Содержание
Внимание! Приведенную ниже систему расчетов нельзя воспринимать как образец.
Введение. 2
Раздел 1. Технологическая цепочка и производительность машин. 3
1.1. Технологическая цепочка.3
1.2. Технологическое оборудование и нормы его производительности.4
Раздел 2. Заправочные данные суровых тканей и нормы расхода пряжи. 5
2.1. Заправочные данные суровой ткани базового артикула 062259: оценка взаимосвязей. 5
2.2.Заправочные данные суровой ткани нового артикула 062259H: организационно-экономическое обоснование значений.7
2.3. Нормы расхода пряжи на 100 м суровой ткани нового артикула.9
Раздел 3. Сопряженность ткацких паковок.11
3.1. Сопряженная длина основы и масса пряжи в рулоне суровой ткани.11
3.2. Сопряженная длина и масса основы на ткацком навое.11
3.3. Сопряженная длина и масса основы на сновальном валу.13
Раздел 4. Сопряженность технологического оборудования.17
4.1. Расчет отходов по переходам ткацкого производства. 17
4.2. Объем производства суровой ткани в час и выход полуфабрикатов.20
4.3. Сопряженное количество единиц заправленного оборудования.21
Раздел 5. Мощность производства. 23
Раздел 6. Технико-экономические нормативы организации производства. 25
6.1. Трудоемкость изготовления суровой ткани. 25
6.2. Машиноемкость изготовления суровой ткани. 26
6.3. Длительность технологического цикла. 27
Заключение. 29
Списокиспользованнойлитературы.30
Задание.
Выполнить проектные расчеты по организации льноткацкого производства при выработке суровой ткани артикула 062259.
Заправочные данные суровой ткани базового артикула 062259
Таблица 1.
Наименование ткани
|
Артикул
|
Ширина ткани, см
|
Плот-ность на 10 см
|
Ширина проборки по бедру, см.
|
Вид основной пряжи
|
Основа
|
Уток
|
Общий расход пряжи без отходов на 100 м, кг
|
По основе
|
По утку
|
Фон
|
Кромка
|
Количество нитей в основе
|
Уработка в качестве по нитям основы, %
|
Отходы, %
|
Расход пряжи без отходов на 100 м, кг
|
Отходы, %
|
Условное обозначение пряжи
|
Расход пряжи без отходов на 100 м, кг
|
Фоновых
|
Кромочных
|
Всего
|
Фон
|
Кромка
|
Ткань сорочечная пестротканая малосминаемая |
062259 |
163 |
220 |
175 |
168,2 |
СК 29 х/б |
С 29х2 х/б |
3584 |
16 |
3600 |
12,0 |
1,8 |
11,64 |
0,11 |
1,5 |
ВК 33,5 ВЛ |
10,06 |
21,81 |
Основные параметры готовой продукции базового артикула 062259
Таблица №2.
Наименование ткани
|
Артикул
|
Ширина ткани, см
|
Поверхностная плотность, г/м2
|
Плотность (число) нитей по
|
Техническая притяжка по утку
|
Весовой лоскут, %
|
основе
|
утку
|
Ткань сорочечная пестротканая малосминаемая |
062259 |
150 |
134 |
240 |
178 |
- 1,5 |
0,8 |
Тип ткацкого станка при выработке суровой ткани нового артикула – станок СТБ.
Производственная площадь льноткацкого производства составляет 10200 м2
.
1.1. Технологическая цепочка.
Кромка
С 29х2 х/б
В бобинах
|
|
Фон
СК 29 х/б
На початках
|
|
 |
 |
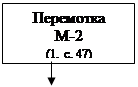 |
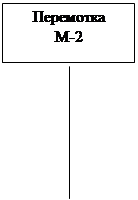 |
Перемотка
МЛМ-2
(1, с. 46)
|
|
Снование
СП-180
(1, с.64)
|
|
 |
 |
Шлихтование
ШБ-11/180
(1, с. 125)
|
|
На выход
 |
Пробирание и привязывание
ПСМ-230, УП2-5
(1, с. 180)
|
|

Примечание: После перематывания формируем основу, на льноткацких предприятиях для партионного снования основ из х/б пряжи применяются быстроходные машины типа СП. Исходя из ширины вырабатываемой ткани подходит машина СП-180.
Для повышения выносливости пряжи производим шлихтование на шлихтовальной машине барабанного типа ШБ – 11/180. Кромочные нити основы поступают на выход шлихтовальной машины, т.к. кромка сформирована из крученых нитей, она не шлихтуется, т.к. уже достаточно прочна.
Для выработки ткани выбираем станок СТБ2-175, в соответствии с заданной шириной.
Технологическое оборудование и нормы его производительности
Таблица № 3.
Марка оборудо-вания
|
Скорость выпускных органов,
м/мин
|
Теоретическая производительность машины, кг/маш.-ч.
|
КПВ
|
Норма производительности машин, кг/маш.-ч.
|
Примечание
|
М-2 |
500-1000
Vкр
=700
Vф
=560
|

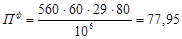
|
0,88 |
171,49
68,6
|
(1, с.47)
Пт
=(V*60*T*mб
)/106
,
где mб
=80
|
МЛМ-2 |
400-800
V=570
|
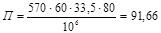 |
0,87 |
79,74 |
(1, с.49)
Пт
=(V*60*T*mб
)/106
|
СП-180 |
350-800
V=400
|
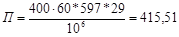 |
0,5 |
207,76
|
(1, с. 64, 2, с. 56)
Чн
=597 число нитей на одном сновальном валу
Пт
=(V*60*Чн
*T)/106
|
ШБ11/180 |
30-150
V=55
|
 |
0,6 |
173,03 |
(1, с. 139)
Пт
=(V*60*T*Но
)/106
|
ПСМ-230 |
- |
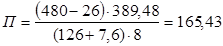 |
- |
165,43 |
Пт
=[(Тсн
–Тб
)*Мн
]/(То
–tв
)*t
Мосн=389,48
(разд.3)
|
УП2-5 |
До 500
V=450
|
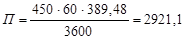 |
0,47 |
1372,92 |
(1, с. 180)
Пт
=(V*60*mо
)/Но
, где mо
- масса пряжи на ткацком навое.
|
СТБ2-175 |
n = до 230 мин-1
n=230
|
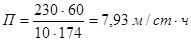 |
0,85 |
6,74 |
Пт
=(n*k*60)/(Ру
*10), где n- частота вращения главного вала, k- число полотен.
Ру
=174
|
Примечание: для ПСМ-230 tосн
=Нвр
*чн
/10, где Нвр
- время на пробирание основ, мин/100 нит; Нвр
=3,5 мин/100 нит; tосн
=3,5*3600/100=126 мин, tвсп
=7,6 мин (1, с. 187), Тб
=Тлн
+Тотд
=10+16=26 мин. (1, с. 183)
2.1. Заправочные данные суровой ткани базового артикула 062259: оценка взаимосвязей
2.1.1. Плотность ткани по основе:
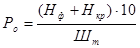
нит/дм, плотность соответствует заданию.
2.1.2. Плотность по утку:

нит/дм, что соответствует заданию.
2.1.3.Ширина кромки:
, см
см, что меньше минимального значения ширины кромки на станках СТБ
2.1.4. Усадка ткани в отделке по основе:
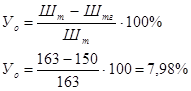
2.1.5. Плотность по основе, исходя из плотности суровой ткани:
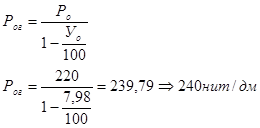
что соответствует исходному значению
2.1.6. Количество зубьев берда:
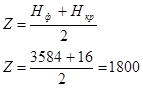
2.1.7. Номер берда:
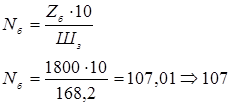
2.1.8. Ширина заправочная:

см, следовательно, ширина проборки нуждается в уточнении
2.1.9. Расход нитей фона:
, где
а0
– уработка основы, %, В – вытяжка на шлихтовальной машине, В=1,5%
кг/100 м
2.1.10. Расход нитей кромки:
, где
Кукр
– коэффициент укрутки,
Кукр
=0,98

2.1.11. Расход нитей утка:
, где
lк
– длина концов зарабатываемых нитей, см
,
где ау
– уработка утка
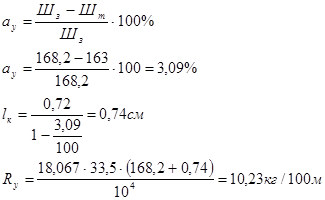
Уменьшим плотность нитей по основе и утку на одну нить, тогда станет: Ро
=219, Ру
=174нит/дм
2.2.1. Усадка ткани в отделке по основе:
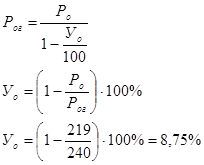
2.2.2. Притяжка ткани по утку:
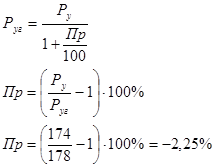
2.2.3. Ширина суровой ткани:
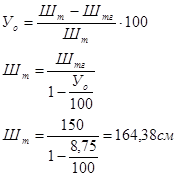
2.2.4. Заправочная ширина суровой ткани:
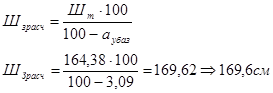
2.2.5. Ширину кромки расчетную принимаю равной 3 см.
2.2.6. Ширина фона:
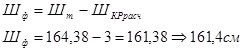
2.2.7. Число нитей фона:
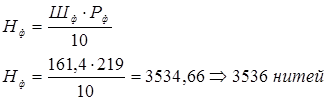
2.2.8. Число нитей кромки:

3,11 больше максимальной ширины кромки, следовательно, принимаю число нитей кромки равным 64, 16 из которых с лин.плотностью 29*2.
Проверка:
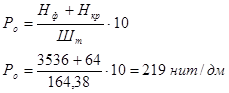
2.9. Определим заправочную ширину суровой ткани:
а) Количество зубьев берда:
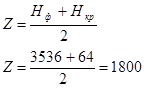
б) Номер берда:
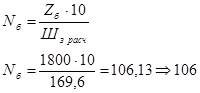
в) Ширина заправочная:
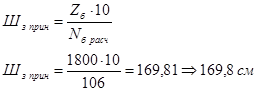
2.2.10. Определим уработку утка:
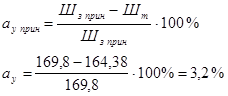
2.2.11.Использование ткацкого станка по ширине.
Станок СТБ2-175, максимальная ширина - 175.
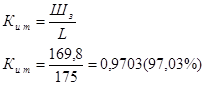
2.3.1. Расход нитей фона:
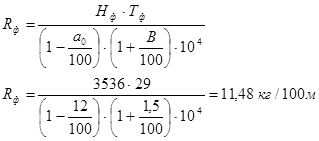
2.3.2. Расход нитей кромки:
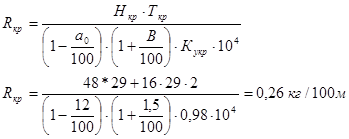
2.3.3. Расход нитей утка:
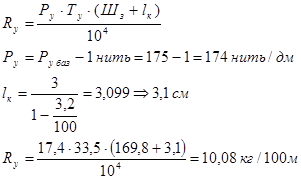
2.3.4. Общий расход:

Заправочные данные суровых тканей
Таблица № 4.
Наименование ткани
|
Артикул
|
Ширина ткани, см
|
Плот-ность на 10 см
|
Ширина проборки по бедру, см.
|
Вид основной пряжи
|
Основа
|
Уток
|
Общий расход пряжи без отходов на 100 м, кг
|
По основе
|
По утку
|
Фон
|
Кромка
|
Количество нитей в основе
|
Уработка в качестве по нитям основы, %
|
Отходы, %
|
Расход пряжи без отходов на 100 м, кг
|
Отходы, %
|
Условное обозначение пряжи
|
Расход пряжи без отходов на 100 м, кг
|
Фоновых
|
Кромочных
|
Всего
|
Фон
|
Кромка
|
Ткань сорочечная пестротканая малосминаемая |
062259 |
163 |
220 |
175 |
168,2 |
СК 29 х/б |
С 29х2 х/б |
3584 |
16 |
3600 |
12,0 |
1,8 |
11,64 |
0,11 |
1,5 |
ВК 33,5 ВЛ |
10,06 |
21,81 |
062259Н |
164,4 |
219 |
174 |
169,8 |
3536 |
64,
48/16
|
3600 |
12,0 |
11,48 |
0,26 |
10,08 |
21,82 |
Исходные данные для расчета рулона ткани
Таблица № 5
Марка ткацкого станка
|
Масса 100 п.м. ткани без учета угаров,
М, кг
|
Условная длина куска, Lк
, м
|
Максимальная масса рулона ткани на товарном валике Мр
, кг
|
СТБ2-175 |
21,82 |
м |
Мр
= 10-25г (2, с. 49) Принимаю Мр
= 16 кг |
Примечание: Sк
=30 м2
по ГОСТу 357-75.
3.1.1.
Длина рулона ткани:
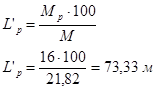
3.1.2.
Количество кусков в рулоне ткани:
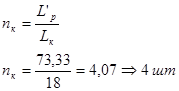
3.1.3.
Длина ткани в рулоне:
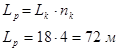
3.1.4.
Масса ткани в рулоне:
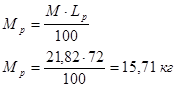
Результаты расчета рулона ткани
Таблица № 6
Артикул ткани
|
L
к
, м
|
L
р
, м
|
n
к
или
nu
в рулоне, шт
|
Мр
, кг
|
062259Н |
18 |
72 |
4 |
15,71 |
Исходные данные для расчета ткацкого навоя
Таблица № 7
Артикул ткани |
Диаметр дисков навоя Dд
, см |
Диаметр ствола навоя
d, см
|
Расстояние между дисками навоя
H, см
|
Диаметр намотки пряжи на навой
Dн
, см
|
Линейная плотность нитей основы Tо
, текс |
Плотность намотки пряжи
γ, г/см3
|
Общее число нитей основы mо
, шт |
062259Н |
70
(1, с. 125)
|
15
(1, с. 229)
|
167
(1, с.126)
|
Dн
= Dд
-(1..3)=70-3=67 |
29 |
0,7
(1, с.125)
|
3600 |
3.2.1.
Объем пряжи на ткацком навое:
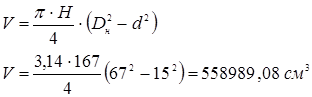
3.2.2.
Масса пряжи на навое:
М' основа
=

М
основа
=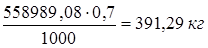
3.2.3.
Длина основы на навое:
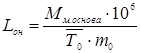
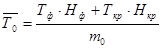
текс
м
3.2.4.
Длина основы в куске ткани:
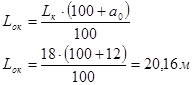
3.2.5.
Возможное число кусков, которое можно получить из одной основы:
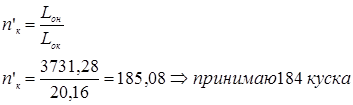
3.2.6.
Сопряженная длина основы на навое:

где nк
– принятое число кусков,
lnp
- длина концов основы, идущих в угары при пробирании или привязывании, lnp
=2,8м, (1, с.361);
lmk
- длина концов основы, идущих в угары в ткачестве, lmk
=1,8 м, (1, с. 363).
3.2.7.
Масса основы на навое с учетом сопряженной длины:
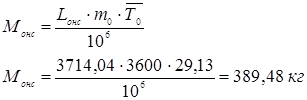
3.2.8.
Коэффициент полезного использования объема ткацкого навоя:

Результаты расчета навоя
Таблица № 8
Артикул ткани |
Т0
, текс |
γ, г/см3
|
V, см3
|
Мон
, кг |
nк
, шт |
Lок
, м |
Lонс
, м |
Монс
, кг |
062259Н |
29,13 |
0,7 |
558989,08 |
391,29 |
184 |
20,16 |
3714,04 |
389,48 |
3.3. Сопряженная длина и масса основы на сновальном валу.
Исходные данные для расчета сновального вала
Таблица № 9
Артикул ткани |
Dд
, см |
d, см |
Н, см |
Dн
, см |
γ, г/см3
|
То
, текс |
mр,
шт |
E, шт |
Lонс
, м |
062259Н |
66
(1, с. 64)
|
24
(1, с. 64)
|
180
(1, с. 64)
|
Dн
= Dд
-(1…3)=66-2=64 |
0,5
(1, с.88)
|
29 |
3584 |
616
(1, с. 67)
|
3714,04 |
3.3.1
Объем пряжи на сновальном валу:
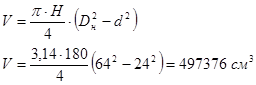
3.3.2.
Масса пряжи на сновальном валу:
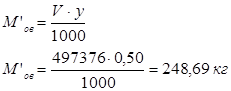
3.3.3.
Количество сновальных валов в партии:
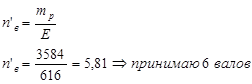
mр
= =3584 (3536 – нити фона и 48 – нити кромки),
Е – емкость шпулярника
3.3.4.
Число нитей на сновальном валу:
597 нитей на валах 1-5, и 599 нитей на 6 валу
3.3.5.
Максимально возможная длина нити на сновальном валу:

3.3.6.
Количество ткацких навоев из партии сновальных валов:
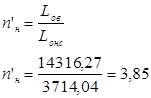
Так как дробная часть больше 0,5, то округление не производим. Уточним длину основы на ткацком навое с целью получения из него целого числа кусков ткани:
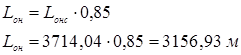
Тогда количество кусков ткани из такого навоя:
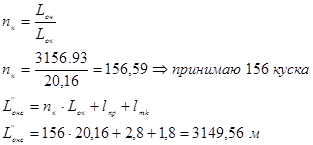
3.3.7.
Сопряженная длина на сновальном валу:
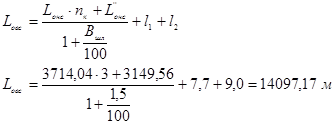
где l1
– длина мягких и клееных концов, идущих в отходы при шлихтовании (1, с.360); l2
– средняя длина нитей основы, остающихся на сновальных валах после шлихтования (1, с.360).
3.3.8.
Масса пряжи на сновальном валу:
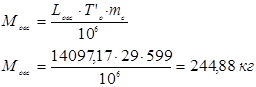
3.3.9.
Коэффициент использования сновального вала:
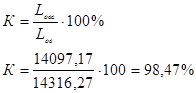
Результаты расчета сновального вала
Таблица № 10
Артикул ткани |
То
, текс |
V, см3
|
γ, г/см3
|
E, шт |
nв,
шт |
nн,
шт |
Lов
, м |
Lовс
, м |
Мов
, кг |
Мовс
, кг |
062259Н |
29 |
497376 |
0,5 |
616 |
6 |
3,85 |
14316,27 |
14097,17 |
248,69 |
244,88 |
3.4.
Сопряженная длина и масса основы на мотальной бобине.
Исходные данные для расчета бобины
Таблица № 11
Артикул ткани |
То
, текс |
D1
, см |
d1
, см |
D2
, см |
d2
, см |
h,
см
|
γ,
см3
|
Lовс
, м |
062259Н |
29 |
23 |
6,4 |
20 |
3,4 |
15,0 |
0,38-0,5 (1, с.47) |
14097,17 |
3.4.2.
Объем пряжи на конической бобине:

3.4.3.
Масса пряжи на бобине: γ принимаю равной 0,5
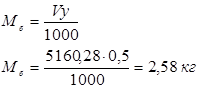
3.4.4.
Длина нити на бобине:
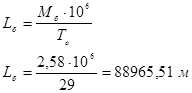
3.4.5.
Количество сновальных валов из ставки бобин:

3.4.6.Сопряженная длина нити (при расчете мотальной паковки необходимо учитывать возможное отклонение плотности намотки на 3-5 %, поэтому длина нити на бобине должна быть больше сопряженной длины на сновальных валах, получаемых из ставки бобин на 3-5 %):

3.4.7.
Сопряженная масса пряжи на бобине:
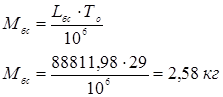
Необходимо, чтобы сопряженная длина нити на бобине была меньше допустимой, но эта разница должна входить в интервал от 0,05 до 0,2%
, т.е. емкость бобины используется достаточно хорошо.
3.4.8.
Коэффициент использования бобины:
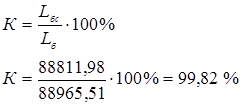
Результаты расчета бобины
Таблица № 11
Артикул ткани
|
То
, текс
|
V
, см3
|
γ,
г/см3
|
Lб
,
м
|
nв,
шт
|
Lбс
,
м
|
Мбс
, кг
|
062259Н |
29 |
5160,28 |
0,50 |
88965,51 |
6 |
88811,98 |
2,58 |
Результаты расчетов третьего раздела приведены в таблице:
Сопряженность ткацких паковок
Таблица № 12
Наименование ткацких паковок
|
Максимальная длина каждой нити основы на паковке, м
|
Сопряженная длина каждой нити основы на паковке, м
|
Максимальная масса всех нитей основы на паковке, кг
|
Масса всех нитей основы на сопряженной паковке, кг
|
Коэффициент полезного использования ткацкой паковки
|
Рулон ткани |
73,33 |
72 |
16 |
15,71 |
- |
Ткацкий навой |
3731,28 |
3714,04 |
391,29 |
389,48 |
99,54 |
Сновальный валик |
14316,27 |
14097,17 |
248,69 |
244,88 |
98,47 |
Бобина |
88965,51 |
88811,98 |
2,58 |
2,58 |
99,82 |
Раздел 4
.
Сопряженность технологического оборудования.
4.1.1. Перематывание
а) основа
где а – длина нити, идущей в отходы при связывании концов, м; а=1,2 м (1, с. 360);
в – длина нити, остающейся на входящей паковке при ее смене, м; в=3 м (1, с 360);
с – длина нити, необходимая для оправки паковки при ее смене, м; с=0,8 м (1, с. 360);
Ln
– длина нити на перематываемой (входящей) паковке, м;
где М – масса пряжи на входящей паковке; М – 1,2 кг
l – длина нити, на которую приходится один обрыв, м
где L=10000 м одиночной нити, чо
- число обрывов на 10000 м одиночной нити
б) уток:
М=160 г; а=1,2 м; в=3 м; с=0,8 м
4.1.2. Снование
где а1
- длина нити, идущей в отходы при смене входящей паковки, м; а1
=0,9 м (1, с.360);
в1
- остаток нити на бобине, идущей в отходы при перезаправке партии бобин; в1
=18 м (1, с. 360);
а2
- длина нити, идущей в отходы при ликвидации обрыва, м; а2
=2,2 м (1, с. 360);
О’с
- число обрывов за время сматывания бобины, приходящихся на длину нити входящей паковки;
где - длина нити, на которую приходится один обрыв, м;
где =10000 м одиночной нити; чо
- число обрывов на 100000 м одиночной нити; чо
=1,2 (6, с. 79);
4.1.3.Шлихтование
l1
- длина клееных концов, идущих в отходы, м (1, с.125); l1
=18 м;
l2
- длина основы между машиной и сновальными валами, отрезаемой при заправке новой партии и идущей в отходы, м;
при 6 сновальных валах l2
=7,7м, (1, с.360);
l3
- средняя длина пряжи, остающаяся на сновальном валике после шлихтования, м;
при 6 сновальных валах l3
=9,0 м, (1, с.360);
l4
- длина нити, идущей в отходы, при ликвидации хомутов, м; l4
=5-6 м, l4
=6м
nв
- количество сновальных валов в ставке;
Lовс
- сопряженная длина основы на сновальном валике, м;
4.1.4. Пробирание (привязывание)
ln
- длина концов, срезанных при пробирании, м;
ln
=0,3-0,6 м;
ln
=0,5 м;
Lонс
- сопряженная длина основы на ткацком навое, м;
4.1.5. Ткачество
а) основа
где l’–длина нити, идущей в отходы при ликвидации обрывов, м; l’ =0,5 м;
l’1
-длина концов нитей основы, остающейся на навое, м; l’1
=1,2 м;
l’2
- длина концов нитей основы на участке скало-ремизы, м; l’2
=0,8-1,5 м;
l’2
= 1,5 м;
l’3
- длина концов нитей основы, идущих в отходы при заправке станка, м; l’3
=2,5 м;
n - число обрывов основы на 1 м одиночной нити; n =1,5 обр/1000 м = 0,0015 обр/м (1, с.268);
б) уток
где l1
-длина уточной нити, идущей в отходы при заправке станка, м; l1
=1-3 м;
l1
=2 м;
l2
- длина уточной нити, идущей на связывание концов при обрыве, м; l2
=0,5-1,5 м;
l2
= 1,5 м;
l3
- длина уточной нити, идущей в отходы при разработке пороков ткани на станке, м; l3
=5-10 м;
l3
=9 м;
l4
- длина уточной нити, остающейся на бобине после ее доработки, м; l4
=2-10 м;
l4
=7 м;
Lб
- длина пряжи на уточной бобине, м
где γ=0,45-0,5 г/см3
; γ=0,5г/см3
(1, с.46);
чоу
- число обрывов уточной нити, приходящихся на длину нити на бобине;
где чоу
- число обрывов утка при выработке 1 м ткани; rоу
=0,40 (1, с.267);
Шз
- ширина заправки по берду, м;
lк
- длина выступающих концов уточной нити, м; lк
= 3,09 м;
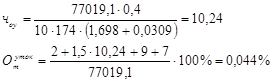
Расчет выхода полуфабрикатов
Таблица № 13
Переходы
|
Отходы, %
|
Уточномотальный
|
0,1
|
Основомотальный
|
0,012
|
Сновальный
|
0,02
4
|
Шлихтовальный
|
0,2
8
|
Проборный
|
0,0
13
|
Ткачество уток
|
0,04
3
|
Ткачество основа
|
0,
22
|
Итого:
основа
уток
|
0,
549
0,14
3
|
4.2. Объем производства суровой ткани в час и выход полуфабрикатов.
4.2.1. Объем производства ткани в расчете на 100 ткацких станков:
По
– норма производительности ткацкого станка в час,
Кро
– коэффициент работающего оборудования
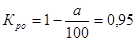
а – процент простоев,

4.2.2. Потребность в полуфабрикатах в час:
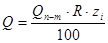
где R –расход пряжи с учетом отходов на 100 м суровой ткани, кг/100м;
zi
– процент отходов на i-м переходе;
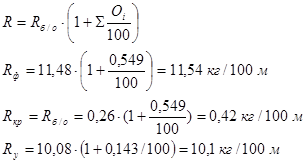
Основа:
а) Перематывание
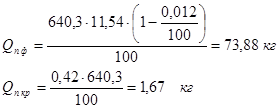
б) Снование
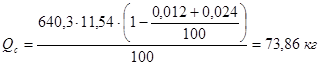
в) Шлихтование

г) Пробирание (привязывание)

Вычислим, сколько основ (кг) пойдет на проборную машину, а сколько на узловязальную. В ткацком производстве пробирают 10-15% основ, остальные привязывают. Принимаю 10%.

д) Ткачество

Уток
а) Перематывание
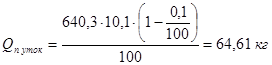
б) Ткачество

4.3. Сопряженное количество единиц заправленного оборудования.
4.3.1. Количество машин в заправке:
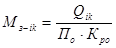
а) Перематывание:
Основа:
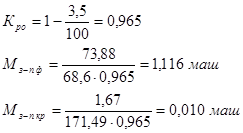
Уток:

б) Снование:
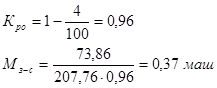
в) Шлихтование:
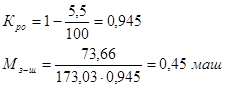
г) Пробирание:
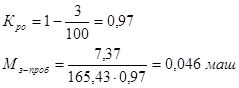
д) Привязывание:
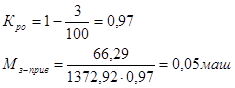
Сопряженность технологического оборудования
Таблица № 14
Марка оборудования
|
Часовая выработка полуфабрикатов, кг
|
Кро
|
Сопряженное
количество заправленного оборудования по расчету, машин
|
М-2,
Т= СК 29 х/б
|
73,88 |
0,965 |
1,116 |
М-2,
Т= С 29х2 х/б
|
1,67 |
0,965 |
0,01 |
МЛМ-2 |
64,61 |
0,965 |
0,840 |
СП-180 |
73,86 |
0,96 |
0,370 |
ШБ11/180 |
73,66 |
0,945 |
0,450 |
ПСМ-230 |
7,37 |
0,97 |
0,046 |
УП2-5 |
73,65 |
0,97 |
0,050 |
СТБ2-175 |
Основа
73,48 уток
64,58
|
100
|
Размеры машин.
Таблица № 15
Марка оборудования
|
Габаритные размеры машин, м2
|
Примечание
|
М-2 |
S=11,7*1,3=15,21 |
(1, с.49) |
МЛМ-2 |
S=11,647*1,23=14,33 |
(1, с.48) |
СП-180 |
S=1,62*2,84=4,6 |
(1, с.64) |
ШБ11/180 |
S=21,905*3,36=73,6 |
(1, с.135) |
ПСМ-230 |
S=1,6*3,02=4,83 |
(1, с.180) |
УП2-5 |
S=2,5*0,5=1,25 |
(1, с.180) |
СТБ2-175 |
S=1,795*3,6=6,46 |
(1, с.229) |
Общая производственная площадь, занимаемая 100 ткацкими станками с соответствующим количеством приготовительного оборудования:

Найдем производственную площадь, занимаемую одной машиной с учетом необходимых проходов между ней и другими проходами ткацкого производства. Для этого делим полученную «габаритную» площадь на коэффициент использования производственной площади. Примем его 0,45 для ткацких станков и 0,35 для приготовительных машин (3, с.12)
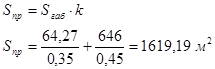
Количество ткацких станков, которое может быть размещено на заданной производственной площади (10200 м2
):
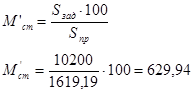
Принимаю 628 станка. Округляем до меньшего числа, кратного 4.
Количество приготовительных машин в каждом переходе, которое может быть размещено одновременно с ткацким оборудованием:
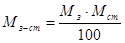
а) Перематывание
Основа:
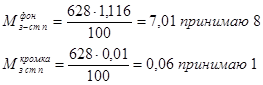
Уток:

б) Снование

в) Шлихтование

г) Пробирание

д) Привязывание

Мощность производства по количеству оборудования
Таблица 16
Марка оборудования
|
Сопряженное количество единиц заправленного оборудования при 100 ткацких станках
|
Габаритные размеры одной машины
|
Габаритная площадь одной машины, м2
|
Габаритная площадь всех заправленных машин и станков
|
Расчетное и принятое к установке количество единиц технологического оборудования
|
М-2 |
1,126 |
11,7*1,3
11,647*1,23
1,62*2,84
21,905*3,36
1,6*3,02
2,5*0,5
1,795*3,6
|
15,21 |
710,27
|
8+1 |
МЛМ-2 |
0,840 |
14,33 |
6 |
СП-180 |
0,370 |
4,6 |
3 |
ШБ11/180 |
0,450 |
73,6 |
3 |
ПСМ-230 |
0,046 |
4,83 |
2 |
УП2-5 |
0,050 |
1,25 |
2 |
СТБ2-175 |
100 |
6,46 |
628 |
Трудоемкость продукции по охвату затрат труда основных рабочих:
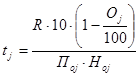
где Но
j
- норма обслуживания для одного работника на j-м переходе ткацкого производства;
а) Перематывание
Основа:
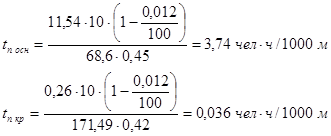
Уток:
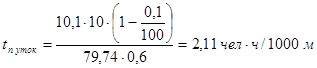
б) Снование

в) Шлихтование

г) Пробирание

д) Привязывание

е) Ткачество

Общая трудоемкость:


а) Перематывание
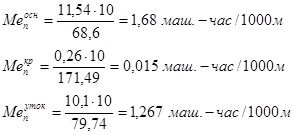
б) Снование

в) Шлихтование

г) Пробирание

д) Привязывание

е) Ткачество

6.3. Длительность технологического цикла
Сопряженность оборудования и длительность технологического цикла
Таблица № 17
Марка оборудования |
Сопряженное количество оборудования |
Длительность технологического цикла, ч |
При заправке 100 ткацких станков |
При заправке 1 шлихтовальной машины |
М-2, Т=СК 29 х/б |
1,116 |
2,480 |
0,70 |
М-2, Т=С 29х2 х/б |
0,010 |
0,022 |
МЛМ-2 |
0,840 |
1,867 |
СП-180 |
0,370 |
0,822 |
ШБ11/180 |
0,450 |
1 |
ПСМ-230 |
0,046 |
0,102 |
УП2-5 |
0,050 |
0,111 |
СТБ2-220 |
100 |
222,222 |
Длительность технологического цикла:
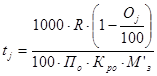
где М’з
- сопряженное количество оборудования при заправке одной шлихтовальной машины.
а) Перематывание
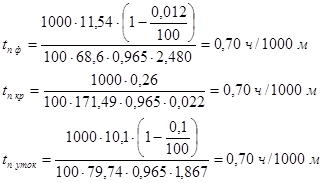
б) Снование
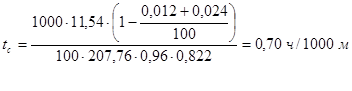
в) Шлихтование

г) Пробирание

д) Привязывание

е) Ткачество

Технико-экономические нормативы организации производства
Таблица № 18
Технико-экономический норматив
|
Значение
|
Трудоемкость, ч/1000 м |
Перематывание
Основа
Кромка
Уток
Снование
Шлихтование
Пробирание
Привязывание
Ткачество
|
3,74
0,036
2,11
0,56
1,33
0,140
0,150
18,55
|
Машиноемкость, ч/1000 м |
Перематывание
Основа
Кромка
Уток
Снование
Шлихтование
Пробирание
Привязывание
Ткачество
|
1,680
0,015
1,267
0,555
0,667
0,070
0,076
148,368
|
Длительность технологического цикла |
0,70 ч/1000 м |
В курсовом проекте выполнены расчеты по проектированию ткацкой фабрики, выпускающей один артикул ткани.
В ходе работы я выбрал технологическую цепочку и рассчитал параметры технологического процесса, а также установил сопряженность длины и массы полуфабрикатов на ткацких паковках.
В пятом разделе рассчитал мощность производства по количеству оборудования.
В последнем разделе рассчитаны некоторые технико-экономические показатели, такие как трудоемкость и машиноемкость изготовления суровой ткани, а также длительность технологического цикла
1. Льноткачество: Справочник./ Под ред. Р.Д. Дружининой.- М.: Легпромбытиздат, 1985
2. Отраслевые нормы расхода и использования сырья в льняной и пенько-джутовой промышленности./ ЦНИИЛВ.-И.: ЦНИИТЭИЛегпром, 1986
3. Белихов Б.А. Организация производства. Курсовой проект: методические указания. - Кострома: КТИ, 1992
4. Методика расчета норм пряжи на выпуск 100 м суровых тканей в ткацком производстве льняной и пенько-джутовой промышленности.- М.:ЦНИИТЭИЛегпром, 1979
5. Нормы технологического проектирования и технико-экономические показатели предприятий текстильной промышленности: льняная промышленность, ткацкое производство./ГПИ – 6 Минлегпрома СССР. –М.:МЛП СССР,1977
6. Брут-Бруляко А.Б., Живетин В.В. Современная техника и технология льноткацкого производства. - М.: Легкая и пищевая промышленность, 1984
7. Алексеева Н.С. и др. Основы проектирования предприятий отрасли: Учебное пособие. – Ярославль: КТИ, 1990
8. Поляк Т.Б., Стерлин Е.А., Летуновская А.А. Организация, планирование и управление ткацким производством. –М.: Легпромбытиздат, 1986
9. Проектирование ткацких фабрик под ред П.В. Власова.- М.: Легкая и пищевая промышленность, 1983
10. Белихов Б.А. Организация производства как система научных знаний и область практической деятельности: Конспект лекции по курсу «Организация производства на предприятиях текстильной промышленности».- Кострома: КГТУ, 2000
|