Реферат по дисциплине «Технология деталей радиоэлектронных средств»
Студент: Юдин Андрей Михайлович
Московский государственный институт радиотехники, электроники и автоматики (технический университет)
Москва 2004
Общие сведения о магнитопроводах
Магнитопроеодом называется деталь или комплект деталей, предназначенных для прохождения с определенными потерями магнитного потока, возбуждаемого электрическим током в обмотках намоточных изделий.
Магнитопроводы являются составными частями схемотехнических элементов РЭА: трансформаторов, дросселей, магнитных головок, фильтров, контуров, запоминающих устройств и др. Форма деталей,
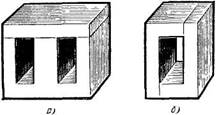
Рис. 1
образующих магнитопровод, а также вид и физические свойства материалов, используемых для их изготовления, обусловлены назначением и конструктивными особенностями схемного элемента. По этим признакам магнитопроводы разделяют на три группы: пластинчатые, ленточные и формованные.
Пластинчатые магнитопроводы представляют собой пакеты, собранные из штампованных плоских пластин. Они бывают двух типов (рис. 1): броневые (а) и стержневые (б).
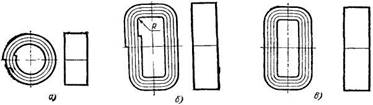
Рис. 2
Ленточные магнитопроводы имеют форму круглых (рис. 2, а) или прямоугольных со скругленными углами колец (рис. 2, б), полученных спиральной навивкой на оправку одной ленточной заготовки или П-образной гибкой нескольких предварительно нарезанных полос. Во втором случае кольца получаются разъемными с плоскостью разреза (рис. 2, в). Неразрезные ленточные магнитопроводы характеризуются лучшими магнитными характеристиками по сравнению с разрезными ленточными и пластинчатыми, так как в последних неизбежны воздушный зазор и частичное замыкание торцов. Однако неразрезные ленточные магнитопроводы имеют следующие недостатки: сложность и большая трудоемкость намоточных работ. Достоинством разрезных ленточных магнитопроводов является то, что катушки для них можно изготавливать на обычных намоточных станках.
Формованные магнитопроводы состоят из одной или нескольких монолитных объемных деталей, изготовленных из порошкообразных магнитодиэлектриков или ферритов с использованием керамической технологии (формование и спекание).
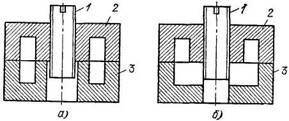
Рис. 3
Забиваем Сайты В ТОП КУВАЛДОЙ - Уникальные возможности от SeoHammer
Каждая ссылка анализируется по трем пакетам оценки: SEO, Трафик и SMM.
SeoHammer делает продвижение сайта прозрачным и простым занятием.
Ссылки, вечные ссылки, статьи, упоминания, пресс-релизы - используйте по максимуму потенциал SeoHammer для продвижения вашего сайта.
Что умеет делать SeoHammer
— Продвижение в один клик, интеллектуальный подбор запросов, покупка самых лучших ссылок с высокой степенью качества у лучших бирж ссылок.
— Регулярная проверка качества ссылок по более чем 100 показателям и ежедневный пересчет показателей качества проекта.
— Все известные форматы ссылок: арендные ссылки, вечные ссылки, публикации (упоминания, мнения, отзывы, статьи, пресс-релизы).
— SeoHammer покажет, где рост или падение, а также запросы, на которые нужно обратить внимание.
SeoHammer еще предоставляет технологию Буст, она ускоряет продвижение в десятки раз,
а первые результаты появляются уже в течение первых 7 дней.
Зарегистрироваться и Начать продвижение
Формованные магнитопроводы нашли широкое применение в высокочастотных устройствах РЭА. На рис. 3 дан пример броневого магнитопровода из магнитодиэлектрика: а — с замкнутой; б — с разомкнутой магнитной цепью (1 — подстроечник, 2 — верхняя чашка, 3 — нижняя чашка). На рис. 4 приведены некоторые образцы магнитопроводов из ферритов: рис. 4, а и б — замкнутый П-образный прямоугольного сечения; рис. 4, в и г — замкнутый П-образный круглого сечения, рис. 4, д — О-образный; рис. 4, е — Г-образный, рис. 4, ж — Е-образный; рис. 4, з — магнитной головки.

Рис. 4
Методы достижения качества магнитопроводов
Магнитопроводы должны иметь высокую магнитную проницаемость, незначительную коэрцитивную силу, стабильные магнитные характеристики в рабочем диапазоне температур и во времени, минимальные потери на гистерезис, рассеивание и вихревые токи, устойчивость к посторонним механическим воздействиям.
Соответствие физических свойств магнитопривода этим требованиям достигается, прежде всего, выбором магнитного материала и построением ТП. При переработке магнитных материалов в детали магнитопроводов исходные магнитные свойства их изменяются под тепловым и силовым воздействием инструментов и технологических сред. По этой причине в ТП изготовления включают ряд операций по контролю и восстановлению магнитных свойств деталей магнитопроводов, а условия выполнения операций формообразования подбирают с расчетом на то, чтобы минимально воздействовать на изменения этих свойств.
В качестве магнитных материалов используют электротехническую сталь, железоникелевые сплавы, магнитодиэлектрики и ферриты. Электротехнические стали и пермаллои применяют в виде горячекатанного и холоднокатанного проката в листах и рулонах толщиной 0,04—0,5 мм. Горячекатанные стали используют в магнитопроводах, работающих на низких частотах, а холоднокатанные — в магнитопроводах с повышенными магнитными характеристиками. Железоникелевые сплавы (пермаллои) характеризуются в 10—20 раз большей магнитной проницаемостью в слабых магнитных полях по сравнению с электротехнической сталью. Высоконикелевые пермаллои (72—80% никеля) марок 79НМ, 80НХС и другие используют для изготовления сердечников малогабаритных дросселей и трансформаторов низкой частоты, магнитных головок и др. Низконикелевые пермаллои (30—50% никеля) марок 38НС, 45Н, 50Н, 50НХС и другие применяют для изготовления магнитопроводов силовых трансформаторов и дросселей, магнитных головок и др.
Сервис онлайн-записи на собственном Telegram-боте
Попробуйте сервис онлайн-записи VisitTime на основе вашего собственного Telegram-бота:
— Разгрузит мастера, специалиста или компанию;
— Позволит гибко управлять расписанием и загрузкой;
— Разошлет оповещения о новых услугах или акциях;
— Позволит принять оплату на карту/кошелек/счет;
— Позволит записываться на групповые и персональные посещения;
— Поможет получить от клиента отзывы о визите к вам;
— Включает в себя сервис чаевых.
Для новых пользователей первый месяц бесплатно.
Зарегистрироваться в сервисе
Электротехнические стали и пермаллои характеризуются малым удельным электрическим сопротивлением (10-7 — 10-6 Ом*м). Использование их в магнитопроводах, работающих на высоких частотах, не представляется возможным из-за больших потерь на вихревые токи, возрастающих пропорционально квадрату частоты. Для магнитопроводов, работающих на высоких частотах, используют магнитодиэлектрики, которые состоят из зерен магнитного материала, разделенных диэлектриком. По сравнению с металлическими магнитными материалами они характеризуются более высоким электрическим сопротивлением (10-3 — 1 Ом*м). В качестве магнитопроводов из магнитодиэлектриков берут карбонильное железо (высокодисперсный порошок, состоящий в основном из частиц сферической формы), альсифер (магнитомягкий сплав с высокой магнитной проницаемостью, содержащий около 9,5% кремния и 5,5% алюминия, остальное — железо; ГОСТ 22187—76) и пермаллои.
Основные достоинства магнитодиэлектриков: малые потери на вихревые токи, стабильные магнитные характеристики в рабочем интервале температур и во времени. К числу недостатков следует отнести небольшую магнитную проницаемость (1,26*10-5 — 7,53*10-6 Гн/м) на радиочастотах, что ограничивает возможность повышения добротности различных индуктивных элементов. Для работы с малыми потерями на высоких частотах до нескольких десятков мегагерц используют магнитные материалы керамического типа, ферриты, получаемые спеканием при высокой температуре смеси окислов железа с окислами никеля, цинка, марганца, магния, меди или другого двухвалентного металла. Ферриты характеризуются высокой магнитной проницаемостью (1,26*10-5 — 2,52*10-3 Гн/м) и удельным электрическим сопротивлением (1 — 105Ом*м).
Для обеспечения требуемой точности формы и размеров при изготовлении пластинчатых магнитопроводов с заданной шероховатостью поверхности используют штамповку, обработку резанием и физико-химические методы. При штамповке и обработке резанием в поверхностных слоях материала в результате силового воздействия инструмента кристаллы правильной формы, характерные для исходного материала, разрушаются и ориентируются в направлении движения инструмента. В результате ухудшаются характеристики магнитопроводов, например, магнитная проницаемость уменьшается, а коэрцитивная сила увеличивается. Для восстановления магнитных характеристик материала проводят отжиг, вызывающий рекристаллизацию материала.
При изготовлении разрезных ленточных магнитопроводов разрезание является одной из ответственных операций. Отклонение режимов этой операции от оптимальных может привести к появлению короткозамкнутых витков и наклепу, в результате возрастут потери на вихревые токи. Разрезание магнитопроводов осуществляют различными способами, например, фрезерованием, абразивным кругом, электроискровой обработкой и т. д. При фрезеровании поверхность разреза получается неровной, а витки магнитопровода оказываются короткозамкнутыми. Кроме того, имеет место наклеп и изменение ориентации зерен в месте разреза. Разрезание магнитопроводов абразивным кругом (шероховатость обработанной поверхности Rа 1,25 мкм) и электроискровой обработкой (Rz 20 мкм) дают лучшие результаты. После разрезания абразивным кругом отпадает необходимость применения последующего шлифования. Электроискровая обработка позволяет избежать механического воздействия на магнитопровод и замыкание отдельных его витков. Поверхностный слой, в котором в результате теплового воздействия происходит изменение ориентации зерен до глубины 0,05—0,08 мм, удаляется при последующем шлифовании торцов магнитопровода.
Точность размеров, формы и качество поверхности формованных магнитопроводов обеспечивается точностью размеров и шероховатостью поверхности оформляющей полости пресс-форм. Магнитные характеристики формованных магиитопроводов обеспечиваются качеством порошка магнитного материала и материала диэлектрической связи. Количество связки при изготовлении магнитопроводов должно быть по возможности минимальным, так как ее увеличение резко снижает магнитную проницаемость магнитопровода и увеличивает диэлектрические потери. Формовочная смесь на основе полистирола обладает хорошей текучестью, поэтому ее используют для изготовления сложных по форме магнитопроводов. Магнитная проницаемость формованных магнитопроводов зависит от их плотности, которая обеспечивается выбором давления при прессовании. С увеличением давления прессования магнитная проницаемость возрастает до определенного значения для данного типа магнитного материала. При дальнейшем увеличении давления прессования возрастают потери на гистерезис, так как имеет место пластическая деформация феррочастиц, возрастает электропроводность и потери на вихревые токи из-за разрушения изоляционной пленки вокруг феррочастиц.
Оптимальное давление прессования для магнитодиэлектриков лежит в интервале 600— 1000 МПа, а для ферритов — 80—200 МПа. Продолжительность выдержки под нагрузкой не влияет на плотность магнитного материала. Обеcпечение равномерной плотности магнитного материала в формованном магнитопроводе осуществляется прессованием в пресс-формах с двойным давлением сверху и снизу. Кроме того, в магнитопроводах из ферритов в случае неравномерной плотности при последующем спекании возникают значительные внутренние напряжения, вызывающие коробление и растрескивание. Для исключения растрескивания магнитопроводов из ферритов проводят следующие технологические мероприятия:
перед спеканием нагревом из них удаляют связку;
при спекании скорость подъема температуры ограничивают 200—300 К/ч из-за быстрого испарения оставшейся связки;
после выдержки при температуре спекания требуется медленное охлаждение со скоростью 50—100 К/ч.
Магнитопроводы с одинаковыми магнитными характеристиками могут быть получены только при одинаковой температуре по всей рабочей зоне печи. Температурный режим поддерживается с точностью ±5 К автоматическим регулированием.
Технологический процесс изготовления деталей методом порошковой металлургии
Четыре основных операции: смешивание, формование, спекание и калибрование.
· Смешивание.
Смешивание – это приготовление однородной механической смеси из металлических порошков различного химического и гранулометрического состава или смеси металлических порошков с неметаллическими.
Формование.
Формование изделий осуществляем путем холодного прессования под большим давлением (30–1000 МПа) в металлических формах. Обычно используются закрытые пресс-формы. Смесь порошков свободно засыпается в полость матрицы, объемная дозировка регулируется ходом нижнего пуансона. Прессование может быть одно- или двусторонним в зависимости от отношения высоты детали к ее диаметру (поперечному размеру). Для формования и калибрования используем прессовое оборудование с механическим, гидравлическим или пневматическим приводом. Полученная прессовка имеет размер и форму готового изделия, а также достаточную прочность для перегрузки и транспортировки к печи для спекания.
· Спекание.
Спекание изделий из однородных металлических порошков производится при температуре, составляющей 70–90% температуры плавления металла. В смесях максимальная когезия достигается вблизи температуры плавления основного компонента, а в цементированных карбидах – вблизи температуры плавления связующего. С повышением температуры и увеличением продолжительности спекания увеличиваются усадка, плотность и улучшаются контакты между зернами. Во избежание окисления спекание проводят в восстановительной атмосфере (водород, оксид углерода), в атмосфере нейтральных газов (азот, аргон) или в вакууме. Прессовка превращается в монолитное изделие, технологическая связка выгорает.
· Калибрование.
При калибровании изделий достигается нужная точность размеров, улучшается качество поверхности и повышается прочность. Примерно 80% нашей продукции проходят эту операцию.
Порошковые изделия готовы к использованию. Однако, для предания заданных свойств, иногда применяются дополнительные операции (пропитка смазками, механическая, термическая, химическая обработка и др.)
Преимущества порошковой металлургии Пять основных преимуществ: безотходность, производительность, высочайшая точность, широкий диапазон свойств, получение уникальных свойств. · Безотходность. Технологию порошковой металлургии можно назвать безотходной. Потери сырья составляют не более 5%. · Производительность. Также экономический эффект можно получить за счет полной автоматизации изготовления деталей на пресс-автоматах (а еще лучше - на роторных линиях). Простые детали можно прессовать свыше 5000 штук в час. · Высочайшая точность. Высокая точность формы и размеров детали обеспечивается особенностями технологии, высокоточным прессовочным и калибровочным пресс-инструментом. Получаем 2-й класс точности (6-7 квалитет) · Широкий диапазон получаемых свойств. Можно регулировать физические, механические, электрические, магнитные и др. свойства производимой продукции. Например, задавать нужные электрические свойства контактов, магнитные свойства магнитопроводов и механические свойства конструкционных деталей. Особенностью порошковой металлургии является возможность изготавливать пористые материалы. Например, можно задавать необходимую пористость для фильтров или самосмазываемых подшипников скольжения. Эксплуатационные характеристики продукции можно сделать более гибкими за счет применения возможностей порошковой металлургии. · Получение уникальных свойств, не достижимых другими традиционными методами. Порошковая технология предоставляет возможности для создания псевдосплавов (из несплавляющихся металлов) и материалов с особыми специальными свойствами, которые нельзя получить, применяя другие известные промышленные методы изготовления. Также она предоставляет возможность получения материалов высокой чистоты.
Технологический процесс изготовления магнитопроводов из ферритов и магнитодиэлектриков
Типовой ТП изготовления магнитопроводов из магнитодиэлектриков включает следующие основные этапы: приготовление порошка магнитного материала, приготовление формовочной смеси, формование, термообработка, пропитка магнитопроводов.
Приготовление порошка магнитного материала осуществляется размолом чистых магнитных материалов (карбонильного железа, альсифера и т. д.).
Приготовление формовочной смеси заключается в том, что порошок магнитного материала смешивают с термопластичной или термореактивной связкой. Термопластичная связка в виде тонкоизмельченного порошка (например, полистирола) или термореактивная — в виде раствора, например бакелитовой смолы в спирте, подается в определенной пропорции с порошком магнитного материала в смеситель, где формовочная смесь тщательно перемешивается для обеспечения полного обволакивания магнитного порошка диэлектрической связкой. Формовочная смесь на основе полистирола после смешивания готова к формованию, а смесь на основе бакелитовой смолы предварительно подсушивается для удаления летучих составляющих на металлических противнях и просеивается, после чего подается на формование.
Формование магнитопроводов осуществляют теми же методами, что и прессование пластмасс, а именно, холодным и горячим прессованием и горячим литьем под давлением. Магнитодиэлектрики с термореактивной связкой обычно формуют холодным и горячим прессованием, а магнитодиэлектрики с термопластичной связкой — литьем под давлением. Холодное прессование проводится при следующих режимах: давление 800—1000 МПа, температура 288—298 К, выдержка под давлением 1—2 с. Режимы горячего прессования формовочной массы на основе полистирола: предварительный нагрев пресс-формы до 453—473 К, давление 400—500 МПа, выдержка под давлением 3—10 мин, охлаждением пресс-формы до 353— 358 К.
Термообработка магнитопроводов проводится в тех случаях, когда используется метод холодного прессования. Отформованные магнитопроводы для полимеризации термореактивной связки помещают в печь с температурой 403—413К и выдерживают 4—8 ч.
Пропитка магнитопроводов проводится с целью повышения влагостойкости и защиты от окисления. При этом используют различные компаунды, кремнийорганические составы, парафин или церизин.
Типовой ТП изготовления магнитопроводов из ферритов включает следующие основные этапы: приготовление порошков соответствующих окислов металлов, приготовление формовочной смеси, формование, термообработка, пропитка магнитопроводов.
Технология изготовления магнитопроводов из ферритов аналогична технологии изготовления деталей из керамики. Формование магнитопроводов осуществляется сухим или сырым прессованием, а также выдавливанием через мундштук. Отпрессованные магнитопроводы спекают в печи с использованием газовой среды в зависимости от состава феррита. Спекание на воздухе с последующим охлаждением в инертной среде проводят для ферритов, содержащих марганец. Спекание в вакууме проводят для марганцево-цинковых ферритов. Конечная температура спекания ферритов 1273—1683 К. Магнитопроводы пропитывают в 80%-ном спиртовом растворе бакелитового лака в течение 30 мин с последующей просушкой в термостате при температуре 413 К в течение 6 ч.
Контроль качества магнитопроводов
Все магнитопроводы подвергают следующим видам контроля: контроль геометрических размеров, внешнего вида, маркировки, массы, контроль магнитных характеристик (магнитной проницаемости и относительного тангенса угла магнитных потерь).
Геометрические размеры магнитопроводов проверяют любым измерительным инструментом, обеспечивающим погрешность измерения, не превышающую установленную ГОСТ 8.051—73. Внешний вид и маркировку проверяют внешним осмотром невооруженным глазом с остротой зрения от 0,8 до 1 и нормальным цветоощущением при освещенности от 60 до 100 лк, сопоставляя с чертежами и образцами внешнего вида. Массу магнитопроводов определяют взвешиванием с погрешностью не более ± 0,5%.
Определение начальной магнитной проницаемости и относительного тангенса угла магнитных потерь рассмотрим на примере кольцевых магнитопроводов из ферритов (см. ГОСТ 14208—77) марок 1000НМ, 1500НМ, 3000НМ, 4000НМ. Начальную магнитную проницаемость определяют измерением коэффициента начальной индуктивности магнитопроводов на одной из частот 1 —100 кГц. Измерение коэффициента начальной индуктивности проводят при помощи мостового измерителя индуктивности (например, низкочастотного измерителя малых индуктивностей ЭМ18-2 или цифрового измерителя индуктивностей ЭМЦ7-2). Магнитопроводы считаются годными, если значения коэффициента начальной индуктивности лежат в пределах, указанных в ТУ.
Относительный тангенс угла магнитных потерь определяют измерением индуктивности Lx, сопротивления rх намагничивающей цепи с испытываемым магнитопроводом при значениях частоты и амплитуды, указанных в ТУ, и сопротивления намагничивающей цепи постоянному току r0. В качестве намагничивающей цепи используют равномерно нанесенную на магнитопровод обмотку. Магнитопроводы перед нанесением обмотки обматывают одним-двумя слоями конденсаторной бумаги толщиной 10—15 мкм. Измерение индуктивности Lx и сопротивления rх обмотки с магнитопроводом проводят мостовым измерителем полных сопротивлений, например типа ЭМ18-5. Измерения Lx, rх проводят сначала при амплитудном значении напряженности переменного магнитного поля Н = 0,8 А/м (10 мЭ), а затем при Н = 8 А/м (100 мЭ). Намагничивающие токи, соответствующие этим напряженностям переменного магнитного поля, даются в ТУ.
Относительный тангенс угла магнитных потерь вычисляют по формуле:
, где
rх — эффективное сопротивление обмотки с сердечником, Ом;
r0 — сопротивление обмотки постоянному току, Ом;
f — частота измерения, Гц;
Lx — индуктивность обмотки с сердечником, Гн;
— начальная магнитная проницаемость, определяемая по формуле:
, в которой
K1 — коэффициент начальной индуктивности, мкГн;
h — высота магнитопровода, мм;
, где D и d — соответственно наружный и внутренний диаметры магнитопровода, мм.
Электрофорез
Электрофорез – движение под действием внешнего электрического поля дисперсных твердых частиц, капель жидкости или пузырьков газа, находящихся во взвешенном состоянии в жидкой или газообразной среде.
Электролитическое осаждение (нанесение покрытия методом электрофореза) означает осаждение краски на поверхности изделия из водного раствора путем электрохимических реакций в процессе погружения и подачи напряжения между изделием, являющимся одним из электродов, и противоэлектродом.
На поверхности изделия осаждается нерастворимое в воде плотное покрытие, которое не может быть растворено повторно.
Покрытие имеет хорошую адгезию к фосфатированной поверхности изделия.
При подъеме изделия из ванны электроосаждения часть жидкой краски захватывается поверхностью изделия; эта пленка легко удаляется при промывке водой.
В процессе последующей сушки при температуре 165-1800С происходит сшивка связующего и получается жесткая, прочная, равномерная по толщине полимерная пленка.
Метод электроосаждения нашел широкое применение в массовом производстве: при грунтовании кузовов автомобилей, "белой техники", дисков колес, радиаторов и т.д. на конвейерных линиях. Это объясняется высокой производительностью, возможностью полной автоматизации процесса, высоким коэффициентом полезного использования лакокрасочного материала (до 92%), высокими защитными свойствами получаемого покрытия.
Установки могут быть непрерывного и периодического действия.
В зависимости от того, является окрашиваемое изделие анодом или катодом, различают анодное и катодное электроосаждение.
В настоящее время все большее распространение получают установки катодного электроосаждения, так как получаемые покрытия отличаются высокой коррозионной стойкостью даже при толщине покрытия 12 мкм.
Установки представляют собой сложный комплекс оборудования, включающий ванну электроосаждения, зоны промывки окрашенных изделий ультрафильтратом и деминерализованной водой, источник питания, токосъемные устройства, систему перемешивания, термостатирования, фильтрации и ультрафильтрации лакокрасочного материала, диализную систему, устройство для предварительной очистки промывных вод, установку для приготовления деминерализованной воды.
Список литературы
Арутюнова И.А., Дальский А.Н. Технология конструкционных материалов, Учебник. – М.: Машиностроение 1985. – 450 с.
Дерягин Б.В., Духин С.С. Электрофорез. - М.: Наука, 1976. 327 с.
Ключников А.В., Привалов В.П., Сергеев В.С., Ушакова С.Е. Технология деталей радиоэлектронной аппаратуры. - М.: Радио и связь, 1986. - 256 с.
|