I.
Общее положение
проекта.
1.1. Общие сведения
о тоннеле.
Мацестинский
тоннель - важное
звено окружной
автомобильной
дороги Новороссийск-Тбилиси-Баку
в обход г. Сочи.
Длина проектируемого
тоннеля составляет
1315,6 м. В плане тоннель
расположен
на кривой радиусом
1000 м. общей длиной-
1088,38 м. с продольным
уклоном i=16
% и на прямой-
227,1 м. (см. лист 1).
Экология
местности-
район строительства
объекта относится
к санитарной
зоне №1А г.Сочи.
Геологические
исследования
показали, что
на пути тоннеля
могли бы встречаться
слабые разрушенные
породы, поэтому
было выбрано
данное направление
тоннеля по
кривой радиусом
1000м. (см. лист 1).
1.2.
Горно-геологические
условия.
Исследуемый
район характеризуется
сложным геологическим
строением,
вызванным
неоднократными
поднятиями
и погружениями
на различных
этапах альпийского
цикла орогена.
В геологическом
строении района
принимают
участие палеогеновые
(Олигоцен- Р3)
и четвертичные
отложения.
Олигоценовые
отложения
распространены
в Абхазской
структурно-фациальной
зоне, где в их
составе выделены
осадки Мацестинской,
Сочинской и
др. свит. Мацестинская
свита отличается
от других
преобладанием
в ее разрезе
песчаников.
По литологическим
признакам свита
подразделена
на две пачки:
а) песчаниковую-
представленную
песчаниками
(80-95%) желтовато-серыми,
кварцевидными,
мелкозернистыми
с тонкой параллельной
слоистостью
и плотными
аргиллитами
желтовато-серыми
и серыми. В подошве
некоторых
пластов песчаников
наблюдаются
маломощные
(5-10 см) черные
гравелиты,
обогащенные
обуглившимися
растительным
детритом. Мощность
пачки 150-180 м.
б) песчаниково-аргиллитовую,
характеризующуюся
резким уменьшением
количества
(до 20-50%) и мощности
(от 1-5 см. до 20-30 см.)
пластов песчаников.
Мощность же
аргиллитовых
слоев увеличивается
до 70 см. Вся мощность
пачки 120-170 м. А общая
мощность свиты
с юго-востока
на северо-запад
уменьшается
от 1000 до 180 м.
Гидрогеологические
условия района
тесно связаны
с геологическим
строением и
климатом.
Исследуемый
район характеризуется
огромным количеством
выпадающих
осадков, играющих
одну из основных
ролей в процессе
накопления
подземных вод.
В районе
пролегания
тоннеля грунтовые
воды приурочены
к коре выветривания
скальной основы,
к делювиальным
и оползневым
глинистым
образованиям,
а также частично
невыветрелой
или слабовыветрелой
зоне многочисленным
трещинам разной
величины.
Проявление
грунтовых вод
в большом количестве,
зафиксированы
буровыми скважинами
в делювиальных
образованиях
на разных глубинах.
На протяжении
всего тоннеля
ожидается
приток воды
в виде капежа
и прерывистых
струй по трещинам
и тектоническим
зонам.
На некоторых
участках Qзаб
достигает до
15 м3/ч. (см. л. 1).
При интенсивном
выпадении
атмосферных
осадков, подземные
воды оказывают
на породы склона
гидростатическое
и гидродинамическое
давление, а
также приводят
к уменьшению
прочности пород
- вследствие
их переувлажнения.
Вдоль прослоек
мергелей, аргиллитов
и песчаников
трещины напластования
образуют своеобразный
канал для
интенсивного
просачивания
атмосферных
осадков в глубокие
толщи коренных
пород.
По химическим
показателям
грунтовые воды
района строительства
тоннеля характеризуются
малой минерализацией
и не агрессивны
к любому цементу
по всем видам
агрессии.
Ввиду близости
к дневной поверхности
(max
глубина от
поверхности
земли 100-110 м.), горные
породы в зоне
заложения
тоннеля и выше
дегазированы
и проявления
взрывоопасных
газов исключается.
1.3. Поперечное
сечение тоннеля.
Сечение в
проходке Sпр=110м2.
Внутреннее
очертание
обделок тоннеля
запроектировано
для автомобильной
дороги I
категории.
Габарит приближения
строения принят
по ГОСТу 24451-80 при
длине тоннеля
свыше 300 м. Принятый
габарит не
требует уширения
проезжей части
на кривой радиусом
R=1000
м. при длине
автопоезда
L=15,0
м.
Принятое
внутреннее
очертание
обделки предусматривает
подвеску осевых
вентиляторов
М8-6/I основной
вентиляции.
Студент Титченко
Д.В. разрабатывает
варианты
проветривания.
В зависимости
от инженерно-геологических
условий и способа
строительства
запроектированы
4 типа тоннельных
обделок. Типы
обделок I-T;
II-T; III-T; IV-T запроектированы
соответственно
для пород с
коэф. крепости
по Протодьяконову
f=1,5;
f=2; f=3; f=4. Эти
типы обделок
подковообразного
очертания,
замкнутые, с
обратным сводом,
имеют одинаковые
геометрические
размеры; друг
от друга отличаются
только армированием.
Размеры
обделок тип
I-T, II-T, III-T
и IV-T
составляют:
ширина- 12,8 м., высота-
9,15 м., толщина в
замке свода-
0,7 м., в стенах- 1,0
м, в обратном
своде- 1,25 м.
В качестве
материала
тоннельных
обделок принят
бетон класса
по прочности
на сжатие В22,5
, марки по
водонепроницаемости
W6,
марки по морозостойкости
F150.
Подземные
воды в районе
строительства
не обладают
агрессивностью
по отношению
к бетону, поэтому
применение
специальных
цементов не
требуется.
С обеих сторон
тоннеля шагом
150 м. в шахматном
порядке размещены
9 камер размером
3,5х3х2,7 (h)м.
Обделка камеры
принята из
монолитного
бетона класса
В22,5. В левой стене
тоннельной
обделки (по
ходу пикетажа)
шагом 40 м. устраиваются
33 ниши, размерами
1,4х1,4 (h)м.,
глубиной 0,3 м.
для размещения
пожарных кранов.
На пк16+00 с левой
стороны тоннеля
(по ходу пикетажа)
расположена
электрокамера
размерами
8,3х4,5х3,7 (h)м.
Свод электрокамеры
железобетонный,
а стены и плоский
лоток бетонные.
1.4. Существующее
положение.
Исходные
данные для
решения проекта:
С южного
портала:
-сооружена
припортальная
стройплощадка
(см. л. 2);
-пройдена
верхняя часть
тоннеля на 200
м. и возведена
вре-
менная
крепь;
-предстоит
осуществить
дальнейшую
проходку и
сбойку.
С северного
портала:
-соорудить
пром. площадку;
-предстоит
осуществить
врезку тоннеля,
проходку и
сбойку.
Учитывая
изложенное
считаем, что
данный дипломный
проект отвечает
условиям
производства,
он является
актуальным,
что и побудило
автора заняться
разработкой
данного проекта.
Данная
технология
отвечает условиям
производства
и горно-геологической
ситуации.
Учитывая
сложность
данного дипломного
проекта, студент
Титченко Д.В.
применительно
к данному тоннелю
разрабатывает
вопросы проветривания.
Таким образом,
данную работу
следует рассматривать
как комплексную.
II.
Сооружение
тоннеля.
2.1. Выбор и
обоснование
способа сооружения
тоннеля.
В данном случае
выбрана схема
сооружения
тоннеля способом
опертого свода
с опережающей
калоттой.
Достоинством
данного способа
является возможность
быстрого возведения
жесткого бетонного
свода, что позволяет
уменьшить
осадки кровли
и окружающего
грунта и обеспечивает
безопасность
ведения работ
по разработке
остальной части
сечения выработки.
В целом способ
опертого свода
характеризуется
надежностью,
простотой и
экономичностью
выполнения
работ.
В основу
разработки
данного проекта
положено, что
со стороны
южного портала
пройдено 200 м.
верхней (калоттной)
части тоннеля.
Проходка
верхней (калоттной)
части тоннеля
осуществлялась
с применением
взрывных работ.
Для этой цели
применялась
буровая установка
“Максиматик”
(см. л. 3), представляющая
собой машину
на пневматическом
ходу, передвигающаяся
от электрического
источника тока
подключаемого
к машине, напряжением
380 В, 50 Гц. Буровая
установка имеет
2 манипулятора
для размещения
на них буровых
машин и 3-ий
манипулятор
для обслуживания
лба забоя, т.е.
для оборки
забоя, прочистки
и заряжания
шпуров и т.д.
С помощью
буровой установки
“Максиматик”
бурятся шпуры
глубиной 1,2 м.,
обеспечивающие
подвигание
забоя до 1м.
Применяемое
ВВ- аммонит
№6ЖВ или аммонит-200.
Технологический
отход машин
ПНБ-3Д2, “Максиматик”
и технологической
тележки перед
взрывными
работами - 50 м.
Во время взрывания
конструкции
обделки и техники
не страдают.
Проветривание
забоя и вывозка
породы путем
погрузки ее
породопогрузочной
машиной ПНБ-3Д2
в подземные
автопоезда
типа МоАЗ.
После уборки
породы возводится
временная
крепь, состоящая
из арки I№30,
которая состоит
из 4-х сегментов.
Для того чтобы
быть собранной,
4 части арки
устанавливают
на 4 направляющие
рандбалки и
соединяют между
собой болтами.
Затем установленную
арку раскрепляют
14-тью металлическими
рошпанами с
ранее установленной
аркой (см. л. 4).
Эти 4 направляющие
рандбалки
прикрепляют
к концам двух
верхних сегментов
арки скобами,
приваренными
к двум предыдущим
аркам (см. л. 3).
В последствии
проходки эти
направляющие
рандбалки
передвигаются
дальше к забою
(опираясь на
2 предыдущие
арки) и на них
устанавливают
следующую арку.
Затем набирается
опалубка из
досок по внутренней
полке арки и
укладывается
бетон класса
В25 с помощью
бетоноукладчика.
Работы по
установке
временного
крепления
ведутся с рабочих
площадок
технологической
тележки.
Технологическая
тележка установлена
на рельсовом
ходу. Основная
несущая часть
представляет
собой портальную
раму к которой
крепятся две
боковые площадки
и одна сверху.
Эти площадки
предназначены
для установки
временной
крепи, возведения
элементов
деревянной
опалубки и др.
работ.
Временный
путь под технологическую
тележку выполняется
из рельс Р53 на
полушпалах
с шагом 0,5 м.
Доставка
строительных
материалов
в забой производится
автотранспортом
и погрузодоставочной
машиной ПД-5.
Бетонная смесь
доставляется
автобетоносмесителями
(миксерами) с
перегрузкой
в бетоноукладчик
или автобетоноукладчиками.
Продолжительность
проходческого
цикла осуществляется
приблизительно
за полутора
суток. Продолжительность
рабочей смены
6 ч. Обычно при
этом задалживается
8-10 рабочих в смену.
После возведения
временной
обделки с отставанием
от забоя 30-40 м.
производится
первичное и
контрольное
(повторное)
нагнетание
(см. л. 4) с помощью
растворонагнетателей
находящихся
на технологической
тележке. Для
выполнения
этой работы
также привлекаются
8-10 человек, которые
работают вслед
за проходческой
бригадой.
С отставанием
от забоя до 50
м. заходками
по 10-15 м. бетонируются
полосы под
стены постоянной
обделки (основание
выработки) с
закладкой в
них элементов
гидроизоляции
обделки.
Эта технологическая
схема отвечает
производственным
и геологическим
условиям сооружения
тоннеля. Поэтому
считаем возможным
эту технологическую
схему использовать
при решении
всех вопросов
в нашей работе.
Расчет
буровзрывных
работ.
N=
;
где q=
1,5;
S= 69 м2;
=
0,78.
N=
= 133 шп.
количество
ВВ: Qобщ=
qSLзах=
1,5691,0=
103,5 кг.
количество
ВВ в шпур: Q=
=
=
0,78 кг. в шпур;
количество
патронов: n=
= 2,6 3
патрона
Принимаем
патроны по 300
гр.
- общее
количество
патронов: nобщ=
Nшпn=
1333=
399 шт.
Qф=
Nn0,3=
13330,3=
119,7 кг.
расход
ВМ на 1 м3: Q1м3=
=
=
1,7 кг.
глубина
шпуров: Lшп=
=
=
1,2 м.;
врубовые
шпуры принимаем
1,3 м.
- общая длина
шпуров: Lобщ=
1271,2+
71,3=
161,5 шпм.
- количество
ЭД: N= =
133 шт.
- количество
ЭД на 1 м3: Nэд
1м3=
=
=
1,9 шт/м3.
Меры безопасности:
перед заряжанием:
обесточить
все машины и
механизмы в
тоннеле, кроме
освещения 36В;
вывести всех
людей за зону
оцепления;
взрывник
свистком подает
сигнал - предупредительный.
2) после заряжания
и монтажа цепи
взрывник подает
второй сигнал
- боевой.
после взрыва
взрывник подает
третий сигнал
– отбой (три
коротких);
4) При обнаружении
«отказа» принимаются
меры согласно
правил ТБ при
ЕПБ взрывных
работ.
2.2. Определение
трудоемкости
работ на 1 п.м.
Табл.
№1.Определение
трудоемкости
работ
в
забое тоннеля.
|
|
Наименование
|
Объем
работ
|
Норма
|
Трудоемкость
|
работ
|
на
1 п.м.
|
времени
|
чел.
см.
|
1.
Бурение шпуров
|
161,5
|
0,5
|
13,32
|
2.
Погрузка породы
|
69
|
0,09
|
1,03
|
3.
Вывоз породы
|
124,2
|
0,42
|
8,85
|
4.
Возведение
крепи:
|
|
|
|
а)
установка
арки
|
1
|
21,6
|
3,6
|
б)
установка
опалубки
|
22
|
0,2
|
0,7
|
в)
укладка бетона
|
6,2
|
2,17
|
2,25
|
г)
разборка опалубки
|
22
|
0,15
|
0,55
|
|
|
|
q=30,3
|
Принимаем
30 чел.
Коэф.
выполнения
выр-тки К=
=
1,01м.
Производительность
1 проходчика
за цикл:
П=1/30=0,03
м.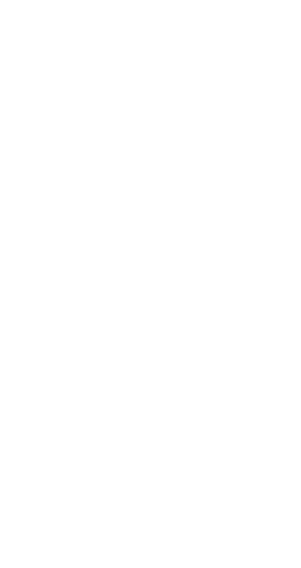
Табл.
№2.
Определение
трудоемкости
работ
по
первичн. и
контр. нагнетанию.
|
|
Наименование
|
Объем
работ
|
Норма
|
Трудоемкость
|
работ
|
на
1 п.м.
|
времени
|
чел.
см.
|
1.
Бурение шпуров
|
5
|
2
|
1,66
|
2.
Нагнетание
цем. р-ра;
|
|
|
|
монтаж
и установка
|
20,68
|
0,84
|
2,17
|
оборудования;
м2.
|
|
|
|
|
|
|
q=3,83
|
|
|
|
|
Табл.
№3.
Определение
трудоемкости
работ
по
постоянной
обделке.
|
Наименование
|
Объем
работ
|
Норма
|
Трудоемкость
|
работ
|
на
1 п.м.
|
времени
|
чел.
см.
|
1.
Установка
опалубки
|
24
|
3,75
|
15
|
2.
Укладка арматуры
|
21,8
|
2
|
7,24
|
3.
Бетонирование
|
18,5
|
0,8
|
2,52
|
4.
Разборка опалубки
|
24
|
1,9
|
7,47
|
|
|
|
q=32,23
|
|
|
|
|
|
|
|
|
Зная объемы
работ и нормы
времени, определяем
продолжительность
цикла в забое
по следующей
формуле:
t=
;
где n-
количество
проходчиков;
- бурение
шпуров t=
=
17,7 ч.
- уборка породы
t=
=
1,38 ч.
- установка
арки t=
=
4,8 ч.
- набор опалубки
t=
=
0,95 ч.
- укладка
бетона t=
=
2,99 ч.
- разборка
опалубки t=
=
0,73 ч.
t=
28,55 ч.
29 ч.
Определение
общего срока
строительства
верхней (калоттной)
части тоннеля.
Зная, что
длина тоннеля
1315 м. и lзах=
1м. имеем:
Т= 1315
29= 38135 ч.
1589 дн.
52,9 мес.
4,4 года.
Т.к. продолжительность
цикла составляет
29 часов, т.е. 5 смен
(продолжительность
смены 6 ч.), то
количество
проходчиков
работающих
в забое составляет:
n=
30/5
6 чел. В состав
работающих
в смену 6-ти
проходчиков
входят еще 3
рабочих из
других бригад
работающих
в эту же смену:
дежурный слесарь,
электрик и
сварщик. Бригада
взрывников
вызывается
отдельно от
рабочей смены
непосредственно
перед ведением
взрывных работ.
Производительность
работ 1-го рабочего
с учетом всех
людей работающих
в забое: П=
=
0,02 м. за цикл.
2.3. Сооружение
врезки со стороны
Северного
портала.
Для безопасного
ведения работ
по врезке тоннеля
выполняются
работы по закреплению
лобового откоса
и устройству
свода из труб
на участке
врезки (см. л.6).
Во избежания
падения породы
по лобовому
откосу укладывается
металлическая
сетка (за исключением
сечения тоннеля)
размером 1001005.
Устанавливаются
балки из
№20 по нижней
грани которых
набирается
опалубка и
укладывается
бетон крепления
лобового откоса
марки В12,5. Укладка
бетона также
производится
с устройством
проема по сечению
тоннеля.
Сверху вниз
производится
бурение скважин
защитного
экрана (см. л.
6). Бурение скважин
осуществляется
станком Тони-Боринг.
Количество
скважин принимается
конструктивно.
Первоначально
шарошкой
191 мм. бурятся
скважины длиной
по 1,5 м., в которые
устанавливаются
кондукторы
(или направляющие)
из труб
1684
длиной 1,8 м. Кондукторы
омоноличиваются
цементно-силикатным
раствором.
После выстойки
продолжается
бурение скважин
шарошкой
145мм. с буровой
трубой
1147.
По достижению
скважиной
проектной
глубины буровая
труба оставляется
в скважине и
через кондуктор
производится
прокачка скважин
цементно-силикатным
раствором.
Нагнетание
производится
насосом НБ-4.
Состав раствора
на 1 м3: вода- 750 л.,
цемент- 750 кг.,
жидкое стекло-
до37,5 кг. Давление
нагнетания-
до 10 атм. Нагнетание
производится
до отказа, либо
до появления
выходов раствора
по лобовому
откосу.
После завершения
работ по созданию
свода из труб,
срезаются балки
крепления
лобового откоса
в пределах
верхнего уступа
(на высоту 3,05 м.),
разрабатывается
грунт верхнего
уступа в пределах
оголовка. Для
крепления лба
забоя верхнего
уступа на время
бетонирования
оголовка, а
также при проходке
на участке
врезки станком
НКР-100М бурятся
5 скважин глубиной
20 м., в которые
устанавливаются
анкерные трубы
764,5
мм. (см. л. 6). Зазор
между трубой
и грунтом
законопачивается
паклей и производится
нагнетание
раствора составом
1:0 с добавками
бентонитовой
глины. Нагнетание
производится
насосом НБ-4
давлением до
10 атм. до излития
раствора через
законопаченное
пространство
между трубой
и грунтом. Срезаются
балки крепления
лобового откоса
в пределах
нижнего уступа,
и разрабатывается
грунт нижнего
уступа в пределах
оголовка.
Устанавливаются
2 сводовых части
арок на верхнем
уступе и 3 полных
арки временной
крепи тоннеля
из I
№30. По боковым
граням оголовка
устанавливаются
вертикальные
балки наружной
опалубки (см.
л.6) из I
№20 шагом 1м., которые
соединяются
с арками временной
крепи с помощью
горизонтальных
связей из стали
10мм. По внутренним
граням арок
и балок из I
№20 набирается
опалубка и
бетонируется
оголовок. Монтажные
работы ведутся
с помощью крана
“Като”.
Врезка в
горный массив
ведется способом
опережающего
верхнего уступа
с применением
самоходной
буровой установки
“Максима-тик”.
Уборка породы-
порододоставочной
машиной ПД-5.
Разработка
ведется заходками
по 1м. с отставанием
нижнего уступа
от верхнего
на 3-4 м. Арки временного
крепления
устанавливаются
с шагом 1 м. После
сооружения
врезки дальнейшая
проходка
осуществляется
сплошным забоем.
2.4. Северная
пром. площадка.
(см. л.5).
2.5. Производство
работ в тоннеле.
1) Производство
работ по возведению
постоянной
обделки сводовой
части тоннеля.
С
опережением
30-40 м. от участка
бетонирования
с помощью
оборудованной
передвижной
технологической
тележки на
временную крепь
(черновой бетон)
наносится
двухслойная
гидроизоляция
(1слой- дренажный
слой геотекстиля,
2 слой- гидроизоляционная
лента).
С помощью
технологической
тележки, оснащенной
подъемником,
впереди опалубки
“Сага”
(см. л. 7) монтируются
армокаркасы.
На установленные
армокаркасы
надвигается
опалубка “Сага”
и укладывается
бетон класса
В25.
Бетон доставляется
автобетоносмесителями
и укладывается
за опалубку
двумя пневмобетоноукладчиками
равномерно
на обе стороны.
Уплотнение
бетонной смеси
производится
вибраторами,
смонтированными
на опалубке,
и при необходимости
глубинными
вибраторами
типа ИВ-47.
2)
Производство
работ по разработке
нижней части
тоннеля.
Разработка
нижней части
тоннеля осуществляется
в 3 этапа (см. л.
7). Работы ведутся
буро-взрывным
способом с
подведением
металлических
ножек под арки
временного
крепления и
их бетонирования.
В
1-ый этап начинается
разработка
средней штроссы
(ядра). Для этого
бурятся вертикальные
шпуры глубиной
3,7м. Длина заходки-
1м. Бурение
осуществляется
с помощью буровой
установки
“Максиматик”.
Применяемое
ВВ- аммонит №6
ЖВ. После взрывных
работ порода
убирается
погрузочной
машиной ПНБ-3Д
в автосамосвалы.
Во
2-ой и 3-ий этапы
разрабатывают
боковые штроссы.
Сначало обуривается
забой левой
бермы горизонтальными
шпурами глубиной
1,2м. После взрыва-ния
и уборки породы
подрабатывается
порода под
металлические
ножки арок.
Затем устанавливается
ножка арки,
набирается
опалубка и
бетонируется.
Аналогично
разрабатывают
правую берму.
Расчет паспорта
буровзрывных
работ по разработке
ядра.
q= 1,50,8=
1,2
S =
8,3
1,0= 8,3 м
Lзах=
1 м.
Q= 1,2
8,3
1= 9,96
10 кг.;
- количество
ВВ в шпур Qшп=
=
= 0,59 кг. в шпур;
- количество
патронов в шпур
n=
=
1,9
2 патрона;
(при массе
патрона 300 гр.)
Табл.
№4.
Определение
трудоемкости
работ
по
разработке
средней штроссы
(ядра).
|
Наименование
|
Объем
работ
|
Норма
|
Трудоемкость
|
работ
|
на
1 п.м.
|
времени
|
чел.
см.
|
1.
Бурение шпуров
|
62,9
|
1,33
|
3,53
|
2.
Погрузка породы
|
22,65
|
0,12
|
0,34
|
q=10,46
Принимаем
10 чел. Коэф.
выполн. выр-тки=
10,46/ 10=1,04
10 чел.- 1 п.м.
30 чел.- Х
(Lзах)
Х=
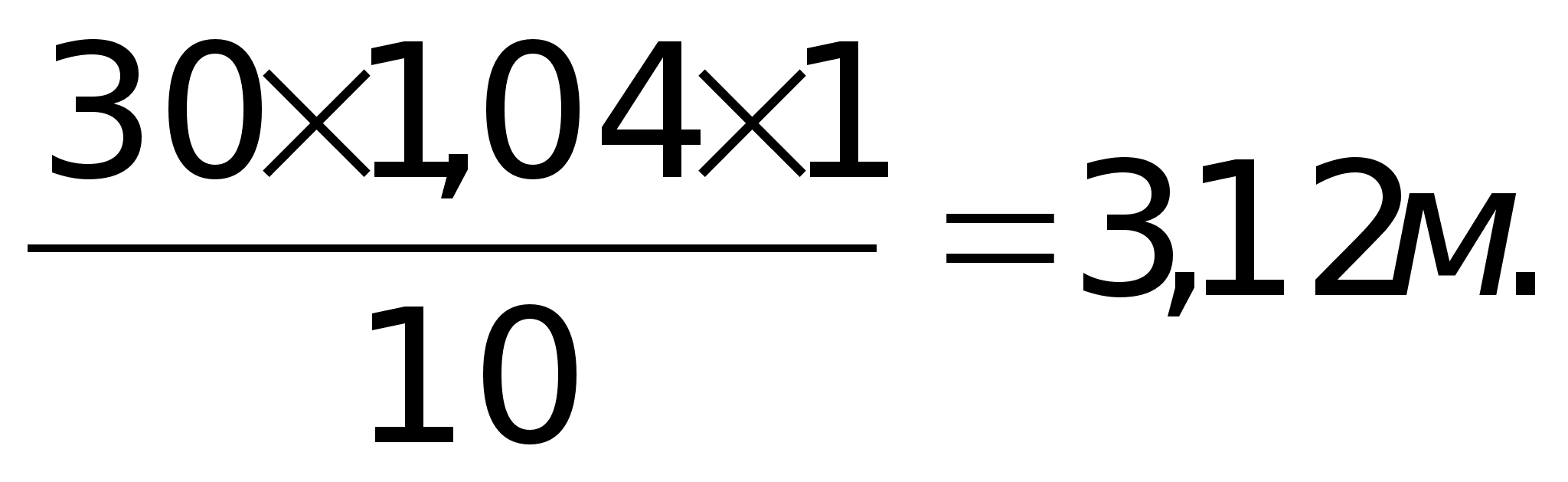
Производительность
1 проходчика
за цикл: П=
0,1 м.
Определение
продолжительности
работ по разработке
ядра:
t=
;
бурение
шпуров t=
=
43,5 ч.
уборка породы
t=
=
1,41 ч.
t=
44,9 ч.
45 ч.
Определение
общего срока
разработки
ядра при строительстве
всего тоннеля:
При Lзах 3,12 м.
за цикл и длине
тоннеля 1315 м. имеем
кол-тво циклов:
Nц=
422
Т= 45
422= 18990 ч.
791 дн.
26,4 мес.
2,2 года.
Расчет
паспорта буровзрывных
работ по разработке
боковой штроссы.
q= 1,50,8=
1,2
S =
( )3=
7,2
м
Lзах=
1 м.
Q= 1,2
7,2
1= 8,64 кг.;
- количество
ВВ в шпур Qшп=
=
= 0,58
0,6 кг. в шпур;
- количество
патронов в шпур
n=
=
2 патрона;
(при массе
патрона 300 гр.)
Табл.
№5. Определение
трудоемкости
работ
по
разработке
боковой штроссы.
|
|
Наименование
|
Объем
работ
|
Норма
|
Трудоемкость
|
работ
|
на
1 п.м.
|
времени
|
чел.
см.
|
1.
Бурение шпуров
|
18,75
|
1,33
|
3,12
|
2.
Погрузка породы
|
7,2
|
0,12
|
0,1
|
3.
Передвижка
опалубки
|
3
|
0,93
|
0,35
|
4.
Сборка бетоновода
|
2
|
0,44
|
0,11
|
5.
Бетонирование
|
3,24
|
2,66
|
1,07
|
6.
Разборка
бетоновода
|
2
|
0,53
|
0,13
|
q=4,88
Общая
трудоемкость
по разработке
ядра и боковой
штроссы: q=8,75
чел.см.
Принимаем
4 чел. Коэф.
выполн. выр-тки=
4,88/ 4=1,22
4 чел.- 1 п.м.
30 чел
1,22.-
Х (Lзах)
Х=

Производительность
1 проходчика
за цикл: П=
0,3 м.
Определение
продолжительности
работ по разработке
боковой штроссы
за цикл:
t=
;
- бурение
шпуров t=
=
38,03 ч.
- уборка породы
t=
=
1,31 ч.
передвижка
опалубки t=
=
4,25 ч.
сборка бетоновода
t=
=
1,34 ч.
укладка
бетона t=
=
13,14 ч.
разборка
бетоновода
t=
=
1,6 ч.
t=
59,67 ч.
60 ч.
Определение
общего срока
разработки
бок. штросс на
протяжении
всего тоннеля:
При длине
Lзах=9,15
м. имеем кол-тво
циклов: Nц=
144
ц.
Т= 144602=
17280 ч.= 720 дн.= 24 мес.=2
года.
3)
Производство
работ по первичному
и контрольному
нагнетанию.
Первичное
нагнетание
производят
в целях заполнения
пустот на контакте
обделки с
поверхностью
выработки,
образовавшихся
в результате
вывалов, обрушений
и неплотной
забутовки.
Растворонагнетатель
присоединяется
к обделке с
помощью растворовода,
который в свою
очередь соединен
с инъектором,
закрепленным
в предварительно
пробуренной
скважине (см.
л.4). Для нагнетания
применяют
цементно-песчаный
раствор состава
1:3.
Контрольное
(повторное)
нагнетание
выполняют для
заполнения
мельчайших
трещин и пустот,
образовавшихся
в результате
твердения и
усадки раствора
первичного
нагнетания.
Нагнетание
производят
цементным
молоком, используя
те же растворонагнетатели,
что и при первичном
нагнетании.
Скважины для
контрольного
нагнетания
бурятся между
скважинами
для первичного
нагнетания
таким образом,
чтобы скважина,
пройдя бетон
обделки и слой
первичного
нагнетания,
вошла в грунт.
Контрольное
нагнетание
производят
до тех пор, пока
не прекратится
поглощение
раствора при
максимально
допустимом
давлении. Это
давление не
должно превышать
0,4 МПа. Порядок
производства
работ по контрольному
нагнетанию
такой же, что
и для первичного
нагнетания.
4) Производство
работ по сбойке
тоннеля.
По мере сближения
двух встречных
забоев взрывание
шпуровых зарядов
в каждом забое
ведется в разное
время с обязательным
определением
размера целика
между встречными
забоями. Взрывание
проводится
лишь после
того, как получено
сообщение о
выводе людей
из противоположного
забоя и выставлении
там поста.
Когда размер
целика между
встречными
забоями составит
7 м, работы должны
проводится
только из одного
забоя. При этом
необходимо
бурить опережающие
шпуры глубиной
на 1 м. больше,
чем глубина
заряжаемых
шпуров.
Введение.
Автор представленной
работы к защите
проходил
преддипломную
практику в
«Южной Горно-Строительной
Компании» в
период с 14 июля
по 14 сентября.
За этот период
времени автор
познакомился
с технологией
и техникой
выполнения
всех проходческих
работ при сооружении
Мацестинского
тоннеля. Кроме
того, автор
имел доступ
ко всей проектно-сметной
документации
данного объекта.
Эти материалы
полностью были
использованы
в данном проекте
и следовательно
отражают существующее
положение.
При выполнении
данного проекта
автор руководствуется
следующими
основными
положениями:
Широкое
использование
отечественной
и передовой
зарубежной
техники.
Широкое
использование
местных строительных
материалов
и стандартных
изделий.
Поточность
производства
при выполнении
всех этапов
работ.
Применение
наиболее передовых
приемов организации
работ.
При выполнении
данной работы
в полной мере
учитывалась
нормативная
и учебная литература.
Кроме того,
автор данного
проекта консультировался
в необходимых
случаях с
руководителями
по соответствующим
разделам.
Таким образом,
данная работа
рассматривается
нами как реальная
работа возможная
к применению.
|
|
|
|
|
|
|
2 |
1,68. |
|
4 |
6.72 |
|
6 |
15.12 |
380 |
8 |
26.8 |
375 |
10 |
42 |
365 |
12 |
60.48 |
350 |
14 |
82.32 |
320 |
16 |
107.5 |
290 |
18 |
136.1 |
240 |
20 |
168 |
160 |
22 |
203.3 |
80 |
24 |
242 |
|
26 |
284 |
|
28 |
329 |
|
30 |
378 |
|
|
|
|
|
|
|
|
|
|
|
|
|
Калькуляция
№1 сметной цены
маш-см буровой
установки
«Максиматик»
(Финляндия).
1
|
2
|
3
|
4
|
5
|
Обоснование
|
Группы,
статьи и
элементы
затрат
|
Формула
подсчета
|
В
т.ч. з/плата руб.
(грн.)
|
Всего
руб. (грн.)
|
СЦПС-I
п.63 с.93 п.149
с.73 |
- Единовременные
затраты.
Перевозка
установки от
ст. Северобайкальск
до ст. Адлер
(6600 км).
|
(18,2+3500,54)
35,8=
7417,76
|
- |
7417,76
(15761,26) |
|
Перевозка
бур. установки
от ст. Адлер
до стройплощадки
(30 км). |
2,071,335,8=
96,34
|
- |
96,34
(204,74) |
ЕРЕР-29
т.ч. таб.1 |
Монтаж бурового
агрегата
а) затраты
труда
слесари
монтажники
– 6 чел.
б)
затраты на
основные и
вспомогатель-
ные
монтажные
материалы
15% и 6%
от
основной з/платы.
в)
амортизация
и ремонт подъемных
и
прочих
приспособлений-
18%.
|
1,2626120=
908,64
908,64(0,450,06)=
190,81
908,640,18=
163,55
908,64+190,81+163,55=
1263
|
908,64 (1930,68) |
1263,0
(2683,62)
|
|
Демонтаж
установки
50% от стоимости
монтажа
в т.ч.
з/плата
|
12630,5=
631,5
908,640,5=
454,32
|
454,32
(965,34)
|
631,5
(1341,81)
|
|
Итого
единовременных
затрат
в т.ч.
з/плата
|
40,54+7417,76+27,21+53,34+96,36++1263+631,5=
9529,71
32,38+19,05+37,34+908,64+454,32=
= 1451,73
|
1451,73
(3084,63)
|
9529,71
(20248,72)
|
|
Единовременные
затраты приходящиеся
на 1 маш.час.
в т.ч.
з/плата
|
9529,71/
8000= 1,19
1451,73/ 8000= 0,18
|
0,18
(0,38)
|
1,19
(2,53)
|
1
|
2
|
3
|
4
|
5
|
|
- Годовые
затраты.
Инвентарно-расчетная
стоимость
установки.
Амортизационные
отчисления
|
315867,410,401=
126662,83
|
|
315867,41
(671155,07)
126662,83
(269133,18)
|
|
Годовые
затраты, приходящиеся
на 1 маш.час.
(в год 4000 ч.). |
126662,83/ 4000= 31,67
|
|
31,67
(67,29)
|
|
- Эксплуатационные
затраты.
Содержание
обслуж. персонала
слесарь
6 разр. – 1 чел.
слесарь
5 разр. – 1 чел.
|
|
1,493
(3,17)
1,262
(2,68)
|
1,493
(3,17)
1,262
(2,68)
|
|
а)
электроэнергия.
б)
технич. обслуживание
и текущий ремонт.
в)
прочие затраты
(диз.топливо,
сжатый воздух,
масло смазочн.
и т.д.).
Итого
эксплуатационных
затрат
в
т.ч. з/плата
Итого
стоимость 1
маш.час.
в т.ч.
з/плата
|
=
=
=
49 квт.час.0,03
= 1,47
0,40+0,49+0,59+0,44+1,89+0,31+
+0,17+0,18+0,05 = 4,52
1,493+1,262+1,47+4,52+2,07=
10,82
1,493+1,262+0,47=
3,23
1,19+31,67+10,92=
43,68
0,18+3,23= 3,41
|
0,47
(0,99)
3,23
(6,86)
3,41
(7,24)
|
1,47
(3,12)
2,07
(4,39)
4,52
(9,6)
10,82
(22,99)
43,68
(93,02)
|
Калькуляция
№2 сметной цены
маш.-см. породопогрузочной
машины
ПНБ-3Д2М.
№
п/п
|
Показатели
|
Един.измер.
|
Машина
погрузочная
шахтная
|
|
Код в
СНИПе
|
|
2720 |
|
|
|
ПНБ3Д2М |
|
Производительность
|
м /мин
|
5,8 |
|
Масса
|
т |
28 |
1 |
Балансовая
стоимость
Норма
аморт. Отчислений
Директивн.
норма выработки
Годовые
затраты
|
грн.
%
час.
грн.
|
138614,4
1260
54,99
|
|
|
|
|
2 |
Миним.
размер оплаты
труда
Среднемес.
норма часов
Кол-во
работающих
З/плата
обслуж. персонала
|
грн.
час.
Чел.
грн.
|
22,57
151,2
1
0,89
|
|
|
|
|
3 |
Размер
надбавки за
рез. х-тер
Норма
выработки в
смену
Оплата
за разн. хар-тер
работ
|
грн.
час.
грн.
|
3,52
6
0,59
|
|
|
|
|
4 |
Норматив
з/платы в ценах
84г.
Коэф.
удорожания
Единовременные
затраты
в т.ч.
з/плата
|
грн.
грн.
грн.
|
0,07
11,67
0,19
0,13
|
5 |
Техобслуж.
и текущ. ремонт
в
т.ч. з/плата
|
грн.
грн.
|
3,40
0,77
|
|
|
|
|
6 |
Норматив.
расхода смаз.
м-лов
Коэф.
удорожания
Затраты
на смаз. материалы
|
грн.
грн.
грн.
|
0,005
0,05
|
7 |
Норма
расхода э/энергии
Стоимость
э/энергии
Затраты
на э/энергию
|
кВт.
грн.
грн.
|
3,94
0,07
0,27
|
|
|
|
|
|
Итого:
|
грн. |
60,4 |
ДЕР
№1 на проходку
1 п.м. тоннеля.
  
№
пп
|
Работы,
машины
|
Объем
|
Нвр
|
Трудоемкость
|
Расценка
грн.
|
Всего,
грн.
|
1. |
Бурение
шпуров |
п.м.
161,5
|
0,5 |
80,75 13,32
|
1,34 |
216,41 |
2. |
Уборка
породы
|
м
69
|
0,09 |
0,21 1.03 |
0,17 |
12,08
|
|
ИТОГО
неучтенные
работы
ВСЕГО
|
% 3
|
|
|
|
228,49
6,85
235,34
|
1.
|
Материалы.
Буровые
коронки
|
шт.
2
|
|
|
6
|
12
|
|
ИТОГО
Неучтенные
материалы
ВСЕГО
|
%
3
|
|
|
|
12
0,36
12,36
|
1.
2.
|
Эксплуатация
машин.
«Максиматик»
«ПНБ-3Д2»
|
маш.см 0,5
маш.см
0,4
|
|
|
93,02
60,4
|
46,51
24,16
|
|
ИТОГО
Неучтенные
машины
ВСЕГО
|
%
3
|
|
|
|
70,67
2,12
72,79
|
|
ВСЕГО
по расценкам |
|
|
|
|
320,49
|
|
|
|
ДЕР
№2 на крепление
1 п.м. тоннеля.
  
№
пп
|
Работы,
машины
|
Объем
|
Нвр
|
Трудоемкость
|
Расценка
грн.
|
Всего,
грн.
|
1.
2.
|
Установка
арки
Укладка
бетона
|
шт
1
м
6,2
|
21,6
2,17
|
21,6 3,6
13,5 2,25
|
7,62
2,13
|
7,62
13,206
|
|
ИТОГО:
Неучтенные
работы
ВСЕГО
|
% 3
|
|
|
|
20,82
0,62
21,44
|
1.
2.
|
Материалы:
Арочная
крепь
Бетон
В25
|
т. 1,14
м
6,2
|
|
|
|
849,92
446,4
|
|
ИТОГО:
Неучтенные
материалы
ВСЕГО:
|
%
3
|
|
|
|
1415,3
42,46
1457,76
|
|
Всего
по расценкам |
|
|
|
|
1479,2
|
Локальная
смета на сооружение
тоннеля.
-
№
п/п
|
Обоснование
|
Ед.
изм.
|
Кол-во
ед.
|
Цена,
грн.
|
Наименование
работ и затрат.
|
Сумма,
млн.
грн.
|
1.
2.
|
ДЕР
№1
ДЕР
№2
|
м.
м.
|
1315
1315
|
320,49
1479,2
|
Проходка
тоннеля
S=
69 м ,
f=
2,5
4
Крепление
тоннеля
Итого
забойных затрат
Общешахтные
расходы 40%.
Итого
прямых затрат
Накладные
расходы 28,5%.
Итого
с накладными
расходами
Плановые
накопления
Всего
по смете
Цена
проходки 1м.
|
0,42
1,95
2,37
0,95
3,32
0,95
4,27
1,28
5,55
0,0042
|
Экономический
эффект: Эобщ=
Эш+Эн;
Эм= 0,3
0,95
=
0,0097 млн. грн.
Эш
= КШ
- экономический
эффект за счет
Эн= 0,3
0,95
=
0,0097 млн. грн.
снижения
общешахтных
расходов;
Эн
= К
Н
- экономический
эффект за счет
Эоющ= 0,0194 млн.
грн.
снижения
накладных
расходов;
К=0,3;
Ш=
0,95 млн. грн. –
относительный
размер общешахтных
расходов;
Н=
0,95 млн. грн. –
нормативные
накладные
расходы;
Тнор=
20 м/мес – нормативные
темпы проходки;
Тпр=
20,7 м/мес.
VII.
Маркшейдерские
работы.
Маркшейдерские
работы при
проведении
тоннеля со
стороны Северного
портала до
конца закругления
R=1000
м.
При проведении
данного тоннеля
маркщейдерская
служба должна
обеспечить
правильное
проектное
направление
выработки,
контроль проведения,
исполнительную
съемку и составление
маркшейдерских
чертежей.
Проведение
тоннеля начинаем
с т.1. На участке
т.1- т.2 тоннель
имеет прямолинейный
участок. Направление
выработки
задается из
начальной т.1
и продолжается
по мере ее проходки
в заданном
направлении.
а) В горизонтальной
плоскости
направление
задается путем
отложения
теодолитом
в натуре горизонтального
проектного
угля.
При отложении
проектного
угла в створе
визирного луча
теодолита
закрепляют
3 точки на расстоянии
5 м друг от друга.
На эти точки
подвешивают
отвесы, создающие
створ, который
в дальнейшем
будут использовать
проходчики
при проведении
тоннеля. Заданные
направления
проходчики
могут использовать
до момента
удаления груди
забоя на расстояние
30-40 м, после чего
процесс задания
направления
оси выработки
повторяется.
б) В вертикальной
плоскости
задание направления
выработке
осуществляется
боковыми реперами.
Задание направление
осуществляется
при помощи
нивелира. В
стенке выработки
закладывается
боковой репер
с уклоном, который
равен проектному
уклону выработки.
На высоте d
от почвы закрепляется
репер R
и определяется
его отметка
H .
Далее на
расстоянии
5-6 м от репера
R
прокладывается
репер R
на высоте, которая
вычисляется
по формуле:
H =
H +
i L,
где
i –
заданный уклон;
L –
горизонтальное
расстояние
между R
и R .
Положение
выработки по
проекту определяется
откладыванием
отрезка d
от репера R .
2. При проведении
криволинейного
участка т.1 –
т.4 тоннеля с
радиусом закругления
R=1000
м и углом поворота
=35
задание направления
круговой линии
ее оси осуществляют
по направлениям
вписанных в
нее хорд одинаковых
длин.
Выбрав минимально
возможное число
хорд n=3,
находим значение
центрального
угла для одной
хорды, равное:
=
=
11,6
Определяем
длину одной
хорды:
l= 2R
Sin/2n
= 21000Sin
35/
23
= 150 м.
Внутренние
углы
при начальной
точке кривой
1 и конечной
точке кривой
4 и углы
при промежуточных
точках 2 и 3 вычисляем
по формулам:
=
180-/2n
= 180-35/23=
174,2
=
180-/n
= 180-35/3=
168,3
На участках
в т.2 – 3 и т.3 – 4 задание
направления
выполняется
аналогично,
как и на участке
в т.1 – 2 .
ОГЛАВЛЕНИЕ.
Введение……………………………………………………………………………..4
Общее положение
проекта
Общие сведения
о тоннеле………………………………………………..5
Горно-геологические
условия…………………………………………….5
Поперечное
сечение
тоннеля……………………………………………...7
Существующее
положение………………………………………………..8
Сооружение
тоннеля.
Выбор и
обоснование
способа сооружения
тоннеля…………………….9
Определение
трудоемкости
работ……………………………………….12
Сооружение
врезки со стороны
Северного
портала……………………15
Северная
пром. площадка………………………………………………..17
Производство
работ в тоннеле:
возведение
постоянной
обделки сводовой
части тоннеля……………...17
разработка
нижней части
тоннеля………………………………………..17
работы по
первичному
и контрольному
нагнетанию…………………...21
сбойка
тоннеля……………………………………………………………..22
Вентиляция.
Общие
сведения…………………………………………………………...23
Расчет системы
вентиляции
тоннеля…………………………………….24
Характеристика
вентиляционного
оборудования………………………30
Охрана труда
Меры безопасности
при ведении
работ в тоннеле……………………...31
Производственная
санитария…………………………………………….32
Противопожарная
защита………………………………………………...34
Подземное
пожарное
водоснабжение
Правила
поведения
работников
при ЧС………………………………...41
Пример
ЧС………………………………………………………………...43
Охрана окружающей
среды…………………………………………………44
Электроснабжение…………………………………………………………..45
Маркшейдерские
работы……………………………………………………48
Технико-экономические
показатели……………………………………….51
Список
использованной
литературы……………………………………………..57
IV.
Охрана
труда.
4.1.Меры
безопасности
при ведении
работ в тоннеле.
Эксплуатация
забойного
оборудования
должна осуществляться
в соответствии
с заводскими
инструкциями,
а ведение работ
– согласно
инструкции
по охране труда
по профессиям.
а)
Меры безопасности
при проходческих
работах с применением
буровой установки
«Максиматик».
- к
работе по проходке
подземных
выработок с
применением
буровой установки
«Максиматик»
допускаются
лица: не моложе
18 лет, прошедшие
медицинское
освидетельствование,
обучение и
инструктаж
по технике
безопасности,
получившие
удостоверение
на право работы;
- при
работе на буровой
установке
проходчики
обязаны быть
в маске, спецодежде
и спецобуви,
предусмотренных
нормами, а также
иметь при себе
средства
индивидуальной
защиты (самоспасатели,
аккумуляторные
лампы, рукавицы,
защитные очки,
предохранительные
пояса) и пользоваться
ими соответственно
месту и характеру
выполнения
работы. Работать
без индивидуальных
средств защиты
или без спецодежды
установленного
образца запрещается;
- запрещается
изменять без
разрешения
технического
персонала
установленную
для буровой
установки
технологию
выполнения
работ;
б) Меры
безопасности
при эксплуатации
породопогрузочной
машины ПНБ-3Д.
- при
работе на
породопогрузочной
машине допускаются
машинисты,
прошедшие
специальный
курс обучения
и получившие
аттестацию
в квалификационной
комиссии. Переход
машиниста к
самостоятельному
управлению
машиной должен
быть отмечен
приказом с
обязательным
закреплением
машиниста за
машиной;
- перед
началом работы
машинист обязан
осмотреть
машину, проверить
надежность
крепления всех
сборочных
единиц, уровень
масла в редукторах
приводов и
состояние
смазки в остальных
трущихся частей
машины. Проверить
плотность
соединений
трубопроводов,
надежность
работы гидроцилиндров
и управления
ими. Проверить
состояние
скребковой
цепи, ее натяжение,
состояние
силового кабеля
и целостность
заземления;
- перед
включением
электродвигателя
машины подать
предупредительный
сигнал для
окружающих;
- машинист
должен ежесменно
выполнять
обслуживание
погрузочной
машины за полчаса
до окончания
смены.
4.2. Производственная
санитария.
Горячая
вода с температурой
75 С для
бани нагревается
бойлерной,
расположенной
в здании АБК.
Сушка
одежды с содержанием
влаги до 0,5 кг
в комплекте,
предусмотрена
в шкафах путем
проветривания;
с содержанием
влаги более
0,5 кг в комплекте
– в специальной
сушильной
камере, оборудованной
нагревательными
элементами
и приточно-
вытяжной вентиляцией.
Обеспыливание
рабочей одежды
производится
при помощи
специальных
обеспыливающих
насадок, присоединенных
к вытяжной
установке,
оборудованной
матерчатыми
фильтрами.
Мойка
обуви производится
на специальной
машине, представляющей
систему вращающихся
щеток, омываемых
водой.
Для обеспечения
питьевой водой
трудящихся
предусматривается
специальная
установка-автомат
для охлаждения
и газирования
питьевой воды.
Производительность
установки 2
м /ч.
Стирка
спецодежды
(1 раз в неделю)
предусматривается
в прачечной,
расположенной
в АБК. В помещении
АБК находятся
также здравпункт
и цех по пошиву
спецодежды.
III.
ВЕНТИЛЯЦИЯ
ГОРНЫХ ВЫРАБОТОК
3.1. Общие сведения.
Проект проходческой
вентиляции
разработан
на основании
исходных данных
по производству
строительно-
монтажных работ
и предусматривает
проветривание
выработок на
всех этапах
строительства
тоннеля.
В начальный
период проходки
во всех забоях
проветривание
осуществляется
свободной
струей, омывающей
призабойное
пространство.
Из-за небольшой
длины выработки,
отработанный
воздух выдавливается
на поверхность
через портал
тоннеля.
В дальнейшем,
для забоя с
Южного портала
принимаем
приточно-вытяжной
способ проветривания.
Приток осуществляем
вентилятором
СВМ-12 главной
вентиляционной
установки ПР1
с помощью
металлических
и гибких воздуховодов.
Воздуховоды
приняты жесткие,
коробчатой
формы из листовой
стали толщиной
2 мм. Применение
воздуховодов
такой формы
обусловлено
тем, что при
движении передвижной
опалубки данный
воздуховод
коробчатой
формы не будет
мешать производству
работ по бетонированию
верхней части
тоннеля. Для
обеспечения
воздухоплотности
соединение
воздуховодов
выполняются
на фланцах
(устанавливаемых
через 6м.) с резиновыми
уплотнителями.
Работу вентсистем
обеспечивают
вентустановки
(напр. ПР1), установленные
на порталах
тоннеля и штольни,
независимые
одна от другой.
В призабойной
зоне тоннеля
с южной стороны
установлены
вентиляторы-
побудители
СВМ-6 (два на забой),
работающие
(30 мин) в режиме
отсоса после
производства
взрыва и способствующие
удалению взрывных
газов из призабойной
зоны. В нормальном
режиме работы
главной вентиляционной
установки ПР1
(на приток)
вентиляторы-побудители
СВМ-6 не работают.
Расчет количества
свежего воздуха
на забой, необходимого
для проветривания
выработок,
рассчитан по
следующим
параметрам:
- обеспечение
свежим воздухом
работающих
в количестве
6м /мин.
на человека;
- обеспечение
минимально-допустимой
скорости движения
воздуха по
выработке,
равной 0.1 м/с;
- разбавление
газов после
взрывных работ
до предельно-допустимых
концентраций;
- удаление
газов после
взрыва;
- разбавление
выхлопных газов
от двигателей
автосамосвалов
до предельно-
допустимых
концентраций;
- разбавление
газов от сварочных
работ до предельно-
допустимых
концентраций.
3.2. Расчет
системы вентиляции
тоннеля.
Вентиляция
забоя тоннеля
с Южного портала.
Исходные
данные:
количество
забоев - 1;
количество
работающих
людей - 14;
площадь забоя
- 111 м2;
способ проходки
- буро-взрывной;
количество
ВВ на одну заходку-
103,5 кг;
сварочные
работы - 1.7 кг/час
электродов
на один пост;
постов-2.
1 .Необходимое
количество
воздуха для
вытяжки после
взрыва.
Q=
=
4,8 м /сек.,
где
t - время
вытяжки после
взрыва, принимаем
равным 30 мин.;
В - количество
взрываемого
ВВ, кг;
I
- газоносность
ВВ, л/кг;
S - площадь
поперечного
сечения выработки,
м2.
Необходимое
количество
воздуха для
работающих
людей:
Q= q
n = 614=84 м /мин=
1.4 м3/сек.; где:
необходимое
количество
воздуха для
одного работающего,
равное 6 м^/мин.;
n - количество
работающих.
Необходимое
количество
воздуха для
обеспечения
минимально
допустимой
скорости движения
воздуха по
выработке:
Q=V
S= 0.1
69= 6,9 м /сек,
где
V - минимально-
допустимая
скорость движения
воздуха по
выработке,
равная 0.1 м/сек.
Необходимое
количество
воздуха для
разбавления
сварочных
аэрозолей до
предельно-
допустимых
концентраций:
Q=
=
2,4 м /сек,
где
а - минимальное
количество
воздуха, подаваемого
на 1 кг отработанных
электродов,
равное 2500 м ;
(Кирин «Рудничная
аэрология»
стр.184);
b - масса
электродов,
расходуемых
за 1 час сварки,
кг;
N - число сварочных
постов.
Общее количество
воздуха для
вентиляции
выработок после
взрыва принимаем
по наибольшим
из рассчитанных
величин, т.е.
11,1 м /с.
Производительность
вентустановки
в режиме реверса
составит:
Q =
=
=
17,3
м /с
Потери напора
на участке
Н= R Q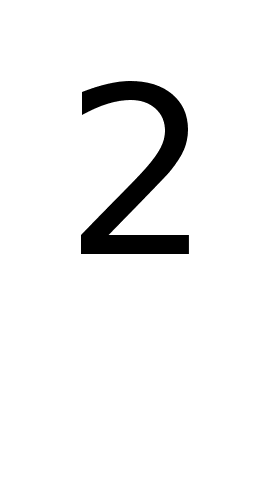 =
0,79 ( ) =
160кг/м2
Необходимое
количество
воздуха для
разбавления
условной окиси
углерода СО,
выделяющейся
при работе
дизельного
двигателя
автосамосвала
МОАЗ-64011:
Q=
k k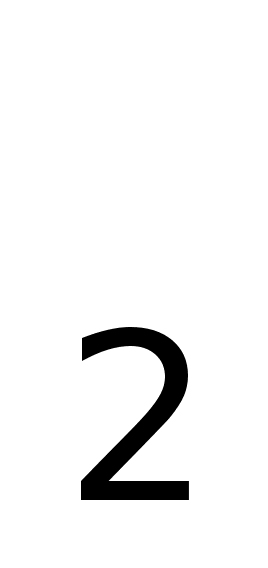 ;
м /с
, где
k
- поправочный
коэффициент,
учитывающий
неравномерность
распределения
концентрации
отработавших
газов по сечению
тоннельной
выработки.
Численное
значение коэффициента
k =
1,3 1,7 (для
выработки до
800 м k =1,6);
k
- коэффициент,
учитывающий
уменьшение
концентрации
отработавших
газов дизельных
машин по длине
транспортной
выработки за
счет поглощения
окислов азота,
акролеина и
дымов мокрыми
стенами тоннеля
и водой по подошве
тоннеля (k =0,75
- стены и
подошва тоннеля
частично увлажнены);
m - количество
одновременно
находящихся
в призабойной
зоне машин,
шт.;
L - длина тоннельной
выработки, м;
V - средняя
скорость движения
груженых и
порожних машин
(V=5км/час= = 1,4
м/с);
qог, qоп
- интенсивность
газовыделений
отработавших
газов на выхлопе
груженых и
порожних машин,
м /с;
Сог, Соп
- начальная
(приведенная
к окиси углерода)
концентрация
отработавших
газов из выхлопной
трубы соответственно
для груженых
и порожних
машин, м /м3;
С доп
- предельно-
допустимая
концентрация
отработавших
газов в атмосфере
транспортной
выработки,
приведенная
к окиси углерода,
(С доп=
1,610
м /м )
q c =
=
=
11,110
м /с
t
- средняя интенсивность
движения транспорта,
сек.
t=
=
=
=
1620 сек,
где
tобв
- время, отведенное
на вывозку
породы;
Vв -
объем взорванной
породы;
Vк -
объем ковша
автосамосвала;
Sв -
площадь поперечного
сечения выработки;
l - длина
заходки;
kр - коэффициент
разрыхления
породы.
Qз=
1,60,75
=
19,4 м /с,
причем по
условиям вентиляции
на участке
возможна работа
не более одного
автосамосвала.
Подбор
главной вентиляционной
установки.
Сопротивление
металлического
воздуховода
определяем
по формуле:
Rтр=
=
=
0,79 , где
а - коэффициент
аэродинамического
сопротивления,
принимаем по
табл. (Кирин,
стр.119)
Коэффициент
доставки на
максимальном
участке:
=
=
=
0,64, где
m - длина
звена воздуховода
= 6м;
L - длина участка
(м);
d - приведенный
диаметр воздуховода;
R - сопротивление
воздуха;
к - коэффициент
удельной стыковой
воздухонепроницаемости
равный 0,0025 (при
удовлетворительной
сборке).
Производительность
главной вентиляционной
установки:
Qв=
=
30,3
м /с,
Потери напора
на участке:
Н= RmрQ ср=
0,79 =
490 кг/м2
Принимаем
к установке
на стройплощадке
Южного портала
вентилятор
СВМ-12 производительностью
30,3 м /с,
давлением 490
кг/м2 с электродвигателем
мощностью 110
кВт.
Технические
характеристики
СВМ-12:
- частота
вращения колеса,
мин
1470
- подача в
рабочую зону,
м /мин
600 - 1920 = 10 – 32 м /сек
- мах КПД
0,82
- масса, кг
2000
Характеристика
вентиляционного
оборудования.
Обозна-
чение
системы
|
Кол. сис-
тем
|
Наименование
обслуживаемо-
го помещения
|
Тип установки
|
Вентилятор |
Электродвигатель |
Прим. |
Тип, исполне-ние
по взрывозащите |
№
|
Положение |
L,
м /час
|
Р,Па
(кгс/
м )
|
n, об/ мин |
Тип, исполнение
по взрывозащите |
N,
кВт
|
п,
об/ мин
|
|
ПР1
|
1
|
Забой Южного
участка тоннеля |
ВЦП-16
|
|
16
|
поворот
лопаток
30°
|
109080
|
490
|
1480
|
АО-114-12/8/6/4 |
200
|
1500/1 000/75 0/500 |
с реверс.
устр-ом |
ПР2
|
1
|
Забой Северного
участка тоннеля |
ВЦП-16
|
|
16
|
поворот
лопаток
50°
|
99000
|
307
|
1480
|
АО-114-12/8/6/4 |
120
|
1500/1 000/75 0/500 |
с реверс.
устр-ом |
П1
|
2
|
Призабоиная
зона южного
участка тоннеля |
ВМ-5М
|
РВ
|
5
|
-
|
13680
|
260
|
|
ВАОМ-52-2
|
13
|
2940
|
|
П2
|
1
|
Забой штольни
|
ВМ-5М
|
РВ
|
5
|
-
|
13680
|
260
|
|
ВАОМ-52-2 |
13
|
2940
|
|
4.3. Противопожарная
защита.
а) объектов
на строй площадке.
Водоснабжение
стройплощадок
осуществляется
от существующих
сетей водопровода.
Давление воды
в трубопроводе
должно быть
не менее 40м. В
качестве резерва
запаса воды
используются
две пожарные
емкости объемом
100м3
каждая.
Схема системы
пожарного
водоснабжения
принята с учетом
требований
п.2,14 и п.8,5 СНиП
2.04.02-84" Водоснабжение.
Наружные сети
и сооружения".
Принят один
пожар на строящемся
тоннеле. Сети
водопровода
приняты тупиковыми.
Наружное
пожаротушение
осуществляется
от пожарного
гидранта ПГ-3000
(Н750мм), установленного
на водопроводной
сети стройплощадок
на расстоянии
50м от портала.
Внутреннее
пожаротушение
производится
при помощи
порошковых
огнетушителей
типа ОП-8Б, установленных
в зданиях
административно-бытового
комплекса и
служебных
вагончиках.
В качестве
резервного
водоснабжение
при пожаре
используется
мотопомпа,
присоединяемая
к тупиковой
разводящей
водопроводной
сети или к емкостям
запаса воды
На стройплощадках
предусмотрена
установка
насосной станции
для повышения
напора в водопроводной
сети при тушении
пожара в подземных
выработках.
В качестве
источника
водоснабжения
в насосной
станции используются
пожарные емкости,
расположенные
рядом с насосной.
Насосная станция
соответствует
второму классу
надежности.
Насосы должны
обеспечиваться
бесперебойным
питанием от
двух независимых
фидеров.
В качестве
мероприятий,
предотвращающих
пожар на стройплощадке,
должны соблюдаться
следующие
требования:
- сооружения,
непосредственно
примыкающие
к порталу должны
сооружаться
из несгораемых
материалов;
- вся территория
около устья
тоннеля должна
быть очищена
от леса, кустарника,
и другой растительности,
а также горючих
материалов;
- склады горючих
и смазочных
материалов,
отвалы горючих
и самовозгорающих
пород, а также
котельных
шлаков разрешается
размещать на
расстоянии
не ближе 100м от
портала и с
учетом господствующего
направления
ветра.
Табл. 1.
Перечень необходимого
оборудования
и материалов
в противопожарном
складе стройплощадок
Северного и
Южного порталов.
№№ |
|
Единица
|
|
п/п |
Наименование
|
измерения |
Количество |
1 |
Передвижной
порошковый |
|
|
|
огнетушитель
марки ОП-500 |
шт. |
1 |
2 |
Ручные
порошковые |
|
|
|
огнетушители
марки ОП-8Б |
шт. |
100 |
3 |
Запас
огнетушащего
порошка |
т |
3 |
|
марки
П-2АП |
|
|
4 |
Насос
электрический |
|
|
|
производительностью
60м час
|
шт. |
1 |
5 |
Мотопомпа
МП-600А |
шт. |
1 |
6 |
Шланг
всасывающий
к насосу |
компл. |
1 |
7 |
Кабель
резиновый
для насоса |
|
|
|
длиной
не менее 100м с
пусковой |
компл. |
1 |
|
электроаппаратурой |
|
|
8 |
Пожарные
рукава (шланги |
|
|
|
резиновые)
диаметром
75мм |
м |
500 |
9 |
Стволы
пожарные |
шт. |
5 |
10 |
Ведра
железные |
шт. |
10 |
11 |
Носилки
рабочие |
шт. |
5 |
12 |
Лопаты
совковые с
черенками |
шт. |
5 |
13 |
Лопаты
штыковые с
черенками |
шт. |
5 |
14 |
Топоры |
шт. |
5 |
15 |
Гвозди
длиной 100-150мм |
кг |
20 |
б) подземных
выработок.
В тоннеле
и штольне
предусмотрена
прокладка
противопожарного
водопровода
Д 100мм.
Кроме того,
в подземных
выработках
размещены посты
с первичными
средствами
пожаротушения,
имеющими в
комплекте:
- огнетушитель
ручной порошковый
марки ОП-8Б - 2шт.;
- ящик с песком
вместимостью
0.2м3 -
1шт.;
- пожарный
щит с противопожарным
инвентарем.
Посты располагаются
в тоннеле и
штольне через
каждые 300м, а также
в забоях выработок
не далее 30м от
груди забоя.
До поступления
в необходимом
количестве
ручных порошковых
огнетушителей
их могут временно
заменять ручные
пенные огнетушители.
В одной из
выработок на
каждом участке
тоннеля и штольни
оборудуется
место для стоянки
передвижной
установки
порошкового
пожаротушения
типа ОП-500. Кроме
того, в связи
с использованием
в тоннеле для
откатки породы
автосамосвалов
МОАЗ, предусмотрена
дополнительно
установка
порошкового
пожаротушения
на каждой
стройплощадке.
Все места
хранения средств
пожаротушения
оснащаются
табличками
с надписями
"Огнетушитель",
"Песок", "Пожарный
щит". Окраска
противопожарного
оборудования
должна выполняться
в соответствии
с ГОСТ" Цвета
сигнальные
и знаки безопасности".
4,4. Подземное
пожарное
водоснабжение.
1). Общие
сведения.
Степень
огнестойкости
тоннельных
выработок -1.
Категория
по пожарной
опасности - В.
Объем выработок
составляет
150 тыс.м3.
Согласно
"Правилам
техники безопасности
при строительстве
метрополитенов
и подземных
сооружений"
принимаем
расход воды
для пожаротушения
тоннеля при
производстве
работ равным
60 м /час.
Согласно
п.6.10 СниП 2.04.01-85 время
тушения пожара
принято 3 часа.
В тоннеле
и штольне
предусмотрена
прокладка
противопожарного
водопровода
Д100 мм, который
при строительстве
используется
для технологических
нужд. Отставание
концов пожарно-технологического
водопровода
от технологического
комплекса
составляет
30м. На концах
водопровода
устанавливаются
пожарные краны
комплектно:
- вентиль 161р
Ду65 - 2 шт.:
- рукав пожарный
Ду65 длиной
20 м - 2 шт.;
- ствол пожарный
РС70 - 2 шт.;
- головка
соединительная
цапковая ГЦ-70
- 2 шт.;
- головка
соединительная
рукавная ГР-70
- 2 шт.
Ящики с пожарными
рукавами и
стволами переносятся
по мере продвижения
забоя.
Кроме того,
пожарные краны
устанавливаются
на пожарно-технологическом
водопроводе
через каждые
100 м, а также на
сопряжении
тоннеля и штольни.
Для отключения
отдельных
участков
пожарно-технологического
водопровода
на трубопроводе
через каждые
400 м устанавливаются
задвижки. При
этом предусматривается
установка
переключающих
устройств для
подачи воды
по трубопроводу
сжатого воздуха.
2). Расчет пожарных
насосов.
1.
Определим
необходимый
напор у пожарного
крана
Hпк=
hр+
hспр, м , где
hр
- потери напора
в рукаве, м
hспр
- необходимый
напор у спрыска
для создания
компактной
струи, м
hр=
kрq =
0,00385
16,62
40 = 42,2 м, где
kр -
коэффициент
сопротивления
рукава (табличное,
по данным Тарасова-
Агалатова).
hспр=
Sспрq =
0,63416,6 =
174,7 м, где
Sспр
- сопротивление
спрыска (табл.
), равное 0,634 для
dспр=19мм.
Нпк=
21,2+174,7=195,9 м.
В связи с
большим потерями
давления в
пожарном кране
(195,5м) при заданном
расходе (60 м /час
или 16,6 л/с) принимаем
к установке
спаренные
пожарные краны,
т.е. 2 комплекта
на каждый пожарный
пост. Тогда
расход через
каждый пожарный
кран составит
30 м /час
или 8,3 л/с.
hр=
kрq =
0,00385
8,32
40 = 5,3 м
hспр=
Sпр q =0,634
8,32 =43,7 м
Нпк= 5,3+43,7=49,0
м
2. Определим
потери напора
в трубопроводе:
- от насосной
на Северном
портале до
забоя тоннеля
и штольни
Н1= 1,1Аq l
= 1,1
0,0002813
16,6
576 = 49,1 м., где
А - удельное
сопротивление
трубопровода
(табл. );
1,1 - потери на
местные сопротивления.
- от насосной
на Южном портале
до забоя тоннеля
Н1= 1,1Аq l
= 1,1
0,0002813
16,62
874 = 74,5м.
3. Определим
геометрическое
превышение
расчетной точки
над насосом
или наоборот
hг;
- для северного
портала:
Hг=
497
0,03 = 14,9м (-)
- для южного
портала:
Hг=
109
0,0258 + 774
0,006= 7,5м (+)
4. Определим
необходимое
давление пожарного
насоса:
- для северного
участка тоннеля
и штольни:
Нну= Нпк
+Н1- Hг=
49,0 + 49,1 - 14,9 = 83,2 м.
- для южного
участка:
Нну=
Нпк+Н1-
Hг=
49,0 + 74,5 - 7,5 =116 м.
5. Принимаем
к установке
насосы – повысители
напора при
пожаре:
- на стройплощадке
северного
портала - насос
типа ЦНС60-99 -2шт.
(1-раб., 1-рез.), подача
60 м /ч,
напор 99 м, электродвигатель
типа 4А180М2 мощностью
N=23,5 кВт, габаритные
размеры - (1620472676h);
-на стройплощадке
южного портала
- насос типа
ЦНС60-132 -2шт. (1-раб.,
1-рез.), подача
60 м /ч,
напор 132 м, электродвигатель
типа 4АМ200L2
мощностью
N=31,3 кВт, габаритные
размеры - (1818492715h).
ВИД АВАРИИ: ПОЖАР. |
|
|
|
|
|
|
|
|
|
Мероприятия |
Ответственные |
Пути и время (мин.) выхода |
Маршрут движения |
по спасению людей |
лица и исполни- |
людей из аварийного и угро- |
отделений ВГСЧ |
и ликвидац. аварии |
тели |
жаемого участков |
и задание |
1. Вызвать ВГСЧ. |
|
Горный мастер |
|
Люди, находящиеся в тонне- |
|
|
Первое отделение ВГСЧ |
|
|
|
Начальник участка |
|
ле выходят на поверхность |
|
|
прибывает в тоннель и при- |
|
|
|
Деж. электрослесарь |
|
в самоспосателях. |
|
|
ступает к тушению пожара |
|
2. Вентилятор СВМ-12 |
|
|
|
Люди, находящиеся за оча- |
|
|
совместно с пожарной |
|
работает нормально. |
|
|
|
гом пожара, при невозмож- |
|
|
частью. |
|
|
|
|
|
ности выхода, открыв. сжа- |
|
|
|
|
3. Энергоснабжение |
|
Деж. электрослесарь |
|
тый воздух, ждут отделение |
|
|
|
|
отключить. |
|
|
|
ВГСЧ и при их помощи вы- |
|
|
|
|
|
|
|
|
ходят на поверхность. |
|
|
|
|
4. Оповестить рабочих |
|
Горный мастер |
|
|
|
|
|
|
в тоннеле и вывести |
|
Бригадир |
|
|
|
|
|
|
их на поверхность. |
|
|
|
|
|
|
|
|
|
|
|
|
|
|
|
|
|
5. Подать воду к очагу |
|
Горный мастер |
|
|
|
|
|
|
пожара. |
|
Электрослесарь |
|
|
|
|
|
|
|
|
|
|
|
|
|
|
|
6. До прибытия ВГСЧ |
|
Горный мастер |
|
|
|
|
|
|
и пожарной части ту- |
|
|
|
|
|
|
|
|
шить пожар своими |
|
|
|
|
|
|
|
|
силами. |
|
|
|
|
|
|
|
|
7. Выставить посты бе- |
|
Горный мастер |
|
|
|
|
|
|
зопасности. |
|
|
|
|
|
|
|
|
|
|
|
|
|
|
|
|
|
8. Сообщить об аварии |
|
Начальник участка |
|
|
|
|
|
|
руководству предприя- |
|
|
|
|
|
|
|
|
тия. |
|
|
|
|
|
|
|
|
4.5. Правила
поведения
работников
при ЧС.
1. Все работники
тоннеля должны
твердо знать
правила поведения
в аварийной
обстановке,
места, где
располагаются
средства
противопожарной
защиты, и уметь
пользоваться
ими. Имеются
первичные
средства
пожаротушения:
песок, пенные
огнетушители
ОП-5,ОУ-5,вода,
средства оповещения
- телефоны
расположены
на портале
тоннеля.
2. Люди, находящиеся
в тоннеле и
заметившие
признаки аварии,
обязаны немедленно
сообщить по
телефону
телефонистке,
главному инженеру
и др.
3. Все работники
обязаны твердо
знать следующие
основные правила
личного поведения
при авариях:
ПОЖАР:
а) при обнаружении
идущего навстречу
дыма необходимо
немедленно
включиться
в самоспасатель
СПП-2 и двигаться
к порталу на
выход;
б) при горении
электропусковой
аппаратуры,
силовых кабелей
необходимо
обесточить
аварийные
агрегаты;
в) при пожаре
в забое тоннеля
необходимо
включиться
в самоспасатель
СПП-2 и начать
тушение первичными
средствами
(песок, огнетушитель,
вода). Если
невозможно
потушить пожар
имеющимися
средствами,
следует выходить
на портал и
отключить
электроэнергию
на механизмы.
ОБРУШЕНИЕ:
а) люди, застигнутые
обрушением,
должны принять
меры к освобождению
пострадавших,
находящихся
под завалом,
установить
характер обрушений
и возможность
безопасного
выхода через
купольную часть
выработки. Если
выход невозможен,
следует установить
дополнительную
крепь и приступить
к разбору завала.
В случае, когда
это невозможно,
ждать прихода
горноспасателей,
подавая сигналы
о местонахождении
посредством
ударов о металлические
предметы: резкие
удары по количеству
находящихся
за обрушением
людей.
ЗАГАЗИРОВАНИЕ:
а) при загазировании,
следует включаться
в самоспасатели
и выйти из
загазированных
выработок,
отключить
электроэнергию
и поставить
знак запрещающий
выход в выработку.
V. Мероприятия
по охране окружающей
среды.
В систему
водоотвода
поступают стоки
от проходческих
механизмов,
вода от мытья
тоннеля и грунтовые
воды, которые
не содержат
вредных примесей
и не требуют
серьезной
очистки.
От забоя с
южного портала
эти воды самотеком
поступают в
систему тоннельного
водоотлива
и на поверхность
в очистные
сооружения.
В забое с северного
портала, где
уклон проезжей
части направлен
от портала к
забою, предусматривается
установка
забойного
насоса марки
1В20/5, производительностью
16 м /час,
напором 50 м. Насос
устанавливается
в забое, откуда
воду перекачивает
в очистные
сооружения
на поверхности.
Трубопроводы
водоотлива
приняты из
стальных
электросварных
труб d=50
мм.
Система
вентиляции
тоннеля запроектирована
таким образом,
что в воздушный
бассейн припортальных
участков, где
размещены
лечебные, курортные
и жилые здания,
вредности не
поступают. Из
порталов
предусматривается
забор чистого
воздуха для
проветривания
тоннеля.
Выброс
отработанного
воздуха происходит
через вентиляционно-транспортную
штольню вентшахты.
Вентшахта
представляет
собой прямоугольную
ж/б трубу высотой
13 м. от проезжей
части штольни,
размерами в
плане: у основания
4,53
м. и устья 22
м. Такие размеры
воздуховыпуска
обеспечивают
рассеивание
вредных веществ
в атмосферу
так, что их
концентрация
в приземном
слое атмосферного
воздуха снижается
до 0,3 м /м .
При этом учитывался
также коэффициент
на рельеф местности
и концентрация
окиси углерода.
- Электроснабжение.
Электроснабжение
строительства
объекта подразделяется
на III категории
электроприемников.
К электроприемникам
I
категории
относятся
вентиляционные
установки
тоннеля, освещение
тоннеля и насосные
установки для
откачки грунтовых
вод из тоннеля.
К электроприемникам
II
категории
относятся
растворо-бетонный
узел, пневмобетонные
установки,
установки
набрызга бетонна,
наружное освещение
площадки
строительства
портала. Электроприемники
III
категории- все
остальные
электроприемники
(напр. проходческое
оборудование
(машины), сварочные
аппараты и
т.д.).
К электроприемникам
работающих
в тоннеле относятся:
буровая установка,
породопогрузочная
машина ПНБ-3Д2,
вентилятор,
освещение
тоннеля и сварка.
Мощность
этих электроприемников
составляет:
Количество
Мощность
Коэф.спроса
Итого Р
(кВт)
(кВт)
- Буровая
установка
1 115 0,5
57,5
- ПНБ-3Д2
1 157 0,4
62,8
- вентилятор
1 24 1
24
- освещение
200 20 1
20
- сварка
3 60 0,8
48
Р=212,3
кВт
Мощность
электроприемников,работающих
на шахтной
поверхности
составляет
210 кВт.
Исходя из
вышеприведенных
нагрузок потребность
в трансформаторных
мощностях
составляет:
Трансформатор
с изолированной
нейтралью –
213 кВт (Т );
Трансформатор
с глухозаземленной
нейтралью –
210 кВт (Т );
Компрессорная
установка
«Ингерсол»
производительностью-
50_+60 мз/н.
Мощность
электродвигателя
250 кВт/6кВт. С учетом
коэф. спроса
потребуется
трансформатор
мощностью- 200
кВт.
Итого:
Т +Т +Т =213+210+200=
623 кВт.
Для питания
проходческих
механизмов
используем
высоковольтные
комплектные
устройства
т. КРУРН-6, трансформаторная
подстанция
т. ТСВП-250/6, устанавливаемые
на портале, и
пункт распределительный
т. ПР-II-7124,
переставляемый
по мере проходки
через 150 м. В качестве
отключающей
аппаратуры
устанавливаем
ящики силовые
т. ЯВШЗ, автоматический
выключатель
т. АВ-400ДО; пусковой
аппаратуры-
пускатели
магнитные т.
ПМЛ, ПВИ.
Распределительную
сеть выполняем
кабелем м. ГРШв.
Питающий кабель
м. АВБбШв наращивается
помере проходки
с помощью
осветительных
коробок т. К654.
Освещение
призабойной
зоны предусматриваем
светильниками
т. НСРО1
100, установленными
через 1 м. по обеим
сторонам забоя.
Осветительную
сеть выполняем
кабелем м. КРПТ.
Освещение
готовых выработок
предусматриваем
от пункта
распределительного
ПР №1 в вентздании
патронами
фарфоровыми
с ушком для
подвеса, расположенными
на высоте через
4 м. по обоим
сторонам тоннеля
в шахматном
порядке на
высоте 2500 мм от
УГР. Напряжение
сети освещения
тоннеля 36В.
Осветительную
выполняем
проводом № АПВ,
проложенным
по кронштейнам
для крепления
проводов освещения.
Трансформаторы
т. ТСШ-4 устанавливаем
в центре осветительных
нагрузок.
Кронштейны
для прокладки
кабелей устанавливаем
через 1 м., низ
кронштейна
на высоте 1500 мм
от УГР.
Все электрооборудование
заземлить.
Магистраль
заземления
выполнить
стальной полосой
сеч. 440
мм, проложенной
по обеим сторонам
тоннеля в двух
местах. Заземляющее
устройство
выполнить из
108 электродов
(сталь угловая
сеч. 50505
мм, длиной 2,5 м),
вбитых в грунт
на расстоянии
3 м друг от друга
и соединенных
между собой
полосой стальной
сеч. 440
мм, проложенной
на глубине 0,7
м от поверхности
земли. Величина
сопротивления
заземляющего
устройства
не должна превышать
2 Ом.
У пожарных
кранов установить
мосты кнопочные
и соединить
их кабелем м.
АВБбШв сеч.
42,5
мм
с насосной
противопожарного
водоснабжения. |