Первичная переработка
|
 |
Нефть представляет собой смесь тысяч различных веществ. Полный состав нефтей даже сегодня, когда имеются в наличии самые изощренные средства анализа и контроля: хроматография, ядерно-магнитного резонанса, электронных микроскопов - далеко не все эти вещества полностью определены. Но, несмотря на то, что в состав нефти входят практически все химические элементы таблицы Д.И. Менделеева, её основа всё-таки органическая и состоит из смеси углеводородов различных групп, отличающихся друг от друга своими химическими и физическими свойствами. Независимо от сложности и состава, переработка нефти начинается с первичной перегонки. Обычно перегонку проводят в два этапа - с небольшим избыточным давлением, близким к атмосферному и под вакуумом, при этом используя для подогрева сырья трубчатые печи. Поэтому, установки первичной переработки нефти носят названия АВТ - атмосферно-вакуумные трубчатки.
Смысл процесса довольно прост. Как и все другие соединения, нефть преимущественно содержит жидкие углеводороды, которые имеют свою температуру кипения, то есть температуру, выше которой они испаряются, переходят в паровую фазу.
Перегонка осуществляется в ректификационной колонне, которая представляет собой высокий цилиндрический аппарат, перегороженный множеством ректификационных тарелок. Их конструкция такова, что поднимающиеся вверх пары углеводородов, могут частично конденсироваться, собираться на этих тарелках и по мере накопления на тарелке жидкой фазы сливаться вниз через специальные сливные устройства. В то же время парообразные продукты продолжают проходить через слой жидкости на каждой тарелке, и по мере прохождения по колонне вверх насыщаются более близкими по температурам кипения фракциями.
Забиваем Сайты В ТОП КУВАЛДОЙ - Уникальные возможности от SeoHammer
Каждая ссылка анализируется по трем пакетам оценки: SEO, Трафик и SMM.
SeoHammer делает продвижение сайта прозрачным и простым занятием.
Ссылки, вечные ссылки, статьи, упоминания, пресс-релизы - используйте по максимуму потенциал SeoHammer для продвижения вашего сайта.
Что умеет делать SeoHammer
— Продвижение в один клик, интеллектуальный подбор запросов, покупка самых лучших ссылок с высокой степенью качества у лучших бирж ссылок.
— Регулярная проверка качества ссылок по более чем 100 показателям и ежедневный пересчет показателей качества проекта.
— Все известные форматы ссылок: арендные ссылки, вечные ссылки, публикации (упоминания, мнения, отзывы, статьи, пресс-релизы).
— SeoHammer покажет, где рост или падение, а также запросы, на которые нужно обратить внимание.
SeoHammer еще предоставляет технологию Буст, она ускоряет продвижение в десятки раз,
а первые результаты появляются уже в течение первых 7 дней.
Зарегистрироваться и Начать продвижение
Температура в ректификационной колонне снижается по её высоте - от куба, до самой верхней тарелки. Для получения из нефти необходимой фракции, кипящей в заданных температурных пределах, достаточно сделать отводы из колонны на определённой высоте. Каждая фракция имеет свое конкретное назначение и в зависимости от него может быть широкой или узкой, то есть выкипать в интервале двухсот или двадцати градусов. И чем более узкие фракции необходимо получить, тем выше должны быть колонны. Чем больше в них тарелок, тем больше раз одни и те же молекулы должны, поднимаясь вверх с тарелки на тарелку контактировать друг с другом, переходя из газовой фазы в жидкую и обратно. Другими словами пройти многократную конденсацию и испарение с массообменом.
На практике перегонку (или, как говорят специалисты, разгонку), проводят в нескольких колоннах. Обычно их пять. На первой колонне выделяется легкая бензиновая фракция, во второй керосиновая и дизельные фракции. Легкая, нестабильная бензиновая фракция конденсируется в специальном холодильнике-конденсаторе и уже в жидком виде отправляется в стабилизационную колонну, откуда стабильная, широкая бензиновая фракция направляется в колонну для разделения на узкие фракции с последующим использованием их на вторичных процессах. Остатки атмосферной перегонки нефти направляют для извлечения более тяжелых масляных фракций в вакуумную колонну.
Сервис онлайн-записи на собственном Telegram-боте
Попробуйте сервис онлайн-записи VisitTime на основе вашего собственного Telegram-бота:
— Разгрузит мастера, специалиста или компанию;
— Позволит гибко управлять расписанием и загрузкой;
— Разошлет оповещения о новых услугах или акциях;
— Позволит принять оплату на карту/кошелек/счет;
— Позволит записываться на групповые и персональные посещения;
— Поможет получить от клиента отзывы о визите к вам;
— Включает в себя сервис чаевых.
Для новых пользователей первый месяц бесплатно.
Зарегистрироваться в сервисе
Омский НПЗ, при существующей переработке 14 млн. тонн нефти в год, способен перерабатывать до 20 млн. тонн нефти. Наличие резервных мощностей по первичной переработке, гарантирует надёжную, стабильную работу всех вторичных процессов и предприятия в целом.
5.2. ХИМИЧЕСКАЯ ПЕРЕРАБОТКА НЕФТИ
5.2.1. Общая характеристика нефтехимического комплекса
Нефти различных месторождений заметно отличаются по фракционному составу - содержанию легких, средних и тяжелых дистиллятов. Большинство нефтей содержит 15-25% бензиновых фракций, выкипающих до 180 °С, и 45-55% фракций, перегоняющихся до 300-350 °С.
Основные химические элементы, входящие в состав нефти, -углерод (82-87%), водород (11-14%), сера (0,1-7%), азот (0,001-1,8%), кислород (0,5-1%).
Общее содержание алканов (парафины) в нефтях достигает 30-50%, циклоалканов (циклопарафины, нафтены) - от 25 до 75%. Арены (ароматические углеводороды) содержатся, как правило, в меньшем количестве по сравнению с алканами и цикло-алканами (10-20%).
Соотношения между группами углеводородов придают неф-тям различные свойства и оказывают влияние на выбор метода переработки нефти и номенклатуру получаемых продуктов.
Нефть является основным источником сырья для нефтеперерабатывающих заводов при получении моторных топлив, масел и мазута. Нефть и продукты ее переработки служат также сырьем для синтеза многочисленных химических продуктов: полимерных материалов, пластических масс, синтетических каучу-ков и волокон, спиртов, растворителей и др. В перспективе большая часть нефтепродуктов (особенно энергетических топлив) может быть замещена альтернативными энергоносителями, в то время как замена нефтяного сырья в качестве источника получения нефтехимических продуктов мало вероятна. Более того, доля нефти, используемой в нефтехимических производствах, в ближайшие годы в мире возрастет до 8% и по прогнозам в 2000 г. достигнет 20-25%. В связи с этим происходит интеграция нефтеперерабатывающей и нефтехимической промышленности и формирование нефтехимических комплексов.
Комбинирование нефтепереработки (первичная переработка, каталитический крекинг, риформинг) с нефтехимическими процессами (пиролиз, синтез мономеров, производство пластмасс и др.) значительно расширяет возможности выбора оптимальных схем глубокой переработки нефти, повышает гибкость произ-водственньгх систем для получения моторных топлив или нефтехимического сырья, способствует увеличению их рентабельности. В настоящее время имеется большое число процессов и их комбинаций, которые потенциально могут обеспечить глубину переработки нефти вплоть до 100%.
5.2.2. Первичная перегонка нефти
Существуют первичные и вторичные методы переработки нефти. Первичными являются процессы разделения нефти на фракции перегонкой, вторичные процессы - это деструктивная (химическая) переработка нефти и очистка нефтепродуктов (фракции перегонки различаются интервалом температур кипения компонентов).
381
Неконденсированные газы и водяной пар в вакуумную систему
Вакуумный га
зойль
» Маловязкая
К
масляная /"^фракция
-ft-Л-*- Средне " вязка;
|
, Тяжелый r
> JA >чбецз
ин
Пар*^ -0-р—*
|
Дёй
Пар-
Пар-»
вязкая
масляная фракция
Чг
/диз.топливо
Тяжелое диз.топливо
|
Пар |
1>
Вязкая масляная фракция
ь&^£удрон
Рис. 5.2.
Схема установки первичной перегонки нефти (АВТ топливно-масляная):
/ - теплообменник; 2
- трубчатая печь; 3 -
холодильник, конденсатор-холодильник; 4 -
атмосферная колонна; 5 - отгонная колонна; 6 -
газосепаратор; 7 - вакуумная колонна
К первичной перегонке относят процессы атмосферной перегонки нефти и вакуумной перегонки мазута. Их назначение состоит в разделении нефти на фракции для последующей их переработки или использования как товарных продуктов. Первичную перегонку осуществляют соответственно в атмосферных трубчатых (AT) и вакуумных трубчатых (ВТ) или атмосферно-вакуумных трубчатых (АВТ)
установках.
На установках ATосуществляют неглубокую переработку нефти с получением бензиновых, керосиновых, дизельных фракций и мазута. Установки ВТ
предназначены для углубления переработки нефти. Получаемые в них из мазута газойлевые, масляные фракции и гудрон используют в качестве сырья в процессах вторичной переработки нефти для производства смазочных масел, кокса, битума и других нефтепродуктов.
Принципиальная схема установки АВТ
первичной перегонки нефти показана на рис. 5.2. Ниже приведен состав (в %) продуктов перегонки западносибирской нефти на установке АВТ-6 (мощность по перерабатываемому сырью 6 млн т/год):
Газ..................................................... 1,1
Фракции, °С.
до 62 4,1
62-85 2,4
85-120 4,5
120-140 3,0
140-180 6
180-240 9,5
240-350 19,0
350-460.................................. 21,0
Гудрон........................................... 28,4
Потери............................................ 1,0
382
Углеводородный газ состоит преимущественно из пропана и бутанов, которые в растворенном виде содержатся в поступающей на переработку нефти. Пропан-бутановую фракцию используют для производства индивидуальных углеводородов на газофракционирующих установках в качестве бытового топлива.
Бензиновые фракции (62-180 °С) служат сырьем во вторичных процессах изомеризации, каталитического риформинга с целью производства индивидуальных ароматических углеводородов (бензола, толуола, ксилолов), высокооктановых компонентов автомобильных и авиационных бензинов; их применяют в качестве сырья пиролиза при получении этилена.
Керосиновые фракции (120-240 °С) используются как топливо для реактивных двигателей в виде осветленного керосина и для производства лаков и красок (уайт-спирит).
Дизельные фракции (140-340 °С) служат дизельным топливом и сырьем для получения жидких парафинов депара-финизацией.
Мазут - остаток атмосферной перегонки нефти - используется как котельное топливо и в качестве сырья во вторичных процессах переработки (каталитический крекинг, гидрокрекинг).
Гудрон - остаток вакуумной переработки мазута - подвергается деасфальтизации, коксованию с целью углубления переработки нефти и используется в производстве битума.
В последнее время нефть перерабатывается на комбинированных установках, сочетающих процессы первичной перегонки нефти с термическими и каталитическими процессами. Комбинированные установки требуют меньших капиталовложений, чем раздельные установки эквивалентной мощности. Они экономичнее и по эксплуатационным затратам, так как более рационально используют тепло потоков и вследствие этого расходуют меньше первичного тепла, воды и электроэнергии. В отечественных установках ЛК-6У комбинируется перегонка нефти с гидроочисткой, каталитическим риформингом и газофракционированием. Мощность этих установок по переработке нефти составляет 6 млн т/год.
4.1. Первичная прямая перегонка нефти
Первичная прямая перегонка осуществляется на трубчатых установках: атмосферная трубчатая печь (АТ – атмосферная трубчатка), вакуумная трубчатка (ВТ), и АВТ (иногда с водяным паром).
В основу метода прямой перегонки нефти и мазута на трубчатых установках непрерывного действия положен принцип однократного испарения нефти (или мазута), нагретый до температуры 350–00 ºС с последующей дробной ректификацией смеси паров, их конденсации и охлаждения. Теоретические основы метода однократного испарения рассмотрены нами в разделе 4.2.1. В результате первичной перегонки нефти на АТ и АВТ получают следующие продукты:
- Сжиженный углеводородный газ (в основном пропан-бутановая смесь);
- Бензиновая фракция (н.к. –180 ºС). Используется после очистки как компонент товарного автобензина и как сырьё для каталитического риформинга;
- Керосиновая фракция (120–315 ºС). После очистки используется как топливо реактивных авиационных двигателей, для освещения, для технических целей.
- Дизельная фракция (атмосферный газойль) — 180–350 ºС. После очистки используется как топливо для дизельных двигателей;
- Мазут – остаток (330–350 ºС). Используется в качестве котельного топлива или сырьё для термического крекинга. Для получения масел.
Рассмотрим обобщенные сведения по теоретическим основам процесса ректификации.
В ректификационных колоннах контактирование потоков пара и жидкости может производится непрерывно (в насадочных колоннах) или ступенчато (в тарельчатых ректификационных колоннах) [20].
В результате каждого контакта компоненты перераспределяются между фазами: пар обогащается низкокипящим, а жидкость – высококипящим компонентом. При длительном контакте и высокой эффективности контактного устройства пар и жидкость, уходящие из тарелки или слоя насадки, могут достичь состояния равновесия, т. е. температуры потоков станут одинаковыми. В этом случае составы компонентов будут связаны уравнениями равновесия (при этом достигается фазовое равновесие) такой контакт в состоянии фазового равновесия принято называть равновесной ступенью или теоретической тарелкой. Подбирая число контактных ступеней и параметры процесса (температурный режим, давление, соотношение потоков, флегмовое число и др.), можно обеспечить требуемую четкость разделения нефтяных смесей.
Место ввода в ректификационную колонну нагретого перегоняемого сырья называют питательной секцией (зоной), где осуществляется однократное испарение. Часть колонны, расположенная выше питательной секции, служит для ректификации парового потока и называется концентрационной (укрепляющей), а другая – нижняя часть, в которой осуществляется ректификация жидкого потока – отгонной, или исчерпывающей секцией.
Различают простые и сложные колонны.
Простые колонны – разделение исходной смеси (сырья) на два продукта. Ректификат (дистиллят) – выводится с верха колонны в парообразном состоянии, и остаток – нижний жидкий продукт ректификации.
Сложные колонны разделяют исходную смесь больше чем на два продукта: 1-ая – ректификационная колонна с отбором дополнительной фракции непосредственно из колонны в виде боковых погонов; 2-ая – ректификационная колонна, у которой дополнительные продукты отбираются из специальных отпарных колонн (стриппингов).
Для разделения многокомпонентных смесей на более чем два компонента (фракции) может использоваться одна сложная колонна либо система простых и сложных колонн, соединенных между собой в определенной последовательности прямыми или обратными паровыми или жидкими потоками. Если не предъявляются сверхвысокие требования к чистоте продукта, используют одну простую колонну для этих целей. Выбор конкретной схемы и рабочих параметров процесса перегонки определяется технико-экономическими и технологическими расчетами с учетом требований по ассортименту и четкости разделения.
Четкость погоноразделения
. В нефтепереработке, например, в качестве достаточно высокой разделительной способности колонны перегонки нефти на топливные фракции считается налегание температур кипения соседних фракций в пределах 10–30 ºС (косвенный показатель четкости (чистоты) разделения). На разделительную способность ректификационных колонн влияют число тарелок (или высота насадки), флегмовое и паровое число.
Флегмовое число
(R
) – соотношение жидкого и парового потоков в концентрационной части колонны (R
= L
/ D
; L
и D
– количество флегмы и ректификата).
Паровое число
(П) – отношение контактируемых потоков пара и жидкости в отгонной секции колонны (П = G
/W
; G
и W – количество соответственно паров и кубового остатка).
Число тарелок
(N
) колонны (или высота насадки) определяется числом Т.Т. (NТ
), обеспечивающим заданную четкость разделения при принятом флегмовом (или паровом) числе, а также эффективностью контактных устройств (обычно КПД реальных тарелок или удельная высота насадки, соответствующая одной Т.Т.). Зависимость числа Т.Т. от флегмового числа колонны можно выразить в виде графика на рис. 4.1.
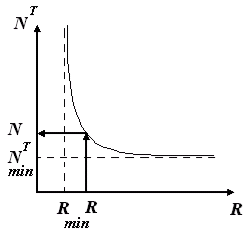 Рисунок 4.1. Зависимость числа теоретических тарелок от флегмового числа
Из графика следует, что граничные пределы нормальной работы ректификационных колонн, т. е. заданная четкость разделения смеси может быть достигнута лишь при одновременном выполнении ограничений по флегмовому числу и числу теоретических тарелок.

Любая точка на кривой может быть выбрана как рабочая. Это означает, что заданная четкость разделения смеси может быть достигнута бесконечным множеством пар чисел NT
и R
. Как видно из рисунка 4.1, флегмовое число (R
) (а значит и количество орошения в колонне) изменяется от минимального значения до бесконечно большой величины. При этом необходимое для обеспечения заданной четкости разделения теоретическое число тарелок (NT
) будет изменяться соответственно от бесконечно большой величины до некоторой минимальной. Но при увеличении количества орошения будут увеличиваться эксплуатационные затраты (расход энергии на перекачку тепла в кипятильнике и холода в конденсаторах). Из опыта эксплуатации ректификационных колонн установлено – оптимальное значение R
, соответствующее минимуму общих затрат на ректификацию не намного превышает min необходимое: R
min
: R
опт
= β R
min
(β – коэффициент избытка флегмы ~1,0–1,3). Фактическое число тарелок N
ф
определяется аналитическим расчетом (на ЭВМ с использованием уравнения равновесия фаз, материального и теплового балансов потоков), либо из опытных данных с учетом эффективного КПД тарелки :
N
ф
= NT
ηT
.
В зависимости от конструкции и места расположения в колонне ηT
изменяется в пределах 0,3–0,9.
На технико-экономические показатели и четкость погоноразделения ректификационной колонны, кроме разделительной способности, значительно влияют физико-химические свойства (плотность, молярная масса, температура кипения, летучесть и т. п.), компонентный состав и др.
В наиболее обобщенной форме разделительные свойства перегоняемого сырья принято выражать коэффициентом относительной летучести (аналог коэффициента селективности в процессах экстракции).
Коэффициент относительной летучести α = K
1
/ K
2
K
1
и K
2
– константы фазового равновесия соответственно низко- и высококипящего компонентов (фракций), т.к. K
1
> K
2
, то α > 1.
α – отношение летучестей компонентов перегоняемого сырья при одинаковых температурах и давлениях. Коэффициент относительной летучести α косвенно характеризует движущую силу процесса перегонки применительно к разделяемому сырью. Сырье, у которого α >> 1 значительно легче разделить на компоненты, чем при его значении близком к 1.
Относительная летучесть зависит от давления и температуры, при которых находятся компоненты, с увеличением давления и температуры величина α снижается. Вблизи критической области значений коэффициента α приближается к единице.
4.1.1. Особенности нефти как сырья процессов перегонки
- Невысокая термическая стабильность нефти, ее высококипящих фракций (≈350–360 ºС), необходимо ограничение температуры нагрева (для повышения относительной летучести - перегонка под вакуумом, перегонка с водяным паром – для отпаривания более легких фракций). Необходимо как минимум две стадии: атмосферная перегонка до мазута (до 350 ºС) и перегонка под вакуумом.
- Нефть – многокомпонентное сырье с непрерывным характером распределения фракционного состава с соответственно летучести компонентов. Коэффициенты относительной летучести непрерывно (экспоненциально) убывают по мере утяжеления фракций и по мере сужения температурного интервала кипения фракций. Поэтому в нефтепереработке отбирают широкие фракции: бензин н.к. – 140 ºС (180 ºС); керосиновые – 140 (180) –240; дизельные – 240–350 ºС; вакуумный газойль – 350–400 ºС, 400–450 ºС и 450–500 ºC; гудрон >490 ºС (>500 ºС). Иногда ограничиваются неглубокой перегонкой нефти с получением в остатке мазута >350 ºС (котельное топливо).
- Высококипящие и остаточные фракции нефти содержат значительное количество гетероорганических смолисто-асфальтеновых соединений и металлов (ухудшают товарные характеристики продуктов и усложняют дальнейшую переработку дистиллятов).
Необходима организация четкой сепарации фаз в секции питания атмосферной и особенно вакуумной колонн. Для увеличения разделительной способности нижних тарелок сепарационной секции колонны необходим избыток орошения (называемый избытком однократного испарения), который достигается путем незначительного перегрева сырья (не выше предельно допустимой величины). Доля отгона при однократном испарении в секции питания колонны должна быть на 2–5 % больше выхода продуктов, отбираемых в виде дистиллята и боковых погонов.
4.1.2. Способы регулирования температурного режима ректификационных колонн.
Регулирование теплового режима – отвод тепла в концентрационной (укрепляющей) зоне, подвод тепла в отгонной (исчерпывающей) секции колонн и нагрев сырья до оптимальной температуры.
Отвод тепла осуществляется путем:
а) использования парциального конденсатора (кожухотрубчатый теплообменный аппарат; применяется в малотоннажных установках, трудность монтажа);
б) организация испаряющегося (холодного) орошения (наиболее распространена в нефтепереработке);
в) организация неиспаряющегося (циркуляционного) орошения, используется широко и не только для регулирования температуры наверху, но и в средних сечениях сложных колонн. На современных установках перегонки нефти применяются комбинированные схемы орошения.
Подвод тепла в отгонной секции:
г) Нагрев остатка ректификации в кипятильнике с паровым пространством (осуществляется дополнительный подогрев кубового продукта в выносном кипятильнике с паровым пространством (рибойлере), где он частично испаряется). Образовавшиеся пары возвращаются под нижнюю тарелку колонны. Особенность этого способа - наличие в кипятильнике постоянного уровня жидкости и парового пространства над этой жидкостью. По своему разделительскому действию кипятильник эквивалентен одной Т.Т. Этот способ широко применяется на установках фракционирования попутных нефтяных и нефтезаводских газов, при стабилизации и отбензинивании нефти, стабилизации бензинов прямой перегонки и вторичных процессов нефтепереработки.
д) Циркуляция части остатка, нагретого в трубчатой печи. В этом случае часть кубового продукта перекачивается через трубчатую печь и подогретая парожидкостная смесь (горячая струя) вновь поступает вниз колонны. Этот способ используют если необходимо обеспечить высокую температуру низа колонны, когда применение обычных теплоносителей (водяной пар и др.) невозможно или нецелесообразно.
Способы регулирования температуры в ректификационной колонне представлены на рис. 4.2.
 г |
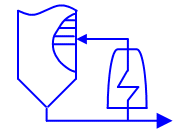 д |
Рисунок 4.2. Регулирование температурного режима по высоте колонны: а, б, в - отвод тепла в концентрационной зоне; г, д - подвод тепла в отгонной секции.
Использование одного острого орошения в ректификационных колоннах неэкономично, т.к. не обеспечивается оптимальное распределение флегмового числа по высоте колонны.
4.1.3. Выбор давления и температурного режима в ректификационной колонне
На экономические показатели перегонки значительное влияние оказывает давление и температурный режим при принятых значениях флегмового числа, числа и типа тарелок. Такие параметры как давление и температура тесно взаимосвязаны: нельзя оптимизировать один из них без учета другого.
При оптимизации технологических параметров колонны ректификации целесообразно выбрать такие значения давления и температуры, которые:
- обеспечивают состояние системы, далекое от критического (должны быть высокие значения коэффициента относительной летучести α).
- исключают возможность термической деструкции сырья и продуктов перегонки или кристаллизации их в аппаратах.
- позволяют использовать дешевые и доступные хладоагенты для конденсации паров ректификата (вода, воздух) и теплоносители для нагрева и испарения кубовой жидкости (водяной пар высокого давления); кроме того, снижать требуемые поверхности холодильников, конденсаторов, кипятильников, теплообменников.
- обеспечивают нормальную работу аппаратов и процессов, связанных с колонной ректификации материальными и тепловыми потоками.
- обеспечивают оптимальный уровень по удельной производительности, капитальным и эксплуатационным затратам.
Повышение или понижение давления в ректификационной колонне сопровождается соответствующим повышением или понижением температуры. Например, для получения в качестве ректификата пропана требуемая температура верха колонны при давлении 0,1 и 1,8 МПа будет соответственно минус 42 ºC и плюс 55 ºС (второй вариант: 1,8 МПа и +55 ºС, более предпочтителен, т. к. повышение давления позволяет использовать воду для конденсации паров пропана, а не специальные хладагенты и дорогостоящие низкотемпературные системы охлаждения). Перегонка, например, под вакуумом позволяет осуществить отбор фракций нефти без заметного разложения, выкипающих при температурах, повышающих температуру нагрева сырья больше чем на 100–150 ºС.
Перегонка нефти при атмосферном давлении осуществляется при температуре в зоне питания ректификационной колонны 320–360 ºС, а вакуумная перегонка мазута – при температуре на выходе из печи не выше 430 ºС.
Расчет температуры нагрева сырья проводится по уравнению, которое выведено совместным решением уравнения материального баланса однократного испарения и уравнения равновесия фаз.
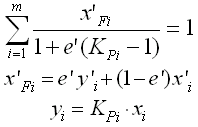
где Kpi
– константа фазового равновесия компонента i
при давлении в системе (П); , – мольные доли компонента i
в исходной смеси, паровой фазе и равновесной жидкости.
4.1.4. Материальный баланс перегонки нефти и использование дистиллятов
Перегонка нефти на АВТ – многоступенчатый процесс (обессоливание, обезвоживание, отбензинивание, АТ и ВТ, стабилизация и вторичная перегонка бензина). Поэтому рассматривают общий или поступенчатый материальный баланс перегонки нефти.
Общий – под ним понимают выход [в % (масс.)] всех конечных продуктов перегонки от исходной нефти, количество которой принимают за 100 %.
Поступенчатый – за 100 % принимают выход (% масс.) продуктов перегонки на данной ступени (продукты могут быть промежуточные). Поступенчатый материальный баланс перегонки нефти составляется при технологических расчетах АВТ.
Рассмотрим общий баланс, приведенный А.К. Мановяном [27].
- Нефть (I) (100 %) поступает на установку с содержанием минеральных солей от 50–300 мг/л и воды 0,5–1,0 % масс.
- Углеводородный газ (II). Содержание его в нефти зависит от того, сколько растворенного газа осталось в ней после промысловой подготовки газа. В легкой нефти (ρ 0,8–0,85) — 1,5–1,8 % масс. Для тяжелой — 0,3–0,8 % масс., а в нефти после стабилизации растворенный газ отсутствует. 90 % этого газа – газ из отбензинивающей колонны. Состав: С1
-С4 с примесью С5
не используется на ГФУ для выделения отдельных углеводородов из-за низкого его давления и мольных количеств; используется как энергетическое топливо в печах АВТ. Если выход 1,5 % и выше газ экономически выгодно компремировать до давления 2–4 МПа и перерабатывать на ГФУ.
- Сухой углеводородный газ стабилизации бензина (III) – это часть легких углеводородов С1
–С3
, оставшаяся растворенной в бензине (выход 0,1–0,2 % масс.) давление до 1,0 МПа можно перерабатывать на ГФУ, но из-за низкого содержания часть направляют в газовую линию II и сжигают в печах.
- Сжиженная головка стабилизации бензина (IV) содержит пропан и бутан с примесью пентанов (0,2–0,3 % масс.) используется для бытовых нужд (сжиженный газ) или газового моторного топлива для автомобилей (СПБТЛ или СПБТЗ).
- Легкая головка бензина (V) – фракция бензина НК–85 ºС (4–6 % масс.) о.ч. не более 70 (моторный метод). Используется для производства нефтяных растворителей или как сырье для каталитической изомеризации (о.ч. 82–85).
- Бензиновая фракция 85-180 ºС (VI) (10-14 % масс., о.ч.м
= 45÷55); на каталитический риформинг (о.ч. до 88-92) и используется как базовый компонент автомобильных бензинов.
- Керосин (Х). Может быть два варианта отбора:
Авиационный керосин 140–230 ºС (10–12 % масс.) марки ТС-1 140–300 ºС (14–18 % масс.)
Дизельное топливо (XI). Атмосферный газойль (180–350 ºС), (22–26 % масс.) – если авиакеросин.
10–12 % масс. – если зимнее или арктическое дизельное топливо.
Легкая газойлевая фракция (XIV) (0,5–1,0 % масс.)
Фракция 100–250 ºС – результат частичной термодеструкции мазута при нагреве его в печи.
- Легкий вакуумный газойль (XV) 240–380 ºС (3–5 % масс.) по качеству близка к летнему дизельному топливу (XI).
- Вакуумный газойль (XVI) – основной дистиллят вакуумной перегонки мазута по топливному варианту (если нельзя получить масло высокого качества 350–500 ºС (550 ºС)) 21–25 % масс.
Используют как сырье для каталитического крекинга, гидрокрекинга.
Если нефть позволяет получить масла, то из вакуумной колонны выводят два потока масляного дистиллята: 350-420°С (10-14%масс.) 420-500°С (12-16%масс.)
· Гудрон (XVII – остаточная часть нефти, остаток, выкипающий выше 500 ºС (10-20%масс.).
Цель переработки нефти (нефтепереработки) — производство нефтепродуктов, прежде всего, различных топлив (автомобильных, авиационных, котельных и т. д.) и сырья для последующей химической переработки Первичные процессы
Первичные процессы переработки не предполагают химических изменений нефти и представляют собой ее физическое разделение на фракции.
[править]Подготовка нефти
Нефть поступает на НПЗ в подготовленном для транспортировки виде. На заводе она подвергается дополнительной очистке от механических примесей, удалению растворённых лёгких углеводородов (С1-С4) и обезвоживанию на электрообессоливающих установках (ЭЛОУ).
[править]Атмосферная перегонка
Нефть поступает в ректификационные колонны на атмосферную перегонку (перегонку при атмосферном давлении), где разделяется на несколько фракций: легкую и тяжёлую бензиновые фракции, керосиновую фракцию, дизельную фракцию и остаток атмосферной перегонки — мазут. Качество получаемых фракций не соответствует требованиям, предъявляемым к товарным нефтепродуктам, поэтому фракции подвергают дальнейшей (вторичной) переработке.
Материальный баланс атмосферной перегонки западно-сибирской нефти
ПРЕДЕЛЫ ВЫКИПАНИЯ, °С
|
ВЫХОД ФРАКЦИИ, % (МАСС.)
|
Газ
|
1,1 % |
Бензиновые фракции
|
<62°С |
4,1% |
62—85°С |
2,4% |
85—120°С |
4,5% |
120—140°С |
3,0% |
140—180°С |
6,0% |
Керосин
|
180—240°С |
9,5% |
Дизельное топливо
|
240—350°С |
19,0% |
Мазут
|
49,4% |
Потери
|
1,0% |
[править]Вакуумная дистилляция
Основная статья
: Вакуум-дистилляция
Вакуумная дистилляция
— процесс отгонки из мазута (остатка атмосферной перегонки) фракций, пригодных для переработки в моторные топлива, масла, парафины и церезины и другую продукцию нефтепереработки и нефтехимического синтеза. Остающийся после этого тяжелый остаток называется гудроном. Может служить сырьем для получения битумов.
Установки первичной перегонки нефти
08 марта 2010 Опубликовал admin
Под первичной перегонкой нефти понимают совокупность физических процессов, направленных на ее разделение по фракциям в соответствии с их температурой кипения: до мазута (получаются светлые нефтепродукты); до гудрона (получаются масла).
При ректификации до мазута давление мало отличается от атмосферного (Рраб=0,11— 0,12 МПа или 1,1— 1,2 ата), поэтому установки по перегонке нефти до мазута называют атмосферными трубчатками (АТ).

При ректификации до гудрона процесс ведется, подвакуумом (РРаб=0,08 МПа или 600 мм рт. ст.), поэтому установки по перегонке нефти до гудрона называют вакуумными трубчатками (ВТ).
Существуют также установки по перегонке нефти сразу до гудрона. Они состоят из двух взаимосвязанных частей — атмосферной й вакуумной. Поэтому такие установки называют атмосферновакуумными трубчатками (АВТ).
В атмосферном блоке АВТ применяют три схемы разделения нефти: с одной сложной ректификационной колонной, с предварительным испарителем и сложной колонной, с предварительной отбензинивающей и сложной колоннами. Схема с предварительной отбензинивающей колонной и сложной ректификационной колонной наиболее распространена в отечественной практике (рис. 4.18).
Обессоленную и обезвоженную нефть прокачивают через теплообменники, где ее нагревают отводимыми с установками дистиллятами до 150—200 °С, затем она поступает в предварительную колонну К-1, в которой от нефти отделяют пары бензина и воды (ее остаточное содержание). Отбензиненную нефть из кубовой части направляют в печь для нагрева до' 250—350 °С и затем — в основную сложную ректификационную колонну К-2, которая состоит из 3—5 простых колонн (в зависимости от числа вводимых дистиллятов). Верхний дистиллят выводят в паровой фазе, остальные — жидкими боковыми погонами через отпарные секции, внутренние или выносные (как показано на схеме). Из нижней, кубовой части колонны, отводят мазут. Его подогревают в трубчатой печи до 400—450 °С и подают в вакуумную колонну К-Ю для получения масляных дистиллятов и вакуумного газойля, являющегося сырьем установок каталитического крекинга.
Для снижения температуры кипения разделяемых компонентов и предотвращения термического разложения сырья перегонку мазута осуществляют в вакууме. С увеличением вакуума температура кипения компонентов снижается, особенно компонентов с большой молекулярной массой. Вакуум в колонне создают барометрическими Конденсаторами и вакуумными насосами (поршневыми, ротационными, эжекторными или струйными), которые можно включать в различной последовательности.
Пожарная опасность установок первичной перегонки нефти характеризуется наличием большого количества ЛВЖ, ГЖ, их паров и углеводородных газов. Так, в некоторых аппаратах (ректификационных колоннах, трубчатых печах) находится одновременно от 20 до 30 т и более нефтепродуктов.
Показатели пожарной опасности нефтепродуктов колеблются в широких пределах. Так, Твсп: у нефтей — от — 35 до +36° и выше, бензинов —от —36 до —7°С, лигроинов —от —7 до +17°С, керосинов — от +15 до + 60°С и выше, мазутов---от+60 до +120 °С, минеральных масел — от + 120 до +220 °С.
Анализ этих цифр показывает, что в производственных условиях даже при нормальной работе технологического оборудования нефтепродукты могут иметь температуру, лежащую в температурных пределах воспламенения. Следовательно, горючая концентрация может образоваться не только в паровоздушном пространстве аппаратов, но и при выходе паров наружу.
При нормальной работе установок возможность образования горючей концентрации существует в дышащих аппаратах и в вакуумных ректификационных колоннах.
При образовании неплотностей или повреждений в вакуумных колоннах АВТ или ВТ будет происходить подсос наружного воздуха внутрь аппаратов. При этом возможны два случая, которые в основном зависят от места повреждения по высоте колонны и от температурного режима. Если Граб>Гсв фракций на соответствующей месту повреждения тарелке, то пары продукта, смешиваясь с воздухом, воспламеняются и установится диффузионное горение внутри колонны в виде факела. Если Tpsk6<TCB нефтепродукта, то подсасываемый воздух, смешиваясь с парами, будет образовывать горючую концентрацию. При этом возможен взрыв внутри аппарата.
При повреждениях аппаратов и трубопроводов нагретые нефтепродукты могут выходить наружу. При этом также возможны два случая. Если Граб выходящей жидкости меньше Гсв, то она будет растека ться и интенсивно испаряться. В этом случае создается опасность образования горючей (в пределах воспламенения) паровоздушной смеси.
Если Граб выходящей жидкости больше или равна ее Гсв, то при контакте с воздухом она воспламеняется и, растекаясь, будет гореть.
Причины повреждения и специфические источники зажигания основных аппаратов установок первичной перегонки нефти (ректификационных колонн, трубчатых печей, теплообменников) раскрыты ранее (см. главу 3).
Развитая сеть различных коммуникаций (трубопроводные эстакады, лотки, система канализации), разлившиеся жидкости и облака парогазовоздушной смеси, образующиеся на аппаратном дворе при авариях технологического оборудования, — характерные пути для распространения пламени.
Установки крекинга нефти. Установки первичной перегонки нефти позволяют получить только 15—20 % светлых нефтепродуктов. Для увеличения выхода светлых нефтепродуктов из нефти, наряду с ее физическим разделением, используют химический способ — процесс расщепления (крекирования) тяжелых молекул углеводородов с целью получения более легких нефтепродуктов с улучшенными свойствами вследствие образования молекул кольчатого и изомерного строения.
В зависимости от условий проведения процесса крекинга различают термический и каталитический крекинг, которым соответствуют установки термического и каталитического крекинга.

Установки термического крекинга (ТК). На установках ТК расщепление молекул тяжелого сырья проводят под воздействием высокой температуры (около 500 °С) и при повышенном давлении (Реаб = 5—7 МПа (50— 70 ат).
Чтобы реакция расщепления проходила до конца, необходима большая длина змеевиков реактора. Для сокращения длины змеевика на практике за реактором устанавливают пустотелую колонну — первичный испаритель, где завершается процесс расщепления вследствие резкого снижения рабочего давления до 0,5—1 МПа (5— 10 ат). Колонну в связи с этим называют реакционной камерой.
Рассмотрим наиболее распространенную схему (рис. 4.19) термического крекинга. Сырье (чаще мазут), пройдя через теплообменник, с температурой около 80 °С поступает в верхнюю часть вторичного испарителя. Верхняя часть испарителя отделена от нижней, поэтому мазут не может стекать вниз, где находится крекинг — остаток с температурой около 400°С. Однако пары крекинг — остатка свободно проходят через слой мазута, нагревая его до 110—120 °С и обогащая своими легкими фракциями.
Из вторичного испарителя направляют в первую ректификационную колонну для его первичного разделения. Образующиеся легкие фракции из головной части этой колонны направляются для повторного разделения во вторую ректификационную колонну. В результате отгонки легких фракций в обеих колоннах, в их кубовых частях, образуются остатки, которые в зависимости от температуры кипения имеют различный состав. В первой колонне остаток называют тяжелым (его температура кипения около 400°С), во второй — легким (температура кипения около 300 °С). Тяжелый остаток подают в печь легкого крекинга (ПЛК), легкий остаток— в печь тяжелого (глубокого) крекинга (ПТК). Проходя по змеевикам печей при избыточном давлении около 5—6 МПа (50—60 ат) и нагреваясь (до 480 °С в ПЛК и до 500°С в ПТК), остатки подвергаются крекированию.
В результате процесса крекинга в змеевиках трубчатых печей образуются сложные смеси углеводородов примерно одинакового состава, которые направляются в первичный испаритель, где происходит завершение процессов расщепления при снижении температуры до 420°С и давления до 0,5—1 МПа (5—10 ат). В реакционной камере при этом идет грубое разделение смеси на две фазы — парогазовую и жидкую, содержащую кокс.
Пары и газы из первичного испарителя, проходя последовательно обе ректификационные колонны, постепенно укрепляются углеводородами бензинового состава и при температуре около 250 °С выводятся из головной,, части второй колонны. После охлаждения парогазовая смесь поступает в газосепаратор для отделения от жидкой фазы (нестабильного бензина) несконденсировавшегося жирного крекинг — газа, который направляется на абсорбционную установку для улавливания паров бензина.
Часть флегмы постоянно отбирают с нижних тарелок второй ректификационной колонны и после охлаждения в виде фракции дизельного топлива выводят с установки. На установке получают также гудрон — тяжелый кревднг-остаток, который выводят из нижней части вторичного испарителя.
|