МИНИСТЕРСТВО ОБРАЗОВАНИЯ И НАУКИ РОССИЙСКОЙ ФЕДЕРАЦИИ
ФЕДЕРАЛЬНОЕ АГЕНТСТВО ПО ОБРАЗОВАНИЮ
Грозненский государственный нефтяной институт
имени акад. М.Д. Миллионщиков
Кафедра «Химическая технология нефти и газа»
КУРСОВАЯ РАБОТА
По курсу
«Технология переработки нефти и газа»
На тему
«Выбор и обоснование варианта и технологической схемы переработки нефти»
Грозный 2009г.
Содержание
Введение
1. Теоретические основы переработки нефти
1.1 Индексация нефтей и ее связь с технологией их переработки
1.2 Физические основы подготовки и первичной переработки нефти
1.3 Основные факторы, определяющие выход и качество продуктов ППН
1.4 Краткие теоретические основы процессов вторичной переработки продуктов ППН и производства масел
2. Характеристика нефти
3. Выбор и обоснование варианта переработки нефти
4. Разработка поточной технологической схемы НПЗ
5. Описание технологических процессов, входящих в схему НПЗ
6. Материальные балансы технологических процессов НПЗ
7. Суммарный материальный баланс НПЗ
Заключение
Список использованной литературы
Введение
Нефть известна человеку с древнейших времен. Учеными установлено, что более 500 тыс. лет тому назад нефть уже была обнаружена на берегу Каспийского моря, а за 6 тыс. лет до нашей эры отмечался выход на поверхности земли нефтяного газа на Кавказе и в Средней Азии. Более 2 тыс. лет тому назад нефть стали применять в строительстве, военном деле и в медицине.
Промышленное значение нефть приобрела лишь в XVIII в. В 1745 г. был построен первый нефтеперегонный завод в России на реке Ухте, затем в 1823 г. – второй на Северном Кавказе около г. Моздок. На этих заводах из нефти отгоняли осветительный керосин, а легко испаряющийся головной продукт перегонки – бензин и тяжелый остаток – мазут сжигали в «мазутных» ямах, так как не находили применение. Первоначально нефть перегоняли в кубах периодического действия, затем, начиная с середины 80-х гг. XIX, на кубовых батареях непрерывного действия.
В 1876 г. В.Г. Шухов изобрел форсунку, которая быстро вытеснила самые разнообразные устройства, применявшиеся для сжигания жидкого топлива. В результате этого балласт производства – мазут стал применяться в качестве топлива для паровых котлов. В том же году Д.И. Менделеев показал возможность получения минеральных смазочных масел перегонкой в вакууме или в токе водяного пара. Нефтяные масла стали вытеснять животные жиры и растительные смазочные масла из всех отраслей техники.
В 1890 г. В.Г. Шухов и С.П. Гаврилов запатентовали трубчатую нефтеперегонную установку непрерывного действия – прообраз современных установок для перегонки нефти. Широкий размах в развитии нефтяной и газовой промышленности определило внедрение карбюраторных, дизельных, газотурбинных, турбореактивных и турбовинтовых двигателей.
1.Теоретические основы первичной переработки нефти
1.1.Индексация нефти и ее связь с технологией их переработки
В зависимости от свойств получаемых нефтепродуктов выбирают наиболее рациональные, экономически выгодные пути переработки нефти. Для определения наиболее приемлемого варианта переработки нефти приводят классификацию. Существует несколько видов классификаций. Когда нефтепереработка только начала развиваться, нефти делили на три вида в зависимости от плотности: легкий, средний, утяжеленные. Позже появилась классификация горного бюро США, затем классификация ГрозНИИ, но в настоящее время наибольшее применение находит технологическая классификация.
Технологические классификации обычно преследуют прикладные цели и часто носят ведомственный характер. В основу их положены признаки, имеющие значения для технологии переработки нефти или получения того или иного ассортимента продуктов.
Рассмотрим принятую в России технологическую классификацию
Таблица 1.1 - Технологическая классификация нефтей
Класс нефти |
Содержание серы, %(масс) |
Нефть |
Бензин (н.к.-180 °C) |
Авиац. кер. (120-240 °C) |
Дизельное топливо (240-350 °C) |
1 (малосернистая) |
≤0,5 |
≤0,1 |
≤0,1 |
≤0,2 |
2 (сернистая) |
0,5-2,0 |
≤0,1 |
≤0,25 |
≤1,0 |
3 (высокосернистая) |
2,0 |
>0,1 |
>0,25 |
>1,0 |
Тип нефть |
Содержание фракций до 350 °C, %(масс) |
1 (легкая) |
≥55,0 |
2 (средняя) |
45-54,9 |
3(тяжелая) |
<45 |
Группа нефти |
Потенциальное содержание базовых масел. % (масс) |
1 |
>25 |
>45 |
2 |
15-24,9 |
45 |
3 |
15-24,9 |
30-44,9 |
4 |
<15 |
<30 |
Подгруппа нефти |
Индекс вязкости |
1 |
>95 |
2 |
90-95 |
3 |
85-90 |
4 |
<80 |
Вид нефти |
Содержание парафина, % (масс) |
Требования подепарафинизации |
не требуется |
требуется |
1 (малопарафинистая) |
≤1,5 |
Для получения реактивного и дизельного топлив и дистиллятных базовых масел |
- |
2 (парафинистая) |
1,51-6.0 |
Для получения реактивного и летнего дизельного топлива |
Для получения зимнего дизельного топлива дистиллятных базовых масел |
3 (высокопарафинистая) |
>6,0 |
- |
Для получения реактивного топлив и дистиллятных базовых масел |
Как видно из этих норм по содержанию серы и парафина, требования касаются не только нефти, но и качества наиболее употребляемых топлив (и базовых масел), причем определяющим для отнесения нефти к тому или иному классу или виду являются требования по дистиллятам.
Шифр нефти по этой классификации записывается пятизначным числом с точками. Например,1.2.2.1.3- малосернистая нефть, со средним содержанием светлых дистиллятов, с достаточно высоким содержанием парафина.
Шифр нефти является как бы ее технологическим паспортом, определяющим направление ее переработки (на топлива или масла), набор технологических процессов (сероочистка, депарафинизация) и ассортимент конечных продуктов.
1.2 Физические основы подготовки и первичной переработки нефти
В нефти, добываемой из недр земли, содержатся вредные примеси, которые затрудняют транспортировку и ухудшают переработку нефти, вследствие чего перед переработкой нефть необходимо подготовить. Подготовка нефти заключается в удалении из нее нежелательных вредных примесей. К ним относятся: вода, минеральные соли, механические примеси. Наличие в нефти механических примесей может привести к отлаганию их в трубопроводах, снижая ее проходимость, а также к эрозии внутренней поверхности труб. Содержание воды в нефти, добываемой из скважин, колеблется в широких пределах и растет с увеличением времени эксплуатации скважин (на старых скважинах содержание воды в нефти может достигать 90%). Вода в нефти приводит к дополнительным экономическим затратам по транспортировке нефти, так как является ненужным балластом. Чрезмерное повышение давления может привести к разрыву змеевика печи или теплообменника. Минеральные соли, содержащиеся в нефти, могут вести себя по-разному. Часть минеральных солей подвергается гидролизу с образованием кислоты, которая приводит к коррозии аппаратуры, т.е. соли, которые не подвергаются гидролизу, могут отлагаться в виде накипи в змеевиках печей и теплообменников, снижая коэффициент теплоотдачи. В нефти, поступающей на первичную переработку, допускается содержание воды не более 0,2%, а минеральных солей не более 5 мг на 1 л.
Нефтяные эмульсии. Нефть с водой образуют 2 типа эмульсий: «нефть в воде», но чаще «вода в нефти». Эмульсией называется система из 2-х нерастворимых жидкостей, одна из которых распределена в другой во взвешенном состоянии в виде мельчайших частиц. Та жидкость, которая находится во взвешенном состоянии в объеме другой, называется дисперсной фазой, а та, в которой распределена эта жидкость, - дисперсной средой. Образованию нефтяных эмульсий предшествует интенсивное перемешивание нефти с водой при добыче. При этом за счет снижения поверхностного натяжения на границе раздела фаз «нефть – вода» адсорбируются вещества, образуя прочный адсорбционный слой, называемый эмульгатором. В случае эмульсии «вода в нефти» в качестве эмульгаторов выступают частицы глины и песка, соли, смолы. Наличие этого адсорбционного слоя препятствует слиянию и укрупнению частиц дисперсной фазы при их столкновении, с последующим их осаждением. Стойкость нефтяных эмульсий зависит от физико-химических свойств (плотности, вязкости), степени дисперсности (чем меньше диаметр частиц дисперсной фазы, тем труднее разрушить эмульсию), а также времени существования эмульсий (эмульсии имеют свойство «стареть», т.е. с увеличением времени существования, увеличивается и ее стойкость к разрушению).
Способы разрушения нефтяных эмульсий. Все способы разрушения нефтяных эмульсий направлены на разрушение адсорбционного слоя с последующим слиянием и укрупнением и осаждением частиц дисперсной среды.
Разработан ряд методов разрушения нефтяных эмульсий, которые делятся на 4 гр.:
1. Механический метод разрушения нефтяных эмульсий. К ним относятся: отстаивание, центрифугирование, фильтрование.
Отстаивание применимо к свежим нестойким эмульсиям, в этом случае отделение воды происходит за счет разности плотностей 2-х сред (частицы воды оседают под действием собственных сил тяжести). Отстаивание применяется на нефтепромыслах в местах добычи нефти.
Центрифугирование основано на разрушении нефтяных эмульсий за счет ее вращения в центрифугах. При этом под действием центробежной силы частицы воды отбрасываются на стенки центрифуги и стекают вниз. Этот метод не нашел применение в промышленности из-за больших энергозатрат, он применяется только в лабораторных условиях.
Фильтрование основано на различной смачиваемости фильтра некоторыми жидкостями. Для разрушения нефтяных эмульсий в качестве фильтра можно использовать опилки древесины, стекловату. В этом случае фильтр смачивается водой и не смачивается нефть. Но из-за быстрого загрязнения фильтра и необходимости его частой смены, метод также применяется только в лабораторных условиях;
2. Термический метод – основан на нагревании нефтяных эмульсий. При этом частицы дисперсной фазы расширяются или адсорбционная пленка лопается, что приводит к слиянию частиц;
3. Химический метод – основан на применении химических реагентов, которые либо разрушают адсорбционный слой, вступая с ним в химическую реакцию, либо вытесняют действующий эмульгатор и становятся на его место, но имеют плотность, меньшую плотности адсорбционной пленки. Эти вещества называются деэмульгаторами;
4. Электрический метод – основан на помещении нефтяных эмульсий в поле электрического тока. В этом случае частицы воды начинают вытягиваться одним концом то к одному, то к другому полюсу (электроду). При смене полюсов они как будто дрожат. При этом происходит столкновение и слияние частиц воды. Разрушение нефтяных эмульсий под действием электрического поля происходит в аппаратах – электродегидраторах.
Принципиальная технологическая схема ЭЛОУ
Разрушение нефтяных эмульсий происходит на блоках ЭЛОУ, которые могут входить в состав установки АТБ или являться отдельными установками. Поступающая на установку нефть нагревается сначала (на установке) в теплообменнике, а затем пароподогревателе до температуры 150-160°C , сливается со щелочью промывкой водой и деэмульгатором и поступает в электродегидратор первой ступени. В Э-1 происходит отделение от нефти основной массы воды и солей. Вода выводится снизу электродегидратора, сверху выводиться частично очищенная нефть. Она вновь смешивается со щелочью промывкой водой и деэмульгатором и поступает в электродегидратор второй ступени. В Э-2 происходит полное отделение от нефти воды и солей. Вода выводится снизу Э-2 , поступает на смещение с нефтью перед Э-1. Сверху Э-2 выводится очищенная нефть, которая в теплообменнике Т-1 отдает тепло поступающей нефти и выводиться с установки. Число степени электродегидрации зависит от степени обводненности нефти и может достигать до четырех. На установке ЭЛОУ применяются все четыре способа разрушения нефтяных эмульсий (рис.1).

щелочь
Очищенная нефть
Рисунок 1- Принципиальная технологическая схема ЭЛОУ
1.3 Основные факторы, определяющие выход и качество продуктов первичной перегонки нефти
Перегонка (дистилляция) – это процесс физического разделения нефти и газов на фракции (компоненты), различающиеся друг от друга и от исходной смеси по температурным пределам (или температуре) кипения. По способу проведения процесса различают простую и сложную перегонку.
Простая перегонка осуществляется постепенным, однократным или многократным испарением.
Перегонка с постепенным испарением состоит в постепенном нагревании нефти от начальной до конечной температуры с непрерывным отводом и конденсацией образующихся паров. Этот способ перегонки нефти и нефтепродуктов в основном применяют в лабораторной практике при определении их фракционного состава.
При однократной перегонке жидкость (нефть) нагревается до заданной температуры, образовавшиеся и достигшие равновесия, пары однократно отделяются от жидкой фазы – остатка. Этот способ, по сравнению с перегонкой с постепенным испарением, обеспечивает при одинаковых температуре и давлении большую долю отгона.
Перегонка с многократным испарением заключается в последовательном повторении процесса однократной перегонки при более высоких температурах или низких давлениях по отношению к остатку предыдущего процесса.
Из процессов сложной перегонки различают перегонку с дефлегмацией и перегонку с ректификацией.
При перегонке с дефлегмацией образующиеся пары конденсируют, и часть конденсата в виде флегмы подают навстречу потоку пара. В результате однократного контактирования парового и жидкого потоков уходящие из системы пары дополнительно обогащаются низкокипящими компонентами, тем самым несколько повышается четкость разделения смесей.
Перегонка с ректификацией – наиболее распространенный в химической и нефтегазовой технологии массообменный процесс, осуществляемый в аппаратах – ректификационных колоннах – путем многократного противоточного контактирования паров и жидкости. Контактирование потоков пара и жидкости может производиться либо непрерывно (в насадочных колоннах) или ступенчато (в тарельчатых ректификационных колоннах).
Классификация ректификационных колонн
Ректификационная колонна представляет собой вертикальный цилиндрический аппарат различного диаметра (1,5-3,5м), высоты (от 10-12 до 30-35м). Изготовляется колонна из специальной марки стали, и она оснащена специальными контактными устройствами.
Все ректификационные колонны делят по нескольким признакам:
1) по технологическому режиму в колонне различают: колонны, работающие при атмосферном давлении или близком к нему; колонны, работающие под избыточным давлением; колонны, работающие под вакуумом;
2) по типу контактных устройств различают: колонны насадочного типа; роторно-дисковые колонны; тарельчатые колонны.
3) по количеству отбираемых продуктов различают простые и сложные колонны. Простой называют колонну, в которой отбирают два продукта – верхний и нижний. Сложной называют колонну, в которой отбирают три и более продукта: сверху, снизу и сбоку колонны.
Простые колонны обеспечивают разделение исходной смеси (сырья) на два продукта: ректификат (дистиллят) - выводимый с верха колонны в парообразном состоянии, и остаток – нижний жидкий продукт ректификации.
Сложные колонны обеспечивают разделение исходной смеси на три и более продукта.

Рисунок 2- Простая ректификационная колонна

Рисунок 3- Сложная ректификационная колонна
Классификация установок первичной переработки нефти
Вариант переработки нефти выбирают в зависимости от шифра нефти. В связи с тем, что светлые фракции (до 350° С) всегда используются в качестве топлив, варианты переработки нефти выбирают в зависимости от группы и подгруппы нефти. Принципиальная технологическая схема АВТ принимается после выбора варианта переработки.
При выборе схемы следует учесть состав и характеристики перегоняемой нефти, а также ассортимент, требования к качеству получаемых продуктов.
I. Атмосферная трубчатка (АТ). Этот блок предназначен для отбора от нефти светлых нефтепродуктов при атмосферном давлении. В атмосферной части схема перегонки может быть с однократным испарением и двухкратным испарением: а) с предварительным отбензиниванием нефти; б) с предварительным испарением легких фракций.
Выбор той или иной схемы зависит от типа нефти и ее класса (особенно по меркаптановой сере), а также содержащихся в нефти растворенных газов. При выборе каждой из этих схем следует учитывать их недостатки и преимущества.
1. Установки с однократным испарением (ОИ) применяются при перегонке стабильных нефтей с незначительным содержанием растворенных газов. Они обеспечивают минимальные энергозатраты и меньшую металлоемкость по сравнению с другими схемами. Существенный недостаток этих установок – отсутствие технологической гибкости для перевода на новое сырье и др. ассортимент продуктов, а также большие потери фракций, выкипающих до 350 °С, с мазутом (рис. 4).
2. При двукратном испарении с предварительным отбензиниванием. Бензиновая фракция и УВ газ отбираются в отбензинивающей колонне, а в основной отбирается легкая, тяжелая керосиновая фракции. Эта схема переработки нефти применяется при наличии в нефти большого количества растворенных газов и бензиновой фракции, а при переработке обводненных, сернистых нефтей. Достоинством этой установки является высокая технологическая гибкость, возможность снижения давления и нагрузки печи от легких фракций, что позволяет тем самым разрушить основную ректификационную колонну и предотвратить ее коррозию. Недостатком этой установки является энергоемкость, обусловленная необходимостью нагрева нижней части отбензинивающей колонны «горячей струей». Отбензиненную нефть приходится нагревать до более высокой температуры (390 ºС), что снижает качество масленых дистиллятов, находящихся в мазуте (рис. 5).


Рисунок 5- Схема установки с двухкратным испарением (предварительным отбензиниванием)3. Разновидностью блока АТ с двухкратным испарением является схема с предварительным испарением легких фракций, т.е. с эвапоратором. По этой схеме, нагретая в теплообменнике или в печи нефть поступает в испаритель, в котором за счет ОИ, разделяется на паровую и жидкостную фазы. Паровая фаза из испарителя подается в питательную секцию сложной ректификационной колонны. Достоинствами являются снижение нагрузки на печь и гидравлическое сопротивление печи. Недостатком является увеличение нагрузки по парам в сложной ректификационной колонне, т.к. в ней происходит ректификация и паров из испарителя и паров, образовавшихся за счет нагревания жидкой фазы в печи. Эта схема переработки нефти применяется крайне редко (рис. 6).
Рисунок 6- Схема установки с двухкратным испарением
(предварительным испарением легких фракций)
|
|
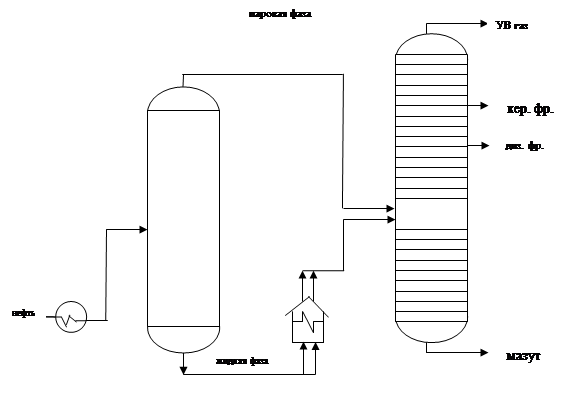 II. Вакуумная трубчатка (ВТ). Этот блок предназначен для перегонки мазута. В зависимости от варианта переработки нефти от мазута отбирают вакуумный газойль (350-500 ºС) – топливный вариант или масленые дистилляты (350-400, 400-450, 450-500 ºС) – топливно-масляный вариант. При отборе от мазута вакуумного газойля применяют схему с ОИ, т.е. мазут после нагрева в печи поступает в вакуумную колонну, где от него отбирается вакуумный газойль, а снизу колонны выводится гудрон (рис.1.7.).
В случае отбора от мазута масляных дистиллятов и когда требуется высокая четкость разделения, применяют схему вакуумного блока с двухкратным испарением. В этом случае в первой вакуумной колонне отбирается от мазута широкая масляная фракция (350-500 и 350-520 ºС), а затем эта фракция разделяется на узкие масляные дистилляты во второй вакуумной колонне, но эксплуатационные расходы на перегонку мазута по этой схеме значительно выше (рис.7).
В настоящее время атмосферные и вакуумные блоки строят в составе одной установки, что позволяет значительно снизить:
а) протяженность трубопроводов;
б) число промежуточных емкостей;
в) эксплуатационные затраты;
г) количество обслуживаемого персонала.
Рисунок 7- Схема установки с ОИ
(при перегонке мазута топливным вариантом)
|
|
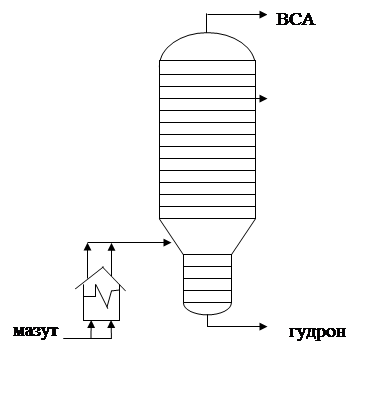
2. Характеристика нефти
Башкирская - одна из богатейших нефтяных областей Советского Союза. На ее территории открыты десятки месторождений, имеющих промышленное значение, из которых такие, как Туймазинское, Шпаковское, Аланское, обладают очень большими запасами нефти.
Карабаевский вал в северо - Западной части раздваивается, одна ветвь включает Орьбашское поднятие, а другая проходит на Касево и Николо-березовку, где залегают одноименные нефтяные месторождения.
На северо - западном продолжении Дюртюлинского вала располагаются Арланская, Уртаульская, Ного - Хазинская, Дюртюлинская и другие структуры, к которым приурочена группа месторождений нефти, получившая название « Большой Арлан».
Исходная нефть, для первичной переработки которой проектируется установка, указывается в задании на курсовое проектирование. В данном случае это Серноводская нефть. Приведем подробную характеристику нефти и составим ее шифр.
Все сведения о Серноводской нефти сводим в следующие таблицы:
· физико-химические свойства нефти;
· потенциальное содержание фракций в нефти;
· характеристика сырья для каталитического крекинга(350-450° С);
· характеристика фракций выкипающих до 200° С
· характеристика керосиновой фракции (180-240 ° С);
· характеристика дизельной фракции(240-350 ° С);
· потенциальное содержание базовых и остаточных масел;
· свойства, определяющие шифр нефти.
Таблица 2.1- Физико-химические свойства нефти
 |
0,8530 |
М |
- |
 |
 |
6 |
Температура
застывания ˚C
|
с обработкой |
-34 |
без обработки |
-16 |
Температура вспышки в закрытом тигле, ˚C |
-13 |
Давление
насыщенных паров
|
При 88 ˚C |
- |
При 50 ˚C |
- |
Парафин
|
Содержание % |
3,40 |
Температура плавления˚C |
52 |
Содержание, % |
серы |
3,04 |
азота |
0,33 |
смол сернокислотных |
76 |
Смол силикагелевых |
16,6 |
асфальтенов |
5,80 |
Коксуемость, % |
6,70 |
Содержание нафтеновых кислот % |
0,010 |
Выход
фракций вес. %
|
до 200 ˚C |
18,7 |
до 350˚C |
42,8 |
Таблица 2.2- Потенциальное содержание фракций в нефти
Отгоняется до температуры, 0
С |
нефть |
Отгоняется до температуры, 0
С |
нефть |
28 (газ до С4
)
60
62
70
80
85
90
95
100
105
110
120
122
130
140
145
150
160
170
180
190
200
210
220
230
240
|
-
3,2
3,7
6,8
7,5
|
250
260
270
280
290
300
310
320
330
340
350
360
370
380
390
400
410
420
430
440
450
460
470
480
490
500
остаток
|
24,9
26,7
28,0
29,9
31,5
33,2
35,1
36,9
38,8
40,2
42,8
44,8
46,2
48,6
50,5
52,5
55,8
55,0
57,5
59,2
60,8
-
-
-
-
-
39,2
|
Таблица 2.3- Характеристика керосиновой фракции (180-240 ° С)
Наименование |
Значение |
Выход на нефть, % масс |
16,5 |
Плотность,  |
0,8138 |
Фракционный состав
н.к.
10%
50%
90%
98%
|
180
192
220
277
288
|
Октановое число |
25 |
Отгоняется до 270° С,% масс |
85 |
Кислотное число, мг КОН/100мл фракции |
3,3 |
Температура,° С
начала помутнения
вспышки в закрытом тигле
Высота некоптящего пламени, мм
Содержание серы, % масс
|
-12
70
-
1,45
|
Таблица2.4-Характеристика фракций выкипающих до 200° С
Температура отбора °С |
Выход(на нефть), % |
 |
Фракционный состав, °С |
Содержание серы % |
Октановые число |
Кислотность, мг КОН на 100 мл фракции. |
н.к |
10% |
50% |
90% |
Без ТЭС |
с 0,6 г ТSC на 1 кг |
С 2,7 г ТSC на 1 кг |
28-85 |
4.8 |
0.6680 |
44 |
56 |
64 |
79 |
0.017 |
62.4 |
- |
- |
- |
28-120 |
8.5 |
0.6913 |
49 |
66 |
89 |
113 |
0.020 |
54,0 |
70.5 |
83.5 |
0.2 |
28-150 |
12.2 |
0,7110 |
52 |
71 |
107 |
139 |
0.042 |
43.0 |
60.0 |
80.2 |
0.4 |
28-180 |
14.9 |
0.7220 |
51 |
76 |
126 |
171 |
0.12 |
40.0 |
56.0 |
72.0 |
- |
28-200 |
17.5 |
0.7320 |
62 |
90 |
139 |
184 |
0.17 |
39.0 |
52.0 |
68.0 |
0.7 |
Таблица 2.5- Характеристика дизельной фракции(240-350 ° С)
Наименование |
Значение |
Выход на нефть, % масс |
19,80, |
Плотность,  |
0,8222 |
Фракционный состав
10%
50%
90%
96%
|
190
230
272
283
|
Содержание серы, % масс |
0,016 |
Цетановое число |
47 |
Дизельный индекс |
55,9 |
Кислотное число, мг КОН/100мл фракции |
- |
Анилиновая точка, °С
Температура застывания, °С
У20
,сст
У5
0 ,
сст
|
60,9
-38
2,65
1,56
|
Таблица 2.5- Потенциальное содержание базовых и остаточных масел
tотбора
, °С |
Выход дистил. фр. или остатка, % |
Характеристика базовых масел |
Содер. базовых масел |
 |
ν50
,
сст
|
ν100
,
сст
|
ν50/ ν100
|
ив |
ввк |
tзаст
, °С |
на д.ф. |
на нефть |
350-400 |
9,7 |
0,8560 |
13,30 |
3,80 |
3,5 |
85 |
0,796 |
-26 |
33,0 |
3,2 |
400-450 |
8,3 |
0,8800 |
30,10 |
6,50 |
4,7 |
85 |
0,817 |
-24 |
36,3 |
3,0 |
Остаток выше 500 |
18,2
|
00,9135 |
3314,8 |
30,38
|
10,2
|
66
|
0,840
|
-17
|
25,0
|
4,5
|
Характеристика сырья для каталитического крекинга Таблица 2.7
Наименование |
Значение |
Выход (на нефть), % |
1,8 |
Плотность,  |
0,9175 |
Температура застывания, 0
С |
29 |
Содержание, %
Серы
|
3,71
|
Содержание парафино-нафтеновых углеводородов,% |
39,8 |
Содержание ароматических углеводородов, %
I группа
II группа
|
17,8
38,6
|
Таблица-2.8.Общие свойства Арланской товарной нефти
Наименование |
Значение |
1. Плотность,  |
0,8918 |
2. Температура застывания, 0
С |
-16 |
3. Температура вспышки, 0
С |
-13 |
4. Коксуемость, % масс |
6,70 |
5. Содержание, % масс
- смол силикагелевых
- асфальтенов
- парафинов
- серы
- азота
|
16,6
3,80
3,40
3,04
0,33
|
6. Кислотное число, мг/г |
– |
7. Фракционный состав, 0
С
- н.к.
- 10 % об.
- 20 % об.
- 30 % об.
- 40 % об.
- 50 % об.
- 60 % об.
- 70 % об.
- 80 % об.
- 90 % об.
- к.к.
|
Свойства, определяющие шифр Арланской товарной нефти нефти Таб. 2.9
Наименование |
Значение |
1 |
2 |
1. Содержание серы, % масс.
- в нефти
- в бензине (н.к.-120°С)
- в керосине (180-240°С)
- в дизельном топливе (240-350°С)
|
3,04
0,020
1,45
1,91
|
Класс нефти: |
1 |
2. Содержание фракций, выкипающих до 350 °С, % масс. |
42,8 |
Тип нефти: |
2 |
3. Суммарное содержание базовых масел, % масс.
- на нефть
- на мазут
|
3,2
5,59
|
Группа нефти: |
2 |
4. Индекс вязкости базовых масел: |
85 |
Подгруппа нефти: |
4 |
5. Содержание парафина в нефти, % масс. |
3,40 |
6. Температура, °С
-начала кристаллизации авиакеросина
-застывания дизельного топлива
- застывания базовых масел
|
-60
-25
-26
|
Вид нефти: |
1 |
Шифр нефти: |
1.2.2.4.1. |
На основании определенного выше шифра, можно сказать, что Серноводская нефть, малосернистая со средним содержанием светлых дистиллятов с высоким содержанием низкокачественных масел и с высоким содержанием парафина. Следовательно, перерабатывается по топливному варианту.
3. Выбор и обоснование варианта переработки нефти
Выбор направления переработки нефти и ассортимента получаемых нефтепродуктов определяется физико-химическими свойствами нефти, уровнем развития техники нефтепереработки и потребностями в товарных нефтепродуктах данного экономического района. Различают три основных варианта переработки нефти: 1) топливный; 2) топливно-масляный; 3) нефтехимический (комплексный).
По топливному варианту нефть перерабатывают в основном на моторные и котельные топлива. При одной и той же мощности завода по нефти топливный вариант переработки отличается наименьшим числом технологических установок и низкими капиталовложениями. Переработка нефти по топливному варианту может быть глубокой и неглубокой. При глубокой переработке нефти стремятся получить максимально возможный выход высококачественных авиационных и автомобильных бензинов, зимних и летних дизельных топлив и топлив для реактивных двигателей. Выход котельного топлива в этом варианте сводится к минимуму. Таким образом, предусматривается такой набор процессов вторичной переработки, при котором из тяжелых нефтяных фракций и остатка – гудрона получают высококачественные легкие моторные топлива. Сюда относятся каталитические процессы – каталитический крекинг, каталитический риформинга, гидрокрекинг и гидроочистка, а также термические процессы, например, коксование. Переработка заводских газов в этом случае направлено на увеличение выхода высококачественных бензинов. При неглубокой переработке нефти предусматривается высокий выход котельного топлива.
По топливно-масляному варианту переработки нефти наряду с топливами получают смазочные масла. Для производства смазочных масел обычно подбирают нефти с высоким потенциальным содержанием масляных фракций. В этом случае для выработки высококачественных масел требуется минимальное число технологических установок. Масляные фракции (фракции, выкупающие выше 350 °C), выделенные из нефти, сначала подвергаются очистке избирательными растворителями: фенолом или фурфуролом, чтобы удалить часть смолистых веществ и низкоиндексные углеводороды, затем проводят депарафинизацию при помощи смесей метил этил кетона или ацетона с толуолом для понижения температуры застывания масла. Заканчивается обработка масляных фракций отбеливающими глинами.
При любом из двух разобранных вариантов переработки нефти следует предусматривать процессы по производству сырья для нефтехимической промышленности: этилена, пропилена, бутиленов, бензола, толуола и др. Из года в год увеличивается доля нефти, используемой как сырье для нефтехимической промышленности.
Нефтехимический вариант переработки нефти по сравнению с предыдущими вариантами отличается большим ассортиментом нефтехимических продуктов и в связи с этим наибольшим числом технологических установок и высокими капиталовложениями.
Выбор того или иного варианта переработки нефти, а, следовательно, и схемы промышленной установки первичной переработки нефти, обусловлен качеством исходной нефти и зависит также от ассортимента намеченных к выработке продуктов с заданными интервалами выкипания.
Экономически целесообразным вариантом переработки Серноводской нефти является топливный, в связи с недостаточным содержанием в ней масляных фракций. Исходя из шифра нефти (1.2.2.4.1.) и для получения выбранных конечных продуктов с приведенными выше свойствами, выберем трехступенчатую схему атмосферно – вакуумной перегонки нефти. В основу разрабатываемой схемы положим одну из промышленных схем АВТ с трехкратным испарением.
Нефть будет подвергаться предварительному обезвоживанию и обессоливанию, поэтому блок ЭЛОУ опускаем.
По принятой схеме нефть проходит три ступени перегонки: предварительной отбензинивание, собственно разделение на фракции и последующую вакуумную перегонку мазута.
Продукты установки АВТ
1. УВ газ, выделяемый из нефти, содержит значительное количество пропана и бутана, частично пентана. Этот газ направляется на ГФУ. Полученные из него фракции используют как бытовые и промышленные топлива, сырье на установках пиролиза, алкилирования (получения алкил - бензина). Полимеризации (получения полимер - бензина).
2. Бензиновая фракция (28-180°C). В основном подвергается вторичной перегонке с получением фракций.
3. Керосиновая фракция (180-240°C) используется для получения реактивных топлив, а также в качестве осветительного керосина.
4. Дизельных фракции (240-350°C) используется для производства различных сортов дизельных топлив.
5. Мазут (остаток выше 350°C) используется для получения котельного топлива, а также в качестве сырья установок термокрекинга.
6. Вакуумный газойль(350-500°C) используется в качестве сырья установок каталитического крекинга для получения высокооктановых бензинов.
7. Гудрон (остаток выше 500°C) используется в качестве сырья установок термокрекинга.
Описание технологической схемы АВТ
Обезвоженная и обессоленная нефть насосом Н-1 прокачивается через теплообменники Т-1 и Т-2, где она нагревается до температуры 180-200 °С, в простую отбензинивающую колонну К-1 на разделение. От нефти отбирают низкокипящие фракции. Давление газов поддерживается в колонне чуть выше атмосферного. Сверху колонны отбирают пары бензиновой фракции с растворенными углеводородными газами, которые далее отделяют от фракции. Часть бензиновой фракции подается обратно в колонну, в качестве холодного орошения, а балансовое количество выводится с установки. Остатком отбензинивающей колонны является отбензиненная нефть, которая подается в печь П-1, где доиспаряется и нагревается до температуры 350 °С и далее поступает в сложную колонну К-2. Часть отбензиненной нефти возвращается в простую колонну К-1 в качестве горячей струи. В сложной ректификационной колонне К-2 отбирают три дистиллята, сверху колонны отбирают пары легкой керосиновой фракции и воды, которые охлаждаются в аппарате воздушного охлаждения, доохлаждаются в конденсаторе – холодильнике и поступают в емкость-водоотделитель. Часть легкой керосиновой фракции возвращается в колонну К-2 в качестве орошения, а балансовое количество выводится с установки. Тяжелая керосиновая и дизельная фракции выводятся с установки через боковые погоны, которые поступают в теплообменники Т-1 и Т-2, где отдают свое тепло нефти, доохлаждаются в АВО-3 и АВО-4 и выводятся с установки. Остатком сложной ректификационной колонны является мазут, который поступает в печь П-2, где нагревается до температуры 420 ° С и поступает в вакуумную колонну К-3. Температура в печи П-2 поддерживается в пределах 420 ° С во избежание термического разложения молекул. В вакуумной колонне К-3 работает специально вакуум создающая аппаратура. Сверху колонны пароструйным эжектором через барометрический конденсатор выводятся пары – разложения. Вакуумный газойль выводится боковыми погонами, остатком вакуумной колонны является гудрон, который охлаждается до температуры 20-40° С в холодильнике погружного типа и выводится с установки, (рис.3.1).

Рисунок3.1. Принципиальная технологическая схема АВТ
4. Разработка поточной технологической схемы (НПЗ)
Сырая нефть с промыслов поступает на ЭЛОУ. Обезвоженная и обессоленная нефть направляется на первичную переработку, т.е. на АВТ.
Углеводородный газ, полученный на установке АВТ, направляется на ГФУ, где он разделяется на сухой (метан - этана) и сжиженный газы (пропановая, бутановая, изопентановая фракции). Сухой газ используется как бытовое и промышленное топливо. Сжиженный газ направляется на блок сжиженных углеводородных газов. Они (сжиженные газы) могут использоваться как баллонное топливо, направляться на установки алкилирования.
Бензиновая фракция (28-180°C) направляется на вторичную перегонку. Она разделяется на две части: бензиновую фракцию 28-85°C, направляемую на изомеризацию (но мы ее на изомеризацию не будем отправлять, чтобы лишний процесс не добавлять, а направим сразу на добавление к товарным бензинам для улучшения их пусковых свойств). Бензиновую фракцию 85-180°C, направляемую на каталитический риформинга, где из нее получают высокооктановый бензин и ВСГ. Бензин риформинга направляется в блок «товарных бензинов», где он смешивается с бензиновой фракцией 28-85 °C . Углеводородный газ направляется вместе с другими газами на ГФУ, а ВСГ- на гидроочистку.
Керосиновая фракция (180-240°C). В зависимости от содержанием серы в ней определяют проводить гидроочистку или нет. В соответствии с шифром нефти гидроочистка для керосиновой фракции не требуется. Далее необходимо провести депарафинизацию, но в данном случае мы этот процесс опустим и направим ее в блок «реактивного топлива».
Дизельная фракция (240-350°C) – требуется гидроочистка. Образующийся углеводородный газ направляются на ГФУ а бензиновая фракция на каталитического риформинга для повышения октанового числа. Дизельное топливо направляется на депарафинизацию (в зависимости от содержания в нем парафина). Обычно для дизельного топлива проводится карбамидная депарафинизация, в результате чего получается само дизельное топливо и парафин. Вакуумный газойль (350-500°C) является сырьем для каталитического крекинга, продуктами которого являются углеводородный газ, бензин, легкий и тяжелый газойли. Легкий газойль используется как компонент дизельного топлива, а тяжелый – как котельное топливо. Гудрон (>500°C) направляется на замедленное коксование, где получают углеводородный газ, бензин, легкий и тяжелый газойли и кокс, (рис.4.1).

5. Описание технологических процессов, входящих в схему НПЗ
Вторичная перегонка бензина (теория. схемы. описание)
Продукты первичной переработки нефти направляются на дальнейшую вторичную переработку. Все процессы вторичной переработки можно разделить по следующим признакам:
· по условиям проведения различают термические (протекают при высоких температурах и давлении), термокаталитические (протекают при высоких температурах, давлении и в присутствии катализатора) и гидрогенизационных (протекают в присутствии водорода) процессы;
· по цели вторичной переработки различают: процессы, направленные на повышение качества продуктов; процессы, направленные на углубление переработки нефти; процессы переработки газов.
Каталитический риформинг
Прямогонные бензиновые фракции имеют низкие октановые числа, так как состоят в основном из низкооктановых, парафиновые, и нафтеновые УВ. Назначением процесса каталитического риформинга является получение высокооктановых бензинов путем ароматизации прямогонных бензинов. Процесс каталитического риформинга может быть также направлен на получение индивидуальных ароматических углеводородов (бензола, толуола, ксилола).
Сырье процесса. В качестве сырья процесса используются прямогонные бензиновые фракции, причем присутствие в сырье С6
–С7
нежелательно, т.к. в условиях процесса они подвергаются гидрокрекингу и дают большой выход газов. Поэтому на процесс риформинга направляют бензиновые фракции с пределами выкипания 85-180°C. Для получения индивидуальные ароматические УВ используют узкие бензиновые фракции.
Продукты процесса. В процессе риформинга получают два целевых и один побочный продукт:
1. бензин риформинга имеет высокое октановое число, содержит большое количество ароматических УВ (до 60%) и имеет тяжелый фракционный состав. Все это приводит к тому, что бензины риформинга не могут использоваться в качестве товарных бензинов в чистом виде, а используются только как компоненты;
2. водородсодержащий газ (ВСГ) является очень важным продуктом риформинга, который используется в гидрогенизационных процессах;
3. углеводородный газ риформинга не содержит непредельных углеводородов и направляется на газофракционирующую установку (ГФУ).
Принципиальная технологическая схема каталитического риформинга
Сырье риформинга после блока гидроочистки смешивается с циркулирующего ВСГ и нагревается в первой секции печи П-1 до температуры 510 °C, затем поступает в первый по ходу движения реактор Р-1, в котором находится стационарный (не движущийся, постоянный) слой катализатора. При контакте сырья с катализатором часть сырья подвергается превращению, но так как реакция эндотермическая, температура сырья снижается до 470-480 °C. Поэтому пары продуктов риформинга и сырья выводятся из реактора, нагреваются во второй секции печи П-1 до температуры 510°C и подаются в реактор Р-2. Пары продуктов и сырья на выходе из Р-2 также имеют пониженную температуру. Поэтому они вновь нагреваются в третьей секции печи П-1 и поступают в реактор Р-3. Пары продуктов и ВСГ из реактора поступают на разделение в сепаратор С-1, сверху которого выводится ВСГ. Избыточная часть ВСГ выводится с установки, а циркулирующая часть возвращается (бензин), который поступает в разделительную колонну, сверху которой выводится углеводородный газ, головка стабилизации, а снизу реформат, (рис.5.1).
 |
 |
  
     
 |
 |
  -
П-1 -Р-3 -Р-2 Р-1
ЦВСГ
ВСГ
     баланс. кол.-во
ВСГ
у/в гол.-а
    сырье после гидроочистки
-С-1
   
нестабильный
платформат
бензин
реформат
Рисунок 5.1. Принципиальная технологическая схема реакторного блока каталитического риформинга
Гидроочистка
Этот процесс предназначен для удаления сернистых, азотистых, кислородсодержащих соединений и гидрирования непредельных углеводородов. В качестве сырья процессов могут использоваться как нефтяные фракции, так и нефтепродукты.
Сырье гидроочистки смешивается с циркулирующим ВСГ, нагревается в печи до заданной температуры и поступает в реактор Р-1. В реакторе Р-1 катализатор укладывается послойной, что позволяет, во-первых, снизит сопротивление слоя катализатора, а во-вторых, для снижения температуры в реакторе между слоями катализатора подается охлажденный ВСГ (т.е. реакции гидрогенолиза изотермические). В реакторе протекают реакции гидрогенолиза и гидрирования. Паропродуктовая смесь, выводимая из реактора, охлаждается в конденсаторе – холодильнике КХ-1 и поступает в сепаратор высокого давления С-1, где происходит отделение от продуктов процесса циркулирующего ВСГ. ЦВСГ очищается от сероводорода на блоке моноэтаноламинной очистки (МЭА). Так как в процессе часть ВСГ расходуется, в ЦВСГ попадается свежая порция ВСГ, а для поддержания количества циркулирующего ВСГ, производится, отдув части ВСГ; затем ВСГ поступает на смешивание с сырьем. Продукты из сепаратора С-1 поступают в сепаратор низкого давления С-2, где за счет снижения давления от продуктов отделяется основная часть углеводородного газа, который ниже поступает на блок МЭА. Продукты из С-2 поступают в сложную ректификационную колонну К-1. сверху К-1 выводится углеводородный газ и бензиновая фракция. Небольшие размеры концентрационной части колонны объясняются небольшим количеством верхнего продукта колонны. Снизу колонны К-1 выводится продукт гидроочистки (гидрогенизат), часть которого нагревается в печи П-2 и возвращается вниз колонны в качестве горячей струи, (рис.5.2).

Рисунок 5.2 Принципиальная технологическая схема гидроочистки
Каталитический крекинг. Качество сырья
а) Фракционный состав сырья. Бензиновые фракции в сырье каталитического крекинга нежелательны, так как в процессе химический состав их не изменяется, следовательно, и октановое число, т.е. они, являются балластом на установке. Но в последнее время в сырье каталитического крекинга стали вовлекать бензиновые фракции вторичных процессов термокрекинга и коксования с целью облагораживания их как по химическому составу, так и по октановому числу. В сырье крекинга их содержание достигает 15%. Керосиновые и дизельные фракции не вовлекаются в сырье каталитического крекинга, так как являются сырьем для производства реактивных и дизельных топлив. Ограничивающим фактором по концу кипения каталитического крекинга является содержание гетероатомных соединений смол, Асфальтенов и тяжелых металлов.
б) Химический (групповой) состав сырья. Наиболее реакции свободными в процессе каталитического крекинга являются изопарафиновые и алкинафтеновые углеводороды; ароматизированные углеводороды в составе сырья каталитического крекинга приводят к увеличению выхода кокса. Таким образом, наиболее благоприятным сырьем каталитического крекинга являются сырье парафин нафтенового основания и нежелательно ароматическое сырье.
в) Содержание нежелательных компонентов. Нежелательные компоненты сырья каталитического крекинга можно условно разделить на две группы:
1) вызывающие только повышенное коксоотложение на катализаторе;
2) вызывающие отравление катализатора.
К первой группе относятся полициклические, ароматические УВ, смолы и асфальтены.
Ко второй группе относятся сернистые соединения, тяжелые металлы и азотистые соединения основного характера (адсорбируется на кислотных центрах катализатора, блокируя их).
Продукты каталитического крекинга:
1. углеводородный газ содержит значительное количество пропана, изобутана и бутана. После фракционирования на ГФУ сухой газ используется в качестве сырья нефтехимии, бытового топлива; изобутан используется в качестве сырья нефтехимии и процесса алкилирования;
2. бензиновая фракция (н.к.-195 ˚C) используется в качестве компонента авто- и авиабензинов;
3. легкий газойль (пределы выкипания 195-350, 195-270, 270-420˚C) используется в качестве компонента дизельного топлива, для производства «игольчатого» кокса и в качестве флогента;
4. тяжелый газойль используется в качестве компонента котельного топлива.
Принципиальная технологическая схема установки каталитического крекинга
Сырье каталитического крекинга с блока гидроочистки поступает в узел смещения лифт - реактора Р-1. перед подачей сырья в узел смешения подается водяной пар, сюда же из регенератора ссыпается горячий регенерированный катализатор. При контакте с горячей катализатором сырье испаряется, пары сырья и катализатор начинают подниматься по лифт - реактору. За время прохождения лифт-реактора (1,5-3 сек.) сырье успевает полностью крекироваться. Пары продуктов и катализатор попадают в отстойную зону реактора. За счет увеличения диаметра отстойной зоны скорость движения катализаторной смеси уменьшается и под действием силы тяжести катализатор ссыпаются парную секцию; за счет контакта с водяным паром тяжелые УВ отпаривается на поверхности катализатора. Для улучшения контакта катализатора и водяного пара парная секция снабжена каскадными горелками. Дисорбированный катализатор из парной зоны ссыпается в регенератор. Регенерация катализатора осуществляется выжигом с поверхности катализатора горячим воздухом образовавшегося кокса. Дымовые газы, образовавшиеся при выжигании кокса, проходят двухступенчатую систему циклонов для улавливания каталитического пыли, затем подаются в котел-утилизатор КУ, в котором за счет тепла отходящих дымовых газов образуется водяной пар, затем дымовых водяной пар, затем дымовые газы проходят электрофильтры для полного управления каталитической пыли и выбрасываются в атмосферу. Регенерированный катализатор возвращаются в лифт-реактор. Пары продуктов крекинга в отстойной зоне реактора также проходят двухступенчатую систему циклонов для улавливания каталитической пыли, затем подаются в ректификационную колонну на разделение. Сверху колонны выводится углеводородный газ, бензиновая фракция и водяной пар, которые после охлаждения и конденсации разделяются в водогазосепараторе. Боковыми погонами колонны являются легкие и тяжелые газойли, выводимые через стриппинги, нижняя часть колонны представляет собой отстойник каталитического шлама. Он возвращается в парную секцию колонны. Сверху отстойника выводится остаток выше 400 или 420 ˚C, (рис.5.3).

Рисунок5.3 Принципиалтьная технологическая схема каталитического крекинга
Состоит из четырех блоков:
1) блока подготовки сырья (гидроочистки);
2) реакторно-регенераторного блока;
3) блока ректификации продуктов крекинга;
4) блока газофракционирования (ГФУ).
Процесс замедления коксования
Коксования предназначено для получения высокоуглеродистого твердого материала, называемого коксом. В качестве сырья процесса используют остатки от прямой перегонки нефти (мазут, гудроны) и тяжелые фракции термокаталитических процессов (тяжелые газойль, крекинг - остатки, пиролизная смола), остатки масляного производства (экстракты, асфальты). По назначению кокс можно разделить на четыре группы:
1) электродный кокс, предназначенный для производства электродов для выплавки Аlи других металлов;
2) металлургический кокс, предназначен для выплавки сталей;
3) конструкционный кокс, предназначенный для футеровки аппаратов, работающих в агрессивных средах;
4) кокс как твердое топливо.
Существуют три модификации этого процесса:
1) периодическое коксование в обогреваемых камерах;
2) непрерывное (замедленное коксование в не обогреваемых камерах);
3) непрерывное коксование в реакторах.
Замедленное коксование – это широко применяемый в настоящее время процесс коксования. Он осуществляется в вертикальных цилиндрических не обогреваемых камерах. На установках замедленного коксования работают параллельно две камерах. На установках замедленного коксования работают параллельно две камеры. Во время работы одной камеры, вторая камера готовится к работе.
Таким образом, камеры работают периодически, а установка в целом непрерывно. Основными аппаратами установки замедленного коксования являются: нагревательные печи, не обогреваемые камеры и разделительная колонна.
Продукты коксования:
1) кокс, углеродный продукт;
2) углеродный газ богат непредельными углеводородами и может использоваться в качестве топлива, но в основном направляются на ГФУ;
3) бензиновая фракция содержит значительное количество непредельных углеводородов и имеет низкое октановое число. После гидроочистки используется в качестве компонента товарных бензинов или установок риформинга;
4) легкий газойль используется после гидроочистки в качестве компонента дизельного топлива;
5)тяжелый газойль может использоваться для производства кокса или в качестве компонента сырья каталитического крекинга и гидрокрекинга.
Принципиальная технологическая схема установки замедленного коксования
Сырье замедленного коксования (гудрон) с вакуумного блока установки АВТ паровым насосом подается в печь П-1, где нагревается до температуры 350-360 ˚С, и затем поступает в ректификационную колону К-3 под тарелку с патрубком; в нижнюю часть ректификационной колонны подаются горячие пары продуктов разложения из коксовых камер; при контакте горячих паров с сырьем происходит конденсация из паров наиболее тяжелых углеводородов; получается вторичное сырье, обогащенное тяжелыми углеводородами.
Для улучшения компонентов между паровой и жидкой фазами, нижняя часть колонны снабжена тарелками и представляет собой конденсатор смешения.
Вторичное сырье снизу ректификационной колонны вновь подается в печь, где нагревается до температуры 500-510˚С, и поступает в коксовую камеру. Коксовая камера заполняется сырьем только на для предотвращения заноса капелек тяжелой жидкости в линию паров; в верхнюю часть коксовой камеры подается антипенный препарат. Заполнение камеры продолжаются 24-36 часов, затем камера выключается, и в ней за счет аккумулированного сырьем тепла протекают реакции коксообразования. Сырье включается на параллельную камеру, предварительно подготовленную к работе, подогретую сначала водяным паром, а затем парами продуктов из рабочей камеры.
После завершения образования кокса, коксовую камеру охлаждают сначала продувкой водяным паром, а затем подачей холодной воды. Продукты из коксовой камеры подаются для разделения в ректификационную колонну, сверху которой отбираются углеводородный газ, водяной пар и пары бензиновой фракции, которые охлаждается и конденсируется в конденсаторе-холодильнике, и разделяются в водогазосепараторе. Сборку колонны выводится легкий и тяжелый газойли. Оставшийся в камере кокс выгружается следующим образом: в коксовую камеру под высоким давлением подают воду, которая как бы «пробуривает скважину»; вверху камеры устанавливается аппаратура («колпачок») и при помощи гидрорезка кокс режется на слои и выводится снизу камеры через специальное «отверстие» и погружается на тележки, (рис.5.4).

Рисунок 5.4.Технологическая схема установки замедленного коксования
Депарафинизация карбамидом
Депарафинизацию называется процесс удаления из нефтяных фракций твердых углеводородов, выпадающих из раствора при понижении температуры. К числу углеводородов, выделяющихся в кристаллическом состоянии из нефтяных фракций, относятся высокомолекулярные парафины и церезины, а также нафтеновые, ароматические и нафтеновые, ароматические и нафтеноароматические углеводороды с длинными боковыми алифатическими радикалами нормального и слаборазветвленного строения.
Дизельные фракции парафинистых нефтей содержат значительное количество алканов нормального строения, благодаря чему имеют сравнительно высокую температуру застывания (-10 -11 ˚С). Чтобы получить из таких фракций дизельное зимнее топливо с температурой застывания -45˚С и дизельное арктическое топливо с температурой застывания -60˚С, эти фракции подвергают депарафинизации с применением карбамида. Необходимым условием успешного ведения процесса является чистота применяемого карбамида. Незначительные примеси делают его непригодным.
Различают депарафинизацию с кристаллическим карбамидом и депарафинизацию в спиртоводном растворе карбамида.
Основные этапы процессы – образование карбамидного комплекса, отделения его, промывка и деструкция. (Схема)
Газофракционирующая установка (ГФУ) схемы
Процесс предназначен для получения индивидуальных легких углеводородов или углеводородов – фракций высокой чистоты из нефтезаводских газов.
Сырье и продукция. Источниками углеводородного газа на НПЗ являются газа, растворенные в нефти и выделяющиеся при первичной перегонке на установках АТ и АВТ. и газы, полученные в процессе деструктивной переработки.
ГФУ нефтеперерабатывающих заводов подразделяются на установки предельных и непредельных газов по типу перерабатывающего сырья.
На ГФУ предельных газов выделяются узкие углеводородные фракции:
этановая; пропановая; бутановая; изопентановая; пентановая; изобутановая.
На ГФУ непредельных газов выделяются следующие фракции:
1. пропан-пропиленовая;
2. бутан-бутиленовая.
6. Материальные балансы технологических процессов НПЗ
Материальный баланс процесса ППН (установка АВТ) Таб.6.1
Наименование продуктов |
% масс. на сырье процесса |
т/сут. |
1 |
2 |
3 |
Взято: |
1. Обезвоженная, обессоленная нефть |
100,0 |
10882,4 |
Получено: |
1. газ до С4
|
1,2 |
130,6 |
2. фр. н.к.-180˚С |
_ |
_ |
3. фр. 180-240˚С |
14,9 |
1621,5 |
4. фр.240-350˚С |
7,2 |
783,5 |
5.фр.350-420˚С |
19,5 |
2122,1 |
6. фр. свыше 420˚С |
18 |
1958,8 |
7. потери |
39,2 |
4265,9 |
Итого: |
100,0 |
10882,4 |
Материальный баланс процесса вторичной перегонки бензина Таб.6.2
Наименование продуктов |
% масс. на сырье процесса |
т/сут. |
1 |
2 |
3 |
Взято: |
1.Фр. н.к.-180˚ С |
100 |
1621,5 |
Получено: |
1. фр. н.к.-85˚ С |
25,4 |
411,9 |
2. фр. 85-180˚ С |
73,9 |
1198,3 |
3. потери |
0.7 |
11,4 |
Итого: |
100 |
1621,5 |
Материальный баланс установки каталитического риформинга Таб.6.3
Наименование продуктов |
% масс. на сырье процесса |
т/сут. |
1 |
2 |
3 |
Взято: |
1. Фр. 85-180˚ С |
100 |
1198,3 |
Итого: |
100 |
7277,0 |
Получено: |
1. дебутанизированный бензин |
84.5 |
1012,6 |
2. водородсодержащий газ (в т.ч. водород) |
11.0- |
131,8- |
3. головка стабилизации |
- |
- |
4. потери |
0.5 |
5,99 |
Итого: |
100 |
1198,3 |
Материальный баланс процесса гидроочистки дизельного топлива Таб.6.4
Наименование продуктов |
% масс. на сырье процесса |
т/сут. |
1 |
2 |
3 |
Взято: |
1.Фр.240-350˚ С |
99.5 |
783,5 |
2.Водород |
0.5 |
3,9 |
Итого: |
100 |
787,4 |
Получено: |
1. дизельное топливо |
97.0 |
763,8 |
2. бензин |
1.5 |
11,8 |
3. сероводород |
1.0 |
7,9 |
4. потери |
0.5 |
3,9 |
Итого: |
100 |
787, |
Материальный баланс процесса каталитического крекинга Таб.6.5
Наименование продуктов |
% масс. на сырье процесса |
т/сут. |
1 |
2 |
3 |
Взято: |
1. Фр. 350-500˚ С |
100 |
2122,1 |
Итого: |
100 |
2122,1 |
Получено: |
1. сухой газ С1
-С2
|
3.5 |
74,3 |
2. жирный газ С3
-С4
|
14.5 |
307,7 |
3. бензин |
40.0 |
848,8 |
4. легкий газойль |
26.0 |
551,8 |
5. тяжелый газойль |
8.5 |
180,4 |
6. кокс сжигаемый |
6.0 |
127,3 |
7. потери |
1.5 |
31,8 |
Итого: |
100 |
2122,1 |
Материальный баланс процесса замедленного коксования Таб.6.6
Наименование продуктов |
% масс. на сырье |
т/сут. |
1 |
2 |
3 |
Взято: |
1. Фр. свыше 420˚С |
100 |
1958,8 |
Итого: |
100 |
1958,8 |
Получено: |
1. газ |
9.5 |
186,1 |
2. бензин |
15.0 |
293,8 |
3. легкий газойль |
25.0 |
489,7 |
4. тяжелый газойль |
24.0 |
470,1 |
5. кокс |
25.0 |
489,7 |
6. потери |
1.5 |
29,4 |
Итого: |
100 |
1958,8 |
Материальный баланс установки карбомидной депарафинизации
Таб.6.7
Наименование продуктов |
% масс. на сырье |
т/сут. |
1 |
2 |
3 |
Взято: |
1. Фр. 180-350˚С (после ГО) |
100 |
787,4 |
Итого: |
100 |
787,4 |
Получено: |
1. дизельное топливо |
82.5 |
649,6 |
2. компонент дизельное топливо летнего |
7.0 |
55,1 |
3. жидкий парафин |
10.0 |
78,7 |
4. потери |
0.5 |
39,9 |
Итого: |
100 |
787,4 |
Материальный баланс установки сероочистки газа Таб.6.8
Наименование продуктов |
% масс. на сырье |
т/сут. |
1 |
2 |
3 |
Взято: |
1. Сухой газ с АВТ (до С4
) |
1.3 |
130,6 |
2. Жирный газ КК |
12.0 |
- |
3. Сухой газ КК |
11,6 |
74,3 |
4. Газ замедленного коксования |
18,2 |
186,1 |
5. Газ термического крекинга |
9,0 |
79,4 |
Итого: |
100 |
470,4 |
Получено: |
1. сероочищенный газ |
94.2 |
443,1 |
2. сероводород |
5.3 |
24,9 |
3. потери |
0.5 |
2,4 |
Итого: |
100 |
470,4 |
Материальный баланс ГФУ Таб.6.9
Наименование продуктов |
% масс. на сырье |
т/сут. |
1 |
2 |
3 |
Взято: |
1. Сероочищенный газ |
100 |
443,1 |
Итого: |
100 |
443,1 |
Получено: |
1. сухой газ С1
-С2
|
30.5 |
135,2 |
2. пропан- пропиленовая фракция |
25.5 |
112,99 |
3. бутан-бутиленовая фракция |
37.5 |
166,2 |
4. С5
и выше |
5.5 |
24,4 |
5. потери |
1.0 |
4,4 |
Итого: |
100 |
443,1 |
7. Суммарный материальный баланс НПЗ
Таблица 1. Материальный баланс НПЗ
Наименование продукта |
Наименование процесса |
т/сут |
% масс. на сырье процесса |
Взято: |
1. Обезвоженная, обессоленная нефть |
10882,4 |
100 |
Итого: |
1088,2 |
100 |
Получено: |
1.Сухой газ С1
-С2
|
ГФУ |
135,2 |
1,2 |
2. Пропан-пропиленовая фракция |
ГФУ |
112,99 |
1,04 |
3.Бутан-бутеленовая фракция |
ГФУ |
- |
- |
4. Головка стабилизации |
Кат. риформинг |
- |
- |
5.С5
и выше |
ГФУ |
24,4 |
0,2 |
6.Сероводород |
Сероочистка газа |
131,8 |
1,2 |
7. Водородсодержащий газ |
Кат. риформинг |
411,9 |
3,8 |
8. Фр. н.к.-850
С |
Вторичн.переработка бензина |
1012,6 |
9,3 |
9.Бензин |
Кат. крекинг |
11,8 |
0,1 |
10. Бензин |
Кат. риформинг |
848,8 |
7,8 |
11.Бензин |
Замедл. коксование |
98,9 |
0,9 |
12.Керосин |
АВТ |
293,8 |
2,7 |
13.Легкий газойль |
Кат. крекинг |
- |
- |
14.Легкий газойль |
Замедл.коксование |
- |
- |
15. Тяжелый газойль |
Кат.крекинг |
551,8 |
5,1 |
16. Тяжелый газойль |
Замедл.коксование |
489,7 |
4,5 |
17.Парафин жидкий |
Карбамидная депарфинизация |
78,7 |
0,7 |
18.Диз.топливо летнее |
Карбамидная депарфинизация |
- |
- |
19.Диз.топливо зимнее |
Карбамидная депарфинизация |
55,1 |
0,5 |
20.Кокс сжигаемый |
Кат.крекинг |
649,6 |
5,97 |
21.Кокс |
Замедлен.коксование |
260,2 |
2,4 |
22.Потери |
АВТ |
39,2 |
0,4 |
Вторичная перегонка |
11,4 |
0,1 |
Гидроочистка диз. топл. |
3,9 |
0,04 |
Кат.крекинг |
31,8 |
0,3 |
Замедл.коксование |
29,4 |
0,27 |
Карбамидн.депарафинизация |
39,9 |
0,4 |
Термокрекинг |
3,9 |
0,04 |
Кат.риформинг |
5,99 |
0,06 |
Сероочистка газа |
2,4 |
0,02 |
ГФУ |
4,4 |
0,04 |
Итого: |
10882,4 |
100 |
Заключение
Мухановская угленосная товарная нефть, как выяснилось в ходе проделанной работы, богата содержанием светлых фракций (67.0%). Выбран топливный вариант переработки, с максимальным отбором светлых фракций. Как уже отмечалось в основной части данной работы, при глубокой переработке нефти получить максимально возможный выход высококачественных авиационных и автомобильных бензинов, зимних и летних дизельных топлив и топлив для реактивных двигателей. Выход котельного топлива в этом варианте сводится к минимуму. Таким образом, предусматривается такой набор процессов вторичной переработки, при котором из тяжелых нефтяных фракций и остатка – гудрона получают высококачественные легкие моторные топлива. Сюда относятся каталитические процессы – каталитический крекинг, каталитический риформинг и гидроочистка, а также термические процессы, например коксование. Переработка заводских газов в этом случае направлена на увеличение выхода высококачественных бензинов. В ходе проделанной работы мы видим, что был выбран максимально экономичный вариант, подобрано оптимальное количество установок для переработки, на которых из данной нефти отбирают конечные продукты. А также можно утверждать, что топливный вариант для Арланской товарной нефти возможен и экономически выгоден.
Список использованной литературы
1. Нефти СССР: Т. III. Нефти Оренбургского района СССР.- М.: Химия, 1972.-432с.
2. Технология переработки нефти. Первичная переработка нефти. Под ред. О.Ф. Глаголевой и В.М. Капустина. - М.:Химия, Колос С, 2006.-400с.
3. Ластовкин Г.А., Радченко Е.Д., Рудин М.Г. Л.: Химия, 1984.-348с.
4. Мановян А.К. технология переработки природных энергоносителей.- М.: Химия, Колос С, 2004.-456с.
5. Рудин М.Г., Сомол В.Е., Фомин А.Е. Карманный справочник нефтепереработчика.- М.: Энефтехим, 2004.-336с.
|