облицовочный материал.
Мел –
землистая горная порода, состоящая из мельчайших обломков раковин и скелетов морских микроорганизмов, представляет собой почти чистый кальцит CaCO3
. Использую при производстве извести, цемента, стекла и благодаря высокой дисперсности для приготовления красок и шпатлевок.
Диатомиты и трепелы –
рыхлые землистые породы белого, серого или желтоватого цвета, в основном состоящие из аморфного кремнезема SiO2
×n
H2
O; по внешнему виду и физическим свойствам похожи на мел. Применят как гидравлическую добавку к вяжущим, а так же используют при производстве теплоизоляционных материалов.
Известковый туф –
хемогенная осадочная горная порода, образовавшаяся в результате выпадения CaCO3
из источников подземных углекислых вод. Туфы пористы и имеют ноздреватое строение. Они легко поддаются распиловке и используются доля внутренней облицовки помещений, улучшая их акустические свойства.
Магнезит –
химические механические осадочные горные породы, состоящие в основном из минерала магнезита MgCO3
. Используют для огнеупорных материалов и магнезиальных вяжущих.
Доломит –
порода, состоящая из минерала доломита CaCO3
× MgCO3
, с примесью глины, оксидов железа и др. по структуре и физическим свойствам близок к плотным известнякам: кг/м3
; МПа. Применяют в качестве строительного камня и щебня для бетона.
Гипс –
горная порода обычно белого или серого цвета, состоящая из минерала CaCO4
×2
H2
O. Использую как сырье для получения гипсовых вяжущих.
Ангидрит –
плотная хемогенная осадочная горная порода, состоящая из минерала ангидрита CaCO4
. Использую для получения вяжущих, для внутренне отделки и скульптурных работ. На открытом воздухе быстро выветривается, переходя в гипс.
2.
Производство глиняного кирпича способом пластического формования.
Глиняный кирпич имеет форму прямоугольного параллелепипеда размерами 250х120х65. Кирпич утолщенный 250х120х88 с обязательными технологическими пустотами.
Масса утолщенного кирпича в высушенном состоянии должна быть не более 4,3 кг.
По согласованию предприятия-изготови
теля с потребителем, от
раженному в договоре на поставку, допускается изготовлять утолщенный
полнотелый кирпич массой более 4,3 кг.
По прочности изделия изготовляют марок: 75, 100, 125, 150, 175, 200, 250, 300.
По морозостойкости
изделия изготовл
яют марок
: F15, F
25, F
35, F
50
. За марку по морозостой
кости
прин
имают чи
сло циклов
по
пе
ре
менного замораживания
и оттаивания,
п
ри
к
оторых в изд
елиях отсутствуют признаки видимых повреждений
(шелуше
ние, расслоение, выкрашивание
и д
р).
В зависимости от средней плотности полнотелые изд
ели
я подразделяют на:
- пористые со средней пл
отностью до 1500 кг/мм3
;
- плотные свыше 1500 кг/м3
.
Теплопроводность 0,71-0,82 Ват/м· ºС.
Предел прочности при сжатии и изгибе 75-300 кг/м2
.
Водопоглащение должно быть не менее 6%.
Изделия относят к группе негорючих строительных материалов
по ГОСТ 30244 «Материалы строительные. Методы испытаний на горючесть».
Производство ведется на хорошо проработанной пластичной массе с влажностью 15-25% из легкоплавких глин средней пластичности, содержащих 40-50% песка. Подготовка сырья
: глину увлажняют паром и интенсивно обрабатывают на бегунах, дезинтеграторах и валках до получения пластичной удобоформуемой массы без крупных каменистых включений (кусочки CaCO3
должны быть удалены или измельчены в порошок).
Качество массы и будущих изделий зависит от тщательности проработки сырьевых компонентов.
Формование кирпича-сырца
производят на ленточном прессе. Увлажненная и тщательно размятая глиняная масса продавливается винтовым конвейером через решетку в вакуумную камеру, где жгуты глины разбиваются вращающимся ножом для удаления воздуха из глиняной массы. Далее масса винтовым валом подается в конусную головку пресса, где окончательно уплотняется и продавливается сквозь формующую часть пресса – мундштук. Мундштук придает глиняной ленте, выходящей из пресса, определенную высоту и ширину. В мундштуке могут быть установлены керны, образующие каналы в выдавливаемой ленте; так получают пустотелый кирпич и трубы.
Глиняная лента нарезается автоматическим устройством на кирпич-сырец. Размер таких кирпичей несколько больше требуемого, т.к. в последующей обработке глина дважды (при сушке и обжиге) претерпевает усадку, достигающую 10-15 %.
Сушка
– важный и сложный этап производства кирпича. В глине перенос влаги затруднен и поэтому быстрое высыхание глины с поверхности приводит не к ускорению сушки, а к растрескиванию кирпича-сырца. Это происходит из-за того, что поверхностный слой дает усадку при высыхании (до 7-10%), а влажное ядро препятствует ей. Простейший способ предохранить кирпич от растрескивания – сушить его медленно, так, чтобы скорость испарения воды не превышала скорости ее миграции внутренних слоев. Но этот путь снижает процессы производства.
Ускорить сушку можно, вводя в сырьевую смесь вещества, облегчающие миграцию влаги к поверхности (опилки), или путем формования в кирпиче сквозных отверстий. Улучшение условий сушки пустотелого кирпича – залог более высокого качества материала.
При влажности кирпича-сырца 6-8% его можно подавать на обжиг.
Обжиг
является завершающим этапом технологического процесса производства глиняного кирпича. Процесс обжига можно разделить на три периода: прогрев сырца, обжиг, охлаждение обожженных изделий. При прогреве сырца температуру до 90-120ºС поднимают медленно, при этом из него удаляется свободная влага. Дальнейшее повышение температуры до 750ºС приводит к удалению химически связанной воды и выгоранию органических примесей. В процессе собственного обжига при температуре 800-900ºС легкоплавкие соединения начинаю расплавляться и обволакивать нерасплавившиеся частицы, при этом уменьшаются линейные размеры изделия и оно уплотняется. При дальнейшем повышении температуры глиняная масса спекается. Температура обжига зависит от состава сырьевой массы и обычно находится в пределах 950-1000ºС. Необходимую температуру обжига следует строго выдерживать. Для обжига использую печи различной конструкции от самых старых кольцевых, в которые кирпич укладывают и вынимают вручную, что является тяжелым и трудоемким процессом, и до современных туннельных и щелевых, где кирпич обжигается в процессе продавливания его по печи. Туннельная печь представляет собой канал длиной до 100 м, в котором по рельсам движутся вагонетки, с обжигаемым изделием. Операции – загрузка, подогрев, обжиг, охлаждение и выгрузка. Длительность процесса обжига 1,5-3 суток. Туннельные печи значительно производительнее и экономичнее кольцевых печей.
В результате обжига глиняный кирпич приобретает камневидное состояние, высокие прочность, водостойкость, морозостойкость и другие строительные свойства.
При выгрузке из печи керамические кирпичи сортируют
. Качество изделий устанавливают по степени обжига, внешнему виду, форме, размерам, а так же по наличию в них различных дефектов, в соответствии с требованиями ГОСТа. По степени обжига они могут быть разделены на изделия нормально обжига, недожог (алого цвета, пониженной плотности и морозостойкости) и пережог (отличается большой плотностью и высокой теплопроводностью). Кирпич недожог и пережог являются браком.
На складах кирпич хранят в штабелях высотой до 1,6 м уложенными на ребро. При механизированной погрузке, разгрузке и транспортировании используют деревометаллические поддоны, на которые кирпич укладывают на ребро с перевязкой или «в елочку» (с наклоном в 45º к центру пакета).
3.
Шлакопортландцемент: состав, свойства и область применения.
Шлакопортландцемент – получают путем совместного помола доменного гранулированного шлака (21-80%), портландцементного клинкера (79-20%) и гипса (не более 5%).
Доменный шлак – отход производства чугуна (на 1 т чугуна приходится около 0,6 т шлака), поэтому шлакопортландцемент экономически выгоднее, чем портландцемента. Выпуск шлакопортландцемента в России составляет около 1/3 общего выпуска цемента. При производстве чугуна в доменную печь загружают железную руду, флюсовый камень (известняк и/или доломит) и кокс. Получаемая на выходе из печи продукция - расплавленный чугун и шлак. Шлак состоит в основном из кварца и оксидов алюминия (от железной руды) и оксидов кальция и магния (от флюсового камня). Из печи шлак выходит в расплавленном состоянии, причем температура расплава может превышать 14807С (27007F). Существует четыре основных способа обработки расплавленного шлака: охлаждение воздухом, быстрое охлаждение холодной водой (вспучивание шлака), дробление и помол. При каждом из данных методов обработки получается уникальный шлаковый материал, обладающий отличительными свойствами. Химический состав доменного гранулированного шлака близок к составу клинкера. Основные составляющие доменного шлака - кварц, оксиды алюминия, кальция и магния, на которые приходится 95 % всего состава шлака. Остальные 15 % - марганец, соединения железа и серы и следовое количество других элементов. Однако, следует отметить, что основные оксиды, входящие в состав шлака не встречаются в свободной форме. В доменном шлаке, охлажденном воздухом, оксиды объединяются в различные силикаты и алюмосиликатные минералы, такие как мелилит, мервинит, волластонит и др., которые также существуют в виде природных пород. В дробленом и молотом шлаках, данные элементы присутствуют в виде стекла. Химический состав шлаков варьируется в очень узких пределах, поскольку все сырье, загружаемое в доменную печь, очень тщательно отбирается и смешивается.
Типичный химический состав доменного шлака, % |
Кварц (SiO2
) |
32-42 |
оксид алюминия (А12
О3
) |
7-16 |
оксид кальция (СаО) |
32-45 |
окись магния (MgO) |
5-15 |
сера (S)* |
1-2 |
оксид железа (Fe2
03
) |
1-1,5 |
оксид марганца (МnО) |
0,2-1,0 |
К самостоятельному твердению шлак не способен, но в присутствии цемента и гипса он проявляет вяжущие свойства.
Шлакопортландцемент выпускают трех марок: 300, 400 и 500. По коррозионной стойкости и водостойкости он превосходит обычный портландцемент, но твердеет несколько медленнее и при этом выделяет меньше теплоты. Недостаток шлакопортландцемента – пониженная по сравнению с обычным портландцементом морозостойкость. В очень сухой воздушной среде отвердевший шлакопортландцемент иногда может обнаруживать не только недобор, но и «сброс» прочности. Причины этого явления объясняются, главным образом, дегидратацией части воды из гидросиликатов кальция, образовавшихся при взаимодействии аморфной двуокиси кремния с гидроокисью кальция. Когда из таких гидросиликатов кальция отщепляется вода, то получаются новообразования с уменьшенным объемом, поэтому в материале возникают внутреннее напряжения, приводящие к возникновению трещин и деградации прочности.
Имеются разновидности шлакопортландцемента: быстротвердеющий, сульфатостойкий.
Шлакопортландцемент обладает следующими специфическими свойствами (в сравнении с портландцементом):
- Более стойки в пресных водах, особенно в мягких, а от части в водах с небольшим содержанием сульфатов. Не имеют преимущества перед портландцементом в водах углекислых, а также содержащих много солей магния;
- Медленнее твердеют при нормальной температуре; в особенности замедляется твердение при околонулевых положительных температурах;
- По скорости твердения при повышенной температуре (при тепловлажностной обработке) превосходит портландцемент;
- В процессе твердения необходима влажная среда. В отдельных случаях при определенных условиях применения, например в строительных растворах, когда вода из него отсасывается кирпичом и ее не хватает для гидрации вяжущего, возможен недобор прочности и даже небольшой ее сброс;
- Тепловыделение шлакопортландцемента меньше, чем портландского;
- Несколько меньшая морозостойкость. Однако применение поверхностно-активных добавок это свойство может быть улучшено.
- Экономичность.
По прочности при сжатии в 28-суточном возрасте подразделяют на марки:
> шлакопортландцемент - 300, 400 и 500;
> шлакопортландцемент быстротвердеющий - 400
Шлакопортландцемент применят в тех областях строительства, где наиболее рационально и полно используются их положительные свойства: в массивных бетонных конструкциях, в виде подземных, подводных сооружений и в производстве пропариваемых изделий, для гидротехнических сооружений и для сборных железобетонных изделий (например, бетонные трубы). По прочности они не уступают портландцементу, но нуждаются в более тщательном уходе при повышенных и пониженных температурах.
4.
Строительный гипс: получение, свойства и применение.
Гипсовые вяжущие вещества – это тонкоизмельченные продукты термической обработки естественных или искусственных разновидностей сульфатов кальция, которые при затворении водой образуют пластичное тесто, твердеющее и сохраняющее свою прочность на воздухе.
Гипс – быстротвердеющее воздушной вяжущее, состоящее из полуводного сульфата кальция CaSO4•0,5H2O, получаемого низкотемпературной (<200ºС) обработкой гипсового сырья.
Сырьем для гипса служит в основном осадочные горные породы - природный гипсовый камень по ГОСТ 4013-82, состоящий из двуводного сульфата кальция (CaSO4•2H2O) и различных механических примесей (глины и др.). В качестве сырья могут так же использоваться гипосодержащие промышленные отходы, например фосфогипс, а также сульфат кальция, образующийся при химической очистке дымовых газов от оксидов серы с помощью известняка.
Получение гипса включает две операции:
- Термообработку гипсового камня на воздухе при 150-160ºС; при этом он теряет часть химически связанной воды, превращаясь в полуводный сульфат кальция β-модификации CaSO4
•2H2
O→ CaSO4
•0,5H2
O+1,5 H2
O
- Тонкий размол продукта, который можно производить как до, так и после термообработки; гипс – мягкий минерал (твердость по шкале Мооса – 2), поэтому размалывается он очень легко.
Таким способом производится основное количество гипса; обычно для этого использую гипсоварочные котлы.
Доступность сырья, простота технологии и низкая энергоемкость производства делают гипс дешевым и перспективным вяжущим.
Разница между количеством воды, необходимым для твердения вяжущего и для получения из него удобоформуемого теста, - основная проблема технологии материалов на основе минеральных вяжущих.
Для гипса проблема снижения водопотребности и, соответственно, снижения пористости и повышения прочности была решена путем получения гипса термообработки не на воздухе, а в среде насыщенного пара (в автоклаве при давлении 0,3-0,4МПа) или в растворах солей. В этих условиях образуется другая кристаллическая модификация полуводного гипса – α-гипс, имеющий водопотребность 35-40%.
Гипс α-модификации называют высокопрочным гипсом, т.к. благодаря пониженной водопотребности он образует при твердении менее пористый и более прочный камень, чем обычный гипс β-модификации. Из-за трудностей производства высокопрочный гипс не нашел широкого применения в строительстве.
Технические свойства гипса.
Истинная плотность полуводного гипса 2,65-2,75 г/см3
; насыпная плотность полуводного гипса 800-1100 кг/м3
.
По строкам схватывания, определяемым на приборе Вика, гипс делят на три группы (А, Б, В)
Вид гипса
|
Начало схватывания
|
Конец схватывания
|
Быстротвердеющий (А) |
Не ранее 2 мин |
Не позднее 15 мин |
Нормальнотвердеющий (Б) |
Не ранее 6 мин |
Не позднее 30 мин |
Медленнотвердеющий (В) |
Не ранее 20 мин |
Не нормируется |
Замедляют схватывание гипса добавкой столярного клея, сульфтноспртовой барды (ССБ), технических лигносульфонатов (ЛСТ), кератинового замедлителя, а также борной кислоты, буры и полимерных дисперсий (например, ПВА).
Марку гипса определяют испытанием на сжатие и изгиб стандартных образцов-балочек 4х4х16см спустя 2 ч после их формования. За это время гидратация и кристаллизация гипса заканчивается.
Установлено 12 марок гипса по прочности от Г-2 до Г-25:
марка |
Г-2 |
Г-3 |
Г-4 |
Г-5 |
Г-6 |
Г-7 |
Г-10 |
Г-13 |
Г-16 |
Г-19 |
Г-22 |
Г-25 |
Предел прочности, МПа, не менее:
При сжатии
|
2 |
3 |
4 |
5 |
6 |
7 |
10 |
13 |
16 |
19 |
22 |
25 |
При изгибе
|
1,2 |
1,8 |
2 |
2,5 |
3 |
3,5 |
4,5 |
5,5 |
6 |
6,5 |
7 |
8 |
В строительстве использую в основном гипс марок от Г-4 до Г-7.
По тонкости помола, определяемой максимальным остатком пробы гипса при просеивании на сите с отверстиями 0,2 мм, гипсовые вяжущие делят на три группы:
Группа |
I |
II |
III |
Помол |
Грубый |
Средний |
Тонкий |
Остаток на сите 0,2% |
23 |
14 |
2 |
Нормальная густота
– количество воды в % необходимое для получения теста стандартной консистенции. Определяют на приборе вискозиметре Суттарда.
Маркируют гипсовые вяжущие по всем трем показателям: скорости схватывания, тонкости помола и прочности.
Плотность затвердевшего гипсового камня низкая (1200-1500 кг/ м3
) из-за значительной пористости (60-30% соответственно).
Гипсовое вяжущее – одно из немногих вяжущих, расширяющихся при твердении: увеличение в объеме достигает 0,2%. Эта особенность гипсовых вяжущих позволяет применять их без заполнителей, не боясь растрескивания от усадки.
При увлажнении затвердевший гипс не только существенно снижает прочность, но и проявляет нежелательное свойство – ползучесть
– медленное необратимое изменение размеров и формы под нагрузкой. Характер водной среды во влажном гипсе – нейтральный (рН=6,5-7,5), и она содержит ионы Ca+2
и SO-2
4
, поэтому стальная арматура в гипсе коррозирует. Увлажнение гипса способствует его гигроскопичности
– способность поглощать влагу из воздуха.
Гипс хорошо сцепляется с древесиной и поэтому его целесообразно армировать деревянными рейками, картоном или целлюлозными волокнами и наполнять древесными стружками и опилками.
Гипс – негорючий
материал, но в силу своей пористости замедляют передачу теплоты, а при действии высоких температур выделяют воду, тем самым тормозя распространение огня.
Область применения.
Главнейшая область применения гипса – устройство перегородок. Они могут быть заводского изготовления, из гипсовых камней или из гипсокартонных листов. Гипсоволокнистые материалы используют как выравнивающий слой под чистые полы. Из гипса делают акустические плиты, применяют для огнезащитных покрытий металлических конструкций, а так же декоративные архитектурные детали (лепнина) и скульптура.
Гипс использую для изготовления форм (например, для керамики) – формовочный гипс и в медицине для фиксации при переломах – медицинский гипс.
5.
Искусственные пористые заполнители, получаемые из глины. Их производство и области применения.
Пористые заполнители для легких бетонов получают главным образом искусственным путем. Из природных пористых заполнителей применяют щебень из пемзы, туфа и пористых известняков, которые используют в качестве местного материала. Марку пористых заполнителей устанавливают по их насыпной плотности (кг/м3
).
Для пористых заполнителей имеет значение правильный зерновой состав. Пористые заполнители выпускают в виде фракций размерами 5-10мм; 10-20 мм и 20-40 мм.
Керамзитовый гравий –
изготовляют путем обжига гранул, приготовленных из вспучивающихся глин. Это легкий и прочный заполнитель. Его объемная насыпная масса 250-800 кг/м3
.
Керамзитовый песок –
(зерна до 5 мм) получают при производстве керамзитового гравия, а также по методу кипящего слоя обжигом сырья во взвешенном состоянии. Кроме того, его можно получать дроблением некондиционного продукта 0 зерен гравия размером более 40 мм и сваров.
Керамзит –
гранулы округлой формы с пористой сердцевиной и плотной спекшейся оболочкой. Прочность керамзита сравнительно высокая при небольшой насыпной плотности (250-600 кг/м3
). Получают керамзит быстрым обжигом во вращающихся печах легкоплавких глинистых пород с большим содержанием оксидов железа и органических примесей до их вспучивания.
Керамзит выпускают в виде гравия (гранулы 5-40 мм) и песка (зерна менее 5 мм). Марки керамзита от 250 до 600 кг/м3
. Морозостойкость – не менее F15.
Шлаковая пемза –
пористый щебень, получаемый вспучиванием расплавленных металлургических шлаков путем их быстрого охлаждения водой или паром. Этот вид экономически очень эффективен, т.к. сырьем служат промышленные отходы, а переработка их крайне проста. Марки шлаковой пемзы от 400 до 1000. Прочность ее соответственно от 0,4 до 2 МПа.
Гранулированный металлургический шлак –
получают в виде крупного песка с пористыми зернами размером 5-7 мм, иногда 10 мм в результате быстрого охлаждения расплавов металлургических шлаков.
Аглопорит –
пористый заполнитель в виде гравия, щебня, получаемый спеканием сырьевой шихты из глинистых пород и топливных отходов. Марки аглопорита от 400 до 900.
Вспученные перлитовый песок и щебень –
пористые зерна белого или светло-серого цвета, получаемые путем быстрого (1-2 мин) нагрева до температуры 1000-1200ºС вулканических горных пород, содержащих небольшой количество (3-5%) гидратной воды (перлит и др.). При обжиге исходная порода увеличивается в объёме в 5-15 раз, в пористость образующихся зерен достигает 85-90%.
По размеру зерен природные пористые заполнители подразделяют на щебень фракций 5-10; 5-20; 5-40; 10-20; 20-40 мм и песок: крупный, средний и мелкий. По объемной насыпной массе природные пористые заполнители подразделяют на марки согласно таблице
Марка по объемной насыпной массе
|
Значение объемной насыпной массы, кг/м3
|
щебня |
песка |
300 |
- |
Менее 300 |
350 |
- |
Св. 300 до 350 |
400 |
- |
» 350 » 400 |
500 |
500 |
» 400 » 500 |
600 |
600 |
» 500 » 600 |
700 |
700 |
» 600 » 700 |
800 |
800 |
» 700 » 800 |
900 |
900 |
» 800 » 900 |
1000 |
1000 |
» 900 » 1000 |
1100 |
1100 |
» 1000 » 1100 |
1200 |
1200 |
» 1100 » 1200 |
- |
1300 |
» 1200 » 1300 |
1400 |
» 1300 » 1400 |
Щебень, выпускаемый двух фракций (5-10 и 10-20 мм), имеет насыпную плотность от 200 до 500 кг/м3
. Щебень не должен содержать пылевидных и глинистых частиц более 3 % по массе. Содержание глины в комках не должно быть более 0,25 % по массе.
По содержанию зерен пластинчатой (лещадной) формы щебень должен удовлетворять требованиям табл.
Группа щебня по форме зерен
|
Содержание зерен пластинчатой (лещадной) формы, % по массе, не более |
Обычная |
30 |
Улучшенная |
20 |
Кубовидная |
15 |
Окатанная |
10 |
К зернам пластинчатой (лещадной) формы относятся зерна щебня, у которых ширина или толщина менее длины в три и более раза.
Щебень в зависимости от прочности, определяемой сдавливанием в цилиндре, подразделяют на марки согласно табл.
Марка щебня по прочности
|
Прочность щебня (при сдавливании в цилиндре), кгс/см2
; даН/см2
|
из пемз и шлаков |
из туфов, крупнопористых базальтов, карбонатных и кремнеземистых пород |
П 25 |
Св. 2 до 3 |
Св. 2 до 3 |
П 35 |
» 3 » 4 |
» 3 » 4 |
П 50 |
» 5 » 8 |
» 4 » 6 |
П 75 |
» 8 » 10 |
» 6 » 8 |
П 100 |
» 10 » 12 |
» 8 » 10 |
П 125 |
» 12 » 15 |
» 10 » 12 |
П 150 |
» 15 » 20 |
» 12 » 16 |
П 200 |
» 20 » 25 |
» 16 » 20 |
П 250 |
» 25 » 30 |
» 20 » 25 |
П 300 |
» 30 » 35 |
» 25 » 30 |
П 350 |
» 35 |
» 30 |
Перлитовый песок – особо легкий вид мелкого заполнителя: его насыпная плотность от 75 до 200 кг/м3
.
Зерновой состав песка должен находиться в пределах, указанных в табл.
Размер отверстий контрольных сит, мм
|
Полные остатки на ситах (% по объему) для песка |
крупного |
среднего |
мелкого |
5,0 |
0-10 |
0-10 |
0-5 |
2,5 |
10-50 |
10-40 |
5-10 |
1,25 |
30-70 |
20-60 |
10-40 |
0,63 |
50-80 |
30-70 |
15-60 |
0,315 |
70-90 |
50-85 |
40-75 |
0,14 |
90-95 |
75-90 |
70-90 |
Проход через сито 0,14 |
10-5 |
25-10 |
30-10 |
Зерновой состав песка для теплоизоляционных легких бетонов не нормируется.
К пористым заполнителям могут предъявлять требования по морозостойкости, водонепроницаемости и др.
Список используемой литературы
1. ГОСТ 10178-85 «Портландцемент и шлакопортландцемент. Технические условия».
2. ГОСТ 125-79 (СТ СЭВ 826-77) «Вяжущие гипсовые. Технические условия».
3. ГОСТ 22263-76 «Щебень и песок из пористых горных пород. Технические условия».
4. ГОСТ 22688-77 «Известь строительнаяметоды испытаний».
5. ГОСТ 379-95 «Кирпич и камни силикатные. Технические условия».
6. ГОСТ 8267-93 «Щебень и гравий из плотных горных пород для строительных работ. Технические условия».
7. ГОСТ 9179-77 «Известь строительная».
8. ГОСТ Р 50544-93
«Породы горные. Термины и определения».
9. Журнал «Ценообразование и сметное нормирование в строительстве», № 5, май 2008 г.
10. СП 23-101-2004 «Проектирование тепловой защиты зданий».
11. Справочник проектировщика промышленных, жилых и общественных зданий и сооружений. Расчетно-теоретический/ под ред. Уманского А.А.– М.: Издательство литературы по строительству, 1972.
12. Строительные материалы и изделия/ Попов, К.Н., Каддо М.Б. – М.: Высшая школа, 2002.
13. Строительные материалы/ Горчаков Г.И. – М.: Высшая школа, 1982.
|