Министерство образования и науки Российской Федерации
Омский государственный технический университет
Кафедра «Авиа- и ракетостроение»
Допускается к защите
Зав. кафедрой «АВиРС»
_______ ______________
«____» ________ 2008 г.
ДИПЛОМНЫЙ ПРОЕКТ
на тему: Проектирование двигательной установки и элементов конструкции второй ступени баллистической ракеты с ЖРД
Студента
Пояснительная записка
Шифр проекта: ДП-2068998.45.02.00.00.000.ПЗ
Специальность: 160801 – Ракетостроение
Омск 2008 г
Омский государственный технический университет
Кафедра «Авиа- и ракетостроение»
Утверждаю:
Зав. кафедрой «АВиРС»
__________
« ___» __________ 2007 г.
Задание
на выполнение выпускной квалификационной работы дипломированного специалиста
Студент
Тема проекта: Проектирование двигательной установки и элементов конструкции второй ступени баллистической ракеты с ЖРД
Утверждена распоряжением по Аэрокосмическому факультету № ___ от ____.11. 2007 г.
Срок сдачи студентом законченного дипломного проекта – 12 февраля 2007 г.
Исходные данные к проекту:
Дальность полета - 7000 км; Масса ступени - 12867 кг; Масса головной части - 2000 кг;
Тяга ступени - 208 кН; Время работы - 169 с; Диаметр баллистической ракеты - 1,97 м;
Длина баллистической ракеты - 19,7 м; Топливо - Азотная кислота + Керосин;
Содержание пояснительной записки (перечень подлежащих разработке разделов):
Введение.
1. Проектирование двигательной установки второй ступени (Выбор основных параметров проектируемого двигателя, тепловой расчет камеры сгорания, расчет центробежного насоса окислителя, расчет газовой турбины, расчет охлаждения двигателя, описание проектируемой двигательной установки).
2. Расчет элементов конструкции второй ступени (выбор конструктивно силовой схемы хвостового отсека по условию минимальной массы, расчет фермы полезной нагрузки, компенсация отверстий в баке окислителя).
3. Технологическая часть.
4. Экономическая часть.
5. Раздел безопасность жизнедеятельности.
Перечень графического материала (с указанием обязательных чертежей):
Общий вид второй ступени- 3 л.
ЖРД- 2 л.
Насос окислителя- 1 л.
Турбина- 1 л.
Технологический часть- 1 л.
Схемы, графики- 1-2 л.
Консультанты по дипломному проекту:
1. Технологическая часть – ст. преподаватель
2. Экономическая часть –
3. Раздел охраны труда –
Дата выдачи задания « ___ » ______ 2007 г.
Руководитель ______________.(подпись)
Задание принял к исполнению студент ________________ (подпись)
Задание консультантов по дипломному проектированию:
Технологическая часть дипломного проекта
Технологический процесс сборки фермы полезной нагрузки
Ст. преподаватель кафедры
«Авиа – и ракетостроение» __________________ (подпись, дата)
Экономическая часть дипломного проекта
Расчёт затрат на разработку инженерного проекта.
Ст. преподаватель кафедры «Экономика и организация труда» ____________________ (подпись, дата)
Раздел охраны труда
1. Охрана труда.
2. Защита в чрезвычайных ситуациях.
Ассистент кафедры
«Безопасность жизнедеятельности» ____________________ ( )
Аннотация
В качестве выпускной квалификационной работы был разработан жидкостный ракетный двигатель второй ступени баллистической ракеты, а также рассчитаны отдельные элементы конструкции второй ступени. Проект состоит из пяти разделов: проектирование ЖРД, проектирование элементов конструкции второй ступени, технологического, экономического и раздела охраны труда.
В разделе проектирования ЖРД выполнены следующие задачи: произведен выбор основных параметров проектируемого двигателя, тепловой расчет представленный в виде окончательных результатов, расчет насоса окислителя и газовой турбины, расчет геометрии и прочности охлаждающего тракта, расчет охлаждения двигателя. Расчет элементов конструкции второй ступени.
В технологическом разделе проекта был разработан технологический процесс сборки фермы полезной нагрузки, содержащий сведения о последовательности проводимых операций во время сборки. Спроектировано приспособления для сборки – сварки фермы.
Экономический раздел содержит расчеты затрат на разработку данного проекта: заработная плата проектировщика, амортизация помещения, оборудования, программного обеспечения и т.д.
В разделе охраны труда отражены основные моменты безопасности и экологичности проекта. Рассмотрены факторы окружающей среды, влияющие на проектировщика, а также меры по устранению действия вредных факторов. Произведен расчет искусственного освещения рабочего места. Рассмотрены способы оценки и повышения устойчивости экономических систем.
Общий объём проекта содержит в себе: 117 листов пояснительной записки, оформленной на формате А4 (плюс Приложения), содержащих в себе 38 таблиц и 33 рисунка; 10 листов графического материала, включающих в себя сборочные чертежи проектируемого двигателя, общий вид второй ступени, чертежи насоса и турбины, а также график изменения тепловых потоков и распределения температур по длине КС.
В конечном итоге, после проведённых расчётов были получены следующие технические характеристики ЖРД:
Число камер сгорания1
Время работы169 с
Тяга двигателя в пустоте208 кН
Удельный импульс в пустоте2817 м/с
Окислитель Азотная кислота
Горючее Керосин
Весовое соотношение компонентов топлива
Длина двигателя1,508 м
Давление в камере сгорания6 МПа
Давление на срезе сопла0,02 МПа
Геометрическая степень расширения сопла26,24
Суммарная мощность ТНА
Частота вращения турбины11600 об/мин
Частота вращения насоса горючего11600 об/мин
Частота вращения насоса окислителя11600 об/мин
Abstract
As exhaust skilled work was designed project liquid missile engine second step ballistic rocket, as well as is calculated separate elements to designs second step. The Project consists of five sections: designing LME, designing element to designs second step, technological, economic and labor guard section.
In section of the designing LME are executed following problems: is made choice main parameter designed engine, heat calculation presented in the manner of final result, calculation of the pump окислителя and gas turbine, calculation to geometries and toughness cooling tract, calculation of the cooling the engine.
The technological process of the assembly of the farm of the service load was designed In technological section of the project, containing information about the sequences conducted operation during assembly. The Designed adjustment for assembly of the welding of the farm.
The Economic section contains the calculations of the expenses on development given project: salary of the designer, amortizations of the premises, equipment, software and etc.
In section labor guard reflected main moments to safety and ecological capacities of the project. The Considered factors surrounding ambiences, influencing upon designer, as well as measures on eliminating the action bad factor. Calculation made of the artificial illumination worker place. The Considered ways of the estimation and increasing to stability of the economic systems.
The General volume of the project contains in itself: 116 sheets of the explanatory note, executed on format A4 (the plus of Exhibit), containing in itself 38 tables and 33 drawings; 10 sheets of the graphic material, comprising of itself assembly drawings of the designed engine, the general type second step, drawings of the pump and turbines, as well as graphs heat flow and sharing the temperature on length CC.
Finally, after called on calculation were received following technical features LME:
Number of the cameras of combustion 1
Time of the work 169 sec.
Pulling of the engine in emptiness 208 kN
Specific pulse in emptiness 2817 м/с
Oxygen Nitric acid
Combustible Kerosene
Сcorrelation component fuel 4,75
Length engine 1,508 m
Pressure in camera of combustion 6 MPa
Pressure on cut sniffled 0,02 MPa
Geometric degree of the expansion sniffled 26,24
Total powers
Frequency of the rotation of the turbine 11600 turn/min
Frequency rotations of the pump combustible 11600 turn/min
Frequency rotations of the pump oxygen11600 turn/min
Введение
Жидкостным ракетным двигателем называют реактивный двигатель использующий для своей работы энергию и массу, запасенные на борту аппарата. Основными, характерными особенностями ракетных двигателей являются:
- автономность от окружающей среды, т. е. ЖРД способен работать без использования окружающей среды, но, тем не менее, выходные параметры зависят от окружающего давления (противодавления).
- независимость тяги от скорости движения аппарата, так как тяга создается в нем за счет расхода запасов рабочего тела и энергии, имеющихся на этом аппарате.
- высокая концентрация подводимой энергии на единицу массы рабочего тела и, как следствие, большая энергонапряженность рабочего процесса и малая удельная масса двигателя, приходящаяся на единицу развиваемой тяги.
На сегодняшний день ЖРД, использующие химическую энергию топлива, являются единственными двигателями способными выводить полезные грузы на околоземную орбиту и за ее пределы.
В данном дипломном проекте произведен расчет ЖРД с заданными техническими характеристиками, используемого на второй ступени баллистической ракеты, с применением упрощенных методик. Во время выполнения дипломного проекта необходимо провести различные расчеты для определения основных конструктивных параметров проектируемого ЖРД, обеспечивающие надежную работу на всех рабочих режимах по заданным проектным параметрам. Произвести прочностные расчеты элементов конструкции самой ракеты.
1. Выбор основных параметров проектируемого ЖРД
1.1 Выбор схемы двигателя и системы подачи топлива
По типу агрегата, создающего давление подачи, различают газовытеснительную и турбонасосную подачу топлива.
Отличительной особенностью вытеснительной системы подачи топлива является то, что баки с компонентами топлива находятся под большим давлением, значительно превышающим давление в КС. По этой причине топливные баки приходится делать толстостенными и, как следствие, большой массы.
Применение вытеснительной системы подачи топлива целесообразно при давлениях в КС не больше . Газовытеснительные системы подачи топлива находят в основном применение в двигателях небольшой тяги, рассчитанных на малое время _еботы, с малым удельным импульсом тяги.
При насосной системе подачи топлива нет необходимости поддерживать в баках высокое давление. Небольшое давление воздушной подушки в баках , создаётся для обеспечения бескавитационной работы насосов. Насосная система подачи топлива значительно сложнее вытеснительной, но для двигателей средних и больших тяг она предпочтительнее, т. к. вес всей системы питания ЖРД, включая баки с топливом, будет меньше.
Системы питания ЖРД с насосной подачей топлива бывают:
- с автономной (независимой) турбиной (схема “без дожигания”);
- с предкамерной турбиной (схема “с дожиганием”).
Системы ЖРД с автономной турбиной применяются для маршевых двигателей средней тяги (максимальное значение давления в КС ). Следует учитывать то, что автономные турбины являются высокоперепадными и малорасходными, а также то, что они снижают удельный импульс тяги двигателя на 2-6 % из-за выброса “мятого” газа за борт ракеты.
Системы ЖРД с предкамерной турбиной используются в двигателях большой тяги с высоким давлением в КС . Предкамерные турбины являются высокорасходными и низкоперепадными. Двигатели данной схемы более экономичны, так как в них исключаются потери удельного импульса тяги из-за расходования топлива на питание турбин.
Так как проектируемый двигатель является двигателем средней тяги с давлением в КС , то выбираем насосную систему подачи топлива без дожигания генераторного газа (рис. 1).

Рис.1.1 Схема ЖРД с автономной турбиной: 1- насос горючего, 2- насос окислителя, 3- камера сгорания, 4-газогенератор, 5-турбина, 6-выхлопной патрубок.
1.2 Выбор давления в камере сгорания и на срезе сопла
Величина давления в камере сгорания влияет на удельный импульс, габариты и массу ДУ. Увеличение давления в КС ведет к росту удельного импульса двигателя, уменьшению линейных размеров КС и соответственно, к уменьшению массы двигателя.
Уменьшение площади критического сечения ведет к уменьшению расхода топлива. Но для подачи топлива в КС насосы должны создавать большие давления подачи, что требует повышения мощности турбины и расхода топлива на нее.
Уменьшение размеров КС вызывает трудности с размещением форсунок на форсуночной головке, а также может вызвать проблему охлаждения двигателя, так как растет теплонапряженность.
Выбирая давление в камере сгорания, необходимо учитывать, что выигрыш в увеличении удельного импульса, уменьшения габаритов и массы ДУ может быть потерян из-за увеличения расхода топлива на турбину и увеличения массы ТНА. В зависимости от схемы ЖРД и системы подачи топлива, существуют рекомендации на величину давления в камере сгорания:
- Для вытеснительной системы подачи топлива .
- Для насосной системы подачи топлива без дожигания генераторного газа (с автономной турбиной) .
- Для насосной системы подачи топлива с дожиганием генераторного газа с предкамерной турбиной работающей по схеме «газ-жидкость» .
- Для насосной системы подачи топлива с дожиганием генераторного газа с предкамерной турбиной работающей по схеме «газ-газ» .
Для проектируемого двигателя работающего без дожигания генераторного газа принимаем давление в камере .
Величина давления на срезе сопла, как и величина давления в камере сгорания, влияет на удельный импульс, габариты и массу ДУ.
При малых значениях давления на срезе сопла увеличивается величина удельного импульса. Но при этом размеры закритической части сопла увеличиваются, что приводит к росту массы ЖРД, а также к увеличению габаритов сопловой части двигателя.
Выбираем давление на срезе сопла минимальным при условии, что прирост удельного импульса компенсирует потери появившиеся за счет увеличения массы двигателя, а его габариты не окажут трудностей при компоновке.
В зависимости от назначения ДУ существуют рекомендации по выбору оптимального давления на срезе сопла:
- для первой ступени давление на срезе сопла принимают .
- на второй ступени давление на срезе сопла принимают .
Для проектируемого двигателя выбираем давление на срезе сопла равным .
1.3 Выбор количества камер сгорания двигательной установки
В зависимости от числа камер сгорания ДУ бывают:
- однокамерные – могут иметь один или два турбонасосных агрегата (ТНА);
- многокамерные – имеют один или два общих ТНА на все камеры ДУ;
- блочные – состоят из нескольких автономных независимых двигателей, объединённых общей рамой и общей системой управления.
При одной и той же тяге однокамерный двигатель большей тяги требует большего времени на доводку, чем многокамерная связка двигателей. При этом также повышается вероятность возникновения высокочастотных колебаний. Кроме того, связка двигателей имеет меньшие габаритные размеры по высоте и лучше заполняет объём двигательного отсека. Масса связки сопоставима с массой однокамерного двигателя. Но увеличение числа камер приводит к увеличению количества различных агрегатов, обеспечивающих работу двигателя, что снижает надёжность установки, также существенно усложняется система подачи топлива из-за разветвленной системы трубопроводов.
При выборе схемы двигательной установки мы будем руководствоваться значением тяги проектируемого двигателя. По существующим рекомендациям одна камера двигательной установки должна создавать тягу в интервале от 200 до 300 кН. Проектируемый двигатель имеет тягу равную 208кН, следовательно, выбираем число камер двигательной установки Z=1.
1.4 Управление вектором тяги
Для того, чтобы обеспечить заданную траекторию полёта ракеты, необходимо создать требуемые по величине и направлению управляющие силы и моменты.
Основными способами управления вектором тяги для ЖРД имеющих одну камеру сгорания являются следующие:
1) Основная камера неподвижна, управляющее усилия создаются четырьмя поворотными двигателями (рис.2а) или поворотными соплами, установленными в шарнирных подвесах. В случае использования рулевых двигателей возможно применять для них собственный ТНА, в этом случае возможен раздельный запуск основного и управляющих двигателей. К недостаткам можно отнести худшие массовые характеристики.
2) Основная камера неподвижна, вместо четырех камер используется две камеры (рис. 2б). В этом случае камеры качаются в двух плоскостях (камеры устанавливаются в карданном подвесе). Достоинством данной схемы является то, что сохраняется возможность управления при отказе одного из рулевых двигателей.
3)Основной двигатель расположен в карданном подвесе, следовательно камера качается в двух плоскостях создавая управляющие моменты по рысканью и тангажу. Для управления по крену применяются два качающихся в одной плоскости сопла (рис. 2в).
4) Основной двигатель расположен в карданном подвесе. Для управления по крену применяются управляющие сопла работающие на генераторном газе или двигатели ориентации (рис.2г).

Рис. 1.2 Способы управления вектором тяги
Из представленных вариантов управления вектором тяги на мой взгляд наиболее удобно осуществлять вторым из представленных способов т. к. данная схема обладает большими по сравнению с другими схемами достоинствами.
1.5 Регулирование тяги двигательной установки по величине
Регулирование тяги ЖРД необходимо как для сохранения постоянства тяги при изменении условий работы двигательной установки, так и для изменения тяги с целью обеспечения заданного режима полёта ракеты.
Существуют следующие способы регулирования тяги:
1. Изменение отношения . Однако практически выполнить конструкцию, позволяющую изменять , сложно.
2. Изменение площади критического сечения :
а) размещение в критическом сечении профилированной иглы (рис. 3). При этом обеспечивается возможность большого диапазона изменения тяги. Главный недостаток этого способа – значительное усложнение конструкции, в первую очередь, из-за трудности охлаждения подвижной иглы.
б) впрыском рабочего тела выше по потоку (метод вихревого клапана).

Рис. 1.3. Схема изменения профилированной иглой: 1 – игла, 2 – уплотнение иглы
Данные способы регулирования тяги сложны, и ведут к изменению рабочих параметров КС (рост давления, уменьшение перепада давления на форсунках и т.д.) поэтому практически не применяются.
3. Изменение давления в КС путём изменения расхода компонентов (табл. 1.1). Это наиболее распространённый способ, который даёт возможность регулировать тягу в широком диапазоне изменений в 3 – 5 раз.
Таблица №1.1
Способы регулирования тяги путём изменения давления в камере сгорания
Способы регулирования |
Особенности способа регулирования |
1. Изменение числа оборотов ТНА:
а) изменение расхода рабочего тела на турбину при постоянной температуре
б) изменение температуры рабочего тела путём изменения соотношения расходов компонентов
|
Реагирование быстрое. Изменение тяги до 10…15 %. Ухудшение рабочих характеристик ДУ вследствие работы ТНА на нерасчётных режимах. Способ а) более приемлем при открытой схеме, способ б) – при замкнутой |
2. Дросселирование расхода компонентов в камеру сгорания |
Реагирование быстрое. Возможно и при вытеснительной подаче и при подаче с ТНА. В первом случае лишнее давление в баках, т.е. лишняя масса. Во втором случае – непроизводительная затрата мощности ТНА |
3. Отключение части форсунок |
Аналогично п. 2. Возникает опасность прогара головки |
4. Изменение перепада давления на форсунках |
Аналогично п. 2 |
5. Закольцовка части расхода компонентов |
Реагирование быстрое. Лишняя затрата мощности ТНА для прокачки закольцованного компонента |
6. Изменение давления в баках при вытеснительной подаче |
Очень медленный процесс. Необходимо изменять давление наддува баков. Лишний запас прочности баков, т.е. лишняя масса |
7. Изменение соотношения компонентов, подаваемых в камеру сгорания |
Реагирование быстрое. Ухудшение рабочих характеристик камеры сгорания |
Принимая во внимание достоинства и недостатки указанных способов, а также учитывая схему ЖРД, для регулирования тяги ДУ по величине будем изменять число оборотов ТНА за счёт варьирования расхода рабочего тела на турбину при постоянной температуре
Схема крепления ЖРД на ракете
Для того, чтобы передать силу тяги ДУ на корпус ракеты используют различные конструктивные схемы крепления двигателя (рис. 4).

Рис. 1.4 Некоторые конструктивные схемы крепления двигателя: а, в – поворотные двигатели; б – крепление с помощью конической оболочки; г – крепление кронштейнами; д – крепление в виде фермы.
Передачу силы тяги от ДУ на корпус ракеты будем осуществлять с помощью конической оболочки, которой является нижнее днище бака горючего. Все остальные агрегаты будут крепится к камере сгорания.
1.6 Размещение ТНА на ДУ
При размещении ТНА, помимо компактности, с целью уменьшения габаритов и массы всей установки, необходимо по возможности обеспечить наиболее прямой путь топлива от баков к насосам (для уменьшения потерь давления), удобный подвод рабочего тела к турбине и отвод газов от неё. Кроме того, следует учитывать возникновение при работе ТНА крутящего момента, сообщаемого ракете, что может потребовать дополнительной компенсации.
Так как проектируемый двигатель имеет одну камеру сгорания, то в хвостовой части УБР остается достаточно пространства для размещения ТНА сбоку от камеры сгорания на самой камере.
На рис. 6 приведены возможные схемы совместной компоновки ТНА и камеры двигателя.

Рис. 1.5. Схемы размещения ТНА относительно камеры двигателя
1.7 Система зажигания
Воспламенение компонентов, поступающих в КС – ответственный момент пуска двигателя. Система зажигания должна гарантированно обеспечить воспламенение топлива во время выхода на рабочий режим.
В зависимости от используемого топлива, типа двигателя и условий эксплуатации зажигание бывает (для несамовоспламеняющихся топлив):
- химическое;
- пиротехническое;
- электроискровое.
Химическое зажигание происходит за счёт самовоспламенения пускового горючего с окислителем, используемым в двигателе, после чего в КС подаются основные компоненты топлива. Схемы исполнения этого метода достаточно надёжны и отработаны, _ей_я_твют осуществлять многократный запуск в полёте.
Пиротехническое зажигание осуществляется с помощью пирозапального устройства (ПЗУ). Мощный факел из продуктов пиротехнического заряда воспламеняет смесь основных компонентов, поступающих через форсуночную головку. Пиротехническое зажигание надёжно, отличается простотой. Электрическая мощность, необходимая для срабатывания пиропатронов, невелика. Но такая система зажигания требует повышенной предосторожности во избежании случайного срабатывания при регламентных проверках заправленной ракеты. Главный недостаток – однократность запуска.
Электроискровое зажигание производится с помощью пусковой электрической свечи. Схема используется преимущественно при запуске кислородно – водородных двигателей. Данный способ допускает многократное включение, может быть использован после длительного хранения двигателя, достаточно прост и безопасен.
С учётом приведённых характеристик различных способов зажигания, остановим свой выбор на химическом зажигании с использованием пускового топлива.
1.8 Характеристика топлива
В современном ракетостроении наиболее широкое применение получили двухкомпонентные жидкие ракетные топлива, состоящие из двух раздельно хранящихся компонентов: окислителя и горючего. Такие топлива наиболее опробованы на практике, а, следовательно, относительно безопасны в эксплуатации; дают возможность широкого выбора компонентов, что позволяет получать высокие значения удельного импульса тяги.
Требования к компонентам жидких ракетных топлив в значительной мере определяются назначением летательного аппарата (ЛА). В зависимости от его назначения различны требования к характеристикам топлива.
Представленное в дипломном проекте топливо “АК + керосин” является:
- азотнокислым;
- высококипящим;
- токсичным;
- стабильным;
- коррозионноактивным.
Большое преимущество данного топлива в том, что оно не дефицитно для отечественных ресурсов, обеспечивает безопасность при эксплуатации, имеет низкую стоимость и возможность утилизации в народном хозяйстве.
Энергетическая характеристика топлива представлена в табл. 1.2.
Физико-химические характеристики окислителя и горючего приведены в табл. 1.3.
Таблица №1.2
Энергетическая характеристика топлива
Топливо |
 |
 |
 |
 |
 |
 |
 |
АК+ Керосин |
2730 |
315 |
1,13 |
3087 |
1513 |
800 |
5,37 |
Таблица №1.3
Физико-химические характеристики окислителя и горючего
Азотная кислота |
Керосин |
Формула |
 |
 |
Температура кипения ,  |
357,25 |
420,15 |
Температура плавления ,  |
231,56 |
200,15 – 220,15 |
Критическая температура , |
531,15 |
713,15 |
Давление паров , Па |
 |
 |
Критическое давление , Па |
 |
 |
Теплопроводность , |
0,25 |
0,12 |
Теплоемкость , |
1763 |
2380 |
Вязкость , |
 |
 |
Поверхностное натяжение ,Н/м |
 |
 |
Коррозионная активность |
Очень активен |
Не активен |
Токсичность |
Токсичен |
Слабо токсичен |
Чувствительность к удару |
Не чувствителен |
Не чувствителен |
Выбор прототипа проектируемого двигателя
Выбор прототипа проектируемого двигателя будем проводить, руководствуясь следующими требованиями:
- минимальная разность тяг прототипа и проектируемого двигателя;
- по назначению двигателя.
Таблица №1.4
Характеристика двигателя – прототипа
Марка двигателя |
LR-105-NA |
Страна производитель |
США |
Назначение ДУ |
РН «Атлас», вторая ступень |
Начало (окончание) разработок |
1954 – 1958 |
Окислитель |
 |
Горючее |
Керосин |
Весовое соотношение компонентов топлива |
2,27 |
Тяга двигателя на земле |
267 кН |
Тяга двигателя в пустоте |
375 кН |
Удельный импульс на земле |
2153 м/с |
Удельный импульс в пустоте |
3025 м/с |
Масса сухого двигателя |
465 кг |
Масса залитого двигателя |
- |
Длина двигателя |
2,5 м |
Диаметр двигателя |
1,20 м |
Давление в камере сгорания |
5,1 Мпа |
Давление на срезе сопла |
- |
Геометрическая степень расширения сопла |
25 |
Время работы |
290 с |
Число камер сгорания |
1 |
Суммарная мощность ТНА |
- |
Частота вращения ТНА |
10500 об/мин |
Частота вращения насоса горючего |
10500 об/мин |
Частота вращения насоса окислителя |
10500 об/мин |
2. Тепловой расчет камеры сгорания
Цель расчета: Расчет проводят с целью определения размеров сопла, удельного импульса тяги и расхода топлива.
Исходные данные для расчета:
Топливо АК + Керосин
Тяга двигателя
Удельный импульс в пустоте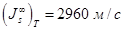
Давление в КС
Давление на срезе сопла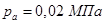
Коэффициент избытка окислителя
- в ядре
- в пристеночном слое
- среднее по КС
Относительный расход топлива
- в ядре
- в пристеночном слое
Весовое соотношение компонентов топлива
- в ядре
- в пристеночном слое
- среднее по КС
Угол раствора на срезе сопла
Тепловой расчет двигателя проводился с использованием таблиц справочника Глушко для данной топливной пары.
Результаты расчета:
Действительное значение удельного импульса тяги в пустоте:
.
Массовый секундный расход топлива:
;
массовый секундный расход горючего:
.
массовый секундный расход окислителя:
.

Рис. 1.6 Расчетная схема определения продольных размеров двигателя.
Диаметр цилиндрической части камеры сгорания:
.
Диаметр критического сечения:
.
Диаметр среза сопла:
.
Длина форсуночной головки:
.
Длина цилиндрической части камеры сгорания:
.
Длина входа в сопло:
.
Длина раструба сопла:
.
Длина сопла:
.
Длина двигателя:
.

Рис.1.7 Профиль сверхзвуковой части сопла построенной графическим методом
Радиус горловины сопла:
.
Угол раскрытия сопла:
.
3. Расчет центробежного насоса окислителя
Цель расчета: Целью данного расчета является определение основных параметров центробежного насоса окислителя второй ступени УБР, к которым относятся: частота вращения вала насоса, геометрические характеристики основных элементов насоса (подвода, центробежного колеса, отвода), а также определение формы колеса в меридиональном сечении, профиля лопаток, размеров улитки, мощности и КПД насоса.
Исходные данные:
Рабочее тело насоса Азотная кислота
Массовый секундный расход окислителя
Максимальная температура окислителя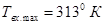
Плотность окислителя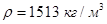
Давление насыщенных паров окислителя при  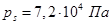
Кинематическая вязкость 
Объемный расход компонента через насос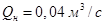
Определение основных расчетных характеристик насоса
Минимальное давление на входе в насос :
,
где - давление наддува в топливном баке;
- давление столба жидкости;
- гидравлические сопротивления магистрали, подводящей к насосу жидкость;
- скорость потока жидкости на входе. Принимаем ;
- плотность окислителя;
- высота столба жидкости от зеркала жидкости в баке до входа в насос;
- коэффициент осевой перегрузки.
Полное давление подачи компонента :
;
где - давление в камере сгорания;
- перепад давления на форсунках;
- сопротивление топливной магистрали от выхода из насоса до ФГ;
Коэффициент быстроходности:
;
где
– напор насоса.
- частота вращения насоса.
где - число оборотов вала насоса.
Коэффициент лежит в диапазоне от 40 до 80, следовательно, колесо является тихоходным.
Объемный КПД определяем по формуле:
.
Приведенный диаметр (эквивалентный диаметр входа):
,
где - безразмерный коэффициент. Принимаем .
Расчетный гидравлический КПД:
.
Механический КПД насоса принимаем: .
Полный КПД насоса:
.
Мощность, затрачиваемая на привод насоса:
.
Крутящий момент на валу насоса:
.
Диаметр вала насоса:
,
где - допускаемое напряжение материала вала насоса на кручение.
материал вала – легированная сталь с .
Диаметр втулки выбирается в диапазоне . Принимаем:
.
Действительный, объемный расход жидкости через колесо:
.
3.1 Размеры и параметры входа на колесо
Диаметр входа на колесо:
.
Скорость движения жидкости на входе в насос:
.
Выбираем колесо с наклонной формой лопатки: 
Определяем ширину входа на колесо
.
где = ;
- скорость потока жидкости при входе на лопатку рабочего колеса;
- относительное уменьшение ширины проточной части колеса.
Окружная скорость колеса на расчетном диаметре:
.
Угол входа жидкости на лопатки без учета стеснения потока лопатками:
.
Величина дополнительного угла атаки:

Угол наклона лопатки на входе в рабочее колесо:
.
Принимаем .
Задаемся толщиной лопатки на входе: .
Предварительно выбираем число лопаток: .
Коэффициент стеснения потока на входе в колесо:
;
Действительная скорость потока жидкости при входе на лопатку:
.
Действительный угол атаки при условии :
.
где - меридиональная скорость, с которой жидкость поступает на лопатки.
Действительная разность (действительный угол атаки):
.
Величина находится в рекомендованных пределах .
3.2 Расчет основных размеров выхода из колеса
Окружная скорость на выходе из колеса:
;
где - коэффициент, определяемый конструкцией насоса. Принимаем =0,5.
Условие прочности колеса выполняется.
Наружный диаметр колеса:
.
Задаемся углом выхода потока колеса (угол лопатки) из диапазона .
Принимаем .
Проверяем выбранное число лопаток:
;
Принятое число лопаток считаем допустимым.
Коэффициент стеснения потока на выходе из колеса:
,
где - толщина лопатки на выходе. Принимаем = =0,003.
Необходимая ширина колеса на выходе при :
;
принимаем (ширина проточной части - условие технологического минимума выполняется).
3.3 Уточнение параметров выхода из колеса
Действительная меридиональная скорость на выходе колеса:
.
Теоретический напор насоса при конечном числе лопаток:
.
Теоретический напор бесконечном числе лопаток:
,
где р – поправочный коэффициент, учитывающий снижение напора за счет конечного числа лопаток:
.
- коэффициент, учитывающий качество обработки колеса и величину выходного угла лопатки
.
Окружная скорость на выходе из колеса (уточненная формула):
.
Уточненный диаметр на выходе колеса:
.
Сравниваем диаметры колеса и :
.
полученный результат считаем удовлетворительным. Принимаем .
Уточняем ширину колеса:
.
Ширина колеса не изменилась.
3.4 Расчет центробежного насоса на кавитацию
Условие работы центробежного насоса без кавитационного срыва:
;
где - давление срыва на входе в насос;
- коэффициент, определяющий кавитационные качества насоса:
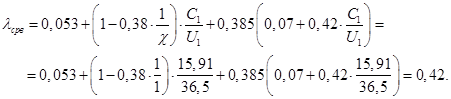
где
.
Проверяем выполнение условия:
;
- условие работы без кавитационного срыва выполняется.
3.5 Профилирование колеса в меридиональном сечении
Для определения формы меридионального сечения, строим линейный график изменения меридиональной скорости и коэффициента стеснения в зависимости от радиуса колеса насоса и находим их значения для каждой расчетного сечения. По полученным значениям , , находим ширину колеса в каждом расчетном сечении по формуле
.
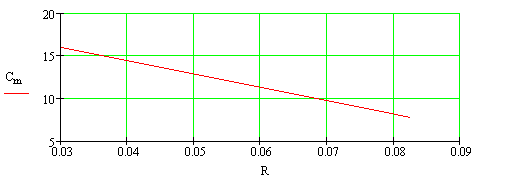
Рис.1.8 График изменения скорости в меридиональном сечении.
Таблица №1.5
Характеристики расчетных сечений
, (м) |
0,3 |
0,0405 |
0,051 |
0,0615 |
0,072 |
0,0825 |
, (м/с) |
15,911 |
14,287 |
12,663 |
11,039 |
9,416 |
7,792 |
 |
0,726 |
0,768 |
0,809 |
0,851 |
0,892 |
0,933 |
, (м) |
0,019 |
0,015 |
0,013 |
0,012 |
0,011 |
0,01 |
Далее строим плавную кривую – среднюю линию меридионального сечения. На расстоянии от оси колеса насоса строим окружности радиусом с центром на средней линии меридионального сечения. К построенным окружностям строим две касательные, которые образуют контур меридионального сечения колеса насоса окислителя.
3.6 Профилирование лопаток колеса
Для построения профиля лопатки строим линейный график изменения угла наклона лопатки в зависимости от изменения радиуса колеса насоса. Находим величину угла наклона лопатки для каждого расчетного сечения.
Таблица №1.6
Угол наклона лопатки в расчетном сечении
, (м) |
0,3 |
0,0405 |
0,051 |
0,0615 |
0,072 |
0,0825 |
, (град) |
24 |
26,2 |
28,4 |
30,6 |
32,8 |
35 |
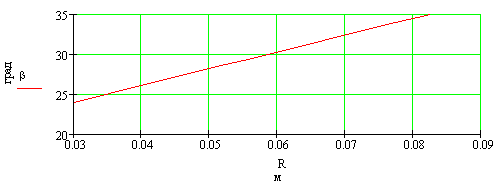
Рис.1.9 График изменения угла наклона лопатки.
На чертеже, в плане, на окружности радиусом , выбираем начальную точку построения ; из нее проводим луч, составляющий с касательной к данной окружности угол , и продолжаем его до пересечения со вспомогательной окружностью радиусом (точка ). Из точки проводим другой луч под углом до пересечения с окружностью (точка ).
3.7 Подвод насоса
Так как ТНА размещается сбоку от камеры сгорания и ось вала параллельна оси двигателя, будем использовать осевой подвод. Данный подвод обладает целым рядом преимуществ: наиболее прост в изготовлении, обладает наименьшим гидравлическим сопротивлением.
3.8 Профилирование улитки насоса
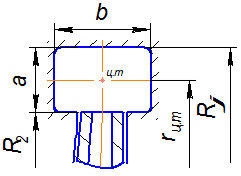
Рис. 1.10 Расчетная схема спирального отвода
Принимаем вид сечения улитки в виде прямоугольника с фиксированной шириной и, изменяемой в зависимости от угла, высотой . Построим ряд подобных по гидравлической форме сечений, для каждого сечения найдем площадь , размеры стороны , радиус центра тяжести сечения , и радиус (наиболее удаленной точки сечения от оси вращения колеса).
Принимаем ширину спирального отвода 
Таблица №1.7
Характеристики спирального отвода по сечениям
№ сечения |
, град) |
, (м) |
,( ) |
, (м) |
, (м) |
, ( ) |
,( ) |
1 |
0 |
0,015 |
0,00038 |
0,0975 |
0,09 |
0,0 |
81,29 |
2 |
45 |
0,020 |
0,0005 |
0,1025 |
0,0925 |
0,005 |
79,10 |
3 |
90 |
0,025 |
0,00063 |
0,1075 |
0,095 |
0,01 |
77,02 |
4 |
135 |
0,03 |
0,00075 |
0,1125 |
0,0975 |
0,015 |
75,05 |
5 |
180 |
0,035 |
0,00088 |
0,1175 |
0,1 |
0,02 |
73,17 |
6 |
225 |
0,040 |
0,001 |
0,1225 |
0,1025 |
0,025 |
71,38 |
7 |
270 |
0,045 |
0,00113 |
0,1275 |
0,105 |
0,03 |
69,68 |
8 |
315 |
0,050 |
0,00125 |
0,1325 |
0,1075 |
0,035 |
68,06 |
9 |
360 |
0,055 |
0,00138 |
0,1375 |
0,11 |
0,04 |
66,52 |
По полученным значениям строим графики функций , .
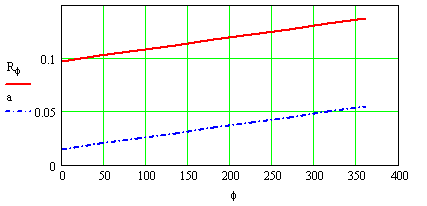
Рис.1.11 График зависимости , от угла .
С помощью данных графиков можно получить необходимые размеры улитки в любом ее сечении и выполнить построение улитки.
В спроектированной улитке получились весьма большие скорости, что может вызвать ухудшение гидравлического КПД за счет высоких гидравлических потерь. Для уменьшения этих потерь целесообразно применять лопаточный диффузор.
3.9 Профилирование выходного патрубка улитки
Скорость движения окислителя в трубопроводах ЖРД:
, принимаем .
Площадь выходного сечения патрубка выполненного в виде круга:
.
Диаметр выходного сечения патрубка:
;
принимаем .
Находим длину конического выходного патрубка. Принимаем угол , , получаем:
.
4. Расчёт газовой турбины
Цель расчета: Определение потребного расхода газа через турбину, параметров газового потока в осевом зазоре между сопловым аппаратом и колесом турбины, спрофилировать сверхзвуковые лопатки рабочего колеса турбины. Определить размер соплового аппарата состоящего из конических сопел, работу, мощность и КПД турбины. Произвести расчет на прочность лопаток рабочего колеса турбины.
Исходные данные:
Мощность насоса окислителя
Мощность насоса горючего
Угловая скорость вращения вала турбины
Наружный диаметр колеса насоса горючего
Топливо газогенератора АК + Керосин
Давление в камере сгорания ЖРД
Стехиометрическое соотношение КТ
Коэффициент избытка окислителя
Материал лопаток турбины ЭИ – 598.
Плотность материала лопаток .
4.1 Параметры рабочего тела турбины
В качестве рабочего тела турбины выбираем генераторный газ восстановительного типа. Принимаем температуру генераторного газа . Энергетические характеристики генераторного газа при данной температуре:
- газовая постоянная;
- показатель адиабаты.
Определение основных расчетных характеристик
Давление на входе в турбину:
.
где
,
, .
.
Двигатель второй ступени УБР, как правило, осуществляет работу при низком давлении окружающей среды или в безвоздушном пространстве. Следовательно, давление окружающей среды достаточно мало. Принимаем давление за бортом УБР равным .
Исходя из этого, находим:
;
где
, .
Перепад давлений на турбине:
.
Перепад давлений для существующих турбин лежит в пределе от 20 до 50. Полученный перепад давлений на турбине лежит в данном диапазоне.
Средний диаметр колеса турбины:
.
Окружная скорость:
.
Проектируемая турбина может быть одноступенчатой так как .
Адиабатная работа турбины:
.
где
.
Адиабатная скорость газового потока:
.
Отношение скоростей:
.
Задаёмся минимальным осевым и радиальным зазорами между колесом и корпусом турбины из условия . Принимаем .
Определяем относительный минимальный зазор:
.
Определяем коэффициент быстроходности турбины:
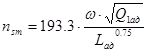
где ряд значений адиабатного расхода газа на входе в рабочее колесо турбины.
,
где - массовый секундный расход турбинного газа (варьируемый параметр);


.
.
где
.
- критическая скорость звука на входе в турбину:
.
Внутренняя (располагаемая) мощность турбины:
;
где - КПД турбины. Принимаем .
Задаёмся начальным значением и, с шагом , для каждого из значений определяем адиабатный расход газа на входе в рабочее колесо, коэффициент быстроходности, внутреннюю (располагаемую) мощность турбины результат занесем в таблицу 1.8.
Таблица №1.8
Результаты расчета
, (кг/с) |
1,0 |
1,05 |
1,1 |
1,15 |
1,2 |
1,25 |
, (м/с) |
6,42 |
6,74 |
7,07 |
7,39 |
7,71 |
8,03 |
 |
11,93 |
12,22 |
12,51 |
12,79 |
13,07 |
13,34 |
, (Вт) |
5,51 |
5,79 |
6,06 |
6,34 |
6,61 |
6,89 |
Потребная мощность турбины:
.
По таблице 1.8 выбираем значение , при котором наиболее совпадает с потребной мощностью . Принимаем .
Погрешность выбранной мощности:
.
Удельная работа турбины:
.
Коэффициент работы турбины:
.
Параметры газового потока в осевом зазоре между сопловым аппаратом и колесом турбины.
Принимаем угол установки сопел . Скоростной коэффициент соплового аппарата .
Скорость на выходе из соплового аппарата:
.
Приведенная скорость:
.
Коэффициент полного давления:
.
Полное давление в осевом зазоре:
.
Статистическая температура в зазоре:
.
Плотность газа в зазоре:
.
Скорость звука в осевом зазоре:
.
Число Маха:
- турбина сверхзвуковая.
Угол потока на выходе из соплового аппарата:
,
где , при .
Угол потока на входе в колесо в относительном движении:
.
Относительная скорость на входе в колесо:
.
Температура торможения в относительном движении:
.
Критическая скорость:
.
Приведенная скорость на входе в колесо:
.
Число Маха в относительном движении:

Полное давление в относительном движении:
.
4.2 Профилирование сверхзвуковых лопаток рабочего колеса турбины
Ширина лопаточной решетки:
,
где - относительная ширина решетки.
Относительный шаг решетки:
.
Высота лопатки колеса турбины на входе лопаточной решетки:
,
где - относительная высота лопатки (выбирается из условия ).
Высота лопатки колеса турбины на выходе лопаточной решетки:
.
Таким образом
- лопатка выбрана с постоянным профилем.
Проверка:
Высота лопатки по отношению к ширине колеса турбины:
- необходимое условие выполняется.
Высота лопатки по отношению к диаметру колеса турбины:
- необходимое условие выполняется.
Выбираем углы входа и выхода лопатки рабочего колеса:
, .
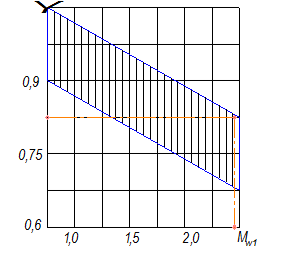
Рис.1.12 Зависимость коэффициента от .
По графику (рис.11) выбираем скоростной коэффициент потерь на лопатках колеса в зависимости от числа . При , .
Относительная скорость потока на выходе:
.
Действительная скорость газа на выходе из колеса:
.
Приведенная скорость:
.
Действительная приведенная скорость:
.
Температура торможения в относительном движении на выходе для активной осевой турбины:
.
Полная температура торможения потока на выходе колеса:
.
Угол потока на выходе из колеса в относительном движении:
.
Угол потока на выходе из рабочего колеса :
.
Абсолютная скорость потока:
.
Оптимальный шаг лопаток рабочего колеса:
.
Число лопаток:
.
Принимаем , тогда шаг лопаток .
Профилирование лопаток рабочего колеса:
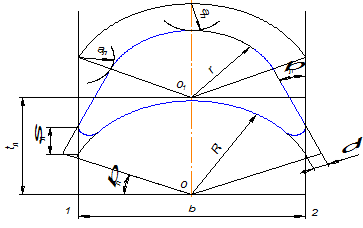
Рис.1.13 Профилирование лопатки.
Радиус вогнутой стороны лопатки:
.
Принимаем толщину лопатки:
, .
Ширина канала:
.
где
.
Определение размеров соплового аппарата состоящего из конических сопел.
Высота соплового аппарата:
.
где , .
Суммарное минимальное сечение сопел соплового аппарата:
.
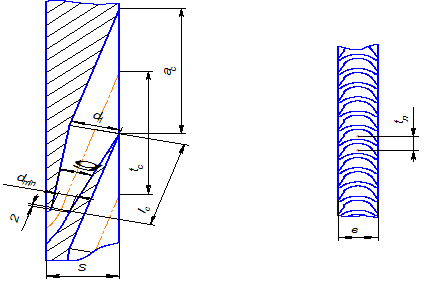
Рис.1.14 Развертка соплового аппарата.
Степень уширения сопла:
;
где , . Принимаем .
Площадь сопел в конце конической части:
.
Площадь выхода из сопел:
.
Степень парциальности турбины:
.
Количество сопел:
.
Принимаем: .
Большая ось сечения эллипса сечения сопел на выходе:
.
Шаг сопел:
.
Минимальный диаметр сопла:
.
Диаметр сопла в конце конической части:
.
Длина сопла:
.
где .
Определение работы, мощности и КПД турбины
Определяем окружной КПД:
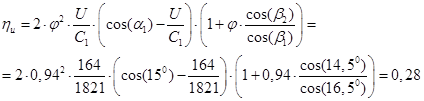
Окружная работа:
.
Выбираем коэффициент расхода утечек через зазор. По рекомендации , принимаем .
Расход утечек через турбину:
.
Расход газа через решетку колеса:
.
Расходный КПД:
.
Окружная мощность:
.
Мощность дискового трения:
.
где
- коэффициент дискового трения.
Значением числа Рейнольдса задаемся на основании рекомендаций.
Мощность потерь связанных с парциальным впуском газа на турбинное колесо:

Эффективная мощность турбины:
.
Эффективная работа турбинного газа:
.
Полученное значение лежит в диапазоне , что отвечает данным статистики.
Коэффициент работы:
.
Полученное значение удовлетворяет данным статистики.
Эффективный КПД турбины:
,
где
.
5. Расчет охлаждения КС
Организация охлаждения камер является одной из важнейших задач проектирования ЖРД и по сравнению с другими типами тепловых машин значительно усложняется особенностями процесса теплообмена в ЖРД.
Первая особенность состоит в том, что процесс в КС протекает при высоких температурах (3000…4000К) и давлениях (до 25 Мпа и более). Поскольку продукты сгорания движутся по КС с очень большой скоростью, резко возрастают коэффициент конвективной теплоотдачи от горячих продуктов сгорания в стенки КС.
Второй особенностью теплообмена в ЖРД является высокий уровень лучистого теплового потока достигающего 20 – 40% общего теплового потока направленного в стенку КС.
Третья особенность теплообмена в ЖРД состоит в том, что вследствие мощных суммарных конвективных и лучистых тепловых потоков в стенку камеры температура может достигать недопустимо высоких величин. Поэтому для ЖРД следует применять жаропрочные материалы, обладающие возможно большей теплопроводностью.
Четвертая особенность теплообмена вытекает из условия применения ЖРД как ДУ ЛА (ракеты, спутника, самолета). Поэтому использовать для охлаждения КС специальную жидкость в большинстве случаев нерационально. Обычно ЖРД охлаждают каким-либо из компонентов топлива, пропуская его до подачи в КС ЖРД через полость охлаждения. Такой принцип охлаждения усложняет конструкцию камеры и выдвигает дополнительные требования к применяемым компонентам топлива.
Температуру стенок КС можно поддерживать в допустимых пределах с помощью одного из следующих способов:
- наружного (или регенеративного) охлаждения.
- внутреннего охлаждения.
- смешанного охлаждения.
- радиационного охлаждения.
- абляционного охлаждения.
- защита внутренних стенок термостойкими покрытиями.
- емкостного охлаждения.
- транспирационного охлаждения.
На процесс теплообмена в КС также оказывает влияние форма и размеры охлаждающего тракта. В оребренном охлаждающем тракте теплообмен увеличивается за счет увеличения поверхности охлаждения и возможности выполнения более тонкой огневой стенки. Помимо улучшения теплообмена применение оребрения увеличивает прочность и жесткость камеры.
Для расчета эффективности системы охлаждения ЖРД необходимо определить конструкцию и основные размеры охлаждающего тракта, выбрать способ охлаждения.
Для проектируемого двигателя, в качестве основного, принимаем наружное охлаждение с помощью одного из компонентов топлива. Данный способ организации охлаждения получил название проточного.
Охлаждающий тракт с продольными ребрами, выполненными фрезерованием. Данный выбор обусловлен тем, что КС охлаждается небольшим количеством охладителя т. е. предъявляются высокие требования к точности изготовления охлаждающего тракта.
Достоинствами КС с фрезерованными пазами являются:
-высокая (по сравнению с КС имеющих гофрированные проставки) прочность.
-качество тракта охлаждения. Пазы любой конфигурации получают механической обработкой, т. е. наиболее точным способом (особенно на станках с программным управлением).
К недостаткам конструкции данного типа относятся большая масса и значительная трудоемкость изготовления.
5.1 Расчет максимального шага оребрения КС
Максимальный шаг ребер рассчитывается для закритической части сопла в режиме гидроопрессовки.
Исходные данные:
Толщина внутренней стенки: .
Материал огневой стенки:12Х18Н10Т
Предел прочности материала огневой стенки (при ): .
Давление в КС: .
Материал припоя:ПЖК-1000
Предел прочности материала припоя: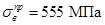
Рабочее давление в межрубашечном зазоре:

где - гидравлические потери в охлаждающем тракте.
- перепад давления на форсунках.
Давление гидроопрессовки:
.
По рекомендациям давление гидроопрессовки . Расчетное давление гидроопрессовки получилось выше рекомендуемого. Принимаем давление гидроопрессовки равным наибольшему рекомендуемому значению .
Максимальный шаг ребер из условия прочности внутренней стенки:
;
где - толщина ребра, - коэффициент запаса прочности.
Максимальный шаг ребер из условия прочности спая:
.
Из двух полученных расчетных значений выбираем наименьшее, которое и будет определять местную прочность КС. По данным статистики шаг ребер лежит в диапазоне от 2 до 6,5 мм. Принимаем максимальный шаг ребер, с учетом рекомендаций, равным .
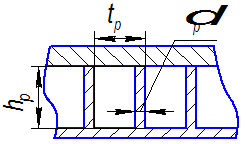
Рис. 1.15 Геометрические параметры охлаждающего тракта
Расчет местной прочности внутренней оболочки КС
Изгибающий момент в зоне защемления внутренней стенки КС:
.
где
.
Момент сопротивления защемленной балки единичной ширины, толщиною :
.
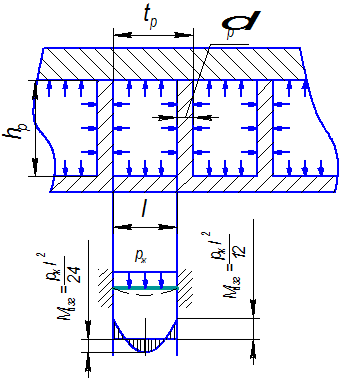
Рис.1.16 Схема нагружения огневой стенки при гидроопрессовке
Напряжение местного изгиба в точке защемления:
.
Напряжение среза во внутренней стенке в месте защемления:
.
Эквивалентное напряжение для внутренней стенки:
.
Коэффициент запаса прочности:
.
5.2 Расчет числа секций оребрения в закритической части сопла
Под секцией будем понимать участок, в пределах которого число ребер охлаждающего тракта остается постоянным. Изменение числа ребер в секциях связано с увеличением шага ребер по диаметру , при движении от критического сечения к срезу сопла вдоль образующей, что ведет к уменьшению прочности огневой стенки. Увеличение количества ребер происходит в момент, когда шаг ребер достигает критического значения определенного выше и равного .
Число каналов критического сечения:
;
где - диаметр критического сечения.
- размер паза ребра охлаждающего тракта. По рекомендациям в критическом сечении .
Принимаем число каналов в критическом сечении равным .
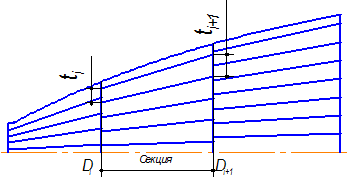
Рис.1.17 Изменение числа ребер по длине КС
Шаг ребер в крайнем сечении i-ой секции докритической части сопла:
.
где - некоторый запас по шагу.
Диаметр крайнего сечения первой секции:
.
Количество ребер второй секции:
.
Диаметр крайнего сечения второй секции:
.
Количество ребер третьей секции:
.
Диаметр крайнего сечения третьей секции:
.
Диаметр крайнего сечения третьей секции больше диаметра среза сопла. Следовательно, необходимость расчета последующей секции отпадает.
Шаг ребер на срезе сопла:
.
5.3 Расчет числа проставок для докритической части сопла
Для докритической части сопла расчет ведется по тем же зависимостям, что и для закритической части.
Уменьшим шаг крайнего сечения секции до , что не повлияет на кол-во секций (как видно из предыдущего расчета) но увеличит скорость движения охладителя и, как следствие, возрастет теплообмен между огневой стенкой и охладителем.
Шаг ребер в крайнем сечении i-ой секции в докритической части сопла:
.
где - запас по шагу.
Диаметр крайнего сечения первой секции:
.
Количество ребер второй секции:
.
Диаметр крайнего сечения второй секции:
.
5.4 Расчет охлаждения КС
Исходные данные:
Материал огневой стенки:12Х18Н10Т.
Толщина огневой стенки: .
Теплопроводность материала огневой стенки: .
Охладитель:Керосин.
Плотность охладителя: .
Расход охладителя в охлаждающем тракте: .
Температура охладителя на входе в охлаждающий тракт: .
Теплоемкость охладителя: .
Теплопроводность охладителя: .
Динамическая вязкость охладителя: .
Высота межрубашечного тракта .
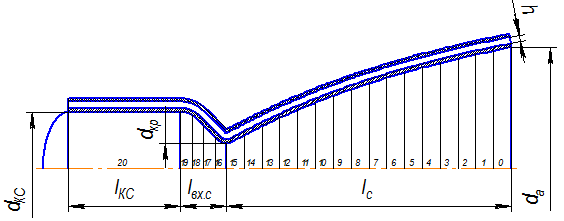
Рис.1.18 Расчетная схема к расчету охлаждения
Камеру двигателя разбиваем на участки. Шаг разбиения камеры на участки, в пределах каждой из частей сопла (дозвуковой и сверхзвуковой) остается постоянным. Дозвуковую часть сопла разбиваем на 4 участка, сверхзвуковую часть сопла на 16 участков. Камеру сгорания на участки не разбиваем. Всего участков j=21. Сечений i=22.
Для расчета необходимо определить диаметр КС , температуру газовой стенки , значение теплоемкости , коэффициент динамической вязкости , а также мольные доли и парциальное давление газообразных индивидуальных веществ (H2O; СО2) продуктов сгорания (ПС) для каждого из сечений. Параметры ПС, а также температуру газовой стенки определяем для трех сечений (вход в сопло, критическое сечение, срез сопла). В дальнейшем будем считать, что параметры ПС по длине КС изменяются по линейному закону.
Термодинамические параметры ПС определяем по справочнику Глушко. Температурой газовой стенки задаемся на основании рекомендаций.
Диапазон температур газовой стенки для жаропрочных сталей:
- в камере сгорания . Принимаем .
- в критическом сечении . Принимаем .
- на срезе сопла . Принимаем .
Парциальное давление газов рассчитывается по следующим зависимостям:
- в камере сгорания .
- в критическом сечении .
- на срезе сопла .
Таблица №1.9
Термодинамические параметры ПС
  |
  |
 |
 |
атм. |
атм. |
КС |
1,1097 |
9,20 |
0,4299 |
0,2024 |
25,790 |
12,14 |
Кр. сечение |
1,0335 |
8,80 |
0,4409 |
0,2153 |
13,227 |
6,459 |
Срез сопла |
0,4279 |
5,20 |
0,4580 |
0,2684 |
0,0916 |
0,0537 |
Значение термодинамических параметров ПС и температуры газовой стенки по расчетным сечениям занесем в таблицу №1.10
Таблица №1.10
№ сеч. |
м |
К |
  |
  |
 |
 |
атм. |
атм. |
0 |
0,35 |
800 |
1,11 |
9,20 |
0,4299 |
0,2024 |
25,79 |
12,14 |
1 |
0,35 |
800 |
1,11 |
9,20 |
0,4299 |
0,2024 |
25,79 |
12,14 |
2 |
0,3318 |
900 |
1,091 |
9,10 |
0,4326 |
0,2052 |
22,65 |
10,72 |
3 |
0,269 |
1000 |
1,072 |
9,00 |
0,4354 |
0,2079 |
19,51 |
9,302 |
4 |
0,1975 |
1100 |
1,053 |
8,90 |
0,4381 |
0,2107 |
16,37 |
7,88 |
5 |
0,155 |
1200 |
1,033 |
8,80 |
0,4409 |
0,2134 |
13,23 |
6,459 |
6 |
0,2054 |
1163 |
0,9956 |
8,58 |
0,442 |
0,2164 |
12,41 |
6,059 |
7 |
0,2618 |
1125 |
0,9578 |
8,35 |
0,443 |
0,2174 |
11,59 |
5,658 |
8 |
0,3139 |
1088 |
0,9199 |
8,13 |
0,4441 |
0,2185 |
10,76 |
5,258 |
9 |
0,3631 |
1050 |
0,8821 |
7,90 |
0,4452 |
0,2196 |
9,943 |
4,858 |
10 |
0,4088 |
1013 |
0,8442 |
7,68 |
0,4462 |
0,2206 |
9,122 |
4,457 |
11 |
0,4516 |
975 |
0,8064 |
7,45 |
0,4473 |
0,2217 |
8,301 |
4,057 |
12 |
0,4915 |
937,5 |
0,7685 |
7,23 |
0,4484 |
0,2228 |
7,48 |
3,657 |
13 |
0,5289 |
900 |
0,7307 |
7,00 |
0,4495 |
0,2238 |
6,659 |
3,256 |
14 |
0,5639 |
862,5 |
0,6928 |
6,78 |
0,4505 |
0,2249 |
5,838 |
2,856 |
15 |
0,5966 |
825 |
0,655 |
6,55 |
0,4516 |
0,226 |
5,017 |
2,456 |
16 |
0,6273 |
787,5 |
0,6171 |
6,33 |
0,4527 |
0,2271 |
4,196 |
2,055 |
17 |
0,656 |
750 |
0,5793 |
6,10 |
0,4537 |
0,2281 |
3,375 |
1,655 |
18 |
0,6829 |
712,5 |
0,5414 |
5,88 |
0,4548 |
0,2292 |
2,554 |
1,255 |
19 |
0,7078 |
675 |
0,5036 |
5,65 |
0,4559 |
0,2303 |
1,734 |
0,8543 |
20 |
0,7312 |
637,5 |
0,4657 |
5,43 |
0,4569 |
0,2313 |
0,9126 |
0,454 |
21 |
0,753 |
600 |
0,4279 |
5,20 |
0,458 |
0,2324 |
0,0916 |
0,05368 |
Для каждого из участков определим средние значения параметров: диаметра КС , температуры газовой стенки , теплоемкости , коэффициента динамической вязкости , а также парциальных давлений .
Результат занесем в таблицу №1.11
Таблица №1.11
№ сеч. |
м |
м |
К |
  |
  |
атм. |
атм. |
0 |
0,35 |
0,35 |
800 |
1,11 |
9,20 |
25,79 |
12,14 |
1 |
0,03575 |
0,3409 |
850 |
1,1 |
9,15 |
24,22 |
11,43 |
2 |
0,03575 |
0,3004 |
950 |
1,081 |
9,05 |
21,08 |
10,01 |
3 |
0,03575 |
0,2333 |
1050 |
1,062 |
8,95 |
17,94 |
8,591 |
4 |
0,03575 |
0,1763 |
1150 |
1,043 |
8,85 |
14,8 |
7,17 |
5 |
0,05575 |
0,1802 |
1181 |
1,015 |
8,69 |
12,82 |
6,259 |
6 |
0,05575 |
0,2336 |
1144 |
0,9767 |
8,46 |
12 |
5,859 |
7 |
0,05575 |
0,2878 |
1106 |
0,9389 |
8,24 |
11,17 |
5,458 |
8 |
0,05575 |
0,3385 |
1069 |
0,901 |
8,01 |
10,35 |
5,058 |
9 |
0,05575 |
0,386 |
1031 |
0,8632 |
7,79 |
9,533 |
4,658 |
10 |
0,05575 |
0,4302 |
993,8 |
0,8253 |
7,56 |
8,712 |
4,257 |
11 |
0,05575 |
0,4715 |
956,3 |
0,7875 |
7,34 |
7,891 |
3,857 |
12 |
0,05575 |
0,5102 |
918,8 |
0,7496 |
7,11 |
7,07 |
3,457 |
13 |
0,05575 |
0,5464 |
881,3 |
0,7118 |
6,89 |
6,249 |
3,056 |
14 |
0,05575 |
0,5803 |
843,8 |
0,6739 |
6,66 |
5,428 |
2,656 |
15 |
0,05575 |
0,612 |
806,3 |
0,6361 |
6,44 |
4,607 |
2,256 |
16 |
0,05575 |
0,6416 |
768,8 |
0,5982 |
6,21 |
3,786 |
1,855 |
17 |
0,05575 |
0,6694 |
731,3 |
0,5604 |
5,99 |
2,965 |
1,455 |
18 |
0,05575 |
0,6954 |
693,8 |
0,5225 |
5,76 |
2,144 |
1,055 |
19 |
0,05575 |
0,7195 |
656,3 |
0,4847 |
5,54 |
1,323 |
0,6542 |
20 |
0,05575 |
0,7421 |
618,8 |
0,4468 |
5,31 |
0,5021 |
0,2538 |
Коэффициент конвективной теплоотдачи от горячих газов к стенке :
;
где - абсолютная температура заторможенного потока (величина известная из теплового расчета двигателя);
- имеет размерность .
Конвективный тепловой поток в стенку КС:
.
Лучистый тепловой поток в стенку КС:
;
где и - тепловые потоки излучаемые газами.
Лучистые тепловые потоки газов:

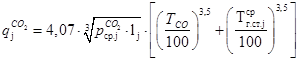
где - приведенная длина луча на j-ом участке.
Парциальные давления газов и имеют размерность – атм.
Суммарный тепловой поток для j-го участка КС:
.
Площадь боковой поверхности j-го участка:
.
Температура охладителя на выходе из охлаждающего тракта:
.
Давление на выходе из охлаждающего тракта:

где - перепад давлений на форсунках.
Температура кипения охладителя на выходе из охлаждающего тракта .
- компонента достаточно для охлаждения.
Подогрев охладителя на j-ом участке:
.
Температура охладителя на j-ом участке:
.
Результаты расчетов заносим в таблицу №1.12.
Таблица №1.12
№ сеч. |
, кВт/м2К |
, Вт/м2 |
, Вт/м2 |
, Вт/м2 |
, Вт/м2 |
, м2 |
, К |
, К |
0 |
1,570 |
3,616 |
6,309 |
9,174 |
5,164 |
0,3848 |
0 |
313 |
1 |
1,597 |
3,598 |
5,885 |
8,895 |
5,076 |
0,03829 |
6,421 |
319,4 |
2 |
1,896 |
4,083 |
4,841 |
8,116 |
5,379 |
0,03374 |
5,995 |
325,4 |
3 |
2,845 |
5,841 |
3,618 |
7,041 |
6,907 |
0,0262 |
5,978 |
331,4 |
4 |
4,498 |
8,785 |
2,588 |
5,985 |
9,642 |
0,0198 |
6,306 |
337,7 |
5 |
4,149 |
7,973 |
2,327 |
5,745 |
8,781 |
0,03156 |
9,156 |
346,9 |
6 |
2,507 |
4,912 |
2,593 |
6,15 |
5,787 |
0,04091 |
7,822 |
354,7 |
7 |
1,660 |
3,314 |
2,791 |
6,462 |
4,239 |
0,05041 |
7,06 |
361,7 |
8 |
1,194 |
2,429 |
2,908 |
6,671 |
3,387 |
0,05929 |
6,634 |
368,4 |
9 |
0,9074 |
1,88 |
2,957 |
6,8 |
2,856 |
0,06761 |
6,378 |
374,7 |
10 |
0,7177 |
1,514 |
2,949 |
6,86 |
2,495 |
0,07535 |
6,21 |
381 |
11 |
0,5842 |
1,254 |
2,889 |
6,86 |
2,229 |
0,08259 |
6,082 |
387 |
12 |
0,4858 |
1,061 |
2,783 |
6,805 |
2,02 |
0,08936 |
5,964 |
393 |
13 |
0,4108 |
0,9127 |
2,636 |
6,695 |
1,846 |
0,0957 |
5,836 |
398,8 |
14 |
0,3519 |
0,795 |
2,448 |
6,53 |
1,693 |
0,1016 |
5,684 |
404,5 |
15 |
0,3044 |
0,6992 |
2,223 |
6,304 |
1,552 |
0,1072 |
5,495 |
410 |
16 |
0,2654 |
0,6195 |
1,959 |
6,009 |
1,416 |
0,1124 |
5,258 |
415,3 |
17 |
0,2326 |
0,5517 |
1,656 |
5,627 |
1,28 |
0,1172 |
4,958 |
420,2 |
18 |
0,2048 |
0,4933 |
1,31 |
5,125 |
1,137 |
0,1218 |
4,574 |
424,8 |
19 |
0,1807 |
0,4421 |
0,9103 |
4,425 |
0,9756 |
0,126 |
4,062 |
428,9 |
20 |
0,1595 |
0,3964 |
0,4278 |
3,264 |
0,7655 |
0,13 |
3,287 |
432 |
Коэффициент теплопередачи от жидкой стенки к охладителю:
;
где - средняя площадь охлаждающего тракта на j-ом участке;
- количество ребер на j-ом участке;
- средний шаг ребер на j-ом участке;
- комплекс физических параметров охладителя;
- средний гидравлический диаметр охлаждающего тракта на j-ом участке;
Средняя температура жидкой стенки на j-ом участке:
.
Средняя температура газовой стенки на j-ом участке:
.
Средняя температура материала огневой стенки на j-ом участке:
.
Разница между принятой и расчетной температурой «газовой» стенки:
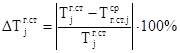
Результат расчета считаем удовлетворительным если разница между принятым значением температуры газовой стенки и расчетным будет составлять менее 5%. Если разница превышает 5% расчет проводим заново приняв за температуру газовой стенки среднюю между принятой и расчетной температурами.
Результаты расчетов заносим в таблицу №1.13.
Таблица №1.13
№ сеч. |
, шт. |
, м |
, м2 |
, м |
, кВт/м2К |
, К |
, К |
, К |
% |
0 |
290 |
0,003792 |
0,002024 |
0,002638 |
6,979 |
1053 |
1268 |
1161 |
36,9 |
1 |
290 |
0,003693 |
0,001953 |
0,002593 |
7,207 |
1024 |
1235 |
1130 |
31,1 |
2 |
290 |
0,003254 |
0,001634 |
0,002371 |
8,458 |
961,3 |
1185 |
1073 |
19,8 |
3 |
290 |
0,002527 |
0,001107 |
0,001896 |
12,08 |
903,1 |
1191 |
1047 |
11,8 |
4 |
290 |
0,001909 |
0,000659 |
0,001334 |
19,62 |
829,2 |
1231 |
1030 |
6,57 |
5 |
145 |
0,003904 |
0,001053 |
0,002687 |
11,73 |
1096 |
1461 |
1279 |
19,1 |
6 |
145 |
0,005061 |
0,001472 |
0,003095 |
8,719 |
1018 |
1259 |
1139 |
9,18 |
7 |
145 |
0,006236 |
0,001898 |
0,003384 |
6,99 |
968,3 |
1145 |
1057 |
3,37 |
8 |
290 |
0,003667 |
0,001934 |
0,002581 |
7,27 |
834,2 |
975,4 |
904,8 |
9,57 |
9 |
290 |
0,004182 |
0,002307 |
0,0028 |
6,211 |
834,5 |
953,5 |
894 |
8,15 |
10 |
290 |
0,00466 |
0,002654 |
0,002971 |
5,486 |
835,7 |
939,6 |
887,6 |
5,76 |
11 |
290 |
0,005108 |
0,002978 |
0,003108 |
4,958 |
836,7 |
929,5 |
883,1 |
2,87 |
12 |
290 |
0,005527 |
0,003282 |
0,003221 |
4,554 |
836,5 |
920,7 |
878,6 |
0,21 |
13 |
290 |
0,005919 |
0,003566 |
0,003315 |
4,237 |
834,5 |
911,4 |
872,9 |
3,30 |
14 |
290 |
0,006286 |
0,003832 |
0,003395 |
3,981 |
829,7 |
900,2 |
865 |
6,27 |
15 |
580 |
0,003315 |
0,003356 |
0,002404 |
4,743 |
737,2 |
801,8 |
769,5 |
0,54 |
16 |
580 |
0,003475 |
0,003589 |
0,002488 |
4,465 |
732,5 |
791,5 |
762 |
2,87 |
17 |
580 |
0,003626 |
0,003808 |
0,002561 |
4,234 |
722,6 |
775,9 |
749,2 |
5,75 |
18 |
580 |
0,003766 |
0,004011 |
0,002626 |
4,041 |
706,1 |
753,5 |
729,8 |
7,93 |
19 |
580 |
0,003897 |
0,004201 |
0,002684 |
3,877 |
680,5 |
721,2 |
700,8 |
9,00 |
20 |
580 |
0,00402 |
0,004379 |
0,002735 |
3,737 |
637 |
668,9 |
653 |
7,49 |
Как видно из таблицы №1.3, разница между заданной и расчетной температурами газовой стенки значительна. Задаемся новыми значениями температуры и повторяем расчет.
Таблица №1.14
№ сеч. |
, К |
, кВт/м2К |
, Вт/м2 |
, Вт/м2 |
, Вт/м2 |
, Вт/м2 |
, м2 |
, К |
, К |
0 |
1034 |
1,435 |
2,969 |
6,182 |
9,057 |
4,493 |
0,3848 |
0 |
313 |
1 |
1042,6 |
1,487 |
3,063 |
5,781 |
8,794 |
4,521 |
0,03829 |
5,719 |
318,7 |
2 |
1067,7 |
1,82 |
3,705 |
4,781 |
8,05 |
4,988 |
0,03374 |
5,56 |
324,3 |
3 |
1120,4 |
2,781 |
5,514 |
3,586 |
6,999 |
6,572 |
0,0262 |
5,688 |
330 |
4 |
1190,4 |
4,444 |
8,499 |
2,573 |
5,961 |
9,353 |
0,0198 |
6,117 |
336,1 |
5 |
1321,3 |
3,989 |
7,108 |
2,273 |
5,647 |
7,9 |
0,03156 |
8,238 |
344,3 |
6 |
1201,6 |
2,464 |
4,686 |
2,571 |
6,114 |
5,554 |
0,04091 |
7,507 |
351,8 |
7 |
1125,5 |
1,65 |
3,262 |
2,784 |
6,451 |
4,186 |
0,05041 |
6,97 |
358,8 |
8 |
1022 |
1,213 |
2,524 |
2,923 |
6,695 |
3,486 |
0,05929 |
6,827 |
365,6 |
9 |
992,3 |
0,9197 |
1,941 |
2,97 |
6,818 |
2,92 |
0,06761 |
6,522 |
372,1 |
10 |
966,6 |
0,7247 |
1,548 |
2,957 |
6,872 |
2,531 |
0,07535 |
6,3 |
378,4 |
11 |
942,8 |
0,587 |
1,268 |
2,893 |
6,866 |
2,244 |
0,08259 |
6,122 |
384,6 |
12 |
919,7 |
0,4856 |
1,06 |
2,783 |
6,805 |
2,019 |
0,08936 |
5,961 |
390,5 |
13 |
896,3 |
0,4084 |
0,9012 |
2,633 |
6,69 |
1,833 |
0,0957 |
5,797 |
396,3 |
14 |
871,9 |
0,3478 |
0,776 |
2,443 |
6,522 |
1,673 |
0,1016 |
5,616 |
401,9 |
15 |
804 |
0,3047 |
0,7005 |
2,223 |
6,305 |
1,553 |
0,1072 |
5,5 |
407,4 |
16 |
780,1 |
0,264 |
0,6133 |
1,958 |
6,007 |
1,41 |
0,1124 |
5,234 |
412,7 |
17 |
753,5 |
0,2302 |
0,5408 |
1,654 |
5,623 |
1,269 |
0,1172 |
4,914 |
417,6 |
18 |
723,6 |
0,2018 |
0,4801 |
1,308 |
5,12 |
1,123 |
0,1218 |
4,518 |
422,1 |
19 |
688,7 |
0,1777 |
0,4289 |
0,909 |
4,421 |
0,962 |
0,126 |
4,005 |
426,1 |
20 |
643,8 |
0,1573 |
0,3869 |
0,4274 |
3,262 |
0,7559 |
0,13 |
3,246 |
429,4 |
Таблица №1.15
№ сеч. |
, шт. |
, м |
, м2 |
, м |
, кВт/м2К |
, К |
, К |
, К |
% |
0 |
290 |
0,003792 |
0,002024 |
0,002638 |
6,979 |
956,8 |
1144 |
1050 |
9,612 |
1 |
290 |
0,003693 |
0,001953 |
0,002593 |
7,207 |
946 |
1134 |
1040 |
8,089 |
2 |
290 |
0,003254 |
0,001634 |
0,002371 |
8,458 |
914 |
1122 |
1018 |
4,826 |
3 |
290 |
0,002527 |
0,001107 |
0,001896 |
12,08 |
874 |
1148 |
1011 |
2,387 |
4 |
290 |
0,001909 |
0,000659 |
0,001334 |
19,62 |
812,8 |
1202 |
1008 |
1 |
5 |
145 |
0,003904 |
0,001053 |
0,002687 |
11,73 |
1018 |
1347 |
1183 |
1,912 |
6 |
145 |
0,005061 |
0,001472 |
0,003095 |
8,719 |
988,8 |
1220 |
1105 |
1,529 |
7 |
145 |
0,006236 |
0,001898 |
0,003384 |
6,99 |
957,6 |
1132 |
1045 |
0,5705 |
8 |
290 |
0,003667 |
0,001934 |
0,002581 |
7,27 |
845,1 |
990,3 |
917,7 |
3,204 |
9 |
290 |
0,004182 |
0,002307 |
0,0028 |
6,211 |
842,3 |
963,9 |
903,1 |
2,951 |
10 |
290 |
0,00466 |
0,002654 |
0,002971 |
5,486 |
839,8 |
945,2 |
892,5 |
2,269 |
11 |
290 |
0,005108 |
0,002978 |
0,003108 |
4,958 |
837,2 |
930,7 |
883,9 |
1,31 |
12 |
290 |
0,005527 |
0,003282 |
0,003221 |
4,554 |
833,9 |
918 |
875,9 |
0,1895 |
13 |
290 |
0,005919 |
0,003566 |
0,003315 |
4,237 |
829 |
905,4 |
867,2 |
1,007 |
14 |
290 |
0,006286 |
0,003832 |
0,003395 |
3,981 |
822 |
891,7 |
856,9 |
2,212 |
15 |
580 |
0,003315 |
0,003356 |
0,002404 |
4,743 |
734,9 |
799,6 |
767,3 |
0,5523 |
16 |
580 |
0,003475 |
0,003589 |
0,002488 |
4,465 |
728,4 |
787,2 |
757,8 |
0,8937 |
17 |
580 |
0,003626 |
0,003808 |
0,002561 |
4,234 |
717,2 |
770,1 |
743,6 |
2,141 |
18 |
580 |
0,003766 |
0,004011 |
0,002626 |
4,041 |
700 |
746,8 |
723,4 |
3,102 |
19 |
580 |
0,003897 |
0,004201 |
0,002684 |
3,877 |
674,2 |
714,3 |
694,3 |
3,584 |
20 |
580 |
0,00402 |
0,004379 |
0,002735 |
3,737 |
631,6 |
663,1 |
647,4 |
2,91 |
Как видно из таблицы №1.15, разница между заданной и расчетной температурами газовой стенки на некоторых участках больше 5%. Задаемся новыми значениями температуры и повторяем расчет.
Таблица №1.16
№ сеч. |
, К |
, кВт/м2К |
, Вт/м2 |
, Вт/м2 |
, Вт/м2 |
, Вт/м2 |
, м2 |
, К |
, К |
0 |
1089 |
1,409 |
2,838 |
6,142 |
9,018 |
4,354 |
0,3848 |
0 |
313 |
1 |
1088,5 |
1,465 |
2,95 |
5,75 |
8,761 |
4,402 |
0,03829 |
5,568 |
318,6 |
2 |
1094,7 |
1,805 |
3,624 |
4,765 |
8,032 |
4,904 |
0,03374 |
5,466 |
324 |
3 |
1134,1 |
2,769 |
5,452 |
3,58 |
6,99 |
6,509 |
0,0262 |
5,634 |
329,7 |
4 |
1196,4 |
4,436 |
8,458 |
2,571 |
5,957 |
9,31 |
0,0198 |
6,089 |
335,8 |
5 |
1334,2 |
3,976 |
7,033 |
2,267 |
5,637 |
7,823 |
0,03156 |
8,157 |
343,9 |
6 |
1210,9 |
2,458 |
4,65 |
2,568 |
6,108 |
5,518 |
0,04091 |
7,458 |
351,4 |
7 |
1128,8 |
1,648 |
3,254 |
2,783 |
6,449 |
4,177 |
0,05041 |
6,956 |
358,3 |
8 |
1006,1 |
1,22 |
2,557 |
2,928 |
6,702 |
3,52 |
0,05929 |
6,895 |
365,2 |
9 |
978,1 |
0,9243 |
1,964 |
2,974 |
6,825 |
2,944 |
0,06761 |
6,575 |
371,8 |
10 |
955,9 |
0,7275 |
1,562 |
2,96 |
6,877 |
2,546 |
0,07535 |
6,337 |
378,1 |
11 |
936,7 |
0,5884 |
1,275 |
2,894 |
6,868 |
2,251 |
0,08259 |
6,141 |
384,3 |
12 |
918,8 |
0,4858 |
1,061 |
2,783 |
6,805 |
2,02 |
0,08936 |
5,963 |
390,2 |
13 |
900,8 |
0,4077 |
0,8977 |
2,632 |
6,689 |
1,83 |
0,0957 |
5,785 |
396 |
14 |
881,8 |
0,3465 |
0,7696 |
2,441 |
6,518 |
1,666 |
0,1016 |
5,592 |
401,6 |
15 |
801,8 |
0,305 |
0,7018 |
2,223 |
6,305 |
1,555 |
0,1072 |
5,505 |
407,1 |
16 |
783,6 |
0,2636 |
0,6114 |
1,957 |
6,006 |
1,408 |
0,1124 |
5,226 |
412,3 |
17 |
761,8 |
0,2293 |
0,5369 |
1,653 |
5,622 |
1,264 |
0,1172 |
4,898 |
417,2 |
18 |
735,2 |
0,2006 |
0,4751 |
1,307 |
5,119 |
1,118 |
0,1218 |
4,497 |
421,7 |
19 |
701,5 |
0,1765 |
0,4239 |
0,9084 |
4,42 |
0,9567 |
0,126 |
3,983 |
425,7 |
20 |
653,4 |
0,1565 |
0,3834 |
0,4272 |
3,261 |
0,7522 |
0,13 |
3,23 |
429 |
Таблица №1.17
№ сеч. |
, шт. |
, м |
, м2 |
, м |
, кВт/м2К |
, К |
, К |
, К |
% |
0 |
290 |
0,003792 |
0,002024 |
0,002638 |
6,979 |
936,9 |
1118 |
1028 |
2,621 |
1 |
290 |
0,003693 |
0,001953 |
0,002593 |
7,207 |
929,3 |
1113 |
1021 |
2,174 |
2 |
290 |
0,003254 |
0,001634 |
0,002371 |
8,458 |
903,8 |
1108 |
1006 |
1,201 |
3 |
290 |
0,002527 |
0,001107 |
0,001896 |
12,08 |
868,5 |
1140 |
1004 |
0,4892 |
4 |
290 |
0,001909 |
0,000659 |
0,001334 |
19,62 |
810,3 |
1198 |
1004 |
0,1477 |
5 |
145 |
0,003904 |
0,001053 |
0,002687 |
11,73 |
1011 |
1337 |
1174 |
0,2028 |
6 |
145 |
0,005061 |
0,001472 |
0,003095 |
8,719 |
984,2 |
1214 |
1099 |
0,2594 |
7 |
145 |
0,006236 |
0,001898 |
0,003384 |
6,99 |
955,9 |
1130 |
1043 |
0,09845 |
8 |
290 |
0,003667 |
0,001934 |
0,002581 |
7,27 |
849,4 |
996,1 |
922,8 |
1,013 |
9 |
290 |
0,004182 |
0,002307 |
0,0028 |
6,211 |
845,8 |
968,4 |
907,1 |
1,002 |
10 |
290 |
0,00466 |
0,002654 |
0,002971 |
5,486 |
842,1 |
948,2 |
895,2 |
0,8191 |
11 |
290 |
0,005108 |
0,002978 |
0,003108 |
4,958 |
838,3 |
932,1 |
885,2 |
0,5064 |
12 |
290 |
0,005527 |
0,003282 |
0,003221 |
4,554 |
833,7 |
917,9 |
875,8 |
0,1031 |
13 |
290 |
0,005919 |
0,003566 |
0,003315 |
4,237 |
827,9 |
904,1 |
866 |
0,3563 |
14 |
290 |
0,006286 |
0,003832 |
0,003395 |
3,981 |
820 |
889,3 |
854,6 |
0,8424 |
15 |
580 |
0,003315 |
0,003356 |
0,002404 |
4,743 |
734,9 |
799,7 |
767,3 |
0,2713 |
16 |
580 |
0,003475 |
0,003589 |
0,002488 |
4,465 |
727,6 |
786,3 |
757 |
0,3374 |
17 |
580 |
0,003626 |
0,003808 |
0,002561 |
4,234 |
715,9 |
768,6 |
742,2 |
0,8763 |
18 |
580 |
0,003766 |
0,004011 |
0,002626 |
4,041 |
698,3 |
744,9 |
721,6 |
1,302 |
19 |
580 |
0,003897 |
0,004201 |
0,002684 |
3,877 |
672,5 |
712,4 |
692,4 |
1,523 |
20 |
580 |
0,00402 |
0,004379 |
0,002735 |
3,737 |
630,3 |
661,6 |
645,9 |
1,229 |
Погрешность между принятой и расчетной температурами менее 5%, точность расчета считаем удовлетворительной.
Из таблицы №9 видно, что температура жидкой стенки значительно превышает допустимую температуру перегрева охладителя , в связи с чем охлаждение двигателя не будет надежным.
Для уменьшения теплового потока в стенку КС и, как следствие, уменьшения температуры жидкой стенки необходима организация внутреннего охлаждения.
Внутреннее охлаждение организуется созданием пристеночного слоя и позволяет уменьшить тепловой поток на 50-70%. Организовать пристеночный слой возможно двумя способами: периферийными форсунками горючего или с помощью поясов завесы. Первый из способов конструктивно более прост, но менее экономичен, второй наоборот, конструктивно более сложен, но создает равномерный пристеночный слой по длине КС и более экономичен.
Выбираем первый способ для создания пристеночного слоя. Уменьшаем суммарный тепловой поток на 55% и повторяем расчет.
Таблица №1.18
№ сеч. |
, Вт/м2 |
, м2 |
, К |
, К |
, кВт/м2К |
, К |
, К |
, К |
0 |
1,959 |
0,3848 |
0 |
313 |
6,979 |
593,8 |
675,4 |
634,6 |
1 |
1,981 |
0,03829 |
2,505 |
315,5 |
7,207 |
590,3 |
672,9 |
631,6 |
2 |
2,207 |
0,03374 |
2,46 |
318 |
8,458 |
578,8 |
670,8 |
624,8 |
3 |
2,929 |
0,0262 |
2,535 |
320,5 |
12,08 |
563 |
685 |
624 |
4 |
4,19 |
0,0198 |
2,74 |
323,2 |
19,62 |
536,8 |
711,4 |
624,1 |
5 |
3,52 |
0,03156 |
3,671 |
326,9 |
11,73 |
627,1 |
773,8 |
700,4 |
6 |
2,483 |
0,04091 |
3,356 |
330,3 |
8,719 |
615 |
718,5 |
666,8 |
7 |
1,879 |
0,05041 |
3,13 |
333,4 |
6,99 |
602,3 |
680,6 |
641,5 |
8 |
1,584 |
0,05929 |
3,103 |
336,5 |
7,27 |
554,4 |
620,4 |
587,4 |
9 |
1,325 |
0,06761 |
2,959 |
339,5 |
6,211 |
552,8 |
608 |
580,4 |
10 |
1,146 |
0,07535 |
2,852 |
342,3 |
5,486 |
551,1 |
598,8 |
575 |
11 |
1,013 |
0,08259 |
2,764 |
345,1 |
4,958 |
549,4 |
591,6 |
570,5 |
12 |
0,909 |
0,08936 |
2,683 |
347,8 |
4,554 |
547,3 |
585,2 |
566,3 |
13 |
0,8234 |
0,0957 |
2,603 |
350,4 |
4,237 |
544,7 |
579 |
561,8 |
14 |
0,7495 |
0,1016 |
2,516 |
352,9 |
3,981 |
541,1 |
572,4 |
556,7 |
15 |
0,6996 |
0,1072 |
2,477 |
355,4 |
4,743 |
502,9 |
532 |
517,4 |
16 |
0,6335 |
0,1124 |
2,352 |
357,7 |
4,465 |
499,6 |
526 |
512,8 |
17 |
0,569 |
0,1172 |
2,204 |
359,9 |
4,234 |
494,3 |
518 |
506,1 |
18 |
0,5029 |
0,1218 |
2,024 |
361,9 |
4,041 |
486,4 |
507,4 |
496,9 |
19 |
0,4305 |
0,126 |
1,792 |
363,7 |
3,877 |
474,8 |
492,7 |
483,7 |
20 |
0,3385 |
0,13 |
1,454 |
365,2 |
3,737 |
455,8 |
469,9 |
462,8 |
По результатам расчета, приведенным в таблице №1.18 видно, что температура жидкой стенки не превышает температуру кипения охладителя по всей длине КС. Температура огневой стенки не превышает критическую температуру для материала стенки равную 1073 0К.
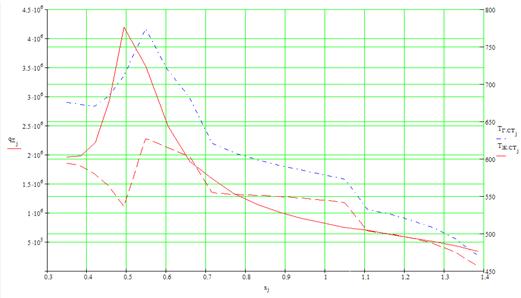
Рис.1.19 Изменение суммарного теплового потока, температуры газовой и жидкой стенок по длине КС
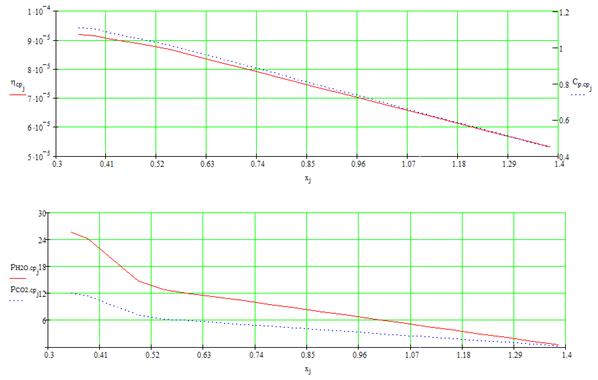
Рис.1.20 Изменение термодинамических параметров продуктов сгорания по длине КС
5.5 Расчет периферийных форсунок горючего
Относительный расход газа в пристеночном слое (для камер с тягой кН)
; выбираем 
Суммарный расход через периферийные форсунки горючего:
.
Для создания пристеночного слоя используются струйные форсунки установленные по концентрической окружности с шагом t=3…4мм.
Количество периферийных форсунок:
.
Расход через одну форсунку:
.
Потребный диаметр форсунки:
;
где - коэффициент расхода; - перепад давления на форсунках.
Полученные геометрические параметры форсунок пристеночного слоя, удовлетворяют среднестатистическим данным для струйных форсунок и, следовательно, могут быть изготовлены.
6. Описание камеры сгорания и ТНА проектируемого двигателя
Проектируемый двигатель предназначен для использования на второй ступени УБР. Двигатель состоит из камеры, турбонасосного агрегата, газогенератора, работающего на основных компонентах топлива, четырех поворотных сопел системы управления.
Таблица №1.19
Основные параметры двигателя.
Тяга двигателя в пустоте |
208 кН |
Топливо |
окислитель |
Азотная кислота |
горючее |
Керосин |
Секундный расход |
окислителя |
 |
горючего |
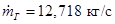 |
Весовое соотношение компонентов топлива |
 |
Коэффициент избытка окислителя |
 |
Давление газов |
в камере сгорания |
6 Мпа |
на срезе сопла |
0,02 Мпа |
Удельная тяга в пустоте |
287,3 с |
Удельный импульс двигателя в пустоте |
 |
Относительная расходонапряженность по КС |
 |
Объем КС (до критического сечения) |
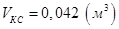 |
Коэффициент полноты давления в камере |
 |
Коэффициент сопла |
 |
6.1 Газодинамический профиль камеры
Дозвуковая часть сопла выполнена в виде плавных переходов с прямолинейным участком под углом для обеспечения наименьших потерь при течении газа в сужающемся канале.
Сверхзвуковая часть сопла спрофилирована графическим методом. Камера представляет собой паяно-сварную конструкцию, состоящую из форсуночной головки, цилиндрического и докритического участков с закритической частью, и закритической части сопла.
6.2 Форсуночная головка
Форсуночная головка состоит из силового кольца, огневого днища, среднего днища, сферического наружного днища и двухкомпонентных форсунок.
Полость горючего образована наружным сферическим и средним днищами. Полость окислителя – средним и огневым днищами.
Среднее и огневое днища связаны между собой однокомпонентными форсунками посредством развальцовки и пайки кислотостойким припоем, устанавливаемым в местах соединений в виде колец. Пайка производится в вакууме. Всего форсунок 499, из них 409 центробежных и 90 струйных.
Из 409 однокомпонентных центробежных форсунок 325 выполнены с увеличенным расходом и установлены в центре ФГ по сотовой схеме. Вокруг ядра по двум концентрическим окружностям установлены 84 центробежных форсунок окислителя уменьшенного расхода, аналогичных по конструкции форсункам увеличенного расхода. На периферии огневого днища по концентрической окружности установлены 90 форсунок горючего для создания пристеночного слоя. Такое расположение форсунок обеспечивает эшелонированный фронт пламени по длине камеры сгорания, что приводит к устойчивой форме горения, к ликвидации высокочастотных колебаний и создания защитного пристеночного слоя.
В центре огневого днища приварен стакан с 6 антидетонационными ребрами, которые дополнительно привариваются к огневому днищу прерывистым швом с двух сторон и к силовому кольцу по внутренней его поверхности. В силовом кольце для подвода компонентов к форсункам окислителя и горючего просверлено по 45 отверстий во взаимно перпендикулярных плоскостях. Между сферическим днищем и средним установлены два перфорированных стакана для придания жесткости блоку плоских днищ. К силовому кольцу приварен коллектор горючего с двумя патрубками с двумя трубопроводами, к которым приварен наконечник с дроссельной шайбой. К наконечнику приварен штуцер для отвода горючего к стабилизатору соотношения компонентов.
Кроме того, на головке камеры приварены штуцер для замера давления окислителя в полости перед форсунками, штуцер для замера давления перед форсунками горючего и три кронштейна для крепления к раме ракеты. Все детали головки, кроме форсунок соединены между собой аргонно-дуговой сваркой.
6.3 Цилиндрический и докритический участки камеры с частью закритического участка сопла
Цилиндрический участок камеры выполнен из двух оболочек, связанных между собой с помощью ребер при помощи пайки кислотостойким припоем.
Докритический участок сопла с частью закритического участка выполнен также из двух оболочек, связанных между собой кислотостойким припоем. Внутренняя оболочка выполнена из легированной стали. Каналы для охлаждения указанной части сопла на внутренней оболочке выполнены фрезерованием. Закритический участок внутренней оболочки из первоначальной цилиндрической доводится до заданного профиля после сборки с внешней оболочкой путем обкатки роликом. Наружная оболочка также выполнена стальной. К внутренней оболочке цилиндрической части камеры сгорания с двух сторон приварены кольца большей толщины для обеспечения более качественной сварки оболочки с силовым кольцом головки, с одной стороны, и для осуществления сварки внутренней стальной цилиндрической оболочки с внутренней оболочкой докритической части сопла с другой стороны. На цилиндрической части камеры сгорания установлено два штуцера для замера давления в ней.
6.4 Закритическая часть сопла
Указанная часть сопла аналогична по конструкции цилиндрической части камеры. Выполнена она из двух стальных конических оболочек, соединенных между собой ребрами при помощи кислотостойкого припоя. Каналы ребер выполнены вдоль образующей сопла.
Коллектор с двумя трубопроводами, переходящими в патрубок с наконечником и дроссельной шайбой, служит для подвода горючего в межрубашечное пространство. К наконечнику приварен штуцер для отбора окислителя к стабилизатору соотношения компонентов. Сопло заканчивается кольцом жесткости, к которому приварены обе оболочки. В кольце жесткости для образования поворотной полости коллектора, выполнена кольцевая проточка.
6.5 Соединение узлов камеры сгорания
Цилиндрический участок камеры соединяется с головкой при помощи сварки: внутренняя оболочка с силовым кольцом – через кольцо большей толщины, чем сама оболочка, а внешняя оболочка с силовым кольцом – через переходное кольцо.
Цилиндрический участок соединяется с докритическим участком также при помощи сварки: внутренние оболочки, стальная цилиндрическая и стальная докритическая – через кольцо из пластичной нержавеющей стали, а внешние оболочки через переходное разрезное кольцо.
Закритическая часть сопла присоединяется также сваркой: по внутренним оболочкам через переходное кольцо из пластичной стали, а по внешним оболочкам – через переходное разрезное кольцо, имеющее продольный шов. Вокруг критического сечения приварено кольцо с кронштейнами. К кронштейну крепится турбонасосный агрегат, регулятор и шар-баллон. Кроме того, к кронштейну крепится сигнализатор давления.
6.6 Система охлаждения
Охлаждение двигателя наружное и внутреннее. Наружное охлаждение осуществляется горючим, идущим по межрубашечному зазору со стороны среза сопла. Внутреннее охлаждение осуществляется при помощи пристеночного слоя создаваемого рядом периферийных струйных форсунок. Внутренние оболочки цилиндра и сопла выполнены толщиной 0,8 мм, высота межрубашечного зазора постоянная – 2,5 мм. Ребра выполнены фрезерованием толщиной 1 мм. Внутренняя оболочка входа докритической части сопла покрыта блестящим хромом толщиной 40-60 микрон.
Таблица №1.20
Материалы, примененные в конструкции прототипа
Внутренние оболочки цилиндра и сопла, гофр, огневое днище, среднее днище, все корпуса форсунок, сетки фильтров. |
Ст.12Х18Н10Т |
Наружное сферическое днище, силовое кольцо, коллекторы, наружная оболочка цилиндрической части, докритической и закритической части сопла, соединительное кольцо цилиндрической и докритической частей камеры. |
Ст.1Х17Н5М8 |
Переходные кольца внутренней оболочки |
Ст. 1Х21Н5Т |
Припой |
Г40НХ |
6.7 Описание насоса окислителя
Таблица №1.21
Основные параметры проектируемого насоса
Тип рабочего колеса |
Центробежное закрытое с осевым преднасосом |
Расход |
 |
Давление |
на входе |
 |
на выходе |
 |
Мощность потребляемая |
 |
Коэффициент полезного действия |
 |
6.8 Корпус
Корпус насоса изготовлен из алюминиевого сплава совместно с улиткой. На наружной поверхности корпус насоса усилен семью ребрами жесткости. В корпусе насоса в полости импеллера выполнено отверстие диаметром 10 мм для образования перепускной магистрали из полости подшипника на вход в насос. Эта полость с входом в насос соединена внешним трубопроводом. Фланец трубопровода крепится к корпусу насоса двумя шпильками.
Входной патрубок насоса окислителя выполнен стальным за одно целое с развитым фасонным фланцем. На входе в патрубок установлена конусная втулка на трех пилонах под передний подшипник вала ротора насоса окислителя.
По наружной поверхности входного патрубка приварен коллектор для приема компонента из импеллерной полости. Трубопровод приваривается к этому коллектору. Под коллектором в корпусе входного патрубка выполнено 36 отверстий диаметром 2 мм под углом 450 к оси патрубка.
Улитка спрофилирована переменным радиусом при постоянной ширине канала. Диффузор выполнен за одно целое с улиткой. Входная его часть имеет прямоугольную форму. Заканчивается диффузор фасонным фланцем с шестью шпильками М8.
6.9 Рабочее колесо
Рабочее колесо представляет собой единый узел, состоящий из центробежного колеса и осевого шнекового преднасоса. Центробежное колесо насоса выполнено из алюминиевого сплава. Крыльчатка имеет 7 фрезерованных лопаток. Закрытые каналы колеса образованы при помощи пайки к лопаткам крыльчатки двух крышек.
На ступицы крышек насоса напрессованы стальные втулки для образования плавающих уплотнений.
Стальной шнек двухзаходный, с правым направлением винтовой линии постоянного шага. Цапфа шнека запрессована в вал ротора насоса. При запрессовке вал нагревается до температуры 1500 С.
Фиксация шнека относительно вала ротора насоса осуществлена радиальным штифтом, который закрыт дистанционным кольцом, установленным между ступицей колеса и внутренней обоймой фиксирующего подшипника. Крутящий момент от вала передается на вал насоса через рессору. Вал насоса воспринимает крутящий момент через шлицы, нарезанные на его внутреннем диаметре, а передает к насосу через шлицы, нарезанные по наружному диаметру вала. Для устранения осевых перемещений рессоры в процессе работы ТНА рессора со стороны насоса окислителя прижата к диску турбины пружиной, вставленной в цилиндрическую проточку цапфы шнека.
6.10 Уплотнения
Для уменьшения перетекания компонента из полостей высокого давления насоса в полости пониженных давлений на колесе выполнены узлы плавающих уплотнений. Плавающее уплотнение, установленное со стороны входа, имеет внутреннее плавающее кольцо. Уплотнение по валу насоса окислителя осуществлено аналогично уплотнению насоса горючего манжетным узлом и импеллером. Просочившийся через манжетное уплотнение окислитель по кольцевому каналу между внутренним диаметром трубки разделительного корпуса уплотнения и рессорой отводится к диску турбины и через отверстие в валу ротора выбрасывается в полость турбины.
На рабочем режиме насосная полость уплотняется импеллером, установленным на резьбовой части вала окислителя. Импеллер относительно вала фиксирован пластинчатым замком по пазу на валу.
Окислитель, просочившийся через плавающее уплотнение на ступице центробежного колеса, проходит через подшипник в импеллерную полость, осуществляя смазку и охлаждение подшипника, и отводится на вход насоса. Окислитель, просочившийся через плавающее уплотнение передней крышки колеса, сразу попадает на вход в колесо насоса.
6.11 Описание турбины ТНА
Таблица №1.22
Параметры проектируемой турбины
Тип турбины |
Осевая, активная, одноступенчатая |
Частота вращения |
 |
Окружная скорость на среднем диаметре лопаток |
 |
Расход газа |
 |
Давление |
на входе |
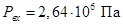 |
на выходе |
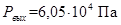 |
Мощность |
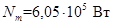 |
Коэффициент полезного действия |
 |
6.12 Описание конструктивного прототипа турбины
Одноступенчатая, активная турбина состоит из корпуса с сопловым и выхлопным аппаратами и рабочего колеса с валом.
6.13 Корпус
Корпус турбины выполнен из жаропрочной стали в виде фасонной цилиндрической втулки. К левому торцу корпуса турбины приварен корпус выхлопного аппарата. К правому торцу по наружной поверхности его, приварен сопловой аппарат турбины.
Сопловой аппарат выполнен в форме венца с семью фрезерованными рабочими соплами и одним пусковым соплом.
К пусковому соплу приваривается корпус пиростартера, а к корпусу соплового венца – входной газовый коллектор переменной площади сечения. К цилиндрической части входного газового коллектора приварен фланец, к которому, в свою очередь приваривается газогенератор. Сопловой венец выполнен из поковки (может выполняться и из штамповки) с последующей механической обработкой (точением и фрезерованием).
Входной газовый коллектор выполнен в виде патрубка из двух штампованных секторов, сваренных между собой. Двумя конусными диафрагмами сопловой аппарат приварен к стальному фасонному корпусу подшипника. В наружной конусной диафрагме выполнено семь окон для возможности крепления при помощи шпилек насоса горючего. Наружная диафрагма усилена семью ребрами жесткости. Жесткость внутренней конической диафрагмы повышена двенадцатью радиальными выштамповками. На корпусе соплового аппарата приварен штуцер для замера давления газа перед турбиной.
Выхлопной аппарат состоит из выхлопного коллектора с двумя выхлопными патрубками. Для увеличения жесткости выхлопного аппарата к нему приварены четыре ребра, цилиндрическая втулка и точеное кольцо Г- образного профиля, которое используется для крепления ТНА к раме двигателя.
Выхлопные патрубки установлены в двух диаметрально противоположных плоскостях. Они имеют коническую форму и состоят из трех штампованных секторов, сваренных между собой. Патрубки заканчиваются цилиндрическими участками, к которым привариваются фланцы для стыковки их с выхлопными трубами.
6.14 Рабочее колесо с валом
Ротор турбины состоит из диска и вала. Лопатки (96 шт.) выполнены электроэрозионным способом зацело с диском. Крепление бандажа к лопаткам диска осуществляется пайкой.
В диске турбины выполнена проточка для напрессовки его на вал. Фиксация диска относительно вала осуществлена шестью штифтами (диаметром 8 мм). Штифты от выпадения защищены кольцом, которое, в свою очередь, зафиксировано от осевых перемещений двумя штифтами (диаметром 3 мм). Штифты после запрессовки заварены по наружной поверхности, места сварки зачищены.
Внутри вала выполнены эвольвентные шлицы для передачи через рессору крутящего момента к насосу окислителя. В валу выполнено шесть отверстий диаметром 4мм для отвода в полость турбины компонентов, просочившихся из насосов сквозь манжетные уплотнения. Кроме того, на внешнем диаметре вала просверлено одно глубокое отверстие диаметром 3мм под штифт для передачи крутящего момента от вала к коллектору. На внешнем диаметре вала выполнены эвольвентные шлицы для передачи крутящего момента колесу насоса горючего.
7. Расчет элементов конструкции второй ступени
7.1 Выбор конструктивно-силовой схемы корпуса хвостового отсека
Сухие отсеки – это приборные, межбаковые, хвостовые отсеки, различного рода обтекатели. Сухие отсеки стрингерной и лонжеронной конструкции в связи с их легкостью, прочностью, простотой и технологичностью нашли наиболее широкое применение на ракетах большой дальности. С расширением возможностей технологий все чаще используют монолитные, гофрированные и многослойные обечайки.

Рис.2.1 Классификация сухих отсеков
При выборе материала необходимо учитывать множество требований, которые очень сложно оптимально сочетать в одном материале. Поэтому, в зависимости от конструктивного применения материала выделяют определяющие требования. Как правило, определяющим является требование минимальной массы при условии неразрушаемости конструкции. Наиболее эффективными являются конструкционные материалы с большой удельной жесткостью . Это отношение позволяет выбрать оптимальный материал не только по жесткости, но также и по массе. По этому показателю используемые для сухих отсеков материалы располагаются в следующем порядке: бериллиевые сплавы (5,24); магниевые сплавы (МА8-3,64); алюминиевые сплавы (Д16Т-3,16); стали (Х18Н9Т-1,72).
Выбираем для обшивки и силовых элементов сплав Амг6, руководствуясь его хорошей свариваемостью и большим модулем упругости. Этот материал широко распространен в ракетостроении, недорог и обладает хорошими прочностными показателями.
Характерным воздействием для сухих отсеков ракеты является сжатие этих отсеков. Поэтому разрушающим усилием будет являться усилие, приводящее к потере устойчивости. Потеря устойчивости может привести к разрушению всей системы, в то время как, например, явление текучести в растянутом элементе не всегда опасно для конструкции.
В приведенных ниже расчетах рассмотрены гладкая, стрингерная и вафельная конструктивно-силовые схемы хвостового отсека с определением массы каждой из схем. Расчет приводится для случая максимального нагружения хвостового отсека второй ступени, которое он испытывает в конце активного участка траектории первой ступени.
Для определения параметров конца активного участка траектории первой ступени воспользуемся программой Полет R.
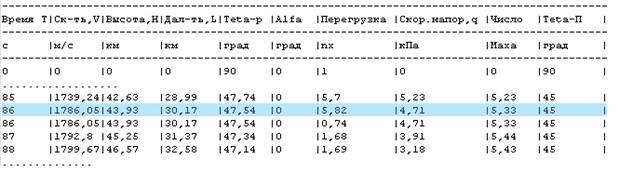
Рис.2.2 Фрагмент отчета программы Полет R.
Исходные данные:
Перегрузка в конце АУТ первой ступени .
Скоростной напор .
Масса второй ступени и полезной нагрузки .
Коэффициент безопасности .
Длина хвостового отсека .
Материал обшивки хвостового отсекаАмг6.
Плотность материала
Предел прочности (при )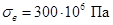
Предел текучести (при ) .
Модуль упругости (при ) .
Коэффициент Пуассона .
Сжимающая расчётная сила:
;
где

ускорение свободного падения в расчетной точке.
Расчет хвостового отсека с неподкрепленной, «гладкой» оболочкой
Толщина обшивки хвостового отсека:
.
где - коэффициент устойчивости.
Масса хвостового отсека с неподкрепленной обечайкой:
.
Расчет хвостового отсека подкрепленного стрингерами
Принимаем разрушающее напряжение для отсека из условия:
.
Шаг стрингеров из условия местной устойчивости обшивки:
;
где - толщина обшивки хвостового отсека.
Определяем число стрингеров:
.
Принимаем .
Сжимающее усилие, действующее на один стрингер:
.
Площадь поперечного сечения стрингера:
.
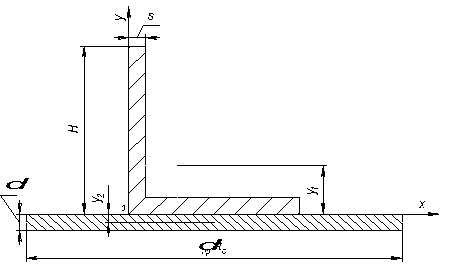
Рис.2.3 Расчётная схема стрингерного отсека
В качестве стрингера выбираем равнобокий уголок 410078 по ГОСТ 13737-90.
Таблица №2.1
Параметры профиля
Высота полки |
 |
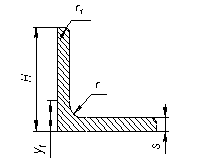 |
Толщина полки |
 |
Радиус скругления |
 |
Радиус скругления |
 |
Площадь сечения |
 |
Момент инерции сечения |
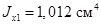 |
Координата центра тяжести |
 |
Ширина присоединенной обшивки:
.
Площадь присоединенной обшивки:
.
Определяем совместную площадь стрингера и присоединённой обшивки:
.
Вычисляем момент инерции стрингера с присоединённой обшивкой относительно наружной поверхности обшивки:
момент инерции присоединённой обшивки относительно собственной центральной оси:
;
координата центра тяжести присоединённой обшивки относительно наружной поверхности обшивки:
;
координата центра тяжести совместного сечения присоединённой обшивки и стрингера относительно наружной поверхности обшивки:
.
момент инерции стрингера с присоединённой обшивкой относительно центральной оси совместного сечения стрингера и обшивки:
.
Общая устойчивость стрингерного отсека
Критическое напряжение потери общей устойчивости отсека:
;
где – коэффициент, зависящий от характера закрепления концов стрингера.
- гибкость стрингера;
где
- радиус инерции сечения.
Условие общей устойчивости хвостового отсека:
- условие не выполняется.
Разделим хвостовой отсек по длине на несколько участков при помощи промежуточных шпангоутов:
- общее число шпангоутов отсека:
- число панелей по длине отсека:
- длина отдельной панели хвостового отсека:
Проводим повторные вычисления гибкости стрингера и критического напряжения потери общей устойчивости хвостового отсека.
Гибкость стрингера:
.
Критическое напряжение потери общей устойчивости отсека:
;
Условие общей устойчивости хвостового отсека:
- условие выполняется.
Коэффициент запаса общей устойчивости отсека:
.
Местная устойчивость стрингера
Критическое напряжение потери устойчивости ребра панельного отсека:
.
где - коэффициент устойчивости полки стрингера.
Коэффициент запаса устойчивости стрингера:
.
Местная устойчивость обшивки между соседними стрингерами
Критическое напряжение потери устойчивости обшивки:

Коэффициент запаса устойчивости обшивки:
.
Масса отсека стрингерной конструкции
Масса обшивки хвостового отсека:
.
Масса стрингеров:

Масса отсека:
.
Расчет хвостового отсека вафельной конструкции
Вафельные оболочки являются предельной формой стрингерно-шпангоутного силового набора. Вафельные оболочки изготавливают фрезерованием толстых листов, методом электрохимического фрезерования и др. При химическом травлении радиус сопряжения между ребром и обшивкой равен высоте ребра. В настоящее время такие оболочки практически не применяются, поскольку, из-за нерациональной формы ребер, они проигрывают в массе механически фрезерованным оболочкам.
По типу расположения ребер, вафельные оболочки различают на оболочки с продольно кольцевым, с перекрестным и с перекрестно кольцевым расположением ребер.
Для проектируемого хвостового отсека выбираем оболочку с перекрестно кольцевым расположением ребер.
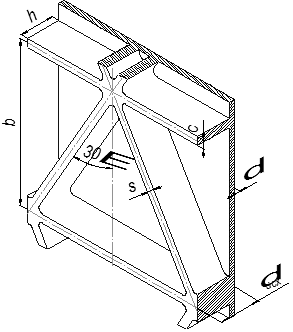
Рис.2.4 Расчетная схема вафельной оболочки
Толщина стенки панельной оболочки:
.
где - безразмерный коэффициент, определяющий отношение толщины исходного листа к толщине стенки вафельной оболочки. Выбирается из диапазона .
- безразмерный коэффициент, определяющий отношение шага ребер к их толщине.
- коэффициент устойчивости вафельной оболочки. Выбирается из диапазона .
.
Толщина исходного листа:
.
Принимаем соотношение коэффициентов подкрепления в осевом и продольном направлении , так как оболочка нагружена осевой силой.
Шаг ячейки:
.
где
.
- безразмерный коэффициент. Выбирается из диапазона .
Толщина ребра в поперечном направлении:
.
Толщина ребра в кольцевом направлении:
.
Местная устойчивость обшивки
Критическое усилие потери местнойустойчивости оболочки:
.
Запас прочности:
.
Местная устойчивость продольных ребер
Критическое усилие потери устойчивости продольного ребра:
.
Запас прочности:
.
Масса отсека вафельной конструкции
Масса обшивки хвостового отсека:
.
Масса силового набора:

где
- площадь ребер в поперечном и кольцевом направлении.
- количество ребер в поперечном направлении.
- количество ребер в кольцевом направлении.
Масса отсека:
.
По результатам проведенных расчетов наименьшую массу имеет отсек вафельной конструкции.
Если определяющим критерием выбора конструктивно-силовой схемы отсека _ей_яется минимальная масса, то предпочтительнее использовать вафельную оболочку. Но если выбор вести и по критерию стоимости изготовления то предпочтительнее использовать оболочку, подкрепленную стрингерами, так как ее стоимость значительно ниже.
7.2 Расчет фермы полезной нагрузки
Рамные конструкции применяются в ЛА для крепления полезной нагрузки в герметичных контейнерах, приборов и аппаратуры, а также для установки двигателей в отсеках в отсеках больших габаритных размеров.
Конструктивные схемы рам определяются требуемой жесткостью конструкции. При выборе конструктивно-силовой схемы фермы учитывается назначение конструкции и требуется в основном определить необходимое число стержневых элементов, их взаимное расположение и число шпангоутов по заданным параметрам прочности и жесткости. При этом требуется обеспечить геометрическую неизменяемость системы, для чего фермы должны быть осесимметричными.
Силовая ферменная конструкция состоит из труб, штампованных фитингов с трубчатыми отростками для соединения сваркой с трубчатыми стержнями и из опор, с помощью которых ферма крепится к стыковочному шпангоуту.
Стержни, как правило, выполняются из труб, а при значительных нагрузках – из прессованных профилей: двутавров, швеллеров и т. д.
Фитинги ферменной конструкции обеспечивают не только жесткую механическую связь, но и также более равномерное распределение и передачу нагрузок.
Исходные данные:
Перегрузка в конце АУТ второй ступени .
Масса полезной нагрузки .
Радиус нижнего основания фермы .
Радиус верхнего основания фермы .
Высота фермы .
Число узлов фермы на меньшем основании .
Число стержней фермы .
Температура рабочей среды .
Марка материала фермыАмг6.
Предел прочности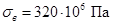
Предел текучести .
Модуль упругости .
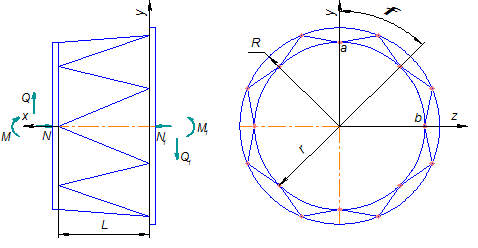
Рис.2.5 Расчетная схема фермы ПН
Расчетное усилие, действующее на ферму
Вес полезной нагрузки:
,
Осевая сила:

где - коэффициент динамичности ( ).
Перерезывающая сила:
.
где - коэффициент поперечной перегрузки ( ).
Изгибающий момент относительно меньшего основания фермы:
.
где - расстояние от центра тяжести ПН до верхнего основания фермы.
Расстояние между узлами по меньшему диаметру фермы:
.
Длина стержней:

Наибольшее касательное усилие на узел фермы в сечении :
;
;
.
Принимаем: .
Наибольшая осевая нагрузка на узел с угловой координатой (точка а):
.
Наибольшая осевая нагрузка на узел угловой координатой (точка b):

;
;
;
;
Принимаем за наибольшее расчетное усилие в стержне .
Расчет стержня фермы трубчатого сечения
Предельная гибкость стержня:

где - коэффициент заделки стержня, учитывающий жесткость закрепления стержня на опоре .
Потребная площадь поперечного сечения стержня:
.
Потребный момент инерции стержня трубчатого сечения:
.
По сортаменту стандартного проката подбираем трубу с максимально близкими значениями площади и момента инерции .
Для изготовления стержня фермы принимаем трубу Амг6 18х1,5 ГОСТ 18482-79, имеющую площадь сечения , момент инерции .
Действительные напряжения сжатия в стержне:
.
Действительная гибкость стержня:
.
Критическое напряжение при условии :
.
Условие устойчивости выполняется.
Коэффициент запаса устойчивости:
;
Коэффициент запаса находится в допустимых пределах .
7.3 Компенсация отверстий в баке окислителя второй ступени
При наличии отверстий в оболочках, сопротивляемость неподкреплённых стенок значительно снижается, поэтому возникает необходимость компенсировать это ослабление. Как показывают эксперименты, вблизи неподкреплённых отверстий имеет место значительная концентрация напряжений, причём местные напряжения имеют быстро затухающий характер.
Для компенсации ослабления и уменьшения концентрации напряжений, отверстие окантовывается добавочным материалом. Частично или полностью ослабление компенсируется также за счёт увеличения толщины оболочки. Однако увеличение толщины всей оболочки нерационально, так как приводит к излишней затрате материала и увеличению массы конструкции, поэтому увеличивают толщину оболочки только в некоторой зоне вблизи отверстия.
В баке окислителя второй ступени можно выделить следующие отверстия, выполненные в оболочке: боковой вырез под люк лаз, выполненный в верхнем днище и центральный вырез в нижнем днище под топливную магистраль.
Определение меридиональных и кольцевых погонных усилий в днищах бака окислителя будем проводить по безмоментной теории оболочек. Неточности вызванные допущениями при расчетах, компенсируются коэффициентом безопасности.
Исходные данные:
Радиус сферического днища бака .
Высота сферического днища .
Коэффициент безопасности .
Материал днищаАмг6.
Предел прочности материала днища .
Усиление отверстия под топливную магистраль
Так как нижнее днище бака окислителя нагружается гидростатическим давлением столба жидкости (давление наддува не учитывается, так как днище совмещенное, а давления наддува в баках горючего и окислителя равны), то наибольшие погонные усилия, _ействующие в оболочке, возникают в момент, когда достигает своего максимума произведение . Гидростатическое давление достигает своего максимума в конце активного участка траектории первой ступени и равняется .

Рис.2.6 Изменение произведения по времени полета.
Диаметр отверстия под ЗУ окислителя .
Диаметр соединения ЗУ и нижнего днища .
Наружный диаметр накладки .
Толщина нижнего днища .
Толщина накладки .
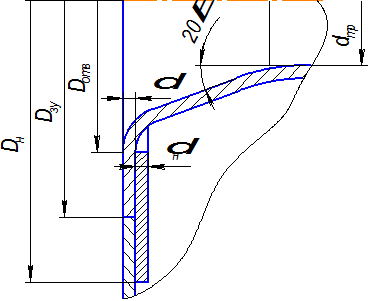
Рис.2.7 Геометрические параметры трубопровода окислителя
Общая площадь усиливающего элемента (кривизной фигур пренебрегаем):
.
Угол широты на границе отверстия:
;
где
.
Меридиональные погонные усилия на границе отверстия:
.
Нормальная растягивающая сила, действующая в кольце:
.
Напряжение, возникающее в кольце:
.
Максимальная расчетная нагрузка для материала накладки:
.
Условие прочности:
- не выполняется. Необходимо увеличить толщину накладки.
Принимаем новую толщину накладки .
Увеличенная площадь усиливающего элемента:
.
Напряжение, возникающее в кольце:
.
Условие прочности:
-выполняется.
Усиление отверстия под люк-лаз
Люк-лаз выполнен в верхнем днище бака окислителя, и расположен в стороне от оси симметрии днища. Такое отверстие подвержено комбинированному воздействию меридиональных и кольцевых усилий. При этом усиление такого отверстия будет воспринимать, наряду с растягивающими нагрузками и изгибающие моменты.
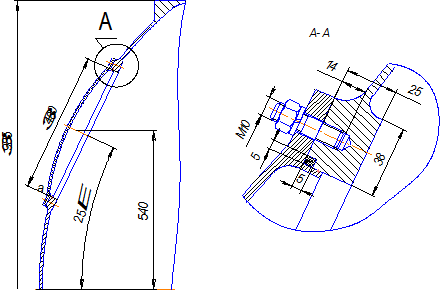
Рис.2.8 Верхнее днище и поперечное сечение фланца люка-лаза
Крышки люков-лазов должны герметично закрывать люк. Простейшая герметизация с помощью плоской прокладки не дает надежного уплотнения, поэтому герметизацию осуществляют установкой прокладки в замкнутом объеме и с применением выступов, врезающихся в прокладку.
Фланцы люков необходимы для размещения крепежных шпилек и для восприятия усилий от давления наддува. Минимальное сечение фланца определяется путем вычерчивания в натуральную величину, с учетом крепежных элементов и уплотнений, расположенных в нем. Далее определяем интересующие нас параметры сечения:
- - момент инерции относительно оси Х (ось перпендикулярна плоскости люка);
- - площадь эффективного (с учетом места под резьбу и пазов под уплотнения) сечения фланца.
Площадь образующего прямоугольника:

Площадь поперечного сечения резьбовой части:
.
Площадь выреза под уплотнение:
.
Площадь эффективного сечения фланца:
.
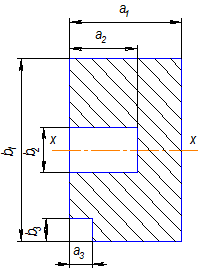
Рис.2.9 Расчетное сечение люка лаза
Момент инерции образующего прямоугольника:
.
Момент инерции сечения резьбовой части:
.
Момент инерции выреза под уплотнение:

Момент инерции сечения фланца относительно оси х:
.
Определим нормальные и касательные напряжения, действующие в сечениях фланца. Для этого построим эпюры изгибающих моментов, нормальных и перерезывающих сил на основании следующих зависимостей:
;
;
.
где - погонная нагрузка, вызванная действием меридиональных, кольцевых усилий. Определяется как среднее арифметическое погонных меридиональных (кольцевых) усилий, действующих на длине диаметра рассматриваемого выреза.

- диаметр средней линии фланца;
- диаметр проходного сечения.
- ширина фланца.
- угол в плоскости выреза, однозначно определяющий положение рассматриваемого сечения.
Таблица №2.2.
Распределение изгибающих моментов, нормальных и перерезывающих сил
 |
 |
 |
 |
 |
 |
 |
 |
 |
 |
0 |
0 |
0 |
6250 |
0 |
0 |
-1333 |
0 |
0 |
4917 |
10 |
-2922 |
16572 |
5873 |
623 |
-3534 |
-1252 |
-2298 |
13037 |
4620 |
20 |
-11336 |
31145 |
4788 |
2417 |
-6643 |
-1021 |
-8918 |
24502 |
3766 |
30 |
-24227 |
41962 |
3125 |
5167 |
-8950 |
-666 |
-19059 |
33012 |
2458 |
40 |
-40040 |
47718 |
1085 |
8540 |
-10177 |
-231 |
-31500 |
37540 |
853 |
50 |
-56868 |
47718 |
-1085 |
12129 |
-10177 |
231 |
-44738 |
37540 |
-853 |
60 |
-72681 |
41962 |
-3125 |
15502 |
-8950 |
666 |
-57179 |
33012 |
-2458 |
70 |
-85572 |
31145 |
-4788 |
18251 |
-6643 |
1021 |
-67320 |
24502 |
-3766 |
80 |
-93986 |
16572 |
-5873 |
20046 |
-3534 |
1252 |
-73940 |
13037 |
-4620 |
90 |
-96908 |
0 |
-6250 |
20669 |
0 |
1333 |
-76239 |
0 |
-4917 |
Наиболее нагруженное сечение (характеризуется максимальными изгибающим моментом и нормальной силой ):
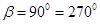   
Напряжение от действия момента :
.
Напряжения от действия растягивающей силы:
.
Напряжение от перерезывающей силы:
.
Эквивалентное нормальное напряжение:
.
Максимальная нагрузка для материала фланца:
.
Условие прочности:
- не выполняется. Необходимо изменить геометрические параметры фланца (целесообразнее изменять ширину фланца). При условие прочности выполняется .
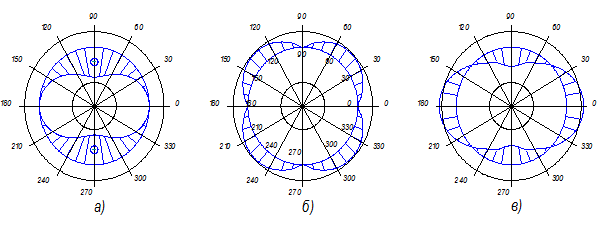
Рис 2.10 Эпюры сил и моментов действующих в вырезе под люк-лаз: а) нормальная сила; б) перерезывающая сила; в) изгибающий момент
8. Технологический процесс сборки фермы крепления ПН
Анализ служебного назначения и технологичности изделия
Ферма предназначена для крепления под оболочкой головного обтекателя полезного груза, а также передачи и равномерного распределения усилий от его веса по несущей оболочке ракеты через верхний шпангоут бака окислителя.
Так как рамы являются сильно нагруженными конструкциями, основным материалом для них является высокопрочная конструкционная сталь. Алюминиевые и магниевые сплавы применяются значительно реже. Применение титановых сплавов и композитов связано со значительными конструктивными и технологическими трудностями, хотя они и дают значительный выигрыш в весе.
Рамы представляют собой пространственную трубчатую конструкцию, работающую в основном на сжатие. Их основной конструктивный элемент — силовой треугольник из труб, связанных между собой в узлах специальными деталями, такими, как пяты и опоры.
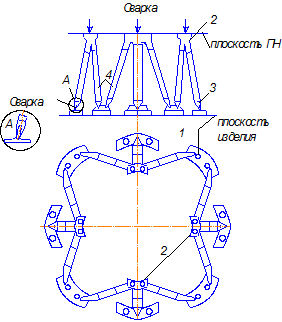
Рис.3.1 Схема односекционной цельносварной рамы: 1- пята; 2- опора; 3- коническая законцовка трубы; 4- раскосы.
Рамы бывают цельные и секционные, что определяется особенностями сборки и их габаритными размерами. Секционные рамы не имеют силовой связи между секциями до полной сборки.
В большинстве своем рамы - это сварные конструкции. Пяты и опоры, как правило, литые или штампованные (с механически обработанными стыковочными элементами).
Основные требования, предъявляемые к рамам:
- высокая жесткость конструкции, то есть обеспечение минимальных упругих деформаций;
- высокая прочность - способность противостоять значительным статическим и динамическим (вибрация) силовым воздействиям;
- обеспечение собираемости с изделием; стыковочные геометрические параметры должны лежать в строго определенных пределах (например, непараллельность поверхности пят относительно их общей поверхности не более 0,2 мм и др.).
Технологический процесс изготовления сварных рам включает в себя:
- обработку деталей (заготовка труб, разделка концов, обработка опор, кронштейнов, косынок и др.);
- сборку и сварку узлов;
- общую сборку и сварку рамы;
- механическую обработку стыковочных мест;
- контроль геометрических параметров и испытания.
Опоры обычно выполняются из стального литья с последующей механической обработкой стыковочных мест (расточка патрубков). Часто используется сталь 08Х14Н7МЛ. Пяты чаще всего являются штампованными деталями, прошедшими механическую обработку из стали 12Х2НВ. Стальное литье проверяется рентгенографированием, штамповка проверяется магнитной порошковой дефектоскопией.
Особо ответственными элементами рамы являются трубы. Заготовки из труб подвергаются 100%-ному контролю. Трубы подвергаются термо- , пескоструйной и механической обработкам и подаются па сборку. Конические заготовки, которые нельзя сделать непосредственно из трубы, штампуются из круга и привариваются к трубе. Трубы и конусы часто изготавливаются из стали 12Х2НВФА.
Сборка является ответственным технологическим процессом, который во многом определяет геометрическую точность размеров рамы. Сборка осложняется тем, что рама является пространственной стержневой конструкцией с большим количеством сварных швов, что приводит к значительным сварочным деформациям.
Сварка рамы производится в специальном приспособлении, предназначенном для закрепления и ориентации узловых деталей, пят и опор. После их установки в приспособление проводится примерка труб, вставляемых между узлами. Трубы обрабатываются до необходимого размера и ввариваются между пятой и опорой (или между опорами); первыми выполняются кольцевые швы. Сваренную раму вынимают из приспособления; при этом неизбежно возникают сварочные деформации, исправляемые механической обработкой опор и пят в специальных приспособлениях. Пяты подвергаются обычно токарной обработке. Если рама секционная, обрабатывают одновременно все секции, используя специальное приспособление, обеспечивающее единство их баз. Опоры, как правило, фрезеруют; при этом для увеличения точности обработки увеличивают жесткость рамы, добавляя в конструкцию рамы специальные трубы-стяжки, крепящиеся на трубах рамы хомутами. При сверлении отверстий в опорах используются кондукторы, базирующиеся по предварительно фрезерованным поверхностям, а при получении отверстий в пятах кондукторы имитаторы стыковочной плоскости изделия (отсека).
Дополнительно для снятия внутренних напряжений в раме после сварки применяется термическая обработка в приспособлении для сборки.
Послесварочные деформации рамы не позволяют выдержать необходимую точность положения мест стыкования рамы с корпусом ракеты и мест присоединения камер сгорания. Поэтому в конструкции двигателя предусматривают устройства для регулирования положения опор. Если таких устройств нет, то стыковочные места механически обрабатываю с целью достижения заданной точности.
Выбор способа обработки опор зависит от величины послесварочных деформаций. Если они небольшие, то можно применить шлифование. При больших деформациях перед шлифованием целесообразно ввести операцию фрезерования. Соответствующий припуск на механическую обработку опор предусматривается при изготовлении опор, подставляемых на сборку и сварку рамы. Приспособление для фрезерования и шлифования опор может быть одно. Установка рамы на опоры может оказаться недостаточно жесткой, вследствие чего при обработке могут возникнуть нежелательные вибрации стоек. В этих случаях следует установить в приспособлении подводимые опоры к стойкам. При этом нужно следить, чтобы эти подводимые опоры не влияли при установке на основные опоры и не деформировали стойки.
После сборки раму обмеряют, проверяют на собираемость при входном контроле (при этом допускается определенный натяг).
Все рамы в цеховых условиях проходят проверку на укомплектованность, осматриваются, проверяется качество сборки и сварки. В доступных местах все швы проверяют рентгеноконтролем, а в недоступных капиллярной дефектоскопией. Одна рама из 10... 20 штук подвергается разрезке на металлографию сварных швов.
Не реже чем раз в год одна рама из партии проходит статические испытания на специальном стенде с имитаторами изделия. Нагрузки прикладываются ступенчато до момента разрушения рамы. Рама должна разрушаться при нагрузке, значительно больше рабочей. После разрушения рамы производят выборочное металлографическое исследование сварных швов и мест разрушения.
Динамическим испытаниям рама подвергается только в период ее доводки.
Маршрутно-технологический процесс сборки фермы полезной нагрузки
№ операции |
Наименование операции |
Содержание операции |
Tопер, мин. |
001 |
Подготовка узлов. |
1. Провести визуальный осмотр на предмет отсутствия механических повреждений.
2. Свариваемые кромки деталей зачистить механическим способом (металлической щеткой, шабером, фрезой).
3. Произвести химическую обработку (травление, промывка, сушка, пассивация).
|
20
60
120
|
005 |
Сборка опор и конических законцовок. |
1. Закрепить детали в приспособлении согласно операционной карте.
2. Проверить смещение свариваемых кромок.
|
10
5
|
010 |
Сварка опор и конических законцовок. |
1. Установить параметры сварки согласно операционной карте.
2. Сварить опору и коническую заготовку в среде защитных газов.
|
3
8
|
015 |
Контроль качества сварных швов |
1. Произвести визуальный контроль качества сварного шва.
2. Зачистить сварной шов.
3. Провести рентгенконтроль сварных швов.
|
8
45
60
|
020 |
Сборка опор и раскосов |
1. Установить и закрепить нижние и верхние опоры в сборочном приспособлении.
2. Установить стержни на опорах и закрепить с помощью стяжек.
|
45
60
|
025 |
Сварка опор и раскосов |
1. Сварку произвести ручной аргонодуговой сваркой в порядке указанном в операционной карте |
200 |
030 |
Термическая обработка |
1. Поместить ферму в сборочном приспособлении в муфельный шкаф.
2. Выдержать при температуре 1500С.
|
10
180
|
035 |
Контроль качества швов |
1. Произвести визуальный контроль качества сварных швов.
2. Зачистить сварные швы.
3. Провести рентгенконтроль сварных швов.
|
15
45
120
|
040 |
Термическая обработка |
1. Поместить ферму в сборочном приспособлении в муфельный шкаф.
2. Выдержать при температуре 3000 С.
3. Выдержать при температуре 180 С.
|
5
8ч.
72ч.
|
045 |
Фрезерование опор |
1. Установить ферму на столе торцефрезеровального станка.
2. Выровнять плоскость опор относительно плоскости фрезерования.
3. Установить параметры хода фрезы.
|
8
10
5
|
050 |
Сверление отверстий в опорах |
1. Установить кондукторы на опорах фермы.
2. Просверлить отверстия в опорах фермы по кондуктору.
|
60 |
055 |
Контроль. |
1. Произвести контроль геометрических параметров.
2. Провести прочностные испытания.
|
60
|
060 |
Окраска |
1. Окрасить поверхность изделия краской.
2. Нанести номер изделия
|
60
15
|
065 |
Контроль ОТК |
1. Оформить дело.
2. Собранный узел предъявить ОТК.
3. Передать узел на общую сборку.
|
45
30
15
|
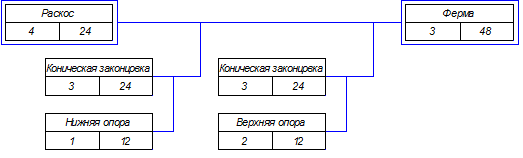
Рис.3.2 Схема сборки фермы полезной нагрузки
Конструкция сборочного приспособления
Сборка и сварка рам может, производится как из отдельных деталей, так и из деталей, предварительно соединенных в узлы. Простые рамы обычно собираются из отдельных деталей. Сложные рамы целесообразно разбивать на простые узлы и сваривать их отдельно. Это упрощает и удешевляет технологию, а также сокращает цикл сборки рамы.
Приспособления для общей сварки и сборки рам большей частью сложные, т.к. фиксаторы для удержания элементов рамы в заданном положении расположены не в плоскости, а в трехмерном пространстве.
Кроме того, эти фиксаторы должны быть сконструированы таким образом, чтобы не мешать изъятию сваренной рамы из приспособления. Для удобства сварки в некоторых случаях приспособление должно позволять поворачивать раму вокруг центральной оси, а иногда ещё и наклонять эту ось под разными углами к горизонту.
Сварка рамы сопряжена с местным нагревом ее элементов и последующим охлаждением, что порождает сварочные деформации. Эти деформации могут изменить геометрию рамы, заданную фиксаторами. Чтобы удержать стыковочные точки рамы от перемещений, вызываемых сварочными деформациями, требуются мощные фиксаторы и жесткая рама, что утяжеляет приспособление.
В некоторых случаях нет нужды удерживать элементы от перемещений, т.к. при этом силы, порождающие перемещения, будут действовать на не вполне оформившиеся и горячие сварные швы, вызывая в них разрывы и трещины.
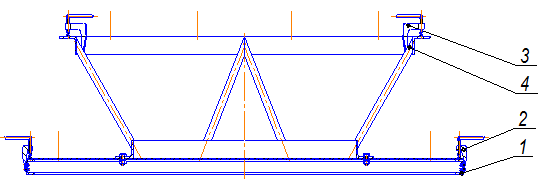
Рис.3.3 Сборочное приспособление фермы полезной нагрузки: 1- основание; 2- нижняя струбцина; 3- верхняя струбцина; 4- рама
Сборка фермы полезной нагрузки производится сваркой, после закрепления элементов в сборочном приспособлении.
Сборочное приспособление состоит из основания (поз.1) изготовленного сваркой из кольца, полученного гибкой швеллера, и круга вырезанного из металлической плиты.
К основанию прикреплены струбцины (поз. 2) и рама (поз. 4). Каждая струбцина крепится к основанию с помощью двух болтов. Всего нижних струбцин двенадцать. Рама крепится по центру основания восьмью болтами. На верхней части рамы также расположены двенадцать струбцин (поз. 3), которые крепятся на раме тем же способом, что и к основанию.
Рама представляет собой сварную конструкцию, состоящую из двух колец изготовленных из равнобоких уголков и восьми стержней трубчатого сечения. Плоскости основания и верхнего кольца рамы параллельны. На основании и верхнем кольце рамы нанесены метки для точной установки опор.
Верхняя и нижняя струбцины конструктивно подобны и имеют Г – образную форму, отличаются они тем, что верхняя струбцина имеет более длинную горизонтальную часть. Струбцины имеют винт с подвижной пятой и шарнирно закрепленную рукоять.
9. Экономическая часть
Расчет затрат на разработку инженерного проекта
Стоимость научно-технического проектирования, как правило, рассчитывается по поэлементной классификации затрат, представляя собой приблизительную смету произведенных или планируемых затрат.
Для расчетов затрат на проектирование может использоваться следующая формула:
Сп = ЗПосн
+ ЗПдоп
+ ЕСН + А + РМ +Э +НР; |
|
где Сп – стоимость научно-технического проектирования
ЗПосн – основная заработная плата проектировщика;
ЗПдоп – дополнительная заработная плата проектировщика;
ЕСН – отчисления на единый социальный налог;
А – амортизация основных фондов: помещения и оборудования (ПК);
РМ – расходные материалы;
Э – стоимость электроэнергии;
НР – накладные расходы.
Стоит отметить, что данная формула не является чем-то жестко фиксированным. Она может быть дополнена целым рядом показателей, вычлененных из так называемых «накладных расходов»
Произведём расчёт затрат по каждому элементу.
Заработная плата проектировщика
Начнем с затрат на заработную плату, поскольку для определения оплаты труда нам нужно будет рассчитать трудоемкость работ или длительность проектирования, от которой будут рассчитываться еще некоторые группы расходов, в частности, амортизация.
Расчет трудоемкости проектирования
Трудоёмкость показывает, сколько времени требуется для производства учётной единицы продукции.
Основное содержание отработки конструкции изделия на технологичность на различных стадиях разработки конструкторской документации приводится ниже (ГОСТ 14.201–83).
Таблица №4.1
Коэффициенты корректировки трудоемкости работ
Масштаб |
Поправочный коэффициент сложности работ, К1 |
Использование в работе аппликаций и оригиналов, % |
Коэффициент использования готовых разработок, К2 |
1:1 |
1.0 |
До 20 |
0.9 |
1:2; 1:10; 1:20; 1:100; 1:100; |
1.05 |
21 – 40 |
0.8 |
1:2.5; 1:4; 1:5; 1:40; 1:50; |
1.1 |
41 – 60 |
0.6 |
1:200; 1:400; 1:500; 1:800; |
1.1 |
61 – 80 |
0.4 |
2:1; 4:1; 5:1; |
1.1 |
свыше 80 |
0.3 |
1:15; 1:25; 1:75; |
1.15 |
Заимствовано |
0.2 |
Данные для расчёта суммарной трудоёмкости собственной работы представлены в табл.
Таблица № 4.2
№ |
Наименование работ |
Трудоемкость, чел. час/стр. |
К стр. |
К1 |
К2 |
Трудозатраты, чел.час |
1 |
Техническое задание |
6 |
2 |
- |
- |
12 |
2 |
Техническое предложение |
2.1 |
Ознакомление с проблемами поставленной задачи |
6 |
2 |
- |
0.9 |
10.8 |
2.2 |
Поиск необходимой литературы |
8 |
1 |
- |
1 |
8 |
3 |
Эскизный проект |
3.1 |
Предварительные замечания |
5 |
3 |
- |
0.9 |
13.5 |
3.2 |
Подготовка к проведению предварительных расчётов |
2 |
- |
- |
- |
2 |
3.3 |
Расчеты |
3 |
70 |
- |
0.9 |
189 |
3.4 |
Технологический раздел |
6 |
7 |
- |
0.9 |
37,8 |
3.5 |
Экономический раздел |
5 |
9 |
- |
0.8 |
36 |
3.6 |
Охрана труда |
5 |
10 |
- |
0.6 |
30 |
4 |
Технический проект |
4.1 |
ЖРД второй ступени |
12 |
2 |
1.1 |
0.6 |
15,8 |
4.2 |
Турбина |
12 |
1 |
1.05 |
0.6 |
7,6 |
4.3 |
Насос окислителя |
12 |
1 |
1.05 |
0.6 |
7,6 |
4.4 |
Вторая ступень баллистической ракеты с ЖРД |
12 |
3 |
1.1 |
0.6 |
23,8 |
4.5 |
Сборочное приспособление фермы полезной нагрузки |
12 |
1 |
1.05 |
0,9 |
11,3 |
5 |
Документация |
5.1 |
Спецификации |
0.5 |
4 |
- |
- |
2 |
ИТОГО |
395,2 |
Перемножая данные столбцов 3, 4, 5, 6 получаем столбец 7, складывая данные которого определим суммарную трудоёмкость собственной работы проектировщика :
Количество рабочих дней:

Отработанное время, мес.:
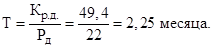
где: Рд=22 – количество рабочих дней в месяце.
Расчет заработной платы проектировщика
Определяем основную заработную плату одного проектировщика:
,
где: О – оклад проектировщика, руб.;
Т – отработанное время, мес;
– районный коэффициент.
По данным бухгалтерии ПО «Полет» оклад инженера-конструктора 3-й категории составляет 3500 руб., районный коэффициент равен 0.15:

Дополнительная заработная плата – выплата за непроработанное время отпуска, перерыва в работе на выполнение общественных обязанностей, и т. д.
Учтем дополнительную заработную плату (оплата отгулов, отпусков). Считаем через соответствующий коэффициент:

где Tпв= 120 – количество праздников и выходных в году;
Тотп= 28 – количество дней в отпуске;
Тбольн = 2 – количество дней по болезни оплачиваемых, не более 2-х дней;
ТГО = 1 – выполнение гос. обязанностей, за которые предоставляется оплачиваемый отгул (не более 1 дня в год).


Отчисления на единый социальный налог
В отчисления на единый социальный налог с 01.01.05 входят следующие статьи:
- пенсионный фонд – 20 % от фонда оплаты труда;
- налог на социальное страхование – 3.2 % от фонда оплаты труда;
- обязательное медицинское страхование – 2.8 % от фонда оплаты труда;
Итого базовая ставка ЕСН для налогоплательщиков (организаций, индивидуальных предпринимателей, физических лиц, не признаваемых индивидуальными предпринимателями), производящих выплаты физическим лицам, равна 26 %.

Амортизация основных средств
При проектировании чаще всего используются следующие основные средства: рабочее помещение, компьютер, калькулятор. К этому списку может добавляться принтер, сканер, дорогостоящий чертежный инструмент, лицензионное программное обеспечение.
Применяется линейный способ начисления амортизации согласно принятой учетной политике на большинстве предприятий; тогда сумма начисления амортизационных отчислений определяется по балансовой (первоначальной) стоимости объекта основных средств и норме амортизации, исчисленной исходя из срока полезного использования объекта.
Расчет амортизации здания
По данным всероссийского классификатора основных средств (ОС) рабочее помещение относится к амортизационной группе № 10 (более 30 лет), n=50 лет – срок эксплуатации рабочего помещения, тогда норма амортизации рабочего помещения:
Норма амортизации за год:
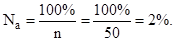
Балансовую (первоначальную) стоимость рабочего помещения определяем по нормативной стоимости метра квадратного:
;
где Нст=7400 руб/м2 – нормативная стоимость метра квадратного соответствующего типа зданий.
Рассчитаем амортизацию рабочего помещения за срок проектирования в нем, выраженный в месяцах (Т):
.
Расчет амортизации компьютера
В соответствии с порядком расчёта амортизации от 01.01.2002 г. на основе классификации основных средств, включаемых в амортизационные группы, ПК относятся к группе № 3 (3 – 5 лет эксплуатации); берем за срок эксплуатации n=5 лет.
Норма амортизации за год:
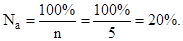
Балансовая (первоначальная) стоимость компьютера равна его первоначальной стоимости и складывается из цены всех комплектующих.
Составляющие ПК (по данным прайс-листа фирмы «Интерсофт»):
Системный блок (процессор “Intel Celeron D320 2400+”, оперативная память 768 МБ, жесткий диск 80 Гб) – 19540 руб.
ЭЛТ монитор «LG» – 5560 руб.
Струйный принтер «Lexmark» –1500 руб.
Итого – цена комплектующих компьютера 
.
Расчет амортизации программного обеспечения
По данным всероссийского классификатора основных средств (ОС) программное обеспечение относится к 1 амортизационной группе ОС (1–2 года), срок эксплуатации программного обеспечения n=2 года.
Амортизация программного обеспечения:
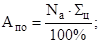
где ∑ц – суммарная цена программного обеспечения.
Норма амортизации программного обеспечения за год равна:
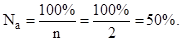
В табл. сведена стоимость программного обеспечения, используемого при разработке дипломного проекта.
Таблица № 4.3
Стоимость программного обеспечения
Наименование ПО |
Цена, руб |
Операционнаясистема
Microsoft® Windows® XP Professional
|
4600.00 |
Офисныйпакет
Microsoft® Office XP Professional
|
9500.00 |
АСКОН ® Система трехмерного твердотельного моделирования КОМПАС–3D V8 |
50000.00 |
Mathsoft® Mathcad 12 |
7500.00 |
Итого, ∑ц |
71600.00 |
Амортизация программного обеспечения за период проектирования:

Расчет затрат на ремонт ПК
Нормативные отчисления на ремонт оборудования (ЭВМ) составляют 2%.
Затраты на ремонт оборудования (ЭВМ):

Расходы на электроэнергию
Потребляемая мощность (Nк) компьютера составила 350Вт.
Коэффициент использование компьютерной техники в проектировании равен 0.7. Таким образом, компьютер использовался в среднем 5.6 часа в день (t).
Определяем полное время его работы.
,
где РД – число рабочих дней в месяце;
n – число месяцев выполнения дипломного проекта.

Стоимость электроэнергии за расчетный период составляет С=1.36 р/кВт/ч.
Определяем затраты на электроэнергию:

Расчет затрат на расходные материалы
РМ = Б + КТ ,
где Б = 130 руб. – затраты на бумагу (за 1 пачку);
КТ – затраты на канцелярские товары и чертёжные принадлежности:
- линейка 24 руб.
- скрепки 6 руб.
- ручка 25 руб.
карандаш автоматический 25 руб.
КТ =24+6+25+25 = 80 руб.
РМ = 130+80 = 210 руб.
Результаты расчетов сводим в табл.
Таблица №4.4
Расходный материал |
Количество |
Цена за единицу, руб. |
Стоимость |
Бумага |
1 пачка |
130 |
130 |
Линейка |
1 шт. |
24 |
24 |
Ручка |
1 шт. |
25 |
25 |
Карандаш автоматический |
1 шт. |
25 |
25 |
Скрепки |
1 упаковка |
6 |
6 |
Итого, РМ |
210 |
Накладные расходы
В накладные расходы входят затраты по управлению и содержанию проектной организации, а также затраты на содержание помещения, на освещение, хозяйственные расходы и т.д.
По данным бухгалтерского отдела ПО «Полет»:
НР = ЗПосн ∙ 300% = 9056,25∙3=27168,75 руб.
Определяем суммарные расходы на проектирование:
Сп = ЗПосн + ЗПдоп + ЕСН + Ап + Э + РМ + НР;
Сп=9056,25+893,85+2587+276+997,5+6712,5+1197+131,95+210+27168,75=49230,8 руб.
Таблица №4.5
Смета затрат на проектирование
Группы затрат |
Затраты, руб. |
1. Основная заработная плата ИТР |
9056,25 |
2. Дополнительная заработная плата ИТР |
893,85 |
3. Отчисления на единый социальный налог |
2587 |
4. Амортизация рабочего помещения |
276 |
5. Амортизация ПК |
997,5 |
6. Амортизация ПО |
6712,5 |
7. Эксплуатация и ремонт ПК |
1197 |
8. Электроэнергия |
131,95 |
9. Расходные материалы |
210 |
10. Накладные расходы |
27168,75 |
Итого:
|
49230,8
|
10. Безопасность жизнедеятельности
10.1 Охрана труда
Негативные производственные факторы при проектировании.
Производственная среда – это часть техносферы, обладающая повышенной концентрацией негативных факторов. Основными носителями травмирующих и вредных факторов в производственной среде являются машины и другие технические устройства, химически и биологически активные предметы труда, источники энергии, нерегламентированные действия работающих, нарушение режимов и организации деятельности, а также отклонения от допустимых параметров микроклимата рабочей среды.
Игнорирование негативных производственных факторов, а также несвоевременное проведение мероприятий по их устранению или снижению могут привести к понижению трудоспособности, ухудшению здоровья работников, а иногда и к человеческим жертвам.
Травмирующие и вредные факторы подразделяют на физические, химические, биологические и психофизиологические (в соответствии с ГОСТ 12.0.003 – 74).
Травмирующие и вредные факторы производственной среды, характерные для большинства конструкторских бюро, приведены в табл. 5.1.
Таблица №5.1
Группа факторов |
Факторы |
Источники и зоны действия фактора |
Мероприятия |
Физические |
Повышенная или пониженная температура воздуха |
Не достаточно эффективная работа отопительной системы в помещении |
Установка дополнительных обогревателей |
Повышенная или пониженная влажность воздуха |
Неправильная организация вентиляционной системы помещений |
Повышение эффективности работы вентиляции установка, при необходимости, кондиционеров |
Повышенный уровень статического электричества |
Зоны около электротехнического оборудования на постоянном токе |
Установка специальных экранов |
Недостаток естественного света |
Неправильное или нерациональное расположение рабочих мест в помещении |
Эффективность естественного освещения можно повысить за счёт применения окраски стен более светлых тонов. |
Физические |
Недостаточная освещённость рабочей зоны |
Неправильная организация освещения рабочих мест |
Рабочее место следует располагать так, чтобы источник освещения рабочей зоны находился слева |
Электромагнитные поля и излучения, повышенная пульсация светового потока |
Зоны около телеэкранов, дисплеев компьютеров, антенн |
Установка специальных защитных экранов на дисплеи |
Психофизиоло-гические |
Статические физические перегрузки |
Продолжительная работа с дисплеями, работа в неудобной позе |
Правильная планировка рабочих мест, организация труда и отдыха. Выбор удобной мебели (рабочие столы, стулья). Минимальная площадь рабочей зоны конструктора 6м2. Наиболее рационально размещать в помещении 10 – 15 конструкторов. |
Нервно-психические перегрузки: |
1) умственное перенапряжение |
Создание научных трудов, разработка сложных инженерных расчётов и чертежей |
2) перенапряжение анализаторов |
Продолжительная работа с дисплеями |
3) монотонность труда |
Продолжительная работа с чертежами |
4) эмоциональные перегрузки |
Ответственность за выполняемую вычислительную работу |
Оптимальные показатели микроклимата на рабочих местах с ВДТ и ПЭВМ
Таблица №5.2
Период года |
Категория работ по уровню энергозатрат, Вт |
Температура воздуха,
°С |
Температура поверхностей,
°С |
Относительная влажн
ость воздуха, % |
Ск
орость движения воздуха, м/с |
Холодный |
Iа (до 139) |
22-24 |
21-25 |
60-40 |
0,1 |
Теплый |
20-22 |
19-23 |
60-40 |
0,2 |
Допустимые показатели микроклимата на рабочих местах с ВДТ и ПЭВМ
Таблица
№5.3
Период года |
Температура воздуха, 0С. |
Температура поверхностей, 0С. |
Относительная влажность воздуха, % |
Скорость движения воздуха, м/с |
Холодный |
20-25 |
19-26 |
15-75*(2) |
0,1*(3) |
Теплый |
21-28 |
20-29 |
15-75*(2) |
0,2*(3) |
Нормируемые показатели освещения основных помещений общественных, жилых, вспомогательных зданий
Таблица №5.4
Помещения |
Нормирование освещенности и КЕО, высота плоскости над полом (В – вертикальная плоскость, Г – горизонтальная плоскость) |
Искусственное освещение |
Разряд и Подразряд зрительной работы |
Естественное освещение |
Совместное освещение |
Помещения для работы с дисплеями |
Освещенность рабочих поверхностей |
Цилиндрическая освещенность |
Показатель дискомфорта |
Коэффициент пульсации |
При верхнем или комбинированном освещении |
При боковом освещении |
При верхнем или комбинированном освещении |
При боковом освещении |
При комбинированном |
При общем освещении |
В-1,2 (на экране дисплея) |
- |
200 |
- |
- |
- |
Б-2 |
- |
- |
- |
- |
Г-0,8 (на рабочих столах) |
500/300 |
300 |
- |
15 |
5 |
А-2 |
3,5 |
1,2 |
2,1 |
0,7 |
Уровни ионизации воздуха помещений при работе на ВДТ и ПЭВМ
Таблица № 5.5
Уровни |
Число ионов в 1 см3 воздуха |
n+ |
n- |
Минимальный |
400 |
600 |
Оптимальный |
15000-30000 |
30000-50000 |
Максимальный |
50000 |
50000 |
Временные допустимые уровни электромагнитного потока, создаваемого ПЭВМ
Таблица №5.6
Наименование параметров |
ВДУ ЭМП |
Напряженность электрического поля |
в диапазоне частот 5 Гц -2кГц |
25 В/м |
в диапазоне частот 2кГц -400кГц |
2,5В/м |
Плотность магнитного потока |
в диапазоне частот 5 Гц -2кГц |
250 нТл |
в диапазоне частот 2кГц -400кГц |
25 нТл |
Электростатический потенциал экрана монитора |
500 В |
Мероприятия по устранению действия опасных и вредных факторов.
Для поддержания нормального микроклимата в рабочей зоне ИТР необходимо применение вентиляции. Вентиляция достигается удалением загрязненного и нагретого воздуха из помещений и подачи в него свежего воздуха. Также для эффективной работы системы вентиляции важно учитывать технические и санитарно-гигиенические требования, такие как:
количество приточного воздуха должно соответствовать количеству удаляемого;
система вентиляции не должна вызывать переохлаждения или перегрева работающих;
система вентиляции не должна создавать шум на рабочих местах;
система вентиляции должна быть электро-, пожаро- и взрывобезопасной.
Кроме применения вентиляции, в создании комфортных (оптимальных) санитарно-гигиенических условий, осуществление которых с помощью обычной вентиляции невозможно входит кондиционирование.
Наиболее рациональным методом по борьбе с шумом является метод акустической обработки помещения, а в частности установка в помещении штучных шумопоглотителей.
Очень важным мероприятием по борьбе с ОВПФ является защита от электромагнитных полей. Наиболее эффективным и часто применяемым методом является установка экранов.
Мероприятием по борьбе с недостаточной освещенностью является применение люминесцентных ламп и ламп ДРЛ. Также предусматривается установка эритемного (профилактического ультрафиолетового) облучения для компенсации солнечной недостаточности. Ультрафиолетовое облучение положительно влияет на обмен веществ, дыхательные процессы, активацию кровообращения и другие функции организма.
Для повышения равномерности естественного освещения осуществляется комбинированное освещение. Светлая окраска потолка, стен и оборудования способствует созданию равномерного распределения яркостей в поле зрения.
Смягчение теней осуществляется с помощью применения светильников со светорассеивающими стеклами, а также предусмотрения на окнах солнцезащитных устройств, которые предотвращают проникновение прямых солнечных лучей, создающих на рабочих местах резкие тени.
Расчет искусственного освещения
При проектировании искусственного освещения необходимо решить задачи: выбрать систему освещения, тип источников света, тип светильников, расположить светильники, определить мощность источников света.
В гигиеническом отношении система общего освещения более совершенна, так как более равномерно распределяет световую энергию, но система комбинированного освещения экономичнее.
Равномерность общего освещения достигается при l<2H, где l - расстояние между центрами светильников, H - высота подвеса светильника над рабочей плоскостью. Рекомендуется размещать светильники с лампами накаливания параллельными рядами, принимают: l=(1,4…1,8)H, для люминесцентных светильников l=0,5l при удалении их от стены.
Для расчета искусственного освещения наиболее распространены методы светового потока, точечный и удельной мощности.
Метод светового потока предназначен для расчета общего освещения горизонтальных поверхностей и позволяет учесть как прямой световой поток, так и отраженный от стен и потолка.
Световой поток одного источника света рассчитывается по формуле:

где Е=400 лк - нормированная освещенность, лк;
Кз=1,5 - коэффициент запаса, учитывающий старение ламп и загрязнение светильников (определяем по табл.5.1);
S=20 м2 - площадь освещаемого помещения;
Z=1,1 - коэффициент минимальной освещенности, для люминесцентных ламп;
N=6 - число источников света в помещении;
η=0,6 - коэффициент использования светового потока.
Коэффициент η зависит от типа светильника, коэффициентов отражения R от стен, потолка, пола и от геометрической характеристики помещения, определенной индексом помещения:
Таблица №5.7
Значение коэффициента запаса Kз.
Характеристика объекта |
Лампы накаливания |
Люминесцентные лампы |
Помещения с большими выделениями пыли, дыма, копоти
Помещения со средними выделениями пыли, дыма, копоти
Помещения с малыми выделениями пыли
Наружное освещение светильниками
Прожекторное освещение
|
1,7
1,5
1,3
1,3
1,5
|
2,0
1,8
1,5
1,5
-
|
Таблица №5.8
Коэффициенты отражения поверхностей Rj.
Поверхность |
Коэффициент отражения |
Поверхность |
Коэффициент отражения |
Свежая побелка
Чистый бетон, побелка помещения
Грязные бетон, светлые обои
Кирпич неоштукатуренный
|
0,7
0,5
0,3
0,1
|
Цвет окрашенной поверхности:
Белый
Розовый
Желтый
Красный (светлый)
Голубой, серый
Зеленый (светлый)
Коричневый
Темно-коричневый
Темно-зеленый
|
0,79-0,84
0,69
0,6
0,56
0,53
0,41
0,23
0,15
0,1
|
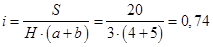
где a=4м и b=5м - длина и ширина помещения.
H=3,0 м - высота подвеса ламп.
Коэффициенты отражения некоторых поверхностей Rj приведены в табл.5.3, а коэффициенты использования светового потока для рассмотренных выше светильников и ряда сочетаний коэффициентов отражения – в табл.5.3.
По полученному световому потоку F подбирают ближайшую стандартную лампу (табл. 5.4). Допускается отклонение светового потока выбранной лампы от расчетного не более чем на (-10…+20)%. Если такое приближение не реализуется, то корректируется число источников света.
Таблица №5.9
Электрические и световые характеристики ламп.
Лампы накаливания (ГОСТ 2239-79) |
Люминесцентные лампы (ГОСТ 6825-79) |
Мощность  |
Световой поток , при  |
Тип лампы |
Световой поток  |
Длина  |
15
25
40
60
75
100
150
200
300
500
750
1000
1500
|
105
210
380
650
950
1320
2000
2950
4500
8200
13100
18500
28000
|
ЛД30-4
ЛБ30-4
ЛД40-4
ЛБ40-4
ЛД65-4
ЛБ65-4
ЛД80-4
ЛДЦ80-4
ЛБ80-4
ЛХБ80-4
ЛТБ80-4
|
1640
2100
2340
2680
3570
3980
4070
3560
6220
4444
4440
|
895
1199
1500
|
По полученному световому потоку F=6111лк по (табл.5.4) подбираем ближайшую стандартную лампу ЛБ80-4.
Защита в чрезвычайных ситуациях.
Устойчивость функционирования объектов экономики. Общие принципы повышения устойчивости.
Большое значение для существования и развития государства имеет его экономический потенциал. Устойчивая экономика позволяет в мирное и военное время решать следующие задачи:
обеспечивать всем необходимым население и армию, в том числе оружием и боеприпасами, транспортными средствами, горючим, средствами связи и др.;
поддерживать производство по планам мирного времени и в кризисных ситуациях;
осуществлять в допустимые сроки восстановительные работы на хозяйственных объектах;
осуществлять разработку новой техники, технологий, в том числе для нужд оборонного комплекса государства и др.
Под устойчивостью технической системы понимают её способность сохранять работоспособность при нештатном воздействии. Соответственно под устойчивостью функционирования объекта экономики будем понимать его способность выпускать продукцию в объёмах и номенклатуре, соответствующих планам, в условиях чрезвычайной ситуации, а также возможности его восстановления после воздействия поражающих факторов. Для объектов, не связанных с выпуском продукции, устойчивость определяется их способностью выполнять свои функции в условиях чрезвычайной ситуации.
В соответствии с этим различают:
Устойчивость функционирования хозяйственного комплекса страны в целом – это способность обеспечить жизнедеятельность государства, выпуск промышленной и сельскохозяйственной продукции, работу энергетики, транспорта и др.;
Устойчивость функционирования отдельной отрасли экономики государства – это способность в условиях кризисной ситуации производить основную продукцию в запланированном объёме;
Устойчивость объекта экономики – это способность всего его комплекса, то есть зданий, сооружений, оборудования, транспорта, коммуникаций противостоять воздействию поражающих факторов чрезвычайной ситуации;
Устойчивость функционирования объекта экономики – это его способность в условиях чрезвычайной ситуации производить продукцию в запланированном объёме и номенклатуре, а так же восстанавливать производство в допустимые сроки после частичных разрушений.
В свою очередь устойчивость функционирования объекта экономики определяется рядом условий:
возможностью защиты работников от всех поражающих факторов;
способностью его строений, оборудования, коммунально-энергетических сетей противостоять поражающим факторам;
надёжностью системы управления, снабжения, оповещения и связи;
возможностью восстановить производство продукции после разрушения и др.
На устойчивость промышленного объекта влияют многие внешние и внутренние факторы.
Район расположения предприятия определяет уровень и вероятность опасности проявления негативных факторов природного происхождения: ураганов, землетрясений, оползней, наводнений и др.
Характер застройки территории определяет наличие смежных производств, естественных укрытий, транспортных магистралей и др. Должны создаваться противопожарные разрывы путём снижения плотности застройки городов, создания отдельных микрорайонов, полос зелёных насаждений, сохранения естественных водоёмов и т.п.
Устройство широких магистралей и создание необходимой транспортной сети имеет цель не допустить образования сплошных завалов, затрудняющих действия спасателей и эвакуацию населения. Ширина таких магистралей (улиц) определяется по формуле:
Ш = Нmax + 15 м,
где Нmax – высота самого высокого здания на магистрали (улице), м.
Планировка зданий и сооружений на территории объекта экономики должна учитывать противопожарные разрывы, ширина которых определяется по формуле:
Шпр = Н1 + Н2,
где Н1 и Н2 - высоты соседних зданий (сооружений), м.
Наиболее значимые сооружения пониженной этажности или заглубленными, их форма должна иметь минимальную парусность, чтобы противостоять воздействию ударной волны.
Для повышения устойчивости элементов зданий и сооружений к световому излучению применяют огнестойкие конструкции, несгораемые материалы, огнезащитные покрытия для сгораемых элементов. Большие здания и сооружения рекомендуется разделять на секции несгораемыми стенами.
С целью исключения проникновения во внутренние помещения радиоактивных элементов, вредных (опасных) химических веществ или бактериологических средств, необходимо предусматривать возможность герметизации зданий, складов и т.п.
Наиболее ценное оборудование целесообразно размещать в прочных сооружениях заглубленного типа или, напротив, в сооружениях из лёгких несгораемых конструкций, так как оборудование более устойчиво к воздействию ударной волны, чем к обломкам обрушившегося здания.
Сооружения, предназначенные для хранения или переработки горючих жидкостей, рекомендуется размещать ниже по уклону местности, чем другие здания и сооружения. Подъездные дороги на территории таких объектов рекомендуется планировать по насыпям, чтобы исключить их затопление при разливе горючих жидкостей.
Толстые стены зданий и сооружений, применение специальных перекрытий и прокладок значительно увеличивает коэффициент ослабления проникающей радиации.
Повышение устойчивости снабжения электроэнергией имеет особое значение, как в быту, так и для хозяйственной деятельности. Прекращение электроснабжения зачастую приводит к прекращению деятельности объекта экономики. Соответственно снабжение электроэнергией больших населённых пунктов и крупных хозяйственных объектов целесообразно осуществлять от двух независимых источников. Наиболее значимые объекты экономики должны иметь автономное электрообеспечение.
Система электроснабжения включает:
электростанции;
линии электропередачи, кабельную и внутреннюю электросеть;
трансформаторные и распределительные станции;
диспетчерские пункты.
Электроснабжение подразделений объекта экономики следует осуществлять по независимым подземным кабельным линиям. Устойчивость трансформаторных подстанций и распределительных устройств предусматривается не ниже устойчивости самого объекта.
Повышение устойчивости снабжения объектов экономики и жилых комплексов водой в настоящее время стало жизненно важной задачей. Производственный цикл большинства предприятий требует надёжного водообеспечения. Отсутствие воды для жителей современных городов сопоставимо с серьёзной чрезвычайной ситуацией.
Современный комплекс водообеспечения включает в себя целый ряд наземных и подземных сооружений. Различают два типа водных источников: от поверхностных (открытых) водоёмов и от подземных источников.
Наиболее слабым звеном системы водоснабжения являются наземные сооружения, что предполагает их особую защиту. Крупные города и уникальные объекты экономики должны иметь не менее двух источников водоснабжения. Системы водоснабжения должны предусматривать возможность отключения повреждённых участков без нарушения функционирования всей системы. Сети водоснабжения должны быть закольцованы и иметь резервные ёмкости с водой, находящиеся под землёй на возвышенных участках местности. Система водоснабжения должна иметь приборы сигнализации и автоматического отключения повреждённых участков.
Сооружения водозабора из открытых источников выполняются из прочных конструкций, выдерживающих воздействие поражающих факторов чрезвычайных ситуаций. Предусматриваются специальные режимы очистки и обеззараживания воды, подаваемой для нужд населённых пунктов, если поступление воды происходит только от поверхностных вод. При этом необходимо учитывать, что для обеззараживания применяется жидкий хлор, хранящийся под высоким давлением, что может привести к химическому заражению в аварийных ситуациях.
Повышение устойчивости газоснабжения населённых пунктов и хозяйственных объектов является необходимым условием нормальной жизнедеятельности и ритмичной работы предприятий. При разрушении элементов системы газоснабжения не только нарушается весь технологический цикл производства, но и появляется опасность возникновения пожаров, взрывов, повышенной загазованности территорий.
Система газоснабжения включает:
источники газа;
магистральные газопроводы;
компрессорные, газгольдерные и газораспределительные станции;
городские газовые сети и сети промышленных предприятий;
запорные устройства.
Надёжность работы системы газоснабжения обеспечивается следующим:
двери, окна, фрамуги в наземных газораспределительных пунктах должны открываться наружу;
газовые сети располагаются под землёй, закольцовываются, оборудуются запорной и предохранительной аппаратурой;
газораспределительные станции размещаются вне зоны возможных разрушений;
осуществляется газоснабжение от нескольких источников;
создаются резервы газа, хранящиеся в подземных сооружениях.
Для повышения устойчивости функционирования как городского хозяйства в целом, так и отдельных хозяйственных объектов, необходимо предусматривать возможность перехода на альтернативные виды топлива (уголь, мазут, торф, дрова).
Устойчивое функционирование объектов экономики также зависит от устойчивой работы канализации и системы теплоснабжения. Выход из строя системы канализации может привести к возникновению очагов инфекционных заболеваний. Повышение надёжности работы канализации обеспечивается использованием нескольких коллекторов. Станции перекачки канализационных и сточных вод должны иметь автономное электроснабжение.
Система теплоснабжения включает в себя теплоэлектроцентрали, котельные и теплотрассы. В результате чрезвычайной ситуации может быть серьезно повреждена система теплоснабжения населенного пункта или предприятия, что создает серьезные трудности для их функционирования, особенно в холодный период года. Так, разрушение трубопроводов с горячей водой или паром может повлечь их затопление и затруднить локализацию и ликвидацию аварии. Наиболее уязвимые элементы систем теплоснабжения - теплоэлектроцентрали и районные котельные. Аварии, связанные с разлитием горячей воды представляют серьёзную опасность для жителей, работников предприятий и затрудняют проведение спасательных работ.
Основным способом повышения устойчивости внутреннего оборудования тепловых сетей является их дублирование. Необходимо также обеспечить возможность отключения поврежденных участков теплосетей без нарушения ритма теплоснабжения потребителей, а также создать системы резервного теплоснабжения. Повышение надёжности теплоснабжения так же обеспечивается кольцеванием сетей, возможностью перекрывать аварийные участки и др.
Для повышения устойчивости работы объектов в чрезвычайных ситуациях необходимо уделять значительное внимание защите рабочих и служащих. Для этого на объектах строятся убежища и укрытия, предназначенные для защиты персонала, создается и поддерживается в постоянной готовности система оповещения рабочих и служащих объекта, а также проживающего вблизи объекта населения о возникновении чрезвычайной ситуации. Персонал, обслуживающий объект, должен знать о режиме его работы в случае возникновения чрезвычайной ситуации, а также быть обученным выполнению конкретных работ по ликвидации очагов поражения. Порядок действия работников в аварийных и иных чрезвычайных ситуациях должен быть рассмотрен при их инструктировании по охране труда и пожарной безопасности, а так же изложен отдельным вопросом в инструкциях по охране труда.
Заключение
В ходе работы над дипломным проектом было выполнено изучение материала связанного с вопросами выбора параметров и схемы двигательной установки, системы подачи топлива в КС, управление вектором тяги УБР, системы запуска и регулирования тяги ДУ. Исследованы свойства используемого топлива. Изучены конструктивные схемы крепления двигателя и ТНА на борту ракеты.
В ходе теплового расчета, определения потребного объема и линейных размеров были получены основные диаметральные и линейные размеры камеры сгорания и параболического сопла, значение удельного импульса, и расхода топлива. Выполнено построение входа в сопло и закритической части сопла графическим методом.
В разделе посвященному охлаждению КС были рассчитаны параметры охлаждающего тракта исходя из условия обеспечения прочности КС. Произведена оценка тепловых потоков в стенку КС. С учетом полученных данных было принято решение о способе организации охлаждения.
В ходе дальнейших расчетов были определены параметры элементов системы подачи топлива: центробежного насоса окислителя и турбины ТНА.
Для центробежного насоса были определены: частота вращения вала и размеры основных элементов насоса (центробежного колеса, отвода, а также определение формы колеса в меридиональном сечении, профиля лопаток, размеров улитки, мощности и КПД насоса).
Для турбины были определены: потребный расход газа через турбину, параметры газового потока в осевом зазоре между сопловым аппаратом и колесом турбины. Выполнено профилирование сверхзвуковых лопаток рабочего колеса турбины. Определены размеры соплового аппарата состоящего из конических сопел, работа, мощность и КПД турбины.
Осуществлен выбор конструктивного прототипа проектируемого двигателя, центробежного насоса окислителя и турбины ТНА.
В разделе проектирования элементов конструкции второй ступени были спроектированы: хвостовой отсек вафельной конструкции, 24 стержневая ферма полезной нагрузки, размеры усилений вырезов в баке окислителя.
В технологическом разделе был разработан технологический процесс сборки фермы полезной нагрузки, содержащий сведения о последовательности проводимых операций во время сборки. Спроектировано приспособления для сборки – сварки фермы.
Экономический раздел содержит расчеты затрат на разработку данного проекта: заработная плата проектировщика, амортизация помещения, оборудования, программного обеспечения и т.д.
В разделе охраны труда отражены основные моменты безопасности и экологичности проекта. Рассмотрены факторы окружающей среды, влияющие на проектировщика, а также меры по устранению действия вредных факторов. Произведен расчет искусственного освещения рабочего места. Рассмотрены способы оценки и повышения устойчивости экономических систем.
Список использованной литературы
1. Васильев А.П., Кудрявцев В.М., Кузнецов В.А. и др. Основы теории и расчёта ЖРД: Учеб. для авиац. спец. вузов. в 2 кн. Кн. 1.– 4-е изд., перераб. и доп.– М.: Высш. шк.,1993.– 383 с.: ил.
2. Васильев А.П., Кудрявцев В.М., Кузнецов В.А. и др. Основы теории и расчёта ЖРД: Учеб. для авиац. спец. вузов. в 2 кн. Кн. 2.– 4-е изд., перераб. и доп.– М.: Высш. шк.,1993.– 383 с.: ил.
3. Конструкция и работа ЖРД: Методические указания к лабораторным работам по дисциплине “Жидкостные ракетные двигатели”/ Сост.Л.И. Гречух, И.Н. Гречух.– Омск,Изд-во ОмГТУ, 2005.- 100 с.: ил.
4. Добровольский М.В. Жидкостные ракетные двигатели. Основы проектирования: Учеб. для вузов.– 2-е изд., перераб. и доп.– М.: Изд-во МГТУ им. Н.Э. Баумана, 2005.– 488 с.: ил.
5. Атлас конструкций ЖРД (описание)/ Под ред. Г.Г. Гахуна. М.: МАИ, Ч.1.– 1969.– 286 с.: ил.
6. Термодинамические и теплофизические свойства продуктов сгорания в 10-ти томах. Т.4. Изд – во ВИНИТИ
7. Атлас конструкций ЖРД (описание)/ Под ред. Г.Г. Гахуна. М.: МАИ, Ч.2.– 1973.– 152 с.: ил.
8. Расчёт центробежного насоса ЖРД: Методические указания к курсовому и дипломному проектированию/ Сост.Л.И. Гречух, И.Н. Гречух.– Омск: Изд-во ОмГТУ, 2004.– 48 с.: ил.
9. Конструкция и пример расчёта на прочность турбины ЖРД: Методические указания к курсовому и дипломному проектированию/ Сост.Л.И. Гречух, И.Н. Гречух.– Омск: Изд-во ОмГТУ, 2003.– 48 с.: ил.
10. Анурьев В.И. Справочник конструктора-машиностроителя: В 3 т. Т.1. – 8 – е изд., перераб. и доп.– М.: Машиностроение, 2001. – 920 с.: ил.
11. Анурьев В.И. Справочник конструктора-машиностроителя: В 3 т. Т.3. – 8 – е изд., перераб. и доп.– М.: Машиностроение, 2001. – 864 с.: ил.
12. Курсовой проект по дисциплине: “Теория, расчёт и проектирование РД”.- Омск. ОмГТУ. 2006. – 65 с.: ил.
13. Лизин В. Т., Пяткин В. А. Проектирование тонкостенных конструкций: Учеб. пособие для студентов вузов. – 4-е изд. перераб. и доп. – М,: Машиностроение, 2003. – 448 с.: ил.
14. Конспект лекций по дисциплине «Расчет оболочек», Омск, ОмГТУ, 2005г.
15. Конспект лекций по дисциплине «Основы проектирования и конструирования ЛА», Омск, ОмГТУ, 2006 г.
16. http://engenegr.ru/
17. http://ssga.ru/
|