МИНИСТЕРСТВО ОБРАЗОВАНИЯ И НАУКИ УКРАИНЫ
ДОНЕЦКИЙ НАЦИОНАЛЬНЫЙ ТЕХНИЧЕСКИЙ УНИВЕРСИТЕТ
КУРСОВАЯ РАБОТА
по дисциплине: “Теория проектирования автоматизированных станочных комплексов”
на тему: “Расчет и проектирования автоматической системы технологического оборудования”
ДОНЕЦК 2005
РЕФЕРАТ
Курсовая работа содержит: с., 7 табл., 4 источника, 4 приложения.
В данной курсовой работе рассматривается процесс проектирования автоматической линии технологического оборудования, которая позволила бы при минимальных затратах добиться заданной производительности.
Цель работы: спроектировать оптимальную структурно-компоновочную схему автоматической линии для условий серийного производства детали «переходник». Реализовать структурную схему на практике, выбрав конкретное технологическое оборудование; описать ее работу с помощью циклограммы.
Курсовая работа включает: данную пояснительную записку, которая содержит все необходимые сведения о проектировании автоматической линии; чертеж компоновки автоматической линии с обозначением всех позиций; циклограмма работы автоматической линии.
Кроме того, для всех операций представлены эскизы карт наладок.
ПЕРЕХОДНИК, ПРОИЗВОДСТВО, ПРОИЗВОДИТЕЛЬНОСТЬ, АТОМАТИЧЕСКАЯ ЛИНИЯ, ЦИКЛОГРАММА
ИСХОДНЫЕ ДАННЫЕ
- чертеж детали (приложение Б);
- базовый технологический процесс обработки детали;
- заданная производительность обработки Qтр
=250 деталей/смена.
СОДЕРЖАНИЕ
ВВЕДЕНИЕ
1. Анализ конструкции детали на технологичность.
2. Базовый технологический процесс обработки штока в условиях неавтоматизированного производства.
3. Операционный технологический процесс, реализуемый в условиях автоматизированного производства.
4. Расчет машинного времени выполнения операций.
5. Анализ базового операционного технологического процесса по критерию обеспечения заданной сменной производительности обработки.
6. Основные положения относительно выбора рационального варианта структуры автоматической линии.
7. Расчет экономических показателей.
ПРИЛОЖЕНИЕ А – Эскизы наладки на агрегатную операцию
ПРИЛОЖЕНИЕ Б – Чертеж детали
ПРИЛОЖЕНИЕ В – Общий вид автоматической линии со спецификацией
ПРИЛОЖЕНИЕ Г – Эскизы наладки на агрегатную операцию
ПРИЛОЖЕНИЕ Д - Циклограмма работы линии
ВВЕДЕНИЕ
Современное производство отличается сложностью производства и технологических процессов. В этих условиях решаются проблемы повышения продуктивности работы и качества производства изготавливаемой продукции при минимальных затратах автоматизации. Для этого необходимо уметь проектировать и широко использовать автоматизированные системы технологического оборудования, в состав которых входит сами станки – автоматы, автоматизированные загрузочные устройства, транспортно – накопительные системы и др.
1. Анализ конструкции детали на технологичность
Цель анализа конструкции детали на технологичность – выявление недостатков конструкции по сведениям, содержащихся в чертежах и технических требованиях, а также возможное улучшение технологичности рассматриваемой конструкции [1].
Технологический контроль чертежей сводится к тщательному их изучению. Чертеж детали содержит все проекции и разрезы, совершенно четко и однозначно объясняющие ее конфигурацию. На чертеже указаны все размеры с необходимыми отклонениями и требуемая шероховатость обрабатываемых поверхностей. Чертеж содержит все необходимые сведения о материале детали, термической обработке и массе детали.
Деталь – переходник является частью гидросистемы угольного комбайна и выполняет роль распределителя – представляет собой призматическую деталь. Она изготавливается ковкой из стали 45. Химический состав материала занесен в таблицу 1.
Таблица 1. 1 – Химический состав, %.
С
|
Si
|
Mn
|
S
|
P
|
0,42-0,50
|
0,17-0,37
|
0,50-0,80
|
не более
|
0,040
|
0,035
|
Деталь имеет две наклонные поверхности которые требуют применения специальных приспособлений, что достаточно нетехнологично.
Деталь имеет глухое отверстие Ø18 мм и длиной 140 мм которое необходимо предварительно рассверлить или обрабатывать за несколько раз, что тоже нетехнологично.
Упрощение конструкции детали или замена ее элементов ввиду её служебного назначения и тяжелых условий эксплуатации нецелесообразно.
Итак, в целом деталь достаточно технологична, допускает применение высокопроизводительных методов обработки и довольно проста по конструкции.
2. Базовый технологический процесс обработки штока в условиях неавтоматизированного производства
005 Заготовительная операция.
010 Вертикально – фрезерная
Станок вертикально – фрезерный 6Н13П
А 1. Фрезеровать поверхность 155х125, фреза торцевая 2214-0157 Т5К10 ГОСТ 9473-80 выдержав размер 45,7 мм
Б 2. Фрезеровать поверхность 155х125, фреза торцевая 2214-0157 Т5К10 ГОСТ 9473-80 выдержав размер 44-0,62
мм.
015 Вертикально – фрезерная
Станок вертикально – фрезерный 6Н13П
А 1. Фрезеровать поверхность 115х44, фреза торцевая 2214-0157 Т5К10 ГОСТ 9473-80 выдержав размер 156,8 мм
Б 2. Фрезеровать поверхность 115х44, фреза торцевая 2214-0157 Т5К10 ГОСТ 9473-80 выдержав размер 155-1
мм.
020 Вертикально – фрезерная
Станок вертикально – фрезерный 6Н13П
А 1. Фрезеровать поверхность 155х44, фреза торцевая 2214-0157 Т5К10 ГОСТ 9473-80 выдержав размер 116,8 мм
Б 2. Фрезеровать поверхность 155х44, фреза торцевая 2214-0157 Т5К10 ГОСТ 9473-80 выдержав размер 115-0,87
мм.
025 Вертикально – фрезерная
Станок вертикально – фрезерная 6Н13П
А 1. Фрезеровать поверхность 450
х650
на проход, фреза торцевая 2214-0157 Т5К10 ГОСТ 9473-80
030 Вертикально – фрезерная
Станок вертикально – фрезерный 6Н13П
А 1. Фрезеровать поверхность 650
х150
на проход, фреза торцевая 2214-0157 Т5К10 ГОСТ 9473-80
035 Радиально сверлильная
Станок вертикально – фрезерный 2А53
А 1. Сверлить 3 отв. Æ18 последовательно сверло 2301-0025 ГОСТ 10903-77
2. Зенкеровать 3отв. Æ 36мм последовательно на глубину 13+1,1
мм, зенкер 2320-2392 ГОСТ 3231-71
040 Радиально – сверлильная
Станок радиально сверлильный 2А53
А 1. Сверлить отв. Æ9,5мм на глубину 5…7мм, сверло 2301-0015 ГОСТ 10903-77.
2. Сверлить отв.Æ18мм на глубину 140мм, сверло 2301-0025 ГОСТ 10903-77
3. Рассверлить отв. Æ22мм на глубину 6мм, сверло 2301-0026 ГОСТ10903-77
045 Радиально – сверлильная
Станок радиально – сверлильный 2А53
А 1. Сверлить отв. Æ18мм до ранее просверленного, сверло 2301-0025 ГОСТ 10903-77.
2. Зенкеровать отв. Æ 48мм на глубину 5мм, зенкер 2345-2392 ГОСТ 3231-71
3. Рассверлить отв. Æ 25Н12 на глубину 9мм, сверло 2301-0077 ГОСТ
10903-77.
050 Радиально – сверлильная
Станок радиально – сверлильный 2А53
А 1. Сверлить отв. Æ18мм до ранее просверленного, сверло 2301-0025 ГОСТ 10903-77.
2. Зенкеровать отв. Æ 31,5мм на глубину 30мм, зенкер 2320-0052
ГОСТ 3231-71
3. Зенковать фаску 1,6х450
, зенковка 2353-0021 ГОСТ 14953-80
4. Зенкеровать отв. Æ34,4мм на глубину 18мм, 2320-0054 ГОСТ 3231-71
5. Развернуть отв. Æ32Н9 на глубину 30мм, развертка 2363-0472
ГОСТ1672-71
6. Нарезать резьбу М36х1,5 на глубину 15мм, метчик М36х1,5 2620-2039 ГОСТ 3266-71
055 Радиально – сверлильная
Станок радиально – сверлильный 2А53
А 1. Сверлить отв. Æ16мм до ранее просверленного, сверло 2301-0022 ГОСТ 10903-77.
2. Зенкеровать отв. Æ24,5 мм на глубину 29мм, зенкер 2320-0042
ГОСТ 3231-71
3. Зенковать фаску 1,6х450
, зенковка 2353-0021 ГОСТ 14953-80
4. Зенкеровать отв. Æ28,4мм на глубину 18мм, 2320-0044 ГОСТ 3231-71
5. Развернуть отв. Æ32Н9 на глубину 29мм, развертка 2363-0239
ГОСТ1672-71
6. Нарезать резьбу М30х1,5 на глубину 15мм, метчик М36х1,5 2620-1935 ГОСТ 3266-71.
060 Радиально – сверлильная
Станок радиально – сверлильный
А 1. Сверлить отв. под резьбу G1/2-B до ранее просверленного
2. Нарезать резьбу G1/2-B на глубину 16мм.
065 Радиально – сверлильная
Станок радиально – сверлильный
А 1. Сверлить отв. под резьбу G1/2-B до ранее просверленного
2. Нарезать резьбу G1/2-B на глубину 16мм.
3. Операционный технологический процесс, реализуемый в условиях автоматизированного производства
Разработка операционного технологического процесса ведется для случая реализации на агрегатных станках.
При разработке операционного технологического процесса используются наиболее перспективные схемы и методы обработки, а также конструкции инструмента и инструментальные материалы, которые предусматривают возможность максимальной интенсификации режимов резания.
Например: Применение комбинированного инструмента, обработка в одной позиции нескольких отверстий, применение инструмента из быстрорежущей стали .
Рассматривая данный процесс для автоматического производства все фрезерные операции относим к заготовительным (005 –025), а операции выполняемые на радиально – сверлильных (030 – 070) будем реализовывать в автоматическом режиме.
4. Расчет машинного времени выполнения операций
Выбор режимов резания произведен в соответствии с машиностроительными нормативами для технического нормирования работ на металлорежущих станках [2]. Все параметры занесены в таблицу 2.
Машинное время для фрезерных и сверлильных работ [3]:
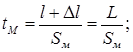
где l – длина обрабатываемой поверхности, мм;
∆l – суммарная величина врезания и перебега, мм;
Sм
– минутная подача, мм/мин.
Минутная подача при сверлении:
Sм
=So
·n;
где Sо
– оборотная подача, мм/об;
n – частота вращения сверла, об/мин.
Таблица 4. 1 – Расчет машинного времени выполнения операций.
Наименование
|
Инструмент
|
Параметры режимов
|
, мм
|
, мм
|
, мин
|
Операции
|
Переход
|
, мм
|
, мм/
об
|
, м/
мин
|
, об/
мин
|
, мм/
мин
|
1. Радиально Сверлильная
|
1.Св. Æ18
2.Св.Æ18
3.Св.Æ18
4.Зен.Æ36
5.Зен.Æ36
6.Зен.Æ36
|
СверлоÆ18
Т5К10
Зенкер Æ36
Т5К10
|
9
9
9
6
6
6
|
0,4
0,4
0,4
0,5
0,5
0,5
|
20
20
20
36
36
36
|
350
350
350
320
320
320
|
|
18
18
18
36
36
36
|
49
49
49
15
15
15
|
0,35
0,35
0,35
0,09
0,09
0,09
|
2. Радиально
сверлильная
|
1. Св. Æ9,5
2. Св. Æ18
3. Расс. Æ22
|
Св.Æ9.5Т5К10
Св.Æ18Т5К10
Св.Æ22Т5К10
|
4,75
9
2
|
0,4
0,4
0,5
|
20
20
18
|
350
350
260
|
|
9,5
18
22
|
7
145
10
|
0,07
1,04
0,05
|
3. Радиально сверлильная
|
1.Св.Æ18
2.Зен.Æ48
3.Расс.Æ25
|
Св.Æ18 Т5К10
Зен.Æ48 Т5К10
Св.Æ25 Т5К10
|
9
15
3,5
|
0,4
0,5
0,5
|
20
30
30
|
350
200
380
|
|
18
48
25
|
25
8
10
|
0,17
0,08
0,05
|
4. Радиально сверлильная
|
1.Св.Æ18
2.ЗенÆ31,5
3.Зен1,6х45
4.ЗенÆ34.4
5.Раз.Æ32
6.Мет.М36
|
Св.Æ18 Т5К10
ЗенÆ31,5Т5К10
Зен.1,6х45
ЗенÆ34,4Т5К10
Раз.Æ32Т5К10
МетчикМ36х1,5
|
9
7,25
3,2
1,45
0,25
1,5
|
0,4
0,5
1
0,5
0,5
1,5
|
20
10
35
15
10
10
|
350
100
280
140
100
110
|
|
18
31,5
40
34,4
32
36
|
70
35
4,5
23
15
40
|
0,5
0,7
0,02
0,32
0,1
0,24
|
5. Радиально
сверлильная
|
1.Св.Æ16
2.ЗенÆ24,5
3.Зен1,6х45
4.ЗенÆ28.4
5.Раз.Æ32
6.Мет.М30
|
Св.Æ16 Т5К10
ЗенÆ24,5Т5К10
Зен.1,6х45
ЗенÆ28,4Т5К10
Раз.Æ25Т5К10
МетчикМ30х1,5
|
8
2,75
3,2
1,95
0,25
1,5
|
0,4
0,5
1
0,5
0,5
1,5
|
20
12
35
14
7
10
|
350
100
280
160
100
100
|
|
16
24,5
40
2,4
25
30
|
55
34
4,5
18
13
40
|
0,39
0,37
0,02
0,22
0,7
0,24
|
6. Радиально сверлильная
|
1.Св.Æ19.5
2.МетG1/2B
|
СверлоÆ19.5
Метчик G1/2B
|
9.75
1.5
|
0.4
1.5
|
20
10
|
325
150
|
|
19.5
20.95
|
35
40
|
0.27
0.17
|
7. Радиально сверлильная
|
1.Св.Æ19.5
2.МетG1/2B
|
СверлоÆ19.5
Метчик G1/2B
|
9.75
1.5
|
0.4
1.5
|
20
10
|
325
150
|
|
19.5
20.95
|
35
40
|
0.27
0.17
|
Простейшим вариантом построения технологического процесса неавтоматизированного производства при принятых методах, технологическом маршруте и режимах обработки является полная обработка детали на одной позиции при последовательном выполнении всех составных операций.
Критерием оценки технологического процесса является технологическая производительность kо
, которая определяется по формуле:
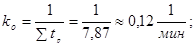
где ∑tр
– суммарное машинное время выполнения всех операций, мин.
Значение технологической производительности может быть основой для расчета оптимальной степени дифференциации и концентрации операций в автоматической линии.
5. Анализ базового операционного технологического процесса по критерию обеспечения заданной сменной производительности обработки
Определение ожидаемой сменной производительности системы технологического оборудования в условиях неавтоматизированного производства делается по формуле:
деталей/смена,
где - время выполнения холостых (вспомогательных) операций в условиях неавтоматизированного производства.
Сравнивая полученное значение (35 деталей/смена) с заданной сменной производительностью обработки (250 деталей/смена), приходим к выводу, что в неавтоматизированном производстве нельзя обеспечить требуемую производительность. Следовательно, необходимо разработать оптимальный структурно-композиционный вариант автоматической линии, который должен обеспечивать заданную производительность обработки.
6. Основные положения относительно выбора рационального варианта структуры автоматической линии
При обработке на автоматической линии переходника технологический процесс дифференцируется на составные части, которые выполняются в разных позициях на разных станках. В процессе обработки – от заготовки к готовой продукции – изделие передается последовательно из позиции в позицию, где получает заданный объем технологического воздействия таким образом, что на каждой позиции выполняется лишь определенная часть обработки. При этом принятые методы, маршрут и режимы обработки, технологические базы и режущий инструмент должны обеспечить выполнение заданных требований качества (точность размеров, шероховатость поверхности и др.).
Известно, что увеличение степени дифференциации технологического процесса обработки сопровождается возрастанием технологической производительности обработки k0
. Максимально дифференцировав операции, получим следующую структурную схему:
Данную структуру можно реализовать на практике двумя способами:
- с использованием станков, возле которых находятся промышленные роботы для загрузки и выгрузки заготовок, и транспортная система для перемещения заготовок от позиции к позиции;
- с использованием специальных силовых головок, которые производят обработку заготовок прямо на транспортере.
1 ВАРИАНТ
Технологический процесс.
010 Агрегатная
1 позиция – Сверлильная операция tр
=0,35мин
Обработать 3 отв. Æ18/36мм, на глубину 13+1,1
мм, комбинированным инструментом сверло – зенкер.
2 позиция – Сверлильная операция tр
=0,38мин
Сверлить отв. Æ9/18мм, на глубину 85мм, комбинированным инструментом сверло-сверло.
3 позиция – Сверлильная операция tр
=0,21мин
Сверлить отв. Æ9/18мм, на глубину 45мм, комбинированным инструментом сверло-сверло.
4 позиция – Сверлильная операция tр
=0,18мин
Сверлить отв. Æ18мм, на глубину 45мм, инструмент сверло спиральное
5 позиций – Сверлильная операция tр
= 0,04мин.
Рассверлить отв. Æ22 на глубину 6 мм, инструмент сверло спиральное.
020 Агрегатная
1.1 позиций – Сверлильная операция tр
= 0,5мин.
Сверлить отв. Æ18мм, инструмент сверло спиральное.
1.2 позиций – Сверлильная операция tр
= 0,39мин.
Сверлить отв. Æ16мм, инструмент сверло спиральное.
1.3 позиций – Сверлильная операция tр
= 0,27мин.
Сверлить отв. Æ19,5мм под резьбу, инструмент сверло спиральное.
2.1 позиций – Сверлильная операция tр
= 0,7мин.
Обработать отв. Æ31,5/34,4/1,6Х450
, комбинированным инструментом зенкер – зенкер – зенковка, на глубину 30мм.
2.2 позиций – Сверлильная операция tр
= 0,37мин.
Обработать отв. Æ24,5/28,4/1,6х450
, на глубину 29 мм, инструмент зенкер – зенкер – зенковка.
2.3 позиций – Сверлильная операция tр
= 0,27мин.
Сверлить отв. Æ19,5мм под резьбу, инструмент сверло спиральное.
2.4 позиций – Сверлильная операция tр
= 0,17мин.
Нарезать резьбу G1/2-B, на глубину 16+1,1
мм, инструмент метчик.
3.1 позиций – Сверлильная операция tр
= 0,24мин.
Обработать отв. Æ32Н9/М36х1,5, на глубину 18 мм, инструмент развертка – метчик.
3.2 позиций – Сверлильная операция tр
= 0,24мин.
Обработать отв. Æ25Н9/М30х1,5, на глубину 18мм, инструмент развертка – метчик.
3.3 позиций – Сверлильная операция tр
= 0,17мин.
Нарезать резьбу G1/2-B, на глубину 16+1,1
мм, инструмент метчик.
030 Агрегатная
1 позиций – Сверлильная операция tр
= 0,17мин.
Сверлить отв. Æ18 мм, на глубину 22мм, инструмент сверло спиральное.
2 позиций – Сверлильная операция tр
= 0,08мин.
Зенкеровать отв. Æ48мм, на глубину 5мм, инструмент зенкер.
3 позиций – Сверлильная операция tр
= 0,05мин.
Рассверлить отв. Æ25Н12, на глубину 4мм, инструмент сверло спиральное.
Лимитирующей позицией является сверлильная операция, для которой tр
=0,7 мин. Производим укрупненный расчет цикловой производительности QЦ
для данного варианта по формуле:
деталей/смена,
где ТЦ
– время рабочего цикла АЛ, мин;
мин,
tр
(q) - время машинной обработки на лимитирующей позиции, мин;
- время несовмещенных вспомогательных ходов цикла.
Кисп
=0,75 – ожидаемый коэффициент использования АЛ.
Уточненный расчет полной производительности выполним по формуле:
,
где Кзаг
=0,85 – коэффициент загрузки линии как характеристика технических и организационных условий ее эксплуатации;
- время несовмещенных вспомогательных ходов цикла;
∑tр
– суммарные собственные внецикловые затраты (простой на единицу продукции), мин/шт.
Внецикловые затраты определяются по формуле:
,
где ∑tин
– ожидаемые суммарные внецикловые затраты по инструменту;
∑tос
– ожидаемые усредненные внецикловые затраты по оснащению.
Затраты времени из-за выхода из строя инструмента определяются по формуле:
,
где tр
– машинное время выполнения составной операции конкретным инструментом, мин;
Т - нормативная стойкость инструмента, мин;
tз
- время, необходимое для замены инструмента при его износе, мин;
tпр
- средняя продолжительность простоев из-за случайных сбоев в работе и поломок инструмента, которые приходятся на период его стойкости, мин.
Значение tз
и tпр
для разных типов инструментов занесены в таблицу 4.
Таблица 6. 1 – Расчет времени затрат по инструменту.
№
п/п
|
Инструмент
|
tр
мин.
|
Т
мин.
|
tз
+tпр
мин.
|
tин
мин.
|
1
2
3
4
5
|
Сверло – зенкер
Сверло – сверло
Сверло – сверло
Сверло
Сверло
|
0,35
0,38
0,21
0,18
0,04
|
45
45
45
45
45
|
1,12
1,12
1,12
1,12
1,12
|
0,008
0,01
0,005
0,0045
0,001
|
1.1
1.2
1.3
2.1
2.2
2.3
2.4
3.1
3.2
3.3
|
Сверло
Сверло
Сверло
Зенкер – зенкер – зенковка
Зенкер – зенкер – зенковка
Сверло
Метчик
Развертка – метчик
Развертка – метчик
Метчик
|
0,5
0,39
0,27
0,7
0,37
0,27
0,17
0,24
0,24
0,27
|
45
45
45
50
50
45
90
50
50
90
|
1,12
1,12
1,12
1,18
1,18
1,12
1,27
1,68
1,68
1,68
|
0,012
0,0097
0,0067
0,0165
0,008
0,0067
0,005
0,008
0,008
0,005
|
1
2
3
|
Сверло
Зенкер
Сверло
|
0,17
0,08
0,05
|
45
50
45
|
1,12
1,18
1,12
|
0,004
0,0018
0,0012
|
|
|
|
|
|
0,1211
|
Расчет ожидаемых внецикловых затрат по оборудованию (для одной позиции) tос
производим по формуле:
tос
,
где tп
– средняя продолжительность простоев j-го нормализованного узла, который входит в состав оснащения конкретной позиции;
tр
– время работы j-го нормализованного узла при выпуске единицы продукции;
k – общее количество нормализованных узлов в оснащении конкретной позиции.
Таблица 6. 2 – Расчет затрат по оснащению первого варианта.
Позиция
|
Наименование механизмов
|
tп
,
мин.
|
tр
,
мин.
|
tос
,
мин.
|
1
|
1. Узел подачи и загрузки заготовки
2. Механизм фиксации
3. Гидравлическое оборудование
4. Электрооборудование
5. Система охлаждения
6. Транспортер стружки
7. Силовой стол с гидроприводом
8. Поворотный стол
9. Силовая головка
|
0,55
0,18
0,23
1,43
0,48
0,24
1,2
0,1
1,25
|
0,1
0,05
0,7
0,7
0,7
0,7
2
0,18
2
|
0,0005
0,0001
0,0007
0,01
0,0034
0,0017
0,024
0,0002
0,025
|
2
|
1. Узел подачи и загрузки заготовки
2. Механизм фиксации
3. Гидравлическое оборудование
4. Электрооборудование
5. Система охлаждения
6. Транспортер стружки
7. Силовой стол с гидроприводом
8. Конвейерный стол
9. Силовая головка
|
0,55
0,03
0,23
1,43
0,8
0,24
2,4
0,1
2,5
|
0,1
0,05
0,7
0,7
0,7
0,7
4
0,3
4
|
0,0005
0,0001
0,0016
0,01
0,0056
0,0016
0,096
0,0003
0,1
|
3
|
1. Узел подачи и загрузки заготовки
2. Механизм фиксации
3. Гидравлическое оборудование
4. Электрооборудование
5. Система охлаждения
6. Транспортер стружки
7. Силовой стол с гидроприводом
8. Поворотный стол
9. Силовая головка
|
0,55
0,03
0,23
1,43
0,24
0,24
0,72
0,1
0,75
|
0,1
0,05
0,7
0,7
0,7
0,7
1,2
0,12
1,2
|
0,0005
0,0001
0,0007
0,01
0,0017
0,0017
0,0086
0,0001
0,009
|
|
|
|
|
0,32
|
Таким образом:
мин.
Производительность данного варианта:
деталей/смена.
2 ВАРИАНТ
Технологический процесс
010 Агрегатная
1 позиция – обработать 3 отв. Æ18/36мм
2 позиция – сверлить отв. Æ9/18мм
3 позиция – сверлить отв. Æ9/18 мм
4 позиция – сверлить отв. Æ18 мм
5 позиция – рассверлит отв. Æ22мм
020 Агрегатная
1 позиция – сверлить отв. Æ18 мм
2 позиция – обработать отв. Æ 31,5/34,4/1,6х450
3 позиция – обработать отв. Æ32/М36х1,5
030 Агрегатная
1 позиция – сверлить отв. Æ16мм
сверлить отв. Æ19,5мм
2 позиция – обработать отв. Æ24,5/28,6/1,6х450
сверлить отв. Æ19,5 мм
нарезать резьбу G1/2-B
3 позиция – обработать отв. Æ25/М30х1,5
нарезать резьбу G1/2-B
040 Агрегатная
1 позиция – сверлить отв. Æ 18мм
2 позиция – зенкеровать отв. Æ 48 мм
3 позиция – рассверлить отв. Æ 25 мм
Таблица 6.3 – Расчет затрат по оснащению второго варианта.
Позиция
|
Наименование механизмов
|
tп
,
мин.
|
tр
,
мин.
|
tос
,
мин.
|
1
|
1. Узел подачи и загрузки заготовки
2. Механизм фиксации
3. Гидравлическое оборудование
4. Электрооборудование
5. Система охлаждения
6. Транспортер стружки
7. Силовой стол с гидроприводом
8. Поворотный стол
9. Силовая головка
|
0,55
0,18
0,23
1,43
0,48
0,24
1,2
0,1
1,25
|
0,1
0,05
0,7
0,7
0,7
0,7
2
0,18
2
|
0,0005
0,0001
0,0007
0,01
0,0034
0,0017
0,024
0,0002
0,025
|
2
|
1. Узел подачи и загрузки заготовки
2. Механизм фиксации
3. Гидравлическое оборудование
4. Электрооборудование
5. Система охлаждения
6. Транспортер стружки
7. Силовой стол с гидроприводом
8. Поворотный стол
9. Силовая головка
|
0,55
0,03
0,23
1,43
0,24
0,24
0,72
0,1
2,5
|
0,1
0,05
0,7
0,7
0,7
0,7
1,2
0,3
1,2
|
0,0005
0,0001
0,0016
0,01
0,0056
0,0016
0,096
0,0003
0,1
|
3
|
1. Узел подачи и загрузки заготовки
2. Механизм фиксации
3. Гидравлическое оборудование
4. Электрооборудование
5. Система охлаждения
6. Транспортер стружки
7. Силовой стол с гидроприводом
8. Поворотный стол
9. Силовая головка
|
0,55
0,03
0,23
1,43
0,56
0,24
1,68
0,1
1,75
|
0,1
0,05
0,7
0,7
0,7
0,7
2,8
0,3
2,8
|
0,0005
0,0001
0,0016
0,01
0,004
0,0016
0,04
0,0003
0,049
|
4
|
1. Узел подачи и загрузки заготовки
2. Механизм фиксации
3. Гидравлическое оборудование
4. Электрооборудование
5. Система охлаждения
6. Транспортер стружки
7. Силовой стол с гидроприводом
8. Поворотный стол
9. Силовая головка
|
0,55
0,03
0,23
1,43
0,24
0,24
0,72
0,1
0,75
|
0,1
0,05
0,7
0,7
0,7
0,7
1,2
0,12
1,2
|
0,0005
0,0001
0,0007
0,01
0,0017
0,0017
0,0086
0,0001
0,009
|
|
|
|
|
0,43
|
Таким образом:
мин.
Производительность данного варианта:
деталей/смена.
7. Расчет экономических показателей
Показателем экономической эффективности являются неполные приведенные затраты.
Неполные приведенные затраты (с учетом принятых допущений):
=
где К – стоимость технологического оборудования;
З – заработная плата (считаем постоянной).
Составим таблицу 7 и 8, в которой укажем стоимость каждой единицы оборудования.
Таблица 7. 1 – Стоимость оборудования для первого варианта
№
обор.
|
Наименование оборудования
|
Наименование
Узла
|
Стоимость узла, у.е.
|
Количество
узлов в
оборудовании
|
Стоимость
оборудования
|
1
|
Агрегатный станок
|
Стол поворотный
|
240
|
1
|
240
|
Силовая головка
|
1200
|
5
|
6000
|
Насадка
|
500
|
1
|
500
|
Стол силовой
|
600
|
5
|
3000
|
2
|
Агрегатный – станок
|
Стол конвейерный
|
1000
|
1
|
1000
|
Силовая головка
|
1200
|
10
|
12000
|
Стол силовой
|
600
|
10
|
6000
|
3
|
Агрегатный станок
|
Стол поворотный
|
240
|
1
|
240
|
Силовая головка
|
1200
|
3
|
3600
|
Стол силовой
|
600
|
3
|
1800
|
|
34380
|
Таблица 7. 2 – Стоимость оборудования для второго варианта
№
обор.
|
Наименование оборудования
|
Наименование
Узла
|
Стоимость узла, у.е.
|
Количество
узлов в
оборудовании
|
Стоимость
оборудования
|
1
|
Агрегатный станок
|
Стол поворотный
|
240
|
1
|
240
|
Силовая головка
|
1200
|
5
|
6000
|
Насадка
|
500
|
1
|
500
|
Стол силовой
|
600
|
5
|
3000
|
2
|
Агрегатный – станок
|
Стол поворотный
|
240
|
1
|
240
|
Силовая головка
|
1200
|
3
|
3600
|
Стол силовой
|
600
|
3
|
1800
|
3
|
Агрегатный станок
|
Стол поворотный
|
240
|
1
|
240
|
Силовая головка
|
1200
|
7
|
9400
|
Стол силовой
|
600
|
7
|
4200
|
4
|
Агрегатный станок
|
Стол поворотный
|
240
|
1
|
240
|
Силовая головка
|
1200
|
3
|
3600
|
Стол силовой
|
600
|
3
|
1800
|
|
34860
|
Из таблицы окончательно выбираем первый вариант, который отличается наиболее низкими значениями приведенных затрат. Для данного варианта приведены эскизы карт наладок.
Чертеж компоновки автоматической линии приведен в приложении Б. Циклограмма работы автоматической линии приведена в приложении Д. Эскизы наладок в приложениях А.
ВЫВОДЫ
В данной курсовой работе рассматривался процесс проектирования автоматической линии технологического оборудования.
Поставленная цель работы - спроектировать оптимальную структурно-компоновочную схему автоматической линии для условий серийного производства детали типа «переходник» - была полностью достигнута, при этом было выполнено основное требование к проектируемой линии: обеспечена требуемая производительность при наилучших экономических показателях.
Курсовая работа включает данную пояснительную записку, которая содержит все необходимые сведения о проектировании автоматической линии; эскизы карт наладок; чертеж компоновки автоматической линии с обозначением всех позиций; циклограмма работы автоматической линии.
ПЕРЕЧЕНЬ ССЫЛОК
1. Горбацевич А.Ф., Шкред В.А. Курсовое проектирование по технологии машиностроения. - Мн: Выш. школа, 1983. - 256 с.
2. СТМ. Т. 1 /Под ред. А.Г. Косиловой и Р.К. Мещерякова. - Г.: Машиностроение, 1985. - 656 с.; СТМ. Т. 2 /Под ред. А.Г. Косиловой и Р.К.Мещерякова. - Г.: Машиностроение, 1985. - 496 с.
3. Справочник Технолога-машиностроителя. Т. 1 /Под ред. А.Г. Косиловой и Р.К. Мещерякова. - Г.: Машиностроение, 1985. - 656 с.; Справочник Технолога-машиностроителя. Т. 2 /Под ред. А.Г. Косиловой и Р.К. Мещерякова. - Г.: Машиностроение, 1985. - 496 с.
4. Балабанов А.Н. Краткий справочник технолога-машиностроителя. - Г.: Издательство стандартов, 1992. - 464 с.
|