Министерство транспорта РФ
Федеральное Агентство железнодорожного транспорта ГОУВПО
Самарский Государственный Университет Путей Сообщения
Кафедра "Путь и строительство железных дорог"
Курсовой проект
по дисциплине: "Организация, планирование и управление
путевым хозяйством"
на тему: "Организация и планирование ремонтов пути
и текущего содержания"
Выполнила: студентка
Группы 264
Хайбрахманова Я.Р.
Проверил: Маёров Г.Р.
Самара 2010
Содержание
1. Планирование ремонтов пути
1.1 Общие положения
1.2 Определение класса пути
1.3 Определение типа пути
1.4.Планирование ремонтов на участках дистанции пути
1.4.1 Нормы периодичности выполнения ремонтно-путевых работ
1.4.2 Усиленный капитальный ремонт пути
1.4.3 Капитальный ремонт пути
1.4.4 Средний ремонт пути
1.4.5 Подъемочный ремонт пути
1.5 Определение приведенной длины дистанции пути
1.6. Расчет численности монтеров пути на дистанции
2. Ресурсосбережение
2.1 Сварка рельсов нового поколения
Библиографический список
Исходные данные
1. Грузонапряженность:
1.1 Четный путь - 76 млн.т км брутто/км в год,
1.2 Нечетный путь - 72 млн.т км брутто/км в год,
1.3 Однопутный участок - 29 млн.т км брутто/км в год.
2. Скорость движения:
Пассажирских:
2.1 Четный путь - 93 км/ч,
2.2 Нечетный путь - 93 км/ч,
2.3 Однопутный участок - 76 км/ч.
Грузовых:
2.4 Четный путь - 78 км/ч,
2.5 Нечетный путь - 78 км/ч,
2.6 Однопутный участок - 63 км/ч.
3. Протяженность участков:
3.1 Четный путь - 169 км,
3.2 Нечетный путь - 169 км.
3,3. Однопутный - 64 км.
4. Количество стрелочных переводов - 164 шт.
5. Минимальный радиус на кривых участках - 650 м.
6. Наличие искусственных сооружений - 0 шт.
7. Природные климатические условия: - 25є.+25єС, метель умеренная, снегопад умеренный.

Путевое хозяйство является одной из ведущих подотраслей железнодорожного транспорта. Железная дорога с его многочисленными сооружениями, обустройствами, комплекс хозяйственных предприятий и производственных формирований, предназначенных для обеспечения нормальной работы пути, проведение его планов предупредительных работ и составляет путевое хозяйство. Существенную роль ПХ подтверждает тем, что свыше 50% основных фондов ж.д. принадлежат ПХ. Основные фонды ПХ.
Таблица 1
Наименование |
Доля в % |
Износ в % |
Земл. Полотно |
26,2 |
30,6 |
ВСП |
45,6 |
58,6 |
Мосты |
8,1 |
47,9 |
ИССО |
14,8 |
45,8 |
Маш. Обор |
3,7 |
48,3 |
Здания |
1,6 |
37,3 |
В ПХ доля эксплуатационных расходов составляет около 25%. Доля сотрудников, занятых в ПХ около 20%.
Доля хозяйств в эксплуатационных расходов.
Таблица 2
Хозяйства |
% |
Локомотивное |
26,7 |
Путевое |
24,6 |
Вагонное |
11,3 |
Пассажирское |
8,5 |
Главнейшей задачей ПХ является обеспечение бесперебойности и безопасности процесса ж/д перевозок, которая регламентируется соответствующей экономически обоснованной системой его ведения включающей в себя высококачественное текущее содержание пути, различные ремонты, снего - и водоборьбу на основании постоянного внедрения прогрессивных конструкций, технологий и методов организации работ.
Текущее содержание пути должно осуществляться при наиболее рациональном сочетании 2х условий:
1. Обеспечение безопасности движение поездов с установленной скоростью;
2. Ресурсосбережение.
Задача текущего содержания пути: систематический надзор за комплексом сооружения пути, путевых устройств, содержание состояния гарантированной безопасности и бесперебойности движения с максимально допустимой скоростью.
Текущее содержание осуществляется круглогодично и на всем протяжение пути, включая участки находящиеся в ремонте. Оно включает изучение причин появления неисправностей и выполнение работ по их устранению и предупреждению. Все сооружения и устройства должны содержаться в соответствии с нормами и допусками установленными правилами технической эксплуатации ж/д. России и инструкции по текущему содержанию пути. От технического состояния пути зависит не только безопасность движения, но и экономическая эффективность использование состава.
Задачи и перспективы развития ПХ по состоянию на 2004 г:
1. Протяженность главного пути с ж/б основанием 48%; 12,5% с негодными деревянными шпалами.
2. На щебне эксплуатируется ≈80%.
3. Степень загрязненности балластной призмы 19,6%.
4. Процент просроченного капитального ремонта 12%.
5. Количество дефектных стрелочных переводов 8,8%.
6. Общая продолжительность дефектного земляного полотна 8,7%.
К 2007г. грузонапряженность возрастет с 44,4% до 57%.
Средняя скорость перевозки должна возрасти на 10%.
Для решения поставленных задач необходимо:
полностью ликвидировать просрочку по капитальному ремонту на всех дорогах. Для этого необходимо оздоровить к 2007 году 16 тыс. км. Это позволит довести протяженность главного пути с ж/б основанием до 75% при условии выпуска ж/б шпал до 5,1 тыс. км. в год.
доукомплектовать современной техникой около 70% ПМС, в том числе средствами диагностики.
намечено сокращение затрат на эксплуатацию ж/д пути за счет применения б/с пути.
применение и использование старогодных рельс.
совершенствование ВСП.
дооснащение дорог рельсошлифовальными поездами, которые позволят репрофилировать профиль рельсов.
в 2001г. принята программа реконструкции земляного полотна на период до 2015г.
намечено коренное изменение подходов к текущему содержанию пути.
мотивация труда (повышение окладов, премирование).
На сети железных дорог должно осуществляться перспективное и текущее планирование путевых работ.
Перспективное (на 3-5 лет вперед) планирование осуществляется на основе нормативных межремонтных сроков с целью рационального образования и использования ремонтного фонда и других ресурсов.
Текущее планирование на предстоящий год производится исходя из фактического состояния пути по критериям назначения того или иного вида ремонта, определяемым по результатам комиссионных осмотров и проверок диагностическими средствами параметров устройства и содержания пути, а также на основе паспортных данных о классе, конструкции верхнего строения, плане и профиле пути, наработанном тоннаже и др. При этом при планировании усиленного капитального или капитального ремонта пути следует учитывать прогнозируемые изменения размеров и скоростей движения поездов на предстоящие 5 лет, которые могут привести к изменению класса пути.
Разработка плана на предстоящий год и выдача заданий на проектирование ремонтов должны быть осуществлены не позднее апреля года, предшествующего году ремонта.
При одинаковых значениях критериев назначения, ремонтов на путях разных классов они должны планироваться в первую очередь на путях более высокого класса.
Ремонтно-путевые работы с применением машин выполняются в специально предоставляемые и в технологические "окна" в графике движения поездов. Порядок их предоставления регламентируется Правилами технической эксплуатации железных дорог Российской Федерации и Инструкцией о порядке предоставления и использования "окон" для ремонтных и строительно-монтажных работ на железных дорогах Российской Федерации.
На работы по ремонту пути: усиленному капитальному, капитальному, усиленному среднему, среднему, подъемочному, планово-предупредительной выправке, по отдельным видам ремонта земляного полотна и искусственных сооружений разрабатываются проекты, калькуляции, сметы по материалам натурного и инженерно-геологического обследований; на другие работы составляются объемные ведомости и калькуляции.
При проектировании, планировании, организации и выполнении ремонтно-путевых работ должны соблюдаться требования*:
Правил технической эксплуатации железных дорог Российской Федерации;
Инструкции по сигнализации на железных дорогах Российской Федерации;
Инструкции по движению поездов и маневровой работе на железных дорогах Российской Федерации;
Инструкции по обеспечению безопасности движения поездов при производстве путевых работ;
перечень нормативно-технических документов ОАО "РЖД", на которое дается ссылка в настоящих Технических условиях;
Правил и технологии выполнения основных работ при текущем содержании пути;
Правил по охране труда при содержании и ремонте железнодорожного пути и сооружений;
Правил электробезопасности для работников железнодорожного транспорта на электрифицированных железных дорогах;
Методических указаний по комплексной оценке состояния пути с использованием диагностических средств;
Методики автоматизированного определения потребности в проведении планово-предупредительной выправки пути по данным ВПС ЦНИИ-4 г.;
Технических указаний по определению и использованию характеристик устройства и состояния пути, получаемых вагонами-путеобследовательскими станциями системы ЦНИИ-4;
Технического руководства по использованию результатов измерений путеобследовательских станций ЦНИИ-4 в качестве предпроектной документации по ремонту железнодорожного пути и оценки соответствия отремонтированного пути проекту;
другие нормативно-технические документы и указания ОАО "РЖД", связанные с производством ремонтно-путевых работ.
Объемы производства работ по усиленному капитальному и капитальному ремонтам пути и стрелочных переводов, усиленному среднему, среднему, подъемочному и планово-предупредительной выправке утверждаются ОАО "РЖД". При этом участки производства работ по усиленному капитальному и капитальному ремонтам пути и стрелочных переводов, усиленному среднему согласовываются по представлению начальников железных дорог Департаментом пути и сооружений МПС России (далее - ЦП МПС)., а после акционирования - его правопреемником.
Работы по ремонту и планово-предупредительной выправке планируются в соответствии с техническими условиями, которые являются нормативно-техническим документом, разработанным в соответствии с утвержденным МПС РФ 27.04.01г. "Положением о системе ведения путевого хозяйства на железных дорогах РФ" основанным на классификации путей.
Классы путей на участках совмещенного движения
Таблица 3
Группа пути |
Грузонапря- женность млн.т. км брутто/км в год |
Категории пути - допускаемые скорости движения поездов (числитель - пассажирские, знаменатель - грузовые)
|
С |
1 |
2 |
3 |
4 |
5 |
40 и менее |
141-200 |
121-140 |
101-120 |
81-100 |
61-80 |
41-60 |
до 140 |
до 100 |
до 90 |
до 80 |
до 60 |
до 60 |
Главные пути |
А |
Более 80 |
1 |
1 |
1 |
1 |
2 |
2 |
3 |
Б |
51 - 80 |
1 |
1 |
1 |
2 |
2 |
3 |
3 |
В |
26 - 50 |
1 |
1 |
2 |
2 |
3 |
3 |
4 |
Г |
11 - 25 |
1 |
1 |
2 |
3 |
3 |
4 |
4 |
Д |
6 - 10 |
1 |
2 |
3 |
4 |
4 |
4 |
4 |
Е |
5 и менее |
- |
- |
- |
4 |
4 |
5 |
5 |
На двухпутном участке:
четный путь - 2Б3, при грузонапряженности 76 млн.т.бр.на км в год и скорости движения пассажирских поездов 93 км/ч и грузовых поездов 78км/ч;
нечетный путь - 2Б3 при грузонапряженности 72 млн.т.бр.на км в год и скорости движения пассажирских поездов 93 км/ч и грузовых поездов 78км/ч;
На однопутном участке: 2В4 при грузонапряженности 29 млн.т.бр.на км в год и скорости движения пассажирских поездов 76 км/ч и грузовых поездов 63км/ч;
На двухпутном участке классы путей устанавливаются одинаковыми с классом пути имеющим большую Грузонапряженность при условии, если разница грузонапряженности не превышает 30%.
Технические требования и нормативы по конструкциям, типам и элементам пути для усиленного капитального и капитального ремонта пути.
Таблица 4
Классы путей |
1 |
2 |
3 |
4 |
5 |
1. Конструкция верхнего строения пути |
Бесстыковой путь на железобетонных шпалах 1)
|
Звеньевой путь
на железобе-
тонных шпалах
|
2. Типы и характеристика верхнего строения пути |
Рельсы Р65,новые,
термоупроч-
ненные,
категории В и
Т1
|
Рельсы Р65,новые,
термоупроч-
ненные,
категории В и
Т1 и Т22)
|
Рельсы Р65,старогодные I
группы
годности;
I и II
репрофили-
рованные2)
|
Рельсы
старогодные
Р65 3)
I и II группы
годности
|
Рельсы
старогодные
Р65 3)
III группы
годности
|
Скрепления новые
|
Скрепления новые и старогодные (в т.ч.
отремонтированные), укладываемые в объёмах,
устанавливаемых техническими условиями на ремонт
и планово-предупредительную выправку пути
|
Шпалы железобетонные новые I сорта
|
Шпалы железобетонные старогодные4)
|
Балласт щебеночный 5) с толщиной слоя;
40 см - под железобетонными шпалами;
35 см - под деревянными шпалами
|
Балласт
щебеночный с
толщиной слоя
под шпалой:
30 см - под
железобетонны
ми; 25 см - под
деревянными
|
Балласт всех
типов с
толщиной слоя
под шпалой не
менее 20 см
|
Размеры балластной призмы - в соответствии с типовыми поперечными профилями |
3. Виды работ при замене верхнего строения пути |
Усиленный капитальный ремонт
Пути
|
Капитальный ремонт пути
|
4. Конструкции и типы стрелочных переводов |
Р65 новые;
рельсовые элементы закаленные.
Брусья железобетонные новые6)
|
Рельсы и металлические части
старогодные.
Брусья железобетонные -
новые и старогодные6)
|
5. Виды работ при замене стрелочных переводов |
Усиленный капитальный ремонт стрелочных переводов |
Капитальный ремонт стрелочных переводов
|
6. Земляное полотно и искусственные сооружения |
Земляное полотно, искусственное сооружение и их обустройства должны удовлетворять
допускаемым осевым нагрузкам и скоростям движения поездов в зависимости от групп и
категорий путей
|
Примечания:
1. Применение звеньевого пути на деревянных шпалах согласовывается с.
Департаментом пути и сооружений ОАО "РЖД", при этом на путях 1-3 классов деревянные шпалы должны быть I типа.
2. В зависимости от балласта на железной дороге старогодных рельсов I и II групп годности допускается по согласованию с Департаментом пути и сооружений: укладка на путях 2 класса категорий Г и Д старогодных репрофилированных рельсов I группы годности;
укладка на путях 3 класса новых рельсов категорий Т1 и Т2.
3. Для звеньевого пути на деревянных шпалах - не легче Р50.
4. При недостатке старогодных железобетонных шпал: новые железобетонные 1 сорта на путях 3 класса, новые 2 сорта - на путях 4 и 5 классов; при недостатке новых железобетонных шпал 2 сорта - новые 1 сорта; при недостатке старогодных и новых железобетонных шпал - новые деревянные.
5. По согласованию с Департаментом пути и сооружений ОАО "РЖД" допускается на путях 3-5 классов укладка асбестового балласта.
6. По согласованию с Департаментом пути и сооружений ОАО "РЖД" допускается укладка деревянных брусьев.
В соответствии с полученными данными устанавливаем конструкцию и тип верхнего строения пути. На мой взгляд, рациональным будет использование бесстыкового пути, так как это наиболее прогрессивная конструкция железнодорожного пути. Полное отсутствие стыков при хорошо отшлифованной поверхности головки рельса и отличном содержании пути позволяют практически не иметь каких-либо дополнительных динамических воздействий на пассажиров, уменьшить сопротивление движению поезда на 8-12 ٪, сократить на 9-10٪ расходы на ремонты подвижного состава и пути.
Для участка железнодорожного пути 2Б3 соответствует бесстыковая конструкция на новых железобетонных шпалах 1 сорта, тип рельсов Р65. Для главных путей я выбрала новые, термоупрочненные рельсы категории Т1 без дополнительных добавок, т.к. путь обладает средней грузонапряженностью и не требует повышенной износостойкости рельсов. в соответствии с таблицей 5 такие рельсы имеют норму гарантийной наработки - 240млн. т брутто. Для моих условий для участка пути 2В4 в соответствии с таблицей 4 выбираю бесстыковую конструкцию пути тип рельсов Р65 категории Т1.
В кривых участках пути используем тип рельсов Р65К, имеющие достаточные моменты инерции и сопротивления, следовательно, возникающие в них напряжения изгиба и кручения не превышают допустимых значений.
Характеристики поперечного профиля рельса Р65

Нормы по гарантии качества изготовителей железнодорожных рельсов представлены в таблице 5
Таблица5
тип термоупрочненных рельсов |
категория качества |
норма гарантийной наработки, млн. т брутто |
на прямых и кривых R>1000м |
на участках пути с кривыми |
радиусом 650м <R<1000м |
R<650м |
Р75, Р65 |
В |
350 |
300 |
- |
Т1
, Т2
|
240 |
150 |
120 |
СС |
310 |
190 |
- |
НЭ, НК |
280 |
170 |
140 |
Р65К |
Т1,
Т2
|
- |
220 |
180 |
Р65 и Р65К |
ИЭ |
- |
- |
180 |
Примечание:
В - рельсы высшей категории качества
Т1,
Т2
- термоупрочненные рельсы, выпускаемые по ГОСТ Р51685-2000
СС - рельсы для скоростного совмещенного движения
НЭ, НК - рельсы низкотемпературной надежности
ИЭ - рельсы повышенной износостойкости и контактной выносливости.
Химический состав рельсов (%) представлен в таблице 6
Таблица 6
марка стали |
тип рельса |
С, % |
Mn, % |
Si, % |
P, % |
S, % |
As,% |
М 76 |
Р75, Р65 |
0,69-0,82 |
0,75-1,5 |
0,13-0,28 |
0,035 |
0,045 |
0,15 |
Значительную твердость, сопротивление износу и вязкость высокоуглеродистых сталей достигаются приданием им специальной термической обработкой однородной сорбитной структуры.
Укладываемый в путь балластный материал должен удовлетворять утвержденным техническим условиям и государственным стандартам.
Балластная призма должна содержаться в соответствии с типовыми поперечными профилями, приведенными на Рис.1.11.
При ширине плеча балластной призмы на звеньевом пути в прямых участках и со стороны внутренней нити в кривых менее нормативного работы по восстановлению нормальной ширины плеча производятся в плановом порядке в течение трех месяцев положительных температур.
При отступлениях от нормативной ширины балластной призмы на протяжении более 10м на звеньевом пути в кривых со стороны наружной нити и на бесстыковом пути в прямых и кривых должны обеспечиваться меры безопасности движения поездов в зависимости от величин отступлений и ожидаемых температур: для звеньевого пути при ширине плеча менее 20см, а для бесстыкового - менее 25см и ожидаемом повышении температуры на 15°С и более относительно температуры закрепления рельсовых плетей скорость ограничивается до 60 км/ч или менее в зависимости от конкретной ширины плеча балластной призмы или ожидаемого повышения температуры.
Верх балластной призмы должен располагаться: при деревянных шпалах - ниже верха шпалы на 3см; при железобетонных шпалах - в одном уровне с верхом средней части шпал.
Загрязненный щебеночный балластный слой необходимо своевременно (не допуская образования выплесков) очищать от загрязнителей, а загрязненный асбестовый и песчаный балласт - заменять. Поверхность балластной призмы должна периодически очищаться от засорителей и растительности.
Для отвода ливневой и образовавшейся при таянии снега воды с путей и междупутий на перегонах и станциях должны устраиваться и содержаться в исправности продольные и поперечные дренажные канавки и лотки.
Балластный слой предназначен для восприятия давления от шпал и передачи его на основную площадку земляного полотна; упругой переработки ударов о рельсы колес подвижного состава; обеспечение устойчивости рельсошпальной решетки; отвода воды от верхнего строения пути. В соответствии с этим материал балластного слоя должен быть прочным, упругим, хорошо сопротивляться смещениям, быть водо - и морозоустойчивым, плохим проводником тока. Этим тербованиям в разной степени удовлетворяют щебень, отходы асбестовой промышленности (асбестовый балласт), гравий, песок, ракушка и шлаки. Наиболее предпочтительным будет выбор щебеночного балласта.
Щебень изготовляют из твердых каменных пород: гранита, кварцита, порфира, диорита, базальта, известняка и др. нормальный размер частиц 26-60 мм. Щебень - наилучший балласт. Он в наибольшей степени (особенно по упругости и обеспечению устойчивости рельсо-шпальной решетки) удовлетворяет предъявляемым к балластному слою требованиям.
Поперечные профили балластной призмы из щебня на песчаной подушке для особо тяжелого типа верхнего строения пути на однопутных участках: а
, б
- соответственно в прямых и кривых на деревянных шпалах; в
, г
- то же на железобетонных шпалах; h
- возвышение наружного рельса; 1
- щебень; 2 –
песок

Поперечные профили балластной призмы из щебня на песчаной подушке для тяжелого типа верхнего строения пути на однопутных участках: а
, б
- соответственно в прямых и кривых на деревянных шпалах; в
, г
- то же на железобетонных шпалах; h -
возвышение наружного рельса; 1
- щебень; 2
– песок

Поперечные профили балластной призмы из щебня на песчаной подушке для нормального типа верхнего строения пути на однопутных участках: а
, б
- соответственно в прямых и кривых на деревянных шпалах; в
, г -
то же на железобетонных шпалах; h -
возвышение наружного рельса; 1
- щебень; 2
– песок

Поперечные профили балластной призмы из щебня на песчаной подушке для особо тяжелого типа верхнего строения пути на двухпутных участках: а
, б
- соответственно в прямых и кривых на деревянных шпалах; в
, г
- то же на железобетонных шпалах; А -
уширение междупутья в кривых; h
- возвышение наружного рельса; 1
- щебень; 2
– песок
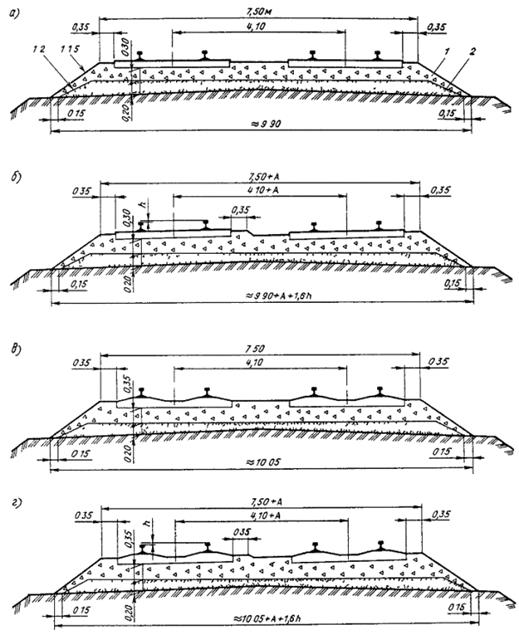
Поперечные профили балластной призмы из щебня на песчаной подушке для тяжелого типа верхнего строения пути на двухпутных участках: а
, б
- соответственно в прямых и кривых на деревянных шпалах; в
, г
- то же на железобетонных шпалах; А
- уширение между.

Поперечные профили балластной призмы из щебня на песчаной подушке для нормального типа верхнего строения пути на двухпутных участках: а
, б
- соответственно в прямых и кривых на деревянных шпалах, в
, г
- то же на железобетонных шпалах, А
- уширение междупутья в кривых, h
- возвышение наружного рельса, 1
- щебень, 2
– песок упутья в кривых; h
- возвышение наружного рельса; 1
- щебень; 2
– песок

Образец поперечного профиля балластной призмы из щебня с покрывающим слоем из асбестового балласта на песчаной подушке для тяжелого типа верхнего строения пути: 1
- асбест; 2 -
щебень, 3 –
песок

Образец поперечного профиля балластной призмы из асбеста на песчаной подушке для нормального типа верхнего строения пути: А -
уширение междупутья в кривых, h
- возвышение наружного рельса, 1
- асбест; 2
– песок
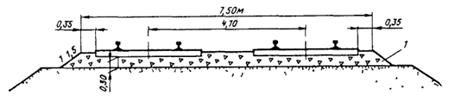
Образец поперечного профиля балластной призмы из щебня на земляном полотне из скальных грунтов, чистого крупно - и среднезернистого песка для тяжелого типа верхнего строения пути: 1
– щебень
Образец поперечного профиля балластной призмы из щебня с выпуском гравийной подушки для тяжелого типа верхнего строения пути: 1
- щебень, 2
- гравий
Таблица 7. Основные размеры балластной призмы
Показатель
|
Типы верхнего строения пути |
Особо тяжелый |
Тяжелый |
Нормальный |
Толщина балластного слоя под шпалой при двухслойной балластной призме и деревянных шпалах, см: |
щебеночный или асбестовый слой |
35 |
30 |
25 |
подушка из песка |
20 |
20 |
20 |
То же при железобетонных шпалах: |
щебеночный или асбестовый слой |
40 |
35 |
30 |
подушка из песка |
20 |
20 |
20 |
Ширина плеча балластной призмы, см1
|
45 |
35 |
25*
|
Крутизна откосов балластной призмы |
1: 1,5 |
1: 1,5 |
1: 1,5 |
Рекомендуемая ширина земляного полотна на прямых участках пути, м: |
на однопутных линиях |
7,5 |
7,0 |
6,5 |
на двухпутных линиях |
11,6 |
11,1 |
10,6 |
1
Ширина плеча указана для случая применения шпал длиной 2,70 м; при шпалах другой длины (2,75 или 2,80 м) плечо уменьшается. |
*
На кривых участках пути радиусом менее 600 м плечо балластной призмы с наружной стороны кривой принимается равным 35 см. |
Примечание. При подушке из гравия толщину слоя щебня или асбеста можно уменьшать на 5 см за счет увеличения на эту величину толщины подушки. |
В соответствии с "Техническими требованиями и нормативами по конструкциям, типам и элементам пути для УК и К ремонтов пути" для участка пути 2Б3 и 2В4 выбираю балласт щебеночный с толщиной слоя под шпалой соответственно 40 см и 30 см под железобетонными шпалами. При этом в соответствии с классом пути определяем ширину плеча балластной призмы, которая составляет 40-45 см, толщину песчаной подушки - 20 см, минимальную длину обочины - 50 см. фракция щебня кубовидная, нормального размера - 25-65 см.
Выбор скреплений




Я думаю, что для двухпутного участка следует выбрать скрепления новые АРС-4, для однопутного участка - старогодние АРС-4. Этот тип
промежуточных скреплений достаточно надежен и в последнее время наиболее часто применяется в конструкции железнодорожного пути. Выбранные скрепления обеспечивают надежную упругую связь рельсов со шпалами, имеют наиболее простую, малодетальную (12 деталей) и удобную при монтаже и эксплуатации конструкцию. Однако АРС-4 имеют такие недостатки, как уширение рельсовой колеи до 1545 мм из-за износа и изломов изолирующего уголка, сползание клемм с подошвы рельсов, нестабильная подуклонка.
Работы по ремонту пути и стрелочных переводов, выполняемых за счет средств ремонтного фонда, подразделяются на следующие основные виды:
усиленный капитальный ремонт пути (условное обозначение - УК);
сплошная замена рельсов в период между усиленными капитальными ремонтами бесстыкового пути на участках с грузонапряженностью более 50 млн. т км бр/км год и металлических частей стрелочных переводов, сопровождаемая работами в объемах среднего (или усиленного среднего) ремонта пути (условное обозначение - PC);
капитальный ремонт пути (условное обозначение - К);
усиленный средний ремонт пути (условное обозначение - УС);
средний ремонт пути (условное обозначение - С);
подъемочный ремонт пути (условное обозначение - П);
сварка рельсовых плетей до длины блок-участка и перегона на фронтах ремонтов предыдущих лет;
шлифовка рельсов (условное обозначение - ШР);
алюминотермитная сварка стрелочных переводов (условное обозначение - АТСп);
сплошная смена рельсов в кривых с боковым износом на новые или старогодные;
сплошная смена переводных деревянных брусьев;
постановка стрелочных переводов на щебень.
Основные виды работ, выполняемых за счет средств, относимых на текущее содержание:
планово-предупредительная выправка пути (условное обозначение - В);
замена негодных и дефектных рельсов, шпал, скреплений и др;
осмотры и диагностика пути (кроме отдельных видов, входящих в предпроектное обследование);
перекладка рельсов с боковым износом из кривых в прямые с заменой рабочего канта и наоборот;
снего-, водо-, пескоборьба;
обслуживание переездов;
другие виды работ текущего содержания пути.
Основные виды работ, выполняемых за счет капитальных вложений:
реконструкция плана и профиля пути на перегонах и станциях, требующих досыпки земляного полотна и перекоса опор контактной сети в объеме более 5% в плане и изменения отметок пути в профиле, требующих досыпок земляного полотна;
перенос стрелочных переводов на новые ординаты;
реконструкция профиля горок;
замена пролетных строений и опор мостов;
переустройство малых мостов в трубы;
строительство путепроводов;
реконструкция тоннелей и других видов искусственных сооружений.
Нормативная периодичность выполнения ремонтно-путевых работ для среднесетевых условий, по которой определяется их ежегодная общая потребность при перспективном и текущем планировании, дифференцируется по различным участкам с учетом технологии ранее выполненных на них ремонтов:
на участках, где усиленный капитальный и капитальный ремонты пути выполнялись с соблюдением требований Положения о системе ведения путевого хозяйства на железных дорогах Российской Федерации.
на участках, где ранее был выполнен капитальный ремонт пути, то есть в соответствии с Положением о планово-предупредительном ремонте верхнего строения пути, земляного полотна и искусственных сооружений на железных дорог России (ППР 64).
По нормативной периодичности выполнения ремонтно-путевых работ в соответствии с классностью путей и вышеприведенной дифференциацией участков определяются расчетные объемы ремонтно-путевых работ, потребность материально-технических, трудовых и финансовых ресурсов.
Среднесетевые нормы периодичности выполнения усиленного капитального и капитального ремонтов пути и основные схемы промежуточных видов ремонтно-путевых работ для определения их потребности при перспективном и текущем планировании на участках, где усиленный капитальный и капитальный ремонты пути уже выполнялись с соблюдением требований ППР 94.
В соответствии с "Техническими условиями на работы по ремонту и планово-предупредительной выправке пути" среднесетевые нормы периодичности выполнения усиленного капитального и капитального ремонтов пути и схемы промежуточных видов ремонтно-путевых работ для определения их потребности при перспективном и текущем планировании заданного полигона будут следующие
Для двухпутного участка при классе пути 2Б3 периодичность выполнения усиленного капитального и капитального ремонта пути 700 млн. т.
Для однопутного участка при классе пути 2В4 периодичность выполнения усиленного капитального и капитального ремонта пути 700 млн т.
Схемы выполнения путевых работ и их очерёдность за межремонтный цикл будет следующая (числитель - путь; знаменатель - стрелочные переводы):
Для однопутного участка:
(УК) ВСВ (РУС) ВСВ (УК)
УК) ВВ (РС) ВВ (РУС) ВВ (РС) ВВ (УК)
(УК) ВСВ (УК)
Для двухпутного участка: (УК) ВВ (РС) ВВ (УК)

Примечания.
1. Указанные нормативы для участков I-II классов приведены для рельсов категории Т1. При освоении выпуска и укладки рельсов категории "В" нормативные межремонтные сроки для участков бесстыкового пути I-II классов составят 1100 млн.т бр.
2. На участках с грузонапряженностью более 50 млн. ткм бр. допускается после наработки тоннажа (700млн.т) вместо усиленного капитального ремонта пути производить сплошную смену рельсов, сопровождаемую усиленным средним ремонтом пути.
3. На железнодорожных линиях федерального значения - 1 раз в 30 лет.
4. На деревянных шпалах - 1 раз в 25 лет.
5. Промежуточные ремонты назначаются по критериям фактического состояния пути, приведенным в технических условиях на работы по ремонту и планово-предупредительной выправке пути.
В соответствии со схемами производства работ в курсовом проекте будут рассматриваться следующие виды капитальных работ: усиленный капитальный ремонт пути (условное обозначение - УК); капитальный ремонт пути (условное обозначение - К); средний ремонт пути (условное обозначение - С); подъемочный ремонт пути (условное обозначение - П); планово-предупредительная выправка пути (условное обозначение - В).
Четный путь (2Б3), t=

Нечетный путь (2Б3), t=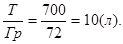

Однопутный участок (2В4), t=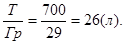
1.4.2
Усиленный капитальный ремонт пути предназначен для комплексного обновления верхнего строения пути на путях 1 и 2 (стрелочных переводов 1-3) классов с повышением несущей способности балластной призмы и земляного полотна, включая основную площадку.
Назначение усиленного капитального ремонта при текущем планировании в первую очередь производится при прочих равных условиях:
на участках, подготавливаемых к скоростному движению пассажирских поездов;
на участках, подготавливаемых к обращению вагонов с повышенной осевой нагрузкой.
Состав входящих в усиленный капитальный ремонт пути работ определяется проектно-сметной документацией.
Работы по ремонту водоотводов и осушению основной площадки выполняются по специальным проектам и сметам в рамках проекта усиленного капитального ремонта, как правило, за год до производства ремонтно-путевых работ.
Работы по ликвидации сложных деформаций земляного полотна выполняются по отдельным проектам.
При усиленном капитальном ремонте пути выполняются следующие основные работы:
замена рельсошпальной решетки на новую, собранную на производственной базе;
комплексная замена стрелочных переводов;
очистка щебеночной призмы на глубину ниже подошвы шпал не менее указанной в таблице 4 настоящих Технических условий или замена асбестового балласта или щебня слабых пород на щебеночный с устройством, при необходимости, разделительного слоя между очищенным и неочищенным массивами балласта или основной площадкой земляного полотна;
положение кривых, удлинение переходных кривых и прямых вставок, если это не требует дополнительного завоза грунта из карьеров и замены или перестановки опор контактной сети в объеме более 5%;
доведение балластной призмы до требуемых размеров;
ликвидация пучинистых мест в земляном полотне и повышение несущей способности основной площадки земляного полотна в местах повышенной деформативности;
положение или укрепление откосов насыпей за счет использования отсева от очистки балластной призмы;
срезка обочин;
выправка, подбивка и стабилизация пути с постановкой на проектные отметки в профиле;
постановка пути на ось в плане и приведение длин переходных кривых и прямых вставок между смежными кривыми в соответствие с максимальными проектируемыми скоростями движения поездов;
ремонт и восстановление водоотводов и дренажных устройств;
срезка и уборка отложений загрязнителей балласта на откосах выемок и насыпей;
ремонт железнодорожных переездов;
очистка русел и планировка конусов малых искусственных сооружений;
сварка плетей до длины блок-участка или перегона, включая стрелочные переводы;
шлифование поверхности катания рельсов и другие работы, предусмотренные проектом.
При последующих усиленных капитальных ремонтах пути состав входящих в них работ должен определяться проектно-сметной документацией с учетом фактического состояния верхнего строения пути, земляного полотна и водоотводов.
Технические условия и требования, предъявляемые к конструкции и элементам верхнего строения при усиленном капитальном и капитальном ремонте пути, приведены в таблице 11, критерии назначения участков пути к усиленному капитальному ремонту пути - в таблице 11.
Критерии выбора участков, подлежащих усиленному капитальному ремонту при текущем планировании
Таблица11
Основные критерии |
Дополнительные критерии |
Количество негодных и дефектных |
Класс |
Одиночный выход рельсов (в сумме за срок службы - в среднем на участке ремонта), шт/км * |
элементов на 1 км верхнего строения пути, более |
Пропущенный тоннаж,
%
Ф *Г V
|
Негодные дерев, шпалы, % |
Негодные скрепления,% |
Кол-во
шпал с выплесками, %
|
2 класс |
6 и более |
18 |
20 |
5 |
100 |
* Одиночный выход рельсов, а также количество дефектных рельсов определяется без |
учета выхода рельсов по боковому износу в кривых, а на участках бесстыкового пути - и без |
учета выхода рельсов уравнительных пролетов; ** На пути с железобетонными шпалами подсчитывается суммарный процент подкладок |
и закладных болтов, на пути с деревянными шпалами - подкладок, костылей и противоугонов, |
при этом, процент негодных костылей и противоугонов учитывается с коэффициентом 0,6. Пример. На звеньевом пути негодных подкладок - 20 %, костылей - 15 %, |
противоугонов - 10
%. Следовательно, сумма процентов негодных элементов составит: 20 + (15 ■ 0,6) +
|
(10-0,6) = 35%. *** По таблице 1.4.1 или 1.4.2 определяется нормативный срок службы в пропущенном тоннаже с учетом понижающих или повышающих коэффициентов или срок службы в годах. |
Примечания:
1. Процент негодных элементов скреплений определяется выборочным порядком путем детального обследования на каждом километре скреплений на двух 25-метровых звеньях (на бесстыковом пути - на двух отрезках пути длиной по 25 м), произвольно выбранных в начале и середине плети (вне уравнительных рельсов)
2. Если приведенные в таблице дополнительные критерии по количеству дефектных и негодных шпал и скреплений, выплесков окажутся меньше табличных на 1/3 и более, то вместо усиленного капитального ремонта пути может быть назначена сплошная смена рельсов, сопровождаемая сопутствующими работами в объеме подъемочного или среднего ремонта.
3. Участки пути, ограничение скорости, на которых введено в приказ начальника дороги, рассматриваются в качестве основного критерия.
Капитальный ремонт пути предназначен для замены рельсо-шпальной решетки на более мощную или менее изношенную на путях 3-5 классов (стрелочных переводов на путях 4-5 классов), смонтированную из новых или старогодных рельсов, новых и старогодных шпал и скреплений.
Капитальный ремонт пути может выполняться как комплексно со снятием и укладкой путевой решетки кранами, так и раздельным способом с заменой рельсов, скреплений, шпал.
В состав работ по капитальному ремонту пути на участках 3-4 классов входят те же работы, что и при усиленном капитальном ремонте, кроме уположения кривых.
На путях 5 класса при капитальном ремонте пути производятся замена материалов верхнего строения пути, не обеспечивающих безопасное движение поездов с установленными скоростями, а также сопутствующие.работы по комплексной выправке пути с ремонтом водоотводных и дренажных сооружений, ликвидацией пучин и балластных выплесков, срезкой лишнего грунта на обочинах и междупутьях.
Таблица 12. Критерии выбора участков, подлежащих реконструкции и капитальному ремонту на новых материалах при текущем планировании
┌──────┬───────────────────────────────────┬───────────────────────────────────┐
││ Основные критерии │ Дополнительные критерии │
│├─────────────────┬─────────────────┼───────────────────────────────────┤
││ Пропущенный │ Одиночный │ Количество негодных и дефектных │
│ Класс│ тоннаж, │ выход рельсов │элементов на 1 км верхнего строения│
│ пути │ срок службы │ (в сумме за │ пути, % и более │
││ в годах, % от │ срок службы - в ├──────────┬──────────┬─────────────┤
││ нормативного (1)│ среднем на │ Негодные │ Негодные │ Число │
│││участке ремонта),│деревянные│скрепления│ шпал с │
│││ шт/км (2) │ шпалы, % │ (3), % │выплесками, %│
├──────┼─────────────────┼─────────────────┼──────────┼──────────┼─────────────┤
│ 1 │ 2 │ 3 │ 4 │ 5 │ 6 │
├──────┼─────────────────┼─────────────────┼──────────┼──────────┼─────────────┤
│ 1 │Не менее 100 │ 4 и более │ 15 │ 15 │ 4 │
│класс ││││││
├──────┼─────────────────┼─────────────────┼──────────┼──────────┼─────────────┤
│ 2 │Не менее 100 │ 6 и более │ 18 │ 20 │ 5 │
│класс ││││││
└──────┴─────────────────┴─────────────────┴──────────┴──────────┴─────────────┘
(1) - По таблице 5.1 определяется нормативный срок службы в пропущенном тоннаже с учетом понижающих и повышающих коэффициентов или срок службы с годах. Для скоростных участков пути нормативных срок службы определяется по таблице 5.2.
(2) При этом учитываются дефекты, образование и развитие которых зависит и возрастает по мере наработки тоннажа (дефекты: 10; 11.1-2; 17; 20; 21.1-2; 41), дефекты пятой группы (кроме дефектов 55; 56.3; 69), дефекты седьмой группы. Выход уравнительных рельсов не учитывается.
(3) На пути с железобетонными шпалами со скреплениями КБ подсчитывается суммарный процент подкладок и закладных болтов, при бесподкладочных скреплениях - клемм и прикрепителей (болтов, шурупов, анкеров), на пути с деревянными шпалами - подкладок и костылей.
Пример. На звеньевом пути негодных подкладок - 20 %, костылей - 15 %. Следовательно, сумма процентов негодных элементов составит: 20+15=35%.
Примечания:
1. Процент негодных элементов скреплений определяется выборочным порядком путем детального обследования на пикете скреплений на двух 25-метровых звеньях (на бесстыковом пути - на двух отрезках пути длиной по 25 м), произвольно выбранных в начале и середине плети (вне уравнительных рельсов)
2. Если приведенные в таблице дополнительные критерии по количеству дефектных и негодных шпал и скреплений окажутся меньше табличных на 1/3 и более, то вместо капитального ремонта пути на новых материалах может быть назначена сплошная смена рельсов, сопровождаемая сопутствующими работами в объеме подъемочного или среднего ремонта.
3. Участки пути, ограничение скорости по состоянию пути на которых введено в приказ начальника дороги, имеют приоритеты на уровне основного критерия.
Таблица 13 Критерии выбора участков, подлежащих капитальному ремонту пути на старогодных материалах
┌────────────┬───────────────────────────────────┬───────────────────────────────────┐
││ Основные критерии │ Дополнительные критерии │
│├─────────────────┬─────────────────┼───────────────────────────────────┤
││ Пропущенный │ Одиночный │ Количество негодных и дефектных │
│ Класс │ тоннаж, │ выход рельсов │элементов на 1 км верхнего строения│
│ пути │ срок службы │ (в сумме за │ пути, % и более │
││ в годах, % от │ срок службы - в ├──────────┬──────────┬─────────────┤
││ нормативного (1)│ среднем на │ Негодные │ Негодные │ Число │
││ не менее │участке ремонта),│деревянные│скрепления│ шпал с │
│││ шт/км (2) │ шпалы, % │ (3), % │выплесками, %│
├────────────┼─────────────────┼─────────────────┼──────────┼──────────┼─────────────┤
│ 1 │ 2 │ 3 │ 4 │ 5 │ 6 │
├────────────┼─────────────────┼─────────────────┼──────────┼──────────┼─────────────┤
│Главные │ Не менее 100 │ 6 и более │ 20 │ 25 │ 6 │
│пути 3 ││││││
│класса ││││││
├────────────┼─────────────────┼─────────────────┼──────────┼──────────┼─────────────┤
│Главные │ Не менее 100 │ 8 и более │ 25 │ 35 │ 8 │
│пути 4, 5 ││││││
│класса, ││││││
│станционные ││││││
│и ││││││
│специальные ││││││
│пути 3-4 ││││││
│класса ││││││
├────────────┼─────────────────┴─────────────────┴──────────┴──────────┴─────────────┤
│Остальные │ Не лимитируется │
│станционные,│ Капитальный ремонт пути назначается начальником службы │
│подъездные и│ пути на основе заявки начальника дистанции пути │
│прочие пути ││
└────────────┴───────────────────────────────────────────────────────────────────────┘
Сноски и примечания аналогичны приведенным в таблице 12.
Средний ремонт пути предназначен для сплошной очистки щебеночной балластной призмы, замены дефектных шпал и элементов скреплений в объемах, предусмотренных настоящими Техническими условиями и обеспечивающих отсутствие потребности в замене шпал в последующие 3 года.
Средний ремонт включает в себя:
сплошную очистку щебеночного балласта на глубину под шпалой не менее 25 см с добавлением балласта, или обновление загрязненного балласта других видов на глубину не менее 15 см под шпалой;
очистку водоотводов;
сплошную замену пружинных шайб на двухвитковые и резиновых подрельсовых прокладок на уравнительных пролетах, на концах плетей по 50-75 м и в зонах сварных стыков;
ремонт переездов;
одиночную замену дефектных рельсов шпал и скреплений;
введение плетей бесстыкового пути в оптимальную температуру и сварку до длины блок участка или перегона, включая стрелочного перевода;
шлифовку рельсов;
регулировку зазоров на звеньевом пути;
снятие пучинных карточек и регулировочных прокладок;
смазку и закрепление закладных и клеммных болтов;
другие работы, предусмотренные проектом и сметной документацией.
Критерии назначения работ по среднему ремонту приведены в таблице 14.
Критерии назначения работ по среднему ремонту.
Таблица14
Класс пути |
Основные критерии |
Дополнительные |
Загрязненность щебня, %
по массе
|
Количество шпал с выплесками %, более |
Количество негодных, %, более |
деревян. шпал |
скреплении |
2 |
> 30 |
6 |
12 |
15 |
> 30 |
8 |
15 |
20 |
* Подсчет процента |
негодных скреплений ведется аналогично |
приведенному в таблице 2.5. |
Примечание.
Загрязненность щебня и количество выплесков оценивается в год, предшествующий назначению ремонта пути. При этом выплески, устраненные в течение года, также входят в эту сумму.
Расчетная периодичность и глубина очистки щебня при среднем ремонте пути в зависимости от условий эксплуатации на участках, где ранее был выполнен усиленный капитальный ремонт пути с обеспечением нормативной толщины щебня приведены в табл.15.
Таблица15
Среднесетевые оптимальные схемы очистки щебня
Нормативные сроки выполнения |
Схема очистки (см/млн.тонн брутто) или (см/годы) |
Класс, группа и
катего-
|
усиленного капитального и капитального ремонта пути, млн.т./годы |
Бесстыковой путь |
Звеньевой путь |
рия пути |
Бессты
ковой путь
|
Звеньевой путь на деревянных шпалах |
1 |
2 |
1 |
2 |
1 |
2 |
4 |
5 |
6 |
7 |
2В4 |
700 |
600/18 |
40/390 |
30/330 |
35/390 |
25/310 |
3Г6 |
700/35** |
1 раз в18 лет |
40/370 |
35/340 |
35/18 лет |
- |
** - глубина очистки щебня при среднем ремонте пути и пропущенный тоннаж до усиленного капитального, усиленного среднего или капитального ремонта пути. |
На стрелочных переводах, расположенных на путях, подлежащих среднему ремонту, также должна назначаться сплошная очистка щебеночного балласта и одиночная замена дефектных элементов в объеме среднего ремонта пути и сварка стыков алюмине-термитной сваркой на стрелочных переводах.
Подъемочный ремонт пути предназначен для восстановления равноупругости подшпального основания путем сплошной подъемки и выправки пути с подбивкой шпал, а также для замены негодных деревянных шпал и частичного восстановления дренирующих свойств балласта.
При подъемочном ремонте пути выполняются:
сплошная выправка пути с подъемкой на 5-6 см, подбивкой шпал и добавлением балласта;
локальная очистка загрязненного щебня в шпальных ящиках и за торцами шпал в местах появившихся выплесков на глубину не менее 10 см ниже подошвы шпал, а при других видах балласта - частичная замена загрязненного балласта на чистый;
замена дефектных рельсов, негодных шпал и элементов скреплений;
регулировка стыковых зазоров;
удаление регулировочных прокладок из-под подошвы рельсов и сплошное закрепление клеммных и закладных болтов при скреплении КБ;
очистка водоотводов;
правка рельсовых и сварных стыков;
шлифовка рельсов;
другие работы в объемах, предусмотренных настоящими Техническими условиями.
Основным критерием назначения работ по подъемочному ремонту пути при их планировании является количество отступлений от норм содержания пути по просадкам, перекосам, отклонениям по уровню и в плане по показаниям путеизмерительного вагона, а дополнительными - количество концов шпал с выплесками, дефектных шпал и скреплений (таблица 16). При превышении показателей негодности и дефектности элементов ВСП значений, указанных в таблице 16, должен проводится средний ремонт пути.
Критерии выбора участков, подлежащих подъёмочному ремонту пути на стрелочных переводах, расположенных на пути, подлежащем подъемочному ремонту, должны также назначаться работы либо в объеме подъемочного ремонта, либо в объеме планово – предупредительной выправки.
Таблица 16
Определим сроки всех ремонтов на однопутном и двухпутном участках.
Класс пути |
Основные критерии |
Дополнительные критерии |
, от и до % |
Количество
отступлений 2 степени *, шт/км, более
|
Загрязнен - ность щебня по массе, % |
Негодных
деревянных шпал
|
Шпал с выплесками |
Негодных скреплений |
1 и 2 |
Группа Б, В |
35 |
<30 |
6-10 |
2-4 |
1.0 - 15 |
Группа Г, Д |
40 |
45 |
<30 |
10-15 |
4-8 |
15-20 |
* По показаниям вагона - путеизмерителя в среднем ширине колеи |
за 3 месяца без |
учета отступлений по |
T= 700/Гр
На однопутном:
Период капитальных ремонтов - 35 лет;
Период среднего ремонта - 17-18 лет;
Период от капитального до выправки ~ 6 лет;
Период до второй выправки - 6 лет;
Период от среднего ремонта до выправки - 6 лет;
Период от выправки до подъемочного ремонта - 6 лет.
На двухпутном участке, на четном пути:
Период усиленных капитальных ремонтов - 15 лет;
Период среднего ремонта - 7-8 лет;
Период от усиленного капитального ремонта до выправки ~ 2-3 года;
Период до второй выправки - 2-3 года;
Период от среднего ремонта до выправки - 2-3 года;
Период от выправки до подъемочного ремонта - 2-3 года.
Основные критерии назначения работ по подъемочному ремонту пути табл.16
На двухрутном участке, на нечетном пути:
Период усиленных капитальных ремонтов - 20-21 год;
Период среднего ремонта - 10-11 лет;
Период от усиленного капитального ремонта до выправки ~ 3-4 года;
Период до второй выправки - 3-4 года;
Период от среднего ремонта до выправки - 3-4 года;
Период от выправки до подъемочного ремонта - 3-4 года.
В понятие приведенной длины входит все протяжение железнодорожного пути, искусственных сооружений и обустройств суммированных с учетом переводных коэффициентов.
В курсовом проекте за единицу приведенной длины будем считать 1 км главного пути однопутного участка звеньевого пути на деревянных шпалах на щебеночном балласте.
Бесстыковой путь переводится в приведенную длину за счет применения коэффициента - 1,2. На Двухпутный участках используется понижающий коэффициент 0,75.10 стрелочных переводов приравниваются к 1 км пути. Для определения приведенной длины станционных путей используют коэффициент 0,33.
Для фактического определения приведенной длины определяется множество факторов в том числе эксплуатационная работа - это состояние пути в плане, профиле и другие показатели.
В курсовом проекте приведенная длина определяется в соответствии с исходными данными, без учета инженерных и искусственных сооружений. По исходным данным приведенная длина составит:
Lприв.км
= а1
*Lгл
+ а2
*Lгл
+ аст
*Lст
+ ас.п
*Nс.п.
Для двухпутного участка:
Lприв.км
= 169*1,2+ 169*0,75= 329,6 км
Для однопутного участка:
Lприв.км
=1,2*64= 76,8 км;
Для стрелочных переводов:
Lприв.км
= 126*1/10= 12,6 км;
Lприв.км
= 38*1/15=2,53 км;
Т.о. получаем: Lприв.км
= 329,6+76,8+12,6+2,53=421,53 км;
Выбираем организационно-структурную форму машинизированной дистанции пути 2м.

Для выполнения НР
Текущее содержание по своей сущности противостоит процессу непрерывного накопления остаточных деформаций в пути. Поэтому структура ПЧ должна обеспечивать состояние пути на заданном техническом уровне соответствующими рациональными и эффективными формами организации работ своих производственных подразделений.
На формирование организационной структуры ПЧ и ее подразделений влияют наличный парк путевых машин, механизмов, транспортных средств, численность рабочей силы, определяемая развернутой длиной путей и их конструкцией, числом стрелочных переводов, протяженностью искусственных сооружений, параметрами эксплуатационных условий и т.д. Наибольшая протяженность ПЧ определяется возможностью оперативного управления ее производственными подразделениями и необходимостью выполнения своевременного натурного осмотра пути, ее обустройств и сооружений.
В зависимости от оснащенности путевыми машинами, для выполнения комплексных планово-предупредительных работ текущее содержание осуществляется механизированными и машинизированными дистанциями пути.
Одна из основных задач путевого хозяйства - обеспечить перевод его практически полностью на машинизированный способ текущего содержания, при котором выполнение наиболее трудоемких работ производится машинными технологическими комплексами.
Границы ПЧ и ее подразделений (участков, околотков, рабочих отделений) устанавливаются на основе расчетов приведенной длины пути (прив.км).
Рекомендуемая приведенная длина современных ПЧ с учетом их укрупнения указана в табл.
Приведенная длина дистанции пути и ее подразделений, привед.км
Участки |
Подразделение |
Однопутные |
Двухпутные |
Дистанция пути (ПЧ) |
200…300 |
300…400 |
Околоток (ПД) |
21…25 |
24…31 |
Рабочее отделение (ПДБ) |
7…8 |
8…10 |
Участок (ПЧУ) |
состоит из 3-4 околотков |
Указанные рекомендации учитываются при обосновании организационной структурной формы ПЧ в увязке с результатами расчетов производственного контингента различных бригад, необходимого для выполнения всего планируемого объема работ текущего содержания.
Для механизированных ПЧ рекомендовано 5 основных структурных форм, из них три для перегонных участков с малыми станциями и две - для крупных станций и околотков.
Характерным для каждой из них является деление механизированной ПЧ на околотки, которые, в свою очередь, могут делиться или не делиться на рабочие отделения.
Каждая организационно-структурная форма имеет свою рациональную сферу применения. Форма 2м - участковая с околотками и рабочими отделениями. Планово-предупредительные работы выполняет укрупненная бригада, а неотложные на каждом рабочем отделении - бригада из 5-7 чел. Во главе с освобожденным бригадиром.
Расчет возможной численности монтеров пути, а точнее расчетный контингент как в целом для дистанции, так и для конкретного ее подразделения определяется по дифференцированным формам затрат труда на текущее содержание пути и искусственных сооружений на основе приказа МПС №8 от 3 апреля 1997г.


Расчет численности монтеров пути для механизированных дистанций ведется по формулам:
а) для главных путей
Ргл
= Lгл-1
*Nгл1
+ Lгл-2
*Nгл2
+ Lго п
*Nгл п
,
где Ргл
- численность монтеров пути, чел.; 133128
N - норма расхода рабочей силы.
Ргл
= 169*0,786+169*0,753+64*0,470= 292 чел.
б) для стрелочных переводов
Рсп
= Псп-1
*Nсп1
+ Псп-
j
*Nсп
j
,
где Псп-1,
Псп -
j
- число стрелочных переводов по каждому типу и марке;
Nсп
- нормы расхода рабочей силы.
Рсп
= 63*0,153+63*0,17+38*0,34=33 чел.
Схема условной железной дороги

Одной из главных проблем путейцев является выход дорогостоящих рельсов. Их дефекты известны, квалифицированны. Задача заключается в технологическом обеспечении условий, предотвращающих образование дефектов.
Известно, что прочность и твердость рельсовых сталей взаимосвязана. Однако показатель твердости однозначно не характеризует прочность и обеспечение высокой надежности. Высокая твердость материала при определенных условиях может быть причиной повышенной хрупкости и излома при динамических нагрузках. Только сочетание высокой твердости и необходимой вязкости материала позволяет получать высокопрочные изделия.
Специфической особенностью изготовления рельсовых плетей из объемнозакаленных сталей оказывающей существенное влияние на возникновение остаточных напряжений и локальное разупрочнение сталей, является повторный нагрев торцов под сварку.
Электроконтактной сварке оплавлением присуще следующие недостатки:
Снижение твердости в зоне шва;
Образование крупнозернистой структуры;
Образование грата;
Недостаточная прочность и пластичность сварных стыков.
Для достижения более высоких эксплуатационных свойств предложен комбинированный способ сварки давлением с последующим объемным легированием сварного стыка методом сверхглубокого проникновения частиц, полученных методом самораспространяющегося высокотемпературного синтеза.
Комбинированный способ обеспечивает:
Формирование мелкодисперсной структуры;
Повышение твердости, прочности, износостойкости сварного шва;
Предотвращение образования грата и снижение затрат на его удаление.
Особенности сварки современных рельсов.
С увеличением количества плетей из новых и старогодных рельсов, внедрением рельсов из кислородно-конверторной стали и стали, выплавленной в электропечах, стал острее вопрос о качестве сварных стыков. В настоящее время на сети дорог действует 20 рельсосварочных предприятий, изготавливающих в год около 5000 км плетей из новых объемнозакаленных рельсов. При этом сваривают около 500 тыс. стыков по технологии, включающей контактную сварку, механическую и термическую обработку, дефектоскопирование. Каждая из операций ответственная, и несоблюдение или нарушение технологии может привести к браку в стыках.
Статистические данные об остродефектных рельсах, обнаруженных средствами дефектоскопии в пути, показывают, что в зоне сварных стыков становится больше дефектов 26.3 (в головке), 56.3 (в шейке) и 66.3 (в подошве).
Причины их образования следующие:
несоблюдение технологии контактной сварки - неметаллические включения, непровары, рыхлости, кратерные усадки;
несоблюдение технологии абразивной обработки - местные неровности на поверхности металла (врезание в тело, концентраторы напряжений в виде острых кромок), поджоги поверхностного слоя металла;
несоблюдение технологии термической обработки - образование мартенсита в поверхностном слое металла головки;
отсутствие термической обработки - смятие и повышенный износ головки, развитие усталостной трещины в области поджога поверхностного слоя металла сварного стыка.
На рис.1 показаны некоторые из перечисленных дефектов. Все упомянутые дефекты можно разделить на появившиеся в результате нарушения технологии сварки и на образовавшиеся в результате нарушения; технологии послесварочных операций.
При электроконтактной сварке оплавлением в ряде случаев в стыке возникают дефекты из-за неполного выравнивания кратеров на концах изделия. Газ и окисленный жидкий металл, находящиеся в кратерах, при кристаллизации образуют такие дефекты как газовый пузырь, рыхлость, кратерная усадка.
Неполное выдавливание из стыка жидкого металла при осадке приводит к появле- шию скоплений неметаллических включений, ориентированных по оси стыка.
В отличие от других способов сварки давлением при нагреве непрерывным оплавлением соприкасающиеся поверхности свариваемых деталей (рельсов) всегда неровные из-за взрывообразного разрушения контактов, большая часть которых покрыта жидким слоем металла (расплава).
На поверхности торца слой металла неоднороден по толщине. Толщина расплава на торцах рельсов зависит от особенностей разрушения элементарных контактов и может изменяться от нуля в местах, где наблюдается срыв жидкого слоя при взрыве контакта, до миллиметра на участках, где металл скапливается в углублениях на поверхности оплавления.
Все участки этой поверхности имеют высокую температуру, близкую к температуре плавления металла, и могут интенсивно окисляться, так как при сварке рельсов оплавлением воздух проникает к соприкасающимся поверхностям, а зазор между ними (искровой зазор) на отдельных участках может достигать нескольких миллиметров.
Учитывая, что при взаимодействии кислорода воздуха с жидким металлом окисление протекает более интенсивно, чем при взаимодействии с твердым металлом, можно ожидать низкокачественной сварки.
По лини шва при сварке углеродистых низколегированных рельсовых сталей непрерывным оплавлением многие дефекты представляют собой оксиды металла и других легирующих элементов.

Рис.1. Основные дефекты в сварных стыках: а -
рыхлость; б -
кратерная усадка; в -
следы термомеханического воздействия абразивного круга при шлифовке; г -
выкрашивание поверхности катания головки сварного стыка в области образования неблагоприятных закалочных структур при нарушении технологии упрочнения воздушно-водяной смесью
С массовым внедрением рельсов из стали, выплавленной в электропечах, и
в 2002-2003 гг. дороги столкнулись с проблемой их свариваемости (образование дефектов сварочного характера и недостаточная прочность и пластичность сварных стыков).
В 2000 г. был принят ГОСТ Р 51685-2000 "Рельсы железнодорожные. Общие технические условия", и все рельсы массовых поставок для железных дорог изготавливаются в соответствии с ним. По техническим требованиям к химическому составу и механическим свойствам рельсы мартеновского, конвертерного и электропечного производства не различаются. Кроме того, фактическая прочность и твердость металла почти такие же, как у рельсов, выпущенных по старым стандартам.
Однако рельсы электропечного производства НКМК отличаются большей чистотой по неметаллическим включениям и содержанием ряда примесей легирующих элементов по верхнему пределу, регламентированному ГОСТ. Поэтому рельсовый металл имеет склонность к подкаливанию зоны сварного шва. В результате при контактной сварке необходим более концентрированный нагрев м^т^ма-*-выоспшпшч11Лъная-€4шрость осадки (минимально около 35-40 мм/с).
Во время испытаний рельсов на статический поперечный изгиб и при изломах в пути в плоскости излома видны матовые пятна серого цвета. При исследовании микроструктуры образцов в зоне этих пятен в сварном шве обнаружены неметаллические включения, не выдавленные при осадке в процессе сварки.
Анализ карт поверхности изломов в характерном рентгеновском излучении с помощью прибора САМЕВАХ 8X50 показал наличие различных, но преимущественно алюмино-кальциевых неметаллических включений. Такие включения значительно снижают прочность сварного стыка рельсов. Это характерно для контактной стыковой сварки рельсов из электростали непрерывным оплавлением и необеспечением достаточных скоростей закрытия искрового зазора при осадке.
Микроисследования подтверждают, что разрушение после статических - испытаний проходит по сварному шву. Во время исследования микроструктуры шва помимо неметаллических включений, часто встречаются рыхлости, что указывает на недостаточно уплотненный металл (см. рис.1, я).
В стационарных условиях рельсосварочных поездов проблему сварки рельсов электропечного производства удается решить с помощью сварочных машин типов К-1000 и МСР-6301, обладающих большой электрической мощностью, имеющих гидроаккумуляторы и выполняющих сварку методом пульсирующего оплавления, а также термообработки сварных стыков.
При разработке технологии сварки современных российских, а также импортных рельсов для достижения высокого качества шва необходимо предусмотреть регулировку интенсивности и ширины разогрева концов рельсов в процессе оплавления. Применяемый на контактных машинах старого поколения (типов К-190, К-355) способ непрерывного оплавления уже не может в полном Iобъеме обеспечить эти требования.
Контактные машины типа К-355, составляющие более 80 % парка оборудования для сварки в пути, были созданы более 30 лет назад, они не имеют гидроаккумуляторов (максимальная начальная скорость осадки 25 мм/с) и не могут выполнять сварку методом пульсирующего оплавления. Поэтому при сварке 1 некоторых партий новых рельсов возникают проблемы, связанные с получением нужных прочности и пластичности стыков.
Наиболее перспективный способ пульсирующего оплавления разработан в ИЭС им. Е.О. Патона НАН Украины. В России он применяется с 1997 г. на стрелочных заводах для сварки деталей стрелочных переводов. Сущность способа заключается в том, что сопротивление между рельсами во время оплавления непрерывно поддерживается на уровне, обеспечивающем максимальную полезную мощность, генерируемую в месте контакта деталей. При одинаковых мощности и напряжения в сварочной цепи сила тока при пульсирующем оплавлении выше в 1,5-2,5 раза, чем при непрерывном, и поддерживается во время Iсварки постоянной. Увеличивается скорость нагрева и уменьшаются припуски на оплавление рельсов. Можно получать концентрированный нагрев в зоне разогрева. Это сокращает время сварки. Изменение скорости оплавления регулируется по кривой тока. В компьютерной системе задается скорость оплавления Vи наклон кривой силы тока I. Меняя эти параметры, можно изменить интенсивность нагрева в зависимости от необходимого тепловложения в стык для разных марок сталей.
Новые марки сталей, которые начали или планируют использовать металлургические комбинаты (в частности, Э76, Э76Ф), требуют более интенсивного и равномерного разогрева концов рельсов.
Непрерывное регулирование параметров сварки, в том числе и перед осадкой, достигаемое быстродействующими регуляторами, обеспечивает более ровную поверхность оплавления торцов рельсов. Кроме того, кратеры на торце во время оплавления имеют меньшую глубину, что понижает вероятность образования различных дефектов в сварном стыке.
В Комплексном отделении "Сварка" ВНИИЖТа исследовали металл сварных соединений рельсов, выполненных пульсирующим оплавлением. При разработке режимов сварки в РСП испытывали контрольные образцы рельсов на поперечный статический изгиб с расстоянием между опорами 1 м. Средние значения разрушающей нагрузки для новых рельсов типа Р65 при растяжении подошвы составляют 2400 кН, при растяжении головки - 2200 кН; стрелы прогиба в среднем равны 36 мм и 35 мм соответственно. Для новых рельсов типа Р75 эти значения составляют соответственно 2720 кН и 2100 кН, 38 мм и 22 мм.
При макроисследованиях темплетов сварных рельсов дефекты сварочного характера не обнаружили, ширина зоны термического влияния узкая и составляет 13-15 мм в одну сторону от сварного шва, что в 1,5 раза меньше чем при "классическом" непрерывном оплавлении. На рис.2 представлены продольные макротемплеты и распределение твердости по поверхности катания сварных стыков после различного вида оплавления. В образцах, вырезанных из сварного рельса, после травления 4-процентным раствором азотной кислоты выявляются шесть участков, из которых состоит околошовная зона.
Микроструктура сварного шва - это крупнозернистый сорбитообразный перлит и ферритная сетка вокруг зерен. Ширина сварного шва 0,3-0,5 мм. Металл шва хорошо уплотнен, неметаллических включений нет. За зоной шва следует зона неполного расплавления, структура которой также состоит из крупнозернистого сорбитообразного перлита с обрывками ферритной сетки. Усадочных рыхлостей и загрязнений неметаллическими включениями нет.
В этой зоне неполного расплавления нарушается связь между волокнами, и от ее осадки зависит качество сварного стыка.
При недостаточной осадке могут остаться незаваренными мелкие усадочные пустоты, а иногда скопления загрязнений на месте бывших очагов плавления.
Следующие зоны - рекристаллизации или крупного зерна, далее нормализации или мелкого зерна, потом - неполной нормализации и основной металл.
Средняя твердость сварного шва - 290 НВ, зон перехода к основному металлу - 270 НВ, что характерно для стыков рельсов, термически не обработанных после сварки.
Ширина зоны разупрочнения металла стыка рельса, сваренного методом непрерывного оплавления, составляет 80 мм, методом пульсирующего - 50 мм (см. рис.2, б).
Существенное уменьшение ширины этой зоны при пульсирующем оплавлении значительно увеличит эксплуатационную стойкость рельсов.

Рис.2. Макроструктура и твердость сварных стыков; а -
характер зоны термического влияния после сварки рельсов соответственно пульсирующим и непрерывным оплавлениями; бив -
распределение твердости металла по поверхности катания сварных стыков соответственно после пульсирующего и непрерывного оплавлений
По результатам механических испытаний и металлографическим исследованиям можно сделать вывод, что качество сварки пульсирующим оплавлением соответствует нормативно-технической документации.
В 2002 г. сотрудники ВНИИЖТа, ИЭС им. Е.О. Патона и Каховский завоД электросварочного оборудования начали внедрять такое оплавление в РСП и на машинах К-1000. Были разработаны режимы сварки рельсов типов Р65 и Р75. К настоящему времени этот метод применяется почти^на^всех машинах. Для сварки рельсов в пути без единовременной замены устаревшего оборудования существует техническое предложение, не требующее больших капиталовложений. Это модернизация контактных машин К-355 (гидросистемы и системы управления) для сварки рельсов методом пульсирующего оплавления и оборудование ПРСМ индукционными установками для термической обработки стыков.

Рис.3. Оборудование нового поколения: а -
стационарная индукционная установка типа
УИН-001 - 100/РТ
Первый опыт модернизации головки К-355 осуществлен на ЗАО "Техэлектро" (г. Псков). На рис.3, я представлена сварочная головка К-355А1М с системой управления и контроля на базе промышленного компьютера. Она оснащена гидроаккумулятором для достижения высоких скоростей осадки. Модернизация выполнена в соответствии с техническим заданием Департамента пути и сооружений ОАО "РЖД". Машина испытывается в полевых условиях.
Доказана необходимость применения дифференцированной термической обработки сварных стыков, заключающейся в упрочнении головки стыка с повторного перекристаллизационного индукционного нагрева всего его сечения с последующей нормализацией подошвы и шейки рельса. В результате такой операции повышается твердость металла головки до необходимого уровня. Вследствие измельчения структуры металла в шейке и подошве сварного стыка при нормализации индукционным нагревом возрастает усталостная и хрупкая прочность.
Бесстыковой путь у нас работает в сложных климатических и эксплуатационных условиях. На дорогах Сибири и Дальнего Востока годовые амплитуды температуры рельсов колеблются от 105 до 125 °С. Максимальные суточные амплитуды температур равны 35-60 °С. Такие перепады создают критический уровень температурных сил, приводящий к выбросам плетей или их изломам с образованием зазоров 60-80 мм, причем почти 30 % их приходится на места сварки.
Следует также отметить, что в морозы увеличивается вероятность хрупких разрушений как самих рельсов, так и сварных стыков. Критическая температура поднимается с образованием в стали крупнозернистой структуры металла при сварке и с появлением в месте дефекта неблагоприятных остаточных напряжений.
Проведенные ВНИИЖТом комплексные исследования показали, что незакаленные рельсы становятся хрупкими при минус 15-20 °С, термически упрочненные - при минус 30-35 °С, сварные стыки закаленных рельсов - при минус 20-40 °С.
В морозы сопротивляемость удару сварных стыков значительно ниже, чем целых несварных объемнозакаленных рельсов. При температуре - 60 °С, являющейся основным охрупчивающим фактором, охватывающей все климатические зоны нашей страны и лежащей заведомо ниже критической температуры хрупкости объемнозакаленных рельсов и их сварных стыков, сопротивляемость удару сварных рельсов в 6 раз меньше, чем несварных.
Хрупкие разрушения во время эксплуатации происходят очень редкоблагодаря строгому соблюдению технологии, режимов сварки и обработки стыков, а также отсутствию в них дефектов. Если была нарушена технология при изготовлении сварных плетей и в стыках появились дефекты, то разрушения такого типа возможны, особенно в виде хрупких доломов, которыми заканчивается развитие усталостной трещины, образовавшейся от дефекта.
Дифференцированная термическая обработка сварных стыков рельсов с упрочнением головки и нормализацией шейки и подошвы устраняет зональную структурную неоднородность металла. При этом упрочненный слой головки представляет собой мелкозернистый сорбит отпуска с тонкой сеткой феррита вокруг зерен, микротвердость составляет Н5
о =
3200-3450 МПа. Данная структура типична для упрочненной рельсовой стали. Микроструктура металла шейки и подошвы стыка - это сорбитообразный перлит с разрозненной сеткой феррита, микротвердость равна Н5
о - 2600-2800 МПа, что характерно для неупрочненной рельсовой стали.
Конструкционная прочность сварных стыков - важнейший фактор, влияющий на их эксплуатационную надежность. Долговечность в области ограниченной выносливости и предел выносливости у термообработанных стыков выше: на 45-50 %, чем у незакаленных и на 15-20 %, чем у цельнокатанных серийных рельсов.
Испытания на копровую прочность рельсовых проб длиной 1200 мм со сварным стыком по середине при температуре - 60 °С выявили, что показатели хрупкой прочности после термообработки увеличиваются на 300 %. Повышение усталостной и хрупкой прочности сварных стыков, подвергнутых дифференцированной термической обработке, благоприятно сказывается на живучести рельсов в северных районах нашей страны.
Применяемые в рельсосварочных предприятиях индукционные установки типа ИТТЗ-250/2,4 не отвечают современным требованиям ресурсосбережения.
Основные причины заключаются в следующем: высока потребляемая мощность (250 кВт); для эффективного охлаждения трансформаторного блока, индукторов и токопреобразователя частоты нужна дистиллированная вода с отдельными накопителями и подающими гидросистемами из нержавеющих сплавов; фор'сунки воздушно-водяного распылителя для закалки головки стыка часто засоряются, что приводит к образованию неблагоприятных закалочных структур на поверхности катания. Имеется 30 таких установок в 17 РСП из 20. В 10 РСП из 17 данное оборудование по приведенным выше причинам не применяется. Анализ остродефектных рельсов показал, что наибольшее количество дефектов в зоне сварных стыков выявлено на тех дорогах, где в РСП не используют или ограниченно используют индукционное оборудование. То есть технология дифференцированной термической обработки стыков в большинстве РСП не применяется из-за несовершенства оборудования.
На основании новейших достижений в электротермии и совместных разработок ВНИИЖТа и НИИ АЭМ (г. Томск) изготовлено индукционное оборудование нового поколения типа УИН-001-100/РТ (см. рис.3,6), отвечающее требованиям ресурсосберегающей политики
ОАО "РЖД".
Прогрессивным направлением усиления верхнего строения пути является замена болтовых стыков сварными. Применение сварки, наряду с увеличением мощности рельсов и термическим их упрочнением, повышением чистоты стали и качества металла, улучшает работу пути и снижает затраты на содержание. Сварка позволяет увеличить длину рельсов, уменьшить количество дорогостоящих болтовых стыков и снизить уровень динамического взаимодействия пути и подвижного состава. В нашей стране большое распространение получила укладка в путь бесстыковых плетей из термически упрочненных рельсов.
Прочность и надежность рельсов, сваренных контактным способом, достигается правильным выбором и строгим соблюдением технологии и режимов сварки, термической и механической обработки сварных стыков. В результате дифференцированной термической обработки сварных стыков на индукционных установках до уровня прочности основного металла термически упрочненных рельсов восстанавливается твердость а головке и структура сорбита закалки. Пределы текучести металла и выносливости сварных рельсов не ниже прокатных. „Лри качественной контактной сварке и обработке стыков усталостных изломов рельсов по сварке в пути практически не бывает. Для обеспечения прочности и надежности работы в пути термическая обработка стыков при сварке рельсов современного и перспективного производства с высоким содержанием углерода и других легирующих элементов является обязательной.

Рис.1. Макро- и микроструктура сварного соединения рельсов без термической обработки: 1 - шов; 2, 3, 4, 5 - соответственно: зоны неполного расплавления металла, крупного и мелкого зерна, неполной нормализации; 6 - основной металл- (XI00).
На дорогах России и других стран разработана и внедрена технология контактной сварки закаленных и термически не упрочненных рельсов, обеспечивающая высокие технико-экономические показатели процесса, механизацию, автоматизацию и компьютеризацию работ.
Сварное соединение рельсов без термической обработки стыков имеет крупнозернистое строение (рис.1) и более низкие механические свойства, чем основной металл.
Зоны сварного стыка по сравнению с прокатными рельсами обладают меньшей пластичностью, вязкостью и большей склонностью к хрупким разрушениям.
У рельсов обычной прочности в зоне сварки разброс твердости колеблется в небольших пределах (НВ 10-30).
При сварке рельсов повышенной и высокой прочности в стыках происходит значительное снижение твердости (соответственно на НВ100 и 150), износостойкости и предела выносливости металла в головке (рис.2).


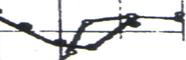
0 100 80 60 40 20 0 20 40 60 80 100 l, мм
Рис.2. Твердость металла головки сварных запаленных рельсов.
Единичные измерения твердости металла показаны на графике кружками (белые - сварные стыки без термической обработки, черные - сварные стыки после термической обработки): а-д - рельсы типа Р65, а-г из стали М76, д - из стали" 75ХГСТ; а - термически не упрочненные - малый разброс твердости металла; б-е - закаленные; б, в - сварка прерывистым подогревом и непрерывным оплавленном, закалка с тепла сварки; г, д - закалки с индукционного нагрева с широкой и узкой зоной нагрева в головке и тепла сварки - после пропуска 400 млн. т груза брутто; в процессе эксплуатации твердость металла в головке дополнительно выравнивается и повышается; е - закалка с индукционного нагрева - большое выравнивание и повышение твердости металла; 1 - стыки без термической обработки; 2 - стыки после упрочнения (выравнивание и повышение твердости металла); мм - расстояние
Для повышения прочности (долговечности развития усталостной трещины), живучести, износостойкости и надежности работы в пути на дорогах России и стран СНГ разработана и внедрена сварка бесстыковых плетей с термической и механической обработкой стыков. При термической обработке твердость металла головки сварных стыков рельсов повышается и выравнивается, а в процессе эксплуатации пути твердость металла еще дополнительно выравнивается (см. рис.2, г, д).
В результате исследований, проведенных ВНИИЖТом, ВНИИ ТВЧ им. Вологдина, Департаментом пути и сооружений МПС России и рельсосварочными предприятиями дорог, создан способ и оборудование для сварки рельсов с дифференцированным термическим упрочнением и механической обработкой стыков.
Техническая характеристика индукционной установки
Была создана индукционная установка нового поколения для термической 'бработки сварных стыков рельсов на технологических линиях рельсосварочных предприятий ИТСМ-250/2,4, кроме того, создана передвижная путевая машина ИТП-250/2,4.
Тип обрабатываемых рельсов Р75, Р65, Р65К, Р50
Переходные стыки рельсов Р75/Р65, Р65/Р50
Мощность источника питания токами
средней частоты 250 кВА
Частота тока 2,4 кГц
Рабочий зазор между витками индуктора
и рельсом 5-10 мм
Температура нагрева сварных стыков 850-875 °С
Продолжительность нагрева сварных стыков 120-240 с
Продолжительность охлаждения металла головки:
закаленные рельсы
воздушно-водяной смесью 40-80 с
воздухом 80-120 с
Продолжительность подстуживания металла головки
воздушно-водяной смесью (термически
не упрочненные рельсы) 10-20 с
Разработку осуществили и внедрили ВНИИЖТ, ВНИИ ТВЧ им. В.П. Вологдина, Департамент пути МПС России и РСП-20 Куйбышевской дороги. При сварке рельсов обычной, повышенной и высокой прочности производится дифференцированная термическая обработка. Она включает нагрев всего сварного стыка рельсов токами средней частоты с помощью специальных индукторов и принудительное охлаждение металла головки воздушно-водной смесью. Индукционные установки снабжены компьютерной техникой. Это обеспечивает рациональный выбор параметров нагрева в зависимости от температуры металла стыков. Различная термическая обработка сечения сварных стыков рельсов, например упрочнение головки с самоотпуском, повышение пластичности металла в подошве и шейке путем нормализации, выполняются в виде единой технологической операции по установленной программе на одном и том же индукционном оборудовании для различных типоразмеров рельсов и марок стали.
Механически обработанные торцы.

Рис.3.5 Сварка с предварительным азотированием и динамическим легированием торцов (механическая обработка торцов с нанесением нанопорошков)

Рис.3.6 Сварка с предварительным азотированием и динамическим легированием торцов (азотирование торцов рельса для достижения в сварных швах мелкодисперсной структуры)

Рис.3.7 Сварка с предварительным азотированием и динамическим легированием торцов (динамическое микролегирование торцов микро - и нанопорошками для повышения износостойкости, прочности и твёрдости)

Рис.3.8. Твердость в зоне сварного стыка при электроконтактной сварке и сварке давлением с подогревом

Рис.3.9. Крупнозернистая структура металла и грат, образующийся при электроконтактной сварке рельсов
1. И.Б. Лехно “Путевое хозяйство”, 1990.
2. Н.П. Кондаков “Проектирование, организация и планирование путевого хозяйства”, 1974.
3. В.Г. Альбрехт “Бесстыковой путь”, 2000.
4. З.Л. Крейнис “Техническое обслуживание и ремонт жд пути”, 2001.
5. Инструкция по техническому содержанию жд пути, М. -2000.
6. Положение о системе ведения путевого хозяйства на ЖД РФ, утвержденное 27.04.2001.
7. Инструкция по тех. обслуживанию и эксплуатации сооружений, устройств, подвижного состава и организации движения на участках движения скоростных пассажирских поездов, 1991.
8. Технические условия на работу по ремонту и планово-предупредительной выправке пути/МПС России, 2000.
9. Технические условия по устройству, укладке, содержанию и ремонту бесстыкового пути / МПС России, 2000.
10. Среднесетевые нормы расхода материалов и изделий на текущее содержание, планово-предупредительную выправку пути и других устройств путевого хозяйства / МПС РФ, 1998.
11. Правила и технологии выполнения основных работ при текущем содержании пути / МПС РФ, 1998.
12. Отраслевые нормы времени на работы по ремонту ВСП (Технолого-нормировочные карты).
13. Типовые технические обоснования нормы времени на работы по текущему содержанию и ремонту земляного полотна и ИССО. М-1999.
14. Технические указания по устройству, укладке, содержанию и ремонту пути. - М.: Транспорт:, 2000.
15. Новакович В.И. Бесстыковой путь со сверх длинными рельсовыми плетями: Учебное пособие. - Ростов - На - Дону: Ростовский государственный университет путей сообщения, 2001. - 92с.
16. Бесстыковой путь / Под ред. В.Г. Когана. - М.: Транспорт, 2000. -408с.
|