(Лекции)
ВВЕДЕНИЕ
Установки, в которых происходит превращение электрической энергии в другие виды с одновременным осуществлением технологических процессов, называют электротехнологическими. Эти установки имеют довольно сложное оборудование, включающее в себя рабочий орган - плазмотрон, плазменный реактор, электронную пушку, электродные системы дуговых и ионных агрегатов, специфические источники питания, автоматически поддерживающие заданный режим работы или управляемые с помощью микропроцессорной техники. В состав вспомогательного оборудования входят системы обеспечения водой, газом, создания и поддержания вакуума и др. Правильные монтаж, наладка и эксплуатация оборудования без знания выполняемого им технологического процесса затруднительны.
Производственная деятельность человека и его быт стремительно насыща- ются электротехнологическими установками. Развитие электротехнологических процессов обеспечивается развивающейся энергетикой страны, строительством новых атомных и тепловых электростанций, сооружением мощных линий электропередач.
Совершенствование электротехнологии повлекло за собой создание мате- риалов, обладающих новыми свойствами: более высокими прочностью, термо- стойкостью, устойчивостью к агрессивному действию химических реакций, и имеющих высокие электроизоляционные свойства и низкую теплопроводность. промышленности и науки достигнуты благодаря применению электротехнологи- ческих процессов.
Если бы эти системы монтировались из компонентов, выпускаемых по технологии, которая была 30-40 лет тому назад, то масса таких устройств достигла десятков тонн, объем - десятков кубометров, потребляемая мощность - сотен киловатт.
.
Входящие в микросхему элементы (транзисторы, диоды, конденсаторы, резисторы и др.) не имеют внешних выводов, а вся микросхема имеет общую герметизацию, защиту от механических повреждений, влияний окружающей среды и входит в состав комплексов. Поэтому стали привычными миниатюрные наручные часы, многофункциональные, снабженные микрокалькулятором, микротелевизором; малогабаритные цветные телевизоры и ЭВМ, обладающие огромным быстродействием и памятью.
Благодаря внедрению контактной сварки достигнут высокий уровень механизации сборочных работ в автомобильной промышленности и авиастроении, обеспечивающий высокую скорость изготовления транспортных средств. В получении высококачественных металлов исключительно важна роль электрошлакового переплава.
На основе явлений поляризации диэлектриков, электромагнитной индукции разработаны такие прогрессивные электротехнологические процессы, как высокочастотная сушка сыпучих и пористых неэлектропроводных материалов, индукционный нагрев и плавка ме- таллов, превратившиеся в настоящее время в базовые технологические процессы.
Как известно, вещество может находиться в четырех агрегатных состояниях - твердом, жидком, газообразном и плазменном.
Твердое состояние - проводники, полупроводники и диэлектрики, металлы и неметаллы, кристаллические и аморфные вещества.
Жидкое состояние - проводники (расплавы металлов, солей, щелочей, оксидов), диэлектрики (минеральные и органические), особая разновидность - жидкие кристаллы.
Газообразное состояние - сложные активные вещества.
Плазменное состояние - электропроводная среда, позволяющая проводить обменные реакции и транспортные процессы на ионном уровне, быть источником лучистой энергии и средством нагрева веществ.
Посредством электрических и магнитных полей с веществом, находящимся в каждом из агрегатных состояний, можно совершать бесчисленное мно- жество операций - изменение температуры, формы, структуры, состава, свойств в разных направлениях и т. д.
Их группируют по результирующему действию электрического тока и магнитного поля, проявляющемуся в различных условиях.
1. Установки, основанные на тепловом действии тока
. К ним относят бытовые нагревательные приборы, печи сопротивления прямого и косвенного действия, установки для нагрева жидкостей и газов - электрические котлы разных типов и калориферы. Установки электрошлакового переплава металлов и электрошлаковой сварки используют явление выделения тепловой энергии преимущественно в шлаке, заполняющем пространство между электродами. В установках контактной сварки электрическая энергия преобразуется в тепловую в переходном сопротивлении в точке контакта двух деталей.
В установках индукционного нагрева используется преобразование энергии переменного тока промышленной или повышенной частоты в энергию переменного магнитного поля, которая преобразуется вновь в электрическую, а затем в тепловую в нагреваемом теле. Этот способ применим для нагрева проводящих тел.
Для нагрева диэлектриков применяются установки, использующие высокочастотное электрическое поле, где преобразование электрической энергии в тепловую идет через процессы поляризации веществ.
Установки, принцип действия которых основан на нагреве электрической дугой, включают в себя электродуговые и рудно-термические печи для выплавки металлов, огнеупоров, получения фосфора и других материалов, а также вакуумно-дуговые печи для переплава и рафинирования металла. Сюда же относятся установки плазменной и плазмодуговой обработки металлов и неметаллических материалов, которыми производят переплав металлов, нанесение защитных покрытий, наплавку и другие операции.
В установках электроэрозионной обработки тепловая энергия выделяется в канале разряда в жидкости при импульсном протекании тока большой силы.
2. Установки, основанные на электрохимическом действии тока
. К ним относят электролизные ванны, заполняемые растворами или расплавами, установки для нанесения защитных и декоративных покрытий, а также установки для изготовления изделий методом гальванопластики, установки электрохимикомеханической обработки изделий в электролитах.
3. Электромеханические установки
, где прохождение импульсного тока вызывает возникновение механических усилий в обрабатываемом материале. Особый класс составляют установки ультразвукового воздействия, осуществ- ляющие технологический процесс путем создания в веществе механических колебаний высокой частоты, получаемых от ультразвуковых генераторов.
4. Электрокинетические установки
, принцип действия которых основан на преобразовании энергии электрического поля в энергию движущихся частиц. К ним относят установки электронно-ионной технологии - электрофильтры, установки по разделению сыпучих материалов и эмульсий, очистке сточных вод, электроокраске.
ЭЛЕКТРОТЕРМИЧЕСКИЕ ПРОЦЕССЫ И УСТАНОВКИ ФИЗИКО-ТЕХНИЧЕСКИЕ ОСНОВЫ ЭЛЕКТРОТЕРМИИ 1.1. Электротермические установки и области их применения
Понятие «электротермия» объединяет большой класс технологических процессов в различных отраслях промышленности, основой которых служит нагрев материалов и изделий с помощью электрической энергии. Применение электронагрева вместо пламенного в некоторых технологических процессах позволяет получить большую экономию топлива и сократить обслуживающий персонал.
В электротермии можно выделить следующие способы преобразования электрической энергии в тепловую.
Нагрев сопротивлением
происходит за счет выделения теплоты в проводящем материале при протекании по нему электрического тока. Этот вид нагрева основан на законе Джоуля-Ленца и применяется в установках прямого и косвенного действия.
.
Индукционный нагрев
, основанный на преобразовании энергии электромагнитного поля в тепловую посредством наведения в нагреваемом теле вихревых токов и тепловыделения в нем по закону Джоуля-Ленца.
Диэлектрический нагрев
помещенных в высокочастотное электрическое поле непроводящих материалов и полупроводников, происходящий за счет сквозных токов проводимости и смещения при поляризации.
Дуговой нагрев
, при котором материал нагревается за счет теплоты, поступающей в него из опорных пятен дуги.
Электронно- и ионно-лучевой нагрев
, в результате которого тепловая энергия выделяется при столкновении быстродвижущихся электронов или ионов, ускоренных электрическим полем, с поверхностью нагреваемого объекта. Плазменный нагрев
, основанный на нагреве газа за счет пропускания его через дуговой разряд или высокочастотное электромагнитное или электрическое поле.
Лазерный нагрев
, происходящий за счет нагрева поверхности объектов при поглощении ими высококонцентрированных потоков световой энергии, полученных в лазерах - оптических квантовых генераторах.
1.2. Теплопередача в электротермических установках
Основные параметры электротермических установок (мощность, коэффи- циент полезного действия, удельный расход электроэнергии) определяют в ре- зультате расчета теплоты. Теплообмен определяется законами теплопередачи. Процесс теплообмена являет- ся сложным, поэтому в инженерных расчетах его подразделяют на более простые составляющие - теплопроводность, конвекцию и излучение (лучистый теплообмен).
Теплопроводность
- это передача теплоты внутри твердого тела или неподвижной жидкости (газа) от областей с более высокой температурой к областям с более низкой температурой.
Она больше у плотных тел (например, металлов) и меньше у пористых (например, пенопласта).
Тепловой поток (Вт) через однослойную плоскую стенку при установившемся режиме определяется по формуле Фурье:
Q = (t1
-t2
)/(lFλ), (1.1)
где t1
и t2
- температуры поверхностей стенки, К; l - ее толщина, м; F - площадь проводящей стенки, м2; λ - коэффициент теплопроводности, зависящий от природы вещества и температуры, Вт/(м·К).
Для большинства применяемых в печестроении материалов
λ=λ0
(1+βtср
).
Здесь λ0
- коэффициент теплопроводности при 273 К; β - температурный коэффициент; tср
= 0,5 (t1
+ t2
) - средняя температура стенки, К.
Конвекция
- теплопередача в жидкостях и газах, при которой перемещаются отдельные частицы и отдельные элементы объема вещества, переносящие присущий им запас тепловой энергии. Перенос теплоты вместе с переносом массы вещества называют конвективным теплообменом
.
Тепловой поток конвективного теплообмена определяют на основании закона Ньютона-Рихмана:
Q = αк
(tс
-tr
)F, (1.3)
где αк
- коэффициент теплоотдачи конвекцией, Вт/(м2
·К); tс
- температура стенки;
(tr
- температура окружающей среды; F - поверхность конвективного теплообмена, м2
.
По закону Ньютона-Рихмана, тепловой поток Q прямо пропорционален поверхности омывания, режиму движения теплоносителя и разности температур стенки и газа или жидкости.
Коэффициент теплоотдачи αк
представляет собой количество теплоты, передаваемой в единицу времени через единицу поверхности при разности температур между поверхностью и омывающей жидкостью в 1 К.
Формула (1.3) может быть применена при естественной и вынужденной конвекциях. Так, для плоских вертикальных стенок в условиях естественной конвекции коэффициент теплоотдачи для диапазона температур Δt = tс
-tr
= 288 -
358 К определяется выражением
αк
= 3,45(tс
-tr
)0,13
,
а для Δt = 358 - 423 К
αк
= 2,05(tс
-tr
)0,25
.
При вынужденной конвекции коэффициент теплоотдачи в первую очередь зависит от скорости движения омывающей среды.
Излучение
- передача теплоты в невидимой (инфракрасной) и видимой частях спектра. При передаче теплоты излучением энергия передается в форме электромагнитных волн. Для передачи тепловой энергии наиболее существенными являются тепловое излучение с длиной волны 0,4-400 мк. При излучении нагретого тела в неограниченное пространство (при односторонней теплопередаче) лучистый тепловой поток (Вт/м2
)
Q = сs
ε(T/100)4
, (1.4)
здесь сs
- постоянный коэффициент излучения абсолютно черного тела; ε - степень черноты тела, численно равная его поглощающей способности (для абсолютно черного тела ε = 1); Т - абсолютная температура, К.
Рассмотренные виды теплопереноса во многих случаях осуществляются совместно. Например, в потоках жидкостей и газов наблюдается теплопроводноконвективный перенос теплоты. В потоках высокотемпературных газов имеет место радиационно-конвективный перенос энергии и т. д.
1.3. Материалы, применяемые в электропечестроении
При изготовлении электротермических установок (ЭТУ) применяется ряд специфических материалов, предназначенных для работы при высоких температурах. В их числе огнеупорные и теплоизоляционные материалы для теплоизоляции нагреваемых тел от окружающей среды и жаропрочные материалы, идущие на изготовление нагревателей и элементов конструкций печей.
Роль огнеупоров в экономии электроэнергии очень высока. Потери теплоты через стенки агрегата составляют 15-25 % и могут быть значительно снижены применением огнеупорной и высокоогнеупорной теплоизоляции.
Огнеупорные материалы
. Огнеупорными называют материалы, используемые для сооружения различных печей и аппаратов, работающих в условиях высокотемпературного (выше 1200 К) нагрева.
По специфическим условиям работы они должны удовлетворять следующим требованиям.
1. Огнеупорность
. Это способность без деформации и оплавления противостоять воздействию высоких температур. В зависимости от степени огнеупорности их подразделяют на три класса: огнеупорные (огнеупорностью 1580-1770 К); высокоогнеупорные (1770-2000 К включительно); высшей огнеупорности (выше 2000 К).
Материалы с огнеупорностью ниже 1580 К называют теплоизоляционными. 2. Механическая прочность
. Максимальной рабочей температурой огнеупорного материала принята температура, при которой начинается деформация материала от сжимающей нагрузки 20 кПа.
3. Термическая устойчивость
. Это способность материала без разрушения выдерживать резкие колебания темп
4. Химическая нейтральность
. Не разрушаться путем химической эрозии. 5. Малая электропроводность
. Огнеупорный материал в электрических печах часто одновременно является и электроизоляционным материалом.
6. Малая теплопроводность
. Она способствует снижению тепловых потерь через стенки электрической печи без чрезмерного увеличения их толщины. Наиболее полно изложенным требованиям удовлетворяют огнеупорные материалы, изготовляемые на основе кремнезема SiO2
(2000 К), глинозема А12
O3
(2300 К), оксида магния МgО (2600 К).
Массовыми огнеупорами для электроплавильных печей являются динас (2000 К), магнезит (2570 К), хромомагнезит, доломит и шамот (2000 К). Для печей сопротивления основным огнеупорным материалом является шамот, представляющий собой глубоко обожженную огнеупорную глину. Теплоизоляционные материалы
. Они должны обладать малой теплопроводностью при достаточной огнеупорности. Поэтому теплоизоляционные материалы - это, как правило, рыхлые легкие массы, сильно пористые изделия или крупнозернистые порошки.
Наибольшее распространение в качестве теплоизоляционных материалов получили диатомит, шлаковые и минеральные ваты, пеностекло, зонолит, а также комбинированные материалы на основе асбеста.
Диатомит
- осадочная горная порода; по химическому составу — почти чистый кремнезем (SiO2
), используется для стен электропечей в виде насыпной изоляции.
Шлаковые и минеральные ваты
получают из топочных и доменных шлаков.
Стекловата
. Максимальная температура ее применения 700-800 К.
Пеностекло.
Максимальная рабочая температура 900-1000 К.
Зонолит
- легкая чешуйчатая масса, выдерживает температуру до 1400 К.
Асбест
- волокнистый материал, с максимальной рабочей температурой 900 К.
Жаропрочные материалы
. Жаропрочность - свойство материала сохранять высокую механическую прочность при высоких температурах. Жароупорность - устойчивость к химическим реакциям при высоких температурах.
Основные жаропрочные материалы - сплавы железа со специальными легирующими добавками. Легирующими материалами служат хром, алюминий, никель. Добавки хрома и алюминия придают сплавам способность противостоять высокотемпературной коррозии. Никель улучшает обрабатываемость материала, повышает его механическую прочность при работе в условиях высокой температуры.
Жаропрочные материалы подразделяют на жаростойкие и жароупорные. Основной легирующей добавкой в первой группе сплавов служит хром. Эти сплавы хорошо противостоят окислению при высоких температурах. Увеличение процентного содержания хрома в стали повышает его жаростойкость.
Для высокотемпературных электропечей в качестве жароупорных материлов применяют молибден, ниобий, вольфрам (работающие в защитных газах-аргоне, азоте, водороде), высокоогнеупорную керамику, карбиды и бориды некоторых материалов.
УСТАНОВКИ НАГРЕВА СОПРОТИВЛЕНИЕМ 2.1. Физическая сущность электрического сопротивления
Электрический ток - это направленное движение положительных или отрицательных электрических зарядов под действием электрического поля. Он может обеспечиваться движением только электронов, как это имеет место в вакууме при эмиссии электронов накаленным катодом, металлах и материалах, проявляющих свойство сверхпроводимости. Вещества, обладающие электронной проводимостью, называют проводниками первого рода
. Проводящие среды, в которых прохождение тока обеспечивается движением частиц вещества - ионов, называют проводниками второго рода
. К ним относятся электролиты-растворы и расплавы. Плазма имеет смешанную проводимость.
В соответствии с электронной теорией у металлов, которые являются кристаллическими веществами, ядра атомов находятся в узлах кристаллических решеток, а пространство между ними заполнено электронами (электронный газ). Число свободных электронов в металле очень велико. Так, для меди оно составляет приблизительно 1029
/м3
.
Проводники второго рода - электролиты-растворы или расплавы кислот солей, щелочей, оксидов и плазма-имеют два вида электропроводности - электронную и ионную. При постоянном токе у растворов и расплавов наблюдается преимущественно ионная проводимость в соответствии с законом Фарадея. Доля электронного тока в этом случае невелика. При переменном токе появляется существенная доля электронного тока, увеличивающаяся с повышением частоты тока.
Количество выделяющейся в проводнике теплоты при прохождении по нему электрического тока зависит от сопротивления проводника, электрического тока в цепи, времени его прохождения и определяется законом Ленца-Джоуля:
Q = I2
Rη,
где I - ток, А; R. - сопротивление, Ом; η - время, с.
Если выразить R через удельное сопротивление проводника, учесть его геометрические размеры l - длину, м, и S - площадь сечения, м2
, то выделяющаяся в проводнике мощность
Р = U2
S/(ρl), (2.8)
где S - площадь сечения, м2
; l - длина проводника, м.
2.2. Нагревательные элементы
Выбор материала и конструкции нагревательного элемента определяется особенностями технологического процесса и конструкции установки.
Идущие на изготовление нагревателей материалы должны обладать рядом специфических свойств: высоким удельным электрическим сопротивлением; малым температурным коэффициентом удельного сопротивления; постоянным электрическим сопротивлением нагревательного элемента в процессе длительного срока его службы - отсутствием старения.
По температурным пределам работы нагревательные элементы подразделяют на три группы:
низкотемпературные - нагрев до 500-700 К и преимущественно конвективный способ теплообмена;
среднетемпературные - нагрев до 900-1300 К с теплообменом конвекцией, теплопроводностью и излучением;
высокотемпературные - нагрев до 2500-3300 К с преимущественно радиационным способом теплопередачи.
Для изготовления нагревателей с рабочей температурой до 1500 К наиболее распространенными материалами являются нихромы (сплавы никеля и хрома), фехрали (хромоалюминиевые сплавы), а также хромоникелевые жаропрочные
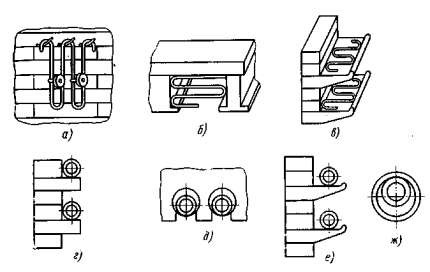
Рис. 2.2. Расположение нагревателей в электрических печах
Для низкотемпературного нагрева широко применяются трубчатые
электронагреватели
- ТЭНы, представляющие собой металлическую трубку 1
, заполненную теплопроводным электроизоляционным материалом 2
, в котором находится электронагревательная спираль 3
(рис. 2.3). В качестве наполнителя применяется плавленый периклаз. По сравнению с открытыми
электронагревателями ТЭНы более злектробезопасны, могут работать в воде, жидких углеводородах, жидком металле, расплавах солей, оксидов и других средах. ТЭНы стойки к вибрациям и механическим нагрузкам. Мощность ТЭНов составляет от 100 Вт до 15 кВт, рабочее напряжение 36-380 В, рабочая температура 400-1000 К. Срок службы ТЭНов составляет 10-40 тыс. ч.
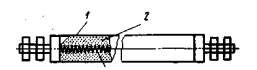
3
Рис. 2.3. Схема трубчатого электронагревателя (ТЭНа)
Для высокотемпературных печей с максимальной рабочей температурой до
1700 К применяются нагревательные элементы из карборунда
(карбид кремния
SiС, получаемый спеканием кремнезема и угля при температуре 1900-2000 К). Для высокотемпературных установок (с максимальной рабочей температурой 2300 К и выше) нагреватели изготовляют из тугоплавких металлов
, угля
или графита
.
При изготовлении нагревательных элементов из тугоплавких материалов применяют молибден, тантал, вольфрам в виде проволоки, ленты, стержней и листов различных сечений.
.
Графитовые электронагреватели
применяются в установках с рабочей температурой 1800-2700 К.
2.3 Установки электроотопления и электрообогрева
Электрические нагревательные установки применяют для: сушки изделий после окраски, пропитки; сушки помещений при строительных работах; подогрева газов для различных технологических целей; отопления помещений; разогрева емкостей с жидкостью, пластичными и вязкими материалами, а также для нагрева твердых тел и устройств - прессов, штампов; прогрева технологических трубопроводов; прогрева бетона, грунтов и дорожных покрытий.
В электроотоплении и электрообогреве используется большое разнообразие различных электронагревательных устройств. К ним относятся электрокалориферы, фены, различные устройства радиационного обогрева, электрокотлы, электрические теплоаккуму-лирующие устройства, устройства для оттаивания грунта, обогрева бетона, дорожных покрытий и т. д.
Электрокалорифер
. Это электронагревательный аппарат, состоящий из нагревательного элемента и вентилятора. Он предназначен для нагрева воздуха и различных газов в технологических процессах. Такие электрокалориферы с вынужденной конвекцией, обеспечивающей интенсивный теплообмен, обладают в несколько раз меньшей поверхностью нагрева по сравнению с поверхностями электронагревательных устройств со свободноконвективным способом теплообмена. При невысоких температурах нагревательных элементов (500 К) в калориферах применяется подвешенная на изоляторах открытая проволочная спираль. Калориферы этого типа обладают небольшим гидравлическим сопротивлением.
В калориферах могут применяться простые и оребренные трубчатые электронагреватели, обладающие развитой поверхностью нагрева.
Отопительный калорифер с трубчатыми оребренными нагревателями предназначен для нагрева воздуха до 400 К в системах воздушного отопления, вентиляции, искусственного климата и в сушильных установках. Он состоит из кожуха и трубчатых нагревательных элементов. Заданная температура выходящего воздуха поддерживается автоматически электроконтактными термометрами, датчики которых установлены на выходе воздуха из калорифера. Для нагрева воздуха до высоких температур (1200 К) применяется калорифер с нагревательными элементами в виде металлических труб; воздух нагревается, протекая внутри них. Межтрубное пространство заполняется фасонными керамическими блоками. Отдельные трубы соединены между собой на концевых участках.
Радиационные электронагреватели.
В различных отраслях промышленности и сельском хозяйстве широко используются радиационные нагреватели, передающие энергию в окружающее пространство излучением. Светлый
(ламповый
) излучатель
представляет собой лампу накаливания с вольфрамовой нитью и стеклянной колбой. Нижняя прилегающая к цоколю часть колбы изнутри алюминирована для создания направленного излучения.
Температура вольфрамовой нити - около 2200 К, максимум излучения приходится на длину волны 1,3 мкм. Основная часть энергии излучается в диапазоне длин волн 0,8-3,5 мкм.
Светлый кварцевый излучатель
представляет собой трубку из кварцевого стекла, внутри которой размещаются вольфрамовые, нихромовые или хромоалю- миниевые спирали. По сравнению с ламповым излучателем он имеет больший срок службы, меньшие габаритные размеры при одной и той же мощности и позволяет получить большую плотность лучистого потока (до 60 кВт/м2
). Темный излучатель
представляет собой трубчатый электронагреватель, расположенный в фокусе полированного отражателя. Рабочая температура поверхности излучателя 700-1000 К, максимум излучения приходится на длины волн 2-5 мкм.
Электрические сушила
. Установки для сушки изделий могут быть радиационного или смешанного действия, когда передача теплоты излучением сочетается с конвекцией (установки конвективно-радиационного типа).
Рис. 2.4. Переносная излучательная панель:
1 - отражатель; 2 - нагреватель; 3 - корпус; 4 - ограждение
При большой
производительности сушила могут быть непрерывно действующими
(методическими). В этом случае высушиваемые изделия или материалы помещены вдоль стенок камеры, на которых расположены нагревательные элементы, и перемещаются с помощью транспортирующих устройств (транспортеров,
конвейеров и пр.). В качестве установок для сушки различного рода поверхностей могут применяться специальные излучательные панели (рис. 2.4). Нагреватели панелей выполняют в виде нихромовой спирали, намотанной на керамические трубки. Источником теплоты в панелях могут служить трубчатые электронагреватели, а в отдельных случаях открытые нагреватели и лампы различ- ных типов.
Электрические отопительные устройства
. Электрическое отопление экономически оправдано в тех случаях, когда для использования другого вида энергии требуются значительные капитальные затраты (строительство новой котельной), возникают значительные трудности в обеспечении топливом, когда необходимо учитывать экологический фактор - чистоту окружающей среды, а также когда использование электрической энергии в ночное время выравнивает суточный график нагрузки электрической станции и системы. Для отопления помещений используются также теплоаккумулирующие уст- ройства. Они в ночное время подключаются к электрической сети, работают на обогрев помещений и одновременно запасают теплоту в теплоаккумуляторе. Затем в дневное время они отдают запасенную теплоту в отапливаемое помещение, бу- дучи отключенными от электрической цепи. Принципиальная схема электроот- опительной установки с теплоаккумулирующим элементом показана на рис. 2.5.
Выбор мощности и теплоаккумулирующей способности установки определяется площадью отапливаемого помещения и климатическими условиями местности. В ряде случаев в качестве теплоаккумулирующего элемента могут служить электрокотлы большой емкости.
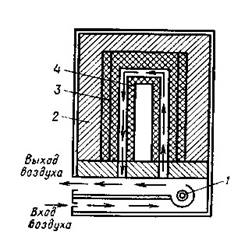
Рис. 2.5. Электрический тепло-аккумулирующий нагреватель:
1 - вентилятор; 2 - теплоизоляция; 3 - запасающий теплоту элемент; 4 - тепловыделяющий элемент
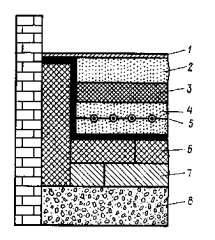
Рис. 2.6. Схема обогрева помещения:
1 - настил пола; 2, 4 - мастика; 3 - теплораспределяющий слой; 5 - плоский тепловыделяющий проводник; 6 - водозащитный слой; 7 - стекло-волокнистая прокладка; 8 - бетон
Использование систем с теплоаккумуляторами положительно сказывается на работе электростанций, снабжающих электрической энергией данный район, поскольку в этом случае повышается электрическая нагрузка станций в ночное время, что приводит к выравниванию суточного графика нагрузки и более рациональному использованию мощности электрической системы.
При осуществлении электроотопления с использованием низкотемпературного обогрева в качестве нагревающих поверхностей используются пол, потолок и стены помещения, в которые монтируются нагревательные элементы. Такой способ отопления позволяет получить хорошее распределение температуры в помещении, уменьшить массу нагревательной установки, достигнуть хороших гигиенических условий.
Установки для обогрева труб, прогрева бетона и грунта
. Для нагрева потока жидкости применяют специальные электрические обогреватели трубопроводов. Они представляют собой плоские металлические обручи толщиной до 5 мм. Между двумя такими обручами размещен нагреватель, намотанный на миканитовую полосу толщиной 0,5 мм. Элементы имеют стяжные обручи, с помощью которых достигается плотное облегание обогреваемой поверхности.
Наиболее рациональный способ электропрогрева бетона - пропускание через него тока. Для ввода энергии в массу прогреваемого бетона служат различные электроды. Их изготовляют из арматурной диаметром 6-10 мм или полосовой стали.
При необходимости оттаивать грунт на всю глубину его промерзания более экономично применение вертикальных глубинных электродов. Электроды забивают в грунт сквозь толщу мерзлого слоя на 15-20 см в слой талого грунта. В начале прогрева ток, проходящий в талом слое, нагревает его и оттаивает расположенную непосредственно над ним часть мерзлого слоя. В связи с этим сечение, по которому проходит ток, постепенно увеличивается и происходит последовательное оттаивание мерзлого грунта.
Электроды диаметром 12-20 мм забивают в грунт и соединяют в три группы для подключения к трехфазной сети. Длина электродов должна превышать глубину промерзания грунта к моменту начала оттаивания на 0,2-0,3 м.
Продолжительность нагрева зависит от толщины оттаиваемого слоя и влажности грунта.
2.4. Электрические печи сопротивления
Электрические печи сопротивления (ЭПС) применяются для
технологических операций в машиностроении, металлургии, легкой и химической промышленности, строительстве, коммунальном и сельском хозяйстве. Разнообразие материалов, обрабатываемых в ЭПС, и видов технологических процессов привело к большому разнообразию конструкций ЭПС, выпуску их малыми сериями и даже в индивидуальном порядке.
При технологических процессах, проводимых в ЭПС, используется только нагрев посредством электричества. В ряде случаев используется возможность нагрева в вакууме или защитных газах. Поэтому рассмотрим общие принципы построения печных установок без детального рассмотрения конструкций, а также схемы электроснабжения и принципы автоматизации.
Электропечи сопротивления выпускают в двух исполнениях: ЭПС косвенного и прямого действия. В ЭПС косвенного действия электрическая энергия превращается в тепловую в специальных нагревателях, а затем передается в рабочее пространство посредством теплопроводности, конвекции и излучения. В ЭПС прямого действия нагреваемое тело включается непосредственно в электрическую цепь. Нагревательные элементы в печах косвенного действия и нагреваемые тела, включаемые в цепь ЭПС прямого действия, могут быть проводниками первого и второго родов.
По уровню достигаемых температур ЭПС можно расположить в следующем порядке: низкотемпературные (900-1000 К), сред-нетемпературные (1000-1600 К) и высокотемпературные (выше 1600 КСреди ЭПС непрерывного действия различают конвейерные, толкатель-ные, рольганговые, карусельные, с шагающим подом, пульсирующим подом, барабанные, протяжные.
В печах с контролируемой атмосферой применяются инертные газы, а также специальные газовые смеси, назначение которых - термохимическая обработка поверхности изделий - азотирование, цементация и нитроцементация, проводимые с целью повышения поверхностной прочности и износоустойчивости деталей .
Электропечи сопротивления периодического действия
. Колпаковая печь - печь периодического действия с открытым снизу подъемным нагревательным
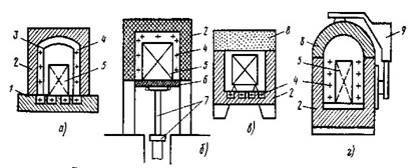
колпаком н неподвижным стендом (рис. 2.7, а
).
Рис. 2.7. Печи сопротивления периодического действия:
а - колпаковая; б - элеваторная; в - камерная; г - шахтная; 1 - стенд; 2 - камера печи; 3 - жаропрочный муфель; 4 - нагревательные элементы; 5 - нагреваемое изделие (садка); 6 - опускающийся под; 7 - подъемное устройство; 8 - свод; 9 -
механизм подъема свода
Нагреваемые детали (садка) 5
с помощью подъемно-транспортных устройств помещаются на стенд 1
. Поверх них сначала устанавливается жаропрочный колпак-муфель 3
, а затем основной колпак 2
камеры печи, выполненной из металлического каркаса с огнеупорной футеровкой.
Нагревательные элементы 4
расположены по боковым стенкам колпака и в кладке стенда.
Элеваторная электропечь
- печь периодического действия с открытой снизу неподвижной камерой нагрева 2
и с опускающимся подом 6
. Она представляет собой цилиндрическую или прямоугольную камеру, установленную на колоннах на высоте 3-4 м над уровнем пола цеха (рис. 2.7,б
).
Камерная электропечь
(рис. 2.7, б
) - печь периодического действия с камерой нагрева, загрузка и разгрузка садки которой производятся в
горизонтальном направлении. Камерная печь состоит из прямоугольной камеры 2
с огнеупорной футеровкой и теплоизоляцией, перекрытой сводом 8
и помещенной в металлический кожух. Печь загружается и выгружается через закрываемое дверцей отверстие в передней части.
.
Шахтную печь
выполняют в виде круглой, квадратной или прямоугольной шахты, перекрываемой сверху крышкой. Нагревательные элементы в ней установлены обычно по боковым стенкам. Принципиальная схема такой печи показана на рис. 2.7, г
.
Электропечи сопротивления непрерывного действия (методические печи).
При установившемся технологическом процессе термообработки для увеличения производительности предпочтительно применять непрерывно действующие печи.
Конвейерная печь
- печь непрерывного действия с перемещением садки на горизонтальном конвейере (рис. 2.8).
Под печи представляет собой конвейер - полотно, натянутое между двумя валами, которые приводятся в движение специальными двигателями. Нагреваемые изделия укладываются на конвейер и передвигаются на нем через рабочее пространство печи. Конвейерная лента может быть выполнена плетеной из нихромо-вой сетки, штампованных пластин и соединяющих их прутков, а также для тяжелых нагреваемых изделий - из штампованных или литых цепных звеньев.
1 2
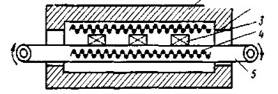
Рис. 2.8. Схема конвейерной электропечи:
1 - теплоизолированный корпус; 2 – загрузочное окно; 3 - нагреваемое изделие; 4 - нагревательные элементы; 5 - конвейер
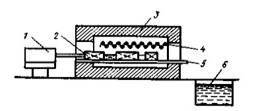
Рис. 2.9. Схема толкательной печи:
1 - толкатель с приводным механизмом; 2 - нагреваемые изделия; 3 - теплоизолированный корпус; 4 - нагревательные элементы; 5 —- подина печи; 6 -
закалочная ванна
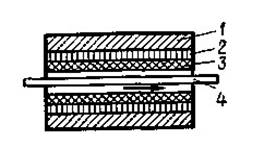
Рис. 2.10. Протяжная электропечь;
1 - теплоизолирующий корпус; 2 - нагреватель; 3 - муфель; 4 - нагреваемое изделие
Конвейер размещается целиком в камере печи и не остывает. Однако валы конвейера находятся в очень тяжелых условиях и требуют водяного охлаждения. Конвейерные нагревательные печи в основном применяются для нагрева сравнительно мелких деталей до температуры около 1200 К.
Перемещение поддонов обеспечивается электромеханическими или гидравлическими толкающими устройствами. Основное преимущество таких печей перед другими типами - их относительная простота, отсутствие сложных деталей из жароупорных материалов. Их недостатки - наличие поддонов, применение которых ведет к увеличению тепловых потерь и к повышенному расходу электрической энергии, ограниченный срок службы поддонов. Толкательные печи, предназначенные для нагрева крупных заготовок правильной формы, выполняют без поддонов. При этом нагреваемые изделия укладывают в пень вплотную непосредственно на направляющие. При использовании в качестве защитного газа водорода или диссоциированного аммиака на загрузочных и разгрузочных камерах печи предусмотрены «свечи» для контроля заполнения ее рабочим газом. Состав рабочего газа каждой печи регулируется самостоятельно и расход его контролируется с помощью расходомеров для водорода и азота. Разгрузочные камеры печей имеют предохранительные клапаны для защиты от разрушения в случае образования в них взрывоопасной смеси.
Протяжная электропечь
- печь непрерывного действия для нагрева проволоки, прутков или ленты путем непрерывной протяжки через камеру нагрева. Она представляет собой муфель с нагревателями, через который пропускается нагреваемое изделие (рис. 2.10).
Электропечи сопротивления для плавки металлов
. В установках этого типа производится выплавка олова, свинца, цинка и различных сплавов на их основе, а также других металлов, имеющих температуру плавления 600-800 К. Важное значение имеют ЭПС для плавки алюминия и его сплавов, поскольку позволяют достичь высокой степени очистки. Большим достоинством печей является простота конструкции, источников питания и технологического процесса. Это дало возможность создать автоматизированные разливочные агрегаты с применением микропроцессоров и роботов-манипуляторов. С большой эффективностью они используются при изготовлении поршней двигателей внутреннего сгорания и других деталей.
По конструктивному исполнению ЭПС можно подразделить на тигельные и камерные (или ванные).
Тигельные печи
(рис. 2.11) представляют собой металлический сосуд - тигель (из чугуна с внутренней обмазкой оксидами), помещаемый в цилиндрический корпус, выполненный из огнеупорного материала 5
, покрытый снаружи металлическим кожухом 6
. Между тиглем и футеровкой размещены электрические нагреватели 4.
Рис. 2.11. Тигельная электрическая печь сопротивления: 1 - желоб; 2 - механический вытеснитель; 3 – тигель; 4 - нагреватель; 5 -
футеровка; 6 – корпус
Приведенная на рисунке конструкция тигельной ЭПС оборудована механическим дозатором и применяется в числе многих других конструкций при массовом производстве, где дозирование металла в промежуточный ковш роботаманипулятора или литейную форму производится с помощью механических, пневматических или электромагнитных устройств. В нашем примере механический вытеснитель 2
размещен на каретке, движущейся вверх и вниз по направляющей колонке. После расплавления металла и доведения его температуры до необходимого уровня вытеснитель опускается в тигель и вытесняет порцию металла, которая по обогреваемому желобу 1
поступает в литейную машину. Удельный расход электроэнергии при плавке алюминия 700750 кВт·ч/кг, КПД печи 50-55 %. Тигельные ЭПС других конструкций имеют механизм наклона, позволяющий наклонять печь и сливать расплавленный металл. Камерные печи
по объему больше тигельных и применяются для переплавки алюминия на слитки.
Удельный расход электроэнергии при работе ЭПС ванного типа составляет 600-
650 кВт·ч/кг, а КПД – 60-65 %. Во всех типах ЭПС возможны два способа
обогрева - внутренний и внешний. При внутреннем обогреве нагреватели - ТЭНы размещены в расплавленном металле и работают при температуре не выше 800- 850 К. При внешнем расположении открытые высокотемпературные нагреватели позволяют получить температуры в рабочем пространстве печи 1100-1200 К. Установки прямого (контактного) нагрева.
Установками прямого нагрева принято называть такие, в которых преобразование электрической энергии в тепловую происходит в нагреваемом материале или изделии при
непосредственном подключении их к источнику питания электроэнергией за счет прохождения через них электрического тока по закону Джоуля-Ленца.
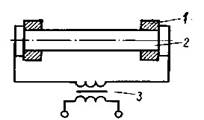
Рис. 2.12. Схема прямого нагрева:
1 - водоохлаждаемые зажимы; 2 - нагреваемое изделие; 3 - печной трансформатор
Прямой нагрев эффективен для термообработки изделии, обладающих равномерным сечением по длине и значительным омическим сопротивлением.
обмоткой, охлаждаемой водой, и несколькими ступенями напряжения в диапазоне
5-25 В, обеспечивающий нагрев тел,, имеющих разное сопротивление.
2.5. Электрооборудование и регулирование параметров печей сопротивления
.
в) включение в цепь нагревателей дополнительных сопротивлений в виде дросселей и реостатов;
г) импульсное регулирование с использованием тиристорных регуляторов.
Использование трансформаторов с плавным бесконтактным регулированием под нагрузкой, автотрансформаторов и потенциал-регуляторов связано со
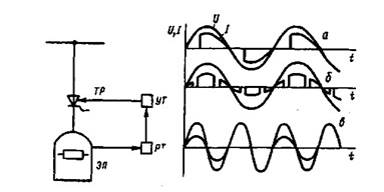
значительными капитальными затратами, наличием дополнительных потерь и потреблением реактивной мощности. По этой причине такое регулирование температуры применяется сравнительно редко.
Включение в цепь нагревателей дополнительного индуктивного или актив- ного сопротивления связано с дополнительными потерями и потреблением реактивной мощности, что также ограничивает применение этого способа регулирования.
Импульсное регулирование на базе тиристорных регуляторов осуществляется с помощью управляемых полупроводниковых вентилей, периодичность работы которых выбирают в зависимости от тепловой инерционности электропечи. Можно выделить три основных способа импульсного регулирования мощности, потребляемой от сети переменного тока .
.р
2.6. Нагрев сопротивлением жидких сред
Электрические котлы.
Они применяются в различных отраслях народного хозяйства для подогрева воды (электроводонагреватели) и получения насыщенного технологического пара низкого давления (электропарогенераторы). Жидкость - вода, расплавы солей, щелочей, оксидов могут быть нагреты прямым пропусканием тока через их объем. Установки такого типа служат для кипячения воды, варки стекла, термообработки металлов.
Электроводонагреватель прямого действия представляет собой цилиндрический стальной сосуд, на верхней крышке которого расположены стержневые электроды и охватывающие их трубчатые антиэлектроды. Между ними находятся стеклотекстолитовые цилиндры. Мощность, развиваемую котлом, регулируют, изменяя положение изоляционных цилиндров относительно системы электродов и антиэлектродов.
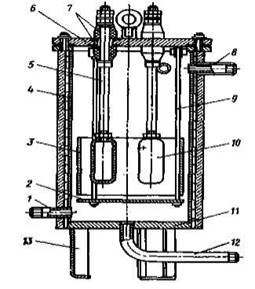
Рис. 2.15. Схема электродного парогенератора:
1 - подвод воды; 2 - дно обечайки; 3 - нулевой электрод; 4 - корпус, 5 - токоподвод; 6 - крышка; 7 - изоляторы; 8 - отвод пара; 9 - шпилька; 10 - фазный электрод; 11 - днище; 12 - дренаж; 13 - опора
Номинальный режим работы котла рассчитан на нагрев воды с удельным электрическим сопротивлением 3000 Ом·см. Изменение солесодержания в рабочей воде для получения номинального значения удельного электрического сопротивления достигается добавлением в систему либо раствора соли, либо дистиллированной воды. Возможна работа котла и на воде с иным удельным сопротивлением, однако во избежание чрезмерного увеличения поверхностной плотности тока на электродах и образования гремучего газа значение его должно составлять 1000-5000 Ом·см.
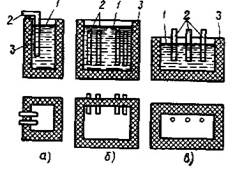
Рис. 2.16. Схемы однофазных электродных ванн с близко расположенными электродами:
а, б - однофазные; в - трехфазные; 1 - уровень расплава соли; 2 - электроды; 3 - футеровка
Температура выходящей воды автоматически поддерживается в нужных пределах датчиком регулирующего термометра.
Электрический парогенератор представляет собой комплект оборудования и аппаратов, в который входит сам парогенератор, питательный бак, насос, соединительные трубопроводы, приборы контроля и управления. Принципиальная схема электродного парогенератора приведена на рис. 2.15. Парогенератор имеет электроды цилиндрической формы 10
и нулевой электрод 3
, выполненный в форме обечайки. Мощность парогенераторов регулируется за счет изменения уровня воды между электродами и нулевым электродом. Работа парогенераторов осуществляется в автоматическом режиме.
Электродные котлы могут иметь трехфазную и однофазную системы электродов, работающие на низком и высоком напряжении. Котлы низкого напряжения (30 В) мощностью 25-400 кВт с КПД 95-98 % имеют малые габаритные размеры, низкую тепловую инерционность.
Высоковольтные котлы, рассчитанные на напряжение 3-35 кВ, применяют в бытовых и производственных целях для систем централизованного отопления и горячего водоснабжения,
Стекловаренные печи.
Их выполняют в виде ванны, выложенной изнутри огнеупорным материалом.
Жидкостные ЭПС для нагрева металла.
Для быстрого и равномерного нагрева металлических изделий и заготовок применяются электродные ванны, представляющие собой металлический или керамический тигель, наполненный солью или стекломассой, в который опущены металлические или металлокерами- ческие электроды. В холодном состоянии соль почти не электропроводна, но если ее нагреть и расплавить, то между электродами начинает протекать электрический ток и в расплаве, как в активном сопротивлении, выделяется тепловая энергия. ЭПС с жидким нагревателем применяют для нагрева до 1100-1600 К изделий из легированных сталей перед закалкой, ковкой или штамповкой, а также для отжига деталей из стали и чугуна. В качестве рабочей среды наиболее о применяют хлористые, фторис- тые, азотно-кислые соли, щелочи либо в чистом виде, либо в различных смесях, преследуя цель снижения температуры плавления, обеспечения необходимого уровня электропроводности. К достоинствам соляных ванн следует отнести:
а) высокую скорость нагрева и большую производительность по сравнению с другими нагревательными установками при равных габаритных размерах; б) легкость осуществления различных способов термической и термохимической обработки;
в) защита изделий от окисления в процессе их нагрева.
Недостатками соляных ванн являются:
а) повышенный удельный расход электроэнергии вследствие увеличенных тепловых потерь с зеркала ванны и необходимости непрерывной работы установки;
б) высокий расход расплавообразующего материала;
в) тяжелые условия труда обслуживающего персонала.
2.7. Электрошлаковые установки
Использование явления разогрева расплава соединений шлака до 2000-2300 К проходящим по нему током легло в основу высокоэффективных технологических процессов электрошлакового переплава (ЭШП) и электрошлаковой сварки (ЭШС Сущность ЭШП состоит в следующем (рис. 2.17). Расходуемый электрод из переплавляемого металла 1
погружается в слой электропроводного шлака 2
, находящегося в водоохлаждаемом кристаллизаторе 3
, закрытом водоохлаждаемым поддоном 4
. Электрический ток протекает между электродом и поддоном через шлак, который имеет высокое электрическое сопротивление и интенсивно разогревается по закону Джоуля - Ленца.
Находящийся в расплаве шлака торец электрода расплавляется, и капли металла, стекающие с электрода, проходят через шлак, где дополнительно разогреваются, очищаются от нежелательных примесей и собираются на дне кристаллизатора в виде слитка. В результате отвода теплоты в поддон и стенки кристаллизатора скапливающийся металл застывает в виде слитка 6
, в верхней части которого находится ванна расплавленного металла 5
. По мере оплавления электрод подается вниз. Между стенкой кристаллизатора и слитком образуется слой гарнисажа 7
.

Рис. 2.17. Схема установки электрошлакового переплава
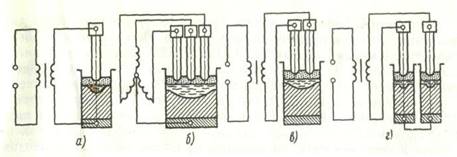
Рис. 2.18. Электрические схемы печей ЭШП:
а - одноэлектродная однофазная; б - трехэлектродная трехфазная; в - двухэлект-
родная однофазная с бифилярным токопроводом; г - то же, для получения двух
слитков
Основными факторами, определяющими улучшение качества металла при обработке в установках ЭШП, являются: химическое взаимодействие со шлаком; направленная кристаллизация слитка; формирование слитка в шлаковом гарнисаже с образованием гладкой поверхности.
Поэтому основное назначение установок ЭШП - производство слитков из высококачественных сталей - валковых, шарикоподшипниковых, нержавеющих, Электрошлаковая сварка
(ЭШС). Она широко используется в
промышленности для соединения металлов большой толщины: стали, чугуна, меди, алюминия, титана и их сплавов. В качестве тепловыделяющего элемента здесь используются расплавленные шлаки, нагревающиеся до заданной температуры при протекании по ним переменного тока. Принципиальная схема ЭШС показана на рис. 2.19.
Электрод 3
и части свариваемого металла 1
включаются в электрическую цепь через шлак 2
, нагреваемый проходящим током выше температуры плавления свариваемого и электродного металла. В результате электродный и свариваемый металлы расплавляются и стекают на дно сварочной ванны 5
, заполняя шов 4
.
Боковые стороны шва закрываются охлаждаемыми ползунами. ЭШС осуществляется автоматами и полуавтоматами, подающими электродную проволоку, дозирующими флюс. Они имеют соответствующую аппаратуру управления. У источников питания ЭШС бывают разные внешние характеристики от крутопадающей до жесткой, мощность их 60-550 кВ·А, вторичное напряжение 8-63 В.
УСТАНОВКИ КОНТАКТНОЙ СВАРКИ 3.1. Физические основы электрической контактной сварки и ее разновидности
Электрическая контактная сварка представляет собой процесс образования неразъемного соединения в результате нагрева металлических деталей протекающим по ним электрическим током, расплавления и сдавливания деталей с последующим охлаждением зоны сварки за счет теплопроводности в тело свариваемых деталей.
Контактная сварка объединяет большую группу методов сварки, отличительной особенностью которых являются надежность получаемых соединений, высокий уровень автоматизации и механизации, высокая производительность процесса и культура производства.
По способу получения соединений различают стыковую, точечную и шовную контактную сварки (рис. 3.1.)
Контактная сварка
 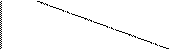
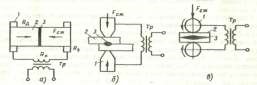
Рис. 3.1. Виды контактной сварки:
а - стыковая; б - точечная; в – шовная
Так как площадь точек очень мала, то в них возникает большое сопротивление прохождению тока, что вызывает сильный локальный нагрев металла. С повышением температуры в месте сварки его сопротивление возрастает, что ускоряет выделение теплоты и нагрев металла до температуры сваривания. Когда металл нагреется до пластического или оплавленного состояния, при сжатии деталей произойдет их сваривание. Застывание металла в точке сварки после отключения тока происходит за счет теплопроводности свариваемых деталей.
Сварочные установки для контактной сварки имеют две основные части: электрическую и механическую
. Электрическая часть состоит из сварочного трансформатора специальной конструкции, токопроводящих частей и устройств для включения и выключения сварочного тока. Механическая часть установок представляет собой устройство для импульсного сжатия свариваемых деталей.
3.2. Стыковая сварка
Стыковая сварка - это способ контактной сварки, при котором детали соединяются по всей площади их касания. Различают два способа стыковой сварки - сопротивлением и оплавлением
.
При сварке сопротивлением
(рис. 3.1, а
) свариваемые детали 2
укрепляют в токоподводах 1
и сжимают с усилием Fсж
При сварке непрерывным оплавлением
детали сближаются при включенном сварочном трансформаторе и путем сжатия осуществляется их контакт. При этом стык разогревается за счет протекания тока. Затем силу сжатия уменьшают, вследствие чего увеличивается контактное сопротивление и снижается сварочный ток. При снижении давления
соприкосновение деталей по плоскости заменяется соприкосновением в отдельных точках При сварке оплавлением с подогревом
детали предварительно подогревают методом кратковременных замыканий их торцов, а затем оплавляются.
Сварка с оплавлением стыка деталей по сравнению со сваркой без оплавления имеет следующие преимущества: более прочный шов, не требующий большой механической обработки; меньшая мощность сварочной установки; пониженный удельный расход электроэнергии; возможность сваривания различных металлов.
К недостаткам следует отнести неизбежную хотя и небольшую потерю металла и наличие «грата» на стыке свариваемых деталей.
Конструктивная схема и сварочный контур машины стыковой сварки показаны на рис. 3.2.
Машины для стыковой сварки могут быть подразделены по способу сварки
(без оплавления стыка и с его оплавлением), назначению
(универсальные и специализированные) и способу установки
(стационарные и переносные).
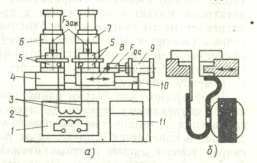
Рис. 3.2. Конструкция (а
) и сварочный контур (б
) машин стыковой сварки:
1 - источник тока; 2 - станина; 3 - токоподводы; 4 - неподвижная плита; 5 - губки; 6, 7 - зажимные устройства; 8 - подвижная плита; 9 - привод подачи; 10 - направляющие; 11 - аппаратура управления
3.3. Точечная сварка
При осуществлении точечной сварки свариваемые детали помещают между двумя электродами, закрепленными в электрододержателях (рис. 3.1, б
). Посредством нажимного механизма электроды плотно сжимают свариваемые детали. После сжатия на электроды подается напряжение и проходящий через детали ток нагревает место сварки до необходимой температуры, при достаточном сжатии в этом месте образуется неразъемное сварное соединение. В центре сварочной точки температура несколько выше температуры плавления свариваемого металла, ее диаметр близок к диаметру электродов.
Машины точечной сварки различаются по способу подвода тока
. Наиболее широко распространена одноточечная двусторонняя
(нормальная) сварка (см. рис.
3.1, б
). Верхний и нижний электроды имеют рабочую поверхность,
обеспечивающую необходимую плотность тока для концентрированного разогрева места сварки. При необходимости уменьшить вмятины от электродов с одной стороны свариваемого изделия применяют один из способов «бесследной» сварки (рис. 3.4, а-в
). Это достигается увеличением рабочей поверхности одного из электродов (рис. 3.4, а
), сваркой на плоском электроде (рис. 3.4, б
) либо введением промежуточной плоской пластины между одним из электродов и деталью (рис.
3.4, в
). Необходимая плотность тока для обеспечения концентрированного нагрева создается вторым электродом с нормальной рабочей поверхностью.

Рис. 3.4. Принципиальные схемы основных способов точечной сварки
В случае невозможности осуществления нормальной одноточечной сварки применяется точечная сварка с косвенным токоподводом
. При этом, с одной стороны, ток подводится электродом с нормальной контактной поверхностью, а с другой - электродом с большей контактной поверхностью (рис. 3.4, г
). Для уменьшения местных остаточных деформаций от сварки применяются способы, показанные на рис. 3.4, д
, е
.
При сварке тонколистовых изделий применяется односторонняя многоточечная сварка
(рис. 3.4, ж
). Одновременная сварка двух точек при двустороннем токопроводе от спаренного трансформатора (рис. 3.4, з
) позволяет сваривать металлические изделия большой толщины.
3.4. Шовная сварка
В процессе шовной сварки соединение двух свариваемых деталей (обычно двух листов) осуществляется с помощью вращающихся роликов за счет пропускания через место сварки электрического тока, как показано на рис. 3.5. Машины для шовной сварки имеют два токопроводящих ролика, из которых один приводной, а другой вращается за счет силы трения при передвижении свари- ваемых листов. По своему принципу шовная сварка аналогична точечной сварке. При осуществлении процесса шовной сварки могут иметь место следующие режимы: непрерывное движение роликов с непрерывной подачей тока; непрерывное движение роликов при прерывистой подаче тока; прерывистое движение роликов с прерывистой подачей тока (шаговая сварка)
.
Рис. 3.5. Схема шовной сварки: 1- сварочный трансформатор; 2 - контактные ролики; 3 - прижимное устройство; 4 - свариваемые детали
Рис. 3.6. Схема расположения роликов и свариваемых деталей при различных способах шовной сварки
Первый из указанных режимов применяется при сварке листов суммарной толщиной до 1,5 мм, поскольку при большей толщине после выхода из-под роликов сваренные листы могут расслоиться вследствие медленного остывания нагретого до пластического состояния стыка. Кроме того, при непрерывной подаче тока может происходить значительное коробление свариваемых листов. Наиболее распространен второй из указанных режимов. При сварке этим способом швы получаются с незначительным короблением листов, а расход электроэнергии - наименьшим.
Наиболее эффективно применение шовной сварки при изготовлении тонкостенных сосудов, сварных металлических труб и других подобных изделий. Взаимное расположение роликов и свариваемых деталей при осуществлении различных способов шовной сварки показано на рис. 3.6.
3.5. Электрооборудование установок контактной сварки
Контактная сварка обладает высокой производительностью, а во многих случаях является единственно возможным и экономически целесообразным способом соединения.
Выпускаемые машины контактной сварки подразделяют на машины общего назначения и высокопроизводительные специализированные машины, предназначенные для сварки конкретных изделий.
В машинах контактной сварки общего назначения
с целью повышения надежности широко применяются сварочные трансформаторы с витыми сердечниками и обмотками, залитыми эпоксидным компаундом, используется аппаратура управления на элементах «Логика» и с интегральными схемами; прерыватели тока с применением тиристоров, высокопроизводительная пневматическая и гидравлическая аппаратура и уплотнительные манжеты повышенной надежности.
По роду питания, преобразования или накопления энергии различаются следующие машины контактной сварки: а) однофазного переменного тока промышленной или пониженной частоты; б) постоянного тока (с выпрямлением тока во вторичном контуре); в) трехфазного тока, низкочастотные с тиристорным преобразователем; г) с накоплением энергии (в конденсаторах, электромагнитных системах, вращающихся массах).
.
Применение однофазных машин контактной сварки ограничивается возможностями включения в заводские трехфазные сети однофазных нагрузок большой мощности вследствие возможного перекоса фаз. Сложность электроснабжения однофазных сварочных машин обусловлена повторнократковременным режимом их работы, вызывающим периодические изменения напряжения сети,, что оказывает вредное влияние на работу параллельно с машиной других электроприемников.
УСТАНОВКИ ИНДУКЦИОННОГО И ДИЭЛЕКТРИЧЕСКОГО НАГРЕВА 4.1. Физико-технические основы индукционного нагрева
Индукционный нагрев проводящих тел - проводников первого и второго рода - основан на поглощении ими электромагнитной энергии, возникновении наведенных вихревых токов, нагревающих тело по закону Джоуля - Ленца. Переменное магнитное поле создается индуктором, который по отношению к нагреваемому телу является первичной обмоткой трансформатора. Нагреваемое тело выполняет роль вторичной обмотки трансформатора, содержащей один короткозамкнутый виток (рис. 4.1).
Рис. 4.1. Принципиальная схема индукционного нагрева:
1 - индуктор; 2 - магнитный поток в нагреваемом теле; 3 - нагреваемое тело; 4 - наведенный ток; 5 - воздушный зазор
Переменный магнитный поток Ф (2
), создаваемый первичной обмоткой - индуктором 1
, пропорционален его МДС и обратно пропорционален сопротивле- нию магнитной цепи. Возникающая в нагреваемом теле ЭДС Е = 4,44Фwf ·10-8
В при известном значении сопротивления нагреваемого тела обеспечивает возникновение в нем вихревого тока I (4
) и выделение соответствующей мощности
Р = I2
r = Е2
r/z2
.
Таким образом, индукционный нагрев является прямым нагревом сопротивлением, а включение нагреваемого тела в цепь тока производится за счет магнитной связи. Индукционный нагрев обладает достоинствами прямого нагрева сопротивлением - высокая скорость нагрева, пропорциональная вводимой мощности, неограниченный уровень достигаемых температур, достаточных для нагрева металлов, плавления металлов и неметаллов, перегрева, расплава, испарения материалов и получения плазмы.
Режим выделения мощности при индукционном нагреве обладает большим быстродействием и легко поддается автоматизации по требованию
технологических процессов, проходящих в открытой атмосфере, в защитных газах и вакууме.
Особенностью индукционного ввода энергии является возможность регули- рования пространственного расположения зоны протекания вихревых токов. Вопервых, вихревые токи протекают в пределах площади, охватываемой индукто- ром. Нагревается только та часть тела, которая находится в магнитной связи с индуктором независимо от общих размеров тела. Во-вторых, глубина зоны цирку- ляции вихревых токов и, следовательно, зоны выделения энергии зависит кроме других факторов от частоты тока индуктора (увеличивается при низких частотах и уменьшается с повышением частоты). Эффективность передачи энергии от индук- тора к нагреваемому току зависит от величины зазора между ними и повышается при его уменьшении. Как и нагрев сопротивлением, индукционный нагрев обеспе- чивает высокую производительность и хорошие санитарно-гигиенические условия труда, хотя для его осуществления требуются более сложные источники питания и повышенный удельный расход электроэнергии на технологические операции. Принципиальная схема индукционного нагрева включает в себя индуктор, зазор и нагреваемое тело. Эти элементы определяют эффективность преобразова- ния электрической энергии, получаемой от источника питания, в тепловую. Индуктор
создает переменный во времени магнитный поток, т. е. электромагнит- ную волну, падающую на нагреваемое тело. Сам индуктор, находящийся в созданном им электромагнитном поле, тоже поглощает энергию, которая выделяется в нем в виде потерь.
Формы индукторов весьма разнообразны - цилиндрическая, плоская, фасонная. Как правило, индукторы изготовляют из меди - немагнитного металла и охлаждаются водой. В большинстве случаев индукторы имеют много витков и изоляцию между витками. При выполнении нагревательных операций индуктор может находиться снаружи нагреваемого тела либо внутри его. В последнем случае внутри индуктора помещают сердечник из листовой трансформаторной стали. Наиболее распространенным является внешнее расположение индуктора на цилиндрическом нагреваемом теле. При прохождении по индуктору переменного тока в соответствии с теорией, изложенной в [33], напряженность магнитного поля в полости одинакова во всех его точках. Поток энергии (квар) внутрь полости индуктора через его поверхность на единицу длины составляет
Рq1,0 = 7,9·10-9(Iw1,0)2f(πD2в/4),
где (Iw1,0
)2
- квадрат ампер-витков индуктора; f - частота тока; πD2
в
/4 - площадь поперечного сечения полости индуктора.
Отсюда следует, что мощность в полости индуктора чисто реактивная и идет на создание переменного магнитного поля.
Потери в многовитковом индукторе, создаваемые поглощением электромагнитной энергии на 1 м его длины,
____
Ри 1,0 = 6,2·10-6(Iw1,0)2Dа√
ρиfFи/kэи;
____
Риq 1,0 = 6,2·10-6(Iw1,0)2Dа√
ρиfGи/kэи.
Здесь Dа
= 2Rа
- «активный» диаметр индуктора (для индуктора снаружи нагреваемого тела Dа
= Dв
= 2Rа
, для индуктора, помещенного в полость цилиндра, Dа
= Dн
= 2Rн
); ρи
- удельное сопротивление материала индуктора; Fк
, Gи
- комплексы, образованные из функции Бесселя, приведены в виде таблиц и графиков в справочной литературе. Потери мощности в зазоре между индуктором и нагреваемым телом зависят от взаимных размеров сопрягающихся деталей. Если в полости индуктора находится нагреваемый металлический цилиндр, то потери в зазоре
Рзq 1,0 = 6,2·10-9(Iw1,0)2 fd20[(Dв/d0)2-1].
При нахождении индуктора в полости нагреваемого цилиндра потери энергии в зазоре
Рзq 1,0 = 6,2·10-9(Iw1,0)2 fd2в[1-(Dн/dв)2].
Здесь d0
, dв
, Dв
и D- характерные размеры нагреваемого тела и индуктора. Энергия, вводимая в нагреваемое тело, определяется в инженерных расчетах через значение мощности, выделяющейся в металлическом цилиндре на 1 м его длины. Для активной мощности
___
Р1,0 = 6,2·10-6(Iw1,0)2d0√
ρμf F0ц
и реактивной мощности
____
Рq1,0 = 6,2·10-6(Iw1,0)2d0√
ρμf G0ц,
где ρ - удельное сопротивление нагреваемого материала; μ - магнитная проницаемость; f - частота поля; (Iw1,0
) - ампер-витки индуктора; F0ц
, G0ц
- сложные комплексы, образованные из функции Бесселя, определяются по таблицам и графикам.
Электрический КПД системы индуктор - металлический цилиндр определяется из соотношения полезной активной мощности Р1,0, выделяющейся в металле, и активных потерь в индукторе Ри1,0
:
ηэ=1/(1+ Ри1,0/ Р1,0).
Максимальное значение КПД составляет 0,70-0,881. Для получения высоких КПД частота при уменьшении диаметра цилиндра должна повышаться до некоторого предела, после которого КПД остается неизменным.
Чем больше зазор между индуктором и нагреваемым цилиндром, тем больше реактивная мощность Рз
q 1,0 и тем ниже соз ф. В слое металла толщиной Δэ
поглощается 86,4 % энергии, прошедшей через поверхность тела. Используя соотношение μа
= μμ0
и ω = 2πf, где μ - относительная магнитная проницаемость нагреваемого металла; μ0
- магнитная постоянная, равная 0,4π10-6
Гн/м, глубина проникновения
_____
Δэ
= 503√ρ/(μf).
Отсюда следует, что глубина нагрева тела увеличивается с ростом его удельного сопротивления и понижается с ростом частоты тока. Кроме того, эта формула позволяет определить необходимую частоту тока для нагрева тела на заданную глубину. Для ферромагнитных материалов, когда с ростом температуры увеличивается ρ, а при достижении точки Кюри значение μ падает от 50-100 до 1, глубина проникновения тока резко увеличивается, однако поглощаемая мощность при этом уменьшается.
Индукционный способ нагрева применяется при следующих технологических процессах: плавка металлов и неметаллов; поверхностная закалка; нагрев заготовок под пластическую деформацию или термохимическую обработку; сварка и пайка; зонная очистка металлов и полупроводников, плавка во взвешенном состоянии; получение монокристаллов из тугоплавких оксидов; получение плазмы.
4.2. Индукционные плавильные установки
По конструктивным особенностям индукционные плавильные печи подразделяют на два типа: канальные и тигельные
. Конструкции этих печей в значительной мере определяют их электрические параметры, энергетические характеристики и технологические возможности.
Необходимость получения полупроводниковых материалов, металлов высокой чистоты, сплавов на основе химически активных и тугоплавких металлов, а также плавленых огнеупорных материалов повышенной чистоты, получение которых в печах с керамической футеровкой весьма затруднительно, привела к созданию новых методов и установок индукционной плавки, обеспечивающих получение указанных материалов без примесей и при гораздо более высоких температурах, чем в тигельных или канальных индукционных печах. К такого типа процессам относятся индукционная гарниссажная плавка, индукционная струйная плавка, плавка во взвешенном состоянии, зонная плавка в холодном тигле, кристаллизационная плавка.
Индукционные канальные печи.
В этих печах канал с расплавленным металлом является короткозамкнутым витком вторичной обмотки
трансформатора, в нем поглощается 90-95 % подведенной к печи электрической энергии. По электротехническим характеристикам канальные печи подобны силовым трансформаторам с распределенной по длине вторичной обмотки нагрузкой. Принципиальная схема индукционной канальной печи (ИКП) приведена на рис. 4.2. С целью уменьшения потока рассеяния Фs
первичную ω1
и вторичную ω2
обмотки располагают одном стержне магнитопровода М, по которому протекает основной магнитный поток Ф1
.
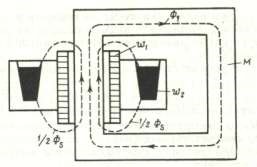
Рис 4 2. Схема индукционной канальной печи
Наиболее важным достоинством индукционных канальных
печей является их высокий энергетический КПД, достигающий в зависимости от рода переплав- ляемого металла значений 60-95 %.
Следует также отметить малый угар металла в индукционных канальных печах, поскольку здесь нет большого перегрева металла и его сильного окисления на поверхности ванны печи.
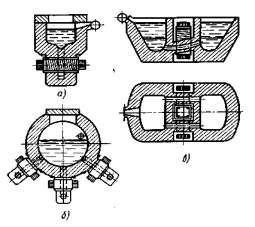
Рис. 4.6. Основные типы конструкций ИКП: а - шахтная; б - барабанная; в - двухкамерная
Рис. 4.7. Схема индукционной тигельной печи
В промышленности находят применение также электромиксеры
и копильники
жидкого металла - устройства для подогрева и выравнивания его температуры перед разливкой, когда объем отливаемой детали больше емкости плавильной печи. Электромиксеры могут быть использованы для литья в кристаллизатор машин непрерывного действия, требующих регулирования скорости литья. Миксеры всегда работают в комплексе с плавильными печами.
Так, для плавки меди и ее сплавов печи имеют максимальную емкость до 16 т, максимальную удельную мощность 30 кВт/т, производительность до 10 т/ч при плавке меди и 13-15 т/ч при плавке латуни, В зависимости от емкости печи удельный расход электроэнергии при плавке меди в них составляет 270-330 кВт
·ч/т, а при плавке сплавов на медной основе 190—210 кВт
·ч/т. Для плавки цинка применяются ИКП емкостью до 100 т и производительностью 30 т/ч, удельный расход электроэнергии при этом составляет 95-110 кВт
·ч/т. Алюминий и его сплавы переплавляются в ИКП емкостью от 170 кг до 40 т, производительностью от 75-100 кг/ч до 10 т/ч при удельном расходе электроэнергии 360-500 кВт
·ч/т.
При разливе чугуна применяют ИКП-миксеры емкостью до 250 т, мощностью 4400 кВт. Удельная мощность при плавке твердой шихты составляет 30-100 кВт/т, а в дуплекс-процессе при жидкой загрузке 20-50 кВт/ч. Максимальная производительность находящихся в эксплуатации в чугунолитейном производстве ИКП составляет 10 т/ч, емкость 100 т. Для плавки катодного цинка применяются ИКП емкостью до 100 т с шестью индукционными единицами общей мощностью 3000 кВт, производительностью 30 т/ч и удельным расходом электроэнергии 100 кВт
·ч/т.
Индукционные тигельные печи.
Характерным электротехническим признаком индукционных тигельных печей является то, что нагреваемые в них электропроводящие тела образуют с индуктором, создающим переменное электромагнитное поле, систему двух индуктивно связанных контуров с током. Индукционная тигельная печь (ИТП) (рис. 4.7) состоит из следующих основных частей: индуктора 1
, подключаемого к источнику переменного тока, расплавляемого металла 2
, находящегося внутри огнеупорного тигля 3
, и внешнего магнитопровода 4
, применяемого в печах большой емкости для экранирования и уменьшения потерь энергии, а также токопроводов и устройства для наклона печи при сливе металла.
Нагрев и расплавление металлической загрузки происходят за счет прохождения в ней индуцированного электромагнитным полем электрического тока и выделения при этом в загрузке теплоты по закону Джоуля-Ленца.
Кроме того, можно отметить следующие положительные свойства индукционных тигельных печей:
а) возможность получения чистых по химическому составу металлов и сплавов, поскольку отсутствует соприкосновение с топливом или электродами; б) возможность проведения плавки в нейтральной среде или вакууме для получения металлов высокого качества;
в) отсутствие перегрева футеровки, что повышает срок службы печи. Практически вся поглощаемая энергия выделяется в слое металла толщиной Δэ.гор
- глубина проникновения тока в горячий металл. По мере нагрева садки меняются магнитная проницаемость и удельное электрическое сопротивление металла, поэтому частота тока индуктора определяется из условий оптимального режима плавки, соответствующего максимальной скорости расплавления. Для обеспечения достаточно высокого КПД нагрева частоту питающего тока определяем по формуле
f ≈ 25*106
ρгор
/d2
0
.
Эта формула справедлива при условии
_
r0
√2/Δэ.гор
≥7,
_____
где r0
= d0
/2 и Δэ.гор
= 503√ ρгор
μf , м (d0
- диаметр тигля, м); ρгор
– удельное электрическое сопротивление горячего металла, Ом·м. Из формулы следует, что частота источника питания печи зависит от геометрических размеров (диаметра d0
). В ИТП большой емкости (больших диаметров) применяются источники питания промышленной частоты, в печах средней и малой емкости - повышенной и высокой частот.
Тепловой КПД определяется видом футеровки и температурой расплава и составляет ηтеп
= 0,84÷0,85. Общий КПД тигельной печи ηп
= ηэ
ηтеп
= 0,48÷0,68. Индукционные тигельные печи имеют естественный коэффициент мощности соs θп
= 0,8÷0,3 и требуют установки батареи конденсаторов для компенсации реактивной мощности.
Тигельные электропечи могут работать с «болотом» и без «болота». «Болото» по объему обычно составляет 25-30 % емкости тигля. При этом в тигель можно загружать шихту любых габаритных размеров: отходы литейного производства, чушки, мелкую стружку и т. д.
Плавильные тигельные печи вне зависимости от частоты питающего тока, начиная от 50 Гц до 400 кГц при емкости тигля от десятков тонн до нескольких килограммов расплавленного металла, имеют одни и те же конструктивные элементы.
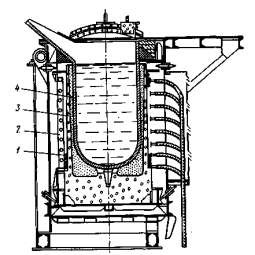
Рис. 4.8. Индукционная тигельная печь со стальным тиглем для плавки магния:
1 - индуктор: 2 - магнитопровод; 3 - набивная футеровка: 4 - стальной тигель
Индукторы
из медной водоохлаждаемой трубки круглого, квадратного или прямоугольного сечения изготовляют однослойными, состоящими из нескольких катушек, имеющих раздельное водяное охлаждение. Толщина стенок медной трубки не должна быть менее 1,3Δэи
(Δэи
- глубина проникновения тока в медь при. рабочей частоте).
В плавильных индукционных печах тепловые и электрические потери составляют 15-20 и 30-35 % соответственно Индукционные тигельные печи выпускаются различных емкостей, мощностей и частот питающего тока. Так, для плавки стали созданы печи емкостью 0,06-6 т, мощностью 90-2230 кВт, частотой тока 2400-500 Гц и производительностью 0,132-3,5 т/ч.
Индукционная плавка без соприкосновения расплава с футеровкой
. Гарнисажная плавка - плавка, при которой расплавленный металл соприкасается только с твердой фазой такого же химического состава, что и расплав, отделяющий его от конструктивных элементов печи.
При индукционной гарнисажной плавке металла с введением энергии через боковой гарнисаж предусматривается создание внутри цилиндрического индукто- ра или охватываемого им тигля слоя гарнисажа из порошка переплавляемого
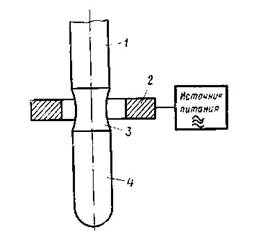
Рис. 4.9. Схема зонной плавки:
1 - поликристалл; 2 - индуктор; 3 - расплавленная зона; 4 – монокристалл
Высококачественные монокристаллы выращивают и с помощью бестигельной зонной плавки
с индуктивным способом передачи энергии в расплав
(рис. 4.9). Для зонной плавки характерно медленное перемещение узкой расплавленной зоны через сравнительно длинный твердый образец, в результате чего достигается перераспределение примесей и изменение кристаллической структуры исходного материала. Из-за излучения с поверхности, а также вследствие небольшой теплопроводности переплавляемых материалов (кремний, германий и др.) и сильной зависимости их удельного сопротивления от температуры зона максимальной температуры, образующаяся под поверхностью кристалла, имеет форму кольца.
Большие возможности при выращивании высокотемпературных кристаллических веществ открывает индукционная плавка в металлических водоохлаждаемых тиглях.
4.3. Индукционные нагревательные установки
Индукционные нагревательные установки широко применяются в различных технологических процессах в машиностроительной и других отраслях промышленности. Их подразделяют на два основных типа: установки сквозного
и поверхностного
нагрева.
Индукционные установки сквозного нагрева применяются для нагрева заготовок под последующую пластическую деформацию: ковку, штамповку, прессовку, прокатку и т. д.
По сравнению с другими видами нагрева (в пламенных печах и печах резис- торного нагрева) индукционный нагрев имеет малый угар металла и меньший брак из-за попадания окалины в обрабатываемое изделие.
В зависимости от геометрических параметров нагреваемых деталей и их материала источники питания индукционных установок выполняют на частоту 5010 000 Гц. Для установок сквозного нагрева выбор рабочей частоты производят таким образом, чтобы выделение теплоты происходило в слое достаточной толщины по сечению детали при отсутствии большого градиента температуры между поверхностью и слоем определенной толщины. При этом будет меньше перегрев поверхности заготовки и выше КПД установки.
Нагрев считают глубинным, если соблюдается условие
_
r0
√2/Δэ.гoр
= 3÷5,
где r0
- радиус нагреваемой заготовки; Δэ.гoр
- глубина проникновения тока в металл горячей заготовки. Необходимая частота для сквозного нагрева цилиндрических стальных заготовок ориентировочно может быть определена по соотношению
f = 3*104
/d2
0
,
где d0
- диаметр нагреваемой заготовки, см.
По режиму работу установки сквозного нагрева подразделяют на установки периодического и непрерывного действия. В установках периодического действия

Рис. 4.10. Схемы индукционных нагревательных установок непрерывного действия:
а, в, г - в продольном; б, д - в поперечном магнитном поле; 1 - индуктор; 2 - нагреваемое изделие; 3 - теплоизоляция; 4 - механизм перемещения заготовки; 5 - магнитопровод
В установках непрерывного действия
одновременно находится несколько заготовок, расположенных в продольном или поперечном магнитном поле (рис.
4.10). В процессе нагрева они перемещаются по длине индуктора, нагреваясь до заданной температуры. В нагревателях непрерывного действия полнее используется мощность источника питания, поскольку средняя мощность, потребляемая ими от источника питания, выше, чем средняя мощность, потребляемая нагревателем периодического действия.
Индукционные нагреватели непрерывного действия имеют более высокий КПД источника питания и производительность их выше, чем установок периодического действия. Применяется питание нескольких нагревателей от одного источника, а также подключение нескольких генераторов к одному нагревателю, состоящему из нескольких секций (рис. 4.10, в
, секции А, В, С). Конструкция индуктора для сквозного нагрева зависит от формы и размеров деталей. Индукторы выполняют круглого, овального, квадратного или прямоугольного сечения. Для нагрева концов заготовок индукторы выполняют щелевыми или петлевыми (рис. 4.10, г
, д
).
Индукционный поверхностный нагрев сопровождается проявлением поверхностного эффекта и эффекта близости
.
Индукционные установки поверхностного нагрева применяются для нагрева деталей под последующую термохимическую обработку (закалка, цементация, азотирование и т. п.).
Индукционная закалка заключается в быстром нагреве поверхности изделия с последующим быстрым охлаждением на воздухе, в воде или масле. При этом поверхность приобретает высокую твердость и способность хорошо работать на трение, а «сырая» (мягкая) сердцевина обеспечивает высокую сопротивляемость ударным нагрузкам. При таком нагреве удается во много раз уменьшить объем нагреваемого металла (по сравнению со сквозным нагревом) и значительно сократить расход электроэнергии.
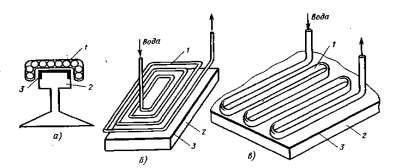
Рис. 4.11. Технологические схемы поверхностного индукционного нагрева:
1 - индуктор: 2 - нагреваемое изделие; 3 - нагретый слой изделия
Необходимость поддержания высокого электрического и теплового КПД системы индуктор - нагреваемое тело определяет исключительно большое количество форм и размеров индукторов.
Схемы некоторых индукторов для поверхностного нагрева показаны на рис. 4.11, а-в
.
Индукторы характеризуются удельной поверхностной мощностью (Вт/м2
), которая зависит от частоты тока, глубины прогрева, размеров нагреваемых изделий и изменяется в очень широких пределах.
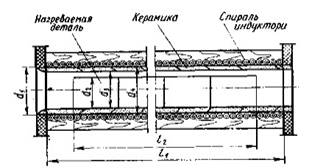
Рис. 4.12. Схема индукционного нагревателя:
d1
- внутренний диаметр индуктора; d2
- диаметр детали; d3
- внутренний
диаметр огнеупорного цилиндра; d4
- внутренний диаметр теплоизолирующего цилиндра; l1
- длина индуктора; l2
- общая длина садки
Выбор основных геометрических соотношений индуктора, т. е. его внутреннего диаметра и длины, а также размеров его теплоизоляции производят следующим образом (рис. 4.12). Внутренний диаметр огнеупорного цилиндра определяют из соотношений
d3
= (1,1 - 1,2)d2
; d3
– d2
> 5 см.
Между индуктором и огнеупорным цилиндром проложен слой теплоизолирующего материала (2-5 мм), что снижает тепловые потери и защищает электрическую изоляцию индуктора.
Оптимальная частота fопт
, необходимая для нагрева на заданную
глубину Δопт
,
fопт
= ρ/(πμΔ2
э
),
где ρ - удельное электрическое сопротивление нагреваемого материала, Ом*м.
Для поверхностного нагрева сталей под закалку (μ = 1)
fопт = 4/Δ2э
Выбор оптимальной частоты для нагрева металла осуществляют по максимальному значению общего КПД, соответствующему минимальному удельному расходу энергии.
Чем больше р нагреваемого изделия, тем выше ηэ
. Так, при нагреве стали предельный ηэ
= 0,7÷0,8, а при нагреве цветных металлов могут быть случаи, когда он только несколько выше 0,5.
Коэффициент мощности системы индуктор-садка и реактивная мощность конденсаторной батареи.
Индукционные установки имеют, как правило, низкий естественный коэффициент мощности, причем значения его изменяются в довольно широких пределах в зависимости от частоты тока, зазора между индуктором и изделием, магнитной проницаемости, удельного сопротивления и размеров нагреваемых изделий.
4.4. Физические основы диэлектрического нагрева
Использование электрического тока, проходящего через диэлектрики и полупроводники в переменном электрическом поле, является основой диэлектри- ческого нагрева, который имеет преимущества перед другими способами нагрева. Это быстрота, равномерность и высокая производительность. С энергетической точки зрения такой нагрев является наиболее эффективным, поскольку при его осуществлении вся энергия вносится в массу нагреваемого материала. По технологическим признакам установки высокочастотного диэлектрического нагрева подразделяют на три вида.
Установки первого вида
используются в процессах промышленной обработ- ки крупных изделий, требующих быстрого нагрева в однородном электрическом поле: сушка волокон шерсти или хлопка, целлюлозы и лесоматериалов, обжиг крупных электроизоляторов и фарфоровых изделий, производство звуко- и теплоизоляционных материалов, сварка пластмасс и полимерных пленок. Установки второго вида
применяются для нагрева протяженных плоских изделий: сушка текстильного волокна, рисунков на тканях, бумаги, фотопленки, химических и фармацевтических препаратов, полимеризации клеев, нагрев каучука, пастеризация и т. д.
В установках третьего вида
проводятся процессы, не требующие быстрого и однородного нагрева: размораживание продуктов, разогрев и быстрое приго- товление блюд, обжиг простых керамических изделий, сушка грибов, чая и т. п. Использование высококачественного нагрева позволяет повысить качество продукции, ускорить технологические процессы и получить при массовом производстве большую экономию, несмотря на высокую стоимость оборудования. Частицы диэлектрика, помещенного в электрическое поле, испытывают механическое воздействие, смещающее положительно заряженные частицы в одну сторону, а отрицательно - в другую. В результате центры электрического действия положительных и отрицательных частиц не совпадают и во внешнем пространстве такая молекула воспринимается как диполь, т. е. как система двух равных, но противоположных зарядов +q и –q, смещенных друг относительно друга на расстояние l (рис. 4.13, а).
Такой диэлектрик, имеющий ориентированные в одном направлении диполи, называют поляризованным. Произведение заряда частицы на смещение l называют электрическим моментом диполя m = gl (Кл*м), который связан с напряженностью электрического поля Е соотношением m = αЕ, где α - мера упругой деформации молекулы или атома - их поляризуемость.
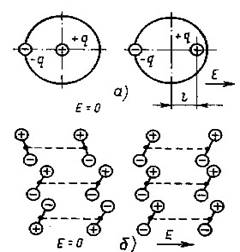
Рис. 4.13. Виды поляризации диэлектрика в электрическом поле:
а - поляризация атомов; б - ориентационнаяполяризация
Различают несколько видов поляризации.
Электронная поляризация
атомов вызвана смещением электронного облака относительно ядра атома и приобретением последним индуцированного дипольного момента (рис. 4.13,а
). Время собственных колебаний электронов составляет 10-14
-10-15
с, за это же время устанавливается электронная поляризация. Ионная поляризация
молекул вызвана упругим смещением ионов в твердых диэлектриках с ионной кристаллической решеткой (ионы Na+
и Сl-
в поваренной соли).
Период собственных колебаний решетки составляет 10-12
- 10-13
с. Время ионной упругой поляризации того же порядка.
Ориентационная поляризация
имеет место в диэлектриках с молекулами, представляющими собой жесткие диполи, независимо от наличия внешнего электрического поля. Поляризация проявляется в частичном повороте и упорядочении диполей под влиянием внешнего электрического поля (рис. 4.13,б
). Это поляризация упругого смещения, возникающая в твердых или жидких диэлектриках, полярные молекулы которых связаны друг с другом так, что под действием электрического поля могут поворачиваться лишь на небольшой угол. Поляризация диэлектрика происходит не только в постоянном, но и в переменном электрическом поле. В этом случае направление поляризации меняется с частотой поля, упругие диполи вибрируют, жесткие поворачиваются в прямом и обратном направлениях. Происходит перемещение зарядов, т. е. через диэлектрик проходит электрический ток. При расположении диэлектрика между обкладками конденсатора, на которые подано напряжение от высокочастотного генератора, цепь тока замкнется через этот генератор.
Поляризация сопровождается потерями энергии, вызванными трением между молекулами (потери трения) и перемещением диполей (дипольные потери). Потери энергии выражаются в нагреве диэлектрика или полупроводника, скорость которого определяется, в частности, частотой изменения поля. Потери при поляризации приводят к запаздыванию смещения молекул по отношению к внешнему полю. С ростом частоты отставание увеличивается, пока не достигнет максимума. Дальнейшее повышение частоты из-за вязкости среды приводит к обратному результату - уменьшению поляризации, что ведет к резкому снижению диэлектрической проницаемости вещества. При отсутствии потерь ток опережает напряженность поля на угол 90°. Если поляризация сопряжена с потерями и несколько запаздывает, ток опережает напряженность на угол, меньший 90°. Разница δ-θ (рис. 4.14) характеризует потери в диэлектрике и называется углом диэлектрических потерь.
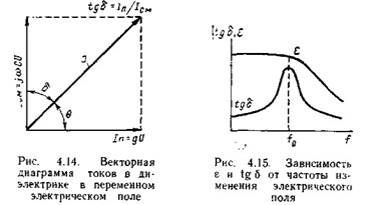
Происходящие в диэлектрике, помещенном в переменное электрическое поле, процессы определяются диэлектрической проницаемостью ε = ε'-jε".
Вещественная часть комплекса ε' характеризует отношение емкостей конденсатора до и после введения в него диэлектрика - относительная диэлектрическая проницаемость вещества.
Мнимая часть ε" = ε'tgδ характеризует поглощение энергии поля диэлектриком и называется коэффициентом потерь
диэлектрика. Проходящий через конденсатор с диэлектриком ток имеет две составляющие: ток смещения Iсм
= jωСU и ток проводимости Iп
= gU. Полный ток, проходящий через диэлектрик,
I = Iп
+ Iсм
= (g + jωС)U.
Отношение тока проводимости к току смещения Iп
/Iсм
= tgδ также определяет коэффициент потерь в диэлектрике.
Показатели ε и tgδ зависят от рода и физического состояния вещества (влажности, температуры), а также от частоты поля. Их зависимость от частоты поля показана на рис. 4.15. Величина tgδ имеет максимум при так называемой релаксационной частоте
f0
, характерной для каждого материала.
Выделяющуюся в диэлектрике мощность можно получить из векторной диаграммы
P = Uicosθ ≈ UItgδ = ωCU2
tgδ,
где ω = 2πf - угловая скорость, рад/с; С - емкость плоского конденсатора, Ф; С = εε0
S/d (S - площадь пластин конденсатора, м2; d - расстояние между ними, м; ε0
= 8,85·10-12
Ф/м - диэлектрическая проницаемость вакуума). Имея в виду, что объем диэлектрика равен 5й и напряженность электрического поля Е= U/d (В/м), мощность Р0
(Вт/м3
), выделяющаяся в единице объема диэлектрика,
Р0
=5,56·10-11
fE2
εtgδ, (4.1)
Подводимая удельная мощность Р0
расходуется на нагрев материала, испарение влаги или других летучих компонентов. При затратах теплоты только на нагрев удельная мощность, поступающая в материал, должна соответствовать
Р нагр
= Cр
γ(ΔT/Δη)/ ηt
. (4.2)
где Ср
- удельная теплоемкость материала, Дж/(г·К); γ - плотность материала, г/см3
; ΔT/Δη - скорость нагрева материала, К/с; ηt
- термический КПД процесса, учитывающий потери теплоты в окружающую среду. При затратах теплоты только на испарение
Рисп
= (L/ηt
) · ( ΔT/Δη), (4.3)
где L - скрытая теплота парообразования при данной температуре нагрева, Дж/г; ΔT/Δη - скорость испарения, Г/(см3
·с).
Анализ уравнений (4.1) - (4.3) позволяет сделать вывод, что мощность, выделяющаяся в диэлектрике, помещенном в переменное электрическое поле, определяется только его электрическими характеристиками ε и tgδ и параметрами поля: напряженностью и частотой.
Выделяющаяся мощность не зависит от теплопроводности материала, которая у диэлектриков, как правило, имеет низкие значения. Эта особенность является существенным преимуществом диэлектрического нагрева, позволяющим значительно ускорить процесс нагрева материала по сравнению с другими традиционными видами нагрева.
4.5. Установки диэлектрического нагрева
Установки диэлектрического нагрева подразделяют на два вида: собственно установки диэлектрического нагрева, работающие на высокой частоте (ВЧ-установки - частота 66 кГц - 100 мГц), и установки сверхвысокочастотного нагрева (СВЧ-нагрев-частота 1000 мГц и выше). Последние применяются при нагреве диэлектриков со сравнительно малым коэффициентом потерь, нагреве пищевых продуктов.
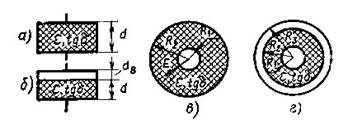
Рис. 4.16. Схемы рабочих конденсаторов установок диэлектрического нагрева
Выбор рабочих параметров установки определяется рядом физических свойств нагреваемого материала.
Одним из условий равномерного нагрева по всему объему однородного материала является превышение глубины проникновения электромагнитной волны в материал под его толщиной. Глубина проникновения (см) определяет расстояние, на котором напряженность электрического поля ослабевает в е
раз относительно ее значения на поверхности:
_
Δ = 9,55·1011
f√ε tgδ.
Допустимая напряженность поля в воздушном зазоре определяется значени- ем пробивной напряженности Eпр.в
. При ее достижении происходит электрический пробой. Напряженность пробоя воздуха ниже, чем Епр
большинства нагреваемых материалов. На практике при процессах сушки с выделением водяных паров или других летучих продуктов напряженность поля в воздушном зазоре не должна пре вышать 1,0-1,5 кВ/см, в других процессах нагрева она может достигать 5,0 кВ/см. Допустимую напряженность поля в материале Eм.доп
принимают в два раза меньшей пробивной напряженности этого материала: Eм.доп
= Eм.пр
/2. Выбрав допустимое значение напряженности поля в материале Ем
по формулам (4.1) - (4.3) определяют рабочую частоту тока (Гц) при нагреве и сушке материала соответственно:
fн
= 7,53*1012
γCΔT ;
ε tgδ ηt
η E2
м
fc
= 7,53*1012
LΔT .
ε tgδ ηt
η E2
м
В комплект установок диэлектрического нагрева входят высокочастотный генератор; система защиты и сигнализации; технологический узел. Принципиальная схема высокочастотного генератора на триоде и его эквивалентная схема нагрузки показаны на рис. 4.17. Технологический узел конденсатор с нагреваемым материалом - включен в колебательныи контур.
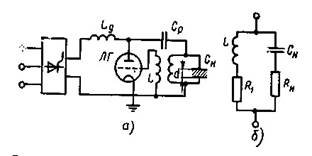
Рис. 4.17. Схема высокочастотного генератора для диэлектрического нагрева (а
) и
эквивалентная схема нагрузки (б
):
Lд
- индуктивность дросселя, защищающего выпрямитель от высокой частоты
;
ЛГ - ламповый генератор
; Ср
- разделительный конденсатор
; Сн
- емкость нагревательного конденсатора
; Lк
- индуктивность колебательного контура
; Rн
- активное сопротивление нагрузки
; R1
- активное сопротивление индуктивной катушки и соединительных проводов
Полное активное сопротивление контура
Rк
= Rн
+R1
Если оно незначительно:
_____
Rк
<<2√Lк
/Сн
,
то частоту генератора с достаточной точностью определяют по условию резонанса контура без потерь:
1/(ωСн
) = ωLк
или
____
f = 1/2π√Lк
Сн
.
Эквивалентное сопротивление контура с учетом потерь
Rэ
= 1/(ωСн
) ·ωLк
/Rк
= Lк
/(Сн
Lк
),
где ωLк
/Rк
- отношение реактивного и активного сопротивлений, т. е. добротность контура. Эквивалентное сопротивление контура должно соответствовать паспортным данным генератора.
Выходная мощность генератора (Вт)
Pг
= P0
υк
/ηк
,
где υк
- объем конденсатора, м3
; ηк
- КПД колебательного контура.
Конструкция технологического узла определяется в основном родом и видом нагреваемого материала. Различные схемы осуществления технологических узлов установок диэлектрического нагрева показаны на рис. 4.18.
Схемы технологических узлов для нагрева и сушки крупногабаритных изделий и порошкообразных материалов показаны на рис. 4.18, а
, б
. При диэлектрическом нагреве температура внутри нагреваемого материала выше, чем в поверхностных слоях, с которых происходит удаление влаги. Совместное влияние градиентов давления, влагосодержания и температуры способствует высокой производительности сушки с использованием высокочастотного нагрева. На рис. 4.18, в
показана схема технологического узла для изготовления изделий из пенопласта. При формировании различных видов изделий исходное сырье помещается в формы, рабочие полости которых повторяют конфигурацию изделия.
Рис. 4.18. Схемы технологических узлов установок диэлектрического нагрева
Существуют установки диэлектрического нагрева для термообработки пористых резин, предварительного нагрева таблетирован-ных пресс-материалов, нагрева в процессе прессования, термообработки изделий и нагрева перед штамповкой, склеивания термореактивными клеями, обработки сельхозпродуктов и т. д.
Применяемые установки диэлектрического нагрева по рабочим частотам условно подразделяют на установки средневолнового (f = 0,3÷3,0 МГц), коротковолнового (f = 3÷30 МГц) и метрового (f = 30÷300 МГц) диапазонов. Первые из них применяются для нагрева материалов с большим фактором потерь εtgδ, к которым относятся очень влажные изделия при их относительно небольших габаритных размерах. Генераторы этих установок имеют сравнительно высокий КПД (0,5-0,6) и выполнены мощностью до нескольких сотен киловатт. Нагрев производится на низких удельных мощностях (р0
= 0,01÷1,0 Вт/см3
) при длительности нагрева в десятки часов и высоком напряжении на рабочем конденсаторе (10-15 кВ). Коротковолновые установки применяются для нагрева материалов со средним значением фактора потерь. КПД таких установок 0,4-0,55. Мощность генератора составляет несколько десятков киловатт, объем одновременно нагреваемого материала небольшой. Удельная мощность р0
= 1÷100 Вт/см3
. Сушка с испарением длится в течение нескольких часов, без испарения - доли часа. Установки удобны при работе с воздушным зазором и для осуществления методического нагрева.
Установки метрового диапазона имеют КПД, равный 0,3-0,4. Применяются для нагрева материалов с малым значением εtgδ. Объем рабочей камеры невелик (р0
= 0,1÷3 кВт/см3
), время нагрева - секунды, могут работать с воздушным зазором.
Особенностью установок сверхвысокой частоты
является соизмеримость геометрических размеров колебательных систем с длиной волны используемых колебаний. Колебательная система автогенератора объединена с генераторной лампой в один вакуумированный блок. Нагрев в электромагнитном поле осуществляется электромагнитным лучом в волноводе или резонаторе. При нагреве лучом нагреваемое тело находится под воздействием электромагнитного луча, излучаемого рупорной антенной, которой заканчивается волновод. Нагрев в волноводе осуществляется бегущей волной и применяется при термообработке листовых материалов, жгутов, лент, жидкостей (рис. 4.18, г
). В объемных резонаторах нагреваются предметы произвольной формы.
В установках СВЧ-нагрева напряженность электрического поля меньше, чем в установках метрового диапазона, что снижает опасность электрического пробоя. В таких установках производится нагрев материалов с низким значением фактора потерь - продуктов, слоистых материалов, медицинских препаратов и т. д.
4.6. Источники питания установок индукционного и диэлектрического нагрева
Индукционная плавильная или нагревательная установка состоит из: источника питания; согласующего устройства (согласующий трансформатор; автотрансформатор); конденсаторной батареи для компенсации реактивной мощности установки; индуктора нагревательной или плавильной установки; сети, связывающей источник питания с индуктором; аппаратуры защиты, регулирования и автоматического управления; механизмов загрузки, выгрузки и перемещения нагреваемого материала.
По частоте потребляемого тока установки индукционного нагрева подразделяют на установки промышленной, повышенной и высокой
частоты. Установки канальных и большинство тигельных печей большой и средней мощности имеют промышленную частоту 50 Гц. Питаются они от сетей внутризаводского электроснабжения напряжением 220, 380 или 660 В непосредственно или через специальные трансформаторы или автотрансформаторы. Установки большой мощности питаются от сетей напряжением 6-10 кВ через высоковольтные печные подстанции.
Нагрузочный блок включает в себя трансформатор с индуктором и конденсатором.
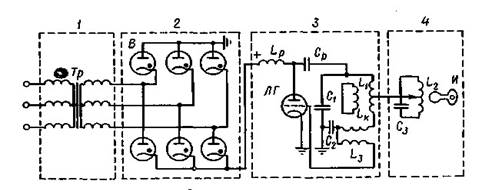
Рис. 4.21. Схема лампового генератора:
1 - блок питания; 2 - выпрямительный блок; 3 - блок генератора; 4 - нагрузочный блок; Тр
- силовой трансформатор; В - вентили; Lр
- разделительная индуктивность; Ср
- разделительная емкость; С1,2,3
- емкости колебательного и нагрузочного контуров; Lк
- короткозамкнутая катушка индуктивности; L1,2
- индуктивности контуров связи и нагрузочного; И - индуктор; ЛГ - генераторная лампа
Высокочастотные ламповые генераторы бывают двух видов: с независимым возбуждением
и с самовозбуждением
(автогенераторы). Отличием автогенератора от генератора с независимым возбуждением является то, что в нем напряжение возбуждения на лампу подается не от постороннего источника ЭДС, а от собствен- ной системы колебательных контуров через обратную связь. В индукционных установках обычно применяются генераторы с самовозбуждением. Поэтому в его состав входят элементы, обеспечивающие возбуждение генератора и управление его работой, а также элементы согласования нагрузки с параметрами лампового генератора.
В контур обратной сеточной связи входят конденсаторы, резисторы и катушки связи, подающие напряжение обратной связи на сетку генераторной лампы. К генератору относятся также катушки регулирования мощности в нагрузке, стабилизаторы напряжения накала и регулятор анодного напряжения, контрольно-измерительная, коммутационная аппаратура и измерительные приборы.
Для высокочастотного нагрева диэлектриков применяются ламповые генераторы на более высокие частоты (5,28-300 мГц). Они состоят в основном из тех же узлов, что и генераторы для индукционного нагрева проводящих материалов (рис. 4.17), но в отличие от последних нагрузкой в них является рабочий конденсатор, в котором находится нагреваемый материал. Так как в процессе нагрева емкость Сн
(рис. 4.17, б
) и активное сопротивление Rн
изменяются, то меняются эквивалентное сопротивление контура и режим работы генератора.
Для поддержания неизменным диапазона частот генератора в течение всего режима нагрева необходимо поддерживать неизменным эквивалентное сопротивление нагрузки, что достигается специальным регулированием - согласованием нагрузки.
Существуют различные схемы колебательной системы с обеспечением самовозбуждения, выбор которых определяется в основном необходимой частотой автоколебаний и требованиями к ее стабильности.
В одноконтурных схемах, используемых для генерирования колебаний с частотой до 1 мГц, применяется в основном трансформаторная или автотрансформаторная связь.
Многоконтурные схемы автогенераторов позволяют плавно и в широких пределах регулировать эквивалентное сопротивление контура без заметного снижения его КПД. Однако они имеют несколько резонансных частот, что может вызвать переход генератора с одной частоты на другую, поэтому необходимо осуществлять обратную связь от вторичного контура с индуктивной связью между контурами. Плавное регулирование сопротивления нагрузки осуществляется за счет перемещения короткозамкнутой индуктивной катушки (см. рис. 4.21). Установки для диэлектрического нагрева выпускают с унифицированными узлами, предназначенными для совместной работы с различным оборудованием
(прессовым и т. п.).
УСТАНОВКИ ДУГОВОГО НАГРЕВА ОСНОВЫ ТЕОРИИ И СВОЙСТВА ДУГОВОГО РАЗРЯДА 5.1. Ионизация газов. Понятие плазмы
В обычных условиях различные газы и их смеси (воздух, аргон, водород, гелий, углекислый газ и др.) не проводят электрический ток. Проводимость возникает тогда, когда в газовой среде помимо молекул и атомов появляются свободные заряженные частицы - электроны, положительные и отрицательные ионы и газ превращается в плазму.
Плазмой принято называть вещество, находящееся в четвертом состоянии (в дополнение к твердому, жидкому и газообразному), характеризующееся наличием нейтральных молекул и атомов, а также заряженных частиц - электронов и ионов, проводящее электрический ток и подчиняющееся законам магнитной газодинамики. Превращение газа в плазму проходит несколько стадий. Для молекулярных газов первым процессом является диссоциация - образование атомов. Возникновение в газе заряженных частиц - ионизация газа - может происходить в результате его нагрева, поглощения энергии рентгеновского или ультрафиолетового излучения, космических лучей, лучей оптического квантового генератора (лазера), действия электрического поля и др.
.
Так как все виды ионизации: тепловое движение частиц, электрическое поле, световое излучение - повышают скорость взаимного перемещения частиц, то следует предположить, что и наложение
высокочастотного напряжения должно приводить к ионизации пространства. Так это и происходит на самом деле. Приложение ВЧ-напряжения приводит к значительной ионизации - появлению ВЧ-короны даже при низких напряжениях.
5.2. Структура электродугового разряда
В ряде электротермических процессов, идущих с поглощением большого количества тепловой энергии, применяется электродуговой разряд, или
электрическая дуга, которая позволяет нагревать различные среды до высоких температур, недостижимых при сжигании топлива. Такие возможности электрической дуги пробудили значительный интерес к изучению ее физических свойств и энергетических возможностей.
Термины «разряд», «дуговой разряд» возникли как описание явления потери
«заряда» батареей гальванических элементов или конденсаторов через газы и вакуум.
В большинстве случаев формы существования электрической дуги самые разнообразные, однако сохранилось первоначальное название «дуга», данное этому явлению В. В. Петровым еще в 1802 г. при описании разряда между
горизонтальными электродами в воздухе, когда высокотемпературный газ в межэлектродном промежутке конвективными потоками воздуха изгибался
выпуклостью вверх, принимая форму дуги или арки.
В последние годы все большее количество производственных процессов переводится на дуговой нагрев. Этому соответствует повышение наших знаний о дуговом разряде, найденные возможности регулирования и использования его многочисленных свойств.
Электрическая дуга является одним из явлений, возникающих при прохождении электрического тока через газ, пары или вакуум.
По внешнему признаку и особенностям электрические разряды в газах очень разнообразны. В общем случае их подразделяют на самостоятельные и
несамостоятельные.
В самостоятельных разрядах заряженные частицы в разрядном промежутке образуются за счет энергии источника тока. Для поддержания несамостоятельного
разряда необходимо воздействие внешних факторов, обеспечивающих ионизацию газов. Дуговой разряд или электрическая дуга характеризуется высокой
плотностью тока в канале разряда (порядка 102-106 А/см2
), низким катодным
падением потенциала (менее 20 В), высокой температурой газовой среды в межэлектродном пространстве, достигающей в зависимости от условий существования дуги значений порядка (3÷5) 103
К и выше.
В цепи, состоящей из проводниковых материалов, передача электрической энергии осуществляется электронами. Другое дело, если в цепь включен проводник второго рода. В этом случае прохождение электрического тока по такой цепи сопровождается протеканием сложных явлений, в процессе
которых электроны превращаются в носители электрических зарядов другого вида, а затем снова в электроны.
Изучение протекающих в приэлектродных областях и на электродах процессов и их закономерностей применительно к электротехнологическим установкам преследует две цели:
1) выявление закономерностей переноса теплоты и материала электрода при электродуговой сварке, плазменно-дуговой и плазменной сварке и резке металлов, переплаве металлов в дуговых печах;
2) создание тугоплавких нерасходуемых или малорасходуемых электродов для электродуговых печей, плазменных генераторов (плазмотронов) и т. д. Контакт электрической дуги с электродами происходит в электродных пятнах (катодном и анодном), которые различаются проходящими в них явлениями и элементарными процессами.
Электроды дуговых установок.
Электроды дуговых установок, применяемых в технологических процессах, подразделяют на два типа: легкоплавкие и тугоплавкие.
Тугоплавкие электроды
изготовляют из графита и материалов на его основе, металлов, имеющих высокую температуру плавления - вольфрам, молибден, тантал и др., используя их способность выдерживать большие тепловые потоки и обеспечивать высокий уровень плотности тока термоэлектронной эмиссии. Можно выделить два вида технологического использования тугоплавких электродов:
1) в технологических процессах, проходящих в установках с
использованием материала электрода (вакуумные дуговые печи). Такие технологические установки называют установками с расходуемым электродом
;
2) в технологических процессах, происходящих в установках с нерасходуемыми электродами
(электродуговой нагрев различных газов в плазмотронах, вакуумные дуговые печи, некоторые виды сварки и электрической резки металлов).
Рассмотрим электроды, применяемые в электродуговых нагревателях газа.
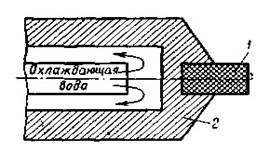
Рис. 5.3. Конструкция катодного узла плазмотрона
На рис. 5.3 показан вольфрамовый катод, выполненный в виде вольфрамового стержня 1
, выступающего на несколько миллиметров из охлаждаемого наконечника 2
. Он предназначен для работы в электродуговых нагревателях газа при токах до 100-2000 А в среде аргона, водорода и азота, исключающих присутствие кислорода.
Легкоплавкие электроды используются в технологических процессах с рас- ходуемыми электродами (электродуговая сварка, переплав металлов и их сплавов в вакуумных дуговых печах и др.) и в процессах с нерасходуемыми электродами (нагрев газов в плазмотронах). Кроме указанных случаев электроды из легкоплав- ких металлов, в частности из ртути, применяются в выпрямительных устройствах. Термохимический катод.
При горении дуги в активных газах на поверх- ности электродов возможно образование соединений, существенно влияющих на электрофизические свойства электродов - работу выхода, плотность тока эмиссии, температуру поверхности.
Термохимическим катодом
называют электрод, активная зона которого образуется при взаимодействии материала электрода с окружащим газом, расходуется во время работы и регенерируется по мере разрушения.
Так, если температура плавления циркония около 2500 К, то диоксид циркония плавится при температуре около 4800 К.
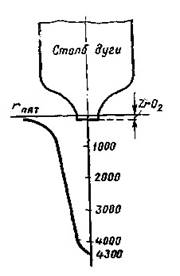
Рис. 5.4. Температурное поле термохимического катода
Термохимический катод не может работать без взаимодействия с окружающей средой.
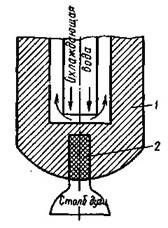
Рис. 5.5. Разрез термохимического катода
На рис. 5.5 показан термохимический катод дуговой установки для нагрева газов. В массивную водоохлаждаемую втулку 1
запрессовывается активная вставка из циркония или гафния 2
, так как охлаждение ее возможно лишь методом контактного теплообмена.
5.5. Особенности дуги переменного тока
В отличие от дуги постоянного тока дуга переменного тока имеет меняющиеся во времени ток и напряжение: iд
= f(η) и uд
= f(η). При этом дважды за период ток и напряжение дугового разряда проходят через нуль и меняют направление, соответственно меняется и полярность электродов. При этом каждый раз происходит погасание и вновь зажигание электродугового разряда. После угасания дуги в межэлектродном промежутке происходят два процесса: деионизация промежутка (увеличение его диэлектрической прочности) и нарастание потенцила на электродах.
Поскольку дуга дважды за период гаснет и загорается, кривая напряжения имеет пики зажигания и угасания. После зажигания дуги происходит снижение напряжения на ней, поскольку имеет место дальнейшее увеличение тока (по синусоиде) и, следовательно, повышение температуры (падающая вольт-амперная характеристика). После прохождения тока через максимум напряжение на дуге остается практически постоянным и повышается при снижении тока перед погасанием дуги.
Дуга может существовать с паузой тока и без паузы в момент перехода тока через нулевое значение. Продолжительность паузы определяется соотношением процессов нарастания диэлектрической прочности дугового промежутка и напряженности электрического поля между электродами, а также температуры электродов, обеспечивающих эмиссию электронов.
Для облегчения зажигания и непрерывного горения дуги в цепь последовательно с ней включают индуктивность.
Мощность электрической дуги можно регулировать несколькими способами.
1. Изменением напряжения питающей сети при постоянном балластном сопротивлении.
2. Изменением балластного сопротивления при неизменном напряжении источника питания.
Для осуществления этого способа регулирования необходимо иметь сопротивление с переключением ступеней. По сравнению с рассмотренным этот способ менее экономичен, поскольку источник вырабатывает постоянную мощность и при уменьшении мощности дуги избыток энергии рассеивается на балластном сопротивлении.
3. Воздействием на дугу различными факторами, в результате чего изменяются условия ее горения при постоянных напряжениях источника и сопротивления в цепи.
Среди факторов, воздействующих на дугу, отметим такие, как наложение на дуговой разряд магнитного поля, поток газа, изменение давления среды и самой среды, в которой горит дуга, а также изменение длины дугового столба.
Влияние этих факторов на вольт-амперную характеристику рассматривалось при обсуждении баланса энергии электродугового столба.
При питании дуги от индивидуальных источников энергии создание падающей характеристики цепи и регулирование мощности дуги необходимо
производить на стороне переменного тока включением дросселей с регулируемым
индуктивным сопротивлением или изменяемой индуктивностью трансформаторов, входящих в источник питания. Это позволяет повысить КПД системы источник питания - электрическая дуга и увеличить крутизну характеристики питающей
цепи. Более крутые или вертикальные характеристики источников сварочного тока позволяют точнее поддерживать заданное значение тока дуги независимо от изменения условий горения дуги. С этой целью разработаны специальные источники питания дуги - параметрические источники тока, тиристорные преобразователи, применяемые в конкретных установках.
Способы зажигания дуги.
В промышленных установках применяются следующие способы возбуждения дугового разряда: импульсное касание электродов; взрыв проводника малого сечения - проволочки; высокочастотный
высоковольтный пробой дугового промежутка.
1.При касании электродов под напряжением в точке их касания в переходном контакте выделяется тепловая энергия, вызывающая расплавление участка электрода. При последующем разведении мостик из расплавленного
металла взрывается. Под действием электрического поля между электродами
горячие участки электрода эмиттируют электроны, увеличивающие ионизацию
продуктов электрического взрыва жидкого металла и создают цепь тока через образовавшуюся плазму. При ожидаемом токе дуги более 50 А скорость разведения электродов не должна превышать 0,01 м/с.
2.В случаях, когда электроды неподвижны или бросок тока, возникающий при их замыкании, превосходит допустимые пределы, зажигание дуги
производится включением источника питания на закороченные тонким
проводником электроды или электроды, находящиеся под напряжением,
замыкаются тонкой проволокой. Для успешного возбуждения дуги необходимо, чтобы проволочка взрывалась при токе, близком к номинальному току дуги.
Материал проволочки должен иметь высокую температуру плавления, чтобы после ее взрыва температура продуктов взрыва была близкой к температуре плазмы дугового разряда.
3.Зажигание дуги импульсным пробоем дугового промежутка, находящегося под напряжением источника питания дуги, производится с
помощью осциллятора. Осциллятор - это преобразователь тока промышленной частоты низкого напряжения (60-220 В) в ток высокой частоты (150-500 кГц)
высокого напряжения 2000-8000 В.
ЭЛЕКТРОДУГОВЫЕ И РУДНО
-ТЕРМИЧЕСКИЕ ПЕЧИ
6.1. Классификация дуговых печей
Электродуговые печи применяются в металлургической, химической, машинострительной и ряде других отраслей промышленности. Они могут быть классифицированы следующим образом:
Дуговые печи косвенного действия
, где электродуговой разряд горит между электродами, расположенными над нагреваемым материалом, и теплообмен между электрической дугой и материалом осуществляется в основном за счет излучения. Дуговые пени прямого действия
. В них электрическая дуга горит между концами электродов и нагреваемым материалом. Нагрев материала осуществляется при выделении энергии в опорных пятнах дуги, протекании тока через расплав, а также за счет излучения плазмы дуги, конвекции и теплопроводности.
Дуговые печи сопротивления
. В них дуга горит под слоем электропроводной шихты; теплота выделяется в дуговом разряде и преимущественно при прохождении тока через шихту в расплавленных материалах. Передача теплоты в объем печи осуществляется за счет теплопроводности, излучения и в меньшей мере конвекции.
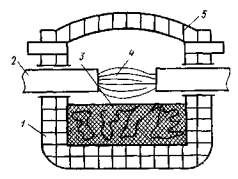
Рис. 6.1. Схема дуговой печи косвенного действия
Из числа дуговых печей можно выделить вакуумные дуговые печи
. В них электрическая дуга горит в инертном газе или парах переплавляемого материала при низком давлении между расходуемым электродом, изготовленным из переплавляемого металла, и ванной жидкого металла, либо между нерасходуемым электродом и ванной жидкого металла.
Приведенную классификацию необходимо дополнить широко внедряемыми в настоящее время плазменными печами
или плазменно-дуговыми плавильными установками
. В этих установках нагрев металла осуществляется электрической дугой, совмещенной со струей плазмы инертного газа. Это позволяет исключить засорение переплавляемого металла материалом электрода, увеличить интенсивность передачи энергии на ванну печи.
Дуговая печь косвенного действия
предназначена для переплава цветных металлов и их сплавов, а также для выплавки некоторых сортов чугуна и никеля. Ее основное преимущество - небольшой угар металла, так как электродуговой разряд не соприкасается непосредственно с переплавляемым материалом. Однофазная дуговая печь косвенного действия (рис. 6.1) представляет собой горизонтально расположенную ванну, футерованную изнутри огнеупором 1
. В противоположных боковых стенках ее установлены электроды 2
, перемещаемые по мере обгорания механизмами подачи. Переплавляемый материал 3
загружают на дно ванны через отверстие в боковой поверхности корпуса 5
. На электроды подается напряжение, затем они сводятся до соприкосновения и возникновения тока в цепи и затем разводятся, что приводит к возникновению электрической дуги 4
. Вследствие поглощения выделяемой дугой энергии происходит нагрев и расплавление металла. После расплавления металла печь наклоняется механизмом наклона и из нее сливается расплав. Регулирование мощности печи производится с помощью источника питания за счет изменения тока дуги, а также ее длины при сближении и удалении электродов.
К электрооборудованию дуговых печей косвенного действия относятся печной трансформатор, регулировочный реактор и электропривод механизма подачи электродов.
Ток к электродам подводится по гибким кабелям от печной трансформаторной подстанции. Регулирование расстояния между электродами осуществляют с помощью электропривода, управляемого персоналом дистанционно, или автоматическим регулятором режима.
Дуговые печи косвенного действия производят емкостью 0,25 и 0,5 т. В них применяются графитизированные электроды. Они снабжены трансформаторами мощностью 175-250 и 250-400 кВ·А.
6.2. Дуговые печи прямого действия
Основное назначение дуговой печи прямого действия (рис. 6.2) - выплавка стали в слитки для последующего передела в прокатных цехах, а также для фасонного литья на машиностроительных заводах; получение металлургического сырья, химических продуктов.
Дуговая сталеплавильная печь
(ДСП) состоит из стального кожуха, имеющего цилиндрическую, расширяющуюся или ступенчатую форму 1
. Внутри кожуха располагается огнеупорная футеровка 2
. Поверх футерованного кожуха печи расположен свод печи 3
, через который пропущены электроды 4
. Для зажигания дуги электроды вначале опускаются до соприкосновения с расплавляемым материалом, а затем немного поднимаются до возбуждения дуги 6
. В процессе плавки электроды перемещаются с помощью механизма подъема электродов 5
. Каждая печь имеет рабочие окна и сливное отверстие. Через рабочее окно производится загрузка печи, а через сливное отверстие - ее выгрузка. Иногда печь загружается сверху при снятом или отодвинутом своде. Слив готового металла производится путем наклона печи.
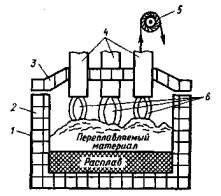
Рис 6.2. Схема дуговой сталеплавильной печи
Для выравнивания химического состава и температуры расплавляемого металла в печах большой емкости имеются электромагнитные устройства для перемешивания расплава.
Электродуговая печная установка снабжена механизмами наклона печи для слива металла, подъема и отворота свода, перемещения электродов. Они могут иметь электромеханический или гидравлический привод. Электроды крепятся в специальных электрододержателях, которые связаны с механизмом перемещения электродов. Ток подводится к электрододержателю с помощью пакета медных шин или водоохлаждаемых труб.
Процесс выплавки электростали в дуговой печи состоит из следующих операций: расплавление скрапа, удаление содержащихся в нем вредных примесей и газов, раскисление металла, введение в него нужных легирующих компонентов, рафинирование, выливание металла в ковш для последующей разливки. Под действием развивающейся в опорном пятне дуги температуры скрап расплавляется и жидкий металл стекает в подину. В шихте образуются колодцы, в которые углубляются опускающиеся электроды до тех пор, пока они не достигнут поверхности расплавленного металла на подине печи.
Расплавление скрапа и шихты приводит к повышению уровня расплавленного металла и для предотвращения короткого замыкания электроды поднимаются. В конце периода расплавления для окончательного доведения состава металла до требуемого в него вводят легирующие добавки и приступают к разливке. Плавка в крупных печах длится 4-6 ч: из них 1,5-2,5 ч длится расплавление и 2-4 ч - окисление и рафинирование металла.
Дуговые сталеплавильные печи являются трехфазными и имеют подину из непроводящего материала. Ванна с металлом в такой печи образует естественную нулевую точку трехфазной цепи, и печь оказывается включенной по трехпроводной системе трехфазного тока без нулевого провода.
Электроды
в дуговых печах служат для ввода электроэнергии в зону ее потребления, для расплавления шихты и получения необходимых материалов. Электроды подразделяют на нерасходуемые
и расходуемые
. Основные требования, предъявляемые к ним: достаточная механическая прочность, способность выдерживать высокие температуры, низкое активное сопротивление. В дуговых печах применяются непрерывно наращиваемые графитизированные электроды. Они имеют круглое сечение и обработанные торцы, в которых по оси имеются отверстия с резьбой. В отверстия ввинчены ниппели, выполненные из материала электрода. Ниппели ввинчены до половины своей длины. На выступающую из торца электрода половину ниппеля навинчен следующий электрод и т. д. Таким способом изготовляется электродная свеча, состоящая из нескольких электродов.
В зависимости от диаметра электроды изготовляют длиной 1000-1800 мм. По мере обгорания в печи нижней части свечи электродов она опускается вниз с помощью механизмов перемещения. Когда электрододержатель подходит к своду печи, производится наращивание и перепуск электродов.
Графитизированные электроды изготовляют из искусственного электрографита в специальных электрических печах. Несмотря на то что они дороже угольных, в современных печах в подавляющем большинстве применяются графитизированные электроды. Основное их достоинство - меньшее удельное сопротивление.
Иногда применяемые графитоугольные электроды диаметром 100-1200 мм изготовляют из антрацита, термоантрацита (прокаленного антрацита), нефтяного кокса, каменноугольного пека и смолы в специальных печах путем обжига заготовок без доступа кислорода при температуре до 1600 К.
В нашей стране в эксплуатации находятся дуговые печи для выплавки стали емкостью до 200 т, питаемые от трансформаторов мощностью до 80 МВ·А. В будущем должны быть созданы печи емкостью 300-400 т. Основные данные ряда
ДСП приведены в табл. 6.1.
6.3. Электрооборудование дуговых печных установок
Электродуговая печь представляет собой мощный энергопотребитель, относящийся ко второй категории по надежности электроснабжения.
Электрооборудование и схемы электроснабжения ДСП имеют ряд особенностей. Основное электрооборудование дуговых печных установок (рис. 6.5) включает печь с электродами и ванной, в которой горят дуги и находится перерабатываемый материал; отдельный для каждой печи понизительный трансформатор, вместе с которым часто размещены дроссели; короткую сеть, соединяющую вторичные выводы трансформатора с электродами печи; коммутационную, измерительную и защитную аппаратуру.
В печных установках применяются трансформаторы и дроссели, изготовленные в виде отдельных аппаратов, а также трансформаторы со встроенными дросселями.

Рис. 6.5. Схема электропечной установки:
1, 6 - выключатели; 2 - высоковольтные шины; 3 - разъединитель; 4 - высоковольтная сеть; 5 - реактор; 7 - печной трансформатор; 8 - короткая сеть; 9 - электроды; 10 - электродуговая печь
В дуговых электропечных установках различают главную и вспомогательные цепи тока (рис. 6.6).
Короткой сетью называют токопровод от выводов вторичной стороны трансформаторов до электродов дуговой печи.
По короткой сети идут очень большие токи (до 100 кА и выше), поэтому токопроводы короткой сети имеют большое сечение и выполнены в виде пакетов медных лент, медных шин или водоохлаждаемых труб.
Короткая сеть состоит из участков жестко закрепленных шинопроводов и гибких проводов, соединяющих концы шинопроводов с передвигающимися во время работы печи электродами.
Подвод питающей линии высокого напряжения от ввода производится через разъединители и выключатели высокого напряжения, установленные вместе с защитными аппаратами в распределительном устройстве электропечной установки.
Электроснабжение трансформаторов печной подстанции производится от сети 6,10-35 кВ, а для мощных подстанций - 110 кВ. Присоединение измерительных и защитных приборов к проводам высокого напряжения производится через трансформаторы тока и напряжения.
Для поддержания наивыгоднейшего режима печи устанавливаются автоматические регуляторы мощности печи. Такие регуляторы воздействуют на механизм передвижения электродов, изменяют длину дуги и поддерживают заданное значение мощности дуговой печи. Для повышения точности регулирования в системы управления вводятся вычислительные машины. Печные трансформаторы
предназначены для питания электродуговых печей. Для печей небольшой и средней мощности трансформаторы выполняют трехфазными. Для печей большой мощности применяются группы однофазных трансформаторов, которые позволяют получить повышенный коэффициент мощности за счет более рациональной конструкции короткой сети и регулировать независимо мощности и напряжения каждой фазы. Мощные печные трансформаторы оборудованы установками принудительного охлаждения с искусственной циркуляцией масла через теплообменник. Они снабжены регуляторами напряжения под нагрузкой, производящими 100-160 переключений в сутки.
Обмотки трехфазных трансформаторов соединяются по схеме «треугольник - треугольник» с возможностью переключения по схеме «треугольник - звезда», что позволяет регулировать вторичное напряжение.
Разъединители
в схемах электроснабжения дуговых печных установок служат для создания видимого разрыва силовой цепи электропечи. Коммутация цепи разъединителем осуществляется только при отключенном высоковольтном выключателе.
Дроссель
или реактор
, служит для ограничения бросков тока при эксплуатационных коротких замыканиях и стабилизации горения дуг за счет создания падающей характеристики цепи питания. Короткая сеть
дуговых печей служит для передачи электрической энергии от вторичной обмотки трансформатора в рабочее пространство печи. Несмотря на небольшую длину короткой сети, ее активное и особенно индуктивное сопротивление является одним из определяющих составных частей общего сопротивления участков печной установки. Они оказывают существенное влияние на энергетические показатели работы печи: мощность, коэффициент мощности, энергетический КПД и т. д.
Короткая сеть должна иметь минимальную длину и наиболее рациональное расположение проводников для снижения индуктивности, равномерной загрузки фаз и проводников в фазах током.
Потребляемая активная мощность Р складывается из активной мощности дуг и активных потерь в подводящей сети:
Р = Рд
+ Рм
,
где Рд
= I2
Rд
; Рм
= I2
r (I - полный ток цепи):
___________
I = Uф
/√(Rд
+ r)2
+ x2
, (6.9)
6.5. Магнитное перемешивание металла в дуговых сталеплавильных печах
После расплавления большей части шихты перемешивание ванны является эффективным средством ускорения процесса. В последующие периоды перемешивание позволяет выравнять химический состав, ускорить выведение газов и вредных компонентов из расплава.
Жидкий металл в ванне дуговой печи приводится в движение с помощью электромагнитных устройств переменного тока с перемещающимся магнитным полем.
Индукторы электромагнитного перемешивания выполняют в виде цилиндрических или плоских конструкций. Первые охватывают боковую поверхность расплава, вторые располагаются под его донной поверхностью. При расположении статора под дном ванны печи в зависимости от используемой частоты, конструкции статора и направления движения магнитного поля могут быть получены разные схемы движения расплава, эффективные для разных периодов плавки. Скорость движения расплава зависит от тока индуктора и составляет 0,2-1 м/с. Возможность магнитного перемешивания достигается только при низких частотах питающего тока, зависящих от глубины ванны расплава.
Автоматизация управления электрическим режимом ДСП.
Задачами автоматизации установки являются следующие: 1) поддержание мощности печи на уровне, определяемом программой; 2) регулирование напряжения трансформатора; 3) быстрое устранение всех отклонений от нормального режима. Поставленные задачи решаются с помощью автоматических регуляторов мощности, снабженных программно-управляющими устройствамиПерспективным направлением автоматизации ДСП является создание АСУ цеха дуговых печей и предприятия в целом.
6.8. Рудно-термические печи
Рудно-термические печи (РТП) являются основными технологическими агрегатами в металлургии и химии, обладающими высокой единичной мощностью и относящимися ко второй категории по надежности электроснабжения. В РТП нагрев перерабатываемых материалов производится за счет теплоты, возникающей при протекании тока по электродам, шихте, электрической дуге и расплавленному материалу.
Номенклатура продуктов, получаемых в РТП, весьма широка: они могут выпускаться из печи в виде пара или газа, жидкости-расплава, твердого тела, извлекаемого целым слитком.
РТП в металлургии черных металлов применяются для получения ферросплавов - сплавов железа с кремнием, марганцем, хромом, вольфрамом и др. Сырьем для получения ферросплавов служат руды или концентраты. При производстве основных сплавов - ферросилиция, ферромарганца и феррохрома - пользуются рудами с большим содержанием металла.
При производстве ферровольфрама, ферромолибдена, феррованадия, ферротитана и т. п. руду вследствие малого содержания в ней полезного компонента обогащают, получая концентрат с высоким содержанием оксидов основного элемента.
Ферросплавы получают восстановлением оксидов соответствующих металлов, используя восстановители - углерод, кремний и алюминий. Реакции восстановления углеродом требуют подвода большой теплоты.
Значительное место в сфере использования РТП занимает получение электроплавленых огнеупоров, идущих на футеровку стекловаренных печей, металлургических агрегатов. Сырьем здесь являются глинозем, циркон и кварцевый песок. Получаемые методом плавки открытой дугой огнеупоры - корунд и бакор разных марок в печах ОКБ-2130, ДС-0,5 имеют высокую чистоту, плотность.
Удельный расход электроэнергии при их получении находится в пределах 1800-2300 кВт·ч на тонну. Здесь перечислены только основные наиболее массовые и энергоемкие производства, тогда как перечень других процессов, осуществляемых в дуговых печах сопротивления, значительно шире и включает производство графита, сероуглерода и многих других веществ.
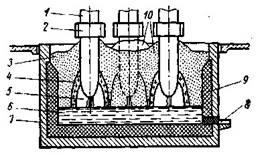
В РТП применяются электроды трех видов, угольные, диаметром до 12001400 мм, графитизированные диаметром до 800 мм и самоспекающиеся диаметром до 2000 мм или прямоугольные размером 3200×850 мм. Самоспекающиеся элект- роды представляют собой круглый или прямоугольный кожух из стали толщиной 1,5-5 мм, заполняемый сверху пастообразной электродной массой. При входе в печь под действием тока и теплоты печи электродная масса спекается и допускает плотность тока до 7,6 А/см2
. По мере сгорания кожух электрода наращивается и заполняется массой, что обеспечивает непрерывную работу печи. Удельное электрическое сопротивление самоспекающихся электродов в 2-3 раза выше, чем у угольных, и в 5-10 раз выше, чем у графитизированных

Рис. 6.12. Схема короткой сети рудно-термической печи:
1 - трансформатор; 2 - гибкие компенсаторы; 3 - пакет трубчатых шин; 4 - неподвижный башмак; 5 - гибкие ленты; в – подвижный башмак; 7 - электроды
Наиболее мощные РТП с прямоугольной ванной имеют шесть электродов, расположенных в линию, и питаются либо двумя трехфазными, либо тремя однофазными трансформаторами. В этом случае каждый трансформатор питает два соседних электрода.
Электрические характеристики РТП определяются особенностями распределения тока в рабочем пространстве печи я соответствующей этому схемой электрического питания.
ВАКУУМНЫЕ ДУГОВЫЕ ПЕЧИ 7.1. Области применения и устройство вакуумных дуговых печей
Для повышения качества металла, полученного в других установках (например, в ДСП), его переплавляют при низком давлении в вакуумных дуговых печах (ВДП), в результате чего в металле уменьшается содержание вредных примесей и растворенных газов. ВДП применяют в основном для выплавки слитков высокореакционных металлов (титана, ниобия, вольфрама, циркония, тантала, молибдена), а также для переплава специальных высококачественных сталей, в результате чего они не только очищаются, но и приобретают более плотную структуру. Рабочее давление в камере печи может составлять 1,0-0,001 Па в зависимости от требований к получаемому металлу. С помощью современных ВДП получают слитки массой от нескольких сотен килограммов до 50-60 т.
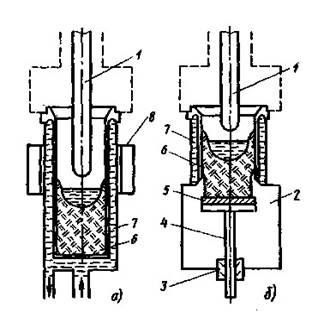
Рис. 7.1. Схема ВДП с глухим кристаллизатором (а
) и с вытягиванием слитка (б
):
1 - электрод: 2 - холодильник; 3 - вакуумное уплотнение штока: 4 - тянущий шток: 5 - поддон; 6 - слиток: 7 - кристаллизатор; 8 - соленоид
В качестве материалов электродов в ВДП используются различные продук-
ты металлургического передела. Так, при плавке титана круглые электроды изго- товляют прессованием титановой губки. При переплавке вольфрама, молибдена и ниобия электроды изготовляют из штабиков путем стыковой сварки и сборки электродов-пакетов. При переплавке сталей в качестве электродов применяют прокат или специальные штанги, полученные методом непрерывной разливки или ковки. В некоторых установках применяют нерасходуемые электроды, а переплавляемый металл кусками подается в кристаллизатор. Каждый из этих способов, в свою очередь, может быть осуществлен по двум схемам: плавка в глухой кристаллизатор (рис. 7.1, а
) и плавка с вытягиванием слитка (рис. 7.1, б
). Основной частью печи является рабочая камера, к которой присоединена вакуумная система. Электрод 1
подвешен к подвижному штоку. Шток проходит через вакуумное уплотнение, расположенное в верхней части камеры. К нижней части рабочей камеры присоединяется водоохлаждаемый кристаллизатор 7
с рубашкой водяного охлаждения. К электроду подается отрицательный, а к кристаллизатору положительный полюс источника питания. В печи, работающей по схеме с вытягиваемым слитком (рис. 7.1, б
), имеется проходящий через вакуумное уплотнение 3
шток 4
для вытягивания слитка. Металл наплавляется на поддон 5
и по мере роста слитка 6
опускается вниз. Процесс вакуумной плавки начинается с создания вакуума в рабочей камере печи и опускания электрода до крайнего нижнего положения. После короткого замыкания или пробоя межэлектродного промежутка возникает дуга. Под действием выделяющейся теплоты электрод расплавляется и металл небольшими каплями перетекает на слиток.
Объем кристаллизатора и размеры электрода, как правило, согласованы. В конце плавки весь электрод переходит в расплав, а испаряющиеся примеси и газы откачиваются вакуумной системой. Такая печь называется печью с расходуемым электродом.
В практике широко применяются ВДП с расходуемыми электродами, поскольку при работе с нерасходуемыми есть опасность загрязнения переплавляемого металла материалом электрода.
Основные элементы печи
. К ним относятся: рабочая камера, штокэлектрододержатель, расходуемые электроды, кристаллизатор, поддон, соленоид.
Рабочая камера
представляет собой водоохлаждаемую сварную конструкцию цилиндрической формы. В верхней части рабочей камеры установлены подсветы и смотровые окна, позволяющие наблюдать за горением дуги и наплавлением слитка. Для дистанционного наблюдения за ходом процесса к гляделкам пристраиваются специальные перископы, проектирующие изображение рабочей зоны на экран. К нижнему фланцу камеры прикреплен кристаллизатор.
Шток
- электрододержатель служит для закрепления и перемещения расходуемого электрода и подвода к нему тока. Он состоит из нескольких коакси- ально расположенных труб, причем медная наружная труба является токоведущей. Внутренние стальные трубы обеспечивают механическую прочность конструкции штока. Между трубами имеются полости для прохода охлаждающей воды. Расходуемые электроды
могут быть прикреплены к штоку различными способами. Они могут быть приварены к огарку, который крепят к хвостовику штока с помощью резьбы, могут удерживаться с помощью специального клиновидного или цангового зажима. Перемещение штока и расходуемого электрода обеспечивается электрическим или гидравлическим приводом. Кристаллизатор
состоит из внутренней гильзы и наружного стального немагнитного кожуха. Между ними имеется полость для охлаждающей воды. Гильзу изготовляют из материала с хорошей теплопроводностью, не смачивающегося жидким металлом.
Поддон
закрывает низ кристаллизатора, входит внутрь или примыкает к торцу его гильзы. Основа поддона - массивный медный диск, снабженный стальной рубашкой водяного охлаждения. Для предотвращения возможного прожога медного диска электрической дугой в начале плавки на него укладывают темплет из переплавляемого металла толщиной 50-100 мм.
Соленоид устанавливают на боковой поверхности кристаллизатора. Он создает аксиальное с ним магнитное поле. Взаимодействие поля соленоида с током дуги и током, растекающимся в ванне расплавленного металла, приводит к повышению напряжения на дуге (для стали с 19-20,5 до 24-25 В), предотвращает переброски дуги на стенку кристаллизатора, стабилизирует дугу. При этом возникает вращение жидкого металла в ванне, что улучшает структуру переплавляемого металла. Питание соленоида производится от полупроводниковых выпрямителей, позволяющих при необходимости производить резкое увеличение и реверсирование тока намагничивания. Для литья в вакууме существуют специальные вакуумные дуговые печи, которые подразделяют на две группы: печи с разливкой при горящей дуге и печи с разливкой после отключения дуги.
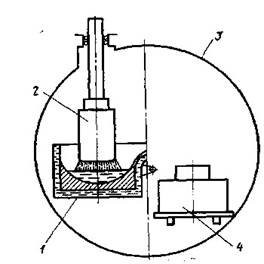
Рис. 7.2. Схема вакуумной дуговой печи для фасонного литья:
1 - тигель; 2 - электрод; 3 - камера; 4 - форма
Такая печь (рис. 7.2) состоит из камеры 3
, в которой размещены собственно плавильный агрегат, включающий тигель 1
, и электрод 2
. Расплавленный металл сливается в форму 4
.
7.2. Особенности дугового разряда в вакуумной дуговой печи
Особые свойства дугового разряда в ВДП обусловлены тем, что электродная система образуется концентрически расположенными стержневым электродом и кристаллизатором. При этом электрическая дуга горит в парах переплавляемого металла при низком давлении в камере ВДП в присутствии осевого магнитного поля.
Плавка с электродом-катодом называется плавкой с дугой прямой полярности, а с электродом-анодом - с дугой обратной полярности.
В зависимости от давления в рабочей камере в ВДП наблюдается три формы дугового разряда.
1. Диффузный, при давлении 0,0133-13,3 Па, представляющий собой слабосветящийся столб, распределенный по всему электроду.
2. Отшнурованный разряд при давлении более 133 Па, представляющий
собой яркосветящийся столб небольшого диаметра.
3. Разряд переходной формы, наблюдающийся при давлении 13,3-2660 Па. Такой разряд имеет признаки диффузного разряда, но занимающего лишь часть торца электрода.
Разряд неустойчив и быстро перемещается в пространстве. Длину дуги, т. е. расстояние между электродами, выбирают такой, при которой ток проходил бы
через ванну, а утечка электронов на стенку кристаллизатора была минимальной.
Такие условия создаются, если зазор между электродом и боковой стенкой камеры больше расстояния между электродом и поверхностью ванны расплава.
Следовательно, ВДП необходимо работать при коротких дугах. В действующих
печах при этом режиме длина дуги составляет около 30-50 мм.
При слишком короткой дуге капли, стекающие с расходуемого электрода, начинают замыкать дуговой промежуток. Вследствие сильного тепловыделения
мостик взрывообразно испаряется. На осциллограмме наблюдаются кратковремен ные броски тока и напряжения. Такой режим не соответствует рабочему. Его прекращают разведением электродов, при этом расстояние между торцом расходуемого электрода и зеркалом ванны расплава должно быть больше длины капли.
При увеличении длины дугового промежутка или при повышении давления в рабочей камере резко уменьшается концентрация паров металла. Катодное пятно
в этом случае переходит с торца электрода на его боковую поверхность и быстро
(со скоростью до 50 м/с) устремляется вверх по электроду. Длина дуги увеличивается и появляется общее свечение газов в камере. Ток дуги при этом
уменьшается, а напряжение пульсирует с большой частотой и повышается на 2030 В. Такой режим называют режимом объемной ионизации (рис. 7.3, б
).
При чрезмерном удлинении дугового промежутка, если длина дуги становится больше зазора между электродом и стенкой, дуга может перейти на стенку кристаллизатора. Возникает аварийный так называемый режим боковой дуги. Если боковую дугу немедленно не погасить, она может прожечь стенку
рабочей камеры или кристаллизатора, а попадание воды внутрь камеры может привести к взрыву установки. Погасить боковую дугу можно уменьшением длины дугового промежутка путем опускания электрода.
Высокочастотную составляющую в кривых тока и напряжения печи выделяют фильтрами и используют в качестве сигнала для управления положением электрода.
Градиент напряжения в столбе дуги при остаточном давлении, состав- ляющем 1-120 Па для всех переплавляемых в ВДП металлов, равен 0,97-3 В/см и не зависит от величины тока. При общем напряжении на дуге 30-50 В большая
часть его приходится на область катодного падения потенциала. Она составляет: для стали - 19 В, титана - 13,5 В, молибдена - 14,4 В и т. д. Анодное падение напряжения значительно меньше и, как правило, не превышает работы выхода
электрона переплавляемого метал.
7.3. Электрооборудование вакуумных дуговых печей
Силовая цепь ВДП включает в себя: источник питания, токопровод от источника питания до печи, токоведущие участки конструкции, токоведущии шток, электрододержатель, расходуемый электрод, слиток, кристаллизатор, вакуумную камеру.
Конструкция токоподвода обеспечивает равномерный контакт по периметру поддона, кристаллизатора и вакуумной камеры, что снижает уровень магнитных полей и способствует стабилизации дугового разряда.
В настоящее время еще находятся в эксплуатации машинные преобразователи серии ГПН-550 мощностью 645-675 кВт, рассчитанные на токи 6500 и 14 000 А, с напряжением холостого хода 85 и 40 В. Все новые установки имеют агрегаты одного из трех типов: выпрямительный на неуправляемых вентилях, выпрямительный на тиристорах, параметрический источник тока.
Выпрямительный агрегат на неуправляемых вентилях
серии ВАКП основан на принципе стабилизации и регулирования тока с помощью дросселей. Крутизна падающего участка внешней характеристики определяется наклоном ненасыщенной части кривой намагничивания железа. Для ограничения тока короткого замыкания (к. з.) до двукратного значения Iн
предусмотрено повышенное реактивное сопротивление, для чего к трансформатору присоединен реактор. Агрегаты, выполненные по этой схеме, работают при токах до 12,5; 25,0 и 37,5 кА и состоят из отдельных блоков: трансформатор, дроссели насыщения, выпрямительный шкаф, устройство для измерения, шкаф и пульт управления, системы водоснабжения.
Силовой трансформатор со ступенями регулирования напряжения состоит из магнитопровода с концентрически расположенными обмотками высокого (ВН) и низкого (НН) напряжения. В схеме переключающего устройства предусмотрен трехфазный токоограничивающий реактор, состоящий из магнитопровода и двойных дисковых катушек. Дроссель насыщения состоит из однофазных дросселей, каждый из которых собирается из элементов, представляющих собой кольцевой магнитопровод с обмотками управления и смещения. Изменение сопротивления дросселя осуществляется регулированием тока в обмотке управления. Если возможностей регулирования дросселя оказывается недостаточно для поддержания требуемого тока, ступени трансформатора автоматически переключаются в нужную сторону.
Выпрямительный агрегат имеет параллельные звезды, лучи которых состоят из параллельно соединенных вентилей, установленных на шинах, охлаждаемых водой. Равномерная загрузка вентилей обеспечивается индуктивными делителями тока. Цепь каждого вентиля защищена плавким предохранителем.
Выпрямительный агрегат имеет защиту от перегрузки по току. При к.з. на стороне постоянного тока длительностью более двух секунд масляный выключатель отключает агрегат. При к.з. на стороне переменного тока агрегат отключается максимально-токовой защитой мгновенного действия.
Агрегаты серии АВП
дают более высокую точность поддержания тока и имеют токоограничивающие дроссели только на стороне низкого напряжения (рис. 7.7). Автоматическая стабилизация тока в процессе плавки обеспечивается системой управления дросселями насыщения, состоящей из измерительных трансформаторов постоянного тока (ТПТ) и тиристоров, регулирующих ток в управляющей обмотке дросселей, включенных последовательно в цепь каждой ветви вторичной обмотки трансформатора. Силовые трансформаторы с первичным напряжением 10 кВ (звезда) и 6 кВ (треугольник) имеют 17 ступеней напряжения, переключаемых под нагрузкой. Вторичные обмотки выполнены по схеме «две обратные звезды» с уравнительным реактором. Плавное регулирование напряжения с дросселями насыщения производится внутри ступени напряжения трансформатора. Выпрямительный шкаф рассчитан на ток 12,5 кА и содержит шесть групп вентилей, каждая из которых через дроссель насыщения соединена с соответствующей обмоткой трансформатора.
Агрегаты на токи 25 и 37,5 кА имеют соответственно два и три шкафа. Номинальное выпрямленное напряжение - 75 В, напряжение на дуге - 25-35 В, мощность агрегата - 940-2800 кВт.
Выпрямительный агрегат имеет необходимые виды защит и блокировок. Для повышения коэффициента мощности на стороне высокого напряжения установлена автоматически управляемая батарея конденсаторов.
Выпрямительные агрегаты на тиристорах
, входят в состав всех новых ВДП.
Агрегаты на тиристорах наряду с высокой точностью стабилизации тока имеют высокий КПД, минимальные габаритные размеры и массу.
Питание агрегатов марок ТВ9-12500/75Т, ТВ9-2500/75Т, ТВ9-37500/75Т, ТВ9-50000/75Т, ТВ9-2500/115Т, ТВ9-50000/115Т осуществляется на напряжении 6 или 10 кВ, первичная обмотка трансформатора имеет устройство РПН. Вторичная обмотка состоит из групп двух обратных звезд с уравнительными реакторами. Каждая группа рассчитана на ток 12,5 кА (ТВ9-12500/75Т). Сглаживающие реакторы L1
и L2
предохраняют источник от резких бросков тока, возникающих при капельных коротких замыканиях. Номинальный ток (12,5-50 кА) и вторичное напряжение (75 или 115 В) указаны в марке агрегата источника.
Шунты ШН1, ШН2 и датчики тока ДТ1
и ДТ2
(трансформаторы постоянного тока), а также измерители, основанные на эффекте Холла (для токов
37,5 и 50 кА), служат для измерения тока Параметрические источники тока
(ПИТ). Для получения крутопадающих или вертикальных ВАХ источников питания ВДП используются резонансные схемы, главным признаком которых является постоянство тока нагрузки при изменяющемся ее сопротивлении.
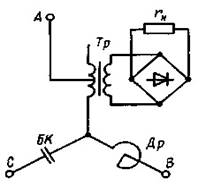
Рис. 7.9. Принципиальная электрическая схема силовых цепей параметрического источника тока
Принципиальная схема ПИТ показана на рис. 7.9. В его состав входит трансформатор нагрузки Тр
в одном луче звезды А с регулятором напряжения под нагрузкой (РПН), включенный на группу неуправляемых вентилей, питающих постоянным током дуговую печь rн
. В луче фазы В включен дроссель Др, имеющий обмотку нодмагничивания для регулирования тока фазы. В фазе С включена конденсаторная батарея БК, емкость которой можно также регулировать. Основным условием регулирования является соблюдение соотношения хL
=хC
. В этом случае ток нагрузки не меняется с изменением ее сопротивления, длины дуги, условий горения.
Система автоматического управления
(САУ) ВДП должна так регулиро- вать мощность, чтобы требуемая скорость наплавления металла равнялась скорос- ти кристаллизации слитка. Кроме того, САУ должна обеспечивать устойчивое горение дуги, поддерживать в заданных пределах непрерывно изменяющуюся длину дуги, режим ее горения. Поэтому в состав САУ входят следующие компо- ненты: управляемый источник тока, регулятор длины дугового промежутка (скорость перемещения электрода), регулятор тока соленоида. ВДП как объект управления представляется в виде системы, состоящей из четырех динамических звеньев с внутренней обратной связью: электрическая дуга, межэлектродный промежуток, электрод, ванна жидкого металла – слиток.
ПЛАЗМЕННЫЕ ТЕХНОЛОГИЧЕСКИЕ ПРОЦЕССЫ И УСТАНОВКИ 8.1. Устройства для получения низкотемпературной плазмы и области их применения
Плазменная технология - молодая отрасль промышленности, интенсивное ее развитие началось в 50-х годах нашего столетия и бурно продолжается в разных странах. Свидетельством тому служит большой поток патентной и научной
информации, а также расширяющиеся области промышленного использования.
Предпосылкой для развития плазменной технологии стало развитие космической техники, что потребовало создания различных типов двигателей, в
том числе и плазменных, материалов и конструкций космических аппаратов, сохраняющих работоспособность при входе в плотные слои атмосферы,
испытаний летательных аппаратов при больших скоростях полета, исследований в
области термоядерного синтеза, газодинамики при высоких скоростях, физики газового разряда, химической технологии высоких режимных параметров. С
использованием плазменной технологии созданы не только новые материалы, обладающие высокими технологическими свойствами (огнеупорностью, твердостью, прочностью), но и аппаратура эффективной обработки этих
материалов.
Плазменная резка черных (нержавеющих) и цветных металлов впервые разработана в СССР в 1956-1957 гг. Она позволяет резать с высокими скоростями
стали больших толщин, медь и ее сплавы, алюминий и другие металлы (например, плазмотрон мощностью 100 кВт режет сталь толщиной 30 мм со скоростью 4 м/мин). При этом сокращаются подгоночные работы в сварочных цехах, поскольку после плазменной резки заготовки имеют большую точность размеров. Плазменная резка широко применяется в судостроении, на предприятиях тяжелого и атомного машиностроения, химической и электротехнической промышленности.
Плазменная сварка обеспечивает соединение деталей из меди, латуни, бронзы, алюминия и его сплавов. Плазменная наплавка и напыление обеспечивают покрытие деталей износостойким, жаропрочным и антикоррозионным составом с минимальным перемешиванием наносимого и основного материала.
Важным направлением использования плазменных потоков является вакуумная плазменная технология с использованием электромагнитных
ускорителей. В облако плазмы в вакууме помещают деталь, которой сообщают
отрицательный потенциал. Тогда положительные ионы вытягиваются из объема
плазмы, ускоряются электрическим полем и поступают к детали. В такой системе
удается получить потоки частиц со скоростями до сотни километров в секунду и энергиями до десятков тысяч электрон-вольт. Это позволяет проводить
технологические процессы, основанные на конденсации атомарных частиц на поверхности, испарение поверхности металлов, внедрение атомов в глубь кристаллической решетки, имплантацию ионов нужного вида.
В вакуумных плазменных установках может быть получена плазма всех известных металлов, сплавов, органических и неорганических веществ. При этом плазмы различных веществ могут вступать в интенсивное химическое взаимодействие, которое невозможно в других обстоятельствах.
Методом плазменной технологии в вакууме могут быть успешно решены следующие наиболее актуальные задачи:
получение особо чистых слоев материалов, обладающих специальными свойствами и выполняющих активные функции (магнитные, оптические, эмиссионные, сверхпроводящие и другие слои);
защита элементов конструкций барьерными слоями от воздействия
агрессивных сред, больших скоростей газовых потоков, высоких температур;
изменение структурно-энергетического состояния поверхности материалов
(упрочнение поверхности, ионное легирование полупроводников и др.); получение материалов в виде многослойных структур, обладающих высокими механическими и эксплуатационными свойствами; получение пленочных монокристаллических структур.
Вакуумная плазменная технология, несмотря на некоторую сложность, позволяет существенно пополнить арсенал методов бесконтактной обработки материалов.
Плазменные технологические процессы в химии состоят из следующих основных стадий: 1) генерация плазмы необходимого состава и параметров по температуре и давлению; 2) ввод реагентов - веществ в твердом, жидком или
газообразном состоянии и обеспечение необходимого времени их контакта; 3) вывод целевого продукта или нескольких продуктов из зоны реакции.
Для получения плазмы используются плазмотроны с различными принципиальными схемами. Плазмохимические реакции могут осуществляться
двумя способами: подача всех компонентов плазмы в зону электрического разряда
с прохождением тока его через реагирующую плазму и подача реагентов в струю плазмы вне зоны разряда. В первом случае плазмотрон совмещается с
реакционным объемом - реактором, во втором применяются плаз-моструйные реакторы, представляющие собой цилиндрический охлаждаемый сосуд, где происходит смешение плазменного потока с вводимым материалом.
Закалка и охлаждение продуктов реакции производятся путем введения в плазму вне зоны разряда дополнительного количества какого-либо газа или жидкости, а также охлаждаемых экранов-теплообменников.
Для получения оксидов азота, идущих в дальнейшем на производство азотных удобрений, используется воздушная плазма с температурой 3000-3500 К при давлении (20÷30) 104
Па, охлаждаемая в процессе закалки со скоростью 108
К/с до температуры 2000-1800 К и остывающая далее в теплообменниках.
Существующие способы получения плазмы можно классифицировать следующим образом: 1) взрыв проводника в электрической цепи; 2) электрическая искра; 3) высокочастотный факельный разряд; 4) коронирующий разряд; 5) дуговой разряд.
Для технологических целей наиболее приемлемыми оказались способы получения плазмы с помощью высокочастотного и дугового разрядов. В настоящее время последний способ имеет ряд преимуществ:
1) возможность получения плазмы в течение длительного времени с высоким коэффициентом полезного действия из твердых, жидких и газообразных сред любого химического состава;
2) возможность получения плазмы в вакууме и при высоких давлениях; 3) возможность использования стандартных источников электрического питания.
Для получения плазмы в плазмотронах используют газы, т. е. плазмообразующую среду. Она может быть одно- и многокомпонентной. В качестве однокомпонентной плазмообразующей среды применяют аргон, гелий, азот и водород.
Подбором состава многокомпонентной плазмообразующей среды в плазменно-технологическом реакторе можно получить любую атмосферу: окислительную, восстановительную или нейтральную.
Одним из наиболее важных тепловых параметров плазмы является ее энтальпия, т. е. количество теплоты, содержащееся в единице ее объема или массы.
Рассмотрим характеристики некоторых плазмообразующих газов.
Аргон
имеет низкое значение энтальпии, что делает его малопригодным для использования в качестве однокомпонентной плазмообразующей среды. Высокая электропроводность аргона при высоких температурах обусловливает низкую напряженность электрического поля в столбе дугового разряда. Аргон является одним из наиболее дефицитных и дорогостоящих газов и применяется в основном в тех случаях, где наибольшую роль играет его химическая инертность. Азот
часто применяется в качестве однокомпонентной плазмообразующей среды. Его теплопроводность и теплоемкость при высоких температурах довольно высоки. По этой причине в атмосфере азота электрический разряд обеспечивает эффективное преобразование электрической энергии в тепловую.
Гелий
имеет более высокие энергетические характеристики, чем аргон. Однако вследствие дефицитности и высокой стоимости
применение его в плазменных установках ограничено. Он применяется в основном как добавка к аргону для улучшения эффективности нагрева в инертной атмосфере рабочего пространства плавильных печей.
Водород
- самый высокоэнтальпийный плазмообразующий газ.
Напряженность электрического поля в водородной дуге в несколько раз выше, чем в аргоновой. Теплопроводность водорода также гораздо выше, чем у других газов. Он сравнительно дешев и недефицитен. Однако чистый водород при высоких температурах разрушающе действует на электроды плазмообразующего аппарата и поэтому он применяется в смеси с аргоном.
Важной характеристикой плазмы является зависимость коэффициента теплопередачи от температуры (рис. 8.2). Из рисунка следует, что процессы диссоциации молекулярных газов увеличивают теплоотдачу от плазмы при ее охлаждении.
При использовании сложных плазмообразующих смесей для обеспечения оптимальных параметров плазмы по энергетическим показателям, стабильности горения электрической дуги и устойчивости электродов подбирают соответствующие компоненты и их соотношения.
Генератор низкотемпературной плазмы или плазмотрон
-
электротехнический аппарат, в котором происходит нагрев плазмо-образующей среды электрическим разрядом. Основными компонентами дуговых плазмотронов являются: электроды; вмещающая их или совмещенная с электродом разрядная камера, формирующая поток плазмы; система впуска плазмообразующего газа; система управления дуговым разрядом. Различные варианты конструктивного выполнения этих компонентов и различные их комбинации обусловили большое количество принципиальных схем плазмотронов.
Для обеспечения длительного ресурса работы электродных систем дуговых плазмотронов применяют электроды из тугоплавких материалов (С, Мо, W, Zr, Hf) либо перемещают опорные пятна дуги для распределения теплового потока на большую площадь электрода, выполненного из меди и охлаждаемого водой. Поэтому тугоплавкие электроды изготовляют в виде стержней или цилиндров малых размеров, запрессованных или вваренных в медный электрододержатель. Легкоплавкие электроды из меди (стали) выполняются в виде цилиндров или торов, по внутренней (или боковой для тора) поверхности которых перемещается опорный конец электрической дуги.В этом классе плазмотронов можно выделить два типа, отличающихся друг от друга методами стабилизации электрической дуги: водоохлаждаемои стенкой и вихревым потоком газа или жидкости.
Рис. 8.3. Схема плазмотрона со стабилизацией дуги стенкой
В плазмотроне (рис. 8.3) дуговой разряд горит между электродами (-) и (+), разделенными водоохлаждаемои стенкой, состоящей из ряда медных секций, разделенных изолятором. Из-за охлаждения около стенки образуется слой холодного газа с относительно низкой электропроводностью, поэтому дуга занимает лишь часть сечения канала, чем достигается принудительное увеличение плотности тока в столбе дуги и значительный рост температуры плазмы. Если длинный канал не имеет секций, то проходящий через него газ нагревается и теряет диэлектрическую прочность. При этом происходит пробой слоя нагретого газа между столбом дуги и водоохлаждаемой стенкой. Это явление получило название «шунтирование дуги стенкой». Процесс шунтирования влияет на работу плазмотрона, в частности он формирует падающую ВАХ дуги, ограничивает температуру плазмы, мощность плазмотрона и снижает его КПД.
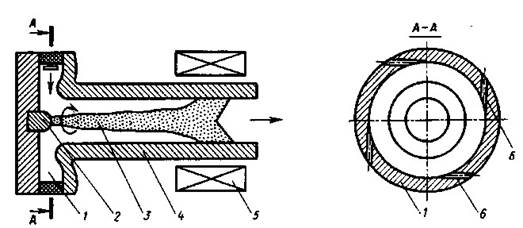
Рис. 8.4. Плазмотрон с газовихревой стабилизацией дуги:
1 - вихревая камера; 2 - внутренний стержневой электрод; 3 - столб дуги; 4 - выходной трубчатый электрод; 5 - соленоид; 6 - тангенциальные каналы
На рис. 8.4 показана принципиальная схема плазмотрона со стабилизацией дуги вихревым потоком газа. Газ, подаваемый через тангенциальные отверстия 6 в вихревую камеру 1
, создает в канале плазмотрона вихревой поток, по оси которого между электродами 2
и 4
горит электрическая дуга 3
. Вследствие интенсивных процессов теплообмена газ нагревается и плазма в виде струи истекает из сопла через электрод 4
. В вихревой камере и канале электрода 4
существует градиент плотности газа, поскольку основная часть его движется в пристеночной области. В результате этого столб дуги «выталкивается» на ось электрода. Стабилизирующее действие газового вихря сохраняется до тех пор, пока не произойдет прогрев всего газа и появится его заметная проводимость, либо пока не произойдет угасание тангенциальной составляющей скорости газового потока. Под действием тангенциальной составляющей скорости газового потока опорное пятно дуги в выходном электроде перемещается по поверхности канала и сносится вниз по потоку осевой компонентной скорости. Этим обеспечивается долговечность трубчатых электродов. Среднемассовая температура плазмы при работе на азоте и воздухе в таких плазмотронах не превышает 5·103
-6·103
К. Коэффициент полезного действия η = ΔНG/Nэл
(где ΔН - разность энтальпий нагретого и холодного газа; G - секундный расход газа; Nэл
= VI - электрическая мощность плазмотрона) достигает 0,75-0,85. Более совершенным является плазмотрон с секционированным электродом и распределенной между секциями подачей плазмообразующего газа, что позволяет значительно поднять напряжение на дуге. Уменьшение эрозии электродов в плазмотронах с вихревой стабилизацией может быть осуществлено за счет наложения на радиальные участки дуги осевого магнитного поля. Конструктивная простота, достаточно высокий тепловой КПД и большой ресурс работы электродов определили широкое распространение рассмотренных типов плазмотронов.
Модификацией плазмотронов со стабилизацией дуги стенкой и вихревым потоком газа является плазмотрон с межэлектродными вставками. В плазмотроне с поперечно-обдуваемыми дугами и коаксиальным расположением электродов управление характеристиками дугового разряда производится осевым магнитным полем, в котором движется как проводник с током столб дугового разряда.
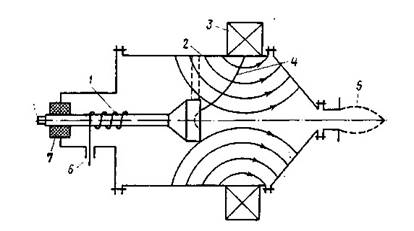
Рис. 8.6. Схема плазмотрона с магнитной стабилизацией дуги:
1 - центральный электрод; 2 - внешний электрод; 3 - соленоид; 4 - столб дуги; 5 - струя плазмы; 6 - подвод газа; 7 - изолятор
Схема плазмотрона с магнитной стабилизацией дуги показана на рис. 8.6. Между электродами 1
и 2
горит электрическая дуга 4
. Магнитное поле создается соленоидом 3
. Газ проходит между электродами, интенсивно нагревается в межэлектродном зазоре электрической дугой и выходит в виде высокотемпературной струи 5
через сопло.
Пространственное положение дуги в таких плазмотронах определяется тремя факторами: геометрическим положением центрального электрода, аэродинамическими силами и формой магнитного поля. Дуга удерживается вблизи середины оси магнитной катушки и под действием набегающего потока сносится в сторону его течения. Скорость вращения дуги пропорциональна току разряда и напряженности магнитного поля. При изготовлении центрального электрода из тугоплавкого материала КПД плазмотрона составляет 0,52-0,76 и преимущественно зависит от потерь в цилиндрический электрод.
Плазмотроны, работающие на переменном однофазном токе, конструктивно схожи с рассмотренными.
В плазменной технологии получили применение трехфазные плазмотроны
, которые представляют собой комбинации из трех однофазных.
По конструктивным особенностям различают одно- и многокамерные
трехфазные плазмотроны. В случае однокамерных плазмотронов все три дуги горят в одном объеме. Устойчивость дугового разряда обеспечивается применением тугоплавких электродов, сохраняющих высокую эмиссионную способность при перемене полярности тока.
Кроме рассмотренных в практике нашли применение плазмотроны, для питания которых одновременно используют постоянный и переменный токи, а также переменный ток промышленной и высокой частоты.
Мощность сопровождающей дуги в этом случае составляет 5-8 % от мощности силовой дуги.
Регулирование мощности в плазмотронах осуществляется изменением сопротивления в цепи питания (регулируемые дроссели), напряжением источника питания, мощностью дуги сопровождения.
Энергетические и вольт-амперные характеристики плазмотронов зависят от многих взаимосвязанных параметров. Кроме того, они являются нелинейными, поэтому теоретическое их исследование затруднено, а порой и невозможно.
Поэтому плазмотроны обычно разрабатываются по целевому назначению.
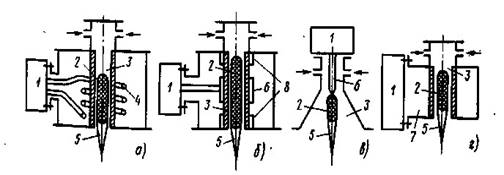
Рис. 8.9. Схемы высокочастотных плазмотронов
Высокочастотные плазмотроны
(рис. 8.9) подразделяют на индукционные, емкостные, факельные, сверхвысокочастотные (СВЧ).
Высокочастотные плазмотроны включают в себя электромагнитную катушку-индуктор 4
или электроды 6
, 8
, подключенные к источнику высокочастотной энергии 1
, разрядную камеру
В высокочастотном индукционном плазмотроне
(рис. 8.9, а
) газ нагревается вихревыми токами, как при индукционном нагреве проводящей среды в переменном электромагнитном поле индуктора при частоте от 6,3 кГц до 20 МГц.
В начале процесса для образования проводящей среды в зоне индуктора создается область высокотемпературного проводящего газа с помощью постороннего источника (например, дуговой разряд). Этот процесс называют зажиганием. После зажигания в камере возникает самоподдерживающийся стационарный безэлектродный разряд 2
. Глубина проникновения (δ, см) вихревых токов в плазму определяется по формуле
_____ δ = (1/2√ρ/(μf),
где ρ - удельное электрическое сопротивление плазмы; f - частота, Гц; μ - магнитная проницаемость, для плазмы μ = 1. Удельное сопротивление аргона, азота и водорода при 15 000 К равно соответственно 0,01, 0,025 и 0,1 Ом·см. Продувая газ через разрядную камеру, на выходе из нее получают струю плазмы 5
с температурой (7,5÷15,0) 103
К со скоростью 10-60 м/с.
Высокочастотный емкостный плазмотрон
(рис. 8.9, б
) имеет высоковольтный 6
и заземленный 8
электроды, между которыми возникает высокочастотное электрическое поле. Электроны, находящиеся в газе, получают энергию от высокочастотного электрического поля и при столкновениях обмени- ваются ею с нейтральными частицами, повышая тем самым температуру газа. В высокочастотном факельном плазмотроне
(рис. 8.9, в
) при давлении, близком к атмосферному, факельный разряд имеет форму пламени свечи. Наиболее легко факельный разряд возникает на электродах с большой кривизной поверхности (на остриях и т. д.) при частотах электрического поля порядка 10 мГц и выше.
В сверхвысокочастотном плазмотроне (рис. 8.9, г
) энергия от источника питания в зону разряда подается по волноводу 7
.
Высокочастотные плазмотроны имеют широкие перспективы применения в химической и металлургической промышленности благодаря большому ресурсу работы (2-3 месяца без замены деталей), возможности получения чистой плазмы агрессивных газов, таких, как хлор, кислород и др., т. е. без засорения продуктами разрушения электродов. Однако пока они имеют более низкий, чем дуговые плазмотроны, энергетический КПД и сложные источники питания.
8.2. Энергетические характеристики плазмотронов и источники питания
К энергетическим характеристикам плазмотрона относятся зависимости параметров дуги от условий работы - рода плазмообразующего газа, давления, геометрических размеров электродов, напряженности управляющего магнитного поля, материала электродов, их температуры и эмиссионной способности, скорости разрушения. Одновременный учет всех этих факторов в настоящее время не представляется возможным, поэтому для расчета ВАХ разряда и определения некоторых размеров электродов пользуются эмпирическими формулами, получаемыми в результате критериального обобщения многочисленных экспериментальных данных.
В настоящее время уравнения ВАХ и КПД составлены для плазмотронов определенных схем и справедливы в строгих границах геометрического подобия, диапазонах изменений токов и расходов газа, для однокомпонентных или стандартных плазмо-образующих сред, а также внутрикамерных давлений, напряженностей магнитных полей.
Мощность плазмотронов определяется соотношением тока дуги и напряжением: Р = IU = IЕl, которое, в свою очередь, определяется длиной дуги l и напряженностью электрического поля Е. Мощность, выделяющаяся в электродах, как было показано, зависит от тока дуги и материала электрода. Так как электроды плазмотронов должны иметь длительный срок работы, а скорость их разрушения прямо пропорциональна току дуги, то при определении параметров разряда следует ориентироваться на минимальные токи и максимальные напряжения, обеспечивающие заданную температуру плазмы и необходимую мощность дуги при заданных габаритных размерах электродов.
Как было показано, напряженность электрического поля Е дуги зависит от рода газа, давления и скорости обдува. Для плазмотронов в этой зависимости появляется дополнительный фактор - температура окружающего газа. В плазмотронах с продольным обдувом напряженность поля дуги имеет максималь- ное значение вблизи зоны подачи газа и постепенно уменьшается в направлении истечения плазмы. Значение Е для дуги, обдуваемой осевым потоком аргона при токах 100-300 А и расходе его 0,25- 1,23 г/с, составляет 4,5-14 В, уменьшаясь при росте тока и снижении расхода газа. Отсюда следует, что для получения необходимой мощности выходной электрод должен иметь необходимые длину и диаметр канала для размещения в нем электрической дуги длиной l. Как правило, длину электрода выбирают несколько большей, чем длина дуги, для предотвраще- ния выхода ее на торец электрода в неуправляемую зону. При конструировании плазменных технологических аппаратов следует учитывать, что напряженность электрического поля дуги растет с увеличением рабочего давления. Выбор схемы источников питания плазмотронов основан на анализе устойчивости дуги, находящейся в интенсивном потоке газа при наличии внешних магнитных полей. Из теории «малого возмущения» условие устойчивости дуги имеет вид
dUист
/dI < dUд
/dI,
здесь (Uист
- статическое напряжение источника питания; Uд
- статическое напряжение дуги.
Для устойчивой работы плазмотрона с падающей ВАХ необходимо иметь крутопадающую внешнюю характеристику источника питания. Это требование усиливается необходимостью строгого поддержания заданной мощности в технологическом процессе, что также требует жесткой стабилизации тока. Поэтому для питания плазмотронов используют следующие типы источников питания с крутопадающей внешней характеристикой: 1) источники на базе управляемого выпрямителя с автоматической стабилизацией тока; 2) установки с дросселями насыщения и магнитоуправ-ляемыми трансформаторами; 3) параметрические источники тока, работающие на принципе резонанса напряжения в трехфазных электрических цепях.
Источник первого типа изготовляют индивидуально к каждой плазменной технологической установке, содержащей мощные высоковольтные плазмотроны; они включаются в общую схему автоматического управления технологическим процессом.
Источники второго и третьего типов стандартные и применяются для питания низковольтных плазмотронов, используемых в технологических процессах плазменного напыления, наплавки, резки, сварки, переплава металла и другие. Нелинейный характер ВАХ дуги приводит к возникновению высокочастотных колебаний, которые могут проникать в питающую сеть и отрицательно влиять на работу других потребителей. Поэтому для создания источников питания первого типа применяется схема со сглаживающим дросселем в цепи дуги (рис. 8.12). Сглаживающий дроссель в цепи дуги в значительной степени сужает частотный спектр возмущений, влияющих на электрическую систему в целом.
Зажигание дуги в плазмотронах производится путем пробоя межэлектродного промежутка осциллятором.
В плазмотронах с секционированным выходным электродом во время запуска анодную цепь питания подключают к первой, ближней к катоду секции, а затем по мере развития дуги последовательно переключают вниз по потоку плазмы и устанавливают на последнем аноде.
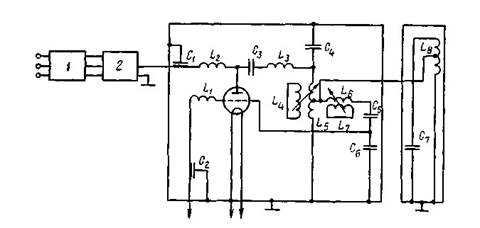
Рис. 8.13. Принципиальная схема ВЧИ-установки, работающей на частоте 1,76 МГц:
1 - анодный трансформатор; 2 - анодный выпрямитель
Высокочастотные плазменные установки питаются от ламповых преобразователей частоты. Принципиальная схема одного из них показана на рис.
8.13. Установка ВЧИ-63/1,76-ИГ-Л01 мощностью 103 кВт с частотой тока 1,76-2,5 МГц включает в себя анодный трансформатор с напряжением 0,38/1,4 кВ, анодный выпрямитель на тиратронах с напряжением 10,5 кВ и рассчитана на анодный ток 8 А и колебательную мощность 63 кВт. Колебательный контур, являющийся основной нагрузкой лампового генератора, образован эквивалентной индуктивностью плазмотрона L8
и емкостью С7
. Генераторная лампа является основным элементом источника питания, определяющим его КПД на уровне 0,6-
0,7 и срок службы порядка 2000 ч.
8.3. Плазменные плавильные установки
Существует два основных направления использования плазмы в металлургии:
1) интенсификация известных процессов плавки с помощью плазменного подогрева или замены в металлургических агрегатах прежних источников теплоты плазменными;
2) создание принципиально новых металлургических агрегатов, а также плазмотехнологических процессов.
Существует несколько типов установок для обработки и получения металлов с помощью плазмотронов.
Наиболее перспективны те из них, в которых применяются плазмотроны прямого действия (анодом является ванна расплавленного металла). На этой схеме основаны плазменно-дуговые печи (ПДП) для выплавки и переплавки высококачественных металлов.
Плавка плазменной дугой в плазменных печах аналогична вакуумно-дуго-гой плавке с нерасходуемым вольфрамовым электродом, но плазменная дуга имеет существенные преимущества перед вакуумной: лучшая жесткость и стабильность дуги, большая длина дуги, предохранение металла от загрязнения вольфрамом электрода, более высокие напряжение и мощность.
Состав плазменной струи может задаваться по-разному, что позволяет поддерживать в печи практически любую атмосферу. Поскольку парциальные давления кислорода, водорода и азота в плазменной печи, работающей на инертном газе, невелики, то условия дегазации жидкого металла в ПДП приближаются к условиям дегазации в вакуумных печах, оборудованных сложными и дорогостоящими вакуумными системами. В отличие от вакуумной индукционной, дуговой и электронной плавки при плавке в ПДП наблюдается меньшее испарение ценных компонентов расплава, а применение плазмотронов позволяет получить высокие, легко регулируемые температуры и решить проблему стабильности и регулирования параметров процесса.
Плазменные и дуговые печи могут быть двух типов: плавильная печь с огнеупорной футеровкой и печь для переплава с водо-охлаждаемым кристаллизатором (глухим или с вытягиванием слитка).
Рис. 8.14. Схема плазменной печи с керамическим тиглем:

а - с одним плазмотроном в своде; б - с плазмотронами, установленными в
стенках; 1 - кожух; 2 — футеровка; 3 - свод; 4 - плазмотрон; 5 - подовый электрод
При выплавке металла в ПДП с огнеупорной футеровкой (рис. 8.14) форма печи и материал огнеупорной футеровки идентичны форме и материалу обычной дуговой печи. Водоохлаждаемый медный анод - подовый электрод 5
монтируется заподлицо с подиной и контактирует с переплавляемым металлом. Камера печи, из которой откачан воздух, заполняется вытекающим из плазмотрона 4
газом, и после достижения определенного давления начинается процесс плавки.
Плазменная дуга вначале проплавляет в шихте узкий канал, и стекающий вниз жидкий металл скапливается на подине ванны, после чего расплавляется весь металл. Дегазация и рафинирование металла особенно интенсивно происходят на поверхности ванны в месте контакта жидкого металла с высокотемпературной струей. Для плавки применяются плазмотроны постоянного и переменного токов различных мощностей. Промышленные печи СССР и ГДР емкостью 5, 10 и 30 т оснащены плазмотронами постоянного тока, работающими на прямой полярности. Наиболее ответственными и теплонапряженными деталями плазмотрона являются катод 2
и сопло 3
, через кольцевой зазор между которыми вытекает плазмообразующий газ. При запуске печи первичная дуга зажигается осциллятором между катодом и соплом и затем сносится газом до
соприкосновения с металлом печи. После этога пусковая дуга отключается и горит только рабочая дуга между катодом и расплавом в потоке плазмы. Длина дуги, а следовательно, напряжение на ней определяются размерами и конструкцией печи (а не плазмотрона), поэтому для плазмотрона существует один рабочий параметр - ток дуги. Некоторые данные по плавильным плазмотронам приведены в табл. 8.1.
Катоды изготовлены из торированного или лантанированного вольфрама. Прочие конструкции плавильных плазмотронов имеют дополнительные каналы для подачи в плавильное пространство других газов, необходимых для металлургического процесса. Напряжение на дуге 150-660 В, вводимая мощность в период расплава равна 12-15 МВт, удельный расход энергии составляет 625 кВт·ч/т.
Таблица 8.1
Параметры |
Режим |
Ток, А
Диаметр катода, мм
Расход аргона, л/с
|
800 2000 4000 5000 10000
5-6 10-12 18-20 24-25 48-50
1 2 3 4 6
|
При плазменно-дуговом переплаве с целью получения особо чистых металлов используются ПДП с кристаллизаторами (рис. 8.16).
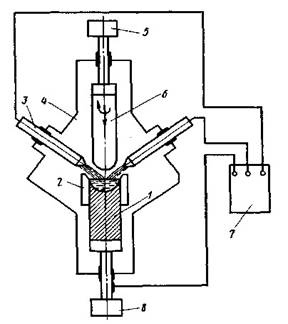
Рис. 8.16. Схема печи для плавки в кристаллизаторе:
1 - слиток; 2 - кристаллизатор; 3 - корпус печи; 5 - плазмотрон; 4 - корпус печи; 5 - механизм подачи и вращения заготовки; 6 - переплавляемая заготовка; 7 - источник питания; 8 - механизм вытягивания слитка
Переплавляемый металл в виде штанги 6 с сечением любой формы подается с постоянной скоростью и оплавляется одной или несколькими плазменными дугами. Анодом в этом случае является поверхность ванны жидкого металла в кристаллизаторе. Стекающий со штанги металл прогревается плазменной струей и растекается по поверхности ванны. В контакте с газовой атмосферой металл рафинируется и затем затвердевает и вытягивается в виде слитка. Рабочее давление в этих печах может изменяться в широких пределах от избыточного (1÷3)105
Па до пониженного 1- 10 Па. По сравнению с печами других типов плазменные печи обладают рядом преимуществ: хорошая поверхность слитков; незначительная потеря металлом легирующих компонентов (Сr, Аl, Ti, Мn, Si и
т. д.); возможность легирования металла газообразным азотом; гибкая связь между мощностью дуг и скоростью плавления слитка, позволяющая регулировать время пребывания металла в жидком состоянии.
Недостатками этих печей являются большая сложность и стоимость эксплуатации.
Для повышения экономичности плазменных печей разрабатываются плазмотроны с полыми катодами и схемы установок с комбинированным питанием постоянным и переменным током.
8.4. Установки плазменной резки и сварки металлов
Плазменная резка осуществляется путем выплавления и испарения металла в полости реза за счет энергии, выделяющейся в опорном пятне дуги и вносимой струей плазмы Энергетический баланс резки складывается из энергии дуги, химических реакций плазмы с металлом (если они возможны) и расхода энергии на расплавление, перегрев, испарение металла в полости реза, теплопередачу в твердый металл и унос с отработавшим потоком плазмы.
Отсюда следует, что процесс плазменной резки необходимо вести с макси- мальной мощностью и максимальной скоростью, обеспечиваемой вспомогатель- ными операциями и применением ЭВМ. Это условие выполняется при выборе тока, напряжения, плазмообразующего газа и конструкции режущего плазмотрона. Ширина реза, определяющая экономичность процесса, связана с диаметром сопла плазмотрона, током дуги и скоростью перемещения плазмотрона.
При оптимальном соотношении между толщиной металла, мощностью дуги, диаметром сопла и скоростью резки струя плазмы погружается на всю толщину металла, а анодная область дуги располагается вблизи нижней кромки реза. Уменьшение мощности дуги, равно как и увеличение скорости продвижения плазмотрона, ведет к сужению полости реза.
Чрезмерное увеличение мощности и снижение скорости движения плазмотрона приводит к увеличению ширины реза, особенно в нижней его части, и перегреву всего разрезаемого металла. Коэффициент полезного действия плазменной резки возрастает с повышением мощности дуги и скорости движения плазмотрона, достигая 80-90 %, тепловой КПД принимают равным 40 %. Для увеличения мощности струи плазмы в пределах заданного тока дуги целесообразно принимать меры по повышению линейного градиента потенциала столба дуги применением высокоэнтальпийных плазмообразующих газов (азота, водорода, воздуха, углекислого газа, паров воды и др.) и интенсивным сжатием столба дуги соплом плазмотрона.
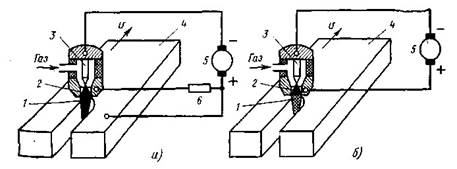
Рис. 8.17. Схема резки металла плазменной дугой (а
) и плазменной струей (б
):
1 - струя плазмы; 2 - дуга; 3 - катод; 4 - разрезаемый материал; 5 - источник питания; 6 - сопротивление, ограничивающее ток дежурной дуги
Режущий плазмотрон (рис. 8.17) с газовой стабилизацией дуги имеет стержневой вольфрамовый (или циркониевый) электрод 3
, соосно расположенный в полости сопла 2
. Стабилизирующий газ подается между ними и обеспечивает проникновение плазмы в глубину металла. При включении установки существует такая последовательность операций: включается подача воды, охлаждающей сопло и электрод, устанавливается необходимый расход газа; поджигается дежурная дуга, ток которой ограничивается сопротивлением 6
, и возникает факел плазмы. При касании дежурным факелом кромки металла возникает цепь силовой плазменной дуги и начинается интенсивный процесс резки. При случайных погасаниях режущей дуги дежурная дуга восстанавливает процесс. При резке металла малых толщин применяется плазменная струй без включения металла в цепь тока (рис. 8.17, б
).
Промышленные установки разных типов работают на токах до 1000 А при напряжении холостого хода до 350 В, обеспечивая скорость резки от 3-4 до 10 м/мин.
Наряду с мощными плазмотронами для автоматизированной машинной резки применяется плазморежущая аппаратура для переносных машин и ручной резки. Плазмотроны этих установок имеют низкое (до 180 В) напряжение холостого хода источника питания, ток - до 400 А.
Плазмотроны, выполняемые по схеме (рис. 8.17, а), являющейся основной при плазменной резке, рассчитывают на рабочий ток, а напряжение дуги формируется в полости реза. Вследствие этого вольт-амперные характеристики дуги здесь падающие, а источники питания имеют вертикальные или крутопадающие внешние ВАХ.
Плазменную сварку металлов проводят с помощью плазмотронов по схеме, приведенной на рис. 8.18.
Высокая мощность плазмотрона и динамическое воздействие плазмы позволяют сваривать металлы разных толщин без подачи присадочной проволоки в сварочный шов, заваривать отогнутые кромки состыкованных деталей, сваривать детали без разделки кромок, осуществлять сварку металла большой толщины за один проход.
Рис. 8.18. Схема проведения плазменной сварки:
а - электрическая схема; 1 - сварочный источник питания; 2 - высокочастотный генератор; 3 - неллавящийся электрод; 4 - плазмообразутощий газ; 5 -
охлаждающая вода; 6 - защитный газ; 7 - сопло для защитного газа; а - изделие; б
- схема газовых потоков, окружающих плазменную дугу; 1 - наружный холодный лоток; 2 - внутренний горячий поток: 3 - столб дуги; в - схема плазменной дуги; 1
- плазмообразующий газ, 2 - фокусирующий газ; 3 - защитный газ; 4 - очертание
факела при отсутствии фокусирующего газа
Применение вторичного фокусирующего газового потока, направленного под углом к оси плазмотрона, позволяет сконцентрировать нагрев на малой площади сварочной ванны. Применяемые газы обеспечивают защиту сварочного шва от воздействия атмосферы.
В зависимости от рода свариваемого металла применяют аргон, смеси аргона с гелием или водородом.
В состав установки по схеме рис. 8.18, а
входит источник питания 1
, представляющий собой трехфазный двухполупериодный выпрямитель с регулируемым значением сварочного тока и крутопадающей ВАХ;
высокочастотный генератор 2
- осциллятор, служащий для возбуждения дежурной дуги между внутренним соплом и электродом 3
в потоке аргона. Ток дежурной дуги ограничивается сопротивлением R, а емкость С служит для облегчения пробоя напряжением высокой частоты межэлектродного промежутка. Для начала процесса сварки необходимо коснуться свариваемого изделия 8
светящейся частью струи плазмы. Тогда по цепи потечет сварочный ток, разогревающий металл 8
в точке воздействия плазмы и образующий сварочную ванну, если бы в плазменную горелку подавался только один газ, как это делалось ранее (рис. 8.18,
б
), то помимо чрезмерно большого расхода аргона технологические свойства плазменной дуги были бы недостаточны для выполнения качественной сварки. Столб дуги 3,
окруженный потоками холодного газа 2
и 1
, имеет возможность самопроизвольно перемещаться по поверхности сварочной ванны.
Для более четкого ориентирования плазмы в точку сварки и улучшения проникновения столба дуги в глубину сварочного шва с одновременным уменьшением расхода аргона применяются плазменные горелки, выполненные по схеме рис. 8.18, в
. Здесь помимо аргона, подаваемого для зажигания дежурной дуги и образования плазмы, подается фокусирующий менее дефицитный газ 2
, производящий сжатие и фокусировку плазменной струи. При этом значительно повышается температура плазмы, что благоприятно влияет на процесс сварки. Защитный газ 3
предотвращает возможность попадания в зону сварки вредных компонентов из окружающей среды. Размеры электродов зависят от тока дуги и расхода газов, а расстояние между горелкой и деталью выбирают в пределах 80-15 мм из условия формирования качественного сварочного шва.
В цепях включения источника питания имеется блокировка, не позволяющая включить плазмотрон без подачи охлаждающей воды и газов.
Источники питания обеспечивают сварочный ток до 450-600 А при напряжении дуги 60-80 В и скорость сварки, например алюминиевого сплава толщиной 4 мм при токе 250 А и расходе плазмообразующего газа 5 л/мин, равную 70 м/ч.
В институте электросварки им. Е. О. Патона АН УССР разработан способ и создана аппаратура микроплазменной сварки на постоянном токе 0,5-10 А деталей из нержавеющей стали, меди, титана, никеля толщиной 0,2-0,6 мм.
8.5. Установки плазменного нанесения покрытий
Нанесение коррозионно-стойких, жаропрочных и других защитных
покрытий осуществляется методами напыления и наплавки.
При напылении плазмой частицы наносимого материала расплавляются и разгоняются до высоких скоростей, а деталь, на которую наносится покрытие - подложка, разогревается до высоких температур. При доведении подложки до состояния плавления процесс напыления переходит в наплавку. Наносимый на подложку материал может представлять собой электропроводную проволоку или стержни, а также неэлектропроводный в холодном состоянии порошок.

При использовании проволоки или прутков процесс образования двухфазного напыляющего потока (плазма+наносимый материал в жидком состоянии) проходит по схемам, показанным на рис. 8.19.
Рис. 8.19. Схемы распыления нейтральной (а
) и токоведущей (б
) проволоки
дуговой плазмой
На пути к подложке мелкие капли расплавленного материала несколько остывают, но предварительный перегрев позволяет донести их до подложки в жидком состоянии.
Напыление неэлектропроводных материалов производится путем ввода порошков в разрядный канал плазмотрона двумя способами: в дугу и в участок плазменной струи за дугой (рис. 8.20).

Рис. 8.20. Схема ввода напыляемого порошка в-столб плазменной дуги (а
) и плазменную струю (б
)
Различие в способах введения порошка определяется его теплофизическими свойствами. Тугоплавкие порошки вводятся в зону дуги, легко расплавляемые - в струю плазмы. При этом обеспечиваются разное время пребывания в зоне высоких температур и разный уровень теплового воздействия на частицу.
При плазменной наплавке изделие и наносимый материал включаются в цепь тока через токоограничивающие сопротивления (рис. 8.21). Скорость подачи материала и перемещения горелки по обрабатываемой поверхности согласуется с тепловой мощностью плазменной струи и контролируется технологом.

Рис. 8.21. Схема наплавки с присадочной проволокой:
а - изделие под током: б - изделие обесточено; 1 - горелка; 2 - ввод
плазмообразующего газа; 3 - канал для ввода защитного газа; 4 - ограничительное сопротивление; 5 - источник питания; 6 - балластное сопротивление; 7 - присадочная проволока
Совмещенные схемы плазменного напыления и наплавки позволяют получить прочно сплавленный с подложкой слой наплавленного материала. Размеры его можно регулировать в широких пределах (по ширине - от 8 до 45 мм, по глубине - от 0,5 до 6 мм), изменяя количество подаваемого присадочного материала и амплитуду движения плазмотрона перпендикулярно направлению его основного движения.
Компонентами установок плазменного нанесения покрытий являются дозаторы наносимого материала, источники электрического питания, система газоснабжения и охлаждения плазмотрона.
Кроме описанных имеется большое количество других плазменных процессов, в результате которых происходит модификация материала (сфероидизация частиц, травление и испарение поверхности). Описание этих процессов можно найти в специальной литературе.
УСТАНОВКИ ДУГОВОЙ ЭЛЕКТРИЧЕСКОЙ СВАРКИ 9.1. Физико-технические основы дуговой сварки
Электрической дуговой сваркой
называют процесс получения неразъемных соединений деталей из различных материалов за счет их сплавления с помощью электрической дуги. Это один из ведущих технологических процессов в машиностроении и строительной индустрии.
При дуговой сварке тепловая энергия, необходимая для плавления металла, получается в результате дугового разряда, возникающего между свариваемым металлом и электродом. Расплавляясь под действием опорных пятен дуги, кромки свариваемых деталей и торец плавящегося электрода образуют сварочную ванну, которая некоторое время находится в расплавленном состоянии. При затвердевании металла образуется сварное соединение. Сварка плавлением представляет собой комплекс металлургических и физико-химических процессов, протекающих в металле при высоких температурах и значительной концентрации тепловой энергии.
Вместе с металлом плавится электродное покрытие при ручной сварке или флюс при дуговой сварке под флюсом.
Расплавленный металл электрода переходит в сварочную ванну в виде капель. Размер капель и их количество зависят от силы тока, химического состава электрода и покрытия (флюса), электромагнитных явлений в дуге и т. п. При совместном переходе капель расплавленного электродного металла и шлака через дуговой промежуток между металлом, шлаком и газами, окружающими дугу, протекают химические реакции. В процессе сварки сварочная ванна перемещается вдоль шва с определенной скоростью, равной скорости сварки При сварке в газовой среде защитное действие обеспечивается применением аргона, аргонгелия, азота, углекислого газа, паров воды.
Капельный перенос обеспечивает поступление в сварочную ванну до 80- 95 % всего металла плавящегося электрода. Остальные 5-20 % теряют в виде брызг и пара. Механизм переноса капли металла включает в себя следующие стадии: оплавление торца электрода, стенание металла, образование капли грушевидной формы. У основания капли образуется тонкая шейка, имеющая высокое электрическое сопротивление. В области шейки плотность тока резко возрастает, перегревая шейку и удлиняя каплю, которая, касаясь (или не касаясь) сварочной ванны, обрывается, на мгновение замыкая накоротко цепь тока. Одновременно шейка взрывается с образованием большого количества паров и газов, отбрасывающих каплю в направлении сварочной ванны. Затем процесс повторяется. При ручной сварке электрод длиной 450 мм расплавляется за 1,5-2 мин. Давлением дуги р=kI2
, где k - эмпирический коэффициент, жидкий металл выдавливается со дна кратера дуги на боковую поверхность, создавая определенную глубину сварочной ванны. Количество расплавляемого за единицу времени металла
С = αп
Iη,
здесь αп
- коэффициент плавления, г/ч; I - ток дуги, А; η - время горения дуги, ч. Вследствие потерь расплавленного металла количество фактически наплавленного металла оценивается коэффициентом наплавки сен, который на 520 % меньше коэффициента плавления.
Значение αн
для электродов с различными покрытиями составляет 7-13 г/(А·ч). Знание коэффициента наплавки важно при нормировании сварочных работ. Скорость сварки (см/ч)
υ = αн
I/(γF),
где αн
- коэффициент наплавки г/(А·ч); γ - удельная масса наплавленного металла (γстали
= 7,85 г/см3
); F - площадь поперечного сечения сварочного шва, см2
. Длина дугового промежутка при сварке должна быть больше длины капли, отрывающейся от электрода, и на практике составляет 4-7 мм.
По сравнению с плазмой сварочной дуги при температуре (4,5÷8) 103
К капля металла является холодной, однако вследствие высокой концентрации электронов имеет более высокую электропроводность и шунтирует часть столба электрической дуги. Это определяет низкое значение линейного градиента потенциала столба дуги. Вследствие малой протяженности столба дуги (4-7 мм) и низкого значения линейного градиента потенциала между приэлектродными пятнами дуги реализуется напряжение 8-12 В. Если учесть, что в структуру напряжения дуги входят компоненты анодного и катодного падений напряжения, значения которых зависят от тока дуги, материала электродов и изменяются в узких пределах (Uа
= 2÷12 В, Uк
= 8÷14 В), то напряжение на сварочной дуге составляет 18-45 В. При некотором увеличении тока напряжение, необходимое для горения дуги, снижается и ВАХ дуги приобретает падающий характер. В области больших токов ВАХ становится жесткой и слабо-возрастающей. Так как интенсивность плавления электрода и свариваемого металла определяется преимущественно мощностью, выделяющейся в опорных пятнах дуги на электродах, а столб дуги выполняет в основном технологические, а не энергети- ческие функции, то главным энергетическим показателем установок дуговой сварки является значение сварочного тока, а напряжение холостого хода источни- ка питания является производным от напряжения на дуге, обеспечивающим ее устойчивое горение. Для падающего и жесткого участков ВАХ дуги напряжение холостого хода источника питания должно быть Uх
= (1,4÷2,2) Uд
при крутопадающей внешней характеристике. Это дает напряжение 55-80 В, что и обеспечивается источниками сварочного тока. Следует отметить, что напряжение источников питания дуговой сварки безопасно для человека; это обусловило широкое развитие ручной дуговой сварки.
Особенности дуги переменного тока и меры, принимаемые для повышения ее устойчивости, описаны ранее. Отметим, что напряжение зажигания при переходе тока через нуль зависит от ряда факторов, в первую очередь от силы тока. С увеличением тока напряжение зажигания дуги снижается. Зависимость между напряжением зажигания и напряжением горения дуги для сварки открытой дугой имеет вид Uз
= (1,3÷2,5) Uд
. При сварке на больших токах под флюсом напряжения зажигания дуги почти равно напряжению горения.
По степени механизации
различают сварку ручную, полуавтоматическую и автоматическую. Отнесение процесса к тому или иному виду зависит от того, каким образом выполняются: зажигание и поддержание определенной длины дуги, манипуляции электродом для придания шву нужной формы, перемещение электрода по линии наложения шва и прекращение процесса сварки. При ручной сварке
операции, необходимые для образования шва, выполняются рабочимсварщиком вручную. Ручная сварка производится плавящимся электродом с покрытием (рис. 9.1) или неплавящимся электродом с газовой защитой.

Рис. 9.1. Схема ручной дуговой сварки:
1 - основной металл; 2 - сварочная ванна; 3 - кратер; 4 – сварочная дуга; 5 - проплавленный металл
Fпр
; 6 - наплавленный металл
Fп
; 7 - шлаковая корка; 8 - жидкий шлак; 9 — покрытие электрода; 10 - стержень электрода; 11 - электрододержатель; 12 - сварочная цепь; 13 - источник питания
При полуавтоматической сварке
плавящимся электродом механизирована часть операций, например операция по подаче электродной проволоки или флюса в сварочную зону, перемещение горелки по свариваемой детали и др. Остальные операции процесса сварки осуществляются сварщиком вручную.
При автоматической сварке
под флюсом (рис. 9.2, а
) автоматизировано большинство технологических операций. Сварочная проволока 2
и
гранулированный флюс 1
подаются в зону дуги, горящей в полости 3
, заполненной парами металла и материалов флюса. По мере перемещения дуги расплавленный флюс всплывает на поверхность сварочной ванны, образуя легко отделяющуюся от шва шлаковую корку 5
, а металл сварочной ванны кристаллизуется в виде сварного шва 4
. Шлак защищает металл от воздействия кислорода и азота воздуха, легирует и замедляет охлаждение металла шва, что способствует получению качественного наплавленного металла при высокой производительности.
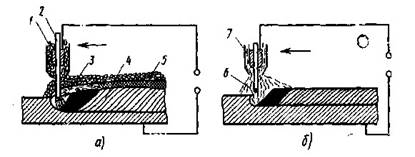
Рис. 9.2. Схема сварки под флюсом (а
) и в среде защитных газов (б
)
При сварке в защитном газе (рис. 9.2, б
) возникающая между электродом и основным металлом (или двумя электродами) дуга окружена газом 6
, подаваемым под небольшим давлением из сопла 7
. Газовая защита применяется при сварке плавящимися и неплавящимися электродами. Роль газа сводится в основном к физической защите сварочной ванны от воздействия воздуха. Рассмотрим наиболее распространенные способы сварки. Сварка в камерах с контролируемой атмосферой
применяется для соединения легкоокисляющихся металлов и их сплавов. В камере можно создать атмосферу из инертных газов, что обеспечит высокое качество сварного соединения.
Сварка трехфазной дугой
применяется при ручном и механизированном способах сварки. Сущность этого способа состоит в том, что к двум электродам, закрепленным в специальном устройстве, и к свариваемому изделию подводится переменный ток от трехфазного источника питания. После возбуждения горит не одна дуга, как обычно, а одновременно три дуги: между каждым из электродов и изделием и дуга между обоими электродами. Эта дуга по отношению к свариваемому изделию является независимой и обеспечивает расплавление электродов.
Сварка трехфазной дугой характеризуется высокой стабильностью процесса, так как дуговой промежуток всегда поддерживается в ионизированном состоянии. При сварке неплавящимся электродом
дуга горит между вольфрамовым электродом и изделием. Электрод проходит через насадок, по которому в зону сварки подается аргон. Поэтому такая сварка называется аргоновой. Диаметр вольфрамового электрода составляет 1-4 мм. Аргоновая сварка металлов толщиной 3 мм и больше успешно выполняется плавящимся электродом на автоматах и полуавтоматах. Этот вид сварки отличается высокой
производительностью, превышающей производительность оварки вольфрамовым электродом, и пригоден для сварки всех металлов, в том числе всевозможных легированных сталей, меди, никеля и их сплавов, титана, алюминия, алюминиевых и магниевых сплавов, которые свариваются без применения флюсов. Важным преимуществом такой сварки является то, что в процессе работы сварщик может видеть место сварки и регулировать процесс.
Газоэлектрической сваркой может быть назван способ, при котором теплота для плавления металла получается не только за счет дугового разряда, но и за счет химических реакций, присходящих в газовой фазе.
Дуговая сварка в углекислом газе
выполняется как неплавящимся, так и плавящимся электродом на автоматах и полуавтоматах.
9.2. Источники питания дуговой сварки
Специфическим свойством сварочных источников тока является способность выдерживать многочисленные технологические короткие замыкания
во вторичной цепи. Они происходят при зажигании дуги касанием электродов, а также во время сварки, когда скорость подачи плавящегося электрода не
согласуется со скоростью его плавления. Кроме того, вследствие нелинейности ВАХ дуги, имеющей падающий, жесткий и восходящий участки, ВАХ источника
питания должна иметь соответствующий вид.
При автоматической сварке под флюсом с саморегулированием дуги, имеющей жесткую характеристику, ВАХ ИП должна быть пологопадающей (рис. 9.3, а
, кривая 3
) для повышения саморегулирования дуги. При сварке в среде защитных газов в условиях большой плотности постоянного тока в электроде ВАХ дуги возрастающая (рис. 9.3, б
, кривая 1
). В этом случае внешняя характеристика ИП для еще большей интенсивности саморегулирования должна быть жесткой или возрастающей (рис. 9.3, б
, кривые 2
, 3
). Источники питания должны обеспечивать возможность настройки различных режимов сварки - установление заданных значений тока и напряжения, обеспечивающего этот ток.
Наиболее распространенным способом настройки режима сварки является комбинированное регулирование
. Оно заключается в том, что весь диапазон регулирования по току разбивают на ряд ступеней (грубое регулирование), а в пределах каждой ступени осуществляют плавное регулирование.
В зависимости от особенностей технологического процесса сварочные работы выполняются на постоянном либо переменном токе. Основными
технологическими показателями источников питания сварочной дуги являются кроме внешней характеристике и напряжения холостого хода относительная продолжительность работы (ПР) и относительная продолжительность включения (ПВ) в прерывистом режиме.
Критерием оценки динамических свойств источника питания служит скорость нарастания напряжения на его зажимах при переходе от режима короткого замыкания к режиму холостого хода. Особенно важно время нарастания напряжения от нуля до значения, достаточного для возбуждения дуги, и время восстановления напряжения. По ГОСТу оно не должно превышать 0,03 с. Поэтому для дуговой оварки создаются специальные источники питания постоянного и переменного токов, которые должны:
а) иметь напряжение холостого» хода в момент зажигания дуги, достаточное для ее возбуждения, но не превышающее пределов, безопасных для жизни сварщика;
б) надежно работать в режимах частых технологических коротких замыканий;
в) иметь внешнюю характеристику, соответствующую В АХ дуги, и иметь достаточную мощность;
г) снабжаться специальными устройствами для плавного изменения тока;
д) соответствовать требованиям удобства эксплуатации и экономичности.
Тепловой режим источника питания оценивается относительными ПР и ПВ, обусловленными прерывистым рабочим процессом сварки. Продолжительность работы определяют как отношение продолжительности рабочего периода источника питания к длительности полного цикла работы. Она выражается в процентах:
ПР = (ηр
/ηц
)100,
где ηр
- время работы под нагрузкой; ηц
- длительность полного цикла.
Условно принято считать, что в среднем ηр
= 3 мин, ηц
= 5 мин, т. е. среднее оптимальное значение ПР = 60 %. ПР отличается от ПВ тем, что в первом случае
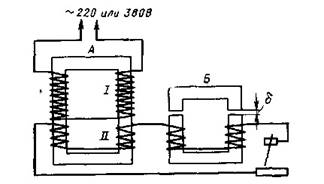
источник питания во время паузы не отключается от сети, а работает в режиме холостого хода, во втором случае источник питания полностью отключается от сети.
Источники питания сварочной дуги переменного тока
- это сварочные трансформаторы, которые подразделяют на одно- и трехфазные, а по количеству питаемых сварочных постов - на одно- и многопостовые.
По способу получения падающих внешних характеристик и регулирования тока различают источники питания двух типов: трансформаторы с нормальным магнитным рассеянием, выполненные в виде двух раздельных аппаратов (трансформатор и дроссель), и трансформаторы с развитым магнитным рассеянием (с подвижными катушками, с магнитными шунтами, с витковым ступенчатым регулятором).
Рис. 9.4. Схема сварочного аппарата с отдельным регулятором
Трансформаторы с отдельным дроссельным регулятором (рис. 9.4), сопротивление которого может изменяться в широких пределах, состоит из сердечника А с двумя обмотками: первичной I
и вторичной II
, создающей напряжение холостого хода 60-65 В. Первичную обмотку подключают к сети переменного тока напряжением 220 или 380 В.
Регулятор тока - дроссель Б состоит из магнитопровода (ярма) и обмотки, расположенной на неподвижной части магнитопровода (якоре). Между ярмом и якорем имеется воздушный зазор δ, изменяя который с помощью регулирующего винта осуществляется плавное регулирование сварочного тока.
При увеличении зазора δ между подвижной и неподвижной частями сердечника электрическое сопротивление (индуктивное) дросселя уменьшается, в результате чего увеличивается ток в сварочной цепи. При уменьшении зазора δ электрическое сопротивление дросселя увеличивается, а ток уменьшается.
Регулирование сварочного тока осуществляется изменением воздушного зазора δ между магнитопроводом и якорем С.
К преимуществам трансформаторов этой системы следует отнести компактность, меньший расход меди и трансформаторной стали; при
регулировании тока с большого значения на минимальное напряжение холостого хода несколько увеличивается, что повышает устойчивость горения дуги.
Трансформаторы с повышенным магнитным рассеянием
получили наиболее широкое распространение при ручной дуговой сварке, где регулирование сварочного тока осуществляется изменением расстояния между первичной и вторичной обмотками или подвижным магнитным шунтом. Это изменяет
сопротивление потока рассеяния и индуктивность трансформатора. Чем больше сопротивление шунтирующей цепи, тем меньше индуктивность рассеяния трансформатора и больше сварочный ток.
Для многопостовой оварки можно использовать любой сварочный трансформатор с жесткой внешней характеристикой. При этом к каждому посту должен быть подсоединен дроссель, обеспечивающий падающую характеристику цепи.
Источники питания постоянного тока
подразделяют на две основные группы: сварочные преобразователи и сварочные выпрямители.
Сварочный преобразователь
состоит из собственно генератора постоянного тока и первичного двигателя (электродвигателя или двигателя внутреннего сгорания).
Однопостовые сварочные генераторы в зависимости от схемы формирования падающей внешней характеристики подразделяются на три основные группы:
1. Генераторы с ращепленными полюсами и с поперечным полем, у которых падающая внешняя характеристика достигается за счет размагничивания основного поля генератора магнитным полем реакции якоря.
2. Генераторы с независимым возбуждением, падающая внешняя характеристика которых достигается за счет уменьшения основного магнитного потока генератора потоком последовательной обмотки. Питание независимой обмотки возбуждения осуществляется от генератора - возбудителя или выпрямителя.
3. Генераторы с намагничивающей параллельной и размагничивающей последовательной обмотками, в которых падающая внешняя характеристика создается за счет размагничивающего действия потоков последовательной обмотки и реакции якоря генератора.
В генераторах с расщепленными полюсами предусмотрен двойной способ регулировки сварочного тока: сдвигом щеток (грубая регулировка) и реостатом в цепи регулируемой обмотки (тонкая регулировка), что позволяет расширить пределы изменения тока без существенного изменения напряжения холостого хода генератора. Сдвиг щеток против направления вращения якоря генератора ослабляет размагничивающее действие потока реакции якоря и увеличивает ток короткого замыкания (сварочный ток). Сдвиг же щеток по направлению вращения якоря уменьшает ток короткого замыкания.
Централизованная схема питания сварочных постов с помощью многопостовых сварочных генераторов имеет ряд преимуществ перед однопостовыми сварочными агрегатами: снижаются затраты на приобретение, ремонт и обслуживание сварочных постов; уменьшается потребность в производственных площадях; увеличивается коэффициент использования сварочного оборудования и т. д.
Сварочные посты СП подключаются к генератору через балластные реостаты РВ, сопротивление которых можно изменять в широких пределах, изменяя тем самым сварочный ток. Балластный реостат создает падающую характеристику, служит регулятором тока, ограничивает и регулирует ток короткого замыкания сварочной цепи поста в момент зажигания дуги.
Одновременно с этим в нем имеются потери электрической энергии.
Сварочные выпрямители
основаны на использовании полупроводниковой техники, применение которой позволяет значительно расширить номенклатуру источников питания для дуговой сварки. К их преимуществам следует отнести равномерную загрузку силовой сети переменного тока и лучшее использование трансформатора, питающего выпрямитель. Динамические свойства выпрямителей из-за меньшей электромагнитной инерции лучше, чем генераторов постоянного тока. Ток и напряжение изменяются при переходных процессах практически мгновенно. КПД выпрямителей также несколько выше, чем у сварочных преобразователей с генератором постоянного тока.
По сравнению со сварочными трансформаторами трехфазные выпрямители обеспечивают большую стабильность дуги, особенно на малых токах, вследствие чего напряжение холостого хода их может быть снижено.
Тиристорные выпрямители
представляют собой замкнутую систему автоматического регулирования с отрицательной обратной связью по гоку при падающих внешних характеристиках и положительной обратной связью по выходному напряжению при жестких внешних характеристиках. Возможна и одновременная работа обратной связи по току и напряжению для получения заданной крутизны наклона пологопадающих внешних характеристик. Для сглаживания пульсаций и обеспечения стабильного процесса сварки в цепь включается индуктивность, значение которой зависит от технологических особенностей и режимов процесса.
Наиболее широкое распространение получили схемы, обеспечивающие минимальную пульсацию выпрямленного тока для ручной и автоматической сварки (ВСС, ВКС, ВД).
Для аргонно-дуговой сварки металлов малых толщин постоянным и импульсным токами применяются транзисторные преобразователи серии АП
9.3. Ручная дуговая сварка
С помощью ручной сварки выполняются многообразные операции соединения деталей в приспособленных для этой цели цехах, а также непосредственно на конструкциях и стройплощадках. Это обусловило специфические требования к применяемому оборудованию и технологии сварки. Сварочные агрегаты переносного исполнения снабжены сварочными проводами соответствующего сечения (табл. 9.2).
Таблица 9.2
Сила тока, А |
Сечение провода, мм2 |
Одинарный |
двойной |
200
300
400
500
|
25
50
75
95
|
-
2×16
2×25
2×35
|
Например, длина провода марки ПРГ (провод резиновый гибкий) или ПРГН (провод резиновый гибкий нейритовый), сплетенного из большого количества отожженных и облуженных проволочек диаметром 0,18-0,22 мм, не должна быть более 30 м, так как чрезмерная его длина вызывает значительные электрические потери и снижает КПД сварочного аппарата.
Электрододержатели при всех технологических приемах надежно удерживают электроды диаметром 0,3-6 мм, приготовленные из холоднотянутой или горячекатаной проволоки, материал которой соответствует материалу свариваемых деталей.
Условные обозначения присадочного материала и легирующих элементов приведены в табл. 9.3.
Таблица 9.3
Элемент
|
Условное обозначение |
Элемент
|
Условное обозначение |
в таблице
Менделеева
|
в марке
стали
|
в таблице
Менделеева
|
в марке
стали
|
Марганец
Кремний
Хром
Никель
Молибден
Вольфрам
Селен
Алюминий
|
Мn
Si
Сr
Ni
Мо
W
Sе
Аl
|
Г
С
Х
Н
М
В
Е
Ю
|
Титан
Ниобий
Ванадий
Кобальт
Медь
Бор
Азот
|
Ti
Nb
V
Со
Сu
В
N
|
Т
Б
Ф
К
Д
Р
А
|
Обозначение марки сварочной проволоки может состоять из цифры, соответствующей ее диаметру в мм, букв Св, означающих «сварочная», цифр, показывающих содержание углерода, и буквенных обозначений компонентов, входящих в состав проволоки (например, 2Св-08ГС). Например, для сварки алюминия и его сплавов применяется проволока марок СвАМц, СвАМб, АЛ9 и др.; для сварки меди и ее сплавов - проволока М1, М2; для сварки бронзы - проволока БрКМцЗ-1; латуни - проволока Л63, Л60-1 и др.
Проволоки для механизированной сварки имеют маркировку, состоящую из букв: Э - электродная, О - омедненная, Ш - электрошлаковая, ВД - воздушнодуговая, ВИ - вакуум-индукционная.
Электроды классифицируют в зависимости от материала, из которого они изготовлены, металла, для сварки которого они предназначены, от количества покрытия, нанесенного на стержень^ от химического состава стержня и покрытия, характера шлака, образующегося при расплавлении покрытия.
Название электродов для сварки конструкционных сталей состоит из обозначения марки электрода, типа электрода, диаметра стержня, типа покрытия и номера ГОСТа. Например,
УОНИ-13/45-Э42А-4,0ФГОСТ9467-60
расшифровывается так: УОНИ-13/45 - марка электрода; Э42А - тип; 4,0-Ф - диаметр и покрытие электрода.
Силу сварочного тока выбирают в зависимости от марки и диаметра электрода, при этом учитывают положение шва в пространстве, вид соединения, толщину и состав свариваемого металла, температуру окружающей среды. При этом необходимо работать на максимально возможном токе. Ток для электродов выбирают, исходя из соотношений
Iсв
= 50dэл
; Iсв
= (20 + 6dэл
)dэл
.
Режим сварки металлов разной толщины и свойств определен в специальных руководствах, а качество сварочных работ в большой степени зависит от квалификации сварщика.
9.4. Установки механизированной и автоматической сварки
При механизации и автоматизации сварки совершенствуется не только подача проволоки в зону горения дуги, но и возбуждение и поддержание горения дуги, перемещение дуги относительно изделия со скоростью сварки, заварка конечного кратера и разрыв дуги, подача и отсос флюса.
Производительность механизированной и автоматической сварки в 5-20 раз выше, чем ручной, при высоком качестве шва и экономном расходовании электроэнергии и материалов. При этих видах сварки флюсы и присадочную электродную проволоку выбирают по тем же критериям, что и при ручной сварке, с тем отличием, что плотность тока в электроде выбирают значительно большей, диаметр применяемой проволоки при токах 100-3000 А составляет 1-6 мм. Сварочная установка состоит из трех основных частей: сварочного агрегата, обеспечивающего процесс сварки, источника питания и аппаратного ящика с пультом управления.
Установки для механизированной и автоматизированной сварки включают в себя следующие разновидности: сварочные полуавтоматы; сварочные автоматы; сварочные тракторы.
Сварочные полуавтоматы
обеспечивают сварку и наплавку с механизированной подачей проволоки и других сварочных материалов в зону горения дуги и ручным перемещением дуги вдоль линии сварного шва.
Полуавтоматы
для сварки под флюсом состоят из тех же узлов, но вместо газовой аппаратуры они снабжены устройствами для подачи флюса.
Горелки для сварки изготовляют на определенный ток, который выбирают из стандартного ряда токов: 125, 160, 220, 250, 315, 400, 500, 630 А. Горелки
имеют естественное или принудительное воздушное или водяное охлаждение. На рис. 9.14 приведена конструкция наиболее распространенной горелки,
применяемой в полуавтоматах А547У и А1197П. Проволока подается к месту сварки по оси шланга, проходит через наконечник /. Шланг, как правило, имеет длину 3 м
Сварочные автоматы обеспечивают механизированное возбуждение и поддержание дугового разряда, подачу сварочных материалов и перемещение дуги вдоль линии сварки. С помощью автоматической сварки изготовляют наиболее ответственные конструкции - корпуса котлов, трубы большого диаметра, цистерны, несущие конструкции сооружений, корпуса морских судов и др.
Диаметр электродной проволоки йэ (мм) можно приближенно вычислить из формулы
Iсв
= 11dэ
+ 10d2
э
.
Скорость подачи электродной проволоки зависит от ее диаметра, тока дуги и составляет 0,5-4-5 м/мин. Ее увеличивают с ростом тока и уменьшением диаметра электродов.
Сварочный трактор
- самоходный агрегат для сварки в основном под флюсом, несущий на самоходной тележке подающий механизм, сварочную горелку, механизм настроечных и корректировочных перемещений, флюсовую аппаратуру, систему управления. Многие конструкционные узлы трактора унифицированы с узлами автоматов и полуавтоматов. Существуют тракторы, перемещающиеся по изделию и перемещающиеся по рельсам. На рис. 9.15 показан сварочный трактор АДС-1000-2. Тележка трактора снабжена отдельным приводом от регулируемого электродвигателя постоянного тока. С помощью цепной передачи вращение передается на обе оси тележки.
УСТАНОВКИ ВЫСОКОИНТЕНСИВНОГО НАГРЕВА УСТАНОВКИ ЭЛЕКТРОННО-ЛУЧЕВОГО НАГРЕВА 10.1. Физико-технические основы электронно-лучевого нагрева
Электронно-лучевой нагрев применяется для обработки тугоплавких и химически активных металлов, сварки, испарения металлов и оксидов, выращивания монокристаллов, металлизации и напыления и т. д.
С технологической точки зрения основными преимуществами электроннолучевого нагрева следует считать:
а) возможность в широких пределах плавно изменять удельную-энергию в зоне нагрева;
б) большую удельную мощность (от десятков ватт до нескольких мегаватт) в месте взаимодействия электронного луча с обрабатываемым изделием);
в) возможность управления пространственным положением луча с помощью магнитной системы;
г) возможность использования вакуума как рабочей среды;
д) возможность получения малоразмерной (прецизионной) зоны воздействия электронного луча на обрабатываемый материал.
К временным недостаткам этого вида нагрева следует отнести прежде всего необходимость обеспечения высокого вакуума, а также сложность изготовления, эксплуатации и высокую стоимость электронно-лучевого оборудования. В нагревательных установках с использованием электронного луча последний представляет собой направленный поток электронов, переносящий энергию от излучателя электронов к изделию. Ускоренные электроны приобретают кинетическую энергию, пропорциональную их скорости, которую они передают веществу обрабатываемого объекта.
Так как электроны теряют свою энергию при столкновении с молекулами и атомами вещества, то в пространстве рабочей камеры должен поддерживаться глубокий вакуум, который необходим также для защиты катода от бомбардировки положительными ионами.
Вышедший из катода электронной трубки электрон ускоряется в электрическом поле и приобретает энергию Wе
(эВ)
Wе
= mе
υ2
/2 = е0
U, (10.1)
где mе
и e0
- масса и заряд электрона; U - пройденная электроном разность потенциалов, В.
Излучаемые катодом электроны ускоряются в электрическом поле и формируются электрическими и магнитными полями в электронный луч.
Мощность электронного луча
Рл
= Iл
Uу
, (10.2)
здесь Pл
- ток луча, А; Uу
- ускоряющее напряжение, В.
Удельная мощность в луче
Рл
= Рл
/Sл
= Iл
Uу
/(πr2
л
), (10.3)
где Sл
и rл
- поперечное сечение и радиус луча на обрабатываемой поверхности. Сформированный пучок проходит через рабочую камеру и попадает на поверхность обрабатываемого объекта. Скорость электронов при попадании на поверхность детали
_______
υ = √2е0
Uу
/mе
.
Глубина проникновения электронов (м) с энергией 5-100 эВ, что имеет место в электронно-лучевых установках (ЭЛУ), может быть определена по формуле Шонланда:
b = 2,1·10-17
Uу
γ, (10.4)
где γ - плотность вещества, мишени, кг/м3
.
Следовательно, в ЭЛУ глубина проникновения электронов и протяженность зоны интенсивного выделения тепловой энергии составляет около 10-6
м, и для твердых тел нагрев является чисто поверхностным. Мощность рентгеновского излучения в энергетическом балансе ЭЛУ составляет доли процента и его можно не учитывать. Однако его биологическое воздействие представляет опасность для обслуживающего персонала. Поэтому при конструировании и изготовлении ЭЛУ должны быть предусмотрены специальные мероприятия по защите обслуживающего персонала от воздействия рентгеновского излучения. Рассмотрим явления, связанные со вторичной эмиссией электронов с бомбардируемой электронным лучом поверхности металла. Значительно перегретая (на 200-1000 К) выше температуры плавления поверхность ванны расплавленного металла представляет собой мощный источник термоэлектронной эмиссии. Мощность (Вт) термоэлектронной эмиссии, уносимая потоком электронов,
Pтэ
=Iтэ
/e0
(θ +2kT), (10.5)
здесь Iтэ
- ток термоэлектронной эмиссии, А; e0
- заряд электрона; θ - работа выхода электрона, эВ; k - постоянная Больцмана; Т - температура, К. Несмотря на малую мощность термоэлектронной эмиссии, ее ток, поглощаемый стенками камеры, может достигать десятков и сотен ампер, поэтому заземление ЭЛУ должно быть надежным и рассчитанным на этот ток. Часть электронов луча отражается от поверхности металла и поглощается стенками камеры. Это приводит к довольно большим потерям мощности электронного луча (для легких металлов 5-10 %, для тяжелых 15-25 %) и значительно влияет на энергетический баланс ЭЛУ.
В камере ЭЛУ происходят сложные процессы взаимодействия электронов луча с атомами остаточных и выделяющихся в процессе плавки и нагрева газов, с атомами металлических паров, находящихся над поверхностью расплавленного металла и т. п.
10.2. Конструкции электронно-лучевых установок
Во всех ЭЛУ имеются общие системы, сходные по своему функционально- му назначению и принципу действия. Среди них можно выделить два комплекса - энергетический и электромеханический.
Энергетический комплекс
ЭЛУ включает в себя электронную пушку с блоками питания и управления лучом. Электронной пушкой называется устройство, в котором эмиттируемый катодом пучок электронов формируется в электрическом и магнитном полях в луч, который ускоряется в электрическом поле, выводится через отверстие в аноде и направляется на нагреваемый объект.
Многочисленным семейством ЭЛУ являются плавильные установки. Наиболее простая схема электронной плавильной установки с кольцевым катодом и автоэлектронным нагревом,- у которой анодом служит сам расплавляемый металл. ЭЛУ с кольцевым катодом
работают на ускоряющем напряжении 5-15 кВ. Их преимуществами являются простота устройства и высокая проводимость, вследствие чего в них можно получить значительные токи пучка при низком напряжении. Их недостаток - нахождение катода в плавильной камере, из-за чего при газовыделении с поверхности ванны он оказывается в зоне повышенного давления. Вышедшие из катода электроны сталкиваются с частицами газов и ионизируют их. Образующиеся положительные ионы направляются к катоду и оседают на нем, что сильно снижает его эмиссионную способность и сокращает срок службы. Поэтому плавильные ЭЛУ с кольцевым катодом имеют ограниченное применение для переплава металлов с малым выделением газов.
ЭЛУ с радиальными пушками
в меньшей мере подвержены этому недостатку. В этих установках вокруг электрода по радиусу установлено несколько катодов и анодов с отверстиями, через которые движущиеся прямолинейно электроны проходят к концу электрода и к ванне. Таким образом, здесь анод отделен от расплавляемого металла, хотя и тот и другой находятся под одинаковым потенциалом. Анод является направляющим и формирующим устройством. В данном случае система анод-катод соответствует понятию электронной пушки.
Часть установки, в которой находятся электронные пушки, отделена от плавильного пространства перегородкой с отверстиями для электрода и пучка электронов. Верхняя и нижняя части камеры имеют индивидуальные системы откачки газов. При значительном выделении газов из ванны лишь часть паров металла попадает через отверстия в верхнюю камеру и откачивается из нее насосом. Радиальные пушки работают при относительно низком ускоряющем напряжении (около 15 кВ), поэтому они имеют ограниченную мощность. Для увеличения мощности всей ЭЛУ необходимо увеличить количество радиальных пушек.
В качестве плавильных наибольшее распространение получили ЭЛУ с
аксиальными пушками
. В отличие от радиальной аксиальная пушка образует сильно сфокусированный электронный луч. В ней имеются два катода. Основной катод К выполнен в виде массивной вогнутой снизу вольфрамовой пластины и разогревается до 2300-2500 К электронной бомбардировкой от вспомогательного катода Ки который выполнен в виде нагреваемой током вольфрамовой спирали. Между катодами прикладывается напряжение 3,5-5,0 кВ. Вспомогательный катод имеет отрицательный потенциал относительно основного, так что основной катод является анодом для вспомогательного. Анод А имеет специальную форму для создания в пространстве между ним и катодом такого электрического поля, которое сфокусировало бы электронный пучок так, чтобы он практически весь проходил через отверстие анода. Пройдя через анод, электронный луч попадает в лучепровод Л, соединяющий катодную камеру с плавильной камерой установки, в которой находится переплавляемый электрод Э. Он может перемещаться горизонтально: его можно вводить под пучок или выводить из-под него. Часть электронов луча проходит мимо электрода и попадает на поверхность ванны жидкого металла, расположенной в кристаллизаторе в нижней части камеры. Лучепровод должен защищать катодный узел от прорыва в него газов из плавильной камеры. С этой целью лучепровод снабжается откачивающим насосом, кроме того, имеются насосы, откачивающие газы и пары из катодного узла и рабочей камеры. В луче-проводе производится дополнительная магнитная фокусировка с помощью магнитных линз М, поскольку на своем пути через лучепровод электронный пучок расширяется. ЭЛУ с аксиальными пушками работают при ускоряющем напряжении 30-40 кВ.
Плавильные ЭЛУ
применяются главным образом для переплавки стали, молибдена, ниобия и других тугоплавких и химически активных металлов. Их мощность составляет от 50 (в лабораторных условиях) до 2000 кВт. Сварочные ЭЛУ
с особо остросфокусированным лучом работают при ускоряющем напряжении 70-100 кВ.
Для питания ЭЛУ используются высоковольтные источники питания постоянного тока. Они состоят из повышающих трансформаторов и высоковольтных выпрямителей, собираемых на тиратронах, селеновых элементах или кремниевых диодах. На крупных установках для стабилизации тока пучка применяются параметрические источники тока.
Катод является одним из основных узлов электронной пушки. Для них катоды изготовляют из тугоплавких металлов (W, Та, Мо), оксидов редкоземельных металлов (Zr, Lа), а также интерметаллических соединений, например гексаборида лантана. Металлические катоды прямого нагрева применяются при небольших токах эмиссии (до 20 мА), а косвенного нагрева — при больших токах (100-200 мА). Заданная сходимость электронного луча обеспечивается подбором конфигурации катодного электрода и анода. После прохождения анода электроны движутся в пространстве, в котором отсутствует электрическое поле. Поскольку электронный луч обладает объемным пространственным зарядом, вследствие столкновения электронов происходит расфокусировка луча. Поэтому после электростатической фокусировки луч фокусируется также электромагнитной линзой, которая представляет собой катушку в магнитопроводе, питающуюся от выпрямителя, обеспечивающего стабильное напряжение и минимальную пульсацию.
Из всех видов электрических печей ЭЛУ являются наиболее сложным комплексом электротехнического оборудования. В системах электроснабжения ЭЛУ выделяются основные и вспомогательные цепи. К основным относятся цепи накала катода, питания преобразователя постоянного тока, а также цепи питания, получения, измерения и контроля вакуума; к вспомогательным - цепи фокусировки, отклонения и развертки электронного луча.
Системы питания ЭЛУ и обеспечения вакуума должны работать надежно и стабильно, поскольку от этого зависит качество переплавляемого материала. В состав электромеханического комплекса
входят рабочая камера, вакуумная система, системы позиционирования и перемещения заготовки, система наблюдения за ходом процесса, система защиты оператора от рентгеновского излучения и ряд вспомогательных устройств и механизмов.
Вакуумная камера
как базовый элемент ЭЛУ определяется видом осуществляемого технологического процесса и является одним из наиболее важных и сложных узлов электромеханического комплекса. Камера должна быть герметичной, механически прочной и жесткой. Материал камеры должен поглощать рентгеновское излучение.
Основная функция вакуумной системы - создание и поддержание в рабочем объеме и в электронной пушке необходимого вакуума, поскольку давление в зоне взаимодействия электронного луча с обрабатываемым изделием должно составлять 10-1
-10-4
Па.
Конструкция систем позиционирования и перемещения заготовок определяется видом операции. Наиболее просты устройства, применяемые при электронно-лучевой плавке (вытягивание слитка). Самые сложные системы используются при размерной обработке - они обеспечивают 5-6 видов различных перемещений с погрешностью позиционирования 1-5 мкм.
10.3. Технологическое применение электронно-лучевого нагрева
Основные технологические операции электронно-лучевой обработки можно
условно подразделить на четыре группы: плавка (технологические операции плавки в вакууме, локального переплава); испарение
(испарение в вакууме, размерная обработка электронным лучом); термообработка
(без изменения агрегатного состояния вещества); сварка
.
Плавка
электронным лучом в вакууме применяется в тех случаях, когда необходимо получить особо чистые металлы. Она имеет преимущества перед плавкой в вакуумных дуговых и индукционных печах, поскольку позволяет производить рафинирование жидкого металла в ванне после прекращения плавления электрода, а также осуществлять другие физико-химические процессы, которые при иных методах плавки не успевают проходить полностью или не протекают вообще. Переплавляемый материал может быть использован практически в любой форме (шихта, пруток, лом, спеченные штабики, губка). Таким образом, основные параметры, определяющие размеры участка, расплавляемого электронным лучом, определяются теплопроводностью и температурой плавления.
Важную роль при электронно-лучевой плавке играет вакуум:
1. В вакууме происходит интенсивное удаление растворенных в металле газов, что значительно улучшает его механические свойства, особенно пластичность. Многие сплавы на основе вольфрама, молибдена, ниобия и других химически активных металлов получили промышленное применение только благодаря тому, что их выплавляют в вакууме.
2. Некоторые из вредных примесей (нитриды, карбиды, оксиды) при нагреве в вакууме разлагаются, при этом происходит вакуумное рафинирование переплавляемого металла.
3. При плавке металла в вакууме непрерывно происходит удаление газообразных продуктов из зоны реакции.
Электронно-лучевая плавка удобна при выращивании монокристаллов
(рис. 10.6), когда на затравку 2
наплавляется материал 5
из тигля 7
и вытягивается с заданной скоростью вертикально вверх с получением монокристалла 3
.
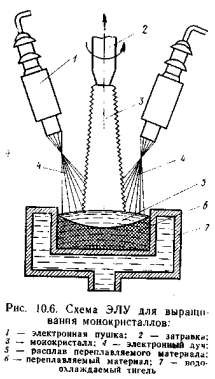
На различных ЭЛУ для плавки в вакууме при давлении 10-4
-10-7
Па получают слитки массой до 20 т.
Локальный переплав
обрабатываемых поверхностей с помощью электронного луча дает возможность получать чрезвычайно высокие скорости кристаллизации металла в зоне плавления. Образующиеся при этом структуры значительно отличаются от структур, получаемых в обычных условиях: расширяются границы растворимости для твердых растворов, измельчается микроструктура, значительно повышаются пластичность и твердость. Такое поверхностное оплавление материала называют
«облагораживающим», что позволяет для изготовления ответственных конструкций с высокими показателями износостойкости использовать недорогие исходные металлы и сплавы.
Испарение в вакууме
материалов при нагреве их электронным лучом широко используют для получения тонких пленок. В отличие от других способов испарения, где энергия подводится к испаряемои поверхности через стенку тигля или высокотемпературный нагревательный элемент, при электронно-лучевом испарении осуществляется прямой нагрев поверхности испаряемого материала. Это позволяет испарять материалы из водо-охлаждаемых тиглей, что особенно важно при работе с химически активными и тугоплавкими материалами.
При электронно-лучевом испарении удается управлять электронным пучком в пространстве и во времени, регулируя тем самым интенсивность ввода энергии в испаряемое вещество, а следовательно, скорость испарения и распределение плотности потоков пара.
Электронно-лучевое испарение применяют в микроэлектронике для нанесения различных металлических покрытий на стальную ленту, для изготовления фольги из псевдосплавов сложного состава. Электронным лучом можно испарять с последующим осаждением на подложку различные неметаллические материалы: диоксид кремния, оксид алюминия, различные виды стекла. Конденсационные покрытия применяют в оптической промышленности и в различных областях электроники.
С помощью размерной обработки заготовки электронным лучом в ней получают глухие или сквозные отверстия заданных размеров или заданный контур. Размерная обработка основана на том, что при достаточно большой удельной поверхностной мощности скорость испарения обрабатываемого материала и давление пара возрастают настолько, что весь жидкий металл с потоком пара выбрасывается из зоны обработки. Строгое дозирование подводимой энергии осуществляется импульсным воздействием электронного луча на поверхность или его перемещением по поверхности с заданной скоростью. Можно выделить три режима размерной электронно-лучевой обработки:
1. Моноимпульсный режим - обработка ведется одиночным импульсом,
т. е. отверстие получают за время действия одного импульса.
2. Многоимпульсный режим - отверстие получают воздействием на заданное место заготовки несколькими импульсами.
3. Режим обработки с перемещением электронного луча по заготовке с заданной скоростью.
Электронный луч нашел применение в первую очередь для размерной обработки твердых материалов - алмазов, кварца, керамики, кристаллов кремния и германия.
Особой разновидностью размерной электронно-лучевой обработки является перфорация
(получение мелких сквозных отверстий) различных материалов. Этим способом изготовляют металлические и керамические элементы фильтров, пористый материал для охлаждения камер сгорания и лопаток турбин. Электронно-лучевая термообработка
заключается в локальном нагреве обрабатываемых участков поверхности с целью получения структурных превращений материала. Она применяется также для отжига материалов в вакууме, повышая их пластичность и очищая поверхность от адсорбированных газов.
Электронно-лучевая сварка
является одним из самых распространенных технологических применений элекронного луча. Ее производят с помощью тонкого пучка электронов, который фокусируется на стыке соединяемых деталей и нагревает их до плавления. Сварочный шов при электронно-лучевой сварке получается чистым и свободным от газов, оксидов и летучих примесей. Общее количество энергии, необходимое для расплавления материала, гораздо меньше, чем при других видах нагрева в процессе сварки. Это обусловлено высокой концентрацией энергии в фокусе электронного луча.
ОПТИЧЕСКИЕ КВАНТОВЫЕ ГЕНЕРАТОРЫ (ЛАЗЕРЫ) 11.1. Основные принципы работы лазеров
Основой работы оптического квантового генератора (ОКГ) является генерирование монохроматических волн оптического диапазона под воздействием индуцированного (вынужденного) излучения.
Согласно законам квантовой механики энергия относительного движения любой системы связанных частиц не является произвольной, а принимает определенный ряд значений, которые называются уровнями энергии Е0
, Еи
Е2
и
т. д. Весь набор допустимых значений энергий принято называть энергетическим спектром системы
.
Электромагнитные волны любой частоты, в том числе и свет, представляют собой поток отдельных порций энергии - квантов или фотонов, энергия которых равна hν.
Согласно квантовой теории Эйнштейна процесс взаимодействия электромагнитных волн с веществом состоит из трех элементарных актов поглощения фотона, а также его спонтанного или индуцированного излучения. Если микрочастица находится в возбужденном состоянии, а ее энергия превышает минимально допустимое значение Е0
, то такое состояние не может сохраняться в течение значительного времени. Даже полностью изолированная от внешней среды возбужденная частица через некоторое время перейдет в состояние с меньшей энергией, при этом переходе она испускает фотон. Такой переход называют самопроизвольным
или спонтанным излучением
. Спонтанное излучение носит шумоподобный характер. Отдельные акты спонтанного излучения различными частицами происходят случайно. Момент излучения кванта каждой из возбужденных частиц, направление его движения и поляризация не связаны с актами испускания квантов другими такими же частицами. Все традиционные источники света (нагретые тела, плазма газовых разрядов) дают спонтанно излучаемый свет.
Иначе происходит процесс индуцированного излучения. Если возбужденная частица находится под воздействием внешних электромагнитных волн резонансной частоты, то она может перейти в состояние с меньшей энергией. При этом она испускает квант, не отличимый от приходящих извне, т. е. имеющий такую же частоту, поляризацию и направление распространения. Вероятность испускания индуцированного излучения пропорциональна интенсивности внешнего излучения - числу квантов в единицу времени. Фаза возникающих при индуцированных переходах электромагнитных волн строго согласована с фазой внешних волн. Поток индуцированного излучения отличается от первичного только возросшей интенсивностью.
Однако в любой находящейся в термодинамическом равновесии или вблизи его колонии частиц заселенности более высоких уровней энергии меньше заселенности уровней, расположенных ниже. Поэтому процессы поглощения квантов происходят чаще, чем индуцированное излучение. По этой же причине электромагнитные волны резонансной частоты взаимодействуя с такими частицами, рассеивают свою энергию и затухают.
Чтобы индуцированное излучение преобладало над поглощением, необходимо за счет внешних сил вывести систему частиц из состояния термодинамического равновесия. При этом за счет внешнего источника энергии создается более высокая заселенность одного из возбужденных состояний, чем заселенность хотя бы одного из состояний с меньшей энергией, т. е. создается инверсная заселенность в системе микрочастиц. И лишь в этом случае состоящая из таких частиц среда становится активной, т. е. способной усиливать волны резонансной частоты.

Рис. 11.1
Принципиальная схема лазера с рубиновым стержнем
В любом ОКГ используется явление индуцированного излучения среды, поддерживаемой в состоянии с инверсной заселенностью уровней за счет работы стороннего источника энергии. Принцип работы ОКГ рассмотрим на примере конструкции лазера с рубиновым стержнем (рис. 11.1).
Синтетический рубиновый стержень представляет собой плавленый оксид алюминия с добавкой (0,04-0,05 %) атомов трехвалентного хрома.
Атомы хрома, находящиеся в состоянии покоя на нижнем энергетическом уровне, под действием испускаемых импульсной лампой фотонов возбуждаются и переходят на более высокий энергетический уровень. Для изготовления лазеров подбирают такие вещества, атомы которых переходят из возбужденного состояния в основное не сразу, а через промежуточное метастабильное
состояние. Атомы находятся в этом состоянии до тех пор, пока они не будут вынуждены перейти в основное состояние. Длина волны излучаемого света при переходе из метастабильного состояния в основное равна длине волны света, благодаря которому этот переход стал возможен. В лазерах достаточно лишь одному атому перейти из метастабильного состояния в основное и испустить при этом фотон, как это стимулирует такой же переход других атомов.

Весь процесс излучения света лазером происходит в два этапа, как показано на энергетической диаграмме (рис. 11.2). Три горизонтальных линии на этом рисунке соответствуют трем энергетическим уровням системы, а стрелками обозначены возможные переходы между ними. Нижний уровень соответствует основному состоянию атома: верхний - возбужденному, а средний - метастабильному.
Если подействовать на находящиеся в метастабильном состоянии атомы квантами световой энергии, частота которых равна частоте перехода из метастабильного состояния в основное, то атомы мгновенно переходят в основное состояние, излучая при этом световую энергию.
Таким образом, метастабильное состояние атомов является определяющим в работе лазера. Процесс перевода атомов в метастабильное состояние осуществляется с помощью подсветки разрядной трубки и представляет собой процесс заселения метастабильного уровня.
При вспышке разрядной трубки, подключенной к источнику питания, возбуждается активный элемент - рубиновый стержень. Возникший в нем луч усиливается, многократно отразившись от световых экранов, и выходит через поверхность, частично отражающую свет, в виде когерентного светового излучения. Когерентным называют излучение с одной частотой, одним направлением и с одинаковыми фазами или постоянной разностью фаз. Основные процессы, происходящие в активном веществе лазера, при его освещении импульсной вспышкой показаны на рис. 11.3. Находящиеся в невозбужденном состоянии атомы хрома (на рисунке они показаны черными точками) под действием фотонов (стрелки на рисунке) переходят в возбужденное состояние (белые точки) (рис. 11.3, а
). После поглощения импульса света возбужденные атомы хрома переходят на более низкий уровень, излучая при этом избыток энергии в форме электромагнитных колебаний, в том числе и в видимой области спектра.
Часть излучаемой атомами энергии рассеивается наружу через стенки стержня (рис. 11.3, б
). Другая часть, направленная в виде фотонов параллельно оси стержня (рис. 11.3, б-г
), по пути своего движения вызывает цепную реакцию образования новых фотонов за счет взаимодействия с находящимися в стержне возбужденными атомами. Возникший поток световой энергии многократно отражается от отражателей на концах рубинового стержня, лавинообразно нарастает при каждом отражении и в конечном счете в виде мощного светового луча выходит из торца стержня в том месте, где отражатель имеет меньшую толщину (штриховка на рис. 11.3). Если теперь на пути этого светового потока поставить линзу, то всю энергию потока можно сфокусировать на очень маленькой площади.
Наименьший теоретически возможный диаметр площадки, на которой можно сфокусировать монохроматическое излучение, равен длине его волны λ при условии, что диаметр входного отверстия объектива В = 2,26F, где F - фокусное расстояние.
11.2. Типы оптических квантовых генераторов
Любой ОКГ независимо от конструктивного выполнения содержит следующие основные элементы: 1) рабочее тело, состоящее из ансамбля атомов или молекул, для которых может быть создана инверсия заселенностей; 2) систему, позволяющую осуществлять инверсию (ее обычно называют системой накачки); 3) оптический резонатор; 4) устройство для вывода энергии из резонатора; 5) систему управления концентрацией энергии и пространственным положением полученного пучка света; 6) различные специальные системы, связанные с конкретным применением ОКГ.
Для инверсии населенности в ОКГ применяют следующие виды накачки: а) оптическую - за счет облучения вещества мощным световым потоком; б) электрическую, осуществляемую при прохождении через вещество электрического тока; в) химическую, когда инверсия возникает за счет химической реакции, в которой принимает участие рабочее вещество, и т. д.
В зависимости от режима работы ОКГ различают устройства, работающие в непрерывном и импульсно-периодическом режимах. Существующие лазеры по роду материалов, используемых для получения индуцированного излучения, подразделяют на четыре основных типа: твердотельные с оптическим возбуждением
, полупроводниковые
(инжекционные
), жидкостные и газовые
(рис. 11.4).

Рис. 11.4. Принципиальные схемы твердотельных лазеров:
а - с рубиновым стержнем; б - полупроводникового
1. Лазеры твердотельные с оптической накачкой
. В лазерах этого типа излучателем - активным элементом - является твердое тело. Принципиальная схема твердотельного оптического квантового генератора показана на рис. 11.4, а
. Стержень 2
, изготовленный из рабочего вещества, помещен между двумя зеркалами 1
, 3
. Зеркало 1
полностью отражает все падающие на него лучи, а зеркало 3
является полупрозрачным. Для накачки энергии используется газоразрядная лампа-вспышка 6
, которая для большей эффективности облучения кристалла помещена вместе с ним внутрь отражающего кожуха 4
с поперечным сечением в форме эллипса. При размещении лампы и кристалла в фокусах эллипса создаются наилучшие условия равномерного освещения кристалла. Питание лампы-вспышки осуществляется от импульсного высоковольтного-источника 5
. Длительность импульса твердотельных ОКХ определяется индуктивностью, включаемой в цепь конденсаторной батареи, и обычно колеблется в пределах 0,1-10 мс. Частота повторения импульсов зависит в основном от условий охлаждения и характеристик импульсной лампы. В современных ОКГ она доходит до 600 импульсов в минуту.
2. Твердотельные полупроводниковые лазеры
. Лазеры этого типа отличаются от рубиновых тем, что в качестве излучающего свет вещества в них используется кусочек полупроводника.
Полупроводниковые лазеры, в которых возбуждение осуществляется при инжекции носителей заряда через р-л-переход, называют инжещионными. Примером лазеров такого типа может служить полупроводниковый квантовый генератор на р-л-переходе в арсениде галлия (рис. 11.4, б
). Акцепторными примесями в арсе-ниде галлия являются цинк, кадмий, индий и др., донорными примесями - теллур, селен и др.
Кристалл инжекционного лазера, схема которого приведена на рис. 11.4, б
, имеет размеры 0,5-1 мм2
. Электрод 7
крепится к контакту 8
, верхняя часть 9
представляет собой проводник р-типа, нижняя часть 11
- проводник n-типа. Между ними имеется р-n-переход 10
, толщина которого составляет 0,1 мкм. Излучающий слой имеет толщину 1-2 мкм вследствие проникновения электронов и дырок через р-n-переход в глубь кристалла.
Недостатком полупроводниковых лазеров является связанная с их малыми размерами невысокая направленность излучения, а также трудность получения высокой монохроматичности.
3. Жидкостные лазеры
. Их основное преимущество - возможность циркуляции жидкости с целью ее охлаждения, что позволяет получать большие энергии и мощности излучения в импульсном и непрерывном режимах 4. Газовые лазеры
. Принципиальное устройство лазеров этого типа гораздо проще уже рассмотренных. Стеклянная трубка наполняется специальной газовой смесью. В ее торцы впаивают два электрода и к ним подводят напряжение от источника питания (рис. 11.5). В трубке возбуждается газовый разряд. Для газовых лазеров подбирают специальные активные смеси, атомы или молекулы которых могут некоторое время находиться в метастабильном состоянии. По сравнению с твердыми телами и жидкостями газы обладают меньшей плотностью и более высокой однородностью, что не вызывает искажения светового луча, его рассеяния и потерь энергии. В результате направленность лазерного излучения в газах резко увеличивается, достигая предела, обусловленного дифракцией. В качестве активных газов в ОКГ применяют аргон, неон, криптон, ксенон, смеси гелия и неона, углекислый газ с добавкой азота и гелия. Газовые ОКГ подразделяют на три большие группы: лазеры на атомных, ионных и молекулярных переходах.
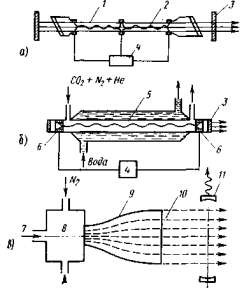
Рис. 11.5. Схемы газовых лазеров:
а - гелий-неонового; б - углекислотного; в - газодинамического
Примером атомного лазера является гелиево-неоновый ОКГ (рис. 11.5, а
). В этом лазере рабочим веществом являются нейтральные атомы неона. Атомы гелия служат для передачи энергии возбуждения. Гелиево-неоновый ОКГ имеет небольшую мощность, но из-за простоты устройства, надежности и достаточно высоких параметров излучения он получил широкое распространение.
В ионных газовых
ОКГ используются переходы между энергетическими уровнями ионов благородных газов (ксенона, аргона, неона, криптона), а также фосфора, серы и хлораГазовый ОКГ на аргоне генерирует излучение мощностью до 150—500 Вт в непрерывном режиме.
Наибольшие мощность и КПД имеют газовые ОКГ, генерирующие колебания на молекулярных переходах. К этой группе относят ОКГ, работающие на углекислом газе
.
11.3. Основы технологии светолучевой обработки
Мощные лазеры применяются в технологических процессах обработки различных материалов. В частности, с их помощью производят сварку, закалку, резку и сверление различных материалов без возникновения в них механических напряжений и с очень большой точностью, вплоть до нескольких длин световых волн. Лазерами обрабатывают материалы практически любой твердости, металлы, алмазы, рубины и т. д.
Лазерное излучение абсолютно стерильно, поэтому оно
используется в медицине для глазных операций, при остановке кровотечений, а также в сельском хозяйстве для предпосевной обработки семян.
Высокая мощность и экономичность СО2
-лазеров делают возможным их использование для разрушения сверхпрочных горных пород при работах в шахтах и тоннелях.
УСТАНОВКИ ЭЛЕКТРОХИМИЧЕСКОЙ И ЭЛЕКТРОФИЗИЧЕСКОЙ ОБРАБОТКИ ЭЛЕКТРОЛИЗНЫЕ УСТАНОВКИ 12.1. Основы электрохимической обработки
Электрохимия изучает поведение ионов в растворах и явления на границе между твердым телом и раствором. Она основана на применении электролитов. Электролитами
называются вещества, растворы и расплавы которых могут проводить электрический ток ионами, образующимися в результате электролитической диссоциации. В отличие от металлов и полупроводников растворы и расплавы электролитов обладают ионной проводимостью. Итак, электрический ток в электролитах представляет собой направленное движение ионов в электрическом поле. В отличие от металлов и полупроводников прохождение электрического тока через электролит сопровождается переносом массы вещества.
С увеличением температуры проводимость электролитов растет, что объясняется увеличением подвижности (уменьшением вязкости жидкости) и возрастанием степени диссоциации.
12.2. Электролиз растворов и расплавов
Явление выделения вещества на электродах при прохождении через электролит тока, а также процессы окисления или восстановления на электродах, сопровождающиеся приобретением или потерей частицами вещества электронов, называются электролизом.
В промышленности электролиз применяется в основном для анодного растворения металла и его катодного осаждения из растворов и расплавов. Если в электролизной ванне процесс происходит с поглощением
электрической энергии, ванна называется электролизером
.
Принципиальная схема электролизера показана на рис. 12.1.
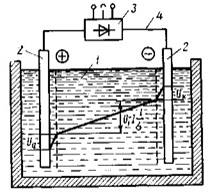
Рис. 12.1. Схема электролизной установки и распределение потенциала между электродами:
1 - электролит; 2 - электроды; 3 - источник питания: 4 - проводящие шины
На аноде переход металла из металлического состояния (Ме0
) в ионное
происходит в результате отдачи 'металлов электронов Ме0
- nе→Меn+
(анодное растворение), где п — число единичных зарядов. На катоде ион приобретает электроны и переходит в металлическое состояние Меn+
+nе→Ме0
(катодное осаждение).
Напряжение на электролизной ванне можно представить состоящим из трех составляющих: напряжение электрохимического разложения вещества, приэлектродные падения потенциала и падение напряжения в электролите:
U = U1
+ Ua
+ Uк
= I l/ζ, (12.6)
где U1
- напряжение электрохимического разложения вещества; Uа
, Uк
- анодное и катодное падения потенциала соответственно; I - сила тока в ванне; l - расстояние между электродами; ζ - проводимость электролита. Мощность, выделяющаяся в электролизной ванне,
Рэ
= I(U1
+ Ua
+ Uк
+ I l/ζ). (12.7)
Только часть этой мощности (IU1
) идет на электрохимическое разложение вещества, остальная же мощность расходуется на нагрев электролита и транспортировку ионов через раствор.
Характерной величиной, определяющей интенсивность электролиза, является электродная плотность тока
(А/м2
):
jэ
= I/S, (12.10)
где I - сила тока; S - поверхность погруженной в электролит части электрода. Электролиз меди
. Целью электролиза меди является снижение содержания примесей в черновой меди, полученной плавкой в отражательных печах, извлечение находящихся в ней благородных и других ценных металлов и получение чистой электролитической меди.
.
При пропускании через ванну постоянного электрического тока происходит растворение черновой меди анодов и осаждение чистой меди на катодах. Благородные металлы и некоторые примеси в виде шлама выпадают в осадок, некоторые другие примеси (никель) переходят в раствор.
Электролиз цинка
. Высококачественный цинк получают путем
электролиза водных растворов его солей. В ваннах устанавливаются алюминиевые катоды и свинцовые аноды. Затем они заполняются водным раствором сернокислого цинка ZnSO4
(5-6 ). Во время электролиза на катоде осаждается металлический цинк, на аноде выделяется газообразный кислород, а в растворе образуется серная кислота Н2
SO4
.
Электролиз алюминия
Так как нормальный потенциал алюминия -1,67 В, то его получают путем электролиза расплавленных солей. В этом случае электролитом является раствор оксида алюминия Аl2
O3
в расплавленном криолите (Nа3
АlF6
).
Поскольку фторидные расплавы являются сильно агрессивными средами, электролиз алюминия ведут с расходуемым угольным электродом, а внутренние поверхности ванн футеруют угольными плитами и блоками.
Производство алюминия является энергоемким. Фактический расход электроэнергии на производство алюминия составляет 14000-16000 кВт·ч/т. Выход металла на 1 кВт·ч составляет 60-77 г, что типично для удельного расхода электроэнергии (16000±500) кВт·ч на 1 т алюминия.
12.3. Электрооборудование электролизных производств
Питание электролизных установок постоянным током осуществляется от генераторов постоянного тока или полупроводниковых выпрямительных агрегатов, преобразующих переменный ток промышленной частоты в постоянный. Наибольшее распространение получили кремниевые выпрямительные агрегаты, имеющие КПД 97-99 %.
12.4. Применение электрохимической обработки материалов в машиностроении
Электрохимическими способами обработки материалов условно принято называть группу новых методов электротехнологии, которые применяются для удаления материала с обрабатываемых поверхностей, его переноса,
формообразования деталей или структурных преобразований, осуществляемых с помощью электрической энергии, вводимой непосредственно в зону обработки. В большинстве новых методов используется преимущественно процесс анодного растворения, т. е. перехода металла, помещаемого в электролизер в
качестве анода, из металлического состояли в различные неметаллические соедин Анодное растворение в нейтральных электролитах сопровождается образованием гидратов оксида металла Ме(ОН)n
, которые практически не растворяются в электролите, выпадают в осадок, пассивируют растворяемую поверхность и забивают межэлектродный промежуток. Для удаления из зоны обработки выпавшего осадка электролиту придается большая скорость движения в межэлектродном промежутке, что позволяет выполнять обработку при повышенных плотностях тока (до сотен ампер на квадратный сантиметр), поскольку при этом происходит интенсивное охлаждение электролита. При электрохимической обработке металлов в кислых растворах, когда продукты реакции достаточно хорошо растворимы в электролите, плотности тока относительно невелики (2-3 А/см2
) и обработка производится в стационарном либо медленно перемешиваемом электролите.
По этим признакам операции электрохимической обработки подразделяют на две группы: 1) электрохимическая обработка при невысокой плотности тока в стационарном электролите; 2) электрохимическая обработка при высокой плотности тока в проточном электролите.
На рис. 12.5 показана схема электрохимической обработки в стационарном электролите для наиболее типичной операции - электролитического шлифования или полирования.
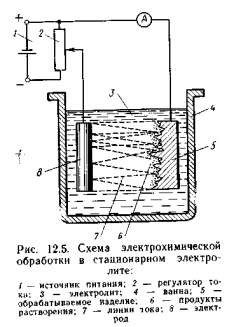
Рис. 12.5. Схема электрохимической обработки в стационарном электролите:
1 - источник питания; 2 - регулятор, тока; 3 - электролит; 4 - ванна; 5 - обрабатываемое изделие; 6 - продукты растворения; 7 - линии тока; 8 - электрод
При прохождении электрического тока через электролит 3
и электроды 8
и 5
происходит растворение поверхности анода в электролите и образование продуктов растворения 6
. Они задерживаются в углублениях поверхности анода и изолируют ее от прохождения тока по всей поверхности, сосредоточивая силовые линии тока 7
на незащищенных участках поверхности анода. Выступы растворяются быстрее впадин, в результате чего происходит сглаживание поверхности изделия - ее полирование.
Электрохимическим способом могут проводиться следующие операции.
Очистка поверхности металла анодным травлением от оксидов, ржавчияы, жировых пленок и других загрязнений.
Ее призводят путем анодного растворения поверхности изделия.
Заострение и затачивание режущего инструмента
, изготовление игл из цилиндрических прутков. Это выполняется за счет создания на режущем лезвии и острение повышенных плоскостей тока.
Профилирование металлических заготовок.
При этом способе обрабатываемое изделие помещено внутрь катода. Анодное растворение происходит интенсивнее в участках, более близких к катоду.
Гравирование и маркирование по металлам
. На изделие, которое является анодом, наносят слой воска, лака или другого изолирующего вещества. Анодное растворение происходит в тех местах, Где металл обнажен.
Изготовление сеток
(аналогично электрохимическому гравированию). Сетку-рисунок наносят изолирующим составом на поверхность анода. Она предохраняет металл от растворения. Обнаженные участки внутри лаковой сетки растворяются.
Изготовление листового металла малой толщины путем анодного растворения.
Нанесение металлопокрытий и анодирование
. Процесс нанесения металлопокрытий на поверхность изделий методом электролиза называется гальванотехникой. В свою очередь, гальванотехника подразделяется на гальваностегию и гальванопластику.
Гальваностегия
- электрохимическое нанесение металлов на металлические изделия с целью повышения их механической прочности, антикоррозионных свойств и декоративных качеств.
Гальванопластика
- электрохимический процесс нанесения металлов на шаблоны, применяемые при изготовлении штампов различных изделий (музыкальные пластинки-диски, типографские клише, статуи и т. д.). При нанесении металлов шаблоны (из воска, гипса, дерева и т. п.) предварительно покрывают слоем графита для придания их поверхностям электропроводности. Анодирование
- процесс получения оксидных антикоррозионных покрытий на поверхности металлических изделий путем их анодной обработки в соответствующих растворах. Оно широко применяется для защиты от коррозии изделий из алюминия, магния и их сплавов. При анодировании на поверхности алюминия образуется двойной оксидный слой: верхний - толстый пористый слой и нижний - тонкий плотный. Алюминиевая оксидная пленка обладает хорошими антикоррозионными и электроизолирующими свойствами.
12.5. Источники питания установок электрохимической обработки
Электрохимическая обработка, основанная на анодном растворении, ведется на постоянном, импульсном, пульсирующем или асимметричном переменном токе. Источники питания (ИП) преобразуют электрическую энергию промышленной сети в необходимую для электрохимической обработки.
ЭЛЕКТРОЭРОЗИОННАЯ ОБРАБОТКА МЕТАЛЛОВ 13.1. Общая характеристика и физические основы процесса
Для обработки металлов с высокими механическими свойствами применяется метод размерной обработки при непосредственном использовании теплового эффекта электрической энергии - электроэрозионная обработка
. Она основана на эффекте расплавления и испарения микропорций материала под тепловым воздействием импульсов электрической энергии, которая выделяется в канале электроискрового заряда между поверхностью обрабатываемой детали и электродом-инструментом, погруженным в жидкую непроводящую среду. Следующие друг за другом импульсные разряды определенной длительности и формы производят выплавление и испарение микропорций металла.
Электроэрозионный способ позволяет обрабатывать токопроводящие материалы любой механической прочности, вязкости, хрупкости, получать детали сложных форм и осуществлять операции, не выполняемые другими методами. При его использовании значительно снижается трудоемкость по сравнению с обработкой резанием, возможно осуществление механизации и автоматизации с целью глубокого регулирования параметров процесса.
Однако по сравнению с механической электроэрозионная обработка имеет ряд существенных недостатков: производительность при такой обработке обычных материалов (стали, цветных металлы и т. д.) значительно ниже, чем при обработке резанием, а расход энергии выше; для получения высокой чистоты поверхности приходится затрачивать больше времени, чем, например, при абразивной обработке.
Картина происходящих поэтапно в межэлектродном зазоре физических процессов при электроэрозионной обработке показана на рис. 13.1. По достижении импульсным напряжением и определенного значения между электродом-инструментом 4
и электродом-деталью 1
в диэлектрической жидкости 2
происходит электрический пробой. При этом от электрода, который в данный момент является катодом, отделяется стриммер 3
и направляется к аноду, ионизируя на своем пути жидкость. В результате этой фазы (ее длительность 10-9
- 10-7
с) образуется канал сквозной проводимости и сопротивление межэлектрод- ного промежутка снижается от нескольких мегаом до долей ома (рис. 13.1. а
).
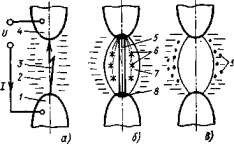
Рис. 13.1. Схема физических процессов Iмежэлектродном промежутке при электроэрозионной обработке
Рис. 13.1. Схема физических процессов в межэлектродном промежутке при электроэрозионной обработке
Через канал проводимости в виде импульса выделяется электрическая энергия, накопленная в источнике питания (рис. 13.1. б
). При этом происходит электрический разряд 5, длительность которого составляет 10-6
-10-4
с, для которого характерна падающая вольт-амперная характеристика. Разряд проходит искровую и дуговую стадии. Благодаря высокой концентрации энергии в зоне разряда и приэлектродных областях развиваются высокие температуры. Под их воздействием образуется парогазовая полость 7
. В приэлектродных областях 8
происходит плавление и испарение микропорций металла на поверхности электрода. В результате развивающегося давления капли жидкого металла 6
выбрасываются из зоны разряда и застывают в окружающей электроды жидкой среде в виде мелких сферических частиц 9
(рис. 13.1, а
).
§ 13.4. Разновидности электроэрозионной обработки и элементы ее оборудования
Формообразование обрабатываемой детали электроэрозионным методом можно осуществить по трем схемам.
1. Копирование формы электрода-инструмента, представляющего собой обратное отображение формы детали. При этой схеме обработки путем поступательного движения электрод-инструмент внедряется в заготовку по мере удаления металла под воздействием импульсов электрической энергии. Точность формы получаемой детали в этом случае зависит от точности изготовления электрода-инструмента и его износа.
2. Взаимное перемещение заготовки и электрода-инструмента по определенному закону. Схема формообразования имеет сходные черты с рядом процессов механической обработки. Съем металла с заготовки, в отличие от механических процессов, осуществляется за счет эрозии удаляемого металла под действием подводимых импульсов электрической энергии.
3. Сочетание обеих схем формообразования. Осуществляя взаимное перемещение специального инструмента и заготовки по определенному закону, получают изделие сложной формы. Эта схема требует сложного оборудования и электродовинструментов.
Наиболее широкое распространение в практике получила первач схема, а выполняемые с ее помощью операции называют ко-пировально-прошивочными. Электроэрозионное прошивание круглых отверстий сплошным электродоминструментом — одна из наиболее широко применяемых в машиностроении операций. Ее частным случаем является прошивание отверстий с криволинейной осью. Принципиальные схемы проведения этих операций показаны на рис. 13.6, а, б.
Последнюю из этих операций производят аналогично первой, но электродинструмент, являющийся катодом, имеет криволинейную форму, повторяемую в изделии.
По второй технологической схеме электроэрозионной обработки проводят резание с использованием в качестве электрода-инструмента металлического диска или проволоки (рис. 13.6,в, г). Обработка проволочным ЭИ позволяет вырезать сложноконтурные детали высокой точности.
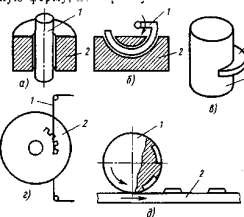
Рис. 13.6. Схема электроэрозионной обработ / — электрод-инструмент; 2 —
электродизделие
Рис. 13.6. Схема электроэрозийной обработки: 1 – электрод – инструмент;
2 – электрод – изделие.
Недостатком операций по этой схеме является ограничение их использования только вырезными или отрезными работами.
§ 13.5. Электроконтактная обработка
Электроконтактная обработка (ЭКО) применяется для съема материала с электропроводной заготовки. В этом виде обработки используется электроэрозионный принцип формообразования, поэтому для ЭКО справедливы многие закономерности электроэрозионной обработки.
Схема простейшего устройства для ЭКО показана на рис. 13.8. Напряжение 11с от промышленной сети поступает на трансформатор /. С его вторичной обмотки напряжение V с амплитудой до 40 В подается на два электрода, один из которых — диск 2 выполнен из электропроводного материала, второй — листовая заготовка 3. Дисковый ЭИ вращается от приводного двигателя с частотой п.
Механическими средствами создается прижимающая диск к заготовке сила Спр. Кроме вращения диску сообщается поступательное движение вдоль обрабатываемой поверхности со скоростью Уин- Межэлектродный промежуток заполнен непроводящей рабочей средой — воздухом, жидкостью, газожидкостной смесью.
Электроды в общем случае подвергаются одновременно механическому и электрическому воздействию. Мощность электрического воздействия определяется произведением сЯсозср, где И и / — действующие значения напряжения и тока.
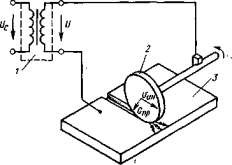
Рис. 13.8. Схема электроконтактной обработки
Рис. 13.8. Схема электроконтактной обработки
ЭЛЕКТРОХИМИКО-МЕХАНИЧЕСКАЯ ОБРАБОТКА В ЭЛЕКТРОЛИТАХ
Под электрохимико-механической обработкой понимают процессы обработки металлических деталей в электролитах в совокупности с механическими и электроэрозионными процессами.
Различают анодно-абразивную и анодно-механическую обработку.
14.1. Анодно-абразивная обработка
Этот тип обработки основан на анодном растворении и механическом
(абразивном) воздействии на обрабатываемое изделие. При этом на поверхность электрода-заготовки (ЭЗ) могут воздействовать: электрический ток,
обеспечивающий анодное растворение; механическая сила, создаваемая частицами абразива, режущими или царапающими поверхность ЭЗ; тепловой поток, приводящий к тепловой эрозии поверхностных слоев ЭЗ.
Схема межэлектродного промежутка при анодно-аб-разивной обработке (ААО) показана на рис. 14.1, а, б. Электрод-инструмент, поверхность которого со скоростью vи
движется вдоль поверхности ЭЗ, подключен к отрицательному полюсу, а к положительному полюсу подключен ЭЗ. Межэлектродный промежуток заполняется раствором электролита.
Приложенная к электроду-инструменту (ЭИ) извне сила О поджимает его к ЭЗ, но так, чтобы между обоими телами не было обширного контакта и их электропроводные поверхности оказались разделенными зазором амин
. При этом через межэлектродный промежуток проходит ток /, а рас-
Рис. 14.1. Схема межэлектродного промежутка при анодно-абразивной обработке: / — электрод-инструмент (ЭИ); 2 — источник постоянного тока; 3 — электродзаготовка (ЭЗ); 4 — раствор электролита; 5 — межэлектродный промежуток
(МЭП)
ходуемая на обработку электрическая мощность Р= UI, где U — напряжение источника питания.
Внешняя сила О вызывает силу трения Отр, которая приложена к поверхности ЭИ, движущегося со скоростью Vи. Таким образом, для обработки детали затрачивается также и механическая энергия Л = оиОТр (обычно она меньше электрической).
При ААО удаляются выступы 5 на ЭЗ (рис. 14.1, а). Во впадинах материал снимается менее интенсивно.
Снятое с поверхности ЭИ вещество может находиться в трех конечных состояниях: химически связанном с составляющими электролита (как при ЭХО), в виде застывших капель металла (как при ЭЭО) и в виде металлических сколотых частиц. Каждое из состояний соответствует одному из уже упомянутых воздействий. Менять роль любого из воздействий можно подбором режима. Интенсивное снятие металла с микровыступов обеспечивается подбором электрического и механического режимов, применением ЭИ, изготовленного из различных абразивных материалов, а также созданием рабочих сред различного состава.
14.2. Анодно-механическая обработка
Анодно-механическая обработка (АМО) основана на одновременном использовании электроэрозионных и электрохимических процессов, происходящих в заполненном электролитом МЭП между ЭИ и ЭЗ.
При этом виде обработки в межэлектродном промежутке происходит образование нерастворимых соединений элементов металла заготовки с анионами электролита. Такой процесс обеспечивается применением в качестве электролита водного раствора жидкого стекла.
Ионы железа, переходящие в раствор благодаря анодному растворению, соединяются с силикат-анионами и образуют нерастворимое соединение, выпадающее на ЭЗ в виде пленки (рис. 14.2).
Формообразование при АМО происходит в основном за счет удаления микровыступов с поверхности ЭЗ термоэрозионным способом.
При высоком напряжении и большом давлении ЭИ на деталь плотность тока на выступах достигает значений, при которых преобладающими становятся электротермические явления, обусловленные местным выделением теплоты.
Рис. 14.2. Схема анодно-механической обработки:
' — обрабатываемая деталь; 2 — пассивная пленка; 3 — электролит; 4 — электродинструмент; 5 — канавка
Рис. 14.3. Схема электроэрозионно-химической обработки:
/ — катод — электрод-инструмент (ЭИ);
2 — отверстие для подачи электролита;
3 — межэлектродный промежуток; 4 — анод — электрод-заготовка; 5 — канал разряда
Электроэрозионно-химическая обработка. В процессах формообразования с применением совмещенной электроэрозионно-хими-ческой обработки (ЭЭХО) удаление металла происходит благодаря анодному растворению и электроискровой эрозии ЭЗ в потоке электролита, прокачиваемого через МЭП.
14.3. Характеристика операций электрохимической обработки Особенностями электрохимической обработки являются:
а) высокая производительность при высокой чистоте обработки;
б) возможность широкого регулирования режимов обработки от черновой до чистовой без прекращения процесса и без снятия детали со станка;
в) возможность обработки токопроводящих материалов (металлических и металлокерамических) любой твердости;
г) пониженное количество отходов по сравнению с механической обработкой на металлорежущих станках.
Рассматриваемым методом можно проводить анодно-механиче-ское резание заготовок (рис. 14.4).
Деталь /соединяется с положительным полюсом источника тока 4 напряжением 20—30 В, а инструмент 2 — с отрицательным. В зазор, образованный между инструментом и поверхностью обрабатываемого изделия, вводят электролит 3, представляющий собой водный ра-
Рис. 14.4. Схема анодно-механического разрезания
Рис. 14.5. Анодно-механическое шлифование:
1 - вращающийся металлический диск (катод); 2 — обрабатываемая деталь створ жидкого стекла. Регулирование тока производят резистором 5.
Электроду-инструменту придают форму диска и сообщают быстрое вращение. Вращающийся диск увлекает в зазор электролит. Съем металла в месте разрезания происходит в результате протекания рассмотренных выше процессов. В качестве ЭИ может быть использована и бесконечная металлическая лента. Чистовая анодно-меха-ническая обработка происходит за счет анодного растворения металла при прохождении электрического тока через электролиты. Обработка происходит в результате непрерывного удаления пленки вращающимся диском-инструментом и электролиза, вызывающего растворение металла анода в местах, очищенных от пленки.
Обдирку — черновое шлифование (рис. 14.5, а—г) производят с помощью вращающегося металлического диска-катода, который прикасается к поверхности обрабатываемого изделия в среде электролита. При черновом шлифовании применяется повышенная плотность тока, благодаря чему процесс по характеру протекания приближается к электроэрозионному и при высокой производительности обрабатываемая поверхность получается шероховатой. Электрохимико-механическую обработку (ЭХМО) проводят с применением электрически нейтральных инструментов. Она предназначена для получения поверхностей высших классов чистоты. Сюда можно отнести такие операции, как полирование в электролите с суспензией абразива, хонингование катодными головками с абразивными вставками и т. д.
Общим для всех разновидностей этого метода обработки является разделение функций токопроводящей и механической частей инструмента.
Основными положительными чертами ЭХМО являются возможность получения наивысшей чистоты поверхности по сравнению с получаемой другими методами анодно-механической обработки; использование неагрессивных электролитов; работа при низких напряжениях (2—16 В); возможность обработки сплавов повы-
шенной вязкости, обработки плоских деталей большой площади при небольшой мощности установок и т. д.
§ 14.4. Оборудование электрохимико-механической обработки
Источниками питания установок ЭХМО могут быть генераторы постоянного тока, двухполупериодные выпрямители, импульсные генераторы и т. д.
ЭЛЕКТРОМЕХАНИЧЕСКИЕ ПРОЦЕССЫ И УСТАНОВКИ
УСТАНОВКИ МАГНИТОИМПУЛЬСНОЙ ОБРАБОТКИ МЕТАЛЛОВ
15.1. Физико-технические основы
Магнитоимпульсная обработка металлов (МИО) — это способ пластической деформации металлов и их сплавов, осуществляемый при прямом преобразовании электрической энергии в механическую непосредственно в самом обрабатываемом изделии.
Физическими основами МИО являются электродинамические силы, возникающие в проводящем теле, помещенном в переменное электромагнитное поле.
Рассмотрим эти силы.
Рис. 15.2. Принципиальная схема электрической цепи установки для магнитоимпульсной обработки металлов
15.2. Элементы оборудования установок магнитоимпульсной обработки Установки для магнитоимпульсной обработки (МИО) состоят из двух основных узлов: подготовительного (накопление энергии и формирование импульсного напряжения и тока) и узла исполнительного —¦ технологического. К первому узлу относятся генераторы импульсных токов, ко второму — индукторы и связанная с ними технологическая оснастка.
15.3. Характеристика операций магнитоимпульсной обработки
Операциями, которые выполняются методом электро-
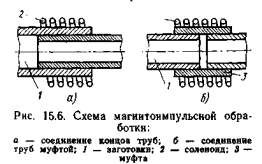
Рис. 15.6. Схема магнитоимпульсной обработки: а — соединение концов труб; б — соединение труб муфтой; 1 — заготовки; 2 — соленоид; 3 —муфта
ния, могут быть развальцовка тонкостенных металлических заготовок любых форм, опрессов-ка, выдавливание гофров, раздача труб, че-каНКа, штамповка. Этим методом можно также выполнять оп-рессовку кабельных наконечников, обжатие тонкостенных металлических труб с образованием резьбы, на-прессовку металлических колпачков на фарфоровые изоляторы, многогранные торцовые ключи из цилиндрических заготовок, соединение деталей напрес-совкой соединительных колец, соединение металлических деталей с неметаллическими, сборку узлов и изделий, напрессовку втулок на тросы. Принципиальные схемы таких операций предназначены на рис. 15.6.
Метод формообразования импульсным магнитным полем можно применять для штамповки из металлического листа (рис. 15.7). Для таких операций индуктор выполняют в виде плоской спирали /. При подаче импульса тока магнитное поле наводит в заготовке 2, помещенной напротив торца катушки, кольцевые вихревые токи. Их взаимодействие с магнитным полем создает усилия, способные деформировать заготовку.
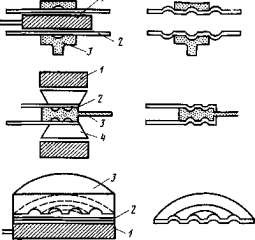
Рис. 15.7. Схема магнитоимпульсного формообразования:
/ — индуктор; 2
— заготовка; 3 — матрица; 4
— концентратор магнитного поля
ЭЛЕКТРОГИДРАВЛИЧЕСКАЯ ОБРАБОТКА МАТЕРИАЛОВ
Физические основы электрогидравлического эффекта
Электрогидравлический эффект — это возникновение высокого давления в результате высоковольтного электрического разряда между погруженными в непроводящую жидкость электродами. За счет энергии импульсной ударной волны, распространяющейся вокруг канала разряда в рабочей среде, возникает давление до 300 МН/м2.
По существу, электрический разряд в жидкости — это новый способ преобразования электрической энергии в механическую, которое совершается без промежуточных звеньев и с высоким КПД. Принципиальная схема осуществления электрогидравлического эффекта показана на рис. 16.1. Элементами схемы являются повышающий трансформатор Тр, выпрямитель Д, накопитель энергии С, формирующий промежуток ФП и разрядный промежуток РП.
Искровой высоковольтный разряд в жидкости характеризуется очень быстрым преобразованием запасенной в накопителе электрической энергии в тепловую, световую, механическую и т. д.
При пробое практическая несжимаемость жидкостей приводит к появлению такого явления, как электрогидравлический удар, что еще больше усиливает действие электрического взрыва.
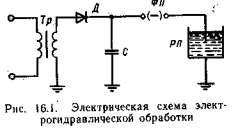
Рис. 16.1. Электрическая схема электрогидравлической обработки
Для питания импульсной энергией установок обработки различных материалов электрогидравлическим методом применяются специальные генераторы, принципиальные схемы которых аналогичны схеме на рис. 16.1. Конденсатор-накопитель С заряжается от сети через автотрансформатор, повышающий трансформатор и выпрямитель. Значения импульсов тока в зарядной цепи ограничиваются зарядным сопротивлением. При пробое формирующего промежутка ФП конденсатор разряжается на рабочий искровой промежуток РП технологического устройства.
Энергетические возможности электрического разряда в непроводящей жидкости (воде) ограничиваются допустимым напряжением зарядки и емкостью конденсаторных батарей установок.
§ 16.2. Технологическое использование высоковольтного электрического разряда в жидкости
Очистка литья. Очистка литья от формовочной земли производится в воде и полностью исключает пылеобразование. При этом методе очищаемые отливки помещают в бак. После установки электродов относительно деталей последние очищаются от формовочной земли серией импульсов. Применение многоэлектродных трехфазных установок позволяет производить обработку сразу нескольких отливок, устанавливаемых относительно электродов в произвольном положении.
Формообразование — это процесс получения фасонных изделий из
тонколистового материала с использованием направленных ударных волн высокой интенсивности, возникающих в жидкости при импульсном электрическом разряде. Основными факторами формообразования методом электрогидравлического разряда являют-
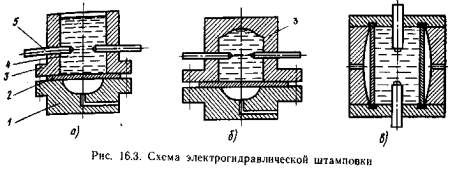
Рис. 16.3. Схема электрогидравлической штамповки
ся сверхвысокие ударные гидравлические давления, мощные ка-витационные процессы, ультразвуковое излучение.
Для получения различных по форме изделий создаются различные формы волн: с острым фронтом, сферические и др. Это достигается различным расположением электродов, а также различными формами проволочек, закорачивающих межэлектродный промежуток. Схема электрогидравлической штамповки детали показана на рис. 16.3. Листовую заготовку 2 укладывают на матрицу/и прижимают к ней с помощью прижимных устройств. Над заготовкой расположена жидкая передающая среда 4, в которой на определенном расстоянии от заготовки размещены положительный и отрицательный электроды 5, соединенные с генератором импульсов тока электрогидравлической установки.
При высоковольтном разряде между электродами возникает то-копроводящий искровой канал, мгновенное расширение которого приводит к возникновению в жидкости ударной волны. Деформация листовой заготовки происходит под действием ударной волны, образующейся при расширении газовой сферы, и сопутствующего гидропотока (рис. 16.3,а).
Более эффективному использованию энергии разряда способствует размещение рабочих электродов в замкнутой камере 3 (рис. 16.3,6) или внутри самой заготовки (рис. 16.3, в).
Изменяя расстояние между концами рабочих электродов, можно получить различную форму фронта ударной волны. Если расстояние между электродами достаточно мало, то возникает волна со сферическим фронтом. Если же электроды удалены друг от друга на несколько сантиметров, то образуется волна с цилиндрическим фронтом. Плоский фронт можно получить, применив тонкую проволочную сетку, которая мгновенно испаряется при прохождении импульса тока.
Форму фронта ударной волны можно привести в соответствие с формой рабочей полости матрицы, для чего проволоку, закорачивающую концы электродов, изгибают таким образом, чтобы разряд следовал по возникшему плазменному каналу.
Кроме рассмотренных установок с непосредственным воздействием рабочей среды на заготовку существуют устройства, в которых деформация заготовки производится посредством промежуточного звена (рис. 16.4). Под действием давления, возникающего в верхней части матрицы 2, пуансон 4 движется вниз и придает заготовке 5 необходимую форму.
Тонкое измельчение. При этом технологическом приеме материал диспергируется или разрушается волной, которая возникает при электрогидравлическом ударе в жидкости. Разрушающая способность волны зависит от параметров разрядного контура, а энергия импульса—-от напряжения и емкости конденсатора. Для дробления различных минеральных сред применяются специальные электрогидравлические вибраторы (ЭГ-вибраторы). Эти устройства просты и надежны.
УЛЬТРАЗВУКОВЫЕ ЭЛЕКТРОТЕХНОЛОГИЧЕСКИЕ УСТАНОВКИ
Физическая сущность ультразвуковой обработки
Ультразвуковой метод обработки является методом механического воздействия на материал. Ультразвуковым он называется потому, что частота ударов соответствует диапазону неслышимых звуков, т. е. ( составляет от 16 до 105 кГц. Звуковые волны представляют собой механические упругие колебания, которые могут распространяться только в упругой среде в отличие от электромагнитных колебаний. Длина звуковой волны Х=у//, где V — скорость распространения волны; /—частота волны. При распространении звуковой волны в упругой среде материальные частицы совершают упругие колебания около своих положений равновесия со скоростью, которая называется колебательной. Сгущение и разряжение среды в продольной волне характеризуется избыточным, так называемым звуковым давлением. Между колебательной скоростью и звуковым давлением существует взаимосвязь, определяемая свойствами среды. При распространении в материальной среде звуковая волна переносит определенную энергию, которая может использоваться в технологических процессах.
Преимуществами ультразвуковой ообработки следует считать:
1) возможность получения акустической энергии различными техническими приемами;
2) широту диапазона технологического применения ультразвука— от размерной обработки до получения неразъемных соединений (сварка, пайка и т. д.); 3) простоту эксплуатации и автоматизации промышленных установок. К недостаткам этого метода относятся: повышенная стоимость акустической энергии по сравнению, с другими видами энергии; необходимость изготовления специальных установок и аппаратов для генерации ультразвуковых колебаний, их передачи и распределения.
Ультразвуковые колебания сопровождаются рядом эффектов, которые могут быть использованы как базовые для разработки различных процессов.
Кавитация — нарушение сплошности жидкости, возникающее при давлении ниже некоторого критического значения.
Поглощение ультразвуковых колебаний веществом—необратимый процесс, в котором часть энергии превращается в тепловую энергию, другая же часть расходуется на изменение структуры вещества. Разделение молекул и частиц различной массы в негомогенных суспензиях в звуковом поле зависит от состава суспензий и частоты поля.
Коагуляция заключается в образовании из мелкодиспергиро-ванных частиц (дыма, пыли, тумана) значительно более крупных частиц. Движение частиц при наличии между ними сил притяжения приводит к соударению и в результате к их объединению и укрупнению.
Дегазация жидкостей или расплавов с помощью ультразвуковых колебаний происходит вследствие вытеснения газовых пузырьков, которые приходят в движение, объединяются в пузырьки больших размеров и всплывают. Диспергирование является эффектом, противоположным коагуляции, и заключается в мелком дроблении вещества и перемешивании его с другими.
17.2. Элементы оборудования ультразвуковых установок
Основными элементами колебательной системы являются источник ультразвуковых колебаний, акустический трансформатор скорости и детали крепления.
Источники ультразвуковых колебаний могут быть двух видов: механические и электрические.
К механическим источникам относятся ультразвуковые сирены и свистки, принцип действия которых основан на преобразовании механической энергии
(например, скорости движения жидкостей или газов). Электрические источники УЗК: преобразуют электрическую энергию в механические упругие колебания соответствующей частоты. Для этих целей служат различные преобразователи: электродинамические, магнитострикционные, пьезоэлектрические. Наиболее распространенными являются магнитострикционные и пьезоэлектрические. Принцип действия магнитострикционных преобразователей основан на продольном магнитострикционном эффекте, который проявляется в изменении длины металлического тела из ферромагнитных материалов (без изменения их объема) под действием магнитного поля. Магнитострикционный эффект у разных металлов различен. Высокой магнитострикцией обладают никель и пермен-дюр, которые нашли широкое применение в производстве магнитострикционных преобразователей. Действие пьезоэлектрических преобразователей основано на способности некоторых веществ изменять свои геометрические размеры (толщину и объем) в электрическом поле. Пьезоэлектрический эффект обратим, т. е. если пластину из пьезоматериала подвергнуть деформациям сжатия или растяжения, то на ее гранях, появятся электрические заряды. Если пьезоэлемент поместить в переменное электрическое поле, то он будет деформироваться, возбуждая в окружающей среде ультразвуковые колебания. Широкое распространение получили пьезоэлементы на основе титана-та бария, цирконата-титаната свинца (ЦТС).
Колеблющаяся пластинка из пьезоэлектрического материала является электромеханическим преобразователем
Существуют ультразвуковые генераторы на транзисторах и тиристорах, ламповые и машинные.
17.3. Технологическое использование ультразвуковых колебаний
Технологическое использование ультразвука в промышленности осуществляется по трем основным направлениям: силовое воздействие на материал; интенсификация технологических процессов; ультразвуковые методы контроля. Ультразвуковые процессы с силовым воздействием на обрабатываемый материал применяются для механической обработки твердых и сверхтвердых сплавов, диспергирования и эмульгирования, удаления поверхностных пленок, загрязнений и др.
Ультразвуковое диспергирование и эмульгирование происходят под действием. интенсивных ультразвуковых волн, вызывающих дробящее действие кавитации и турбулентное движение жидкостей. Этим методом удается получить стойкие эмульсии таких несмешивающихся обычными способами жидкостей, как вода и масло, ртуть и вода, бензол и вода и др.
Ультразвуковые методы контроля. С помощью ультразвуковых колебаний можно непрерывно контролировать ход технологического процесса без проведения лабораторных анализов проб.
Установив предварительно зависимость параметров звуковой волны от физических свойств среды, измеряя затем амплитуду колебаний частиц, интенсивность ультразвуковых колебаний или скорость звука, можно достаточно точно судить о состоянии среды и ее изменениях.
Как правило, ультразвуковые методы контроля осуществляются с помощью ультразвуковых колебаний небольшой интенсивности. В зависимости от физикохимических характеристик среды скорости звука в ней будут различными. Измерив скорость звука, можно судить о происшедших физико-химических превращениях в данной среде, контролировать ее концентрацию, определять наличие примесей, следить за ходом технологического процесса.
ЭЛЕКТРОКИНЕТИЧЕСКИЕ МЕТОДЫ ОБРАБОТКИ МАТЕРИАЛОВ
ОСНОВЫ ЭЛЕКТРОННО-ИОННОЙ ТЕХНОЛОГИИ
18.1. Характеристика электронно-ионных процессов
При воздействии электрического поля высокой напряженности на вещество, находящееся в твердом, жидком или газообразном состоянии, возникают процессы, при которых наряду с изменением физических и химических свойств материала происходит изменение распределения образующих его частиц в пространстве. Это применение электрических полей высокой напряженности в технологических процессах получило общее название электронно-ионной технологии (ЭИТ).
Электронно-ионная технология включает в себя три характерных процесса: электризацию материала в момент диспергирования или уже находящегося в дисперсном состоянии; организацию различных форм движения частиц в электрическом поле; формирование готового продукта или изделия.
Получили развитие следующие виды ЭИТ: электрогазоочистка — выделение из газового (воздушного) потока содержащихся в нем твердых или жидких частиц;
электросепарация — разделение многокомпонентных систем на компоненты, путем использования электрофизических и физико-химических свойств частиц компонентов;
электроокраска — нанесение твердых или жидких покрытий на изделия; электропечать — формирование изображения, получение многократных копий, выполнение матриц для размножения; электроформообразование.
В основе электронно-ионной технологии лежат следующие явления. Электроосмос — движение жидкости по отношению к твердому телу под действием электрического поля.
Электрофорез, или катафорез, — движение частиц, взвешенных в жидкости или газе под воздействием электрического поля.
Электродиализ—явление, которое составляют диализ (очистка растворов от электролитов) и электрофорез.
Указанные явления протекают в электростатических установках. При массопереносе в таких установках электрическое поле перемещает не ионы, как это происходит при электролизе, а макрочастицы вещества, состоящие из большого количества молекул.
Электроосмос используется для удаления избыточной влаги из почв при прокладке транспортных магистралей и гидротехническом строительстве, для сушки торфа, обезвоживания пористых материалов, очистки воды, технических жидкостей и т. д.
В электростатических установках протекание процессов обусловлено возникающими кулоновскими силами. Для их возникновения частицы должны быть заряжены.
На практике используются в основном три принципа зарядки частиц: 1) путем осаждения на поверхности частицы ионов из объема газа, окружающего частицу; 2) путем электростатической индукции, т. е. разделения зарядов в электрическом поле; 3) путем механической, химической и тепловой электризации.
ЭЛЕКТРОСТАТИЧЕСКИЕ ПРОМЫШЛЕННЫЕ УСТАНОВКИ
19.1. Принцип действия и устройство электрофильтров
Электрофильтр, как агрегат, состоит из следующих основных элементов (рис.
19.1):
1) система подготовки газов для подачи в электрофильтр, в которую входят устройства для увлажнения газа и выравнивания профиля скоростей; 2) источник питания — повышающий трансформатор в комплекте с регулирующим автотрансформатором и высоковольтный выпрямитель; 3) собственно электрофильтр.
Процесс воздействия поля на частицы вещества в электрофильтрах включает две стадии: а) предварительная бесконтактная зарядка частиц; б) осаждение частиц за счет кулонов-ского взаимодействия их зарядов с электрическим полем. Принцип действия
электрофильтра заключается в следующем. От источника питания через изолирующий ввод на коронирующий электрод и осадительный электрод подается высокое напряжение постоянного тока.

Рис. 19.1. Принципиальная схема электрофильтра:
1 — регулирующий автотрансформатор; 2 — повышающий трансформатор; 3 — высоковольтный выпрямитель; 4 — кабель с ограничительным сопротивлением; 5 — изолирующий ввод; В — коронирующий электрод; 7 — осадительный электрод; 8 — механизм встряхивания; 9 — бункер
Между электродами возникает резко неоднородное электрическое поле. Необходимая разность потенциалов U0
для возникновения коронного разряда в электрофильтре определяется по известному значению Е0
для соответствующей системы электродов. По мере повышения напряжения после возникновения коронного разряда ток быстро возрастает. При дальнейшем повышении напряжения коронный разряд может перейти в искровой. Рабочие токи в электрофильтре обычно составляют порядка 0 1—0,5 мА/м длины электрода. По достижению разностью потенциалов между электродами электрофильтра значения 50—80 кВ напряженность электрического поля способна сообщить свободным электронам и ионам газа скорость выше критической. Энергия таких электронов становится достаточной для ударной ионизации нейтральных частиц.
Образующиеся при этом ионы и свободные электроны разгоняются электрическим полем до критических скоростей и ионизируют, в свою очередь, другие атомы и молекулы. Этот процесс нарастает лавинообразно. Подобная ионизация называется коронированием. После образования короны в электрофильтре возникают две различные зоны. Первая из них расположена вокруг коронирующего электрода. Она заполнена положительно и отрицательно заряженными ионами и электронами. Вторая зона занимает пространство между короной и осадительным электродом, она заполнена только отрицательными ионами и электронами. Поэтому при прохождении через полость электрофильтра запыленного газа большинство пылинок получает отрицательный заряд и направляется к положительному осадительному электроду 7. Осадительные электроды периодически встряхиваются специальными механизмами 8 и осевшая на них пыль осыпается в бункер 9.
Достигаемый установкой электрофильтров экономический эффект весьма значителен, поскольку пыль, улавливаемая электрофильтром, часто представляет большую ценность, в ней содержатся серебро, медь, никель, сурьма, цинк, свинец, магний и др.
Социально-общественный гигиенический эффект электрофильтров трудно переоценить, так как предприятия энергетической (тепловые электростанции) и металлургической промышленности выбрасывают в воздух огромное количество всевозможных газов, загрязняющих атмосферу и окружающую среду. Созданы и успешно эксплуатируются электрофильтры для очистки воздуха в животноводческих помещениях и на птицефермах с большой запыленностью и бактерицидной осемененностью. Такие агрегаты (U =7 кВ, I = 804-100 мкА) улавливают более 90 % пылевых частиц с диаметром более 1 мк и 80 % микроорганизмов, имея при этом производительность 350—420 м3/ч воздуха.
Оборудование электрофильтров.
Конструкцию электрофильтра конкретного назначения в основном определяют технологические условия его работы: состав и свойства очищаемых газов и содержащихся в газах взвешенных частиц, температура, давление и влажность очищаемых газов, требуемая степень очистки и т. д.
Электрофильтры подразделяют на две группы:
однозонные, в которых зарядка и осаждение частиц происходят в одной конструктивной зоне, где расположены коронирующая и осадительная системы; двухзонные, в которых зарядка и осаждение частиц происходят в двух конструктивных зонах: в первой располагается коронирующая система — ионизатор, во второй ¦— осадительная система — осадитель.
По конструкции осадительного электрода электрофильтры подразделяют на трубчатые и пластинчатые.
Трубчатый электрофильтр изготовляют из стальных труб, называемых осадительными электродами. По оси труб натянута проволока — коронирующий электрод.
Пластинчатый электрофильтр собирают из ряда параллельных металлических пластин или частого ряда проволок, являющихся осадительными электродами. Между рядами осадительных электродов подвешивают проволочные коронирующие электроды. 19.2. Источники питания электрофильтров и регулирование их параметров Агрегаты питания электрофильтров, их схемы, конструкции блоков и способы регулирования напряжения определяют надежность и эффективность процесса электроочистки газовых сред.
В состав агрегата питания входят регулятор напряжения, повышающий трансформатор, выпрямитель и интегратор.
19.3. Электростатические технологические процессы и их оборудование Электрические установки, основанные на явлении электроосмоса, применяются для очистки воды, выделения растворенных в ней веществ, получения питьевой воды для населения и пресной воды для промышленности.
Принципиальная схема установки для окраски металлически* изделий в высоковольтном электрическом поле показана н| рис. 19.8. На заземленном конвейере / подвешивают подготовлен ные к окраске изделия 2. Конвейер движется от входа камеры. 1 ее выходу 3. Внутри камеры сверху и снизу конвейера на изоляторах 5 подвешены рамы с металлическими сетками 6, соединенными с высоковольтным выпрямителем 4 и являющимися коронирующими электродами. При заданном напряжении между сетками и конвейером начинается коронный разряд.
Вдуваемые пневматическим распылителем через сопло 8 частицы краски заряжаются в электрическом поле и, превратившись в отрицательные ионы, движутся к положительно заряженным изделиям (аноду). Заряженные частицы падают на изделия со всех сторон и равномерно окрашивают плотным слоем краски всю его поверхность. В камере окраски установлен вытяжной вентилятор 7, удаляющий из камеры пары растворителей и обеспечивающий заданный состав атмосферы.
Электронно-ионная технология с успехом применяется в сельском хозяйстве при опрыскивании растений, в кабельной и резиновой промышленности для припудривания изделий из резины и для других тонких операций.
ЛИТЕРАТУРА
1 Б о л о т о в А. В., Ш е п е л ь Г. А. Электротехнологические установки. --АлмаАта: Мектеп, 1983.
2. Евтюкова И. П. и др. Электротехнологические промышленные установки. — М.:
Энергоиздат, 1982.
|