Федеральное агентство по образованию
Государственное образовательное учреждение
Среднего профессионального образования
Каменск-Уральский Политехнический Колледж
Специальность: 150102
Металлургия цветных металлов
Группа Мт-42
КУРСОВОЙ ПРОЕКТ
По дисциплине «Металлургия алюминия»
Выполнил:
Проверил:
2009
Электролизер для получения алюминия с боковым токоподводом на силу тока 80000А
СОДЕРЖАНИЕ
1 Пояснительная записка
Введение…………………………………………………..4
1.1 Госты на алюминий и сырье…………………………6
1.2 Обоснование состава электролита и технологичес-
ких параметров ……………………………………..10
1.3 Описание конструкции………………………………16
1.4 Обслуживание при нормальной работе, неполадки,
способы устранения ………………………………....19
1.5 Вопросы БЖД………………………………..……....26
2 Расчетная часть
2.1 Конструктивный расчет……………………………...33
2.2 Материальный расчет………………………………..35
2.3 Электрический расчет………………………………..37
2.4 Тепловой расчет………………………………………44
2.5 Расчет числа электролизеров в серии……………….45
3 Графическая часть проекта
Библиография……………………………………………47
Спецификация……………………………………………48
ВВЕДЕНИЕ
Алюминий (AI) – химический элемент 3 группы периодической системы Д.И. Менделеева. Порядковый номер его 13, атомная масса 26,97.
Алюминий – серебристо – белый металл, в чистом виде – с синеватым оттенком.
Важнейшие физические свойства алюминия представлены в таблице 1 Таблица 1 – Свойства алюминия
Показатели
|
Значение
|
Температура плавления (градус Цельсия)
Температура кипения (градус Цельсия)
Плотность при 20 градусах Цельсия, г / куб.см.
при 1000 градусах Цельсия, г / куб. см.
Удельная теплоёмкость при 20 градусах Цельсия
Дж / моль * К
Теплота плавления, Дж / г
Теплота испарения, Дж / г
Коэффициент теплопроводности в температурном интервале
0 – 100 градусов Цельсия, Вт. см. * град.
Удельное электрическое сопротивление при 20 градусах Цельсия, мкОм * м.
Коэффициент линейного термического расширения
Твердость по Бринеллю, кг / кв. мм.
Электрохимический эквивалент, г / А * ч
|
660,24
2497
2,6996
2,289
24,35
386
10900
2,35 – 2,40
0,0265
6
23 * 10
15
0,3354
|
Пластические свойства алюминия зависят от его частоты: чем меньше примесей включает металл, тем легче он подвергается ковке, штамповке, прокатке и резанию. Введение в алюминий меди, цинка, магния и других металлов в
сочетании с термической обработкой даёт получение высококачественных
сплавов, в которых отношение прочности к плотности выше, чем у легированных
сталей. Отражательная способность алюминия на 15–20 % меньше, чем у серебра ,
однако, зеркало из алюминия более стойко и не тускнеет.
Электропроводность алюминия составляет 65 % от электропроводности меди, а, следовательно, провода одинаковой проводимости из алюминия в 2,16 раза легче медных.
В электрохимическом аспекте – алюминий электроотрицательный элемент, его стандартный электронный потенциал равен – 1,67 В. На воздухе алюминий покрывается тонкой (порядка 10-5 см) и плотной плёнкой оксида алюминия, которая защищает поверхность алюминия от окисления. Чем чище алюминий, тем тоньше и прочнее плёнка оксида и выше коррозионная стойкость металла.
Алюминий обладает, значительным химическим сродством к кислороду теплота образования алюминия, составляет 1670 кДж / моль. Это свойство алюминия широко используется в процессах алюминотермического восстановления металлов.
Малая плотность, высокая электропроводность, низкая коррозионная стойкость, достаточно высокая механическая прочность, пластичность обеспечили высокое применение, как чистого металла, так и сплавов на его основе. К тому же алюминий, как известно, относится к числу наиболее распространенных элементов. Содержание его в земной коре достигает 7,45%, и по распространенности он занимает третье место после кислорода (49,3%) и кремния (26%).Чистый алюминий применяется в электротехнической промышленности для изготовления проводов и кабеля, шинопроводов, конденсаторов, выпрямителей. В силу большой коррозионной стойкости он широко применяется в химическом машиностроении, для изготовления бытовых приборов, в пищевой промышленности для хранения пищевых продуктов (упаковочные материалы).Алюминиевые сплавы – литейные и деформируемые – также находят широкое применение в различных областях техники, главным образом в авиа-строении, автомобильной промышленности, транспортном машиностроении, в промышленном и гражданском строительстве. В данном проекте рассматривается конструкцию электролизера с боковым токоподводом
1 ОПИСАТЕЛЬНАЯ ЧАСТЬ
1.1 Государственные стандарты на алюминий и сырьё
Для получения алюминия путём электролиза применяется сырьё которое должно соответствовать определенным требованиям ГОСТа.
ГОСТы на алюминий и сырьё приведены в следующих таблицах.
Жидкий алюминий – сырец, ГОСТ 11070 – 01. Обычно получают марки А7, А6, А5, А35, А0. Процентное содержание алюминия и примесей в техническом алюминии сведено в таблицу 2.
Таблица 2-Технический алюминий, ГОСТ 11070-01
Si
|
Fe
|
Cu
|
Mn
|
Mg
|
Zn
|
Ga
|
Ti
|
проч.
|
AI
|
А85
|
0,06
|
0,08
|
0,01
|
0,02
|
0,02
|
0,02
|
0,03
|
0,008
|
0,02
|
99,85
|
А8
|
0,10
|
0,12
|
0,01
|
0,02
|
0,02
|
0,04
|
0,03
|
0,01
|
0,02
|
99,80
|
А7
|
0,15
|
0,16
|
0,01
|
0,03
|
0,02
|
0,04
|
0,03
|
0,01
|
0,02
|
99,70
|
А7Е
|
0,08
|
0,20
|
0,01
|
-
|
0,02
|
0,04
|
0,03
|
0,01
|
0,02
|
99,70
|
А7Э
|
0,10
|
0,20
|
0,01
|
0,03
|
-
|
0,03
|
0,04
|
0,01
|
0,03
|
99,70
|
А6
|
0,18
|
0,25
|
0,01
|
0,03
|
0,03
|
0,05
|
0,03
|
0,02
|
0,03
|
99,60
|
А5Е
|
0,10
|
0,35
|
0,02
|
-
|
0,03
|
0,04
|
0,03
|
0,015
|
0,02
|
99,50
|
А5
|
0,25
|
0,30
|
0,02
|
0,05
|
0,03
|
0,06
|
0,03
|
0,02
|
0,03
|
99,50
|
А35
|
0,65
|
Si+Fe
|
0,05
|
0,05
|
0,05
|
0,10
|
-
|
0,02
|
0,03
|
99,35
|
А0
|
0,95
|
Si+Fe
|
0,05
|
0,05
|
0,05
|
0,10
|
-
|
0,02
|
0,03
|
99,00
|
Исходным сырьем для получения алюминия является глинозем
Требования предъявляемые к глинозему приведены в таблице 3
Таблица 3-Глинозем металлургический ГОСТ 30558-98
Марка
|
Массовая доля примеси, %, не более
|
Потеря
массы
при
прокали-вании
(300- 1000), % не более
|
Код ОКП
|
SiO2
|
Fe2O3
|
TiO2+
V2O5+
MnO
|
Zno
|
P2O5
|
Cсумма
Na20+
K2O в
Перес-чёте
на Na2O
|
Г-000
|
0,02
|
0,01
|
0,01
|
0,01
|
0,001
|
0,3
|
0,6
|
1711230011
|
Г-00
|
0,02
|
0,03
|
0,01
|
0,01
|
0,002
|
0,4
|
1,2
|
1711230012
|
Г-0
|
0,03
|
0,05
|
0,02
|
0,02
|
0,002
|
0,5
|
1,2
|
1711230013
|
Г-1
|
0,05
|
0,04
|
0,02
|
0,03
|
0,002
|
0,4
|
1,2
|
1711230014
|
Г-2
|
0,08
|
0,05
|
0,02
|
0,03
|
0,002
|
0,5
|
1,2
|
1711230015
|
В качестве электролита используют криолит искусственный технический
В таблице 4 приведены данные на технический криолит
Таблица 4.Криолит искусственный технический ГОСТ 10561-80
Наименование показателей
|
Норма для марки и сорта
|
КАэ
|
КА
|
КП
|
Высший
сорт
|
Первый
сорт
|
1
|
2
|
3
|
4
|
5
|
Внешний вид
|
Мелкокристаллический порошок от слабо розового до серовато – белого цвета
|
Массовая доля фтора, %
|
54 - 56
|
Не менее 54
|
Не менее 54
|
Не менее 52
|
Массовая доля алюминия, %
|
16 - 18
|
Не более 18
|
Не более 19
|
Не более 23
|
Массовая доля натрия, %
|
23 - 25
|
Не менее 23
|
Не менее 22
|
Не менее 13
|
Криолитовый модуль, не менее
|
Не норм
|
1,7
|
1,5
|
Не норм
|
Массовая доля двуокиси кремния (SiO2), не более
|
0,5
|
0,5
|
0,9
|
1,5
|
Массовая доля окиси железа (Fe2O3), %, не более
|
0,06
|
0,06
|
0,08
|
0,1
|
Массовая доля сульфатов в пересчёте на SO2 , %, не более
|
0,5
|
0,5
|
1,0
|
1,0
|
Массовая доля воды, %, не более
|
0,2
|
0,2
|
0,5
|
0,8
|
Массовая доля пятиокиси фосфора (Р2О5), %, не более
|
0,05
|
0,05
|
0,2
|
0,6
|
Все данные на фтористый алюминий сведены в таблице 5
Таблица 5.Алюминий фтористый технический ГОСТ 19181-78
Наименование показателей
|
Норма
|
Высший сорт ОКП
2154350120
|
Первый сорт ОКП
2154350138
|
Потери при прокаливании, %, не более
|
2,5
|
3,5
|
Массовая доля фтористого алюминия (AIF3), %, не более
|
93
|
88
|
Массовая доля свободной окиси алюминия (AI2O3), %, не более
|
4
|
7
|
Массовая доля суммы двуокиси кремния и окиси железа (SiO2 + Fe2O3) , %, не более
|
0,3
|
0,4
|
Массовая доля сульфатов SO4 , %, не более
|
0,1
|
0,2
|
Массовая доля пятиокиси фосфора
(Р2О5), %, не более
|
0,05
|
0,05
|
Добавки
- Алюминий фтористый технический ГОСТ 19181-78
- Фтористый натрий технический ТУ 113 – 08 – 586 – 86
- Сода кальцинированная, техническая ГОСТ 5100 – 85
- Магнезит ГОСТ 1216 – 87
- Фтористый кальций (шпат плавиковый) ГОСТ 29219-91
- Анодная масса ТУ 48 – 5 – 80 – 86
1.2 Обоснование состава электролита и технологических параметров
К электролиту предъявляют следующие требования:
- Электролит не должен содержать ионов металла более электроположительных, чем алюминий.
-Температура плавления электролита должна быть близкой к температуре плавления алюминия или ниже.
- В расплавленном состоянии электролит должен иметь плотность меньше плотности алюминия, что упрощает конструкцию ванны.
- Должен хорошо растворять глинозем, чтобы не было осадка.
- Должен быть мало летучим и не гигроскопичным.
- Должен обладать высокой электропроводностью.
- Должен быть дешевым и не дефицитным.
Чистый NaF плавится при температуре 992 °С. При добавлении к нему AlF3
температура плавления снижается, и при содержании AlF3
14,5% образуется эвтектика с температурой плавления 888°С. При концентрации AlF3
25% имеем стойкое химическое соединение криолит. При концентрации AlF3
37,5% образуется нестойкое химическое соединение хиолит. При содержании AlF3
50% образуется нестойкое химическое соединение метафторалюминат Na. Т.к. чистый AlF3
при температуре 1260 °С возгоняется не плавясь, то дальнейшее изучение диаграммы затруднено из-за высокой летучести AlF3
.
Температура плавления криолита составляет 1010°С. При добавлении к криолиту глинозема температура его снижается примерно на 5°С на каждый 1% массы глинозема. Наиболее низкая температура плавления около 938°С получается при концентрации глинозема 14,5%. Дальнейшее увеличение концентрации глинозема приводит к резкому повышению температуры плавления смеси.
Глинозем снижает температуру плавления но имеет в нем ограниченную растворимость. При содержании глинозема 14,5% по массе образуется эвтектика с температурой плавления 938 °С. При снижении концентрации Al2
O3
менее 1% электролит перестает смачивать подошву анода и возникает анодный эффект.
Максимальная растворимость глинозема в криолите при 1000°С составляет около 16,5% по массе, поэтому во избежание образования на подине больших глиноземистых осадков содержание Al2
O3
в электролите поддерживают в пределах от 1 до 5 %. Следовательно, если электролит будет состоять только из смеси криолита и глинозема, то его температура при указанной концентрации глинозема будет равна 985-1005 °С. Однако это слишком высокая температура, чтобы успешно вести технологический процесс. Температуру плавления электролита можно так же уменьшить за счет изменения криолитового отношения, т.е. увеличения содержания в нем NaF или AlF3
.
Но первый путь не желателен т.к. при увеличении содержания NaF возрастает вероятность выделения на катоде Na и как следствие снижение выхода по току.
Поэтому на практике применяют второй путь – увеличивают содержание фтористого алюминия, т.е. уменьшают криолитовое отношение. Снижение криолитового отношения на 0,1 уменьшает температуру плавления электролита на 3-5 °С. На практике криолитовое отношение поддерживают в пределах 2,5÷2,7, т.к. дальнейшее снижение его приводит к ухудшению растворения глинозема и увеличению потерь фтор солей за счет летучести.
С целью снижения температуры в электролит так же вводят добавки фтор солей: фтористого кальция CaF2
, фтористого магния MgF2
. Например 1% CaF2
снижает температуру плавления примерно на 3 °С; 1% MgF2
на 5 °С.
Очень эффективной добавкой для снижения температуры электролита являются соли лития, например углекислый литий Li2
CO3
, алюминат лития Li2
O· Al2
O3
. Но эти соли дороги и пока не нашли широкого применения.
Общее содержание добавок в электролите не рекомендуется увеличивать более 7-8%, т.к. они снижают растворимость глинозема и при большом содержании затрудняют ведение технологического процесса.
Летучесть электролита
Наиболее летучим компонентом является AlF3
, таким образом чем меньше
к.о. тем больше содержание AlF3
и тем выше летучесть электролита.
Добавки глинозема снижают его летучесть. Обычно электролит перегрет на 13-15 °С по сравнению с его температурой плавления, а летучесть его незначительна. При повышении температуры плавления свыше 980 °С летучесть его резко увеличивается, поэтому вводят добавки CaF2
и MgF2
которые несколько снижают температуру и тем самым уменьшают летучесть.
Плотность электролита
Важным свойством электролита является его плотность. Необходимо стремиться к тому чтобы она была наименьшей, поскольку электролит в ванне находится сверху расплавленного алюминия, имеющего плотность 2,3 г/см3
. Плотность криолита в твердом виде составляет 2,95 г/см3
а при температуре 1000°С 2,09 г/см3
. Добавление к криолиту глинозема снижает плотность расплава. Так, при 10% Al2
O3
плотность его равна 2,04 г/см3
.
Плотность уменьшается так же при снижении КО меньше 3. В этом случае уменьшение КО на 0,1 позволяет снизить плотность примерно на 0,007 г/см3
. Добавка MgF2
изменяет плотность незначительно. Даже 10% этой соли увеличивает плотность всего на 0,03 г/см3
. Но CaF2
существенно изменяет плотность электролита: каждый его процент увеличивает плотность на 0,008 г/см3
.
Плотность электролита так же зависит и от температуры. Повышение ее на каждые 10 °С уменьшает плотность на 0,01 г/см3
. Причем у электролита плотность зависит от температуры в большей степени чем у алюминия.
Таким образом при температуре 1000 °С плотность Al на 10% больше
плотности электролита это обеспечивает нормальное разделение продуктов
электролизом, и упрощает конструкцию электролизера т.к. металл собирается под слоем электролита. Расплав с содержанием глинозема 5%, КО 2.4-2.6 при температуре 960 °С имеет плотность 2,11 г/см3
.
При значительном снижении температуры может произойти выравнивание плотностей металла и электролита, что приведет к всплыванию алюминия, а это
не желательно т.к. нарушается технологический процесс.
Вязкость электролита
Вязкость электролита оказывает существенное влияние на расслоение
продуктов электролиза. Минимальной вязкостью обладает чистый NaF, а с увеличением содержания AlF3
вязкость повышается. Поэтому наиболее вязкими являются кислые электролиты.
Добавки глинозема до 10% практически не изменяют вязкости. Однако дальнейшее увеличение концентрации глинозема значительно повышает вязкость электролита. Например при температуре 1000°С и содержании глинозема 17% вязкость составляет около 5 сантипуаз . Несколько большее влияние на вязкость оказывает температура, так повышение температуры на 10 °С уменьшает вязкость примерно на 3%.
Промышленные электролиты обычно имеют вязкость 3,2-3,4 сантипуаз.
Электропроводность
Это свойство оказывает большое влияние на расход энергии и температурный режим электролизера. В слое электролита имеется наибольшее падение напряжения. Для процесса электролиза нужен электролит с наибольшей электропроводностью.
Наилучшей электропроводностью обладает NaF. При температуре 1000°С его электропроводность 4,46 Ом-1
·см-1
. Для криолита эта величина составляет 2,5 Ом-1
·см-1
.
С повышением содержания AlF3
электропроводность ухудшается. Так же большое влияние на электропроводность оказывают добавки Al2
O3
. При содержании глинозема 5% электропроводность электролита 2,45 Ом-1
·см-1
.
Добавки CaF2
и MgF2
так же несколько снижают электропроводность. Обычно промышленные электролиты несколько загрязнены угольной пеной,
которая так же снижает электропроводность и нарушает токораспределение.
В практических расчетах пользуются величиной обратной электропроводности – электросопротивление. Для промышленных электролитов оно составляет 0,5 Ом.
Поверхностное или межфазное натяжение
При электролизе криолит-глиноземных расплавов поверхностное натяжение рассматривается на четырех границах. Нагляднее это можно посмотреть на рисунке 1-Зоны поверхностного натяжения
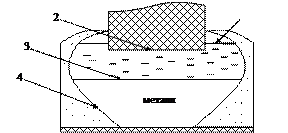
1-Электролит – анодные газы, 2-Электролит – анод, 3- Электролит - металл. 4-Электролит – угольная футеровка – металл.
Рисунок 1- Зоны поверхностного натяжения.
На границе 1 наибольшим поверхностным натяжением обладает NaF, он плохо смачивает электролит. AlF3
снижает натяжение и способствует лучшему удалению анодных газов – это наблюдается в кислых электролитах.
На границе 2 в щелочных электролитах смачиваемость лучше, чем в кислых – это приводит к пропитыванию анода и его разрушению.
Большое влияние на смачиваемость анода оказывает содержание глинозёма
в электролите. При уменьшении концентрации глинозема электролит хуже смачи-
вает анод и при содержании глинозема менее 1% электролит перестает смачивать анод. В результате возникает анодный эффект. Из-за разрушения анода в электролите всегда присутствует угольная пена .Она легче выделяется из кислых электролитов чем из щелочных. На границе 3 электролит – металл кислые электролиты плохо смачивают жидкий алюминий. Это положительный фактор т.к. снижается растворимость алюминия в электролите. На границе 4 металл – угольный блок поверхностное натяжение металла большое, поэтому он не смачивает падину. Под слой металла может попасть электролит который смачивает падину хорошо, пропитывает ее и разрушает.
Состав электролита:
-1 Глинозем 1,929
-2 Фтор соли 0,021
-3 Криолит 0,031
Основные технологические параметры нормально работающего электролизера
Состав электролита поддерживается в пределах криолитовое отношение 2,40-2,50
Содержание: CaF2 = 5,2-6 %
MgF2 = 1,4-2 %
CaF2+MgF2 = не >8 %
- Уровень металла после выливки не < 28 см (32-34 см)
- Уровень электролита 16-20 см
- Частота анодного эффекта не >1 раза в сутки на электролизере
- Длительность анодного эффекта не >2 минут
- Напряжение анодного эффекта не <30 В
- Рабочее напряжение 4,12-4,52 В
- Температура электролита не >9600
С
1.3 Описание конструкции
Основными элементами электролизера являются: катодное устройство, анодное устройство, ошиновка и металлический грузонесущий каркас со смонти-
рованным на нем механизмом перемещения анода, шторными укрытиями, бункерами для хранения глинозема и т.д.
1.3.1 Катодное устройство
Катодное устройство алюминиевого электролизера предназначено для создания условий, необходимых для протекания процесса электролиза в криолит-глиноземном расплаве. Поскольку электролиз идет в весьма агрессивной среде при 950-1000 С0
, катодное устройство должно быть устойчиво к действию расплавленных фтористых солей; обладать достаточно высоким теплоизоляционными свойствами, чтобы до минимума сократить потери тепла; быть электропроводным в зоне протекания процесса и иметь надежную изоляцию во избежание утечек тока; иметь достаточно жесткую конструкцию, способную выдержать напряжения, возникающие от протекания физико-химических реакций; обеспечивать продолжительную работоспособность между ремонтами и мобильность при замене в целях сокращения простоя электролизера в ремонте
На рисунке 2 показан продольный разрез катодного устройства с кожухом без днища.
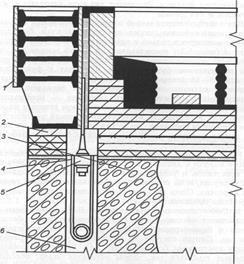
/ - катодный кожух; 2 -цоколь; 3 -
бетонный фундамент; 4
- анкерная лапа;
5 - изоляционная втулка и шайба; 6-
анкерный колодец.
Рисунок 2 Продольный разрез катодного устройства с кожухом без днища
Катодное устройство состоит из стального кожуха, футерованного внутри угольными подовыми блоками, боковыми плитами. В нижнюю часть подовых блоков перед их установкой в электролизер устанавливаются стальные стержни(блюмсы) которые заливают чугуном. Блюмсы служат для отвода тока от подины. Швы между подовыми блоками и периферийный шов набивают холодной набивной подовой массой. к катодной ошиновке подключаются с помощью пакетов гибких медных лент стальные блюмсы катодного устройства.
При разработке данного мною проекта я использовал девять катодных блоков.
Внутренние размеры катодного кожуха:
- Lкож = 5850 мм
- Вкож = 3970 мм
1.3.2 Анодное устройство электролизеров с боковым токоподводом
Анодное устройство алюминиевого электролизера, являясь одним из электродов, предназначено для подвода тока в зону непосредственного протекания процесса электролиза. Основным материалом анода служит углеродистый материал. По мере протекания процесса электролиза анод постепенно окисляется, и его необходимо периодически опускать. Для этого служит специальный подъемный механизм анодного устройства.
Рисунок 3 - Электролизер с боковым подводов тока.
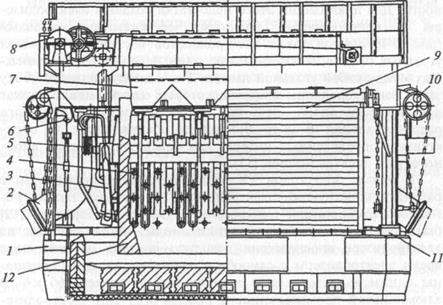
катодный кожух; 2 -
газоотводный патрубок; 3 -
токоподводящие спуски; 4
- штыри; 5 - анодная ошиновка; 6-
крюк для подвески временных тяг; 7 - бункер для глинозема; 8
- механизм подъема анода; 9 -
штора; 10 -
механизм подъема штор; 11
- стойка опорной лапы
Размеры анода:
Площадь подошвы анода = 105263 см2
Ширина анода Ва = 240 см
Высота анода На = 170 см
Количество токоподводящих шин 7 шт
Анодное устройство электролизеров с боковым токоподводом состоит из анодной рамы с «перьями», подвешенной на винтовых домкратах к грузонесущему каркасу. В анодной раме по периметру ее устанавливается алюминиевая обечайка, в которой формируется анод. Анод подвешивается к анодной раме за нижний ряд штырей, которые лежат на сережках, вывешенных на нижних концах перьев рамы или при помощи клиновой подвески. Общее количество работающих штырей составляет 67 шт. Токоведущими являются два нижних ряда штырей. Они подключаются к анодной ошиновке с помощью медных спусков. Анодные спуски подключаются к штырям с помощью клинового контакта.
Электролизеры с боковым токоподводом снабжены укрытием для сбора и эвакуации вредных веществ, Выделяющихся в процессе электролиза: укрытие
монтируется на каркасе и имеет вверху газосборный колпак и шторы навивного или створчатого типа, закрывающие боковые и продольные стороны электролизера
Ошиновка электролизера
Ошиновка является токонесущим элементом конструкции электролизера и состоит из двух частей – анодной и катодной. Электролизеры, располагаемые рядами один за другим, соединены токопроводами из алюминиевых шин различного сечения и включены в электрическую цепь последовательно: катодные шины одного электролизера соединены с анодными шинами другого. Группа электролизеров, объединенная в одну цепь, называется серией.
Газоулавливающие устройства
Назначение газоулавливающих устройств как составной часки электролизера–сбор
выделяющихся в процессе электролиза газов (максимально достижимой концентрации) на месте их возникновения и последующая эвакуация газов в газоочистную систему.
1.4. Обслуживание при нормальной работе, неполадки, способы устранения.
Обслуживание электролизеров включает в себя следующие операции:
- наблюдение за технологическим процессом;
- поддержание технологических параметров электролиза в заданных пределах;
пробивка корки электролита и загрузка сырья и материалов;
-ликвидация анодных эффектов;
- переключение анодных спусков;
- извлечение и забивка штырей;
- перетяжка анодной рамы;
- наращивание алюминиевой обечайки;
- загрузка анодной массы;
- перетяжка анодной рамы;
- наращивание алюминиевой обечайки;
- загрузка анодной массы;
- выливка металла;
- устранение возможных нарушений технологического режима.
Наблюдение за технологическим процессом.
В течение смены обслуживающий персонал ведет наблюдение за работой каждого электролизера, поддерживает на электролизерах заданное рабочее
напряжение, уровни металла, электролита и его состав, состояние анода, настылей, гарниссажей. осадков на подине, междуполюсного расстояния.
Нормальная работа электролизера должна характеризоваться следующими внешними признаками:
- Огни, отведенные вблизи углов анода (два с каждой продольной стороны), должны выбиваться с силой из-под корки электролита и иметь фиолетово-голубой цвет.
- Рабочее напряжение должно быть устойчивым, без частых колебаний.
- Корка должна быть равномерной по толщине вокруг анода.
- Электролит должен равномерно бурлить вокруг анода.
- Угольная пена должна хорошо отделяться от электролита и выгорать.
- Покраснения поверхности анода над расплавом должны отсутствовать.
- Электролит, настывающий на ломике при кратковременном опускании его в расплав, должен иметь четко различимую линию границы металла с электролитом.
- Застывшая проба электролита в изломе не должна содержать угольных частиц.
О нарушениях технологического режима обслуживающий персонал ставит в известность мастера смены и по его распоряжению принимает меры по их устранению. Обслуживающий персонал должен особое внимание уделять герметизации технологического оборудования и системы газоотсоса, оказывающих влияние на состояние воздушной среды в корпусах электролиза. Количество электролизеров, одновременно разгерметизированных в корпусе по различным причинам (обработка электролизеров, выливка металла, извлечение и забивка анодных штырей и т.п.) не должно превышать 15% от общего количества электролизеров. Администрация цеха (корпуса) должна постоянно следить за состоянием шторных укрытий и своевременно принимать меры по устранению неисправностей. При отключении электролизеров на капитальный ремонт газоочистные патрубки должны быть закрыты.
Обработка электролизеров и загрузка глинозема.
При обработке электролизеров пробивку криолитоглиноземной корки осуществляется самоходными пневматическими машинами. После пробивки корки на электролизере устанавливается нормальное рабочее напряжение (перемещением анода). При этом необходимо руководствоваться не только показанием вольтметра, но и наблюдать за работой анода (электролит должен равномерно бурлить вокруг анода).
На электролизерах, работающих в режиме периодического питания,
обработка производится регламентировано 8 раз в сутки через каждые три часа и заключается в пробивке корки электролита всей продольной стороны с чередованием сторон. Торцы пробиваются не реже одного раза в двое суток с обязательной расчисткой угольной пены и кусков электролита: подошва и углы анода, прилегающие обрабатываемому торцу, продираются кочергой и скребком.
Разовая загрузка глинозема около 120 кг. Не разрешается простой электролизера
без обработки более чем 12 часов.
Пусковые электролизеры обрабатываются согласно инструкции по обжигу и пуску электролизеров и по указанию старшего мастера. На электролизерах с расстроенным технологическим ходом разрешается пробивка с продольных
сторон и обоих торцов с уменьшенной загрузкой глинозема на корку электролита, уменьшение или увеличение числа обработок против принятого схемой, снятие угольной пены с поверхности электролита и так далее.
Перед обработкой электролизера электролизник обязан проверить на закрепленных электролизерах:
- уровень металла и электролита:
- величину и постоянство рабочего напряжения;
- на всех электролизерах использовать информацию о режимных
параметрах, полученных при приемке смены, записей на панели электролизера и визуальных наблюдений за состоянием технологического хода.
При обработке электролизера необходимо выполнить следующие операции - пробить криолитоглиноземную корку электролита, погружая ее в электролит и не допуская попадания кусков корки под анод;
- удалить из электролита куски спекшейся анодной массы и анода;
- при наличии скоплений угольной пены выгарнуть ее из-под углов анода и
торца на середину продольной стороны;
- оплескать электролитом оголенную часть боковой поверхности анода во
избежание выгорания «шеек»;
- подобрать с бортов электролизера горячий глинозем и оборот на поверхность
электролита, после чего загрузить глинозем из бункеров. Простаивание
электролизеров без загрузки глинозема на корке не допускается.
Во время обработки электролизера необходимо проверить работу анода (равномерное бурление электролита по периферии анода). В случае неравномерной работы электролизник обязан доложить мастеру и принять меры к устранению данного явления.
После окончания обработки и загрузки новой порции глинозема на электро-
лизере отводятся «Огни» в корке электролита, по два с каждой продольной
сторона на расстоянии не ближе 10 см от анода.
«Огни» на электролизере должны поддерживаться постоянно во избежание выгорания «шеек» на аноде и вытекания электролита через борт.
На табличке каждого электролизера в обязательном порядке должны отмечаться дата, смена и характер последнего анодного эффекта, общее их количество на данном электролизере с начала месяца, а также характер последней обработки электролизера, дата обработки торцов.
На электролизерах должна быть создана и постоянно поддерживаться прочная круто падающая бортовая настыль. Образование подовой настыли не допускается, с целью профилактики образовавшийся осадок ежедневно подтягивают к борту электролизера с помощью специального скребка. Контроль за чистотой подин и состоянием настылей осуществляется ежедневно электролизниками на закрепленных за звеном электролизерах и не реже одного раза в неделю - сменным мастером, 2-х раз в месяц - старшим мастером. Состояние чистоты подин по каждому электролизеру проверяется и регистрируется в технологическом журнале ежемесячно.
Устранение анодного эффекта.
Для устранения анодного эффекта необходимо :
- на электролизерах, питающихся способом пробивки криолитоглиноземной
корки, произвести дополнительную внеочередную обработку в объеме не менее ½
продольной стороны, обработанной перед анодным эффектом;
- если после извлечения жерди вспышка возникает вновь, в электролизер
добавляется глинозем и операция ее гашения повторяется. Для гашения анодного эффекта жердь вводится под анод кратковременно. Категорически запрещается оставлять деревянную жердь в расплаве после устранения анодного эффекта. При отсутствии жердей устранение анодного эффекта производится скребком или «шумовкой». Время ликвидации анодного эффекта - не более 2,0 минут.
Корректировка электролита.
Необходимый уровень электролита в электролизерах поддерживается загрузкой свежего, регенерированного криолита, оборотного твердого и жидкого электролита; для поддержания заданного состава могут использоваться добавки
фтористого алюминия, фтористого натрия или соды, каустического магнезита, фтористого кальция.
Свежий криолит состоит из собственно криолита и фтористого алюминия, что позволяет использовать свежий криолит как добавку для корректировки электролита. Кусковой оборотный электролит загружается вдоль продольных сторон электролизера.
Свежий криолит, фтористый алюминий, регенерированный криолит, фтористый натрий, фтористый кальций, каустический магнезит загружаются после обработки электролизера по регламенту на поверхность электролита, предварительно присыпанную горячим глиноземом. Загрузка фтористого натрия целесообразна после анодного эффекта. При использовании соды она разбрасывается тонким слоем по поверхности электролита с соблюдение мер предосторожности (возможен выброс электролита в случае увлажненности соды).
Загруженные на присыпанную глиноземом корку электролита ровным слоем фторсоли укрываются затем полной дозой глинозема. Разовая загрузка фторсолей не должна превышать (40 - 90) кг. Максимальная загрузка фторсолей (120-150) кг (2 продольные стороны и торец).
Выливка металла.
Выливка металла из электролизеров производится по установленному графику.
В особых случаях, в зависимости от состояния технологического хода электролизеров, график выливки может быть изменен старшим мастером серии.
При выливке металла попадание электролита в вакуум-ковш не допускается
Напряжение при выливке металла не должно превышать нормальное более, чем на 0,2 В. После выливки металла рабочее напряжение устанавливается такое
же, что и до выливки.
Отверстие в корке электролита для выливки металла пробивается между 2 и 3 штырями от угла анода со стороны вольтметра.
Уровень металла в электролизерах после выливки должен быть по
вертикали при ежедневном графике выливки - не менее 28 см.
После выливки металла на электролизере проверяется положение углов анода и отсутствие перекоса анода. Соприкосновение углов анода с настылью не
допускается.
Обслуживание анода.
Обслуживание анода включает в себя следующие операции: переключение анодных спусков с одного ряда штырей на другой, извлечение и забивка штырей, перетяжка анодной рамы, наращивание алюминиевого кожуха (обечайка), загрузка анодной массы.
Переключение анодных спусков производится при расстоянии от подошвы анода до 1-го ряда штырей (20 — 22) см. Анодные спуски переключаются в этом случае с 1-го ряда штырей на 3-й. Переключение спусков сводится к разборке, зачистке и сборке контакта «шинка - штырь». Особое внимание следует уделять зачистке и сборке, так как плохое качество контакта определяет дополнительные потери электроэнергии.
Неисправные анодные спуски ремонтируются и подключаются немедленно при и: обнаружении.
Извлечение анодных штырей нижнего ряда осуществляется при помощи специальных машинок. Перед извлечением штырей их освобождают от нагрузки веса анода. С этой целью анод подвешивают на временные тяги. Количество временных тяг для подвески анода -10 штук.
Извлеченные из анода штыри правятся и отправляются на чистку.
После извлечения штырей осуществляется перетяжка анодной рамы на новый горизонт до тех пор, пока серьги не будут подняты под штыри второго ряда, и временные тяп не освободятся от веса анода. После этого временные тяги
снимают. При операции перетяжки анодной рамы необходимо следить за равномерностью ее перемещения, не допуская перекосов и неравномерной
нагрузки на анодные штыри. При невозможности тщательного подбора сережек под не подошедшие под штыри сережки должны быть подложены алюминиевые прокладки необходимой толщины.
После перетяжки рамы забивают верхний ряд штырей. Штыри в анод забивают под углом не менее 5° по отношению к горизонту. Оптимальный угол забивки штырей - (5 - 11)°. Длина не забитой части штыря должна быть - (240 - 250) мм.
Наращивание алюминиевой обечайки производится через 30 - 50 дней в зависимости от скорости сгорания анода, а также ширины алюминиевого листа, используемого для изготовления секций обечайки. Новую секцию устанавливают в обечайку так, чтобы шов перекрывался на (250 - 300) мм. Шов по всему
периметру анода проклёпывается алюминиевыми заклепками.
Для создания качественного тела анода загрузка анодной массы должна производиться равномерно, 2 раза за период между перетяжками анодной рамы, но не позднее одних суток после нее. Разовая доза не более 2 брикетов весом (1 - 1,3) т каждый.
Загрузка производится так, чтобы слой жидкой анодной массы выдерживался в пределах (45±75) см. С целью получения анодов высокого качества и избежании расслоений поверхность расплавленной массы в анодах перед загрузкой очередных порций анодной массы тщательно очищается струей сжатого воздуха от пыли.
Корректировка жидкого слоя анодной массы производится добавками массы с большим или меньшим (по сравнению с рядовой) содержанием связующего, а при отсутствии такой массы - добавкой пека.
Добавление в анод пека допускается только в исключительных случаях с разрешения начальника цеха или заместителя начальника цеха по производству.
Неполадки в работе ванн.
Все электролизеры с расстроенным технологическим ходом отключаются от автоматического регулирования и обрабатываются под руководством мастера
смены.
Основные нарушения технологического режима, возникающие в практике из-за неправильного обслуживания электролизеров:
- «зажатие» электролизера, т.е. замыкание части анода или непосредственно на «зеркало» металла (катод) при чрезмерном занижении межполюсного расстояния или через куски угля, скопление пены и насыщенный металлом осадок в межполюсном пространстве;
- образование «конуса» на подошве анода и отставание в сгорании углов анода; - «горячий ход» и работа «в бока», т.е. нарушение теплового равновесия электролизера;
- «холодный ход» и образование на подине под анодом осадка, настыли, «коржей»;
- «негаснущая вспышка», т.е. вспышка, возникшая из-за перенасыщения электролита глиноземом и увеличение его электросопротивления.
Если на электролизере обнаружено расстройство технологического режима, то необходимо немедленно выяснить его причины, т.е. характер технологического нарушения и принять меры по его ликвидации.
«Зажатие» электролизера, приводящее к снижению напряжения, «замиранию» анода и повышению температуры электролита ликвидируется увеличением междуполюсного расстояния за счет поднятия анода. Поднимать анод нужно до тех пор, пока не начнется бурление электролита вокруг анода. При этом напряжение на электролизере может повыситься до (6±7) В, а иногда и выше. По мере того как электролизер начнет улучшать ход, напряжение будет
самопроизвольно снижаться, а электролит охлаждаться. Если при снижении напряжения ухудшается бурление электролита, то анод нужно снова поднять.
Необходимо снизить температуру электролита. Это достигается за счет загрузки криолита на поверхность электролита и переплавки твердого алюминия.
Для ликвидации «зажатия», вызванного замыканием через куски угля, скопление пены и так далее, необходимо поднять анод до бурления электролита и очистить междуполюсное пространство с помощью кочерги и скребка, вскрыв для этого корку электролита в местах. где электролизер «желтит»
или при необходимости полностью. Куски корки электролита не должны попадать под анод.
Угольную пену необходимо снять, загрузку глинозема уменьшить. Напряжение постепенно снизить до нормального.
«Конус» на подошве и отставание в сгорании углов анода образуются в результате длительного скопления угольной пены или осадка под анодом, т.е. вследствие «зажатия» электролизера или низкой электропроводности в этом месте анода.
«Конус» и отставание в сгорании углов анода приводят к «горячему ходу» электролизера.
На таком электролизере необходимо: против места образования конуса или в углах вскрыть корку, не опуская ее в электролит, возможно больше поднять анод; сбить «конус» или отставшие углы с помощью специальных ломов, тщательно продрать подошву анода скребками, очистить междуполюсное пространство, снять пену, засыпать уменьшенную порцию глинозема на корку и постепенно снизить напряжение до нормального.
Если «конус» срубить не удается, то электролизер оставляют работать на завышенном MПP при напряжении (5-6) В для сжигания «конуса» и обрабатывают его, как «горячо идущий».
«Конус» систематически продирают кочергой или скребком. В исключительных случаях, когда длительное время не удается восстановить
нормальный технологический режим, с разрешения заместителя начальника цеха по производству электролизер временно отключают от токовой нагрузки, поднимается анод из электролита и срубается «конус».
Работа производится под руководством старшего мастера серии.
«Горячо» работающий электролизер исключается из общего графика обработки и обрабатывается по указанию старшего мастера серии или мастера смены. «Горячий ход», как правило, следствие «зажатия» электролизера, образования «конуса» на подошве анода, отставания в сгорании углов анода, образования «коржей» и осадка на подине, а также работы на завышенном напряжении из-за
неверного показания вольтметра. Порядок обработки «горячо»
идущего электролизера:
- тщательно снимают глинозем с корки электролита, полностью или частично вскрывают корку и снимают пену ;
- проверяют пространство под анодом, выявляют причину «горячего хода» и устраняют ее;
- тщательно очищают междуполюсное пространство, не допуская замешивания осадка в электролите, во избежание возникновения «негаснущей» вспышки;
- обрубают гарниссаж и места его оплавления запековывают оборотным электролитом;
- на образовавшуюся корку дают небольшую загрузку глинозема;
- если «горячий ход» электролизера вызван наличием на подине электролизера “коржей”, то необходимо повысить уровень электролита, уменьшить до минимума загрузку глинозема, повысить криолитовое отношение электролита и удалить «коржи».
Если на «горячем» электролизере науглерожен электролит, то производят частичную или полную его замену, во избежание карбидообразования («грибов»), путем его отливки и добавки свежего порошкового криолита или заливки чистого электролита из другого электролизера.
Частоту обработок «горячего» электролизера необходимо увеличить, до минимума снизить загрузку глинозема, если надо, увеличить или уменьшить «зеркало» металла, контролировать и восстанавливать боковой гарниссаж путем запековки оборотным электролитом.
«Горячий» электролизер, как правило, обрабатывается кругом. Порядок такой обработки сохраняется до тех пор, пока электролизер не даст нормальную вспышку.
«Холодный ход» электролизера возникает вследствие недостаточного прихода тепла или недостаточного перегрева электролита по сравнению с температурой его кристаллизации, в связи с изменением состава электролита.
На «холодно» идущем электролизере следует на (0,1в - 0,2в) В поднять напряжение, уменьшить частоту обработки, тщательно отгребать глинозем с корки электролита при обработке. Снизить постепенно уровень металла и повысить криолитовое отношение к установленному инструкцией. Увеличить
загрузку глинозема на корку электролита с целью утепления электролизера. Если на подине большой осадок и настыль, следует после разогрева электролизера осторожно очистить от них подину, избегая замешивания осадка в электролите.
Порядок ликвидации «негаснущей» вспышки:
- снять с корки электролита глинозем, возможно выше поднять анод, вскрыть
и снять корку с обеих сторон электролизера, при «кислом» электролите добавить фтористый натрий или соду для увеличения криолитового отношения электролита;
- охлаждать и освежать электролит путем непрерывной подсыпки свежего криолита равномерно вокруг анода;
- места с сильным движением расплава у борта электролизера закладывать крупными кусками оборотного электролита;
- отливать перенасыщенный глиноземом электролит;
- для охлаждения электролизера использовать также оборотный электролит,
хорошо просеянную угольную пену и твердый металл;
- гашение «негаснущей» вспышки обычным методом запрещается;
- при ликвидации «негаснущей» вспышки необходимо все работы выполнять быстро, действовать исходя из конкретно сложившейся обстановки по указанию мастера смены или старшего мастера серии.
В случае, если указанным порядком вспышку не удается погасить, и на электролизере создается аварийное положение, в виде исключения, мастер смены с разрешения диспетчера завода и старшего мастера на (5-10) минут может отключить серию от токовой нагрузки Для ликвидации «негаснущей» вспышки.
После ликвидации вспышки напряжение постоянно, с учетом хода электролизера, снижается до нормального, и устанавливается нормальный режим
обработки. При необходимости в электролизере плавится металл. После установления нормального режима на электролизере, как правило, чистится подина.
Прорыв металла и электролита на электролизере.
Признаки нарушения:
Быстрое падение уровня, повышение напряжения до вспышечного, оголение погруженной части анода, появление дыма и газов из-под рифления и вокруг ванны.
Причины, вызывающие нарушения – не однократный горячий ход электролизера. Работа ванны «в бока». Изношенное состояние футеровки или подины.
Способы ликвидации нарушения:
Быстро прорубить корку над местом вытекания расплава и забить дырку либо оборотным кусковым электролитом с добавкой окиси магния, либо глиноземом или магнезитом. Если авария носит серьезный характер, электролит и металл очень быстро уходит из ванны, опустить анод до замыкания с металлом или подиной, чтобы не разорвать цепь серии. Защитить катодную ошиновку от расплавления. Если опускание анода не поспевает за убылью металла и электрол-
та, необходимо отключить серию.
Серию подключить снова, когда анод будет поставлен на подину или металл. Место прорыва забить подовой массой, затем в ванну залить электролит, анод поднять до нормального напряжения.
Прорыв жидкой анодной массы из анода.
Признаки нарушения:
Вытекания жидкой анодной массы на поверхности корки электролита, попадание ее в электролит, протекание через борт ванны на рефленки, в шинные каналы и на асфальтовое покрытие пола.
Причины, вызывающие нарушения:
Неосторожная забивка анодного штыря, забивка анодных штырей, подлежащих отбраковке, некачественная подготовка алюминиевой обечайки,
разрыв обечайки при перетяжке рамы, отслоение обечайки от конуса спекания при перетяжке анодной рамы.
Способы ликвидации нарушения:
Забивка места вытекания массы «кляпом» из бумаги или ткани, перекапывание поверхности анода напротив места вытекания, недопущение попадания массы на оголенную поверхность электролита, подсыпка глиноземом
рефленок и асфальтового пола для предотвращения прочного прилипания массы к их поверхности при остывании. При ликвидации прорыва тщательная очистка корки и электролита от попавшей анодной массы, постоянное наблюдение за местом ухода массы.
В алюминиевых электролизерах допускается переплавка твердого
алюминия в виде бракованных и недолитых чушек, обрезков слитков, заготовок и отходов производства катанки, проката, прессованной стружки и фольги, сплавов и съемов из ковшей и миксеров, проливов, шлаков из литейного отделения, а
также «пушонки» и «козлов». Переплавка других видов твердого алюминия, в частности бракованных изделий, имеющих полости и каналы, не разрешается.
Материалы перед загрузкой в электролизер должны быть хорошо просушены и прогреты на борту электролизера или на корке электролита не менее 6 часов; «козлы» перед опусканием в расплав должны быть прогреты на борту электролизера или на корке электролита не менее 12 часов; «пушонки» в начале подсушивается тонким слоем на перекрытии шинных каналов в течение суток, а затем прогревается на корке электролита не менее 16 часов.
В послепусковой период работы электролизеров запрещается плавить «козлы» и «пущонку».
Переплавка твердого алюминия в электролизерах производится в следующих случаях:
- в послепусковой период работы электролизеров при снижении рабочего напряжения. Для ускорения вывода электролизеров на сортность переплавляемый твердый металл должен быть не ниже марки А5;
- на нормально работающих ваннах для восполнения металла, отобранного для заливки в пусковые электролизеры;
- при обслуживании электролизеров с нарушенным технологическим режимом («зажатие» электролизера, «горячий» ход, негаснущая «вспышка») для охлаждения электролизера и снижения температуры электролита.
2 РАСЧЕТНАЯ ЧАСТЬ
2.1Конструктивный расчет
Конструктивный расчет выполняется для определения размеров
конструктивных элементов ванн, для этого необходимы следующие показатели: сила тока на ванне, анодная плотность тока. Анодную плотность тока принимаем 0,76 А/см2
, I=80 000 кА
2.1.1
На основании этих данных определяем размеры анода.
Sа
= I/dа
= -А/А*см2
где:
I – сила тока, А
dа
– плотность тока, А/см2
Sа
= 80000/0,76 = 105263 см2
Ва
– ширина анодного массива принимаем 210-250 см, тогда длина анодного массива будет:
Lа
= Sа
/Ва
= 105263/240 = 438 см
Высота анода На
= hт
+hж
= (115-120)+(35-50) = 120+50 =170 см
2.1.2
Определяем внутренние размеры шахты ванны.
Внутренние размеры шахты ванны определяются исходя из размеров анодного массива и расстояния до боковой футеровки, которое составляет: по продольной стороне 55см, а по торцевой 50см.
Ширина шахты – Вш
Вш
= Ва
+ 2 · 55 = 240 + 110 = 350 см = 3500 мм
Длина шахты – Lш
Lш
= Lа
+ 2 · 50 = 438 + 100 = 538 см = 5380 мм
Глубина шахты – Нш
Нш
= hме
+ hэл
+hк
= 32 + 16 + 10 =58 см
hк
=8-10 см
2.1.3
Конструкция подины.
Число блоков. В настоящее время длина катодных блоков l = 600 – 2200мм, шириной b = 550 мм, высотой h = 400 мм.
Число блоков в ряду:
l = Lш
/вб
+4 = 538/55+4 = 538/59 = 9 шт
Определяем расстояние между катодными и боковыми блоками в торцах шахты:
l = Lш
-(вб
*nб
+(nб
-1)*4)/2 = 538-(55*9+(9-1)*4)/2 = 5,5 см
2.1.4
Определяем внутренние размеры катодного кожуха.
Lкож
= Lш
+2*(200+hтепл
) =
Вкож
= Вш
+2*(200+hтепл
) =
Lкож
= 5380+2*(200+35) = 5850 мм
Вкож
= 3500+2*(200+35) = 3970 мм
Нn
= Нш
+Нб
+30+(5*65)+50
где:
Нш
– шахта
Нб
– блок
30 – угольная засыпка
(5*65) – пять рядов кирпичей
50 – шамотная засыпка
Нn
= 580+400+30+(5*65)+50 = 1385 мм
2.
2 Материальный расчет
Проводится для определения производительности электролизера и расхода сырья на производство алюминия. Исходными данными является сила тока, выход по току и расходные нормы по сырьевым материалам и анодной массе.
Расходные нормы:
1.
AI2
O3
- 1,929 т
2.
Анодная масса -0,496 т
3.
Фторсоли - 0,021 т
4.
Криолит - 0,031 т
5.
Выход по току - 90%
2.2.1
Приходная часть
Производительность электролизера определяется по формуле
Рм
= I*c*η*10-3
где:
I – сила тока, А;
с – электрохимический эквивалент, равный 0,3354 г/А-ч
η – выход по току доли единицы
Рм
= 80000*0,3354*0,9*10-3
= 24,1 кг/г
Определяем приход материалов в ванну
Р AI2
O3
= Р AI * Рг
= 24,1 * 1,929 = 46,489 кг
РАНОД
= Р AI * Ра
= 24,1 * 0,496 = 11,953 кг
РФТОР
= Р AI * РФ
= 24,1 · 0,052 = 1,25 кг
Ра
, Рг
, Рф
– расход глинозема, анодной массы, фтористых солей в кг/кг алюминия.
В процессе работы в электролизере нарабатывается Al, выделяются анодные газы сгорает анод и расходуются фториды.
2.2.2
Расход материалов. Алюминий. Количество полученного алюминия определяется производительностью электролизера РAl кг/ч.
Анодные газы количество СО и СО2
в моль/г определяется из уравнений.
МCO
= NCO
/2-NCO
* РAl
/18 = 0,2/2-0,2* 24,1/18 = 0,149 моль/г
МCO
2
= NCO
2
/1+NCO
2
* РAl
/18 = 0,8/1+0,8* 24,1/18 = 0,595 моль/г.
где:
NCO
и NCO
2
– мольные доли СО СО2
в анодных газах соответственно
NCO
= 0,4 и NCO
2
= 0,6.
Весовое количество СО и СО2
РСО
= МСО
* 28
РСО
= 0,149 * 28 = 4,172 кг
РСО2
= МСО2
* 44
РСО2
= 0.595 * 44 = 26,18 кг
где:
28 и 44 – молекулярные массы СО и СО2
Потери глинозема в виде пыли и механические потери принимаются как разность между приходом глинозема в электролизере Рт и теоретическим расходом глинозема РAl
2
O3
(теор.).
ΔРAl
2
O
3
= РAl
2
O
3
-РAl
2
O
3
(теор.) = 46,489-45,549 = 0,94 кг
РAl
2
O
3
(теор.) = 1,89-РAl
2
O
3
= 1,89-24,1 = 45,549
Потери фторсолей принимаются равными приходу фторсолей 7,977 кг. Потери углерода, определяются как разность между приходом Ра и количеством израсходованного с газами углерода Рс
Рс = Ра-Ра = 11,953-8,928 = 3,025
Ро = (Мсо+Мсо2
)*12 = (0,149+0,595)*12 = 8,928
Таблица.6 Материального баланса
Приход
|
Кг/г
|
%
|
Расход
|
Кг/г
|
%
|
Глинозем
|
46,489
|
Алюминий
|
24,1
|
Фторсоли
|
1,25
|
Анодные газы
СО СО2
|
4,172
26,18
|
Анодная масса
(обожженные аноды)
|
11,953
|
Потери Al2
O3
,
фторсолей,
анодной массы (обожженные аноды)
|
0,94
1,25
3,025
|
Итого
|
59,692
|
100%
|
Итого
|
59,667
|
100%
|
2.
3 Электрический расчет
Цель: определение конструктивных размеров ошиновки, определение падения напряжения на всех участках цепи, составление баланса напряжений. Определение рабочего греющего и среднего напряжения. Определение выхода по энергии и удельного расхода по электроэнергии.
dAl
= 0,415 А/мм2
dFe
= 0,18 А/мм2
dCu
= 0,7 А/мм2
41,5А/см2
18 А/см2
70 А/см2
2.3.1
Определяем падение напряжения в анодном устройстве.
2.3.1.1
Падение напряжения в стояках.
ΔUст
= I*Rt*a/Sобщ
где:
I – сила тока, А
Rt – удельное сопротивление проводника, Ом · см
а – длина участка шинопровода, см
Sобщ
– общее сечение проводника, см2
Sэк
–экономически выгодное площадь сечение проводника, см2
Сечение стояка:
Sэк
= I/dAl
= 80000/41,5 = 1927,71 см2
nШ
– число алюминиевых шин, шт
nш
= Sэк
/Sпр
= 1927,71/258 = 7,47 ≈ 7
где:
Sпр
– сечение одной шины, см2
Sобщ
– общее сечение стояка, см2
Sпр
= 43*6 = 258
Sобщ
= nШ
· SПР
SОб
= 7 · (43 · 6) = 1806 см2
а = 265 см
RtAI
– удельное сопротивление алюминиевых шин определяется по формуле
Rt AI
= 2,8 (1 + 0,0038 · t) · 10-6
= 2,8*(1+0,0038)*10-6
= 3,44*10-6
Ом*см
где:
t - стояка 60 °
С
ΔUст
= (80000*3,44*10-6
*265)/1806 = 0,04 В
2.
3.1.2
Определяем падение напряжения в анодных шинах.
ΔU = I*Rt*a/Sобщ
Sобщ
= 43*6*7 = 1806
Sобщ
– сечение анодных шип равно сечению стояка
RtAl
= 2,8 (1 + 0,0038 · t) · 10-6
= 2,8*(1+0,0038*80)*10-6
= 3,65*10-6
Ом*см
Длина анодных шин принимается равная длине кожуха + 100 см
Lа.ш.
= Lкож
+ 100см = 5850+ 100 = 5950 мм = 595 см
Падение напряжения в анодных шинах
ΔUа.ш
. = (I*3,65*10-6
*Lа.ш
.)/Sобщ
= (80000*3,65*10-6
*595)/1806 = 0,096 В
Определяем количество рабочих штырей
nшт
= 2*(P-8*24)/35 =
где:
2 – количество рабочих рядов, шт
Р – периметр анода
35- расстояние между штырями
Р = 2*(Ва
+Lа
) = 2*(240+438) = 1356 см
nшт
= 2*(1356+8*24)/35 = 67 шт
Среднее сечение 1-го штыря
Sшт
= I/dFe
*nшт
= 80000/18*67 = 66,3 см2
Д = Sшт
*4/π = 66,3*4/3,14 = 9,19 см
Длинна штырей составляет 105 см
2.3.1.3
Определяем падение напряжения в анодных спусках.
Удельное сопротивление анодных спусков при t = 120 °
С
RtCu
= 1,82 · (1 + 0,004· 120) · 10-6
= 2,7 · 10-6
Ом · см
Сечение анодных спусков
Sанод.
спу.
= I/dCu
= 80000/70 = 1142,86 см2
Lанод. спу.
= 210 см
При длине анодных спусков 210 см определяем падение напряжения.
ΔUанод. спу.
= (80000*2,7*10-6
*210)/1142,86 = 0,039 В
Определяем количество медных шинок приходящихся на 1 штырь, если сечение одной шинки 1см2
nшинок
= Sа.сп.
/1*nшт
= 1142,86/1*67 = 17 шинок
2.3.1.4
Определяем падение напряжения в самообжигающемся аноде.
Определяется по формуле
ΔUа
= (146*Ва
+7,3*Sа
/к)*(180*5,47*lср
+0,08*lср
2
)*Rt*dа
*10-3
/D
Где:
ВА
– ширина анода, см = 240
SА
– площадь анода, см2
К- количество токоведущих штырей, (шт)
lСР
– среднее расстояние от токоведущих штырей до подошвы анода – (35см)
ρt
– удельное электро сопротивление анода (0,007 Ом · см)
dА
– анодная плотность тока – А/см2
D – длина забитой части штыря –(105-26 = 79см)
ΔUа
= (146*240+7,3*105263/67)*(180*5,47*35+0,08*1225)*
*0,007*0,76*10-3
/79 = 0,108 В
2.3.1.5
Определяем падение напряжения в контактах анодного узла.
Принимается по практическим данным:
1) Анодная шина – анодный стояк
2) Анодный стояк – катодная шина
3) Анодная шина – анодный спуск
Принимаем по 0,005 в на каждом участке, тогда
ΔUконт
= 0,005*3+0,007 = 0,015 В
В контакте шинка – штырь 0,007 В, тогда общее падение напряжения в контактах составляет
ΔUш-ш
= 0,007 В
2.3.1.6
Полное падение напряжения в контактах
ΔUа.у.
= ΔUконт
+ ΔUш-ш
= 0,015+0,007 = 0,022 В
2.3.2
Падение напряжения в электролите.
ΔЭЭл
= I*Rt*L/Sа
+2*(Lа
+Ва
)*(2,5+L) =
= 80000*0,5*48/105263+2*(438+240)*(2,5+4,8) = 1,67 В
где:
I – сила тока 80000 А
Rt – удельное сопротивление электролита 0,5 Ом · см
L – межполюсное расстояние см
SА
– площадь анода, см2
LА
– длина анода см
ВА
– ширина анода 240 см
2.3.3
Падение напряжения в катодном устройстве.
ΔUпод
= (Lпр
*Rt*10-3
+(3,83*10-2
*А2
+2,87*а*3
√а)*В/Sст
)*dа
*10-3
Lпр
= 2,5*0,92*Н-1,1*h+132/b
Приведенная длинна пути тока по блоку (см)
Где:
Н - высота катодного блока (40 см)
H - высота катодного стержня с учетом чугунной заливки (13 см)
B - ширина катодного стержня с учетом чугунной заливки (26 см)
Lпр
= 2,5*0,29*40-1,1*13+132/26 = 30,07 см
Rt-удельное электро сопротивление угольного блока
Rt = (Ом*см) = 3,72*10-3
А - 1/2 ширины шахты см (350/2 = 175)
В - ширина угольного блока с учетом шва (59 см)
а - ширина бортовой настыли (50 см)
Sст
– площадь поперечного сечения стального стержня с учетом чугунной заливки (338 см2
)
dа
- анодная плотность тока (0,76)
ΔUпод
= (30,07*3,72*10-3
+(3,83*10-2
*1752
+2,87*503
√50)*59/338*0,76*10-3
= 0,23 В
2.3.3.1
Падение напряжения в стержнях не заделанных в подину.
ΔUст
= I*Rt*L/S
RtFe
= 13(1+0,004*t)*10-6
(Ом * см) = 20,8*10-6
(t = 150)
S – сечение катодных стержней = 23*11,5*nбл
= 23*11,5*18 = 4761
L – длинна катодных стержней (50 см)
ΔUст
= 80000*20,8*10-6
*50/4761 = 0,017 В
2.3.3.2
Падение напряжения в катодных спусках
ΔUспу
= I*Rt*h/S
RtCu
= 1,82*(1+0,004*150)*10-6
= 2,9*10-6
Ом * см
t – катодный спуск – 1500
с
S – сечение катодных спусков
Sк
= I/dCu
= 80000/0,7 = 1142,85 см2
Определяем количество лент в катодных спусках
ΔUст
= 80000*2,9*10-6
*60/1142,85 = 0,012 В
ρAI
- удельное сопротивление АI шин при t = 150 °
С
ρt
AI
= 2,8*(1 + 0,0038 * 150) *10-6
= 4,4 * 10-6
Ом * см
t = 1500
с
Длинна катодной шины
L = Lкож
+100 = 5850+100 = 5950 см = 595 мм
Сечение катодных шин
Sкш
= I/dAl
= 80000/41,5 = 1927,71 см2
Количество шин
nш
= Sкш
/Sш
= 1927,71/258 = 7,4 ≈ 7 шин
Sкш
= nш
*43*6 = 7*43*6 = 1806 см2
ΔUпа
= I*Rt*L/Sкш
= 80000*4,4*10-6
*595/1806 = 0,1 В
2.3.3.3
Падение напряжения в контактах катодного узла
1) Катодный стержень – спуск - 0,005 В
2) Спуск – катодная шина – 0,005 В
ΔUкат. узл.
= 2*0,005 = 0,01 В
2.3.4
Падение напряжения за счет анодных эффектов.
ΔUа.э.
= К*(Uа.э.
-Uраб
)*τ*10-3
/1440*10-3
где:
UА.Э.
– напряжение анодного эффекта до 40 в
К – количество анодных эффектов в сутки 1 шт
UРАБ
– рабочее напряжение
τ – продолжительность анодного эффекта, принимаем 2 мин.
1440 – количество минут в сутках
ΔUан.эф.
= 1*(40-4,18)*2*10-3
/1440*10-3
= 0,05 В
2.3.5
Определяем основные показатели
ηэ
= 10*с*ηi
/Uср
т/кВ*ч = 10*0,336*90/4,114 =73,75 т/кВт*ч
Wуд
= 106
/ηэ
кВт*ч/т = 106
/73,75 = 13559,32 кВт*ч/т
Падения напряжения в общесерийной ошиновки
ΔUоб..ошн
= 0,05 В
Uразложения
= 1,68 В
Данные из расчета сводим в таблицу 7
Таблица 7 –Электрический баланс электролизера
Uгр
|
Uраб
|
Uср
|
1. анодный узел
1.1 Падение напряжения в стояках
1.2 Падение напряжения в анодных шинах
1.3 Падение напряжения в анодных спусках
1.4 Падение напряжения в аноде
1.5 Падение напряжения в анодном узле
|
0,108
|
0,03
0,096
0,039
0,108
0,022
|
0,03
0,096
0,039
0,108
0,022
|
Всего в анодном узле:
|
0,108
|
0,295
|
0,295
|
2.Катодный узел
2.1Падение напряжения в подине
|
0,23
|
0,23
|
0,23
|
2.2Падение напряжения в катодных стержнях
|
0,017
|
0,017
|
2.3Падение напряжения в катодных спусках
|
0,012
|
0,012
|
2.4Падение напряжения в катодных шинах
|
0,1
|
0,1
|
2.5Падение напряжения в катодах
|
0,01
|
0,01
|
Всего в катодном узле:
|
0,23
|
0,369
|
0,369
|
3 Напряжение разложения
|
1,68
|
1,68
|
1,68
|
4 Падение напряжения в электролите
|
1,67
|
1,67
|
1,67
|
5 Падение напряжения за счет анодных эффектов
|
0,05
|
0,05
|
6 Падение напряжения в общесерийной ошиновке
|
0,05
|
Итого:
|
3,738
|
4,014
|
4,114
|
2.4 Тепловой баланс электролизера
2.
4.1
Приход.
2.
4.1.1
Тепло от электроэнергии.
QЭЛ
= 3,6 * 103
* I * UГР
= 3,6 * 103
* 80 * 3.738 = 1076544 кДж/ч
I – сила тока 73 000 А
UГР
– напряжение греющее 3.79в
2.
4.1.2
Используемое тепло анодных газов
Qсм
= PСО2
* ΔНСО2
+ PCO
* ΔНCO
РСО2
– РC
О
– количество СО и СО2 кг
Где:
ΔНСО
2
и ΔНСО
– изменение теплосодержания СО2
и СО в интервале температур от Т2 до Т1 кДж/кг
Qан
= 26,18*8941+4,172*3946 = 250538,092 кДж/кг
Расход тепла
1) Тепло на разложение глинозема.
Qраз.
Al
2
O
3
= РAl
*ΔHAl
2
O
3
РAl
– производительность электролизера кг/час
ΔHAl
2
O
3
– теплота реакции образований
Al2O3 кДж/кг
Qразл
Al
2
O
3
= 24,1*1393,3 = 33578,53
2) Тепло уносимое вылитым металлом Qмет
Qмет
= РAl
*ΔHТ1
Т2
Al
РAl
– количество вылитого Al в час
ΔHТ1
Т2
Al – изменение теплосодержания в интервале температур
Qмет
= 24,1*1393,3 = 33578,53
3) Потери тепла с отходящими анодными газами
QСО2
= РСО2
*ΔHТ1-Т2
СО2
QCO
= РCO
*ΔHТ1-Т2
СО
ΔHТ1-Т2
СО2
; ΔHТ1-Т2
СО
– изменения теплосодержания СО и СО2 в интервале температур от Т2 до Т1 кДж/кг
РСО
,РСО2
– количество СО и СО2 кг/ч
QСО2
= 26,18*418,4 = 10953,712
QСО
= 4,179*627 = 2620,233
4) Определение потерь тепла с поверхности и конструктивных элементов электролизера
Qпот
= Qприх
-(Qразл
+Qме
+Qгаз
) = 1327082,092- (745364,8+33578,53+13573,945) =
=534564,817
Таблица 7 – тепловой баланс
Статьи прихода
|
Приход
|
Статьи расхода
|
Расход
|
кДж/час
|
%
|
кДж/час
|
%
|
1 От прохождения
электрического тока
|
1076544
|
81,07
|
1 На разложение
глинозема
2 Потери с вылитым металлом
|
745364,8
33578,53
|
56,4
2,5
|
2 От сгорания угольного анода
|
250538,092
|
18,93
|
3Потери с газами
отходящими
4 Потери с поверхностей и конструктивных элементов электролизера
|
13573,945
534564,817
|
1
40,1
|
3 Итого
|
1327082,092
|
100%
|
1327082,092
|
100%
|
2.5 Расчет количества электролизеров в цепи
Определение напряжения на входе в серию
Uсерию
850-(8,5+40+8,5) = 793 В
2.5.1
Число рабочих электролизеров в серии составит
nраб
= 793/Uср
-ΔUа.э.
= 793/4,25-0,05 = 188 шт
Число резервных электролизеров
nр
= nраб
*18/4,5*365 = 188*18/4,5*365 = 2,1 ≈ 2 шт
365 – число дней в году
18 – длительность простоя при КАП ремонте (дни)
4,5 – продолжительность межремонтной эксплуатации (год)
Общее число электролизеров
n = nраб
+nр
= 188+2 = 190 шт
2.5.2
Годовая производительность серии Р:
Р = I*8760*0,336*ηi
*nраб
*10-6
I – сила тока в серии (А)
8760 – число часов в году
0,336 – электрохимический эквивалент
ηi
– выход по току
nраб
– число рабочих электролизеров
Р = 80000*8760*0,336*0,9*188*10-6
= 39841,32 т
Библиография.
1. «Металлургия алюминия» И.А. Троицкий, В.А. Железнов.
2. «Производство алюминия» В.Г. Терентьев и др.
3. В.А. Кубернский, М.М. Воронова. Сравнительный анализ научно-технического уровня и эксплуатационных характеристик, существующих на предприятиях ОАО ”СУАЛ-ХОЛДИНГ” АСУТП ЭЛЕКТРОЛИЗА АЛЮМИНИЯ, 2002
4. Г.М. Глинков, М.Д. Климовицкий «Теоретические основы автоматического управления металлургическими процессами», Издательство «Металлургия», М., 1998
5. И.В.Николаев, В.И. Москвитин, Б.А. Фомин
«Металлургия легких металлов»,
Издательство «Металлургия», М., 1999
6. Инструкция оператору-технологу по работе с АСУТП «Электролиз» электролизного цеха завода УАЗ, ОАО УАЗ-СУАЛ редакция от 21.03.2003
7. Общие правила по технике безопасности
и эксплуатации электроустановок потребителей ОАО “СУАЛ-УАЗ”
|