СОДЕРЖАНИЕ
ВВЕДЕНИЕ
РАЗДЕЛ 1.
ТЕХНИКО-ТЕХНОЛОГИЧЕСКИЙ
1.1 Общие сведения о районе
1.2 Обоснование конструкции скважины
1.3 Промывочные растворы
1.3.1 Нормирование глинистых растворов
1.3.2 Приготовление и утяжеление глинистого раствора (расчеты)
1.3.3 Химическая обработка глинистого раствора
1.4 Обоснование выбора способа и проектирование режимов бурения
1.5
Методы ликвидации аварий
1.6 Выбор типов и параметров буровых растворов
1.7 Обоснование выбора типоразмеров ПВО
1.8 Обоснование вхождения в продуктивный пласт
1.9 Способ освоения скважины
1.10 Контроль качества цементирования
1.11 Выбор буровой установки
РАЗДЕЛ 2. СПУСК ОБСАДНОЙ КОЛОННЫ
2.1Обоснование режима спуска обсадных колонн
2.2 Обоснование режима спуска эксплуатационной колонны
2.3 Расчет допустимой глубины опорожнения колонны
2.4 Оснастка обсадных колонн
2.5 Цементирование обсадной колонны
РАЗДЕЛ 3. ЭКОНОМИЧЕСКАЯ ЧАСТЬ
3.1 Исходные данные для расчета стоимости строительства 1м скважины
3.2 Расчет затрат для определения сметной стоимости
(цены) строительства 1 м. скважины
3.3 Расчет сметной стоимости (цены) строительства 1 м. скважины
РАЗДЕЛ 4. ОХРАНА ОКРУЖАЮЩЕЙ СРЕДЫ
4.1 В процессе проводки, промывки и крепления ствола скважин
4.3 При эксплуатации НГС
РАЗДЕЛ 5. ОХРАНА ТРУДА
5.1 Правила безопасной эксплуатации бурового оборудования и инструмента
5.2 Техника безопасности при приготовлении, очистке и обработке буровых растворов
5.3 Техника безопасности при спускоподъемных операциях
5.4 Техника безопасности при креплении скважину
5.5 Меры безопасности при опробовании, испытании иосвоении скважин
5.6 Меры безопасности при ликвидации аварий и осложнений
5.7 Обеспечение пожарной безопасности на объекте бурения
РАЗДЕЛ 6. БЕЗОПАСНОСТЬ ЖИЗНЕДЕЯТЕЛЬНОСТИ
6.1 Промышленная санитария
Список использованной литературы
Введение
Начало добычи нефти в нашей стране уходит в далекое прошлое. Но рождением нефтяной промышленности считают 1861 год, когда Грозном на старых промыслах была пробурена первая скважина, а позже в 1864 г, скважин на Кубани. 20 июня 1918г. нефтяная промышленность в России была национализирована.
В 1944г, правительство поручило УЗТМ- Уральскому заводу тяжелого машиностроения г. Свердловск, выпуск комплектных БУ, для бурения скважин на глубину от 3000м, и выше . Соответственно в1947-48г., выпускаются уникальные установки БУ-ЗД, Бу-4Э,Бу-5Д, Бу-бЭ, предназначенные для бурения на 3000-4000м.
Установки 5Д-6Э сняты с производства, а Бу-ЗД, 43, составляют около 60%, от всего парка БУ в России. Кинематическая, пневматическая схемы, те же, а оборудование, входящее в комплект БУ более новое и мощное. Раньше в комплект этих установок входил насос У 8-3, а сейчас У 8-7 МА2.
Позже УЗ ТМ выпускают комплектные установки, для бурения скважин глубиной на 4, 5; 6, 7; 8,10 и 15 тысяч м, с дизель-гидравлическим проводом и дизель- электрическим проводом, а так же БУ для кустового бурения, для работы на севере. В 1980г УЗТМ выпускает БУ -125 А- уникальную установку, где все технологические процессы автоматизированы, а управление дистанционно с пульта дисплея. Все буровые выпускаемые УЗТМ, за исключением БУ ЗД, 43, снабжены комплектом АСП автомат спуска подъема. В 1985г. УЗТМ каждые сутки выпускало одну комплектную БУ, следовательно в год 365-3 70 комплексных БУ и это в плане завода составляло всего 10%. В 1950г. Волгоградский завод Баррикады, а позлее В ЗБТ- Волгоградский завод буровой техники, приступил к выпуску установок для мелкого бурения, глубиной ОТ 1600 до 2500м, с электроприводом постоянного тока, с дизельным приводом и для кустового бурения БУ 2500 Бр ЗУ (ДУ) (ЭУК), снабжены комплексом АСПЗ. В 1974г. на Кольском полуострове закладывается уникальная СГ- сверх,- тлубокая скважина, проектной глубиной 15000м., по последним данным забой составляет более 13000 м.
В 1978г закладывается вторая СГ- Саатлинская в Азербайджане, в настоящее время забой около 12000м. В 90-х годах закладывается в центральной России еще три таких СГ.
Без преувеличения можно сказать, что углеводороды, углеводородное сырье является становым хребтом современной цивилизации на Земле. Под знаком Большой Нефти прошло XX столетие. Природные У В вступили в третье тысячелетие как основные энергоносители и источники химического сырья. Будущее, - во всяком случае, близкое, - почти безраздельно принадлежит им.
За последние полвека мировое потребление энергии возросло вчетверо главным образом благодаря развитию добычи и использования углеводородного сырья - нефти и газа. Альтернативные источники энергии, невзирая на технологическую эффективность и экономическую рентабельность их эксплуатации, до настоящего времени не составили сколько-нибудь серьёзной конкуренции углеводородному топливу. Характерным примером может служить многообещающее - площадь земной поверхности в 1 м2
получает - 1 кВт при вертикальном освещении в безоблачную погоду- использование энергии Солнца. Мощность наиболее крупных солнечных энергоустановок в Испании не превышает 7-9 МВт, и только в США в пустыне Мохаве построено пять энергетических станций мощностью 30 МВт. Даже достаточно просто «снимаемая» и используемая геотермальная энергия по сию пору выступает не альтернативой, а скорее дополнением к углеводородному сырью. В частности, реализация проекта разбуривания гидротермальной зоны Тиви на о. Лусон (Филиппины) позволила в период 1979- 1982 гг. ввести в эксплуатацию при ГеоТЭС мощностью по ПО МВт каждая. Пароводяная смесь извлекалась с глубин 200 - 2500 м из андезитов антропогенового возраста при помощи 85 скважин. Однако показательно, что по состоянию на 1983 г. Филиппинам удалось снизить импорт нефти благодаря использованию геотермальной энергии только на 7%.
Таким образом, нефть и газ останутся и в реально обозримом будущем главными энергоносителями, если даже не учитывать их роли как сырья для химического синтеза.
Различают возобновляемые и невозобновляемые источники энергии. К возобновляемым
относятся Солнце, ветер, геотермальные источники, приливы и отливы, реки. Невозобновляемыми
источниками энергии являются уголь, нефть и газ.
Специалисты видят выход в создании космических солнечных электростанций
(КЭС). Дело в том, что в космосе нет восходов и закатов Солнца, нет облаков, препятствующих прохождению лучей.
Поэтому на единиц поверхности космической площадки поступает в 10 раз больше энергии, чем на такую же площадь земной поверхности. Уже сегодня разработаны проекты КЭС массой до 60000 т с площадью солнечных батарей до 50 км. Поднятая над поверхностью Земли на 36000 км такая станция будет иметь мощность 5 млн. кВт, т.е. на млн. кВт больше, чем самая крупная в Европе Ленинградская АЭС. Станция, выведенная на стационарную орбиту «повиснет» над одной точкой земной поверхности. Передавать полученную энергию на Землю предполагается с помощью лазеров или сверхвысокочастотного излучения. Реализация данного проекта сдерживается тем, что добытая в космосе энергия окупит сгоревшее при запусках ракет (с элементами для монтажа КЭС) топлива только через 30 лет безаварийной работы станции.
В реально обозримой перспективе не предвидится альтернатива нефти и газу как природным источникам углеводородов, служащих энергоносителей сырьем для органического синтеза.
РАЗДЕЛ 1.
ТЕХНИКО-ТЕХНОЛОГИЧЕСКИЙ
1.1
Общие сведения о районе
Тушиловское нефтегазоконденсатное месторождение расположено в пределах Ногайского района РД, в 131 км. К Юго-Востоку от городаЮжно-Сухокумск, где сосредоточены центральные базы снабжения и ремонта УБР и НГДУ объединение «Дагнефть-Роснефть». Ближайшая железнодорожная станция Кочубей расположена 86 км от поселка Южно-Сухокумск и сообщается с последней асфальтированной дорогой. Гидрогеографическая сеть развита 'слабо. Севернее месторождения протекает река Сухая Кума, водный баланс которой после пуска в эксплуатацию Терско-Кумуского оросительного канала стал относительно постоянным.
В орографическом отношении район заложения разведочной скважины представляет слабо всхолмленную полупустынную равнину с абсолютными отметками +10 +12 м. над уровнем моря. Климат района континентальный, с холодной малоснежной зимой и жарким сухим летом, с частыми и сильными ветрами. Среднегодовая температура составляет + 10 °С, максимальная летом +35° + 40 °С, зимой - 25 - 28 °С. 'Среднегодовое количество осадков 200 мм.
Промерзаемость почвы не превышает 0,5 м.
Водоснабжение осуществляется за счет артезианских скважин, залегающих на глубинах 250- 450 м. и приуроченных к древнекаспийским и апшеронским отложениям.
Население в районе сконцентрировано в рабочих поселках и на кутанах отгонных пастбищ. Имеющиеся грунтовые дороги на площади большей частью пригодны для автотранспорта, проложены по ровной степи. Связь с УБР осуществляется по телефону. Доставка вахт осуществляется автотранспортом из поселка Южно-Сухокумск.
Бурения скважин ведется на ДВС. Отопительный период 129 дней.
1.2 Обоснование конструкции скважины
На основании изучения проектных геолого-технических условий бурения проектируемых скважин, накопленного производственного опыта бурения скважин на площадях ОАО «НК Роснефть» - Дагнефть», исходя из совмещенного графика давлений, принята радикальная конструкция скважины.
При выборе конструкции учитывалось:
• необходимость осуществления по возможности меньшего выхода долот из-под башмака обсадных колонн;
• рационально возможный диаметр эксплуатационной колонны;
• возможность бурения высокопроизводительными долотами по возможности максимального диаметра;
tнеобходимость и возможность ггрименения равнопрочных компоновок бурильных колонн при бурении и насосно-компрессорных при испытании.
I. Шахтное направление 630 мм спускается на глубину 7 м в целях предохранения устья скважины от размыва циркулирующим буровым раствором при бурении под кондуктор. Бетонируется на глубину погружения в грунт -4 м.
П. Кондуктор 426 мм спускается на глубину 0 м для предохранения устья скважины от размыва циркулирующим буровым раствором, предотвращения грифонообразования и сообщений скважин с шурфом при бурении под следующую колонну.
III. I промежуточная колонна 299мм. спускается на глубину Ю*/о м в кровлю майкопской серии для перекрытия неустойчивых пород вышележащей части разреза, где возможны поглощения глинистого раствора плотностью более 1240 кг/м , для перекрытия источников питьевой воды, а также для уменьшения выхода открытого ствола скважины.
IV. II промежуточная колонна 219*245 мм спускается на глубину 3835 м.с целью перекрытия осыпающихся майкопских, меловых и юрских отложений и изоляции их от триасового комплекса, который разбуривается на глинистом растворе более низкой плотности ИЗО кг/м3
.
Спускается колонна в две секции:
I секция в интервале 3835-
2355 м.
II секция в интервале 2355-
0м.
V. Эксплуатационная колонна 146 мм. спускается до проектной глубины 4100 м. с целью перекрытия перспективных в нефтегазоносном отношении объектов, дальнейшего опробования и эксплуатации их.
Спускается колонна в две секции:
Iсекция в интервале 4100 -
2800м
IIсекция в интервале2800 -
0м.
Секционный спуск связан с невозможностью зацементировать ее в один прием.
Скважина по назначению является поисковой.
Так как промывка скважин – одна из самых ответственных технологических операций, выполняемых при бурении, поэтому выбору промывочной жидкости уделяется особое внимание при строительстве скважин.
В проекте приводятся расчеты по определению весового и объемного количества глины и химреагентов при бурении поисковой скважины на площади «Тушиловская».
1.3 Промывочные растворы
Назначение промывочного раствора при бурении скважин: 1) очистка забоя от выбуренной породы; 2) вынос частиц породы на дневную поверхность; 3) охлаждение рабочих элементов долота; 4) создание противодавления на пласт при разбуривании многопластовых месторождений, в пластах которых содержатся различные вещества (вода, нефть, газ); 5) глинизирование стенок скважины с целью временного разобщения пластов друг от друга; 6) удержание выбуренной породы во взвешенном состоянии в периоды прекращения циркуляции промывочного агента и т. п.
Исследования и практика бурения показывают, что для очистки забоя от шлама пригодны газ, вода, нефть, глинистые и многие другие растворы.
При бурении в нормальных (неосложненных) с геологической точки зрения условиях, когда разбуриваемое месторождение сложено плотными сланцами и скальными породами, не обваливающимися при контакте с водой, а различных водо-, газо-, нефтепроявлений п пластов, сложенных агрессивными породами (гипсы, пласты соли, ангидриты и другие), до эксплуатационного горизонта не встречается, к промывочному агенту предъявляются самые элементарные требования. Он должен очищать забой скважины от выбуренной породы, транспортировать ее на поверхность (выносить из скважины) и охлаждать долото. В данном случае в качестве промывочной жидкости следует использовать воду.
При проходке глубоких скважин в нормальных условиях бурения промывочный раствор должен обладать, кроме того, способностью при прекращении циркуляции удерживать частицы выбуренной породы во взвешенном состоянии. В таких случаях в качестве промывочного раствора используют так называемые нормальные глинистые растворы
(водная суспензия глин).
К промывочным растворам, используемым в осложненных условиях бурения, предъявляются дополнительные требования. Они должны выполнять роль временного крепления неустойчивых стенок скважины (глинизировать их), предохраняя ствол скважины от обвалов, предотвращать поступления из пластов в скважину газа, нефти и воды, предупреждая тем самым проявления и выбросы их, облегчать разрушение пород, оказывая на них физико-химическое воздействие, обеспечивать нормальные условия вскрытия и освоения продуктивных горизонтов и т. п.
Для осложненных условий бурения промывочные растворы с соответствующими свойствами выбирают в зависимости от вида осложнений, применительно к конкретным условиям района или отдельной бурящейся скважины.
Если свойства промывочного агента удовлетворяют геологическим условиям бурения, то они оказывают косвенное и прямое влияние на показатели бурения (механическую скорость и проходку на долото).
Косвенное влияние свойств промывочного раствора на показатели бурения проявляется в том, что с увеличением главным образом плотности и вязкости возрастают сопротивления в циркуляционной системе, вследствие чего приходится уменьшать количество промывочного агента, подаваемого в скважину в единицу времени.
Непосредственное влияние свойств промывочного раствора на показатели бурения проявляется в том, что с изменением плотности п вязкости его изменяются условия очистки долота и скважины от выбуренной породы. Чем меньше вязкость, т. е. чем выше подвижность промывочного агента, тем быстрее он удаляет из забоя шлам и тем лучше его очищает. Значение плотности промывочного раствора в этом процессе ниже значения вязкости.
Наиболее успешно очистка забоя от выбуренной породы осуществляется газом, а затем водой, глинистым раствором, тяжелым глинистым раствором. Механическая скорость бурения в зависимости от вида промывочного раствора изменяется в таком же порядке.
Вынос шлама на поверхность также может успешно осуществляться любым из указанных выше промывочных растворов, если поддерживать необходимую скорость восходящего потока.
При бурении с использованием воды или раствора охлаждение долота происходит в результате теплообмена между промывочной жидкостью и рабочей поверхностью разрушающего инструмента.
При использовании в качестве промывочного раствора газа происходит резкое понижение температуры и долото охлаждается также в достаточной мере вследствие адиабатического процесса расширения газа при истечении его из отверстий долота.
Продувку скважин газом вместо промывки их жидкостью можно выполнять при бурении электробурами и роторным способом. Она особенно эффективна при прохождении геологических разрезов, содержащих горизонты с низкими пластовыми давлениями и зоны, поглощающие промывочную жидкость. В целях пожарной безопасности для продувки скважин часто используют выхлопные газы от двигателей внутреннего сгорания или смеси этих газов* с небольшим количеством воздуха.
В разрезах газонефтяных месторождений часто встречаются горизонты с высоким пластовым давлением, при разбуривании которых нельзя применять продувку газом. В этих случаях промывают скважины жидкостью, плотность которой определяют обычно по формуле
, (1)
гдеρ— плотность промывочной жидкости в т/м3
;
ρ
пл— пластовое давление в бар;
L
— глубина скважины в м;
р
— допускаемая разность между гидростатическим и пластовым давлениями.
Единые технические правила ведения работ при бурении скважин на нефтяных, газовых и газоконденсатных месторождениях, предусматривают, что для скважин глубиной до 1200 м
гидростатическое давление в скважине, создаваемое весом столба промывочной жидкости, должно на 10—15% превышать ожидаемое пластовое давление, а для скважин большей глубины на 5—10%.
Еслиρ< 1, а разбуриваемое месторождение сложено плотными сланцами и скальными породами, то в качестве промывочной жидкости следует использовать водуили аэрированный раствор.
Если ρ = 1 1,25 т/м3
и в разрезе разбуриваемого месторождения нет поглощающих и обваливающихся горизонтов, то для промывки скважин применяют нормальный глинистый раствор.
Еслиρ= 1,25 1,8 т/м3
,
то рекомендуется использовать утяжеленный глинистый раствор, получаемый из нормального глинистого раствора путем введения в него утяжелителя (барита, гематита, магнетита и т. п.). Глинистый раствор сϱy
.р
= 1,5 1,6 т/м3
можно приготовить и без утяжелителя, если для этого использовать специальную тяжелую глину.
Еслиϱ > 1,8 т/м3
следует применять тяжелый глинистый раствор сϱт
.р
. до 2,2 2,3 т/м3
.
m
Кроме необходимой плотности, промывочная жидкость должна обладать способностью удерживать частицы пород во взвешенном состоянии при прекращении циркуляции. Для этого статическое напряжение сдвига υ1
, измеряемое через 1 мин,
должно удовлетворять следующему условию:
м
н
/с
(2)
гдеm
— опытный коэффициент, зависящий от формы частиц; для частиц породы диаметром от 2 до 40 мм
величина т
колеблется в пределах 2,5—1,6; d
0
— диаметр частиц породы, удерживающихся во взвешенном состоянии, в см.
Если в процессе бурения используется глинистый раствор сϱp
и υ1
,то после прекращения циркуляции все частицы породы с плотностьюϱп
и диаметромd
0
остаются во взвешенном состоянии.
Для нормального глинистого раствора υ1
≤ 490 мн/см2
.
Использовать растворы с υ1
> 490 мн/см2
при нормальных условиях бурения не рекомендуется, так как это ведет к некоторому снижению механической скорости бурения, увеличению продавочных и гидродинамических давлений. Чрезмерный рост последних может оказаться причиной возникновения поглощений промывочной жидкости.
Глинистые растворы с υ1
≥ 785 1180 мн/см2
применяют при прохождении поглощающих горизонтов.
Для утяжеления считаются пригодными глинистые растворы с υ1 = 195 390 мн/см2
.
Наряду сϱи υ1
важнейшими показателями, характеризующими промывочную жидкость, являются условная вязкость Т
и водоотдача В.
Рекомендуется поддерживать вязкость по СПВ-5: для нормального раствора Т
≤ 30 сек,
для утяжеленного Т =
30 50 сек.
Для борьбы с поглощениями промывочной жидкости применяют растворы с большей вязкостью вплоть до состояния, когда раствор не течет (через воронку СПВ-5).
Для нормальных глинистых растворов водоотдача В
рекомендуется до 10 см3
за 30 мин.
При бурении в породах, где возможны обвалы и прихваты, В
рекомендуется снижать до 5—6 см3
и даже 2—3 см3
за 30 мин.
Загрязнение неутяжеленных растворов твердыми частицами не должно превышать 4% при роторном и 2% при турбинном способах бурения.
В РФ глинистые растворы приготовляют как из комовой глины, добываемой в глинокарьерах, расположенных в районах буровых работ, так и из глинопорошков, выпускаемых специальными заво- дами. Глинопорошки представляют собой высушенную и измель- ченную глину с химическими реагентами или без них, которая обра- зует с водой устойчивую суспензию. Глинопорошки выпускают по техническим условиям, утвержденным Госкомитетом нефтедобывающей промышленности
Таблица 1
Сорт |
Плотность глинистого раствора (при вязкости 25сек
по СПВ-5), m
/м3
|
Выход раствора из 1 т
глинопорошка, м3
|
Остаток на сите, %
|
Влажность, % |
Содержание песка в глинистом растворе, % |
№ 0,5 |
№ 0,075 |
общее |
В том числе отмытого |
1
2
3
4
|
До 1,06
1,06 – 1,08
1,08 – 1,15
Свыше 1,5
|
> 10
10 – 8
8 – 4
< 4
|
0
0
0
0
|
До 10
» 10
» 10
» 10
|
5,0–8,0
5,0–8,0
5,0–8,0
5,0–8,0
|
До 0,8
» 1,5
» 3,0
» 4,0
|
До 0,5
» 0,8
» 1,5
» 3,0
|
Показатели, которым должны отвечать глинопорошки и глинистые растворы, приготовленные из них, приведены в табл. 1
1.3.1 Нормирование глинистых растворов
Параметры глинистых растворов выбираются в зависимости от вида осложнений и конкретных условий бурения. Для этого в каждом нефтегазодобывающем или разведочном районе разработаны специальные инструкции, которыми и следует руководствоваться в практической работе. В настоящем параграфе приводятся лишь ориентировочные сведения по данному вопросу. Исследованиями и многолетней практикой установлены следующие требования (нормы), предъявляемые к основным свойствам глинистых растворов.
В нормальных
(с геологической точки зрения) условиях бурения плотность глинистого раствора в зависимости от качества разбуриваемых (или применяемых для приготовления глинистого раствора) глин принимается равнойϱp
= 1,10 1,35 т/
м3
. Статическое напряжение сдвига, замеряемое через 1 мин
, υ1
= 145 195 мн/см2
,
а замеряемое через 10 мин υ10
=
295 490 мн/см2
.
Условная вязкость по СПВ-5 равна 20—25 сек
для растворов, не обработанных химическими реагентами, и 25—50 сек
для химически обработанных глинистых растворов. Водоотдача В
≤ 10 см3
за 30 мин.
Толщина глинистой корки К
равна 1—2 мм,
а липкость ее Кл
=
0,25 (по А. А. Линевскому). Процентное содержание песка П
≤ 4% для роторного и П
≤ 2% для турбинного способов бурения. Стабильность С
≤ 0,03. Отстой О
≤ 5%. Концентрация водородных ионов рН ≥ 7 (обычно 7,5—9,0).
Для предупреждения водо-, газо-
и нефтепроявлений
и борьбы с ними необходимая плотность глинистого раствора определяется по формуле (1). Водоотдача принимается равной В
= 10 см3
за 30 мин.
Процентное содержание песка П
≤ 4% для роторного и П
≤ 2% для турбинного способов бурения. Концентрация водородных ионов рН = 9,0 9,5. Статическое напряжение сдвига υ
1
= 295 490 мн/см2
.
Величина условной вязкости изменяется в зависимости от вида проявления. В случае газопроявлении Т ≤
30 сек,
нефтепроявлений Т
≤ 50 сек,
водонроявлений Т
≥ 50 сек.
Для предупреждения обвалов
стенок скважин и борьбы с ними плотность глинистого раствора выбирают в зависимости от величины горного давления (при этом обычно руководствуются опытом бурения в данном районе) и определяют по формуле (1).
Другие параметры глинистого раствора должны быть примерно такими: = 195 295 мн/см2
; Т
= 25 26 сек; В
≤ 5 см3
за 30 мин; П
≤ 4% для роторного и П
≤ 2% для турбинного способов бурения; рН = 10; К
≤ 2 мм; Кл
=
0,25 (по А. А. Линевскому); для уменьшения липкости глинистой корки в ряде районов рекомендуется вводить в глинистый раствор добавки нефти или дизельного топлива в количестве 3—
4%.
В целях предупреждения прилипаний
и прихватов
бурового инструмента в отдельных районах также рекомендуются добавки маслянистой нефти > 5% от объема глинистого раствора.
Для борьбы с поглощениями
плотность глинистого раствора должна быть минимально возможной (иногда используется аэризо-ванный раствор сϱp
= 0,8 0,6 т/м3
).
Статическое напряжение сдвига принимается равным υ
1
= 785 1180 мн/см2
,
причем в течение 10 мин
эта величина должна возрастать не менее чем в 1,5—2 раза. Условная вязкость раствора должна быть Т
≥ 100 сек.
Водоотдача В
≤ 10 см3
за 30 мин.
При роторном бурении рекомендуются добавки в глинистый раствор различных инертных наполнителей (опилки, слюда, целлофан, подсолнечная лузга, отходы асбеста, хлопка, кожевенного производства, торф и т. п.).
При бурении глубоких скважин в сложных геологических условиях, при проходке направленных скважин для вскрытия продуктивных горизонтов в качестве промывочного агента часто используют растворы на нефтяной основе: высококальциевые, эмульсионные и известковые растворы.
В районах, сложенных мощными толщами карбонатных или сульфатных пород, можно применять естественные карбонатные, сульфатные или сульфатно-карбонатные водные растворы.
При разбуривании нефтегазоносных месторождений, содержащих продуктивные горизонты с весьма низким пластовым давленном, а также площадей, где наблюдаются катастрофические поглощения промывочной жидкости, исключающие применение последней, в качестве промывочного агента используются воздух или газ
. Эти промывочные агенты практически незаменимы также при бурении в трещиноватых и кавернозных породах в районах, где с целью охраны поверхностных и грунтовых вод от загрязнения категорически запрещено использовать промывочные растворы, в пустынях и на других площадях, ощущающих острую нехватку воды, в районах Крайнего Севера и вечной мерзлоты с исключительно холодным климатом и т. д.
1.3.2 Приготовление и утяжеление глинистого раствора (расчеты)
Весовое количество глины, потребное для приготовления 1 м3
глинистого раствора заданной плотности, определяем по формуле
(3)
а весовое количество воды, потребное для приготовления 1м3
глинистого раствора заданной плотности, находим по формуле
(4)
гдеq
г
— количество сухой глины, потребное для приготовления 1 м
3
глинистого раствора;
qB
— количество воды, потребное для приготовления 1 м3
глинистого раствора;
ϱr
, ϱb
, ϱp
— плотности соответственно глины, воды и глинистого раствора;
п
— влажность глины в долях единицы.
Плотность наиболее распространенных глин (в плотном теле - изменяется обычно в пределах 2,5—2,8 т/м3
,
а в раздробленном виде она колеблется в пределах 1,65—1,90 т/м3
.
Количество сухой глины, потребное для приготовления 1 м3
глинистого раствора заданной плотности, может быть подсчитано также по формуле (3), если принять п
= 0.
В промысловых условиях иногда удобнее пользоваться не весовыми, а объемными количествами глины, которые нетрудно подсчитать, пользуясь формулой
, (5)
гдеV
г
— объемное количество глины в раздробленном ϱвиде;
ϱcp
= 1,9 — средняя плотность глины в т/м3
.
Для определения массового и объемного количества глины, потребной для приготовления 1 м3
глинистого раствора заданной плотности, можно пользоваться также и следующими приближенными формулами:
qг
= l,6(ϱp
– 1)m
, (6)
Vг
= 0,94(ϱp
– l)м3
. (7)
Принимаяϱг
= 2,6 Т/м3
иϱcp
= 1,7 Т/м3
,
можно получить следующие расчетные формулы для определения весовых и объемных количеств глины, потребных для приготовления 1 м3
глинистого раствора заданной плотности:
а) для приготовления 1 м3
глинистого раствора на пресной воде
, (8)
(9)
б) для приготовления 1 м3
глинистого раствора на морской воде
(10)
(11)
Нормы потребного количества глины и воды для приготовления 1 м3
глинистого раствора заданной плотности (в м3
)
могут быть взяты также из справочника укрупненных сметных норм (СУСН) на строительство нефтяных и газовых скважин.
Количество утяжелителя, потребное для утяжеления 1 м3
глинистого раствора от плотностиϱp
доплотностиϱут
.р
, определяется по следующей формуле [40]:
, (12)
гдеq
у
т
— масса влажного утяжелителя, потребная для приготовления 1 м3
раствора;
p
—
плотность глинистого раствора до утяжеления;
—
плотность глинистого раствора после утяжеления;
yt
—
плотность утяжелителя;
п
— влажность утяжелителя в долях единицы.
Если qут
определяем для утяжеления 1 м3
раствора, то размерность его выражается в т.
Когда расчет ведем на 1 л
глинистого раствора, тоqут
— в г.
Количество утяжелителя, необходимое для утяжеления 1 м3
глинистого раствора, можно определить, пользуясь номограммой С. Ю. Жуховицкого.
Для быстрых ориентировочных подсчетов потребного количества утяжелителей удобно пользоваться также специальными таблицами, составленными в расчете на сухой утяжелитель.
Объем, который займет 1 м3
глинистого раствора после утян-ге-ления, определяется по следующей формуле:
(13)
или для некоторых утяжелителей по специальным таблицам.
Плотности барита и других утяжелителей определяются при помощи пикнометров по следующим формулам:
, (14)
, (15)
, (16)
гдеp
— масса пикнометра в г;
р1
— масса пикнометра с утяжелителем в г;
р2
— масса пикнометра с водой в г;
р3
— масса пикнометра с водой и утяжелителем в г;
V
п
— объем пикнометра в см3
;
ϱк
— плотность керосина в г/см3
или т/м3
\
р4
— масса пикнометра с керосином и утяжелителем в г;
ϱб— плотность барита в г 1см3
или т/м3
;
ут
— плотность утяжелителя, содержащего примеси, реагирующие с
водой, в г/см3
или т/м3
.
Влажность п
утяжелителя подсчитывается по формуле
, (17)
В табл. 2 приведены технические условия, которым должен удовлетворять соответствующий сорт баритового утяжелителя.
Параметры |
Сорт |
I |
II |
III |
Плотность, не менее, г/см3
……………………..
Содержание сернокислого бария в пересчете на сухое вещество не менее, % …………….
Содержание влаги не более, %
а) в подсушенном ………………………...
б) в неподсушенном ……………………..
Содержание водорастворимых солей не более, % ………………………………………...
В том числе кальция ………………………..
Тонкость помола – остаток на сите 170 меш при размере ячеек в свету 0,074 мм
не более, % ………………………………………...
Содержание фракции минус 5мк
не более, %..
Растекаемость по конусу АзНИИ не менее…..
|
4,2
90
5,0
14,0
0,35
0,05
10,0
10,0
14
|
4,00
5,0
14,0
0,4
0,05
10,0
15,0
–
|
3,80
5,0
14,0
0,45
0,06
10,0
20,0
–
|
Ожидаемую плотность глинистого раствора, разгазированного в процессе бурения после выхода его из скважины на поверхность, определяем но формуле
. (18)
Количество газа, поступающего в глинистый раствор из пласта в течение 1 ч,
равно
, (19)
гдеQ
— количество промывочной жидкости, подаваемой в скважину, в л1сек;
ϱy
г.
р
—
плотность раствора, закачиваемого в скважину, в т/м3
;
D
— диаметр скважины в м;
υ
— механическая скорость бурения в м/ч;
b
— пористость породы в %;
α
— коэффициент растворимости газа в нефти в м3
/м3
-йгА/;
для свободного газа а = 1;
ρ
пл
— пластовое давление в атм
;
W
г
— количество газа, приведенного к атмосферному давлению,, поступающего в скважину за 1 ч
работы, в м3
.
Определим количество (массу) и объем глины (плотность которой равна 2,7 Т/м3
, а влажность 16%), потребные для приготовления 1 м
3
глинистого раствора плотностью 1,27 Т/м3
,
затворяемого па морской воде плотностью 1,03 Т/м3
.
Весовое количество глины, потребное для приготовления 1 м3
глинистого раствора заданной плотности, подсчитываем по формуле (3), а объемное по формуле (5):
,
.
Определив количество сухой глины, плотность которой равна 2,6 Т/м3
,а также количество пресной воды, потребные для приготовления 1 м3
глинистого раствора плотностью 1,24 т/м3
.
Количество сухой глины, необходимое для приготовления 1 м3
глинистого раствора, находим по формуле (3), приняв в ней n = 0:
.
Количество пресной воды, потребное для приготовления 1 м3
глинистого раствора, определяем но формуле (4):
.
Подсчитаем количество гематита, плотность которого равна 4,5 т/м3
,
а влажность 12%, потребное для увеличения плотности глинистого раствора от 1,3 до 1,8 т/м3
.
Определим также объем, который займет 1 м3
глинистого раствора после утяжеления.
Количество влажного гематита, потребное для утяжеления 1 м3
глинистого раствора в необходимых пределах, подсчитываем по формуле (12):
.
Объем, который займет 1 м3
глинистого раствора после утяжеления его, найдем по формуле (13):
.
Решим эту задачу, пользуясь графическим и табличным способами Жуховицкого. По номограмме, составленной для сухого утяжелителя, находим, что для утяжеления 1 м3
глинистого раствора в заданных пределах надо израсходовать 0,84 m сухого утяжелителя. Чтобы учесть влажность утяжелителя, нужио полученную цифру увеличить на 12% (рекомендуется увеличение от 10 до 20% в зависимости от влажности утяжелителя). Тогда потребный расход влажного утяжелителя составит 1,01 т
(как видим, результат несколько занижен по сравнению с аналитическим расчетом).
Найдем затем потребный расход утяжелителя. Он равен 0,82 т
сухого утяжелителя. Учитывая влажность утяжелителя, находим, что потребный расход его составляет 0,82 • 1,12 = 0,92 т
(результат также занижен по сравнению с аналитическим расчетом).
Объем, который займет 1 м3
глинистого раствора после утяжеления, оказывается равным 1,178 м3
,
что достаточно близко к определенному по формуле (13).
Определим плотность гематита, если в пикнометр массой 68 г
и объемом 72 см3
,
заполненный керосином, плотность которого равна 0,83 т/м3
,
введено некоторое количество утяжелителя. Масса пикнометра с навеской гематита оказалась равной 103 г,
а масса пикнометра с керосином и гематитом 156 г.
Плотность гематита при заданных условиях задачи определяем по формуле (16):
.
Определим влажность гематита, если масса пробы утяжелителя до просушивания составляла 735 г,
а после просушивания 638 г.
Влажность гематита согласно формуле (17) равна
.
Найти ожидаемую плотность разгазированного глинистого раствора по выходе его из скважины диаметром 0,3 м,
если в нее прокачивается 40 л/сек
глинистого раствора, плотность которого равна 1,75 т/м3
.
Средняя механическая скорость бурения равна 7,5м
/ч, а ожидаемое пластовое давление 165 атм
.Пористость породы принять равной 27%, а коэффициент растворимости газа в нефти 0,95 м3
/м3
• атм
.
Количество газа, поступающего в глинистый раствор из пласта в течение 1 ч, определим по формуле (19):
.
Плотность разгазированного глинистого раствора после выхода его из скважины находим по формуле (18):
.
1.3.3 Химическая обработка глинистого раствора
По характеру действия на промывочные растворы реагенты подразделяются на три основные группы: понизители водоотдачи, понизители вязкости, реагенты комбинированного действия.
Основные данные о реагентах для снижения водоотдачи промывочных растворов
В качестве понизителя водоотдачи применяются: углещелочной (УЩР), торфощелочной (ТЩР), карабоксиметилцеллюлоза (КМЦ), конденсированная сульфит-спиртовая барда (КССБ), крахмал, гид-ролизованный полиакрилонитрил (гипан).
УЩР — наиболее распространенный в РФ реагент для обработки промывочных растворов. Применяется для общего улучшения буровых растворов, повышения их дисперсности и агрегативной устойчивости, снижения водоотдачи и вязкости. По принципу действия этот реагент является реагентом-стабилизатором суспензии, но имеет и пептизирующие функции. УЩР служит для регулирования вязкости и напряжения сдвига растворов, загустевших от выбуренной породы. УЩР готовится из бурого угля обработкой щелочно-каустической или кальцинированной содами. Соотношение угля и щелочи должно быть в определенных пропорциях. Если щелочи мало, то не все количество кислот будет извлечено. Если же щелочи взять много, коллоидные вещества реагентов коагулируют.
УЩР пригоден при бурении пород, содержащих пресные и небольшой минерализации воды (до 1,5—2% соли). Реагент обеспечивает сохранение низкой водоотдачи пресных растворов при высокой забойной температуре (373—473° К). Хорошо совмещается с другими реагентами.
Каждый раз при получении новой партии бурого угля проверяют егокачество. Лучшим считается такой уголь, из которого можно больше извлечь гуминовых кислот.
Прежде всего определяют влажность п
бурого угля по формуле
, (20)
Где а
– масса сухого угля (после просушки);
b – масса влажного угля.
Затем подсчитывают концентрацию гуминовых кислот по формуле
, (21)
где с
— концентрация гуминовых кислот в исследуемом растворе в %;
V
— объем взятого для определения исследуемого раствора в см3
;
V
1
— объем раствора после разбавления его водой в см3
; с1
— концентрация гуминовых кислот в эталоне в %.
Реагент, состоящий из бурого угля, каустической соды и воды, условно обозначают УЩР. Для первичной обработки глинистого раствора готовят реагент по одному из следующих рецептов: УЩР-9-2, УЩР-11-2, УЩР-13-2 и УЩР-15-2 (здесь в первом рецепте цифры 9 и 2 обозначают, что в 1000 см3
реагента содержится 90 г
сухого бурого угля, содержащего 45% гуминовых кислот, и 20 г кристаллической каустической соды, остальное вода). Для повторной обработки глинистого раствора используют реагент, приготовленный обычно по рецепту УЩР-10-1.
Количество влажного бурого угля Р,
потребное для приготовления единицы объема химического реагента, вычисляем по формуле
,
где Р
— необходимое количество влажного бурого угля;
Q
— процентное содержание сухого бурого угля в реагенте по
рецепту;
п
— влажность бурого угля;
N
— объем реагента, который необходимо приготовить.
Если N
выражено в л, то Р
в кг;
если N
в м
3
, то Р
в т.
Каустическая сода поступает на буровую обычно в растворенном .виде. Для определения требуемого объема раствора необходимо знать содержание кристаллической соды в нем, для чего определяют плотность раствора и по таблице находят содержание соды.
Объем раствора каустической соды, необходимый для пригото-вления единицы объема химического реагента, определяем по формуле
,
где V
— объем раствора каустической соды;
R — процентное содержание каустической соды в реагенте;
N—
объем реагента, который необходимо приготовить;
т
— процентное содержание сухой каустической соды в растворе соды.
Если N
в л,
то и V
в л;
если N
вм3
,
то и V
в м3
.
При первичной обработке глинистого раствора в него добавляют УЩР в
зависимости от условий бурения данной скважины в количествах 100, 200 пли 300 см3
на 1 л, а при дополнительной обработке в 5—6 раз меньше.
Реагенты из торфа (ТЩР). Способ приготовления торфощелочного реагента (ТЩР) ничем не отличается от приготовления УЩР. Определение влажности торфа и подсчет необходимых количеств торфа и каустической соды производятся точно так же, как и для бурого угля, т. е. по формулам (20)- (23).
Первичная обработка глинистых растворов производится ТЩР, приготовляемым по одному из рецептов: ТЩР-10-1, ТЩР-10-2; ТЩР-10-3 и ТЩР-10-4 (первая цифра — процентное количество сухого торфа, вторая — кристаллической каустической соды).
При первичной обработке глинистого раствора в него добавляют ТЩР взависимости от условий бурения данной скважины в количествах 100, 150 или 200 см3
на 1 л,а при дополнительной обработке в 5—6 раз меньше.
КМЦ — натриевая соль целлюлозо-гликолевой кислоты — представляет собой рассыпчатое твердое вещество кремового цвета, хорошо растворимое в воде при перемешивании. Применяется для снижения водоотдачи промывочных растворов при малых и средних концентрациях соли.
При большой солености КМЦ комбинируют с другими защитными реагентами. Добавка КМЦ в пресные растворы загущает их, а в соленые — разжижает. Совместима со всеми реагентами и видами химической обработки. Малоэффективна при хлоркальциевой агрессии. Обычные улучшающие добавки для пресных условий 0,5—0,75%, в соленой среде 1—2%. Первичная обработка глинистого раствора производится 10%-ным водным раствором КМЦ. Термостойка до393—403° К.
КССБ
—
продукт конденсации сульфит-спиртовой барды (ССБ) с формалином и фенолом в кислой среде с последующей нейтрализацией каустиком. КССБ представляет собой жидкость плотностью 1,12 т/м3
,
вязкостью50—10 спз
приt
—
293° К, с сухим остатком 15—25%. Выпускается в трех модификациях.
КССБ-1
предназначается для улучшения качества обычных глинистых и известковых растворов на пресной воде, а также при содержании в них до 10% солей.
Для приготовления 1 м3
реагента берут 600 л
ССБ 30%-ной концентрации, 48 л
формалина той же концентрации, 30 л
серной кислоты. Нейтрализуется воднымраствором едкого натра дорН = = 8 9, добавляется вода до общего объема готового продукта 1 м3
.
КССБ-2предназначается для обработки глинистых растворов, содержащих выше 10% солей, а также для известковых и высококальциевых глинистых растворов.
Для приготовления смеси берут 600 л
ССБ 30%-ной концентрации, 12 л
фенола, 48 Л
формалина 30%-ной концентрации и 18 лсерной кислоты плотностью 1,84 т/м3
.
Нейтрализуется едким натром. Добавляется вода до общего объема готовой продукции 1 м3
.
КССБ-3
предназначается для улучшения качества глинистого раствора при забойной температуре выше 400° К, применяется как для пресных, так и для высокоминерализованных растворов.
Для приготовления смеси берут 600 л
30%-ной ССБ, 100 л. 20%-ного раствора хромпика, 12 л фенола, 48 л формалина 30%-ной концентрации и 18 л серной кислоты. Нейтрализуется едким натром. Добавляется вода дообщего объема готовой продукции 1 м3
.
КССБ эффективна при комбинированной обработке совместно с другими реагентами. В неутяжеленных растворах добавка КССБ может вызвать образование пены. Для борьбы с пеной рекомендуется применять пеногасители, разработанные Волгоградским научно-исследовательским институтом нефтяной и газовой промышленности (ВНИИНП), представляющие собой десятипроцентную суспензию в соляровом масле резины (PC) и полиэтилена (ПЭС). Содержание воздуха при применении указанных пеногасителей легко регулируется на уровне 0—3%. Другие пеногасители (соансток, жирные кислоты и их соли, кремнийорганические полимеры марки МПС-4000 . н МПС-9000) менее термостойки. Оптимальные добавки ПЭС иPCв растворе составляют соответственно 0,1—0,15 и 0,2—
0,3% на объем раствора в расчете на сухое вещество (полиэтилен, резину). Для обработки растворов в зависимости от минерализации и температуры необходимо вводить от 1 до 3% КССБ (в пересчете на сухой продукт).
Крахмальные реагенты
. Крахмал применяют двух видов: обычный технический и модифицированный. Обычный технический крахмалне раствортгм в воде и может быть добавлен в промывочный раствор только предварительно клейстеризованным щелочью с концентрацией активного вещества не более 8—10%, он ферментативно неустойчив. Под действием микроорганизмов и энзимов разрушается, теряя стабилизирующие свойства. Из-за низкой термостабильности приt
=
393 403°
К крахмал претерпевает расщепление с потерей стабилизирующих свойств.
Модифицированный крахмал — растворимую модификацию крахмала — готовят путем высушивания крахмальной суспензии при t
= 403 423° К с добавкой в суспензию перед высушиванием алюмокалиевых квасцов.
Для получения ферментативно устойчивой модификации вместе с квасцами вводится бактерицид (диоцид). Модифицированный крахмал представляет собой белый порошок влажностью 8—12%, не требующий добавки щелочи при обработке растворов, хорошо растворим в холодной воде и глинистом растворе. Модифицированный крахмал является высокоэффективным защитным реагентом, обеспечивающим низкую водоотдачу промывочных растворов любой модификации включая и хлоркальциевую агрессию. Не термостоек, вследствие этого не рекомендуется применять его при высокой забойной температуре (более 373° К).
Для сохранения плотности раствора его можно обрабатывать непосредственно добавкой порошкообразного реагента в циркуляционную систему.
Добавка в раствор модифицированного крахмала колеблется в пределах 0,5—2% (на сухое вещество). Крахмальный реагент из обычного технического крахмала обычно готовят по рецепту: в 100 частях водного раствора содержится 5—10% сухого крахмала и 1 — 2% кристаллической каустической соды. Иногда для снижения вязкости к крахмальному реагенту добавляют 5—6% раствора ССБ.
Гипан — продукт щелочного гидролиза полиакрилонитрила — представляет собой вязкую жидкость со слабым аммиачным запахом, желтого цвета с содержанием 10%-ного сухого вещества, вязкостью 9—16 спз
1%-ного водного раствора. Основное назначение гипана — обеспечение низкой водоотдачи пресных растворов при забойной температуре до 523° К, когда другие реагенты-стабилизаторы недейственны. Гипан хорошо защищает промывочные растворы от агрессивного воздействия минерализации (сульфата, хлористого натрия). Менее эффективен гипан при хлоркальциевой агрессии. При значительных количествах соли гипан добавляется в количестве 1 %. В маломинерализованные глинистые растворы при температурах 373—393° К добавляется в количестве 0,5%, а при высокой забойной температуре 0,75—2%.
Пресные растворы гипан загущает, соленые — разжижает, но не столь интенсивно как КМЦ. Весьма полезно сочетание гипана с известковой обработкой, хроматами и реагентами (крахмалом, КМЦ, УЩР и др.). Гипан морозоустойчив и не подвергается ферментативному разложению. Вследствие незначительных расходов и длительного действия гипана при обработке им раствора применение его в ряде случаев оказывается более выгодным, чем КМЦ.
Сухие гуматощелочные реагенты. Большое удобство в работе буровиков представляют сухие гуматощелочные реагенты, УЩР или ТЩР, которые готовятся на специальных заводах и доставляются на буровые в виде сухого крупнозернистого порошка. Технология получения их заключается в перемешивании сухого или подсушенного бурого угля (с содержанием влаги 15—18%) или торфа с концентрированной щелочью (42—45%). Соотношение бурого угля, торфа и каустической соды в них то же самое, что и жидких реагентов. Поэтому необходимые расчеты производятся по формулам (20) —(23). Сухой УЩР и ТЩР можно добавлять непосредственно в циркуляционную систему.
Реагенты-понизители вязкости
Следует различать два вида реагентов понизителей вязкости и предельного напряжения сдвига промывочных растворов — общего и специального назначения.
Реагенты общего назначения
К числу реагентов, служащих для единовременного разжижения (перед спуском колонн, электрометрическими работами и т. п.) и для систематической обработки растворов, относятся: сульфит-спиртовая барда (ССБ), полифенольный лесохимический реагент (ПФЛХ), сульпор, синтаны (синтетические таннины), натуральные растительные экстракты, окисленный лигнин.
Реагенты, предназначенные для обработки пресных и маломинерализованных растворов (в том числе на морской воде), загустевших в результате поступления в них разбуриваемых пород, преимущественно глинистых. Не пригодны они для разжижения растворов, загустевших от действия солей. Термостойкость растворов, обработанных этими реагентами, равная 383—403° К, может быть повышена комбинированием с хроматами. Добавки реагентов разжижают выходящие из скважины растворы, загустевшие от действия высокой забойной температуры. Единовременные добавки реагентов колеблются в пределах 0,2—0,5% (по массе сухого вещества). Все реагенты совместимы со всеми другими продуктами, применяемыми для химической обработки промывочных растворов (содой, УЩР, КССБ, крахмалом, КМЦ, гипаном и др.) с различными рецептурами их (известковыми, хлоркальциевыми, хроматными, эмульсионными и т. п.). Реагенты применяются в щелочных растворах 5—10 % -ной концентрации в соотношении со щелочью от 1 : 0,1 до 1 : 0,5 (на сухое вещество). Обработка ведется добавкой тонкой струи реагента в циркулирующий раствор.
Реагенты из сульфит-спиртовой барды (ССБ). ССБ является отходом целлюлозной промышленности. Поступает с завода с различным содержанием твердого вещества. Для первичной обработки пресных глинистыхрастворов реагент ССБ готовится но одному из рецептов: ССБ-30-4, ССБ-30-5, ССБ-30-6 (первая цифра — процентное содержание сухой ССБ, вторая — процентное содерл^ание кристаллической каустической соды), а иногда ССБ-20-3, ССБ-20-4 и ССБ-20-5. В соленых растворах применяется без щелочи. При высоких за'бойных температурах не разжижает.
Объем раствора ССБ, необходимый для приготовления единицы объема химического реагента, определяется по формуле
, (24)
где V
— объем раствора ССБ;
R
— процентное содержание сухой ССБ в реагенте;
N—
количество реагента, которое необходимо приготовить;
mi
— процентное содержание сухой ССБ в растворе барды.
Если N в л,
то V
в л,
если N
в м3
,
то и V
в м3
.
Величинуm
1
находят по таблице, исходя из плотности раствора ССБ
Определение плотности густой или твердой ССБ несколько затруднительно. В таких случаях количество ССБ, необходимое для приготовления реагента, подсчитывают по формуле
(25)
где Р
— количество ССБ, необходимое для приготовления реагента;
Q
— процентное содержание сухой ССБ в рецепте реагента (обычно 30%);
N
— количество реагента, которое надо приготовить;
т2
— количество воды в кг,
добавленное к 0,2 кг
барды для снижения плотности ее до 1,28—1,30 т/м3
.
Если N
в л,
то Р
в кг;
если N
в м3
,
то Р
получают в т.
При первичной обработке глинистого раствора в него добавляют реагент ССБ в зависимости от условий бурения данной скважины в количествах 40, 60 и 80 см3
на 1 л,
а при дополнительной обработке в 5—6 раз меньше. Недостатком ССБ является ее пенообразующее действие. Требует применения пеногасителей.
Иногда обработка глинистых растворов может производиться аналогом ССБ — сульфит-целлюлозным экстрактом (СЦЭ) марки «известковый» (из серии дубителей).
Рецепт химического реагента из него таков: СЦЭ-20-5 (первая цифра — процентное содержание сухого СЦЭ, вторая — процентное содержание кристаллической каустической соды). Определение необходимых количеств СЦЭ иNaOH производится точно так же,-как и для реагента ССБ.
ПФЛХ
является продуктом формальдегидиой конденсации полифенолов растворимых смол — отхода при газификации древесины. Темно-коричневое твердое вещество, растворимое в воде и водных растворах щелочи. Для обработки глинистых растворов ПФЛХ применяется 5—10%-ной концентрации. Соотношение ПФЛХ и щелочи варьируют от 1 : 0,1 до 1 : 0,5 (на воздушно-сухие вещества) в зависимости от состава глинистого раствора, его щелочности и требуемой вязкости.
Сулькор — сульфитироваыный щелочной экстракт одубины. Темно-коричневое твердое вещество. Аналог ПФЛХ.
Окисленный лигнин
готовится путем обработки гидролизного лигнина разбавленной или концентрированной азотной кислотой, смесью азотной и серной кислоты, газообразным хлором или хлорной водой. В зависимости от применяемого окислителя полученный продукт условно называется нитро или хлорлигнином. Окисленный лигнин представляет собой желто-коричневый порошок, растворяющийся в водных растворах щелочи. Наиболее часто применяется реагент 5%-ной концентрации при соотношении лигнина и щелочи 1 : 0,3 (воздушно-сухие вещества).
Синтан-5 — продукт омегасульфирования новолачной смолы на основе фенолов буроугольногопроисхождения. Синтетический дубитель. Твердоекоричневое вещество,растворимое в воде и щелочных растворах. Аналог ПФЛХ.
Еловый экстракт
— сульфитированный водный экстракт еловой коры, темно-коричневый сухой продукт, растворимый в воде и водных растворах щелочей. Аналог ПФЛХ.
Реагенты-понизители вязкости специального
назначения
Комплексные фосфаты
(полифосфаты) — натриевые гексомето-фосфат, пирофосфат, триполифосфат. Добавка к
глинистым растворам не более 1—1,2%; превышение этого количества вызывает загу-стевание растворов. Применение полифосфатов наиболее эффективно при единовременной обработке (спуске колонн, электрометрических работах и т. п.), но они могут применяться также при бурении неглубоких скважин. Полифосфаты нецелесообразно применять для разжижения соленых растворов, так же как и в условиях высокой забойной температуры, при которой они разлагаются; не могут они применяться также в известковых, гипсовых, высококальциевых и других растворах, так как с растворимыми солями кальция дают осадки. »
Хроматиые реагенты (анионные соединения хрома) — хроматы и бихроматы калия и натрия.
Оранжевые поршни или сплавы, хорошо растворимые в воде. Применяются в условиях высокой забойной температуры для предотвращения вызванного ею загустевания растворов. Наиболее эффективны при температуре свыше 373° К, когда другие реагенты, служащие для разжижения вязкости, перестают действовать. Хроматные реагенты можно добавлять к различного рода промывочным растворам (пресным, известковым, минерализованным, утяжеленным) раздельно или совместно с реагентами-стабилизаторами в виде хромгуматов, хромлигносульфонатов и др.
Применяют хроматные реагенты в виде водных растворов 10%-ной концентрации. Единовременные добавки их 0,05—0,2% (по массе сухого вещества па объем раствора).
Комбинированные реагенты
Исследованиями установлено, что одновременное применение УЩР и ССБ для обработки глинистых растворов позволяет регулировать толщину сольватных оболочек и тем самым достигать снижения водоотдачи раствора без повышения его вязкости.
Оптимальные количества УЩР и ССБ подбираются в лаборатории. Содержание бурого угля в комбинированном реагенте составляет 10%, каустической соды обычно 2%, а ССБ от 0,2 до 4%.
Рецепты комбинированных реагентов принято обозначать так: К-10-2-0,2, К-10-2-0,5 и т. д. (первая цифра — процентное содержание сухого бурого угля, вторая — процентное содержание кристаллической каустической соды, третья — процентное содержание сухой ССБ). Необходимые количества ССБ подсчитывают по формулам (24) или (25), каустической соды — по (23), бурого угля — по (2), (21) и (20).
Специальные промывочные растворы
Известковые глинистые растворы
. При разбуривании сильно набухающих глин и солевых отложений, для борьбы с обвалами стенок и сужениями стволов скважин, а также в случае притока в скважину высокоминерализованных вод применяют известковые глинистые растворы в сочетании сNaOH, ССБ, КССБ и другими реагентами, а также понизителями липкости.
Растворы, обработанные известью, обладают небольшими вязкостью, статическим и динамическим напряжениями сдвига, легко управляемы и весьма стабильны.
Рецептура первичной обработки глинистого раствора известью подбирается в зависимости от его качества, степени минерализации, концентрации глинистой фазы и т. п. Примерное соотношение между' химическими реагентами (в процентах от объема раствора) таково: ССБ (50%-ной концентрации) от 0,3 до 4,0%, каустическая сода (кристаллическая) от 0,05 до 0,5%, известь (сухая) от 0,1 до 0,8%.
При последующих обработках раствора известью с целью поддержания постоянства стабильных свойств его на каждый метр углубления скважины добавляют следующее количество компонентов: ССБ (КССБ) 10—35 л, каустической соды 4—7 кг,
извести 6— 10 кг.
Если известкование раствора производится с использованием КССБ, то добавки каустической соды колеблются в пределах 1— 3 кг
на 1 м
проходки.
Недостатком глинистых растворов, обработанных пзвестыо, является тенденция их к загустевапию при температурах порядка 393° К и выше.С помощью различных добавок (например, хромпика) процесс загустевают может задерживаться.
Высококальциевые растворы (ВКР).
Обычные глинистые растворы для перевода в высококальциевые обрабатывают хлористым кальцием, известьюи реагентом-стабилизатором (КМЦ, крахмал, КССБ и другими реагентами, устойчивыми к действию солей). При необходимости в эти растворы можно добавить понизители вязкости (ССБ, ПФЛХ, окисленный лигнин и др.), утяжелитель или нефть. ВКР может быть применен при бурении в самодиспергирующихся глинистых сланцах с целью предотвращения осыпей и обвалов стенок скважины: в пластичных набухающих глинах препятствует быстрому переходу глины в раствор и росту его вязкости в условиях минеральной агрессии. Отличительной особенностью ВКР является его состояние регулируемой коагуляции, обусловленное повышеннымсодержанием иона кальция в фильтрате глинистого раствора. При проникновении фильтрата ВКР в пласт происходит его активное взаимодействие с частицами глины на стенках скважины. Адсорбция кальция в количестве, превышающем порог коагуляции глинистых частиц, уменьшает гидратацию глины вплоть до полного разрушения диффузного слоя. Создаются условия для слипания и агрегирования глинистых частиц на поверхности раздела.
Резкое изменение, структурно-агрегатного состояния глины вызывает увеличение ее механической прочности, предотвращает процесс самопроизвольного осыпания сланцев. Расход реагентов для поддержания необходимых параметров обусловливается содержанием иона Са в фильтрате раствора и рН среды. Для бурения в сыпучих глинистых сланцах содержание иона Са колеблется в пределах 0,08—0,15% при рН = 8 9. При этом расход реагентов составляет 0,3-0,6% СаС12
, 0,1-0,15% Са (ОН)2
, 0,1-0,3% ССБ и 1 — 1,5% КМЦ (добавки реагентов даны в процентах сухого вещества на объем глинистого раствора). ВКР, стабилизированные КМЦ, обладают сравнительно низкой термостойкостью. Уже приt
= 330 350° Кпроисходит резкое повышение водоотдачи, а для КССБ-1 приt
= 373 393° К 5 < 15—18 см
3
. Более термостойкими оказываются растворы, стабилизированные КССБ-2, при которой необратимое увеличение водоотдачи наблюдается лишь приt
>
423° К.
Для забойной температурыt
< 373 393° К рекомендуется следующая рецептура ВКР: концентрация 0,75—1% СаС12
, 0,2— 0,5% Са (ОН)2
и 10—12% КССБ-1. При этом параметры раствора: плотность 1,2—1,25 т/м3
,
вязкость 35—50 сек, водоотдача 5—8 еж3
, содержание ионов Са в фильтрате 0,25—0,3%, рН = 7 9. Для забойной температуры до 423° К концентрация реагентов в растворе должна быть 0,75-1% СаС12
и 12% КССБ-2-10.
Эмульсионные растворы
. В ряде случаев в водную дисперсионную среду химически обработанных глинистых растворов вводят равномерно распределенные капельки нефти, стабилизированной Эмульгаторами, или нефтепродуктов (до 10—30% по весу от объема раствора). Такиерастворы называют эмульсионными.
Хороший эмульсионный раствор может быть получен лишь на базе высококачественного исходного химически обработанного глинистого раствора путем поддержания в нем оптимального количества нефтянойфазы (в среднем 10—20%), высокой стабильности и дисперсности эмульсии (размеры глобул должны быть в пределах 10—100 мкм).
Нефтяной компонент не только улучшает параметры раствора, но и придает ему новые свойства. Перед введением нефти глинистый раствор обрабатывают химическими реагентами (УЩР, ССБ, КМЦ), соответствующими условиям бурения. При этом нередко обходятся безспециальных реагентов-эмульгаторов. Если же стабильность эмульсин недостаточна или необходима более тонкая эмульсия, то в раствор добавляют эмульгаторы — сульфатно-нафтеновые кислоты, их солии различные контакты (газойлевый, керосиновый, НЧК, детергент ДС) в количестве 0,1—1,0%.
С введением 5% нефти (по весу от объема раствора) резко снижается липкость раствора, при 7—8% прекращается образование сальников. При дальнейшем увеличении количества нефти заметно увеличиваются механические скорости проходки, уменьшается износ долот.
Оптимальное количество нефти в растворе устанавливается опытным путем в зависимости от условий бурения. Нефть добавляется в процессе циркуляции со скоростью, позволяющей ввести расчетное количество нефти за два-три цикла циркуляции.
Растворы на нефтяной основе
предназначены: для бурения в осложненных условиях, в частности при проходке обваливающихся соленосных и других пород; для вскрытия продуктивных пластов (особенно с низким пластовым давлением); для бурения глубоких п сверхглубоких скважин при высоких забойных температурах; для увеличения проходок на долото.
Параметры растворов па нефтяной основе в зависимости от конкретных условий бурения могут изменяться в широких пределах: плотность от 0.9 до 2,2 т/м
3
, вязкость по СПВ-5 от 35 сек
до «нетечет», фильтрация за 30 мин
нуль, статическое напряжение сдвига1
от нуля до нескольких сот мн/см2
,
стабильность практически равна нулю. Растворы на нефтяной основе при низких температурах приготовляются следующим образом: смесь битума с дизельным топливом в глиномешалке нагревается до 303—313° К открытым паром, а затем вводится известь. При гашении извести водой (конденсатом пара) температура в глиномешалке поднимается до 373—393° К„ Свободная вода испаряется, получается безводный раствор на нефтяной основе. При сравнительно высоких температурах в скважине процесс приготовления может быть упрощен. В приемные емкости заливается дизельное топливо, в которое в процессе циркуляции вводится расчетное количество известково-битумных порошков и воды. В настоящее время наиболее освоенной рецептурой растворов на нефтяной основе является приготовление их из известково-битумных порошков. На 1 м3
раствора на нефтяной основе расходуется 0,65 м3
дизельного топлива, 4,9 кг
известково-битумных порошков, в которых отношение извести к битуму по массе для растворов с плотностью меньше 1,5 т/м3
берется 2 : 1, а для растворов с плотностью более 1,5 т/м3
это отношение равно 1 : 1, к раствору добавляют 20% воды от массы извести. При этом используются окисленный битум с температурой размягчения 413—433° К, негашеная известь активностью не менее 60%, которая получается путем обжига природного известняка; дизельное топливо можно применять как зимнее, так и летнее. Битум п известь применяются в порошках. Известково-битумные порошки изготовляются путем раздельного или совместного помола битума и извести в молотковых дробилках.
Безглинистые промывочные растворы
. В последнее время в нефтяных районах Украины, Саратовской, Пермской и других областях начинают применяться безглинистые промывочные растворы.
Ниже приводятся некоторые рецептуры указанных жидкостей.
Меловой раствор.
Сырьем для приготовления этого раствора являются отходы мелоцементных заводов или меловая крошка. Химическая обработка исходной меловой суспензии состоит в добавлений 15—20% УЩР. Параметры обработанного мелового раствора: плотность 1,2—1,34 т/м3
,
вязкость 30—40 сек, водоотдача 7—12 см9
за 30 мин.
Высококалъциевые безглинистые эмульсионные растворы.
Исходным Материалом для получения этих растворов служит крахмально-нефтяная эмульсия следующего состава: воды 80—85%, нефти 15 — 20%, крахмала 4—5%, каустической соды 0,5—0,6% (по массе крахмала).
Крахмально-нефтяная эмульсия имеет следующие параметры: плотность 1,0 т/м3
,
вязкость 250—300 сек,
водоотдача 2—3 см3
за 30 мин,
статическое напряжение сдвига 0 мм/см2
.
Высококальциевые эмульсионные растворы применяются при бурении солей и ангидрита. За счет насыщения солью и обогащения выбуренной породой плотность увеличивается до 1,2—1,26 т/м3
,
вязкость снижается до 25—40 сек
и водоотдача увеличивается до 4—8 см3
.
Естественные аргиллитовые растворы.
Естественная аргил-литовая суспензия, получаемая при бурении аргиллитов, обрабатывается 15% УЩР; в результате раствор приобретает следующие параметры: плотность 1,22 т/м3
,
вязкость 18—20 сек,
водоотдача 5—8 см3
.
Возможно утяжеление исходного естественного аргиллитового раствора до плотности 1,4 т/м3
путем добавления мела. Иногда для стабилизации естественного аргиллитового раствора применяют реагент 2%-иой концентрации следующего состава: 20 ч. гидролизованного полиакриламида, 2 ч.NaOH и 2 ч. триполифосфатнатрия, условно названногоPG-2. Стабилизированный реагент РС-2 аргиллитовый раствор устойчив к воздействию высокой температуры до 373—383° К, допускает утяжеление гематитом до плотности 1,5— 1,55 т/м3
,
при этом вязкость его не превышает 50—70 сек,
а водоотдача 6—8 сл3
. Расход реагента РС-2 (сухого, вещества) для обработки естественного аргиллитового раствора составляет 0,6—1,6 кг
на 1 м
обрабатываемого интервала.
Безглинистый крахмально-силикатный раствор.
Составными материалами указанного раствора являются: крахмал 3—4%, кристаллическая каустическая сода 1,5 — 2%, жидкое стекло 15—20% и вода 80-85%.
Параметры крахмально-силикатного раствора: плотность 1,12 т/м3
,
вязкость 48 сек,
водоотдача 4 см3
,
статическое напряжение сдвига 20,5 мм/см2
.
Плотность можно регулировать добавками утяжелителя в пределах до 1,7 т/м3
.
Раствор не восприимчив к соляной агрессии.
Додавки графита в глинистый раствор
Иногда для уменьшения липкости и снижения статического напряжения сдвига корки глинистого раствора в него добавляют серебристый графит в количестве 0,8—1,5% по весу к объему промывочной жидкости.
Для обработки глинистого раствора предварительно готовят так называемый графитовый раствор. Его приготовляют на основе глинистого раствора, разбавленного УЩР.
Предварительные наблюдения показывают, что оптимальное количество графита, вводимого в
1 м3
глинистого раствора, равно примерно 40 кг.
Расчет скорости подачи реагента и воды в глинистый раствор при химической обработке его
При химической обработке глинистого раствора, циркулирующего в скважине, очень важен правильный расчет скорости подачи реагента и воды.
Скорость подачи химического реагента и воды в глинистый раствор должна обеспечивать соблюдение рецепта обработки при условии введения их в течение времени, равного целому числу оборотов циркуляции, и определяется по следующей формуле:
, (26)
гдеv
— скорость добавления химического реагента или воды к
глинистому раствору в л/ч\
Q
— объем циркулирующего глинистого раствора в м
3
;
п
— количество химического реагента или воды, добавляемое к глинистому раствору, в % от объема раствора;
т
— число циклов движения глинистого раствора, в течение которых должна быть проведена химическая обработка;
Т
— продолжительность одного оборота циркулирующего глинистого раствора в ч.
Продолжительность одного- цикла циркуляции глинистого раствора в скважине определяется по таблице.
Расход жидкости определяют мерной посудой по времени ее Заполнения, пользуясь специальными таблицами.
Определить влажность бурого угля, а также концентрацию гуминовых кислот в нем, если навеска влажного угля в 68,7 г
после просушки равна 58,8 г,
а для придания исследуемой вытяжке гуминовых кислот одинакового с эталоном цвета понадобилось к 2 см
3
исследуемого раствора добавить 6 см
3
воды. Концентрация гуминовых веществ в эталоне составляет 0,08%.
Влажность бурого угля определим по формуле (20)
.
Концентрацию гуминовых кислот найдем по формуле (21)
.
Подсчитать количество бурого угля влажностью 20% и объем каустической соды, плотность раствора которой равна 1,16 т/м3
,
необходимые для приготовления 1 м3
химического реагента по рецепту УЩР-15-3.
Потребное количество влажного бурого угля найдем по формуле (22):
.
Объем раствора каустической соды, необходимый для приготовления 1 м3
химического реагента, определим по формуле (23):
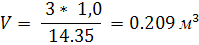
Здесь величинаm
= 14,35% найдена по таблицеB
зависимости от плотности раствора каустической соды (1,16 т/м3
)
.
Определить объем раствора ССБ плотностью 1,19 т/м3
и объем раствора каустической. ,соды плотностью 1,24 т/м3
,
необходимые для приготовления 1 м3
химического реагента по рецепту ССБ-30-5.
По величине плотности раствора ССБ, равной 1,19 т/м3
, находим процентное содержание сухой ССБ в растворе (тх
=
40%). Затем по формуле (24) подсчитываем потребный объем раствора ССБ:
.
По величине плотности раствора каустической соды, равной 1,24 т/м3
,
по таблице находим процентное содержание сухой каустической соды в растворе (т =
21,55%). Затем по формуле (23) подсчитываем потребный объем раствора:
.
Определить количество ССБ, необходимое для приготовления 1 м3
химического реагента по рецепту ССБ-30-6, если к 0,2 кг
раствора ССБ для снижения плотности его до 1,29 т/м3
необходимо добавить 0,5 кг
воды.
КоличествоССБ, необходимое для приготовления 1 м3
реагента, подсчитываем по формуле (25):
.
Определить потребные количества раствора ССБ плотностью 1,23 т/м3
,
бурого угля влажностью 20% и раствора каустической соды плотностью 1,4 т/м3
,
необходимые для приготовления 1 м3
комбинированного реагента по рецепту К-10-2-0,5.
Объем раствора ССБ, необходимый для приготовления 1м
3
химического реагента по заданному рецепту, находим по формуле (24):
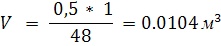
Здесь процентное содержание тх
= 48% сухой ССБ в растворе барды найденопо величине плотности раствора ССБ, равной 1,23 т/м3
.
Количество бурого угля влажностью 20%, необходимое для приготовления 1м
3
химического реагента, подсчитываем по формуле (22):
.
Объемное количество раствора каустической соды плотностью 1,4 т/м3
,
потребное для приготовления 1 м3
комбинированного химического реагента по заданному рецепту, подсчитываем по формуле (23):
.
Здесь процентное содержание т
= 50,7% сухой каустической соды в раствореNaOH найдено по таблице по плотности раствора, равной 1,4 г/см3
.
Определить скорость подачи химического реагента и воды в глинистый раствор, циркулирующий в скважине глубиной 1300 м,
бурящейся долотом № 8. Объем раствора, находящийся в процессе циркуляции, равен 115 м3
.
К нему необходимо добавить 6% химического реагента и 3,5% воды. Обработку требуется произвести за два цикла циркуляции раствора. Производительность буровых насосов 30 л/сек.
По таблице находим, что продолжительность одного цпкла циркуляции глинистого раствора в скважине равна 35 мин.
Тогда скорость подачи реагента по формуле (26) равна
л/ч
,
а скорость добавления воды окажется равной
л/ч
.
Реагенты-структурообразователи
Основное назначение реагентов-структурообразователей сводится к увеличению вязкости (иногда до такого состояния, что глинистый раствор не течет через воронку СПВ-5) и повышению тиксотропных свойств глинистых растворов при борьбе с поглощениями.
К структурообразователям относятся каустическая сода, кальцинированная сода, жидкое стекло, известь, цемент, поваренная соль, хлористый кальций и др.
Для получения растворов с очень большой вязкостью и высоким началом сдвига применяют следующие добавки:
а) жидкое стекло до 5% по массе от объема циркулирующего раствора;
б) кальцинированную соду до 6% по массе от объема циркулирующего раствора;
в) каустическую соду до 4% по массе от объема циркулирующего раствора (имеется в виду кристаллическая сода); если сода подается на буровую в жидком виде, то производим перерасчет по формуле (23);
г) каустическую соду до 2% и нефть до 10%;
д) кальцинированную соду до 3% и нефть до 10%;
е) различные инертные добавки — опилки, рисовую шелуху, кордное волокно, отходы кожевенной промышленности, торф, паклю, слюду и т. д. — в количестве 2—3% по массе от объема глинистого раствора (обычно количество инертных добавок определяется в зависимости от конкретных условий бурения).
Профилактические
глинистые растворы для бурения в поглощающих горизонтах готовят из химически обработанных растворов путем введения в них структурообразующих добавок.
В качестве последней прежде всего проверяют эффективность действияNaCl, так как она в ряде случаев значительно повышает структуру раствора.
Когда действиеNaCl недостаточно эффективно, в раствор добавляют жидкое стекло в количестве 3—5% по массе от объема глинистого раствора. Если при этом не будет обеспечена необходимая растекаемость раствора по конусу АзНИИ (10—11 см)
, тов раствор добавляют 0,5—1,0% известкового молока.
В качестве коагулирующей добавки можно использовать известь в сухом виде или в виде известкового молока. Рецепт обработки раствора предварительно разрабатывают в лаборатории. Обычно известь добавляют в количестве 10—20 кг
на 1 м3
раствора (1—2% по массе от объема глинистого раствора), приготовленного на пресной воде, и 35—38 кг
па 1 м3
раствора, приготовленного на морской воде.
Если в процессе бурения возникают поглощения средней интенсивности с более или менее значительным снижением уровня раствора в скважине, то для их ликвидации готовят гель-цементы.
Основными компонентами гель-цементов являются глинистый раствор, жидкое стекло и цемент. Количество тампонажного цемента в 1 м3
гель-цемента должно быть 0,5—0,9 m, а глинистого раствора 700—800 л.
Для обеспечения более широких возможностей регулирования сроков схватывания в гель-цемент рекомендуется добавлять алебастр 15—25% по весу от веса цемента.
1.4 Обоснование выбора способа бурения и проектирование режимов бурения
Основные требования к выбору способа бурения - необходимость обеспечения успешной проводки ствола скважины при возможных осложнениях с высокими технико-экономическими показателями. Поэтому способ бурения выбирается на основе анализа статистического материала по уже пробуренным скважинам исоответствующих экономических расчетов.
Из анализа приведенных данных следует, что для геологического разреза характерны многочисленные интервалы, представленные мягкими породами, твердость которых ниже третьей категории по классификации Л. А. Шрейнера. Разбуривание таких пород целесообразно вести энергоемкими долотами.
Эти, а также другие особенности геологического разреза позволяют считать наиболее обоснованным выбор роторного способа бурения.
В основу выбора породоразрушающего инструмента положены физико-механические свойства горных пород, литологический разрез, перемежаемость пород, а также способ бурения, компоновка низа бурильной колонны, режимные параметры бурения и степень износа долот.
Выбор управляемых оптимальных параметров режима бурения (осевая нагрузка на долото и скорость его вращения) производится на основании анализа фактических данных бурения на площади Равнинная.
Выбор способа бурения производится с учетом условий проводки скважины, особенностей каждого из способов бурения, а также на основании выбранных долот и режимов бурения.
Потребный расход бурового раствора определяется из зависимости
Q = d *F
Где в – удельный расход жидкости л/с на см2
F – площадь забоя, см2
.
В соответствии со способом бурения, режимными параметрами и естественнымиусловиями искривления скважин, на основании анализа фактических данных бурения скважин производится выбор компоновки
низа бурильной колонны.
Бурение в интервале 7-50 м.
Бурение осуществляется долотом III -490 С-ЦВ роторным способом со следующей компоновкой низа бурильной колонны: долото 490 С-ЦВ, бурильные трубы 140 мм.
Осевая нагрузка с 2-3 т, производительность - 34,1 л/с. число оборотовротора - 60-80 об/мин. Бурение в интервале 50-1010 м.
Бурение в интервале 50-1080 м ведется роторным способом долотами III 393,7 М-ЦВ (М-ГВ).
Режим бурения:
осевая нагрузка 4-12 тс;
производительность насосов 59,3 л/с;
число оборотов ротора 80 - 120 об/мин;
допустимое давление на насосах 114 кгс/см2
;
диаметр втулок 170мм;
число двойных ходов 65 х/мин.
Бурение в интервале 1080-1010 м ведется роторным способом долотами III -393,7 С-ЦВ (С-ГВ).
Режим бурения:
осевая нагрузка 15 -18 тс;
производительность насосов 51,8 л/с;
допустимое давление на насосах 114 кгс/см2
;
число оборотов ротора 90 - 100 об/мин;
диаметр втулок 170мм;
число двойных ходов 65 х/мин.
Компоновка низа бурильной колонны при бурении в интервале 50-1300м:
долото диаметром 393,7 мм + УБТС 1-229 40 м + УБТС 1 - 203 72 м + УБТС 1-178 8м + бурильные трубы диаметром 140 мм.
Проработка ствола скважины в интервале 30-1250 м производится в два этапа:
1. долото диаметром 393,7 мм + УБТС 1-229 8 м + ЦС - 392 + УБТС 1-229 8м + УБТС 1-203 32 м УБТС 1- 178 8 м + бурильные трубы диаметром 140 мм.
2.долото диаметром 393,7 мм + ЦС - 392 +УБТС 1-229 8 м + ЦС -392 +УБТС 1-229 8м + УБТС 1- 203 32 м УБТС 1- 178 8 м + бурильные трубы диаметром 140 мм.
Бурение под колонну 245*219 мм в интервале 1010-3835 м
Бурение в интервале 1300-2625 м производится роторным способом
долотом 269,9 М-ГВ (МГ-Н)
Режим бурения:
осевая нагрузка 15-18 тс;
производительность насосов 35,3 л/с;
число оборотов ротора 100-120 об/мин:
Интервал 2625-4130 м бурится долотом 111-269,9 С-ГНУ (С-ГНУ, СЗ-ГНУ) с нагрузкой на долото 18-22 тс, производительность насосов -33,5 л/с, число оборотов ротора 80-90 об/мин.
Расход раствора будет обеспечен двумя насосами на втулках 140 мм, допустимое давление на насосах до 180 кгс/см , -число двойных ходов -55-60 х/мин.
Компоновка низа бурильной колонны при бурении в интервале 1300-4100м:
долото диаметром 269,9 мм + УБТС 1-203 72 м + УБТС 1-178 112 м + ПЖЦ (противожелобной центратор) + бурильные трубы диаметром 127,140мм.
Отбор керна в интервале бурения под II промежуточную колонну производится следующей компоновкой бурильного инструмента: колонковое долото К 212,7/80 СТ + КД ИМ - 190/80 «Недра» + УБТС 1-203 72 м +УБТС 1-178 32 м + ПЖЦ - 243 + б/т диаметром 127,140мм. Бурение под эксплуатационную колонну 140 мм.
Бурение производится долотами 1-190,5 СЗ-Н и 111-190,5 С-ГВ роторным способом с нагрузкой на долото -10-15 тс, производительность насосов -16,7л/с, число оборотов ротора - 60-70 об/мин.
Расход бурового раствора будет обеспечен работой одного насоса с диаметром втулок 130 мм, допустимое давление на насосах - 200 кгс/см2
, число двойных ходов - 60 х/мин.
Отбор керна в интервале бурения под эксплуатационную колонну производится следующей компоновкой бурильного инструмента: колонковое ДОЛОТО К 187,3/80 СЗ + КД 11М - 190/80 «Недра» + УБТС 1-146 108 м + УБТС 1-120 32 м + бурильные трубы диаметром 114,127 мм.
1.5 Методы ликвидации аварий
В процессе бурения нефтяных и газовых скважин аварией считают нарушение технологического процесса, вызываемое прихватом или поломкой с оставлением в скважине инструментов, элементов бурильной колонны или других предметов, для извлечения которых требуются специальные работы.
Аварии происходит в основном вследствие брака в работе или исполнителей технологического процесса, или изготовителей инструментов, оборудования и механизмов.
Основное число аварий в бурении возникают в результате нарушения технических и технологических проектов.
Прежде чем приступить к ликвидации аварии, необходимо тщательно проанализировать ее на основе современного состояния техники ловильных работ и опыта ликвидации аварии. При этом надо иметь в виду, что применение и несоответствующего ловильного инструментаприводит к усложнению аварии, а нередко и к ликвидации скважины.
При подозрении на поломку инструмента в скважине бурильщик обязан немедленно приступить к подъему бурильной колонны. Одновременно, не прекращая основных работ и не оставляя своего поста, бурильщик должен уведомить мастера, а при отсутствии его -руководство предприятия об аварии.
Работы по ликвидации аварии ведутся буровым мастером под руководством старшего инженера (мастера) по сложным работам или главного (старшего) инженера предприятия. Если на буровой присутствует несколько руководящих работников, то ответственным является старший по должности, через которого мастеру передаются указания по ликвидации аварии.
Перед спуском ловильного инструмента в скважину буровой мастер составляет эскиз общей его компоновки и ловильной части с указанием основных размеров. Из спускаемой колонны удаляют переводники с уменьшенными площадями сечения проходных отверстий.
Перед проведением ловильных работ проверяют состояние талевого каната и спускоподъемного оборудования, а также крепление штропа вертлюга в зеве крюка.
Все замковые соединения бурильной колонны и соединения частей ловильного инструмента крепятся машинными, или автоматическими ключами.
Извлечение прихваченной части бурильной колонны
Выбор того или иного вида ловильного инструмента зависит от -характера слома колонны и состояния скважины.
Для подъема неприхваченных бурильных труб применяют освобождающиеся и неосвобождающиеся ловильные инструменты.
Ловители являются наиболее распространенными ловильными инструментами. Их не применяют, если вес оставшихся и скважине труб больше допустимой нагрузки на ловитель или если аварийная труба имеет сильно разорванный конец со сложной конфигурацией излома.
В первую очередь рекомендуется использовать наружные ловильные инструменты (ловители, наружные труболовки, колокола резьбовые и колокола гладкие), причем желательно с центрирующими приспособлениями.
Предпочтение отдается освобождающимся ловильным инструментам.
Извлечение прихваченной бурильной колонны.
Прихват - сложный вид аварии, которая не происходит мгновенно. Прихват требует анализа обстоятельств аварии, изучения состояния ствола, показателей и особенностей работы бурильной колонны в период, предшествующий аварии. Особенно подробно надо изучать наличие осыпей, обвалов, нефте - водо - и газопроявлений, сужений ствола, расположения неустойчивых пластов и уступов; состояние бурильной колонны продолжительность ее работы, время и качество проведения профилактики четких проверок; состояние циркуляции, изменение подачи насосов и давления прокачиваемой промывочной жидкости.
1
.6
Выбор типов и параметров буровых растворов
Буровые растворы выполняют функции, которые определяют не только . успешность и скорость бурения, но и ввод скважины в эксплуатацию с максимальной продуктивностью. Основные из этих функций - обеспечение острого углубления при устойчивом состоянии ствола скважины и хранение коллекторских свойств продуктивных пластов.
Тип бурового раствора, его компонентный состав и границы возможного применения устанавливают исходя из геологических условий: физико-химических свойств пород и содержащихся в них флюидов, пластовых и горных давлений, забойной температуры.
Рецептуры и методы их обработки выбирают поинтервально в зависимости от геолого-технических условий проходки скважины на основании обобщения опыта на данном районе.
В связи с тем, что разрез сложен породами, склонными к потери устойчивости при снижении противодавления в скважине, а также наличием в разрезе высоконапорных нефтегазопроявляющих горизонтов, исключающих снижение давления в скважине, для бурения выбирается глинистый раствор на водной основе, хорошо зарекомендовавший себя при бурении скважин в аналогичных геологических условиях.
Интервал 0 - 1010 м.
Интервал сложен глинами и песчаниками акчагыла, мэотиса, сармата, карагана и чокрака, где возможны осыпи, обвалы пород, поглощение бурового раствора и водопроявления. В плиоценовых отложениях (песчаники Апшеронского яруса) находятся залежи воды гидрокарбонатнонатриевого типа, которые используются для питья.
С учетом вышеизложенного для бурения интервала 0 - 1010 м выбираем экологически чистый полимерглинистый раствор.
Обработку раствора до глубины 1010 м производим экологически чистыми реагентами - бентонитовая глина, КМЦ - 300, (УЩР), ФК-1.
Рекомендуемые параметры раствора при бурении данного интервала:
• плотность, гс/см3
- 1,19±0,02;
• вязкость по СПВ-5, с – 30 45;
• водоотдача, см за 30 мин - 4,0 5,0;
• СНС, мг/см2
через 1 и 10 мин - 15 20 / 20 30;
• рН раствора, ед – 8 9;
• содержание песка, % - до 2; ч
• толщина корки, мм - 1,5 2,0.
Интервал 1010- 3835 м.
Интервал представлен отложениями Майкопа, фораминиферовых слоев, меловых и юрских отложений. Здесь в процессе бурения возможны осложнения в виде осыпей, поглощений бурового раствора, прилипание бурового инструмента и нефтегазоводопроявления.
С учетом вышеизложенного для бурения интервала 1010- 3835 м выбираем гуматный раствор.
Обработку раствора в интервале бурения 1010- 3835 м производим реагентами - УЩР, сода каустическая, хроматы, Лакрис-20 и Лигнотин. Облагораживание бурового раствора производим бентонитовой глиной. В качестве смазывающей добавки используем ФК-1, который предназначен для обработки буровых растворов с целью улучшения их смазочных, ингибирующих и фильтрационных свойств, а также для исключения нефти, СМАДа и других экологически опасных смазывающих добавок.
Рекомендуемые параметры раствора при бурении данного интервала:
• плотность, гс/см3
- 1,24±0,02;
• вязкость по СГТВ-5, с - 35 45;
• водоотдача, см3
за 30 мин - 3,0 4,0;
• СНС, мг/см2
через 1 и 10 мин – 152 0 / 30 5 0;
• рН раствора, ед - 8 10;
• содержание песка, % - до 2;
• толщина корки, мм - 1,01 5.
Интервал 3835 -4100 м.
Интервал представлен отложениями нижней юры и триасовых обложений. Здесь в процессе бурения возможны осложнения в виде поглощений бурового раствора, прилипание бурового инструмента и нефтегазоводопроявления.
С учетом вышеизложенного, а также для сохранения коллекторских свойств продуктивныхпластов для бурения интервала 3835 - 4100 м выбираем полимерхромгуматный раствор.
Обработку раствора в интервале бурения 3835 -4100 м производим реагентами - УЩР, сода каустическая, КМЦ-600, хроматы, Лакрис-20, и Литнотин. Облагораживание бурового раствора производим бентонитовой глиной. В качестве смазывающей добавки используем ФК-1, который предназначен для обработки буровых растворов с целью улучшения их смазочных, ингибирующих и фильтрационных свойств, а также для исключения нефти, СМАДа и других экологически опасных смазывающих добавок. При бурении данного интервала для сохранения коллекторских свойств продуктивных пластов в раствор добавляется мел.
Рекомендуемые параметры раствора при бурении данного интервала:
• плотность, гс/см3
-1,13±0,02;
• вязкость по СПВ-5, с – 30 40;
• водоотдача, см3
за 30 мин - 2,0 34,0;
• СНС, мг/см2
через 1 и 10 мин – 152 0 / 30 50;
• рН раствора, ед – 81 0;
• содержание песка, % - до 2;
• толщина корки, мм - 1,0 1,5.
Кроме того, перед спуском обсадных колонн, в раствор добавляется серебристый графит.
При разбуривании цементных стаканов и мостов в раствор добавляется кальцинированная сода.
1.7 Обоснование выбора типоразмеров ПВО
При замещении бурового раствора пластовым флюидом устьевое давление
Ру
= 0,1х 4100 х (1,1-0,72) = 16,45 МПа.
Рабочее давление ПВО определяется по формуле:
РРаб
=1,1хРу
= 1,1x16,45 = 18,1 МПа.
По конструкции скважиныи рабочему давлению подходит обвязка колонной головки типа ОКК2х350-168x245x324.
Согласно «Правилбезопасности нефтяной и газовой промышленности» выбираем схему превенторной установки, обеспечивающую герметизации скважины при спущенной колонне и без нее (два превентора - с трубными и глухими плашками, универсальный превентор).
Диаметр долота 190,5 мм. По рабочему давлению подходит ПВО типа ОП2 - 230 х 35, включающее в себя: превентор универсальный ТУ 1 -230 х 35; два плашечных превентера 11111 - 230 х 35; манифольд МПБ 2 -80 х 35. Масса комплекта 17150 кг.
Данный комплект ПВО имеет номинальный диаметр проходного сечения 230 мм, а, следовательно, в случае выброса может загерметизировать устье как при спущенной бурильной колонне, так и при колонне обсадных труб.
1.8 Обоснование способа вхождения в продуктивный пласт
Вхождение в продуктивный пласт - это порядок операций, проводимых в скважине непосредственно перед бурением и во время разбуривания продуктивной толщи.
Вскрытие продуктивных пластов является завершающим и наиболее ответственным этапом бурения скважины. В зависимости от условий бурения и эксплуатации применяют следующие основные схемы заканчивания скважин.
• перекрытие обсадной колонной вышележащих горных пород до кровли продуктивного пласта с последующим вскрытием продуктивного пласта и перекрытием его эксплуатационной колонной или хвостовиком. Если продуктивные пласты представлены устойчивыми породами, эксплуатационную колонну не спускают в скважину;
• полное вскрытиепродуктивного пласта с последующим спуском комбинированной обсадной колонны и применением манжетного способа цементирования. Манжетаустанавливается на уровне кровли продуктивного пласта;
• полное вскрытие продуктивного пласта со спуском колонны сплошным цементированием и последующим простреливанием отверстий против продуктивных пластов.
Методы вскрытия пласта в зависимости от пластового давления, степенью и дренирования и других факторов могут быть различными, но все они должны удовлетворять следующим основным требованиям.
1. При вскрытии пласта с высоким давлением должна быть предотвращена возможность открытого фонтанирования скважины;
2. При вскрытии пласта должны быть сохранены на высоком уровне природные фильтрационные свойства пород призабойной зоны.
3. Иногда в кровле продуктивного пласта, вскрыв продуктивный пласт, спускают хвостовик или после вскрытия пласта.
Фильтры могут быть как с круглыми, так и со щелевидными отверстиями. Щелевидные фильтры не всегда надежно предотвращают поступления песка в скважину или часто засоряются. Поэтому применяют также и другие способы оборудования забоя для предотвращения поступления песка в скважину.
1
.9 Способ освоения скважины
После спуска колонны-подъемника из насосно-компрессорных труб и скончания монтажа фонтанной арматуры приступают к выполнению последней и очень важной операции - освоению скважины.
Под освоением понимают проведение ряда мероприятий для вызова притока нефти с доведением ее отбора до наибольшего значения (для данной категории скважины) и подъема ее на дневную поверхность в сборные резервуары, а газа — в газопроводы.
При освоении скважины, параметры бурового раствора приводят в соответствие с требуемыми.
При отсутствии притока глинистый раствор заменяют на воду. В случае отсутствия притока из пласта снижают уровень жидкости в скважине «спя уменьшения давления на забой. Проектом предусмотрено снижение уровня в эксплуатационной колонне на 1500 м.
Вытеснение жидкости из скважины сжатым азотом производят с помощью передвижного компрессора высокого давления - АГУ-8К Освоение скважинынагнетанием сжатого азота осуществляется по следующей схеме. Через задвижку компрессором в затрубное пространство нагнетают сжатый азот, который вытесняет воду через спущенные в эксплуатационную колонну компрессорные трубы. Давление на забое сильно снижается, что вызывает интенсивный приток нефти и газа из пласта. В результате при наличии высокого давления в пласте происходит фонтанирование.
В случае отсутствия притока из пласта применением методов, основанных на снижении забойного давления, проводят различные операции по воздействию на призабойную зону пласта, т.е. осуществляют гидромеханическое, химическое или комбинированное воздействия, после чего вновь используют способы, направленные на снижение забойного давления и вызов притока из пласта
1.10 Контроль качества цементирования
нефтяная скважина бурение пласт
Наличие цементного камня проверяется с помощью АКЦ после ОЗЦ.
Сцепление цементного кольца с обсадной колонной и стенками скважины проверяется АКЦ после ОЗЦ.
Герметичность крепи проверяется опрессовкой после ОЗЦ. Герметичность цементного кольца проверяется опрессовкой после разбуривания цементного стакана и углубления под следующую колонну на 1-3 м.
В случае недоподъема цементного раствора до устья скважины необходимо провести ОЦК для определения высоты подъема цементного раствора.
1.11 Выбор буровой установки
Исходными данными при выборе буровой установки являются проектная глубина и конструкция скважины.
Буровую установку выбирают по ее максимальной грузоподъемности [GKp], обусловливающей вес в воздухе наиболее тяжелой колонны бурильных или обсадных труб:
Gбк
. (илиGок
.)<[Gкр
].
Вес кондуктора
Gк
= 5,22т
Вес I промежуточной колонны
G1пр
= 98,42т
Вес II промежуточной колонны
GII
пр
= 132,29т
Вес эксплуатационной колонны
Gэ
.к
.= 115,25т
Максимальный вес бурильной колонны с УБТ
Gб
.к
=159, 26т
Из приведенного расчета следует, что наибольшую нагрузку БУ будет испытывать при бурении под вторую промежуточную колонну.
Максимальные нагрузки с учетом расхаживания:
от веса бурильной колонны
Gбк
= 159, 26 х 1,25 - 199,08 т;
от веса наиболее тяжелой обсадной колонны
Gб
.к
= 132, 29 х 1,25 - 165,36 т;
Для бурения данной скважины используем буровую установку ВМ -53 Д. Грузоподъемность установки ВМ - 53 Д - 320 Т.
РАЗДЕЛ 2. СПУСК ОБСАДНОЙ КОЛОННЫ
2.1 Обоснование режима спуска обсадных колонн
Под режимом спуска обсадной колонны понимают сборку обсадных труб в колонну СПУСК ее в скважину на длину каждой трубы, долив бурового раствора и промывку ствола.
Проектные решения должны обеспечить спуск обсадной колонны в заданный интервал ствола скважины без осложнений, удовлетворительную подготовку обсадной колонны и затрубного пространства к цементированию при выполнении технологических требований и инструктивных указаний по продолжительности проведения отдельных операций.
Обеспечение этих требований учитывается введением соответствующих ограничений:
• на предельные давления Р в гидравлическом канале скважины; обеспечивающие отсутствие гидроразрыва пород, поглощений бурового раствора и нефтегазопроявлений при спуске колонны и промывке скважин:
Р≤[Рпол
]i
- где[Рпол
]i
— допустимые давления поглощения любогоi-гo пласта в разрезе
• на предельные напряжения (ti
) в обсадных трубах, их соединениях, элементах подъемной системы буровой установки:
Τ≤[Τпол
]i
,
гдеΤ
i
-
проектные напряжения в каждом 1
-м элементе
колонны и оборудования;
• на недопущение повреждения элементов колонной и заколонной технологической оснастки при спуске колонны в скважину.
Как правило, практика эксплуатации оборудования и проводка скважины позволяет учесть эти требования в виде ограничений на скорость спуска труб, частоту вращения барабана лебедки и других элементов подъемной системы, разгрузку индикатора веса, интенсивность торможения.
Технологическим обоснованием ограничения скоростей спуска обсадных колонн служит то обстоятельство, что при движении колонны повышается роль всякого рода неровностей ствола скважины, которые являются возможным источником образования сальников и закупорки затрубного пространства, а также причиной глубокого внедрения колонны в стенку скважины и остановки процесса спуска. При этом с ростом диаметра колонны следует уменьшить скорость ее спуска.
Исходя из практического опыта, можно принять в качестве верхней границы средней скорости спуска, следующие значенияVT
(м/с).
Кондуктор............................................ 0,5
Промежуточная колонна.................... 0,8
Эксплуатационная колонна................. 1,0
2.2 Обоснование режима спуска эксплуатационной колонны
Спуск колонны будет осуществляться с применением клиновых захватов или спайдеров, в том числе спайдера - элеватора на крюке талевой системы.
Допускается применение элеваторов в начале спуска до достижения массы колонны (с учетом облегчения ее в буровом растворе), соответствующей коэффициенту запаса прочности на страгивание (растяжение) верхних резьбовых соединений не менее 1,5.
До смазки резьба должна быть очищена неметаллической щеткой или другим приспособлением, обезжирена и протерта насухо с принятием мер по предотвращению загрязнения и попадания влаги перед смазкой и свинчиванием.
Для свинчивания и закрепления резьбовых соединений необходимо использовать специальные автоматические ключи, как правило, с гидравлическим приводом, оборудованные моментомером с показывающим и записывающим устройствами.
Допускается закрепление машинными ключами резьбовых соединений труб кондукторов и промежуточных колонн, после которых не ожидается вскрытие газовых и газоконденсатных пластов, а также нефтяных пластов с АВПД.
«Усиление» резьбовых соединений при ненормальном свинчивании труб любой марки стали и любым способом запрещается.
При ненормальном свинчивании трубу следует отсоединить и забраковать.
Перед подачей на мостки буровой предохранительные кольца на ниппелях должны быть ослаблены для легкого отвинчивания «от руки», а предохранительные ниппели из муфт полностью вывернуты.
На муфту затаскиваемой к ротору трубы должен одеваться легкий безрезьбовый колпак.
До подачи на мостки буровой к ротору длина каждой трубы и встраиваемых в колонну элементов технологической оснастки должны быть подвергнуты контрольному измерению стальной рулеткой.
Башмак обсадной колонны должен навинчиваться «на весу» после затаскивания обсадной трубы и закрепляться на роторе.
Центраторы, турболизаторы и скребки необходимо одевать и закреплять на трубах, на мостках буровой перед затаскиванием труб.
Спуск обсадной колонны необходимо осуществлять со скоростью, рассчитанной поинтервально в соответствии с РД 39 - 00147001 - 767 -2000.
Максимально допустимая скорость спуска обсадной колонны [V]i из условия предотвращения поглощения бурового раствора и непревышения репрессии на продуктивные пласты, имеющей место при их вскрытии и углублении скважины, вычисляется по формуле:
 
где [P]i
- допустимое давление на рассматриваемый пласт, МПа; принимается равным величине максимального гидравлического давления, имевшего при последних долблениях;
PRI
- гидростатическое давление на рассматриваемый пласт, МПа, при последних долблениях;
Ii
- длины участков спущенной части колонны до подошвы рассматриваемого пласта с одинаковыми для данного участкаDi
иdi
м; спущенная ниже кровли пласта часть колонны, не учитывается;
di
иDi
- соответственно диаметр обсадной колонны, в том числе бурильных труб, на которых спускается секциями потайная колонна, и средневзвешенный на длине Ii
, диаметр ствола скважины, м;
рб
- плотность бурового раствора в скважине, кг/м3
;
£ - коэффициент гидравлических сопротивлений; рассчитывается для измеренных реологических параметров бурового раствора по известным зависимостям; при отсутствии данных принимается равным 0,055.
Выбор скорости спуска обсадной колонны осуществляется дифференцированно в зависимости от длины спущенной части колонны относительно рассматриваемого пласта в следующем порядке.
Исходя из условия безопасного спуска, примем скорость спуска, равную 0,5-1,0 м/с.
При промывках скважины, технологических или вынужденных остановках и после окончания спуска обсадную колонну необходимо периодически расхаживать.
После окончания допуска колонны, в том числе оборудованной устройством для ступенчатого цементирования, до проектной глубины необходимо сбросить в обсадные трубы запорный шар обратного клапана.
2.3 Расчет допустимой глубины опорожнения колонны
Спуск колонны с заранее помещенным шаром или преждевременное сбрасывание его в трубы запрещается без крайней необходимости.
При вынужденном спуске (допуске) колонны без самозаполнения необходимо осуществлять периодический долив колонны с обеспечением четырехкратного запаса прочности порциями бурового раствора V, м3
, определяемыми из выражения
м
3
гдеd - внутренний диаметр доливаемых обсадных или бурильных труб, м;
Р - меньшая из двух величин, давление смятия обсадных труб или паспортный допустимый перепад давления на обратный клапан, МПа;
р - плотность бурового раствора, кг/м3
g - ускорение свободного падения, м/с2
Долив колонны осуществляется черезL, м, спущенных труб
м
Колонну следует доливать через каждые 650 м.
2.4 Оснастка обсадных колонн
Кондуктор диаметром 426 мм
Кондуктор спускается на глубину 30 м в одну секцию. Низ кондуктора оборудуется стальным башмаком с цементной направляющей пробкой БКМ 426. На 10 м от башмака устанавливается ЦКОД - 426 - 2, он же является и «стоп» кольцом.
Первая промежуточная колонна диаметром 299 мм
Спускается на глубину 1010 м в одну секцию. Низ секции оборудуется стальным башмаком с цементной направляющей пробкой БКМ 324. На 20 м от башмака устанавливается ЦКОД-324-2, он же является и «стоп» кольцом. Пружинные центраторы ЦЦ-324/394-1 установить на глубинах: 10 м, 50 м, 100 м, далее через 50 м - 25 центраторов, выше башмака через 20 м - 3 центратора. Общее количество центраторов - 31 шт.
Вторая промежуточная колонна диаметром 219x245 мм
Спускается на глубину 3835 м в две секции.
Первая секция длиной 1480 м устанавливается в интервале 3835 – 2355м. Низ секции оборудуется стальным башмаком с чугунной направляющей пробкой БП-219. На 20 м от башмака устанавливается ЦКОД-219-2, он же является и «стоп» кольцом. Пружинные центраторы ЦЦ-219/270-1 установить через 25 м. Общее количество пружинных центраторов - 59 шт. Секция спускается при помощи левого разъединителя РРГ-219.
Вторая секция длиной 2355м устанавливается в интервале2355- 0 м. Низ секции оборудуется стыковочным башмаком от РРГ-219. ЦКОД-219-2 устанавливается на 20 м от башмака, он же является и «стоп» кольцом. Пружинные центраторы ЦЦ-219/270-1 установить через 25 м в интервале 2650-1250 М, а В интервале 0-1250 м через 45 м. Муфту ступенчатого цементирования МСЦ 1-245 установить на глубине 1200 м. По одному пружинному центратору на трубу выше и ниже МСЦ 1—245. Всего пружинных центраторов 84 шт.
Эксплуатационная колонна диаметром 146 мм
Спускается на глубину 4100 м.
Низ колонны оборудуется стальным башмаком с чугунной направляющей пробкой - БП-219. На 30 м от башмака устанавливается ЦКОД-140-1, он же является и «стоп» кольцом. Пружинные центраторы ЦЦ-140/191-1 установить через 25 м в интервале 4100-3835 м, а в интервале 3835-^00 м - через 45 м. Общее количество пружинных центраторов - 45шт.
2.5 Цементирование обсадной колонны
Цементирование обсадных колонн является одним из важнейших процессов при проходке нефтяных и газовых скважин.
Чтобы предохранить стенки скважины от обрушения пород, предупредить возможность сообщения продуктивных и водоносных пластов между собой и чтобы создать канал, по которому нефть или газ могли бы подниматься с забоя до устья скважины без потерь, необходимо крепить ствол.
Скважину крепят металлическими трубами, называемыми обсадными. Но при креплении их только обсадными трубами не получают надежной изоляции пластов и эти пласты не разобщаются. Для их разобщения необходимо в затрубное пространство между обсадными трубами и стенками скважины закачать цементный раствор.
После определенного срока твердения (ОЗЦ) цементный раствор, превратившись в цементный камень, разобщает водоносные, нефтеносные и газоносные пласты в интервале подъема цементного раствора.
Перед проведением цементирования обсадных колонн определяют необходимую высоту подъема тампонажного раствора за колонной с учетом требований охраны недр; выбирают способ цементирования и тампонажные материалы в зависимости от геологических и физико-химических условий.
В настоящее время существуют несколько способов цементирования. К ним относятся: одно и двухступенчатое цементирование, манжетное цементирование, цементирование под давлением, цементирование хвостовиков.
Процесс одноступенчатого цементирования заключается в следующем. После того как обсадная колонна спущена, скважину подготавливают к цементированию, промывая ее после спуска обсадной колонны труб.
Двухступенчатое цементирование скважин рекомендуется применять в следующих случаях: если возникают трудности технического порядка, не позволяющие поднять уровень цементного раствора; на забое высокая температура. При нормальном цементировании ствола скважины может возникнуть опасность цементирования малодебитных или сильно дренированных пластов. В этом случае нижняя часть эксплуатационной колонны, в пределах нефтеносного и газоносного пласта составляется из перфорированных труб - фильтра, т.е. производится манжетное цементирование скважин.
Манжета представляет собой воронку, изготовленную из эластичного материала (брезента, кожи и т.п.), высотой 60-70 см, причем верхний диаметр манжеты несколько больше диаметра скважины
РАЗДЕЛ 3. ЭКОНОМИЧЕСКАЯ ЧАСТЬ.
3.1. Исходные данные для расчета стоимости строительства 1м скважины
№ |
Наименование показателей |
Единица
измерений
|
Показатели |
1 |
Затраты на подготовительные работы к строительству скважины - всего |
т.р. |
70,0 |
2 |
Строительство и разборка вышки и привышечных сооружений, монтаж и демонтаж бурового оборудования |
т.р. |
66,0 |
3 |
Подготовительные работы к бурению (постоянные по сметной документации) |
т.р. |
40,0 |
4 |
Промыслово – геофизические работы - всего |
% |
6,0 |
5 |
Дополнительные затраты при производстве строительно – монтажных работ в зимнее время |
% |
0,65 |
6 |
Испытание скважин на продуктивность |
т.р. |
50,0 |
7 |
Накладные расходы в %-х от прямых затрат |
% |
18,0 |
8 |
Плановые накопления |
% |
8,0 |
9 |
Резерв на непредвиденные работы и затраты |
% |
2,0 |
10 |
Налог на добавленную стоимость |
% |
18,0 |
3.2
Расчет затрат для определения сметной стоимости (цены) строительства 1м. скважины
1. Общая сумма затрат на подготовительные работы к строительству скважины (строка 1) задаются в дипломном проекте и составляют 70 т.р.
2. Затраты на строительство и разборку вышки и привышечных сооружений, монтаж и демонтаж бурового оборудования задаются и составляют 66 т.р.(строка 2).
3. Затраты на подготовительные работы к бурению (постоянные по сметной документации) задаются и составляют 40т.р. (строка З).
4. Затраты на бурение скважины определяются поинтервально и зависят от глубины скважины.
а) при бурение под кондуктор (глубина спуска 30 м.) - составили 2,1 т.р.
б) при бурение 1 пром. колонны - 314,0 т.р.
в) при бурении 2 пром. колонны - 885,9 т.р
г) под эксплуатационную колонну - 71,9 т.р.
Общая сумма затрат на бурение скважины составила 1273,9 т.р.
5.
Затраты по креплению скважины также рассчитываются в зависимости от глубины спуска и затем суммируются
а) затраты по креплению кондуктора до 30 м. составляют 6 т. р.,
А затраты на спуск и крепление промежуточных колонн составляют:
б) при спуске 1-й промежуточной колонны на глубину до 1010 м. затраты на крепление составляют 190,2 т.р.
в) при спуске 2-й промежуточной колонны до глубины 3835м. - 484,5 т.р.
г) при спуске эксплуатационной колонны до 4100 м. - 51,2т.р.
Общая сумма затрат по креплению скважины составляет - 731,9 т.р.
6. Общая сумма промыслово-геофизических работ (строка 4) рассчитывается в % от суммы затрат на бурение, крепление и испытание первого объекта, т.е.
5,4% *( 1273,9 + 731,9 + 45)/100 = 110,7 т.р.
7. Дополнительные затраты при производстве строительно-монтажных работ в зимнее время (строка 9) берутся в размере 0,85% от суммы затрат по строке 3 и 4, т.е.
0,85% * 106/100 = 0,9 т.р.
Общая сумма прямых затрат составляет 2288,4 т.р. (строка 11).
Накладные расходы берутся в размере 18,0% от суммы прямых затрат, т.е.
18,0% * 2288,4/100 = 411,9 т.р. (строка 12).
Итого с накладными расходами 2288,4 + 411,9 = 2700,3 т.р.
Плановые накопления составляют 8% от общей суммы, т.е.
8 * 2700,3/100-216,0 т.р.
Итого с плановыми накоплениями 2700,3 + 216,0 = 2916,3 т.р.
Затраты на транспортировку вахт наземным способом рассчитываются следующим образом:
а) в вышкостроении - 6% от суммы (стр.3 + стр.4): 6 * 106/100 = 6,4 т.р.
б) в бурении и креплении - 5% от суммы (стр.6 + стр.7)
5 * ( 1273,9 + 731,9)/100= 100,3 т.р.
в) в испытании - 5% от строки 10: 5 * 45/100 = 2,3 т.р.
Общая сумма затрат составляет - 109,0 т.р.
Резерв на непредвиденные расходы и затраты, оставляемые в распоряжении буровой организации берется в размере 2% от стоимости выполненных работ, т.е.
2 * 3025,3/100 = 60,5 т.р.
Итого затрат на строительство скважины : 3025,3 + 60,5 = 3085,8 т.р.
Налог на добавленную стоимость берется в размере 18% и составляет
18 *3085,8/100 = 555,4 т.р.
Всего затрат на строительство скважины, зафиксированных в базе для расчета цены 1м. строительства скважины составляет 3085,8 + 555,4 = 3641,2 т.р.
В связи с инфляцией необходимо сделать перерасчет всех затрат с учетом переводного коэффициента Кпер
= 22,4, т.е.
3641,2 * 22,4 = 81562,9 т.р.
Сметная стоимость (цена) строительства 1 м. скважины составляет 81562,9/4100= 19893 руб/м.
№
п/п
|
Наименование показателей |
един.
измер.
|
Показатели
задания расчетные
|
1 |
2 |
3 |
4 |
5 |
1
2
3
4
5
6
7
8
9
10
11
12
13
14
15
16
17
18
19
20
21
22
23
|
Глубина скважины
Глубина спуска обсадной колонны
б) кондуктор
в) I промежуточная колонна
г) II промежуточная колонна
д) Эксплуатационная
Затраты на подготовительные работы
к строительству скважины - всего
Строительство и разборка вышки и привышечных сооружений, монтаж и демонтаж бурового оборудования
Подготовительные работы к бурению
(постоянные по сметной документации)
Затраты на бурение скважины -всего:
в том числе:
а) при бурении под кондуктор
б) при бурении под I пром. колонну
в) при бурении под II пром. колонну
г) при бурении под экспл. Колонну
Затраты по закреплению скважины -всего
в том числе:
а) по крепленю кондуктора
б) по креплению I пром. колонны
в) по креплению II пром. колонны
г) по креплению экспл. Колонны
Промыслово- геофизические работы-всего
Дополнительные затраты при производстве строительно-монтажных работ в зимнее время
Испытание скважины на продуктивность
Итого прямые затраты (3+…..+11)
Накладные расходы в % от прямых затрат
Итого с накладными расходами
Плановые накопления
Итого с плановыми накоплениями
Транспортировка вахт наземным транспортом
в том числе:
а) в вышкостроении
б) в бурении и креплении
в) в испытании
Резерв на непредвиденные работы и затраты,
оставляемые в распоряжении буровой организации (в % от стоимости выполненных работ)
Прочие работы и затраты
Итого затрат на строительство скважины
Налог на добавленную стоимость
Всего затрат на строительство скважины, зафиксированных в базе для расчета цены 1м. скважины
Всего затрат на строительство скважины с учетом переводного коэффициента
(Кпер
= 22,4)
Сметная стоимость (цены) строительства 1м. скважин
|
м
м
м
м
м
м
т.р.
т.р.
т.р.
т.р.
т.р.
т.р.
т.р.
т.р.
т.р.
т.р.
т.р.
т.р.
%,т.р.
%,т.р.
т.р.
т.р.
%,т.р.
т.р.
%,т.р.
т.р.
т.р.
%,т.р.
%,т.р.
%,т.р.
%,т.р.
т.р.
т.р.
%,т.р.
т.р.
т.р.
р/м
|
4100
30
1010
3835
4100
40,0
66,0
20,0
5,4
0,85
45,0
18,0
8,0
6,0
5,0
5,0
2,0
18,0
|
40,0
66,0
20,0
1273,9
2,1
314,0
885,9
71,9
731,9
6,0
190,2
484,5
51,2
110,7
0,9
45,0
2288,4
411,9
2700,3
216,0
2916,3
109,0
6,4
100,3
2,3
60,5
3085,8
555,4
3641,2
81562,9
19893
|
РАЗДЕЛ 4. ОХРАНА ОКРУЖАЮЩЕЙ СРЕДЫ И НЕДР
4.1
В процессе проводки ствола скважины
Источниками выбросов вредных веществ в атмосферу при бурении и испытании скважин являются: двигатели внутреннего сгорания буровой установки, амбары для буровых сточных вод, циркуляционная система, амбар для запасного глинистого раствора, топливо масло установка, емкость для хранения нефти, глиномешалка, факельная установка, ёмкость для сбора нефти, устье скважины, привенторный амбар.
Проектом предусматривается проведения следуювдих основных мероприятий по защите воздушного бассейна:
• строгое соблюдения режимно-технологических регламентов и требований инструкций по предотвращению нефтегазопроявлений в процессе строительства скважин; обязательная установка на устье бурящихся- скважшг противовыбросовое оборудование с гидравлическим приводом;
• установка барботажной ёмкости на концах выхлопных коллекторов дизельных установок, для нейтрализации выхлопных газов в 10 % «известковом молочке;
• установка на всех ёмкостях и резервуарах для хранения нефти и ГСМ дыхательных клапанов и герметично закрывающихся люков;
• покраска резервуаров и ёмкостей светоотражающей краской;
• хранение химреагентов и сыпучих материалов для приготовления буровых растворов в не нарушенной таре в крытом сарае с бетонированным полом; обязательный вывоз этих материалов по окончанию строительства скважины;
• производство испытания скважин только через передвижную трапную установку, обеспечивая сбор нефти в закрытые ёмкости и сжигания попутного газа на специальном факельном устройстве.
Охрана водной среды
Сточные воды, загрязнённые нефтепродуктами, минеральными и органическими примесями в процессе поверхностной миграции и инфильтрации загрязняют поверхностные и подземные воды. В результате этого изменяются химические и органолептические свойства воды. При сбросе сточных вод в водоем ухудшаются физические свойства воды; в ней растворяются токсичные вещества, образуется поверхностная плёнка нефти и осадок на дне водоёма. Биохимическое окисление токсичных веществ в водоёме сопровождается непрерывной миграцией тяжёлых её фракций с поверхности на дно и обратно. Токсичные вещества, скопившиеся на дне водоёма в анаэробных условиях, сохраняются длительное время и являются источниками вторичного загрязнения водоёмов.
Таким образом, при бурении скважины возможно загрязнение поверхностных и грунтовых вод за счёт некачественной гидроизоляции амбара, технологических площадок, при аварийных разливах нефти, поступление нефти и минерализованных вод в подземные воды в результате перетоков по затрубному пространству и др.
С целью не допущения загрязнения водной среды, охраны и рационального использования водных ресурсов проектом предусматривается проведение следующих основных мероприятий:
• обеспечения оборотного водоснабжения на буровой;
• с целью исключения загрязнения водоносных горизонтов, почвы, скважина будет буриться глинистым раствором с применением экологически безвредным заменителем нефти ФК-1 (ТУ-39-00147001 -164-97);
• гидроизоляция буровых амбаров для сброса бурового шлама (БШ), отработанного бурового раствора (ОБР) и БСВ устройством противофильтрационных экранов из цементно-бентонитовой пасты толщиной 0,15м;
•бетонирование площадок под вышечным, агрегатным, насосными блоками буровой установки;
•устройство бетонированных стоков из под бурового оборудования с уклоном в сторону амбара для БСВ;
•сооружение бетонированного амбара у блока ГСМ буровой на случай аварийного разлива нефтепродуктов;
•реагентная очистка (осветление) БСВ коагулянтоми и флокулянтами с целью экономии воды.
Охрана недр в процессе бурения
Ресурсы недр могут быть истощены за счет грифонообразования, открытого фонтанирования скважин, межпластовых перетоков, нерационального использования минеральных ресурсов.
В процессе бурения скважины в результате нарушений технологических требований и единых технических норм возможны загрязнения пластов с питьевыми водами, а также за счёт заколонных перетоков флюидов.
Проектом предусматривается проведения следующих мероприятий по охране недр:
• строгое соблюдение режимно-технологических регламентов бурения и выполнение всех мероприятий по предупреждению газоводонефтепроявлений и открытых фонтанов;
• использование при креплении скважин высокопрочных обсадных труб с герметичными резьбовыми соединениями;
• использование для цементирования обсадных колонн высококачественных тампонажных материалов, соответствующих условиям скважины;
• обеспечение высоты подъёма цемента за колоннами при цементировании обсадных колонн строго по проекту;
• обязательная установка на устье скважин и качественное цементирование 7- метровых шахтных направлений для надёжной изоляции грунтовых вод и предотвращения грифонообразования;
• прохождение водоносных горизонтов с запасами пресных вод в процессе бурения с использованием буровых растворов, не содержащих токсичных химических реагентов;
Обеспечение для надёжной изоляции водоносных горизонтов обязательного спуска в скважину кондуктора на необходимую глубину и цементирования его на всю длину
4.2 Охрана недр
в процессе эксплуатации скважины
Задача охраны недр состоит из осуществления системы мероприятий по предотвращению потерь нефти и газа из-за низкого качества проводки скважины, неправильной разработки нефтяных залежей и эксплуатации скважины.
Для предотвращения осложнений, возникающих в процессе эксплуатации месторождения, необходимо:
• обеспечить постоянную оптимизацию режима эксплуатации скважин и технологического режима разработки месторождения с целью достижения максимального коэффициента извлечения нефти;
• при обнаружении в межколонном пространстве скважин давления или выделения вокруг них следует выяснить причину этих явлений и незамедлительно принять меры по их ликвидации;
• при проведении работ по увеличению производительности скважины путем воздействия на призабойную зону должны быть обеспечены:
• целостность обсадных колонн и цементного камня за ними;
• сохранность устойчивости пород в призабойной зоне.
4.3 При эксплуатации НГС
Все способы освоения скважин основаны на принципе снижения противодавления на ее забой для получения притока жидкости из пласта. В одних случаях это достигается снижением уровня жидкости.
Освоение скважин заменой жидкости в стволе жидкостью меньшей плотности.
После перфорации эксплуатационной колонны и спуска насосно - компрессорных труб приступают к замене жидкости в стволе скважины жидкостью меньшей плотностью.
Во избежание нежелательных явлений при освоении скважин необходимо осуществлять плавный запуск скважины (плавно продавливать столб жидкости в скважине), для чего следует регулировать отбор жидкости устьевыми штуцерами с одновременным регулированием расхода рабочего агента.
Поэтому перед освоением скважины этим методом необходимо установить на газовоздухопроводе обратный клапан и манометр, отпрессовать линию и обвязку на полуторакратное давление от ожидаемого максимального рабочего давления.
Освоение скважин аэрацией.
Освоение скважин этим способом заключается в постепенном уменьшении плотности смеси в колонне труб одновременным нагнетанием в скважину воды или нефти и сжатого газа или воздуха. Благодаря постепенному переходу на смесь меньшей плотности давление на забой плавно уменьшается, что и способствует постепенному увеличению потока в скважину.
Освоение скважин с поршневанием
. При поршневании скважин, когда устье остается негерметизированным, загрязняются рабочая площадка, территория вокруг скважины, создаются опасные условие работы (скользкость) и возникают опасности пожара и отправление рабочих газом, особенно содержащим сероводород.
РАЗДЕЛ 5. ОХРАНА ТРУДА
5.1
Правила безопасной, эксплуатации- бурового оборудования и инструмента
При бурении нефтяных и газовых скважин значительное число несчастных случаев гфоисходит в процессе эксплуатации оборудования.
Главные механики и энергетики отвечают за исправное состояние и своевременное испытание паровых котлов, аппаратов, компрессорных, насосных и газовых установок. Начальник транспортного цеха отвечает за правильное содержание и безопасную эксплуатацию транспортных средств. Буровой мастер обязан организовать проведение всех работ в точном соответствии с требованиями технологии и правил безопасности, продлить в установленные сроки инструктаж рабочих.
Новые работники к самостоятельной работе допускаются только после прохождения инструктажей по безопасному ведению работ, проверки знаний, в необходимых случаях, и соответствующего производственного обучения и стажировки. На предприятии проводится целый спектр инструктажей: вводный и инструктаж на рабочем месте, который в свою очередь подразделяется на первичный, периодический, внеочередной и специальный (целевой).
Обеспечение пожаробезопасности
Мероприятия по пожарной безопасности разделяются на четыре основные группы:
а) предупреждение пожаров;
б) ограничение сферы распространения огня;
в) максимальное сохранение ценностей в зоне пожара;
г) создание условий эффективного тушения пожаров.
Своевременный профилактический осмотр оборудования и уход за НИМ создают условия для безопасной и безаварийной работы
5.2 Техника безопасности при приготовлении, очистке и обработке буровых растворов
При приготовлении промывочного раствора непосредственно на буровой последняя до начала проводки скважины обеспечивается требуемым количеством доброкачественной глины, На буровой устанавливается глиномешалка, сооружается навесы, сараи, площадки и емкости для хранения глины, бурого угля, химических реагентов и т.д.
Для удобства обслуживания глиномешалки должны оборудоваться трапом шириной не менее 1,5 м с перилами. Угол наклона трапа не должен превышать 30°.
Для улучшения качества промыв очных жидкостей их обрабатывают химическими реагентами.
Приготовление химических реагентов для обработки промывочной жидкости в условиях буровой является трудоемким, опасным процессом.
При подготовке химических реагентов рабочие должны соблюдать меры предосторожности.
Необходимо учитывать, что едкий натр в сильной концентрации дает ожоги всех степеней, а в умеренных концентрациях обезжиривает кожу.
При работе с едким натром рабочие не должны допускать попадания его на открытые части тела.
При приготовлении химических реагентов возникает опасность ожогов рук, лица и глаз рабочих от попадания отлетевших частиц каустической соды и других реагентов для защиты от ожогов рабочие должны обязательно работать в резиновых сапогах, фартуке, перчатках и защитных очках или специальных масках сочками, причем всегда стоять с наветренной стороны.
Перед ремонтом гидромешалки необходимо перекрыть нагнетательный трубопровод, а на проходной задвижке или пусковом устройстве насоса вывесить предупредительный плакат: «Не включать — работают люди».
При размещении на буровой установок для дегазации необходимо обеспечить удобства при их обслуживании, а также отвод в сторону выделенного газа и легких углеводородов. В случае применения для дегазации промывочного раствора химических веществ, обладающих токсичными свойствами, необходимо применять соответствующие меры безопасности.
5.3 Техника безопасности при спускоподъемных операциях
Спускоподъемные операции являются наиболее трудоемкими и их выполнение требует значительных физических усилий.
Согласно проведенному во ВНИИТБ анализу травматизма по некоторым предприятиям нефтедобывающей промышленности выявлено, что при бурении на спускоподъемные операции приходится примерно 30 -40% всех несчастных случаев.
Неправильные приемы работы, несоблюдение правил безопасности, возможность обрыва канатов при креплении и раскреплении машинных ключей, свинчивание свечей круговым ключом , нахождение рабочих в опасных зонах рабочей площадки приводит к значительному травматизму
Важным фактором, на который следует обратить внимание при спускоподъемных операциях, чтобы исключить возможность травмирования рабочих, является состояние рабочей площадки буровой
Запрещается находиться в радиусе действия подвесного бурового ключа и вблизи натяжного каната при свинчивании и развинчивании бурильных или обсадных труб.
При посадке бурового инструмента, а также колонны обсадных труб на ротор, подводе и отводе механизированных буровых ключей люди не должны находиться на роторе и в зоне действия ключей.
Запрещается проворачивать стол ротора, а также производить подъем бурового инструмента до ввода обоих штропов в проушины элеватора и их страховки шпильками или другими приспособлениями.
Запрещается подавать руками бурильные свечи с подсвечника к устью скважины и обратно. При отсутствии механизма для установки бурильных свечей на подсвечник и перемещения их к ротору указанные операции должны производиться с помощью отводного ключа.
Находящиеся на полатях крючки и другие приспособления для завода и установки свечей за палец должны привязываться пеньковым или оцинкованным канатом к элементам вышки.
По окончании спускоподъемных операций и при вынужденных остановках необходимо перекрыть главный кран воздушной линии и выпустить воздух из линии пневматического бурового ключа, а ручки управления ключом зафиксировать в нейтральном положении.
5.4 Техника безопасности при креплении скважин
С точки зрения техники безопасности крепление скважин особенно газовых является одной из самых ответственных работ. Спуск обсадных колонн с точки зрения техники безопасности характеризуется использованием тяжелого инструмента и наличием повышенных нагрузок на буровое оборудование.
Перед спуском колонны обсадных труб в скважину буровой мастер и механик должны проверить исправность всей буровой установки, талевой системы и инструмента, предназначенных для выполнения операции по спуску колонны.
Обнаруженные неисправности должны быть устранены до начала спуска обсадной колонны. Спуск в скважину обсадной колонны разрешается при наличии у бурового мастера утвержденного плана проведения этой работы.
Запрещается рабочим находиться у нижнего конца обсадной трубы, поднимаемой для навинчивания.
До начала работ по цементированию скважины около буровой установки должна быть подготовлена площадка для цементировочных агрегатов, цементосмесительных машин и другого оборудования.
Цементирование скважин должно производиться в дневное время. При вынужденном цементировании скважины в вечернее и ночное время площадка для установки агрегатов должна иметь освещенность не менее 25 лк.
Кроме того, каждый цементировочный агрегат должен иметь индивидуальное освещение.
Во время цементирования скважины запрещается ремонтировать агрегаты, цементировочную головку и трубопроводы, находящиеся под давлением.
В целях безопасности обслуживания агрегатов и возможности отъезда какого-либо из них в сторону, в случае необходимости следует соблюдать следующие расстояния:
• от устья скважины до блок-манифольда - не менее 10 м;
• от блок-манифольда до агрегатов - не менее 5 10 м;
• между цементировочными агрегатами и цементосмесительными машинами - не менее 1,5 м.
5.5 Меры безопасности при опробовании, испытании и освоении скважин
После опрессовки эксплуатационной колонны проводятся подготовительные работы по ее перфорации, применяют
Для перфорации скважины применяют кумулятивную и гидропескоструйную перфорацию.
При кумулятивной перфорации вблизи скважины у приемного моста подготовляется площадка для установки на ней оборудования, аппаратуры и инструмента промыслово-геофизической партии.
Во время работ по перфорации вокруг скважины устанавливается запретная зона в радиусе 50 м, а работы в опасной зоне, не связанные с производством пристрелочных работ, должны быть прекращены.
При спуске перфоратора в скважину (или подъеме) возможно травмирование рабочих движущимся кабелем.
После перфорации к скважине разрешается подойти только руководителю геофизической партии и рабочему, поставленному на управление задвижками. Остальные рабочие могут подойти к скважине лишь после команды руководителя взрывными работами.
При гидропескоструйном вскрытии пласта применяются цементировочные агрегаты. Запрещается устанавливать агрегаты, пескосмесители и автоцистерны под силовыми и осветительными линиями, находящимися под напряжением, и на расстоянии менее 10 м от устья скважины. Включать агрегаты можно лишь после удаления людей, не связанных непосредственно с выполнением работ у агрегатов, за пределы опасной зоны.
При прокачивании и продавливании жидкости запрещается обслуживающему персоналу находиться у устья скважины.
Во время работы агрегатов во избежание несчастных случаев запрещается проводить ремонт или крепление обвязки устья скважины.
При освоении скважины путем замены промывочной жидкости в стволе жидкостью меньшего удельного веса необходимо предварительно опрессовать нагнетательный трубопровод на полуторакратное давление от ожидаемого максимального рабочего давления.
При освоении скважины с помощью компрессора также необходимо предварительно опрессовать воздухопровод на полуторакратное давление от максимального рабочего и установить на воздухопровод обратный клапан.
При освоении скважин с помощью передвижного компрессора последний должен устанавливаться не ближе 25 м от скважины.
5.6 Меры безопасности при ликвидации аварий и осложнений
Для предупреждения несчастных случаев с персоналом, участвующим в ликвидации аварии, необходимо проводить следующие мероприятия.
1. Работы по ликвидации аварий в скважине буровой мастер должен вести под руководством старшего инженера по сложным работам или главного инженера.
2. До спуска ловильного инструмента в скважину необходимо проверить состояние бурового оборудования и инструмента. После проверки исправности оборудования в скважину спускают ловильный инструмент.
3. Площадка внутри вышки должна быть свободной от посторонних предметов.
4. Помимо изложенного, при работах по освобождению прихваченной брильной или обсадной колонны необходимо удалить всех рабочих, кроме бурильщика, из опасной зоны на расстояние не ближе 60 м от вышки Необходимо также дополнительно укрепить штроп вертлюга от выпадения из зева крюка петлями из прядей талевого каната, которые закрепляются в серьгах вертлюга.
5. При применении кислотных ванн рабочие, участвующие в смешивании и закачивании кислоты в скважину, должны работать в костюмах из кслотостойкой ткани, исключающей поражение участков тела кислотой. Лица работающих должны быть защищены маской, руки - резиновыми перчатками, а ноги - резиновыми сапогами с брюками на выпуск.
6. При отбивке бурильной колонны ротором с подъемного крюка должны быть сняты штропы.
7. При нефтяных и кислотных ваннах под заливочной головкой или под ведущей трубой устанавливается обратный клапан.
5.7 Обеспечение пожарной безопасности на объекте бурения
Пожарная безопасность при бурении скважины определяется двумя основными факторами: наличием на буровой площадке горючих материалов, как в условиях нормальной работы, так и при возникновении аварийных ситуаций, а также возможностью образования источников зажигания в горючей среде.
Горючими материалами, присутствие которых вызывается производственной необходимостью, являются запасы топлива для двигателей, промывочные растворы на углеводородной основе, нефтепродукты, обтирочные материалы и т.д.
Причинами, способствующими появлению в горючей среде источников зажигания, могут быть падение и соударение плохо закрепленных частей оборудования, нагрев трущихся деталей в механизмах неисправное или неправильно используемое электрооборудование, нарушения правил пожарной безопасности и т.д.
Важным условием обеспечения пожарной безопасности является правильное устройство и размещение двигателей внутреннего сгорания (ДВС).
Топливо от места хранения к напорному бачку должно подаваться через топливопровод. Топливопровод оборудуется запорным вентилем, устанавливаемым в 5 м от стены машинного помещения.
Установка и обвязка две должны обеспечить достаточное удаление нагревающихся частей двигателя и потока выхлопных газов от горючих материалов.
Выхлопные трубы всех две должны оборудоваться искрогасителями.
Необходимым условием обеспечения пожарной безопасности является строгое соблюдение требований, предъявляемых к электрооборудованию.
Буровые установки должны быть обеспечены аварийным освещением напряжением не выше 12 В и переносными взрывозащитными светильниками того же напряжения.
Осветительную и силовую электропроводку на буровой площадке выполняют проводами и кабелями, сечения и защиту которых выбирают как для невзрывоопасных помещений и установок.
Безопасность сварочных работ обеспечивается строгим соблюдением «Типовой инструкции о порядке ведения сварочных и других огневых работ на взрывоопасных, взрывопожароопасных и пожароопасных объектах нефтяной промышленности».
Комплекс пожарно-профилактических мероприятий на буровых включает в себя организацию поста или стенда с комплектом противопожарного инвентаря. Набор первичных средств пожаротушения, приходящихся на одну бурящуюся скважину, должен включать: шесть пенных огнетушителей, 2 м3
песка в ящиках, четыре лопаты, два лома, два топора, два багра, четыре пожарных ведра.
РАЗДЕЛ 6. БЕЗОПАСНОСТИ ЖИЗНЕДЕЯТЕЛЬНОСТИ
6.1
Промышленная санитария
Предметом гигиены труда является изучение всей производственной обстановки с целью разработки комплекса организационных, санитарно-гигиенических и лечебно-профилактических мероприятий, необходимых для оздоровления производственных условий и повышения производительноститруда.
Одной из задач гигиены труда является установление допустимых концентраций химических веществ в воздухе и параметров физических факторов, к которым относятся: неблагоприятные метеорологические условия, воздействия большой интенсивности и ультрафиолетового излучения, токов высокой частоты, шума вибрации, ультразвука, повышенное или пониженное атмосферное давление. Не только факторы внешней среды, но и организация технологического и трудового процесса влияют на здоровье работающих, их работоспособность и производительность труда.
Поэтому задачей гигиены труда является разработка и внедрение комплекса мероприятий направленных на обеспечение оптимальных условий труда: устранение или оздоровление тех участков производственного процесса, которые могут нанести ущерб здоровью работающих; рациональная организация труда отдыха; разработка индивидуальных средств защиты; проведение медицинских мероприятий, направленных на предупреждение заболеваний; получение научно обоснованных материалов для законодательных актов по оздоровлению условий труда.
На производственных объектах должны быть санитарно-бытовые помещения для обслуживающего персонала.
Санитарно-бытовые помещения необходимо ежедневно убирать и проветривать
Гардеробные, душевые и другие санитарно-бытовые помещения и устройства должны периодически дезинфицироваться.
Администрация предприятия обязана обеспечивать всех работников вблизи мест работы питьевой водой, отвечающей санитарным нормам.
Для питьевой воды должны применяться эмалированные или алюминиевые бачки, снабженные кранами фонтанчикового типа с ограждением, препятствующим прикосновению к крану ртом.
Устройство санузлов должно соответствовать санитарным нормам.
Работы, связанные с выделением вредных для здоровья газов, паров, пыли, должны производиться в вытяжных шкафах, оборудованных надежной вентиляцией.
Спецодежда и спецобувь должны соответствовать действующему ГОСТ и выдаваться для каждой профессии работников в пределах установленных норм.
Во время работы рабочие обязаны пользоваться выданной им спецодеждой и спецобувью.
Запрещается носить кашне и платки со свисающими концами. Рабочие бригад бурения, капитального и подземного ремонта скважин, а также вышкомонтажники должны работать в защитных касках. В холодное время следует применять каски с теплыми подшлемниками.
При работе со щелочами и кислотами работающие должны быть в защитных очках, спецодежде и спецобуви, перчатки должны быть заправлены в рукава, а брюки поверх голенищ сапог.
Список использованной литературы
1. Вадещаш Ю.В..Бурение нефтяных и газовых скважин. - М: Издательский центр «Академия», 2004 – 352 с.
2. Справочник инженера по бурению в 2-х томах под редакцией В. И. Мищевича. - М.: Недра, 1973 – (518+374) с.
3. Элияшевский М. Н., Сторонский М. Н., Орсуляк Я. М. Типовые задачи и расчеты в бурении - М. Недра, 1982 – 295 с.
4. Иогаисен К. В. Спутник буровика. Справочник. –М: Недра, – 1990 –303 с.
5. Правила безопасности в нефтяной и газовой промышленности. -М.,2004–305 с.
6. Правила пожарной безопасности в нефтяной промышленности ГШБО-85.ML, 1987г.
7. Ганджумян Р. А, Калинин А. Г., Никитин Б. А.Инженерные расчеты при бурении глубоких скважин. Справочноепособие – М.: Недра 2000 –487 с.
8. Калинин А. Г., Левицкий А. 3., Мессер А. Г., Соловьев Н. В. Практическое руководство по технологии бурения скважин на жидкие и газообразные полезные ископаемые. Справочное пособие. – М.г Недра 2001 –448 с.
9. Пустовойтенко И. П.Предупреждение и ликвидация аварий в бурении . – М.: Недра, 1983 –278 с.
10. 10. Калинин А. Г., Ганджумян Р. А., Мессер А. Г.Справочшгк шгженера–технолога по бурению глубоких скважин. –М.:Недра –807 с
11. Материалы ОАО «Дагнефтегаз»
|