Введение
Станочные приспособления являются одним из основных элементов оснащения металлообрабатывающего производства, позволяющих эффективно использовать в производственном процессе станки общего назначения.
Применение приспособлений дает возможность специализировать и настраивать станки на заданные процессы обработки, обеспечивающие выполнение технологических требований и экономически рентабельную производительность.
Правильно выбранное приспособление должно способствовать повышению производительности труда и точности обработки; ликвидации предварительной разметки заготовок и выверки их при установке на станке.
Приспособления с механизированным управлением во многих случаях позволяет автоматизировать процессы закрепления и освобождения деталей, что во многом приближает станки с такими приспособлениями к условиям работы специализированного оборудования.
Затраты на обслуживание и ремонт приспособлений вполне окупается экономическим эффектом их применения.
При всех условиях производства, станки, оснащенные приспособлением, могут успешно конкурировать со специализированным оборудованием.
Ступень оснащенности станков приспособлениями и их выбор в каждом случае решается условиям и программой производства.
В зависимости от масштабов производства (серийное, мелкосерийное, индивидуальное и опытное) и технологических факторов станочные приспособления по назначению и конструкции подразделяются на следующие группы: универсальное приспособление; универсально-наладочные; универсально-групповые приспособления; сборно – разборные приспособления.
1. Основные требования к конструкции приспособления
Станочные приспособления – это орудие производства для установки и закрепления заготовок и инструментов при обработке на металлорежущем станке. Станочные приспособления должны быть удобными в изготовлении, безопасными в работе, быстродействующими, точными, виброустойчивыми, износостойкими, ремонтопригодными. По своим конструктивно – технологическим параметрам станочные приспособления должны быть совместимы с другими компонентами технологической системы.
Сокращению сроков изготовления и снижению затрат на технологическую подготовку производства, выполнение оснащаемых операций с достижением заданных показателей производительности и точности способствуют унификация, стандартизация приспособлений, их деталей и сборочных единиц. Станочные приспособления классифицируют по технологическим и конструктивным признакам, степени универсальности и уровню механизации.
По группам оснащаемых станков станочные приспособления бывают токарными, сверлильными, расточными, фрезерными, строгальными, долбежными, протяжными, шлифовальными и др.
В данном проекте используется одноместные одноместное приспособление, предназначенную для обработки одной заготовки.
2. Правило 6 точек
Для того, чтобы точно определить положение валика в пространстве, необходимо задать пять координат которые лишают валик пяти степеней свободы: возможности перемещаться в направлении осей OX, OY, OZ и вращаться вокруг осей OX и OZ.
Шестая степень свободы – возможность вращаться вокруг собственной оси – отнимается у валика координатой, проведенной от поверхности шпоночной канавки.
Цилиндрическая поверхность валика, несущая четыре опорные точки, называется двойной направляющей базирующей поверхностью; торцовая поверхность валика является упорной базой. Для ориентирования детали в угловом положении необходима вторая упорная база под шпонку или штифт.
При базировании по наружной цилиндрической поверхности или по отверстию в различных самоцентрирующих патронах и на оправках эти поверхности также являются двойными направляющими базами; торец или уступ детали используют в качестве упорной базы.
Схема базирования коротких цилиндрических деталей.
В этом случае торцовая поверхность детали, несущая три опорные точки является главной базирующей поверхностью. Короткая цилиндрическая поверхность несет две опорные точки и называется центрирующей базой. Боковая поверхность шпоночной канавки эквивалентна одной опорной точке и является упорной базой.
3. Проверка правила 6 точек
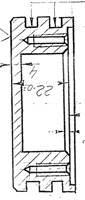 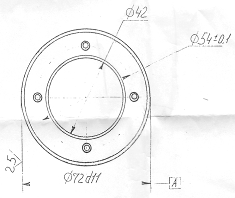
4
. Выбор установочных и направляющих элементов приспособления
Детали и механизмы приспособления, обеспечивающие правила и однообразное положение заготовки относительно инструмента, называются установочными элементами (опорами).
К установочным элементам предъявляют следующие требования:
– число и расположение установочных элементов должно обеспечивать необходимую ориентацию заготовки согласно принятой в технологическом процессе схемы базирования, а также достаточную ее устойчивость;
– при использовании черновых баз с шероховатостью до 3-го класса установочным элементам целесообразно выполнять с ограниченной опорной поверхностью в целях уменьшения влияния погрешностей этих баз на устойчивость заготовки
– установочные элементы по возможности не должны повреждать технологические базы заготовки, что особенно важно при ее установке на точные базы не подвергаются дальнейшей обработке.
– установочные элементы должны быть жестко зафиксированы. Для повышения жесткости крепления целесообразно улучшать качество сопряжения установочных элементов с корпусом приспособления применяя шлифование, а в отдельных случаях шабрение или притирку поверхности стенки.
– для повышения износостойкости опоры выполняют из сталей 45 или 20 (20 Х) и подвергают термической обработке для получения твердости HRC 58…62.
Несущие поверхности опор целесообразно шлифовать доводя шероховатость их поверхности до 8-го класса.
– в целях упрощения и ускорения ремонта приспособления его установочные элементы должны быть легкосменными.
Соблюдение этих требований предохраняет приспособление от брака при обработки и сокращает время и средства затрачиваемые на ремонт.
Опоры сопрягаются с технологическими базами устанавливаемой заготовки. Различают опоры основные с помощью которых заготовку лишают степеней свободы и вспомогательную ужесточающую технологическую систему. Опоры выбирают исходя из схем установочных требований к оснащаемым операциям, формам и гостам технологических баз массы и материала заготовки ожидаемые силовые реакции в опорах.
Направляющие элементы приспособления придают режущему инструменту определяет положение относительно заготовки а также уменьшает его упругие перемещения при обработке.
Направляющими элементами токарных патронов являются кулачки.
5. Компоновка конструкции приспособления
На чертеже показан трехкулачковый рычажный патрон с механизированным приводом для перемещения кулачков при зажиме и разжиме деталей, обрабатываемых на токарных и револьверных станках. Пневмопривод, закрепленный на фланце, установленном на заднем конце шпинделя токарного станка, состоит из пневмоцилиндра 4, в котором размещается поршень 8 со штоком 9, крышки 3, в отверстие которой запрессован хвостовик 1, невращающейся воздухораспределительной муфты 2 с двумя штуцерами 20 и 22 для подвода сжатого воздуха.
Для герметизации полостей А и Б пневмоцилиндра 4 на поршне установлены манжеты 7 с промежуточным кольцом 6, закрепленные кольцом 5. Герметизация штока осуществляется манжетой 17 и невращающейся муфтой 2 с вращающимся хвостовиком 1, манжетами 19 и 21. Невращающаяся распределительная муфта 2 установлена на наружном кольце шарикоподшипника 18, внутреннее кольцо которого вращается вместе с хвостовиком 1.
От распределительного крана сжатый воздух по трубопроводу подводится к штуцеру 22, а затем, пройдя по каналам в хвостовике 1, крышке 3 и пневмоцилиндре 4, поступает в штоковую полость А и перемещает поршень 8 со штоком 9 влево. При этом шток через тягу 16 и винт перемещает втулку 10 в корпусе влево. В корпусе патрона на осях установлены три рычага 11 с отношением плеч 3: 1. На концах рычагов подвижно установлены сухари, которые входят в пазы втулки 10 и в пазы основания кулачков 13. При движении влево втулка 10 поворачивает на осях рычаги 11, короткие плечи которых перемещают кулачки к центру, и деталь зажимается. После обработки детали распределительный кран переключается сжатый воздух подводится штуцеру 20 и, пройдя по каналу в хвостовике 1, поступает в безштоковую полость Б пневмоцилиндра и перемещает поршень 8 со штоком 9 вправо. При этом шток через тягу 16 перемещает втулку 10 с вертикальными плечами рычагов 11 вправо, а горизонтальные плечи этих рычагов разводят кулачки 13, и деталь разжимается.
Установка кулачков 13 патрона на требуемый размер обрабатываемых деталей производится вращением винта 12, на конце которого имеется зубчатое колесо 14, находящееся в зацепление с плоским центральным зубчатым колесом 15. При вращении зубчатое колесо 15 через зубчатые колеса 14 поворачивает остальные винты 12, которые перемещают все кулачки в положение, соответствующее размеру обрабатываемой детали.
При разжиме деталей по внутреннему диаметру необходимо переставить в пазах патрона кулачки 13, повернуть их на 1800
. Диаметр зажимаемой детали кулачками патрона 10 – 240 мм. Диаметр зажимаемого прутка 10–40 мм. Максимальное усилие на штоке 44000 Н (4500 кгс)
Исходные данные
1. Оборудование – токарный винторезный станок 16 К 20
2. Режущий инструмент – расточной резец из быстрорежущей стали Р9
3. Сечение державки 25х 25
4. Обрабатываемый материал – Бронза Бр АЖ 9–4
Порядок расчета:
1 Определяем силу действующую на заготовку
Pz
= 9,81 x Cpz
x tx
x S0
y
x Kpz
Kpz
= Kmpz
x Kф
pz
x K pz
где Cpz
– коэффициент характеризующий металл и условия его обработки
t – глубина резания в мм
S – подача в мм/ об
x, y – показатели степеней при глубине резания и подаче
Pz
= 9,81 x 200 x 2 x 0,405 x 0,9 = 0, 891= 637 H
Kmpz
= (170)
1,1
190
Kф
pz
= 0,9
2. Рассчитываем силу зажима.
W= Q
[K1
(1+3aM1
/h(l1
/l2
) = 628
= 1544 H
[0,875 (1+3x20x 0,75/64/25)
где: Wсум
– сила зажима принято 628
M1
– коэффициент трения между направляющей поверхностью кулачка и пазом патрона
K1
козффициент учитывающий дополнительные силы трения в патроне
принято 0,875
l1
и l2
– длины короткого и длинного плеч двуплечего рычага длина направляющей части кулачка соприкасающаяся с пазом корпуса патрона. принято 25 a – вылет кулачка тот середины его опоры в пазу патрона до центра приложения силы зажима W на одном кулачке.
Q – осевая сила принято 628
Расчет погрешностей
При расчете приспособления на точность SE при обработке не должна превышать величину допуска T размером SE<T
Суммарная погрешность S E зависит от нескольких факторов
S E= Eуст
+ Eобр
+ Eпр
где: Eуст
– погрешности установки детали в приспособление
Eобр
– погрешности обработки детали
Eпр
– расчетная погрешность приспособления
Погрешность установки представляет собой отклонение фактического положения закрепленной детали в приспособлении от требуемого теоретического.
Погрешность установки Eуст
включает погрешности базирования Eб
, закрепления Eз
и положения детали в приспособлении Eп
Eуст
= Eб
+ Eз
+ Eп
Погрешность положения Eп
детали в приспособлении по выбранному параметру Eпр
установки приспособления на планке Eу
и положения детали из-за износа приспособления Eu
Eп
= Eпр
+ Eу
+ Eu
Погрешность базирования Eб
= 0,04
Погрешность закрепления Eз
= 0,025
Установка приспособления Eу
= 0
т. к приспособление плотно прижато к столу.
Смещение инструмента Eп
= 0
Погрешность износа установки диаметров Eu
= И= 0,06
И= И0
К1
К2
К3
К4
(N / N0
)
где:
И – средний износ установочных элементов для заготовки при усилии P0
=10 кН и базовом числе установок N= 1000000
К1
; К2
; К3
; К4
– коэффициенты учитывающие влияние материала заготовки, оборудования, условий обработки, числа установок заготовки
N – число установок заготовки
К1
=0,97; К2
=1,25; К3
= 0,94; К4
=2,8
И=И0
К1
К2
К3
К4
(N/N0)
= 0.040 0.97 1.25 0.94 2.8 (50 103
/ 100 103
)=0.12 0.5 = 0.06
w – экономическая точность оборудования = 0,018
Для расчета точности приспособления Eпр
можно использовать упрощенную формулу
[Eпр
]< Т – Кm
√(Кm
1
* Eб
)2
* Eз
2
+ Eу
2
+ Eu
2
+ Enu
2
+ (Km
1
* w)2
где:
Т – допуск выполненного размера,
Eб
; Eз;
Enu
;
Eу
– погрешности базирования закрепления установки приспособления на станке. Положения детали из – за износа установочных элементов приспособления и от переноса инструмента Кm
= 1…1,2- коэффициент учитывающий отклонения рассеяния значений соответствующих величин закона нормального распределения.
Кm
1
= 0.8… 0,85 – коэффициент учитывающий изменение предельного значения погрешностей базирования при работе на настроечных станках
Кm
2
= 0,6… 0,8 – коэффициент учитывающий долю погрешностей обработки в суммарной погрешности вызываемой факторами не зависящими от приспособления
Подставляем данные в формулу
[Eпр
]= 0,16–1,2√(0,8*0,04)2
+ 0,0252
+02
+0,062
02
+ (0,6*0,018)2
= 0,16–0,095=0,065
Eпр
< [Eпр
]
En
= Eпр
+ Eу
+ Eu
= 0.02 + 0+0,06= 0,08
Eуст
= Eб
+ Eз
+ En
= 0.04 + 0.025 + 0.08 = 0.125
S E = Eуст
+ Eобр
+ Eпр
= 0,125 + 0,005 + 0,02 =0,15 Þ обработка возможна, т. к. допуск больше чем суммарная погрешность
Т>
å
E
= 0.16>0.15
Расчет погрешности на размер 20-0,33
E= И=0,06
И=И0
К1
К2
К3
К4
(N/N0
) = 0.04 0.97 1.25 0.94 2.8 (50 103
/ 100 103
)=0.06
[Eпр
] = Т – Кm
√(Кm
* Eб
) E2
з
+ E2
у
+ Eu
2
+ E2
m
1
+ (Кm
2
* w)2
= 0.33 – 1.3 0.075= 0.23
En
= Eпр
+ Eу
+ Eu
= 0.05 + 0.06 = 0.11
Eуст
= Eб
+ Eз
+ En
= 0,04 + 0,03 = 0.18
åE = Eуст
+ Eобр
+ Eпр
= 0.18 + 0.005 + 0,05= 0. 255 Þ обработка возможна
Т>
å
E
= 0.33>0.255
Рассчитываем экономическую эффективность проектируемого приспособления
Эп
= (Тшт
– Тп
шт
) Сч.з
N
= (0,45–0,25) 16,0*20000 = 64000 руб.
60
P = Sпр
(А+B) = 80000 (0.5 + 0.5)= 40000 руб.
Dп
= Эп
– P= 64000 – 40000= 24000 руб.
Сч.з
= Сb
.
y
чз
Rм
= 17,85* 0,9=16,0 руб./ч
где
Сч.з
– часовые затраты по эксплуатации рабочего места руб./ч
Сby
ч.з
– практические скорректированные часовые затраты на базовом рабочем месте
Rм
– машино-коэффициент, показывающий, во сколько раз затраты, связанные с работой данного станка, больше, чем аналогичные расходы у базового станка
Эп
- годовая экономия (без учета годовых затрат на приспособление), руб.
P – годовые затраты на приспособление, руб.
Тшт
– штучное время при обработке детали без приспособления или в универсальном приспособлении, мин
Тп
шт
– штучное время на операции после внедрения приспособления
N – годовая программа, шт.
Sпр
– стоимость приспособления
А – коэффициент амортизации
В-коэффициент, учитывающий ремонт и хранение приспособления
Dп
– экономический эффект от применения приспособления
Заключение
Я спроектировал механизированное станочное приспособление
Для обработки детали Поршень.
Данное приспособление применяется в серийном производстве рабочая среда – сжатый воздух давления 0,4 МПа. В данной работе я рассчитывал погрешности приспособления, усилие зажима параметры зажимного механизма необходимые для усилия зажима.
Одну из деталей «шток» рассчитывал на прочность расчет показал что данная деталь выдерживает все возникающие во время работы приспособления напряжения. Так ж в данной работе проанализирована деталь обрабатываемая в данном приспособлении, материал из которого изготовлена деталь и технологию операцию мной выбран станок 16К20.
В данной работе содержится также графическая часть. В нее вошли чертежи детали и приспособления
Список использованной литературы
1. Горбацевич А.Ф. Курсовое проектирование по Технологии машиностроения.
2. Белоусов А.П Проектирование станочных приспособлений Москва «Высшая Школа» 1980 г.
3 Добрыднев А.Г. Курсовое проектирование по Технологии машиностроения.
4. Ансеров М.А. Приспособления для металлорежущих станков
5. Горошкин А.К Приспособления для металлорежущих станков
6. Корсаков В.С. Основы конструирования приспособлений
|