Министерство науки и образования Украины
Приднепровская государственная академия
строительства и архитектуры
Кафедра технологии строительных материалов, изделий и
конструкций
Расчетно-пояснительная записка
К курсовой работе по дисциплине
«Технологии заполнителей бетона»
на тему:
«Цех по производству керамзита»
Проектировала студентка 771 гр. Руководитель проекта к.т.н., доцент
Лукьяненко А.А.
Еременко В.А.
Днепропетровск 2010
Содержание
1. Введение 3
2. Общая часть.................................................................................... $
2.1 Состав предприятия....................................................................... £
2.2 Номенклатура и характеристика продукции................................... б
2.3 Характеристика использованного сырья......................................... •?
3. Технологическая часть...................................................... (%,
3.1 Обоснование принятой технологии производства............................ {%,
3.2 Принятая технологическая часть..................................................... /(/
3.3 Описание технологии..................................................................... \$
3.4 Технологические режимы и расчеты............................................... \%
3.5 Выбор и характеристика основного технологического оборудования....... %о
3.6 Контроль производства.................................................................. %х
4. Потребность в энергоресурсах........................................................... £3
5. Штатная ведомость цеха................................................................... £3
6. Охрана труда и окружающей среды.................................................. & ?
7. Строительная часть.......................................................................... Я #
8. Технико-экономическая часть........................................................... $0
9. Список литературы........................................................................... 33
 Введение
Вспучивание глины при обжиге известно с незапамятных времен. Самопроизвольное вспучивание нередко наблюдается в керамическом производстве - образование пузырей, вздутий и других пороков изделий.
В результате вспучивания получается легкий поризованный материал с мелкоячеистой структурой, обладающей малой плотностью при значительной прочности и высокими теплозащитными свойствами.
Вспучивание глин при обжиге связано с двумя процессами: газовыделением и переходом глины в пластическое состояние.
Источниками газовыделения являются реакции восстановления оксидов железа при их взаимодействии с органическими примесями, окисление этих примесей, дегидратации гидрослюд и других водосодержащих глинистых минералов, диссоциации карбонатов и т. д. В пиропластическое состояние глины переходят, когда при высокой температуре в них образуется жидкая фаза (расплав), в результате чего глина размягчается, приобретает способность к пластической деформации, в то же время становится газонепроницаемой и вспучивается выделяющими газами.
В отличие от плотных, пористых и пустотелых керамических материалов и изделий, вырабатываемых из глин, вспученный при обжиге глинистых пород материал ячеистого строения называют керамзитом.
Термин керамзит обозначает не какой-либо вид готового материала или изделия, а вспученную при обжиге глинистых пород массу ячеистого строения. Название же готовых видов материала образуется по общепринятому в технике словосочетанию материал -готовый продукт. Например, стальная проволока, стальной рельс, в рассматриваемом случае - керамзитовый гравий, керамзитовый песок, керамзитовые блоки, керамзитовый щебень и т. д.
Длительный опыт освоения керамзита показал, что методы его получения, а также области использования его технических свойств
могут быть самыми разнообразными. С развитием науки и техники они непрерывно совершенствуются и расширяются. Так, если в период
зарождения промышленности керамзита вспучивания глин вели в горнах периодического действия и туннельных печах и на решетках с принудительным прососом воздуха, то в настоящее время предложены и внедряются новые перспективы методы вспучивания: в двухбарабанных печах, в кипящем слое, в кольцевых, шахтных и других печах.
В последние десятилетия в производство керамзитового гравия наряду с классическими легкоплавкими глинистыми породами вовлекаются различные отходы углеобогащения, золы и шлаки тепловых электростанций, а также трепела, диатомиты т. д.
Вместе с тем, несмотря на очевидные успехи в организации производства и применении керамзита, технический уровень действующих керамзитовых предприятий и качество выпускаемой ими продукции, особенно в последнее десятилетие, далеко не отвечают возросшим требованиям современной строительной индустрии.
2. Общая часть
2.1. Состав предприятия
В данном разделе мы даем представление об отделениях, в которых исполняются отдельные технологические операции, которые составляют производство, которое проектируется.
При производстве керамзита основными технологическими отделениями являются такие как:
- склад сырья;
- подготовительное отделение;
- отделение тепловой обработки;
- сортировочное отделение;
- склад готовой продукции (силоса)
На складе сырья хранятся материалы, которое необходимо для производства керамзита: глина, уголь и вода. Глину можно хранить в открытых складах. Воду в специально предназначенных для нее емкостях.
Подготовительное отделение включает в себя первичную переработку, приготовление глиняного теста, формование сырцовых гранул и опудривание (сухой глиной).
К отделению тепловой обработки относятся сушка во вращающем барабане (Wнач=15-16%, Wкон=3%) обжиг во вращающей печи (t обж. =1200-1250°С) и охлаждение в специальных холодильниках ( от t нач.=900°С до t кон. =50-60°С).
В сортировочном отделении находится грохот, который делит уже готовый продукт по крупности на фракции: до 5мм, 5-10мм, 10-20мм, 20-40мм.
После сортировки керамзит поступает на склад готовой продукции т. е. в силоса, где каждая фракция хранится в отдельных силосах в зависимости от ее размера. Затем его уже транспортируют заказчику в зависимости от расстояния автомашинами или железнодорожными вагонами.
2.2. Номенклатура и характеристика продукции
Согласно ГОСТ 9759-83 предусмотрены следующие фракции керамзитового гравия по крупности зерен: 5... 10, 10...20, и
20...40мм. В каждой фракции допускается до 10% более крупных зерен по сравнению с номинальными размерами. Из-за невысокой эффективности грохочения материала в барабанных грохотах трудно добиться более тщательного разделения керамзита на фракции.
По насыпной плотности керамзитовый гравий подразделяется на 8 марок: М250...600, причем к М250 относится керамзитовый гравий с насыпной плотностью до 250 кг/м3
, к МЗОО - до 300 кг/м3
и т. д. Насыпную плотность определяют по фракциям в мерных сосудах. Чем крупнее фракция керамзитового гравия, тем, как правило, меньше насыпная плотность, поскольку крупные фракции содержат наиболее вспученные гранулы.
Для каждой марки по насыпной плотности стандарт устанавливает требования к прочности керамзитового гравия при сдавливании в цилиндре. По заказам потребителей для приготовления конструкционных легких бетонов стандарт допускает выпуск керамзитного гравия так же М700 и 800 с прочностью при сдавливании в цилиндре соответственно не менее 3,3 и 4,5 МПа.
Стандартная методика предусматривает свободную засыпку керамзитового гравия в цилиндр а затем сдавливание его с уменьшением первоначального объема на 20%. Под действием нагрузки прежде всего происходит уплотнение гравия за счет некоторого смещения зерен и их более компактной укладки. Основываясь на опытных данных, можно полагать, что за счет более плотной укладки керамзитового гравия достигается уменьшение объема свободной засыпки в среднем на 7%. Следовательно, остальные 13% уменьшение объема приходятся на смятие зерен. Если первоначальная высота зерна Д, то после смятия она уменьшается на 13%.
Из этих соображений в ГОСТ 9757-83 «Заполнители пористые неорганические для легких бетонов. Общие технические условия» предусмотрена маркировка пористых заполнителей не только по насыпной плотности, но и по прочности, причем для керамзита и подобного ему пористого гравия числа, определяющие марку по прочности, в среднем в 4,5 раза превышают показатели прочности, полученные при испытании сдавливанием в цилиндре.
Маркировка по прочности позволяет сразу наметить область рационального применения того или иного керамзита в бетонах
соответствующих марок. Более точнее данные получают при испытании заполнителя в бетоне.
Для быстрого определения прочности отдельных зерен керамзитового гравия в СибЗНИИЭП разработан метод испытания их гидростатическим давлением в жидкости (масле), в НИИкерамзите – аналогичный метод объемного сжатия гидропластмассой.
В зависимости от особенностей сырья и технологии производства действительная прочность керамзита может отличаться от расчетной, но предварительная ориентировочная ее оценка все же дает представление о возможности и целесообразности использования данного керамзита для получения бетона требуемых классов по прочности. Приведенные числовые значения расчетной прочности керамзитового гравия показывают, что этот пористый заполнитель может быть достаточно прочным для высокопрочных легких конструкционных бетонов, несмотря на низкие показатели прочности при стандартном испытании.
Зерна керамзитового гравия могут иметь шарообразную или вытянутую форму, что зависит от формы сырцовых гранул. По стандарту среднее значение коэффициента должно быть не более 1,5, зерна с коэффициентом формы более 2,5 в керамзитовом гравии первой категории качества таких зерен допускается не более 15% по массе.
Содержание расколотых зерен в керамзитовом гравии допускается не более 10... 15% по массе в зависимости от категории качества.
Керамзитовый гравий должен выдерживать не менее 15 циклов попеременного замораживания и оттаивания в насыщенном водой состоянии с потерей массы данной фракции не более 8%.
При испытании кипячением потеря массы не должна превышать 5%. Таким испытанием выявляется наличие опасных известняковых включений - «дутиков».
Ограничивается водопоглощение (не более 20...30% по массе за 1ч в зависимости от марки), содержание водорастворимых сернистых и сернокислых соединений. Эти и другие требования стандарта обеспечивают стойкость и долговечность керамзита.
По данным исследователей, изучавших качество керамзита на многих предприятиях, керамзит везде неоднороден. Очевидно, это предопределенно самой технологией получения керамзитового
гравия, когда каждая гранула вспучивается по-разному при неоднородности сырья и непостоянстве температурных условий в печи. В результате керамзитовый гравий - это совокупность неодинаковых вспученных гранул различной плотности и прочности.
Для получения однородности керамзита есть два пути:
- первый путь состоит в совершенствовании технологии производства, усреднение сырья, более тщательно его переработке и грануляции, стабилизации режимов термоподготовки, обжига и охлаждения, улучшения фракционирования.
- второй путь - разделение готовой продукции на фракции не только по крупности, но и по плотности зерен.
Применительно к керамзитовому гравию термин «обогащение» означает разделение его на классы по плотности зерен. Более легкий будет богаче, хорошо вспученными зернами, более тяжелый - богаче менее вспученными, зато более прочными зернами.
Считается, что керамзитовый гравий и другие пористые заполнители подлежат обогащению только в условиях сухой сепарации, что их нельзя увлажнять, поскольку по ГОСТ 9759-83 влажность поставляемого керамзитового гравия должна быть не более 2%. Однако это ограничение касается поставляемого гравия, а при использовании его можно увлажнять, как того требует технология. В технологии легких бетонов нередко рекомендуется предварительно увлажнять пористые заполнители, чтобы уменьшить поглощение ими воды из бетонной смеси.
2.3. Характеристика используемого сырья
Сырьем для производства керамзита служат глинистые породы, относящиеся в основном к осадочным горным.
Для производства керамзита наиболее пригодны монтмориллонитовые и гидрослюдистые глины, содержащие не более 30% кварца.
Основной критерий пригодности глинистого сырья для производства керамзита - способность вспучиваться при
термической обработке в пределах 1050-1250°С и образовывать при этом материал, имеющий ячеистое строение с плотностью в куске в пределах 200-1350 кг/м3
.
Различают слабо-, средне- и хорошовспучивающиеся
глинистые породы с коэффициентом вспучивания соответственно до 2,5; 2,5 - 4,5 и Кв свыше 4,5; чем выше коэффициент вспучивания
сырья, тем меньше плотность керамзита, и тем более ценно это сырью для производства керамзита.
При отсутствии хорошо- и средневспучивающих глинистых пород для производства керамзита, используемого в конструктивно-теплоизоляционных бетонах, сырьем могут служить слабовспучивающиеся глинистые породы с железистыми, органическими и другими добавками.
Установить ценность керамзитового сырья по какому-либо одному признаку весьма затруднительно, поэтому в большинстве случаев определяют ряд свойств: генезис, внешний вид, минералогический, химический и гранулометрический состав, огнеупорность, интервал вспучивания, содержание свободного керамзита засоренность крупнозернистыми (камневидными и карбонатными) включениями, а также структурно-механические свойства, большинство из которых оказывает прямое и притом весьма существенное влияние на основные критерии керамзитового сырья - плотность и коэффициент вспучивания.
Физико-механические и важнейшие технологические свойства глинистого сырья в основном определяется его вещественным, минералогическим, гранулометрическим и химическим составами.
Вещественный состав.
По вещественному составу легкоплавкие глинистые породы делят на следующие группы. К супесям
относят мелкообломочные горные породы с содержанием частиц глинистых минералов 3-10%. Супеси занимают промежуточное положение между песками и суглинками. Они непластичны, обладают слабой связующей способностью и при некоторой оптимальной влажности комкаются. Для производства керамзитового гравия они не пригодны.
Суглинки
- тонкообломочные глинистые породы различного химико-минералогического состава и генетического происхождения с содержанием частиц глинистых минералов 10-30%. По ряду основных свойств они занимают промежуточное положение между глинами и суглинками. Суглинки обладают средней пластичностью и слабой связующей способностью.
Лессовидные глины и суглинки
- пылевидные глинистые породы с преобладанием частиц размером 0,05-0,001мм, от которых зависят основные свойства этих пород. Содержание карбоната кальция в лессах обычно превышает 10%. Поэтому из-за возможного оплавления и деформации при обжиге
заполнителя они в чистом виде без добавок других пород не пригодны для производства керамзита во вращающихся печах.
Сланцы -
обширная группа метаморфических пород разного состава с характерной сланцеватой текстурой, обусловленной параллельным расположением чешуйчатых и таблитчатых минералов.
По минералогическому составу сланцы подразделяют на глинистые, кремнистые, хлоритовые, шунгитовые и др.
Аргиллиты-
глины, затвердевшие в результате природного прессования, дегидратации, перекристаллизации и цементации.
Основную массу аргиллитовых пород составляют глинистые минералы - гидрослюда, монтмориллонит, каолинит, хлориты с примесью кварца, полевых шпатов, слюд и т. д. Они также содержат до 50-80% кремнезема, до 20% и более глинозема и незначительное количество щелочей.
Трепел
- высокопористая, слабо сцементированная, рыхлая, осадочная порода. Основной оксид породы – SiO2 (70-90%).
Диатомиты -
легкая, рыхлая, слабосцементированная порода, состоящая преимущественно из микроскопических кремнистых панцирей одноклеточных диатомитовых водорослей.
Опока
- осадочная кремнистая горная порода с полураковым изломом, на 90% состоящая из мелкозернистого аморфного водного кремнезема с примесями глинистых веществ, карбонатов, кварца, полевого шпата, вулканического стекла, органических остатков и др.
Минералогический состав.
Глинистые горные породы -механическая смесь различных глинообразующих минералов и сопутствующих примесей. Мономинеральные глины в природе встречаются редко. Поэтому минеральный тип глины обычно характеризуют преобладающим в рассматриваемой породе глинообразующим минералом.
С появлением новых методов исследования, главным образом рентгеноструктурного и термографического анализов, было установлено, что основу большинства глинистых пород составляют различные глинистые материалы, находящиеся не в аморфном, а в кристаллическом состоянии, и что именно эти минералы те или другие основные свойства глинистым породам. Наиболее распространенны минералы монтмориллонита, гидрослюд или иллита, хлорита, каолинита и вермикулита.
Гранулометрический состав.
Все минералы, входящие в состав полиминеральных легкоплавких глин, можно подразделить на первичные и вторичные.
К первичным относят минералы, входившие в состав минеральных пород, подвергшихся выветриванию: кварц, полевые шпаты, слюды, роговые обманки, авгиты, граниты, эпидот, турмалин, рутил, циркон, апатит, кальцит, доломит, серпентин, ставролит, титанит, магнетит, бетит, ангидрит, амфиболы и многие др.
К вторичным - минералы, образовавшиеся в процессе выветривания, переотложения и преобразования различных пород, в первую очередь глинообразующие минералы группы монтмориллонита, гидрослюд, гидрохлорида, вермикулита, каолинита, а также водные оксиды алюминия, оксиды и гидроксиды железа, и многие другие.
Первичные материалы в глинах, как правило, более прочны и химически устойчивы, чем вторичные, что проявляется в том, что первичные минералы сосредотачиваются главным образом в более крупных фракциях глинистого сырья размером более 0,001мм, тогда как вторичные минералы составляют основу самых тонкодисперсных фракций.
Частицы крупнее 0,01мм представлены в глинах преимущественно кварцем при незначительном содержании слюды, полевых шпатов и некоторых других первичных минералов.
Химический состав
легкоплавких пород обусловлен их минералогическим составом, количеством и составом примесей и так же разнообразен, как и минералогический состав.
В легкоплавких глинистых породах, как показали исследования, состав основных составляющих, определяемых химическим анализом, варьируется в весьма широких пределах: SiO2
- 48-80%; А12
O3
- 7-27%; Fе2
O3
и FeO - 0,5-13,5%; CaO- 0,5-20%; MgO- 0,3-12%; К2
О и Na2
О- 0,5-7,5%.
В ряде случаев природное глинистое сырье может быть улучшено введением добавок.
Например коэффициент вспучивания
можно повысить, добавив в глину примерно 1% мазута, солярового масла и других органических веществ, железистые добавки, в частности отходы производства серной кислоты из спирта - пиритные огарки.
Если золы и шлаки вводятся в больших дозах, сопоставимых с расходом глинистого сырья, то получаемый керамзит обычно называют глинозольным или глиношлаковым. Чаще всего добавки вводятся в сравнительно небольших дозах, и основным сырьем для производства керамзитового гравия остаются глинистые породы.
Для расширения температурного интервала вспучивания используют такой прием, как опудривание сырцовых глиняных гранул порошком огнеупорной глины, мелким кварцевым песком или иным тугоплавким порошком, что позволяет повысить температуру обжига и при этом избежать оплавление гранул.
Химический, минералогический и гранулометрический составы легкоплавких глинистых пород в решающей степени влияют на их вспучивание и образование ячеистой структуры керамзита.
Химический состав глинистых пород оказывает значительное влияние на процесс вспучивания главным образом потому, что он обуславливает образование пиропластической массы при обжиге с оптимальной для порообразования вязкостью в пределах определенного интервала температур (50-200°).
Однако, каким бы благоприятным не было сочетание химических составляющих, создающих необходимые
реологические условия для порообразования размягченной массы, этого не достаточно, чтобы произошло само вспучивание.
Химический состав вспучивающихся глинистых пород колеблется в широких пределах. Поэтому важно установить пределы содержания каждого из компонентов и их соотношения для вспучивающегося и невспучивающегося глинистого сырья, а для сырья, обладающего различной вспучиваемостью.
3. Технологическая часть
3.1. Обоснование принятой технологии производства
Основное оборудование керамзитовых предприятий оборудование для обжига. В настоящие время наиболее распространен метод обжига керамзитового гравия в одно- и двухбарабанных вращающихся печах; кроме того, осваивается промышленное производство керамзитового гравия и песка в печах кипящего слоя.
Достоинство вращающихся печей как аппаратов для вспучивания глинистых пород - возможность получать заполнителей, зерновой состав, которого в основном соответствует нормативным требованиям.
Другое важное достоинство вращающихся печей состоит в том, что зерна материала в них вспучиваются в свободном объеме, не ограниченном стенками или неподвижной массой таких же зерен. Поэтому процесс может быть очень интенсивным, что позволяет получать 500 кг/м3
при коэффициенте выхода 2-3.
К недостаткам вращающихся печей помимо их низкой тепловой экономичности относится трудность обжига в них слабо- и средневспучивающихся глинистых пород с малым интервалом вспучивания.
При обжиге керамзитового гравия во вращающихся печах важнейшим признаком для типизации керамзитового производства служат применяемые способы переработки сырья и приготовление полуфабриката. Опыт показал, что какого-либо универсального метода переработки глин и их грануляции в полуфабрикатах, пригодный для вспучивания, не существует. Более того способы изготовления полуфабриката, его размеры, форма, влажность и другие параметры могут и должны изменятся в зависимости от свойств употребляемого сырья.
Решающее значение при выборе способов изготовления полуфабриката имеют физические, главным образом структурно-механические свойства глинистых пород: плотность, однородность, влажность, пластичность, структура и т.д.
Выбор способа переработки сырья определяется свойствами
исходного сырья, а качество заполнителя зависит от режима термической обработки, при котором создаются оптимальные условия вспучивания подготовленных сырцовых гранул (зерен).
Различают четыре основных технологических схемы подготовки сырцовых гранул, или четыре способа производства керамзита: сухой, пластический, порошково-пластический и мокрый.
В своей курсовой работе я принимаю производство керамзита пластическим способом, потому, что он допускает использование широко встречающегося рыхлого глинистого сырья, корректирующих добавок и позволяет получать керамзит с различной гаммой свойств.
Классификация способов производства и добавок разработаны достаточно детально, однако обобщающей работы по систематизации достигнутых технологических решений пластическим способом пока нет.
Пластический способ подготовки сырья и приготовления полуфабриката применяют при использовании увлажненных пластичных и рыхлых глинистых пород как однородного, так и неоднородного состава.
3.2. Описание технологии
Пластический способ подготовки сырья и приготовления полуфабриката применяют при использовании увлажненных пластичных и рыхлых глинистых пород как однородного, так и неоднородного состава. При пластическом способе производства керамзита в глиняную массу могут вводиться добавки, повышающие склонность к вспучиванию исходного сырья, тогда как при сухом способе, когда полуфабрикат получают непосредственно из природной породы, это исключается.
При переработке по пластическому способу вспучиваются, однородные глинистые породы гранулируются в полуфабрикат определенной формы размером 7-15мм в поперечнике. Более тщательной переработки такому сырью не требуется, так как оно уже самой природой гомогенизировано, и химико-минералогические составляющие в нем распределены равномерно. Это обстоятельство значительно упрощает изготовление гранулированного материала из подобного сырья.
Таки образом, технология обработки однородных глин сводится к их грануляции на упрощенных механизмах типа дырчатых и прессующих вальцов. При этом куски материала можно направлять непосредственно во вращающуюся печь на обжиг или сначала сушить в отдельных сушильных установках. Следует, однако, иметь в виду, что однородное керамзитовое сырье встречается весьма редко. Переработка глинистых пород неоднородного состава по пластическому способу имеет целью разрушение природной структуры сырья, его гомогенизацию и изготовление полуфабриката с размером зерен в пределах примерно 7-15 мм в поперечнике, пригодного для обжига со вспучиванием во вращающихся печах.
Механизм и оборудование для переработки и грануляции сырья выбирают в зависимости от склонности к вспучиванию и физико-механических свойств исходного сырья: влажности, плотности, вязкости, пластичности, однородности состава и т.д. При этом необходимо учитывать, что основная задача переработки неоднородного глинистого сырья по пластическому способу -тщательная его гомогенизация в целях разрушения природной структуры, равномерного распределения по всей массе химических и минералогических составляющих, влаги, а также твердых и жидких добавок, применяемых для интенсификации процессов образования керамзита и улучшения его качества.
Степень переработки глинистого сырья оказывает исключительно большое влияние на качественные показатели заполнителя - его плотность, прочность, водопоглощение, морозостойкость и т.д. Чем однороднее глинистая масса и равномернее распределены в не составляющие, влага и добавки, тем интенсивнее протекают физико-химические процессы при обжиге, равномернее поризация материала, мельче образующие поры, ниже плотность и выше прочность керамзита, меньше разброс качественных показателей готового продукта. Опыт показывает, что улучшением переработки глинистого сырья можно достигнуть снижение плотности керамзита, получаемого из рада неоднородных по составу, особенно трудно перерабатываемых, уплотненных, плохо размокаемых глин, в 1,5-2 раза и настолько же повысить его относительную прочность.
Переработка глинистого сырья - мероприятие комплексное. Оно начинается еще на карьере при добыче и кончается при формировании гранулированного сырца.
Глина подается автосамосвалами непосредственно из карьера в пластичный ящичный подаватель. Над решеткой бункера ящичного подавателя установлена рыхлительная машина. Ящичным подавателем и ленточным конвейером глина подается в камневыделительные вальцы типа СМ-416А (производительность 35,5 м3
/ч). После камневыделительных вальцов второй ленточный конвейер транспортирует глину в подготовительное отделение, где она обрабатывается на установленных друг за другом глиномешалке и дырчатых вальцах. Двухвальная глиномешалка с пароувлажнением перемешивает глину и подогревает и оттаивает ее в зимний период. В случае применения средневспучивающихся глинистых пород в глиномешалку подают жидкие органические добавки, а при необходимости доувлажнения ( например, в летнее время) - воду. Производительность мешалки 8-22 м3
/ч. Гранулы формуются в дырчатых вальцах типа СМ-369А
производительностью 40 м/ч. Сырьевые гранулы из дырчатых вальцов опудривают порошком огнеупорной глины, затем они поступают в загрузочную камеру сушильного барабана, который установлен на нулевой отметке параллельно вращающейся печи. Подсушенные гранулы транспортируются ленточным конвейером в промежуточную емкость. Равномерная подача сухих гранул во вращающуюся печь из бункера промежуточной емкости
осуществляется тарельчатым питателем диаметром 1700 мм. Гранулы обжигают во вращающейся печи длиной 40 и диаметром 2,5м. Обожженные гранулы керамзита охлаждаются в холодильнике шахтного типа, из которого керамзит подается пневмотранспортом в силосный склад.
Для получения фракционированного продукта керамзит рассевают на четыре фракции с размером зерен до 5, 5-10, 10-20, 20-40мм распределяют по силосам двумя ленточными конвейерами. Склад керамзита состоит из девяти силосов по 200т каждый. Из силосов керамзит выдают в автомашины или железнодорожные вагоны.
3.3. Технологические режимы работы и расчеты.
Режим работы предприятия определяется технологическими особенностями производства и характеризуется количеством рабочих дней в году, количеством смен в день и продолжительностью смены в часах.
|
|
|
|
|
|
Таблица 1
|
|
|
Режим работы предприятия
|
|
|
№
|
Наименован
|
Кол-во
|
Кол-
|
Продолжи-
|
Годовой
|
Коэф.
|
Годовой
|
пп
|
цехов и
|
рабочих
|
во
|
тельность
|
фонд
|
использов
|
фонд
|
|
отделений
|
дней
|
смен
|
смен в ч.
|
эксплуат.
|
эксплуат.
|
рабочего
|
|
|
в году
|
в день
|
|
времени, ч
|
времени
|
времени
|
1
|
2
|
3
|
4
|
5
|
6
|
7
|
8
|
2
|
Склад сырья
|
365
|
3
|
8
|
8760
|
0,92
|
8059,2
|
3
|
Подготови
тельное отделение
|
365
|
3
|
8
|
8760
|
0,92
|
8059,2
|
4
|
Отделение тепловой обработки
|
365
|
3
|
8
|
8760
|
0,92
|
8059,2
|
5
|
Отдел сортировки
|
365
|
3
|
8
|
8760
|
0,92
|
8059,2
|
6
|
Силосные склады
|
365
|
3
|
8
|
8760
|
0,92
|
8059,2
|
Производительность цеха или завода рассчитывается исходя из заданного годового объема продукции и принятого режима работы предприятия.
Возможные производственные потери на готовую продукцию устанавливаются на основании «Норм технологического проектирования».
Таблица 2
Производительность предприятия
№пп
|
Наименование продукции
|
Единицы измерения
|
Производительность
|
в час
|
в смену
|
в день
|
в год
|
1
|
керамзит
|
м3
|
11,53
|
92,2
|
276,7
|
101000
|
Потери сырьевых материалов определяется исходя из годовой программы и потери на единицу продукции. При расчете необходимо учитывать производственные потери при переработке и транспортировке.
Ориентировочно количество потерь материала, могут быть принятые следующие:
-при дроблении и последующему транспортированию - до 1%;
-при подготовке, переработке и формовании гранул - до 1%;
-при хранении сыпучих материалов на складах - до 1%.
Таблица 3
Потери сырьевых материалов на единицу времени
№ пп
|
Наименование материала
|
Единицы измерения
|
Количество на ед. продукции
|
Примечание
|
1
|
Глина
|
м3
/т
|
0,34/0,544
|
Р=1600
|
2
|
Уголь
|
м3
/т
|
0,065/0,054
|
10%, Р=1200
|
3
|
Вода
|
м3
|
0,108
|
W=16-18%
|
Таблица 4
Потери сырьевых материалов и полуфабрикатов
№ пп
|
Наименование продукции
|
Единицы измерения
|
|
Потребность
|
|
в час
|
в смену
|
вдень
|
в год
|
1
|
Глина
|
м3
|
4,37
|
35,09
|
105,27
|
35370,2
|
2
|
Уголь
|
м3
|
0,84
|
6,71
|
20,12
|
6761,95
|
3
|
Вода
|
м3
|
1,35
|
10,82
|
32,46
|
10908
|
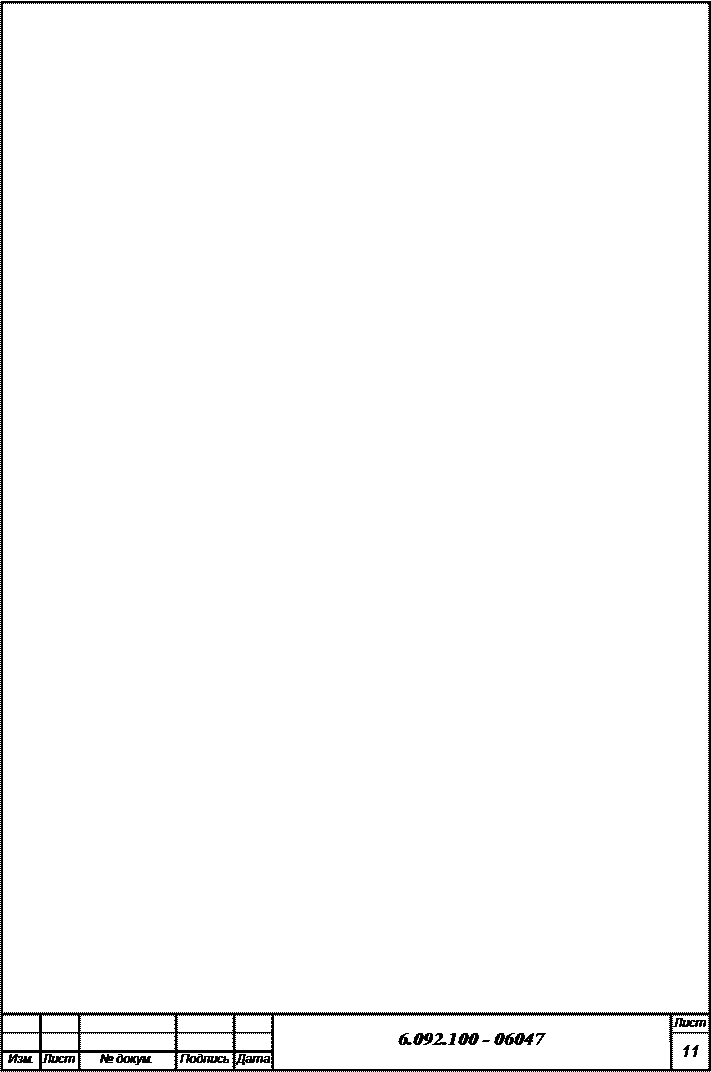
Потери сырьевых материалов и полуфабрикатов:
Глина = 0,34*10100*1,03=35370,2 м3
/год
Уголь = 0,054*101000*1,01=6761,95 м3
/год
Вода = 0,108*101000=10908 м3
/год
|