ВВЕДЕНИЕ
Приспособлениями в машиностроении называют дополнительные устройства к технологическому оборудованию, применяемые при выполнении технологических операций (обработка заготовок, сборка изделий, контроль). За счет использования приспособлений устраняется необходимость разметки заготовок, расширяются технологические возможности металлообрабатывающего оборудования, возрастает производительность труда, повышаются точность обработки и качество изделий. Используя приспособления, можно сократить основное технологическое время за счет совмещения обработки нескольких заготовок и различных поверхностей одной заготовки; увеличение числа одновременно работающих инструментов, повышения параметров режимов обработки. В общем объёме средств технологического оснащения примерно 50 % составляют станочные приспособления.
Для обработки отверстий на сверлильном станке чаще всего применяют кондукторы. Кондуктор-это приспособление, служащее для установки деталей, обрабатываемых на сверлильных станках, и имеющие кондукторные втулки для направления режущего инструмента. Кондукторная втулка предохраняет инструмент от увода в начале резания.Для уменьшения износа втулок и уменьшения смещения оси обрабатываемого отверстия из-за возможного перекоса инструмента во втулке между ее нижним торцом и поверхностью заготовки оставляют зазор. Тогда стружка не проходит через втулку, а сбрасывается в сторону. При сверлении стали зазор увеличивается до размера диаметра.
Иногда при обработке отверстий, расположенных на различных поверхностях деталей, требуется изменять ее положение на станке относительно режущего инструмента. Для этого применяют кондукторы различных видов: накладные, стационарные, передвижные, поворотные, групповые.
В моём случае для обработки детали «Фланец» выгодно применить кондуктор для сверления отверстий по окружности детали. Применение кондуктора позволяет надёжно базировать и закреплять обрабатываемую деталь с сохранением её жёсткости в процессе обработки, повысить производительность и облегчить условия труда рабочего в результате механизации приспособлений.
1 ОБЩАЯ ЧАСТЬ
1.1 Назначение, устройство, принцип действияпроектируемого приспособления

Рисунок 1 Кондуктор для сверления отверстий по окружности
На сверлильных станках широкое распространение получили кондукторы.
Кондуктор - это станочное приспособление, предназначенное для закрепления деталей, обрабатываемых на сверлильных станках, и имеющие кондукторные втулки для предотвращения увода сверла.
Кондуктор состоит из трёх основных частей: ползуна с кондукторной планкой, вертикально перемещающегося по скалкам приспособления; консольной планки для закрепления деталей и делительного устройства. Планка с кондукторной втулкой перемещается по направляющим ползуна; отсчет перемещений производится по нониусу.
В два отверстия корпуса 3 запрессованы две параллельные направляющие втулки 18,по которым в вертикальном направлении перемещается ползун 10.Кондукторная планка 9 устанавливается на требуемый диаметр расположения осей отверстий по окружности вручную по нониусу, нанесенному на боковой прикрывающей планке и миллиметровой шкале на кондукторной планке. Кондукторная планка 9 после перестановки закрепляется винтом 14 с накатной головкой, который через промежуточный плунжер 13 и шарик 12 действует на зажимной шарик 11,который заклинивается в продольномV-
образном пазу ползуна 16.
В постоянную кондукторную втулку 7 устанавливается сменная кондукторная втулка 8.
Регулируемый по высоте ползун 10 зажимается в требуемом положении винтом 15 с накатной головкой, действующим через шарик 16.
Шарик 16 как клин передаёт давление на два промежуточных шарика 17,
расположенных в поперечном канале ползуна 10,
прижимающих плунжеры, расположенные в этом канале, к колонкам 18.
1.2 Маршрутная технология для изготовления детали «Фланец»
005 Заготовительная
Заготовка-штамповка
010Токарная
015Сверлильная
Сверлить 12отв.Ø26 на l=32
020Контрольная
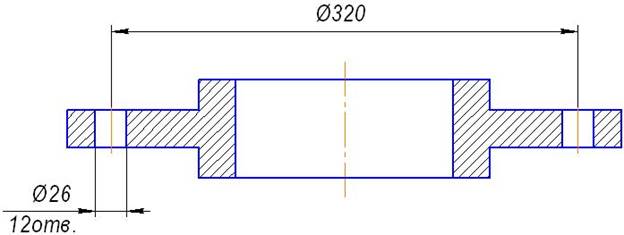
Рисунок 2 Операционный эскиз детали «Фланец»
1.3 Проверка условия лишения возможности перемещения заготовки в приспособлении по шести степеням свободы.
Требуемая точность обработки обеспечивается определённым положением заготовки относительно режущего инструмента. Положение заготовки при обработке характеризуется шестью степенями свободы. Каждое свободное, твердое тело имеет 6 степеней свободы, т.е. 3-хкоординатное перемещение вдоль осей X,Y,Z. Поэтому чтобы лишить деталь всех 6-и степеней свободы, необходимо обеспечить силовой контакт поверхности детали в приспособлении с 6-ю неподвижными точками. В этом заключается правило 6-и точек. Причем эти 6 точек должны быть расположены в 3-х взаимоперпендикулярных плоскостях.
Закрепляем деталь в трёхкулачковом патроне, кулачки работают на разжим, деталь зажимается за внутреннюю поверхность. Заготовка лишается всех 6 степеней свободы: возможности перемещения относительно осей X, Y, Zи вращение вокруг X, Y, Z.Сверло при обработке направляется кондукторной втулкой, что позволяет уменьшить смещение инструмента при сверлении.
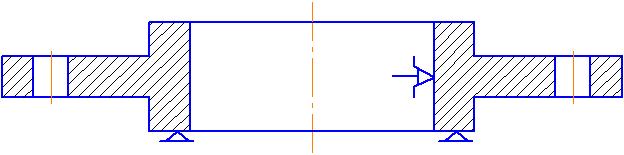
рисунок 3 Схема базирования детали «Фланец»
2 РАСЧЁТНАЯ ЧАСТЬ
2.1 Расчёт погрешности базирования заготовки в приспособлении
В процессе обработки заготовки возникают отклонения от геометрической формы и размеров, заданных чертежом, которые должны находиться в пределах допусков, определяющих наибольшие допустимые значения погрешностей размеров и формы заготовки или детали.
Сумма всех погрешностей определяется по формуле
∑ =kбаз.
+ y
ст.
+ обр.
+[ ]пр.
,(1)
где k=0,8÷0,85 – коэффициент уменьшения погрешности баз
вследствии того, что действительные размеры установочной поверхности редко равны предельным;
баз.
- погрешность базирования при выполнении данной операции;
баз
=0
уст
- погрешность установки, возникающая под действием зажимных сил и сил резания. Она зависит от типа приспособления, и главным образом, от характера зажима и не зависит от схемы базирования и метода обработки.
уст.
=0,13мм
обр
- погрешность обработки детали на данной операции.
Эту величину можно определить следующим образом
обр.
=k,
* , (2)
где -табличное значение средней экономической точности.
k,
=0,6÷0,8 – коэффициент уменьшения величины , которым учитывается изменение табличных данных, k,
=0,8
обр.
=0,2436мм
[ ]пр.
, т. к причины, вызывающие эту погрешность своевременно устраняются, то при расчёте погрешности этой составляющей обычно пренебрегают.
∑ =0,8*0+0,13+0,2436=0,3736мм.
Для обеспечения необходимой точности обрабатываемой детали при конструировании приспособления необходимо выбрать такую схему, при которой будет соблюдено условие
баз
< баз.доп
. (3)
где баз
-действительное значение погрешностей базирования обрабатываемой детали в приспособлении;
баз.доп.
- допускаемое значение погрешностей базирования обрабатываемой детали в приспособлении.
Допускаемое значение погрешностей базирования обрабатываемой детали в приспособлении определяется по формуле
баз.доп
=δ , (4)
где δ- Допуск на размер обрабатываемого отверстия;
- точность обработки детали достижимая при выполнении данной операции.
Определяем для размера Ø320.
δ(14квалитет)=1мм
(12квалитет)=0,406мм
0<0,594, условие выполнено.
Если допуск на размер детали равен δ, а сумма всех погрешностей ∑ , то необходимо чтобы соблюдалось условие
∑ ≤ δ (5)
0,3736≤1, условие выполнено, значит, приспособление обладает требуемой точностью.
2.2 Расчёт усилия зажима
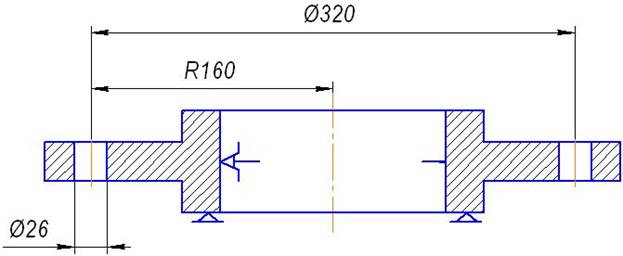
Рисунок 4 Схема усилия зажима
При установке детали в кондуктор должно обеспечиваться надежное закрепление детали от действия крутящего момента, способствующего проворачиванию детали при сверлении и сдвига в осевом направлении под действием осевой составляющей силы резания.
Так как мы обрабатываем отверстие сверлом то в зоне резания возникает момент, который старается повернуть деталь.
При расчёте усилия зажима опираюсь на литературу [6]
Силу зажима в Н, рассчитываем по формуле
.
(6)
где k- коэффициент запаса;
Мк
- крутящий момент, создаваемый сверлом;
Мк
= , (7)
где 
=
26мм
=0,041;
q=2;
y=0,7;
=0,43;
=0,75
Мк
=114Н*м.
-коэффициент трения;
=(0,1÷-0.,15)=0,1.
-расстояние от сверла до оси или до точки закрепления сверла;
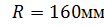
k=k0
*k1
* k2
* k3
* k4
* k5,
(8)
где k0
=1,5-гарантированный коэффициент запаса для всех случаев;
k1
- коэффициент, учитывающий состояние поверхности заготовки(для чистовой обработки 1);
k2
- коэффициент, учитывающий увеличение сил резания от прогрессирующего затупления инструмента (k2
=1-1,9);
k3
- коэффициент, учитывающий увеличение сил резания при прерывистом резании. При точении k3
=1,2;
k4
- коэффициент, учитывающий постоянство силы зажима, развиваемой силовым приводом приспособления (k4
=1,3 для ручного привода с удобным расположением рукояток);
k5
-коэффициент, учитывающий только при наличии моментов, стремящихся повернуть обрабатываемую деталь.
k5
=1, обрабатываемая деталь установлена базовой плоскостью на опоры с ограниченной поверхностью контакта;
k=1,5*1*1*1,2*1,3*1=2,34
=5,5Н
2.3 Прочностные расчёты одной детали приспособления
При расчёте опираюсь на литературу [1].
Рассчитываем на прочность винт с внутренним шестигранником.
Материал винта- Сталь 45.
Коэффициент запаса прочности рассчитывается по формуле
, (9)
где σпред.
-прдельное напряжение,
σпред.
=610МПа;
σ-расчётное напряжение
Допускаемое напряжение [σ] находится по формуле
 (10)
= 300МПа
2МПа (2000Па)
Расчётное напряжение находится по формуле
, (11)
где -это нагрузка. которую выдерживает материал, не разрушаясь;
-площадь поперечного сечения
, (12)
Где m-масса винта;
-ускорение свободного падения;

=0,68Н
= , (13)
где d-диаметр винта;
= .

=0,073МПа(72Па)
Прочность элемента конструкции обеспечивается, если наибольшее напряжение, возникающее в нём, не превышает допускаемого,
σ ≤[σ] , (14)
72≤2000,выполнено.
3 ТЕХНИКА БЕЗОПАСНОСТИ
1. Наружные элементы конструкции приспособления не должны иметь поверхностей с неровностями (острые кромки, углы и др.),
2. Способ соединения со станком и со с сменными наладками должен исключать возможность самопроизвольного ослабления крепления
3. Конструкция приспособления должна обеспечивать свободное удаление СОЖ и стружки.
4. Конструкция приспособления должна быть безопасной при складировании с транспортировке.
5. Контролю выполнения требований безопасности должны подвергать вновь изготовленные, модернизированные и прошедшие ремонт приспособления.
6. Неоговоренные радиусы скруглений, размеры фасок наружных, поверхностей, должны быть не менее 1мм.
7. При массе приспособления свыше 12кг должна быть предусмотрена возможность закладки и съёма стропов и других захватных устройств грузоподъёмных механизмов.
8. Усилие закрепления заготовок следует рассчитывать из условия превышения максимальных сил резания не менее, чем в 2,5раза.
9. Устройства, нагревающиеся в процессе эксплуатации свыше 45°С должны быть теплоизолированы или ограждены.
ЗАКЛЮЧЕНИЕ
В данной курсовой работе мною было спроектировано приспособление для сверления 12 отверстий Ø26 мм в детали «Фланец».
Для того чтобы правильно и надёжно закрепить деталь в приспособлении при такой операции, как сверление, необходимо использовать кондуктор.
Для направления режущего инструмента в корпусе кондуктора имеются кондукторные втулки, которые обеспечивают точную обработку отверстий в соответствии с чертежом. Конструкция и размеры этих втулок стандартизованы. С целью снижения стоимости изготовления кондуктора проводится широкая нормализация деталей и основных узлов кондуктора.
В ходе проектирования станочного приспособления кондуктор, были выявлены некоторые преимущества применения такого приспособления:
применение специализированного приспособления позволит
снизить трудоёмкость обработки на данной операции.
упрощают процесс сверления отверстий и позволяют получить увеличение производительности.
позволяет стабильно обеспечивать высокое качество обрабатываемых деталей при минимальной зависимости качества от квалификации рабочего;
применение кондуктора исключает разметку осей отверстий.
Но, несмотря на ряд преимуществ, кондуктор имеет и недостатки:
Невысокая жесткость;
Чувствительность к биению сверла.
В процессе проектирования приспособления для сверления отверстий
в детали «Фланец», изучены и освоены принципы проектирования станочных приспособлений, а также ряд смежных тем, таких как: расчет погрешности базирования; расчеты на прочность; расчет сил зажима; основы конструирования; получено представление о технологических процессах механической обработки деталей и требованиях безопасности предъявляемых к приспособлениям при их проектировании и при работе на них.
Список используемых источников
1. Ансеров М.А. Приспособление для металлорежущих станков.- Москва: Машиностроение, 1975.-638с.
2. Аркуша А.И. Техническая механика, теоретическая механика и сопротивление материалов. – Москва : Высшая школа,2005г.-351с.
3. Белоусов А.П.Проектирование станочных приспособлений. - Москва: Высшая школа,1980.-240с.
4. Горошкин А.К. Приспособления для металлорежущих станков. -Москва:Машиностроение,1971.-384с.
5. Справочник технолога – машиностроителя. В 2-х т. Т.2/ под ред. А.Г. Косиловой, Р.К. Мещерякова.-4-е изд., перераб. и доп. – Москва:Машиностроение,1986.-496с.,ил.
6. Ревин С.А.Методические указания по проектированию технологических процессов механической обработки деталей машин. - Москва: Высшая школа, 1979.-287с.
|