Федеральное агентство по образованию
ГОУ ВПО "Российский государственный профессионально-педагогический
Университет"
Кафедра технологии и оборудования машиностроения
Пояснительная записка к курсовому проекту
ПРОЕКТИРОВАНИЕ ТЕХНОЛОГИЧЕСКОГО
ПРОЦЕССА МЕХАНИЧЕСКОЙ ОБРАБОТКИ ДЕТАЛИ
"КРЫШКА ПОДШИПНИКА"
Выполнил:
"___"______20___г.
Проверил:
"___"______20___г.
Екатеринбург
2010 г.
Содержание
Введение
Раздел I. Исходная информация
1.1 Служебное назначение и технологическая характеристика детали
1.2 Определение типа производства
Раздел II. Анализ исходных данных
2.1 Анализ рабочего чертежа детали
Раздел III. Разработка технологического процесса обработки детали
3.1 Выбор исходной заготовки
3.2 Выбор технологических баз
3.3 Выбор методов обработки поверхностей
3.4 Составление технологического маршрута обработки
3.5 Выбор средств технологического оснащения
Раздел IV. Технологические расчеты
4.1 Расчет припусков
4.2 Расчет режимов резания
4.3 Расчет технических норм времени
Заключение
Список литературы
Особенности науки технологии машиностроения в нашей стране является то, что эта наука опирается на работы, которые ведутся не только в научно-исследовательских, проектно-технологических и учебных институтах, но и в многочисленных заводских технологических лабораториях и цехах. Наряду с учеными вносят свой вклад в развитие науки и техники передовые рабочие производств. При работе металлорежущих станках они применяют высокие режимы резания, создают инструменты и приспособления собственных конструкций, принимают участие в разработке рациональных технологических процессов, способствующих повышению производительности труда.
Для достижения высокого уровня производства и производительности труда необходимо непрерывно обеспечивать всемерное повышение темпов технического прогресса, ускорять внедрение достижений науки и техники во все отрасли народного хозяйства.
Технический прогресс всего народного хозяйства зависит от уровня развития машиностроительной промышленности.
В процессе изучения механической обработки деталей возникает множество вопросов, связанных с необходимостью выполнения заданных технологических требований, с эксплуатацией сложного оборудования, режущего и измерительного инструмента, оснастки и др.
Целью курсовой работы является разработка технологического процесса изготовления детали "Крышка подшипника".
Для этого необходимо решить следующие задачи:
изучение технологии механической обработки;
применение приобретенных знаний при проектировании технологического процесса.
Раздел
I. Исходная информация
Крышка подшипника - это деталь тело вращения. Конструкция детали представляет собой взаимное пересечение цилиндрических и конических поверхностей, так же имеется отверстие, расположенное под углом к оси вращения детали. На этом отверстии нарезается коническая трубная резьба.
Имеются шесть отверстии диаметром 7 мм, которые предназначены для крепления крышки к корпусу редуктора. Центрирование детали происходит по цилиндрической поверхности диаметром 100 мм и торцевой.
Отсюда можно сказать, что крышка выполняет роль опоры при вращении других деталей в сборочном узле.
Материал заготовки - серый чугун СЧ 20 ГОСТ 1412-85
Чугун серый - сплав железа с графитом, который присутствует в виде пластинчатого или волокнистого графита.
Серый чугун характеризуется высокими литейными свойствами (низкая температура кристаллизации, текучесть в жидком состоянии, малая усадка) и служит основным материалом для литья. Он широко применяется в машиностроении для отливки станин станков и механизмов, поршней, цилиндров. Кроме углерода, серый чугун всегда содержит в себе другие элементы. Важнейшие из них это кремний и марганец. В большинстве марок серого чугуна содержание углерода лежит в пределах 2,4-3,8%, кремния 1-4% и марганца до 1,4%. Цена за тонну СЧ составляет от 6000 до 15000 рублей в зависимости от региона. Заменители: СЧ 25, СЧ 30, СЧ 35.
Определяем тип производства, в зависимости от габаритов, массы (веса) и размера годовой программы выпуска изделий, из этих данных необходимо установить тип производства:
Единичное - определяется выпуском деталей (продукции) в малом количестве.
Серийное - производство характеризуется ограниченным выпуском продукции, но большими сериями. Серийное производство подразделяется на крупносерийное и мелкосерийное.
Крупносерийное - относительно постоянный выпуск продукции большими сериями, либо изготовлением изделий, производство которых часто повторяется. По характеру ближе остальных к массовому. При выборе технологического оборудования специального и специализированного, дорогостоящего приспособления или вспомогательного приспособления и инструмента необходимо производить расчёт затрат и сроков окупаемости, а также ожидаемый экономический эффект от использования оборудования и технологического оснащения.
Мелкосерийное - широкая номенклатура, большой размер серии, редкая периодичность выпуска. По характеру близко к единичному.
Массовое - характеризуется выпуском одной и той же продукции как правило длительное время (годами).
Согласно массе детали 0,4 кг, и годовой программе 5000 шт. в год, тип производства - среднесерийное.
Таблица 3 - Определение типа производства
Масса детали,
кг.
|
Тип производства
|
Единичное
|
Мелко-
серийное
|
Средне-серийное
|
Крупно-
серийное
|
Массовое
|
< 1,0
|
< 10
|
10 - 2000
|
1500 - 100000
|
75000 - 200000
|
200000
|
1,0 - 2,5
|
< 10
|
10 - 1000
|
1000 - 5000
|
50000 - 100000
|
100000
|
2,5 - 5,0
|
< 10
|
10 - 500
|
500 - 35000
|
35000 - 75000
|
75000
|
5,0 - 10
|
< 10
|
10 - 300
|
300 - 25000
|
25000 - 50000
|
50000
|
> 10
|
< 10
|
10 - 200
|
200 - 10000
|
10000 - 25000
|
25000
|
В соответствии с таблицей 3 тип производства среднесерийный.
Серийное производство характеризуется изготовлением ограниченной номенклатуры деталей партиями, повторяющимися через определенные промежутки времени. Это позволяет использовать наряду с универсальным специальное оборудование. При проектировании технологических процессов предусматривают порядок выполнения и оснастку каждой операции.
Для организации серийного производства характерны следующие черты. Цехи, как правило, имеют в своем составе предметно-замкнутые участки, оборудование на которых расставляется по ходу типового технологического процесса. В результате возникают сравнительно простые связи между рабочими местами и создаются предпосылки для организации прямоточного перемещения деталей в процессе их изготовления.
Предметная специализация участков делает целесообразной обработку партии деталей параллельно на нескольких станках, выполняющих следующие друг за другом операции. Как только на предыдущей операции заканчивается обработка нескольких первых деталей, они передаются на следующую операцию до окончания обработки всей партии. Таким образом, в условиях серийного производства становится возможной параллельно-последовательная организация производственного процесса. Это его отличительная особенность.
Применение той или иной формы организации в условиях серийного производства зависит от трудоемкости и объема выпуска закрепленных за участком изделий. Так, крупные, трудоемкие детали, изготовляемые в большом количестве и имеющие сходный технологический процесс, закрепляют за одним участком с организацией на нем переменно-поточного производства. Детали средних размеров, многооперационные и менее трудоемкие объединяют в партии. Если запуск их в производство регулярно повторяется, организуются участки групповой обработки. Мелкие, малотрудоемкие детали, например нормализованные шпильки, болты, закрепляют за одним специализированным участком. В этом случае возможна организация прямоточного производства.
Для предприятий серийного производства характерны значительно меньшие, чем в единичном, трудоемкость и себестоимость изготовления изделий. В серийном производстве, по сравнению с единичным, изделия обрабатываются с меньшими перерывами, что снижает объемы незавершенного производства.
С точки зрения организации основным резервом роста производительности труда в серийном производстве является внедрение методов поточного производства.
Количество деталей в партии (n, шт) для одновременного запуска определяется упрощенным способом по формуле:
n = ,
где N - годовая программа выпуска;
а - периодичность запуска в днях (рекомендуется следующая периодичность запуска деталей: 3,6, 12,24 дня)
254 - количество рабочих дней в году.
Расчет:
n = 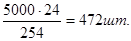
Размер партии может быть скорректирован с учетом удобства планирования и организации производства. С этой целью размер партии принимают не менее сменной выработки.
Раздел
II. Анализ исходных данных
"Крышка подшипника" является телом вращения, при эксплуатации данная деталь испытывает постоянные нагрузки, деталь также испытывает колебательные нагрузки (вибрация).
Габаритные размеры детали - Ø145мм, длина 42 мм
Все фаски подрезаются под углом 450
.
Детали после отливки подвергают отжигу, для снятия внутренних напряжении и выровнять структуру металла.
Основные технологические задачи включают требования по обеспечению:
точности размеров (цилиндрическая поверхность Ø60Н7, Ø100h6);
параллельность торцевых поверхностей 0,01мм;
качества поверхностного слоя (шероховатость цилиндрической поверхности Ra = 1,6 мкм, внутреннего диаметра Rа = 1,6 мкм, отверстия Ra=6,3; для остальных Rа = 6,3…10мкм).
Технологический процесс обработки данной детали строится на основе типового технологического процесса обработки детали "Крышка"
Основные этапы обработки
черновая обработка поверхностей;
чистовая обработка поверхностей
отделочные операции.
Деталь технологична, т.к имеет небольшие габаритные размеры. Соотношение размеров детали оптимально для применения наиболее рациональных и экономически выгодных методов обработки.
Раздел
III. Разработка технологического процесса обработки детали
Метод литья по выплавляемым моделям, благодаря преимуществам по сравнению с другими способами изготовления отливок, получил значительное распространение в машиностроении и приборостроении.
Промышленное применение этого метода обеспечивает получение из любых литейных сплавов сложных по форме отливок массой от нескольких граммов до десятков килограммов со стенками, толщина которых в ряде случаев менее 1 мм, с шероховатостью от Rz = 20 мкм до Ra = 1,25 мкм (ГОСТ 2789-73) и повышенной точностью размеров (до 9-10-го квалитетов по СТ СЭВ 144-75)".
Указанные возможности метода позволяют максимально приблизить отливки к готовой детали, а в ряде случаев получить литую деталь, дополнительная обработка которой перед сборкой не требуется. Вследствие этого резко снижаются трудоемкость и стоимость изготовления изделий, уменьшается расход металла и инструмента
Отливки по выплавляемым моделям изготовляют практически из всех литейных сплавов: углеродистых и легированных сталей, коррозионно-стойких, жаростойких и жаропрочных сталей и сплавов, чугуна, цветных сплавов, например алюминиевых, медных, титановых и др.
При проектировании литых деталей учитывают условия их работы, в связи с чем некоторые свойства металла отливок приобретают первостепенное значение. Показатели их регламентируют, в то время как другие свойства считают менее важными.
Выбор заготовки для дальнейшей механической обработки является одним из важнейших этапов проектирования технологического изготовления детали. От правильного выбора заготовки, установления ее форм, размеров припусков на обработку, точности размеров и твердости материала в значительной степени зависят характер и число операций или переходов, трудоемкость изготовления детали, величина расхода материала инструмента, и в итоге, стоимость изготовления детали.
При выборе заготовки предпочтение следует отдавать той заготовке, которая обеспечивает меньшую технологическую себестоимость детали. Если же сопоставимые варианты по технологической себестоимости равноценны, то предпочтительным следует считать вариант заготовки с более высоким Ким
.
Существуют несколько методов получения заготовок:
№ п/п
|
Вид заготовки
|
|
Заготовка, полученная литьем
|
1
|
Литье
|
в песчаную форму
|
2
|
в форму из жидких самотвердеющих смесей
|
3
|
в песчаную форму, изготовленную под высоким удельным давлением
|
4
|
в металлическую форму
|
5
|
полученное центробежным методом
|
6
|
в оболочковую форму
|
7
|
по выплавляемым моделям
|
8
|
штамповкой жидкого металла
|
9
|
под давлением
|
Для изготовления заготовки детали "Крышка подшипника" используем метод литья по выплавляемым моделям.
Область применения этого метода серийное и массовое производство.
Для чернового базирования возьмем внутреннею цилиндрическую поверхность Ø92 и правый торец, потому как эти поверхности обеспечат хорошую устойчивость детали при обработке.

При выборе баз руководствуются следующими рекомендациями: - соблюдение принципа единства баз, т.е. по возможности обеспечивать совмещение технологической и конструкторской баз. Это значит задавать положение обрабатываемой поверхности по возможности теми же размерами, которые проставлены на чертеже детали.
Отступление от этих правил приводит к ужесточению допусков на исходные размеры, так как вместо конструкторских размеров приходится вводить технологические размеры, на которые назначаются меньшие допуски. Во-вторых, технологическая база, по возможности, должна обеспечивать неизменность положения заготовки в процессе её обработки, т.е. должна быть постоянной.
Способ базирования заготовки (детали) определяется, в основном, её формой. Используются типовые способы базирования заготовок, включающие в себя поверхности или совокупность поверхностей трех видов: плоскость, цилиндрическое отверстие и цилиндрическая наружная поверхность. В моем технологическом процессе основной установочной базой данной детали является внутренняя цилиндрическая поверхность Ø92. В качестве вспомогательных базовых поверхностей принимаю торцевые поверхности. Принятые схемы базирования на операциях обеспечат выполнение всех размеров согласно чертежу.
Выбор методов обработки поверхностей зависит от конфигурации детали, ее габаритов и качества обрабатываемых поверхностей, вида принятой заготовки.
Необходимее качество поверхностей в машиностроении достигается преимущественно обработкой резанием.
В зависимости от технических требований предъявляемых к детали и типа производства выбирают один или несколько возможных методов обработки и тип соответствующего оборудования.
Таблица 8 - Методы обработки поверхностей детали "Крышка подшипника"
Номер поверхности
|
Вид поверхности
|
Квалитет точности
|
Шероховатость
|
Метод обработки поверхности
|
1.
|
Ø145, Ø71, Ø45
|
h14
h 12
|
Ra
20
Ra
12,5
|
Обтачивание:
черновое
чистовое
|
2.
|
Ø100
|
h 14
h 11
h8
h6
|
Ra
20
Ra
10
Ra
3,2
Ra
1,25
|
Точение:
Черновое
п/чистовое
чистовое
тонкое
|
3.
|
Ø60
|
Н14
Н12
Н10
Н7
|
Ra
20
Ra
10
Ra
3,2
Ra
1,25
|
Растачивание:
Черновое
п/чистовое
чистовое
тонкое
|
Таблица 6 - технологический маршрут обработки детали "Крышка подшипника" вариант 1
№ операции
|
Наименование и краткое содержание операции. Технологические базы
|
Наименование оборудования
|
005
|
Заготовительная.
|
Литье
|
010
|
Термическая.
|
Печь
|
015
|
Токарно-револьверная
Наружная и внутренняя обработка цилиндрических поверхностей.
Внутренняя цилиндрическая поверхность и торец.
|
Токарно-револьверный станок 1Н325
|
020
|
Фрезерная.
Фрезеровать плоскость концевой фрезой
Базирование по диметру 100 мм и по торцу.
|
Вертикально-фрезерный станок
6Н12ПБ
|
025
|
Сверлильная
Сверление отверстий и нарезание резьбы
Базирование по диметру 100 мм и по торцу.
|
Радиально-сверлильный станок
2В56
|
030
|
Слесарное
Притупить острые кромки и зачистка от грязи
|
Стол слесарный и шлифовальная машинка ИП 124
|
035
|
Промывка
|
УБР - 200, машина моечная
|
040
|
Контрольная
Контроль деталей согласно чертежа
|
|
045
|
Упаковывание
|
|
Таблица 7 - технологический маршрут обработки детали "Крышка подшипника" вариант 2
№ операции
|
Наименование и краткое содержание операции. Технологические базы
|
Наименование оборудования
|
005
|
Заготовительная.
|
Литье
|
010
|
Термическая.
|
Печь
|
015
|
Токарная с ЧПУ
Наружная и внутренняя обработка цилиндрических поверхностей.
Внутренняя цилиндрическая поверхность и торец.
|
Токарный станок ч ЧПУ 16К20Ф3
|
020
|
Фрезерная с ЧПУ
Фрезеровать плоскость концевой фрезой
Сверление отверстий и нарезание резьбы
Базирование по диметру 100 мм и по торцу.
|
Многоцелевой сверлильно-фрезерно-расточный станок 2254ВМФ4
|
025
|
Слесарное
Притупить острые кромки и зачистка от грязи
|
Стол слесарный и шлифовальная машинка ИП 124
|
030
|
Контрольная
Контроль деталей согласно чертежа
|
|
035
|
Упаковывание
|
|
Выбираю вариант технологического маршрута, приведенный в таблице 6 (вариант 1), так как данные станки позволяют использовать принцип дифференциации операции, т.е. простые переходы можно распределить на несколько станков, тем самым добиться повышения производительности труда.
К средствам технологического оснащения относятся: технологическое оборудование; технологическая оснастка; средства механизации и автоматизации технологических процессов.
При выборе станочного оборудования необходимо учитывать:
характер производства;
методы достижения заданной точности при обработке;
соответствие станка размерам детали;
мощность станка;
удобство управления и обслуживания станка;
возможность оснащения станка высокопроизводительными приспособлениями и средствами механизации и автоматизации.
1. Токарно-револьверные станки
Токарно-револьверные станки применяются в серийном производстве для обработки деталей из прутков или из штучных заготовок. На этих станках можно выполнить все основные токарные операции.
Револьверные станки отличаются от токарно-винторезных тем, что не имеют задней бабки и ходового винта, а имеют револьверную головку, в гнездах которой может быть установлен разнообразный инструмент. При наличии специальных комбинированных державок можно в одном гнезде головки, закрепить несколько инструментов. Заготовки зажимаются патронами или специальными цанговыми зажимными устройствами. Револьверная головка может поворачиваться вокруг своей оси, и тогда инструмент последовательно подводится к детали, обрабатывая ее за несколько переходов. Инструмент крепится также и в резцедержателе поперечного суппорта. Применение токарно-револьверных станков считается рациональным в том случае, если по технологическому процессу обработки детали требуется применение большого количества режущего инструмента.
К преимуществам токарно-револьверных станков, по сравнению с токарными, относятся: возможность сокращения машинного времени за счет применения многорезцовых державок и одновременной обработки детали инструментом, установленным на револьверной головке и поперечном суппорте, а также сравнительно малые затраты времени за счет предварительной настройки станка на обработку детали многими инструментами.
Токарно-револьверные станки в зависимости от вида обрабатываемых заготовок бывают прутковые или патронные. Обычно станки малого размера - прутковые, а среднего размера могут быть как прутковые, так и патронные. Крупные револьверные станки обычно патронные. Все эти станки делятся на станки с вертикальной и горизонтальной осью вращения револьверной головки (рис.16).

3 2 1
Рис.16. Токарно-револьверный станок 1Н325
В условия серийного производства в качестве приспособлений используются универсальные стандартные приспособления.
Выбор оснастки:
№ операции
|
Установочно-зажимное приспособление
|
015
|
7100-0015 - трех кулачковый самоцентрирующий патрон ГОСТ 2675-80.
|
020, 025
|
Специальное установочно-зажимное приспособление
|
Таблица 6
Выбор режущего инструмента
№ операции
|
Средства технологического оснащения
|
Краткая техническая характеристика
|
Код, ГОСТ
|
Источник
|
015
|
Расточной резец
|
Н=20мм, В=20мм,
L=100мм
|
2142-0191
ГОСТ 9795-84
|
[4, с.239]
|
Резцы отрезные
|
Н=25мм, В=16мм,
L=80мм
|
2177-0503
ГОСТ 18890-73
|
[4, с.258]
|
Резец проходной упорный, Т5К10
|
Н=25мм, В=25мм,
L=150мм
|
2103-0712
ГОСТ 18890-73
|
[4, с.267]
|
Резец канавочный
|
Н=20мм, В=12мм,
L=мм
|
2177-0001
ГОСТ 18894-73
|
[4, с.262]
|
Фреза концевая
|
d=32 мм, L=155мм,
l=53 мм
|
ГОСТ 17026-71
|
[4, с.224]
|
020
|
Фреза концевая
|
d=32 мм, L=155мм,
l=53 мм
|
ГОСТ 17026-71
|
[4, с.224]
|
025
|
Сверло с коническим хвостовиком
|
d=10 мм, L=120мм,
l=55 мм
|
ГОСТ 11183-71
|
[4, с.234]
|
025
|
Метчик RC
1 1/2
|
|
ГОСТ 3266-81
|
[4, с.310]
|
Раздел
IV. Технологические расчеты
Определение общего припуска на сторону.
Общий припуск на сторону определяется с учетом следующих данных:
1) допуск размера детали от базы до обрабатываемой поверхности;
2) вид окончательной обработки;
3) метод установки отливки при обработке;
4) общий допуск элемента поверхности;
5) уровень точности обработки;
6) ряд припуска;
7) тип производства;
8) тип обрабатываемой поверхности;
9) соотношение между требуемой точностью обработанной поверхности детали и исходной точностью поверхности отливки.
Допуск размера детали - 0,022 мм. При обработке тел вращения базой является ось детали. Следовательно, допуск размера от базы до обрабатываемой поверхности равен 0,022/2=0,011 мм.
Вид окончательной обработки определяется
в зависимости от соотношения между допусками размера детали и отливок и от базы обработки до обрабатываемой поверхности и допуска размера отливки.
Соотношение ITJIT3
=
0,011/1,2 = 0,009 (допуск на размер отливки 1,2 мм).
По табл.3.10 при допуске размера отливки свыше 1,0 мм и соотношения допусков до 0,01 вид окончательной механической обработки - тонкое точение.
Заготовка на станке устанавливается без выверки при односторонних отклонениях формы и расположения обрабатываемой поверхности относительно номинальной. В этом случае припуск назначают с учетом полного значения допуска формы и расположения обрабатываемой поверхности относительно номинальной. При индивидуальной обработке отливок, когда установка осуществляется с выверкой по обрабатываемой поверхности, припуски назначают с учетом половинных значений допуска формы и расположения обрабатываемой поверхности.
Общий допуск элемента поверхности
определяется на размер от обрабатываемой поверхности до базы обработки, при этом допуски размеров отливки, изменяемых обработкой, определяют по номинальным размерам детали. Так как отклонения формы и расположения поверхностей не регламентируются, то общий допуск равен допуску на размер детали.
Уровень точности обработки.
Обработка детали ведется на станке нормальной точности с ручным управлением. В соответствии с табл.3.12 уровень точности обработки - пониженный.
При пониженном уровне точности обработки значения припуска следует принимать на 1 строку ниже интервала действительного допуска (см. примечание 2 к табл.3.12).
Тип производства - серийное.
Для отливок мелкосерийного и единичного производства допускается назначать увеличенные значения припусков, соответствующие интервалам общих допусков, расположенным в табл.3.14 соответственно на 1 и 2 строки ниже интервала действительного допуска.
Тип обрабатываемой поверхности -
поверхность вращения. С учетом примечания, половинный допуск равен 1,2/2 = 0,6 мм.
По табл.3.14 для допуска 0,6 мм чистовой обработки для 6-го ряда припуска общий припуск равен 2,2 мм. С учетом уровня точности обработки припуск должен назначаться на 1 строку ниже интервала действительного допуска, т.е. в диапазоне свыше 1,5 до 2,2 мм, т.е. общий припуск на сторону составит 2,2 мм - это суммарный припуск на все переходы обработки: черновой, получистовой, чистовой и тонкой. В соответствии с табл.3.14 составляющими для каждого вида обработки будут:
черновая -
0,5 мм;
получистовая - 0,3
мм;
чистовая -
0,2 мм
тонкая - 0,1мм
Таблица 9 - Припуски и допуски на обрабатываемые поверхности
Поверх-
ность
|
Размер, мм
|
Припуск, мм
|
Допуск, мм
|
Предельное отклонение, мм
|
Верхнее
|
Нижнее
|
1.
|
Ø 145
|
4,0
|
0,9
|
0,6
|
0,3
|
2.
|
Ø 71
|
3,0
|
0,5
|
0,25
|
0,25
|
3.
|
Ø 45
|
2,0
|
0,3
|
0,1
|
0,2
|
4.
|
Ø 60
|
3,0
|
0,5
|
0,25
|
0,25
|
5.
|
Ø 100
|
2,2
|
0,6
|
0,3
|
0,3
|
6.
|
42
|
2,5
|
0,5
|
0,2
|
0,3
|
7.
|
16
|
2
|
0,3
|
0,2
|
0,1
|
Режимы резания оказывают влияние на точность и качество обработанной поверхности, производительность и себестоимость обработки.
Режимы резания определяются глубиной резания t, мм; подачей на оборот Sо
, мм/об и скоростью резания V, м/мин.
Операция 015: Токарно-револьверная.
Оборудование - Токарно-револьверный станок 1Н325, приспособление - Трех кулачковый самоцентрирующий патрон.
Исходные данные: деталь - корпус подшипника, материал заготовки - СЧ 20 ГОСТ 1412-85, получаемая шероховатость Ra
1,6мкм.
Содержание операции: обтачивание наружной поверхности Ø 145.
Режущий инструмент: резец проходной упорный материал режущей части Т5К10.
Глубина резания t = 1,5 мм.
Sтабл.
= 0,65 мм/об. [3, с.365]
Нормативный период стойкости: Тн.
= 60 мин.
Скорость резания:
Vтабл.
= 170 м/мин, [3, стр.60]
Частота вращения:
,
где D - диаметр обрабатываемой поверхности, D = 145 мм.
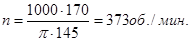
Уточнение частоты вращения по паспорту станка: n = 350об/мин.
Пересчет скорости резания с учетом уточненной частоты вращения:

Определение минутной подачи:


Длина рабочего хода:
Lр. х.
= Lрез.
+ у, где
Lрез.
= 5 мм.
y = длина врезания и перебега инструмента
y = 5+2 = 7 мм.
Lр. х
= 5 + 7 = 12 мм.
Расчет основного времени обработки:
,
Кр
=1 - число рабочих ходов
Содержание перехода: расточить внутреннюю цилиндрическую поверхность Ø62Н7+0,03
мм.
Режущий инструмент: резец расточной проходной, материал режущей части Т5К10.
Глубина резания t = 2,0 мм.
Sтабл.
= 0,3 мм/об. [3, с.365]
Нормативный период стойкости: Тн.
= 60 мин.
Скорость резания: Vтабл.
= 142 м/мин, [3, стр.60]
Частота вращения:
,
где D - диаметр обрабатываемой поверхности, D = 62 мм.
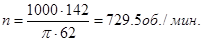
Уточнение частоты вращения по паспорту станка: n = 730 об/мин.
Пересчет скорости резания с учетом уточненной частоты вращения:

Определение минутной подачи:


Длина рабочего хода:
Lр. х.
= Lрез.
+ у, где
Lрез.
= 32 мм.
y = длина врезания и перебега инструмента
y = 3+2 = 5 мм.
Lр. х
= 32 + 5 = 37 мм.
Расчет основного времени обработки:
,
Кр
=2 - число рабочих ходов
Сверлильная. Содержание перехода: сверлить отверстие Ø12 мм.
Режущий инструмент: сверло с коническим хвостовиком, режущая часть Р6М5.
Sтабл.
= 0,3 мм/об. [3, с.425]
Нормативный период стойкости: Тн.
= 60 мин.
Скорость резания:
Vтабл.
= 10 м/мин, [3, стр.120]
Частота вращения:
,
где D - диаметр обрабатываемой поверхности, D = 12 мм.
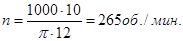
Уточнение частоты вращения по паспорту станка: n = 250 об/мин.
Пересчет скорости резания с учетом уточненной частоты вращения:

Определение минутной подачи:


Длина рабочего хода:
Lр. х.
= Lрез.
+ у, где
Lрез.
= 20 мм.
y = длина врезания и перебега инструмента
y = 3+2 = 5 мм.
Lр. х
= 20 + 5 = 25 мм.
Расчет основного времени обработки:
,
Кр
=1 - число рабочих ходов
Под технически обоснованной нормой времени понимается, время необходимое для выполнения заданного объема работы при определенных организационно - технических условиях.
В серийном производстве определяется норма штучно-калькуляционного времени Тш-к
:
Тш-к
= (Тп-з
/n) +Тшт
Определяем Твс
Твс = tуст
+tпер
+ tизм
Твс = 0,7+0,12+0,26+0,26+0,11+0,8 = 2,2 мин.
Определяем Тшт. к по наибольшему времени То и наименьших режимах резания:
Топер. (токарная)
= То+Твс = 10,5 + 1 = 11,5 мин
Топер. (расточная)
= То+Твс = 1,66 + 2 = 3,66 мин
Топер. (сверлильная)
= То+Твс = 8,6 + 1,4 = 10 мин
Топер. (шлифовальная)
= То+Твс = 5,5 + 2,5 = 8,0 мин
Топер. (алмазно-расточная)
= То+Твс = 4,8 + 1,7 = 6,5 мин
Тдоп = Топер х4% = 1,1 х 4% = 0,04 мин
Тшт = Топер + Тдоп = 45+0,04 = 45,04 мин.
Тп. з = tнал
+ tпол. инст
+ tпод. нал
= 5+7,5+8 = 20 мин.
Тшт. к = Тп. з /n+ Тшт = 20/100 + 45,04 = 45,24 мин.
Ведущая роль в ускорении научно-технического прогресса, поднятию России на мировой уровень в сфере производства призвано сыграть машиностроение, которое в кратчайшие сроки необходимо поднять на высший технический уровень. Цель машиностроения - изменение структуры производства, повышение качественных характеристик машин и оборудования. Предусматривается осуществить переход к экономике высшей организации и эффективности со всесторонне развитыми силами, зрелыми производственными отношениями, отлаженным хозяйственным механизмом. Такова стратегическая линия государства.
Предметом исследования и разработки в технологии машиностроения являются виды обработки, выбор заготовок, качество обрабатываемых поверхностей, точность обработки и припуски на неё, базирование заготовок; способы механической обработки поверхностей - плоских, цилиндрических, сложнопрофильных и др.; методы изготовления типовых деталей - корпусов, валов, зубчатых колёс и др.; процессы сборки (характер соединения деталей и узлов, принципы механизации и автоматизации сборочных работ); конструирование приспособлений.
Основными направлениями развития современной технологии: переход от прерывистых, дискретных технологических процессов к непрерывным автоматизированным, обеспечивающим увеличение масштабов производства и качества продукции; внедрение безотходной технологии для наиболее полного использования сырья, материалов, энергии, топлива и повышения производительности труда; создание гибких производственных систем, широкое использование роботов и роботизированным технологических комплексов в машиностроении и приборостроении.
1. ГОСТ 26645-85. Отливки из металлов и сплавов.
2. Справочник технолога - машиностроителя. В 2-хт. Т.1 / Под ред. А.М. Дальского, А.Г. Суслова, А.Г. Косиловой, Р.К. Мещерякова. - 5-е изд., исправл. - М.: Машиностроение - 1, 2003 г.912 с., ил.
3. Справочник технолога - машиностроителя. В 2-х т. Т.2 / Под ред. А.М. Дальского, А.Г. Суслова, А.Г. Косиловой, Р.К. Мещерякова. - 5-е изд., исправл. - М.: Машиностроение - 1, 2003 г.944 с., ил.
4. Расчет припусков и межоперационных размеров в машиностроении: Учеб. пособие для машиностроит. спец. Вузов / Я.М. Радкевич и др.; под редакцией В.А. Тимирязева. - М.: Высшая школа, 2004. - 272 с.
5. Ансеров М.А. Приспособления для металлорежущих станков. - Л.: Машиностроение, 1975.
6. Анурьев В.И. Справочник конструктора - машиностроителя. М.: Машиностроение, 1992 - Т1.
7. Выбор литья и проектирование чертежа отливки: Метод. указания. / Сост.: В.А. Литвиненко, Ю.С. Косоротова; ОмГТУ. - Омск, 1996. - 44с.
8. Добрыднев И.С. Курсовое проектирование по предмету "Технология машиностроения": Учебн. Пособие для техникумов по специальности "Обработка металлов резанием". - М.: Машиностроение, 1985.184с., ил
9. Зуев А.А. Технология машиностроения. 2-е изд., испр. И доп. - СПб.: Издательство "Лань, 2003. - 496с.
10. Козлова Т.А. Курсовое проектирование по технологии машиностроения: Учеб. пособие. - Екатеринбург: Изд-во Урал. Гос. Проф. - пед. ун-та, 2001. - 169с.
11. Куклин Н.Г., Куклина Г.С. Детали машин: Учеб. для машиностроит. спец. техникумов. - 4-е изд., перераб и доп. - М.: Высш. шк., 1987. - 383с.: ил.
12. Общемашиностроительные нормативы режимов резания: Справочник: В 2 т.: Т.1/А.Д. Локтев, И.Ф. Гущин, В.А. Батуев и др. - М.: Машиностроение, 1991. - 640 с.
13. Общемашиностроительные нормативы времени вспомогательного, на обслуживание рабочего места и подготовительно-заключительного для технического нормирования станочных работ: Сер. пр-во. М.: Машиностроение, 1974. 420 с.
14. Общемашиностроительные нормативы времени и режимов резания на токарно-автоматные работы. Часть I. Серийное, крупносерийное, массовое производство.: "Экономика", 1989. - 298чс.
15. Технологические наладки: Методические указания к курсовому и дипломному проектированию по технологии машиностроения / Сост. Ф.В. Беляков; ОмПИ, - Омск, 1980, 1,2ч.
|