МИНИСТЕРСТВО ОБРАЗОВАНИЯ И НАУКИ УКРАИНЫ
Национальный аэрокосмический университет им Н.Е. Жуковского
ПРОЕКТИРОВАНИЕ И ИССЛЕДОВАНИЕ МЕХАНИЗМА ДВИГАТЕЛЯ ВНУТРЕННЕГО СГОРАНИЯ
Пояснительная записка к курсовому проекту
Дисциплина – «Теория машин и механизмов»
Харьков 2009
Введение
Среди рычажных механизмов различных типов одним из наиболее распространенных в технике являются кривошипно-ползунные механизмы (КПМ). Они используются в двигателях внутреннего сгорания (ДВС), компрессорах, насосах, ряде станков (например, прессах) и других машинах различного назначения, включая наземные и воздушные транспортные средства.
Поршневые ДВС служат для преобразования теплоты, выделяющейся при сгорании топлива в цилиндрах, в механическую работу. Механизмы одноцилиндровых ДВС имеют сравнительно небольшую мощность . Они применяются в основном в энергоустановках для привода в движение электрогенераторов, компрессоров, воздуходувных установок, в самоходных шасси, служат для перемещения грузов и т.д.
Одним из эффективных средств повышения мощности ДВС является увеличение числа их цилиндров. Поэтому многоцилиндровые ДВС широко распространены в современной технике. В авиации ДВС сейчас применяются в вертолетах, легких транспортных, спортивных и учебных самолетах.
1. Проектирование кривошипно-ползунного механизма ДВС
1.1 Определение линейных размеров звеньев механизма
Проектирование кинематической схемы кривошипно–ползунного механизма (КПМ) заключается в выборе в соответствии с заданными условиями и требованиями значений линейных размеров кривошипа и шатуна.
Определяем ход поршня:
,
где: – диаметр поршня.
Запишем ход поршня через длину кривошипа:

Из отношения длины шатуна к радиусу кривошипа определим длину шатуна:

В качестве начального звена в КПМ выбрано кривошип. Условие существования КПМ:

1.2
Структурный анализ механизма

Рисунок 1.2.1. Механизм ДВС – кривошипно-шатунный механизм
1.2.1. Определяем число подвижных звеньев: 
1.2.2. Подсчет и классификация кинематических пар 5 и 4 класса:
1. (0–1) – НКП, вращательная, 5 класса;
2. (1–2) – НКП, вращательная, 5 класса;
3. (1–4) – НКП, вращательная, 5 класса;
4. (2–3) – НКП, вращательная, 5 класса;
5. (3–0) – НКП, поступательная, 5 класса;
6. (4–5) – НКП, вращательная, 5 класса;
7. (5–0) – НКП, поступательная, 5 класса.
Таким образом, 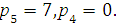
Определение степени подвижности:


Выделение основного механизма – основной механизм это первое звено и стойка с соединяющей их кинематической парой.
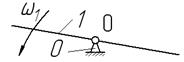
Рисунок 1.2.2. Основной механизм первого класса
Выделение 1-й в порядке наслоения группы Ассура – звено 2–3, 4–5.

Рисунок 1.2.3. Первая в порядке наслоения группа Ассура 2-го класса 2-го вида
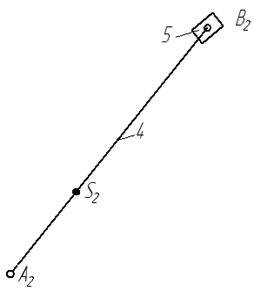
Рисунок 1.2.4. Вторая в порядке наслоения группа Ассура 2-го класса 2-го вида
Определение класса механизма в целом. Механизм 2-го класса, так как в его состав входит структурная группа второго класса.
1.3 Кинематический анализ механизма
Метод замкнутых контуров устанавливает связь между геометрическими и кинематическими параметрами механизма и основан на условии замкнутости контуров. В механизмах 2-го класса количество замкнутых контуров равно количеству структурных групп 2-го класса, образующих механизм. Если звенья механизма принять за векторы, то в процессе движения конфигурация векторного многоугольника изменяется, но условие замкнутости сохраняется, т.е. в любом положении механизма геометрическая сумма векторов равна нулю.

Рисунок 1.3.1. Замкнутый векторный многоугольник
Кинематическая схема механизма приведена на рис. 1.3.1. Направляющие ползунов наклонены относительно системы координат . Целесообразно выбрать новую систему координат , начало которой совмещено с осью вращения кривошипа 1, а ось абсцисс ориентирована параллельно направляющим ползуна 3. Для однозначного определения направляющих углов и со звеньями 1 и 2 связываются векторами . Длину шатуна 2 и положение точки на шатуне выражено через длину кривошипа: 

Направляющий угол вектора :

где: координаты начала и конца вектора которые выражены в виде соотношений:




После подстановки уравнений в имеется:

или

Функция положения точки ползуна 3 соответствует выражению

Функция положения точки на шатуне 2


Кинематические передаточные функции получаются путем дифференцирования соотношений по обобщенной координате .
Передаточное отношение угловых скоростей шатуна и кривошипа
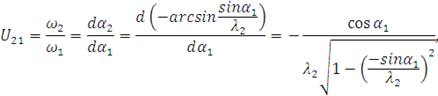
или окончательно

Передаточные функции скорости некоторых точек: точки на ползуне

или окончательно

точки на шатуне:


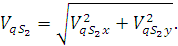
Угловое ускорение шатуна 2:

или

Передаточная функция углового ускорения шатуна 2 определяется соотношением

где:


Окончательно получается

Отношение ускорения к квадрату угловой скорости точки на ползуне равно

Действительные значения углового ускорения шатуна 2 и линейного ускорения точки ползуна 3 соответственно становят:


Следуя методике, изложенной выше, получим



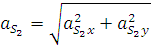
Результаты вычислений для 24 положений кривошипно-ползунного механизма приведены в таблицах ниже
Таблица 1.3.1. Результаты расчетов

|

|

|

|

|

|

|

|

|
0
|
0
|
14,3
|
0
|
2,9633
|
-10
|
-1,792
|
-144
|
7,8606
|
30
|
-7,18
|
11,0
|
-1,754
|
2,5674
|
-8,729
|
-6,549
|
-114,6
|
-69,42
|
60
|
-12,5
|
4,91
|
-2,813
|
1,2173
|
-5,121
|
-9,431
|
-43,21
|
-130,6
|
90
|
-14,5
|
-2,49
|
-2,88
|
-0,623
|
0
|
-9,857
|
29,745
|
-140,6
|
120
|
-12,5
|
-9,25
|
-2,175
|
-2,21
|
5,1215
|
-7,761
|
71,987
|
-93,77
|
150
|
-7,18
|
-13,6
|
-1,126
|
-2,944
|
8,7287
|
-3,519
|
84,907
|
-16,91
|
180
|
0
|
-14,3
|
0
|
-2,709
|
10
|
1,7916
|
86,4
|
47,869
|
210
|
7,18
|
-11,0
|
1,1258
|
-1,845
|
8,7287
|
6,5491
|
84,907
|
78,683
|
240
|
12,5
|
-4,91
|
2,1748
|
-0,753
|
5,1215
|
9,4315
|
71,987
|
85,921
|
270
|
14,5
|
2,49
|
2,88
|
0,3769
|
0
|
9,8574
|
29,745
|
86,308
|
300
|
12,5
|
9,25
|
2,8135
|
1,492
|
-5,121
|
7,7613
|
-43,21
|
82,728
|
330
|
7,18
|
13,6
|
1,7542
|
2,4682
|
-8,729
|
3,5187
|
-114,6
|
61,896
|
360
|
0
|
14,3
|
0
|
2,9633
|
-10
|
-1,792
|
-144
|
7,8606
|
390
|
-7,18
|
11,0
|
-1,754
|
2,5674
|
-8,729
|
-6,549
|
-114,6
|
-69,42
|
420
|
-12,5
|
4,91
|
-2,813
|
1,2173
|
-5,121
|
-9,431
|
-43,21
|
-130,6
|
450
|
-14,5
|
-2,49
|
-2,88
|
-0,623
|
0
|
-9,857
|
29,745
|
-140,6
|
480
|
-12,5
|
-9,25
|
-2,175
|
-2,21
|
5,1215
|
-7,761
|
71,987
|
-93,77
|
510
|
-7,18
|
-13,6
|
-1,126
|
-2,944
|
8,7287
|
-3,519
|
84,907
|
-16,91
|
540
|
0
|
-14,3
|
0
|
-2,709
|
10
|
1,7916
|
86,4
|
47,869
|
570
|
7,18
|
-11,0
|
1,1258
|
-1,845
|
8,7287
|
6,5491
|
84,907
|
78,683
|
600
|
12,5
|
-4,91
|
2,1748
|
-0,753
|
5,1215
|
9,4315
|
71,987
|
85,921
|
630
|
14,5
|
2,49
|
2,88
|
0,3769
|
0
|
9,8574
|
29,745
|
86,308
|
660
|
12,5
|
9,25
|
2,8135
|
1,492
|
-5,121
|
7,7613
|
-43,21
|
82,728
|
690
|
7,18
|
13,6
|
1,7542
|
2,4682
|
-8,729
|
3,5187
|
-114,6
|
61,896
|
720
|
0
|
14,3
|
0
|
2,9633
|
-10
|
-1,792
|
-144
|
7,8606
|
Таблица 1.3.2. Результаты расчетов

|

|

|

|

|

|

|
0
|
1,92
|
2,8978
|
124,8
|
76,387
|
0
|
-405,6
|
30
|
2,2696
|
2,6337
|
111,48
|
93,313
|
191,98
|
-303,8
|
60
|
2,7721
|
2,0938
|
84,887
|
118,61
|
349,01
|
-129,7
|
90
|
2,88
|
1,9668
|
77,437
|
123,21
|
413,12
|
65,303
|
120
|
2,5735
|
2,4593
|
91,237
|
102,66
|
349,01
|
250,69
|
150
|
2,1325
|
2,862
|
102,35
|
78,892
|
191,98
|
383,71
|
180
|
1,92
|
2,8137
|
105,6
|
81,111
|
0
|
405,62
|
210
|
2,1325
|
2,4236
|
102,35
|
95,849
|
-192
|
303,83
|
240
|
2,5735
|
2,0196
|
91,237
|
104,2
|
-349
|
129,68
|
270
|
2,88
|
1,9458
|
77,437
|
105,26
|
-413,1
|
-65,3
|
300
|
2,7721
|
2,2719
|
84,887
|
99,58
|
-349
|
-250,7
|
330
|
2,2696
|
2,7078
|
111,48
|
86,086
|
-192
|
-383,7
|
360
|
1,92
|
2,8978
|
124,8
|
76,387
|
0
|
-405,6
|
390
|
2,2696
|
2,6337
|
111,48
|
93,313
|
191,98
|
-303,8
|
420
|
2,7721
|
2,0938
|
84,887
|
118,61
|
349,01
|
-129,7
|
450
|
2,88
|
1,9668
|
77,437
|
123,21
|
413,12
|
65,303
|
480
|
2,5735
|
2,4593
|
91,237
|
102,66
|
349,01
|
250,69
|
510
|
2,1325
|
2,862
|
102,35
|
78,892
|
191,98
|
383,71
|
540
|
1,92
|
2,8137
|
105,6
|
81,111
|
0
|
405,62
|
570
|
2,1325
|
2,4236
|
102,35
|
95,849
|
-192
|
303,83
|
600
|
2,5735
|
2,0196
|
91,237
|
104,2
|
-349
|
129,68
|
630
|
2,88
|
1,9458
|
77,437
|
105,26
|
-413,1
|
-65,3
|
660
|
2,7721
|
2,2719
|
84,887
|
99,58
|
-349
|
-250,7
|
690
|
2,2696
|
2,7078
|
111,48
|
86,086
|
-192
|
-383,7
|
720
|
1,92
|
2,8978
|
124,8
|
76,387
|
0
|
-405,6
|
1.
4
Силовой расчет механизма при
,
,
и
Цель этого этапа исследования – определение реакций в кинематических парах механизма и величины действующего момента, приложенного к кривошипу механизма.
Определение движущей силы при помощи давления рабочего тела в цилиндре и диаметра поршня :

Таблица 1.4.1. Движущие силы и давления в цилиндрах

|

|

|

|

|
0
|
1,38
|
15607,43
|
0,03
|
339,292
|
30
|
2,64
|
29857,7
|
0,03
|
339,292
|
60
|
1,14
|
12893,1
|
0,02
|
227,33
|
90
|
0,54
|
6107,256
|
0
|
0
|
120
|
0,3
|
3392,92
|
-0,01
|
-112
|
150
|
0,21
|
2375,044
|
-0,03
|
-339,292
|
180
|
0,15
|
1696,46
|
-0,03
|
-339,292
|
210
|
0,03
|
339,292
|
-0,03
|
-339,292
|
240
|
0,03
|
339,292
|
-0,02
|
-227,33
|
270
|
0,03
|
339,292
|
-0,01
|
-112
|
300
|
0,03
|
339,292
|
0,03
|
339,292
|
330
|
0,03
|
339,292
|
0,04
|
451,26
|
360
|
0
|
0
|
0,13
|
1469,134
|
390
|
0
|
0
|
0,45
|
5089,38
|
420
|
-0,03
|
-339,292
|
1
|
11308,6
|
450
|
-0,03
|
-339,292
|
1,8
|
20357,52
|
480
|
-0,03
|
-339,292
|
2,14
|
24201,7
|
510
|
-0,03
|
-339,292
|
0,94
|
10630,02
|
540
|
0
|
0
|
0,46
|
5201,346
|
570
|
0,03
|
339,292
|
0,27
|
3053,628
|
600
|
0,03
|
339,292
|
0,19
|
2147,718
|
630
|
0,06
|
678,584
|
0,11
|
1245,202
|
660
|
0,27
|
3053,628
|
0,03
|
339,292
|
690
|
0,81
|
9160,884
|
0,03
|
339,292
|
720
|
1,38
|
15607,43
|
0,03
|
339,292
|
Используя построенный план ускорений, определим силы и моменты сил инерции, действующие на звенья механизма в процессе движения:


положение 2:






положение 5:






положение 21:






положение 24:






Определив направления сил и моментов сил инерции с помощью плана ускорений (силы инерции противоположно направлены ускорениям центров масс звеньев механизма, а моменты сил инерции противоположно направлены угловым ускорениям звеньев механизма), и перенеся их на схему механизма. Разобьем его на части согласно проведенному структурному анализу. Рассмотрим группу Ассура звенья 2–3. Запишем сумму моментов относительно точки :

Рисунок 1.4.1. Плечи сил
положение 2:

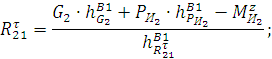

положение 5:

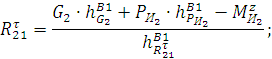

положение 21:

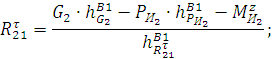

положение 24:

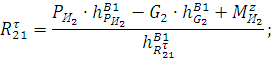

где: и – плечи силы тяжести и силы инерции , соответственно. – проекция момента на ось z, направление которой к нам перпендикулярно плоскости чертежа.
Запишем уравнение суммы сил:

В уравнении (1.4.4) неизвестны по модулю силы и , так как в уравнении два неизвестных, то можно построить план сил, откуда и определим неизвестные силы.
Для каждого положения выбрано масштаб плана сил :
Тогда отрезки соответствующие известным силам будут равны:
положение 2:






положение 5:






положение 21:






положение 24:






Построив план сил, определяем:
положение 2:



положение 5:



положение 21:



положение 24:



Рассмотрим звено 3, записав уравнение суммы сил, определим реакцию используя ранее построенный план сил:

Из плана сил определяем:
положение 2:

положение 5:

положение 21:

положение 24:

Рассмотрим группу Ассура звенья 4–5. Запишем сумму моментов относительно точки :
положение 2:

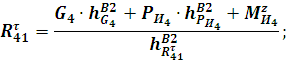

положение 5:

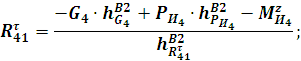

положение 21:

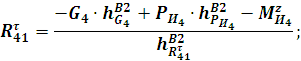

положение 24:



где: и – плечи силы тяжести и силы инерции , соответственно.
– проекция момента на ось z, направление которой к нам перпендикулярно плоскости чертежа.
Запишем уравнение суммы сил:

В уравнении (1.37) неизвестны по модулю силы и , так как в уравнении два неизвестных, то можно построить план сил, откуда и определим силы и .
Для каждого положения выбрано масштаб плана сил :
Тогда отрезки соответствующие известным силам будут равны:
положение 2:






положение 5:



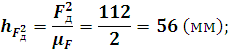


положение 21:






положение 24:






Построив план сил, определяем:
положение 2:



положение 5:



положение 21:



положение 24:



Рассмотрим звено 5, записав уравнение суммы сил, определим реакцию , используя ранее построенный план сил:

Из плана сил определяем:
положение 2:

положение 5:

положение 21:

положение 24:

Рассмотрим основной механизм первое звено.
Составим сумму моментов относительно точки О, учитывая,
что и :
Рисунок 1.4.2. Плечи сил

При этом плечи будут равны:



положение 5:

При этом плечи будут равны:



положение 21:

При этом плечи будут равны:



положение 24:

При этом плечи будут равны:



Для нахождения реакции составим уравнение суммы сил действующих на основной механизм:

Для построения каждого плана сил выберано масштабный коэффициент :
Тогда отрезки соответствующие силам и будут равны:
положение 2:


положение 5:


положение 21:


положение 24:


Из плана находим:
положение 2:

положение 5:

положение 21:

положение 24:

1.5 Приведенный момент сил
Определение приведенного момента сил трения, осуществляется нахождением моментов во вращательных КП и сил трения в поступательных КП:

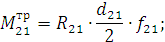
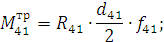
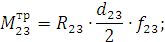
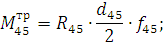

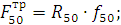
где: коэффициент трения во вращательных КП;
коэффициент трения в поступательных КП;
диаметр шатунной шейки;
диаметр поршневого пальца;
диаметр коренной шейки.



Используя значения найденных в силовом расчете реакций в КП для положений 2, 5, 21, 24, определяются значения моментов сил трения и сил трения в КП для этих положений:
положение 2:







положение 5:







положение 21:







положение 24:







Зная моменты сил трения и силы трения в КП, определяется приведенный момент сил трения исходя из того что элементарная работа приведенного момента сил трения равна суммарной элементарной работе сил трения в КП:


где: угловая скорость 2-го звена относительно 1-го;
угловая скорость 4-го звена относительно 1-го;
угловая скорость 2-го звена относительно 3-го;
угловая скорость 4-го звена относительно 5-го.
Положение 2:




Положение 5:




Положение 21:




положение 24:




Следовательно, приведенный момент сил трения будет равен:
положение 2:


положение 5:


положение 21:


положение 24:


1.6 Динамическая модель
В качестве динамической модели выбрано механизм, совпадающий с основным механизмом (согласно проведенному структурному анализу), который совершает вращательное движение с той же угловой скоростью и обладающий кинетической энергией равной суммарной кинетической энергии исходного механизма. При этом момент инерции замещающего механизма совпадает с приведенным моментом инерции исходного механизма, если в качестве звена приведения выбрать первое звено. В процессе движения механизма будем считать, что на него действует момент равный приведенному моменту исходного механизма, если в качестве звена приведения выбрать первое звено.
Для нахождения приведенного момента инерции механизма (в качестве звена приведения выберем первое звено) воспользуемся тем, что суммарная кинетическая энергия механизма должна быть равна кинетической энергии звена приведения. Откуда и определим приведенный момент инерции для первого и второго цилиндров.


Следовательно:


Учитывая, что получается:
Приведенный момент сил тяжести и сил давления газов в цилиндрах определим из условия равенства мощности приведенного момента и суммарной мощности сил тяжести и давления газов в цилиндрах двигателя. Используя то, что мощность силы есть скалярное произведение силы на скорость точки приложения силы, получим:


Для третьего и четвертого цилиндров приведенные величины найдем с учетом сдвига по фазе между соответствующими цилиндрами.
Для всех исследуемых положений значения приведенного момента инерции механизма и приведенного момента активных сил, указаны в таблице:
Таблица 1.5.1. Результаты расчетов
№
|

|

|

|

|

|

|


|


|


|


|
1
|
90
|
40
|
130
|
136,6
|
90
|
180
|
0,013213
|
0,040855
|
1,5
|
-54,0
|
2
|
50
|
2,93
|
130
|
157,88
|
0
|
180
|
0,022786
|
0,033788
|
2622,1
|
-47,4
|
3
|
50
|
29,73
|
130
|
170,5
|
0
|
180
|
0,03798
|
0,017818
|
1817,7
|
-16,6
|
4
|
50
|
50
|
50
|
124,33
|
0
|
0
|
0,039419
|
0,014419
|
882,9
|
-0,8
|
5
|
50
|
71,9
|
50
|
86,73
|
0
|
180
|
0,028345
|
0,028435
|
370,9
|
13,8
|
6
|
50
|
101,7
|
50
|
63,27
|
0
|
180
|
0,017313
|
0,040414
|
133,9
|
52,9
|
7
|
90
|
140
|
50
|
43,2
|
90
|
180
|
0,013213
|
0,036496
|
-1,5
|
49,5
|
8
|
130
|
178,77
|
50
|
19,38
|
180
|
180
|
0,017313
|
0,024148
|
-21,9
|
34,6
|
9
|
130
|
151,9
|
50
|
13,3
|
180
|
180
|
0,028345
|
0,01505
|
-40,4
|
10,9
|
10
|
130
|
130
|
130
|
53,57
|
180
|
0
|
0,039419
|
0,013674
|
-52,3
|
3,1
|
11
|
130
|
109,73
|
130
|
89,65
|
180
|
180
|
0,03798
|
0,020391
|
-50,2
|
-26,1
|
12
|
130
|
82,93
|
130
|
115,97
|
180
|
180
|
0,022786
|
0,03262
|
-30,4
|
-58,2
|
13
|
90
|
40
|
130
|
136,6
|
90
|
180
|
0,013213
|
0,040855
|
1,5
|
-221,4
|
14
|
50
|
2,93
|
130
|
157,88
|
0
|
180
|
0,022786
|
0,033788
|
3,3
|
-657,2
|
15
|
50
|
29,73
|
130
|
170,5
|
180
|
180
|
0,03798
|
0,017818
|
51,7
|
-691,0
|
16
|
50
|
50
|
50
|
124,33
|
180
|
0
|
0,039419
|
0,014419
|
52,3
|
633,7
|
17
|
50
|
71,9
|
50
|
86,73
|
180
|
0
|
0,028345
|
0,028435
|
38,9
|
2676,3
|
18
|
50
|
101,7
|
50
|
63,27
|
180
|
0
|
0,017313
|
0,040414
|
19,3
|
1567,9
|
19
|
90
|
140
|
50
|
43,2
|
90
|
0
|
0,013213
|
0,036496
|
-1,5
|
708,3
|
20
|
130
|
178,77
|
50
|
19,38
|
180
|
0
|
0,017313
|
0,024148
|
-21,9
|
285,0
|
21
|
130
|
151,9
|
50
|
13,3
|
180
|
0
|
0,028345
|
0,01505
|
-40,4
|
83,2
|
22
|
130
|
130
|
130
|
53,57
|
180
|
180
|
0,039419
|
0,013674
|
-101,2
|
-22,5
|
23
|
130
|
109,73
|
130
|
89,65
|
180
|
180
|
0,03798
|
0,020391
|
-432,1
|
-26,1
|
24
|
130
|
82,93
|
130
|
115,97
|
180
|
180
|
0,022786
|
0,03262
|
-804,2
|
-44,4
|
Определим работу приведенного момента активных сил. Для этого построим диаграмму приведенного момента активных сил в зависимости от угла поворота звена приведения (первого звена), для исследуемых 24 положений (два полных оборота) пользуясь тем, что работа приведенного момента равна:

Выполним графическое интегрирование построенной диаграммы приведенного момента активных сил в зависимости от угла поворота звена приведения. Для этого на каждом участке отметим середины хорд, которые перенесем на вертикальную ось. Полученные точки на вертикальной оси соединим лучами с полюсом S, взятом на расстоянии от начала координат .
Возле диаграммы момента строим новые оси. Из точки О новой системы координат проводим прямую параллельную первому лучу перенесенной точки до пересечения ее с вертикалью соответствующего значения угла. Из полученной точки проводим вторую прямую аналогично первой и т.д. Ломаную заменим близкой к ней плавной кривой. В результате получим диаграмму работы момента.
Масштабный коэффициент полученной диаграммы будет равен:

Интегрируя диаграмму приведенного момента сил трения, получим диаграмму работы приведенного момента сил трения. Так как приведенный момент сил трения противоположно направлен угловой скорости, то его работа будет отрицательна. Следовательно, для нахождения полной работы необходимо вычесть из работы движущих сил работу сил трения. Таким образом, получим диаграмму суммарной работы всех активных сил.
Так как за полный цикл установившегося движения изменение кинетической энергии равно нулю то, используя диаграмму суммарной работы активных сил можно сказать, что при условии постоянства момента сил производственного сопротивления диаграмма их работы будет прямой проходящей через начало и конец диаграммы работы движущих сил. Следовательно, проведя эту прямую можно продифференцировав ее определить момент сил производственного сопротивления. Для этого совершим параллельный перенос полученной прямой в точку S, найдя точку пересечения с осью приведенного момента активных сил, определим значение момента производственного сопротивления. Так как момент производственного сопротивления противоположно направлен угловой скорости звена приведения, то отложим найденный отрезок в отрицательном направлении оси приведенного момента активных сил. Проведя горизонтальную прямую через найденную точку, получим диаграмму момента производственного сопротивления. Таким образом, момент производственного сопротивления будет равен:


Мощность двигателя будет равна:


Изменение кинетической энергии за полный цикл установившегося движения определим как разность между диаграммой работы приведенного момента активных сил и диаграммой работы момента производственного сопротивления.
1.7 Определение момента инерции маховика
Для определения момента инерции махового колеса необходимо построить диаграмму для одного полного цикла времени установившегося движения механизма, при этом достаточно знать только изменение кинетической энергии и изменение приведенного момента инерции. Построим диаграмму приведенного момента инерции механизма повернутую на (т.е. ортогонально диаграмме кинетической энергии). Далее проводя проекционные прямые двух диаграмм до их точек пересечения и соединяя полученные точки плавной кривой, получаем участок диаграммы для установившегося движения механизма.
Для определения величины приведенного момента инерции маховика воспользуемся следующими формулами:


где: – средняя угловая скорость звена приведения;
– коэффициент неравномерности вращения кривошипа (звена приведения основного механизма),
Подставляя данные значения для и определим углы и :


Далее проведем одну касательную к диаграмме под углом , а другую – под углом и определим их точки пересечения с осью (точки K и L). Используя длину найденного отрезка, определим момент инерции маховика.

1.8 Определение механического КПД
Механический коэффициент полезного действия (КПД) – это отношение абсолютного значения работы сил полезного сопротивления к работе движущих сил, определенных за время, равное или кратное периоду установившегося движения:

Механический КПД характеризует относительную величину энергии, используемую в машине по прямому назначению. Он является основным показателем механического совершенства машин.
2. Синтез оптимальных чисел зубьев и кинематический анализ механизма
Для синтеза планетарного механизма по схеме А+II, с заданным передаточным отношением и , включающего в свой состав 3 сателлита, необходимо определить количество чисел зубьев зубчатых колес обеспечивающее безотказную работу механизма.
Передаточное отношение , раскладывается на две составляющих;
передаточное отношение первой ступени;
передаточное отношение второй ступени.
Общее передаточное отношение определяется следующим образом:
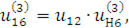
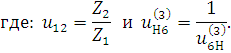
Определение передаточное отношения :
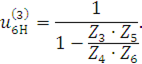
Для выполнения синтеза планетарного механизма необходимо определить числа зубьев всех колес, а также выбрать модули зубчатых колес. При этом требуется, чтобы были выполнены условия сборки, соосности и соседства для данного количества сателлитов и выбранного числа зубьев.
Так как для механизма II с заданным числом сателлитов передаточное отношение может быть реализовано в пределах , то выбирается передаточное отношение .
Определение возможные значения, с использованием графиков приложения [5] для данной схемы. Откуда , выбрано .
Для определения числа зубьев планетарного механизма применяются генеральные уравнения, при этом





Из полученных соотношений видно, что число зубьев шестого колеса должно быть кратно 3, 9, и 15 (наименьшее общее кратное 45), при этом необходимо учесть, что число зубьев зубчатых колес должно быть не меньше 18. Возможные комбинации чисел зубьев колес планетарного механизма для данного передаточного отношения определены в таблице 3.1.
Таблица 7.1. Возможные числа зубьев зубчатых колес

|

|

|

|
45
|
15
|
12
|
42
|
90
|
30
|
24
|
84
|
135
|
45
|
36
|
126
|
180
|
60
|
48
|
168
|
Окончательно выбрано

Определение диаметров зубчатых колес





Определение передаточного отношения первой ступени
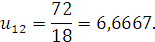
Следовательно выбрано тогда диаметры колес равны:
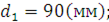

Проверка необходимых условий
условие соосности:



условие соседства
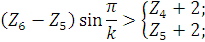

условие сборки
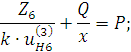

где: произвольные целые числа, такие, что 
число сателлитов планетарного механизма;
отношение количества зубьев четвертого колеса к третьему;
отношение модулей зубчатых колес первой ступени к второй.
3. Исследование качественных характеристик внешнего эвольвентного зацепления
Зубчатые передачи являются наиболее распространенным видом механических передач. В зависимости от условий эксплуатации при проектировании зубчатых передач учитываются различные факторы, влияющие на повышение их прочности, надежности и износостойкости. Широко распространенным методом улучшения эксплуатационных качеств и расширения конструктивных возможностей зубчатых передач является смещение режущего инструмента при их изготовлении.
При проведении геометрического расчета взято во внимание, что зубчатые колеса эвольвентные цилиндрические прямозубые, нарезаны стандартным реечным инструментом.

Геометрический расчет зубчатой передачи с учетом выбранных коэффициентов смещения
.
Определение угла эксплуатационного зацепления :

Определение коэффициента воспринимаемого смещения :
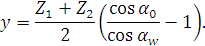
Определение коэффициента уравнительного смещения 

Определение величины радиального зазора С:

Определение межосевого расстояния :
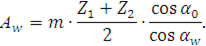
Определение радиусов делительных окружностей :


Определение радиусов основных окружностей :
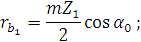
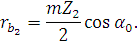
Определение радиусов начальных окружностей :
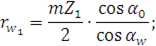
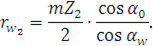
Определение радиусов окружностей вершин :


Определение радиусов окружностей впадин :


Определение толщины зубьев по делительным окружностям:


Определение шага зацепления по делительной окружности:

Определение коэффициента перекрытия:
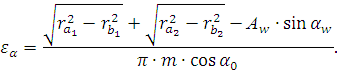
Так как рабочие участки профилей зубьев перекатываются друг по другу со скольжением, то на этих участках возникают силы трения и происходит процесс изнашивания. Характеристикой вредного влияния скольжения являются коэффициенты относительного скольжения, которые определяются по формулам:
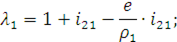
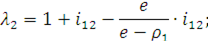
где: и абсолютные значения передаточного отношения зубчатой пары колес;
длина теоретической линии зацепления;
расстояние от точки касания теоретической линии зацепления с основной окружностью первого колеса, отсчитываемое в направлении к точке (радиус кривизны сопряженного профиля в точке контакта);
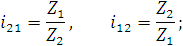

Геометрический коэффициент удельного давления определяет влияние геометрических параметров зацепления на контактную прочность зубьев.

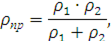
где: радиусы кривизны профилей зубьев в точке контакта;
приведенный радиус кривизны.

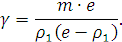
Результаты расчетов коэффициентов относительного скольжения и удельного давления для разных коэффициентов смещения приведены в таблице 3.1.
Таблица 3.1. Результаты расчета.

|

|
0
|
11,062
|
22,124
|
33,186
|
44,248
|
55,311
|
66,373
|
77,4347
|
88,497
|
99,559
|

|

|
-5,609
|
-1,891
|
-0,652
|
-0,033
|
0,3391
|
0,587
|
0,76397
|
0,8967
|
1
|

|
1
|
0,8487
|
0,6541
|
0,3947
|
0,0316
|
-0,513
|
-1,421
|
-3,2368
|
-8,684
|

|

|

|
1,017
|
0,5811
|
0,452
|
0,4068
|
0,4068
|
0,452
|
0,5811
|
1,017
|

|

|

|
0
|
7,981
|
15,961
|
23,941
|
31,922
|
39,902
|
47,883
|
55,863
|
63,844
|
71,824
|

|

|
-5,609
|
-1,891
|
-0,652
|
-0,033
|
0,339
|
0,587
|
0,764
|
0,897
|
1
|

|
1
|
0,849
|
0,654
|
0,395
|
0,032
|
-0,513
|
-1,421
|
-3,237
|
-8,684
|

|

|

|
1,41
|
0,806
|
0,627
|
0,564
|
0,564
|
0,627
|
0,806
|
1,41
|

|

|

|
0
|
10,903
|
21,806
|
32,709
|
43,612
|
54,515
|
65,418
|
76,321
|
87,223
|
98,126
|

|

|
-5,609
|
-1,891
|
-0,652
|
-0,033
|
0,339
|
0,587
|
0,764
|
0,897
|
1
|

|
1
|
0,849
|
0,654
|
0,398
|
0,032
|
-0,513
|
-1,421
|
-3,237
|
-8,684
|

|

|

|
1,032
|
0,590
|
0,459
|
0,413
|
0,413
|
0,459
|
0,590
|
1,032
|

|
Коэффициент в полюсе зацепления :

Минимальное значение коэффициента удельного давления будет достигаться при контакте профиля зубьев в средине граничного участка линии зацепления:
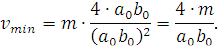
Определение длины активного участка линии зацепления
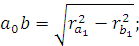
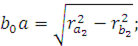

Определение значения коэффициента относительного скольжения на концах активного участка линии зацепления:
профиль колеса :

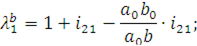
профиль колеса :
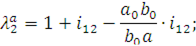

Определение значения коэффициента удельного давления на концах активного участка линии зацепления:
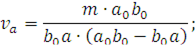
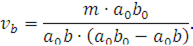
Результаты расчета параметров зубчатого зацепления для разных коэффициентов смещения занесены в таблицу 3.2.
Таблица 3.2. Результаты расчета
Параметр
|

|


|

|

|
0,037
|
0,015
|
0,036
|

|
26,7717
|
20
|
26,4392
|

|
1,10277
|
0
|
1,03862
|

|
0,18723
|
0
|
0,16738
|

|
2,5
|
2,5
|
2,5
|

|
221,028
|
210
|
220,386
|

|
95
|
95
|
95
|

|
115
|
115
|
115
|

|
89,2708
|
89,2708
|
89,2708
|

|
108,065
|
108,065
|
108,065
|

|
99,9887
|
95
|
99,6985
|

|
121,039
|
115
|
120,688
|

|
110,098
|
105
|
112,866
|

|
129,058
|
125
|
125,846
|

|
89,47
|
82,5
|
92,04
|

|
108,43
|
102,5
|
105,02
|

|
20,7817
|
15,708
|
22,6525
|

|
20,0247
|
15,708
|
17,5424
|

|
1,20026
|
1,56767
|
1,20007
|

|
0,82609
|
0,82609
|
0,82609
|

|
1,21053
|
1,21053
|
1,21053
|
, мм
|
31,4159
|
31,4159
|
31,4159
|

|
99,5589
|
71,8242
|
98,1264
|

|
0,40545
|
0,56201
|
0,41137
|

|
0,40177
|
0,55692
|
0,40764
|

|
64,4378
|
55,2786
|
69,0615
|

|
70,5544
|
62,8254
|
64,4926
|

|
35,4333
|
46,2798
|
35,4277
|

|
-1,0095
|
-4,7673
|
-0,584
|

|
0,54975
|
0,75274
|
0,65234
|

|
0,50236
|
0,82661
|
0,36869
|

|
-1,221
|
-3,0443
|
-1,8764
|

|
0,48651
|
1,27043
|
0,45238
|

|
0,43992
|
0,78529
|
0,48886
|
В результате подбора коэффициентов смещения исходного контура было достигнуто минимальной разности коэффициентов относительного скольжения вследствие чего можно обеспечить заданное условие – минимальный износ зубьев. Так же было проведено исследование нулевого зацепления и зацепления со смещением исходных контуров 
, которые показали менее подходящие результаты нежели принятое смещение.
Список литературы
1. Шебанов И.Г. Основы кинематики и синтеза дифференциальных зубчатых механизмов авиационных устройств. Учебное пособие. – Харьков: ХАИ, 2002. – 30 с.
2. Шебанов И.Г. Синтез авиационных механизмов. Учебное пособие. – Харьков: ХАИ, 1999. – 120 с.
3. Теория механизмов и машин: Учеб. для ВТУЗОВ/ К.В. Фролов, С.А. Попов, А.К. Мусатов и др.; Под ред. К.В. Фролова. – М.: 1987. – 496 с.
4. Алферов В.В. Определение геометрических параметров и качественных показателей смещенного эвольвентного зацепления. – Харьков: ХАИ, 1999. –36 с.
5. А.И. Чайка. Проектирование и исследование кривошипно-ползунных механизмов машин различного назначения. Учебное пособие. – Харьков: ХАИ, 1993. – 94 с.
6. Курсовое проектирование по теории механизмов и машин. Кореняко А.С. и др. «Вища школа», 1970, – 332 с.
|