 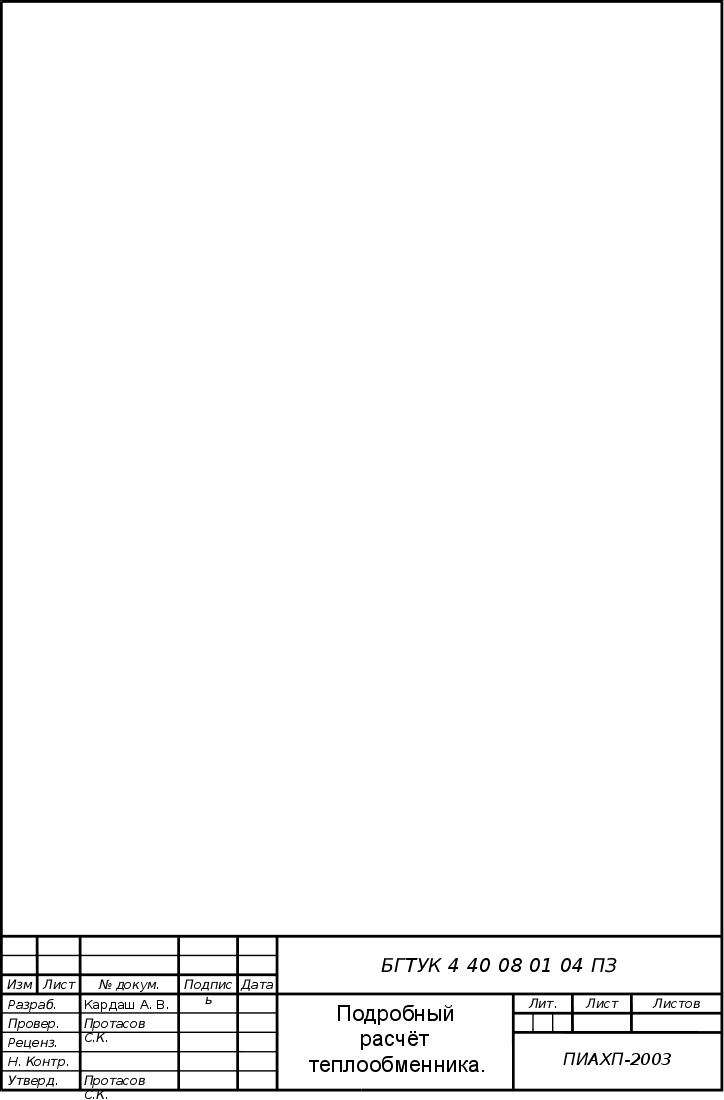 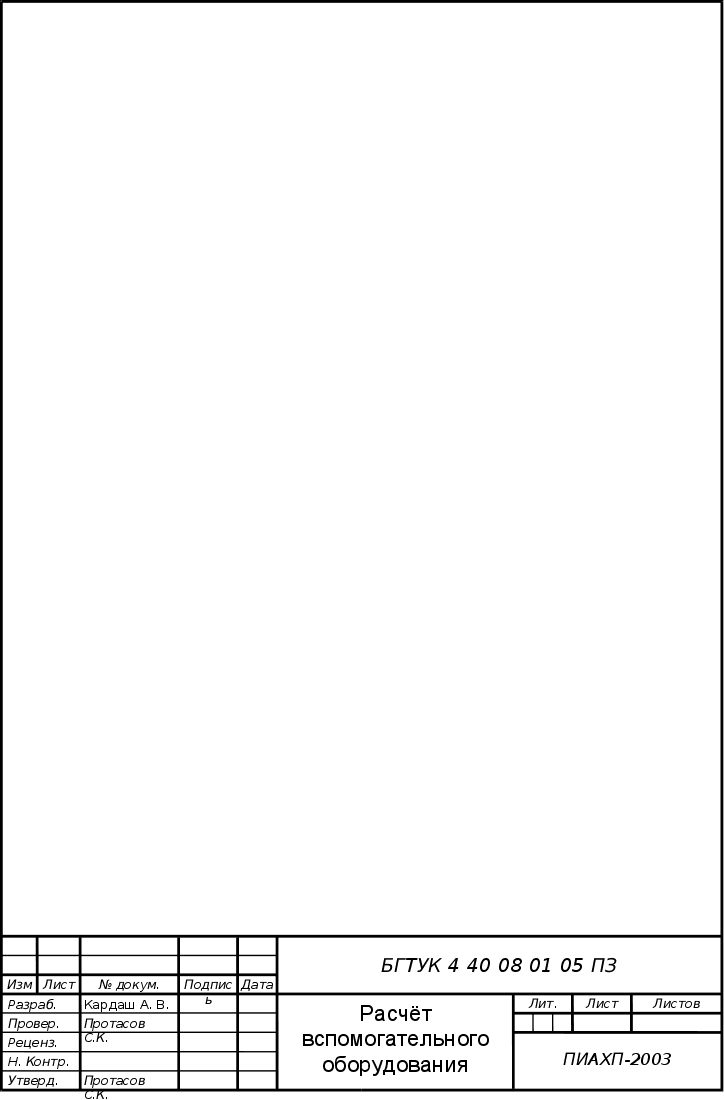 1.
ЛИТЕРАТУРНЫЙ
ОБЗОР
1.1. Теоретические
основы разрабатываемого
процесса
1.1.1.
Общие сведения
о процессе
ректификация
Ректификация
представляет
собой процесс
многократного
частичного
испарения
жидкости и
конденсации
паров. Процесс
осуществляется
путем контакта
потоков пара
и жидкости,
имеющих различную
температуру,
и проводится
обычно в колонных
аппаратах. При
каждом контакте
из жидкости
испаряется
преимущественно
легколетучий,
или низкокипящий,
компонент (НК),
которым обогащаются
пары, а из паров
конденсируется
преимущественно
труднолетучий,
или высококипящий,
компонент (ВК),
переходящий
в жидкость.
Такой двухсторонний
обмен компонентами,
повторяемый
многократно,
позволяет
получить в
конечном счете
пары, представляющие
собой почти
чистый НК. Эти
пары после
конденсации
в отдельном
аппарате образуют
дистиллят
(ректификат)
и флегму – жидкость,
возвращаемую
для орошения
колонны и
взаимодействия
с поднимающимися
парами. Пары
получают путем
частичного
испарения снизу
колонны остатка,
являющегося
почти чистым
ВК.
Как
отмечалось,
достаточно
высокая степень
разделения
однородных
жидких смесей
на компоненты
может быть
достигнута
путем ректификации.
Сущность процессов,
из которых
складывается
ректификация,
и получаемые
при этом результаты
можно проследить
с помощью t
— х —
у
-диаграммы
(рис. 1.1).
Нагрев
исходную смесь
состава х1
до
температуры
кипения получим
находящийся
в равновесии
с жидкостью
пар (точка b).
Отбор
и конденсация
этого пара дают
жидкость состава
x2
обогащенную
НК (х2
> х1).Нагрев
эту жидкость
до температуры
кипения t2,
получим пар
(точка d),
конденсация
которого дает
жидкость с еще
большим содержанием
НК, имеющую
состав ха,
и т.
д. Проводя таким
образом последовательно
ряд процессов
испарения
жидкости и
конденсации
паров, можно
получить в
итоге жидкость
(дистиллят),
представляющую
собой практически
чистый НК.
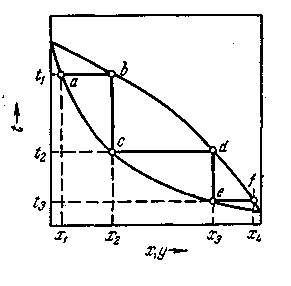
Рис. 1.1.
Изображение
процесса
разделения
бинарной
смеси путем
ректификации
на диаграмме
t—Х—у.
Аналогично,
исходя из паровой
фазы, соответствующей
составу жидкости
x4,
путем проведения
ряда последовательных
процессов
конденсации
и испарения
можно получить
жидкость (остаток),
состоящую почти
целиком из ВК.
В простейшем
виде процесс
многократного
испарения можно
осуществить
в многоступенчатой
установке, в
первой ступени
которой испаряется
исходная смесь.
На вторую ступень
поступает на
испарение
жидкость, оставшаяся
после отделения
паров в первой
ступени, в третьей
ступени испаряется
жидкость, поступившая
из второй ступени
(после отбора
из последней
паров) и т. д.
Аналогично
может быть
организован
процесс многократной
конденсации,
при котором
на каждую следующую
ступень поступают
для конденсации
пары, оставшиеся
после отделения
от них жидкости
(конденсата)
в предыдущей
ступени.
При достаточно
большом числе
ступеней таким
путем можно
получить жидкую
или паровую
фазу с достаточно
высокой концентрацией
компонента,
которым она
обогащается.
Однако выход
этой фазы будет
мал по отношению
к ее количеству
в исходной
смеси. Кроме
того, описанные
установки
отличаются
громоздкостью
и большими
потерями тепла
в окружающую
среду.
Значительно
более экономичное,
полное и четкое
разделение
смесей на компоненты
достигается
в процессах
ректификации,
проводимых
обычно в более
компактных
аппаратах
— ректификационных
колоннах.
Процесс
ректификации
осуществляется
путем многократного
контакта между
неравновесными
жидкой и паровой
фазами, движущимися
относительно
друг друга.
При
взаимодействии
фаз между ними
происходит
массо- и теплообмен,
обусловленные
стремлением
системы к состоянию
равновесия.
В результате
каждого контакта
компоненты
перераспределяются
между фазами:
пар несколько
обогащается
НК, а жидкость
— ВК. Многократное
контактирование
приводит к
практически
полному разделению
исходной смеси.
Таким
образом, отсутствие
равновесия
(и соответственно
наличие разности
температур
фаз) при движении
фаз с определенной
относительной
скоростью и
многократном
их контактировании
являются необходимыми
условиями
проведения
ректификации.
1.1.2. Равновесие
в системах
жидкость-пар
В
общем случае
жидкая смесь
может состоять
из нескольких
компонентов.
В простейшем
случае из двух,
например из
компонентов
А и
В. Характер
поведения
жидкой смеси
зависит главным
образом от
природы составляющих
ее веществ и
давления.
Для идеальных
растворов
характерно
то, что сила
взаимодействия
между всеми
молекулами
(одноименными
и разноименными)
равна. При этом
общая сила, с
которой молекула
удерживается
в смеси, не зависит
от состава
смеси. Очевидно,
что парциальное
давление в этом
случае должно
зависеть лишь
от числа молекул,
достигающих
в единицу времени
поверхности
жидкости со
скоростью,
необходимой
для преодоления
сил внутреннего
притяжения
молекул, т. е.
при данной
температуре
давление
соответствующего
компонента
возрастает
пропорционально
его содержанию
в жидкой смеси
(закон Рауля):
рА
= РАхА (1.1)
и рВ
= РВ(1-хА) (1.2.)
Закон
Рауля справедлив
и для газов с
температурой
ниже критической
(т. е.
такой температуры,
выше которой
газ при увеличении
давления не
сжижается).
По степени
растворимости
компонентов
смеси жидкости
подразделяют
на взаиморастворимые
в любых соотношениях,
частично растворимые
и практически
взаимонерастворимые.
В свою очередь
смеси со взаиморастворимыми
компонентами
в любых соотношениях
делятся на:
идеальные
растворы, которые
подчиняются
закону Рауля;
так называемые
нормальные
растворы - жидкие
смеси, частично
отклоняющиеся
от закона Рауля,
но не образующие
смесей: с постоянной
температурой
кипения (азеотропов);
неидеальные
растворы
- жидкости
со значительными
отклонениями
от закона Рауля,
в
том числе смеси
с постоянной
температурой
кипения (азеотропы).
(Отметим, что
полностью
взаимонерастворимых
жидкостей нет,
обычно все
жидкости хотя
бы в незначительных
количествах,
но растворяются
друг в друге.
Однако в этих
случаях на
практике для
удобства принимают
такие жидкости
взаимонерастворимыми.)
Смесь
двух жидкостей,
взаиморастворимых
в любых соотношениях,
представляет
собой систему,
состоящую из
двух фаз и двух
компонентов,
и по правилу
фаз:
С=К-Ф+2=2-2+2=2
(1.3.)
имеет
две степени
свободы (из
трех - давления
Р,
температуры
t,
концентрации
х). Однако
при анализе
и расчете процессов
перегонки
жидкостей одну
из переменных
обычно закрепляют
и строят диаграмму
фаз в плоской
системе координат.
При этом возможны
следующие
варианты фазовых
диаграмм: Р
— t
(х = const),
Р — —
x(t
= const),
t
— х(Р = const).
Для технических
расчетов наиболее
важной является
диаграмма t
— х, у, так
как обычно
процессы перегонки
в промышленных
аппаратах
протекают при
Р = const,
т. е. в изобарных
условиях. На
этой диаграмме
(рис. 5.2.) по оси
абсцисс отложены
концентрации
жидкой х
и паровой
у фаз,
отвечающие
различным
температурам.
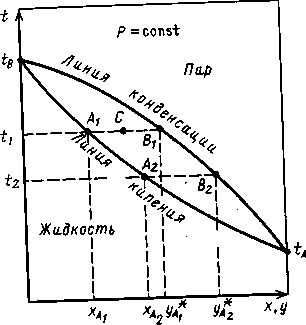
Рис. 1.2.
Фазовая диаграмма
t
— х, у
По закону
Дальтона рА
= Рy*A,
и тогда
y*A=
pA/P=(PA/P)
xA,
(1.4.)
но
Р
=
pA+pB=PAxA+PB(1-xB)=PB+(PA-PB)xA
(1.5.)
тогда
xA=(P-PB)/(PA-PB)
(1.6.)
По уравнению
(1.6.)) по известным
РА
и РB
при
заданной температуре
t1
, t2
и т.д.
находят хA
, хB
и т.д.,
а затем по уравнению
(1.4.) -соответствующие
значения у*A1
, у*А2
и т.д.
и по найденным
точкам строят
линии кипения
жидкости (кривая
tAA2A1tB)
и
конденсации
паров (кривая
tAB2BltB).
Отметим,
что уравнение
(1.6.) устанавливает
связь между
концентрациями
(по жидкости)
и заданными
давлениями
(общим Р
и
насыщенных
паров РА
и РB).
Отрезки А1В1
, А2
В2
и т.
д., соединяющие
точки равновесных
составов жидкой
и паровой фаз,
являются изотермами.
Отметим,
что точки, лежащие
на кривой tAA2A1tB,,
отвечают
жидкой фазе,
находящейся
при температуре
кипения. Очевидно,
что любая точка,
лежащая ниже
этой кривой,
характеризует
систему, состоящую
только из жидкой
фазы. Аналогично,
любая точка
лежащая выше
кривой tA
B2
В1
tB
, характеризует
систему, темпера
тура которой
выше температуры
начала конденсации
пара, т. е пары
в этой точке
являются перегретыми,
и система состоит
только из паровой
фазы. Точки,
находящиеся
между кривыми
кипения и конденсации
(например, точка
С на рис. 1.2.), характеризуют
системы, температуры
которых выше
температуры
кипения жидкости
данного состава
и ниже температуры
конденсации
паров этого
же состава.
Таким образом,
эти точки отвечают
равновесным
парожидкостным
системам.
Основные
положения
фазового равновесия
были рассмотрены
в гл. 2 (правило
фаз Гиббса,
законы Генри
и Рауля и др.).
Там же для идеальных
бинарных систем
получено уравнение
(1.7.), которое описывает
линию равновесия:
у*А
= ахА/[1+хА(а-1)],
(1.7.)
где а
= РА/РВ
-
относительная
летучесть
компонента
А (иногда
а
называют
коэффициентом
разделения).
Очевидно,
что для смеси,
состоящей из
n
компонентов,
например, А,
В, С, D,
на
основе законов
Рауля и
Дальтона имеем
yA
= (РA/Р)хA;
yB
= (РB/Р)хB;
yC
= (РC/Р)хC;
yD
= (РD/Р)хD.
(1.8.)
Поскольку
P=PAxA+
PBxB+
PCxC+
PDxD+
…=
(1.9.)
то для
любого j-го
компонента
yj
= PjXj/ .
(1.10.)
Разделив
числитель и
знаменатель
правой части
уравнения
(1.10) на
величину РА,
получим
yj
= а
jXj/ ,
(1.11.)
где а
A
= РА/РВ
; а
в
= РВ/РА
; а
C
= РС/РА
и т. д.
Например,
зависимость
давления насыщенного
пара от температуры
хорошо описывается
эмпирическим
уравнением
Антуана
lnРА
= А - В/(Т+ C),
(1.12.)
где А
- постоянная,
не зависящая
от температуры;
В и
С -константы,
определяемые
по справочникам;
T-
абсолютная
температура.
Уравнение
(5.12) описывает
температурную
зависимость
давлений паров
в интервале
температур
до нескольких
десятков градусов
и при давлениях,
не слишком
близких к
критическим.
Взаимное
положение
кривых на фазовых
диаграммах
t
— х — у и
у — х
как
для идеальных,
так и для реальных
систем могут
быть определены
с помощью законов
Коновалова.
Законы Коновалова
устанавливают
связи между
изменениями
состава, давления
или температуры
в двухфазных
системах, они
лежат в основе
теории перегонки
и ректификации
бинарных смесей.
Первый
- закон Коновалова
формулируется
так: пар
обогащается
тем компонентом,
при добавлении
которого к
жидкости повышается
давление
пара над ней
или снижается
ее температура
кипения, или
пар всегда
более обогащен
НК, чем соответствующая
ему равновесная
жидкая фаза.
Первый
закон Коновалова
дополняется
первым
правилом Вревского,
отражающим
влияние температуры
на равновесные
составы фаз:
при
повышении
температуры
бинарной смеси
в парах возрастает
относительное
содержание
того компонента,
парциальная
молярная теплота
испарения
которого больше.
Это можно
проиллюстрировать
с помощью фазовой
диаграммы (рис.
1.2.). Для идеальной
смеси очевидно,
что при одной
и той же температуре
t
содержание
НК в парах у*A1
(точка
B1
больше
его содержания
ха
в равновесной
с парами жидкости
(точка А1).
При
добавлении
к смеси НК ее
температура
кипения снижается,
но содержание
НК в паре остается
выше, чем в жидкости.
Реальные
жидкие смеси
могут значительно
отклоняться
от закона Рауля.
Если зависимость
полного давления
(или сумма
парциальных
давлений) паров
от состава
жидкой смеси
проходит выше
линий, характеризующих
те же зависимости
для идеальных
смесей (рис.
1.3.), то такое отклонение
называют
положительным,
если
ниже - отрицательным
отклонением
от
закона Рауля.
Эти отклонения
определяются
изменением
активности
молекул в растворе,
диссоциацией,
гидратацией
и др. Степень
отклонения
реальной системы
от закона Рауля
выражают величиной
коэффициента
активности
:
pA
= PAxA
. (1.13.)
Для смесей
с положительным
отклонением
от закона Рауля
> 1, для смесей
с отрицательным
отклонением
—
< 1. Отметим, что
определение
значений у
часто затруднительно,
поэтому диаграммы
P
— х
обычно
строят по
экспериментальным
(справочным)
данным.
Рис. 1.3.
Диаграмма р
— х для
смеси с положительным
отклонением
от закона Рауля
(пунктиром
показаны
соответствующие
линии
для идеального
раствора)
Для многих
реальных смесей
отклонение
от закона Рауля
настолько
существенно,
что приводит
к качественно
новому состоянию
системы, а на
фазовых диаграммах
Р — х
и t
— х появляются
(рис. 1.4.,б, в) относительный
максимум или
минимум. При
этом кривые
жидкости и пара
соприкасаются
друг с другом
в экстремальных
точках, в которых
составы равновесных
фаз одинаковы.
Такие смеси,
как известно,
называют
азеотропными,
или
азеотропами.
Их
основная особенность
состоит в том,
что при испарении
такая смесь
(азеотроп) не
изменяет своего
состава, поэтому
для ее разделения
требуются
специальные
методы (азеотропная
и экстрактивная
ректификация,
изменение
давления и
др.).
Рис. 1.4. Фазовые
диаграммы
равновесия
жидкость-пар
для идеальной
(а) и реаль- ных
(б, в) систем
Эта особенность
азеотропных
смесей постулируется
вторым
законом Коновалова,
который можно
сформулировать
следующим
образом: если
давление и
температура
сосуществования
двух бинарных
фаз имеют экстремум
(максимум или
минимум), то
составы фаз
одинаковы. Это
справедливо
для фаз любой
природы. Для
систем жидкость
- пар второй
закон Коновалова
определяет
основное
свойство азеотропов.
При изменении
внешних условий
- температуры
(или давления)
значение
а
изменяется
различно по
разные стороны
от точки азеотропа;
одна часть
«рыбки» (рис.1.4.,
б, в)
должна
становиться
шире, другая
- уже. Очевидно,
что в части
диаграммы, где
в паре содержится
больше, чем в
растворе, компонента
с меньшей теплотой
испарения, при
понижении
температуры
(давления), а
увеличивается.
5.1.3. Материальный
и тепловой
балансы ректификационной
колонны
Пусть,
согласно схеме
на рис. (1.5.), в колонну
поступает F
кмоль
исходной
смеси, состав
которой хF
мол.
долей НК. Сверху
из колонны
удаляется G
кмоль
паров,
образующих
после конденсации
флегму и дистиллят.
Количество
получаемого
дистиллята
Р кмоль,
его
состав хP
мол.
долей НК. На
орошение колонны
возвращается
флегма в количестве
Ф кмоль,
причем
ее состав равен
составу дистиллята
(хф=
xP
мол.
долей). Снизу
из колонны
удаляется
W
кмоль
остатка
состава xw
мол.
долей НК.
Тогда
уравнение
материального
баланса колоны
будет:
Ф+F
=
G+W.
(1.14)
Поскольку
G=P+Ф,
то
F =
P+W.
(1.15.)
Соответственно
по НК
материальный
баланс:
FxF
=
PxP+WxW
(1.16.)
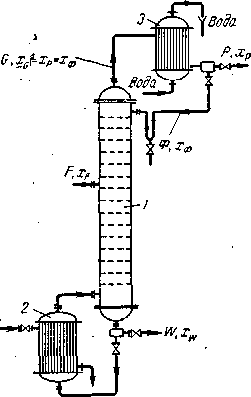
Рис.
1.5. К
составлению
материального
баланса
ректификационной
колонны:
/ — колонна;
2 — куб;
3 —
дефлегматор.
Для колонны
непрерывного
действия с
учетом потерь
тепла в окружающую
среду имеем:
Приход
тепла
Расход
тепла
С теплоносителем
в кипя-
С
парами, поступающими
из
тальнике .……… QКИП..
колонны в
дефлегматор
QG
= GI
С исходной
смесью……….QF=FiF
С
остатком…………………
QW
=Wiw
С флегмой .................
. QФ
= ФiФ
Потери
в окружающую
среду QП
Кроме
известных
величин, в выражения
для количеств
тепла входят:
I,
iF,
iф
и iw
—
энтальпии
соответственно
паров, выходящих
из колонны,
исходной смеси,
флегмы и остатка.
Таким
образом, уравнение
теплового
баланса:
Qкип
+ QF
+ QФ
= QG
+ QW
+ QП
. (1.17.)
Подставляя
вместо Q
их
значения и
учитывая, что
F=Р
+ W,
G
= P(R+
1) и Ф =
PR,
получим
Qкип
+ (Р
+ W)iF
+ РRiФ
= P(R+\)I
+ WiW
+ QП (1.18.)
Решая
уравнение
(5.18.) относительно
Qкип,
находим расход
тепла в кипятильнике
Qкип
= Р(I
–
iF)
+ PR( I -iФ)
+ W(iW
- iF)
+ QП
( 1.18а.
)
Из уравнения
теплового
баланса (5.18а.)
видно, что тепло,
подводимое
в кипятильник,
затрачивается
на испарение
дистиллята
[Р(I—iF)],
испарение
флегмы [PR(I
— iф)],
нагревание
остатка до
температуры
кипения
[W(iw
— iF)],
а также
на компенсацию
потерь тепла
в окружающую
среду.
Флегма
из дефлегматора
поступает в
колонну при
температуре
ее кипения.
Поэтому энтальпия
выходящих из
колонны паров
I
== iФ
+ rф,
где
rф
— теплота
испарения
флегмы.
Потери
тепла в окружающую
среду обычно
выражают в
долях тепла,
подводимого
в кипятильник,
т. е. принимают
QП
= aПQкип,
где при наличии
хорошей тепловой
изоляции коэффициент
аП
= 0,03—0,05.
Делая
соответствующие
подстановки
в уравнение
(1.18а.), окончательно
получим
QКИП
=[P(I
–
iF)
+ PRrФ
+ W(iW
- iF)]
/ (1-aП)
(1.19.)
Энтальпии
жидкостей,
входящих в
уравнение
(1.18.) и (1.19.), равны
произведениям
их мольных
теплоемкостей
с на
температуры
t
(в °С).
Теплоемкости
с и
теплоты испарения
для бинарных
смесей вычисляют
по
правилу аддитивности
исходя из свойств
чистых
компонентов
А и В:
с = сАх+сВ(1—х)
r
= rАх+rВ(1—х)
где х
— мольная
доля компонента
А в
смеси.
Количество
тепла QДЕФ,
отнимаемого
охлаждающей
водой в дефлегматоре,
зависит от
количества
конденсирующихся
в нем паров.
При
полной конденсации
паров, выходящих
из
колонны, находим
QДЕФ
= P(R+1)rФ
= P(R+1)(I-iФ)
(1.20.)
Уравнения
рабочих линий.
Для получения
уравнений
рабочих линий
воспользуемся
общим для всех
массообменных
процессов
уравнением
():
y= ,
(1.21)
где L
и G
— расходы
жидкой и паровой
фаз; у,
х, уа
и хк
—соответственно
текущие концентрации
паровой и жидкой
фаз и их концентрации
на верхнем
конце колонны
.
Применяя
это уравнение
к процессу
ректификации,
выразим все
входящие
в него величины
в мольных единицах.
Укрепляющая
часть колонны.
Количество
жидкости (флегмы),
стекающей
по этой части
колонны
L
= Ф = PR,
(1.22)
где R=
-флегмовое
число, представляющее
собой отношение
количества
флегмы к
количеству
дистиллята.
Количество
паров, поднимающихся
по колонне
G=P+Ф=P+PR=P(R+1),
(1.23)
Для верхнего
конца укрепляющей
части колонны
состав паров
yG=yP
и,
согласно принятому
выше допущению,
ур
= хр.
Следовательно,
в данном
случае ун
= хр.
В том же
сечении колонны
состав жидкости
(флегмы), поступающей
из дефлегматора,
xф
= хр,
т. е.
хк
= хр.
Учитывая
значения L,
G,
yk
и хk
получаем
уравнение
(1.24), получим
y=
(1.24)
откуда
y=
(1.25)
Зависимость
(1.24) является
уравнением
рабочей
линии
укреплящей
части
колонны.
В этом уравнении
= tg
а = А
— тангенс
угла наклона
рабочей линии
к оси абсцисс,
а
=В
— отрезок,
отсекаемый
рабочей линией
на оси ординат
диаграммы
у —
х (рис.
1.6).
Исчерпывающая
часть колонны.
Количество
орошающей
жидкости L'
в этом
части колонны
больше количества
флегмы Ф, стекающей
по укрепляющей
части на количество
исходной смеси,
поступающей
на питающую
тарелку. Если
обозначить
количество
питания, приходящегося
на 1
кмоль
дистиллята
через f=
F/P,
то F
= Pf
и
количество
жидкости, стекающей
по исчерпывающей
части колонны,
составит:
L
=
Ф
+
F
=
PR
+
Pf
=
P
(R + I) (1.26)
Количество
пара, проходящего
через нижнюю
часть колонны,
равно количеству
пара, поднимающегося
по верхней
(укрепляющей)
ее части. Следовательно
G’=G=P(R+1)
Для низа
колонны состав
удаляющейся
жидкости (остатка)
х'к
= xw
и,
согласно допущению,
состав поступающего
сюда из кипятильника
пара у’н=yw
=xw
.Подставив
значения L',
G',
х’к
и у’н
в общее
уравнение ,
получим
(1.27)
После
приведения
к общему знаменателю
и сокращения
подобных членов
находим:
(1.28)
Зависимость
(1.25) представляет
собой уравнение
рабочей
линии
исчерпывающей
части
колонны.
В этом
уравнении
= tg
a'
= А'
—тангенс
угла наклона
рабочей линии
к оси
ординат, а
=
В' —
отрезок, отсекаемый
рабочей линией
на оси
абсцисс (см.
рис.1.6).
Умножив
числитель и
знаменатель
выражений для
А' и
А (для
укрепляющей
части колонны)
на количество
дистиллята
Р, можно заметить,
что
они представляют
собой отношения
количеств
жидкой и паровой
фаз, или
удельный расход
жидкости, орошающей
данную часть
колонны.
Построение
рабочих линий
на диаграмме
у —
х. Для
построения
рабочих
линиоткладывают
на оси абсцисс
диаграммы (см.
рис. 1.6) заданные
составы жидкостей
xw,
xf
и хр.
Учитывая
принятые допущения
о равенстве
составов пара
и жидкости на
концах колонны,
из точки х
восстанавливают
вертикаль до
пересечения
с диагональю
диаграммы в
точке а
с координатами
ур
= хр.
Величину
R
считаем
известной.
Откладывая
на оси ординат
отрезок
В=
, соединяют
прямой конец
отрезка
(точку
d)
с точкой
а. Из точки,
отвечающей
заданному
составу хf,
проводят
вертикаль до
пересечения
с линией ad
в точке
b.
Прямая
аb
— рабочая
линия укрепляющей
части колонны.
Согласно допущению
yw
= xw
,из точки, соответствующей
составу xw
, восстанавливают
вертикаль до
пересечения
с диагональю
диаграммы и
получают точку
с —
конечную точку
рабочей линии
исчерпывающей
части колонны.
Соединяют точку
с прямой
с точкой b,
принадлежащей
одновременно
рабочим линиям
укрепляющей
и исчерпывающей
частей колонны.
Прямая bc
представляет
собой рабочую
линию исчерпывающей
части колонны.
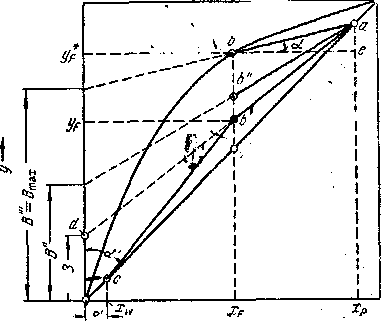
Рис. 1.6
Построение
рабочих линий
ректификационной
колонны на
у—x
диаграмме.
Рабочие
линии ab
и bc
в отличие
от рабочих
линий процесса
абсорбции
располагаются
под линией
равновесия.
В данном случае,
как уже отмечалось,
НК переходит
в паровую фазу,
стремящуюся
к равновесию
с жидкой фазой,
т. е. по существу
десорбируется
из жидкости.
1.2. Основные
технологические
схемы для проведения
разрабатываемого
процесса
Процессы
ректификации
осуществляются
периодически
или непрерывно
при различных
давлениях: при
атмосферном
давлении, под
вакуумом
(для разделения
смесей высококипящих
веществ), а также
под давлением
больше атмосферного
(для разделения
смесей, являющихся
газообразными
при нормальных
температурах).
1.2.1. Непрерывная
ректификация
Рассмотрим,
как реализуются
указанные
выше условия
в ректификационных
колоннах непрерывного
действия
(рис. 1.7.), которые
наиболее широко
применяются
в промышленности.

Рис.1.7. Схема
непрерывно
действующей
ректификационной
установки:
1— ректификационная
колонна (а —
укрепляющая
часть, б —
исчерпывающая
часть); 2 —кипятильник;
3 —
дефлегматор;
4 —
делитель флегмы;
5 —
подогреватель
исходной смеси;6
—
холодильник
дистиллята
(или холодильник-конденсатор);
7 — холодильник
остатка (или
нижнего продукта);
8, 9 сборники;
10 —
насосы.
Ректификационная
колонна 1 имеет
цилиндрический
корпус, внутри
которого установлены
контактные
устройства
в виде тарелок
или насадки.
Снизу
вверх по колонне
движутся пары,
поступающие
в нижнюю часть
аппарата из
кипятильника
2, который
находится вне
колонны, т. е.
является выносным
(как показано
на рисунке
1.7.), либо размещается
непосредственно
под колонной.
Следовательно,
с помощью
кипятильника
создается
восходящий
поток
пара.
Пары проходят
через слой
жидкости на
нижней тарелке,
которую
будем считать
первой, ведя
нумерацию
тарелок условно
снизу вверх.
Пусть
концентрация
жидкости на
первой тарелке
равна х1
(по
низкокипящему
компоненту),
а ее температура
t1.
В результате
взаимодействия
между жидкостью
и паром, имеющим
более высокую
температуру,
жидкость частично
испаряется,
причем в пар
переходит
преимущественно
НК. Поэтому на
следующую
(вторую) тарелку
поступает пар
с содержанием
НК у1>
х1.
Испарение
жидкости на
тарелке происходит
за счет тепла
конденсации
пара. Из пара
конденсируется
и переходит
в жидкость
преимущественно
ВК, содержание
которого в
поступающем
на тарелку паре
выше равновесного
с составом
жидкости на
тарелке. При
равенстве
теплот испарения
компонентов
бинарной смеси
для испарения
1 моль
НК
необходимо
сконденсировать
1 моль
ВК, т.
е. фазы на тарелке
обмениваются
эквимолекулярными
количествами
компонентов.
На второй
тарелке жидкость
имеет состав
x2,
содержит
больше НК, чем
на первой (х2
> x1),
и
соответственно
кипит при более
низкой температуре
(t2
1).
Соприкасаясь
с ней, пар состава
у1
частично
конденсируется,
обогащается
НК и удаляется
на вышерасположенную
тарелку, имея
состав y2
> x2,
и т. д.
Таким
образом пар,
представляющий
собой на выходе
из кипятильника
почти чистый
ВК, по мере движения
вверх все более
обогащается
низкокипящим
компонентом
и покидает
верхнюю тарелку
колонны в виде
почти чистого
НК, который
практически
полностью
переходит в
паровую фазу
на пути
пара от кипятильника
до верха колонны.
Пары
конденсируются
в дефлегматоре
3, охлаждаемом
водой, и получаемая
жидкость разделяется
в делителе 4
на
дистиллят и
флегму, которая
направляется
на верхнюю
тарелку колонны.
Следовательно,
с помощью -
дефлегматора
в колонне создается
нисходящий
поток
жидкости.
Жидкость,
поступающая
на орошение
колонны (флегма),
представляет
собой
почти чистый
НК. Однако, стекая
по колонне и
взаимодействуя
с паром,
жидкость все
более обогащается
ВК, конденсирующимся
из пара. Когда
жидкость достигает
нижней тарелки,
она становится
практически
чистым
ВК и поступает
в кипятильник,
обогреваемый
глухим паром,
или
другим теплоносителем.
На некотором
расстоянии
от верха колонны
к жидкости из
дефлегматора
присоединяется
исходная смесь,
которая поступает
на так называемую
питающую тарелку
колонны. Для
того чтобы
уменьшить
тепловую
нагрузку
кипятильника,
исходную смесь
обычно предварительно
нагревают в
подогревателе
5 до температуры
кипения жидкости
на питающей
тарелке.
Питающая
тарелка как
бы делит колонну
на две части,
имеющие различное
назначение.
В верхней части
1а (от
питающей до
верхней тарелки)
должно быть
обеспечено
возможно большее
укрепление
паров, т. е. обогащение
их НК с тем, чтобы
в дефлегматор
направлялись
пары, близкие
по
составу к чистому
НК. Поэтому
данная часть
колонны называется
укрепляющей.
В нижней части
1б (от
питающей до
нижней тарелки)
необходимо
в максимальной
степени удалить
из жидкости
НК, т.
е. исчерпать
жидкость для
того, чтобы в
кипятильник
стекала жидкость,
близкая
по составу к
чистому ВК.
Соответственно
эта часть колонны
называется
исчерпывающей.
В дефлегматоре
3 могут
быть сконденсированы
либо все пары,
поступающие
из колонны,
либо только
часть их соответствующая
количеству
возвращаемой
в колонну флегмы.
В первом случае
часть конденсата,
остающаяся
после отделения
флегмы, представляет
собой дистиллят
(ректификат),
или верхний
продукт, который
после охлаждения
в холодильнике
6 направляется
в сборник дистиллята
9. Во втором случае
несконденсированные
в дефлегматоре
пары одновременно
конденсируются
и охлаждаются
в холодильнике
6, который
при таком варианте
работы служит
конденсатором-холодильником
дистиллята.
Жидкость,
выходящая из
низа колонны
(близкая по
составу ВК)
также делится
на две части.
Одна часть, как
указывалось,
направляется
в кипятильник,
а другая — остаток
(нижний продукт)
после охлаждения
водой в
холодильнике
7 направляется
в сборник 8.
На рис.
(1.7.) приведена
лишь принципиальная
схема непрерывно-действующей
ректификационной
установки.
Такие установки
оснащаются
необходимыми
контрольно-измерительными
и регулирующими
приборами,
позволяющими
автоматизировать
их работу и
проводить
процесс с помощью
программного
управления
в оптимальных
условиях.
1.2.2. Периодическая
ректификация
Периодически
действующие
ректификационные
установки
применяют,
как правило,
для разделения
жидких смесей
в тех случаях,
когда использование
непрерывнодействующих
установок
нецелесообразно.
Обычно это
характерно
для технологических
процессов, в
которых количества
подлежащих
разделению
смесей невелики
и требуется
определенное
время для накопления
этих продуктов
перед разделением
или в условиях
часто меняющегося
состава исходной
смеси. Последний
случай специфичен
для гибких
технологических
процессов, в
которых спектр
получаемых
продуктов
весьма разнообразен.

Периодическую
ректификацию
проводят на
установках
с практически
идентичной
принципиальной
схемой. Один
из возможных
вариантов
такой установки
показан на рис.
(1.8.).
Рис. 1.8. Схема
установки для
проведения
периодической
ректификации:
1-куб-кипятильник;
2-подогреватель;
3-ректификационная
колонна; 4-дефлегматор;
5-делитель
потока; 6-холодильник;
7-сборники.
Исходную
смесь периодически
загружают в
куб-кипятильник
1, снабженный
подогревателем
2, в который подается
теплоноситель,
например насыщенный
водяной
пар. Исходную
смесь доводят
до кипения.
Образующиеся
пары поднимаются
по колонне 3, в
которой происходит
противоточное
взаимодействие
этих паров
с жидкостью
(флегмой), поступающей
из дефлегматора
4. Часть
конденсата
после делителя
потока возвращается
в колонну в
виде флегмы,
другая часть
- дистиллят
Р - через
холодильник
6 собирается
в сборниках
7 в виде отдельных
фракций. Процесс
ректификации
заканчивают
обычно после
того, как будет
достигнут
заданный средний
состав дистиллята.
Таким образом,
колонна 3
является
аналогом укрепляющей
части колонны
непрерывного
действия, а куб
выполняет роль
исчерпывающей
части.
Периодическая
ректификация
может осуществляться
двумя способами:
1) при
постоянном
составе дистиллята
(хр
= const)
и 2) при
постоянном
флегмовом числе
(RP
= const).
В первом
случае количество
флегмы по мере
уменьшения
содержания
легколетучего
компонента
в кубе должно
постепенно
возрастать.
В промышленных
условиях установки
для проведения
такого процесса
необходимо
оснащать управляющими
автоматизированными
системами,
способными
осуществлять
непрерывное
и строго программированное
изменение
питания колонны
флегмой и подачи
теплоносителя
в испаритель
(куб колонны).
Изменение
основных расходных
параметров
можно проводить,
например, по
данным о качественном
составе легколетучего
компонента
либо в кубовой
жидкости, либо
в дистилляте.
1.2.3. Экстрактивная
и азеотропная
ректификация
Уровень
трудности
разделения
смесей с близкими
температурами
кипения может
быть оценен
с помощью
коэффициента
относительной
летучести =
РА/РВ. Если значение
невелико, то
такую смесь
можно разделять
под вакуумом.
Вместе с тем
часто экономически
целесообразнее
в этом случае
оказывается
использование
метода, основанного
на введении
в разделяемую
смесь
дополнительного-разделяющего-компонента
избирательного
действия.
В разделяющем
компоненте,
который является
высококипящим
по отношению
к одному из
двух компонентов
исходной смеси,
этот последний
хорошо растворим,
а второй компонент
либо нерастворим,
либо труднорастворим.
Присутствие
третьего -
разделяющего,
или экстрагирующего,
- компонента
приводит к
снижению сил
притяжения
нерастворимого
компонента
в растворе к
остальным
частицам и в
результате
этого - к увеличению
его относительной
летучести в
системе (рис.
1.9.).
Таким образом,
разделяющий
агент обладает
избирательным
действием -
повышает давление
пара НК в большей
степени, чем
давление пара
ВК. Резкое увеличение
облегчает
разделение
исходных компонентов,
но влечет за
собой последующий
процесс разделения
смеси хорошо
растворимого
и экстрагирующего
компонентов,
которые удаляются
с остатком.
Описанный метод
разделения
называют
экстрактивной
ректификацией.

Рис. 1.9.
Положение
кривой равновесия
без добавки
(1) и с добавкой
(2) разделяющего
агента
В отличие
от экстрактивной,
азеотропная
ректификация
заключается
в осуществлении
процесса в
присутствии
разделяющего
компонента,
образующего
с компонентами
разделяемой
смеси один или
несколько
азеотропов,
которые в основном
отбираются
в виде дистиллята.
Схема установки
для проведения
экстрактивной
ректификации
представлена
на рис. (1.10.).
Исходную
смесь, состоящую
из компонентов
А и
В, подают
на тарелку
питания колонны
7 для экстрактивной
ректификации.
Несколько
выше тарелки
питания вводят
разделяющий
агент С.
Низкокипящий
компонент
отбирают в виде
дистиллята,
а смесь высококипящего
компонента
В и
разделяющего
компонента
С из нижней
части колонны
1 направляют
на разделение
в колонну 2.
Разделяющий
компонент,
отбираемый
в виде кубового
остатка, возвращают
на орошение
колонны 1.

Рис. 1.10. Схема
установки для
экстрактивной
ректификации
бинарной смеси
1-колонна
для экстрактивной
ректификации;
2-колонна для
разделения
продукта В
и
экстрагирующего
компонента
С;
3-насосы;
4-кипятильники;
5-конденсаторы
При
азеотропной
ректификации
(рис. 1.11.) исходную
азеотропную
смесь подают
на тарелку
питания колонны,
которая орошается
сверху
разделяющим
агентом С.
Расход
разделяющего
агента в
основном зависит
от состава
исходной смеси.
Так, при азеотропной
ректификации
расход разделяющего
компонента
увеличивается
с повышением
в исходной
смеси концентрации
тех компонентов,
которые
отбираются
в дистиллят.
При экстрактивной
ректификации,
наоборот, расход
разделяющего
компонента
возрастает
при увеличении
в исходной
смеси концентрации
компонентов,
отбираемых
в виде кубового
остатка.

Рис. 1.11. Схема
установки для
азеотропной
ректификации:
1-колонна;
2-конденсатор;
3-отстойник;
4-кипятильник
Наиболее
сложной задачей
при использовании
методов экстрактивной
и азеотропной
ректификации
является выбор
разделяющего
компонента,
который должен
удовлетворять
следующим
требованиям:
1) обеспечивать
возможно большее
повышение
коэффициента
относительной
летучести
разделяемых
компонентов;
2) достаточно
легко регенерировать;
3) хорошо растворять
разделяемые
компоненты
для предотвращения
расслаивания
жидкой фазы
при темпе
температурных
условиях в
колонне; 4) быть
безопасным
в обращении,
доступным,
дешевым, термически
стабильным.
Обычно при
выборе разделяющего
агента основываются
на справочных
данных.
Если в
качестве разделяющего
агента используют
растворимые
твердые
вещества, то
такой процесс
разделения
называют солевой
ректификацией.
1.3. Типовое
оборудование
для проектируемой
установки
Для проведения
процессов
ректификации
применяются
аппараты
разнообразных
конструкций,
основные типы
которых не
отличаются
от соответствующих
типов абсорберов.
В ректификационных
установках
используют
главным образом
аппараты двух
типов: насадочные
и тарельчатые
ректификационные
колонны. Кроме
того, для ректификации
под вакуумом
применяют
пленочные и
роторные колонны
различных
конструкций.
Насадочные,
барботажные,
а также некоторые
пленочные
колонны по
конструкции
внутренних
устройств
(тарелок, насадочных
тел и т. д.) аналогичны
абсорбционным
колоннам. Однако
в отличие от
абсорберов
ректификационные
колонны снабжены
теплообменными
устройствами
— кипятильником
(кубом) и дефлегматором.
Кроме того, для
уменьшения
потерь тепла
в окружающую
среду ректификационные
аппараты покрывают
тепловой изоляцией.
Кипятильник
или куб, предназначен
для превращения
в пар части
жидкости, стекающей
из колонны, и
подвода пара
в ее нижнюю
часть (под насадку
или нижнюю
тарелку). Кипятильники
имеют поверхность
нагрева в виде
змеевика или
представляют
собой кожухотрубчатый
теплообменник,
встроенный
в нижнюю часть
колонны (рис.
1.12., а).
Более
удобны для
ремонта и замены
выносные кипятильники
(см. рис. 1.7.), которые
устанавливают
ниже колонны
с тем, чтобы
обеспечить
естественную
циркуляцию
жидкости.
В периодически
действующих
колоннах куб
является не
только испарителем,
но и емкостью
для исходной
смеси. Поэтому
объем куба
должен быть
в 1,3—1,6 раза больше
его единовременной
загрузки (на
одну операцию).
Обогрев кипятильников
наиболее часто
производится
водяным насыщенным
паром.
Дефлегматор,
предназначенный
для конденсации
паров и подачи
орошения (флегмы)
в колонну,
представляет
собой кожухотрубчатый
теплообменник,
в межтрубном
пространстве
которого обычно
конденсируются
пары, а в трубах
движется охлаждающий
агент (вода).
Однако вопрос
о направлении
конденсирующихся
паров и охлаждающего
агента внутрь
или снаружи
труб следует
решать в каждом
конкретном
случае, учитывая
желательность
повышения
коэффициента
теплопередачи
и удобство
очистки поверхности
теплообмена.
В
случае частичной
конденсации
паров в дефлегматоре
его располагают
непосредственно
над колонной
(рис. 1.12., а), чтобы
обеспечить
большую компактность
установки, либо
вне колонны
(см. рис. 1.7.). При
этом конденсат
(флегму) из нижней
части дефлегматора
подают непосредственно
через гидравлический
затвор наверх
колонны, так
как в данном
случае отпадает
необходимость
в делителе
флегмы.
В случае
полной конденсации
паров в дефлегматоре
его устанавливают
выше колонны
(см. рис. 1.7.), непосредственно
на колонне (см.
рис. 1.12., а)
или
ниже
верха колонны
(рис. 1.12., б)
для
того, чтобы
уменьшить общую
высоту установки.
В последнем
случае флегму
из дефлегматора
1 подают в колонну
2 насосом.
Такое размещение
дефлегматора
часто применяют
при установке
ректификационных
колонн вне
зданий, что
более экономично
в условиях
умеренного
климата.
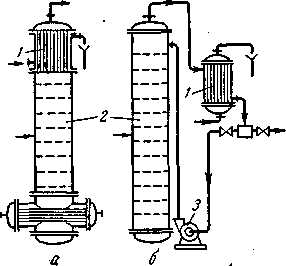
Рис. 1.12.
Варианты установки
дефлегматоров:
а —
на колонне;
б —
ниже верха
колонны;
1 — дефлегматоры;
2 —
колонны;
3 —
насос.
Б а р б о
т а ж н ы е колонны
в процессах
ректификации
наиболее
широко распространены.
Они
применимы для
больших
производительностей,
широкого диапазона
изменений
нагрузок по
пару и жидкости
и могут обеспечить
весьма
четкое разделение
смесей. Недостаток
барботажных
аппаратов—относительно
высокое гидравлическое
сопротивление—в
условиях
ректификации
не имеет такого
существенного
значения, как
в процессах
абсорбции,
где величина
р
связана со
значительными
затратами
энергии на
перемещение
газа через
аппарат. При
ректификации
повышение
гидравлического
сопротивления
приводит лишь
к некоторому
увеличению
давления
и соответственно
к повышению
температуры
кипения жидкости
в кипятильнике
колонны. Однако
тот же недостаток
(значительное
гидравлическое
сопротивление)
сохраняет свое
значение для
процессов
ректификации
под вакуумом.
В н а с
а д о ч н ы х
колоннах (рис.
1.13.) используются
насадки различных
типов, но в
промышленности
наиболее
распространены
колонны с насадкой
из колец Рашига.
Меньшее гидравлическое
сопротивление
насадочных
колонн по сравнению
с барботажными
особенно важно
при
ректификации
под вакуумом.
Даже при значительном
вакууме в верхней
части колонны
вследствие
большого
гидравлического
сопротивления
ее разрежение
в кипятильнике
может оказаться
недостаточным
для требуемого
снижения температуры
кипения исходной
смеси.
Для уменьшения
гидравлического
сопротивления
вакуумных
колонн в них
применяют
насадки с возможно
большим свободным
объемом.
В самой
ректификационной
колонне не
требуется
отводить тепло,
как в абсорберах.
Поэтому трудность
отвода тепла
из насадочных
колонн является
скорее достоинством,
чем недостатком
насадочных
колонн в условиях
процесса
ректификации.
Однако
и при ректификации
следует считаться
с тем, что равномерное
распределение
жидкости по
насадке в колоннах
большого диаметра
затруднено.
В связи с этим
диаметр промышленных
насадочных
ректификационных
колонн обычно
не превышает
0,8—1 м.
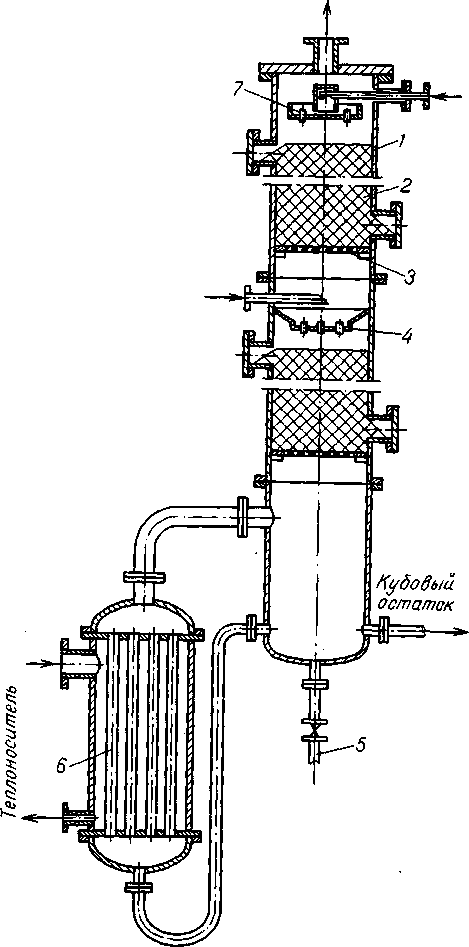
Рис. 1.13.
Насадочная
ректификационная
колонна с
кипятильником
1-корпус;
2-насадка; 3-опорная
решетка;
4-перераспределитель
флегмы; 5-патрубок
для слива кубового
остатка; 6-кипятильник;
7-ороситель.
Как уже
отмечалось,
в насадочных
колоннах поверхностью
контакта фаз
является смоченная
поверхность
н а с а д к
и. Поэтому насадка
должна иметь
возможно большую
поверхность
в единице объема.
Вместе с тем
для того, чтобы
насадка работала
эффективно,
она должна
удовлетворять
следующим
требованиям:
1) хорошо смачиваться
орошающей
жидкостью, т.е.
материал
насадки по
отношению к
орошающей
жидкости должен
быть
лиофильным;
2) оказывать
малое гидравлическое
сопротивление
газовому потоку,
т.е. иметь возможно
большее значение
свободного
объема или
сечения насадки;
3) создавать
возможность
для высоких
нагрузок аппарата
по жидкости
и газу; для этого
насадка должна
также иметь
большие значения
или SCB;
4) иметь малую
плотность;
5) равномерно
распределять
орошающую
жидкость; 6) быть
стойкой к агрессивным
средам; 7) обладать
высокой механической
прочностью;
8) иметь невысокую
стоимость.
Очевидно,
что насадок,
которые бы
полностью
удовлетворяли
всем
указанным
требованиям,
не существует,
так как соответствие
одним требованиям
нарушает соответствие
другим (например,
увеличение
удельной поверхности
а насадки
влечет за собой
повышение
гидравлического
сопротивления,
а также снижение
предельно
допустимых
скоростей газа
и т.д.).
Поэтому
в промышленности
используют
большое число
разнообразных
по форме и размерам
насадок, изготовленных
из различных
материалов
(металла, керамики,
пластических
масс и др.), которые
удовлетворяют
основным требованиям
при проведении
того или иного
процесса
ректификации.
В качестве
насадки наиболее
широко применяют
тонкостенные
кольца
Рашига
(Приложение
1, а), имеющие
высоту, равную
диаметру, который
изменяется
в пределах
15-150 мм. Кольца
малых размеров
засыпают в
колонну навалом.
Большие кольца
(от 50х50 мм и
выше) укладывают
правильными
рядами, сдвинутыми
друг относительно
друга. Такой
способ заполнения
аппарата насадкой
называют
загрузкой в
укладку, а
загруженную
таким способом
насадку - регулярной.
Регулярная
насадка имеет
ряд преимуществ
перед нерегулярной,
навалом засыпанной
в колонну: обладает
меньшим гидравлическим
сопротивлением,
допускает
большие скорости
газа. Однако
регулярная
насадка требует
более сложных
по устройству
оросителей,
чем насадка,
засыпанная
навалом.
Хордовую
насадку
(см.
Приложение
1, б) обычно применяют
в колоннах
большого диаметра.
Несмотря на
простоту ее
изготовления,
хордовая насадка
вследствие
небольших
удельной поверхности
и свободного
сечения вытесняется
более сложными
и дорогостоящими
видами фасонных
насадок, часть
из которых
представлена
в Приложение
1, б. В табл. 1.1. приведены
основные
характеристики
насадок некоторых
типов.
Таблица
1.1. Характеристики
насадок
|
|
Удельная
|
Свобод-
|
Эквивалент-
|
Масса
\
|
Насадка
|
Размеры
элемен-
|
поверхность,
|
ный
|
ный
диаметр,
|
1 м3
на
-
|
|
та,
мм
|
М2/М3
|
объем,
|
м
|
садки,
кг
|
|
|
|
М3/М3
|
|
|
.
Регулярная
насадка
|
Деревянная
хордовая
|
10
|
100
|
0,55
|
0,022
|
210
|
(шаг
в свету
|
20
|
65
|
0,68
|
0,042
|
145
|
10
х 100 мм)
|
|
|
|
|
|
Керамические
кольца
|
50 х
50 х 50
|
НО
|
0,735
|
0,027
|
650 |
Рашига
|
80 х
80 х 8
|
80
|
0,720
|
0,036
|
670 |
|
100
х 100 х 100
|
60
|
0,720
|
0,048
|
670
|
Засыпка
в навал
|
Керамические
кольца
|
15 х
15 х 2
|
330
|
0,700
|
0,009
|
690 |
Рашига
|
25 х
25 х 3
|
200
|
0,740
|
0,015
|
530
|
|
50 х
50 х 5
|
90
|
0,785
|
0,035
|
530
|
Стальные
кольца
|
10 х
10 х 0,5
|
500
|
0,880
|
0,007
|
960
|
Рашига
|
15 х
15 х 0,5
|
350
|
0,920
|
0,009
|
660 |
|
25 х
25 х 0,8
|
220
|
0,920
|
0,017
|
640
|
Керамические
кольца
|
25 х
25 х 3
|
220
|
0,740
|
0,014
|
610 |
Палля
|
50 х
50 х 5
|
120
|
0,780
|
0,026
|
520
|
Стальные
кольца
|
25 х
25 х 0,6
|
235
|
0,900
|
0,01 |
525
|
Палля
|
50 х
50 х 1
|
108
|
0,900
|
0,033
|
415
|
Керамические
седла
|
12,5
|
460
|
0,680
|
0,006
|
720
|
Берля
|
25
|
260
|
0,690
|
0,011
|
670
|
|
38
|
165
|
0,700
|
0,017
|
670 |
При выборе
размеров насадки
необходимо
учитывать, что
с увеличением
размеров ее
элементов
увеличивается
допустимая
скорость газа,
а гидравлическое
сопротивление
насадочной
колонны снижается.
Общая стоимость
колонны с крупной
насадкой будет
ниже за счет
снижения диаметра
колонны, несмотря
на то, что высота
насадки несколько
увеличится
по сравнению
с таковой в
колонне, заполненном
насадкой меньших
размеров.
Если
необходимо
провести глубокое
разделение
газовой смеси,
требующее
большого числа
единиц переноса,
то в этом случае
рациональнее
использовать
мелкую насадку.
При выборе
размера насадки
необходимо
соблюдать
условие, при
котором отношение
диаметра D
колонны
к эквивалентному
диаметру dЭ
насадки
D/dЭ
10.
Пленочные
аппараты.
Эти аппараты
применяются
для ректификации
под
вакуумом смесей,
обладающих
малой термической
стойкостью
при нагревании
(например, различные
мономеры и
полимеры, а
также другие
продукты
органического
синтеза).
В ректификационных
аппаратах
пленочного
типа достигается
низкое гидравлическое
сопротивление.
Кроме того,
задержка жидкости
в единице
объема работающего
аппарата мала.
К числу
пленочных
ректификационных
аппаратов
относятся
колонны с регулярной
насадкой
в виде пакетов
вертикальных
трубок диаметром
6—20 мм
(многотрубчатые
колонны),
а также пакетов
плоскопараллельной
или сотовой
насадки с каналами
различной
формы, изготовленной
из перфорированных
металлических
листов или
металлической
сетки.
Одна из распространенных
конструкций
роторно-пленочных
колонн показана
на рис. 1.14.
Она состоит
из колонны, или
ректификатора
1, снабженного
наружным обогревом
через
паровые рубашки
2 и
ротором 3,
роторного
испарителя
4 и
конденсатора
5. Ротор, представляющий
собой полую
трубу с лопастями,
охлаждаемую
изнутри водой,
вращается
внутри
корпуса колонны.
Исходная
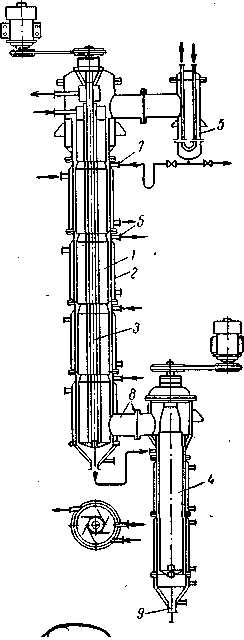
Рис.1.14. Схема
роторно-пленочной
ректификационной
колонны.
1-колонна;
2-рубашка для
обогрева; 3-ротор;
4-роторный
испаритель;
5-конденсатор-дефлегматор;
6-штущер для
ввода исходной
смеси; 7- штуцер
для ввода флегмы;
8-штуцер для
ввода пара;
9-штуцер для
вывода остатка.
смесь
подается в
колонну через
штуцер
6. Сверху
колонна орошается
флегмой, поступающей
из конденсатора
5 через штуцер
7. Пар подается
в колонну через
штуцер 8 из
испарителя
4, снабженного
неохлаждаемым
ротором и
аналогичного
пленочному
выпарному
аппарату. Поднимаясь
в пространстве
между ротором
3 и
корпусом колонны
1, пар конденсируется
на наружной
поверхности
ротора. Образующаяся
пленка конденсата
отбрасывается
под действием
центробежной
силы по поверхности
лопастей ротора
к периферии.
Попадая на
обогреваемую
внутреннюю
поверхность,
жидкость испаряется
и образующийся
пар поднимается
кверху. Таким
конденсационно-испарительным
способом (при
работе вне
адиабатических
условиях) достигается
четкое разделение
смеси при малом
времени ее
пребывания
в аппарате
и незначительном
перепаде давлений
по высоте колонны,
так как большая
часть
внутреннего
пространства
корпуса заполнена
потоком пара.
Роторные
испарители
типа испарителя
4 могут
быть использованы
в качестве
самостоятельных
аппаратов для
вакуумной
дистилляции
смесей, чувствительных
к высоким
температурам.
Недостатки
роторных колонн:
ограниченность
их высоты и
диаметра (из-за
сложности
изготовления
и требований,
предъявляемых
к прочности
и жесткости
ротора), а также
высокие эксплуатационные
расходы.
В случае
загрязненных
сред целесообразно
применять
регулярные
насадки, в том
числе при работе
под повышенным
давлением. Для
этих сред можно
использовать
также так называемые
колонны с
плавающей
насадкой.
В качестве
насадки в таких
колоннах обычно
применяют
легкие полые
шары из пластмассы,
которые при
достаточно
высоких скоростях
газа переходят
во взвешенное
состояние.
Вследствие
их интенсивного
взаимодействия
такая насадка
практически
не загрязняется.
В колоннах
с плавающей
насадкой возможно
создание более
высоких скоростей,
чем в колоннах
с неподвижной
насадкой. При
этом увеличение
скорости газа
приводит к
расширению
слоя шаров, что
способствует
снижению скорости
газа в слое
насадки. Поэтому
существенное
увеличение
скорости газового
потока в таких
аппаратах
(до 3-5 м/с) не приводит
к значительному
возрастанию
их гидравлического
сопротивления.
ПРИЛОЖЕНИЕ
1
Виды
насадок
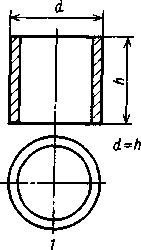
2 3
a.
5
б
а -
насадка
из колец Рашига:
1-отдельное
кольцо; 2-кольца
навалом; 3-регулярная
насадка; б
- фасонная насадка:
1-кольца Палля;
2 -седлообразная
насадка; 3-
кольца
с крестообразными
перегородками;
4 -керамические
блоки; 5-витые
из проволоки
насадки; 6-кольца
с внутренними
спиралями;
7-пропеллерная
насадка; 8-деревянная
хордовая насадка
Б Г ТУ
ФАКУЛЬТЕТ
УТВЕРЖДАЮ
Зав.кафедрой
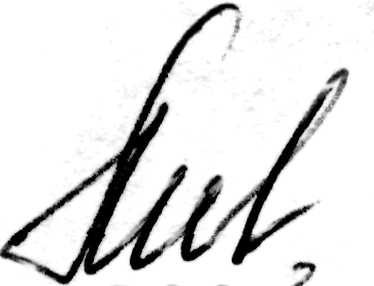
“_______"___________
"
2003 г “
ЗАДАНИЕ
ПО КУРСОВОМУ
ПРОЕКТИРОВАНИЮ
Студенту
Кардашу А. В.
1. Тема
проекта: Рассчитать
и спроектировать
ректификационную
установку
непрерывного
действия
для разделения
бинарной смеси
_______________________________
____________________________
2. Сроки
сдачи cтудентом
законченного
проекта
3. Исходные
данные к проекту:
3.1. Производительность:
______________
по исходной
смеси ___________________
по
дистилляту________________________
по кубовому
остатку_______6000
кг/ч_____
3.2. Содержание
легколетучего
компонента
в:
а) исходной
смеси __0.22____ % Мольные
б) дистилляте_______0.9___
% Мольные
в) кубовом
остатке _0.08____
% Мольные
3.3. Температура
исходной
смеси__35_С______
3.4. Температуры
греющего пара
и охлаждающей
воды во вспомогательном
оборудовании
выбрать самостоятельно.
3.5.Исходная
смесь перед
подачей в колонну
подогревается
в теплообменнике
с использованием
тепла кубового
остатка (паров
флегмы и дистиллята).
3.6. Тип
колонны
______________________
3.7. Тип
контактных
устройств____________
3.S.
Давление вверху
колоны ___________
* - параметры
выбрать самостоятельно
4. Содержание
расчётно-пояснитсльной
записки изложено
на обороте
бланка задания
5. Перечень
графического
материала:
5.1. Схема
установки 1
лист (А1).
5.2. Общий
вид аппарата
с необходимыми
разрезами
сечениями
отдельными
узлами
(по указанию
преподавателя.
А1 )
5.3.
Чертеж
сборочной
единицы, рабочие
чертежи деталей
(А 1. только для
спец.:
Т.05.03.01
МиАХП).
6. Консультанты
по проекту:
Протасов С. К.
7. Дата
выдачи задания
7.09.2003
8. Календарный
график работы
нал проектом:
8.1. Литературный
обзор
24.09.2003
8.2. Обоснование
и описание
установки
1.10.2003
8.3. Подробный
расчёт ректификационной
колонны 29.10.2003
8.4. Подробный
расчет теплообменника
19.11.2003
8.5. Расчёт
и подбор вспомогательного
оборудования
3.12.2003
8.6. Выполнение
графической
части
22.12.2003
8.7. Защита
проекта
РУКОВОДИTЕJIЬ
__Протасов C.
К.___________________
Задание
принял к исполнению
______________________________ « 9 » Сентября
2003 г
Содержание
расчетно-пояснительной
записки
Пояснительная
записка включает:
титульный лист,
задание на
проектирование,
реферат, содержание,
введение,
литературный
обзор, описание
технологической
схемы установки,
расчет основного
аппарата, подробный
расчет одного
из теплообменников,
расчет и подбор
вспомогательного
оборудования,
заключение
и список использованных
источников.
При необходимости
в состав пояснительной
записки включают
список условных
обозначений
и приложения.
Список основных
обозначений
помещают после
содержания,
а приложения
после списка
использованных
источников.
Задание на
проектирование
выдается
руководителем
проекта.
2. Реферат
содержит сведения
об объеме проекта,
перечень ключевых
слов, краткую
аннотацию
материалов
проекта.
3. Содержание
включает перечень
наименований
разделов и
подразделов,
в которых состоит
пояснительная
записка.
4. Во введении
кратко отражаются
роль и перспективы
развития химической
промышленности,
роль технологического
процесса и
назначение
проектируемой
установки.
Объем введения
не должен
превышай, двух
листов.
5. В литературном
обзоре приводится
описание: 1)
теоретических
основ разрабатываемого
процесса; 2) основных
технологических
схем для для
проведения;
3) типового
оборудования
для проектируемой
установки.
По заданию
преподавателя
литературный
обзор может
быть дополнен
патентным
обзором по
современному
аппаратурно-технологическому
оформлению
процесса.
6. Обоснование
и описание
технологической
схемы включают:
обоснование
ее выбора,
обоснование
выбора основного
аппарата и
вспомогательного
оборудования
с кратким описанием
их конструкций
и принципа
действия; подробное
описание принципа
действия
разрабатываемой
установки.
Описание
технологической
схемы завершается
кратким обоснованием
мероприятий
по охране окружающей
среды, т.е. по
предотвращению
и обезвреживанию
вредных промышленных
выбросов.
7. Расчет
основного
аппарата зависит
от его назначения,
типа и конструкции.
Он содержит
технологический
и конструктивный
расчеты по
существующим
методикам.
8. Подробный
расчет теплообменника
включает в себя
как теплотехнический,
так и гидравлический
расчеты.
9. Подбор
вспомогательного
оборудования
(обычно стандартного
и нормализованного)
производится
на основе
ориентировочных
расчетов.
10. В заключение
приводятся
характеристики
установки,
основного
аппарата и
вспомогательного
оборудования.
11. Список
использованных
источников
включает перечень
литературы
и других источников,
использованных
при выполнении
курсового
проекта.
ПРИ ВЫПОЛНЕНИИ
КУPCОВОГО
П РОЕКТА ПО
ВСЕМ ТЕМАМ
РУКОВОДСТВОВАТЬСЯ:
1. Калишук
Д. Г. , Протасов
С.К., Марков В.А.
Процессы и
аппараты химической
технологии.
Методические
указания к
курсовому
проектированию
по одноименной
дисциплине
для студ. очного
и заочного
обучения. - Мн.:
Ротапринт БГТУ,
1992.
2. Основные
процессы и
аппараты химической
технологии.
Пособие по
проектированию
/ Под ред. Ю.И.
Дытнерского.
- М.: Химия, 1991.
Министерство
образования
Республики
Беларусь
Учреждение
образования
: “Белорусский
государственный
технологический
университет”
Кафедра
ПИАХП
Расчётно-пояснительная
записка
К курсовому
проекту по
курсу ПИАХТ
на
тему: Расчёт
и проектирование
ректификационной
установки
непрерывного
действия для
разделения
бинарной смеси
бензол-толуол.
Разработал:
студент
Факультета
ТОВ 4к. 1 гр.
Кардаш
А. В.
Проверил:
Протасов С К
Минск
2003
РЕФЕРАТ
Записка
содержит:
5 – таблиц;
20 - рисунков; 2
приложения;
67 листов.
РЕКТИФИКАЦИЯ,
КОЛОНА, ТАРЕЛКА,
НАСАДКА, ДИСТИЛЯТ,
ФЛЕГМА, НАСОС,
ТЕПЛООБМЕННИК,
ШТУЦЕР, ТРУБОПРОВОД,
ПАР, КОНДЕНСАТ.
В данной
расчетно-пояснительной
записке приведен
тепловой,
материальный,
гидравлический
расчет ректификационной
установки
включающую
в себя теплообменную
аппаратуру,
трубопроводы,
ёмкости для
продуктов
перегонки и
саму колону.
Выполнен также
подбор стандартного
оборудования
и оптимальной
технологической
схемы для проведения
процесса. Проведен
полный гидравлический
и тепловой
расчёт теплообменника
СОДЕРЖАНИЕ
Введение…………………………………………………………………………
|
6 |
1.
Литературный
обзор………………………………………………………… |
7 |
1.1
Теоретические
основы разрабатываемого
проц6есса……………………. |
7 |
1.1.1
Общие сведения
о процессе
ректификации…………..……………
|
7 |
1.1.2
Равновесие
в системах
жидкость-пар……………………………… |
8 |
1.1.3
Материальный
и тепловой
балансы ректификационной
колоны... |
11 |
1.2 Основные
схемы для
проведения
процесса………………………………. |
17
|
1.2.1
Непрерывная
ректификация………………………………………... |
18
|
1.2.2
Периодическая
ректификация……………………………………… |
19
|
1.2.3
Экстрактивная
и азеотропная
ректификация……………………… |
20 |
1.3
Типовое оборудование
для проектируемой
установки…………………..
|
23
|
2.Описание
и обоснование
установки………………………………………… |
29
|
3.Расчёт
ректификационной
колонны……………….…………………………
|
31 |
3.1
Особенности
расчёта тарельчатой
ректификационной
колоны………….
|
31 |
3.1.1
Материальный
баланс колонны
и………………………………….
|
31 |
3.1.2.
Определение
рабочего
флегмового
числа…..…………………….
|
32 |
3.1.3.
Определение
среднемассового
расхода по
жидкости……………. |
35
|
3.1.4. Определение
среднемассового
расхода по
пару…….…………….
|
35
|
3.1.5. Скорость
пара и диаметр
колонны………………………………….
|
36
|
3.2.Определение
высоты
колоны……………………………………………… |
38
|
3.2.1
Определение
высоты колоны
по кинетической
кривой…………..
|
38
|
3.2.2.
Высота светлого
слоя жидкости
на тарелке и
паросодержание
барботажного
слоя……………………………………………………….. |
40 39
|
3.2.3
Определение
коэффициентов
массопередачи……………………..
|
43
|
3.2.4
Определение
эффективности
тарелки……………………………..
|
45
|
3.3.
Расчет гидравлического
сопротивления
тарелок колонны……………..
|
50 |
3.4.
Расчёт
штуцеров…………………………………………………………….
|
51 |
3.5
Тепловой баланс
ректификационной
колоны……………………………..
|
51 |
4.Подробный
расчёт
теплообменника…………………………………………
|
54
|
5.
Расчёт и подбор
вспомогательного
оборудования…………………………
|
58
|
5.1.
Расчёт кожухотрубчатого
испарителя……………………………………..
|
58
|
5.2.
Расчёт теплообменника
подогревателя……………………………………. |
58
|
5.3.
Расчёт кожухотрубчатого
конденсатора
(дефлегматора)………………... |
59
|
5.4.
Расчёт холодильника
дистиллята…………………………………………..
|
60 |
5.5
Выбор насоса
для перекачивания
исходной
смеси………………………. |
60 |
5.6
Определение
высоты
всасывания…………………………………………... |
63
|
Заключение………………………………………………………….……………
|
64
|
Список
использованных
источников…………………………………………..
|
65
|
Приложение
1……………………………………………………………………
|
66
|
Приложение
2……………………………………………………………………
|
67
|
ВВЕДЕНИЕ
На всем протяжении
своего развития
химия служит
человеку в его
практической
деятельности.
Еще задолго
до новой эры
возникли ремесла,
в основе которых
лежали химические
процессы: получение
металлов, стекла,
керамики, красителей.
Роль современной
химии в различных
отраслях
промышленности
и сельского
хозяйства
исключительно
велика. Без
развития химии
невозможно
развитие
топливно-энергетического
комплекса,
металлургии,
транспорта,
связи, строительства,
электроники,
сферы быта и
услуг и т. д.
Химическая
индустрия
снабжает народное
хозяйство
различными
материалами
и сырьем. Это
кислоты, щелочи,
растворители,
топливо, масла,
пластмассы,
химические
волокна, синтетические
каучуки, минеральные
удобрения и
многие другие.
В различных
отраслях
промышленности
используются
химические
методы, например
катализ (ускорение
процессов),
защита металлов
от коррозии,
обработка
деталей химическим
способом.
Исключительно
большое значение
химия имеет
в энергетике,
которая использует
энергию химических
реакций. В связи
с истощением
природных
запасов нефти
возрастает
потребление
синтетического
топлива, которое
вырабатывает
химическая
индустрия.
Существенной
экономии нефти
позволяет
достичь внедрение
новых процессов
получения
жидкого топлива
из бурого и
каменного угля.
Таким образом,
химической
и нефтехимической
промышленности
отводится
важная роль
в реализации
энергетической
программы РБ.
Современная
химическая
промышленность
характеризуется
весьма большим
числом разнообразных
производств,
различающихся
условиями
протекания
технологических
процессов и
многообразием
физико-химических
свойств перерабатываемых
веществ и выпускаемой
продукции.
Вместе с тем
технологические
процессы различных
производств
представляют
собой комбинацию
сравнительно
небольшого
числа типовых
процессов
(нагревание,
охлаждение,
фильтрование
и т. д.). За последние
десятилетия
развитие химической
технологии
привело к появлению
принципиально
новых процессов,
что поставило
химическую
технологию
на качественно
более высокий
уровень. В этом
отношении
весьма перспективным
является бурное
развитие
вычислительной
техники, которая
создает невиданные
до недавнего
времени возможности
для исследования,
моделирования
и расчета процессов
и аппаратов
химической
технологии.
Ректификация
— массообменный
процесс, который
осуществляется
в большинстве
случаев в
противоточных
колонных аппаратах
с контактными
элементами
(насадки тарелки)
аналогичными
используемым
в процессе
абсорбции.
Ректификационная
установка даёт
наиболее полное
разделение
смесей жидкостей,
целиком или
частично растворимых
друг в друге.
Процесс заключается
в многократном
взаимодействии
паров с жидкостью
- флегмой, полученной
при частичной
конденсации
паров.
2.ОПИСАНИЕ
И ОБОСНОВАНИЕ
УСТАНОВКИ
Для разделения
смеси толуол
– бензол, применяется
ректификационное
разделение.
Процесс разделения
требуется
проводить
непрерывным
способом. Так
как нам не известны
предыдущие
стадии процесса,
то перед подачей
на колонну
необходимо
предусмотреть
накопительный
бак, который
будет обеспечивать
непрерывную
подачу смеси
на ректификационную
колонну в случае
сбоев на предыдущих
этапах производства,
так как эти
сбои могут
привести к
остановке
колонны. По
этой же причине
необходимо
предусмотреть
два нагнетательных
насоса, передающих
исходную смесь
с накопительного
бака, через
теплообменники
на ректификацию
(на случай выхода
одного из них
из строя). Для
возможности
очистки накопительного
бака, предусматривается
отвод в канализацию
из последнего
предусматривается
отвод в канализацию
для воды.
Питание
требуется
подавать в
колонну при
температуре
кипения, для
этого необходимо
подогреть его.
С этой целью
перед подачей
на колонну
устанавливается
теплообменник.
Так как исходная
смесь толуол
– бензол кипит
при температуре
99 С, то для подогрева,
с целью экономии
греющего пара,
целесообразно
использовать
тепло кубового
остатка. Для
отвода конденсата
предусматриваем
отдельную
канализационную
систему, позволяющую
возвращать
конденсат
обратно на
парогенерацию.
В колонне исходная
смесь разделяется
на два потока:
толуол содержащий
и бензол, отбираемых
соответственно
с нижней и верхней
частей колонны.
толуол как
более труднолетучий
компонент,
собирается
внизу (в кубовой
части) колонны,
а бензол как
легколетучий
компонент в
верхней части
колонны. Для
обеспечения
потока пара
через колонну,
устанавливается
кипятильник
кубового остатка.
Часть кубового
остатка в виде
продукта отводится
и собирается
в бак. Целесообразно
предусмотреть
установку
сборных баков,
как для толуола,
так и для бензола,
т.к. не известно
по технологической
линии, куда
направляются
продукты
ректификации.
Для транспортировки
по дальнейшей
технологической
линии продуктов,
из сборных
баков продукта
транспортируются
насосами. Перед
подачей бензола
в сборную ёмкость
его необходимо
охладить, что
осуществляется
также при помощи
теплообменников.
В целях экономии
энергии, рационально
использовать
тепло кубового
остатка для
нагревания
питания. При
этом также
уменьшается
количество
теплообменников,
если этого
тепла достаточно,
чтобы нагреть
питание до
температуры
кипения, или
уменьшается
поверхность
теплообменника
при использовании
дополнительного
подогрева с
помощью греющего
пара. Для образования
флегмы пары,
содержащие
преимущественно
легколетучий
компонент,
конденсируют
в теплообменнике-дефлегматоре,
и разделяют
на отводимый
в виде продукта
поток и на поток,
возвращаемый
как флегму
обратно в колонну.
Так как в
дефлегматоре
продукт только
конденсируется,
но не охлаждается,
то перед подачей
в сборную ёмкость
его необходимо
охладить. Охлаждение
продукта в
теплообменнике
и дефлегматоре
осуществляется
с помощью воды,
как наиболее
дешевого
теплоносителя.
Для оборотной
вода после
выхода из
теплообменников
и отвода предусматриваем
отдельную
канализационную
систему, для
возможности
раздельного
направления
на регенерацию.
Для сборных
ёмкостей продуктов
также устанавливаем
отвода для
промывных вод.
Так как в
технологическом
процессе используются
легко текучие
и чистые жидкости
с не большим
расходом, то
используем
центробежные
насосы. В качестве
теплообменников
используем
кожухотрубчатые
теплообменники
как наиболее
распространённые
и вполне подходящие
для реализации
нашей технологической
схемы. Технологическая
схема приведена
на чертеже.
Министерство
образования
Республики
Беларусь
Учреждение
образования
: “Белорусский
государственный
технологический
университет”
Кафедра
ПИАХТ
Пояснительная
записка
К курсовому
проекту по
курсу ПИАХТ
Тема:
Непрерывная
ректификация
Разработал:
студент
Факультета
ТОВ 4к. 1 гр.
Кардаш
А. В.
Проверил:
Протасов С К
Минск
2003
РЕФЕРАТ
РЕКТИФИКАЦИЯ,
КОЛОНА, ТАРЕЛКА,
НАСАДКА, ДИСТИЛЯТ,
ФЛЕГМА, НАСОС,
ТЕПЛООБМЕННИК,
ШТУЦЕР, ТРУБОПРОВОД,
ПАР, КОНДЕНСАТ.
В данной
расчетно-пояснительной
записке приведен
тепловой,
материальный,
гидравлический
расчет ректификационной
установки
включающую
в себя теплообменную
аппаратуру,
трубопроводы,
ёмкости для
продуктов
перегонки и
саму колону.
Выполнен также
подбор стандартного
оборудования
и оптимальной
технологической
схемы для проведения
процесса. Проведен
гидравлический
и тепловой
расчёт теплообменника
Записка
содержит:
5 – таблиц;
20
- рисунков;
2 приложения;
67 листов.
СОДЕРЖАНИЕ
Реферат
………………………………………………………………………….
|
2 |
Введение…………………………………………………………………………
|
6 |
1.
Литературный
обзор………………………………………………………… |
7 |
1.1
Теоретические
основы разрабатываемого
проц6есса……………………. |
7 |
1.1.1
Общие сведения
о процессе
ректификации…………..……………
|
7 |
1.1.2
Равновесие
в системах
жидкость-пар……………………………… |
8 |
1.1.3
Материальный
и тепловой
балансы ректификационной
колоны... |
11 |
1.2 Основные
схемы для
проведения
процесса………………………………. |
17
|
1.2.1
Непрерывная
ректификация………………………………………... |
18
|
1.2.2
Периодическая
ректификация……………………………………… |
19
|
1.2.3
Экстрактивная
и азеотропная
ректификация……………………… |
20 |
1.3
Типовое оборудование
для проектируемой
установки…………………..
|
23
|
2.Описание
и обоснование
установки………………………………………… |
29
|
3.Расчёт
ректификационной
колонны……………….…………………………
|
31 |
3.1
Особенности
расчёта тарельчатой
ректификационной
колоны………….
|
31 |
3.1.1
Материальный
баланс колонны
и………………………………….
|
31 |
3.1.2.
Определение
рабочего
флегмового
числа…..…………………….
|
32 |
3.1.3.
Определение
среднемассового
расхода по
жидкости……………. |
35
|
3.1.4. Определение
среднемассового
расхода по
пару…….…………….
|
35
|
3.1.5. Скорость
пара и диаметр
колонны………………………………….
|
36
|
3.2.Определение
высоты
колоны………………………………………………
|
38
|
3.2.1
Определение
высоты колоны
по кинетической
кривой…………..
|
38
|
3.2.2.
Высота светлого
слоя жидкости
на тарелке и
паросодержание
барботажного
слоя……………………………………………………….. |
40 39
|
3.2.3
Определение
коэффициентов
массопередачи……………………..
|
43
|
3.2.4
Определение
эффективности
тарелки……………………………..
|
45
|
3.3.
Расчет гидравлического
сопротивления
тарелок колонны……………..
|
50 |
3.4.
Расчёт
штуцеров…………………………………………………………….
|
51 |
3.5
Тепловой баланс
ректификационной
колоны……………………………..
|
51 |
4.Подробный
расчёт
теплообменника…………………………………………
|
54
|
5.
Расчёт и подбор
вспомогательного
оборудования…………………………
|
58
|
5.1.
Расчёт кожухотрубчатого
испарителя……………………………………..
|
58
|
5.2.
Расчёт теплообменника
подогревателя……………………………………. |
58
|
5.3.
Расчёт кожухотрубчатого
конденсатора
(дефлегматора)………………... |
59
|
5.4.
Расчёт холодильника
дистиллята…………………………………………..
|
60 |
5.5
Выбор насоса
для перекачивания
исходной
смеси………………………. |
60 |
5.6
Определение
высоты
всасывания…………………………………………... |
63
|
Заключение………………………………………………………….……………
|
64
|
Список
использованных
источников…………………………………………..
|
65
|
Приложение
1……………………………………………………………………
|
66
|
Приложение
2……………………………………………………………………
|
67
|
ВВЕДЕНИЕ
На всем протяжении
своего развития
химия служит
человеку в его
практической
деятельности.
Еще задолго
до новой эры
возникли ремесла,
в основе которых
лежали химические
процессы: получение
металлов, стекла,
керамики, красителей.
Роль современной
химии в различных
отраслях
промышленности
и сельского
хозяйства
исключительно
велика. Без
развития химии
невозможно
развитие
топливно-энергетического
комплекса,
металлургии,
транспорта,
связи, строительства,
электроники,
сферы быта и
услуг и т. д.
Химическая
индустрия
снабжает народное
хозяйство
различными
материалами
и сырьем. Это
кислоты, щелочи,
растворители,
топливо, масла,
пластмассы,
химические
волокна, синтетические
каучуки, минеральные
удобрения и
многие другие.
В различных
отраслях
промышленности
используются
химические
методы, например
катализ (ускорение
процессов),
защита металлов
от коррозии,
обработка
деталей химическим
способом.
Исключительно
большое значение
химия имеет
в энергетике,
которая использует
энергию химических
реакций. В связи
с истощением
природных
запасов нефти
возрастает
потребление
синтетического
топлива, которое
вырабатывает
химическая
индустрия.
Существенной
экономии нефти
позволяет
достичь внедрение
новых процессов
получения
жидкого топлива
из бурого и
каменного угля.
Таким образом,
химической
и нефтехимической
промышленности
отводится
важная роль
в реализации
энергетической
программы РБ.
Современная
химическая
промышленность
характеризуется
весьма большим
числом разнообразных
производств,
различающихся
условиями
протекания
технологических
процессов и
многообразием
физико-химических
свойств перерабатываемых
веществ и выпускаемой
продукции.
Вместе с тем
технологические
процессы различных
производств
представляют
собой комбинацию
сравнительно
небольшого
числа типовых
процессов
(нагревание,
охлаждение,
фильтрование
и т. д.). За последние
десятилетия
развитие химической
технологии
привело к появлению
принципиально
новых процессов,
что поставило
химическую
технологию
на качественно
более высокий
уровень. В этом
отношении
весьма перспективным
является бурное
развитие
вычислительной
техники, которая
создает невиданные
до недавнего
времени возможности
для исследования,
моделирования
и расчета процессов
и аппаратов
химической
технологии.
Ректификация
— массообменный
процесс, который
осуществляется
в большинстве
случаев в
противоточных
колонных аппаратах
с контактными
элементами
(насадки тарелки)
аналогичными
используемым
в процессе
абсорбции.
Ректификационная
установка даёт
наиболее полное
разделение
смесей жидкостей,
целиком или
частично растворимых
друг в друге.
Процесс заключается
в многократном
взаимодействии
паров с жидкостью
- флегмой, полученной
при частичной
конденсации
паров.
2.ОПИСАНИЕ
И ОБОСНОВАНИЕ
УСТАНОВКИ
Для разделения
смеси толуол
– бензол, применяется
ректификационное
разделение.
Процесс разделения
требуется
проводить
непрерывным
способом. Так
как нам не известны
предыдущие
стадии процесса,
то перед подачей
на колонну
необходимо
предусмотреть
накопительный
бак, который
будет обеспечивать
непрерывную
подачу смеси
на ректификационную
колонну в случае
сбоев на предыдущих
этапах производства,
так как эти
сбои могут
привести к
остановке
колонны. По
этой же причине
необходимо
предусмотреть
два нагнетательных
насоса, передающих
исходную смесь
с накопительного
бака, через
теплообменники
на ректификацию
(на случай выхода
одного из них
из строя). Для
возможности
очистки накопительного
бака, предусматривается
отвод в канализацию
из последнего
предусматривается
отвод в канализацию
для воды.
Питание
требуется
подавать в
колонну при
температуре
кипения, для
этого необходимо
подогреть его.
С этой целью
перед подачей
на колонну
устанавливается
теплообменник.
Так как исходная
смесь толуол
– бензол кипит
при температуре
99 С, то для подогрева,
с целью экономии
греющего пара,
целесообразно
использовать
тепло кубового
остатка. Для
отвода конденсата
предусматриваем
отдельную
канализационную
систему, позволяющую
возвращать
конденсат
обратно на
парогенерацию.
В колонне исходная
смесь разделяется
на два потока:
толуол содержащий
и бензол, отбираемых
соответственно
с нижней и верхней
частей колонны.
толуол как
более труднолетучий
компонент,
собирается
внизу (в кубовой
части) колонны,
а бензол как
легколетучий
компонент в
верхней части
колонны. Для
обеспечения
потока пара
через колонну,
устанавливается
кипятильник
кубового остатка.
Часть кубового
остатка в виде
продукта отводится
и собирается
в бак. Целесообразно
предусмотреть
установку
сборных баков,
как для толуола,
так и для бензола,
т.к. не известно
по технологической
линии, куда
направляются
продукты
ректификации.
Для транспортировки
по дальнейшей
технологической
линии продуктов,
из сборных
баков продукта
транспортируются
насосами. Перед
подачей бензола
в сборную ёмкость
его необходимо
охладить, что
осуществляется
также при помощи
теплообменников.
В целях экономии
энергии, рационально
использовать
тепло кубового
остатка для
нагревания
питания. При
этом также
уменьшается
количество
теплообменников,
если этого
тепла достаточно,
чтобы нагреть
питание до
температуры
кипения, или
уменьшается
поверхность
теплообменника
при использовании
дополнительного
подогрева с
помощью греющего
пара. Для образования
флегмы пары,
содержащие
преимущественно
легколетучий
компонент,
конденсируют
в теплообменнике-дефлегматоре,
и разделяют
на отводимый
в виде продукта
поток и на поток,
возвращаемый
как флегму
обратно в колонну.
Так как в
дефлегматоре
продукт только
конденсируется,
но не охлаждается,
то перед подачей
в сборную ёмкость
его необходимо
охладить. Охлаждение
продукта в
теплообменнике
и дефлегматоре
осуществляется
с помощью воды,
как наиболее
дешевого
теплоносителя.
Для оборотной
вода после
выхода из
теплообменников
и отвода предусматриваем
отдельную
канализационную
систему, для
возможности
раздельного
направления
на регенерацию.
Для сборных
ёмкостей продуктов
также устанавливаем
отвода для
промывных вод.
Так как в
технологическом
процессе используются
легко текучие
и чистые жидкости
с не большим
расходом, то
используем
центробежные
насосы. В качестве
теплообменников
используем
кожухотрубчатые
теплообменники
как наиболее
распространённые
и вполне подходящие
для реализации
нашей технологической
схемы. Технологическая
схема приведена
на чертеже. |