Содержание
|
Введение……………………………………………………………………………
|
5
|
1 Выбор электродвигателя. Кинематический и силовой
|
расчет привода…………………………………………………………………
|
6
|
2 Расчет зубчатой передачи редуктора…………………………………
|
9
|
3 Проектный расчет валов редуктора…………………………………
|
15
|
4 Конструирование зубчатых колес……………………………………
|
16
|
5 Эскизная компоновка редуктора………………………………………
|
17
|
6 Проверочный расчет подшипников качения…………………….
|
20
|
7 проверочный расчет шпоночных соединений………………….
|
24
|
8 Проверочный расчет валов редуктора………………………………
|
25
|
9 Назначение посадок основных деталей редуктора……………
|
28
|
10 Смазка и сборка редуктора………………………………………………
|
29
|
Список литературы……………………………………………………………
|
30
|
Введение
Заданием на курсовой проект предусмотрена разработка конструкции одноступенчатого цилиндрического прямозубого редуктора привода для цепного конвейера. Привод (рисунок 1) состоит из электродвигателя 1
, одноступенчатого цилиндрического редуктора 3
, цепной передачи 4
и приводного вала 5
. Для соединения вала электродвигателя с быстроходным валом редуктора используется упругая муфта 2
.
Исходными данными для проектирования являются мощность на ведомом валу привода PB
= кВт и число оборотов ведомого вала привода nB
= об/мин.

Рисунок 1 – Кинематическая схема привода конвейера
Редуктор предназначен для передачи мощности от вала двигателя к приводному валу конвейера, понижения угловых скоростей и, соответственно, повышения вращающегося момента ведомого вала по сравнению с ведущим валом. Редуктор состоит из корпуса в котором помещаются элементы передачи – зубчатые колеса, валы, подшипники и т.д. В корпусе редуктора размещают так же устройство для смазывания зацепления и подшипников.
1 Выбор электродвигателя, кинематический и силовой расчеты привода
1.1 Определение расчетной мощности электродвигателя
Определяем общий КПД привода
, (1)
где ηм
– КПД муфты, принимаем ηм
= 0,99;
ηзп
– КПД зубчатой передачи редуктора, принимаем ηзп
= 0,97;
ηоп
– КПД открытой цепной передачи, принимаем ηоп
= 0,93;
ηп
– КПД пары подшипников, принимаем ηп
= 0,99;
Определяем расчетную мощность электродвигателя, кВт
, (2)
1.2 Выбор электродвигателя
Подбираем электродвигатели серии 4А с номинальной мощностью P
ном
= 2,2 кВт. Параметры выбранных электродвигателей сводим в таблицу 1
Таблица 1 – Электродвигатели серии 4А с номинальной мощностью P
ном
= 2,2 кВт
Вариант
|
Тип
двигателя
|
Номинальная
мощность, кВт
|
Частота вращения, об/мин
|
синхронная
|
номинальная
|
1
|
4A112MA8
|
2,2
|
750
|
710
|
2
|
4A100L6
|
2,2
|
1000
|
960
|
3
|
4A90L4
|
2,2
|
1500
|
1425
|
4
|
4A80B2
|
2,2
|
3000
|
2865
|
Для окончательного выбора электродвигателя, необходимо определить передаточное число привода и его ступеней для всех типов двигателей.
Определяем передаточное число привода для первого варианта электродвигателя
, (3)
.
Передаточное число редуктора принимаем u
ред
= 4, тогда передаточное число открытой передачи составит:
, (4)
.
Аналогично определяем передаточные числа для остальных вариантов электродвигателя, оставляя при этом передаточное число редуктора постоянным. Результаты расчетов сводим в таблицу 2
Таблица 2 – Определение передаточного числа привода и его ступеней
Передаточное число
|
Варианты
|
1
|
2
|
3
|
4
|
Общее для привода u
общ
|
8,875
|
12
|
17,813
|
35,813
|
Редуктора u
ред
|
4
|
4
|
4
|
4
|
Открытой передачи u
оп
|
2,219
|
3
|
4,453
|
8,953
|
Окончательного выбираем второй вариант электродвигателя. Характеристики принятого электродвигателя и все параметры, необходимые для дальнейших расчетов, сводим в таблицу 3
Таблица 3 – Результаты энергетического расчета
Параметр
|
Обозн.
|
Значение
|
Тип электродвигателя
|
–
|
4A100L6
|
Присоединительные размеры, мм
|
d
1
l
1
|
28
60
|
Номинальная мощность электродвигателя, кВт
|
Рном
|
2,2
|
Расчетная мощность электродвигателя, кВт
|
Рэд
|
1,845
|
Номинальная частота вращения электродвигателя, об/мин
|
n
эд
|
960
|
Передаточное число привода
|
u
общ
|
12
|
Передаточное число редуктора
|
u
ред
|
4
|
Передаточное число открытой передачи
|
u
оп
|
3
|
1.3 Определение кинематических и силовых параметров привода
Расчет элементов привода выполняем по расчетной мощности Рэд
электродвигателя. Обозначим валы привода (рисунок 2): 1
– быстроходный вал редуктора; 2
– тихоходный вал редуктора; 3
– приводной вал конвейера. Для каждого вала определяем частоту вращения n
, мощность Р
и вращающий момент Т.
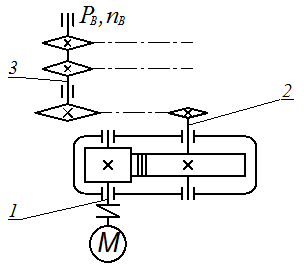
Рисунок 2 – Обозначение валов привода
Определяем частоту вращения каждого вала:
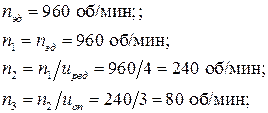
Определяем мощность на каждом валу:
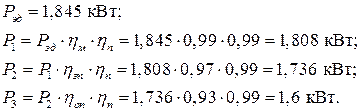
Определяем крутящий момент на каждом валу:
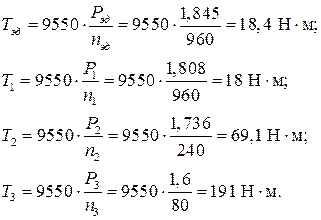
Результаты расчетов сводим в таблицу 4
Таблица 4 – Кинематические и силовые параметры привода
№ вала
|
n
, об/мин
|
Р
, кВт
|
Т
, Н·м
|
Эд.
|
960
|
1,845
|
18,4
|
1
|
960
|
1,808
|
18
|
2
|
240
|
1,736
|
69,1
|
3
|
80
|
1,6
|
191
|
2 Расчет зубчатой передачи редуктора
2.1 Выбор материалов для изготовления шестерни и колеса
Принимаем для шестерни сталь 45, а для колеса сталь 45Л. Механические характеристики материалов представлены в таблице 5
Таблица 5 – Механические характеристики материалов зубчатых колес
Наименование
|
Марка
стали
|
Вид ТО
|
Диаметр
заготовки
|
Твердость
НВ
|
Расчетная
твердость НВ
|
шестерня
|
45
|
У
|
60…90
|
207…236
|
210
|
колесо
|
45Л
|
Н
|
любой
|
155…195
|
180
|
Для обеспечения одинаковой долговечности зубьев шестерни и колеса прямозубых передач и ускорения их приработки должно выполняться условие:
, (5)
Поэтому принимаем HB
1
= 210; H
B2
= 180.
2.2 Определение допускаемых контактных напряжений
Определяем предел контактной выносливости при базовом числе циклов перемены напряжений для шестерни и колеса
; (6)


Определяем допускаемые контактные напряжения для шестерни и колеса
, (7)
где K
Н
L
– коэффициент долговечности, учитывающий влияние срока службы и режима работы; при длительном сроке службы и постоянном режиме работы K
Н
L
= 1;
S
Н
– коэффициент безопасности; для нормализованных или улучшенных колес S
Н
= 1,1;


Для прямозубых передач из нормализованных или улучшенных сталей за расчетное допускаемое контактное напряжение принимается меньшее из напряжений, определенных по материалу шестерни [σ
H
1
], и колеса [σ
H
2
].
Принимаем 
2.3 Определение допускаемых напряжений изгиба
Определяем предел выносливости при изгибе, соответствующий базовому числу циклов перемены напряжений для шестерни и колеса
; (8)


Определяем допускаемые напряжения изгиба для шестерни и колеса
(9)
где KFL
– коэффициент долговечности, при длительном сроке службы и постоянном режиме работы KFL
= 1;
SF
– коэффициент безопасности; определяется как произведение двух коэффициентов:
(10)
где – коэффициент, учитывающий нестабильность свойств материала зубчатых колес при вероятности неразрушения 99%; для нормализованных и улучшенных колес = 1,75;
– коэффициент, учитывающий способ получения заготовки зубчатого колеса: для поковок и штамповок ; для литых заготовок ;
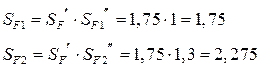


2.4 Проектировочный расчет на контактную выносливость
Определяем межосевое расстояние передачи, мм
, (11)
где Ka
– вспомогательный коэффициент, для прямозубых передач Ka
= 49,5 МПа1/3
;
ψ
ba
– коэффициент ширины венца колеса, принимаем ψ
ba
= 0,25;
u
ред
– передаточное число зубчатой передачи редуктора, u
ред
= 4;
Т
2
– вращающий момент на валу колеса, Т
2
= 69,1 Н∙м;
[σ
H
] – допускаемые контактные напряжения, [σ
H
] = 390,9 МПа;
K
Нβ
– коэффициент, учитывающий неравномерность распределения нагрузки по длине зуба, для прирабатывающихся колес K
Нβ
= 1;
принимаем aw
= 120 мм.
По эмпирическому соотношению определяем модуль зацепления, мм
(12)

принимаем m
= 2 мм.
Определяем числа зубьев шестерни и колеса
(13)
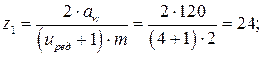

принимаем z
1
= 24; z
2
= 96.
Определяем фактическое передаточное число зубчатой передачи
; (14)
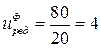
Определяем расхождение с ранее принятым передаточным числом

Определяем делительные диаметры колес, мм
(15)


Уточняем межосевое расстояние
(16)
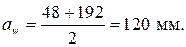
Определяем рабочую ширину венца колеса
; (17)

принимаем b
2
= 30 мм.
Определяем ширину венца шестерни
; (18)
;
принимаем b
1
= 34 мм.
Определяем диаметры вершин зубьев для шестерни и колеса, мм
(19)


Определяем диаметры впадин зубьев для шестерни и колеса, мм
(20)


Определяем окружную скорость колес, м/с
. (21)
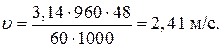
В зависимости от полученного значения окружной скорости назначаем 8-ю степень точности передачи.
2.5 Проверочный расчет на контактную выносливость
Для обеспечения контактной выносливости должно выполняться условие
, (22)
где KHα
– коэффициент, учитывающий неравномерность распределения нагрузки между зубьями, для прямозубых передач KHα
= 1;
K
Нβ
– коэффициент, учитывающий неравномерность распределения нагрузки по длине зуба, для прирабатывающихся колес K
Нβ
= 1;
KHυ
– коэффициент, учитывающий динамическую нагрузку, возникающую в зацеплении, принимаем KHυ
= 1,113;
ZH
– коэффициент, учитывающий форму сопряженных поверхностей зубьев, для прямозубых передач ZH
= 1,76;
Z
М
– коэффициент, учитывающий механические свойства материалов зубчатых колес, для стальных колес Z
М
= 275 МПа1/2
;
Zε
– коэффициент, учитывающий суммарную длину контактных линий, для прямозубых передач определяется по формуле:
, (23)
где εα
– коэффициент торцевого перекрытия;
; (24)
;
;
.
Недогрузка передачи составляет:
.
2.6 Проверочный расчет на выносливость при изгибе
Определяем для шестерни и колеса коэффициент формы зуба
при z
1
= 24; YF
1
= 3,938;
при z
2
= 96; YF
2
= 3,602.
Определяем отношения:
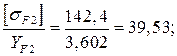
Дальнейший расчет выполняем по материалу колеса
Выносливость зубьев по напряжениям изгиба обеспечена при выполнении условия:
, (25)
где Yβ
– коэффициент, учитывающий наклон зуба, для прямозубых колес Yβ
= 1;
KF
α
– коэффициент, учитывающий неравномерность распределения нагрузки между зубьями, для прямозубых передач KF
α
= 1;
KF
β
– коэффициент, учитывающий неравномерность распределения нагрузки по длине зуба, для прирабатывающихся передач KF
β
= 1;
KF
υ
– коэффициент, учитывающий динамическую нагрузку, возникающую в зацеплении, принимаем KF
υ
= 1,274;

Все параметры зацепления передачи сводим в таблицу 6
Таблица 6 – Параметры зацепления зубчатой передачи
Наименование параметра
|
Обозн.
|
Единица
измерения
|
Значения
|
шестерня
|
колесо
|
Межосевое расстояние
|
aw
|
мм
|
120
|
Модуль зацепления
|
m
|
мм
|
2
|
Степень точности по ГОСТ 1643-81
|
–
|
–
|
8
|
Передаточное число
|

|
–
|
4
|
Угол наклона зубьев
|
β
|
град
|
0
|
Число зубьев
|
z
|
–
|
24
|
96
|
Делительный диаметр
|
d
|
мм
|
48
|
192
|
Диаметр окружности вершин
|
da
|
мм
|
52
|
196
|
Диаметр окружности впадин
|
df
|
мм
|
43
|
187
|
Ширина венца
|
b
|
мм
|
34
|
30
|
3 Проектный расчет валов
Определение размеров ступеней валов приведено в таблице 7
Таблица 7 – Определение размеров ступеней валов
Ступень
вала
|
Вал-шестерня
|
Вал колеса
|
1-я
под полумуфту и звездочку цепной передачи
|
Из расчета на прочность
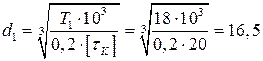
Из условия установки полумуфты d
1
= 28 мм
принимаем d
1
= 28 мм
|
Из расчета на прочность
принимаем d
1
= 28 мм
|
По ГОСТ 12080–66
принимаем l
1
= 42 мм
|
По ГОСТ 12080–66
принимаем l
1
= 42 мм
|
2-я
под уплотнение и подшипник
|
d
2
= d
1
+ 2t
= 28 + 2·3,5 = 35 мм
принимаем d
2
= 35 мм
|
d
2
= d
1
+ 2t
= 28 + 2·3,5 = 35 мм
принимаем d
2
= 35 мм
|
3-я
для упора подшипника и под колесо
|
d
3
= d
2
+ 3∙r
= 35 + 3·2,5 = 42,5 мм
принимаем d
3
= 42 мм
|
принимаем d
3
= 38 мм
|
4-я
для упора колеса
|
–
|
d
4
= d
3
+ 3∙f
= 38 + 3·1,2 = 41,6 мм
принимаем d
4
= 42 мм
|
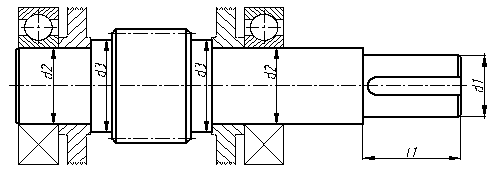
Рисунок 3 – Конструкция быстроходного вала
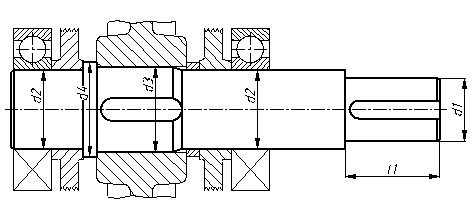
Рисунок 4 – Конструкция тихоходного вала
4 Конструирование зубчатых колес
Рисунок 5 – Конструкция зубчатого колеса
Определяем размеры конструктивных элементов зубчатых колес (рисунок 5)
– диаметр ступицы: 
принимаем d
ст
= 65 мм;
– длина ступицы: 
принимаем l
ст
= 40 мм;
– толщина обода: 
принимаем δ0
= 8 мм;
– толщина диска: 
принимаем с
= 10 мм;
– диаметр окружности отверстий: 
принимаем D
отв
= 120 мм;
– диаметр отверстий: 
принимаем d
отв
= 25 мм;
– размер фаски, мм: n
≈ m
= 2 мм;
5 эскизная компоновка редуктора
5.1 Определение размеров конструктивных элементов корпуса редуктора
Определяем толщину стенки редуктора (δ ≥ 8 мм):
δ
= (0,025∙a
w
+ 1) = (0,025∙120 + 1) = 4 мм.
принимаем δ
= 8 мм.
Толщину стенки крышки принимаем δ
1
= δ
= 8 мм.
Определяем диаметры болтов, соединяющих:
– редуктор с плитой: d
1
= 2 ∙ δ
= 2 ∙
8 = 16 мм,
принимаем болты М16.
– корпус с крышкой у бобышек подшипников: d
2
= 1,5 ∙
δ
= 1,5 ∙ 8 = 12 мм,
принимаем болты М12.
– корпус с крышкой по периметру соединения: d
3
= 1,0∙
δ
= 1,0∙
8 = 8 мм,
принимаем болты М10.
Определяем ширину фланцев редуктора:
Si
= δ
+2 + к
i
,
– фундаментного S
1
= 8 + 2 + 40 = 50 мм;
– корпуса и крышки (у подшипников) S
2
= 8 + 2 + 32 = 42 мм;
– корпуса и крышки (по периметру) S
3
= 8 + 2 + 28 = 38 мм.
Определяем толщину фланцев редуктора:
– фундаментного δ
фл1
= 2,3∙δ = 2,3∙8 = 18,4 мм;
принимаем δ
фл1
= 20 мм;
– корпуса (соединение с крышкой) δ
фл2
= 1,5∙δ = 1,5∙8 = 12 мм;
принимаем δ
фл2
= 12 мм;
– крышки (соединение с корпусом) δ
фл3
= 1,35∙δ = 1,35∙8 = 10,8 мм;
принимаем δ
фл3
= 10 мм;
Для установки крышки относительно корпуса применяем два штифта 8h
7х30 по ГОСТ 9464–79.
5.2 Определение расстояний между элементами редуктора
Толщина стенки корпуса редуктора δ
= 8 мм;
Расстояние от внутренней поверхности стенки редуктора до боковой поверхности вращающейся части:
С
= (1,0…1,2)∙δ
= (1,0…1,2)∙8 = 8…9,6 мм;
принимаем С
= 10 мм.
Радиальной зазор от поверхности вершин зубьев до внутренней поверхности стенки редуктора:
С5
= 1,2∙δ
= 1,2∙8 = 9,6 мм.
принимаем С5
= 10 мм.
Радиальной зазор от поверхности вершин зубьев до внутренней нижней поверхности стенки корпуса:
С6
= (5…10)∙m
= (5…10)∙2 = 10…20 мм.
5.3 Предварительный выбор подшипников качения
Для опор валов принимаем радиальные шариковые подшипники легкой серии. Параметры выбранных подшипников сводим в таблицу 8
Таблица 8 – Параметры подшипников качения
№ вала
(рисунок 2)
|
Обозн.
|
Размеры, мм
|
Грузоподъемность
С
r
, кН
|
d
|
D
|
В
|
r
|
1
|
207
|
35
|
72
|
17
|
2
|
25,5
|
2
|
207
|
35
|
72
|
17
|
2
|
25,5
|
5.4 Определение размеров конструктивных элементов крышек подшипников
В зависимости от размера D
отверстия в корпусе под подшипник, определяется толщина стенки δ
, диаметр d
, и число z
винтов крепления крышки. Размеры других конструктивных элементов определяются по соотношениям:
Толщина фланца крышки δ1
= 1,2∙δ
;
Толщина цилиндрической части δ
2
= (0,9…1,0)∙δ
;
Диаметр установки винтов D
1
= D
+ 2,5∙d
;
Диаметр фланца D
2
= D
1
+ 2∙d
;
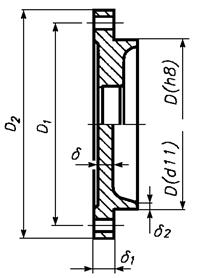
Рисунок 6 – Конструкция крышек подшипников
Размеры конструктивных элементов подшипниковых крышек быстроходного и тихоходного валов сводим в таблицу 9
Таблица 9 – Размеры основных конструктивных элементов крышек
№ вала
рисунок 2
|
D
, мм
|
d
, мм
|
z
|
δ
, мм
|
δ
1
, мм
|
δ
2
, мм
|
D
1
, мм
|
D
2
, мм
|
1
|
72
|
М8
|
4
|
6
|
8
|
6
|
92
|
110
|
2
|
72
|
М8
|
4
|
6
|
8
|
6
|
92
|
110
|
5.5 Выбор способа смазывания передачи и подшипников
Так как окружная скорость зубчатых колес υ
1
< 10…15 м/с (υ
1
= 2,41 м/с), то смазывание зубчатой передачи осуществляется погружением зубчатого колеса в масляную ванну. Глубина погружения при этом не должна превышать 0,25 радиуса колеса. Объем масляной ванны должен составлять 0,3…0,8 дм3
/кВт, что при известных размерах поперечного сечения редуктора определяет положение его дна.
Так как окружная скорость зубчатых колес υ
1
< 3 м/с, то смазывание подшипников осуществляется пластичным смазочным материалом. С целью предотвращения вымывания смазки из подшипникового узла, устанавливаем мазеудерживающие кольца.
5.6 Выбор уплотнений валов
В качестве уплотнений валов выбираем резиновые армированные манжеты по ГОСТ 8752-79, конструктивные размеры которых сводим в таблицу 10
Таблица 10 – Размеры основных конструктивных элементов манжет
Вал
|
Внутренний
диаметр d
, мм
|
Наружный
диаметр D
, мм
|
Толщина
h
, мм
|
Быстроходный
|
35
|
58
|
10
|
Тихоходный
|
35
|
58
|
10
|
6 Проверочный расчет подшипников качения
6.1 Определение сил, нагружающих валы редуктора
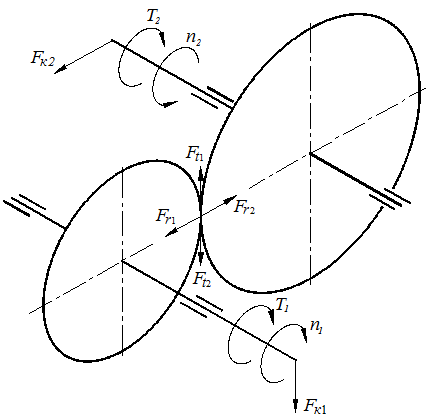
Рисунок 7 – Схема нагружения валов редуктора
Определяем силы в зубчатом зацеплении
Окружная сила:
(26)
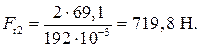

Радиальная сила:
(27)
где α
– угол зацепления передачи; для передач без смещения α
= 20˚;
;

Определяем консольные силы
(28)
на быстроходном валу от муфты

на тихоходном валу от цепной передачи

6.2 Проверка подшипников быстроходного вала
6.2.1 Определение реакций опор
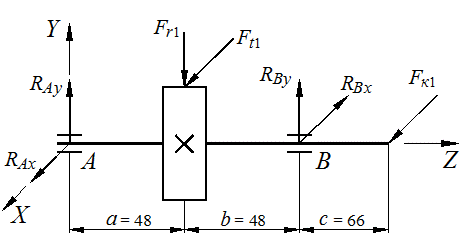
Рисунок 8 – Схема нагружения быстроходного вала
Определяем опорные реакции в вертикальной плоскости




Проверка: Σ
Yi
= R
А
y
– Fr
1
+ R
В
y
= 338,2 – 676,4 + 338,2 = 0.
Определяем опорные реакции в горизонтальной плоскости




Проверка: Σ
Х
i
= R
А
x
+ Ft
1
– R
В
x
+ F
к
1
= 4,7 + 719,8 – 1254,8 + 530,3 = 0.
Определяем суммарные радиальные реакции


6.2.2 Определение динамической грузоподъемности подшипников
Исходные данные для расчета:
Частота вращения вала – n
= 960 об/мин;
Требуемая долговечность подшипника – Lh
= 10000 ч;
Подшипник 207
Базовая динамическая грузоподъемность Cr
= 25500 Н;
Коэффициент вращения V
= 1 (вращается внутреннее кольцо).
Расчет ведем для опоры В
, как наиболее нагруженной
Радиальная реакция Fr
= RB
= 1299,6 Н;
Определяем эквивалентную динамическую силу
(29)
где КБ
– коэффициент безопасности, принимаем КБ
= 1,3;
КТ
– температурный коэффициент, принимаем КТ
= 1,0;
Х
– коэффициент радиальной нагрузки, Х
= 1;

Определяем требуемую динамическую грузоподъемность
; (30)
где k
– показатель степени; для шариковых подшипн6иков k
= 3;

Т.к. С
тр
< С
r
, то предварительно выбранный подшипник подходит.
6.3 Проверка подшипников тихоходного вала
6.3.1 Определение реакций опор
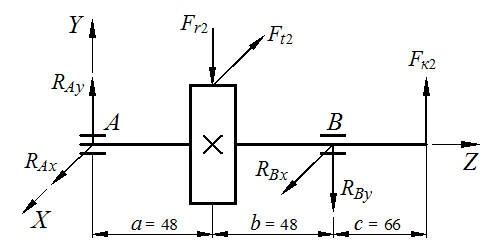
Рисунок 9 – Схема нагружения тихоходного вала
Определяем опорные реакции в вертикальной плоскости




Проверка: Σ
Yi
= R
А
y
–Fr
2
– RBy
+ F
к
2
= 1055,7 – 676,4 – 1422,9 + 1043,6 = 0.
Определяем опорные реакции в горизонтальной плоскости




Проверка: Σ
Х
i
= – R
А
x
+ Ft
2
– R
В
x
= – 359,9 + 719,8 – 359,5 = 0.
Определяем суммарные радиальные реакции


6.3.2 Определение динамической грузоподъемности подшипников
Исходные данные для расчета:
Частота вращения вала – n
= 240 об/мин;
Требуемая долговечность подшипника – Lh
= 10000 ч;
Подшипник 207
Базовая динамическая грузоподъемность Cr
= 25500 Н;
Коэффициент вращения V
= 1 (вращается внутреннее кольцо).
Расчет ведем для опоры B
, как наиболее нагруженной
Радиальная реакция Fr
= RB
= 1467,7 Н;
Определяем эквивалентную динамическую силу по формуле (29)

Определяем требуемую динамическую грузоподъемность по формуле (30)

Т.к. С
тр
< С
r
, то предварительно выбранный подшипник подходит.
7 Проверочный расчет шпоночных соединений
Принимаем шпонки призматические со скругленными торцами. Размеры сечений шпонки, пазов и длины шпонок – по ГОСТ 23360-78
Материал шпонок - сталь 45 нормализованная.
Допускаемые напряжения [σсм
] = 120 МПа.
Прочность шпоночного соединения обеспечена при выполнении условия:
(31)
где l
р
– рабочая длина шпонки;
Быстроходный вал, d
= 28 мм шпонка 8×7×40, t
1
= 4 мм;

Тихоходный вал, d
= 28 мм шпонка 8×7×40, t
1
= 4 мм;

Тихоходный вал, d
= 38 мм шпонка 10×8×36, t
1
= 5 мм;

Как видно из расчетов, во всех случаях прочность шпоночных соединений обеспечена.
8 Проверочный расчет валов редуктора
8.1 Построение эпюр внутренних силовых факторов
Расчет будем вести для тихоходного вала, как наиболее нагруженного.
Строим эпюру изгибающих моментов в вертикальной плоскости “M
х
”
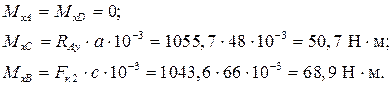
Строим эпюру изгибающих моментов в горизонтальной плоскости “My
”

Определяем суммарные изгибающие моменты в опасных сечениях
 
Строим эпюру крутящих моментов “T
”
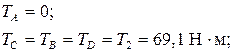
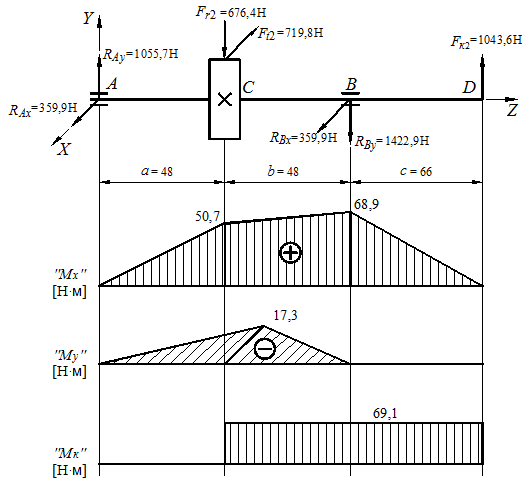
Рисунок 10 – Эпюры внутренних силовых факторов
8.2 Расчет вала на усталостную прочность
Расчет вала на усталостную прочность заключается в определении коэффициентов запаса прочности s
для опасных сечений и сравнении их с допускаемыми значениями [s
]. Прочность обеспечена при s
> [s
] = 2,5.
Исходные данные:
– Материал вала сталь 45 улучшенная;
– предел прочности σв
= 780 МПа;
– предел выносливости стали при симметричном цикле перемены напряжений изгиба σ
-1
= 353 МПа;
– предел выносливости стали при симметричном цикле перемены напряжений кручения τ
-1
= 216 МПа;
– коэффициенты, характеризующие чувствительность материала к асимметрии цикла изменения напряжения: ψσ
= 0; ψτ
= 0;
Расчет ведем для сечения вала B
(рисунок 10), т.к. в этом сечении возникает наибольший изгибающий момент. Концентрация напряжений обусловлена посадкой подшипника с гарантированным натягом. Диаметр вала d
= 35 мм.
Определяем коэффициент запаса прочности по напряжениям изгиба
(32)
где kσ
– коэффициент концентрации напряжений при изгибе;
εσ
– масштабный фактор, учитывающий влияние размеров сечения валов,
принимаем kσ
/εσ
= 3,38;
β
– коэффициент, учитывающий упрочнение поверхности, применение специальных технологических методов; при отсутствии специального упрочнения или термообработки β
= 0,95…0,98 (шлифование); принимаем β
= 0,97;
σа
– амплитуда напряжений изгиба, МПа;
σ
m
– среднее напряжение цикла напряжений изгиба, МПа; т.к. осевая нагрузка на вал отсутствует, то принимаем σ
m
= 0;
Амплитуда напряжений изгиба определяется по формуле:
(33)
где Ми
– изгибающий момент в расчетном сечении, Ми
= 68,9 Н∙м;
W
– осевой момент сопротивления сечения изгибу, мм3
;
Определяем осевой момент сопротивления сечения изгибу по формуле:
(34)
;
;
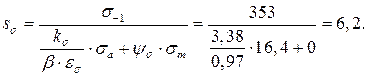
Определяем коэффициент запаса прочности по напряжениям кручения
(35)
где k
τ
– коэффициент концентрации напряжений кручения;
ετ
– масштабный фактор, учитывающий влияние размеров сечения валов,
принимаем k
τ
/ετ
= 2,43;
τа
– амплитуда напряжений кручения, МПа;
τ
m
– среднее напряжение цикла напряжений кручения, МПа.
Амплитудное и среднее значение касательных напряжений определяется по формуле:
(36)
где Т
– крутящий момент в расчетном сечении, Т
= 69,1 Н∙м;
Wp
– полярный момент сопротивления сечения кручению, мм3
;
Определяем полярный момент сопротивления сечения по формуле:
(37)
;
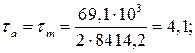
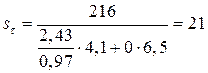
Определяем суммарный коэффициент запаса прочности по напряжениям изгиба и кручения
(38)
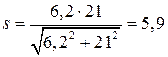
Как видно из расчетов, прочность вала обеспечена.
9 Назначение посадок основных деталей редуктора
Посадки основных деталей редуктора представлены в таблице 11
Таблица 11 – Посадки основных деталей передач
Соединение
|
Посадка
|
Зубчатые колеса на вал
|
H
7
p6
|
Распорные кольца
|
H
8
k6
|
Мазеудерживающие кольца на вал
|
H7
k6
|
Сквозные крышки подшипников в корпус
|
H7
h8
|
Глухие крышки подшипников в корпус
|
H7
d9
|
Полумуфта на вал
|
H7
n6
|
Звездочка на вал
|
H7
h6
|
Внутренние кольца подшипников на вал
|
L0
k6
|
Наружные кольца подшипников в корпус
|
H7
l0
|
Манжеты на вал
|
отклонение вала h11
|
10 Смазка и сборка редуктора
10.1 Смазка редуктора
Смазывание зубчатого зацепления производится разбрызгиванием жидкого масла. При контактных напряжениях σ
Н
до 600 МПа и окружной скорости колес u
до 5 м/с вязкость масла должна быть приблизительно равна 28∙10-6
мм2
/с. Принимаем масло И–Г–А–32.
Смазывание подшипников производится пластичным смазочным материалом, закладываемым в подшипниковые камеры при сборке.
10.2 С
борка и регулировка редуктора
Сборка редуктора производится в соответствии со сборочным чертежом. Перед сборкой внутреннюю полость корпуса редуктора тщательно очищают и покрывают маслостойкой краской.
На быстроходный вал 4 насаживают мазеудерживающие кольца 5 и напрессовывают шарикоподшипники 29 предварительно нагретые в масле до температуры 80 – 100°С.
В начале сборки тихоходного вала закладывают шпонку 26 и напрессовывают зубчатое колесо 10 до упора в буртик вала. Затем надевают распорное кольцо 11, мазеудерживающие кольца 5 и устанавливают шарикоподшипники 29, нагретые в масле.
Собранные валы укладывают в основание корпуса редуктора 2 и надевают крышку корпуса редуктора 3. Для центровки крышку корпуса устанавливают на основание корпуса с помощью двух конических штифтов 27 и затягивают болты 17 и 18.
Затем вставляют в сквозные подшипниковые крышки резиновые манжеты 28 и устанавливают крышки 7 и 8 с прокладками 8, предварительно заложив пластичный смазывающий материал в подшипниковые камеры.
Ввертывают пробку 14 маслоспускного отверстия с прокладкой 15 и крепят маслоуказатель 12 с прокладкой 13. Заливают в редуктор масло и закрывают смотровое отверстие крышкой 1.
Осевой зазор в подшипниках регулируют за счет выбора суммарной толщины набора регулировочных прокладок. Пятно контакта зубчатых зацеплений регулируется осевым перемещением валов с помощью перестановки регулировочных прокладок.
Собранный и отрегулированный редуктор обкатывают и испытывают на стенде по программе испытаний.
Список литературы
1. Тростин В.И. Методика расчетов параметров зацепления закрытых цилиндрических и конических зубчатых передач. – Гомель: ротапринт ГФ БПИ, 1980. – 43 с.
2. Чернавский С.А. Боков К.Н., Чернин И.М., Курсовое проектирование деталей машин: Учеб. Пособие для учащихся машиностроительных специальностей техникумов. – 3-е изд., стереотипное. Перепечатка с издания 1987 г. – М.: ООО ТИД «Альянс», 2005, 416 с.
3. Дунаев П.Ф., Леликов О.П. Конструирование узлов и деталей машин: Учеб. пособие. для техн. спец. вузов – М.: Высшая школа, 2000. – 447с., с ил.
4. Куклин Н.Г., Куклина Г.С. Детали машин: Учеб. для машиностроит. спец. техникумов. – 4-е изд., перераб. и доп. – М.: Высш. шк., 1987. – 383 с.: ил.
5. Иванов М.Н. Детали машин. Учеб. для студентов высш. техн. учеб. завед. – 5-е изд., перераб. – М.: Высш. шк., 1991. – 383 с.: ил.
6. Гулиа Н.В. Детали машин. Учебник для студ. сред. проф. образования. – М.: Издательский центр «Академия», 2004. 416 с.
7. Курсовое проектирование деталей машин: Справ. пособие. Ч 1/ А.В. Кузьмин, Н.Н. Макейчик, В.Ф. Калачев и др. – Мн.: Высшая школа, 1982. – 2085с.
8. Шейнблит А.Е. Курсовое проектирование деталей машин: Учеб. пособие. – Калининград: Янтар. сказ, 2002. – 454с.
9. Курмаз Л.В., Скойбеда А.Т. Детали машин. Проектирование. Учеб. пособие. – Мн.: УП «Технопринт», 2002. – 290 с.
|