ВВЕДЕНИЕ
Развитие спроса на строительно-дорожную технику заставило отечественных машиностроителей расширять линейку типоразмеров выпускаемой продукции, а также создавать принципиально новые для нашей страны машины. За последние годы стало производиться множество разнообразной техники, но в относительно небольших количествах. Основной проблемой при модернизации существующих и создании новых типов машин и оборудования являлось и является отсутствие широкой базы комплектующих агрегатов и элементов гидропоивода. Именно гидросистема является самым слабым звеном в отечественной технике.
Современная дорожная и строительная техника уже на стадии проектирования учитывает все тенденции технического развития. Иначе она не будет соответствовать современным требованиям. Модельный ряд машин должен быть широким, элементная база – непременно новой, собранной из высокоточных, надежных компонентов. Все эти требования всецело относятся и к элементам объемного гидропривода, являющегося неотъемлемой частью современной мобильной техники
Применение в конструкциях машин импортных комплектующих, безусловно, повышает надежность техники, но в то же время ведет к ее удорожанию и, как следствие, снижению конкурентоспособности на внутреннем рынке.
Темой курсового проекта выбрано проектирование регулируемого аксиально-поршневого насоса с наклонным блоком, как альтернативы для насоса Bosch - Rexroth, используемого в настоящее время в гидроприводе экскаватора ЕТ-25.
1.ВЫБОР ПРОТОТИПА
В гидроприводах строительных, дорожных и других мобильных машин применяются насосы различных типов, которые являются наиболее сложным гидравлическим оборудованием. Условно насос принято считать "сердцем" любого гидропривода машины: при отключенном насосе или в случае его отказа ни один из гидродвигателей не может быть приведен в действие. Работоспособность насоса определяет безотказность работы всего гидропривода машины. Отсюда вытекает важность изучения конструкции, знание принципа действия и умелого обслуживания насосов, гидромоторов, а также другого гидрооборудования.
Насос предназначен для обеспечения перемещения рабочей жидкости в процессе преобразования механической энергии приводного двигателя внутреннего сгорания или электромотора в энергию потока рабочей жидкости, поэтому назначение насоса - нагнетание рабочей жидкости в трубопроводы.
Обычно насос считается источником создания давления в гидравлической системе. Однако такое определение неточно, так как для получения давления должно быть создано сопротивление потоку рабочей жидкости в виде внешней нагрузки на валу гидромотора.
Основными параметрами любого насоса являются рабочий объем V, номинальное давление Рном и номинальная частота вращения nном, а производными - производительность (подача) Qном, потребляемая мощность Nном, а также полный КПД.
В гидроприводах мобильных машин применяют роторно-вращательные и роторно-поступательные насосы, которые по виду рабочих органов разделяют на шестеренные, шиберные (пластинчатые) и поршневые. По углу между осями блока и поршня различают радиальные и аксиальные поршневые насосы. По механизму передачи движения радиально-поршневые насосы классифицируют на кулачковые и кривошипные, а аксиально-поршневые - с наклонным блоком и с наклонным диском.
Насосы могут быть выполнены с нерегулируемым и регулируемым рабочим объемом и предназначены для работы как в режиме объемного насоса, так и в режиме объемного гидромотора (насоса-мотора) с реверсивным и нереверсивным направлениями вращения и с постоянным и реверсивным направлениями потока.
Сравнительная оценка основных параметров гидромашин различных типов показывает, что каждый тип имеет определенные конструктивные особенности, которые определяют область их использования, целесообразную с технической и экономической точек зрения.
Шестеренные насосы широко используют в мобильных машинах небольшой мощности при низком и среднем давлении в гидросистеме. Они достаточно надежны в эксплуатации, менее требовательны к чистоте рабочей жидкости и имеют меньшую стоимость по сравнению со стоимостью гидронасосов других типов.
Применение аксиально-поршневых гидронасосов наиболее целесообразно при среднем и высоком давлении в гидросистемах мобильных машин и цикличном характере изменения внешней нагрузки. Дополнительные устройства обеспечивают реверсирование потока и изменение подачи.
Аксиально-поршневые насосы имеют более высокий полный КПД, по сравнению с КПД шестеренных и пластинчатых насосов. Объемный КПД аксиально-поршневых насосов начинает заметно снижаться только при вязкости рабочей жидкости менее 10 мм²/с, для пластинчатых насосов этот предел вязкости составляет 50-80 мм²/с, а для шестеренных - 80 мм²/с.
В результате анализа современных конструкций аксиально-поршневых насосов установлено следующее:
1. Основным направлением совершенствования конструкций аксиально-поршневых гидронасосов является улучшение энергетических показателей, главным образом, путем увеличения номинального давления, частоты вращения и угла наклона блока цилиндров. По критерию наименьшей стоимости объемного гидропривода максимальное давление следует повысить до 32-40 МПа. Частоту вращения можно повысить 20-30% путем создания избыточного давления во всасывающей гидролинии. Повышение частоты вращения связано с необходимостью соединения насосов непосредственно с коленчатым валом двигателей внутреннего сгорания, а также увеличения мощности гидравлических приводов.
2. Аксиально-поршневые насосы с наклонным блоком цилиндров получили наиболее широкое применение в объемных гидроприводах машин, работающих в средних и тяжелых режимах внешних нагрузок с большой частотой включения. Их следует предпочитать при выборе перспективного типа гидромашин с учетом номинального давления, так как они более надежны в условиях переменных нагрузок и менее чувствительны к загрязнению рабочей жидкости, чем аксиально-поршневые насосы с наклонным диском.
Традиционная схема исполнения насосов с наклонным блоком цилиндров и торцевым распределением рабочей жидкости позволяет использовать номинальное давление до 35 МПа.
3. При выборе предпочтительной конструкции из наиболее распространенных конструкций аксиально-поршневых насосов следует учитывать, что при прочих равных условиях насосы с шатунной кинематикой имеют следующие преимущества:
возможность работы в насосном и моторном режимах в открытой и замкнутой гидросистемах;
высокая всасывающая способность, обеспечивающая удовлетворительное заполнение рабочего объема при широком диапазоне изменения вязкости рабочей жидкости, что особенно важно для гидроприводов мобильных машин, эксплуатируемых на открытом воздухе при широком диапазоне изменения температуры;
относительно меньшая чувствительность к чистоте рабочей жидкости (могут надежно работать при тонкости фильтрации до 40 мкм);
возможность встраивания регуляторов давления и расхода, а также вспомогательного насоса для питания системы управления и подпитки.
2. РАСЧЕТ ОСНОВНЫХ ЧАСТЕЙ И ПАРАМЕТРОВ
ГИДРОМАШИНЫ
2.1 Расчет размеров блока цилиндров
Если рабочий объем гидронасоса известен, то задача расчета состоит в определении размеров основных деталей и узлов, обеспечивающих получение требуемой частоты вращения вала при заданном номинальном потоке, удовлетворяющих условиям прочности при расчетном давлении в напорной линии, учитывающих необходимость обеспечения минимальных потерь мощности и оптимальной долговечности.
Определяющее влияние на размеры гидромашины оказывает блок цилиндров и принятая схема компоновки. Исходными данными для расчета блока служат: рабочий объем насоса q, число цилиндров z, давление нагнетания и угол наклона .
Рисунок 2.1.1 - Блок цилиндров
Общий вид блока цилиндров показан на рисунке 2.1. Его конструкция мало зависит от типа аксиально-поршневой машины. Основными размерами блока являются: диаметр цилиндра d, диаметр делительной окружности , диаметр внутренней расточки , наружный диаметр , длина цилиндра и высота блока Н.
Рабочий объем определим по формуле:
, (2.1.1)
где
теоретическая подача;
фактическая подача, которая нам задана в техническом задании, т.е. подача без учета утечек;
объемный КПД гидромотора, принимаем , как у аналогичных насосов 313 серии.
см3
.
л/мин.
Так как это основной параметр гидромашины, то выбираем его по ГОСТ 13824 – 80: = 125 .
2.1.1 Определение диаметров поршней
, (2.1.2)
где
- угол наклона блока цилиндров, принимается равным от 15 до 25°, для насоса, выбранного мною за прототип g = 25°;
z- количество поршней, принимаем z = 11, рабочий объем одного цилиндра будет равен:
КD
– дезаксиал. КD
=1,05.
мм,
Из ряда стандартных диаметров по ГОСТ 12447 – 80 выберем dп
=20 мм.
2.1.2 Определение основных размеров блока цилиндров
Определим диаметр делительной окружности блока цилиндров:
, (2.1.3)
где
z- количество поршней;
диаметр поршня.
мм.
Наружный диаметр блока цилиндров:
, (2.1.4)
где
b – размер перемычки между двумя соседними цилиндрами,
, (2.1.5)
где
Kb
– конструктивный коэффициент, предварительно принимаю 0,3.

мм.
Внутренний диаметр блока цилиндров:
, (2.1.6)
мм.
2.1.3 Расчет блока цилиндров на прочность и жесткость
Проверка блока цилиндров на прочность проводится по формуле:
, (2.1.7)
где
А – относительная толщина стенки цилиндра, А≤2,9.
Pp
– максимальное давление нагнетания с учетом коэффициента запаса равным 1,5; Pp
=60 МПа.
,
,
МПа,
для бронзы 60 МПа, а для стали 150 МПа. Принимаю в качестве материала сталь 20Х.
Проверка блока цилиндров на жесткость проводится по формуле:
, (2.1.8)
где
µ - коэффициент Пуассона, для стали µ=0,28,
Е – модуль упругости, Е=2×105
МПа.
мкм
Дно цилиндра принимается не менее 2×b, то есть не менее 13.6 мм.
Радиус сферы под распределительный диск примем ориентировочно равным:
,
мм.
Во всех случаях уточнения размеров при конструировании необходимо следить, чтобы толщина материала на всех участках, разделяющих внутреннюю полость цилиндров и внешние поверхности блока, включая проточки, фаски и т.п., была не меньше, чем , во избежание нарушения прочности блока.
2.1.4. Определим максимальный ход поршней и длину шатуна
Определю максимальный ход поршня hмах
(2.1.9)
= 40 мм.
2.2 Расчет и конструирование поршневых групп
2.2.1 Расчет сил действующих на поршень
Основными силами, действующими в насосах с наклонным блоком являются, как и во всех других случаях, силы давления жидкости. Они приложены к поршням и через шатуны предаются на упорный диск, вызывая напряжения сжатия в материалах шаровых шарниров.
Сила Fn
действующая на поршень раскладывается на две составляющие: FN
и FA
, и находится с ними в следующих зависимостях:
, (2.2.1)
где
Sп
– площадь поршня.
Н,
, (2.2.2)
Н,
, (2.2.3)
Н.
2.2.2 Определение основных размеров поршня
Поршневая группа является ответственным узлом гидромашины, так как от ее исполнения во многом зависят объемный и механический КПД и общий ресурс.
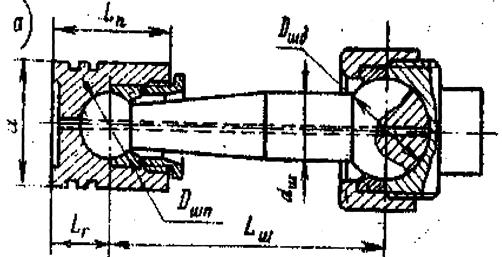
Рисунок 2.2.1 – Конструкция поршневой группы.
Определим диаметр головки шатуна со стороны упорного диска.
, (2.2.4)
примем мм.
Определим диаметр головки шатуна со стороны поршня.
, (2.2.5)
мм.
Длину поршня принимаю =100мм.
Длину шатуна выбираем исходя из условия, что:
, (2.2.6)
где
диаметр делительной окружности блока цилиндров
мм.
Диаметр шатуна определяем конструктивно:
мм.
Диаметр отверстия для подвода смазки в шатуне конструктивно принимаем мм.
Определю угол наклона шатуна к оси поршня
, (2.2.7)
где
- длина шатуна;
дезаксиал;
диаметр окружности заделки шатунов в диске.
.
2.2.3 Проверка на прочность
Проверка прочности по опорным поверхностям сферических шарниров.
, (2.2.8)
где
площадь поршня;
Кс
– коэффициент использования площади опорной поверхности; принимаю Кс
= 1.
МПа,
Определим момент трения в шарнирах, возникающий при вращении блока цилиндров:
, (2.2.9)
где
fтр
= 0,13 – коэффициент трения(сталь по стали);
сила продольного сжатия;
диаметр головки шатуна со стороны упорного диска.
.
Напряжение сжатия определим по формуле:
, (2.2.10)
где
сила продольного сжатия;
диаметр шатуна;
диаметр отверстия для подводки смазки в шатуне.
,
Напряжение изгиба.
, (2.2.11)
где
Wмин
– момент сопротивления наиболее ослабленного сечения при изгибе;
Wмин
= , (2.2.12)
м3
.
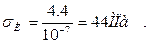
Суммарные напряжения:
, (2.2.13)
где
yб
– коэффициент снижения допускаемого напряжения, зависит от гибкости l и определяется (приближенно) по таблице.
, (2.2.14)
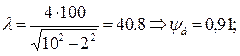
КШ
- запас прочности, приму КШ
= 1,8;
предел усталостной прочности при продольном сжатии и пульсирующем характере нагружения, s-1
= 700 МПа.
МПа.

Условие прочности выполняется.
Принимаем материал шатунов – сталь марки 12 ХН3А ГОСТ 4543-61.
2.3 Расчет геометрии торцевого распределителя
Определю диаметр окружности, на котором размещается ось окон всасывания и нагнетания. Так как прочностные показатели блока цилиндров не позволяют уменьшить средний диаметр окон нагнетания, то принимаю D0
=95мм.
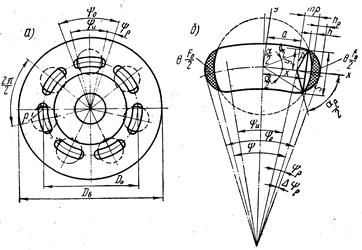
Рисунок 2.3.1 – Торец цилиндрического блока и его геометрия.
Углы j1
и d1
показывают, насколько момент перекрытия окон цилиндра опережает момент прихода его оси в нейтральное положение, а углы j2
и d2
- углы запаздывания показывают, насколько момент открытия окон отстает от момента прохода цилиндром нейтрального положения. При увеличении углов j2
и d1
повышается компрессия жидкости в цилиндрах перемещающимися поршнями, а при увеличении углов j1
и d2
повышается разряжение в цилиндре.
Для предотвращения повышения давления выше давления нагнетания принимаю d2
= 1, а также для избежания возможности недозаполнения цилиндров и следовательно снижения объемного КПД принимаю j1
= 1.
Рассчитаю радиус закругления окна r по формуле:
, (2.3.1)
где
отношение площади окна и площади цилиндра, принимаю равным 0,5.
r мм.
Вычислим углы , и . принимаю равным 85мм для сниженияокружных скоростей.
=
arcsin = arcsin
12,25°; (2.3.2)
=
arcsin = arcsin = 6,1°; (2.3.3)
=
= 12,25-6,1 = 6,15°. (2.3.4)
Скорость жидкости в окне цилиндра не должна превышать 7,5 м/с.
, (2.3.5)
где
V0
– Скорость жидкости в окне цилиндра;
F0
– площадь окна цилиндра, мм2
.
м/с,
т.е. предельная скорость не превышена.
Толщина окна цилиндра:
см.
Рассчитаю угол запаздывания j2
(2.3.6)
где
номинальное давление насоса в полости нагнетания, МПа;
давление в полости всасывания, пренебрегу им;
Е – модуль упругости жидкости, Е = 1500 МПа;
- мертвый объем. =1,1 

Вычислим угол упреждения j1
, (2.3.7)
где V - объём жидкости в цилиндре в конце хода всасывания. V=12.5

2.4 Расчет сил действующих в распределительном узле
Срок службы и герметичность аксиально-поршневой гидромашины во многом зависит от сил, действующих в распределительном узле, ввиду чего правильное определение усилий, действующих на стыке между цилиндровым блоком и распределительным диском, а также гидростатическое уравновешивание этих сил, являются общей проблемой для всех типов этих машин.
Расчет сил действующих в распределительном узле затруднен, поскольку цилиндровый блок находится под сложным воздействием: 1) сил давления жидкости в цилиндрах и стыковом зазоре между поверхностями контакта блока и золотника; 2) сил трения поршней о стенки цилиндров и в шаровых опорах; 3) боковые составляющие сил давления; 4) центробежные силы поршней; 5) сил, обусловленных динамической и статической несбалансированностью цилиндрового блока.
Из всех указанных основными являются силы, обусловленные давлением жидкости в цилиндрах и в стыковом зазоре, по этому в первом приближении учитывают только эти силы.
Цилиндровый блок находится под действием: а) силы Fпр
давления жидкости на донышки цилиндров; б) противодействующих им сил Fотж
давления жидкости в рабочем окне и в стыковом зазоре. При этом должно быть обеспечено Fпр
>Fотж
.
, (2.4.1)
Где: n – минимальное число цилиндров, одновременно соединяющихся с полостью нагнетания, n=5;
Sц
– Площадь сечения цилиндра, Sц
=314мм2
;
Sокн
– площадь распределительного окна золотника, Sокн
=1020 мм2
;
Sконт
– площадь контакта цилиндрового блока с распределительным золотником со стороны рабочего окна, Sконт
=1385 мм2
;
Pн
– давление нагнетания;
Рср
– среднее давление в стыковом зазоре, Рср
=0,5×Рн
=0,5×40=20 МПа.



Превышение сжимающей силы над раскрывающей не должно вызывать излишних сил трения и износа сопряженных деталей.
Оценку распределителя по этому параметру производят в практике по так называемому коэффициенту поджима m, примем m=15%.
, (2.4.2)

Дополнительное прижатие обеспечим пружиной.


2.5 Расчет вала насоса
Предварительно диаметр вала будем считать из расчета на чистое кручение:
(2.5.1)
где
М – момент на валу насоса. Определяется по формуле:
, (2.5.2)
Н×м,
допускаемые напряжения при изгибе. Определяется приближенно по формуле:
, (2.5.3)
где
σТ
– предел прочности. Для стали 40Х σТ
=800 МПа,
KT
– коэффициент прочности, ориентировочно примем 3.
Тогда:
МПа
мм
2.6 Подбор подшипников
Так как в зоне нагнетания может находится одновременно 6 поршней, следовательно силы FA
и FN
следует также увеличить в 6 раз.
Н,
Н,
Определим реакции в опорах подшипников:
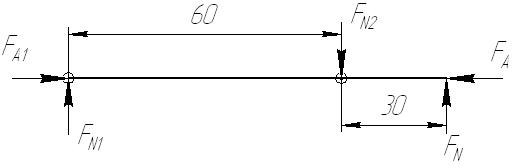
Рисунок 2.6.1 – Силы нагружения
Н,
Н,
Н,
Для первой опоры выбираю роликовый радиальный подшипник 42313. Для второй роликовый конический 7613А.
При подборе подшипников по динамической грузоподъемности учитывается нагрузка и число ее циклов. Для роликовых подшипников справедливы равенства:
, (2.6.1)
Где Lh
– расчетное число часов;
n – частота оборотов мин-1
, (2.6.2)
где Lna
– число циклов, млн. оборотов;
с- динамическая грузоподъемность подшипника, Н;
Р – эквивалентная радиальная динамическая нагрузка на подшипник, Н;
Эквивалентную радиальную нагрузку для роликовых подшипников определяем по формуле:
, (2.6.3)
Kб
– коэффициент безопасности, учитывающий динамические нагрузки, Kб
=1 ;
КТ
– температурный коэффициент, при t<105°С КТ
=1;
V=1 – коэффициент вращение кольца;
X; Y- коэффициенты, учитывающие разное повреждающее действие ради альной и осевой нагрузок. Х=0.4, Y=0,72.
Н,
млн. оборотов.
ч.
2.7 Выбор зазоров
Масла обладают хорошей смазывающей способностью в гидродинамических условиях при обеспечении достаточно больших зазоров между трущимися парами более 0,5 мкм. При повышении нагрузок и уменьшении зазоров наступает переход к граничному трению, характеризующемуся соприкосновению граничных пленок, которые предотвращают контакт чистых металлов и их схватывание.
При уменьшении зазора между блоком цилиндров и поршнем, это приведет к увеличению утечек, то есть к уменьшению объемного КПД.
При повышении точности обработки цилиндра позволяет повысить КПД и обеспечить взаимозаменяемость при сборке поршневой группы.
Технологический диаметр поршня назначают так, чтобы между поршнем и цилиндром обеспечивался гарантированный зазор:
.
Оптимальным считаю зазор так как в данном сопряжении (плунжер-блок) температурное расширение не оказывает влияние на изменение зазоров.
В сопряжении блок-диск принимаю .
2.8 Расчет объемных потерь
Утечки масла в аксиально-поршневых гидромашинах происходят по зазорам между цилиндрами и поршнями и между блоком цилиндров и сферическим распределителем. Эти утечки в зазорах определяются по формуле:
, (2.8.1)
где
D– высота щели;
m- динамическая вязкость; определяется по формуле:
m= , (2.8.2)
где
r - плотность жидкости, r =850кг/м3
;
кинематическая вязкость , = 16сСт;
(2.8.3)
= p d – периметр щели;
l – средняя длина поршня, находящаяся в цилиндре, l=70 мм .
Определю утечки по зазорам между цилиндрами и поршнями:
(2.8.4)

Определю утечки по зазорам в распределительном узле:
(2.8.5)
где
– периметр щели на распределителе, найдем по формуле:
(2.8.6)
где
– угол полукольцевого окна входа на распределителе, примем равным 

– длина щели, примем равной величине уплотняющего пояска, l2
=4.5 мм;
.
Определю суммарные утечки
(2.8.7)

2.9 Расчет механических и гидравлических потерь
Преобразование энергии – гидравлической в механическую в гидронасосах обеспечивается за счет движения рабочих элементов, которое сопровождается потерями энергии на трение механических частей.
Определим момент трения, развиваемый при движение поршней в цилиндрах блока.
(2.9.1)
где
– коэффициент трения; = 0,05.
Определим максимальный момент трения при Sin =1
 
(2.9.2)
где
pср
– среднее значение прижимающего усилия
- площадь опорной поверхности сферического распределителя; Fоп
= p Dоп
;
Dоп
– средний диаметр опорной поверхности; Dоп
= 9 см;
- ширина опорного пояска; принимаю = 5 мм;

площадь контакта цилиндрового блока с распределительным золотником со стороны окна нагнетания;
.

2.10 Ориентировочный расчет коэффициентов полезного действия
В гидромашине имеют место потери мощности на трение в подшипниковых парах: hп
=0,98 – КПД дного подшипника;
, (2.10.1)
где
Мкр
– теоретический крутящий момент на валу мотора;

Так как мы не учитывали гидравлические потери, принимаю =0,90.
Определю объемный КПД насоса

(2.10.2)
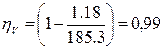
Определю общий КПД насоса
(2.10.3)
.
2.11 Кинематика движения поршня
2.11.1. Кинематика относительного движения поршня
За один оборот.
Определю перемещение поршня
(2.11.1)
Рисунок 2.12.1 График перемещения поршня за один оборот.
Определю скорости поршня
(2.11.2)
Рисунок 2.12.2 График скорости поршня за один оборот 
Определю ускорение поршня
(2.11.3)
Рисунок 2.12.3 - График ускорения поршня за один оборот
Мгновенная подача одним поршнем определяется по формуле
(2.12.4)
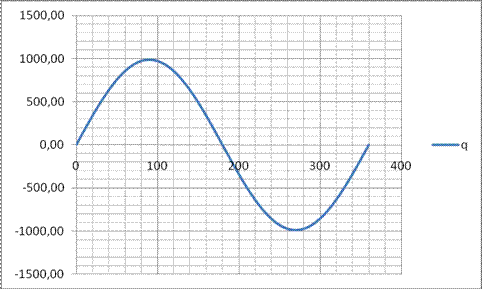
Рисунок 2.12.4 - График мгновенной подачи одним поршнем за один оборот
Таким образом, мгновенная подача всего насоса будет следующей:
(2.11.5)
где
α – угол между осями поршней, α=32,73 ;
Рисунок 2.12.5 - График мгновенной подачи всего насоса за один оборот
2.12.2. Расчет неравномерности подачи жидкости
Подача жидкости в аксиально-поршневых машинах имеет пульсирующий характер, и слагается из подач отдельных поршней, совершающих рабочий цикл в текущий момент. Это непостоянство подачи, не зависит от давления нагнетания и оценивается коэффициентом неравномерности подачи, который для насоса с 11 поршнями составляет 0,5%.
Расчетная формула выглядит следующим образом:
(2.12.1)
2.13 Ориентировочный расчет ресурса машины
, (2.13.1)
Так как протототип моего насоса был рассчитан на давление 20 МПа, то из равенства 2.13.1 можно справедливо полагать, что ресурс моего насоса в работе такой же гидросистемы будет минимум в 2 раза больше, ввиду того, что коэффициент загрузки его уменьшится в 2 раза.
3. ВЫБОР РАБОЧЕЙ ЖИДКОСТИ
В зависимости от эксплуатационных свойств и состава (наличия соответствующих функциональных присадок) гидравлические масла делят на группы А, Б и В.
Группа А (группа НН по ISО) - нефтяные масла без присадок, применяемые в малонагруженных гидросистемах с шестеренными или поршневыми насосами, работающими при давлении до 15 МПа и максимальной температуре масла в объеме до 80 °С.
Группа Б (группа HL по ISO) - масла с антиокислительными и антикоррозионными присадками. Предназначены для средненапряженных гидросистем с различными насосами, работающими при давлениях до 2,5 МПа и температуре масла в объеме свыше 80 °С.
Группа В (группа HM по ISO) - хорошо очищенные масла с антиокислительными, антикоррозионными и противоизносными присадками. Предназначены для гидросистем, работающих при давлении свыше 25 МПа и температуре масла в объеме свыше 90 °С.
В масла всех указанных групп могут быть введены загущающие (вязкостные) и антипенные присадки. Загущенные вязкостными полимерными присадками гидравлические масла соответствуют группе НV по ISO 6743/4.
Таким образом, учитывая наличие в насосе пар трения «сталь по стали» считаю необходимым применение масел группы В (НМ по ISO), то есть содержащие противоизносные присадки.
Учитывая вышеизложенные требования и вязкостные характеристики масел выбираю следующие масла для использования в качестве рабочей жидкости:
Лето – масло «Р» (МГ-22-В по ГОСТ 17479.3-85)
Зима – масло «ВМГЗ» (МГ-15-В по ГОСТ 17479.3-85)
Масло гидравлическое ВМГЗ (ТУ 38.101479-86) - маловязкая низкозастывающая минеральная основа, вырабатываемая посредством гидрокаталитического процесса, загущенная полиметакрилатной присадкой. Содержит присадки: противоизносную, антиокислительную, антипенную. Масло предназначено для систем гидропривода и гидроуправления строительных, дорожных, лесозаготовительных, подъемно-транспортных и других машин, работающих на открытом воздухе при температурах в рабочем объеме масла от -40 до +50 °С в зависимости от типа гидронасоса. Для северных регионов рекомендуется как всесезонное, а для средней географической зоны - как зимнее.
Выбираю 11 класс чистоты рабочей жидкости, применяемой в гидросистеме с проектируемым насосом. Но учитывая, что в гидросистеме экскаватора ЕТ-25 номинальное давление равно 20 МПа, считаю возможным применение масла с классом чистоты 12 (минимальный класс чистоты рабочей жидкости для гидроаппаратуры, применяемой на экскаваторе ЕТ-25).
Класс |
Дисперсный состав (число частиц загрязнений в объеме жидкости 100 см3
)×103
|
Размер частиц, мкм |
5…10 |
10…25 |
25…50 |
50…100 |
100…200 |
Гранулометрический состав, % |
64,2 |
32,1 |
3,2 |
0,4 |
0,1 |
11 |
31,5 |
16 |
1,6 |
0,2 |
0,05 |
12 |
63 |
31.5 |
3.15 |
0.4 |
0.1 |
|