Содержание
Лист
Введение
|
5
|
1. Кинематическая схема привода
|
6
|
2. Выбор электродвигателя по каталогу
|
7
|
3. Выбор материалов. Определение допускаемых напряжений
3.1 Допускаемые контактные напряжения
3.2 Допускаемые напряжения при изгибе
|
8
8
9
|
4. Расчет зубчатой передачи
|
10
|
4.1 Определение межосевого расстояния
4.2 Определение геометрических параметров
4.3 Определение геометрических размеров зацепления
4.4 Силы, действующие в зацеплении
4.5 Проверка прочности зубьев по напряжениям изгиба
|
10
10
11
11
11
|
5. Проектный расчет валов
|
13
|
6. Выбор подшипников
|
14
|
7. Расчет ременной передачи
|
15
|
8. Проверочный расчет валов
|
17
|
8.1 Быстроходный (ведущий) вал
8.2 Расчет ведущего вала на выносливость
8.3 Тихоходный (ведомый) вал
|
17
18
21
|
9. Проверочный расчет подшипников
9.1 Быстроходный (ведущий) вал
9.2 Тихоходный (ведомый) вал
|
23
23
23
|
10. Выбор системы смазки
Приложение 1
Приложение 2
|
25
27
29
|
Введение
Курсовое проектирование имеет очень большое значение в развитии навыков самостоятельной творческой работы студентов, тат как прививает им навыки научно-исследовательской работы, рационализации, изобретательства, пользования справочной литературой, ГОСТами, нормами, таблицами и номограммами, а также навыки расчетов и составления расчетно-пояснительных записок к проектам.
Курсовой проект по Прикладной механике является важной самостоятельной инженерной работой студента, охватывающей вопросы расчета на прочность, жесткость, износостойкость, долговечность и другие виды работоспособности деталей машин и базирующейся на всех видах уже изученных студентами дисциплинах, подготавливает студентов к выполнению курсовых проектов по специальным дисциплинам, а также к выполнению дипломного проекта.
1.
Кинематическая схема привода
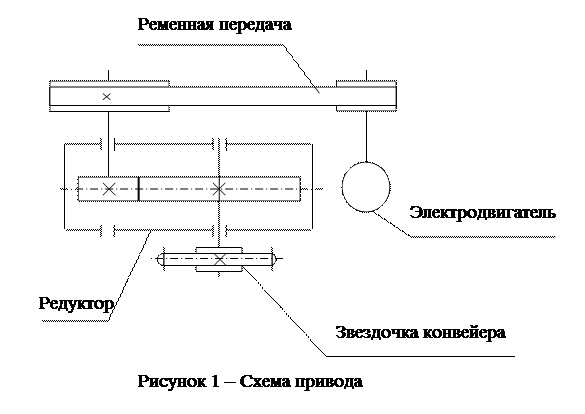
Спроектировать привод к ленточному конвейеру.
Мощность на ведомом валу редуктора Р3
= 4,5 кВт и угловая скорость вращения этого вала ω
= 2,8π.
2.Выбор электродвигателя по каталогу
Требуемая мощность электродвигателя [1,с.89]
(2.1)
где η – общий КПД редуктора [1,с.89].
(2.2)
где η1
= 0,97 – К.П.Д. ременной передачи;
η2
= 0,99 – К.П.Д. пары подшипников;
η3
= 0,96 – К.П.Д. редуктора;

Ртр
=4,5/0,913=4,93 кВт.
Из табл. [1,с.93] выбираем электродвигатель (по требуемой мощности) типа А02-52-8 имеющий мощность Р1
=5,5 кВт при частоте вращения n=730 об/мин и угловой скорости ω=76 рад/с .Угловая скорость ведущего вала привода
(2.3)
Число оборотов ведущего вала привода
(2.4)
Общее передаточное число [1,с.90]
В соответствии с ГОСТ 2185-86, U=8,69 [1,c.97]. При этом передаточное число ременной передачи U1
=2,4, редуктора U2
=3,62 [1,с.97]
Частота вращения ведущего вала редуктора
(2.5)
Угловая скорость каждого из валов
(2.6)

Мощность каждого из валов
(2.7)
Вращающие моменты, Н/м
(2.8)
3.Выбор материалов. Определение
допускаемых напряжений
Так как мощность привода небольшая в качестве материалов шестерен и колес целесообразно назначить материалы с твердостью НВ<350. При этом каждая зубчатая передача будет прирабатываться, а стоимость редуктора будет невысокой.
Шестерни: Сталь 40Х, термообработка – улучшение; твердость 270 НВ; временное сопротивление σв
=950МПа; предел текучести σТ
=700МПА [2,c.56].
Для лучшей приработки зубьев рекомендуется назначать для материалов колеса твердость на (20…50)НВ ниже, чем для шестерен [1,с.55].
Колеса: Сталь 40Х; улучшение; 250НВ; σв
=850МПа; σТ
=550МПА [2,c.96].
3.1Допускаемые контактные напряжения
Для расчета на контактную прочность [3,с.143], МПа
[σ]Н
=(σН0
/
S
Н
)
KHL
,
(3.1)
где σН0
–
предел контактной выносливости при пульсирующем цикле напряжений;
S
Н
– коэффициент безопасности;
KHL
– коэффициент долговечности в расчете на контактную прочность.
Для нормализованных и улучшенных материалов
σН0
=2НВ+70МПа; (3.2)
σН0
=2·250+70=570МПа.
S
Н
=1,1[3,с.147].
Число циклов нагрузки зубьев шестерни в течение срока службы
NH
1
=60
Lh
n
1
(3.3)
Lh
=8ч/сут · 300дней в году · 5 лет=12000ч срок службы
NH
1
=60·970 об/мин·12000 ч = 7·108
NH
1
=60·242,5 об/мин·12000 ч = 1,75·108
В расчете на контактную прочность NHG
=10. При НВ<350 и NH
1
> NHG
, назначаем KHL
=1,0 [3,с.148].
[σ] определяем по материалу колес, как менее прочному [3,с.145]
[
σ
Н
]=(570/1,1)·1,0=518 МПа.
Назначаем [σ] =[σН
]=518 МПа.
3.2Допускаемые напряжения при изгибе
Для расчета на изгиб [3,с.145], МПа
[
σF
]=(
σF
0
/
SF
)
KFC
KFL
,
(3.4)
где σF
0
– предел выносливости материала при нулевом цикле напряжений при изгибе;
SF
– коэффициент безопасности;
KFC
– коэффициент, учитывающий характер напряжений, считая передачи реверсивными (симметричный цикл напряжений), получаем KFC
=1 [3,с.151];
KFL
– коэффициент долговечности;
При НВ<350 и NF
1
>NFG
, принимаем KFL
=1,0 [3,с.151].
Для нормализованных и улучшенных материалов SF
=1,75;
Для колеса, МПа
σF
0
=1,8НВ=18·250=450; (3.5)
[
σF
]
=(450/1,75)·1,0·1,0=257 МПа.
Для шестерни, МПа
σF
0
=
1,8·270=486 МПа;
[
σF
]
=(486/1,75)·1,0·1,0=277 МПа.
4.
Расчет зубчатой передачи
4.1Определение межосевого расстояния
Межосевое расстояние из условия контактной прочности [1,c.187]
(4.1)
где KHβ
– коэффициент расчетной нагрузки;
Ψва
– коэффициент ширины зубчатого колеса по межосевому расстоянию;
T 2
– вращающий момент на колесе.
(4.2)
где T1
– вращающий момент на шестерне;
η3
–К.П.Д. редуктора.
В проектном расчете предварительно принимаем KHβ
=1,04, Ψa
=0,43 [1,с.187].

Назначаем а
w
=
160 мм
4.2Определение геометрических параметров
Модуль зацепления [2,с.38], мм
m
=(0,01÷0,02)aw
; (4.3)
m
=
(0,01÷0,02)·160=1,6÷3,2.
Назначаем по ГОСТ 2185-86 m
=1,6.
Числа зубьев [2,c.38],угол наклона зубьев β
=0°
(4.4)
(4.5)
Определяем делительные диаметры
(4.6)
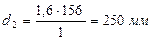
Ширина колеса
(4.7)
Ширина шестерни
(4.8)
4.3Определение геометрических размеров зацепления
Геометрические размеры зацепления [1,с.174], мм
Диаметры окружностей выступов
dai
=di
+2m
; (4.9)
da1
=69+2·1,6=72 мм;
da
2
=250+2·1,6=253 мм.
Диаметры окружностей впадин
dri
=
di
- 2,5
m
; (4.10)
dr
1
=69-2,5·1,6=65 мм;
dr
2
=250-2,5·1,6=246 мм.
4.4Силы, действующие в зацеплении
по[3,c.113]
Окружная:
Ft
=2
T
2
/
d
1
=2·165600/69=4994 Н. (4.11)
Радиальная:
Fr
=
Ft
·
tgα
/
cosβ
=
4994·0,364/1=1818 Н. (4.12)
Осевая:
Fa
=
Ft
·
tgβ
=4994·tg
0°=0 Н. (4.13)
4.5Проверка прочности зубьев по напряжениям изгиба
по [3,с.157]
(4.14)
где YF
– коэффициент формы зуба;
KF
– коэффициент нагрузки, принимаем равным 1,1;
Yβ
– коэффициент наклона зубьев,при β=0 принимаем равным 1.
Значение коэффициента формы зуба по таблице1.5[3,c.158]
YF
1
=3,7 – для шестерни;
YF
2
=3,6 – для колеса; (4.15)

75>71.
Проверку проводим по зубьям колеса как по менее прочному
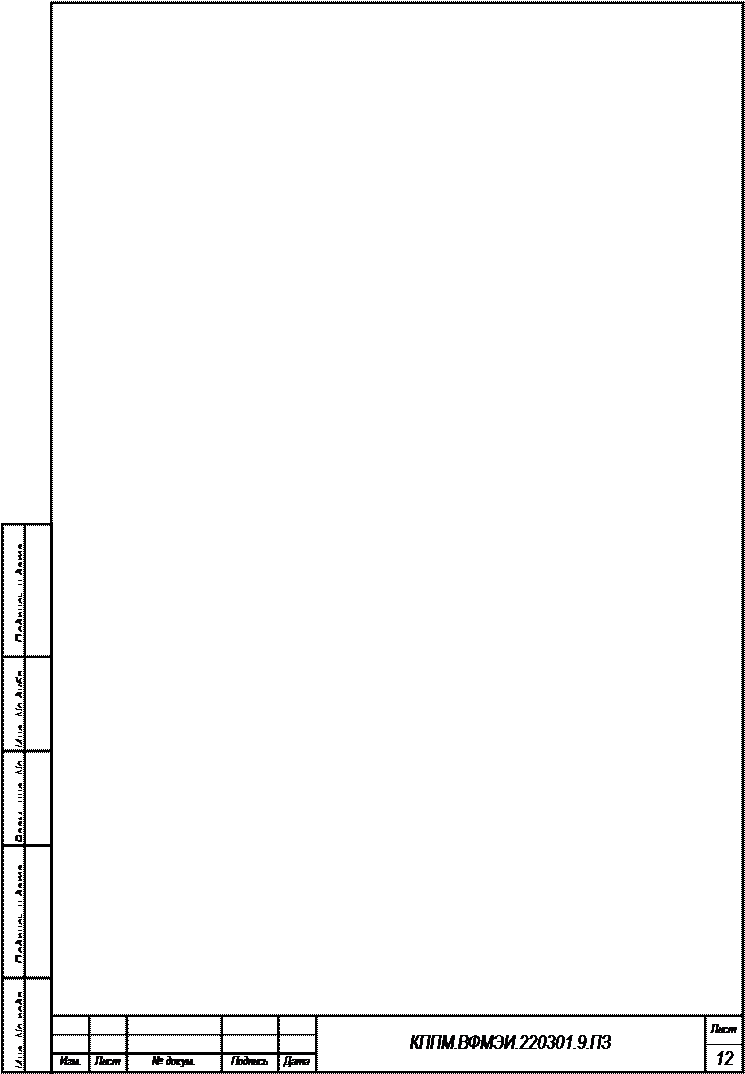 
Прочность зубьев колеса по напряжениям изгиба обеспечена.
5.Проектный расчет валов
В редукторах общего назначения обычно применяются валы из сероуглеродистой стали 45, улучшение, с твердостью 200 НВ[3,c.121].
Предварительные значения диаметров различных участков стальных валов редуктора определяют по формулам [1,c.42].
для быстроходного вала
(5.1)
(5.2)

для тихоходного вала
(5.3)


Диаметры остальных участков вала назначают по конструктивным соображениям с учетом удобства посадки на вал шестерен, зубчатых колес, подшипников и т.д. [2,c.158].Все диаметры назначают в соответствии с ГОСТ 6636-89 [1,с.289].
6.Выбор подшипников
Для опор валов цилиндрической прямозубой передачи редуктора предварительно намечаем радиальные шариковые подшипники, легко серии по посадочному диаметру dП
.
Таблица 1
Обозначение
|
d
|
D
|
B
|
C
|
C0
|
209
|
45
|
85
|
19
|
33,2
|
18,6
|
210
|
50
|
90
|
20
|
35,1
|
19,8
|
7.расчет ременной передачи
По номограмме [4,c.330] в зависимости от частоты вращения меньшего шкива n1
=730об/мин и передаваемой мощности P=5,5кВт принимаем сечение клинового ремня Б.
Вращающий момент
(7.1)
Диаметр меньшего шкива
(7.2)
Диаметр большого шкива
(7.3)
согласно таблице 7.8[4,c.133] принимаем d2
=315мм.
Уточняем передаточное число
(7.4)
при этом угловая скорость вала будет
(7.5)
Межосевое расстояние
(7.6)
где T0
– высота сечения ремня по таблице 7.7[4,c.132] ,
(7.7)
Принимаем предварительно близкое значение ар
=450мм.
Расчетная длина ремня

ближайшее значение по стандарту таблица 7.7[4,c.132] L=1600м.
Уточнение межосевого расстояния с учетом стандартной длинны ремня
(7.8)
где W=0,5π(d1
+d2
)=0,5 π(125+297)=663мм,
y=(d2
-d1
)2
=(297-125)2
=29584мм2
,

Угол обхвата меньшего шкива
(7.9)
Число ремней в передаче

 (7.10)
где Кд
– коэффициент динамичности и режима работы;
Р0
– мощность передаваемая одним ремнем;
К=Кα
·Кl
·Кz
=0,92·0,95·0,95=0,8303 – корректирующий коэффициент,
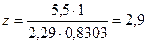
принимаем три ремня.
Предварительное натяжение одного ремня
(7.11)
где Ki
– коэффициент передаточного отношения, изменяется от 1,12 до 1,14;
Fv
– дополнительное натяжение ремня от действия центробежных сил;
Кα
– коэффициент угла обхвата, таблица 3.7[4,c.23];
Кl
– коэффициент, учитывающий влияния длины ремня на его ресурс, таблица 3.8[4,c.23].
(7.11)
где ρ – плотность ремня, для клиновых ремней равна 11000…1250 кг/м3
;
А – площадь поперечного сечения ремня(для сечения Б А= 138 мм2
).

Радиальная сила, действующая навал
где (7.12)


8.Проверочный расчет валов
8.1
Быстроходный (ведущий) вал
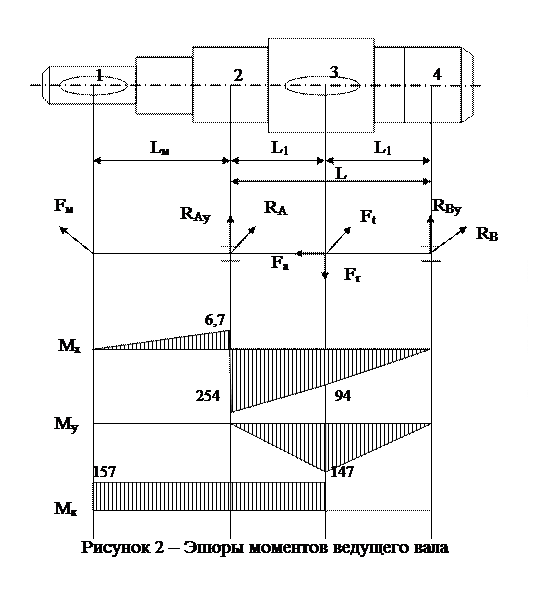
8.1.1 Определяем реакции в подшипниках
Дано: Ft
=4994H,
Fr
=1818H, Fa
=0H, L
=118мм, L
1
=59мм, d
1
=63мм,
L
м
=66,5мм, Fм
=1411Н.
Вертикальная плоскость:
∑M3
=0;
(8.1)
∑M1
=0;
(8.2)
8.1. 2 Строим эпюру изгибающих моментов относительно Х:
Мx1
=0; Mx2
=RAy
·L1
=114·59·10-3
=6,7H·м; Mx4
=0;
Mx
3
=-Fм
·Lм
=-1411·66,5·10-3
=-93,8Н·м;
Mx
2
=-Fм
(Lм
+L1
)+RBy
·L1
=-1411· (66,5+59)-1297·59=-254Н·м.
Горизонтальная плоскость:
RAx
=RBx
=Ft
/2=4994/2=2497H. (8.3)
8.1.3 Строим эпюру изгибающих моментов относительно оси Y:
My2
=0; My3
=-RAx
·L1
=-2497·59·10-3
=-147Н·м; My4
=0.
8.1.4 Строим эпюру крутящих моментов:
Mк
=Ft
·d1
/2=4994·63/2=157Н·м. (8.4)
8.1.5 Определяем суммарные реакции:
(8.5)
(8.6)
8.2
Расчет ведущего вала на выносливость
В этом расчете для опасных сечений вала вычисляем общий коэффициент запаса выносливости [1,c.288]
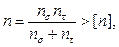
(8.7)
где [n]=1,5÷5[1,c.288]-рекомендуемая величина коэффициента выносливости;
nσ
-коэффициент запаса выносливости с учетом только нормальных напряжений (изгиб) [1,c.288];
nτ
-коэффициент запаса выносливости с учетом только касательных напряжений (кручение) [1,c.288];
(8.8)
В этих формулах σ-1
и τ-1
предел выносливости материала вала при симметричном цикле напряжений изгиба и кручения соответственно, МПа
σ
-1
=
0,43σ
в
; (8.9)
τ
-1
=(0,5÷0,58) σ
-1
; [1,c.288] (8.10)
σa
τa
и σm
τm
– амплитуда и среднее напряжение циклов нормальных и касательных напряжений;
Kσ
;Kτ
– эффективный коэффициент концентрации напряжений изгиба и кручения в опасном сечении [1,c.290];
εσ
;ετ
- масштабный коэффициент [1,c.290];
ψσ
;ψτ
– коэффициент ассиметрии цикла [1,c.292].
Можно считать, что нормальные напряжения в поперечных сечениях вала изменяются по симметричному циклу. Тогда
σm
=0, а σa
=σU
=M/W·2 [1,c.290],
где
(8.11)
Напряжения кручения изменяются по пульсирующему (отнулевому) циклу, поэтому [1,c.289]
(8.12)
где
(8.13)
Суммарный
(8.14)

Изгиб:
σ-1
=
0,43·570=245,1 МПа,
Kσ
=
1,75;
εσ
=
0,89;
ψσ
=
0,2;

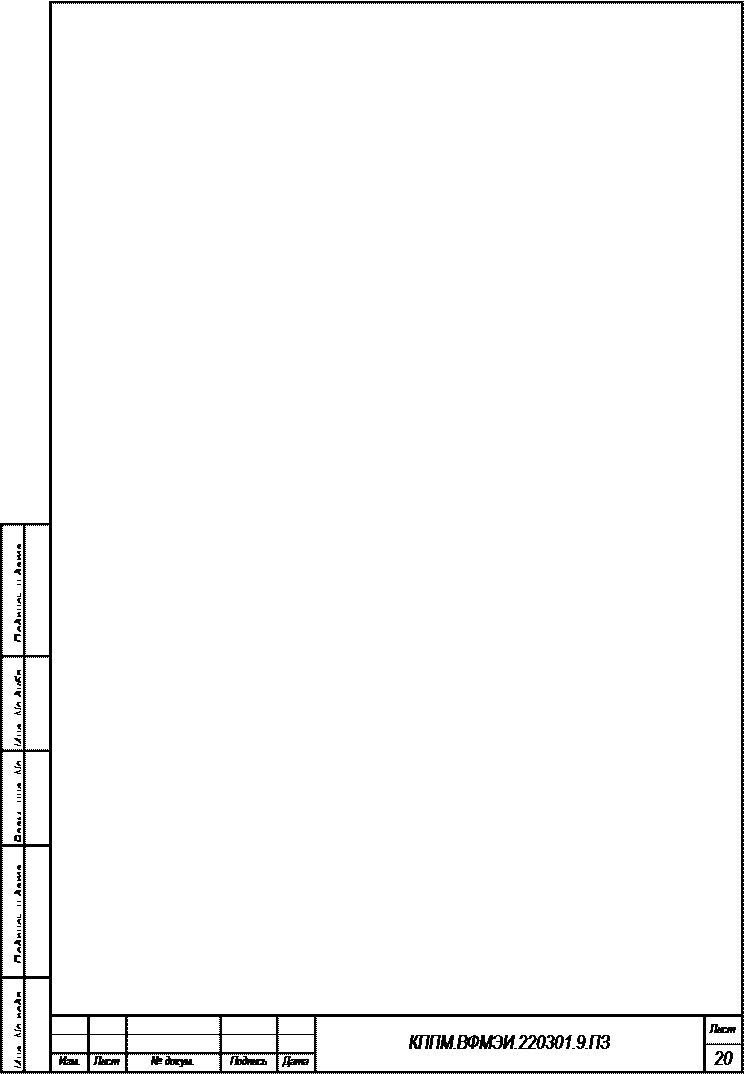 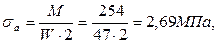
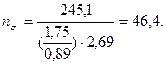
Кручение:
τ-1
=0,5·245,1=122,6 МПа,

Kτ
=
1,75;
ετ
=
0,78;
ψτ
=
0;
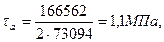
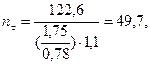
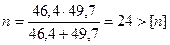
Следовательно, выносливость обеспечена.
8.3
Тихоходный (ведомый) вал
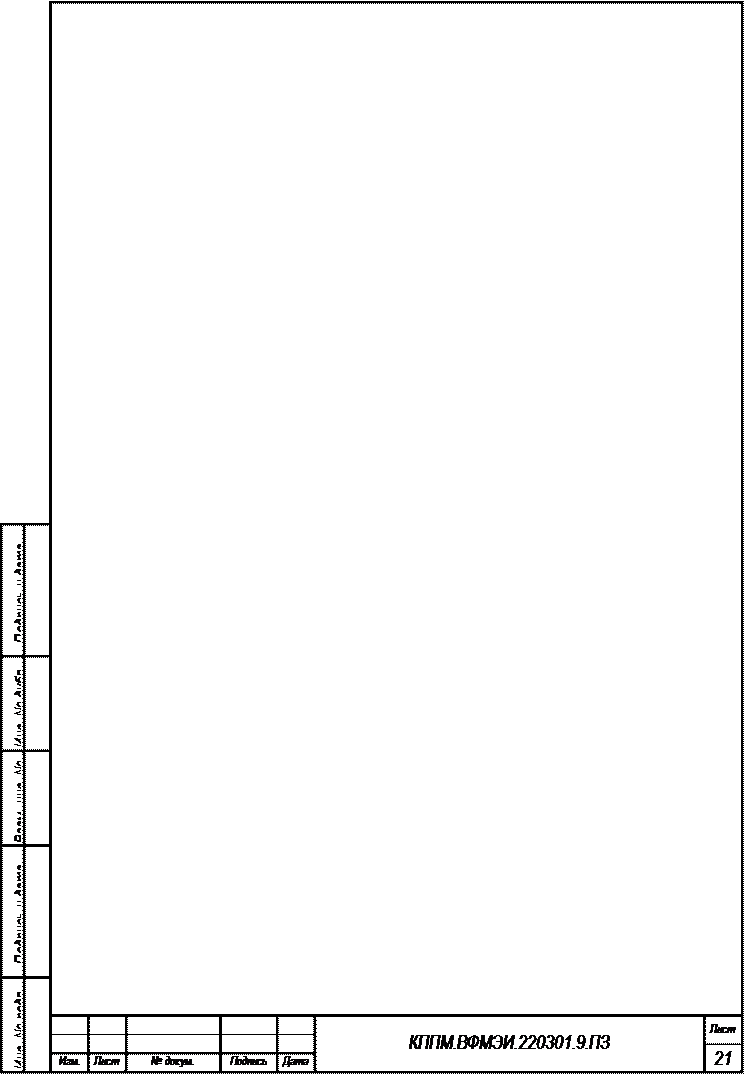 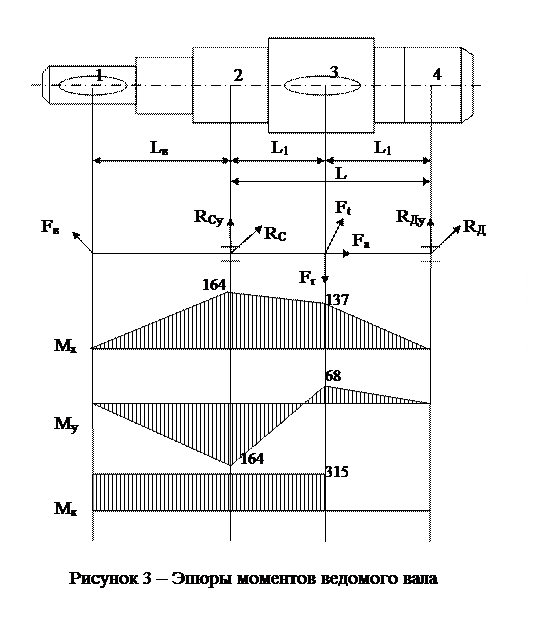
8.3.1 Определяем реакции в подшипниках
Дано: Ft
=4994H,
Fr
=1818H, Fa
=0H, L
=120мм, L
1
=60мм, d
2
=126мм,
L
в
=69,5мм, F
в
=2359Н.
Вертикальная плоскость:
∑M4
=0;

(8.15)
∑M2
=0;
 (8.16)
8.3.2 Строим эпюру изгибающих моментов относительно оси Х:
Мx
1
=0; Mx
2
=Fв
·Lв
=2359·69,5·10-3
=164H·м; Mx
4
=0;
Mx
3
=Fв
· (Lв
+L1
)-RCy
·L1
=2359· (69,5+60) ·10-3
-2816·60·10-3
=137Н·м;
Mx
3
=RД
y
·L1
=2275·60·10-3
=137Н·м.
Горизонтальная плоскость:
∑M4
=0;
(8.17)
∑M2
=0;
(8.18)
8.3.3 Строим эпюру эпюру изгибающих моментов относительно Y:
Мy1
=0; My2
=-Fв
·Lв
=-2359·69,5·10-3
=-164H·м; My4
=0;
My3
=-Fв
· (Lв
+L1
)+RCx
·L1
=-2359· (69,5+60) ·10-3
+6221·60·10-3
=68Н·м.
8.3.4 Строим эпюру крутящих моментов:
Mк
=Ft
·d2
/2=4994·126·10-3
/2=315Н·м. (8.19)
8.3.5Определяем суммарные реакции, Н:
(8.20)
(8.21)
9.Проверочный расчет подшипников
9.1
Быстроходный (ведущий) вал
Намечаем радиальные шариковые подшипники легкой серии 209.
Эквивалентная нагрузка
Рэ
= V · Pr
· KT
· Кб
=1·2450·1,05·1=2573H. (9.1)
где Pr
=RA
=2450H- радиальная нагрузка на подшипник;
Pa
=Fa
=0H- осевая нагрузка на подшипник;
V=1-коэффициент вращения [5, c.197];
Кб
=1- коэффициент безопасности для ленточных конвейеров.
Номинальная долговечность подшипников в млн.об
L=(C/Pэ
)р
=(33200/2573)3
=2148 млн.об. (9.2)
где С-каталожная динамическая грузоподъемность данного типоразмера подшипника;
р-степенной показатель, для шарикоподшипников принимается равным трем [5, c.196].
Номинальная долговечность подшипника, ч
(9.3)
что больше установленных ГОСТ 16162-85.
Следовательно, долговечность подшипника обеспечена.
9.2
Тихоходный (ведомый) вал
Намечаем радиальные шариковые подшипники легкой серии 210.
Эквивалентная нагрузка
Рэ
= V · Pr
· KT
· Кб
=1·4482·1,05·1=4706H. (9.4)
где Pr
=RД
=4482H- радиальная нагрузка на подшипник;
Pa
=Fa
=0H- осевая нагрузка на подшипник;
V=1-коэффициент вращения [5, c.197];
Кб
=1- коэффициент безопасности для ленточных конвейеров.
Номинальная долговечность подшипников в млн.об
L=(C/Pэ
)р
=(35,1/4706)3
=415 млн.об. (9.5)
где С-каталожная динамическая грузоподъемность данного типоразмера подшипника;
р-степенной показатель, для шарикоподшипников принимается равным трем [5, c.196].
Номинальная долговечность подшипника, ч
(9.6)
что больше установленных ГОСТ 16162-85.
Следовательно, долговечность подшипника обеспечена.
10.Выбор системы смазки
Для редуктора общего назначения применяют картерную систему смазки (окунанием). Этот способ применяется для зубчатых передач при окружных скоростях от 0,3 до 12,5 м/с.
Сорт масла и его кинематическая вязкость зависят от величины контактных напряжений в зацеплении и окружной скорости. Эти характеристики можно определить по рекомендациям [6, c.255].
Объем масла для редуктора
V=(0,4…0,8)Pтр
=0,6·4,93=3л (10.1)
Скорость редуктора
υ=ω3
·d2
/2000=8,8·250/2000=1,1м/с (10.2)
По υ=1,1 м/c и кинематической вязкости ν=34 [6,c.334],выбираем масло: И-Г-А-68 [6,c.317].
список литературы
1. Дунаев П.Ф., Леликов О.П. Конструирование узлов и деталей машин.-М.: Высшая школа., 1998.-443с.
2. Чернин И.М. Расчеты деталей машин: Справочное пособие.-М.: Высшая школа, 1978.-472.
3. Анурьев В.И. Справочник конструктора-машиностроителя. В 3-х т. Т.2-М.: Машиностроение, 2001.
4. Иванов М.Н. Детали машин.-М.: Высшая школа, 1984.-336 с.
5. Баласанян Р.А., Киркач Н.Ф. Расчет и проектирование деталей машин.-М.: Высшая школа, 1991-354 с.
6. Шейнблит А.Е. Курсовое проектирование деталей машин-М.: Высшая школа.,1991.-432 с.
|