Введение
Термин "технология" происходит от двух греческих слов: tecoh – искусство, мастерство, умение и logoz – наука. В производственных процессах он применяется для обозначения технологических процессов: операционных, маршрутных, полных, а также методов и способов их выполнения.
Интегральная схема (микросхема) – микроэлектронное изделие, выполняющее определенную функцию преобразования, обработки сигнала, накапливания информации и имеющее высокую плотность электрически соединенных элементов (или элементов и компонентов), которые с точки зрения требований к испытаниям, приемке, поставке и эксплуатации рассматриваются как единое целое.
Важным показателем качества технологии и конструкции ИС является плотность упаковки элементов на кристалле – число элементов, приходящихся на единицу его площади. Кроме уменьшения размеров элементов для повышения плотности элементов на кристалле используется совмещение нескольких (обычно двух) функций некоторыми областями полупроводникового кристалла, а также трехмерные структуры, разделенные диэлектрическими прослойками.
Конструктивно-технологическая классификация ИС отражает способ изготовления и получаемую при этом структуру. По этому критерию различают полупроводниковые и гибридные ИС. В полупроводниковых ИС все элементы и межэлементные соединения изготовлены в объеме и на поверхности полупроводника. В гибридных ИС на диэлектрической подложке изготовляются пленочные пассивные элементы (резисторы, конденсаторы) и устанавливаются навесные активные и пассивные компоненты. Промежуточным типом ИС являются совмещенные интегральные схемы, в которых транзисторы изготовляются в активном слое кремния, а пленочные резисторы и диоды – как и проводники на изолирующем слое двуокиси кремния.
По типу применяемых активных элементов (транзисторов) интегральные схемы делятся на ИС на биполярных транзисторах (биполярных структурах) и ИС на МДП-транзисторах (МДП-структурах).
Данная работа посвящена описанию основных технологических операций производства интегральных микросхем:
· выращивание монокристаллов;
· изготовление пластин;
· обработка поверхности пластин;
· 4
· 5
· 6
· 7
· 8
· 9
· 10
1
Выращивание монокристаллов
Качество полупроводниковых приборов в значительной степени зависит от качества исходных полупроводниковых материалов. Поэтому создание полупроводниковой интегральной схемы начинается с изготовления монокристаллических слитков полупроводников. Особую проблему при этом представляет их очистка от примесей.
В настоящее время для промышленного изготовления большинства полупроводниковых микросхем применяют кремний. Это объясняется тем, что кремний по сравнению с также хорошо изученным и освоенным полупроводниковой промышленностью германием обладает рядом преимуществ. Так, кремний имеет большую ширину запрещенной зоны, что обеспечивает более широкий интервал рабочих температур, меньшие обратные токи переходов и меньшую их зависимость от температуры, а также позволяет изготавливать резисторы с большими значениями сопротивлений, слабо зависящими от тока утечки. Кремниевые переходы имеют большие пробивные напряжения, их пробой наступает при больших температурах. Кроме того, кремний является самым распространенным в природе элементом после кислорода. Содержание кремния в земной коре составляет по массе 27,7 %, что обеспечивает неограниченную возможность расширения его производства по сравнению с другими полупроводниками, относящимися к рассеянным элементам. Помимо дешевизны и недефицитности, кремний обладает существенно большим значением напряжения образования дислокаций, чем другие полупроводники. Это делает возможным выращивание бездислокационных монокристаллических слитков диаметром до 150 мм и более с массой более 100 кг. Известно несколько способов получения монокристаллических слитков, основанных на следующем принципе.
Растворимость большинства примесей гораздо больше в жидкой фазе, чем в твердой. Поэтому если постепенно охлаждать расплавленный полупроводник, то в затвердевшей части будет меньше примесей, чем в оставшейся жидкой части, словно примеси оттесняются в жидкую фазу. Отрезая же от полностью затвердевшего слитка ту часть, которая затвердела последней (и в которой, соответственно, сконцентрирована основная масса примесей) и повторяя операцию несколько раз, можно получить очень чистый материал. В рамках данной работы остановимся на двух методах: методе Чорхальского и зонной плавке.
1.1 Метод Чорхальского
Схема процесса изображена на рис 1. В расплавленное нагревателем вещество, которое находится в тигле и имеет температуру, близкую к температуре плавления, опускают монокристаллическую затравку того же состава, что и расплав. Далее приводится в действие механизм подъема и вращения затравки; при этом затравка смачивается расплавом и увлекает его вверх, вследствие чего расплав на затравке нарастает в виде кристаллической фазы. Метод обеспечивает получение полупроводникового материала в форме совершенных монокристаллов с определенной кристаллической ориентацией и минимальным числом дефектов. Нагреватель может быть резистивным, высокочастотным, электронно-лучевым.
При этом необходимо выдерживать должный температурный режим на поверхности соприкосновения кристалл-расплав, скорость вращения стержня и скорость вытягивания. Вращение стержня обуславливает перемешивание расплава, а также вывод дислокаций за пределы кристалла. Процесс производится в атмосфере инертных газов или водорода, которые также должны быть достаточно чистыми.
1.2 Метод зонной плавки (метод перекристаллизации)
На рис 2 показана схема безтигельной вертикальной зонной плавки. Достоинством метода является совмещение процесса глубокой очистки полупроводника с последующим выращиванием его монокристалла. Отливка в форме стержня из предварительно очищенного и легированного поликристаллического полупроводника прикрепляется одним концом к затравочному кристаллу. Небольшая зона контакта на границе затравочного кристалла разогревается до температуры плавления полем высокой частоты или электронным пучком и медленно сдвигается к противоположному концу стержня. На затравочной стороне происходит отвердение кремния в виде монокристалла. Как уже было сказано, большинство примесей обладают хорошей растворимостью в жидкой фазе по сравнению с твердой. Поэтому по мере продвижения зона плавления все больше насыщается примесями, которые по завершении процесса концентрируются на конце слитка. Обычно процесс зонной плавки повторяют несколько раз, по окончании очистки загрязненный конец слитка отрезают.
Обычно изготовляют монокристаллы с равномерным распределением легирующей примеси (донорной или акцепторной). Легирование кремния или германия элементами осуществляется введением в расплав соответствующей примеси. Таким образом, слитки могут иметь электронную электропроводность (n-тип) или дырочную (р-тип). Максимальная длина может достигать 100, 150 см, а диаметр слитка до 150 мм и более.
2 Изготовление пластин
Полученные путем метода Чорхальского и метода зонной плавки массивные монокристаллические слитки непосредственно не используются. Их нарезают на множество тонких пластин, на основе которых уже изготавливаются отдельные интегральные микросхемы.
Механическая обработка полупроводников затруднена их высокими твердостью и хрупкостью. Использовать обычные методы механической обработки, применяемые в металлообрабатывающей промышленности, такие, например, как прокатка, штамповка, вырубка, нельзя. Для изготовления пластин из монокристаллических слитков применяют метод абразивной обработки, т.е. обработки более твердым, но менее хрупким, чем обрабатываемая поверхность, материалом, а также другие эффективные методы.
Перед началом резки слиток необходимо прочно закрепить на неподвижном основании, причем очень важно обеспечить точное расположение слитка относительно полотен или дисков с тем, чтобы пластины имели необходимую кристаллографическую ориентацию. Как правило, пластины нарезаются в плоскости <111> или <100>.
Наиболее распространенным способом крепления является закрепление с помощью различных наклеечных материалов, например, воска, канифоли, шеллака, глифталевой смазки, клея БФ, эпоксидных смол и крепежных мастик на их основе. Наклеечное вещество расплавляется и наносится на заготовки и крепежные приспособления и, застывая, скрепляет их в заданном положении.
После механической обработки материал нагревают, расплавляя наклеечный материал. Затем заготовки отмывают от наклеечного материала в специально подобранных растворителях. Для закрепления на держателе рабочего стола слиток сначала ориентированно приклеивают к специальной оправке торцом или цилиндрической поверхностью, а слитки большого диаметра – одновременно торцевой и цилиндрической поверхностями (рис 4).
Держатель рабочего стола станка с помощью поворотной головки позволяет поворачивать слиток и устанавливать его относительно плоскости отрезного круга так, чтобы получить пластины с заданной ориентацией поверхности.
Обычно, резка слитка на пластины осуществляется либо с помощью комплекта тонких длинных стальных полотен, либо с помощью "алмазных дисков".
2.1 Резка стальными полотнами и дисками
На рис 3 показана схема резки стальными полотнами или наборами полотен с использованием абразивной суспензии. Этот метод применяется в лабораторных условиях для сквозного разделения пластин и подложек. Метод не обеспечивает высокой производительности и качества. Точность размеров кристаллов невысокая из-за неравномерности натяжения полотен в обойме, их вибрации, неравномерности износа. Абразивная суспензия загрязняет структуры.
Первоначально широкое применение в промышленности имела резка металлическими дисковыми пилами с применением абразивной суспензии. Это объясняется простотой и доступностью этого метода резания. Однако в настоящее время его применяют только в случае резки пластин на кристаллы. Принцип резки практически тот же, что и при резке стальными полотнами. В зону резания подают абразивную суспензию, которая, ускоряясь за счет вращения диска, с силой ударяет в обрабатываемый материал и откалывает от него микрочастицы. Процесс резания ускоряют частицы абразива, постепенно обновляемые в зазоре между металлическим диском и полупроводниковой пластиной. Абразивная суспензия достаточно хорошо отводит тепло из зоны резания и специального охлаждения не требует.
Жесткость металлических дисков, как правило изготавливаемых из стальных холоднокатных лент, недостаточна для резания слитков на пластины, и удовлетворительное качество резания достигается только при небольших глубинах резания, как было указано выше, при резании на кристаллы. Абразивные порошки изготавливаются из карбида бора В4
С3
, карбида кремния SiC, и электрокорунда Al2
O3
. По размерам зерна абразивные порошки подразделяются на четыре группы:
· шлифзерно;
· шлифпорошки;
· микропорошки;
· тонкие микропорошки.
2.2 Резка диском с наружной алмазной кромкой
Резание диском с наружной алмазной кромкой обладает по сравнению с процессом резания диском с применением абразивной суспензии более высокой производительностью и позволяет разделять толстые, а следовательно большого диаметра, пластины, обеспечивает воспроизводимые размеры и форму кристаллов и плат со строго вертикальными боковыми гранями, а также большой выход годных структур, достигающий 98 ¸ 100 %. Схема процесса изображена на рис 4.
Диск закрепляется на шпинделе станка своей центральной частью. Такое закрепление не обеспечивает высокой жесткости диска. Жесткость режущей кромки обеспечивается его конструкцией. Режущая кромка выступает за наружный диаметр прижимных фланцев не более чем на 1,5 глубины резания. Алмазоносный режущий слой на металлический диск наносится с помощью специальной связки. Из всех видов связок (органическая, керамическая, металлическая) только металлическая связка полностью обеспечивает прочность сцепления алмазосодержащего слоя с металлическим диском и хорошую самозатачиваемость в процессе резания. Рекомендуемые режимы резки для слитков кремния: частота вращения диска – 5000 ¸ 8000 об/мин, скорость продольной подачи слитка – 30 ¸ 60 мм/мин, расход СОЖ около 3 л/мин. Натяжение диска периодически контролируется с помощью электронного прибора и регулируется не менее одного раза за рабочую смену. Перед началом каждой резки диск проверяют на степень выработанности алмазной кромки, отсутствие трещин, задиров. Для точности размеров отрезаемых пластин, качества их поверхности и ширины реза важна правильная установка диска на барабан режущего станка. В процессе резки диск не должен вибрировать и отклоняться от плоскости. Охлаждение при резке осуществляется путем подачи СОЖ.
2.3 Резка диском с внутренней алмазной кромкой
В настоящее время способ резания диском с внутренней режущей алмазной кромкой является наиболее перспективным и прогрессивным из всех существующих. Этим способом можно производить самые универсальные процессы резания слитков на пластины до резания пластин на отдельные кристаллы. Основой диска служит стальная фольга толщиной 0,1 ¸ 0,2 мм. Алмазосодержащую режущую кромку на металлическую основу наносят гальваническим способом, применяя в качестве связки никель.
Механизм резки состоит в хрупком разрушении обрабатываемой поверхности под действием нормальных усилий и в срезании микровыступов закрепленными в режущей кромке алмазными зернами (тангенциальные усилия). Нормальные усилия, передаваемые от диска через зерна алмаза на слиток, вызывают появление микротрещин, которые, увеличиваясь в процессе отрезания пластины, распространяются вглубь, смыкаются, образуя выколки. Затем эти выколки выкрашиваются и удаляются из зоны обработки. Помимо прочего, СОЖ, проникая в микротрещины обрабатываемой поверхности и оказывая капиллярное расклинивающее действие, интенсифицирует процесс резки. С увеличением частоты вращения диска нормальные и тангенциальные усилия уменьшаются, что повышает качество обработки поверхности и за счет уменьшения деформаций диска улучшает параллельность сторон пластин. Вместе с тем увеличение частоты вращения диска повышает производительность процесса. Однако, увеличение частоты вращения диска свыше 5000 об/мин вызывает возрастание вибрации станка и температуры в зоне резания. Схема процесса резки представлена на рис 5. К преимуществам резки диском с внутренней алмазной кромкой относятся высокая скорость резания (до 40 мм/мин), хорошее качество обработки поверхности (8 класс шероховатости), малый разброс по толщине пластин (±20 мкм), небольшие отходы материала.
Недостатки резки: сложность установки алмазного диска, его натяжения и центровки, зависимость качества и точности обработки от точности и качества инструмента.
2.4 Резка при помощи ультразвука
Одной из новейших технологий является резание при помощи ультразвуковых колебаний частиц абразива. Ультразвуковая резка применяется при обработке полупроводниковых пластин в тех случаях, когда необходимо получить кристаллы сложной конфигурации и заданного профиля.
На рис 6 показана схема процесса. Под режущую кромку инструмента подается абразивная суспензия. Торец инструмента помещается на небольшом расстоянии от обрабатываемой поверхности, что необходимо для достижения акустического контакта. Частицы абразивного вещества под влиянием ультразвуковой энергии, приобретаемой с инструмента, приобретают колебательное движение. Это движение вызывается способностью ультразвуковых волн при распространении в упругих средах (а абразивная суспензия есть упругая среда) вызывать разрежение и сгущение этих сред. В результате разрежения в абразивной суспензии образуются кавитационные пузырьки, которые в момент исчезновения создают большие давления.
Благодаря кавитационным явлениям частицы абразива с силой ударяются в обрабатываемый материал и выбивают из него микрочастицы. Поскольку в этом участвует большое количество частиц абразива, а частота ударов равна частоте ультразвука, то, не смотря на незначительные размеры откалываемых частиц, процесс резки происходит быстро (около 1 мм/мин). Так как инструменту можно придать любую форму, то при помощи этого метода можно вырезать детали любой конфигурации.
Станки для ультразвуковой резки обычно выполняют в виде двух отдельных частей: магнитостриктора и усилителя ультразвуковых колебаний.
2.4 Лазерное разделение пластин
Разделение с помощью лазерного излучения относится к бесконтактным способам, при которых отсутствуем механическое воздействие на обрабатываемый материал. Разделение можно выполнить либо с предварительным получением рисок (лазерное скрайбирование), либо путем сквозного прохода всей толщи материала (лазерная резка). Образование рисок происходит в результате испарения материала сфокусированным лазерным лучом большой мощности. При сквозной резке имеет место также и плавление.
С помощью лазерного луча можно производить резку сквозь слой оксида или металла. Благодаря отсутствию механического воздействия отсутствуют микросколы и микротрещины. Оплавление материала по краям риски уменьшает вероятность отслаивания пленочных покрытий. Кристаллографическая ориентация не оказывает влияния на качество разделения и форму кристаллов. Получаемые кристаллы имеют практически вертикальные боковые поверхности, что весьма облегчает автоматическую сборку.
К недостаткам лазерного разделения относятся: высокая стоимость и сложность оборудования, необходимость защиты поверхности специальной пленкой от загрязнений продуктами испарения и расплавления, возникновение зон со структурными нарушениями кремния.
Лазерное скрайбирование применяется в крупносерийном производстве для разделения пластин кремния диаметром до 76 мм. Арсенид галлия нельзя скрайбировать лазерным лучом из-за выделения токсичных соединений мышьяка.
3 Обработка поверхности пластин
Полученные полупроводниковые пластины нельзя сразу использовать для производства интегральных микросхем. Сначала они должны пройти предварительную обработку.
Поверхность пластин после резки весьма неровная: размеры царапин, выступов и ямок иногда намного превышают размеры будущих структурных элементов. Поэтому перед началом основных технологических операций пластины многократно шлифуют, а затем полируют. Цель шлифовки помимо удаления механических дефектов состоит также в том, чтобы обеспечить необходимую толщину пластины (200 ¸ 300 мкм), недостижимую при резке и параллельность плоскостей.
3.1 Шлифовка
Под шлифованием понимают процесс обработки поверхностей заготовок на твердых дисках – шлифовальниках из чугуна, стали, латуни, стекла и других материалов с помощью инструментов – шлифовальников и абразивной суспензии (обработка свободным абразивом) или с помощью алмазных шлифовальных кругов (обработка связанным абразивом).
Раньше в большинстве случаев шлифовка была односторонней, т.е. каждая из двух плоскостей пластины шлифовалась отдельно. Однако современная технология промышленного производства предусматривает двусторонню шлифовку пластин кремния свободным абразивом (рис 7). По сравнению с другими методами такое шлифование более производительно, обеспечивает высокую точность обработки поверхностей, не требует наклейки пластин. Остаточные механические напряжения распределены более равномерно, что позволяет получать пластины с меньшим изгибом.
Подаваемая через верхний шлифовальник суспензия равномерно окружает все пластины, образуя прослойку между шлифовальниками и обрабатываемыми поверхностями. При работе станка движение верхнего шлифовальника и кассет для пластин-сепараторов передается зернам абразива. Свободно перемещаясь и переворачиваясь они создают определенное давление на обрабатываемые поверхности. Это приводит к появлению микротрещин и микровыколок, которые отрываются от поверхности и уносятся в сборник с отработанной суспензией. Движение шлифовальника через цевочные колеса передается сеператорам. Пластины, увлекаемые сепараторами, совершают сложные перемещения между шлифовальниками, чем достигается равномерность их обработки и износа шлифовальников. Шлифование проводят в несколько этапов, постепенно уменьшая зернистость абразива.
По окончании шлифовки на поверхности все же остается механически нарушенный слой толщиной до нескольких микрон и выше, под которым расположен еще более тонкий, так называемый "физически нарушенный" слой. Последний характерен наличием "незримых" искажений кристаллической решетки и механических напряжений, возникающих в процессе шлифовки.
Удаление обоих нарушенных слоев и снижение неровностей поверхности до уровня, свойственного оптическим системам и составляющего сотни, а иногда десятки ангстрем осуществляется обезжириванием и полировкой.
3.2 Обезжиривание поверхности
Как уже было сказано, поверхность отшлифованной пластины не удовлетворяет качеством. Для ее доводки необходимо удалить молекулярные органические и химически связанные с поверхностью загрязнения, а затем – остаточные ионные и атомарные. Для этого применяют обезжиривание поверхности.
Обезжиривание (отмывка) в органических растворителях (толуоле, дихлорэтане, спиртах: этиловом, метиловом и др) применяется для удаления с поверхности пластин жиров животного и растительного происхождения, минеральных масел, смазок, воска, парафина и других органических и механических загрязнений и наиболее часто выполняется погружением, в парах, с помощью ультразвука, струйной обработкой.
Обезжиривание погружением (рис 8) выполняют в специальных герметичных установках с двумя-четырьмя сваренными в единый блок ваннами с повышающимся уровнем жидкости. Полупроводниковые пластины в химически инертных кассетах, например из фторопласта, погружают в ванну с
наименьшим уровнем и по мере очистки последовательно переносят в ванны с большим уровнем растворителя. В ванну с наивысшим уровнем из перегонного куба поступает чистый растворитель, а из нее избыток растворителя стекает в ванну с меньшим уровнем и т.д. Из ванны с наименьшим уровнем загрязненный растворитель сливается в отстойник, из которого поступает для очистки дисцилляцией в перегонный куб. Процесс обезжиривания интенсифицируют подогревом и перемешиванием растворителя. Ультразвуковое обезжиривание выполняют в специальных ваннах, дно и стенки которых совершают механические колебания с УЗ-частотой (рис 9).
В жидкости возникают вихревые акустические потоки с высокими скоростями, которые интенсивно перемешивают жидкость, а также упругие волны (сгустки и разрежения за счет смещения частиц жидкости). В местах разрежения жидкости появляются кавитационные пузырьки. Под действием сил, которые стремятся вернуть смещенные частицы в исходное положение, эти пузырьки после кратковременного существования захлопываются. При интенсивных колебаниях и захлопывании кавитационных пузырьков возникают ударные волны, сообщающие большие ускорения молекулам жидкости, которые с силой ударяются о поверхность обрабатываемых пластин и сбивают с них частицы загрязнений. Благодаря кавитации жидкость способна проникать в глубокие поры, каналы, углубления, которые при обычных методах остаются неочищенными.
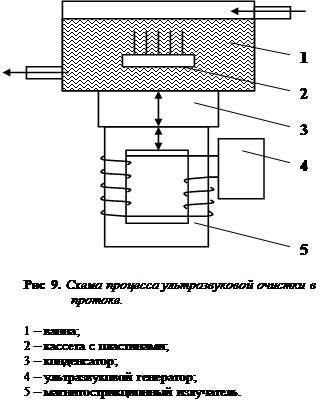
3.3 Полировка
Обезжиренные пластины подвергаются окончательной обработке – полировке. Чаще всего используется химическая полировка (травление), т.е. по существу растворение поверхностного слоя полупроводника в тех или иных реактивах. Обязательными компонентами таких реактивов являются окислитель (обычно азотная кислота) и растворитель образующегося окисла (обычно плавиковая кислота. Кроме этих компонентов в состав травителей входят ускорители и замедлители реакции. Выступы и трещины на поверхности стравливаются быстрее, чем основной материал, и в целом поверхность выравнивается. Чтобы раствор не застаивался у поверхности травления, применяется динамическое травление, т.е. вращение ванны во время процесса (рис 10)
Иногда химическую полировку сочетают с предварительной механической. Для этого тканые или нетканые материалы (сатин, батист, сукно, замшу и др) натягивают на обычный шлифовальный круг и закрепляют хомутиком. Полирование выполняют в несколько этапов, постепенно уменьшая размер зерна и твердость абразива, а на последнем этапе полностью исключают абразивное воздействие на обрабатываемый материал (рис 7).
4 Фотолитография
Именно внедрение литографии в полупроводниковое производство в 1957 г. определило дальнейшее развитие элементной базы электроники и позволило перейти от дискретных элементов к интегральным.
В производстве современных микросхем литография – самый универсальный технологический процесс. Она позволяет воспроизводимо и с большой точностью выполнять сложные рисунки с размерами элементов до одного и менее микрометра в разнообразных материалах. Литография применяется при изготовлении полупроводниковых и пленочных структур, для получения всевозможных канавок и углублений в полупроводниковых и иных материалах. С ее помощью изготавливают шаблоны – инструменты для проведения самого процесса литографии, получают сквозные отверстия в фольге при изготовлении прецезионных свободных масок, выводных рамок или лент, применяемых для автоматизированной сборки и герметизации интегральных микросхем.
Основное назначение литографии при изготовлении структур микросхем – получение на поверхности пластин контактных масок с окнами, соответствующими топологии формируемых технологических слоев, и дальнейшая передача топологии (рисунка) с маски на материал данного слоя.
Сущность процесса литографии заключается в следующем. Литография представляет собой сложный технологический процесс, основанный на использовании явлений, происходящих в актинорезистах при актиничном облучении.
Актинорезисты, на практике называемые просто резистами, представляют собой материалы, чувствительные к излучению определенной длины волны (к актиничному излучению), и стойкие (резист – сопротивляться) к технологическим воздействиям, применяемым в процессе литографии. Под действием излучения происходящие в резистах процессы необратимо меняют их стойкость к специальным составам – проявителям.
Резисты, растворимость которых в проявителе увеличивается после облучения, называются позитивными. Негативные резисты после облучения становятся практически нерастворимыми в проявителе.
В зависимости от типа применяемого излучения различают оптическую, рентгеновскую, электронную и ионную литографии. Более подробно мы рассмотрим оптическую литографию или фотолитографию. Фоторезисты представляют собой сложные полимерные композиции, в составе которых имеются фоточувствительные и пленкообразующие компоненты, растворители и специальные добавки.
Фотошаблоны являются основными инструментами фотолитографии, с их помощью производится локальное облучение фотослоя в соответствии с топологией микросхемы. Фотошаблон для изготовления структур микросхем – плоскопараллельная пластина (или гибкая пленка) из прозрачного для УФ-излучения материала с нанесенным на ее рабочую поверхность непрозрачным пленочным рисунком, соответствующим топологии одного из слоев структуры микросхемы и многократно повторенным со строго определенным шагом в пределах рабочей области пластины (пленки).
Для основы фотошаблонов применяют оптическое боросиликатное стекло или полимерные пленки, которые хорошо обрабатываются и не изменяют свойств под действием излучения. Для выполнения рисунка применяют галоидно-серебряную фотографическую эмульсию (эмульсионные фотошаблоны), металлы (металлизированные фотошаблоны) и полупрозрачные для видимого света оксиды или другие материалы (транспарентные, цветные фотошаблоны).
Рис 11 наглядно демонстрирует процесс фотолитографии. На поверхность двуокиси кремния наносится равномерный слой фоторезиста. Сверху на него накладывается фотошаблон. Сквозь него фоторезист засвечивается ультрафиолетовым светом. После этого пластину с фоторезистом проявляют; в процессе проявления засвеченные участки фоторезиста стравливаются и в этих местах обнажается поверхность двуокиси кремния. Оставшийся (незасвеченный) слой фоторезиста подвергают термическому дублению – полимеризации, в результате чего этот слой становится нечувствительным к химическим травителям. Поэтому, когда на следующем этапе пластину подвергают травлению, растворяются лишь обнаженные участки двуокиси кремния, вплоть до поверхности самой пластины, вследствие чего в оксидной маске получается необходимая совокупность «окон», через которые в дальнейшем проводят локальную диффузию или напыление контактов. Далее удаляется задубленный слой фоторезиста и пластина с оксидной маской готова к дальнейшей обработке.
5 Методы получения полупроводниковых слоев и переходов
Все рассмотренные ранее этапы технологии производства ИС можно охарактеризовать как предварительные. Действительно, проделав эти действия мы получим лишь заготовку интегральной схемы. Теперь же надо монтировать на ней элементы, которые и будут определять работу готового изделия. Для этого на пластине необходимо создать полупроводниковые слои и переходы. Данные этапы являются предварительными и основными этапами сборки микросхемы.
Полупроводниковые структуры интегральных микросхем нельзя изготовить, не применив хотя бы один из трех процессов: эпитаксиальное наращивание полупроводниковых слоев, диффузионное и ионное легирование. Рассмотрим каждый из них.
5.1 Эпитаксия
Эпитаксия – процесс наращивания монокристаллических слоев на монокристаллических подложках. Монокристаллические подложки в процессе роста эпитаксиального слоя выполняют ориентирующую роль затравки, на которой происходит кристаллизация.
Эпитаксиальные слои можно наращивать в вакууме, из парогазовои и жидкой фазы.
В зависимости от состава материалов слоя и подложки различают процессы автоэпитаксии и гетероэпитаксии. Если составы материалов практически одинаковы, например слой кремния на кремниевой пластине, процесс называют автоэпитаксией. Гетероэпитаксия – процесс ориентированного нарастания вещества, отличающегося по химическому составу от вещества подложки.
Для осаждения слоев кремния из парогазовой фазы в промышленном производстве используют кремнийсодержащие соединения: тетрахлорид кремния, силан. В соответствии с применяемыми исходными продуктами называют и методы: хлоридный и силановый.
Хлоридный метод основан на использовании химического взаимодействия паров тетрахлорида кремния с чистым водородом.

В результате реакции на подложке осаждается чистый кремний, а пары HCl уносятся потоком водорода. Эпитаксиальный слой осажденного кремния монокристалличен и имеет ту же структуру и ориентацию, что и подложка.
Если к парам тетрахлорида кремния добавить пары галоидных соединений бора (BBr3
) или фосфора (PCl3
), то эпитаксиальный слой будет иметь уже не собственную, а примесную проводимость, поскольку в ходе химической реакции в кремний будут внедряться акцепторные атомы бора или донорные атомы фосфора.
5.2 Диффузионное легирование
Внедрение примесей в исходную пластину (в эпитаксиальный слой) путем диффузии при высокой температуре является одним из основных способов создания диодных и транзисторных структур в интегральной технологии.
Диффузия может быть локальной и общей. В первом случае она осуществляется на определенных участках пластины через специальные маски (рис 12 а, б), во втором – по всей поверхности (рис 10 в).
Диффузию можно проводить и однократно и многократно (двойная, тройная диффузия). Например, в исходную пластину n-типа можно во время первой диффузии внедрить акцепторную примесь и получить р-слой, а затем во время второй диффузии внедрить в полученный слой (на меньшую глубину) донорную примесь и тем самым обеспечить трехслойную структуру (рис 10 г).
5.3 Ионное легирование
Основной особенностью ионного легирования является возможность воспроизводимого получения заданной концентрации примеси на данной глубине практически на любой площади пластины. Это обусловлено тем, что можно с большой точностью задавать ток ионного луча. Возможно получение неглубоких однородно легированных слоев, а также резких р-n переходов. Распределениями примесей можно легко управлять в широких пределах, изменяя дозу облучения, энергию и угол падения ионов.
Ионное легирование осуществляется путем бомбардировки пластины ионами примеси, ускоренными в специальных установках (ускорителях частиц) до значительной энергии. На схеме установки ионного легирования (рис 13) ионы примеси из источника ионов входят в анализатор по массе. Необходимость разделения ионов по массе вызвана тем, что вытягиваемый из источника поток ионов неоднороден по составу; в нем присутствуют ионы различных элементов и соединений и многозарядные ионы. Для разделения ионов по отношению массы к заряду применяют различные сепараторы, которые основаны на взаимодействии движущегося иона с магнитными и электрическими полями или с комбинацией этих полей. В большинстве установок сепараторами являются секторные магнитные системы, в которых происходит Поворот пучка ионов на угол менее 180° (например, 45°, 6О0
или 90°).
Ионы с определенным отношением массы к заряду входят в электростатический ускоритель ионов, к электродам которого от отдельного высоковольтного источника подводится напряжение, в отдельных установках до 200 кВ и выше. Ускоренные ионы через щель поступают в фокусирующую систему, а затем в сканирующую систему, которая обеспечивает перемещение сфокусированного пучка ионов по полупроводниковой пластине, расположенной в приемной камере. В установке обеспечивается необходимый высокий вакуум. Получаемый ток пучка ионов в различных установках составляет от десятков микроампер до нескольких миллиампер. Сканирование пучка в одном поперечном направлении механическое, а в другом электростатическое, площадь сечения пучка 1 ¸ 2 мм2
. Число одновременно закладываемых в камеру пластин с диаметром 75 ¸ 150 мм в разных установках составляет 96 ¸ 24. Следует заметить, что глубина проникновения ионов, зависящая от их энергии, составляет 0,1 ¸ 0,5 мкм, т.е. очень мала и недостижима при диффузионном легировании. Это позволяет получать резкие профили (большие градиенты) распределения примеси.
Ионное легирование характеризуется универсальностью и гибкостью, позволяет с высокой точностью управлять количеством легирующей примеси (путем регулировки тока пучка ионов) и глубиной внедрения – изменением энергии (напряжения источника). Процесс ионного легирования может осуществляться при низких температурах, вплоть до комнатных, благодаря чему сохраняются исходные электростатические свойства кристаллов. Это большое преимущество метода перед диффузионным легированием. Низкая температура позволяет проводить ионное легирование на любом этапе технологического цикла. Однако недостатком метода (кроме необходимости сканирования пучка) является возникновение обилия радиационных дефектов в облученном полупроводнике, вплоть до образования аморфного слоя. Такие дефекты полностью удается устранить путем кратковременного отжига (в кремнии при 900 ¸ 1100°С).
6 Технология полупроводниковых биполярных и МДП ИМС
Итак, теперь мы подошли вплотную к основным технологическим операциям изготовления интегральных микросхем.
Современные интегральный микросхемы (в дальнейшем – ИМС) можно разделить на два класса: полупроводниковые и гибридные. К гибридным относятся ИМС, в которых содержатся отдельные навесные элементы. К полупроводниковым относятся ИМС, все элементы которой выполняются в объеме или на поверхности единой полупроводниковой подложки. В процессе изготовления такой схемы необходимо избирательно формировать транзисторы, диоды, резисторы, конденсаторы и их соединения на одной полупроводниковой пластине – подложке и обеспечивать достаточно хорошую изоляцию, исключающую паразитное взаимодействие между ними.
6.1 Элементы ИМС
Технология ИМС предполагает значительное отличие элементной базы от обыкновенной электротехники. На рис 13 представлены основные элементы ИМС.
Полупроводниковая ИМС имеет общую подложку из кремния р-типа. На ней выполняются транзисторы (рис 14 а), резисторы (рис 14 б), конденсаторы (рис 14 в) и диоды.
Диоды образуют из транзисторных структур, используя различные способы соединений их электродов.
Имеется пять способов включения транзистора как диода, отличающихся различной крутизной прямой ветви ВАХ и временем восстановления обратного сопротивления. Наименьшее время переключения имеет диод, одним электродом которого служит эмиттер, а другим – соединенные вместе коллектор и база.
Полупроводниковые резисторы изготовляют одновременно с активными элементами. Они обычно выполняются в виде прямоугольного слоя полупроводника при базовой диффузии и называются диффузионными. В таких резисторах используется объемное сопротивление материала, имеющего определенную степень легирования. Диффузионные резисторы могут иметь номинальные значения сопротивлений от нескольких ом до двух десятков килоом.
Конденсаторы полупроводниковых ИМС выполняются двух видов. Часто в качестве конденсаторов используют смещенный в обратном направлении р-n переход. Емкость такого конденсатора зависит от величины обратного напряжения, а последовательно с ней всегда оказывается включенным большое объемное сопротивление полупроводникового материала. Таким образом можно изготовить конденсаторы емкостью до сотни пикофарад. Другой разновидностью являются металл-окисел-полупроводниковые конденсаторы, которые образуются областью n+
-типа (от эмиттерной диффузии) и металлической пленкой алюминия, разделенными слоем двуокиси кремния. Эти конденсаторы могут иметь емкость до нескольких сотен пикофарад.
Рассмотренные элементы полупроводниковых ИМС обладают паразитными компонентами, ограниченным диапазоном номинальных значений и весьма малыми рассеиваемыми мощностями. При разработке топологии ИМС необходимо стремиться к исключению паразитных связей между ее элементами и к обеспечению требуемого теплоотвода.
6.2 Изготовление биполярных ИМС с изоляцией
p
-
n
переходами
На рис 15 показана структура интегрального n-р-n-транзистора изолированного p-n переходом. В этом транзисторе подложкой является кремний р-типа; на ней созданы эпитаксиальный n-слой и так называемый скрытый n+
-cлoй. Изолирующий р-n-переход создается путем диффузии акцепторной примеси на глубину, обеспечивающую соединение образующихся при этой диффузии р-областей с р-подложкой. В этом случае эпитаксиальный n-слой разделяется на отдельные n-области (изолирующие «карманы»), в которых и создаются потом транзисторы. Эти области будут электрически изолированы только в том случае, если образовавшиеся р-n переходы имеют обратное включение. Это достигается, если потенциал подложки n-р-n транзистора будет наименьшим из потенциалов точек структуры. В этом случае обратный ток через р-n переход незначителен и практически исключается связь между n-областями (карманами) соседних транзисторов.
Теперь, зная принцип изоляции p-n переходом, и воспользовавшись материалом предыдущих пунктов, можно дать развернутое описание технологии.
а)
Изготовление биполярных ИМС методом разделительной диффузии насквозь эпитаксиального слоя (рис 16) состоит из двух этапов: изготовления эпитаксиальной структуры со скрытыми n+
-областями (а-в) и изготовления биполярной ИМС на этой структуре (г-з).
Эпитаксиальные структуры обычно изготавливают в отдельном процессе. Легирующая примесь для скрытых n+
-областей должна иметь высокую растворимость в кремнии при малой глубине диффузии. Поверхностная концентрация скрытого слоя не должна быть слишком высокой, так как это увеличивает диффузию в растущий эпитаксиальный слой, а также механические напряжения и плотность дислокаций, вызванные несоответствием атомных радиусов кремния и примеси. В связи с этим для получения скрытого n+
-слоя применяют сурьму и мышьяк, которые имеют меньшие, чем фосфор, коэффициенты диффузии. Однако при использовании мышьяка в скрытых слоях наблюдается большое количество дефектов. Поэтому для создания высоковольтных биполярных микросхем скрытые слои легируют преимущественно сурьмой. Эпитаксиальный n-слой выращивают обычно хлоридным методом. Толщина слоя 3 ¸ 25 мкм в зависимости от назначения ИМС.
По рассмотренной технологии изготавливают ИМС первой и второй степени интеграции. Возможности процесса для получения более высоких степеней интеграции ограничены из-за ряда недостатков ИМС: наличия больших токов утечки, большой площади изолирующего р-n перехода, а значит и емкости паразитной связи, низкой радиационной стойкости.
б)
Изготовление биполярных ИМС методом коллекторной изолирующей диффузии (КИД) – изолированные карманы и одновременно коллекторные n+
n++
-области формируются в процессе диффузии донорной примеси сквозь тонкий (1 ¸ 2 мкм) эпитаксиальный p-слой (рис 17). Для изолирующей диффузии необходимы окна в SiO2
-маске (на рисунке не указаны), перекрывающие скрытые n+
-области. После диффузии получаются изолированные n+
p-карманы. Базовая p+
-диффузия проводится без SiO2
-маски, что исключает фотолитографию и упрощает технологический процесс.
В КИД-технологии число фотолитографий уменьшается по сравнению с предыдущим процессом. Область коллектора сильно легирована, поэтому нет необходимости для повышения быстродействия ИМС проводить дополнительную диффузию золота или другой понижающей время жизни неосновных носителей тока примеси. Однако в эпитаксиальной базе дрейф носителей от эмиттера к коллектору уменьшен, что понижает быстродействие ИМС. Кроме этого тонкий эпитаксиальный слой ограничивает пробивное напряжение коллектор-база из-за распространения объемного заряда в базовую область.
6.3 Изготовление биполярных ИМС с диэлектрической изоляцией
Диэлектрическая изоляция обеспечивает лучшие параметры ИМС.
а)
Изоляция пленкой диэлектрика с использованием поликристаллического кремния реализуется в эпик-процессе. Исходной заготовкой является однослойная nn+
-структура (рис 18). После локального травления на глубину около 15 мкм и удаления SiO2
-маски термически выращивают или осаждают из паро-газовой фазы пленку диоксида кремния толщиной 1 ¸ 2 мкм. Поверх нее осаждают слой высокоомного поликремния толщиной 175 ¸ 200 мкм. Для получения изолированных n+
n-карманов лишнюю часть кремния сошлифовывают. Полученная при этом подложка структуры ИМС, как и при изоляции p-n-переходом, проводящая, хотя и имеет более высокое удельное сопротивление. Для улучшения изоляции слой SiO2
иногда заменяют слоем Si3
N4
, двойными слоями SiO2
–Si3
N4
или SiO2
–SiC.
Таким образом, получение кремниевых карманов в поликристаллическом кремнии выполняется по меза-эпитаксиальной технологии. Элементы ИМС в этих карманах далее формируются по планарной технологии. В целом процесс можно охарактеризовать как меза-эпитаксиально-планарный. Наряду с приведенным маршрутом имеются его модификации. Например получение комплементарных биполярных ИМС, в составе которых имеются p-n-p и n-p-n транзисторы (рис 19).
Эпик-процессы относительно сложны и трудоемки. Основная сложность заключается в необходимости прецизионной механической обработки. К недостатку метода также относится относительно небольшая степень интеграции. ИМС.
Эпик-процессы относительно сложны и трудоемки. Основная сложность заключается в необходимости прецизионной механической обработки. К недостатку метода также относится относительно небольшая степень интеграции. ИМС.
б) Необходимо отметить, что эпик-технология требует прецезионной механической обработки, которая затруднена из-за наличия прогиба подложки в результате различия коэффициентов температурного линейного расширения монокристаллического и поликристаллического кремния и оксида кремния. Различие микротвердости этих материалов приводит к наличию ступенек на поверхности, что затрудняет получение качественной металлизации. С целью устранения отмеченных недостатков разработаны технологические процессы, в которых вместо поликристаллического кремния для изолирующих областей и основания кристаллов используют стекло, ситалл или керамику, т.е. проводят изоляцию диэлектрическим материалом. Такие процессы имеют общее название «кремний в диэлектрике» (КВД). У них много общего с обычным эпик процессом. Отличие состоит в том, что сначала фор мируют элементы ИМС (рис 20,а), а затем пластину с элементами со стороны выводов подвергают локальному травлению – создают мезаобласти (рис 20,б). После этого пластину со стороны мезаобластей прикрепляют к вспомогательной пластине (рис 20,в), а ее обратную сторону подвергают шлифованию (рис 20,г) с последующим нанесением изолирующего диэлектрика (рис 20,д). Завершают процесс удалением вспомогательной пластины (рис 20,е) и металлизацией.
Диэлектрическая изоляция по сравнению с p-n изоляцией технологически сложнее; площадь, занимаемая элементами, больше. Но, благодаря лучшим электрическим свойствам, она постоянно совершенствуется и широко применяется в производстве биполярных ИМС.
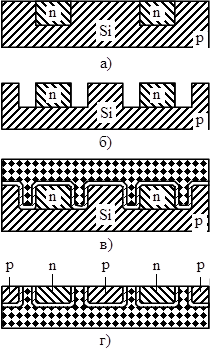
6.4 Изготовление биполярных ИМС с комбинированной изоляцией
В основу изготовления полупроводниковых биполярных ИМС с комбинированной изоляцией положены процессы, обеспечивающие формирование элементов с изоляцией p-n переходами их горизонтальных участков и диэлектриком – вертикальных боковых областей.
а)
Изопланарные процессы основаны на использовании кремниевых пластин с тонким (2 ¸ 3 мкм) эпитаксиальным слоем, селективного термического окисления кремния на всю глубину эпитаксиального слоя вместо разделительной диффузии, проводимой в обычном планарно-эпитаксиальном процессе. Реализация такого процесса достигается использованием при маскировании на первых стадиях формирования структуры ИМС специфический свойств нитрида кремния Si3
N4
. Нитрид кремния препятствует превращению кремния в SiO2
в местах, где Si3
N4
служит в качестве защитного слоя. Кроме того, нитрид кремния легко удаляется травителем на основе фосфорной кислоты, который не воздействует на оксид. Изопланарная технология позволяет создавать тонкие базовые области и небольшие коллекторные области с оксидными боковыми стенками и тем самым обеспечивает получение транзисторных структур малых размеров и высокого быстродействия. Имеются две разновидности изопланарной технологии: «Изопланар I» и «Изопланар II». При изготовлении ИМС по процессу «Изопланар I» в качестве исходной используют кремниевую пластину p-типа с эпитаксиальным n-слоем и скрытым n+
-слоем. Начинают процесс с наращивания на поверхности пластины слоя нитрида кремния., в котором с помощью фотолитографии формируют окна под изолирующие области. Затем производят травление кремния на глубину, превышающую половину толщины эпитаксиального слоя, после чего окислением вытравленные канавки заполняют оксидом кремния. После удаления слоя нитрида при маскировании оксидом кремния в локализованных островках кремния («карманах») формируют транзисторные структуры и осуществляют металлизацию.
Процесс «Изопланар II» позволяет получать структуры с эмиттерными областями, выходящими боковой стороной на слой изоляции. Приконтактные n+
-области коллекторов расположены в самостоятельных карманах, соединенных с эмиттер-базовыми карманами, скрытыми n+
-областями. Этот процесс предъявляет менее жесткие требования к точности совмещения слоев, так как окно смещается в диоксид, диффузия эмиттерной примеси в который не происходит. Базовую диффузию можно проводить по всей площади карманов, что также упрощает процесс.
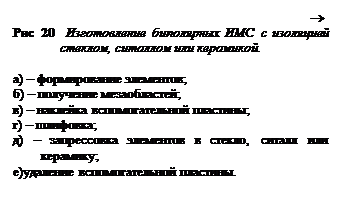
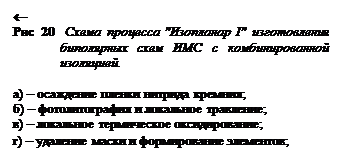 
Изопланарная технология совмещает преимущества планарной и меза-технологии, она позволяет избежать неоднородности электрического поля на периферии планарного p-n перехода, снизить паразитные емкости между активными областями структуры, повысить качество изоляции и степень интеграции ИМС.
Процессы «Изопланар I» и «Изопланар II» иллюстрируют рис 21 и рис 22 соответственно.
6.5 Изготовление толстооксидных
p
-МОП-ИМС и
n
-МОП-ИМС
Рассмотрим наиболее простые типовые процессы изготовления ИМС с металлическими затворами и толстой пленкой оксида между металлизацией и пластиной кремния. Это уменьшает паразитные емкости, а также дает некоторые другие преимущества перед ранее применяемой тонкооксидной технологией.
|