Содержание
Введение
1.
Формирование блока исходных данных:
1.1 Информация о судне и грузах
1.2 Выбор технологии грузоперевалки
1.3
Определение расчетной загрузки судна
2. Определение показателей плана стивидорного обслуживания судна:
2.1 Параметры кордонного грузового фронта
2.2 Удельная себестоимость грузоперевалки
2.3 Стивидорный тариф
2.4 Финансовый результат
3. Календарное планирование стивидорного обслуживания судна:
3.1 Моделирование задачи составления ПСОС
3.2 Подготовка исходных данных к составлению ПСОС
3.3 решение задачи и составление рабочей формы ПСОС
4. Оперативный анализ результатов стивидорного обслуживания судна:
4.1 Исходные положения
4.2 Версия реализации ПСОС
4.3 Анализ полученных результатов
Заключение
Литература
Приложение 1. Расчетное судно
Приложение 2. РТК перегрузки колес железнодорожных
Приложение 3. РТК перегрузки пробки в кипах
Введение
Основной задачей производственно-оперативного планирования в порту является установление объема и характера перегрузочных работ на планируемый период, распределение технических и трудовых ресурсов и разработка мероприятий для выполнения этого объема работ.
Обработка судов в портах возможна по различным вариантам, выбор которых определяется рядом факторов (номенклатурой грузов, типом судна, специализацией причала, возможностями технических средств и трудовых ресурсов, действующими нормами одновременной обработки судов, судо-часовыми нормами и др.). Отдельные варианты обычно не равнозначны по экономической эффективности. Кроме того, эффективность одного и того же варианта для порта и для флота может быть совершенно различной. Поэтому оптимальным может быть признан такой вариант, который обеспечивает достижение суммарной экономической эффективности по порту и флоту в целом.
Основными мероприятиями, касающимися организации труда, являются: подготовка, обслуживание и оснащение рабочего места; расстановка по рабочим местам в соответствии со знаниями и квалификацией каждого работающего; создание оптимального режима труда, позволяющего поддерживать работоспособность и состояние здоровья работающих на высоком уровне; разработка и внедрение научно обоснованных норм труда, правильно отражающих затраты труда работающих; материальное стимулирование и его совершенствование; улучшение бытовых, культурных и социальных условий жизни и труда работающих; всемерное улучшение методов охраны труда и техники безопасности; организация высокой дисциплины труда; создание условий творческой инициативы трудящихся и всемерное развитие всех форм соревнования; непрерывное повышение квалификации и знаний трудящихся.
Все указанные выше мероприятия направлены на повышение производительности труда.
Специфика перегрузочных работ обусловливает ряд особенностей в организации труда портовых рабочих.
Также необходимо отметить, что к оперативному планированию относят распределение перегрузочных ресурсов порта между объектами работ, отдельно по погрузке и выгрузке, разработка сменно-суточного плана работы порта, составление оптимального плана обработки каждого судна.
1. Формирование блока исходных данных
1.1. Информация о судне и грузах
Приводим основные эксплуатационно-технические характеристики заданного судна – «Бежица», необходимые для решения организационно-технологических вопросов стивидорного обслуживания судов (СОС) (табл.1.1-1.2.)
Таблица 1.1. Основные характеристики судна
Наименование параметра
|
Значение
|
Специализация
|
сухогруз
|
Количество палуб
|
2
|
Количество отсеков
|
6
|
Чистая грузоподъемность, т
|
10514
|
Киповая вместимость, м3
|
16790
|
Таблица 1.2. Параметры грузовых помещений и люков
№
|
Трюма
|
Твиндеки
|
Люки
|
L
, м
|
B
, м
|
H
, м
|
W
, м3
|
L
, м
|
B
, м
|
H
, м
|
W
, м3
|
L
, м
|
B
, м
|
1
|
16,1
|
15
|
4
|
610
|
16,1
|
15
|
3,6
|
790
|
8,4
|
6
|
5
|
17,3
|
15
|
6,6
|
1 630
|
17,3
|
15
|
3,3
|
1 210
|
13,7
|
2х6,1
|
3
|
18,4
|
15
|
6,6
|
2 140
|
16,8
|
15
|
3,1
|
1 160
|
13,7
|
2х6,1
|
4
|
28,8
|
15
|
6,6
|
3 360
|
27,2
|
15
|
3,1
|
1 900
|
24,9
|
2х6,1
|
5
|
17,6
|
15
|
6,6
|
1 880
|
17,6
|
15
|
3,1
|
1 190
|
13,7
|
2х6,1
|
6(реф)
|
10,5
|
12,2
|
3
|
350
|
-
|
12,2
|
2,4
|
570
|
8,6
|
6,2
|
Полное техническое описание судна приведено в приложении 1.
В данном курсовом проекте для анализа результатов стивидорного обслуживания судна используются два груза: пробка в кипах и колеса железнодорожные. Приводим краткую характеристику этих грузов.
Железнодорожные колеса
- нейтральный тяжелый груз. Грузовые места должны укладываться только на пайол или палубы твиндеков. Погрузка должна производиться в сухую погоду, на грузовых местах не должно быть следов снега, льда и пр. В некоторых случаях (короткий рейс, низкие температуры во время предстоящего морского перехода и пр.) возможна погрузка при незначительных метеоосадках по письменному требованию грузовладельца. Этот факт должен быть зафиксирован в судовом журнале (как и случаи подачи увлажненных грузовых мест в трюм: со следами льда, снега и пр.). Целесообразна погрузка поверх этого груза других, легких грузов после соответствующей сепарации.
Металл, из которого изготовляются колеса, обычно подвержен коррозии. Процесс коррозии активизируется при повышении температуры и относительной влажности воздуха, особенно в условиях засоленности окружающего (и трюмного) воздуха при морском переходе. Поэтому не рекомендуется мойка трюмов соленой водой перед погрузкой; при невозможности использовать пресную воду, имеет смысл, по возможности, ограничиться тщательной сухой зачисткой грузовых помещений. Этот факт также следует отразить в судовом журнале.
Рекомендуемый режим перевозки – герметизация трюмов, во избежание активизации процесса коррозии грузовых мест в результате засоленности трюмного воздуха (водяная пыль, брызги и пр.).
При резких (более 10 °С) суточных изменениях температуры наружного воздуха целесообразно вентилирование грузовых помещений в режиме «рециркуляция» во избежание образования конденсата на грузе (при повышении температуры наружного воздуха). В последнем случае иногда бывает необходимо включать вентиляцию в режиме «освежение» (на короткое время – 10-15 мин.) с целью снижения содержания влаги в трюмном воздухе, при этом следует принимать во внимание погодные условия и конструктивные особенности трюмной системы вентиляции (место расположения воздухозаборников и пр.).
Учитывая высокую теплопроводность груза, правильное вентилирование обычно дает положительный результат. Факт включения вентиляции и режим вентилирования следует фиксировать в судовом журнале.
Пробка
– ценный наружный слой покровной ткани тропических растений (пробковый дуб, амурское дерево, бархатное дерево и пр.). Очень легкая, непроницаемая для газов, используется как изоляционный материал в промышленности, также в медицине и быту.
Гигроскопический груз; при увлажнении, а тем более подмочке, плесневеет; подвержен деятельности микроорганизмов, активность которых возрастает с повышением температуры и относительной влажности; при перевозке в условиях высоких температур и низкой относительной влажности – крошится, при этом ухудшается товарный вид и снижается качество и стоимость. Оптимальная относительная влажность около 75 %. Предъявляется к перевозке в кипах, обшитых паковочной тканью, стянутых металлическими лентами.
Вентиляция должна быть использована для предотвращения (уменьшения интенсивности) образования конденсата и поддержания (по возможности) оптимальной относительной влажности.
Груз, как правило, требует фитосанитарного (карантинного) контроля.
Прием и сдача груза производятся счетом мест, при этом необходимо обращать внимание на качество упаковки кип (упаковочная ткань должна быть прочной и чистой, а металлические ленты и проволока на кипах – целыми).
Основные транспортные характеристики грузов указаны в табл.1.3.
Таблица 1.3. Транспортные характеристики грузов
Колеса (стопки)
|
Пробка (кипы)
|
наружный диаметр, мм
|
750
|
длина, мм
|
700
|
внутренний диаметр, мм
|
590
|
ширина, мм
|
700
|
высота стопки, мм
|
1000
|
высота, мм
|
1150
|
масса стопки, кг
|
1000
|
масса, кг
|
80
|
1.2. Выбор технологии грузоперевалки
С целью получения наилучших результатов при обработке судна, которые будут выражаться в минимальном сроке обработке при минимальных затратах производственных ресурсов порта, мы производим отбор технологических схем перевалки груза по производительности, которая должна быть максимальной, и по количеству задействованных людей и механизмов, которое соответственно должно быть сведено к минимуму.
Поскольку судно, которое используется для перевозки предложенных грузов, имеет недостаточное раскрытие люков, а соответственно значительные подпалубные пространства, при выборе технологических схем по вариантам судно-вагон и судно-склад будут отобраны по две схемы: одна для загрузки подпалубных пространств, другая – для работы на просвете люка.
Для варианта склад-вагон выбирается только одна схема.
Вариант склад-склад не рассматривается, поскольку его использование может привести лишь к снижению эффективности работы порта, а значит, его необходимо исключить.
Выбранные технологические схемы и показатели работы на этих схемах представлены в табл.1.4.
Таблица 1.4. Выбранные технологические схемы и их параметры
№ п/п
|
Наименование технологических схем
|
Расстановка докеров/машин по технологическим операциям
|
Производительность ТЛ, т/смену
|
ВГН
|
ВТП
|
СКЛ
|
КРД
|
СДВ
|
Всего
|
Железнодорожные колеса в стопках
|
Вариант судно-вагон
|
1
|
трюм-кран-полувагон
|
2/-
|
-
|
-
|
2/1
|
3/-
|
7/1
|
158
|
2
|
трюм(погрузчик)-кран-полувагон
|
2/-
|
-
|
-
|
2/1
|
4/1
|
8/2
|
158
|
Вариант судно-склад
|
1
|
трюм-кран-склад
|
-
|
-
|
2/-
|
2/1
|
3/-
|
7/1
|
184
|
2
|
трюм(погрузчик)-кран-склад
|
-
|
-
|
2/1
|
2/1
|
4/1
|
8/3
|
184
|
Вариант склад-вагон
|
1
|
склад-кран-полувагон
|
2/-
|
-
|
3/1
|
-
|
-
|
5/1
|
161
|
Пробка в кипах
|
Вариант судно-вагон
|
1
|
трюм-кран-полувагон
|
2/-
|
-
|
-
|
2/1
|
4/-
|
8/1
|
106
|
2
|
трюм(погрузчик)-кран-полувагон
|
2/-
|
-
|
-
|
2/1
|
6/2
|
10/3
|
106
|
Вариант судно-склад
|
1
|
трюм-кран-склад
|
-
|
-
|
2/-
|
2/1
|
4/-
|
8/1
|
118
|
2
|
трюм(погрузчик)-кран-склад
|
-
|
-
|
2/-
|
2/1
|
6/2
|
10/3
|
118
|
Вариант склад-вагон
|
1
|
склад-кран-полувагон
|
2/-
|
-
|
3/1
|
-
|
-
|
5/1
|
96
|
Выбранные схемы предполагают использование перегрузочных машин и технологической оснастки, указанных в табл.1.5.
Таблица 1.5. Технические средства
Наименование механизма
|
Грузоподъемность, т
|
Колеса
|
кран портальный
|
5-15
|
кран пневмоколесный (гусеничный)
|
5-25
|
погрузчик трюмный
|
1,5-5
|
крановая подвеска
|
5-10
|
захват крановый
|
1,5
|
вилочный захват к трюмному погрузчику
|
1,5-5
|
стропы стальные
|
5-15
|
подвеска для доставки в трюм погрузчика
|
5
|
Пробка
|
кран портальный
|
5-15
|
кран пневмоколесный (гусеничный)
|
5-25
|
погрузчик трюмный
|
до 7,0
|
распорная рама
|
5,0
|
захват крановый ящичный
|
0,5
|
боковой захват к трюмному погрузчику
|
1,5
|
багры
|
-
|
ручной инструмент (ломики, крюки ручные)
|
-
|
лестницы приставные
|
-
|
Поскольку из всех операций технологического процесса обработки груза основу стивидорного обслуживания судов (СОС) составляет судовая операция, приводим краткую характеристику ее для каждого груза.
Железнодорожные колеса
Выгрузка колес осуществляется с помощью захватов, навешенных на раму. Для фиксации захвата в нерабочем положении служит защелка, которая входит в зацепление с балкой. Захват вводится внутрь стопки и, опираясь консолями балки на верхнее колесо, занимает наклонное положение. Рабочий вручную переводит защелку в верхнее положение. При натяжении краном шток перемещается вверх. Поворачивая тяги; зацепы рычагов входят под нижний бандаж и захватывают груз. При этом защелка, связанная с балкой тросиком, при натяжении последнего защелкивается. После опускания груза по назначению шток под действием собственного веса перемещается вниз, рычаги выходят из-под груза, защелка автоматически входит в зацепление с балкой и захват принимает нерабочее положение.
При невозможности завести захват из-за смещения отдельных мест стопки больше допускаемого, выгрузка может проводится стальными стропами, навешенными на крюк крана. При одновременной строповке 2-х стопок конец стропа пропускается внутрь одной стопки и выводится наружу из соседней стопки колес. Затем свободный конец крепится к стропу с помощью роликовой скобы «в удав». Аналогично производится строповка стопок вторым стропом. Таким образом «подъем» состоит из 4-х стопок.
Более подробное описание всех операций, а также все возможные технологические схемы перегрузки железнодорожных колес приведены в приложении 2.
Пробка в кипах
Выгрузка пробки с просвета люка производится следующим образом. Кран подает в грузовое помещение распорную раму с захватами. Рабочие производят застропку необходимого количества кип. После ухода рабочих в безопасное место кран выносит «подъем» из грузового помещения.
После выгрузки кип из грузового помещения до требуемого уровня (количество кип по высоте от пайола определяет производитель работ с учетом технических возможностей погрузчика и устойчивости штабеля) и выгрузки кип с просвета люка до пайола, очистки пайола от остатков сепарации, в грузовое помещение краном подаются трюмные погрузчики с боковыми гидрозахватами. До этого выгрузка кип из подпалубных пространств ведется вручную с помощью деревянных ломиков и ручных крючков. Перед спусканием погрузчиков производитель работ должен определить и указать безопасные места и укрытия для рабочих и погрузчиков. Погрузчик захватывает под палубой 1-2 кипы за торцы либо за боковые грани, транспортирует их на просвет люка, где укладывает рядами, формируя «подъем». После этого погрузчик отъезжает на безопасное расстояние, а водитель выходит из кабины. Рабочие стропят груз и уходят в безопасное место. Кран выносит «подъем» из грузового помещения. По окончании работ погрузчики краном выгружаются из грузового помещения. Россыпь груза собирается с помощью лопат и метел в металлические ковши, которые краном подаются на причал.
Более подробное описание всех операций, а также все возможные технологические схемы перегрузки пробки в кипах приведены в приложении 3.
1.3. Определение расчетной загрузки судна
Данная задача охватывает комплекс вопросов, связанных с расчетом весовых нагрузок (распределенной массы) грузовых отсеков судна, определением массы принимаемых к погрузке грузов по наименованиям и распределением отобранных грузов между грузовыми помещениями судна. Задача решается исходя из обеспечения максимального использования чистой грузоподъемности и грузовместимости судна при соблюдении требований, регламентирующих сохранение его необходимой остойчивости, прочности и дифферента, безопасности плавания судна и сохранности груза.
Для заданного судна рассчитывается его удельная грузовместимость:
, (1)
где - киповая вместимость судна, м3
;
- чистая грузоподъемность судна, т
1,597 м3
/т
Полученное значение удельной грузовместимости судна принимаем одинаковым для всех грузовых помещений (отсеков).
Определяем весовую нагрузку (распределенную массу) грузовых отсеков судна:
, ( ) (2)
где - номер грузового отсека;
- грузовместимость -го трюма и твиндека, соответственно.
876,6 т
1778,3 т
2066,4 т
3293,7 т
1992,35 т
Отсек №6 – рефрижераторный и поэтому в расчетах не используется.
Рассчитываем массу принимаемых к погрузке грузов по наименованиям и одновременно производим их распределение между грузовыми отсеками судна. Для этого предварительно определяем УПО грузов (колеса – груз №1, пробка – груз №2):
, (3)
где - соответственно, наружный и внутренний диаметр стопки, м;
- высота стопки, м;
- масса стопки, т;
= 1,25 – коэффициент трюмной укладки.
0,21 м3
/т
, (4)
где - линейные размеры кипы, м;
- масса кипы, т;
8,8 м3
/т
Полученные результаты сравниваем с удельной грузовместимостью судна и получаем: < < , т.е. груз №1 (колеса) – «тяжелый», груз №2 (пробка) – легкий.
В этом случае задача загрузки отсеков решается, исходя из предпосылки о полном использовании грузоподъемности и грузовместимости судна и каждого его грузового отсека. Для решения задачи используется система двух уравнений:
, (5)
где 0,003 - коэффициенты учитывающие долю материалов, необходимых для сепарации и крепления грузов обоих наименований.
Для отсека №1 эта система будет решаться следующим образом:

= 732,85 т
= 141,13 т
Определяем массу сепарационных и крепежных материалов для каждого груза в каждом отсеке:
, (6)
где - шифр груза.
= 2,2 т
= 0,42 т
Результаты расчетов по всем отсекам и судну в целом приведены в табл.1.6.
2. Определение показателей плана стивидорного обслуживания судна
2.1. Параметры кордонного грузового фронта
Основными параметрами кордонного грузового фронта являются производительность и количество технологических линий (ТЛ), необходимое для обеспечения загрузки-разгрузки судна в минимальные сроки при минимальных затратах производственных ресурсов.
1. Расчетная производительность ТЛ определяется на основе выбранных ранее технологических схем.
Для определения производительности ТЛ как средневзвешенной величины по технологическим схемам в рамках каждого варианта грузоперевалки необходимо предварительно найти доли груза, перегружаемые по каждой технологической схеме (т.е. доли груза, размещаемые в подпалубных пространствах грузовых отсеков и на просветах люков судна).
Примем указанные доли одинаковыми по прямому и складскому вариантам, а также по всем грузовым отсекам судна. Тогда их значения можно рассчитать по формулам:
, (7)
, (8)
где - соответственно, длина и ширина i-го грузового люка, м
- высота i-го грузового отсека, м

= 0,51
Рассчитываем средневзвешенную по технологическим схемам производительность ТЛ для каждого варианта грузоперевалки:
, (9)
где - шифр варианта грузоперевалки
Для прямого варианта по перевалке груза №1 эта величина составит:
22,6 т/ч
Находим доли груза, которые необходимо перегрузить по прямому и складскому вариантам грузоперевалки путем расчета коэффициентов транзитности и складирования:
, (10)
, (11)
где - техническая норма загрузки вагона, т (количество груза в одном вагоне);
- количество вагонов в одной подаче;
- количество е
-го груза которое необходимо перегрузить в ходе СОС
, (12)
где - длина причала, у которого обрабатывается судно, м;
- длина вагона, используемого для перевозки е
-го груза, м;
, (13)
где = 155,7 м – наибольшая длина расчетного судна;
= 20 м – запас свободной длины причала при наибольшей длине расчетного судна.
175,7 м
Для перевозки железнодорожных колес используется 8-осный полувагон, а для пробки в кипах – 6-осный полувагон, основные характеристики которых представлены в табл.2.1.
Таблица 2.1. Характеристики полувагонов
Наименование
|
Единицы измерения
|
Значение
|
8-осный полувагон
|
6-осный полувагон
|
Грузоподъемность
|
т
|
125
|
94
|
Объем кузова
|
м3
|
1375
|
106
|
Длина по осям автосцепок
|
мм
|
20240
|
16400
|
Внутренние размеры:
|
|
|
|
длина
|
мм
|
18758
|
2902
|
ширина
|
мм
|
2790
|
14586
|
высота
|
мм
|
2450
|
2365
|
Методом моделирования мы получили, что т, т,
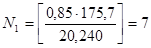
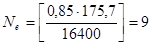
0,063
0,937
0,065
0,935
Определяем средневзвешенную по вариантам грузоперевалки производительность ТЛ:
, (14)
Для груза №1 эта величина составит:
т/ч
Полная плановая производительность ТЛ как средневзвешенная по наименованиям грузов величина рассчитывается по формуле:
, (15)
где - соответственно доли грузов №1 и №2
, (16)
, (17)
где - весовая загрузка судна, т
0,839
0,161
= 23,91 т/ч
Расчеты всех средневзвешенных значений производительности по всем параметрам представлены в табл.2.2.
Таблица 2.2. Производительность ТЛ
Наименование груза (шифр)
|
Вариант грузоперевалки
|
Номер ТС
|
Производительность ТЛ, т/ч
|
ТС
|
Вариант
|
Груз
|
Судно
|
колеса (1)
|
судно-вагон
|
1
|
22,6
|
22,6
|
26,03
|
23,91
|
2
|
22,6
|
судно-склад
|
1
|
26,3
|
26,3
|
2
|
26,3
|
склад-вагон
|
1
|
23
|
23
|
пробка (2)
|
судно-вагон
|
1
|
15,1
|
15,1
|
16,8
|
2
|
15,1
|
судно-склад
|
1
|
16,9
|
16,9
|
2
|
16,9
|
склад-вагон
|
1
|
13,7
|
13,7
|
2. Расчетное количество ТЛ определяется на основании предела концентрации их на судне, который зависит от характеристик судна: с одной стороны, линейных и архитектурных, лимитирующих протяженность грузового фронта ТЛ; с другой стороны, конструктивных, обуславливающих люковую неравномерность загрузки судна и величину предела концентрации ТЛ на его грузовых люках.
Поэтому определяем предел концентрации ТЛ на грузовых люках исходя из правил техники безопасности ( ) и исходя из конструктивных характеристик судна обуславливающих неравномерность загрузки грузовых отсеков по трудоемкости ( ), а затем находим расчетное количество ТЛ по формуле:
, (18)
По правилам техники безопасности возможно одновременно обрабатывать люки следующим количеством ТЛ:
Люк №1 – 1
Люк №2 – 1
Люк №3 – 1
Люк №4 – 2
Люк №5 – 1
Таким образом, .
, (19)
где - трудоемкость загрузки-разгрузки судна, ч
- трудоемкость загрузки-разгрузки i-го отсека, ч
- предел концентрации ТЛ на люке по правилам техники безопасности.
, ( ) (20)
, (21)
36,66 ч
74,37 ч
86,42 ч
137,75 ч
83,33 ч
ч

= 5
2.2. Удельная себестоимость грузоперевалки
Данный показатель в курсовом проекте рассматривается в двух модификациях:
а) как полная удельная себестоимость грузоперевалки, т.е. с учетом всех расходов по комплексу стивидорных и терминальных операций, производимых с грузом с момента его прибытия в порт и до момента отправления из порта;
б) как удельная себестоимость стивидорных работ, т.е. с учетом расходов по судовой и частично кордонной технологическим операциям, составляющим основу СОС
Полная удельная себестоимость грузоперевалки определяется путем расчета удельной себестоимости грузоперевалки по каждой технологической схеме вариантов судно-вагон, судно-склад, средневзвешенных значений по технологическим схемам прямого и складского вариантов, средневзвешенных значений этого показателя по всем трем вариантам грузоперевалки, а затем собственно полной удельной себестоимости.
Приводим расчет удельной себестоимости грузоперевалки по ТС №1 по варианту судно-вагон для груза №1 (колеса).
, (22)
где - шифр технологической схемы
- оплата труда докеров грн/т
- оплата работы тальмана, грн/т
- оплата работы стивидора, грн/т
- расходы по стивидорному оборудованию (перегрузочным машинам и средствам внутрипортового транспорта), грн/т
- накладные расходы
, (23)
где = 0,25 – коэффициент, учитывающий отчисления по заработной плате докеров;
= 1,335 – коэффициент, учитывающий доплаты к заработной плате докеров;
= 2,15 грн/чел-ч – тарифная ставка докера;
= 1,1 – коэффициент, учитывающий надбавку к заработной плате бригадира;
- численность бригады докеров;
= 1 – количество бригад докеров, участвующих в обслуживании судна.
0,257 грн/т
, (24)
где = 1,95 грн/чел-ч – тарифная ставка тальмана;
0,086 грн/т
, (25)
где = 0,25 – коэффициент, учитывающий заработную плату стивидора;
0,086 грн/т
, (26)
где 25,54 грн/маш-ч – стоимость содержания портального крана;
– количество портальных кранов в составе ТЛ;
9,44 грн/маш-ч – стоимость содержания погрузчика;
– количество погрузчиков в составе ТЛ;
грн/маш-ч
, (27)
где = 2,4 – коэффициент, учитывающий процент накладных расходов;
грн/т
грн/т
Расчет всех значений удельной себестоимости грузоперевалки по всем технологическим схемам всех вариантов для всех грузов производится аналогично (см. табл.2.3.)
Определяем средневзвешенную удельную себестоимость перевалки груза в рамках вариантов:
, (28)
Для груза №1 по варианту судно-вагон эта величина составит:
грн/т
По каждому грузу находим средневзвешенную по всем трем вариантам перевалки себестоимость:
, (29)
Для груза №1 эта величина составит:
грн/т
Расчеты всех средневзвешенных значений удельной себестоимости по всем параметрам представлены в табл.2.3.
Таблица 2.3. Полная удельная себестоимость грузоперевалки
Наименование груза (шифр)
|
Вариант грузоперевалки
|
Номер ТС
|
Статьи удельной себестоимости грузоперевалки, грн/т
|
Удельная себестоимость грузоперевалки, грн/т
|

|

|

|

|

|
ТС
|
Вариант
|
Груз
|
колеса (1)
|
судно-вагон
|
1
|
0,257
|
0,086
|
0,086
|
1,13
|
3,74
|
5,299
|
5,927
|
4,168
|
2
|
0,289
|
0,086
|
0,094
|
1,55
|
4,85
|
6,688
|
судно-склад
|
1
|
0,221
|
0,074
|
0,074
|
0,97
|
3,21
|
4,549
|
5,148
|
2
|
0,248
|
0,074
|
0,081
|
1,33
|
4,16
|
5,893
|
склад-вагон
|
1
|
0,19
|
0,085
|
0,069
|
0,67
|
2,43
|
3,444
|
3,444
|
пробка (2)
|
судно-вагон
|
1
|
0,432
|
0,129
|
0,14
|
1,69
|
5,74
|
8,131
|
9,983
|
8,632
|
2
|
0,527
|
0,129
|
0,164
|
2,94
|
9,02
|
12,78
|
судно-склад
|
1
|
0,386
|
0,115
|
0,125
|
1,51
|
5,13
|
7,266
|
8,924
|
2
|
0,471
|
0,115
|
0,147
|
2,63
|
8,07
|
11,43
|
склад-вагон
|
1
|
0,319
|
0,142
|
0,115
|
1,86
|
5,85
|
8,286
|
8,286
|
Удельная себестоимость стивидорных работ определяется аналогично, но отличие методики состоит в том, что рассматриваются только варианты судно-вагон и судно-склад с выделением в технологических схемах двух операций – кордонной и судовой. Которыми охватывается комплекс стивидорных операций. При таком условии формулы для расчета статей и преобразуются и принимают следующий вид:
, (30)
где - численность, соответственно, трюмного и кордонного звеньев бригады докеров;
, (31)
где - количество погрузчиков, используемых трюмным звеном докеров.
Остальные статьи себестоимости и ее средневзвешенные значения по схемам находятся аналогично полной удельной себестоимости.
Приводим расчет удельной себестоимости стивидорных работ по ТС №1 по варианту судно-вагон для груза №1 (колеса).
грн/т
0,086 грн/т
0,07 грн/т
грн/т
грн/т
грн/т
грн/т
По каждому грузу находим средневзвешенную по всем трем вариантам перевалки себестоимость:
, (32)
Для груза №1 эта величина составит:
грн/т
Расчеты всех средневзвешенных значений удельной себестоимости по всем параметрам представлены в табл.2.3.
Таблица 2.3. Удельная себестоимость стивидорных работ
Наименование груза (шифр)
|
Вариант грузоперевалки
|
Номер ТС
|
Статьи удельной себестоимости стивидорных работ, грн/т
|
Удельная себестоимость стивидорных работ, грн/т
|

|

|

|

|

|
ТС
|
Вариант
|
Груз
|
колеса (1)
|
судно-вагон
|
1
|
0,194
|
0,086
|
0,07
|
0,565
|
2,2
|
3,115
|
3,75
|
3,244
|
2
|
0,225
|
0,086
|
0,078
|
0,982
|
3,29
|
4,661
|
судно-склад
|
1
|
0,166
|
0,074
|
0,06
|
0,485
|
1,88
|
2,665
|
3,215
|
2
|
0,194
|
0,074
|
0,067
|
0,844
|
2,83
|
4,009
|
пробка (2)
|
судно-вагон
|
1
|
0,337
|
0,129
|
0,117
|
0,845
|
3,43
|
4,858
|
6,475
|
5,818
|
2
|
0,432
|
0,129
|
0,14
|
2,1
|
6,72
|
9,521
|
судно-склад
|
1
|
0,301
|
0,115
|
0,104
|
0,755
|
3,06
|
4,335
|
5,779
|
2
|
0,386
|
0,115
|
0,125
|
1,873
|
6
|
8,5
|
2.3. Стивидорный тариф
Данный показатель так же, как и удельная себестоимость грузоперевалки, рассчитывается в двух модификациях, которым соответствуют:
а) консолидированная стивидорная ставка, определяемая на базе полной удельной себестоимости грузоперевалки;
б) стивидорный тариф, рассчитываемый на базе удельной себестоимости стивидорных работ.
Численные значения этих величин находятся по формулам:
, (33)
, (34)
где = 1,6 коэффициент, учитывающий процент прибыли стивидорной компании (порта);
= 1,2 – коэффициент, учитывающий налог на добавленную стоимость.
= 8,0 грн/т
= 16,57 грн/т
= 6,23 грн/т
= 11,17 грн/т
2.4. Финансовый результат
Данным показателем, который характеризует соотношение между результатами СОС (доходами) и затратами, на его осуществление (расходами), определяется плановая прибыль. Которая может быть достигнута в случае обеспечения обработки судна в соответствии с расчетными показателями СОС.
В случае, когда процессом СОС охватываются стивидорные и терминальные операции, плановая прибыль находится из соотношения:
, (35)
44 795,1 грн
Если же СОС ограничивается только стивидорными операциями, то плановая прибыль определяется по формуле:
, (36)
33 573,6 грн
3. Календарное планирование стивидорного обслуживания судна
В календарном плане стивидорного обслуживания судна (ПСОС) отражается планируемый процесс обработки судна, «расписанный» во времени с выделением суток и смен. В нем фиксируются плановые значения показателей СОС для судна и его грузовых отсеков (люков). Основными среди этих показателей являются:
· расчетная продолжительность обработки судна и его люков;
· последовательность и календарные сроки начала-окончания обработки люков судна;
· количество ТЛ и способы их распределения между люками в процессе производства стивидорных операций;
· сменно-суточные задания (объемы грузоперевалки) по люкам и судну в целом.
3.1. Моделирование задачи составления ПСОС
В содержательном плане существо задачи составления ПСОС состоит в обеспечении гармоничного сочленения двух процессов загрузки-разгрузки люков судна и работы используемых для этой цели ТЛ – при соблюдении организационно-технологических и экономических требований, оговариваемых при обосновании условий СОС. Такая цель может быть достигнута на основе увязки в единую систему характеристик судна, груза и ТЛ, которые одновременно являются параметрами процесса СОС. К числу указанных характеристик-параметров относятся:
- количество люков предъявляемых судном к обработке ( );
- плановая загрузка судна и люков, соответственно;
- предел концентрации ТЛ на судне и люках;
- количество ТЛ, выделяемых для обработки судна ( );
- производительность ТЛ на люках (принимаем )
- коэффициент, учитывающий снижение производительности ТЛ при их совместной работе (2 и более ТЛ) на одном люке (принимаем =0,9).
Конкретный вид связи между перечисленными параметрами удается определить и формализовать, введя понятие исходного способа организации СОС, под которым подразумевается любой допустимый вариант расстановки ТЛ на судне (закрепления ТЛ за люками судна) с учетом предела концентрации линий на люках.
Определив множество такого рода способов организации СОС, можно утверждать, что для построения оптимального ПСОС необходимо, во-первых, установить подмножество (сочетание) наиболее рациональных вариантов расстановки ТЛ на судне, во-вторых, определить время, в течение которого следует использовать каждый из найденных вариантов. В такой постановке задача поддается решению при наличии адекватной процессу СОС математической модели.
Для построения упомянутой модели необходимо дополнить перечень параметров СОС следующими характеристиками:
- шифр расстановки ТЛ на судне ( );
- промежутки времени, в течение которых расстановка ТЛ на судне не изменяется;
- количество ТЛ одновременно работающих на люке i
по варианту ;
- интенсивность обработки судна, дифференцируемая по люкам и вариантам расстановки ТЛ
Т
– продолжительность СОС как сумма отрезков времени, в течение которых используются различные варианты расстановки ТЛ на судне.
Значения интенсивности загрузки-разгрузки люков судна по вариантам расстановки ТЛ находятся из соотношения вида:
(37)
, 
При оговоренных выше условиях рассматриваемой задаче соответствует линейная модель вида:
; (38)
, ; (39)
³ 0, (40)
Эта модель «читается» следующим образом: необходимо минимизировать продолжительность СОС (38) при обязательном обеспечении плановой загрузки люков судна (39). Условием (40) обеспечивается неотрицательность переменных (параметров управления) модели.
В результате реализации модели (38)-(40) отыскивается оптимальный план , компонентам которого соответствуют отрезки времени , на протяжении каждого из которых расстановка ТЛ на судне остается неизменной. При этом указанными отрезками времени охватываются своего рода «полосы» ПСОС с постоянным закреплением ТЛ за люками судна. Склейка таких «полос» в определенной последовательности позволяет получить календарный ПСОС в обобщенной форме.
3.2. Подготовка исходных данных к составлению ПСОС
В данном курсовом проекте ПСОС составляется для выгрузки судна по данным табл.3.1.
Таблица 3.1. Исходные условия построения ПСОС
Параметры
|
Обозначения
|
Значения параметров по люкам
|
1
|
2
|
3
|
4
|
5
|
Загрузка отсеков, т
|

|
876,6
|
1778,3
|
2066,4
|
3293,7
|
1992,35
|
Предел концентрации ТЛ на люках
|

|
1
|
1
|
1
|
2
|
1
|
Производительность ТЛ, т/ч
|

|
23,91
|
23,91
|
23,91
|
23,91
|
23,91
|
Коэффициент снижения производительности ТЛ
|

|
1
|
1
|
1
|
0,9
|
1
|
Количество ТЛ
|

|
5 ( )
|
Определяем множество допустимых вариантов расстановки ТЛ на судне. Эта операция выполняется путем перебора комбинаций распределения ТЛ между люками от носа к корме с соблюдением ограничений на предел концентрации ТЛ на люках.
Полное множество допустимых вариантов расстановки ТЛ на судне для заданного количества ТЛ представлено в табл.3.2.
Таблица 3.2. Варианты расстановки ТЛ на судне
№ люка
|
Предел концентрации ТЛ
|
Номера вариантов расстановки ТЛ по люкам
|
1
|
2
|
3
|
4
|
5
|
1
|
1
|
1
|
|
1
|
1
|
1
|
2
|
1
|
1
|
1
|
|
1
|
1
|
3
|
1
|
1
|
1
|
1
|
|
1
|
4
|
2
|
2
|
2
|
2
|
2
|
1
|
5
|
1
|
|
1
|
1
|
1
|
1
|
Располагая данными табл.3.1-3.2 можно рассчитать по формуле (37) интенсивность обработки люков для каждого варианта расстановки ТЛ.
Для люка №1:
т/ч

Результаты расчетов по всем люкам сведены в табл.3.3.
Таблица 3.3. Интенсивность обработки люков
№ люка
|
Интенсивность обработки люков по вариантам расстановки ТЛ, т/ч
|
Плановая загрузка люка, т
|
1
|
2
|
3
|
4
|
5
|
1
|
23,91
|
0
|
23,91
|
23,91
|
23,91
|
876,6
|
2
|
23,91
|
23,91
|
0
|
23,91
|
23,91
|
1778,3
|
3
|
23,91
|
23,91
|
23,91
|
0
|
23,91
|
2066,4
|
4
|
43,04
|
43,04
|
43,04
|
43,04
|
23,91
|
3293,7
|
5
|
0
|
23,91
|
23,91
|
23,91
|
23,91
|
1992,35
|
По данным о загрузке люков судна и интенсивности их обработки модель (38)-(40) в развернутой форме принимает следующий вид:
;





³ 0,
3.3. Решение задачи и составление рабочей формы ПСОС
Реализация построенной модели достигается с использованием симплекс-метода программы «Microsoft Exel 2000». Решив задачу с помощью этой программы, получили оптимальный план:

Таким образом минимальна продолжительность СОС составляет 87 ч и достигается при использовании первой, второй, третьей и пятой расстановок ТЛ в течение соответственно 3, 50, 12 и 22 часов. По этой информации и данным по вариантам расстановки ТЛ строим ПСОС в обобщенной форме (табл.3.4.)
Таблица 3.4. План стивидорного обслуживания судна
Отрезки времени
, ч
|
Календарное время в часах
|
Рабочие смены
|
Расстановка ТЛ на судне
|
Сменные задания ,т/смену
|
Порядковый номер, 
|
Время работы , ч
|
Объем грузоперевалки , т/см
|
люк №1
|
люк №2
|
люк №3
|
люк №4
|
люк №5
|

|
0-3
|
1
|
3
|
ТЛ №1
|
ТЛ №2
|
ТЛ №3
|
ТЛ №4
|
-
|
344,31
|
ТЛ №5
|
71,73
|
71,73
|
71,73
|
129,12
|

|
4-8
|
4
|
-
|
ТЛ №1
|
ТЛ №2
|
ТЛ №3
|
ТЛ №5
|
459,08
|
ТЛ №4
|
95,64
|
95,64
|
172,16
|
95,64
|
9-16
|
2
|
7
|
-
|
ТЛ №1
|
ТЛ №2
|
ТЛ №3
|
ТЛ №5
|
803,39
|
ТЛ №4
|
167,37
|
167,37
|
301,28
|
167,37
|
17-24
|
3
|
7
|
-
|
ТЛ №1
|
ТЛ №2
|
ТЛ №3
|
ТЛ №5
|
803,39
|
ТЛ №4
|
167,37
|
167,37
|
301,28
|
167,37
|
0-8
|
4
|
7
|
-
|
ТЛ №1
|
ТЛ №2
|
ТЛ №3
|
ТЛ №5
|
803,39
|
ТЛ №4
|
167,37
|
167,37
|
301,28
|
167,37
|
9-16
|
5
|
7
|
-
|
ТЛ №1
|
ТЛ №2
|
ТЛ №3
|
ТЛ №5
|
803,39
|
ТЛ №4
|
167,37
|
167,37
|
301,28
|
167,37
|
17-24
|
6
|
7
|
-
|
ТЛ №1
|
ТЛ №2
|
ТЛ №3
|
ТЛ №5
|
803,39
|
ТЛ №4
|
167,37
|
167,37
|
301,28
|
167,37
|
0-8
|
7
|
7
|
-
|
ТЛ №1
|
ТЛ №2
|
ТЛ №3
|
ТЛ №5
|
803,39
|
ТЛ №4
|
167,37
|
167,37
|
301,28
|
167,37
|
9-12
|
8
|
4
|
-
|
ТЛ №1
|
ТЛ №2
|
ТЛ №3
|
ТЛ №5
|
459,08
|
ТЛ №4
|
95,64
|
95,64
|
172,16
|
95,64
|

|
13-16
|
3
|
ТЛ №1
|
-
|
ТЛ №2
|
ТЛ №3
|
ТЛ №5
|
344,31
|
ТЛ №4
|
71,73
|
71,73
|
129,12
|
71,73
|
17-24
|
9
|
7
|
ТЛ №1
|
-
|
ТЛ №2
|
ТЛ №3
|
ТЛ №5
|
803,39
|
ТЛ №4
|
167,37
|
167,37
|
301,28
|
167,37
|
0-2
|
10
|
2
|
ТЛ №1
|
-
|
ТЛ №2
|
ТЛ №3
|
ТЛ №5
|
229,54
|
ТЛ №4
|
47,82
|
47,82
|
86,08
|
47,82
|

|
3-8
|
5
|
ТЛ №1
|
ТЛ №2
|
ТЛ №3
|
ТЛ №4
|
ТЛ №5
|
597,75
|
119,55
|
119,55
|
119,55
|
119,55
|
119,55
|
9-16
|
11
|
7
|
ТЛ №1
|
ТЛ №2
|
ТЛ №3
|
ТЛ №4
|
ТЛ №5
|
836,85
|
167,37
|
167,37
|
167,37
|
167,37
|
167,37
|
17-24
|
12
|
7
|
ТЛ №1
|
ТЛ №2
|
ТЛ №3
|
ТЛ №4
|
ТЛ №5
|
836,85
|
167,37
|
167,37
|
167,37
|
167,37
|
167,37
|
0-3
|
13
|
3
|
ТЛ №1
|
ТЛ №2
|
ТЛ №3
|
ТЛ №4
|
ТЛ №5
|
358,65
|
71,73
|
71,73
|
71,73
|
71,73
|
71,73
|
4. Оперативный анализ результатов стивидорного обслуживания судна
4.1. Исходные положения
Данная задача решается в предположении, что процесс СОС завершился. При таком условии становятся известными фактические значения параметров-показателей ПСОС, к числу которых относятся:
· продолжительность обработки судна ( );
· загрузка судна ( );
· производительность ТЛ ( );
· количество ТЛ ( );
· уровень организации СОС, оцениваемый коэффициентом £ 1.
Перечисленные показатели СОС связываются зависимостью
, (41)
Аналогично определяется связь и между плановыми показателями СОС
, (42)
В обоих случаях показатель продолжительности СОС ( ) является в понятиях теории экономического анализа результативным показателем, а параметры, от которых он зависит ( ), выступают в качестве факторных показателей.
Анализ результатов СОС состоит, с одной стороны, в сопоставлении планового и фактических значений продолжительности СОС, а с другой, в оценке влияния на ее приращение факторных показателей.
4.2. Версия реализации ПСОС
Фактические значения показателей СОС определяются расчетным путем.
, (43)
где = 0,95 – коэффициент, с помощью которого имитируется уровень выполнения плана загрузки судна.
9 506,98 т
, (43)
где = 1,35 – коэффициент, с помощью которого имитируется уровень выполнения плановой производительности.
, (44)
т/ч
31,05 т/ч
, (45)
где = 0,75 – коэффициент, с помощью которого имитируется уровень выполнения плана по использованию ТЛ.
4
, (46)
где = 0,85 – коэффициент, с помощью которого имитируется уровень выполнения плана по организации СОС.
0,85
По формуле (41) определяем фактическую продолжительность СОС:
90,05 ч
4.3. Анализ полученных результатов
Анализ результатов СОС производится на основе полученных данных по отклонению факторных показателей ( ), которые определяются как разность между их фактическими и плановыми значениями. Результаты таких расчетов приведены в табл.4.1.
Таблица 4.1. Уровень выполнения плановых показателей
Показатели
|
Обозначения
|
Значения
|
Отклонения ( )
|
Коэффициенты
|
план
|
факт
|
Загрузка судна, т
|

|
10007,35
|
9506,98
|
-500,37
|
0,95
|
Производительность ТЛ, т/ч
|

|
23
|
31,05
|
8,05
|
1,35
|
Количество ТЛ
|

|
5
|
4
|
-1
|
0,75
|
Коэффициент, учитывающий уровень организации СОС
|

|
1
|
0,85
|
-0,15
|
0,85
|
Продолжительность СОС, ч
|

|
87
|
90,05
|
3,05
|
|
Используя интегральный метод анализа, определяем влияние факторов и на приращение результата показателя .
, (47)
-4,5 ч
, (48)
-26,9 ч
, (49)
19,95 ч
, (50)
14,5 ч
Полное приращение результата показателя определяем по формуле:
, (51)
3,05 ч
Таким образом за счет уменьшения загрузки судна и увеличения фактической производительности ТЛ плановая продолжительность СОС должна была сократиться на 31,4 ч. Однако, вследствие уменьшения планового количества ТЛ и снижения уровня организации СОС время обработки судна могло возрасти на 34,45 ч. В итоге же фактическая продолжительность СОС под совокупным воздействием всех четырех факторов увеличилась на 3,05 ч.
Заключение
В ходе выполнения данного курсового проекта нами была проведена работа по планированию и анализу результатов стивидорного обслуживания судна.
Основываясь на данных о предложенных грузах (колеса железнодорожные и пробка в кипах) и расчетном судне («Бежица»), а также используя информацию о способах перегрузки указанных грузов в Ильичевском морском торговом порту, мы определили наилучшие варианта обработки грузов с целью минимизировать время стоянки судна в порту и расходы порта на производственные ресурсы.
Поскольку в стивидорном обслуживании судна приоритетную роль играют судовая и частично кордонная операции, то себестоимость работ была рассчитана в виде полной удельной себестоимости перегрузки по каждому грузу (4,168 и 8,632 грн/т, соответственно), а также в виде удельной себестоимости стивидорных работ (3,244 и 5,818 грн/т, соответственно). При этом прибыль порта в составит: полная – 44 795,1 грн., от стивидорных работ – 33 573,6 грн.
Полученные результаты послужили основой для построения календарного плана стивидорного обслуживания судна. Для его построения нами была разработана математическая модель, которая позволила получить в результате минимальную продолжительность обработки судна – 87 ч.
Однако реализация плановых значений на 100 % не всегда возможна. Поэтому нами был проведен анализ влияния изменений различных факторов на время стивидорного обслуживания судна. В результате мы получили, что при уменьшении загрузки судна на 5 %, увеличении средневзвешенной производительности на 35 %, уменьшении планового количества технологических линий на 25 % и снижении уровня организации СОС на 15 % суммарное время обработки судна возрастет на 3,05 ч.
Полученные результаты свидетельствуют о том, что при изменении факторных показателей, которое часто имеет место при практической реализации плановых заданий, результирующее значение времени стивидорного обслуживания судна может меняться.
Однако в рассматриваемом случае мы можем говорить о том, что отклонение фактического значения от оптимального не окажет губительного влияния на дальнейшую работу судна и порта, т.к. это отклонение незначительно.
Таким образом, полученные результаты являются допустимыми и их можно принять к реализации.
Литература:
1.
Ветренко Л.Д., Ананьина В.З., Степанец А.В. Организация и технология перегрузочных процессов в морских портах. – М.:Транспорт, 1989.
2.
Шматов Э.М. Справочник стивидора – М.: Транспорт, 1975.
3.
Гаврилов М.Н. Транспортные характеристики грузов: Справочное руководство – М.: В/О «Мортехинформреклама». Морской транспорт, 1994.
4.
Магамадов А.Р. Оптимизация оперативного планирования работы порта. – М.: Транспорт, 1979.
5.
Механик Л.А., Токман Г.И. Портовые перегрузочные работы (планирование, организация и технология).-М.: Транспорт, 1983.
|