
Кафедра “Управление качеством, стандартизация и метрология”
Курсовая работа
по дисциплине
«Экономика качества, стандартизации и сертификации»
Тема: «Расчет и анализ затрат, связанных с качеством в процессах разработки и изготовления изделия «Домкрат» в условиях мелкосерийного производства на ФГУП “192 центральный завод железнодорожной техники”»
Руководитель: к.т.н. доц. Ефимова Г.В.
«___»__________2009 г.
___________
Студент группы 05-СТС: Жиденко А.В.
«___»__________2009 г.
_____________
Брянск 2009 г.
Содержание
Введение. 3
1.Краткая характеристика ФГУП «192 ЦЗЖТ». 3
2. Функциональная модель процесса изготовления «Домкрат». 3
3. Сведения о численности, доле участия в процессе и заработной плате исполнителей процессов. 3
4. Классификация и расчет затрат, связанных с качеством в процессах3
5. Анализ данных о затратах, связанных с качеством... 3
5.1 Анализ суммарных затрат на качество в процессе. 3
5.2 Анализ затрат на качество в сравнении с показателями бизнеса. 3
5.3 Анализ доли затрат на качество в затратах на процесс. 3
5.4 Анализ баланса затрат на соответствие и несоответствие качества.3
5.5 Анализ структуры затрат на качество по категориям.. 3
5.6 Анализ «дефектного» процесса. 3
6. Рекомендации по улучшению деятельности.. 3
Само понятие "экономика качества" (economics of quality) внесло определенные противоречия в систему деловых и экономических ценностей, которыми оперируют менеджеры по качеству. Некоторые из них убеждены в том, что нет никакой самостоятельной "экономики качества", поскольку ни один экономист не станет игнорировать качество продукции. Присутствует и другая, альтернативная точка зрения, согласно которой достижение абсолютного качества представляется экономически невозможным. Менеджеры, придерживающиеся таких взглядов, считают себя свободными в принятии решений относительно допустимого уровня качества продукции или услуг и по собственному усмотрению обозначают этот уровень термином "приемлемое или достаточное качество". Принятие любого из этих крайних взглядов может создать определенные проблемы для менеджмента, но настоящая проблема возникает в тех случаях, когда менеджеры, работающие в одной команде, придерживаются различных точек зрения на проблемы качества. В этом случае можно с уверенностью сказать, что качество никогда не сыграет своей оптимизирующей роли в достижении деловых целей компании.
Понятие "цена качества" (cost of quality)*, имеющее прямое отношение к экономике качества, независимо от точек зрения разных специалистов на эту проблему, тоже относится к числу терминов, вызывающих неизбежные споры. В основных выводах Национальной конференции по качеству (1982 г.) утверждалось, что само словосочетание "цена качества" недопустимо, поскольку качество должно приносить прибыль, а не создавать лишние расходы. Некоторые специалисты, включая X. Дж. Харрингтона (Н. J. Harrington) и Фрэнка М. Грайна (Frank M. Gryna), предпочитают применять такие термины, как "цена низкого качества" или "издержки, обусловленные низким качеством". Министерство обороны США употребляет термин "расходы, связанные с качеством". Но независимо от применяемой терминологии стоит всегда помнить о том, что цена качества не сводится только к организационным расходам на его обеспечение.
Чтобы с самого начала прояснить существо дела, следует напомнить содержание понятий "менеджмент качества" и "цена качества". Реальная ценность любой программы качества определяется ее способностью удовлетворить потребителей продукции и принести прибыль предприятию. Регулирование затрат, связанных с качеством, служит для менеджмента инструментом, позволяющим решать задачи повышения качества продукции с учетом обеспечения требуемой прибыльности работы компании.
При разработке концепции "цены качества" следует четко различать затраты, связанные с качеством, и расходы, обусловленные организацией работ по обеспечению качества. Недопустимо сводить цену качества исключительно к затратам, связанным с осуществлением функций менеджмента качества. В принципе любые переделки уже выполненной работы влекут увеличение цены качества. Очевидные примеры таких переделок - исправление дефектных изделий, повторные испытания собранной продукции, перенастройка оборудования или изменение банковских обязательств. В сфере услуг подобными очевидными примерами служат переделки уже предоставленных услуг, например, переоформление договора о предоставлении займа в банке или замена поданных по заказу блюд в ресторане. Не столь явными примерами переделок могут показаться повторные закупки материалов взамен бракованных, реагирование на претензии потребителей или внесение конструктивных изменений в продукцию для устранения выявленных недостатков. Тем не менее в цену качества входят любые расходы, которых можно было бы избежать при условии идеального качества продукции или услуг.
Практически любые нарушения любого функционального подразделения компании могут стать причиной переделок уже произведенной продукции или предоставленной услуги, следовательно, и соответствующих дополнительных расходов. В этом - существо той составляющей цены качества, которую называют "потерями от дефектов" (failure cost).
Утилизация или переделки дефектной продукции - это общепринятые понятия в компаниях, занятых в сфере производства. Более того, соответствующие расходы даже планируются многими из них. Аналогичный феномен присутствует и в индустрии услуг, хотя для его обозначения там иногда применяется другая терминология. Могут, например, переписываться условия страховки, переделываться или чиниться сшитая на заказ одежда, поданные в ресторане блюда могут возвращаться обратно на кухню, может теряться багаж пассажиров, номера в отеле оказываются не подготовленными к приему гостей и т.д. Иными словами, в компаниях, работающих в сфере услуг, могут присутствовать затраты, эквивалентные издержкам от дефектов в сфере производства и представляющие собой ту долю операционных расходов, которая обусловлена несоответствием предоставляемых услуг действующим стандартам.
Проще говоря, затраты, связанные с качеством, служат измерителями экономических последствий, вызванных выполнением или невыполнением требований к качеству производимой продукции или оказываемых услуг, включая их соответствие внутренним требованиям компании и ее обязательствам перед потребителями и обществом в целом.
Выявление и анализ затрат, связанных с качеством в процессах разработки и изготовления «Домкрат» в условиях мелкосерийного производства на ФГУП 192 «ЦЗЖТ»является целью выполнения данной курсовой работы. Для ее достижения необходимо сделать следующее:
- построить функциональную модель процессов в методологии IDEF0;
- определить численность, долю участия в процессах и заработную плату исполнителей процессов;
- проанализировать суммарные затраты на качество в подразделении, и провести сравнение по показателям бизнеса;
- выполнить сравнительный анализ затрат на качество в процессах на основе структуры затрат и баланса затрат «на соответствие/несоответствие»
- выявить наиболее «дефектный» процесс и провести его анализ;
- сделать выводы и предложить рекомендации по улучшению деятельности.
Федеральному государственному унитарному предприятию «192 Центральный завод железнодорожной техники» в 2009 году исполняется 90 лет. Завод ведет свою историю с августа 1919 года, когда на базе бывшего Второго коренного парка царской армии был сформирован Третий коренной железнодорожный парк, вошедший в состав РКК А.
В настоящее время завод является единственным предприятием в системе Железнодорожных войск РФ, выпускающим высокопроизводительную технику для сборки и укладки железнодорожного полотна, строительства мостов, погружения свай.
За эти годы завод освоил много образцов военной техники для Железнодорожных войск и народного хозяйства. Путевые машины ПРМ-РМ, ВПРМ-Г, звеносборочные стенды ЗС-500, ЗС-500М, путеукладчики ПБ-3М, краны сборно-разборные СРК-20, СРК-50М, СРК-70 поступают на вооружение, хорошо зарекомендовали себя в работе. Трубчатые и штанговые молоты с ударной массой от 1,25 до 3,0 тонны широко применяются не только в войсках, но и в народном хозяйстве. Изготовленная по заказу гражданских железнодорожников полуавтоматическая звеносборочная линия ЗЛЖ для сборки звеньев железнодорожного пути на железобетонных шпалах оснащена гидравлическим оборудованием, решетку она может собирать с различными видами крепления. После успешного проведения испытаний завод приступил к серийному изготовлению наплавного железнодорожного моста-ленты МЛЖ-ВТ.
Завод постоянно участвует в различных выставках, на которых его продукция получает достойную оценку. За высокие показатели в работе в течение многих лет заводу присуждаются дипломы и переходные вымпелы Военного совета Железнодорожных войск. Лучшие специалисты – передовики производства отмечены правительственными и ведомственными наградами. Завод плодотворно сотрудничает с предприятиями ближнего и дальнего зарубежья. Заключаются контракты с фирмой «Жейсмар» (Франция) и Республикой Беларусь.
Получаемая заводом прибыль позволяет производить техническое перевооружение и поддерживать имеющиеся мощности в работоспособном состоянии. В 2008 году на эти цели направлено более 15 млн. рублей.
На заводе организована и постоянно ведется работа по обучению молодых рабочих, а также повышению квалификации и получению смежных дефицитных профессий.
Значительно расширились социальные блага для работников, предусмотренные коллективным договором. Большое внимание уделяется на заводе материальному и моральному поощрению работников.
Все это в целом позволяет решать сложные задачи, стоящие перед коллективом завода, воспитывает высокое чувство гордости за свое предприятие.
SADT
– модель изготовления «Домкрат»
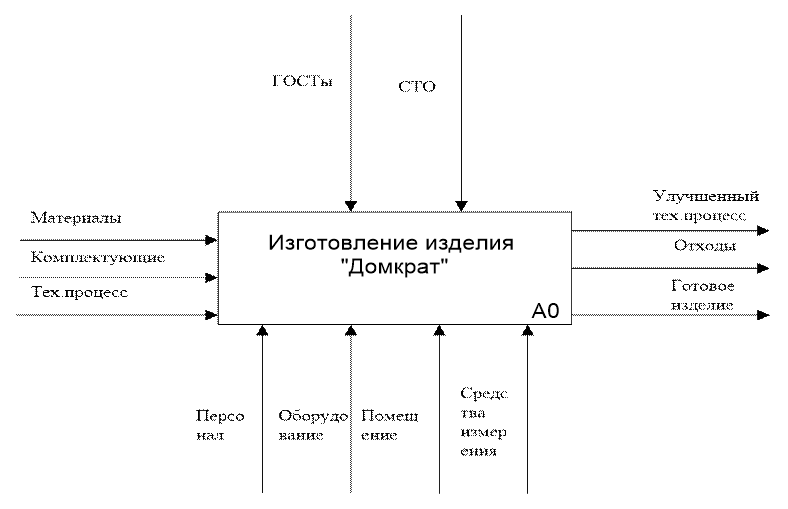
Второй уровень декомпозиции
SADT
– модели разработки и изготовления «Домкрат»
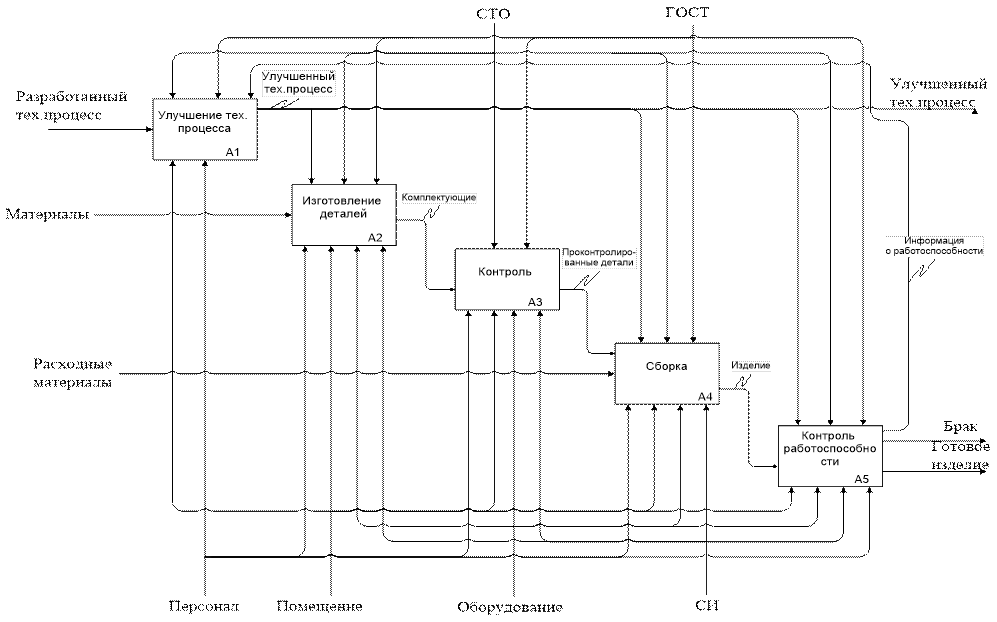
В представленных ниже таблицах собраны данные об исполнителях принимающих непосредственное участие разработки и изготовления изделия «Домкрат» в условиях мелкосерийного производства на ФГУП «192 ЦЗЖТ»
Таблица 1
А1 «Улучшение тех.процесса»
Должность |
Численность,
чел.
|
Доля участия в
процессе, %
|
Заработная
плата одного
исполнителя,
руб.
|
Календарная
трудоемкость
исполнителей в
данном процессе, чел.-дн./ мес.
|
Заработная плата в процессе, руб. |
Зам. ген. директора по финансам |
1 |
10 |
33000 |
22*0,10 = 2,2 |
0,1*33000 = 3300 |
Главный инженер |
1 |
15 |
23000 |
22*0,15 = 3,3 |
0,15*23000 = 3450 |
Бухгалтер |
1 |
15 |
21000 |
22*0,15 = 3,3 |
0,15*21000 = 3150 |
Инженер по подготовке производства |
2 |
20 |
14000 |
2*(22*0,20) = 8,8 |
2*(0,2*14000) = 5600 |
Начальник цеха |
1 |
25 |
14000 |
22*0,25 = 5,5 |
0,25*14000 = 3500 |
Технолог |
2 |
50 |
13000 |
2*(22*0,5) = 22 |
2*(0,5*13000) = 13000 |
Нормировщик труда |
1 |
15 |
10000 |
22*0,15 = 3,3 |
0,15*10000 = 1500 |
Уборщица |
1 |
10 |
4200 |
22*0,10 = 2,2 |
0,1*4200 = 420 |
Итого по процессу
|
10
|
50,6
|
33920
|
Таблица 2
А2 «Изготовление деталей»
Должность |
Численость,
чел.
|
Доля участия в
процессе, %
|
Заработная
плата одного
исполнителя,
руб.
|
Календарная
трудоемкость
исполнителей в
данном процессе, чел.-дн./ мес.
|
Заработная плата в процессе, руб. |
Нач. цеха |
1 |
20 |
14000 |
4,4 |
2800 |
Зам. нач. цеха |
1 |
25 |
13000 |
5,5 |
3250 |
Мастер |
2 |
70 |
12000 |
30,8 |
16800 |
Токарь |
2 |
100 |
12000 |
44 |
24000 |
Фрезеровщик |
3 |
60 |
12000 |
39,6 |
21600 |
Слесарь |
4 |
60 |
12000 |
52,8 |
28800 |
Закальщик |
1 |
40 |
12000 |
8,8 |
4800 |
Уборщица |
1 |
30 |
4200 |
6,6 |
1260 |
Итого по процессу
|
15
|
192,5
|
103310
|
Таблица 3
А3 «Контроль»
Должность |
Численность,
чел.
|
Доля участия в
процессе, %
|
Заработная
плата одного
исполнителя,
руб.
|
Календарная
трудоемкость
исполнителей в
данном процессе, чел.-дн./ мес.
|
Заработная плата в процессе, руб. |
Зам. начальника цеха |
1 |
5 |
13000 |
0,05*22=1,1 |
650 |
Мастер |
2 |
10 |
12000 |
2*0,1*22=4,4 |
2400 |
Контролер ОТК |
2 |
100 |
7000 |
3*1,0*22=66 |
14000 |
Уборщица |
1 |
10 |
4200 |
0,1*22=2,2 |
420 |
Итого по процессу
|
6
|
73,7
|
17470
|
Таблица 4
А4 «Сборка»
Должность |
Численность,
чел.
|
Доля участия в
процессе, %
|
Заработная
плата одного
исполнителя,
руб.
|
Календарная
трудоемкость
исполнителей в
данном процессе, чел.-дн./ мес.
|
Заработная плата в процессе, руб. |
Нач. цеха |
1 |
20 |
14000 |
0,2*22=4,4 |
2800 |
Зам. нач. цеха |
1 |
25 |
13000 |
0,25*22=5,5 |
3250 |
Мастер |
2 |
20 |
12000 |
2*0,2*22=8,8 |
2400 |
Слесарь-сборщик |
3 |
100 |
12000 |
3*1,0*22=66 |
36000 |
Грузчик |
1 |
50 |
6000 |
0,5*22=11 |
3000 |
Уборщица |
1 |
20 |
4200 |
0,2*22=4,4 |
840 |
Итого по процессу
|
9
|
100,1
|
48290
|
Таблица 5
А5 «Контроль работоспособности»
Должность |
Численность,
чел.
|
Доля участия в
процессе, %
|
Заработная
плата одного
исполнителя,
руб.
|
Календарная
трудоемкость
исполнителей в
данном процессе, чел.-дн./ мес.
|
Заработная плата в процессе, руб. |
Мастер |
2 |
10 |
12000 |
2*0,1*22=4,4 |
2400 |
Контролер ОТК |
2 |
100 |
7000 |
3*1,0*22=66 |
14000 |
Уборщица |
1 |
10 |
4200 |
0,1*22=2,2 |
420 |
Итого по процессу
|
5
|
72,6
|
16820
|
В приведенных ниже таблицах 6 – 10 представлены данные о классификации затрат на качество по элементам PAF-модели.
Затраты на качество по j
-му виду работ в i
-той категории определяются по формуле:
,
где – трудоемкость по j
-му виду работ в i
-той категории, чел.-дн./мес.;
– календарная трудоемкость, чел.-дн./мес.;
– заработная плата в исследуемом подпроцессе, руб.
Кроме затрат, связанных с трудоемкостью исполнителей, в таблицах также представлены абсолютные финансовые затраты по некоторым показателям (материалы израсходованные на контроль и испытания, стоимость брака), полученные по результатам опроса сотрудников экономического отдела ФГУП “192 ЦЗЖТ”
Таблица 6
Исходные данные о трудоемкости и затратах на подпроцесс:
А1 «Улучшение тех.процесса»
Наименование категории затрат |
Трудоемкость, чел.- дн. |
Затраты, руб. |
1
|
2
|
3
|
1.Предупредительные затраты |
1.1 Разработка и внедрение мероприятий по СМК, СТО, программ повышения качества, плана качества |
2,5 |
1675,9 |
1.2 Аудит СМК |
1 |
670,36 |
1.3 Ознакомление с новыми технологиями |
0,2 |
134,07 |
1.4 Участие в совершенствовании действующих технологических процессов и производственных графиков |
1,5 |
1005,54 |
1.5 Участие в совещаниях "День качества" и подготовка к нему необходимых данных |
0,2 |
134,07 |
Продолжение таблицы 6
1
|
2
|
3
|
1.6 Прохождение обучения (в т.ч. По СМК), повышение квалификации |
1 |
670,36 |
1.7 Проведение анализа качества процессов и рассмотрение предложений, касающихся улучшения |
0,5 |
335,18 |
1.8 Проведение анализа качества процессов и рассмотрение предложений, касающихся улучшения |
0,2 |
134,07 |
1.9 Сбор исходных данных по показателям процессов, о затратах на качество, заполнение отчетности для анализа. |
0,9 |
603,32 |
Итого предупредительные затраты |
8 |
5362,86 |
2. Затраты на оценку и контроль качества |
2.1 Контроль соблюдения технологических процессов, выявление и устранение причины их нарушения. |
1 |
670,36 |
2.2 Контроль за выполнением плановых показателей |
0,1 |
67,03 |
2.3 Контроль за расходованием средств |
1 |
670,36 |
2.4 Испытание изготовленной оснастки и смонтированного (отремонтированного) оборудования |
0,5 |
134,07 |
Итого затраты на оценку и контроль качества |
2,3 |
1742,93 |
3. Внутренние потери от дефектов |
3.1 Поиск источника возникновения брака |
0,7 |
469,25 |
3.2 Выявление виновников брака, выяснение причин отклонения от технической документации |
0,2 |
134,07 |
3.3 Анализ причин и продолжительности простоев |
0,7 |
469,25 |
3.4 Разрешение внутренних конфликтных ситуаций |
0,2 |
134,07 |
3.5 Перепроверка информации в отчетной документации |
0,3 |
201,11 |
3.6 Анализ причин отсутствия комплектующих и материалов на рабочем месте |
0,2 |
134,07 |
3.7 Урегулирование спорных вопросов со службами завода |
1 |
670,36 |
3.8 Перепроверка информации в отчетной документации |
0,5 |
335,18 |
Итого внутренние потери |
3,8 |
2547,36 |
4. Внешние потери |
4.1 Рассмотрение претензий потребителей |
1,5 |
1005,54 |
4.2 Доработка продукции, отличающейся
1 |
0,8
2
|
536,29
3
|
характеристиками от требований потребителя. |
Итого внешние потери |
2,3 |
1541,83 |
Затраты на качество
|
16,4 |
10993,9 |
Затраты на нормальное функционирование процесса |
34,2 |
22926,10 |
Итого затраты на нормальное функционирование
|
34,2 |
22926,10 |
ИТОГО на процесс
|
50,6 |
33920 |
Таблица 7
Исходные данные о трудоемкости и затратах на подпроцесс:
А2 «Изготовление деталей»
Наименование категории затрат |
Трудоемкость, чел.-дн. |
Затраты, руб. |
1
|
2
|
3
|
1.Предупредительные затраты |
1.1 Аудит СМК |
0,5 |
268,34 |
1.2 Ознакомление с новыми технологиями |
0,2 |
107,34 |
1.3 Участие в совершенствовании действующих технологических процессов и производственных графиков |
0,1 |
53,67 |
1.4 Участие в совещаниях "День качества" и подготовка к нему необходимых данных |
0,1 |
53,67 |
1.5 Прохождение обучения, повышение квалификации |
3 |
1610,04 |
1.6 Проведение работ по аттестации персонала и рабочих мест |
0,3 |
161,01 |
1.7 Осуществление производственного инструктажа рабочих (в т.ч. по предупреждению брака) |
0,1 |
53,67 |
1.8 Проверка оснастки и оборудования до начала работы |
0,8 |
429,34 |
Итого предупредительные затраты |
5,1 |
2737,08 |
2. Затраты на оценку и контроль качества |
1 |
2 |
3 |
2.1 Входной контроль материалов и покупных изделий |
2 |
1073,36 |
2.2 Контроль соблюдения технологических процессов, выявление и устранение причины их нарушения |
0,3 |
161,01 |
2.3 Контроль за обеспечением производства материалами и покупными изделиями |
1,5 |
805,02 |
2.4 Испытание изготовленной оснастки и отремонтированного оборудования |
2 |
1073,36 |
2.5 Контроль наличия технологической, рабочей, нормативной документации на рабочих местах |
0,3 |
161,01 |
2.6 Инвентаризация инструмента и материалов. |
2 |
1169,86 |
2.7 Проведение периодических контрольных проверок, например «летучего контроля».
|
0,1 |
53,67 |
2.8 Проверка режима работ и распорядка |
0,2 |
107,34 |
Итого затраты на оценку и контроль качества |
8,4 |
4604.63 |
3. Внутренние потери от дефектов |
3.1 Поиск источника возникновения брака |
0,7 |
375,67 |
3.2 Выявление виновников брака, выяснение причин отклонений от технической документации. |
0,2 |
107,34 |
3.3 Выход из строя оснастки, механизмов и оборудования (в т.ч. компьютерного), вызов ремонтных служб и оценка дальнейшей работы |
3 |
1610,04 |
3.4 Дополнительная работа в связи с изменением плана |
0,5 |
268,34 |
3.5 Разрешение внутренних конфликтных ситуаций |
0,2 |
107,34 |
3.6 Доработка документации, выданной инженерными службами |
4 |
2146.72 |
Итого внутренние потери |
8,6 |
4597,45 |
4. Внешние потери |
0 |
0 |
Итого внешние потери |
0 |
0 |
Затраты на качество
|
22,2 |
11939,16 |
1 |
2 |
3 |
Затраты на нормальное функционирование процесса |
170,3 |
91370,84 |
Материалы основные, израсходованные на нормальное функционирование |
950000,00 |
Материалы вспомогательные, израсходованные на нормальное функционирование |
54000,00 |
Итого затраты на нормальное функционирование
|
170,3 |
1095370.84 |
ИТОГО на процесс
|
192,5 |
1107309.84 |
 |
Таблица 8
Исходные данные о трудоемкости и затратах на подпроцесс:
«А
3
Контроль»
Наименование категории затрат
|
Трудоемкость, чел.-дн. |
Затраты, руб. |
1 |
2 |
3 |
1.Предупредительные затраты |
1.1 Ознакомление с новыми технологиями |
0,2 |
47,41 |
1.2 Участие в совершенствовании действующих технологических процессов |
0,8 |
189,63 |
1.3 Прохождение обучения, повышение квалификации |
1,6 |
561,24 |
1.4 Проверка оснастки и оборудования до начала работы |
2 |
474,08 |
1.5 Сбор исходных данных по показателям процессов, о затратах на качество, заполнение отчетности для анализа |
0,7 |
165,93 |
Итого предупредительные затраты |
3,7 |
877,06 |
2. Затраты на оценку и контроль качества |
2.1 Контроль и оценка качества деталей |
12 |
2844,50 |
2.2 Операции по оценке качества в процессе производства |
4,6 |
1090,39 |
2.3 Инвентаризация инструмента и материалов |
3 |
711,13 |
2.4 Контроль за правильностью и своевременностью оформления всей необходимой документации
|
1,5 |
355,56 |
Итого затраты на оценку и контроль качества
|
21,1 |
5001,59 |
1 |
2 |
3 |
3. Внутренние потери от дефектов |
3.1 Анализ бракованных изделий, определение мер по устранению |
3 |
711,13 |
3.2 Определение способа устранения дефекта, составление дефектной ведомости. |
1 |
237,04 |
3.3 Поиск источника возникновения брака. |
0,8 |
189,63 |
3.4 Выявление виновников брака, выяснение причин отклонений от технической документации. |
0,3 |
71,11 |
3.5 Пересмотр требований по качеству для изделий в отношении которых эти требования не выдерживаются |
0,6 |
142,23 |
3.6 Разрешение внутренних конфликтных ситуаций |
0,6 |
142,23 |
Итого внутренние потери |
6,3 |
1493,36 |
4. Внешние потери |
4.1 Расследование причин грубых ошибок контроля |
0,4 |
94,82 |
Итого внешние потери |
0,4 |
94,82 |
Затраты на качество
|
31,5 |
7466,82 |
ИТОГО на процесс
|
73,7 |
17470 |
Таблица 9
Исходные данные о трудоемкости и затратах на подпроцесс:
«А4 Сборка»
Наименование категории затрат |
Трудоемкость, чел.-дн. |
Затраты, руб. |
1.Предупредительные затраты |
1.1 Ознакомление с новыми технологиями |
0,6 |
289,45 |
1.2 Участие в совещаниях "День качества" и подготовка к нему необходимых данных |
0,2 |
96,49 |
1.2 Прохождение обучения, повышение квалификации |
0,4 |
192,97 |
1.3 Проведение работ по аттестации персонала и рабочих мест |
1 |
482,42 |
1.4 Осуществление производственного инструктажа рабочих |
0,6 |
289,45 |
1 |
2 |
3 |
1.5 Проверка оснастки и оборудования до начала работы |
1,0 |
463,12 |
Итого предупредительные затраты |
3,8 |
1833,19 |
2. Затраты на оценку и контроль качества |
2.1 Контроль за обеспечением производства материалами и покупными изделиями |
1 |
482,42 |
2.2 Контроль соблюдения технологических процессов, выявление и устранение причины их нарушения. |
3,5 |
1688,46 |
2.3 Проверка режима работ и распорядка |
0,2 |
96,48 |
2.4 Прочие действия, направленные на оценку и контроль качества. |
0,4 |
192,97 |
Итого затраты на оценку и контроль качества |
5,1 |
2460,33 |
3. Внутренние потери от дефектов |
3.1 Повторное выполнение сделанной работы |
3 |
1447,25 |
3.2 Выход из строя оснастки, механизмов и оборудования (в т.ч. компьютерного), вызов ремонтных служб и оценка дальнейшей работы |
2 |
964,84 |
3.3 Дополнительная работа в связи с изменением плана |
0,2 |
96,48 |
3.4 Разрешение внутренних конфликтных ситуаций |
0,5 |
241,21 |
Итого внутренние потери |
5,7 |
2749,78 |
4. Внешние потери |
Итого внешние потери |
0 |
0,00 |
Затраты на качество
|
14,6 |
7043,3 |
Затраты на нормальное функционирование процесса |
85,5 |
41246,7 |
Полуфабрикаты собственного производства, израсходованные на нормальное функционирование |
120000 |
Покупные изделия, израсходованные на нормальное функционирование |
53000 |
Итого затраты на нормальное функционирование
|
85,5 |
214246,7 |
ИТОГО на процесс
|
100,1 |
221290 |
Таблица 10
Исходные данные о трудоемкости и затратах на подпроцесс:
«А5 Контроль работоспособности»
Наименование категории затрат |
Трудоемкость, чел.-дн. |
Затраты, руб. |
1.Предупредительные затраты |
1.1 Участие в совещаниях "День качества" и подготовка к нему необходимых данных |
0,6 |
139,01 |
1.2 Прохождение обучения, повышение квалификации |
0,4 |
92,67 |
1.3 Проведение работ по аттестации персонала и рабочих мест |
1 |
231,68 |
1.4 Осуществление производственного инструктажа рабочих |
1,8 |
417,03 |
Итого предупредительные затраты |
3,8 |
880,39 |
2. Затраты на оценку и контроль качества |
2.1 Инвентаризация инструмента и материалов |
1 |
231,68 |
2.2 Контроль и оценка качества готовой продукции |
3,5 |
810,88 |
2.3 Проверка режима работ и распорядка |
0,2 |
46,34 |
2.4 Контроль наличия технологической, рабочей, нормативной документации на рабочих местах |
0,4 |
92,67 |
Итого затраты на оценку и контроль качества |
5,1 |
1181,57 |
3. Внутренние потери от дефектов |
3.1 Повторное выполнение сделанной работы (в т.ч. повторное оформление документации) |
3 |
695,04 |
3.2 Выход из строя оснастки, механизмов и оборудования (в т.ч. компьютерного), вызов ремонтных служб и оценка дальнейшей работы |
2 |
463,36 |
3.3 Дополнительная работа в связи с изменением плана |
0,2 |
46,34 |
3.4 Позднее начало и раннее окончание работ |
0,5 |
115,84 |
1
|
2 |
3 |
Итого внутренние потери |
5,7 |
1320,58 |
4. Внешние потери |
Итого внешние потери |
0 |
0,00 |
Затраты на качество
|
14,6 |
3382,54 |
Итого затраты на нормальное функционирование
|
63 |
13437,46 |
ИТОГО на процесс
|
77,6 |
16820 |
Для сравнения данных о затратах, связанных с качеством различных подпроцессов и проведения анализа затрат по каждому подпроцессу, заносим полученные данные в сводную таблицу 11.
Таблица 11
«
Сводная таблица по затратам на качество в процессе изготовления «Домкрат» в условиях мелкосерийног производства на ФГУП “192 ЦЗЖТ”»
Наименование процесса |
Затраты на предупреждение |
Затраты на оценку |
Внутренние потери |
Внешние потери |
Затраты на качество |
Затраты на процесс, руб |
Доля затрат на качество в затратах на процесс, % |
руб |
% |
руб |
% |
руб |
% |
руб |
% |
руб |
% |
1 |
2 |
3 |
4 |
5 |
6 |
7 |
8 |
9 |
10 |
11 |
12 |
13 |
Улучшение тех.процесса |
5362,86 |
48,78 |
1742,93 |
15,85 |
2547,36 |
23,17 |
1541,83 |
14 |
10993,9 |
100,00 |
33920 |
32,41 |
Изготовление деталей |
2737,08 |
22,82 |
4604,63 |
38,39 |
4597,45 |
38,33 |
0 |
0 |
11993,9 |
100,00 |
1107309,84 |
1,08 |
Контроль |
877,06 |
11,75 |
5001,59 |
66,98 |
1493,36 |
20 |
94,82 |
1,27 |
7466,82 |
100,00 |
17470 |
42,74 |
Сборка |
1833,19 |
26,02 |
2460,33 |
34,93 |
2749,78 |
39,04 |
0 |
0 |
7043,3 |
100,00 |
221290 |
3,18 |
Контроль работоспособности |
880,39 |
26,02 |
1181,5 |
34,93 |
1320,58 |
39,04 |
0 |
0 |
3382,54 |
100,00 |
16820 |
20,11 |
Итого |
11690,58 |
28,6 |
14990,98 |
36,67 |
12708,53 |
31,09 |
1636,65 |
4 |
40880,46 |
100,00 |
1396809,84 |
2,93 |
Анализируются затраты на качество в целом по процессу подразделения в абсолютном (в рублях) и относительном выражениях (в процентах).
Суммарные затраты на качество в подразделении составляет 40880,46 рублей что составляет 2,93% от общих затрат на процесс. Эта цифра является довольно маленькой, но здесь следует иметь в виду, что цена комплектующих подвергающихся обработке, а потом и сборке, очень большая, в результате чего затраты в сопоставлении с их стоимостью очень малы.
Чтобы соотнести величину затрат на качество с положением дел в подразделении, необходимо затраты на качество сопоставить с показателями бизнеса для данного подразделения.
1. Показатель бизнеса – себестоимость
.
Себестоимость может быть определена как сумма величин оплаты труда, непосредственно затраченного на производство продукции, стоимости материалов и комплектующих, накладных расходов.
В различные периоды времени, на себестоимость могут оказывать влияние следующие факторы:
· автоматизации процессов;
· внедрение новых технологий;
· применение альтернативных материалов;
· смены обслуживающего персонала.
Тем не менее, поскольку в эту категорию вовлечена целая группа затрат, влияние временных изменений не настолько существенно, как если бы в качестве базы измерений был использован только лишь один элемент затрат.
Цеховая себестоимость – руб.
Найдем коэффициент, базирующийся на себестоимости:

В итоге можно сделать вывод что затраты на качество занимают малую долю от себестоимости. А вот достаточна ли эта доля станет ясно из последующих анализов.
Берутся данные о затратах на качество в подпроцессах и о процентах затрат на качество в затратах на процесс и наглядно изображаются в виде графика (рис.1) и столбчатой диаграммы (рис.2) соответственно.
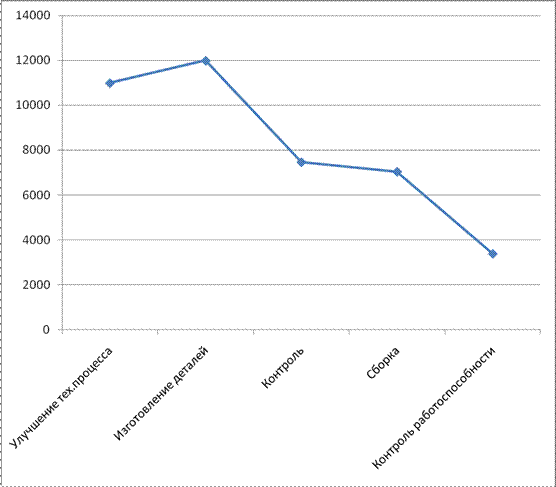
Рис.1 Затраты на качество в процессе «Изготовление деталей»
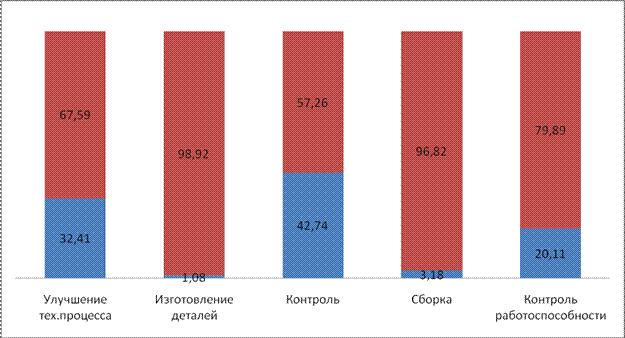
Рис.2 Доля затрат на качество в затратах на процесс «Изготовление деталей»
По результатам данных в сводной таблице, а также посредством графика, можно выявить процесс, на который затрачено больше всего средств на качество. Этим процессом является «Изготовление деталей», но в отношении с общей суммой средств, приходящейся на его функционирование, эта доля является очень маленькой за счет дороговизны сырья. Такая же ситуация наблюдается и в процессе «Сборка», где также применяются дорогостоящие комплектующие. В процессе «Контроль» затраты на качество и нормальное функционирование процесса практически равны. В процессе «Улучшение тех.процесса» затраты на качество составляют 32,41%, что может говорить о том, что изготовление «Домкрат» является очень важным процессом и покупатели заинтересованы в том, чтобы качество выпускаемой продукции отвечало их требованиям, и требуют постоянного улучшения покупаемой продукции.
Затраты на процесс сами по себе не отражают реального положения дел в процессе, для более наглядного сопоставления используется баланс затрат на соответствие и затрат вследствие несоответствия.
В затраты на соответствие входят затраты на предупреждение и оценку, а в затраты вследствие несоответствия входят затраты на внутренние и внешние отказы.
Рассчитывается процентное соотношение между собой затрат на соответствие и вследствие несоответствия качества, эти данные представляются в виде таблицы.
Таблица 12
Баланс затрат на соответствие и несоответствие
Улучшение тех.процесса |
Изготовление деталей |
Контроль |
Сборка |
Контроль работоспособности |
руб |
% |
руб |
% |
руб |
% |
руб |
% |
Затраты на соответствие |
7105,79 |
63,47 |
7341,71 |
61,49 |
5878,65 |
78,73 |
4293,52 |
60,96 |
2061,89 |
60,96 |
Затраты на несоответствие |
4089,19 |
36,53 |
4597,45 |
38,51 |
1588,18 |
21,27 |
2749,78 |
39,04 |
1320,58 |
39,04 |
Итого |
11194,98 |
100,00 |
11939,16 |
100,00 |
7466,83 |
100,00 |
7043,30 |
100,00 |
3382,47 |
100,00 |
Результаты анализа представляем в виде столбчатых диаграмм (рис.3).

Рис. 3 Баланс затрат на соответствие и несоответствие
Исходя из данных сводной таблицы и столбчатой диаграммы видно, что наименьшие затраты на несоответствие имеет процесс «Контроль». Наибольшие затраты в % отношении на несоответствие имеют процессы «Сборка» и «Контроль работоспособности». Самые же большие затраты в денежном эквиваленте принадлежат процессу «Изготовление деталей». Это может объясняться различными факторами, которые будут выявлены в результате построения причинно - следственной диаграммы. В процессе «Контроль» уровень затрат на несоответствие обусловлен высоким уровнем несоответствий в предшествующем процессе «Изготовление деталей».
Данный вид анализа может проводиться как для отдельных подпроцессов, так и для процесса в целом.
Проведем анализ по процессу в целом. Данные для анализа берутся из таблицы 11 «Сводная таблица по затратам на качество».
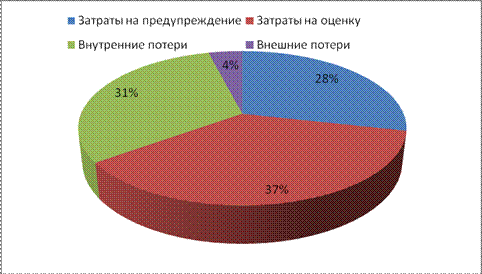
Рис.4 Доля затрат на качество по категориям в процессе «Изготовление изделия домкрат»
Наибольшую часть затрат представляют собой затраты на оценку, что в совокупности с серьезными затратами на предупреждение свели к нулю внутренние потери. Однако внешние потери все еще довольно велики, но являются приемлимыми.
По проведенному сравнительному анализу процессов выбирается процесс для более глубокого анализа.
Для более глубокого анализа выбираем оказавшийся «дефектным» подпроцесс, «Изготовление деталей».
Для анализа данного подпроцесса сравним элементы затрат, входящих в каждую из категорий.
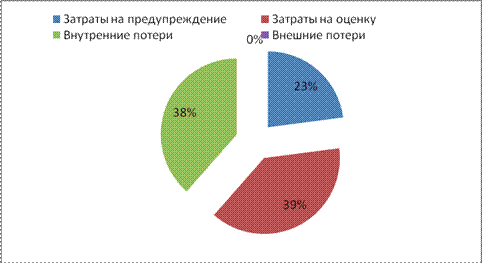
Рис.5 Доля затрат на качество по категориям в «дефектном» процессе
Из круговой диаграммы видно что наибольшую сумму негативных затрат представляют собой затраты на внутренние потери. Необходимо проанализировать все затраты входящие в эту группу и выявить какой же из этих элементов имеет наибольшее негативное влияние.
Таблица 13
«Внутренние потери от дефектов в процесс «Изготовление деталей»
Наименование категории затрат |
Трудоемкость, чел.-дн. |
Затраты, руб. |
Доля во внутренних потерях, % |
1 |
2 |
3 |
4 |
1. Поиск источника возникновения брака |
0,7 |
375,67 |
8,17 |
2. Выявление виновника брака, выяснение причин отклонений от технической документации. |
0,2 |
107,34 |
2,33 |
3. Выход из строя оснастки, механизмов и оборудования |
3 |
1610,04 |
35,02 |
4. Дополнительная работа в связи с изменением плана |
0,5 |
268,34 |
5,84 |
5. Разрешение внутренних конфликтов |
0,2 |
107,34 |
2,33 |
6. Доработка документации, выданной инженерными службами |
4 |
2146,72 |
46,69 |
Итого внутренние потери |
8,6 |
4597,45 |
100,00 |
Представим данные в виде столбчатых диаграмм (рис.6,7).
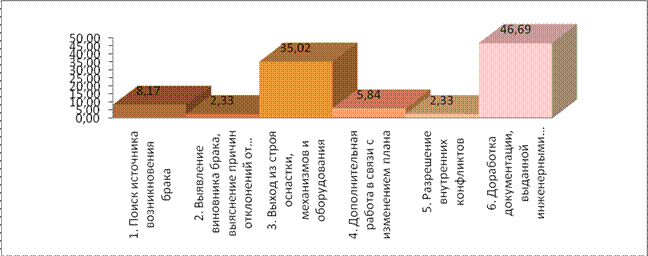
Рис.6 Затраты на внутренние потери от дефектов
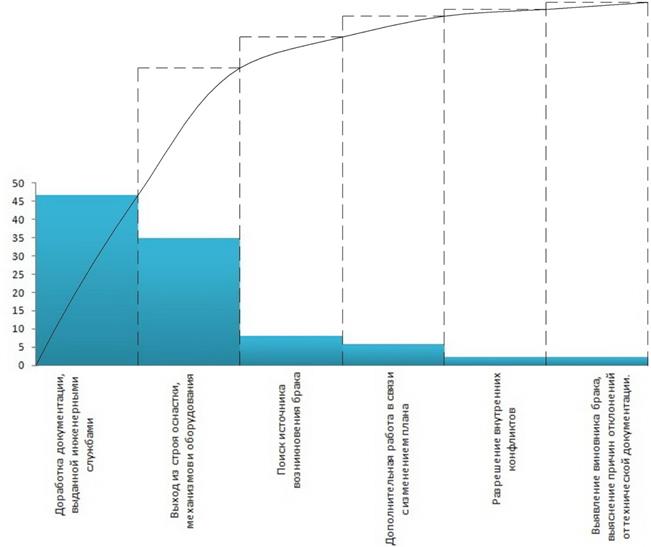
Рис.7 Диаграмма Парето
Из этих диаграмм наглядно видно, что больше всего средств в «дефектном» процессе затрачивается на доработку документации выданной инженерными службами. Соответственно необходимо рассмотреть этот пункт расходов как можно подробнее, чтобы выявить причины, приводящие к его возникновению. Для этого анализа целесообразно использовать причинно-следственную диаграмму, часто называемую диаграммой Исикавы (по имени её автора японского профессора - специалиста в области качества).
Диаграмма Исикавы является графическим изображением, которое в сжатой форме и логической последовательности распределяет причины.
Основная цель диаграммы – выявить влияние причин на всех уровнях технологического процесса. Главным достоинством ее, является то, что она дает наглядное представление не только о тех факторах, которые влияют на изучаемый объект, но и о причинно-следственных связях этих факторов (что особенно важно).
Эту диаграмму из-за ее формы часто называют «рыбьей костью» или «рыбьим скелетом». Схема представляет собой графическое упорядочение факторов, влияющих на объект анализа.
При вычерчивании схемы Исикавы следует выбрать один показатель качества или одно из следствий, которые необходимо проконтролировать, и поместить его справа в конце горизонтальной линии. Основные группы причин распределяются, тогда как рыбий скелет, отдельные причины стрелками указывают на основную причину (подводят большие первичные стрелки, обозначающие главные факторы, влияющие на объект анализа).
Далее к каждой первичной стрелке необходимо подвести стрелки второго порядка, к которым, в свою очередь подводят стрелки третьего порядка и т. д. до тех пор, пока на диаграмму не будут нанесены все стрелки, обозначающие факторы, оказывающие заметное влияние на объект анализа в конкретной ситуации. Каждая из стрелок, нанесенная на схему, должна представлять собой в зависимости от ее положения либо причину, либо следствие: предыдущая стрелка по отношению к последующей всегда выступает как причина, а последующая как следствие. В каждую границу факторов включаются конкретные причины, которые можно проконтролировать и принять мероприятия по их устранению.
В результате построенной диаграммы Исикавы были выявлены причины, приводящие к выходу оборудования из строя в процессе «Изготовление деталей». Основными причинами, приводящими к выходу из строя являются:
- изношенность инструмента;
- некачественное сырьё, материалы и заготовки;
- не соответствующие нормам условия труда;
- не достаточно квалифицированные рабочие;
- несовершенство технологии.
В результате были предложены следующие рекомендации.
1. Необходимо провести анализ оборудования, выявить точность, которую оно может обеспечить, определить возможность его дальнейшего использования в производстве в целом, а в частности, возможность наладки.
2. Провести переговоры с поставщиками, согласовать требуемое качество поставляемых запасных частей и оснастки. В случае невозможности обеспечения поставщиком требуемого качества поставок, произвести его замену.
3. Направить работников, занятых в самых ответственных операциях на повышение квалификации, что так же приведет к повышению качества производимой продукции и уменьшит вероятность неправильного использования оборудования.
4. Повысить мотивацию участников процесса к качественному и добросовестному выполнению своих обязательств. Это приведет к самосовершенствованию, возможным предложениям по совершенствованию технологии производства, а также к качественному выполнению работниками своих обязательств.
6. Повысить условия труда на рабочих местах. Провести технический осмотр вентиляции и отопления, установить необходимое количество осветительных приборов.
7. Необходимо проверять сотрудников на знание ими должностных инструкций и выполнение технологических процессов. Знание работниками своих обязанностей и технологий производства, один из гарантов качественного выполнения ими своих обязательств.
8. Предприятие должно создавать производственную среду, необходимую для достижения соответствия требованиям к продукции, и управлять ею. Состояние среды один из ключевых моментов во всем цикле изготовления продукции и оно должно соответствовать требованиям нормативной документации, чтобы снизить риск возможного выхода из строя оборудования, режущего инструмента, ухудшения характеристик заготовок, комплектующих и готовой продукции.
Список используемой литературы
1. ГОСТ Р 52380.2-2005 «Руководство по экономике качества. Часть 2. Модель предупреждения, оценки и отказов»
2. Лекции доц., к.т.н. Ефимовой Г.В. по дисциплине «Экономика качества, стандартизации и сертификации»
|