Содержание:
Введение...................................................................................... 2
Раздел 1. Классификация устройств для очистки воздуха от пыли............................................................................................... 4
Раздел 2. Виды воздушных фильтров......................... 7
2.1. Ячейковые фильтры.................................................................................... 7
2.2. Самоочищающиеся масляные фильтры.............................................. 7
2.3. Рулонные фильтры....................................................................................... 8
2.4. Воздушные фильтры высокой эффективности с материалами ФП 9
2.5. Электрические воздушные фильтры................................................... 12
Раздел 3. Пылеуловители для очистки выбросов в атмосферу.......................................................................................................... 14
3.1. Общая характеристика пылеуловителей.......................................... 14
3.2. Пылеосадочные камеры.......................................................................... 15
3.3. Инерционные пылеуловители............................................................... 16
3.4. Циклоны......................................................................................................... 19
3.4.1. Общая характеристика........................................................................... 19
3.4.2. Батарейные циклоны (мультициклоны)................................................. 21
3.5. Ротационные пылеуловители............................................................... 22
3.6. Вихревые пылеуловители....................................................................... 23
3.7. Фильтрационные пылеуловители....................................................... 24
3.7.1. Волокнистые фильтры............................................................................ 25
3.7.2 Тканевые фильтры.................................................................................... 27
3.7.3. Зернистые фильтры................................................................................. 28
3.8. Аппараты мокрой очистки газов........................................................... 29
3.8.1. Полые и насадочные аппараты.............................................................. 30
3.8.2. Барботажные и пенные аппараты........................................................ 31
3.8.3. Аппараты ударно-инерционного типа................................................... 32
3.8.4. Аппараты центробежного типа............................................................ 34
3.8.5. Скруббер Вентури.................................................................................... 35
3.8.6. Электрические фильтры......................................................................... 36
Приложение............................................................................. 38
Список используемой литературы:....................... 45
Введение
Большое число современных химико-технологических процессов связано с дроблением, измельчением и транспортированием сыпучих материалов. При этом неизбежно часть материалов переходит в аэрозольное состояние, образуя пыль, которая с технологическими или вентиляционными газами выбрасывается в атмосферу.
Пылевые частицы имеют большую суммарную поверхность, вследствие чего их химическая и биологическая активность очень высока. Некоторые вещества в аэродисперсном состоянии приобретают новые свойства, например способность взрываться. Частицы промышленной пыли имеют различные форму и размеры. Понятие размера частицы ввиду большого разнообразия форм условно. В пылеулавливании принято характеризовать размер частицы величиной, определяющей скорость ее осаждения. Такой величиной служит седиментационный диаметр (диаметр шара, скорость осаждения и плотность которого равны скорости осаждения и плотности сравниваемой частицы). При этом сама частица может иметь произвольную форму. Пылевые частицы различной формы при одной и той же массе оседают с разной скоростью. Чем ближе их форма к сферической, тем быстрее они оседают. Наибольший и наименьший размеры частиц характеризуют диапазон дисперсности данной пыли.
В настоящее время известно несколько сотен различных конструкций аппаратов для очистки газов от пыли. Несмотря на многообразие, все они являются вариантами аппаратурного оформления, где использованы немногие основные принципы осаждения или задержания взвешенной фазы.
Естественными движущими силами процесса осаждения пылевых частиц в потоке являются силы тяжести и диффузии. Эти силы, однако, являются недостаточными для самопроизвольной очистки газов. Хотя улавливание наиболее крупных частиц иногда и осуществляют посредством естественного осаждения в гравитационном поле, в большинстве аппаратов современной пылеочистной техники используют более интенсивное силовое поле, создаваемое искусственно.
Так, для пылеулавливания широко применяют инерционные силы, проявляющиеся при изменении направления и скорости пылегазового потока, а также силы электрического притяжения предварительно заряженных частиц к осадительному электроду.
Находит применение в пылеулавливании и процесс коагуляции, в результате которого происходит образование укрупненных агрегатов, состоящих из нескольких частиц пыли. Этот процесс интенсифицируют с помощью инерционных, электрических или термических сил. В пылеулавливающих устройствах основной процесс осаждения частиц часто сопровождается побочными нежелательными процессами. Так, например, уже осажденные частицы могут вновь увлекаться газовым потоком, а агрегаты частиц, образовавшиеся в процессе коагуляции, разрушиться и т. д.
Для подавления вторичных процессов, мешающих пылеулавливанию, принимают специальные меры — смачивают осадительные поверхности, снижают скорость газа, повышают электропроводность частиц, вводят в газ жидкость для увеличения прочности агрегатов частиц и т. п.
Чтобы выделить пылевидные частицы из газов, осуществляют фильтрование газов через пористые перегородки. В этом случае используют инерционный, электрический или диффузионный механизм осаждения частиц. Выбор механизма осаждения зависит от размеров пылевых частиц, скорости газового потока и других факторов.
В зависимости от природы сил, используемых в пылеулавливающих аппаратах для отделения частиц пыли от газового потока, их подразделяют на четыре основные группы пылеосадительные камеры и циклоны, аппараты мокрой очистки газов, пористые фильтры, электрические фильтры.
Раздел 1. Классификация устройств для очистки воздуха от пыли.
Пылеулавливающее оборудование при всем его многообразии может быть классифицировано по ряду признаков: по назначению, по основному способу действия, по эффективности, по конструктивным особенностям. Классификация пылеулавливающего оборудования дана в ГОСТ 12.2.043-80. Оборудование пылеулавливающее. Классификация.
Оборудование, применяемое для очистки от пыли воздуха в системах вентиляции, кондиционирования и воздушного отопления, а также для защиты от загрязнения пылью воздушной среды зданий, сооружений и прилегающих к ним территорий, метрополитенов, подземных и открытых горных выработок, подразделяется на следующие типы:
· оборудование, применяемое для очистки от взвешенных частиц пыли воздуха, подаваемого в помещения системами приточной вентиляции, кондиционирования и воздушного отопления – воздушные фильтры
;
· оборудование, применяемое для очистки от пыли воздуха, выбрасываемого в атмосферу системами вытяжной вентиляции – пылеуловители
.
Пылеулавливающее оборудование в зависимости от способа отделения пыли от воздушного потока применяют следующих исполнений: оборудование для улавливания пыли сухим
способом, при котором отделенные от воздуха частицы пыли осаждаются на сухую поверхность; оборудование для улавливания пыли мокрым
способом, при котором отделение частиц от воздушного потока осуществляется с использованием жидкостей.
Пылеулавливающее оборудование по принципу действия подразделяется на группы, по конструктивным особенностям – на виды и действует по сухому (табл. 1) и мокрому (табл. 2) способу.
Таблица 1.
Группы и виды пылеулавливающего оборудования для улавливания пыли сухим способом.
Группа оборудования
|
Вид оборудования
|
Область применения
|
воздушных фильтров
|
пылеуловителей
|
Гравитационное
|
Полое
Полочное
|
-
-
|
+
+
|
Инерционное
|
Камерное
Жалюзийное
Циклонное
Ротационное
|
-
-
-
-
|
+
+
+
+
|
Фильтрационное
|
Тканевое
Волокнистое
Зернистое
Сетчатое
Губчатое
|
-
+
-
+
+
|
+
-
+
-
-
|
Электрическое
|
Однозонное
Двухзонное
|
-
+
|
+
+
|
Примечание. Знак «+» означает применение; знак «-» означает неприменение.
Таблица 2.
Группы и виды пылеулавливающего оборудования для улавливания пыли мокрым способом.
Группа оборудования
|
Вид оборудования
|
Область применения
|
воздушных фильтров
|
пылеуловителей
|
Инерционное
|
Циклонное
Ротационное
Скрубберное
Ударное
|
-
-
-
-
|
+
+
+
+
|
Фильтрационное
|
Сетчатое
Пенное
|
+
-
|
-
+
|
Электрическое
|
Однозонное
Двухзонное
|
-
+
|
+
+
|
Биологическое
|
Биофильтр
|
-
|
+
|
Примечание. Знак «+» означает применение; знак «-» означает неприменение.
Пылеулавливающее оборудование, в котором отделение пыли от воздушного потока осуществляется последовательно в несколько ступеней, отличающихся по принципу действия, конструктивным особенностям и способу очистки, относят к комбинированному
пылеулавливающему оборудованию.
Классификация пылеулавливающего оборудования согласно ГОСТ 12.2.043-80 приведена на схеме. На схеме дополнительно показан вид пылеулавливающего оборудования – биофильтр, применяемый для очистки выбросов, от ряда органических пылей.
Раздел 2. Виды воздушных фильтров.
2.1. Ячейковые фильтры
Ячейковые фильтры являются старейшим видом воздушных фильтров. В настоящее время применяют унифицированные ячейковые фильтры с фильтрующим слоем из различных материалов. Ячейка фильтра представляет собой разъемную металлическую коробку. В корпус ячейки укладывается фильтрующий слой. Рамка ячейки имеет ручки для установки и извлечения из панели.
Фильтр ФяР
(фильтр Река). Фильтрующим слоем являются металлические гофрированные сетки. Сетки промасливаются специальными маслами (висциновым и др.). Регенерация осуществляется путем промывки запыленных ячеек фильтра в содовом растворе.
Фильтры ФяВ
заполнены гофрированными винипластовыми сетками. По эффективности и пылеемкости идентичны фильтрам ФяР. Могут применяться как в замасленном, так и сухом виде. При применении в сухом виде эффективность несколько ниже.
В фильтрах ФяП
в качестве фильтрующего материала применен губчатый пенополиуретан, обработанный в растворе щелочи для придания ему воздухопроницаемости. Фильтр обладает меньшей пылеемкостью, чем ФяВ. Регенерация производится промывкой водой. Простота регенерации облегчает эксплуатацию фильтра.
Фильтр ФяУ
заполнен стекловолокнистым упругим фильтрующим материалом ФСВУ. Пылеемкость фильтра меньше, чем ФяВ и ФяР. Запыленный материал подлежит замене.
Ячейки фильтров устанавливают в плоские или в V
-образные панели.
2.2. Самоочищающиеся масляные фильтры
Самоочищающиеся фильтры лишены основного недостатка ячейковых фильтров – необходимости выполнения трудоемкой операции по ручной промывке запыленных панелей. Кроме того, они компактны, допускают большую удельную воздушную нагрузку, чем ячейковые фильтры.
Применяют два вида самоочищающихся масляных фильтров – с фильтрующим слоем, образованным пружинной сеткой, и слоем из сетчатых шторок.
Самоочищающиеся масляные фильтры с пружинной сеткой.
Очистка воздуха производится при его последовательном прохождении через две движущиеся бесконечные пружинные сетки, смоченные маслом (воздух проходит через четыре плоскости, смоченные маслом). Каждая сетка приводится в движение с помощью двух пар валов, получающих вращение от электродвигателя через редуктор. Необходимо обеспечить равномерное движение воздуха по всему сечению фильтра со скоростью до 3 м/с.
При движении пружинных сеток их нижние части погружаются в масляную ванну и при этом очищаются от осевшей на них пыли. Масло в ванне периодически сменяется. Применяют масло висциновое, веретенное, трансформаторное, турбинное и др. Сорт масла должен соответствовать времени года согласно рекомендации завода-изготовителя фильтров.
Самоочищающийся масляный фильтр с сетчатыми шторками.
Фильтрующий слой создают сетчатые шторки, прикрепленные к втулочным цепям, надетым на приводные шестеренки. На вертикальных участках движения цепей шторки перекрывают друг друга. В нижней и верхней частях фильтра шторки разъединяются. При прохождении шторок через масляную ванну они промываются, и слой масла обновляется. Шторки движутся периодически – через 12 минут.
Фильтрующая панель поворачивается за 12 – 20 с. (в зависимости от размеров фильтра). Удельная воздушная нагрузка фильтра 8350 м3
/(ч×м3
). Установка фильтров снабжается системой маслоснабжения с его подогревом, циркуляцией и очисткой.
Рекомендуемая скорость воздуха при прохождении фильтра 2,5 – 2,6 м/с.
Самоочищающиеся фильтры со шторками выпускает ряд зарубежных фирм и отечественных предприятий.
2.3. Рулонные фильтры
Промышленность до недавнего времени изготовляла рулонный фильтр ФРУ, предназначенный для очистки приточного и рециркуляционного воздуха с запыленностью менее 0,5 мг/м3
. Возможно применение фильтра и при большей запыленности при технико-экономическом обосновании. Серийно выпускались фильтры производительностью 20-120 м3
/ч. Фильтры могут устанавливаться в вентиляционных камерах и в кондиционерах.
Фильтр собирают из двух или трех секций в зависимости от требуемой производительности. Секция состоит из сварного корпуса, подвижной решетки. Решетка натянута между нижним и верхним валами. Нижний вал – ведущий. В верхней и нижней частях каркаса установлены катушки с фильтрующим материалом. Перемещение решеток и вращение катушек осуществляется с помощью электродвигателя мощностью 0,25 кВт через редуктор. По мере загрязнения материал перематывается с верхних катушек на нижние. В фильтре применяют фильтрующий материал типа ФСВУ. Он представляет собой слой из стеклянного волокна толщиной 30 – 50 мм, промасленный и пропитанный в процессе изготовления связующими веществами. Слой обладает рыхлостью и упругостью. Материал изготовляется в виде полотнищ длиной 15 м. Подвижная решетка обеспечивает необходимую жесткость и прочность фильтрующего слоя.
Перемотка катушек производится периодически при достижении определенного значения гидравлического сопротивления в результате накопления пыли. Скорость перемещения материала при перемотке около 0,5 м/мин.
2.4. Воздушные фильтры высокой эффективности с материалами ФП
Материалы ФП
и процесс их получения разработаны в Физико-химическом институте им. Л. Я. Карпова. Материалы ФП представляют собой исключительно равномерные слои ультратонких полимерных волокон.
Поскольку механическая прочность слоя волокон материала ФП невелика, он нанесен на тканевую подложку (марля, бязь, перкаль), которая и обеспечивает необходимую прочность.
В большинстве материалов ФП волокна сцеплены между собой за счет сил трения, и фильтрующий слой выдерживает значительную деформацию. Удлинение при разрыве – от 30 – 50%. Высокая пластичность обеспечивает надежную эксплуатацию фильтров, снаряженных материалами ФП.
Материалы ФП в зависимости от того, из какого полимера они изготовлены, стойки к различным химическим веществам, к высоким температурам – до 250 - 270°C.
Волокна ФП имеют вид ленты, ширина которой в 3 – 5 раз больше толщины. Материалы ФПП обычно обозначают по размеру волокон, а именно по ширине: например, ФПП-15, ФПП-25, ФПП-70 – обозначает фильтр Петрянова из перхлорвиниловых волокон шириной волокон соответственно 1,5; 2,5; 7,0 мкм.
Материалы ФП, изготовленные из полимеров с высокими изоляционными свойствами (перхлорвинил, полистирол), могут получать и удерживать электрические заряды. В результате повышается эффективность фильтра.
При длительном хранении, механическом воздействии, при высокой влажности, под воздействием ионизирующих излучений фильтровальные материалы теряют электрические заряды. Это же происходит и при накоплении в фильтре пыли в результате длительной эксплуатации.
Данные для выбора материалов ФП, применяемых в фильтрах систем вентиляции, приведены в табл. 3.
Таблица 3.
Выбор материалов ФП
Название фильтра
|
Рекомендуемая марка материала ФП
|
Удельная нагрузка по воздуху, нм3
/(ч*м2
)
|
Эффективность очистки*, % (не менее)
|
Очистка приточного воздуха и нетоксичных вентиляционных выбросов.
|
ФПП-70-0,2
|
до 150
|
90
|
Очистка рецеркуляционного и систем кондиционирования.
|
ФПП-70-0,5
|
до 150
|
99
|
Очистка вентиляционных выбросов, содержащих токсичные или радиоактивные аэрозоли.
|
ФПП-15-1,5
|
до 150
|
99-99,9
|
Стерилизация вентиляционного воздуха.
|
ФПП-15-3
|
до 150
|
99,9-99,99
|
Очистка вентиляционного воздуха и других газов с целью улавливания и возврата ценных продуктов.
|
ФПП-25-3
|
до 150
|
99,9-99,99
|
Очистка вентиляционных выбросов «горячих» камер, боксов, каньонов и т.п.
|
ФПА-15-4
|
до 150
|
99,9-99,99
|
Очистка вентиляционного воздуха, содержащего аэрозоли особо опасных веществ
|
ФПП-15-4,5
|
до 150
|
99,9-99,995
|
* - данные по аэрозолям относятся к высокодисперсным аэрозолям с размером частиц 0,1-0,2 мкм.
|
Широко распространен фильтр тонкой очистки – рамочный фильтр ЛАИК
(лаборатория института Карпова). В одном м3
фильтра расположено до 100 м2
поверхности фильтрующего материала. П-образные рамки размещаются с чередованием открытых и закрытых сторон в двух противоположных направлениях. Техническая характеристика фильтра ЛАИК дана в табл. 4.
Таблица 4.
Характеристики фильтра ЛАИК
Марка фильтра
|
Фильтрующая поверхность
|
Фильтрующий материал
|
Производительность, нм3
/ч
|
Сопротивление Па
|
Габариты, мм
|
Допустимая температура, 0
С
|
Назначение
|
При нагрузке 150 м3
/ч*м2
|
Входное сечение
|
Длина
|
ЛАИК
СП-3/15
|
15,1
|
2250
|
180
|
565*735
|
780
|
60
|
Для приточной и вытяжной вентиляции
|
ЛАИК
СП-6/15
|
15,1
|
2250
|
240
|
565*735
|
780
|
ЛАИК
СП-3/17
|
17,5
|
ФПП-15
|
2550
|
150
|
615*995
|
355
|
ЛАИК
СП-6/17
|
17,5
|
2550
|
210
|
615*995
|
355
|
ЛАИК
СП-3/21
|
21,0
|
3150
|
290
|
650*690
|
625
|
Для стерилизации воздуха и систем кондиционирования
|
ЛАИК
СП-6/21
|
21,0
|
3150
|
340
|
650*690
|
625
|
ЛАИК
СП-3/26
|
26,0
|
3950
|
400
|
660*665
|
750
|
ЛАИК
СП-6/26
|
26,0
|
3950
|
460
|
660*665
|
750
|
ЛАИК СЯ
|
16,0
|
2400
|
130
|
550*630
|
310
|
Для приточной вентиляции и систем кондиционирования
|
Для очистки значительных количеств воздуха из отдельных фильтров устраивается фильтровальная перегородка, в которой устанавливают несколько десятков или более фильтров.
2.5. Электрические воздушные фильтры
Фильтры, применяемые для очистки от пыли приточного воздуха, устроены несколько иначе, чем электрические пылеуловители, используемые для очистки выбросов в атмосферу.
Электрический воздушный фильтр – двухзонный. Вначале поток воздуха, подвергающегося очистке, проходит зону 1, которая представляет собой решетку из металлических пластин с натянутыми между ними коронирующими электродами из проволоки. К электродам подведен постоянный ток напряжением 13-15 кВ положительного знака от выпрямителя 2. Получив электрический заряд при прохождении ионизационной зоны, пылевые частицы в потоке воздуха направляются в осадительную зону 3. Она представляет собой пакет металлических пластин, расположенных параллельно друг другу на расстоянии 8 – 12 мм. К каждой второй пластине подведен ток напряжением 6,5 – 7,5 кВ положительного знака. Пыль осаждается на заземленных пластинах, к которым ток не подведен.
Вокруг коронирующего электрода происходит электрический разряд, сопровождающийся свечением («корона»). В результате электрических разрядов происходит выделение атомарного кислорода (одноатомные молекулы), образование озона O
3
, а также оксидов азота. При напряжении, применяемом в воздушных фильтрах, и при наличии в нем двух зон озон и оксиды азота выделяются в небольших количествах и опасности для людей не представляют. В электрических пылеуловителях, применяемых для очистки выбросов, используют ток напряжением 80-100 Вт, кроме того, в этих аппаратах к коронирующим электродам подведен ток отрицательного знака, что по имеющимся данным сопровождается более интенсивным выделением вредных веществ (в 8 раз).
Сила электрического тока и потребляемая мощность в электрических фильтрах невелики и находятся в пределах соответственно 0,8 мА и 10 Вт на 1000 м3
/ч очищаемого воздуха.
Фракционная эффективность электрического фильтра дана в табл. 5.
Таблица 5.
Фракционная эффективность электрического фильтра
Размер частиц, мкм
|
Число частиц в воздухе
|
Эффективность улавливания,%
|
перед фильтром
|
после фильтра
|
0,5
|
4000
|
405
|
89,9
|
0,6
|
2505
|
107
|
95,7
|
0,7
|
1000
|
46
|
95,4
|
0,8
|
500
|
27
|
94,6
|
0,9
|
180
|
12
|
93,5
|
1
|
140
|
7
|
95
|
1,5
|
45
|
3
|
93,3
|
2
|
28
|
1
|
96,6
|
Электрический фильтр ФЭ
собирают из унифицированных ячеек. Основные технические показатели фильтра ФЭ приведены в табл. 6.
Таблица 6.
Основные технические показатели фильтров типа ФЭ
Показатели
|
Ф1Э1
|
Ф3Э2
|
Ф5Э3
|
Ф8Э4
|
Ф10Э5
|
Ф14Э6
|
Ф18Э7
|
Номинальная пропускная способность, тыс. м3
/ч
|
10
|
19
|
33
|
55
|
66
|
100
|
130
|
Площадь рабочего сечения (округлено), м2
|
1
|
3
|
5
|
8
|
10
|
14
|
13
|
Количество ячеек шириной, мм: 758
965
|
7
-
|
14
-
|
-
18
|
24
12
|
-
36
|
-
54
|
-
72
|
Потребляемый ток, мА
|
7
|
14
|
24
|
42
|
54
|
81
|
110
|
Потребляемая мощность, Вт
|
100
|
200
|
350
|
600
|
600
|
1100
|
1500
|
Масса, кг
|
205
|
367
|
583
|
963
|
1120
|
1640
|
2125
|
Габаритные размеры, мм:
А
Н
|
820
1840
|
1580
1840
|
2090
2344
|
2625
3098
|
3125
3098
|
3125
4598
|
4125
4598
|
Электрический фильтр может быть снабжен противоуносным фильтром, который представляет собой разъемную рамку с заполнением фильтрующим материалом ФСВУ или пенополиуретаном. На входе в фильтр установлена защитная проволочная сетка.
Уловленную пыль удаляют с помощью промывки водой. Расход воды 0,5 м3
на 1 м3
входного сечения фильтра, 0,08 м3
на 1000 м3
очищаемого воздуха, при давлении воды 300 кПа. Продолжительность промывки 3 – 5 мин. Промывка обычно производится раз в 1 – 2 мес., а при отсутствии противоуносного фильтра – 1 раз в неделю. Полная очистка ячеек фильтра производится 1 - 2 раз в год.
Раздел 3. Пылеуловители для очистки выбросов в атмосферу
3.1. Общая характеристика пылеуловителей
Пылеуловители, применяемые для очистки воздуха, удаляемого системами вытяжной вентиляции, делятся на пять классов в зависимости от размеров эффективно улавливаемых частиц пыли, отнесенной к соответствующей группе по дисперсности (табл. 7).
Таблица 7.
Классификация пылеуловителей
Класс пылеуловителей
|
Размеры эффективно улавливаемых частиц, мкм
|
Эффективность по массе пыли, %
при классификационной группе пыли по дисперсности
|
I
|
II
|
III
|
IV
|
V
|
I
|
Более 0,3-0,5
|
-
|
-
|
-
|
99,9-80
|
<80
|
II
|
Более 2
|
-
|
-
|
99,9-92
|
92-45
|
-
|
III
|
Более 4
|
-
|
99,9-99
|
99-80
|
-
|
-
|
IV
|
Более 8
|
>99,9
|
99,9-95
|
-
|
-
|
-
|
V
|
Более 20
|
>99
|
-
|
-
|
-
|
-
|
Под эффективным улавливанием понимают улавливание с эффективностью более 95%. Однако, эффективность улавливания частиц данной группы пыли, приведенная в табл. 7 является в основном ориентировочной, поскольку зависит от концентрации пыли в очищаемом воздухе, от ее слипаемости, волокнистости, которые значительно влияют на коагуляцию пыли.
Разработаны и эксплуатируются значительное количество пылеуловителей во всех отраслях промышленности. Число конструкций составляет тысячи. Имеется возможность рассмотреть здесь лишь наиболее распространенные, характерные и перспективные. Будут рассмотрены аппараты, применяемые преимущественно для очистки вентиляционных выбросов, а также устройства, используемые главным образом в системах очистки технологических выбросов. Четкой границы провести нельзя. Например, циклоны широко применяются, как в системах вентиляции, так и в технологических установках. В то же время некоторые аппараты преимущественно служат для технологической очистки (пылеуловители Вентури, электрофильтры и др.). Это подтверждает необходимость изучения будущими специалистами по теплогазоснабжению и вентиляции основных видов оборудования, применяемого для очистки воздуха и газов в системах различного назначения.
3.2. Пылеосадочные камеры
Пылеосадочные камеры являются простейшими пылеулавливающими устройствами. Они относятся к группе гравитационного оборудования, в которую входят два вида оборудования – полое и полочное.
Пылевая частица, внесенная в камеру потоком воздуха, находится под действием двух сил: силы инерции, под воздействием которой она стремится перемещаться горизонтально, и силы тяжести, под действием которой она осаждается на дно камеры.
Равнодействующую сил можно получить из параллелограмма сил. В горизонтальном направлении частица проходит путь l
, м
;
в вертикальном h
, м
;
где – время пребывания частицы в камере, с;
– скорость движения частицы в горизонтальном направлении, м/с;
– скорость движения частицы в вертикальном направлении, м/с.
Из приведенных выше зависимостей получена формула для определения длины камеры, необходимой для того, чтобы пылевая частица, совершая движение в камере, осела на дно.
(1)
Из формулы (1) видно, что длина камеры прямо пропорциональна ее высоте, т. е. чем ниже камера, тем быстрее пылевая частица при своем движении в камере встретит дно камеры. Из этого следует, что для уменьшения высоты целесообразно разделить камеру на несколько параллельных каналов с помощью горизонтальных перегородок. По этому принципу устроена полочная
пылеосадочная камера. Для удобства удаления пыли полки устраивают наклонными или поворотными.
Для осаждения тонких фракций пыли в камере должно быть обеспечено ламинарное движение воздуха, при котором не было бы перемещения воздуха поперек потока. Для этого пришлось бы устраивать камеры громадных размеров, что практически неосуществимо.
В реальных условиях в пылеосадочных камерах наблюдается турбулентный или переходный режим.
Для увеличения эффекта осаждения за счет использования сил инерции применяются камеры, к потолку которых подвешены цепи, стержни.
В. В. Батурин предложил камеру лабиринтного типа. В этой камере происходит быстрое затухание скоростей в струе, настилающейся на щит, так как струя растекается во все стороны. В результате проведенных испытаний установлено, что эффективность очистки в камере лабиринтного типа выше, чем в обычных пылеосадочных камерах. Известны также пылеосадочные камеры, в которых осуществляется мокрая очистка. Так, для улавливания пыли, растворимой в воде, например, сахарной, применяют пылеосадочную камеру, в которой нижняя часть заполнена горячей водой. Осаждающаяся сахарная пыль поглощается водой, которую по достижении высокой концентрации в ней сахара периодически возвращают в производство и заменяют новой.
Для нормальной работы пылеосадочной камеры необходимо, чтобы воздух равномерно двигался через камеру. Для этого при входе в камеру устанавливают сетки, решетки и другие устройства для выравнивания потока воздуха. Максимальная скорость движения воздуха через пылеосадочную камеру обычно не превышает 3 м/с.
Преимуществом пылеосадочной камеры является простота устройства, несложность эксплуатации, долговечность. Пылеосадочные камеры могут быть изготовлены из кирпича, бетона и других неметаллических материалов, устойчивых к коррозии. Потери давления в пылеосадочных камерах обычно не превышают 20 – 150 Па. В то же время пылеосадочные камеры имеют существенные недостатки, из-за которых применение этого вида пылеуловителей значительно сократилось.
В пылеосадочной камере, даже усовершенствованной конструкции, можно осуществить осаждение наиболее крупных фракций пыли преимущественно со значительной плотностью. Мелкие фракции выносятся из камеры воздушным потоком. Пылевые камеры занимают много места. Степень очистки воздуха в пылеосадочных камерах не превышает 50 – 60 %. Это устройство может применяться лишь для предварительной очистки воздуха от крупнодисперсной пыли со значительной плотностью. Для осаждения взрывно- и пожароопасной пыли устройство пылеосадочных камер не допускается.
3.3. Инерционные пылеуловители
Действие инерционного пылеуловителя основано на том, что при изменении направления движения потока запыленного воздуха (газа) частицы пыли под действием сил инерции отклоняются от линии тока и сепарируются из потока. К инерционным пылеуловителям относится ряд известных аппаратов: пылеотделитель ИП, жалюзийный пылеуловитель ВТИ и др., а также простейшие инерционные пылеуловители (пылевой мешок, пылеуловитель на прямом участке газохода, экранный пылеуловитель и др.).
Инерционные пылеуловители улавливают крупную пыль – размером 20 – 30 мкм и более, их эффективность обычно находится в пределах 60 – 95 %. Точное значение зависит от многих факторов: дисперсности пыли и других ее свойств, скорости потока, конструкции аппарата и др. По этой причине инерционные аппараты применяют обычно на первой ступени очистки с последующим обеспыливанием газа (воздуха) в более совершенных аппаратах. Преимуществом всех инерционных пылеуловителей является простота устройства и невысокая стоимость аппарата. Этим и объясняется их распространенность. Рассмотрим основные конструкции инерционных пылеуловителей.
Инерционный пылеуловитель ИП
представляет собой конус, образованный коническими кольцами постепенно уменьшающегося диаметра. Очищаемый воздух входит в основание конуса со скоростью 18 м/с и движется к основанию конуса.
По ходу движения воздух выходит через щели между кольцами, а пылевые частицы под действием сил инерции, продолжая движение в прямолинейном направлении, ударяются о стенки и отбрасываются в массу потока. По мере движения потока концентрация в нем пыли возрастает. У вершины конуса в пылевоздушной смеси остается лишь 5 – 10 % воздуха, поступившего в аппарат. Выйдя из аппарата, пылевоздушная смесь направляется в циклон. Пыль отделяется от воздуха и поступает в бункер, а обеспыленный воздух возвращается к вентилятору.
Таким образом, в установке ИП-циклон воздух подвергается двухступенчатой очистке, общая эффективность которой порядка 90 %. При улавливании пескоструйной пыли эффективность, как показывали испытания, находилась в пределах 92,5 – 95,9 %.
Преимуществом ИП является компактность и простота устройства. Аппарат может применяться в качестве первой ступени при очистке воздуха от крупнодисперсной пыли. Разработано несколько номеров ИП, рассчитанных на различную производительность.
Жалюзийный пылеуловитель ВТИ
по устройству и принципу действия аналогичен ИП. Аппараты, предназначенные для очистки газов с высокой температурой, изготовляют из чугуна или железнопрочной стали. Пылеуловитель расположен в газоходе, между стенкой газохода и решеткой образуется канал с постепенно уменьшающимся сечением, в который поступает газ, обеспыленный при прохождении решетки. В конической части пылеуловителя, по мере движения потока и выхода части газа через щели в решетке, концентрация пыли возрастает. Эта пылегазовая смесь направляется затем на очистку в циклон. Очищенный газ отсасывается дымососом. Гидравлическое сопротивление жалюзийного пылеуловителя ВТИ находится в пределах 100 – 500 Па. О фракционной эффективности пылеуловителя (eф
) свидетельствуют такие данные. При очистке газов от золы с плотностью r = 2600 кг/м3
фракционная эффективность составляла:
d
, мкм
|
10
|
15
|
20
|
25
|
30
|
40
|
50
|
60
|
eф
|
47
|
63
|
78
|
86,5
|
91,3
|
94,8
|
96,5
|
97,7
|
Приведенная эффективность отмечена при гидравлическом сопротивлении 400 – 500 Па. При уменьшении гидравлического сопротивления фракционная эффективность снижается на 10 – 5 %.
Простейшие инерционные пылеуловители.
Один из пылеуловителей такого типа известен под названием «пылевой мешок». Очищаемый газ входит в корпус аппарата по центральной трубе, прямой или конической. Сепарация пыли происходит при повороте потока на 180° и последующем его подъеме к выходному патрубку. Скорость потока во входном патрубке 10 м/с, в цилиндрической части корпуса 1 м/с. Эффективность очистки газов с пылевыми частицами более 30 мкм находится в пределах 65 – 80 %. Гидравлическое сопротивление – 150 – 390 Па. Пылевые мешки целесообразно применять для предварительной очистки газов с высокой концентрацией пыли – несколько сот граммов на 1 м3
. Используется преимущественно в металлургии.
Экранный инерционный пылеуловитель.
Основной элемент аппарата – V
-образный профиль. Струи, на которые разбивается поток запыленного газа, сталкиваются с основанием V
-образного элемента. В результате столкновения и кругового движения пыль отделяется от потока и попадает в бункер, расположенный внизу. В случае необходимости для более полного удаления пыли из V
-образных каналов прибегают к постукиванию или вибрации. Применяют также впрыскивание жидкости, что способствует удалению пыли и предотвращает ее повторный унос газовым потоком. Преимуществом аппарата является возможность его использования при высоких температурах и агрессивных средах.
Гидравлическое сопротивление аппарата 25 – 100 Па. Эффективность очистки при запыленности газа 20 – 70 г/м3
и содержании фракций более 10 мкм 62 % составляла 80 – 91 %.
Таблица 8.
Техническая характеристика инерционных газоочистных аппаратов
Пылеуловители
|
Циклоны
|
тип
|
производительность, м3
/ч
|
масса, кг
|
тип
|
производительность, м3
/ч
|
масса, кг
|
гидравлическое сопротивление, Па
|
ИП-1
|
745
|
27
|
ЦИП-1
|
45
|
6,1
|
700
|
ИП-2
|
1030
|
35
|
ЦИП-2
|
62
|
7,8
|
630
|
ИП-3
|
1730
|
55
|
ЦИП-3
|
104
|
12,6
|
570
|
ИП-4
|
2600
|
101
|
ЦИП-4
|
156
|
20,4
|
530
|
ИП-5
|
3670
|
132
|
ЦИП-5
|
220
|
35,7
|
510
|
ИП-6
|
6340
|
209
|
ЦИП-6
|
380
|
58,6
|
480
|
ИП-7
|
9400
|
398
|
ЦИП-7
|
582
|
95,6
|
460
|
ИП-8
|
12750
|
495
|
ЦИП-8
|
380
|
58,6
|
480
|
ИП-9
|
15000
|
562
|
ЦИП-9
|
582
|
95,6
|
460
|
3.4. Циклоны
3.4.1. Общая характеристика
Сепарация пылевых частиц в циклоне осуществляется на основе использования центробежной силы.
Циклоны широко применяются для очистки от пыли вентиляционных и технологических выбросов во всех отраслях народного хозяйства. Можно утверждать, что циклоны являются наиболее распространенным видом пылеулавливающего оборудования. Их широкое распространение в значительной мере объясняется тем, что они имеют многие преимущества – простота устройства, надежность в эксплуатации при сравнительно небольших капитальных и эксплутационных затратах. Надежность циклонов обусловлена, в частности, тем, что в их конструкции нет сложного механического оборудования.
Капитальные и эксплутационные затраты на пылеулавливающие установки, оборудованные циклонами, значительно меньше соответствующих расходов для установок с рукавными фильтрами, а тем более электрофильтрами. Циклоны делятся на циклоны большой производительности и циклоны высокой эффективности. Первые имеют обычно большой диаметр и обеспечивают очистку значительных количеств воздуха. Вторые – сравнительно небольшого диаметра (до 500 – 600 мм). Очень часто применяют групповую установку этих циклонов, соединенных параллельно по воздуху.
Циклоны, как правило, используют для грубой и средней очистки воздуха от сухой неслипающейся пыли. Принято считать, что они обладают сравнительно небольшой фракционной эффективностью в области фракций пыли размером до 5 – 10 мкм, что является основным их недостатком. Однако циклоны, особенно циклоны высокой эффективности, улавливают не такую уж малую часть пыли размером до 10 мкм – до 80 и более процентов.
В современных высокоэффективных циклонах, в конструкции которых учтены особенности улавливаемой пыли, удалось существенно повысить общую и фракционную эффективность очистки. Отмеченный выше недостаток обусловлен особенностями работы циклонов, в частности, турбулизацией потока запыленного воздуха, которая препятствует сепарации пыли.
Разработано и применяется в технике обеспыливания большое число различных типов циклонов, которые отличаются друг от друга формой, соотношением размеров элементов и т. д.
Корпус циклона состоит из цилиндрической и конической частей.
По форме циклоны разделяются на цилиндрические (H
ц
> H
к
) и конические (H
к
> H
ц
), H
ц
и H
к
соответственно высота цилиндрической и конической части циклона. Коническая часть аппарата выполняется в виде прямого конуса, обратного конуса или может состоять из двух конусов – прямого и обратного. Строение конической части определяет особенности движения пылевоздушного потока в этой части циклона и оказывает существенное влияние на процесс сепарации, а также коагуляцию некоторых видов пыли в аппарате, на устойчивость его работы при улавливании данных видов пыли.
Запыленный воздух поступает в циклон через патрубок, очищенный – удаляется через выхлопную трубу. В зависимости от способа подведения воздуха к циклону различают циклоны с тангенциальным и спиральным подводом воздуха. При прочных равных условиях циклоны со спиральным подводом обладают более высокой эффективностью очистки. Поток запыленного воздуха входит в корпус циклона обычно со скоростью 12 – 14 м/с.
Применяют циклоны правые (вращение потока запыленного воздуха по часовой стрелке, если смотреть сверху) и левые (вращение против часовой стрелки).
Ниже рассматриваются теоретические основы циклонного процесса и наиболее распространенные и характерные виды циклонных аппаратов.
Запыленный воздух, войдя в корпус, движется по спирали вниз вдоль стенок корпуса. Крупные пылевые частицы (более 100 мкм) под действием центробежных сил движутся у стенок корпуса, а мелкие частицы (менее 10 мкм) – на некотором расстоянии от стенок. Достигнув уровня прорезей в стенках корпуса, крупные пылевые частицы с частью воздуха удаляются из корпуса через отверстия в пылесборник. Здесь происходит сепарация частиц, и они через патрубок удаляются.
Мелкие пылевые частицы продолжают движение в составе воздушного потока в корпусе циклона, а затем в пылесборнике. Мелкие частицы совместно с крупными покидают аппарат через пылевыпускной патрубок. Воздушный поток через выхлопную трубу выходит из аппарата.
Сферический циклон был испытан в производственных условиях на пыли древесной, цементной, известковой, угольной, песка, щебня, золы и шлака, горелой формовочной смеси. Эффективность очистки находилась в пределах 98 – 99 % (для частиц 10 – 50 мкм).
Повышение эффективности очистки, особенно в области мелких фракций, достигается благодаря более равномерной подаче, распределению и закручиванию пылевоздушного потока (наличие нескольких входных патрубков). Сферическая форма корпуса и пылесборника способствует интенсификации процесса коагуляции частиц.
Таблица 9.
Техническая характеристика основных типов циклонов
Тип циклона
|
Отношение коэффициента гидравлического сопротивления к скорости потока
|
Скорость газового потока, м/с
|
Степень очистки (медианный размер частиц 8 мкм) при гидравлическом сопротивлении 100 Па и расходе воздуха 1800 м3
/ч, %
|
в сечении корпуса
|
во входном отверстии
|
в сечении корпуса
|
во входном отверстии
|
ЦН-11
|
250
|
6,1
|
2,9
|
16,2
|
73,1
|
ЦН-15
|
160
|
7,6
|
3,1
|
13,5
|
71,7
|
ЦН-24
|
80
|
10,9
|
4,4
|
12,0
|
63,7
|
ЦН-15У
|
170
|
8,2
|
3,2
|
14,6
|
65,2
|
СК-ЦН-34
|
1200
|
25
|
1,1
|
8,0
|
75
|
СДК-ЦН-33
|
600
|
20,3
|
1,6
|
9,8
|
74
|
ЛИОТ
|
460
|
4,2
|
5,1
|
21,5
|
67,7
|
ВЦНИИОТ
|
-
|
9,3
|
13,5
|
-
|
71,9
|
СИОТ
|
-
|
6,0
|
3,9
|
17,0
|
71,7
|
3.4.2. Батарейные циклоны (мультициклоны)
Батарейный циклон (мультициклон) состоит из большого количества циклонных элементов небольшого диаметра, расположенных в общем корпусе с единым подводом и отводом газа и общим бункером.
Корпус батарейного циклона разделен на несколько секций, которые частично могут отключаться при изменении нагрузки на аппарат.
Наиболее распространены циклонные элементы с направляющими аппаратами типа «винт» и «розетка». Обычно применяют циклонные элементы диаметром 100, 150, 250 мм.
Циклонный элемент состоит из корпуса, направляющего аппарата и выхлопной трубы. Элементы с направляющим аппаратом «розетка» имеют более высокую эффективность, но они более склонны к забиванию пылью, чем элементы с аппаратом «винт».
Целесообразность применения батарейных циклонов объясняется тем, что эффективность циклонных аппаратов малого диаметра выше, чем большого. Кроме того, габариты батарейного циклона, в частности, по высоте, меньше, чем группы циклонов при той же производительности.
Недостатком батарейных циклонов является более высокий удельный расход металла по сравнению с одиночными циклонами, а также неравномерное распределение очищаемого воздуха между элементами, что приводит к некоторому снижению эффективности очистки по сравнению с одиночными циклонами того же диаметра, что и элементы батарейного циклона.
Батарейные циклоны могут применяться для улавливания слабо- и среднеслипающихся пылей. Их используют для очистки газов от летучей золы, пыли цемента, доломита, известняка, шамота и др. Для улавливания сильнослипающихся пылей их применять не рекомендуется.
Ряд аппаратов предназначен для очистки газов с температурой до 400°С. Часть аппаратов выпускается во взрывоопасном исполнении.
Батарейный циклон БЦ-2 включает (в зависимости от типоразмера) от 20 до 56 чугунных литых циклонных элементов диаметром 250 мм с направляющими аппаратами «розетка».
3.5. Ротационные пылеуловители
В ротационных пылеуловителях очистка газов (воздуха) от пыли основана на использовании центробежных сил и сил Кориолиса, возникающих при вращении рабочего колеса аппарата.
Характерной особенностью ротационных пылеуловителей является то, что в одном аппарате совмещен побудитель (вентилятор) и пылеуловитель. Благодаря этому аппарат более компактен, чем установка, состоящая из вентилятора и пылеулавливающего устройства. Ротационный пылеуловитель потребляет меньше электроэнергии, чем вентилятор и пылеуловитель в сумме.
Ротационные пылеуловители делятся на две основные группы в зависимости от места подвода запыленного потока к аппарату. Большая часть ротационных пылеуловителей относится к группе, в которой запыленный поток поступает в центральную часть колеса, вращающегося в кожухе. Пылевые частицы под действием центробежных сил и сил Кориолиса отбрасываются на периферию диска и оттуда поступают в пылесборник.
Применяются также аппараты ротационного типа, в которых для повышения эффективности очистки запыленный поток соприкасается с водной поверхностью, отдавая воде часть содержащейся в нем пыли.
Ротационные пылеуловители служат для очистки воздуха (газов) от неслипающихся и слабослипающихся пылей при их значительной концентрации в потоке. Эффективность очистки от пыли с частицами размером 8 – 12 мкм составляет 83 %. Для размера 20 мкм – до 97 %.
Таблица 10.
Техническая характеристика ротационных пылеотделителей
Производительность, м3
/ч
|
Напор, Па
|
Частота вращения ротора, об/мин
|
Вид пыли
|
Концентрация пыли, г/м
|
Степень очистки,%
|
Расход электроэнергии,
кВт*ч/м3
|
на входе
|
на выходе
|
870
|
2460
|
3000
|
Зола
|
28
|
5,0
|
80
|
1,6
|
720
|
2310
|
3000
|
»
|
24
|
4,0
|
84
|
1,56
|
570
|
2310
|
3000
|
»
|
6
|
0,1
|
78
|
1,44
|
870
|
2310
|
3000
|
»
|
140
|
20,0
|
82
|
1,6
|
363
|
2460
|
3000
|
Стекло
|
10
|
0,02
|
99
|
1,2
|
725
|
500
|
3000
|
Кварц
|
12
|
0,1
|
99
|
1,4
|
275
|
500
|
3000
|
Уголь
|
10
|
0,1
|
99
|
0,8
|
550
|
500
|
3000
|
Тальк
|
12
|
0,14
|
99
|
0,85
|
2000
|
500
|
730
|
Суперфосфат
|
4,3
|
0,16
|
98
|
0,95
|
2000
|
500
|
730
|
Огарок
|
50
|
0,1
|
99
|
0,9
|
3.6. Вихревые пылеуловители
В вихревом пылеуловителе, как и в циклоне, сепарация пыли основана на использовании центробежных сил. Основное отличие вихревых пылеуловителей от циклонов заключается в наличии вспомогательного закручивающего газового потока.
Применяют два вида вихревых пылеуловителей: сопловые и лопаточные.
В аппарате и того и другого типа запыленный газ поступает в камеру через входной патрубок с завихрителем типа «розетка» и обтекателем. В кольцевом пространстве между корпусом аппарата и входным патрубком расположена подпорная шайба, которая обеспечивает безвозвратный спуск пыли в бункер.
Обтекатель направляет поток газа к периферии. Пылевые частицы за счет воздействия центробежных сил перемещаются из центральной части потока к периферии.
Далее процесс в аппаратах двух видов несколько отличается. В сопловом аппарате на запыленный поток воздействуют струи вторичного воздуха (газа), выходящие из сопел, расположенных тангенциально. Поток переходит во вращательное движение.
Отброшенные под воздействием центробежных сил к стенкам аппарата пылевые частицы захватываются спиральным потоком вторичного воздуха (газа) и вместе с ним движутся вниз в бункер. Здесь частицы пыли выделяются из потока, а очищенный воздух (газ) снова поступает на очистку.
Эксперименты показали положительную роль повышения давления вторичного воздуха до 30 – 40 кПа сверх атмосферного. Эффективное пылеулавливание может быть обеспечено и при меньшем давлении. Сопла для подачи вторичного воздуха нужно расположить по нисходящей спирали. Оптимальной явилась установка 8 сопел диаметра 11 мм двумя спиральными рядами под углом наклона 30°.
В аппарате лопаточного типа вторичный воздух, отобранный в периферии очищенного потока, подается кольцевым направляющим аппаратом с наклонными лопатками. По основным показателям аппараты лопаточного типа оказались более эффективными: при одинаковом диаметре камеры – 200 мм и производительности 330 м3
/ч гидравлическое сопротивление соплового аппарата составило 3,7×103
Па, эффективность 96,5 %, а лопаточного соответственно 2,8×103
Па и 98% (при улавливании особо мелкодисперсной пыли).
Применяют следующие способы подведения к вихревому пылеуловителю воздуха, необходимого для закручивания обеспылеваемого потока: из окружающей среды, из очищенного потока, из запыленного потока. Первый вариант целесообразен, если очистке подвергается горячий газ, который необходимо охладить. Применяя второй вариант, можно несколько повысить эффективность очистки, так как для использования в качестве вторичного воздуха отбирают периферийную часть потока очищенного воздуха с наибольшим содержанием остаточной пыли. Третий вариант наиболее экономичен: производительность установки повышается на 40 – 65 % с сохранением эффективности очистки.
Вихревой пылеуловитель может применяться для очистки вентиляционных и технологических выбросов от мелкодисперсной пыли в химической, нефтехимической, пищевой, горнорудной и других отраслях промышленности. В вихревых пылеуловителях достигается весьма высокая для аппаратов, основанных на использовании центробежных сил, эффективность очистки – 98 – 99 % и выше. На эффективность очистки оказывает незначительное влияние изменение нагрузки (в пределах от 50 до 115 %) и содержания пыли в очищаемом воздухе (газе) – от 1 до 500 г/м3
. Аппарат может применяться для очистки газов с температурой до 700°С. В вихревом пылеуловителе не наблюдается износа внутренних стенок аппарата, что связано с особенностями его воздушного режима. Аппарат более компактен, чем другие пылеуловители, предназначенные для сухой очистки выбросов.
3.7. Фильтрационные пылеуловители
В фильтрационных пылеуловителях очистка воздуха (газа) от пыли происходит при прохождении запыленного потока через слой пористого материала. В качестве фильтрующего слоя используют ткани, кокс, гравий и др.
Процесс фильтрации основан на многих физических явлениях (эффект зацепления, в том числе ситовый эффект, - аэрозольные частицы задерживаются в порах и каналах, имеющих сечение меньше, чем размеры частиц; действие сил инерции – при изменении направления движения запыленного потока частицы отклоняются от этого направления и осаждаются; броуновское движение – в значительной мере определяет перемещение высокодисперсных субмикронных частиц; действие гравитационных сил, электростатических сил – аэрозольные частицы и материал могут иметь электрические заряды или быть нейтральными).
По мере накопления в фильтрующем слое задержанных частиц режим фильтрации меняется. Для поддержания его в требуемых пределах производят регенерацию фильтра, которая заключается в периодическом или систематическом удалении задержанных частиц.
Большинство фильтров обладает высокой эффективностью очистки. Фильтры применяют как при высокой, так и при низкой температуре очищаемой среды, при различной концентрации в воздухе взвешенных частиц.
Соответствующим подбором фильтровальных материалов и режима очистки можно достичь требуемой эффективности очистки в фильтре практически во всех необходимых случаях.
Во многих конструкциях фильтровальных пылеуловителей режим работы фильтра, в частности, режим регенерации, поддерживается автоматически.
Обладая многими положительными качествами, фильтрующие устройства в то же время не лишены недостатков: стоимость очистки в фильтрах выше, чем в большинстве других пылеуловителей, в частности, в циклонах. Это объясняется большей конструктивной сложностью фильтров по сравнению с другими аппаратами, большим расходом электроэнергии. Многие конструкции фильтрационных пылеуловителей более сложны в эксплуатации и требуют квалифицированного обслуживания.
Фильтрационные пылеуловители в зависимости от материала фильтрующего слоя подразделяются на волокнистые, тканевые, зернистые.
3.7.1. Волокнистые фильтры
В волокнистых фильтрах фильтрующий слой образован относительно равномерно распределенными тонкими волокнами фильтрующих материалов. Эти фильтры предназначены для улавливания частиц мелкодисперсной и особо мелкодисперсной пыли при ее концентрации в очищаемом воздухе (газе) в пределах 0,5 – 5 мг/м3
.
Волокнистые фильтры могут быть подразделены на тонковолокнистые, глубокие и грубоволокнистые фильтры.
Тонковолокнистые фильтры
служат для улавливания высокодисперсной пыли и других аэрозольных частиц размером 0,05 – 0,1 мкм с эффективностью не менее 99 %. В качестве фильтровального материала используется ФП (фильтр Петрянова).
Для тонкой и условно грубой очистки применяют фильтры ПФТС, снаряженные стекловолокном. Производительность фильтров 200 – 1500 м3
/ч, сопротивление 200 – 1000 Па. Фильтры применяют в тех случаях, когда температура очищаемой среды выше 60°С и в ней находятся вещества, разрушающие материалы ФП.
Основного недостатка тонковолокнистых фильтров (короткий срок службы фильтрующего слоя из-за неприменимости регенерации) лишены глубокие фильтры
. Они рассчитаны на срок службы 10 – 20 лет. Это достигается благодаря наличию нескольких фильтрующих слоев общей высотой 0,3 – 2,0 м. Диаметр волокон 8 – 19 мкм. Первый слой фильтра на пути движения очищаемой среды состоит из грубых волокон, последний слой – из тонких. Фильтр применяется в системах стерилизации воздуха в производстве антибиотиков, витаминов и других био- и медицинских препаратов. Фильтр периодически стерилизуют острым паром, затем просушивают сухим воздухом.
Грубоволокнистые фильтры.
Эти фильтры называют также предфильтрами, так как их устанавливают перед тонковолокнистыми фильтрами для предварительной очистки воздуха (газов). Благодаря этому снижается стоимость очистки, поскольку стоимость грубоволокнистых фильтров почти в 10 раз ниже тонковолокнистых, их легче заменять или регенерировать. Фильтровальный материал предфильтра состоит из смеси волокон диаметром от 1 до 20 мкм.
Фильтры-туманоуловители.
Многие технологические процессы сопровождаются образованием туманов. Так, например образование тумана происходит при испарении масел, производстве и концентрировании различных кислот, производстве хлора и др. Жидкие частицы в тумане имеют размер менее 10 мкм.
Для улавливания частиц тумана в настоящее время применяют волокнистые фильтры-туманоуловители различных конструкций, для которых характерен непрерывный вывод уловленной жидкости.
Применяют в основном два типа фильтров-туманоуловителей: низкоскоростные и высокоскоростные.
Низкоскоростные фильтры
снаряжены смесью в определенной пропорции грубых и тонких волокон. В элементе низкоскоростного фильтра соосно расположены две проволочные сетки, пространственно между которыми заполнено волокнами. Трубка в нижней части корпуса аппарата оборудована гидрозатвором, через который уловленная жидкость поступает в корпус аппарата.
Высокоскоростные туманоуловители.
Увеличение скорости фильтрации приводит к уменьшению размеров волокнистых фильтров. Высокоскоростные фильтры выпускает фирма «Монсанто». Фильтр состоит из плоских элементов. Они установлены в каркасе, под которым расположен поддон, куда стекает уловленная жидкость. Фильтрующим слоем являются иглопробивные материалы-войлоки. По химической стойкости наиболее универсален полипропиленовый войлок. Толщина слоя – 3 – 12 мм, диаметр волокон 20 – 75 мм. Сопротивление фильтра 500 Па, эффективность улавливания частиц более 3 мм около 100 %.
3.7.2 Тканевые фильтры
Тканевые фильтры по форме фильтрующей поверхности могут быть рукавными и рамочными. Наибольшее распространение в промышленности получили рукавные фильтры. Рукавный фильтр состоит из ряда тканевых рукавов, подвешенных в металлической камере. Верхняя часть рукавов обычно заглушена
Запыленный газ поступает в нижнюю часть аппарата и проходит через ткань рукавов. На поверхности ткани и в ее порах осаждается пыль. По мере увеличения толщины слоя пыли возрастает сопротивление фильтра, поэтому осевшую на ткани пыль периодически удаляют. Процесс фильтрации газа зависит от типа ткани и вида пыли. Гладкие и неворсистые ткани сравнительно легко пропускают запыленный газ. В порах таких тканей задерживаются только крупные частицы пыли. Фильтр начинает хорошо задерживать мелкую пыль только после накопления на поверхности фильтрующих элементов слоя пыли. Для ворсистых, шерстяных тканей с мелкими порами влияние начального слоя пыли менее заметно Ворсистые ткани целесообразно применять при улавливании зернистой гладкой пыли, а при улавливании волокнистой пыли — лучше гладкие ткани.
Фильтрация тонкой пыли (частицы менее 1—2 мкм) возможна лишь на поверхности ранее осажденной пыли.
Ткани, используемые в качестве фильтровальных материалов, должны отличаться высокой пылеемкостью, воздухопроницаемостью, механической прочностью, стойкостью к истиранию, стабильностью свойств при повышенной температуре и агрессивном воздействии химических примесей, а также минимальным влагопоглощением и способностью к легкому удалению накопленной пыли. Не все применяемые в промышленности материалы удовлетворяют перечисленным требованиям, поэтому каждый материал используют в определенных, наиболее благоприятных для него условиях.
Тканевые фильтры различаются между собой по следующим признакам:
· форме тканевых фильтрующих элементов (рукавные, плоские, клиновые и др.);
· месту расположения вентилятора относительно фильтра (всасывающие и нагнетательные);
· способу регенерации ткани (встряхиваемые, с обратной продувкой, с вибровстряхиванием, с импульсной продувкой и др.);
· форме корпуса для размещения фильтрующих элементов (прямоугольные, цилиндрические, открытые);
· числу секций в установке (одно- и многосекционные);
· виду используемой ткани (шерсть, бязь, стеклоткань и т. д.).
Отечественной промышленностью серийно выпускаются рукавные фильтры типа ФВ, МФУ, РФГ, ФВК, ФРМ, ФВВ, МФВ, МФС, ПФР, ФР.
Рукавные фильтры типа ФВ предназначены для средней и тонкой очистки газов от волокнистой пыли. Рукава выполняют из суровой бязи. Фильтры МФУ применяют для тонкой очистки газов и воздуха от сухой и слипающейся пыли с размером частиц до 1 мкм (цемент, мука, зола).
Таблица 13.
Техническая характеристика рукавных фильтров
Тип фильтра
|
Фильтрующая поверхность, м2
|
Число секций
|
Число рукавов в секции
|
Диаметр рукава, мм
|
Длина рукава, мм
|
Масса фильтра, кг
|
ФВК-30
|
15
|
2
|
18
|
135
|
2060
|
1053
|
ФВК-60
|
45
|
4
|
18
|
135
|
2060
|
1682
|
ФВК-90
|
75
|
6
|
18
|
135
|
2060
|
2300
|
ФРМ-1-6
|
105
|
6
|
10
|
-
|
-
|
5776
|
ФРМ1-8
|
147
|
8
|
10
|
-
|
-
|
7137
|
ФРМ1-10
|
189
|
10
|
10
|
-
|
-
|
8633
|
ФВВ-45
|
30
|
3
|
18
|
135
|
2090
|
1735
|
ФВВ-90
|
75
|
6
|
18
|
135
|
2090
|
2935
|
МФВ-204
|
350
|
12
|
17
|
220
|
3000
|
-
|
МФС-45
|
30
|
3
|
16
|
172
|
1850
|
4778
|
3.7.3. Зернистые фильтры
Фильтрующий слой в этих фильтрах образован зернами сферической или другой форме. Могут использоваться при высоких температурах – до 500 – 800°С, в условиях воздействия агрессивной среды. Зернистые фильтры распространены значительно меньше, чем тканевые фильтры. Различают насыпные
зернистые фильтры, в которых элементы фильтрующего слоя не связаны жестко друг с другом, и жесткие зернистые фильтры, в которых эти элементы прочно связаны между собой путем спекания, прессования, склеивания и образуют прочную неподвижную систему.
Зернистые жесткие фильтры керамические, металлокерамические и др. обладают значительной устойчивостью к высокой температуре, коррозии, механическим нагрузкам. Их недостаток – высокая стоимость, большое гидравлическое сопротивление, трудность регенерации.
В насадке насыпных фильтров используют песок, гравий, шлак, дробленые горные породы, кокс, крошку резины, пластмасс, графита и др. материалы в зависимости от требуемой устойчивости и к воздействию температуры, химических веществ и др.
Зернистый фильтр может быть единственной ступенью в установке или первой ступенью перед более эффективным фильтром, например с материалами ФП.
Регенерация осуществляется путем рыхления слоя вручную или механически, промывки водой, замены слоя.
Пример такого фильтра – зернистый гравийный фильтр для улавливания пылей с наличием абразивных частиц и агрессивных газов от дробилок, грохотов, сушилок, мельниц, транспортирующих устройств предприятий по производству цемента, извести, гипса, фосфорных удобрений и др. Удельная нагрузка на фильтр – 17 – 50 м3
/(м2
×ч), сопротивление фильтра – в пределах 0,5 – 1,5 кПа. Эффективность очистки – до 99,8 %.
3.8. Аппараты мокрой очистки газов
Одним из простых и эффективных способов очистки промышленных газов от взвешенных частиц является мокрый способ, получивший в последние годы значительное распространение в отечественной промышленности и за рубежом.
Аппараты мокрой очистки газов отличаются высокой эффективностью улавливания взвешенных частиц и небольшой стоимостью по сравнению с аппаратами сухой очистки.
Некоторые типы аппаратов мокрой очистки (турбулентные газопромыватели) могут быть применены для очистки газов от частиц размером до 0,1 мкм.
Аппараты мокрой очистки газов по степени очистки могут не только успешно конкурировать с такими высокоэффективными пылеуловителями, как рукавные фильтры, но и использоваться в тех случаях, когда рукавные фильтры не могут быть применены вследствие высокой температуры, повышенной влажности или взрывоопасности очищаемых газов.
В аппаратах мокрой очистки газов одновременно со взвешенными частицами можно улавливать парообразные и газообразные компоненты. К недостаткам мокрой очистки следует отнести: необходимость обработки образующихся сточных вод, повышенный брызгоунос и необходимость защиты аппаратов от коррозии при обработке агрессивных сред. Несмотря на эти недостатки, мокрые газоочистные аппараты с успехом применяют в химической промышленности.
Аппараты мокрой очистки часто используют в газоочистных системах для одновременного охлаждения и увлажнения газов. В этом случае газоочистные аппараты служат еще и теплообменниками смешения, где охлажденный газовый поток непосредственно контактирует с охлаждающей жидкостью.
Среди аппаратов для очистки газов от пыли мокрые пылеуловители отличаются наибольшим многообразием, что обусловливается силами, воздействующими на газо-жидкостные потоки. При этом жидкая фаза находится в аппарате в виде пленки, струи, капель, пены или различных сочетаний.
По принципу работы аппараты мокрой очистки газов делятся на следующие группы: полые и насадочные, барботажные и пенные, аппараты ударно-инерционного типа, центробежного типа, динамические и турбулентные промьватели.
3.8.1. Полые и насадочные аппараты
В полых и насадочных аппаратах запыленные газы пропускают через поток распыляемой, разбрызгиваемой или стекающей по насадке жидкости. При этом частицы пыли захватываются потоками промывной жидкости и осаждаются в аппарате, а очищенные газы выбрасываются в атмосферу.
В полых скрубберах промывку газов осуществляют с помощью разбрызгивания жидкости навстречу движущемуся очищаемому потоку. Для орошения скрубберов применяют форсунки грубого распыления. Высокая эффективность очистки газов достигается в том случае, если промывная жидкость распыливается с образованием капель 0,5 — 1 мм. Обычно скруббер представляет собой вертикальный аппарат круглого или прямоугольного сечения. Форсунки устанавливают в одном или нескольких сечениях по высоте аппарата.
Для снижения брызгоуноса скорость газа в аппарате не должна превышать 1 - 1,2 м/с. Гидравлическое сопротивление полого скруббера невелико и обычно не превышает 250 Па. Расход воды составляет 5 - 10 м3
/ч на 1 м2
площади поперечного сечения. Наиболее полно в этих аппаратах улавливаются частицы пыли более 10 мкм.
Характерной особенностью насадочных скрубберов является то, что процесс выделения пыли происходит на смоченной поверхности насадки в результате многочисленных изменений движения газового потока в аппарате. Насадочные скрубберы заполняют насадочными элементами различной конфигурации, которые удерживаются на опорных решетках. К беспорядочной насадке относятся кольцевая (при загрузке навалом), седлообразная, кусковая; в регулярной - хордовая, блочная, уголковая.
Недостатками насадочных скрубберов являются частые забивки насадки при обработке запыленных газов, что ограничивает область их применения в технике пылеулавливания. Насадочные колонны целесообразно применять только при улавливании хорошо смачиваемой пыли, особенно в тех случаях, когда процессы улавливания сопровождаются охлаждением или очисткой газов от других компонентов.
3.8.2. Барботажные и пенные аппараты
В барботажных аппаратах очищаемые газы в виде пузырьков проходят через слой жидкости; при этом вследствие большой поверхности соприкосновения газов с жидкостью протекает процесс очистки газов от взвешенных частиц. Очищаемые газы барботируют в жидкость через трубки, опущенные в слой жидкости. Для дробления газов на мелкие пузырьки край барботажной трубки часто делают зубчатым. Эффективность подобных аппаратов достаточно велика, однако из-за сложности изготовления они имеют ограниченное применение в промышленности.
В пенных аппаратах пылеулавливающий эффект достигается в результате движения очищаемого газа через слой пены. Пена в этих аппаратах может формироваться различными способами: на решетке, куда подается жидкость, продуваемая снизу воздушным потоком или при ударе воздушного потока о зеркало жидкости.
Пенные пылеуловители широко распространены в химической промышленности. Они просты по конструкции и достаточно эффективны. В отличие от барботеров в пенных пылеуловителях газы проходят через жидкость со скоростью, превышающей скорость свободного всплывания пузырьков, что создает условия для образования высокотурбулизованной пены.
Пенные газопромыватели представляют собой вертикальный аппарат круглого или прямоугольного сечения, во внутренней полости которого установлены перфорированные или щелевые решетки. Очищаемые газы поступают к решеткам снизу. В результате интенсивного перемешивания газа с жидкостью в слое пены происходит смачивание и выделение из потока пылевидных частиц, которые выводятся из аппарата в виде шлама, а очищенные газы выходят через патрубок, расположенный в верхней части аппарата.
Существуют пенные пылеуловители с провальной (а)
и переливной (б)
решетками. В первом из них жидкость как бы «проваливается» сквозь отверстия в решетке, через которые поступает очищенный поток. Аппараты с переливными решетками могут работать со свободным сливом пены через сливной порог. Для эффективной работы аппаратов как с провальными, так и переливными решетками важно, чтобы жидкость и газ равномерно распределялись по поверхности решеток.
В пенных аппаратах с переливными решетками расходуется примерно в три раза меньше жидкости и допустимы значительные колебания нагрузки по газу и жидкости, чем в аппаратах с провальными решетками. Однако решетки провального типа меньше забиваются пылью, поскольку стекающая в отверстия вода смывает осадок с решеток.
Необходимо отметить, что при скорости газа более 1,0—1,2 м/с в пенных аппаратах возможен сильный унос капель воды. Поэтому в сечении аппарата над слоем пены должен быть установлен каплеуловитель. Последними исследованиями в области совершенствования пенных аппаратов было установлено, что над основной решеткой должен быть расположен специальный выпрямитель высотой 60 мм в виде сот с ячейками (35х35 мм). Соты выравнивают слой пены по всей площади решетки и позволяют увеличить скорость газа в сечении корпуса аппарата до 3 м/с.
В целях интенсификации массо- и теплообменных процессов в последние годы получил распространение аппарат, в котором подвижной насадкой служат полые и сплошные шары из полиэтилена, полистирола и других пластические масс.
В корпусе аппарата между нижней опорно-распределительной решеткой и верхней ограничительной решеткой помещается слой полых шаров. Эти аппараты успешно применяли для мокрого обеспыливания газов в процессах, сопровождающихся образованием взвесей и осадков, когда другие аппараты оказывались непригодными.
При гидравлическом сопротивлении от 1500 до 2000 Па в аппарате с псевдоожиженной шаровой насадкой улавливается до 99% частиц размером от 2 мкм и более.
Пенные пылеуловители ЛТИ используют для тонкой очистки технологических, дымовых и выхлопных газов, а также вентиляционного воздуха от пыли, туманов и других загрязнений, обеспечивая более высокую степень очистки по сравнению с мокрыми пылеуловителями другие типов.
3.8.3. Аппараты ударно-инерционного типа
Мокрые газоочистные аппараты ударно-инерционного типа работают по принципу инерционного осаждения частиц во время преодоления очищаемыми газами препятствия или при резком изменении направления движения газового потока над поверхностью жидкости.
Мокрый ударно-инерционный пылеуловитель представляет собой вертикальную колонну, в нижней части которой находится слой жидкости. Запыленные газы со скоростью 20 м/с направляются сверху вниз на поверхность жидкости. При резком изменении направления движения газового потока (на 180°) взвешенные частицы, содержащиеся в газах, проникают в воду и осаждаются в ней, а очищенные газы натравляются в выходной газопровод. Пылеуловители этого типа удовлетворительно работают в случае хорошо смачивающейся пыли с размером частиц более 20 мкм. Шлам из аппарата удаляется периодически или непрерывно через гидрозатвор. Для удаления уплотненного осадка со дна применяют смывные сопла.
Среди мокрых пылеуловителей ударного действия можно выделить еще два наиболее распространенных в промышленности аппарата: статический пылеуловитель ПВМ, типа ротоклон и скруббер ударного действия (скруббер Дойля).
Производительность промышленных ротоклонов составляет от 2500 до 90000 м3
/ч. Эксплуатационным достоинством ротоклонов является возможность изменения производительности (в пределах 25% от номинальной) без заметного снижения эффективности. Институтом Гипротяжмаш был разработан пылеуловитель производительностью до 40000 м3
/ч. Он оборудован устройством для автоматической водоподпитки и поддержания уровня воды в аппарате. Аппарат показал хорошие результаты по эффективности очистки аспирационного воздуха и рекомендован к применению для очистки вентиляционных выбросов от неслипающихся и нецементирующихся пылей.
В скруббер Дойля газ на очистку поступает через трубы, в нижней части которых установлены конусы, увеличивающие скорость газовых потоков (до 35—55 м/с). С этой скоростью газовый поток ударяется о поверхности жидкости, создавая завесу из капель. Уровень жидкости в скруббере на 2—3 мм ниже кромки газоподводящей трубы, а гидравлическое сопротивление составляет 1500 Па. Техническая характеристика скруббера Дойля приведена в табл. 11
Таблица 11.
Техническая характеристика скруббера Дойля
Вид пыли
|
Запыленность, г/м3
|
Эффективность очистки, %
|
Расход воды, м3
/ч на 100 м3
газа
|
на входе
|
на выходе
|
Зола
|
23,1
|
0,342
|
98,4
|
4,0
|
Свинцовый агломерат (от дробилок)
|
1,91
|
0,0071
|
99,6
|
0,8
|
Свинцовый агломерат (от сушильных печей)
|
4,75
|
0,101
|
97,9
|
1,36
|
Фосфорит
|
17,5
|
0,468
|
97,4
|
1,92
|
Уголь
|
4,4
|
0,06335
|
98,6
|
1,36
|
3.8.4. Аппараты центробежного типа.
Принцип использования центробежной силы для улавливания пыли, широко используемый в циклонах, нашел применение и в аппаратах мокрой очистки. Вращение газового потока в аппаратах центробежного типа осуществляется с помощью специальных направляющих лопаток либо путем тангенциального подвода газа. Орошение аппаратов осуществляют форсунками, установленными в центральной части аппарата или вдоль его стенок.
Над форсунками предусматривается свободная от орошения зона, которая служит для сепарации капельной жидкости. Наибольшее применение в промышленности получили центробежные скрубберы с тангенциальным подводом газов.
Пылеуловитель с водяной пленкой (ПВП) рассчитан на очистку запыленного вентиляционного воздуха от любых видов неслеживающейся пыли. Корпус такого циклона представляет собой цилиндр, в нижней части которого тангенциально закреплен патрубок для подвода запыленного газа. Внутренняя стенка циклона орошается водой, стекающей по ней в виде пленки.
Если содержание пыли превышает 2 г/м3
, перед циклоном с водяной пленкой рекомендуется устанавливать первую ступень очистки в виде сухого циклона или другого инерционного пылеотделителя. Циклоны ЦВП не применяют для очистки агрессивных газов.
Центробежный скруббер ВТИ предназначен для очистки дымовых газов от золы. Аппарат можно применять для очистки дымовых газов при сжигании твердого топлива с содержанием серы не более 1% и температуре поступающих на очистку газов не выше 200 °С. Скруббер ВТИ состоит из стального цилиндра с коническим днищем, входного патрубка, оросительной системы и гидравлического затвора. Входной патрубок аппарата приваривается тангенциально к внутренней поверхности.
Степень очистки газов в скруббере ВТИ достигает 90% и не зависит от смачиваемости пыли, изменения плотности орошения (в пределах от 0,06 до 0,14 кг/м3
) и концентрации пыли в газах (до 20 г/м3
). Техническая характеристика центробежных скрубберов приведена в табл. 12.
Таблица 12.
Техническая характеристика центробежных скрубберов ВТИ
Внутренний диаметр, мм
|
Максимальная производительность, м3
/с
|
Расход воды на орошение, м3
/ч
|
Отношение коэффициента гидравлического сопротивления к скорости газа на входе
|
Внутренний диаметр, мм
|
Максимальная производительность, м3
/с
|
Расход воды на орошение, м3
/ч
|
Отношение коэффициента гидравлического сопротивления к скорости газа на входе
|
500
|
1,10
|
0,7
|
46,5
|
1200
|
6,30
|
2,1
|
35,2
|
700
|
2,15
|
1,1
|
40,3
|
1300
|
7,40
|
2,35
|
34,7
|
900
|
3,55
|
1,5
|
37,3
|
1400
|
8,60
|
2,65
|
34,1
|
1000
|
4,40
|
1,7
|
36,6
|
1500
|
9,85
|
2,95
|
33,8
|
1600
|
11,20
|
3,25
|
33,5
|
3.8.5. Скруббер Вентури
Скруббер Вентури является наиболее распространенным аппаратом этого класса. Его выполняют в виде трубы, имеющей плавное сужение на входе (конфузор) и плавное расширение на выходе (диффузор). Наиболее узкая часть трубы Вентури называется горловиной. В конфузор на некотором расстоянии от горловины с помощью форсунок подводится жидкость. Запыленный поток с большой скоростью проходит через горловину и входит в диффузор. В процессе истечения газа через горловину происходит тесный контакт между газом и жидкостью. Процесс очистки газа в аппарате можно рассматривать как фильтрование газа через объемный фильтр, состоящий из мельчайших капелек; образующихся при дроблении жидкости.
При очистке горячего влажного газа повышению эффективности процесса способствует охлаждение газа ниже точки росы и выделение сконденсированной влаги. При движении газа через диффузорный участок трубы скорость потока снижается, в результате происходит агрегация мелких капель. Для их улавливания за трубой Вентури обычно устанавливают циклоны или другие аппараты подобного типа. |
По конструкции разные типы турбулентных промывателей отличаются конфигурацией поперечного сечения трубы-распылителя (круглое, прямоугольное), местом подачи орошающей жидкости (в конфузор или горловину) и конструкцией каплеуловителя.
Эффективность улавливания пыли в скрубберах Вентури увеличивается с ростом скорости газов в горловине и плотности орошения. Оптимальное соотношение между скоростью газов в горловине трубы и плотностью орошения определяют для каждого вида пыли, оно зависит от ее дисперсного состава. Так, при улавливании частиц пыли, размеры которых меньше 0,1 мкм, большое значение приобретает продолжительность контакта запыленных газов с поверхностью диспергированной жидкости. В этом случае повышение эффективности может быть достигнута при снижении скорости газов до 50 м/с и увеличении плотности орошения до 3,5 л/м3
газа.
В зависимости от способа подвода орошающей жидкости можно различать основные типы аппаратов с центральным подводом жидкости в конфузор, с периферийным орошением (в конфузоре или в горловине), с пленочным орошением, с бесфорсуночным и форсуночным орошением.
3.8.6. Электрические фильтры
Одним из наиболее совершенных способов очистки промышленных газов от пыли и туманов является электрическая очистка в электрофильтрах.
Широкое применение электрофильтров для улавливания твердых и жидких частиц обусловлено их универсальностью и высокой степенью очистки газов при сравнительно низких энергозатратах. Эффективность установок электрической очистки газов достигает 99%, а в ряде случаев и 99,9%. Такие фильтры способны улавливать частицы различных размеров, в том числе и субмикронные, при концентрации частиц в газе до 50 г/м3
и выше.
Промышленные электрофильтры широко применяют в диапазоне температур до 400—450°С и более, а также в условиях воздействия коррозийных сред.
Электрофильтры могут работать при разрежении и под давлением очищаемых газов. Они отличаются относительно низкими эксплуатационными затратами, однако капитальные затраты на сооружение электрофильтров довольно высоки, так как эти аппараты металлоемки и занимают большую площадь, а также снабжаются специальными агрегатами для электропитания. При этом с уменьшением производительности установок по газу удельные капитальные затраты сильно возрастают.
Преимущественной областью применения электрофильтров с точки зрения экономической целесообразности является очистка больших объемов газа.
К недостаткам электрофильтров наряду с их высокой стоимостью следует отнести высокую чувствительность процесса электрической очистки газов к отклонениям от заданного технологического режима, а также к механическим дефектам внутреннего оборудования.
Иногда свойства газопылевого потока являются серьезным препятствием для осуществления процесса электрогазоочистки (например, при высоком удельном электрическом сопротивлении пыли или когда очищаемый газ представляет собой взрывоопасную смесь).
Улавливание пыли в электрофильтрах основано на известной способности разноименно заряженных тел притягиваться друг к другу. Пылевидным частицам сначала сообщается электрический заряд, после чего они осаждаются на противоположно заряженном электроде.
Когда в межэлектродном пространстве проходит газ со взвешенными пылевидными частицами, ионы газа адсорбируются на поверхности пылинок, вследствие чего пылинки заряжаются и приобретают способность перемещаться под воздействием электрического поля к осадительным электродам. Осевшую на электродах пыль периодически удаляют. Таким образом, электрогазоочистка включает процессы образования ионов, зарядки пылевидных частиц, транспортирования их к осадительным электродам, периодическое разрушение слоя накопившейся на электродах пыли и удаление ее в пылесборные бункеры.
С увеличением напряженности электрического поля и величины заряда, получаемого частицами, скорость движения заряженных частиц к электроду возрастает. Электрофильтр будет тем лучше улавливать пыль, чем больше его длина, выше напряженность поля и меньше скорость газа в аппарате.
Различные конструкции электрофильтров отличаются направлением хода газов (вертикальные, горизонтальные), формой осадительных электродов (пластинчатые, С-образные, трубчатые, шестигранные), формой коронирующих электродов (игольчатые, круглого или штыкового сечения), числом параллельно работающих секций (одно- и многосекционные). Электрофильтры подразделяются на сухие и мокрые.
В сухих электрофильтрах обычно улавливаются твердые частицы, которые удаляются с электродов встряхиванием. Очищаемый в сухом электрофильтре газ должен иметь температуру, превышающую точку росы, во избежание конденсации влаги, появление которой может вызвать коррозию аппарата.
В мокрых электрофильтрах можно улавливать твердые и жидкие частицы, смываемые с поверхности электродов орошающей жидкостью (обычно водой). Температура газа, поступающего в мокрый электрофильтр, должна быть близкой к точке росы или равна ей. Если жидкие частицы самостоятельно стекают с электродов по мере их накопления, то мокрые электрофильтры могут не иметь специальных устройств для промывания.
Существуют два основных типа осадительных электродов - пластинчатые и трубчатые. Пластинчатые электроды используются, как в горизонтальных, так и в вертикальных электрофильтрах, а трубчатые — только в вертикальных. Трубчатые осадительные электроды предпочтительнее пластинчатых вследствие лучших характеристик электрического поля. Однако обеспечить хорошее встряхивание трубчатых электродов сложно, и поэтому их редко применяют в сухих электрофильтрах и довольно широко в мокрых.
Приложение
Расчеты пылеулавливающего оборудования
1. Расчет скоростного пылеуловителя
При расчете скоростного пылеуловителя определяют размеры, гидравлическое сопротивление, эффективность турбулентного промывателя.
Режим работы трубы – коагулятора (скорость газа в сечении горловины и удельный расход воды) выбирают в зависимости от характеристики пыли и ее дисперсного состава, а также от требуемой эффективности очистки газа.
Расчет эффективности работы скруббера Вентури может быть осуществлен на основании данных фракционной степени очистки газов и при помощи энергетической теории мокрого пылеулавливания. Суть энергетической теории мокрого пылеулавливания, основанной на законе сохранения энергии, заключается в следующем.
Эффективность любого мокрого аппарата газоочистки при улавливании определенного вида пыли зависит только от потери давления и не зависит от размера и конструкции пылеуловителя. В общий расход энергии на очистку газа включается как энергия, затрачиваемая на преодоление сопротивления при проходе запыленного газа через аппарат, так и расходуемая на распыление воды.
Затрату энергии на мокрую очистку газа от пыли без учета энергии, расходуемой на создание движения газа, определяют выражением

где Кт
- удельная энергия соприкосновения, затрачиваемая на очистку в мокром пылеуловителе 1000м^3 газов, кДж;
Δpап
- гидравлическое сопротивление аппарата, Н/мІ;
рж
- давление распыливаемой жидкости, Н/мІ;
Vж,
Vг
- расход соответственно жидкости и газа, мі/с.
Первое слагаемое в выражении (1) характеризует степень турбулизации газо-жидкостного потока в аппарате, второе – качество диспергирования жидкости. Их влияние на величину зависит от типа аппаратов. Например, в скруббере Вентури оснсвное влияние оказывает гидравлическое сопротивление аппарата. Зависимость между степенью очистки газа и затратами энергии выражают формулой
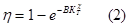
где B, ? - константы, определяемые видом и дисперсным составом пыли и не зависящие от типа и размеров мокрого пылеуловителя.
Таблица 1
Параметры
B
и
c
для некоторых пылей
Номер кривой на рис. 1
|
Вид пыли или тумана
|
B
|
c
|
1
2
3
4
5
6
7
8
9
10
11
12
13
14
15
16
17
18
19
20
21
22
23
-
-
-
-
|
Конверторная пыль (при продувке кислородом сверху)
Тальк
Туман фосфорной кислоты
Ваграночная пыль
Мартеновская пыль
Колошниковая (доменная) пыль
Пыль известковых печей
Пыль, содержащая окись цинка, из печей, выплавляющих латунь
Щелочной аэрозоль из известковых печей
Аэрозоль сульфата меди
Дурнопахнущие вещества мыльных фабрик
Пыль мартеновских печей, работающих на дутье, обогащенном кислородом
Пыль мартеновских печей, работающих на воздушном дутье
Пыль из доменных печей
Пыль из томасовского конвертора
Пыль, образующаяся при выплавке 45%-ного ферросилиция в закрытых электропечах
Пыль, образующаяся в содорегенерационных котлоагрегатах сульфатно-целлюлозного производства
Пыль от производства черного щелока при обработке предварительно увлажненных газов
То же, при обработке сухих газов
Частицы поташа из МГД-установок открытого цикла
Пыль, образующаяся при выплавке силикомарганца в закрытых ферросплавных печах
Пыль каолинового производства
Улавливание сажи, образующейся при электрокрекинге метана
Возгоны свинца и цинка из шахтных печей
Пыль дымовых газов карбидной печи
Пыль закрытой печи, выплавляющей углеродистый феррохром
Зола дымовых газов ТЭЦ
|
9,88·10 -2
0,206
1,34·10 -2
1,355·10 -2
1,915·10 -2
6,61·10 -3
6,5·10 -4
2,34·10 -2
5,53·10 -5
2,14·10-4
1,09·10-5
1,565·10-6
1,74·10-6
0,1925
0,268
2,42·10-5
4·10-4
1,32·10-3
9,3·10-4
0,016
6,9·10-3
2,34·10-4
10-5
6,06·10-3
0,823·10-3
6,49·10-5
0,17
|
0,4663
0,3506
0,6312
0,6210
0,5688
0,891
1,0529
0,5317
1,2295
1,0679
1,4146
1,619
1,594
0,3255
0,2589
1,26
1,05
0,861
0,861
0,554
0,67
1,115
1,36
0,4775
0,914
1,1
0,3
|
Эти константы определяют только экспериментальным путем. Их значения для некоторых пылей и туманов приведены в табл. 1.
Величина h незначительно характеризует качество очистки в интервале высоких степеней очистки (0,98 – 0,99), поэтому в этом случае используют понятие числа единиц переноса:
Из уравнений (2) и (3) величину единиц переноса можно выразить формулой
В логарифмических координатах формула (4) представляет собой прямую линию, тангенсом угла наклона которой к оси абсцисс является c , а величину B находят при пересечении прямой с линией, соответствующей значению KТ
=1,0
Зная NЧ
, удельную энергию KТ
можно определить при помощи графиков, изображенных на рис. 1 (номера линий соответствуют определенной пыли по табл. 1).
Величина KТ
учитывает способ ввода жидкости в аппарат, диаметр капель, вязкость, поверхностное натяжение и другие свойства жидкости.
Технологический расчет мокрых центробежных циклонов и скрубберов
Расчет мокрых центробежных аппаратов заключается в определении их основных размеров, расхода воды, гидравлического сопротивления и эффективности по очистке газа. Диаметр цилиндрической части циклонов и скрубберов рассчитывают по формуле
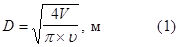
где V – количество газа, подлежащего очистке при рабочих условиях, м^3/c;
υ – средняя скорость газа в сечении цилиндрической части аппарата, м/с.
Расход воды, необходимой для орошения стенок аппаратов, определяется в зависимости от их диаметра по формуле
Gв=0,14?D, л/с (2)
При таком расходе воды толщина пленки будет не менее 0,3 мм, что исключит разрывы на пути ее движения по стенкам.
Гидравлическое сопротивление циклонов и скрубберов находят по формуле
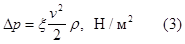
где р – плотность газа в рабочих условиях, Нсм ,
υ - скорость газа во входном патрубке, м/с;
ξ – коэффициент местного сопротивления аппарата.
Значение коэффициента местного сопротивления циклонов зависит от диаметра:
Диаметр циклона , м . 0,6 0,8 1,0 1,2 1,4 1,6
ξ 3,4 3,0 2,9 2,8 2,7 2,6
Значение скрубберов типа МП – ВТИ ?=9, а для типа ЧС – ВТИ ?=2,6ч2,8.
Если в формуле (3) принять скорость газа в цилиндрической части корпуса аппарата, то значение коэффициента гидравлического сопротивления следует принимать для циклонов ?=30ч32 ? для скрубберов ?=33,5ч35,2.
Чтобы определить степень очистки газа или воздуха в циклонах и скрубберах, необходимо знать их фракционную эффективность. Для мокрых центробежных циклонов и скрубберов диаметром 1 м, по данным ВТИ, фракционная эффективность в зависимости от скорости витания частиц пыли приведена в табл. 2.
Таблица 2
Фракционная эффективность очистки газа от пыли в мокрых циклонах и скрубберах диаметром 1м,
%
Скорость газа во входной патрубке,м/с
|
Фракционная эффективность при скорости витания частиц, см/с
|
0 - 0,5
|
0,5 - 2
|
2 - 5
|
5 - 10
|
10-15
|
15-20
|
>20
|
15
17
19
21
23
|
65,5
75,7
81,5
85
87,4
|
80
85,2
88,2
90,3
91,6
|
88
90
91,5
92,8
93,7
|
91
92
93,2
94,3
95,3
|
92,7
93,7
94,5
95,5
96,4
|
94
95
95,8
96,7
97,6
|
98
98,5
99
99,5
100
|
Скорость витания частиц в зависимости от их размера и плотности находят по номограмме. По этим данным общую степень очистки газа определяют по формуле (4).
Для циклонов другого диаметра D м степень очистки газа может быть уточнена по формуле

В некоторых случаях требуется знать конечную температуру газа на выходе из циклона или скруббера. Ее можно определить по эмпирической формуле

где tВЫХ
- температура газа на выходе из аппарата, С;
tВХ
- температура газа перед аппаратом, С;
tН
- температура воды, поступающей на орошение, С;
tК
-температура волы на выходе из аппарата, принимаемая на 5 – 10 С меньше температуры мокрого термометра газа, С;
с - теплоемкость газа, Дж/(кг· С);
- плотность газа перед аппаратом, кг/м?.
Расчет полого скруббера
Количество тепла, которое необходимо отнять от газа в процессе его охлаждения и передать жидкости (воде), рассчитывают по формуле
Q=V0
(c+f1
cП
)(t1
-t2
); Дж/с (1)
где V0
- количество сухого газа при нормальных условиях, м?(н)/с;
с – объемная теплоемкость сухого газа при нормальных условиях, Дж/(м?(н)·°C);
сП
- теплоемкость водяного пара, Дж/(кг·°C);
f1
- начальное влагосодержание газа, кг/м?(н);
t1
, t2
- соответственно начальная и конечная температуры газа на выходе в скруббер и на выходе из него, °C.
Пренебрегая теплопотерями в окружающую среду, полезный рабочий объем скруббера рассчитывают по формуле
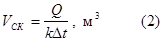
где k – объемный коэффициент теплопередачи в скруббере, Вт/(м?·°С);
?t – средняя разность температур газа и жидкости, °C.
Зависимость объемного коэффициента теплопередачи от плотности орошения и массовой скорости в скрубберах была получена Г.Ф. Алексеевым и В.А. Оленевым опытным путем при исследованиях охлаждения и очистки доменного газа водой:
ккал/(м3
*ч*0
С), (3)
где U – плотность орошения, кг/(м?·ч);
ρГ
– плотность газа, кг/м?;
υГ
– скорость газа, м/с.
Таблица 3
Коэффициент теплопередачи и испарения в полых скрубберах (практические данные)
Для некоторых газов объемный коэффициент теплопередачи в скрубберах приведен в табл. 3. Коэффициент теплопередачи зависит от режимных параметров жидкости и газа в скруббере.
Его значение увеличивается с ростом относительной скорости газа и капель, а также с уменьшением размера капель и снижается с ростом величины удельного орошения.
Среднюю разность температур газа и воды в скруббере (газ и вода движутся противотоком) определяют из выражения
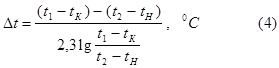
где t1
, t2
– начальная и конечная температура газа, °C;
tН
, tК
– начальная и конечная температура воды, °C.
Список используемой литературы:
Алиев Г.М. Устройство и обслуживание газоочистительных и пылеулавливающих установок - М.: Металлургия, 1983
Гордон Г.М., Пейсахов И.Л. Пылеулавливание и очистка газов – М.: Металлургия, 1968
Денисов С.И. Улавливание и утилизация пылей и газов – М.: Металлургия, 1991
Дубальская Э.Н. Очистка отходящих газов – М.,1991
Коузов П.А., Малыгин А.Д., Скрябин Г.М. Очистка от пыли газов и воздуха в химической промышленности – Л.: Химия, - Ленинградское отделение. 1982
Ю.В. Красовицкий, А.В. Малинов, В.В. Дуров Обеспыливание промышленных газов в фаянсовом производстве – М.: Химия, 1994
Лаптев А.А., Приемов С.И., Родичкин И.Д., Шемшученко Ю.С. Охрана и оптимизация окружающей среды – Киев.: Либедь, 1990
Охрана окружающей среды :Справочное пособие / Сост. Л.П. Шариков. – Л.: Судостроение, 1978
Пирумов А.И. Обеспыливание воздуха – М.: Стройиздат, 1974
Пирумов А.И. Обеспыливание воздуха – 2-е изд., испр. и доп. – М.:Стройиздат,1981
Родионов А.И., Клушин В.Н., Торочешников Н.С. Техника защиты окружающей среды – М.: Химия, 1989
Справочник по пыле- и золоулавливанию – М.: Энергия, 1975
Старк С.Б. Газоочистительные аппараты и установки в металлургическом производстве – М.: Металлургия,1990
Страус В. Промышленная очистка газов – М.: Химия, 1981
Штокман Е.А. Очистка воздуха – М.: Изд. АСВ, 1999
|