Федеральное агентство по образованию
ГОУ ВПО «Пермский государственный технический университет – ПГТУ»
Кафедра строительных материалов и специальных технологий
Проектирование бетоносмесительной установки для производства лестничных маршей производительностью 13000 м3
/год
КУРСОВОЙ ПРОЕКТ
ПОЯСНИТЕЛЬНАЯ ЗАПИСКА
270106 589121 06057 ПЗ
Руководитель:
В.А. Шаманов
Студентка
Гр ПСК – 07 – 1:
Д.В. Ширинкина
Пермь 2010
СОДЕРЖАНИЕ
ПЕРЕЧЕНЬ ЛИСТОВ ГРАФИЧЕСКИХ МАТЕРИАЛОВ.. 4
ВВЕДЕНИЕ. 5
1. ОСНОВНЫЕ ХАРАКТЕРИСТИКИ ИЗДЕЛИЯ.. 6
1.2 Транспортировка и хранение. 11
2. ТРЕБОВАНИЯ К КОНСТРУКЦИОННЫМ МАТЕРИАЛАМ.. 12
2.1. Бетонная смесь. 12
2.1.1. Вяжущие вещества. 12
2.1.2. Крупный заполнитель. 13
2.1.3. Мелкий заполнитель. 14
2.1.4. Вода. 16
2.1.5. Добавка. 16
2.2 Арматура. 17
3. ПОДБОР СОСТАВА БЕТОНА.. 19
3.1. Исходные данные. 19
3.2. Подбор состава бетона без учета добавки. 19
3.3. Расчет состава бетона с учетом добавки. 22
4 ОСНОВНЫЕ РАСЧЕТЫ БЕТОНОСМЕСИТЕЛЬНОГО УЗЛА.. 24
4.1. Режим работы предприятия. 24
4.2. Составление рабочей программы предприятия. 24
4.3. Расчет по складу сырьевых материалов. 25
4.3.1. Расчет склада цемента. 25
4.3.2. Расчет склада крупного и мелкого заполнителей. 26
4.4 Расчет расходных бункеров. 28
5 ПОДБОР ТЕХНОЛОГИЧЕСКОГО ОБОРУДОВАНИЯ.. 30
5.1 Подбор дозаторов. 30
5.2 Подбор бетоносмесителей. 31
6 ОХРАНА ТРУДА И ТЕХНИКА БЕЗОПАСНОСТИ.. 33
ЗАКЛЮЧЕНИЕ. 35
БИБЛИОГРАФИЧЕСКИЙ СПИСОК.. 35
Наименование документа
|
Обозначение документа
|
Формат листа
|
Линия по приготовлению бетонной смеси для производства лестничных маршей
|
270106 589121 06076 ТС
|
А1
|
Целью данного курсового проекта является проектирование бетоносмесительной установки для производства лестничных маршей. Производительность установки должна быть 13000 м3
/год по заданию курсового проекта.
Лестничные марши применяют в промышленном и гражданском строительстве, для зданий коммерческого назначения. Лестничные марши применяют двух типов - плитной конструкции без фризовых ступеней и ребристой конструкции с фризовыми ступенями. Марши первого типа являются основным унифицированным решением для кирпичных, крупнопанельных и крупноблочных зданий, второго типа - для общественных зданий.
Наиболее рациональным способом производства при заданной производительности будет являться агрегатно-поточный способ. Этот способ позволяет использовать различное технологическое оборудование, различные по размерам формы, изготовлять широкую номенклатуру изделий. Агрегатно-поточный способ для мелкосерийного производства является наиболее выгодным. При несложном технологическом оборудовании, небольших производственных площадях и затратах на строительство этот способ дает высокий съем продукции с 1 м2
производственной площади цеха. Здесь сочетаются небольшие затраты труда со сравнительно низкими размерами удельных капитальных вложений. Этот способ позволяет разделить технологические операции по специализированным постам, создать условия для организации четкого пооперационного контроля качества изделий, обеспечивает высокий коэффициент использования оборудования и оборачиваемость форм. Годовая производительность агрегатно-поточной технологии определяется номенклатурой выпускаемой продукции, режимом формования изделий и продолжительностью работы формовочного поста.
Лестничные марши подразделяют на следующие типы:
- ЛМ - плоские без фризовых ступеней;
- ЛМФ - ребристые с фризовыми ступенями;
- ЛМП - ребристые с полуплощадками.
Марши предназначены для применения в лестницах на расчетные временные нагрузки (при коэффициенте надежности по нагрузке =1,2 и без учета собственного веса):
- 3,5 кПа (360 кгс/м ) - для жилых зданий;
- 4,7 кПа (480 кгс/м ) - для общественных зданий, производственных и вспомогательных зданий промышленных предприятий.
Марка элементов лестниц состоит из буквенно-цифровых групп, разделенных дефисами.
Первая группа содержит обозначение типа элемента лестницы и габаритные размеры: длину и ширину в дециметрах (значения которых округляют до целого числа), а для маршей дополнительно указывают координационную высоту марша (высоту вертикальной проекции) в дециметрах. Длину маршей типа ЛМП без нижней полуплощадки указывают в марке, равной длине основного марша этого типа (с двумя полуплощадками). Для конечных площадок и накладных проступей, укладываемых на верхние конечные ступени маршей, первую группу дополняют строчной буквой "в".
Во второй группе указывают:
- расчетную временную нагрузку, обозначаемую цифрами 4 при нагрузке 3,5 кПа (360 кгс/м ) и 5 при нагрузке 4,7 кПа (480 кгс/м ), а для маршей и площадок, изготовляемых из легкого бетона, - вид бетона, обозначаемый прописной буквой "Л";
В третьей группе указывают:
- левое исполнение и вид отделки верхней лицевой поверхности;
- для маршей типа ЛМП - цифрами обозначают: 1 - марш с верхней удлиненной полуплощадкой, 2 - марш с нижней удлиненной полуплощадкой, 3 - марш без нижней полуплощадки.
Для маршей, предназначенных для эксплуатации в среде с агрессивной степенью воздействия на железобетонные конструкции, в марке дополнительно указывают показатель проницаемости бетона (например, - пониженной проницаемости), а для маршей, предназначенных для зданий с расчетной сейсмичностью 7 - 9 баллов, - строчную букву "с".
Пример условного обозначения (марки) марша типа ЛМ длиной 2720 мм, шириной 1050, высотой вертикальной проекции 1400 мм, под расчетную нагрузку 3,5 кПа (360 кгс/м ), из легкого бетона, с гладкой бетонной поверхностью: ЛМ27.11.14-4Л
В соответствии с заданием необходимо спроектировать БСУ для производств лестничных маршей. Эскиз изделия представлении на рисунке 1. Выберем марку марша ГОСТ ЛМ 30.11.15-4. Размеры изделия, мм: l = 3030 мм, b = 1050 мм, hом = 1500мм, lом = 2700 мм. Марка бетона – 300. Расход бетона на изделие – 0, 59м3, стали – 16,25 кг.

Рисунок 1.1 - Эскиз изделия
1.1 Технические требования
Лестничные марши следует изготовлять в соответствии с требованиями ГОСТ 9818-95 и технологической документации, утвержденной в установленном порядке, по типовой проектной документации.
Лестничные марши должны удовлетворять требованиям ГОСТ 13015.0:
· по показателям фактической прочности бетона (в проектном возрасте и отпускной);
· по морозостойкости и водонепроницаемости бетона;
· по плотности легкого бетона;
· по истираемости бетона;
· к маркам сталей для арматурных и закладных изделий, в т.ч. для монтажных петель;
· по отклонению толщины защитного слоя бетона до рабочей арматуры;
· по защите от коррозии.
Лестничные марши должны удовлетворять установленным при проектировании требованиям по прочности, жесткости и трещиностойкости. При этом испытания элементов лестниц нагружением не проводят.
Марши должны выпускаться с законченной отделкой верхних лицевых поверхностей.
Допускается по согласованию с потребителем производить поставку маршей без уложенных накладных проступей, которые должны поставляться в комплекте с маршами или отдельно с предприятия - изготовителя накладных простулей и устанавливаться на марши на строительной площадке.
Лестничные марши следует изготовлять из тяжелого бетона по ГОСТ 26633 или из легкого бетона плотной структуры по ГОСТ 25820.
Нормируемая отпускная прочность бетона лестничных маршей должна составлять (в процентах от класса или марки бетона по прочности на сжатие):
- 70 - при поставке элементов лестниц в теплый период года;
- 80 - при поставке накладных проступей в холодный период года;
- 85 - при поставке маршей и площадок в холодный период года.
Истираемость мозаичного декоративного конструкционного слоя бетона маршей на щебне из мрамора не должна превышать 1,8 г/см .
Для армирования лестничных маршей следует применять:
- стержневую горячекатаную арматурную сталь классов А-I, А-III по ГОСТ 5781 и А-IIIв, изготовляемую из арматурной стали класса А-III, упрочнением вытяжкой, с контролем величины напряжения и предельного удлинения;
- стержневую термомеханически упрочненную арматурную сталь классов Ат 400С, Ат 500С и Ат 600С по ГОСТ 10884;
- проволоку класса Вр-1 по ГОСТ 6727 и класса Врп-1 по ТУ 14-4-1322.
Значения действительных отклонений геометрических параметров элементов лестниц не должны превышать предельных, указанных в табл. 1.2.
Таблица 1.2 Допустимые отклонения геометрических параметров
Наименование отклонения геометрического параметра
|
Наименование геометрического параметра
|
Предельное отклонение
|
Отклонение от линейного размера
|
Марши и площадки
|
Длина
|
до 4000
|
±5
|
св. 4000
|
±6
|
Ширина
|
±5
|
Толщина
|
±3
|
Размеры ребер, полок, выступов, отверстий и каналов
|
±5
|
Положение выступов, выемок и отверстий
|
5
|
Положение закладных изделий:
|
в плоскости поверхности для закладных изделий размерами до 100
|
5
|
то же, для закладных изделий размерами св. 100
|
10
|
из плоскости поверхности
|
3
|
Отклонение от прямолинейности
|
Прямолинейность профиля лицевой поверхности:
|
ступени марша, площадки или накладной проступи длиной до 2500 на участке 1000
|
2
|
марша или площадки длиной св. 2500 до 4000 на всей длине
|
±3
|
то же, длиной св. 4000 на всей длине
|
±4
|
В бетоне маршей, поставляемых потребителю, трещины не допускаются, за исключением усадочных и других поверхностных технологических трещин на нижней и торцовых поверхностях элементов, ширина которых не должна превышать 0,2 мм.
1.2 Транспортировка и хранение
Транспортировать и хранить элементы лестниц следует в соответствии с требованиями ГОСТ 13015.4 и ГОСТ 9818-95.
Марши (кроме маршей типа ЛМП) следует транспортировать и хранить в штабелях в горизонтальном положении, при этом марши следует располагать ступенями вверх. Высота штабеля при хранении маршей не должна превышать 2,5 м.
Марши с полуплощадками (типа ЛМП) следует транспортировать и хранить в положении "на ребро". Допускается хранить марши других типов в положении "на ребро" при надежном их закреплении в этом положении.
Подкладки и прокладки между рядами маршей должны быть толщиной не менее 30 мм и установлены в местах расположения строповочных отверстий или монтажных петель.
2.1. Бетонная смесь
Бетоны, применяемые при изготовлении лестничных маршей, должны иметь следующие показатели качества:
- Марка бетона по прочности на сжатие должна быть М300, соответственно класс бетона должен быть В 22,5.
- Удобоукладываемость принимается в диапазоне от 5 до 9 см в соответствии со СНиПом 3.09.01-85.
[4]
- Показатель раствороотделения не должен превышать 6-8 %
- Средняя плотность в диапозоне от 1600 до 2000 кг/м .
- Показатель истираемости бетона лестничных маршей не должен превышать 0,8 г/см , а для лестничных маршей высшей категории качества - 0,6 г/см .
- Морозостойкость и водонепроницаемость бетона при эксплуатации лестничного марша при температуре ниже минус 40°С – F 200, W 4; от минус 20°С до минус 40°С - F 200, W 4; от минус 5°C до минус 20°С – F 100, W 4.
- Лестничные марши относятся к первой категории требований к трещиностойкости, в которой не допускается образование трещин.
- Содержание вовлеченного воздуха
В задании предложено взять бетонную смесь В15 П1 W4, но данная смесь не пригодна для изготовления изделия, так как не удовлетворяет требованиям по прочности на сжатие. Рекомендуется взять бетонную смесь марки М300. Марка по удобоукладываемости П1 предполагает осадку конуса в пределах 1-4 см, что не соответствует требованиям СНиПа. Поэтому целесообразно назначить марку П2.
2.1.1. Вяжущие вещества
В бетонных смесях для ЖБК используются следующие виды вяжущих: портландцемент, гидрофобный цемент, шлаковый цемент, быстротвердеющий цемент, пуццолановые цементы, глинозёмистый цемент, сульфатостойкий цемент, расширяющиеся цементы, напрягающий цемент, магнезиальный цемент. К изделию не предъявляется никаких специфических требований, и бетонная смесь не должна обладать особыми свойствами, следовательно, наиболее целесообразным будет применить для производства обыкновенный портландцемент.
Активность вяжущего вещества должна приниматься в пределах 1,2…2 прочности бетона. Следовательно, так как требуемая прочность бетона равна 300 кгс/см2
, активность цемента должна лежать в пределах от 360 до 600 кгс/см2
.
В задании предложено взять цемент ЦЕМ II / А – Ш В32,5, Rцем
= 417кгс/см2
, который удовлетворяет требованиям, предъявляемым к вяжущим веществам. Он должен удовлетворять требованиям ГОСТ 10178-85. Цемент должен показывать равномерность изменения объема при испытании образцов кипячением в воде. Начало схватывания цемента должно наступать не ранее 45 мин, а конец - не позднее 10 ч от начала затворения.
2.1.2. Крупный заполнитель
[6]
Прочность на сжатия крупного заполнителя должна не менее чем в два раза превышать прочность бетона. Так как бетон должен быть марки не меньше, чем М300, крупный заполнитель должен быть марки не ниже, чем Д600.
В качестве крупного заполнителя для бетона применяют щебень, гравий или щебень из гравия. Щебень (материал в виде кусков с размерами 5—70 мм) получают путем дробления плотных горных пород, мартеновских или доменных шлаков, отходов керамической промышленности, кирпича и т. п. При дроблении горных пород обломки щебня получаются неправильной формы с шероховатой поверхностью. Щебни, имеющие зерна, приближающиеся по форме к кубу или тетраэдру, считаются лучшими для бетона. Гравий— рыхлые обломки окатанной формы крупностью от 5 до 70 мм, образовавшиеся в результате естественного разрушения (выветривания) горных пород. Крупный заполнитель должен иметь среднюю плотность от 2000 до 2800 кг/куб.м. Щебень вследствие шероховатой поверхности зерен лучше сцепляется с цементным камнем и позволяет при прочих равных условиях получить более прочные бетоны, чем с гравием. Однако бетонные смеси на гравии имеют большую подвижность и лучшую удобоукладываемость, чем на щебне.
Содержание пылевидных и глинистых частиц в щебне из изверженных и метаморфических пород, щебне из гравия и в гравии не должно превышать для бетонов всех классов 1% по массе. Содержание пылевидных и глинистых частиц в щебне из осадочных пород не должно превышать для бетонов класса В22,5 и выше - 2% по массе; класса В20 и ниже - 3% по массе.
Содержание зерен пластинчатой (лещадной) и игловатой формы в крупном заполнителе не должно превышать 35% по массе.
Содержание зерен слабых пород в гравии и щебне из гравия не должно превышать 10% по массе для бетонов всех классов.
В задании в качестве крупного заполнителя предложено взять щебень из гравия фр 5-20мм. По составу щебень из гравия состоит из 75% зерен осадочных пород (известняки, доломиты) и около 25% зерен изверженных пород (граниты). Примем марку щебня из гравия Д800. Он соответствует требованиям, предъявляемым к крупному заполнителю.
2.1.3. Мелкий заполнитель
Мелкие заполнители должны иметь среднюю плотность зерен от 2000 до 2800 кг/куб.м.
Допустимое содержание пород и минералов, отнесенных к вредным примесям в заполнителях:
· аморфные разновидности диоксида кремния, растворимого в щелочах (халцедон, опал, кремень и др.) - не более 50 ммоль/л;
· сера, сульфиды, кроме пирита (марказит, пирротин и др.) и сульфаты (гипс, ангидрит и др.) в пересчете на SO(3) - не более 1,5% по массе для крупного заполнителя и 1,0% по массе - для мелкого заполнителя;
· пирит в пересчете на SO(3) - не более 4% по массе;
· слоистые силикаты (слюды, гидрослюды, хлориты и др., являющиеся породообразующими минералами) - не более 15% по объему для крупного заполнителя и 2% по массе - для мелкого заполнителя;
· магнетит, гидрооксиды железа (гетит и др.), апатит, нефелин, фосфорит, являющиеся породообразующими минералами, - каждый в отдельности не более 10%, а в сумме - не более 15% по объему;
· галоиды (галит, сильвин и др.), включающие водорастворимые хлориды, в пересчете на ион хлора - не более 0,1% по массе для крупного заполнителя и 0,15% по массе - для мелкого заполнителя;
· свободное волокно асбеста - не более 0,25% по массе;
· уголь - не более 1% по массе. [7]
Зерновой состав мелкого заполнителя должен соответствовать графику (см. рис.2). [6]
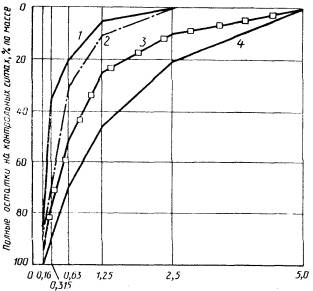
Рисунок 2 – График зернового состава мелкого заполнителя
В задании в качестве мелкого заполнителя предложено взять песок известняковый с модулем крупности(Мк
) 2,3. Он удовлетворяет требованиям, предъявляемым к мелкому заполнителю.
2.1.4. Вода
[8]
Содержание в воде органических поверхностно-активных веществ, сахаров или фенолов, каждого, не должно быть более 10 мг/л.
Вода не должна содержать пленки нефтепродуктов, жиров, масел.
В воде, применяемой для затворения бетонных смесей и поливки бетона не должно быть окрашивающих примесей, если к бетону предъявляют требования технической эстетики.
Окисляемость воды не должна быть более 15 мг/л.
Водородный показатель воды (pH) не должен быть менее 4 и более 12,5.
Вода не должна содержать также примесей в количествах, нарушающих сроки схватывания и твердения цементного теста и бетона, снижающих прочность и морозостойкость бетона.
2.1.5. Добавка
[9]
Пластифицирующие добавки – добавки, увеличивающие подвижность бетонной смеси. В задании предложено взять добавку ЛСТ, которая относится к 3 группе классификатор по эффективности, т.е. средним пластификатором.
Для пластификации бетонной смеси и раствора ее вводят в небольшом количестве — 0,1-0,5 % от массы цемента. В расчете на 1 м3 бетона расход добавки составляет всего 0,5... 1 кг. В качестве аналогов можно применить СДБ (Сульфитно-дрожжевая бражка) и УПБ (Мелассная упаренная последрожжевая барда). Из таблицы 2.1.5.1 делаем вывод, что наиболее выгодно применить добавку ЛСТ, предложенную в задании.
Таблица 2.1.5 Сравнительные характеристики пластифицирующих добавок
Добавки
|
Условное обозначение
|
Содержание сухого вещества, %
|
Снижение водопотребности, %
|
Ориентировочное количество добавки в расчете на сухое вещество, % массы цемента
|
Достигаемый эффект
|
Примерная стоимость в пересчете на сухое вещество, руб./т
|
Сульфитно-дрожжевая бражка
|
СДБ
|
76
|
На 5-15
|
0,1-0,2
|
Улучшение удобоукладываемости, снижение расхода цемента, повышение прочности, сокращение цикла формования
|
65
|
Лигносульфонат технический марки В
|
ЛСТ
|
50
|
На 5-10
|
0,1-0,2
|
То же
|
53
|
Мелассная упаренная последрожжевая барда
|
УПБ
|
50
|
На 5-10
|
0,2-0,3
|
Улучшение удобоукладываемости, снижение расхода цемента, повышение прочности, морозостойкости, сокращение цикла формования бетонной смеси
|
100
|
2
.2 Арматура
Для армирования лестничных маршей следует применять:
· стержневую горячекатаную арматурную сталь классов А-I, А-III по ГОСТ 5781-82 и А-IIIв, изготовляемую из арматурной стали класса А-III, упрочнением вытяжкой, с контролем величины напряжения и предельного удлинения;
· стержневую термомеханическую упрочненную арматурную сталь классов Ат-IIIС и Ат-IVС по ГОСТ 10884-81;
· проволоку класса Вр-I по ГОСТ 6727-80 и класса Врп-I по ТУ 14-4-1322-85.
3.1. Исходные данные
· Бетон B22,5 (Rб
= 29,4 МПа).
· Подвижность бетонной смеси П2 (5…9 см)
· Цемент ЦЕМ II / А – Ш В32,5. Rц
= 41,7 МПа
· Крупный заполнитель – щебень из гравия. НКЗ = 20мм. Марка по прочности на сжатие – Д800. Истинная плотность 2,6 кг/л, плотность 1,48 кг/л.
· Мелкий заполнитель – песок речной. Мк =2,3, водопотребность –7%. Рп
= 2,63 кг/л.
· Добавка суперпластификатор ЛСТ. Дозируется в количестве 0,1-0,2% от массы вяжущего. Среднее уменьшение расхода воды – 8%.
3.2. Подбор состава бетона без учета добавки
Определяем В/Ц
В/Ц=А*Rц
/( Rб
+ А*0,5*Rц
) (3.1)
где В/Ц - водоцементное отношение
Rб
– активность бетона, кгс/см2
Rц
– активность цемента, кгс/см2
А – коэффициент, учитывающий качество материалов для бетона.
В/Ц = 0,6*41,7 /(29,4 + 0,6*0,5*41,7) = 0,6
По графику на рисунке 3.1. определяем необходимое количество воды. Принимаем осадку конуса раной 7 см, откуда следует, что водопотребность смеси составляет 195л/м3
. Поскольку в качестве крупного заполнителя используется щебень из гравия, водопотребность следует увеличить на 10 л, после чего она будет составлять 205л/м3
.
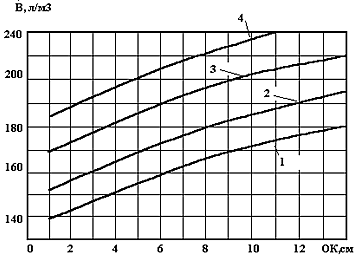
Рисунок 3.1. - График водопотребности В пластичной бетонной смеси, изготовленной с применением портландцемента, песка средней крупности (водопотребность 7%) и гравия наибольшей крупности: 1-70 мм; 2-40 мм; 3-20 мм; 4-10 мм ОК — осадка конуса.
Определяем расход цемента по формуле
Ц= В: В/Ц (3.2)
Ц = В : В/Ц = 205 / 0,6 = 341 кг/м3
. Проверим, удовлетворяет ли полученный результат требованиям СНиПа 82-02-95. Согласно СНиПу минимальный расход цемента ЦЕМ II / А – Ш В32,5 на бетонную смесь с маркой по водонепроницаемости W4 равен 330 кг/м3
. [10] Полученное значение удовлетворяет требованиям СНиПа.
Коэффициент раздвижки α находим по таблице 3.1. путем интерполяции. α=1,42.
Пустотность щебня
Пщ= 1- ρн
/ ρи
(3.3)
Пщ
= 1 - pср
/рнас
= 1 – 1,48 / 2,6 = 0,43
Таблица 3.1. Оптимальные значения коэффициента α для пластичных бетонных смесей
Расход цемента, кг/м3
|
Оптимальные значения коэффициента α при В/Ц
|
0,4
|
0,5
|
0,6
|
0,7
|
0,8
|
250
|
-
|
-
|
1,26
|
1,32
|
1,38
|
300
|
-
|
1,3
|
1,36
|
1,42
|
-
|
350
|
1,32
|
1,38
|
1,44
|
-
|
-
|
400
|
1,4
|
1,46
|
-
|
-
|
-
|
500
|
1,5
|
1,56
|
-
|
-
|
-
|
Определяем расход щебня по формуле
Щ= 1000/(α*Пщ
/ ρн
+ 1/ ρи
) (3.4)
Щ = 1000 / (1,42 * 0,43 / 1,48 + 1 / 2,6) = 1254 кг/м3
Определим расход песка по формуле
П = ρи
п
( 1 - Ц/ ρи
ц
– Щ/ ρи
щ
– В) (3.5)
П = 2,63(1000 – 341/3,1 – 205 – 1298 / 2,6) = 533 кг/м3
Посчитаем соотношение между мелким и крупным заполнителями
r = П/Щ = 0,42 (3.6)
Соотношение соответствует оптимальному.
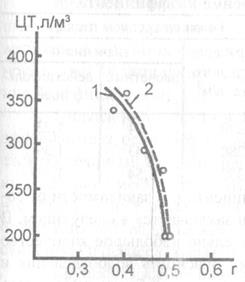
Рисунок 3.2. Зависимость оптимального соотношения крупного и мелкого заполнителя от расхода цементного теста.
3.3. Расчет состава бетона с учетом добавки
Добавка ЛСТ. Оптимальная дозировка – 0,15% от массы цемента. Среднее уменьшение расхода воды К = 8%.
Определим новый расход воды
B1
= B*(1-K) (3.7)
B1
= B*(1-K) = 205*(1-0,08) = 189л/м3
В/Ц = const = 0,6, откуда Ц’ = B : B/Ц = 189 / 0,6 = 314,3 кг/м3
Коэффициент раздвижки α’ = 1,38
Щ’ = 1000 / (1,38 * 0,43 / 1,48 + 1 / 2,6) = 1273 кг/м3
П’ = 2,63(1000 – 314/3,1 – 189 – 1273 / 2,6) = 580 кг/м3
r = П/Щ = 0,56 , соответствует оптимальному
Определим количество вводимой добавки
mд
= Ц*Д (3.8)
mд
= 314*0,0015 = 0,472
Определим количество вводимого концентрированного раствора добавки
A=ЦД/(kpp
) (3.8)
A= 314*0,15/(14*1,063)=3,16 л/м3
Определим недостающее для затворения количество воды
В2
= В1
– Арр
(1 – k/100)
(3.9)
В2
= 189 -3,16*1,063(1-14/100) = 185,7 л/м3
Таблица 3. Результаты расчета состава бетонной смеси
Цемент, кг/м3
|
Добавка л/м3
|
Песок, кг/м3
|
Щебень, кг/м3
|
Вода, л/м3
|
Плотность, кг/м3
|
314,3
|
3,16
|
580
|
1273
|
185,7
|
2399,8
|
4.1. Режим работы предприятия
Для бетоносмесительного цеха по производству лестничных маршей производительностью 13000 м3
/год принимаем количество рабочих суток в году – 260 при односменной работе (смена – 8 часов). [11] Годовой фонд рабочего времени будет составлять (260-7)*1*8 = 2024 ч. (с учётом 7 суток на ремонт и обслуживание оборудования).
4.2. Составление рабочей программы предприятия
В течении года должно быть произведено 13тыс. м
3
бетонной смеси. В таблице 4.1. представлена рабочая программа, обеспечивающая данную производительность.
Таблица 4.1. Рабочая программа предприятия
Расход
|
На 1м3
|
В год
|
В месяц
|
В сутки
|
В смену
|
В час
|
на замес
|
БС, м3
|
-
|
13000
|
1083.333
|
35.616
|
35.6164
|
4.452
|
0.24734
|
С учетом потерь 2%
|
-
|
13260
|
1105
|
36.329
|
36.3288
|
4.541
|
0.25228
|
Цемент, т
|
0.3143
|
4086.3333
|
340.5278
|
11.195
|
11.1954
|
1.399
|
0.07775
|
С учетом потерь 1%
|
0.3175
|
4127.1967
|
343.9331
|
11.307
|
11.3074
|
1.413
|
0.07852
|
Вода, л
|
185.7
|
2414147.4
|
201178.9
|
6614.1
|
6614.1
|
826.8
|
45.9313
|
С учетом потерь 1%
|
187.56
|
2438288.8
|
203190.7
|
6680.2
|
6680.24
|
835
|
46.3906
|
Щебень, т
|
1.273
|
16548.676
|
1379.056
|
45.339
|
45.3388
|
5.667
|
0.31485
|
С учетом потерь 2%
|
1.2984
|
16879.65
|
1406.637
|
46.246
|
46.2456
|
5.781
|
0.32115
|
Песок, т
|
0.5796
|
7535.3512
|
627.9459
|
20.645
|
20.6448
|
2.581
|
0.14337
|
С учетом потерь 2%
|
0.5912
|
7686.0582
|
640.5049
|
21.058
|
21.0577
|
2.632
|
0.14623
|
Добавка, кг
|
0.4715
|
6129.5
|
510.7917
|
16.793
|
16.7932
|
2.099
|
0.11662
|
С учетом потерь 1%
|
0.4762
|
6190.795
|
515.8996
|
16.961
|
16.9611
|
2.12
|
0.11779
|
Раствор добавки, л
|
3.1683
|
41187.34
|
3432.278
|
112.84
|
112.842
|
14.11
|
0.78363
|
С учетом потерь 1%
|
3.1999
|
41599.214
|
3466.601
|
113.97
|
113.97
|
14.25
|
0.79146
|
4.3. Расчет по складу сырьевых материалов
[5]
4.3.1. Расчет склада цемента
Склад должен обеспечивать запас цемента на 7 суток беспрерывной работы, следовательно он должен вмещать 79,15т цемента. С учетом коэффициента возможных потерь при разгрузочных и транспортных операциях, равного 1,04 и коэффициента заполнения емкости 0,9 итоговая вместимость склада должна составлять 91,46т цемента. В качестве склада цемента будут использованы 2 силоса вместимостью 60т каждый. Тогда суммарная вместимость силосов будет составлять 120т.
Cхема силоса приведена на рисунке 4.1.
Рассчитаем габаритные размеры силосов при h=3d из формулы:
Vсил
=πd2
h/4 (4.2)
где Vсил
– объем силоса, м3
d – диаметр силоса, м
h – высота силоса, м
Vсил
= π*d3
*3/4 (4.3)
(4.4)
В соответствыы и ГОСТом 10704.91 принимаем диаметр трубы равным 2,19м. [12]
h= 2,19*3 = 6,57 м
4.3.2. Расчет склада крупного и мелкого заполнителей
Запас заполнителей, требуемый для выполнения производственной программы завода железобетонных изделий:
Щ = QЗщ
n/р (4.5)
где Щ – запас щебня на складе, м3
Q – производительность завода, м3
/год
Зщ
– средний расход щебня, м3
/м3
бетонной смеси
n – запас заполнителей при поступлении их на склад автомобильным транспортом, сутки
р – расчетный годовой фонд рабочего времени, сутки
Щ= 13260ּ0,9ּ7/365 = 228,9 м3
П = QЗп
n/р (4.6)
где П – запас песка на складе, м3
Q – производительность завода, м3
/год
Зп
– средний расход песка, м3
/м3
бетонной смеси
n – запас заполнителей при поступлении их на склад автомобильным транспортом, сутки
р – расчетный годовой фонд рабочего времени, сутки
П=13260ּ0,45ּ7/365=114,4 м3
Угол естественного откоса заполнителей - 40º. Высоту штабеля принимаем 4 м. Схема склада заполнителей приведена на рисунке 4.2.
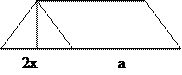 |
Рисунок 4.2 – Схема склада заполнителей
|
|
Рассчитаем площадь склада:
а=(Щ+П)/S (4.7)
где а – длина склада, м
Щ – расход щебня, м3
П – расход песка, м3
S – площадь боковой стороны склада, м2
a= (228,9 +114,4)/19,08 = 17,99 м
Sскл
=2хa (4.8)
где Sскл
– площадь склада, м2
2х – ширина склада, м
a – длина склада, м
Sскл
= 4*ctg40*2*17,99 =171,65 м2
Площадь склада заполнителей с учетом коэффициента, учитывающего устройство проездов и проходов К=1,5:
Sскл
=257,48 м2
4.4 Расчет расходных бункеров
Объем расходных бункеров рассчитывается по формуле:
V=tQчас
З/γ (4.9)
где V – запас материала в расходных буккерах, м3
t – время запаса материала в бункере, час
Qчас
– часовая производительность бетонной смеси, м3
/ч
З – расход материала на м3
бетонной смеси, м3
γ – коэффициент заполнения бункера
Запас заполнителей в расходных бункерах на 3 часа:
Vщ
= 3*4,541*0,9/0,9 = 13,62 м3
Vп
= 3*4,541*0,45/0,9= 6,81 м3
Запас цемента в расходном бункере на 3 часа:
Vц = 3*4,541*0,265/0,9 = 4,01 м3
Запас добавки в сухом виде, воды и раствора добавки в расходных баках на 3 часов:
Vд = 3*4,541ּ0,476/0,9 = 7,208 кг = 0,006 м3
Vв = 3ּ4,541ּ0,188/0,9 = 2,84 м3
Vр-р=3ּ4,541ּ0,0032/0,9 = 0,0484 м3
Схема расходного бункера представлена на рисунке 4.2.
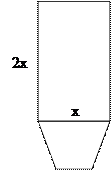
Рисунок 4.2 – Схема расходного бункера.
Рассчитаем габаритные размеры расходных бункеров при высоте, равной двум ширинам основания
V = SH (4.8)
где V – объем расходного бункера, м3
S – площадь основания бункера, м2
Н – высота расходного бункера, м
(4.9)
Хщ
=2,4 м Н=4,8 м
Xп
=1,9 м Н=3,8 м
Хц
=1,6 м Н=3,2 м
Для поддержания эстетичности конструкции цеха принимаем два бункера для щебня размерами 2*2*4 м и один расходный бункер для песка с габаритными размерами 2*2*4 м.
Для цемента приминаем расходный бункер габаритными размерами 2*2*4 м.
Для добавки в сухом виде принимаем бак емкостью 20 л.
Для воды используем бочку емкостью 3 м3
.
Для хранения готового раствора добавки принимаем бак емкостью 100 л.
5.1 Подбор дозаторов
Технические характеристики применяемого дозатора приведены в таблице 5.1. [13]
Таблица 5.1 – Технические характеристики дозатора воды
Наименование параметра
|
исполнение
|
с одним питателем
|
АД-30-БЖ
|
Наибольший предел дозирования (НПД), кг
|
30
|
Наименьший предел дозирования (НмПД), кг
|
4,0
|
Время дозирования, с, не более
|
45
|
Дискретность отсчета, кг
|
0,01
|
Класс точности по ГОСТ 10223-97
|
1
|
Погрешность дозирования, %
|
±0,5
|
Управление заслонками
|
электропневматическое
|
Установленная мощность, кВт
|
0,3
|
Рабочее давление сжатого воздуха, МПа
|
0,4-0,6
|
Габаритные размеры (LxCxH), мм, не более
|
960 * 810 * 1250
|
Масса, кг, не более
|
120
|
Таблица 5.2 – Технические характеристики дозатора цемента [14]
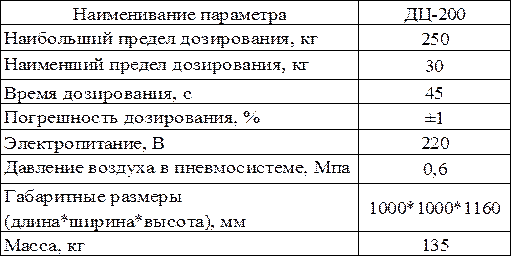
Таблица 5.3 – Технические характеристики дозатора заполнителей
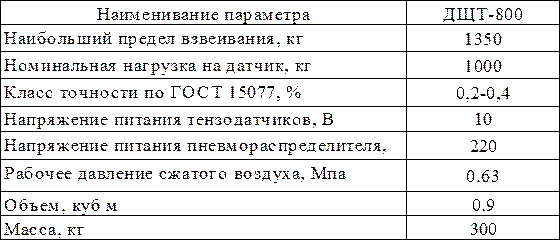
5.2 Подбор бетоносмесителей
Для жестких смесей следует применять бетоносмесители принудительного действия. Для данного бетоносмесительного цеха принимаем бетоносмеситель принудительного действия БС-4М [14]
Таблица 5.4 – Технические характеристики бетоносмесителя БС-4М
БС-4М
|
Объем готовой бетонной смеси, л
|
300
|
Крупность заполнителя, мм, не более
|
30
|
Угловая скорость вала, об/мин.
|
30
|
Мощность электродвигателя, кВт
|
3
|
Габаритные размеры:, мм
|
1400х940х1470
|
Масса, кг
|
450
|
Расчет количества замесов в час:
Nзам
= Vбс/ч
/Vзам
β (5.1)
где Nзам
– количество замесов в час
Vбс/ч
– часовая производительность бетонной смеси, м3
/ч
Vзам
– объем замеса, м3
β – коэффициент выхода бетона
Nзам
=4,541/0,3ּ0,55=9,623 => Nзам
=9
Количество циклов в час должно удовлетворять неравенству:
Vзам
βNзам
>Vбс/зам
(5.2)
где Vзам
– объем замеса, м3
β – коэффициент выхода бетона
Nзам
– количество замесов в час
Vбс/зам
– производительность бетонной смеси за один замес, м3
/замес
0,3ּ0,55ּ9>0,194 – условие выполнено, значит, число замесов в час принимаем равным 9.
Техника безопасности – комплекс технических и организационных мероприятий, направленный на обеспечение безопасности условий труда. В состав таких мероприятий могут входить: разработка правил безопасного проведения работ, ограждение вращающихся частей машин и механизмов, защитное заземление электроустановок, изучение персоналом правил техники безопасности.
Для создания безопасных условий труда при приготовлении бетонной смеси соблюдают следующие правила:
· Площадки в пределах рабочей зоны бетоносмесителей содержат в чистоте и не загромождают. Все работающие механизмы освещают.
· Подъемники, бункера, лотки и другие устройства для подачи материалов ограждают, а все корпуса электродвигателей заземляют.
· Закрытые помещения, в которых работают с пылящими материалами и добавками, оборудуют вентиляцией и устройствами, предупреждающими распыление материалов. Пылеобразование в основном возникает при транспортировании и перегрузки цемента, поэтому во время таких операций рабочие должны пользоваться противопылевой спецодеждой, защитными очками с плотной оправой, а для защиты дыхательных путей – респираторами.
· При приготовлении бетонных смесей с химическими добавками соблюдают меры предосторожности против ожогов, повреждения глаз и отравления.
· До пуска в эксплуатацию каждую установленную или отремонтированную машину осматривают и испытывают.
· При выгрузке бетонной смеси из бетоносмесителя запрещается ускорять опорожнение вращающегося барабана лопатой или другим приспособлением.
· Не допускается проверять, смазывать и ремонтировать электропневматические сборочные единицы дозаторов во время их работы.
· Силосы и бункера для хранения цемента оборудуют устройствами для обрушения сводов цемента.
· Загрузочные отверстия емкостей для хранения пылевидных материалов закрывают защитными решетками, люки в защитных решетках запирают на замок.
При подаче бетонной смеси автотранспортом с мостов и эстакад движение людей по ним не допускается. Выгружать бетонную смесь можно только тогда, когда в бетонируемом сооружении на месте выгрузки никого нет.
Изготовление лестничных маршей должно производиться в соответствии с требованиями, обеспечивающими безопасность производственного оборудования и производственного процесса, при создании эффективных средств защиты рабочих [2].
Транспортирование маршей осуществляют всеми видами транспорта при условиях, исключающих воздействие на марши атмосферных выпадающих осадков.
Условия транспортирования в части воздействия механических факторов устанавливают в нормативных документах на конкретное изделие в соответствии с ГОСТ 23170.
Крепление лестничных маршей в транспортном средстве и сам процесс транспортирования должны обеспечивать сохранность формы, размеров и товарного вида маршей.
Потребитель должен хранить лестничные марши под навесами или в помещениях, защищающих поверхность от воздействия атмосферных выпадающих осадков.
Условия хранения и транспортирования маршей в части воздействия климатических факторов внешней среды устанавливают в нормативных документах на конкретное изделие в соответствии с ГОСТ 13015.
Перед допуском к выполнению работ все работники должны пройти инструктаж по технике безопасности. Все работающие должны соблюдать указания по технике безопасности, изложенные в заводских инструкциях.
В ходе выполнения курсового проекта на тему «Проектирование бетоносмесительной установки для производства лестничных маршей» была запроектирована бетоносмесительная установка производительностью 13000 м3
/год с расчетом производственного состава бетона, емкости силосов цемента, складов заполнителей, расходных бункеров; были подобраны дозаторы воды и добавки, цемента, заполнителей и бетоносмеситель, обеспечивающий заданную производительность бетонной смеси.
Как результат проведенной работы представлен чертеж линии по приготовлению бетонной смеси для производства лестничных маршей, на котором изображена компоновочная схема бетоносмесительной установки, площадью менее 200 м2
в плане и высотой около 10 м, что соответствует партерной схеме производства бетонной смеси, а также изображены силосы для цемента и склад заполнителей, расчет которых произведен в курсовом проекте.
БИБЛИОГРАФИЧЕСКИЙ СПИСОК
1. Баженов Ю.М. Технология бетона: учебник / Ю.М. Баженов. М.: АСВ, 2003. 500 с.
2. Горяйнов К.Э. Проектирование заводов железобетонных изделий: учеб. пособие для инженерно-строительных ВУЗов / К.Э. Горяйнов, В.И. Сорокер, Б.В. Коняев. М.: Высшая школа, 1970. 390 с.
3. ГОСТ 9818-85: Марши и площадки лестниц железобетонные
4. СНиП 3.09.01-85: Строительные нормы и правила. Производство сборных железобетонных конструкций и изделий. Дата введения 1986-01.
5. Баженов Ю.М. Технология бетонных и железобетонных изделий: учебник для ВУЗов / Ю.М. Баженов, А.Г. Комар. М.: Стройиздат, 1984. 672 с.
6. ГОСТ 26633-91. Бетоны тяжелые и мелкозенистые. Технические условия.
7. ГОСТ 8736-93 Песок для строительных работ. Технические условия.
8. ГОСТ 23732 – 79: Вода для бетонов и растворов. Технические условия. Введен 01.01.1980. Переиздание - июль 1993. М.: Изд-во стандартов, 1980. 3с.
9. Официальный сайт компании ОАО ПОЛИПЛАСТ [Электронный ресурс] / Строительная химия: добавки для бетона, синтетические вещества, клеи, 2010. Режим доступа: http://www.polyplast-un.ru/
10. СНиП 82 – 02 – 95: Федеральные элементные нормы расхода цемента при изготовлении бетонных и железобетонных изделий и конструкций. Приняты и введены в действие постановлением Минстроя России от 1 декабря 1995 г. № 18-101. Взамен СНиП 5.01.23-81. М.: Изд-во стандартов, 1996. 17с.
11. ОНТП 07 – 85: Общесоюзные нормы технологического проектирования предприятий сборного железобетона. Взамен ОНТП 07-80. Введены 01.01.1986. М.: Изд-во стандартов, 1986. 33с.
12. ГОСТ 10704 - 91: Трубы стальные электросваные прямошовные, сортамент. Утвержден и введен в действие Постановлением Комитета стандартизации и метрологии СССР от 15.11.91 № 1743. Взамен ГОСТ 10704 – 76.
13. Официальный сайт компании ОАО Кировоградский завод дозирующих автоматов [Электронный ресурс] / Дозирующее оборудование, 2010. Режим доступа: www.dozator.com.
14. Официальный сайт компании ЗАО «Стройтехника» [Электронный ресурс] / Стройтехника. СПб, 2009. Режим доступа: www.stroytehnika.ru
|