Содержание
Задание
1 Описание конструкции и назначение узла
2 Расчет и выбор посадок подшипников качения
3 Выбор посадок для сопряжений узла и их расчёт
4 Выбор средств измерений деталей
5 Расчёт рабочих и контрольных калибров
6 Расчёт и выбор посадки с зазором
7 Расчёт и выбор посадки с натягом
8 Расчёт точности зубчатой передачи
9 Расчёт размерной цепи вероятностным методом
Список используемых стандартов
Список используемой литературы
Приложение
1. Описание конструкции и назначения узла
Данный узел (
натяжной вал цепного транспортера
) предназначен для обеспечения необходимого натяжения цепи.
Натяжной вал цепного транспортера состоит из: оси 1, корпуса 6,двух подшипников 15, крышки корпуса 8, звездочки 5, манжеты 14, шайбы 17,винта 11, а так же натяжного устройства, состоящее из: болтов 12, контргайки 13, пружины 16.
Ось 1 вмонтирована в корпус цепного транспортера. На неё посажены два подшипника 15, которые запрессованы в корпус 6.На корпус 6 напрессовывается звездочка 5,которая передает вращательное усилие цепи транспортера. Корпус 6 с помощью болтов 11 закрывается двумя крышками 8. Для более плотной посадки крышки 8 на ось 1 устанавливают манжету 14.
Чтобы не происходил быстрый износ колец подшипников 2 в конструкции данного узла предусмотрена их смазка через масленку 10 и отверстие во втулке 2 и оси 1.
2. Расчёт и выбор посадок подшипников качения
Исходные данные:
Подшипник №306
Класс точности 5
Радиальная реакция R = 11,2 kH
Осевое усилие A = 14 kH
Характер нагрузки - с умеренными толчками и вибрациями, перегрузка до 150%.
Размеры подшипника [2]:




2.1 Для циркуляционно нагруженного кольца определяется интенсивность нагружения PR
, H.
, (2.1)
где R – радиальная реакция опоры на подшипник, кН
В – ширина подшипника, мм
r – радиус фасок колец подшипника, мм
KП
– динамический коэффициент посадки [1,табл.3.5]
F – коэффициент ослабления посадочного натяга при полом вале или тонкостенном корпусе
FA
– коэффициент неравномерности распределения радиальной нагрузки между рядами роликов или между сдвоенными шарикоподшипниками при наличии осевой нагрузки на опору [1,табл. 3.2]
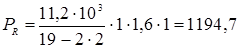 
2.2 По величине интенсивности нагружения PR
выбираем вид посадки [1,табл.3.3,]
«k» - посадка на вал
2.3 Для колец, воспринимающих колебательное и местное нагружение, выбирается вид посадки в зависимости от характера нагружения и вида корпуса [1, табл. 3.6]
«H» - посадка в корпус
2.4 Выбор квалитета для посадок колец подшипников
Для вала – 5 квалитет
Для корпуса – 6 квалитет
2.5 По ГОСТ 520 – 89 и ГОСТ 25347 – 82 определяем отклонения ES, EI, ei, es, строим поля допусков по наружному (D) и внутреннему (d) диаметрам и определяем табличные натяги Nmax
и Nmin
Отклонения для внутреннего кольца подшипника:
ES = 13 мкм, EI = 2 мкм
Отклонение для наружного кольца подшипника:
es = 19 мкм, ei = 0 мкм
Определяем поле допуска внутреннего (L5) и наружного (l5) колец [1,табл.
3.9]
L5 = 8 мкм, l5 = 9 мкм

Nmin
=dmin
- Dmax
=ei-ES (2.2)
Nmax
=dmax
-Dmin
=es-EI (2.3)
Nmin
=0,002-0=0,002 [мм]
Nmax
=0,013-(-0,008)=0,021 [мм]
2.6 Вычислим минимальный допустимый натяг:
(2.4)
- конструктивный фактор,
где d0
– приведенный диаметр внутреннего кольца
(2.5)

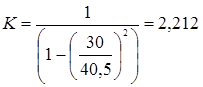
(2.6),
где R – радиальная реакция
 =21 [мкм]
Т.к. условие Nmin
≥ не выполняется, то вводим поправку на
 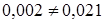
шероховатость:
(2.7),
где и - шероховатость соответственно вала и корпуса [1,табл. 3.1]:
мкм, мкм
[мкм] или 0,0147 [мм]
Т.к. условие Nmin
≥ не выполнено, то вводим поправку на

шероховатость:
[мкм] или 0,0084 [мм]
Т.к. условие Nmin
≥ не выполнено, то вводим поправку на

шероховатость:
[мкм] или 0,0021 [мм]
Nmin
≥ - условие выполнено

2.7 Вычислим максимальный допустимый натяг:
(2.8),
где –предел прочности шарикоподшипниковой стали
[мм]
- условие выполнено.
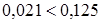
2.8 Проверяем наличие посадочного рабочего зазора:
По внутреннему диаметру (d)определяем min и max радиальный зазор [1,табл. 3.11]:
Gmin
=10 мкм, Gmax
=24 мкм
Определяем начальный радиальный зазор:
(2.9)
[мкм] или 0,017 [мм]
Определи эффективный натяг:
(2.10),
где - усреднённый натяг
(2.11)
 
 
Определим рабочий радиальный зазор:
(2.12),
где  
 
Условие - выполнено.
Определим усилие запрессовки подшипника на вал ( ):
(2.13),
Где - коэффициент трения при запрессовке
- модуль упругости стали
 
2.9 Определим температуру нагрева подшипника в масле для установки его на вал:
(2.14),
где - температурный коэффициент линейного расширения подшипниковой стали
- сборочный зазор
 
3 Выбор посадок для сопряжений узла и их расчёт
В соответствии с заданием на курсовую работу назначаем посадки для десяти сопряжений сборочной единицы. Результаты выбора посадок представляем в виде таблицы 1.
Таблица 1 – Выбранные посадки
Номер сопрягаемых
деталей
|
Наименование
сопрягаемых деталей
|
Выбранные посадки по ГОСТ 25347 – 82
(СТ СЭВ144 – 88)
|
15 – 1 |
Подшипник – вал |
30 L5/k5 |
15 – 6 |
Подшипник – крышка |
72 H6/l5 |
8 – 6 |
Крышка – корпус |
72 H7/k6 |
11 – 6 |
Болт – корпус |
M6 H8/m7 |
5 – 6 |
Звездочка – корпус |
97 H7/m6 |
1 – 14 |
Вал – манжета |
30 H8/m6 |
14 – 8 |
Манжета – крышка |
52 E9 |
11 – 8 |
Болт – крышка |
M6 H8/js7 |
1 – 2 |
Вал – втулка |
30 H9/js8 |
3 – 6 |
Втулка – корпус |
72 H9/n7 |
Расшифровка буквенных обозначений посадок, расчет предельных размеров, зазоров или натягов, построение полей допусков для десяти выбранных сопряжений оформляем в виде таблицы 2
Таблица 2 – Расчет выбранных посадок
номера
Сопря-гаемых
деталей
|
номиналь-
ный размер с отклонени-
ями
|
Предельные размеры, мм |
Схемы полей допусков |
Dmax
|
Dmin
|
dmax
|
dmin
|
Smax
|
Smin
|
15-01 |

|
30,013 |
30,002 |
30 |
29,992 |
0,021 |
0,002 |
 |
15-06 |

|
72,019 |
72 |
72 |
71,991 |
0,028 |
0 |
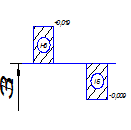 |
08-06 |

|
72,03 |
72 |
72,021 |
72,002 |
0,028 |
-0,021 |
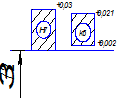 |
11-06
d
|

|
6,022 |
6 |
6,021 |
6,006 |
0,016 |
-0,021 |
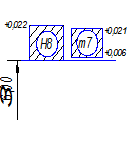
|
11-06
d2
|

|
5,531 |
5,513 |
5,529 |
5,517 |
0,014 |
-0,016 |
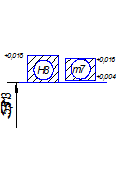
|
11-06
d1
|

|
5,206 |
5,188 |
5,204 |
5,192 |
0,014 |
-0,016 |
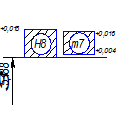 |
05-06 |
 |
97,035 |
97 |
97,035 |
97,013 |
0,022 |
-0,035 |
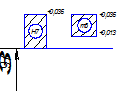 |
01-14 |

|
30,033 |
30 |
30,035 |
30,013 |
0,02 |
-0,035 |
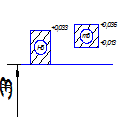 |
14-08 |

|
52,154 |
52,06 |
0 |
0 |
52,154 |
52,06 |
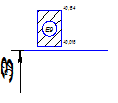 |
11-08
d
|

|
6,022 |
6 |
6.007 |
5,993 |
0,029 |
-0.007 |
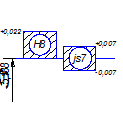 |
11-08
d2
|

|
5,531 |
5,513 |
5,519 |
5,507 |
0,024 |
-0,006 |
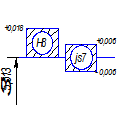 |
11-08
d1
|

|
5,206 |
5,188 |
5,194 |
5,182 |
0,024 |
-0,006 |
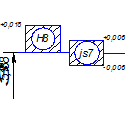
|
01-02 |

|
30,062 |
30 |
30,019 |
29,981 |
0,081 |
-0,019 |
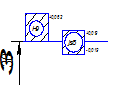 |
03-06 |

|
72,074 |
72 |
72,05 |
72,02 |
0,054 |
-0,05 |
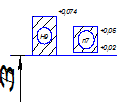 |
Производим выбор измерительных средств с учетом допустимой погрешности измерений, а также погрешности измерительных средств. Значение допустимой погрешности измерения dизм
зависит от величины допуска на изготовление изделия IT, который в свою очередь связан с номинальным размером и квалитетом.
Результаты выбора измерительных средств оформляются в виде таблицы 3.
Таблица 3 – Характеристики измерительных средств
Номера сопрягаемых деталей |

|
Средства измерения
|
Цена деления
|
Пределы
измерения
|
15 – 01 |
0,011 |
- |
- |
- |
0,008 |
Микрометры гладкие (ГОСТ 6507-78) |
0,1 |
25-50 |
15 – 6 |
0,019 |
Нутромеры микрометрические (ГОСТ 10-75) |
0,01 |
75-100 |
0,009 |
- |
- |
- |
08 – 06 |
0,025 |
Нутромеры индикаторные
(ГОСТ 868-72)
|
0,01 |
35-50 |
0,016 |
Штангенциркуль (ГОСТ 166-75) |
0,05 |
0,042 |
Нутромеры индикаторные (ГОСТ 868-72) |
0,01 |
35-50 |
0,043 |
Штангенциркуль (ГОСТ 166-75) |
0,05 |
0,021 |
Нутромеры индикаторные (ГОСТ 868-72) |
0,01 |
35-50 |
0,013 |
Микрометры рычажные (ГОСТ 4381-68) |
0,01 |
25-50 |
0,021 |
Нутромеры индикаторные
(ГОСТ 868-72)
|
0,01 |
35-50 |
0,013 |
Микрометры рычажные (ГОСТ 4381-68) |
0,01 |
25-50 |
0,062 |
Индикаторы часового типа (ГОСТ 166-75) |
0,01 |
0,062 |
Штангенциркуль (ГОСТ 166-75) |
0,05 |
0,039 |
Нутромеры индикаторные
(ГОСТ 868-72)
|
0,01 |
35-50 |
0,025 |
Микрометры гладкие (ГОСТ 6507-78) |
0,1 |
25-50 |
- |
0,013 |
- |
Микроскопы нструмент. ММИ и БМИ(ГОСТ 2014-71) |
0,005 |
0-25 |
- |
5 Расчет рабочих и контрольных калибров
5.1 Выбираем сопряжение: корпус – вал Æ
Стоим поля допусков для данного сопряжения
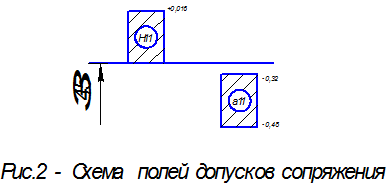
5.2 Размечаем нулевые линии для построения полей допусков калибров:
- Калибр – пробка (для контроля отверстий):
Проходная сторона (наименьшее отверстие):
Dmin
=Dн
+EI (5.1)
Dmin
=Dн
+EI=45+0=45 [мм]
Непроходная сторона (наибольшее отверстие):
Dmax
=Dн
+ES (5.2)
Dmax
=Dн
+ES=45+0,16=45,16 [мм]
- Калибр – скоба (для контроля вала):
Проходная сторона (наименьший вал):
dmin
=dн
+ei (5.3)
dmin
=dн
+ei=45+(-0,32)=44,68 [мм]
Непроходная сторона (наибольший вал):
dmax
=dн
+es (5.2)
dmax
=dн
+es=45+(-0,48)=44,52 [мм]
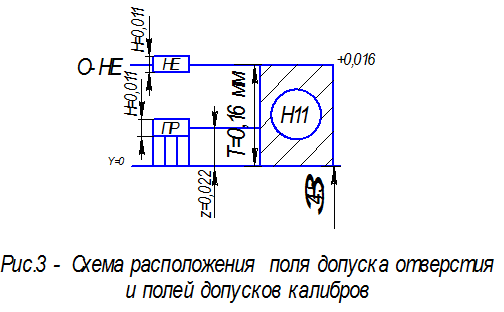
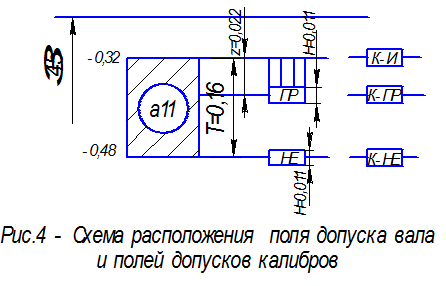
5.3 По таблицам допусков на калибры (ГОСТ 24853-81) берем отклонения:
- Для пробок Z=22 мкм, Y=0 мкм, H=Hs=11 мкм
- Для скоб Z=22 мкм, Y=0 мкм, H1
=Hs=11 мкм
Поля допусков калибров строятся от соответствующих нулевых линий.
Участок износа штрихуется вертикальными линиями.
5.4 Рассчитываем предельные размеры калибров, результаты оформляем в виде таблицы 2.
Размеры калибра-пробки
мм
мм
мм
мм
мм
Размеры калибра-скобы
мм
мм
мм
мм
мм
Таблица 4 – Предельные размеры калибров
Размеры, мм |
Для пробок |
Для скоб |
Проходная сторона |
Наибольший |
45,1875 |
44,6635 |
Наименьший |
45,0275 |
44,6525 |
Изношенный |
45 |
44,68 |
Непроходная сторона |
Наибольший |
45,1545 |
44,5255 |
Наименьший |
44,9945 |
44,5145 |
5.5 Определяем исполнительные размеры калибров для простановки их на чертежах:
Исполнительный размер калибра-пробки


Исполнительный размер калибра-скобы


6 Расчёт и выбор посадки с зазором
Исходные данные:
Номинальный диаметр сопряжения d=60 мм;
Длина сопряжения l=40 мм;
Угловая скорость вращения n=1000 об/мин;
Нагрузка на опору R=2 Кн;
Марка смазочного масла: индустриальное 30
Шероховатость поверхности втулки RzD
=3,2 мкм; вала Rzd
=1,6 мкм
Материал втулки – чугун, вала – сталь 30.
6.1 Рассчитываем угловую скорость:
(6.1),
где n – угловая скорость вращения
[рад/с]
6.2 Определяем среднее удельное давление:
(6.2),
где R – нагрузка на опору
[Н/м2
]
6.3 Устанавливаем допустимую минимальную толщину маслянистого слоя – h:
(6.3),
где RzD
и Rzd
– соответственно шероховатость втулки и вала.
[мм]
6.4 В соответствии с заданием определяем вязкость масла [1,табл. 1.3]:
[Па·с]
(6.4),
где tп
=500
С – температура нагрева подшипника в масле
[Па·с]
6.5 Определяем функциональный комплекс:
(6.5)
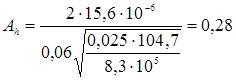
6.6 По графику [1, рис. 1.1] определяем относительные эксцентриситеты:
и 
6.7 Рассчитываем минимальный допустимый зазор:
(6.6),
где - относительный эксцентриситет при Smin
.
[м]
(6.7)
[м],
где вычисляется по таблице [1, табл. 1.6] в зависимости от эксцентриситета и отношения l/d.
6.8 Определяем температурное изменение зазора:
(6.8),
Где a1
и a2
– соответственно коэффициент линейного расширения материала вала и втулки
[м]
6.9 Рассчитываем минимальный действующий зазор:
(6.9)
[м]
6.10 Рассчитываем максимальный допустимый зазор:
(6.10),
Где - относительный эксцентриситет при Smax
.
[м]
6.11 Рассчитываем максимальный действующий зазор:
(6.11)
[м]
[мм] и [мм]
По таблицам ГОСТ 25347 – 82 [3] выбираем предельные зазоры:
Для [мкм] и [мкм] выбираем посадку в системе отверстия H8/h7.
Строим выбранную посадку:
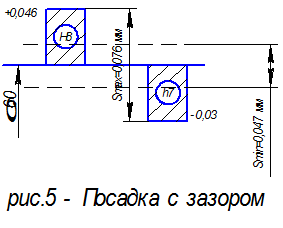
7 Расчёт и выбор посадки с натягом
Исходные данные:
Номинальный диаметр сопряжения D=100 мм;
Наружный диаметр втулки D2
=250 мм;
Длина сопряжения L=160 мм;
Передаваемый крутящий момент Mкр
=4500 Н·м;
Материал втулки и вала – сталь 30;
Диаметр осевого отверстия D1
=0 мм; осевое усилие P=0.
Шероховатость поверхности втулки RzD
=10 мкм, Rzd
=6,3 мкм
7.1 Определяем величину удельного контакта эксплуатационного Pз
между поверхностями сопряжения вала и втулки:
(7.1),
где d – номинальный диаметр сопряжения, – длина сопряжения, - коэффициент трения при запрессовке.
[Па]
7.2 По графику деформаций [1, рис. 2.1] и величинам Pэ
/sт
; d1
/d2
и d/d2
определяем характер деформирования отверстия и вала, вызванный удельным давлением:
(7.3)
По графику [1, рис. 2.1], учитывая отношения (7.3), делаем вывод что характер деформирования отверстия и вала, - упругий.
7.3 По графику деформаций [1, рис. 2.1] определяем наибольшее допустимое значение на границе допустимой зоны деформирования (кривая «а» или «б») и рассчитываем значение :
Наибольшее допустимое значение - кривая «а».
По графику [1, рис. 2.1] определяем, что .
[Па] – предел текучести материала.
[Па]
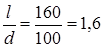
7.4 По графику [1, рис. 2.1] находим значение коэффициента неравномерности распределения удельного давления æ, затем рассчитываем наибольшее (для этого коэффициента) значение удельного давления Pнб доп
:
æ=0,95
PНБ
ДОП
= PНБ
· æ(7.4)
PНБ
ДОП
=0,88·108
·0,95=0,83 [Па]
7.5 Определяем коэффициенты формы отверстия и вала
CA
= (7.5)
CВ
= (7.6),
где - коэффициент Пуассона [1, табл. 2.2].
CA
= =0,58
CВ
= =0,3
7.6 Рассчитываем величину натягов:
Nmin
= Рэ
(7.7),
где EA
=EB
=2·1011
Па – модуль упругости стали.
Nmin
= 2.2·107
[мм] или 1 [мкм]
Nmax
= Pнб
.доп
(7.8)
Nmax
= 0,83·108
=0,036 [мм] или 36 [мкм]
7.7 Рассчитываем поправку на смятие микронеровностей сопрягаемых поверхностей и находим расчетные величины натягов для выбора посадки:
(7.9),
где К1
и К2
коэффициенты, учитывающие поправку на смятие микронеровностей.
Определяем по таблице [1, табл. 2.4]коэффициенты K1
и K2
:
K1
=K2
=0,25
[мкм] или 0,008 [мм]
Nmin
р
= Nmin
+ ΔШ
(7.10)
Nmin
р
= 0,001 + 0,008=0,009 [мм]
Nmax
р
= Nmax
+ ΔШ
(7.11)
Nmax
р
= 0,036 + 0,008=0,044 [мм]
7.8 Проверяем выполнение условий и выбираем стандартную посадку:
Nmax
р
Nmax
– условие выполнено
0,044 мм>0,036 мм
Nmin
р
Nmin
– условие выполнено
0,009 мм>0,001 мм
По таблицам ГОСТ 25347 – 82 [3] выбираем стандартную посадку по ГОСТ 25347 – 82 и строим её поля допусков с указанием размеров, натягов и отклонений:
Для Nmin
=1 [мкм] и Nmax
=36 [мкм] выбираем посадку в системе отверстия H6/n5.

7.9 Определяем наибольшее удельное давление на сопрягаемых поверхностях при наибольшем натяге выбранной посадки
(7.12)
[Па]
7.10 Вычисляем наибольшее напряжение во втулке:
σд
= (7.13),
где sД
– наибольшее напряжение во втулке.
Σд
= [Па]
7.11 Проверяем прочность втулки по выполнению неравенства:
σд
- условие выполнено
0,74·108
Па<2,94·108
Па
8 Расчёт точности зубчатой передачи
Исходные данные:
Число зубьев ведущего колеса Z1
=36;
Число зубьев ведомого колеса Z2
=50;
Окружная скорость колеса Vокр
=30 м/с;
Модуль зубчатой передачи m=5 мм;
Ширина колеса В=20 мм;
Рабочая температура колеса: T=800
C; корпуса: T=600
C;
Материал колеса: Силумин; корпуса: Чугун; Вид передачи: Грузовые машины
8.1 По величине окружной скорости Vокр
выбираются степени точности зубчатой передачи и затем корректируются по виду передачи [1, табл. 5.1]:
Для Vокр
=30 м/с соответствует 6 степень точности.
8.2 Определяем межосевое расстояние аw
:
аw
= (8.1),
где Z1
и Z2
– соответственно число зубьев ведущего и ведомого колеса, m – модуль.
Аw
= [мм]
8.3 Определяем температурную компенсацию зазора jn
1
и оптимальную толщину смазки jn
2
:
jn
1
=аw
[ (tкол
– 200
С) – (tкорп
– 200
С)]2sina (8.2),
где a1
и a2
– температурные коэффициенты линейного расширения материала втулки и вала соответственно, tкол
и tкорп
– температура колеса и корпуса соответственно, a – угол зацепления.
jn
1
=215[ (60 – 200
С) – (80 – 200
С)]2sin200
=0,103 [мм]
Для силовых передач:
jn
2
=20 (8.3)
jn
2
=20 =100 [мм]
8.4 Определяем минимальный боковой зазор передачи Smin
:
Smin
jn1
+ jn2
(8.4)
Smin
0,103+100 [мм]
Smin
100,103 [мм]
8.5 Определим диаметр делительной окружности для ведущего колеса:
D=mZ1
(8.5)
D=mZ1
= мм
8.6 Определим длину дуги:
L= (8.6)
L= мм
По таблицам ГОСТ 1643 – 81 [1] подбирается вид сопряжения:
5 – 6 – 6
8.5 Выберем контролируемые параметры и средства их измерения:
Таблица 5 – Обозначение контролируемых параметров
№
п. п.
|
Наименование параметра |
Обозначение |
1 |
Наибольшая кинематическая погрешность колеса |
 |
2 |
Рекомендуемая погрешность шага по зубчатому колесу |
 |
3 |
Накопленная погрешность К шагов |
 |
Таблица 6 – Значения параметров Fр
и Fрк
Степень
точности
|
Обозначение |
Модуль m, мм |
Диаметр делительной окружности
(для Fр
) или длинна дуги (дл Fрк
), мм
|
Св.125 до 200 |
5 |
Fр
|
от 1 до 16 |
25 |
Fрк
|
от 1 до 16 |
22 |
Таблица 7 – Нормы плавности работы (по ГОСТ 1643 – 72), мкм
Степень
точности
|
Обозначение |
Модуль m
мм
|
Диаметр делительной
окружности, мм
|
Св.125 до 280 |
5 |
 |
От 3,55 до 6 |
17 |
9 Расчет размерной цепи вероятностным методом
Назначение предельных отклонений составляющих звеньев размерной цепи при известном допуске замыкающего звена называется прямой задачей, которая может быть решена либо методом полной взаимозаменяемости, либо методом вероятностного расчёта. В данной курсовой работе производим расчет размерной цепи вероятностным методом, что позволяет установить на составляющие звенья более широкие допуски, чем те, которые получаются при решении задачи методом полной взаимозаменяемости. В основе этого метода служат теоремы математической статистики, устанавливающие свойства дисперсии. Замыкающее звено размерной цепи принимается за случайную величину, являющуюся суммой независимых случайных переменных, т.е. суммой независимых составляющих звеньев цепи. Как известно из теории вероятности, при любых законах распределения случайных погрешностей отдельных составляющих звеньев погрешность замыкающего звена также будет случайной погрешностью, подчиняющейся определённому закону распределения.
Распределение размеров в пределах допуска может происходить по одному из следующих законов:
а) нормального распределения;
б) равнобедренного треугольника (Симпсона);
в) равной вероятности.
Исходные данные:
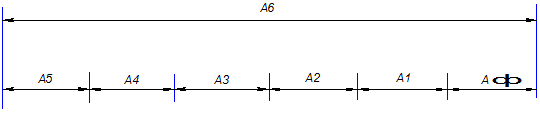
А1
|
А2 |
А3 |
А4 |
А5 |
А6 |
А |
70 |
120 |
40 |
100 |
70 |
400 |
 |
РВ |
РТ |
Н |
РТ |
РТ |
Н |
А4=5% |
Выполнение расчета:
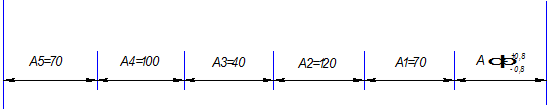
9.1 Номинальный размер замыкающего звена рассчитывается по формуле:
А∆
= А6
– (А1
+А2
+А3
+А4
+А5
) (9.1)
А∆
=400-(70+120+40+100+70)=0 мм.
9.2 Расчет средней точности размерной цепи. Введем следующие коэффициенты - коэффициент относительного рассеивания, который равен для:
Нормального распределения – 0,333
Закона равнобедренного треугольника – 0,408
Закона равной вероятности – 0,577
9.3 В зависимости от процента брака определяем для каждого звена добавочный множитель t:
А1: 0,27% - 3,00
А2: 0,27% - 3,00
А3: 0,27% - 3,00
А4: 5% - 1,96
А5: 0,27% - 3,00
А6: 0,27% - 3,00
9.4 Определяем произведение . Возводим это произведение в квадрат, где - единица допуска, которая выбирается в зависимости от номинальных размеров по ГОСТ 23347 – 82.
А1 |
А2 |
А3 |
А4 |
А5 |
А6 |
70 |
120 |
40 |
100 |
70 |
400 |
1,86 |
2,17 |
1,56 |
2,17 |
1,86 |
3,54 |
9.4.1 Суммируем все значения и определяем значение среднего коэффициента точности цепи – аср
по формуле:
аср
= (9.2),
где [TA ] – замыкающее значение допуска, мкм

мм = 1600 мкм
Таблица 8 – Расчет средней точности размерной цепи.
Аi ном
|
i |
t |
λi
|
(i·t·λi
)2
|
70 |
1,86 |
3,00 |
0,577 |
10,37 |
120 |
2,17 |
3,00 |
0,408 |
7,06 |
40 |
1,56 |
3,00 |
0,333 |
2,43 |
100 |
2,17 |
1,96 |
0,408 |
3,01 |
70 |
1,86 |
3,00 |
0,408 |
2,28 |
400 |
3,54 |
3,00 |
0,333 |
3,54 |

аср
= = мкм
По полученному значению аср
из табл.1.2[4] выбираем ближайший более точный квалитет допусков звеньев размерной цепи.
Принимаем а = 250, что соответствует 13 квалитету.
9.5 Определение вероятностного допуска замыкающего звена.
По табл.1.3[4] (ГОСТ 25347 – 82) определяем допуски составляющих звеньев размерной цепи.
Таблица 9 – Расчет вероятностного допуска замыкающего звена
Аi ном
|
TAi
|
λi
|
t |
(TAi
· λi
·t)2
|
70 |
460 |
0,577 |
3,00 |
634029,99 |
120 |
540 |
0,408 |
3,00 |
436868,12 |
40 |
390 |
0,333 |
3,00 |
151795,95 |
100 |
540 |
0,408 |
1,96 |
186474,73 |
70 |
460 |
0,408 |
3,00 |
317014,04 |
400 |
890 |
0,333 |
3,00 |
790516,59 |
9.6 Рассчитываем вероятностный допуск замыкающего звена по формуле:
(9.3)

мкм
Условие TA [TA ] выполняется.
1586,4 1600
9.7 Полученные допуски составляющих звеньев разбиваем на отклонения, пользуясь следующими правилами:
а) если среднее отклонение звена , то отклонение для всех звеньев принимаются симметрично, т.е. ;
б) если то отклонения принимаются
- для увеличивающихся звеньев ;
- для уменьшающихся звеньев ;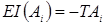
в) если , то отклонения принимаются
- для увеличивающихся звеньев ;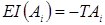
- для уменьшающихся звеньев ;
Звено А6 – увеличивающееся
Звенья А1-А5 – уменьшающиеся
мм = 0 мкм, то отклонения:
А1: ES(70) = +230 мкм EI(70) = -230 мкм
А2: ES(120) = +270 мкм EI(120) = -270 мкм
А3: ES(40) = +195 мкм EI(40) = -195 мкм
A4: ES(100) = +270 мкм EI(100) = -270 мкм
A5: ES(70) = +230 мкм EI(70) = -230 мкм
A6: ES(400) = +445 мкм EI(400) = -445 мкм
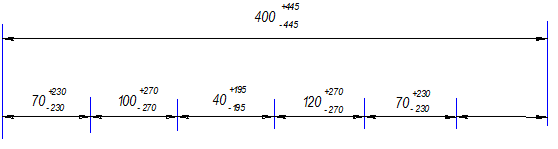
Так как разбивка отклонений произвольна, то обязательное условие может не выполняться.
мкм
– условие выполняется
0 мкм = 0 мкм
9.8 Процент годных деталей при сборке размерной цепи вычисляют в следующей последовательности:
а) Определяем средне квадратичное отклонение звена :
(9.4),
Где [ ] – заданное значение допуска, мкм:
мкм
б) Находим границы нового допуска:
Х= (9.7),
где - вероятный допуск, мкм
Х= мкм
в) Находим пределы интегрирования расчетного вероятностного допуска Z:
(9.8)
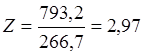
Г) Рассчитываем вероятность изготовления годных деталей по формуле:
(9.9),
Где Ф(Z) – значение функции Лапласа
Ф(2,97) = 0,4982; 
д) Процент годных деталей:
(9.10)

е) Брак:
(9.11)

Список используемой литературы
1. Расчет посадок с зазорами и натягами. Допуски и посадки подшипников качения. Выбор средств измерения. Допуски зубчатых передач: Произв. – техн. Материалы к учеб. Занятиям по курсу «Взаимозаменяемость, стандартизация и технические измерения»: для студентов спец. 170500, 170600/Воронеж. Гос. Технол. Акад.; Сост. А.А. Афанасьев, В.И. Логинова, Ю.М. Веневцев, И.М. Комарчев. Воронеж, 1997. 40 с.
2. Курсовое проектирование деталей машин: Учеб. Пособие для учащихся машиностроительных специальностей техникумов/С.А. Чернавский, К.Н. Боков, И.М. Чернин и др. – 2-е изд., перераб. и доп. – М.: Машиностроение, 1988. – 416 с.: ил.
3. Допуски и посадки: Справочник: В 2-х ч./В.Д. Мягков, М.А. Палей, А.Б. Романов, В.А. Брагинский. – 6-е изд. П.: Машиностроение, 1982. – Ч.1,1983. – Ч. 2.
4. Афанасьев А.А., Веневцев Ю.М. Допуски отверстий, валов, резьб, калибров: учебное пособие ВГТА/А.А. Афанасьев, Ю.М. Веневцев. Воронеж, 1994. – 44 с.
5. Методические указания к оформлению расчетно-проектных, расчетно-графических работ, курсовых и дипломных проектов/Воронеж. Гос. Технол. Акад.; Сост. Ю.Н. Шаповалов, В.Г. Савенков, Е.В. Вьюшина. Воронеж, 1998. – 50 с.
6. Взаимозаменяемость, стандартизация и технические измерения: Учебник для вузов/А.И Якушев, Л.Н. Воронцов, Н.М. Федотов. – 6-е изд., перераб. и доп. – М.: Машиностроение, 1986. – 352 с.
7. Справочник контролера машиностроительного завода. Допуски, посадки, линейные измерения/А.Н. Виноградов, Ю.А. Воробьев, Л.Н. Воронцов и др.; под ред. А.И. Якушева. – 3-е изд. – М.: Машиностроение, 1980. – 367 с.
|