1 ИСХОДНЫЕ ДАННЫЕ
Необходимо разработать производственный процесс и правильно организовать работу производственного участка предприятия по выпуску копира 08-75. Вид заготовки – отливка.
Годовая программа 270тыс.шт.
Исходные данные технологического процесса обработки детали на механическом участке представлены в таблице 1.1.
Таблица 1.1 – Технологический процесс обработки деталей на механическом участке
Деталь
|
Номер детали
|
Черновой вес, кг
|
Чистовой вес, кг
|
Закрепление операций и затраты времени по
операциям по видам оборудования, мин.*
|
вертикально-сверлильный
|
протяжной
|
токарный
|
токарный
|
вертикально-сверлильный
|
фрезерный
|
Основная деталь
|
копир
|
08-75
|
0,92
|
0,67
|
1-1,5
|
2-2,0
3-1,8
|
4-2,5
|
5-1,9
|
6-2,9
7-2,7
|
8-1,6
|
Догружаемая деталь
|
муфта
|
08-127
|
1,9
|
1,58
|
1-1,8
|
2-2,9
3-1,4
|
4-1,9
|
5-1,9
|
6-1,6
7-1,3
|
8-1,5
|
Примечание:* Первая цифра – номер операции, вторая – штучное время (tшт.i
), мин.
2
ОРГАНИЗАЦИОННАЯ ЧАСТЬ
2.1
Технико-экономическая характеристика типа производства
Одной из основных характеристик типа производства является коэффициент специализации, показывающий среднее число операций, закрепленных за одним рабочим местом. Различные типы производства характеризуются следующими коэффициентами специализации (серийности) Кс
: массовое – Кс
≤ 1; крупносерийное – Кс
= 2 ÷ 10; среднесерийное – Кс
= 10 ÷ 20; мелкосерийное – Кс
= 20 ÷ 40; единичное – Кс
> 40.
В массовом производстве коэффициент специализации определяется:
,
|
(1)
|
где τ – такт выпуска деталей, мин.
,
|
(2)
|
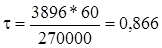
где Fд
– действительный годовой фонд времени работы оборудования, час. При двухсменной работе Fд
= 3896 час.;
N – годовая программа, N=270 тыс. шт.
t шт. ср.
– среднее штучное время по операциям, мин.
,
|
(3)
|

m – число операций (i = 1, 2, …, n).
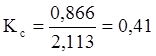
Тип производства: массовое.
2.2
Расчет потребного количества оборудования
и определение его загрузки
В поточном производстве потребное количество оборудования определяется по каждой технологической операции, причем количество оборудования должно соответствовать числу рабочих мест. Расчетное число рабочих мест на i-й операции (nрi
) определяется:
,
|
(4)
|
При определении npi
после запятой необходимо взять два знака.
По результатам npi
определяем принятое количество оборудования nпpi
.
Коэффициент загрузки оборудования по i-й операции (Кзi
):
,
|
(5)
|
Результаты расчетов сведем в таблицу 2.2.1.
Таблица 2.2.1 – Расчет количества оборудования (рабочих мест) и коэффициента их загрузки по участку
№ операции
|
Тип станка
|
τ, мин.
|
t шт,i
, мин.
|
npi
|
nпpi
|
Кзi
|
1
|
2
|
3
|
4
|
5
|
6
|
7
|
1
|
вертикально-сверлильный
|
0,866
|
1,50
|
1,73
|
2
|
0,87
|
2
|
протяжной
|
0,866
|
2,00
|
2,31
|
3
|
0,77
|
3
|
протяжной
|
0,866
|
1,80
|
2,08
|
3
|
0,69
|
4
|
токарный
|
0,866
|
2,50
|
2,89
|
3
|
0,96
|
5
|
токарный
|
0,866
|
1,90
|
2,19
|
3
|
0,73
|
6
|
вертикально-сверлильный
|
0,866
|
2,90
|
3,35
|
4
|
0,84
|
7
|
вертикально-сверлильный
|
0,866
|
2,70
|
3,12
|
4
|
0,78
|
8
|
фрезерный
|
0,866
|
1,60
|
1,85
|
2
|
0,92
|
Итого:
|
16,9
|
19,52
|
24
|
0,81
|
По полученным показателям проверяем возможность применения многостаночного обслуживания, совмещения профессий и дозагрузки оборудования.
Дозагрузка осуществляется при Кзi
< 1 с учетом данных о пропускной способности станков, их загрузки основной деталью. Определение возможности дозагрузки выполняем в следующей последовательности:
1 Определяем пропускную способность оборудования (Рi
) по каждой операции, исходя из годового фонда времени их работы, станко-часы, (графа 5):
,
|
(6)
|
2 Определяем загрузку оборудования основной деталью по каждой операции (Qoi
), станко-часы, (графа 6):
,
|
(7)
|
3 Рассчитаем объем возможной дозагрузки станков по каждой операции (Qв.д.i
), (графа 7):
,
|
(8)
|
4 Выбираем деталь для дозагрузки оборудования. Исходные данные технологического процесса обработки догружаемой детали даны в таблице 1.1.
5 Определяем загрузку операций догружаемой деталью (N'д), единиц:
,
|
(9)
|
Для обеспечения равной пропускной способности между операциями принимаем количество догружаемых деталей по минимальному значению N'д, полученному в расчете, т.е. Nд = minN'д. Результаты заносим в графу 10.
6 Определяем фактический объем дозагрузки по каждой операции (Qф.д.i
), ст.-час. (графа 11):
,
|
(10)
|
7 Определяем неиспользуемое время по операциям (∆Qi
), ст.-час. (графа 12):
,
|
(11)
|
8 Определяем коэффициент загрузки оборудования и рабочих мест с учетом принятой дозагрузки по каждой операции, Кзi
:
,
|
(12)
|
Таблица 2.2.2 – Расчет дозагрузки оборудования
№ операции
|
Наименование оборудования
|
Количество станков, nпрi.
|
Штучное время, tшт.i
|
Пропускная способность станков Рi,
ст.-час. (3896 х гр.3)
|
Загрузка станков основной деталью, Qoi, час ; .N х
t
шт.,
i
(гр.5 – гр.6) 60
|
Объем возможной дозагрузки станков, ст.-час. Qв.д.
|
Вид догружаемой детали
|
Штучное время догружаемой детали, мин.tд
. шт..i
|
Принятое количество догружаемых деталей, шт., Nд
|
Фактический объем дозагрузки станков, ст.-час., Qф.д.
Nд. х
t
д
шт.i
60
|
Неиспользуемое время, ст.-час., ∆Qi
(гр.7 – гр.11)
|
Коэффициент загрузки оборудования и рабочих мест, Кзi:
|
1
|
2
|
3
|
4
|
5
|
6
|
7
|
8
|
9
|
10
|
11
|
12
|
13
|
1
|
вертикально-сверлильный
|
2
|
1,50
|
23376
|
6750
|
1042
|
муфта
|
1,8
|
13831
|
414,9
|
627,1
|
0,92
|
2
|
протяжной
|
3
|
2,00
|
7792
|
9000
|
2688
|
муфта
|
2,9
|
13831
|
668,5
|
2019,5
|
0,83
|
3
|
протяжной
|
3
|
1,80
|
11688
|
8100
|
3588
|
муфта
|
1,4
|
13831
|
322,7
|
3265,3
|
0,72
|
4
|
токарный
|
3
|
2,50
|
7792
|
11250
|
438
|
муфта
|
1,9
|
13831
|
438,0
|
0,0
|
1,00
|
5
|
токарный
|
3
|
1,90
|
11688
|
8550
|
3138
|
муфта
|
1,9
|
13831
|
438,0
|
2700,0
|
0,77
|
6
|
вертикально-сверлильный
|
4
|
2,90
|
7792
|
13050
|
2534
|
муфта
|
1,6
|
13831
|
368,8
|
2165,2
|
0,86
|
7
|
вертикально-сверлильный
|
4
|
2,70
|
15584
|
12150
|
3434
|
муфта
|
1,3
|
13831
|
299,7
|
3134,3
|
0,80
|
8
|
фрезерный
|
2
|
1,60
|
15584
|
7200
|
592
|
муфта
|
1,5
|
13831
|
345,8
|
246,2
|
0,97
|
Итого
|
24
|
16,9
|
101296
|
76050
|
17454
|
14,3
|
13831
|
2858,4
|
14157,6
|
0,85
|
Таким образом, дозагрузка технологического процесса другой деталью позволила повысить загрузку оборудования на участке до уровня, соответствующего массовому производству.
2.3 Расчет загрузки поточной линии
Поток, в котором с учетом дозагрузки изготавливается два вида продукции, относится к многопредметному.
Многопредметные потоки подразделяются на одновременные и переменно-поточные.
Одновременные многопредметные потоки по способу запуска изделия подразделяются на следующие виды:
а) с суммарным запуском – когда в каждую рабочую зону загружаются все виды предметов труда в соответствии с их ассортиментными числами. При этом за каждый такт осуществляется выпуск продукции в полном ассортименте;
б) с запуском изделий пропорциональными партиями – когда в каждую рабочую зону загружается один вид продукции в наименьшем количественном отношении, но во все зоны, равные числу видов продукции, загружается полная ассортиментная сумма;
в) с циклическим запуском – когда в каждую рабочую зону загружается по одному изделию в количественном соотношении, равном ассортиментному числу.
Работа в переменных многопредметных потоках может быть организована в двух вариантах;
1-ый – последовательным переключением после запуска всего объема задания по отдельным видам продукции;
2-ой – последовательно-ассортиментным запуском всех видов продукции в течение каждой смены.
В первом случае поток рассчитывается как специализированная однопредметная линия при запуске отдельных видов изделий; имеются только особенности определения такта по каждому виду продукции и коэффициента загрузки линии.
Во втором случае особенности расчета связаны с определением объема задания по каждому виду изделий по каждой смене и времени, необходимого для их производства.
В данном примере расчет проведем по переменному многопредметному потоку с последовательным переключением после выпуска всего объема задания по отдельным видам продукции.
Расчет производим в следующем порядке:
1 Определим трудоемкость программы по основной (Тосн.
) и догружаемой (Тдогр.
) детали, час.:
,
|
(13)
|
,
|
(14)
|
где Νосн.
, Νд.
– соответствие программы выпуска по основной и догружаемой детали;
, – норма времени по i
-й операции основной и догружаемой детали.
мин.
мин.
2 Определяем общую трудоемкость:
Тоб.
= Тосн.
+ Тдогр
,
|
(15)
|
мин.
3 Определяем удельный вес трудоемкости каждой детали в общей их трудоемкости, %:
а) основной (dосн.
):
,
|
(16)
|
,
|
б) догружаемой (dдогр.
):
,
|
(17)
|
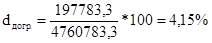
|
4 Распределим годовой фонд времени работы (Fэф
= 3896 час.) по отдельным видам изделий пропорционально их удельному весу в общей трудоемкости программы, час:
а) по основной детали:
,
|
(18)
|
час
|
б) по догружаемой детали:
,
|
(19)
|
час
|
5 Определим такт по каждой детали, мин:
а) по основной:
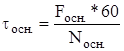
|
(20)
|
,мин
|
б) по догружаемой:
,
|
(21)
|
мин
|
6 Проведем уточненный расчет количества оборудования на потоке (таблица 2.3.1) в соответствии с методикой, описанной в 2.2.
Таблица 2.3.1 – Расчет количества оборудования на потоке
№ операции
|
Наименование
операции
|
Основная деталь
τосн
=0,830, мин.
|
Догружаемая деталь τдогр
=0,702, мин.
|
Устанавливается в потоке единиц оборудования, nпот.
і
|
tшт.
і
|

|
nпр.і
|
tшт.і
|

|
nпр.і
|
1
|
2
|
3
|
4
|
5
|
6
|
7
|
8
|
9
|
1
|
вертикально-сверлильная
|
1,5
|
1,81
|
2
|
1,8
|
2,56
|
3
|
2
|
2
|
протяжная
|
2
|
2,41
|
3
|
2,9
|
4,13
|
5
|
5
|
3
|
протяжная
|
1,8
|
2,17
|
3
|
1,4
|
1,99
|
2
|
3
|
4
|
токарная
|
2,5
|
3,01
|
4
|
1,9
|
2,71
|
3
|
4
|
5
|
токарная
|
1,9
|
2,29
|
3
|
1,9
|
2,71
|
3
|
3
|
6
|
вертикально-сверлильная
|
2,9
|
3,49
|
4
|
1,6
|
2,28
|
3
|
4
|
7
|
вертикально-сверлильная
|
2,7
|
3,25
|
4
|
1,3
|
1,85
|
2
|
4
|
8
|
фрезерная
|
1,6
|
1,93
|
2
|
1,5
|
2,14
|
3
|
3
|
ИТОГО
|
16,9
|
20,36
|
25
|
14,3
|
20,37
|
24
|
28
|
В графе 9 устанавливаемое количество оборудования принимается по каждой группе оборудования по максимальному значению nпр.
і
основной или догружаемой детали.
7 Расчет коэффициента загрузки линии проводится по следующей зависимости:
а) при выпуске отдельных видов деталей:
- основная деталь:
,
|
(22)
|
- догружаемая деталь:
,
|
(23)
|
где m – число операций;
б) средний коэффициент загрузки линии в целом (Кпот.
):
,
|
(24)
|
где k – число разновидностей изделий.
,
|
Сравнивая итоговый показатель загрузки поточной линии Кпот
с итоговыми показателями, полученными в таблицах 2.2.1 и 2.2.2, следует сделать вывод о целесообразности производства догружаемой детали в данном потоке.
Дозагрузка считается целесообразной, так как отклонение Кпот
от итоговых показателей Кзагр
(таблицы 2.2.1 и 2.2.2) не превышает 15% (0,85-0,73=0,12 или 12%)
На основе таблицы 2.2.1 составляем сводную ведомость потребного оборудования на участке (таблица 2.3.2).
Таблица 2.3.2 – Технико-экономическая характеристика оборудования
Тип станка
|
Габаритные размеры, мм
|
К-во оборудования, ед., на участке
|
Мощность, М, кВт
|
Категория ремонтной сложности
|
Сумма единиц ремонтной сложности
|
Стоимость оборудования, Цоб
.,тыс.у.е.
|
Балансовая стоимость оборудова-ния с учетом установки, Соб
., тыс.у.е.
|
Одного станка
|
Всех станков, гр.3хгр.4
|
Меха-ничес-кой части, Rм
|
Элек-триче-ской части, Rэ
|
Меха-ничес-кой части, гр.3 х гр.6
|
Элек-триче-ской части, гр.3 х гр.7
|
Одного станка
|
Всех стан-ков, гр.3х гр.10
|
1
|
2
|
3
|
4
|
5
|
6
|
7
|
8
|
9
|
10
|
11
|
12
|
Вертикально-сверлильный
|
3200х1250
|
10
|
20,5
|
205
|
15
|
13
|
150
|
130
|
810
|
8100
|
9234
|
Протяжной
|
3250х2250
|
6
|
20
|
120
|
16
|
12
|
96
|
72
|
630
|
3780
|
4310
|
Токарный
|
2800х1480
|
6
|
24,4
|
146,4
|
18
|
16
|
108
|
96
|
1230
|
7380
|
8414
|
Фрезерный
|
2665х4700
|
2
|
16
|
32
|
13
|
10
|
26
|
20
|
670
|
1340
|
1528
|
Итого
|
24
|
503,4
|
380
|
318
|
20600
|
23486
|
2.4 Расчет численности работающих на участке
2.4.1 Расчет численности основных производственных рабочих
Количество основных производственных рабочих может устанавливаться по трудоемкости работ, по нормам обслуживания, по нормативам численности, по рабочим местам.
Численность основных производственных рабочих по трудоемкости работ определяется следующим образом:
,
|
(25)
|
где Тп.
– трудоемкость производственной программы основной детали (н-часы);
Fэф.
– годовой полезный фонд времени работ0ы среднесписочного рабочего в плановом периоде; Fэф. = 1955 час.;
Кn
– планируемый коэффициент выполнения норм; Кn
= 1,15.
Если на участке, в цехе можно определить объем работ в натуральном выражении, численность основных производственных рабочих рассчитывается по норме выработки:
,
|
(26)
|
где Vn – плановый объем работ в натуральном выражении ( шт.);
Вч
– часовая норма выработки.
Списочная численность рабочих, занятых на аппаратурных процессах (металлургия, химическая промышленность и др.), определяется по нормам обслуживания:
,
|
(27)
|
где nоб.i
– число единиц i-го вида оборудования;
nсм
- число смен;
Нo
- норма обслуживания;
Ксп
- коэффициент приведения явочной численности к списочной.
На поточных линиях численность основных производственных рабочих определяется по числу рабочих мест с учетом сложности работы линии, многостаночного обслуживания и совмещения профессий.
2.4.2
Расчет численности вспомогательных рабочих
Численность вспомогательных рабочих определяем по процентному соотношению к основным производственным рабочим. Для массового производства это соотношение изменяется в пределах 30 – 50 %.
Полученную численность вспомогательных рабочих распределяем по профессиям:
а) наладчики – 24/5=4,8. Принимаем 5 чел.
Принимаем: один наладчик обслуживает 5 станков.
б) слесари-ремонтники – (380+318)/500=1,49. Принимаем 2 чел.
Норма обслуживания на одного слесаря-ремонтника 500 ремонтных единиц. Фактическое количество единиц ремонтной сложности необходимо взять по таблице 2.3.2 как сумму итогов по графам 8 и 9. Тогда количество слесарей-ремонтников определяется как отношение: (гр. 8 + гр. 9)/500.
в) контролеры – 34/18=1,88чел. Принимаем 2 чел.
На 18 человек основных производственных рабочих предусматривается 1 контролер.
Расчет транспортных средств показывает, что для перемещения предметов труда между рабочими местами, удаления стружки и других перемещений нужны 2 транспортные единицы. При двухсменном режиме работы нужны 4 транспортных рабочих.
Итак, общее количество вспомогательных рабочих составит 13 человек (5+2+2+4=13).
2.4.3 Расчет численности специалистов, руководителей и служащих
Наиболее распространенный метод определения численности специалистов, руководителей и служащих – по нормам численности или нормам управляемости, которые отражают количество человек, необходимых для выполнения работ, закрепленных за отделом или другим структурным подразделением. Так, норма управляемости для мастера – 25 рабочих, старшего мастера – 100 человек, начальника участка – 180 человек.
В настоящем расчете принимаем количество руководителей, специалистов и служащих – 7 % от общего числа рабочих, т.е. суммы основных и вспомогательных рабочих.
Полученную численность распределим по категориям: старший мастер – 1 чел; мастер – 1 чел; бухгалтер – 1 чел.
2.5
Построение плана-графика работы линии
Построим план-график работы поточной линии только по основной детали.
1 Определение периода обслуживания.
Под периодом обслуживания понимаем промежуток времени, в течение которого достигается равенство выпуска деталей по всем операциям и рабочий-оператор завершает полный цикл обслуживания закрепленных за ним станков.
Период обслуживания (Тп.о.) зависит от величины детали и ее веса (таблица 2.5.1).
Таблица 2.5.1 – Рекомендуемые значения периода обслуживания
Величина детали
|
Примерный вес детали, кг
|
Продолжительность периода обслуживания, Тп.о.
|
Крупная
|
свыше 15
|
1 – 2 часа
|
Средняя
|
3 - 15
|
½ - 1 смена
|
Мелкая
|
менее 3
|
1 – 2 смены
|
Продолжительность одной смены – 492 мин.
Исходя из конкретных условий принимаем Тп.о
. =1 смены=492мин.
2 Расчет выработки за период обслуживания.
Выработка за период обслуживания по основной детали определяется:
,
|
(28)
|
ед.
|
Определим загрузку оборудования основной деталью по каждой группе оборудования. Для этого рассчитаем трудоемкость работы по производству основной детали в течение периода обслуживания по каждой операции (Тcmi
):
,
|
(29)
|
Результаты расчетов представлены в таблице 2.5.2 (графа 5).
Таблица 2.5.2 – Расчет графика работы оборудования за период обслуживания
№ операции
|
Наимено-вание
операции
|
Ппр.
і
|
tшт.
і
|
Тс
m
і
|
Время работы недогруженного станка, Тнедогр
.i
|
Номер рабочего
|
График работы оборудования, Тп.о
. = 492 мин.
|
Приме-чание
|
1
|
2
|
3
|
4
|
5
|
6
|
7
|
8
|
9
|
1
|
вертикально-сверлильная
|
2
|
1,5
|
852
|
360
|
1
|
492
|
2
|
360
|
2
|
протяжная
|
3
|
2
|
1137
|
153
|
3
|
492
|
4
|
492
|
5
|
153
|
3
|
протяжная
|
3
|
1,8
|
1023
|
39
|
6
|
492
|
7
|
492
|
5
|
39
|
4
|
токарная
|
3
|
2,5
|
1421
|
437
|
8
|
492
|
9
|
492
|
10
|
437
|
5
|
токарная
|
3
|
1,9
|
1080
|
96
|
11
|
492
|
12
|
492
|
2
|
96
|
6
|
вертикально-сверлильная
|
4
|
2,9
|
1648
|
172
|
13
|
492
|
14
|
492
|
15
|
492
|
5
|
172
|
7
|
вертикально-сверлильная
|
4
|
2,7
|
1534
|
58
|
16
|
492
|
17
|
492
|
19
|
492
|
20
|
58
|
8
|
фрезерная
|
2
|
1,6
|
909
|
417
|
21
|
492
|
22
|
417
|
ИТОГО
|
24
|
16,9
|
Определяем время работы недогруженного станка по каждой операции (Тнедогр.i)
:
Тнедогр.i
= Tcmi
– Tn
.
o
.
x ,
|
(30)
|
где - количество единиц оборудования, полностью загруженных в течение периода обслуживания.
Время работы недогруженного станка (графа 6),Тнедогр
., определяется следующим образом. Например, на операции имеется 2 станка, время работы которых за период обслуживания (Тобсл
. = 1 смене = 8,2 часа = 492 мин.) составляется 692 мин. Следовательно, один станок будет полностью загружен, то есть 492 часа, а второй недогружен. Время работы недогруженного станка составит 692 – 492 = 200 час. В случае, если Тст
і
< Тп.о.
, то время работы недогруженного станка Тнедогр
. = Тст
і
(см. операции 2 и 3).
3 Проверим по каждой операции соответствие количества оборудования nпр
.
(а, следовательно, рабочих мест) и численности основных производственных рабочих Чопр
i
.. Если nпр
i
> Чопр
i
., то надо расставить рабочих по рабочим местам таким образом, чтобы время, необходимое для выполнения планового задания (выработки за период обслуживания), не превышало Тп.о
. При этом допускается совмещение работ, многостаночность обслуживания (см. таблица 2.5.2.1).
В графе 7 – «номер рабочего» – проставляется фактический номер рабочего по каждой единице оборудования в соответствии с его закреплением по операциям и рабочим.
4 Рассчитать межоперационные оборотные заделы (Zобор
.) и построить график, их изменения.
График движения оборотного задела в прерывно-поточной линии строится на основе графика работы оборудования. Образуются оборотные заделы из-за различной производительности смежных рабочих мест. Их величина определяется между двумя смежными операциями с учетом выделенных фаз, на которые расчленен период работы в каждой паре смежных операций в соответствии с графиком. Размер максимального оборотного задела между парой смежных операций с различной производительностью определяется по формуле:
,
|
(31)
|
где Zобор
. – величина изменения межоперационного оборотного задела между двумя смежными операциями за время фазы;
Fc
– продолжительность фазы, мин., т.е. отрезок времени, в течение которого не происходит никаких изменений в распорядке выполнения операций;
nn-1; nn – количество параллельно работающих станков соответственно на предшествующей и последующей операций;
tшт.n-1; tшт.n – штучное время соответственно на предшествующей и последующей операций, мин.
Таблица 2.5.3– Расчет и построение графика изменения величины оборотного задела между каждой парой смежных операций
№ операции
|
Ппр.
і
|
tшт.
і
|
График работы оборудования, Тп.о
. = 492 мин.
|
1
|
2
|
3
|
4
|
1
|
2
|
1,5
|
 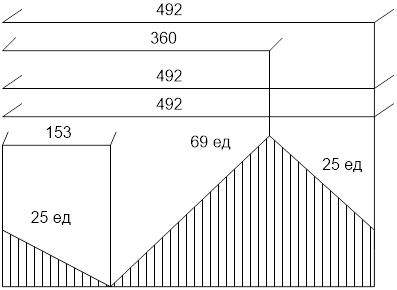
|
2
|
3
|
2
|
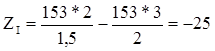 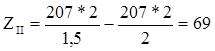 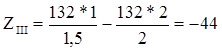
|
2
|
3
|
2
|
 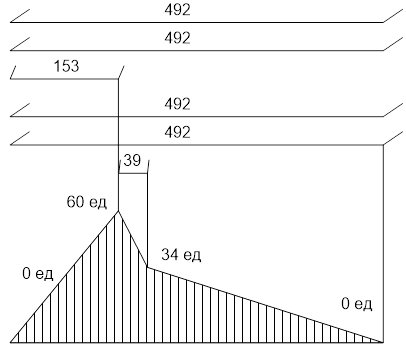
|
3
|
3
|
1,8
|
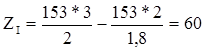 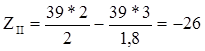 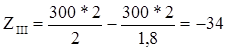
|
Продолжение таблицы 2.5.3
1
|
2
|
3
|
4
|
3
|
3
|
1,8
|
 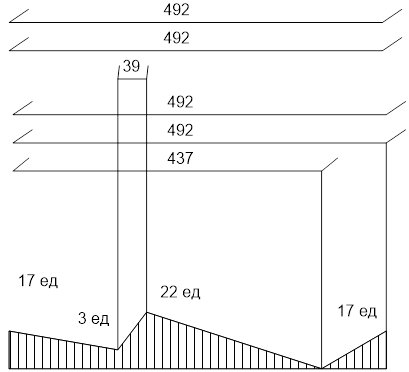
|
4
|
3
|
2,5
|
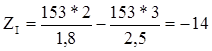 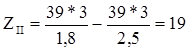 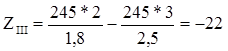 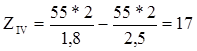
|
4
|
3
|
2,5
|
 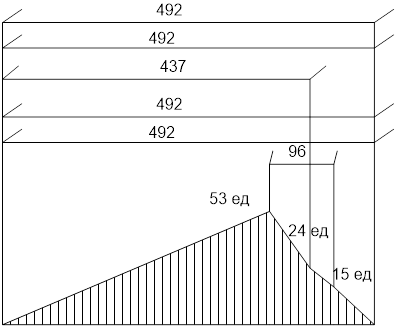
|
5
|
3
|
1,9
|
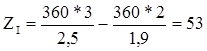 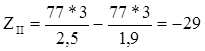 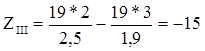 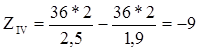
|
Продолжение таблицы 2.5.3
1
|
2
|
3
|
4
|
5
|
3
|
1,9
|
 
|
6
|
4
|
2,9
|
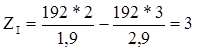 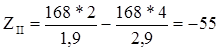  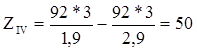 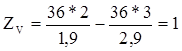
|
6
|
4
|
2,9
|
 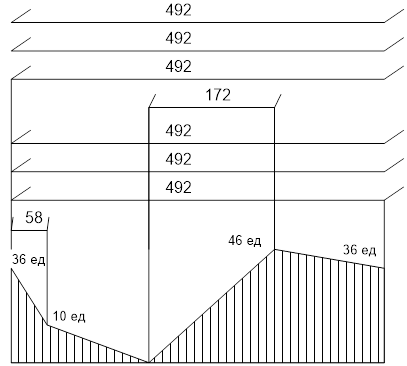
|
7
|
4
|
2,7
|
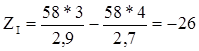 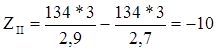 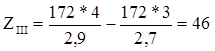 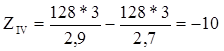
|
Окончание таблицы 2.5.3
Общая величина Zоб. на линии определяется как сумма задела на начало смены на всех операциях.
5 Рассчитать величину технологического задела (Zтехн.) на начало периода обслуживания. Его величина определяется:
где m - количество операций;
с - количество рабочих мест на операции;
n' - количество одновременно обрабатываемых на каждом рабочем месте деталей.
В нашем примере n' =1 шт.
шт.
|
6 Рассчитать величину транспортного задела (Zmp.).
Величина Zmp. зависит от принятого порядка передачи деталей с операции на операцию и характера транспортного средства (таблица 2.5.4).
Таблица 2.5.3 – Рекомендуемые размеры транспортных партий, штук
Вес детали, кг
|
Размеры транспортной партии при средней трудоемкости
операций по данной детали
|
До 1 мин.
|
1,0 – 2,5 мин.
|
2,5 – 5,0 мин.
|
5,0 – 11,0 мин.
|
1
|
2
|
3
|
4
|
5
|
До 0,1
|
100
|
50
|
20
|
10
|
0,1 – 0,2
|
50
|
20
|
20
|
10
|
0,2 – 0,5
|
20
|
20
|
10
|
5
|
0,5 – 1,0
|
10
|
10
|
5
|
2
|
1,0 – 2,0
|
5
|
5
|
2
|
1
|
2,0 – 5,0
|
2
|
2
|
2
|
1
|
При периодической транспортировке
,
|
(32)
|
где р – размер передаточной транспортной партии.
В остальных случаях рекомендуется поштучная передача.
6 Рассчитать общую величину цикловых заделов (Zц.) прямоточной линии:
,
|
(33)
|
шт.
|
Таким образом, в массовом производстве одна и та же продукция выпускается через одинаковый промежуток времени – такт. Каждое рабочее место выполняет свою операцию. Если, например, ежесуточно выпускается 200 единиц продукции, то это значит, что на каждом рабочем месте закрепленная операция выполняется 200 раз.
2.6
Организация и планирование обеспечения инструментом
В условиях массового производства комплектация и доставка нужного инструмента осуществляется согласно сменному заданию или на основании карты подготовки выполнения сменного задания. Снабжение рабочих мест инструментом и заточка инструмента осуществляются централизованно.
2.6.1 Расчет потребности режущего инструмента
Расход режущего инструмента (Иреж.) по каждому виду для массового и крупносерийного производства определяется:
,
|
(34)
|
где dм – доля машинного времени в общем штучном времени (tшт) по операции, на которой применяется данный инструмент;
Тизн – расчетное время работы инструмента до полного износа.
,
|
(35)
|
L – общая величина рабочей части инструмента, стачиваемая при переточке, мм;
l – величина слоя, снимаемого при каждой переточке, мм;
tст – стойкость инструмента, т.е. время машинной работы инструмента между двумя переточками, час.;
Ку - коэффициент случайной убыли инструмента (Ку = 0,05).
Расчет Иреж проведем в следующей последовательности.
Определяем время работы инструмента до полного износа (таблица 2.6.1).
Таблица 2.6.1 – Время работы инструмента до полного износа
Наименование инструмента
|
L, мм
|
l,
мм
|
tст
., час.
|
Расчет Тизн
., час.
|
Резец подрезной
|
36
|
2,5
|
3,0
|
46,20
|
Резец проходной
|
26
|
4,0
|
2,0
|
15,00
|
Сверла
|
34
|
0,7
|
2,5
|
123,93
|
Фреза
|
7,3
|
0,6
|
4,0
|
52,67
|
1 Определяем расход режущего инструмента на программу (таблица 2.6.2).
Таблица 2.6.2 – Расчет потребности режущего инструмента
Наименование
инструмента
|
Деталь
|
N
, шт.
|
tшт
., мин.
|
dм
|
Тизн
., час.
|
Иреж.
, шт.
|
Резец подрезной
|
основная
|
270000
|
2,5
|
0,65
|
46,20
|
166,6
|
Резец проходной
|
основная
|
270000
|
1,9
|
0,60
|
15,00
|
360,0
|
Сверла
|
основная
|
270000
|
7,1
|
0,7
|
123,93
|
190,0
|
Фреза
|
основная
|
270000
|
2,3
|
0,7
|
52,67
|
144,8
|
Примечание:
условно принимаем, что резец подрезной устанавливается на одной токарной операции, а резец проходной – на другой (или на двух других).
3 Определяем запас инструмента на рабочих местах.
Количество инструмента, находящегося на рабочих местах при периодической его подноске (Zр.м.
), определяется:
,
|
(36)
|
где tnn
- периодичность подноски инструмента к рабочим местам, час.
Обычно tnn
выбирается в зависимости от периодичности съема и принимается равной или кратной длительности смены;
tс
- периодичность съема инструмента со станка, час. Устанавливается в соответствии с величиной стойкости инструмента:
,
|
(37)
|
где n р.м
. – число рабочих мест, на которых применяется данный инструмент;
mи
- количество одноименного инструмента, применяемого на рабочем месте (mи
= 2);
Кс.з.
- коэффициент страхового запаса инструмента на рабочих местах. Обычно Кс.з
. = 1; на многорезцовых станках Кс.з
. = 2~ 4. В Принимаем Кс.з
. = 1.
Расчет проводится в следующей последовательности.
а) определим периодичность съема и подачи инструмента со станка (таблица 2.6.3).
Таблица 2.6.3 – Периодичность съема инструмента со станков
Наименование
инструмента
|
tст
., час.
|
tшт
., мин.
|
dм
|
tс
, час.
|
tпп
, час.
|
Zр.м
|
Резец подрезной
|
3,0
|
2,5
|
0,65
|
4,62
|
492
|
216
|
Резец проходной
|
2,0
|
1,9
|
0,6
|
3,33
|
492
|
298
|
Сверла
|
2,5
|
7,1
|
0,7
|
3,57
|
492
|
298
|
Фреза
|
4,0
|
2,3
|
0,7
|
5,71
|
492
|
175
|
Если резец или сверло применяется на нескольких операциях технологического процесса изготовления детали, расчет надо вести по каждой операции ввиду различия tшт.i
:
б) определяем запас инструмента на рабочих местах по приведенной формуле (таблица 2.6.3).
2.6.2
Расчет потребности измерительного инструмента
Расход измерительного инструмента на программу (для производственных целей) определяется по формуле:
,
|
(38)
|
где N - годовая программа выпуска изделий, шт.;
ав
- количество измерений на одну деталь, шт. (принимаем – 3 измерения);
Кпр.
– выборочность контроля (например, Кпр.
= 0,8);
Тм
- количество измерений, выдерживаемых данным мерителем до полного износа (норма износа):
,
|
(39)
|
где ад
- величина допустимого износа мерителя, мКм;
γ - коэффициент допустимого износа мерителя, при достижении которого инструмент передается контролерам (γ = 0,7);
a - коэффициент ремонта и восстановления носителя (a = 2);
b - норматив стойкости мерителя (число измерений на 1 мКм износа инструмента);
Ку
- коэффициент преждевременного выхода инструмента из строя (Ку
= 0,05).
Результаты занесем в таблицы 2.6.4 и 2.6.5.
Таблица 2.6.4 – Норма износа измерительных инструментов по видам
Наименование инструмента
|
ад
, мКм
|
b, шт.
|
α
|
γ
|
Тм
, шт.
|
Скоба
|
10
|
2630
|
2
|
0,7
|
36820
|
Калибр
|
12
|
900
|
2
|
0,7
|
15120
|
Таблица 2.6.5 – Расход измерительного инструмента по видам для основной и догружаемой детали
Наименование инструмента
|
ав
, шт.
|
Кпр
.
|
Тм
.,шт.
|
Киз
., шт.
|
для основной детали
|
Скоба
|
2
|
0,75
|
36820
|
12
|
Калибр
|
1
|
0,8
|
15120
|
16
|
2.7
Выбор и расчет межоперационных транспортных средств
Транспортные средства определяют в зависимости от типа производства, формы его организации, веса и габаритов изделия, объема грузооборота, вида передачи изделия, расположения и планировки участка.
Пусть на участке обработки деталей при межоперационном перемещении применяется тара. Для перемещения деталей между операциями выбираем электроталь грузоподъемностью 0,5 – 1,0 т.
Для перемещения крупных партий деталей, погрузки стружки на транспортные средства для удаления ее с участка применим кран-балку. Количество кран-балок (Пкр
) определится:
,
|
(40)
|
где l
– длина пути крана туда и обратно (l
= 50 м);
v – скорость передвижения тельфер – v = 30 м/мин.; кран-балка – v = 50 м/мин.;
tз
, tсн
- время на захват и снятие с крана груза ( tз
= tсн.
= 0,5 мин.);
а - число одновременно захватываемых деталей (а = 300).
ед.
|
Ввиду небольшого объема производства продукции в работе принимает одну кран-балку.
Стоимость транспортных средств: кран-балки – 652 тыс. у.е., электротали – 234 тыс. у.е., затраты на доставку и монтаж транспортных средств составляют 10 % от их стоимости. Общие затраты на транспортные средства (Зтр
.) составят:
тыс.у.е.
|
2.8
Расчет площади участка
Площадь участка (Sу
) состоит из основной производственной площади (Sпр
.) и вспомогательной (Sвсп.
):
,
|
(41)
|
Основная производственная площадь по операции (таблица 2.8.1) составляет (Sпр.
j
):
,
|
(42)
|
где S1
и S2
- площадь, занимаемая соответственно станками и проходами, м²;
n пр
j
– принятое количество станков по операции.
Основная производственная площадь по всем операциям Sпр
составит:
,
|
(43)
|
Таблица 2.8.1 – Расчет производственной площади участка
№№
операции, j
|
Наименование
оборудования
|
Габаритные размеры, мм
|
Принятое кол-во станков, nпр
.
|
Площадь, м²
|
одного станка, S1
|
прохода, S2
|
общая,
Sпр
j
|
1
|
вертикально-сверлильное
|
3200х1250
|
2
|
4
|
12
|
32
|
2
|
протяжное
|
3250х2250
|
3
|
7,3125
|
12
|
57,9375
|
3
|
протяжное
|
3250х2250
|
3
|
7,3125
|
12
|
57,9375
|
4
|
токарное
|
2800х1480
|
3
|
4,144
|
12
|
48,432
|
5
|
токарное
|
2800х1480
|
3
|
4,144
|
12
|
48,432
|
6
|
вертикально-сверлильное
|
3200х1250
|
4
|
4
|
12
|
64
|
7
|
вертикально-сверлильное
|
3200х1250
|
4
|
4
|
12
|
64
|
8
|
фрезерное
|
2665х4700
|
2
|
12,5255
|
12
|
49,051
|
24
|
Итого
|
421,79
|
Площадь проходов принимается на 1 станок в среднем 12 м².
Вспомогательная площадь (Sвсп
.):
,
|
(44)
|
где Sскл.
. – складская площадь под заготовки и готовые детали (примем 15% от производственной);
Sирк.
– площадь ИРК (примем в массовом производстве 0,35 м² на станок);
Sконтр.
– площадь одного контрольного пункта ( 6 м² );
Sбыт.
– площадь бытовых и конторских помещений (примем 1,22 м² на 1 рабочего).
Произведем расчет вспомогательной площади участка. Определим общую площадь участка Sу
.
м²
|
м²
|
м² * 2=12 м²
|
м²
|
м²
|
м²
|
Определим объем здания (Оз
):
,
|
(45)
|
где h - высота здания – 9,25 м.
м3
|
Стоимость здания определим по формуле:
,
|
(46)
|
где Цз
- цена 1 м ³ здания – 800 у.е.
у.е.
|
2.9
Разработка графика ремонта оборудования
Сроки ввода оборудования в эксплуатацию нового (или после капитального ремонта) по основному производству представлены в таблице 2.9.1.
Таблица 2.9.1 – Сроки ввода оборудования в эксплуатацию по основному производству
Наименование станков
|
Количество единиц
|
Категория сложности ремонта
|
Месяцы установки или капитального ремонта
станков по годам (предлагаемые)
|
01
|
02
|
03
|
04
|
Вертикально-сверлильные
|
10
|
8
|
II, V, XI
|
IV, VIII
|
I, X
|
II, IV, X
|
Протяжные
|
6
|
12
|
I, VI
|
III, V
|
IV, VII
|
-
|
Токарные
|
6
|
11
|
XI, III
|
V, X
|
III, VIII
|
-
|
Фрезерные
|
2
|
10
|
-
|
II
|
V
|
-
|
Итого:
|
24
|
Структура ремонтного цикла имеет следующий вид:
К – О – М1
– О – М2
– О – С1
– О – М3
– О – М4
– О – С2
– О – М5
– О – М6
– О – К
Продолжительность ремонтного цикла Тц = 24 000 час. или 6 лет при двухсменной работе оборудования.
1 Рассчитываем продолжительность в месяцах межремонтного (Тм.р.) и межосмотрового (Тм.о.) периодов по формулам:
,
|
(47)
|
,
|
(48)
|
где nм
, nс
, nо
– соответственно количество малых, средних ремонтов и осмотров в структуре ремонтного цикла.
мес
|
мес
|
2 Составляем график ремонта оборудования, установленного в первом году (таблица 2.9.2), во втором году (таблица 2.9.3), в третьем году (таблица 2.9.4) и в четвертом году (таблица 2.9.5).
3 Составляем график ремонта оборудования на планируемый (пятый) год.
Таблица 2.9.2 – График ремонта оборудования, установленного в 01-ом году
Наименование
оборудования
|
|
К
|
О
|
М1
|
О
|
М2
|
О
|
С1
|
О
|
М3
|
О
|
М4
|
О
|
С2
|
О
|
М5
|
О
|
М6
|
О
|
К
|
Вертикально-сверлильное
|
1
|
II 01
|
VI 01
|
X 01
|
II 02
|
VI 02
|
X 02
|
II 03
|
VI 03
|
X 03
|
II 04
|
VI 04
|
X 04
|
II 05
|
VI 05
|
X 05
|
II 06
|
VI 06
|
X 06
|
II 07
|
2
|
V 01
|
IX 01
|
I 02
|
V 02
|
IX 02
|
I 03
|
V 03
|
IX 03
|
I 04
|
V 04
|
IX 04
|
I 05
|
V 05
|
IX 05
|
I 06
|
V 06
|
IX 06
|
I 07
|
V 07
|
3
|
XI 01
|
III 02
|
VII 02
|
XI 02
|
III 03
|
VII 03
|
XI 03
|
III 04
|
VII 04
|
XI 04
|
III 05
|
VII 05
|
XI 05
|
III 06
|
VII 06
|
XI 06
|
III 07
|
VII 07
|
XI 08
|
Протяжное
|
1
|
I 01
|
V 01
|
IX 01
|
I 02
|
V 02
|
IX 02
|
I 03
|
V 03
|
IX 03
|
I 04
|
V 04
|
IX 04
|
I 05
|
V 05
|
IX 05
|
I 06
|
V 06
|
IX 06
|
I 07
|
2
|
VI 01
|
X 01
|
II 02
|
VI 02
|
X 02
|
II 03
|
VI 03
|
X 03
|
II 04
|
VI 04
|
X 04
|
II 05
|
VI 05
|
X 05
|
II 06
|
VI 06
|
X 06
|
II 07
|
VI 07
|
Токарное
|
1
|
XI 01
|
III 02
|
VII 02
|
XI 02
|
III 03
|
VII 03
|
XI 03
|
III 04
|
VII 04
|
XI 04
|
III 05
|
VII 05
|
XI 05
|
III 06
|
VII 06
|
XI 06
|
III 07
|
VII 07
|
XI 07
|
2
|
III 01
|
VII 01
|
XI 01
|
III 02
|
VII 02
|
XI 02
|
III 03
|
VII 03
|
XI 03
|
III 04
|
VII 04
|
XI 04
|
III 05
|
VII 05
|
XI 05
|
III 06
|
VII 06
|
XI 06
|
III 07
|
Таблица 2.9.3 – График ремонта оборудования, установленного во 02-ом году
Наименование
оборудования
|
К
|
О
|
М1
|
О
|
М2
|
О
|
С1
|
О
|
М3
|
О
|
М4
|
О
|
С2
|
О
|
М5
|
О
|
М6
|
О
|
К
|
Вертикально-сверлильное
|
4
|
IV 02
|
VIII 02
|
XII 02
|
IV 03
|
VIII 03
|
XII 03
|
IV 04
|
VIII 04
|
XII 04
|
IV 05
|
VIII 05
|
XII 05
|
IV 06
|
VIII 06
|
XII 06
|
IV 07
|
VIII 07
|
XII 07
|
IV 08
|
5
|
VIII 02
|
XII 02
|
IV 03
|
VIII 03
|
XII 03
|
IV 04
|
VIII 04
|
XII 04
|
IV 05
|
VIII 05
|
XII 05
|
IV 06
|
VIII 06
|
XII 06
|
IV 07
|
VIII 07
|
XII 07
|
IV 08
|
VIII 08
|
Протяжное
|
3
|
III 02
|
VII 02
|
XI 02
|
III 03
|
VII 03
|
XI 03
|
III 04
|
VII 04
|
XI 04
|
III 05
|
VII 05
|
XI 05
|
III 06
|
VII 06
|
XI 06
|
III 07
|
VII 07
|
XI 07
|
III 08
|
4
|
V 02
|
IX 02
|
I 03
|
V 03
|
IX 03
|
I 04
|
V 04
|
IX 04
|
I 05
|
V 05
|
IX 05
|
I 06
|
V 06
|
IX 06
|
I 07
|
V 07
|
IX 07
|
I 08
|
V 08
|
Токарное
|
3
|
V 02
|
IX 02
|
I 03
|
V 03
|
IX 03
|
I 04
|
V 04
|
IX 04
|
I 05
|
V 05
|
IX 05
|
I 06
|
V 06
|
IX 06
|
I 07
|
V 07
|
IX 07
|
I 08
|
V 08
|
4
|
X 02
|
II 03
|
VI 03
|
X 03
|
II 04
|
VI 04
|
X 04
|
II 05
|
VI 05
|
X 05
|
II 06
|
VI 06
|
X 06
|
II 07
|
VI 07
|
X 07
|
II 08
|
VI 08
|
X 08
|
Фрезерное
|
1
|
II 02
|
VI 02
|
X 02
|
II 03
|
VI 03
|
X 03
|
II 04
|
VI 04
|
X 04
|
II 05
|
VI 05
|
X 05
|
II 06
|
VI 06
|
X 06
|
II 07
|
VI 07
|
X 07
|
II 08
|
Таблица 2.9.4 – График ремонта оборудования, установленного в 03-ем году
Наименование
оборудования
|
К
|
О
|
М1
|
О
|
М2
|
О
|
С1
|
О
|
М3
|
О
|
М4
|
О
|
С2
|
О
|
М5
|
О
|
М6
|
О
|
К
|
Вертикально-сверлильное
|
6
|
I 03
|
V 03
|
IX 03
|
I 04
|
V 04
|
IX 04
|
I 05
|
V 05
|
IX 05
|
I 06
|
V 06
|
IX 06
|
I 07
|
V 07
|
IX 07
|
I 08
|
V 08
|
IX 08
|
I 09
|
7
|
X 03
|
II 04
|
VI 04
|
X 04
|
II 05
|
VI 05
|
X 05
|
II 06
|
VI 06
|
X 06
|
II 07
|
VI 07
|
X 07
|
II 08
|
VI 08
|
X 08
|
II 09
|
VI 09
|
X 09
|
Протяжное
|
5
|
IV 03
|
VIII 03
|
XII 03
|
IV 04
|
VIII 04
|
XII 04
|
IV 05
|
VIII 05
|
XII 05
|
IV 06
|
VIII 06
|
XII 06
|
IV 07
|
VIII 07
|
XII 07
|
IV 08
|
VIII 08
|
XII 08
|
IV 09
|
6
|
VII 03
|
XI 03
|
III 04
|
VII 04
|
XI 04
|
III 05
|
VII 05
|
XI 05
|
III 06
|
VII 06
|
XI 06
|
III 07
|
VII 07
|
XI 07
|
III 08
|
VII 08
|
XI 08
|
III 09
|
VII 09
|
Токарное
|
5
|
III 03
|
VII 03
|
XI 03
|
III 04
|
VII 04
|
XI 04
|
III 05
|
VII 05
|
XI 05
|
III 06
|
VII 06
|
XI 06
|
III 07
|
VII 07
|
XI 07
|
III 08
|
VII 08
|
XI 08
|
III 09
|
6
|
VIII 03
|
XII 03
|
IV 04
|
VIII 04
|
XII 04
|
IV 05
|
VIII 05
|
XII 05
|
IV 06
|
VIII 06
|
XII 06
|
IV 07
|
VIII 07
|
XII 07
|
IV 08
|
VIII 08
|
XII 08
|
IV 09
|
VIII 09
|
Фрезерное
|
2
|
V 03
|
IX 03
|
I 04
|
V 04
|
IX 04
|
I 05
|
V 05
|
IX 05
|
I 06
|
V 06
|
IX 06
|
I 07
|
V 07
|
IX 07
|
I 08
|
V 08
|
IX 08
|
I 09
|
V 09
|
Таблица 2.9.5 – График ремонта оборудования, установленного в 4-ом году
Наименование
оборудования
|
К
|
О
|
М1
|
О
|
М2
|
О
|
С1
|
О
|
М3
|
О
|
М4
|
О
|
С2
|
О
|
М5
|
О
|
М6
|
О
|
К
|
Вертикально-сверлильное
|
8
|
II 04
|
VI 04
|
X 04
|
II 05
|
VI 05
|
X 05
|
II 06
|
VI 06
|
X 06
|
II 07
|
VI 07
|
X 07
|
II 08
|
VI 08
|
X 08
|
II 09
|
VI 09
|
X 09
|
II 10
|
9
|
IV 04
|
VIII 04
|
XII 04
|
IV 05
|
VIII 05
|
XII 05
|
IV 06
|
VIII 06
|
XII 06
|
IV 07
|
VIII 07
|
XII 07
|
IV 08
|
VIII 08
|
XII 08
|
IV 09
|
VIII 09
|
XII 09
|
IV 10
|
10
|
X 04
|
II 05
|
VI 05
|
X 05
|
II 06
|
VI 06
|
X 06
|
II 07
|
VI 07
|
X 07
|
II 08
|
VI 08
|
X 08
|
II 09
|
VI 09
|
X 09
|
II 10
|
VI 10
|
X 10
|
Таблица 2.9.6 – График ремонта оборудования на планируемый 5
год
Наименование
оборудования
|
Номер станка
|
Месяцы
|
I
|
II
|
III
|
IV
|
V
|
VI
|
VII
|
VIII
|
IX
|
X
|
XI
|
XII
|
Вертикально-сверлильное
|
1
|
С
|
О
|
М
|
2
|
О
|
С
|
О
|
3
|
М
|
О
|
С
|
4
|
О
|
М
|
О
|
5
|
М
|
О
|
М
|
6
|
С
|
О
|
М
|
7
|
М
|
О
|
С
|
8
|
О
|
М
|
О
|
9
|
О
|
М
|
О
|
10
|
О
|
М
|
О
|
Протяжное
|
1
|
С
|
О
|
М
|
2
|
О
|
С
|
О
|
3
|
О
|
М
|
О
|
4
|
М
|
О
|
М
|
5
|
С
|
О
|
М
|
6
|
О
|
С
|
О
|
Токарное
|
1
|
М
|
О
|
М
|
2
|
С
|
О
|
М
|
3
|
М
|
О
|
М
|
4
|
О
|
М
|
О
|
5
|
С
|
О
|
М
|
6
|
О
|
С
|
О
|
Фрезерное
|
1
|
О
|
М
|
О
|
2
|
О
|
С
|
О
|
4 Рассчитываем годовую трудоемкость ремонта оборудования по видам работ: слесарные - (Qслес.
) – таблица 2.9.7; станочные - (Qстан.
) – таблица 2.9.8; прочие - (Qпр.
) – таблица 2.9.9. Исходные данные для расчета – в таблице 2.9.6.
Годовой объем слесарных, станочных и прочих работ по ремонту и межремонтному обслуживанию оборудования определяется исходя из состава оборудования, его ремонтной сложности, структуры и продолжительности межремонтного цикла, межремонтных периодов, действующих трудовых нормативов по следующей формуле:
,
|
(49)
|
где n – число видов оборудования;
tк
, tс
, tм
, tо
– трудоемкость соответственно капитального, среднего, малого ремонта и осмотров на одну ремонтную единицу, час.;
nк
, nс
, nм
, nо
– число соответственно капитальных, средних, малых ремонтов и осмотров в течение межремонтного цикла в плановом периоде.
R – категория сложности ремонта.
Таблица 2.9.7 – Расчет трудоемкости слесарных работ
Наименование
станков
|
Количество ремонтных операций по видам ремонта
|
Категория сложности
ремонта,
R
|
Расчет
трудоемкости, час., Qслес
.
|
малый
nм
|
средний
nс
|
осмотр
nо
|
Сверлильные
|
10
|
5
|
15
|
8
|
650
|
Протяжные
|
5
|
4
|
9
|
12
|
609
|
Токарные
|
7
|
3
|
8
|
11
|
572
|
Фрезерное
|
1
|
1
|
4
|
10
|
130
|
Нормы времени на
слесарные работы,
час.
|
4,0
|
6,0
|
0,75
|
Итого:
|
1961
|
Таблица 2.9.8 – Расчет трудоемкости станочных работ
Наименование
станков
|
Количество ремонтных операций по видам ремонта
|
Категория сложности
ремонта,
R
|
Расчет
трудоемкости, час.,
Qстан
.
|
малый
nм
|
средний
nс
|
осмотр
nо
|
Сверлильные
|
10
|
5
|
15
|
8
|
452
|
Протяжные
|
5
|
4
|
9
|
12
|
466,8
|
Токарные
|
7
|
3
|
8
|
11
|
393,8
|
Фрезерное
|
1
|
1
|
4
|
10
|
94
|
Нормы времени на
станочные работы,
час.
|
2,0
|
7,0
|
0,1
|
Итого:
|
1406,6
|
Таблица 2.9.9 – Расчет трудоемкости прочих работ
Наименование
станков
|
Количество ремонтных операций по видам ремонта
|
Категория сложности
ремонта,
R
|
Расчет
трудоемкости, час.,
Qпр
.
|
малый
nм
|
средний
nс
|
Сверлильные
|
10
|
5
|
8
|
28
|
Протяжные
|
5
|
4
|
12
|
30
|
Токарные
|
7
|
3
|
11
|
24,2
|
Фрезерное
|
1
|
1
|
10
|
6
|
Нормы времени на
слесарные работы,
час.
|
0,1
|
0,5
|
Итого:
|
88,2
|
5 Общая годовая трудоемкость всех ремонтных работ (Qгод.
) составляет:
,
|
(50)
|
час
|
6 Расчет продолжительности простоя (Тпр.
) из-за ремонта (таблица 2.9.10). Определяется исходя из данных таблицы 2.9.6. Расчет аналогичен как и при определении годового объема ремонтных работ по видам.
Таблица 2.9.10 – Продолжительность простоя оборудования, суток
Наименование
оборудования
|
Количество ремонтных операций
|
Категория
сложности
ремонта,
R
|
Расчет продолжительности
простоя, сутки Тпр.
|
малый ремонт,
nм
|
средний ремонт,
nс
|
Сверлильное
|
10
|
5
|
8
|
24,4
|
Протяжное
|
5
|
4
|
12
|
24,24
|
Токарное
|
7
|
3
|
11
|
21,67
|
Фрезерное
|
1
|
1
|
10
|
4,7
|
Норма простоя оборудования в ремонте, суток на 1 ремонтную машину при двухсменной работе
|
0,14
|
0,33
|
Всего:
|
75,01
|
|