Строительные композиты на основе минеральных техногенных заполнителей
Р.Г. Еромасов*, Э.М. Никифорова, Е.Д. Кравцова, Ю.Е. Спектор
Сибирский федеральный университет
В настоящее время отсутствует системный подход к процессам получения облицовочных керамических материалов на базе природного и техногенного сырья, базирующегося на установлении критериев формирования структуры, прогнозирования и направленного регулирования состава керамических материалов и технологических процессов их получения. В статье представлены результаты исследований по оптимизации зернового состава кремнеземистых техногенных продуктов для получения облицовочных керамических материалов с направленно регулируемыми эксплуатационными свойствами. Описана модель облицовочного керамического композиционного материала на базе наполнителя из зерен кварца. Выявлен оптимальный зерновой состав кремнеземистых отходов для регулирования плотности упаковки керамических масс на стадии подготовки сырья, формования и обжига.
Введение
Значительным резервом управления эксплуатационными характеристиками керамических облицовочных материалов является направленное регулирование процесса формирования структуры спеченной керамики. Основа разработки научного подхода к формированию плотных упаковок керамических облицовочных материалов - моделирование различных вариантов структур облицовочных композиционных материалов из многокомпонентных смесей.
Исследование моделей создания укладок, эффективно снижающих пустотность, базируется на принципе формирования структур различных типов, основанных как на заполнении объема зернами всех размеров, так и при отсутствии зерен промежуточных размеров между зернами заданных фракций. При этом показателем степени упаковки керамического порошка принято соотношение твердой составляющей и пустоты в единице объема с учетом зависимости степени уплотнения от свойств порошка, размеров частиц, его составляющих [1].
Методика исследований
Подготовку и измельчение исходных сырьевых материалов осуществляли на щековой дробилке ЩД-6 и кольцевой мельнице ROCKLABS. Фракционирование сырьевых материалов проведено на ситовом анализаторе ВПТ 220. Металлографическое исследование спеченных материалов осуществлено на микроскопе Axio observer. Alm. Оптимизация фракционного состава керамической шихты проведена методом симплекс-решетчатого планирования с математической обработкй экспериментальных данных в программе «Статистика».
Результаты исследований и их обсуждение
Исходным сырьем для проведения исследований стала тугоплавкая глина Компановско- го месторождения, а также техногенные продукты в виде стеклобоя, кварц-полевошпатовых флотационных отходов обогащения Сорского молибденового комбината, высококварцевой (до 90 масс. % SiO2CB) горелой формовочной земли - отхода литейного производства машиностроительных предприятий.
Разработанная модель облицовочного композиционного материала на базе высококремнеземистого сырья может быть представлена в следующем виде. В качестве заполнителя композита выступает свободный оксид кремния, источником которого являются техногенные продукты: кварц-полевошпатовый сорский песок и горелая земля, а также крупнозернистые кремнеземистые примеси из глинистого компонента. Крупные зерна кварца составляют практически неизменяемый скелет, или «наполнитель», мало вовлекаемый в физико-химические процессы. Наличие скелета из крупных зерен кварца, преобладающего в керамических массах, предопределяет возможность получения облицовочных материалов с незначительными объемными изменениями при обжиге и связанными с этим малыми внутренними напряжениями и деформациями. Роль связующей матрицы выполняют плавни из кварц-полевошпатового сор- ского песка, стеклобой, а также глинистые минералы. Многочисленные исследования упаковки зерен одинакового размера, близких по форме к сферическим, показали фактический объем в 58-63 %, занятый зернами [2, 3]. Принцип достижения наиплотнейшей упаковки высококремнеземистых облицовочных масс базировался на достижении строго определенных соотношений отдельных фракций и размеров исходного зерна. В работе реализовывался принцип подбора так называемой прерывной укладки, при которой между зернами заданных фракций зерна промежуточных размеров отсутствуют. В соответствии с представлениями зерна самой крупной фракции образуют скелет, пустоты которого заполняются следующей фракцией. Новые пустоты могут заполняться третьей фракцией и т.д. На рис. 1 а изображена модель упаковки двухфракционной системы: отход (-0,315+0,08 мм) - глина, стеклобой (-0,056 мм и менее). Из рисунка видно, что реализуется принцип наиболее плотной упаковки, зерна мелкой фракции заполняют пустоты между зернами более крупной фракции. На рис. 1 б изображена модель упаковки двухфракционной системы: отход (-0,08+0,056 мм) - глина, стеклобой (-0,056 мм и менее); принцип наиболее плотной упаковки реализуется в меньшей степени ввиду недостаточной разницы между размерами двух фракций. На рис. 1 в - модель упаковки однофракционной системы: отход, глина, стеклобой (-0,056 мм), принцип наиболее плотной упаковки не выполняется. Рисунок 1 г показывает наибольший эффект уплотнения с использованием трехфракционной системы с «прерывной» укладкой, соответствующей содержанию фракций
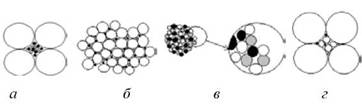
Рис. 1. Модель упаковки структуры: - отход; * - глина; О - стеклобой
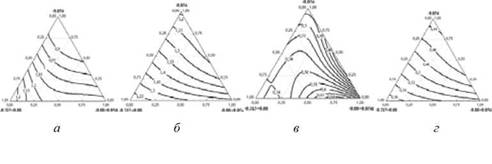
Рис. 2. Проекции линий, равных значений: насыпнойплотности (а), плотности утряски шихты (б), Ктв горелой земли (в) и Ктв шихты на основе горелой земли (а), на трехкомпонентный симплекс
(масс. %): отход фр. (-0,315+0,08 мм)-36, отход фр. (-0,08+0,056 мм)-19, глина, стеклобой фр. (-0,056 мм и менее)-45. Выбор прерывной укладки базировался на извеслных представлениях возможности достижения при ней большей плотно сти упаковки. Вариант «непрерывной» укладкл доя реализации в кремнеземистыл облицовочных массах признан неперспективным ввиду невозможности получения задаиного соотношения фракций, обеспечивающих максимальную плотность укладки порошка бее рассевь и пофракционной дозировки.
Оптимизацию фракционного состава проводили на фиксированном составе шихты, соответствующем соотношению ко мпонентов (масс. %): глина - 20; кварцсодержащие отходы - 55; стеклобо й - 25. Для оптзмизаць и фракционного со става гореиой земли реализован с имплекс- решетчатый план третьего порядке для трехкомпонентной смеси. Выбор факторов осуществляли с учетом рекомендкции пл достижению наиболее плотной упакооки сзрессьванных керамических масс. Были исследованы следующие факторы: содержание фр. -0,3У5 + 0,еь мм (х1С; содеежание фр. -0,08 + 0,С56 мм (х2); содержание фр. менее -0,Ь56 мм (х3). Результаты оптимизации фракционного состава отходов для получения максимальной плотности утряски кремнеземистого скелета и шихты на его основе с добавлением глины и стеклобоя, а также достижения максимальной плотно сти обожженных образцов представлены на рис. 2.
Анализ данных риз. 2 свидезельствует, что диопазон достигнутой плотности утряски шинты на ллнове горелой формовочной земли сеставляет от 1,2 до 1,55 г/см 3. Пе сравнению с чистой годесой землей максимальная плотность утряски снизилась с 1,7 до 1,55 г/см 3, что объясняется наличием мелкой (фр. менее 0,056 мм) фракции глины и стеклобоя. Максимальная плотность утряски достигается при использовании крупной монофракции горелой формовочной земли х1 = -0,315+0,08 мм - 100 масс. %. Для интерпретации результатов степень упаковки выразили через безразмерный коэффициент Ктв, характеризующий долю объема в системе, за-
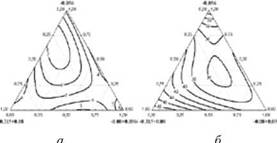
Рис. 3. Проекции лииий равных значений: водопоглошанию(а) и прочности (б) обожженных образцов шихты на основе горелой земли, на трехкомпонентный симплекс
нятую твердым веществом [2, 3]. Этот коэффициент численно равен отношению плотности р (кажущейся, насыпной и т.д.) к истинной плотности твердого вещества утв. Диапазон достигнутой плотности упаковки зернистого каркаса из горелой земли составляет от 0,46 до 0,64. При этом достижение максимального коэффициента упако вки достигается при использовании двухфракционной системы -0 ,315+0,08 мм - 70-80 масс. % и фракции -0,08+0,056 мм - 20-30 масс. %. Достижение максимально плотной упаковас непластичных кремнеземистых облицовочных масс на основе преимущественно кру пной фрткции гартлой земли подтварждает и одновременно расширяет уже существующие представления о достижении плотной укладки в глинистых системах. Несколько иная картина достижения максимально возможной плотности упаковки наблюдается для шихты, имеющий помимо кварц-содержащих отходов мелкую (менее 0 ,056 мм) фракцию глины и стеклобоя при суммарном ее количестве в шихте 45 масс. %. Существенное увеличение содержания мелкой фракции в шихте приводит к значительному снижению плотности упаковки шихты. Наблюдаемые закономерности объясняются вполне известным механизмом ебразования частицами малых размерон тыхлых коагпляционных структур в виде Цеспорядочныа сеток, препятствующих плотной упаковке частиц. Результаты оптимизации фракционного состава отходов для достижения максимальной прочности обожженных образцов и их минимального водопоглощения представлены на рис. 3.
Диапазон достигнутой прочности обожженных образцов на основе горелой земли составляет от 32 до 48 МПа. При этом достижение максимальных значений прочности происходит при использовании как крупной монофракции горелой земли, так и двухфракционной системы -0,315+0,08 мм - 70-80 масс. % и фракции -0,056 мм - 20-30 масс. %. Граничным пределом максимального водопоглощения выбрано его значение, соответствующее 5 % (требования стандарта). Достижение заданного показателя возможно в достаточно широких областях, представленных на экспериментальном симплексе. Наиболее предпочтительным является использование двухфракционного состава горелой земли в следующем соотношении: фракция х1 - 55-60 масс. % и х3 - 40-45 масс. %.
Заключение
На базе разработанной модели композиционного облицовочного материала с кварцевым скелетом и предложенного метода осуществления в нем наиболее плотной упаковки выявлены закономерности взаимосвязи величины коэффициента упаковки Ктв кварцевого скелета, керамической шихты в целом и эксплуатационных свойств спеченных образцов в зависимости от соотношения фракций определенного размера, взятых в оптимальных пределах.
Список литературы
Патент № 2431625 РФ Способ изготовления облицовочной керамики / Р.Г. Еромасов,
Э.М. Никифорова. Заявл. 26.04.2010; опубл. 20.10.2011, Бюл. № 21.
Кондратенко В.А. Керамические стеновые материалы: оптимизация их физикотехнических свойств и технологических параметров производства. М.: Композит, 2005. 508 с.
Патент № 2420484 РФ Керамическая масса / Э.М. Никифорова, Р.Г. Еромасов. Заявл. 01.02.2010; опубл. 10.06.2011, Бюл. № 16.
Патент № 2422399 РФ Керамическая масса / Э.М. Никифорова, Р.Г. Еромасов. Заявл. 05.02.2010; опубл. 27.06.2011, Бюл. № 18.
Патент № 2426706 РФ Смесь для изготовления теплоизоляции / Э.М. Никифорова, Р.Г. Еромасов. Заявл. 05.02.2010; опубл. 20.08.2011, Бюл. № 23.
Пивинский Ю.Е. Керамические и огнеупорные материалы. СПб.: Стройиздат2003. Т1. 686 с.
|