ФЕДЕРАЛЬНОЕ АГЕНТСТВО ОБРАЗОВАНИЯ
Коломенский институт (филиал)
Государственного образовательного учреждения
высшего профессионального образования
«МОСКОВСКИЙ ГОСУДАРСТВЕННЫЙ ОТКРЫТЫЙ УНИВЕРСИТЕТ»
Экономический факультет
Кафедра менеджмента
Специальность 080502 «Экономика и управление на предприятии машиностроения»
КУРСОВАЯ РАБОТА
по дисциплине
«Организация производства»
Тема: «Организация производства на участке механического цеха по обработке детали «Вал шлицевый»»
Выполнил: __________________
Проверил: __________________
Сдано: ______________________
Дата защиты__________________
Оценка ______________________
Коломна
2009
Реферат
Курсовая работа, 56 страниц, 5 рисунков, 1 таблица, 7 источников литературы, 33 формулы, 2 приложения.
Основные определения:
тип производства, производственный цикл, технологический цикл, цех, производственная структура цеха, организационная структура управления цехом, планировка цеха, многостаночное обслуживание, энергетическое хозяйство предприятия.
Объект исследования
- участок механического цеха
Цель курсовой работы
- рациональная организация производства деталей типа «Вал шлицевый» на участке механического цеха.
Методологическая и теоретическая база
- учебники, учебные и методические пособия, справочная литература по вопросам организации производства в машиностроении, курс лекций по дисциплине «Организация производства на предприятии отрасли».
Практическое значение работы
- разработка мероприятий по сокращению длительности производственного цикла изготовления деталей, рациональному размещению оборудования на участке цеха, обеспеченияпропорциональности, прямоточности, ритмичности, непрерывности и параллельности в организации производства с целью улучшения технико-экономических показателей работы цеха.
Содержание
Введение
1. Раздел 1. Разработка принципов рациональной организации производства на участке механического цеха при обработке детали «Вал шлицевый»
1.1 Исходные данные для расчета
1.2 Обоснование типа производства
1.3 Расчет партии запуска детали
1.4 Расчет необходимого количества оборудования для выполнения годовой программы и его загрузки
1.5 Расчет производственной мощности участка
1.6 Расчет необходимого количества оборудования и его загрузки по мощности участка
1.6.1 График загрузки оборудования с учетом догрузки
1.7 Выявление «узких» и «широких» мест на производственном участке. Разработка мероприятий по их ликвидации
1.7.1 График загрузки оборудования на участке с учетом ликвидации «широких» и «узких» мест
1.8 Расчет длительности технологического и производственного циклов обработки партии деталей до и после ликвидации «широких» и «узких» мест
1.9 Производственная структура цеха
1.10 Организационная структура цеха
1.11 Принципы организации цехов и участков предприятия
1.12 Пути рациональной организации производственного процесса
1.13 Планировка оборудования на участке цеха
1.14 Организация многостаночной работы
Выводы по разделу 1.
2. Раздел 2. Организация энергетического хозяйства
2.1 Состав энергетического хозяйства предприятия
2.2 Задачи и функции энергетической службы
2.3 Планирование потребности предприятия в энергии различных видов
2.4 Технико-экономические показатели энергетического хозяйства цеха
2.5 Пути экономии энергии
Выводы по разделу 2
Заключение
Список литературы
Введение
Рыночная экономика по своей сущности является средством, стимулирующим рост производительности труда, повышение эффективности производства. В этих условиях важным является определение принципов рациональной организации производства для повышения эффективности деятельности предприятия и его подразделений.
Рациональная организация производства включает комплекс мероприятий по эффективному сочетанию трудовых процессов с материальными элементами производства, осуществляемый в конкретных социально-экономических условиях в целях производства продукции с установленными качественными показателями при экономичном использовании ресурсов.[5]
Сокращение длительности производственных процессов представляет собой одну из наиболее важных задач организации современного производства, от надлежащего решения которой в большой мере зависит его эффективная рентабельная работа.
Производственный цикл как неотъемлемая часть производственного процесса широко используется в планировании при составлении оперативных планов, определении нормативов незавершенного производства и других планово-производственных расчетах. Сокращение производственного цикла даёт возможность предприятию ускорить оборачиваемость оборотных средств, выполнить установленный план с меньшими затратами этих средств, высвободить часть оборотных средств. [4]
Целью выполнения данной курсовой работы является разработка рациональной организации производства деталей типа «Вал шлицевый» на участке механического цеха на основе применения общих принципов организации производственного процесса - специализации, пропорциональности, параллельности, прямоточности, непрерывности и ритмичности.
К основным задачам, решаемым в ходе курсовой работы, относятся:
выявление «узких» и «широких» мест на производственном участке и разработка мероприятий по их ликвидации;
сокращение длительности производственного цикла;
разработка плана размещения оборудования на участке механического цеха;
расчет потребности предприятия в энергии различных видов;
поиск путей экономии энергии.
Раздел 1. Разработка принципов рациональной организации производства на участке механического цеха при обработке детали « Вал шлицевый»
1.1 Исходные данные для расчета
Название детали:
Вал шлицевый
Годовая программа:
18400 шт.
Тип производства:
серийное
Масса детали:
9,85 кг.
Масса заготовки:
11,22 кг.
Материал
: сталь 40Х
Технологический процесс обработки детали «Вал шлицевый»
№. операции |
Наименование операции |
Раз
ряд
|
Наименование станка |
Модель
станка
|
ВРЕМЯ мин. |
Тосн |
Твсп |
Ттт |
Тпз |
5 |
Радиально-сверлильная |
3 |
Радиально-сверлильный |
2554 |
4,4 |
0,63 |
5 ,53 |
16 |
10 |
Токарно-винторезная |
3 |
Токарио-винторезный |
16К201 ФЗ |
6,93 |
5,54 |
12,47 |
16 |
15 |
Радиально-сверлнльная с ЧПУ |
2 |
Радиально-сверлильный с ЧПУ |
2554Ф1 |
0,73 |
3,19 |
4,3 1 |
11 |
25 |
Шлицефрезерная |
4 |
Шлицефрезерный |
5350А |
20,11 |
1,52 |
23,8 |
23 |
30 |
Шлицешлифовальная |
4 |
Шлицешлифовальный |
3451 |
10,2 |
1, 62 |
13 |
22 |
1.2 Обоснование типа производства
Под типом производства
понимается совокупность признаков, определяющих организационно-технологическую характеристику производственного процесса, осуществляемого как на одном рабочем месте, так и на совокупности их в масштабе участка, цеха, завода.
В зависимости от широты номенклатуры, регулярности, стабильности и объема выпуска изделий современное производство подразделяется на следующие типы: единичное, серийное, массовое. От типа производства во многом зависит характер технологического процесса и его построение. [4]
Определим тип производства, исходя из объема выпуска и массы детали (Табл. 1).
Таблица 1

Так как объем выпуска детали составляет 18400 шт., а масса детали равна 9,85 кг., следовательно, тип производства – среднесерийное.
Данный тип характеризуется ограниченной номенклатурой изделий, изготовляемых или ремонтируемых периодически повторяющимися партиями и сравнительно большим объемом выпуска. Серийное производство является основным типом современного машиностроительного производства и предприятиями этого типа выпускается 75-80% всей продукции машиностроительного производства. По всем технологическим и производственным характеристикам серийное производство занимает промежуточное положение между единичным и массовым производством.
Объем выпуска предприятий серийного производства колеблется от десятков и сотен до тысяч регулярно повторяющихся изделий, используется универсальное, специализированное и частично специальное оборудование.
Широко используются станки с ЧПУ, обрабатывающие центра. Оборудование расставляется по технологическим группам с учетом направления основных грузовых потоков цеха по предметно-замкнутым участкам. Технологическая оснастка в основном универсальная и создается высокопроизводительная специальная оснастка, при этом целесообразность ее создания должна быть предварительно обоснована технико-экономическими расчетами. Большое распространение имеет универсально-сборная, переналаживаемая технологическая оснастка, позволяющая существенно повысить коэффициент оснащенности серийного производства. В качестве исходных заготовок применяют горячекатаный и холоднотянутый прокат, литье в землю и под давлением, точное литье, поковки, штамповки. Требуемая точность достигается как методом автоматического получения размерам, так и методом пробных ходов и промеров с частичным применением разметки.
Средняя квалификация рабочих – 3-5 разряд. Наряду с рабочими высокой квалификации, работающих на сложных станках и наладчиков, используются рабочие операторы, работающие на настроенных станках.
Серийное производство значительно экономичнее, чем единичное, так как лучшее использование оборудования, специализация рабочих, увеличение производительности труда обеспечивают уменьшение себестоимости продукции.[6]
1.3 Расчет партии запуска детали
, где (1)
- подготовительно - заключительное время на подготовку и наладку станка для обработки партии деталей;
- сумма штучного времени по всем операциям технологического процесса;
- коэффициент серийности ( =15)
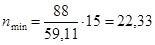
= 18400 шт., = 22 , подбираем значения таким образом, чтобы годовая программа делилась на
нацело без остатка. Итак,
, т.к. партий.
1.3.1 Расчет штучно-калькуляционного времени
, мин., где (2)
- сумма штучного времени по всем операциям технологического процесса;
- сумма подготовительно – заключительного времени по всем операциям технологического процесса.
мин.
мин.
мин.
мин.
мин.
мин.
1.4 Расчет необходимого количества оборудования для производства заданной годовой программы
, единиц оборудования (станков), где (3)
- годовая программа
- штучно-калькуляционное время
- годовой эффективный фонд времени работы единицы оборудования
= 4000 час.
- коэффициент выполнения норм
=1,2
станков
станков
станков
станков
станков
станков
1.4.1 Принимаем необходимое количество оборудования по каждой операции
(5) = 0,398 (5) = 1
(10) = 0,841 (10)= 1
(15) = 0,306 (15)= 1
(25) = 1,584 (25)= 2
(30) = 0,892 (30)= 1

1.4.2 Расчет загрузки оборудования по каждой операции
, где (5)
-необходимое количество оборудования для производства заданной годовой программы
- принятое количество оборудования для производства заданной годовой программы





1.4.3 Расчет среднего процента загрузки оборудования по программе
(6)
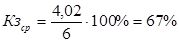
1.5 Расчет производственной мощности участка
, шт. (7)
шт.
1.6 Расчет необходимого количества оборудования при его загрузке по программе, равной производственной мощности участка
, ед.об. (8)
ед. об.
ед.об.
ед. об.
ед.об.
ед. об.
1.6.1 Расчет загрузки оборудования при его догрузке по мощности участка с учетом ранее принятого количества станков
(9)
, , 
1.6.2 График загрузки оборудования с учетом догрузки

Рис 1.1. График загрузки оборудования с учетом догрузки
1.7 Выявление «узких» и «широких» мест на производственном участке. Разработка мероприятий по их ликвидации
На полученном графике загрузки оборудования с учетом догрузки наблюдаем наличие «узких» (перегруженных) и «широких» (недогруженных) групп оборудования в цехе.
«Узкое» место характеризуется загрузкой оборудования более 100 %, а «широкое» - менее 60 %.
Оптимальная загрузка в серийном производстве составляет 80-85 %.
Для обеспечения равномерной загрузки оборудования необходимо ликвидировать «узкие» (операция №10 и №30) и «широкие» (операция №5 и №15) места.
«Узкие» места можно ликвидировать путем:
пересмотра технологии с целью уменьшения t шт-к ;
увеличения количества смен на операциях с «узкими» местами;
увеличения количества оборудования до оптимальной загрузки;
использования и 3-й смены, и увеличения количества станков.
Воспользуемся одним из предложенных методов, а именно, 2-м методом.
В данном случае применяем не 2-х сменный, а 3-х сменный режим работы на операциях № 10 и №30, при этом значение = 5600 час.
, ед.об. (10)
ед. об.
ед. об.
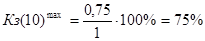

Таким образом, в результате применения 3-х сменного режима работы оборудования произошло снижение его загрузки до оптимального уровня, а именно, по операции № 10 на 30 %, а по операции № 30 на 32 %. «Широкие» места можно ликвидировать путем их догрузки аналогичной работой с других участков. Чтобы узнать, сколько деталей необходимо привести на каждое недогруженное рабочее место, составляем пропорцию вида:
(по операции № 5)
М
= 22879 шт. – 49 % загрузки, Х
дет. – 85 % , следовательно,
Х
дет.= ед.
= Х
дет – М = 39688-22879 = 16809 ед.
(по операции № 15)
М
= 22879 шт. – 38 % загрузки, Х
дет. – 85 % , следовательно,
Х
дет.= ед.
= Х
дет – М = 51177-22879 = 28298 ед.
Таким образом, по операции № 5 необходима догрузка рабочих мест в размере 16809 ед., а по операции № 15 – в размере 28298 ед. Рассчитаем средний % загрузки оборудования с учетом ликвидации «широких» и «узких» мест:
(11)

Средний процент загрузки оборудования составил 87%, что является оптимальным значением для серийного производства.
1.7.1 График загрузки оборудования с учетом ликвидации «широких» и «узких» мест

догрузка оборудования по мощности (ликвидация «широкого» места) |
|
Условные обозначения:
Рис 1.2. График загрузки оборудования с учетом ликвидации «широких» и «узких» мест
1.8 Расчет длительности технологического и производственного циклов обработки партии деталей до и после ликвидации «узких» и «широких» мест
Производственным циклом
называется календарный период времени, в течение которого выполняется производственный процесс или любая часть его – операция, процессы изготовления заготовок, механической обработки деталей, сборки, испытаний.
, час., (12)
Где S - число смен в рабочих сутках (S=2)
Тсм – продолжительность одной смены (Tсм =8 ч.)
f – коэффициент перевода рабочего времени в календарное (f=0,7)
- наиболее короткий операционный цикл из каждой пары смежных операций
m – число операций (m=5)
- межоперационное время (среднее)
= 10% от , т.е.
=10% от 62,94 = 6,3мин.= 0,105 ч.
Основной составляющей производственного цикла является длительность технологических операций, которая составляет технологический цикл.
,
час., где (13)
n – количество деталей в партии ( )
m – количество операций (m=5)
- норма по всем операциям
– количество рабочих мест на каждой операции
р –
размер передаточной партии (р=2)
1.8.1 Рассчитаем длительность технологического и производственного циклов обработки партии деталей до ликвидации «узких» и «широких» мест
ч.
1.8.2 Рассчитаем длительность технологического и производственного циклов обработки партии деталей после ликвидации «узких» и «широких» мест
Так как после ликвидации «широких» и «узких» мест количество оборудования не изменилось, то технологический цикл остался тем же, т.е.
= 570,01 мин.= 9,5 ч.
ч.
В результате применения 3-х сменного режима работы оборудования по двум операциям (№ 10 и № 30) длительность производственного цикла сократилась на 4,71 часа.
1.9 Производственная структура цеха
Производственная структура цеха
–
состав основных и вспомогательных участков и обслуживающих подразделений, их специализация и взаимосвязь. [2]
Рис. 1.3. Производственная структура цеха
Цех
- это основная структурная производственная единица предприятия, административно обособленная и специализирующаяся на выпуске определенной детали или изделий либо на выполнении технологически однородных или одинакового назначения работ.
Цехи делятся на участки, представляющие собой объединенную по определенным признакам группу рабочих мест. Производственная структура цеха показана на рис. 1.3.
По назначению цехи подразделяются на:
- основные
(производство основной профильной продукции или законченной части производственного процесса).
- вспомогательные
(обеспечивают условия для функционирования основного производства (инструменты, энергия, ремонт оборудования)).
- обслуживающие
(обеспечивают основное и вспомогательное производства транспортом, складами (хранение), техническим контролем и т.д.).
В зависимости от вида специализации выделяют следующие типы производственной структуры основных цехов:
технологическая;
предметная (или подетально-узловая, если предприятие специализируется на выпуске деталей или узлов к изделиям);
смешанная (предметно-технологическая). [2]
В цехах с технологической специализацией
выполняется определенная часть производственного процесса. Продукция, выпускаемая цехом, часто меняется и не закреплена за рабочими местами. Этот вид промышленной структуры наименее эффективен по сравнению с предметным и подетально-узловым.
Предметная или подетально-узловая структура
основных цехов характерна для массового выпуска продукции устойчивой номенклатуры, при таком типе производственной структуры каждый цех специализируется на выпуске одного или нескольких конструктивно подобных изделий. В цехах участки создаются по предметно-замкнутому принципу.
Наиболее распространенной является смешанная структура
(предметно-технологическая). При ней заготовительные цехи имеют технологическую структуру, обрабатывающие — подетально-узловую, а выпускающие — предметную. Цехи (участки), организованные по данному принципу специализации, обладают значительными экономическими преимуществами, так как при этом сокращается длительность производственного цикла в результате полного или частичного устранения встречных или возвратных перемещений, снижаются потери времени на переналадку оборудования, упрощается система планирования и оперативного управления ходом производства.[3]
Производственная структура вспомогательных цехов включает:
Заготовительный цех
осуществляет предварительное формообразование деталей изделия (литье, горячая штамповка, резка заготовок и т.д.)
Цех ремонтный
осуществляет технические мероприятия по уходу, надзору, обслуживанию и ремонту оборудования для поддержания его в состоянии постоянной готовности к работе.
Энергетический цех.
Его задачами являются бесперебойное и надежное обеспечение предприятия всеми видами энергии, а так же выполнение правил эксплуатации энергетического оборудования, организация его технического обслуживания и ремонта.
К производственной структуре обслуживающих цехов относятся:
Цех технического контроля,
основными функциями которого являются: контроль за качеством и комплектностью выпускаемых изделий, учет и анализ возвратов продукции, а так же предупреждение брака и дефектов в производстве.
Складские подразделения
занимаются приемкой, хранением, учетом материалов и регулированием уровня их запаса, подготовкой к отправке потребителю готовой продукции.
Транспортный цех
. Основной его задачей является обеспечение своевременного и бесперебойного обслуживания транспортом основных и вспомогательных производств.[2]
1.10 Организационная структура управления цехом
Организационная структура управления
- форма разделения и кооперации управленческой деятельности, в рамках которой осуществляется процесс управления по соответствующим функциям, направленным на решение поставленных задач и достижение намеченных целей. [5]
С этих позиций структура управления представляется в виде системы оптимального распределения функциональных обязанностей, прав и ответственности, порядка и форм взаимодействия между входящими в ее состав органами управления и работающими в них людьми.
Организационная структура цеха определяется типом производства, техническим уровнем и сложностью выпускаемой продукции, численностью рабочих, уровнем механизации и автоматизации производства и другими факторами, связанными с отраслевыми особенностями.
На рис. 1.4. представлена наиболее распространенная схема управления цехом. Цехи и его подразделения работают в соответствии с положением о цехах и производственных участках, утвержденным директором предприятия.
Начальник цеха подчинен директору предприятия. Он руководит цехом на основе единоначалия и персонально отвечает за состояние цеха, психологический климат в коллективе и за результаты всех видов его производственно-хозяйственной деятельности.

Рис.1.4. Схема управления механосборочным цехом
В подчинении начальника цеха находится следующий аппарат управления:
- технологическое бюро
, которое ведает разработкой рабочей технологии, инструктажем мастеров по ее применению, осуществляет контролем за соблюдением технологической дисциплины на производственных участках; в подчинении начальника техбюро находятся группа инженеров-технологов, техник по инструменту, мастерская по ремонту несложной технологической оснастки; архив технической документации цеха; инструментальные кладовые;
- бюро труда и заработной платы
, которое ведает нормированием, тарификацией и материальным стимулированием труда, выявлением заниженных норм, контролем за рациональным использованием фонда заработной платы фонда материального поощрения;
- бюро планово-экономическое
(экономист цеха),
которое ведает разработкой плана экономического и социального развития цеха, доведением показателей плана до участков и бригад, учетом и контролем выполнения плана, внедрением хозрасчета в подразделениях цеха, анализом конечных результатов работы цеха;
- производственно-диспетчерское бюро (ПДБ)
, которое ведает разработкой оперативно-календарных планов цеха, участков и бригад, их материальным обеспечением на каждую смену, использованием оборудования по мощности и времени, организацией бесперебойной, ритмичной работы всех участков, выполнением ими сменно-суточных заданий и месячных планов выпуска продукции в установленной номенклатуре и качеству; в ведении ПДБ цеха находятся цеховые склады материалов, заготовок и готовой продукции, а также внутрицеховой транспорт;
- бюро цехового контроля
, которое занимается межоперационным и окончательным контролем продукции цеха, его оборудования и технологической оснастки, разработкой и реализацией профилактических мероприятий по предупреждению брака; работники бюро цехового контроля в части соблюдения трудовой дисциплины и правил внутреннего распорядка подчиняются начальнику цеха, а в части оценки качества продукции только главному контролеру предприятия (объединения);
- механик цеха
, который руководит слесарями и электриками и организует техническое обслуживание, текущий и средний ремонт оборудования цеха по графику, утвержденному главным механиком и главным энергетиком предприятия, контролирует эксплуатацию оборудования;
- завхоз цеха
, который руководит обслуживающими рабочими и отвечает за санитарное состояние помещений цеха.[4]
1.11 Принципы организации цехов и участков предприятия
В зависимости от формы специализации производственные подразделения предприятия организуются по:
технологическому (на выполнении отдельной операции или вида работ),
предметному (на изготовлении отдельного вида продукции или ее составной части),
поточному (при разделении участков на поточные линии),
смешанному (предметно-технологическому) принципам.
По технологическому принципу
на машиностроительных предприятиях специализируются литейные, кузнечные, термические, сборочные цехи; на текстильных предприятиях — прядильные, ткацкие, отделочные (красильные) цехи. При использовании технологического принципа оборудование располагают исходя из выполнения однородных технологических операций для обработки разных деталей. Оборудование формируют по однотипным группам, например, в механическом цехе на одном участке могут быть сгруппированы только токарные станки, на другом — строгальные, на третьем — фрезерные.
Технологический принцип облегчает руководство цехом или участком: мастер, отвечающий за группу однородных станков, может всесторонне изучить их; при чрезмерной загрузке одного станка работа может быть передана на любой освободившийся станок. Однако технологический принцип имеет и недостатки. Так, при большом разнообразии продукции нужны частые переходы от одних технологических операций к другим. Это требует дополнительного времени на переналадку станков, удлиняет цикл изготовления, усложняет планирование и производственные связи подразделений и др. Поэтому этот принцип неэкономичен. Его применяют в условиях единичного и мелкосерийного типа производства с большой номенклатурой деталей.
При использовании предметного принципа
построения цехов каждый из них специализируется на изготовлении какого-либо определенного изделия или его составной части. По этому принципу сформированы цехи в крупносерийном и массовом производстве.
При организации цехов и участков по предметному принципу создаются благоприятные условия для применения передовых методов организации производства и труда. Расстановка оборудования по ходу выполнения технологических операций резко сокращает путь движения обрабатываемых деталей и затраты времени на их транспортировку. Возникают благоприятные предпосылки для организации поточных и автоматических линий, более полно используется оборудование, рабочие специализируются на выполнении узкого круга операций, в результате чего повышается их квалификация, улучшается организация труда, усиливается ответственность за качество выпускаемых изделий. При этом мастер полностью отвечает за весь цикл изготовления изделия. Все это ведет к росту производительности труда и снижению себестоимости продукции. К недостаткам, присущим предметным цехам и участкам, можно отнести неполную загрузку оборудования на отдельных операциях вследствие небольшого объема работ. Организация таких участков наиболее целесообразна при относительно постоянной и небольшой номенклатуре выпускаемых изделий, т. е. она присуща крупносерийному и частично массовому производству.
При поточном принципе
построения цехов происходит разделение участков на поточные линии. Поточные линии организуют или в виде отдельных поточных участков, специализированных на обработке одного или нескольких изделий, или в виде одной сквозной поточной линии. Поточные методы работы свойственны массовому производству.
Начальным звеном производственной структуры служит рабочее место. Расположение рабочих мест зависит от типа производства. Например, на поточных линиях они расположены по ходу технологического процесса и по времени связаны единым тактом потока. На предприятиях, где не используется поточной метод организации производства, рабочие места размещают преимущественно по группам однотипного оборудования.
При предметно-технологическом (смешанном) принципе
построения цехов заготовительные цехи (литейные, штамповочные, прессовые, кузнечные) специализируются по технологическому принципу, а обрабатывающие — по предметному. [7]
1.12 Пути рациональной организации производственного процесса
Организация производственного процесса предусматривает рациональное сочетание в пространстве и во времени всех основных, вспомогательных и обслуживающих процессов, обеспечивающее наименьшее время его осуществления. Главная цель организации производственного процесса — всемерная экономия времени, обеспечение высокого качества и эффективности производства продукции.
Рациональная организация производственных процессов на предприятиях базируется на следующих общих принципах:
специализации,
пропорциональности,
параллельности,
прямоточности,
непрерывности,
ритмичности процесса.
1)Специализация процесса
— это минимизация разнообразия работ и операций, а также режимов обработки и других элементов производственного процесса. Разнообразие операций в процессе зависит прежде всего от номенклатуры изделий, закрепленных за одним производственным подразделением (участком, линией, цехом и др.). В этих условиях процессы ну ждаются в частых переналадках, перестройках, что всегда приводит к повышенным потерям. Снижению потерь при этом способствуют совершенство системы оперативного планирования и конструктивно-технологическая унификация.
2)Пропорциональность
— это согласованность всех элементов процесса и прежде всего по производительности и производственной мощности. Нарушение этого требования приводит к диспропорциям, образованию «узких мест» в производстве, вследствие чего ухудшается использование оборудования и рабочего времени, увеличиваются производственные заделы, удлиняется производственный цикл и др. Все это ведет к снижению эффективности производства.
Для обеспечения пропорциональности производственных процессов необходима оптимизация номенклатурно-количественных заданий по критерию полноты загрузки оборудования. Пропорциональность производственного процесса способствует широкому внедрению комплексной механизации и автоматизации производства, охватывающей основные, вспомогательные и обслуживающие процессы.
3)Параллельность
работ в процессе означает одновременность выполнения операций и частей производственного процесса. Параллельность может иметь место при выполнении самой операции, при протекании смежных операций при выполнении основных, вспомогательных и обслуживающих процессов.
При выполнении технологической операции параллельность выражается в одновременной работе нескольких станков на операции, в многопредметной обработке на станках, в совмещении машино-автоматической обработки с выполнением рабочим ручных, вспомогательных элементов операции. В простых производственных процессах (при обработке деталей партиями) помимо изложенного имеет место одновременность обработки партии на смежных операциях процесса, а также выполнения вспомогательных и обслуживающих процессов. Возможность параллельного протекания частичных процессов во многом зависит от степени унификации и взаимозаменяемости элементов конструкции, позволяющих независимое их изготовление.
4)Прямоточность
означает пространственное сближение операций, стадий процесса, исключающее возвратные движения предмета труда в процессе производства. Для этого операции и частичные процессы пространственно располагают в порядке следования операций технологического процесса, вследствие чего сокращается время прохождения изделия в производстве, а также упорядочиваются грузопотоки и уменьшается грузооборот. В этом случае возникает задача оптимизации расстановки оборудования и расположения рабочих мест.
Принцип прямоточности в организации процесса применим не только к простым процессам, но и к сложным, выполняемым в масштабе предприятия. В соответствии с этим проектируются расположение цехов и служб на территории завода (генплан), размещение участков в цехах. Наиболее полно этот принцип может быть реализован при устойчивой номенклатуре изготовляемой продукции и развитой типизации технологических процессов.
5)Непрерывность
в организации производственного процесса выражается в непрерывности движения предмета труда в производстве (т. е. без пролеживаний и ожиданий обработки), а также в непрерывности работы рабочих и оборудования. Только комплекс этих трех факторов обеспечивает полную непрерывность производственного процесса.
Таким образом, принцип непрерывности выражается в сведении к минимуму всех видов перерывов в производстве изделий: внутриопера-ционных, межоперационных, межлинейных, межцеховых. При соблюдении принципа пропорциональности создаются объективные предпосылки к непрерывности процесса, так как равная производительность по операциям исключает межоперационные ожидания обработки, например, на непрерывных поточных линиях.
6)Принцип ритмичности
и равномерности
выступает как важнейшее требование к организации производственного процесса. Следует различать понятия: ритмичность выпуска продукции, ритмичность работы (производства) и равномерность производства.
Ритмичность выпуска
означает выпуск одинакового объема продукции за равные интервалы времени (месяцы, декады, смены и др.). Ритмичность работы
— это выполнение равных объемов работы по количеству (суммарно в нормо-часах) и составу (видам работ) за равные интервалы времени. Ритмичность работы непосредственно связана с ритмичностью выпуска, и эта взаимосвязь предопределяет равномерность производства. Равномерность производства
означает соблюдение ритмичности выпуска и работы, причем объем работы, выполняемый за определенный интервал времени, по количеству и составу полностью соответствует трудоемкости выпускаемой продукции за этот интервал. При этом в каждом интервале времени происходит компенсация трудоемкости выпуска изделий выполнением комплекса соответствующих работ. Часто ритмичность выпуска характеризуется одинаковым выпуском продукции за декаду. Однако ритм выпуска продукции может быть различным; он зависит от сложности продукции и длительности процессов ее изготовления.
Следовательно, ритм выпуска продукции как бы задает нужный ритм работы на участке, в цехе, заводе. Он обусловлен планом предприятия и может сохраняться лишь при условии ритмичной работы на всех участках, рабочих местах основного процесса и сопряженных с ним вспомогательных, обслуживающих процессов.
Основные принципы ложатся в основу организации любого производственного процесса, но в разной мере могут быть реализованы. Они действуют взаимозависимо и однонаправленно. Например, достигая количественной пропорциональности в процессе, одновременно создают предпосылки для непрерывности и ритмичности производственного процесса, к прямоточности движения предмета труда.
Система организации производственного процесса должна обладать необходимой надежностью, т. е. способностью противостоять различным помехам, нарушающим ее основные принципы. Для этого в системе должны быть предусмотрены механизмы саморегулирования, опирающиеся на качественную нормативную базу, оптимальные методы планирования и управления, необходимые резервы, обеспечивающие бесперебойность процесса при случайных или неизбежных помехах и др. [4]
1.13 Планировка оборудования на участке цеха
Планировка цеха
- это план расположения производственного, подъемно-транспортного и другого оборудования, инженерных сетей, рабочих мест, проездов, проходов. [1]
План участка механического цеха представлен в Приложении 2.
Технологическая планировка участка разрабатывается при проектировании или реконструкции участков. Планировка решает вопросы: технологических процессов организации производства, техники безопасности, выбора транспортных средств, научной организации труда и производственной этики. [1]
Проектируемая планировка участка механического цеха по изготовлению детали «Вал шлицевый» определяется технологическим процессом и заданным серийным типом производства.
В цехе, где располагается проектируемый участок, ширина пролета составляет 16 м, шаг колонн 10,5 м. Пролетом называется часть здания, ограниченная в продольном направлении двумя параллельными рядами колонн.
В начале участка предусматривается – склад заготовок (готовой продукции); в удобном месте для подъезда транспортных средств – место сбора готовой продукции (контейнер), а так же:
- место мастера;
- участок окончательного контроля;
- стеллажи для деталей на промежуточных операциях;
- контейнеры для стружки.
Станки на проектируемом участке располагаются в порядке выполнения технологических операций. При разработке плана расположения станков, учитывалось их положение относительно колонн, проездов, проходов, вспомогательных помещений с использованием нормативов.
При передаче детали в другой пролет участка сохраняется общая прямоточность движения деталей. Передача деталей из пролета в пролет осуществляется на данном участке следующими способами: поворотным краном, рольгангом и автотележкой (электрокаром).
Рабочие места станочников спланированы таким образом, чтобы обеспечить безопасность работающих, максимальное удобство в работе, возможность выполнения ремонта, а так же быстрой эвакуации рабочих в экстремальных случаях.
Для обеспечения пожарной безопасности на территории цеха располагаются:
- противопожарный щит;
- ящик с песком;
- огнетушители.
На участке предусмотрена зона психологической разгрузки.
1.14 Организация многостаночной работы
Многостаночное обслуживание
— одновременная работа одного рабочего или бригады на нескольких станках без снижения при этом производственной мощности оборудования. Переход к многостаночному обслуживанию требует высокой квалификации работника, хорошего знания используемых машин, четкой, продуманной организации труда. [6]
Техническими предпосылками развития многостаночного обслуживания являются повышение уровня автоматизации используемого оборудования, улучшение системы управления оборудованием и конструкции технологической оснастки, в результате которых, уменьшается доля ручного труда по обслуживанию оборудования и увеличивается доля автоматической его работы.
Организационными предпосылками введения многостаночного обслуживания является:
- рациональная планировка оборудования на рабочем месте, обеспечивающая удобство его обслуживания;
- кратчайшие маршруты перехода от станка к станку;
- реализация наиболее эффективной системы обслуживания рабочих мест;
- изменение форм разделения и кооперации труда таким образом, чтобы большинство функций (наладка, подналадка станков, передача деталей, заточка инструментов и др.) выполнялись вспомогательными рабочими.
Экономическая целесообразность многостаночного обслуживания заключается в возможности обеспечения полной занятости рабочих-станочников и обслуживаемого ими оборудования.
Особенностью организации многостаночной работы является определение рациональных маршрутов перемещений рабочего при обслуживании оборудования. Затраты времени на подходы к станкам имеют большой удельный вес в общем времени занятости рабочего.
Эффективность многостаночной работы в значительной степени зависит от организации системы обслуживания. Обслуживание рабочих мест многостаночников проектируется таким образом, чтобы большинство функций (наладка, регулировка, контроль, подача деталей и др.) выполнялись вспомогательными рабочими. Совершенствование трудовых процессов рабочих-многостаночников направлено на сокращение времени занятости при обслуживании каждого станка, расширение фронта многостаночного обслуживания, обеспечение равномерной загрузки рабочего в цикле, снижение монотонности труда.[6]
1.15.1 Расчет нормы обслуживания станков одним рабочим
, ед.об. (станков) (15)
- основное время
- вспомогательное время
станка
Принимаем = 2 станка на одного рабочего-фрезеровщика.
1.15.2 Циклограмма многостаночного обслуживания (на операцию № 25)
Условные обозначения:
  
Рис. 1.5. Циклограмма многостаночного обслуживания
Выводы по разделу 1
В ходе выполнения данного раздела были проведены последовательные расчеты, направленные на выявление «узких» и «широких» местна производственном участке и разработку мероприятий по их ликвидации.
Для обеспечения равномерной загрузки оборудования «узкие» места были ликвидированы путем применения 3-х сменного режима работы оборудования на операциях № 10 и № 30. В результате этого произошло снижение загрузки оборудования до оптимального уровня (по операции № 10 на 30%, а по №30 - на 32%).
«Широкие» места были ликвидированы путем их догрузки аналогичной работой с других участков.
Одной из важных задач данного раздела было определение длительности производственного и технологического циклов до и после ликвидации «узких» и «широких» мест.
В результате было установлено, что длительность технологического цикла не изменилась в обоих случаях = 570,01 мин. = 9,5 ч., так как осталось неизменным количество оборудования.
Длительность производственного цикла сократилась на 4,71 часа в результате применения 3-х сменного режима работы оборудования по 2-м операциям (№ 10 и № 30). Переход цеха на 3-х сменный режим работы значительно увеличит загрузку оборудования, общепроизводственные расходы, а так же увеличатся расходы на з/п рабочих и электроэнергию.
Сокращение производственного цикла имеет большое экономическое значение:
сокращается оборачиваемость оборотных средств за счет сокращения объемов незавершенного производства;
увеличивается фондоотдача основных производственных фондов;
снижается себестоимость изделий за счет сокращения условно-постоянной части издержек на одно изделие.
Раздел 2. Организация энергетического хозяйства
2.1 Состав энергетического хозяйства предприятия
Энергетическое хозяйство предприятия
-
совокупность установок, служащих для преобразования и передачи энергии, и соответствующих служб, обеспечивающих бесперебойное снабжение предприятия всеми видами энергии и энергоносителей (электроэнергией, топливом, паром, газом и т. д.) установленных параметров и при наименьших затратах. [3]
Промышленные предприятия — основные потребители энергетических ресурсов. Их потребность в энергии и энергоносителях непрерывно возрастает, причем энерговооруженность труда на предприятиях является одним из главных показателей научно-технического прогресса.
Структура энергетического хозяйства крупного машиностроительного предприятия, включает:
энергетические цехи (электросиловой, теплосиловой, газовый, электромеханический, слаботочный);
преобразовательные и генерирующие установки (компрессорная, котельная, генераторная станция и др.);
цеховые и общезаводские энергопередающие сети;
потребители энергии (оборудование, станки, печи и др.).[3]
Энергетическое хозяйство крупных предприятий находится в ведении главного энергетика, мелких предприятий — в ведении главного механика. В состав отдела главного энергетика вводят бюро (группы) энергоиспользования, энергооборудования, электрическая и тепловая лаборатории.
Группа энергоиспользования занимается:
нормированием расходов энергоресурсов;
планированием энергоснабжения;
разработкой энергобалансов;
учетом и анализом использования энергии.
Группа энергооборудования осуществляет:
руководство ППР (планово-предупредительным ремонтом) энергоустановок и энергосетей;
контроль за техническим состоянием сетей, оборудования и правилами их эксплуатации;
разработкой мероприятий по совершенствованию энергохозяйства и экономии энергосресурсов.
Энерголаборатории выполняют исследовательские работы по снижению расходов энергии и топлива, проводят измерения, испытания оборудования и сетей, проверку контрольно-измерительных приборов.
Обеспечение бесперебойного питания крупного завода необходимыми энергоресурсами возлагается на дежурных инженеров, руководящих эксплуатацией всего энергетического хозяйства в течение смены. [2]
2.2 Задачи и функции энергетической службы
Основными задачами энергетического хозяйства предприятия являются:
определение потребности предприятия в энергоресурсах и наиболее экономичных способов ее покрытия;
организация устойчивого энергоснабжения предприятия и его подразделений в точном соответствии с потребностью;
рациональная организация эксплуатации, технического обслуживания и ремонта энергетического оборудования и сетей на предприятии;
разработка и проведение мероприятий, направленных на сокращение энергопотребления, экономию энергии и всех видов топлива;
использование вторичных энергоресурсов и нетрадиционных источников энергии;
сокращение затрат на энергоснабжение предприятия и содержание энергохозяйства;
снижение энергоемкости и энергетической составляющей в себестоимости продукции.
Важной особенностью энергоснабжения является невозможность создания существенных запасов энергии, что вынуждает производить и потреблять энергию одновременно, а также обеспечивать соразмерность по величине ее производства и потребления. Режим производства энергии в каждый отрезок времени зависит от режима ее потребления. Потребление энергии в производстве неравномерно по часам суток, дням недели, месяцам и сезонам года. Поскольку изменяется во времени потребность в энергии (спрос), соответственно должно изменяться ее предложение (производство, закупка, отбор из внешней сети энергоснабжения). Еще одной важной особенностью, определяющей требования к организации энергетического хозяйства предприятия, является недопустимость сбоев в энергопитании технологических средств, участвующих в производстве товарной продукции: энергетическое хозяйство должно обеспечивать надежность и бесперебойность энергоснабжения.
Функции энергетической службы предприятия
:
разработка нормативов, касающихся энергетической службы;
планирование потребности во всех видах энергии и энергоносителей, составление энергетического баланса предприятия;
планирование потребности в запчастях;
организация выработки (обеспечения) предприятия всеми видами энергии;
оперативное планирование и диспетчирование обеспечения предприятия всеми видами энергии;
организация ремонтных работ оборудования;
разработка технической документации для проведения монтажных, ремонтных работ оборудования и энергетических коммуникаций (сетей);
организация обслуживания энергетического оборудования, сетей, линий связи;
контроль за качеством ремонтных работ;
организация монтажных, пусконаладочных работ нового оборудования, демонтаж и утилизация списанного энергетического оборудования;
надзор за правилами эксплуатации оборудования;
контроль за расходами всех видов энергии. [3]
2.3 Планирование потребности предприятия в энергии различных видов
При планировании потребности в энергии необходимо детально анализировать ее расход за период, предшествующий плановому. Плановые показатели по расходу энергии должны обеспечивать нормальный ход производственных процессов, исключать сверхнормативные потери.[3]
Определение потребности в энергии, топливе основывается на использовании балансового метода планирования. Для этих целей составляются сводные балансы и по отдельным видам энергии, топлива. В расходной части баланса рассчитывается потребность в энергии на производственную, хозяйственно-бытовую и непроизводственную деятельность предприятия. В приходной части баланса определяются источники покрытия этой потребности, производится расчет обеспечения необходимой потребности в энергии:
- за счет ее получения от районных систем;
- за счет собственных источников;
- за счет использования вторичных энергоресурсов.
Потребность в энергии зависит от мощности предприятия, энергоемкости выпускаемой продукции, характера технологических процессов и других факторов и определяется на основе таких исходных данных как:
генеральный план завода;
план цехов и помещений с размещением и спецификацией производственного, вспомогательного и сантехнического оборудования с указанием потребной мощности электродвигателей;
потребность в энергии каждого вида в соответствии с расчетами;
режима работы потребителей энергии;
среднего максимального часового и годового расхода энергии.[2]
1) Годовой расход технологической и осветительной электроэнергии для цеха на шинах низкого напряжения определяется по формуле:
, кВт/час (16)
- сумма активных мощностей на шинах низкого напряжения, кВт.
- действительный годовой фонд времени работы оборудования для одной смены, час.
- количество смен работы оборудования
- коэффициент загрузки оборудования по времени (0,75-0,85)


Сжатый воздух применяется для обдувки станков от стружки, деталей после мойки, узлов и изделий при сборке, а также для пневмо-устройств и пневмо-инструмента. Общую потребность в сжатом воздухе для каждого цеха и завода в целом определяют, исходя из расхода воздуха при непрерывной работе всех воздухоприемников, коэффициенте использования их в каждой смене годового фонда времени работы воздухоприемника.[2]
3) Коэффициент использования воздухоприемников оборудования:
(17)
- число часов фактической работы воздухоприемников
- число часов рабочей смены
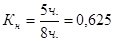
4) Средний часовой расход сжатого воздуха для одного воздухоприемника:
(18)
- расход воздуха в час при непрерывной работе, (10 )
 

5) Средний часовой расход (действительный) сжатого воздуха для всего количества воздухоприемников:
(19)
1,5 – коэффициент, учитывающий утечку воздуха, а так же выполнение непредусмотренных работ
 
6) Наибольший часовой расход воздуха применяется на 30% больше 
, (20)
 
По этому расходу подбирается оборудование компрессорной установки.
7) Годовая потребность в сжатом воздухе:
(21)
- количество смен
- коэффициент загрузки оборудования по времени
 
Вода в цехах употребляется на производственные и бытовые нужды. На производственные нужды вода используется для приготовления охлаждающих смесей, промывки деталей, охлаждения и закалки в установках ТВЧ, испытания узлов и изделий, для гидрофильтров распылительных камер.[2] 8) Годовой расход воды для охлаждающих жидкостей при резании металлов:
(22)
- часовой расход воды на один станок в литрах (0,6 л./час)
- количество станков
- действительный годовой фонд времени одного станка в одну смену
- количество смен
- коэффициент загрузки повремени

Для других целей расход воды определяется укрупненно по существующим нормам расхода.
Пар расходуется на производственные нужды цеха (для подогрева воды и смесей), а так же для отопления и вентиляции.[2]
9) Годовая потребность пара на отопление и вентиляцию (в тоннах) составляет:
,т. (23)
- расход тепла на 1 здания в килокалориях на час (0,5 Ккал/час)
- количество часов в отопительном периоде (H= 4320 час.)- для средней полосы РФ.
V- объем здания ( )
- теплота испарения в Ккал/кг.; =540 Ккал/кг.
 
т.
10) Годовая потребность в топливе на отопление:
, т. (24)
- теплотворная способность условного топлива; К=7000 Ккал/кг.
- КПД котельной установки [2]
т.
2.4 Технико-экономические показатели энергохозяйства цеха
Показатели производства и распределения энергии (удельные расходы топлива на производство всех видов энергии) КПД генерирующих установок.
(25)

Удельные расходы топлива и энергии на производство продукции предприятия.
удельный расход осветительной энергии:
кВт/ед.прод., где
N
– годовая программа(26)
удельный расход сжатого воздуха:
кВт/ед.прод. (27)
удельный расход воды для охлаждающих жидкостей:
кВт/ед.прод. (28)
удельный расход пара на отопление и вентиляцию:
кВт/ед.прод. (29)
удельный расход топлива на отопление:
кВт/ед.прод. (30)
Показатели себестоимости производства энергии (тепловой, электрической, энергии сжатого воздуха и пара).
Показатели энерговооруженности:
Коэффициент электровооруженности труда
(31)
- суммарная мощность электрических установок, кВт.
- число рабочих, работающих в наибольшую по численности смену
Коэффициент энергоемкости продукции
(32)
- выпуск продукции в неизменных ценах, тыс.руб.
- электроэнергия, фактически затраченная на производство, кВт.
Коэффициент энерговооруженности производства
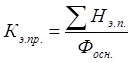 (33)
- суммарная мощность энергетических установок, кВт.
- стоимость основных производственных фондов, тыс. руб. (в неизменных ценах) [2]
2.5 Пути экономии энергии
Экономия электроэнергии может осуществляться за счет следующих мероприятий:
совершенствования техники, технологии и организации производства;
установки на оборудование электродвигателей соответствующей мощности;
рационального сочетания общего и местного освещения;
отключения электродвигателей на время перерывов, а также лишнего освещения;
содержания в чистоте стекол в оконных рамах;
соблюдения графиков профилактического обслуживания и ремонта электродвигателей.
Основные мероприятия экономии теплоэнергии:
повышение эффективности котельного оборудования за счет применения механизации;
использования возвратного конденсата;
своевременной очистки котлов от накипи;
лучшей очистки технической и питьевой воды;
соблюдение графиков ремонтов всех видов;
внедрение контрольно-измерительных приборов и др.
При снижении удельных норм расхода электрической и тепловой энергии на предприятии образуется экономия на их стоимости.[3]
Выводы по разделу 2
Энергохозяйство промышленного предприятия — это не только вспомогательный и обслуживающий участок предприятия, но и элемент энергетических систем района и представляет собою сложную совокупность процессов производства, преобразования, распределения и использования всех видов энергетических ресурсов.
Энергохозяйство обеспечивает производство на данном предприятии энергией в различных видах и энергоносителях, осуществляет ремонтно-эксплуатационное обслуживание и монтаж энергооборудования в производственных цехах. В то же время оно оказывает активное влияние на развитие предприятия (углубление взаимосвязи энергетики и технологии, комплексная механизация и автоматизация производственных процессов).[3]
Значительное влияние на повышение эффективности предприятия оказывает снижение затрат на энергоснабжение и улучшение использования энергоустановок как составной части основных производственных фондов предприятия.
Большое значение имеет экономия, и рациональное использование энергоресурсов на промышленных предприятиях, являющихся основными потребителями топлива и энергии. Поэтому снижение расхода энергоресурсов на предприятиях позволит уменьшить затраты на развитие топливно-энергетического комплекса (ТЭК) страны.
Таким образом, энергохозяйство занимает важное место в экономике предприятия и производстве и оказывает существенное влияние на развитие, как предприятия, так и топливно-энергетического комплекса страны.
Заключение
В данной курсовой работе рассмотрены и изучены принципы рациональной организации производства деталей типа «Вал шлицевый» на участке механического цеха.
Изучены теоретические материалы по организации энергетического хозяйства предприятия, его состав, основные функции и задачи; рассчитана потребность предприятия в энергии различных видов и топлива, определены основные технико-экономические показатели энергохозяйства цеха, а так же пути экономии электро- и теплоэнергии.
В ходе выполнения работы решены поставленные задачи по обеспечению равномерной загрузки оборудования на производственном участке и сокращению длительности производственного цикла. Разработан план участка механического цеха.
Современный производитель должен рационально применять методы и соблюдать требования принципов организации производства в комплексе, только в этом случае возможна оптимизация производственных процессов и, соответственно, достижение максимальной эффективности производства.
Список использованной литературы
1. Егоров М.Е. Основы проектирования машиностроительных заводов. Изд. 6-е, перераб и доп. Учебник для машиностроит. вузов. М., «Высшая школа», 1969.
2. Курс лекций по дисциплине «Организация производства на предприятии машиностроения»
3. Организация и планирование энергохозяйства промышленных предприятий/В.Т.Мелехин, Г.Л.Багиев, В.А.Полянский.-2-е изд., перераб. и доп. – Л.: Энергоатомиздат. Ленингр. отд-ние, 1988. – 224с.: ил.
4. Организация, планирование и управление предприятием машиностроения: Учебник для студентов машиностроительных специальностей вузов / И. М. Разумов, Л. А. Глаголева, М. И. Ипатов, В. П. Ермилов. – М.: Машиностроение, 1982. – 544 с., ил.
5. Райзберг Б.А., Лозовский Л.Ш., Стародубцева Е.Б. Современный экономический словарь.-5-е изд., перераб. и доп.-М., 2006
6. Организация и планирование машиностроительного производства (производственный менеджмент): Учебник/К.А.Грачева, М.К.Захарова, Л.А.Одинцова и др., Под ред. Ю.В.Скворцова, Л.А.Некрасова. – М.: Высш.шк., 2003. – 470 с.: ил.
7. Фатхутдинов Р.А. Организация производства: Учебник. – М.: ИНФРА-М, 2002. – 672с. – (Серия «Высшее образование»).
|