Расчётно-графическая работа
з дисциплины ВСТИ
Тема: «
Рассчёт технологических размеров и допусков»
Задание:
рассчитать технологические размеры и допуски, при выполнении которых выдерживались бы заданные чертежом размеры, и обеспечивалось снятие минимальных припусков.
Исходные данные:
S1
=42-0,062
мм, S2
=10-0,07
мм, S3
=25 мм, S4
=16-0,43
мм, D1
=125-0,53
мм; D2
=92Н12мм; D3
=100 мм; D4
=88Н12 мм, D5
=82 мм.
Материал – СЧ18
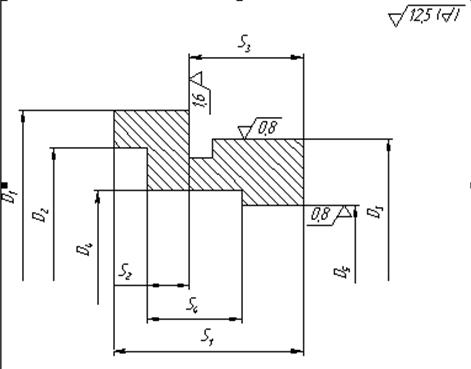
Рисунок 1 – Эскиз детали
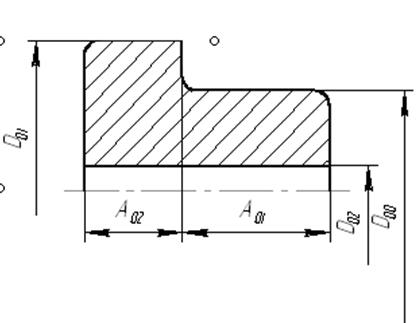
Рисунок 2 – Эскиз заготовки
Основная цель сборки - выдержать точность всех замыкающих звеньев сборочной размерной цепи. Замыкающее звено и его точность определяется служебным назначением сборочной единицы, ее собираемость и эксплуатацией.
Размерная цепь строится, начиная с замыкающего (исходного) звена. Затем по чертежу находят примыкающую к нему слева деталь, размер которой непосредственно влияет на размер замыкающего звена. Далее находят размер второй детали, сопряженной с размером первой. И так последовательно выявляют детали сборочного соединения, сопряженные Друг с другом, размеры которых непосредственно влияют на размер замыкающего звена. Последний из этих размеров должен примкнуть к размеру замыкающего звена, замкнув цепь. В состав размерной цепи от каждой детали входит только один размер.
В зависимости от пространственного расположения звеньев размерные цепи могут быть плоскими, пространственными. У изделия, как правило, несколько размерных цепей. Каждой цепи присваивается определенная буква. Звеньям линейной цепи обычно присваивают букву русского алфавита, угловым - греческого. Каждому составляющему звену присваивают индекс в виде порядкового номера, отсчет которого производится, от левой границы замыкающего звена. Замыкающему звену присваивают индекс. Увеличивающие звенья обозначают стрелками, проставленными над буквенным обозначением звена и направленными вправо, а также знаком "+" уменьшающие - стрелками влево и знаком "-".
Расчет и анализ размерной цепи позволяет:
1. установить количественную связь между размерами деталей изделия
2. установить номинальные значения
3. допуски взаимосвязанных размеров, исходя из эксплуатационных требований и экономической точности обработки деталей и сборки изделия
Забиваем Сайты В ТОП КУВАЛДОЙ - Уникальные возможности от SeoHammer
Каждая ссылка анализируется по трем пакетам оценки: SEO, Трафик и SMM.
SeoHammer делает продвижение сайта прозрачным и простым занятием.
Ссылки, вечные ссылки, статьи, упоминания, пресс-релизы - используйте по максимуму потенциал SeoHammer для продвижения вашего сайта.
Что умеет делать SeoHammer
— Продвижение в один клик, интеллектуальный подбор запросов, покупка самых лучших ссылок с высокой степенью качества у лучших бирж ссылок.
— Регулярная проверка качества ссылок по более чем 100 показателям и ежедневный пересчет показателей качества проекта.
— Все известные форматы ссылок: арендные ссылки, вечные ссылки, публикации (упоминания, мнения, отзывы, статьи, пресс-релизы).
— SeoHammer покажет, где рост или падение, а также запросы, на которые нужно обратить внимание.
SeoHammer еще предоставляет технологию Буст, она ускоряет продвижение в десятки раз,
а первые результаты появляются уже в течение первых 7 дней.
Зарегистрироваться и Начать продвижение
4. определить, какой вид взаимозаменяемости (полный, неполный) будет наиболее экономичен
5. добиться наиболее правильной простановки размеров на рабочих чертежах
6. определить операционные допуски и сделать пересчет размеров при несовпадении технологических, конструкторских, измерительных баз.
Технологический процесс изготовления втулки
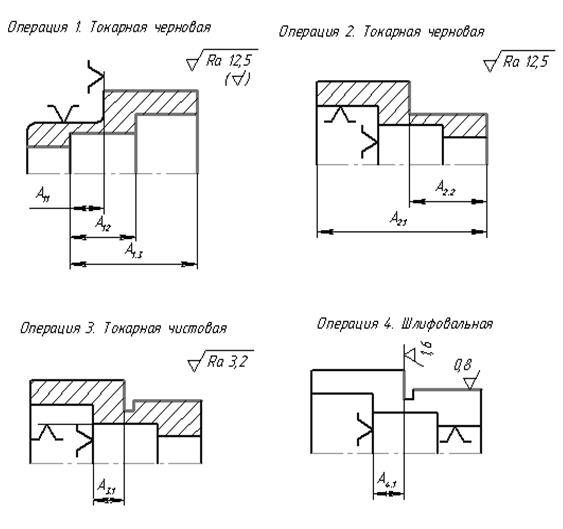
1. Составим схему обработки (рис. 3)
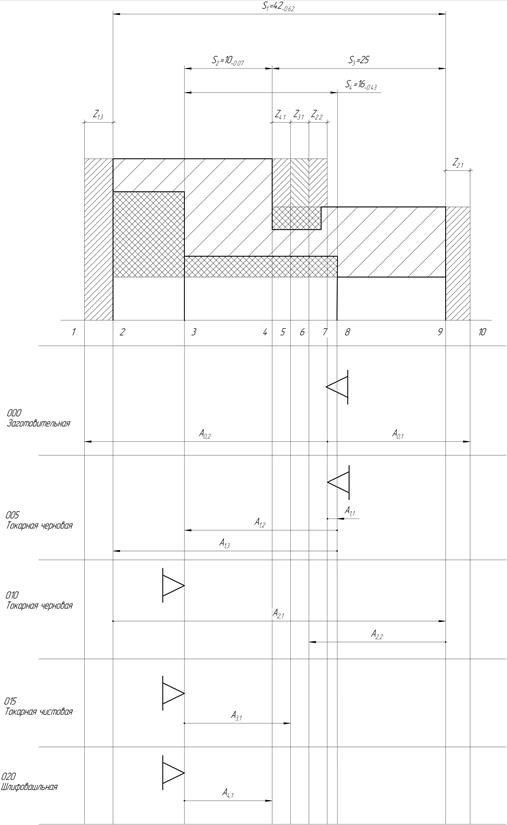
Рисунок 3 – Схема обработки
3. Построим граф технологических размерных цепей (рис.4)
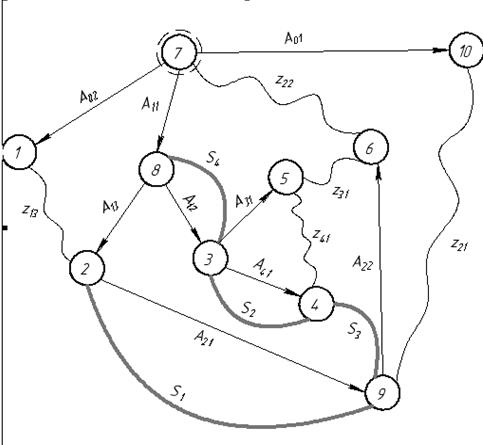
Рисунок 4 - Граф технологических размерных цепей
Уравнение размерных цепей:
1) A2.1
-S1
=0; A2.1
=S1
2) A1.2
-S4
=0; A1.2
=S4
3) A4.1
-S2
=0; A4.1
=S2
4) A3.1
-z4.1
-A4.1
=0; A3.1
=z4.1
+A4.1
5) A1.3
-A1.2
+A4.1
+S3
-A2.1
=0; A1.3
=A1.2
-A4.1
-S3
+A2.1
6) A2.2
+z3.1
+A3.1
-A4.1
-S3
=0; A2.2
=-z3.1
-A3.1
+A4.1
+S3
7) A1.1
+z2.2
-A2.2
-A1.3
+A2.1
=0; A1.1
=-z2.2
+A2.2
+A1.3
-A2.1
8) A0.2
+A1.1
-A1.3
-z1.3
=0; A0.2
=-A1.1
+A1.3
+z1.3
9) A0.1
-A1.1
+A1.3
-A2.1
-z2.1
=0; A0.1
=A1.1
-A1.3
+A2.1
+z2.1
4. Заполнимтаблицу 1
Для размеров А12
и А1.3
доминирующей погрешностью будет погрешность базирования, численно равная допуску на размер, который связывает измерительную и технологическую базы. Таким размером является размер А11
. Но поскольку данные размеры обрабатываются с одного установа и размеры А12
и А1.3
проставлены от чистовой базы, определяющей для которой является размер А11
, то можно считать, что погрешность базирования будет равна нулю.
На размер А21
доминирующей будет погрешность базирования, численно равная допуску на размер А13
. Что составляет 0,27 мм. Для размеров А31
и А41
измерительная база совпадает с технологической. Значит погрешность базирования на эти размеры будет равна нулю.
Таблица 1 – Расчет допусков на технологические размеры
Индекс размера |
Способы обработки |
Точность размеров заготовки |
Шероховатость |
Величина размера, мм |
Величина допуска, мм |
Доминирующая погрешность |
Расчетный допуск |
А01
|
Отливка в кокиль |
І кл |
Rz 200
h=300
|
До 30 |
0,15 |
0,31 |
0,46 |
А02
|
Отливка в кокиль |
І кл |
Rz 200
h=300
|
До 30 |
0,15 |
0,31 |
0,46 |
А11
|
Растачивание черновое |
IT10 |
Rz50
h=50
|
До 18 |
0,27 |
- |
0,27 |
А12
|
Однократное подрезание |
IT10 |
Rz50
h=50
|
До 18 |
0,27 |
- |
0,27 |
А13
|
Однократное подрезание |
IT10 |
Rz50
h=50
|
До 30 |
0,27 |
- |
0,27 |
А21
|
Однократное подрезание |
IT10 |
Rz50
h=50
|
До 50 |
0,25 |
0,27 |
0,52 |
А22
|
Черновое подрезание |
IT14 |
Rz50
h=50
|
До 30 |
0,62 |
- |
0,62 |
А31
|
Чистовое подрезание |
IT10 |
Rz12,8
h=50
|
До 18 |
0,07 |
- |
0,07 |
А41
|
Шлифование |
IT8 |
Rz6,4
h=25
|
До 10 |
0,022 |
- |
0,022 |
Таблица 2 – Расчет технологических размеров
Известные (заданные) размеры |
Неизвестные (искомые размеры) |
Размеры |
Величинаи допуска |
Ожидаемая погрешность |
Средний расчетный |
Допустимая корректировка |
Средний скорректированный размер |
Размер |
Допуск |
Уравнение контура |
Средний расчетный раз мер |
Номинальный расчетный размер |
Номинальный скорректированный размер |
Средний скорректированный размер |
1 |
2 |
3 |
4 |
5 |
6 |
7 |
8 |
9 |
10 |
11 |
12 |
13 |
S1
|
42-0.62
|
0,52 |
41.69 |
±0,05 |
41,74 |
А21
|
-0,52 |
А21
=S1
|
41,69 |
41,95-0,52
|
42-0,52
|
41,74 |
S2
|
10-0,07
|
0,022 |
9,965 |
±0,024 |
9,989 |
А41
|
-0,022 |
А41
=S2
|
9,965 |
9,976-0,022
|
10-0,022
|
9,989 |
S3
|
25-1,12
|
1,022 |
24,44 |
±0,049 |
24,489 |
А13
|
-0,21 |
А13
=А12
+А21
-А41
-S3
|
23,176 |
23,281-0,21
|
23,33-0,21
|
23,225 |
S4
|
16-0,43
|
0,27 |
15,785 |
+0,08 |
15,865 |
А12
|
-0,27 |
А12
=S4
|
15,785 |
15,92-0,27
|
16-0,27
|
15,865 |
Z13
|
0,5 |
0,94 |
0,97 |
+ |
0,94 |
А02
|
-0,46 |
А02
=А13
+Z13
-A11
|
20,06 |
20,29-0,46
|
20,3-0,46
|
20,07 |
Z21
|
0,5 |
1,46 |
1,23 |
+ |
1,46 |
А01
|
-0,46 |
A01
=Z21
+A21
+A11
-A13
|
23,88 |
24,11-0,46
|
24,2-0,46
|
23,97 |
Z22
|
0,5 |
1,62 |
1,31 |
+ |
1,62 |
А11
|
+0,27 |
A11
=A22
+A13
-Z22
-A21
|
4,085 |
3,95+0,27
|
4+0,27
|
4,135 |
Z31
|
0,1 |
0,712 |
0,456 |
+ |
0,712 |
А22
|
+0,62 |
A22
=A41
+S3
-Z31
-A31
|
23,908 |
23,598+0,62
|
23,6+0,62
|
23,91 |
Z41
|
0,025 |
0,092 |
0,071 |
+ |
0,092 |
А31
|
-0,07 |
A31
=Z41
+A41
|
10,06 |
10,095-0,07
|
10,1-0,07
|
10,065 |
Сделаем проверочный расчет (выборочно)
Z41
=A31
-A41
=10,1-0,07
-10-0,022
=0,1-0,92
Снятие минимального припуска Z41
=0,025 обеспечено.
S1
=A21
=42-0.52
(мм)
Припуск – слой материала, назначаемый для компенсации погрешностей, возникающих в процессе изготовления детали, в целях обеспечения заданного качества.
Расчету подлежит минимальный припуск на обработку. Колебание же размера обрабатываемой поверхности заготовки в пределах допуска на ее изготовление создает колебание величины припуска. Поэтому различают:
Сервис онлайн-записи на собственном Telegram-боте
Попробуйте сервис онлайн-записи VisitTime на основе вашего собственного Telegram-бота:
— Разгрузит мастера, специалиста или компанию;
— Позволит гибко управлять расписанием и загрузкой;
— Разошлет оповещения о новых услугах или акциях;
— Позволит принять оплату на карту/кошелек/счет;
— Позволит записываться на групповые и персональные посещения;
— Поможет получить от клиента отзывы о визите к вам;
— Включает в себя сервис чаевых.
Для новых пользователей первый месяц бесплатно.
Зарегистрироваться в сервисе
- припуск минимальный (Zmin ),
- номинальный (Zном ),
- максимальный (Zmax).
Они удаляются с поверхности заготовки в процессе её обработки для получения детали.
S1
выдерживается в заданных пределах 42-0,62
, следовательно размер A21
рассчитан правильно.
Список литературы
1. Справочник технолога - машиностроителя. В 2-х т. Т. 1 / Под ред. А. Г. Косиловой и Р. К. Мещерякова. - 4-е изд., перераб. и доп. - М.: Машиностроение, 1986. - 496 с., ил.
2. Горбацевич А.Ф., Шкред В.А. Курсовое проектирование по технологии машиностроения. – 4-е изд., перераб. – Минск: Вышейш. Школа, 1983. – 256 с.
|