СОДЕРЖАНИЕ
Введение 4
1. Анализ исходных данных для выбора материала. 6
2. Выбор способа формообразования. 7
3 Выбор марки материала. 8
4. Назначение вида и режима термической обработки. 10
5. Описание структуры и свойств готовых деталей. 11
Литература 12
Задание № 174
Выбрать способ формообразования, марку материала и режим термической или химико-термической обработки для высоконагруженного диска плуга диаметром 85 мм, работающего без значительных ударных нагрузок. Наибольшая толщина 10 мм. Требования: механические свойства в сечении – σв
≥ 1000МПа, σТ
≥ 800 МПа, δ ≥ 8%.
Ротационный плуг модели ПР-1,2 "Super-krot"
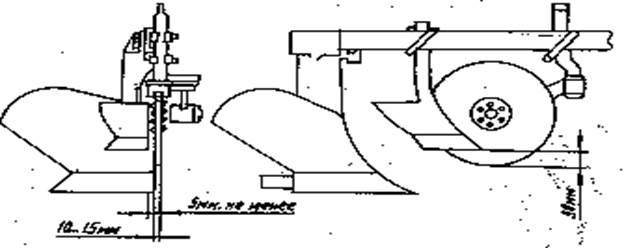
ВВЕДЕНИЕ
Еще в начале XVIII в. в Англии и в других европейских странах был распространен деревянный однолемешный конный плуг. Все части плуга, кроме лемеха, были деревянными. Поэтому основной задачей его усовершенствования стало стремление найти такой материал, который обеспечил бы более длительный срок работы орудия. В России работа над усовершенствованием плуга велась с конца XVIII в. Вольное экономическое общество дважды, в 1773 и в 1791 гг., объявляло конкурс на создание лучшего плуга. В начале XIX в. были распространены передковые плуги конструкции Лукьяна Рудницкого, Трофима Петренко и беспередковый плуг. В 30-х годах XVIII в. в Шотландии появился плуг, у которого наиболее изнашивающиеся части – лемех и отвал были сделаны целиком из железа. Некоторое время в Англии, а потом и в США были распространены так называемые железные плуги. Однако они не отличались большой прочностью, а их лемех быстро изнашивался. В 1803 г. англичанин Роберт Рансон сделал цельный плуг из чугуна. Хотя это повысило его прочность, однако чугунный плуг был пригоден лишь для вспашки чернозема. При обработке глинистой почвы он увязал в ней, а по песку — скользил. Поэтому плуг Рансона не получил большого распространения. В 1819 г. американский фермер П. Вуд сконструировал чугунный плуг оригинального типа. Этот плуг делался из чугуна, причем все его части изготовлялись отдельно. По мере изнашивания отдельных частей их можно было заменять другими. Однако чугунные плуги обладали некоторыми существенными недостатками: лемехи при обработке рыхлой земли скоро притуплялись, а в каменистой, твердой почве чугун ломался. В 1833 г. кузнец Джон Лен из Чикаго в лемех деревянного плуга вделал острое стальное лезвие в чугунной оправе. Это был первый шаг к изготовлению цельного стального плуга. В том же 1833 г. в США кузнец Джон Дир создал первый цельностальной плуг. Вначале плуги изготавливались из так называемой пильной стали, считавшейся наиболее прочной, но затем, в 1868 г., американец Вильям Морисон получил специальную плужную сталь, из которой и начали делать плуги. Наряду с поисками нового материала для изготовления плуга шла работа над усовершенствованием его конструкции.
Современные плуги изготавливаются из чугуна или стали в зависимости от обрабатываемой почвы. Современные плуги делятся на лемешные, дисковые, роторные и комбинированные. Для обработки сухой твердой почвы используют дисковые, а не лемешные плуги. У дисковых плугов рабочим органом вместо остроконечных лезвий является стальной диск с острыми краями.
Конструкция плугов функциональна и не сложна в сборке, настройке, эксплуатации и обслуживании. В конструкции рабочих органов применяются износостойкие материалы, элементы рабочих органов, наиболее подверженные износу, выполнены сменными. Использование новых видов стали, применение новых методов обработки и окраски поверхности приводит к увеличению срока службы почвообрабатывающих агрегатов
1. Анализ исходных данных для выбора материала.
Задание предусматривает выбор материала для высоконагруженного диска плуга диаметром 85 мм, работающего без значительных ударных нагрузок. Прокаливаемость детали плуг равна толщине сечения 10мм.
На основании требований приведенных в задании, высокие значения прочностных характеристик (σВ
≥1000 МПа, σТ
≥800 МПа) и пластичности (δ≥8%,) характерны для среднеуглеродистых низколегированных сталей.
Серийные почвообрабатывающие детали отечественного производства изготавливают из среднеуглеродистых низколегированных сталей марок 5, 35, 40Х, 45, Л53, 65Г, 40Г2, 55С2 и др. Изделия закаливают и подвергают среднему отпуску. Твердость закаленной поверхности находится в пределах 39,5…48 HRC. Показатель прочности не превышает 900…1200 МПа.
2. Выбор способа формообразования.
Наиболее оптимальным способом формообразования детали плуг является листовая штамповка. Листовой штамповкой получают разнообразные детали из различных сталей и сплавов для авиационной, автомобильной, тракторной промышленности, производства товаров широкого потребления и других отраслей народного хозяйства. Основной признак листовой штамповки - неизменность толщины заготовки в ходе обработки. В качестве заготовки используют лист, ленту, полосу, фасонный профиль.
Процесс листовой штамповки характеризуется высокой производительностью (до 40000 деталей в смену с одного штампа), легко поддается механизации и автоматизации, обеспечивает высокую точность размеров и хорошее качество поверхности отштампованных деталей, большой экономией металла, низкой себестоимостью изготовляемых изделий. Другие способы формообразования не подходят, так как они наиболее дорогие и энергоемкие.
3. Выбор марки материала.
Рессорно-пружинные углеродистые и легированные стали имеют высокий модуль упругости, ограничивающий упругую деформацию. Они недорогие и достаточно технологичные, применяются для изготовления жестких (силовых) упругих элементов в авто- и тракторостроении, железнодорожном транспорте, станкостроении, для силовых упругих элементов приборов. Часто эти материалы называют пружинными сталями общего назначения.
Стали должны иметь высокие пределы упругости, выносливости и релаксационную стойкость. Этим требованиям удовлетворяют стали с повышенным содержанием углерода (0,5-0,7%), углеродистые стали (65, 70, 75, 80, 85, 6ОГ, 65Г, 70Г) характеризуются невысокой релаксационной стойкостью, особенно при нагреве. Они не пригодны для работы при температурах выше 100°С.
Таблица 1 – назначение и общая характеристика
Марка
|
60Г
|
Заменитель
|
65Г
|
Классификация
|
Сталь конструкционная рессорно-пружинная
|
Применение
|
Плоские и круглые пружины, рессоры, пружинные кольца и другие детали пружинного типа, от которых требуются высокие упругие свойства и износостойкость; бандажи, тормозные барабаны и ленты, скобы, втулки и другие детали общего и тяжелого машиностроения
|
Таблица 2 – Химический состав в % стали 60Г ГОСТ 14959 – 79.
C
|
Si
|
Mn
|
Ni
|
S
|
P
|
Cr
|
Cu
|
0.57 0.65
|
0.17 - 0.37
|
0.7 - 1
|
до 0.25
|
до 0.035
|
до 0.035
|
до 0.25
|
до 0.2
|
Таблица 3 – Температура критических точек
Критическая точка
|
°С
|
Ac1
|
726
|
Ac3
|
765
|
Ar3
|
741
|
Ar1
|
689
|
Mn
|
270
|
Таблица 4 – Механические свойства
Термообработка, состояние поставки
|
Сечение, мм
|
s0,2
, МПа
|
sB
,
МПа
|
d5
, %
|
y, %
|
HB
|
HRCэ
|
Сталь категорий: 3,3А,3Б,3В,3Г,4,4А,4Б. Закалка 830 °С, масло, отпуск 470 °С.
|
|
785
|
980
|
8
|
30
|
|
|
Закалка 790-810 °С, вода. Отпуск 360-400 °С, воздух.
|
20
|
1180
|
1370
|
5
|
10
|
|
42-47
|
Закалка 800-820 °С, вода. Отпуск 530-600 °С, воздух.
|
60
|
640
|
830
|
9
|
37
|
|
30-35
|
Нормализация
|
80
|
390
|
390
|
11
|
35
|
229
|
|
Таблица 5 – Механические свойства в зависимости от температуры отпуска
t отпуска, °С
|
σ0,2
, МПа
|
σВ
, МПа
|
δ5
, %
|
y, %
|
HB
|
400
|
1460
|
1710
|
2
|
5
|
440
|
500
|
1270
|
1460
|
4
|
10
|
420
|
600
|
1120
|
1240
|
7
|
16
|
380
|
700
|
980
|
1130
|
5
|
22
|
350
|
4. Назначение вида и режима термической обработки.
Оптимальным вариантом окончательной (упрочняющей) термообработки, обеспечивающей получение требуемых свойств, является, закалка в масле при температуре 840о
С с охлаждением в воде или масле и среднему отпуску при температуре 420-520о
С.
5. Описание структуры и свойств готовых деталей.
Материал и свойства деталей рабочих органов плугов должны быть адекватны изнашивающей способности обрабатываемых почв. Из-за низкой прочности и абразивной износостойкости почворежущие элементы, изготовленные из среднеуглеродистой стали с традиционным способом упрочнения (закалка+отпуск), в результате такого вида термообработки образуется структура троостита
.
Для обработки песчаных и супесчаных почв при комплексном учете материаловедческих, конструкторских, технологических, триботехнических, эксплуатационных и экономических факторов, можно применять почворежущие изделия с наплавочными материалами (почворежущие профили изделий с лицевой стороны подлежат наращиванию износостойким сплавом). Основной металл в этом случае обеспечивает необходимую прочность, а твердое металлопокрытие - абразивную износостойкость. В результате, появляются резервы снижения стоимости рабочих органов почвообрабатывающих машин.
ЛИТЕРАТУРА
1. Арзамасов Б.Н. Материаловедение. М. Машиностроение.1986
2. Журавлев В.Н., Николаева О.И. Машиностроительные стали. Справочник. –
М.: Машиностроение, 1992.
3. Карпенко А.Н. Справочник механизатора. М. Агропромиздат, 1986
4. Кузьмин Б.А. Технология металлов и конструкционные материалы. М. Машиностроение. 1981
5. Шапиро А.А. Пособие для сельского кузнеца. М. Высшая школа, 1967
6. http://s-metall.com.ua
|