А.Г. Солодянкин
КУРСОВОЙ
ПРОЕКТ
2003
СОДЕРЖАНИЕ
Введение 3
1 Анализ производственной деятельности предприятия 5
1.1 Общая характеристика предприятия 5
1.2 Организация ТО и ТР машин 7
1.3 Обоснование темы проекта 9
2 Планирование и организация ТО и ТР автомобилей на предприятии 10
2.1 Расчетно-технологическая часть 10
2.1.1 Корректирование межремонтного пробега 10
2.1.2 Расчет производственной программы 11
2.1.3 Определение трудоемкости работ по ТР за год 17
2.1.4 Определение трудоемкости диагностирования 21
2.1.5 Определение годовой трудоемкости мастерской 23
2.1.6 Расчет численности рабочих 24
2.2 Организация и выполнение работ по ТО и ТР 25
2.2.1 Выбор и обоснование метода организации ТО и ТР подвижного состава
25
2.2.2 Технологический процесс ТО и ТР 26
2.2.3 Планирование и контроль проведения ТО и ТР подвижного
состава 27
2.2.4 Установление режимов работ 28
2.2.5 Расположение исполнителей по специальностям и квалификациям 29
2.2.6 Подбор технологического оборудования 30
2.2.7 Расчет производственных площадей 34
3 Технологическая разработка процесса ТР сцепления автомобиля
ГАЗ-3110 35
3.1 Анализ принимаемого технологического процесса 35
3.2 Составление документации технологического процесса 36
3.3 Описание разрабатываемого технологического процесса 37
3.4 Нормы времени на одну операцию 41
4 Безопасность жизнедеятельности на производстве 43
4.1 Организация работ по созданию здоровых и безопасных условий
труда 43
4.2 Инструкция по охране труда при выполнении технологического
процесса 44
4.2.1 Общие требования безопасности 46
4.2.2 Требования безопасности перед началом работы 49
4.2.3 Требования безопасности во время работы 50
4.2.4 Требования безопасности в аварийных ситуациях 51
4.2.5 Требования безопасности по окончании работ 52
4.3 Пожарная безопасность 53
5 Охрана окружающей среды 54
6 Технико-экономическая оценка проекта 56
Заключение 61
Литература 62
ВВЕДЕНИЕ
Автомобильный транспорт в отличии от других видов транспортных средств является наиболее массовым и удобным для перевозки грузов и пассажиров на относительно небольшие расстояния. Он обладает большей маневренностью, хорошей приспосабливаемостью и проходимостью в различных климатических и биографических условиях.
Автомобильный транспорт играет важную роль в транспортной системе страны. Работой автомобильного транспорта обеспечивается нормальное функционирование предприятий. Свыше 80% объема всех перевозимых грузов приходится на этот вид транспорта, именно автомобильный подвоз является началом и завершением любых перевозок (железнодорожных, морских, воздушных). Ежедневно автобусы и легковые автомобили перевозят десятки миллионов людей.
Повышение надежности автомобиля и снижение затрат на их содержание составляют одну из важнейших задач народного хозяйства. С целью решения данной проблемы, заводы изготовители транспортных средств установили нормы технического обслуживания и ремонта с учетом эксплуатации.
Безотказная работа автомобиля в значительной степени зависит от своевременного и качественного выполнения технического обслуживания.
Техническое обслуживание предназначено для поддержки автомобилей в работоспособном состоянии приличном внешнем виде. Для уменьшения интенсивного изнашивания деталей, а также для выявления отказов и неисправностей с целью их своевременного устранения.
Техническое обслуживание является профилактическим мероприятием, проводится в плановом порядке через определенный пробег или срок службы. Из-за несвоевременного или некачественного технического обслуживания происходит быстрый износ агрегатов и узлов двигателя, а также увеличивается вероятность поломок автомобиля.
Курсовое проектирование – составная часть учебного процесса на завершающем этапе подготовки специалиста. В процессе курсового проектирования, учащийся должен закрепить, углубить и обобщить знания в области и технологии технического обслуживания и текущего ремонта автомобилей и двигателей, развивать навыки самостоятельных работ для решения практических задач при решение вопросов производственного практического характера.
Курсовой проект содержит различную работу прогрессивной технологии и организации рабочих на производственных участках.
1. Анализ производственной деятельности предприятия
1.1 Общая характеристика предприятия
Предприятие организовано для перевозки грузов и пассажиров. По характеру перевозок предприятие смешанное, а по принадлежности и назначению обслуживающее клиентуру независимо от ведомственной принадлежности и восполняющее перевозки для организаций, в состав которого они входят.
Основные задачи предприятия; организует и выполняет перевозки в соответствии с планом, хранение, техническое обслуживание и ремонт собственного подвижного состава, материальное техническое снабжение.
Для выполнения этих задач на предприятии предусмотрены службы эксплуатации, техническая и управления.
Задачи этого предприятия сводятся к поддержанию своего подвижного состава в исправном состоянии и выпуску его на линию, где его работой руководит центральная диспетчерская.
Служба эксплуатации занимается вопросами выполнения перевозок грузов и пассажиров. Они принимают заказы на перевозки, и заключает договоры с клиентурой, составляет планы перевозок и руководит их выполнением, ведет учет выполненной работы.
Техническая служба обеспечивает исправное состояние подвижного состава и подготовку выполнения перевозок. Она разрабатывает график технического обслуживания и обеспечивает их восполнение, ведет учет автомобилей, занимается техническим нормированием. В распоряжении технической службы находятся зоны: зона стоянки технического обслуживания подвижного состава, зона ремонта, мастерские и другие производственные участки, связанные с поддержанием подвижного состава в исправном состоянии, а также отдел главной механики.
Отдел снабжения обеспечивает всеми необходимыми эксплуатационными и другими материалами.
Предприятие повышает квалификацию своих рабочих. Увеличивает свой автопарк. Ведет учет материальных и других ценностей предприятия. Составляет финансовые отчеты.
 1.2 Организация обслуживания и текущего ремонта автомобилей на предприятии
   
Рисунок 1.1 - схема организации ТО и ТР
Согласно схеме организации процесса технического обслуживания (ТО) текущего ремонта (ТР) автомобиля в автотранспортном предприятии (АТП), автомобиля прибывшего с линии в первую очередь проходят контрольно пропускной пункт (КПП). Здесь на автомобиль, требующий техническое обслуживание (по плану, графику) или текущего ремонта (по заявке водителя или заключению контролера механика), выписываем листок учета с указанием неисправности или требуемого по плану, графику, вида обслуживания.
Автомобили, требующие по графику ТО-1 или То-2, направляются сначала на выполнение ЕО, то есть уборочно-моющих, обтирающих и заправочных работ. После выполнения ежедневного обслуживания машины направляются в зону ожидания, а затем в соответствующие производственные зоны предприятия (на посты диагностики или ТО), а после выполнения ТО, а зону стоянки. Автомобили, проходящие через контрольно пропускной пункт и требующие в результате заявки водителя и осмотра контролера механика ТР с соответствующей отметкой в листе учета, направляют на посты ЕО и далее через зону ожидания в зону ремонта, для устранения неисправностей. После устранения неисправностей с соответствующей отметкой в листе учета автомобиль устанавливается на стоянку. В зону ремонта автомобили могут поступать из зоны ТО при обнаружении неисправностей требующих текущего ремонта.
При неисправности, возникающей на линии, водитель вызывает автомобиль технической помощи. Дежурный механик КПП выписывает листок учета автомобиля, на ремонт автомобиля на линии, который переходит механику автомобиля технической помощи листок учета переходит дежурному механику КПП.
Исправный автомобиль, не требующий ТО, отправляют в зону ЕО, после чего устанавливается в зону стоянки.
1.3 Выбор и обоснование темы курсового проекта
Автомобильная промышленность страны постоянно совершенствует конструкцию выпускаемых автомобилей с целью снижения расхода топлива, уменьшения загрязнения окружающей среды, повышения безопасности дорожного движения.
Однако эффективное использование автомобилей зависит не только от совершенства конструкции. Во многом оно зависит от качества и своевременного ТО и ремонта. В качестве обслуживания и своевременности ремонта важную роль играет эффективность диагностирования.
На безопасность дорожного движения прямое влияние оказывает состояние тормозной системы. Для того, чтобы свести на ноль влияние не- эффективности тормозной системы на автомобильную аварийность я считаю необходимо развить (новое направление проблемы надежности диагностики) как вследствие своей молодости, а также из-за исключительного разнообразия и сложности объектов диагностирования автомобилей пока еще не превратилась в строго формализованную систему. Поэтому для успешного диагностирования необходим пока только малый опыт и инженерная интуиция.
Марка автомобиля
|
Количество штук
|
Пробег тыс. км.
|
1
|
2
|
3
|
ГАЗ-3102
ГАЗ-3307
ГАЗ-3110
ИЖ-2126
ИЖ-412
ИЖ-2715
КамАЗ-5511
КамАЗ-54112
ЗИЛ-433480
ЗИЛ-130
УАЗ-3151
ПАЗ-3205
УРАЛ-4320
АЗЛК-2141
ВАЗ-2107
ВАЗ-2109
ВАЗ-2106
КВЗ-3207
Прицеп
|
2
7
1
3
4
2
2
3
5
2
1
1
3
6
2
3
6
1
4
|
25
15
25
20
75
80
35
60
40
5
45
50
55
65
70
10
15
20
30
|
2.Планирование и организация ТО и ТР автомобилей на предприятии.
2.1 Расчетно-технологическая часть
2.1.1 Корректирование межремонтного пробега
Таблица 2.1
Список автомобилей
Действительный пробег автомобилей до капитального ремонта вычисляем по формуле [1 с 16]
(1)
где K1
=0.9-коэффициент корректирования нормативов в зависимости от условий эксплуатации с.26[7].
K1
= 1- коэффициент корректирования нормативов в зависимости от модификации состава и организации его работы с.26 [1].
K3
=0.9- коэффициент корректирования нормативов в зависимости от природно-климатических условий с.27 [1].
км - нормативный пробег до КР с.17 [1]

Корректированный удельный простой на ТО и ТР по формуле с.62[2]

где - нормативный удельный простой в ТР с.332[11]
- коэффициент корректирования нормативов простоя в техническом обслуживании и ремонте в зависимости от пробега с начала эксплуатации с.27[1].
дней/1000км
Коэффициент технической готовности по формуле с.3 [78]

где Dэ
– число дней эксплуатации за цикл нахождения автомобиля в исправном состоянии.

где - среднесуточный пробег автомобилей

- число дней простоя в ТР


- число дней простоя в КР

Определяем коэффициент выпуска подвижного состава по формуле. с. 60 [7].

где - количество рабочих дней в году; для автобусов
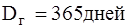
KГ
=0,95 – коэффициент неэксплуатационных простоев

Ожидаемый годовой пробег автомобилей в группе по формуле

где N - количество автомобилей в группе
2.1.2 Расчет производственной программы
Количество ЕО по формуле с.113 [4]


Действительный пробег подвижного состава до ТО-1 и ТО-2 по формуле сю28 [6]

где - нормативный пробег до ТО-1

Действительный пробег до ТО-2 по формуле с. 25[3]


Количество ТО-2 для групп автомобилей по формуле с. 172 [6]


Количество ТО-1для групп автомобилей по формуле с. 132 [2]


Количество СТО для групп автомобилей по формуле Сю 80[4]


Действительная трудоемкость ЕО по формуле с. 263 [5]

где - нормативная трудоемкость ЕО
K2
– коэффициент корректирования нормативов в зависимости от модификации подвижного состава и организации его работы.
K5
- коэффициент корректирования нормативов трудоемкости ТО и ТР в зависимости от количества обслуживаемых автомобилей на АТП и количества технологических групп подвижного состава.

Действительная трудоемкость ТО-2 по формуле с. 16 [3]


Действительная трудоемкость ТО-2 по формуле с. 132[6]


Действительная трудоемкость ЕО по формуле с.168 [1]

Полная трудоемкость ЕО для групп автомобилей за год по формуле с.29 [1]

где NЕО
- количество ЕО за год
tЕО
- действительная трудоемкость ЕО

Полная трудоемкость ТО-1 для групп автомобилей за год по формуле с. 268 [2].

где tТО-1
- действительная трудоемкость ТО-1
NТО-1
– количество ТО-1 для групп автомобилей за год.

Полная трудоемкость ТО-2 для групп автомобилей за год по формуле с. 183[3].


Полная трудоемкость СТО для групп автомобилей за год по формуле с. 321[4].

где tСТО
=2,415 чел/ч - см. формулу (17)
NСТО
=2 – см. формулу (13)

Действительная трудоемкость ТР по формуле с. 59[7]

где -нормативная трудоемкость ТР
K4
- коэффициент корректирования нормативов удельной трудоемкость ТР и продолжительности простоя в То и ремонте в зависимости от пробега с начала эксплуатации.
K5
- коэффициент корректирования нормативов трудоемкости ТО и ТР в зависимости от количества обслуживаемых автомобилей на АТП и количества технологических совместных групп подвижного состава

Общая годовая трудоемкость ТР на 1000км пробега

где tТР
- действительная трудоемкость ТР
Lг
– ожидаемый годовой пробег количества автомобиля в группе

2.1.3 Определение трудоемкость работ по ТО и ТР за год
Таблица 2.2
Характеристика автопарка
Группа автомобилей
|
Нормативный пробег до КР
|
Число автомобилей прошедших КР
|
Число автомобилей не прошедших КР
|
ГАЗ-3102
ГАЗ-3107
ГАЗ-3110
ИЖ-2126
ИЖ-412
ИЖ-2715
КаМАЗ-335511
КаМАЗ-54112
ЗИЛ-433480
ЗИЛ-130
УАЗ-3151
ПАЗ-3205
УРАЛ-4320
АЗЛК-2141
ВАЗ-2107
ВАЗ-2109
ВАЗ-2106
КВЗ-3207
Прицеп
|
300
100
300
125
125
100
300
250
250
300
300
320
250
125
125
125
125
320
100
|
0
0
0
0
0
0
0
0
0
0
0
0
0
0
0
0
0
0
0
|
2
7
1
3
4
2
2
3
5
2
1
1
3
6
2
3
6
1
4
|
Годовая трудоемкость ТО-1 по формуле с. 36[4]
, 
где tТО-1
- действительная трудоемкость ТО-1
NТО-1
– количество ТО-1 за год
Tспр
(1) – трудоемкость сопутствующего ремонта при ТО-1

где LТР
– регламентируемая доля сопутствующего ремонта при ТО-1 и ТО-2

Трудоемкость сопутствующего ремонта при ТО-1


Трудоемкость сопутствующего ремонта при ТО-2

где Tспр
(2) - трудоемкость сопутствующего ремонта при ТО-2


где Tспр
(2) - трудоемкость сопутствующего ремонта при ТО-2
NТО-2 –
количество ТО-2 для групп автомобилей

Общая годовая трудоемкость всех ТО по формуле С. 38[1]

где ТЕО
- полная трудоемкость ЕО для групп автомобилей за год
TТО-1
– полная трудоемкость ТО-1 для групп автомобилей за год
TТО-2
- полная трудоемкость ТО-2 для групп автомобилей за год
Tсто - – полная трудоемкость СТО для групп автомобилей за год

Годовая трудоемкость постовых работ после ТР по формуле с.178[1]

где Tспр
(1) - трудоемкость сопутствующего ремонта при проведении ТО-1
Tспр
- трудоемкость сопутствующего ремонта при проведении ТО-2

Общи объем рабат по техническим воздействиям на подвижной состав по формуле с. 311[1]

где - общая годовая трудоемкость всех ТО
- годовая трудоемкость постовых работ после ТР

Таблица 2.3 Действительная трудоемкость выполненных работ
Марка автомобиля
|
(t) Трудоемкость чел/ч
|
ЕО
|
ТО-1
|
ТО-2
|
СО
|
1
|
2
|
3
|
4
|
5
|
ГАЗ-3102
ГАЗ-3107
ГАЗ-3110
ИЖ-2126
ИЖ-412
ИЖ-2715
КаМАЗ-335511
КаМАЗ-54112
ЗИЛ-433480
ЗИЛ-130
УАЗ-3151
ПАЗ-3205
УРАЛ-4320
АЗЛК-2141
ВАЗ-2107
ВАЗ-2109
ВАЗ-2106
КВЗ-3207
Прицеп
|
0,4
0,5
0,4
0,3
0,6
0,2
0,4
0,5
0,6
0,5
0,4
0,8
0,6
0,3
0,3
0,3
0,3
0,8
0,5
|
2,9
2,4
2,9
2,6
3,3
2,5
2,9
3,8
4,0
2,9
2,9
6,3
4,0
2,6
2,6
2,6
2,6
6,3
1,8
|
12,1
10,4
12,1
10,6
13,5
8,3
12,5
16,1
16,9
12,2
12,1
20,7
16,9
10,6
10,6
10,6
10,6
20,7
7,0
|
2,4
2,1
2,4
2,1
2,7
1,7
2,5
3,2
3,4
2,4
2,4
4,1
3,4
2,1
2,1
2,1
2,1
4,1
1,4
|
2.1.4 Определение трудоемкости диагностирования
Трудоемкость диагностирования комплексных работ Д-1 по формуле с. 124[3]

где CД-1
=8 – доля трудоемкости диагностирования в общей трудоемкости ТО-1

трудоемкость поэлементного диагностирования комплекса работ Д-2 по формуле с. 131[2]

где СД-2
=10 - доля трудоемкости диагностирования в общей трудоемкости ТО-2
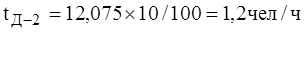
Количество общего диагностирования за год комплексных работ Д-1 по формуле с. 142[2]

где NТО-1
и NТО-2
– количество ТО-1 и ТО-2 соответственно за год

Количество поэлементного диагностирования комплекса работ Д-2 по формуле с. 72[1]

где NТО-2
– количество ТО-2 для групп автомобилей за год

Трудоемкость общего диагностирования комплекса работ Д-1 и поэлементного диагностирования комплекса работ Д-2 по формуле с. 38[1]

где tД-1
- трудоемкость диагностирования комплекса работ Д-1
NД-1
– количество общего диагностирования за год комплекса работ Д-1
TД-2
– трудоемкость поэлементного диагностирования комплекса работ Д-2
NД-2
- трудоемкость поэлементного диагностирования комплекса работ Д-2
2.1.5 Определение годовой трудоемкости мастерской
где Tдоп
– объем дополнительных работ, определенный из расчета от основной трудоемкости работ
где 8-10% - уходит на ремонт оборудования
5-7% - на восстановления и изготовление деталей
3-5% - на ремонт и изготовление технической оснастки и инструмента
10% - на прочие (неучтенные) работы
 
2.1.6 Расчет численности производственных рабочих
Явочное количество рабочих по формуле с. 210[6]

где Фн
=2070ч – номинальный годовой фонд рабочего времени

Списочное количество рабочих по формуле с. 215[6]

где Фд
=1700ч – действительный годовой фонд рабочего времени

2.2 Организация выполнения работ по техническому обслуживанию и ремонту подвижного состава.
2.2.1 Выбор метода организации технического обслуживания и ремонта подвижного состава.
Организация технического обслуживания и ремонта подвижного состава основывается на принципах моральной и материальной ответственности конкретных исполнителей за качество выполнения технического обслуживания и ремонта подвижного состава. Этот способ организации хорош тем, что рабочие будут качественнее выполнять работу, которую им назначили. Будет серьезный подход даже к самой простой детали. Рабочие будут заинтересованы в своем деле.
Вследствие этих факторов предприятие обретает авторитет качественного предприятия.
Организация предприятия использует метод универсальных постов, так как организация предприятия данным методом предусматривает то, что все работы, предусмотренные для данного вида ТО, выполняются в полном объеме на одном посту группой исполнителей, состоящих из рабочих разных специальностей или рабочих-универсалов. Этот метод эффективен тем, что на предприятии работает определенное минимальное количество рабочих, что обеспечивает минимальные затраты на заработную плату и вследствие отсутствия рабочего, его можно заменить другим человеком.
ТО на данном предприятии тупикового типа из-за малого количества рабочих. Транспортное средство загоняют на станцию технического обслуживания, и специалисты проводят ремонт одновременно, не создавая помех друг другу, за более короткое время.
2.2.2 Технологический процесс технического обслуживания
Автомобиль, прибывающий с линии, направляется на ТО, ремонт или стоянку. В любом случае автомобиль проходит наружную очистку и мойку, затем устанавливается на техническое обслуживание или ремонт. Ежедневное обслуживание проводит водитель на месте стоянки автомобиля в гараже, при этом осуществляются все необходимые записи в путевом листе. Проводится внешний осмотр, проверка действия систем сигнализации и управления. Заправку топливом и маслом производят на заправочной станции.
Автомобиль после мойки для прохождения диагностики в зависимости от номера ТО направляют на соответствующие линии, оборудованные установками.
На линии технического обслуживания №1 выполняют контрольно-осмотровые, крепежно-регулировочные, смазочно-очистительные и другие виды работ. Также выполняют экспресс-диагностирование и сезонное обслуживание.
На линии технического обслуживания №2 и текущего ремонта проверяют схождение колес, тормозные и тяговые качества автомобиля.
Текущий ремонт автомобиля производят тупиковым методом на специальном участке, имеющем необходимое технологическое оборудование.
Данные работы проводятся в соответствии со схемой организации технического обслуживания и текущего ремонта на автотранспортном предприятии в соответствии с рисунком 1.1.
2.2.3 Планирование и контроль проведения ТО и ТР подвижного состава.
Полученное расчетом среднее количество технического обслуживания, которое следует выполнять ежедневно, необходимо уточнять в процессе оперативного планирования с учетом изменения пробега по месяцам. Конкретный день постановки автомобиля на ТО как правило устанавливается на основании фактического пробега с учетом условий эксплуатации каждого автомобиля. День установки автомобиля определяется по плану-графику. Для определения дня постановки автомобиля на ТО по графику, принятый пробег между обслуживаниями, делят на среднесуточный пробег одной группы автомобилей. План-график составляют на весь год, но чаще – на два-три месяца. Планирование ТО по плану-графику не позволяет учесть фактическое количество дней работы и среднесуточный пробег автомобилей, поэтому фактический пробег автомобиля по плану-графику значительно отличается от принятого пробега при планировании. Однако он позволяет запланировать и определить предварительные затраты на техническое обслуживание и ремонт.
2.2.4
Установление режимов работы.
Режим работы предприятия – это характер рабочей недели, число рабочих дней, смен и их продолжительность.
На автотранспортных предприятиях режим работы планируют по прерывной рабочей неделе в одну смену.
Рабочая неделя состоит из пяти рабочих дней и двух выходных. Рабочий день длится восемь часов.
Также один час отводится на обед и существует два производственных перерыва с 9.20 до 9.40 и с 14.20 до 14.40. Последний рабочий день недели бывает укороченным и длится семь часов.
2.2.5 Распределение исполнителей по специальностям и квалификациям
Штат пункта ТО и ТР
Таблица 2.1
Специальность
|
Разряд
|
IV
|
V
|
VI
|
Слесарь - ремонтник
|
________
|
1
|
1
|
Карбюраторщик
|
________
|
1
|
________
|
Слесарь - диагростик
|
________
|
________
|
1
|
Электрогазосварщик
|
________
|
1
|
________
|
Аккумуляторщик
|
1
|
________
|
________
|
Всего
|
1
|
3
|
2
|
На пункте ТО и ТР работает 6 человек. Средний разряд рабочих составляет 5,16. Это говорит о том, что все рабочие хорошо обучены и способны справится с работой и сделать ее качественно.
2.2.6 Подбор технологического оборудования
Подбор осуществляется на основании имеющегося оборудования и согласно рекомендации по оснащению мастерских всем необходимым оборудованием. Оборудование располагают в соответствии с требованиями и нормами по размещению технологического оборудования. Расстояние от капитальной стены составляет 0,6 метров, расстояние между оборудованием – не менее 1,2 метра .
Перечень оборудования
Таблица 2.2
№
|
Наименование оборудования
|
Марка мод.
|
Краткая тех. Характеристика
|
Кол-во шт.
|
Габариты ,мм
|
1
|
2
|
3
|
4
|
5
|
6
|
1
|
Пароводоструйная очистительная установка
|
ОМ-
3360
|
Производительность:
1000кг/ч .рабочее давление
16-20кгс/см2
|
1
|
1400*830*1300
|
2
|
Компрессоваккумная установка
|
КИ-
4942
|
Производительность:
3м3
/ч
|
1
|
796*336*556
|
3
|
Стробоскоп
|
КИ-
4890
|
1
|
500*320*200
|
4
|
Индикатор расхода
газов
|
КИ-
4887
|
1
|
235*180*190
|
5
|
Приспособление для регулировки теплового зазора клапанов
|
ПИМ-
4816
|
1
|
220*125*80
|
6
|
Стетоскоп
|
КИ-
1154
|
1
|
635*50
|
7
|
Компрессиметр
|
КИ-
861
|
1
|
8
|
Прибор для опреде-
ления технического
состояния цилиндро-
поршневой группы
|
К-
69М
|
1
|
258*125*132
|
9
|
Стенд для проверки
электро оборудова-
ния и системы зажи-гания
|
537
|
Масса 66кг
|
1
|
755*1000*
*1600
|
10
|
Токарно-винторез.
станок
|
16К20
|
РМЦ 1000
|
1
|
2380*1093*
*2400
|
11
|
Вертикально-сверлильный станок
|
2Н125
|
d сверла 25мм
|
2
|
1355*885*
*2400
|
12
|
Точильно-шлифовальрый станок
|
3М634
|
d круга 400мм
|
1
|
900*600*
*1200
|
13
|
Наковальня
двурогая
|
ГОСТ
11548-
65
|
2
|
600*150
|
14
|
Стенд для испытания ТНВД
|
КИ-
921М
|
1
|
1200*600
*850
|
15
|
Верстак
|
ОРГ-
4968
|
4
|
1710*750
*850
|
16
|
Шкаф
|
ОРГ
4991
|
4
|
1700*900*
*950
|
17
|
Стенд универсальный для разборки и сборки двигателей, КПП, и компресоров
|
ОПР-
647
|
3
|
1006*680*
*950
|
18
|
Шкаф для зарядки АКБ
|
ПИМ-
222М
|
1
|
1060*812*
*2100
|
19
|
Стенд для разборки и сборки задних и передних мостов
|
ОПР-689
|
2
|
970*680*
*1130
|
20
|
Электровулканизатор
|
М6140
|
1
|
350*320*450
|
21
|
Комплект ручного шиноремонтного инструмента
|
ОШ-
1319А
|
1
|
680*280*130
|
22
|
Таль электрическая передвижная
|
ТЭЗ-
511
|
Qгп
=3,0т
|
1
|
23
|
Тележка ручная
|
Д-
1145
|
3
|
1150*500*
*700
|
24
|
Верстак на 2 рабочих места
|
ОРГ-
1268-
01-070
|
3
|
2400*800*
*805
|
25
|
Ванна для проверки камер
|
Р-908
|
1
|
900*700*
*700
|
26
|
Электромеханический солидолонагнетатель
|
НИИАТ
390
|
2
|
690*380*
*782
|
27
|
Подъемник электромеханический двухстоячный стационарный
|
П180Е-
17
|
Qгп
=3,5т; высота подъема: 1820мм;мощность:
2*15кВт
|
2
|
3722*3130*
*2593
|
28
|
Подъемник электромеханический
Четырехсеоячный со
Стендом для контроля углов установки колес
|
П178
Д-он
|
Qгп
=3,5т;
мощность:
2*15кВт
|
2
|
4930*2960*
*2095
|
29
|
Комплект изделий для очистки и проверки свечей зажигания
|
3203
|
Давление: 3-6кгс/см2
мощность:
0,15кВт
|
1
|
30
|
Однопостовой сварочный трансформатор
|
ТС-
300
|
20кв*А
110…385А
|
1
|
600*324*
*1020
|
31
|
Стол для электрогазосварочных работ
|
ОКС-
7523
|
1
|
1100*750*
*650
|
32
|
Инструмент автомеханика
|
И-
132
|
6
|
33
|
Тиски
|
П-140
|
6
|
Оборудование подобрано согласно рекомендаций и общая площадь оборудования составляет 84,6м2
2.2.7 Расчет производственных площадей
Площадь производственного участка определяется по площади занимаемого оборудования и переходным коэффициентом.

где Fоб
- площади оборудования, м2
;
Fм
=19,5 (площадь самого крупного автомобиля КаМАЗ – 5511) – площадь машин, м2
;
- коэффициент, учитывающий проходы и проезды;

Площади складов материалов и запчастей определяют исходя из количества материалов и запчастей.

где Qг
– (принимаем массу материала 12,5% массы автомобиля, массу запчастей 17% от массы автомобиля) – годовая потребность в материалах и запчастях, кг;
tм
=3 – срок хранения материалов и запчастей, мес.;

Площадь склада
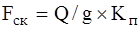
где g=2 – допустимая нагрузка на 1м2
площади склада
Kп
=0,3 – коэффициент проходов и проездов;

3. Технологическая разработка процесса ТР сцепления автомобиля ГАЗ-3110
3.1 Анализ применения технологических процессов
Текущий ремонт (ТР) автомобилей в АТП производится по потребности, выявляемой водителем в процессе эксплуатации, при ежедневных контрольных осмотрах механиками (при возвращении автомобиля с линии), а также в процессе проведения ТО-1 и ТО-2 при обнаружении сверхобъемных работ.
В целях повышения коэффициента технической готовности парка (и т.п.), ТР стараются по возможности проводить в межсменное время, обычно в вечернее и ночное. Исключение составляют трудоемкие работы по замене крупных агрегатов. Их следует проводить в дневную смену, наиболее благоприятную для работы. К тому же в это время функционирует основной склад и склад агрегатов. Проводят ТР в специально отведенных зонах на подъемниках или осмотровых канавах, преимущественно на постах тупикового типа. Поточный метод при проведении ТР не приемлем ввиду слишком большой разницы как по объему, так и по видам работ в каждом конкретном случае проведения ТР. Для уменьшения простоя автомобиля в ТР все большее распространение находит использование специализированных постов для выполнения конкретных трудоемких работ с использованием соответствующего современного высокопроизводительного оборудования, а также внедрение агрегатного метода ремонта, когда вместо неисправного узла или агрегата сразу же ставят на автомобиль, заранее отремонтированный из оборотного фонда.
3.2 Составление документации технологического процесса
Проектирование технологических процессов выполняют в соответствии с требованиями стандартов ЕСКД (ГОСТ 2.601-68…ГОСТ 2.605-68) и ЕСКД (ГОСТ 3.1401-74 и ГОСТ 3.1423-75).
Проектирование технологических процессов ТР заключается в составлении карт эскизов, ведомости оснастки, карты типового технологического процесса ТР и ведомости деталей к этому процессу.
Разработку нормы эскизов выполняют по форме 5 (ГОСТ 3.1105-74). Эскиз сборочной единицы или всего изделия выполняют от руки без соблюдения масштаба. При необходимости на карте эскизов справа от изображения или под ним приводят технические требования по ГОСТ 2.316-68. На карте необходимо указать наименование и номер по каталогу сборочной единицы, число листов и номера операций, к которому сделан эскиз.
Разработка карты типового технологического процесса ТР. Карты типовых технологических процессов (КТП) составляют на каждый вид ТР, определяемый характером сложности ТР (ГОСТ 3.115-79, форма 8).
На карте указывают: номер операции (кратный пяти), наименование оборудования с указанием инвентарного номера по действующему классификатору.
3.3 Описание разрабатываемого технологического процесса
Ремонт сцепления и гидропривода. Снятие сцепления необходимо для проведения ремонтных работ. Сцепление можно снять с автомобиля, не снимая двигатель. Для этого автомобиль следует установить на эстакаду, подъемник или смотровую яму, чтобы обеспечить удобный доступ к сцеплению снизу.
Для снятия сцепления необходимо:
- отсоединить от коробки передач рычаг переключения передач. Для этого изнутри кузова поднять к рукоятке рычага наружный резиновый уплотнитель, отвернуть колпак, расположенный на горловине механизма переключения передач, и вытащить рычаг вверх;
- отсоединить оттяжную пружину и трос от промежуточного рычага привода ручного тормоза;
- снять карданный вал, выполняя указания по его снятию, изложенные в разделе «Карданная передача»;
- отсоединить от коробки передач гибкий вал привода спидометра и провод включателя света заднего хода;
- отвернуть два болта крепления рабочего цилиндра к картеру и поднять вверх рабочий цилиндр с толкателем, не отсоединяя его от трубопровода;
- вынуть вилку выключения сцепления; отвернуть болты крепления и снять штампованную нижнюю часть картера сцепления; снять соединительный кронштейн подвески трубы глушителя; отсоединить поперечину задней опоры двигателя от кронштейнов лонжеронов; отвернуть гайки шпилек крепления коробки передач к картеру сцепления и снять коробку передач вместе с муфтой и подшипником включения сцепления; снять прокладку между картером сцепления и коробкой передач;
- проверить наличие на маховике двигателя, кожухе нажимного диска совмещенных меток «О» и, если они отсутствуют, нанести их; постепенно отвернуть болты крепления кожуха сцепления к маховику, проворачивая при этом коленчатый вал двигателя; вынуть ведомый и ведущий диски сцепления из картера сцепления через нижний люк.
Для снятия гидравлического привода с автомобиля необходимо:
- отсоединить от рабочего цилиндра выключения сцепления трубопровод; слить жидкость из гидравлической системы через отсоединенный конец трубопровода в чистый сосуд, отсоединить и снять рабочий цилиндр выключения сцепления и толкатель рабочего цилиндра; снять оттяжную пружину педали выключения сцепления; отсоединить толкатель главного цилиндра от педали; вынуть две пластмассовые втулки из проушины толкателя; расшплинтовать и отвернуть гайку оси педалей сцепления и тормоза; снять с оси педали сцепления, вынуть две пластмассовые втулки из головки педали; отсоединить от главного цилиндра выключения сцепления трубопроводов и снять трубопровод; отсоединить и снять главный цилиндр выключения сцепления.
Разборка сцепления состоит из разборки ведущего и ведомого диска и разборки главного и рабочего цилиндров.
При разборке главного цилиндра необходимо:
- снять крышку и сетчатый фильтр наполнительного бачка главного цилиндра; вывернуть штуцер крепления бачка к корпусу, снять бачок и прокладку штуцера; снять с корпуса и сдвинуть к проушине толкателя резиновый защитный чехол; вынуть из корпуса главного цилиндра стопорное кольцо упорной шайбы; вынуть из корпуса главного цилиндра упорную шайбу и толкатель; вынуть из корпуса главного цилиндра поршень с уплотнительными манжетами, клапан поршня, возвратную пружину с держателем. Во избежании повреждения уплотнительных манжет для удаления поршня необходимо подвести сжатый воздух в отверстие присоединения трубопровода. Штуцер главного цилиндра с прокладкой при разборке отвертывать не следует, если на автомобиле не наблюдалось подтекания через него рабочей жидкости.
При разборке рабочего цилиндра необходимо:
- отсоединить от рабочего цилиндра резиновый защитный чехол и вынуть толкатель вместе с чехлом; снять чехол с толкателя; вынуть из корпуса рабочего цилиндра стопорное кольцо; вынуть поршень с уплотнительной манжетой из рабочего цилиндра. Во избежании повреждения поршня и манжеты необходимо подвести сжатый воздух в отверстие присоединения трубопровода; снять с поршня уплотнительную манжету; вынуть из цилиндра пружину; вывернуть из рабочего цилиндра клапан прокачки; снять с клапана резиновый защитный колпачок.
Сборка гидравлического привода выключения сцепления выполняется в порядке обратном разборке. Пред сборкой зеркало цилиндров должно быть смазано касторовым маслом или свежей тормозной жидкостью.
При сборке главного цилиндра необходимо убедиться, что возвратная пружина уверенно возвращает поршень в исходное положение. Далее следует проверить при помощи мягкой проволоки диаметром 0,3…0,5мм, не перекрывает ли манжета компенсационное отверстие. Использование главного цилиндра с перекрытым компенсационным отверстием совершенно невозможно.
При сборе рабочего цилиндра убедится, что пружина уверенно перемещает поршень в цилиндре.
Причина неисправности – неполное выключение сцепления. Сцепление «ведет» (не включается или включается с трудом передача переднего хода, передача заднего хода включается с треском).
Наличие воздуха в системе гидравлического привода – прокачать систему гидравлического привода сцепления, убедиться, что перемещение конца вилки не менее 14 мм.
Заедание ступицы ведомого диска на шлицах ведущего вала – устранить заедание на шлицах (зачистить шлицы).
Коробление ведомого диска – заменить ведомый диск или провести его правку.
Неодновременное нажатие подшипника выключения сцепления на рычаги выключения сцепления – отрегулировать взаимное расположение концов рычагов выключения сцепления.
Ослабление нажимных пружин – заменить пружины новыми с проверенной нагрузкой.
Замасливание фрикционных накладок ведомого диска – заменить ведомый диск или фрикционные накладки. При небольшом замасливании промыть поверхность накладок керосином и зачистить шкуркой.
3.4 Расчет норм времени на выполнение операций
Проведем расчет времени на примере операции слива масла; для остальных операций расчет производится аналогично.
Определяем оперативное время по формуле с. 42[6]

где Тосн
– основное время, мин;
Твс
– вспомогательное время, мин.

находим дополнительное время по формуле с. 50[6]
Вычисляем штучное время по формуле с. 58[6]
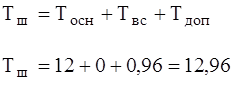
определяем норму времени по формуле с. 70[6]

где Тш1,
Тш2
, Тшп2
, Тпз1
, Тпз2
, Тпз3
, Тпз
n
– штучное и подготовительное время – заключительное время выполняемых операций, мин;
N – количество операций

4. Безопасность жизнедеятельности на производстве
4.1. Организация работ по созданию здоровых и безопасных условий труда
Здоровье и безопасность условий труда зависит от своевременного прохождения инструктажа по охране труда (ОТ ) и техники безопасности (ТБ ).
При поступлении на предприятие с рабочим проводится вводный инструктаж. В нем описываются все особенности предприятия, в том числе и те, которые представляют опасность. Производится запись в журнале, когда и кому был проведен вводный инструктаж и проинструктированный ставит свою подпись в отчетном журнале о том, что проинструктирован.
Вводный инструктаж проводит инженер по ТБ данного предприятия и ставит отметку в книжке рабочего о том, что инструктаж проведен.
После вводного инструктажа с рабочим проводят инструктаж на рабочем месте. Его проводит мастер данного участка. Инструктаж по ОТ и ТБ на рабочем месте проводится один раз в квартал и рабочий расписывается в отчетном журнале за каждый проведенный с ним инструктаж.
Инструктаж на рабочем месте включает в себя особенности данного участка, факторы, представляющие собой угрозу здоровью и различные опасные приспособления и агрегаты ( кран- балки, тельфер и т.д.).
Также существуют внеплановый инструктаж, который проводится после несчастного случая либо серьезного нарушения ОТ и ТБ.
4.2 Инструкция по охране труда при выполнении технического процесса
При разработке новых технологий для ремонта и технического обслуживания сельскохозяйственной техники безопасность работников должна обеспечиваться путем:
- устранения непосредственного контакта работников с исходными материалами, заготовками, полуфабрикатами, комплектующими изделиями, агрегатами, травмоопасными узлами, элементами и отходами производства, оказывающими опасное и вредное воздействие;
- замены технологических процессов и операций, в которых постоянно действуют опасные и вредные производственные факторы, процессами и операциями, в которых указанные факторы отсутствуют или не превышают предельно допустимых уровней;
- комплексной механизации, автоматизации процессами и операциями при невозможности устранения из технологического процесса опасных и вредных производственных факторов;
- герметизация оборудования или создание изолированных помещениях повышенного (избыточного по сравнению с атмосферным) давление воздуха;
- указание перечня средств коллективной и индивидуальной защиты работников;
- указаний по применению средств защиты и устройств, автоматически устраняющих воздействие на работников опасных факторов, в том числе и в случае аварии;
- защиты от возможных отрицательных воздействий природного характера и погодных условий.
При использовании в технологическом процессе новых исходных данных материалов, препаратов, а также при образовании после их применения промежуточных веществ, обладающих опасными и вредными факторами, должны быть разработаны регламентирующие документы с целью организации обучения работников безопасным приемом выполнения работ и обеспечения их соответствующий специальной одеждой и другими средствами индивидуальной защиты.
Использование в технологических процессах новых веществ и препаратов разрешается только после утверждения в установленном порядке соответствующих гигиенических нормативов.
Маршруты движения машин по территории должны исключить случаи их столкновения, наезды на работников и отдыхающих.
В технологических процессах должны быть заложена согласованность работы и оборудования, при которой исключается возможность возникновения опасных производственных факторов.
4.2.1 Общие требования безопасности
Инструкция содержит требования по охране труда работников всех профессий, занятых ремонтом и техническим обслуживанием техники и растениеводческих хозяйств.
Все вновь поступающие на работу работники, допускаются к работе только после прохождения медицинского осмотра, вводного и первичного (на рабочем месте) инструктажей с росписью в журнале регистрации проводимых инструктажей по охране труда. В дальнейшем работники проходят повторный инструктаж и проверку знаний по охране труда не ранее одного раза в три месяца и периодические медицинские осмотры в соответствии с приказом Минздрава РФ.
Работники, связанные с выполнением работ или обслуживанием объектов (установок, оборудования) повышенной опасности, а также объектов подконтрольном органам государственного надзора должны ежегодно проходить курсовое обучение и проверку знаний по безопасности труда.
Работнику, успешно прошедшему проверку знаний, выдается удостоверение на право самостоятельной работы.
Работники и имеющие перерыв в работе, на которую они нанимаются, более 3-х лет, и повышенной опасности – более 12 месяцев должны пройти обучение и проверку знаний по безопасности труда до начала самостоятельных работ.
При изменении технологического процесса или модернизации оборудования, приспособлений, переводе на новую временную или постоянную работу, нарушении работающим требований безопасности, может привести к травме, аварии или пожару, а также при перерывах в работе более чем на 30 календарных дней, работник обязан пройти внеплановый инструктаж.
В процессе производственной деятельности на работников воздействуют следующие опасные и вредные факторы:
- движущиеся машины и механизмы;
- подвижные части производственного оборудования;
- разрушающиеся материалы конструкции;
- отлетающие осколки;
- повышенная запыленность и загазованность рабочей зоны;
- повышенный уровень шума и вибрации на рабочем месте;
- повышенная или пониженная температура воздуха рабочей зоны;
- пониженная или пониженная подвижность воздуха;
- недостаточная освещенность рабочего места;
- загрязненные химическими веществами, радиацией и пестицидами поверхности оборудования, машин и материалов;
Опасное состояние машин, оборудования.
- открытые вращающиеся и движущиеся части машин и оборудования;
- скользкие поверхности;
- захламленность рабочего места посторонними предметами;
- отдых в неустановленных местах;
- выполнение работы в состоянии алкогольного опьянения.
Не допускается ТО и ремонт машин и оборудования, работающих в зоне радиоактивного, химического загрязнения, загрязнения пестицидами и нейтрализация загрязнения.
На рабочее место не допускаются лица, не имеющие отношения к выполняемой работе. Не перепоручайте выполнение своей работы другим лицам.
Выполняйте требования знаков безопасности.
Не заходите за ограждения электрооборудования.
Будьте внимательны к предупредительным сигналам грузоподъемных машин, автомобилей, тракторов и других видов движущегося транспорта.
Рабочий, допустивший нарушение требований инструкции по охране труда, может быть привлечен к дисциплинарной ответственности согласно правилам распорядка предприятия, а если эти нарушения связаны с причинением материального ущерба предприятию, рабочий несет и материальную ответственность в установленном порядке.
4.2.2 Требования безопасности перед началом работы
Наденьте спецодежду и другие установленные для данного предприятия средства индивидуальной защиты.
Одежда должна быть застегнута на все пуговицы и заправлена, брюки должны быть поверх обуви, застегните обшлаги рукавов, уберите волосы под плотно облегающий головной убор.
Проверьте, чтобы применяемый при работе инструмент и приспособления были исправны, не изношены и отвечали безопасным условиям труда.
Деревянные рукоятки инструментов должны быть изготовлены из выдержанной древесины твердых и вязких пород, гладко обработаны, на их поверхности недолжно быть выбоин, сколов и других дефектов. Инструмент должен быть правильно насажен и прочно закреплен.
Ударные инструменты (зубила, бородки) не должны иметь трещин, заусениц, наклепы, затылочная их часть должна быть гладкой, не иметь трещин, заусениц и сколов.
Концы ручных инструментов, служащих для заводки в отверстия при монтаже (ломики для сборки и т.д.), не должны быть сбитыми.
Съемники должны иметь исправные лапки, винты, тяги и упоры.
4.2.3 Требования безопасности во время работы
Постоянно следите за исправностью оборудования и не оставляйте его без надзора. При уходе с рабочего места оборудование остановите и обесточьте.
Работайте при наличии и исправности ограждений, блокировочных и других устройств, обеспечивающих безопасность труда, и при достаточной освещенности рабочего места.
Не прикасайтесь к находящимся в движении механизмов и вращающихся частей машин, а также находящимся под напряжением токоведущим частям оборудования.
Содержите в порядке и чистоте рабочее место.
Проходы проезды, проезды и рабочие места должны быть свободными.
Посторонние предметы и инструмент располагайте на расстоянии движущихся механизмов.
При пуске машины, агрегата, станка лично убедитесь в отсутствии работников в зоне работы машины.
В случае плохого самочувствия прекратите работу, приведите рабочее место в безопасное состояние, обратитесь к врачу, поставьте в известность руководителя работ.
4.2.4 Требования безопасности в аварийных ситуациях
При замеченных неисправностях производственного оборудования и инструмента, а также, если при прикосновении к машине, станку, агрегату ощущается действие электрического тока, либо имеет место сильный электроприборов, электродвигателей, электроаппаратуры, появление искрения или обрыв проводов и т. Д. предупредите работающих об опасности, немедленно поставьте в известность руководителя работ.
При необходимости организуйте эвакуацию людей из опасной зоны.
При несчастных случаях с людьми, окажите им доврачебную помощь, немедленно поставьте в известность руководителя работ сохраняйте обстановку, при которой произошел несчастный случай, если это не угрожает жизни и здоровью окружающих и не нарушает технического процесса до прибытия лиц, расследование причин несчастного случая.
При поражении электрическим током как можно быстрее освободите пострадавшего от действия тока, так как продолжительность его Действия определяется тяжестью травмирования. Для этого быстро отключите рубильником или другим отключающим устройствам ту часть электроустановки, которой касается пострадавший.
4.2.5 Требование безопасности по окончанию работы
Приведите в порядок рабочее место (очистите от пыли и грязи оборудование, инструмент, соберите и вынесите в отведенное место мусор и отходы, соберите и сложите в установленное место инструмент, приспособление и необработанные детали, обработанные детали сдайте в кладовую).
Установите ограждения и знаки безопасности у открытых проемов, отверстий и люков.
Обесточьте оборудование, выключите вентиляцию и местное освещение.
Снимите спецодежду и другие средства индивидуальной защиты, уберите их в шкаф закрытого типа, если спецодежда требует стирки или ремонта, сдайте ее в кладовую.
Поставьте в известность руководителя работ о состоянии оборудования.
Выполните правила личной гигиены.
4.3 Пожарная безопасность
Работник обязан знать сигналы оповещения о пожаре, место нахождения средств для тушения пожара и уметь ими пользоваться. Не допускается использование пожарного инвентаря для других целей.
Не загораживайте проходы и доступ к противопожарному оборудованию.
Засыпайте песком пролитые на землю топливо и смазочные материалы. Пропитанный нефтепродуктами песок немедленно уберите ми вывезите в место, согласованное с санэпидстанцией.
Уберите использованный обтирочный материал в специальные металлические ящики с крышками.
Не разводите огонь в секторах хранения сельскохозяйственной техники на территории машинного двора и в помещениях.
Не храните на рабочем месте легковоспламеняющиеся предметы и горючие жидкости, кислоты и щелочи в количествах, превышающих сменную потребность готовом к употреблению виде.
Не применяйте для тушения пожара в электроустановке, находящейся под напряжением, химические пенные или химические воздушно – пенные огнетушители.
Рабочий, допустивший нарушения требований инструкций по охране труда, может быть привлечен к дисциплинарной ответственности согласно правилам внутреннего распорядка предприятия, а если эти нарушения связаны с причинением материального ущерба предприятию, рабочий несет и материальную ответственность в установленном порядке.
5. Охрана окружающей среды
Охрана природы – система мер, направленных на поддержание рационального взаимодействия между деятельностью человека и окружающей природной средой, обеспечивающих сохранение и восстановление природных богатств, разумное использование природных ресурсов, предупреждающих вредное влияние результатов деятельности общества на природу и здоровье человека.
Все это делается в интересах настоящих и будущих поколений людей. Эти мероприятия должны научно обосновываться, и могут осуществляться на разных уровнях: международном, государственном, ведомственном, производственном, общественном, индивидуальном.
В связи с научно-техническим прогрессом и ростом населения потребности общества быстро возрастают. В хозяйственную деятельность вовлекаются все природные ресурсы, индустриализация и интафикация сельского хозяйства сопровождаются существенными изменениями природной среды.
Автотранспорт бурно развивается в индустриальных странах. В настоящее время общая численность автомобилей в мире составляет свыше 300 млн. Автомобиль – это удобное средство транспорта, но он отрицательно влияет на окружающую среду.
В некоторых странах загрязнение воздуха автотранспортом достигает угрожающих размеров. Это особенно относится к США, где численность автопарка – свыше 100 млн. В городах России эта проблема не стоит так остро. В РФ основная транспортная система – общественные виды транспорта (автобусы), что создает условие для предотвращения угрожающего уровня загрязнения. Однако и в России существует проблема загрязнения воздуха автотранспортом. Проведенные исследования позволили установить, что выхлопные газы автомобилей представляют весьма сложную смесь, в состав которой входят много компонентов. Однако многообразие продуктов выброса может быть сведено к нескольким группам.
Атмосфера крупных городов развитых стран загрязнена до такой степени, что в ряде случаев регулировщики уличного движения должны вдыхать кислород. В этих целях в местах наиболее интенсивного автомобильного движения установлены баллоны с кислородом.
6. Техника экономичности проекта
Стоимость основных производственных фондов по формуле с. 60[5]

где Сзд
, Соб
– стоимость производственного задания и установленного оборудования в руб.
Спи
- стоимость приборов инвентаря и приспособлений штучная оптовая цена превышает 100руб.
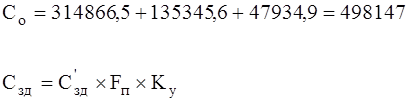
где - средняя стоимость строительно-монтажных работ отнесенных к 1м2
производственной площади 1руб на м2
принять 75руб м2
Fп
– производственная площадь м2
Ку
=13,4 – коэффициент удорожания оборудования

стоимость установленного оборудования, приспособлений, инструментов, инвентаря по формуле с. 79[5]
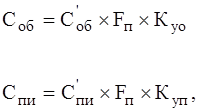
где Соб
- стоимость оборудования отнесенного к 1м2
производственной площади принимаем 45руб. м2
Спи –
стоимость приборов, приспособлений инструментов и инвентаря отнесенная 1м2
производственной площади 15руб. 1м2
Куо
=9,6 – коэффициент удорожания приспособлений, инструментов, инвентаря.
Куо
=10,2
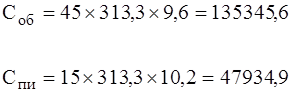
Производительная годовая программа по формуле с. 90[5]

где Тоб
– общая трудоемкость работ чел/ч
Т – трудоемкость обслуживания и ремонта

Цеховая себестоимость обслуживания по формуле с. 100[5]

где Спрн
– полная заработная плата с начислениями
Сзн
, Спр
– нормативные затраты на запчасти и ремонтные материалы
Соп
– общепроизводственные накладные расходы

где Спр
- основная зарплата рабочих в руб.
Сдоп
– дополнительная зарплата принимается 10% от основной зарплата платы в руб.
Сур
– зональный коэффициент принимаем 15% от основной зарплата платы

где tизд
– трудоемкость ТО и ТР сцепления UFP – 3110
Cч
– часовая ставка рабочих коп./ч
Кt
– коэффициент учитывающий доплату за сверхурочные и другие работы, принимаем 1,025
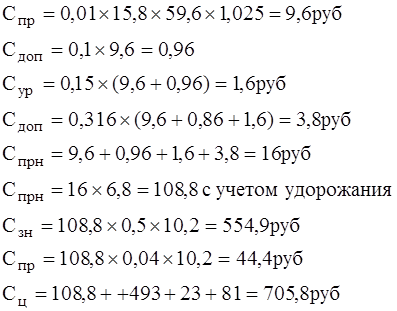
Стоимость общепроизводственных накладных расходов

где Rоп
– процент общепроизводственных накладных расходов равных 28%
Стоимость запасных частей и ремонтных материалов с учетом удорожания принимаем из соотношения, что запасные части составляют 50% от полной зарплаты, и материалы 4%

Определяем удельные показатели пункта ТО
Фонды отдачи по формуле с. 120[5]
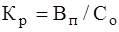
где Вп
– валовая продукция
Со
– стоимость основных производственных фондов

Стоимость валовой продукции по формуле с. 125[3]
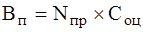
где Соц
– оптовая цена соответствующего обслуживания и ремонта

Производительность труда по формуле с. 134[139]
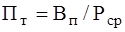
где Рср
– среднегодовое число производственных рабочих

Использование площади по формуле с. 140[5]
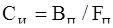
где Fп
– производственная площадь

Техника - экономические показатели
Таблица 6.1
Показатели
|
По проекту
|
1
|
2
|
1.Среднегодовая стоимость основных производственных фондов, 1000 руб.
2.Производственная площадь, м2
3.Численность работников
4.Использование площади, руб./м2
5.Валовая продукция,1000 руб.
6.Себестоимость ТО-2, руб.
7.Фондоотдача, руб./чел
8.Производительность труда, руб./чел
9.Средняя зарплата рабочих за год, руб.
|
355,5
223,6
6
361,2
80,7
697,8
0,23
13462,2
1281.6
|
В целом предприятие выдает неплохие результаты. При небольшой площади, количестве работников фондоотдача 0,23 руб./руб., срок окупаемости предприятия около 2-х лет и это при нормативном сроке в 7 лет.
Заключение
Выполнив курсовое проектирование, я понял, что главное направление в развитии агропромышленного комплекса страны- интенсификация сельскохозяйственного производства на основе технического перевооружения, что непосредственно связано с производством новых машин, увеличением автоматизированных средств механизации и совершенствованием инженерной службы. Научились определять количество ремонтно - обслуживающих воздействий на машинно - тракторный парк. Уяснил, как правильно нужно определить годовую загрузку центральной ремонтной мастерской. Научился эффективно использовать производственные площади и оборудования. Выбирать необходимое оборудование и расставить так, чтобы облегчить условия труда рабочих. Нужно рационально использовать рабочие места. Узнал, какие мероприятия необходимы для того, чтобы обезопасить жизнь человека. Выполнив технологический процесс по восстановлению детали, научился выбирать нужные наиболее эффективные и не требующие дорогостоящего оборудования и затрат способов восстановления.
В мастерских должна быть обеспечена необходимая техника безопасности, и мероприятия, направленные на обеспечение безопасности жизнедеятельности человека, а также должны быть созданы все условия для труда рабочих.
В настоящее время, в связи с трудным положением многих хозяйств, нехваткой средств, на приобретение новой техники, в хозяйствах проводят восстановление деталей в силу возможностей ремонтных мастерских своими средствами.
Литература
1. Антонов С.Л., Трофимов В.А.
2. Бабусенко С.М. Проектирование ремонтных предприятий.
3. Епифанов Л.И., Епифанова Е.А. Техническое обслуживание и ремонт автомобилей.
4. Канаров Ф.М., Перехогин М. А. Охрана труда.
5. Купреев З. Ч. Справочник по оплате труда.
6. Смелов А. П. Курсовое и дипломное проектирование по ремонту машин.
7. Положение о техническом обслуживании и ремонте подвижного состава автомобильного транспорта.
|