Министерство образования и наук Украины
Национальный горный университет
Кафедра транспортных систем и технологий
Пояснительная записка
курсового проекта
по дисциплине
«Транспортные системы
горных предприятий»
Вариант №10
Выполнил:
Проверил:
Днепропетровск
2004
СОДЕРЖАНИЕ
Введение
Исходные данные
1.Обработка исходных данных
1.1 Расчет технологических параметров выемочного участка
1.2 Обоснование транспортной системы шахты
2. Участковый транспорт
3.1 Участковый транспорт очистных забоев
3.2 Расчет участкового ленточного конвейера
3.3 Участковый транспорт подготовительных забоев
3. Магистральный транспорт
4.1 Расчет конвейерного уклона
4.2 Расчет конвейера главного конвейерного штрека
4. Технико-экономические показатели
5. Правила безопасности
Список литературы
|
3
4
5
5
11
12
12
13
19
22
22
26
30
31
36
|
ВВЕДЕНИЕ
Горная отрасль играет важнейшую роль в развитии топливно-энергетического комплекса Украины. Одним из главных энергоносителей в Украине является уголь, но предприятия, добывающие уголь, в настоящее время находятся в состоянии затяжного кризиса. Одним из способов выхода из кризисного состояния – это техническое перевооружение угольной промышленности.
В техническом перевооружении угольной промышленности важнейшее место принадлежит проблеме дальнейшего развития и совершенствования внутреннего шахтного транспорта как одного из основных звеньев технологического комплекса производственных процессов угольной шахты.
Основные требования, предъявляемые к шахтным транспортным системам: обеспечение бесперебойной высокопроизводительной работы очистных, подготовительных забоев; минимальные потери качества и сохранения сортности полезного ископаемого в процессе его доставки; высокий уровень безопасности, простота управления и обеспечения комфортных условий для обслуживающего персонала.
Исходные данные
Годовая добыча шахты, млн. т.
Размеры шахтного поля, км:
· по простиранию
· по падению
Мощность пластов, м:
1. пласт
2. пласт
3. пласт
Расстояние между пластами
1 – 2
2 – 3
Угол падения пластов, град
Средняя плотность угля, т/м3
Начальная глубина ведения работ, м
Крепость боковых пород
Категория шахты по газу
Способ вскрытия
Способ подготовки
|
1,5
8,0
3,0
1,5
1,2
1,3
70
70
15
1,55
100
5
III
Вертикальными
стволами
Панельный
|
1. ОБРАБОТКА ИСХОДНЫХ ДАННЫХ
1.1 Расчет технологических параметров выемочного участка
Выбор очистного комплекса.
Для очистных работ в пределах разрабатываемого шахтного поля для пластов мощностью 1,3 м и 1,5 м принимаем очистной комплекс 2МКД90, для пласта мощностью 1,1 м принимаем комплекс 1МКД90 в состав которых входят: механизированные крепь поддерживающе-оградительного типа 2КД90 и 1КД90 соответственно, узкозахватный очистной комбайн ГШ200Б, скребковый конвейер СП250.13, а также гидро- и электрооборудование, смонтированное на энергопоезде в конвейерном штреке.
1.1.1 Техническая характеристика крепей 1КД90 и 2КД90:
Вынимаемая мощность, м
Угол падения пласта, град
- при подвигании забоя по простиранию
- при подвигании забоя по восстанию
Категория пород основной кровли
Категория пород непосредственной кровли
Рабочее сопротивление крепи
- поддерживающей части, кН/м2
- посадочного ряда секции крепи, кН/м
Шаг установки секций, м
Шаг передвижки секций, м
Коэффициент затяжки кровли
Длина комплекта поставки, м
Длина выемочного столба (не менее), м
Тип насосной установки
|
0,80 – 1,25
35
10 / 10
А1
, А2
Б2
, Б3
, Б4
490
2800
1,5
0,63; 0,80
0,9
150 - 200
800
СНТ32
|
1,1 – 1,5
35
10 / 10
А1
, А2
Б2
, Б3
, Б4
530
3000
1,5
0,63; 0,80
0,9
150 - 200
800
СНТ32
|
1.1.2 Техническая характеристика комбайна ГШ200Б:
Вынимаемая мощность, м
Угол падения пласта, град
- при подвигании забоя по простиранию
- при подвигании забоя по восстанию / падению
Сопротивляемость угля резанию, кН/м
Диаметр барабанов по резцам, мм
Ширина захвата, мм
Рабочее напряжение сети, В
Частота тока, Гц
Тип системы подачи
Мощность привода комбайна, кВт
- на резание
- системы подачи
Габаритные размеры, мм
- длина
- ширина (по корпусу)
- высота
Масса Комбайна, т
|
0,95 – 1,50
35
10 / 10
300
800
630
660
50
БСП
2 110
2 36
6800
920
690
14,7
|
1.1.3 Техническая характеристика конвейера СП250.13:
Максимальная производительность, т/мин
Длина комплекта поставки, м
Угол падения пласта, град
- при подвигании забоя по простиранию
- при подвигании забоя по восстанию / падению
Скорость движения скребковой цепи, м/с
Тяговый орган
- калибр цепи
- количество цепей
- шаг скребков, мм
Привод конвейера
- тип электродвигателя
- мощность электродвигателя, кВт
- количество электродвигателей
Рештачный став
- высота рештака, мм
- ширина рештака, мм
- длина рештака, мм
|
7,1
150 – 250
35
10 / 10
1,0
18 64 – С15 2
2
1024
2ЭДКОФ 250В
55
3
190
642
1500
|
Определение скорости подачи комбайна.
Скорость подачи комбайна по силовому фактору.
Скорость подачи комбайна по силовому фактору определяется по следующей формуле:
, м/мин. (1.1)
где Руст
– установленная мощность комбайна, кВт, определяется по формуле:
, кВт. (1.2)
Рп
– паспортная мощность привода комбайна, Рп
=
220, кВт; Нw
– удельная энергоемкость разрушения угля, определяется по следующей формуле:
Нw
= 0,00185Ар
(0,77+0,008R)
, кВт/т. (1.3)
Ар
– средневзвешенная сопротивляемость угля резанию, Ар
= 190
, кН/м;
R
– показатель хрупкости угля;
R = 0,25АР
, кВт/т (1.4)
m
– вынимаемая мощность пласта, m2
= 1,5
м; m3
= 1,2
м; m1
= 1,3
м; r
– ширина захвата, r = 0,63
, м; – средневзвешенный, объемный вес угля в целике, =1,55
т/м3
; k
0
– коэффициент ослабления пласта врубом, k
0
=1,0
.
4,8 м/мин; 5,98 м/мин; 5,5 м/мин.
Скорость подачи комбайна по проветриванию лавы.
Скорость подачи комбайна по фактору проветривания лавы определяется по следующей формуле:
,м/мин (1.5)
где v
– максимально допустимая скорость движения воздуха по лаве, v=4
,м/с; d –
максимально допустимая концентрация метана в исходящей струе воздуха, d = 1%
; φ
–
коэффициент, учитывающий сужение воздушной струи в лаве из-за загромождения ее механизмами, j
= 0,9
; в –
ширина призабойного пространства, в = 4,2
м; kвп
–
коэффициент, учитывающий движение воздушной струи по выработанному пространству, kвп
= 1,3
; q
– относительная метанообильность пласта, q = 11
м3
/т.с.д.; mг
–геологическая мощность пласта, mг
= 1,1
м; kнм
– коэффициент неравномерности метановыделения, kнм
= 1,15
.
1,6 м/мин; 1,3 м/мин; 1,4 м/мин.
Скорость подачи комбайна по креплению лавы.
Скорость подачи комбайна по креплению лавы определяется по следующей формуле:
, м/мин. (1.6)
где В –
шаг установки секций крепи, В = 1,5
м; - суммарная продолжительность выполнения цикла передвижки секции крепи; определяется по следующей формуле:
 = 0,7 мин. (1.7)
где t
1
– продолжительность перемещения ГРОЗ от секции к секции, t
1
= 6 сек.;
t
2
– продолжительность зачистки секции (карманов), t
2
= 18 сек.; t
3
– время снятия секции с распора, t
3
= 6 сек.; t
4
– время подтяжки секции, t
4
= 5 сек.; t
5
– время распора секции, t
5
= 6 сек.;
2,15 м/мин.
Из всех полученных значений скорости подачи комбайна принимаем наименьшее значение: 1,6 м/мин; 1,3 м/мин; 1,4 м/мин.
Определение продолжительности цикла.
Продолжительности цикла определяется по следующей формуле:
, мин (1.8)
где tв
– продолжительность выемки угля комбайном, определяется по следующей формуле:
, мин. (1.9)
где L
– длина лавы, L = 200
м; å
l
н
– суммарная длина ниш, å
l
н
= 0. vк
–
скорость подачи выемочной машины vк
=2,4
м/мин.; t
3
– продолжительность зачистки лавы комбайном, t
3
= 0. tвп
– время вспомогательных процессов, определяется по формуле:
=16 мин. (1.10)
k
0
– коэффициент отдыха, k
0
= 10 %; k
1
– коэффициент, учитывающий обводненность, k
1
= 1,0; k
2
– коэффициент, учитывающий устойчивость пород кровли, k
2
= 1,1; k
3
– коэффициент, учитывающий гипсометрию пласта, k
3
= 1,0;
k
4
– коэффициент, учитывающий угол падения пласта, k
4
= 1,2; å
tк
– продолжительность концевых операций, определяется по формуле:
, мин. (1.11)
где lк
– длина корпуса комбайна, lк
= 6,8 м; lик
– длина изгиба конвейера, lик
= 15 м.
Тц1
= 185,7 мин; Тц2
= 224,6 мин; Тц3
= 209,8 мин.
Определение количества циклов в сутки.
Определение количества циклов в сутки осуществляется по следующей формуле:
. (1.12)
где t
р
– продолжительность ремонтно-подготовительной смены, t
р
= 360 мин.;
tпм
– время противовыбросных мероприятий, t
пм
= 0; t
пз
– время подготовительно-заключительных операций, t
пз
= 20 мин.; t
тп
– технологические перерывы, t
тп
= 15 мин.; n
– количество выемочных смен за сутки, n =
3.
Получаем: NЦ1
=
5; NЦ2
=
4; NЦ3
=
4.
Определение нагрузки на очистной забой.
Определение суточной нагрузки на забой.
Определение суточной нагрузки на забой производится по следующему выражению:
,т/сут. (1.16)
Qсут 1
= 1276т/сут; Qсут 2
= 817 т/сут; Qсут 3
= 885 т/сут.
Определение сменной нагрузки на забой.
Определение сменной нагрузки на забой производится по следующему выражению:
, т/см. (1.17)
Qсм 1
= 425 т/см; Qсм 2
= 272 т/см; Qсм 3
= 295 т/см.
1.2 Обоснование схемы внутришахтного
транспорта шахты
Исходя из заданных горнотехнических параметров предприятия: размеры шахтного поля по простиранию/падению – 8,0/3,0 км; угол падения пластов – 190
; вскрытие – вертикальными, центрально-сдвоенными стволами; способ подготовки – панельный; производственная мощность шахты – 1,5 млн.т./год, принимаем схему транспорта, обеспечивающую полную конвейеризацию основного грузопотока. Транспортная цепочка основного грузопотока следующая: отбитый в очистном забое уголь скребковым конвейером СП250.13 транспортируется на конвейерный ходок, где посредствам скребкового перегружателя КСП уголь перегружается на участковый ленточный конвейер; далее, уголь транспортируется на главный конвейерный штрек, далее конвейерный квершлаг, по которому – к разгрузочным ямам главного наклонного ствола. С подготовительных забоев горная масса грузится в вагонетки ВДК2.5 и посредствам напочвенной дороги ДКНЛ транспортируется к вспомогательному ходку, далее посредствам одноконцевой откатки, горная масса транспортируется к главному откаточному штреку, затем к клетьевому стволу. Оборудование и вспомогательные материалы транспортируются в специализированных площадках, люди – в вагонетках ВПГ18.
Количество очистных забоев по пласту определяется по следующей формуле:
=2 (2.1)
где А
Г
– производственная мощность шахты, АГ
= 1500000 тыс. т./год; N
р
– количество рабочих дней в году, N
р
= 300; п
– количество пластов, п
= 3;
kp
– коэффициент ритмичности работы лавы, kp
= 0,8. Qсут
– средняя суточная нагрузка на забой, определяется:
= 1011 т/сут. (2.2)
Для обеспечения своевременной подготовки следующих выемочных столбов, принимаем четыре подготовительных забоев (по 2 на пласт).
2. Участковый транспорт.
2.1 Участковый транспорт очистных забоев.
Из очистного забоя отбитый уголь, посредствам скребкового конвейера СП250.13(технические характеристики приведены в разделе 1.1) перегружается в скребковый перегружатель КСП2М, находящийся в участковом конвейерном штреке; далее, уголь перегружается на участковый ленточный конвейер, с помощью которого транспортируется на конвейерный уклон. Вспомогательные материалы, оборудование, люди, перевозятся по выработкам в специализированных вагонах при помощи напочвенной дороги ДКНЛ. Технические характеристики выше перечисленного оборудования представлены ниже.
Техническая характеристика КСП2М:
Максимальная производительность, т/мин
Длина комплекта поставки, м
Скорость движения скребковой цепи, м/с
Тяговый орган
- калибр цепи
- количество цепей
- шаг скребков, мм
Привод конвейера
- тип электродвигателя
- мощность электродвигателя, кВт
- количество электродвигателей
Масса, т
|
8,0
68
1,25
18 64 – 7
2
1022
ЭДКОФ 43/4
55
2
32,5
|
Техническая характеристика ДКНЛ:
Расстояние транспортирования, не более, м
Масса транспортируемого груза, не более, т
Скорость транспортирования, м/с
Приводная станция:
- тип электродвигателя
- мощность, кВт
- гидромуфта
Тормоз:
- рабочий
- предохранительный
Диаметр шкива трения, мм
Диаметр тягового каната, мм
Колея, мм
Наибольшее количество людских вагонеток, шт
Число мест в пассажирской вагонетке
Масса оборудования дороги длиной 1,5 км, т
|
1500
15
0,25 – 1,85
ЭДКОФ 42/4
45
ТЛ32М
Ленточный
Колодочный
750
15
900
3
12
19,5 – 22,3
|
2.2 Расчет участкового ленточного конвейера
Определение расчетного грузопотока.
Расчетный грузопоток вычисляется по следующей формуле:
166,7 т/ч (2.1)
где k
– коэффициент неравномерности, k
= 2,0; kм
– коэффициент машинного времени, kм
= 0,8.
Теоретическая производительность выбираемого конвейера Q
T
принимается равной расчетному грузопотоку: Q
T
= Qp
.
Выбор ленточного конвейера.
Выбор конвейера производится исходя из неравенства QT
QП
, с учетом угла наклона трассы и приемной способности. Исходя из этого принимаем конвейер 1Л80П, (QП
= 420 т/ч) 185,0 < 420,0.
Техническая характеристика ленточного конвейера 1Л80П:
Максимальная производительность, т/ч
Приемная способность, м3
/мин
Скорость движения ленты, м/с
Мощность привода конвейера, кВт
Угол установки конвейера, град
Длина поставки, м
Тип конвейерного става
Лента:
· Тип ленты
· Ширина ленты, мм
Масса ленты, кг/м2
Расчетная разрывная прочность, кН/см
Число тканевых прокладок
Толщина наружных обкладок, мм
Роликоопоры:
Диаметр роликов, мм
Масса вращающихся частей роликоопор:
- груженая ветвь, кг
- порожняя ветвь, кг
Расстояние между роликоопорами
- груженая ветвь, мм
- порожняя ветвь, мм
Приводная станция:
Количество приводных барабанов
Связь между барабанами
Угол обхвата барабанов лентой, град
Диаметр приводных барабанов, мм
Поверхность барабанов
Натяжная станция:
Расположение
Натяжное устройство
Тип двигателя
|
420
11,5
2,0
110
от -16 до +18
750 - 1000
жесткий, подвесной
2Ш 800 4 ТК-200 4,5-3,5 ГЗ
800
16
200
4
4,5/3,5
89
14,70
11,62
1400
2800
2
жесткая
240/240
400
без футировки
в хвосте
автомат.
ВРП160S4
|
Проверка ширины ленты по кусковатости груза
Для рядовых углей проверка ширины ленты по кусковатости груза производится исходя из следующего неравенства:
м (2.2)
где d
max
– максимальное значение кусковатости груза, d
max
= 0,2 м;
0,60 < 0,80 – условие выполняется.
Исходя из рекомендаций, выработанным опытом применения ленточных конвейеров в угольных шахтах, в участковых горных выработках следует применять конвейеры с минимальной шириной ленты 0,80 м.
Линейные массы движущихся частей
верхних роликоопор:
, кг/м; (2.3)
нижних роликоопор:
, кг/м; (2.4)
ленты:
, кг/м; (2.5)
груза:
, кг/м (2.6)
где mp
1
и mp
11
– массы вращающихся частей одной роликоопоры соответственно верхней и нижней ветвей; mp
1
=14,7 кг, mp
11
=11,62 кг; lp
1
и lp
11
– расстояние между роликоопорами соответственно верхней и нижней ветвей; lp
1
= 1,4 м, lp
11
= 2,8 м; m
– масса 1м2
ленты; m
= 16 кг/м2
; В
– ширина ленты; В
= 0,8 м;
Расчет силы тяги для перемещения ветвей
нижней:
F
2-1
= L qл
g(c
2
w
cosb
+
sinb
)+ c
2
Lqp
11
gw =
22961Н; (2.7)
верхней:
F
4-3
= L g( qл
+ q
гр
)(c
2
w
cosb –
sinb)+ c
2
Lqp
1
gw =
61120, Н; (2.8)
где: c
2
– коэффициент, учитывающий местные сопротивления; c
2
=
1.1; w
– коэффициент сопротивления движению ветвей, w
= 0,06; L
– длина транспортирования, L
= 2000 м; g
– ускорение свободного падения, g
= 9,8 м/с.
Тяговое усилие на приводных барабанах
Тяговое усилие на приводных барабанах определяется по формуле:
F0
= F4-1
= F2-1
+ F4-3
=
84082, Н; (2.8)
Минимальное начальное натяжение ленты
Минимальное начальное натяжение ленты определяется по условиям сцепления и провеса груженой ветви:
По условию сцепления на приводе:
, Н (2.10)
где kt
–
коэффициент запаса тяговой способности привода, kt
=
1,3; f
– коэффициент трения сцепления ленты и барабана, f
= 0,3; a1
и a2
– углы обхвата лентой приводных барабанов, a1
= a2
= 4,19 рад.;
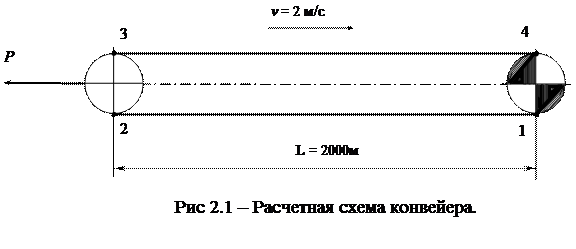 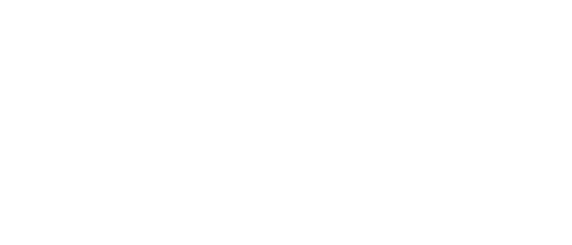
По условию ограничения провеса ленты на груженой ветви:
Fгр
=
3500 В
= 3500 .
0,8 = 2800, Н (2.11)
Максимальное усилие на приводных барабанах
Fmax
=
F4-3
+
F
гр.
min
=
93709 Н (2.12)
Определение разрушающего натяжения ленты
Определение разрушающего натяжения ленты производится по формуле:
Fразр.
=
1000Вi
sвр
=
640000, Н (2.13)
где i
– количество тканевых прокладок в ленте, i
= 4; sвр
– временное сопротивление на разрыв одной прокладки, sвр
= 200Н/мм.
Количество конвейеров на заданную длину транспортирования
Осуществляется по следующей формуле:
n = m Fmax.
/ Fразр.
=
1,17 (2.14)
На заданную длину транспортирования принимаем два конвейера, длиной 1000 м.
Силы тяги для перемещения ветвей одного конвейера:
, Н (2.15)
= 30560, Н (2.16)
Сила тяги на приводном барабане одного конвейера:
=42041, Н (2.17)
Минимальное начальное натяжение ленты одного конвейера по условию сцепления:
= 4813, Н (2.18)
Максимальное натяжение ленты одного конвейера:
= 46854, Н (2.19)
Запас прочности ленты одного конвейера:
(2.20)
Мощность привода одного конвейера:
, кВт (2.21)
где vн
–
номинальная скорость движения ленты, vн
=
2м/с; kреж
– коэффициент режима, учитывающий неравномерность распределения мощности двигателей в многоприводных конвейерах, kреж
= 1,0; h -
коэффициент полезного действия передачи, h =
0,9. При этом должно соблюдаться следующее неравенство:
Np
1
< Nуст
1
(2.22)
86 < 110 – требуемое условие соблюдается, принимаем два конвейера на заданную длину транспортирования, по 1000 м
Усилие на натяжной станции:
Р1
=
2F1
=
9627 Н (2.23)
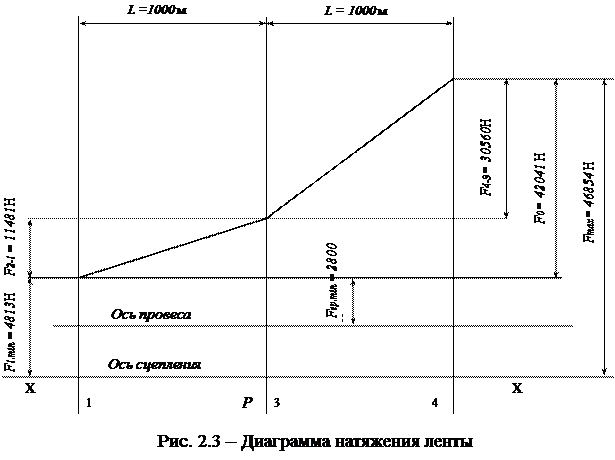
2.3 Участковый транспорт подготовительных забоев.
Учитывая крепость боковых пород (f
= 5), проведение горных выработок будет осуществляться с помощью проходческого комбайна нового технического уровня КСП32. Для погрузки горной массы с перегружателя комбайна в вагонетки, принимаем ленточный перегружатель УПЛ2М, техническая характеристика которого приведена ниже. По участковой (проводимой) выработке горная масса транспортируется напочвенной дорогой ДКНЛ, производительности которой достаточно для использования в качестве основной транспортной единицы; также она используется для доставки оборудования, крепежных материалов, людей. От участков горная масса в вагонетках ВГ2,5, электровозом АРП7 транспортируется к стволу. Технические данные вышеперечисленного оборудования представлены ниже, за исключением напочвенной дороги ДКНЛ, характеристика которой имеется в разделе 3.1.
Техническая характеристика УПЛ2М:
Максимальная производительность, м3
/ч
Ширина ленты, мм
Скорость движения ленты, м/с
Привод конвейера
- мощность электродвигателя, кВт
- количество электродвигателей
- потребляемое напряжение, В
Колея, мм
- основного пути
- дополнительного пути
Габаритные размеры, мм
- длина
- ширина
- высота
Масса, т
|
180
800
1,5
15
1
660
900
1640
14000 - 23300
1340 - 2000
1990
7
|
Техническая характеристика ВГ2,5:
Вместимость кузова, м3
Колея, мм
Жесткая база, мм
Длина, мм
Масса (тара), т
|
2,5
900
800
3150
1,15
|
Техническая характеристика АРВ7:
Сцепная масса, т
Ширина колеи, мм
Данные часового режима:
Суммарная мощность, кВт
Сила тяги, Н
Скорость движения, км/ч
|
7
900
20
9100
7,5
|
Тяговые двигатели:
Количество двигателей
Потребляемое напряжение, В
Тяговая батарея:
Тип батареи
Номинальная ёмкость, А ч
Энергоемкость батареи, кВт ч
Исполнение батареи
|
2
130
102ТНЖШ-550
550
50
РВ
|
3. магистральный транспорт
3.1 Расчет конвейерного уклона.
Аналогично предыдущему, выполнен расчет конвейерного уклона. Сменный грузопоток в данном случае будет равный сменной нагрузке на очистной забой и составляет Q
см
= 850 т/см. С учетом коэффициента неравномерности грузопотока в каждой лаве k
= 1,5 и коэффициента машинного времени kм
= 0,85 производительность расчетного грузопотока составляет Qp
= QТ
= 250 т/ч.
Результаты расчета конвейера сведены в таблицу 3.2. Для транспортирования груза, в данном случае принят специальный конвейер для работы в наклонных стволах – 2Л100У, с паспортной производительностью 850т/ч
Техническая характеристика ленточного конвейера 2Л100У:
Максимальная производительность, т/ч
Приемная способность, м3
/мин
Скорость движения ленты, м/с
Мощность привода конвейера, кВт
Угол установки конвейера, град
Длина поставки, м
Лента:
· Тип ленты
· Ширина ленты, мм
Масса ленты, кг/м2
Расчетная разрывная прочность, кН/см
Число тканевых прокладок
Толщина наружных обкладок, мм
Роликоопоры:
Масса вращающихся частей роликоопор:
- груженая ветвь, кг
- порожняя ветвь, кг
Расстояние между роликоопорами
- груженая ветвь, мм
- порожняя ветвь, мм
Приводная станция:
Количество приводных барабанов
Связь между барабанами
Угол обхвата барабанов лентой, град
Диаметр приводных барабанов, мм
Поверхность барабанов
Расположение натяжной станции
|
850
15,8
2,0
2 110
от -16 до +18
до 1000
2Ш 1000 4 ТК-200 4,5-3,5 Г
1000
18,2
200
4
4,5/3,5
37,70
21,9
1500
3000
2
жесткая
210/210
630
без футировки
в хвосте
|
На рисунке 3.2 изображена диаграмма натяжения ленты при длине транспортирования L
= 1400м.
Таблица 3.2 – Расчет технологических параметров конвейера
№ |
Наименование показателя |
Обозначение |
Единица измерения |
Численное значение |
1
2
3
4
5
6
7
8
9
|
Расчетный грузопоток
Тип ленточного конвейера
Линейные массы движущихся частей
Верхних роликоопор
Нижних роликоопор
Ленты
Груза
Сила тяги для перемещения ветвей
Верхней
Нижней
Тяговое усилие на приводных барабанах
Минимальное натяжение ленты
По условию сцепления на приводе
По условию ограничения провеса
Максимальное натяжение ленты
Разрушающее натяжение ленты
Количество конвейеров
|
Qp
2Л100У
qp
1
qp
11
q
л
q
гр
F
4-3
F
2-1
Fo
F
1
min
F
гр.
min
Fmax
F
разр
n
|
т/ч
---
кг/м
кг/м
кг/м
кг/м
H
H
H
H
H
H
Н
---
|
250
---
25,1
7,3
18,2
34,7
325929
–98910
227019
59671
3500
322429
800000
3,25
|
Принимаем четыре конвейера длиной по 350 м каждый |
10
11
12
13
14
15
|
Сила тяги для перемещения ветвей
Верхней
Нижней
Тяговое усилие на приводных барабанах
Минимальное натяжение ленты
По условию сцепления на приводе
По условию ограничения провеса
Запас прочности ленты
Мощность привода одного конвейера
Паспортная мощность привода конвейера
|
F4-3
1
F2-1
1
Fo
1
F1 min
1
F
гр
.miт
1
m1
N1
N
п
|
Н
Н
Н
Н
Н
---
кВт
кВт
|
81482
–24727
56755
14918
3500
10,3
145
220
|
Принимаем четыре конвейера 2Л100У по 350 м каждый.
3.2 Расчет конвейера главного конвейерного штрека.
Сменный грузопоток в данном случае будет равный сменной нагрузке на очистной забой и составляет Q
см
= 850 т/см. С учетом коэффициента неравномерности грузопотока в каждой лаве k
= 1,5 и коэффициента машинного времени kм
= 0,85 производительность расчетного грузопотока составляет Qp
= QТ
= 250 т/ч.
Результаты расчета конвейера сведены в таблицу 3.1. Для транспортирования груза, в данном случае принят специальный конвейер для работы в наклонных стволах – 2Л100У, с паспортной производительностью 850т/ч
Техническая характеристика ленточного конвейера 2Л100У:
Максимальная производительность, т/ч
Приемная способность, м3
/мин
Скорость движения ленты, м/с
Мощность привода конвейера, кВт
Угол установки конвейера, град
Длина поставки, м
Лента:
· Тип ленты
· Ширина ленты, мм
Масса ленты, кг/м2
Расчетная разрывная прочность, кН/см
Число тканевых прокладок
Толщина наружных обкладок, мм
Роликоопоры:
Масса вращающихся частей роликоопор:
- груженая ветвь, кг
- порожняя ветвь, кг
Расстояние между роликоопорами
- груженая ветвь, мм
- порожняя ветвь, мм
Приводная станция:
Количество приводных барабанов
Связь между барабанами
Угол обхвата барабанов лентой, град
Диаметр приводных барабанов, мм
Поверхность барабанов
Расположение натяжной станции
|
850
15,8
2,0
2 110
от -16 до +18
500 – 750
2Ш 1000 4 ТК-200 4,5-3,5 Г
1000
18,2
200
4
4,5/3,5
37,70
21,9
1500
3000
2
жесткая
210/210
630
без футировки
в хвосте
|
На рисунке 3.2 изображена диаграмма натяжения ленты при длине транспортирования L
= 2000м.
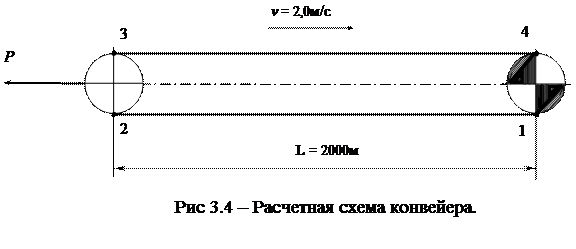
Таблица 3.2 – Расчет технологических параметров конвейера
№ |
Наименование показателя |
Обозначение |
Единица измерения |
Численное значение |
1
2
3
4
5
6
7
8
9
|
Расчетный грузопоток
Тип ленточного конвейера
Линейные массы движущихся частей
Верхних роликоопор
Нижних роликоопор
Ленты
Груза
Сила тяги для перемещения ветвей
Верхней
Нижней
Тяговое усилие на приводных барабанах
Минимальное натяжение ленты
По условию сцепления на приводе
По условию ограничения провеса
Максимальное натяжение ленты
Разрушающее натяжение ленты
Количество конвейеров
|
Qp
1Л1000П
qp
1
qp
11
q
л
q
гр
F
4-3
F
2-1
Fo
F
1
min
F
гр.
min
Fmax
F
разр
n
|
т/ч
---
кг/м
кг/м
кг/м
кг/м
H
H
H
H
H
H
Н
---
|
250
---
25,1
7,3
18,2
34,7
104410
47755
152166
39996
3500
192162
800000
1,92
|
Так как расчетная мощность привода превышает паспортную, принимаем два конвейера длиной по 1000 м каждый |
10
11
12
13
14
15
|
Сила тяги для перемещения ветвей
Верхней
Нижней
Тяговое усилие на приводных барабанах
Минимальное натяжение ленты
По условию сцепления на приводе
По условию ограничения провеса
Запас прочности ленты
Мощность привода одного конвейера
Паспортная мощность привода конвейера
|
F4-3
1
F2-1
1
Fo
1
F1 min
1
F
гр
.miт
1
m1
N1
N
п
|
Н
Н
Н
Н
Н
---
кВт
кВт
|
52205
23878
76083
19988
3500
9
194
220
|
Принимаем два конвейера на заданную длину транспортирования по 1000м каждый.
4 технико-экономические показатели
Таблица 4.1
Основные технико-экономические показатели
№
п/п
|
Наименование оборудования |
Кол-во
шт
|
Производи-тельность
т/см
|
Цена
тыс.грн
|
1
2
3
4
5
6
7
8
|
СП250.13
КСП2М
1Л80П
2Л100У
АРВ7
ВГ2,5
ВПГ18
ДКНЛ
|
6
6
12
6
6
116
6
16
|
272 – 425
272 – 425
272 – 425
816 – 1275
582
582
---
97
|
468
360
1120
2450
980
67
86
950
|
5. ПРАВИЛА БЕЗОПАСНОСТИ
5.1 Охрана труда при эксплуатации локомотивного транспорта
Горизонтальные выработки, по которым производится откатка локомотивами, должны иметь уклон не более 0,005.
Тормозной путь состава на максимальном уклоне при перевозке грузов не должен превышать 40 м, а при перевозке людей - 20 м.
Локомотив во время движения должен находиться в голове состава. Нахождение локомотива в хвосте состава разрешается только при маневровых операциях, выполнять которые разрешается на участке протяжением не более 300 м при скорости движения не более 2 м/с.
Запрещается эксплуатация локомотивов при:
а) нарушениях взрывобезопасности оборудования на локомотивах;
б) снятой крышке батарейного ящика аккумуляторного электровоза или неисправном ее блокировочном устройстве;
в) неисправности электрооборудования, блокировочных устройств и средств защиты, скоростемеров;
г) неисправных или неотрегулированных тормозах;
д) неисправности песочниц или отсутствия песка в них;
е) неисправности сцепных устройств;
ж) неисправности буферов;
з) изношенных более чем на 2/3 толщины колодках и более чем на 10 мм - бандажах;
и) несветящихся или неисправных фарах;
к) неисправности сигнальных устройств.
Управление локомотивом должно производиться только из кабины локомотива, машинист не должен выходить из нее на ходу, а также самовольно передавать управление локомотивом другому лицу и выполнять ручные операции по сцепке и расцепке локомотива с составом из кабины.
Каждый локомотив, находящийся в эксплуатации, должен осматриваться в следующие сроки:
а) ежесменно машинистом при приемке локомотива;
б) дежурным электрослесарем при выпуске локомотива на линию;
в) еженедельно начальником электровозного депо, а где его нет - механиком участка шахтного транспорта;
г) один раз в квартал начальником участка совместно с механиком шахтного транспорта.
5.3 Охрана труда при перевозке людей по горизонтальным и наклонным выработкам
Перевозка людей по горным выработкам должна осуществляться пассажирскими средствами, предназначенными и допущенными в установленном порядке для этих целей, в соответствии с указаниями, содержащимися в заводских инструкциях по их эксплуатации.
При перевозке людей в пассажирских вагонетках (поездах) по горизонтальным выработкам скорость движения не должна превышать 20 км/ч, а при перевозке людей в оборудованных грузовых вагонетках - 12 км/ч.
Поезд (вагонетка) должен обслуживаться специально обученным горнорабочим (кондуктором), который во время перевозки людей должен находиться в передней части первой вагонетки по направлению движения. В этом же месте должна находиться рукоятка ручного привода парашютов.
Тип рельсов и способ настилки рельсовых путей в наклонных выработках, где производится перевозка людей пассажирскими вагонетками, должны соответствовать типу парашютного устройства.
Конвейеры для перевозки людей должны оборудоваться в соответствии с «Инструкцией по перевозке людей ленточными конвейерами в подземных выработках угольных и сланцевых шахт».
Запрещается:
а) перевозка в поездах с людьми инструментов и запасных частей, выступающих за борт вагонеток, взрывчатых, легковоспламеняющихся и едких материалов;
б) прицепка грузовых вагонеток к людским составам, за исключением не более двух вагонеток в конце состава для перевозки инструмента в горизонтальных выработках;
в) переноска громоздких и длинных предметов по путям во время перевозки людей;
г) езда людей на локомотивах, в необорудованных вагонетках, на платформах (площадках) и т.п.
Допускается с разрешения машиниста электровоза проезд на локомотиве инженерно-техническим работникам и стажерам машиниста локомотива при наличии второй кабины (сиденья);
д) проходить между вагонетками и перелазить через них во время движения состава.
Для доставки материалов и выдачи породы при ремонтах людских ходков, оборудованных механической, доставкой, грузовую вагонетку разрешается прицеплять к незагруженному пассажирскому поезду. При этом должны соблюдаться следующие условия:
а) скорость движения поезда не должна превышать 3 м/с;
б) для прицепки грузовой вагонетки должны применяться прицепные устройства, изготовленные заводами или ремонтными предприятиями по технической документации завода-изготовителя пассажирских вагонеток;
в) нагрузка на прицепное устройство головной пассажирской вагонетки и на подъемную машину (лебедку) не должна превышать расчетную;
г) перевозка людей в пассажирском поезде (вагонетке) с прицепленной грузовой вагонеткой не допускается. Это требование не распространяется на лиц, занятых на ремонте данной выработки.
Ежесуточно осмотр указанного оборудования и проверка парашютных устройств включением ручного привода должны производиться механиком подъема или ИГР. Такая же проверка один раз в месяц должна производиться главным механиком или ИГР, назначенным для этой цели.
5.4 Охрана труда при перевозке грузов по горизонтальным и наклонным выработкам
Запрещается допускать в работу грузовые вагонетки, транспортные единицы секционных поездов, монорельсовых и напочвенных дорог:
а) с неисправными полускатами (расшатанными колесами, недостающими крепежными болтами и валиками, изогнутыми осями колесных пар и трещинами на осях, глубокими выбоинами на колесах и пр.);
б) с неисправными сцепками, серьгами и другими тяговыми частями, а также со сцепками, изношенными сверх допустимых норм;
в) с неисправными буфетами и тормозами;
г) с неисправными запорными механизмами и неплотно прилегающими днищами вагонеток (секционных поездов) с разгрузкой через дно;
д) с деформированными или разрушенными подвагонными упорами;
е) с разрушенными или выгнутыми наружу более чем на 50 мм стенками кузовов вагонеток;
ж) с неисправными межсекционными перекрытиями секционных поездов.
Запрещается:
а) проталкивание несцепленных составов, прицепка непосредственно к локомотиву платформ или вагонеток с длинномерными материалами, а также платформ и вагонеток, груженных лесом или оборудованием, выступающим за верхний габарит транспортных средств;
б) ручная сцепка и расцепка вагонеток во время движения состава, а также сцепка и расцепка крюковых сцепок без применения специальных приспособлений;
в) сцепка и расцепка вагонеток в наклонных выработках и в выработках с самокатным уклоном и на закруглениях;
г) оставлять подвижной состав на участках выработок, имеющих самокатный уклон;
д) формирование составов из вагонеток со сцепками разных типов;
е) проталкивание составов локомотивами с помощью стоек, распилов, досок, а также локомотивом, движущимся по параллельному пути;
ж) сцепка и расцепка вагонеток на расстоянии ближе б м от опрокидывателей, вентиляционных дверей или других препятствий;
з) применение для затормаживания и удержания подвижного состава подручных средств;
и) оставлять вагонетки, составы или локомотивы на разминовках ближе 4 м от рамного рельса стрелочного перевода.
В выработках с углом наклона до 10° при небольшом (1-2 вагонетки) количестве вагонеток в составе допускается иметь барьеры жесткого типа;
в) ниже верхних приемных площадок, а также в заездах промежуточных выработок могут устанавливаться барьеры жесткого типа, прочность которых должна определяться расчетом. Управление такими барьерами должно быть дистанционным. В выработках длиной до 30 м, предназначенных для транспортировки вспомогательных материалов и оборудования, допускается применение барьеров е ручным управлением.
На нижних и промежуточных приемных площадках на горизонтальных участках выработок должны устраиваться ниши для укрытия работающих и размещения пультов. управления и связи.
Требования настоящего параграфа не распространяются на наклонные выработки, используемые для перевозки людей в людских либо грузолюдских транспортных средствах, оборудованных парашютными устройствами.
СПИСОК ЛИТЕРАТУРЫ
1. Методические указания к самостоятельной работе по теме "Расчет ленточного конвейера" для студентов специальности 09.02 "Подземная разработка месторождений полезных ископаемых", Н. Я. Биличенко, Г. М. Широков Днепропетровск ГГАУ (НГУ) 1994г
2. Транспорт на горных предприятиях. Под общей редакцией Б. А. Кузнецова Москва, "Недра" – 1969г.656с
3. Справочник по шахтному транспорту. Г. Я. Пейсахович, И. П. РемизовМосква, "Недра" – 1977г
4. Правила безопасности в угольных шахтах. Киев 1996.
5. К. Ф. Сапицкий, В. П. Прокофьев, И. Ф. Ярембаш Донецк 1999. Задачник по подземной разработке угольных месторождений.
|