1. Структура стали.
Структура стали зависит от температуры. Чистое железо имеет температуру плавления ~ 1535°; по мере увеличения количества углерода и других компонентов температура плавления уменьшается и малоуглеродистая сталь с содержанием углерода 0,2% начинает застывать при температуре ~ 1520°. Сначала образуются кристаллы чистого железа - феррита, затем они обогащаются углеродом и при температуре 1490° вся сталь переходит в твердый раствор углерода в железе, называемый аустенитом (Feg), в котором атом углерода располагается в центре атомной кубической решетки железа. Атомы железа располагаются весьма плотно по углам куба решетки и в центре граней, всего 14 атомов (гранецентрированная система атомной решетки, рис. 1); при меньшем содержании углерода переход в аустенит совершается при более низких температурах (до 1400°). Аустенит сохраняется до температуры ~900°; после этого начинается распад его и замена гранецентрированной решетки аустенита более рыхлой решеткой чистого железа — феррита (Fea) имеющей, кроме атома в центре куба, еще атомы по углам куба, всего 9 атомов (рис.2), Почти весь углерод при этом выделяется из раствора.

Рис..1. Атомная решетка аустенита Рис.2. Атомная решетка феррита
Распад аустенита заканчивается при температуре ~700°. Выделившийся углерод входит в химическое соединение с железом, образуя карбид железа Ре3С, называемый цементитом. Таким образом, при более низких температурах сталь состоит из двух компонентов: феррита (почти чистого железа), содержащего ничтожно малое количество углерода (до 0,003%), и цементита. Феррит весьма мягок и пластичен, цементит же очень тверд и хрупок.
Количество цементита зависит от содержания в стали углерода. Феррит образует зерна (кристаллиты), занимающие почти весь объем металла, с различной ориентацией в них кристаллов (ячеек) в зависимости от направления кристаллизации; цементит располагается между зернами феррита. При распаде аустенита при температуре 900 — 700°, поскольку более плотная структура аустенита заменяется более рыхлой структурой феррита, происходит увеличение объема, несмотря на понижение температуры. В малоуглеродистых сталях углерода немного, не все ячейки аустенита содержат углерод, поэтому цементит образуется только в некоторых местах. Там вместе с частицами феррита, не имеющими на границах зерен правильного строения, цементит образует смесь — перлит, который размещается между зернами феррита в виде отдельных включений или прослоек. При травлении шлифа стали (при металлографических исследованиях) феррит получает светлую окраску, а перлит — темную (рис.3), что весьма облегчает определение величины ферритовых зерен, а также количества углерода, поскольку феррит почти не растворяет углерода, который весь в виде цементита находится в перлите. Перлит, так же как и цементит, достаточно прочен и упруг.
Рис.3. Микроструктура стали
Зерна феррита получаются различной величины в зависимости от числа очагов кристаллизации. Каждое зерно как кристаллическое образование резко анизотропно, имея различные сопротивления и модули упругости по разным направлениям. Однако в целом сталь, состоящая из весьма большого числа зерен, ориентированных по разнообразным направлениям, статистически имеет в среднем по всем направлениям одинаковые сопротивления. Сталь при упругой работе ведет себя как типично квазиизотропное тело: чем зерна мельче и чем их число больше, тем сталь более изотропна. Модули упругости феррита по различным направлениям меняются от 29000 до 13 500 кг/мм2, составляя в среднем примерно 19 000 кг1мм2. Предел прочности феррита в среднем равен всего 25 кг1мм2 при относительном удлинении 50%, предел прочности цементита 80 — 100 кг/мм2 при удлинении 1%; таким образом, цементит почти совершенно хрупок. Перлит имеет средние характеристики между ферритом и цементитом.
Структура низколегированных сталей, также состоящих из феррита и перлита, аналогична структуре стали 3. Низколегированные стали содержат мало углерода и повышение их прочности получается за счет легирующих добавок (марганца, кремния, никеля, хрома и т. д.), которые, как правило, находятся в твердом растворе с ферритом и этим его упрочняют; некоторые из них, кроме, того, образуют карбиды и упрочняют также прослойки между зернами феррита. Распад аустенита и образование феррита в низколегированных сталях происходит при более низких температурах, чем у стали 3 (500 — 450°).
2.
Модель строения чугуна.
Чугун отличается от стали только наличием графитовых включений, определяющих специальные свойства чугунов.
В зависимости от формы графита и условий его образования различают следующие группы чугунов: серый –
с пластинчатым графитом; высокопрочный –
с шаровидным графитом; ковкий
– с хлопьевидным графитом.
Схемы микроструктур чугуна в зависимости от металлической основы и формы графитовых включений представлены на рис. 4
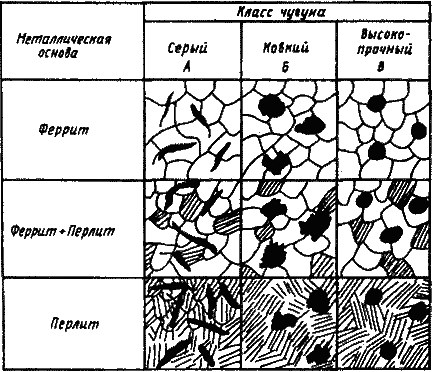
Рис. 4.
3.
Марки стали в зависимости от легирующих элементов.
По химическому составу стали делят на углеродистые и легированные.
Углеродистые стали подразделяют на низкоуглеродистые (< 0,3% C), среднеуглеродистые (0,3—0,7% С) и высокоуглеродистые (>0,7% C).
Легированной называют сталь, в которую вводят с целью придания ей тех или иных свойств один или несколько легирующих элементов.
Легированные стали с суммарным содержанием легирующих элементов менее 5% называют низколегированными, от 5 до 10% - среднелегированными и более 10% - высоколегированными (в этих сталях углерод не считается легирующим элементом).
Марки конструкционных сталей обозначают буквами Ст, после которых ставят цифры: Ст1, Ст2 и т. д. С возрастанием номера увеличиваются предел прочности и содержание углерода в стали. Марки качественных конструкционных сталей обозначают двузначным числом, указывающим на среднее содержание углерода. Например, марка Ст07 означает, что в углеродистой качественной стали содержится около 0,7% углерода.
Инструментальные углеродистые стали обозначают буквой У и цифрами,указывающими среднее содержание углерода в десятых долях процента. Например, маркой У8 обозначают углеродистую инструментальную сталь со средним содержанием 0,8% углерода. Буква А, стоящая в конце марки (У8А, У12А и др.), указывает на высокое качество стали.
Легированные конструкционные стали обозначают цифрами и буквами, которые указывают на химический состав стали. При этом первые две цифры обозначают среднее содержание углерода в сотых долях процента; стоящие далее буквы обозначают легирующие элементы. Цифры, следующие за этими буквами, указывают на процентное содержание обозначенного буквой элемента. Для легирующих элементов приняты следующие буквенные обозначения: X — хром, Н — никель, Г — марганец, С — кремний, В — вольфрам, М — молибден, Ф — ванадий, К — кобальт, Т — титан, Ю — алюминий, Д — медь, П — фосфор, Р — бор, Б — ниобий, А — азот, Е — селен, Ц — цирконий.
Например, марка 35Х обозначает хромовую сталь, содержащую около 0,35% углерода и 1,5% хрома; марка 45Г2 обозначает марганцевую сталь, содержащую около 0,45% углерода и 2% марганца.
Легированные инструментальные стали маркируют аналогично легированным конструкционным сталям, но среднее содержание углерода указывают в десятых долях процента (если его содержание не превышает 0,9%) или совсем не указывают (если содержание углерода около или более 1%). Быстрорежущие стали маркируют буквой Р, после которой ставят цифры, указывающие на среднее содержание вальфрама в процентах.
4. Диаграмма Железо – цементит. Феррит, ледебурит.
Диаграмма состояния железоуглеродистых сплавов, позволяет определять состояние и структуру сплавов при любой температуре и при любом содержании углерода в пределах до 6,67%.
В диаграмме крайняя левая ордината при отсутствии углерода (С=0% соответствует чистому железу, а крайняя правая при С-6,67% — цементиту. Необходимо иметь в виду, что в железоуглеродистых сплавах при охлаждении углерод чаще выделяется не в чистом виде, а в виде цементита, поэтому ось абсцисс ограничена чистым цементитом, содержание углерода в котором равно 6,67% .
Линию АСО диаграммы называют линией ликвидуса; выше этой линии сплавы находятся в жидком состоянии. Когда температура сплава соответствует линии АС, начинается процесс кристаллизации аустенита, а на линии СО — цементита.
Линию АВЕСР называют линией солидуса, так как она соответствует моменту полного затвердения сплава. В зависимости от температуры и содержания углерода железоуглеродистые сплавы содержат следующие структурные составляющие:
аустенит
— твердый раствор углерода в гамма-железе. Сталь, имеющая структуру аустенита, немагнитна и обладает большой пластичностью; кристаллы аустенита и жидкий сплав находятся ниже линии ВС;
феррит
— твердый раствор углерода в альфа-железе. Он характеризуется незначительной твердостью, невысокой прочностью, но большой пластичностью; линия GS диаграммы показывает температуры начала выделения феррита из аустенита;
цементит
— химическое соединение железа с углеродом (карбид железа Fе3С); он весьма тверд и хрупок. Сплав цементита и жидкого сплава находится ниже линии СО;
перлит
— механическая смесь феррита и цементита — продукт распада медленно охлаждаемого аустенита при 723 градусах и содержании углерода 0,83%;
ледебурит
— механическая смесь аустенита и цементита (эвтектика) при температуре 1120 градусов и содержании углерода 4,3%;
графит
— свободный углерод в основной массе металла в виде пластинок или зерен.
5.
Выплавка чугуна. Доменная печь и химическая реакция.
Чугун – сплав железа и углерода с сопутствующими элементами (содержание углерода более 2,14 %).
Для выплавки чугуна в доменных печах используют железные руды, топливо, флюсы.
Топливом
для доменной плавки служит кокс, возможна частичная замена газом, мазутом.
Чугун выплавляют в печах шахтного типа – доменных печах
.
Сущность процесса получения чугуна в доменных печах заключается в восстановлении оксидов железа, входящих в состав руды оксидом углерода, водородом и твёрдым углеродом, выделяющимся при сгорании топлива.
При выплавке чугуна решаются задачи:
1. Восстановление железа из окислов руды, науглероживание его и удаление в виде жидкого чугуна определённого химического состава.
2. Оплавление пустой породы руды, образование шлака, растворение в нём золы кокса и удаление его из печи.
Устройство и работа доменной печи.
Доменная печь (рис. 6) имеет стальной кожух, выложенный огнеупорным шамотным кирпичом. Рабочее пространство печи включает колошник 6
, шахту 5
, распар 4
, заплечики 3,
горн 1
, лещадь 15
. В верхней части колошника находится засыпной аппарат 8
, через который в печь загружают шихту. Шихту подают в вагонетки 9
подъемника, которые передвигаются по мосту 12
к засыпному аппарату и, опрокидываясь, высыпают шихту в приемную воронку 7
распределителя шихты. При опускании малого конуса 10
шихта попадает в чашу 11
, а при опускании большого конуса 13
– в доменную печь, что предотвращает выход газов из доменной печи в атмосферу. При работе печи шихтовые материалы, проплавляясь, опускаются, а через загрузочное устройство подают новые порции шихты, чтобы весь полезный объём был заполнен. Полезный объем печи – объем, занимаемый шихтой от лещади до нижней кромки большого конуса засыпного аппарата при его опускании. Полезная высота доменной печи (Н
) достигает 35 м, а полезный объем – 2000…5000 м3
. В верхней части горна находятся фурменные устройства 14
, через которые в печь поступает нагретый воздух, необходимый для горения топлива. Воздух поступает из воздухонагревателя, внутри которого имеются камера сгорания и насадка из огнеупорного кирпича, в которой имеются вертикальные каналы. В камеру сгорания к горелке подается очищенный доменный газ, который, сгорая, образует горячие газы. Проходя через насадку, газы нагревают ее и удаляются через дымовую трубу. Через насадку пропускается воздух, он нагревается до температуры 1000…1200 0
С и поступает к фурменному устройству, а оттуда через фурмы 2
– в рабочее пространство печи. После охлаждения насадок нагреватели переключаются.
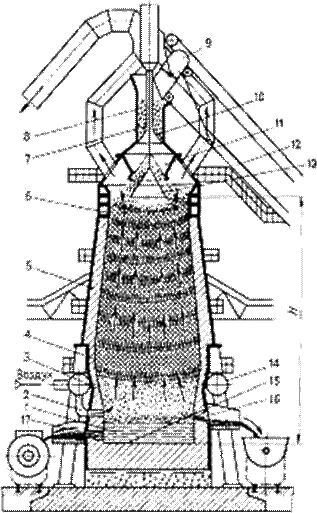
Рис. 6. Устройство доменной печи
В верхней части колошника находится засыпной аппарат 8
, через который в печь загружают шихту. Шихту подают в вагонетки 9
подъемника, которые передвигаются по мосту 12
к засыпному аппарату и, опрокидываясь, высыпают шихту в приемную воронку 7
распределителя шихты. При опускании малого конуса 10
шихта попадает в чашу 11
, а при опускании большого конуса 13
– в доменную печь, что предотвращает выход газов из доменной печи в атмосферу.
Горение топлива
.
Вблизи фурм природный газ и углерод кокса, взаимодействуя с кислородом воздуха, сгорают.
В результате горения выделяется большое количество теплоты, в печи выше уровня фурм развивается температура выше 2000 0
С.
Продукты сгорания взаимодействуют с раскаленным коксом по реакциям:
CO2
+C=2CO-Q
H2
O+C=CO+H2
-Q
Образуется смесь восстановительных газов, в которой окись углерода CO является главным восстановителем железа из его оксидов. Для увеличения производительности подаваемый в доменную печь воздух увлажняется, что приводит к увеличению содержания восстановителя. Горячие газы, поднимаясь, отдают теплоту шихтовым материалам и нагревают их, охлаждаясь до 300…400 0
С у колошника.
Шихта (агломерат, кокс) опускается навстречу потоку газов, и при температуре около 570 0
С начинается восстановление оксидов железа.
Восстановление железа в доменной печи
.
Восстановление железа происходит по мере продвижения шихты вниз по шахте и повышения температуры от высшего оксида к низшему, в несколько стадий:
Fe2
O3
→Fe3
O4
→FeO→Fe
Температура определяет характер протекания химических реакций.
Восстановителями окcидов железа являются твердый углерод, оксид углерода и водород. Восстановление твердым углеродом (коксом)называется прямым восстановлением,
протекает в нижней части печи (зона распара), где более высокие температуры, по реакции:
FeO+C=Fe+CO-Q
Восстановление газами (CO и H2
) называется косвенным восстановлением
, протекает в верхней части печи при сравнительно низких температурах, по реакциям:
3Fe2
O3
+CO=2Fe3
O4
+CO2
+Q
Fe3
O4
+CO=3FeO+CO2
-Q
FeO+CO=Fe+CO2
+Q
За счет CO и H2
восстанавливаются все высшие оксиды железа до низшего и 40…60 % металлического железа.
При температуре 1000…1100 0
C восстановленное из руды твёрдое железо, взаимодействуя с оксидом углерода, коксом и сажистым углеродом, интенсивно растворяет углерод. При насыщении углеродом температура плавления понижается и на уровне распара и заплечиков железо расплавляется (при температуре около 1300 0
С). Капли железоуглеродистого сплава, протекая по кускам кокса, дополнительно насыщаются углеродом (до 4%), марганцем, кремнием, фосфором, которые при температуре 1200 0
C восстанавливаются из руды, и серой, содержащейся в коксе. В нижней части доменной печи образуется шлак в результате сплавления окислов пустой породы руды, флюсов и золы топлива. Шлаки содержат Al2
O3
, CaO, MgO, SiO2
, MnO, FeO, CaS . Шлак образуется постепенно, его состав меняется по мере стекания в горн, где он скапливается на поверхности жидкого чугуна, благодаря меньшей плотности. Состав шлака зависит от состава применяемых шихтовых материалов и выплавляемого чугуна. Чугун выпускают из печи каждые 3…4 часа через чугунную летку 16
, а шлак – каждые 1…1,5 часа через шлаковую летку 17
(летка – отверстие в кладке, расположенное выше лещади). В настоящее время чугун и шлак выпускаю т в одну ледку и разделяют. Летку открывают бурильной машиной, затем закрывают огнеупорной массой. Сливают чугун и шлак в чугуновозные ковши и шлаковозные чаши. Чугун поступает в кислородно-конвертерные или мартеновские цехи, или разливается в изложницы разливочной машиной, где он затвердевает в виде чушек-слитков массой 45 кг.
6.
Печь для выплавки стали. Мартеновские и другие электрические печи.
Мартеновская печь
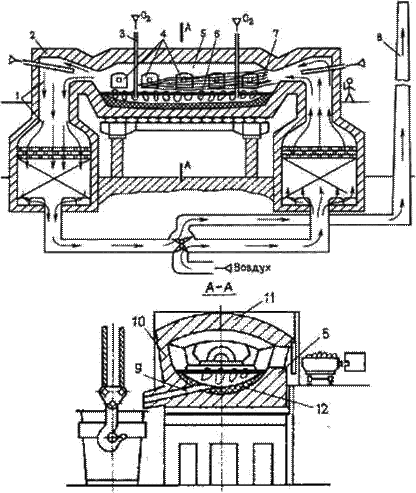
Рис.7. Схема мартеновской печи
Мартеновская печь по устройству и принципу работы является пламенной отражательной регенеративной печью. В плавильном пространстве сжигается газообразное топливо или мазут. Высокая температура для получения стали в расплавленном состоянии обеспечивается регенерацией тепла печных газов.
Современная мартеновская печь представляет собой вытянутую в горизонтальном направлении камеру, сложенную из огнеупорного кирпича. Рабочее плавильное пространство ограничено снизу подиной 12, сверху сводом 11,
а с боков передней 5 и задней 10 стенками. Подина имеет форму ванны с откосами по направлению к стенкам печи. В передней стенке имеются загрузочные окна 4 для подачи шихты и флюса, а в задней – отверстие 9 для выпуска готовой стали.
Дуговая сталеплавильная печь
При строительстве металлургических заводов отдают предпочтение, как правило, двум типам печей:
– печи постоянного тока с одним катодом (ДППТ)
– дуговой печи трёхфазного переменного тока с высоким сопротивлением контура (ДСП)
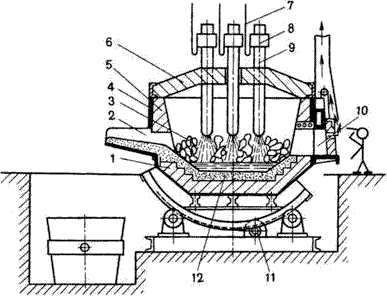
Рис. 8. Схема дуговой печи трёхфазного переменного тока
Дуговая печь питается трёхфазным переменным током. Имеет три цилиндрических электрода 9
из графитизированной массы, закреплённых в электрододержателях 8
, к которым подводится электрический ток по кабелям 7
. Между электродом и металлической шихтой 3
возникает электрическая дуга. Корпус печи имеет форму цилиндра. Снаружи он заключён в прочный стальной кожух 4
, внутри футерован основным или кислым кирпичом 1
. Плавильное пространство ограничено стенками 5
, подиной12
и сводом 6.
Съёмный свод 6
имеет отверстия для электродов. В стенке корпуса рабочее окно 10
(для слива шлака, загрузки ферросплавов, взятия проб), закрытое при плавке заслонкой. Готовую сталь выпускают через сливное отверстие со сливным желобом 2
. Печь опирается на секторы и имеет привод 11
для наклона в сторону рабочего окна или желоба. Печь загружают при снятом своде.
Индукционные тигельные плавильные печи
Выплавляют наиболее качественные коррозионно-стойкие, жаропрочные и другие стали и сплавы.
Вместимость от десятков килограммов до 30 тонн.
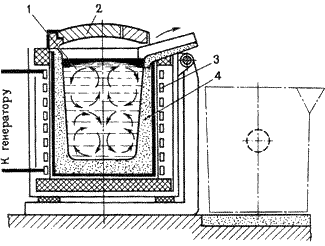
Рис. 9. Схема индукционной тигельной печи.
Печь состоит из водоохлаждаемого индуктора 3
, внутри которого находится тигель 4
(основные или кислые огнеупорные материалы) с металлической шихтой, через индуктор от генератора высокой частоты проходит однофазный переменный ток повышенной частоты (500…2000 Гц).
При пропускании тока через индуктор в металле 1
, находящемся в тигле, индуцируются мощные вихревые токи, что обеспечивает нагрев и плавление металла. Для уменьшения потерь тепла, печь имеет съёмный свод 2
.
7.
Цветные сплавы – алюминий, медь, олово и др.
Медь
(ГОСТ i859—66)—металл красного цвета, мягкий поддающийся протяжке в холодном состоянии. Плотность зависит от способа получения и колеблется от 8,3 до 8,9
Предел прочности чистой меди на растяжение составляет 20—35 кгс/мм2. Медь обладает большой электропроводностью, поэтому ее широко применяют в электротехнической промышленности. Медь хорошо сопротивляется коррозии, образуя на поверхности защитную пленку. Медные листы используют для покрытия монументальных зданий
Цинк
(ГОСТ ,3640—65)—металл синевато-серого цвета с плотностью 7,14. В зависимости от химической чистоты цинк делится на шесть марок: ЦВ, ДО, Ц1, Ц2, ЦЗ и Ц4.
Предел прочности чистого цинка при растяжении 1 кгс/мм2. Технологические свойства цинка изменяются от температуры. В пределах 100—150° С цинк хорошо куется и прокатывается в тонкие листы. От влажного воздуха на цинковой поверхности появляется окисная пленка, которая приостанавливает коррозию металла. Цинковые листы,могут, быть использованы в качестве кровельного материала.
Олово
(ГОСТ 860—60) — блестящий металл серебристо-белого цвета с плотностью 7,31. При изгибаний олово издает характерный треск
При температуре 13,2° С белое олово превращается в порошок, серое олово, с объемной массой 6,75. Чтобы этого не произошло, олово нужно хранить в теплом помещении и изолировать от серого.
При обычных условиях олово устойчиво к воздействиям химических веществ, поэтому его применяют для лужения посуды. В технике олово используют для припоев, а также оно входит в состав различных сплавов.
Свинец
(ГОСТ 3778—65)—металл синевато-серого цвета с плотностью 11,9.
Свинец — легкоплавкий и мягкий металл; он ковок, легко режется и прокатывается. При действий на него влажного воздуха поверхность металла покрывается тонкой пленкой, предохраняющей свинец от дальнейшей коррозии
Свинец применяют во многих отраслях промышленности: при изготовлении аккумуляторов, кабелей, красок, взрывчатых веществ, а также при производстве сплавов.
Алюминий
(ГОСТ 11069—64) —мягкий и легкий металл; его плотность 2,72. Алюминий обладает высокой электропроводностью, теплопроводностью и коррозионной стойкостью. Чистый алюминий в литом состоянии имеет пониженную прочность, деформированный (прокатанный) он приобретает механическую прочность, достаточную для широкого применения в технике. В зависимости от химической чистоты алюминий имеет девять марок: АВОООО, AB000, AB00, AB0, А00, АО, Al, A2 и A3.
Алюминий легко окисляется на воздухе. Окисная пленка обладает плотностью и предохраняет его от дальнейшей коррозии.
Листовой алюминий используют для покрытия некоторых типов гражданских зданий.
8. Сварка. Основные типы сварки.
Сварку подразделяют на 3
класса:
1.
Термический
класс. Также разделяется на:
а. Дуговая электросварка: ручная дуговая, сварка неплавящимся электродом, сварка плавящимися электродами, электродуговая сварка с использованием флюса;
б. Газопламенная сварка;
в. Электрошлаковая сварка;
г. Плазменная;
д. Электро–лучевая;
е. Лучевая.
2.
Термомеханический
класс. В свою очередь подразделяется на:
а. Контактная сварка: точечная, рельефная, стыковая;
б. Диффузионная сварка;
в. Кузнечная сварка;
г. Сварка с использованием высокочастотного тока;
д. Сварка трением.
3.
Механический
. Механический класс также делится на:
а. Сварка взрывом;
б. Ультразвуковая;
в. Холодная сварка.
Электродуговая сварка.
Рис. 10. Ручная дуговая сварка металлическим электродом с покрытием(стрелкой указано направление сварки): 1 - металлический стержень; 2 - покрытие электрода; 3 - газовая атмосфера дуги; 4 - сварочная ванна; 5 - затвердевший шлак; 6 - закристаллизовавшийся металл шва; 7 - основной металл; 8 - капли расплавленного электродного металла; 9 - глубина проплавления
Источником теплоты является электрическая дуга, возникающая между торцом электрода и свариваемым изделием при протекании сварочного тока в результате замыкания внешней цепи электросварочного аппарата. Сопротивление электрической дуги больше, чем сопротивление сварочного электрода и проводов, поэтому бо́льшая часть тепловой энергии электрического тока выделяется именно в плазму электрической дуги. Этот постоянный приток тепловой энергии поддерживает плазму (электрическую дугу) от распада.
Выделяющееся тепло (в том числе за счёт теплового излучения из плазмы) нагревает торец электрода и оплавляет свариваемые поверхности, что приводит к образованию сварочной ванны - объёма жидкого металла. В процессе остывания и кристаллизации сварочной ванны образуется сварное соединение.
Газопламенная сварка.
Рис. 11. Правый (а) и левый (б) способы газовой сварки
Источником теплоты является газовый факел, образующийся при сгорании смеси кислорода и горючего газа. В качестве горючего газа могут быть использованы ацетилен, водород, пропан, бутан, блаугаз, МАФ, бензин, бензол, керосин и их смеси. Тепло, выделяющееся при горении смеси кислорода и горючего газа, расплавляет свариваемые поверхности и присадочный материал с образованием сварочной ванны. Пламя может быть окислительным, «нейтральным» или восстановительным, это регулируется количеством кислорода.
Электрошлаковая сварка.
Источником теплоты служит флюс, находящийся между свариваемыми изделиями, разогревающийся проходящим через него электрическим током. При этом теплота, выделяемая флюсом, расплавляет кромки свариваемых деталей и присадочную проволоку. Способ находит своё применение при сварке вертикальных швов толстостенных изделий.
Плазменная сварка.
Рис. 12. 1. Электрод; 2. Плазменное сопло; 3. Фокусирующее сопло; 4. Защитное сопло; 5. Деталь.
Источником теплоты является плазменная струя, получаемые при ионизации рабочего газа в промежутке между электродами, одним из которых может быть свариваемое изделие либо оба электрода находятся в плазменной горелке — плазмотроне. Струя плазмы сжимается и ускоряется под действием электромагнитных сил, оказывая на свариваемое изделие как тепловое так и газодинамическое воздействие. Помимо собственно сварки этот способ часто используется для технологических операций наплавка, напыление и резка.
Электронно-лучевая сварка.
Источником теплоты является электронный луч, получаемый за счёт термоэлектронной эмиссии с катода электронно-лучевой пушки. Сварка ведётся в высоком вакууме – Па в вакуумных камерах. Известна также технология сварки электронным лучом в атмосфере нормального давления, когда электронный луч покидает область вакуума непосредственно перед свариваемыми деталями.
Лазерная сварка.
Источником теплоты служит лазерный луч. Применяют лазерные установки всех видов.
Контактная сварка.
При сварке происходят два последовательных процесса: нагрев свариваемых изделий до пластического состояния и их совместное пластическое деформирование. Основными разновидностями контактной сварки являются: точечная контактная сварка, стыковая сварка, рельефная сварка, шовная сварка.
Диффузионная сварка.
Сварка осуществляется за счёт диффузии — взаимного проникновения атомов свариваемых изделий при повышенной температуре. Сварку проводят в вакуумной установке, нагревая места соединения до 800 °C. Вместо вакуума может быть использована среда защитных газов. Методом диффузной сварки можно пользоваться при создании соединений из разнородных металлов, отличающихся по своим физико-химическим свойствам, изготавливать изделия из многослойных композитных материалов.
Способ был разработан в СССР в 1950-х годах Н. Ф. Казаковым.
Сварка высокочастотными токами.

Рис. 13. Схема высокочастотной сварки труб с индукционным (а) и контактным (б) способами подвода тока: 1 - индуктор; 2 и 3 - контакты; 4 - ферритовый стержень; 5 - сжимающие ролики; 6 - труба; 7 - направляющий ролик
Источником теплоты служит высокочастотный ток проходящий между свариваемыми изделиями. При последующем пластическом деформировании и остывании образуется сварное соединение.
Сварка трением.
Если жестко закрепить одну деталь, а другую, прижав к ней, вращать, то за счет механической работы сил трения детали в месте прикосновения сильно разогреются, оплавятся и сварятся.
Способ достаточно экономичный. Автоматизированые установки для сварки трением потребляют электроэнергии в 10 раз меньше, чем установки для контактной сварки. Соединяются детали за считанные секунды, при этом практически нет газовых выделений.
Способ позволяет сваривать разнородные материалы: медь и алюминий, медь и сталь, алюминий и сталь и т. д.
Идея сваривать детали трением была высказана токарем-изобретателем А. И. Чудиковым. В 1950-е годы на простом токарном станке ему удалось прочно соединить два стержня из низкоуглеродистой стали.
Сварка взрывом.
Сварка осуществляется сближением атомов свариваемых изделий на расстояние действия межатомных сил за счёт энергии, выделяемой при взрыве. С помощью данного способа сварки часто получают биметаллы.
Ультразвуковая сварка металлов.
Сварка осуществляется сближением атомов свариваемых металлических изделий на расстояние действия межатомных сил за счёт энергии ультразвуковых колебаний, вводимых в материалы. Ультразвуковая сварка характеризуется рядом положительных качеств, что несмотря на высокую стоимость оборудования, обуславливает её применение в производстве микросхем (сварка проводников с контактными площадками), прецизионных изделий, сварка металлов разных типов и металлов с неметаллами.
Холодная сварка.
Холодная сварка представляет собою соединение однородных или неоднородных металлов при температуре ниже минимальной температуры рекристаллизации; сварка происходит благодаря пластической деформации свариваемых металлов в зоне стыка под воздействием механического усилия.
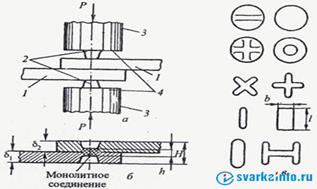 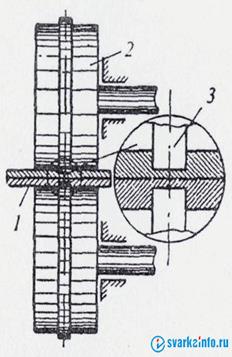
Рис. 14. Схема холодной точечной сварки (а), геометрия сварного соединения (б) и формы пуансонов (в)
Рис. 15. Схема холодной шовной сварки: 1 - детали; 2 - ролики; 3 - выступы
Технология обработки заготовок, деталей машин на металлорежущих станках.
9.
Станки токарные, инструмент и обработка заготовок.
Главным движением токарного станка является вращение заготовки, а режущие инструменты (обычно однолезвийные) регулируемо закрепляются на неподвижной станине. Резец может подаваться по направляющим вдоль или поперек оси шпинделя. Заготовка закрепляется либо в патроне шпинделя, либо в центрах передней и задней бабки. Скорость подачи может регулироваться вручную или автоматически посредством ряда клиноременных или зубчатых передач, приводящих в движение ходовой винт и поперечные салазки суппорта. Скорость вращения заготовки регулируется в широких пределах в соответствии с выбранными режимами резания. Приводной электродвигатель может иметь как фиксированную, так и переменную частоту вращения. На токарных станках (а они составляют основу станочного парка) обычно выполняют операции обработки цилиндрических поверхностей, поперечной обточки и обрезки, нарезания винтовой резьбы и расточки осевых отверстий.
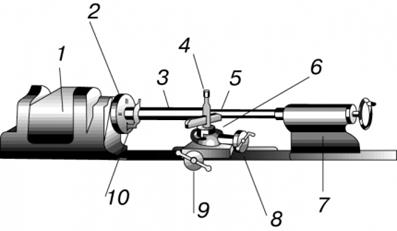
УНИВЕРСАЛЬНЫЙ ТОКАРНО-ВИНТОРЕЗНЫЙ СТАНОК. Такие станки составляют основу станочного парка. Резец закреплен на поворотном суппорте, позволяющем автоматически или вручную подавать его вдоль или поперек детали, либо под углом при точении конических поверхностей. 1 – передняя бабка; 2 – планшайба; 3 – деталь (вал); 4 – резцедержатель; 5 – резец; 6 – суппорт; 7 – задняя бабка; 8 – делительная головка; 9 – поперечная подача; 10 – токарный хомутик.
Существуют токарные станки разных видов, типов и размеров. Токарно-револьверный станок, часто применяемый для изготовления одинаковых деталей, снабжается несколькими режущими инструментами, закрепленными в поворотном (револьверном) суппорте. Блок управления револьверного токарного станка с ЧПУ дает команды движения шпинделя, поворота и перемещения револьверных суппортов, перемещения задней бабки. В тех случаях, когда очень велик вес заготовки или ее форма такова, что заготовку легче обрабатывать на горизонтальном столе, применяются большие токарно-карусельные станки. Рабочий стол такого станка вращается вместе с заготовкой, а режущие инструменты подаются либо сбоку, либо с торца заготовки.
10.
Станки расточные, инструмент и обработка заготовок.
Расточные станки — группа металлорежущих станков, предназначена для обработки заготовок крупных размеров в условиях индивидуального и серийного производства. На этих станках можно производить растачивание, сверление, зенкерование, нарезание внутренней и наружной резьб, обтачивание цилиндрических поверхностей, подрезку торцов, цилиндрическое и торцовое фрезерование. Иногда на расточных станках можно произвести окончательную обработку заготовки корпусной детали без перестановки ее на другие станки.
Отличительной особенностью расточных станков является наличие горизонтального (или вертикального) шпинделя, совершающего движение осевой подачи. В отверстии шпинделя закрепляется режущий инструмент — борштанга с резцами, сверло, зенкер, развертка, фреза и др.
Перемещения, обеспечивающие установку шпинделя в заданное положение, и движения подачи сообщаются различным узлам расточных станков в зависимости от назначения, компоновки, размеров станка, а также характера операции.
Рис. 10. Станок универсальный расточный с неподвижной передней стойкой с крестовым поворотным столом:1, 5 — салазки, 2 — станина, 3 — задняя стойка, 4 — люнет, 6 — поворотный стол, 7 — расточная оправка с резцом, 8— шпиндель, 9 —планшайба с суппортом, 10 — неподвижная передняя стойка, 11 — расточная бабка; В — ширина стола, D — диаметр шпинделя, s — подача, v — вращательное движение шпинделя
11.
Резьбонарезание - инструменты и станки.
Ручной клупп-
представляет собой резьбонарезной инструмент, состоящий из рукояти и гнезда, в котором закрепляются резьбонарезные плашки. Простейшие модели головок клуппа имеют жестко фиксированные резьбонарезные плашки. Такие головки резьбонарезного инструмента предназначены для нарезки резьбы на деталях одного диаметра. Более сложные головки клуппа имеют механизм подачи плашек. Благодаря возможности подачи плашек резьбонарезного инструмента, их можно отводить для быстрого снятия резьбонарезного инструмента после нарезки резьбы. Эта особенность головки клуппа уменьшает время выполнения операции нарезки резьбы.
Часто головки резьбонарезного инструмента и
меют направляющие плашки или направляющий хвостовик для центрирования детали в резьбонарезном инструменте, для повышения качества нарезки резьбы.
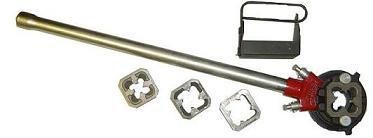
Электрический клупп. К этому классу резьбонарезного инструмента можно отнести компактные, мобильные аппараты, головки которых получают привод от электродвигателя через понижающий редуктор. Частота вращения головки такого резьбонарезного инструмента в среднем 20-30 оборотов в минуту. Качество и скорость нарезки резьбы электрическим резьбонарезным инструментом выше, чем ручным клуппом. Этому способствует центрованная головка резьбонарезного инструмента, равномерный ход плашек и распределение усилия. Двигатель электроклуппа, в большинстве случаев, имеет значительный запас мощности, который и обеспечивает резьбонарезному инструменту равномерность нарезки резьбы при увеличении нагрузки.
Электроклуппы приспособлены для нарезки резьбы в тесных местах – не нужно пространство для поворота рукояти. Электрические резьбонарезные инструменты совместимы с унифицированными резьбонарезными головками непосредственно или через специальные адаптеры, что расширяет их функциональные возможности нарезки резьбы разных видов.
12.
Зубонарезание, станки для нарезки зубчатых колес.
Зубонарезание - процесс обработки зубьев зубчатых колёс и др. деталей, имеющих зубья, на зубообрабатывающем станке путём снятия стружки зуборезным инструментом. Зубонарезание бывает черновое (предварительное) и чистовое. При черновом З. снимается большая часть припуска, а профиль зуба ещё не получает окончательной формы. Чистовое З. бывает либо окончательным процессом, либо после него производят упрочняющую обкатку зубьев, термическую обработку с последующим зубошлифованием или доводкой. Черновое З. осуществляют методами обкатки или копирования, чистовое З. — обычно методом обкатки. При копировании инструментом является дисковая или пальцевая фреза, которая в радиальной плоскости имеет профиль, соответствующий впадине между зубьями нарезаемого зубчатого колеса. При обкатке используют червячные фрезы, зубонарезные гребёнки, долбяки, зубострогальные резцы с режущей частью, производящая поверхность которой представляет собой как бы профиль зуба сопряжённой зубчатой рейки (колеса). Профиль зуба, получаемый после З. по методу обкатки, близок к огибающей линии, образованной последовательными положениями режущей кромки инструмента
В зависимости от применяемого инструмента различают зубофрезерные, зубодолбёжные, зубострогальные, зубоотделочные (зубошевинговальные, зубошлифовальные, зубохонинговальные, зубопритирочные, зубообкаточные и зубозакругляющие) станки.
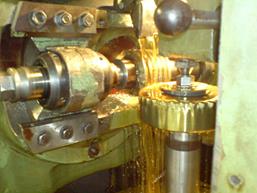
Рис. 1. Зубофрезерный станок.
Рис. 2. Принципиальная схема работы вертикального зубодолбёжного станка.
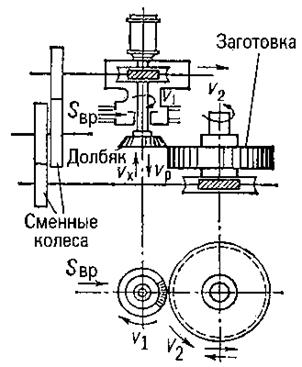
Рис. 3. Нарезание зубьев фасонной зуборезной головкой.
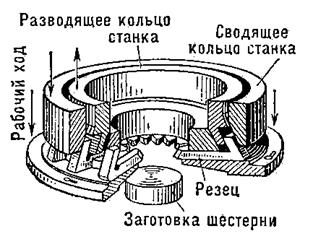
Рис. 4. Зубострогальный станок. Схема нарезания зубьев на коническом зубчатом колесе: 1 — обрабатываемое зубчатое колесо; 2 — производящее зубчатое колесо; 3 — зубострогальные резцы производящего колеса.
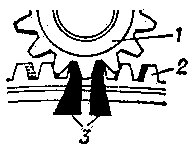
Рис. 5. Схемы шевингования цилиндрических зубчатых колёс: а — реечным шевером; б — дисковым шевером.
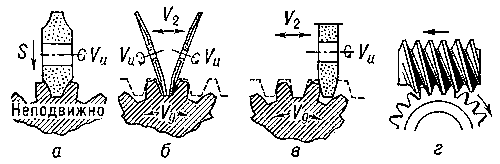
Рис. 6. Схемы зубошлифования: а — по методу профильного копирования фасонным шлифовальным кругом; б — по методу обкатки двумя тарельчатыми шлифовальными кругами; в — по методу обкатки одним дисковым шлифовальным кругом, имеющим профиль зуба рейки; г — по методу обкатки абразивным червяком; Vu
и Vg
— скорости вращения соответственно инструмента (шлифовального круга) и детали (зубчатого колеса); S — поперечная подача шлифовального круга; V2
— скорость возвратно-поступательного движения шлифовальных кругов.
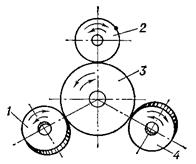
Рис. 7. Схема притирки зубчатых колёс: 1, 2, 4 — притиры; 3 — обрабатываемое колесо.
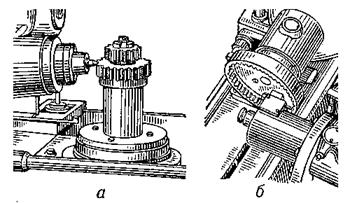
Рис. 8. Схемы зубозакругления наружных (а) и внутренних (б) зубьев.
13.
Электроэрозионные способы обработки.
Электроэрозионная
обработка основана на том, что при сближении электродов, находящихся под током, происходит искровой разряд, разрушающий в наибольшей мере анод, которым служит обрабатываемая заготовка. Разряд происходит при накоплении тока в особом конденсаторе (магазине емкостей). Таким способом производят главным образом образование отверстий в металлах любой твердости. Этот способ малопроизводителен и обеспечивает достижение 3-го класса точности и 8-го класса чистоты. Его применяют в производственных цехах в тех случаях, когда обработка другими, более производительными, способами не осуществима.
Рабочим инструментом в большинстве случаев служит латунная тонкая проволока, способная многократно изгибаться под нужным углом. Выбор латуни обусловлен высоким уровнем теплопроводности. Мягкий материал находится под высоким напряжением, показатели которого выбираются таким образом, чтобы нагрев из-за собственного сопротивления не расплавил проволоку. Разогрев до 10000 градусов происходит мгновенно, поэтому некоторые металлы не просто испаряются, а сублимируют. С точки зрения физической химии высокое термическое воздействие разрушает кристаллическую решетку, и ионы металла отрываются от поверхности. Визуально же кажется, что латунная проволока «разъедает» основной металл, словно кислота. Это и дало название методу. Т.о. проволока медленно погружается в заготовку, отверстие в которой в точности повторяет контур латунного инструмента.
Для гарантированного охлаждения испаряемого металла и его удаления из зоны контакта используются диэлектрические жидкости – керосин или машинное масло – в которые и погружается заготовка. Жидкий диэлектрик влияет на расстояние пробоя, снижая его до 150 мкм и меньше, чем ограничивает зону контакта.
Электроэрозионная технология включает в себя несколько методов, одни из которых позволяют выполнять сложнофасонные прожиги и вырезать отверстия, другие – разделять заготовки, выполненные из жаропрочных аустенитных сталей или титановых соединений.
В основе метода электроискровой обработки лежит образование катод-анодной системы, где заготовка заряжается положительно, а эрозионный инструмент – отрицательно. При этом в месте контакта возникает дуговой разряд короткой продолжительности. Температура в середине дуги минимально достигает 8 тысяч градусов. Поскольку расстояние пробоя достаточно низкое, разница в температуре поверхности металла в зоне контакта и в центре дуги небольшая.
Другой разновидностью электроэрозионной обработки в системе катод-анод является анодно-механическая технология, когда отрицательно заряжена не проволока, а диск или замкнутая лента. Диэлектрическая пленка в местах контакта вращающегося инструмента временно разрушается. В местах же открытия чистого металла образуются дуговые разряды, испаряющие тонкий поверхностный слой.
При электроимпульсной обработке сменяется полярность системы катод-анод. Образуемые дуговые разряды прерываются перемещением инструмента и отключением тока. Средняя температура разряда достигает 5000 градусов.
Министерство образования РФ
СПб ГАСУ
Кафедра Конструкционных материалов
Курсовая работа
по предмету: “Технологии конструкционных материалов”.
Выполнил: Шарин С.Ю.
Группа: 3ПГС-у 2
Санкт-Петербург 2010 г.
Содержание:
1. Структура стали
2. Модель строения чугуна
3. Марки сталей в зависимости от легирующих элементов
4. Диаграмма железо-цементит. Феррит, ледебурит
5. Выплавка чугуна. Доменная печь и химическая реакция
6. Печь для выплавки стали. Мартеновские и другие электрические печи
7. Цветные сплавы – алюминий, медь, олово и др.
8. Сварка. Основные типы сварки
9. Станки токарные, инструмент и обработка заготовок
10. Станки расточные, инструмент и обработка заготовок
11. Резьбонарезание - инструменты и станки
12. Зубонарезание, станки для нарезки зубчатых колес
13. Электроэрозионные способы обработки
|