Содержание
Цели проектирования
1.Анализ служебного назначения детали, технические требования к точности относительного положения поверхностей
2. Формирование содержания операций
2.1 Определение метода получения заготовок
2.3 Определение количества переходов
3. Расчет технологических параметров
3.1 Расчет припусков на обработку
3.2 Расчет технологических режимов резания
3.3 Определение силы резания
3.4 Расчет мощности резания
3.5 Расчет нормы времени на обработку
4. Разработка чертежа для пневматического трехкулачкового патрона
5. Расчет усилий закрепления заготовки
Заключение
Библиографический список
Цель проектирования
Цель курсового проектирования – закрепление и систематизация знаний по предмету, разработка технологического процесса обработки детали типа диск в условиях автоматизированного производства с подробной разработкой позиционного приспособления и схвата промышленного робота.
1. Анализ служебного назначения детали
Изготовление данной детали производится из прутка – прокатом, способом резки проката на пресс – ножницах с прямыми и фасонными ножами.
Точность и размеры детали выполняются в соответствии с требованиями чертежа.
2. Формирование содержания операций
2.1 Определение метода получения заготовок
Заготовку можно получить различными методами: из проката, штамповкой, литьем.
Данная задача решается из условий:
- коэффициента использования материала, который должен быть
Vд/V3>70%
где тд – масса детали;
тз – масса заготовки.
- себестоимости.
В данных условиях себестоимость не рассчитывается, в связи с отсутствием необходимых данных.
Рассчитываем коэффициент использования материала из условия, что заготовка получается из полосы.
т = V/p,
где т- масса заготовки или детали;
V- объем заготовки или детали;
р - плотность материала заготовки или детали, которая для стали 45
составляет 7,8Ч10-3 кг/м3.
Рассчитаем объем заготовки, принимая, что она имеет форму цилиндра,
объем которого:
V=πЧr2Чh,
где π =3,14;
r – радиус цилиндра;
h – высота цилиндра.
V3=3,14Ч0,023Ч0,1252 =1128437,5 мm 3;
Vd= V1- V2= 20Ч3,14Ч (1202-282)= 855084,28 мм3;
тд= кг;
Таким образом, коэффициент использования материала будет:
Ким=(Vд/V3)Ч100%
Ким=(855084,28 /1128437,5)Ч100%=75,78%
Относительно проведенных нами расчетов, можно сделать вывод об экономичности и целесообразности данного способа получения заготовки.
2.2 Определение количества переходов
Согласно заданию, поверхность 120 мм получается способом токарной обработки. На основании этого обосновываем количество переходов внутри операции через понятие уточнение. Понятие уточнения может быть определенно как отношение допуска на предыдущем переходе к допуску, формируемому на настоящем переходе (переход – законченная часть операции, в результате которой формируется новая поверхность или сочетание поверхностей).
ε∑=Tзаг/Tдет;
Поле допуска на поверхность детали составляет 0,023 мм. Для заготовки допуск будет составлять 2,8 мм. Тогда суммарное уточнение:
ε∑=121,7.
Определим сколько понадобиться переходов, чтобы как можно экономичнее из заготовки получить деталь.
εчер=Tзаг/Tчер;
Допуск при черновой обработке составляет 0,4 мм, отсюда:
εчер=2,8/0,4=7;
Как видно одного чернового обтачивания не достаточно, поэтому необходима еще получистовая обработка:
εп/ч=Tчер/Tп/ч;
Для получистовой обработке точность поверхности составит 0,25 мм.
εп/ч=0,4/0,25=1,6;
Данного перехода также будет не достаточно, поэтому необходимо чистовое обтачивание, где Tчис=0,063:
εчис=Tп/ч/Tчис;
εчис=1,6/0,063=25,4;
Проверим достаточность переходов из условия, что:
εчерЧεп/чЧ εчис> ε∑;
εчерЧεп/чЧ εчис=7Ч1,6Ч 25,4=284,48;
284,48>121,7.
Таким образом для получения из заготовки детали требуется 3 перехода.
3. Расчет технологических параметров
3.1 Расчет минимальных припусков и межпереходных размеров для переходов
Припуск – слой материала, удаляемый с поверхности заготовки в целях достижения заданных свойств обрабатываемой поверхности детали.
Для расчета припуска используются формулы, в зависимости от вида точения. Для нашего случая:
2zmin =2[(Rz+h)i-1+√( Δ2∑(i-1) +ε2i )];
где i – индекс принадлежности к текущему переходу;
i-1 – индекс принадлежности к предыдущему переходу;
Δ∑(i-1) – суммарное отклонение расположения поверхностей;
εi – погрешность установки на выполняемом переходе;
hi-1 – величина дефектного слоя на предыдущем переходе;
Rz – высота микронеровностей предыдущей операции.
Рассчитаем отклонение расположения поверхностей, l = 23 мм:
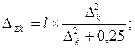
Для проката кривизна профиля на 1 мм составляет 1, поэтому:

;
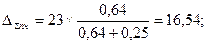
;
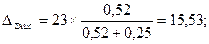
Расчетная формула для определения размеров поверхности имеет следующий вид:
Dmin(i-1)= Dmin(i)+2ЧZmin(i) ;
где Dmin(i-1) – наименьший предельный размер, полученный на предшествующем технологическом переходе;
Dmin(i) – наименьший предельный размер, полученный на выполняемом технологическом переходе.
Dmin(чист)=120-0,038=119,962 мм;
Dmin(п/ч)=119,962+0,221=120,183 мм;
Dmin(чер)=120,183+0,493=120,676 мм;
Dmin(прок)= 120,676+1,046=121,722 мм.
Рассчитываем наибольший предельный размер:
Dmax(i)= Dmin(i)+Td(i) ;
Dmax(прок)=121,722+2,8=124,522 мм;
Dmax(чер)=120,676+0,4=121,076 мм;
Dmax(п/ч)=120,183+0,16=120,343 мм;
Dmax(чис)=119,962+0022=119,984 мм.
Максимальный припуск на обработку поверхности, находят как разность наибольших предельных размеров:
Zmax(i)= Dmax(i-1) –Dmax(i) ;
Соответственно получаем:
Zmax(чер)=124,522-121,076=3,446 мм;
Zmax(п/ч)=121,076-120,343=0,732 мм;
Zmax(чис)=120,343-119,984=0,359 мм.
Все полученные значения оформляем в виде таблицы:
Таблица 1
Обработка
|
Rz
|
h
|
Δ
∑(
i
-1
)
|
ε
|
2
Zmin
, мкм
|
Dmin
,
мм
|
Td
, мм
|
Dmax
,
мм
|
Полученные предельные припуски
|
2
Zmax
|
2
Zmin
|
Прокат
|
200
|
300
|
23
|
0
|
-
|
121,722
|
2,8
|
124,522
|
-
|
-
|
Черновая
|
128
|
100
|
18,4
|
0
|
1045,38
|
120,676
|
0,4
|
121,076
|
3446
|
1045
|
Получистовая
|
64
|
30
|
16,54
|
0
|
492,8
|
120,183
|
0,16
|
120,343
|
732
|
493
|
Чистовая
|
0,8
|
20
|
15,53
|
0
|
221,08
|
119,962
|
0,022
|
119,984
|
359
|
221
|
Правильность проведения расчетов можно проверить по формуле:
Tdзаг –Tdдет =∑2 Zmax(i)–∑2 Zmin(i);
Воспользуемся данной формулой:
Tdзаг –Tdдет =2,800 –0,022 =2,778 мм;
∑2 Zmax(i)–∑2 Zmin(i)=2,778 мм;
На основе полученных результатов можно сделать вывод о правильности проведенных расчетов.
3.2 Расчет технологии режимов резания
При назначении элементов режимов резания учитывается характер обработки, тип и размеры инструмента, материала его режущей части, материал и состояние заготовки, тип и состояние оборудования.
Скорость резания при точении рассчитывают по формуле:
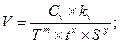
где Cv – коэффициент;
т, х, у - коэффициенты, принимаемые в зависимости от вида обработки и характеристики подачи;
T – среднее значение периода стойкости(работа до затупления), при одноинструментальной обработке выбирается любое в диапазоне от 30 до 60, мин;
kv – коэффициент, являющийся произведением коэффициентов:
kv=kmvЧknvЧkuv ;
kmv=kГ(750/σB)nv;
где kmv – коэффициент, учитывающий влияние материала заготовки;
knv – коэффициент, учитывающий влияние состояния поверхности заготовки на скорость резания;
kuv - коэффициент, учитывающий влияние инструментального материала на скорость резания;
σв - параметр, характеризующий обрабатываемый материал, σв = 750МП;
kГ – коэффициент, характеризующий группу сталей по обрабатываемости.
Принимаем значения коэффициентов:
kmv ≈1;
knv = 0,9;
kuv =1;
Тогда рассчитываемый коэффициент:
kv=1Ч0,9Ч1=0,9 .
Т=50 мин.
При черновом точении назначают глубину резания t по возможности максимальную, равную всему припуску на обработку или большей части его. При чистовой (окончательной) обработке – в зависимости от требований точности размеров и шероховатости обработанной поверхности.
tчерн= 1,446 мм;
tп.ч= 0,23 мм;
tчист=0,11мм ;
Подачу при черновой обработке выбирают максимально возможную, исходя из жесткости и прочности системы СПИД, мощности привода станка, прочности твердосплавной пластинки и других ограничивающих факторов.
При чистовой обработке – в зависимости от требуемой степени точности и шероховатости обработанной поверхности.
При наружном черновом точении резцами с пластинками из твердого сплава Т15К6 выбираем, для детали D = 120 мм:
S черн=1 мм/об; Cv =340; x=0,15; y=0,45;m=0,2.
Отсюда рассчитываем скорость резания при черновом точении:
мм/мин;
При получистовом точении:
Sп.ч= 0,9 мм/об; Cv =340; x=0,15; y=0,45;m=0,2.
Отсюда рассчитываем скорость резания при получистовом точении:
мм/мин;
Для чистового точения:
Sп.ч= 0,8 мм/об; Cv =340; x=0,15; y=0,45;m=0,2.
Отсюда рассчитываем скорость резания при черновом точении:
мм/мн;
3.3 Расчет силы резания
Силу резания принято раскладывать на составляющие силы, направленные по осям координат станка – тангенциальную Pz, радиальную Py и осевую Px.
При наружном, продольном и поперечном точении, растачивании, эти составляющие рассчитывают по формуле:
Pz(Py ,Px)=10CpЧtxЧSyЧVnЧkp ;
В зависимости о обрабатываемого материала (конструкционная сталь, σв=750 МПа), материала рабочей части резца (твердый сплав Т15К6) и вида обработки (наружное, продольное, поперечное точение), выбираем:
для тангенциальной составляющей:
Cp=300 ; x=1; y=0,75; n=-0,15 ;
для радиальной составляющей:
Cp=243; x=0,9; y=0,6; n=-0,3 ;
для осевой составляющей:
Cp=339; x=1; y=0,5; n=-0,4 ;
Поправочный коэффициент kp представляет собой произведение ряда коэффициентов, учитывающих фактические условия резания:
kv=kmpЧkφpЧkvpЧkλp ,
где kmp – поправочный коэффициент, учитывающий влияние качества обрабатываемого материала на силовые зависимости:

n – показатель степени, для твердого сплава равный 0,75;
kφp,kvp,kλp – поправочные коэффициенты, учитывающие влияние геометрических параметров режущей части инструмента на составляющие силы резания при обработке стали.
Для режущей части инструмента из твердого сплава:
При главном угле в плане φ=450, переднем угле γ= -150, а угле наклона главного лезвия λ= -50 :
для Pz: kφp=1,0;
kvp =1,25;
kλp = 1,0.
Для Px: kφp=1,0;
kvp =2,0;
kλp = 1,07.
Для Py: kφp=1,0;
kvp =2,0;
kλp = 0,75.
Следовательно получим:
для Pz: kp=1,25;
Px: kp=1,5;
Py: kp=2,14.
Имея все данные, рассчитываем силы резания:
Pz черн=3000Ч1,4461Ч10,75Ч132,41-0,15Ч1,25= 2605,62 Н ;
Px черн=2430Ч1,4460,9Ч10,6Ч132,41-0,3Ч1,5= 1172,92 Н;
Py черн=3390Ч1,4461Ч10,5Ч132,41-0,4Ч2,14=1485,98 Н ;
Pz пч=3000Ч0,231Ч0,90,75Ч183-0,15Ч1,25=364,82 Н ;
Px пч=2430Ч0,230,9Ч0,90,6Ч183-0,3Ч1,5= 181,02 Н;
Py пч=3390Ч0,231Ч0,90,5Ч183-0,4Ч2,14= 197,01 Н;
Pz чис=3000Ч0,111Ч0,80,75Ч215,5-0,15Ч1,25= 155,86 Н ;
Px чис=2430Ч0,110,9Ч0,80,6Ч215,5-0,3Ч1,5= 87,25Н;
Py чис=3390Ч0,111Ч0,80,5Ч215,5-0,4Ч2,14=83,21 Н ;
3.4 Расчет мощности резания
Мощность резания рассчитывается по формуле:
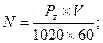
В нашем случае для чернового точения:
кВт;
Для получистового:
кВт;
Для чистового:
кВт.
3.5 Расчет нормы времени на обработку
Время рабочих ходов равно длительности лимитирующей операции дифференцируемого технологического процесса и определяется по формуле:
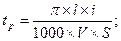
где l – длина рабочего хода, мм;
n – частота вращения шпинделя, об/мин;
S – подача, мм/об;
V – скорость резания, м/мин;
i – количество переходов.
Выполним расчет для черновой обработки:
мин;
для получистовой обработки:
мин;
для чистовой обработки:
мин.
Теперь подсчитаем n:

для черновой получим:
об/мин;
для получистовой:
об/мин;
и для чистовой получаем:
об/мин.
4. Разработка чертежа для пневматического трехкулочкого патрона
Cамоцентрирующиеся трехкулачковые токарные патроны из стали и чугуна предназначены для установки на универсальные токарные, револьверные, внутришлифовальные станки, делительные головки и различные приспособления для закрепления штучных заготовок и пруткового материала.
Патроны токарные трехкулачковые изготавливаются с цилиндрическим центрирующим пояском и устанавливаются на шпиндели станков через переходные фланцы по ГОСТ 3889-80.Все основные детали патронов изготавливаются из конструкционных, легированных термически обработанных сталей.
Пневмо – кинематическая схема автоматизированного устройства для установки заготовок на технологическом оборудовании представлена на чертеже.
Устройство:
Воздухоприемное кольцо неподвижно закреплено через промежуточное кольцо на торце бабки станка, с корпусом патрона центрируется на фланце шпинделя и закрепляется гайками с помощью поворотной шайбы. С правой стороны корпус- цилиндр закрыт крышкой 4, в которой имеются обычные радиальные пазы под кулачки 5. На ступице поршня 3 образованы три продольных паза, расположенных относительно друг друга под углом 1200 и наклонены по отношению к оси на 150. В эти пазы заходят концы кулачков, образуя несамотормозящие клиновые соединения. При линейном перемещении поршня сцепленные с его пазами кулачки, совершают перемещения в радиальном направлении, зажимая или освобождая обрабатываемую деталь.
Принцип работы:
При включении электромагнита притягивается перекрывающая рамка 5 и сжатый воздух через штуцер подводится к невращающемуся воздухоприемнику 1, заполняет кольцевой паз и далее через отверстия в резиновом уплотненном кольце и отверстия в корпусе 2 поступает в левую полость цилиндра; кулачки при этом расходятся. При переключении распределительного крана воздух из цилиндра уходит в атмосферу, а поршень под действием сильных пружин 3 возвращается в исходное положение, кулачки перемещаются к центру и зажимают изделие.
5. Расчет усилий закрепления заготовки
Закрепление заготовки осуществляется в трех кулачковом патроне схема закрепления и действующие при этом силы показаны в приложении. В общем виде формула для расчета силы закрепления заготовки рассчитывается по формуле:
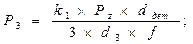
где k1 - коэффициент, принимаем равным 1,5;
f – коэффициент, принимаем равным 0,1;
Pz – сила резания, берем значение при черновой обработке;
Pz черн= 2605,62 Н ;
Отсюда рассчитываем силу закрепления:
12710,4 Н.
Закрепление заготовки осуществляется в трех кулачковом патроне.
Теперь, зная силу закрепления, найдем диаметр цилиндра, принимая, что давление в цилиндре ρ=5 кг/см2:
мм.
Данный диаметр соответствует стандарту.
Заключение
Цель и задача курсового проекта выполнены. А именно, были закреплены и систематизированы знания по предмету, применены теоретические знания при решении вопросов, воплощенные в данном проекте.
Осуществлена разработка технологического процесса обработки детали диск в условиях автоматизированного производства с подробной разработкой позиционного приспособления.
Библиографический список
1. Косилова А.Г., Мещерякова Р.К. Справочник технолога-машиностроителя. В 2-х томах. М.: Машиностроение, 1986., 496 с.
2. ГОСТ 2675-80 Патроны самоцентрирующие трехкулачковые.
|