ФЕДЕРАЛЬНОЕ АГЕНТСТВО ПО ОБРАЗОВАНИЮ
Белгородский государственный технологический университет
им. В.Г. Шухова
ЭКСПЛУАТАЦИЯ И НАЛАДКА СИСТЕМ ТГСВ
Учебное пособие для студентов заочной формы обучения
с применением дистанционных технологий специальностей
270109 (290700) – Теплогазоснабжение и вентиляция
Белгород 2007
УДК 696+697(07)
ББК 38.76Я7
Э 41
Составитель: Скляр Б. Д.
Эксплуатация и наладка систем ТГСВ: Учебное пособие /Б. Д. Скляр. – Белгород: Изд-во БГТУ им. В.Г. Шухова, 2007. - с.
Рассмотрены вопросы устройства, эксплуатации и наладки систем теплогазоснабжения, вентиляции и кондиционирования. Освещены вопросы испытания подземных трубопроводов, газопроводов и внутридомового оборудования систем ТГВ. Описываются контрольно-измерительные приборы, трубы и фасонные изделия, запорная и запорно-регулирующая арматура, газогорелочное оборудование используемых в системах ТГВ.
Учебное пособие предназначено для подготовки студентов высших учебных заведений по эксплуатации и наладке систем теплогазоснабжения и вентиляции.
УДК 696+697(07)
ББК 38.76Я7
Ó Белгородский государственный
технологический университет
(БГТУ) им. В.Г. Шухова, 2007
Оглавление
ВВЕДЕНИЕ
ГЛАВА I. СИСТЕМЫ ТЕПЛОСНАБЖЕНИЯ
I.1.КЛАССИФИКАЦИЯ СИСТЕМ ТЕПЛОСНАБЖЕНИЯ
I.2 ОБЩИЕ СВЕДЕНИЯ О ТЕПЛОСНАБЖЕНИИ
I.3 КЛАССИФИКАЦИЯ ТЕПЛОВЫХ СЕТЕЙ
I.4. СПОСОБЫ ПРОКЛАДКИ И КОНСТРУКЦИИ НАРУЖНЫХ ТЕПЛОВЫХ СЕТЕЙ
I.5. ПУСК ТЕПЛОВЫХ СЕТЕЙ, ТЕПЛОВЫХ ПУНКТОВ И СИСТЕМ ТЕПЛОПОТРЕБЛЕНИЯ
I.6. ОРГАНИЗАЦИЯ НАЛАДОЧНЫХ РАБОТ
I.7. ОБСЛУЖИВАНИЕ ТЕПЛОВЫХ ПУНКТОВ
I.8. ИСПЫТАНИЯ ТРУБОПРОВОДОВ И ОБОРУДОВАНИЯ ВОДЯНЫХ ТЕПЛОВЫХ СЕТЕЙ
I.9. РЕГУЛИРОВАНИЕ СИСТЕМ ТЕПЛОСНАБЖЕНИЯ
I.10. АНАЛИЗ РЕЖИМОВ РАБОТЫ СИСТЕМЫ ТЕПЛОСНАБЖЕНИЯ КИП И А
ГЛАВА II. СИСТЕМЫ ГАЗОСНАБЖЕНИЯ
II.1 КЛАССИФИКАЦИЯ СИСТЕМ ГАЗОСНАБЖЕНИЯ
II.2 ЭКСПЛУАТАЦИЯ И НАСТРОЙКА ГРП
II.3 ПРОФИЛАКТИЧЕСКОЕ ОБСЛУЖИВАНИЕ ГАЗОПРОВОДОВ
II.4. КОНСТРУКЦИЯ ТРУБЫ И ФАССОННЫЕ ИЗДЕЛИЯ
II.5. ЭКСПЛУАТАЦИЯ И РЕМОНТ ГАЗОПРОВОДОВ
II.5.1.ЗАЩИТА ГАЗОПРОВОДОВ С ИСПОЛЬЗОВАНИЕМ ИЗОЛЯЦИИИ
II.5.2.ЭЛЕКТРИЧЕСКИЕ МЕТОДЫ ЗАЩИТЫ
II.5.3. ЭКСПЛУАТАЦИЯ УСТАНОВОК СЖИЖЕННЫХ ГАЗОВ. ПРОФИЛАКТИЧЕСКОЕ ОБСЛУЖИВАНИЕ
II.6. РЕМОНТНЫЕ РАБОТЫ НА ПОДЗЕМНЫХ ГАЗОПРОВОДАХ
II.7. КОНТРОЛЬНО-ИЗМЕРИТЕЛЬНАЯ АППАРАТУРА
II.8. ГАЗОГОРЕЛОЧНЫЕ УСТРОЙСТВА
II.9. УСРОЙСТВО И ЭКСПЛУАТАЦИЯ ДЫМОХОДОВ. ПРАВИЛА ЭКСПЛУАТАЦИИ ВНУТРИДОМОВОГО ГАЗОВОГО ОБОРУДОВАНИЯ
II.10. ПРИЕМ В ЭКСПЛУАТАЦИЮ ГАЗОПРОВОДОВ ГАЗОРЕГУЛЯТОРНЫХ ПУНКТОВ
II.11.ТЕХНИКА БЕЗОПАСНОСТИ ПРИ ЭКСПЛУАТАЦИИ ПОДЗЕМНЫХ ГАЗОПРОВОДОВ
II.11.1 ОСНОВНЫЕ СВОЙСТВА ГАЗОВ
II.11.2. ЭКСПЛУАТАЦИЯ И НАЛАДКА ГРП
II.11.3. ПРОФИЛАКТИЧЕСКОЕ ОБСЛУЖИВАНИЕ ГАЗОПРОВОДОВ
ГЛАВА III. СИСТЕМЫ ВЕНТИЛЯЦИИ И КОНДИЦИОНИРОВАНИЯ
III.1 КЛАССИФИКАЦИЯ СИСТЕМ КОНДИЦИОНИРОВАНИЯ
III.2 КЛАССИФИКАЦИЯ СИСТЕМ ВЕНТИЛЯЦИИ
III.2.1. ЕСТЕСТВЕННАЯ ВЕНТИЛЯЦИЯ
III.2.2. МЕХАНИЧЕСКАЯ ВЕНТИЛЯЦИЯ
III.2.2.1. КЛАССИФИКАЦИЯ ПРОМЫШЛЕННЫХ ПЫЛЕУЛОВИТЕЛЕЙ
III.2.2.2. ОСНОВНЫЕ МЕХАНИЗМЫ ОСАЖДЕНИЯ ЧАСТИЦ
III.2.2.3. СУХИЕ МЕХАНИЧЕСКИЕ ПЫЛЕУЛОВИТЕЛИ
III.2.2.4. ИНЕРЦИОННЫЕ ПЫЛЕУЛОВИТЕЛИ
III.2.2.5. ЦИКЛОНЫ
III.2.2.6. ВИХРЕВЫЕ ПЫЛЕУЛОВИТЕЛИ
III.2.2.7. ДИНАМИЧЕСКИЕ ПЫЛЕУЛОВИТЕЛИ
III.2.2.8. МОКРЫЕ ПЫЛЕУЛОВИТЕЛИ
III.2.2.9. ФИЛЬТРЫ
III.2.2.9.1 ВОЛОКНИСТЫЕ ФИЛЬТРЫ
III.2.2.9.2. ЭЛЕКТРОФИЛЬТРЫ
III.2.3. ПРИТОЧНАЯ ВЕНТИЛЯЦИЯ
III.2.4. ВЫТЯЖНАЯ ВЕНТИЛЯЦИЯ
III.2.5. МЕСТНАЯ ВЕНТИЛЯЦИЯ
III.2.5.1. МЕСТНАЯ ПРИТОЧНАЯ ВЕНТИЛЯЦИЯ
III.2.5.2. МЕСТНАЯ ВЫТЯЖНАЯ ВЕНТИЛЯЦИЯ
III.2.6. ОБЩЕОБМЕННЫЕ СИСТЕМЫ ВЕНТИЛЯЦИИ
III.2.6.1. ОБЩЕОБМЕННАЯ ПРИТОЧНАЯ ВЕНТИЛЯЦИЯ
III.2.6.2. ОБЩЕОБМЕННАЯ ВЫТЯЖНАЯ ВЕНТИЛЯЦИЯ
III.2.7. КАНАЛЬНАЯ И БЕСКАНАЛЬНАЯ ВЕНТИЛЯЦИЯ
ГЛАВА IV. ПРИБОРЫ ИЗМЕРЕНИЯ И КОНТРОЛЯ, ИСПОЛЬЗУЕМЫЕ В СИСТЕМАХ ОТОПЛЕНИЯ, ВЕНТИЛЯЦИИ И КОНДИЦИОНИРОВАНИЯ
IV.1. ОЩИЕ ТРЕБОВАНИЯ В КОНТРОЛЮ ПАРАМЕТРОВ МИКРОКЛИМАТА
IV.2. ИЗМЕРИТЕЛЬНЫЕ ПРИБОРЫ СИСТЕМ ОТОПЛЕНИЯ, ВЕНТИЛЯЦИИ И КОНДИЦИОНИРОВАНИЯ
IV.3. ПРИБОРЫ И СРЕДСТВА КОНТРОЛЯ НАЛИЧИЯ ВРЕДНЫХ ВЕЩЕСТВ И ПЫЛИ В ВОЗДУХЕ
IV.4. ПРИБОРЫ ДЛЯ ИЗМЕРЕНИЯ ТЕПЛОВЫХ ПОТЕРЬ
ТЕСТ ПО ДИСЦИПЛИНЕ «ЭКСПЛУАТАЦИЯ И НАЛАДКА СИСТЕМ ТГВ»
ЭКЗАМЕНАЦИОННЫЕ ВОПРОСЫ ПО ДИСЦИПЛИНЕ «ЭКСПЛУАТАЦИЯ И НАЛАДКА СИСТЕМ ТГВ»
КОНТРОЛЬНАЯ РАБОТА
ВВЕДЕНИЕ
Каждое инженерное сооружение имеет свои специфические особенности, от которых в значительной степени зависят их приемка в эксплуатацию, наладка и пуск в действие. Это в полной мере касается и систем теплоснабжения, газоснабжения, вентиляции и кондиционирования.
В последние годы наблюдается процесс разукрупнения систем теплоснабжения из-за значительного подорожания теплоты в системах централизованного теплоснабжения и в связи с массовой загородной индивидуальной застройкой.
Бурное развитие газовой промышленности и газоиспользование в стране обуславливает интенсивное расширение сети газопроводов различного назначения, газораспределительных станций, газорегуляторных пунктов и установок, газохранилищ, систем связи и телемеханизации внутриобъектных газопроводов с газоиспользующими устройствами, а также обеспечение защиты подземных газопроводов от коррозии. В связи с взрыво- и пожароопасностью на линейных газовых сооружениях, вызванной свойствами горючих газов, предъявляются особые требования.
Без применения современных вентиляционных систем и систем кондиционирования воздуха немыслимы новые технологии производств и комфортные условия в помещениях для работы и проектирования, предназначенных для производственной деятельности или проживания и отдыха человека.
Учебное пособие по дисциплине «Эксплуатация и наладка систем тепло- газоснабжения и вентиляции» предназначено для качественной подготовки технически грамотных специалистов в области обслуживания систем теплогазоснабжения и вентиляции.
ГЛАВА
I
. СИСТЕМЫ ТЕПЛОСНАБЖЕНИЯ
1.1 КЛАССИФИКАЦИЯ СИСТЕМ ТЕПЛОСНАБЖЕНИЯ
Назначение любой системы теплоснабжения заключается в обеспечении потребителей теплоты необходимым количеством тепловой энергии требуемых параметров.
Существующие системы теплоснабжения в зависимости от взаимного расположения источника и потребителей теплоты можно разделить на централизованные и децентрализованные системы. В централизованных системах теплоснабжения один источник теплоты обслуживает теплоиспользующие устройства ряда потребителей, расположенных раздельно, поэтому передача теплоты от источника до потребителей осуществляется по специальным теплопроводам — тепловым сетям.
Централизованное теплоснабжение состоит из трех взаимосвязанных и последовательно протекающих стадий: подготовки, транспортировки и использования теплоносителя. В соответствии с этими стадиями каждая система централизованного теплоснабжения состоит из трех основных звеньев: источника теплоты (например, теплоэлектроцентрали или котельной), тепловых сетей (теплопроводов) и потребителей теплоты.
В децентрализованных системах теплоснабжения каждый потребитель имеет собственный источник теплоты.
Основными видами теплоносителей для целей теплоснабжения являются вода и водяной пар. При этом, вода используется преимущественно для удовлетворения нагрузок отопления, вентиляции, кондиционирования воздуха, и горячего водоснабжения, а пар, кроме того,— для удовлетворения технологической нагрузки.
1.2 ОБЩИЕ СВЕДЕНИЯ О ТЕПЛОСНАБЖЕНИИ
Потребители теплоты. Под тепловым потреблением понимают использование тепловой энергий для разнообразных коммунально-бытовых и производственных целей: отопление, вентиляция, кондиционирование воздуха, горячее водоснабжение, технологические процессы.
Потребители теплоты по характеру их загрузки во времени можно разделить на сезонные и круглогодичные. К сезонным потребителям относятся системы отопления, вентиляции и кондиционирования воздуха, а к круглогодичным — системы горячего водоснабжения и технологические аппараты. Тепловые нагрузки потребителей не остаются постоянными.
Расходы теплоты на отопление, вентиляцию и кондиционирование воздуха зависят в основном от климатических условий: температуры наружного воздуха, направления и скорости ветра, влажности воздуха и др. Из названных факторов основное значение имеет температура наружного воздуха, Сезонная нагрузка имеет сравнительно постоянный суточный график и переменный годовой график. Отопление и вентиляция являются зимними тепловыми нагрузками, для кондиционирования воздуха в летний период требуется искусственный холод.
Нагрузка горячего водоснабжения зависит от степени благоустройства жилых и общественных зданий, режима работы бань, прачечных и т. д. Технологическое потребление теплоты зависит в основном от характера производства, типа оборудования, вида выпускаемой продукции.
Горячее водоснабжение и технологическая нагрузка имеют переменный суточный график, а их годовые графики в определенной мере зависят от времени года. Летние нагрузки, как правило, ниже зимних вследствие более высокой температуры водопроводной воды и перерабатываемого сырья, а также благодаря меньшим тепловым потерям теплопроводов и технологических трубопроводов.
Максимальные тепловые потоки на отопление, вентиляцию и горячее водоснабжение жилых, общественных и производственных зданий должны приниматься по соответствующим проектам.
1.3 КЛАССИФИКАЦИЯ ТЕПЛОВЫХ СЕТЕЙ
По количеству параллельно проложенных теплопроводов тепловые сети могут быть однотрубными, двухтрубными и многотрубными. Однотрубные сети наиболее экономичны и просты. В них сетевая вода после систем отопления и вентиляции должна полностью использоваться для горячего водоснабжения. Однотрубные тепловые сети являются прогрессивными, с точки зрения значительного ускорения темпов строительства тепловых сетей. В трехтрубных сетях две трубы используют в качестве подающих для подачи теплоносителя с разными тепловыми потенциалами, а третью трубу — в качестве общей обратной, так называемой «обратки». В четырехтрубных сетях одна пара теплопроводов обслуживает системы отопления и вентиляции, а другая — систему горячего водоснабжения, а также используется на технологические нужды.
В настоящее время наибольшее распространение получили двухтрубные тепловые сети, состоящие из подающего и обратного теплопровода для водяных сетей и паропровода с конденсатопроводом для паровых сетей. Благодаря высокой аккумулирующей способности воды, позволяющей осуществлять дальнее теплоснабжение, а также большей экономичности и возможности центрального регулирования отпуска теплоты потребителям, водяные сети имеют более широкое применение, чем паровые.
Водяные тепловые сети по способу приготовления воды для горячего водоснабжения разделяются на закрытые и открытые. В закрытых сетях для горячего водоснабжения используется водопроводная вода, нагреваемая сетевой водой в водоподогревателях. При этом сетевая вода возвращается на ТЭЦ или в котельную. В открытых сетях вода для горячего водоснабжения разбирается потребителями непосредственно из тепловой сети и после ее использования в сеть не возвращается. Качество воды в открытой тепловой сети должно отвечать требованиям ГОСТ 2874—82*.
Тепловые сети разделяют на магистральные, прокладываемые на главных направлениях населенных пунктов, распределительные — внутри квартала, микрорайона и ответвления к отдельным зданиям.
Радиальные сети сооружают с постепенным уменьшением диаметров теплопроводов в направлении от источника теплоты. Такие сети наиболее просты и экономичны по начальным затратам. Их основной недостаток — отсутствие резервирования. Во избежание перерывов в теплоснабжении (в случае аварии на магистрали радиальной сети прекращается теплоснабжение потребителей, присоединенных на аварийном участке) согласно СНиП 2.04,07—86 должно предусматриваться резервирование подачи теплоты потребителям за счет устройства перемычек между тепловыми сетями смежных районов и совместной работы источников теплоты (если их несколько). Радиус действия водяных сетей во многих городах достигает значительной величины (15—20 км).
Устройством перемычек тепловая сеть превращается в радиально-кольцевую, происходит частичный переход к кольцевым сетям. Для предприятий, в которых не допускается перерыв в теплоснабжении, предусматривают дублирование или кольцевые (с двусторонней подачей теплоты) схемы тепловых сетей.
Несмотря на то, что кольцевание сетей существенно увеличивает их стоимость, тем не менее на крупных системах теплоснабжения значительно повышается надежность теплоснабжения, создается возможность резервирования, а также повышается качество гражданской обороны.
Паровые сети устраивают преимущественно двухтрубными. Возврат конденсата осуществляется по отдельной трубе — конденсатопроводу. Пар от ТЭЦ по паропроводу со скоростью 40—60 м/с и более идет к месту потребления. В тех случаях, когда пар используется в теплообменниках, его конденсат собирается в конденсатных баках, откуда насосами по конденсатопроводу возвращается на ТЭЦ.
Направление трассы тепловых сетей в городах и других населенных пунктах должно предусматриваться преимущественно по районам наибольшей тепловой нагрузки с учетом вида прокладки, данных состава грунтов и наличия грунтовых вод.
1.4 СПОСОБЫ ПРОКЛАДКИ И КОНСТРУКЦИИ НАРУЖНЫХ ТЕПЛОВЫХ СЕТЕЙ
Трубопроводы тепловых сетей размещают в отведенных для инженерных сетей технических полосах параллельно красным линиям улиц, дорог и проездов вне проезжей части и полосы зеленых насаждений. Трассы тепловых сетей под проезжей частью улиц, дорог и тротуарами прокладывают при соответствующем обосновании. По территории населенных мест предусматривают подземную прокладку тепловых сетей — бесканальную, в непроходных каналах, в общегородских или внутриквартальных коллекторах совместно с другими инженерными сетями. На площадках промышленных предприятий предусматривают надземную прокладку тепловых сетей по опорам и эстакадам. Иногда допускается подземная прокладка сетей.
Надземную прокладку тепловых сетей в городах и населенных пунктах выполняют при соответствующем обосновании. Тепловые сети (Dу
<500 мм) преимущественно прокладывают бесканальным способом. Бесканальная прокладка не допускается на подрабатываемых территориях и в просадочных грунтах II типа. При сейсмичности 8 баллов и выше бесканальную прокладку применяют только для труб Dу
<400 мм. Подземная и надземная прокладка водяных тепловых сетей применяется независимо от параметров теплоносителя.
1.5 ПУСК ТЕПЛОВЫХ СЕТЕЙ, ТЕПЛОВЫХ ПУНКТОВ И СИСТЕМ ТЕПЛОПОТРЕБЛЕНИЯ
Пуск тепловых сетей в эксплуатацию после строительства и ремонта производит пусковая бригада по специальной программе, утверждаемой главным инженером эксплуатирующей организации. Пуск водяных тепловых сетей состоит из следующих основных операций: заполнения сети водой, установления циркуляции сети, включения абонентов, пусковой регулировки сети.
Пуск производят по программе, предусматривающей:
- режим работы насосно-подогревательной установки источника тепла при включении ее схему сети;
- оперативную схему тепловой сети во время пуска;
- очередность и порядок пуска каждой отдельной магистрали и ее ответвлений;
- время наполнения каждой магистрали, исходя из ее емкости и скорости заполнения;
расчетное статическое давление каждой заполненной магистрали и влияние этого давления на смежные участки сети;
- состав пусковой бригады, расстановку и обязанности исполнителей;
- выбор соответствующих средств связи (сигнализация, телефон, радио) между отдельными членами пусковой бригады, а также с дежурным персоналом района и источника тепла.
Перед пуском проверяют исправность всего оборудования пускаемого участка сети и подготовку приспособления для откачки воды из нижних точек трассы и камер, оборудованных спускной арматурой. При пуске наблюдают за наполнением и прогревом трубопроводов, состоянием арматуры, компенсаторов, дренажных устройств и другого оборудования.
Последовательность и скорость проведения пусковых операций должны исключать возможность появления больших термических деформаций в тепловых сетях и системах теплопотребления. При включении в эксплуатацию сетей сначала следят за установлением циркуляции воды в сети, а затем включают пар на подогреватель источника тепла. При останове сети сначала прекращают подогрев сетевой воды, а затем отключают сетевые насосы. Изменение температуры воды в тепловой сети должно производиться постепенно и равномерно со скоростью, не превышающей 30°С/ч.
Заполнение сети водой. Трубопроводы тепловой сети заполняют химически очищенной, деаэрированной водой. Для предотвращения запотевания труб температура заполняющей воды должна быть не ниже 40 °С, а все каналы и камеры перед заполнением трубопроводов тщательно вентилируют. Не допускается заполнять сеть водой с температурой выше 70°С. Заполнение сети водой производится через обратную линию под напором подпиточного насоса или подпиточного бака. Давление, под которым подается вода в заполняемый трубопровод, не должно превышать статического давления данной сети более чем на 2 МПа. Во избежание гидравлических ударов и для лучшего удаления воздуха расход воды при занолнении трубопроводов не должен превышать пределы, указанные в табл. 1.1.
Таблица 1.1.
Максимальный часовой расход воды при заполнении трубопроводов тепловой сети
Диаметр трубопровода •Ду, мм
|
Расход воды, ма
/ч
|
Диаметр трубопровода Dу
, мм
|
Расход воды, м3
/ч
|
100
|
10
|
500
|
100
|
150
|
15
|
600
|
150
|
200
|
20
|
700
|
200
|
250
|
25
|
800
|
250
|
300
|
35
|
900
|
300
|
350
|
50
|
1000
|
350
|
400
|
65
|
1100
|
400
|
450
|
85
|
1200
|
500
|
Основную магистраль теплопровода заполняют водой в следующем порядке. На заполняемом участке трубопровода закрывают все дренажные устройства, отключают все ответвления или тепловые пункты и открывают все секционирующие задвижки, кроме головных. Открывают все воздушные краны на сети. Закрывают задвижки на перемычках между подающим и обратным трубопроводами. Постепенно открывают головную задвижку на обратном трубопроводе заполняемого участка и заполняют сеть. По мере заполнения сети и прекращения вытеснения воздуха воздушные краны закрывают, через 2—3 мин после закрытия воздушные краны вновь открывают для дополнительного выпуска воздуха. Эту операцию повторяют до тех пор, пока не будет выпущен весь воздух.
По окончании заполнения обратной магистрали открывают перемычку между подающим и обратным трубопроводами и заполняют водой подающую магистраль. Заполнение производится в том же порядке, что и обратной магистрали. После окончания заполнения трубопроводов необходимо периодически в течение 2—3 ч открыть воздушные краны для окончательного удаления воздуха. Распределительные сети заполняют водой после заполнения магистральных теплопроводов, а ответвлений к абонентам — после заполнения распределительных сетей.
Выполнение циркуляции в сети. Установление циркуляции в основных магистральных теплопроводах осуществляют через концевые перемычки при отключенных ответвлениях и системах теплопотребленик.
Циркуляцию в сети производят в следующем порядке:
а) открывают головные и секционирующие задвижки на включаемой сети, а также задвижки на концевой перемычке между подающим и обратным трубопроводами;
б) открывают задвижку на обводной линии подогревателей бойлерной, а при отсутствии обвода — задвижки на входе и выходе воды из каждого подогревателя;
в) открывают задвижки на всасывающих патрубках сетевых насосов, задвижки на нагнетательных патрубках оставляют полностью закрытыми;
г) включают подпиточный насос и в обратном коллекторе сети с помощью регулятора подпитки, а при его отсутствии — задвижкой на нагнетательном патрубке подпиточного насоса или с помощью задвижки на подпиточной линии устанавливают давление в соответствии с заданным статическим режимом;
д) включают один сетевой насос;
е) постепенно открывают задвижку на нагнетательном патрубке сетевого насоса;
ж) после установления циркуляции величина подпитки должна быть отрегулирована таким образом, чтобы давление в обратном коллекторе сети соответствовало заданному динамическому режиму;
з) включают подачу пара на сетевые подогреватели и начинается подогрев сетевой воды со скоростью не более 30°С/ч.
Если на теплопроводе установлены автоматические регуляторы давления, одновременно с установлением циркуляции происходит их настройка для обеспечения требуемых давлений на тепловых пунктах.
В ответвлениях от основной магистрали циркуляция устанавливается через концевые перемычки на этих ответвлениях под напором, давлением, имеющимся в магистрали. При этом все задвижки на тепловых пунктах абонентов должны быть плотно закрыты. Для осуществления циркуляции в ответвлениях поочередно медленно открывают головные задвижки ответвления сначала на обратном, а затем на подающем трубопроводе. Установление циркуляции в ответвлениях к абонентам, не имеющим перемычек между подающим и обратным трубопроводами, производится через линию подсоса элеватора (задвижки после элеватора должны быть плотно закрыты), а для безэлеваторных вводов — через местные системы с включением последних в работу. Во избежание подъема давления в отключенных системах (из-за неплотности запорной арматуры) открывают спускные краны, расположенные за отключающими задвижками.
Включение насосов на насосных станциях, расположенных на пускаемых теплопроводах, производят в следующем порядке:
а) подмешивающих и подкачивающих насосов, установленных на обратных трубопроводах, — после установления циркуляции в сети основными сетевыми насосами и до включения систем теплопотребления;
б) насосов, установленных на подающих трубопроводах, — после включения систем теплопотребления, по мере необходимости увеличения располагаемого напора в сети. Пуск насосов производится при закрытой задвижке нагнетательного патрубка и открытой задвижке всасывающего патрубка.
Особенности пуска сети при отрицательных температурах наружного воздуха. Пуск сети при отрицательных температурах наружного воздуха производят только в исключительных случаях: после аварийной остановки и ремонта и необходимости ввода в действие вновь построенных теплопроводов. Наполнение и установление циркуляции в магистрали и протяженных ответвлениях производят по отдельным разделенным секционирующими задвижками участкам. Магистрали заполняют водой с температурой 50—60°С одновременно по подающему и обратному трубопроводам. Величина подачи воды должна иметь максимальное значение, указанное в табл. 1.1.
Подающий и обратный трубопроводы пускаемой сети оборудуют через каждые 200—250 м секционирующими задвижками и дополнительными дренажными кранами, которые при наполнении сети закрываются лишь после того, как температура дренируемой из них воды достигнет 40°С. Тотчас после пуска головного секционированного участка сети для восполнения теплопотерь в трубопроводах включают сетевые подогреватели источника тепла. После установления циркуляции необходимо периодически в течение 2—3 дней производить выпуск воздуха через все воздушные краны, установленные в сети и системах абонентов.
Включение тепловых пунктов и систем теплопотребления. Перед включением в эксплуатацию все тепловые пункты и системы теплопотребления должны быть отремонтированы, промыты, опрессованы. На тепловых пунктах и в системах теплопотребления устанавливают смесительные и дросселирующие устройства, рассчитанные на обеспечение нормальной работы.
Заполнение и включение системы теплопотребления производят при установившейся циркуляции в сетях до подъема температуры воды по заранее разработанному графику с учетом производительности водоподготовки и подпиточного устройства источника тепла. Отключение концевых перемычек, через которые осуществляется начальная циркуляция в сети, производят после того, как расход воды через включенные системы абонентов достигнет необходимого минимума для устойчивой работы сетевых насосов и для поддержания избыточного давления на всем протяжении обратного теплопровода.
Заполнение систем теплопотребления сетевой водой производят постепенным открытием задвижек на обратном трубопроводе теплового пункта при закрытой задвижке на подающей линии. Воздушные краны в системе должны быть открыты до момента прекращения выхода воздуха и появления воды. В тех случаях, когда давление в обратном трубопроводе на тепловом пункте ниже статического давления системы теплопотребления, ее верхнюю часть заполняют из подающей линии путем частичного открытия задвижки на подающем трубопроводе теплового пункта при одновременном прикрытии задвижки на обратной линии. При этом необходимо следить по манометрам за давлением в системе, чтобы оно не превысило максимального для прочности нагревательных приборов.
Необходимый подпор при работе системы обеспечивается настройкой регулятора подпора, в случае его отсутствия — дроссельной диафрагмой. После наполнения системы теплопотребления открывается задвижка на подающей линии теплового пункта, и в системе устанавливается циркуляция.
Для обеспечения пусковой регулировки сети на тепловых пунктах и в системах теплопотребления устанавливают расчетные сопла элеваторов и дроссельные диафрагмы, и автоматические регуляторы. До включения всех абонентов избыточные располагаемые напоры на тепловых пунктах снижают с помощью задвижек, расположенных на подающих линиях. Окончательную регулировку тепловых сетей и систем теплопотребления производят после их вывода на нормальный режим работы.
1.6 ОРГАНИЗАЦИЯ НАЛАДОЧНЫХ РАБОТ
Обслуживание тепловых сетей.
В объем работ по обслуживанию тепловых сетей входят:
- поддержание в исправном состоянии всего оборудования, строительных и других конструкций тепловых сетей путем проведения своевременного их осмотра и ремонта;
- наблюдение за работой компенсаторов, опор, арматуры, дренажей, контрольно-измерительной аппаратуры и других элементов оборудования со своевременным устранением замеченных неисправностей;
- устранение сверхнормативных потерь тепла путем своевременного отключения неработающих участков сети, удаления скапливающейся в каналах и камерах воды, ликвидации проникания грунтовых и верховых вод в каналы и камеры, своевременного восстановления разрушенной изоляции;
- устранение сверхнормативных гидравлических потерь в сети за счет регулярной промывки и очистки трубопроводов;
- своевременное удаление через воздушники воздуха из теплопроводов и недопущение присоса воздуха путем постоянного поддержания избыточного давления во всех точках сети и системах потребителей;
- поддержание в сети и на тепловых пунктах потребителей необходимых гидравлического и теплового режимов при систематической проверке требуемых параметров в характерных точках сети и на тепловых пунктах потребителей;
- обеспечение расчетного распределения теплоносителя по тепловым пунктам потребителей;
- принятие мер по предупреждению, локализации и ликвидации неполадок и аварий в сети.
Тепловые сети обслуживает бригада слесарей-обходчиков (не менее двух человек на закрепленных за ними участках сети). Обход теплопроводов производят по графику не реже одного раза в две недели в течение отопительного сезона и одного раза в месяц в межотопительный период. При обходе сети проверяют затяжку болтов (поочередно, крест-накрест) всех фланцевых соединений, без особых усилий затягивают сальниковые компенсаторы до прекращения течи, смазывают маслом с графитом движущуюся часть стаканов компенсаторов, проверяют состояние дренажных и воздушных кранов и вентилей, выпускают воздух из сети, проверяют состояние контрольно-измерительных приборов (термометров, манометров и др.) и правильность их показаний по контрольным приборам.
Для контроля состояния подземных теплопроводов, теплоизоляционных и строительных конструкций периодически производят шурфовки на тепловой сети. Число ежегодно проводимых плановых шурфовок устанавливают в зависимости от протяженности сети, типов прокладки и теплоизоляционных конструкций и количества коррозионных повреждений труб. На каждые 5 км трассы должно быть не менее одного шурфа. На новых участках сети шурфовки производят, начиная с третьего года эксплуатации. Эксплуатационное предприятие должно иметь специальную схему тепловой сети, на которой отмечают места и результаты шурфовок, места аварийных повреждений и затопления трассы, переложенные участки.
По результатам осмотра оборудования тепловой сети и самой трассы при обходах, а также проведенных шурфовок оценивают состояние оборудования, трубопроводов, строительно-изоляционных конструкций, интенсивность и опасность процесса наружной коррозии труб и намечают необходимые мероприятия по устранению выявленных дефектов или неполадок. Дефекты, которые не могут быть устранены без отключения теплопровода, но не представляющие непосредственной опасности для надежной эксплуатации, заносят в журнал ремонтов для ликвидации в период ближайшего останова теплопровода или в период ремонта. Дефекты, которые могут вызвать аварию в сети, устраняют немедленно.
Для предотвращения коррозии металлических строительных конструкций тепловой сети (балок, перекрытий, неподвижных опор, эстакад, мачт и т. д.) их бетонируют по металлической сетке, приваренной к конструкции, или периодически окрашивают антикоррозионными красками. Окраску металлических конструкций подземных сооружений производят не реже 1 раза в 2 года. Для предупреждения внутренней коррозии трубопроводов подпитку тепловой сети производят деаэрированной водой. Содержание кислорода в воде не должно превышать 0,05 мг/кг. Содержание кислорода в воде проверяют не реже 1 раза в неделю отбором проб из подающего и обратного трубопроводов каждой магистрали.
Во избежание подсоса воздуха избыточное давление в сети и во всех присоединенных системах теплопотребления должно быть не ниже 0,5 кгс/см2
как при гидродинамическом, так и при статическом режиме работы системы теплоснабжения. Состояние внутренней поверхности трубопроводов следует определять в период текущих и капитальных ремонтов, а также при шурфовках тепловых сетей путем осмотра вырезаемых труб и торцов труб у снятой арматуры. Для систематического контроля внутренней коррозии на подающем и обратном трубопроводах, в том числе сетей горячего водоснабжения, в характерных точках устанавливают индикаторы коррозии. Установку индикаторов в контрольных точках и их изъятие производят один раз в год во время останова сети на профилактический ремонт. Во избежание усиленного процесса коррозии трубопроводов систем горячего водоснабжения запрещается даже периодическое повышение температуры воды в системе свыше 65 °С.
Эксплуатирующая организация составляет список камер и участков проходных каналов, подверженных опасности проникания газа, и согласовывает его с газоснабжающей организацией. Все газоопасные камеры и каналы отмечают на оперативной схеме. Опасные камеры должны иметь специальную окраску люков и содержаться под надежным запором. Эксплуатацию газоопасных тепловых сетей следует производить в строгом соответствии с требованиями «Правил техники безопасности при обслуживании тепловых сетей».
Скапливающуюся в камерах тепловой сети воду непрерывно или периодически удаляют с помощью стационарных или передвижных средств. Дренажи необходимо содержать в полной исправности, регулярно прочищать и ремонтировать. В процессе эксплуатации необходимо постоянно следить за планировкой и состоянием поверхности земли по всей трассе тепловой, сети.
Систематический контроль за утечками теплоносителя производится в зависимости от величины подпитки тепловых сетей. При утечке теплоносителя, превышающей установленные нормы, следует принять срочные меры к обнаружению места утечки и устранению неплотностей. Качество воды для подпитки тепловых сетей должно удовлетворять требованиям, приведенным в табл. 1.2. проверяют нагрузку электрооборудования, температуру подшипников, наличие смазки, состояние сальников, действие системы охлаждения, наличие диаграммных лент в регистрирующих приборах. На неавтоматизированных насосных станциях организуют круглосуточное дежурство слесаря-машиниста.
Таблица 1.2.
Качество воды для подпитки водяных тепловых сетей при различной максимальной температуре подогрева сетевой воды.
Показатель качества воды
|
До 75 °С
|
76-100 о
С
|
101—200 °С
|
|
Не более
|
Растворенный кислород,
мг/кг
Взвешенные вещества,
мг/кг
Карбонатная жесткость,
м.г/(экв-кг)

Остаточная общая жесткость при использовании воды для продувки котлов (допускается в закрытых системах теплоснабжения), мг/(экв-кг)
Условная сульфатно-кальциевая жесткость
Свободная углекислота
|
0,1
5
1,5
6.5÷ 8,5
—
—
|
0,1
5
0,7
6.5÷ 85
0,1
|
0,05
5
0.5
6.5 ÷8,5
0,05
В пределах величин, исключающих выпадение из раствора CaSO
|
Перед каждым пуском насосов, а при работе насосов — не реже 1 раза в сутки проверяют состояние насосного и другого связанного с ним оборудования. В дренажных насосных станциях не реже 1 раза в две недели проверяют работу поплавкового устройства автоматического включения насосов. В насосных станциях ведут оперативный журнал и суточные ведомости. В журнале дежурный персонал записывает распоряжения диспетчера тепловой сети, делает пометки о всех переключениях, пуске и останове насосов, а также отмечает приемку и сдачу дежурств по насосной станции. В суточных ведомостях записывают показания контрольно-измерительных приборов.
Баки-аккумуляторы. Учитывая, что баки-аккумуляторы горячей воды являются источником повышенной опасности в аварийных ситуациях, в процессе эксплуатации им следует уделять особое внимание и заполнять их только деаэрированной водой. Ежегодно необходимо вести визуальный осмотр баков, компенсирующих устройств, вестовых труб, один раз в три года проводить инструментальное обследование баков для проверки толщины металлоконструкций и их коррозионного износа с помощью приборов «Кварц-6» и «Кварц-15». Внеочередные инструментальные обследования проводят по результатам визуального осмотра. Коррозионный износ при инструментальном обследовании определяют по отношению максимального уменьшения толщины металла к исходной толщине кровли и соответствующего пояса стенки бака.
Пригодность баков к дальнейшей эксплуатации после визуального осмотра и инструментального обследования оценивают по следующим параметрам. При коррозионном износе стенок, кровли, днища меньше 20 % толщины металла разрешается дальнейшая эксплуатация бака при обеспечении противокоррозионной защиты. При коррозионном износе стенок бака более 20 °/о толщины металла в верхней части бака (более 50 % высоты бака, считая от днища) допускается временная эксплуатация только со сниженным уровнем, т.е, при максимальном заполнении на 1 м ниже зоны, где имеет место указанный износ; в дальнейшем после ремонта баки должны быть обеспечены защитой от коррозии.
При износе стенок бака более 20 % толщины металла в нижней части (менее 50 % высоты бака) его необходимо немедленно ремонтировать. При износе днищ и кровли более 20 % толщины металла бак также снимают с эксплуатации и ремонтируют. После ремонта баки допускаются к эксплуатации при условии защиты их от коррозии.
1.7 ОБСЛУЖИВАНИЕ ТЕПЛОВЫХ ПУНКТОВ
Основными задачами обслуживания тепловых пунктов являются: обеспечение для каждого теплового пункта, а следовательно, и системы теплопотребления расхода теплоносителя требуемых параметров в пределах установленного лимита; обеспечение рационального использования теплоносителя и температурного перепада в системе теплопотребления; снижение до минимума тепловых потерь и устранение утечек; обеспечение бесперебойной и нормальной работы всего оборудования теплового пункта и систем теплопотребления.
Эксплуатацию тепловых пунктов осуществляет персонал потребителей под контролем организации, эксплуатирующей тепловые сети, или непосредственно персонал, эксплуатирующий тепловые сети. Последняя форма эксплуатации является наиболее эффективной и прогрессивной. Постоянное дежурство обслуживающего персонала на тепловом пункте, как правило, не обязательно. Необходимость дежурства и его продолжительность устанавливают в зависимости от характера работы систем теплопотребления, степени автоматизации и диспетчеризации, а также местных условий эксплуатации.
Обход тепловых пунктов производят слесари-обходчики по мере необходимости, но не реже одного раза в две недели в соответствии с утвержденным графиком. При обходе проверяют состояние помещения теплового пункта и всего оборудования, режим работы системы, герметичность всех соединений трубопроводов и арматуры, состояние контрольно-измерительных приборов и автоматических регуляторов. В открытых системах теплоснабжения во избежание перетекания воды на тепловом пункте из подающей трубы в обратную необходимо регулярно проверять герметичность закрытия обратного клапана, установленного на ответвлении от обратного трубопровода.
В журнале теплового пункта записывают обнаруженные при обходе неисправности и дают указания по их устранению с последующей проверкой выполнения абонентом этих указаний. В процессе эксплуатации показания контрольно-измерительных приборов периодически заносят в журнал. При постоянном дежурстве записи делают с интервалами, определяемыми режимом теплового потребления, но не реже 4 раз в смену; при отсутствии постоянного дежурства — не реже одного раза в сутки.
В процессе эксплуатации систематически уточняют тепловую нагрузку зданий путем контрольных замеров температур обратной воды и воздуха в отапливаемых помещениях. При неравномерном прогреве отдельных частей и приборов системы теплопотребления производят соответствующую регулировку. Регулировку выполняет персонал, эксплуатирующий систему теплопотребления. Спускные краны, элеваторы, дроссельные диафрагмы, установленные на тепловых пунктах и системах теплопотребления, должны быть опломбированы. При возникновении аварийной ситуации обслуживающий персонал потребителя должен сообщить об этом диспетчеру организации, эксплуатирующей тепловую сеть, для принятия мер по устранению аварии.
Включение и выключение тепловых пунктов и абонентских систем, а также регулирование расхода теплоносителя производит, как правило, персонал организации, эксплуатирующей тепловую сеть. Ежегодно оборудование тепловых пунктов ремонтируют. Объем и время проведения ремонта устанавливают и согласовывают потребитель и эксплуатирующая организация совместно.
Приемку тепловых пунктов и систем теплопотребления после монтажа и ремонта производят с участием персонала эксплуатирующей организации. С целью проверки подготовленности к отопительному сезону проверяют выполнение плана ремонтных работ, а также качество выполненных работ.
1.8 ИСПЫТАНИЯ ТРУБОПРОВОДОВ И ОБОРУДОВАНИЯ ВОДЯНЫХ ТЕПЛОВЫХ СЕТЕЙ
Гидравлические испытания.
Гидравлическими испытаниями тепловой сети определяют фактические значения коэффициента трения и эквивалентной шероховатости для использования их при расчете гидравлического сопротивления трубопроводов. Кроме того, определяют гидравлическое сопротивление водоподогревательной установки и ее коммуникаций и уточняют фактические характеристики сетевых и подпиточных насосов. Испытания тепловой сети, коммуникаций водоподогревательной установки, сетевых и подпиточных насосов сводятся к одновременному измерению расхода, давления и температуры сетевой воды.
Расход воды при испытаниях определяют нормальными измерительными диафрагмами с острой кромкой и подключенными к ним дифманометрами. Температуру теплоносителя измеряют техническими термометрами с ценой деления 0,5—1 °С. Давления при испытании тепловой сети и водоподогревательной установки замеряют пружинными образцовыми и контрольными манометрами. При испытании насосных установок используют технические манометры.
Выбор участков, гидравлических режимов и измерительных приборов для испытаний. Гидравлические испытания производят на магистральных и разводящих трубопроводах тех участков, где предполагается самое плохое состояние внутренней поверхности труб, которое находится в зависимости: от времени прокладки и включения в эксплуатацию участков теплосети, от качества подпиточной воды с учетом отдельных случаев подпитки сырой неумягченной или загрязненной воды; от случаев длительного простоя тепловой сети в опорожненном состоянии; от способа и периодичности промывки тепловой сети. При выборе участков должны быть учтены также сведения эксплуатационников о завышенных гидравлических потерях, об интенсивности коррозии. Намеченные для испытаний участки осматривают на месте, уточняя их длины и диаметры, местные сопротивления (компенсаторы, задвижки, повороты), места присоединения ответвлений и их диаметры. Результаты осмотра наносят на схему испытуемой части сети. По схеме выбирают места установки циркуляционных перемычек и манометров.
Перемычки, как правило, устанавливают на концах испытуемых трубопроводов. В этом случае, когда диаметр испытуемого трубопровода значительно уменьшается по длине трассы, предусматривают дополнительные перемычки где-либо в середине трассы, чтобы при испытаниях можно было создать в головной части трубопровода (большого диаметра) достаточно большие скорости воды, как это показано на рис. 1.1. Диаметр концевой перемычки ориентировочно принимают на параметр меньше диаметра трубопровода в месте ее врезки. Промежуточные перемычки рассчитывают не на полный расход воды, который будет при испытании, а лишь на часть его, поскольку при испытаниях вода будет циркулировать не только через промежуточные, но и через концевые перемычки. На каждой перемычке предусматривают установку задвижки одинакового с ней диаметра.
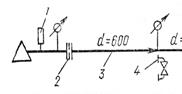
Рис. 1.1. Схема расположения перемычек и контрольно-измерительных приборов для проведения гидравлических испытаний: 1
- место установки манометров и термометров; 2
— измерительная диафрагма; 3 -
подающий и обратный трубопроводы испытуемой теплосети; 4
— циркуляционная перемычка
Манометры устанавливают на подающем и обратном трубопроводах в следующих характерных точках испытуемой магистрали: в местах изменения внутреннего диаметра трубопровода; в местах изменения количества циркулирующей воды (если одновременно испытывают несколько магистралей и ответвлений); в местах установки циркуляционных перемычек; на трубопроводах неизменного диаметра, но большой протяженности — через каждые 500—600 м трассы. В источнике теплоснабжения манометры устанавливают: на подающем и обратном коллекторах тепловой сети, на входе и выходе каждой водонагревательной установки (водогрейного котла, основного и пикового подогревателей); на напорном и всасывающем патрубках сетевых насосов; до и после грязевиков и охладителей конденсата. Места установки манометров наносят на схему тепловой сети и источника теплоснабжения.
Для измерения расхода воды при испытаниях измерительные приборы устанавливают: на подающем или обратном трубопроводе тепловой сети на выходе из источника теплоснабжения; на трубопроводе подпитки тепловой сети; на подающем или на обратном трубопроводе ответвлений, которые намечаются для испытания одновременно с основной магистралью. Возможность использования существующих измерительных диафрагм, ожидаемый расход циркуляционной воды во время испытаний, правильность выбранных мест установки перемычек и их диаметров, а также необходимые (по пределам измерений) для измерения манометры устанавливают в результате ориентировочного гидравлического расчета. При этом задаются эквивалентной шероховатостью трубопроводов (исходя из указанных выше сведений об эксплуатации) и таким расходом воды, чтобы удельные потери напора были не меньше 15 мм на 1 м.
Полученную в результате расчета величину потерь напора в тепловой сети и в перемычке сопоставляют с напором сетевых насосов при заданной величине циркуляции. Достаточно близкие совпадения этих величин указывают на то, что диаметр перемычки и расход сетевой воды приняты правильно. В противном случае необходимо произвести повторный гидравлический расчет, задаваясь другим расходом воды или другим диаметром (местом врезки) перемычки. Для увеличения циркуляции воды подключают крупных потребителей, расположенных за последней точкой измерения давления по испытуемой части магистрали, а из элеваторов этих потребителей удаляют сопла.
Возможность использования существующих диафрагм для замера максимального и минимального расходов воды, намечаемых при испытательных режимах, проверяется расчетом по формуле
, (1.1)
где G —расход воды, м3
/ч; А — коэффициент, зависящий от типа заполнителя, примененного в дифференциальном манометре (для дифманометров. заполненных ртутью над которой находится вода А = 0,04435: для дифманометров. заполненных водой, над которой находится воздух, А-0,01251); а — коэффициент расхода, определяемый по графику рис. 1.2 в зависимости от величины
где D
—
внутренний диаметр трубопровода; d
—
диаметр мерного отверстия диафрагмы, мм; h — разность высот столбов жидкости в дифференциальном манометре, мм; γ — плотность циркуляционной воды, кгc/м3
.
Измерительная диафрагма может быть использована для испытаний, если перепад давлений в дифманометре, подключенном к диафрагме, будет находиться в пределах 50—600 мм. Если существующая диафрагма не удовлетворяет условиям минимального расхода воды, следует проанализировать возможность, не заменяя диафрагмы при испытаниях на минимальных расходах, применить в качестве рабочей среды в дифманометре не ртуть, а какую-либо другую жидкость с меньшей плотностью или же, перевернув дифманометр, превратить его в водо-воздушный. Если же существующую диафрагму
по условиям перепада давлений при испытательных режимах использовать невозможно, она должна быть заменена другой, рассчитанной по формуле (1.1). Манометры для испытаний выбирают для каждого участка, исходя из того, чтобы измеренное давление не превышало 2/3 предела шкалы. Ожидаемое давление принимают по результатам предварительного гидравлического расчета с учетом профиля тепловой сети и расчетных показаний манометров при статическом режиме.
Проведение испытаний. Испытания начинают с определения геодезических отметок точек наблюдения относительно нулевой точки, за которую, как правило, принимают отметку манометра, установленного на выводном коллекторе источника тепла, или самую низкую точку сети. Геодезические отметки определяют путем

Рис. 1.2. График для определения расхода нормальных острых диафрагм
одновременного снятия показаний манометров при статическом режиме (сетевые насосы остановлены) и поддержании заданного давления в обратном коллекторе с помощью подпиточных насосов. Отметки определяют при двух режимах, различающихся на 0,5—1 кгс/см2
.
При статическом режиме должно быть снято не менее 10 показаний манометров с интервалом 5 мин. Задвижки в источнике тепла на испытуемых магистралях и циркуляционных перемычках при статическом режиме должны быть открыты.
По данным статических испытаний, геодезическую поправку определяют по формуле
,
где и - манометрические давления при статическом режиме соответственно в нулевой и данной точках, кгс/см2
; у
— плотность воды, соответствующая ее температуре во время испытаний, кгс/м8
.
На результаты измерений значительное влияние оказывают утечки воды. Поэтому при испытаниях следует тщательно следить за величиной подпитки, чтобы она при статическом режиме была близка к нулю, а при работе сетевых насосов не превышала 1 % количества воды, циркулирующей в сети. При больших утечках испытания должны быть приостановлены до их устранения.
Перед проведением основных испытаний производят пробные испытания при работе сетевых насосов со снятием показаний всех установленных приборов, во время которых проверяют достаточность потерь напора на участках (удельные потери напора должны быть не меньше 15 мм на 1 м), правильность выбора пределов измерения манометров и работу дифманометра. Если пробные испытания покажут, что при принятом режиме удельные потери недостаточны, необходимо принять меры к увеличению скорости (расхода) воды в тепловой сети путем включения дополнительных перемычек или крупных потребителей, увеличения напора на выводах с источника тепла и т. п.
Основные гидравлические испытания проводят при максимально возможном расходе воды и при расходе, сокращенном до 70—80 % максимального. Испытания при максимальном расходе воды позволяют получить наиболее надежные результаты за счет наибольшего падения давления. Испытания с сокращенным расходом воды проводят для проверки величин падения давления, полученных при максимальном расходе. По каждому режиму должно быть снято не менее 15 показаний с интервалом 5 мин.
Соответствие результатов испытаний при максимальном расходе воды результатам, полученным при сниженном расходе, проверяют по квадратичной зависимости
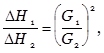
где и — потери напора на участке соответственно при максимальном и сниженном расходах воды, м; и — соответственно максимальный и сниженный расходы воды при испытаниях, м3
/ч.
Сетевые и подпиточные насосы испытывают при расходах воды, изменяемых в пределах от нуля до максимально возможного расхода и от максимально возможного до нуля. Производительность насоса изменяют с помощью задвижки на нагнетательном патрубке насоса. При испытаниях измеряют расход сетевой (подпиточной) воды, давление на всасывающем и нагнетательном патрубках (манометры располагают на одной высоте), мощность, потребляемую электродвигателем при различных режимах. При изменении расхода сетевой воды от нуля до максимального производят не менее пяти замеров одновременно по всем приборам и столько же при изменении расхода от максимального до нуля.
Гидравлическое сопротивление коммуникаций сетевой воды в источнике тепла определяют от обратного до подающего коллектора на выводах тепловой сети. Испытания проводят при различных схемах включения оборудования, соответствующих условиям эксплуатации при двух режимах работы сетевых насосов и одном статическом. На каждом режиме производят не менее пяти измерений. Каждый подогреватель (водогрейный котел, бойлер) испытывают отдельно. При испытаниях измеряют расход воды через испытуемый подогреватель и давление воды на входе и выходе из подогревателя. Остальные параллельно присоединенные подогреватели должны быть надежно отключены.
Обработка материалов испытаний. Для расчетов используют показания приборов при максимальном расходе воды, которые являются наиболее надежными. Показания приборов обрабатывают следующим образом. Выбирают 10 показаний приборов, последовательных по времени и соответствующих наиболее стабильному режиму. Среднеарифметическое значение выбранных показаний принимают за основу дальнейших расчетов. К усредненному показанию манометра вносят поправку согласно паспорту госповерки, а затем градусные показания манометра переводят в кгс/см2
. По величинам давлений с учетом поправок на погрешность и на положение манометра по формуле (1.2) определяют полные напоры в начале и конце каждого участка:
, (1.2)
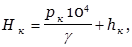
где и — истинное давление (с учетом погрешности манометра) в трубопроводе соответственно в начале и конце участка, кгс/см2
; и — геодезические поправки на положение манометров в начале и конце участка, м; у
— плотность воды при испытаниях, кгс/м3
.
По величине разности полных напоров в начале и конце участка находят величину общей потери напора на участке:
. (1.3)
Для участков, на которых установлены измерительные диафрагмы, потеря напора в диафрагме должна исключаться из вычисленной по формуле (1.3) общей потери напора на участке. С достаточной степенью точности потеря напора в диафрагме равна
,
где h
— перепад давлений по дифманометру, мм рт. ст.;d — диаметр мерного отверстия измерительной диафрагмы, мм; — внутренний диаметр трубопровода в месте установки диафрагмы, мм; 12,6 — коэффициент перевода, мм рт. ст. в мм вод. ст.
Затем определяют потери напора (в м) в местных сопротивлениях каждого участка:
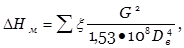
где — сумма коэффициентов местных сопротивлений: G—расход воды, мэ
/ч; — внутренний диаметр трубы м.
Далее определяют линейные (на трение) потери напора:

рассчитывают удельные линейные потери напора на участке:
,
где L
— длина участка, м.
Находят коэффициент трения:
,
Эквивалентную шероховатость (К,
мм) определяют из соотношения
,
где r— внутренний радиус трубопровода, мм.
Для анализа результатов испытаний строят график напоров в тепловой сети при испытаниях (рис. 1.3). Повышенные удельные потери напора на отдельных участках свидетельствуют о местных засорах трубопровода, неисправности запорной арматуры, наличии внутренних наплывов в сварных соединениях и др.
Фактические величины коэффициентов используют при последующей разработке гидравлических режимов тепловой сети для определения поправочного коэффициента к гидравлическим потерям в трубопроводах.
Тепловые испытания.
Общие положения. Тепловые испытания проводят с целью определения фактических потерь тепла в водяных тепловых сетях, пересчета этих потерь на различные режимы эксплуатации и сопоставления их с нормативными значениями. Фактические тепловые потери определяют не реже чем через 5 лет в связи с расширением и реконструкцией тепловых сетей, изменением теплотехнических
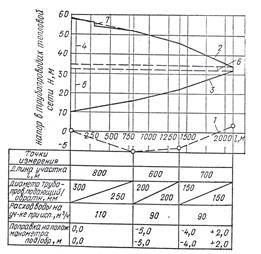
Рис. 1.3. График напора в тепловых сетях 1 — условный профиль испытуемой магистрали; 2
—- линия напоров в подающей магистрали; 3
-- линия напоров в обратной магистрали; 4
— потери напора в подающей магистрали; 5
— потери напора в обратной магистрали; 6 —
потери напора в перемычке; 7 -
потери напора в диафрагме показателей изоляции трубопроводов сетей в процессе их эксплуатации, заменой изоляции на отдельных участках и т. п.
Тепловые испытания водяных сетей проводят непосредственно после окончания отопительного сезона. Перед испытаниями восстанавливают разрушенную тепловую изоляцию, осушают камеры тепловых сетей, приводят в порядок дренажи, организуют сток поверхностных вод с трассы и т. п.
Для определения тепловых потерь водяных сетей выполняют следующие работы:
а) анализируют материалы по системе теплоснабжения;
б) выбирают участки сетей, подлежащие испытаниям;
в) рассчитывают параметры испытаний;
г) подготавливают сети, оборудование и измерительную аппаратуру к испытаниям;
д) проводят тепловые испытания;
е) обрабатывают данные, полученные при испытаниях;
ж) сопоставляют величины фактически измеренных при испытаниях тепловых потерь с нормативными величинами;
з) разрабатывают предложения по нормированию эксплуатационных потерь тепла.
Анализ материалов по системе теплоснабжения. Подготовку к испытаниям начинают с детального анализа схемы тепловых сетей, оборудования теплоприготовительной установки, типов прокладки, конструкции изоляции и состояния ее на отдельных участках сетей.
В процессе подготовки составляют таблицу с данными по характеристике сетей, в которой указывают диаметры и длины труб по участкам, конструкцию изоляции и типы прокладки (подземная бесканальная и в непроходных каналах, надземная внутри и вне помещений). Образец таблицы приведен ниже, в примере расчета тепловых потерь водяных тепловых сетей.
Для перерасчета полученных при испытаниях результатов на различные эксплуатационные режимы работы сетей и для определения температурных параметров испытаний используют: климатологические данные для того населенного пункта, в котором расположены испытуемые сети; среднегодовые температуры грунта на среднем уровне оси теплопроводов при подземной прокладке и наружного воздуха при надземной прокладке вне помещений; среднемесячные температуры грунта на среднем уровне оси теплопроводов при подземной прокладке и наружного воздуха по каждому месяцу в отдельности. Эти данные принимают как многолетние по материалам ближайшей к данному населенному пункту метеостанции или пользуются данными справочников по климату.
Среднемесячные температуры воды в подающей и обратной линиях двухтрубных водяных тепловых сетей определяют по графикам температур воды в этих линиях применительно к среднемесячным температурам наружного воздуха. Среднегодовые температуры воды в подающей и обратной линиях сетей определяются как среднеарифметические из среднемесячных температур ее в соответствующих линиях за весь период работы сетей в течение года.
Выбор участков сетей для испытаний. Испытаниям, как правило, подвергают те участки сетей, у которых тип прокладки и конструкции изоляции являются преобладающими для данных сетей. Определение тепловых потерь двухтрубных водяных тепловых сетей проводят на циркуляционном кольце, состоящем из подающей и обратной линий с перемычками между ними на начальном и конечном участках кольца. Начальный участок циркуляционного кольца содержит оборудование и трубопроводы теплоприготовительной установки (рис. 1.4).
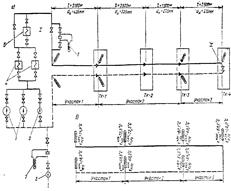
Рис. 1.4.
Схема испытуемого циркуляционного кольца: а —
движение воды и расстановка измерительных приборов при испытаниях; б
— измерение температур воды: !
— теплоприготовительяая установка; II
— циркуляционная перемычка; 1
— сетевые насосы: 2
— летний насос малой производительности; 3 —
подпиточный насос; 4 —
основные подогреватели сетевой воды; 5
— пиковый подогреватель сетевой воды или водогрейный котел; 6
— дифманометр на подающей линии; 7 — дифманометр на подпиточной линии
Циркуляционное кольцо состоит из ряда последовательно соединенных участков, отличающихся типом прокладки и конструкцией изоляции, а иногда и диаметром трубопроводов. Рекомендуется проводить испытания циркуляционного кольца, которое включает в себя основную магистраль тепловых сетей, состоящую из труб наибольшего диаметра и максимальной протяженности от источника тепла. При этом все ответвления и отдельные абоненты, присоединенные к циркуляционному кольцу, на время испытаний отсоединяют от него. Благодаря этому расходы воды на всех участках кольца во время испытаний в основном одинаковы и могут различаться между собой только незначительной утечкой воды из кольца, покрываемой его подпиткой.
Снижение температуры воды по мере ее движения по кольцу обусловливается при этом только тепловыми потерями трубопроводов и арматуры в окружающую среду. Величины этих тепловых потерь подсчитывают, исходя из измеренного во время испытаний расхода воды и снижения ее температуры на отдельных участках кольца. При таком режиме работы, в отличие от условий нормальной эксплуатации двухтрубных водяных тепловых сетей, температуры воды в обратной линии кольца лишь незначительно ниже температур в подающей линии соответствующего участка, поскольку это снижение вызвано только тепловыми потерями соответствующей части кольца.
Типы прокладок и конструкции изоляции, подвергаемые испытаниям, выбирают, исходя из отношения , где: материальная характеристика для подающей или обратной линии сетей, просуммированная по всем участкам с данными типом прокладки и конструкцией изоляции, м2
; dH
— наружный диаметр труб в пределах одного участка сети (по подающей или обратной линии при равных диаметрах труб этой линий), м; l — протяженность участка сети с данными типом прокладки и конструкцией изоляции, м.
При отношении <0,15 данные типы прокладки и конструкции изоляции, как правило, испытаниям не подлежат, а эксплуатационные потери тепла для них определяют, исходя из нормативных данных; при 0,15 соответствующие типы прокладки и конструкции изоляции, как правило, должны подвергаться испытаниям.
Расчет параметров испытаний. Основные параметры испытаний определяют расчетным путем. Ими являются величины температуры воды в подающей линии сетей на выход из теплоподготовительной установки и величины расхода воды на начальном участке испытуемого циркуляционного кольца. Кроме того, выявляют ожидаемые в процессе испытаний значения температуры воды в обратной линии на входе в теплоподготовительную установку и величину расхода подпиточной воды, а также ориентировочную продолжительность испытаний. Температурный режим циркуляционного кольца во время испытаний задается исходя из следующих условий:
- разность между средней температурой воды по всем участкам кольца и температурой окружающей среды должна быть по возможности близка к среднегодовому значению разности средней по подающей и обратной линиям температуры воды и температуры окружающей среды для данных сетей;
- снижение температуры воды в циркуляционном кольце за счет его тепловых потерь при испытаниях должно составлять не менее 8 и не более 20 °С.
При наличии на испытуемом кольце участков с различными типами прокладки и конструкциями изоляции величину снижения температуры воды в кольце выбирают в соответствии с величиной, рассчитанной по формуле
(1.4)
воды а подающей или обратной линии на участке с наименьшей материальной характеристикой  принимаем неравным 2°С из соображений обеспечения надлежащей точности измерений температуры; — наименьшая в пределах кольца величина отношения материальной характеристики для подающей или обратной линии отдельного участка испытуемого кольца ММНН
к суммарной материальной характеристике подающей и обратной линий для всего кольца в целом.
При величине отношения <0,1 тепловые потери на соответствующих участках испытуемого кольца, как правило, отдельно не измеряют.
Температуры воды в подающей и обратной .и линиях испытуемого кольца на выходе из теплоподготовительной установки и на входе в нее определяют по формулам:
; (1.5)
, (1.6)
где и — среднегодовые температуры воды в подающей и обратной линиях для испытуемых сетей, °С; ожидаемая усредненная по всем участкам кольца температура окружающей среды во время испытаний, °С: — усредненная по тем же участкам среднегодовая температура окружающей среды, °С.
При наличии в пределах испытуемого кольца участков, как с подземной, так и с надземной прокладкой тепловых сетей усредненные температуры окружающей среды: и подсчитывают соответственно по формулам:
; (1.7)
, (1.8)
где и — соответственно среднемесячные температуры грунта на среднем уровне оси теплопроводов и наружного воздуха в период проведения испытаний, °С; и соответственно среднегодовые температуры грунта и наружного воздуха, °С; и — материальные характеристики для подающей или обратной линии по всем участкам соответственно подземной и надземной прокладки, расположенным в пределах испытуемого циркуляционного кольца, м2
; — суммарная материальная характеристика для подающей или обратной линии по всем участкам испытуемого кольца, м2
.
Расчетный расход воды ( ,
ккал/ч), циркулирующей по испытуемому кольцу, принимают, исходя из ориентировочной величины тепловых потерь этого кольца при режиме испытаний которую подсчитывают по формуле
, (1.9)
Где и — нормативные величины удельных тепловых потерь двухтрубных водяных тепловых сетей соответственно по подающей и обратной линиям для каждого диаметра труб и типа прокладки, ккал/(м-ч).
Указанные величины определяют, исходя из действующих «Норм проектирования тепловой изоляции для трубопроводов и оборудования электростанций и тепловых сетей» (Госэнергонздат, 1959), отдельно для участков надземной (табл. 1.3) и подземной прокладки (табл. 1.3) применительно к температурному режиму, поддерживаемому во время испытаний в циркуляционном кольце. В упомянутых нормах значения удельных тепловых потерь для двухтрубных водяных сетей даны для каждого наружного диаметра труб и нескольких значений среднегодовой температуры воды отдельно по подающей и обратной линиям при заданной температуре окружающей среды (воздуха при надземной и грунта при подземной прокладке). Поскольку приведенные в нормах значения разности температур воды и окружающей среды, как правило, не соответствуют разностям температур, имеющим место при испытаниях, эти значения пересчитывают для условий испытаний по следующим формулам:
для участков надземной прокладки, ккал/(м.ч):
; (1.10)
, (1.11)
где , и нормативные значения
удельных тепловых потерь при надземной прокладке труб данного наружного диаметра и среднегодовых температурах воды соответственно 100, 75 и 50 ºC , ккал/(м ч) (см. табл. 1.3);
и — средние температуры воды при режиме испытаний соответственно в подающей и обратной линиях испытуемого кольца, ºС
; (1.12)
, (1.13)
Формулы (1.10) и (1.11) действительны для температур 75°С 100°С и °С, при которых, как правило, работают двухтрубные водяные тепловые сети, регулируемые по графикам температур 150/70 º
С или 130/70 ºС. В отдельных случаях, когда величина <75°C, значения определяют по формуле (1.2);
для участков подземной прокладки, ккал/(м-ч):
, (1.14)
где и — нормативные значения удельных тепловых потерь при подземной прокладке для труб данного наружного диаметра соответственно для подающей линии при среднегодовой температуре воды 90 °С и для обратной линии при среднегодовой температуре воды 50 °С (см. табл. 1.2).
Формула (1.14) действительна для температур 65°С 110°С и <50°С, при которых, как правило, работают двухтрубные водяные тепловые сети. При расчетах по формуле (1.9) суммирование осуществляют по всем участкам длиной I
испытуемого кольца, отличающимся наружным диаметром труб или типом прокладки, но не конструкцией изоляции, так как последняя не влияет на нормативные значения тепловых потерь. Входящий в формулу (1.9) коэффициент местных тепловых потерь β учитывает эти потери в арматуре, опорах и компенсаторах, находящихся в пределах испытуемого кольца. Величину этого коэффициента в соответствии со СНиП И-36-73 («Тепловые сети. Нормы проектирования») определяют по табл. 1.3.
Таблица 1.3.
Коэффициент β местных тепловых потерь
|
Тип прокладки
|
|
β
|
Бесканальная
В тоннелях и каналах
Надземная
|
1,15
1,20
1,25
|
Расчетный расход воды (т/ч) в циркуляционном кольце, назначаемый на время испытании, определяют по формуле
, (1.15)
Предполагаемую величину часовой подпитки сети при испытаниях принимают равной 0,5 % суммарной вместимости трубопроводов в пределах испытуемого циркуляционного кольца.
Ожидаемое время (ч) пробега частиц воды по испытуемому циркуляционному кольцу находят по формуле
, (1.16)
где V
— суммарная вместимость труб испытуемого циркуляционного кольца в пределах от выхода до входа их в теплоподготовительную установку, м3
; — расчетный расход воды при испытании, т/ч
; у
— плотность воды в испытуемом кольце при средней температуре воды в нем кг/м3
.
Подготовка сетей и оборудования к испытаниям.
Циркуляцию воды в испытуемом кольце создает летний сетевой насос небольшой производительности. При отсутствии такого насоса необходимый расход воды может быть обеспечен основным сетевым насосом, оборудованным циркуляционной перемычкой с регулировочной задвижкой. На конечном участке испытуемого кольца для перепуска воды из подающей линии в обратную устанавливают циркуляционную перемычку, рассчитанную на потери напора в ней 1—2 м. Для перепуска воды из подающей линии в обратную могут быть использованы также элеваторные перемычки вводов, расположенных за конечным участком испытуемого кольца. Сопла элеваторов при этом должны быть удалены. Непосредственно перед началом испытаний все тепловые вводы абонентов сетей, кроме используемых в качестве перемычек за конечным участком, а также все ответвления, не подвергающиеся испытаниям, и перемычки между подающей и обратной линиями отсоединяют от испытуемого кольца. Плотность отсоединения тщательно проверяют.
Подготовка измерительной аппаратуры. При тепловых испытаниях сетей измеряют расход воды, циркулирующей по испытуемому кольцу, расход подпиточной воды и температуры воды в точках наблюдения. Расход сетевой и подпиточной воды измеряют посредством диафрагм, установленных на подающей или обратной линии, а также на подпиточной линии. К измерительным диафрагмам присоединяют ртутные дифманометры ДТ-50 с разгрузочными вентилями. Измерительные диафрагмы должны быть рассчитаны на величины расходов сетевой и подпиточной воды, которые были выявлены при определении параметров испытаний, и на перепад давлений, соответствующий примерно 400 мм рт. ст.
1.9 РЕГУЛИРОВАНИЕ СИСТЕМ ТЕПЛОСНАБЖЕНИЯ
Наладку водяных тепловых сетей производят для обеспечения нормального теплоснабжения потребителей. В результате наладки создаются необходимые условия для работы систем отопления, приточной вентиляции, кондиционирования воздуха и горячего водоснабжения и повышаются технико-экономические показатели централизованного теплоснабжения за счет увеличения пропускной способности тепловых сетей, ликвидации перетопа потребителей, снижения расхода электроэнергии на перекачку теплоносителя.
Наладку производят во всех звеньях централизованного теплоснабжения: в теплоприготовляющей установке источника тепла, тепловой сети, тепловых пунктах и системах теплопотребления.
Наладочные работы выполняют в три этапа:
1) обследуют и испытывают систему централизованного теплоснабжения с последующей разработкой мероприятий, обеспечивающих эффективность ее работы;
2) выполняют разработанные мероприятия;
3) регулируют систему.
В результате обследования выявляют фактические эксплуатационные режимы, уточняют тип и состояние оборудования системы теплоснабжения, определяют характер и величину тепловых нагрузок, необходимость и объем испытаний тепловых сетей и оборудования.
В процессе наладочных работ испытывают пропускную способность теплосети и коммуникаций источника тепла, определяют фактическую характеристику сетевых насосов, испытывают калориферные установки. При необходимости тепловые сети испытывают на теплопотери, прочность и компенсирующую способность при максимальной температуре сетевой воды.
Разработку режимов и мероприятий, обеспечивающих эффективность работы тепловой сети, проводят на основе данных обследования и испытаний в следующем порядке: рассчитывают фактические тепловые нагрузки; разрабатывают режим отпуска тепла; определяют расчетные расходы сетевой воды; производят гидравлический расчет наружных тепловых сетей, а при необходимости — систем теплопотребления промышленных зданий; разрабатывают гидравлический режим работы тепловых сетей; рассчитывают дроссельные и смесительные устройства для тепловых пунктов потребителей и отдельных теплоиспользующих установок; определяют места установки автоматических регуляторов на источнике тепла, тепловых сетях и у потребителей; составляют перечень мероприятий, выполнение которых должно предшествовать регулировке. При выполнении мероприятий по наладке производят следующие работы: устраняют дефекты строительных конструкций и оборудования; приводят схемы и оборудование водоподогревательной установки, тепловых сетей, подкачивающих насосных станций, тепловых пунктов и систем теплопотребления в соответствие с рекомендациями, основывающимися на выполненных расчетах и разработанных тепловых и гидравлических режимах: оснащают все звенья системы теплоснабжения необходимыми контрольно-измерительными приборами в соответствии с требованиями нормативных документов; автоматизируют отдельные узлы системы теплоснабжения; устраивают насосные и дроссельные станции; устанавливают дроссельные и смесительные устройства.
К регулировке систем централизованного теплоснабжения приступают только тогда, когда проверкой выявляют выполнение всех разработанных мероприятий по наладке. В процессе регулировки проверяют прогрев теплоиспользующих установок при работе источника тепла в разработанных тепловых и гидравлических режимах, а также соответствие фактических расходов теплоносителя расчетным, корректируют диаметры отверстий сопел элеваторов и дроссельных диафрагм, настраивают автоматические регуляторы.
Эффективность наладки тепловых сетей характеризуется следующими показателями: сокращением расходов топлива за счет ликвидации перегрева систем теплопотребления; сокращением расхода электроэнергии на перекачку теплоносителя за счет снижения удельного расхода сетевой воды и отключения излишних насосных станций; обеспечением возможности подключения к сетям дополнительных теплопотребителей; сокращением расходов топлива на выработку электроэнергии за счет снижения температуры воды в обратных трубопроводах тепловой сети (в теплофикационных системах).
1.10 АНАЛИЗ РЕЖИМОВ РАБОТЫ СИСТЕМЫ ТЕПЛОСНАБЖЕНИЯ КИП И А
Измерение технологических параметров.
При наблюдении за технологическим режимом в процессе эксплуатации и во время специальных испытаний в системе централизованного теплоснабжения контролируют следующие параметры.
1. На тепловой сети:
- давление на подающем и обратном магистральных трубопроводах до и после секционирующих задвижек и во всех местах изменения диаметра трубопроводов, на ответвлениях диаметром 300 мм и более до и после задвижек;
- температуру в подающих и обратных трубопроводах перед секционирующими задвижками, перед ответвлениями (по ходу воды) диаметром 300 мм и более, на всех обратных трубопроводах перед задвижкой (по ходу волы), а также в местах изменения типа прокладки или изоляционной конструкции;
- величину расхода теплоносителя в подающем и обратном трубопроводах ответвлений диаметром 500 мм и более.
На каждом трубопроводе выводов тепловых сетей ТЭЦ или котельной, кроме того, регистрируют температуру, давление и расходы воды.
2. На насосных станциях:
- температуру на подающем трубопроводе смесительной насосной станции, до и после точки смешения, в подающем и обратном трубопроводах, до и после подкачивающих и смесительных насосов;
- давление в напорном коллекторе подкачивающих и смесительных насосных станций, а также в трубопроводах до и после клапанов рассечки;
- давление во всасывающих и нагнетательных патрубках каждого насоса, в общих напорных коллекторах подкачивающих и смесительных насосных станций;
- величину расхода теплоносителя в подающем трубопроводе, до и после точки смешения в смесительных насосных станциях.
3. На центральных тепловых пунктах (ЦТП) манометры устанавливают в следующих местах:
ЦТП с зависимым присоединением систем отопления
|
ЦТП с независимым присоединением систем отопления
|
- на подающем трубопроводе тепловой сети
-на обратном трубопроводе тепловой сети
- на (ГВС) горводопровода
- на подающем трубопроводе системы горячего водоснабжения (ГВ), на выходе из бойлера
-на циркуляционном трубопроводе системы ГВС до насосов или регулятора подпора
-на напорном коллекторе хозяйственных насосов
- на напорном коллекторе циркуляционных насосов ГВС
- на выходе холодной воды из ЦТП
- на регуляторе температуры
- на регуляторе перепада давления (расходов)
- на подающем трубопроводе систем отопления на выходе из ТП;
- на обратном трубопроводе систем отопления на входе в ТП;
|
- на подающем трубопроводе систем перед отопительным бойлером;
- на подающем трубопроводе систем отопления (по местной воде);
- на обратном трубопроводе от систем отопления (по местной воде);
- на подающий коллектор отопительных насосов;
- на подающем коллекторе подпиточных насосов;
|
Температуру измеряют:
ЦТП с зависимым присоединением систем отопления
|
ЦТП с независимым присоединением систем отопления
|
- в подающем трубопроводе тепловой сети;
- в обратном трубопроводе тепловой сети;
- вода поступает в систему горячего водоснабжения;
- сетевой воды на систему отопления;
- обратной воды от каждой системы отопления.
|
- сетевой воды на отопительные водоподогреватель;
- обратной сетевой воды после отопительного водоподогревателя;
- местной воды на систему отопления;
- местной воды от каждой системы отопления.
|
Измеряют величину расхода: сетевой воды на тепловой пункт (на обратном трубопроводе тепловой сети); сетевой воды на подпитку независимой системы отопления; водопроводной воды; воды, идущей на горячее водоснабжение.
На индивидуальных тепловых пунктах измеряют:
- давление в подающем и обратном трубопроводах после входных задвижек (кроме того, устанавливают штуцеры для манометров, до и после смесительного устройства);
- температуру в подающем и обратном трубопроводах после входных задвижек. На подающем трубопроводе смешанной воды, кроме того, устанавливают гильзы для термометров, до задвижек на всех обратных трубопроводах, идущих от отдельных теплопотпебляющих систем или отдельных частей систем);
- величину расхода — в закрытых системах на подающем или обратном трубопроводах, а в открытых системах — на подающем трубопроводе и на линии горячего водоснабжения после смесительного устройства.
Каждая из ступеней подогревателя горячего водоснабжения оборудована показывающими манометрами и термометрами на входе и выходе сетевой и водопроводной воды. Перед подогревателями на трубопроводе холодной воды устанавливают водомер.
При монтаже и эксплуатации приборов необходимо учитывать следующее:
1) измеряемое давление должно соответствовать последней трети шкалы прибора;
2) показания прибора от нуля до первого цифрового деления недействительны;
3) манометр следует устанавливать только в вертикальном положении штуцером вниз;
4) манометры присоединять к трубопроводам только через трехходовые краны (технические манометры имеют резьбу М20; трехходовые краны имеют с одного конца резьбу ½" для присоединения к штуцеру на трубопроводе, с другого — М20 для присоединения манометра);
5) заворачивать манометр за корпус или газовыми ключами запрещается, для этого применяют гаечный ключ размером 17 мм;
6) во избежание закипания трехходовых кранов их следует смазывать техническим вазелином;
7) все манометры раз в год должны проходить проверку, после которой на них должно стоять клеймо госповерителя.
Термометры монтируют таким образом, чтобы обеспечить хорошую видимость показаний. Для защиты от механических повреждений термометры защищены гильзой с защитным кожухом, снабженным с лицевой стороны вырезом для наблюдения за показаниями. Кожух жестко прикреплен к гильзе. Для улучшения теплопередачи гильзу очищают от грязи и заполняют машинным маслом или глицерином. Хвостовик термометра должен быть полностью утоплен в гильзе, при этом резервуар термометра должен находиться в центре потока. Гильзу изготавливают из нержавеющей стали или латуни и ввинчивают в бобышку, приваренную к трубопроводу. При монтаже гильзы на трубопроводе малого диаметра следует применять угловую бобышку, при этом гильза должна быть направлена навстречу потоку. Не допускается приваривать гильзу непосредственно к трубопроводу. При снятии показаний запрещается вытаскивать термометр из гильзы.
ГЛАВА 2. СИСТЕМЫ ГАЗОСНАБЖЕНИЯ
2.1 КЛАССИФИКАЦИЯ ГАЗОВЫХ СИСТЕМ
Все газопроводы, прокладываемые в городах и населенных пунктах, различаются по их назначению и величине давления газа.
По назначению газопроводы разделяют на магистральные, распределительные и вводы (ответвления). Однако такое деление является условным, так как одни и те же газопроводы одновременно выполняют функции передачи и распределения газа.
В особую группу следует также выделить внутриобъектовые газопроводы.
Распределительные газопроводы служат для транспортировки газа по проездам; ответвления и вводы – для подачи газа от распределительных газопроводов к потребителям, а внутриобъектовые газопроводы – для подачи газа от отключающего устройства на вводе до газовых приборов различного назначения.
Определенное давление, создаваемое в подземных газопроводах, обеспечивает движение газа. Величина давления газа зависит от расстояния, на котором находятся потребители от источника газоснабжения и режима работы потребителей. Чем больше расстояние, тем выше давление.
Повышение давления позволяет по газопроводам небольших диаметров подавать значительное количество газа. Уменьшение диаметров труб значительно снижает стоимость прокладки газопроводов. Однако по соображениям безопасности газ под высоким давлением нельзя подавать в жилые дома, мелкие коммунально-бытовые учреждения. Номинальное давление газа для таких потребителей составляет 130-200 мм вод. ст., а давление газа в распределительных газопроводах достигает 12 атм. Поэтому на распределительных газопроводах сооружают специальные газорегуляторные установки для снижения давления газа до требуемой величины.
Снижение давления требует увеличения диаметра газопроводов, а подача газа только по газопроводам низкого давления привела бы к завышению стоимости их сооружения. Поэтому в городах и населенных пунктах прокладываются газопроводы низкого, среднего и высокого давления.
Существует следующая классификация газопроводов по величине давления газа:
- газопроводы низкого давления (до 2000 Па – для искусственного газа; до 3000 Па – для природного газа и 3500 – 4000 Па – для сжиженного газа).
При установке у бытовых коммунально-бытовых потребителей индивидуальных или групповых регуляторов-стабилизаторов в распределительных газопроводах низкого давления допускается давление до 0,05 Па.
- газопроводы среднего давления (от 5000 до 300000 Па);
- газопроводы высокого давления (от 300000 до 600000 Па);
Газопроводы высокого давления для подачи газа газгольдерным станциям и промышленным предприятиям (от 600000 до 1200000 Па).
В особых случаях разрешается прокладка газопроводов давлением более 1200000 Па при обосновании их необходимости и согласовании с органом Гостехнадзора.
По газопроводам низкого давления подается газ жилым домам и коммунально-бытовым предприятиям.
Газопроводы среднего давления служат для питания распределительных газопроводов низкого давления через регуляторные пункты (ГРП). По этим газопроводам также подается газ через ГРП или регуляторные установки (РГУ) в газопроводы промышленных и крупных коммунально-бытовых предприятий, а также для отопленных котельных.
Газопроводы высокого давления предназначены для подачи газа через ГРП в газопроводы высокого и среднего давления, а также непосредственно крупным промышленным предприятиям и газгольдерным станциям.
2.2 ЭКСПЛУАТАЦИЯ И НАСТРОЙКА ГРП
При эксплуатации газорегуляторных пунктов выполняются следующие работы:
- обход регуляторных пунктов и устранение выявленных неисправностей;
- плановая проверка работы оборудования;
- профилактический ремонт оборудования;
- проверка контрольно-измерительных приборов и приборов телеизмерения и телеуправления;
- контроль за состоянием помещения регуляторных пунктов.
Обход регуляторных пунктов. Обслуживают оборудование ГРП два слесаря один раз в два дня по утвержденному графику, если газорегуляторные пункты оборудованы телемеханическими установками, то проверять их работу можно один раз в неделю.
При обслуживании выполняются следующие работы:
- смена картограмм, заливка чернила, завод часовых механизмов;
(по картограммам периодически анализируется работа оборудования ГРП);
- проверка плотности резьбовых и фланцевых соединений при помощи мыльной эмульсии;
- проверка наличия газа в помещении ГРП.
Два раза в месяц концентрацию газа необходимо проверять газоанализатором или лабораторным анализом. Максимальная концентрация газа в помещении ГРП должна быть не более 0,5%;
- проверка правильности показаний манометров. Проверка манометров на нуль производится при каждом посещении ГРП. Два раза в год правильность показаний манометра сверяется с контрольным манометром.
Раз в год после ремонта производится клеймение манометров. Особое внимание необходимо уделять на выходное давление газа, которое устанавливается диспетчерской службой и поддерживается на заданном уровне. В некоторых случаях слесари по указанию своего мастера или диспетчерской службы изменяют выходное давление газа;
- осмотр всего установленного оборудования и выявление различных дефектов;
- проверка работы отопительной системы и температуры помещения ГРП. Температура в помещении должна быть не менее +5°С, а наружной поверхности отопительных приборов— не более 80 °С;
- проверка уровня жидкости в гидрозатворе. Этот уровень устанавливается в зависимости от выходного давления и должен обеспечить срабатывание гидрозатвора раньше срабатывания запорно-предохранительного клапана.
Однако, для выполнения сборки-разборки узлов, необходимо получить заказ-наряд и выполнять работы.
При обходе проверяют также помещения ГРП, освещение, вентиляцию, телефон и т. д. Результаты обхода заносятся в журнал по установленной форме.
Все выявленные неисправности устраняют немедленно сами слесари или, в зависимости от сложности, дежурная бригада.
Плановая проверка и профилактический ремонт оборудования ГРП. Плановая проверка оборудования проводится два раза в год, ее цель — выявить и устранить неисправности, а также провести настройку оборудования на заданный режим. Работы ведутся бригадой слесарей под руководством инженерно-технических работников. При плановой проверке проводятся следующие работы:
- определение плотности и чувствительности мембран. Плотность мембран проверяют внешним осмотром и мыльной эмульсией, чувствительность мембран — путем изменения нагрузки на мембрану и наблюдением за давлением. Так, мембраны регуляторов низкого давления должны быть чувствительны при изменении нагрузки, соответствующей изменению давления до З мм вод. ст. Колебание выходного давления газа за регулятором должно быть не более 5% в ту или другую сторону;
- проверка плотности прилегания клапана к седлу. Для проверки достаточно закрыть клапан, уменьшив нагрузку на мембрану, и проследить за регулятором. Если клапан закрыт, то шума не должно быть. Существуют и другие способы определения плотности закрытия: по картограммам регистрирующих приборов, выходному давлению газа, с помощью листа чистой бумаги, вложенного между клапаном и седлом, и т. д. Во всех случаях при обнаружении неплотности закрытия клапана, его необходимо отремонтировать или заменить;
- проверка работы запорно-предохранительных, выхлопных и сбрасывающих устройств. Для проверки работы запорно-хранительного клапана достаточно повысить выходное давление газа и посмотреть, при каком давлении клапан сработает. При выходном низком давлении клапан должен сработать при давлении газа на 50 мм вод. ст. выше рабочего давления газа. Если выходное давление газа среднее, то клапан должен сработать при давлении на 25 выше рабочего давления. Гидравлический затвор и пружинный выхлопной клапан настраиваются на давление 10—15 мм вод. ст.
меньше давления в запорно-предохрапительном клапане;
- осмотр и очистка фильтра. Состояние фильтра определяется путем замера перепада давления газа в нем, если перепад большой, то фильтр чистят;
- проверка хода и плотность закрытия задвижек и предохранительного клапана. Прочистка импульсных линий, проверка плотности арматуры и соединений и т. д.
Профилактический ремонт проводится один раз в год. При этом разбираются все узлы оборудования, смазываются трущиеся части, ремонтируются или заменяются негодные, проверяется работа оборудования на различных режимах и т. д. При производстве работ, связанных с изменением давления газа, разрешается пользоваться байпасом при условии обеспечения бесперебойности и надежности снабжения газом. После окончания работ необходимо взять анализ пробы воздуха из помещения ГРП и произвести запись о выполненных работах в специальный журнал.
3.3 ПРОФИЛАКТИЧЕСКОЕ ОБСЛУЖИВАНИЕ ГАЗОПРОВОДОВ
Цель профилактического надзора за газопроводами — своевременное выявление различных неисправностей и утечек газа. Эти работы проводит бригада линейных слесарей, за которыми закрепляются определенные трассы газопроводов. Для удобства обслуживания все газопроводы делятся на маршруты, составляются маршрутные схемы, в них, кроме газопровода, нанесены все прилегающие к нему сооружения и коммуникации на расстоянии 15 м от оси газопровода в обе стороны.
Сроки профилактических осмотров подземных газопроводов и их сооружений приведены в табл. 2.4.
Обход трассы газопроводов проводится по специальному графику, составленному с учетом вышеперечисленных норм на периодичность обслуживания.
Таблица 2.1
Сроки профилактических осмотров подземных газопроводов
Сооружения и устройства
|
Сроки осмотров (не реже)
|
Периодичность обхода трасс:
а) газопроводы среднего и высокого давления:
в пределах застроенной части территории
в пределах незастроенной части территории
б) газопроводы низкого давления
в) газопроводы низкого давления, где должна быть установлена активная защита (до ее устройства). То же при реконструкции дорожного покрова
Ревизия газопроводов:
а) стальные газопроводы (шурфовой осмотр и буровая проверка)
б) чугунные газопроводы (шурфовой осмотр и буровая проверка)
Проверка на загазованность:
телефонные и теплофикационные колодцы (при канальной прокладке). Общие коллекторы и тоннели для подземных сооружений. Водопроводные колодцы.
Шахты колодцев и устьев мостов. Подвалы домов с газовой разводкой, без газовой разводки.
Осмотры и откачка сборников конденсата
Одновременные замеры давления по всей газовой сети
Подводные переходы газопроводов через реки и каналы:
а) береговые части переходов
б) обследование подводной части переходов газопроводов всех давлений производится: при длине более 30 м
с расчетной положительной плавучестью
При длине менее 30 м
с расчетной отрицательной плавучестью
Арматура, установленная на газопроводах, в колодцах (задвижки, краны, компенсаторы), периодический осмотр и ремонт
|
1 раз в 2 дня
1 раз в 3 дня
2 раза в месяц
Ежедневно
Через 3 года после ввода в эксплуатацию; в последующее время через 5 лет
1 раз в 5 лет – 1 раз в год
При каждом обходе газовой сети
2 раза в месяц
2 раза в год (зимой) и при вводе новых газопроводов в эксплуатацию
В сроки обходы трассы
1 раз в 2 года
1 раз в 5 лет
1 раз в год
|
При обходе и обслуживании трассы выполняются следующие работы:
- осмотр и проверка на загазованность колодцев, подвалов, контрольных трубок и других сооружений;
- наблюдение за состоянием трассы и установленных на ней коверов и настенных знаков;
- проверка и откачка конденсата или воды из конденсатосбориков и гидрозатворов;
- проверка давления газа на различных участках газопроводов;
- выявление и устранение различных закупорок;
- буровой осмотр и устранение утечек газа;
- определение наличия блуждающих токов;
- проверка и мелкий ремонт арматуры газопроводов;
- составление необходимой технической документации.
В зависимости от сложности перечисленных работ они могут выполняться двумя слесарями или целой бригадой. Так, например, обход трассы производится двумя слесарями, из которых один назначается старшим. Слесари должны знать не только трассу газопровода, но и основные физико-химические свойства газа, так как эти знания помогут определить утечку газа по многим косвенным признакам. Известно, что при значительных утечках из газопроводов среднего и высокого давлений газ иногда выходит на поверхность с шипением, а в лужах и дюкерах образуются пузыри. Если трасса покрыта снегом, то на нем могут быть бурые пятна, летом — желтая трава и т. д.
Практикой установлено, что из газопроводов среднего и высокого давлений газ при утечке распространяется со скоростью до 6 м/ч. Передвигаясь с такой скоростью, он распространяется на большие
расстояния, проникает в различные сооружения и коммуникации.
Поэтому, кроме газовых колодцев, проверяют и другие сооружения. В случае обнаружения утечки газа необходимо проверить все прилегающие к газопроводу сооружения в радиусе до 50 м.
Наличие газа и его концентрацию определяют специальными приборами — газоанализаторами. Определение наличия газа огнем категорически запрещается! Если в колодцах или других сооружениях обнаружен газ, то сооружения необходимо срочно проветрить и сообщить о наличии взрывоопасной концентрации в соответствующую службу или участок.
Особую осторожность и оперативность необходимо проявить при обнаружении газа в подвалах зданий. Срочно проветрить подвалы, проверить газоанализаторами проникновение газа в квартиры вышележащих этажей.
На особо ответственных и труднодоступных участках газопроводов устанавливают контрольные трубки, с их помощью легко наличие газа в газопроводах, заключенных в футляр.
Кроме периодических работ, составляется специальный график осмотра и проверки газовых колодцев два раза в год. При этом выполняются такие работы, как: очистка колодцев от грязи и других посторонних предметов, проверка состояния задвижек и компенсаторов, покраска колодцев и установленного в них оборудования. Результаты проверки состояния оборудования и трассы газопровода и сведения о проведенном ремонте записываются в специальные журналы.
Различные сооружения газопроводов, газовые колодцы, ковера, люки зимой могут быть покрыты снегом, поэтому для их быстрого отыскания устанавливаются настенные указатели с цифрами величин привязки этих сооружений (рис. 2.1). Эти на стенные указатели должны также регулярно проверяться и корректироваться. В случае их поломки или отсутствия необходимо их восстановить.
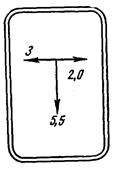
Рис. 2.1. Настенный указатель
Очень важной задачей является проверка конденсатосборников и гидрозатворов. Удаляют конденсат из газопроводов по специальному графику, имеющемуся в эксплуатационной организации. Откачивают конденсат из гидрозатворов и конденсатосборников низкого давления ручным насосом (рис. 2.2) или мотонасосом, а из газопроводов высокого давления и среднего давления — мотонасосом. Конденсат удаляется в специальную емкость и опорожняется в заранее отведенном месте.
При откачке конденсата нельзя допускать к месту работы посторонних лиц, курить и пользоваться открытым огнем!
Перед откачкой конденсата из конденсатосборников высокого и среднего давлений необходимо открыть крышку и, закрыв кран, отвернуть пробку на кране. В кран вворачивается отвод высотой до 1,5 м и к нему присоединяется конец гибкого шланга, второй конец шланга вставляется в цистерну. Только после этого открывается кран и начинается откачка конденсата. После окончания откачки кран закрывается, отворачивается отвод с гибким шлангом и ввертывается дюймовая пробка. Крышку ковера можно закрыть, только убедившись, что нет никаких утечек и неисправностей. Характерными неисправностями конденсатосборников являются утечки газа из кранов и резьбовых соединений.
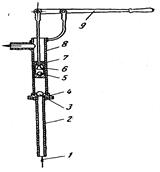
Рис. 2.2. Ручной насос для откачки конденсата: 1
– нарезка, 2
– трубка, 3
– шарик, 4
– гнездо, 5
– шар диаметром 25 мм
, 6
– поршень, 7
– кожа, 8
– цилиндр, 9
– рычаг
На рис. 2.3 показан специальный ключ для разборки крана конденсатосборника без снятия коверов. При выполнении таких работ давление газа необходимо снизить до 1 кГ/см2
.
Часто конденсатосборники забиваются песком и грязью. В этом случае под определенным давлением их заполняют водой для разжижения осадка. Разжиженный осадок удаляется насосом. В случае замерзания конденсата в стояках необходимо применять такие растворители, как этиловый спирт, метанол и др.
Все работы по проверке и обслуживанию конденсатосборников и гидрозатворов записываются в журнал установленной формы.
Слесари должны следить также за состоянием дорожного покрытия вдоль трассы газопровода. Особое внимание надо обращать на участки, где производятся работы другими организациями. К таким работам относятся: снос или строительство зданий, прокладка или ремонт различных коммуникаций, реконструкция дорожного покрытия и др. Организации до начала этих работ должны получить у эксплуатационников эскизы расположения газопровода и уведомление, в котором указываются меры безопасности при производстве работ на трассе газопровода.

Рис. 2.3. Ключ для отвертывания головки конденсатосбоников среднего и высокого давления
Одна из наиболее важных и ответственных задач работников газового хозяйства — обеспечение и поддержание постоянной величины давления газа в сетях. Особенно это важно для газопроводов низкого давления, так как от них питаются наиболее многочисленные потребители — жилые дома и коммунально-бытовые потребители. Изменение давления газа резко ухудшает условия работы газовых приборов, уменьшает к. п. д., а порой и не обеспечивает нормальное горение. Очень часто это объясняется большим перепадом давления газа на отдельных участках газопроводов. В таких случаях проводятся замеры давления газа в заранее намеченных точках газопроводов газорегуляторных пунктах, конденсатосборниках, гидрозатворах, вводах в дома, газовых приборах и т. д. В среднем на каждые 500 пог. м газопровода выбирается одна точка замера. Все работы по замерам давления газа тщательно планируются и проводятся по специальной инструкции, утвержденной главным инженером треста или конторы. Для замера давления газа необходимо выбрать такое время, когда все потребители работают на полную мощность, причем работы должны быть закончены за 1—2 ч.
Для полного и всестороннего изучения режима работы газопроводов проводят одновременные замеры давления газа не реже двух раз в год, в период наибольшего расхода — зимой и наименьшего — летом. По данным замера величины давления газа в разных точках газопроводов строятся карты давлений в газовых сетях. По картам легко определяются участки, где имеется наибольший перепад давления газа.
Для ликвидации этих перепадов и улучшения режима газоснабжения проводятся следующие работы:
- изменяют выходное давление раза на газорегуляторных пунктах, питающих газопроводы;
- заменяют отдельные участки газопроводов для увеличения их пропускной способности;
- кольцуют газовые сети или устанавливают устройство дополнительной подпитки газопроводов;
- устраняют обнаруженные закупорки.
2.4 КОНСТРУКЦИИ ТРУБЫ И ФАСОННЫЕ ИЗДЕЛИЯ
Трубы. Для сооружения газопроводов применяют трубы, изготовленные из хорошо свариваемых малоуглеродистых и низколегированных сталей. Максимальное содержание углерода в сталях, применяемых для изготовления труб, должно быть не более 0,27%, а минимальная величина относительно их удлинения должна быть 18%.
Трубы могут быть бесшовные и электросварные. В табл. 2.2 приведена номенклатура, а в табл. 2.3 — размеры труб. Наиболее употребительные диаметры труб для городского газового хозяйства с условным проходом от 100 до 400 мм. Под условным проходом труб понимают их номинальный внутренний диаметр, однако для характеристики труб необходимо знать также их наружный и внутренний диаметры. Наиболее постоянной величиной является наружный диаметр, а внутренний зависит от толщины стенки газопровода. Объясняется это тем, что газопроводы могут работать под различными давлениями и чем больше будет давление газа, тем больше должна быть толщина стенок при прочих равных условиях.
Таблица 2.2
Номенклатура труб, применяемых для сооружения газопроводов
Виды трубы
|
ГОСТ на сортамент и технические требования
|
Область применения
|
Бесшовные:
|
|
|
горячекатаные
|
8731-58
8732-58
|
Подземные и надземные газопроводы всех категорий давления
|
холоднотянутые и холоднокатаные
|
8733-58
8734-58
|
Подземные и надземные газопроводы высокого давления
|
Стальные:
|
|
|
электросварные
|
10704-63
|
Подземные и надземные газопрово-
|
прямошовные
|
10706-63
|
ды всех категорий давления
|
электросварные
|
10704-63
10705-63
|
Подземные и надземные газопроводы низкого и среднего давления
|
электросварные со спиральным швом диаметром 426-720
|
8696=62
|
Подземные и надземные газопроводы все категорий давления
|
Водогазопроводные (газовые)
|
3262-62
|
Внутренние газопроводы и прямолинейные участки подземных газопроводов низкого и среднего давления
|
Для сооружения подземных газопроводов сейчас применяют трубы с минимальным условным диаметром 50 мм и толщиной стеки 3 мм, а если трубы используют для сооружения подводных переходов, то минимально допустимая толщина стенок должна быть 5 мм, для прокладки ответвлений можно использовать грубы диаметром 25 мм.
Тощина стены в мм
|
10
|
Теоретический вес 1 пог. м трубы в кг ( при плотности стали 7,85)
|
12,33
|
16,28
|
19,48
|
24,17
|
30,33
|
36,75
|
51,54
|
64,86
|
77,78
|
90,51
|
-
|
9,5
|
11,83
|
15,58
|
18,63
|
23,08
|
28,93
|
35,05
|
49,08
|
61,73
|
73,92
|
-
|
-
|
9
|
11,32
|
14,87
|
17,76
|
21,97
|
27,52
|
33,29
|
46,61
|
58,60
|
70,14
|
-
|
(92,55)
|
8,5
|
10,80
|
14,15
|
16,87
|
20,86
|
26,10
|
31,55
|
-
|
-
|
-
|
-
|
-
|
8
|
10,26
|
13,42
|
15,98
|
19,73
|
24,66
|
29,79
|
41,63
|
52,28
|
62,54
|
-
|
-
|
7,5
|
9,71
|
12,67
|
15,07
|
18,59
|
23,21
|
28,02
|
-
|
-
|
-
|
-
|
-
|
7
|
9,15
|
11,91
|
14,16
|
17,44
|
21,75
|
26,24
|
33,60
|
45,92
|
-
|
-
|
-
|
6,5
|
8,58
|
11,14
|
13,22
|
16,27
|
20,28
|
24,45
|
-
|
-
|
-
|
-
|
-
|
6
|
7,99
|
10,36
|
12,28
|
15,09
|
18,79
|
22,64
|
31,52
|
-
|
-
|
-
|
-
|
5,5
|
7,89
|
9,56
|
11,33
|
13,90
|
17,29
|
20,82
|
-
|
-
|
-
|
-
|
-
|
5
|
6,78
|
8,75
|
10,36
|
12,70
|
15,78
|
18,99
|
-
|
-
|
-
|
-
|
-
|
4,5
|
6,16
|
7,93
|
9,38
|
11,49
|
14,26
|
17,15
|
-
|
-
|
-
|
-
|
-
|
4
|
5,52
|
7,10
|
8,38
|
10,26
|
12,73
|
-
|
-
|
-
|
-
|
-
|
-
|
Наружный диаметр
|
в мм
|
60
|
76
|
89
|
108
|
133
|
159
|
219
|
273
|
325
|
377
|
426
|
Диаметр условного прохода
|
50
|
70
|
80
|
100
|
125
|
150
|
200
|
250
|
300
|
350
|
400
|
По внешнему виду труб трудно определить их химический состав и механические свойства, поэтому на все трубы имеются паспорта или, как их часто называют, сертификаты заводов-изготовителей.
Если сертификаты отсутствуют, то качество каждой трубы можно определить механическим испытанием и химическим анализом. Соединяют трубу электродуговой, контактной и газовой сварками, причем газовой сваркой можно варить трубы диаметром до 150 мм и толщиной стенки 5 мм. Все эти виды сварки обеспечивают предел прочности сварного соединения не ниже предела прочности металла трубы.
Фасонные части. Фасонные части служат для соединения отдельных частей газопроводов при ответвлениях, поворотах (или переходах на другие диаметры). К фасонным частям относятся: фитинги, отводы, тройники, переходы, фланцевые соединения, заглушки и т. д.
Фитинги служат для соединения труб на цилиндрической резьбе. Отводы применяют, когда необходимо изменить направление газопровода на определенный угол. По способу изготовления отводы бывают гнутые и сварные. Гнутые делаются из бесшовных труб диаметром до 400 мм. Наиболее распространенные углы поворота отводов 30, 45, 60, 75, 90°. Сварные отводы изготавливают для газопроводов диаметром более 150 мм. Предпочтительнее использовать гнутые отводы, так как они имеют меньше сварочных соединений и создают незначительные сопротивления потоку газа.
Тройники или кресты применяют для устройства ответвлений от газопровода в одну или две стороны. Они могут быть проходными и переходными. У проходных тройников диаметры ствола равны диаметрам ответвлений. У переходных тройников диаметр ответвления меньше диаметра ствола и они выполняются размерами от 80 50 до 900 800 мм. Тройники следует устанавливать в ограниченном количестве, так как в них происходят большие потери давления газа.
Переходы изменяют диаметр газопроводов. На практике их часто изготавливают из труб путем вырезки клиньев и сваркой остальных частей. Наибольшее распространение имеют переходы, изготовленные из листовой стали, с одним или двумя продольными швами.
Фланцевые соединения применяют для установки различной арматуры и аппаратуры. Качество фланцевых соединений зависит от подготовки уплотнительных поверхностей, поэтому на каждом фланце делается не менее двух уплотнительных канавок. Недостаток их сильная утечка газа. Герметичность фланцевых соединений обеспечивается различными прокладочными материалами, наибольшее применение имеют паранитовые прокладки толщиной 3—5 мм. Перед установкой паранита для придания прочности и плотности его необходимо подержать в растительном масле.
Арматура газопроводов. В процессе эксплуатации газовых сетей и сооружений часто возникает необходимость в прекращении или изменении потока газа. Для этих целей на газопроводах устанавливается запорная арматура: задвижки, краны, гидравлические затворы и вентили.
Все эти запорные устройства должны обеспечивать герметичность отключения на длительное время, быстроту отключения и включения, надежность в обслуживании и минимальные сопротивления потоку газа.
Выполнить эти требования поможет правильный выбор запорной арматуры для отдельных участков и сооружений. Так, в газопроводах среднего и высокого давления преимущественно устанавливают задвижки, на газопроводах низкого давления, помимо задвижек, устанавливают и гидрозатворы, на газопроводах диаметром до 80 мм, прокладываемых внутри помещений – краны.
Наиболее распространенный вид запорной арматуры – краны и задвижки. Регулирование потока газа или полное его прекращение достигается путем изменения затвора вдоль уплотняющих поверхностей. Это достигается вращением штока, который может быть выдвижным и невыдвижным. При установке задвижек в колодцах целесообразно применять задвижки с выдвижным шпинделем, так как они удобны в обслуживании и по ним легко определяется степень открытия задвижки.
На газопроводах низкого давления преимущественно устанавливают чугунные задвижки, а на газопроводах среднего и высокого давления – стальные. Задвижки запорный шибер в виде двух дисков с впрессованными в них уплотнительными кольцами. В нижней части задвижки подвижный клин соединен с дисками через шток. При открытии задвижки шток тянет шибер вверх и открывается проход для газа. При закрытии шибер опускается, плотно прижимает диск к корпусу задвижки. Плотность прилегания штока и крышки обеспечивает сальник. Шток задвижек вращается при помощи маховика или ключа с квадратным отверстием. У больших задвижек для вращения маховика применяют различные виды зубчатых червячных или пневматических передач. На рис. 2.3 представлены наиболее распространенные типы задвижек с выдвижным и невыдвижным шпинделем.
Недостаток задвижек в том, что они не всегда обеспечивают полную герметичность отключения. Объясняется это тем, что в нижней части их корпуса собираются различные мелкие твердые частицы в виде пыли и грязи, которые, занимая определенный объем, не дают дискам плотно сесть на свое место и в результате задвижки не дают полного отключения. Кроме того, при эксплуатации задвижек с неплотным открытым проходным сечением диск под действием потока газа, особенно на газопроводах среднего и высокого давлений, истирается и тем более не может гарантировать надежную герметичность. Вот почему установка задвижек должна быть ограничена.
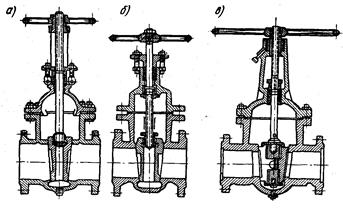
Рис. 2.3. Типы задвижек: а
– с выдвижным шпинделем, б
– с невыдвижным шпинделем, в
– с выдвижным шпинделем и с разрезным клином
Установка задвижки в колодце показана на рис. 2.4. Колодцы должны быть водонепроницаемыми, однако на практике, особенно в местах высоким уровнем грунтовых вод, они часто заливаются водой.
Наличие воды в колодце крайне недопустимо, так как быстро портится и выходит из строя установленная в нем арматура, кроме того, вода, заполняя колодец, значительно сокращает объем колодца, что может привести к созданию взрывной концентрации при незначительных утечках газа.
Учитывая недостатки газовых колодцев, на газопроводах диаметром до 100 мм при транспортировке осушенного газа устраивают небольшие колодцы—приямки с установкой арматуры в верхней части, что обеспечивает ее обслуживание с поверхности земли (рис. 2.5). В таких колодцах используют краны, имеющие значительное преимущество перед задвижками. Особенно удобны в эксплуатации краны с принудительной смазкой, обеспечивающие полную герметичность, даже при содержании в газе различных примесей. Один из новых типов кранов со смазкой под давлением показан на рис. 2.6.
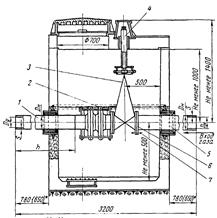
Рис.2.4. Установка задвижек в газовом колодце: 1, 5
– газопроводы, 2
– компенсатор, 3
– задвижка, 4
– шток, 6
– фланец, 7
- болт
Гидравлические затворы представляют собой стальной горшок с отростками для присоединения к газопроводу при сварке. Через верхнюю часть горшка проходит трубка диаметром 25 мм, нижняя часть которой скошена для увеличения ее площади и предотвращения засорения. Трубка выводится под ковер и закрывается дюймовой пробкой. При установке гидравлических затворов в нижних точках газопровода они могут выполнять 4 сборника конденсата и запорного устройства.
При использовании гидравлических затворов в качестве запорных устройств необходимо, чтобы высота плеча была на 200 мм
больше, чем максимальное рабочее давление в газопроводах. Понятно, что для газопроводов среднего и высокого давления гидравлические затворы не пригодны, так как высота запирающего столба возрастает настолько, что гидрозатвор становится неконструктивным.
Для отключения подачи газа отворачивается пробка на стояке и через него заливается в горшок вода или другая жидкость, уровень которой будет зависеть от давления газа в газопроводе. Уровень воды можно замерить металлическим прутиком, опущенным через трубку. Для возобновления подачи газа жидкость из гидрозатвора (рис. 2.7, а) удаляется ручным насосом или мотонасосом. Такая относительная сложность и длительность работ по заливу и откачке воды - основной недостаток этих затворов.
К преимуществам гидрозатворов можно отнести простоту их устройства и герметичность затвора, хотя при аварийном повышении величины давления в сетях не исключена возможность выброса воды, к недостаткам — полное прекращение подачи газа при не своевременной откачке воды или конденсата. Очень неудобно пользоваться гидравлическими затворами при присоединениях вводов и ответвлений к действующим газопроводам, так как в этих случаях гидравлические затворы заливаются водой и газопровод невозможно продуть от места врезки до ввода. Этот недостаток ликвидирован на гидравлических затворах нового типа.
Новый тип гидрозатвора (рис. 2.7, 6) видоизменен за счет установки дополнительной продувочной трубки диаметром 40 мм, к которой в верхней части приваривается отвод диаметром 20 мм с резьбой для муфты с пробкой. Дюймовая трубка для откачки воды проходит через продувочный стояк и в верхней части приваривается к нему. Плечи гидрозатвора приваривают к газопроводу на разных уровнях, что обеспечивает одновременное отключение газопровода и продувку через него газа. Для этого достаточно залить водой только часть гидрозатвора и вывернуть пробку для продувки газовоздушной смеси.

Рис. 2.5. Установка кранов в мелком колодце: 1
– отвод, 2
– кран, 3
– прокладка, 4
– болт с гайкой
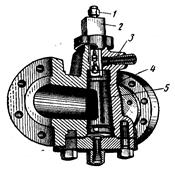
Рис. 2.6. Кран со смазкой и опрокинутым расположением пробки:
1
– смазочный болт, 2
– шпиндель, 3
– смазочная камера, 4
– пробка, 5
– смазочные канавки
 
Конденсатосборники. Конденсатосборник устанавливают в низших точках газопроводов для сбора и удаления воды, В зависимости от влажности транспортируемого газа они могут быть двух видов: для влажного газа большей емкости и для сухого газа меньшей емкости.
Конденсатосборники могут быть низкого, среднего и высокого давлений. Конденсатосборники низкого давления (рис. 2.8) представляют собой емкость или, как часто называют, горшок, снабженный трубкой диаметром 1. Как и у гидрозатвора, эта трубка выводится под ковер и заканчивается муфтой и пробкой. Через эту трубку удаляется конденсат, продувается газопровод, замеряется давление газа. При необходимости трубку можно использовать для замера величины блуждающих токов путем определения разности потенциалов труба-грунт.

Рис. 2.8. Конденсатосборник низкого давления: 1
– корпус; 2
– трубка; 3
– подушка под ковер; 4
– ковер малый; 5
– пробка; 6
– муфта
Конденсатосборники среднего (рис. 2.9) и высокого давлений по конструкции несколько отличаются от конденсатосборников низкого давления. В этих конденсатосборниках установлена дополнительная защитная трубка и кран на внутреннем стояке. Под действием давления газа конденсат, имеющийся в горшке, отжимается во внутреннюю трубку вод определенным напором (в зависимости от величины давления газа) автоматически откачивается.


Рис. 2.9. Конденсатосборник среднего давления: 1 – корпус, 2 – кожух, 3 – внутренняя трубка, 4 – муфта, 5 – болт, 6 – гайка, 7 – прокладка, 8 – пробка, 9 – ковер большой,10 – головка, 11 – подушка
В старых конструкциях конденсатосборников зимой конденсат замерзал в верхних местах трубки, что порой сопровождалось разрывом стояков. В современных конструкциях конденсатосборников возможность исключается, так как газ через отверстие в верхней части внутреннего стояка производит противодавление на конденсат и тот под действием своего веса опускается вниз. При открытии крана на внутреннем стояке противодавление прекращается, и конденсат выходит на поверхность. Чем больше давление в газопроводе, тем быстрее и лучше будет опорожняться конденсатосборник.
Компенсаторы. Как подземные, так и надземные газопроводы при изменении температуры окружающей среды изменяют свою длину.
Так, например, стальной газопровод длиной в 1 км при увеличении температуры на 1°С удлиняется на 12 см. Под действием температурных изменений возникают различные усилия, которые могут привести к изгибу или растяжению газопроводов.
В процессе эксплуатации газопроводов величина изменения температуры может достигать несколько десятков градусов, что вызывает напряжение в несколько сотен атмосфер. Поэтому для предотвращения разрушения газопровода необходимо обеспечить свободное перемещение.
Устройствами, обеспечивающими свободное перемещение труб, являются компенсаторы. Они бывают тарельчатые, линзовые и лирообразные.
На подземных газопроводах наибольшее распространение получили линзовые компенсаторы (рис.2.10). Компенсатор имеет волнистую поверхность, изменение длины которого предохраняет газопровод от воздействия температурных деформаций. Кроме того, компенсаторы при установке их рядом с задвижками или другими видами запорных и регулирующих устройств не только предохраняют арматуру, но и обеспечивают возможность свободного демонтажа фланцевой арматуры и замены прокладок.
Необходима установка компенсаторов при наличии чугунной арматуры в колодцах и на гидрозатворах, укладываемых по мостам и эстаках. В колодцах компенсаторы устанавливают в свободном состоянии, чтобы обеспечить их полную компенсирующую способность.
Гнутые П-образные и линзовые компенсаторы изготавливаются из бесшовных труб и устанавливаются вместе с кранами и задвижками в мелких колодцах.

Рис.2.10. Линзовый компенсатор: 1 – гайка, 2 – тяга, 3 – полулинза, 4 – кронштейн, 5 – царга, 6 – рубашка, 7 - кронштейн, 8 – патрубок
2.5 ЭКСПЛУАТАЦИЯ И РЕМОНТ ГАЗОПРОВОДОВ.
2.5.1 ЗАЩИТА ГАЗОПРОВОДОВ С ИСПОЛЬЗОВАНИЕМ ИЗОЛЯЦИИИ
Изоляционные покрытия и их характеристика. Подземные газопроводы защищают от коррозии двумя способами: пассивным и активным. Пассивный заключается в изоляции газопроводов, при активном методе, помимо изоляции, применяют также электрические методы защиты.
В качестве противокоррозионной изоляции используют битумные, битумно-резиновые и полимерные материалы.
Противокоррозионные покрытия не должны проводить электрический ток, должны иметь необходимую механическую прочность и хорошую прилипаемость (адгезию), не подвергаться разрушению от биологических воздействий, быть эластичными и водонепроницаемыми и т. д.
В зависимости от степени коррозионности грунтов применяются три типа изоляции: нормальная, усиленная и весьма усиленная. Выбор типа изоляции производится по табл. 2.3.
Таблица 2.
3
Применяемые типы изоляции
Минимальная годовая величина удельного сопротивления в Ом/м
|
Степень коррозионной активности грунта
|
Рекомендуемые защиты
|
Более 100
От 20 до 100
От 10 до 20
От 5 до 10
Менее 5
|
Низкая
Средняя
Повышенная
Высокая
Весьма высокая
|
Нормальная изоляция для газопроводов низкого давления из труб с толщиной стенки не менее 5 мм
и усиленная для стальных газопроводов
Усиленная изоляция
Весьма усиленная изоляция
Весьма усиленная изоляция и активная защита
То же
|
Из табл. 2.3 видно, что защита газопроводов зависит от коррозионной активности грунта. Однако газопроводы, прокладываемые через различные преграды (водные, железнодорожные, автострады и т. д.) и в районах с опасностью повреждений блуждающими токами, независимо от коррозионности грунтов, должны иметь весьма усиленную изоляцию. Поэтому в городах и населенных пунктах в основном применяются усиленная и весьма усиленная изоляции, даже при низкой коррозионности грунтов.
Таблица 2.
4
Толщина различных типов изоляции
Толщина изоляции
|
Толщина в мм
|
нормальная
|
усиленная
|
весьма усиленная
|
Битумная с минеральным заполнителем и усиливающей оберткой ………………
|
3
|
6
|
9
|
Битумно-резиновая с бризолом и гидроизолом ……………………………..
|
-
|
5,5
|
8,5
|
Пластмассовая лента с учетом толщины слоя клея …………………………………
|
0,12-0,3
|
0,4-0,6
|
0,4-0,8
|
В табл. 2.4 приведены толщины различных типов изоляции. Изоляция из пластмассовых лент имеет различные пределы толщины, они зависят от технологии производства и свойств применяемых материалов.
Таблица 2.5
Характеристика и состав битумных типов изоляции
Типы изоляции
|
Последовательность слоев
|
Минимальная толщина в мм
|
Типы битумной изоляции
|
Нормальная
|
Грунтовка
Битумное покрытие
Крафт-бумага
|
3
|
Усиленная
|
Грунтовка
Битумное покрытие
Гидроизол
Битумное покрытие
Крафт-бумага
|
6
|
Весьма усиленная
|
Грунтовка
Битумное покрытие
Гидроизол
Битумное покрытие
Гидроизол
Битумное покрытие
Крафт-бумага
|
9
|
Типы битумно-резиновой изоляции
|
Нормальная
|
Грунтовка
Битумно-резиновая мастика (3 мм
)
Крафт-бумага
|
3
|
Усиленная
|
Грунтовка
Битумно-резиновая мастика
Бризол (1,5 мм
)
|
5,5-6
|
Весьма усиленная
|
Грунтовка
Битумно-резиновая мастика (3 мм
)
Бризол (1,5 мм
)
Битумно-резиновая мастика (2,5 мм
)
Бризол (1,5 мм
)
|
8,5-9
|
Характеристика и состав битумной и битумно-резиновой изоляции приведены в табл. 2.5. Первым слоем изоляции является грунтовка, ее применяют для улучшения прилипаемости битумной изоляции к телу газопровода. Грунтовка представляет собой раствор битума в бензине в соотношении 1 : 3 по объему. Для приготовления грунтовки необходимо куски битума марки IV или смеси битумов марок III и V загрузить в котел и разогреть до температуры 200 °С, после чего расплавленный битум охлаждается до 80 °С, вливается тонкой струей в бензин и перемешивается.
Вливать бензин в битум категорически запрещается, так как это может привести к несчастным случаям!
Для повышения прочности изолирующего покрытия в битум добавляют различные наполнители: каолин 12—20% по весу, цемент, мелкий асбест и т. д. Такая смесь называется битумной мастикой.
При температурах наружного воздуха +5°С и ниже добавляют пластификаторы (соевое масло, зеленое масло) до 3% по весу, что придает битумной мастике пластические свойства.
Указания по выбору типа изоляции в зависимости от коррозионности грунта и характеристики газопровода приведены в табл. 2.6.
Таблица 2.6
Указания по выбору типа изоляции
Коррозионная активность грунтов и характеристика участков газопроводов
|
Тип изоляции
|
Газопроводы в грунтах с низкой и средней коррозионной активностью
Газопроводы в грунте с повышенной и высокой коррозионной активностью
Участки газопроводов в грунтах с низкой и средней коррозионной активностью на вводах во дворы и здания
Газопроводы в грунте с весьма высокой коррозионной активностью
Участки газопроводов в грунте с повышенной и высокой коррозионной активностью на вводах во дворы и здания, а также на пересечениях с железнодорожными и трамвайными путями, автомагистралями
Участки газопроводов на подводных переходах через реки и каналы, на затапливаемых поймах рек, в болотах. Участки явно выраженной опасностью повреждения блуждающими токами
|
Нормальная
Усиленная
То же
Весьма усиленная
То же
То же
|
Для увеличения прочности изолирующего покрытия применяют усиливающие обертки бризол, гидроизол и различные стеклоткани. Бризол готовят из битума с дроблением вулканизованной резины, гидроизол представляет собой толстый слой бумаги из асбеста с добавлением до 20% целлюлозы, пропитанной нефтяным битумом.
Для защиты изоляции от солнечных лучей и стекания применяют защищающую обертку, обычно из крафт-бумаги. Хранят ее в сухом помещении и в случае увлажнения до накладки на битумное покрытие просушивают.
Выполнение изоляционных работ. Изоляция газопроводов производится в следующей последовательности. Газопровод очищается до металлического блеска от загрязнений и ржавчины. Для очистки применяют трубоочистные машины или специальные щетки. Затем на газопровод наносится грунтовка толщиной 0,1—0,2 мм и после ее высыхания битумная эмаль. Эмалью покрывают в несколько слоев толщиной по 1,5 мм, после чего на горячую мастику накладывают усиливающую обертку. Оберткой из крафт-бумаги обертывают трубу по спиральной ленте так, чтобы она прилетала плотно без морщин и складок.
В последнее время получили широкое распространение различные пластмассовые изоляционные покрытия (полихлорвиниловые, полиэтиленовые и др.), которые выпускаются в виде липкой ленты шириной 450 мм и толщиной до 0,5 мм.
Работы по изоляции газопроводов полностью механизированы, ручной способ применяется только при изоляции отдельных стыков и участков газопровода.
Контроль за качеством изоляции. При проверке качества изоляции труб необходимо произвести:
- наружный осмотр изоляции путем проверки гладкости и равномерности покрытия и отыскания поврежденных участков;
- проверку толщины изоляционного покрытия не реже, чем через каждые 100 м
и не менее четырех точек по окружности трубы;
- проверку прилипаемости изоляционного покрытия к трубе и слипаемости усиливающих оберток с битумной мастикой. Эту проверку надо проводить в сомнительных местах путем надреза изоляции двумя сходящимися под углом 60° линиями и отдиранием изоляции от трубы. Если изоляция хорошая, то очень трудно отодрать изоляцию от тела трубы и усиливающий материал от битума;
- сплошную проверку качества изоляции специальными приборами. Так, например, если проверяемый газопровод не уложен в траншею и не засыпан, то пользуются дефектоскопом, а если газопровод уже уложен в траншею и присыпан, то испытывается на проскок искры через изоляцию.
На рис. 2.11 приведена схема искрового дефектоскопа для контроля изоляции газопроводов. Работы по отысканию мест повреждения изоляции проводятся в следующем порядке: к зачищенному концу газопровода 8
прикрепляется провод высокого напряжения 7
. Электрическая цепь дефектоскопа замыкается выключателем 2
. Искатель 9
дефектоскопа устанавливается над трубой 8
и перемещается вдоль нее. В местах с плохой изоляцией произойдет искровой пробой и в результате вспыхнет сигнальная неоновая лампа 14
, вмонтированная в рукоятку 12
. Таким образом, отыскиваются поврежденные места изоляции, которые после исправления снова проверяются
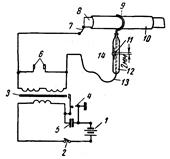
Рис. 2.11. Схема дефектоскопа: 1
– аккумулятор, 2
– выключатель, 3
– катушка, 4
– прерыватель, 5
– конденсатор, 6
– предохранительный зазор, 7
, 13
– провода высокого напряжения, 8
– газопровод, 9
– искатель, 10
– изоляция газопровода, 11
– воздушный зазор, 12
– рукоятка дефектоскопа, 14
– неоновая лампочка
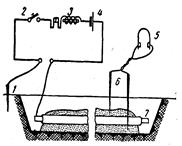
Рис. 2.12. Схема искателя повреждений ИПИТ: 1
, 6
– электроды, 2
– выключатель, 3
– реле прерывателя, 4
– батарея, 5
– наушники, 7
- газопровод
Принципиальная схема искателя повреждения показана на рис 2.12. Принцип работы прибора заключается в том, что па газопровод 7
подается пульсирующий ток, который стекает с газопровода в грунт в тех местах, где повреждена изоляция. Этот ток возвращается на прибор через заземляющий электрод. В тех местах вокруг газопровода, где ток стекает в грунт, образуется электрическое поле, которое отыскивается с помощью наушников 5
и подключенных к ним двух индикаторных электродов 6
, погружаемых по обе стороны газопровода 7
. Надежной работе прибора мешают различные помехи (шумы). Поэтому при работе с искателем нельзя становиться на газопровод; газопровод должен быть присыпан на высоту до 30 см
, за исключением его концов и явно оголенных участков; присыпку газопровода грунтом необходимо производить за 5—б ч до начала проверки.
2.5.2 ЭЛЕКТРИЧЕСКИЕ МЕТОДЫ ЗАЩИТЫ
Для защиты газопроводов от коррозии блуждающими токами применяются электрические дренажи, катодные станции и протекторы.
Электродренажная защита. Дренажная защита наиболее распространенный способ защиты газопроводов от блуждающих токов. Через электродренажные установки осуществляется отвод токов, попавших на газопровод, обратно к источнику. Отвод ведется через специальный проводник, соединяющий газопровод с минусовой шиной подстанции или рельсами электрифицированной дороги.
При отводе тока ликвидируется возможность электрической коррозии, так как прекращается выход токов из газопровода в грунт.
В настоящее время в основном применяют поляризованные дренажи, обладающие односторонней проводимостью (рис. 2.13).

Рис. 2.13. Схема поляризованного дренажа УПДУ-57: 1
– газопровод, 2
, 4
– предохранители, 3
– сопротивление, 5
, 7
– контакты, 6
– диод, 8
– дренажная обмотка, 9
– выключающая обмотка, 10
– шунт амперметра, 11
– амперметр, 12
– рубильник, 13
- рельс
Принцип работы дренажной установки заключается в следующем: если на газопроводе 1
возникает положительный потенциал по отношению к рельсу 13
, то ток пройдет через, предохранитель 2
, сопротивление 3
, предохранитель 4
, диод 6
с обмоткой 9
, шунт 10
и рубильник 12
на рельс 13
.
Движение тока будет продолжаться до тех пор, пока разность потенциалов не достигнет 1—1,2 в
, в противном случае замыкаются контакты 5
и 7
и ток потечет через обмотку 8
, а по ответвлению — к диоду 6
через шунтирующие контакты 5
. Если разность потенциалов снизится до 0,1 в
, то контакты размыкаются и дренажная цепь разрывается. Если потенциал рельса будет больше потенциала трубы, то диод 6
тока не пропустит.
Катодная защита. Схема действия катодной защиты показана на рис. 2.14. На газопровод 2
накладывается отрицательный потенциал от специального источника постоянного тока 5
и тем самым защищаемый участок газопровода превращается в катодную зону. Путем помещения в грунт старых труб или рельсов и подключением их к положительному источнику постоянного тока через провода 4
поблизости от газопровода создается анодная зона. Таким образом, искусственно создается электрическая цепь и ток течет следующим образом: от положительного полюса источника питания по изолированному кабелю на анодное заземление 6
, от анодного заземления ток стекает в грунт и через поврежденные участки 1
газопровода на защищаемый газопровод, а от газопровода по изолированному кабелю на отрицательный полюс источника питания.
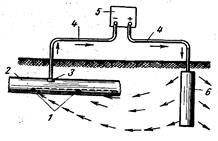
Рис. 2.14. Схема действия катодной защиты: 1
– места повреждения изоляции, 2
– газопровод, 3
– точка дренажа, 4
– провода, 5
– источник постоянного тока, 6
– заземление из старых труб
Таким образом, происходит постепенное разрушение не газопровода, а вкопанных в землю старых труб (анода). Однако необходимо отметить, что этот вид за щиты имеет существенные недостатки, — небольшую зону действия в большие расходы на электроэнергию.
Протекторная защита. Схема действия протекторной защиты показана на рис. 2.15. Принцип ее действия основан на том, что газопроводу путем подключения к нему протекторов, обладающих более отрицательным потенциалом, придается отрицательный потенциал. Таким образом, участок газопровода превращается в катод без постороннего источника тока. Протектор представляет собой цилиндр из магния, алюминия, цинка и их сплавов, в центре которого расположен стальной сердечник в виде стержня или спирали. Сердечник выступает с одного или с обоих концов протектора, что дает возможность соединить их по нескольку штук. Протекторы располагаются на расстоянии до 4,5 м от газопровода. В настоящее время выпускаются протекторы типа МГА (гальванические аноды). Средний срок их службы 8—10 лет, вес 5—7 кг
.

Рис. 2.15. Схема протекторной защиты:
1
– газопровод, 2
– контрольный пункт, 3
– проводники, 4
– заполнитель, 5
– протектор
ЭКСПЛУАТАЦИЯ СРЕДСТВ ЗАЩИТЫ
Эксплуатация средств электрозащиты осуществляется специально обученными работниками. На каждую установку необходимо иметь паспорт и журнал контроля работы. В паспорт заносятся техническая характеристика и режим работы этих установок, В журнал необходимо заносить все работы, связанные с осмотром и проверкой установок.
Обслуживание установок состоит из периодических осмотров и контрольных замеров. Катодные установки осматривают один раз в месяц, а протекторные и дренажные два раза в месяц.
При периодическом осмотре дренажа проверяется:
целостность монтажа, отсутствие различных повреждений, плотность контактов;
наличие предохранителей и их исправность;
состояние контактов реле;
чистка контактов реле, смена предохранителя, очистка дренажа от пыли, грязи и снега.
При осмотре катодной установки проверяется:
наличие тока и напряжение источника питания;
- целостность монтажа установки и отсутствие различных неисправностей;
- плотность контактов.
При профилактическом осмотре протекторной защиты проверяется, плотность контакта и отсутствие различных повреждений
в контактном устройстве.
При периодических контрольных замерах на дренажных установках измеряется:
- величина и направление тока;
- величины и разности потенциала между газопроводом и рельсами, при котором срабатывает дренажная установка, а также определяется средняя величина этой разности. Проверяется так же, разорвется ли цепь дренажа при перемене полярности газопровода относительно рельсов;
- разность потенциалов между газопроводом и землей. Проверяется исправность имеющихся контрольно-сигнальных устройств.
Если в цепи дренажа отсутствует шунт, величину дренажного
тока измеряют переносным шунтом, подключаемым в дренажную цепь параллельно предохранителю или рубильнику.
При периодических контрольных замерах на катодных установках производится:
- измерение величины выходного напряжения;
- измерение величины тока;
- измерение разности потенциалов между землей и газопроводом;
- проверка состояния анодного заземления;
- проверка имеющихся контрольно-сигнальных устройств.
Периодическими контрольными замерами на установках протекторной защиты предусматривается:
- измерение потенциала газопровода относительно земли при включенной и отключенной защите;
- измерение тока, протекающего по цепи протектор — газоровод;
- измерение сопротивления в цепи протектор — газопровод.
Если потенциал трубопровода на участке подключения электродов будет меньше минимального защитного потенциала, то проверяется исправность провода между протектором и газопроводом, а также места его соединений с газопроводом и протектором. При уменьшении объема протекторов до 10% от его первоначального объема их заменяют новыми. Кроме того, не реже одного раза в год проверяется эффективность действия протекторной установки.
Все результаты осмотра и контрольных замеров заносятся в специальный журнал.
2.5.3 ЭКСПЛУАТАЦИЯ УСТАНОВОК СЖИЖЕННЫХ ГАЗОВ
.
ПРОФИЛАКТИЧЕСКОЕ ОБСЛУЖИВАНИЕ
Профилактическое обслуживание баллонных и резервуарных установок производится службой «Горгаз». Профилактическое обслуживание относится к важнейшим мероприятиям, обеспечивающим безопасную эксплуатацию оборудования баллонных и резервуарных установок.
Слесари, за которыми закреплены индивидуальные и групповые баллонные установки и резервуарные установки, обязаны по графикам проверять состояние газового оборудования, уровень и давление в них сжиженного газа.
Перед выходом на объект слесарь должен получить наряд (задание) на работу от мастера (бригада от диспетчера), узнать от него о наличии заявок от потребителей газа. Эти заявки, особенно заявки на устранение утечек газа, выполняются в первую очередь. Слесарь должен иметь при себе исправный набор инструментов, необходимые запасные части и служебное удостоверение.
Основная работа слесаря, обслуживающего газовые приборы баллонных и резервуарных установок:
выявление и устранение утечек газа в арматуре головки резервуара и в местах присоединения баллонов к рампе;
контроль по жидкостному манометру за давлением газа в дворовых сетях или перед газовыми приборами;
настройка регулятора давления на номинальное давление в сети в ЗОО мм вод. ст.
;
проверка исправности предохранительных клапанов;
проверка наличия и комплектности противопожарного инвентаря;
проверка по указателю уровня и манометру наличия жидкости в резервуарах и своевременное принятие мер к наполнению их газом;
проверка надежности установки шкафов и, если потребуется, подбивка грунта под брусья и крепление шкафа к стене разъемных хомутов установленного в кухне баллона;
контроль окраски кожухов и ограждений, ящиков для баллонов, наличия действующих замков на дверцах;
проверка мыльной эмульсией (под давлением) плотности соединений на обвязке резервуаров и баллонов, устранение обнаруженных неисправностей;
смазка кранов, прочистка газовых горелок, их регулировка;
замена изношенных деталей газовых приборов;
проверка состояния тяги дымоходов водонагревателей.
Обслуживание подземных газопроводов от групповых установок сжиженного газа производится так же, как и дворовых газопроводов
сетевого газа.
Такие работы, как проверка плотности, устранение утечек и контроль за величиной давления, производятся три раза в месяц.
При накоплении в резервуарах групповых установок тяжелых остатков (что обнаруживается по малому давлению в резервуарах) их необходимо удалить.
Для этого автоцистерну соединяют шлангом, привернутым к наполнительно-сливному штуцеру цистерны, а другим концом к сливному штуцеру подземного резервуара. Переток жидкости происходит за счет увеличения давления паров сжиженного газа в опорожняемом резервуаре. Увеличение давления достигается за счет перепуска паров из соседнего резервуара или группы резервуаров, заправленных до этого сжиженным газом.
Самым серьезным нарушением в работе регулятора давления является замерзание его в зимнее время при наличии влажного газа. В результате в отверстии сопла у входа образуются кристаллы льда. Чем шире сопло в регуляторе, тем труднее оно замерзает, следовательно, замерзать будут небольшие регуляторы.
Для предупреждения замерзания регуляторов необходимо воспрепятствовать попаданию влаги в резервуары. Если регуляторы замерзнут, то необходимо в резервуары ввести метиловый спирт из расчета 1,3 л на 1000 л емкости резервуара (3,3 л спирта на резервуар емкостью 2,5 м3
и 5,7 л на резервуар емкостью 4,4 м3
).
В борьбе с замерзанием регуляторов часто прибегают к отогреванию. Замерзшие участки или регулятор следует отогревать горячим полотенцем. Иногда для ликвидации замерзания регуляторов вскрывают входное соединительное устройство и вливают в сопло несколько капель метилового спирта.
Для предупреждения замерзания пружины регулятора следует вводить в верхнюю камеру регулятора небольшое количество глицерина. Чтобы не образовывался лед под клапаном регулятора, можно смазывать его сопло смазками, которые при меняются в авиации для борьбы с обледенением самолетов.
Нарушение работы регулятора может быть вызвано расстройством рычага и неправильной подгонкой частей клапана. Иногда аналогичное нарушение вызывается скоплением краски в дыхательном отверстии верхней полости диафрагмы или если выходное и дыхательное отверстия забиваются грязью.
Устранение мелких неисправностей, отмораживание и настройка регуляторов производятся на месте их установки. При значительном расстройстве и неисправности регулятора они проверяются на специальных стендах и ремонтируются в мастерских.
2.6 РЕМОНТНЫЕ РАБОТЫ НА ПОДЗЕМНЫХ ГАЗОПРОВОДАХ
Ремонт, проводимый на газопроводах, подразделяется на профилактический (текущий) и капитальный.
Профилактический ремонт проводится периодически по заранее составленному графику, в соответствии с нормами и сроками, приведенными в табл. 2.4.
При профилактическом ремонте производятся: осмотр с использованием бурения скважин газопроводов, устранение причин утечек газа, устранение закупорок, ремонт арматуры и сооружений на газопроводах, ремонт тела трубы и изоляции, пополнение и восстановление технической документации.
Осмотр с использованием бурения скважин проводится для точного определения мест утечек газа, выявленных при проверке колодцев и других сооружений. С этой целью вдоль трассы газопровода через каждые 2 м, а при наличии сварочной схемы газопровода над каждым стыком бурятся скважины. Диаметры скважин обычно составляют 20—ЗО мм, а глубина зависит от расстояния до верха трубы. Если бурят при мерзлом грунте, то скважина должна быть ниже нижней образующей газопровода на 20 см, так как мерзлый грунт не дает распространиться газу вверх. В летних условиях глубину скважин можно уменьшить, т. е. не доводить до верхней образующей на 20 см. Скважины необходимо располагать в шахматном порядке параллельно оси газопровода на расстоянии 300 мм от стенки газопровода. Несоблюдение этих условий может привести к повреждению газопровода и серьезным последствиям.
Наличие газа в скважинах определяется газоанализаторами, а если скважины расположены на расстоянии более З м от зданий, колодцев и других сооружений, то и огнем, так как в этом случае исключается возможность образования взрывоопасной концентрации. Во избежание получения ожогов зажженную спичку надо отвести на расстояние вытянутой руки и только после этого опустить ее в скважину. Наличие газа в скважинах проверяется и различными реактивами, однако эти способы пока не имеют широкого распространения, так как связаны с дополнительными затратами и временем.
В настоящее время скважины бурят специальными пневматическими бурами, электровибраторами, электробурами, перфораторами, а также вручную.
Чаще всего из механических приспособлений для бурения используют электровибратор (рис. 2.17), с его помощью скважина бурится за 1 мин. Особенно удобно бурить им скважины в мягких грунтах, так как его легко извлекать, но при бурении скважин в плотных грунтах возникает ряд неудобств по извлечению клиньев, поэтому приходится механизировать и процесс выемки клиньев из скважин.
Однако сам процесс бурового осмотра, связанный с бурением большого количества скважин, особенно по усовершенствованными дорожным покрытиям, связан с большими неудобствами и затратами. Поэтому в настоящее время изучают возможность определения мест утечек газа без производства буровых работ.

Рис. 2.17. Электровибратор для бурения: 1
– электровибратор, 2
– рукоятка, 3
– оголовок, 4
– патрубок, 5
– шпилька, 6
- клин
По результатам бурового осмотра или другими способами определяется наиболее вероятное место повреждения газопровода. Иногда место повреждения определяется неправильно, а работы по раскопке и засыпке отдельных участков трудоемки и дорогостоящи. Поэтому необходимо тщательно проверить все скважины, путем сравнения определить участок с наибольшей концентрацией газа и только после этого приступить к раскопкам шурфов, длина которых должна составляет 1,5—2 м. Способ устранения утечки газа зависит от вида повреждения и величины давления газа в газопроводе.
Практика показывает, что наиболее распространенные повреждения газопроводов - разрывы стыков стальных труб, неплотности в арматуре, повреждения оголовков стояков конденсатосборников, гидрозатворов, контрольных трубок и коррозия труб.
Разрывы стыков стальных газопроводов устраняются путем сварки катушки длиной не менее 400 мм. Если работы ведутся на газопроводах высокого и среднего давлений, то можно временно установить муфты. Для этого предварительно на стык приваривается металлический бандаж, затем на бандаж надевается разъемная муфта и приваривается. Плотность приваренной муфты проверяется опрессовкой воздухом через пробку, которая в дальнейшем заваривается. Лепестковые муфты (рис. 2.18) применяют также, когда на стыках имеются не только трещины, но и сквозные отверстия в виде пор. Во всех случаях категорически запрещается подварка стыков!
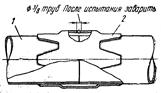
Рис. 2.18. Лепестковая муфта: 1
– газопровод, 2
– муфта
Если на газопроводе обнаружены продольные трещины размером более 0,8 м, необходимо отключить подачу газа и вварить на место трещины катушку требуемой длины. Сварные соединения испытывают на плотность, продувая газ через весь отключенный участок газопровода. Неплотности в арматуре устраняют, заменяя отдельные детали, прокладки, подтягивая болты фланцевых соединений, уплотняя сальник и т. д.
Если дефекты деталей нельзя устранить на месте, то эти детали заменяют новыми. Очень часто меняют задвижки; новую задвижку устанавливают вместе с компенсатором. Конденсатосборники и гидрозатворы, как правило, не ремонтируют, а заменяют новыми.
Одна из наиболее важных задач эксплуатационников — выявление и устранение различных закупорок в газопроводах. Измеряя давление газа на от дельных участках газопроводов, по перепаду давления определяют место закупорки.
Закупорки могут быть водяные, смоляные, нафталиновые и снежно-ледяные. При водяных и снежно-ледяных закупорках необходимо своевременно откачивать воду из конденсатосборников и гидрозатворов. Если на отдельных участках образуются провесы, заполненные водой, то следует выправить уклон газопровода или установить дополнительные конденсатосборники.
Смоляные и нафталиновые закупорки образуются часто в газопроводах искусственного газа, а при транспортировании влажного газа могут образоваться снежно-ледяные закупорки или, как их часто называют, гидраты. Эти закупорки устраняются заливкой специальных растворителей в газопровод или отогревом места закупорки.
На вводах к домам закупорки устраняют шуровкой газопровода проволокой диаметром до 10 мм или прочисткой ершом. Очень серьезную опасность представляют закупорки из нерастворимых предметов, которые извлекают из газопровода путем его демонтажа или вырезки окна, а иногда, продувая инертным газом под давлением.
Все вышеперечисленные виды ремонтных работ фиксируются в паспорте газопровода. На основании этих данных планируется его капитальный ремонт.
При капитальном ремонте заменяют поврежденные коррозией участки газопровода, восстанавливают изоляцию на отдельных участках, заменяют арматуру, ремонтируют газовые колодцы и заменяют или устанавливают средства защиты газопроводов от электрической коррозии.
2.7 КОНТРОЛЬНО-ИЗМЕРИТЕЛЬНАЯ АППАРАТУРА
Для контроля работы газорегулирующего оборудования применяют контрольно-измерительные приборы. Этими приборами измеряются давление, температура, разность (перепад) давлений и расход газа. В зависимости от способа передачи показаний приборы разделяются на показывающие, самопишущие и суммирующие. Технические стационарные приборы предназначены для постоянных замеров, а переносные — для периодических замеров.
Приборы для измерения давления газа. О нормальной работе регуляторной установки можно судить лишь на основе анализа изменения давлений, замеряемых контрольно-измерительными приборами в соответствующих точках. Своевременное обнаружение отклонения замеряемого давления от нормы позволяет принять меры к устранению причин, вызвавших нарушение заданного режима.
Измерение давления газа производится показывающими или регистрирующими манометрами и напоромерами. Манометры для замера начального давления присоединяются к подводящему газопроводу перед входной задвижкой. Манометры для замера конечного давления целесообразно ставить за выходной задвижкой регулятора.
Контроль за работой регуляторной установки заключается в сопоставлении давления на входе и выходе из регулятора.
Степень засоренности фильтра измеряется либо одним манометром с переключающим устройством, либо с помощью дифманометра. При установке манометров для проверки правильности их показаний следует предусматривать трехходовые краны для периодического подключения контрольного прибора. Из-за неблагоприятного влияния газовых завихрений импульсные трубки манометров не следует присоединять к тройникам или крестовинам.
Приборы для измерения расхода газа. Учет расхода газа ведется объемными счетчиками или расходомерами с нормальными диафрагмами. В качестве объемных счетчиков на ГРП используют в основном ротационные счетчики. Измерительное устройство счетчиков работает под действием давления протекающего газа. Суммарный объем газа, прошедшего через счетчик, определяется по числу объемов, вытесненных из измерительной камеры. В настоящее время ротационные счетчики типа РС выпускают на следующие номинальные расходы: 40, 100 250, 400, 600 и 1200 м3
/ч.
Любой расход газа, давление которого превышает 0,1 МПа, а также расход больший, чем суммарная пропускная способность двух параллельно работающих ротационных счетчиков при давлении, меньшем, чем 0,1 МПа измеряется методом перепада давления.
2.8 ГАЗОГОРЕЛОЧНЫЕ УСТРОЙСТВА
Рациональное, экономичное и безопасное сжигание газа в различных энергетических установках зависит в первую очередь от правильного выбора и условий установки на агрегате газогорелочного устройства.
Перевод на отопление газом промышленных и котельных агрегатов, ранее работавших на твердом или жидком топливе, значительно повышает их производительность. Применение газа (природного, сжиженного и др.) в ряде отраслей промышленности дает возможность ввести в эксплуатацию новые высокопроизводительные газоиспользующие агрегаты, облегчает автоматизацию процессов нагрева, значительно улучшает технико-экономические показатели.
Поэтому по мере увеличения удельного веса газа в топливном балансе нашего народного хозяйства вопросы рационального использования и экономии этого ценнейшего топлива приобретают все большее значение. Несмотря на кажущуюся простоту сжигания газа, этот процесс может варьироваться в весьма широких пределах, давая для одной и той же установки раз личный эффект.
Опыт показывает, что почти любой котел или любая промышленная установка, переведенная на отопление природным газом, может работать с более высокими показателями.
Основными критериями оценки работы теплотехнического агрегата являются эффективность топливоиспользования и максимальная интенсификация заданного технологического процесса. Например, при проектировании и эксплуатации котельных установок необходимо стремиться к обеспечению максимальной производительности котла и получению наивысшего коэффициента его полезного действия.
Для промышленных печей основной задачей является максимальное ускорение процесса нагрева с соблюдением технологических особенностей и с наименьшим расходом топлива, т. е. также получение наивысшего коэффициента их полезного действия.
Естественно, что эти задачи должны решаться с наименьшими материальными затратами и с соблюдением условий безопасности, надежности работы и т. д.
Выбор способа сжигания газа, организация аэродинамики топки или рабочего объема далеко не безразличны с точки зрения указанных выше показателей, так как свойства и условия формирования факела горящего газа приводят к разным температурным режимам и тепловым эффектам процесса. Поэтому для каждого типа теплотехнической установки, а подчас для каждого конкретного случая должны быть проанализированы и применены наиболее выгодные приемы сжигания газа.
Несомненно, эффективность использования газа не может быть получена только в результате выбора той или иной конструкции горелки, она достигается при правильном решении всего комплекса вопросов, связанных с теплообменом и аэродинамикой установки, начиная от подачи воздуха и газа и кончая удалением продуктов сгорания в атмосферу. Несмотря на исключительное значение начальной стадии процесса, т. е. сжигания газа, очень важно правильно выбрать оборудование при проектировании к квалифицированно эксплуатировать газогорелочные устройства.
В настоящее время для удовлетворения различных требований, как в отношении тепловых нагрузок, так и в отношении давления газа перед горелками и способов смешения его с воздухом применяют многообразные конструкции газовых горелок.
Исходя из способа подачи воздуха, горелки всех конструкций можно классифицировать как:
а) диффузионные (или внешнего смещения);
б) подовые;
в) однопроводные и двухпроводные инжекционные;
г) двухпроводные с принудительной подачей воздуха (смесительные);
д) комбинированные (газомазутные, пылегазовые и т. д.).
По давлению газа перед соплом горелок их делят на:
— горелки низкого давления — до 500 мм вод. ст.;
— горелки среднего давления от 500 мм вод, ст. до 0,3 МПа
— горелки высокого давления — свыше 0,3 Мпа
В зависимости от метода сжигания газа горелки бывают факельные и бесфакельные.
Диффузионные горелки применяют редко и в настоящей главе они не рассмотрены.
Наибольшее распространение при газоснабжении коммунально-бытовых и промышленных предприятий получили инжекционные горелки, в которых воздух, необходимый для сжигания газа, подсасывается непосредственно в горелку газовой струей.
В горелках, в которых необходимый для сжигания газа воздух (полностью или частично) подается под давлением, газ можно сжигать как пламенным, так и беспламенным способом.
Комбинированные горелки (пылегазовые, газомазутные и т. д.), работающие по принципу либо инжекционных горелок, либо горелок с принудительной подачей воздуха, применяют редко и главным образом для специальных целей.
Анализируя опыт сжигания газов и, в частности, природного газа у нас и за рубежом, можно считать, что наиболее перспективны в промышленных и энергетических установках инжекционные горелки среднего давления, работающие на давлениях порядка 0,3 —1,0 кГ/см2
.
Современные горелки проектируют многосопловыми, с керамическими стабилизаторами горения и лопаточными устройствами, обеспечивающими хорошее перемешивание газовоздушной смеси.
Газовые горелки всех конструкций имеют общие основные элементы: форсунку, смеситель и горелочную насадку со стабилизирующим устройством.
В зависимости от технологических, эксплуатационных и других условий эти элементы могут быть конструктивного различного решения; некоторые из них могут совсем отсутствовать или компоноваться в одной детали.
Все элементы горелок связаны между собой определенными соотношениями, полученными на основании расчета и практических данных.
В инжекционных горелках форсунка, регулятор первичного воздуха, смеситель и горелочная насадка бывают различных форм и сечений. Роль стабилизатора выполняют одно или несколько отверстий или щелей определенных размеров.
Горелки с принудительной подачей воздуха имеют одну или несколько форсунок, смеситель, металлическую или керамическую горелочную насадку со стабилизирующим устройством в виде отверстий определенного размера.
Комбинированные горелки имеют одну или несколько форсунок не только для газа, но и для других видов топлива, смесительное устройство самых разнообразных конструкций (в зависимости от требований) и горелочную насадку со стабилизирующим устройством также самой разной формы.
Все горелки при сжигании газа в условиях, соответствующих открытому пространству (перепад давления равен нулю), должны удовлетворять следующим общим требованиям.
1. Изготовляемые серийно или по отдельным чертежам они должны пропускать необходимое количество газа и обеспечить полноту его сгорания с минимальным избытком воздуха; количество горючих компонентов при неполном сгорании в отходящих продуктах допускается в следующих пределах:
а) для газогорелочных устройств, применяемых в бытовых приборах содержание СО в сухих продуктах горения при не должно быть более 0,05% по объему как без отвода продуктов сгорания в дымоотводящий канал, так и при дымоотводящем канале ;
б) для газогорелочных устройств, применяемых в коммунально-бытовых и промышленных установках, с отводом продуктов сгорания в дымоотводящий канал сумма всех горючих компонентов не должна превышать 1,5%.
2. Регулирование тепловой нагрузки, характеризуемой количеством сжигаемого газа в единицу времени, должно быть легким при достаточно высоком пределе регулирования.
Для газовых горелок различают три вида тепловой нагрузки: номинальную (расчетную), минимальную и максимальную. Минимальная тепловая нагрузка определяется возможностью длительной работы горелки без проскоков пламени на форсунку.
Максимальная тепловая нагрузка определяется возможностью длительной работы горелки без отрыва пламени от горелки.
Отношение величин минимальной и максимальной тепловых нагрузок определяет пределы регулирования горелки. Это отношение должно бы: как правило, не менее 1 : 2 для инжекционных горелок низкого и среднего давления, 1 : 2,5 для диффузионных и по горелок, 1 : 4 для двухпроводных и комбинированных горелок.
3. Обеспечивать устойчивость пламени при максимальной тепловой нагрузке, а также хорошее смешение и полноту сгорания при минимальной тепловой нагрузке. Устойчивость горелки определяется длительностью ее работы без проскоков и отрыва пламени при изменениях теплоты сгорания газа и его давления на от заданных параметров на всех указанных выше режимах. При этом настройка горелки должна оставаться без изменения.
4. Конструкция должна быть проста и удобна в монтаже и эксплуатации.
5. Уровень звукового давления от шума от газогорелочных устройств, работающих на номинальном режиме, должна быть в каждом случае в пределах, допускаемых санитарными нормами, т. е. до 85 дб
.
В заключение следует отметить, что выбор соответствующей конструкции газовой горелки не всегда будет удачным, если при этом исходить только из параметров газа и требуемой тепловой нагрузки горелки, и не учитывать конструкцию топочного пространства.
Нормальная работа газогорелочных устройств в большей степени зависит от конструкции топочного пространства и правильного расположения в нем горелок. Например, газовые горелки надо располагать на достаточном расстоянии от теплопередающих поверхностей, чтобы не было затухания концов факела; в экранированной топке может быть отрыв и потухание пламени при его соприкосновении водогрейными трубами, что вызывает необходимость подачи вторичного воздуха в зону горения. В топках без футеровки на пути факела применяют огнеупорные туннели, решетки и горки из боя шамотного кирпича, небольшие шамотные своды, чередующиеся с открытыми проемами, что не только повышает полноту сгорания газа, но и стабилизирует процесс горения.
Бесфакельное сжигание газа применяют, как правило, при малом топочном объеме или при необходимости получения очень высоких температур в нагревательных печах металлообрабатывающей промышленности.
При бесфакельном сжигании газа каждую горелку снабжают керамическим туннелем, а её конструкция должна обеспечить полное смешение газа с необходимым количеством воздуха.
2.9 УСРОЙСТВО И ЭКСПЛУАТАЦИЯ ДЫМОХОДОВ. ПРАВИЛА ЭКСПЛУАТАЦИИ ВНУТРИДОМОВОГО ГАЗОВОГО ОБОРУДОВАНИЯ
При сжигании природного или искусственных газов образуются продукты сгорания газа, состоящие из углекислого газа , водяных паров и азота , оставшегося после химических реакций кислорода воздуха с горючими компонентами сжигаемого газа. Если процесс сжигания проводился с избытком воздуха, то в продуктах сгорания будет «лишний» кислород , не вступивший в реакцию с горючим.
Кроме того, при сжигании газов образуется большое количество продуктов сгорания. Так, при нормальном сжигании 1 м3
природного газа расходуется около 9,5 м3
воздуха и образуется примерно 8,5 м3
продуктов сгорания газа и около 2 м3
водяных паров.
По правилам безопасности газового хозяйства требуется отводить продукты сгорания газа от каждого прибора, агрегата или печи по обособленному дымоходу, находящемуся, как правило, во внутренних стенах зданий. Чтобы обеспечить надежный и полный отвод продуктов сгорания газа через дымоход, необходимо правильно его построить и правильно эксплуатировать. Нарушение этих условий приводит к тому, что часть продуктов сгорания попадет в помещение и может быть причиной отравления людей. Продукты сгорания газа с температурой выше 150 °С имеют плотность значительно меньшую, чем плотность атмосферного воздуха. Это обусловливает подъемную силу, благодаря которой уходящие газы уходят по вертикальному каналу (дымоходу) от газового прибора наружу. Следовательно, чем больше разница между температурой уходящих газов и температурой наружного воздуха, тем с большей скоростью уходящие газы будут проходить вверх по дымоходу, и, наоборот, чем меньше разница этих температур, тем с меньшей скоростью будет идти поток уходящих газов в дымоходе. Это одна из величин, характеризующих мощность (производительность) дымохода.
Другой величиной является площадь сечения дымохода, с увеличением или уменьшением которой изменяется мощность дымохода (при условии неизменности скорости потока отходящих газов в дымоходе).
Различные газовые приборы сжигают неодинаковое количество газа, а значит у них неодинаковое количество уходящих газов и температура, с которой они направляются в дымоход. Таким образом, для разных газовых приборов требуется строить дымоходы соответствующих площадей сечений. При заниженной площади сечения дымоход «задохнется» и не сможет пропустить все выделяющиеся из прибора продукты сгорания газа. Дымоходы могут быть прямоугольного и круглого сечения.
Большое влияние на работу дымоходов оказывает охлаждение отходящих газов при потоке в дымоходе. Если дымоход сделан приставным снаружи здания, не выдержана толщина стенок дымохода при строительстве или они не имеют утепления, то уходящие газы будут сильно охлаждаться в зимнее время, разность температур между ними и атмосферным воздухом будет уменьшаться, а значит уменьшаться и мощность дымохода. В особенно холодные дни охлаждение уходящих газов может быть настолько значительным (ниже точки росы), что водяные пары из продуктов сгорания будут конденсироваться (превращаться из пара в воду) и оседать на стенках дымохода, в результате наступит закупорка дымохода кристаллами льда. Сильное охлаждение отходящих газов может произойти и за счет подсоса наружного воздуха в дымоход через его неплотности, а также за счет большого подсоса воздуха через тягопрерыватель газового прибора.
Образование неплотностей (трещин) или завал дымохода может также произойти в результате разрушения его стенок при воздействии на них отходящих газов, если дымоход выполнен из непрочных материалов. Поэтому категорически запрещается строить дымоходы из силикатного кирпича, шлакобетонных и других неплотных или пористых материалов. Потоку отходящих газов в дымоходе оказывает сопротивление шероховатость стенок, наличие внутренних сужений, выступов, выемок и изгибов, допущенных при небрежном строительстве.
Завышенная величина сечения дымохода, а также его вытянутая прямоугольная форма (одна сторона сечения больше другой в два раза) вызывают турбулизацию потока уходящих газов и тем самым повышают сопротивление дымохода потоку уходящих газов. Любой дымоход можно оценить по его суммарному, результирующему показателю, выражающемуся в величине разрежения, которое создается вначале дымохода при потоке отходящих газов. Это разрежение называют тягой дымохода.
Для каждого газового прибора экспериментально устанавливается минимально необходимое разрежение (тяга), при котором обеспечивается нормальная работа прибора и полный отвод продуктов сгорания газа. Так, например, минимально необходимая тяга в дымоходе для водонагревателя КГИ-56 должна быть равной 0,3 мм вод. ст.
, для АГВ-80 — 0,2 мм вод. ст.
Если дымоход по своему сечению соответствует по размерам величине патрубка прибора, но не создает требуемой тяги, то в этом случае недостаточна высота дымохода. Следовательно, дымоход должен обеспечить такую тягу у места подключения прибора, которая будет достаточной для преодоления сопротивления газового прибора проходу продуктов сгорания газа и преодоления сопротивления самого дымохода
Таким образом, работоспособность дымохода характеризуется тремя величинами: разностью температур между уходящими газами и наружным воздухом, сечением и высотой дымохода. «Правила безопасности в газовом хозяйстве» предъявляют ряд требований к устройству дымохода.
При устройстве дымоходов в наружных стенах толщина стенок должна определяться расчетом с тем, чтобы температура продуктов сгорания на выходе из дымохода была не ниже температуры точки росы. В строящихся зданиях отвод продуктов сгорания газа должен предусматриваться от каждого прибора, агрегата или печи по обособленному дымоходу. В существующих зданиях допускается присоединение к одному дымоходу не более двух водонагревателей или отопительных печей, расположенных на одном или разных этажах, при условии ввода продуктов сгорания в дымоход на различных уровнях, не ближе 50 см друг от друга и устройства в дымоходе на такую высоту рассечек.
Сечение дымоходов должно определяться расчетом или по утвержденным таблицам, но не быть меньше, чем у патрубка газового прибора, печи и др., присоединяемого к дымоходу. Если к дымоходу присоединяются два прибора, то должна учитываться их совместная работа. Газовые приборы предприятий общественного питания могут присоединяться к общим дымоходам.
Толщина стенки дымохода от его внутренней поверхности до наружной, выходящей в помещение, должна быть не менее 0,25 м. Шов кирпичной кладки дымохода должен быть полным и толщиной не более 10 мм.
Для присоединения газовых приборов к дымоходам используют трубы из кровельной стали. Суммарная длина их горизонтальных участков не должна быть более 3 м во вновь строящихся и не более 6 м в существующих домах.
В дымоходах, к которым подключаются приборы, не имеющие тягопрерывателей для регулирования тяги устанавливаются шиберы, имеющие отверстия диаметром не менее 15 мм. На соединительных трубах или дымоходах от приборов, имеющих тягопрерыватели, установка шиберов не допускается. Присоединять к дымоходу соединительную трубу от газового прибора следует так, чтобы ниже Ввода трубы в дымоходе оставался «карман» глубиной не менее 250 мм, и люк для очистки (рис. 2.18).
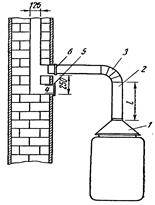
Рис. 2.18. Присоединение газопровода к дымоходу 1
– тягопрерыватель, 2
– соединительная труба, 3
– отвод, 4
– карман, 5
– дверка чистки дымохода, 6
– упорный валик
Дымоходы, выходя выше крыши здания, подвергаются воздействию воздушных потоков различного направления. Одни потоки могут создавать у оголовка дымохода зону пониженного давления и тем самым облегчать работу дымохода, другие, наоборот, могут создавать зону повышенного давления (подпор) и тем самым затруднять выход продуктов сгорания газа. Нисходящие вертикальные потоки не только могут воспрепятствовать выходу продуктов сгорания наружу, но и «опрокинуть» тягу, создать в дымоходе поток обратного направления и тем самым нарушить работу газового прибора и вызвать аварийное положение в помещениях здания.
Ветровой подпор создается обычно у оголовка дымохода, когда он расположен вблизи высокой стены здания. При отсутствии ветра или при расположении с заветренной стороны дымоход будет работать нормально. Для устранения вредного влияния ветрового подпора на работу дымохода последний надо в этих случаях поднимать (наращивать) выше зоны ветрового подпора, которая ограничивается прямой, проведенной от конца близко расположенной стены под углом 45° к горизонтали.
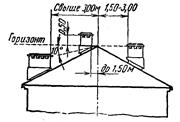
Рис. 2.19. Расположение дымовых труб на крыше здания
При нормальных условиях дымоходы выводят с соблюдением следующих требований (рис. 2.19):
- на 0,5 м выше конька крыши при их расположении (считая по горизонтали) не далее 1,5 м от конька крыши;
- в уровень с коньком крыши, если они отстоят на 1,5—3,0 м от конька крыши;
- ниже конька крыши, но не ниже прямой, проведенной от конька вниз под углом 10° к горизонту, при расположении их от конька далее 3 м.
Во всех случаях высота трубы дымохода над прилегающей частью крыши должна быть не менее 0,5 м. Дымоходы должны быть защищены от воздействия атмосферных осадков.
В существующих зданиях пригодность дымоходов для присоединения к ним газовых приборов, отопительных печей, работающих на газовом топливе, проверяется обученными этому виду работ инженерно-техническими работниками, организаций, эксплуатирующих эти здания, и трубоочистных секторов жилищно-эксплуатационных контор, РЖУ или добровольными пожарными обществами.
Периодическая проверка и прочистка дымоходов проводится домоуправлениями в следующие сроки:
дымоходы от газовых водонагревателей: кирпичные — один раз в квартал, асбоцементные — один раз в год;
дымоходы от отопительных печей — один раз в год перед отопительным сезоном;
дымоходы отопительно-варочных печей — три раза в год перед началом и среди отопительного сезона, а также в весеннее время;
в зимнее время не реже одного раза в месяц должен производиться осмотр оголовков дымоходов с целью предотвращения замерзания и закупорки устьев дымоходов. Результаты проверки состояния оголовков и их ремонт должны отмечаться в специальном журнале домоуправления или ЖЭК.
ЭКСПЛУАТАЦИЯ ВНУТРИДОМОВОГО ГАЗОВОГО ОБОРУДОВАНИЯ
Ответственность за состояние и правильную эксплуатацию внутридомового газового оборудования в городах и поселках несут эксплуатационные организации газового хозяйства. Ведомственные и частные дома обслуживаются соответствующими домоуправлениями (ЖЭК) или эксплуатационными организациями газового хозяйства по договору с ними или владельцами домов.
Обслуживание газового оборудования. Основной формой обслуживания газооборудования жилых домов является периодический профилактический осмотр и ремонт газовых приборов, производимый в плановом порядке и по заявкам потребителей.
Периодичность профилактического осмотра в жилых домах установлена:
газовые плиты и быстродействующие водонагреватели — раз в два месяца;
емкостные водонагреватели, отопительные и отопительно-варочные печи, котлы и другие приборы, имеющие автоматические устройства, один раз в месяц.
При профилактическом осмотре в обязательном порядке выполняется следующий комплекс работ:
а) По газопроводам
Осмотр всех газопроводов, начиная от крана на вводе; обмыливание всех соединений на вводе с целью проверки состояния и герметичности соединений и арматуры на газопроводе.
Смазка кранов (задвижек) на вводе, кранов на ответвлениях в квартиры и к стоякам
Смазка кранов перед счетчиком и на опусках к приборам
Проверка крепления газопроводов
Проверка работы запорной арматуры, кранов (задвижек) на стояках и вводах, если требуется, перенабивка сальников
б) По газовым плитам
Разборка и смазка всех кранов
Снятие горелок и прочистка форсунок
Проверка плотности соединений
Проверка плотности закрытия дверок духового шкафа
Регулировка всех горелок плиты
Смена мелких деталей (ручек, кранов, пружин, дверки духового шкафа, форсунок, регуляторов воздуха, ручек духового шкафа, газораспределителей конфорочных горелок)
в) По газовым проточным водонагревателям
Расборка и смазка кранов
Проверка плотности всех соединений
Прочистка отверстий газовых горелок, запальников и форсунок
Очистка радиатора от сажи и окалины
Проверка исправности автоматики блок-крана, а у автоматических приборов – проверка автоматики безопасности
Регулировка подачи газа и воды с проверкой работы водонагревателя на разных режимах
Проверка тяги дымохода и состояния соединительных труб, притока свежего воздуха и состояния приточной вентиляции
Перенабивка сальника и проверка работы водяного вентиля, смена мембраны, пружин и других деталей
г) По емкостным водонагревателям и квартирным отопительным котлам
Разборка и смазка кранов
Проверка плотности всех соединений
Извлечение и прочистка удлинителя потока продуктов сгорания у АГВ
Прочистка отверстий горелок и форсунок, включая запальник, очистка спая термопары
Проверка исправности автоматики безопасности и регулирования, настройка ее на заданный режим
Исправление и смена деталей
Проверка тяги, а также притока свежего воздуха и вытяжной вентиляции
д) По газифицированным печам
Смазка кранов
Проверка плотности всех соединений
Проверка и прочистка всех отверстий горелок и форсунок
Проверка тяги дымохода и отсутствие трещин в кладке печи внешним осмотром
Проверка исправности автоматики и устранение выявленных неисправностей, настройка автоматики
е) По газовым счетчикам
Наблюдение за состоянием и работой счетчика
|
При каждом посещении по графику
По мере надобности
По мере надобности, но не реже одного раза в три месяца
При каждом посещении по графику
Один раз в три месяца
По мере надобности, но не реже одного раза в три месяца
То же
При каждом посещении по графику
То же
По мере надобности
То же
По мере надобности, но не реже одного раза в три месяца
При каждом посещении по графику
По мере надобности
То же
При каждом посещении по графику
То же
То же
По мере надобности
По мере надобности, но не реже одного раза в три месяца
При каждом посещении по графику
По мере надобности
То же
При каждом посещении по графику
По мере надобности
При каждом посещении по графику
По мере надобности, но не реже одного раза в три месяца
При каждом посещении по графику
По мере надобности
При каждом посещении по графику
То же
При каждом посещении по графику
|
Пуск газа в газовые приборы. Пуск газа в газооборудование зданий производится бригадой квалифицированных слесарей, допущенных к выполнению газоопасных работ, в составе менее двух человек, возглавляемой инженерно—техническим работником, ответственным за пуск газа.
До пуска газа в газовое оборудование жилого дома необходимо:
проверить соответствие согласованного проекта и исполнительно-технической документации на газификацию жилого дома, выполненным строительно—монтажным работам;
проверить внешним осмотром отсутствие механических повреждений и незаглушенных участков газопровода от задвижки или крана на вводе в здание до кранов на спусках к приборам в правильность установки газовых приборов в соответствии с проектом;
проверить наличие и исправность инструмента, резиновых шлангов и необходимых материалов для производства работ при пуске газа в газопровод и газовые приборы строения;
проинструктировать пусковую бригаду о правилах безопасности при пуске газа в газопроводы и газовые приборы зданий;
проверить укомплектованность газовых приборов и их исправное состояние;
наличие тяги в каналах вытяжной вентиляции помещений, в которых эксплуатируются газовые приборы;
проверить наличие, исправное состояние и закрытое положение пробковых кранов на газопроводах и кранов перед горелками газовых приборов;
каждый газовый ввод должен быть обязательно разъединен с внутридомовым газопроводом. Кран на вводе должен быть закрыт, а отсоединенная сторона корпуса крана от газопровода заглушивается глухой металлической пробкой. При наличии задвижки на газовом вводе после нее по ходу газа устанавливается заглушка;
проверить отключение снабжения газом от общего распределительного газопровода, газовые вводы в строения, в которых внутреннее газовое оборудование не находится в эксплуатации.
при обнаружении неисправностей газопровода или приборов пуск газа не производится до полного устранения неисправностей.
Перед пуском газа в газопровод и приборы ответственный руководитель пусковой бригады производит контрольную опрессовку газопровода воздухом под давлением 400 мм вод. ст.
, при этом опрессовывается весь газопровод до кранов перед горелками газовых приборов. Газопроводы считаются выдержавшими испытания, если в течение 5 мин падение давления не превысит 20 мм вод. ст.
Сброс газовоздушной смеси из газового ввода газооборудования здания производится через наиболее удаленный газовый стояк и высоко расположенный газовый прибор.
Продувка газом дворовых газопроводов и вводов производится через газовые вводы с установкой приспособления короткого сгона с переходом, на который после крана надевается резиновый шланг длиной не менее 10 м. Свободный конец шланга выводится на расстояние 8 м от строения. При продувке в пространстве радиусом 10 м от места выброса газовоздушной смеси не должно допускаться появления огня. Продувка дворового газопровода считается законченной, если отобранная проба газа в ведре с эмульсией при поджигании загорается спокойным желтым пламенем без вспышки «хлопком». Проба газовоздушной смеси, введенная в мыльную эмульсию емкости, поджигается за пределами загазованной воздушной атмосферы.
Продувку внутридомового газового оборудования проводят в следующем порядке:
перед продувкой ответственный за пуск газа дает указание монтажно-строительной организации удалить глухую прокладку, установленную после задвижки на газовом вводе, или вывернуть пробку на кране ввода и присоединить (фланец) между вводом и внутридомовым газопроводом; затем задвижка или кран открывается и немедленно мыльной эмульсией проверяется плотность фланцевого соединения, а также сальника задвижки или крана и плотность соединений стона. Продувают газовые вводы и стояки последовательно, начиная с наиболее отдаленного ввода и стояка. На остальных газовых вводах стояки должны быть разъединены, краны перекрыты и заглушены пробками (при наличии задвижек устанавливается глухая прокладка);
продувка газом внутридомовых газопроводов и газовых приборов в доме начинается с квартир, расположенных на верхнем этаже наиболее удаленного стояка;
если одна или несколько квартир (секций), в которые производится пуск газа, окажутся закрытыми (не заселены), пускать газ в такие стояки можно лишь при получении от домоуправления расписки, что оно обеспечит сохранность газопроводов и при боров в этих квартирах. Газовые приборы незаселенных квартир должны быть отключены от газоснабжения путем затяжки кранов перед приборами с опломбированием. Отключение оформляется актом. До выполнения этого требования пуск газа в эти газовые стояки запрещается, и краны на газовых стояках должны быть закрыты;
внутридомовые газопроводы должны продуваться газом через спуск к газовой плите через резиновый шланг, свободный конец которого выпускается в окно. Присоединение шланга к опуску производится через специальный переход. Продувка участка газопровода после крана на опуске к газовой плите производится через форсунку газовой плиты и резиновый шланг диаметром 8—10 мм с выводом шланга в окно. Газ пускают после присоединения шланга.
Продувка проводится в следующем порядке: сначала открывают кран на квартирном вводе, потом на опуске к прибору, а затем у прибора. У быстродействующего водонагревателя один конец шланга присоединяются к патрубку перед блок-краном газового водонагревателя, а другой (свободный) выводят в окно.
При наличии в доме газооборудовавных отопительных печей один конец шланга присоединяют к рампе горелки, а другой (свободный) выводят за окно.
Продувка газа в дымоход или в вентиляционный канал строго запрещается!
После окончания продувки внутридомовых газопроводов поочередно зажигают газ на горелках газовых приборов. После первичного зажигания необходимо:
отрегулировать горение газа на всех горелках приборов;
проверить давление газа на приборах по водяному манометру; повесить накидные ключи на краны перед газовыми приборами;
проверить мыльным раствором плотность всех резьбовых соединений газопровода;
сообщить и практически показать всем жильцам квартиры, как безопасно зажигать газ на конфорочных горелках газовых плит, горелках духовых шкафов и других приборов;
подробно проинструктировать всех жильцов квартир, как пользоваться установленными в квартире газовыми приборами, как определить утечку газа мыльной эмульсией и какие нужно принимать меры в случае появления запаха газа.
После окончания работ по пуску газа составляется акт по установленной форме о вводе в эксплуатацию газового оборудования дома.
2.10 ПРИЕМ В ЭКСПЛУАТАЦИЮ ГАЗОПРОВОДОВ И ГАЗОРЕГУЛЯТОРНЫХ ПУНКТОВ
Газопроводы и газорегуляторные пункты (ГРП) принимаются в эксплуатацию комиссией, в состав которой входят представители строительно-монтажной организации, представителем эксплуатирующей организации и Ростехнадзором.
Строительно-монтажная организация предъявляет комиссии всю необходимую исполнительно-техническую документацию:
- утвержденный проект;
- сварочные схемы газопроводов с копиями дипломов сварщиков, протоколами лабораторных испытаний контрольных стыков
и заключений по просвечиванию стыков;
- журнал сварочных работ;
- сертификаты на трубы, электроды, изоляционные материалы;
- журнал изоляционных работ;
- акты проверки постели, уклонов и очистки внутренней полости газопроводов;
- паспорта или акты на испытание арматуры;
- исполнительные чертежи в объеме проекта;
- акты испытаний газопроводов на прочность и плотность.
Если в процессе строительства были некоторые отступления от проекта, то предъявляются также документы, разрешающие эти отступления.
Все представленные документы рассматриваются комиссией для выявления соответствия выполненных работ проекту и требованиям правил техники безопасности, газового хозяйства.
После ознакомления с документацией и проверки ее члены комиссии осматривают все газопроводы, сооружения и арматуру. К моменту приема газопроводы должны быть испытаны на прочность, плотность и засыпаны грунтом. В то же время, комиссия имеет право проверить любые участки газопроводов путем вырезки стыков, повторного испытания и т. д. Прием нового объекта оформляется специальным актом, он одновременно является разрешением на ввод в эксплуатацию газопровода.
На прочность проверяют качество сварных соединений и механическую прочность тела трубы, поэтому в этот период все места соединений должны быть доступны для осмотра, а сам газопровод присыпается на высоту 20—25 см.
Если испытывается газопровод низкого или среднего давлений, то стыки не изолируются и не засыпаются, кроме случая, когда стыки проверяются физическими методами контроля. При испытании на прочность время испытания не ограничено, оно проводится до тех пор, пока не будут выявлены дефекты (но не менее 1 ч).
На плотность подземные газопроводы испытывают после их полной засыпки и выравнивания температуры воздуха в трубе с температурой грунта (рис. 2.20).

Рис. 2.20. Схема установки для испытания подземных газопроводов на плотность: 1
– газопровод, 2
– конденсатосборник, 3
– задвижки, 4
– заглушки, 5
– пружинный манометр, 6
– трубопровод от компенсатора, 7
– краны, 8
– водяной (или ртутный) манометр, 9
– дорожное покрытие, 10
– продувочная свеча
Это вызвано тем, что из-за разницы температур можно получить искаженные показания падения давления. Продолжительность выравнивания температуры воздуха с температурой грунта зависят от диаметра газопровода и в среднем составляет 6—12 ч. После выравнивания температур газопровод должен выдерживаться при заданном давлении в течение 24 ч.
Таблица 2.8
Нормы испытания газопроводов на прочность и плотность
Давление в газопроводе
в кГ/см2
|
Давление газа в кГ/см2
|
Расчетная величина падения давления по формуле (для газопроводов одного диаметра)
|
на прочность
|
на плотность
|
Низкое – до 0,05 (диаметр до 150мм)
Низкое – до 0,05
Среднее – от 0,05 до3
Высокое – от 3 до 6
Высокое – от 6 до 12
|
1,0
3,0
4,5
7,5
15,0
|
0,2
1,0
3,0
6,0
12,0
|
Не более 1 мм вод. ст. в ч
Для подземных газопроводов:
мм рт .ст.
|
В табл. 2.8 показаны нормы и условия испытания и допустимые падения давления для различных газопроводов.
Газопровод считается выдержавшим испытание и принятым в эксплуатацию, если истинная потеря давления будет меньше предельно допускаемого падения давления. Если потеря давления больше допустимой, то газопровод не принимается в эксплуатацию до выяснения и устранения дефектов.
2.11 ТЕХНИКА БЕЗОПАСНОСТИ ПРИ ЭКСПЛУАТАЦИИ ПОДЗЕМНЫХ ГАЗОПРОВОДОВ
При эксплуатации распределительных газопроводов необходимо соблюдать меры безопасности производства работ, предотвращать возможные аварии, связанные со специфическими свойствами газов.
2.11.1 ОСНОВНЫЕ СВОЙСТВА ГАЗОВ
Все виды газообразного топлива могут взрываться, если они смешаны с воздухом в определенных соотношениях (табл. 2.9).
Горючие газы могут воспламеняться или взрываться тогда, когда они смешаны в определенных соотношениях с воздухом и нагреваются не ниже определенной температуры, называемой температурой воспламенения.
Минимальные и максимальные количества газа в газовоздушных смесях, при которых может произойти их воспламенение, называются нижним и верхним пределом взрываемости (табл. 2.9).
Очень важной характеристикой горения газов является скорость распространения пламени, т. е. скорость движения фронта горения по отношению к невоспламененной газовоздушной смеси. Скорость распространения пламени зависит от условий горения, характера движения газовоздушной смеси, ее состава и температуры, а также от содержания в ней негорючих (балластных) примесей.
Таблица 2.9.
Температуры воспламения и пределы взрываемости (воспламеняемости) газов и паров в смеси с воздухом
Íàèìåíîâàíèå ãàçîâ
|
Òåìïåðàòóðû âîñïëàìåíåíèÿ, î
Ñ
|
Ïðåäåëû âçðûâàåìîñòè (îáúåì. % ãàçà â ñìåñè) ïðè 20 î
Ñ è äàâëåíèè 760 ìì ðò.ñò.
|
íèæíèé
|
âåðõíèé
|
Àöåòèëåí………………………………
Áóòàí………………………………......
Áóòèëåí……………………………......
Âîäîðîä……………………………......
Ìåòàí……………………………….....
Îêèñü óãëåðîäà…………………......
Ïðîïèëåí……………………………...
Ïðîïàí………………………………...
Ñåðîâîäîðîä………………………......
Ýòàí……………………………………
Ýòèëåí…………………………………
Êîêñîâûé ãàç……………………….....
Ñëàíöåâûé ãàç………………………...
|
335
490
445
510
645
610
455
510
290
530
540
640
700
|
2,3
1,5
1,7
4,0
5,0
12,5
2,0
2,1
4,3
3
3
5-6
6-8
|
82
8,5
9,9
75
15
75
9,7
9,5
45,5
13
28,6
30-32
30-40
|
Для суждения об относительных величинах максимальных скоростей распространения пламени и различных газов в табл. 2.10 приведены значения этих скоростей, определенные в трубе диаметром 25 мм.
Таблица 2.10.
Максимальные скорости распространения пламени смесей горючих газов с воздухом
Íàèìåíîâàíèå ãàçà
|
Îáúåìíûé ïðîöåíò ãàçà â ñìåñè ñ ìàêñ. ñêîðîñòüþ ðàñïðîñòðàíåíèÿ ïëàìåíè
|
Ìàêñèìàëüíàÿ ñêîðîñòü, ì/ñåê
|
Âîäîðîä……………………………………
Îêèñü óãëåðîäà…………………………....
Ìåòàí……………………………....
Ýòàí…………………………………………..
Ïðîïàí………………………………………..
Ýòèëåí………………………………………..
|
38,5
45,0
9,8
6,5
4,6
3,6
7,1
|
4,83
1,25
0,67
0,85
0,82
0,82
1,42
|
Токсические (ядовитые) свойства некоторых газов характеризуются данными, приведенными в таблице 2.11.
Таблица 2.11.
Степень воздействия вредных газов на организм человека
Äëèòåëüíîñòü è õàðàêòåð âîçäåéñòâèÿ íà ÷åëîâåêà ïðè äûõàíèè
|
Ñîäåðæàíèå âðåäíûõ ãàçîâ â âîçäóõå, % (ïî îáúåìó)
|
ÑÎ
|
SO2
|
H2
S
|
NO2
|
CO2
|
Íåñêîëüêî ÷àñîâ áåç çàìåòíîãî âëèÿíèÿ…………………….
Ïðèçíàêè ëåãêîãî îòðàâëåíèÿ èëè ðàçäðàæåíèÿ ñëèçèñòûõ îáîëî÷åê ÷åðåç 2-3 ÷àñà…………………………
Îïàñíîñòü ñåðüåçíîãî îòðàâëåíèÿ ÷åðåç 30 ìèí…………………………..
Îïàñíî äëÿ æèçíè ïðè êðàòêîâðåìåííîì âîçäåéñòâèè………
|
0,01
0,01-0,05
0,2-0,3
0,5-0,8
|
0,0025
0,005
0,008-0,015
0,06
|
0,0015
0,005-0,008
0,02-0,03
0,05
|
0,0008
0,001
0,005
0,015
|
0,5-1,0
2-3
4-5
7-10
|
Удушье может наступить при нахождении людей в загазованной среде без противогазов. Объясняется это тем, что газ, состоящий в основном из метана, заполняя помещение, вытесняет кислород, необходимый для нормального дыхания. При значительном содержании метана в воздухе (свыше 10%) человек испытывает при дыхании недостаток кислорода и может задохнуться.
Особенно опасна окись углерода, она содержится в искусственных газах и продуктах неполного сгорания газов. Окись углерода не имеет запаха и цвета, поэтому присутствие ее в воздухе часто ощущается по признакам отравления.
Признаки отравления наступают уже при вдыхании воздуха с содержание 0,05% окиси углерода, а при более высоких концентрациях (0,4-0,5%) может произойти острое отравление. Признаки отравления окисью углерода: головокружение, тошнота, слабость, шум в ушах, а иногда и потеря сознания.
Большинство работ, выполняемых на подземных газопроводах, являются газоопасными, т. е. или выполняются в загазованной среде, или при их производстве возможен выход газа из газопроводов и агрегатов.
К газоопасным относятся следующие работы:
- присоединение новых газопроводов к действующим;
- ввод газопроводов в эксплуатацию;
- ремонт действующих газопроводов;
- ремонт арматуры газопроводов;
- ликвидация различных закупорок;
- откачка конденсата из конденсатосботников и гидрозатворов;
- разборка действующих газопроводов.
2.11.2 ЗАЩИТНЫЕ СРЕДСТВА И ПРИСПОСОБЛЕНИЯ
При выполнении газоопасных работ все работники обеспечиваются защитными средствами и приспособлениями (противогазы, спасательные пояса, веревки, спецодежда и др.).
Перед пользованием противогазом необходимо убедиться в его исправности. Годность противогаза определяют, зажимая конец гофрированной трубки и контрольного входа, если при этом в маску попадает воздух, то пользоваться противогазом нельзя. Необходимо проверить также, нет ли прорывов и проколов на маске, начиная от подбородка и постепенно натягивая ее на лицо.
К средствам защиты относятся также спасательные пояса (рис.2.21) и веревки, которые применяются для быстрого извлечения рабочих, находящихся в колодцах или котлованах. Каждый раз до и после применения спасательные пояса и веревки необходимо проверять. Кроме того, спасательные пояса испытывают два раза в год на прочность путем подвески к ним груза весом 200 кг на 5 мин. Если после снятия груза на поясе не обнаружатся повреждения, то он считается годным.
Спасательные веревки испытывают четыре раза в год в течение 15 мин при нагрузке 200 кг. Веревка считается удовлетворительной, если ее длина увеличилась на более чем на 5% от первичной. Испытания проводит специальная комиссия, результаты заносятся в акт.
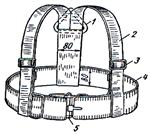
Рис. 2.21. Спасательный пояс: 1
– кольцо, 2
– лямка, 3
– пряжка, 4
– пояс, 5
– замок
Для безопасного выполнения различных работ не менее важное значение имеет качество спецодежды и инструмента. К спецодежде относятся: брезентовые рукавицы, костюмы, резиновые сапоги, защитные очки и маска и т. д.
До начала и в процессе работы необходимо определять величину концентрации газа в воздухе. Для этих целей применяют различные газоанализаторы.
При помощи газоанализатора можно определить концентрацию газа в пределах от 0,1 до 11%.
2.11.3 ВЫПОЛНЕНИЕ ГАЗООПАСНЫХ РАБОТ
Газоопасные работы выполняют бригады рабочих в составе не менее двух человек, а при работах в колодцах и траншеях – не менее трех. Для выполнения этих работ назначается ответственный, обычно инженерно-технический работник. Перед работой выдается наряд, в котором указывается время начала работы и основные меры безопасности. На наиболее сложные и ответственные работы – ремонт газопроводов среднего и высокого давления, врезки в газопроводы диаметром 400 мм и т. д., кроме наряда, составляется специальный план производства работ. Наряды и планы выдаются заблаговременно. После получения наряда ответственный за выполнение работы собирает рабочих, знакомит их с предстоящей работой и подробно инструктирует каждого из членов бригады.
Газоопасные работы, как правило, ведутся в дневное время, однако могут быть случаи, когда их необходимо выполнить в ночное время. Это требует принятия дополнительных мер: ограждения и освещения места производства работ. Если работы производятся в закрытых и трудноосвещаемых помещениях, то применяются переносные электролампы во взрывобезопасном исполнении или аккумуляторные лампы шахтерного типа. Действующее освещение необходимо оставлять в том виде, в каком оно было до начала работ, так как при включении или выключении может образоваться искра.
При выполнении газоопасных работ в колодцах, котлованах и других подземных сооружениях и закрытых помещениях работающие должны быть в противогазах и спасательных поясах, обувь не должна иметь подковок и гвоздей, в противном случае на обувь надевают галоши. Если в колодцах и котлованах отсутствуют специальные приспособления для спуска и подъема, то до начала работ устанавливается металлическая лестница соответствующей высоты. Категорически запрещается производство газоопасных работ в колодцах с неразобранными перекрытиями, а также в тесных котлованах и траншеях!
Если работы предусматривают снижение давления газа, то его снижают до начала работ, однако даже при сниженном давлении могут быть случаи воспламенения выходящего в атмосферу газа. Поэтому необходимо иметь на месте средства для тушения воспламенившегося газа. Пламя тушится замазыванием глиной, засыпкой землей, набрасыванием асбестовых или брезентовых одеял, а также струей инертного газа.
Несоблюдение правил безопасности в газовом хозяйстве может привести к таким серьезным последствиям, как удушье, отравление, ожоги, ранение, ушибы, поражения электрическим током и т. д.
ГЛАВА 3. СИСТЕМЫ ВЕНТИЛЯЦИИ И КОНДИЦИОНИРОВАНИЯ
3.1 КЛАССИФИКАЦИЯ СИСТЕМ КОНДИЦИОНИРОВАНИЯ
Кондиционирование воздуха – это создание и автоматическое поддержание (регулирование) в закрытых помещениях всех или отдельных его параметров (температуры, влажности, чистоты, скорости движения воздуха) на определенном уровне с целью обеспечения оптимальных метеорологических условий, для самочувствия людей или ведения технологического процесса.
Кондиционирование воздуха осуществляется комплексом технологических средств, называемых системой кондиционирования воздуха (СКВ). В состав СКВ входят технологические средства забора воздуха, подготовки, т.е. придания необходимых кондиций (фильтры, теплообменники, увлажнители или осушители воздуха), перемещения (вентиляторы) и его распределения, а также средства хладо- и теплоснабжения, автоматики, дистанционного управления и контроля. СКВ больших общественных, административных и производственных зданий обслуживаются, как правило, комплексными автоматизированными системами управления.
Автоматизированная система кондиционирования поддерживает заданное состояние воздуха в помещении независимо от колебаний параметров окружающей среды (атмосферных условий).
Основное оборудование системы кондиционирования для подготовки и перемещения воздуха агрегатируется (компонуется в едином корпусе) в аппарат, называемый кондиционером. Во многих случаях все технические средства для кондиционирования воздуха скомпонованы в одном блоке или в двух блоках, и тогда понятия «СКВ» и «кондиционер» однозначны.
Прежде чем перейти к классификации систем кондиционирования, следует отметить, что общепринятой классификации СКВ до сих пор не существует и связано это с многовариантностью принципиальных схем, технических и функциональных характеристик, зависящих не только от технических возможностей самих систем, но и от объектов применения (кондиционируемых помещений).
Современные системы кондиционирования могут быть классифицированы по следующим признакам:
- по основному назначению (объекту применения):комфортные и технологические;
- по принципу расположения кондиционера по отношению к обслуживаемому помещению: центральные и местные;
- по наличию собственного (входящего в конструкцию кондиционера) источника тепла и холода: автономные и неавтономные;
- по принципу действия: прямоточные, рециркуляционные и комбинированные;
- по способу регулирования выходных параметров кондиционированного воздуха: с качественным (однотрубным) и количественным (двухтрубным) регулированием;
- по степени обеспечения метеорологических условий в обслуживаемом помещении: первого, второго и третьего класса;
- по количеству обслуживаемых помещений (локальных зон): однозональные и многозональные;
- по давлению, развиваемому вентиляторами кондиционеров: низкого, среднего и высокого давления.
Кроме приведенных классификаций, существуют разнообразные системы кондиционирования, обслуживающие специальные технологические процессы, включая системы с изменяющимися во времени (по определенной программе) метеорологическими параметрами.
Комфортные СКВ предназначены для создания и автоматического поддержания температуры, относительной влажности , чистоты и скорости движения воздуха, отвечающих оптимальным санитарно-гигиеническим требованиям для жилых и административно-бытовых зданий или помещений.
Технологические СКВ предназначены для обеспечения параметров воздуха, в максимальной степени отвечающих требованиям производства. Технологическое кондиционирование в помещениях, где находятся люди, осуществляется с учетом санитарно-гигиенических требований к состоянию воздушной среды.
Центральные СКВ снабжаются извне холодом (доставляемым холодной водой или хладагентом), теплом (доставляемым горячей водой, паром или электричеством) и электрической энергией для привода электродвигателей вентиляторов, насосов и пр.
Центральные СКВ расположены вне обслуживаемых помещений и кондиционируют одно большое помещение, несколько зон такого помещения или много отдельных помещений. Иногда несколько центральных кондиционеров обслуживают одно помещение больших размеров (производственный цех, театральный зал, закрытый стадион или каток).
Центральные СКВ оборудуют центральными неавтономными кондиционерами, которые изготавливаются по базовым (типовым) схемам компоновки оборудования или их модификациям.
Центральные СКВ обладают следующими преимуществами:
1) возможностью эффективного поддержания заданной температуры и относительной влажности воздуха в помещениях;
2) сосредоточением оборудования и ремонта, как правило, в одном месте (подсобном помещении, техническом этаже и т.п.);
3) возможностями обеспечения эффективного шумо- и виброгашения. С помощью центральных СКВ при надлежащей акустической обработке воздуховодов, устройстве глушителей шума и гасителей вибрации можно достигнуть наиболее низких уровней шума в помещениях и обслуживать такие помещения, как радио- и телевизионные студии и т.п.
Несмотря на ряд достоинств центральных СКВ, надо отметить, что крупные габариты и проведение сложных монтажно-строительных работ по установке кондиционеров, прокладке воздуховодов и трубопроводов часто приводят к невозможности применения этих систем в существующих реконструируемых зданиях.
Местные СКВ разрабатывают на базе автономных и неавтономных кондиционеров, которые устанавливают непосредственно в обслуживаемых помещениях. Достоинством местных СКВ является простота установки и монтажа.
Такая система может применяться в большом ряде случаев:
в существующих жилых и административных зданиях для поддержания теплового микроклимата в отдельных офисных помещениях или в жилых комнатах;
во вновь строящихся зданиях для отдельных комнат, режим потребления холода в которых резко отличается от такого режима в большинстве других помещений, например, в сервисных и других насыщенных тепловыделяющей техникой комнат административных зданий. Подача свежего воздуха и удаление вытяжного воздуха при этом выполняется, как правило, центральными системами приточно-вытяжной вентиляции;
во вновь стоящихся зданиях, если поддержание оптимальных тепловых условий требуется в небольшом числе помещений, например, в ограниченном числе номеров-люкс небольшой гостиницы;
в больших помещениях как существующих, так и вновь строящихся зданий: кафе и ресторанах, магазинах, проектных залах, аудиториях и т.д.
Автономные СКВ снабжаются извне только электрической энергией, например, кондиционеры сплит-систем, шкафные кондиционеры и т.п. Такие кондиционеры имеют встроенные компрессионные холодильные машины, работающие, как правило, на фреоне-22.
Автономные системы охлаждают и осушают воздух, для чего вентилятор продувает рециркуляционный воздух через поверхностные воздухоохладители, которыми являются испарители холодильных машин. В переходное и зимнее время они могут производить подогрев воздуха с помощью электрических подогревателей или путем реверсирования работы холодильной машины по циклу так называемого «теплового насоса».
Наиболее простым вариантом, представляющим децентрализованное обеспечение в помещениях температурных условий, можно считать применение кондиционеров сплит-систем.
Неавтономные СКВ подразделяются на:
воздушные, при использовании которых в обслуживаемое помещение подается только воздух. (Мини-центральные кондиционеры, центральные кондиционеры);
водовоздушные, при использовании которых в кондиционируемые помещения подается воздух и вода, несущие тепло и холод, либо то и другое вместе (системы чиллеров-фанкойлов, центральные кондиционеры с местными доводчиками и т.п.).
Однозональные центральные СКВ применяются для обслуживания больших помещений с относительно равномерным распределением тепла, влаговыделений, например, больших залов кинотеатров, аудиторий и т.п. Такие СКВ, как правило, комплектуются устройствами для утилизации тепла (теплоутилизаторами) или смесительными камерами для использования в обслуживаемых помещениях рециркуляции воздуха.
Многозональные центральные СКВ применяют для обслуживания больших помещений, в которых оборудование размещено неравномерно, а также для обслуживания ряда сравнительно небольших помещений. Такие системы более экономичны, чем отдельные системы для каждой зоны ил каждого помещения. Однако с их помощью не может быть достигнута такая же степень точности поддержания одного или двух заданных параметров (влажности и температуры), как автономными СКВ (кондиционерами и сплит-системами и т.п.).
Прямоточные СКВ полностью работают на наружном воздухе, который обрабатывается в кондиционере, а затем подается в помещение.
Рециркуляционные СКВ, наоборот, работают без притока или с частичной подачей (до 40 %) свежего наружного воздуха или на рециркуляционном воздухе (от 60 до 100 %), обработки в кондиционере вновь подается в это же помещение.
Классификация кондиционирования воздуха по принципу действия на прямоточные и рециркуляционные обусловливается, главным образом, требованиями к комфортности, условиями технологического процесса производства либо технико-экономическими соображениями.
Центральные СКВ с качественным регулированием метеорологических параметров представляют собой широкий ряд наиболее распространенных, так называемых одноканальных систем, в которых весь обработанный воздух при заданных кондициях выходит из кондиционера по одному каналу и поступает далее в одно или несколько помещений.
При этом регулирующий сигнал от терморегулятора, установленного в обслуживаемом помещении, поступает непосредственно на центральный кондиционер.
СКВ с качественным регулированием подают в одно или несколько помещений холодный или подогретый воздух по двум параллельным каналам. Температура в каждом помещении регулируется комнатным терморегулятором, воздействующим на местные смесители (воздушные клапаны), которые изменяют соотношение расходов холодного и подогретого воздуха в подаваемой смеси.
Двухканальные системы используются очень редко из-за сложности регулирования, хотя и обладают некоторыми преимуществами, в частности, отсутствием в обслуживаемых помещениях теплообменников, трубопроводов тепло-холодоносителя; возможностью совместной работы с системой отопления, что особенно важно для существующих зданий, системы отопления которых при устройстве двухканальных систем могут быть сохранены.
Недостатком таких систем являются повышенные затраты на тепловую изоляцию параллельных воздуховодов, подводимых к каждому обслуживаемому помещению.
Двухканальные системы так же как и одноканальные, могут быть прямоточными и рециркуляционными.
Кондиционирование воздуха, согласно СНиП 2.04.05-91*
, по степени обеспечения метерологических условий подразделяются на три класса:
Первый класс – обеспечивает требуемые для технологического процесса параметры в соответствии с нормативными документами.
Второй класс – обеспечивает оптимальные санитарно-гигиенические нормы или требуемые технологические нормы.
Третий класс – обеспечивает допустимые нормы, если они не могут быть обеспечены вентиляцией в теплый период года без применения искусственного охлаждения воздуха.
По давлению, создаваемому вентиляторами центральных кондиционеров, СКВ подразделяются на системы низкого давления (до 100 кг/м2
), среднего давления (от 100 до 300 кг/м2
) и высокого давления (выше 300 кг/м2
).
3.2 КЛАССИФИКАЦИЯ СИСТЕМ ВЕНТИЛЯЦИИ
Вентиляцией называется совокупность мероприятий и устройств, используемых при организации воздухообмена для обеспечения заданного состояния воздушной среды в помещениях и на рабочих местах в соответствии со СНиП (Строительными нормами).
Системы вентиляции обеспечивают поддержание допустимых метеорологических параметров в помещениях различного назначения.
При всем многообразии систем вентиляции, обусловленном назначении помещений, характером технологического процесса, видом вредных выделений и т.п., их можно классифицировать по следующим характерным признакам:
1. По способу создания давления для перемещения воздуха: с естественным и искусственным (механическим) побуждением.
2. По назначению: приточные и вытяжные.
3. По зоне обслуживания: местные и общеобменные.
4. По конструктивному исполнению: канальные и бесканальные.
3.2.1 ЕСТЕСТВЕННАЯ ВЕНТИЛЯЦИЯ
Перемещение воздуха в системах естественной вентиляции происходит:
вследствие разности температур наружного (атмосферного) воздуха и воздуха в помещении, так называемой аэрации;
вследствие разности давлений «воздушного столба» между нижним уровнем (обслуживаемым помещением) и верхним уровнем – вытяжным устройством (дефлектором), установленным на кровле здания;
в результате воздействия так называемого ветрового давления.
Аэрацию применяют в цехах со значительными тепловыделениями, если концентрация пыли и вредных газов в приточном воздухе не превышает 30% предельно допустимой в рабочей зоне. Аэрацию не применяют, если по условиям технологии производства требуется предварительная обработка приточного воздуха или, приток наружного воздуха вызывает образование тумана или конденсата.
В помещениях с большими избытками тепла воздух всегда теплее наружного. Более тяжелый наружный воздух, поступая в здание, вытесняет из него менее плотный теплый воздух. При этом в замкнутом пространстве помещения возникает циркуляция воздуха, вызываемая источником тепла, подобная той, которую вызывает вентилятор.
В системах естественной вентиляции, в которых перемещение воздуха создается за счет разности движений воздушного столба, минимальный перепад по высоте между уровнем забора воздуха из помещения и его выбросом через дефлектор должен быть не менее 3 м. При этом рекомендуемая длина горизонтальных участков воздуховодов не должна быть более 3 м, а скорость воздуха в воздуховодах – не превышать 1 м/с.
Воздействие ветрового давления выражается в том, что на наветренных (обращенных к ветру) сторонах здания образуется повышенное, а на подветренных сторонах, а иногда и на кровле, - пониженное давление (разрежение).
Если в ограждениях здания имеются проемы, то с наветренной стороны атмосферный воздух поступает в помещение, а с заветренной – выходит из него, причем скорость движения воздуха в проемах зависит от скорости ветра, обдувающего здание, и, соответственно, от величин возникающих разностей давлений.
Системы естественной вентиляции просты и не требуют сложного дорогостоящего оборудования и расхода электрической энергии. Однако зависимость эффективности этих систем от переменных факторов (температуры воздуха, направления и скорости ветра), а также небольшое располагаемое давление не позволяют решать с их помощью все сложные и многообразные задачи в области вентиляции.
3.2.2 МЕХАНИЧЕСКАЯ ВЕНТИЛЯЦИЯ
В механических системах вентиляции используются оборудование и приборы (вентиляторы, электродвигатели, воздухонагреватели, пылеуловители, автоматика и др.), позволяющие перемещать воздух на значительные расстояния. Затраты электроэнергии на их работу могут быть довольно большими. Такие системы могут подавать и удалять воздух из локальных зон помещения в требуемом количестве, независимо от изменяющихся условий окружающей воздушной среды. При необходимости воздух подвергают различным видам обработки (очистке, нагреванию, увлажнению и т.д.), что практически невозможно в системах с естественным побуждение.
Следует отметить, что в практике часто предусматривают так называемую смешанную вентиляцию, т.е. одновременно естественную и механическую вентиляцию.
В каждом конкретном проекте определяется, какой тип вентиляции является наилучшим в санитарно-гигиеническом отношении, а также экономически и технически более рациональным.
3.2.2.1 КЛАССИФИКАЦИЯ ПРОМЫШЛЕННЫХ ПЫЛЕУЛОВИТЕЛЕЙ
. В технике пылеулавливания применяется большое число аппаратов, отличающихся друг от друга как по конструкции, так и по принципу осаждения взвешенных частиц. По способу улавливания пыли их обычно подразделяют на аппараты сухой, мокрой и электрической очистки газов.
В основе работы сухих пылеуловителей лежат гравитационные, инерционные и центробежные механизмы осаждения. Самостоятельную группу аппаратов сухой очистки пылеуловители фильтрационного действия. В основе работы мокрых пылеуловителей лежит контакт запыленных газов с промывной жидкостью, при этом осаждение частиц происходит на капли, поверхность газовых пузырей или пленку жидкости. В электрофильтрах осаждение частиц пыли происходит за счет сообщения им электрического заряда.
3.2.2.2 ОСНОВНЫЕ МЕХАНИЗМЫ ОСАЖДЕНИЯ ЧАСТИЦ.
Работа любого пылеулавливающего аппарата основана на использовании одного или нескольких механизмов осаждения взвешенных в газах частиц.
Гравитационное осаждение (седиментация) происходит в результате вертикального оседания частиц под действием силы тяжести при прохождении их через газоочистной аппарат.
Осаждение под действием центробежной силы отмечается при криволинейном движении аэродисперсного потока, когда развиваются центробежные силы, под действием которых частицы отбрасываются на поверхность осаждения.
Инерционное осаждение происходит в том случае, когда масса частицы или скорость ее движения настолько значительны, что она не может следовать вместе с газом по линии тока, огибающей препятствие, а, стремясь по инерции продолжить свое движение, сталкивается с препятствием и осаждается на нем.
Зацепление (эффект касания) наблюдается, когда расстояние частицы, движущейся с газовым потоком, от обтекаемого тела равно или меньше ее радиуса.
Диффузионное осаждение. Мелкие частицы испытывают непрерывное воздействие молекул газа, находящихся в броуновском движении, в результате которого возможно осаждение этих частиц на поверхности обтекаемых тел или стенок аппарата.
Электрическое осаждение. В процессе ионизации газовых молекул электрическим зарядом происходит заряд частиц, содержащихся в газах, а затем под действием электрического поля они осаждаются на электродах. Электрическое осаждение возможно и при взаимодействии частиц с каплями (или пузырями), причем электрические заряды могут быть подведены к частицам, к орошающей жидкости, или одновременно и к частицам, и к жидкости. Электрическое осаждение частиц может происходить и при прохождении аэрозоля через фильтрующие перегородки.
3.2.2.3 СУХИЕ МЕХАНИЧЕСКИЕ ПЫЛЕУЛОВИТЕЛИ. К сухим механическим пылеуловителям относятся аппараты, использующие различные механизмы осаждения: гравитационный (пылеосадительные камеры), инерционный (осаждение пыли за счет изменения направления движения газового пока или на препятствие) и центробежные (одиночные, групповые и батарейные циклоны, вихревые и динамические пылеуловители).
В табл. 3.1 приведены некоторые характерные параметры сухих механических пылеуловителей.
В настоящее время пылеосадительные камеры (рис. 3.1) применяются только в качестве аппаратов предварительной очистки, особенно при высокой начальной концентрации пыли.
В осадительных камерах достаточно эффективно улавливаются частицы пыли размером 30 – 50 мкм.
Основные достоинства осадительных камер заключаются в простоте конструкции, низкой стоимости, в небольших расходах энергии и в возможности улавливания абразивной пыли. Кроме того, работа камер не подвержена влиянию температуры и обеспечивает улавливание пыли в сухом виде. Однако, для достижения высокой эффективности при улавливании относительно мелкой пыли необходимы очень громоздкие камеры.
Таблица 3.1
Характерные параметры сухих механических пылеуловителей
Òèï ïûëåóëîâèòåëÿ
|
Ìàêñèìàëüíàÿ ïðîèçâîäèòåëüíîñòü ì3
/÷
|
Ýôôåêòèâíîñòü ïûëåóëàâëèâàíèÿ ÷àñòèö ðàçëè÷íûõ ðàçìåðîâ
|
Ãèäðàâëè÷åñêîå
ñîïðîòèâëåíèå, Ïà
|
Âåðõíèé ïðåäåë òåìïåðàòóðû ãàçîâ, î
Ñ
|
Îñàäèòåëüíàÿ êàìåðà
|
Îïðåäåëÿåòñÿ âîçìîæíîé ïëîùàäüþ äëÿ ðàçìåùåíèÿ
|
>50 ìêì
(80-90%)
|
50-130
|
350-550
|
Öèêëîí
|
85000
|
10 ìêì (50-80%)
|
250-1500
|
350-550
|
Âèõðåâîé ïûëåóëîâèòåëü
|
30000
|
2 ìêì
(90%)
|
äî 2000
|
äî 250
|
Áàòàðåéíûé öèêëîí
|
170000
|
5 ìêì (90%)
|
750-1500
|
350-550
|
Èíåðöèîííûé ïûëåóëîâèòåëü
|
127500
|
2 ìêì
(90%)
|
750-1500
|
äî 400
|
Äèíàìè÷åñêèé ïûëåóëîâèòåëü
|
42500
|
Òî æå
|
-
|
äî 400
|
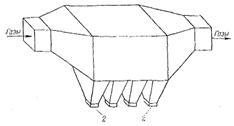
Рис. 3.1. Пылеосадительная камера: 1
– корпус; 2
– пылеотводящие бункера
3.2.2.4 ИНЕРЦИОННЫЕ ПЫЛЕУЛОВИТЕЛИ
. При резком изменении направления движения газового потока частицы пыли под действием инерционной силы будут стремиться двигаться в прежнем направлении и в дальнейшем могут быть выделены из этого потока. На этом принципе работает целый ряд пылеуловителей.
Камера с перегородкой по эффективности не на много отличается от обычной осадительной горизонтальной камеры, но имеет более высокое гидравлическое сопротивление. Плавный поворот в камере позволяет снизить гидравлическое сопротивление.
В осадителе запыленный газовый поток направляется сначала вниз по расширяющемуся конусу, а затем поворачивает на 180о
и выводится сверху. В результате этого частицы пыли подвергаются дополнительному усилию, направляющему их в сторону бункера камеры. Это усилие обеспечивает дополнительное ускорение порядка g
/3. Расширяющийся конус позволяет постепенно снизить скорость газового потока и препятствует вторичному уносу частиц.
В подобных пылеуловителях, устанавливаемых непосредственно за доменными печами, скорость газов в свободном сечении кмеры составляет примерно 1,0 м/с, а во входной цилиндрической трубе – около 10 м/с. При этом частицы пыли крупнее 25-30 мкм улавливаются на 65-85%. Гидравлическое сопротивление подобного пылеуловителя с диаметром камеры 10 м и приблизительно такой же высотой цилиндрической части составляет от 150 до 390 Па.
Эффективность пылеуловителя с заглубленным бункером, в зависимости от скорости газов на входе, приведена ниже:
Ïûëü
|
Ñêîðîñòü ãàçîâ íà âõîäå, ì/ñ
|
Êîíöåíòðàöèÿ ïûëè, ã/ì3
|
Ýôôåêòèâíîñòü, %
|
Ðàñïûëèâàåìûé óãîëü (ñîäåðæàíèå ÷àñòèö ðàçìåðîì ìåíåå
60 ìêì – 75,4%)
|
7,3
9,9
12,2
|
34,9
91,0
23,4
|
74,3
63,0
47,0
|
Çîëà (ñîäåðæàíèå ÷àñòèö ðàçìåðîì ìåíåå 60 – 60,6%)
|
5,3
8,6
13,5
|
19,8
21,1
10,3
|
79,7
70,5
55,5
|
Решающее влияние на вторичный унос частиц пыли из подобного пылеуловителя оказывает глубина цилиндрической части камеры, где гасится турбулентный поток газа. Наличие же вторичного уноса подтверждается снижением эффективности с ростом скорости газов.
3.2.2.5 ЦИКЛОНЫ
. Циклонные аппараты благодаря дешевизне и простоте устройства и обслуживания, сравнительно небольшому сопротивлению и высокой производительности являются наиболее распространенным типом сухого механического пылеуловителя.
Циклонные аппараты имеют следующие преимущества:
1) отсутствие движущихся частей в аппарате;
2) надежное функционирование при температурах газов вплоть до 500 о
С без каких-либо конструктивных изменений (если предусматривается применение более высоких температур, то аппараты можно изготовлять из специальных материалов);
3) возможность улавливания абразивных материалов при защите внутренних поверхностей циклонов специальными покрытиями;
4) пыль улавливается в сухом виде;
5) гидравлическое сопротивление аппаратов почти постоянно;
6) аппараты успешно работают при высоких давлениях газов;
7) пылеуловители весьма просты в изготовлении;
8) рост запыленности газов не приводит к снижению фракционной эффективности очистки.
Правильно спроектированные циклоны могут эксплуатироваться надежно в течение многих лет.
Вместе с тем необходимо иметь в виду, что гидравлическое сопротивление высокоэффективных циклонов достигает 1250 – 1500 Па, и частицы размером меньше 5 мкм улавливаются циклонами плохо.

Рис. 3.2. Основные виды конструкций циклонов (по подводу газов): а
– спиральный; б
– тангенциальный; в
– винтообразный; г
– розеточный (циклон с возвратом газов); д
– розеточный (прямоточный циклон)
На рис. 3.2 схематично представлены основные виды конструкций циклонных пылеуловителей. Циклоны различаются по способу подвода газа в аппарат, который может быть спиральным (рис. 3.2, а
), тангенциальным, обычным (рис.3.2, б
) и винтообразным (рис. 3.2, в
), а также осевым (рис.3.2, г, д
). Циклоны с осевым (розеточным) подводом газов работают как с возвратом газов в верхнюю часть аппарата, та и без него (рис. 3.2, д
). Последний тип аппаратов («прямоточные циклоны») отличается низким гидравлическим сопротивлением и меньшей по сравнению с циклонами других типов эффективностью пылеулавливания. Недостатком прямоточных циклонов является необходимость отсоса части газов через бункер для отвода пыли, что способствует их абразивному износу.
Удаление пыли из газов в циклоне протекает в две стадии. На первой стадии частицы переносятся в зону осаждения. Этот процесс осуществляется за счет центробежной силы. Вторая стадия – отделение частиц – начинается, когда концентрация частиц в газовом потоке превышает предельную нагрузку, т.е. то количество пыли, которое в состоянии переносить газовый поток в данных условиях с учетом пристенногоэффекта.
Принципиально циклон работает последующей схеме (рис. 3.3). Газы, направляющиеся в аппарат, поступают в цилиндрическую часть циклона и совершают движение по спирали с возрастающей скоростью от периферии к центру, спускаются по наружной спирали, затем поднимаются по внутренней спирали и выходят через выхлопную трубу. Обычно в циклонах центробежное ускорение в несколько сот, а то и тысячу раз больше ускорения силы тяжести. Поэтому, даже весьма маленькие частицы пыли не в состоянии следовать за линиями тока газов и под влиянием центробежной силы выносятся из кривой движения газов по направлению к стенке.
В цилиндрической камере циклона статическое давление, как и в каждом искривленном течении, сильно падает в направлении от периферии к центру. В основном потоке направленные во внутреннюю сторону сжимающие усилия приходят в равновесное состояние с центробежными силами газов. Более медленно текущий у стенки циклона пограничный слой соответственно испытывает меньшие центробежные силы.
Однако у конической стенки циклона и у его крышки начинает уже сказываться перепад давления, сжимающее поток усилие становится значительно больше центробежной силы, и поток в виде сильного вторичного вихря направляется внутрь, захватывая с собой много частиц пыли. Но так как затем поток еще несколько раз по пути вниз обернется вокруг выхлопной трубы, частицы могут быть вновь отброшены к стенке аппарата.
Вторичный поток, искривленный вдоль конической стенки, захватывает отброшенную к стенке пыль и направляет ее вниз к пылеосадительной камере (бункеру). Без этого потока отдельные частицы, находящиеся у стенки, не смогли бы попасть вниз, поскольку направленная вверх составляющая центробежной силы является большей по сравнению с силой тяжести.
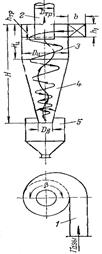
Рис. 3.3. Схема работы циклона: 1
– входной патрубок; 2
– выхлопная труба; 3
– цилиндрическая камера; 5
– пылеосадительная камера
О большом влиянии вторичного потока свидетельствует тот факт, что пыль выносится из лежащих и даже из перевернутых циклонов.
В пылеосадительной камере вследствие сужения в месте соединения газовый поток циркулирует слабее, чем в цилиндрической камере. Однако и в этом случае на оси вихрь имеет пониженное давление. Часть вторичного потока цилиндрической камеры в пылеосадительной камере перемещается вниз и вновь возвращается в ядро вихря. Благодаря этому же отсепарированная пыль может быть вновь захвачена и вынесена в район оси вихря.
3.2.2.6 ВИХРЕВЫЕ ПЫЛЕУЛОВИТЕЛИ
. Основным отличием вихревых пылеуловителей от циклонов является наличие вспомогательного закручивающего газового потока.
На рис. 3.4 показаны две основные разновидности вихревых пылеуловителей. В вихревом аппарате соплового типа (рис. 3.4, а
) запыленный газовый поток закручивается лопаточным завихрителем и двигается вверх, подвергаясь при этом воздействию вытекающих из тангенциально расположенных сопел 3
струй вторичного газа (воздуха). Под действием центробежных сил взвешенные в потоке частицы отбрасываются к периферии, а оттуда – в возбуждаемый струями спиральный поток вторичного газа, направляющий их вниз в кольцевое межтрубное пространство. Вторичный газ в ходе спирального обтекания потока очищаемого газа постепенно полностью проникает в него. Кольцевое пространство вокруг входного патрубка оснащено подпорной шайбой 6
, обеспечивающей безвозвратный спуск пыли в бункер 7
.
Наилучшие результаты по эффективности улавливания достигается при установке сопел, распыливающих вторичный газ, не менее чем в четыре ряда и под углом 30о
. В качестве оптимальной рекомендуется установка лопаток завихрителя по углом 30-40о
при отношении диаметра завихрителя к диаметру аппарата, равном 0,8-0,9.

Рис. 3.4. Конструкция вихревых пылеуловителей: а
– соплового типа; б
– лопаточного типа; 1
– камера; 2
– выходной патрубок; 3
– сопла; 4
– лопаточный завихритель типа «розетка»; 5
– входной патрубок; 6
– подпорная шайба; 7
– пылевой бункер; 8
– кольцевой лопаточный завихритель
Вихревой пылеуловитель лопаточного типа (рис. 3.4, б
) отличается тем, что вторичный газ отбирается с периферии очищенного газа и подается кольцевым направляющим аппаратом с наклонными лопатками 8
.
Как и у циклонов, эффективность вихревых аппаратов с увеличением диаметра падает.
3.2.2.7 ДИНАМИЧЕСКИЕ ПЫЛЕУЛОВИТЕЛИ
. В динамических пылеуловителях очистка газов от пыли осуществляется за счет центробежных сил и силы Кориолиса, возникающих при вращении рабочего колеса (рис. 3.5).

Рис.3.5. Динамический пылеуловитель: 1
корпус вентилятора; 2
– патрубок для отвода пыли; 3
– патрубок для отвода части газового потока на рециркуляцию; 4
– колесо вентилятора
Динамические пылеуловители помимо осаждения частиц пыли из газового потока выполняют еще роль тягодутьевого устройства.
Динамический пылеуловитель потребляет больше энергии, чем обычный вентилятор с идентичными параметрами по производительности и напору. Но это расход энергии меньше, чем требуется при раздельном функционировании центробежного сепаратора и вентилятора.
Наибольшее распространение в отечественной промышленности из динамических аппаратов получил дымосос-пылеуловитель (рис. 3.6). Аппарат предназначен для улавливания частиц пыли со средним диаметром крупнее 15 мкм. Дымосос-пылеуловитель применяется для очистки дымовых газов малых котелен, в литейных производствах для очитки аспирационных выбросов и на асфальтобетонных заводах для очистки сушильных барабанов.

Рис. 3.6. Дымосос-пылеуловитель.
Работа дымососа-пылеуловителя основана на следующем принципе. За счет разности давлений, создаваемых рабочим колесом 2
на валу 1
, запыленный поток поступает в улитку 5
и приобретает криволинейное движение. Под действием центробежных сил частицы пыли отбрасываются к периферии и вместе с небольшим количеством газов (8-10 %) отводятся для окончательного отделения через патрубок 9
в выносной малогабаритный циклон 8
, соединенный с улиткой газоходами. Разгрузка циклона производится через спускной стояк с затвором-мигалкой 10
. Очищенный газовый поток из циклона возвращается в центральную часть улитки.
Аэрозоль протягивается через циклон под действием перепада давлений между центром улитки и ее периферией, который повышается за счет работы вспомогательной крыльчатка 6
. Из центральной зоны улитки очищенные газы через направляющий аппарат 4
поступают в рабочее колесо дымососа, а затем через кожух 3
выбрасываются в дымовую трубу 11
.
Регулировка производительности дымососа осуществляется шибером 7
. При закрывании шибера газовый поток отжимается к периферии улитки, и соответственно эффективность аппарата возрастает.
Для предотвращения обратного выброса отсепарированной пыли с периферии улиточного пылеуловителя и защиты его стенок от абразивного износа предусмотрены защитные козырьки из полосовой стали, которые располагаются на боковинах улитки в периферийной зоне.
3.2.2.8 МОКРЫЕ ПЫЛЕУЛОВИТЕЛИ
. Процесс мокрого пылеулавливания основан на контакте запыленного газового потока с жидкостью, которая захватывает взвешенные частицы и уносит их из аппарата в виде шлама. Метод мокрой очистки газов от пыли считается достаточно простым и в то же время весьма эффективным способом обеспыливания.
Мокрые пылеуловители имеют ряд преимуществ перед аппаратами других типов.
1. Аппараты мокрого типа отличаются сравнительно небольшой стоимостью и более высокой эффективностью улавливания взвешенных частиц по сравнению с сухими механическими пылеуловителями.
2. Мокрые пылеуловители (например, скрубберы Вентури) могут быть применены для очистки газов от частиц размером до 0,1 мкм.
3. Мокрые пылеуловители не только могут успешно с такими высоэффективными пылеуловителями, как рукавные фильтры или электрофильтры, но и использоваться в тех случаях, когда эти аппараты обычно не применяются, например, при высокой температуре и повышенной влажности газов, при опасности возгораний и взрывов очищенных газов или улавливаемой пыли.
4. Аппараты мокрого типа могут одновременно с очисткой газов от взвешенных частиц улавливать парообразные и газообразные компоненты, т.е. их можно использовать в качестве абсорбентов, а также для охлаждения и увлажнения газов качестве теплообменников смешения.
Однако метод мокрого обеспыливания имеет и ряд недостатков.
1. улавливаемый мокрыми пылеуловителями продукт выделяется в виде шлама, что связано с необходимостью обработки сточных вод и, следовательно, с удорожанием процесса очистки.
2. При охлаждении очищаемых газов до температуры, близкой к точке росы, а также при механическом уносе из газоочистного аппарата газовым потоком капель жидкости пыль может осаждаться в газопроводах, дымососах и дымовых трубах. Кроме того, брызгоунос приводит к безвозвратным потерям орошающей жидкости.
3. В случае очистки агрессивных газов аппаратуру и коммуникации необходимо защищать антикоррозионными материалами.
В качестве орошающей жидкости в мокрых пылеуловителях чаще всего применяется вода; при совместном решении вопросов пылеулавливания и химической очистки газов выбор орошающей жидкости (абсорбента) обусловливается процессом абсорбции.
Общепринятой классификации мокрых пылеуловителей до настоящего времени не имеется. Обычно они подразделяются на группы в зависимости от поверхности контакта или по способу действия:
1) полые газопромыватели (оросительные устройства; промывные камеры; полые форсуночные скрубберы);
2) насадочные скрубберы;
3) тарельчатые газопромыватели (барботажные и пенные аппараты);
4) газопромыватели с подвижной насадкой;
5) мокрые аппараты ударно-инерционного действия (ротоклоны);
6) мокрые аппараты центробежного действия;
7) механические газопромыватели (механические скрубберы, динамические скрубберы);
8) скоростные газопромыватели (скрубберы Вентури, эжекторные скрубберы).
Помимо перечисленных групп к мокрым пылеуловителям в какой-то степени могут быть отнесены также мокрые электрофильтры, орошаемые волокнистые фильтры и аппараты конденсационного действия. Что касается аппаратов конденсационного действия, то они до настоящего времени не получили какого-либо широкого применения в промышленности.
Иногда мокрые пылеуловители подразделяют по затратам энергии на низконапорные, средненапорные и высоконапорные. К низконапорным аппаратам относятся пылеуловители, гидравлическое сопротивление которых не превышает 1500 Па. В эту группу входят форсуночные скрубберы, барботеры, мокрые центробежные аппараты и др. К средненапорным мокрым пылеуловителям с гидравлическим сопротивлением от 1500 до 3000 Па относятся некоторые динамические скрубберы, газопромыватели ударно-инерционного действия, эжекторные скрубберы. Группа высоконапорных газопромывателей с гидравлическим сопротивлением больше 3000 Па включает в основном скруббера Вентури и дезинтеграторы.
3.2.2.9 ФИЛЬТРЫ
. В основе работы пористых фильтров всех типов лежит процесс фильтрации газов через пористую перегородку – фильтрующую среду, в ходе которого твердые или жидкие частицы, взвешенные в газе, задерживаются в ней, и газ полностью проходит сквозь нее.
Применяемые фильтрующие пористые перегородки по своей структуре весьма разнообразны, но в большинстве своем они состоят из волокнистых или зернистых элементов, которые условно могут быть разделены на следующие типы.
Гибкие пористые перегородки:
а) тканевые материалы из природных, синтетических и минеральных волокон;
б) нетканевые волокнистые материалы (войлоки, клееные и иглопробивные материалы, бумага, картон, волокнистые маты);
в) ячеистые листы (губчатая резина, пенополиуретан, мембранные фильтры).
Полужесткие пористые перегородки – слои волокон, стружка, вязаные сетки, расположенные на опорных устройствах или зажатые между ними.
Жесткие пористые перегородки:
а) зернистые материалы – пористая керамика и пластмасса, спеченные или спрессованные порошки металлов (металлокерамика), пористые стекла, углеграфитовые материалы и др.;
б) волокнистые материалы – сформированные слои из стеклянных металлических волокон;
в) металлические сетки и перфорированные листы.
Зернистые слои:
а) неподвижные, свободно насыпанные материалы;
б) периодически или непрерывно перемещающиеся материалы.
Поток аэрозоля в объеме фильтрующего материала многократно дробится на мелкие струйки, которые непрерывно сливаются, обтекая отдельные элементы (волокна или зерна), что способствует приближению взвешенных частиц к поверхности элементов или пор, их осаждению на них и удержанию силами адгезии.
В фильтрах уловленные сухие частицы накапливаются в порах или образуют пылевой слой на поверхности перегородки, и таким образом сами становятся для вновь поступающих частиц частью фильтрующей среды. Однако по мере накопления частиц размер пор и общая пористость перегородки неизбежно уменьшается, а сопротивление движению газов возрастает; поэтому в определенный момент возникает необходимость разрушения и удаления пылевого осадка (для снижения перепада давления и сохранения начальной скорости фильтрации). В ряде случаев требуется замена забитого пылью фильтра или переснаряжение его новыми фильтрующими материалами. Таким образом, процесс фильтрации в большинстве случаев предусматривает периодическую регенерацию фильтров. При улавливании жидких частиц накапливающаяся жидкость может удалятся из пористой перегородки самопроизвольно, т.е. фильтр подвергается саморегенерации.
Современные фильтры в зависимости от назначения и величин входной и выходной концентраций улавливаемой дисперсной фазы условно разделяют на три класса.
Фильтры тонкой очистки (высокоэффективные или абсолютные фильтры) – предназначены для улавливания с очень высокой эффективностью (обычно выше 90%) в основном субмикробных частиц из промышленных газов и воздуха при низкой входной концентрации (менее 1 мг/м3
) и малой скорости фильтрации (менее 10 м/с). Такие фильтры применяют для улавливания особо токсичных частиц, а также для ультратонкой очистки воздуха при проведении некоторых технологических процессов или в особо чистых помещениях, в которых воздух служит рабочей средой; обычно эти фильтры не подвергаются регенерации.
Фильтры для очистки атмосферного воздуха (воздушные фильтры) – используются в системах приточной вентиляции и кондиционирования воздуха. Они рассчитаны на работу при концентрации пыли менее 50 мг/м3
, часто при высокой скорости фильтрации (до 2,5-3 м/с). Фильтры этого класса бывают нерегулируемые, а также периодически или непрерывно регулируемые.
Промышленные (тканевые, зернистые, грубоволокнистые) фильтры применяются для очистки промышленных газов в основном с высокой концентрацией дисперсной фазы (до 60 г/м3
). Для периодического или непрерывного удаления накапливающейся в фильтрующей перегородке пыли фильтры этого класса имеют устройства для регенерации, позволяющие поддерживать производительность на заданном уровне и возвращать ценные продукты в производство; фильтры этого класса нередко являются составной частью технологического оборудования.
3.2.2.9.1 ВОЛОКНИСТЫЕ ФИЛЬТРЫ
. Волокнистые фильтры (набивные, маты, из картона, бумаги и др.) представляют собой различные толщины, в которых более или менее однородно распределены волокна. Это фильтры объемного действия, так как они рассчитаны на улавливание и накапливание частиц преимущественно по всей глубине слоя. Сплошной слой пыли образуется только на поверхности наиболее плотных материалов, обычно при фильтрации относительно крупных частиц и к концу срока службы фильтра.
Волокнистые фильтры используют при концентрации дисперсной твердой фазы 0,5-5 мг/м3
. при таких концентрациях основная доля частиц обычно имеет размеры менее 5-10 мкм, значительную долю составляют субмикронные частицы.
Для фильтров используют естественные или специально получаемые волокна толщиной от 0,01 до 100 мкм, а также их смеси. Толщина фильтрующих сред составляет от десятков долей миллиметра (бумага) до двух метров (многослойные глубокие насадочные фильтры долговременного использования).
Волокнистые фильтры, применяемые для улавливания твердых или жидких частиц из газов и воздуха во время проведения технологических процессов или выбрасываемых в атмосферу, называются промышленными, в отличие от воздушных, предназначены для очистки атмосферного воздуха от пыли в системах приточной вентиляции.
Различают следующие виды промышленных волокнистых фильтров:
1) сухие – тонковолокнистые, электростатические, глубокие фильтры предварительной очистки (предфильтры);
2) мокрые – сеточные, самоочищающиеся, с периодическим или непрерывным орошением.
3.2.2.9.2 ЭЛЕКТРОФИЛЬТРЫ.
Коронный разряд и принцип действия электрофильтров. Электрофильтры – устройства, в которых очистка газов от взвешенных в них частиц происходит под действием электрических сил. Для этого частицам сообщается электрический заряд. В результате действия электрического поля на заряженные частицы они выводятся из очищаемого газового потока и осаждаются на осадительных электродах.
Зарядка частиц в электрофильтрах происходит в поле коронного заряда.
Коронный заряд представляет собой специфическую форму незавершенного электрического заряда, характерного для систем электродов с резко неоднородным полем. В качестве примера на рис. 3.7 представлено распределение напряженности электростатического поля в промежутке между коаксиальными цилиндрами. Напряженность поля существенно возрастает по направлению к проводу (внутреннему цилиндру) и достигает максимального значения у его поверхности.
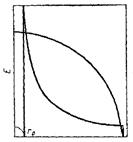
Рис. 3.7. распределение напряженности электростатического поля в промежутке между коаксиальными цилиндрами
Ионизационные процессы при коронном заряде сосредоточены в узкой области, где напряженность поля наибольшая, т.е. вблизи коронирующего электрода.
В зоне ионизации присутствуют положительные ионы и электроны, которые при выходе из зоны ионизации превращаются отрицательные ионы. При отрицательной полярности коронирующего электрода положительные ионы быстро достигают его. Во внешней области коронного заряда присутствуют только отрицательные ионы, которые создают в межэлектродном пространстве униполярный объемный заряд.
Во внешней области коронного заряда ионизационные процессы отсутствуют, так как напряженность поля там для ионизации недостаточна. Ток коронного разряда обеспечивается за счет движущегося в промежутке между электродами униполярного объемного заряда. Если во внешней области коронного разряда, занимающей преобладающую часть межэлектродного пространства, находятся твердые или жидкие частицы, то ионы из объемного заряда, осаждаясь на поверхности этих частиц, сообщают им электрический заряд.
В преобладающем большинстве случаев в одном и том же поле коронного разряда происходит и зарядка частиц и их выделение из газового потока за счет движения их под действием поля в направлении, перпендикулярном потоку газа. Это позволяет упростить конструкцию аппаратов, сделать их более компактными. Кроме того, при униполярном коронном разряде удается получить распределение поля, способствующее степени очистки газов в электрофильтрах.
Конструктивная схема электрофильтра представлена на рис. 3.8. Между двумя осадительными плоскостями натянут ряд проводов. В пространство между каждой из плоскостей и проводами поступает запыленный газ. В поле коронного разряда, возникающего при подаче высокого напряжения на проводе, частицы заряжаются и под действием поля движутся к осадительным плоскостям, с которых они периодически удаляются. Таким образом, концентрация пыли в газе при прохождении его через электрофильтр значительно уменьшается.
Электрофильтры рассмотренного вида носят название пластинчатых. Второй тип электрофильтров – трубчатые (рис.3.9), в которых используется система электродов «коаксиальные цилиндры».
В трубчатых электрофильтрах удается получить более высокие значения рабочего напряжения, чем в пластинчатых. Вместе с тем, в пластинчатых электрофильтрах более просто решаются проблемы очистки очень больших объемов газов и удаления пыли с осадительных электродов.

Рис. 3.8. Принципиальная схема электрофильтра: 1
– осадительные электроды; 2
– коронирующие электроды; 3
– источник высокого напряжения
Рис. 3.9. Трубчатый электрофильтр: 1
– цилиндрический осадительный электрод; 2
– коронирующий электрод; 3
– узел подвода газа и сбора пыли
Осаждение частиц на электроды происходит под действием электрического поля из области газа, непосредственно примыкающей к электродам. Убыль частиц из этой области восполняется в результате перемещения частиц из остального межэлектродного пространства под действием поля и за счет увлечения частиц турбулентными пульсациями газа.
3.2.3 ПРИТОЧНАЯ ВЕНТИЛЯЦИЯ
Приточные системы служат для подачи в вентилируемые помещения чистого воздуха взамен удаленного. Приточный воздух в необходимых случаях подвергается специальной обработке (очистке, нагреванию, увлажнению и т.д.).
3.2.4 ВЫТЯЖНАЯ ВЕНТИЛЯЦИЯ
Вытяжная вентиляция удаляет из помещения (цеха, корпуса) загрязненный или нагретый обработанный воздух.
В общем случае в помещении предусматриваются как приточные, так и вытяжные системы. Их производительность должна быть сбалансирована с учетом возможности поступления воздуха в смежные помещения или их смежных помещений. В помещениях может быть также предусмотрена только вытяжная или только приточная система. В этом случае воздух поступает в данное помещение снаружи или из смежных помещений через специальные проемы или удаляется из данного помещения наружу, или перетекает в смежные помещения.
Как приточная, так и вытяжная вентиляция может устраиваться на рабочем месте (местная) или для всего помещения (общеобменная).
3.2.5 МЕСТНАЯ ВЕНТИЛЯЦИЯ
Местной вентиляцией называется такая, при которой воздух подают на определенные места (местная приточная вентиляция) и загрязненный воздух удаляют только от мест образования вредных выделений (местная вытяжная вентиляция).
3.2.5.1 МЕСТНАЯ ПРИТОЧНАЯ ВЕНТИЛЯЦИЯ
. К местной приточной вентиляции относятся воздушные души (сосредоточенный приток воздуха с повышенной скоростью). Они должны подавать чистый воздух к постоянным рабочим местам, снижать в их зоне температуру окружающего воздуха и обдувать рабочих, подвергающихся интенсивному тепловому облучению.
Метеорологические условия и скорость движения воздуха на рабочем месте должны соответствовать характеру работы и особенностям вредных выделений. Так, при воздействии на рабочего теплового облучения интенсивностью более 300 ккал/м2
ч, температура воздуха на рабочем месте и подвижность воздуха должны удовлетворять требованиям санитарных норм промышленного проектирования, приведенным в табл. 3.2.
К местной приточной вентиляции относятся и воздушные оазисы – участки помещений, отгороженные от остального помещения передвижными перегородками высотой 2-2,5 м, которых нагнетается воздух с пониженной температурой.
Местную приточную вентиляцию применяют также в виде воздушных завес (у ворот, печей и пр.), которые создают как бы воздушные перегородки или изменяют направление потоков воздуха. Местная вентиляция требует меньших затрат, чем общеобменная.
Таблица 3.2.
Температура Т (о
С) и скорость движения воздуха V (м/с) при воздушном душировании
Период года
|
Категория работы
|
При тепловом облучении интенсивностью
|
от 300 до
600 ккал/м3
ч
|
от 600 до
1200 ккал/м3
ч
|
от 1200 до
1800 ккал/м3
ч
|
t (о
С)
|
V (м/с)
|
t (о
С)
|
V (м/с)
|
t (о
С)
|
V (м/с)
|
Теплый (температура наружного воздуха +10о
С и выше)
|
Легкая
|
22-24
|
0,5-1
|
21-23
|
1-2
|
19-20
|
2-3
|
Средней тяжести
|
21-23
|
1-2
|
20-22
|
2-3
|
19-21
|
3
|
Тяжелая
|
20-22
|
2-3
|
19-21
|
3
|
18-20
|
3
|
Холодный (температура наружного воздуха ниже +10о
С)
|
Легкая
|
19-21
|
0,1-1
|
18-20
|
1-2
|
17-18
|
2-2,5
|
Средней тяжести
|
17-19
|
0,5-1
|
16-18
|
1-2
|
16-17
|
2-3
|
Тяжелая
|
16-18
|
1-2
|
16-17
|
2-3
|
16
|
3
|
В производственных помещениях при выделении вредностей (газов, влаги, теплоты и т.д.) обычно применяют смешанную систему вентиляции – общую для устранения вредностей во всем объеме помещения и местную (местные отсосы и приток) для обслуживания рабочих мест.
3.2.5.2 МЕСТНАЯ ВЫТЯЖНАЯ ВЕНТИЛЯЦИЯ
. Местную вытяжную вентиляцию применяют, когда места выделений вредностей в помещении локализованы и можно не допустить их растворение по всему помещению.
Местная вытяжная вентиляция в производственных помещениях обеспечивает улавливание и отвод вредных выделений: газов, дыма, пыли и частично выделяющегося из оборудования тепла.
Для удаления вредностей применяют местные отсосы (укрытия в виде шкафов, зонты, бортовые отсосы, завесы, укрытия в виде кожухов у станков и др.).
Основные требования, которыми они должны удовлетворять:
Место образования вредных выделений должно быть полностью укрыто.
Конструкция местного отсоса должна быть такой, чтобы отсос не мешал нормальной работе и не снижал производительность труда.
Вредные выделения необходимо удалять от места их образования в направлении их естественного движения (горячие газы и пары надо удалять вверх, холодные и тяжелые газы и пыль - вниз).
Конструкции местных отсосов условно делят на три группы:
Полуоткрытые отсосы (вытяжные шкафы, зонты, см. рис. 3.10). Объемы воздуха определяются расчетом.
Открытого типа (бортовые отсосы). Отвод вредных выделений достигается лишь при больших объемах отсасываемого воздуха (рис. 3.11).
Система с местными отсосами изображена на рис. 3.12.
Основными элементами такой системы являются местные отсосы-укрытия (МО), всасывающая сеть воздуховодов (ВС), вентилятор (В) центробежного или осевого типа, ВШ – вытяжная шахта.

Рис. 3.10. Зонты-козырьки у нагревательных печей: а
– у щелевого отверстия при выпуске через него продуктов горения; б
– у отверстии, снабженного дверкой при выпуске продуктов горения через газовые окна
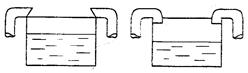
рис. 3.11. Бортовые отсосы
При устройстве местной вытяжной вентиляции для улавливания пылевыделений удаляемый из цеха воздух, перед выбросом его в атмосферу, должен быть предварительно очищен от пыли. Наиболее сложными вытяжными системами являются такие, в которых предусматривают очень высокую степень очистки воздуха от пыли с установкой последовательно двух или даже трех пылеуловителей (фильтров).
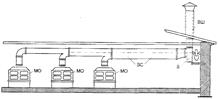
Рис. 3.12. Схема местной вытяжной вентиляции
Местные вытяжные системы, весьма эффективны, так как позволяют удалять вредные вещества непосредственно от места их образования или выделения, не давая им распространиться в помещении. Благодаря значительной концентрации вредных веществ (паров, газов, пыли), обычно удается при небольшом объеме удаляемого воздуха достичь хорошего санитарно-гигиенческого эффекта. Однако, местные системы не могут решить всех задач, стоящих перед вентиляцией: не все вредные выделения могут быть локализованы этими системами, например, вредные выделения, рассредоточенные на значительной площади или в объеме; подача воздуха в отдельные зоны помещения не может обеспечить необходимые условия воздушной среды, если работа производится на всей площади помещения или ее характер связан с перемещением и т.д.
3.2.6 ОБЩЕОБМЕННЫЕ СИСТЕМЫ ВЕНТИЛЯЦИИ
Как приточные, так и вытяжные, предназначены для осуществления вентиляции в помещении в целом или в значительной его части.
Общеобменные вытяжные системы относительно равномерно удаляют воздух из всего обслуживаемого помещения, а общеобменные приточные системы подают воздух и распределяют его по всему объему вентилируемого помещения.
3.2.6.1 ОБЩЕОБМЕННАЯ ПРИТОЧНАЯ ВЕНТИЛЯЦИЯ
. Общеобменная приточная вентиляция устраивается для ассимиляции избыточного тепла и влаги, разбавления вредных концентраций паров и газов, не удаленных местной и общеобменной вытяжной вентиляцией, а также для обеспечения расчетных санитарно-гигиенических норм и свободного дыхания человека в рабочей зоне.
при отрицательном тепловом балансе, т.е. при недостатке тепла, общеобменную приточную вентиляцию устраивают с механическим побуждением и с подогревом всего объема приточного воздуха. Как правило, перед подачей воздух очищают от пыли.
При поступлении вредных выделений в воздух цеха количество приточного воздуха должно полностью компенсировать общеобменную и местную вытяжную вентиляцию.
3.2.6.2 ОБЩЕОБМЕННАЯ ВЫТЯЖНАЯ ВЕНТИЛЯЦИЯ.
Простейшим типом общеобменной вытяжной вентиляции является отдельный вентилятор (обычно осевого типа) с электродвигателем на одной оси (рис. 3.13), расположенный в окне или в отверстии стены. Такая установка удаляет воздух из ближайшей к вентилятору зоны помещения, осуществляя лишь общий воздухообмен.
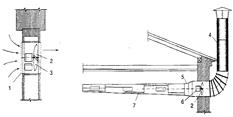
Рис. 3.13. Простейшие схемы вытяжной вентиляции: 1
– утепленный клапан; 2
– вентилятор; 3
– лопасти вентилятора; 4
– вытяжная шахта; 5
– шибер; 6
– электродвигатель; 7
– вытяжная сеть
В некоторых случаях установка имеет протяженный вытяжной воздуховод. Если длина вытяжного воздуховода превышает 30-40 м и, соответственно, потери давления в сети составляют более 30-40 кг/м2
, то вместо осевого вентилятора устанавливается вентилятор центробежного типа.
Когда вредными выделениями в цехе являются тяжелые газы или пыль и нет тепловыделений от оборудования, вытяжные воздуховоды прокладывают по полу цеха или выполняют в виде подпольных каналов.
В промышленных зданиях, где имеются разнородные вредные выделения (теплота, влага, газы, пыль и т.п.) и их поступление в помещение происходит в различных условиях (сосредоточено, рассредоточено, на различных уровнях и т.п.), часто невозможно обойтись какой-либо одной системой, например, местной или общеобменной.
В таких помещениях для удаления вредных выделений, которые не могут быть локализованы и поступают в воздух помещения, применяют общеобменные вытяжные системы.
В определенных случаях в производственных помещениях, наряду с механическими системами вентиляции, используют системы с естественным побуждением, например, системы аэрации.
3.2.7 КАНАЛЬНАЯ И БЕСКАНАЛЬНАЯ ВЕНТИЛЯЦИЯ
Системы вентиляции имеют либо разветвленную сеть воздуховодов для перемещения воздуха (канальные системы), либо каналы (воздуховоды) могут отсутствовать, например, при установке вентиляторов в стене, в перекрытии, при естественной вентиляции и т.д. (бесканальные системы).
Таким образом, любая система вентиляции может быть охарактеризована по указанным выше четырем признакам: по назначению, зоне обслуживания, способу перемещения воздуха и конструктивному исполнению.
ГЛАВА 4. ПРИБОРЫ ИЗМЕРЕНИЯ И КОНТРОЛЯ, ИСПОЛЬЗУЕМЫЕ В СИСТЕМАХ ОТОПЛЕНИЯ, ВЕНТИЛЯЦИИ И КОНДИЦИОНИРОВАНИЯ
4.1 ОЩИЕ ТРЕБОВАНИЯ В КОНТРОЛЮ ПАРАМЕТРОВ МИКРОКЛИМАТА
В соответствии с требованиями СНиП 2.04.05 подлежат контролю параметры теплоносителя (холодоносителя) и воздуха в следующих системах:
- внутреннего теплоснабжения
— температура и давление теплоносителя в общих подающем и обратном трубопроводах в помещении для приточного вентиляционного оборудования; температура и давление теплоносителя на выходе из теплообменных устройств;
- отопления с местными отопительными приборами
- температура воздуха в контрольных помещениях (по требованию технологической части проекта);
- воздушного отопления и приточной вентиляции
— температура приточного воздуха и воздуха в контрольном помещении (по требованию технологической части проекта);
- воздушного душирования
— температура подаваемого воздуха;
- кондиционирования
— температура воздуха наружного, рециркуляционного, приточного после камеры орошения или поверхностного воздухоохладителя и в помещениях; относительная влажность воздуха в помещениях (при ее регулировании);
- холодоснабжения
— температура холодоносителя до и после каждого теплообменного или смесительного устройства; давление холодоносителя в общем трубопроводе;
- вентиляции и кондиционирования с фильтрами, камерами статического давления, теплоутилизаторами
— давление и разность давлений воздуха (по требованию технических условий на оборудование или по условиям эксплуатации).
4.2 ИЗМЕРИТЕЛЬНЫЕ ПРИБОРЫ СИСТЕМ ОТОПЛЕНИЯ, ВЕНТИЛЯЦИИ И КОНДИЦИОНИРОВАНИЯ
В системах отопления для измерения температуры воды и пара применяют ртутные и спиртовые термометры: ртутные — для температур выше 35 о
С спиртовые — ниже —35 о
С.
Термометры устанавливают на трубопроводах навстречу потоку. При измерении температуры среды с избыточным давлением нижнюю
часть термометра помещают в гильзу, погруженную в измеряемую среду. По форме нижней части термометры могут быть прямыми и изогнутыми под углом 90 или 135° (табл. 4.1).
Таблица 4.1.
Технические данные термометров
Номер термометра
|
Интервалы измерения температуры, о
С
|
Цена деления шкалы, о
С, при длине верхней верхней части термометра, мм
|
Длина погружаемой части термометра, мм
|
240
|
160
|
прямого
|
углового
|
1
|
-90…+30
|
1
|
-
|
66
|
104
|
2
|
-30…+50
|
0,5
|
1
|
103
|
141
|
3
|
-60…+500
|
1
|
1
|
163
|
201
|
4
|
0…+100
|
1
|
1
|
253
|
291
|
5
|
0…+160
|
1
|
2
|
403
|
441
|
6
|
0…+200
|
1
|
2
|
633
|
680
|
7
|
0…+300
|
2
|
-
|
1000
|
1050
|
8
|
0…+350
|
5
|
-
|
1600
|
1300
|
Примечание: Диаметр погружаемой части термометра (7,5 0,5) мм
Манометры, мановакуумметры, вакуумметры (табл. 4.2) предназначены для измерения избыточного и вакуумметрического давления в системах отопления.
Таблица 4.2.
Пределы измерения манометров и вакуумметров
Прибор
|
Марка
|
Предел измерения, МПа
|
Манометр
|
ОБМ1-100, МОШ1-100
ОБМ1-160, Мош1-160
М-250
|
0…1; 0,16; 0,25; 0,4; 0,6; 1; 1,6; 2,5; 4; 6
0…0,1; 0,16; 0,25; 0,4; 0,6; 1; 1,6; 2,5; 4; 6; 10
0…0,6; 1; 1,6; 2,5; 4; 5; 10
|
Мановакууметр
|
ОБМ В1, МВОШ1
|
-0,1…0,06; 0,15; 0,34 0,5; 0,9; 1,5; 2,4
|
Вакууметр
|
ОБВ1, ВОШ1
|
-0,1…0
|
В системах вентиляции и кондиционирования для определения давления широко применяют U-образные манометры (рис.4.1).
Давление определяют по разности уровней в коленах манометра:
, (4.1)
где - плотность заливаемой жидкости (для воды =1000 кг/м3
, для ртути = 13600 кг/м3
, для спирта =800…810 кг/м3
); g – ускорение свободного падения, равное 9,81 м/с2
.

Рис. 4.1. U-образный манометр: 1
– стеклянная трубка; 2
– деревянная планка; 3
– шкала
Ртуть применяют для измерения больших давлений, а спирт – в случае выполнения измерений при низких температурах.
Модификацией U-образного манометра является напорометр (рис. 4.2). В нем одно из колен манометра заменено резервуарчиком, площадь поперечного сечения которого во много раз больше, чем у трубки. Это позволяет не учитывать изменение уровня в резервуаре по сравнению с изменением уровня в трубке и вести отчет только по уровню в ней. Для большей точности и простоты отсчетов трубку делают наклонной с постоянным или переменным углом наклона .

Рис.4.2. Наклонный напорометр: 1
– стеклянный резервуар; 2
– трубка; 3
– колодка; 4
– шкала; 5
– клин
Для определения давлений и скоростей воздуха применяют несложную по конструкции пневмометрическуб трубку (рис.4.3). Она представляет собой две спаянные трубки – трубку 1
, имеющую полушаровую поверхность с отверстием посередине и предназначенную для измерения полных давлений, и трубку 2
, имеющую скошенный с двух сторон глухой конец для измерения статических давлений.На определенном расстоянии от скошенного конца выполнены четыре отверстия диаметром 0,5…0,8 мм.
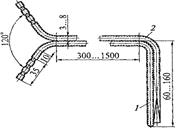
Рис.4.3. Пневмометрическая трубка
Схемы присоединения пневмометрической трубки к напопрометру приведены на рис. 4.4.
Для измерения полного положительного давления
трубку полного давления 1
присоединяют к штуцеру 2
резервуара напорометра, а штуцер трубки 3
напорометра оставляют открытым (см. рис. 4.4, а). Полное отрицательное давление
определяют присоединением трубки полного давления 1
к штуцеру трубки 3
напорометра при открытом штуцере 2
(см. рис. 4.4, б). Присоединив трубку статического давления 4
к штуцеру 2
резервуара напорометра при открытом штуцере трубки 3
(см. рис. 4.4, в), замеряют статическое положительное давление
. Если присоединить трубку статического давления 4
к штуцеру трубки 3
, а штуцер 2
открыть (см. рис. 4.4, г), то можно замерить статическое отрицательное давление
. Присоединив трубку полного давления 1
к штуцеру 2
напорометра, а трубку 4
к штуцеру трубки 3
(см. рис. 4.4, д), измеряют скоростное (динамическое давление
).
Во всех случаях пневмометрическую трубку нужно вводить в воздуховод открытым концом против потока воздуха. Если прибор установлен в помещении, в котором поддерживается разрежение или, наоборот, подпор, то открытый штуцер прибора следует соединить с атмосферой.
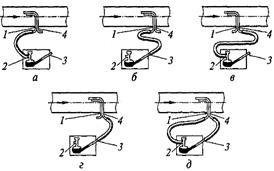
Рис. 4.4. Схемы присоединения пневмометрической трубки к напорометру при замерах давления: а
– полного положительного; б
– полного отрцательного; в
– статического положительного; г
– статического отрицательного; д
– скоростного; 1
– трубка полного давления; 2
– штуцер резервуара напорометра; 3
– трубка напорометра; 4
– трубка статического давления
Определить линейную , м/с, или массовую U
, кг/(м2
с), скорость воздуха в интересующей точке вентиляционной системы можно, измерив динамическое давление в ней , Н/м2
:
; (4.2)
. (4.3)
Принимая плотность воздуха =1,3 кг/м3
, получаем и . Этими формулами можно пользоваться при температурах воздуха 15…25о
С.
Для определения расхода воздуха приборы устанавливают по возможности на длинном прямом участке воздуховода постоянного сечения, так как отводы и тройники искажают скоростное поле на значительной длине воздуховода.
Среднее значение скоростных давлений, замеряемых в различных точках сечения воздуховода, определяют по формуле
, (4.4)
где - скоростные давления, замеряемые соответственно в точках 1, 2, …, n
сечения, n
– число точек замеров.
Для измерения скорости движения можно пользоваться анемометром, который представляет собой вертушку, вращающуюся под действием набегающего потока воздуха. Вертушка соединена со счетным механизмом. Замеры этим прибором производят следующим образом. Записывают начальное показание счетчика анемометра, с выключенным механизмом устанавливают его в воздушном потоке и через 5…10 с выключают счетчик одновременно с секундомером. Через 1…2 мин счетчик выключают и записывают его конечное показание. Затем разность конечного и начального отсчетов делят на время замера в секундах. Пользуясь тарировочным графиком, которым снабжается каждый анемометр, переводят полученный результат от деления в значение скорости в метрах в секунду.
Для измерения скоростей от 1 до 20 м/с используют чашечные анемометры. Измерение анемометром производят в открытых концах воздуховодов, в приточных и вытяжных отверстиях, в проемах внешних ограждений. Для большей точности показаний анемометры должны
быть укреплены на рейках. Счетный механизм пускают и выключают с помощью штуцера. Ось колеса чашечного анемометра должна быть перпендикулярна оси потока, а ось колеса крыльчатого анемометра должна совпадать с направлением потока. В каждом поеме замер нужно производить два раза. Разница между результатами не должна превышать %, в противном случае производят дополнительный замер. В открытых проемах и отверстиях площадью до 1…2 м2
скорость воздуха замеряют при медленном равновесном передвижении анемометра по всему сечению отверстия или проема.
Для замера малых скоростей движения воздуха (до 1 м/с) может быть использован кататермометр. Это термометр с цилиндрическим или шаровым резервуаром внизу, который переходит в капилляр с расширением в верхней части. Шкала кататермометра проградуирована от 35 до 40о
С в цилиндрическом приборе и от 33 до 40о
С – в шаровом. Принцип действия прибора основан на зависимости скорости охлаждения его резервуара от метеорологических условий, в частности от скорости движения воздуха.
На таком же принципе основано действие термоанемометров (рис. 4.5). В этих приборах приемником служит проволока, нагреваемая электрическим током до заданной температуры. Измерение температуры производят электрометром или термопарой.

Рис. 4.5. Термоанемометр: 1
– гальванометр; 2
– вилка измерительного преобразователя; 3
– зажим для включения прибора в сеть; 4
– переключатель питания; 5
– переключатель для измерения температуры или скорости движения воздуха; 6
– переключатель «Измерение - Контроль»;7
– ручка регулирования напряжения; 8
– ручка регулировании подогрева; 9
– защитный футляр измерительного преобразователя; 10
– измерительный преобразователь (микросопротивление)
Объем воздуха V
, м3
, проходящего в течение 1 с через проем, отверстие или сечение воздуховода, подсчитывают по формуле
, (4.5)
где - средняя скорость воздушного потока, м/с, замеряемая анемометром; F
– площадь сечения воздуховода, м2
.
Для измерения относительной влажности воздуха в вентиляционных установках применяют психрометр (рис. 4.6), имеющий шкалу от -15 до+50о
С с ценой деления 0,2о
С или шкалу от 0 до 45о
С. Он состоит из двух одинаковых ртутных термометров – сухого и влажного (смоченного).
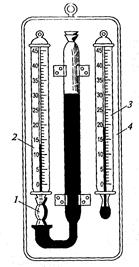
Рис. 4.6. Психрометр: 1
– резервуар для ртути; 2
влажный термометр; 3
– сухой термометр;4
– планка
Резервуар влажного ртутного термометра обернут гигроскопической тканью, конец которой опущен в стаканчик с дистиллированной водой. Вследствие испарения влаги смоченный термометр показывает более низкую температуру, чем сухой. По разности показаний этих термометров, пользуясь специальными таблицами или графиками, определяют относительную влажность воздуха.
Аспирационный психрометр (рис. 4.7) в верхней части имеет вентилятор 3
, который приводят в действие заводным механизмом 2
или электромотором. Вентилятор с равномерной скоростью протягивает через прибор исследуемый воздух. Этот прибор более точен, чем стационарный, так как конструкция его исключает влияние на показания неравномерной скорости воздуха и теплового облучения.
При необходимости более точного определения относительной влажности воздуха могут быть использованы термовлагометры ТВ-2 и датчики влажности ДИВ-3 (абсолютная погрешность % в диапазоне температур 5…35о
С), а также автоматические непрерывно действующие гигрометры «Волна-1М» (абсолютная погрешность % в диапазоне температур 0…60о
С). Чувствительным элементом термовлагометра ТВ-2 является пленочный хлористолитиевый влагочувствительный элемент сорбционного типа, сопротивление которого изменяется в зависимости от относительной влажности воздуха. Для компенсации зависимости сопротивления влагочувствительного элемента от температуры последовательно с ним включены два терморегистра.
В качестве чувствительного элемента гигрометра «Волна-1М» используется пьезоэлектрический резонанс, покрытый слоем гигроскопического вещества. Принцип действия прибора основан на измерении изменения частоты колебаний резонанса в результате сорбции влаги пленкой, нанесенной на его поверхность.
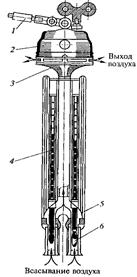
Рис. 4.7. Аспирационный психрометр с вентилятором: 1
– ручка-подвеска; 2
– заводной механизм вентилятора; 3
– вентилятор; 4
– сухой термометр; 5
– влажный термометр; 6
– смоченная марля
4.3 ПРИБОРЫ И СРЕДСТВА КОНТРОЛЯ НАЛИЧИЯ ВРЕДНЫХ ВЕЩЕСТВ И ПЫЛИ В ВОЗДУХЕ
При контроле воздушной среды на содержание вредных веществ применяют различные методы: лабораторные, индикационные, экспрессные, инструментальные.
Лабораторные методы
дают возможность точно определить микроколичества токсичных веществ в воздухе, но при этом требуют значительного времени и применяются, главным образом, в исследовательских работах.
Для качественного и количественного анализа органических и неорганических газообразных смесей в лабораторных условиях может быть использован, например, универсальный хроматограф «Биохром-1». В основу принципа действия прибора положен хроматографический метод, который заключается в разделении веществ в потоке газоносителя.
Индикационные методы
отличаются простотой, с их помощью можно быстро производить качественные определения. Например, бумажка, пропитанная уксуснокислым свинцом, чернеет в присутствии следов сероводорода; бумажка, пропитанная парадиметиламинобензальдегидом (бумажка Прокофьева), краснеет в присутствии следов фосгена и т.д. Индикационные методы применяются, когда нежелательно присутствие токсичных веществ даже в очень малых концентрациях, а при их наличии требуются особые срочные меры (пуск аварийной вентиляции, нейтрализация загазованного участка, применение средств индивидуальной защиты и др.). Количественные определения токсичных веществ в воздухе при помощи индикационных методов можно произвести только ориентировочно.
В практической деятельности для проведения экспрессных методов
химического анализа используют переносные универсальные газоанализаторы УГ-1 УГ-2 УГ-3, ГХ-4, ГХ-5, ГХ-6, ГХ-СО-5, рудничный индикатор и другие приборы. К ним прилагают наборы индикаторных трубок, реактивной бумаги, специальные растворы со стандартными шкалами.
Принцип действия широко применяемого газоанализатора УГ-3 основан на протягивании через индикаторную трубку строго определенного объема исследуемого воздуха. Побудителем расхода воздуха является резиновый сильфон, растягиваемый пружиной. Объем воздуха задается по шкале прибора в диапазоне 0...400 см3
путем измерения угла поворота барабана, на который натягиваются два тросика, соединенных с подвижным концом сильфона. Цена одного деления шкалы прибора 10 см3
. По длине окрашенного столбика порошка в индикаторной трубке судят о концентрации анализируемого газа (пара) в воздухе. Газоанализатор УГ-3 имеет небольшие размеры (204 104 94 мм) и массу (1,7 кг), прост и удобен в обращении.
Наиболее совершенными являются инструментальные методы
контроля загазованности воздушной среды, выполняемые с помощью газоанализаторов и газосигнализаторов, принцип действия которых основан на фотоколориметрическом, термохимическом, ионизационном, эмиссионном, кулонометрическом и других способах анализа.
Различают автоматические газоанализаторы и газоанализаторы периодического действия. Автоматические газоанализаторы осуществляют обычно непрерывную регистрацию уровня загазованности, выдавая результаты на бумаге.
Газосигнализаторы настраивают на определенный уровень загазованности (ПДК, взрывоопасное содержание газа и др.), при достижении которого они дают световой или звуковой сигнал.
На практике используют достаточно много приборов, рассчитанных на определение различных химических веществ. К ним следует отнести: ФЛ-5501М (универсальный газоанализатор); ТХ-2104, ПГ-1, Г-СОМ, «Паллади-2»; ФЛ 2106 (окись углерода); ГСФ-З (фосген); ФК-560, ФЛ 6602 (сероводород); ИКРП (ртуть); ФКГ—3, ФЛ 6201 (хлор); ФГЦ-1Е, 2, 3, 4 (сероуглерод); ФК-450, ФЛ 4504 (окислы азота); ГПК-1 (сернистый газ); «Гамма-1», «Сигма- 1» (органические вещества) и др. Получили распространение газосигнализаторы взрывоопасных газов и паров: ПГФ2М 1, ИВП-1, СВК-ЗМ1, ИВК-1, ПИВ-1, ГБ-3, СТХ-5У4, СТХ-6, ТХ-2102 (2104), ГИК-1 и др.
Ленточные фотометры типа ФЛ являются стационарными автоматическими показывающими и самопишущими приборами, предназначенными для непрерывного измерения в циклическом режиме микроконцентраций окиси углерода (ФЛ 2106), двуокиси азота (ФЛ 4504), хлора (ФЛ 6201), Сероводорода (ФЛ 6602), фреона (ФЛ 6803), двуокиси азота, сернистого ангидрида, аммиака, гидразингидрата, озона и других газов (ФЛ 550 1М). Конструктивно универсальный ленточный фотометр ФЛ 5501М имеет газовую, электрическую и кинематическую схемы.
Газовая схема (рис. 4.8) включает в себя: реакционную камеру 1
с поджимным устройством, в которой происходит обработка газом ленты 2
, смоченной индикаторным составом; побудитель расхода 7
для просасывания анализируемой газовой смеси через прибор; ротаметр 3
для контроля количества просасываемого газа; химический 5
и контрольный 6
фильтры для защиты побудителя расхода и регулирующего дросселя 4
. В фотометре предусмотрена байпасная газовая линия с контрольным фильтром 9
с запорно-регулирующим вентилем 8
для регулирования расхода газовой смеси.
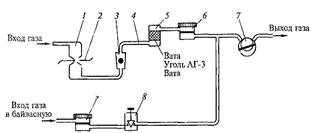
Рис. 4.8. Газовая схема универсального фотометра ФЛ 5501М: 1
– реакционная камера; 2
– лента; 3
– ротаметр; 4
– дроссель; 5,6,9
– фильтры; 7
– побудитель расхода; 8
– запорно-регулирующий вентиль
В электрическую схему фотометра входят: датчик; блок питания вспомогательных устройств; электронный самопишущий прибор.
Кинематическая схема фотометра обеспечивает требуемую последовательность работы основных узлов прибора с помощью программного механизма.
Фотометр выпускают в пылезащищенном, брызгозащищенном взрывозащищенном и искробезопасном исполнениях. Пределы измеряемых концентраций: метан 0…3 %; водород — 0...2%; углекислый газ — 0...1%.
Запыленность воздуха оценивают количеством пыли в миллиграммах на 1 м воздуха. Измеряют концентрацию пыли, ее дисперсность и состав. Для промышленно-санитарного анализа чаще всего используют весовой способ при оценке запыленности. Для выделения пыли из воздуха применяют следующие методы:
- аспирационный
— основан на просасывании воздуха через фильтры (из стеклянной или хлопчатобумажной ваты, ткани и др.) или через жидкости (воду, масла);
- седиментационый
— основан на естественном оседании пыли на стеклянные пластинки или банки. После оседания пыли рассчитывают ее массу на 1 м поверхности;
- электроосаждения
— заключается в создании поля высокого напряжения, в котором пылевые частицы электризуются и притягиваются затем к электродам.
Прибор контроля запыленности воздуха ПКЗВ-906 предназначенного для оперативного измерения запыленности помещений, дисперсного анализа порошков, аэрозолей и контроля фильтров. Его используют в приборостроении, электронной и химической промышленности, порошковой металлурги, биологии, медицине, фармакологии. Он позволяет измерять концентрацию твердых частиц пыли в единице объема помещения и размер взвешенных в воздухе частиц от 0,3 до 100 мкм в семи размерных диапазонах. Индикация результатов измерения — цифровая. Расход воздуха составляет (1 0,1) л/мин. Автоматизированная система контроля чистоты воздуха и газов (АСКЧВГ) предназначена для контроля фракционного состава дисперсной фазы аэрозолей. Она состоит из вычислительного комплекса, пульта управления, датчиков счетной концентрации аэрозоля и обеспечивает полную автоматизацию процесса измерения. По сравнению с зарубежными аналогами система имеет рас ширенные функциональные возможности за счет одновременного определения пофракционного состава аэрозоля и его массовой концентрации. Время цикла измерения — не более 5 мин; диапазоны измеряемых частиц аэрозоля—0,5…1, 1...2, 2...5, 5...10, 10...25, 25...40, 40...80 и более 80 мкм; диапазон измеряемых массовых концентраций — 0,001...100 мг/м3
.
4.4 ПРИБОРЫ ДЛЯ ИЗМЕРЕНИЯ ТЕПЛОВЫХ ПОТЕРЬ
В процессе эксплуатации оборудования систем отопления, вентиляции и кондиционирования необходимо следить за состоянием его изоляции. Нарушение изоляции приводит к значительным потерям теплоты.
Для определения тепловых потерь через изоляцию оборудования и теплопроводов применяют измеритель тепловых потерь ИТП-6 (рис. 4.9).
Прибор ИТП-6 предназначен для непосредственных измерений локальных потерь теплоты, уносимой за счет свободной конвекции и излучения в окружающую среду через тепловую изоляцию теплоиспользующего оборудования и трубопроводов.

Рис. 4.9. Измеритель тепловых потерь ИТП-6: а
– общий вид; б
– схема прибора; Д
– датчик; В
– клавишный переключатель; R
1
…
R
7
– резисторы; mA
– миллиамперметр
Пределы измерения плотности тепловых потоков прибором ИТП-6: 0…1000; 0…2000;0…5000 Вт/м2
при цене деления шкалы соответственно 20; 40; 100 Вт/м2
.
Прибор работает при относительной влажности воздуха до 80%, температуре окружающего воздуха от -30 до+50о
С и температуре поверхности контролируемой изоляции до +80о
С.
Действие прибора основано на явлении термоэлектрического эффекта, возникающего в датчике при прохождении через него теплового потока. Датчик теплового потока представляет собой батарею из большого числа последовательно соединенных элементов. Тепловой поток, пронизывая датчик, возбуждает в цепи прибора термоэлектрический ток, линейно зависящий от плотности теплового потока.
Разновидностью приборов, измеряющих интенсивность теплового излучения, являются актинометры различной конструкции. Действие их основано на поглощении лучистой энергии и превращения ее в теплоту, количество которой регистрируется различными способорами.
Наибольшее распространение получили актинометры, принцип действия которых, как и у ИТМ-6, основан на термоэлектрическом эффекте (рис. 4.10). В качестве приемника теплового излучения в приборе использована термоэлектрическая батарея в виде ряда термопар, соединенных между собой последовательно, причем положительные спаи термопар присоединены к пластинам, близким по свойствам к абсолютно черному телу, а отрицательные – к пластинам с высокой отрицательной способностью. При воздействии теплового излучения черные пластины интенсивно нагреваются, и в цепи возникает электрический ток, измеряемый гальванометром, шкала которого отградуирована в единицах тепловой радиации.
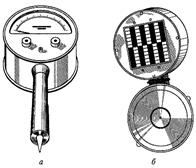
Рис. 4.10. Актинометр: а
– вид спереди; б
– вид сзади (приемник актинометра)
ТЕСТ ПО ДИСЦИПЛИНЕ «ЭКСПЛУАТАЦИЯ И НАЛАДКА СИСТЕМ ТГВ»
1. Водяные тепловые сети по способу приготовления воды для горячего водоснабжения подразделяются на:_______________________
а) однотрубные, двухтрубные и многотрубные;
б) магистральные, распределительные и ответвления;
в) закрытые и открытые.
2. Радиальные тепловые сети сооружают:_____________________
а) с постепенным увеличением диаметров теплопроводов в направлении от источника теплоты;
б) с постепенным уменьшением диаметров теплопроводов в направлении от источника теплоты;
в) с неизменяемыми диаметрами теплопроводов в направлении от источника теплоты.
3. Радиальные тепловые сети характеризуются:________________
а) отсутствием резервирования подачи теплоносителя;
б) наличием резервирования подачи теплоносителя.
4. Из каких основных операций состоит пуск тепловых сетей?
а) гидравлическое испытание, включение абонентов;
б) гидравлическое испытание, тепловое испытание, включение абонентов;
в) заполнение сети водой, установление циркуляции сети, включение абонентов, пусковая регулировка сети.
5. Заполнение тепловой сети водой производится через:________
а) подающую линию;
б) обратную линию;
в) расширительный бак.
6. Температура воды для заполнения тепловой сети должна быть:
а) < 40 o
C;
б) > 70 o
C;
в) . 40 o
C и < 70 o
C.
7. Давление заполняющей воды тепловой сети не должно превышать____________________________________________________
а) 2 МПа;
б) 2,5 МПа;
в) 3 МПа.
8. Установление циркуляции в основных магистральных теплопроводах осуществляется через:_____________________________
а) системы теплопотребления;
б) ответвления;
в) кольцевые перемычки.
9. Обход теплопроводов производят по графику не реже:_______
а) одного раза в две недели (отопительный сезон) и одного раза в месяц (межотопительный сезон);
б) одного раза в месяц (отопительный сезон) и одного раза в два месяца (межотопительный сезон).
10. Какое избыточное давление в тепловой сети и во всех присоединенных системах теплопотребления должно быть во избежание подсоса воздуха в системе отопления?
а) не ниже 0,002 МПа;
б) не ниже 0,003 МПа;
в) не ниже 0,005 МПа.
11. Состояние внутренней поверхности трубопроводов следует определять____________________________________________________
а) в отопительный период путем осмотра вырезаемых контрольных участков труб;
б) в период текущих и капитальных ремонтов, а также при шурфовках тепловых сетей;
в) затрудняюсь ответить.
12. Во избежание усиленного процесса коррозии трубопроводов систем горячего водоснабжения запрещается даже периодическое повышение температуры воды в системе свыше:____________________
а) 65 о
С;
б) 70 о
С;
в) 75 о
С.
13. При утечке теплоносителя, превышающей установленные нормы, следует:________________________________________________
а) произвести подпитку в зависимости от величины утечки теплоносителя;
б) принять срочные меры к обнаружению места утечки и устранению неплотностей;
в) прекратить подачу теплоносителя потребителю.
14. Состояние насосов и связанного с ним насосного оборудования проверяют:________________________________________
а) перед каждым пуском насосов, а при работе насосов не реже 1 раза в сутки;
б) 1 раз в неделю;
в) 2 раза в неделю.
15. Кто осуществляет эксплуатацию тепловых пунктов?
а) организация, эксплуатирующая тепловые сети, под контролем потребителя;
б) персонал потребителей под контролем организации, эксплуатирующей тепловые сети;
в) затрудняюсь ответить.
16. Кто устанавливает и согласовывает объем и время проведения ремонта тепловых пунктов?
а) потребитель;
б) эксплуатирующая организация;
в) потребитель и эксплуатирующая организация совместно.
17. Кто производит включение и выключение тепловых пунктов и абонентских систем, а также регулирование расхода теплоносителя?
а) персонал потребителей;
б) персонал организации, эксплуатирующей тепловую сеть;
в) совместно.
18. Гидравлические испытания тепловой сети, коммуникаций водоподогревательной установки, сетевых и подпиточных насосов сводятся к_____________________________________________________
а) измерению давления и температуры сетевой воды;
б) измерению расхода и температуры сетевой воды;
в) измерению давления и расхода сетевой воды;
г) одновременному измерению расхода, давления и температуры сетевой воды.
19. Какими приборами определяют расход сетевой воды при испытаниях?
а) расходомерами турбинными;
б) расходомерами крыльчатыми;
в) измерительными диафрагмами и подключенными к ним дифманометрами;
г) ведрами и тазиками.
20. Какими приборами прииспытании тепловой сети водоподогревательной установки измеряют давление?
а) контрольными манометрами;
б) пружинными образцовыми манометрами;
в) тонометрами;
г) пружинными образцовыми и контрольными манометрами;
д) техническими манометрами.
21. С какой целью производят тепловые испытания теплосети?
а) с целью восстановления разрушенной тепловой изоляции, осушения камер тепловых сетей, приведения в порядок дренажей и организации стока поверхностных вод с трассы;
б) с целью определения фактических потерь тепла в водяных тепловых сетях, пересчета этих потерь на различные тепловые режимы эксплуатации и сопоставления их с нормативными значениями;
в) с целью определения изменений в связи с расширением и реконструкцией тепловых сетей, снижением теплотехнических показателей изоляции трубопроводов сетей в процессе их эксплуатации и заменой изоляции на отдельных участках.
22. Когда проводят тепловые испытания водяных тепловых сетей?
а) непосредственно после окончания отопительного сезона;
б) непосредственно перед началом отопительного сезона;
в) непосредственно во время отопительного сезона.
23. С какой целью производят наладку водяных тепловых сетей?
а) с целью ликвидации перетопа потребителей;
б) с целью определения фактических характеристик сетевых насосов;
в) с целью определения величины тепловых нагрузок;
г) с целью обеспечения нормального теплоснабжения потребителей.
24. Какой из перечисленных показателей отрицательно влияет на эффективность наладки тепловых сетей?
а) сокращение расхода топлива за счет ликвидации перегрева систем теплопотребления;
б) сокращение расхода электроэнергии на перекачку теплоносителя за счет снижения удельного расхода сетевой воды и исключения излишних насосных станций;
в) обеспечения возможности подключения к сетям дополнительных потребителей;
г) снижение температуры теплоносителя с одновременным снижением расхода;
д) сокращение расходов топлива на выработку электроэнергии за счет снижения температуры воды в обратных трубопроводах тепловой сети.
25. При монтаже и эксплуатации приборов необходимо учитывать, что манометр следует устанавливать:____________________
а) в горизонтальном положении штуцером в сторону;
б) в вертикальном положении штуцером вверх;
в) в вертикальном положении штуцером вниз.
26. Каким образом присоединяются к трубопроводам манометры?
а) только через вваренный в трубопровод штуцер;
б) только через трехходовой кран.
27. Периодичность госповерки манометров:___________________
а) 2 раза в год;
б) 1 раз в год;
в) 1 раз в два года.
28. По каким критериям различаются все газопроводы, прокладываемые в городах и населенных пунктах?
а) по диаметрам труб газопроводов;
б) по способу прокладки газопроводов;
г) по составу и расходу перекачиваемого газа;
д) по назначению и величине давления газа.
29. Что такое «ГРП»?
а) городской распределительный пункт;
б) газопровод районного потребления;
в) газовый ремонтный пункт;
г) газорегуляторный пункт.
30. Чем пользуются при проверке концентрации газа в ГРП?
а) манометром;
б) дифманометром;
в) барометром-анероидом;
г) спичкой;
д) газоанализатором.
31. Какая максимально допустимая концентрация газа в ГРП?
а) не более 0,5%;
б) не более 0,75%;
в) не более 0,85%.
32. какая минимальная температура допускается в помещении ГРП?
а) +10 о
С;
б) +5 о
С;
в) 0 о
С.
33. Как часто необходимо проверять концентрацию газа в ГРП?
а) два раза в месяц;
б) один раз в месяц;
в) один раз в два месяца.
34. Плановая проверка оборудования ГРП проводится:_________
а) один раз в год;
б) два раза в год;
в) один раз в три месяца.
35. Профилактический ремонт оборудования ГРП проводится:___
а) один раз в год;
б) два раза в год;
в) один раз в три месяца.
36. Целью профилактического осмотра газопровода является:___
а) деление газопроводов на маршруты и составление маршрутных схем;
б) закрепление линейных трасс газопроводов за бригадами слесарей;
в) своевременное выявление различных неисправностей и утечек газа.
37. Назовите наиболее важную и ответственную задачу работников газового хозяйства:___________________________________
а) выявление злостных неплательщиков-потребителей газа;
б) обеспечение и поддержание постоянной величины давления газа в сетях.
38. Какие трубы применяют для сооружения газопроводов?
а) стальные из малоуглеродистых и низколегированных сталей;
б) стальные из высокоуглеродистых сталей;
в) стальные из легированных сталей.
39. Каким видом сварки соединяют трубы?
а) электродуговой сваркой;
б) контактной сваркой;
в) газовой сваркой;
г) электродуговой, газовой и контактной сварками.
40. К какому виду арматуры относятся краны и задвижки?
а) к запорно-регулирующему;
б) к предохранительному;
в) к арматуре обратного действия;
г) к аварийному.
41. Наиболее полную герметичность отключения обеспечивают:_
а) задвижки;
б) краны;
в) затрудняюсь ответить.
42. Подземные газопроводы защищают от коррозии двумя способами:____________________________________________________
а) пассивным и активным;
б) пассивным и интенсивным.
43. Противокоррозионные покрытия должны иметь следующие свойства:______________________________________________________
а) являться диэлектриками, иметь необходимую механическую прочность и хорошую адгезию, быть эластичными и водонепроницаемыми;
б) должны проводить электрический ток, иметь невысокую механическую прочность и плохую прилипаемость, иметь низкую эластичность и высокую капиллярность.
44. Какой перечень ремонтных работ характерен для капитального ремонта подземных газопроводов?
а) осмотр газопроводов с использованием бурения скважин; устранение причин утечек газа; устранение закупорок; ремонт арматуры и сооружений на газопроводах; ремонт тела трубы и изоляции; пополнение и восстановление технической документации;
б) замена поврежденных коррозией участков газопровода; восстановление изоляции; замена арматуры; ремонт газовых колодцев; замена или установка средств защиты газопроводов от электрической коррозии.
45. Работоспособность дымохода характеризуется тремя величинами:___________________________________________________
а) разностью влажностей между уходящими газами и наружным воздухом, сечением и длиной дымохода;
б) разностью температур между уходящими газами и наружным воздухом, сечением и высотой дымохода.
46. Сечение дымохода должно определяться:__________________
а) расчетом или по таблицам, но не быть меньше, чем у патрубка газового прибора, присоединяемого к дымоходу;
б) расчетом или по таблицам, но не быть больше, чем у патрубка газового прибора, присоединяемого к дымоходу.
47. Кто несет ответственность за состояние и правильную эксплуатацию внутридомового газового оборудования?
а) МЧС;
б) органы местного самоуправления;
в) эксплуатационные организации газового хозяйства.
48. Кто осуществляет пуск газа в газовое оборудование зданий?
а) бригада квалифицированных слесарей, допущенных к выполнению газоопасных работ; в составе не менее двух человек, возглавляемая инженерно-техническим работником, ответственным за пуск газа;
б) главный инженер газового хозяйства лично.
49. Внутридомовые газопроводы должны продуваться через спуск к газовой плите через резиновый шланг, свободный конец которого выпускается:__________________________________________
а) в окно;
б) в дымоход или вентиляционный канал;
в) в канализацию.
50. После окончания работ по пуску газа:_____________________
а) производится регулировка горения газа на всех горелках приборов;
б) практически показывается всем жильцам, как безопасно зажигать газ;
в) составляется акт по установленной форме о вводе в эксплуатацию газового оборудования дома.
51. Кто входит в состав комиссии, принимающей в эксплуатацию газопроводы и ГРП?
а) представители проектной организации; представители эксплуатирующей организации; представители органов самоуправления;
б) представители строительно-монтажной организации; представители эксплуатирующей организации; Ростехнадзор.
52. Прием нового объекта газоснабжения оформляется специальным актом, который:____________________________________
а) является одновременно разрешением на ввод в эксплуатацию;
б) не является разрешением на ввод в эксплуатацию.
53. К моменту приема в эксплуатацию газопроводы должны быть испытаны на прочность и плотность и засыпаны грунтом, при этом:____
а) комиссия не имеет право проверять любые участки газопроводов;
б) комиссия имеет право проверять любые участки газопроводов путем вырезки стыков, повторного испытания и т.д.
54. При выполнении газоопасных работ все работники обеспечиваются:_______________________________________________
а) спецодеждой, специнструментом, защитными средствами и приспособлениями;
б) спецодеждой, средствами пожаротушения и дополнительным пайком.
55. Газоопасные работы в колодцах и траншеях выполняют бригады рабочих в составе:______________________________________
а) не менее двух человек;
б) не менее трех человек;
в) не менее пяти человек.
56. Наиболее дорогостоящими и энергоемкими являются:_______
а) системы естественной вентиляции;
б) системы механической вентиляции;
в) системы смешанной вентиляции.
57. Какой параметр воздуха в системе воздушного душирования подлежит контролю в соответствии с требованиями СНиП?
а) влажность подаваемого воздуха;
б) температура подаваемого воздуха.
58. Какой параметр воздуха в системе вентиляции подлежит контролю в соответствии с требованиями СНиП?
а) относительная влажность воздуха;
б) температура воздуха;
г) давление или разность давлений.
59. Какие применяют приборы для определения давления в системах вентиляции и кондиционирования?
а) манометры, мановакуумметры, вакуумметры;
б) U-образные манометры, напорометры, микроманометры.
60. Определить линейную скорость υ. м/с, или массовую скорость воздуха U, кг/м8
с, в интересующей точке вентиляционной системы можно, измерив:________________________________________________
а) динамическое давление в этой точке;
б) статическое давление.
61. Можно ли измерить скорость движения воздуха анемометром?
а) да;
б) нет;
в) затрудняюсь ответить.
62.Каким прибором пользуются для определения относительной влажности воздуха в вентиляционных установках?
а) термоанемометром;
б) психрометром.
63. Можно ли для замера малых скоростей движения воздуха (до 1 м/с) использовать кататермометр?
а) нет;
б) да;
в) затрудняюсь ответить.
64. В каких единицах измеряется запыленность воздуха?
а) мг/м3
;
б) г/м3
;
в) кг/м3
.
65. Для определения запыленности воздуха необходимо измерить:_____________________________________________________
а) концентрацию пыли;
б) дисперсность пыли;
в) состав пыли;
г) концентрацию, дисперсность и состав пыли.
66. Какие параметры необходимо учитывать при выборе сухого механического пылеуловителя?
а) гидравлическое сопротивление, температуру газа, производительность, концентрацию пыли, эффективность пылеулавливания;
б) скорость газа на входе в пылеуловитель, концентрацию пыли.
67. Радиальные вентиляторы высокого давления (ВВД) могут развивать давление:
а) до 2000 Па;
б) до 3000 Па;
в) до 30000 Па.
68. Что означает номер в маркировке радиального вентилятора ВЦ4-70 № 6,3:
а) удельную быстроходность;
б) коэффициент полного давления;
в) КПД вентилятора;
г) наружный диаметр рабочего колеса.
69. Какое из нижеперечисленных определений является верным:
а) правильным является вращение рабочего колеса по ходу разворота спирального корпуса радиального вентилятора;
б) правильным является вращение рабочего колеса против хода разворота спирального корпуса радиального вентилятилятора.
70. Используются ли при действии осевых вентиляторов центробежные силы:
а) да;
б) нет;
в) затрудняюсь ответить.
71. По сравнению с радиальными вентиляторами, осевые…
а) проще в конструктивном исполнении, имеют меньшую массу на единицу мощности, реверсивны и более удобны в регулировке;
б) сложнее в конструктивном исполнении, имеют большую массу на единицу мощности, нереверсивны и менее удобны в регулировке.
ЭКЗАМЕНАЦИОННЫЕ ВОПРОСЫ ПО ДИСЦИПЛИНЕ «ЭКСПЛУАТАЦИЯ И НАЛАДКА СИСТЕМ ТГВ»
Раздел «Теплоснабжение»
Системы теплоснабжения. Основные элементы.
Трубопроводы. Категории трубопроводов. Цвета обязательной окраски.
Опоры теплосетей. Опоры подвесные.
Компенсаторы линейных удлинений. Типы компенсаторов. Физика процесса компенсации.
Арматура систем теплоснабжения. Виды арматуры. Маркировка.
Центральные тепловые пункты (ЦТП). Оборудование ЦТП.
Насосы, грязевики, элеваторы. Конструктивные особенности, технические характеристики, особенности эксплуатации.
Гидравлические испытания систем теплоснабжения.
Тепловые испытания систем теплоснабжения.
Приемка в эксплуатацию тепловых сетей, тепловых пунктов и систем теплоснабжения и теплопотребления.
Пуск водяных тепловых сетей, тепловых пунктов и систем теплопотребления.
Обслуживание тепловых пунктов.
Обслуживание тепловых сетей.
Контрольно-измерительные приборы для измерения температуры, давления и расхода теплоносителя.
Защита наружных тепловых сетей от коррозии при канальной и бесканальной прокладке.
Особенности эксплуатации тепловых сетей.
Регулирование систем теплоснабжения.
Основные направления технической политики Минтопэнерго России в области теплоснабжения на перспективу до 2020 г.
Использование металлополимерных труб в системах отопления.
Раздел «Газоснабжение»
Классификация систем газоснабжения.
Трубы арматура систем газоснабжения. Цвета обязательной окраски.
ГРП. Эксплуатация и наладка.
Испытание и приемка в эксплуатацию газопроводов и ГРП.
Испытание городских газопроводов.
Испытание газопроводов промышленных предприятий.
Испытание домовых газовых сетей.
Ввод в эксплуатацию систем газоснабжения.
Профилактические работы на подземных газопроводах. Сроки и методика проведения профилактических работ.
Капитальный ремонт газопроводов.
Ремонтные работы по видам защит подземных газопроводов от коррозии.
Техника безопасности при эксплуатации подземных газопроводов.
Эксплуатация газопроводов промышленных предприятий.
Эксплуатация внутрицеховых газопроводов.
Эксплуатация внутридомового газового оборудования.
Устройство и эксплуатация дымоходов.
ГПРС. Устройство и эксплуатация.
Эксплуатация установок сжиженных газов.
Службы эксплуатации газового хозяйства.
Производство аварийных работ. Ремонтные работы в зимних условиях.
Перечень документов инвентаря и инструментов при ремонтных работах в системах газоснабжения.
Раздел «Вентиляция и кондиционирование»
Назначение и классификация систем вентиляции.
Определение необходимого воздухообмена.
Конструктивные особенности естественной вентиляции.
Конструктивные особенности механической вентиляции.
Аварийная вентиляция и особенности её устройства.
Требования, предъявляемые к выбору вентиляционного оборудования.
Приборы измерения и контроля, используемые в системах вентиляции и кондиционирования.
Испытание и наладка систем вентиляции.
Паспорт вентиляционной установки.
Паспорт газоочистной установки.
Пусконаладочные работы (ПНР) систем вентиляции.
Конструктивные особенности оборудования систем вентиляции.
Приборы для выбора проб пыли. Внешняя и внутренняя фильтрации.
Оборудование для очистки воздуха от пыли. Классификация пылеуловителей.
Классификация систем кондиционирования воздуха.
Особенности эксплуатации центральных систем кондиционирования воздуха.
Наладка и испытания СКВ и СВ.
Требования СНиП к контролю параметров микроклимата.
КОНТРОЛЬНАЯ РАБОТА ПО ДИСЦИПЛИНЕ
«Эксплуатация и наладка систем ТГВ» на тему:
«Определение верхнего и нижнего предела воспламеняемости газовой смеси»
1. Краткие теоретические сведения.
Наинизшая температура смеси газа и воздуха, при которой выделение тепла за счет реакции горения газа несколько превышает теплоотдачу, называется температурой воспламенения. Превышение выделяющегося тепла должно при этом не только покрывать потери тепла в окружающую среду, но и быть достаточным для активизации соседних частиц газа и воздуха и для нагрева их до температуры воспламенения. Только при этих условиях возможно устойчивое горение газа. Однако температура воспламенения топлива является вполне определенной величиной, характерной для данного вида топлива. В практических условиях она зависит не только от химического состава и физических свойств топлива, но и от ряда других условий: концентрации газа и наличия кислорода, степени перемешивания газа и воздуха, формы и размеров топочного пространства, быстроты и способа нагрева смеси, давления газа и воздуха, а также наличия катализаторов, ускоряющих или замедляющих химические процессы горения.
Температура воспламенения горючих газов в кислороде и воздухе приведена в табл. 1.
Таблица 1
Температура воспламенения горючих газов
№ п/п
|
Газы
|
Температура воспламенения в воздухе в о
С
|
Температура воспламенеия в кисроде в о
С
|
№ п/п
|
Газы
|
Температура воспламенения в воздухе в о
С
|
Температура воспламенения в воздухе в о
С
|
1
|
Метан…..
|
650
|
550
|
8
|
н
-Бутан
|
490
|
460
|
2
|
Этилен…
|
540
|
500
|
9
|
Водород
|
510
|
450
|
3
|
Этан……
|
530
|
485
|
10
|
Окись углерода
|
610
|
590
|
4
|
Пропилен
|
455
|
420
|
11
|
Сероводород
|
290
|
220
|
5
|
Пропан…
|
540
|
490
|
12
|
Коксовый газ
|
640
|
-
|
6
|
1-Бутилен
|
440
|
400
|
13
|
Природный газ
|
610
|
-
|
7
|
u-Бутан
|
540
|
-
|
|
|
|
|
Как видно из приведенной таблицы, температура воспламенения газов в кислороде на 50-100 о
С ниже температуры воспламенения газов в воздухе. Увеличение содержания в горючих газах балластных примесей (особенно СО2
) повышает температуру их воспламенения.
Нагретые газовоздушные смеси могут воспламеняться только при определенном содержании газа в воздухе или кислороде. При уменьшении содержания в смеси горючей части может наступить такой момент, когда смесь теряет способность гореть, т.е. не будет воспламеняться без подвода тепла извне. При увеличении содержания горючего компонента в смеси также может наступить момент, когда смесь потеряет способность воспламеняться и гореть.
Поэтому различают низший предел воспламеняемости, соответствующий минимальному содержанию горючего компонента, при котором смесь еще остается горючей, и высший предел воспламеняемости, соответствующий максимальному содержанию горючего компонента, при котором смесь еще остается горючей.
Существование верхнего и нижнего предела воспламеняемости (взрываемости) объясняется тепловыми потерями при горении. По мере уменьшения горючего компонента в смеси все больше увеличивается расход тепла на нагрев не горючей части смеси, скорость распространения пламени все время уменьшается, и, наконец, наступает момент, когда горение прекращается.
С увеличением содержания горючего компонента в смеси также наступает момент, когда происходит полное сгорание горючих компонентов из-за недостатка кислорода (воздуха). При этом расход тепла не нагрев несгоревших негорючих компонентов будет все время увеличиваться, скорость распространения пламени уменьшаться, и, наконец, наступит момент, когда горение прекратится.
При равных условиях определения величина пределов воспламенения (взрываемости) газовоздушных смесей зависит в основном от свойств горючих компонентов, т.е. от свойств испытываемого газа.
В табл. 2 приведены пределы воспламеняемости (взрываемости) компонентов, входящих в состав технических газов.
Пределы взрываемости компонентов сжиженного газа по сравнению с природным и коксовым газами кажутся узкими (2 – 9 %). Но если эти пределы выразить в калориях на 1 нм3
газовоздушной смеси, то они будут достаточно широкими. для компонентов сжиженного газа они лежат в границах от 500 до 2300 ккал/нм3
, в то время как для природного газа – от 500 до 1500 ккал/нм3
и для коксового - от 350 до 1200 ккал/нм3
.
Таблица 2
Пределы воспламеняемости горючих газов и паров при стандартных условиях
№ п/п
|
Газы
|
% объемных газов в смеси с воздухом
|
Разни
ца между пределами
|
Нижний предел
|
Верхний предел
|
1
|
Метан
|
5,3
|
15,0
|
9,7
|
2
|
Ацетилен
|
2,5
|
81,0
|
78,5
|
3
|
Этилен
|
2,8
|
28,6
|
25,8
|
4
|
Этан
|
3,0
|
12,5
|
9,5
|
5
|
Пропилен
|
2,4
|
10,3
|
7,9
|
6
|
Пропан
|
2,2
|
9,5
|
7,3
|
7
|
u-Бутан
|
1,8
|
8,4
|
6,6
|
8
|
н
-Бутан
|
1,9
|
8,5
|
6,6
|
9
|
u-Пентан
|
1,3
|
8,0
|
6,7
|
10
|
н
-Пентан
|
1,4
|
7,8
|
6,4
|
11
|
Водород
|
4,1
|
74,6
|
70,2
|
12
|
Окись углерода
|
12,5
|
74,2
|
61,7
|
13
|
Сероводород
|
4,3
|
45,5
|
41,2
|
14
|
Коксовый газ
|
5,6
|
31,0
|
25,4
|
15
|
Водяной газ
|
6,2
|
72,0
|
65,8
|
16
|
Генераторный газ
|
20,7
|
73,7
|
53,0
|
17
|
Природный газ
|
4,5
|
17,0
|
12,5
|
|
|
|
|
|
Пределы воспламеняемости горючих газовых смесей, не содержащих балластных примесей, определяют исходя из следующего соотношения:
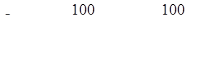
где - верхний или нижний предел воспламеняемости горючей смеси;
- верхние или нижние пределы воспламеняемости компонентов, входящих в газовую смесь;
- мольные концентрации компонентов, входящих в газовую смесь, в процентах.
Если в газовой смеси содержатся не горючие компоненты (балластные примеси), то пределы воспламеняемости (взрываемости) могут быть определены по следующему уравнению:
,
где - верхний или нижний предел воспламеняемости газовой смеси, содержащей балластные примеси;
а - содержание балластных примесей в долях единицы.
С повышением содержания балластных примесей в газовой смеси пределы взрываемости (воспламеняемости) растут, как растет и разность между их значениями. Увеличение температуры газовоздушной смеси приводит к расширению пределов воспламеняемости; при температуре воспламенения и более высоких температурах горючие газы при любом их содержании в газовоздушной смеси.
Обогащение воздуха кислородом приводит к увеличению верхнего предела воспламеняемости газа, а соответственно и к расширению пределов их горючести.
При повышении давления наблюдается сужения пределов воспламеняемости горючих газов за счет роста нижнего предела и уменьшения верхнего предала воспламеняемости.
Учитывая важность вышесказанного, студенты должны получить практические навыки при определении пределов воспламеняемости газовой смеси в данной контрольной работе.
2. Задание к контрольной работе:
- определить верхний и нижний пределы воспламеняемости газовой смеси, состоящей из нескольких компонентов.
Вариант состава газовой смеси определяется цифрой зачетной книжки студента по табл.3.
Контрольная работа выполняется на стандартных листах формата А4 и сдается преподавателю на проверку.
К экзамену по дисциплине «Эксплуатация и наладка систем ТГВ» допускаются студенты, правильно выполнившие контрольную работу, сдавшие тест по курсу данной дисциплины.
Таблица 3
Газы, входящие в состав смеси, %
|
Предпоследняя цифра зачетной книжки
|
0
|
1
|
2
|
3
|
4
|
5
|
6
|
7
|
8
|
9
|
Метан
|
10
|
|
|
|
|
5
|
15
|
|
10
|
|
Ацетилен
|
|
15
|
|
|
|
|
|
10
|
|
5
|
Этилен
|
|
|
20
|
|
|
|
15
|
10
|
|
10
|
Этан
|
20
|
|
|
|
10
|
|
5
|
|
|
|
Пропилен
|
|
15
|
10
|
|
|
|
|
10
|
|
10
|
Пропан
|
|
|
|
15
|
20
|
10
|
5
|
|
15
|
|
u-Бтан
|
|
|
|
|
10
|
|
5
|
|
15
|
|
н
-Бутан
|
|
|
|
25
|
|
10
|
|
|
|
|
Водород
|
5
|
5
|
5
|
10
|
5
|
5
|
5
|
5
|
5
|
10
|
Окись углерода
|
30
|
25
|
20
|
15
|
20
|
15
|
25
|
25
|
20
|
30
|
Сероводород
|
10
|
15
|
20
|
15
|
10
|
20
|
5
|
5
|
10
|
|
Коксовый газ
|
|
5
|
|
|
5
|
|
|
15
|
5
|
|
Двуокись углерода + азот
|
25
|
20
|
15
|
20
|
15
|
25
|
15
|
20
|
15
|
20
|
Природный газ
|
|
|
10
|
|
5
|
10
|
5
|
|
5
|
15
|
|