Маршрут обработки конического зубчатого колеса прямозубого Размеры, мм 
Опе-рация | Содержание или наименование операции | Станок, оборудование | Оснастка | 005 | Отрезать заготовку | Абразивно-отрезной 8Б262 | Тиски | 010 | Кузнечная |
|
| 015 | Термическая обработка |
|
| 020 | Подрезать торцы 6032Н7 и 87.66/66 предварительно. Точить поверхность 60 предварительно. Сверлить, зенкеровать, развернуть отверстие 32Н7 предварительно. Расточить и точить фаски. | Токарный полуавтомат с ЧПУ КТ141
| Трех кулачковый патрон | 025 | Подрезать торец 87,66/32Н7. Точить поверхность 87,66 предварительно.
| Токарный полуавтомат с ЧПУ КТ141
| Трех кулачковый патрон | 030 | Протянуть шпоночный паз В=10js9 окончательно. | Горизонтально-протяжной 7512 | Жесткая опора | 035 | Опилить заусенцы на шпоночном пазе | Вибробункер |
| 040 | Подрезать торец 60/32Н7 предварительно, торец 87,66/60 и точить поверхность 60, 87,66 окончательно. | Токарный полуавтомат с ЧПУ КТ141 | Трёхкулачковый патрон | 045 | Подрезать торец 87,66/32Н7 предварительно | Токарный с ПУ КТ141 | Трёхкулачковый патрон. | 050 | Контроль |
|
| 055 | Строгать 35 зубьев (m=2,5) под шлифование | Зубострогальный 5Т23В | Оправка | 060 | Зачистить заусеницы на зубьях | Вибробункер |
| 065 | Шлифовать торец 60/32Н7 окончательно и отверстие 32Н7 окончательно | Внутришлифовальный | Трёхкулачковый патрон | 070 | Шлифовать торец 87,66/32Н7 окончательно | Плоскошлифовальный 3Б740 | Магнитный стол | 075 | Шлифовать 35 зубьев (m=2,5) окончательно | Зубошлифовальный 58П70В | Оправка | 080 | Промыть деталь | Моечная машина |
| 085 | Технический контроль |
|
| 090 | Нанесение антикоррозионного покрытия |
|
| Содержаниеработы
Деталь : коническое зубчатое колесо Обосновать и выбрать способ получения заготовки. Определить припуски и допуски на механическую обработку, выбрать чертеж заготовки с указанием размеров и предельных отклонений. Определить последовательность и содержание технологических операции (составить план механической обработки с указанием эскизов установов, наименований операций и переходов) Выбрать станки и станочные приспособления для всех операции. Выбрать технологические базы и способы установки заготовки на станке. Для трех операций выбрать режущий инструмент с маркой инструментального материала, геометрию параметров (угол заточки), привести расчёт режимов резания для трёх операций (токарная, сверильная , протягивание). Спроектировать приспособление для металлорежущего станка и выполнить его чертёж. оформить спроектированный технологический процесс в виде маршрутных карт и трех операционных карт для операций указанных в п. 5. Составить пояснительную записку, отразив вопросы: а). содержание задания; б).выбор способа получения заготовки и определение её припусков и допусков; в).расчёт режима резания согласно п. 5. г).выбор режущего инструмента и проектирование одного из них; д.).выбор приспособлений и проектирование одного из них; е).список литературы . _PAGE __ Введение
Машиностроение, поставляющее новую технику отраслями народного хозяйства, определяет технический прогресс страны .Технологическая подготовка представляет собой часть производственного процесса. Её задачей является обеспечения технологичности конструкции изделия, разработке технологических процессов . Разработка технологического процесса включает в себя: анализ исходных данных, выбор заготовки, выбор технических баз, составления маршрута обработки, разработку переходов, выбор оборудования и инструментов, определение режима резания и т.д.
Выбор наиболее эффективных методов и средств изготовления детали, цель разработки технологического процесса.
Деталь : Коническое зубчатое колесо Изготовлено из стали Ст 45 (ГОСТ 1050-74) sв 610 Мпа 200 НВ
Поскольку данное производство характеризуется малым объёмом выпуска одинаковых изделий, повторное изготовление которых не предусматривается, значит технологическое оборудование данного производства будет универсальным и на рабочем месте выполнятся будут разнообразные операции без их периодического повторения с использованием универсальной оснастки. Исходя из этого всего сказанного делается вывод о типе производства - единичное производство. 1. Выбор способа получения заготовки и опредиление её припусков и допусков.
Способ получения заготовки: Прокат Припуски определяем по ГОСТ 7829-70
Припуски должны быть разделены на общие и межоперационные. Под общим припуском понимают припуск, снижаемый в течении всего процесса обработки данной поверхности - от размера заготовки до окончательного размера готовой детали. Межоперационным называют припуск, который удаляют при выполнении отдельной операции. Припуск должен иметь размеры, обеспечивающие выполнение необходимой для данной детали механической обработки при удовлетворении установленных требований к шероховатости и качеству поверхности металла и точности размеров деталей при наименьшем расходе материала наименьшей себестоимости детали. При установлении размеров припусков на обработку указывают допустимое отклонение от них, т.е. допуски на размеры заготовки, т.к. получить заготовку точно установленных размеров невозможно. При установлении размеров припусков на обработку указывают допустимые отклонения от них, т.е. допуски на размеры заготовки, т.к. получить заготовку точно установленных размеров невозможно. Размер припуска зависит от толщены поверхностного поврежденного слоя, т.е. от толщены корки для литых заготовок, обезуглероженного слоя для проката, глубины поверхностных неровностей, раковин, трещин, пор, и пр., а также от неизбежных производственных и технологических погрешностей, зависящих от способа изготовления заготовки, её формы и размеров, способа обработки, геометрических погрешностей станка и других факторов . В производственных условиях размеры припусков устанавливают на основании опыта; при этом используются различные нормативные таблицы, входами в которые являются геометрические размеры детали конструктивные формы, точность обработки и чистоты поверхности. На рис. 1 показаны схемы расположения межоперационных припусков и допусков при обработке заготовок типа вала (рис. 1, а) и отверстия ( рис. 1б ). Необходимо иметь в виду , что показанные на рис.1 . припуски являются наименьшими . Из схемы рисунка следует , что общий припуск на обработку - Z0 равен сумме наименьших межоперационных припусков и межоперационных допусков без допуска на определенную операцию
Z0=Z1+d1+Z2+d2+Z3
На практике размер заготовки (например вала) определяют:
B1=B6+Z3+d2+Z2+d1+Z1=B6+Z0
Рис 1а. Рис 1б. 
Условия обозначения : B1 - размер заготовки ( вала) ; B2 и B3 - наибольший и наименьший предельные размеры операции; B4 и B5 - то же, после второй операции; B6 и B7 - то же, после третьей операции; Z1 и d1 - межоперационный припуск и допуск на первую операцию; Z2 и d2 - то же, на вторую операцию; Z3 и d3 - то же на третью операцию; A1 - размер отверстия в заготовке; A2 и A3, A4 и A5, A6 и A7 - наименьшие и наибольшие предельные размеры отверстий после первой, второй и третьей операции соответственно. Имея в виду то, что B6 - это один из размеров детали, указанный в чертеже. Графическое построение поле припусков и допусков проводят в последовательности обратной последовательности обработки. При проектировании технологического процесса межоперационные размеры определяют следующим образом. Для вала :
B4 = B6 +Z3 + d2 B2 = B6 +Z3 +d2 + Z2 + d1 = B6 + Z1
Эти размеры и указывают в технологической документации, как предельные, которые должны быть получены в результате выполнения соответствующей операции (перехода). Полученный размер заготовки (прутка) B1 уточняют по сортометру, выбирая ближайший больший. Оринтеровочные значения общего припуска для проката характеризуются следующими средними данными.
Вид заготовки | Материал | Припуск на толщину дефектного слоя на сторону в мм.
| Общий припуск на сторону в мм.
| Прутковый металл | Сталь | 0,5 | 1 - 2
| То для максимально нагруженного размера получаем:
Ж86,66 + 1,4 + 1,0 = Ж 89,06 мм ;
По ГОСТ 7417 - 75 находим ближайшую большую Ж 90 мм; следовательно для изготовления детали используем припуск :
круг 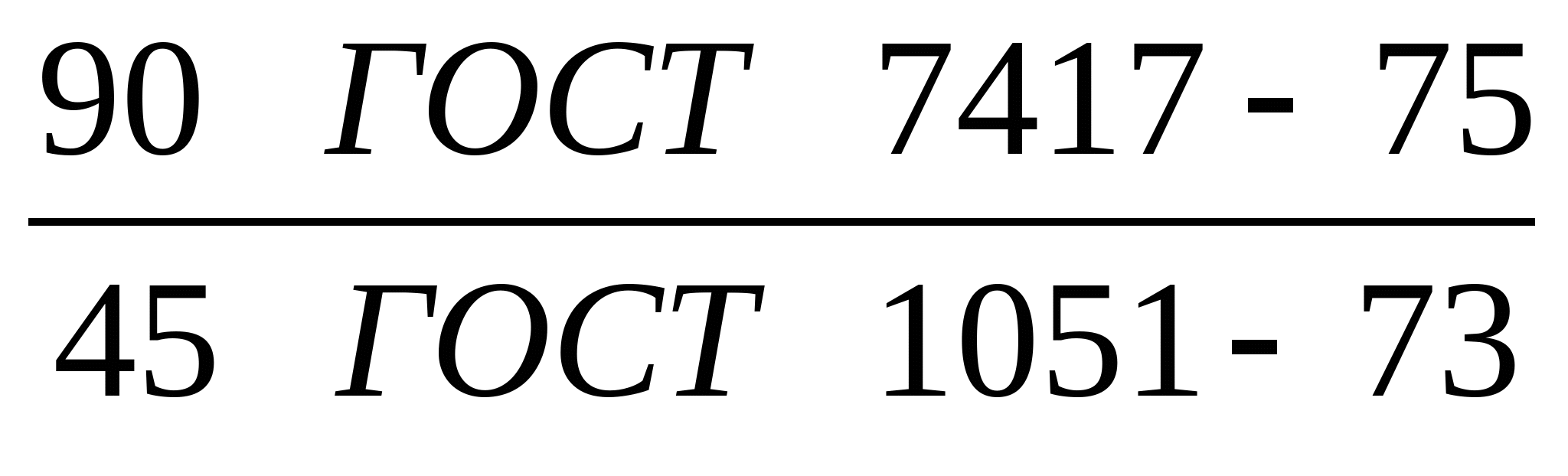 Для изготовления детали используем сталь 45 со следующими технологическими свойствами:
температура ковки , С 0 :начала 1250 , конца 700 свариваемость - трудно свариваемая . способы сварки - ручная дуговая .
Необходим подогрев с последующей термообработкой . К отпускной хрупкости не склонна .
Химический состав
C | Si | Mn | Cr | S | P | Cu | Ni | As |
|
|
|
|
|
| Не более |
|
| 0,42ё0,50
| 0,17ё0,37 | 0,50ё0,80 | 0,25 | 0,04 | 0,035 | 0,25 | 0,25 | 0,08 |
Назначение - изготовление вал - шестерён, коленчатых и распределительных валов, шестерён, шпинделей, бандажей, цилиндров, кулаков, и других нормализуемых, улучшаемых и подвергаемых поверхностной термообработке деталей, от которых требуется поверхностная прочность. _PAGE __ Оборудование и инструмент для механической обработки заготовки .
Заданием предусмотрены для расчёта следующие операции:
токарная - Ж 90 до Ж60 мм сверлильная - Ж 32 мм протягивание шпоночного глаза B = 10jr 9;
Согласно рекомендаций разработки «Методика расчётов режимов резания при механической обработке металлов« ( к. т. н. Моисеев В.В.) выбираем следующее оборудование:
А) Для токарной обработки токарно винторезный станок 1М61 со следующими параметрами: Наибольший диаметр обрабатываемой детали - 320 мм Расстояние между центрами 1000 мм Число ступеней частот вращения шпинделя 24 Частота вращения шпинделя 12,5 - 1600 об/мин Число ступеней подач суппорта 24 подача суппорта : продольная - 0,08 - 1,9 мм/об поперечная - 0,04 -0,95 мм/об Мощность главного электро двигателя - 4 квт КПД станка - 0,75 Наибольшая сила подачи механизма подачи - 150 кг-с.
В качестве режущего инструмента для токарной обработки используем токарный проходной резец, прямой, правый . Материал рабочей части - твердый сплав Т5К10, материал корпуса резца - сталь 45, сечение корпуса резца (державки) :
B ґ H = 16 ґ25мм
длинна резца - 150 мм
Геометрические параметры:
j = 600 g1 = - 50 a = 120 ¦ = 0,6мм R = 6 мм j1 = 150 g = 15 0 t = 00 B = 2,5мм r = 1мм
Форма передней поверхности - радиусная с фаской В качестве дополнительной оснастки для токарной обработки выбираем:
а ) патрон самоцентрирующийся трех кулачковый по ГОСТ 2675 - 80; 7100 - 0005; б ) оправку с разрезными цангами по ГОСТ 31. 1066.02 - 85; 7112 - 1458;
Б) .Для сверления - вертикальносверильный станок 2Н135 со следующими параметрами:
наибольший условный диаметр сверления - 35 мм вертикальное перемещение сверлильной головки - 250 мм число ступеней частоты вращения шпинделя - 12 частота вращения шпинделя - 31,5 - 1400 об/мин число ступеней подач - 9 подача шпинделя - 0,1 ё 1,6 мм/об крутящий момент на шпинделе - 40 кг-с/м наибольшая допустимая сила подачи - 1500 кг-с мощность электродвигателя - 4 квт КПД станка - 0,8;
В качестве режущего инструмента используем сверло спиральное из быстро режущей стали Р18: по ГОСТ 2092 - 77 2301 - 4157; В качестве дополнительной оснастки используем тисы станочные с ручным приводом: по ГОСТ 14904 - 80 7200 - 0213;
В) Для протягивания: выбираем горизонтально - протяжной станок модели 7Б510 со следующими характеристиками :
номинальное тяговое усилие - 10000 кг-с длинна рабочего хода ползуна - 1250 мм диаметр отверстия под планшайбу в опорной плите - 150 мм размер передней опорной плиты - 420 мм пределы рабочей скорости протягивания - 1ё9 м/мин мощность главного электродвигателя - 17 кВт КПД станка - 0,9;
В качестве режущего инструмента используем протяжку: по ГОСТ 24820 - 81;
В качестве дополнительного оборудования (оснастки) используем тисы станочные с ручным приводом: по ГОСТ 14.904 - 80 7200 - 0213;
Г) Выбор измерительного инструмента:
Измерительный инструмент - это техническое устройство, используемое при измерениях и имеющие нормированные метрологические свойства. При выборе измерительного инструмента учитываются формы контроля (сплошной или выборочный масштаб производства, конструктивные характеристики детали, точность её изготовления ). В соответствии с линейными размерами нашей детали:
максимальный измеряемый диаметр - D1 max= 90 мм минимальный измеряемый диаметр - D min = 32 мм максимальный линейный размер - Lmax = 38,0 мм минимальный линейный размер - Lmin = 10 мм и классом точности размеров (смотри выше) - 5
В качестве основного измерительного инструмента выбираем: Штангенциркуль.
Штангенциркуль Ш Ц - 1 по ГОСТ 166 - 80 с ценой делений 0,1 мм.
Для измерения диаметра отверстий шпоночного паза выбираем нутромеры индикаторные:
тип параметры | НИ - 50 М | НИ - 18 |
|
|
|
|
|
| диапазон измерений
цена деления
допускаемая погрешность
глубина измерения | 18 ё 50 мм
0,01мм
±0,012 мм
150мм | 10 ё 18 мм
0,01мм
±0,012мм
130мм |
Для измерения параметров зубчатого колеса выбираем универсальный прибор для измерения зубчатых колёс по ТУ - 2 - 034 - 544 - 81 типа ЗИП - 1 со следующими характеристиками:
Модуль 1 - 8; Диаметр делительной окружности 20 - 320 мм ; Степень точности 6 Цена деления 0,001 мм; Допускаемая погрешность 0,0035 мм
1. Расчет режимов резания.
Расчет режима резания при токарной обработке.
Деталь - коническое зубчатое колесо . Материал сталь 45;
s в = 61 кг-с/ мм 2 ;
Режущий инструмент - токарный проходной резец из быстрорежущей стали Т5К10, правый, стойкость резца - 90 мин .
Оборудование - токарно - винторезный станок 1М 61 Необходимо рассчитать режим резания при токарной обработке цилиндрической поверхности с диаметра Ж 87,66 мм; до диаметра Ж 60 мм; по 5 классу, на длине 12 мм .
1) .Определяем припуск на механическую обработку и глубину резания :
мм
Учитывается что припуск до 2мм срезается за один проход, принимаем i = 7, где i - число проходов, то;
мм
2. Назначаем подачу для первого точения: - 0,4 мм/об проверяем выбранную подачу с паспортной подачей станка 1М 61:
Sст = 0,08 ё 1,9 мм/об Z = 24 ( число ступеней подач ) Smax = Smin ґ jz - 1 ;
;
Рассчитаем значение подач по ступеням :
S10 = S1 ґ j 9 = 0,08 ґ 1,15 9 = 0,28 мм/об S11 = S10 ґ j = 0,28 ґ 1,15 = 0,32 мм/об S12 = S11 ґ j = 0,32 ґ 1,15 = 0,368 мм/об S13 = S12 ґ j = 0,368 ґ 1,15 = 0,423 мм/об
В качестве расчетной принимаем ближайшую меньшую : Sp = S12 = 0,368 мм/об
3) . Определяем расчётную скорость резания: , где
Kv - поправочный кооэфициент, учитывающий реальные условия резания
; где
- поправочный коэффициент, учитывающий влияние обрабатываемого материала.
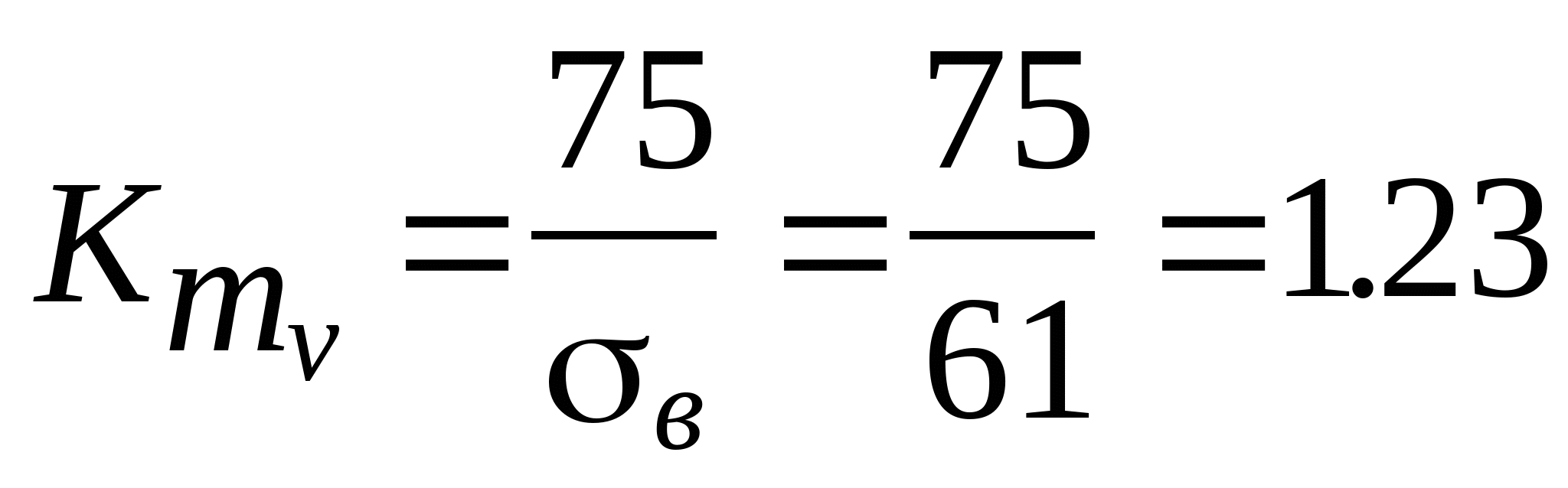
- поправочный коэффициент на материал режущей части инструмента. Для Т5К10 = 0.65; (таб. 2)
= поправочный коэффициент, учитывающий влияние периода стойкости резца: Для Т = 90 мин. = 0.92 (таб. 3)
= поправочный коэффициент, учитывающий состояние поверхности заготовок (таб. 4) = 1.0
Находим:
= 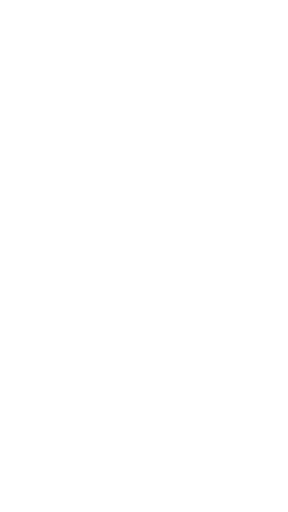
- коэффициент зависящий от качества обрабатываемого материала и материала режущей части инструмента; Т - принятый период стойкости резца (Т = 90 мин) Значения - находим по таблице 5, для стали при S > 0.3;
то ; Определяем расчётную частоту вращения ;
, где D - диаметр детали.
;
По паспорту станка 1М61 = 12.5 об/мин; = 1600 об/мин
Z = 24 (число ступеней вращения)
= ґ ;
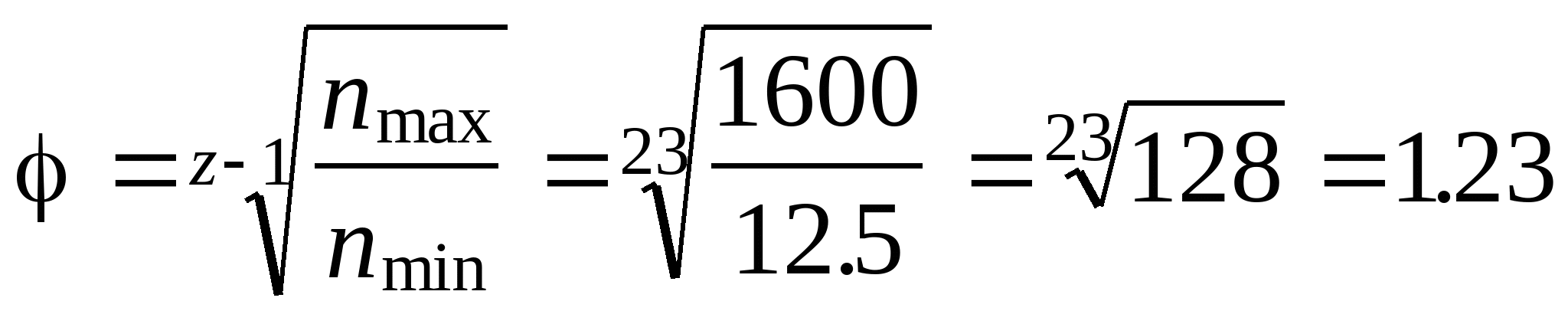
Определяем частоту вращения по ступеням.
    
В качестве расчётной принимаем ближайшее меньшее значение
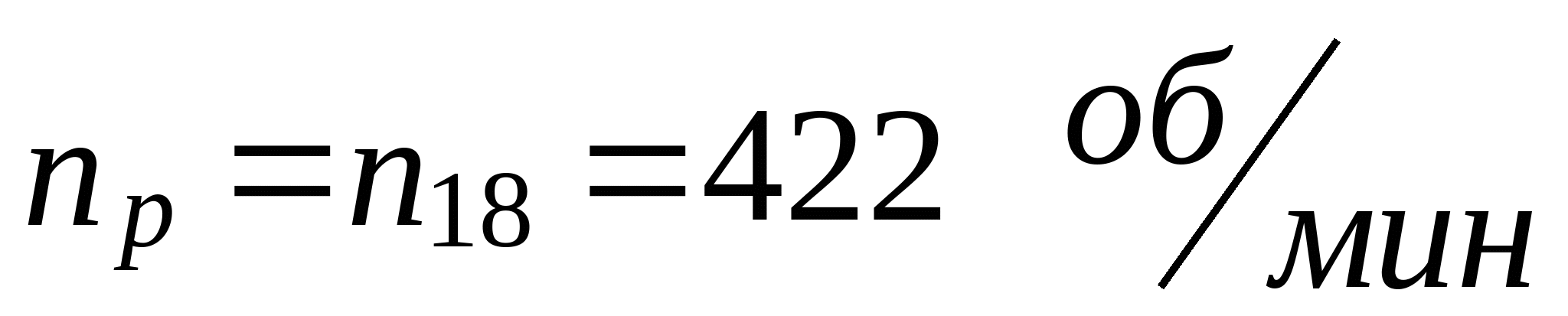
5. Определяем фактическую скорость резанья:
;
Основные режимы резания при точении:
t = 1.98 мин. Sp = S12 = 0.368 мм/об = 116 м/мин = = 422 об/мин Проверяем выбранный режим по мощности, потребляемой на резание:
, где
Кр - поправочный коэффициент , где - поправочный коэффицент на обрабатываемый материал, по таб. 6 находим = 0.89 (sв = 61 кг-с/мм2) - поправочный коэффициент на главный угол в плане резца (таб. 7) = 1.0; (j = 450);
То Кр = ґ = 0.89 ґ 1.0 = 0.89;
Значения находим по таблице 8
То кг-с;
Определяем осевую составляющую силы резания ;
кг-с, =17.14 кг-с
По паспорту станка кг-с следовательно расчёт произведён верно. Определяем эффективную мощность на резании Nэ;
квт Определяем мощность потребляемую на резание.
КПД станка = 0.75 квт.
определяем коэффициент использования станка
,
где - мощность главного электродвигателя станка; N=4 квт (по паспорту)
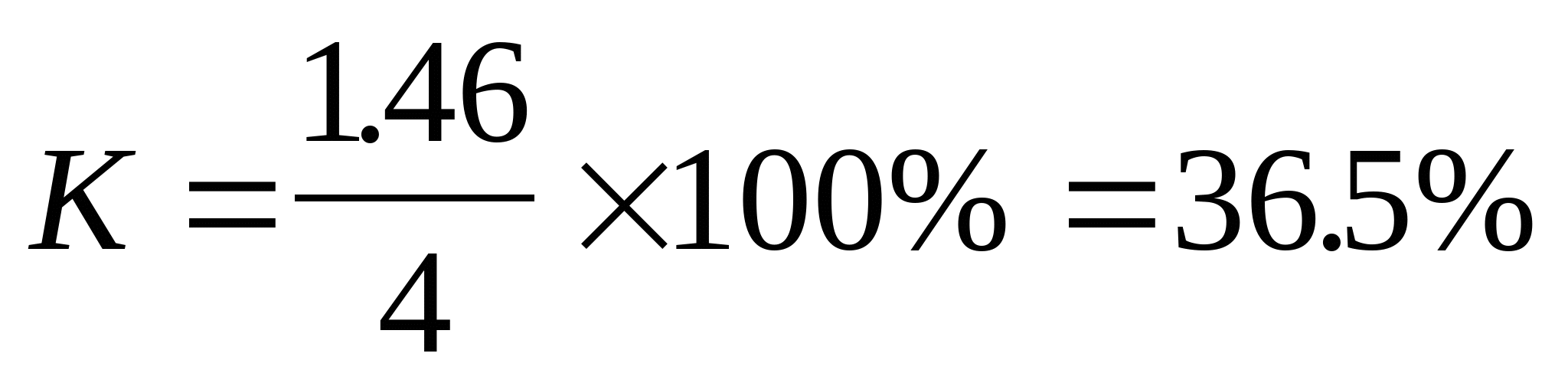 Определяем технологическое (машинное) время
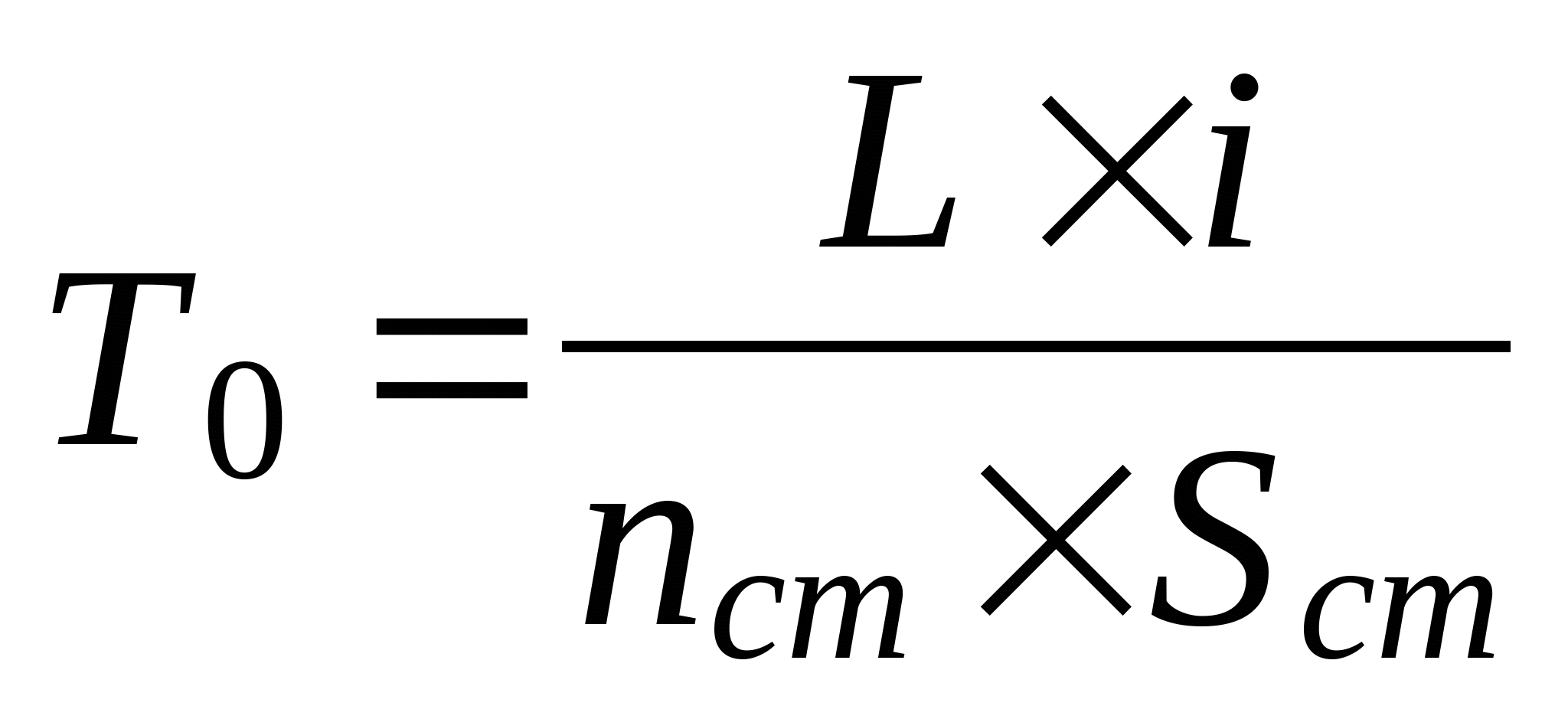
где L - расчётная длина обрабатываемой поверхности.
L = l + l1 + l2, где
l - действительная длина обрабатываемой поверхности; l = 12 мм; l1 - величина врезания
l1 = t ґ ctgj = 1.98 ґ ctg450 = 1.98 мм;
l2 - выход инструмента; l2 = (2ё3) Sст = 2 ґ 0.37 = 0.74 мм; i = 7 (количество проходов) L = l + l1 + l2 = 12 + 1.98 + 0.74 = 14.72 мм;
минут.
(Приложение) Операционная карта механической обработки : 010 ТОКАРНАЯ _PAGE __ Расчёт режима резания при сверлении
Деталь - заготовка конического зубчатого колеса. Материал - сталь 45: sв = 61 кг-с/мм2; Станок вертикально сверлильный модели 2Н135; Сверло - спиральное из быстрорежущей стали Р18; Ж 30 Определяем глубину резания при сверлении:
15 мм Подача при сверлении : S = 0.02 ґ = 0.02 ґ 30 = 0.6 мм/об;
Корректируем подачу по паспорту станка 2Н135;
Sпас = 0.1 ё 1.6 мм/об; Z =9; S = 0.6, т.е. 0.1 < S < 1.6
Выбираем подачу по ступеням:
Smax = jz-1 ґ Smin;
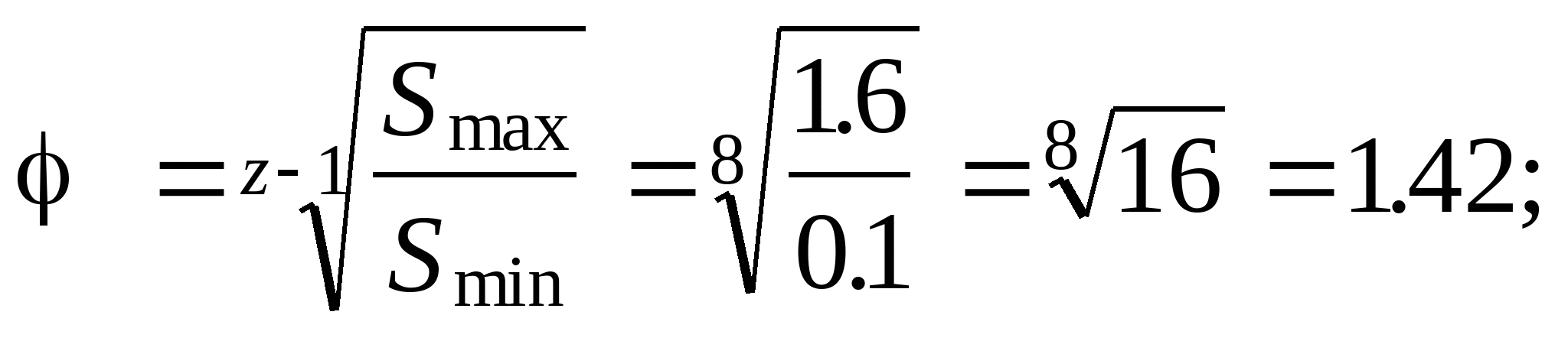
S2 = 0.1 ґ 1.42 = 0.142 мм/об S3 = 0.142 ґ 1.42 = 0.202 мм/об S4 = 0.202 ґ 1.42 = 0.286 мм/об S5 = 0.286 ґ 1.42 = 0.406 мм/об S6 = 0.406 ґ 1.42 = 0.577 мм/об S7 = 0.577 ґ 1.42 = 0.820 мм/об
В качестве рассчётной принимаем ближайшую меньшую
Sp = S6 = 0.577 мм/об
3 . Определяем расчётную скорость резанья при сверлении
где 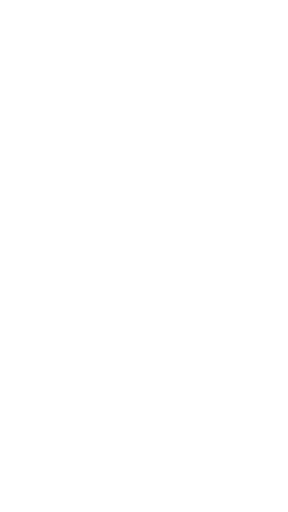
Кv = KLv ґ KMv ґ KHv - поправочный коэффициент. KLv - коэффициент, учитывающий глубину отверстия в зависимости от диаметра сверла. По таблице 9 находим KLv = 1.0; KMv - коэффициент учитывающий влияние материала.
Для стали ; где a = 0.9 (таб. 10)
sв = 61; ;
KMv - коэффициент учитывающий материал сверла. Для сверла из быстрорежущей стали KMv = 1.0; то Кv = KLv ґ KMv ґ KMv = 1.0 ґ 1.14 ґ 1.0 = 1.14;
По табл. 11 находим для S > 0.2;
Cv = 9.8; bv = 0.4; Xv = 0; Yv = 0.7; m = 0.2;
м/мин; Определяем расчётную частоту вращения шпинделя
 По паспорту станка
nmin = 31.5 об/мин; nmax = 1400 об/мин; Z = 12; число ступеней вращения nmax = nmin ґ jz-1

Частота вращения по ступеням:
n2 = n1 ґ j = 31.5 ґ 1.41 = 44.42 об/мин; n3 = n2 ґ j = 44.4 ґ 1.41 = 62.62 об/мин; n4 = n3 ґ j = 62.6 ґ 1.41 = 88.3 об/мин; n5 = n4 ґ j = 88.3 ґ 1.41 = 124.5 об/мин; n6 = n5 ґ j = 124.5 ґ 1.41 = 175.6 об/мин; n7 = n6 ґ j = 175.6 ґ 1.41 = 247.5 об/мин; n8 = n7 ґ j = 247.5 ґ 1.41 = 349.0 об/мин;
В качестве рассчётной принимаем ближайшую меньшую частоту вращения
np = n7 = 247.5 об/мин Определяем фактическую скорость резания.

Основные режимы резанья при сверлении:
S = 0.6 мм/об; V = 23.31 м/мин; n = 247.5 об/мин; Определяем осевую силу резания:
Р0 = Ср ґ DZp ґ Syp ґ KMp
по таблице 6 КMp = 0.89: по табл. 12 находим:
Ср = 51; Zp = 1.4; Yp = 0.8, то Р0 = 51 ґ 301.4 ґ 0.60.8 ґ 0.89 = 51 ґ 116.9 ґ 0.665 ґ 0.89 = 352.8 кг-с; Рдоп = 1500 кг-с; то Р0 < Р0 доп; Определяем крутящий момент

где ;
то табл. 12 находим для стали СМ = 40; ВМ = 2.0; Yм = 0.8; Мкр = 40 ґ 302.0 ґ 0.60.8 ґ 0.89 = 8.54 кг-с ґ м;
по паспорту станка Мкр п = 40 кг-с ґ м; Определяем мощность на шпинделе станка.

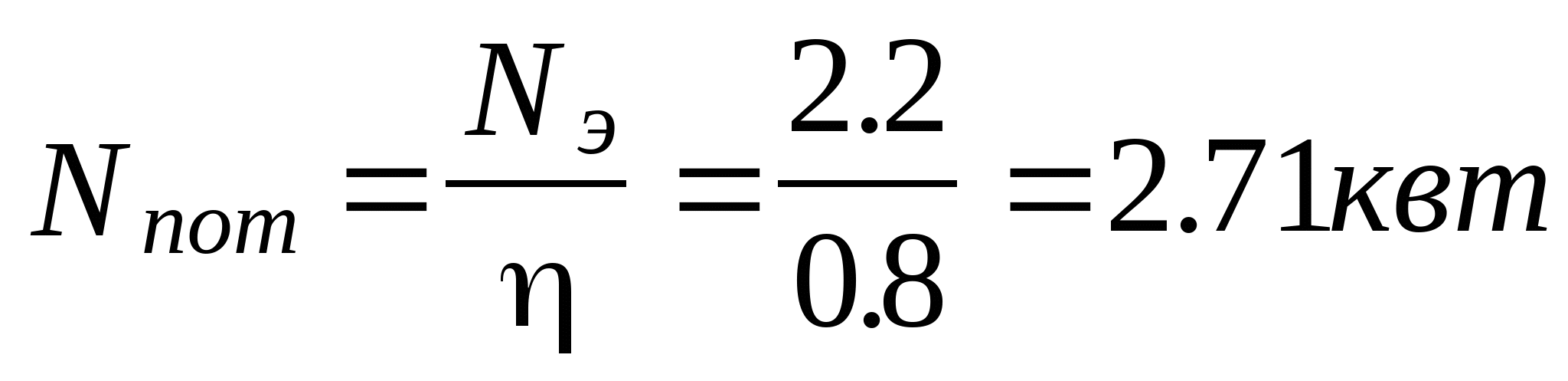
h = 0.8 (КПД станка по паспорту) Коэффициент использования станка по мощности

где - мощность главного электродвигателя станка по паспорту. Определяем основное техническое время
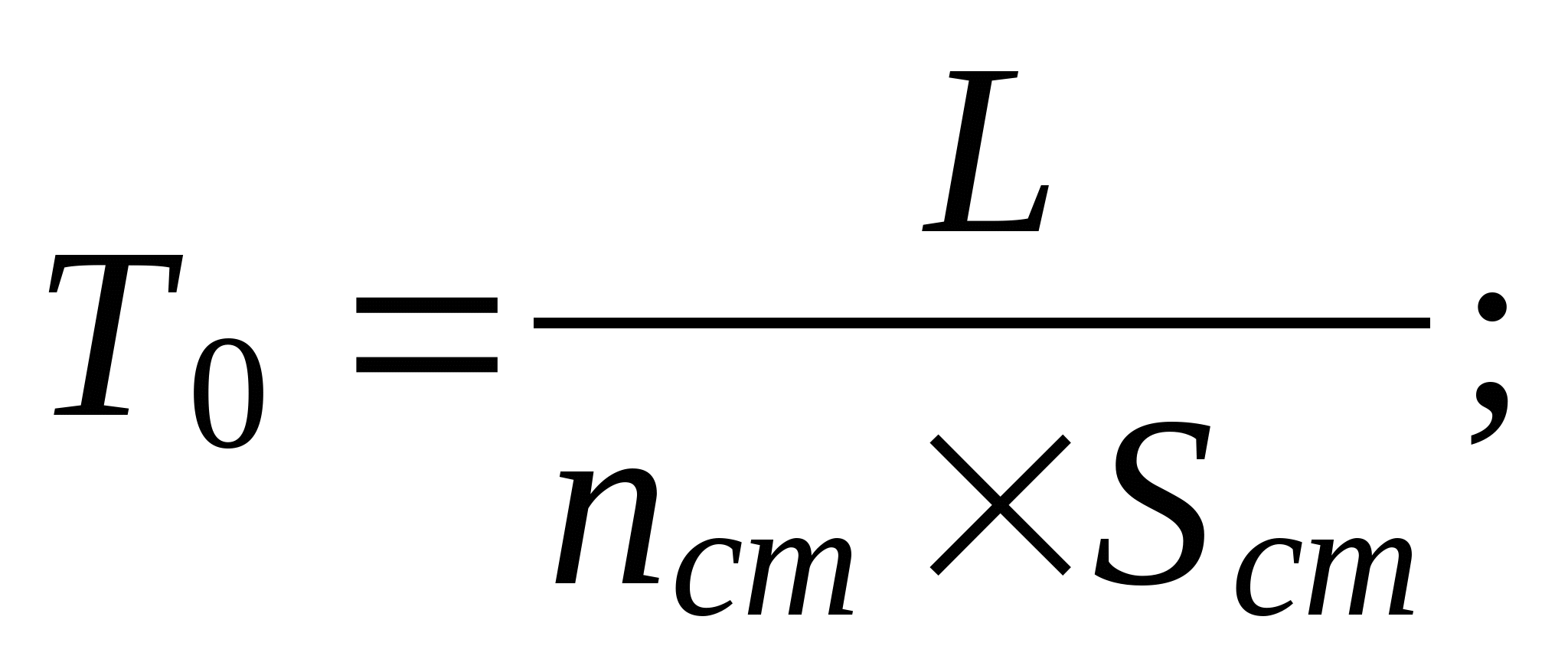
где L - расчётная длинна обрабатываемой поверхности.
;
l -действительная длина (чертёжный размер) l = 33 мм; l1 - величина врезания; l2 - выход инструмента;
l1 + l2 = 0.4 ґD = 0.4 ґ 30 = 12 мм 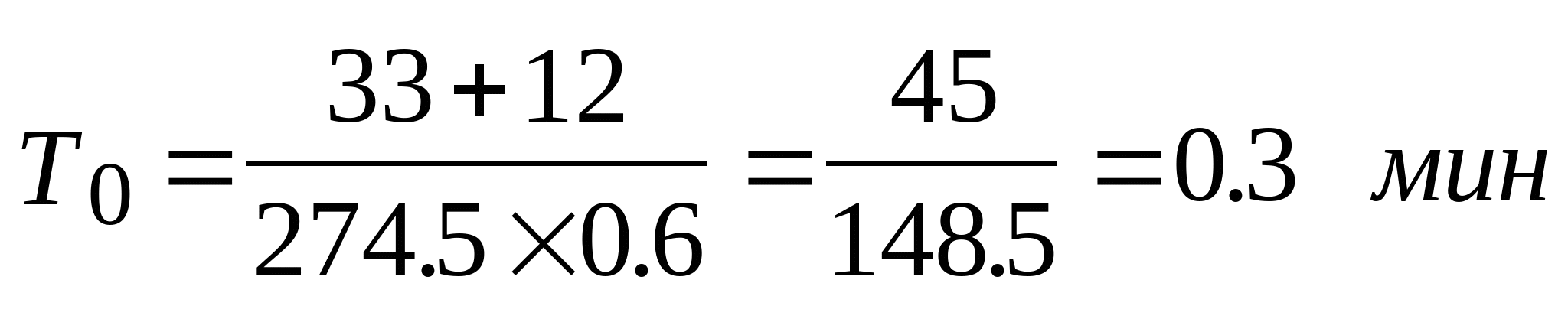
(Приложение) Операционаая карта механической обработки (сверлильная) _PAGE __ Расчёт режима резания при протягивании По таблице 15 выбираем подачу на зуб ; = 0.1 мм Определяем расчётную скорость резания:
;
где Т = стойкость протяжки; назначаем Т =300 мин, по таблице 16 находим  ;
По паспорту станка 1 < < 9, то расчёт верен. Определяем силу резания :  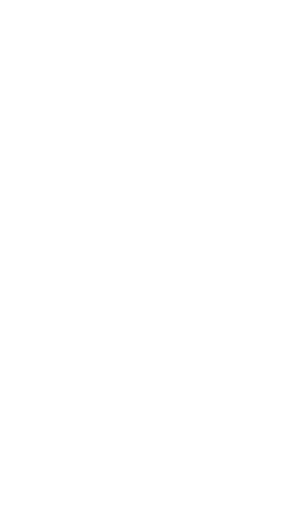 по таблице 17 находим
=177; = 0.85; = 0.1 мм; b = 10; n = 1

- коэффициенты, характеризующие влияние соответственно износа, смазочно охлаждающей жидкости заднего и переднего углов.
=1.0; =1; =1.0 = 1.13 (охлаждение эмульсолам)
;
По паспорту станка =10000 кг-с, то расчёт верен. Определяем эффективную мощность.
; Потребляемая мощность
;
где h = 0.9 - КПД станка по паспорту. Коэффициент использования по мощности главного электродвигателя.
 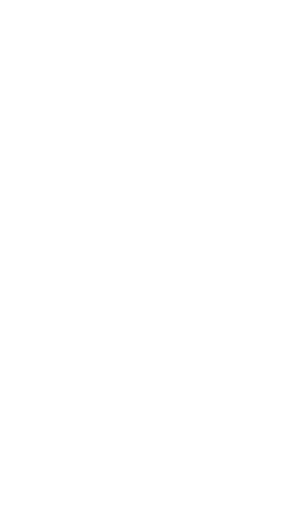
В связи с низким коэффициентом использования электродвигателя в качестве протяжного станка можно выбрать менее мощный, например 7Б505 с мощностью 7 квт. Определяем основное технологическое время Т;
; где
= l + - длина рабочего хода инструмента; l - действительное определение (чертёжная) длина протягиваемой детали. l = 33; - длина режущей части протяжки
 мм; - длина калибрующей части мм; l = 10 мм - длина перебегов протяжки.
мин;
(Приложение) Операционная карта механической обработки при протягивании. _PAGE __ Расчёт и конструирование сверла.
Расчёт и конструирование сверла из быстрорежущей стали с коническим хвостовиком для обработки сквозного отверстия Ж 30, глубиной L = 33 мм. В заготовке из стали 45 с пределом прочности s = 610 Мпа; Определяем диаметр сверла по ГОСТ 2092-77 находим необходимый диаметр сверла Ж 30 мм: сверло 2301-4157. Определяем осевую составляющую силы резания
DХp ;
; где по таблице ; - по расчётам режима резания; ; Момент силы сопротивления резания DZм , где   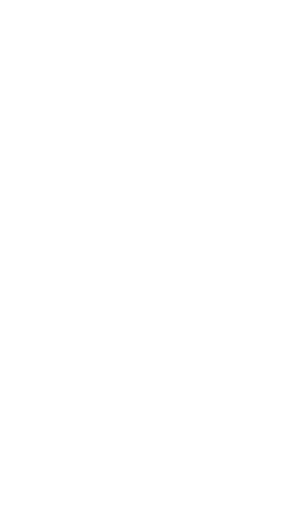 Определяем № конуса Морзе хвостовика; осевую составляющую силу резания можно разложить на две силы: Q - действующую нормально к образующей конуса , где q угол конусности хвостовика, и силу R действующую в радиальном направлении и уравновешивающую реакцию на противоположной точке поверхности конуса. Сила Q создаёт касательную составляющую T силы резания; с учётом коэффициента трения поверхности конуса о стенки втулки m имеем: ; Момент трения между хвостовиком и втулкой:

Приравниваем момент трения к максимальному моменту сил сопротивления резанию, т.е. к моменту, создающимуся при работе затупившимся сверлом, который увеличивается до трёх раз по сравнению с моментом, принятым для нормативной работы сверла

средний диаметр конуса хвостовика: или ; =9.225 кг-сґм; = 654 кг-с m = 0.096 - коэффициент трения стали по стали; Рq = 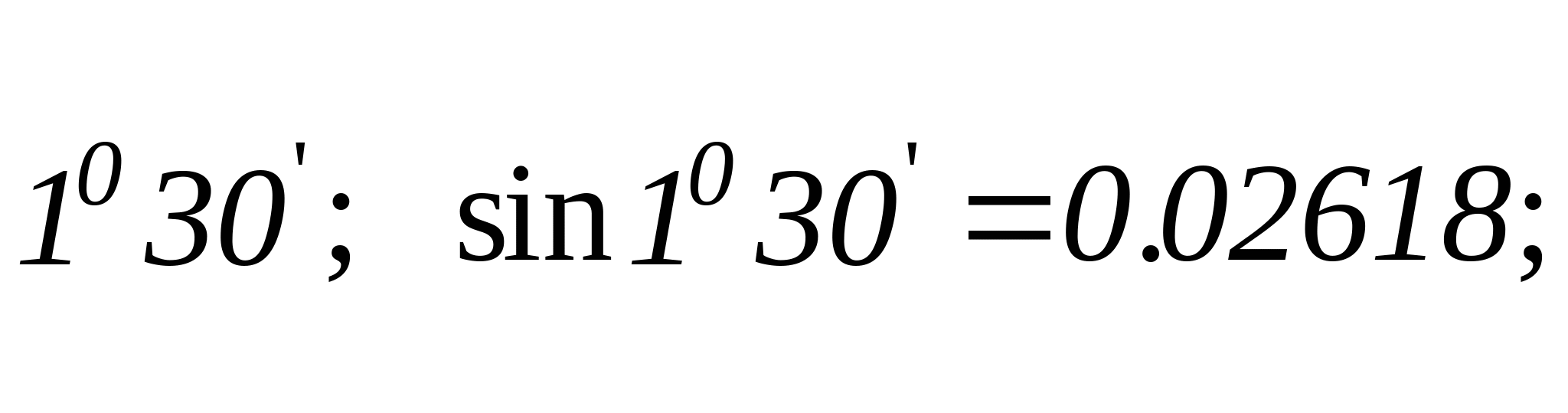 - отклонение угла конуса
мм
По ГОСТ 25557-82 выбираем ближайший больший конус т.е. конус Морзе №3:
5.5 Определяем длину сверла по ГОСТу находим
L = 395 мм l = 275 мм
5.6 Определяем геометрические и конструктивные параметры рабочей части сверла; Форма заточки - ДП (двойная с подточкой перемычки), Угол наклона винтовой канавки 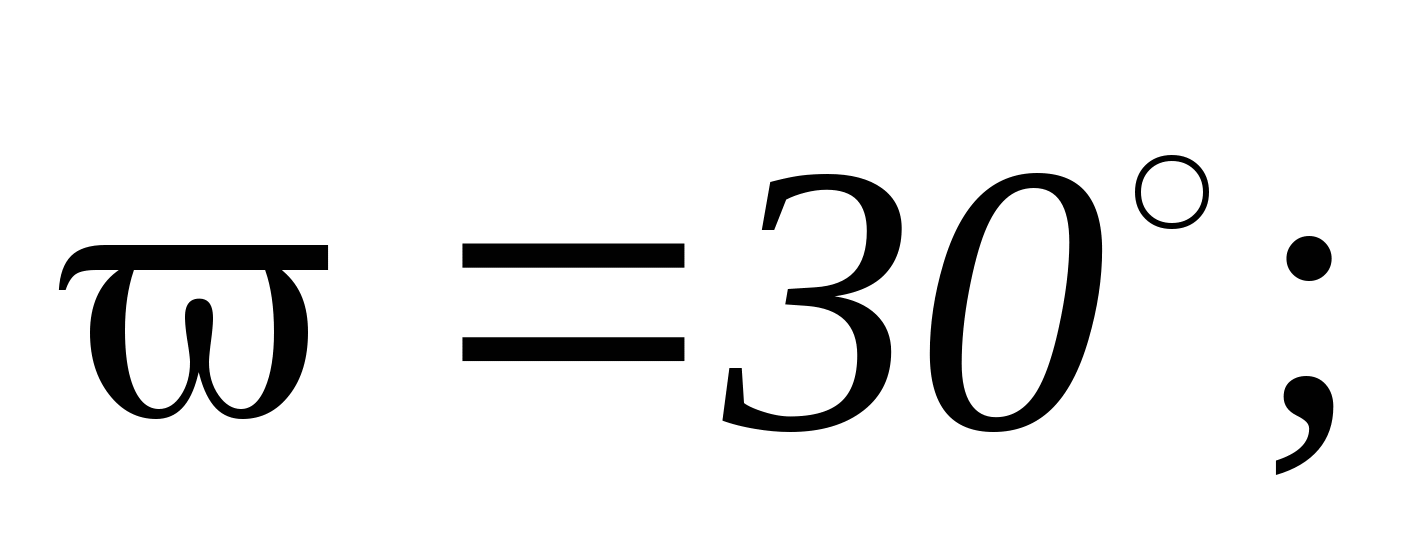 - угол между режущими кромками - задний угол - угол наклона поперечной кромки.
Шаг винтовой канавки
мм;
Толщина - сердцевина сверла выбирается в зависимости от диаметра сверла; мм;
Утолщение сердцевины по направлению хвоставику 0.5 - 0.8 мм на 100 мм длины рабочей части:
мм;
ширина ленточки (вспомогательная задняя поверхность лезвия , выбираем по таблице в зависимости от диаметра сверла мм;
5.7 Предварительное отклонения размеров конуса хвостовика устанавливаем по ГОСТ 2848-75. Радиальное биение рабочей части сверла относительно оси хвостовика не должно превышать 0.15 мм; Углы ;
Угол наклона винтовой канавки ; Предельные отклонения размеров подточки перемычки режущей части сверла + 0.5 мм; Твёрдость рабочей части сверла ;
(Приложение) Операционная карта сверлильная, Маршрутная карта. _PAGE __ Выбор станочного приспособление для зубофрезерования.
Станочные приспособления - это положительные устройства к станкам, позволяющие достаточно точно устанавливать и закреплять заготовки деталей при их обработке . При необходимости станочные приспособления обеспечивают направления режущего инструмента и периодический поворот заготовки в процессе обработки . Станочные приспособления обеспечивают правильное взаимное расположение заготовки, стола и инструмента, расширяют технологические возможности станков. Они повышают точность обработки, производительность и экономическую эффективность, облегчают условия труда рабочих. По группам оснащаемых станков, приспособления подразделяются на токарные, фрезерные, сверлильные (кондукторы), шлифовальные и т.д.. По количеству устанавливаемых деталей: одноместные и многоместные. По степени универсальности (специализации) приспособления подразделяются на: - универсальные безналадочные (УБП) и универсально наладочные приспособления (УНП); - специализированные безналадочные (СБН) и наладочные приспособления (СНП); - специализированные приспособления: универсальные сборные (УСП); сборноразборные (СРП) и необратимые специальные (НСП).
Для установки и закрепления установок, обрабатываемых на зубофрезерных, зубодолбёжных, зубошевенговых и зубошлифовальных станках, применяются разнообразные оправки, обеспечивающие высокую степень базирования. Для точного центрирования применяют оправку с упругой оболочкой - с гидропластом, жесткие для посадки заготовок с небольшим зазором. Заготовку закрепляют ручным зажимом или используют приспособление с пневматическим, гидравлическим приводом. На точность зубообработки непосредственно влияет точность центрований приспособлений, ось которых должны совпадать с осью вращения стола. В качестве приспособления для зубофрезирования выбираем оправку зубчатую центровую по ГОСТ 18438-73; обозначение 7150-0421
Расчёт усиления зажима
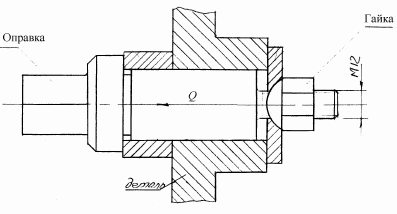
Для винтового зажима ;
где F = 200 Н на усилие на ключе;
l - длина плеча ключа; l = 150 мм; - средний диаметр резьбы; =10.98 мм; a - угол подвига резьбы; ; - угол трения резьбовой пары; ; - половина угла профиля резьбы
кг-с; (Приложение) Чертёж оправка зубчатоя центровая. _PAGE __ Список исследуемой литературы. Добрыднев И.С. курсовое проектирование по предмету “Технология машиностроения” М. Машиностроение 1985 г. Ансеров М.А. “Приспособление для машинорежущих станков” М. “Машиностроение” 1975 г. Моисеев В.В. “Методика расчётов режимов резания при механической обработке металлов” Ю-Сах. ЮСГПИ 1990 г. Моисеев В.В. “Проектирования приспособлений для металлорежущих станков” Методическое пособие. Ю-Сах ЮСГПИ 1994 г. Панова А.А. “Обработка деталей резанием” Справочник технолога. М. “Машиностроение” 1998 г. Анурьев В.И. “Справочник конструктора - машиностроителя в 3-х томах”, М. “Машиностроение” 1980 г. Красикова А.Г. “Справочник технолога машиностроителя” в 2-х томах М. “Машиностроение” 1986 г. _PAGE __ |