КЛАССИФИКАЦИЯ БОЛТОВ
ВИДЫ БОЛТОВ И ТИПОРАЗМЕРЫ
К болтам относятся стержни с винтовой канавкой на одном конце и головкой на другом, служащие для разъемных соединений отдельных частей машин и конструкций при помощи гайки.
По форме головки болты разделяются на болты с многогранной головкой, чаще всего с шестигранной, и болты с фасонной головкой (полукруглой, потайной, клеммные, закладные, стыковые и др.).
Наибольшее распространение получили болты с шестигранной головкой, которые применяются в соединениях, испытывающих нагрузки самого различного характера: статические, циклические, динамические (ударного характера). Болты с шестигранной головкой используются как тяжелонагруженные детали в двигателях внутреннего сгорания (шатунные болты), в ходовой части гусеничных тракторов (башмачные болты), во фланцевых соединениях сосудов, находящихся под давлением, и др.
Болты с шестигранной головкой различаются:
1. По диаметру резьбы и безрезьбовой части стержня.
Стандарты включают болты с диаметром резьбы от 1,6 до 160мм. Наибольшее применение имеют болты с диаметром резьбы до 48 мм. Стандарты на эти 'болты выделены в самостоятельную группу.
По диаметру гладкой (безрезьбовой) части стержня болты разделяются на:
а) болты с диаметром гладкой части стержня, равным наружному диаметру резьбы (ГОСТ 7796—70, ГОСТ 7798—70, ГОСТ 7805—70, ГОСТ 7808—70 и др.);
б) болты с диаметром гладкой части стержня, приблизительно равным среднему диаметру резьбы (ГОСТ 7795—70, ГОСТ 7811— 70, ГОСТ 15590—70). Эти болты для улучшения центрирования стержня в отверстии скрепляемых деталей имеют направляющий подголовок длиной не менее половины диаметра.
2. По длине стержня и длине резьбы.
Длина стержня болтов колеблется в широком диапазоне от 1,0 d
до 10—30 d (d—
диаметр резьбы).
Абсолютная длина резьбовой части стержня увеличивается с увеличением диаметра стержня, а относительная длина — уменьшается и составляет от 5 d до 2 d. Различают болты с резьбой до головки и имеющие безрезьбовой участок стержня.
3. По размеру «под ключ» S.
Существуют болты с нормальным размером «под ключ» S=
1,5—1,6 d и с уменьшенным S = 1,3—1,4 d.
Болты с уменьшенным размером «под ключ» имеют соответственно меньшую опорную поверхность и поэтому могут применяться в соединениях с пониженными требованиями к прочности на смятие под головкой.
Болты с шестигранной головкой изготовляются в нескольких исполнениях: основное (рис. 1,а) (без отверстий или углублений), с отверстиями в стержне или головке (рис. 1,6, в)
или с углублением в головке '(рис. 1, г, д).
Болты с отверстиями в головке или в стержне применяются в соединениях, требующих предохранения от самоотвинчивания. Стопорение осуществляется с помощью шплинтов (проволоки), вставляемых в отверстие, просверленное в стержне или головке болта. Углубление в головке выполняется для облегчения оформления шестигранника в процессе безотходной высадки головки.
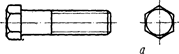
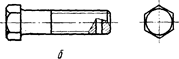
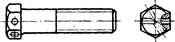

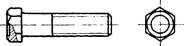
г д
Рис. 1. Виды болтов с шестигранной головкой
Головка болта может иметь опорную шайбу (рис. 1,а). При изготовлении головки болтов с опорной шайбой уменьшается величина смещения оси опорной поверхности относительно оси стержня и снижается вероятность появления заусенцев на опорной поверхности.
4. По точности изготовления (повышенной, нормальной, грубой).
Болты разной степени точности отличаются:
а) точностью выполнения размеров (диаметра, длины, высоты головки и др.);
б) величиной отклонения от правильной геометрической формы (несоосности головки и стержня, резьбовой и безрезьбовой частей стержня, неперпендикулярности опорной поверхности головки относительно оси стержня, уклона граней и т. д.);
в) дефектами внешнего вида (срезами или сколами металла на гранях, заусенцами на опорной поверхности, выкрашиванием ниток резьбы и др.).
Дефекты внешнего вида и величины отклонений от правильной геометрической формы для болтов с диаметром резьбы до 48 мм регламентируются ГОСТ 1759—70.
Болты с фасонной головкой в зависимости от вида головки и подголовка предназначаются преимущественно для соединения конструкций из дерева и листового металла. Стандарты на болты с фасонной головкой охватывают болты с диаметром резьбы от 5 до 24 мм длиной от 2 d
до 30 d.
В зависимости от формы и размера головки и типа подголовка болты изготавливают: с полукруглой головкой и усом (рис. 2,а); с полукруглой головкой и квадратным подголовном (рис. 2,6);
с потайной головкой и усом (рис. 2,в); с потайной головкой и квадратным подголовком (рис. 2,г); шинные (с потайной головкой) D=1,7—1,8 d,
где D—
диаметр головки.
Стандарты на болты с полукруглой головкой включают болты с облегченной головкой .D=1,7—1,8 d,
с нормальной головкой D=
2,2—2,3 d
и увеличенной головкой (.D=3,0 d).
Потайные головки бывают облегченные и нормальные.

Рис. 2. Виды болтов с фасонной головкой
Болты с фасонной головкой изготавливают грубой точности с резьбой крупного шага по ГОСТ 16093—70.
Болты с увеличенным диаметром головки (свыше 2d) применяют преимущественно для крепления деревянных конструкций, так как большая опорная поверхность под головкой уменьшает вероятность смятия древесины. Болты с диаметром головки менее 2 d
применяют в основном для соединения конструкций из металла.
Болты закладные, клеммные и стыковые применяют для рельсовых скреплений железнодорожного пути. Клеммные и закладные болты изготовляют одного диаметра резьбы — 22 мм с крупным шагом (преимущественно горячей штамповкой). Стыковые болты изготавливают горячей штамповкой.
МАТЕРИАЛ И КЛАССЫ ПРОЧНОСТИ БОЛТОВ
Механические свойства крепежных изделий с диаметром резьбы до 48 мм и материалы для их производства регламентируются ГОСТ 1759—70.
Для болтов установлены три группы материалов: углеродистые и легированные стали; коррозионно-стойкие, жаропрочные, жаростойкие и теплоустойчивые стали; цветные сплавы.
В основном применяют болты из углеродистых и легированных сталей; болты, изготовленные из материалов второй и третьей группы, применяют в специальных случаях при жестких требованиях к жаропрочности, коррозионной стойкости, габаритам и весу соединений.
Болты изготавливают как из спокойных, так и из кипящих сталей. Учитывая, что кипящие стали более склонны к хладноломкости,
чем стали спокойной выплавки, их применение для крепежных изделий ограничено.
Из углеродистых и легированных сталей в ГОСТ 1759—70 предусмотрено изготовление болтов двенадцати классов прочности, из коррозионно-стойких, жаропрочных и жаростойких сталей шести групп и цветных металлов также шести групп материалов.
Классы прочности охватывают диапазон временного сопротивления от 30 до 160, кгс/мм2
. Под классам прочности понимается комплекс механических свойств, включающий временное сопротивление, предел текучести, относительное удлинение после разрыва, твердость, напряжение от пробной нагрузки, а для ряда классов — ударную вязкость.
Временным сопротивлением о-в называется отношение максимальной нагрузки Рmах, которую выдерживает материал (болт) в момент наступления разрушения, 'к первоначальному поперечному сечению Fo
.
Предел текучести От
представляет собой наименьшее напряжение, при котором деформация материала происходит без заметного увеличения растягивающей нагрузки Рт .
Предел текучести определяется на специальных образцах. Часто при растяжении образцов действующая нагрузка изменяется вплоть до момента разрушения, при этом пользуются значением условного предела текучести.
Ударная вязкость материала характеризуется полной работой, затраченной на деформацию и разрушение специального призматического образца с односторонним надрезом (выточкой), деленной на площадь сечения в надрезе. Образцы вытачиваются из болтов с удалением резьбы.
Относительное удлинение — это отношение увеличения длины образца после разрыва к его начальной длине.
Класс прочности болтов обозначается двумя числами. Первое число, умноженное на 10, определяет величину минимального временного сопротивления (кгс/мм2
). Второе число, умноженное на 10, определяет отношение предела текучести к временному сопротивлению (%), а произведение чисел определяет величину минимального предела текучести (кгс/мм2
).
Введение классов прочности облегчает выбор и расчет резьбовых соединений, позволяет регламентировать усилия предварительной затяжки, что значительно повышает надежность и долговечность соединении.
Группы материалов обозначаются двузначным числом, первая цифра которого указывает вид материала, а вторая цифра — прочность.
При оформлении заказов на продукцию, а также в различной конструкторской документации болты обозначаются по условной схеме. Условное обозначение болтов включает: наименование детали, исполнение, диаметр резьбы, шаг резьбы, поле допуска резьбы, длину болта, класс прочности или группу, марку стали или сплава, обозначение вида покрытия, толщину покрытия и номер размерного стандарта.
Для упрощения обозначения часто применяемых деталей в условной схеме не указываются крупный шаг резьбы, поле допуска 8g,
исполнение 1, марка углеродистой стали и цветного сплава.
Дополнительно в условном обозначении может отмечаться применение спокойной (буквой С) или автоматной (буквой А) сталей.
Например, болт по ГОСТ 7796—70 исполнения 2, имеющий диаметр резьбы 1Й мм с шагом 1,25мм и поле допусков 6 g,
при длине 60 мм и классе прочности 5.8 (записывается без точки) с цинковым покрытием (вид покрытия 01) толщиной, 9 мкм обозначается: болт 2М 12Х1,25—6 ХбО.58,019 ГОСТ 7796—70.
ГОСТ 1759—70 рекомендует технологию изготовления болтов в зависимости от их класса прочности.
В производственных условиях болты изготавливаются холодной или горячей штамповкой и точением без термической обработки или с термической обработкой после получения крепежных изделий одним из перечисленных выше способов.
Болты, изготовляемые холодной штамповкой без термической обработки, имеют пониженные пластические свойства вследствие наклепа, полученного при холодной деформации. Величина предела текучести материала болтов при этом приближается к величине временного сопротивления и составляет в большинстве случаев 0,8— 0,9 Gs.
Поэтому указанным методом можно изготовлять только болты классов прочности 4.8, 5.8, 6.9 и в ряде случаев 8.8.
В ряде случаев эти же болты могут быть изготовлены и холодной штамповкой, но с обязательным отжигом исходного металла.
Высокопрочные болты из среднеуглеродистых и легированных сталей (классы прочности 8.8, 10.9 и 12.9, 14.9) изготовляются с закалкой и отпуском.
ИСХОДНАЯ ЗАГОТОВКА ДЛЯ ХОЛОДНОЙ ШТАМПОВКИ БОЛТОВ
ТРЕБОВАНИЯ, ПРЕДЪЯВЛЯЕМЫЕ К КАЧЕСТВУ МЕТАЛЛА
Стабильность технологического процесса штамповки и качество штампуемых болтов во многом определяются качеством исходного металла. Холодная штамповка предъявляет специфические требования к исходному металлу. Материал, применяемый для холодной штамповки, должен обладать высокой пластичностью, иметь равномерные механические свойства и химический состав и не иметь поверхностных и внутренних дефектов.
Деформируемость металла в холодном состоянии, т. е. его способность претерпевать пластическое формоизменение без разрушения, зависит от многих факторов: качества поверхности заготовки; химического состава; структуры; механических свойств и технологических параметров процесса штамповки.
Дефекты поверхности металла заготовки являются одной из основных причин возникновения надрывов и трещин при холодной штамповке. Они могут образовываться на разных стадиях переработки металла, начиная от разливки стали и кончая калибровкой перед высадкой.
Дефектами разливки являются газовые пузыри, расположенные внутри или на поверхности металла, неметаллические включения, пористость и др. Газовые пузыри возникают обычно в кипящей стали, в спокойной образуется неравномерно расположенная пористость. При прокатке дефекты слитков способствуют образованию на поверхности проката трещин, закатов, глубоких рисок, волосовин, которые необходимо удалять перед процессом холодной деформации.
Исследование влияния глубины и конфигурации поверхностных дефектов на деформируемость углеродистой стали проводят путем осадки образцов с искусственно нанесенной трещиной различной глубины, различным углом и радиусом при вершине. Установлено, что дефекты (волосовины, риски, плены и др.) глубиной 0,05 мм и более при высадке с большими степенями деформации раскрываются, образуя трещины.
Для снижения брака при холодном прессовании необходимо удалять дефекты с поверхности обрабатываемого металла. Поэтому поверхность слитков перед прокаткой необходимо зачищать. На металлургических заводах зачистку проводят механическим или огневым способом.
При нагреве слитков перед прокаткой необходимо добиваться наименьшего обезуглероживания. На обезуглероженной поверхности вследствие ее пониженной твердости при прокатке образуются более глубокие риски и царапины.
Количество дефектов, образующихся при прокатке, зависит также от степени износа валков. По мере износа на поверхности ручьев прокатных валков появляются надрывы металла, выступы, углубления и т. д. Эти неровности отпечатываются на горячем металле и закатываются на последующих переходах, что приводит к нарушению сплошности металла.
Поверхностные дефекты могут образоваться при калибровке металла перед штамповкой. К таким дефектам относятся риски и царапины, имеющие иногда большую протяженность по длине. Устранению этих дефектов способствуют: качественное травление (при неудовлетворительном травлении на металле остаются частицы окалины, способствующие образованию рисок и царапин на волочильном инструменте и металле);
применение волок с правильной геометрией рабочего канала; применение качественной смазки при калибровке.
Пластичность стали, во многом определяется ее химическим составом. Так, увеличение содержания углерода в стали снижает ее пластичность и деформируемость, приводит к увеличению прочностных характеристик. Стали с содержанием углерода ^0,25i% необходимо отжигать для увеличения пластичности. Практически стали с содержанием углерода C 0,5% можно штамповать только после предварительного подогрева.
Повышенное содержание кремния
в стали резко снижает ее пластичность; при деформировании в холодном состоянии вызывает значительный разогрев заготовки, снижает стойкость инструмента, повышает усилия штамповки и приводит к образованию трещин.10702—63. «Сталь для холодной высадки», ГОСТ 1050—74. «Сталь углеродистая качественная конструкционная», ГОСТ 360—71. «Сталь углеродистая обыкновенного качества», ГОСТ 4543—71 «Сталь легированная конструкционная». Сортамент калиброванного металла регламентируют ГОСТ 10702—63, ГОСТ 7417—75. Преимущественное применение для 'штамповки имеет сталь по ГОСТ 10702—63.
Калиброванная сталь для штамповки болтов поставляется в натартованном (наклепанном) состоянии. Наклеп возникает, за счет обжатия при волочении горячекатаной стали. Твердость нагартованной стали, величины временного сопротивления и относительного сужения не должны превышать норм, установленных соответствующими стандартами.
Поверхность калиброванной стали должна быть чистой, гладкой, светлой или матовой без трещин, волосовин, закатов, плен, окалины. Допускаются отдельные мелкие риски механического происхождения в пределах '/4 'предельных отклонений на диаметр, а также отдельные вмятины и рябизна в пределах полусуммы допусков.
Макроструктура не должна иметь усадочной раковины и рыхлости, трещин, пузырей, расслоений, неметаллических включений и флокенов, видимых без применения увеличительных приборов при проверке на изломах или протравленных образцах.
Необходимо отметить, что показатели, нормируемые стандартами, и, в
частности, ГОСТ 10702—63, не полностью удовлетворяют требованиям к металлу, предназначенному для холодной высадки. Так, величина относительного сужения для ряда сталей нормируется меньшей 50%, испытание на осадку предусмотрено только до Va первоначальной высоты, нет требования обязательной зачистки поверхности и др.
ПОДГОТОВКА МЕТАЛЛА К ШТАМПОВКЕ
Металл, предназначенный для штамповки, должен иметь чистую и блестящую поверхность, свободную от окалины, жировых и других загрязнений, я содержать прочно удерживаемую на поверхности технологическую смазку.
Подготовка поверхности заготовки включает операции: очистку поверхности от окалины, жировых и других загрязнений; нанесение подсмазочного слоя (носителя смазки); нанесение технологической смазки.
Прокат или термически обработанный металл имеет на поверхности окисную пленку — окалину, которая должна быть удалена для предупреждения преждевременного износа технологического инструмента и получения чистой и точной заготовки. Основным способом удаления окалины с заготовок, предназначенных для холодной штамповки болтов, является травление.
Травление углеродистых сталей производят главным образом в растворе, содержащем 8—20% серной кислоты, при температуре 50—80°С в течение 10—120 мин, или в концентрированной соляной кислоте при 20— 30° С в течение 5—30 мин. Продолжительность травления зависит от марки стали, диаметра и состояния поставки (прутки, бунты) металла и концентрации раствора.
Травление меди, латуни Л63, Л62 производят в растворе, содержащем 3—10% H2
S04
при температуре 20—40° С.
Травление алюминиевых сплавов проводят в растворе с 5—10% едкого натра и c последующим погружением в раствор с 10—15% азотной кислоты (пассивированием).
После травления для удаления травильного шлама и кислоты металл промывают в горячей и холодной воде. Промывка стальных заготовок в горячей воде производится при температуре 50—70° С в течение 1—2 мин, холодная промывка осуществляется водой под давлением 5—7 атм. в течение 1—2 мин.
Для нейтрализации остатков серной кислоты и уменьшения коэффициента трения при калибровке и холодной штамповке металл подвергается известкованию в растворе, содержащем 3—5% извести (СаО), при температуре 100° С (2—3 погружения). Допускается выработка раствора до концентрации СаО 0,5— 1%. На поверхности металла должна быть сплошная пленка извести. Нейтрализацию кислоты можно производить в водном растворе мыла с концентрацией 0,5—0,8 г/л при температуре раствора 70—80° С в течение 2—3 мин. После нейтрализации с целью предупреждения коррозии металл подвергается сушке при температуре 100—120° С в течение 15—20 мин.
Для повышения надежности сцепления смазки с деформируемым металлом заготовку целесообразно покрывать подсмазочным слоем. Подсмазочное покрытие способствует снижению трения при штамповке и повышает стойкость штампового инструмента. Особенно эффективно, применение подсмазочного слоя при штамповке болтов с редуцированием стержня.
Нанесение подсмазочного слоя производится перед волочением или после волочения (перед штамповкой).
Наибольшее распространение получило нанесение подсмазочного слоя перед волочением, так как при этом слой носителя смазки получается более равномерным по толщине и надежно сцепленным с основным металлом.
Заготовки из углеродистых и низколегированных сталей чаще всего подвергают фосфатированию. Фосфатирование заключается в обработке металла в 2,5— 3%-ном растворе кислой фосфорнокислой соли цинка, температура раствора 60—80° С. Продолжительность фосфатирования равна 5—15 мин. Фосфатный слой может деформироваться без разрушения вместе с основным металлом. Фосфатное покрытие действует как непрерывный разделяющий слой между контактными поверхностями инструмента и заготовки, уменьшая трение, предотвращая налипание металла на инструмент и хорошо удерживая смазочное вещество. Фосфатирование в 1,2—1,3 раза снижает усилия деформирования.
Процесс подготовки металла с нанесением фосфатного слоя состоит из следующих операций: 1) травление при фосфатировании волоченого металла — обезжиривание); 2) промывка водой; 3) фосфатирование;
4) промывка водой; 5) известкование или омыление;
6) сушка.
Фосфатное покрытие считается качественным, если после волочения сохраняется зеркальный цвет (от черного до серого), при этом чем темнее цвет волочения, тем лучше покрытие.
При подготовке поверхности заготовок из нержавеющих сталей (12Х18Н9Т, 12Х18Н10Т и др.) вместо фосфатирования используют известково-солевое покрытие. Оно не требует дополнительных операций для химического разрушения пленки, образующейся на поверхности нержавеющей стали в процессе травления (пассивирования), и позволяет работать на высоких скоростях при волочении.
Нержавеющие и жаростойкие стали подготавливаются к штамповке по следующей технологии: 1) травление, 2) промывка в горячей воде, 3) пассивирование, 4) промывка в горячей воде, 5) нанесение известково-солевого покрытия, 6) сушка, 7) калибровка.
Известково-солевое покрытие имеет существенные недостатки. Поваренная соль ускоряет процесс коррозии металла, в сырую погоду впитывает влагу и затрудняет процесс волочения. Кроме того, известь очень пылит, засоряет воздух и помещение цеха и тем самым ухудшает условия труда.
При подготовке к штамповке нержавеющих сталей может применяться омеднение. На Дружковском метизном заводе омеднение металла, идущего на холодную штамповку болтов (с редуцированием стержня); производится по следующей технологии: а) травление;
б) промывка в горячей и холодной воде; в) омеднение;
г) промывка в холодной воде; д) нейтрализация (известкование) ; е) сушка.
После калибровки металл подвергается вторичному мед нению. Омеднение производится в растворе, содержащем 120—150 г/л медного купороса, 50—60 г/л серной кислоты и 2—3 г/л столярного клея при температуре раствора 18—22°С в течение 1—1,5 мин (двукратное погружение). Омеднение считается удовлетворительным, если поверхность металла покрыта сплошной медной пленкой без отслоения, рыхлости и просвечивания основного металла (через пленку).
Омеднение уступает фосфатированию по эффективности снижения коэффициента трения, кроме того, при нанесении медного покрытия трудно контролировать его свойства.
Положительные результаты при штамповке трудно деформируемых сталей дают лаковые покрытия и обработка в растворе щавелевой кислоты (оксалатирование). Указанные покрытия применяются и при штамповке цветных сплавов.
На калиброванный металл перед штамповкой или в процессе штамповки наносится технологическая смазка. В качестве смазки часто используется мыльная эмульсия. Хорошие результаты дает применение раствора сульфида молибдена в машинном масле.
В последние годы находят применение в процессах штамповки специальные смазки—укринолы. На московском заводе «Станконормаль» используется смазочно-охлаждающая жидкость на основе парафина (СОЖ В23 К) и укринол 5/5, позволяющие штамповать металл без фосфатного покрытия.
Для получения заготовки с требуемыми для штамповки болтов размерами
При изготовлении болтов из низкоуглеродистых сталей 10, Юкп, 20, 20 кп волочение, как правило, проводится с обжатием 12—20% без промежуточного отжига. Подкат из среднеуглеродистых и легированных марок стали для облегчения процесса волочения отжигается.
Оптимальная схема подготовки к штамповке среднеуглеродистых и легированных сталей включает:
1) отжиг горячекатаного металла; 2) подготовку поверхности металла к волочению; 3) волочение с обжатием 25—30%; 4) промежуточный сфероидизиру-ющий отжиг; 5) подготовку поверхности (фосфатирование); 6) волочение с обжатием 5—8%.
В результате промежуточного отжига после волочения стабилизируются структура металла и механические свойства, способствуя (совместно с последующим фосфатированием) снижению усилий штамповки, улучшению качества изделий и повышению износостойкости инструмента.
По рекомендациям ВНИИметиза применение промежуточного отжига целесообразно и при штамповке болтов (с редуцированием) из сталей 20, ЗО кп (классы прочности 5.8, 6.8).
При отжиге низкоуглеродистых сталей, протянутых с обжатием 8—16%, следует учитывать возможность интенсивного роста зерна, вследствие чего снижается пластичность стали. Поэтому перед отжигом не следует проводить волочение при указанных величинах деформаций.
ИЗГОТОВЛЕНИЕ БОЛТОВ
ХАРАКТЕРИСТИКИ ПРОЦЕССА ХОЛОДНОЙ ШТАМПОВКИ
Холодной пластической деформацией в практике штамповочного производства называют процесс, протекающий без принудительного нагрева металла.
В процессе деформации происходит механическое упрочнение (наклеп), повышаются твердость деформируемого металла, пределы прочности и текучести и снижаются относительное удлинение и сужение.
Процесс деформации сопровождается нагревом металла и инструмента, температура которых может достигать 300° С..
При холодной объемной штамповке всей заготовке придается заданная форма и размеры путем заполнения материалом рабочей полости штампов. Высадка, в отличие от штамповки, заключается в осадке части заготовки между подвижным (пуансоном) и неподвижным (матрицей) инструментом.
Основными достоинствами холодной штамповки являются высокая производительность, точность размеров и чистота поверхности изделий, повышенная прочность штампуемых деталей, низкий расход металла, широкий диапазон изготовляемых типоразмеров. Холодной штамповкой изготовляются болты с диаметром стержня до 30 мм. Однако в последнее время таким способом изготовляют болты с метрической резьбой, имеющие .стержень диаметром до 52 мм.
Основной недостаток холодной деформации — снижение пластичности металла вследствие наклепа и соответственно повышение опасности хрупкого разрушения болтов при эксплуатации. Особенно возрастает опасность хрупкого разрушения для болтов из среднеуглеродистых и легированных сталей, которые, как правило, .необходимо подвергать термообработке, способствующей исключению неблагоприятных последствий холодной деформации.
Процесс штамповки болтов заключается в том, чтобы из заготовки диаметром меньше диаметра отверстия в матрице (на величину зазора) и значительно меньше диаметра наибольшего сечения головки болта можно получить изделие необходимых размеров.
При выборе технологического процесса холодной штамповки необходимо учитывать следующие параметры:
1. Отношение длины свободной осаживаемой части заготовки к ее диаметру lo/dy.
Под свободно осаживаемой частью заготовки понимается отрезок, заключенный между матрицей и пуансоном, т. е. отрезок, не контактирующий с инструментом. Величина этого отношения характеризует трудность процесса формообразования головки болта и устойчивость свободного отрезка металла к продольному изгибу. Чем меньше величина lo/dy,
тем легче протекает процесс деформации и лучше оформление конечной заготовки. При большой величине отношения возможен изгиб стержня и нарушение правильной конфигурации заготовки (возникновение прогибов, складок), что ведет к браку продукции.
Для предотвращения указанных нарушений процесса высадки отношение длины свободной осаживаемой части к диаметру не должно превосходить определенной величины. При превышении этой величины процесс формообразования головки разделяется на несколько переходов.
Следует отметить, что при высадке болтов с предельным отношением lo/do необходимо обеспечить чистый срез заготовки и перпендикулярность плоскости отреза к продольной оси. При осадке заготовки с косым срезом торцовой площадки возможен ее изгиб и, как следствие, брак продукции.
Возможность изгиба заготовки при осадке увеличивается со снижением сил трения по контактируемым поверхностям заготовки и пуансона. Поэтому при неблагоприятных условиях для исключения продольного изгиба заготовки ее концевую часть защемляют в пуансоне.
Неблагоприятные условия снижают допустимую длину свободной осаживаемой части заготовки. Например, при косой отрезке заготовки и неудовлетворительном состоянии рабочей поверхности пуансона предельная величина отношения lo/do при высадке за один, удар может снизиться до 1,5 do и ниже.
При высадке головки болта за несколько переходов первые переходы носят подготовительный характер. На подготовительных переходах заготовка принимает промежуточную форму, при этом вследствие осадки происходит уменьшение отношения lo/do (для последующего перехода). Окончательное оформление головки осуществляется на последнем переходе высадки.
2. Отношение диаметра высаживаемой головки к ее высоте.
Чем больше отношение D/H, т. е. чем меньше высота головки болта и больше диаметр, тем труднее протекает процесс высадки, тем больше усилие для формообразования головки.
Практически влияние величины D и Н оценивают через отношение D/do и H/do. Отношение H/do, особенно для нержавеющей стали, не должно быть меньше 0,5. Отношение D/do при высадке за один удар должно составлять не более 2,2, за два удара 2,2—2,6, за три удара 2,6—4,0.
3. Относительная и истинная деформация.
Отношение lo/do не характеризует интенсивности процесса деформирования 'и является в основном технологическим фактором. Деформация при формообразовании головки оценивается величинами относительной деформации или истинной (логарифмической) деформации.
Кроме того, при оценке процесса осадки необходимо учитывать и величину деформации в поперечном направлении (уширение q= {Fi—Fo)jFi,
где Fo и Fi — соответственно начальная и конечная площадь поперечного сечения заготовки.
При высадке полукруглых, потайных, полупотайных и шестигранных головок болтов величины поперечной деформации различны в различных сечениях головки. В сечении с наименьшим поперечным размером происходит минимальная деформация, в сечении с наибольшим размером — максимальная. В этих случаях необходимо учитывать среднюю и максимальную величину поперечной деформации.
Очевидно, что для цилиндрических головок болтов поперечная деформация во всех сечениях головки имеет одинаковую величину. Чем больше величина средней деформации, тем выше усилие формообразования головки, тем больше вероятность появления трещин при осадке, тем важнее пластические свойства металла.
Максимальная поперечная деформация для нецилиндрических головок имеет место на ограниченных участках высаживаемой головки и вероятность появления трещин на этих участках зависит главным образом от количества и величины дефектов поверхности исходного материала.
Таким образом, по величинам деформации определяют 'возможность высадки головки болтов без нарушений сплошности материала и оценивают силовые параметры высадки. При выборе технологического процесса необходимо стремиться к получению минимальной степени деформации.
Степень деформации при высадке головок может быть снижена путем увеличения диаметра исходного металла. Увеличение диаметра исходного металла возможно при процессе штамповки, включающем редуцирование или прямое выдавливание стержня.
Редуцирование представляет операцию заталкивания заготовки в редуцирующую матрицу (рис. 4, а),сопровождающуюся уменьшением диаметра стержня соответственно диаметру редуцирующего пояска (без осадки заготовки). Качество процесса редуцирования
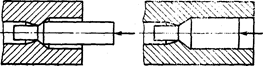
а
д
Рис. 4. Редуцирование (в) и прямое выдавливание (б)
определяется, главным образом, продольной устойчивостью заготовки (отсутствием изгиба стержня) 'и зависит от 'степени уменьшения сечения стержня при редуцировании.
Предельная величина уменьшения диаметра стержня при свободном редуцировании составляет 15—16%. Превышение этой величины может привести к изгибу стержня и наплыву металла перед матрицей.
Редуцируются, как правило, болты с длиной стержня, не превышающей 10 диаметров резьбы. Редуцирование более .длинных заготовок требует повышенной точности изготовления инструмента и часто затруднительно из-за изгиба стержня при выталкивании заготовки из матрицы. В отечественной и зарубежной практике редуцирование больших длин производится редко и только при значительном снижении скорости редуцирования.
При прямом выдавливании заготовка полностью заполняет канал матрицы (ом. рис. 4, б), свободная часть отсутствует и опасности потери устойчивости при заталкивании заготовки практически нет. Выдавливанием можно уменьшать диаметр- стержня до 50% и более.
Благоприятные условия протекания процесса прямого выдавливания (неравномерное трехстороннее сжатие) способствуют увеличению пластичности металла, поэтому трещины при этом процессе на поверхности изделий, не возникают. При прямом выдавливании возможны относительные деформации до 95%. Так же как и редуцирование, выдавливание больших длин не производится.
ТЕХНОЛОГИЧЕСКИЕ ПРОЦЕССЫ ХОЛОДНОЙ ШТАМПОВКИ БОЛТОВ
Технологический процесс изготовления заготовок болтов с шестигранной головкой (без резьбы) включает в себя образование промежуточной формы головки, окончательное оформление головки (шестигранника), получение стержня с требуемыми размерами, образование фаски.
Шестигранную головку можно получить обрезкой предварительно высаженной цилиндрической головки, или пластической деформацией .Фаска на конце стержня также может выполняться как пластической деформацией (при штамповке болтов), так и резанием. Предпочтительным является образование фаски резанием на встроенном в высадочный автомат приспособлении, так как при образовании фаски выдавливанием в матрице усложняется изготовление матриц, а при накатке резьбы на стержне с выдавленной фаской снижается стойкость накатного инструмента.
При получении фаски выдавливанием на каждую длину болта требуется своя матрица, в то время как при штамповке без оформления фаски перестройка автомата по длине болта не влечет смены матрицы. Однако при штамповке болтов из низкоуглеродистой стали и при ограниченных перестройках автомата целесообразно образование фаски выдавливанием.
Известны следующие основные технологические процессы штамповки болтов: без редуцирования; с однократным редуцированием; с двукратным редуцированием; с выдавливанием и редуцированием,.
Технологический процесс высадки без редуцирования применяется для изготовления болтов М6-М24 с уменьшенной головкой с диаметром гладкой части
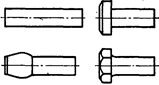
стержня, равным среднему диаметру резьбы (ГОСТ 7795—70, ГОСТ 7811—70), и коротких болтов с резьбой до головки или с малой величиной гладкого участка (ГОСТ 7796—70 и ГОСТ 7808—70) из низкоуглеродистых сталей Юкп и 20 кп. Болты изготовляются преимущественно без термической обработки классов срочности 4.8, 5.8 и 6.8. Технологические переходы штамповки приведены на рис. 5.
Цилиндрическая головка высаживается за два удара, размеры стержня изменяются незначительно. При изготовлении болтов с направляющим подголовком одновременно с высадкой головки происходит образование подголовка.
Прочность болтов, как правило, несколько ниже прочности исходного калиброванного металла, так как снижается вследствие осадки предварительно упрочненного при волочении металла (эффект Баушингера).
Достоинством метода является простота изготовления технологического инструмента.
Недостатками процесса являются:
1. Невозможность изготовления болтов с диаметром гладкой части стержня, равным наружному диаметру •резьбы (за исключением коротких болтов, у которых гладкая часть стержня может образоваться одновременно с высадкой головки).
2. Большая степень деформации при высадке головки и, как следствие, большие нагрузки на инструмент и повышенная опасность возникновения трещин на головке, особенно при высадке болтов из среднеуглеродистых и легированных сталей, большая неравномерность свойств головки и стержня.
3. Необходимость обязательной термообработки болтов из среднеуглеродистых сталей из-за значительного охрупчивания металла и повышенной опасности разрушения под головкой.
4. Трудность изготовления болтов с нормальной головкой.
Недостатки этого процесса штамповки болтов привели к постепенному вытеснению его более прогрессивными, включающими операцию редуцирования стержня.
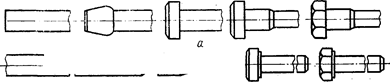
Рис. 6. Технологические схемы изготовления болтов высадкой с однократным редуцированием стержня
Процесс изготовления болтов высадкой с однократным редуцированием в настоящее время получил наибольшее распространение для изготовления болтов с диаметром стержня, равным наружному диаметру резьбы (ГОСТ 7796—70, ГОСТ 7798—70, ГОСТ 7805—70, ГОСТ 7808—70).
Болты могут изготовляться как из низкоуглеродистых, так и из среднеуглеродистых и легированных марок стали. Технологические переходы штамповки показаны на рис. 6.
Наиболее распространенным является процесс высадки с однократным редуцированием из металла диаметром, равным наружному диаметру резьбы (см. рис. 6, а). При данном процессе высадка цилиндрической головки осуществляется за два удара, диаметр гладкой части стержня почти не изменяется. Участок под накатывание резьбы образуется редуцированием на диаметр под накатку. Размеры диаметров под накатывание метрической резьбы регламентируются ГОСТ 19256—73.
Для болтов из низкоуглеродистых сталей одновременно с высадкой головки может осуществляться выдавливание фаски на конце стержня.
Степень деформации головки при высадке с однократным редуцированием и охрупчивание под головкой меньше, чем при высадке без редуцирования, однако еще достаточно велика, особенно для болтов с нормальной головкой.
Болты из среднеуглеродистых сталей при этом процессе целесообразно термически обрабатывать для снятия наклепа. Механические свойства болтов соответствуют свойствам исходного калиброванного металла. Редуцирование повышает прочность стержня сравнительно с прочностью проволоки лишь в случае обжатий менее 20%.
Технология штамповки болтов с однократным редуцированием по методу ЗИЛа (см. рис. 6, б) применяется для изготовления коротких болтов с резьбой до головки. При этом способе диаметр исходного металла больше наружного диаметра резьбы, и поэтому степень деформации головки сравнительно с предыдущим процессом снижается.
Вследствие уменьшения отношения lo/do головка может оформляться за один переход. Отличительной особенностью этого процесса штамповки является наличие позиции, на которой происходит выдавливание фаски.
При высадке с редуцированием на однопозиционных автоматах (в одной матрице) редуцирование стержня производится первым ударом одновременно с высадкой конической головки. Окончательное оформление головки происходит при втором ударе.
Совмещение на одной позиции операций высадки головки с редуцированием нежелательно, так как при этом увеличиваются нагрузки на инструмент и снижается его стойкость. Кроме того, при высадке головки происходит раздача конца редуцированного стержня, и при выталкивании заготовки из матрицы это приводит к дополнительному истиранию редуцирующего пояска.
Высадка с редуцированием осуществляется, как правило, на многопозиционных автоматах. При многопозиционных процессах заготовка штампуется в нескольких матрицах. Эти процессы получили в настоящее время наибольшее распространение в специализированном производстве болтов.
Процесс изготовления болтов высадкой с двукратным редуцированием в последнее время получил широкое распространение для штамповки болтов с диаметром стержня, равным наружному диаметру резьбы. Высадкой с двукратным редуцированием изготовляют болты из среднеуглеродистых и легированных сталей в широком диапазоне классов прочности (от 4.6 до 10.9). Технологические переходы штамповки представлены на рис. 7.
Диаметр исходной заготовки при этом процессе на 10—15% больше наружного диаметра резьбы, поэтому высадка головки осуществляется за один удар. При первом редуцировании (относительное обжатие не более 30%) происходит уменьшение диаметра части заготовки, идущей на образование стержня болта, до

Рис. 7. Технологические схемы изготовления болтов высадкой с двукратным редуцированием стержня
размера наружного диаметра резьбы, второе редуцирование (аналогично предыдущему процессу) служит для образования участка под накатку резьбы (см. рис. 7, а).
Степень деформации и упрочнение материала головки меньше, чем при высадке без редуцирования и с однократным редуцированием, что позволяет в ряде случаев избежать термообработки болтов, изготовленных из среднеуглеродистых сталей. Прочность болтов выше прочности исходного калиброванного металла вследствие упрочнения стержня при редуцировании.
При высадке с двукратным редуцированием снижаются нагрузки на инструмент и вероятность возникновения трещин на головке вследствие уменьшения степени деформации при высадке.
Однако по сравнению с однократным редуцированием усложняется инструмент (две редуцирующие матрицы), что сдерживает распространение этого процесса.
Кроме того, при изготовлении болтов из легированных сталей (с термической обработкой) затрудняется процесс накатки резьбы вследствие упрочнения металла при двойном редуцирований участка под резьбу.
Штамповка с двукратным редуцированием по методу ЗИЛа (см. рис. 7, б) отличается от рассмотренного способа введением операции выдавливания фаски, что вызывает необходимость совмещения на одной позиции редуцирования с выссадкой головки. Как уже указывалось выше, это ведет к "снижению стойкости инструмента.
Процесс высадки с выдавливанием и однократным редуцированием обеспечивает получение болтов повышенной прочности без термообработки с временным сопротивлением до 100 кгс/мм2
(рис. 8).

Рис. 8. Технологическая схема изготовления болтов высадкой с выдавливанием и редуцированием стержня
Исходным материалом служит заготовка диаметром (1,2-1,3) do.
Заготовка осаживается на первой прессовой позиции с относительной деформацией 10% с образованием фаски. Осадка заготовки облегчает проведение последующих операций выдавливания и редуцирования. Выдавливание стержня на диаметр, равный наружному диаметру резьбы, производится в закрытой матрице с относительной деформацией до 50% 'и более. При этом процессе неравномерность свойств головки и стержня практически отсутствует, прочность на много выше прочности исходного калиброванного металла.
Основными недостатками процесса, препятствующими его распространению, является необходимость применения выдавливающих пуансонов малого диаметра и матриц с большим перепадом диаметров, сложных в изготовлении, необходимость обеспечения высокой соосности пуансонов и матриц.
У всех рассмотренных выше процессов изготовления болтов образование многогранника происходит путем обрезки граней. Масса отходов при обрезке достигает 6—8% от массы болта.
Процесс обрезки характеризуется большими ударными нагрузками на малые рабочие площадки инструмента, что определяет его низкую стойкость (значительно ниже стойкости высадочного инструмента).
Образование углубления необходимо для лучшего заполнения ребер шестигранника. Недостатками процесса является большая степень деформации головки, неблагоприятные условия течения металла при образовании шестигранника (растягивающие напряжения по граням), приводящие к появлению надрывов и трещин на головке и особенно на кромках углубления. Процесс
характеризуется большими нагрузками на инструмент при оформлении шестигранника и высокими требованиями к пластичности металла и качеству поверхности. Высаженные болты по своему внешнему виду уступают изготовленным с обрезкой граней (нет четкого оформления ребер шестигранника, имеются надрывы на кромках углубления и т. д.).
В связи с указанными недостатками процесс не получил широкого распространения.
Метод фирмы «Хатебур» для изготовления болтов из низкоуглеродистой стали безоблойной высадкой осуществляется со следующими технологическими переходами (см. рис. 9,6): отрезка заготовки, редуцирование стержня, предварительная высадка шестигранной головки, вторая высадка шестигранной головки с большой торцовой фаской, окончательная высадка головки и редуцирование части стержня под резьбу.
При этом методе степень деформации головки значительно ниже, чем при высадке с углублением, так как исходный материал имеет диаметр, равный 1,10—1,15 диаметра резьбы, а высаженные болты упрочнены редуцированием.
Недостатками процесса являются большие нагрузки на инструмент вследствие трудности заполнения металлам углов шестигранника, неблагоприятные условия течения металла при образовании шестигранника.
Кроме того, при штамповке необходимо обеспечение точной отрезки для сохранения постоянства объема головки и точного переноса, так как вследствие возможного поворота заготовки болта при выталкивании может не произойти полного совмещения граней предварительного шестигранника с гранями инструмента на последующей операции высадки. Последнее ведет к срезу металла по граням и браку продукции.
При редуцировании головки происходит смещение слоев металла по боковой поверхности головки, что может привести к образованию заусенцев на торцовой поверхности. Для предотвращения появления заусенцев на цилиндрической заготовке предусмотрена фаска.
В процессе редуцирования происходит вытеснение металла по граням с заполнением фаски и искажением опорной поверхности. Для .исправления опорной поверхности и торцовой фаски на головке предусматривается дополнительная операция доштамповки шестигранника. С целью предотвращения появления заусенцев на опорной поверхности при доштамповке цилиндрическая заготовка болта высаживается с опорной шайбой. Процесс осуществляется из заготовки диаметром 1,10— 1,15 диаметра резьбы с двукратным редуцированием стержня.
По сравнению с методом фирмы «Хатебур» при изготовлении болтов способом, разработанным во ВНИИ-метизе, снижается усилие высадки и улучшаются условия течения металла при образовании многогранника, а также исключается одна операция предварительной высадки головки болта-
Болты с фасонной головкой по конструкции отличаются от болтов с шестигранной головкой формой головки и подголовка .В зависимости от размера головки и технологии штамповки болты могут изготовляться без термообработки или с термообработкой (отжигом) с целью исключения неблагоприятных последствий холодной деформации, создающих опасность хрупкого разрушения под головкой.
Технологические процессы изготовления болтов с фасонной головкой принципиально не отличаются от процессов, применяемых для штамповки болтов с шестигранной головкой. В последнее время внедряют процессы штамповки болтов с фасонной головкой на многопозиционных автоматах с применением двукратного редуцирования.
При штамповке болтов на многопозиционных автоматах для повышения качества оформления головки применяют в качестве завершающей операции обрезку кромок головки.
ДЛЯ ИЗГОТОВЛЕНИЯ БОЛТОВ
При изготовлении болтов с применением холодной штамповки выполняются операции образования стержня, получения промежуточной и окончательной форм головки, накатки резьбы. Указанные операции производятся на одном автомате — комбайне или нескольких прессах-автоматах, образующих автоматическую линию из последовательно расположенных машин, соединенных транспортными механизмами для передачи заготовки.
Автоматическая линия может включать холодновысадочные, обрезные и резьбонакатные автоматы.
Холодновысадочный автомат служит для высадки головки болта (промежуточной или окончательной формы) и оформления стержня (без резьбы). На обрезном прессе производится оформление многогранной головки обрезкой. Образование резьбы осуществляется на резьбонакатном автомате. При получении окончательной формы головки болта на холодновысадочном автомате обрезной автомат в состав линии не включается.
Часто в состав линии включается оборудование для подрезки торца и обточки концевой фаски, а также для сверления контровочных отверстий.
После выполнения основных технологических операций в ряде случаев проводят дополнительные операции термической обработки и покрытия поверхности, которые осуществляются на специальных термических и гальванических агрегатах.
Холодновысадочные прессы-автоматы отличаются количеством позиций формообразующего инструмента, числом ударов, необходимых для образования заготовки, конструкцией высадочных матриц и расположением позиций штамповки.
По количеству позиций автоматы делятся на однопозиционные и многопозиционные.
Однопозиционные автоматы в зависимости от числа ударов могут быть одноударными, двух ударными и трех ударными.
Для изготовления, одной детали на одноударном прессе требуется один оборот коленчатого вала (один ход высадочного ползуна), на двух ударном — два, на трех ударном — три. Для штамповки болтов применяются в основном двух ударные автоматы. Многопозиционные автоматы могут быть одно- и двух ударными, преимущественное применение для штамповки 'болтов имеют одноударные многопозиционные прессы.
По конструкции высадочных матриц прессы-автоматы делятся на автоматы с цельными и разъемными матрицами. Многопозиционные автоматы изготовляют главным образом с цельными матрицами.
Применение разъемных (раздвижных) матриц, раскрывающихся при выталкивании высаженной заготовки, позволяет снизить усилие выталкивания и изготовлять болты с длиной стержня более 10 диаметров. К недостаткам процесса штамповки в разъемных матрицах относятся пониженные по сравнению со штамповкой в цельных матрицах точность размеров и качество поверхности (овальность стержня, шов на стержне вследствие зазора между полуматрицами), изготовляемых изделий.
Многопозиционные автоматы изготавливают с горизонтальным и с вертикальным расположением позиций штамповки. Болтовые автоматы с горизонтальным расположением позиций штамповки бывают двух-, трех и четырехпозиционные. Автоматы с вертикальным расположением позиций бывают двух- и четырехпозиционными.
На однопозиционных высадочных автоматах получают заготовку окончательной формы только при изготовления болтов с фасонной головкой. Многогранную головку получают обрезкой цилиндрической головки на обрезном автомате.
В некоторых случаях на двух ударных холодновысадочных автоматах вторым ударом производят обрезку шестигранника или окончательную высадку шестигранной головки с углублением.
На многопозиционных автоматах изготавливают болты с полностью оформленной шестигранной головкой. На многопозиционных автоматах с резьбонакатным устройством (автоматах-комбайнах) выполняются все операции изготовления болтов, включая накатку резьбы.
Автомат с цельной матрицей состоит из узла подачи материала, механизма отрезки и переноса заготовки с линии подачи на линию штамповки, узла высадки.
При штамповке болтов на прессах-автоматах с цельной матрицей длина стержня изделия, регулируемая выталкивателем, не должна превышать 8—10 диаметров, и в одной матрице можно штамповать болты разной длины.
Известны отдельные конструкции двух ударных автоматов с цельной матрицей, позволяющие штамповать болты с длиной стержня до 30 d (на автомате А1020 штампуют болты диаметром 8 мм, длиной до 200 мм).
Нижний предел длины стержня ограничивается необходимой длиной заталкивания, равной диаметру или несколько большей его.
На двух ударных прессах-автоматах длинные болты изготовляются, как правило, без редуцирования. При изготовлении болтов с шестигранной головкой редуцирование длинных болтов может выполняться одновременно с операцией обрезки или высадки шестигранника на обрезном автомате.
Прессы-автоматы с разъемной матрицей имеют механизм перемещения (сжатия и разжима) матриц. Пря работе пресса (рис. 11) бунтовой металл 1 направляется подающими роликами через отрезную матрицу и раскрытые высадочные полуматрицы 2 и 4 до поворотного упора S. По окончании подачи материала подвижная полуматрица 2, перемещаясь к линии штамповки, торцовой поверхностью отрезает заготовку. Отрезанная заготовка переносится между обеими полу матрицами на линию штамповки, где полу матрицы сжимаются. После штамповки заготовки первым и вторым ударами пуансонов 5 и 6 разъемная матрица вместе с заготовкой .возвращается в исходное положение и разжимается. Выталкивание заготовки из разжатой матрицы происходит подаваемым металлом, выталкивающая шпилька отсутствует.
На высадочных автоматах с разъемной матрицей можно изготовлять болты большей длины, чем на автоматах с цельной матрицей. Кроме того, они производительнее, так как цикл работы у этих автоматов сокращен за счет совмещения подачи материалов с выталкиванием высаженной заготовки. На прессах-автоматах с цельной матрицей можно штамповать более короткие заготовки, чем на автоматах с разъемной матрицей, у которых из-за отсутствия выталкивателя для каждой длины стержня одного и того же диаметра требуется своя высадочная матрица. При коротких стержнях высота этой матрицы, равная длине стержня, будет незначительной, и при штамповке матрица может расколоться.
Однопозиционные двух ударные холодновысадочные прессы-автоматы применяются чаще для штамповки болтов с фасонной головкой.
Болты с шестигранной головкой, требующие многооперационной технологии, штампуют на многопозиционных прессах-автоматах.

Рис. 12. Схема многопозиционной штамповки болтов
При работе многопозиционных автоматов (рис. 12) калиброванный металл направляется подающими роликами 2 в отрезную матрицу 3 до упора 4. Нож 5 отрезает заготовку 6 и переносит ее на первую позицию 1, где пуансоном 7 заталкивается в высадочную матрицу 8. Высаженная заготовка 9 выталкивается из матрицы 8 первой позиции механизмом переноса переда-
ИНСТРУМЕНТ ДЛЯ ХОЛОДНОЙ ШТАМПОВКИ БОЛТОВ
Рабочий инструмент для холодной штамповки болтов на прессах-автоматах включает: а) ролики задающие, подающие и правильные; б) отрезные матрицы;
в) отрезные ножи; г) высадочные матрицы; д) пуансоны предварительные (черновые) и окончательные (чистовые); е) выталкиватели.
Ролики задающие служат для облегчения заправки и проталкивания металла через правильные ролики. Задающие ролики применяются для заправки металла крупного размера (диаметром 12 мм и более) и выполняются с индивидуальным приводом, отключающимся после окончания заправки конца металла. Правильные ролики служат для устранения кривизны металла и располагаются обычно в шахматном порядке чаще всего без привода. Подача металла в автомат осуществляется одной или двумя парами приводных подающих роликов, периодически поворачивающихся на определенный угол. Две пары роликов устанавливаются для подачи материала диаметром более 20 мм, чтобы предупредить соскальзывание металла. Задающие и подающие ролики изготавливают с канавкой (желобком), соответствующей профилю металла, при этом задающие ролики выполняют с одной канавкой, подающие — чаще всего с двумя . Профиль желобка правильных роликов целесообразно выполнять в форме углового паза, что делает ролики универсальными и позволяет применять их для правки металла различных диаметров.
Отрезные матрицы служат для приема металла и отрезки его (в паре с ножом). Матрицы изготавливают цельными стальными (или из твердого сплава для мелких размеров), сборными или с запрессованной твердосплавной вставкой . Диаметр канала отрезной 'матрицы принимается 'больше диаметра отрезаемого металла на величину зазора, необходимого для свободной подачи металла. Зазор принимают равным 0,05—0,20 мм в зависимости от диаметра металла. При работе матрицы в паре с отрезным ножом-втулкой величину зазора уменьшают в два раза. Для крепления в матричном блоке отрезная матрица имеет наружную кольцевую проточку; по мере затупления режущей кромки матрицу поворачивают.
Отрезные ножи изготавливают двух типов: открытый нож с прижимной лапкой, закрытый нож-втулка с прижимом или без прижима. Для увеличения стойкости ножей рабочую часть армируют пластинками из твердого сплава.
Качество отрезки зависит от зазора между материалом 'и ручьем отрезной матрицы и от зазора между рабочим торцом матрицы и ножом, который принимают равным 0,03—0,1 мм в зависимости от диаметра разрезаемой заготовки.

Рис. 17. Отрезные ножи:
а — открытый; б — закрытый нож-втулка с прижимом; в— закрытый нож-втулка без прижима (1 — вставка из твердого сплава)
В процессе работы величины зазоров увеличиваются: зазор между матрицей и материалом изменяется вследствие износа ручья матрицы, а зазор между матрицей и ножом — вследствие динамического характера нагрузок при отрезке. Зазор между заготовкой и отверстием закрытого ножа втулки принимают на 0,04— 0,06 мм больше зазора между материалом и матрицей.
В процессе отрезки материал подается в профильную выточку ножа (центр сечения круглого металла совпадает с центром окружности выточки) или впереди ножа (перед прижимной лапкой).
В высадочных матрицах в зависимости от вида болта и технологии штамповки оформляется стержень, подголовок, головка или ее часть. На 1рис. 18 приведены формы рабочих каналов высадочных матриц. Размеры ручья матрицы последней позиции принимают по соответствующим минимальным размерам высаживаемых пуансоном в матрицу 2 (позиция I) она входит в канал пуансона, сжимая пружину 3. Высадка цилиндрической головки на позиции II происходит в пуансоне 4 и зазоре между матрицей и пуансоном, а образование опорной шайбы — в матрице 5.
Величину зазора между пуансоном и матрицей устанавливают при наладке. На позицииIII производится редуцирование заготовки, которая заталкивается в редуцирующую матрицу 6 плоским пуансоном 7. Обрезка цилиндрической головки под шестигранник осуществляется на позиции IV обрезным пуансоном 8.
В обрезной матрице 9 предусмотрена выточка под опорную шайбу. После окончания процесса обрезки заготовка болта выталкивается из матрицы через полость пуансона.
Для цельного инструмента и корпусов сборного инструмента применяют следующие 'материалы. Задающие, правильные и подающие ролики изготавливают из чугуна С4 44-24 или из стали 18ХГТ (HRC
59—62), цельные отрезные матрицы из сталей У 10, У10А (HRC
58—62), корпуса сборных отрезных матриц из стали ЗОХГСА или из сталей 35ХГСА, 40Х (HRC A3.—
45), цельные отрезные ножи из сталей У8А, У10А и У 10 (твердость режущей кромки HRC
59—62), корпуса сборных отрезных ножей — из стали ЗОХГСА или из сталей 35ХГСА, 40Х, У10А (HRC
40—45), прижимные лапки к ножам из сталей 65Г, 60С2 или из У8, У8А (твердость рабочей части H.RC
56—59), цельные высадочные матрицы—из сталей Х12М, Х12Ф1 или У 10, У10А (HRC
54—62), корпус и бандаж сборных высадочных матриц—из стали ЗОХГСА или из сталей 40Х, 35ХГСА (HRC
40—45); цельные предварительные высадочные пуансоны — из стали Х12М или из сталей У 10, У10А (HRC
59—62), цельные окончательные высадочные пуансоны—из стали 40Х или У10 (HRC
42—45), корпуса сборных высадочных пуансонов — из стали ЗОХГСА или из сталей 40Х, 35ХГСА (HRC
40—45), выталкиватели—из стали Х12М или из сталей У8А, У10, У10А (HRC
56—58), пробки и проставки— из сталей Х12М, Х12Ф или У8, У10 (HRC
59-62).
Стойкость инструмента—
важнейший фактор, влияющий на стабильность технологического процесса, производительность автомата, а также на качество высаживаемых болтов. Количественно стойкость инструмента характеризуется количеством изготовленных заготовок или изделий за время его эксплуатации до полного износа.
От материала, применяемого для изготовления инструмента, его твердости, прочности и качества обработки в значительной степени зависит стойкость инструмента. Применение вставок из твердого сплава взамен стальных позволяет повысить стойкость высадочного инструмента в 20—60 раз. Средняя стойкость болтовых высадочных матриц с вставками из твердого сплава достигает несколько сот тысяч штук; стойкость отрезных ножей и отрезных втулок доходит до 4 и более миллионов резов.
На стойкость инструмента оказывают влияние точность изготовления и настройки отрезного инструмента, от которых зависит качество отрезки заготовок. Косой срез, вмятины и заусенцы на отрезанной заготовке способствуют преждевременному выходу из строя матриц и пуансонов.
Существенное влияние на стойкость оказывают степень деформации, число и последовательность технологических операций; указанные характеристики определяются формой и размерами болтов и принятым технологическим процессом изготовления.
Долговечность отрезного инструмента (ножей, матриц) из твердого сплава определяется в основном усталостной прочностью; инструмент выходит из строя вследствие образования усталостных трещин без изменений размеров вблизи рабочих поверхностей или при незначительном их изменении. При отрезке заготовок на холодновысадочных автоматах допустимым числом резов до перешлифовки твердосплавного инструмента считается 200—500 тыс. резов (в зависимости от материала и диаметра разрезаемой заготовки).
Высадочные стальные матрицы выходят из строя в основном вследствие изменения их размеров сверх допустимых, т. е. по .износу и редко из-за поломок. Высадочные твердосплавные матрицы выходят из строя как вследствие износа и изменения размеров по диаметру, так и из-за выкрашивания твердого сплава, особенно в канале вставки вблизи рабочего торца. При этом матрицы, армированные твердым сплавом ВК15, ВК20 и предназначенные для штамповки болтов из заготовки диаметром до 12 мм, выходят из строя в основном по износу; матрицы, армированные твердым сплавом ВК20, ВК25 и предназначенные для штамповки болтов из заготовки диаметром до 14—16 мм, выходят из строя в основном из-за выкрашивания твердого сплава и появления усталостных трещин; матрицы, армированные твердым сплавом ВК20К и предназначенные для штамповки болтов из исходной заготовки диаметром более 10 мм, выходят из строя главным образом вследствие износа.
Для редуцирующей матрицы 1максимальный износ наблюдается на редуцирующем пояске в зонах, граничащих с цилиндрическими каналами, и вблизи торца матрицы.
Линейный износ канала твердосплавного высадочного инструмента очень незначителен и после выполнения 500—800 тыс. ударов составляет до 0,04—0,06 мм.
Выше уже отмечалось отрицательное влияние на стойкость инструмента некачественной отрезки заготовки. Колебание ее длины и диаметра также отрицательно сказывается на стойкости. Завышение диаметра заготовки приводит к снятию смазки с поверхностного слоя, увеличению сил трения и усилий в процессе штамповки, затрудняется заталкивание заготовки в канал матрицы. Занижение диаметра заготовки вызывает увеличение степени деформации при высадке, ухудшение качества отрезки, что приводит к снижению стойкости пуансонов и матриц. При недостаточной длине заготовки возможно соударение пуансона и матрицы, что может привести к их поломке; завышенная длина может привести к появлению заусенца между торцами матрицы и пуансона, вызывающего значительное увеличение удельных нагрузок на инструмент.
Состояние поверхности заготовки существенно влияет на стабильность процесса штамповки и удельные усилия на инструмент (см. главу II, п. 3). Отсутствие подсмазочного покрытия, поверхностные дефекты на исходной заготовке вызывают налипание металла на инструмент, появление задиров, что приводит к быстрому выходу инструмента из строя.
С повышением прочности и твердости штампуемого материала возрастают нагрузки на инструмент и снижается его стойкость.
Повышение содержания в металле вредных примесей, снижающих его пластические свойства, также оказывает отрицательное воздействие на стойкость инструмента.
Правильная установка и систематическая регулировка инструмента положительно сказываются на стойкости инструмента. Техническое состояние автомата, величина зазоров в направляющих ползуна, салазках, в подшипниках влияют на точность размеров заготовки, а также на стабильность процесса штамповки, что в свою очередь оказывает влияние на стойкость инструмента.
НАПРАВЛЕНИЯ РАЗВИТИЯ ПРОИЗВОДСТВА БОЛТОВ
Производство болтов развивается в направлении улучшения прочности и пластичности материала, совершенствования антикоррозионной защиты, технологических процессов и оборудования.
Прочность болтов определяет размеры соединения и имеет тенденцию к неуклонному росту. В ближайшие годы следует ожидать постепенного вытеснения болтов с шестигранной головкой классов прочности 3.6, 4.6, 4.8, 5.8, 6.8, составляющих в специализированном производстве до 90% общего выпуска болтов, болтами классов прочности 8.8 и 10.9.
Защита болтов от коррозии необходима для продления сроков эксплуатации изделий и осуществляется применением антикоррозионных покрытий или материалов с антикоррозионными свойствами.
Следует ожидать расширения производства болтов, как с антикоррозионным покрытием, так и из антикоррозионных материалов.
Пластичность материала болтов значительно влияет на надежность и долговечность соединений. Особенно велико влияние пластических свойств при эксплуатации болтов в условиях низких температур, при которых работают свыше 30% самых различных машин.
Повышенные требования к пластичности материала болтов, предназначенных для работы в условиях низких температур, вызывают необходимость расширения выпуска болтов с гарантированной величиной ударной вязкости как при нормальной, так и при пониженной температурах.
Развитие производства болтов требует совершенствования технологических процессов изготовления, оборудования и инструмента для осуществления технологии.
Технологические процессы холодной штамповки развиваются в направлении расширения применения многопозиционных процессов, обеспечивающих получение болтов повышенной прочности без термической обработки и безоблойных процессов высадки, освоения процессов штамповки из металла, упрочненного термической обработкой.
Оборудование для холодной штамповки болтов совершенствуется в направлении повышения производительности, расширения диапазона изготовляемых размеров изделий, улучшения условий труда, механизации и автоматизации процессов.
Основные направления совершенствования оборудования для холодной штамповки болтов могут быть сведены к следующим:
1. Создание многопозиционных автоматов, позволяющих высаживать болты с диаметром резьбы до 48 мм и длиной до 300 мм.
2. Создание участков и цехов с полностью автоматическим циклом.
3. Увеличение выпуска автоматов-комбайнов.
4. Разделение прессов на коротко ходовые (длина стержня изготовляемых болтов до 5d) с резким увеличением производительности (до 350—600 шт/мин) и длинно ходовые с расширением изготовляемых длин болтов.
5. Оснащение автоматов сменными матричными блоками и освоение внестаночной настройки.
6. Оснащение автоматов устройствами для отсоса паров, шумопоглощающими, предохранительно-сигнальными устройствами и счетчиками изделий.
7. Повышение уровня унификации узлов и агрегатов прессов.
ОСОБЕННОСТИ ПРОИЗВОДСТВА СПЕЦИАЛЬНЫХ ВИДОВ БОЛТОВ
К специальным видам болтав могут быть отнесены:
а) высокопрочные; б) из нержавеющих сталей; в) самоконтрящиеся.
Основным методом получения болтав повышенной прочности является их изготовление из среднеуглеродистых и легированных сталей с доследующей термической обработкой (закалкой и отпуском) готовой продукции.
Применяемые для холодной штамповки качественные стали имеют повышенное сопротивление деформации и для облегчения процесса штамповки исходный металл необходимо подвергать промежуточному сфероидизирую-щему отжигу (см. гл. II).
Штамповку высокопрочных болтов проводят гари минимальных ходах высадочного ползуна. Наибольший диаметр стержня болта, который возможно штамповать на данном автомате, уменьшается на 1—2 (размера. Например, на автомате QPBA-161 штампуют болты из низкоуглеродистых сталей диаметрам до 24 мм, а из легированных сталей диаметром до 20 мм. При штамповке высокопрочных болтов в связи c повышенной трудностью деформирования по сравнению с изготовлением болтов из низкоуглеродистых сталей уменьшается коэффициент использования оборудования (КИО). При разработке технологического процесса холодной штамповки болтов из сталей с повышенным сопротивлением деформации нельзя совмещать на первой позиции высадку головки с редуцированием стержня в 'связи с трудностью выталкивания заготовки из матрицы.
Термическая обработка болтов является трудоемкой и дорогостоящей операцией. Болты после такой обработки имеют невысокую усталостную прочность. При термической обработке болтов, особенно длинных, наблюдается изгиб (искривление) стержня и искажение размеров резьбы, в связи с этим в некоторых случаях болты подвергаются повторной накатке.
Для обеспечения хорошего качества поверхности и геометрических размеров резьбы при термической обработке применяют защитные среды.
В последние годы проведены исследования по разработке технологии изготовления высокопрочных болтав из низкоуглеродистых сталей путем термического упрочнения (подката. При этом исключается операция термической обработки болтав, что снижает их себестоимость. Опытные партий болтов М12 из термически упрочненной с прокатного нагрева стали 20 кп, изготовленные на Дружковском метизном заводе, по прочности соответствовали требованиям классов прочности 8.8—10.9 при высоких пластических характеристиках. К недостаткам этого метода получения в высокопрочных болта в относятся повышенные сопротивление деформации при штамповке и нагрузка на инструмент.
Нержавеющие стали характеризуются интенсивным упрочнением три холодной деформации. При штамповке болтов из этих сталей увеличивается энергия, необходимая для деформации, что требует применения более мощных прессов. Вследствие повышенного прилипания заготовки с инструментом и высоких нагрузок на инструмент увеличивается его износ и возрастает число поломок.
Штамповка .болтов из нержавеющих сталей возможна только при соответствующей подготовке поверхности исходного металла (см. гл. II) и применении оптимальных смазок. Чаще всего при штамповке применяют масляные смазки на основе коллоидного графита или дисульфида молибдена с различными присадками.
Штамповку болтав необходимо проводить гари пониженных скоростях, КИО при штамповке болтав из нержавеющих сталей снижается.
При свинчивании с гайкой болтов из нержавеющих сталей происходит прилипание резьбы болта и гайки, поэтому резьбу болтов изготавливают с гарантированным зазорам, т. е. с полем допуска g и е по ГОСТ 16093—70.
Самоконтрящиеся болты применяют для уменьшения самоотвинчивания резьбового соединения в процессе эксплуатации.
Наибольшее распространение получили болты с зубчатой опорной поверхностью под головкой. Известны также и другие виды самоконтрящихся болтав (с конической опорной поверхностью и шлицами в головке, с резьбой переменного шага и др.), применяющиеся реже. Болты с зубчатой опорной поверхностью изготавливают из низкоуглеродистых сталей с последующей цементацией. Болты штампуют на двух ударных автоматах безоблойным способом. Технологический процесс характеризуется повышенными нагрузками на инструмент вследствие безоблойной высадки шестигранной головки с зубчатой опорной шайбой и повышенными требованиями к качеству исходного металла.
При изготовлении болта в с антикоррозионным покрытием в результате нанесения покрытия размеры резьбы увеличиваются, при этом абсолютное увеличение примерно равно четырехкратной толщине покрытия. Это увеличение размеров компенсируется предварительным уменьшением размеров резьбы при изготовлении .болтов. Создается гарантированный зазор, величина которого больше четырехкратной толщины покрытия. Размеры диаметров металла под накатку резьбы приведены в ГОСТ 19256—73. При возрастании толщины покрытия необходимо соответствующее увеличение гарантированного зазора. Это достигается уменьшением диаметра стержня под накатывание резьбы.
В связи с неравномерностью распределения покрытия по длине болта при изготовлении болтов с длиной стержня l>5 d необходимо увеличивать гарантированный зазор, т. е. дополнительно занижать размеры резьбы.
ТЕХНИКА БЕЗОПАСНОСТИ НА РАБОЧЕМ МЕСТЕ ПРЕССОВЩИКА
Правила техники безопасности в цехе и на рабочем месте прессовщика устанавливаются специальными инструкциями и Правилами, знание и соблюдение которых периодически контролируется администрацией цеха. Правила техники безопасности разделяются на общие, применимые на всех участках цеха, и специальные, действительные только для данного рабочего места.
Наиболее важные из общих правил следующие:
1. Необходимо содержать в чистоте рабочее место, не допускать наличия посторонних предметов в зоне обслуживания автоматов.
Нельзя оставлять на станине автомата или около нее технологический и другой инструмент, который может попасть в подвижные части пресса и привести к аварии и травмированию.
2. Не следует допускать загромождения проходов посторонними предметами, сырьем или готовой продукцией, а также их загрязнения (маслом, СОЖ).
3. Следует носить и содержать спецодежду в исправном состоянии.
4. Во время работы оборудования прессовщик должен находиться на своем рабочем месте. Не следует переходить на другой участок без разрешения руководителя.
5. При выполнении работы не по прямой специальности (во время простоев или ремонта пресса) необходимо ознакомиться с правилами безопасного выполнения новой работы.
Перед пуском пресса в работу необходимо обеспечить чистоту рабочего места и проверить готовность пресса к пуску.
Запрещается:
1. Работать на оборудовании:
а) при отсутствии ограждений, предусмотренных данным автоматам, или при их неисправном состоянии;
б) при неисправных тормозных, блокирующих и предохранительных устройствах;
в) при неисправном электрооборудовании и отсутствии заземления;
г) при неисправном креплении технологического инструмента;
д) при увеличенных зазорах в направляющих высадочного ползуна.
Большой износ направляющих высадочного ползуна ведет к повышению несоосности пуансонов и матриц и может вызвать поломку инструмента с опасными последствиями. При неисправном креплении инструмента может произойти его вылет из гнезда, поломка автомата и травмирование прессовщика.
2. Производить настройку и крепление инструмента во время работы механизмов или неполной их остановке.
Проверка правильности установки технологического инструмента должна производиться по специальным меткам, а инструменте или положению крепящих гаек и стопоров.
Настройка прессов и пробная штамповка заготовок должна производиться на минимальной скорости, на одиночных ходах автомата.
Для проверки взаимодействия механизмов и наладки инструмента на прессах, не оснащенных микроприводом или толчковым включением, должны быть установлены штурвалы или устройства для ручного поворота маховика.
3. Вскрывать электрооборудование автоматов.
4. Включать автомат, не убедившись в отсутствии посторонних предметов в рабочих зонах.
Прессовщик может приступить к работе только после устранения всех недостатков.
При работе на прессах-автоматах необходимо следить за исправным состоянием:
1) инструмента для наладки автомата;
2) пульта управления механизмами автомата (работы кнопок включения и выключения, световой сигнализации);
3) ограждений механизмов пресса, блокирующих и предохранительных устройств;
4) токоведущих частей электрооборудования, заземления оборудования;
5) тормозных устройств.
При выполнении ремонтных и наладочных работ необходимо применять инструмент, предназначенный для этих работ.
По окончании работ рабочее место должно быть приведено в порядок, поставлены на место ограждения, восстановлены предохранительные устройства.
Наблюдение за работой автомата следует вести либо через защитные стекла, либо при их отсутствии в защитных очках на безопасном расстоянии.
Особенностью работы автоматов является наличие обильной смазки инструмента и заготовок. Недопустимо разбрызгивание СОЖ на неподвижные части оборудования и рабочую площадку;
изделия должны поступать в коробку без выноса излишней смазочно-охлаждающей жидкости; с целью исключения травмирования заусенцами и острыми кромками металла его задачу следует производить в рукавицах. Для снижения влияния шума рекомендуется применять противошумныс наушники, антифоны, «беруши» и другие устройства.
|