Введение
Машиностроению принадлежит ведущая роль среди других отраслей экономики, так как основные производственные процессы выполняют машины. Поэтому и технический уровень многих отраслей в значительной мере определяет уровень развития машиностроения .
Повышение эксплуатационных и качественных показателей, сокращение времени разработки и внедрение новых машин, повышение их надежности и долговечности – основные задачи конструкторов –машиностроителей. Одним из направлений решения этих задач является совершенствование конструкторской подготовки инженеров высших заведений .
Большие возможности для совершенствования труда конструкторов дает применение ЭВМ, позволяющие оптимизировать конструкций, автоматизировать различную часть процесса проектирования. Объектами курсового проектирования являются приводы различных машин и механизмов, использующие большинство деталей и узлов общего машиностроительного применения.
Важной целью выполнения проекта является развитие инженерного мышления, включающее умение использовать предшествующий опыт, находить новые идей, моделировать, используя аналоги. Курсовому проекту по деталям машин свойственна многовариантность решения при одном и том же заданий развивает у студентов мыслительную деятельность и инициативу.
Важнейшей задачей курсового проектирования- развитие умения разрабатывать техническую документацию. Базируясь на исходных предпосылках из курса графики машиностроительного черчения, в процессе самостоятельной работы над курсовым проектом, студенты овладевают свободным чтением и выполнением чертежей неограниченной сложности.
1.ВЫБОР ЭЛЕКТРОДВИГАТЕЛЯ И КИНЕМАТИЧЕСКИЙ РАСЧЕТ ПРИВОДА
1.1 Определение общего КПД привода
,
где - КПД прямозубой цилиндрической зубчатой передачи
- КПД клиноременной передачи
- КПД пары подшипников качения
m-число пар подшипников
, 
m=2
Принимаем , 
0.96 0.95
1.2 Определение расчетной мощности электродвигателя
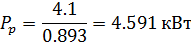
1.3 Определение среднеквадратичной мощности электродвигателя
,
где -частные значения нагрузок на i-тых участках циклограммы нагружения
частные значения длительности нагрузок на i-тых участках циклограммы нагружения
наибольшее значение длительно действующей нагрузки
- срок службы передачи


Принимаем номинальную мощность трех фазного асинхронного электродвигателя серии 4А по ГОСТ 19523-81 P=4 кВт.
1.4 Выбор электродвигателя и разбивка общего передаточного числа привода по ступеням
По принятой номинальной мощности электродвигателя из каталога выбирают четыре электродвигателя серии 4А по ГОСТ 19523-81 с различной частотой вращения вала.
Для них выполняем сравнительный расчет. Результаты сведем в таблицу.
Таблица .1
Определяемый параметр
|
Тип электродвигателя
|
4А100S2УЗ
|
4А100L4Y3
|
4A112MВ6Y3
|
4A132S8Y3
|
1.Частота вращения вала эл.двигателя 
|
2880
|
1430
|
950
|
720
|
2.общее передаточное число клиноременной передачи 
|
27.96
|
13.88
|
9.22
|
6.99
|
3.Рекомендуемое передаточное число клиноремнной передачи 
|
2
|
2
|
2
|
2
|
4. Расчетное значение передаточного числа редуктора
|
13.98
|
6.94
|
4.61
|
3.49
|
Продолжение таблицы.1
|
5.Передаточное число редуктора ГОСТ 2185-66
|
-
|
-
|
4
|
3.55
|
6.Расчетное значение передаточного числа клиноременной передачи 
|
-
|
-
|
2.30
|
1.96
|
Анализируя полученные результаты, приходим к выводу, что может быть использован только электродвигатель: 4A132S8Y3
Выбранный электродвигатель проверим на достаточность пускового момента.
Должно соблюдаться условие:

где = 2.6

1.5 Определение частоты вращения валов привода
Вал электродвигателя (ведущего шкива)

Входной вал редуктора (вал шестерни)

Выходной вал редуктора

1.6 Определение крутящих моментов валов привода
Вал электродвигателя

Входной вал редуктора (вал шестерни)

Выходной вал редуктора

2.РАСЧЕТ КЛИННОРЕМЕННОЙ ПЕРЕДАЧИ
2.1.Выбор сечения ремня
Исходя из заданной передаваемой мощности и пологая, что скорость ремня V=5….10 М/с принимаем предварительно три сечения ремня. А, Б и. В, ГОСТ 1284-80
2.2.Определение расчетного диаметра ведущего шкива.
Принимаем следующие диаметры шкивов для всех трех форм сечений ремня: ; ; ; ;
2.3.Определение скорости ремня



Дальнейший расчет ведем для всех трех форм сечений
2.4.Определение диаметра ведомого шкива
; ; ;
где - относительное проскальзывание ремня
Для резиновых ремней принимаем 



Принимаем , ГОСТ 17383-73
2.5.Определение фактического передаточного числа и отклонения от заданного значения






Допустимое отклонение фактического передаточного числа от заданного не должно превышать 5%.
2.6.Определение межосевого расстояния

Для сечения А

Принимаем 
Для сечения Б

Принимаем 
Для сечения В

Принимаем 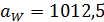
2.7.Определение минимальной длинны ремня



2.8.Определение расчетной длинны ремня






Принимаем 
2.9.Определение частоты пробега ремня
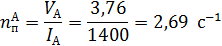
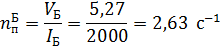
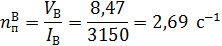
2.10.Уточнение межосевого расстояния






2.11.Определение угла обхвата меньшего шкива



2.12.Определение полезного допускаемого напряжения в ремне



Принимаем предварительное напряжение в ремне 
тогда =1.48 МПа. =1.48 МПа. =1.48 МПа.
-коэффициент, зависящий от угла обхвата.
Принимаем = 0.96 = = 0.962
-скоростной коэффициент, учитывающий ослабление сцепления ремня со шкивом под действием центробежных сил
Принимаем =1.042 =1.036 =1.014



2.13.Определение окружной силы



2.14.Определение числа ремней

Округляем до 13;

Округляем до 6;

Округляем до 2;
где 
2.15.Определение силы предварительного натяжения

2.16.Определении максимального напряжения в ремне

где -полезное напряжение от центробежных сил.

Для резинотканевого клинового ремня 
- напряжение от центробежных сил

-
напряжение изгиба при отгибаний ремнем ведущего щкива.

E
-
модуль упругости
Тогда 
2.17.Определение срока службы ремня
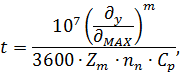
где -предел выносливости ремня зависящий от его материала;
-число шкивов в передаче
- частота пробегов ремня;
- коэффициент учитывающий режим работы;
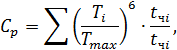

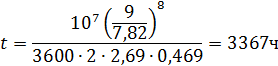
Полученная долговечность ремня вполне приемлема
3.Расчет закрытой прямозубой цилиндрической передачи
Данные для расчета:
u-передаточное число 3,55
-частота вращения шестерни, 367,3
- крутящий момент на валу шестерни, Н м 60,89
- срок службы передачи, ч 13.5
3.1.ПРОЕКТИРОВОЧНЫЙ РАСЧЕТ
Определение межосевого расстояния из условия контактной выносливости зубьев:
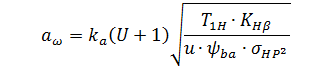
где
-вспомогательный коэффициент, имеющий размерность МПа;
- предаточное число;
- крутящий момент на валу шестерни при расчете на контактную выносливость, Н м
- допустимое контактное напряжение, МПа. Так как в зацеплений участвуют шестерни и зубчатое колесо, то необходимое опрелделить соответствующей им
=495 МПа для рпямозубой передачи;
=
3,55- по данным расчета;
= =60,89- по данным расчета.
;
В расчетную формулу определения межосевого расстояния подставляется меньшее из получаемых значений 
где и пределы контактной выносливости поверхностей зубьев, соответствующих эквивалентному числу циклов перемены напряжений МПа.
При выполнений проектировочного расчета предварительно принимается:
где -коэффициент учитывающий шерховатость сопрягаемых поверхностей зубьев;
-коэффициент учитывающий окружную скорость;
коэффициент учитывающий влияние смазки;
- коэффициент учитывающий размеры зубчатого колеса;
- коэффициент безопасности;
Для зубчатых колес с однородной структурой материала =1.1
;
;
где и -пределы выносливости поверхности зубьев шестерни и колеса, соответствующему базовому числу циклов перемены напряжений, МПа при
- Коэффициент долговечности;
;
;
где и - твердость рабочих поверхностей зубьев шестерни и колеса.
Стремясь получить сравнительно небольшие размеры передачи и не высокую ее стоимость, принимаем для изготовления шестерни – сталь 40 ХН с улучшением, при этом =260, а для изготовлений зубчатого колеса –сталь 40ХС с улучшением, при =240
При выборе материала и термообработки необходимо выполнять условие:

Тогда:


,
где - базовое число циклов перемены напряжений, соответствующее длительному пределу выносливости;
- эквивалентное число циклов перемены напряжения.
Определяется в зависимости о данных графика нагрузки.
При постоянном значении частоты вращения зубчатых колес 

где - частные значения нагрузок на шестерне или колесе, соответствующие i-тым участкам графика нагрузки, Н М;
- наибольшее значение длительно действующих нагрузок на шестерни или колесе, Н м;
- частные значения длительности нагрузок на i-тых участках графика
нагрузки, час;
В соответствии с графиком нагрузки.
Для шестерни:

60
Для колеса:

60
При для непосредственной нагрузки принимаем 

Тогда:


При этом

=550/1.1
В расчетную формулу межосевого расстояния подставляем МПа
Для зубчаты колес из улучшенной к нормальной стали при несимметричном расположений зубчатых колес относительно опор для зубчатых колес с закаленной сталью 
При симметричном расположений зубчаты колес относительно опор для подвижных зубчатых колес на валах коробок скоростей
. В редукторах для каждой последующей степени увеличивают на 20%.....30%.
Принимаем для одноступенчатого редуктора симметричное расположение зубчатых колес относительно опор.
Тогда 
зависит от расположения зубчатых колес относительно опор, твердости зубьев и величины 
= отношение ширины зубчатого венца к начальному диаметру шестерни.
Но 
При =0.6 и симметричном расположений зубчатых колес принимаем =1.05
Тогда

Принимаем 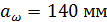
Определение модуля зацепления

По ГОСТ 9563-60 принимаем

Суммарное число зубьев.
Число зубьев шестерни и колеса.
Округляем 

Делительные диаметры шестерни и колеса


Ширина зубчатых колес .
Ширина венца колеса:

Ширина венца шестерни:
мм
Диаметры вершин зубьев.
=62+2 2=66мм
=218+4=222мм
Диаметры впадин зубьев.


Фактическое межосевое расстояние.

Окружная скорость и степень точности передачи.
По таблице принимаем 9-ю степень точности.
3.2.Проверочный расчет
Определение контактны напряжений, действующих в зацеплений.
Условие прочности при контактной выносливости.
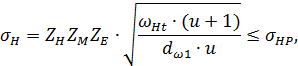
-коэффициент, учитывающий форму сопряженных поверхностей в полосе зацепления;
- коэффициент, учитывающий механические свойства сопряженных материалов поверхностей зубьев;
- коэффициент, учитывающий суммарную длину контактных линий
-удельная расчетная окружная сила, Н/мм.
Принимаем
=1.76
=275
Для прямозубой передачи:
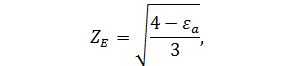
где -коэффициент торцевого перекрытия.
Для прямозубой передачи =1.74
Тогда:


где -исходная расчетная окружная сила при расчете на контактную выносливость, Н
-коэффициент, учитывающий распределения нагрузки между зубьями.
-коэффициент, учитывающий динамическую нагрузки, возникающую в зацеплений;
= =1964 H
=1 – для прямозубой передачи;

– ранее принято;
,
где - динамическая добавка.
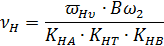
где - удельная окружная динамическая сила Н/мм.
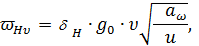
где -коэффициент учитывающий влияние вида зубчатой передачи и модификаций профиля головки зуба;
-коэффициент учитывающий влияние разности шагов зацепления зубьев шестерни и колеса.
При для прямых зубьев шестерни =0.006 и 9-й степени точности =73
Ранее принято , u=3,55

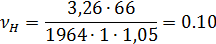



Условие прочности выполнено.
Расчет зубьев на выносливость при изгибе.
Условие прочности:

где -напряжение при изгибе, МПа;
-Коэффициент, учитывающий перекрытие зубьев
m- модуль зацепления, мм;
Принимаем =3.79 , =3.60
Для прямозубой передачи 
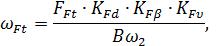
где -исходная окружная расчетная сила при расчете на изгиб, Н.
Предварительно полагаем, что в зацеплении находится одна пара зубьев и принимаем для прямозубой передачи =1.
При и при симметричном расположений зубчатых колес относительно опор принимаем =1.06


По аналогий расчетом на контактную выносливость :
= Н/мм; = Н; = мм
Тогда: 




где - предел выносливости материала зубьев при изгибе, соответствующий эквивалентному числу циклов перемены напряжений , МПа.
-коэффициент, учитывающий шероховатость.

-предел выносливости материала, МПа.
-коэффициент, учитывающий влияние шлифования переходной поверхности.
- коэффициент, учитывающий влияние деформационного упрочнения электрохимической обработки.
В зависимости от принятых материалов и термообработки


Для улучшенных и нормализованных зубчатых колес :

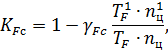
-коэффициент, учитывающий влияние амплитуд напряжений противоположного знака;
-исходная расчетная нагрузка, действующая в прямом направлений вращения, Н м;
Так как график нагрузки соответствует прямому направлению вращения, так и реверсивному.
и -числа циклов перемены напряжений соответственно при прямом направлений движения и при реверсе.
Для вышесказанного 
Для зубчатых колес из нормализованной и улучшенной сталей
=0.35
Тогда:
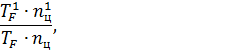
=1-0.35 =0.65
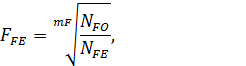
При 
При 
где -базовое число циклов перемены напряжений изгиба, ;
-
эквивалентное число циклов перемены напряжений.
При постоянном значений частоты вращения зубчатых колес 
Для шестерни:

Для колеса:

+

При =1
Принимаем 
Тогда: 


где -коэффициент учитывающий нестабильность свойств материалов зубчатого колеса и ответственность передачи 
Принимаем 
При m=2мм, .
При 
Тогда


Условие прочности выполнено:


4.Предварительный расчет валов
Предварительный расчет валов проведем на кручение по пониженным допускаемым напряжениям.
Диаметр валов при допускаемом напряжении вычисляем по формуле:
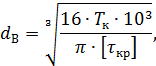
Ведущий вал.
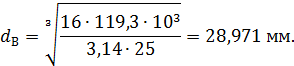
Под свободный (присоединительный) конец вала выбираем диаметр вала:28 мм
Под 2-й элемент (подшипник) выбираем диаметр вала: 30 мм.
Под 3-й элемент (шестерня) выбираем диаметр вала: 35 мм.
Под 4-й элемент (подшипник) выбираем диаметр вала: 30 мм.
Выходной вал.
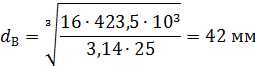
Под свободный (присоединительный) конец вала выбираем диаметр вала:42 мм
Под 2-й элемент (подшипник) выбираем диаметр вала: 45 мм.
Под 3-й элемент (колесо) выбираем диаметр вала: 50 мм.
Под 4-й элемент (подшипник) выбираем диаметр вала: 45 мм.
5.Конструктивные параметры элементов передач
5.1. Цилиндрическая шестерня редукторной передачи
Диаметр ступицы:


Длина ступицы:


Длину ступицы, из конструктивных соображений, принимаем равной ширине зубчатого венца .
Фаска

где - нормальный модуль зацепления.

5.2. Цилиндрическое колесо редукторной передачи
Диаметр ступицы:


Длина ступицы:


Длину ступицы, из конструктивных соображений, принимаем равной ширине зубчатого венца 
Толщина обода:


Толщина диска:


Внутренний диаметр обода:

где диаметр впадин зубьев, мм.
Диаметр впадин зубьев:


тогда

Диаметр центровой окружности:


Диаметр отверстий:
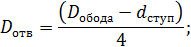

Фаска

где - нормальный модуль зацепления.

5.3. Ведущий шкив клиноременной передачи
Диаметр ступицы:


Длина ступицы:


Толщина обода:

где - высота обода,

Внутренний диаметр обода:


5.4. Ведомый шкив клиноременной передачи
Диаметр ступицы:


Длина ступицы:


Толщина обода:

где - высота обода,

Внутренний диаметр обода:


Диаметр центровой окружности:


Диаметр отверстий:
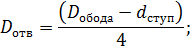

6.ПРОВЕРКА ШПОНОЧНЫХ СОДИНЕНИЙ
Цилиндрическое шестерня 1-ой передачи
Для данного элемента подбираем шпонку призматическую с округленными торцами .
Размеры сечений шпонки и пазов и длинны шпонок по ГОСТ 23360-78
Материалы шпонки –Сталь 45 нормализованная.
Напряжение на смятие и условие прочности проверяем по формуле:
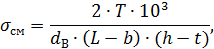

Где -диаметр вала; =8 мм-высота шпонки; -ширина шпонки; -длинна шпонки;
Допускаемые напряжения смятия при переменной нагрузке и при стальной ступице .
Проверим шпонку на срез.
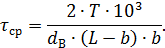


Все условия прочности выполнены.
Цилиндрическое колесо 1-ой передачи.
Для данного элемента подбираем шпонку призматическую с округленными торцами .
Размеры сечений шпонки и пазов и длинны шпонок по ГОСТ 23360-78
Материалы шпонки –Сталь 45 нормализованная.
Напряжение на смятие и условие прочности проверяем по формуле:
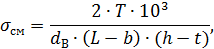

Где -диаметр вала; =9 мм-высота шпонки; -ширина шпонки; -длинна шпонки;
Допускаемые напряжения смятия при переменной нагрузке и при стальной ступице .
Для данного элемента принимаем две шпонки расположенные под углом 180 градусов друг к другу.
Проверим шпонку на срез.
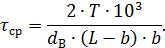


Все условия прочности выполнены.
6.2 РАСЧЕТ ШПОНОК ДЛЯ ГИБКИХ ПЕРЕДАЧ
Для ведущего шкива.
Для данного элемента подбираем шпонку призматическую с округленными торцами .
Размеры сечений шпонки и пазов и длинны шпонок по ГОСТ 23360-78
Материалы шпонки –Сталь 45 нормализованная.
Напряжение на смятие и условие прочности проверяем по формуле:
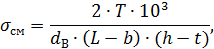

Где -диаметр вала; =8 мм-высота шпонки; -ширина шпонки; -длинна шпонки;
Допускаемые напряжения смятия при переменной нагрузке и при стальной ступице .
Проверим шпонку на срез.
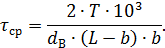


Все условия прочности выполнены.
Для ведомого шкива.
Для данного элемента подбираем шпонку призматическую с округленными торцами .
Размеры сечений шпонки и пазов и длинны шпонок по ГОСТ 23360-78
Материалы шпонки –Сталь 45 нормализованная.
Напряжение на смятие и условие прочности проверяем по формуле:
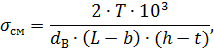

Где -диаметр вала; =7 мм-высота шпонки; -ширина шпонки; -длинна шпонки;
Допускаемые напряжения смятия при переменной нагрузке и при стальной ступице .
Для данного элемента принимаем две шпонки расположенные под углом 180 градусов друг к другу.
Проверим шпонку на срез.
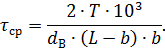


Все условия прочности выполнены.
7.КОНСТРУИРОВАНИЕ КОРПУСА РЕДУКТОРА
Для одноступчатого цилиндрического редуктора толщину стенки корпуса и крышки, отвечают требованиям технологии литья, необходимой прочности и жесткости вычисляют по формулам:



После проведенного расчета получили, то принимаем 8 мм.
Толщина верхнего пояса (фланца) корпуса:

Толщина нижнего пояса (фланца) крышки корпуса:

Толщина нижнего пояса корпуса без бобышки:

при наличии бобышки:


Толщина рёбер основания корпуса:

Округляем до 4.
Учитывая неточности литья, размеры сторон опорных платиков для литых корпусов должны быть на 2…4 мм больше размеров опорных поверхностей прикрепляемых деталей. Обрабатываемые поверхности выполняются в виде платиков, высота h которых принимается

Плоскости стенок, встречающихся под тупым углом, сопрягают радиусом 
Плоскости стенок, встречающихся под прямым углом, сопрягают радиусом

Толщина внутренних рёбер из – за более медленного охлаждения металла корпуса и крышки: 
Принимаем 6 мм.
Диаметр фундаментных болтов (их число ≥4):

Диаметр болтов у подшипников

Диаметр винтов крепления крышки корпуса вычисляем в зависимости от вращающего момента на выходном валу редуктора:


Принимаем 10 мм.
Размер q, определяющий положение болтов 

где - диаметр винтов крепления подшипника M10.

Высота бобышек под болт выбирают конструктивно так, чтобы образовалась опорная поверхность под головку болта и гайку. Желательно,
чтобы у всех бобышек иметь одинаковую высоту .
Диаметр штифтов:


8.ВЫБОР ПОДШИПНИКОВ КАЧЕНИЯ
Для ведущего вала выбираем шарикоподшипник №307.
d = 35 мм;
D = 80 мм;
B = 21 мм;
r = 2.5 мм;
Рисунок. 1. Шарикоподшипник радиальный однорядный.
Грузоподъемность:
Динамическая C = 2620 кгс;
Статическая
Предельная частота вращения, (об/мин), при:
Пластической смазке – 8000
Жидкой смазке – 10000
Масса (приблизительно), кг – 0,44.
Для ведомого вала выбираем шарикоподшипник №310.
d = 50 мм;
D = 110 мм;
B = 27 мм;
r = 3.0 мм
Рисунок. 2. Шарикоподшипник радиальный однорядный.
Грузоподъемность:
Динамическая C = 4850 кгс;
Статическая
Предельная частота вращения, (об/мин), при:
Пластической смазке – 5000
Жидкой смазке – 6300
Масса (приблизительно), кг – 1,08
9.ВЫБОР СОРТА МАСЛА
Для смазывания передач при окружной скорости вращения зубчатых колес 0,3 м/c <
V <
12,5 м/с рекомендуется применять картерную смазку. В корпус редуктора масло заливают так, чтобы венец зубчатого колеса был в него погружен. При вращении колес масло увлекается зубьями, разбрызгивается, попадает на внутренние стенки корпуса, откуда стекает в нижнюю его часть. Внутри корпуса образуется взвесь частиц масла в воздухе, которая покрывает поверхность расположенных внутри корпуса деталей.
Смазывание элементов передач редуктора в проектируемом приводе производиться окунанием нижних элементов в масло, заливаемое внутрь корпуса до уровня, обеспечивающего погружение элемента передачи примерно на 10-20 мм. Объем масляной ванны V определяется из расчета 0,25 масла на 1 кВт передаваймой мощности:

По таблице 10.8 устанавливаем вязкость масла. При контактных напряжениях и скорости рекомендуемая вязкость масла должна быть примерно равно . По таблице 10.10 принимаем масло ЦИЛИНДРОВАННОЕ - 11 ( по ГОСТ 20799-75).
Подшипники смазываются тем же маслом, которым смазываются детали передачи. При окружной скорости вращения колес брызгами масла покрываются все детали передачи и внутренние поверхности стенок корпуса. Стекающее с колес, валов и со стенок корпуса масло попадает в подшипники.
При необходимости для смазки подшипников качения выбираем пластическую смазку ЦИАТИМ – 201 по ГОСТ 6267-74. Камеры подшипников заполняются данной смазкой и периодически пополняют ей.
10. ВЫБОР ПОСАДОК
10.1 Выбор посадок колец подшипников.
Быстроходный и тихоходный валы редуктора устанавливаются на
шариковые подшипники. Внутреннее кольца подшипников вращаются вместе с валом относительно действующей радиальной нагрузки и имеют, следовательно, циркуляционное нагружение. По таблице 6.5 выбираем поле допуска вала: шейки валов под подшипники выполняем с отклонением вала k6.
Наружное кольцо подшипника неподвижно относительно радиальной
Нагрузки и подвергается местному нагружению. По таблице 6.6 определяем поле допуска отверстия – H7, что по СТ СЭВ 144-75 соответствует легкопрессовой посадке.
10.2 Выбор посадки зубчатого колеса на вал.
Примем, что вращательный момент передается от колеса к валу
соединением с натягом. Для подбора посадки материала вала сталь 40Х ( Материал колеса – сталь 40ХС ( . Сборка осуществляется нагревом колеса. Используем методику подбора посадок с натягом, изложенную в параграфе 3 гл. 5 .
Устанавливаем колесо на вал с натягом k6 через шпонку.
10.3 Посадка муфты на выходной вал редуктора – .
Посадка муфты на выходной редуктор - .
Остальные посадки назначаем, пользуясь данными таблицы 8.11 .
11.ТЕХНОЛОГИЯ СБОРКИ
Перед сборкой внутреннюю полость корпуса редуктора тщательно очищают и покрывают маслостойкой краской.
Сборку производят в соответствий с чертежом общего вида редуктора, начиная с узлов вала.
На валы закладывают шпонки и напрессовывают элементы передач редуктора. Мазеудерживающие кольца и подшипники следует насаживать, предварительно нагрев в масле до 80-100 градусов по Цельсию, последовательно с элементами передач. Собранные валы укладывают в основание корпуса редуктора и надевают крышку корпуса, покрывая предварительно поверхности стыка крышки и корпуса спиртовым лаком. Для центровки устанавливаю крышку на корпус с помощью двух конических штифтов; затягивают болты, крепящие крышку к корпусу. После этого в подшипниковые камеры закладывают смазку, ставят крышки подшипников с комплектом металлических прокладок, регулируют тепловой зазор. Перед постановкой сквозных крышек в проточки закладывают войлочные уплотнения, пропитанные горячим маслом. Проверяют проворачиванием валов отсутствие заклинивания подшипников (валы должны проворачиваться от руки) и закрепляют крышку винтами. Затем ввертывают пробку маслоспускного отверстия с прокладкой и жезловой маслоуказатель. Заливают в корпус масло и закрывают смотровое отверстие крышкой с прокладкой, закрепляют крышку болтами. Собранный редуктор обкатывают и подвергают испытанию и подергают на стенде по программе, устанавливаемой техническими условиями.
Заключение
В настоящем курсовом проекте мной разработан привод, состоящий из клиноременной передачи и одноступенчатого цилиндрического редуктора.
В результате расчетов нами определены следующие параметры:
· Передаточное число клиноременной передачи – 1,96;
· Передаточное число передачи – 2;
· Межосевое расстояние плоскоременной передачи – 761 мм;
· Межосевое расстояние зубчатой цилиндрической передачи –135 мм;
· Для привода предлагается использовать электродвигатель марки 4А132S8Y3, мощностью 4 кВт и частотой вращения 720 мин-1
.
|