Введение
1. Особенности сварки алюминия и его сплавов, применяемые материалы
1.1 . Удаление окисной пленки с поверхности свариваемого металла
1.2. Конструктивные и технологические особенности сварки алюминия и его сплавов
1.3. Материалы для сварки алюминия и его сплавов
2. Обзор наиболее распространенных способов сварки алюминия и его сплавов
2.1. Ручная дуговая сварка покрытыми электродами алюминия и его сплавов
2.2. Аргонодуговая сварка неплавящимся вольфрамовым электродом с подачей присадочной проволоки
2.2.1. Сварка вольфрамовым электродом переменным симметричным током
2.2.2. Сварка вольфрамовым электродом переменным асимметричным током
2.2.3. Импульсная сварка вольфрамовым электродом
2.3. Плазменная сварка алюминия и его сплавов
2.4. Механизированная аргонодуговая сварка плавящимся электродом
2.4.1. Механизированная сварка плавящимся электродом
2.4.2. Механизированная импульсно-дуговая сварка плавящимся электродом
3. Оценка способов дуговой сварки алюминия и его сплавов
4. Техника безопасности и пожарные мероприятия при выполнении сварочных работ
Список литературы
Введение.
Алюминий и его сплавы играют важную роль в современной промышленности. Это обусловлено тем, что большинство промышленных сплавов алюминия обладает рядом уникальных свойств: сочетание высоких механических свойств (высокая удельная прочность .В/.) и физических свойств (малая плотность ., высокая теплопроводность, которая в 3-3.5 раза выше, чем у стали).
В работе [1] приведены данные о потреблении алюминия и его сплавов в мире за 1998 год.
Рис.1. Применение алюминия и его сплавов в 1998 году в разных частях мира
Основными областями применения являются транспорт (авиационная промышленность, кораблестроение, вагоностроение), строительство (металлоконструкции общего назначения) и упаковочная промышленность.
Рис.2. Применение алюминия и его сплавов в промышленности
Большинство промышленных сплавов представляют собой сложные металлургические системы. В качестве основных легирующих элементов для алюминия используют магний, марганец, медь, кремний, цинк, реже никель, титан, бериллий, цирконий. Большинство легирующих элементов образуют с алюминием твердые растворы ограниченной растворимости, а также промежуточные фазы с алюминием и между собой (например, Mg2Si, CuAl2). Суммарное содержание легирующих элементов, как правило, не превышает15%. алюминия марганцем или магнием способствует повышению его прочности.Дополнительного упрочнения, как и для технического алюминия, можно достичь нагартовкой (наклепом). Однако применение нагартованного металла в сварных конструкциях менее удобно, чем использование ненагартованного или отожженного. Нагартованный металл, в особенности с повышенным содержанием легирующих примесей, труднее деформировать при изготовлении заготовок под сварку. Кроме того, эффект нагартовки легко снимается сварочным нагревом. Временное сопротивление сплава АМг6 в отожженном и нагартованном состояниях 320 и 380 МПа соответственно.
Максимальную прочность термически упрочняемых сплавов получают в результате закалки и последующего старения. В закаленном и состаренном сплаве упрочнение обеспечивается образованием зон Гинье – Престона (зонное упрочнение) или мелкодисперсных фаз (фазовое упрочнение). Закалку сплава осуществляют погружением его в воду. При этом создается пересыщенный твердый раствор алюминия. При последующей выдержке на воздухе и комнатной температуре (естественное старение) или при температуре 100 – 190°С (искусственное старение) прочность полуфабрикатов повышается в 2 2,5 раза. Временное сопротивление термически упрочняемых сплавов достигает 400 – 500 МПа и более.
Чем меньше примесей в алюминиевом сплаве, тем, как правило, выше его пластичность. Технический алюминий, алюминиево-марганцевый и низколегированные сплавы с магнием вплоть до АМг5 легко деформируются в холодном состоянии. Образцы сплава АМг6 в зависимости от толщины, содержания сопутствующих примесей могут быть изогнуты на 100—180°. Термически упрочняемые сплавы допускают деформацию только в закаленном состоянии, а в состаренном состоянии изгибу не подлежат. Их можно деформировать после небольшого нагрева (150 – 200°С).
В связи с тенденцией замены черных металлов алюминием и его сплавами во многих отраслях техники, строительства и транспорта эту замену следует осуществлять с учетом технико-экономических преимуществ того или иного сплава перед сталью. При использовании алюминиевых сплавов необходимо также учитывать их коррозионную стойкость и свариваемость.
Коррозионная стойкость алюминия и его сплавов определяется наличием на поверхности изделий плотной окисной пленки. Алюминий совершенно нетоксичен, чем определяется широкое применение его в пищевой промышленности. Он весьма стоек в окислительных средах. В связи с этим его используют в сосудах для транспортировки и получения азотной кислоты и т.п. Как правило, чем меньше примесей в техническом металле, тем выше его коррозионная стойкость. Алюминий и его сплавы совершенно непригодны для работы в щелочной среде.
Под свариваемостью понимают совокупность свойств, определяющих возможность получения сварных соединений определенного качества при данном способе сварки. Чем легче получаются качественные соединения, тем выше свариваемость сплава. Многогранное понятие «свариваемость» включает склонность сплавов к образованию трещин, пористости, механические свойства сварных соединений, коррозионную стойкость и пр. При сварке плавлением свариваемость зависит от химического состава сплава и его структуры, которая создается в результате металлургического передела слитка. Среди физико-химических характеристик металла наибольшее влияние на свариваемость оказывают наличие окисной пленки, химический состав, теплопроводность, температура плавления, плотность, коэффициенты теплопроводности и линейного расширения. Последнее приводит к тому, что уровень деформации алюминиевых сварных конструкций в 1.5-2 раза выше, чем у аналогичных стальных конструкций.
Чтобы обеспечить алюминиевым сварным конструкциям требуемую форму и размеры, используют конструктивные и технологические методы уменьшения сварочных деформаций. К числу этих методов относят правильный выбор толщины свариваемых деталей, соответствующее конструирование сварного соединения при сварке разнотолщинных деталей, предварительный подогрев свариваемых поверхностей.
При сварке алюминия и его сплавов также существует такое понятие, как критический сварочный ток. Этот ток определяется рядом факторов, которые недостаточно изучены. Увеличение сварочного тока выше критического значения нарушает процесс формирования сварочного шва, его поверхность покрывается морщинистыми складками, а глубина проплавления резко уменьшается. Величина критического тока зависит от вида сварки, качества защиты поверхности сварочной ванны инертным газом, состава этого газа, толщины свариваемых элементов.
В настоящее время в Украине наиболее распространена аргонодуговая сварка неплавящимся электродом алюминия и его сплавов на переменном токе. Этот метод не является оптимальным для всех видов сварных соединений, т.к. имеет недостаточно высокую производительность. Механизированная сварка плавящимся электродом в среде аргона, например, обеспечивает в 4-5 раз большую производительность, но худшее удаление окисных пленок. Это должно отрицательно сказываться на механических свойствах сварных соединений. Механизированная импульсно-дуговая сварка плавящимся электродом, которая мало применяется в Украине, устраняет этот недостаток, однако свойства сварных соединений изучены недостаточно. Появившиеся в последнее время современные источники питания, например, ВД-306ДК, использующие комбинированную вольтамперную характеристику (ВАХ имеет ряд участков, каждый из которых отвечает за определенную стадию массопереноса, включая формирование капли, ее отрыв от электрода и перенос в сварочную ванну), вообще не исследованы в области технологических свойств при сварке алюминия и его сплавов. Инверторные источники питания ввиду минимального распространения в Украине, также не имеют практического опыта промышленного применения в области сварки указанных соединений. Метод плазменной сварки алюминия известен более широко, но имеет распространение в основном за рубежом.
Поэтому, тема настоящего обзора определена необходимостью систематизации и обобщения основных технологических параметров сварки алюминия и его сплавов в свете достижений техники за последние годы, рассмотрения влияния различных видов аппаратурного оформления процесса сварки алюминия и его сплавов на свойства сварных соединений, экономической целесообразностью применения тех или иных методов сварки.
1. Особенности сварки алюминия и его сплавов,
применяемые материалы.
Технология сварки алюминия и его сплавов достаточно многообразна, виды сварки перечислены выше и имеют ряд особенностей. К числу основных особенностей сварки алюминия и его сплавов любым из перечисленных методов относятся: необходимость удаления окисной пленки с поверхности свариваемых изделий, тщательная подготовка под сварку, предварительный подогрев и др. В работе [2] приведены основные трудности сварки алюминия и его сплавов. К ним относятся:
1. Наличие и возможность образования тугоплавкого окисла Al2O3 (Tпл = 2050ºС) с плотностью больше, чем у алюминия, затрудняет сплавление кромок соединения и способствует загрязнению металла шва частичками этой пленки.
2. Резкое падение прочности при высоких температурах может привести к разрушению (проваливанию) твердого металла нерасплавившейся части кромок под действием веса сварочной ванны. В связи с высокой жидкотекучестью, алюминий может вытекать через корень шва.
3. В связи с большой величиной коэффициента линейного расширения [. = (21 . 24.7)10-6 .
С-1] и низким модулем упругости сплав имеет повышенную склонность к короблению. Уровень сварочных деформаций в 1.5-2 раза выше, чем у аналогичных стальных конструкций.
4. Необходима самая тщательная химическая очистка сварочной проволоки и механическая очистка и обезжиривание свариваемых кромок. В связи с резким повышением растворимости газов в нагретом металле и задержкой их в металле при его остывании возникает интенсивная пористость, обусловленная водородом, приводящая к снижению прочности и пластичности металла. Предварительный и сопутствующий подогрев замедляет кристаллизацию металла сварочной ванны, что способствует более полному удалению газов и снижению пористости.
5. Вследствие высокой теплопроводности алюминия необходимо применение мощных источников теплоты. С этой точки зрения в ряде случаев желательны подогрев начальных участков шва до температуры 120-1500С или применение предварительного и сопутствующего подогрева.
6. Металл шва склонен к возникновению трещин в связи с грубой столбчатой структурой металла шва и выделением по границам зерен легкосплавных эвтектик, а также развитием значительных усадочных напряжений в результате высокой литейной усадки алюминия (7%).
В настоящем разделе приводятся основы технологии сварки алюминия и его сплавов и применяемые сварочные материалы.
1.1. Удаление окисной пленки с поверхности
свариваемого металла
.
В естественных условиях производства и хранения алюминий покрывается слоем окиси, предохраняющим его от коррозии. На воздухе зачищенная поверхность сразу же покрывается новым слоем окиси, толщина которого восстанавливается практически в течение нескольких дней, надежно защищая металл от дальнейшего окисления. На рис.1.1 показана кинетическая зависимость окисления алюминия при 200ºС. 
Рис.1.1. Кинетическая зависимость окисления алюминия при 200ºС.
Окисная пленка на поверхности алюминия и его сплавов затрудняет процесс сварки. Обладая высокой температурой плавления (20500ºС) она не растворяется в жидком металле в процессе сварки. Попадая в ванну, она затрудняет сплавление между собой частиц металла и ухудшает формирование шва.
Важной характеристикой окисной пленки алюминия является ее способность адсорбировать газы, в особенности водяной пар. Поэтому, окисная пленка является источником газов, растворяющихся в металле, и косвенной причиной возникновения в нем несплошностей различного рода.
Естественная защитная пленка имеет значительную толщину и ее удаление в процессе сварки весьма затруднительно. Поэтому поверхность соединяемых деталей и проволоки очищают от слоя окиси непосредственно перед сваркой и создают на ней искусственный слой окиси, который сохраняется достаточно тонким в течении 8-16 ч. Полученный тонкий слой окиси алюминия сравнительно легко удаляется электрической дугой или с помощью флюса во время сварки.
Обработка поверхности свариваемых деталей и проволоки производится следующим образом [3]. Сначала производится механическая зачистка с помощью металлических щеток. Затем свариваемые детали и проволока обезжириваются в водном растворе следующего состава: 40-50 г/л тринатрийфосфата (Na3PO4 . 12H2O), 35-50 г/л кальцинированной соды (Na2CO3) и 25-30 г/л жидкого стекла (Na2SiO3). Время обезжиривания примерно 5 минут, температура раствора 60-700С. Далее свариваемые детали и проволоку подвергают травлению в течении 1-3 мин в 5% растворе щелочи NaOH или KOH. После этого остатки щелочи и продукты реакции смывают сначала горячей, а потом холодной водой. После промывки детали пассивируют 20% азотной кислотой (HNO3), нагретой до температуры 600С. При этом детали покрываются новым тонким слоем окисной пленки. Извлеченные из азотной кислоты детали промывают холодной, затем горячей водой и сушат.
Так как в атмосферных условиях толщина образованной пленки, хотя и более медленно, но все же увеличивается, подготовленные к сварке детали необходимо сварить в течение 24 часов, а сварочную проволоку использовать в течение 8 часов. Различие в сроке хранения подготовленных к сварке деталей и проволоки обусловлено тем, что непосредственно перед сваркой соединяемые кромки деталей дополнительно очищают от окисных пленок механическим путем – проволочной щеткой, а затем шабером. Образовавшаяся после механической зачистки тончайшая пленка окиси легко удаляется сварочной дугой, горящей в среде инертных газов. Весьма эффективно происходит удаление окиси с поверхности металла, имеющего отрицательный потенциал. Присутствующие в дуге положительные ионы инертных газов разгоняются катодным напряжением и ударяют в поверхностный слой окисной пленки. Процесс обработки свариваемого металла положительными ионами называют катодным распылением. Результаты этого процесса остаются в виде беловатых полос по сторонам шва.
Менее эффективно удаление окиси алюминия с поверхности свариваемого металла происходит, когда он имеет положительный потенциал. Окись алюминия в этом случае разрушается при взаимодействии с расплавленным алюминием. В результате образуется газообразный субокисел Al2O. Поскольку эта реакция возможна только при температурах свыше 17000С, область очищенной поверхности практически ограничена анодным пятном. Естественно, для такого метода сварки применяются мощные горелки и высокие токи дуги для обеспечения большой плотности теплового потока в области анодного пятна дуги. Такой метод удаления окисной пленки называется термической очисткой. Поэтому, этот метод более эффективен при использовании в качестве защитного газа гелия, так как он наиболее высокоэнтальпийный газ и способствует более стабильному поддержанию дугового промежутка.
При ручной дуговой сварке покрытыми электродами и автоматической дуговой сварке по слою флюса расплавленный алюминий защищают от окружающей атмосферы флюсами из хлоридов и фторидов щелочных и щелочноземельных металлов, которые под действием дуги расплавляются и энергично реагируют с окисью алюминия, образуя комплексные соединения, переходящие в шлак, либо летучие соединения. Так, например, при использовании флюсов состава 50% KCl; 15% NaCl; 35% Na3AlF2 происходит разрушение Al2O3 по реакции
Al2O3 + 6KCl = 2AlCl3ЃЄ + 3K2O и растворение Al2O3 в криолите Na3AlF2 с образованием легкоплавкого шлака (NaCl снижает температуру плавления криолита). Криолит не только растворяет Al2O3, но, изменяя поверхностное натяжение металла, способствует образованию мелкокапельного переноса электродного металла. Остатки флюса и шлака, как правило, при комнатных температурах способствуют коррозии алюминия. Поэтому их остатки необходимо тщательно удалять с поверхности сваренных изделий, протирая загрязненные участки волосяными щетками в струе горячей воды или пара. Очищающее действие дуги зависит от глубины ее проникновения в соединяемый металл. Эту глубину регулируют, изменяя силу сварочного тока. Как правило, сварочный ток для сварки алюминия и его сплавов не превышает 550-750А. Увеличение сварочного тока выше этих критических значений нарушает процесс формирования шва.
При сварке плавлением алюминиевых сплавов наиболее рациональным типом соединений являются стыковые. Для устранения окисных включений в металле швов используют удаляемые подкладки из коррозионно-стойкой стали, других металлов с повышенной температурой плавления, а также меди, благодаря ее высокой теплопроводности. Используют также остающиеся подкладки из свариваемого алюминиевого сплава или разделку кромок с обратной стороны шва, что обеспечивает удаление окисных включений из стыка в канавку подкладки. 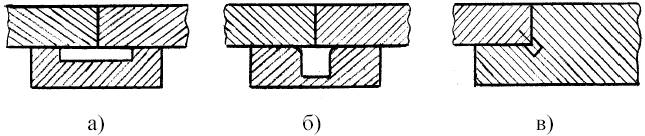
Рис.1.2. Форма поперечного сечения канавки в подкладке,
формирующей обратную сторону стыкового шва:
а – прямоугольная; б – квадратная со скругленными кромками; в – квадратная, наклонная
Подкладка, формирующая обратную сторону стыкового шва, имеет канавку, различные формы которой представлены на рис.1.2. Чаще всего используют канавки прямоугольной формы (рис. 1.2, а), которые обеспечивают стабильные условия для формирования шва и удаления окисных пленок при довольно значительных смещениях линии стыка и дуги от оси канавки. Канавка, поперечное сечение которой показано на рис.1.2 б, обеспечивает плавный переход от усиления шва к основному металлу. Но из-за малой ширины ее надо применять вместе с дополнительной центрующей оснасткой. Для удаления окисных пленок в стыковых соединениях с остающейся подкладкой, изготовленной как единое целое со свариваемым элементом, используют прямоугольные и наклонные канавки (рис.1.2, в), которые просты в изготовлении. Кроме удаления окисных пленок такая канавка уменьшает теплоотвод от сварочной ванны в сторону более толстого элемента замкового соединения. удаления окисных пленок из корня шва при односторонней сварке стыковых соединений на подкладке с канавкой показан на рис.1.3. Канавка, как уже говорилось ранее, препятствует отводу теплоты от свариваемых кромок в подкладку и способствует опусканию окисных пленок вместе с расплавленным металлом сварочной ванны в нижнюю часть сварного шва. 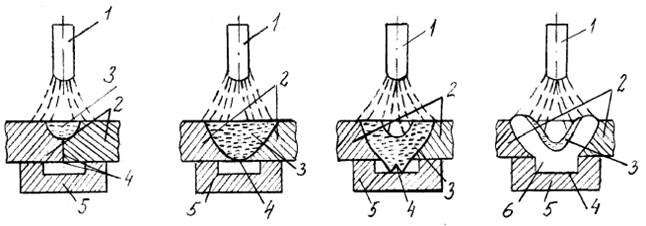
Рис.1.3. Схема удаления окисных пленок из корня шва при односторонней
сварке стыковых соединений на подкладке с канавкой:
1 – электрод; 2 – свариваемый металл; 3 – расплавленный металл сварочной ванны; 4 – окисные пленки на поверхности соединяемых кромок; 5 – подкладка с канавкой; 6 – металл шва.
Вероятность полного удаления окисных пленок с торцевых поверхностей свариваемых кромок повышается с увеличением глубины канавки. В то же время слишком глубокая канавка требует дополнительного расхода сварочной проволоки для ее заполнения, а чрезмерно высокий валик на обратной стороне шва будет способствовать концентрации напряжений в зоне сплавления. На практике обычно применяют подкладки с глубиной канавки 1.2-2 мм. При правильно выбранном и стабильном режиме сварки такая глубина канавки более чем в 1.5 раза превышает высоту оставшихся под дугой окисных пленок и обеспечивает их полное удаление в поверхностный слой нижнего усиления шва. Канавка должна иметь достаточную ширину, чтобы обеспечить нормальное прогибание окисных пленок на нижней поверхности состыкованных кромок в условиях возможного смещения стыка в процессе сварки.
1.2. Конструктивные и технологические особенности сварки алюминия
.
Как было сказано выше, из-за большого коэффициента теплопроводности и линейного расширения алюминия, существенно искажается форма, и изменяются размеры сварных конструкций из алюминиевых сплавов. Поэтому, необходимо использовать конструктивные и технологические методы уменьшения сварочных деформаций вне зависимости от выбранного вида сварки.
Конструктивные способы уменьшения деформаций и напряжений предусматриваются при проектировании сварного соединения. К ним относятся уменьшение количества сварных швов в изделии, симметричное расположение ребер жесткости, швов, косынок. Для уравновешивания деформаций припуски деталей на усадку должны быть равны усадке с тем, чтобы размеры конструкции после сварки соответствовали проектным. Необходимо предусматривать возможность использования зажимных сборочно-сварочных приспособлений для предотвращения смещения свариваемых кромок относительно друг друга в процессе сварки. Повышенная склонность к деформации свариваемых соединений алюминия и его сплавов способствует появлению в них горячих трещин. Особенно склонны к образованию горячих трещин стыковые швы, близко расположенные друг к другу из-за пересечения зон термического влияния. Необходимо конструктивно располагать швы на максимально возможном удалении друг от друга. Если нельзя разнести швы, соединяемые элементы изготавливают как единое целое (рис.1.4). а) б)
Рис.1.4. Конструкция соединения близко расположенных патрубков с листом
а – не рекомендуемая; б рекомендуемая
Отличительной чертой сварки алюминия является то, что описанные выше конструктивные способы необходимо применять в совокупности с описанными в предыдущем разделе методами удаления окисной пленки из сварного соединения. Это наглядно иллюстрируется на примере соединения трубы с трубной доской (такие устройства широко применяются как теплообменники в энергетике и представляют собой два круглых фланца с просверленными в них отверстиями, в которые вставлены теплообменные трубки). На рис.1.5 показаны различные виды соединения трубы с трубной доской. 
Рис.1.5. Соединение трубы с трубной доской
а) замковое; б) стыковое с канавкой, полученное гибкой; в) стыковое с канавкой, полученной резанием.
На рис.1.5 а показано соединение трубы с трубной доской, где наклонная канавка выполняет две функции: первая функция – удаление окисных пленок, вторая функция – создание равнотолщинности сварного соединения (сварка выполняется по кольцу с торцевой верхней поверхности). На рис.1.5 б, в показан другой вид соединения, где кольцевая канавка служит для удаления окисных пленок, а кольцевая проточка в трубной доске – для обеспечения равнотолщинности сварного соединения (сварка также выполняется с торцевой поверхности по кольцу). Вообще, в связи с низкой температурой плавления для алюминия проблема равнотолщинности очень актуальна. Это вызвано тем, что для высококачественного сварочного соединения необходимо проплавить обе сопрягаемые поверхности. Из-за низкой температуры плавления более тонкая деталь может просто расплавиться. Поэтому, свариваемые кромки разнотолщинных элементов должны иметь одинаковую толщину. На рис.1.6 показаны варианты стыкового соединения разной толщины. а) б)
Рис.1.6. Стыковое соединение металла разной толщины
а – допускаемое; б рекомендуемое
Для стыковых соединений ширину утоненной части более массивного элемента можно ориентировочно определить по формуле [8] где S1, S2 – толщины свариваемых соединений, l
– длина утоненной части.
Не менее важны технологические меры уменьшения деформаций. Необходимо подобрать оптимальный режим сварки, с тем, чтобы зона термического влияния была минимальной. Для этого стремятся использовать методы сварки, обеспечивающие высокую концентрацию энергии в дуге, а соединения сваривают на повышенных скоростях. На деформацию соединения существенно влияет порядок выполнения швов. При выполнении швов большой протяженности целесообразно использовать обратно-ступенчатый способ сварки. Сварку конструкций, имеющих несколько последовательно расположенных швов, целесообразно начинать со среднего шва, а затем поочередно, с каждой стороны, выполнять остальные швы, двигаясь к краям конструкции. Также необходимо учитывать, что соединения со скосом кромок более склонны к деформации, чем без скоса кромок и соединения с симметричной двусторонней разделкой кромок менее склонны к деформациям, чем с односторонней разделкой кромок. Для предотвращения продольного прогиба соединений применяют предварительный обратный выгиб свариваемых элементов, который подбирают опытным путем.
Для устранения остаточных деформаций применяют ударную и тепловую правку. Чтобы не повредить поверхность, алюминиевые соединения правят ударами резиновых и деревянных молотков. Правку стальными молотками можно выполнять только через алюминиевые или деревянные подкладки. Тепловую правку применяют для тех алюминиевых соединений, работоспособность которых не ухудшается сопровождающим нагрев разупрочнением, например, при правке малонагруженных элементов или конструкций из отожженного металла. Максимальная температура подогрева должна быть не выше температуры отжига для применяемого алюминиевого сплава.
К числу технологических особенностей сварки алюминия необходимо отнести и предварительный подогрев. Он имеет важное значение в виду того, что окисная пленка на поверхности свариваемых алюминиевых металлоконструкций прекрасно адсорбирует влагу и необходимо применять меры по удалению этой влаги. Если этого не делать, то в сварном соединении могут возникнуть дефекты. Поэтому, свариваемые кромки перед сваркой подогревают, используя газовые горелки (восстановительное пламя), горячий воздух или электроконтактные нагреватели.
Температура и время подогрева зависят от марки и толщины свариваемого металла (табл.1.1). Температуру контролируют с помощью контактных термопар или термокарандашей.
Таблица 1.1
Максимальная температура подогрева некоторых алюминиевых сплавов. [8]
Сплав |
Толщина металла, мм |
Температура, 0С |
Продолжительность нагрева, мин |
А99, АД1 |
Любая |
350 |
60 |
АМц |
Любая |
250 |
60 |
АМг3, АМг4, АМг5 |
< 12 > 12 |
100 150 |
30 10 |
АД31, АД33, АВ |
< 12 > 12 |
180 200 |
60 30 |
1915 |
< 12 > 12 |
140 160 |
30 20 |
1.3. Материалы для сварки алюминия и его сплавов.
Сварочная проволока.
При дуговой сварке большинства соединений требуется проволока, металл которой заполняет зазоры, а также обеспечивает формирование шва в соответствии с размерами, установленными ГОСТ 14806-80. Кроме того, проволока позволяет изменять состав шва, что особенно важно при сварке различных алюминиевых сплавов. Требуемый для легирования состав проволоки выбирают с учетом химического состава свариваемых кромок и доли участия проволоки в образовании шва. Для дуговой сварки в инертных газах содержание каждого элемента в проволоке можно рассчитать из уравнения [8] 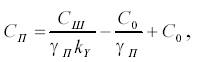
где СП – расчетное содержание элемента в проволоке; С0 – содержание элемента в свариваемом металле; СШ – содержание элемента в металле шва; kY – суммарный коэффициент усвоения элемента металлом шва при сварке; .П – доля проволоки в металле шва.
Доля проволоки в металле шва зависит от типа соединения, толщины свариваемых кромок, формы и размеров шва, зазоров.
Под действием высоких температур часть легирующих элементов улетучивается с поверхности расплавленного металла сварочной ванны и электродной проволоки. Эти потери учитывает суммарный коэффициент усвоения элемента металлом шва, который учитывает, какое количество данного элемента перешло в шов. Величина потерь зависит от способа и режима сварки, физико-химических свойств элемента и его содержания в проволоке. Обычно коэффициент усвоения kY определяют экспериментальным путем, сравнивая фактическое содержание элемента в шва с расчетным.
Определенный по уравнению состав проволоки чаще всего не совпадает с составом проволок, выпускаемых промышленностью. В связи с этим для сварки подбирают ту марку проволоки, у которой состав наиболее соответствует расчетному.
С введением легирующих элементов прочность металла шва повышается, а пластичность и коррозионная стойкость снижаются. Для большинства алюминиевых сплавов суммарное содержание в шве или зоне сплавления 5-8% легирующих элементов достаточно, чтобы по границам зерен образовался сплошной ободок из вторичных фаз. При такой структуре дальнейшее легирование не только не увеличивает, а даже несколько снижает прочность в результате концентрации напряжений по малопластичным вторичным фазам. Таким образом, для получения пластичных коррозионно-стойких соединений алюминиевые сплавы целесообразно сваривать менее легированными проволоками. Когда требуются сварные соединения повышенной прочности, наоборот, применяют более легированные проволоки с суммарным содержанием легирующих элементов не выше 6 –7%.
Наличие максимума трещинообразования при сварке алюминиевых сплавов в каждой системе легирования определяет выбор проволоки, способной обеспечить соединениям повышенную стойкость против трещин. Чтобы повысить стойкость соединений против образования горячих трещин, при сварке сплавов менее легированных, чем сплав с максимальным показателем трещинообразования, применяют проволоку с пониженным содержанием легирующих элементов, тогда как более легированные сплавы сваривают проволоками с более высоким содержанием легирующих элементов.
В зависимости от предъявляемых к соединениям требований, для сварки каждого из алюминиевых сплавов обычно применяют несколько марок проволок. Наиболее простым подходом является применение универсальной проволоки, которая обеспечивает сварным соединениям достаточно высокие значения всех основных характеристик: стойкость против горячих трещин, прочность, пластичность и коррозионную стойкость. Остальные рекомендованные проволоки обеспечивают соединениям повышенные значения одной из названных характеристик при удовлетворительных значениях всех остальных (табл. 1.2.).
Таблица 1.2.
Рекомендуемые марки проволок для сварки распространенных алюминиевых сплавов.
Свариваемый Металл |
Универсальная проволока, обеспечивающая удовлетворит. характеристики соединения |
Проволока, обеспечивающая удовлетворительные характеристики соединения и повышенные показатели |
Стойкость против горячих трещин |
Временное сопротивление разрыву |
Относительное удлинение |
Коррозион. стойкость |
А99, А97, А95 |
А99 |
А99 |
СвА85Т |
А99 |
А99 |
АД0,АД1 |
СвА5 |
СвА5 |
СвА5 |
СвА97 |
СвА97 |
Амц |
СвАМц |
СвАМц |
СвАМц |
СвАМц |
СвАМц |
АМг3 |
СвАМг3 |
СвАМг5 |
СвАМг5 |
АВч |
АВч |
АМг5 |
СвАМг5 |
СвАМг63 |
СвАМг6 |
СвАМг5 |
Св1557 |
АМг6 |
СвАМг6 |
СвАМг63 |
СвАМг61 |
СвАМг63 |
Св1557 |
АВ, АД31, АД33 |
СвАК5 |
СвАК5 |
Св1557 |
Св1557 |
АВч |
1915 |
Св1557 |
СвАМг5 |
СвАМг6 |
СвАМг5 |
Св1557 |
Прим. Проволоку с обозначением «Св» поставляют по ГОСТ 7871-75, остальную по ТУ |
Проволока может применяться в двух назначениях:
как электродная проволока при полуавтоматической или автоматической сварке в защитных газах (в шведском стандарте называется «Autrod»)
как присадочный материал при аргонодуговой сварке неплавящимся электродом (в шведском стандарте называется «Tigrod»)
Применяют также импортную сварочную проволоку фирмы «ESAB» (Швеция), (табл.1.3).
Таблица 1.3
Рекомендуемые марки проволок фирмы «ESAB» для сварки распространенных алюминиевых сплавов [4].
Свариваемый металл |
Марка проволоки |
Чистый алюминий А995 |
OK Autrod 18.01 (состав проволоки Al99,5) |
Чистый алюминий A995 |
OK Autrod 18.11 (состав проволоки Al99,5Ti) |
Силумин, с содержанием Si до 7% |
OK Autrod 18.04 (состав проволоки AlSi5) |
Сплав АМг3 (до 3%Mg) |
OK Autrod 18.13 (состав проволоки AlMg3) |
Сплав АМг5 (до 5%Mg) |
OK Autrod 18.15 (состав проволоки AlMg5) |
Сплавы АМг4, АМг5 |
OK Autrod 18.16 (состав проволоки AlMg4,5Mn) |
2.
Обзор наиболее распространенных способов сварки
алюминия и его сплавов
.
Для алюминия и его сплавов применяют практически все промышленные способы сварки плавлением. К основным методам сварки относятся: ручная дуговая сварка покрытыми электродами (ММА), аргонодуговая сварка неплавящимся вольфрамовым электродом с подачей присадочной проволоки (ТIG),плазменная сварка, полуавтоматическая сварка в защитном газе – бывает как минимум четырех разновидностей (импульсная полуавтоматическая сварка, традиционная полуавтоматическая сварка, полуавтоматическая сварка с управляемым массопереносом на инверторном источнике питания, полуавтоматическая сварка на источниках питания типа ВД-306ДК с комбинированной вольтамперной характеристикой). Другие виды сварки алюминия и его сплавов, такие как автоматическая сварка под слоем флюса и газовая сварка применяются значительно реже и рассматриваться не будут. Каждый способ сварки имеет свои особенности, которые необходимо учитывать для наиболее эффективного их использования при изготовлении изделий различного назначения.
2.1 .
Ручная дуговая сварка покрытыми электродами
алюминия и его сплавов
.
Ручную дуговую сварку покрытыми электродами применяют при изготовлении конструкций из технического алюминия, сплавов АМц и АМг, содержащих до 5 % магния, а также силумина. Толщина свариваемого металла лимитируется диаметром электрода. Минимальный диаметр электрода обычно составляет 4 мм, что вызвано трудностями сварки электродами малого сечения вследствие высокой скорости их плавления. Алюминиевый электрод расплавляется в 2-3 раза быстрее стального. В связи с этим толщина свариваемого металла должна быть свыше 4 мм.
Наиболее приемлемым типом сварного соединения для алюминия является стыковое. Соединений внахлестку и тавровых избегают, так как возможно затекание шлака в зазоры, из которых его трудно удалить при промывке после сварки. Наличие шлака в зазоре может вызвать коррозию металла. Поэтому, этот метод сварки алюминия наиболее редко применяется в промышленности. Отличие от ручной дуговой сварки стальных металлоконструкций заключается в том, что алюминий имеет значительно более высокую теплопроводность, чем сталь (см. п.1). Это приводит к тому, что шлак при ручной дуговой сварке не успевает, в ряде случаев, удаляться из расплавленного металла сварного соединения ввиду малого времени нахождения сварочной ванны в расплавленном состоянии и остается в соединении в виде дефектов.
Защитные (инертные) газы.
Для защиты расплавленного металла сварочной ванны и проволоки при сварке алюминия и его сплавов применяются инертные газы и их смеси: аргон высшего или первого сорта по ГОСТ 10157 –79 и гелий особой или высокой чистоты по ГОСТ20461-75. Инертные газы аргон и гелий поставляются в баллонах.
Вольфрамовые электроды.
Вольфрам – самый тугоплавкий из известных металлов (по температуре плавления он уступает только углероду). Температура плавления вольфрама равна 36000С, удельный вес 19,3 г/см3, он обладает весьма малой летучестью при высоких температурах и имеет низкий коэффициент теплопроводности. Вольфрамовые электроды изготавливаются по ГОСТ 23949-80. Они различаются по легированию, которое уменьшает работу выхода электронов и соответственно срок службы электродов. Электроды бывают чистые (ЭВЧ), лантанированные(ЭВЛ), иттрированные (ЭВИ), торированные (ЭВТ). Характеристики наиболее распространенных электродов в табл. 1.5.
Таблица 1.5
Характеристики наиболее распространенных электродов [8]
Марка электрода |
Содержание примесей, мас. % |
Диаметр прутка или проволоки, мм |
ЭВЧ |
0,5; |
1,0; 1,6; 2,0; 2,5; 3,0; 4,0; 5,0; 6,0; 8,0;10,0 |
ЭВЛ |
(1,1-1,4) окиси лантана (LaO) |
1,0; 1,6; 2,0; 2,5; 3,0; 4,0; 5,0; 6,0; 8,0;10,0 |
ЭВИ-1 |
(1,5-2,3) окиси иттрия (Y2O3) |
2,0; 3,0; 4,0; 5,0; 6,0; 8,0;10,0 |
ЭВИ-2 |
(2,0-3,0) окиси иттрия (Y2O3) |
2,0; 3,0; 4,0; 5,0; 6,0; 8,0;10,0 |
ЭВИ-3 |
(2,5-3,5) окиси иттрия (Y2O3) |
2,0; 3,0; 4,0; 5,0; 6,0; 8,0;10,0 |
ЭВТ-15 |
(1,5-2,0) двуокиси тория(ThO2) |
2,0; 3,0; 4,0; 5,0; 6,0; 8,0;10,0 |
Электроды, применяемые при аргонодуговой сварке необходимо затачивать. Это повышает стабильность работы аргонодуговой установки и качество сварного соединения.
Покрытые электроды.
Для сварки алюминия и его сплавов применяют следующие наиболее распространенные марки покрытых электродов, производства России и других стран [4,5]:
Электрод Свариваемый сплав
ОЗА 1 Технический алюминий
ОК 96.10 («ESAB») Технический алюминий
ОЗА2 Литой сплав типа АЛ-4
ОК 95.50 («ESAB») Литой сплав типа АЛ-4
МВТУ Сплавы типа АМц
АФ1 Сплавы типа АМг, АМц
ОК 96.20 («ESAB») Сплавы типа АМг, АМц
А1Ф Сплавы типа АМц, силумин
Состав электродных покрытий для сварки алюминия и его сплавов для некоторых из перечисленных марок электродов приведен в табл. 1.6.
Таблица 1.6
Состав некоторых электродных покрытий для сварки алюминия и его сплавов, мас. % [5]
Компонент |
Марки покрытия |
ОЗА1 |
ОЗА 2 |
МВТУ |
АФ1 |
А1Ф |
Хлористый натрий |
18,2 |
30 |
18,0 |
Хлористый калий |
32,5 |
50 |
20,0 |
32,0 |
Хлористый литий |
9,1 |
24,0 |
9,0 |
Фтористый калий |
39,0 |
Криолит |
35,0 20 |
35,0 33,0 |
Фтористый натрий |
5,2 |
17,0 |
5,0 |
Ферросилиций |
3,0 |
Флюс АФ-4А |
65,0 |
С течением времени при хранении электроды увлажняются, поэтому перед сваркой их необходимо подсушить при температуре 150 – 200 0С.
Сварочные флюсы.
Для полуавтоматической сварки под слоем флюса применяют флюсы АН-А1, АН-А4, 48-АФ-1, МАТИ-1а, МАТИ-10.Состав флюсов в табл. 1.7.
Таблица 1.7
Состав флюсов для сварки алюминия и его сплавов, мас.% [5]
Компонент |
Марка флюса |
АН-А1 |
АН-А4 |
48-АФ-1 |
МАТИ-1а |
МАТИ-10 |
Хлористый натрий 20,0 |
Хлористый калий |
50,0 |
57,0 |
47,0 |
47,0 |
30,0 |
Хлористый литий |
8,0 |
Фтористый барий |
28,0 47,0 |
68,0 |
Фтористый натрий |
42,0 |
Фтористый калий |
2,0 |
Фтористый литий |
7,5 |
Фтористый алюминий |
7,5 |
2,0 |
Криолит |
30 |
3,0 |
Фторцирконат калия |
2,0 |
Окись хрома |
2,0 |
Флюс должен храниться в герметически закрываемой таре, а перед употреблением просушиваться при температуре 200 – 250 0С в течении 2 часов.
Наиболее приемлемым типом сварного соединения для алюминия является стыковое. Соединений внахлестку и тавровых избегают, так как возможно затекание шлака в зазоры, из которых его трудно удалить при промывке после сварки. Наличие шлака в зазоре может вызвать коррозию металла. Поэтому, этот метод сварки алюминия наиболее редко применяется в промышленности. Отличие от ручной дуговой сварки стальных металлоконструкций заключается в том, что алюминий имеет значительно более высокую теплопроводность, чем сталь (см. п.1). Это приводит к тому, что шлак при ручной дуговой сварке не успевает, в ряде случаев, удаляться из расплавленного металла сварного соединения ввиду малого времени нахождения сварочной ванны в расплавленном состоянии
и остается в соединении в виде дефектов.
2.2. Аргонодуговая сварка неплавящимся вольфрамовым электродом с подачей присадочной проволоки (ТIG).
Аргонодуговая сварка неплавящимся вольфрамовым электродом с подачей присадочной проволоки (ТИГ) наиболее распространенный способ сварки, применяющийся для изготовления сварных конструкций из алюминиевых сплавов ответственного назначения. Основным преимуществом процесса дуговой сварки вольфрамовым электродом в среде защитного газа является отсутствие шлаковых включений, возможность работы на малых токах дуги (от 5А), возможность сварки тонких листов, включая фольгу, высокая устойчивость горения дуги во всем диапазоне токов, технологичность процесса. Благодаря этому процесс широко используется при сварке алюминия и его сплавов.
2.2.1. Сварка вольфрамовым электродом переменным
симметричным током.
Питание дуги осуществляется переменным током от источников с падающими внешними характеристиками. Существует справедливое мнение, что аргонодуговую сварку необходимо производить на штыковых или крутопадающих внешних вольт-амперных характеристиках. Это обусловлено тем, что в указанном случае минимален пусковой бросок тока, что резко улучшает свойства сварного соединения. Переменный ток дуги при сварке алюминия обеспечивает разрушение окисной пленки. Для повышения стабильности горения электрической дуги и эффективного разрушения окисной пленки, кроме падающей внешней характеристики источника и постоянной работы осциллятора используют дополнительную индуктивность (дроссель) в цепи дуги (обеспечивает дополнительную ЭДС самоиндукции и не позволяет погаснуть электрической дуге). Осцилляторы выполняют две функции – бесконтактное зажигание электрической дуги и стабилизацию сварочного тока в момент прохождения через ноль специальными стабилизаторами, синхронизированными со сварочным током и включенными, как правило, параллельно электрической дуге. Последние устройства обычно совмещают с осцилляторами. Электрическая дуга горит между изделием и неплавящимся вольфрамовым электродом. Для повышения стабильности горения электрической дуги рекомендуется тщательно затачивать конец вольфрамового электрода. Симметричность тока обеспечивает равную проплавляющую и очищающую способность электрической дуги. Это самый простой и распространенный способ аргонодуговой сварки.
2.2.2. Сварка вольфрамовым электродом переменным
асимметричным током.
По сравнению с аргонодуговой сваркой неплавящимся электродом симметричным током, сварка асимметричным током алюминиевых сплавов расширяет технологические возможности за счет регулирования параметров тока прямой и обратной полярности. Как правило, регулировка асимметричности осуществляется в пределах 30% от амплитудного значения параметра. Преобладание составляющей тока прямой полярности приводит к увеличению глубины проплавления и скорости сварки, а также к повышению стойкости вольфрамового электрода. Преобладание тока обратной полярности улучшает очистку свариваемого металла от окисной пленки и улучшает качество формирования шва. Выбор правильного режима сварки в этом случае является задачей технолога. Для аргонодуговой сварки алюминиевых сплавов неплавящимся вольфрамовым электродом переменным асимметричным током используются установки УДГУ-351АС/DC и УДГУ-501AC/DC.
2.2.3. Импульсная сварка вольфрамовым электродом.
В ряде случаев целесообразно использовать сварку вольфрамовым электродом импульсной дугой. Подача импульсов осуществляется, как правило, с частотой до 50 или свыше 100Гц и эти импульсы накладываются на базовое напряжение на дуге. Импульсы имеют остроугольную или прямоугольную форму и служат для улучшения формирования сварного шва (при частоте следования 1-50 Гц) и для улучшения удаления окисной пленки (при частоте следования более 100 Гц). Наиболее часто такие импульсы применяются при сварке тонколистового металла. Для сварки в импульсном режиме выпускаются приставки к установкам УДГУ-351АС/DC и УДГУ-501AC/DC (типа ППС-01 -пульт пульсирующей сварки). Пульт пульсирующей сварки ППС-01 позволяет
регулировать максимальное и минимальное значения импульсов тока, а также их продолжительность. В стандартном исполнении он позволяет регулировать частоту следования импульсов до 10 Гц, по спецзаказу- до 30Гц. Это обеспечивает снижение вероятности прожогов свариваемого металла и улучшает формирование сварного соединения.
2.3. Плазменная сварка.
Плазменная сварка является дальнейшим развитием и усовершенствованием аргонодуговой сварки вольфрамовым неплавящимся электродом. Плазменная сварка – это сварка плавлением, при которой нагрев производится сжатой дугой. Сжатая дуга – это дуга, столб которой сжат с помощью сопла плазменной горелки, потока газа или внешнего электромагнитного поля. Промышленное развитие получили сварочные плазменные горелки, где стабилизация и сжатие дуги осуществляется с помощью сопла плазменной горелки и потока плазмообразующего газа. При свободном горении дуги температура столба достигает 5000-6000К и столб дуги имеет форму усеченного конуса (рис.2.2, а). При ограничении возможности свободного расширения дуги температура ее возрастает. Кроме того, при сжатии столб дуги принимает практически цилиндрическую форму (рис.2.2, б), стабилизируется анодное пятно на изделии, тепловой поток становится более сосредоточенным, глубина проплавления возрастает, снижается нагрев основного металла, прилегающего к шву.

Рис.2.2. Схемы сопловых частей аргонодуговой (а) и плазменной (б) горелок
Сжимающее дугу сопло, через которое проходит плазма, имеет два важных размера – диаметр выходного отверстия dc
и длину lc
. Расстояние, на котором установлен электрод от выходного отверстия сопла, называется углублением электрода ly
, а расстояние между внешней поверхностью (торцом) сопла и свариваемым изделием – рабочим расстоянием Н
. Рекомендуется длину цилиндрической части сопла lc
выполнять в диапазоне 0.5-2 dc
. Соотношение lc/ dc
носить название калибра и является важной характеристикой сварочной плазменной горелки, так как определяет давление сжатой дуги на сварочную ванну и возможность возникновения аварийного режима работы горелки – двойного дугообразования (дуга горит между электродом и соплом, соплом и изделием). Чем меньше длина цилиндрической части сопла, тем меньше вероятность возникновения этого аварийного режима.
По сравнению с аргонодуговой сваркой неплавящимся вольфрамовым электродом плазменная сварка имеет следующие преимущества:
• Меньшее влияние возможного изменения расстояния от торца сопла до изделия на геометрические размеры зоны проплавления;
• Меньшее влияние изменения тока на форму дуги, а, следовательно, и на стабильность проплавления металла;
• Высокая надежность зажигания дуги благодаря дежурной дуге;
• Отсутствие включений вольфрама в сварном соединении;
• Повышенная скорость сварки;
• Меньшее тепловложение и, следовательно, коробление изделий.
Если принять одинаковую скорость сварки, то при плазменной сварке необходим ток в два раза меньший по сравнению с аргонодуговой сваркой, сварные швы более узкие и с уменьшенной зоной термического влияния, благодаря чему уменьшается деформация конструкций. Недостатком плазменной сварки является то, что применяются водоохлаждаемые плазменные горелки и значительно усложняется и удорожается оборудование.
Плазменная сварка алюминия и его сплавов в связи с необходимостью разрушения и удаления окисной пленки выполняется сжатой дугой постоянного тока обратной полярности. Электрод в такой горелке служит анодом. В табл. 2.4 приведены рекомендуемые значения допустимого сварочного тока прямой и обратной полярности для вольфрамовых электродов различных марок и диаметров.
Таблица 2.4.
Допустимые значения постоянного тока прямой и обратной полярности для электродов различных марок [8]
Диаметр электрода, мм |
Максимальный сварочный ток (А) для вольфрамовых электродов при полярности |
ЭВЧ |
ЭВЛ |
ЭВТ-15 |
ЭВИ-3 |
прямой |
обратной |
прямой |
обратной |
прямой |
обратной |
прямой |
обратной |
2,0 |
50-90 |
20-25 |
110-150 30- |
35 |
140-180 |
35-40 |
160-200 |
40-50 |
3,0 |
160-200 |
30-35 |
240-280 |
40-45 |
300-340 |
45-50 |
320-360 |
50-70 |
4,0 |
320-370 |
40-50 |
470-520 |
50-60 |
530-580 |
60-70 |
600-660 |
70-80 |
5,0 |
570-600 |
50-70 |
680-740 |
60-80 |
770-830 |
70-90 |
860-920 |
80-110 |
6,0 |
70-90 |
80-110 |
90-120 |
100-130 |
8,0 |
110-140 |
120-160 |
140-180 |
160-200 |
10,0 |
160-210 |
170-220 |
200-250 |
220-270 |
Как следует из табл. 2.4, при переходе на обратную полярность происходит многократное снижение допустимого тока. Поэтому, наиболее разумным решением является использование медных сферических водоохлаждаемых анодов. Это обеспечивает возможность изменения сварочного тока в широких пределах (до 300А) при сохранении высокой (более 10 часов) продолжительности работы. Работы в этом направлении, как отмечалось выше, проводит ЗАО НПФ «ИТС» и ВАТТ МО РФ, г. С-Петербург.
Процесс возбуждения дуги в установках обычно происходит следующим образом:
• С помощью высокочастотного высоковольтного напряжения осциллятора в промежутке электрод – сопло возбуждается искровой разряд, который затем переходит в дуговой (под воздействием электрического поля источника питания), т.е. возбуждается так называемая дежурная дуга постоянного тока, горящая между электродом и соплом.
• Потоком плазмообразующего газа катодное пятно дежурной дуги перемещается с внутренней конической поверхности сопла на его цилиндрическую поверхность, одновременно с этим дежурная дуга растягивается и плазменная струя длиной 20-40 мм истекает из сопла.
• При касании факела дежурной дуги изделия замыкается цепь электрод – изделие и возникает основная дуга, ток дежурной дуги снижается до нуля.
Для плазменной сварки алюминия применяют установки типа УПС-301 (токи до 300А) и УПС-501 (токи до 500А). В последнее время наиболее часто применяют источник питания ВД-306ДК или ВД-506ДК и приставку БУСП-ТИГ для аргонодуговой сварки, которая служит для подключения плазменной горелки, регулировки тока дежурной дуги, базового тока, скорости нарастания-снижения базового тока, времени продувки до и после сварки и времени горения дежурной дуги после выключения основной сварочной дуги.
В качестве плазменной горелки часто применяли плазмотрон типа ПС-3, конструкция которого допускает использование медного или вольфрамового электродов. Плазмотрон разработан СПбГТУ, выпускался заводом «Электрик». В настоящее время наибольший интерес вызывает псевдоплазменная горелка с медным анодом разработки ЗАО НПФ «ИТС» и ВАТТ. Существует соглашение, что после промышленных испытаний промышленное производство этой горелки будет осуществлять немецкая фирма «Abicor Binzel»
Рекомендуемые режимы плазменной сварки сплава АМг6 приведены в табл.2.5.
Таблица 2.5.
Ориентировочные режимы плазменной сварки стыковых соединений из сплава АМг6 толщиной 3,2 мм. [5]
Род тока |
IСВ, А UД, В |
VСВ, м/ч |
dПР, мм |
q/v
.103
, Дж/м |
Постоянный (обратная полярность) |
87 |
33 |
23 |
1,8 |
225 |
Переменный |
220 21 |
20 |
2,0 |
415 |
Механические свойства сварных соединений из сплава АМг6 толщиной 3,2 мм, выполненных на постоянном токе обратной полярности следующие: предел прочности .В = 32,3 – 33,4 кгс/мм2 (316,9 – 327,7 МПа), угол загиба . = 78 – 81 град. [5]
2.4. Механизированная аргонодуговая сварка плавящимся электродом.
2.4.1. Механизированная сварка плавящимся электродом
непрерывным током
Механизированную сварку плавящимся электродом применяют для получения стыковых, тавровых, нахлесточных и других соединений алюминия и его сплавов толщиной 4-6 мм и более. Этот способ является самым производительным среди ручных видов сварки. За границей наиболее распространенный среди видов сварки алюминия.
Отличием механизированной сварки алюминия от традиционной механизированной сварки сталей является: использование аргона в качестве защитного газа, тефлоновых подающих каналов вместо стальных, специальной формы роликов в подающем механизме, специальных мундштуков на горелках. В СССР ввиду отсутствия дешевых тефлоновых каналов этот метод сварки был незаслуженно не востребован.
Электрическая дуга при этом способе сварки горит между изделием и плавящимся электродом (проволокой), который подается в зону дуги обычно с постоянной скоростью.
Надежное разрушение пленки окислов при механизированной сварке плавящимся электродом достигается лишь при питании дуги постоянным током обратной полярности. Механизм удаления окисной пленки в этом случае заключается в разрушении и распылении ее тяжелыми положительными ионами, бомбардирующими катод (эффект катодного распыления).
Недостатком способа сварки алюминия плавящимся электродом является некоторое снижение по сравнению со сваркой неплавящимся электродом показателей механических свойств. В частности, уменьшение прочности шва об
ясняется тем, что электродный металл, проходя через дуговой промежуток, перегревается в большей степени, чем присадочная проволока при сварке неплавящимся электродом. Также происходит худшее удаление окисной пленки, т.к. при аргонодуговой механизированной сварке непрерывным током сварочный процесс сопровождается короткими замыканиями, в момент которых катодное распыление отсутствует.
Для устранения этих недостатка в сварочной установке ВД-306ДК применены принципиально новые технические решения: низковольтная постоянная подпитка сварочной дуги напряжением 10-11В, которая накладывается на общую картину сварочного напряжения.
Для сварки, как правило, применяют проволоку диаметром 1.2-1.6 мм, так как из-за недостаточной жесткости сварка алюминиевой проволокой меньшего диаметра затруднена. Применение проволоки большего диаметра принципиально возможно, однако сварные соединения в этом случае получаются крупночешуйчатые, что ухудшает их внешний вид и механические свойства.
Установки для механизированной сварки состоят из выпрямителя (ВД-306ДК и т.д.), механизма подачи (ПДГО-508, ПДГО-510 и т.д.) со специальными роликами.
Конструкция механизма подачи должна обеспечивать надежное и стабильное поступление мягкой алюминиевой проволоки. Обычно в таких механизмах предусматривают две пары специальных ведущих и прижимных роликов, что уменьшает возможность проскальзывания проволоки и ее сминания.
Наиболее применимы сварочные горелки немецкой фирмы «Abicor Binzel» с тефлоновым подающим каналом. Следует отметить, что в виду использования аргона, как защитного газа, чаще всего применяют водоохлаждаемые модели горелок. Сопло горелки должно обеспечивать надежную защиту инертным газом жидкой сварочной ванны. Диаметр сопла горелки для механизированной сварки алюминия обычно 18-22 мм.
Ориентировочные режимы механизированной аргонодуговой сварки алюминия плавящимся электродом приведены в табл. 2.6.
Таблица 2.6.
Ориентировочные режимы механизированной аргонодуговой сварки алюминия и его сплавов плавящимся электродом. [5]
Тип соединения |
b, мм |
dЭЛ.ПР., мм |
IСВ, А |
UД, В |
VCВ, м/ч |
Расход аргона, л/мин |
Число проходов |
Встык, без разделки кромок |
4-6 8-10 12 |
1,5-2,0 1,5-2,0 2,0 |
140-240 220-300 280-300 |
19-22 22-25 23-25 |
20-30 15-25 15-18 |
6-10 8-10 10-12 |
2 2 2 |
Встык, с Vобразной разделкой кромок на подкладке |
5-8 10-12 |
1,5-2,0 2,0 |
220-280 260-280 |
21-24 21-25 |
20-25 15-20 |
8-10 8-12 |
2-3 3-4 |
Встык, с Х образной разделкой кромок |
12-16 20-25 30-60 |
2,0 2,0 2,0 |
280-360 330-360 330-360 |
24-28 26-28 26-28 |
20-25 18-20 18-20 |
10-12 12-15 12-15 |
2-4 4-8 10-40 |
Тавровое, угловое и нахлесточное |
4-6 8-16 20-30 |
1,5-2,0 2,0 2,0 |
200-260 270-330 330-360 |
18-22 24-26 26-28 |
20-30 20-25 20-25 |
6-10 8-12 12-15 |
1 2-6 10-40 |
Особый интерес при механизированной сварке алюминия вызывает использование источника питания ВД-306ДК с механизмом подачи ПДГО-508(510) (полуавтоматический модуль мультисистемы «Сорока»). Использование этого источника вызывает большой промышленный интерес в виду того, что в нем применены принципиально новые технические решения: низковольтная постоянная подпитка сварочной дуги напряжением 10-11В. Особенностью низковольтной подпитки напряжения на сварочной дуге является наложение постоянно действующего отрицательного потенциала. Это обеспечивает непрерывное горение электрической дуги, улучшает удаление окисной пленки, обеспечивает более мягкий переход капель электродного металла в сварочную ванну, уменьшает разбрызгивание и улучшает стабильность горения электрической дуги и качество формирования сварного соединения. Высоковольтная подпитка служит для облегчения зажигания дуги. Таким образом, в указанной схеме стало возможным производить регулирование продолжительности коротких замыканий и их частоты, возможность регулирования тока короткого замыкания. Установка имеет также возможность регулировки угла наклона вольтамперных характеристик и возможность производить сварку на значительном удалении от источника питания (до 20м). Последнее обеспечивается за счет применения обратных связей по току и напряжению на дуге. Для реализации последнего необходимо применять подающий механизм ПДГО-510Т и выпрямитель ВД-306ДК. Следует напомнить, что этот источник обеспечивает высококачественную сварку алюминия и его сплавов в режиме ручной дуговой сварки. Кроме того, его использование позволяет решить проблемы комплектации сварочной техникой цехов, когда все виды сварки (ММА, МИГ,ТИГ) можно производить на базе одного выпрямителя, комплектуя его различными приставками (БУСП-ТИГ, ПДГО) для реализации различных технологических процессов.
Механические свойства сварных соединений из сплава АМг6 толщиной 10 мм, выполненных механизированной сваркой на традиционных источниках питания (типа ВДУ-506) следующие [7]: .В = 30,6 кг/мм2, угол загиба . = 133 град.
2.4.2. Механизированная импульсно-дуговая сварка
плавящимся электродом.
Повысить качество металла шва алюминиевых сплавов удается применением техники управляемого переноса металла при импульсно-дуговой сварке.
Импульсно-дуговая сварка плавящимся электродом отличается от обычной тем, что на постоянный ток обратной полярности, получаемый от основного источника питания, накладываются кратковременные импульсы тока с определенной частотой (как правило, 50 или 100Гц). Импульсы генерируются импульсным устройством для получения мелкокапельного направленного переноса электродного металла через дугу при более низких значениях сварочного тока, чем это имеет место при естественном мелкокапельном переносе. Величину и длительность импульсов сварочного тока выбирают такими, чтобы можно было обеспечить управляемый перенос металла с торца электрода небольшими каплями в широком диапазоне токов. Как правило, в паузах между импульсами значение тока небольшое, но достаточное для поддержания горения сварочной дуги, при котором ввод теплоты в изделие уменьшается и отсутствует перенос металла.
Импульсно-дуговая сварка обеспечивает повышение механических свойств наплавленного металла и сварных соединений в целом, улучшает стабильность процесса, позволяет выполнять сварку в различных пространственных положениях с улучшенным формированием швов, существенно стабилизировать провар корня шва.
Для механизированной импульсно-дуговой сварки плавящимся электродом используют источник питания ВДГИ-302, который комплектуется подающим механизмом ПДИ-304.
Ориентировочные режимы механизированной импульсно-дуговой сварки алюминия и его сплавов плавящимся электродом в аргоне приведены в табл. 2.7.
Таблица 2.7.
Ориентировочные режимы механизированной импульсно-дуговой сварки алюминия и его сплавов плавящимся электродом в аргоне. [5]
b, мм |
dЭЛ.ПР., мм |
Частота импульсов, 1/с |
, А |
UД, В |
, м/ч |
Расход аргона, л/мин |
Число проходов |
4 |
1,4-1,6 |
50 |
130-150 17- |
19 20- |
25 |
10-12 |
1 |
5 |
1,4-1,6 |
50 |
140-170 17- |
19 20- |
25 |
10-13 |
1 |
6 |
1,4-1,6 |
100 |
160-180 18- |
21 20- |
25 |
12-14 |
1 |
8 |
2,0 |
100 160- |
190 22-24 |
25- |
30 12- |
14 2 |
10 |
2,0 |
100 220- |
280 24- |
26 25- |
30 14- |
16 |
2 |
В последние годы широкое распространение при импульсно-дуговой сварке алюминия получили инверторные установки. Наиболее характерным представителем является установка для механизированной сварки типа Sinermig – 401 («OZAS»). Работа источника осуществляется на частоте 26 кГц с возможностью наложения дополнительных импульсов регулируемой амплитуды и скважности. Применение дополнительных импульсов позволяет увеличить производительность на 25% (по данным ОАО «Адмиралтейские верфи»). Использование этого источника позволяет получать кроме указанных выше возможностей, еще и формирование швов с обратным валиком и т.д., что часто требуется при сварке трубопроводов. Это достигается за счет возможности регулировки амплитуды и скважности импульсов, что невозможно на установке ВДГИ-302, где импульсы следуют постоянной амплитуды и частоты. Однако, данных по механическим свойствам изделий из алюминия и его сплавов, сваренных на таком источнике, не существует, ввиду его новизны, поэтому, точно делать выводы о применимости его для сварки конструкций из алюминиевых сплавов нельзя. В данной работе ниже приводится систематические данные по сравнению механических свойств на различных источниках питания при различных видах сварки.
3. Оценка способов дуговой сварки алюминия и его сплавов.
1. Электродуговая сварка алюминия является сложным процессом и требует точного поддержания параметров технологического процесса. Это обусловлено специфическими свойствами алюминия (низкая температура плавления ТПЛ =
VCВ
IСВ6600С, высокая теплопроводность . = 0.52 кал/см.сек.0С, высокая скорость кристаллизации металла шва, высокое сродство к кислороду, высокий коэффициент линейного расширения . = 24,58.10-6). При нарушении технологии швы могут быть плохого качества. Основными дефектами являются непровары, прожоги, поры, трещины, окисные и вольфрамовые включения, а также неудовлетворительное формирование шва.
2. При всех видах электродуговой сварки алюминия применяют специальные технологические и конструктивные меры, способствующие удалению окисной пленки с поверхности свариваемого металла, шлаковых включений, снижению загазованности сварочной ванны, уменьшающие коробление и т.д., которые описаны в настоящей работе.
3. Принципиально дуговая сварка алюминия и его сплавов может осуществляться всеми известными методами: ручная дуговая сварка покрытыми электродами, аргонодуговая сварка неплавящимся электродом (симметричным переменным током, асимметричным переменным током, импульсная), плазменная сварка, полуавтоматическая аргонодуговая сварка плавящимся электродом (с использованием источников питания, выполненных по стандартной схеме выпрямления, с использованием низковольтных и высоковольтных подпиток напряжения на сварочной дуге – комбинированная вольтамперная характеристика, с наложением импульсов на сварочное напряжение). Особое внимание при использовании этих методов необходимо обратить на то, что сварку необходимо осуществлять на обратной полярности или переменном токе. Этот процесс промышленно освоен. Применение сварки на прямой полярности принципиально возможно и обеспечивает высокое качество но находится в стадии лабораторных образцов. В табл. 3.1 приведено сравнение механических свойств сварного соединения из сплава АМГ-5, выполненного различными методами и наличия внутренних дефектов. Сварка производилась на сплаве АМг5, S = 2.5 мм, = 1.2 мм.
Таблица 3.1
Зависимость механических свойств сварного соединения из АМг-5 от вида сварки
Вид сварки |
Установка |
Режим сварки |
.В, кгс/мм2 |
., град |
Дефекты |
Исходный материал |
32 |
Механизированная сварка плавящимся электродом |
ВС-300Б |
=110А, UД = 18В |
19 |
105 |
П1,0; 7П0,3 |
ВДУ-506 |
=125А, UД = 18В |
21 |
125 |
3П0,3; П1,0 |
ВД-506ДК |
=120А, UД = 17В |
26 |
45 |
10П0,3 |
Механизированная импульсно-дуговая сварка плавящимся электродом |
ВДГИ-302 |
f = 100Гц, =100А, UД = 20В |
10 |
90 |
2Н5,0; 6П0,3; 2П1,0 |
ВДГИ-302 |
f = 50Гц, IСВ = 100А, UД = 20В |
27 |
103 |
Синермиг-401 |
= 87А, UД = 16В |
18 |
130 |
3П1,0; 3П0,5 |
IСВ IСВ IСВIСВIСВdПР
Аргонодуговая сварка неплавящимся вольфрамовым электродом с подачей присадочной проволоки |
УДГУ-351 |
Симметричный ток, IСВ = 50А |
16 |
37 |
Ц5В0,5; 5П0,3; В0,5 |
УДГУ-351 |
Асимметричный ток, IСВ = 50А, КАС = 0.56 |
9 |
90 |
3П0,3; В2,0 |
УДГУ-351 |
Асимметричный ток, IСВ = 50А, КАС = 0.43 |
26 |
83 |
4С5В0,5; 2В0,5 |
УДГУ-351 |
Пульсир. режим = 0.15с, tп= 0.15с, IСВ = 50А |
23 |
75 |
2С10В0,5; С20В0,5; П 1,0 |
Из анализа данных таблицы 3.1 следует: . . . .
Наилучший результат обеспечивает стандартная установка для импульсно-дуговой механизированной сварки типа ВДГИ-302 на частоте следования импульсов 50Гц. Сварные соединения, сваренные этим методом, единственные среди исследованных в работе, не имеют внутренних дефектов, имеют самую высокую механическую прочность сварного соединения (84% от прочности основного металла) и один из самых высоких углов загиба.
Ко второй группе установок относятся выпрямители для полуавтоматической сварки (ВД-306(506)ДК, ВДУ-506), которые показали очень неплохие результаты. Механическая прочность составляет 81,2% от прочности основного металла для ВД-306ДК и 65% для ВДУ-506.
К третьей группе установок относится синергетический источник Синермиг-401 на котором производилась импульсно-дуговая механизированная сварка на базовой частоте 26кГц и подача дополнительных импульсов на частоте 100Гц. Полученные данные по этому источнику достаточно противоречивы. С одной стороны получена самая высокая пластичность сварного соединения (данные по углу загиба), с другой стороны – один из самых низких показателей механической прочности (56% от прочности основного металла).
К четвертой группе установок можно отнести метод сварки ТИГ на установках типа УДГУ-501. Самым интересным результатом является факт, что при сварке переменным симметричным током получены одни из самых низких показателей по механической прочности и углу загиба сварного соединения (50% от прочности основного металла). Хуже имеются данные только при коэффициенте асимметрии 0,43, т.е., когда синусоида напряжения на электроде горелки и изделии сдвинута в положительную область, т.е. на изделии присутствует больше положительного потенциала, чем отрицательного (28% от прочности основного металла). Картина качественно меняется, когда коэффициент асимметрии составляет 0,53, т.е. синусоида напряжения на электроде и изделии сдвинута в отрицательную область (81,2% от прочности основного металла) или когда применен пульсирующий режим сварки (72 % от прочности основного металла).
Объяснить полученные результаты можно следующим образом: при сварке алюминиевых конструкций и использовании алюминиевой проволоки для обеспечения формирования плотного малоокисленного сварного соединения перенос должен вестись каплями достаточно однородного размера, причем размер этих капель должен не быть минимальным, а перенос, соответственно, не должен быть струйным. В противном случае, при использовании инверторных источников питания, когда из-за работы источника питания на большой частоте происходит процесс дробления капель, происходит их интенсивное окисление, ввиду резкого увеличения удельной поверхности капель. Сварное соединение формируется из капель минимального размера, которые достаточно окислены, поэтому механические свойства соединения невелики, но внешний вид и пластичность соединения находятся на высоком уровне. Для формирования высококачественного сварного соединения просто не хватает степени газовой защиты, а сварка со специальными дополнительными газовыми поддувами или камерами с контролируемой атмосферой экономически не оправдана.
Косвенно полученный вывод подтверждает результат по использованию другого импульсно-дугового источника, но работающего на промышленной частоте – ВДГИ-302. В этом случае, уменьшение частоты следования импульсов со 100 до 50Гц, т. е. не стремление к струйному переносу, а стремление фиксировать размер капель электродного металла на уровне 0,8-1 мм, позволило получить самые высокие результаты.
В таблице 3.2 приведены экспериментальные характеристики сварочного процесса при механизированной сварке плавящимся электродом (dэ=1.2 мм) в среде аргона сплава АМг5. Таблица 3.2 Экспериментальные характеристики сварочного процесса при механизированной сварке плавящимся электродом (dэ=1.2 мм) в среде аргона сплава АМг5 
ТЕХНИКА БЕЗОПАСНОСТИ И ПОЖАРНЫЕ МЕРОПРИЯТИЯ ПРИ ВЫПОЛНЕНИИ СВАРОЧНЫХ РАБОТ
Леса, подмостки и трапы на судне должны быть надежными, изготовленными по утвержденным чертежам и принятыми представителями отдела техники безопасности. Леса должны иметь бортовые доски высотой 150 мм, чтобы исключить падение вниз инструментов или других предметов. На лесах обязательно устанавливают 2-3 яруса лееров. Трапы или сходни должны быть прочно закреплены и иметь перила по обеим сторонам. Не допускается перегрузка лесов сверх нормы. Необходимо следить, чтобы по одной вертикали на лесах и площадках не работало несколько человек.
Запрещается работать на мокрых, скользких и обледенелых палубах судна и настилах лесов. Лед надо сколоть, а мокрые места посыпать песком, опилками и т.п.
Все рабочие места в цехе и на судне должны быть оборудованы средствами тушения пожаров. В жаркое время года деревянные настилы лесов периодически поливают водой. Все горючие и быстровоспламеняющиеся материалы хранят в специальных помещениях и специальной таре. При использовании огнеопасных материалов нужно строго придерживаться инструкций.
В случае возникновения пожара в цехе или на судне необходимо срочно вызвать пожарную команду завода, а до ее прибытия принять меры по тушению пожара (воспользоваться огнетушителем, песком и водой) и меры по обеспечению безопасности людей и спасению имущества от огня.
Следует помнить, что масло, нефть можно тушить пенными огнетушителями или песком. Горячую электропроводку и электрические машины, находящиеся под напряжением, нельзя тушить водой и пенными огнетушителями, так как это может привести к поражению людей электрическим током. В таких случаях нужно немедленно обесточить проводку и машины и только после этого приступить к тушению огня. При возникновении пожара очень важно сохранить спокойствие, дисциплину и беспрекословно выполнять распоряжения руководителя, ответственного за тушение пожара.
Ответственность за организацию и состояние техники безопасности на предприятиях несет администрация этих предприятий, в составе которой имеются специальные отделы по технике безопасности, или инженеры по технике безопасности.
Все рабочие, перед допуском к работе, должны быть проинструктированы по безопасному ведению работ и в случае необходимости сдать соответствующее испытание по правилам техники безопасности.
Вредное влияние излучения электрической дуги, невидимые ультрафиолетовые лучи, используемые сварочной дугой, вредно действует на сетчатку и роговую оболочку глаз. Если смотреть не защищенными глазами на свет дуги в течение 5-10 минут, то спустя 1-2 часа после этого, появляется боль в глазах, спазмы век, слезотечение, светобоязнь и воспаление глаз. В этом случае нужно обратиться к врачу.
Для защиты зрения служат щитки и маски с защитными стеклами. Стекла совершенно не пропускают ультрафиолетовых лучей, а инфракрасные лучи пропускают лишь в пределах от 0,1 до 3% от общего количества.
Для предохранения от действия лучей сварочной дуги, людей, работающих по соседству с местами сварки, ограждают светонепроникающими щитами, ширмами или кабинами из фанеры и брезентом высотой 1,8 м. Для улучшения вентиляции внутри кабины, стенки не доводят до пола на 25-30 см. чтобы уменьшить разность в яркости света, стенки кабин окрашивают в матовые светлые тона (серый, голубой, желтый) и увеличивают искусственную освещенность рабочего места.
Поражение электрическим током. Предельное напряжение холостого хода при сварке не должно превышать, как правило, 70 В. Особенно опасно поражение током при сварке внутри резервуаров, где сварщик соприкасается с металлическими поверхностями, находящимися под напряжением по отношению к электродержателю.
Список используемой литературы.
1.Anders Norlin. A century of aluminium – a product of the future // A welding review published by Esab. Focus Aluminium, 2000. №2. с. 31-33.
2.Акулов А.И., Бельчук Г.А., Демянцевич В.П. Технология и оборудование сварки плавлением. .: Машиностроение, 1977.
3. Аргоно-дуговая сварка алюминиевых сплавов для строительных конструкций, технологические рекомендации. М.: Госстройиздат, 1963.
4. Каталог ESAB, 1998.
5. Гуревич С.М. Справочник по сварке цветных металлов. Киев: Наукова думка, 1981.
6. Малаховский В.. Плазменная сварка. М.: Высш.шк., 1987.
7. Руссо В.Л. Сварка алюминиевых сплавов в среде инертных газов. Л.: Судпромгиз 1962.
8.Рабкин Д.М., Игнатьев В.Г., Довбищенко И.В. Дуговая сварка алюминия и его сплавов. М.: Машиностроение, 1982.
9. Рабкин Д.М., Игнатьев В.Г., Довбищенко И.В. Сварка алюминия и его сплавов: курс лекций для специалистов-сварщиков. Киев: Наукова думка, 1983.
10.Klas Weman. Equipment for aluminiu welding //A welding review published by Esab. Focus Aluminium , 2000. №2. с. 11-13.
|