Содержание
Аннотация…………………………………………………………………………....2
Введение………………………………………..…………………………...………..2
Литературный обзор…………………………………………………...…...………..3
1.1 Смесители с перемешиванием при свободном падении…..…………………..4
1.2 Смесители с принудительным перемешиванием материалов………………...6
1.3 Смеситель роторный……………………………………………………………..7
1.4Смеситель планетарный…………………………………………..………..……9
1.5 Смеситель планетарно-роторный…………………………………..………….11
1.6 Смеситель для приготовления керамзитобетонной смеси…………………...13
1.7 Бетоносмеситель непрерывного действия………………………………….....15
2. Устройство мешалок………………………………………………………….….18
2.1 Лопастные мешалки………………………………………………………….…18
2.2 Пропеллерные мешалки……………………………………………………......20
2.3 Турбинные мешалки……………………………………………………………21
2.4 Специальные мешалки…………………………………………………………23
3 Блок-схема процесса …………………………………………………….…….…25
4 Расчет аппарата…………………………………………………………………..27
5 Программа расчета…………………..…………………………………………...30
6 Охрана труда и окружающей среды…………………………………………….31
Список использованных источников……………………………………………..34
Введение
Перемешивание широко применяется в строительной промышленности для приготовления суспензий, эмульсий, растворов и паст. Посредством перемешивания достигается тесное соприкосновение частиц и непрерывное обновление поверхности взаимодействия веществ. Вследствие этого при перемешивании значительно ускоряются процессы массообмена, например: растворение твердых веществ в жидкостях, процессы теплообмена и протекание многих химических реакций. Перемешивание используют для ускорения абсорбции, выпаривания и других основных процессов.
Перемешивают вещества, находящиеся в одинаковых и различных агрегатных состояниях: твердые компоненты с твердыми, твердые с жидкими, газообразные с жидкими, жидкие с жидкими и т. п. Например, при изготовлении бетонных изделий смесь готовят из цемента, песка, щебня и т.п. Вяжущее вещество и вода составляют активную часть бетонной смеси.
В результате химических реакций между ними, образуется цементный камень, прочно соединяющий скелетные части (песок и щебень) бетона. На конечную прочность бетона, помимо оптимального состава, большое влияние оказывают однородность смеси, достигаемая при перемешивании.
Курсовое проектирование выполняется с целью закрепления теоретических навыков инженерного анализа, теоретического расчета и проектирования процессов и аппаратов технологии строительных материалов и изделий.
Темой курсового проектирования является изучение процесса перемешивания материалов, проектирование смесительного аппарата.
1. Литературный обзор
Для перемешивания материалов используют машины, называемые смесителями. В зависимости от физических свойств перемешиваемых материалов применяются смесители для пластичных, сухих и жидких материалов. По характеру работы смесители подразделяются на машины периодического (циклического) и непрерывного действия. В машинах периодического действия смешивание материалов происходит в отдельном сосуде, при этом все компоненты загружают в соответствии с рецептурой и перемешивают в течение определенного времени, затем смесь из сосуда выгружается также непрерывно.
По способу смешивания материалов смесители подразделяются на машины, в которых материал перемешивается при свободном его падении (гравитационные), и на машины с принудительным перемешиванием. В первых смесителях материалы поднимаются на определенную высоту, а затем падают под действием сил тяжести, перемешиваясь при этом; во вторых смесителях на материал непосредственно воздействуют рабочие органы машины. /2/
Наиболее распространенным способом перемешивания в жидких средах является механическое перемешивание при помощи мешалок, снабженных лопастями той или иной формы. Помимо механического перемешивания, применяют также перемешивание сжатым воздухом. Иногда жидкости перемешивают многократным перекачиванием их насосом через аппарат, т. е. путем циркуляции в замкнутом контуре. Оба последних способа требуют сравнительно большого расхода энергии, а перемешивание воздухом сопряжено также с возможным окислением или испарением продуктов.
Основными характеристиками любого процесса перемешивания являются: расход энергии и эффективность перемешивания.
В различных процессах эффективность перемешивания определяется по-разному. Например, при суспендировании эффективность перемешивания характеризуется равномерностью распределения твердых частиц в жидкости и скоростью достижения достаточной равномерности
1.1 Смесители с перемешиванием при свободном падении
.
Бетоносмеситель цикличного действия с перемешиванием материала при его свободном падении показан на рисунок 1.1.
Он состоит из рамы 11, смесительного барабана 2, загрузочного устройства 5. Барабан представляет собой два усеченных конуса, соединенных цилиндрической обечайкой. Шесть поддерживающих роликов 4 предотвращают продольное перемещение барабана. Пневмоцилиндр 8 предназначен для поворота барабана на угол 550
при выгрузке бетонной смеси. Внутренняя поверхность смесительного барабана офутерована износостойкими стальными плитами. На ней укреплено шесть лопастей: по три в каждой конусной части. Кромки лопастей наплавляются износостойким сплавом. При работе смесителя компоненты смеси из дозаторов по течке загружаются во вращающийся барабан. Материал лопастями поднимается на угол до 480
и затем ссыпается вниз, перемешиваясь при этом. Время загрузки барабана 10-15 с. Время перемешивания зависит от жесткости бетонной смеси и колеблется в пределах от 60 до 150 с. После окончания перемешивания загрузочная течка пневмоцилиндром отводится от смесительного барабана. Пневмоцилиндр 8 наклоняет вращающийся смесительный барабан, и бетонная смесь под действием силы тяжести выгружается в транспортирующие устройства. Время выгрузки бетонной смеси из барабана 10-15 с.
Производительность Q Бетоносмеситель определяют по формуле
Q= Vk, (1.1)
где V - объем готового замеса, м3
,
k - количество замесов в ч.
Рисунок 1.1 – Бетоносмеситель циклического действия
1- электродвигатель
2-смесительный барабан
4- поддерживающие ролики
5-загрузочное устройство
6- электродвигатель
8- пневмоцилиндр
11-рама
12-стойка
Бетоносмеситель непрерывного действия с перемешиванием при свободном падении, показанный на рисунке 2, состоит из смесительного барабана 3, на который насажены бандаж 2 и зубчатое венцовое колесо 5 с бандажом, загрузочного устройства и привода. Барабан бандажами опирается на роликоопоры 14. Роликоопора состоит из рамы и двух опорных роликов 13, оси которых установлены в подшипниках. На одной роликоопоре смонтированы два упорных ролика 15, предотвращающих продольное перемещение смесительного барабана. Внутренняя поверхность смесительного барабана облицована износостойкими стальными листами. К ней прикреплены лопасти (полки) 1, наплавленные твердым сплавом. К вертикальной стенке загрузочной воронки прикреплена труба 6, предназначенная для подачи воды в смесительный барабан. Конец трубы заканчивается распылительным устройством 4. Все механизмы смесителя смонтированы на фундаментной раме 10 Компоненты бетонной смеси подаются непрерывно через загрузочную воронку в барабан, куда одновременно поступает вода. При вращении смесительного барабана материал перемешивается и направляется к выходному открытому концу.
Рисунок 1.2 – Бетоносмеситель неприрывного действия с перемешиванием при свободном падении.
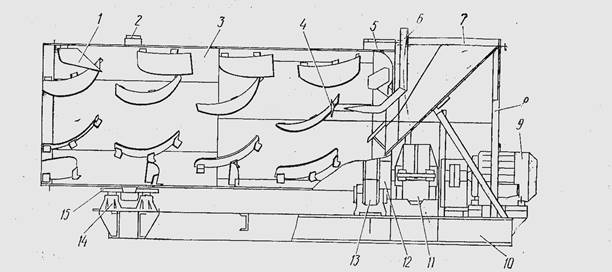
1- лопасти (полки)
2- бандаж
3- смесительный барабан
4- распылительное устройство
5- зубчатое венцовое колесо
6- труба, предназначенная для подачи воды в смесительный барабан
7-корпус
8-рама
9-мотор
10- фундаментная рама
11-стойка
12-привод
13- два опорных ролика
14- роликоопоры
15- два опорных ролика
1.2 Смесители с принудительным перемешиванием материалов
Бетоносмеситель непрерывного действия показан на рисунке 1.3.
Компоненты бетонной смеси подаются непрерывно через загрузочную воронку в барабан, куда одновременно поступает вода. При вращении смесительного барабана материал перемешивается и направляется к выходному открытому концу.
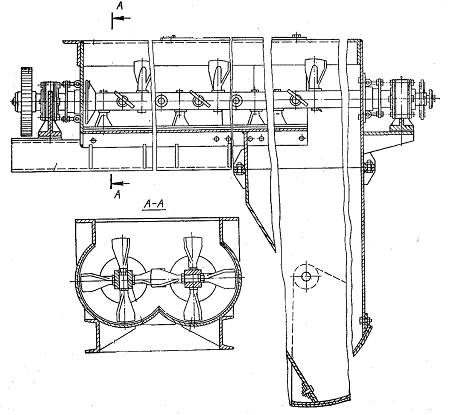
Рисунок 1.3- Бетоносмеситель непрерывного действия
1.3 Смеситель роторный
.
Смеситель роторный для смешивания компонентов бетонной смеси с объемом готового замеса 330 л показан на рисунке 1.4.
Смеситель состоит из неподвижного корпуса 3, рамы 5 и смешивающего механизма, смонтированного на роторе 1. Вращение ротору сообщается от электродвигателя. Материалы смешиваются в кольцевой рабочей камере, образованной внутренней 9 и наружной 4 обечайками. Смешивающий механизм состоит из пяти лопастей, которые к ротору крепятся с помощью держателей 6 и водил 8. Лопасти расположены на разных расстояниях от оси вращения и перекрывают, поэтому все пространство кольцевой камеры. В камеру материал загружается через патрубок 7. Готовую смесь из рабочей камеры выгружают через секторное отверстие, расположенное в днище. Отверстие перекрывается затвором, управляемым пневмоцилиндром 18 через систему тяги рычагов 17. Внутренняя поверхность рабочей камеры футеруется высокопрочными стальными листами.
Корпус смесителя укреплен на трех стойках 2, расположенных под углом 1200
относительно друг друга. Пружинные амортизационные устройства 10 предназначены для предупреждения поломки лопастей, держателей и водил при попадании в рабочую камеру крупных кусков материала (или посторонних предметов).
Рисунок 1.4- Смеситель роторный для смешивания компонентов бетонной смеси
1- ротор
2- стойка
3- неподвижный корпус
4- наружная обечайка
5- рама
6- держатель
7- патрубок
8- водило
9- внутренняяобечайка.
10- пружинные амортизационные устройства
11- система тяги рычагов
12-рама
13- управляемый пневмоцилиндр
14- электродвигатель
1.4 Смеситель планетарный
.
Смеситель планетарный для смешивания компонентов бетонной смеси с объемом готового замеса 660 л, показанный на рисунке 1.5, состоит из сварной металлической рамы 5, чаши 7 и смесительного устройства. На раме смонтировано четыре роликоопоры 4, на них установлена чаша, и две стойки б, 13, на которых смонтирован привод. Смесительное устройство состоит из двух крестовин 18, на них смонтировано по три лопасти 19. Крестовины и чаша вращаются во взаимно противоположных направлениях. Вращение от электродвигателя 21 через клиноременную передачу 1 и одноступенчатый цилиндрический редуктор 2 передается трансмиссионному валу 8, который установлен на трех подшипниках 10. На вал 8 насажены три конических шестерни 11, две из которых входят в зацепление с коническими колесами 9, расположенными на валах крестовин, а третья соприкасается с коническим колесом 12, находящимся на верхнем конце вертикального вала 14. На нижнем конце этого вала насажена цилиндрическая шестерня 15, входящая в зацепление с зубчатым венцовым колесом 16, укрепленным на чаше. Внутри чаши на держателях смонтированы три неподвижных скребка 20, предназначенных для очистки ее вертикальной стенки и подачи смешиваемого материала под смесительные лопасти. Для предохранения смесительных лопастей и неподвижных скребков от поломок, в случае попадания крупных кусков, применяют пружинные амортизаторы.
Загружают материалы, подлежащие смешиванию, сверху, выгружают через центральное отверстие в днище чаши, закрываемое затвором 17. Управляют затвором с помощью пневмоцилиндра 22 через систему тяг и рычагов 3. Давление воздуха в сети 0,35 и 0,7 МПа. Смешивают компоненты лопастями, вращающимися в сторону, противоположную вращению чаши.
Рисунок 1.5- Смеситель планетарный для смешивания компонентов бетонной смеси.
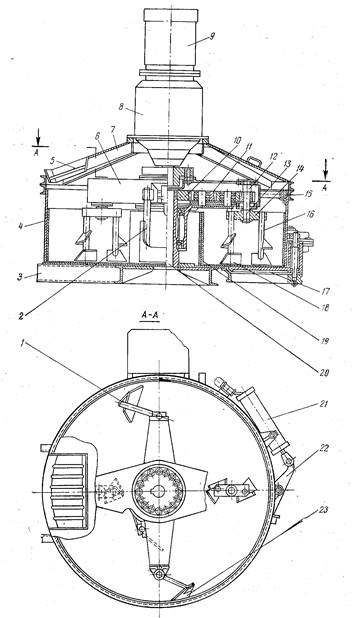
1- клиноременная передача
2- одноступенчатый цилиндрический редуктор
3- система тяг и рычагов
4- роликоопоры
5- сварная металлическая рама
6- стойка
7-чаша
8- трансмиссионный вал
9- конические колеса
10- три подшипника
11- три конических шестерни
12- коническое колесо
13- стойка
14- вертикальный вал
16- зубчатое венцовое колесо
17- цилиндрическая шестерня
18- две крестовины
19- три лопасти
20- три неподвижных скребка
21-электродвигатель
22-пневмоцилиндр
1.5 Смеситель планетарно-роторный.
Смеситель планетарно-роторный, показанный на рисунке 1.6, предназначен для приготовления бетонной смеси с объемом готового замеса 800 л. Он состоит из нижней рамы3,цилиндрического корпуса 4, внутренней цилиндрической обечайки 19 (закрытой сверху), верхней рамы 7, на которой смонтирован привод. Рабочая камера смесителя образуется внутренними стенками и днищем корпуса и наружными стенками обечайки 19. В центре смесителя установлен вертикальный вал 20 и неподвижное цилиндрическое зубчатое колесо 10. От электродвигателя 9 с встроенным редуктором 8 вращение передается траверсе 6. На траверсе в подшипниках смонтированы попарно по две промежуточных 11 и по одной ведомой 12 шестерен. Ведомые шестерни насажены на вертикальные валы 13, на вторых концах которых расположены перекладины 14, к которым прикреплены по две стойки 16,с двумя смесительными лопастями 18 каждая. При работе электродвигателя первые две промежуточные шестерни окатываются по неподвижному колесу и далее через вторые промежуточные и ведомые шестерни передают вращение валам 13. Вследствие этого смесительные лопасти совершают сложное движение вокруг осей валов 13 и центрального вала 20.
Для очистки стенок рабочего пространства на траверсе 6 укреплены скребки: первый 2 - жестко; он предназначен для очистки наружных стенок обечайки 19; второй 23 - через пружинный амортизатор, он служит для очистки внутренних стенок корпуса 4; третий 1 - жестко, он направляет материал под смесительные лопасти. Внутренние поверхности рабочей камеры облицованы листами из износоустойчивой стали.
Загрузка материалов в смеситель осуществляется через патрубок 5, выгрузка- через отверстие в днище корпуса, закрываемое секторным затвором 17, управляемым пневмоцилиндром 21 через систему тяг и рычагов 22. Трубопровод 15 предназначен для подачи воды в смеситель. В последнее время в конструкцию таких смесителей стали вводить дополнительный узел подачи пара для подогрева бетонной смеси во время ее перемешивания с целью уменьшения цикла его работы, а, следовательно, повышения производительности.
Рисунок 1.6- Смеситель планетарно-роторный
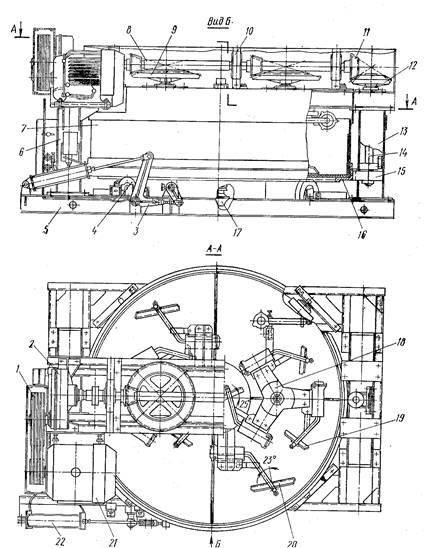
1-скребок, направляющий материал под смесительные лопасти
2-скребок, предназначенный для очистки наружных стенок обечайки
3- нижняя рама
4- цилиндрический корпус
5-патрубок
6-траверс
7- верхняя рама
8- встроенный редуктор
9-электродвигатель
10- неподвижное цилиндрическое зубчатое колесо
11-промежуточная шестерня
12- ведомая шестерня
13- вертикальные валы
14- перекладины
15- трубопровод
16- две стойки
17-секторный затвор
18- две смесительные лопасти
19- внутренняя цилиндрическая обечайка
20- вертикальный вал
21-пневмоцилиндр
22- система тяг и рычагов
23-скребок, служащий для очистки внутренних стенок корпуса
1.6 Смеситель для приготовления керамзитобетонной смеси.
Смеситель, предназначенный для приготовления керамзитобетонной смеси, показанный на рисунке 1.7, состоит из чаши 18, укрепленной на раме 21, и двух катков. Рама 21 установлена на стойки 5. Чаша сверху закрыта кожухом 15. Каждый каток 19 состоит из втулки 8 и двух дисков 17, соединенных между собой по окружности стержнями 16. Каток подшипниками опирается на ось 9, которая одним концом крепится к траверсе 10.
Траверса соединяется с перекладиной 13, насаженной на верхний конец вертикального вала 3. В центре чаши установлена втулка 4. На нижнем конце вала насажено коническое зубчатое колесо 2. Материал в смеситель подается через люк 11, вода - через трубу 14.
Выгружается смесь через отверстие в днище чаши, перекрываемым затвором. Управляют затвором с помощью пневмоцилиндра 7 через систему тяг и рычагов. Регулирование катков по высоте осуществляется винтовыми механизмами 12. Лопасти 6 предназначены для направления смешиваемого материала под катки. Катки приводятся во вращение вокруг вертикальной оси от электродвигателя 20 через двухступенчатый цилиндрический редуктор 22 и коническую шестерню 1. За счет сил трения катки приводятся во вращение вокруг горизонтальных осей. При этом решетчатые катки смешивают компоненты бетонной смеси.
Для приготовления цементных, известковых и других растворов применяют передвижные и стационарные растворосмесители. Передвижные растворосмесители. На заводах широкого распространения не получили.
Рисунок 1.7- Смеситель, предназначенный для приготовления керамзитобетонной смеси
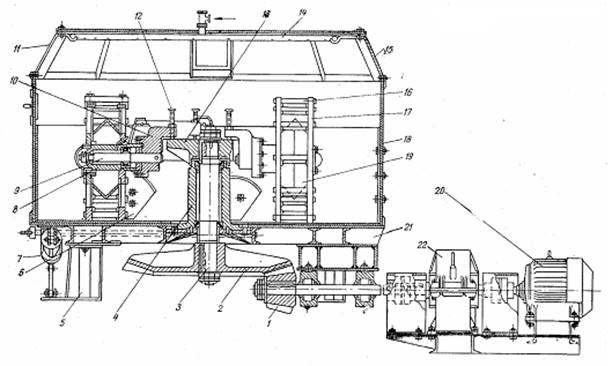
1- коническая шестерня
2- коническое зубчатое колесо
3- вертикальный вал
4-втулка
5-стойки
6- лопасть
7-пневмоцилиндр
8-втулки
9-ось
10-траверс
11-люк
12- винтовые механизмы
13-перекладина
14-труба
15-кожух
16-стержни
17-два диска
18- чаша
19-каток
20- электродвигатель
21-рама
22- двухступенчатый цилиндрический редуктор
1.7 Бетоносмеситель непрерывного действия
.
Бетоносмеситель непрерывного действия показан на рисунке 1.8.
Смеситель состоит из фундаментной рамы 1, корпуса 11 корытообразной формы, копильника 7 с затвором 8, двух валов 10 с лопастями 9 и привода 2, состоящего из электродвигателя, клиноременной передачи, редуктора (на рисунке не показаны) и открытой 'Зубчатой передачи. Корпус изготовлен из листовой стали, он закрыт крышкой б. В передней части корпуса находится загрузочное отверстие 5.
Валы 10 прямоугольного сечения установлены в подшипниках 3, расположенных у внешних торцовых стенок корпуса. Лопасть состоит из пластины и хвостовика с резьбой. Лопасти на валах устанавливают под углом таким образом, чтобы стальные пластины образовывали винтовую линию. Угол установки плоскостей пластин можно регулировать от 0 до 900
. Конусные отражатели 4, укрепленные на валах, предохраняют подшипники от засорения.
Компоненты бетонной смеси перемещаются от загрузочного отверстия к копильнику, перемешиваясь при этом. Готовая бетонная смесь выгружается или непрерывно, или периодически. В последнем случае бетонная смесь собирается в копильнике. Выгружается смесь при открытом затворе. Управление затвором производится от одного из валов через цепную передачу и фрикционную муфту.
растворосмесители непрерывного действия принудительного перемешивания подобны бетоносмесителям непрерывного действия, рассмотренным выше. Растворосмесители могут иметь один или два лопастных вала. При получении бетонов из газобетонных смесей применяют передвижной смеситель, показанный на рис. 75. Газобетоносмеситель состоит из самоходной портальной рамы 7, бункера 2, вертикального вала 3 с лопастями 4 и привода 9.
Рама опирается на колеса. Бункер состоит из верхнего и двух нижних усеченных конусов и средней цилиндрической части коробчатой формы. В верхней части бункера смонтированы загрузочные патрубки 1. К каждому нижнему усеченному конусу бункера прикреплены выгрузочные устройства, состоящие из патрубков 11 и затворов 10; на цилиндрической части бункера.
смонтированы вибраторы б. На внутренних стенках бункера укреплены лопасти 5, предназначенные для улучшения перемешивания смеси. В нижней части вертикального вала 3 укреплен трехлопастной винт 8. Вращение вертикальному валу сообщается от электродвигателя через клиноременную передачу и червячный редуктор.
Газобетоносмеситель работает следующим образом. Устанавливают его на посту загрузки. Через патрубки 1 в корпус смесителя при одновременном вращении вертикального вала подается шлам, а затем связующее (цемент, известь). При подаче цемента включаются вибраторы, через 50-60 с. подается водная суспензия алюминиевой пудры (газообразователь). Смесь перемешивается в течение двух минут, при этом смесительперемещается к формам, заполняемым смесью. Газопенобетоносмеситель после выгрузки смеси в формы возвращается к посту загрузки, и цикл работы повторяется.
Рисунок 1.8- Бетоносмеситель непрерывного действия
1- фундаментная рама
2-привод
3-подшипники
4-отражатель
5- загрузочное отверстие
6-крышка
7-копильник
8-затвор
9-лопасти
10- два вала
11-корпус
2. Устройство мешалок.
Механические мешалки разделяются по устройству лопастей на следующие группы:
1) лопастные - с плоскими лопастями,
2) пропеллерные - с винтовыми лопастями,
3) турбинные.
4) специальные (якорные и др.)
2.1 Лопастные мешалки.
Простейшие лопастные мешалки имеют две плоские лопасти, установленные в вертикальной плоскости, т. е. перпендикулярно к направлению вращения (рисунок 2.1).
Лопасти укреплены на вертикальном валу, который приводится во вращение от зубчатой или червячной передачи и делает 12-80 об/мин. Диаметр лопастей составляет примерно 0,7 диаметра сосуда, в котором вращается мешалка. При малых числах оборотов мешалки жидкость совершает круговое движение, то есть вращается по окружностям, лежащим в горизонтальных плоскостях, в которых движутся лопасти.
В этих условиях отсутствует смешивание различных слоев жидкости и интенсивность перемешивания низкая.
Интенсивное перемешивание достигается в результате появления вторичных потоков и вихревого движения жидкости. Вторичные потоки возникают под действием центробежных сил, вызывающих движение жидкости в плоскости вращения лопасти от центра сосуда к его стенкам. Вследствие этого в центре сосуда возникает пониженное давление, причем в область пониженного давления всасывается из слоев, лежащих выше и ниже лопасти. В результате в сосуде происходит циркуляция жидкости, показанная стрелками на рис. 2.2. Вторичные потоки, складываясь с основным круго\3ым движением жидкости, создают сложное движение, при котором происходит интенсивное перемешивание отдельных слоев. Интенсивность перемешивания возрастает с увеличением числа оборотов; однако еще быстрее увеличивается мощность, потребляемая мешалкой и при круговом движении жидкости на ее поверхности под действием центробежной силы, образуется воронка (рис. 2.2), глубина которой возрастает с увеличением числа оборотов. Образование воронки ведет к ухудшению использования емкости сосуда.
Рисунок 2.1- Стальная и чугунная лопастные мешалки
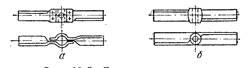
Рисунок 2.2 – Циркуляция жидкости при перемешивании лопастными мешалками
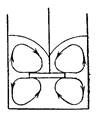
Для каждого случая опытным путем можно найти оптимальное число оборотов, при котором достигается необходимая эффективность перемешивания. Дальнейшее увеличение числа оборотов вызывает излишний расход энергии.
Вихревое движение жидкость приобретает при установке в сосуде с мешалкой отражательных перегородок в виде вертикально поставленных полос. При обтекании жидкостью перегородок за ними образуется зона пониженного давления, в которой возникают вихри. При возрастании числа оборотов вихри отрываются от перегородок и движутся в направлении вращения лопасти. В случае дальнейшего увеличения числа оборотов возникает беспорядочное вихревое движение жидкости, при этом вихри соударяются друг с другом по всему объему жидкости. В этих условиях достигается высокая равномерность и интенсивность перемешивания. В то же время при наличии перегородок, препятствующих вращению всей массы жидкости, резко снижается глубина воронки. Обычно достаточночетырех симметрично установленных радиальных перегородок для улучшения перемешивания. Однако с установкой перегородок возрастает расход энергии на перемешивание.
Для лучшего перемешивания всего объема жидкости в сосуде на валу устанавливают несколько пар горизонтальных лопастей, т. е. применяют многолопастные, а также рамные мешалки (рисунок 2.3), состоящие из нескольких горизонтальных и вертикальных, а иногда и наклонных плоских лопастей. Рамные мешалки отличаются прочностью и пригодны для перемешивания вязких жидкостей.
Рисунок 2.3- горизонтальные лопасти
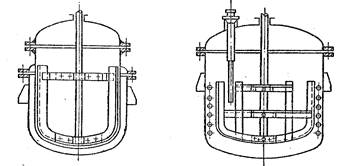
Достоинства лопастных мешалок:
1) простота устройства и дешевизна изготовления,
2) вполне удовлетворительное перемешивание умеренно вязких жидкостей.
Недостатки:
1) малая интенсивность перемешивания вязких жидкостей,
2) непригодность для перемешивания легко расслаивающихся веществ.
Основные области применения лопастных мешалок:
1)Перемешивание жидкостей небольшой вязкости
2)Растворение и суспендирование твердых веществ, обладающих малой плотностью
3) грубое смешение жидкостей.
Лопастные мешалки простого типа наиболее эффективны при перемешивании маловязких сред (до 100 спз).
Для перемешивания жидкостей с вязкостью свыше 2500 спз более пригодны рамные мешалки или лопастные мешалки в сосудах с отражательными перегородками.
В указанных областях применения лопастные мешалки обеспечивают хорошее перемешивание при небольшом расходе энергии. Лопастные мешалки непригодны для быстрого растворения, тонкого диспергирования, а также для получения суспензий, содержащих твердую фазу большой плотности.
2.2 Пропеллерные мешалки
Лопасти пропеллерных мешалок изогнуты по профилю судового винта, то есть с постепенно меняющимся наклоном, почти от 00
у оси до 900
на конце лопасти. Вращаясь в жидкости, лопасти действуют наподобие винта, а жидкость, окружающая пропеллер, как бы является гайкой и перемещается в направлении оси мешалки. Это осевое движение складывается с круговым перемещением жидкости, благодаря чему возникает ее винтовое движение. Если винтовая поверхность пропеллера правая, а вращение его происходит по часовой стрелке, то осевое движение жидкости направлено вверх и в сосуде возникает циркуляция жидкости.
На валу, в зависимости от высоты слоя жидкости, устанавливают один или несколько пропеллеров. Диаметр лопасти пропеллера равен 0,25-0,3 диаметра аппарата. Скорость вращения пропеллера составляет 160-1000 06/мин.
Пропеллерные мешалки создают более интенсивные осевые потоки жидкости, чем лопастные, и, следовательно, более интенсивно перемешивают жидкость. Перемешивание пропеллерными мешалками улучшается при установке в аппарате отражательных перегородок или диффузора - короткого цилиндрического (иногда слегка конического) стакана, в котором помещается пропеллер.
Диффузор направляет циркуляцию жидкости в осевом направлении и благоприятно влияет на перемешивание в аппаратах с большим отношением высоты к диаметру, а также в аппаратах со змеевиками и другими внутренними устройствами.
Эффективность перемешивания в аппаратах большой емкости возрастает при эксцентричной установке пропеллеров или расположении вала пропеллерной мешалки под углом 10 - 200
к вертикали.
Достоинства пропеллерных мешалок:
1) интенсивное перемешивание,
2) умеренный расход энергии, даже при значительном числе оборотов,
3) невысокая стоимость.
Недостатки:
1) малая эффективность перемешивания вязких жидкостей
2) Ограниченный объем интенсивно перемешиваемой жидкости
Пропеллерные мешалки применяются главным образом для следующих целей:
1) интенсивное перемешивание маловязких жидкостей;
2) приготовление суспензий и эмульсий;
3) взмучивание осадков, содержащих да 10% твердой фазы, состоящей из частиц размером до 0,15 мм.
Пропеллерные мешалки перемешивают жидкость быстрее и интенсивнее лопастных мешалок, при умеренном расходе энергии, превышающем, однако, расход ее для лопастных мешалок.
Пропеллерные мешалки пригодны для проведения непрерывных процессов, но неприменимы для гомогенного смешивания, для смешивания вязких жидкостей (более 6000 спз), а также для смешивания жидкостей с твердыми веществами большой плотности.
Рисунок 2.4-. Пропеллерная мешалка.
 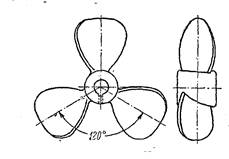
2.3 Турбинные мешалки
Турбинные мешалки бывают двух типов: открытые и закрытые (рисунок 2.5), имеющие лопастное колесо с каналами (наподобие рабочего колеса центробежного насоса). Турбинные мешалки работают при 100-350 об/мин. и производят интенсивное перемешивание жидкости.
Открытые турбинные мешалки представляют собой, по существу, усовершенствованную конструкцию простых лопастных мешалок. Вращение нескольких лопастей, расположенных под углом к вертикальной плоскости, создает наряду с радиальными потоками осевые потоки жидкости, что способствует интенсивному перемешиванию ее в больших объемах. Интенсивность перемешивания возрастает при установке в сосуде отражательных перегородок.
Закрытые турбинные мешалки обычно устанавливают внутри направляющего аппарата, который представляет собой неподвижное кольцо с лопатками, изогнутыми под углом 45-900 (рисунок 2.5). Закрытые турбинные мешалки создают преимущественно радиальные потоки жидкости при небольшой затрате кинетической энергии. Образующиеся радиальные потоки жидкости обладают достаточно большой скоростью и распространяются па всему сечению аппарата, достигая наиболее удалённых его точек. Жидкость входит в мешалку через центральное отверстие и выходит по касательной к колесу. В колесе жидкость плавно меняет направление от вертикального (па оси) до горизонтального (па радиусу) и выбрасывается из колеса с большой скоростью.
При таком направленном и многократно повторяющемся в единицу времени движении жидкости достигается быстрое и эффективное перемешивание ее во всем объеме сосуда.
Для улучшения и ускорения перемешивания (что особенно важно в аппаратах непрерывного действия) применяют турбинные мешалки с лопастями или колесами, расположенными на различной высоте.
Достоинства турбинных мешалок:
1) быстрота перемешивания и растворения,
2.) эффективное перемешивание вязких жидкостей
3) пригадн6сть для непрерывных процессов.
Недостатком турбинных мешалок является сравнительная сложность и высокая стоимость изготовления.
Области применения турбинных мешалок:
1) интенсивное перемешивание и смешивание жидкостей различной вязкости, которая мажет изменяться в широких пределах мешалки открытого типа до 105 спз, мешалки закрытого.
2) тонкое диспергирование и быстрое растворение
3) взмучивание осадков в жидкостях, содержащих 60 % и более твердой фазы (для открытых мешалок - до 60%); допустимые размеры твердых частиц: до 1,5 .мм для открытых мешалок, до 25 .мм для закрытых мешалок.
Нормализованные турбинные мешалки выпускают с диаметром турбины 300, 400, 500 и 600 мм.
Рисунок 2.5- турбинные мешалки
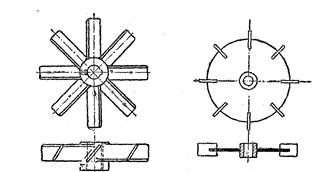 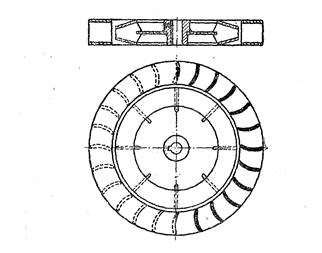
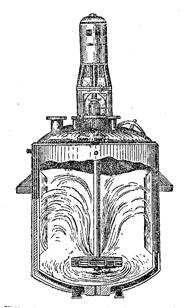
2.4 Специальные мешалки
Для перемешивания вязких жидкостей и пастообразных материалов применяют так называемые якорные мешалки с лопастями, изогнутыми по форме стенок и днища сосуда (рисунок 14). Якорные мешалки очищают стенки аппаратов от налипающего на них материала, благодаря чему улучшается теплообмен, и предотвращаются местные перегревы перемешиваемых веществ.
Барабанная мешалка представляет собой лопастной барабан в виде так называемого беличьего колеса. Мешалки этой конструкции создают большую подъемную силу и потому весьма эффективны при проведении реакций между газом и жидкостью а также при получении эмульсии, обработке быстро расслаивающихся суспензии и взмучивании тяжёлых осадков. Рекомендуемые условия применения барабанных мешалок: отношение диаметра барабана к диаметру сосуда от 1: 4 до 1: 6.
Рисунок 2.6- Специальные мешалки
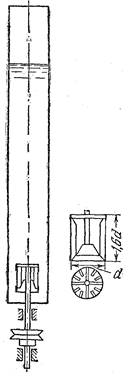
Перемешивание сжатым воздухом
Перемешивание маловязких жидкостей иногда производят сжатым воздухом. Таким способом возможно лишь медленное перемешивание при сравнительно большом расходе энергии; кроме того, как указывалось, перемешивание воздухом может сопровождаться нежелательным окислением или испарением продуктов.
Обычно перемешивание сжатым воздухом проводят в аппаратах, снабженных барботером - трубой с отверстиями для выхода воздуха, или в аппаратах, работающих по принципу воздушных подъемников (эрлифтов). В последнем случае жидкость, смешанная с пузырьками воздуха, поднимается по центральной трубе, расположенной по оси аппарата, и опускается в кольцевом пространстве между трубой и стенками аппарата. Таким образом, жидкость циркулирует в аппарате и перемешивается в нем.
3. Блок-схема процесса
__
H
__
__
X
Y
  
__
Z
Контролируемые нерегулируемые факторы Х:
- температура окружающей среды;
- атмосферное давление;
- число оборотов мешалки;
- отношение твердой фазы к жидкой;
- плотность жидкости;
- вязкость жидкости;
- плотность твердой фазы;
- размеры твердых частиц;
- размеры аппарата;
- коррозия деталей;
- износ деталей;
- ширина и диаметр лопасти
Контролируемые регулируемые факторы Н:
- время перемешивания;
- скорость подачи суспензии;
- глубина погружения лопасти;
- количество жидкости;
- интенсивность перемешивания;
- неполное перемешивание;
Неконтролируемые нерегулируемые факторы
Z
:
- эксплутационные воздействия;
- человеческий фактор
- незначительное измельчение
- примеси
- отключение электроэнергии:
- перепады электроэнергии;
Выходы
Y
:
- степень гомогенизации;
- производительность;
4. Расчет аппарата
Изучить процесс смешения и разработать смеситель непрерывного действия, в котором необходимо равномерно суспезировать твердые частицы в жидкости плотностью Р и вязкостью µ. Наибольший размер твердых частиц d; плотность твердой фазы Ртв. Диаметр аппарата о; высота жидкости в нем H=D; ширина лопастей b мм; шаг изменения диаметра 100 мм;
Исходя из заданной мощности двигателя Р, определить оптимальный диаметр лопаток и число оборотов мешалки. Составить блок-схему алгоритма и программу расчета на ЭВМ. Исходные данные приведены в таблице 4.1:
Таблица 4.1 - Исходные данные
C |
K |
I |
m |
n |
0,105 |
0,6 |
0,8 |
0,4 |
1,9 |
Таблица 4.2- Данные
D, мм d, мм b, мм μ, Н P, кг/м Pтв,
кг/м3
Р., кВт
1650 1,5 100 0,03 1830 2350 3
4.1 Расчет оптимального диаметра лопаток и числа оборотов мешалки.
Для расчета определяющего числа оборотов мешалки находим значение критерия Рейнольдса по формуле:
Rem
= = C∙ GA
h
∙( ρтв
/ ρ )l
( dч
/ d )m
( D / d )n
; (4.1)
Где: GA
= - критерий Галилея;
dч
- диаметр твердой частицы;
Ρтв
- плотность твердой фазы;
Значения коэффициента С и показателей степеней в уравнении (4.1) приводятся
ниже.
С= 0,105; k= 0.6; C= 0.8; m= 0.4; n= 1.9; (4.2)
Для расчета, определяющего числа оборотов n0
мешалки находим значения безразмерных величин, входящих в правую часть уравнения (4.1)

GA
= = = ;
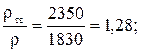 ; 
Rem
= 0.105(3650,3∙107
d3
)0.6
∙(1,28)0.8
( )0.4
∙( )1.9
=53446,88∙d-0.5
;
Рассчитываем определяющее число оборотов мешалки :
n0
= 
d=400мм. = 0,4 м.
n0
== = 8.6585 об
/сек
= 519.51 об
/мин.
Rem
=53446,88∙ 0.4-0.5
= 84506.946=>С= 0,27
fd
= ( )0.93
= 1,345
fn
= 1;
C1
= 0,27∙1,345∙1= 0,363;
NP
=0,363∙0.45
∙8,65853
∙1830= 4415,559 Вт.
Nдв
= = 5,887 кВт.
d= 500мм.= 0,5м.
n0
= = 4,965 об/с
= 297,9 об
/мин.
Rem
= 53446,88∙(0,5)-0,5
= 75585,3 =>С= 0.29;
С1
= С∙f0
∙fn
∙fd
;
fn
= 1;
fd
= ( )0.93
= 1,09268
С1
=0.31∙1,09268∙1= 0,33873;
NP
= C1
d5
n3
ρ
NP
= 0,33873∙0.55
∙4,9653
∙1830= 2370,8961 Вт.
Nдв
= = 3,161 kВт.
d= 600мм.= 0,6м.
n0
= = 3,142 об
/сек
= 188,52 об
/мин.
Rem
= 53446.88∙(0,6)-0,5
= 68999.6014=>С= 0,3;
С1
= С∙f0
∙fn
∙fd
; fn
= 1;
fd
= ( )0.93
= 0,922266
С1
= = 0,27667
NP
= C1
d5
П3
ρ
NP
=0,27667∙0,65
∙ 3,1423
∙1830= 1446,8876Вт.
Nдв
= = 1,9292 kВт
5. Программа расчета
programturb;
varr,Rtv,rr,d,dtv,Diam,dd,ddl:real;
Po,m,Ga,Rem,no,fd,c,cl,N,P:real;
BEGIN {Ввод данных} Writeln(' Введите дaH~e:');
Writе('Диаметраппарата D=');Read(Diam);
Writе('Диаметртвердыхчастиц dч=');Rеаd(dtv);
Writе('Плотность жидкости p=');Read(r);
Writе('Плотность твердой фазы PTB=');Read(Rtv);
Writе('Вязкость жидкости m=');Read(m);
Writе('Мощность двигателя P=');Readln(Po);
d:=O.l; {Расчет} REPEAT GA:=exp(3*ln(d»*sqr(r)*9.81/sqr(m);
rr:=rtv/r;
dd:=dtv/d;
ddl:=diam/d;
Rem:=O.25*exp(O.57*ln(Ga))*exp(O.37*ln(rr))* exp(O.33*ln(dd))*exp(1.15*ln(ddl));
no:=Rem*m/(sqr(d)*r);
fd:=exp(O.93*ln(ddl/3));
cl:=1.15*fd;
N:=cl*exp(5*ln(d))*exp(3*ln(no))*r;
p:=N*1.2/0.9;
Wri teln ( , При диаметре лопастей d= " d: 1 : 1,' м');
Writе('Число оборотов no= ',no:3:2,' об/с ');
Writеlп('Мощность двигателя Р= ',р:3:0,' Вт');
Writeln;
d:=d+O.l;
Until (р<Ро);
end.
Мощность двигателя Р=: 3,161 Вт
Число оборотов no=: 4,965 об/с
6. Охрана труда и окружающей среды
С развитием цивилизации перед охраной труда встают все новые и новые вопросы, в частности проблема сохранения человеческого здоровья на производстве. В процессе труда на человека кратковременно или длительно воздействуют вредные фaктopы. Результатом их отрицательных воздействий могут явиться профессиональные заболевания. Появление профессиональных вредностей связано с нерациональной организацией трудовых процессов или с неблагоприятными условиями окружающей среды. Для отдельных групп профессий характерны определенные соответствующие им заболевания.
Рассмотрим характерные вредные факторы, возникающие на производстве.
Звук или шум возникает при механических колебаниях в твердых, жидких и газообразных средах. Шумом являются различные звуки, мешающие нормальной деятельности человека и вызывающие неприятные ощущения. Установлено, что длительное воздействие шума вызывает в организме различные неблагоприятные для здоровья изменения. Объективно действие шума проявляется в виде повышения кровяного давления, учащенного пульса и дыхания, снижения остроты слуха, ослабления внимания, некоторые нарушения координации движения, снижения работоспособности. Субъективно действие шума может выражаться в виде головной боли, головокружения, бессонницы, общей слабости.
Разработка мероприятий по борьбе с шумом начинается на стадии проектирования технологических процессов и машин, разработки плана
производственного помещения. Этими мероприятиями могут быть: уменьшение шума в источнике возникновения; снижение шума на путях его распространения; совершенствование технологических процессов и машин.
Уменьшение шума в источнике возникновения является наиболее эффективным и экономичным. В каждой машине (электродвигатель) в результате колебаний, как всей машины, так и составляющих ее деталей (зубчатых передач, подшипников, валов шестерен) возникают шумы механического, аэродинамического и электромагнитного происхождения.
При работе различных механизмов снизить шум на 5... 1 О ДБ можно путем: устранения зазоров в зубчатых передачах и соединениях деталей с подшипниками; применения глобоидных и шевронных соединений; широкого использования пластмассовых деталей.
Вибрация возникает при работе машин для приготовления, распределения и уплотнения бетонной смеси, бетоносмесителей, дозаторных установок, компрессоров, и др. строительных машин. Низкочастотные вибрации вызываются инерционными силами, силами трения, периодическими рабочими нагрузками. Высокочастотные вибрации возникают в результате ударов из-за наличия зазоров в соединениях механизмов, ударов в зубчатых и цепных передачах, соударений в подшипниках качения. Вибрация так же, как и шум приводит К снижению производительности труда, виброболезни, ухудшению самочувствия.
Методы уменьшения вредных вибраций от работающего оборудования
можно разделить на две основные группы:
1) методы, основанные на уменьшении интенсивности возбуждающих сил в источнике их возникновения;
2) методы ослабления вибрации на путях их распространения через опорные связи от источника к другим машинам и строительным конструкциям. Если не удается уменьшить вибрацию в источнике или вибрация является необходимым технологическим компонентом, то ослабление вибрации достигается применением виброизоляции, виброгасящих оснований, динамических гасителей вибрации.
Пыль - это мельчайшие твердые частицы, способные некоторое время
находиться в воздухе во взвешенном состоянии. Пыль характеризуется
химическим составом, размером и формой частиц, их плотностью, электрическими, магнитными и другими свойствами.
Пыль представляет собой гигиеническую вредность, так как она отрицательно влияет на организм человека. Помимо этого пыль ухудшает видимость в цехах, повышает абразивный износ трущихся изделий машин и механизмов.
В зависимости от состава пыли изменяется ее вредность. Особую опасность представляет диоксид кремния Si02, который вызывает такое заболевание, как силикоз.
Основными способами защиты от пыли на производстве являются: максимальная механизация, модернизация и автоматизация производственных процессов; применение герметического оборудования для транспортировки материалов; использование увлажненных сыпучих материалов; применение эффективных аспирационных установок; тщательная и систематическая пылеуборка помещений с помощью современных средств; применение в качестве средств индивидуальной защиты респираторов, очков, противопыльной спецодежды. Для очистки воздуха применяют пылеуловители, воздухоочистители, фильтры, пылеосадительные камеры, центробежные пылеосадители- циклоны.
Производственное освещение это система устройств и мер, обеспечивающая благоприятную работу зрения человека и исключающая вредное или опасное влияние на него в процессе труда. При неудовлетворительной освещенности ухудшаются условия для осуществления зрительных функций и жизнедеятельности организма: появляются утомление, глазные болезни, головные боли, что может быть причиной несчастных случаев. Плохо освещенные опасные зоны, слепящие прожекторы и лампы, блики от них, резкие тени ухудшают или вызывают полную потерю ориентации работающих. Основные требования, предъявляемые соответствие освещенности характеру к производственному зрительной работы, освещению: достаточно равномерное распределение яркости на рабочей поверхности, отсутствие резких теней на рабочих поверхностях, отсутствие блесткости, постоянство освещенности во времени, обеспечение электро-, взрыво- и пожаробезопасности, экономичность. Эти требования могут быть соблюдены при правильном выборе типа и системы производственного освещения, которые подразделяются на естественное (дневной свет), искусственное (электрические источники), смешанное (естественное дополняется искусственным).
Выбор источника света зависит от освещаемого предмета и площади освещения. На заводах железобетонных конструкций и строительных материалов должны использоваться лампы накаливания типа ЛН, а также люминесцентные лампы типа ЛЛ, ДР Л, ДРИ.
Электробезопасность это система организационных и технических мероприятий, обеспечивающих защиту людей от поражения электрическим током.
Опасность эксплуатации электроустановок определяется тем, что токоведущие проводники (или корпуса машин, оказавшиеся под напряжением в результате повреждения изоляции) не подают сигналов опасности, на которые реагирует человек. Реакция на электрический ток возникает лишь после его прохождения через ткани человека.
Среди технических способов, обеспечивающих электробезопасность можно выделить изоляцию токоведущих частей или ограждение неизолированных токоведущих частей и расположение их на недоступной высоте; зануление, защитное заземление, защитное отключение; применения малого напряжения, блокировочных устройств, электрического разделения сетей.
Таким образом, можно сделать вывод о том, что вопрос охраны труда является одним из важнейших на современном этапе жизни нашего общества.
Список использованных источников
1. Плановский А.Н. Процессы и аппараты химической технологии. - М.:
Химия 1968.
2. Дроздов Н.Е. Журавлев М.И. Механическое оборудование заводов сборного железобетона. - М.: Стройиздат, 1975. - 302 с.
3. Касаткин А.г. Основные процессы и аппараты химической технологии. М.: Химия 1973.
4. Бауман В.А. Клушанцев Б.В. Мартынов В.Д. Механическое оборудование предприятий строительных материалов изделий и конструкций. - М.:
Машиностроение. 1975. - 351 с.
5. Пчелинцев В.А., Коптев Д.В. Орлов Г-Г. Охрана труда в строительстве. М.: Высш. шк., 1991. - 272 с.
6. ГОСТ 2.105-95 Общие требования к текстовым документам. - М:
Стандарт. - введено 1.07.96. - 10 с.
|