Введение
Целью курсового проекта является разработать цех по производству древесностружечных плит с годовой программой 85 тыс. м³. Для этого нам необходимо выполнить следующее:
- выбрать марку смолы и обосновать выбор;
- рассчитать производительность цеха:
а) выбрать схему главного конвейера и способ производства плит;
б) выбрать режим горячего прессования;
в) рассчитать производительность цеха;
- выбрать отвердитель;
- рассчитать расход сырья и материалов;
- выбрать и рассчитать потребное количество основного технологического оборудования;
- составить схему технологического процесса и план размещения оборудования.
1 Характеристика плит намеченных к производству
1.1 Классификация и виды плит
Плиты подразделяют:
- по физико-механическим показателям – на марки П-А и П-Б;
- по качеству поверхности – на Ι и ΙΙ сорта;
- по виду поверхности – с обычной и мелкоструктурной (М) поверхностью;
- по степени обработки поверхности – на шлифованные (Ш) и не шлифованные;
- по гидрофобным свойствам – с обычной и повышенной (В) водостойкостью;
- по содержанию формальдегида – на классы эмиссии Е1, Е2и Е3.
Размеры плит должны соответствовать указанным размерам таблицы 1.
Таблица 1 – Размеры древесностружечных плит и предельные отклонения от номинальных размеров (по ГОСТ 10632 – 07)
Параметры
|
Значения
|
Предельные отклонения
|
Толщина
|
От 8 до 28 с градацией 1 (для
шлифованных)
|
± 0.3
|
Длина
|
1830, 2040, 2440, 2500,
2600, 2700, 2750, 2840, 3220, 3500, 3600, 3660, 3690, 3750, 4100, 5200, 5500, 5680
|
± 5
|
Ширина
|
1220, 1250, 1500, 1750, 1800, 1830, 2135, 2440, 2500
|
± 5
|
Примечания:
- толщина не шлифованных плит устанавливается как сумма номинального значения толщины шлифованной плиты и припуска на шлифование, который не должен быть более 1.5 мм;
- допускается выпускать плиты размерами меньше основных на 200 мм с градацией 25 мм, в количестве не более 5 % от партии;
- по согласованию с потребителем допускается выпускать плиты форматов, не установленных в таблице 1.
Отклонение от прямолинейности кромок не должно быть более 2 мм.
Отклонение от перпендикулярности комок плит не должно быть более 2 мм на 1000 мм длины кромки.
Перпендикулярность кромок может определяться разностью длин диагоналей пласти, которая не должна быть более 0.2 мм длины плиты.
Плиты должны изготавливаться с применением синтетических смол, разрешённых Минздравом РФ.
Содержание вредных химических веществ, выделяемых плитами в производственных помещениях, не должно превышать допустимо предельно концентраций, утверждённых Минздравом РФ для воздуха рабочёй зоны производственных помещений.
В условиях эксплуатации количество химических веществ, выделяемых плитами в производственных помещениях, не должно превышать в окружающей среде предельно допустимых концентраций, утверждённых Минздравом РФ для атмосферного воздуха.
Физико-механические показатели плит плотностью от 550 кг/м³ до 820 кг/м³ должны соответствовать нормам, указанным в таблице 3.
В зависимости от содержания формальдегида плиты изготавливают трёх классов эмиссии, указанных в таблице 2.
Таблица 2 – Классы эмиссии древесностружечных плит
Классы эмиссии
|
Содержание формальдегида, мг на 100г
|
Е1
|
до 10 включительно
|
Е2
|
св. 10 до 30 включ.
|
В условном обозначении плит указывают:
- марку;
- сорт;
- вид поверхности (для плит с мелкоструктурной поверхностью);
- степень обработки поверхности (для шлифованных плит);
- гидрофобные свойства ( для плит повышенной водостойкости);
- класс эмиссии формальдегида;
- длину, ширину и толщину в миллиметрах;
- обозначение настоящего стандарта.
Таблица 2 – Физико-механические показатели плит общего назначения по ГОСТ 10632-07
Наименование показателя
|
Норма
|
П - Б
|
1
|
2
|
1 Влажность, % Тн*
Тв*
|
5
12
|
2 Разбухание по толщине:
за 24ч (размер образцов 100×100 мм),% (Тв)
за 2ч (размер образцов 25×25 мм),% (Тв)**
|
33
15
|
3 Предел прочности при изгибе, Мпа, для толщин, (Тн):
от 8 до 12
» 13 » 19
» 20 » 30
|
16
14
12
|
4 Предел прочности при растяжении перпендикулярно пласти, Мпа, для толщин, мм (Тн):
от 8 до 12
» 13 » 19
» 20 » 30
|
0.3
0.30
0.25
|
5 Предельное сопротивление выдёргиванию шурупов, , (Тн)***:
из пласти
из кромки
|
55
45
|
6 Покоробленность, мм (Тв)
|
1.6
|
7 Шероховатость поверхности пласти Rm, мкм (Тв), для образцов
с сухой поверхностью:
для шлифованных плит с обычной поверхностью
для шлифованных плит с мелкоструктурной поверхностью
|
63
40
|
для не шлифованных плит
после 2ч вымачивания***:
для шлифованных плит с обычной поверхностью
для шлифованных плит с мелкоструктурной поверхностью
для не шлифованных плит
|
500
180
150
-
|
Примеры условных обозначений:
Плит марки П – А первого сорта с мелкоструктурной поверхностью шлифованных класса эмиссии Е1 размерами 3660×1830×16 мм:
П – А, Ι, М, Ш, Е1, 3660×1830×16, ГОСТ 10632 – 07;
То же, плит марки П – Б второго сорта с обычной поверхность не шлифованных класса эмиссии Е2 размерами 3660×1830×16 мм:
П – Б, ΙΙ, Е2, 3660×1830×16, ГОСТ 10632 – 07.
На кромку плиты наносят в виде чёткого штампа тёмным красителем маркировку, содержащую:
- наименование и (или) товарный знак предприятия-изготовителя;
- марку, сорт, вид, поверхности и класс эмиссии;
- дату изготовления и номер смены.
Плиты на экспорт нормируют по нормативно-технической документации. Плиты, предназначенные для использования в районах Крайнего Севера и приравненных к ним районах, упаковывают по ГОСТ 15846.
На экспорт плиты упаковывают в соответствии с требованиями внешнеэкономических предприятий.
2 Расчет производительности цеха
2.1 Пресс для горячего прессования
Основная цель горячего прессования ДСтП - уплотнение стружечного брикета до заданной толщины плиты и стабилизации этой толщины за счёт склеивания между собой древесных частиц.
В качестве основного оборудования при изготовлении трехслойных древесностружечных плит принимают многоэтажный гидравлический пресс ПР – 6А при прессовании плит на поддонах.
2.2 Выбор режима горячего прессования древесностружечных плит
Продолжительность прессования плит в прессе является важным технологическим параметром, т.к. она определяет не только свойства, но и производительность пресса для горячего прессования.
К параметрам режима горячего прессования относятся следующие: температура прессования, условия прессования (с паровым ударом и без него), величина давления, продолжительность прессования, начальная
влажность стружечных брикетов, загружаемых в пресс горячего прессования и т. д. Температуру плит пресса устанавливают в пределах 160-220 °С (она указана в задании на курсовой проект).
Продолжительность прессования (выдержки) плит в прессе является важнейшим технологическим параметром, определяющим не только производительность пресса горячего прессования и цеха (завода) ДСтП, но и свойства получаемых плит. Продолжительность прессования зависит от многих факторов: плотности плит, температуры плит пресса, конструкции и толщины, влажности стружечных брикетов, применения парового удара, вида связующего и т. д.
Продолжительность прессования tпр
, мин, определяется по формуле
где tуд
– удельная продолжительность прессования, мин/мм;
d – толщина плиты, мм.
Удельную продолжительность прессования (минут на 1 мм толщины плиты) и давление выбирают по таблицам 2.1 и 2.2 /1/, tуд
=0,38 мин/мм
.
После определения всех параметров выписывают режим горячего прессования по форме:
Температура прессования, °С
Начальное удельное давление, МПа
Влажность стружечных брикетов, %
Продолжительность прессования, мин
|
160
2,4 – 2,7
8
6,7
|
2.3 Режим работы цеха и коэффициент использования оборудования
Фонд рабочего времени оборудования определяется вычитанием из числа дней в году количества устанавливается в соответствии со следующим режимом работы цехов:
Число дней в году ............……………….. …… 365
Число дней на капитальный ремонт ....………. 20
Число дней на профилактический ремонт …... 29
Праздничные дни............……………………….. 12
Число рабочих дней в году Т = 365 – 29 – 20 - 12 = 304 дня.
Тогда фонд рабочего времени (число рабочих часов в году), Тэф
, ч, определяется по формуле
где t
– продолжительность рабочей смены, ч;
к
– число рабочих смен в сутки.
Т ЭФ
= 304 ∙ 3 ∙ 8 = 7296.
Итак, годовой фонд рабочего времени составляет 7296 часов.
2.4 Определение производительности цеха
Производительность цеха по производству ДСтП определяется производительностью многоэтажного гидравлического пресса, который является основным агрегатом главного конвейера. В цикл прессования кроме непосредственного прессования входит время, затрачиваемое на загрузку пакетов в загрузочную этажерку и выгрузку склеенных плит из пресса. Производительность гидравлического многоэтажного пресса, ПЧ
, м3
/ч, определяется по формуле
где ПЧ
– часовая производительность пресса, м3
/ч;
n – число рабочих промежутков пресса;
l и b – соответственно длина и ширина чистообрезных ДСтП, м;
d – толщина шлифованных плит, м;
КИ
– коэффициент использования агрегатов главного конвейера;
tПР
– продолжительность прессования плит, мин;
tВСП
– продолжительность вспомогательных операций на 1 цикл
работы пресса, (1,5-2) мин.
.
Годовая производительность пресса, П Г
, м3
/год, определяется по формуле
ПГ
= ПЧ
∙ ТЭФ
где ТЭФ
– число рабочих часов в году, ч.
.
Полученное значение округляют до десятков тысяч м3
/год.
3 Характеристика сырья, древесных частиц, смолы и отвердителя для производства плит
3.1 Характеристика сырья, древесных частиц
Для производства плиты используется следующее сырье:
-для внутренних слоев: шпон-рванина (береза – 70 %, ольха – 30 %);
-для наружных слоев: карандаши фанерного производства (береза – 70 %, ольха – 30 %).
Характеристика древесных частиц, для формирования слоёв древесностружечных плит приведена в таблице 6.
Таблица 6 - Средние размеры древесных частиц для формирования слоев
Параметры
|
Значения параметров, мм
|
Для наружных слоев плит
|
Для среднего слоя плит всех марок
|
С мелкоструктурной поверхностью
|
С обычной поверхностью
|
Толщина, мм не более
|
0,25
|
0,40
|
0,8
|
Ширина, мм не более
|
1,5
|
2
|
10
|
Длина, мм не более
|
5
|
20
|
30
|
3.2 Характеристика смолы и отвердителя
Для производства ДСтП используется карбамидоформальдегидная смола марки КФ-МТ-15.
Физико-химические показатели карбамидоформальдегидной смолы КФ-МТ-15
Внешний вид
|
однородная суспензия от белого до светло-жёлтого цвета
|
Массовая доля сухого остатка, %
|
66±1
|
Коэффициент рефракции
|
1,462-1,465
|
Массовая доля свободного формальдегида, % не более
|
0,3
|
Вязкость условная по ВЗ-4 при 20±50
С, с
после изготовления
после хранения 60 суток
|
30-50
150
|
Концентрация водородных ионов, рН
|
6,5-8,5
|
Стабильность смолы при хранении, мес.
|
до 2
|
Продолжительность желатинизации при добавлении 1%
NH4
Cl, ч, не менее
при 1000
С
при 20±10
С
|
35-55
8
|
Плотность при 200
С, г/см3
|
1,26-1,28
|
Предел прочности при скалывании по клеевому слою после вымач. образцов в воде в теч. 24 ч, МПа не менее
|
1,6
|
В качестве отвердителя для внутреннего слоя используют 20%-й раствор хлористого аммония. Для избежания преждевременного отверждения связующего в поверхностных слоях при загрузке брикетов в пресс для наружных слоев применяют комбинированный отвердитель.
Состав комбинированного отвердителя, в мас.ч.:
хлористый аммоний ……………………………………………… 20
аммиачная вода, 25% - ой концентрации ……………………..25-30
вода ……………………………………………………………50–55.
Расход отвердителя составляет (5 – 6) мас. ч. на 100 мас. ч. рабочего раствора смолы. При температурах прессования выше 160° С допускается прессование плит без добавления отвердителя в наружные слои
4 Расчет расхода сырья, стружки, смолы и химикатов
Для определения потребности в сырье, стружке, синтетических смолах на единицу продукции или для выполнения заданной программы в единицу времени (час, смену, сутки, год) необходимо выполнить соответствующие расчеты.
Для определения требуемого количества оборудования или его загрузки необходимо знать, какое количество материала перерабатывается (проходит) на данной технологической операции.
4.1 Плотность плиты по слоям
ДСтП имеет неодинаковую плотность по толщине: большую в наружном слое и меньшую во внутреннем. Разница в плотности зависит от фракционного состава древесных частиц и других факторов. Плотность плиты по слоям, rн
и rвн
, кг/м3
, определяют по формуле 
где rпл
– плотность плиты, кг/м3
;
rн
и rвн
– плотность соответственно наружных и внутреннего слоёв, кг/м3
;
iн
и iвн
– соответственно доля внутреннего и наружных слоёв.
; ;
. При заданной плотности плиты 650 кг/м3
плотность внутренних и наружных слоев составит соответственно
,
.
4.2 Норма расхода связующего
Норма расхода связующего (по сухому остатку) в процентах к массе абсолютно сухой стружки зависит от породы древесины, слоя и конструкции (типа) плит.
Таблица 7 – Средняя норма расхода связующего (по сухому остатку) по отношению к массе абсолютно сухой стружки
Порода
|
Трёхслойные плиты
|
Наружные слои
|
Внутренний
слой
|
Ель, сосна
|
12,5
|
8,5
|
Береза, ольха
|
13,5
|
9,5
|
Средневзвешенное содержание связующего (по сухому остатку) в стружечной плите rср пл
, % 
где Р1
, Р2
, Рn
– норма расхода связующего;
i1
, i2
, in
– доля сырья данной породы в общем объёме сырья, по спецификации.
Средневзвешенная норма расхода связующего для наружных слоев составит
.
Средневзвешенная норма расхода связующего для внутренних слоев
.
4.3 Пооперационный расчет перерабатываемого материала
Данный расчет позволяет определить количество перерабатываемого сырья на каждой технологической операции для расчета количества технологического оборудования, а также расход сырья и связующего для выполнения заданной программы.
В связи с разным составом внутреннего и наружных слоев и неравномерной их плотностью пооперационный расчет перерабатываемого материала на каждой технологической операции ведут раздельно для каждого слоя.
Количество абсолютно сухого материала в готовых плитах gабс.с.
,кг/ч, (при влажности готовых плит 8%) определяют по формуле
, где ПЧ
– часовая производительность цеха, кг/ч;
dСЛ
– толщина одного слоя, мм;
dПЛ
– толщина готовой плиты, мм;
rСЛ
– средняя плотность данного слоя, кг/м3
;
1,08- коэффициент, учитывающий влажность плиты.
Количество абсолютно сухого материала в готовых плитах для наружных и внутренних слоёв составит
,
.
Масса абсолютно сухого материала в наружных слоях до шлифовки плит, кг/ч, (с учётом припуска на обе стороны 1,5 мм) составит
3126 ∙ (5,12+1,5) / 5,12 = 4042.
Тогда потери абсолютно сухого материала при шлифовки плит, кг/ч, равны
4042 – 3126 = 916.
Потери в виде шлифованной пыли на 50% возвращаются в производство в бункер сухой стружки для наружных слоёв
916 ∙ 0,5 = 458.
Потери материала при обрезке плит по формату, %, составят
[(3,55∙1,8) – (3,5∙1,75) / (3,55∙1,8)] ∙100 = 4,15
где 3,55 ∙ 1,8 – формат плиты до обрезки, м;
3,5 ∙ 1,75 – формат плиты после обрезки, м.
Масса абсолютно сухого материала в плитах до обрезки, кг/ч, составит
для наружных слоёв (4042 ∙ 100) / (100 – 4,15) = 4217,
для внутреннего слоя (5029 ∙ 100) / (100 – 4.15) = 5247.
Отходы при обрезке после измельчения на 90% возвращаются в бункер сухой стружки для внутреннего слоя. При этом количество возвращаемого материала, кг/ч, составляет
[(4217 – 4042) + (5247 – 5029)] ∙0,9 = 354.
Потери при формировании ковра, %, составляют
[(4100 – 350) / 3550] ∙ 100=15,5
где 4100 – длина стружечного пакета с учётом стружечной массы в
разделительной коробки формирующего конвейера.
Масса абсолютно сухого материала, кг/ч, проходящего через формирующие машины, составит
для наружных слоёв (4217 ∙ 100) / (100 – 15,5) = 4991
для внутреннего слоя (5247 ∙ 100) / (100 – 15,5) = 6209.
Потери сухого материала для наружных слоёв, кг/ч, при формировании стружечного ковра равны
4991 – 4217 = 774.
Стружечная масса из разделительных коробок главного конвейера с помощью пневмотранспортной установки возвращается в формирующие машины внутреннего слоя, поэтому количество абсолютно сухого материала, кг/ч, выходящего из смесителя, для внутреннего слоя равно
5247 – 774 = 4473.
Норма расхода связующего составляет для наружных слоёв 13,5%, для внутреннего слоя 9,5% (см 4.2). Тогда часовой расход сухого связующего, кг/ч, составит
для наружных слоёв (4991 ∙ 13,5) / (100 +13,5) = 594
для внутреннего слоя (4473 ∙ 9,5)/(100 + 9,5) = 388.
Количество абсолютно сухих древесных частиц, кг/ч, поступающих в смесители, равно
для наружных слоёв 4875 – 594 = 4281
для внутреннего слоя 4473 – 388 = 4085.
Масса абсолютно сухой стружки, кг/ч, поступающей в бункера, с учётом возврата шлифованной пыли в бункер наружного слоя и дроблёнки от форматной обрезки в бункер для внутреннего слоя составит
для наружных слоёв 4281 – 458 = 3823.
для внутреннего слоя 4085 – 354 = 3731.
Количество крупных древесных частиц, отделяемых при сепарации стружки наружного слоя и направляемых в стружку внутреннего слоя, равно примерно 10%. Тогда масса абсолютно сухой стружки, кг/ч, выходящей из сушильных барабанов, составит
для наружных слоёв (3823 ∙ 100) / (100 – 10) = 4248
для внутреннего слоя 3731 – 425 = 3306.
Потери при сушки стружки составляют для наружных слоёв 3%, для внутреннего слоя 2,5%. Тогда потребность в абсолютно сухой стружке, кг/ч, перед сушкой составит
для наружных слоёв (4248 ∙ 100) / (100 – 3) = 4379
для внутреннего слоя (3277 ∙ 100) / (100 – 2,5) = 3391.
Потери при раскрое и измельчении сырья, изготовлении и транспортировки стружки, а также непредвиденные потери в сумме достигают примерно 7%. Тогда потребность в абсолютно сухой древесине, кг/ч, составит
для наружных слоёв (4479 ∙ 100) / (100 – 7) = 4709
для внутреннего слоя (3391 × 100) / (100 – 7) = 3646.
Результаты расчётов сводятся в таблицу 8.
Часовой расход материала данной влажности на каждой технологической операции gw
, кг, определяют по формуле
, где gw
– расход материала данной влажности, кг;
gабс.с.
– расход абсолютно сухого материала, кг;
W – влажность материала на данной технологической операции на данном потоке, %.
Для наружных слоёв
.
Таблица 8 – Часовой расход абсолютно сухого материала и при данной влажности на каждой технологической операции
Технологически операции
|
Часовой расход абсолютно
сухого материала по слоям,
кг
|
Влажность
материала,
%
|
Часовой расход материала
данной влажности по слоям,
кг
|
Наружные
|
Внутренний
|
Wн.
|
Wвн
|
Наружные
|
Внутренний
|
1
|
2
|
3
|
4
|
5
|
6
|
7
|
Готовые шлифовальные плиты
|
3126
|
5029
|
8
|
8
|
3376
|
5431
|
До шлифовки
|
4042
|
5029
|
8
|
8
|
4365
|
5431
|
До обрезки
|
4217
|
5247
|
8
|
8
|
4554
|
5667
|
В формирующих машинах
|
4991
|
6209
|
14
|
10
|
5689
|
6830
|
До формирующих машин
|
4991
|
4473
|
14
|
10
|
5689
|
4920
|
До смесителя
|
4281
|
4085
|
3
|
2
|
4409
|
4167
|
До бункеров сухой стружки
|
3823
|
3731
|
3
|
2
|
3938
|
3806
|
До сепарации
|
4248
|
3306
|
2
|
2
|
4375
|
3372
|
До сушилок
|
4379
|
3391
|
80
|
80
|
7882
|
6104
|
До измельчения
(потре6ность в сырье)
|
4709
|
3646
|
80
|
80
|
8467
|
6563
|
4.4 Расход древесного сырья, смолы и химикатов на 1 м3
плит
Пооперационный расчёт позволяет не только определить поток материала (стружки) в единицу времени на данной технологической операции, но и по результатам его расчёта определить расход древесного сырья и смолы на 1 м3
плит. Для этого необходимо часовой расход сырья по массе разделить на плотность древесного сырья при данной влажности (80%). Первоначально определяют плотность древесного сырья r, кг/м3
, /1, таблица 4.3/. При использовании смеси пород определяется для каждого слоя средневзвешенная плотность rСП
, кг/м3
, по формуле rСП
= r1
× i1
+ r2
× i2 +
. . . + rn × in
,
где in
– доля древесины в общей массе сырья, %.
Для производства плит марки П-Б в наружных слоях используют карандаши фанерного производства следующего породного состава: береза 70% и ольха 30%. Во внутренних слоях применяется шпон-рванина (береза 70%, ольха 30%)
Средневзвешенная плотность наружных слоев составит
rСП
= 790 × 0,3 + 940 × 0,7 = 895.
Внутренних – rСП
=790 × 0,3 + 940 × 0,7 = 895.
Часовой расход или потребность в древесном сырье V
, м3
/Ч
, определятся по формуле V
=
V
Н
+
V
ВН
,
где V
Н
и V
ВН
– часовой расход древесного сырья соответственно наружных и
внутренних слоев, кг. 
Расход древесного сырья, V Р
, м3
на 1 м3
, плит составит
,
где 12,5 – часовая выработка плит, м3
.
Годовая потребность в древесном сырье, м3
, составит
1,34 × 91000 = 121940,
где 91000 – производительность цеха в год, м3
.
Расход смолы, (в пересчёте на сухой остаток) на изготовление 1 м3
плит равен
,
где 594 и 388 – часовой расход смолы, кг, по сухому остатку, соответственно для наружных и внутренних слоёв.
Расход смолы стандартной концентрации, кг, (К=64%) на 1м3
плит составит
.
Расход смолы рабочей концентрации, кг, (К=54%) на изготовление 1 м3
плит составит
.
При изготовлении 1 м3
плит требуется 1,29 кг хлористого аммония и 1,09 кг аммиачной воды.
Таблица 9 – Сводная ведомость расхода древесины, смолы и химикатов
Компоненты плиты
|
Расход материалов
|
на 1 м3
|
в час
|
в год
|
нар.
|
внутр.
|
нар.
|
внутр.
|
Древесное сырьё, м3
|
0,76
|
0,58
|
9,5
|
7,25
|
122208
|
Смола КФ-МТ-15, т
стандартной концентрации
рабочей концентрации
|
0,07425
0,088
|
0,04845
0,0575
|
0,928
1,1
|
0,606
0,719
|
11190
13270
|
Отвердитель, кг в т.ч. хлористый аммоний
|
1,29
|
16,13
|
117648
|
Аммиачная вода
|
1,09
|
13,63
|
99408
|
5 Выбор и расчёт количества основного технологического оборудования
5.1 Схема технологического процесса
Технологический процесс производства древесностружечных плит отличается стабильностью и последовательностью выполняемых операций независимо от вида изготавливаемой продукции. Технологический процесс предусматривает следующие операции:
1. Доставку, выгрузку, укладку и хранение древесного сырья.
2. Сортировку сырья по видам и породам, подготовку технологической щепы (сортировку и очистку от примесей).
3. Переработку карандашей и шпона-рванины в стружку.
5. Сушку древесных частиц (стружки).
6. Сортирование стружки по фракциям (потокам) и отделение некондиционных древесных частиц (крупных древесных частиц и сколов).
7. Повторное измельчение стружки.
8. Приготовление связующего и добавок.
9. Дозирование стружки смешивание ее со связующим.
10. Формирование стружечного ковра (пакетов).
11. Разделение стружечного ковра на пакеты и контроль их массы.
12. Предварительную подпрессовку стружечного ковра и пакетов.
13. Загрузку подпрессованных стружечных брикетов в пресс и горячее прессование плит.
14. Выгрузку, охлаждение, кондиционирование и выдержку плит.
15. Форматную обрезку, шлифование и сортирование плит.
5.2 Выбор схемы переработки сырья в стружку
В проекте для переработки сырья в стружку выбираем однопоточную схему.
На первом потоке отходы фанерного производства перерабатываются в технологическую щепу в барабанных рубительных машинах типа «Майер». Затем она перерабатывается в стружку в центробежных стружечных станках типа ДС-7, ДС-7А.
5.3 Обнаружение в сырье металлических предметов
В сырье, поступающем на переработку в щепу в рубительные машины или в стружку на стружечные станки, иногда встречаются различные металлические включения, которые, попадая в станки, выводят из строя режущие ножи, а большие металлические предметы выводят из строя (а иногда приводят к аварии) оборудование. Поэтому все сырье, поступающее в переработку на рубительные машины и стружечные станки, должно проходить через металлоискатель.
5.4 Сортировка сырья по породам
Неравномерный породный состав сырья является одной из основных причин разнотолщинности плит. Поэтому сортировка сырья по породам является одной из важнейших технологических операций. Всю древесину, поступающую для производства ДСтП, рекомендуется сортировать на складе по породам на следующие группы: ель, сосна, кедр, пихта; берёза, ольха, липа; осина; дуб, бук и др. Такая сортировка позволяет направлять для изготовления стружки различных слоёв соответствующие породы или же использовать породы в известном соотношении, обеспечивая постоянный породный состав стружки.
5.5 Переработка сырья в щепу
Кусковые отходы лесопильных и деревообрабатывающих цехов перерабатываются в щепу только на барабанных рубительных машинах с
механизмом принудительной подачи.
Требуемое количество барабанных рубительных машин n, шт, определяют по формуле
где Q – объем перерабатываемого сырья. м3
/ ч (таблица 9, графа 5);
П – производительность рубительной машины в час, пл.м3
, (принимается из технической характеристики);
2 – коэффициент, учитывающий неравномерность загрузки рубительной машины.
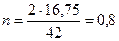
Принимаем один станок фирмы «Майер»коэффициентом загрузки Кз
= 0,8.
5.6 Сортировка щепы
В производстве ДСтП в основном применяют сортировки типа СЩ - 1 и СЩ - 120. Количество сортировок n, шт, определяют по формуле
где Qсырья
– объем сырья в час, м3
, принимается из сводной ведомости, таблица 9, графа 5 – древесное сырье.
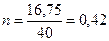
Принимаем один станок марки СЩ-1с коэффициентом загрузки Кз
= 0,42.
5.7 Переработка щепы в стружку
При переработке технологической щепы в игольчатую стружку для внутренних слоев применяют центробежные станки ДС-7, ДС-7А, Пальман.
Количество стружечных станков n, шт, определяют по формуле
, где Qстр
– потребность в абсолютно сухой стружке таблица 8 по операции «До сушилок», кг/ч «внутренние слои»;
П – производительность кг/ ч (принимают из таблицы 5.8 /1/), кг/ч.
.
Принимаем пять станков марки ДС-7А с коэффициентом загрузки Кз
= 0,95.
5.8 Буферное хранение щепы, сырой и сухой стружки
Для создания буферных запасов щепы и равномерной ее выдачи для измельчения в стружку служат вертикальные бункера.
Для хранения сырой стружки используют вертикальные бункера ДБО-60, сухой стружки - бункера ДБОС-60, древесной пыли - бункера ДБОП-60.
В начале задаются временем (1-2) часа, в течение которого необходимо обеспечить бесперебойную работу на данном потоке, и затем определяют требуемое количество бункеров nб
, шт, по формуле
, где gстр
– часовая потребность в стружке на потоке принимается по данным пооперационного расчета, кг/ч;
– время, в течение которого бункера обеспечивают бесперебойную работу потока на данном участке, ч;
Vб
– объем бункера по технической характеристике, м3
;
стр
– насыпная масса стружки, кг/м3
;
Кз
– коэффициент заполнения рабочего объема бункера (0,95).
Такие расчеты необходимо провести для каждого потока в отдельности для бункеров сырой и сухой стружки.
- для хранения щепы
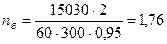
Принимаем два бункера марки ДБО-60 с коэффициентом загрузки Кз
= 0,88.
- для хранения сырой стружки
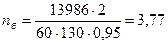
Принимаем четыре бункера марки ДБО-60 с коэффициентом загрузки Кз
=0,94.
- для хранения сухой стружки наружных слоев
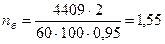
Принимаем два бункера марки ДБОС-60 с коэффициентом загрузки Кз
= 0,78.
- для хранения сухой стружки внутренних слоев
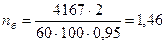
Принимаем два бункера марки ДБОС-60 с коэффициентом загрузки Кз
= 0,73.
5.9 Сушка древесных частиц
Перерабатываемое сырьё имеет важность (60-80) %. Влажность стружки перед смешиванием со связующим должна быть (2-4) % для внутренних и (4-6) % для наружных слоёв, поэтому древесные частицы подвергают сушке. Для сушки измельчённой древесины используют преимущественно газовые сушилки непрерывного действия, которые работают на топочных газах.
Требуемое количество агрегатов «Прогресс» n, шт, определяют для каждого потока в отдельности по формуле
, где Qстр
– потребность в стружке (в абсолютно сухом состоянии) в час на данном потоке. Принимается по таблице 8 по операции «До сепарации», кг/ч;
П – производительность по технической характеристике, кг/ч.
Принимаем производительность агрегата «Прогресс» равной 2000т/час.
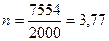
Принимаем четыре агрегата «Прогресс» с коэффициентом загрузки Кз
= 0,94
5.10 Сортировка древесных частиц
Операция сортирования стружки необходима для отделения из общей массы древесных частиц те, которые необходимы для формирования определенных слоев стружечного ковра; отделения древесной пыли и крупной стружки, превышающие допустимые параметры. Для сортирования широко применяют механические сортировки качающегося типа, пневматические сепараторы и комбинированные сортировки. Качественное сортирование стружки по фракциям достигается при сочетании механического и пневматического способов.
Для сортировки сухой стружки для наружных слоев по длине и ширине применяют механическую сортировку ДРС-2, а по толщине – вертикальный пневматический сепаратор «Келлер». Для сортировки стружки внутренних слов применяют двухступенчатый пневматический сепаратор ДПС-1 или двухступенчатый пневматический сепаратор «Келлер».
Требуемое количество n, шт, механических сортировок ДРС-2 и пневматических сепараторов «Келлер» и ДПС-1 для каждого потока в отдельности определяют по формуле
, где Qстр
– потребность в стружке в час на данном потоке, кг/ч, принимают по таблице 8 по операции «До сепарации» из последних колонок.
П – производительность сортировок или сепаратора (выбираем по таблицам их технических характеристик /1/).
Сортировка сухой стружки по длине и ширине для наружных слоев
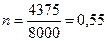
Принимаем одну механическую сортировку марки ДРС-2 с коэффициентом загрузки Кз
= 0,55.
Сортировка сухой стружки по толщине для наружных слоев
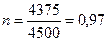
Принимаем один пневматический сепаратор марки «Келлер» с коэффициентом загрузки Кз
= 0,97.
Сортировка стружки для внутренних слоев

Принимаем сортировочную машину ДПС-1 с коэффициентом загрузки Кз
= 0,97 %.
5.11 Повторное измельчение стружки
Для получения древесных частиц с регламентированными размерами при изготовлении плит марок П-А и П-Б стружку дополнительно измельчают по ширине в молотковой дробилке ДМ-8.
Количество определяют для каждого потока в отдельности по формуле
, где Q – потребность в стружке в час на данном потоке, кг/ч;
П - производительность дробилок, кг/ч.
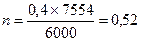
Принимаем один станок марки ДМ-8 с коэффициентом загрузки Кз
= 0,52.
5.12 Приготовление рабочих растворов.
Необходимое количество установок для наружных слоев определяется по формуле
, где Q - расход смолы стандартной концентрации, кг/ч;
П – производительность установки, кг/ч.
Необходимое количество установок для внутренних слоев
Принимаем по одной установке ДКС-2 для наружных и внутренних слоев.
5.13 Смешивание древесных частиц со связующим
Смешивание стружки со связующим (осмоление) является одним из важнейших технологических процессов, так как оно в значительной степени определяет качество и стоимость древесностружечных плит.
Требуемое количество смесителей n, шт, определяют по формуле
Для наружных слоев - .
Принимаем один смеситель марки ДСМ-7 с коэффициентом загрузки Кз
= 0,95.
Для внутренних слоев - .
Принимаем один смеситель марки ДСМ-7 с коэффициентом загрузки Кз
= 0,98.
Схема смесителя представлена на листе КП ТД 101 ССС. Данный смеситель состоит из корпуса в виде барабана длиной 2 метра и диаметром 0,5м. внутри расположен вал с лопастями. Полый вал разделен на две части в одну из них подается холодная вода, с другой стороны – связующее. Вода необходима для охлаждения. Под действием холодной воды образуется конденсат, который не позволяет прилипать древесным частицам к стенкам. На концах лопаток имеются форсунки для разбрызгивания , лопатки имеют возможность изменения угла поворота для обеспечения производительности.
5.14 Формирование стружечного ковра
Задачей формирования стружечного ковра (пакетов) является дозирование и равномерное распределение осмоленных древесных частиц для обеспечения одинаковой толщины, плотности прочности по площади древесностружечных плит при последующем прессовании.
Количество формирующих машин рассчитывают для каждого слоя по формуле
Для наружных слоев - .
Для внутренних слоев - .
Для наружных слоев необходимо принимать не менее 2 формирующих машины даже с небольшим коэффициентом загрузки. Для равномерного распределения по площади осмоленных древесных частиц при формировании внутреннего слоя рекомендуется принимать 4 формирующих машины несмотря на коэффициент загрузки.
Принимаем две формирующие машины марки ДФ-6 для наружных слоев с коэффициентом загрузки Кз
=0,88 и четыре формирующие машины марки ДФ-6 для внутренних слоев с коэффициентом загрузки Кз
= 0,83.
5.15 Подпрессовка и контроль массы стружечных пакетов
Предварительная подпрессовка стружечных пакетов в главном конвейере при способе прессования плит на поддонах производится в прессе ПР-5.
Производительность пресса ПР-5, ППР
, м3
/ч, определяется по формуле
,
где lпл
– длина плиты, м;
δпл
– толщина нешлифованной плиты, м;
Впл
– ширина обрезной нешлифованной плиты, м;
К – коэффициент использования оборудования, 0,9.
Загрузка пресса ПР-5 определяется по формуле
, где Qпл
- часовая выработка чистообрезных нешлифованных плит, м3
.
.
5.16 Охлаждение и выдержка плит
После выгрузки из пресса горячего прессования в отпрессованных древесностружечных плитах имеют место значительные градиенты температуры, влажности и степени поликонденсации (отверждения) связующего. Это является причиной образования внутренних напряжений в плитах, которые с течением времени при охлаждении выравниваются. Поэтому после выгрузки из пресса плиты должны сначала охлаждаться и только потом поступать на механическую обработку (форматную обрезку, шлифование, раскрой и др.).
Охлаждение древесностружечных плит производится в установках веерного типа.
После охлаждения плиты укладывают в плотные стопы (пачки) высотой 400 или 2500 мм, которые затем поступают на участок выдержки перед механической обработкой. Выдерживать плиты удобно на приводных роликовых конвейерах, которыми стопы одновременно продвигаются к участку обработки плит.
5.17 Форматная обрезка и шлифование плит
Производительность форматно – обрезных станков и линии шлифования определяют по формуле ,
где u – скорость подачи, м/мин;
δпл
,bпл
– толщина и ширина обрабатываемых плит, м;
К1
– коэффициент использования станка, (0,8…0,9);
К2
– коэффициент использования рабочего времени, (0,9…0,95).
Скорость подачи линии шлифования ДЛШ-50 зависит от толщины сошлифованных с двух сторон слоев. При суммарной толщине сошлифованных слоев 1,5 мм она составляет 13,5 м/мин.
Загрузку форматно - обрезного станка и линии шлифования проверяют по формуле
, где Qпл
– часовая выработка чистообрезных нешлифованных плит, равная производительности горячего пресса, м3
/ч.
,
.
Основная цель шлифования древесностружечных плит - получение плит заданной толщины с шероховатостью поверхности в соответствии с требованиями стандарта.
Производительность линии шлифования составляет


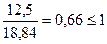
Принимаем один форматно-обрезной станок ДЦ-8 и одну линию шлифования ДЛШ-100.
5.18 Промежуточная выдержка и хранение плит на складе
От линии шлифования и сортировки пачки плит высотой до 600 мм перевозят автопогрузчиками на склад, где их укладывают в штабеля высотой до 4,5 м. Пачки плит укладывают на деревянные поддоны или на деревянные бруски толщиной не менее 80 мм, расстояние между которыми должно быть 500... 600 мм. Плиты хранят в сухом, отапливаемом (в зимнее время), вентилируемом помещении, оснащенном механизмами для погрузки, разгрузки и транспортировки.
Площадь одного пакета или штабеля, F ПАК
, м2
, определяется по формуле
, где lпл
, bпл
– длина и ширина плит, м.
.
Объем одного пакета высотой 400 ... 800 мм, м3
.

Число пакетов, укладываемых в один штабель высотой не более 4,5 м с учетом прокладок толщиной 100 мм между пакетами,
. Объем плит в одном штабеле, м3
. 
Число штабелей для укладки суточного объема производства плит
, где Qсут
– объем производства плит за 1 сутки, м3
.
.
Число штабелей N ШТ
, для укладки пяти - семисуточного объема производства плит определяется по формуле
, где Q - объем производства плит за период времени (5 - 7 суток).
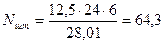
Площадь склада хранения плит, S, м2
, исходя из числа штабелей на пяти - семисуточный запас с учетом проездов и проходов, площадь которых можно принять равной площади, занятой штабелями определяется по формуле
, .
5.19 Сводная ведомость основного технологического оборудования
После выполнения расчётов составляется сводная ведомость основного технологического оборудования по следующей форме.
Таблица 10 – Сводная ведомость основного технологического оборудования
N п/п
|
Наименование
оборудования
|
Марка
|
Принятое
количество
|
Коэффициент
загрузки
|
Установленная мощность, кВт
|
нар.
|
внут
|
нар.
|
внут.
|
единицы
|
всего
|
1
|
Барабанная
рубительная машина
|
Майер
|
1
|
0,8
|
132
|
132
|
2
|
Сортировка
|
СЩ - 1
|
1
|
0,42
|
4,0
|
4
|
3
|
Измельчение щепы в стружку
|
ДС-7А
|
5
|
0,97
|
213
|
1065
|
4
|
Вертикальные
бункера
|
ДБО –60
Бункер щепы
|
2
|
0,88
|
21,9
|
43,8
|
ДБО –60
Бункер сырой стружки
|
4
|
0,94
|
21,9
|
43,8
|
ДБОС-60
|
2
|
2
|
0,78
|
0,73
|
39
|
156
|
5
|
Сушильные
барабаны
|
Прогресс
|
4
|
0,94
|
62
|
62
|
6
|
Пневматический
сепаратор
|
Келлер
|
1
|
-
|
0,97
|
-
|
5.3
|
5,3
|
Механический
сепаратор
|
ДРС – 2
|
-
|
1
|
-
|
0,55
|
4,0
|
4
|
Сортировка внутр. слоев
|
ДПС-1
|
-
|
1
|
-
|
0,97
|
175,5
|
175,5
|
7
|
Повторное измельчение
|
ДМ - 8
|
1
|
0,5
|
132
|
132
|
8
|
Установка для приготовления
связующего
|
ДКС - 2
|
1
|
1
|
0,38
|
0,25
|
5,5
|
11
|
9
|
Смесители
|
ДСМ- 7
|
1
|
1
|
0,95
|
0,98
|
50
|
100
|
10
|
Формирующие
машины
|
ДФ – 6
|
2
|
4
|
0,88
|
0,83
|
10.2
|
61,2
|
11
|
Пресс предвор.
под прессовки
|
ПР-5
|
1
|
0,88
|
86
|
86
|
12
|
Пресс горячего
прессования
|
ПР-6А
|
1
|
1
|
295
|
295
|
13
|
Весы
|
ДВ - 3
|
1
|
|
|
|
14
|
Веерный охладитель
|
|
1
|
|
|
|
15
|
Обрезной станок
|
ДЦ-8
|
1
|
0,7
|
27,2
|
27,2
|
16
|
Линия шлифования
|
ДЛШ-100
|
1
|
0,66
|
625,5
|
625,5
|
|
Итого
|
3026
|
6 Описание технологического процесса
Технологический процесс изготовления древесностружечных плит состоит из следующих основных этапов:
- подготовка сырья;
- поступление стружки;
- сушка и сортировка стружки;
- повторное измельчение стружки;
- приготовление и дозирование связующего;
- дозирование стружки и смешивание ее со связующим (осмоление стружки);
- формирование стружечного ковра;
- холодная подпрессовка ковра;
- контроль массы ковра;
- горячее прессование плит;
- охлаждение (кондиционирование) и выдержка;
- обрезка плит по периметру шлифование и сортировка плит.
- на ряде предприятии дополнительно включается операция раскроя плит на заготовки.
Производство древесностружечных плит, как правило, состоит из двух участков: цех или отделение подготовки сырья и изготовления стружки и главный корпус, где осуществляется изготовление самих плит
6.1 Подготовка сырья и изготовление стружки по однопоточной схеме
Технологический процесс производства древесностружечных плит представлен на листе КП ТД 101 СТП.
Отходы фанерного производства: карандаши и шпон-рванина подаются со склада в барабанную рубительную машину «Майер»(3) при помощи ленточного конвейера(1).
От рубительной машины щепа поступает на сортировочную машину СЩ-1 (4). В этой машине щепа делится на три фракции: крупная( идет на повторное измельчение), кондиционная (направляется на переработку стружки), самая мелкая фракция идет на наружные слои.
Далее щепа с помощью скребковых конвейеров (6), направляется в бункера щепы ДБО-60 (8, устанавливаемые, как правило, в главной корпусе перед сушильными барабанами АКС – 5 (10).
Из бункеров щепа подается на центробежно-стружечный станок ДС-7 (7) для ее измельчения в стружку. После чего она при помощи скребкового транспортера(5) подается в бункер сырой стружки ДБО-60 (9).
Кондиционная щепа от сортировки (4) направляется в вертикальные бункера ДБО-60 (8). Измельчённая стружка на скребковых конвейерах поступает в вертикальные бункера для хранения сырой стружки ДБОС – 60 (9).
6.2 Сушка и сортировка стружки
Из бункеров (9) сырая стружка поступает в сушильный барабаны (10), где высушивается в потоке топочных газов, получаемых от сжигания мазута или природного газа. В зависимости от начальной влажности высушиваемого материала температура агента суши на входе в сушильный барабан устанавливается в пределах 250-350°С. Влажность сухих древесных частиц не более 3-4%.
Сортировка древесных частиц производится в два этапа: сначала по ширине на механическом сепараторе ДРС-2 (18), затем по толщине на пневматической сепараторе (двухступенчатом). На механическом сепараторе ( отделяются мелкие древесные частицы (микростружка), пригодные для формирования наружных слоев древесностружечных плит, и направляется в бункера наружного слоя (13).
В пневматическом сепараторе «Келлер» (19) отделяется кондиционная стружка для внутреннего слоя (при изготовлении трехслойных плит). Оставшаяся на днище камеры крупные древесные частицы и сколы направляются на дополнительное измельчение в зубчато-ситовую мельницу ДМ – 8 (21).
Для сортировки щепы для внутренних слоев используется сортировочная машина ДПС-1.
6.3 Смешивание древесных частиц со связующим (осмоление стружки)
Древесные частицы для наружных и внутреннего слоев смешивают со связующим раздельно в высокооборотных смесителях ДСМ-7 (17). Перед поступлением в смеситель древесные частицы дозируют по массе весами непрерывного действия (14) и затем они направляются в выравнивающий бункер-питатель (16), с помощью которого обеспечивается равномерное объемное дозирование древесных частиц в смеситель.
Дозирование компонентов (смолы и отвердителя) связующего осуществляется с помощью весов типа НД (14) и подачи в смесители с помощью клее приготовительных установок ДКС-2 (15), установленных рядом со смесителями.
6.4 Формирование стружечных пакетов, предварительная их подпрессовка, горячее прессование, охлаждение или кондиционирование плит
Стружечные пакеты формируются послойно машинами ДФ-6 (23, 24) на формирующем конвейере (22).
Сформированные стружечные пакеты проходят под металлоулавителями (25) для удаления из пакетов случайных металлических предметов и направляется на весы ДВ – 3 (28) для взвешивания пакета. Далее поступает в пресс предварительной подпрессовки ПР-5 (26), чтобы придать
им транспортную прочность и обеспечить свободную загрузку в пресс для горячего прессования. Предварительная подпрессовка производится при удельном давлении 1,5 - 2,5 МПа.
Подпрессованные пакеты сначала поперечным, а затем продольным цепным конвейером направляются к загрузочной этажерке пресса ПР-6А (27) для горячего прессования. При перемещении пакетов с их кромок отсасывается осыпавшаяся стружка, которая направляется в формашины (23) для внутреннего слоя.
После размыкания плит пресса поддоны вместе с отпрессованными древесностружечными плитами выгружаются разгрузчиком в разгрузочную этажерку, а затем по мере опусканий ее захватываются и выносятся конвейером из этажерки. Древесностружечные плиты отделяются от поддонов с помощью системы "ныряющего захвата", когда плиты по роликам движутся вперед, а поддон изгибается вниз и проходит под роликовым конвейером, затем поддоны идут на очиститель поддонов (33). После отделения древесностружечные плиты поперечным конвейером направляются на установку для охлаждения веерного типа (29). Температура поверхности древесностружечных плит после охлаждения не должна превышать 50° С.
После охлаждения плиты укладываются штабелеукладчиком (30) в плотные стопы высотой 500 мм.
После выдержки плиты поступают на форматную отрезку (31), а затем шлифовку (32). Для шлифования плит применяют абразивные ленты.
После шлифования плиты здесь же сортируют и маркируют. Качество и чистоту поверхности определяют визуально оператор линии при сортировке.
Заключение
В данном курсовом проекте приведена характеристика ДСтП, сырья и материалов. Произведен расчет производительности пресса. Сделан пооперационный расчет сырья и материалов. Составлена технологическая схема изготовления ДСтП. Произведен расчет необходимого оборудования и дано описание технологического процесса. В графической части представлена схема техпроцесса, разработан план размещения оборудования, который представлен на листе КП ТД 101 ПТХ и приведена схема смесителя для смешивания связующего с древесными частицами, лист КП ТД 101 ССС.
Технико-экономические показатели приведены в таблице 11.
Таблица 11 - технико-экономические показатели.
Показатель
|
Ед. изм
|
Значение
|
Часовая производительность
|
м3
/ч
|
12,5
|
Норма расхода смолы
Наружные слои
Внутренние слои
|
кг/ч
|
3126
5029
|
Суммарная мощность
|
кВт
|
3026
|
Съем продукции с 1 м2
|
м3
/м2
|
17,3
|
Трудозатраты на изготовление 1 м3
|
м3
/ч.час
|
0,32
|
Трудоемкость изготовления 1 м3
|
ч.час/м3
|
3,12
|
Расход электроэнергии на изготовление 1 м3
|
кВт/ч
|
242,1
|
|