Федеральное агенТство по образованию
ГОСУДАРСТВЕННОЕ ОБРАЗОВАТЕЛЬНОЕ УЧРЕЖДЕНИЕ ВЫСШЕГО ПРОФЕССИОНАЛЬНОГО ОБРАЗОВАНИЯ
"ТЮМЕНСКИЙ ГОСУДАРСТВЕННЫЙ НЕФТЕГАЗОВЫЙ УНИВЕРСИТЕТ"
ИНСТИТУТ НЕФТИ И ГАЗА
КАФЕДРА АВТОМАТИЗАЦИИ И УПРАВЛЕНИЯ
ПОЯСНИТЕЛЬНАЯ ЗАПИСКА
к выпускной работе по дисциплине
«Проектирование микропроцессорных систем автоматизации» на тему:
СИСТЕМА УПРАВЛЕНИЯ СЕПАРАТОРОМ НА
ПРОМЫСЛОВОЙ КС
Тюмень 2009
Реферат
Пояснительная записка 45с., 5 рис., 10 табл., 10 источников, 5 прил.
ГАЗОВЫЙ СЕПАРАТОР, СРЕДСТВА АВТОМАТИЗАЦИИ, ДАТЧИК, КОНТРОЛЛЕР, МОДУЛЬ, РЕГУЛИРОВАНИЕ, ДАВЛЕНИЕ, УРОВЕНЬ, ТЕМПЕРАТУРА, ИСПОЛНИТЕЛЬНЫЙ МЕХАНИЗМ.
Объектом исследования является сепарационная установка первой ступени - ГС V 50м3
.
Цель работы - разработка системы автоматизации ГС на компрессорной станции на базе программируемого логического контроллера SLC 500 фирмы Allen Bradley.
В работе произведен выбор технических средств автоматизации, разработан алгоритм управления ГС и программно реализован для контроллера SLC 500, разработана схема внешних электрических соединений, произведен расчет системы автоматического регулирования давления газа в сепараторе.
Содержание
Введение…………………………………………………………………………..
|
6
|
1
|
Технология отделения газа ………………………………………………...
|
7
|
2
|
Автоматизация объекта…………………………………………..................
|
11
|
3
|
Программируемый логический контроллер………………………………
|
17
|
3.1 Обоснование выбора контроллера…………………………………......
|
17
|
3.2 Выбор конфигурации и расчет электропотребления.………………...
|
19
|
3.3 Разработка алгоритма управления технологическим процессом…....
|
22
|
4
|
Расчет контура регулирования давления в сепараторе…………………...
4.1 Определение математической модели объекта……………………….
4.2 Расчет оптимальных настроек регулятора…………………………….
|
2 24
24
26
|
Заключение……………………………………………………………………….
|
30
|
Список используемых источников……………………………………………...
|
31
|
Приложение А Схема автоматизации..…………………………........................
|
32
|
Приложение Б Блок схема алгоритма…………...……………….......................
|
33
|
Приложение В Расчет оптимальных настроек регулятора...………………….
|
34
|
Приложение Г Таблица RTU……………………………… ……………….......
|
35
|
Приложение Д Текст программы для контроллера……....…………………....
|
36
|
Список сокращений
КС – компрессорная станция.
НГС – газовый сепаратор.
ПЛК – программируемый логический контроллер.
ПО – программное обеспечение.
ЧЭ – чувствительный элемент.
АСУ ТП – автоматизированные системы управления технологическими процессами.
МЭОФ – механизм исполнительный электрический однооборотный фланцевый постоянной скорости.
ИМ – исполнительный механизм.
БСПТ – блок сигнализации положения токовый.
БП – блок питания.
БРУ – блок ручного управления.
ПБР – пускатель бесконтактный реверсивный.
БТВИ – блок токовых выходов искробезопасный.
Введение
Развитие газовой и ряда смежных отраслей промышленности сегодня в значительной степени зависит от дальнейшего совершенствования эксплуатации и обслуживания систем трубопроводного транспорта природных газов из отдаленных регионов в промышленные и центральные районы страны.
Для оптимального управления технологическими процессами на КС используются современные технические средства автоматизации, без которых на сегодня невозможен качественный контроль и работа всего процесса добычи и транспорта газа.
При создании автоматизированных объектов ставятся следующие основные цели и задачи:
- Превращение объектов в полностью автоматизированные технологические звенья, работающие в автоматическом режиме в соответствии с заданием вышестоящего уровня.
- Обеспечение надежной работы газодобывающих, газотранспортных и газоперерабатывающих объектов за счет оптимального управления технологическими процессами, автоматического обнаружения и локализации аварийных ситуаций.
- Достижение высоких технико-экономических показателей функционирования предприятий за счет повышения производительности труда, снижения удельных затрат энергоресурсов, эффективного использования установленных мощностей.
В связи с этим, задачей выпускной работы является разработка системы автоматического управления и регулирования, построенной на базе микропроцессорной системы контроля и управления. Для достижения этой цели разработана схема автоматизации, составлена блок схемы алгоритма, управления, написана программа для выбранного контроллера в соответствии с алгоритмом.
1 Технология отделения газа
Сепарация (от лат. separatio - отделение), сепарирование в технике, процессы разделения смесей разнородных частиц твёрдых материалов, смесей жидкостей разной плотности, эмульсий; взвесей твёрдых частиц или капелек в газе или паре. Газовый сепаратор - аппарат для очистки продукции газовых и газоконденсатных скважин от капельной влаги и углеводородного конденсата, твёрдых частиц и др. примесей. Примеси затрудняют транспортировку газа и являются причиной коррозии трубопроводов, закупорки (частичной или полной) скважин, шлейфов и промыслового оборудования вследствие образования пробок гидратов или льда [7].
Каждый пункт вывода отсепарированного газа называется ступенью сепарации газа.
Многоступенчатая сепарация применяется для постепенного отвода свободного газа по мере снижения давления. Она применяется при высоких давлениях на устье скважин.
Газожидкостную смесь из скважины направляют сначала в ГС высокого давления, в котором из нефти выделяется основная масса газа. Этот газ может транспортироваться на большие расстояния под собственным давлением.
Из сепаратора высокого давления нефть поступает в сепаратор среднего и низкого давления для окончательного отделения от газа.
Сепарация газа от жидкости может происходить под влиянием гравитационных, инерционных сил. В зависимости от этого и различают гравитационную, инерционную и сетчатую сепарации, а газосепараторы - гравитационные, сетчатые и роторные.
Гравитационная сепарация осуществляется вследствие разности плотностей жидкости и газа, т.е. под действием их силы тяжести. Газосепараторы, работающие на этом принципе, называются гравитационными.
Инерционная сепарация происходит при резких поворотах газожидкостного потока. В результате этого жидкость, как более инерционная, продолжает двигаться по прямой, а газ меняет свое направление. В результате происходит их разделение. На этом принципе построена работа роторного газосепаратора, осуществляемая подачей газонефтяной смеси в циклонную головку, в которой жидкость отбрасывается к внутренней поверхности и затем стекает вниз в нефтяное пространство газосепаратора, а газ двигается по центру циклона.
Сетчатая сепарация основана на явлении селективного смачивания жидкости на металлической поверхности. При прохождении потока газа с некоторым содержанием жидкости через жалюзийные насадки (каплеуловители) капли жидкости, соприкасаясь с металлической поверхностью, смачивают ее и образуют на ней сплошную жидкостную пленку. Жидкость на этой пленке держится достаточно хорошо и при достижении определенной толщины начинает непрерывно стекать вниз. Это явление называется эффектом сетчатой сепарации.
Сепараторы типа ГС предназначены для отделения газа от продукции газовых скважин на первой и последующей ступенях сепарации жидкости и газа, включая горячую сепарацию на последней ступени.
Выпускается нормальный ряд сепараторов ГС с пропускной способностью по жидкости 2000¸30000 т/сут [1].
Газо-жидкостной сепаратор СЦВ-7 предназначен для глубокой очистки газового потока от капельной, мелкодисперсной, аэрозольной жидкости, масла и тведрдых примесей. При сепарации бинарной смеси (газ - жидкость) одновременно осуществляется и процесс разгазирования жидкой фазы. Используются на предприятиях нефтегазовой, химической, металлургической, машиностроительной, легкой промышленности.
Принцип работы сепаратора:
Газожидкостная смесь, подводится в аппарат через вводной патрубок (5), распложенный в верхней его части. Установка входного патрубка, смещенного по горизонтам относительно осевой линии корпуса на 1/2 его диаметра позволяет решить задачу сохранения величины центробежного эффекта на входе газожидкостной смеси в аппарат, практически не ослабив надежности корпуса сепаратора. Дефлектор (6) препятствует поступлению газа в осевую зону сепарационного пакета (8) без предварительного разделения газовзвеси.
Использование дефлектора с изменяющимся данным сечением (в начале увеличивает свое сечение до максимально допустимой величины, после чего сужается по горизонтали и возрастает по высоте, сохраняя при этом площадь поперечного сечения в максимально широком участке) позволяет удалить по горизонтали на выходе из дефлектора газожидкостный поток от щелевых отверстий сепарационного пакета (8), а по высоте равномерно рассредоточить и в тоже время за счёт минимальной щели «придавить» жидкую фазу к внутренней поверхности сепаратора, что в конечном счете, улучшает процесс сепарации.

Рисунок 1.1 - Сепаратор СЦВ-7 (схематический рисунок)
В пространстве, образованном стенкой корпуса (1) и пластинами (9) из газового потока выделяется основная масса жидкости. Капли жидкости отбрасываются центробежной силой на стенки корпуса (1) сепаратора и под действием гравитационных сил, по ходу газового потока, нисходящей спирали транспортируются через кольцевой зазор (19) к сливному патрубку (18).
Исполнение дефлектора с узкой щелью удаленного от направляющих щелевых сепарационного пакета создает значительный зазор между вращающейся по внутренней поверхности корпуса жидкостной пленке и щелевыми каналами, засасывающими газовый поток в направляющие пакета, при этом условия сепарации отделенной жидкой фазы идеальные.
Из-за того, что по ходу движения жидкостного потока установлена карман-ловушка, состоящая из боковых направляющих корпуса (1) и изогнутой пластины (20), а также крышки, составляющей часть перегородки (2), условия для удаления жидкой фазы идеальные, в этом конструктивном исполнении дефлектор полностью изолирует наличие жидкой фазы вблизи вертикальных лопастей. Направляемая жидкость сливается через открытую нижнюю часть ловушки-кармана.
Мелкодисперсная капельная жидкость, не осевшая на корпусе (1) попадает на наружную поверхность пластин (9) и транспортируется газовым потоком через входные тангенциальные щели, попадая на их внутреннюю поверхность.
В конце верхней суженой части дефлектора (6) установлена дугообразная пластина (7) нисходящая по ходу газожидкостного потока и направленная по отношению к горизонтальной прямой под углом 25°, такое инженерное решение позволило вращающийся между корпусом и сепарационным пакетом вектор газожидкостного потока направить по нисходящей кривой, в результате чего газовый слой, вращающийся непосредственно по внутренней поверхности сепарационного пакета разделился на три слоя со своими векторами осевых скоростей: непосредственно у стенки направлен вниз, далее незначительный слой «неподвижный» и следующий третий основной слой направлен вверх. Наличие первого слоя с направлением вектора осевой скорости вниз позволило сгонять (в зависимости от режима - росу, капли, пленку) вниз избежав дополнительных направляющих, удаляющих по спирали вниз, частицы жидкой фазы. Опускаясь по внутренней поверхности пластин (9) частицы жидкости, приблизившись к нижней кромке, соскальзывают и попадают на поверхность шайбы (17), откуда через кольцевой зазор (19) транспортируются в направлении сливного патрубка (18) [3].
2 Автоматизация объекта
Не существует отрасли промышленности, в которой не было бы потребности применения АСУТП. Одними из главных преимуществ АСУТП являются снижение, вплоть до полного исключения, влияния так называемого человеческого фактора на управляемый процесс, сокращение персонала, минимизация расходов сырья, улучшение качества исходного продукта, и в конечном итоге существенное повышение эффективности производства. Основные функции, выполняемые подобными системами, включают в себя контроль и управление, обмен данными, обработку, накопление и хранение информации, формирование сигналов тревог, построение графиков и отчетов.
Структура автоматизированной системы управления можно разделить на три основные уровня. В первый низший уровень, входят датчики, исполнительные механизмы, первичные и вторичные преобразователи. В средний входят программируемые контроллеры (ПЛК), в верхний ЭВМ. В данной работе рассмотрены первые два уровня.
В С-1 осуществляется дистанционный контроль:
- давления с помощью датчика давления;
- температуры с помощью датчика температуры;
- уровня с помощью датчика уровня;
- предусмотрена сигнализация максимального и минимального давления;
- предусмотрена сигнализация максимального и минимального уровня.
Регулирование и автоматическое поддержание уровня осуществляется при помощи дискового регулирующего затвора с электроприводом, установленного на линии выхода нефти из сепаратора. Выходной сигнал с датчика (4-20мА) поступает на контроллер.
Схема автоматизации системы управления ГС-1 приведена в приложении А.
Для автоматизации работы сепаратора выбирается оборудование удовлетворяющее следующим требованиям:
- способность работать в неблагоприятных условиях;
- надежность;
- диапазон измерения;
- погрешность измерения;
- наличие определенных видов защиты;
- несложный монтаж;
- наличие унифицированного выходного сигнала.
При выборе датчиков, для измерения избыточного давления, уровня и температуры в сепараторе, учитываются диапазон измерений, основная приведенная погрешность, работа во взрывоопасной среде, удобство монтажа и обслуживания, цены. Сравнительные характеристики датчиков приведены в таблице 2.1, 2.2, 2.3.
Таблица 2.1 – Технические характеристики датчиков для измерения давления
Характеристика
|
Метран 100ДИ
|
Rosemount
CDS-3151
|
Сапфир-22ДИ
|
минимальный
|
0-0,04
|
0,25
|
0,15
|
максимальный
|
100
|
40
|
60
|
Основная погрешность измерений, %
|
0,1
|
0,1
|
0,15
|
Взрывозащищенное исполнение
|
Еx, Bh
|
Exd, Exia
|
Exsd
|
Выходной сигнал, мА
|
0-5, 0-20,4-20
|
4-20
|
4-20; 0-5; 0-20;
|
По характеристикам датчики давления серии Метран-100 предназначены для работы в системах автоматического контроля, регулирования и управления технологическими процессами и обеспечивают непрерывное преобразование в унифицированный токовый и/или цифровой на базе HART-протокола выходной сигнал дистанционной передачи следующих измеряемых величин. Датчик Метран-100 является относительно недорогим [4].
Таблица 2.2 – Технические характеристики датчиков для измерения уровня
Характеристика
|
ДУУ2М
|
Rosemount 5400
|
NivoPRESS D
|
Длина чувствительного элемента, м
|
1,5 – 4 (жесткий ЧЭ)
|
До 6 (Радарный уровнемер)
|
0 – 30 (Радарный уровнемер)
|
Продолжение таблицы 2.2
Характеристика
|
ДУУ2М
|
Rosemount 5400
|
NivoPRESS D
|
Темп-ра контролируемой среды, °С
|
-45 ÷ +120
|
-40 ÷ +150
|
-25 ÷ +125
|
Давление контролируемой среды, МПа
|
до 2
|
До 1
|
До 1
|
Темп-ра внешней среды, °С
|
-45 ÷ +75
|
-40 ÷ +70
|
-40 ÷ +50
|
Абсолютная основная погрешность по уровню, %
|
± 1
|
±1
|
±0,2
|
Для измерения уровня в сепарационной установке, использован уровнемер поплавковый ДУУ4М, удовлетворяющий в основном всем требования. Уровнемер состоит из датчика ДУУ2М, обеспечивающего измерение текущих значений контролируемых параметров и блока БТВИ3, обеспечивающего питание подключенного к нему датчика и формирование выходных информационных сигналов. Датчик уровня поплавковый ДУУ4М является относительно не дорогим [2].
Таблица 2.3 – Технические характеристики БТВИ3
Характеристика
|
Значение
|
Температура внешней среды °С
|
+5 ÷ +45
|
Абсолютная основная погрешность по уровню, %
|
± 1
|
Абсолютная основная погрешность по температуре, %
|
± 1
|
Манометры, показывающие сигнализирующие ДМ-2005 предназначены для измерения избыточного и вакуумметрического давления различных сред и управлений внешними электрическими цепями от сигнализирующего устройства прямого действия.
Таблица 2.4 – Технические характеристики манометра ДМ 2005
Характеристика
|
МП3-Уф
|
ДМ 2005
|
Напряжение внешних коммутируемых цепей, В
|
220
|
220
|
Диаметр корпуса, мм
|
100
|
150
|
Класс точности
|
1,5
|
1,5
|
Пределы измерений, кгс/см2
|
0.1; 0..1,6; 0..2,5; 0..4; 0..6; 0..10; 0..16; 0..25, 0..40, 0..60
|
0..1; 0..1,6; 0..2,5; 0..4; 0..6; 0..10; 0..16; 0..25
|
Температура окружающей среды, °С
|
-50° до +60
|
-50° до +60
|
Диапазон измерений избыточного давления
|
0-75% диапазона показаний
|
0-75% диапазона показаний
|
Чувствительный элемент первичного преобразователя и встроенный в головку датчика микропроцессорный преобразователь преобразуют измеряемую температуру в унифицированный выходной сигнал постоянного тока.
Термометры показывающие предназначены для измерения температуры жидких и газообразных сред
Таблица 2.5 – Технические характеристики датчиков для измерения температуры
Характеристика
|
Метран-276
|
ТКП-100 М1
|
Пределы измерения, °С
|
-50...+180/0...+500
|
–25…+35; –25…+75; 0…+50; 0…+100; 0…+120; +100…+200; +200…+300
|
Погрешность, %
|
±0,5; 1
|
1; 1,5
|
Форма представления информации выходной сигнал, мА
|
0..5; 4..20; 4..20
|
0..5; 4..20; 4..20
|
Взрывозащищенное исполнение
|
Exia, Exd
|
Ex
|
Для измерения температуры в сепараторе использован датчик Метран-276, удовлетворяющий всем требованиям, а также является относительно не дорогим.
Для переключения цепей управления исполнительными устройствами в АСУ ТП применен блок ручного управления БРУ-33, который имеет:
- входов: 1;
- выходов: аналоговых – 1, дискретных – 6.
Выполняемые функции:
- ручное переключение режимов управления исполнительным устройством с автоматического на ручной и обратно;
- индикация положения регулирующего органа стрелочным индикатором;
- кнопочное управление интегрирующим исполнительным устройством;
- преобразование выходного сигнала индуктивного или реостатного датчика исполнительного механизма в унифицированный сигнал;
- световая индикация выходного сигнала регулирующего устройства с импульсным выходным сигналом [10].
Таблица 2.6 – Технические характеристики блока ручного управления БРУ-33
Характеристика
|
Значения
|
Питание блока, В
|
220
|
Потребляемая мощность, Вт
|
Не более 4
|
Масса, кг
|
0,7
|
Габариты, мм
|
80x40x197
|
Выходной сигнал, мА
|
0..5, 4..20
|
Также в данной работе применен пускатель ПБР-3А предназначен для управления электроисполнительными механизмами с 3-х фазным асинхронным двигателем (АОЛ, АИР, 4А). Пускатели ПБР-3А обеспечивают пуск, реверс и защиту от перегрузки 3-х фазного асинхронного электродвигателя с короткозамкнутым ротором [8].
Таблица 2.7 – Технические характеристики пускателя бесконтактного реверсивного ПБР-3А
Характеристика
|
Значение
|
Быстродействие, мс
|
25
|
Напряжение источника питания цепей управления, В
|
22-26
|
Электрическое питание, В
|
220/380
|
Потребляемая мощность, Вт
|
57
|
Для соединения приборов нижнего уровня с контроллером используются провода монтажные гибкие с комбинированной волокнистой и поливинилхлоридной изоляцией типа МГШВЭ.
Провода МГШВЭ предназначены для работы при рабочем переменном напряжении до 380 В для сечений 0,08 – 0,14 мм² и 1000 В для сечений 0,2 – 1,5 мм² частоты до 1000 Гц и постоянном напряжении до 500 и 1500 В соответственно.
Конструкция:
- токопроводящая жила – из медных проволок, луженых оловянно-свинцовым припоем;
- изоляция – два слоя полиэфирной нити во взаимно-противоположных направлениях и поливинилхлоридный пластикат;
- экран – поверх изоляции в проводах марки МГШВЭ накладывается экран из медных проволок номинальным диаметром не более 0,15 мм, луженых оловянно-свинцовым припоем;
- количество жил – 1, 2, 3.
Технические характеристики проводов МГШВ:
- Электрическое сопротивление изоляции, пересчитанное на 1 м длины, МОм, не менее: в нормальных климатических условиях – 2х104; при температуре до 70°С – 1х10³; при относительной влажности воздуха 98% и температуре до +35°С – 1х10².
- Провода устойчивы к: синусоидальной вибрации, механическому удару одиночного и многократного действия, линейному ускорению и акустическому шуму – по ОТУ; атмосферным конденсируемым осадкам, статической пыли, соляному туману, плесневым грибам; воздействию бензина, минерального масла и соленой воды.
- Провода не распространяют горение при одиночной прокладке.
- Диапазон рабочих температур: от -50 до +70°С.
- Минимальная наработка проводов – 10 000ч.
- Срок службы проводов – 15 лет [3].
3 Программируемый логический контроллер
3.1 Обоснование выбора контроллера
ПЛК представляют собой устройство, предназначенное для сбора, преобразования, обработки, хранения информации и выработки команд управления. Они реализованы на базе микропроцессорной техники и работают в локальных и распределенных системах управления в соответствии с заданной программой. От небольших до мощных и высокоскоростных систем ПЛК обеспечивают самых требовательных заказчиков исчерпывающими возможностями и гибкостью при реализации современных сетевых решений в распределенных системах управления и контроля [3].
При выборе программируемого логического контроллера необходимо учитывать следующие факторы:
- характер применения (автономно, в качестве станции в распределенной сети, в качестве удаленной станции);
- функциональное назначение (ПИД – регулирование, управление системами тепло и водоснабжения, измерение и счет данных, терморегулирование, аварийная защита и блокировка и т.д.);
- количество входов/выходов (цифровых и аналоговых);
- требуемая скорость передачи данных;
- наличие автономного счетчика времени;
- условия регистрации и хранения данных;
- возможность самодиагностики;
- требования к панели оператора;
- язык программирования;
- интерфейс;
- каналы связи (проводной, беспроводной);
- режим и условия эксплуатации.
ПЛК (PLC) производства Mitsubishi Electric
В зависимости от типа, ПЛК Mitsubishi Electric могут использоваться как на уровне управления отдельными технологическими единицами, так и на уровне управления технологическим процессом в целом. PLC
Mitsubishi Electric отличают исключительно высокое качество, вариативность и гибкость решений, широкие возможности применения, высокое быстродействие. Контроллеры семейства MITSUBISHI ALPHA XL представляют собой небольшие компактные приборы, объединяющие в одном корпусе входы и выходы, центральный процессор, память, электропитание и графический ЖК дисплей. Контроллеры MITSUBISHI
ALPHA XL является идеальным средством для замены контакторов и реле в уже имеющейся установке, а также для использования во вновь создаваемых системах автоматизации. В одной программе ALPHA XL может обрабатываться до 200 функциональных блоков. При этом любую отдельную функцию (таймер, счетчик, обработку аналоговых сигналов, функцию календаря/часов и т. п.) можно сколь угодно часто использовать во всех программах.
ПЛК
производства ТЕКОН
ПЛК
ТЕКОН отвечают требованиям международных стандартов и российских ГОСТов. Для производства программируемых логических контроллеров компания применяет самые современные компоненты, обеспечивающие высокие технические характеристики продукции, что, вкупе с оригинальными схемотехническими решениями и отлаженной технологией производства, позволяет Заказчикам быть уверенными в надежности программируемых контроллеров «ТЕКОН». Система интеллектуальных модулей ввода-вывода ТЕКОНИК® предназначена для построения распределенных автоматических и автоматизированных систем измерения, контроля, регулирования, диагностики и управления производственными процессами, технологическими линиями и агрегатами. Отличительной особенностью системы является наличие мощного процессорного модуля, позволяющего выполнять сложные алгоритмы управления. Модулями ввода-вывода ТЕКОНИК® можно также расширять системы, реализованные как на контроллерах ТЕКОН, так и на контроллерах других производителей.
ПЛК SLC 500
Промышленные контроллеры SLC-500 — широко используются во всем мире.
SLC 500 это:
- популярное решение для расширяемых приложений автоматизации;
- экономичные и легкие в использовании процессоры с большими возможностями;
- исключительная надежность, подтвержденная в сотнях тысяч приложений;
- расширенная система команд, включающая косвенную адресацию, широкие математические возможности и вычисление выражений.
Аппаратура контроллера разработана для эксплуатации в тяжёлых промышленных условиях, для противостояния вибрациям, повышенной температуре и электромагнитным помехам.
- Компактная конструкция контроллера позволяет устанавливать его в ограниченном пространстве.
- Удалённый доступ к контроллеру возможен посредством соединения с ним по сетям Ethernet, ControlNet, DeviceNet, DH+, DH-485.
В состав процессора SLC 5/03 также включен канал RS-232, который обеспечивает асинхронный последовательный коммуникационный интерфейс данных с терминальными устройствами. Процессор SLC 5/04 (каталожный номер 1747-L542 ) обладает теми-же возможностями, что и SLC 5/03, но с некоторыми дополнительными функциями. Например, процессор SLC 5/04 включает сопроцессор для увеличения скорости выполнения математических команд. Он также содержит встроенный порт сети Data Highway Plus (DH+). Непосредственное подключение к сети DH+ обеспечивает связь SLC 5/04 с процессорами семейства PLC-5 по сети DH+ без какого-либо дополнительного оборудования. Любой программируемый контроллер SLC 500 в сочетании с модулем непосредственной коммуникации (DCM), модулем сканера (SN) или модулем распределенного сканера (DSN) для реализации распределенного ввода/вывода может быть интегрирован в сеть дистанционного ввода/вывода [6].
3.2 Выбор конфигурации и расчет электропотребления
Семейство SLC 500 предлагает широкий выбор модулей дискретного В/В, которые позволяют строить системы управления с минимальными затратами. Наличие 32-канальных модулей В/В снижает, кроме того, требования к монтажному пространству. Все дискретные и специализированные модули сертифицированы в соответствии со стандартами индустриальных приложений UL и CSA, а большинство из них одобрено для использования в условиях окружающей среды Класс 1, Дивизион 2.
Модули процессора SLC серии 1746 обеспечивает надёжное управление промышленными объектами. Rockwell Automation предлагает большой выбор процессоров SLC, которые могут подключаться к различным сетям связи для распределённого управления и работать с удалёнными модулями ввода-вывода. Также Rockwell Automation предлагает большую номенклатуру модулей ввода-вывода серии 1746, дискретных и аналоговых (в том числе интеллектуальных) для индустриального применения.
Семейство SLC 500 — это развивающееся семейство малых программируемых контроллеров, построенное на двух аппаратных модификациях: фиксированный контроллер с опцией расширения при помощи 2-x слотного шасси, или модульный контроллер до 960 точек ввода/вывода. Средства программирования и большинство модулей В/В совместимы для обеих модификаций, так что Вы можете реализовать с минимальной стоимостью широкий спектр приложений.
При конфигурации контроллера определяется необходимое количество входов-выходов, требуемый объём памяти и тип сети связи. В последствии при необходимости расширения возможностей контроллера можно добавить в него Вх/Вых, память или интерфейсы связи. Быстрый обмен сообщениями по сети, связь с другими сетями, а также связь между модулями в шасси [6].
Расчет энергопотребления приведен ниже, и полученные результаты сведены в таблицу 3.1.
Таблица 3.1 – Конфигурация контроллера и энергопотребление
№ шасси
|
№
слота
|
Каталожный номер
|
Источник питания
|
Описание
|
5В
|
24В
|
1
1746-А7
|
0
|
1747-L532
|
1000
|
200
|
Процессор SLC
|
1
|
1746 – NI8
|
200
|
100
|
Аналоговый входной модуль
|
2
|
1746 – IB8
|
50
|
0
|
Дискретный входной модуль
|
3
|
1746 – OB8
|
135
|
0
|
Дискретный выходной модуль
|
Итого
|
I, мA
|
1385
|
300
|
Блок питания 1746 – P1
|
БП
|
I, мA
|
2000
|
460
|
Запас
|
I, мA
|
615
|
160
|
Расчеты производились следующим образом:
- для 5В 1000+200+50+135=1385мА;
- для 24В 200+100=300мА.
В зависимости от значений потребляемого тока, с учетом резерва 15%, выбран источник питания 1746 – P1. Его некоторые эксплуатационные характеристики:
- напряжение линии – 85-132/170-265В переменного тока (47-63Гц);
- типичная потребляемая мощность – 137ВА;
- защита предохранителем – 1746-F1 или подобный;
- допустимый ток – 2А при 5В, 0.46А при 24В;
- рабочая температура – 0-60 .
3.3 Разработка алгоритма управления технологическим процессом
Программа – упорядоченная последовательность действий, реализующая алгоритм решения некоторой задачи.
Общая структура программы приведена в таблице 4.1.
Таблица 4.1 – Структура программы для контроллера
Файл
|
Программа
|
LAD 2
|
Основная программа
|
LAD 3
|
Подпрограмма инициализации модулей
|
LAD 4
|
Подпрограмма проверки датчиков
|
LAD 5
|
Подпрограмма масштабирования и проверки соответствия входных значений параметров уставкам
|
LAD 6
|
Подпрограмма опроса системы
|
LAD 7
|
Подпрограммы регулирования уровня
|
LAD 8
|
Подпрограмма регулирования давления
|
Основная программа предназначена для последовательного вызова основных подпрограмм.
Первой запускается подпрограмма инициализации модулей, с помощью нее определяется, в какой форме будет приходить информация от аналоговых датчиков. Данная подпрограмма сработает, только при запуске контроллера.
Затем следует подпрограмма проверки датчиков. С помощью этой подпрограммы происходит диагностика цепей датчиков на обрыв.
Потом вызывается подпрограмма масштабирования входных параметров. Данная подпрограмма преобразует сигнал, пришедший от датчиков в форму необходимую, для последующих операций. Также в ней происходит сравнение полученных параметров с уставками и в случае несоответствия, выставки определенного бита в единицу.
Следующей вызывается подпрограмма опроса системы. Она предназначена для выставления битов аварий при отклонении параметров процесса от уставки. После выполнения отмеченных выше операций происходит вызов подпрограмм регулирования и давления.
В подпрограммах регулирования уровня и давления происходит опрос текущего состояния регулируемого параметра, в зависимости от полученного значения, происходит вычисление и выдача определенного управляющего воздействия на исполнительный механизм.
4 Расчет контура регулирования давления в сепараторе
4.1 Определение математической модели объекта
Объектом регулирования является газосепаратор.
Необходимо рассчитать настройки регулятора, системы автоматического регулирования давления газа в сепараторе. Задано допустимое перерегулирование - 20%.
График переходной характеристики объекта показан на рисунке 4.1.

Рисунок 4.1 – Графики переходных характеристик сепаратора для системы регулирования давления газа P(t) при ступенчатом изменении положения регулирующего органа РО.
Математической моделью объекта регулирования является апериодическое звено первого порядка с запаздыванием.
Передаточная функция такого звена имеет вид:
, (4.1)
где: Коб
– коэффициент усиления объекта,
Тоб
– постоянная времени объекта,
τоб
– постоянная времени запаздывания.
Из графика переходной характеристики объекта регулирования находятся следующие параметры объекта регулирования:
- постоянная времени объекта Тоб
=4с;
- постоянная времени запаздывания τоб
=1с;
- начальное значение выходного сигнала Y
ном
=0,74 МПа;
- установившееся значение выходного сигнала Y
уст
=0,787МПа;
- начальное положение регулирующего органа H
0
=60%;
- конечное положение регулирующего органа H
мах
=64%.
С помощью полученных параметров объекта определяется относительное изменение регулируемого параметра δ
:
. (4.2)
Относительное изменение входной величины μ
:
. (4.3)
Коэффициент передачи объекта:
. (4.4)
Передаточная функция объекта примет вид:
.
4.2 Расчет оптимальных настроек регулятора
Регулятор работает в дискретном режиме, а передаточная функция объекта регулирования непрерывна, поэтому необходимо рассчитать Z-передаточную функцию объекта. Для этого в систему вводится экстраполятор (фиксатор) нулевого порядка с передаточной функцией . Фиксатор нулевого порядка сохраняет измеренную в начале каждого периода квантования амплитуду на весь период квантования. В результате структурная схема САР примет вид, представленный на рисунке 4.2.

Рисунок 4.2 – Структурная схема дискретной САР
Для того чтобы выбрать тип регулятора, определяем отношение τоб
/Тоб
:
.
Отношение 0,2<
t
об
/
T
об
<0,7, следовательно, для регулирования будем использовать ПИ-регулятор.
Приведенная непрерывная часть системы представляет собой последовательное включение фиксатора нулевого порядка и объекта с заданной передаточной функцией:
. (4.5)
Z-передаточная функция приведенной части рассчитывается по формуле:
. (4.6)
Следовательно, Z-передаточная функция приведенной части примет вид:
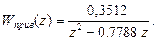
Передаточная функция дискретного ПИ-регулятора имеет вид:
. (4.7)
Передаточная функция разомкнутой системы :
Заменяем и получаем комплексную частотную характеристику (КЧХ) или амплитудно-фазовую частотную характеристику разомкнутой системы (АФЧХ):
Так как Т=1, то частоту при построении КЧХ можно изменять в пределах или .
По номограммам Солодовникова при известном значении допустимого перерегулирования определяется , модуль , запас по фазе и [9].
На комплексной плоскости строится окружность:
. (4.8)
Радиус данной окружности определяется по формуле:
. (4.8)
Центр окружности лежит в точке О: 
КЧХ строится на том же графике, что и запретная область. При этом задается и подбирается такой , чтобы КЧХ касался запретной области, но не пересекал ее границы. Оптимальными являются те значения, для которых отношение Кр
/Ти
является наибольшим. Интервал варьирования будет от 2 до 6, так как наибольшее значение Кр
/Ти
приходится на =3.2. Шаг выберем 0.4.
Результаты сводятся в таблицу 4.1.
Таблица 4.1 – Значения настроек ПИ-регулятора
Tи
|
2
|
2.4
|
2.8
|
3.2
|
3.6
|
4
|
4.4
|
4.8
|
5.2
|
5.6
|
6
|
Кр
|
0.383
|
0.538
|
0.702
|
0.829
|
0.912
|
0.968
|
1.01
|
1.043
|
1.07
|
1.0925
|
1.113
|
Кр
/Ти
|
0.1915
|
0.22417
|
0.25071
|
0.25906
|
0.25333
|
0.242
|
0.2295
|
0.2173
|
0.20577
|
0.19509
|
0.1855
|
Оптимальные настройки, таким образом, равны , .
Для того чтобы убедиться в оптимальности полученных настроек, нужно рассчитать прямые и косвенные показатели качества:
Косвенные показатели качества определяются по АЧХ замкнутой системы (рисунок 4.3).

Рисунок 4.3 – Амплитудно – частотная характеристика замкнутой системы при настройках ПИ-регулятора Кр опт
= 0.829 , Ти опт
=3.2
Фактическое значение частотного показателя колебательности , то есть расчет можно считать удовлетворительным.
Прямые показатели качества определяются по переходной характеристике замкнутой системы (рисунок 4.4).

Рисунок 4.4 – График переходной характеристики замкнутой системы при настройках ПИ-регулятора Кр опт
= 0.829, Ти опт
=3.2
Прямые показатели качества:
- перерегулирование σфакт
=
12.3% < σдоп
=
20%;
- время регулирования tp
=
9с < t
доп
=(3÷4)Тоб
=12 с ÷ 16 с.
Так как полученные показатели качества управления меньше допустимых, настройки ПИ-регулятора можно считать оптимальными.
Заключение
В работе дана общая характеристика объекта. В последующем идет выбор оборудования, которое наиболее подходит данному объекту, необходимое для создания системы автоматизированного управления. Для автоматизации работы сепаратора выбирается оборудование нижнего уровня системы автоматизации удовлетворяющее следующим требованиям:
- способность работать в неблагоприятных условиях;
- надежность;
- диапазон измерения;
- погрешность измерения;
- наличие определенных видов защиты;
- несложный монтаж;
- наличие унифицированного выходного сигнала.
А также идет сравнение и выбор программно-логического контроллера, учитывая его характеристики и соотношения цена-качество. Выбор определен в пользу SLC-500 серии 1746 с типичной потребляемой мощностью 137 ВА.
Приведено описание программы для ПЛК, написанной в программном пакете RSLogix 500 в соответствии с разработанной блок схемой.
Произведен расчет системы автоматического регулирования давления в сепараторе. Регулирование производится с помощью ПИ-закона регулирования. Произведена оценка качества регулирования (σ = 12.3%, tр.
= 12 с). Так как показатели качества не превышают допустимых значений (ε<20%, tр
<(3÷4)Тоб
), настройки регулятора Кр опт
= 0.829, Ти опт
=3.2 - являются оптимальными.
Список использованных источников
1 Технологический регламент КС-7 Федоровского месторождения.
2 Справочник слесаря по контрольно измерительным приборам. Гресько А.А., Долгая А.А. Киев, «Техника – 2005».
3 www
.kipiasoft.su - Библиотека специалиста по КИПиА
4 www.rizur.ru - датчики давления, преобразователи давления
5 Проектирование систем автоматизации технологических процессов: Справочное пособие по содержанию и оформлению проектов. Емельянов А.И., Капник О.В. М.: Энергоатомиздат, 2006.
6 Аналоговые модули ввода – вывода (серия 1746) SLC 500. Руководство пользователя / Allen – Bradley A Rockwell International Company. 2007. – 66c.
7 Кармазин В. В., Кармазин В. И., Бинкевич В. А., Магнитная регенерация и сепарация при обогащении руд и углей, [М.], 2005;
8 Разработка и эксплуатация нефтяных и газовых месторождений, М., 2007.
9 Ротач В.Я. Теория автоматического управления энергетическими процессами, М, Энергоатомиздат, 2004.
10 Приборы и средства автоматизации. Каталог Т1. Приборы для измерения температуры, М.
Приложение А

Рисунок А.1 – Схема автоматизации функциональная
Приложение Б
Приложение В
Расчет оптимальных настроек регулятора
Приложение Г
Приложение Д
Текст программы контроллера
|