Министерство общего и профессионального образования РФ
Алтайский государственный технический университет
им. И. И. Ползунова
Кафедра химической техники и инженерной экологии
Курсовой проект защищён
с оценкой ______________
Руководитель канд. техн.
наук, доцент Андреева Н. Г.
Насадочная ректификационная колонна
для разделения бинарной смеси диоксан – толуола
Пояснительная записка курсового проекта по дисциплине
«Процессы и аппараты химической технологии»
КП 68.170500.29.000.ПЗ
Проект выполнил студент
гр. МАХП -01
Нормоконтролёр
канд. техн. наук, доцент Андреева Н. Г.
Барнаул 2004 Содержание
Введение. 3
1 Физико – химические основы.. 4
2 Технологическая схема ректификационной установки. 6
3 Расчётная часть. 8
3.1 Задание и исходные данные. 8
3.2 Материальный баланс и рабочее флегмовое число. 9
3.3 Скорость пара и диаметр колонны.. 12
3.4 Высота слоя насадки и колонны.. 13
3.5 Гидравлическое сопротивление насадки. 15
3.6 Тепловой расчет установки.15
4 Механический расчет установки. 17
4.1 Расчет толщины обечаек. 17
4.2 Расчет толщина крышки и днища. 18
4.3 Расчёт изоляции колонны.. 18
4.4 Расчёт штуцеров.19
4.4.1 Штуцер для ввода исходной смеси.19
4.4.2 Штуцер для ввода флегмы.. 19
4.4.3 Штуцер для отвода кубового остатка. 19
4.4.4 Штуцер для вывода паров дистиллята. 19
4.4.5 Штуцер для ввода паров кубовой смеси. 20
4.5 Емкости. 20
4.6 Насосы.. 21
Заключение. 23
Список использованной литературы.. 24
Приложение А
Приложение Б
Приложение В
Приложение Г
Приложение Д
Ректификация – процесс разделения гомогенных смесей летучих жидкостей путём двустороннего массообмена и теплообмена между неравновесными жидкой и паровой фазами, имеющими различную температуру и движущимися противоположно друг другу.
Разделение осуществляется обычно в колонных аппаратах при многократном или непрерывном контакте фаз. При каждом контакте из жидкости испаряется преимущественно низкокипящий компонент, которым обогащаются пары, а из паровой конденсируется преимущественно высококипящий компонент переходящий в жидкость. В результате обмена компонентами между фазами в конечном счете пары представляют собой почти чистый низкокипящий компонент. Эти пары выходящие из верхней части колоны после их конденсации в отдельном аппарате дают дистиллят (верхний продукт) и флегму - жидкость, возвращающую для орошения колоны и взаимодействия с поднимающимися в колоне парами. Снизу удаляется жидкость представляющая собой почти чистый высококипящий компонент - кубовый остаток (нижний продукт). Часть остатка испаряют в нижней части колоны для получения восходящего потока пара.
Ректификация известна с начала девятнадцатого века, как один из важнейших технологических процессов главным образом спиртовой и нефтяной промышленности. В настоящее время ректификацию всё шире применяют в самых различных областях химической технологии, где выделение компонентов в чистом виде имеет весьма важное значение (в производных органического синтеза, изотопов, полупроводников и различных других веществ высокой чистоты).
Достаточно высокая степень разделения однородных жидких смесей на компоненты может быть достигнута путем ректификации. Сущность процессов, из которых складывается ректификация, и получаемые при этом результаты можно проследить с помощью t – х – у – диаграммы.
Нагрев исходную смесь состава x1
до температуры кипения получим находящийся в равновесии с жидкостью пар (точка b). Отбор и конденсация этого пара дают жидкость состава х2
обогащенную НК (х2
>х1
).Нагрев эту жидкость до температуры кипения t2
, получим пар (точка d), конденсация которого дает жидкость с еще большим содержанием НК, имеющую состав x3, и т. д. Проводя таким образом последовательно ряд процессов испарения жидкости и конденсации паров, можно получить в итоге жидкость (дистиллят), представляющую собой практически чистый НК.
Аналогично, исходя из паровой фазы, соответствующей составу жидкости x4
, путем проведения ряда последовательных процессов конденсации и испарения можно получить жидкость (остаток), состоящую почти целиком из ВК.
В простейшем виде процесс многократного испарения можно осуществить в многоступенчатой установке, в первой ступени которой испаряется исходная смесь. На вторую ступень поступает на испарение жидкость, оставшаяся после отделения паров в первой ступени, в третьей ступени испаряется жидкость, поступившая из второй ступени (после отбора из последней паров) и т. д. Аналогично может быть организован процесс многократной конденсации, при котором на каждую следующую ступень поступают для конденсации пары, оставшиеся после отделения от них жидкости (конденсата) в предыдущей ступени.
При достаточно большом числе ступеней таким путем можно получить жидкую или паровую фазу с достаточно высокой концентрацией компонента, которым она обогащается. Однако выход этой фазы будет мал по отношению к ее количеству в исходной смеси. Кроме того, описанные установки отличаются громоздкостью и большими потерями тепла в окружающую среду.
Значительно более экономичное, полное и четкое разделение смесей на компоненты достигается в процессах ректификации, проводимых обычно в более компактных аппаратах - ректификационных колоннах.
При взаимодействии фаз между ними происходит массо- и теплообмен обусловленные стремлением системы к состоянию равновесия.
В результате каждого контакта компоненты перераспределяются между фазами: пар несколько обогащается ПК, а жидкость — ВК.
Многократное контактирование приводит к практически полному разделению исходной смеси.
Таким образом, отсутствие равновесия (и соответственно наличие разности температур фаз) при движении фаз с определенной относительной скоростью и многократном их контактировании являются необходимыми условиями проведения ректификации.
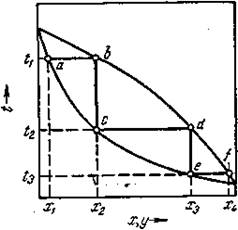
Рис 1.1 Изображение процесса разделения бинарной смеси путем ректификации на диаграмме t—х—у
Процессы ректификации осуществляются периодически или непрерывно при различных давлениях: при атмосферном давлении, под вакуумом (для разделения смесей высококипящих веществ), а также под давлением больше атмосферного (для разделения смесей, являющихся газообразными при нормальных температурах).
Принципиальная схема ректификационной установки приведена на рисунке 2.1:

Рис. 2.1:Принципиальная схема ректификационной установки:
1 - теплообменник-подогреватель; 2,6 - насосы; 3 - емкость для исходной смеси; 4 - кипятильник; 5 - ректификационная колона; 7 - дефлегматор; 8 - холодильник дистиллята; 9 - холодильник кубовой жидкости; 10 - емкость для кубовой жидкости; 11 - емкость для сбора дистиллята
Исходную смесь из промежуточной емкости 1
центробежным насосом 2
подают в теплообменник 3, где она подогревается до температуры кипения. Нагретая смесь поступает на разделение в ректификационную колонну 5, где состав жидкости равен составу исходной смеси xF
.
Стекая вниз по колонне, жидкость взаимодействует с поднимающимся вверх паром, образующимся при кипении кубовой жидкости в кипятильнике 4.
Начальный состав пара примерно равен составу кубового остатка Х
W
,
т. е. обеднен легколетучим компонентом. В результате массообмена с жидкостью пар обогащается легколетучим компонентом. Для более полного обогащения верхнюю часть колонны орошают в соответствии с заданным флегмовым числом жидкостью (флегмой) состава хР
,
получаемой в дефлегматоре 6
путем конденсации пара, выходящего из колонны. Часть конденсата выводится из дефлегматора в виде готового продукта разделения — дистиллята, который охлаждается в теплообменнике 7 и направляется в промежуточную емкость 8.
Из кубовой части колонны насосом 9
непрерывно выводится кубовая жидкость — продукт, обогащенный труднолетучим компонентом, который охлаждается в теплообменнике 10и направляется в емкость 11.
Таким образом, в ректификационной колонне осуществляется непрерывный неравновесный процесс разделения исходной бинарной смеси на дистиллят (с высоким содержанием легколетучего компонента) и кубовый остаток (обогащенный труднолетучим компонентом).
3.1 Задание и исходные данные
Необходимо рассчитать насадочную ректификационную колонну для разделения бинарной смеси диоксан – толуол. GD
=1000 кг/ч, xF
=45% (мол.), xD
=90% (мол.), xW
=2% (мол.). Давление в колонне составляет 600 мм рт. ст., смесь поступает при температуре кипения. Равновесные даны о паре и t-x,y диаграмма представлены ниже.
Таблица 3.1. Данные о
равновесном составе пара
x%, мол. |
y*
%, мол. |
t |
р |

Рис. 3.1. Диаграмма равновесия между паром и жидкостью при постоянном давлении в координатах t-x,y
|
8,7 |
12,9 |
100,72 |
600 |
15,2 |
20 |
99,58 |
23,2 |
31,8 |
98,38 |
31 |
40,6 |
97,38 |
41,8 |
51 |
96,16 |
44,9 |
53,5 |
96,08 |
51,4 |
59,7 |
95,38 |
62,2 |
68,9 |
94,55 |
70,5 |
74,9 |
94,31 |
80,6 |
83,1 |
93,93 |
90,8 |
92 |
93,65 |
Расчет ректификационной колонны сводится к определению ее основных геометрических размеров — диаметра и высоты. Оба параметра в значительной мере определяются гидродинамическим режимом работы колонны, который, в свою очередь, зависит, от скоростей и физических свойств фаз, а также от типа и размеров насадок.
При проведении процессов вакуумной ректификации с целью снижения гидравлического сопротивления выбирают специальные виды насадок, обладающих большим свободным объемом. Наиболее правильно выбор оптимального типа и размера насадки может быть осуществлен на основе технико-экономического анализа общих затрат на разделение в конкретном технологическом процессе.
Ориентировочный выбор размера насадочных тел можно осуществить исходя из следующих соображений. Чем больше размер элемента насадки, тем больше ее свободный объем (живое сечение) и, следовательно, выше производительность. Однако вследствие меньшей удельной поверхности эффективность крупных насадок несколько ниже. Поэтому насадку большого размера применяют, когда требуются высокая производительность и сравнительно невысокая степень чистоты продуктов разделения.
В ректификационных колоннах для разделения агрессивных жидкостей, а также в тех случаях, когда не требуется частая чистка аппарата, обычно применяют керамические кольца Рашига. Но вследствие малой удельной поверхности таких колец и плохой разделяемости данной жидкости для данного случая примем насадку из керамических колец Палля размером 35х35х4. Удельная поверхность такой насадки а=165 м2
/м3
, свободный объём ε=0,76 м3
/м3
, насыпная плотность 540 кг/ м3
, dэ
=0,018, число штук в м3
18500.
Насадочные колонны могут работать в различных гидродинамических режимах: пленочном, подвисания и эмульгирования. В колоннах большой производительности с крупной насадкой осуществление процесса в режиме эмульгирования приводит к резкому уменьшению эффективности разделения, что объясняется существенным возрастанием обратного перемешивания жидкости и значительной неравномерностью скорости паров по сечению аппарата. Ведение процесса в режиме подвисания затруднено вследствие узкого интервала изменения скоростей пара, в котором этот режим существует. Поэтому выберем плёночный режим работы колонны.
3.2 Материальный баланс и рабочее флегмовое число
Обозначим массовый расход дистиллята через GD
кг/с, кубового остатка GW
кг/с, исходной GF
кг/с.
Из уравнений материального баланса ректификационной колонны непрерывного действия:
GF
= GD
+GW
; (3.1)
GF
XF
= GD
XD
+GW
XW
, (3.2)
где GF
, GD
,GW
– массовые расходы питания, дистиллята и кубового остатка; XF
, XD
, XW
– содержание легколетучего компонента в питании, дистилляте и кубовом остатке, массовые доли.
Для расчетов выразим концентрации питания, дистиллята и кубового остатка в массовых долях , X.
X = x∙MД
/(x∙MД
+ (1 – x)∙MТ
), (3.3)
где MД
=88, MТ
=92– мольные массы диоксана и толуола.
XF
= (88∙0,45)/(88∙0,45 + (1 – 0,45)∙92) = 0,439 кг/кг смеси.
XD
= (88∙0,9)/(88∙0,9 + (1 – 0,9)∙92) = 0,896 кг/кг смеси.
XW
= (88∙0,02)/(88∙0,02 + (1 – 0,02)∙92) = 0,019 кг/кг смеси.
Из уравнений материального баланса
GF
= GW
+1000
GF
∙0,439 = GW
∙0,019 +1000∙0,896
GF
=2088 кг/ч = 0,580 кг/с; GW
= 1088 кг/ч = 0,302 кг/с; GD
=0,278 кг/с.
Определяем минимальное число флегмы по уравнению:
RMIN
= (XD
-Y*
F
)/(Y*
F
–XF
); (3.4)
где Y*
F
= 0,54- мольная доля диоксана в паре (из приложения Д).
RMIN
= (0,9 – 0,54)/(0,54 – 0,45) = 4.
Задавшись различными значениями коэффициентов избытка флегмы β, определим соответствующие флегмовые числа. Графическим построением ступеней изменения концентраций между равновесной и рабочей линиям на диаграмме состав параY – состав жидкости X находим N[1]. Определение Nприведены в приложениях А, Б, В, Г, а результаты в таблице 3.2:
Таблица 3.2
β |
1,05 |
1,35 |
1,75 |
2,35 |
R |
4,2 |
5,4 |
7 |
9,4 |
N |
58 |
42 |
32 |
29 |
N(R+1) |
301,6 |
268,8 |
256 |
301,6 |
Используя данные из таблицы, построим зависимостьN(R+1)=f(R):
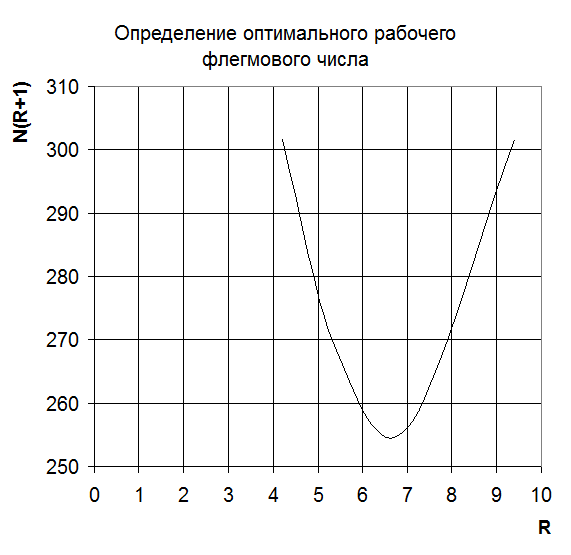
Рисунок 3.2 Зависимость N(R+1) от R
Минимальное произведение N(R+1) соответствует флегмовому числу R
=6,6
(из рис.3.2).
Уравнения рабочих линий:
а) верхней(укрепляющей) части колонны:
y= ((R/(R+1))∙x)+(xD
/(R+1)); (3.5)
y
= 0,868∙
x
+0,118;
б) нижней (исчерпывающей) части колонны:
y = (R+F)/(R+1)∙x - (F-1)/(R+1)∙ xW
,
где F - относительный мольный расход питания.
F = (xD
- xW
)/(xF
-xW
) ; F = (0,9-0,02)/(0,45-0,02)=2,047;
y
= 1,138∙
x
– 0,003
.
Из приложения Д nт
=35 – число теоретических тарелок, nт в
= 20 – число теоретических тарелок в верхней части колонны, nт н
= 15 – в нижней.
Средние массовые расходы (нагрузки) по жидкости для верхней и нижней частей колонны определяют из соотношений:
L
В
=
GD
RM
В
/
MD
;
(3.6)
L
Н
=
GD
RM
Н
/
MP
+
GF
M
Н
/
MF
,
(3.7)
где М
D
и М
F
— мольные массы дистиллята и исходной смеси; МВ
и МН
— средние мольные массы жидкости в верхней и нижней частях колонны. Средние мольные массы жидкости в верхней и нижней частях колонны соответственно равны:
МВ
= МД
xср. в
+ М Т
(1 — xср. в
);
МН
= МД
xср. н
+ М Т
(1 — xср. н
); (3.8)
где МД
и МТ
— мольные массы диоксана и толуола; хср.в
и хср.н
— средний мольный состав жидкости соответственно в верхней и нижней частях колонны:
xc
р. в
=(xD
+xF
)/2 =(0,9 + 0,45)/2 = 0,675 кмоль/кмоль смеси;
xc
р. н
= (
xF
+xW
)/2= (0,45 + 0,02)/2 = 0,235 кмоль/кмоль смеси.
Тогда:
МВ
= 88 ∙ 0,675 + 92 (1 - 0,675) = 89,30 кг/кмоль;
МН
= 88 ∙ 0,235 + 92 (1 - 0,235) = 91,06 кг/кмоль.
Мольная масса исходной смеси и дистиллята:
MF
= 88 ∙ 0,45 + 92(1 — 0,45) = 90,2 кг/кмоль,
MD
= 88 ∙ 0,9 + 92(1 — 0,9) = 88,4 кг/кмоль.
Подставим рассчитанные величины в уравнения (3.6) и (3.7), получим:
L
В
= 0,278
∙ 6,6 ∙ 89,3 / 88,4 = 1,853 кг / с;
L
Н
= 0,278
∙ 6,6 ∙ 91,06 / 88,4 + 0,58 ∙ 91,06 / 90,2 = 2,476 кг / с.
Средние массовые потоки пара в верхней GВ
и нижней GH
частях колонны соответственно равны:
GВ
= GD
(R+1)M’В
/ M D
;
GН
= GD
(R+1)M’Н
/ M D
.(3.9)
Здесь M’В
и M’Н
- средние мольные массы паров в верхней и нижней частях колонны:
М’В
= МД
yср. в
+ М Т
(1 — yср. в
);
М’Н
= МД
yср. н
+ М Т
(1 — yср. н
); (3.10)
где
yc
р. в
=(yD
+yF
)/2 =(0,9 + 0,51)/2 = 0,705 кмоль/кмоль смеси;
yc
р. н
= (yF
+yW
)/2= (0,51 + 0,02)/2 = 0,265 кмоль/кмоль смеси.
Тогда
М’В
= 88∙ 0,705 + 92(1 - 0,705) = 89,18 кг/кмоль;
М’Н
= 88∙ 0,265 + 92(1 – 0,265) = 90,94 кг/кмоль.
GH
= 1,73(2,1 + 1) 87,8/78 = 6,04 кг/с.
Подставив численные значения в уравнение (3.9), получим:
GВ
= 0,278 (6,6+1)89,18 / 88,4 = 2,131 кг/с;
GН
=0,278 (6,6+1) 90,94 / 88,4 = 2,174 кг/с.
3.3 Скорость пара и диаметр колонны
Для ректификационных колонн, работающих в пленочном режиме при атмосферном давлении, рабочую скорость можно принять на 20—30 % ниже скорости захлебывания [5].
Предельную фиктивную скорость пара w
п
, при которой происходит захлебывание насадочных колонн, определяют по уравнению [6]:
, (3.11)
где ρx
, ρy
— средние плотности жидкости и пара, кг/м3
; μx
— в мПа-с.
Поскольку отношения L
/
G
и физические свойства фаз в верхней и нижней частях колонны различны, определим скорости захлебывания для каждой части отдельно.
Найдем плотности жидкости ρх в
, ρx
н
и пара ρy
в
, ρy
н
в верхней и нижней частях колонны при средних температурах в них tв
и tн
. Средние температуры паров определим по диаграмме t
—х, у
(см. рис. 3.2) по средним составам фаз: tВ
= 94°С; tн
=102 °С. Тогда
ρy
в
=М’В
T0
/(22,4(T0
+t0
)); ρy
н
=М’Н
T0
/(22,4(T0
+t0
)). (3.12)
Отсюдаполучим:
ρy
в
= 89,19∙ 273/(22,4∙ (273+94))=2,95 кг/м3
;
ρy
н
= 90,94∙ 273/(22,4∙ (273+102))=2,96 кг/м3
Плотность физических смесей жидкостей подчиняется закону аддитивности:
ρсм
= ρ1
xоб
+ ρ2
(1- xоб
),
где xоб
— объемная доля компонента в смеси.
В рассматриваемом задаче плотности жидких диоксана итолуола близки [7], поэтому можно принять ρx
в
= ρх н
= ρх
= 790 кг/м3
.
Вязкость жидких смесей ц∙ находим по уравнению [8]:
lg μx
=xср
lg μx
д
+ (1-xср
) lg μx
т
, (3.13)
где μx
д
и μx
т
— вязкости жидких диоксана и толуола при температуре смеси [7].
Тогда вязкость жидкости в верхней и нижней частях колонны соответственно равна:
lgμx
в
=0,675 lg0,22 + (1-0,675) lg0,30,
lgμx
н
=0,235 lg0,21 + (1-0,235) lg0,27,
откуда μx
в
= 0,243 мПа∙с; μx
н
= 0,254 мПа∙с.
Предельная скорость паров в верхней части колонны:
;
откуда w
пв
=1,241 м/с.
Предельная скорость паров в нижней части колонны:
;
откуда w
пн
=1,172 м/с.
Примем рабочую скорость но 30% ниже предельной:
w
в
=1,241∙0,7=0,87 м/с; w
н
=1,172∙0,7=0,82 м/с.
Диаметр ректификационной колонны определим из уравнения расхода:
(3.14)
Отсюда диаметры верхней и нижней части колонны равны соответственно:
м; м.
Рационально принять стандартный диаметр обечайки d = l,2 м одинаковым для обеих частей колонны. При этом действительные рабочие скорости паров в колонне равны:
w
в
= 0,87(1,03/1,2)2
= 0,64 м/с; w
н
= 0,82 (1,07/1,2)2
= 0,65 м/с,
что составляет соответственно 52 и 55 % от предельных скоростей.
3.4 Высота слоя насадки и колонны
Высота ректификационной колонны насадочного типа находится из уравнения:
Нк
=Ят+(т-1)рр
+Яв
+Ян
+Нк
+Нд
(3.15)
где Z=5 м – высота насадки в одной секции; n – число секций; hр
=1,215 – высота промежутков между секциями насадки, в которых устанавливают распределители жидкости, м: Zв
= 1,2 м и Zн
= 2 м – соответственно высота сепарационного пространства над насадкой и расстояние между днищем колонны и насадкой, Нк
- высота крышки, Нд
– высота днища.
n=(Hв
+ Hн
)/Z, (3.16)
Hн
=hэ н
∙nт н
Hв
= hэ в
∙nт в
(3.17)
где Hв
и Hн
– высота слоя насадки в верхней и нижней частях колонны; hэ в
и hэ н
– эквивалентная высота насадки [8].
; (3.18)
где - критерий Рейнольдса [8]:
. (3.19)
Отношение L/G в верхней и нижней частях соответственно равны:
G/L=(R+1)/R=(6,1+1)/6,6=1,15;
G/L=(R+1)/(R+F)=(6,6+1)/(6,6+2,047)=0,88. (3.20)
Вязкость паров для верхней и нижней частей колонны:
μy
в
= M’в
/(yв
МД
/ μу Д
+ (1 - yв
) МТ
/ μу Т
);
μy
н
= M’н
/(yн
МД
/ μу Д
+ (1 – yн
) МТ
/ μу Т
), (3.21)
где
yв
=(yD
+ yF
)/2=(0,9+0,51)/2=0,705 кмоль / кмоль смеси;
yн
=(yw
+ yF
)/2=(0,02+0,51)/2=0,265 кмоль / кмоль смеси. (3.22)
μy
в
= 89,18/(0,705∙88/ 0,009 + (1 – 0,705) 92/ 0,0089)=0,009 мП∙с;
μy
н
= 90,94/(0,265∙88/ 0,009 + (1 – 0,265) 92/ 0,0089)=0,0089 мП∙с.
Тогда:
;
.
Для определения m – тангенса угла наклона равновесной линии для верхней и нижней частей колонны добавим линию тренда:
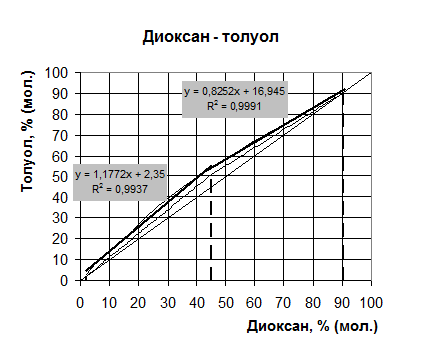
Рис. 3.3. Касательные к линии равновесия
Тогда для верхней и нижней частей колонны mсоответственно равно 0,83 и 1,18. Следовательно:
м;
м.
Высота слоя насадки для верхней и нижней частей колонны равны:
Нв
=20∙0,73=14,6 м и Нн
=15∙0,65=9,75 м.
Н=14,6+9,75=24,35 м.
Примем Н=25 м, то n=25/5=5 секций, 3 в верхней части колонны и 2 в нижней. Конечная высота ректификационной колонны равна:
Нк
=5∙5+(5-1)∙1,215+1,2+2+0,3+0,3=33,66 м. Для дальнейших расчётов примем HК
=40 м.
3.5 Гидравлическое сопротивление насадки
Гидравлическое сопротивление насадки ΔРнаходят по уравнению
ΔР=10169 ∙
U
ΔРс
.(3.23)
Гидравлическое сопротивление сухой неорошаемой насадки ΔРС
рассчитывают по уравнению [1]:
, (3.24)
где λ
—коэффициент сопротивления сухой насадки, зависящий от режима движения газа в насадке.
Критерий Рейнольдса для газа в верхней и нижней частях колонны соответственно равен:
;
. (3.25)
Следовательно, режим движения турбулентный.
Для турбулентного режима коэффициент сопротивления сухой насадки в виде беспорядочно засыпанных колец Рашига находят по уравнению
λ= 16/ 2
. (3.26)
Для верхней и нижней частей колонны соответственно получим:
=16/49680,2
= 2,92; = 16/51200,2
= 2,90.
Гидравлическое сопротивление сухой насадки в верхней и нижней частях колонны равно:
Па;
Па.
Плотность орошения в верхней и нижней частях колонны определим по формулам:
Uв
=Lв
/(ρх
0,785d2
), Uн
=Lв
/(ρх
0,785d2
). (3.27)
Подставив численные значения, получим:
Uв
=1,853/(790∙0,785∙1,22
)=0,0021 м3
/(м2
∙с),
Uн
=2,476/(790∙0,785∙1,22
)=0,0028 м3
/(м2
∙с).
Гидравлическое сопротивление орошаемой насадки в верхней и нижней частях колонны:
ΔР=10169∙ 0,0021
∙2545 = 5762 Па; ΔР=10169∙ 0,0028
∙1744 = 5185 Па.
Общее гидравлическое сопротивление орошаемой насадки в колонне:
ΔР = ΔРв
+ ΔРн
= 5762 + 5185 = 10947≈ 11000 Па.
3.6 Тепловой расчет установки.
Расход теплоты, отдаваемой охлаждающей воде в дефлегматоре-конденсаторе, находим по уравнению:
Qд
=GD
∙ (1+R) ∙ rD
, (3.28)
где rD
-удельная теплота конденсации паров в дефлегматоре, кДж/кг.
rD
=XD
∙ rд
+(1-XD
) ∙ rт
, (3.29)
где rд
–и rт
–удельные теплоты конденсации диоксана и толуола при 94°С [8].
rд
= 360 кДж/кг;
rт
= 321 кДж/кг;
rD
= 0,896 ∙ 360+(1 – 0,896) ∙ 321= 356 кДж/кг;
Qд
= 0,278 ∙ (1+6,6) ∙ 356= 752 кВт.
Расход теплоты, получаемой в кубе-испарителе от греющего пара, находим по уравнению:
Qк
= Qд
+ GD
∙ СD
∙ tD
+ GW
∙ СW
∙ tW
– GF
∙ СF
∙ tF
+Qпот
, (3.30)
где Qпот
приняты в размере 3% от полезно затрачиваемой теплоты; удельные теплоёмкости взяты соответственно при tD
=94°С, tW
=102°С, tF
=96°С, температура кипения исходной смеси tF
определена по t-x-y по диаграмме (рис.3.2).
СW
= (0,54 ∙ 0,019 + 0,45 ∙ (1 - 0,019)) ∙ 4190 = 1893 Дж/(кг ∙ К);
СF
= (0,53 ∙ 0,439 + 0,44 ∙ (1 - 0,439)) ∙ 4190 = 2009 Дж/(кг ∙ К);
CD
= (0,52 ∙ 0,896 + 0,44 ∙ (1 - 0,896)) ∙ 4190 = 2144 Дж/(кг ∙ К).
CD
, СW
, СF
-взяты из справочника [8].
Qк
=(752000 + 0,278 ∙ 2144 ∙ 94 + 0,302 ∙ 1893 ∙ 102 – 0,58 ∙ 1893 ∙ 96) ∙ 1,03= = 760937 Вт ≈ 761кВт.
Расход теплоты в паровом подогревателе исходной смеси:
Q=1,05 ∙ GF
∙ СF
∙ (tF
–tнач
), (3.31)
где тепловые потери приняты в размере 5%, удельная теплоёмкость исходной смеси СF
= (0,5∙ 0,439+0,42 ∙ (1-0,439)) ∙ 4190 = 1907 Дж/(кг ∙ К)
при t = (96+18)/2 =57 °С.
Q=1,05 ∙ 0,58 ∙ 1907 ∙ (96 – 18) = 90586 Вт.
Расход греющего пара, имеющего давление рабс
=4 кгс/см2
и влажность 5%
а) в кубе испарителе:
Gгп
=Q/(rгп
∙ X), (3.34)
где rгп
=2141 ∙ 103
Дж/кг – удельная теплота конденсации греющего пара.
Gгп
= 760937/(2141 ∙ 103
∙ 0,95) = 0,374 кг/с;
б) в подогревателе исходной смеси
Gгп
= 90586/(2141 ∙ 103
∙ 0,95) = 0,045 кг/с.
Всего: 0,374 + 0,045 = 0,419 кг/с или 1,508 т/ч.
Расход охлаждающей воды при нагреве её на 200
С в дефлегматоре:
Vв
=Qд
/(Св
∙ (tкон
-tнач
) ∙ ρв
), (3.35)
где Св
=4190 Дж/(кг ∙ К) - удельная теплота конденсации воды; ρв
- плотность воды.
Vв
=75200/(4190 ∙ 20 ∙ 1000)=0,009 м3
/с или 32,4 м3
/ч. 4 Механический расчет установки
4.1 Расчет толщины обечаек
Исполнительную толщину тонкостенной гладкой цилиндрической обечайки, нагруженной внешним давлением, рассчитываем по формуле:
, (4.1)
где pн
– наружное давление, равное разности атмосферного и данного
760 - 600 = 160 мм. рт. ст. = 0,1- 0,08=0,02 МПа.
Т. к. среда является агрессивной и токсичной, то принимаем сталь 12Х18H10Т, для которой σ*=152 МПа [11],
С – прибавка к расчётным толщинам.
С = П ∙ τ, (4.2)
где П – скорость коррозии или эрозии, П = 0,1мм/год, τ– срок службы аппарата, принимаем τ = 20 лет.
С = 0,1 ∙ 20 = 2 мм.
К2
=0,35 – коэффициент, определяемый по Рис. 13.1 [11].
[σ]=ησ*, (4.3)
где η = 1 – поправочный коэффициент, учитывающий вид заготовки (листовой прокат).
[σ]= 1 ∙ 160=160 МПа.
мм
Примем S = 8 мм.
Для обечаек с диаметром больше 200мм должно соблюдаться условие:
(S-C)/D < 0,1 (4.4)
(8 – 1)/1200 = 0,0058 < 0,1 - условие выполняется.
Проверим конструкцию на устойчивость по формуле:
Рн
/[pн
]+F/[F]+M/[M] 1. (4.5)
Т. к. аппарат имеет большую высоту, то М будет на порядок больше F. Тогда выражением F/[F] пренебрегаем.
Допускаемое наружное давление находят по формуле:
. (4.6)
Допускаемое давление из условия прочности находят по уравнению:
[pн
]σ
=2 ∙ [σ] ∙ (S – C)/(D + S – C) (4.7)
Допускаемое давление из условия устойчивости в пределах упругости определяют по уравнению:
, (4.8)
где В1
– меньшее из двух, вычисленных по формулам:
В1
=1; В1
= , (4.9)
ny
– запас устойчивости, равный 2,4.
Допускаемый момент находят по выражению:
(4.10)
Допускаемый изгибающий момент из условия прочности:
[М]σ
= 0,25 ∙ π ∙ D ∙ [σ] ∙ (S – C) ∙ (D + S – C) (4.11)
Допускаемый изгибающий момент из условия устойчивости:
(4.12)
Определим изгибающий момент.
Вес слоя насадки равен: G=9,8 ∙ Vн
∙ ρ= (3 ∙ 9 ∙ 3,14 ∙ 0,62
) ∙ 540=161514 Н.
Учитывая вес обечаек (при S=16 мм это около 80 кН), днища, крышки, распределительных тарелок, фланцев и т. д., округлим до 0,3 МН. Тогда
M=G ∙ Hк
∙ 0,215 = 0,3 ∙ 34 ∙ 0,215=2,193 МН ∙ м.
Расчёты сведём в таблицу:
Таблица 4.1. Влияние внешнего давления и момента на устойчивость
S, м |
[M]σ
|
[M]E
|
[M] |
M/[M] |
В1
|
[p]E
|
[p]σ
|
[p] |
Pн
/[pн
] |
Pн
/[pн
]+ M/[M] |
0,007 |
0,908 |
1,437 |
0,768 |
2,857 |
0,446 |
0,013 |
1,328 |
0,013 |
1,502 |
4,359 |
0,008 |
1,091 |
2,266 |
0,983 |
2,232 |
0,407 |
0,023 |
1,592 |
0,023 |
0,869 |
3,101 |
0,009 |
1,273 |
3,332 |
1,190 |
1,844 |
0,377 |
0,037 |
1,856 |
0,037 |
0,548 |
2,391 |
0,010 |
1,457 |
4,652 |
1,390 |
1,578 |
0,352 |
0,055 |
2,119 |
0,055 |
0,367 |
1,945 |
0,012 |
1,824 |
8,127 |
1,779 |
1,232 |
0,315 |
0,107 |
2,645 |
0,106 |
0,188 |
1,420 |
0,014 |
2,192 |
12,820 |
2,161 |
1,015 |
0,288 |
0,184 |
3,168 |
0,184 |
0,109 |
1,124 |
0,016 |
2,562 |
18,848 |
2,538 |
0,864 |
0,266 |
0,292 |
3,690 |
0,291 |
0,069 |
0,933 |
При S=16 мм условие устойчивости выполняется.
Примем S=16 мм.
4.2 Расчет толщина крышки и днища
Толщину стенки эллиптического днища определяют по формуле:
, (4.9)
мм.
Принимаем толщину крышки и днища равной толщине стенки = 16 мм.
4.3 Расчёт изоляции колонны
Определить необходимую толщину слоя изоляции аппарата, внутри которого температура 102 С. Изоляционный материал - совелит. Температура наружной поверхности изоляции не должна быть выше 35 С. Примем температуру окружающего воздуха tо
= 20 °C и определим суммарный коэффициент теплоотдачи в окружающую среду лучеиспусканием и конвекцией по уравнению 4.71 [8]:
α = 9,74+0,07 ∙ Δt = 9,74+0,07 ∙ (35-20) = 10,79 Вт/(м2 ∙ К).
Удельный тепловой поток:
q = α ∙ (tст
-to
) = 10,79 ∙ (35-20) = 161,85 Вт/м2
.
Принимая приближенно, что все термическое сопротивление сосредоточено в слое изоляции, можно написать:
q = K(tвн
-to
) = la/б ∙ (tвн
-to
),
откуда толщина слоя изоляции (la = 0,098 теплопроводность совелита)
б = la/q ∙ (tвн
-to
) = 0,098/161,85 ∙ (102-20) = 0.05 м.
Так как наиболее горячая часть колонны это куб, то для всей остальной колонны можно принять ту же толщину слоя изоляции.
4.4 Расчёт штуцеров.
Расчёт штуцеров сводится к определению диаметра штуцера по уравнению:
, (4.10)
где w
- скорость, для жидкости принимаем 1,5м/с, для пара – 15 м/с.
4.4.1 Штуцер для ввода исходной смеси.
VF
= GF
/rF
(4.11)
VF
= 0,58 /790 = 7,34 ∙ 10-4
м3
/с.
0,025 м = 25 мм.
По ОН26-01-34-66 примем штуцер с наружным диаметром 37мм, с условным проходом Dу
=25 мм.
4.4.2 Штуцер для ввода флегмы
(4.12)
VD
= GD
∙ R, (4.13)
где R = 6,6 – флегмовое число
VD
= 0,278 ∙ 6,6 = 1,835 кг/с.
0,044 м = 44 мм.
По ОН26-01-34-66 примем штуцер с наружным диаметром 64 мм, с условным проходом Dу
=50 мм.
4.4.3 Штуцер для отвода кубового остатка
VW
= GW
∙ R, (4.14)
где R – отношение количества кубового остатка и парожидкостной смеси, принимаем её равной 2.
VW
= 0,302 ∙ 2 = 0,604 кг/с.
0,025 м = 25 мм.
По ОН26-01-34-66 примем штуцер с наружным диаметром 37 мм, с условным проходом Dу
=25 мм.
4.4.4 Штуцер для вывода паров дистиллята
V = G/rП
(4.15)
rП
= r’ = 2,95 кг/м3
G = GD
∙ (R+ 1) (4.16)
G = 0,278 ∙ (6,6 + 1) = 2,113 кг/с.
V = 2,113/2,95 = 0,716 м3
/с.
0,245 м = 245 мм.
По ОН26-01-34-66 примем штуцер с наружным диаметром 278 мм, с условным проходом Dу
=250 мм.
4.4.5 Штуцер для ввода паров кубовой смеси
V = G/rП
(4.17)
rП
= r” = 2,96 кг/м3
G = GW
∙ (R+1) (4.18)
G = 0,302 ∙ (6,6+1) = 2,295 кг/с.
V = 2,295/2,96 = 0,775 м3
/с.
0,255 м = 255 мм.
По ОН26-01-34-66 примем штуцер с наружным диаметром 278 мм, с условным проходом Dу
=250 мм.
4.5 Емкости
Ёмкости рассчитываются на непрерывную работу в течении 2 - 8 часов. Предельные объемы емкостей находим из соотношения:
V(max) = G ∙ t(max)/p t(max) = V(max) ∙ p/G
V(min) = G ∙ t(min)/p t(min) = V(min) ∙ p/G (4.19)
G - массовый расход;
t - время работы;
р - плотность при 20 °С.
В данном случае нет необходимости в точном расчете плотности и, так как для всех жидкостей они схожи, возьмем ρ = 790 кг/м3
.
1. Е1
- емкость для исходной смеси.
V(max) = 2088 ∙ 8/790 = 21 м3
,
V(min) = 2088 ∙ 2/790 = 5,3 м3
.
2. Е2
- емкости для кубового остатка:
V(max) = 1088 ∙ 8/790 = 11 м3
,
V(min) = 1088 ∙ 2/790 = 2,8 м3
.
2. Е3
- емкости для дистиллята:
V(max) = 1000 ∙ 8/790 = 10,1 м3
,
V(min) = 1000 ∙ 2/790 = 2,5 м3
.
Примем цилиндрические ёмкости с элептическими днищами, изготовленные из стали 12Х18H10Т:
Таблица 4.2. Ёмкости
Ёмкость для |
Длина L, м |
Внутренний диаметр D, м |
Объём V, м3
|
Толщина стенки S, мм |
исходной смеси |
4,5 |
2,4 |
20,5 |
3 |
дистиллята и
кубового остатка
|
3,5 |
2 |
9 |
3 |
1. Е1 - емкость для исходной смеси:
t = 790 ∙ 20,5/2088 = 7,75 часов.
2. Е2 - емкости для дистиллята:
t = 790 ∙ 9/1000 = 7,11 часов
2. Е3 - емкости для кубового остатка:
t = 790 ∙ 9/1088 = 6,53 часов
Все емкости с целью облегчения технического обслуживания и промывки связаны с магистралями оборотной воды и пара.
4.6 Насосы
Для перекачки кубового остатка и исходной смеси исходя из расходы и высоты, на которую подаётся жидкость, выберем насосы из таблицы соответственно под номером 1 и 2:
Таблица 4.3 Герметичные насосы типа ЦГ
№ |
Наименование |
Р, КВт |
Подача/напор |
Т жидкости, °С |
Масса, кг. |
1. |
ЦГ 6,3/20К-1,1-2 |
1,1 |
6,3 / 20 |
- 50… + 100 |
70 |
2. |
ЦГ 6,3/32К-2,2-2 |
2,2 |
6,3 / 32 |
- 50… + 100 |
79 |
Насосы ЦГ применяются в химической, газовой, топливно-энергетической, фармацевтической, нефтехимической, нефтяной, пищевой, мясо-молочной, холодильной и перерабатывающей промышленности и других производствах. Эксплуатация насосов без утечек и отсутствия обслуживающего персонала позволяет использовать их при работе с высокотоксичными, ядовитыми, химически активными жидкостями и сжиженными газами. Смазка и охлаждение насосов осуществляется перекачиваемой жидкостью. Уровень защиты - взрывобезопасный.
Предназначены для перекачивания в стационарных условиях жидкостей и сжиженных газов, пары которых могут образовывать с воздухом взрывоопасные смеси. Указанные жидкости могут быть нейтральными, агрессивными и вредными всех классов с кинематической вязкостью до 40 сСт и плотностью не более 1800 кг/м3. Допускается наличие твердых неабразивных включений с массовой долей до 0,2% и размером частиц не более 0,2 мм.
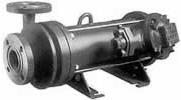
Рис. 4.1 Герметичный насос типа ЦГ
Материал проточной части: 12Х18Н10Т (исп. К) или 10Х17Н13М2Т (исп. Е) или ст. 3-10 (исп. А)
Изготавливаются на одно из напряжений 380 / 660 В.
В комплект поставки насосов входят: паспорт, ЗИП и принадлежности.
Условное обозначение электронасоса на примере 1ЦГ12,5/50К-4-2-У2:
1 - порядковый номер модернизации;
ЦГ - центробежный герметичный;
12,5 - номинальная подача (м3/ч);
50 - номинальный напор (м.);
К - условное обозначение по материалу ("К" - 12Х18Н10Т, "Е" - 10Х17Н13М2Т, "А" - ст. 3-10);
4 - номинальная мощность встроенного электродвигателя (кВт);
2 - конструктивное исполнение в зависимости от температуры и давления перекачиваемой жидкости;
У - климатическое исполнение;
2 - категория размещения;
При выполнении с одним из вариантов наружного диаметра рабочего колеса, после величины напора добавляется "а" или "б".
В процессе проделанной работы была рассчитана ректификационная установка для разделения смеси диоксан-толуол.
Были получены следующие данные:
диаметр колонны - 1200 мм;
высота колонны – 34 м;
толщина цилиндрической обечайки, элептического днища и крышки 16 мм.
Колонна состоит из 5 секций (3 в верхней части колонны и 2 в нижней) по 5 метра каждая, с расстоянием между секциями 1,215 м. В качестве перераспределитель жидкости принята тарелка ТСН-II. Жидкости подаются на тарелки ТСН-III.
Колонна насадочного типа работает в плёночном режиме.
Были выбраны в качестве насадки керамические кольца Палля размером 35х35х4, с удельной поверхностью а=165 м2
/м3
, свободным объём ε=0,76 м3
/м3
, насыпной плотность 540 кг/ м3
, dэ
=0,018, числом штук в м3
18500.
Рассчитали тепловой и механический баланс установки, построили графики и таблицы. Список использованной литературы
1. Касаткин А. Г.,
Основные процессы и. аппараты химической технологии. Изд. 9-е. М.: Химия, 1973. 750 с.
2. Справочник коксохимика. Т. 3. М.: Металлургия, 1966. 391 с.
3. Рамм В. М.
Абсорбция газов. М.: Химия, 1976. 655 с.
4. Коробчанский И. Е
., Кузнецов М. Д.
Расчет аппаратуры для улавливания химических продуктов коксования. М.: Металлургия. 1972. 295 с.
5. Александров И. А.
Ректификационные и абсорбционные аппараты. М.: Химия, 1978. 277 с.
6. Лащинский А. А., Толчинский А. Р.
Основы конструирования и расчета химической аппаратуры. Л.: Машиностроение, 1970. 752 с.
7. Стабников В. Н.
Расчет и конструирование контактных устройств ректификационных и абсорбционных аппаратов. Киев: Техника, 1970. 208 с.
8. Павлов К. Ф., Романков П. Г., Носков А. А.
Примеры и задачи по курсу процессов и аппаратов. Л.: Химия, 1976, 552 с.
9. Бретшнайдер С.
Свойства газов и жидкостей. М.— Л.: Химия, 1970. 535 с.
10. Хоблер Т.
Массопередача и абсорбция. Л.: Химия, 1964. 479 с.
11. Дытнерский Ю.А., Процессы и аппараты химической технологии. 2-е изд., перераб. и дополн.- М.: Химия, 1991-496с.
12. Колонные аппараты. Каталог. М.: ЦИНТИХИМНЕФТЕМАШ, 1978. 31 с.
13. Касаткин А. Г., Дытнерский Ю. И., Кочергин Н. В.
Тепло- и массоперенос. Т. 4. Минск: Наука и техника. 1966. С. 12—17.
|