Глава 5. Логистика производственных процессов
5.1. Цели и пути повышения организованности материальных потоков в производстве
Предметом изучения логистики как науки
является оптимизация потоковых процессов. Принципы логистики: синхронизация, оптимиза ция и интеграция — служат основным методологическим подходом к повышению организованности и эффективности функционирования производственных систем.
Логистика
— это еще и уровень культуры использования знаний о природе и обществе, позволяющий не только принимать и осуществ лять системные решения, но и воспитывающий системное представле ние, на базе которого возможна гармонизация деятельности людей в крупных организациях.
Методология логистики позволяет осуществлять системную раци онализацию сложных производственных систем. Она вооружает нас методами повышения организованности производственных систем и позволяет эффективно завоевывать конкурентные преимущества.
В условиях рыночной экономики выживаемость предприятий, завоевание ими конкурентных преимуществ возможны лишь при условии их обязательной непрерывной организационно-техничес кой перестройки с целью приближения реально существующего производства к его оптимальному проекту, соответствующему достигну тым уровням знаний, техники, технологии, организации и управле ния производством.
Эта организационно-техническая перестройка представляет со бой непрерывный процесс гибкой адаптации предприятия к непре рывно меняющимся условиям рынка, к нестабильным налогам и методам государственного регулирования. Для достижения устойчи вой конкурентоспособности на рынке процесс перестройки органи зации должен идти как процесс сближения существующей модели организации с ее идеальным проектом.
Оптимальный проект организации должен соответствовать со временным уровням технологии, техники и культуры (знаний) орга низации и управления предприятиями.
Разработку оптимального проекта предприятия как высокоорганизованной и гибкой производственной системы (ПС) можно представить в качестве типового процесса, который начинается с опре деления главной специфической цели функционирования системы и предполагает ее типовую дикомпозицию, что сегодня известно как «дерево целей» (см. рис. 25).
Что касается подсистем организации и управления промышлен ным предприятием, то они имеют иные цели первого уровня, но одинаковые цели второго, третьего и четвертого уровней, как это показано на рис. 25.
Исходя из сущности понятия системы и цели ее функционирования, которые раскрываются на основе системного подхода к изуче нию или проектированию ПС, следует выделить триединые части: функциональную, элементную и организационную.
Функциональный аспект организации системы — это структура взаимосвязанных функций, которая устанавливается в соответствии с целью и подцелями функционирования системы. Раскрытие со держания взаимосвязанной совокупности функций с одинаковой целевой направленностью определяет состав простейших функцио нальных задач и последовательность их решения. В итоге формиру ются логика действия каждой функциональной подсистемы и логика функционирования системы в целом.
В нашем примере (рис. 25) для подсистемы организации и управ ления основным производством главной целью функционирования является обеспечение своевременной и комплектной поставки про дукции в соответствии с хозяйственными договорами при миними зации затрат на достижение этой цели.
В условиях непоточного производства минимизация затрат на производство (цель второго уровня) может быть обеспечена за счет организации непрерывной загрузки производственных участков и плановых рабочих мест при максимально возможной непрерывности движения предметов труда в производстве.
Третий уровень целей, как нам представляется, должен быть на правлен на повышение организованности (эффективности) процес сов производства, т. е. на реализацию основных и противоположных принципов организации производства, на основе которых осуществляется рационализация построения и организации гибкого (адап тивного) функционирования и развития ПС.


Рис . 25. Концептуальная схема типового проектирования логистических систем на примере обобщенного алгоритма проектирования логистической подсистемы «организация и управление основным производственным процессом»
Например, целевая организация производственных процессов предполагает всяческое уменьшение неупорядоченности, разнооб разия и неопределенности в движении предметов труда как в прост ранстве, так и во времени. Так, однонаправленное движение предметов труда в производстве обеспечивает: (а) многократное умень шение сложности ПС и трудоемкости управления производством благодаря сокращению в десятки раз количества различных межце ховых и внутрицеховых технологических маршрутов и производст венных связей между участками; (б) создание базы для согласования сроков выполнения работ с непрерывной загрузкой плановых рабо чих мест и производственных участков; (в) повышение технологиче ской однородности работ на каждом рабочем месте и т. д.
Целевая организация производственных процессов осуществля ется в соответствии с главной целью предприятия, т. е. на основании годовой производственной программы предприятия, и формирует или уточняет их производственную структуру, или объектную струк туру предприятия (ПС).
Функциональный состав задач, подлежащих реализации в процессе функционирования предприятия, и спроектированная произ водственная структура предприятия вместе определяют организационную структуру управления предприятием, или его субъектную структуру.
В свою очередь, объектная и субъектная структуры предприятия образуют элементную структуру предприятия.
Гибкость адаптации предприятия к изменениям внешних и внут ренних условий работы обеспечивается за счет многих факторов, основными из которых являются гибкость техники и технологии, уровень профессионализма кадров, гибкость организации и управ ления производством.
Различают тактическую и стратегическую гибкость. Первая оп ределяет время, необходимое предприятию для освоения производства нового изделия или для реконструкции (создания) отдельного производства, связанного с нововведениями в технике, технологии, или то и другое вместе. Вторая определяет значимость возможных капиталовложений, эффекты, объем и время реконструкции пред приятия.
Реализация основных принципов организации производства приводит лишь к повышению организованности (эффективности) функ ционирования предприятия при относительно стабильных воздей ствиях окружающей среды; тогда как реализация основных и проти воположных принципов организации производства повышает еще и внутреннюю гибкость производства, т. е. способность оперативно, с минимальными затратами, адаптироваться к изменениям производ ственной программы, условий на рынке товаров и услуг, норм госу дарственного регулирования.
В итоге формируется динамичная организационная структура предприятия (ПС). Это как бы структура некоторой взаимосвязан ной совокупности методов организации и управления процессами производства в пространстве и во времени, соответствующая до стигнутому уровню знаний и обеспечивающая динамическое взаи модействие между компонентами системы в соответствии с их функ циональным назначением.
Наличие организационной структуры, объединяющей элементы предприятия и их функции в единое целостное образование и опре деляющей правила и направленность динамического взаимодействия элементов, — необходимое условие существования системы.
Четвертый уровень целей — обеспечение функционирования системы, сохранение гибкости и адаптивности системы в заданных параметрах (см. рис. 25). Здесь окончательно уточняется функцио нальный состав задач, решаемых в системе.
Сегодня в промышленных организациях сложилась негативная практика, когда свернуты или реализуются лишь частично такие основные функции управления, как прогнозирование, нормирова ние и планирование. Особенно внушают опасения плохая организация нормирования и недостаток специалистов по организации и нормированию труда.
Следует помнить, что если не реализуется в полном объеме хотя бы одна из основных функций управления, то система организации и управления материальными потоками в производстве начинает деградировать. Это происходит даже в том случае, когда цели более высоких уровней достигнуты и можно было бы пожинать плоды повышения эффективности производства.
5.2. Требования к организации и управлению материальными потоками .
Рациональная организация и управление материальными пото ками сегодня предполагают обязательное использование основных логистических принципов: однонаправленности, гибкости, синхрониза ции, оптимизации, интеграции потоков процессов.
Организации и оперативному управлению материальными пото ками принадлежит ведущая роль в оперативном управлении предприятием, в своевременной поставке продукции и особенно в целях повышения эффективности производства, так как в их рамках реша ются все вопросы, связанные с использованием производственных ресурсов во времени и в пространстве.
Современная организация и оперативное управление производством (материальными потоками) должны отвечать ряду требований.
1. Обеспечение ритмичной, согласованной работы всех звеньев производства по единому графику и равномерного выпуска продукции
Часто ритмичную работу отождествляют с равномерным выпус ком продукции, однако это неправомерно. Ритмичная работа — это прежде всего гармонизация всех процессов производства (основ ных, вспомогательных, обсуживающих и управленческих) и эффек тивное использование располагаемых ресурсов, т. е. работа в соот ветствии с принципами и методами логистики.
Представляется, что под ритмичной работой следует понимать оптимальную (целенаправленную, искусную в соответствии с закономерностями движения производственного процесса) организацию во времени и пространстве единичных 1 , частичных 2 и частных 1 про цессов в единый непрерывный производственный процесс, обеспе чивающий своевременный выпуск каждой конкретной продукции в установленных объемах с минимальными затратами производствен ных ресурсов.
В настоящее время очень сложно реализовать требование рит мичной, согласованной работы всех производственных подразделе ний предприятия из-за статического восприятия производственного процесса и статических методов ведения календарно-плановых рас четов хода производства.
2. Обеспечение максимальной непрерывности процессов производства
Непрерывность производственного процесса имеет две противо речивые стороны: непрерывность движения предметов труда и непрерывность загрузки рабочих мест. Вопрос в том, какой непрерывности производственного процесса отдать предпочтение в тех или в иных условиях.
" Единичный процесс — процесс изготовления партии деталей одного наи менования на производственном участке .
Частичный процесс — процесс изготовления комплекта деталей одного изделия ( заказа ) на производственном участке .
э Частный процесс — процесс изготовления изделия ( заказа ) одного наиме нования на всех стадиях производства , во всех производственных подразделе ниях основного производства .
Исследованиями установлено, что в процессе производства про должительности всех взаимосвязанных операций выравниваются до некоторого календарного предела. Причем минимальный календарный предел выравнивания близок по величине к максимальной продолжительности операции в рассматриваемой совокупности взаимосвязанных операций. Выравнивание продолжительности опера ций может происходить либо за счет простоев рабочих мест, либо за счет пролеживания предметов труда, либо за счет того и другого одновременно.
Следует иметь в виду, что час простоя рабочего места (рабочего и оборудования) в условиях непоточного производства наносит убыт ки во много раз большие, чем убытки производства от часа проле живания предметов труда одного наименования. Поэтому общий критерий оптимизации — минимум затрат производственных ресур сов — в условиях непоточного производства может быть обеспечен за счет организации непрерывной загрузки рабочих мест, тогда как в поточном производстве — выбором варианта с минимальным вре менем межоперационного пролеживания деталей.
3. Обеспечение максимальной надежности плановых расчетов и минимальной трудоемкости плановых работ
Сегодня на машиностроительных предприятиях, как правило, используются статические методы планирования и управления про изводством, которые порождают ряд трудноразрешимых проблем, как-то:
- а) дефицит производственных мощностей. Производство отстает от графика из-за нехватки рабочей силы и оборудования. Это приводит к дополнительным сверхурочным работам, нарушениям сроков по ставок готовой продукции, жалобам потребителей, необходимости вести учет неудовлетворенных заявок и другим аналогичным трудностям;
- б) субоптимальность календарных планов производства. Из-за отсутствия четких приоритетов заказов, неэффективности действующих правил формирования графиков, а также постоянных изменений текущего состояния работ в цехе многие работы назначаются к выполнению неправильно. В результате имеет место прерывание производственных циклов для выполнения таких работ, у которых неожиданно увеличились приоритеты, возрастает число переналадок оборудования, а работы, шедшие по графику, внезапно начинают отставать;
- в) большие длительности производственных циклов. Пытаясь скомпенсировать трудности, связанные с проблемами «а» и «б», планирующий персонал практикует выделение дополнительного времени на выполнение отстающих заказов. По этой причине производство в цехе перегружается, сбиваются приоритеты заказов, что в итоге при водит к чрезмерному увеличению продолжительности производст венных циклов;
- г) неэффективное управление запасами. В то время когда суммарные запасы сырья, полуфабрикатов и готовой продукции чрезмерно велики, по некоторым необходимым в производстве позициям имеет место дефицит. Высокий уровень суммарных запасов оборачивается большими издержками по их содержанию, а нехватка сырья приводит к отставанию от графиков производства;
- д) низкий КПД оборудования. Эта проблема отчасти является следствием плохого календарного планирования (излишне частые переходы с выпуска одного вида продукции на другой, прерывание работ), а также других факторов, которые не могут контролироваться в полной мере (например, движение «узких» и «широких» мест в производстве, поломки оборудования, снижение спроса на выпускаемую продукцию);
- е) отклонения от технологии производства. Это, например, замена постоянных технологических маршрутов на специально подбираемые последовательности операций в обход узких мест. В результате растет объем наладочных работ, на станки устанавливается неподходящая оснастка, уменьшается эффективность процесса обработки.
С этими проблемами сталкиваются не только в России, но, на пример, и в США. В значительной мере они порождены ошибочным представлением о ходе производства как о статичном процессе и свидетельствуют о недостаточной надежности плановых расчетов.
Представление о ходе производства как о статичном процессе ба зируется на следующих предположениях.
Предполагается, что длительность производственного цикла из готовления детали является величиной конечной, окончательной, а на самом деле она является величиной вероятностной — ошибка в определении сроков составляет сорок процентов.
Предполагается, что длительность производственного цикла ве дущей детали комплекта определяет длительность его производственного цикла. Тогда как длительность производственного цикла комплекта деталей как минимум в 1,5 раза больше длительности производственного цикла ведущей детали комплекта, и ошибка воз растает еще в 1,5 раза.
Если первые два предположения приводят только к нарушениям плановых сроков, то следующие повинны в разбаланисировке пла нов, штурмовщине и дефиците деталей на сборке.
Предполагается, что трудоемкость изготовления изделия распре деляется равномерно в пределах каждой стадии длительности производственного цикла. На самом деле плотность (интенсивность) ра бот на протяжении цикла каждой стадии производства меняется в значительных пределах.
Предполагается, что внутри каждой стадии производства структу ра трудоемкости работ изготовления изделия во времени не меняет ся. На самом деле она меняется очень сильно. Так, стартовые опера ции отсутствуют в конце каждой стадии изготовления изделия, а финишные — в начале.
В конечном итоге несовершенство календарно-плановых расче тов хода производства на предприятии приводит к известным порокам: постоянно возникающему дефициту деталей, непредвиденному движению «узких и широких мест», к распределению работ вместо их планирования, штурмовщине и неритмичности в работе, к зна чительным потерям рабочего времени.
4. Обеспечение достаточной гибкости и маневренности в реализа
Анализ условий выполнения первых трех требований, предъявляемых к организации и управлению материальными потоками, пока зал, что используемые методы несовершенны. Чтобы в условиях не совершенного планирования на уровне цехов и производственных участков обеспечить выполнение производственных планов предприятия, всем линейным руководителям и диспетчерскому персона лу цехов и заводоуправления приходится много заниматься регули рованием хода производства и перераспределением работ по различ ным приоритетам с целью уменьшения потерь производства и рабо чего времени.
Это единственное требование к организации и управлению мате риальными потоками, которое реализуется «любой ценой» и за счет которого выполняются производственные планы и программы.
5. Обеспечение непрерывности планового руководства
Каждое производственное подразделение получает план (задание по объему, номенклатуре и срокам выполнения заказов), обес печивается соответствующими ресурсами и нацеливается на дости жение запланированных конечных результатов работы. Но несовершенство календарно-плановых расчетов даже в условиях интенсивного использования вычислительной техники не позволяет плановику и мастеру надежно планировать работу участка, определять последовательность и сроки выполнения конкретных работ (операций) на каждом рабочем месте хотя бы на несколько дней вперед, т. е. непрерывность планирования как бы не доходит до рабочих мест.
Поэтому плановик и мастер участка, как правило, распределяют работу, формируют загрузку каждому рабочему на смену, исходя из сиюминутных приоритетов.
Для повышения уровня непрерывности планового руководства необходимо научиться не только разрабатывать месячные планы- графики хода производства на каждом производственном участке, но и уметь удерживать производственный процесс в рамках составленного плана-графика при воздействии на него различных возму щений. Это позволит должным образом организовать своевремен ную оперативную подготовку производства и предупредительное техническое обслуживание под конкретные производственные зада ния.
6. Обеспечение соответствия системы оперативного управления производством (ОУП) типу и характеру конкретного производства
Разработаны типовые системы ОУП. Каждая соответствует типу и характеру производства, но сложность их использования состоит в том, что на предприятии, как правило, функционируют производст ва разных типов. Даже в отдельных цехах можно выделить продук цию массового, единичного и серийного характера.
С другой стороны, одновременное использование на одном предприятии нескольких типовых систем ОУП невозможно ввиду их несовместимости хотя бы, например, по планово-учетным единицам и методам согласования работы цехов.
Задачу создания единой системы оперативного управления пред приятием с различными типами производства можно решить, если за основу взять не тип производства, а форму организации произ водства, например, маршрутную или поточную.
В условиях рынка ускорение роста эффективности производства обязательно требует повышения научного уровня управления, авто матизации его функций, применения современного математическо го аппарата, средств вычислительной и организационной техники, создания интегрированных систем управления предприятиями (ИСУП). Организация и управление материальными потоками должно совершенствоваться в рамках подсистемы оперативного управле ния основным производством (ОУОП).
5.3. Законы организации производственных процессов и возможности оптимизации организации материальных потоков в пространстве и во времени
5.3.1. Законы организации производства и конкурентоспособность
Любая наука последовательно проходит три этапа развития: накоп ление материала, его систематизация, установление закономернос тей. Логистика как наука
в настоящее время находится на рубеже второго этапа. Систематизация имеющегося материала еще не закон чена, а параллельно уже предпринимаются попытки определить прин ципы и выявить закономерности оптимизации потоковых процессов.
Как наука и практика логистика имеет своей целью повышение организованности производственных систем, и поэтому она тесно взаимодействует с организацией производства как наукой о проек тировании, создании и развитии производственных систем. Законы и закономерности организации производства являются базой для решения логистических проблем.
В настоящее время в теории организации производства можно выделить две группы закономерностей: закономерности организа ции производственных систем и закономерности организации про изводственных процессов.
Закономерности организации производственных систем, напри мер, нашли свое отражение в работах Е.Г. Гинзбурга и В.А. Петрова.
Большим достижением в современной теории.организации производства можно считать выявление и описание того, как проявляются законы организации высокоэффективных, ритмичных произ водственных процессов. Речь идет о:
- законе упорядоченности движения предметов труда в произ водстве;
- законе календарной синхронизации продолжительностей тех нологических операций;
- законе эмерджентности основных и вспомогательных произ водственных процессов;
- законе резервирования ресурсов в производстве;
- законе ритма производственного цикла выполнения заказа.
Природа воздействия этих законов на организацию производственных процессов, на организацию производства описана в работах Ю.Ю. Наймарка.
Использование вышеназванных законов организации производ ственных процессов позволяет спланировать и поддерживать рит мичную работу производственных подразделений предприятия, т. е. работу в форме рациональной организации производственных про цессов, при которой процессы изготовления отдельных деталей, комплектов деталей и выполнения отдельных заказов программы сочетаются по заранее определенному плану. Это сочетание и обеспечивает ритмичную работу как непрерывное возобновление всего производственного процесса одновременно (параллельно) во всех производственных подразделениях и на каждом рабочем месте в строгом соответствии с плановой пропорциональностью, технологической прямоточностью и экономически обоснованной надежностью выпуска изделий в установленные сроки и надлежащего качества.
Организация и поддержание ритмичной работы каждого пред приятия и его производственных подразделений позволяет устра нить традиционные потери ресурсов рабочего времени рабочих и оборудования (а они составляют не менее 40% первоначальной ве личины ресурсов) по организационно-техническим причинам. Ор ганизация и поддержание ритмичной работы каждого предприятия предполагает целенаправленное резервирование ресурсов в плане до 5—8% их первоначальной величины.
И наконец, организация и поддержание ритмичной работы каждого предприятия обеспечивает ему конкурентные преимущества: лидерство по минимуму затрат, гарантированное время доставки заказов, индивидуализацию изделий по требованиям заказчиков, гибкое регулирование объемов производства, расширение сервисных услуг и ряд других преимуществ.
5.3.2. Закон упорядоченности движения предметов труда в производстве
Традиционное отсутствие стандартизации и типизации индиви дуальных технологических маршрутов изготовления разных наименований предметов труда (деталей) вызывает неупорядоченное, поч ти хаотическое их движение в производстве.
В этом нетрудно убедиться, если маршруты движения деталей наложить на планировки предприятия и его производственных под разделений, которые участвуют в их изготовлении. При хаотическом движении деталей время завершения той или иной операции или изготовления изделия в целом может определяться только в порядке прогноза по той или иной вероятностной модели.
Эта особенность организации производственного процесса в пространстве и во времени позволяет сформулировать закон упорядо ченности движения предметов труда в производстве: без предвари тельной организации движения предметов труда по типовым межцехо вым и внутрицеховым технологическим маршрутам вообще невозможно планирование хода производства.
В самом деле, если известны направление движения и средняя его скорость, то, очевидно, можно установить предельные сроки достижения заданного пункта на трасее движения. Это очень важно при планировании хода производства по отдельным заказам.
Традиционно считается, что обработка партии деталей на техно логической операции есть движение этой партии, а время ее межоперационного пролеживания в ожидании освобождения последую щего рабочего места или простой рабочего места в ожидании завер шения обработки этой партии деталей на предыдущей операции — это время перерывов в ходе производственного процесса. Длитель ность перерывов имеет средневероятностный характер, поэтому надежное планирование сроков хода производства возможно лишь при использовании предельно вероятностных сроков выполнения работ.
Упорядоченное движение деталей в производстве может дости гаться двумя способами:
- стандартизацией и типизацией межцеховых и внутрицеховых технологических маршрутов;
- проектированием типовой схемы движения предметов труда в производстве (ТСД ПТ).
Стандартизация и типизация техмаршрутов не позволяет учесть все возможности в формировании однонаправленных материальных потоков, тогда как проектирование и использование ТСД ПТ на основе конструкторско-технологического классификатора предме тов труда на всю производственную программу обеспечивает ис пользование всех потенциальных возможностей организации одно направленных материальных потоков.
ТСД ПТ делает возможным более чем десятикратное сокращение количества различных межцеховых технологических маршрутов (рас- цеховок).
Использование ТСД ПТ также ведет к резкому сокращению количества внутрипроизводственных связей между участками, многократно уменьшает сложность и трудоемкость планирования и управления производством и, кроме того, создает необходимую организа ционную основу согласования сроков выполнения работ с полной загрузкой плановых рабочих мест и производственных подразделений при минимально необходимом и комплектном незавершенном производстве.
Повышению упорядоченности движения предметов труда в про изводстве способствует рациональная очередность запуска деталей в производство. Упорядочение запуска деталей в производство по разным критериям может обеспечивать либо сокращение длительности совокупного цикла изготовления рассматриваемых деталей, либо уменьшение внутрисменных простоев рабочих мест, либо повышение устойчивости осуществления производственного процесса по плану-графику. Использование этих возможностей также способст вует повышению эффективности производства.
5.3.3. Проявление закона непрерывности хода производственного процесса
Производственный процесс протекает во времени и пространст ве. Время протекания производственного процесса характеризуется длительностью производственного цикла, временем простоя рабо чих мест и временем пролеживания предметов труда в производстве. Все три характеристики, особенно две последние, сильно зависят от значения максимальной продолжительности одной из операций, от средней продолжительности всех операций и от степени асинхрон- ности продолжительностей операций.
Пространственное протекание производственного процесса ха рактеризуется (а) производственной структурой, (б) структурой располагаемых ресурсов, (в) последовательностью и структурой трудо вых затрат, необходимых для изготовления выпускаемой продукции при выполнении производственной программы предприятия.
Изменение организации движения предметов труда во времени постоянно приводит к одним и тем же результатам: изменяется длительность производственного цикла, изменяется суммарное вре мя простоя рабочих мест и изменяется суммарное время межопера ционного пролеживания предметов труда. Фактическая длительность производственного цикла по сравнению с расчетной является ито говой оценкой, характеризующей уровень достоверности и качества календарно-плановых расчетов хода производства.
Минимизация потерь производства от суммарного времени про стоев рабочих мест и от суммарного времени межоперационного пролеживания предметов труда характеризует уровень организован ности и эффективности хода производства.
Любые изменения организации движения предметов труда в про странстве, в соответствии с законом упорядоченности движения, не должны нарушать однонаправленности материальных потоков. В противном случае будут потеряны достоверность календарно-пла- новых расчетов и надежность своевременного выполнения обяза тельств по поставкам продукции.
Межоперационное пролеживание предметов труда и простои рабочих мест в процессе изготовления изделий служат своеобразными календарными компенсаторами, выравнивающими календарные дли тельности смежных технологических операций на производственных участках.
Эффективность процесса изготовления зависит оттого, какой из календарных компенсаторов используется в большем или меньшем объеме.
В процессе производства время межоперационного пролежива ния предметов труда и время простоев рабочих мест противопос тавляются друг другу как различные календарные компенсаторы, исключающие из производственного процесса различные элементы производства: либо рабочего и средства труда, либо предметы труда.
Уже при ближайшем рассмотрении очевидно, что в условиях непоточного производства предпочтительнее непрерывная загрузка рабочих мест. Это подтверждается и при более глубоком анализе потерь производства от часа простоя рабочего места и часа пролежи вания партии предметов труда. В условиях же поточного производ ства, напротив, предпочтительнее простои рабочих мест, так как задержка движения одного предмета труда на час равноценна оста новке каждого рабочего места поточной линии на один час.
Сопоставление потерь производства от часа простоя рабочего места и от часа пролеживания партии предметов труда позволяет сформулировать некоторые правила выбора рациональных (эффективных) методов календарной организации производственного про цесса:
- а) во всех типах производства час простоя рабочего места и час пролеживания партии предмета труда противопоставляются друг другу не только как различные компенсаторы, выравнивающие длительности операций, но и как разные по величине потери производства;
- б) в непоточном производстве производственный процесс должен организовываться по принципу непрерывной загрузки рабочих мест в противоположность принципу непрерывного движения предметов труда в поточном производстве;
- в) выбор принципа организации производственного процесса (непрерывная загрузка рабочих или непрерывное движение предметов труда) в конкретных условиях определяется соотношением потерь производства от простоя рабочих мест и от пролеживания предметов труда.
5.3.4. Проявление закона ритма производственного цикла изготовления изделия
Закон ритма производственного цикла изготовления изделия проявляется каждый раз, когда в процессе изготовления отдельного изделия или его частей формируется или фиксируется относительно их производственных циклов (времени их производства) неравно мерность потребления ресурсов рабочего времени рабочих и обору дования.
Закон ритма производственного цикла изготовления изделия — это объективно существующая совокупность существенных причинно-след ственных связей между параметрами производственной программы пред приятия (т.е. составом, сроками, приоритетами, пропорциями объектов производства и их структурной трудоемкости), с одной сторо ны, и структурой элементов производства (например, структурой ре сурсов рабочего времени различных рабочих мест основного произ водства), потребляемых в производстве, — с другой.
Закон ритма производственного цикла изготовления изделия — это существенные связи, которые (а) проявляются при согласовании и гармонизации количественных организационно-технологических пропорций сопрягаемых элементов процесса производства (предме тов труда, рабочих и рабочих мест) в пространстве и во времени и (б) зависят от параметров производственной программы и от осо бенностей организации производства на предприятии и на каждом участке производства.
Общеизвестно, что согласование работ только по срокам — недо статочная гарантия своевременного исполнения заказа. Работы должны быть взаимосвязаны как по срокам, так и по объемам и структуре используемых ресурсов во времени и пространстве.
Неравномерность потребления материальных и трудовых ресурсов в течение производственного цикла изготовления изделия была подмечена уже давно. Так, еще в 1933 г. Непорент О.И. предлагал путем календарного перераспределения процессов изготовления де талей изделия организовать равномерное распределение всей «про изводственной работы» по изделию на протяжении его производственного цикла. Однако он тут же оговаривался, что практически, даже при тщательной проработке календарных графиков изготовления изделий, невозможно получить равномерную по величине «про изводственную мощность процесса».
Неравномерность трудовых затрат по величине и структуре в течение производственного цикла изготовления изделия обусловливается технологией производства (определенной последовательностью технологических операций), которые вызывают, например, рез кие изменения величины и структуры трудовых затрат в моменты завершения технологических операций над комплектом деталей из делия.
Так, в момент запуска ведущих деталей количество рабочих мест, на которых выполняются первые операции над деталями комплекта рассматриваемого изделия, сильно ограничено по сравнению с количеством деталей комплекта.
С одной стороны, число рабочих мест, на которых выполняются первые операции технологического процесса, намного меньше об щего числа рабочих мест, участвующих в производстве; с другой стороны, не все рабочие места, на которых выполняются первые операции, могут быть заняты изготовлением деталей комплекта рас сматриваемого изделия, так как одновременно с деталями данного изделия запускаются детали других изделий.
Поэтому в момент запуска ведущих деталей на механообрабаты- вающем участке фронт рабочих мест, одновременно участвующих в изготовлении деталей рассматриваемого комплекта, незначителен и намного меньше среднего расчетного числа рабочих мест, которые непрерывно на протяжении производственного цикла изготовления изделия должны участвовать в изготовлении деталей комплекта дан ного изделия.
После прохождения ведущими деталями комплекта первых тех нологических операций в работу постепенно запускаются все остальные детали комплекта. С момента запуска первой детали ком плекта на первую операцию процесса и до момента запуска первой детали комплекта на последнюю операцию процесса развертывается процесс изготовления комплекта деталей.
Фронт рабочих мест, одновременно занятых изготовлением дета лей данного комплекта, с момента запуска начинает возрастать и достигает своего максимума в момент завершения первой операции процесса (в момент завершения обработки деталей комплекта на первой операции типового тихнологического маршрута).
Если достигнута наилучшая организованность производственного процесса во времени и пространстве, то действует правило «золотого сечения»: в момент, соответствующий точке «золотого сечения», про изводственный цикл изготовления рассматриваемого комплекта де талей делится на две части; причем производственный цикл изготовления комплекта так относится к своей большей части, как эта большая часть цикла относится к меньшей.
В точке «золотого сечения» количество рабочих мест, привлечен ных к изготовлению деталей комплекта, как правило, в два раза превышает среднее количество рабочих мест, выделяемых в плане для изготовления рассматриваемого комплекта деталей.
Для оптимального процесса изготовления комплекта деталей точ ка «золотого сечения» должна находиться между 2/3 и 3/4 длительнос ти цикла механообработки рассматриваемого комплекта деталей. В этот момент в изготовлении деталей данного комплекта одновре менно участвуют рабочие места, на которых выполняются промежу точные и финишные операции технологического маршрута изготов ления комплекта деталей.
С момента завершения обработки комплекта деталей на первой операции процесс изготовления рассматриваемого комплекта дета лей начинает свертываться. Фронт рабочих мест постепенно сокра щается.
По мере завершения изготовления все большей части деталей рассматриваемого комплекта число одновременно работающих про межуточных рабочих мест сильно сокращается. В конце цикла изго товления рассматриваемого комплекта деталей работают только фи нишные рабочие места.
Из вышеизложенного можно сделать следующий вывод: на про тяжении цикла механообработки комплекта деталей изделия в одном подразделении фронт рабочих мест сильно изменяется по числу и по составу.
Ритм производственного цикла изготовления изделия представля ет собой закономерное сочетание процессов развертывания и свертыва ния изготовления комплектов заготовок, деталей, сборочных единиц изделия по стадиям производства и производственным участкам, а в каждом производственном подразделении — закономерное изме нение объема и состава выполняемых работ над каждым комплектом предметов труда данного изделия относительно производственного цикла изготовления комплекта деталей в данном подразделении.
При этом изменение длительности цикла выполнения работ над комплектом предметов труда данного изделия в любом производст венном подразделении не меняет внутренних пропорций распределе ния объема и состава этих работ относительно одних и тех же долей производственного цикла рассматриваемого комплекта предметов труда. Удлинение производственного цикла изготовления комплекта предметов труда, как правило, связано с уменьшением количества рабочих мест, выделяемых для изготовления этого комплекта.
Существуют три возможных метода моделирования ритма произ водственного цикла изготовления изделия: статистический, статиче ский и динамический.
В качестве статистического метода
используется статистическое моделирование процесса изготовления изделия и на этой основе разрабатывается норматив календарного распределения трудоемко сти изделия относительно его производственного цикла.
Методика статистического моделирования ритма производствен ного цикла изготовления изделия относительно проста. Выбираются все пооперационные наряды, по которым оплачивалось изготовление уже выпущенного изделия. Наряды сортируются по цехам, по груп пам взаимозаменяемого и специального оборудования. Затем проводится дополнительная сортировка нарядов каждой группы по календарным интервалам в соответствии со сроками исполнения. В качестве таких интервалов могут использоваться дни, недели и месяцы, например, для производственных циклов большей длительности.
Трудоемкости работ в пооперационных нарядах, попавших в данный интервал календарного времени, суммируются, и получаются вариационные ряды (абсолютного) распределения трудовых затрат каж дого вида в течение фактической длительности производственного цикла изделия.
Если на график точками нанести каждое значение отдельного вариационного ряда и последовательно соединить эти точки, то получится ломаная линия, отражающая фактическое календарное рас пределение трудоемкости выполнения работ определенного вида отно сительно длительности производственного цикла изготовления из делия.
Фактическая длина производственного цикла изготовления изде лия делится обычно на десять равных частей. Каждому отрезку длины цикла соответствует своя площадь, ограниченная ломаной линией фактического распределения трудоемкости. Таких участков получается также десять. Затем определяется удельный вес каждого участка в общей площади. Получается вариационный ряд, отражаю щий удельное распределение трудовых затрат данного вида работы относительно каждой десятой доли фактического производственного цикла изделия.
Так делается по каждому виду работы, и получается статистичес кая модель распределения трудовых затрат, или статистическая мо дель ритма производственного цикла изготовления изделия.
Статический метод моделирования ритма
производственного цик ла изготовления изделия предполагает предварительное построение статичной модели процесса производства. В качестве такой модели рекомендуется пооперационная схема вхождения (разузлования) в изделие сборочных единиц, деталей, заготовок, полуфабрикатов и т.д. За календарную продолжительность каждой операции в этой схеме обычно принимают одну смену.
Пооперационная схема вхождения напоминает собой «дерево», в котором в качестве «ствола» выступают операции главной сборки, в качестве крупных «ветвей», отходящих от ствола, — операции сбор ки сборочных единиц, а «ветки» — это операции по изготовлению деталей и заготовок. Если за начало отсчета принять момент завер шения последней операции генеральной, сборки и присвоить ей первый номер, то, присваивая номера каждой операции «ствола», «ветки» в последовательности, обратной ходу технологического про цесса, получим привязку каждой технологической операции изго товления изделия к определенному номеру смены, которая прини мается за такт планирования.
Операция, имеющая наибольший номер, по существу определяет длительность производственного цикла изготовления изделия. Если теперь в каждом такте планирования просуммировать трудоемкости операций по видам работ, то получим распределение трудоемкости изготовления изделия по видам работ относительно каждой доли его производственного цикла, т. е. будет сформулирован статичный ритм производственного цикла изготовления изделия.
Статистическая модель отражения ритма производственного цикла изготовления изделия с ошибкой в 40%, а статичная с ошибкой в 30% прогнозируют (улавливают) характер изменения мощности процес са изготовления изделия по фазам производственного процесса. Эти неточности в определении календарного распределения структуры трудоемкости изготовления изделия приводят в планировании к ошиб кам относительно назначения договорных сроков поставки, к непред сказуемому движению «узких» и «широких» мест в производстве, к большим потерям рабочего времени, рабочих мест и оборудования. При использовании статистического метода теряется примерно 40%, а при использовании статического метода примерно 30% рабочего времени рабочих и оборудования.
В отличие от статистической и статичной модели динамическая модель ритма
производственного цикла изготовления изделия поз воляет с большей достоверностью устанавливать предельно вероят ностные (самые поздние) сроки выполнения работ. При этом процессы изготовления каждого изделия увязываются с процессами изготовления всех остальных изделий, входящих в производствен ную программу; учитываются пространственная структура произ водственного цикла, динамика структуры трудоемкости изготовле ния каждого изделия, непрерывная загрузка производственных под разделений производственной программой.
Динамическая модель формирования ритма производственного цикла изготовления изделия строится на основе повышения организованности протекания производственного процесса и в целом способствует надежному определению длительности производственного цикла изготовления каждого изделия, обеспечивая рациональное использование производственных ресурсов (сокращение потерь ра бочего времени до 5-10%, устранение сверхурочных работ, увеличе ние загрузки оборудования, сокращение оборотных средств в неза вершенном производстве).
5.3.5. Проявления закона календарной синхронизации циклов процессов изготовления изделий и их частей
Синхронизация циклов процессов изготовления изделий и их частей имеет место в любом производственном процессе, но ее, как правило, не замечали, т. е. ее как бы вовсе не было. Если процессом синхронизации циклов процессов не управлять, то продолжитель ности циклов увеличатся раза в три, так как при этом календарное выравнивание каждой части процесса превысит величину наиболь шего цикла соответствующей ч'асти процесса. Это справедливо для каждого уровня разбиения процесса изготовления изделия на части: операция, деталь, комплектооперация, комплект деталей, стадия изготовления изделия (заготовительная, механообрабатывающая, сборочная).
Неуправляемая синхронизация приводит к многократному пре вышению рационального уровня незавершенного производства и большим потерям рабочего времени рабочих и оборудования (в настоящее время в непоточном производстве эти потери рабочего вре мени достигают 50%).
Знания о проявлениях закона синхронизации циклов процессов изготовления изделий и их частей необходимы как основа искусства управления производственным процессом с целью минимизации затрат на производство. Для обеспечения конкурентоспособности предприятия возможность минимизации затрат на производство играет, как правило, первостепенное значение.
Синхронизация циклов технологических операций
Межоперационное пролеживание предметов труда и простои рабочих мест в процессе изготовления изделий служат своеобразными календарными компенсаторами, выравнивающими календарные дли тельности смежных технологических операций на производственных участках.
Явление выравнивания календарных продолжительностей смежных технологических операций имеет силу закона. С действием этого зако на можно познакомиться на различных примерах.
Пример 1: непрерывно-поточное производство.
Предварительная принудительная организационно-технологиче ская синхронизация продолжительностей взаимосвязанных технологических операций детали позволяет организовать непрерывно- поточную линию по ее изготовлению. На этой линии обеспечивают ся непрерывность движения (изготовления) каждой детали и непре рывная загрузка каждого рабочего места. Но принудительная син хронизация продолжительностей технологических операций — до вольно дорогое удовольствие. К ней прибегают, когда выигрыш от синхронизации операций перекрывает расходы на нее.
Пример 2: прерывно-поточное производство.
На прямоточной линии синхронизация технологических опера ций происходит при сознательном участии человека. Например, при построении графика прямоточной линии предусматривается синхронизация производительности смежных технологических опера ций.
Календарная организация всех форм поточного производства построена по принципу непрерывного движения деталей: синхрони зация длительностей деталеопераций здесь должна бы осуществляться только за счет простоев рабочих мест, но это неэффективно, так как час простоя рабочего места (рабочего и оборудования) стоит дороже, чем час пролеживания одной детали. Поэтому организуется параллельно-последовательное движение деталей, когда все микро простои рабочих мест концентрируются.
Эта концентрация становится возможной за счет допущения не которого межоперационного пролеживания деталей. Концентрация микропауз простоев каждого рабочего места позволяет высвободить рабочего и на это время перевести его на другую операцию. Здесь синхронизация длительностей деталеопераций до величины такта поточной линии осуществляется как за счет простоев оборудования рабочих мест, так и за счет межоперационного пролеживания дета лей.
Вообще при любой форме организации производства неравные продолжительности технологических операций выравниваются до некото рого календарного предела либо за счет пролеживания деталей, либо за счет простоев рабочих мест, либо за счет того и другого одновременно.
Пример 3: непоточное производство.
В непоточном производстве при неупорядоченном движении де талей календарный передел выравнивания длительностей технологических операций, как правило, больше максимальной длительности технологической операции, взятой из совокупности операций, выполняемых в рассматриваемый плановый период. При упорядо ченном движении деталей минимальным календарным пределом вырав нивания операций можно управлять.
Выравнивание длительностей технологических операций в непо точном производстве имеет две объективные причины. Первая со стоит в том, что подобно поточному производству организация не прерывности протекания производственного процесса в непоточ ном производстве требует синхронизации продолжительностей операции. Вторая причина выравнивания — необходимость комплекто вания предметов труда в процессе их изготовления до размеров планово-учетной единицы (машнокомплект, условный комплект, бригадокомплект, маршрутный комплект и т. д.).
Например, детали, уже прошедшие обработку, вынуждены проле живать в ожидании изготовления самой последней из их комплекта, а те, что не попали на первую операцию сразу в момент запуска комплекта, вынуждены ожидать своей очереди запуска в обработку.
Календарный предел выравнивания длительности технологических операций характеризует ход производственного процесса с двух его противоречивых сторон — как непрерывность загрузки рабочих мест ( R .) и как непрерывность изготовления предметов труда ( R .).
Естественно, что при заданных организационно-технологичес ких условиях минимум затрат на производство достигается при на ибольшей непрерывности использования средств производства (ра бочих мест), а это соответствует единому оптимальному ритму изго товления партий деталей в производстве ( R ).
Объемно-динамический метод планирования и организация хода производства по принципу непрерывной загрузки плановых рабочих мест позволяют обеспечить не только непрерывную загрузку плановых рабочих мест, но и минимальную длительность производственного цикла изготовления рассматриваемого маршрутного комплекта деталей (Т ).
Если на каждой операции процесса изготовления маршрутного комплекта деталей (т. е. на комплектоопрации) используется одно или большее количество рабочих мест, то длительность его производственного цикла можно определить по формуле
m - l
п ' _ ГЛ t ' .
Mj '
|
T Mlw = n t ^f j -^(n > -C j )
j = l j - l
где n ' — количество наименований деталей, подлежащих изготовлению на участке в определенном плановом периоде и составляющих один комплект деталей;
t 4 j — средний интервал времени, через который осуществляется передача партии деталей одного наименования на следующую комплектооперацию после завершения
их обработки на j -й комплектооперации ( t ' j = t /сЛ;
t \„. — меньший из двух средних интервалов времени, через
которые осуществляется передача деталей комплекта со смежных j -й или ( j + ])-й комплектооперации; С — количество рабочих мест, участвующих в обработке дета лей комплекта на меньшей j -й комплектооперации;
tj — средняя продолжительность выполнения технологичес ких операций над деталями комплекта на j -й комплекто операции (или на j -м виде работ); j — порядковый номер комплектооперации или операции ти пового технологического маршрута, по которому детали рассматриваемого комплекта проходят обработку, j = 1, m .
Здесь цикл изготовления комплекта деталей определяется с учетом условий организации производственного процесса: количества номенклатурных позиций в плане (п'); количества рабочих мест, используемых на каждой операции процесса (С); средней продол жительности выполнения одной технологической операции над де талями комплекта на каждой j -й комплектооперации ( R ,). Этой формулой определяется связь между количеством номенклатурных по зиций в плане, плановым сроком выполнения работ и нормативным размером партии деталей.
Синхронизация циклов изготовления деталей
Календарная синхронизация циклов изготовления деталей имеет явный характер. Так, если детали имеют одинаковое количество операций, то их циклы выравниваются вследствие выравнивания длительностей их операций. Детали в производственных подразделениях изготавливаются, как правило, комплектами, а это означает, что длительность цикла изготовления каждой детали комплекта равна длительности цикла изготовления рассматриваемого комплекта деталей.
Синхронизация длительностей комплектоопераций процесса изготовления комплектов деталей
Сегодня еще многих плановиков производства мучает проблема: какой фронт рабочих мест того или иного участка следует выделять для выполнения работ по конкретному изделию (заказу)?
Проблема, как правило, усложняется тем, что одновременно нужно вести работы над несколькими заказами.
Оказывается, и здесь спасает закон синхронизации — надо добиваться синхронизации комплектоопераций, и тогда автоматически сокращаются длительности циклов изготовления комплектов деталей.
Рассмотрим простые примеры взаимосвязи комплектоопераций:
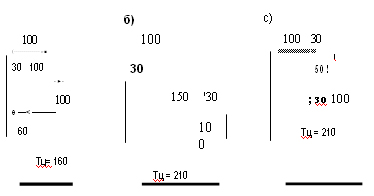
Условные обозначения :
¦+¦ ----- *¦ - длительность комплектоопераций ;
¦*¦ ------ *¦ - опережения между комплектооперациями ;
Тц - совокупный цикл изготовления комплекта деталей на трех операциях
Рис . 26. Иллюстрация синхронизации длительностей комплектоопераций
Из рис. 26 видно, что при нарушениях синхронизации длитель ностей комплектоопераций происходит удлинение совокупного цик ла. Удлинение второй комплектоопераций на 50 ед. в случае «б» и уменьшение длины второй комплектоопераций на 50 ед., в случае «с» дают одинаковый результат — удлинение совокупного цикла на 50 ед.
5.4. Организация рациональных материальных потоков в непоточном производстве
5.4.1. Основы упорядочения материальных потоков
Целевая организация производственных процессов как направ ление развития производственных систем предполагает всяческое уменьшение неупорядоченности, разнообразия и неопределенности в движении предметов труда как в пространстве, так и во времени. Прежде всего движение предметов труда должно быть упорядочено в пространстве, так чтобы оно стало однонаправленным.
Однонаправленное движение предметов труда в пространстве организуется в соответствии с принципами организации производства (специализация, стандартизация, прямоточность) и проектируется в виде типовой схемы движения предметов труда (ТСД ПТ).
Однонаправленное движение предметов труда является обяза тельным и достаточным условием перехода от прогнозирования к планированию хода производственного процесса. Только эта одна возможность планирования хода производства уже делает ТСД ПТ обязательным элементом рациональной организации производства. Помимо этого применение ТСД ПТ гарантирует и другие эффекты в организации и управлении производством.
В современных условиях ТСД ПТ может разрабатываться как для проектируемых, так и для действующих предприятий. ТСД ПТ проектируется по двум структурным группам описательных характери стик (параметров): предметной и маршрутной.
Предметная группа параметров описывает всю годовую номенклатуру данного предприятия и выделяет предметы труда настолько однородные в конструктивно-технологическом отношении, что они могут передаваться между производственными подразделениями по одной расцеховке или по одному организационно-технологическо му маршруту, а внутри каждого производственного подразделения могут изготавливаться по типовому технологическому маршруту либо по групповому технологическому процессу. Предметная группа па раметров обеспечивает организацию однонаправленного движения предметов труда в производстве.
Маршрутная группа параметров определяет рациональную последовательность производственных подразделений, участвующих в изготовлении данной однородной группы деталей и сборочных еди ниц (ДСЕ), а также рациональную последовательность типов и ви дов основного технологического оборудования, применяемого при обработке данной однородной группы ДСЕ в проектируемом или анализируемом производственном подразделении. Маршрутная груп па параметров призвана обеспечить минимизацию затрат на произ водство.
В действующих предприятиях предметная и маршрутная группы параметров уже применяются, но часто обособленно. Их предстоит согласовать, уменьшить разнообразие расцеховок, унифицировать технологические маршруты внутри производственных подразделе ний за счет специализации последних на изготовлении однородной группы деталей и на этой базе создать ТСД ПТ.
Методика формирования ТСД ПТ предусматривает следующую последовательность работ: формирование исходных данных; клас сификация деталей, сборочных единиц (ДСЕ) по конструктивно-технологическим признакам; систематизация состава организаци онно-технологических маршрутов (ОТМ) изготовления предметов производства; уточнение специализации производственных подраз делений; разработка альтернативных вариантов ОТМ для групп од нородных в конструктивно-технологическом отношении ДСЕ; выбор формы (поточной или непоточной) организации производст венного процесса, а также выбор рациональных ОТМ по минимуму приведенных затрат; формирование ТСД ПТ из рациональных ОТМ.
5.4.2. Анализ организационно - плановых признаков группировки деталей
К организационно-плановым характеристикам процесса изготов ления деталей относятся трудоемкость их производства и объем выпуска. Эти факторы в основном и определяют степень стабильно сти производственных условий на рабочих местах и характер повто рения запуска деталей в производство. Концентрация на участке деталей, имеющих примерно одинаковые трудоемкости и объемы выпуска, способствует уменьшению разнообразия ритмов их изго товления и тем самым обеспечивает повышение ритмичности производства и улучшение экономических показателей работы участков и цехов.
5.4.3. Оптимизация состава станочного парка производственных участков
Закрепление номенклатуры деталей за поточно-групповыми гиб кими или маршрутными участками — это исходный момент для выбора состава станочного парка. Из каждой типогруппы деталей, закрепленных за производственным участком, выбирается наиболее сложная деталь, на которую как на типовую разрабатывают разные варианты технологического процесса ее изготовления. Так как за каждым поточно-групповым и каждым гибким участками закрепляют детали только одной типогруппы, то состав их оборудования определяется соответствующей типовой деталью.
За маршрутным участком закрепляются детали разных типогрупп, поэтому каждый вариант изготовления разных типовых деталей дол жен осуществляться по одному типовому технологическому марш руту, в который должны вписываться их технологические процессы изготовления. При этом одноименные операции их технологичес ких процессов базируются на одном и том же технологическом оборудовании.
При выборе варианта технологического процесса изготовления каждой типовой детали требуется ее годовая программа ( Nr ), кото рую определяют исходя из трудоемкости всех m деталей рассматри ваемой типогруппы, закрепленных за данным участком.
'Nr=[J]t UIi -N i /t UIiT ] >
i - l
где1 ш1 — штучная норма времени на i -ю деталь, мин;
t m т — штучная норма времени на типовую деталь, мин.
Очевидно, что такая годовая программа изготовления каждой типовой детали способствует повышению типа производства от единичного к массовому и выбору преимущественно гибкого специали зированного или гибкого специального оборудования.
Оптимальный состав станочного парка производственного участ ка соответствует тому варианту технологического процесса изготов ления типовой детали, который характеризуется минимумом затрат на его реализацию. Для расчетов используют следующую формулу:
Si = Ci + Ек • Ki ,
где Si — сумма затрат на реализацию i - ro варианта изготовления типовой детали;
Ci — технологическая себестоимость изготовления типовой де тали по i -му варианту технологического процесса;
Ек — норма прибыли на капитал;
Ki — капитальные и единовременные затраты на реализацию i - ro варианта изготовления типовой детали.
В связи с возможностью применения машино-коэффициентов и упрощения техники расчета себестоимости машино-часа (станко- часа работы оборудования) формулу технологической себестоимос ти можно представить в следующем виде:
Cj = Vtuijj (3 pj + С б м-ч • KMj • Кмаш; • Pup 1%; +
j = i
+ V(n • tn-3j- KocCoCj),
j = i
где tui — норма штучного времени изготовления i -й детали на
j -й операции, час;
Зр. — часовая (основная и дополнительная с начисления-
ми) заработная плата основного рабочего на j -й опе рации, руб.;
С б м-ч — себестоимость машино-часа базового станка, руб.;
Кмаш. — коэффициент машинного времени на j -й операции;
Ри. — часовые расходы на инструмент на j -й операции;
Nr . — годовая производственная программа i -й детали, штук;
п — число партий или число переналадок станка за год
при изготовлении соответствующей типогруппы де талей;
tn -з. — норма подготовительно-заключительного времени на j -й операции техпроцесса изготовления i -й детали;
Зн. — часовая (основная и дополнительная с начислениями) зарплата наладчика, руб.;
Кос — коэффициент амортизации и эксплуатации специальной оснастки;
Сое. — стоимость оснастки на j -й операции, руб.
В том случае, когда изменение процесса механической обработки вызвано применением разных для каждого из вариантов материалов или заготовок, к результату С надо добавить стоимость материала (заготовки).
С = С. + См. • Nr .,
II I Г
где См ; — стоимость материала заготовки i -й детали.
В соответствии с выбранным оптимальным вариантом технологического процесса изготовления деталей и годовой программой данного участка определяются потребное оборудование и производ ственные площади. Оборудование расставляют по ходу технологиче ского процесса (маршрута). Для того чтобы обеспечить гибкость в перестройке производственной структуры участка при возможном ежегодном изменении производственной программы, оборудование должно устанавливаться на резиновых подушках, а вся подводка коммуникаций к станку должна осуществляться сверху.
5.5. Оптимизация организации производственного процесса во времени
5.5.1. Статическое представление об организации производственного процесса во времени
Основными календарно-плановыми нормативами организации производственного процесса во времени являются длительность производственного цикла детали, нормативный размер партии деталей и длительность производственного цикла изготовления изделия.
Расчет длительности производственного цикла партии деталей
Определение длительности производственного цикла партии деталей (партии одного предмета труда) можно проиллюстрировать применительно к механической обработке партии деталей. Этот рас чет является типовым и применяется с учетом специфики технологий во всех цехах промышленных предприятий.
Длительность совокупного цикла механической обработки пар тии деталей при разных способах (видах) календарной организации процесса определяется по следующим формулам:
T n = n Ј tj ; Tnp = ( n - l ) t rj , + ^ t j ;
j=i j=i
mm rn
Т пп = Т п -( п -1)^1 т ; .= п ^1 ; -( п -1)^^,
j = i j = i j = i
где Т п — длительность цикла обработки партии деталей при по следовательном способе календарной организации про цесса;
Т п — длительность цикла обработки партии деталей при па раллельном способе календарной организации процесса;
Т пп — длительность цикла обработки партии деталей при па раллельно-последовательном способе календарной орга низации процесса;
п — размер партии одинаковых деталей, в штуках;
t — длительность j -й технологической операции детали;
t rji = max t . — наибольшая длительность технологической опера ции детали;
t M . — длительность меньшей из каждой пары смежных техно логических операций детали.
По вышеприведенным формулам (например, для п = 8, j = 4, t , = 3,
t = 1, t = 4, t = 2, когда It ,= 1 + 1+2 = 4и11 = 3+1+4 +
2 > 3 > 4 ' ^ ^ м j *^ J
+ 2 = 10) длительности циклов изготовления рассматриваемой партии деталей примут следующие значения:
Т = 8 • 10 = 80, Т = 7 • 4 + 10 = 38, Т = 80 - 7 • 4 = 52.
п ' пр ' пп
Расчет оптимального размера партии
Для расчета оптимального экономически целесообразного разме ра партии используется расчетно-аналитический метод. Согласно этому методу, все затраты по изготовлению партии деталей можно разделить на две категории. Первая категория затрат остается посто янной при любом размере партии, а в пересчете на одну деталь снижается по мере увеличения размера партии. К этой категории относятся затраты, связанные с запуском партии деталей в произ водство (Сзап), в том числе затраты по переналадке оборудования, оформлению документации, планированию и учету производства, затраты на подготовительно-заключительные действия по каждой операции. Вторая категория затрат — это затраты на содержание и увеличение незавершенного производства.
Экономически целесообразный размер партии (п опт), миними зирующий удельную величину этих затрат и потерь, может быть исчислен по формуле:
С изг ' Л
где С зап — затраты по запуску партии деталей в обработку (затраты на наладку, оформление документации, включение пар тии в график запуска и выдачу нарядов исполнителям, учет движения партии в ходе обработки и т. п.), руб.;
С и1г — затраты по изготовлению одной детали (материалы, зар плата и другие затраты цеховой себестоимости), руб.;
N — количество деталей, которые надо изготовить согласно программе на плановый период, шт.;
ц — коэффициент потерь от связывания средств в незавер шенном производстве, он равен норме прибыли на ка питал.
Из-за необходимости в каждом конкретном случае учитывать ограничения и другие требования, накладываемые на оптимальный размер партии, при практических расчетах используется норматив ный размер партии деталей, который устанавливается методом под бора: определяют минимально допустимый размер партии с точки зрения экономически целесообразного использования оборудова ния и корректируют его в сторону увеличения в зависимости от конкретных производственных условий.
Статическое представление об экономически целесообразном размере партии не учитывает основных конкретных условий произ водства, от которых на самом деле зависит рациональный размер партии деталей. Такими условиями являются: количество наимено ваний деталей, подлежащих изготовлению в данном плановом пери оде; соответствие структуры и величины пропускной способности производственного подразделения суммарной трудоемкости и струк туре трудоемкости производственной программы данного подразде ления; количество операций ведущей детали или количество опера ций в типовом технологическом маршруте. То есть не учитывается динамизм хода производственного процесса.
Расчет длительности производственного цикла изделия
Одним из основных календарно-плановых нормативов непоточ ного производства является длительность цикла изготовления изде лия (выполнения заказа). Расчет длительности производственного цикла изделия завершается построением циклового графика изго товления этого изделия (см. рис. 27). Методика расчета длительно сти производственного цикла изготовления детали в механообраба-тывающем цехе была рассмотрена выше. Длительность цикла изго товления заготовки определяется аналогично длительности цикла механообработки детали. Для ускорения расчетов продолжитель ность цикла изготовления отливок, поковок и штамповок устанавливается укрупненно при помощи нормативов, разработанных для различных видов литья, поковок и штамповок в зависимости от их веса, сложности и других факторов. Длительность цикла сборки (Тц, сб) складывается из длительности цикла генеральной сборки (Тц.г.сб) и из максимальной длительности цикла сборки сборочной единицы (Тц.сб.ед). Длительности циклов генеральной сборки и сборки сборочных единиц определяются как суммы длительностей отдельных операций соответственно генеральной сборки и сборки сборочных единиц (Тсб.о).
Тсб . о = ,
CK B q
где t o — нормативная трудоемкость сборочной операции, час; С — количество рабочих, занятых на данной сборочной операции; q — длительность рабочей смены, час; К в — коэффициент выполнения норм.
Цикл сборки определяется путем построения циклового графика (циклограммы) сборки. Простейший цикловой график сборки изде лия приведен на рис. 27.
Цикловой график сборки строится с конца, с момента завершения общей (генеральной) сборки, по операциям общей сборки и затем по операциям сборки сборочных единиц. Как правило, операции сборки разных сборочных единиц выполняются параллельно. Степень параллельности предопределяется технологической после довательностью вхождения сборочных единиц в изделие.
Производственный цикл изготовления изделия включает длительность цикла изготовления заготовок (Тц.заг), длительность цикла механической обработки (Тц.мех), длительность цикла сборки (Тц.сб).
Тц.изд = Тц.заг + Тц.мех. + Тц.сб. + (т — 1) ¦ tMU ,
где т — количество стадий в производстве;
tMU — время межцеховых перерывов (обычно tMU — 3—5 суток).
Длительность производственного цикла на каждой стадии произ водства определяется по ведущему производственному подразделе нию, в котором комплект деталей (заготовок) рассматриваемого из делия имеет наибольший совокупный цикл. Совокупный цикл меха нообработки комплекта деталей определяется по длительности цик ла ведущей детали, имеющей наибольшую длительность цикла по сравнению с другими деталями этого комплекта.
Ведущие детали — это, как правило, детали, характеризующиеся наибольшей трудоемкостью или наибольшим количеством техноло гических операций. Длительность пребывания деталей в термическом, гальваническом, слесарно-сварочном и других цехах, куда детали (заготовки) передаются для выполнения специальных техноло гических операций, устанавливается укрупненно и включается в длительность цикла соответствующей детали (заготовки).
В длительность производственного цикла детали входит время ее межоперационного пролеживания, продолжительность которого определяется целым рядом факторов: характером специализации участка, уровнем специализации рабочих мест, количеством опера ций в технологическом процессе, степенью загрузки оборудования и другими факторами. В заводской практике длительность межоперационных перерывов в обработке партии деталей часто устанавливается без должного обоснования в размерах, кратных длительности одной смены: 0,5 смены, 1 смена или сутки на каждый межоперационный интервал. Однако значительный удельный вес межоперацион ных перерывов (примерно 70-80%) в длительности цикла изготовле ния детали требует более обоснованного похода к определению его значения. Для повышения обоснованности расчетов длительности циклов и межоперационных перерывов применяют методы математи ческой статистики, в частности множественную корреляцию. Однако нормы времени межоперационного пролеживания по формулам корреля ционной зависимости имеют значительные погрешности.
Первая погрешность состоит в том, что через статистические нор мы межоперационного пролеживания прошлые условия организа ции производства как бы планируются на будущее. При этом игно рируется динамизм номенклатуры выпускаемой продукции, состава рабочих мест, структуры трудоемкости изделий, уровня организации обслуживания рабочих мест и, кроме того, не учитывается степень совершенства оперативного управления производством.
Вторая погрешность состоит в том, что на основе статистических норм времени межоперационного пролеживания определяются лишь средневероятностные величины длительности циклов ведущей и прочих деталей.
С помощью циклового графика изготовления изделия, аналогичного цикловому графику, изображенному на рис. 27, определяется длительность производственного цикла изготовления изделия и ус танавливаются календарные опережения по стадиям производствен ного процесса. Под опережением выпуска понимается промежуток времени между выпуском из сборочного цеха готового изделия и выпуском из соответствующего цеха заготовок, деталей или сбороч ных единиц, предназначенных для сборки данного изделия. Сроки между выпуском изделия в сборочном цехе и запуском заготовок, деталей этого изделия в соответствующих цехах называются опережениями запуска. Графически эти опережения показаны на рис. 27. Расчеты опережений необходимы для определения сроков запуска- выпуска деталей в производстве, таким образом, чтобы каждый цех предыдущей стадии производства своевременно и комплектно обеспечивал цехи последующих стадий производства заготовками, дета лями, сборочными единицами.
В примере (рис. 27) выпуск изделия намечен на 25 октября. Выпуск деталей из механического цеха должен опережать выпуск изделия А на 17 дней, а запуск деталей в механическом цехе — на 35 дней, т. е. детали должны быть запущены 5 сентября. Выпуск заготовок должен опережать выпуск станка на 38 дней, а запуск заготовок на первую операцию в заготовительном цехе на 44 дня, т. е. изготовление заготовок должно быть начато 23 августа.
5.5.2. Динамическое представление об организации и оптимизации процесса изготовления комплекта деталей
Процессы изготовления партий деталей или единичные произ водственные процессы организуются во времени, и их протяжен ность при различных способах обработки труда определяется по соответствующим формулам длительности производственного цик ла: Тп, Тпр и Тпп.
Эти формулы не должны механически переноситься на более сложные частичные и частные производственные процессы. Напри мер, в практике машиностроительных предприятий из-за несовершенства действующих методик большие ошибки допускаются при определении длительности производственного цикла частичного производственного процесса (процесса изготовления комплекта деталей) и особенно при расчете опережений между операциями частичного производственного процесса (видами работ на производст венном участке).
Обычно длительность производственного цикла изготовления комплекта деталей устанавливают по длительности цикла изготовле ния ведущей (наиболее трудоемкой и многооперационной) детали, что приводит к занижению цикла не менее чем в 1,5 раза. За опережениями между операциями частичного процесса вообще, как правило, не следят, отдавая предпочтение отслеживанию прохождения деталями отдельных операций, что приводит к потере контроля за организацией производственного процесса, к нарушению непре рывности производственного процесса (к внутрисменным простоям рабочих, к непредсказуемым движениям «широких» и «узких» мест в производстве), к неритмичной работе производственных участков и предприятия в целом.
Чтобы этого не допустить, длительность производственного цикла частичного процесса при параллельно-последовательном выполнении его операций должна определяться по формуле, аналогичной формуле длительности цикла изготовления партии деталей при па раллельно-последовательном способе обработки предметов труда.
Так, если в формуле длительности цикла изготовления партии деталей при параллельно-последовательном способе организации процесса (Тпп) произвести следующие замены:
п — количество деталей в партии на п' — количество наименований деталей, подлежащих изготовлению на участке в определенном плановом периоде и составляющих один комплект деталей;
tj — продолжительность технологической операции детали на
t : — среднюю продолжительность технологических операций детали на каждой j -й операции частичного производственного процесса (или j - ro вида работ);
t H . — продолжительность меньшей в каждой паре продолжительностей j -й и ( j + 1)-й операции детали на t • — продолжительность меньшей в каждой паре средних продолжительностей технологиче ских операций на j -й и ( j + 1)-й операциях частичного процесса или на j -м и ( j + 1)-м видах раббт, то получится формула для определения длительности производственного цикла изготовления комплекта деталей для случая, когда накаждой операции процесса используется только по одному рабочему месту:
к, к„
j = l j = l
Если на каждой операции частичного процесса используется разное количество рабочих мест, то длительность его производственно го цикла может определяться по формуле:
Ко Ко
T "„„= n ' j ;7;- j ;( n - c j )? Mj ,
j = i j = i
где t '. — средний интервал времени, через который осуществляется выпуск деталей после завершения их обработки на j -й операции частичного процесса ( t ' j = t -/ Cj );
t ' • — меньший из двух средних интервалов времени, через ко торый осуществляется передача деталей с j -й или ( j + 1)-й операций частичного процесса;
С. — количество рабочих мест, участвующих в обработке дета лей на меньшей смежной j -й операции частичного процесса.
Для того чтобы объемно-календарный контур частичного процес са был более устойчив и в него вписывались практически все очеред ности деталей комплекта при Г. < t ': + 1 , опережение между началами смежных операций процесса должно составлять О' • = t - + t '-.
В связи с увеличением О н . совокупный цикл изготовления ком плекта деталей, рассчитываемый по формуле Т" пп , несколько увели чится. Суммируя все t ' j по j -м операциям частичного процесса, для которых t ' j < t ' j + |, получим Е tj = 0" j . На эту величину и надо увеличить размер цикла Т" пп с тем, чтобы расчетный совокупный цикл соответствовал протяженности реального процесса.
Проиллюстрируем это на примере. В верхней части табл. 6 при ведены исходные данные, характеризующие трудоемкость изготов ления деталей комплекта по операциям техпроцесса. В нижней части таблицы произведен расчет параметров процесса, по которым определяется размер цикла Т" пп . Количество рабочих мест на каждой операции процесса устанавливается так, чтобы средние интервалы времени (через которые осуществляется передача деталей по сле завершения их обработки на каждой операции процесса) по величине были как можно ближе к минимальной средней продол жительности одной операции (в нашем примере это t ' 4 = 12,69),
что способствует минимизации совокупного цикла без дробления партий деталей при запуске.
В соответствии с вышеприведенными формулами для данного примера имеем:
О н2 = п' T , 2 -( n > - C 3 ) f з =13- 13,654-(13-2) 9,885 = = 177,5-108,68 = 68,82,
О^п' ? 5 -(п* -С 6 )Г 6 =13- 13,346-(13-4) 12,09 = = 173,5-108,81=64,69;
к„ к„ -1
j = l j = l
К К.
= У Lj -Ј Sj = 950,8-581,69= 369,11;
Т" пп = j 0, lj + n ? 6 = j = i к,- l = У О Hj + L 6 = 211,81+ 157,3 = 369,11.
j = i
Совпадение результатов расчетов одного и того же цикла Тпп указывает на отсутствие ошибок в них.
Для уточнения расчетного цикла Т" пп нужно найти операции частичного процесса, у которых t ':< t ': +1 . В табл. 6 это первая, третья и четвертая операции процесса, и поэтому:
IAO HJ = t ',+ t ' 3 + Г 4 = 11,46+ 9,88 + 12,69 = 34,03.
Реальный совокупный цикл (Т ) изготовления рассматриваемого комплекта деталей составит
Т р = Т" пп +1 AO HJ = 369,11 + 34,03 = 403,14 час.
Использование параллельно-последовательного способа выпол нения операций процесса или объемно-динамического метода (ОДМ) планирования хода производства на примере графического модели рования процесса изготовления рассматриваемого маршрутного ком плекта деталей (МКД) (рис. 28) подтверждает высокую надежность рекомендуемых плановых расчетов.
В настоящее время на машиностроительных предприятиях широ ко распространен объемно-календарный метод (ОКМ) планирования, который базируется на представлении о ходе производства как о статичном процессе.
ОДМ в отличном от ОКМ учитывает технологическую последовательность выполняемых работ и позволяет увязывать сроки и объемы выполняемых работ с загрузкой производственных подразделе ний не только на плановый интервал в целом, но и внутри с учетом динамики распределения работ относительно их производственного цикла.
5.6. Правило 80-20
Иногда такое правило называется «Кривая 80—20» или «Анализ ABC » 1 . Смысл его в следующем. Представьте себе, что вы уронили 100 монет на лужайку. Первые 80 монет вы нашли довольно быстро, но на поиски каждой следующей у вас уходит все больше и больше времени, так как радиус поиска расширяется, трава на лужайке. разной высоты и плотности и т.д. Расход времени на одну монету возрастает, и, наконец, наступает такой момент, когда удельный расход времени на поиск одной монеты превысит стоимость монеты. Об этом надо помнить и вовремя остановиться.
При анализе эффективности производства фирмы, выпускающей изделия разных номенклатур, а равно эффективности их материаль-
'Ronald H. Ballou. Basic business logistics. Prentice-Hall International, 1995.
Рис . 28. График изготовления маршрутного комплекта деталей при параллельно - последовательном способе выполнения операций процесса ( пример использования объемно - динамического метода планирования хода производства , модель «Б» ).
Использованы очередности запуска деталей в производство : на всех операциях процесса - самая малая операция над деталями в первую очередь .
Таблица 6 П ример расчета совокупного цикла изготовления комплекта деталей при параллельно - последовательном способе выполнения операций процесса
N деталей |
Плановая трудоемкость по операциям , час |
Общая трудоем кость , ч |
1 токар . |
2 фрезер . |
3 сверл . |
4 токар . |
5 фрезер . |
6 шлиф . |
1.
2.
3.
4.
5.
6.
7.
8.
9. 10. 11. 12. 13. I
|
60 50
45 80
30 80 80 45 60 66
596
|
40 25
15 60
60 75
80 355
|
5
7 15 40 40 25 25
50 20 30 257
|
20
30 10 40 10
55 165
|
15
35 25
20 90 90
52 20 347
|
40 30 50
50 70 55 90 90 55 28 35 36 629
|
140 120 75 117 180 165 215 285 285 160 213 228 166 2349 |
Параметры |
Значения параметров для расчета совокупного цикла изготовления комплекта деталей по операциям |
п '
h
г .
° .. J
д ° .. о .
| расч .
О .
j прин .
L i s i
t ' .
Mj
|
596
13 45,84
4 11,46 45,84 11,46 57,30
58
149 103,14 11,46
|
355
13
27,308
2 13,654 68,82
68,82 69
177,5 108,73 9,885
|
257
13 19,77
2 9,885 19,77 9,885 29,65
30 128,5 108,73 9,885
|
165
13 12,69
1 12,69 12,69 12,69 25,38
26
165 152,28 12,69
|
347
13 26,692
2 13,346 64,69
64,69 65 173,5 108,81 12,09
|
629
13 48,38
4 12,09
157,3
|
2349
15 73,125 211,81 34,03 245,84
248 950,8 581,69 56,01
|
Группа изделий А: наиболее ценные изделия, на долю которых приходится около 80% общей стоимости изделий, выпущенных фир мой, и они составляют лишь около 15-20% всего выпуска продукции, поступившей на склад готовой продукции.
Группа изделий В: средние по стоимости изделия (примерно 10—15% общей стоимости выпуска), но в количественном отноше нии они составляют 30% общего выпуска.
Группа изделий С: самые дешевые (примерно 5—10% от общей стоимости выпуска) и самые массовые (более 50% общего выпуска) изделия.
Анализ кривой ABC показывает, что группа изделий А должна находиться под строгим контролем и учетом, т. е. изделия этой груп пы — основные в бизнесе фирмы.
Изделия В требуют обычного контроля, налаженного учета и постоянного внимания.
Изделия С нуждаются в самом обыкновенном контроле, как-то: периодическая проверка уровней запаса.
Правило 80—20 используется обычно при составлении оптималь ного заказа с учетом спроса потребителей, оно также помогает в решении задач относительно экстраполяции прошлых тенденций на будущее и др.
Контрольные вопросы к главе 5
- В чем сущность «дерева целей» концепции типового проекти рования логистических систем?
- Каковы роли и взаимосвязи функциональной, элементной и организационной структур производственной системы?
- В чем различие между тактической и стратегической гибкостью производственных систем?
- Какие конкурентные преимущества дает реализация основ ных и противоположных принципов организации производ ственных процессов в логистических системах?
- Раскройте требования, предъявляемые к организации и опе ративному управлению материальными потоками в логистических системах. Охарактеризуйте существующий уровень их реализации.
- Назовите предположения о ходе производства, которые характеризуют этот процесс как статичный. Каким образом статичное восприятие хода производства препятствует оптими зации материальных потоков?
- Как проявления закона упорядоченности движения предме тов труда в производстве влияют на решение проблем опти мизации материальных потоков?
- Как проявления закона синхронизации частей производст венного процесса могут быть использованы при решении проблем оптимизации материальных потоков?
- Охарактеризуйте возможности оптимизации движения мате риальных потоков при использовании зависимостей и взаи мосвязей, определяемых законом ритма производственного цикла выполнения заказа.
- Какие проблемы управления материальными потоками по рождают статические методы планирования хода производства?
- Охарактеризуйте проявления закона непрерывности производственного процесса в производстве.
- Как правило «золотого сечения» можно использовать при выборе оптимального решения по организации производственного процесса?
- Назовите недостатки использования статистического метода определения ритма производственного цикла изготовления изделия.
- Назовите недостатки и преимущества использования стати ческого метода построения ритма производственного цикла изготовления изделия.
- Назовите преимущества динамического метода проектирования и поддержания ритма производственного цикла изготов ления изделия.
- Какой единый ритм изготовления партий деталей в произ водстве способствует решению проблем оптимизации мате риального потока?
- Как определить оптимальный размер партии деталей, если известны плановый период и количество номенклатурных позиций в плане?
- Охарактеризуйте основные преимущества динамического пред ставления об организации процесса изготовления комплекта деталей при оптимизации
Управление товарно-материальными запасами
Здесь мы обсудим, какова роль товарно-материальных запасов в экономике, перечислим виды товарно-материальных запасов, рассмотрим, на какие категории подразделяются товарно-материальные запасы в зависимости от их целевого назначения. Детально оценим, что является одним из важнейших стимулов создания запасов и к каким издержкам приводит дефицит запасов. Мы назовем факторы, определяющие точный уровень резервных запасов, объясним различие в подходах к формированию запасов в различных отраслях экономики и выявим, почему существует разрыв между теорией и практикой принятия решений относительно товарно-материальных запасов. Кроме того, мы перечислим, какие основные недостатки управления производством сдерживают сокращение времени на прохождение изделий и запасов в цехах и на складах, какова статистическая закономерность, определяющая размеры потребности в различных видах товаров, представленных в запасах.
Важный моменты этого раздела сайта: что нового принесла логистика в развитие системы запасов, какие вопросы по проблеме управления запасами являются центральными в логистических системах и в чем именно заключается суть управления товарно-материальными запасами. Мы раскроем механизм функционирования системы «Точно в срок», определим, для каких условий разработаны основные и прочие системы управления запасами, перечислим планируемые параметры в системах управления запасами - bizprofy.ru. Сделаем акцент на том, какие сбои в плановых параметрах можно учесть в системе с фиксированным размером заказа, какие сбои в плановых параметрах можно учесть в системе с фиксированным интервалом времени между заказами и какие сбои в плановых параметрах предусмотрены в системе с установленной периодичностью пополнения запасов до постоянного уровня.
|
На уровне фирм запасы относятся к числу объектов, требующих больших капиталовложений, и поэтому представляют собой один из факторов, определяющих политику предприятия и воздействующих на уровень логистического обслуживания в целом. Однако многие фирмы не уделяют ему должного внимания и постоянно недооценивают свои будущие потребности в наличных запасах. В результате этого фирмы обычно сталкиваются с тем, что им приходится вкладывать в запасы больший капитал, чем предполагалось. Изменения объемов товарно-материальных запасов в значительной степени зависят от превалирующего на данный момент отношения к ним предпринимателей, которое, безусловно, определяется конъюнктурой рынка. Когда основная масса предпринимателей настроена оптимистично относительно возможностей экономического роста, они расширяют свои операции, увеличивают объемы инвестиций в создание запасов. Тем не менее колебания уровней последних не вызываются одним лишь инвестированием. Важными факторами выступают здесь качество принимаемых решений, а также то, какая конкретно технология управления запасами используется.
Будущие потребности в наличных запасах
Товарно-материальные запасы всегда считались фактором, обеспечивающим безопасность системы материально-технического снабжения, ее гибкое функционирование, и являлись своего рода «страховкой». Существует три вида товарно-материальных запасов: сырьевые материалы (в том числе комплектующие изделия и топливо); товары, находящиеся на стадии изготовления; готовая продукция.
Безопасность системы материально-технического снабжения Запасы технологические и переходные. Циклические запасы
Определение точного уровня резервных запасов, необходимых в условиях нестабильности сроков реализации заказов и изменчивого спроса на товары и материалы, - дело нелегкое. Вероятностная природа вышеуказанных колебаний и нестабильности означает, что для нахождения удовлетворительных решений проблем, связанных с резервными товарно-материальными запасами, обычно необходимо соответствующее моделирование или имитация.
Поскольку в фирмах различных отраслей экономики создание товарно-материальных запасов определяется той специфической ролью, которую они играют в процессе выпуска продукции, постольку объяснимы и различия в подходах к политике капиталовложений в данной области и к определению приоритетности задач, решаемых в ходе производства - bizprofy.ru. В фирмах некоторых отраслей народного хозяйства основной задачей является контроль за сырьем, в других - за готовой продукцией, а на предприятиях отраслей, производящих инвестиционные товары, большая часть организационных усилий концентрируется на контроле за незавершенным производством.
Резервные товарно-материальные запасы
Коэффициенты оборачиваемости капитала характеризуются значительной изменчивостью и существенно отличаются не только у преуспевающих и непреуспевающих компаний, но и у фирм различного типа. Последнее объясняется в основном спецификой структуры издержек, существующей в отраслях народного хозяйства, сезонными колебаниями сбыта, нормами конкурентной борьбы, принятыми в той или иной отрасли экономики, уровнем рентабельности, стилем руководства предприятиями и характером деловых операций. Перечисленные обстоятельства следует отнести к весьма важным факторам, оказывающим серьезное влияние на эффективность политики любой фирмы в области создания и реализации запасов.
Управление запасами и оборачиваемость капитала Снижение времени на прохождение изделий и запасов в цехах и на складах
В последние годы произошло заметное усовершенствование методов производства, что позволило снизить производственные расходы. Дальнейшая экономия средств может быть достигнута, если будут реализованы резервы, заложенные в рационализации обеспечивающих процессов. Прежде всего это относится к оптимизации запасов. Решения, принимаемые руководством фирм в этой области, в конечном счете касаются каждого отдельного вида товара или предмета хранения, конкретная единица которых, подлежащая контролю, называется «единицей учета запасов».
Сегодня, благодаря активизации ряда факторов, в том числе и внедрению логистики, многие предприятия последовательно связаны друг с другом, производство и система запасов приобретают взаимозависимый характер. В такой ситуации управление производством означает организацию работы не только каждого звена в отдельности, но и всех вместе как единого целого. Анализируя систему производственных заказов, многие фирмы стали исходить из метода комплексного регулирования, позволяющего гармонично соединить все звенья и соразмерить объемы производства и запасов. Благодаря целенаправленному применению организованных, плановых и контрольных мероприятий возможно, с одной стороны, воспрепятствовать созданию излишних запасов, а с другой - устранить такой недостаток, как отсутствие готовности к поставкам.
Оптимизация запасов Логистический подход к управлению товарно-материальными запасами
Последние новшества в сфере производства таковы: дифференциация продукции на возможно более поздней стадии производства (на базе максимально однотипных комплектующих); использование выгод массового производства не на стадии сборки, а на стадии изготовления комплектующих изделий; стремление к максимальному удовлетворению потребностей клиента на этапе выбора товара для производства.
Производство без складов Точно в срок
Практика показывает, что для эффективного внедрения стратегии «Точно в срок» необходимо изменение способа мышления целого коллектива, занимающегося вопросами производства и сбыта. Традиционный стереотип мышления типа «чем больше, тем лучше» должен быть заменен схемой «чем меньше, тем лучше», если речь идет об уровне запасов, использовании производственных мощностей, продолжительности производственного цикла или о величине партии продукции.
Один из вариантов снижения риска при хранении запасов - использование технологий, основанных на системах гибкого производства, на его роботизации. В данном случае преимуществом является сокращение времени и затрат на подготовительные операции - bizprofy.ru. Это делает экономически выгодным изготовление изделий небольшими партиями, что особенно важно в условиях жесткой конкуренции и постоянных изменений требований рынка. Особенно важно подчеркнуть, что одновременно существенно снижается и риск морального устранения запасов.
Эффективное внедрение стратегии «Точно в срок»
Изучая предыдущие разделы сайта вы, вероятно, обратили внимание на то, что изложение материала следовало логике развития хозяйственного процесса. Действительно, за информационной логистикой, работающей с потоками информации как основой функционирования всех подсистем логистики, следует логистика закупок, далее - логистика производственных процессов и логистика распределения. Именно эти три этапа:
- закупка сырья, материалов и комплектующих; - производство продукции или оказание услуг; - распределение готовой продукции или услуг
- оставляют единый экономический процесс, для осуществления которого и создается любое предприятие. Таким образом, логистику можно рассматривать как реальный хозяйственный процесс производства продукции или оказания услуг. Логистика представляет собой взгляд на производство товаров и услуг как единый и непрерывный процесс движения предметов труда от их исходной формы до конечного продукта, а также связанной с ним информации. В этом смысле логистика является философией существования и развития экономики, так как содержит в себе совокупность методологических принципов, лежащих в основе эффективного функционирования составляющих ее организаций.
Функциональные особенности логистики в системе управления
Цели образования и соответствующие им виды запасов могут быть различными, но независимо от этого запасы представляют собой вторую по значимости после партии обработки расчетную составляющую производственного процесса. Их объем, место расположения и динамичная зависимость от потребностей последующих стадий производства в большей степени определяют эффективность материальных потоков внутри организации и во внешней по отношению к ней среде. Именно запасы сырья, материалов, комплектующих и готовой продукции непосредственно увязывают организацию с ее поставщиками и потребителями, формируя цепи логистических систем экономики в целом - bizprofy.ru. Таким образом, логистика запасов занимает ключевое место в логистической системе как отдельной организации, так и экономики в целом. Обеспечение единого и непрерывного процесса снабжения всех стадий производственного процесса необходимыми запасами в оптимальном количестве и заданного качества - важнейшая гарантия эффективного функционирования организаций и экономик регионов.
Хозяйственный процесс производства продукции или оказания услуг Материальные ценности, ожидающие производственного или личного потребления Классификация запасов по месту их нахождения Классификация запасов по исполняемой ими функции
Логистическая система управления запасами проектируется с целью непрерывного обеспечения потребителя каким-либо видом материального ресурса. Реализация этой цели достигается решением следующих задач:
- учет текущего уровня запаса на складах различных уровней; - определение размера гарантийного (страхового) запаса; - расчет размера заказа; - определение интервала времени между заказами.
Для ситуации, когда отсутствуют отклонения от запланированных показателей и запасы потребляются равномерно, в теории управления запасами разработаны две основные системы управления, которые решают поставленные задачи, соответствуя цели непрерывного обеспечения потребителя материальными ресурсами. Такими системами являются:
1. Система управления запасами с фиксированным размером заказа. 2. Система управления запасами с фиксированным интервалом времени между заказами.
Логистическая система управления запасами с фиксированным размером заказа Оптимальный размер заказа по критерию минимизации совокупных затрат Порядок расчета системы управления запасами с фиксированным размером заказа Система управления запасами с фиксированным интервалом времени между заказами Иллюстрация функционирования системы управления запасами с фиксированным интервалом времени между заказами
Следствием преимущества системы с фиксированным интервалом времени между заказами является то, что в системе с фиксированным размером заказа максимальный желательный запас всегда имеет меньший размер, чем в первой системе - bizprofy.ru. Это приводит к экономии на затратах по содержанию запасов на складе за счет сокращения площадей, занимаемых запасами, что, в свою очередь, составляет преимущество системы с фиксированным размером заказа перед системой с фиксированным интервалом времени между заказами.
Сравнение функционала основных систем управления запасами
Разобранные основные системы управления запасами базируются на фиксации одного из двух возможных параметров - размера заказа или интервала времени между заказами. В условиях отсутствия отклонений от запланированных показателей и равномерного потребления запасов, для которых разработаны основные системы, такой подход является вполне достаточным. Однако на практике чаще встречаются иные, более сложные ситуации. В частности, при значительных колебаниях спроса основные системы управления запасами не в состоянии обеспечить бесперебойное снабжение потребителя без значительного завышения объема запасов. При наличии систематических сбоев в постановке и потреблении основные системы управления запасами становятся неэффективными.
Для таких случаев проектируются иные системы управления запасами, которые мы называем прочими. Их составляют элементы основных систем управления запасами. Каждая из основных систем имеет определенный порядок действий. Так, в системе с фиксированным размером заказа заказ производится в момент достижения порогового уровня запаса, величина которого определяется с учетом времени и возможной задержки поставки. В системе с фиксированным интервалом времени между заказами размер заказа определяется исходя из наличных объемов запаса и ожидаемого потребления за время поставки - bizprofy.ru. Различное сочетание звеньев основных систем управления запасами, а также добавление принципиально новых идей в алгоритм работы системы приводит к возможности формирования по сути дела огромного числа систем управления запасами, отвечающими самым разнообразным требованиям. Сейчас мы остановимся на двух наиболее распространенных прочих системах. Это:
1. Система с установленной периодичностью пополнения запасов до постоянного уровня. 2. Система «Минимум—максимум».
Система управления запасами с установленной периодичностью их пополнения до постоянного уровня Иллюстрация функционирования системы управления запасами с установленной периодичностью их пополнения до постоянного уровня Система пополнения запасов «Минимум-максимум» Иллюстрация функционирования системы управления запасами «Минимум—максимум»
Основные системы управления запасами - с фиксированным размером заказов и с фиксированным интервалом времени между заказами, а также прочие системы управления запасами - с установленной периодичностью пополнения запасов до постоянного уровня и система «Минимум—максимум» разработаны для условий, когда отсутствуют отклонения от запланированных параметров поставки и потребления. Этими параметрами являются:
- размер заказа; - интервал времени между заказами; - время поставки; - возможная задержка поставки; - ожидаемое дневное потребление; - прогнозируемое потребление до момента поставки.
Непрерывное обеспечение потребности в каком-либо виде материального ресурса
Для проектирования логистической системы управления запасами мы рекомендуем применять методику, основанную на имитационном графическом моделировании поведения системы. Она проста в применении, нетрудоемка и, как показал опыт ее применения, дает хорошие результаты.
Рекомендуемая методика проектирования логистической системы управления запасами
Повышение эффективности использования систем управления запасами в логистической системе организации приводит к необходимости разработки оригинальных систем управления запасами. В теории управления запасами имеется достаточное количество специальных способов ведения такой работы.
лава 9. Транспорт в условиях логистики
9.1. Влияние логистики на транспорт
Развитие логистики оказало существенное влияние на транс портную политику и структурные изменения в характере деятельности предприятий данной отрасли, которая в конце 70-х годов пре вратилась в своего рода узкое место в экономике промышленно развитых стран. Ее относительно низкая эффективность была обус ловлена тем, что органы государственного регулирования чрезмерно жестко регламентировали тарифы, расстояния транспортировки, номенклатуру перевозимых грузов, направления капиталовложений и некоторые другие параметры деятельности транспортных компаний, а также проводили политику ограничения числа фирм в ком плексе. В итоге конкурентная борьба была вялой, а действовавшие компании пользовались монопольным положением, что давало им возможность сдерживать объем и ассортимент услуг и компенсиро вать высокие издержки высокими тарифами.
Дерегулирование транспорта сняло все вышеуказанные ограни чения и взяло курс на переориентирование его с количественных на качественные показатели. Например, вопрос о выдаче лицензии фирмам стал всецело зависеть от того, отвечают ли они критерию «соответствует, желает и способен».
Благодаря снижению уровня государственного регулирования транспорта фирмы данной отрасли получили свободу предложений в предоставлении услуг, высвобождающих часть оборотных средств у клиентуры посредством определенной синхронизации в работе транс порта и производственных подразделений фирм. В связи с этим ужесточаются требования к качеству поставок товаров, претерпевает изменение степень важности критериев при выборе видов транспорта, внедряются прогрессивные формы поставки грузов, учащаются поставки продукции мелкими партиями. Все это приводит к изме нению связей в логистической цепи, сдвигам в структуре перевозок и по сути дела к новому взгляду на транспорт и пересмотру транс- Портной политики.
Переход от жесткого государственного контроля к дерегулирова нию транспортом начался с конца 70-х годов. Наиболее заметные сдвиги в этой области произошли в США. В 1977 г. там началось дерегулирование воздушного транспорта, а вслед за ним в 1980 г. — автомобильного и железнодорожного и наконец в 1984 г. — водного. Принятые законы разрешили создавать на всех видах транспорта новые компании и свободно устанавливать тарифы. Кроме того, на воздушном транспорте авиационным экспедиторским агентствам разрешалось иметь в собственном владении и эксплуатировать самолеты. Автотранспортным агентствам позволено участвовать в де ятельности транспортных компаний общего пользования. Экспедиторским агентствам и транспортным компаниям предоставлена возможность создавать совместные предприятия с фирмами, специали зирующимися на экспортной торговле. В Японии в целях повышения конкуренции осуществлена приватизация железных дорог. В Великобритании отменены лицензии, значительно сдерживающие использование автомобилей как по поясам дальности перевозок, так и по номенклатуре грузов.
В целях достижения синхронизации работы транспорта и произ водства в хозяйственной деятельности фирм, как уже отмечалось выше, широко применяются системы «Канбан» и «Точно в срок» (« Just in time »). Суть их в применении к транспорту состоит, кратко говоря, в следующем: если в основном производстве используется технология «Строго по графику» без информации о содержании существенных объемов запасов необходимых материалов, сырья, по луфабрикатов и комплектующих изделий, то в закупочной и сбытовой логистике перевозки осуществляются соответственно через короткие интервалы (система «Канбан») и в строго определенное время (система «Точно в срок»). По указанной технологии подача грузов и тоннажа, клиентуре в необходимых случаях ведется с точнос тью до минут. При этом, например, автомобиль с главного конвей ере автосборочного завода поступает не на склад, а в вагон, и одно временно специальное погрузочное устройство, управляемое ЭВМ, обеспечивает постановку следующего вагона под погрузку очеред ной партии автомашин. Такая технология позволяет обходиться без громоздкого и дорогостоящего складского хозяйства и ускорять оборачиваемость капитала. В результате нормативы запасов материаль ных ценностей резко сокращаются. Например, в Японии они со ставляют 2- и 5-суточную потребность, а на автосборочном заводе «Ниссан» запас комплектующих деталей рассчитан всего на 2 часа работы главного конвейера. При переходе на работу по системе «Точно в срок» время реализации товара сокращается до двух раз.
Своевременное удовлетворение потребностей отраслей, требующих гарантированной доставки грузов к определенному сроку, до стигается также организаций движения грузовых поездов на сети железных дорог по жесткому расписанию. Грузоотправитель брони рует в поезде необходимую ему грузоподъемность и обеспечивает погрузку в технологически необходимое время. Такие поезда не ожидают груза, так что отправитель, не успевший справиться с гру зовой работой, теряет оплаченный тариф так же, как и пассажир, опоздавший на поезд.
Под влиянием логистических систем «Канбан» и «Точно в срок» пользователи транспортных услуг стали отдавать предпочтение таким критериям, как соблюдение временных графиков доставки грузов (в зависимости от продолжительности планируемой поставки считаются допустимыми следующие отклонения: для 8—12 недель — 25%; 4-8 недель — 10%, менее 4 недель — 1%), ответственность за удовлетворение текущих потребностей и возможность отслеживания движения груза. Повышение значимости названных критериев на блюдалось у 90% фирм, принявших на вооружение рассматриваемые логистические системы. Одновременно половина из этих фирм повысила интерес к таким факторам, как близость расположения терминалов, величина тарифов, протяженность маршрутов и наличие специализированного подвижного состава.
Таким образом, в известном смысле можно утверждать, что с рубежа 70—80-х годов начинается органическое срастание транспор та с обслуживаемым производством, превращение его в звено единой системы «производство — транспорт — распределение».
Новый подход к транспорту как к составной части более крупной системы, т. е. логистической цепи,
привел к необходимости рассмат ривать его в разных аспектах. С точки зрения изучения эффективности работы отдельных видов транспорта интерес представляют пере возки грузов между пунктами отправления и назначения на каждом из них (например, от одной железнодорожной станции до другой, из порта в порт или с терминала на терминал). Однако с позиции организации перевозок целесообразно анализировать весь процесс перевозки в целом от двери грузоотправителя до двери грузополучателя. Если же учитывать интересы клиентуры, то здесь необходимо принимать в расчет не только перевозку на магистральных видах транспорта, но и обработку, хранение, упаковку и распаковку, пода чу материалов к станкам в цехе и все связанные с этим процессы информации, сопровождающие материальный поток. Такой подход способствует оптимальному выбору транспортных услуг, ибо качест во перевозок, как правило, в большей мере отражается на общих расходах, чем себестоимость перевозок.
С точки зрения специализации и кооперирования производства изучение транспорта нельзя ограничивать сферой отдельных материально-технических связей. Он должен рассматриваться во всей системе материально-технического снабжения — от первичного по ставщика до конечного потребителя, включая промежуточные эта пы. И, наконец, с целью максимального сокращения издержек за срок службы продукции предлагается расширить понятие «концепция логистики»,
включив в него весь жизненный цикл продукции — от этапа проектирования до использования вторичного сырья и от ходов.
Политика дерегулирования автомобильного транспорта и приме нение системы «Точно в срок» способствовали расширению сферы его деятельности. Особенно это заметно в США с их относительно длинными плечами перевозок по сравнению с западноевропейски ми странами и Японией. В Соединенных Штатах Америки автомо били стали все больше эксплуатироваться не только на коротких и средних расстояниях, но и на расстояниях до 1600 км — для достав ки как комплектующих изделий, так и готовой продукции. В силу чего доля автомобильного транспорта в освоении перевозок грузов несколько возросла. В наибольшей степени это относится к авто транспортным фирмам, работающим по контрактам. В последних оговариваются стимулы и штрафные санкции относительно качест ва перевозок, и это способствует повышению стандартов на предоставляемые услуги. Из общего числа компаний, использующих кон трактные перевозки автотранспортом, 51% повысили к нему инте рес и 49% не изменили своего прежнего отношения. Задействование автомобильного транспорта общего пользования осталось почти не изменным. В то же время 25% промышленных фирм, владеющих собственным парком автомобилей, повысили их использование, а 14% фирм — снизили. Повысилась доля автомобильного транспорта и в западноевропейских странах, и не только во внутренних, но и в международных сообщениях. Предполагается, что и в дальнейшем технико-эксплуатационные особенности автомобильного транспорта обеспечат ему надежное положение в условиях повышенного спроса на перевозки грузов частыми, но мелкопартионными отправ ками, которые, в свою очередь, ускорят развитие автоматической обработки грузов, контейнеризации и пакетизации, а также инфор матики в области грузовой и перевозочной работы. Однако это приведет к увеличению стоимости транспортировки; повысится и значение качественных факторов, например, таких, как надежность и своевременность доставки.
Дерегулирование в основном коснулось автомобильного транс порта как наиболее приспособленного к перевозкам грузов мелкими партиями, способствующим сокращению запасов материальных ре сурсов и повышению скорости их оборачиваемости. Что же касается железных дорог, то они оказались во многих случаях не в состоянии адекватно изменившейся системе материально-технического обес печения удовлетворить спрос на перевозки. На железнодорожный транспорт по-прежнему распространяется ряд правовых и админис тративных требований со стороны государства. В частности, такие требования предписывают надлежащее функционирование линий на конкретных направлениях, освоение всего объема перевозок пас сажиров и грузов, ограничения в соответствующей политики в обла сти цен и соблюдение ряда других требований. В силу указанных причин железнодорожный транспорт стал менее благоприятным по сравнению с автомобильным видом транспорта для использования его по системе «Точно в срок». Так, в конец 80-х годов 49% промыш ленных фирм США, работающих по данной логистической системе, снизили степень пользования услугами железных дорог; столько же фирм сохранили уровень их услуг, и лишь 2% фирм повысили его.
Тем не менее, как считают зарубежные специалисты, это не озна чает, что в новых условиях спроса на перевозки роль железнодорож ного транспорта обречена на снижение. Напротив, такие качествен ные его характеристики, как регулярность и скорость движения поездов в прямом сообщении (в европейском регионе — это международные перевозки), могут оказаться весьма полезными. Более того, в целях ускорения доставки грузов на железнодорожном транспорте может быть расширено применение контрейлерных перевозок, контейнеров и маршрутных составов. Операции по составлению поездов будет целесообразно выполнять на ограниченном числе сортировоч ных станций. Первостепенное значение для повышения использова ния грузоподъемности вагонов приобретает консолидация грузов.
Использование внутреннего водного транспорта в логистической цепи в значительной степени ограничивается сезонностью его рабо ты в ряде стран. Однако внутренние водные пути могут быть ис пользованы в качестве альтернативного вида транспорта по сравнению с автодорожным, на котором действуют такие сдерживающие факторы, как запрещение работы в выходные дни, дорожные налоги и т.д. Благодаря применению системы «Точно в срок» расширились возможности привлечения водного транспорта по сравнению с теми случаями, когда акцент делался на повышение скорости доставки.
Внедрение логистической концепции в практику мирохозяйст венных связей позволит в определенной степени увеличить объем перевозок грузов морским и особенно воздушным транспортом в межконтинентальном сообщении. Не исключен рост авиационных перевозок и во внутренних сообщениях. Например, в США к началу 90-х годов востребование воздушного транспорта возросло у 29% фирм, использующих систему «Точно в срок», и только 5% фирм отказались от его услуг.
В логистических системах, работающих «строго по графику», ос новной фактор, обеспечивающий эффективную работу на линиях снабжения и сбыта товарно-материальных ценностей, — это новые услуги автомобильных и железнодорожных компаний по сбору и распределению грузов. Такие услуги транспортных предприятий обес печивают ускорение перевозки на большие расстояния от постав щиков к производителям или рынкам конечной продукции и часто исключают звенья, существующие в традиционных системах комплектования грузов. В результате проводимые операции обычно яв ляются менее дорогостоящими и обеспечивается более высокое ка чество обслуживания, чем при конкурирующих способах распреде ления. Кроме того, компании, пользующиеся новыми услугами, извлекают прямые выгоды, как-то: уменьшается продолжительность цикла обработки заказа, а хранение запасов товарно-материальных ценностей заменяется транспортными потоками. Учитывая вышеизложенное, представляет интерес более подробное рассмотрение политики транспортных предприятий, приведшей к изменению харак тера деятельности последних.
9.2. Политика транспортных предприятий и изменения в характере их деятельности
Основные положения логистики, характерные для фирм-произ водителей и потребителей продукции (приоритет потребителя, вы сокий уровень сервиса, сокращение времени выполнения заказа и др.) в полной мере относятся и к предприятиям транспортной от расли, задействованным в логистических системах. Отличительной чертой их работы в новых условиях конкуренции на рынке транспортных услуг становится разработка политики комплексного решения транспортных и сопряженных с ними проблем на ином, качест венно высоком уровне. Практика показывает, что такая политика приносит успех, если она достаточно дифференцирована и базируется на таких основных компонентах, как: предоставление нетради ционных новых дополнительных услуг, политика в области комму никаций и политика заключения контрактов.
К политике предоставляемых услуг относятся все решения и дей ствия, направленные на комплексное осуществление транспортного процесса. Это означает, что организация перевозок грузов с учетом расстояния их транспортировки, количества и сроков доставки пла нируется в соединении с дополнительными услугами и потребностя ми спроса.
Анализ участия фирм-перевозчиков в логистической деятельности грузовладельцев США показал, что транспортные предприятия весьма охотно идут на расширенную диверсификацию своей дея тельности. Это повышает потенциал привлечения клиентуры, увеличивает прибыль, ускоряет внедрение новейших транспортных тех нологий, укрепляет положение на рынке транспортных услуг. В свою очередь, фирмы-продуценты не менее заинтересованы в том, чтобы освободиться от многих логистических функций и сосредоточить внимание на основной профилирующей деятельности с целью сни жения затрат и повышения гибкости в работе. Из 350 обследован ных предприятий различных отраслей экономики США 70% переда ли транспортным фирмам функции по выполнению и оформлению расчетов за перевозку грузов. Примерно 20—22% предприятий отка зались в пользу транспортников от работы, связанной с определени ем цены за перевозку, складскими операциями и выбором оптимального маршрута доставки товаров. Фирмы-перевозчики сочли выгодным переключить на себя выполнение контрольных функций за грузами, находящимися в пути следования. Они стали заниматься также организацией электронного обмена данными между всеми участниками логистического процесса и хранением информации. В результате около 12—15% фирм-продуцентов освободились от вы полнения указанных функций. И наконец, от 7 до 11% фирм, под вергшихся обследованию, передали перевозчикам функции по осуществлению контроля за товарно-материальными запасами, выпол нению заказов и эксплуатации парка транспортных средств 1 .
Опыт многих транспортных фирм, взявших на вооружение логистическую концепцию, показывает, что политика дополнительных услуг, не связанных непосредственно с перевозками, имеет большое значение и дает положительные результаты. Она повышает потен циал привлечения клиентуры, увеличивает прибыль, позволяет ус корить внедрение более прогрессивных транспортных технологий и улучшить обслуживание потребителей, находящихся в постоянном контакте с перевозчиком, а также укрепить свое положение на рынке транспортных услуг.
' Traffic Management , 1988, vol . 27, № 10, p . 41.
В свою очередь промышленные фирмы, доверившие часть своих функций транспортным предприятиям, предпочитают специализи роваться на основной своей деятельности для повышения ее эффек тивности и готовы оплачивать квалифицированные услуги сторон них фирм по выполнению ряда логистических функций. Промышленные фирмы видят в этом процессе свою основную выгоду — снижение суммарных затрат и особенно сокращение фонда заработной платы. Кроме того, наряду с чисто экономическими факторами грузовладельцы получают более высокую степень свободы маневра. Так, повышение коммерческой гибкости очень ценно для отраслей, работающих на распределенных по большим территориям рынках и несущих потери от несвоевременного переключения товарных пото ков в соответствии с колебаниями спроса.
По мнению некоторых экспертов-логистиков, главной причиной, препятствующей расширению взаимодействия промышленных и транспортных фирм в области логистики, является опасность по тери грузовладельцем контроля за движением сырья и готовой продукции. Вместе с тем следует отметить, что эта причина носит, по- видимому, субъективный характер, и можно ожидать снижения ее влияния по мере накопления опыта совместной работы и укрепле ния взаимного доверия. Подтверждение этому: в настоящее время процесс передачи транспортным фирмам логистических функций со стороны производственных фирм быстро развивается, эта тенденция, вероятно, сохранится и в перспективе.
Политика транспортных предприятий в области коммуникаций имеет своей целью информировать клиентов о предлагаемых паке тах услуг, а также постоянно оказывать необходимое влияние на клиентуру, чтобы она могла использовать услуги в возможно боль шем объеме. Другая цель этой политики — способствовать расшире нию и совершенствованию взаимодействия транспортных фирм и грузоотправителей на основе использования вычислительной техни ки и главным образом с помощью электронного обмена данными.
Информирование клиентуры о предлагаемых пакетах услуг не только означает постоянное обращение к ней и присутствие на рынках спроса, но и требует переосмысления политики с точки зрения того, что сбыт транспортных услуг вес больше и больше происходит исключительно на рынке покупателей, а не продавцов. Данное требование должно соблюдаться также и в периоды, характеризующиеся недостатком транспортных мощностей, так как стремление сбыть услуги характеризуется продолжительным действием. Кроме того, для сбыта пакета услуг необходимо выполнение еще одного важного требования: в информации должно содержаться нечто новое. Примером этого может быть реклама нового маршрута или нового способа перевозок, способствующая повышению степени известности предлагаемого пакета услуг. Таким образом, политика в области коммуникаций направлена на то, чтобы убедить рынок или определенные группы клиентуры в особой значимости предложенной услуги и, возможно, ее незаменимости.
Предложению пакета транспортных услуг предшествует изучение потребностей клиентуры. В последние годы на транспорте ряда про- мышленно развитых стран исследованием потребностей стали зани маться специальные логистические центры и другие структуры. Во Франции, например, такие центры были созданы на железных доро гах в 80-е годы. Они проводят анализ грузопотоков и распределения их по сети. На основе данных анализа подготавливаются предложе ния по ( I ) организации оптимальных грузопотоков как железнодорожным, так и другими видами транспорта; (2) способам распределения перевозок между различными видами транспорта; (3) комплектованию групп товаров; (4) порядку заключения договоров на перевозку и др. Цель подготавливаемых предложений заключается в том, чтобы обеспечить: повышение уровня работы транспорта; со блюдение сроков доставки грузов; повышение надежности и регуляр ности перевозок; сохранность товаров и т.д.
Представляет интерес порядок перегруппировки товаров в грузо потоках на железнодорожном транспорте Франции с целью повы шения рентабельности перевозок за счет укрупнения грузопотока и реорганизации некоторых операций. Концентрация грузопотоков стимулируется тарифной политикой, в соответствии с которой мас совые перевозки грузов осуществляются по сниженным тарифам. При этом место, где производится перегруппировка грузопотоков, может использоваться одним или несколькими предприятиями.
На железных дорогах развитых стран существуют и другие органи зации, занимающиеся логистическими услугами в соответствии с тре бованиями рынка, например, организации по экспедиторской дея тельности, несущие ответственность за доставку груза, включая его перевозку от поставщика до потребителя, даже в тех случаях, когда груз перевозится в смешанных сообщениях. Во Франции многие та кие организации имеют численность служащих 250 человек и более.
В настоящее время в целях повышения качества обслуживания клиентуры экспедиторские организации строят новые терминалы, которые будут располагать цехами для технического обслуживания большегрузных автомашин. Планируется, что некоторые терминалы будут иметь свою собственную железнодорожную ветку, а для сокра щения времени на таможенные формальности на них предполагается ввести в эксплуатацию электронную систему таможенного контроля.
Экспедиторские организации предоставляют услуги по любой логистической операции, связанной с перевозочным процессом. Например, они берут на себя функции по выполнению таможенных формальностей, отвечают за сохранность груза в пути, гарантируют его доставку необходимой скоростью и т.д. При этом услуги оказы ваются по всей логистической цепочке, начиная от поставщика сырья и кончая доставкой готовой продукции потребителям. Как показывает практика, подключение услуг к информационной автоматизированной системе управления производством позитивно ска зывается на всей ее деятельности.
Интенсификация хозяйственных связей между транспортными фирмами и другими участниками логистического процесса объек тивно привела к увеличению потока информации и одновременно усложнила обмен ею. С целью улучшения качества обслуживания клиентуры потоки бумажной информации стали вытесняться авто матизированными системами, основанными на еовременной ком пьютерной технике. Наиболее важным для транспортных фирм стал обмен данными грузовых накладных с компьютера грузоотправителя на компьютер перевозчика и далее на компьютер грузополучате ля, а также электронный перевод ценных бумаг, сведений о местона хождении грузов и некоторой другой информации.
Использование компьютерной техники для электронной переда чи данных сокращает объем бумажной документации и конторские расходы, помогает избежать традиционных ошибок, возникающих при ручном заполнении документов, способствует ускорению доставки грузов, уменьшению запасов товарно-материальных ценнос тей, повышению производительности труда. Поэтому не случайно в странах с рыночной экономикой уровень применения фирмами электронного обмена данными постоянно растет. Например, в США в конце 1980-х годов средний уровень компьютеризации составил (в %): на фирмах грузополучателей — 30; транспортных фирмах — 26,8; складах общего пользования — 15,3; у грузоотправителей — 15,0; у подрядчиков — 3,9. Ожидается, что к 1996 г. этот уровень на указанных фирмах существенно возрастет и составит соответствен но 36,6%, 35,8%, 32,4%, 23,9% и 15,8%, т. е. в среднем он будет равен 33%'.
' Traffic Management , 1988, vol . 27, № 5, p . 48.
9.3. Новые логистические системы сбора и распределения грузов
Распределение программ производства, снабжения и сбыта, ра ботающих строго по графику («Канбан» и «Точно в срок»), — это результат совершенствования методов производства товаров и до ставки их на рынок. Взаимосвязь и взаимозависимость всех логисти ческих элементов,
включая транспорт, обусловили необходимость комплексного подхода к их дальнейшему развитию, на базе которого и происходило формирование инновационных транспортных систем сбо ра и распределения материальной продукции.
Подготовка к внедрению вышеуказанных программ заключалась в таких мерах, как: налаживание высококачественного и надежного производства; перепланировка производственных помещений и на стройка их на эффективную работу (включая улучшение работы по сбору заказов потребителей); внедрение современных информаци онных систем, обеспечивающих текущее управление и контроль всего логистического процесса в реальном масштабе времени, и, наконец, обеспечение надежной транспортировки грузов.
Первые три пункта подготовительных мероприятий обычно осу ществляются производственными и реже посредническими фирма ми. Перевозки же полностью или частично выполняются транспортными предприятиями общего пользования. Поскольку все элементы логистических каналов, функционирующих по вышеуказан ным программам, должны работать почти идеально, чтобы избежать остановки производственного процесса или исчерпания запасов у потребителей, постольку непосредственный контроль за движением товарно-материальных ценностей является основным объектом пристального внимания. Из этого следует, что транспорт представляет собой важное звено логистической системы; он должен обладать рядом необходимых свойств и удовлетворять определенным требованиям в целях создания инновационных систем сбора и распреде ления грузов.
Прежде всего транспорт должен быть достаточно гибким, чтобы обеспечивать перевозочный процесс, подвергающийся еженедель ной или даже ежедневной корректировке, гарантировать частую и круглосуточную доставку грузов в разбросанные и отдаленные пунк ты, надежно обслуживать клиентуру с целью избежания остановки работы предприятий или дефицита у заказчика. Одновременно транс порт должен обладать способностью перевозить небольшие партии грузов через короткие интервалы времени в соответствии с меняющимися запросами пользователя и условиями мелкосерийного про изводства.
Основными организационными структурами, отвечающими вы шеуказанным требованиям, стали региональные транспортные ком пании по сбору и распределению грузов, обеспечивающие перевоз ки на небольшие расстояния к торговой зоне. Такие компании обычно осуществляют перевозки грузов малыми партиями и дают экономию затрат за счет использования собственного терминала по сбору и распределению грузов вместо распределительного центра промыш ленной фирмы, обслуживающего некоторый регион и несущего боль шие расходы по содержанию запасов. На пунктах сбора региональ ных транспортных компаний грузы хранятся один-два дня, а затем комплектуются и поставляются заказчику на следующие или вторые сутки. Обычно операции транспортной организации по сбору и распределению грузов сокращают продолжительность доставки ма лых партий груза от поставщика до заказчика на 25—50% и более в зависимости от конфигурации обслуживаемой сети. Новые услуги транспортных организаций предоставляют клиентуре возможность осуществлять контроль и проявлять гибкость для быстрой перестрой ки каналов распределения. В реальном масштабе времени заказчики могут изменять объем и сроки поставок, маршруты следования, раз мер партий грузов, подлежащих сдаче, или транзитных услуг.
Появление на рынке услуг региональных транспортных компаний по сбору и распределению грузов и перевозке их к торговым зонам снизили конкурентоспособность промышленных фирм, вла деющих центрами распределения и традиционными транспортными организациями по доставке грузов мелкими партиями. Последние, также, как и автотранспортные компании, осуществляющие магис тральные перевозки, были вынуждены прибегнуть к более диффе ренцированным видам обслуживания. Кроме того, новые регио нальные организации по сбору грузов, установив свои цены и нор мативы обслуживания, начали предлагать специализированные ус луги в данной сфере деятельности, направленные на удовлетворение конкретных потребностей грузоотправителей.
Стремление иметь логистические системы с более высоким уров нем обслуживания и низким уровнем запасов товарно-материальных ценностей на длинных линиях снабжения привело к возникновению различных вариантов управления этими системами, а именно: к изменению традиционных способов консолидации грузов, выполнению операций на вблизи расположенных складах, осуще ствлению новых видов услуг по сбору и распределению грузов, а также объединению систем поставщиков и производителей.
При традиционных способах оказания услуг сокращение време ни доставки грузов достигается путем комбинирования быстрого обслуживания клиентуры транспортными компаниями общего пользования и специальной ускоренной обработки грузов в пунктах их объединения. Ответственность за организацию всей работы канала снабжения обычно несет заказчик. Фирмы по сбору грузов объединяют мелкие партии, поступающие от нескольких поставщиков. Объединенные грузы отправляются непосредственно заказчикам либо на его склады или в случае необходимости в распределительные центры, где они разукрупняются и мелкими партиями в течение одного-двух дней доставляются заказчику силами и техникой цент ра. Часто отправку мелкопартионных грузов осуществляют либо служба доставки, либо транспортные компании, специализирующи еся на перевозке небольших упаковок грузов.
Преимущество скорректированного традиционного способа ока зания услуг состоит в том, что при изменении условий в регионе или потребности в обслуживании клиентуры можно перезаключать контракты на любом участке канала снабжения, так как все расходы по перевозке грузов несут пункты по их сбору и транспортные компа нии общего пользования. Недостатки данного способа — это весьма существенные затраты по привлечению транспортных компаний общего пользования с их высокими тарифами, отсутствие гибкости в операциях на постоянных пунктах и ограничение на качество обслуживания, связанные с большим числом поставщиков.
Операции на складах, расположенных вблизи от поставщиков или производителей, аналогичны традиционным услугам по укрупнению мелких партий грузов. Поставщики, имеющие такой склад в нескольких километрах от предприятия-продуцента, поставляют ему разнообразную продукцию, предварительно укрупнив ее в партии требуемого размера. Фирмы-производители на своих складах осуществляют сбор комплектующих элементов, поступающих от многих поставщиков, объединяют их партии и отправляют потребителям.
Позитивная сторона (для поставщиков или производителей) данного способа обслуживания заключается в простоте изменения вида услуг и размера партий грузов, доставляемых транспортными фир мами, и возможности приспосабливать логистические операции к потребностям предприятия в поставках на повседневной основе. Вместе с тем выполнение операций на расположенных вблизи скла дах имеет и недостатки: необходимость нести капитальные затраты на создание склада, который не всегда может использоваться полно стью; затруднения (с точки зрения поставщика) в обслуживании одного-двух предприятий при любом расположении склада; сложность (с точки зрения фирмы-изготовителя) координации значи тельного объема транспортных операций по доставке грузов собст венным подвижным составом.
К более совершенным способам сбора и распределения грузов относятся смешанные контейнерные железнодорожные перевозки во внутреннем и международном сообщениях, осуществляемые на большие расстояния по системе «Точно в срок», а также межрегио нальные перевозки грузов, выполняемые автотранспортными ком паниями между принадлежащими им региональными пунктами, которые обычно отстоят один от другого на 850 и более километров.
Фирма «Американ президент лайнс» совместно с другими желез ными дорогами перевозит контейнеры от портов западного до пор тов восточного побережья США. С помощью специально оборудо ванных железнодорожных вагонов и быстрого выполнения погру-зочно-выгрузочных работ грузовладельцы могут доставлять контейнеры за 7 суток от побережья до побережья. При транспортировке только морским путем на это уходило 15— 17 суток. С учетом расхо дов на перегрузку контейнеров с судна на железную дорогу и обрат но и затрат на создание специальных небольших причалов данный способ транспортировки дает не только выигрыш во времени, но и обходится намного дешевле, что в конечном итоге приводит к со кращению запасов товарно-материальных ценностей и организации контрейлерных перевозок по конкурентоспособным тарифам. К недостаткам смешанных железнодорожно-морских перевозок контей неров относятся проблема двойной ответственности за груз и огра ниченные возможности осуществлять транспортировку данным спо собом в условиях отсутствия свободной территории в портах.
Автотранспортные компании, выполняющие межрегиональные перевозки грузов укрупненными партиями при полном использова нии грузоподъемности собственных автомобилей, предварительно консолидируют грузы на пунктах сбора и разукрупняют их в местах распределения, доставляя мелкими партиями до получателей.
Основное преимущество такою способа сбора и распределения грузов — это возможность приспосабливать каналы материально-технического снабжения к потребностям заказчика, так как авто транспортные компании способны контролировать работу автомо билей, эксплуатирующихся по системе «Точно в срок». Кроме того, эти компании не применяют жестких тарифов и не заключают тра диционных контрактов, обеспечивая тем самым высокую гибкость в отношениях с заказчиками.
Недостаток данного способа сбора и распределения грузов — срав нительно небольшие размеры автотранспортных компаний (не более 50 автомобилей, часто менее 20 ед.), вследствие чего они по-падают в зависимость от крупных заказчиков. Негативной стороной автотранс портных компаний является также то, что они редко предлагают свои услуги в масштабе всей страны, а сосредоточивают свою деятель ность, как правило, на обслуживании одного-двух регионов, чтобы иметь сбалансированные потоки грузов на основных магистралях.
Самый современный вариант логистического обслуживания кли ентуры по программе «Точно в срок» (при дальних расстояниях перевозок грузов) — это интегрированные системы снабжения поставщика и производителя, появившиеся благодаря внедрению в хозяйственную практику фирм электроники. В таких системах име ются новейшие типы ЭВМ, связанные с центральной «ЭВМ распре деления», которая выдает данные о наличии запасов товарно-мате риальных ценностей, в том числе в пунктах укрупнения партий груза и на всем пути его следования.
Несмотря на то, что отдельные элементы логистической системы (транспорт, пункты обработки грузов, средства связи и т. д.) могли бы принадлежать поставщикам и производителям на индивидуаль ной или совместной основе, фактически в первые годы зарождения системы современных услуг за большинством элементов сохранялась прежняя собственность, а их деятельность координировалась при помощи электронной техники, являющейся общей собственно стью. В дальнейшем стала проявляться тенденция к совместному владению поставщиками и производителями некоторыми элемента ми логистических систем, работающих по программе «Точно в срок» (или осуществлению совместного контроля). Особенно это стало характерным для корпораций с вертикально интегрированными филиалами, поставляющими материалы другим дочерним, фирмам, а также партнерам совместных предприятий, участвующим в разра ботке новейших технологий.
Непосредственные связи с помощью электронных средств между поставщиками и производителями многообразны. Прямая связь между двумя сторонами не только ускоряет процесс прохождения заказов, обеспечивая их более быстрое выполнение при меньшем объеме бумажной документации, но и облегчает управление запасами товарно-материальных ценностей, сокращая затраты на выпол нение заказов и хранение запасов. Кроме того, современная связь обеспечивает поставщику получение большого объема информации, делая для него доступными данные о сбыте продукции. Однако еще более важно то, что обеспечивается мгновенная связь поставщика с конечным потребителем. В результате удается быстро оценить изме нения и тенденции на рынке.
Таким образом, исследование новых логистических систем сбора и распределения грузов показали, что они получили широкое рас пространение в развитых странах с рыночной экономикой, став с точки зрения затрат и уровня обслуживания эффективными альтер нативами прежним системам транспортного сервиса.
Контрольные вопросы к главе 9
- Какое влияние оказала логистика на развитие транспорта?
- Назовите важнейшие мероприятия по дерегулированию транс порта.
- Охарактеризуйте новые критерии оценки работы транспорта, возникающие под влиянием логистических систем «Канбан» и «Точно в срок».
- В чем заключается новый подход к транспорту как составной части логистической цепи?
- Какие изменения произошли в освоении перевозок различ ными видами транспорта в условиях функционирования ло гистики?
- Перечислите новые виды услуг автотранспортных и железно дорожных компаний по сбору и распределению грузов.
- Расскажите об основных компонентах политики решения транспортных проблем.
- Охарактеризуйте политику предоставления новых услуг на транспорте.
- Раскройте содержание политики транспортных фирм в области коммуникаций и политики заключения контрактов.
- Какие требования предъявляются к транспорту в целях повы шения качества его работы в логистических системах?
- Какие организационные структуры транспорта наиболее полно удовлетворяют требованиям, предъявляемым транспорту, функционирующему в логистических системах?
- Назовите преимущества и недостатки нового способа оказания услуг транспортными компаниями общего пользования.
- Раскройте суть смешанных контрейлерных железнодорожных перевозок грузов.
- Расскажите о положительных и отрицательных сторонах перевозок грузов укрупненными партиями в межрегиональном сообщении, выполняемых автотранспортными компаниями.
- В чем существо логистического обслуживания клиентуры при дальних расстояниях перевозок грузов по критерию «Точно в срок» на базе использования электроники?
|