Глава
4.
Введение.
Обработка
давлением один
из основных
способов получения
заготовок и
деталей в
приборостроении.
Широкое применение
заготовок и
деталей, полученных
обработкой
давлением,
объясняется
прежде всего
их малой стоимостью,
большой производительностью
изготовления,
малой материалоемкостью,
высокой точностью
и высоким
качеством
поверхности.
При обработке
давлением
происходит
частичное или
полное изменение
формы заготовки
за счет перераспределения
объема под
действием
внешних сил.
К этому виду
обработки
относят горячую
и холодную
ковку, листовую
и объемную
штамповку,
прокатку, волочение,
ротационное
выдавливание,
штамповку
взрывом взрывчатых
веществ и
газовых смесей,
импульсным
магнитным
полем, электрогидравлическую,
эластичными
рабочимии
средами и др.
- десятки различных
операций. *
В основе
физической
сущности различных
видов обработки
давлением
лежат общие
закономерности,
на основании
которых возможно
управление
физическими
свойствами
деталей и процессом
формообразования.
4.1. Физические
основы обработки
давлением
Строение
деформируемого
металла. Все
применяемые
в промышленности
металлы и сплавы
имеют поликристаллическое
строение, то-есть
состоят из
множества
произвольно
ориентированных
в объеме кристаллов.
В некоторых
случаях кристаллы
имеют преобладающую
ориентацию,
обусловленную
технологией
производства.
Расположение
атомов в' кристалле
определяется
условиями
кристаллизации.
Пластическая
деформация.
Под действием
внешних сил
расстояние
между атомами
меняется и при
переносе атомов
в новые положения
устойчивого
равновесия
изменяется
форма заготовки
- возникает
пластическая
деформация.
Пластическое
деформирование
происходит
за счет двух
механизмов:
скольжения
и двойникования.
Скольжение
представляет
собой параллельное
смещение тонких
слоев кристалла
относительно
смежных (рис.1).
Обычно плоскостями
скольжения
являются плоскости
наибольшей
упаковки атомов.
Пересечение
плоскостей
скольжения
с поверхностью
кристалла
называют полосой
скольжения.
Скольжение
начинается
в одном или
нескольких
участках плоскости
скольжения
и затем распространяется
на всю поверхность.
При сдвиге
атомов одного
слоя относительно
другого величина
необходимого
касательного
напряжения
равна
τmax=(b/a)*(G/2п)
где (a , b - расстояние
между атомами
соответственно
в вертикальном
и горизонтальном
направлении,
G - модуль сдвига
(кГ/мм2) MПa
Из формулы
следует, что
сопротивление
сдвигу на несколько
порядков больше
действительных
значений. Эти
расхождения
объясняются
наличием дислокаций.
Дислокации
- это искажение
кристаллической
решетки (рис.2
), причинами
которых являются:
наличие примесей,
отсутствие
в узлах решетки
атомов, излишние
атомы, граница
зерна между
деформированной
и недеформированной
частью в плоскости
скольжения.
Искажения
в реальных
кристаллах
ослабляют
межатомные
связи; это и
уменьшает
прочность
металлов во
много раз.
Двойникование
- это механизм
пластической
деформации,
приводящий
к симметричному
изменению
ориентировки
одной части
кристалла
относительно
другой (рис.3).
Иногда плестическая
деформация
сопровождается
при двойниковании
увеличением
объема (например
у Fe на 50%).

Пластическая
деформация
поликристалла.
У поликристалла
плоскости
скольжения
в отдельных
зернах ориентированы
не одинаково.
И при приложении
внешних сил
деформация
в зернах будет
происходить
не одновременно;
сначала в зернах
с наиболее
благоприятной
ориентировкой
по отношению
к действующему
напряжению,
а затем во всех
остальных,
когда величина
напряжения
и для их положения
достигает
максимального
значения. В
результате
скольжения
в поликристаллическом
теле на поверхности
появляются
линии скольжения
(рис.4) След скольжения
ухудшает внешний
вид деталей.
При дальнейшем
увеличении
степени деформации
вся поверхность
тела покрывается
линиями скольжения
и поэтому их
следов нельзя
заметить.
Дальнейшее
увеличение
степени деформации
приводит к
вытянутости
зерна в направлении
течения и повороту
кристаллографических
осей зерен. При
некоторой
(значительной)
деформации
разница в
направлениях
кристаллографических
осей уменьшается:
возникает
преимущественная
ориентировка
осей поликристалла,
которую называют
текстурой.
Возникновение
текстуры ведет
к анизотропии
всех свойств
тела. Анизотропия
механических
свойств отрицательно
сказывается
на качестве,
расходе металла,
трудоемкости
изготовления
изделия.
Влияние
холодной пластической
деформации
на физико-механические
свойства.
При пластическом
деформировании
тела с увеличением
деформации:
а) изменяются
механические
характеристики
- увеличивается
предел упругости,
текучести,
прочности,
твердость;
уменьшается
- относительное
удлинение (рис.
5), сужение, ударная
вязкость ,
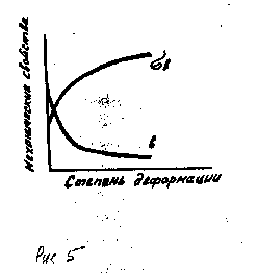
б) изменяются
физические
характеристики
- увеличивается
электрическое
сопротивление
(у вольфрамовой
проволоки на
30-50%), коэрцитивная
сила и гистерезис,
уменьшается
- магнитная
проницаемость,
магнитная
восприимчивость,
магнитное
насыщение и
остаточный
магнетизм,
уменьшается
теплопроводность,
сопротивление
коррозии.
Упрочнение.
Совокупность
всех явлений,
связанных с
изменением
механических
и физико-химических
свойств материалов
называется
упрочнением
(пакленом).
С увеличением
деформации
сопротивление
деформированию
увеличивается
по сравнению
с начальным
в два и более
раза (рис . 5) .
Степень
деформации.
Показателем
степени деформации
в обработке
давлением
наиболее часто
принимается
относительная
и логарифмическая
деформация.
Наиболее
распространено
использование
относительных
деформаций,
например, для
растяжения:
д=(l-lo)/lo
где lo и l - начальная
и конечная
длина образца
при растяжении.
Деформирование
при повышенных
температурах.
С целью уменьшения
деформирующего
усилия и повышения
пластичности
обрабатываемый
металл нагревают.
При повышении
температуры
деформируемого
металла в нем
возникают
процессы
противоположные
упрочнению
- возврат и
рекристаллизация.
При нагреве
до температуры
(0,25-0,30)К° абсолютной
температуры
плавления
металла амплитуда
колебания
атомов при
деформировании
настолько
увеличивается,
что они могут
занимать новые
положения
устойчивого
равновесия.
Это явление
называют возвратом.
Возврат
приводит к
некоторому
уменьшению
сопротивления
деформированию,
однако не влияет
на величину,
форму и размеры
зерна. Поэтому
возврат не
препятствует
образованию
текстуры. С
увеличением
температуры
скорость возврата
увеличивается,
увеличение
скорости
деформирования
может уменьшить
скорость возврата.
Возврат происходит
также и 'при
нагреве ранее
холоднодеформированного
металла.
При температуре
0,4К° и более в
металле протекает
процесс рекристаллизации.
Рекристаллизация
заключается
в появлении
зародышей,
возникновении
и росте новых
зерен взамен
деформированных.
Возможность
рекристаллизации
обусловливается
при увеличении
температуры
повышением
энергетического
баланса атомов,
при котором
атомы получают
возможность
перегруппировок
и интенсивного
обмена местами.
При рекристаллизации
получают равноосные
зерна; величина
образовавшихся
зерен зависит
от температуры,
степени деформации
и скорости
деформации
(рис. 6 ).
Процессу
рекристаллизации
можно подвергать
холоднодеформированные
металлы.
Влияние
горячей пластической
деформации
на свойства
металла. Заготовки
с литой структурой
обычно подвергают
горячей обработке
давлением.
Литая структура
характеризуется
крупными кристаллами
первичной
кристаллизации,
по границам
которых располагаются
прослойки,
обогащенные
примесями и
неметаллическими
включениями.
Деформирование
литой структуры
приводит к
дроблению
кристаллитов
и вытягиванию
их в направлении
наиболее интенсивного
течения металла.
Одновременно
происходит
и вытягивание
в том же направлении
межкристаллитных
прослоек, содержащих
неметаллические
включения. При
достаточно
большой степени
деформации
неметаллические
включения
принимают форму
прядей вытянутых
в направлении
интенсивного
течения металла,
образуя полосчатость
макроструктуры
(полосчатости
микроструктуры
при этом нет).
Полосчатость
макроструктуры
приводит к
анизотропии
металла. Показатели
пластичности
(предел текучести
и удлинение)
вдоль и поперек
волокон значительно
отличаются,
причем разница
их значений
возрастает
с увеличением
степени деформации.
Прочностные
характеристики
металла вдоль
и поперек волокон
отличаются
незначительно,
а увеличение
степени деформации
на их величине
практически
не сказывается.
При горячей
обработке
металлов давлением
стремятся вести
процесс деформирования
таким образом,
чтобы волокна
макроструктуры
были расположены
в направлениях
наибольших
нормальных
напряжений
в условиях
работы детали.
Виды деформаций.
В зависимости
от возможности
протекания
в металле при
деформации
процессов
упрочнения
или разупрочнения
различают
несколько видов
деформации.
Горячая
деформация
- деформация,
при которой
происходит
полная рекристаллизация
деформируемого
металла.
Холодная
деформация
- деформация
при которой
отсутствуют
возврат и
рекристаллизация.
Различают
и промежуточные
виды деформаций:
неполная горячая
деформация
- деформация,
при которой
рекристаллизация
проходит не
полностью;
неполная холодная
деформация
- деформация,
при которой
происходит
только возврат.
Основные
закономерности
пластической
деформации
1. Закон постоянства
объема: объем
металла при
его пластическом
деформировании
остается неизменным.
2. Закон наличия
упругой деформации
при пластическом
деформировании.
При любом
пластическом
деформировании
общая деформация
складывается
из упругой и
остаточной
3. Закон остаточных
напряжений.
При обработке
давлением
однородная
пластическая
деформация
практически
не имеет места,
хотя при решении
она принимается
равномерной.
Неоднородность
деформаций
обусловлена
контактным
трением, неравномерным
распределением
температур,
неоднородностью
химического
состава и
механических
свойств, формой
деформируемого
тела и деформирующего
инструмента.
При неравномерной
деформации
отдельные зерна
деформируются
по-разному.
Однако благодаря
связи между
собой они не
могут самостоятельно
изменять размеры.
В результате
взаимного
влияния возникают
напряжения
со стороны
более деформированных
участков, которые
будут увеличивать
деформацию
менее деформированных
участков и
наоборот. Эти
напряжения
называются
дополнительными.
Дополнительные
напряжения
бывают трех
видов:
напряжения
первого рода
- напряжения,
уравновешивающиеся
между отдельными
частями тела,
напряжения
второго рода
- напряжения
уравновешивающиеся
между отдельными
зернами,
напряжения
третьего рода
- напряжения
уравновешивающиеся
между отдельными
элементами
зерна.
После снятия
деформирующего
усилия дополнительные
напряжения
остаются в
металла; в этом
случае их называют
остаточными,
их характеристика
аналогична
характеристике
дополнительных
напряжений.
Остаточные
напряжения
можно полностью
или частично
снять при
нагреве
металла: при
температуре
возврата снимают
остаточные
напряжения
первого рода,
при температурах
выше температуры
возврата и
ниже температуры
рекристаллизации
снимают остаточные
напряжения
второго и первого
родов* при
температуре
рекристаллизации
снимают остаточные
напряжения
третьего, второго
и первого родов.
Механическим
путем можно
уменьшить
статочные
напряжения
1-го рода за счет
равномерного
деформирования.
4.2. Основные
операции обработки
давлением
Операции
обработки
давлением
классифицируют
в зависимости
от используемого
инструмента,
оборудования,
температуры
обрабатываемого
металла и других
признаков. В
зависимости
от применяемого
инструмента,
деформирующего
металл, различают:
1) штамповую
обработку,
2) бесштамповую
обработку.
При штамповой
обработке на
машине используют
специальный
инструмент
- штамп (отсюда
и происходит
название). С
помощью штампа
можно получать
изделия одинаковых
размеров. При
бесштамповой
обработке на
машине используют
универсальный
деформирующий
инструмент,
позволяющий
получать различные
размеры изделий
одинаковой
формы (круглый,
квадратный,
прямоугольный
пруток, лист,
ленту). К операциям
штамповой
обработки
относят:
1) операции
холодной листовой
штамповки,
2) операции
холодной объемной
штамповки,
3) операции
горячей (листовой
и объемной)
штамповки. При
операциях
листовой штамповки
исходная заготовка
из листового
металла и в
процессе
пластического
деформирования
ее толщина
не меняется
или изменяется
незначительно.
При операциях
объемной штамповки
размеры исходной
заготовки
значитально
изменяются
по трем направлениям.
Основными
операциями
бесштамповой
обработки
являются:
1) прокатка,
2) волочение.
Операции холодной
листовой штамповки
делятся на три
основные группы:
1) разделительные,
2) формообразующие,
3) комбинированные.
К разделительным
операциям
листовой штамповки
относят: отрезку,
разрезку, обрезку,
вырезку, надрезку,
просечку, вырубку,
пробивку,
зачистку и
калибровку
и др.
При разделительных
операциях
происходит
отделение
полное (отрезка,
разрезка, обрезка,
вырезка, вырубка,
пробивка, зачистка,
калибровка)
или частичное
(надрезка, просечка)
металла от
исходной заготовки.
Результатом
этих операций
являются или
готовые детали
или заготовки,
используемые
для последующей
обработки.
К формообразующим
операциям
относят: гибку,
вытяжку, отбортовку,
обжим, формовку
и др.
При формообразующих
операциях
исходная плоская
заготовка
деформируется
в пространственную
деталь. При
этом плоская
заготовка или
локально (гибка,
отбортовка,
обжим, формовка)
или полностью
(вытяжка) деформируется.
К комбинированным
операциям
относят - различные
комбинации
одновременно
выполняемых
в одной или
нескольких
позициях штампа
различных
операций.
Операции
холодной объемной
штамповки:
выдавливание,
высадка, чеканка
и калибровка,
накатка резьб
и зубчатых
колес и др.
4.3.
Материалы,
применяемые
в холодной
штамповке
В холодной
штамповке
применяют
разнообразные
как металлические,
так и неметаллические
материалы.
Наиболее широко
применяют
следующие
металлы и их
сплавы: железо,
медь, алюминий,
магний, цинк,
никель, титан;
обрабатывают
штамповкой
и менее распространенные
металлы и их
сплавы: молибден,
тантал, кобальт,
бериллий, цирконий,
золото, серебро,
платину и др.
Неметаллические
штампуемые
материалы
разделяют на
две группы. К
первой группе
относят: бумагу,
картон, прессшпан,
кожу, фетр, войлок,
резину и прорезиненную
ткань, хлопчатобумажные
и шерстяные
ткани и другие
прокладочные
материалы. Ко
второй группе
относят
конструкционные,
электроизоляционные
и теплоизоляционные
материалы: 1)
слоистые пластмассы
- текстолит,
гетинакс, стекло-
текстолит,
асботекстолит,
фибра, древеснослоистые
пластики и др.,
2) блочные
пластмассы
- органическое
стекло, целлулоид,
винилласт,
поливинилхлорид,
полиэтилен,
3) асбестовые
изделия - бумага
асбестовая,
картон асбестовый,
гидроизол,
паронит, асбометалличес-
кое армированное
полотно, 4) слюда
и миканиты:
слюда (мусковит,
флагонит, биотит),
миканиты
(коллекторный,
прокладочный,
формовочный
и гибкий).
Номенклатура
марок материалов
и сортамент
(форма и размеры)
установлены
соответствующими
Гостами. Наиболее
распространенными
являются различные
сортаменты
черных и цветных
металлов в виде
листов, лент,
полос, круглых,
квадратных
и шестигранных
прутков. В последние
годы созданы
новые листовые
материалы
стальные и
алюминиевые
листы, покрытые
цветной пластмассой
толщиной 0,36 мм.
Технологические
свойства металла
для штамповки
характеризуют:
механические
характеристики,
химический
состав, структура
и величина
зерна, анизотропия,
точность размеров
заготовок.
Механические
свойства металла
характеризуют
в основном:
а)прочностными
показателями-пределом
текучести (бт
, пределом прочности
бв , б) пластическими
показателями
- относительным
удлинением
д и относительным
сужением. В
зависимости
от условий
работы назначения
и технологии
штамповки к
штампуемому
материалу
предъявляют
определенные
механические
и технологические
требования.
При разделительных
операциях
металлы с высоким
пределом
текучести дают
чистый срез;
для формообразующих
операций (гибки,
вытяжки) желателен
низкий предел
текучести - это
способствует
уменьшению
упругой деформации
после штамповки.
Особенно это
важно для операций
гибки, где большой
объем упругодеформируемого
металла. Вытяжка
листового
металла успешно
протекает при
большом относительном
удлинении
(δ>28%) и малом
отношении
предела текучести
к пределу прочности
- бт/бв<0,65. Выбранный
материал должен
также обеспечивать
возможность
выполнения
последующих
технологических
операций отделки,
сборки и т.д.
Химический
состав сильно
влияет на
механические
свойства материала.
Для регламентирования
механических
характеристик
к химсоставу
для штампуемых
сталей предъявляют
жесткие требования.
Структура
в большой степени
влияет на
механические
свойства материала.
В сталях структурное
состояние
углерода (феррит,
перлит, цементит)
определяет
пригодность
к штамповке.
Наиболее
благоприятна
для штамповки
структура
феррита или
структура
феррита и зернистого
перлита.
Величина
зерна и однородность
его оказывают
большое влияние
на штампуемость.
Неоднородность
зерна вызывает
неравномерную
деформацию
объема металла
и является
причиной разрывов
при вытяжке.
Рекомендуют
величину зерна
0,026-0,057 мкм, при величине
зерна менее
0,018 мкм сталь хуже
деформируется
- при вытяжке
возникают
трещины и гофры,
при гибко
значительное
пружинение.
При разделительных
операциях
качество поверхности
скола определяется
величиной
зерна, при вытяжке
и гибко ухудшение
шероховатости
тем больше,
чем больше
величина зерна.
Анизотропия
увеличивает
количество
операций при
вытяжке при
гибко увеличивает
минимальную
величину радиуса
гибки, при вырубке
- пробивке уменьшает
точность размеров.
Точность
размеров заготовки
оказывает
влияние на
точность изготовления
деталей.
4.4. Холодная
листовая штамповка
Виды заготовок.
Для листовой
штамповки
используют
заготовки в
виде листа,
полосы, ленты
или профилей
различного
поперечного
сечения: труба,
уголок, двутавр
и т.д.
Раскрой
материала.
Раскрой материала
- это способ
расположения
деталей (заготовок)
в ленте, полосе
или на листе
с целью рационального
использования
исходного
материала.
Раскрой
полосы (ленты).
В зависимости
от требований
по точности
различают три
типа раскроя:
а) с отходами
перемычками,
б) с частичными
отходами, в)
без отходов.
Раскрой с
отходами (рис.7a)
применяют для
изготовления
деталей повышенной
точности (8-13
квалитет), а
также для деталей
сложной конфигурации,
раскрой с частичными
отходами (рис.7б)
и без отходов
(рис.7в) применяют
для простых
по форме деталей
низкой точности.
Перемычки между
деталями и
краем определяют
по таблицам
в зависимости
от толщины и
конфигурации
детали.
Применяют по
указанным
схемам однорядный
и многорядный
раскрой. Нужную
ширину полосы
(ленты) получают
путем резки
листа (рулона)
на полосы (ленты).
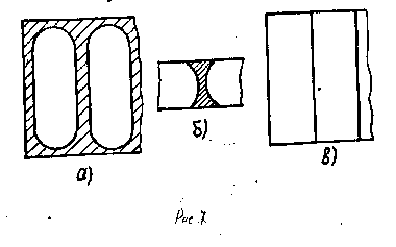
Раскрой
листа (ленты).
При раскрое
листа нужно
стремиться
к получению
целого числа
полос, длина
которых равна
шагу подачи.
Предпочтительным
является продольный
раскрой (рис.8а)
увеличивающий
производительность
труда за счет
меньшего количества
заправок полос
в штамп. Для
уменьшения
отхода по некратности
длины полосы
применяют
поперечный
и комбинированный
раскрой листа
(рис.8б,в). При
раскрое ленты
следует предусматривать
у краев припуск
2-3 мм для удаления
смятых при
транспортировке
торцов.
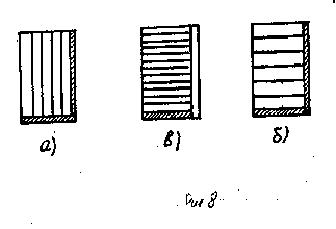
Рациональным
считается
раскрой, для
которого получают
наибольший
коэффициент
использования
материала
N=(n*Fд)/B*A
где n - число
деталей в полосе
или ленте,
Fд - площадь
детали, мм2,
B,A - ширина и длина
полосы, ленты
или листа, мм.
Разделительные
операции
Общие сведения.
Различают
разделительные
операции: 1) со
значительной
шириной отделяемого
металла (более
двух толщин)
- резка, вырубка,
пробивка,
вырезка, надрезка
и др., и 2) операции
с небольшой
шириной отделяемого
металла (менее
0,5 толщина - зачистка,
калибровка.
Механизмы
разделения
в этих случаях
различны.
Первая группа
операций применяется
для разделения
листов и лент
с целью получения
деталей или
заготовок для
последующей
штамповки.
Вторая группа
операций - с
целью отделки
- повышения
качества деталей
Резка.
Механизм разделения
операций резки,
вырубки, пробивки
и др. одинаков.
Процесс резания
- деформирования
заготовки
протекает в
три этапа:
1) упругая
и начало пластической
деформации,
2) пластическая
деформация,
сопровождающаяся
пластическим
врезанием ножей
в материал
заготовки,
3) разделение
металла, происходящее
после исчерпания
пластической
деформации
путем скола.
При упругой
деформации
(1 этап) происходит
упругое сжатие
и изгиб, свободные
концы заготовки
при этом поворачиваются
на некоторый
угол. При пластической
деформации
(2 этап) врезаются
ножи в разделяемый
металл, качество
поверхности
разделения
при этом зависит
в значительной
мере от качества
задней поверхности
ножей. После
исчерпания
пластической
деформации
металла наступает
сдвиг (скол)
металла (3 период).
У режущих кромок
ножей образуются
трещины скола
металла. Эти
трещины располагаются
под некоторым
углом к направлению
движения ножей.
Для качественного
среза они должны
встретиться.
Следовательно,
для обеспечения
качественного
среза между
ножами должен
быть определенный
зазор Z Опытные
данные показывают,
что величина
зазора должна
быть в пределах
Z = (0,05-0,20)S (S - толщина
металла).
Шероховатость
поверхности
среза соответствует
Ra = 2,5-0,32 мкм, шероховатость
поверхности
скола - Rz = 16,0-20,0 мкм
(рис.9д).
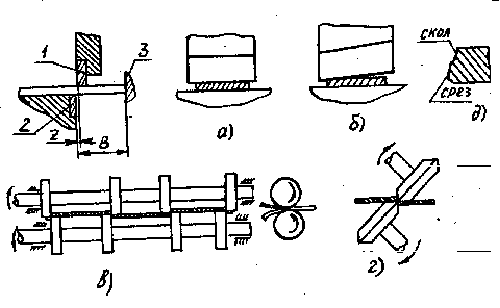
рис. 9
Напряжения
и деформации
в плоскости
листа распространяются
вдоль линии
резки по обе
стороны примерно
на полосе шириной
около одной
толщины металла
(рис.10).
Из этих данных
следует, что
при ширине
отрезаемой
полосы или
ленты равной
или менее двух
толщин поперечное
сечение будет
значительно
искажено.
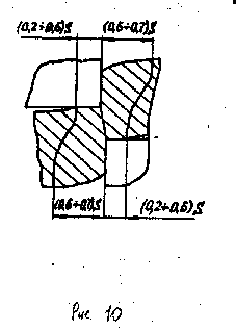
Под действием
силы резания
возникает
опрокидывающий
момент, поворачивающий
лист. Для предотвращения
поворота листа
применяют
прижим.
Основные
технологические
параметры кроме
зазора, точности
и шероховатости
поверхности
- усилие и работа
резки; они
определяются
по формулам:
p=бв*s*L н/(кгс)
(2)
A=(p*s*a)/1000 нм(кгс)
(3)
где бв - предел
прочности
разрезаемого
металла н/м2
(кгс/мм2),
S - толщина
металла (мм), L
- периметр резки
(мм), a - коэффициент,
равный 0,5-0,6.
Усилие и
работа необходимы
для подбора
оборудования
(ножниц).
Для резки
листового
металла применяют
различные типы
ножниц: 1) ножницы
с параллельными
прямыми ножами,
2) ножницы с
наклонными
прямыми ножами,
3) ножницы с
многодисковыми
ножами, 4) ножницы
с парнодисковыми
наклонно
поставленными
ножами и др.
(рис.9а-г), а также
штампы.
Ножницы с
параллельными,
наклонными
и многодисковыми
ножами применяют
для прямолинейной
резки; ножницы
с парнодисковыми
наклонными
ножами - для
криволинейной
резки и вырезки
по замкнутому
контуру. Ножницы
с параллельными
и наклонными
ножами применяют
для резки листов,
ножницы с
многодисковыми
ножами - для
резки лент. Для
выбора ножниц
усилие рассчитывают
по формулам:
а) для ножниц
с параллельными
ножами - по формуле
(2)
б) для ножниц
с наклонными
ножами
P=(1/2)*(бв*S2)/tgL (4)
в) для многодисковых
ножниц
*
P=0,4*m*(бв*S2)/tga
где бв - предел
прочности
материала,
н/м2(кгс/мм2),
S - толщина
материала, мм,
L - угол наклона
ножей, град, α
(альфа) -угол
захвата материала
дисками, град,
м - число пар
ножей.
Точность
резки по ширине
зависит от
толщины и ширины
отрезаемой
заготовки;
более высокая
точность резки
на штампах,
затем на многодисковых
ножницах, затем
на параллельных
ножницах и
наиболее низкая
- на ножницах
с наклонными
ножами. Точность
резки на ножницах
определяется
по справочным
таблицам в
зависимости
от ширины и
толщины разрезаемого
металла. Ориентировочно
она оценивается
12-14 калитетом
точности.
Технологические
требования
(технологичность).
1) Ширина отделяемой
части металла
должна быть
или равна двум
толщинам материала.
2) Точность
резки по ширине
- 12-14 квалитет. Она
уточняется
по справочнику
в зависимости
от применяемого
оборудования
и толщины материала.
3) Шероховатость
поверхности
среза по толщине
неоднородна
- от Rz = 160-20 мкм в зоне
скола до (Ra = 2,5-0,32 мкм
в зоне среза.
Вырубка
и пробивка.
При вырубке
и пробивке
происходит
отделение
металла по
замкнутому
контуру; при
вырубке отделенная
часть - является
деталью, при
пробивке - отходом.
Схема процесса
показана на
рис.11
Механизм
разделения
со всеми его
особенностями
не отличаются
ничем от механизма
разделения
при резке. Напряжения
пластического
деформирования
распространяются
на величину
равную (0,6-0,7) толщины
металла (рис.10),
как и при резке.
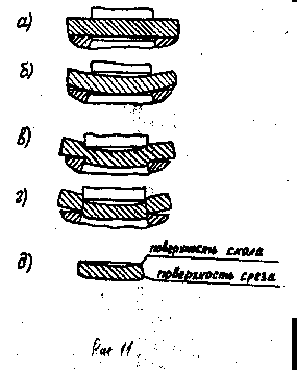
В отличие
от резки изгибающий
момент при
вырубке - пробивке
приложен по
замкнутому
контуру к заготовке,
находящейся
внутри и вне
контура резки,
что приводит
также к изгибу
вырубаемой
и пробиваемой
заготовки -
детали. При
равномерном
сопротивлении
изгибу, что
достигается
соответствующим
расстоянием
от контура
резки до края
заготовки
(перемычке),
получают нормальное
качество поверхности
разделения.
При малой перемычке
ча6ть металла
втягивается
в зазор между
режущими кромками
и в этом случае,
как и при большом
зазоре, получают
заусенцы. Под
действием
изгибающего
момента обе
части заготовки
получают остаточный
прогиб, для
получения
плоской детали
необходима
дополнительная
операция плоскостной
правки. Величина
зазора здесь
также влияет
на качество
разделения.
При нормальном
зазоре Z = (0,05-0,20)S получают
наилучшее
качество поверхности
разделения
- в зоне среза
параметр
шероховатости
Ra = 2,5-0,32 мкм, в зоне
скола параметр
шероховатости
Rz= 80-20 мкм, при увеличенном
зазоре шероховатость
поверхности
разделения
такая же как
и при нормальном
зазоре, и кроме
этого возникает
заусенец; при
уменьшенном
зазоре поверхности
скола не могут
соединиться
и поэтому параметр
шероховатости
ниже Rz =320 мим в
зоне двойного
скола - среза
(рис.12). Точность
размеров при
вырубке - пробивке
зависит от
толщины материала,
формы и размеров
заготовки.
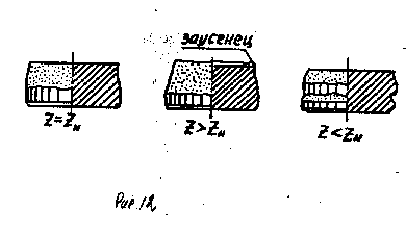
Точность
круглого контура
находится в
пределах 11-14
квалитета. Для
конкретных
условий уточняется
по справочнику.
Так как заготовка
в процессе
вырубки-пробивки
прогибается,
то применение
прижима заготовки
увеличивает
точность размеров.
Усилие и
работа, необходимые
для выбора
оборудования
определяют
по формулам
(2) и (3).
Для выполнения
операций
вырубки-пробивки
используют
механические
- кривошипные
прессы. Прессы
могут быть
оснащены устройствами
для автоматической
подачи ленты
или полосы,
автоматическими
устройствами
выталкивания
детали из верхней
и нижней части
штампа, для
удаления отходов
и деталей под
действием сил
веса изготовляют
прессы с наклоняемой
станиной.
Основной
инструмент
для вырубки
и пробивки -
штамп, который
устанавливается
на пресс. Размеры
штампа должны
вписываться
в рабочее
пространство
пресса - размеры
стола пресса
и быть не более
наименьшего
расстояния
от ползуна
пресса до стола.
Типовая
конструкция
штампа
для серийного
и массового
производства
деталей без
прижима изображена
на рис. 13 Любой
штамп состоит
из следующих
основных деталей:
1 - формообразующих
деталей - пуансона
(1), матрицы (2), П -
деталей ориентирующих
заготовку
относительно
рабочих деталей
- направляющих
(3) или фиксатора,
Ш - деталей
ориентирующих
рабочие детали
друг относительно
друга- направляющих
колонок (4) и
направляющих
втулок (5),
1У - деталей,
снимающих отход
или заготовку
с пуансона -
съемника (6),
У - корпусных
деталей штампа
- верхней плиты
(7), нижней плиты
(8),
У1 - деталей,
обеспечивающих
крепление
штампа к прессу
- хвостовика
(9), прижимных
планок, прокладки,
болтов с гайками,
УП - крепежных
деталей для
крепления всех
деталей в штампе
-винтов,
штифтов,
болтов и др.

Технологичность
деталей, получаемых
вырубкой и
пробивкой
определяется
прочностью
рабочих частей
штампа и технологическим
процессом
штамповки.
1. Плоские
детали должны
иметь простую
конфигурацию,
острые углы,
узкие прорези
и выступы снижают
стойкость
штампов и усложняют
их изготовление.
2. При применении
цельных матриц,
вырубка с
перемычками,
пробивке
выполнять
плавное сопряжение
пересекающихся
элементов
контура детали
(рис.14a). Минимальные
радиусы сопряжения
углов: при α>90°
R=(0,25-0,35)S , при a<90° R=(0,5 - 0,6)S -
для металлов,
для неметаллических
материалов
эти радиусы
больше из-за
малой прочности
штампуемого
материала.
3. При составных
матрицах и при
безотходной
штамповке
пересекающиеся
элементы контура
не сопрягают.
4. Минимальные
размеры отверстий,
пробиваемые
в штампах нормальной
конструкции:
круглых d=(1-1.5)S ,
квадратных
a = (0,9-1,4)S , прямоугольных
b = (0,7-1,2)S , овальных
c = (0,6-1,1)S для сталей
в зависимости
от прочности
( бв = 50-70 кгс/мм2) (рис.
14б).

5. Для пробивки
отверстий
диаметром до
1/3S , применяют
специальные
штампы.
6. Минимальные
расстояния
между раздельно
пробиваемыми
отверстиями
круглой и
прямоугольной
формы a1>(1-1,2)S (рис.14в).
7. Минимальное
расстояние
между пробиваемым
отверстием
и ранее полученным
контуром детали
a2>(0,7-0,9)S (рис.14в).
8. Минимальное
расстояние
между одновременно
пробиваемыми
отверстиями
равно двум-трем
толщинам металла.
*
9. Точность
размеров определяется
в зависимости
от толщины
штампуемого
металла и
конфигурации
детали, для
круглых контуров
она находится
в пределах
11-14 квалитета.
10. Шероховатость
поверхности
среза по толщине
неоднородна:
в зоне среза
Rа = 2,5-0,32 мкм, в зоне
скола - Rz=80-20 мкм.
Технологический
маршрут вырубки*пробивки:
а) вырубка
- укладка полосы
в штамп и установка
ее до упора,
вырубка детали,
удаление детали
из штампа (и
подача полосы
на шаг),
- галтовка
(для снятия
заусенцев),
- рассортировка
деталей и абразивов,
- контроль,
б) пробивка
- укладка заготовки
в штамп,
- пробивка
детали,
-удаление
детали из штампа,
- контроль.
Чистовая
вырубка и пробивка
Чистовую
вырубку и пробивку
применяют для
исключения
недостатков
вырубки-пробивки:
получения
перпендикулярности
поверхности
среза плоскости
детали, устранения
прогиба, получения
шероховатости
поверхности
с параметром
Ra = 2,5-0,32 мкм и точности
6-9 квали-
тета.
Зачистка
Зачистка
и калибровка
применяются
для тех же целей,
что и чистовая
вырубка и пробивка,
т.е. достижения
перпендикулярности
поверхности
среза плоскости
листа, шероховатости
Rа = 2,5-0,32 мкм, точности
8-9 квалитета.
Зачистка
(калибровка)производится
на ранее полученных
вырубкой (пробивкой)
заготовках.
В этом случае
после правки
с обрабатываемой
поверхности
снимают небольшой
слой материала
- припуск.
Зачистка
выполняется
по наружному
или внутреннему
контуру заготовки.
Минимальная
величина припуска
на зачистку
равна зазору
между пуансоном
и матрицей при
вырубке или
пробивке (рис.15).
Зачистку
применяют для
деталей с периметром
до 300 мм и толщиной
до 10 мм. Зачистка
выполняется
за один проход
для деталей
толщиной менее
5 мм с плавным
очертанием
наружного
контура. Многократную
зачистку применяют
для деталей
толщиной более
5 мм и для деталей
со сложной
конфигурацией
наружного
контура независимо
от толщины.
Качество зачистки
зависит от
величины припуска
и распределения
его по периметру,
а при многократной
зачистке от
распределения
по переходам.
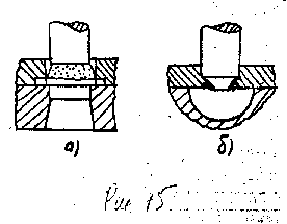
Применяют
также зачистку
обжатием
в матрице с
заваленными
кромками, припуск
в этом случае
составляет
0,04-0,06 мм.
Формообразующие
операции
Гибка.
Гибка - это
формообразующая
операция, при
которой изменяется
кривизна в
одном или нескольких
участках заготовки.
Изменение
кривизны может
происходить
только при
переменных
деформациях
по толщине; эти
переменные
деформации
вызваны переменными
напряжениями
по толщине.
Гибка производится
под действием
силы, момента
или одновременно
силой и моментом.
Наиболее часто
используется
гибка силой
(рис.16а).
Исследование
процесса гибки
показывает,
что по толщине
напряжения
и деформации
не только постепенно
изменяются,
но и различны
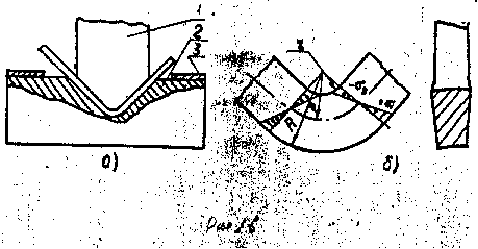
по знаку: в
участках, прилегающих
к матрице, возникают
растягивающие
напряжения
и деформации
растяжения,
а участках,
прилегающих
к пуансону,
напряжения
и деформации
сжатия, что
приводит к
изменению
поперечного
сечения (рис.16б).
Между этими
участками
находятся
слои с напряжениями
и деформациями
равными нулю.
В общем случае,
слои нулевых
напряжений
и деформаций
(нейтральные
слои) не совпадают.
Практическое
значение имеет
положение
нейтрального
радиуса деформаций,
определяемого
по формуле
r1=r+x*s (6)
где r -
радиус пуансона,
S - толщина металла,
x - коэффциент
смещения нейтрального
от серединного
слоя, определяемой
в зависимости
от отношения
r/s , при
r/s = 0,5 x=0,3 при r/s = 10, x=0,5. В
дальнейшем
r1 используется
для определения
размеров заготовки.
В процессах
гибки большое
значение имеет
радиус гибки.
Величина его
ограничивается
минимальным
радиусом. Минимальный
радиус гибки
определяется
из условия
отсутствия
разрушения
металла в зоне
растяжения.
Минимальная
величина этого
радиуса зависит
от пластических
свойств материала
и толщин заготовки.
Для материалов
средней пластичности
( δ = 15-20%) минимальный
радиус гибки
(пуансона)
ориентировочно
равен 0,5 * Для
конкретных
материалов
(условий*) уточняется
по таблицам.
Чем более пластичный
металл, тем
меньше минимальный
радиус гибки
и наоборот.
Минимальный
радиус гибки
зависит и от
расположения
линии гибки
относительно
направления
проката (расположения
волокон макроструктуры);
при параллельных
линию гибки
и направлении
проката - минимально
допустимый
радиус больше,
чем при взаимноперпендикулярном
расположении
направления
проката и линии
гибки, когда
получают наименьшую
величину минимально
допустимого
радиуса гибки.
При промежуточной
величине угла
наклона линии
гибки к направлению
проката надо
брать промежуточные
значения радиуса
гибки, пропорциональные
величине угла.
Для предупреждения
образования
отпечатков
на полочках
детали необходимо
назначать на
кромках матрицы,
по которым
втягивается
материал, радиус
не менее трех
толщин.
Так как напряжения
и деформации
по толщине
неодинаковы
по величине
и знаку, то на
основе закона
о разгрузке,
происходит
уменьшение
растянутой
части, и увеличение
размера сжатой
части заготовки.
Это приводит
к упругому
изменению угла
гибки - пружинению,
приводящему
к уменьшению
угла гибки
(рис.17). Одновременно
происходит
и увеличение
радиуса гибки.
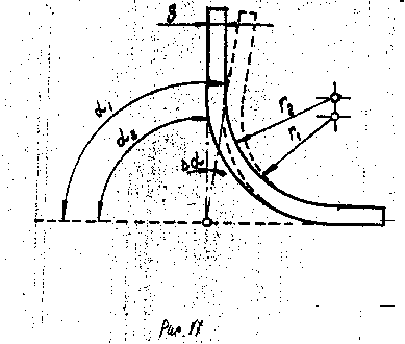
Пружинение
зависит от
относительной
величины радиуса
пуансона r/s ,
материала
детали, угла
гибки и других
факторов. Величина
пружинения
для данных
условие гибки
постоянна.
Величина пружинения
может быть
уменьшена путем
сжатия (правки)
детали в штампе.
При радиусах
гибки менее
r/s<2 изменение
радиуса по
величине
незначительно
и поэтому его
не учитывают.
Растягивающие
и сжимающие
напряжения
и деформации
гибки вследствие
закона о дополнительных
напряжениях,
возникают и
в прямолинейных
участках, прилегающих
к криволинейным,
распространяются
на расстояние
до двух толщин
материала от
линии сопряжения
криволинейного
участка с
прямолинейным.
Усилие гибки
V образной
детали определяют
по формуле:
P= бв*(B*s2)/(r+s) (7)
где B - ширина
летали.
Для других
форм детали
определяют
усилие по
соответствующим
формула в
справочниках.
Размеры
заготовки
рассчитывают
исходя из развертки
детали на плоскость.
Как известно
при гибке изменяется
длина волокон
в криволинейных
участках, а
прямолинейные
остаются по
длине до и после
гибки неизменной
длины. Поэтому
деталь разделяют
на прямолинейные
и криволинейные
участки (рис.18),
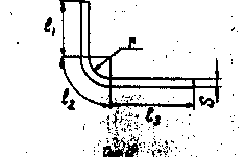
определяют
их длины и суммируют
для получения
общей длины
развертки.
Длины прямолинейных
участков определяют
по данным чертежа,
длины криволинейных
участков по
длине нейтрального
волокна деформации:
lkpi=(п*r1*a)/180
длина развертки
равна
где - сумма
длин прямолинейных
участков, - сумма
длин криволинейных
участков,
r1 - радиус
нейтрального
волокна деформации
формула (6) n,k - число
прямолинейных
и криволинейных
участков.
Оборудование
Для выполнения
операции гибки
используют
кривошипные
прессы. В условиях
массового
производства
используют
специализированные
прессы, а также
специальные
гибочные прессы
- универсально-гибочные
автоматы. Эти
автоматы увеличивают
производительность
в десятки раз.
Оснасткой
для гибки является
штамп. Конструкция
штампа для
гибки содержит
элементы, известные
по конструкции
штампа для
вырубки-пробивки.
Технологичность
деталей получаемых
гибкой
1. Радиус гибки
пуансона не
должен быть
менее допустимого
минимального
для данного
материала.
2. Радиус матрицы
не менее трех
толщин.
3. Длина отгибаемой
части полочки
должна быть
не менее двух
толщин (рис.19а),
если отгибаемая
часть короче
рекомендуемой
величины, то
ее изготовляют
более длинной,
а затем обрезают
по высоте.
4. Расстояние
от края отверстия
до линии сопряжения
полочки с радаусом
должано быть
не менее двух
толщин (рис.19а).
При меньшем
расстоянии
пробивку отверстия
делают после
гибки или
предусматривают
на перегибе
отверстие
(рис.19а) для
предупреждения
искажения
ранее полученного
отверстия.
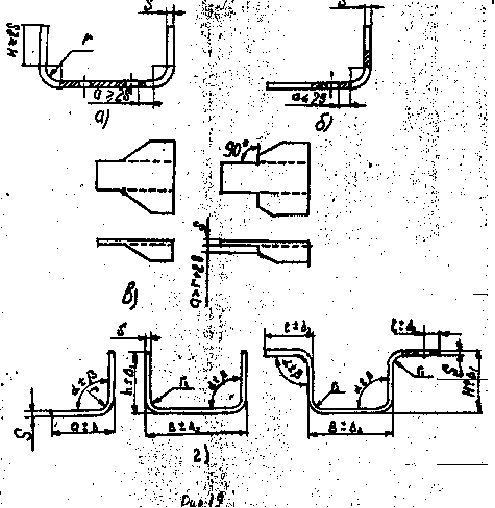
5. При одновременной
двуугловой
(четырехугловой)
гибке длина
линии гибки
противоположных
полочек не
должна резко
отличаться,
так как под
действием сил
трения может
изменяться
высота полочки.
6. Угол между
линиями гибки
и контура домен
быть равен 90˚
для предупреждения
деформации
полочек под
действием сил
трения (рис.19в).
7. Простановка
размеров и
допусков на
чертеже детали:
наиболее технологичны
детали у которых
координаты
центров отверстий
заданы от края
полочки (рис.
), в этом случае
пробивку отверстий
совмещают с
вырубкой заготовки,
при другой
схеме простановки
размеров
отверстия
пробивают в
отдельном
штампе после
гибки для обеспечения
заданной точности;
допуски на
линейные размеры
задают симметричные.
Вытяжка.
Вытяжкой называют
процесс превращения
плоского заготовки
в полое изделие,
или - процесс
превращения
полой заготовки
в полое изделие
меньшего диаметра
и большей высоты.
Различают
вытяжку с
утонением
стенок и без
утонения стенок,
а также комбинированную
вытяжку.
При обычной
вытяжке толщина
стенок детали
гложет быть
больше исходного
толщины заготовки.
При вытяжке
с утонением
толщина стенок
получаемой
детали меньше
толщины стенок
заготовки. При
обычной вытяжке
основная деформация
происходит
за счет значительного
изменения
диаметра заготовки,
при вытяжке
с утонением
- за счет
изменения
толщины заготовки.
При комбинированной
вытяжке происходит
деформирование
заготовки и
за счет изменения
диаметра и за
счет уменьшения
толщины заготовки
одновременно.
В зависимости
от температуры
штампуемого
металла различают
холодную вытяжку
и вытяжку с
подогревом.
Под термином
"вытяжка"
подразумевают
холодную вытяжку
без утонения.
В процессе
вытяжки получают
детали круглого
и других (произвольных)
поперечных
сечений: квадрат,
прямоугольник,
овал и др.
Рассмотрим
процесс вытяжки
на примере
изготовления
круглой детали
(рис.20). В этом
случае круглая
заготовка
втягивается
в зазор Z между
матрицей и
пуансоном под
действием силы
Р; при этом диаметр
заготовки
уменьшается
и высота изделия
увеличивается
за счет сжатия
заготовки в
окружном направлении
и растяжения
в радиальном
направлении;
дно растягивается
в окружной и
радиальном
направлениях.
При некоторых
условиях под
действием
сжимающих
напряжений
теряется устойчивость
фланца-кольцевой
части заготовки.
Это приводит
к образованию
гофров, препятствующих
втягиванию
заготовки в
зазор и приводящих
к разрыву заготовки
- браку. Для
предупреждения
образования
гофров вводят
прижим (рис.
20а), прижим осуществляют
с давлением
q = (0,1-0,3 кгс/мм2) 0,01-0,03 Мн/м2.
Процесс
деформирования
при вытяжке
характеризует
отношение
среднего радиуса
деуали к радиусу
заготовки -
коэффициент
вытяжки; предельная
величина коэффициента
вытяжки
m=r/R3=0,5-0,7 (10)
при этом
отношение
высоты полученной
детали к диаметру
H/d<0,7-0,6.
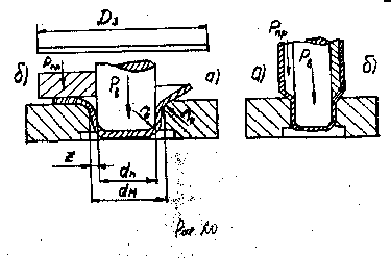
Если необходима
большая высота
детали полученное
полое изделие
подвергают
последующей
вытяжке: второй,
третьей и т.д.
При этом предельная
суммарная
величина коэффициента
вытяжки может
достигать m =
0,25, а отношение
высоты детали
к диаметру до
8-10. Необходимость
прижима. Прижим
на первой операции
нужен, если
(S/D3)*100<2 (11)
прижим на
последующих
операциях
нужен, если
(S/dn-1)*100<1,5 , а mn<0,78 (12)
Усилие прижима
определяют
по формуле
Pnp=q*Fnp (13)
где q - давление
прижима , Fnp - площадь
прижима .
Втягивание
материала в
матрицу возможно
лишь наличии
определенных
радиусов на
пуансоне или
матрице, так
как при радиусах
равных нулю
процесс вытяжки
переходит в
процесс вырубки.
При вытяжке
рекомендуют
назначать:
радиус матрицы
: rm=(4-8)S (14)
радиус пуансона:
rn=(0,7-0,8)rm
Для уменьшения
сил трения при
вытяжке заготовки
смазывают
смазками,
назначаемыми
в зависимости
от марки металла
заготовки.
Усилие вытяжки
определяют
по формуле
(наибольшее)
Pв=бв*п*d (15)
Общее усилие
определяют
с учетом прижима
P=pв+pnp (16)
При вытяжке
одновременно
можно формовать
на дне небольшие
рельефные
впадины и выступы,
деталь может
быть без фланца
и с фланцем.
Особенности
формы
При вытяжке
вследствие
анизотропии
материала
открытый торец
детали получается
по высоте не
одинаковым
, а наружный
диаметр фланца
не круглым .
Поэтому необходим
припуск для
обрезки. Толщина
детали по высоте
также не одинакова
у верхнего
торца от 1 до
1,3 толщины у дна
- 0,85So , толщина дна
уменьшается
до 0,95So (рис.21)
Размеры
заготовки
определяют
из условия
равенства
поверхности
заготовки
поверхности
детали с учетом
припуска на
обрезку; для
круглой детали:
Fзаг=FДЕТ+F;
D3=1,13(Fзаг)1/2 (17)
Зазор между
матрицей и
пуансоном
принимается
равным (1-1,3)So в
зависимости
от коэффициента
вытяжки.
Штампы для
вытяжки имеют
те же, что и при
вырубке - пробивки,
основные элементы.
Вытяжка с
подогревом.
При обычной
вытяжке за один
переход получают
высоту (0,6-0,7)d. При
вытяжке с подогревом
можно за один
переход получить
высоту, равную
(1,3-2,3)d. Способ используется
для вытяжки
заготовок
главным образом
из цветных
сплавов (алюминиевых,
магниевых,
титановых).
Сущность процесса
заключается
в том, что материал
в очаге деформации
нагревается
(рис.22) и тем самым
уменьшается
его предел
текучести а
в зоне сформировавшейся
части детали
металл охлаждается
для увеличения
механических
характеристик.
Температура
нагрева в очаге
деформации
должна быть
выше температуры
рекристаллизации
с тем, чтобы
материал не
получал упрочнения.
Вытяжка делается
на
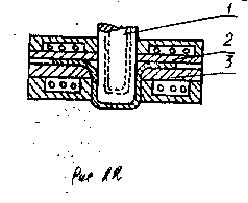
гидропрессах
или на тихоходных
(12-20ход/мин) механических
прессах.
Вытяжка с
утонением.
Вытяжка с уточнение
отличается
от рассмотренной
выше вытяжки
тем, что при
этом процессе
уменьшается
толщина стенки
полого изделия,
а диаметр остается
почти неизменным,
высота детали
значительно
увеличивается.
Зазор между
матрицей и
пуансоном в
этом случае
меньше толщины
заготовки
(рис.23).

Сущность
процесса. Усилие
от пуансона
передается
донышку, при
этом начинает
уменьшаться
толщина стенки
за счет нормальных
сил возникающих
со стороны
конической
части матрицы
и пуансона,
тангенциальных
сжимающих сил
и еще сил трения
на матрице и
пуансоне.
Важно отметить,
что сила трения
на пуансоне
направлена
вниз и способствует
разгрузке
опасного сечения,
так как материал
в очаге деформации
под действием
сдвигающих
напряжений
частично при
движении пуансона
вытесняется
вверх относительно
движения пуансона
(двигающегося
вниз).
Для получения
большей степени
деформации
(U=(Fo-F)/Fo) вытяжку ведут
через две или
три матрицы.
Для вытяжки
с утонением
применяют все
деформируемые
материалы.
Вытяжка с
утонение нашла
широкое применение
в промышленности,
особенно в
приборостроении
для изготовления
заготовок
сильфонов -
упругих чувствительных
элементов
системы автоматики.
Вытяжка с
утонением по
сравнением
с обычной вытяжкой
имеет следующие
преимущества:
1.Не требует
применения
сложных штампов
и прессов.
2.Число вытяжных
операций может
быть меньше
для получения
заданной высоты
по сравнением
с обычной вытяжкой.
3.Качество
металла в вытянутой
стенке лучше.
Особенность
деталей заключается
в том, что толщина
донца в (5-10) раз
толщины стенок.
Точность
при вытяжке
нужно рассматривать
для каждого
параметра
отдельно:
а) Точность
по диаметру,
б) Точность
по толщине
стенок,
в) Точность
по высоте.
Эти параметры
в значительной
степени определяются
степенью точности
инструмента.
С учетом всех
факторов достигаемая
при вытяжке
точность по
диаметру может
соответствовать
6-9 квалитету;
по толщине -
6-11 квалитету;
по высоте - ниже
16 квалитета.
Качество
наружной поверхности
зависит от
качества поверхности
матрицы: внутренней
- определяется
частотой поверхности
исходного
материала и
пуансона;
шероховатостью
по наружной
поверхности
- Ra=0,63-0,16 мкм.
Комбинированная
вытяжка.
При комбинированной
вытяжке за один
переход существенно
уменьшается
диаметр заготовки
и толщина (рис.24).
Так как при
обычной вытяжке
значительная
разнотолщинность
стенки по высоте
(до 0,85S у дна и до
1,3S у верхнего
торца), то в
начальный
момент происходит
только обычная
вытяжка и вытяжка
с уточнением.
При комбинированной
вытяжке создается
благоприятная
схема напряженного
состояния, при
которой обычная
вытяжка разгружает
наиболее нагруженное
сечение вытяжки
с уточнением.
Это позволяет
с получением
высоких качественных
показателей
увеличить
производительность
в 2-3 раза.
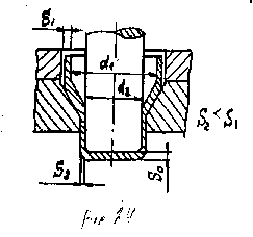
При комбинированной
вытяжке получают
заготовки 6-9
квалитета,
точности по
диаметру , 6-11
квалитета
точности по
толщине стенки,
шероховатость
- Ra=0,63-0,16 мкм.
Технологичность
деталей полученных
вытяжкой.
1.Радиус рабочей
кромки матрицы
rm=(4-8)S, пуансона
rn=0,7rm. Сопряжение
дна со стенкой
без радиуса
можно получить
путем калибровки
или при штамповке
весьма толстых
заготовок с
D3/S>20 , m>0,7.
2.В первую
очередь операцию
вытяжки можно
получить отношение
высоты детали
(H) к диаметру
(d) не более H/d<0,6
(m=0,5); для получения
большей высоты
необходимы
последующие
переходы.
Наиболее
экономично
изготовлять
более высокие
детали с большей
точностью и
лучшим качеством
поверхности
комбинированной
вытяжкой, при
которой за одну
операцию можно
получить в
зависимости
от принятых
степеней деформации
относительную
высоту детали
до 1,5-2,5.
3. Избегать
глубоких вытяжек
с широким фланцем
(Dф>3d при h>2d) , требующих
большого количества
операций.
4.Конфигурация
деталей должна
быть простой:
дно - плоское
или слегка
выпуклое в
наружную сторону,
фланец - плоский,
боковые поверхности
цилиндрические,
конические;
Вместо конических
с малым углом
конусности
предпочтительнее
цилиндрические
поверхности.
5.Размеры
деталей следует
проставлять
так : высоту-от
дна детали,
радиусы закруглений
между дном и
стенкой - по
внутренней
поверхности,
радиус закругления
между фланцем
и стенкой - по
наружной поверхности,
размеры выступов
по высоте лучше
проставлять
между дном и
ступенью снаружи.
6.Допуски на
диаметры выпуклых
деталей следует
устанавливать
не выше 12-13 квалитета
точности.
7.Точность
поперечного
сечения деталей
при комбинированной
вытяжке соответствует
6-9 квалитету
точности, большая
точность относится
к деталям, полученным
с большой степенью
деформации
по диаметру.
8.Шероховатость
поверхности
деталей полученных
комбинированной
вытяжкой и
вытяжкой с
утонением
соответствует
Ra=1,25-0,16 мкм; при обычной
вытяжке шероховатость
на 1-2 интервала
параметра
шероховатости
ниже исходной.
Формовка.
Формовка
- процесс изменения
формы заготовки
за счет местных
деформаций.
К формрвке
относятся
операции:
1.рельефная
формовка,
2.отбортовка
отверстий,
3. закатка
борта,
4. раздача,
5. обжим,
6. правка.
Рельефная
формовка -
операция, которая
обеспечивает
получение на
заготовках
ребер жесткости
различной формы
(рис.25). При рельефной
формовке листового
материала
деформирование
происходит
за счет двухосного
растяжения
(растяжения
в плоскости
листа), при этом
материал значительно
утоняется
(50%).
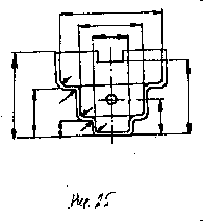
Допустимая
степень деформации
определяется
по формуле:
E=(l-lo)/l0<0,75δ = 15-18% (18)
где lo и l -длина
элемента до
и после деформации
операции, δ -
относительное
удлинение
материала при
растяжении.
Отбортовка
. Различают
отбортовку
отверстий и
отбортовку
наружного
контура.
Отбортовка
отверствий
- процесс формоизменения
листовой заготовки,
при котором
у отверстия
получают борт
(рис.26).
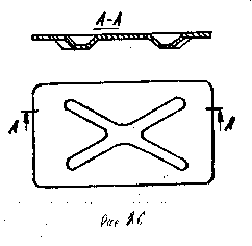
При деформировании
наблюдается
растяжение
в тангенциальном
(окружном)
направлении
и уменьшение
толщины материала.
Степень деформации
определяется
коэффициентом
отборки:
Kот=d/D
При (S/D)*100=2 , Kот=0,75
при сверлении
отверстия и
Kот=0,8 при пробивке.
Допустимая
степень деформации
в значительной
степени зависит
от:
1) качества
поверхности
отверствия,
2)относительной
толщины материала
,
3) материала
и его состояния
,
4)формы рабочей
части пуасона.
Чем меньше
трещин на поверхности
отверствия,
чем меньше Kот.
У сверленных
отверствий
Kот меньше, чем
пробитных. У
пробитной
детали Kот
значительно
изменяется
в зависимости
от положения
блестящего
пояска относительно
матрицы. Если
блестящий
поясок будет
в зоне наибольших
деформаций,
то Kот меньше,
чем при положении
шероховатой
части в зоне
наибольших
деформаций.
Высота борта
определяется
как и при гибке
(приближенно).
Это возможно
благодаря тому,
что материал
утоняется.
Наибольшая
толщина у края
борта определяется
выражением
(на основе
постоянства
объема)
S1=So*(Kот)1/2 (20)
Разновидности
отбортовки:
отбортовка
с утонением.
Отбортовка
с утонением
выполняется
для получения
более высоких
буртов. При
отбортовке
с утонением
одновременно
с образованием
бурта толщина
стенки уменьшается.
Отбортовка
наружного
контура
- это в сущности
процесс неглубокой
вытяжки. К этому
процессу относятся
все характерные
особенности
вытяжки: напряженное
состояние,
деформации
и возможность
гофрообразования.
Раздача
- представляет
собой процесс
увеличения
периметра
поперечного
сечения трубчатой
исходной заготовки
(рис.27).
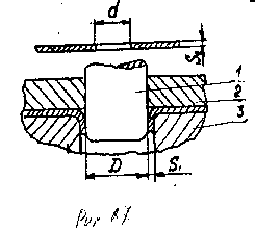
Наименьшая
толщина стенки
прближенно
определяется
выражением
S1=So*(d/d1) (21)
Соотношение
Kр=d/d0 называют
коэффициентом
раздачи, который
может достигать
величины 1,6 при
S/d=0,15 и угле а=20 грд.
(рис.27).
Обжим
- процесс уменьшения
периметра
поперечного
сечения краевой
части полой
заготовки
(рис.28).
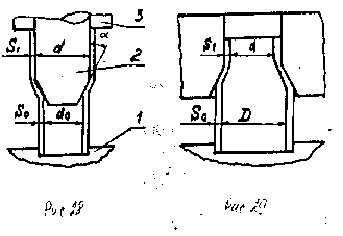
При обжиме
в заготовке
возникают
тангенциальные
сжимающие
напряжения,
в результате
чего уменьшается
периметр и
уменьшается
толщина заготовки.
Увеличение
толщины заготовки
у края можно
определить
из выражения,
полученного
на основе условия
постоянства
объема:
S об=So√(D/d)
(22)
В процессе
обжима вертикальная
часть детали
имеет сжимающие
напряжения,
под действием
которых она
может получить
потерю устойчивости.
Для предупреждения
потери устойчивости
и увеличения
коэффициента
обжима
Kоб=D/d (23)
применяют
подпор наружный,
внутренний
и одновременно
оба.
Коэффициент
обжима для
мягкой стали:
-
без подпора |
подпор наружный |
подпор
внутренний
и наружный |
0,7-0,75 |
0,55-0,6 |
0,3-0,35 |
Правкой
называют
операцию, при
которой происходит
увеличение
точности формы
детали.
При операциях
отрезки или
вырубки, гибки
и пробивки
материал в
очаге деформации
и вблизи него
находится под
действием
изгибающего
момента. Этот
изгибающий
момент нарушает
плоскостность
полученных
деталей, за
счет удлинения
волокон на
одной и укорочение
волокон на
другой сторонах
детали. Операция
правки заключается
в том, сделать
все волокна
одинаковой
длины по толщине
металла (кроме
зон гибки в
гнутых деталях.
Достигается
это на штампах
(рис.29). Штампы
для правки
могут иметь:
плоские
(гладкие) плиты,
точечные
плиты,
вафельные
плиты.
Шаг между
выступами
точечных и
вафельных плит
должен быть
равен: t=(0,5-0,9)S, давление
правки от 50 до
300 мн/м2 (от 5 до 30
кГ/мм2). Плиты
должны быть
массивными
с тем, чтобы
при правке они
не прогибались.
Комбинированная
штамповка.
Для получения
производительности
труда (в 3-10 раз),
уменьшения
количества
штампов и прессов
в месте штамповки
по отдельным
операциям
применяют
комбинированную
штамповку.
Комбинированная
штамповка
заключается
в одновременном
выполнении
нескольких
операций в
одном штампе.
Существует
три способа
комбинирования
операций холодной
штамповки:
последовательный,
совмещенный
и последовательно-совмещенный
(рис.30).
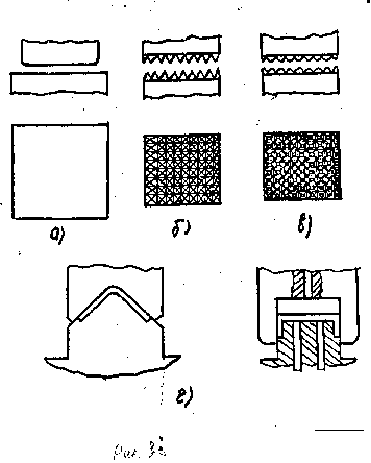
Отличие этих
вариантов
состоит в
последовательности
и месте выполнения
операций. При
последовательном
способе все
операции выполняются
одновременно
в последовательном
штампе на разных
позициях, причем
число переходов
соответствует
числу позиций.
При совмещенном
способе все
операции выполняются
одновременно
в одной и той
же позиции
штампа совмещенного
действия. При
последовательно-совмещенном
способе для
одновременного
выполнения
всех операций
требуется
позиций в инструменте
меньше, чем
операций. Этот
способ представляет
комбинацию
из первых двух.
Для выполнения
технологических
процессов
используется
материал в виде
полосы или
ленты. Использование
полосового
или ленточного
материала
позволяет в
значительной
мере механизировать
и автоматизировать
процесс штамповки.
Ширина полосы
при наличии
вытяжки в
комбинированной
штамповке
принимается
несколько
больше, чем это
необходимо
для получения
детали с той
целью, чтобы
можно было
иметь перемычки
между отдельными
операциями
для перемещения
всех полуфабрикатов
на следующую
позицию.
При выполнении
формоизменяющих
операций в
ленте (полосе)
часто требуется
специальная
подготовка
ленты (выполнение
прорезей, вырубки
промежутков)
для облегчения
процесса
деформирования
материала.
Выбор способа
штамповки
определяется
рядом факторов:
1.точностью
изготовления
детали (особенно
получения
соосности),
2.технической
культурой
инструментального
производства,
3.конструкцией
детали и пр.
В зависимости
от сложности
и размеров
детали комбинированная
штамповка может
быть однорядная
и многорядная.
Точность
комбинированной
штамповки
определяется
точностью
отдельных
элементов
контура детали
и точностью
взаимного
расположения
этих элементов.
Точность отдельных
контуров детали
определяется
точностью
используемого
способа. Точность
взаимного
расположения
отдельных
элементов
контура определяется
способом
комбинированной
штамповки: при
совмещенной
штамповке -
точностью
взаимного
расположения
пуансонов и
матриц; при
последовательной
- точностью
взаимного
расположения
пуансонов и
матриц и точностью
оринтеровки
(базирования)
полуфабриката
(заготовок) на
каждом переходе,
обычно она
соответствует
12-14 квалитету.
Штамповка
в условиях
мелко серийного
производства.
При мелкосерийном
производстве
изготовляют
от 3-5 до 20-10000 штук
деталей.
Использование
в мелкосерийном
производстве
штампов серийного
производства,
стоящих до
200-300 руб., экономически
невыгодно и
увеличивает
срок изготовления
новых деталей
(штамп серийного
производства
изготовляют
ориентировочно
один месяц).
Для быстрого
освоения новых
изделий (опытных
образцов) с
минимальными
производственными
затратами в
условиях
мелкосерийного
производства
применяют два
способа: штамповку
на упрощенных
штампах и на
универсальных
штампах.
К штамповке
на упрощенных
штампах относят
штамповку: а)
на пинцетных
штампах, б) на
литых штампах,
в) на штампах
с использованием
полиуретана,
взрывчатых
веществ, импульсного
магнитного
поля, взрыва
газовых смесей,
электрогидравлического
эффекта и др.
Пинцетные
(листовые) штампы
(рис.31) используют
как для индивидуальной,
так и групповой
штамповки
деталей. Их
применяют для
вырубки - пробивки,
иногда для
гибки, отбортовки,
рельефной
формовки.

Литые штампы
изготовляют
из алюминиевоцинковых
сплавов и используют
для гибочных,
вытяжных, формовочных
работ. Такие
штампы допускают
многократное
восстановление.
Рекомендуют
их армировать
стальными
вставками в
наиболее изнашиваемых
местах.
Универсальные
штампы требуют
первоначально
больших затрат
на изготовление,
чем такого же
назначения
штампы серийного
производства;
однако они
быстро окупаются,
так как используются
для штамповки
большой номенклатуры
деталей. По
конструктивному
оформлению
они подобны
штампам серийного
производства,
однако, имеют
некоторое
отличие.
Универсальные
штампы используют
для двух видов
штамповки:
1)поэлементной
и 2)групповой
штамповке.
Сущность
метода поэлементной
штамповки
заключается
в том, что контур
детали, разделенный
на простейшие
элементы (прямые,
кривые, окружности
и др.) образуется
последовательной
штамповкой
при помощи
набора универсальных
штампов, установленных
на прессах.
Обязательным
условием эффективного
использования
штамповки
является нормализация
элементом
геометрических
форм штампуемых
деталей.
Последовательность
изготовления
детали показана
на рис.32.
Порядок
операций должен
так назначаться,
чтобы последующие
операции не
вызывали изменения
положения уже
изготовленного
элемента контура
относительно
базы.
Точность
взаимного
расположения
элементов
контура детали
при последовательной
штамповке
соответствует
12-14 квалитету.
Сущность
групповой
штамповки
состоит в том,
что, сгруппированные
по технологическим
признакам
детали (вытяжки,
пробивки, и
т.д.) обрабатываются
на групповых
штампах, которые
представляют
собой штампы
состоящие из
двух основных
частей, блока
и комплекта
быстросменных
наладок. Блок,
включающий
плиты, направляющие
элементы и
элементы крепления
штампа и зажима
наладок, закрепляется
постоянно на
прессе. Быстросменные
наладки, выполняющие
функции ориентировки
заготовки и
формирования
детали (вырубки,
гибки, вытяжки
и т.д.) можно быстро
(за несколько
минут) заменять
и таким образом
переналаживать
штамп на выполнение
другой операции.
4.2. Основные
операции обработки
давлением
Операции
обработки
давлением
классифицируют
в зависимости
от используемого
инструмента,
оборудования,
температуры
обрабатываемого
металла и других
признаков. В
зависимости
от применяемого
инструмента,
деформирующего
металл, различают:
1) штамповую
обработку,
2) бесштамповую
обработку.
При штамповой
обработке на
машине используют
специальный
инструмент
- штамп (отсюда
и происходит
название). С
помощью штампа
можно получать
изделия одинаковых
размеров. При
бесштамповой
обработке на
машине используют
универсальный
деформирующий
инструмент,
позволяющий
получать различные
размеры изделий
одинаковой
формы (круглый,
квадратный,
прямоугольный
пруток, лист,
ленту). К операциям
штамповой
обработки
относят:
1) операции
холодной листовой
штамповки,
2) операции
холодной объемной
штамповки,
3) операции
горячей (листовой
и объемной)
штамповки. При
операциях
листовой штамповки
исходная заготовка
из листового
металла и в
процессе
пластического
деформирования
ее толщина
не меняется
или изменяется
незначительно.
При операциях
объемной штамповки
размеры исходной
заготовки
зн*читально
изменяются
по трем направлениям.
Основными
операциями
бесштамповой
обработки
являются:
1) прокатка,
2) волочение.
Операции холодной
листовой штамповки
делятся на три
основные группы:
1) разделительные,
2) формообразующие,
3) комбинированные.
К разделительным
операциям
листовой штамповки
относят: отрезку,
разрезку, обрезку,
вырезку, надрезку,
просечку, вырубку,
пробивку,
зачистку и
калибровку
и др.
При разделительных
операциях
происходит
отделение
полное (отрезка,
разрезка, обрезка,
вырезка, вырубка,
пробивка, зачистка,
калибровка)
или частичвое
(надрезка, просечка)
металла от
исходной заготовки.
Результатом
этих операций
являются или
готовые детали
или заготовки,
используемые
для последующей
обработки.
К формообразующим
операциям
относят: гибку,
вытяжку, отбортовку,
обжим, формовку
и др.
При формообразующих
операциях
исходная плоская
заготовка
деформируется
в пространственную
деталь. При
этом плоская
заготовка или
локально (гибка,
отбортовка,
обжим, формовка)
или полностью
(вытяжка) деформируется.
К комбинированным
операциям
относят - различные
комбинации
одновременно
выполняемых
в одной или
нескольких
позициях штампа
различных
операций.
Операции
холодной объемной
штапмповки:
выдавливание,
высадка, чеканка
и калибровка,
накатка резьб
и зубчатых
колес и др.
4.3. Материалы,
применяемые
в холодной
штамповке
В холодной
штамповке
применяют
разнообразные
как металлические,
так и неметаллические
материалы.
Наиболее широко
применяют
следующие
металлы и их
сплавы: железо,
медь, алюминий,
магний, цинк,
никель, титан;
обрабатывают
штамповкой
и менее распространенные
металлы и их
сплавы: молибден,
тантал, кобальт,
бериллий, цирконий,
золото, серебро,
платину и др.
Неметаллические
штампуемые
материалы
разделяют на
две группы. К
первой группе
относят: бумагу,
картон, прессшпин,
кожу, фетр, войлок,
резину и прорезиненную
ткань, хлопчатобумажные
и шерстяные
ткани и другие
прокладочные
материалы. Ко
второй группе
относят
конструкционные,
электроизолйционные
и теплоизоляционные
материалы: 1)
слоистые пластмассы
- текстолит,
гетинакс, стекло-
текстолит,
асботекстолит,
фибра, древеснослоистые
пластики и др.,
2) блочные
пластмассы
- органическое
стекло, целлулоид,
динилласт,
доливинилхлорид,
полиэтилен,
3) асбестовые
изделия - бумага
асбестовая,
картон асбестовый,
гидроизол,
паронит, асбометалличес-
кое армированное
полотно, 4) слюда
и миканиты:
слюда (мусковит,
флагонит, биотит),
миканиты
(коллекторный,
прокладочный,
формовочный
и гибкий).
Номенклатура
марок материалов
и сортамент
(форма и размеры)
установлены
соответствующими
Гостами. Наиболее
распространенными
являются различные
сортаменты
черных иуветных
металлов в виде
листов, лент,
полос, круглых,
квадратных
и шестигранных
прутков. В последние
годы созданы
новые листовые
материалы
стальные и
алюминиевые
листы, покрытые
цветной пластмассой
толщиной 0,36 мм.
Технологические
свойства металла
для штамповки
характеризуют:
механические
характеристики,
химический
состав, структура
и величина
зерна, анизотропия,
точность размеров
заготовок.
Механические
свойства металла
характеризуют
в основном:
а)прочностными
показателями-пределом
текучести (бт
, пределом прочности
бв , б) пластическими
показателями
- относительным
удлинением
д и относительным
сужением. В
зависимости
от условий
работы назначения
и технологии
штамповки к
штампуемому
материалу
предъявляют
определенные
механические
и технологические
требования.
При разделительных
операциях
металлы с высоким
пределом
текучести дают
чистый срез;
для формообразующих
операций (гибки,
вытяжки) желателен
низкий предел
текучести - это
способствует
уменьшению
упругой деформации
после штамповки.
Особенно это
важно для операций
гибки, где большой
объем упругодеформи-
руемого металла.
Вытяжка листового
металла успешно
протекает при
большом относительном
удлинении
(д>28%) и малом
отношении
предела текучести
к пределу прочности
:бт/бв<0,65. Выбранный
материал должен
также обеспечивать
возможность
выполнения
последующих
технологических
операций отделки,
сборки и т.д.
Химический
состав сильно
влияет на
механические
свойства материала.
Для регламентирования
механических
характеристик
К химсоставу
для штампуемых
сталей предъявляют
жесткие требования.
Структура
в большой степени
влияет на
механические
свойства материала.
В сталях структурное
состояние
углерода (феррит,
перлит, цементит)
определяет
пригодность
к штамповке.
Наиболее
благоприятна
для штамповки
структура
феррита или
структура
феррита и зернистого
перлита.
* Величина
зерна и однородность
его оказывают
большое влияние
на штампуемость.
Неоднородность
зерна вызывает
неравномерную
деформацию
объема металла
и является
причиной разрывов
при вытяжке.
Рекомендуют
величину зерна
0,026-0,057 мкм, при величине
зерна менее
0,018 мкм сталь хуже
деформируется
- при вытяжке
возникают
трещины и гофры,
при гибко
значительное
пружинение.
При разделительных
операциях
качество поверхности
скола определяется
величиной
зерна, при вытяжке
и гибко ухудшение
шероховатости
тем больше,
чем больше
величина зерна.
Анизотропия
увеличивает
количество
операций при
вытяжке .при
гибко увеличивает
минимальную
величину радиуса
гибки, при вырубке
- пробивке уменьшает
точность размеров.
Точность
размеров заготовки
оказывает
влияние на
точность изготовления
деталей.
4.4. Холодная
листовая штамповка
Виды заготовок.
Для листовой
штамповки
используют
заготовки в
виде листа,
полосы, ленты
или профилей
различного
поперечного
сечения: труба,
уголок, двутавр
и т.д.
Раскрой
материала.
Раскрой материала
- это способ
расположения
деталей (заготовок)
в ленте, полосе
или на листе
с целью рационального
использования
исходного
материала.
Раскрой
полосы (ленты).
В зависимости
от требований
по точности
различают три
типа раскроя:
а) с отходами
перемычками,
б) с частичными
отходами, в)
без отходов.
Раскрой с
отходами (рис.7a)
применяют для
изготовления
деталей повышенной
точности (8-13
квалитет), а
также для деталей
сложной конфигурации,
раскрой с частичными
отходами (рис.7б)
и без отходов
(рис.7в) применяют
для простых
по форме деталей
низкой точности.
Перемычки между
деталями и
краем определяют
по таблицам
в зависимости
от толщины и
конфигурации
детали.
Применяют по
указанным
схемам однорядный
и многорядный
раскрой. Нужную
ширину полосы
(ленты) получают
путем резки
листа (рулона)
на полосы (ленты).
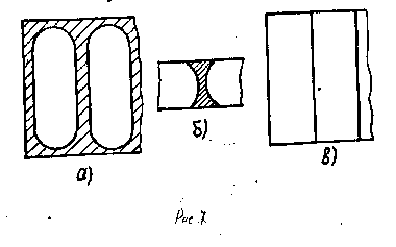
Раскрой
листа (ленты).
При раскрое
листа нужно
стремиться
к получению
целого числа
полос, длина
которых равна
шагу подачи.
Предпочтительным
является продольный
раскрой (рис.8а)
увеличивающий
производительность
труда за счет
меньшего количества
заправок полос
в штамп. Для
уменьшения
отхода по некратности
длины полосы
применяют
поперечный
и комбинированный
раскрой листа
(рис.8б,в). При
раскрое ленты
следует предусматривать
у краев припуск
2-3 мм для удаления
смятых при
транспортировке
торцов.
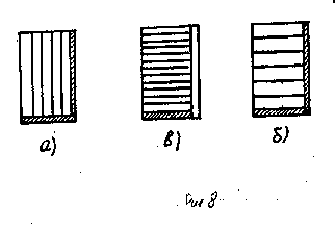
Рациональным
считается
раскрой, для
которого получают
наибольший
коэффициент
использования
материала
N=(n*Fд)/B*A
где n - число
деталей в полосе
или ленте,
Fд - площадь
детали, мм2,
B,A - ширина и длина
полосы, ленты
или листа, мм.
Разделительные
операции
Общие сведения.
Различают
разделительные
операции: 1) со
значительной
шириной отделяемого
металла (более
двух толщин)
- резка, вырубка,
пробивка,
вырезка, надрезка
и др., и 2) операции
с небольшой
шириной отделяемого
металла (менее
0,5 толщина - зачистка,
калибровка.
Механизмы
разделения
в этих случаях
различны.
Первая группа
операций применяется
для разделения
листов и лент
с целью получения
деталей или
заготовок для
последующей
штамповки.
Вторая группа
операций - с
целью отделки
- повышения
качества деталей
Резка.
Механизм разделения
операций резки,
вырубки, пробивки
и др. одинаков.
Процесс резания
- деформирования
заготовки
протекает в
три этапа:
1) упругая
и начало пластической
деформации,
2) пластическая
деформация,
сопровождающаяся
пластическим
врезанием ножей
в материал
заготовки,
3) разделение
металла, происходящее
после исчерпания
пластической
деформации
путем скола.
При упругой
деформации
(1 этап) происходит
упругое сжатие
и изгиб, свободные
концы заготовки
при этом поворачиваются
на некоторый
угол. При пластической
деформации
(2 этап) врезаются
ножи в разделяемый
металл, качество
поверхности
разделения
при этом зависит
в значительной
мере от качества
задней поверхности
ножей. После
исчерпания
пластической
деформации
металла наступает
сдвиг (скол)
металла (3 период).
У режущих кромок
ножей образуются
трещины скола
металла. Эти
трещины располагаются
под некоторым
углом к направлению
движения ножей.
Для качественного
среза они должны
встретиться.
Следовательно,
для обеспечения
качественного
среза между
ножами должен
быть определенный
зазор Z Опытные
данные показывают,
что величина
зазора должна
быть в пределах
Z = (0,05-0,20)S (S - толщина
металла).
Шероховатость
поверхности
среза соответствует
Ra = 2,5-0,32 мкм, шероховатость
поверхности
скола - Rz = 16,0-20,0 мкм
(рис.9д).
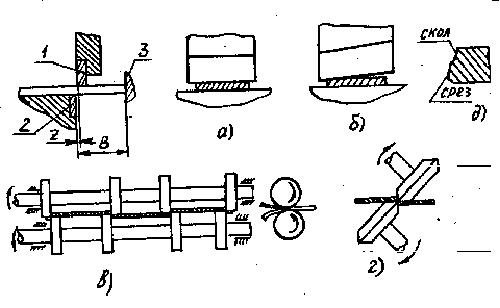
рис. 9
Напряжения
и деформации
в плоскости
листа распространяются
вдоль линии
резки по обе
стороны примерно
на полосе шириной
около одной
толщины металла
(рис.10).
Из этих данных
следует, что
при ширине
отрезаемой
полосы или
ленты равной
или менее двух
толщин поперечное
сечение будет
значительно
искажено.
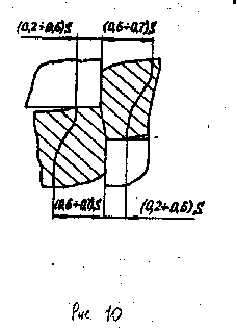
Под действием
силы резания
возникает
опрокидывающий
момент, поворачивающий
лист. Для предотвращения
поворота листа
применяют
прижим.
Основные
технологические
параметры кроме
зазора, точности
и шероховатости
поверхности
- усилие и работа
резки; они
определяются
по формулам:
p=бв*s*L н/(кгс)
(2)
A=(p*s*a)/1000 нм(кгс)
(3)
где бв - предел
прочности
разрезаемого
металла н/м2
(кгс/мм2),
S - толщина
металла (мм), L
- периметр резки
(мм), a - коэффициент,
равный 0,5-0,6.
Усилие и
работа необходимы
для подбора
оборудования
(ножниц).
Для резки
листового
металла применяют
различные типы
ножниц: 1) ножницы
с параллельными
прямыми ножами,
2) ножницы с
наклонными
прямыми ножами,
3) ножницы с
многодисковыми
ножами, 4) ножницы
с парнодисковыми
наклонно
поставленными
ножами и др.
(рис.9а-г), а также
штампы.
Ножницы с
параллельными,
наклонными
и многодисковыми
ножами применяют
для прямолинейной
резки; ножницы
с парнодисковыми
наклонными
ножами - для
криволинейной
резки и вырезки
по замкнутому
контуру. Ножницы
с параллельными
и наклонными
ножами применяют
для резки листов,
ножницы с
многодисковыми
ножами - для
резки лент. Для
выбора ножниц
усилие рассчитывают
по формулам:
а) для ножниц
с параллельными
ножами - по формуле
(2)
б) для ножниц
с наклонными
ножами
P=(1/2)*(бв*S2)/tgL (4)
в) для многодисковых
ножниц
*
P=0,4*m*(бв*S2)/tga
где бв - предел
прочности
материала,
н/м2(кгс/мм2),
S - толщина
материала, мм,
L - угол наклона
ножей, град, α
(альфа) -угол
захвата материала
дисками, град,
м - число пар
ножей.
Точность
резки по ширине
зависит от
толщины и ширины
отрезаемой
заготовки;
более высокая
точность резки
на штампах,
затем на многодисковых
ножницах, затем
на параллельных
ножницах и
наиболее низкая
- на ножницах
с наклонными
ножами. Точность
резки на ножницах
определяется
по справочным
таблицам в
зависимости
от ширины и
толщины разрезаемого
металла. Ориентировочно
она оценивается
12-14 калитетом
точности.
Технологические
требования
(технологичность).
1) Ширина отделяемой
части металла
должна быть
или равна двум
толщинам материала.
2) Точность
резки по ширине
- 12-14 квалитет. Она
уточняется
по справочнику
в зависимости
от применяемого
оборудования
и толщины материала.
3) Шероховатость
поверхности
среза по толщине
неоднородна
- от Rz = 160-20 мкм в зоне
скола до (Ra = 2,5-0,32 мкм
в зоне среза.
Вырубка
и пробивка.
При вырубке
и пробивке
происходит
отделение
металла по
замкнутому
контуру; при
вырубке отделенная
часть - является
деталью, при
пробивке - отходом.
Схема процесса
показана на
рис.11
Механизм
разделения
со всеми его
особенностями
не отличаются
ничем от механизма
разделения
при резке. Напряжения
пластического
деформирования
распространяются
на величину
равную (0,6-0,7) толщины
металла (рис.10),
как и при резке.
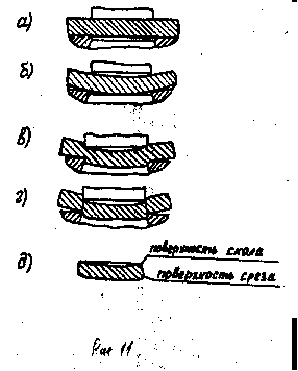
В отличие
от резки изгибающий
момент при
вырубке - пробивке
приложен по
замкнутому
контуру к заготовке,
находящейся
внутри и вне
контура резки,
что приводит
также к изгибу
вырубаемой
и пробиваемой
заготовки -
детали. При
равномерном
сопротивлении
изгибу, что
достигается
соответствующим
расстоянием
от контура
резки до края
заготовки
(перемычке),
получают нормальное
качество поверхности
разделения.
При малой перемычке
ча6ть металла
втягивается
в зазор между
режущими кромками
и в этом случае,
как и при большом
зазоре, получают
заусенцы. Под
действием
изгибающего
момента обе
части заготовки
получают остаточный
прогиб, для
получения
плоской детали
необходима
дополнительная
операция плоскостной
правки. Величина
зазора здесь
также влияет
на качество
разделения.
При нормальном
зазоре Z = (0,05-0,20)S получают
наилучшее
качество поверхности
разделения
- в зоне среза
параметр
шероховатости
Ra = 2,5-0,32 мкм, в зоне
скола параметр
шероховатости
Rz= 80-20 мкм, при увеличенном
зазоре шероховатость
поверхности
разделения
такая же как
и при нормальном
зазоре, и кроме
этого возникает
заусенец; при
уменьшенном
зазоре поверхности
скола не могут
соединиться
и поэтому параметр
шероховатости
ниже Rz =320 мим в
зоне двойного
скола - среза
(рис.12). Точность
размеров при
вырубке - пробивке
зависит от
толщины материала,
формы и размеров
заготовки.
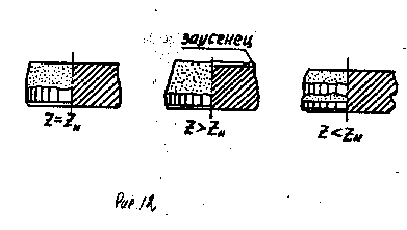
Точность
круглого контура
находится в
пределах 11-14
квалитета. Для
конкретных
условий уточняется
по справочнику.
Так как заготовка
в процессе
вырубки-пробивки
прогибается,
то применение
прижима заготовки
увеличивает
точность размеров.
Усилие и
работа, необходимые
для выбора
оборудования
определяют
по формулам
(2) и (3).
Для выполнения
операций
вырубки-пробивки
используют
механические
- кривошипные
прессы. Прессы
могут быть
оснащены устройствами
для автоматической
подачи ленты
или полосы,
автоматическими
устройствами
выталкивания
детали из верхней
и нижней части
штампа, для
удаления отходов
и деталей под
действием сил
веса изготовляют
прессы с наклоняемой
станиной.
Основной
инструмент
для вырубки
и пробивки -
штамп, который
устанавливается
на пресс. Размеры
штампа должны
вписываться
в рабочее
пространство
пресса - размеры
стола пресса
и быть не более
наименьшего
расстояния
от ползуна
пресса до стола.
Типовая
конструкция
штампа
для серийного
и массового
производства
деталей без
прижима изображена
на рис. 13 Любой
штамп состоит
из следующих
основных деталей:
1 - формообразующих
деталей - пуансона
(1), матрицы (2), П -
деталей ориентирующих
заготовку
относительно
рабочих деталей
- направляющих
(3) или фиксатора,
Ш - деталей
ориентирующих
рабочие детали
друг относительно
друга- направляющих
колонок (4) и
направляющих
втулок (5),
1У - деталей,
снимающих отход
или заготовку
с пуансона -
съемника (6),
У - корпусных
деталей штампа
- верхней плиты
(7), нижней плиты
(8),
У1 - деталей,
обеспечивающих
крепление
штампа к прессу
- хвостовика
(9), прижимных
планок, прокладки,
болтов с гайками,
УП - крепежных
деталей для
крепления всех
деталей в штампе
-винтов,
штифтов,
болтов и др.
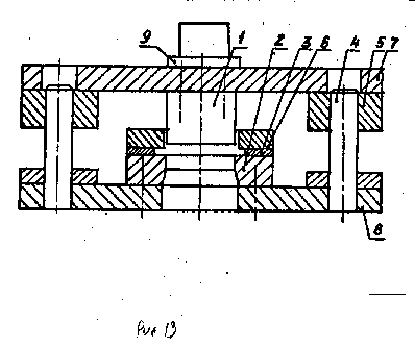
Технологичность
деталей, получаемых
вырубкой и
пробивкой
определяется
прочностью
рабочих частей
штампа и технологическим
процессом
штамповки.
1. Плоские
детали должны
иметь простую
конфигурацию,
острые углы,
узкие прорези
и выступы снижают
стойкость
штампов и усложняют
их изготовление.
2. При применении
цельных матриц,
вырубка с
перемычками,
пробивке
выполнять
плавное сопряжение
пересекающихся
элементов
контура детали
(рис.14a). Минимальные
радиусы сопряжения
углов: при α>90°
R=(0,25-0,35)S , при a<90° R=(0,5 - 0,6)S -
для металлов,
для неметаллических
материалов
эти радиусы
больше из-за
малой прочности
штампуемого
материала.
3. При составных
матрицах и при
безотходной
штамповке
пересекающиеся
элементы контура
не сопрягают.
4. Минимальные
размеры отверстий,
пробиваемые
в штампах нормальной
конструкции:
круглых d=(1-1.5)S ,
квадратных
a = (0,9-1,4)S , прямоугольных
b = (0,7-1,2)S , овальных
c = (0,6-1,1)S для сталей
в зависимости
от прочности
( бв = 50-70 кгс/мм2) (рис.
14б).
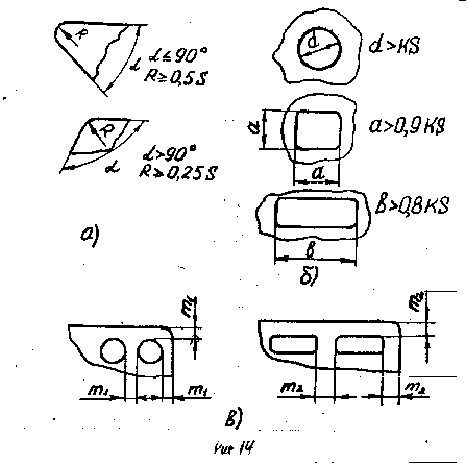
5. Для пробивки
отверстий
диаметром до
1/3S , применяют
специальные
штампы.
6. Минимальные
расстояния
между раздельно
пробиваемыми
отверстиями
круглой и
прямоугольной
формы a1>(1-1,2)S (рис.14в).
7. Минимальное
расстояние
между пробиваемым
отверстием
и ранее полученным
контуром детали
a2>(0,7-0,9)S (рис.14в).
8. Минимальное
расстояние
между одновременно
пробиваемыми
отверстиями
равно двум-трем
толщинам металла.
*
9. Точность
размеров определяется
в зависимости
от толщины
штампуемого
металла и
конфигурации
детали, для
круглых контуров
она находится
в пределах
11-14 квалитета.
10. Шероховатость
поверхности
среза по толщине
неоднородна:
в зоне среза
Rа = 2,5-0,32 мкм, в зоне
скола - Rz=80-20 мкм.
Технологический
маршрут вырубки*пробивки:
а) вырубка
- укладка полосы
в штамп и установка
ее до упора,
вырубка детали,
удаление детали
из штампа (и
подача полосы
на шаг),
- галтовка
(для снятия
заусенцев),
- рассортировка
деталей и абразивов,
- контроль,
б) пробивка
- укладка заготовки
в штамп,
- пробивка
детали,
-удаление
детали из штампа,
- контроль.
Чистовая
вырубка и пробивка
Чистовую
вырубку и пробивку
применяют для
исключения
недостатков
вырубки-пробивки:
получения
перпендикулярности
поверхности
среза плоскости
детали, устранения
прогиба, получения
шероховатости
поверхности
с параметром
Ra = 2,5-0,32 мкм и точности
6-9 квали-
тета.
Зачистка
Зачистка
и калибровка
применяются
для тех же целей,
что и чистовая
вырубка и пробивка,
т.е. достижения
перпендикулярности
поверхности
среза плоскости
листа, шероховатости
Rа = 2,5-0,32 мкм, точности
8-9 квалитета.
Зачистка
(калибровка)производится
на ранее полученных
вырубкой (пробивкой)
заготовках.
В этом случае
после правки
с обрабатываемой
поверхности
снимают небольшой
слой материала
- припуск.
Зачистка
выполняется
по наружному
или внутреннему
контуру заготовки.
Минимальная
величина припуска
на зачистку
равна зазору
между пуансоном
и матрицей при
вырубке или
пробивке (рис.15).
Зачистку
применяют для
деталей с периметром
до 300 мм и толщиной
до 10 мм. Зачистка
выполняется
за один проход
для деталей
толщиной менее
5 мм с плавным
очертанием
наружного
контура. Многократную
зачистку применяют
для деталей
толщиной более
5 мм и для деталей
со сложной
конфигурацией
наружного
контура независимо
от толщины.
Качество зачистки
зависит от
величины припуска
и распределения
его по периметру,
а при многократной
зачистке от
распределения
по переходам.
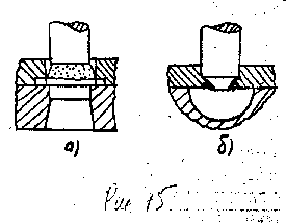
Применяют
также зачистку
обжатием
в матрице с
заваленными
кромками, припуск
в этом случае
составляет
0,04-0,06 мм.
Формообразующие
операции
Гибка.
Гибка - это
формообразующая
операция, при
которой изменяется
кривизна в
одном или нескольких
участках заготовки.
Изменение
кривизны может
происходить
только при
переменных
деформациях
по толщине; эти
переменные
деформации
вызваны переменными
напряжениями
по толщине.
Гибка производится
под действием
силы, момента
или одновременно
силой и моментом.
Наиболее часто
используется
гибка силой
(рис.16а).
Исследование
процесса гибки
показывает,
что по толщине
напряжения
и деформации
не только постепенно
изменяются,
но и различны
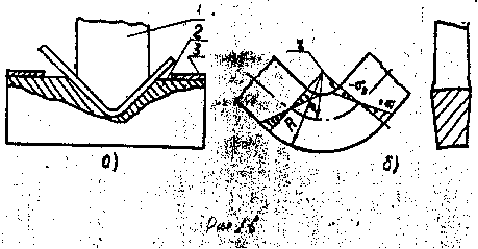
по знаку: в
участках, прилегающих
к матрице, возникают
растягивающие
напряжения
и деформации
растяжения,
а участках,
прилегающих
к пуансону,
напряжения
и деформации
сжатия, что
приводит к
изменению
поперечного
сечения (рис.16б).
Между этими
участками
находятся
слои с напряжениями
и деформациями
равными нулю.
В общем случае,
слои нулевых
напряжений
и деформаций
(нейтральные
слои) не совпадают.
Практическое
значение имеет
положение
нейтрального
радиуса деформаций,
определяемого
по формуле
r1=r+x*s (6)
где r -
радиус пуансона,
S - толщина металла,
x - коэффциент
смещения нейтрального
от серединного
слоя, определяемой
в зависимости
от отношения
r/s , при
r/s = 0,5 x=0,3 при r/s = 10, x=0,5. В
дальнейшем
r1 используется
для определения
размеров заготовки.
В процессах
гибки большое
значение имеет
радиус гибки.
Величина его
ограничивается
минимальным
радиусом. Минимальный
радиус гибки
определяется
из условия
отсутствия
разрушения
металла в зоне
растяжения.
Минимальная
величина этого
радиуса зависит
от пластических
свойств материала
и толщин заготовки.
Для материалов
средней пластичности
( δ = 15-20%) минимальный
радиус гибки
(пуансона)
ориентировочно
равен 0,5 * Для
конкретных
материалов
(условий*) уточняется
по таблицам.
Чем более пластичный
металл, тем
меньше минимальный
радиус гибки
и наоборот.
Минимальный
радиус гибки
зависит и от
расположения
линии гибки
относительно
направления
проката (расположения
волокон макроструктуры);
при параллельных
линию гибки
и направлении
проката - минимально
допустимый
радиус больше,
чем при взаимноперпендикулярном
расположении
направления
проката и линии
гибки, когда
получают наименьшую
величину минимально
допустимого
радиуса гибки.
При промежуточной
величине угла
наклона линии
гибки к направлению
проката надо
брать промежуточные
значения радиуса
гибки, пропорциональные
величине угла.
Для предупреждения
образования
отпечатков
на полочках
детали необходимо
назначать на
кромках матрицы,
по которым
втягивается
материал, радиус
не менее трех
толщин.
Так как напряжения
и деформации
по толщине
неодинаковы
по величине
и знаку, то на
основе закона
о разгрузке,
происходит
уменьшение
растянутой
части, и увеличение
размера сжатой
части заготовки.
Это приводит
к упругому
изменению угла
гибки - пружинению,
приводящему
к уменьшению
угла гибки
(рис.17). Одновременно
происходит
и увеличение
радиуса гибки.
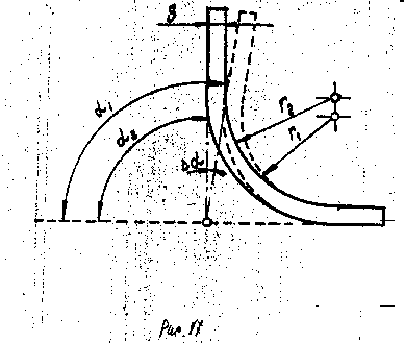
Пружинение
зависит от
относительной
величины радиуса
пуансона r/s ,
материала
детали, угла
гибки и других
факторов. Величина
пружинения
для данных
условие гибки
постоянна.
Величина пружинения
может быть
уменьшена путем
сжатия (правки)
детали в штампе.
При радиусах
гибки менее
r/s<2 изменение
радиуса по
величине
незначительно
и поэтому его
не учитывают.
Растягивающие
и сжимающие
напряжения
и деформации
гибки вследствие
закона о дополнительных
напряжениях,
возникают и
в прямолинейных
участках, прилегающих
к криволинейным,
распространяются
на расстояние
до двух толщин
материала от
линии сопряжения
криволинейного
участка с
прямолинейным.
Усилие гибки
V образной
детали определяют
по формуле:
P= бв*(B*s2)/(r+s) (7)
где B - ширина
летали.
Для других
форм детали
определяют
усилие по
соответствующим
формула в
справочниках.
Размеры
заготовки
рассчитывают
исходя из развертки
детали на плоскость.
Как известно
при гибке изменяется
длина волокон
в криволинейных
участках, а
прямолинейные
остаются по
длине до и после
гибки неизменной
длины. Поэтому
деталь разделяют
на прямолинейные
и криволинейные
участки (рис.18),
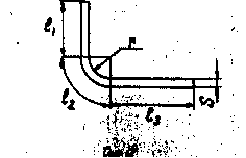
определяют
их длины и суммируют
для получения
общей длины
развертки.
Длины прямолинейных
участков определяют
по данным чертежа,
длины криволинейных
участков по
длине нейтрального
волокна деформации:
lkpi=(п*r1*a)/180
длина развертки
равна
где - сумма
длин прямолинейных
участков, - сумма
длин криволинейных
участков,
r1 - радиус
нейтрального
волокна деформации
формула (6) n,k - число
прямолинейных
и криволинейных
участков.
Оборудование
Для выполнения
операции гибки
используют
кривошипные
прессы. В условиях
массового
производства
используют
специализированные
прессы, а также
специальные
гибочные прессы
- универсально-гибочные
автоматы. Эти
автоматы увеличивают
производительность
в десятки раз.
Оснасткой
для гибки является
штамп. Конструкция
штампа для
гибки содержит
элементы, известные
по конструкции
штампа для
вырубки-пробивки.
Технологичность
деталей получаемых
гибкой
1. Радиус гибки
пуансона не
должен быть
менее допустимого
минимального
для данного
материала.
2. Радиус матрицы
не менее трех
толщин.
3. Длина отгибаемой
части полочки
должна быть
не менее двух
толщин (рис.19а),
если отгибаемая
часть короче
рекомендуемой
величины, то
ее изготовляют
более длинной,
а затем обрезают
по высоте.
4. Расстояние
от края отверстия
до линии сопряжения
полочки с радаусом
должано быть
не менее двух
толщин (рис.19а).
При меньшем
расстоянии
пробивку отверстия
делают после
гибки или
предусматривают
на перегибе
отверстие
(рис.19а) для
предупреждения
искажения
ранее полученного
отверстия.
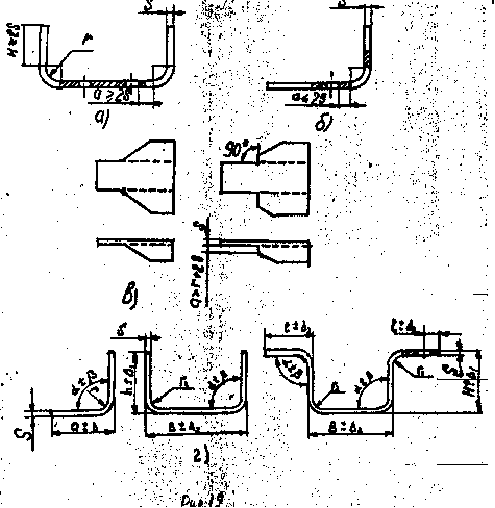
5. При одновременной
двуугловой
(четырехугловой)
гибке длина
линии гибки
противоположных
полочек не
должна резко
отличаться,
так как под
действием сил
трения может
изменяться
высота полочки.
6. Угол между
линиями гибки
и контура домен
быть равен 90˚
для предупреждения
деформации
полочек под
действием сил
трения (рис.19в).
7. Простановка
размеров и
допусков на
чертеже детали:
наиболее технологичны
детали у которых
координаты
центров отверстий
заданы от края
полочки (рис.
), в этом случае
пробивку отверстий
совмещают с
вырубкой заготовки,
при другой
схеме простановки
размеров
отверстия
пробивают в
отдельном
штампе после
гибки для обеспечения
заданной точности;
допуски на
линейные размеры
задают симметричные.
Вытяжка.
Вытяжкой называют
процесс превращения
плоского заготовки
в полое изделие,
или - процесс
превращения
полой заготовки
в полое изделие
меньшего диаметра
и большей высоты.
Различают
вытяжку с
утонением
стенок и без
утонения стенок,
а также комбинированную
вытяжку.
При обычной
вытяжке толщина
стенок детали
гложет быть
больше исходного
толщины заготовки.
При вытяжке
с утонением
толщина стенок
получаемой
детали меньше
толщины стенок
заготовки. При
обычной вытяжке
основная деформация
происходит
за счет значительного
изменения
диаметра заготовки,
при вытяжке
с утонением
- за счет
изменения
толщины заготовки.
При комбинированной
вытяжке происходит
деформирование
заготовки и
за счет изменения
диаметра и за
счет уменьшения
толщины заготовки
одновременно.
В зависимости
от температуры
штампуемого
металла различают
холодную вытяжку
и вытяжку с
подогревом.
Под термином
"вытяжка"
подразумевают
холодную вытяжку
без утонения.
В процессе
вытяжки получают
детали круглого
и других (произвольных)
поперечных
сечений: квадрат,
прямоугольник,
овал и др.
Рассмотрим
процесс вытяжки
на примере
изготовления
круглой детали
(рис.20). В этом
случае круглая
заготовка
втягивается
в зазор Z между
матрицей и
пуансоном под
действием силы
Р; при этом диаметр
заготовки
уменьшается
и высота изделия
увеличивается
за счет сжатия
заготовки в
окружном направлении
и растяжения
в радиальном
направлении;
дно растягивается
в окружной и
радиальном
направлениях.
При некоторых
условиях под
действием
сжимающих
напряжений
теряется устойчивость
фланца-кольцевой
части заготовки.
Это приводит
к образованию
гофров, препятствующих
втягиванию
заготовки в
зазор и приводящих
к разрыву заготовки
- браку. Для
предупреждения
образования
гофров вводят
прижим (рис.
20а), прижим осуществляют
с давлением
q = (0,1-0,3 кгс/мм2) 0,01-0,03 Мн/м2.
Процесс
деформирования
при вытяжке
характеризует
отношение
среднего радиуса
деуали к радиусу
заготовки -
коэффициент
вытяжки; предельная
величина коэффициента
вытяжки
m=r/R3=0,5-0,7 (10)
при этом
отношение
высоты полученной
детали к диаметру
H/d<0,7-0,6.
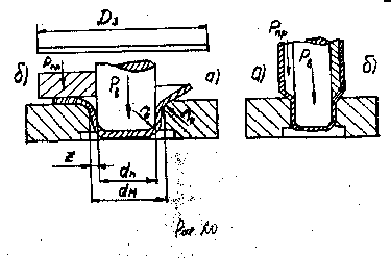
Если необходима
большая высота
детали полученное
полое изделие
подвергают
последующей
вытяжке: второй,
третьей и т.д.
При этом предельная
суммарная
величина коэффициента
вытяжки может
достигать m =
0,25, а отношение
высоты детали
к диаметру до
8-10. Необходимость
прижима. Прижим
на первой операции
нужен, если
(S/D3)*100<2 (11)
прижим на
последующих
операциях
нужен, если
(S/dn-1)*100<1,5 , а mn<0,78 (12)
Усилие прижима
определяют
по формуле
Pnp=q*Fnp (13)
где q - давление
прижима , Fnp - площадь
прижима .
Втягивание
материала в
матрицу возможно
лишь наличии
определенных
радиусов на
пуансоне или
матрице, так
как при радиусах
равных нулю
процесс вытяжки
переходит в
процесс вырубки.
При вытяжке
рекомендуют
назначать:
радиус матрицы
: rm=(4-8)S (14)
радиус пуансона:
rn=(0,7-0,8)rm
Для уменьшения
сил трения при
вытяжке заготовки
смазывают
смазками,
назначаемыми
в зависимости
от марки металла
заготовки.
Усилие вытяжки
определяют
по формуле
(наибольшее)
Pв=бв*п*d (15)
Общее усилие
определяют
с учетом прижима
P=pв+pnp (16)
При вытяжке
одновременно
можно формовать
на дне небольшие
рельефные
впадины и выступы,
деталь может
быть без фланца
и с фланцем.
Особенности
формы
При вытяжке
вследствие
анизотропии
материала
открытый торец
детали получается
по высоте не
одинаковым
, а наружный
диаметр фланца
не круглым .
Поэтому необходим
припуск для
обрезки. Толщина
детали по высоте
также не одинакова
у верхнего
торца от 1 до
1,3 толщины у дна
- 0,85So , толщина дна
уменьшается
до 0,95So (рис.21)
Размеры
заготовки
определяют
из условия
равенства
поверхности
заготовки
поверхности
детали с учетом
припуска на
обрезку; для
круглой детали:
Fзаг=FДЕТ+F;
D3=1,13(Fзаг)1/2 (17)
Зазор между
матрицей и
пуансоном
принимается
равным (1-1,3)So в
зависимости
от коэффициента
вытяжки.
Штампы для
вытяжки имеют
те же, что и при
вырубке - пробивки,
основные элементы.
Вытяжка с
подогревом.
При обычной
вытяжке за один
переход получают
высоту (0,6-0,7)d. При
вытяжке с подогревом
можно за один
переход получить
высоту, равную
(1,3-2,3)d. Способ используется
для вытяжки
заготовок
главным образом
из цветных
сплавов (алюминиевых,
магниевых,
титановых).
Сущность процесса
заключается
в том, что материал
в очаге деформации
нагревается
(рис.22) и тем самым
уменьшается
его предел
текучести а
в зоне сформировавшейся
части детали
металл охлаждается
для увеличения
механических
характеристик.
Температура
нагрева в очаге
деформации
должна быть
выше температуры
рекристаллизации
с тем, чтобы
материал не
получал упрочнения.
Вытяжка делается
на
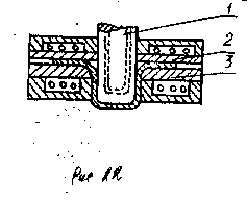
гидропрессах
или на тихоходных
(12-20ход/мин) механических
прессах.
Вытяжка с
утонением.
Вытяжка с уточнение
отличается
от рассмотренной
выше вытяжки
тем, что при
этом процессе
уменьшается
толщина стенки
полого изделия,
а диаметр остается
почти неизменным,
высота детали
значительно
увеличивается.
Зазор между
матрицей и
пуансоном в
этом случае
меньше толщины
заготовки
(рис.23).
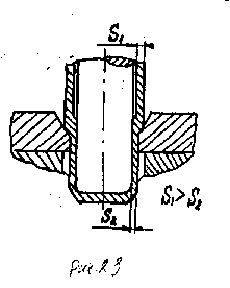
Сущность
процесса. Усилие
от пуансона
передается
донышку, при
этом начинает
уменьшаться
толщина стенки
за счет нормальных
сил возникающих
со стороны
конической
части матрицы
и пуансона,
тангенциальных
сжимающих сил
и еще сил трения
на матрице и
пуансоне.
Важно отметить,
что сила трения
на пуансоне
направлена
вниз и способствует
разгрузке
опасного сечения,
так как материал
в очаге деформации
под действием
сдвигающих
напряжений
частично при
движении пуансона
вытесняется
вверх относительно
движения пуансона
(двигающегося
вниз).
Для получения
большей степени
деформации
(U=(Fo-F)/Fo) вытяжку ведут
через две или
три матрицы.
Для вытяжки
с утонением
применяют все
деформируемые
материалы.
Вытяжка с
утонение нашла
широкое применение
в промышленности,
особенно в
приборостроении
для изготовления
заготовок
сильфонов -
упругих чувствительных
элементов
системы автоматики.
Вытяжка с
утонением по
сравнением
с обычной вытяжкой
имеет следующие
преимущества:
1.Не требует
применения
сложных штампов
и прессов.
2.Число вытяжных
операций может
быть меньше
для получения
заданной высоты
по сравнением
с обычной вытяжкой.
3.Качество
металла в вытянутой
стенке лучше.
Особенность
деталей заключается
в том, что толщина
донца в (5-10) раз
толщины стенок.
Точность
при вытяжке
нужно рассматривать
для каждого
параметра
отдельно:
а) Точность
по диаметру,
б) Точность
по толщине
стенок,
в) Точность
по высоте.
Эти параметры
в значительной
степени определяются
степенью точности
инструмента.
С учетом всех
факторов достигаемая
при вытяжке
точность по
диаметру может
соответствовать
6-9 квалитету;
по толщине -
6-11 квалитету;
по высоте - ниже
16 квалитета.
Качество
наружной поверхности
зависит от
качества поверхности
матрицы: внутренней
- определяется
частотой поверхности
исходного
материала и
пуансона;
шероховатостью
по наружной
поверхности
- Ra=0,63-0,16 мкм.
Комбинированная
вытяжка.
При комбинированной
вытяжке за один
переход существенно
уменьшается
диаметр заготовки
и толщина (рис.24).
Так как при
обычной вытяжке
значительная
разнотолщинность
стенки по высоте
(до 0,85S у дна и до
1,3S у верхнего
торца), то в
начальный
момент происходит
только обычная
вытяжка и вытяжка
с уточнением.
При комбинированной
вытяжке создается
благоприятная
схема напряженного
состояния, при
которой обычная
вытяжка разгружает
наиболее нагруженное
сечение вытяжки
с уточнением.
Это позволяет
с получением
высоких качественных
показателей
увеличить
производительность
в 2-3 раза.
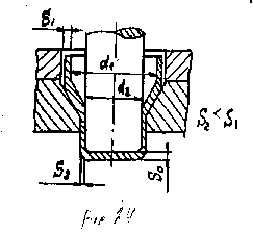
При комбинированной
вытяжке получают
заготовки 6-9
квалитета,
точности по
диаметру , 6-11
квалитета
точности по
толщине стенки,
шероховатость
- Ra=0,63-0,16 мкм.
Технологичность
деталей полученных
вытяжкой.
1.Радиус рабочей
кромки матрицы
rm=(4-8)S, пуансона
rn=0,7rm. Сопряжение
дна со стенкой
без радиуса
можно получить
путем калибровки
или при штамповке
весьма толстых
заготовок с
D3/S>20 , m>0,7.
2.В первую
очередь операцию
вытяжки можно
получить отношение
высоты детали
(H) к диаметру
(d) не более H/d<0,6
(m=0,5); для получения
большей высоты
необходимы
последующие
переходы.
Наиболее
экономично
изготовлять
более высокие
детали с большей
точностью и
лучшим качеством
поверхности
комбинированной
вытяжкой, при
которой за одну
операцию можно
получить в
зависимости
от принятых
степеней деформации
относительную
высоту детали
до 1,5-2,5.
3. Избегать
глубоких вытяжек
с широким фланцем
(Dф>3d при h>2d) , требующих
большого количества
операций.
4.Конфигурация
деталей должна
быть простой:
дно - плоское
или слегка
выпуклое в
наружную сторону,
фланец - плоский,
боковые поверхности
цилиндрические,
конические;
Вместо конических
с малым углом
конусности
предпочтительнее
цилиндрические
поверхности.
5.Размеры
деталей следует
проставлять
так : высоту-от
дна детали,
радиусы закруглений
между дном и
стенкой - по
внутренней
поверхности,
радиус закругления
между фланцем
и стенкой - по
наружной поверхности,
размеры выступов
по высоте лучше
проставлять
между дном и
ступенью снаружи.
6.Допуски на
диаметры выпуклых
деталей следует
устанавливать
не выше 12-13 квалитета
точности.
7.Точность
поперечного
сечения деталей
при комбинированной
вытяжке соответствует
6-9 квалитету
точности, большая
точность относится
к деталям, полученным
с большой степенью
деформации
по диаметру.
8.Шероховатость
поверхности
деталей полученных
комбинированной
вытяжкой и
вытяжкой с
утонением
соответствует
Ra=1,25-0,16 мкм; при обычной
вытяжке шероховатость
на 1-2 интервала
параметра
шероховатости
ниже исходной.
Формовка.
Формовка
- процесс изменения
формы заготовки
за счет местных
деформаций.
К формрвке
относятся
операции:
1.рельефная
формовка,
2.отбортовка
отверстий,
3. закатка
борта,
4. раздача,
5. обжим,
6. правка.
Рельефная
формовка -
операция, которая
обеспечивает
получение на
заготовках
ребер жесткости
различной формы
(рис.25). При рельефной
формовке листового
материала
деформирование
происходит
за счет двухосного
растяжения
(растяжения
в плоскости
листа), при этом
материал значительно
утоняется
(50%).
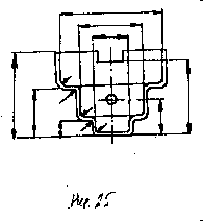
Допустимая
степень деформации
определяется
по формуле:
E=(l-lo)/l0<0,75δ = 15-18% (18)
где lo и l -длина
элемента до
и после деформации
операции, δ -
относительное
удлинение
материала при
растяжении.
Отбортовка
. Различают
отбортовку
отверстий и
отбортовку
наружного
контура.
Отбортовка
отверствий
- процесс формоизменения
листовой заготовки,
при котором
у отверстия
получают борт
(рис.26).
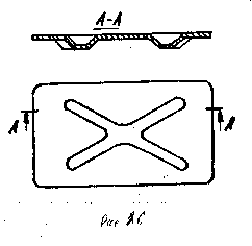
При деформировании
наблюдается
растяжение
в тангенциальном
(окружном)
направлении
и уменьшение
толщины материала.
Степень деформации
определяется
коэффициентом
отборки:
Kот=d/D
При (S/D)*100=2 , Kот=0,75
при сверлении
отверстия и
Kот=0,8 при пробивке.
Допустимая
степень деформации
в значительной
степени зависит
от:
1) качества
поверхности
отверствия,
2)относительной
толщины материала
,
3) материала
и его состояния
,
4)формы рабочей
части пуасона.
Чем меньше
трещин на поверхности
отверствия,
чем меньше Kот.
У сверленных
отверствий
Kот меньше, чем
пробитных. У
пробитной
детали Kот
значительно
изменяется
в зависимости
от положения
блестящего
пояска относительно
матрицы. Если
блестящий
поясок будет
в зоне наибольших
деформаций,
то Kот меньше,
чем при положении
шероховатой
части в зоне
наибольших
деформаций.
Высота борта
определяется
как и при гибке
(приближенно).
Это возможно
благодаря тому,
что материал
утоняется.
Наибольшая
толщина у края
борта определяется
выражением
(на основе
постоянства
объема)
S1=So*(Kот)1/2 (20)
Разновидности
отбортовки:
отбортовка
с утонением.
Отбортовка
с утонением
выполняется
для получения
более высоких
буртов. При
отбортовке
с утонением
одновременно
с образованием
бурта толщина
стенки уменьшается.
Отбортовка
наружного
контура
- это в сущности
процесс неглубокой
вытяжки. К этому
процессу относятся
все характерные
особенности
вытяжки: напряженное
состояние,
деформации
и возможность
гофрообразования.
Раздача
- представляет
собой процесс
увеличения
периметра
поперечного
сечения трубчатой
исходной заготовки
(рис.27).
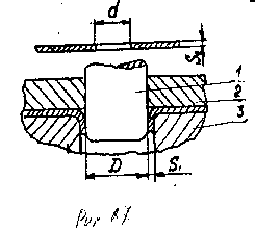
Наименьшая
толщина стенки
прближенно
определяется
выражением
S1=So*(d/d1) (21)
Соотношение
Kр=d/d0 называют
коэффициентом
раздачи, который
может достигать
величины 1,6 при
S/d=0,15 и угле а=20 грд.
(рис.27).
Обжим
- процесс уменьшения
периметра
поперечного
сечения краевой
части полой
заготовки
(рис.28).
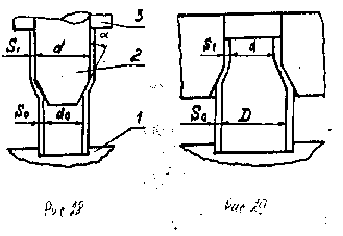
При обжиме
в заготовке
возникают
тангенциальные
сжимающие
напряжения,
в результате
чего уменьшается
периметр и
уменьшается
толщина заготовки.
Увеличение
толщины заготовки
у края можно
определить
из выражения,
полученного
на основе условия
постоянства
объема:
S об=So√(D/d)
(22)
В процессе
обжима вертикальная
часть детали
имеет сжимающие
напряжения,
под действием
которых она
может получить
потерю устойчивости.
Для предупреждения
потери устойчивости
и увеличения
коэффициента
обжима
Kоб=D/d (23)
применяют
подпор наружный,
внутренний
и одновременно
оба.
Коэффициент
обжима для
мягкой стали:
-
без подпора |
подпор наружный |
подпор
внутренний
и наружный |
0,7-0,75 |
0,55-0,6 |
0,3-0,35 |
Правкой
называют
операцию, при
которой происходит
увеличение
точности формы
детали.
При операциях
отрезки или
вырубки, гибки
и пробивки
материал в
очаге деформации
и вблизи него
находится под
действием
изгибающего
момента. Этот
изгибающий
момент нарушает
плоскостность
полученных
деталей, за
счет удлинения
волокон на
одной и укорочение
волокон на
другой сторонах
детали. Операция
правки заключается
в том, сделать
все волокна
одинаковой
длины по толщине
металла (кроме
зон гибки в
гнутых деталях.
Достигается
это на штампах
(рис.29). Штампы
для правки
могут иметь:
плоские
(гладкие) плиты,
точечные
плиты,
вафельные
плиты.
Шаг между
выступами
точечных и
вафельных плит
должен быть
равен: t=(0,5-0,9)S, давление
правки от 50 до
300 мн/м2 (от 5 до 30
кГ/мм2). Плиты
должны быть
массивными
с тем, чтобы
при правке они
не прогибались.
Комбинированная
штамповка.
Для получения
производительности
труда (в 3-10 раз),
уменьшения
количества
штампов и прессов
в месте штамповки
по отдельным
операциям
применяют
комбинированную
штамповку.
Комбинированная
штамповка
заключается
в одновременном
выполнении
нескольких
операций в
одном штампе.
Существует
три способа
комбинирования
операций холодной
штамповки:
последовательный,
совмещенный
и последовательно-совмещенный
(рис.30).
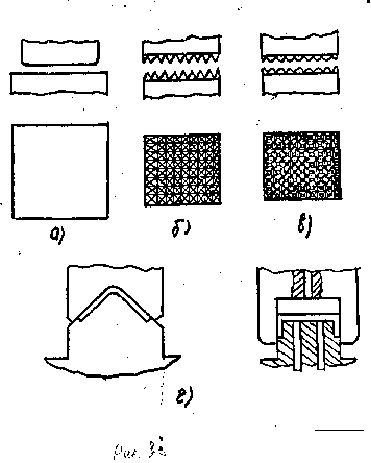
Отличие этих
вариантов
состоит в
последовательности
и месте выполнения
операций. При
последовательном
способе все
операции выполняются
одновременно
в последовательном
штампе на разных
позициях, причем
число переходов
соответствует
числу позиций.
При совмещенном
способе все
операции выполняются
одновременно
в одной и той
же позиции
штампа совмещенного
действия. При
последовательно-совмещенном
способе для
одновременного
выполнения
всех операций
требуется
позиций в инструменте
меньше, чем
операций. Этот
способ представляет
комбинацию
из первых двух.
Для выполнения
технологических
процессов
используется
материал в виде
полосы или
ленты. Использование
полосового
или ленточного
материала
позволяет в
значительной
мере механизировать
и автоматизировать
процесс штамповки.
Ширина полосы
при наличии
вытяжки в
комбинированной
штамповке
принимается
несколько
больше, чем это
необходимо
для получения
детали с той
целью, чтобы
можно было
иметь перемычки
между отдельными
операциями
для перемещения
всех полуфабрикатов
на следующую
позицию.
При выполнении
формоизменяющих
операций в
ленте (полосе)
часто требуется
специальная
подготовка
ленты (выполнение
прорезей, вырубки
промежутков)
для облегчения
процесса
деформирования
материала.
Выбор способа
штамповки
определяется
рядом факторов:
1.точностью
изготовления
детали (особенно
получения
соосности),
2.технической
культурой
инструментального
производства,
3.конструкцией
детали и пр.
В зависимости
от сложности
и размеров
детали комбинированная
штамповка может
быть однорядная
и многорядная.
Точность
комбинированной
штамповки
определяется
точностью
отдельных
элементов
контура детали
и точностью
взаимного
расположения
этих элементов.
Точность отдельных
контуров детали
определяется
точностью
используемого
способа. Точность
взаимного
расположения
отдельных
элементов
контура определяется
способом
комбинированной
штамповки: при
совмещенной
штамповке -
точностью
взаимного
расположения
пуансонов и
матриц; при
последовательной
- точностью
взаимного
расположения
пуансонов и
матриц и точностью
оринтеровки
(базирования)
полуфабриката
(заготовок) на
каждом переходе,
обычно она
соответствует
12-14 квалитету.
Штамповка
в условиях
мелко серийного
производства.
При мелкосерийном
производстве
изготовляют
от 3-5 до 20-10000 штук
деталей.
Использование
в мелкосерийном
производстве
штампов серийного
производства,
стоящих до
200-300 руб., экономически
невыгодно и
увеличивает
срок изготовления
новых деталей
(штамп серийного
производства
изготовляют
ориентировочно
один месяц).
Для быстрого
освоения новых
изделий (опытных
образцов) с
минимальными
производственными
затратами в
условиях
мелкосерийного
производства
применяют два
способа: штамповку
на упрощенных
штампах и на
универсальных
штампах.
К штамповке
на упрощенных
штампах относят
штамповку: а)
на пинцетных
штампах, б) на
литых штампах,
в) на штампах
с использованием
полиуретана,
взрывчатых
веществ, импульсного
магнитного
поля, взрыва
газовых смесей,
электрогидравлического
эффекта и др.
Пинцетные
(листовые) штампы
(рис.31) используют
как для индивидуальной,
так и групповой
штамповки
деталей. Их
применяют для
вырубки - пробивки,
иногда для
гибки, отбортовки,
рельефной
формовки.
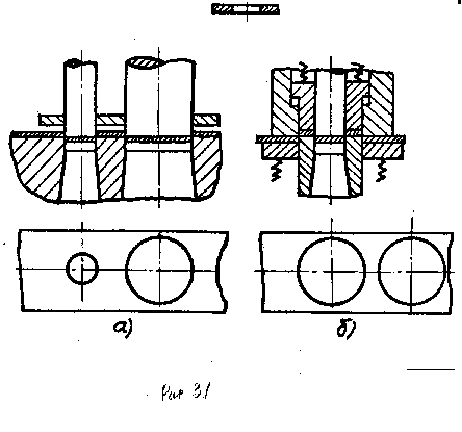
Литые штампы
изготовляют
из алюминиевоцинковых
сплавов и используют
для гибочных,
вытяжных, формовочных
работ. Такие
штампы допускают
многократное
восстановление.
Рекомендуют
их армировать
стальными
вставками в
наиболее изнашиваемых
местах.
Универсальные
штампы требуют
первоначально
больших затрат
на изготовление,
чем такого же
назначения
штампы серийного
производства;
однако они
быстро окупаются,
так как используются
для штамповки
большой номенклатуры
деталей. По
конструктивному
оформлению
они подобны
штампам серийного
производства,
однако, имеют
некоторое
отличие.
Универсальные
штампы используют
для двух видов
штамповки:
1)поэлементной
и 2)групповой
штамповке.
Сущность
метода поэлементной
штамповки
заключается
в том, что контур
детали, разделенный
на простейшие
элементы (прямые,
кривые, окружности
и др.) образуется
последовательной
штамповкой
при помощи
набора универсальных
штампов, установленных
на прессах.
Обязательным
условием эффективного
использования
штамповки
является нормализация
элементом
геометрических
форм штампуемых
деталей.
Последовательность
изготовления
детали показана
на рис.32.
Порядок
операций должен
так назначаться,
чтобы последующие
операции не
вызывали изменения
положения уже
изготовленного
элемента контура
относительно
базы.
Точность
взаимного
расположения
элементов
контура детали
при последовательной
штамповке
соответствует
12-14 квалитету.
Сущность
групповой
штамповки
состоит в том,
что, сгруппированные
по технологическим
признакам
детали (вытяжки,
пробивки, и
т.д.) обрабатываются
на групповых
штампах, которые
представляют
собой штампы
состоящие из
двух основных
частей, блока
и комплекта
быстросменных
наладок. Блок,
включающий
плиты, направляющие
элементы и
элементы крепления
штампа и зажима
наладок, закрепляется
постоянно на
прессе. Быстросменные
наладки, выполняющие
функции ориентировки
заготовки и
формирования
детали (вырубки,
гибки, вытяжки
и т.д.) можно быстро
(за несколько
минут) заменять
и таким образом
переналаживать
штамп на выполнение
другой операции.
4.5.
Обьемная штамповка.
Бесштамповая
обработка
Холодное
выдавливание.
Холодным
выдавливанием
называют процесс,
при котором
холодный металл
вытесняется
из закрытого
объема в зазор
или отверстие,
имеющееся в
инструменте.
При холодном
выдавливании
метал в закрытом
объеме находится
под большим
давлением -
2000-2500 МН/м2 (до 200-250 кг/мм2)
и в следствии
может течь в
том направлении,
в котором
сопротивление
течению найменьшее.
Возможности
получаемых
форм деталей
определяется
способами
выдавливания
(рис.34) : прямым
, обратным и
комбинированным.
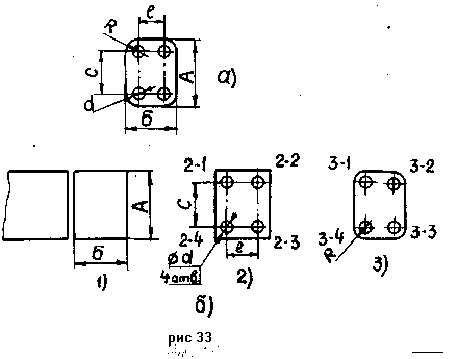
При
прямом выдавливании
металл течет
в напрввлении
движения пуансона
, при обратном
выдавливании
в противоположном
движении : в
направлении
движении и
обратном движении
пуансона.
Для
холодного
выдавливания
используют
деформируемые
алюминий и его
сплавы , медь
и ее сплавы
,никель и его
сплавы, стали
с пределом
прочности до
550-600 МН/м2.
Поперечное
сечение детали
определяется
степенью деформации
U=(Fo-F)/Fo
(24)
где
Fo и F - площадь
поперечного
сечения заготовки
и детали.
Допустимая
степень деформации
зависит от
марки и состояния
металла.
Если при допустимой
степени деформации
не получают
нужных размеров
деталей вводят
дополнительные
операции
выдавливания.
Усилие
выдавливания
определяют
по формуле :
P=q/Fn (25)
где
q-давление течения
, Fn-площадь на
которую давит
пуансон.
Давление
течения один
из важнейших
технологических
параметров
холодного
выдавливания.
Величина давления
зависит от
марки материала
и его состояния,
степени деформации,
силы трения
и др.
Силы
трения увеличивают
усилия в 2-3 раза
,поэтому стремятся
их уменьшать
до минимума.
С этой целью
используют
определенные
смазки. Так как
при холодном
выдавливании
возникают
большие давления,
то смазки легко
выдавливаются
и происходит
контакт инструмента
с несмазанной
заготовкой,
что приводит
к микросвариванию
и резкому увеличению
давления. Для
сохранения
смазки при
выдавливании
на заготовку
наносят пористый
прочнопластичный
разделяющий
слой. Для сталей
разделяющим
слоем является
- слой цинкового
фосфата, для
алюминия и его
сплавов - слой
анодных окислов.
Смазкой для
стали является
раствор хозяйственного
мыла, для алюминия
и его сплавов
- животные жиры
и минеральные
смазки на основе
парафина.
Размеры
заготовки.
Размеры поперечного
сечения заготовки
на 0,05-0,10 мм меньше
размеров матрицы;
высота заготовки
определяется
из условия
равенства
объема заготовки
объема детали
с учетом припуска
на обрезку.
H=(Vд+V)/F3
(26)
где
F3 - площадь заготовки,
Vд,V
- объем заготовки
и припуск на
обрезку.
Для
уменьшения
давления течения
используют
выдавливание
с активными
(направленное
по течению
металла)силами
трения . Это
позволяет
уменьшить
усилие (давления)выдавливания
на 15-40% соответственно
при степенях
деформации
50-70% .
При
холодном выдавливании
получают 6-11
квалитет точности
детали по поперечному
сечению, шероховатость
поверхности
с параметром
Ra=2,5-0,16 мкм, высокую
производительность
,экономию металла.
Для
выдавливания
используют
колоночные
и бесколоночные
штампы. Для
холодного
выдавливания
сталей ,медных
и никелевых
сплавов используют
специальные
прессы, для
мягких алюминевых
сплавов
(бв<10-12кг/мм2)-обычные
кривошипные
прессы.
Высадка
- процесс перераспределения
металла, при
котором на
заготовке
получают местное
утолщение
(рис.35).
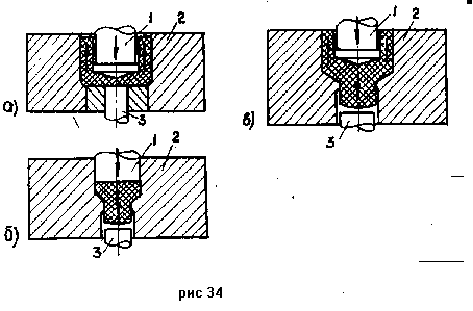
При
высадке можно
получить утолщение
на трубчатых,
плоских заготовках,
заготовках
из прудка и
т.д. Высадка
осуществляется
двумя способами
- открытым и
закрытым. При
открытом способе
металл имеет
возможность
свободно течь
в направлении,
перпендикулярном
движению пуансона;
при закрытом
способе течение
металла перпендикулярно
движению пуансона
ограничивается
инструментом.
Для
высадки используют
калиброванные
прудки. Детали
изготовляют
из стали марок
от 10 до 45 , 20Х , 40Х , 30ХГСА,
ШХ9 , ШХ15 , 12Х18Н9Т,
У10А, дюралюмина
Д1 и Д16 , латуни
Л62 , Л68 , меди и др.
Длина
высаживаемой
части заготовки
ho определяется
из условия
равенства
объемов заготовки
и высаживаемой
части детали.
При ho<2d высадка
выполняется
за один переход,
при 2,5d
ho=4*V/(пd2)
(27)
где
V - объем высаживаемой
части заготовки.
Процесс
высадки изделий
массового
производства
автоматизорован
и выполняется
на холодновысадочных
автоматах.
Изготовляют
автоматы одно-,двух-
и трехударные.
В автоматах
подача материала
, отрезка заготовки,
высадка головки
и удаление
детали выполняются
автоматически
.
Качество
деталей. Точность
поперечных
размеров деталей
в формируемых
в инструменте
в соответствует
8-11 квалитету,
при тщательном
изготовлении
инструмента
- 7 квалитету
точности. Точность
продольных
размеров
соответствует
11-13 квалитету.
Широховатость
поверхности
соответсвует
- Ra=2,5-0,32 мкм.
Прокатка.
Различают три
основные вида
прокатки :продольную,
поперечную
и поперечно-винтовую
(рис.36).

При
продольной
прокатке (рис.35а)
валки одинакового
диаметра вращаются
в противоположных
направления
с одинаковыми
скоростями.
Оси валков
паралельны,
а растояния
между валками
одинаковы.
Металл деформируется
в основном
продольном
направлении
в напрвлении
проката. При
поперечной
прокатке (рис.36,б)
валки с паралельными
осями вращаются
в одном направлении
с одинаковыми
скоростями.
Прокатываемая
заготовка
круглого поперечного
сечения по мере
уменьшения
расстояния
между валками
обжимается
по диаметру;
при этом заготовка
вытягивается
в продольном
направлении.
При поперечно-винтовой
прокатке (рис.36,в)
валки вращаются
, как и при поперечной
прокатке , с
одинаковыми
скоростями
в одну сторону.
Оси валков
наклонены одна
к другой. Заготовка
при вращении
валков подается
в направлении
биссектрисы
угла наклона
валков и одновременно
вращается. При
этой прокатке
уменьшается
поперечное
сечение заготовки.
Основной
технологический
параметр прокатки-
степень деформации:
W=(Fo-F)/Fo (28)
где
Fo и F - площади
поперечного
сечения заготовки
до и после прокатки.
Прокатка
в металургическом
производстве
используется
для получения
листов,
лент, труб, прудков
и других профилей
, используемых
в различных
отраслях
металлообрабатывающей
промышленности.
В приборостроении
используется
для получения
точных пластин,
лент, профилей,
а также для
упрочнения
лент (полос) и
листов.
При
холодной прокатке
достигают 6-9
квалитет точности
и параметр
шероховатости
Ra=1,25-0,32 мкм. При точной
(шариковой и
валковой) прокатке
в приборостроении
получают 5 квалитет
точности и
параметр
шероховатости
Ra=0,63-0,04 мкм.
Волочение.
Волочение - это
процесс притягивания
заготовки через
отверстие
меньшего поперечного
сечения, чем
сечение заготовки
(рис.37). При волочении
получают сплошные
и полые детали
постоянного
поперечного
сечения по
длине. Поперечное
сечение может
быть любым.
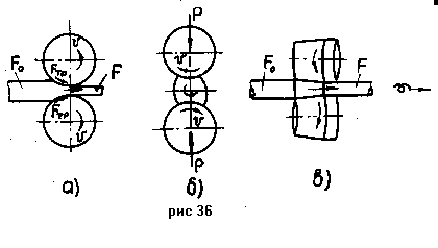
Для
волочения
используют
инструмент
- волоки (цельные
или составные),
устанавливаемые
на волочильные
станы, которые
бывают продольно-волочильные
и барабанные.
Продольно-волочильные
используют
для волочения
труб, прутков,
барабанные
- для волочения
проволоки и
других профилей
сматываемых
в бунты. На
приборостроительных
заводах используют
оба вида станов.
Основной
технологический
показатель
- степень деформации,
которая не
должна быть
более 25%
U=(Fo-F)/Fo
(31)
где
Foи F - площадь
поперечного
сечения заготовки
до и после волочения.
При
волочении
получают точность
поперечных
размеров 6-9
квалитета,
шероховатость
поверхности
соответствует
Ra=0,63-0,16 мкм.
Использование
волоченных
профилей при
производстве
деталей приборов
позволяет
уменьшить
расход металла
до 45% и снизить
трудоемкость
до 20% в сравнении
с изготовлением
деталей резаньем.
Ротационный
обжим.
Ротационный
обжим - это процесс
последовательного
обжатия по
периметру и
длине заготовки,
в результате
которого
увеличивается
длина и уменьшается
поперечное
сечение заготовки.
Этот процесс
выполняют на
ротационно-обжимных
(рис.38)
и радиально
обжимных машинах.
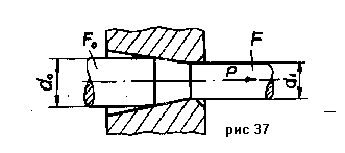
На
этих машинах
получают
удлиненные
изделия не
только круглого,
но и граненного
сечения; изделия
можно получать
диаметром от
0,15 мм до 400 мм сплошного
профиля до 600
мм трубчатого
профиля; изделия
могут быть
постоянного
сечения по
длине и ступенчатые
из металлопорошков
жаропочных
и других малопластичных
сплавов; можно
выполнять
сборочные
операции.
Степень
деформации
(формула 28) может
достигать 90% ,
так как металл
деформируется
при благоприятной
степени нагружения.
При горячей
обработке можно
деформировать
с любой степенью
деформации.
При
ротационном
обжиме достигают
точность 6-9
квалитета при
холодной обработке
и 11-13 квалитета
при горячей
обработке,
шероховатость
поверхности
- Ra=0,32-0,08 мкм при холодной
обработке и
Rz=40-20 мкм при горячей
обработке.
Горячая
объемная штамповка.
Горячую
объемную штамповку
применяют для
изготовления
сложных и
ответственных
деталей
в условиях
серийного и
массового
производства.
При горячей
штамповке
завариваются
внутренние
литейные поры,
что увеличивает
плотность
металла. Формообразование
в этом случае
обусловлено
пластичностью,
которая зависит
не только от
химсостава,
температуры,
скорости деформации,
но и от схемы
воздействия
внешних сил.
Наряду с высокой
пластичностью
при обработке
давлением
стремятся
получить возможно
меньшее сопротивление
деформированию.
Показателем
технологических
свойств в этом
случае является
ковкость. Ковкость
увеличивается
с повышением
пластичности
и уменьшением
сопротивления
деформированию.
Нагрев металла
увеличивает
ковкость.
Объемная
штамповка
заключается
в формоизменении
заготовки в
штампах под
действием
внешних сил.
Полость, формирующая
в штампе заготовку,
называется
ручьем. Отштампованная
заготовка
называется
штампованной
поковкой.
Последовательность
технологического
процесса изготовления
штампованной
поковки: резка
исходного
металла на
заготовки,
нагрев заготовки,
штамповка,
обрезка заусенца,
охлаждение
и термообработка
поковок, очистка
от окалины,
правка и контроль.
Исходным
металлом для
объемной штамповки
являются прокатные
или прессованные
прутки чаще
из углеродистой,
низколегированной
стали, а также
из высоколегированной
стали и сплавов,
жаропрочность
сплавов, алюминиевых,
медных магниевых
и титановых
деформированных
сплавов.
Основные
виды объемной
штамповки. Виды
объемной штамповки
подразделяют
в зависимости
от применяемого
оборудования,
на котором она
производится,
типа штампа
и других факторов.
В
зависимости
от оборудования
объемная штамповка
подразделяется
на следующие
виды: штамповку
на молотах,
штамповку на
горизонтально-ковочных
машинах (ГКМ),
штамповку на
кривошипных
горячештамповочных
прессах (КГШП),
штамповку на
специальных
машинах
(вертикально-ковочных,
ротационно-обжимных,
радиально-обжимных,электровысадочных),
штамповку на
фрикционных
и гидравлических
прессах.
Указанное
обороудование
принципиально
отличается
друг от друга
скоростью
деформирования
металла. Наибольшая
скорость (до
7м/сек) у молота,
наименьшая
- у гидравлического
пресса (десятки
мм в мин.). На молоте
деформирование
производится
за несколько
ударов, на прессе
за одно нажатие
на каждом ручье.
В
зависимости
от типа штампа
различают:
штамповку в
открытых штампах,
штамповку в
закрытых штампах,
штамповку
выдавливанием.
Тип штампа
определяет
условие течения
металла и поэтому
этот вид подразделения
штамповки
является основным.
Штамповку
выдавливанием
применяют
только на прессах,
штамповку в
открытых и
закрытых штампах
можно выполнять
на любом виде
оборудования.
В зависимости
от количества
ручьев в штампе
различают
штамповку в
одноручьевых
штампах и штамповку
в многоручьевых
штампах.
Далее
рассмотрим
содержание
и особенности
выполнения
основных операций
горячей объемной
штамповки.
Расчет
массы и размеров
исходной заготовки.
Масса
исходной заготовки
складывается
из массы
поковки и массы
отходов:
Qзаг=Qп+Qз+Qуг+Qкл
Qп
- масса поковки
определяется
умножением
объема поковки
на плотность;
объем поковки
рассчитывают
по номинальным
горизонтальным
размерам и
номинальным
вертикальным
размерам поковки
плюс половина
положительного
допуска. массу
заусенца Qз
определяют
по формуле:
Qз=(0,75-0,8)*Sзк*pn*p
где
Sзк
- площадь поперечного
сечения заусенечной
канавки, pn - периметр
поковки в плоскости
разъема. Массу
угара Qуг берут
в зависимости
от способа
нагрева: при
нагреве в мазутной
печи масса
угара составляет
2-3% от массы заготовки,
в газовой печи
- 1,5-2%, при электронагреве
- 0,5-1%.
Qкл
- масса клещевины
- участка для
захвата заготовки
клещами, определяет
в зависимости
от диаметра
заготовки или
от тянутой под
клещевину части
заготовки.
Расчет
размеров заготовки.
Размеры заготовки
определяют
в зависимости
от способа
штамповки. При
штамповке
поперек оси
заготовки
(плашмя) длина
заготовки равна
lзаг=ln*K
где
ln -
длина поковки;
К - коэффициент,
зависящий от
вида штамповочного
ручья, изменяется
в пределах
1,02-1,3.
Площадь
поперечного
сечения заготовки
равна:
Sзаг=Vзаг/lзаг
где
Vзаг
- объем заготовки.
При
штамповке вдоль
оси, т.е. при наличии
осадки, соотношение
высоты заготовки
к диаметру
должно удовлетворять
соотношению
1,27
Обычно
Hзаг/Dзаг=2
Деаметр
поперечного
сечения заготовки:
Dзаг=((4*Vзаг)/пK)1/3
После
определения
Dзаг
выбирают ближайший
большой размер
по ГОСТу и вычисляю
скорректированную
длину заготовки.
Резка
исходного
материала на
заготовки
заключается
в подготовке
металла к резке
и непосредственно
резке.
Подготовка
металла к резке
заключается
в зачистке на
поверхности
проката различных
местных дефектов
(плен, трещин
и т.п.) и правки
изогнутых
исходных прутков.
Местные дефекты
удаляют механическим
способом
(пневмозубилом,
абразивным
кругом, на
металлорежущих
станках или
огневым способом
(выплавкой
сварочным
электродом)).
Правку проката
производят
на кривошипных
или гидравлических
прессах.
Резку
исходного
пруткового
металла производят
на прес-ножницах,
кривошипных
прессах, пилах,
абразивными
кругами, в
хладноломах,
газовой резкой
и другими средствами.
Нагрев
заготовок.
Термомеханический
режим ковки.
При
определенных
температурах
металлы обладают
высокой ковкостью
- высокой пластичностью
и низким сопротивлением
деформированию
. Нагрев должен
обеспечивать
требуемую
температуру
заготовка,
равномерное
распределение
ее по сечению,
отсуствие
трещин, минимальное
окисление и
обезуглероживание
поверхности.
Температура
штамповки имеет
верхний и нижний
пределы, между
которыми лежит
температурный
интервал штамповки.
Нижняя граница
интервала для
железоуглеродистых
сплавов (сталей)
не должна быть
ниже температуры
фазовых превращений
(Ас3); верхняя
граница должна
быть ниже температуры
пережога, при
которой возникают
межкристалитные
окислы.
С увеличением
температуры,
как известро,
наблюдается
рост зерен
(рис.6) и металл
получает
крупнозернистую
структуру.
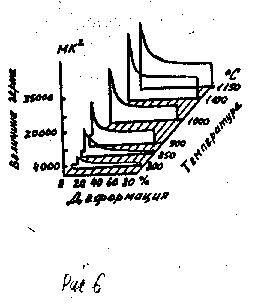
При
правильно
выбранном
температурном
интервале
штамповки путем
пластикой
деформации
можно измельчить
крупное зерно,
возникшее в
металле при
нагреве. С
увеличением
скорости нагрева
меньше окисление
и обезуглероживание
и поэтому экономичнее
нагрев. Однако
при слишком
быстром нагреве
в результате
значительного
температурного
градиента по
сечению заготовки
в металле могут
возникать
термические
напряжения,
которые в некоторых
случаях приводят
к образованию
микро- и макротрещин.
Скорость
нагрева зависит
от типа печи,
обрабатываемого
металла, вида
укладки заготовок
и других факторов.
Температурный
интервал и
скорость нагрева
устанавливают
на основе комплексов
исследований
и поэтому обычно
определяют
по таблицам
в справочниках.
Нагрев
высоколегировнной
стали и сплавов
из-за их низкой
теплопроводности
производят
с предосторожностями,
основная цель
которых
- снятие остаточных
напряжений
и предупреждение
образования
термических
трещин. Поэтому
перед нагревом
заготовок под
штамповку их
подвергают
предварительному
отжиму, а иногда
промежуточному
отжигу. Температурный
интервал штамповки
высоколегированных
сталей и сплавов
узкий, что требует
для формообразования
дополнительных
переходов. Для
повышения
равномерности
деформации
при штамповке
применяют
подогрев штампов
до температуры
200-400 С. При нагреве
необходимо
предохранять
заготовки от
окисления. Для
этого применяют
стеклянные
смазки или газ
аргон.
Нагрев
осуществляют
в мазутных,
газовых, электрических
печах без защитной
и с защитной
против окисления
атмосферой,
а также в растворах
солей.
Штамповка.
Штамповка
в открытых
штампах
характерна
тем, что штамп
в процессе
деформирования
остается открытым,
а зазор между
верхним и нижним
штампом в процессе
деформирования
переменным.
В этот зазор
вытекает металл
из рабочей
полости, образуя
заусениц. Заусениц
закрывает выход
из полости
штампа и этим
способствует
заполению всей
полости штампа
при дальнейшем
сближении
штампов. Заусениц
вытесняется
и избыток металла
из рабочей
полости. Поэтому
заготовку можно
нарезать не
точно, с избытком
металла. Штамповка
в открытых
штампах производится
на молотах,
кривошипных
горячештамповочных
прессах, гидравлических
прессах, фрикционных
прессах и других
машинах.
Штамповка
в закрытых
штампах
характерна
тем, что штамп
в процессе
деформирования
остается закрытым,
а зазор между
подвижной и
неподвижной
частями остается
постоянным
и небольшим.
При избытке
деформируемого
металла, последний
вытекая в зазор,
создает торцевой
заусенец и
вызывает большие
напряжения
в штампе и износ.
Штамповку в
закрытых штампах
выполняют на
ГКМ, КГШП, молотах.
Штамповка
в штампах для
выдавливания
характерна
тем, что штамп
имеет глубокую
полость, которая
заполняется
выдавливанием.
Штамповка
выдавливанием
производится
на гидропрессах,
КГШП, ГКМ. Этот
процесс рекомендуют
для штамповки
малопластичных
сталей и сплавов
(например
высоколегированных
сталей и сплавов).
Возможности
формообразования.
При штамповке
в открытых и
закрытых штампах
можно на штампованных
поковках получить
различной формы
выступы, ребра,
углубления,
отвестия (с
перемычками)
за один или
несколько
ударов.
При
выдавливании
и доштамповке
можно получить
заданную форму
деталей типа
“стакан”, стержень
с головкой и
трубка с фланцем
за один - три
перехода в
зависимости
от K=F/f (F - площадь
проекции поковки
на плоскость
разъема, f - площадь
сечения деформированной
части заготовки).
В зависимости
от условий
деформирования
относительное
обжатие w=100*(F-f)/F
может быть
равно 15-95 %. Следует
обращать внимание
при выдавливании
на скорость
истечения
W=(F/f)*V (V - скорость
движения ползуна
пресса) для
предупреждения
брака по наружным
трещинам.
Высоколегированную
сталь и специальные
сплавы штампуют
при меньших
скоростях, чем
низколегированную
и углеродистую.
Выбор
оборудования
для штамповки.
При Штамповке
на молотах
выбор молота
осуществляется
по массе падающих
частей G для
штамповки в
открытых штампах:
G=10*Fn
[кг]
где
Fn -
площадь проекции
поковки в плане.
При
штамповке на
прессах выбор
пресса осуществляют
по рабочему
усилию , определенному
по формуле в
зависимости
от формы детали
в плане и типа
пресса (КГШП,
фрикционный
и др.).
Обрезка
заусенца и
прошивка отверствий.
Заусенец образуется
при горячей
штамповке в
открытых штампах.
Этот заусенец
обрезают на
обрезных, кривошипных
и иногда гидравлических
прессах. Обрезка
заусенца
подразделяется
на горячую и
холодную. Крупные
и средние по
массе поковки,
штампуемые
на молотах с
массой падающих
частей более
1 т, имеют относительно
толстый заусенец,
который легко
обрезать в
горячем состоянии,
непосредственно
после штамповки.
Обрезной пресс
в этом случае
находится рядом
со штамповочной
машиной. Мелкие
поковки с тонкими
заусенцами
легко обрезаются
в холодном
состоянии; эту
обрезку выполняют
в другом (не
штамповочном)
отделении;
производительность
холодной обрезки
выше, чем горячей.
Число обрезных
прессов для
холодной обрезки
меньше, чем
число штамповочных
машин (прессов,
молотов).
Схема
процесса обрезки
и штампа представлена
на рис. 42. Поковка
3 укладывается
в матрицу 4 и
движение пуансона
1 проталкивается
вниз через нее.
При этом заусенец
срезается.
Режущим элементом
здесь является
матрица,
а пуансон - подающим,
проталкивающим
элементом.
Матрица укрепляется
в нижней плите
7, а пуансон - в
пуансонодержателе.
При обратном
ходе с пуансона
6 снимается
заусенец съемником
5.
Зачистку
поковок обычно
производят
с частичной
зачисткой
штамповочного
уклона. Зазор
между пуансоном
и матрицей
принимают в
зависимости
от формы поковок.
Прошивка
отверствий.
Если в поковке
должно быть
отверствие,
то при штамповке
делают наметки
(углубления)
с одной или
двух сторон
с оставлением
пеленок 2 (рис.41).
Эту пленку
прошивают
(обычно в горячем
состоянии)
после штамповки,
анологично
тому, как обрезают
заусенец. При
этом применяют
те же обрезные
прессы. Схема
прошивки с
одновременной
обрезкой заусенца
показана на
рис.41. Здесь
представлен
совмещенный
штамп, где 1 -
пуансон обрезки,2
- пленка, подлежащая
удалению прошивкой,
3 - поковка, 4 - матрица,
5 - выталкиватель,
6 - пуансон прошивки,
7 - основание
штампа.
В производстве
чаще прошивка
и обрезка заусенца
выполняется
как отдельная
операция.
Усилие
обрезки и прошивка
определяют
по формуле
P=(1,5-1,8)бв*Sф*Pср
где
бв
- предел прочности
на срез при
температуре
обрезки-прошивки,
Sср,Pср
- соответственно
толщина и периметр
среза.
Под
толщиной среза
понимают толщину
пленки или
заусенца с
учетом закругления
и прибавления
величины
положительного
отклонения
допуска на
размер поковки
по высоте.
Охлаждение
и термообработка.
Режим охлаждения
поковок после
штамповки имеет
такое же значение,
как и режим
нагрева. Скорость
охлаждения
влияет на величину
термических
напряжений,
которые в случае
быстрого охлаждения
приводят обычно
к наружным
трещинам. А при
неодновременном
по объему металла
переходе через
критический
интервал температур
- к структурным
напряжениям,
которые могут
сумироваться
с температурными.
Это может привести
к микро- и макротрещинам.
При охлаждении
некоторых марок
сталей могут
образовываться
флокены, белые
пятна; они не
имеют определенной
ориентировки
в связи с деформациями
и не связанные
с ликвационными
зонами. Белые
пятна внешне
похожи на флокены,
но располагаются
исключительно
в ликвационных
участках и
ориентируются
в направлении
деформации.
На появление
флокенов и
белых пятен
оказывает
большое влияние
водород, растворенный
при выплавке
металла. Для
уменьшения
влияния водорода
на образование
флокенов и
белых пятен
применяют
соответствующий
режим охлаждения.
Охлаждения
в зависимости
от марки материала
и размеров
поковок производятся:
на воздухе
(одиночных или
штабелями), в
ящиках с песком,
золой или окалиной,
в термостатах
и неотапливаемых
колодцах, в
подогреваемых
колодцах, вместе
с печью.
После
штамповки для
снятия остаточных
напряжений,
предохранения
от образования
флокенов и
размельчения
зерна (Штамповкой
после дополнительного
нагрева) применяют
отжиг, а для
выравнивания
структуры по
сечению (путем
диффузии легирующих
элементов)
применяют
гомогенизационный
отжиг поковок.
Очистка
поковок от
окалины.
После штамповки
поковки имеют
на поверхности
слой окислов,
который ухудшает
качество поверхности
и препятствует
последующей
механообработке.
Для очистки
поковок применяют
травление,
галтовку и
дробеметную
очистку.
Травление
применяют для
очистки от
окислов сложных
поковок в растворе
кислоты. После
погружения
поковок в раствор
кислоты. После
погружения
поковок в раствор
кислоты (или
кислот), кислота
проходит через
слой окалины
и вступает в
реакцию с металлом,
образуя рыхлую
пленку, которая
имеет большую
толщину, чем
толщина окислившегося
металла. Это
способствует
разрушению
окислов. Для
сталей применяют
раствор серной
и соляной кислот
с присадкой
КС; для никелевых
сталей - такой
же раствор
кислот, но более
концентрированный;
для алюминеевых
сплавов - раствор
щелочи. Затем
для сталей
производят
промывку в
щелочном растворе
и воде, для
алюминиевых
сплавов - в растворе
азотной кислоты
и воде.
Очистка
поковок травлением
это самый
качественный
и самый дорогой
способ очистки.
Галтовку
применяют для
очистки мелких
и средних по
массе поковок
простой формы
(короткие валики,
шестерни).
Загруженные
во вращающийся
вокруг горизонтальной
оси барабан
поковки (иногда
с ними и шары)
удаются и окислы
скалываются.
Недостаток
способа - большой
шум.
Дробеметную
очистку применяют
для очистки
от окислов
мелких и средних
поковок сложной
формы. В этом
случае на очищаемые
поверхности
направляют
движущуюся
с большой скоростью
чугунную дробь,
которая при
ударе о поверхность
поковки скалывает
окислы. Поковки
должны поворачиваться
для очистки
нужных поверхностей.
Качество поверхности
получают хорошее.
Недостатком
способа является
возможность
закрытия трещин,
которые в дальнейшем
трудно обнаружить.
Правка
поковок.
Штампованные
поковки могут
искривляться
в процессе
удаления из
ручья штампа,
обрезке заусенца,
прошивке отверстий
и при их транспортировке.
У изогнутых
поковок при
механообработке
может быть в
некоторых
местах недостаточный
припуск, а в
других - избыточный
припуск.
Правку
производят
в горячем и
холодном состоянии,
более часто
используют
холодную правку.
Горячую
правку после
обрезки заусенца
обычно применяют
для простых
поковок из
высоколегированной
или высокоуглеродистой
стали, при холодной
правке в которых
возможно
возникновение
трещин. Такую
правку выполняют
обычно в окончательном
ручье штампа.
Для
сложных поковок
или поковок
с отверстием
горячую правку
производят
в специальном
штампе.
Холодной
правке подвергают
сложные мелкие
и средние по
массе поковки.
При холодной
правке невозможно
получить из-за
упругих деформаций
при разгрузке
абсолютно не
искривленные
поковки.
Калибровку
поковок
выполняют для
повышения
точности размеров,
улучшение
качества поверхности
отдельных
участков или
всей поковки,
а также снижения
колебания массы
поковки. Калибровку
применяют в
массовом и
крупносерийном
производстве.
Различают
плоскостную
и объемную
калибровку.
Плоскостная
калибровка
производится
в холодном
состоянии на
кривошипно-коленных
чеканочных
прессах для
получения
точных вертикальных
размеров на
одном или нескольких
участках поковки.
Объемную
калибровку
применяют для
увеличения
точности размеров
в разных направлениях,
а при выдавливании
некоторого
излишка металла
в заусенец - и
для получения
точной массы.
Точность
объемной калибровки
ниже, чем плоскостной.
Иногда применяют
комбинированную
калибровку
- сначала объемную,
а затем плоскостную.
Усилие
плоскостной
калибровки
для круглых
поковок:
P=бs*(1+(m/3)*(d/h))*(п*d2)/4
где
d - диаметр поковки;
h - высота; бs
- напряжение
пластического
течения; m - коэффициент
контактного
трения.
Виды
брака. Контроль
качества штампованных
поковок.
Брак может быть
на любом этапе
технологического
процесса. Наиболее
характерны
следующие виды
брака: вмятины,
недоштамповка
выступов, углов,
закруглений
и ребер, смещение
одной половины
поковки относительно
другой в плоскости
разъема, зажимы,
повышенная
кривизна, отклонение
допуска от
заданного,
утяжка, брак
по термообработке
и очистке от
окалины.
Вмятины
на поковках
могут быть в
результате
заштамповки
окалины и
механических
повреждений
при удалении
из штампа и
переброске
горячих поковок.
Недоштамповка
возникает при
недостаточном
нагреве заготовки
и количестве
ударов или
массе падающих
частей молота.
Смещение плоскости
разъема возникает
при износе
направляющих
машины или
штампа. Зажимы
возникают из-за
резких ударов,
несоответствия
чернового ручья
штампа чистовому
ручью и из-за
Эксцентричной
укладки заготовки
в штамповочном
ручье. Повышенная
кривезна возникает
при неравномерном
охлаждении
поковки или
из-за деформации
при переброске
горячих штампованных
поковок. Повышенные
допуски и размеры
возникают при
слишком большом
износе штампов
или при недоштамповке.
При штамповке
на КГШП возможно
также незаполнение
штампа, повышенная
кривизна при
выталкивании,
след от выталкивателя,
зажим типа
“прострел”.
Из-за неправильного
течения металла
при штамповке
выдавливанием
возникает
“утяжка”, “прострел”,
наружные и
внутренние
сколы. Брак при
термообработке
может быть
такой: обезуглероживание,
отклонение
от заданной
твердости и
микроструктуры.
Контроль
штампованных
поковок производят
на всех этапах
технологического
процесса.
С этой целью
выполняют
контроль химического
состава, проверяют
размеры поковок
и визуально
контролируют
поверхностные
дефекты, контролируют
режимы нагрева
и термообработки,
твердость
поковок. Внешние
дефекты, трещины,
зажимы, прострелы
для ответственных
деталей конструируют
магнитным и
люминисцентным
методом, а метод
вихревых токов
позволяет
конторолировать
химический
состав, твердость,
трещины, структурное
состояние,
внутренние
напряжения
в поковках и
размеры их
сечения. Внутренние
дефекты в поковках
определяют
ультразвуковым
методом и
просвечиванием
лучами Рентгена.
Технологичность
поковок.
Чертеж
поковки составляют
по чертежу
детали. Правильно
разработанный
чертеж поковки
позволяет
учесть особенности
течения металла
в штампе, обеспечивает
возможность
ее рационального
изготовления.
Технологичной
считается
паковка в которой
правильно
выбрана поверхность
разъема; назначены
шероховатость
поверхности,
допуски, припуски
и напуски; определены
штамповочные
уклоны и линия
разъема; определены
радиусы скруглений;
назначены
наметки под
прошивку и
определены
размеры пленки
под прошивку;
установлено
направление
волокон в поковке,
толщина волокна
и ребер и другие
вопросы.
Поверхность
разъема
- это поверхность,
по которой
соприкасаются
части штампа.
Обычно за поверхность
разъема принимают
плоскость.
Плоскость
разъема должна
совпадать с
плоскостью
двух наибольших
размеров поковки
и обеспечивать
свободное
удаление штампованной
поковки из
штампа. Если
поковка не
симметрична,
то более глубокие
полости располагают
в верхней части
штампа, т.к. вверх
металл течет
лучше. Правильно
выбранная
плоскость
разъема обеспечивает
возможность
контроля сдвига
между верхним
и нижним штампом
по внешнему
виду поковки
после обрезки
заусенца. На
рис. 44а плоскость
разъема выбрана
правильно и
позволяет
обнаружить
сдвиг при обрезке
заусенца, на
рис.44б - плоскость
разъема выбрана
не правильно,
т.к. не позволяет
обнаружить
сдвиг, на рис.44в
- возможное
расположение
плоскости
разъема при
односторонней
бобышке.
Широховатость
поверхности
обычно при
горячей штамповке
получают в
пределах Rz=160-40
мкм, а точность
в пределах
12-16 квалитета,
болеевысокие
качественные
показатели
относятся к
штамповке в
закрытых штампах.
Допуски учитывают
изменения
размеров при
недоштамповке
по высоте и
износ штампов.
При калибровке
достигают
8-12 квалитет
точности,
широховатость
- Ra=2,5-0,32 мкм. Если
заготовка
детали должна
иметь более
высокие качественные
показатели
(точность и
шероховатость
поверхности),
то эти показатели
достигают
механической
обработкой
путем снятия
припуска со
штампованной
поковки. Припуски
и допуски при
горячей объемной
штамповке
назначают по
ГОСТ 7505-74. Практически
величина припуска
составляет
0,5-6 мм и ориентировочно
может быть
определена
по эмпирической
формуле
П=0,4+0,01h+0,0015l
где
h и l - наибольшие
размеры поковки
по высоте и в
плоскости
разъема.
Стандартом
предусмотрено
разделение
поковок на три
основные группы
в зависимости
от предъявляемых
к ним требованиям
по точности.
Наиболее жесткие
требования
относятся к
поковкам первой
группы; ГОСТ
7505-74 также регламентируем
напуски. К напускам
относят некоторый
объем металла
на поковке для
облегчения
изготовления
детали. Напуск
можно удалить
механической
обработкой.
При диаметре
отверстия менее
30мм устанавливают
напуск, т.е. не
штампуют отверстие
из-за малой
стойкости
штампа; к напускам
относят также
напуски для
штамповочных
уклонов и радиусов
скругления.
Уклоны.
Штамповочные
уклоны назначают
для легкого
и быстрого
удаления поковки,
а также для
облегчения
заполнения
штампа. Различают
наружные и
внутренние
уклоны. Величина
уклона зависит
от наличия
выталкивателей
у оборудования
и относительной
высоты поковки.
При отсуствии
выталкивателей
(молоты)
наружные уклоны
равны 5-7°, внутренние-7-10°;
при наличии
выталкивателей
(КГШП, ГКМ, гидропрессы)
наружные уклоны
равны 3-5°, внутренние-
5-7°.
Для
относительно
более высоких
поковок (отношение
глубины полости
к ширине
принимают
большие величины
уклонов. Выбор
уклонов производят
по таблицам
справочников.
Толщина
полотна и ребер
определяется
условиями
деформирования,
чем меньше
толщина, тем
больше напряжение
течения и меньше
стойкость
инстумента.
Толщину
полотна назначают
в зависимости
от площади
штамповочной
заготовки в
плане и формы
сечения. При
увеличении
площади от 20
до 2000 см2 толщина
увеличивается
от 1,5 до 12 мм.
Высота,
толщина ребра
и расстояние
между ребрами
зависят от
формы поперечного
сечения штампуемого
изделия. В открытых
сечениях толщина
ребра зависит
только от его
высоты, в закрытых
двутавровых
сечениях толщина
ребра определяется
высотой ребер
и расстоянием
между ними.
Ребро хорошо
заполняется
при отношении
его высоты к
толщине не
более 10. Для ребер
небольшой
высоты (менее
10 мм) и малой
толщины (менее
2 мм) из-за трудности
заполнения
полости (возникают
большие давления)
толщину ребра
назначают 2-4
меньше высоты.
Наименьшее
расстояние
между ребрами
зависит от
высоты. (При
высоких ребрах
и небольшом
расстоянии
между ними
выступ штампа,
формирующий
эти ребра быстро
изнашивается).
Наименьшее
расстояние
для высоты
ребер 5-70 мм равно
10-80 мм; наибольшее
для той же высоты
соответственно
-(30-20)S, S-толщина
полотна.
Радиус
закругления
на поковках
назначают, как
и штамповочные
уклоны, для
облегчения
заполнения
штампа и для
обеспечения
удовлетворительной
стойкости
инструмента.
Радиусы закругления
назначают по
ГОСТ 7505-74 в зависимости
от относительной
глубины полости
и абсолютной
глубины полости.
Различают
наружные и
внутренние
радиусы, внутренние
радиусы примерно
в три раза больше
наружных R=3r. После
назначения
внутренних
радиусов их
надо согласовать
с припуском
таким образом,
чтобы величина
припуска была
не меньше, чем
на прилегающих
участках.
Наметки
и пленки под
прошивку. При
штамповке
невозможно
получить сквозное
отверстие.
Для облегчения
последующей
прошивки и
экономии металла
в поковке делают
наметку с
перемычкой-пленкой
небольшой
толщины.
В
зависимости
от формы и размеров
отверстий
поковок применяют
пять типов
наметок: плоскую,
с раскосом, с
магазином, с
карманом, глухую.
Плоскую
наметку применяют
при 50‹
d <80 мм, а при наличии
предварительного
штамповочного
ручья применяют
при 30
При
150 >d>80 мм и отсуствии
предварительного
ручья и всегда
для наметок
в предварительном
ручье примеряют
наметки с раскосом,
толщина пленки
Smax=1,35S, Smin=0,65S, S=0,1d.
Наметку
с магазином
применяют при
150>d>55 мм и наличии
предварительного
ручья, в котором
делается наметка
с расскосом.
Наметку
с карманом
применяют в
окончательном
ручье при D>155 мм
и низких поковках
со сравнительно
малым отношением
высоты к диаметру
H/D<0,07. Толщина
S=0,4(d)1/2.
Глухую
наметку применяют
только с целью
экономии металла,
когда наметку
получают с
относительно
большой глубиной
и большим радиусом
R. Отверстие
получают в
дальнейшем
сверлением.
4.6.
Высокоэнергетические
импульсные
методы штамповки.
Применение
высокоэнергетических
методов штамповки
позволяет
экономично
изготовлять
абаботкой
давлением такие
детали и заготовки,
которых ранее
невозможно
было изготовлять
или для изготовления
которых ранее
требовалось
дорогостоящее
мощное оборудование.
Эти методы
деформирования
используют
в условиях
мелкосерийного
и серийного
производства,
как для листовой
так и для объемной
штамповки.
Штамповка
листового
металла.
Гидровзрывная
штамповка. При
гидровзрывном
формоизменении
энергии, образующаяся
при взрыве,
передается
штампуемой
заготовки через
ударную волну,
давление и
сопутствующий
ей гидропоток.
В качестве
среды, передающей
энергию взрыва,
используют
жидкость, сыпучую,
вязкую или
твердую среду.
Деформируемые
листовые или
трубчатые
заготовки можно
подвергать
различным
операциям:
резке, вытяжке,
рельефной
формовке, раздаче,
обжиму, отбортовке
и др.. Причем
возможно
формоизменение
с нагревом
заготовки с
помощью передающей
среды (песком).
Для
взрывной штамповки
используют
бризантные
и метательные
взрывчатые
вещества. Взрыв
может производиться
в стационарном
или съемном
(разовом) бассейне.
Для формоизменения
заготовки в
зависимости
от выполняемой
операции чаще
всего используют
только матрицу
или пуансон;
для вытяжки,
рельефной
формовки, отбортовки
- матрицу, для
обжима - пуансон.
При вытяжке
обычно получают
за один переход
меньшую предельную
величину коэффициента
вытяжки, чем
в обычных условиях:
материал
|
сплав
ОТ4
|
ст.3
|
2Х13
|
12Х18НIОТ
|
08
|
АМг6-М
|
m
|
0,68
|
0,65
|
0,64
|
0,63
|
0,63
|
0,61
|
Матрицы
для вытяжки
могут быть
металлические
цельнолитые
или составные,
железобетонные,
из льда.
Точность
деталей изготовленных
взрывной штамповкой
по сравнению
с обычной вытяжкой
значительно
выше.
Электрогидравлическая
штамповка
по сравнению
со взрывной
имеет ряд
преимуществ:
а) возможность
применения
в обычных условиях,
б)простота
дозирования
энергии, в)возможность
осуществления
серии разрядов,
следующих друг
за другом, г)
легкость
автоматизации
процесса. Однако
установки для
электрогидравлической
штамповки
дороже установок
для штамповки
взрывом, а размеры
и стоимость
электрогидравлических
установок
ограничивают
энергетические
возможности
метода.
Сущность
метода. При
высоковольтном
электрическом
разряде между
электродами,
помещенными
в жидкость,
возникает
токопроводящий
искровой канал,
мгновенное
расширение
которого приводит
к возникновению
в жидкости
ударной волны.
Деформация
заготовки
происходит,
как и при гидровзрывной
штамповке, под
действием
ударной волны,
давление и
сопутствующего
гидропотока.
Более эффективному
использованию
энергии разряда
по сравнению
с открытой
емкостью для
формоизменения
способствует
размещение
рабочих электродов
в замкнутой
камере или
внутри трубчатой
заготовки,
закрытой с двух
сторон крышками.
Рассматриваемым
методом выполняют
операции вытяжки
деталей из
плоских заготовок,
отбортовку,
раздачу трубчатых
заготтовок,
оформление
сложного контура
на листовых
и трубчатых
заготовках,
калибровку,
пробивку и
некоторые
другие операции.
Этим методом
получают детали
из цветных
металлов, стали
и высокопрочных
сплавов. Толщина
штампуемых
деталей <4-10 мм,
а габариты
большинства
деталей в плане
достигают
1200*2000 мм.
Инструмент.
Обычно для
электрогидравлической
штамповки
используют
матрицы, которые
изготовляют
из стали (иногда
и других
материалов-цинковых,
алюминевых
сплавов, литьевых
эпоксидных
смол). Основной
рабочий инструмент
- электроды,
которые изготовляют
из стали, латуни,
однако найбольшей
электроэрозийной
стойкостью
обладает
металлокерамическая
композиция
на основе вольфрама
ВНМ-3-2.
Для
электрогидравлической
штамповки
используют
отечественные
установки
“Удар 12м” и “
Удар 20” , ” Удар
20с”, “ Удар 150”,
“Удар-II”, позволяющие
изготовлять
детали размером
от 400*400 мм до 2000*1200 мм
с толщиной
стенки от 3 до
10 мм или соответственно
диаметром
заготовки от
300 мм до 1500 мм с
толщиной стенки
от 3 до 10 мм. Запасаемая
энергия указанных
установок
изменяется
соответственно
от 10 до 160 Кдж.
Штамповка
импульсным
магнитным
полем.
Основные преимущества
метода в сравнении
с взрывной и
электрогидравлической
штамповкой
: а)большая скорость
формоизменения
заготовки и
высокая призводительность,
б) возможность
точнее регулировать
параметры
процесса, в)
возможность
широко механизировать
и автоматизировать
операции процесса,
г) возможность
легкого встраивания
устоновки
импульсной
магнитной
штамповки в
автоматические
линии.
Сущность
метода.При
помещении
заготовки в
импульсное
магнитное поле,
создавемое
с помощью разряда
энергии, накопленной
в конденсаторной
батарее, на
катушку индуктивности
(рабочий индуктр),
в заготовке
индуцируются
вихревые токи,
взаимодействие
которых с токами
индуктора
приводит к
возникновению
усилий, деформирующих
заготовку.
Этот
метод штамповки
применяют в
основном для
таких операций,
как обжим и
раздача трубчатых
заготовок,
калибровка
трубчатых
изделий, получение
на деталях
различных
рифлений, штамповка
деталей из
плоских заготовок,
пробивка отверствий
в плоских и
трубчатых
деталях из
различных
металлов и
сплавов, сборка.
Преимущественное
распостранение
имеет обработка
металлов и
сплавов, обладающих
высокой
электропроводностью.
Деформирование
заготовок из
материалов
с недостаточно
высокой электропроводностью
(углеродистых
и нержавеющих
сталей) осуществляется
через передающую
среду или через
так называемый
“спутник”-
промежуточный
материал с
высокой
электропроводностью,
помещаемый
на обрабатываемую
заготовку.
Максимальная
толщина стенки
детали составляет
1,5-2 мм для стали,
1,7-2,5 мм -для латуни
и 2-3 мм - для алюминевых
и медных сплавов.
Инструмент.
Рабочим инструментом
в этом случае
является индуктор
и оправка (матрица).
В установках
магнитно-импульсного
деформирования
используют
индукторы
однократного
и многократного
использования:
первые применяют
в условиях
единичного
производства,
вторые-в условиях
серийного
производства.
Для увеличения
прочности
индукторов
и придания им
универсальности
служат концентраторы
магнитного
поля.
Оборудование.
Для магнитн-импульсной
штамповки
используют
отечественные
магнитно-импульсные
установки и
установки
изготовляемые
в ГДР , ЧССР ,
которые обладают
максимальной
запасаемой
энергией от
4,1 до 22,5 Кдж.
Объемная
штамповка.
Высокоскоростная
объемная штамповка
позволяет
максимально
приблизить
форму и размеры
поковки к форме
и размерам
деталей, что
обеспечивает
экономию металла
и сводит к минимуму
механическую
обработку. Этим
методом изготовляют
поковки с тонкими
стенками из
алюминия, меди,
различных
сталей и сплавов.
Поковки получают
с мелкозернистой
структурой
и высокими
механическими
свойствами;
значительно
улучшается
структура и
свойства сплавов
на основе молибдена,
никеля и титана.
Улучшение
структуры и
увеличение
прочности в
несколько раз
увеличивает
стойкость
деталей (шестерен
в 2-10 раз).
Высокоскоростная
объемная штамповка
выполняется
со скоростями
движения инструмента
9-18 м/сек для изготовления
поковок методом
горячего и
холодного
выдавливания.
Экономически
целесообразно
применять
высокоскоростную
штамповку в
условиях
крупносерийного
производства
для поковок,
которые могут
быть получены
на обычном
горячештамповочном
оборудовании.
Для
нагрева сталей,
жаропрочных
сплавов, титана
рекомендуют
индукционные
печи или печи
с инертной
атмосферой,
алюминевых
сплавов - печи
с принудительной
циркуляцией
воздуха. Во
всех случаях
рекомендуют
безокислительный
нагрев.
Перед
началом работы
пуансон и матрицу
следует подогреть
до 180 град.С и
поддерживать
температуру
в этом пределе
в процесе штамповки
во избежание
перегрева и
потере стойкости
штампа.
Смазки
выбирают с
учетом штампуемого
материала.
Суспензию
графита в воде
применяют в
качестве смазки
при штамповке
большинства
металлов; при
штамповке
труднодеформируемых
металлов
предпочтительнее
суспензия
графита в масле.
При тяжелых
условиях работы
применяют
дисульфид
молибдена (при
температуре
штамповки <
650град.С).
Штампы
для высокоскоростной
штамповки
изготовляют
из сталей 4Х5В2ФС
(ГОСТ 5950-63) и 4Х4М2ВФС.
Оборудование
для высокоскоростной
штамповки
высокоскоростные
молоты с пневматическим
приводом и
энергией удара
2,5-60 кн.м (2,5-60 тс м).
4.6.
Высокоэнергетические
импульсные
методы штамповки.
Применение
высокоэнергетических
методов штамповки
позволяет
экономично
изготовлять
абаботкой
давлением такие
детали и заготовки,
которых ранее
невозможно
было изготовлять
или для изготовления
которых ранее
требовалось
дорогостоящее
мощное оборудование.
Эти методы
деформирования
используют
в условиях
мелкосерийного
и серийного
производства,
как для листовой
так и для объемной
штамповки.
Штамповка
листового
металла.
Гидровзрывная
штамповка. При
гидровзрывном
формоизменении
энергии, образующаяся
при взрыве,
передается
штампуемой
заготовки через
ударную волну,
давление и
сопутствующий
ей гидропоток.
В качестве
среды, передающей
энергию взрыва,
используют
жидкость, сыпучую,
вязкую или
твердую среду.
Деформируемые
листовые или
трубчатые
заготовки можно
подвергать
различным
операциям:
резке, вытяжке,
рельефной
формовке, раздаче,
обжиму, отбортовке
и др.. Причем
возможно
формоизменение
с нагревом
заготовки с
помощью передающей
среды (песком).
Для
взрывной штамповки
используют
бризантные
и метательные
взрывчатые
вещества. Взрыв
может производиться
в стационарном
или съемном
(разовом) бассейне.
Для формоизменения
заготовки в
зависимости
от выполняемой
операции чаще
всего используют
только матрицу
или пуансон;
для вытяжки,
рельефной
формовки, отбортовки
- матрицу, для
обжима - пуансон.
При вытяжке
обычно получают
за один переход
меньшую предельную
величину коэффициента
вытяжки, чем
в обычных условиях:
материал
|
сплав
ОТ4
|
ст.3
|
2Х13
|
12Х18НIОТ
|
08
|
АМг6-М
|
m
|
0,68
|
0,65
|
0,64
|
0,63
|
0,63
|
0,61
|
Матрицы
для вытяжки
могут быть
металлические
цельнолитые
или составные,
железобетонные,
из льда.
Точность
деталей изготовленных
взрывной штамповкой
по сравнению
с обычной вытяжкой
значительно
выше.
Электрогидравлическая
штамповка
по сравнению
со взрывной
имеет ряд
преимуществ:
а) возможность
применения
в обычных условиях,
б)простота
дозирования
энергии, в)возможность
осуществления
серии разрядов,
следующих друг
за другом, г)
легкость
автоматизации
процесса. Однако
установки для
электрогидравлической
штамповки
дороже установок
для штамповки
взрывом, а размеры
и стоимость
электрогидравлических
установок
ограничивают
энергетические
возможности
метода.
Сущность
метода. При
высоковольтном
электрическом
разряде между
электродами,
помещенными
в жидкость,
возникает
токопроводящий
искровой канал,
мгновенное
расширение
которого приводит
к возникновению
в жидкости
ударной волны.
Деформация
заготовки
происходит,
как и при гидровзрывной
штамповке, под
действием
ударной волны,
давление и
сопутствующего
гидропотока.
Более эффективному
использованию
энергии разряда
по сравнению
с открытой
емкостью для
формоизменения
способствует
размещение
рабочих электродов
в замкнутой
камере или
внутри трубчатой
заготовки,
закрытой с двух
сторон крышками.
Рассматриваемым
методом выполняют
операции вытяжки
деталей из
плоских заготовок,
отбортовку,
раздачу трубчатых
заготтовок,
оформление
сложного контура
на листовых
и трубчатых
заготовках,
калибровку,
пробивку и
некоторые
другие операции.
Этим методом
получают детали
из цветных
металлов, стали
и высокопрочных
сплавов. Толщина
штампуемых
деталей <4-10 мм,
а габариты
большинства
деталей в плане
достигают
1200*2000 мм.
Инструмент.
Обычно для
электрогидравлической
штамповки
используют
матрицы, которые
изготовляют
из стали (иногда
и других
материалов-цинковых,
алюминевых
сплавов, литьевых
эпоксидных
смол). Основной
рабочий инструмент-
электроды,
которые изготовляют
из стали, латуни,
однако найбольшей
электроэрозийной
стойкостью
обладает
металлокерамическая
композиция
на основе вольфрама
ВНМ-3-2.
Для
электрогидравлической
штамповки
используют
отечественные
установки
“Удар 12м” и “
Удар 20” , ” Удар
20с”, “ Удар 150”,
“Удар-II”, позволяющие
изготовлять
детали размером
от 400*400 мм до 2000*1200 мм
с толщиной
стенки от 3 до
10 мм или соответственно
диаметром
заготовки от
300 мм до 1500 мм с
толщиной стенки
от 3 до 10 мм. Запасаемая
энергия указанных
установок
изменяется
соответственно
от 10 до 160 Кдж.
Штамповка
импульсным
магнитным
полем.
Основные преимущества
метода в сравнении
с взрывной и
электрогидравлической
штамповкой
: а)большая скорость
формоизменения
заготовки и
высокая призводительность,
б) возможность
точнее регулировать
параметры
процесса, в)
возможность
широко механизировать
и автоматизировать
операции процесса,
г) возможность
легкого встраивания
устоновки
импульсной
магнитной
штамповки в
автоматические
линии.
Сущность
метода.При
помещении
заготовки в
импульсное
магнитное поле,
создавемое
с помощью разряда
энергии, накопленной
в конденсаторной
батарее, на
катушку индуктивности
(рабочий индуктр),
в заготовке
индуцируются
вихревые токи,
взаимодействие
которых с токами
индуктора
приводит к
возникновению
усилий, деформирующих
заготовку.
Этот
метод штамповки
применяют в
основном для
таких операций,
как обжим и
раздача трубчатых
заготовок,
калибровка
трубчатых
изделий, получение
на деталях
различных
рифлений, штамповка
деталей из
плоских заготовок,
пробивка отверствий
в плоских и
трубчатых
деталях из
различных
металлов и
сплавов, сборка.
Преимущественное
распостранение
имеет обработка
металлов и
сплавов, обладающих
высокой
электропроводностью.
Деформирование
заготовок из
материалов
с недостаточно
высокой электропроводностью
(углеродистых
и нержавеющих
сталей) осуществляется
через передающую
среду или через
так называемый
“спутник”-
промежуточный
материал с
высокой
электропроводностью,
помещаемый
на обрабатываемую
заготовку.
Максимальная
толщина стенки
детали составляет
1,5-2 мм для стали,
1,7-2,5 мм -для латуни
и 2-3 мм - для алюминевых
и медных сплавов.
Инструмент.
Рабочим инструментом
в этом случае
является индуктор
и оправка (матрица).
В установках
магнитно-импульсного
деформирования
используют
индукторы
однократного
и многократного
использования:
первые применяют
в условиях
единичного
производства,
вторые-в условиях
серийного
производства.
Для увеличения
прочности
индукторов
и придания им
универсальности
служат концентраторы
магнитного
поля.
Оборудование.
Для магнитн-импульсной
штамповки
используют
отечественные
магнитно-импульсные
установки и
установки
изготовляемые
в ГДР , ЧССР ,
которые обладают
максимальной
запасаемой
энергией от
4,1 до 22,5 Кдж.
Объемная
штамповка.
Высокоскоростная
объемная штамповка
позволяет
максимально
приблизить
форму и размеры
поковки к форме
и размерам
деталей, что
обеспечивает
экономию металла
и сводит к минимуму
механическую
обработку. Этим
методом изготовляют
поковки с тонкими
стенками из
алюминия, меди,
различных
сталей и сплавов.
Поковки получают
с мелкозернистой
структурой
и высокими
механическими
свойствами;
значительно
улучшается
структура и
свойства сплавов
на основе молибдена,
никеля и титана.
Улучшение
структуры и
увеличение
прочности в
несколько раз
увеличивает
стойкость
деталей (шестерен
в 2-10 раз).
Высокоскоростная
объемная штамповка
выполняется
со скоростями
движения инструмента
9-18 м/сек для изготовления
поковок методом
горячего и
холодного
выдавливания.
Экономически
целесообразно
применять
высокоскоростную
штамповку в
условиях
крупносерийного
производства
для поковок,
которые могут
быть получены
на обычном
горячештамповочном
оборудовании.
Для
нагрева сталей,
жаропрочных
сплавов, титана
рекомендуют
индукционные
печи или печи
с инертной
атмосферой,
алюминевых
сплавов - печи
с принудительной
циркуляцией
воздуха. Во
всех случаях
рекомендуют
безокислительный
нагрев.
Перед
началом работы
пуансон и матрицу
следует подогреть
до 180 град.С и
поддерживать
температуру
в этом пределе
в процесе штамповки
во избежание
перегрева и
потере стойкости
штампа.
Смазки
выбирают с
учетом штампуемого
материала.
Суспензию
графита в воде
применяют в
качестве смазки
при штамповке
большинства
металлов; при
штамповке
труднодеформируемых
металлов
предпочтительнее
суспензия
графита в масле.
При тяжелых
условиях работы
применяют
дисульфид
молибдена (при
температуре
штамповки <
650град.С).
Штампы
для высокоскоростной
штамповки
изготовляют
из сталей 4Х5В2ФС
(ГОСТ 5950-63) и 4Х4М2ВФС.
Оборудование
для высокоскоростной
штамповки
высокоскоростные
молоты с пневматическим
приводом и
энергией удара
2,5-60 кн.м (2,5-60 тс м).
|