Федеральное агентство по образованию
Государственное образовательное учреждение
высшего профессионального образования
«ЛИПЕЦКИЙ ГОСУДАРСТВЕННЫЙ ТЕХНИЧЕСКИЙ УНИВЕРСИТЕТ»
Кафедра физического металловедения
Измерение
твердости
металлов
Методические указания к лабораторным работам
для студентов специальностей
150105, 150702
Ю. С. Шатов,
И. П. Горбунов,
А. Г. Гвоздев
Липецк – 2006
669.01(07)
Ш 288
Шатов, Ю.С. Измерение твердости металлов. Методические указания к лабораторным работам для студентов специальностей 150105, 150702. /Ю.С. Шатов, И.П. Горбунов, А.Г. Гвоздев. – Липецк: ЛГТУ, 2006. – 33 с.
Предназначены для студентов 3 курса специальностей 150105, 150702. В методических указаниях приведена методика работы на твердомерах. Указывается цель каждой работы; сообщаются теоретические сведения, необходимые для выполнения эксперимента, приводятся схемы приборов; рассматривается порядок выполнения работ и дается форма отчета. Даны варианты индивидуальных заданий студентам для определения твердости металлов.
Ил. 5. Табл. 7. Библиогр.: 6 назв. Приложений 2.
Методические указания утверждены на заседании кафедры физического металловедения 15 сентября 2006 г., протокол № 1
Рецензент – В.В.Логунов
© Липецкий государственный
технический университет, 2006
Общие указания
Цель работы:
1. Освоить методику измерения твердости на приборах Бринелля, Роквелла, Виккерса и микротвердомере.
2. Научиться правильно выбирать прибор, нагрузку и наконечник при испытаниях твердости различными методами и определять твердость выданных образцов.
3. Уметь измерять твердость отдельных фаз и структурных составляющих.
Твердость определяет способность металла сопротивляться деформации на поверхности образца или изделия.
Испытания на твердость широко применяется в лабораторных и заводских условиях для характеристики механических свойств металлов и сплавов.
Твердость металлов измеряют при помощи воздействия на поверхность изделий наконечником, изготовленного из твердого материала (закаленная сталь, алмаз и др.) и имеющего форму шарика, конуса, пирамиды или иглы. По характеру воздействия наконечника различают несколько способов измерения твердости: а) метод вдавливания; б) метод отскока; в) метод царапания.
Твердость, определенная вдавливанием, характеризует сопротивление металла пластической деформации.
Твердость, определенная по отскоку, характеризует упругие свойства. Твердость, определенная царапанием, сопротивление разрушению. Таким образом, твердость является специфическим свойством металла и при испытаниях на твердость могут измеряться упругие свойства металлов, сопротивление пластическим деформациям, сопротивление разрушению и ар. Широкое применение испытаний на твердость в практике объясняется тем, что они не требует длительного времени, специальных сложных образцов, могут проводиться на готовых изделиях без их разрушения и позволяют по эмпирическим соотношениям судить о других механических свойствах металла. Выбор формы, размеров наконечника и величины нагрузки зависит от целей испытания, структуры, ожидаемых свойств, состояний поверхности и размеров испытуемого образца.
Если металл имеет гетерогенную структуру с крупными выделениями отдельных структурных составляющих, различных по свойствам (например, серый чугун, подшипниковые сплавы), то для измерения твердости выбирают шарик большого диаметра.
При испытаниях металлов с высокой, твердостью (например, закаленная сталь) применяют алмазный конус при снижении общей нагрузки (во избежание образования трещин в образце). Однако значительное снижение нагрузки нежелательно т.к. приведет к резкому уменьшению деформируемого объема и может дать значения, не характерные для основной массы металла.
Измерение микротвердости имеет целью определить плотность отдельных зерен, фаз, структурных составляющих и поверхностных слоев металла при его химико-термической обработке. В этом случае объем, деформируемый вдавливанием, должен быть меньше объема измеряемого зерна, поэтому прилагаемая нагрузка выбирается небольшой.
Значительное влияние на результаты испытаний твердости оказывает состояние поверхности материала. Если поверхность неровная – криволинейная или с выступами – то отдельные участки в различной степени оказывает сопротивление вдавливанию, что приводит к ошибке при измерении твердости.
Поэтому, чем меньше нагрузка, тем тщательнее готовится поверхность. Она должна представлять шлифованную горизонтальную площадку, а для измерения микротвердости и полированную. Измеряемая поверхность должна быть установлена горизонтально, т.е. перпендикулярно действию нагрузки. Противоположная сторона образца должна быть зачищена и не иметь окалины, т.к. последняя при нагружении сминается, что искажает результаты измерения. Метод вдавливания твердого наконечника получил наибольшее распространение в практике испытаний металлов. К этому методу относятся методы Бринелля, Роквелла, Виккерса. Измерение твердости этими методами стандартизированы и устанавливаются ГОСТами:
Бринелля – ГОСТ 9012 – 59, Роквелла – ГОСТ 9013 – 59, Виккерса – ГОСТ 2999 – 59.
На рис. 1 показан диапазон значений твердости этих трех принципиально одинаковых методов, основанных на статическом вдавливании твердого наконечника.

Рис. 1. Диапазон значений твердости
Методические указания по измерению твердости на приборах Бринелля, Роквелла, Виккерса и микротвердомере ПМТ – 3
Общие сведения о методах испытания твердости на приборах Бринелля и Роквелла описано в учебных пособиях [1,4], с которыми студент должен подробно ознакомиться при подготовке к данной работе.
Твердость по Бринеллю – НВ, Н/м2
.
При измерении твердости на приборе Бринелля студент должен руководствоваться следующими советами:
1. Прежде чем приступить к испытанию на твердость, необходимо правильно подобрать по табл. 2 нагрузку (Р) и диаметр шарика (Д) исходя из материала и толщины образца, ГОСТ 9012 – 59. Нагрузку выбирают так, чтобы соблюдался закон подобия
Р/Д2
= const (1)
В этом случае возможно сравнение твердости, полученной при различном диаметре шариков. Минимальная толщина испытуемого образца должна быть не менее десятикратной глубины отпечатка. На обратной стороне испытуемого образца после вдавливания шарика не должно быть следов деформации.
2. Чем больше диаметр шарика, тем выше точность в определении твердости.
3. Твердость материала при измерении по Бринеллю не должна превышать 4500 МН/м2
, т.к. для вдавливания используется стальной закаленный шарик с твердостью НВ = 6000 МН/м2
и при испытании более твердых металлов он будет деформироваться сам.
4. Продолжительность выдержки образца строго постоянна и устанавливается перед измерением от 10 до 60 секунд (согласно табл.2) в зависимости от материала.
5. Диаметр отпечатка (d), полученного после вдавливания, измеряется при помощи специальной лупы с точностью до 0,05 мм. При этом для лучшей освещенности отпечатка окно лупы располагают в направлении к источнику света.
6. Значение твердости находят из таблиц или рассчитывает по формуле Н/м2
(2)
7. Поверхность испытуемого образца должна быть свободна от окалины и других посторонних веществ, при этом поверхность обрабатывается в виде плоскости так, чтобы края отпечатка были отчетливо видны при измерении его диаметра.
8. Расстояние от центра отпечатка до края образца должно быть больше или равно 2,5 d,. а между центрами двух соседних отпечатков – больше или равно 4 d.
9. Диаметры отпечатков (d) должны находиться в пределах
.
В случае несоблюдения этого условия испытание признается неверным и должно быть повторено с применением соответствующей нагрузки.
Порядок измерения твердости на приборе Бринелля
После того, как подобраны нагрузка, диаметр шарика и установлено время выдержки, испытуемый образец помещают на столик и при помощи маховичка приводят в соприкосновение с шариком до упора, создавая этим предварительную нагрузку в 1000 Н. Нажатием кнопки включают электродвигатель. Нагружение образца, выдержка и снятие нагрузки осуществляются автоматически. Длительность выдержки сигнализируется зажиганием лампочки. После отключения электродвигателя столик опускают и измеряют полученный отпечаток специальной лупой. Диаметр отпечатка замеряют в двух взаимно перпендикулярных направлениях и берут среднее значение. Зная диаметр отпечатка и приложенную нагрузку, по табл. 1 находят величину твердости испытуемого образца.
Твердость по Роквеллу –
HRB
, Н
R
А, Н
R
С,
HRF
При измерении твердости на приборе Роквелла студент должен руководствоваться следующими советами:
1. Испытания твердости на этом приборе могут производиться вдавливанием закаленного шарика (D =I,588 мм), алмазного конуса. При этом алмазный конус применяется для испытания твердых металлов (НВ – 2500 МН/м2
).
2. В зависимости от типа индентора и выбранной нагрузки измерения твердости проводят по шкалам A,B,C,F. Полученное значение твердости является величиной безразмерной и выражается в единицах данной шкалы соответственно HRA, HRB, HRC, HRF (см. табл. 3).
3. Прибор измеряет глубину отпечатка. Каждое деление шкалы индикатора соответствует глубине вдавливания (h) в 0,002 мм, поэтому, чем меньше h, тем больше твердость.
4. Соотношение между твердостью и глубиной вдавливания определяется выражениями
для алмазного конуса (3)
для шарика (4)
5. Перед началом испытания необходимо выбрать шкалу измерения, т.е. нагрузку, шкалу отсчета и индентор (шарик или конус). Шкалы А и С применяет для измерения закаленной стали, причем, когда требуется измерить твердость в поверхностном слое, например, после химико-термической обработки, после закалки ТВЧ, нагрузку снижают до 500 Н, т.е. использует для измерения шкалу А. Для определения твердости отожженной и нормализованной стали применяют шкалу В, нагрузку 1000 Н. Дня цветных металлов, имеющих малую твердость, измерения проводят по шкале F. Нагрузка в этом случае снижена до 500 Н, чтобы уменьшить глубину проникновения стального шарика.
6. Поверхность испытуемого образца должна быть очищена шлифовкой от окалины и других посторонних веществ.
7. Перпендикулярность приложения нагрузки обеспечивается за счет создания параллельности опорных поверхностей образца.
8. Минимальная толщина образца должна бить не меньше восьмикратной глубины внедрения наконечника после снятия основной нагрузки. На обратной стороне образца не должно быть заметно после измерения твердости следов деформации. Расстояние от края образца или между соседними отпечатками должно быть не менее 3 мм.
9. Отсчет результатов измерения твердости производится в целых делениях шкалы индикатора с точностью 0,5 единицы шкалы. За число твердости принимается результат отдельного измерения. Причем на каждом образце должно быть произведено не менее трех измерений.
Порядок измерения твердости на приборе Роквелла
После подготовки поверхности образца и выбора шкалы устанавливается соответствующая нагрузка и индентор (шарик или алмазный конус). Образец помещают на столик прибора и при помощи маховичка приводят в соприкосновение с наконечником, создавая предварительную нагрузку в 100 Н, что отмечается на циферблате установкой маленькой стрелки против красной точки. При этом большая стрелка должна занять вертикальное положение, указывая вверх с отклонением ±5 делений шкалы от вертикали. Если отклонение стрелки превышает 5 делений, предварительная нагрузка должна быть снята, а измерение твердости произведено в другой точке образца.
Затем совмещает большую стрелку с нулем черной шкалы (независимо от выбранной шкалы измерения) и нажатием на рычаг дают основную нагрузку.
После полной остановки движения стрелки (через 2–3 с) производится отсчет твердости по шкале индикатора. Необходимо помнить, что при измерении алмазным конусом отсчет твердости производится по черной шкале, а при измерении стальным шариком – по красной шкале. Несмотря на ряд недостатков метода Роквелла: условность величины определяемой твердости, малая точность измерения этот метод широко применяется для массового контроля. Причиной этого является ряд достоинств метода:
1. Быстрое определение твердости благодаря автоматизации приборов.
2. Возможность определения твердости материалов с НВ > 500 ед.
3. Возможность измерения твердости на малых и тонких образцах.
Твердость по Роквеллу HRA, HRB, HRC, HRF может быть переведена в твердость по Бринеллю при помощи таблицы (см. табл. 4), составленной на основании экспериментальных данных
Метод Виккерса
При измерении твердости по Виккерсу согласно ГОСТ 2999 – 59 в испытуемый металл вдавливается четырехгранная алмазная пирамида с углом при вершине 135°. Для испытания могут применяться нагрузки 50, 100, 200, 300, 500, 1000 и 1200 Н. Отпечаток получается в виде квадрата. При помощи микроскопа, находящегося на приборе, измеряется диагональ отпечатка. Твердость по Виккерсу HV определяют как удельное давление, приходящееся на единицу поверхности отпечатка Н/м2
(5)
где Р – нагрузка на пирамиду, Н;
d – длина диагонали отпечатка, мм2
.
Числа твердости по Бринеллю и Виккерсу имеют одинаковую размерность, а для металлов с твердостью до 450 ед. они одинаковы.
Измерение твердости алмазной пирамидой дает более точные значения для металлов с высокой твердостью, чем измерения шариком или конусом, так как диагонали отпечатка достаточно велики даже при малой глубине отпечатка. При вдавливании пирамиды соотношение между диагоналями получающегося отпечатка при изменении нагрузки остается постоянным, что позволяет в широких пределах менять нагрузку. Величину нагрузки выбирают в зависимости от целей исследования, толщины и твердости исследуемого образца. Продолжительность выдержки под нагрузкой составляет: для черных металлов 10–15 с, для цветных металлов 30–60 с.
Прибор Виккерса (рис.2) снабжен рычажным устройством 1 для нагружения алмазной пирамиды 5, специальным микроскопом 6 для измерения диагоналей отпечатка, а также грузовым приводом 7.
Поверхность образцов для определения твердости по Виккерсу предварительно тщательно отшлифовать наждачной бумагой тонкого номера или отполировать. Толщина исследуемого образца должна быть не меньше, чем 1,5 диагонали отпечатка.
На приборе Виккерса можно измерять твердость мягких металлов и очень твердых сплавов и, кроме того, твердость в тонких поверхностных слоях, например при обезуглероживании, поверхностном наклепе, химико-термической обработке и т.д.
Однако каждое определение по Виккерсу занимает сравнительно много времени и требует тщательной подготовки поверхности образца, что является основным недостатком этого метода, препятствующим широкому применению его в цеховых условиях.
Порядок измерения твердости по Виккерсу
1. Определяют необходимую величину нагрузки в зависимости от материала и Форму испытуемого изделия, пользуясь таблицей 5.
2. Образец помещается на столике 4, установленном на винте 3, который перемещается вращением маховичка 2 до тех пор, пока не произойдет соприкосновение алмазной пирамида о поверхность образца.
3. Включается рукоятка 1, и нагрузка системой рычагов передается на образец.
4. Отводят изделие от соприкосновения с алмазным наконечником поворотом маховика против часовой стрелки и, поворачивая головку микроскопа вправо до упора, совмещает объектив микроскопа с отпечатком.
5. Отпечаток фокусируют и измеряют величину диагоналей. Для этого вращением винта подводят к краю диагонали нулевую отметку шкалы, а затем, вращая микровинт, подводят к противоположному концу диагонали подвижную линию. При отсчете пользуются шкалой микроскопа, одно деление которой равно 0,1 мм, и микровинтом, одно деление которого на лимбе соответствует 0,001 мм при увеличении в 100 раз. Для измерения второй диагонали поворачивают головку микроскопа на 90° – по часовой стрелке. После замера двух диагоналей определяет среднее значение d.
6. Пользуясь таблицей, по значению d определяют твердость по Виккерсу (HV) или находят ее по формуле (5).
Метод измерения микротвердости
При определении микротвердости четырехгранная алмазная пирамида (с углом между противоположными гранями при вершине 135°) вдавливается в испытуемый материал под очень небольшой нагрузкой от 0,05 до 5 Н. Число твердости выражается в величинах твердости Н и определяется по формуле (5).
Числа твердости согласно ГОСТ 9450 – 60 обозначают символом Н с указанием в индексе величины нагрузки в граммах (например, H50
= 220 означает, что число микротвердости 220 получено при нагрузке 0,5 Н).
Испытание на микротвердость применяют для контроля качества материала очень мелких деталей, а также для определения твердости структурных составлявших, твердости покрытий и весьма тонких поверхностных слоев. Поверхность образца для определения микротвердости подготавливают так же, как и для микроисследования. Полирование рекомендуется электролитическое во избежание наклепа в тонком поверхностном слое. Для определения микротвердости применяют прибор ПМТ – 3. Это вертикальный микроскоп 1 с нижним положением столика, который

Рис. 2. Прибор Виккерса
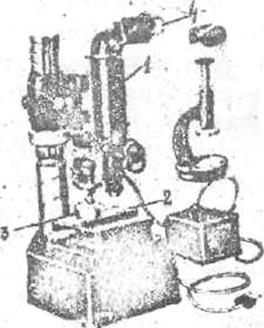
Рис. 3. Общий вид прибора ПМТ – 3
Это вертикальный микроскоп 1 с нижним положением столика, который имеет два сменных объектива с увеличением в 487 и 130 раз (обычно пользуются увеличением в 487) и окуляр – микрометр 4 для измерения диагонали отпечатков. Вращением столика 2 выбранное место на шлифе 3 подводят под индентор – пирамиду. Принцип измерения твердости такой же, как и по Виккерсу, только пирамида отличается более высокой точностью изготовления. На рис. 3 показан общий вид прибора ПМТ – 3.
Выбор нагрузки зависит от задачи измерения. Центр отпечатка должен быть удален от края шлифа или от края соседнего отпечатка не менее чем на две диагонали отпечатка. Если отпечаток получен слишком близко к краю, то вдавливание индентора облегчается и поэтому значение твердости оказывается заниженным. Если первый отпечаток расположен слишком близко от второго, то второй отпечаток будет находиться в зоне, уже наклепанной от первого вдавливания, поэтому твердость получается завышенной.
При малой нагрузке велика относительная погрешность в измерении отпечатка и сильнее сказывается качество шлифа, поэтому желательно брать наибольшую нагрузку.
Вместо определения числа твердости по формуле обычно пользуется таблицами, рассчитанными для нагрузок 0,2; 0,5; 1 и 2 Н. Но если нужно измерить твердость отдельного зерна, приходится снижать нагрузку, пока отпечаток не окажется настолько малым, чтобы до краев зерна оставалось не менее двух диагоналей. Даже отпечаток, далеко отстоящий от видимой границы зерна, может давать завышенное (или заниженное) значение твердости из–за того, что под ним на небольшой глубине под поверхностью шлифа залегает другая фаза (более твердая или более мягкая). Индентор "упирается" в нее или, наоборот, "проваливается" сквозь твердую корку в мягкую подложку. Поэтому разброс измеренных значений микротвердости, как правило, гораздо больше, чем при обычных измерениях твердости. Измерения микротвердости имеют ценность только при правильной статистической обработке диагонального числа размеров.
Среднее значение микротвердости Н вычисляем по формуле (6), среднеквадратичные значения SА
– по формуле (7)
(6)
где n – число измерений,
Нi
– текущее измерение.
Для возможности обработки полученных данных на ЭВМ производили преобразования
(7)
число степеней свободы 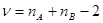
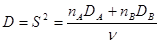
где – дисперсия;
– дисперсия измерений структурной составляющей А;
– дисперсия измерений структурной составляющей B.
Критерий Стьюдента подсчитываем по формуле
(8)
По значениям и находят из таблицы 6 значение Р – вероятности из того, что действительные твердости H1
и H2
одинаковы. Величина Р = 0,9 означает, что с вероятностью более 90 % значения микротвердости первого и второго образцов должны совпадать. Малые значения Р указывают на существование достоверной разницы в твердости.
Порядок замера микротвердости
Перед измерением микротвердости необходимо:
а) Подготовить поверхность исследованного образца так же, как при микроструктурном анализе (шлифовка – полировка – травление),
б) Определить цену деления окуляр – микрометра (см. работу “Количественный анализ”[2]).
в) Подобрать нагрузку в зависимости от размера к предполагаемой твердости.
г) Закрепить шлиф к неметаллической пластине с помощью ручного пресса и пластилина строго параллельно горизонтальной плоскости предметного столика.
После этого приступают к измерениям.
1. Пластину со шлифом устанавливают на столике.
2. Перемещением столика микровинтами подводят выбранное для укола место под перекрестием окуляра.
3. Устанавливают барабанчик окулярного микрометра 7 в нулевое положение.
4. Поворачивают столик до упора (делать плавно), при этом образец располагается под нагрузкой.
5. Нагружают образец медленным (10–15 с) поворотом рукоятки арретира индентора 4 и делают выдержку 5 с., после чего рукоятку арретира возвращают в исходное положение. Каждый раз, прежде чем вращать столик, необходимо убедиться, что алмазная пирамида поднята. Внимание! Вращая столик при опущенном инденторе (наконечнике), можно сломать алмаз.
6. Сняв нагрузку, столик возвращают вращением в исходное положение, т.е. под микроскоп. Если отпечаток значительно удален от перекрестия (см. рис. 4. (1)), винтами 9 (рис. 3) осторожно смещают изображение отпечатка в перекрестие.
7. Микровинтом 7 перемещают перекрестие из положения 1 в положение 2 (рис. 4) и на лимбе микровинта 7 определяют длину диагонали отпечатка в делениях лимба dдел
.
Результаты измерений заносят в таблицу. Величину диагонали отпечатка в микронах определяют по формуле с учетом найденной ранее цены деления
dмкм
= dдел
.

Рис. 4. Приемы последовательного измерения диагонали отпечатков на приборе ПМТ–3 окуляр – микрометром АМ9–2 (АМ9–1)
  
Рис. 5. График для определения микротвердости без пересчета
Сделав перевод каждого измеренного значения диагонали в твердость, находят среднее значение твердости (отдельно дет каждого измерения). Поскольку зависимость твердости от длины диагонали нелинейная, нельзя вычислять сначала среднюю диагональ, а потом находить по ней твердость. Для ускорения работы рекомендуется построить на миллиметровке, используя формулу (5), график в координатах dдел
– твердость и из него находить все значений твердости.
Методика работы
В этой работе студенты знакомятся с техникой определения твердости по Бринеллю, Роквеллу, Виккерсу и микротвердости на приборе ПМТ – З и приобретают навык для того, чтобы при выполнении других работ они могли определять твердость самостоятельно. Кроме, того, студенты знакомятся с устройством прессов Бринелля, Роквелла, Виккерса, прибора ПМТ – 3 и с принципом их работы.
Задание на определение твердости методом Бринелля и Роквелла
Студент изучает индивидуальную задачу (см. приложение 1) и решает ее самостоятельно. Прежде чем начать испытания студент выясняет, какие из образцов надо испытать по Бринеллю и какие по Роквеллу.
1. Измерить твердость на образцах, предварительно измерив штангенциркулем толщину образцов.
2. Пользуясь табл.2, выбрать, диаметр шарика и нагрузку.
3. При испытании по Роквеллу необходимо установить, по какой шкале надо производить измерение твердости (по шкале А, В, С и F), пользуясь при этом табл. 3. Измерить твердость образца по Бринеллю и Роквеллу и сопоставить ее.
4. Твердость по Бринеллю определить по таблице и рассчитать по формуле (2). Сопоставить полученные результаты. Диаметр отпечатка замерить в двух перпендикулярных направлениях и брать среднее значение.
5. Твердость по Роквеллу определить из среднего значения трех измерений.
6. Определить предел прочности и предел выносливости, пользуясь табл.8.
7. Все полученные результаты занести в таблицы.
Задание на определение твердости по Виккерсу
На приборе могут работать одновременно не более 2–3 студентов. Для измерения твердости по Виккерсу образцы шлифуют и полируют. Испытанию на HV подвергаются образцы различных марок углеродистой или легированной стали, проведшие термическую обработку (отжиг, нормализацию, закалку, отпуск).
1. Провести испытания на твердость различных марок углеродистой стали 20, 35, 45, У7, У8, У12 в отожженном состоянии. Сделать вывод о влиянии содержания углерода на твердость стали. Объяснить полученные результаты в связи с изменением структуры.
2. Провести испытания стали 45, У8 в нормализованном, закаленном и отпущенном состояниях. Сделать вывод о влиянии термообработки на свойства стали.
3. Один из отожженных образцов испытать по Бринеллю и Роквеллу, сопоставить, числа твердости, полученные по Виккерсу, по Бринеллю и Роквеллу. Аналогичное задание по пунктам 1, 2, 3 по указанию преподавателя может быть выполнено для легированных марок сталей.
4. При измерении твердости по Виккерсу на каждом образце делается 10–15 отпечатков.
5. Полученные результаты замеров занести в таблицу.
Задание на определение микротвердости
На одном приборе ПМТ – 3 могут работать одновременно не более 2–3 студентов.
1. Измерить микротвердость образцов в соответствии с индивидуальным заданием (см. приложение 2).
2. На шлифе измеряют твердость различных фаз или структурных составляющих. Если это углеродистая сталь (например, ст.45), то определяют твердость феррита и перлита. Студент делает по 15 отпечатков на каждой структурной составляющей.
3. Каждый студент вычисляет среднее значение H, а также все внесенные в табл. 7 величины (отдельно для каждой фазы).
4. Из 30–45 измеренных значений микротвердости перлита и феррита с интервалом в 10 ед. строят гистограмму распределения микротвердости для каждой структурной составляющей.
5. С помощью формул (8), (9), (10) и табл. 6 проверяют, насколько достоверно найденное различие в твердости феррита и перлита, если:
а) использовать по 3 замера, твердости каждой составляющей,
б) использовать 10 замеров,
в) использовать 20, 30, 45 замеров (объединить данные двух – трех студентов).
Полученные результаты изобразить графически.
Форма отчета
Студент представляет письменный отчет о работе, в котором должны быть приведены:
1. Краткое описание определения твердости по Бринеллю, Роквеллу, Виккерсу и микротвердости с изложением теоретических положений и формул.
2. Схема одного из приборов c указанием назначений основных деталей.
3. Письменное обоснование выбора прибора и условий испытаний для решения индивидуальной задачи.
4. Результаты испытаний в виде таблицы и графики с объяснением причин изменения твердости в зависимости от вида термической обработки.
5. Кроме решения индивидуальной задачи каждый студент выполняет дополнительную работу, указанную в заданиях по определению твердости на приборах Бринелля, Роквелла, Виккерса и ПМТ – 3, что должно найти отражение в отчете.
Библиографический список
1. Гвоздев А.Г. Лабораторный практикум по материаловедению. Учебное пособие [Текст] / А.Г. Гвоздев. Липецк: ЛГТУ, 2002.
2. Лившиц Б.Г. Металлография [Текст] / Б.Г. Лившиц. М.: Металлургия, 1971.
3. Захаров A.M. Диаграммы состояния двойных и тройных систем [Текст] / A.M. Захаров. М.: Металлургия, 1978.
4. Кример Б.И. Лабораторный практикум по металлографии и физическим свойствам металлов и сплавов [Текст] / Б.И Кример, Е.В. Панченко, Л.А. Шишко, В.Н. Николаева, Ю.С. Авраамов. М.: Металлургия, 1966.
5. Панченко Е.В. Лаборатория металлографии [Текст] / Е.В. Панченко, Ю.А. Скаков, Б.И. Кример, П.П. Арсентьев, К.В. Попов, М.Я. Цвилинг. М.: Металлургия, 1965.
6. Штремель М.А. Лабораторный практикум по спецкурсу «Прочность сплавов». Часть 1. [Текст] / М.А. Штремель. М.: Металлургия, 1968.
Таблица 1
Числа твердости по Бринеллю, НВ (МН/м2
∙× 10-1
)
Нагрузка 3000 Н
Диаметр шарика 10 мм
|
Нагрузка 7500 Н
Диаметр шарика 5 мм
|
Нагрузка 1875 Н
Диаметр шарика 2,5 мм
|
Диаметр отпечатка
|
твердость НВ
|
Диаметр отпечатка
|
твердость НВ
|
Диаметр отпечатка
|
твердость НВ
|
2,05
|
898
|
1,25
|
602
|
0,65
|
555
|
2,1
|
857
|
1,3
|
555
|
0,7
|
477
|
2,2
|
782
|
1,35
|
515
|
0,75
|
415
|
2,25
|
744
|
1,4
|
477
|
0,8
|
363
|
2,3
|
713
|
1,45
|
455
|
0,85
|
321
|
2,35
|
683
|
1,5
|
451
|
0,9
|
285
|
2,4
|
652
|
1,55
|
390
|
0,95
|
255
|
2,45
|
627
|
1,6
|
363
|
1
|
229
|
2,5
|
600
|
1,65
|
341
|
1,05
|
207
|
2,55
|
578
|
1,7
|
321
|
1,1
|
187
|
2,6
|
555
|
1,75
|
302
|
1,15
|
170
|
2,65
|
532
|
1,8
|
285
|
1,2
|
156
|
2,7
|
512
|
1,85
|
269
|
1,25
|
141
|
2,75
|
495
|
1,9
|
255
|
1,3
|
131
|
2,8
|
477
|
1,95
|
241
|
1,35
|
121
|
2,85
|
460
|
2
|
229
|
1,4
|
111
|
2,9
|
444
|
2,05
|
217
|
1,45
|
103
|
2,95
|
430
|
2,1
|
207
|
1,5
|
95,5
|
3
|
418
|
2,15
|
198
|
1,55
|
88,7
|
3,05
|
407
|
2,2
|
187
|
1,6
|
82,5
|
3,1
|
387
|
2,25
|
178
|
1,65
|
76,8
|
3,15
|
375
|
2,3
|
170
|
1,7
|
71,6
|
3,2
|
364
|
2,35
|
162
|
1,75
|
66,8
|
3,25
|
351
|
2,4
|
156
|
3,30
|
340
|
2,45
|
149
|
3,35
|
332
|
2,5
|
141
|
3,4
|
321
|
2,55
|
136
|
3,45
|
311
|
2,6
|
131
|
3,5
|
302
|
2,65
|
126
|
3,55
|
293
|
2,7
|
121
|
3,6
|
286
|
2,75
|
116
|
3,65
|
277
|
2,8
|
111
|
3,7
|
269
|
2,85
|
107
|
3,75
|
259
|
2,9
|
103
|
3,8
|
255
|
2,95
|
99,7
|
3,85
|
242
|
3
|
95,5
|
3,9
|
241
|
3,05
|
92
|
4
|
235
|
3,1
|
88,7
|
4,05
|
228
|
3,15
|
85,5
|
4,1
|
223
|
3,2
|
82,4
|
4,15
|
217
|
3,25
|
79,5
|
4,2
|
212
|
3,3
|
76,8
|
4,25
|
209
|
3,35
|
74,1
|
4,3
|
202
|
3,4
|
71,6
|
4,35
|
196
|
3,45
|
69,2
|
4,4
|
192
|
3,5
|
66,8
|
4,45
|
187
|
4,5
|
183
|
4,55
|
179
|
4,6
|
174
|
4,65
|
170
|
4,7
|
166
|
4,75
|
163
|
4,8
|
159
|
4,85
|
156
|
4,9
|
153
|
4,95
|
149
|
5
|
147
|
5,05
|
140
|
5,1
|
137
|
5,15
|
134
|
5,2
|
131
|
5,25
|
128
|
5,3
|
126
|
5,35
|
124
|
5,4
|
121
|
5,45
|
118
|
5,5
|
116
|
5,55
|
114
|
5,6
|
112
|
5,65
|
109
|
5,7
|
107
|
Таблица 2
Твердость по Бринеллю
Металлы
|
Твердость НВ
|
Толщина образца, мм
|
Соотношение между нагрузкой Р и квадратом диаметра шарика D2
|
Диаметр шарика D
|
Нагрузка Р Н∙10-1
|
Выдержка под нагрузкой, с
|
Черные
|
140–450
|
6–3
4–2
2
|
Р=30∙D2
|
10
5
2.5
|
3000
750
187.5
|
10
10
10
|
Черные
|
140
|
6
6–3
3
|
Р=10∙D2
|
10
5
2.5
|
3000
250
62.5
|
10
10
10
|
Цветные
|
130
|
6–3
4–2
2
|
Р=30∙D2
|
10
5
2.5
|
3000
750
187.5
|
30
30
30
|
Цветные
|
35–130
|
9–3
6–3
2–3
|
Р=10∙D2
|
10
5
2.5
|
1000
250
62.5
|
30
30
30
|
Цветные
|
8–35
8–35
8–35
|
6
6–3
3
|
Р=2.5∙D2
|
10
5
2.5
|
250
750
5.5
|
60
60
60
|
Таблица 3
Шкалы испытания по Роквеллу
Обозначения
|
Нагрузка,
Н×10-1
|
Наконечник
|
Шкала индикатора для отсчета твердости
|
Шкалы испытания
|
Чисел твердости
|
A
|
HRA
|
60
|
Алмазный конус
|
Черная
|
C
|
HRC
|
150
|
Алмазный конус
|
Черная
|
B
|
HRB
|
100
|
Стальной шарик
|
Красная
|
F
|
HRF
|
60
|
Стальной шарик
|
Красная
|
Таблица 4
Рекомендуемая нагрузка
Толщина образца, мм
|
Рекомендуемая нагрузка (Н∙10-1) при твердости Н
|
20–50
|
50–100
|
100–300
|
300–900
|
0,3–0,5
|
–
|
–
|
–
|
5–10
|
0,5–1
|
–
|
–
|
5–10
|
10–20
|
1–2
|
5–10
|
10–20
|
10–20
|
–
|
2–4
|
10–20
|
0–30
|
20–50
|
20–50
|
4
|
20
|
30
|
50
|
–
|
Таблица 5
Таблица сопоставления чисел твердости, определяемых различными методами
По Виккерсу Н
нагрузка 1–120 Н 10-1
|
По Роквеллу
|
По Шору Н (по склероскопу)
|
По Бринеллю МН/м2∙10-1
|
По Виккерсу HV, нагрузка 1–120 Н 10-1
|
По Роквеллу
|
По Шору Н (по склероскопу)
|
По Бринеллю МН/м2∙10-1
|
HRC
|
HRA
|
HRB
|
HRF
|
HRC
|
HRA
|
HRB
|
HRF
|
1220
|
72
|
89
|
–
|
–
|
107
|
782
|
534
|
49
|
76
|
–
|
–
|
65
|
477
|
1184
|
71
|
86
|
–
|
–
|
105
|
770
|
502
|
48
|
75
|
–
|
–
|
64
|
460
|
1149
|
70
|
87
|
–
|
–
|
102
|
757
|
474
|
47
|
74
|
–
|
–
|
61
|
444
|
1114
|
69
|
87
|
–
|
–
|
100
|
744
|
467
|
46
|
–
|
–
|
–
|
60
|
437
|
1067
|
68
|
86
|
–
|
–
|
98
|
728
|
460
|
45
|
73
|
–
|
–
|
59
|
430
|
1021
|
67
|
85
|
–
|
–
|
96
|
713
|
435
|
44
|
73
|
–
|
–
|
57
|
415
|
980
|
66
|
–
|
–
|
–
|
94
|
698
|
423
|
43
|
72
|
–
|
–
|
55
|
401
|
940
|
65
|
84
|
–
|
–
|
92
|
683
|
412
|
42
|
–
|
–
|
–
|
54
|
395
|
903
|
64
|
–
|
–
|
–
|
90
|
667
|
401
|
41
|
71
|
–
|
–
|
53
|
388
|
867
|
63
|
83
|
–
|
–
|
88
|
652
|
390
|
40
|
71
|
–
|
–
|
52
|
375
|
835
|
62
|
–
|
–
|
–
|
87
|
639
|
380
|
39
|
70
|
–
|
–
|
50
|
363
|
803
|
61
|
82
|
–
|
–
|
85
|
627
|
361
|
38
|
69
|
–
|
–
|
49
|
352
|
775
|
60
|
–
|
–
|
–
|
83
|
613
|
344
|
37
|
69
|
–
|
–
|
47
|
340
|
745
|
59
|
81
|
–
|
–
|
81
|
600
|
335
|
36
|
68
|
–
|
–
|
46
|
332
|
694
|
58
|
80
|
–
|
–
|
78
|
578
|
320
|
35
|
68
|
–
|
–
|
45
|
321
|
671
|
57
|
–
|
–
|
–
|
76
|
567
|
312
|
34
|
67
|
–
|
–
|
44
|
311
|
649
|
56
|
79
|
–
|
–
|
75
|
555
|
305
|
33
|
67
|
–
|
–
|
42
|
302
|
629
|
55
|
–
|
–
|
–
|
73
|
543
|
291
|
31
|
66
|
–
|
–
|
41
|
293
|
606
|
54
|
78
|
–
|
–
|
72
|
532
|
285
|
30
|
66
|
–
|
–
|
40
|
286
|
595
|
53
|
–
|
–
|
–
|
71
|
522
|
278
|
29
|
65
|
–
|
–
|
39
|
277
|
587
|
52
|
77
|
–
|
–
|
70
|
512
|
272
|
28
|
65
|
–
|
–
|
38
|
269
|
551
|
51
|
76
|
–
|
–
|
68
|
495
|
261
|
27
|
64
|
–
|
–
|
37
|
262
|
543
|
50
|
–
|
–
|
–
|
67
|
486
|
255
|
26
|
64
|
–
|
–
|
36
|
255
|
250
|
25
|
63
|
–
|
–
|
36
|
248
|
–
|
–
|
–
|
64
|
–
|
–
|
114
|
Таблица 6
Значения t при данном числе свободы и данной величине вероятности Р
P

|
0,9
|
0,8
|
0,7
|
0,6
|
0,5
|
0,4
|
0,3
|
0,2
|
0,1
|
0,05
|
0,02;
|
0,01
|
0,001
|
1
|
0,158
|
0,325
|
0,510
|
0,727
|
1,000
|
1,375
|
1,963
|
3,078
|
6,314
|
12,705
|
31,821
|
63,657
|
635,519
|
2
|
0,142
|
0,289
|
0,445
|
0,617
|
0,816
|
1,061
|
1,386
|
1,886
|
2,920
|
4,303
|
6,965
|
9,925
|
31,398
|
3
|
0,137
|
0,277
|
0.424
|
0,584
|
0,765
|
0,978
|
1,250
|
1,638
|
2,353
|
3,182
|
4,541
|
5,841
|
12,941
|
4
|
0,132
|
0,271
|
0,414
|
0,569
|
0,741
|
0,941
|
1,190
|
1,533
|
2,132
|
2,776
|
3,747
|
4,604
|
8,510
|
5
|
0,132
|
0,257
|
0,408
|
0,559
|
0,727
|
0,920
|
1,156
|
1,476
|
2,015
|
2,571
|
3,365
|
4,032
|
6,859
|
5
|
0,131
|
0,255
|
0,404
|
0,553
|
0,718
|
0,906
|
1,134
|
1,440
|
1,943
|
2,447
|
3,143
|
3,707
|
6,959
|
7
|
0,130
|
0.263
|
0,402
|
0,549
|
0,711
|
0,896
|
1,119
|
1,415
|
1,895
|
2,365
|
2,998
|
3,499
|
5,405
|
8
|
0,130
|
0,262
|
0,399
|
0,546
|
0,705
|
0,889
|
1,108
|
1,397
|
1,850
|
2,306
|
2,896
|
3,355
|
5,041
|
9
|
0,129
|
0,261
|
0,398
|
0.543
|
0,703
|
0,883
|
1,1
|
1,383
|
1,833
|
2,252
|
2,821
|
3,250
|
4,781
|
10
|
0,129
|
0,260
|
0,397
|
0,542
|
0,700
|
0,879
|
1.093
|
1,372
|
1,812
|
2,228
|
2,754
|
3,159
|
4,587
|
11
|
0,129
|
0,260
|
0,395
|
0,540
|
0,697
|
0,875
|
1,088
|
1,353
|
1,796
|
2,201
|
2,718
|
3,105
|
4,437
|
I2
|
0,128
|
0,259
|
0,395
|
0,539
|
0,695
|
0,873
|
1,083
|
1,356
|
1,782
|
2,179
|
2,681
|
3,055
|
4,318
|
13
|
0,128
|
0,259
|
0,394
|
0,538
|
0,694
|
0,870
|
1,079
|
1,350
|
1,771
|
2,160
|
2,650
|
3,012
|
4,221
|
14
|
0,128
|
0,258
|
0,393
|
0,537
|
0,692
|
0,858
|
1,075
|
1,345
|
1,75I
|
2,145
|
2,624
|
2,977
|
4,140
|
15
|
0,126
|
0,258
|
0,393
|
0,535
|
0,691
|
0,865
|
1,074
|
1,341
|
1,753
|
2,131
|
2,602
|
2,947
|
4,073
|
16
|
0,128
|
0,258
|
0,392
|
0,535
|
0,690
|
0,865
|
1,071
|
1,337
|
1,745
|
2,120
|
2,583
|
2,921
|
4,015
|
17
|
0,128
|
0,257
|
0,392
|
0,534
|
0,689
|
0,863
|
1,059
|
1,335
|
1,740
|
2,110
|
2.567
|
2,898
|
3,955
|
P
|
0,9
|
0,8
|
0,7
|
0,6
|
0,5
|
0,4
|
0,3
|
0,2
|
0,1
|
0,05
|
0,02;
|
0,01
|
0,001
|
18
|
0,128
|
0,257
|
0,392
|
0,534
|
0,688
|
0,862
|
1,057
|
1,330
|
1,734
|
2,101
|
2,552
|
2,878
|
3,922
|
19
|
0,127
|
0,257
|
0.391
|
0,533
|
0,688
|
0,861
|
1,055
|
1,328
|
1,729
|
2,093
|
2,539
|
2,851
|
3,883
|
20
|
0,127
|
0,257
|
0,391
|
0,533
|
0,687
|
0,860
|
1,054
|
1,325
|
1,725
|
2,085
|
2,528
|
2,845
|
3,650
|
21
|
0,127
|
0,257
|
0,391
|
0,532
|
0,686
|
0,859
|
1,063
|
1,323
|
1,721
|
2,060
|
2,.518
|
2,831
|
3,319
|
22
|
0,127
|
0,256
|
0,390
|
0,532
|
0,686
|
0,858
|
1,061
|
1,321
|
1.717
|
2,074
|
2,508
|
2,819
|
3,792
|
23
|
0,127
|
0,256
|
0,390
|
0,532
|
0,685
|
0,858
|
1,060
|
1,319
|
1,714
|
2,069
|
2,500
|
2,807
|
3.767
|
24
|
0,127
|
0,256
|
0,390
|
0,531
|
0,685
|
0,857
|
1,059
|
1,318
|
1,711
|
2,064
|
2,492
|
2,797
|
3,745
|
25
|
0,127
|
0,256
|
0,390
|
0,531
|
0,684
|
0,856
|
1,058
|
1,316
|
1,708
|
2,060
|
2,485
|
2,787
|
3,725
|
26
|
0,127
|
0,256
|
0,390
|
0,531
|
0,684
|
0,856
|
1,058
|
1,315
|
1,706
|
2,056
|
2,479
|
2,779
|
3,707
|
27
|
0,127
|
0,256
|
0,389
|
0,531
|
0,684
|
0,855
|
1,057
|
1,314
|
1,703
|
2,052
|
2,473
|
2,771
|
3,690
|
28
|
0,127
|
0,256
|
0,389
|
0,530
|
0,683
|
0,855
|
1,055
|
1,313
|
1,701
|
2,048
|
2,457
|
2,763
|
3,574
|
29
|
0,127
|
0,256
|
0,389
|
0,530
|
0,683
|
0,854
|
1,055
|
1,311
|
1,699
|
2,045
|
2,462
|
2,755
|
3,559
|
30
|
0,127
|
0,256
|
0,389
|
0,530
|
0,683
|
0,854
|
1,055
|
1,310
|
1,697
|
2,042
|
2,437
|
2,750
|
3,645
|
40
|
0,126
|
0,255
|
0,388
|
0,529
|
0,681
|
0,851
|
1,050
|
1,303
|
1,684
|
2,021
|
2,423
|
2,704
|
3,551
|
50
|
0,126
|
0,254
|
0,387
|
0,527
|
0,679
|
0,848
|
1,046
|
1,296
|
1,671
|
2,000
|
2,390
|
2,560
|
3,450
|
120
|
0,126
|
0,254
|
0,386
|
0,526
|
0,677
|
0,845
|
1,041
|
1,289
|
1,658
|
1,980
|
2,358
|
2,617
|
3,373
|
200
|
0,126
|
0,253
|
0,385
|
0,524
|
0,674
|
0,842
|
1,035
|
1,282
|
1,645
|
1,950
|
2,325
|
2,576
|
3,291
|
Таблица 7
Соотношение между твердостью и прочностью металлов и сплавов
№ п/п
|
Материал
|
Предел прочности МН/м2∙10-1
|
Предел выносливости σ-1,
МН/м2∙10-1
|
1
|
Сталь (НВ=125–175)
|
0,343 НВ
|
0,15 НВ (для с=0,2–0,45%)
|
2
|
Сталь (НВ=175–450)
|
0,362 НВ
|
0,12 НВ (для с=0,2–0,8%)
|
3
|
Серый чугун
|
НВ – 40
40
|
–
|
4
|
Дюралюминий
a) отожженный
b) после закалки и старения
|
0,36 НВ
0,35 НВ
|
0,12 НВ
|
5
|
Медь, латунь, бронза
a) отожженные
b) наклепанные
|
0,55 НВ
0,4 НВ
|
0,15 НВ
–
|
6
|
Цинковые сплавы
|
0,09 НВ
|
–
|
Приложение 1
Индивидуальные задания студентам для определения твердости методом Бринелля и Роквелла
В заданиях 1–10. Измерить твердость металла или сплава на приборах Бринелля и Роквелла и сравнить полученные результаты:
№1– техническое железо, №2– алюминий, №3 – медь,
№4 – мягкая сталь, №5– вольфрам, №6 – титан, №7 – сталь 20,
№8 – сталь 45, №9 – сталь У8, №10 – сталь УI2.
В заданиях 11–14. Измерить твердость образцов, имеющих различную толщину сравнить полученные результаты:
№11 – мягкая сталь, №12 – титановый сплав, №13 – медь,
№14 – состаренный дюралюминий.
В заданиях 15–22. Измерить твердость образцов закаленной стали, используя различные нагрузки. Полученные результаты сравнить:
№15 – сталь 45, №16 – сталь 40Х, №17 – сталь Р18, №18 – сталь У7,
№19 – сталь Р9, №20 – сталь У12, №21 – сталь ХВГ, №22 – сталь 9ХС.
В заданиях 23–26, Измерить твердость поверхностного слоя в образцах, подвергнутых различной термообработке:
№23 – закаленная сталь, №24 – цементация + закалка,
№25 – азотирование, №26 – закалка ТВЧ.
№27 – На образце толщиной 3 мм сделать отпечатки шариком 2,5, 5 и 10 мм. Измерить диаметр отпечатка и вычислить твердость, сравнить полученные результаты и объяснить расхождение.
№28 – На образце мягкой стали сделать серию отпечатков на приборе Бринелля, ставя их на расстоянии 0,5 и 4 мм друг от друга. Сравнить полученные значения твердости и объяснить их различие.
№29 – Измерить твердость образца углеродистой стали (отожженной) шариком и конусом. Сравнить полученные результаты.
В заданиях 30–37. Провести испытания твердости НВ в заданных сплавах при нагрузках 187,5; 750; 1000; 1250 и 1500 Н×10-1
для цветных сплавов и при 750, 1000, 1250, 3000 Н×10-1
для сталей, чугунов шариком D = 10 мм. Подсчитать твердость для каждой нагрузки Р. Построить логарифмическую зависимость lgP – lgd, определить графическим путем константы d и n в математической зависимости между нагрузкой и твердость. P=adn
№30 – алюминиевый сплав, №31 – латунь, №32 – медь,
№33 – трансформаторная сталь, №34 – сталь У12, №35 – серый чугун,
№36 – белый чугун, №37– модифицированный чугун.
В заданиях 38–49. В заданном сплаве провести испытания твердости шариками различных диаметров (2,5;5;10 мм при P=const) и сделать вывод о влиянии диаметра шарика на твердость:
№38 – сталь 20, Р=7500 Н, №39 – сталь 45, P=7500 Н,
№40 – сталь У8, Р=7500 Н.
№41 – Провести испытание образца на твердости шариками различных диаметров:2,5, 5 и 10 мм. Нагрузки, требующиеся для получения одинакового значения твердости, подсчитать из равенства P/D2
= const
№42 – Провести испытание на твердость по Роквеллу различных марок стали: 20, 45, У7, У10, 712 в отожженном состоянии. Сделать вывод о влиянии содержания углерода на твердость стали (построить график HR=φ(%С)).
№43 – Провести испытание по Роквеллу образцов алюминия, стали отожженной и закаленной, выбрав соответствующие инденторы и нагрузки.
№44 – Измерить твердость по Роквеллу трех образцов сплавов системы Рb–Sb с содержанием 5, 20, 50 % Sв. Начертить диаграмму Рb– Sb и по полученным значениям твердости нанести на диаграмме линию, показывающую изменение твердости в зависимости от состава. Объяснить, как связано изменение твердости со структурой сплава.
№45 – В сплавах Сu – Zn содержащих 10, 30 и 42% Zn, выполнить работу, указанную в заданиях №44.
В заданиях 46–49. Измерить твердость двух образцов, один из которых находится в деформированном, а другой – в рекристаллизованном состоянии. Указать, какой образец подвергался рекристаллизации и его примерную температуру. Объяснить, какие изменения в структуре металла в процессе рекристаллизации вызвали изменения твердости. В качестве материала используете: №46 – сталь 20, №47 – .медь, №48 – латунь, №49 – алюминий,
№50 – Образец толщиной 20 мм закален, затем разрушен и со стороны излома зашлифован. Измерить твердость по толщине образца (через каждые 2 мм), построить график в координатах: твердость – расстояние от поверхности образца. Объяснить ход полученной кривой.
№51 – Измерить твердость двух фрез, изготовленных из быстрорежущей стали (измерения вести на зачищенной поверхности).
На основании полученных результатов объяснить, какая из фрез была подвергнута окончательной термообработки, какая еще должна пройти.
№52 – Измерить твердость стали 45, используя шкалы А, В, С и F. Сопоставить полученные значения твердости, предварительно переведя их в числа Бринелля. Объяснить причины расхождения в полученных результатах и какая из шкал в данном случае долина быть применена.
Приложение 2
Индивидуальные задания по измерению, микротвердости
№1 – Измерить микротвердость феррита в стали 20 и перлита в стали У7.
№2 – Измерить микротвердость феррита в стали 30 и перлита в стали У7.
№3 – Измерить микротвердость феррита и перлита в стали 40.
№4 – Измерить микротвердость феррита и перлита в стали 45.
В заданиях №5–8 – Измерить микротвердость феррита и сорбита в стали, подвергнутой отжигу и нормализации:
№5 – сталь 20Х. №6 – сталь 30Х. №7 – сталь 40Х. №8 – сталь 50Х,
В заданиях 9–11. Измерить микротвердость феррита, перлита и структурно-свободных карбидов в сталях, подвергнутых отжигу при t =850° C:
№9 – сталь Р9. №10 – сталь PI8. №11 – сталь ХI2.
В заданиях 12–15. Изучить влияние легирующих элементов на твердость феррита. Образцы подвергают отжигу при температуре 760–780° С.
№12 – сталь 1XI3. №13 – сталь 2X13. №14 – трансформаторная сталь.
№15 – динамная сталь.
№16 – Определить микротвердость структурных составляющих в свинцовистом баббите, содержащем 15% Sb.
№17 – Определить микротвердость фаз в латуни (40% Zn) .
№18 – Сталь 45 подвергнута неполной закалке с температуры 740o
С. Определить твердость феррита и мартенсита.
В заданиях 19–25. Сталь подвернута химико-термической обработке. Определить микротвердость в поверхностном слое и построить график распределения микротвердости по глубине слоя образца подвергнутого:
№19 цементации, №20 цементации и закалке, №21 азотированию,
№22 актированию, №23 борированию.
В заданиях 24–27. Измерить твердость феррита при нагрузках 20, 50, 100 и 200 Н×10-1
и объяснить различие в микротвердости в следующих марках стали;
№24 – сталь 20, №25– сталь 25, №26 – трансформаторная сталь,
№27 – сталь У8 (для перлита).
Техника безопасности при определении твердости на приборах Бринелля, Роквелла, Виккерса и ПМТ–3
1. Соблюдать общие правила безопасности при работе на электроустановках.
2. Во избежание падения гирь, применяемых для создания нагрузки, навеска гирь должна осуществляться с чередованием прорезей (поворот на 90° вокруг оси).
3. При определении твердости цилиндрических поверхностей применять специальные призматические насадки.
Шатов Юрий Семенович
Горбунов Иван Петрович
Гвоздев Анатолий Григорьевич
ИЗМЕРЕНИЕ ТВЕРДОСТИ МЕТАЛЛОВ
Методические указания к лабораторным работам
для студентов специальности 150105, 150702
Лицензия ИД №06179 от 01.11.2001
Компьютерный набор: И.П. Горбунов
Редактор Т.М. Курьянова
Подписано в печать . . 2006 Формат 60x84 1/16. Ризография. Бумага офсетная. Печ. л. 2. Тираж 300 экз. Заказ №
Липецкий государственный технический университет. 398600 Липецк, ул. Московская, 30. Типография ЛГТУ. 398600 Липецк, Московская, 30.
|