Антикоррозийная обработка
Содержание
Введение
Часть I. Кузовной ремонт
1.1 Кузов. Классификация повреждений. Конструкция кузова легкового автомобиля
1.2 Повреждения кузова, возникшие при эксплуатации
1.3 Покупка деталей и стоимость ремонта
1.4 Технология ремонта. Разборка кузова
1.5 Очистка кузова от коррозии и лакокрасочных материалов
1.6 Проверка геометрии кузова
1.7 Подготовка автомобиля к ремонту
1.8 Ремонт съемных деталей кузова
1.9 Ремонт сварных элементов
1.10 Технология восстановления формы деталей
1.11 Рихтовка
1.12 Электронагревом
1.12 Устранение деформации шпатлевкой или оловом
Часть 2. Устранение деформации крыши
2.1 Технология замены узлов и деталей кузова
2.2 Методика правки съемных деталей
2.3 Об автомобильных стеклах
2.4 Герметизирующие уплотнения
2.5 Технология сборки кузова
2.6 Гидравлические системы для рихтовочных стендов
2.7 Аксессуары для рихтовочных стендов
2.8 Системы контроля геометрии кузова
Ремонт отечественных и зарубежных автомобилей - прибыльный вид деятельности. С каждым днем растет количество автомобилей и предприятий, которые занимаются их ремонтом. И если ремонт агрегатов и систем, техническое обслуживание автомобиля многие автолюбители производят самостоятельно, то кузовным ремонтом под силу заняться далеко не каждому. Кроме специфического оборудования, позволяющего восстановить первоначальную форму деталей и цвет автомобиля, требуется опыт работы, знание современных материалов и особенностей их использования. Это особенно важно, если автомобиль новый и дорогой, поэтому и цены на кузовные работы достаточно высоки.
При всех достоинствах современных автомобилей, они уже через несколько лет эксплуатации теряют первоначальный вид, не говоря уже о более заметных повреждениях кузова в результате аварии. Но то, что является бедой для автомобилиста, для работника мастерской, станции техобслуживания - источник дохода. И автолюбитель готов идти на траты, чтобы автомобиль был не только средством передвижения, но и радовал глаз, служил долгие годы. Это возможно только в том случае, если кузовные работы выполнены качественно, мастер знает свое дело. Стоит ли удивляться тому, что на рынке труда всегда востребованы специалисты по ремонту автомобилей? Для человека, который хочет обеспечить себя стабильным заработком, эта сфера деятельности подходит как никакая другая, ведь автомобилей с каждым днем становится все больше, а увеличение парка дорогих и престижных машин позволяет устанавливать достаточно высокие расценки на кузовные работы, ведь ремонт такой автомашины - это еще и огромная ответственность, высокий уровень качества выполненных работ.
В данном учебном пособии рассмотрены все аспекты произведения кузовного ремонта автомобиля - от оценки общего состояния и восстановления частей кузова, в том числе после аварии, до декоративного украшения автомобиля и "наведения лоска". Особое внимание уделено современному ассортименту красок и лаков, шпатлевок, средств по уходу за кузовом автомобиля. Описаны все вопросы подготовки автомобиля к покраске, возможные дефекты и способы их устранения, способы восстановления старых покрытий и т.д.
Отличие этой книги от аналогичных в том, что теоретические вопросы тесно переплетены с практическими, подробно описана технология выполнения каждой операции. Это особенно ценно для молодого специалиста, который после обучения сразу устраивается на работу - сведения, приведенные в книге, помогут без помощи опытного специалиста сразу приступить к своим обязанностям. Эта же особенность подбора, построения и изложения материала - "с нуля", очень подробно и с минимумом терминов - позволяет рекомендовать книгу автолюбителям, которые решились самостоятельно заняться кузовным ремонтом или хотят оценить реальный объем работ, а затем и качество их исполнения в автомастерской.
Назначение кузова современного легкового автомобиля определяется двумя функциями: кузов обеспечивает пассажирам и водителю комфорт и безопасность в аварийных ситуациях.
По назначению и исполнению кузова легковых автомобилей подразделяют на следующие 5 классов:
"седан
" - двух- или четырехдверный, 4-5-местный, с отдельными отсеками для двигателя, пассажиров и багажа;
"универсал
" - автомобиль с вагонной формой кузова, используется для перевозки людей и грузов;
"кабриолет
" - 4-6-местный автомобиль со складной крышей и съемными стенками боковых окон;
"лимузин
" - автомобиль высокого уровня комфортабельности, водитель отделен от пассажиров стеклянной перегородкой;
"купе
" - двухместный автомобиль с двумя дополнительными местами на заднем сидении.
Кузова большинства легковых автомобилей являются несущим элементом конструкции, к ним крепятся элементы ходовой части и шасси. Это уменьшает массу автомобиля, снижает его общую высоту, а значит, и центр тяжести, делая автомобиль более устойчивым. С другой стороны, эта несущая конструкция создает трудности для шумоизоляции салона. Комфортабельные автомобили высокого класса имеют рамную конструкцию
.
Основа кузова - каркас. Требования к нему следующие. Конструкцию каркаса рассчитывают так, чтобы при ударе с любой стороны энергия удара гасилась. Детали кузова, образующие салон, должны получить при этом минимально возможные деформации, другими словами, кузов должен устранить или снизить тяжесть последствий аварии.
Для поглощения энергии удара при столкновении служат бамперы. Для обеспечения безопасности внутри салона - мягкая панель приборов, накладки стоек
, конструкция других элементов. Определенную роль в обеспечении безопасности играют также ремни безопасности.
Для примера охарактеризуем конструкцию кузова автомобиля ВАЗ-2108. Каркас кузова включает следующие элементы: передок, пол, боковины, крышу с рамой ветрового окна, панель задка
и силовые элементы
- лонжероны, поперечины, стойки. Детали оперения: лицевые панели кузова
и навесные узлы
- капот, дверь задка, передние крылья. Все детали и узлы, кроме навесных элементов и передних крыльев, соединены контактной точечной сваркой, а значительно нагруженные детали каркаса дополнительно приварены электродуговой сваркой.
Передок состоит из вертикального щитка, брызговиков, поперечин, коробки воздухопритока, усилителей
и других мелких деталей. Брызговики соединены с передними лонжеронами.
Пол автомобиля включает передний, средний
и задний полы
. В переднем, имеющем корытообразную форму, находится тоннель для размещения выпускных труб, топливных и тормозных трубопроводов. Тоннель служит для предохранения этих деталей от повреждений и увеличения жесткости пола. Задний пол имеет нишу для запасного колеса. Вдоль полов приварены лонжероны. К полу приварены также передняя, средняя и задняя поперечины.
Боковины кузова состоят из наружных
и внутренних панелей
. Наружные являются цельными с центральными и задними стойками и с проемами боковых окон. Внутренние панели кузова конструктивно объединяют в себе наружные арки задних колес и усилители стоек. За усилителем у правой боковины есть ниша для установки улавливателя паров бензина, желобки и фланцы под уплотнители дверей и стекол.
Съемные узлы - это передние двери, дверь задка, капот, передние крылья, бамперы, облицовка радиатора
и др. Крылья прикреплены к каркасу самонарезающими болтами; под крыльями для уменьшения вибрации установлены прокладки. Петли передних дверей и капота допускают регулировку их положения.
Для повышения жесткости и прочности кузова применяют усиливающие накладки, кронштейны, ребра жесткости
.
Для защиты от механических повреждений, создания термо- и шумоизоляции нижняя наружная часть кузова, брызговики колес и внутренние поверхности крыльев покрыты антикоррозионным материалом, а пол салона и багажника - специальными вибродемпфирующими мастиками. Перед сваркой коррозионно-опасных мест свариваемые детали покрывают специальным консервирующим составом. Внешние и внутренние поверхности кузова обрабатывают специальными составами, в результате чего на них образуются не растворимые в воде защитные соединения. Снаружи кузов окрашивают синтетическими эмалями.
Стеклоподъемники отечественных автомобилей
двух типов - рычажные и тросовые. Тросовый привод стеклоподъемника крепят на внутренней панели двери гайками к приварным болтам.
Трос охватывает два ролика на верхнем и нижнем кронштейнах направляющей стеклоподъемника. В механизме привода стеклоподъемника трос наматывается на барабан, на его ведущем валике есть пружинный тормоз, который препятствует самопроизвольному опусканию стекла.
Элементы кузова, повышающие безопасность
Наиболее вероятная скорость автомобилей при соударениях составляет 80 км/ч при лобовых и задних ударах и 64 км/ч при боковых ударах. Эти цифры являются исходными для расчета прочности кузовов и разработки конструктивных мер, обеспечивающих безопасность легковых автомобилей.
Повышение безопасности автомобилей включает в себя меры "активной" безопасности, которые способствуют предотвращению возникновения аварий, и меры "пассивной" безопасности, которые закладываются в конструкцию автомобиля для обеспечения безопасности водителя и пассажиров, если аварию предотвратить не удастся.
Меры "активной" безопасности
автомобиля предусматривают разработку конструкций деталей и узлов, обеспечивающих эффективность торможения и надежность работы тормозного привода, противоблокировочных систем, позволяющих автомобилю двигаться в заданном направлении при торможении, а также меры по увеличению обзора дороги и окружающей обстановки с места водителя. Сюда относят установку двухрежимного стеклоочистителя, отопителя, вентилятора, которые не допускают обледенения и запотевания стекол.
Меры "пассивной" безопасности
предусматривают предотвращение или уменьшение травматизма водителя и пассажиров при аварии. Результат достигается обеспечением защитной зоны вокруг каждого пассажира, ограничением возможности перемещения водителя и пассажиров относительно сиденья, уменьшением уровня травматизма от ударов о внутренние поверхности салона, обеспечением возможности выхода водителя и пассажиров из потерпевшего аварию автомобиля.
Обеспечение защитных свойств кузова заключается в разработке и внедрении таких конструктивных решений, которые позволяют образовать вокруг водителя и пассажиров защитную зону.
Жесткий салон
в сочетании с энергопоглощающими передней и задней частями кузова позволяет снизить ускорения людей в момент соударения и в наилучшей степени обеспечивает защитную зону вокруг пассажиров. Кузова такой конструкции строят по принципу прогрессивной энергоемкости, т.е. с заданной степенью усиления одних деталей при максимально допустимом смятии других в целях поглощения энергии удара.
Очень большие нагрузки при ударах в разных направлениях (продольном, поперечном и вертикальном) действуют на двери, петли дверей и дверные замки. Двери
защищают салон от проникновения внутрь посторонних предметов при аварии и не должны открываться во время соударения, чтобы пассажиры не могли выпасть из кузова. Дверные замки оборудуются надежной системой блокировки, предотвращающей случайное их отпирание под действием инерционных нагрузок или при ударе в момент аварии, так как и сами двери не исключаются из общего контура жесткости салона кузова.
Для защиты водителя и пассажиров при боковых столкновениях в двери кузова встроены защитные брусья коробчатого сечения
. Брус размещен внутри двери между опускным стеклом и наружной панелью. Кроме защиты салона от проникновения ударяющего автомобиля, брусья как бы сдвигают ударенный автомобиль в сторону.
Бамперы
в современных легковых автомобилях обладают защитными свойствами в сочетании с декоративными особенностями, созданными дизайнерами. Сегодня устанавливают бамперы широкого профиля с наиболее закругленными формами. Их защитные свойства высоки, бамперы предохраняют автомобиль от повреждений при легких столкновениях и должны соответствовать международным нормам безопасности.
Системы, ограничивающие перемещение водителя и пассажиров внутри кузова, включают в себя сиденья и ремни безопасности
.
Уровень травматизма при авариях снижается наиболее эффективно, если в конструкции автомобиля предусмотрено надежное крепление пассажира к сиденью, которое, в свою очередь, не должно отрываться от пола кузова под действием аварийных перегрузок. Сиденья
закрепляют так, чтобы они выдерживали требования безопасности по продольным нагрузкам, действующим в обоих направлениях, а также по крутящему моменту.
Ремни безопасности имеют простое замковое устройство, обеспечивающее надежное крепление, а при необходимости позволяющее быстро отстегнуться. В рабочем положении ремни обеспечивают достаточную свободу перемещений водителя и не мешают управлению автомобилем.
Расчеты и практика показывают, что ремни безопасности надежно защищают пассажиров при фронтальном соударении со скоростью до 80 км/ч.
Следующий элемент - руль
. Безопасность руля заключается в исключении случаев тяжелого травмирования водителей при фронтальных столкновениях автомобилей. В соответствии с требованиями во время испытания автомобиля на столкновение с железобетонным барьером массой не менее 70 т при скорости 48,3 км/ч верхняя часть рулевой колонки и рулевого вала не должны перемещаться в заднем направлении горизонтально и параллельно продольной оси транспортного средства более чем на 12,7 см. Если рулевая колонка сталкивается с моделью туловища, которая ударяется об эту колонку с относительной скоростью не менее 24,1 км/ч, то сила, с которой рулевая колонка воздействует на переднюю часть модели туловища, не должна превышать 11,35 кН (1135 кгс).
Ветровые стекла
автомобилей должны соответствовать требованиям правил ЕЭУ ООН. Например, стекла автомобилей ВАЗ трехслойные, они состоят из двух профилированных полированных стекол с прослойкой из липкого прозрачного пластика. Основное преимущество слоистого ветрового стекла заключается в том, что трещины при ударе распространяются из центра удара, осколки удерживаются на пластмассовой прослойке, стекло сохраняет свою прозрачность, форму и не выпадает из проема кузова.
Заднее и боковые стекла изготовляют из закаленного стекла, они проходят специальную термообработку, обеспечивающую повышенную прочность. При разрушении эти стекла распадаются на множество мелких осколков без острых углов и граней, способных вызвать глубокие ранения.
Подголовники
должны исключить тяжелые травмы, выражающиеся в повреждении шейных позвонков и позвонков верхних отделов грудной клетки. Такие травмы наносятся при ударе движущегося автомобиля в заднюю часть стоящего автомобиля. При таком виде дорожно-транспортного происшествия подголовники по прочности должны соответствовать международным правилам ЕЭК ООН, а их конструкция исключать возможность травмирования заднего пассажира при фронтальном столкновении автомобилей.
Важное значение имеет интерьер кузова. Он включает в себя внутреннюю отделку салона, которая должна отвечать современным эстетическим и эргономическим требованиям.
Панель приборов
изготовляют без выступающих деталей и острых кромок, с удобным размещением контрольно-измерительных приборов и органов управления. Энергоемкость панели обеспечивается не только мягкой обивкой, но и введением в конструкцию каркаса стальных тонколистовых панелей, способных при ударе поглощать энергию за счет их частичной деформации.
Подлокотники, двери и противосолнечные козырьки облицовывают мягкими материалами. Ручки дверей, стеклоподъемников, кнопки переключателей и блокировки замков дверей размещают и изготовляют так, чтобы в случае удара пассажир не мог получить травмы.
Повреждения автомобиля при авариях
Наибольшее количество соударений автомобилей приходится на переднюю часть, несколько меньше - на заднюю и наименьшее - на боковые.
Повреждения кузовов, полученные в результате соударения, делят на три категории. К первой относят очень сильные повреждения, в результате которых необходима замена кузова. Ко второй категории относятся повреждения средней тяжести, при которых большая часть деталей требует замены или сложного ремонта. К третьей относятся менее значительные повреждения - пробоины, разрывы на лицевых панелях, вмятины и царапины, полученные при ударе во время движения с малой скоростью. Эти повреждения не представляют опасности для пассажиров и водителя при эксплуатации автомобиля, хотя его внешний вид не отвечает эстетическим требованиям.
Наиболее разрушительные повреждения кузова наблюдаются при фронтальных столкновениях - соударениях, нанесенных автомобилю непосредственно в переднюю часть кузова или под углом не более 40-45° в районе передних стоек. Такие столкновения происходят, как правило, между двумя движущимися навстречу транспортными средствами, скорости которых складываются, что и создает высокие ударные нагрузки. Количество энергии, которое должно поглотиться при таких соударениях, огромно: около 80 100 кДж для автомобиля массой около одной тонны. Эта энергия поглощается при деформации автомобиля за время менее 0,1 с. Кузов автомобиля разрушается, особенно его передняя часть, а действующие при этом большие нагрузки в продольном, поперечном и вертикальном направлениях передаются всем смежным деталям каркаса кузова и особенно его силовым элементам. Рассмотрим сказанное на примерах.
Итак, фронтальное соударение автомобиля произошло передней частью кузова в районе левого переднего крыла, лонжерона и левой фары
. Разрушительные повреждения получают панель передка, крылья, капот, брызговики, передние лонжероны, рама ветрового окна и крыша. Эта деформация устанавливается визуально. Невидимая деформация происходит в передних, центральных и задних стойках с обеих сторон, в левых передней и задней дверях, в левом заднем крыле и даже в задней панели багажника.
Или: соударение произошло передней частью кузова автомобиля под углом 40-45°. Разрушительные повреждения получили передние крылья, капот, панель передка, брызговики, передние лонжероны. Восстановить базовые точки передней части кузова без замены деформированных деталей новыми практически невозможно. При этом необходимо восстановление размеров по проемам передних дверей и положению передних и центральных стоек, так как силовые нагрузки передавались через передние двери на передние и центральные стойки кузова, создавая сжимающие усилия на порог и верхнюю часть боковины кузова.
Еще пример: удар нанесен сбоку в переднюю часть кузова автомобиля в районе сопряжения передней панели с передними частями лонжерона и левого крыла
. Разрушительные повреждения получают оба передних крыла, панель передка, брызговики, лонжероны, капот. Растягивающие усилия нарушают проем левой передней двери, сжимающие усилия вызывают деформацию в проеме правой двери и в боковине левой передней двери. Передние и центральные стойки также получают значительные силовые перегрузки и отклоняются от своего первоначального положения.
Удар получен сбоку в переднюю стойку кузова автомобиля с левой стороны
. При этом значительно деформированы левая передняя стойка, рама ветрового окна, крыша, пол и лонжероны переднего пола, панель передка, капот, крылья, брызговики и передние лонжероны. Передок кузова автомобиля сдвинулся влево, порог и верхняя часть правой боковины восприняли растягивающие нагрузки, а центральные и задние стойки - сжимающие нагрузки; правый брызговик в сопряжении с передней стойкой испытывал разрывающие усилия.
При внешнем осмотре аварийного кузова можно установить наличие перекосов по выдвижению или западанию дверей, крышки багажника и капота относительно неподвижных поверхностей кузовных деталей. Нарушение равномерности зазоров по линиям сопряжения навесных и неподвижных деталей также свидетельствует о наличии деформаций в деталях каркаса кузова, вызванных аварией. При этом следует помнить, что внешним осмотром нельзя определить отклонения линейных размеров проемов кузова и геометрических параметров по базовым точкам основания кузова. Для этих целей необходимо применять измерительные средства, специальные контрольные приспособления и стенды, описания которых даны в соответствующих главах книги.
В этой главе речь идет о менее значительных повреждениях кузова, возникших в процессе эксплуатации автомобиля и ухудшающих внешний вид.
Вмятины появляются в результате остаточной деформации при ударе, неправильном ремонте, а также вследствие некачественной сборки кузова.
Вмятины бывают простыми и легко поддающимися ремонту и сложными - с острыми загибами и складками или располагаться в труднодоступных для ремонта местах.
Трещины - это часто встречающиеся повреждения кузова. Они могут появиться в любом месте в результате перенапряжения металла (ударов, изгибов), а также в результате непрочного соединения узлов и деталей и недостаточной прочности конструкции.
Разрывы и пробоины подразделяют на простые, принимающие после правки металла вид трещины, и сложные, требующие при ремонте поврежденного места постановки заплат.
Обрывы в деталях кузова характеризуются величиной порванной части панели или оперения. Большие обрывы часто устраняют постановкой вставок сложного профиля, а в некоторых случаях производят полную замену детали.
Растянутые поверхности металла различают по месту их нахождения: на поверхности панели в виде бугра и в отбортовках деталей (растянуты борта и кромки).
Коррозия по своему внешнему проявлению может встречаться в виде равномерной, когда металл разрушается равномерно по всей поверхности, и местной, когда металл разрушается на отдельных участках. Последняя форма коррозии обнаруживается по темным пятнам или глубоким черным точкам на металле, она более опасна, так как металл может в короткий срок разрушиться с образованием сквозных отверстий.
Нарушение сварных соединений встречается в узлах деталей, которые соединены точечной сваркой, и в сплошных сварных швах кузова.
Нарушение клепаных швов является результатом ослабления или среза заклепок, а также износа отверстий под болты и заклепки.
Прогибы, перекосы и скручивание обычно появляются в результате аварийной нагрузки. Перекосы бывают межузловые и в плоскости одного узла или детали (перекос в дверном проеме кузова, перекос в самой двери, прогиб пола).
Износы отверстий и стержней возникают в результате трения качения (оси и отверстия в петлях дверей) или ослабления крепления узла заклепками или болтами; износы поверхностей - из-за систематической нагрузки, прилагаемой к поверхности, например, при перевозке абразивных грузов в кузовах автомобилей.
Конструктивные недоработки узлов кузова часто приводят не только к появлению повреждений, но осложняют их ремонт, а иногда и выполнение ремонтных операций вплоть до необходимости замены поврежденного узла новым. Конструктивные недоработки в кузове, осложняющие его ремонт, имеют место, главным образом, в отечественных автомобилях, потому что на автомобильных заводах недостаточно полно учитывают требования автотранспортных и авторемонтных предприятий к конструкции кузова.
Ремонт кузова автомобиля - самый дорогой из ремонтов. Купить можно практически любую деталь кузова, но во сколько она обойдется - вопрос. Стоимость запчастей для всех заднеприводных вазовских моделей примерно на одном уровне, а например, капот для "Нивы" стоит почти в два раза дороже, чем капот "девятки". Цены на оригинальные детали нестандартных "нив" выше, чем на детали для стандартных, в несколько раз. Капот УАЗ-3160 потянет почти на 6000 рублей. [1] 1 Цены приведены на 2004 год.
Почему-то левые крылья и двери на все модели ВАЗ и переднеприводные "москвичи" дороже правых чуть не в два раза.
Если хорошо знать цены и проявить смекалку, можно сократить затраты на ремонт. Скажем, иногда достаточно поменять дверь не целиком, а только ее наружную часть. Так, для ВАЗ-2106 дверь в сборе стоит 800 рублей, а наружная панель 150. Таким образом можно ремонтировать не только двери, но и другие пострадавшие в аварии части автомобиля. Если можно, меняем не весь бампер в сборе, а его основную часть без кронштейнов и накладок.
В фаре часто достаточно поменять стекло, остальное ремонтируется со значительной экономией средств. В иной ситуации достаточно купить рассеиватель, корпус - опять экономия и, возможно, значительная.
Автолюбители часто сомневаются - ремонтировать своими силами или в автосервисе?
Цены на кузовные работы в столичном автосервисе у провинциала могут вызвать головокружение, ибо в провинции расценки заметно ниже. Стоимость услуг частных мастеров, работающих в гаражных кооперативах, процентов на 30 ниже тех же услуг официальных фирм. В некоторые автосервисы владелец отечественной машины вряд ли вообще когда-нибудь нанесет визит, а о ценах в них владельцы недорогих автомобилей говорят шепотом.
Профессиональные кузовщики гарантируют высокое качество работы. Тут подход один: если рихтовка детали дороже ее стоимости и замены, деталь меняют. В некоторых случаях опытный кузовщик все-таки советует переплатить за ремонт и выправить "родные" детали. Это вдвойне оправдано, если автомобиль новенький. Заводские детали сопротивляются коррозии дольше купленных запчастей.
Как говорилось, цены на кузовные работы в провинции дешевле. Калькуляция простая: цены на запчасти столичные, а работа недорогая. Поэтому и мастерам чаще приходится ремонтировать, чем заменять детали.
Есть мнение: поврежден лонжерон - автомобиль ремонту не подлежит. Если лонжерон пострадал несильно, его можно восстановить, не опасаясь последствий. Если в результате удара лонжерон поврежден серьезно, надо менять кузов или продавать автомобиль на запчасти. Если деформированы пол или крыша, даже опытный мастер со специальным оборудованием вряд ли восстановит первоначальную геометрию кузова.
Для ориентации приведем калькуляцию затрат на ремонт и запчасти для "девятки" в рублях.
Стоимость запчастей: крыло - 700, капот - 1300, бампер - 1600, фара - 700, решетка радиатора - 70, радиатор - 860.
Материалы: краска (заказ, 1 кг) и растворитель - 2000, грунтовка (1 кг) - 200, "Тосол" (5 л) - 80.
Работа: замена крыла - 200, замена капота - 200, ремонт брызговика - 1500, ремонт рамки радиатора - 600, покраска деталей - 3000, установка остальных деталей - 700.
Если подбить итог, сумма затрат будет примерно на уровне 450 у. е.
Дорого? Тогда можно посоветовать автолюбителю только засучить рукава и браться за ремонт собственного авто своими силами.
Прием машины в ремонт
Автомобиль, подлежащий ремонту, должен быть чистым, без посторонних вещей в салоне и багажнике. Дополнительные противоугонные средства, специальные части и прочие детали должны быть отключены или сняты.
В автосервисе автомобиль принимает контролер-приемщик или иное доверенное лицо в присутствии заказчика по предъявлению технического паспорта на автомобиль и справки ГИБДД ГАИ о регистрации аварии.
При приемке автомобиля обязательно проверяют документы на автомобиль, комплектность автомобиля, техническое состояние, определяют и согласовывают с заказчиком объем работ, ориентировочно определяют стоимость и сроки выполнения работ.
Автосервис несет ответственность за сохранность и комплектность принятого автомобиля. Хранение принятых в ремонт автомобилей допускается и на открытой площадке. Перечень работ, указанный в заказе-наряде для производства ремонтных операций, должен соответствовать характеристикам прейскуранта цен на услуги и подлежит обязательному выполнению. Запчасти и материалы, перечисленные в заказе-наряде, устанавливаются на ремонтируемый автомобиль в соответствии с технологическими процессами.
Дополнительные работы по устранению неисправностей
, обнаруженных в процессе ремонта, производятся с предварительного согласия заказчика с последующей их оплатой. В этом случае общая стоимость дополнительных работ вместе со стоимостью деталей, узлов и агрегатов, израсходованных в ходе устранения неисправностей, не должна превышать 10% от первоначальной стоимости заказа. При стоимости дополнительных работ свыше 10% с заказчиком согласовывается новая стоимость ремонта.
Неисправности автомобиля, влияющие на безопасность движения, обнаруженные при приемке или в процессе ремонта, подлежат обязательному устранению. В случае отказа заказчика от выполнения работ по устранению неисправностей этой категории или невозможности их устранения в заказе-наряде указывается неисправность и делается запись "До устранения данной неисправности автомобиль эксплуатации не подлежит".
Ремонтные предприятия принимают в ремонт кузова и автомобили в комплектности завода-изготовителя, при этом допускается отсутствие отдельных съемных деталей. По типу и конструкции кузова должны соответствовать моделям завода-изготовителя. Допускается наличие деталей, узлов, механизмов и агрегатов различной конструкции в пределах изменений, произведенных заводом за период выпуска данной модели.
Не принимают в ремонт кузова
, имеющие:
сквозную коррозию кузова по линиям соединения несущих элементов, исключающую возможность присоединения (сварки) ремонтных вставок (одновременно по передним и задним лонжеронам и усилителям пола);
аварийную деформацию с одновременной сквозной коррозией элементов основания кузова, исключающую возможность их правки;
деформацию после пожара со смещением двух и более контрольных точек в разных зонах основания кузова более чем на 30 мм.
Не подлежат ремонту детали кузова
:
изменившие свою форму в результате пожара;
имеющие сквозную коррозию по линиям соединения с другими частями кузова;
ранее ремонтировавшиеся с применением шпаклевок на эпоксидной основе.
В зависимости от объема ремонта и состояния разборка кузовов бывает частичная
и полная
. Частичную производят, когда кузов находится в хорошем состоянии и ремонта требуют только отдельные его части, поврежденные в результате износа, ослабления креплений или аварии. Полную разборку производят, как правило, при капитальном ремонте автомобиля и когда большинство узлов кузова нуждается в ремонте.
До разборки автомобиля на агрегаты в специально оборудованном помещении производят наружную мойку кузова. После мойки кузов подвергают предварительному контролю, при котором производят тщательный внешний осмотр узлов и деталей, подлежащих обязательному снятию с кузова при его капитальном ремонте (внутренняя обивка кузова, стекла, арматура, декоративные накладки и др.), для выяснения их состояния и целесообразности ремонта. Цель предварительного контроля - не загромождать производственные помещения негодными (подлежащими утилизации) деталями. Затем снимают с кузова все узлы и детали, закрывающие корпус с внутренней и наружной сторон, а также все агрегаты ходовой части автомобилей с кузова несущей конструкции. Для тщательной очистки днища кузова от грязи его промывают вторично.
Эффективная разборка аварийного автомобиля на ремонтном предприятии обеспечивается наличием достаточной производственной площади, оборудования, инструмента для разборочно-сборочных работ и инструмента для удаления деформированных элементов кузова. Предприятие, хорошо оснащенное моечным, грузоподъемным и другим гаражным оборудованием, а также механизированным инструментом, способно качественно выполнить разборочные операции с минимальными затратами труда и времени. Конечно, в условиях частного гаража таких условий быть не может, но это не означает, что нельзя, проявив смекалку и находчивость, выполнить эту работу.
Порядок разборки таков. Автомобиль, принятый с повреждениями аварийного характера, автопогрузчиком подают на свободное место арматурного участка, где установлен специальный контейнер для складирования демонтированных деталей, узлов и агрегатов.
Каждая деталь имеет в этом контейнере свое место. Слесарь механосборочных работ даже с небольшим навыком без особого труда может уложить детали при разборке на свое место и быстро, без потерь времени на поиск, взять их при сборке.
С помощью домкрата автомобиль устанавливают передней частью к проезду, а задней частью - к стоящему сзади контейнеру на специальных подставках. Опорными местами (четыре точки) служат кронштейны домкратных гнезд пола кузова. Высота подставок - 600 мм. Такая высота является наиболее оптимальной для слесарей и обеспечивает свободный доступ к абсолютному большинству деталей, подлежащих снятию или установке на автомобиль.
Для снятия и установки двигателя в сборе с коробкой передач и передней подвеской используют тележку БС-135.000 и модернизированный гидравлический гаражный домкрат типа П-302. Модернизация домкрата вызвана необходимостью обеспечить высоту подъема агрегатов до 700 мм и заключается в увеличении длины рамы и исполнительного рычага. Тележка БC-135.000 представляет собой небольшую трехопорную раму, на которую опирается двигатель. Для удобства транспортировки тележка снабжена поворотными колесами.
При выполнении работ по снятию агрегата с автомобиля под двигатель подкатывают тележку и поднимают ее домкратом до упора в силовой агрегат. В это время двигатель отсоединяют от кузова в опорных точках, разъединяют детали системы гидравлического привода тормозов и сцепления, передней подвески и др. Затем тележку опускают вместе с силовым агрегатом в сборе и выкатывают из-под кузова.
Таким способом снимают и задний мост, отсоединив от деталей подвески и гидравлического привода тормозов.
Одновременно с разборкой автомобиля выполняют контроль демонтированных деталей с разделением их на годные, подлежащие выбраковке или ремонту. Узлы и агрегаты, подлежащие ремонту, направляют на агрегатный участок. Годные детали, узлы и агрегаты складируют по своим местам в контейнер, а подлежащие замене выбраковывают. На выбракованные детали обычно составляют ведомость, по которой на складе комплектуют запасные части для ремонта данного автомобиля.
Кузов автомобиля после разборки передается на участок кузовного ремонта. Контейнер с демонтированными деталями закрывают и вывозят автопогрузчиком на склад.
Деформации, встречающиеся при ремонте аварийных автомобилей, настолько разнообразны, что найти кузова с одинаковой степенью повреждений почти невозможно. Почти каждый кузов после аварии при восстановлении требует механических воздействий, т. e. отрезку тех или других деталей, которые мешают снять с автомобиля тот или другой агрегат или узел (например, подвеску, радиатор, двигатель, топливный бак, запасное колесо и многие другие детали в зависимости от места и тяжести повреждения). В таких случаях на стадии разборки автомобиля необходимо отделить переднюю часть кузова или целые панели кузова, являющиеся частью всего корпуса сварной конструкции, механизированным инструментом, ручной ножовкой или зубилами.
С кузова снимают старое лакокрасочное покрытие. Разобранный таким образом и очищенный от старого покрытия кузов проходит подробный контроль, при котором выявляют характер повреждений, намечают порядок ремонта и определяют трудоемкость ремонтных работ. Результаты предварительного и окончательного контроля вносят в ведомость осмотра, являющуюся основным документом, определяющим состояние кузова до ремонта.
Кузов может быть правильно разобран только при строгом соблюдении технологической последовательности, исключающей возможность поломки и повреждения деталей. Порядок разборки устанавливается на каждый тип кузова.
При разборке кузовов и оперения очень трудоемкой работой является отвертывание заржавевших болтов, гаек и шурупов, удаление заклепок, разъединение панелей, сваренных точечной сваркой. Для удаления крепежных деталей, не поддающихся отвертыванию, можно применить один из следующих способов. Надо нагреть гайку пламенем газовой горелки. Этот способ весьма эффективен - после нагрева гайка обычно легко отвертывается. Можно откусить болт с гайкой кусачками или обрезать ножовкой либо отрубить гайку зубилом. Можно просверлить в головке болта отверстие диаметром, равным диаметру стержня болта, после чего головка отпадает, а стержень болта с гайкой выбивают из отверстия бородком. Данный способ успешно применяют для провертывающихся болтов с полукруглой головкой. Можно срезать головку болта или винта газовым резаком.
Для облегчения отвертывания заржавевших болтов и гаек применяют специальные химические составы, которые при нанесении на болтовые соединения удаляют продукты коррозии на резьбе и за счет хорошей проникающей способности смазывают резьбу между болтом и гайкой, облегчая тем самым демонтаж резьбового соединения. Обычно такие составы выпускают в аэрозольной упаковке и наносят распылением.
В шурупах, которые нельзя вывернуть вследствие износа прорези головки, надо просверлить головку, а затем, сняв деталь, вывернуть или выдернуть шуруп.
Заржавленные винты петель дверей нагревают газовым пламенем, после чего их легко вывернуть.
Расшивку клепаных швов производят так, чтобы не повредить разбираемые панели, если они не подлежат замене.
Детали, укрепленные точечной сваркой, отрубают острым тонким зубилом или просверливают места сварки через верхний лист панели с внутренней стороны кузова.
Особая осторожность необходима при разборке хрупких и легко повреждающихся деталей. Наоборот, детали, подлежащие замене, могут быть сняты любым способом, ускоряющим разборку, вплоть до повреждения их, если они не поддаются снятию, но при условии, что при этом не будут повреждены связанные с ними годные детали.
При полной разборке кузовов объем работ и порядок их выполнения в значительной мере зависят от конструкции кузова и от количества и характера повреждений. Последовательность разборки кузова сводится в основном к снятию подушек и спинок сидений, внутреннего оборудования, ручек, поручней, держателей, хромированной арматуры и декоративных накладок, отделочных рамок, подлокотников, плафонов, внутренних перегородок и обивки, разных механизмов, стекол кузова, электропроводки, труб отопителя и других деталей и узлов, установленных внутри салона.
Лакокрасочное покрытие может быть удалено механическим способом с помощью пескоструйных аппаратов
или механизированным ручным инструментом, химической обработкой
специальными смывками и щелочными растворами.
При пескоструйной очистке и очистке механизированным ручным инструментом одновременно с лакокрасочным покрытием удаляются ржавчина и окалина.
Наиболее распространенным абразивным материалом для пескоструйной обработки металлических поверхностей является металлическая дробь с размером зерен 0,2-0,3 мм. Для очистки панелей кузова и оперения, изготовленных из листовой стали толщиной 0,8-1 мм, от старого покрытия и получения необходимой шероховатости оптимальный угол наклона струи дроби к обрабатываемой поверхности должен быть 45°, а давление воздуха - 0,2-0,3 МПа. Шероховатость обработанной поверхности не должна быть больше 20-30 мкм, что обеспечит высокое качество нового защитного покрытия.
Для дробеструйной обработки используют передвижной аппарат с ручным пистолетом. В аппарате предусмотрена автоматическая регенерация абразивной дроби и подача ее в дробеструйный пистолет.
Для удаления продуктов коррозии ручным механическим способом применяют различные установки. Из этих установок наибольший интерес представляет иглофреза. Иглофреза состоит из отрезков высокопрочной проволоки с определенной плотностью набивки. Она может срезать слой ржавчины, окалины, металла толщиной 0,01-1 мм.
Из ручного механизированного инструмента для очистки поверхности и удаления лакокрасочных покрытий используют также шлифовальные машинки МШ-1, И-144, шлифовальные аппараты ШР-2, ШР-6. Этот способ очистки применяют для проведения небольших объемов работ, так как он не обеспечивает необходимого качества и производительности работ.
Для удаления покрытий химическим способом применяют различные смывки
. Смывки наносят на поверхность распылением или кистью. Через несколько часов покрытие вспучивается, и его удаляют механическим способом, а затем поверхность промывают водой.
Крупные авторемонтные предприятия с большим объемом ремонта кузовов для снятия лакокрасочного покрытия используют щелочные растворы. Очистку производят в ваннах с полным погружением в них кузовов, кабин и других деталей. Для снижения времени травления применяют ускорители - глюконат натрия, этиленгликоль. Раствор, состоящий из 20% едкого натра, 0,5% глюконата натрия и 8% этиленгликоля, снимает покрытие толщиной 100-150 мкм за 10-15 мин при температуре раствора 95-98 °C.
Удаляют лакокрасочное покрытие в механизированных агрегатах, которые состоят из последовательно расположенных четырех отсеков: для снятия покрытия окунанием, промывки горячей водой, пассивирования, обдувки горячим воздухом.
При очистке кузова от коррозии надо определять глубину коррозионного разрушения. Для этой цели служат гамма-толщиномеры
.
Если автомобиль побывал в аварии, то часто деформируется при этом не только его кузов. Последствия аварии оказываются более значительными и глубокими, чем это кажется на первый взгляд неискушенному человеку. Последствия могут быть самыми разнообразными и весьма существенными для дальнейшей эксплуатации автомобиля. Выделим основные:
нарушение правильности расположения колес (проявляется в плохой устойчивости автомобиля на дороге и повышенном износе шин);
нарушение диагоналей (контрольных точек). Эти диагонали, указанные на конструкторской базе автомобиля, проводятся под основанием между определенными точками рамы кузова и точками крепления переднего и заднего мостов. Но такое искажение диагоналей может наблюдаться и в других частях - проеме дверей, рамках переднего и заднего стекол.
Деформации сопровождаются образованием складок пола или другого элемента основания или рамы. Оно и понятно, удар не может вызвать значительное утолщение тонкого металла, каким является лист, поэтому в зоне удара образуются крупные складки. Другие складки, сопровождаемые утолщением металла, могут появляться в более отдаленном месте, а именно: в местах наименьшего сопротивления их образованию, в длинномерных деталях кузова, которые легче поддаются сгибу, в больших промежутках между точками сварки, где листы могут сдвигаться относительно друг друга.
Очевидно, уже при первом изучении состояния автомобиля надо обнаружить все деформации - очевидные, как смятый капот, и не бросающиеся в глаза изменения базовых (контрольных) точек.
Первый осмотр рекомендуется проводить следующим образом: автомобиль приподнимается на подъемнике и производится осмотр основания или рамы визуально либо ощупыванием рукой с целью обнаружения возможных складок. (При этом не надо путать небольшие складки, которые есть в местах изгиба некоторых штампованных деталей). Если обнаружены складки, то деформация кузова определенно произошла.
Иногда складки могут быть плохо различимы или хорошо видны, но расположены в местах, не влияющих на основные размеры. Если не обнаружено никаких складок, то для большей достоверности необходимо произвести следующий контроль.
Состояние автомобиля в основном определяет контроль правильности установки колес. Есть много методов этого контроля. Можно провести на контрольном стенде с вращением мостов автомобиля. Электронная модель такого оборудования обеспечивает простоту проведения контроля, а также высокую точность.
После выполнения контроля геометрии переднего моста (развал, схождение) можно произвести проверку соответствия положения заднего моста и установки колес. Замеренные величины должны соответствовать допускам, установленным изготовителем. Эту диагностику можно выполнять с помощью специального штангенциркуля, который состоит из профиля квадратного сечения, по которому скользят две каретки, на каждой из них смонтированы движки со шкалой. Движки перемещаются по направляющим и могут быть зафиксированы. На конце профиля установлен игольчатый стержень, регулируемый по высоте. На профиле закреплена металлическая рулетка. Металлическая лента рулетки проходит через ближнюю каретку и своим концом крепится к дальней каретке. Автомобиль устанавливается так, чтобы передние колеса не были повернуты в какую-либо сторону, а захваты распределены равномерно. Длина профиля должна быть немного больше расстояния между осями автомобиля. Надо отрегулировать эту длину, расположить неподвижный игольчатый стержень так, чтобы его острие находилось по центру передней ступицы или по краю обода на высоте центра ступицы переднего колеса. Потом расположить два движка так, чтобы они острием касались края обода заднего колеса на уровне центра колеса. Зафиксировать каретки и движки.
Контроль заключается в сравнении положения колес на одной стороне автомобиля с положением колес на другой стороне. Первое измерение может быть сделано с любой стороны автомобиля. После первого измерения необходимо отвести зафиксированный штангенциркуль, стараясь не нарушить регулировку, и установить его симметрично с противоположной стороны автомобиля. Если вершины движков прикладываются точно, то колеса расположены правильно и деформация отсутствует. Если вершины движков не совпадают с контролируемыми точками, то имеет место деформация кузова.
Измерение диагоналей без снятия механических узлов производится по инструкции завода-изготовителя автомобилей, в которой контролируемые диагонали проводятся между контрольными точками. Диагонали проводятся между направляющими отверстиями рамы кузова, затем от этих направляющих отверстий - к точкам механических узлов, какими являются крепежные болты (ось крепления рычага подвески), или шарниров. Эти диагонали не измеряют в числовых значениях, а проверяют только их симметричность. После определения расстояния между точками, отмеченными, например, на левой стороне, производят симметричное измерение на правой стороне, чтобы путем сравнения установить идентичность этих размеров. Если измеренные размеры неодинаковы, имеет место деформация кузова.
Эти измерения производятся под автомобилем, установленным на подъемнике или на яме. Инструментом для измерения диагоналей может быть измерительная масштабная рейка. Она состоит из неподвижной центральной части, представляющей собой гильзу, на концах которой нанесены неподвижные шкалы.
К рейке прилагается набор подвижных наконечников, регулируемых по высоте и устанавливаемых в перпендикулярном направлении на концы подвижных линеек или иногда на их продолжение. Они могут быть проградуированы в миллиметрах либо иметь условные риски.
Проверка с помощью измерительной рейки осуществляется следующим образом. Сначала надо осмотреть центральную часть днища рамы кузова. Эта часть наиболее жесткая и является точкой отсчета для других диагоналей. Контроль заключается в определении положения траверс. Надо установить центрирующий измерительный наконечник в центральное отверстие, расположенное под осью пола кузова, и отрегулировать подвижную линейку с измерительными наконечниками до первого контрольного отверстия. Затем надо перенести установленный размер симметрично в другое положение и производить аналогичные измерения других диагоналей между точками, указанными заводом-изготовителем. Диагонали измеряются между точками рамы днища кузова и точками переднего или заднего мостов. Некоторые проверки осуществляются с частичным снятием механических узлов.
Штангенциркули и измерительные рейки могут применяться для контроля основных размеров в параллельном или диагональном направлениях после снятия механических узлов с целью оценки выполненной работы или предстоящей работы.
Контроль диагоналей может быть осуществлен и более простым и менее точным способом с помощью двухметровой рулетки, однако из-за возможных смещений рулетки и неточности центрирования такой способ не обеспечивает требуемой точности.
У некоторых моделей автомобилей расстояние между осями колес распределено несимметрично по отношению к оси кузова. Например, ось симметрии задних колес (встречается в иномарках) может быть несколько смещена относительно оси кузова. Тогда изготовитель задает расстояние между осями для каждой стороны. Разность может быть подсчитана и затем прибавлена или отнята в зависимости от конкретного случая и показаний штангенциркуля, полученных в процессе контроля. При этом регулировка неподвижного наконечника и движков не изменяется.
Контроль поверхности основания кузова позволяет установить коробление или образование складок основания кузова. Автомобиль приподнимается на подъемнике, после чего нивелировочная и центрирующая рейки крепятся к части кузова, образующей раму, при снятых подвижных деталях.
Эти измерительные рейки снабжены двумя подвижными линейками, посредством которых рейка устанавливается на требуемую ширину измеряемой части кузова. В центре подвижных линеек установлено визирное устройство. На каждом конце подвижных линеек установлены стержни, регулируемые по высоте и оканчивающиеся головкой в форме крючка для крепления реек к автомобилю.
По всей длине автомобиля размещают несколько измерительных реек, у которых регулирование стержней с крюками по высоте производится от нулевого размера основания, заданного изготовителем. Длина линеек выставляется симметрично с каждой стороны от острия визира. Ремонтник располагается перед автомобилем и производит непосредственное визирование так, чтобы визирные стержни располагались по одной линии, а измерительные рейки - в одной плоскости. Если же измерительные рейки не находятся в одной плоскости, а стержни визиров не расположены по одной линии, это означает, что произошла деформация основания кузова.
Современные измерительные системы по принципу работы делятся на две группы. Первая ориентирована на применение шаблонов, имеющих посадочные места для базовых точек. При этом кузов как бы надевается на шаблон, и любое несоответствие сразу же становится заметным. Такой порядок позволяет при замене лонжеронов и других силовых элементов использовать стенд в качестве стапеля.
Ко второй группе относятся электронные измерительные системы. Координаты базовых точек определяются лазерным лучом или щупом. Компьютер сравнивает полученные данные с заводскими спецификациями. Чем еще хороша эта система? На любом этапе ремонта можно распечатать результаты замеров (для страховой компании или по желанию клиента). Кстати, лазерная система позволяет проверить углы установки колес.
Однако такие "блага" фирменного сервиса не каждому по карману. Есть варианты проще (например, "Эксперт 2000" производства СПК "Индустрия"). Опытный мастер на таком или подобном оборудовании вполне способен вернуть кузову красоту и пропорции.
Новые измерительные системы хороши, хотя зачастую они мало интересуют хозяина машины. Многие автолюбители считают, что дивиденды от их применения получают прежде всего работники автосервиса, так как они экономят время и силы, а заодно поднимают цену.
Несколько слов о шаблонах (
контрольных калибрах). Эти контрольные устройства специально изготовляются для контроля определенных частей конкретной модели автомобиля. С помощью одного шаблона за одну установку можно проконтролировать множество размеров и форм.
Конструктивно шаблоны могут быть простыми, вырезанными из листа и тщательно подогнанными, как, например, шаблон для контроля рамки переднего стекла. В то же время они могут быть сложными, состоящими из набора сваренных между собой профилей с опорными пятками, в которых выполнены отверстия для крепления шаблонов в определенные места автомобиля, например, в крепежные отверстия передних или задних траверс.
Контроль шаблонами
проводят в следующих случаях:
для точного определения повреждений перед ремонтом;
для оценки выполненной работы в процессе ремонта и определения объема предстоящих работ;
для контроля формы отремонтированной детали или нескольких деталей после ремонта, а также правильности установки в первоначальное положение.
Назовем требования, которые необходимо исполнять при работе с шаблонами
.
Нельзя устанавливать шаблоны с усилием, так как это может вызвать деформацию шаблонов.
Нельзя загонять шаблоны на место с помощью ударов.
Нельзя использовать шаблоны в качестве подкладок под рычаг.
Нельзя применять шаблоны для закрепления деталей при газо- и электросварке (в этих случаях шаблон можно применить только для разметки, после чего его снимают, чтобы дать детали возможность расширения, а затем и сжатия в процессе сварки).
Не должно быть помех установке шаблона на контролируемое место. Перед контролем может быть произведена разборка.
Шаблоны не должны подвергаться деформации.
В автосервисе можно встретить и стенды размерного контроля
.
В отличие от тех же шаблонов, на стендах размерного контроля все проверки основаны на измерениях различных точек основания кузова. Эти системы заимствуют принцип щупов, и поэтому стенды размерного контроля обладают огромными преимуществами, обеспечивая высокую точность и комплексность осуществляемого контроля.
На станциях техобслуживания можно встретить установки БС-123.000 для правки и контроля кузовов
. Такой агрегат позволяет быстро и точно определить перекосы кузова и устранить их. Точность размеров отремонтированного кузова может быть доведена до стандартной, с которой изготавливается новый кузов на заводе-изготовителе. Установка позволяет определить три пространственные координаты базовых точек на нижней части кузова.
Кроме определения взаимного расположения важнейших точек автомобиля, конструкция установки предусматривает возможность жесткой и точной фиксации деталей пола кузова и лонжеронов в течение всего периода ремонта. Установка обеспечивает свободный доступ ко всем базовым точкам пола кузова в процессе ремонта и контроля.
Лучшая грудь - натуральная!
Упражнения для увеличения груди!
Ваша грудь будет красивой!
Помогут 2 упражнения
Nokia Concept
Эксклюзивная Новинка! Такого Вы Ещё Не Видели!
Через 2 недели Ваша грудь не вместится в старый лифчик!
Лучшая грудь - натуральная!
http://www.marketgid.com/ghits/284363/i/3506/k/
" \t "_blank
Футболки "Alchemy Gothic" популярны во всем мире!
Богатый выбор - на самый изысканный вкус!
http://www.marketgid.com/ghits/59814/i/3506/k/
" \t "_blank
Победа за Вами!
12500.00 руб
Перестаньте "содержать" и "кормить" паразитов!
http://www.marketgid.com/ghits/212939/i/3506/k/
" \t "_blank
Отличный Подарок для Дамы!
11500.00 руб
Роскошный Телефон на Две Сим карты!
Тренер сборной Канады нашел методы против Овечкина...
Овечкин подвел команду...
Система боя, равной которой пока не существует...
Просто смотрите на 25 кадр! Жмите!...
"Кузовные работы: Рихтовка, сварка, покраска, антикоррозийная обработка"
Принцип работы установки заключается в том, что одиннадцать опорных точек в нижней части автомобиля располагаются таким образом, чтобы передняя и задняя подвески после ремонта кузова были зафиксированы по координатам базовых точек с точностью, заданной заводом-изготовителем.
Для проведения работ должны быть демонтированы детали и узлы от базовых точек пола кузова, после чего кузов помещают на установку и фиксируют по всем возможным точкам.
Кузов, не имеющий отклонений по базовым точкам, должен быть зафиксирован на раме пальцами в специальных кронштейнах установки по парным точкам крепления: стабилизатора поперечной устойчивости, поперечины передней подвески, кронштейна коробки передач, нижних продольных штанг задней подвески, а также в одной точке крепления поперечной штанги задней подвески. Специальный кронштейн с зажимом используется для закрепления кузова при ремонте.
Применение данной установки обеспечивает достаточно высокую степень точности контроля пола кузова за счет жесткой фиксации базовых точек. При этом соблюдаются важнейшие требования безопасности автомобиля по правильному расположению колес относительно опорной поверхности и обеспечивается правильное взаимное расположение их относительно друг друга.
Широкое распространение имеет установка "Даталинер" фирмы "Блэкхок" (Швеция). С ее помощью контроль геометрических параметров по базовым точкам пола кузова может выполняться без предварительного снятия узлов и агрегатов с автомобиля.
Для выполнения контрольных операций автомобиль, закрепленный на основной раме установки, поднимают двух- или четырехстоечным подъемником на удобную высоту и устанавливают строго в горизонтальной плоскости. К полу кузова, в соответствии с рекомендациями завода-изготовителя, по местам расположения базовых точек прикрепляют подвесные линейки. При этом визирные каретки устанавливают и фиксируют на прозрачных градуированных шкалах линеек, согласно размерам, указанным в контрольных картах завода. Зажимы и фиксаторы подвесок устроены так, что постоянно обеспечивают независимое вертикальное положение линеек.
Затем на опорах выставляют продольный и поперечный брусья измерительной системы. Направляющий брус, по которому перемещается корпус преломляющего устройства, устанавливают горизонтально и параллельно продольной оси автомобиля. При помощи двух винтов, расположенных на продольном направляющем брусе под источником света, направление светового луча регулируется так, чтобы он попал в центр перекрестья на корпусе рулетки, помещенной на конце направляющего бруса. Свет луча должен проецироваться между основной рамой установки и полом кузова автомобиля.
Для измерения выбирают три базовые точки неповрежденной части пола кузова и по ним дополнительно корректируют прибор как в горизонтальной, так и в вертикальной плоскостях. Затем выполняют контрольные замеры оставшихся базовых точек пола кузова. Величины отклонений, зафиксированные по визирным кареткам подвесных линеек, дают четкое представление о степени и направлениях деформаций.
Измерительное устройство, примененное на установке "Даталинер", относится к оптическим прецизионным системам
, работающим по принципу использования лазерного луча. Лазерный луч от источника подается на призму, затем, преломляясь под углом 90°, он попадает в виде точки на подвесные линейки. Такая система обеспечивает высокую точность измерений.
Подытоживая сказанное, отметим, что при ремонте автомобилей применяются два основных направления размерного контроля: механические системы
(щупы, рулетки, шаблоны и т.д.) и оптические системы
, проектирующие луч лазера на контрольные точки.
Прежде всего перед проведением ремонтных работ на автомобиле необходимо отсоединить аккумуляторную батарею и генераторные провода
. Все последующие действия можно назвать стандартными. Рекомендуется тщательно помыть автомобиль, особенно места, требующие ремонта, чтобы точно оценить деформацию кузова и определить объем будущих работ.
Тщательная мойка
, кроме того, устраняет возможность повреждения измерительных приборов, обеспечивает точность измерений.
Помимо поврежденных деталей, необходимо снять все детали и принадлежности, которые могут привести к попаданию инородных предметов между инструментом и обрабатываемым металлом, к возможным повреждениям соседних деталей кузова, мешать работе или создавать опасность.
Как уже отмечалось, надо очистить кузов от грязи. Куски грязи прилипают, в особенности к внутренним полостям крыльев колес и к наиболее выступающим местам днища кузова, а также к некоторым механическим узлам. Грязь легко удаляется мытьем сильной струей воды. Первоначальная обмывка струей воды увлажняет слой грязи, затем грязь легко смывается последующим мытьем.
Сложнее снимать звукоизоляционные покрытия
. Их наносят при изготовлении автомобиля на внутренние поверхности некоторых деталей, таких, как крылья и др. Звукоизоляционные покрытия легко воспламеняются и могут стать источником загорания от пламени кислородно-ацетиленовой горелки в случае ее применения. С другой стороны, под действием теплоты они размягчаются и образуют пластичный слой, препятствующий качественному выравниванию поверхности при рихтовке.
Для удаления этих материалов из-за сильного их сцепления с металлом приходится применять шаберы
. Для этих целей обычно применяют концевые шаберы, которые изготовляют из изношенных плоских напильников, их конец затачивается шлифовальным кругом, чтобы обеспечить угол резания, равный приблизительно 45°. При проведении этой однообразной работы необходимо следить за правильной насадкой ручки шабера, так как в процессе шабрения возвратно-поступательные движения, совершаемые шабером, могут привести к соскакиванию хвостовика напильника с ручки. Выскочивший шабер может поранить руку.
При наличии в мастерской компрессорной установки и пневматического оборудования можно быстро провести шабрение с помощью пневматического пистолета, снабженного инструментом для зачистки поверхности.
Быструю очистку кузова от этих покрытий обеспечивают установки горячего воздуха, при этом температура воздуха достигает 500-800 °C в зависимости от мощности установок.
Также необходимо удалить краски и мастики
, наносимые на наружные поверхности при покраске. Краска или мастика мешает работать кузовщикам, кроме того, поверхность листа получается неровной из-за остатков краски и мастики, что ухудшает условия рихтовки и не дает возможности получить гладкую поверхность. Они удаляются шлифмашинками.
При ремонте могут быть повреждены или могут мешать работать элементы кузова
, прикрепленные болтами, которые мешают доступу к поврежденному участку, либо не позволяют использовать инструмент (установить домкрат, обеспечить размах молотка и т.д.). Это амортизаторы, капот, крышка багажника, двери и другие детали.
Могут быть повреждены либо подлежат замене элементы электрооборудования
. Желательно отсоединить электрические провода, чтобы не повредить изоляцию, или снять прибор полностью, чтобы он не повредился от вибрации при сильных ударах молотка. К таким элементам относятся фары, сигнальные приборы, реле.
Иногда для ремонта кузова достаточно снять одно колесо
, а для проведения крупного ремонта может возникнуть необходимость в снятии части подвески или переднего и заднего мостов.
Снятие механических узлов
должно производиться в порядке, установленном изготовителем в инструкции по ремонту. Последующая установка выполняется очень тщательно, с соблюдением всех заданных регулировок. Исходя из этого, за исключением несложного демонтажа, не требующего применения специализированного инструмента, рекомендуется, чтобы эти работы выполнялись опытным механиком либо под его наблюдением и с применением специализированного инструмента.
Если работы выполняются в салоне, то металл кузова, как правило, не виден, он закрыт декоративной отделкой. Ее необходимо демонтировать, снять двери, снять подножные коврики, панели задних боковых стенок кузова автомобиля
и т.д.
Ремонтные работы приводят к запылению салона, иногда сопровождаются искрообразованием, требуют места для ремонта внутри салона, так что в таких случаях обязательно нужно вынимать сидения
. Если рулевое колесо и щиток приборов не сняты, их необходимо закрыть чехлом.
До сих пор речь шла о деталях, которые могут мешать либо пострадать при проведении ремонтных работ. Но есть еще элементы, создающие опасность при ремонте.
Например, источниками пожара могут быть бак и бензопроводы
, если они располагаются в зоне возможного нагрева горелкой или попадания отлетающих искр, а также материалы, оставшиеся на металле после снятия звукоизоляционных войлочных покрытий. Их необходимо тщательно удалить, так как они легко воспламеняются и могут быть источником пожара, если окажутся в зоне сварки.
Чтобы не быть разбитыми при неосторожных ударах, должны быть сняты стекла
, находящиеся вблизи ремонтируемой зоны.
Съемными называют детали, которые устанавливают на каркас кузова и крепят болтами. К ним относятся: бамперы
или щитки, решетка радиатора, капот, крышка багажника, двери
и крылья (
если они съемные).
Сборка производится с помощью винтов с шестигранными головками, которые ввинчиваются в гайки. В некоторых случаях гайки удерживаются от проворачивания сепараторами квадратной формы из листового материала. Сепараторы приварены к внутренней поверхности листа, к которому крепится съемная деталь. Гайка в сепараторе не проворачивается. Между головкой винта и листовой обшивкой кузова устанавливается лепестковая шайба, предотвращающая откручивание собранных элементов. С течением времени коррозия (ржавчина) в резьбе гайки и винта делает отвинчивание невозможным или очень трудным. Поэтому нежелательно резко увеличивать усилие на ключ, под действием крутящего момента, приложенного к короткому участку винта между его головкой и гайкой, может произойти отрыв винта.
Для облегчения отвинчивания можно попытаться смазать винты и гайки специальными маслами или жидкостями. Перед отвинчиванием немного ждут, чтобы жидкость проникла в заржавленную резьбу. Эффективен другой способ отвинчивания, который заключается в нагреве гайки пламенем кислородно-ацетиленовой горелки. При этом винт удлиняется, а ржавчина отделяется. Но при нагреве гайки докрасна нагревается окружающий материал кузова, что может вызвать обгорание находящихся поблизости резиновых уплотнений, электрических проводов и др. Так что этот способ применять можно очень осторожно и только после снятия деталей, которые способны воспламеняться.
Если винт обломался, необходимо в оставшейся части просверлить отверстие малого диаметра (для направления), а затем просверлить отверстие диаметром под нарезку резьбы и нарезать резьбу. После снятия поврежденного элемента зачищают контактные поверхности. Если эти поверхности не были защищены, их покрывают специальной антикоррозионной краской. При последующей установке необходимо применять новые винты и шайбы. Перед установкой желательно слегка смазать болт, что облегчает завинчивание и задерживает образование ржавчины.
Поврежденные бамперы в некоторых случаях можно выправить. Так как металл бампера достаточно толстый, необходим сильный нагрев зоны правки, что приводит к разрушению хромового покрытия. Детали из коррозионно-стойкой стали с незначительными повреждениями можно отремонтировать, а после восстановления их формы отполировать. Однако эти ремонтные операции редко являются выгодными, так как стоимость правки быстро достигает стоимости новой детали, так что замена является более предпочтительной. Кроме того, не всегда качество правки профилированных бамперов удовлетворительное. При ремонте составных бамперов производят замену только поврежденных деталей, в результате чего снижается стоимость ремонта.
Щитками обычно называют бамперы, изготовленные из пластических материалов. Сегодня они находят все более широкое применение для защиты автомобиля, чем и объясняется это название. Кроме того, они в значительной степени улучшают аэродинамические характеристики кузова.
Ремонт щитков из смолы, армированной стекловолокном, может осуществляться посредством стеклоткани, покрытой смолой. (Более подробно об этой технологии будет рассказано ниже). В то же время другие композиционные материалы, из которых изготовляют щитки, такие, как поликарбонаты, совершенно непригодны для ремонта. Щитки обычно крепятся к кузову двумя центральными и двумя боковыми болтами. Если противотуманная оптика или указатели поворотов встроены в щитки, то при снятии щитка необходимо отключить электрические провода.
Крылья (съемные) часто снимают и заменяют новыми, даже если их можно выправить. Правка крыльев может обойтись дороже, чем замена их новыми.
Крылья крепятся к кузову винтами, которые обычно контрятся, т.е. ввинчены в упругие металлические пластинки. Крылья крепятся к верхней части брызговика, передней стойке и передней панели. Чтобы снять крыло, сначала необходимо снять буфер, а в некоторых случаях и решетку облицовки радиатора, оптические элементы фар и сигнальных приборов. После снятия крыла необходимо обработать места контакта и удалить все следы коррозии.
Перед установкой нового (или бывшего в употреблении) крыла надо покрыть места контакта слоем герметика. Затем надо установить крыло на брызговик, вставить винты в места крепления и слегка завернуть их, не затягивая, чтобы отрегулировать зазоры дверей и капота, а затем затянуть винты окончательно. Потом можно установить расположенные вблизи детали, которые были сняты перед снятием крыла. Присоединить электрические провода к фарам и сигнальным фонарям, соблюдая расцветку проводов, если таковая предусмотрена.
Если крылья приварены и не очень сильно деформированы, то их обычно подвергают правке, так как замена таких крыльев достаточно трудоемка. Если правка приваренных крыльев требует очень много времени и если внутренние детали или передняя и задняя стойки повреждены, то крылья следует заменить.
Не все части крыла выправляются с одинаковой трудоемкостью, если крыло и подвергается правке. Легче выправить верхнюю скругленную часть крыла, чем его боковую поверхность, которая обычно имеет небольшую выпуклость.
Для увеличения жесткости на боковой поверхности крыла часто выполняют линии жесткости. После общей правки с помощью киянки необходимо в первую очередь восстановить окончательную форму линий жесткости, а затем уже выровнять поверхность крыла. Потом выправляют боковые поверхности крыла. Если при этом возникают вздутия, их устраняют посредством точечного нагрева детали.
Если часть поверхности имеет небольшую выпуклость, переходящую за границы линий жесткости, ее можно устранить путем вытяжки металла, не нарушая при этом формы сопряжения линии жесткости с основной поверхностью. Такую операцию можно выполнить только при достаточно большой длине поверхности, так как при малой длине обработки выпуклость может стать больше, чем до правки.
Сказанное означает, что во всех случаях надо с самого начала выбрать правильную стратегию рихтовки конкретной детали. Ошибка может привести к неисправимым дефектам.
Капот и крышка багажника - подвижные детали автомобиля, следовательно, они являются съемными. Капот и крышка багажника выполняются из штампованного листа, усиленного с внутренней стороны листовыми штампованными профилями. Деформация капота почти всегда вызывает и деформацию профилей жесткости. Если произошло складывание капота и крышки багажника, то технически их невозможно выправить.
Правку капота или крышки багажника удобнее производить на верстаке, так что их обычно снимают. Правка осуществляется сначала с помощью пресса, затем - рихтовкой киянкой, спрофилированной по месту. Когда форма детали приблизительно восстановлена, удаляют точки сварки и отрезают пилой части профилей жесткости, мешающие выравниванию поверхности. Отрезают в недеформированной зоне, далее заканчивают правку поверхности и профилей жесткости отдельно. Затем профили жесткости приваривают либо кислородно-ацетиленовой сваркой, либо электросварочным аппаратом в среде защитного газа в те места, из которых они были вырезаны. При этом панель капота или крышки багажника защищают от нагрева либо асбестовым картоном, либо листом металла, который помещают между свариваемым профилем и поверхностью листа, а затем убирают. Точки сварки подвергают зачистке. Экономически такой объем работы по восстановлению формы редко оправдывается для деталей автомобилей массового выпуска. В этом случае практичней заменить поврежденную деталь новой. Так что перед началом ремонтных работ надо точно выяснить стоимость деталей, а затем уже принимать решение, что делать. Другое дело - ремонт собственными силами, которые человек, как правило, не пересчитывает на деньги, особенно когда испытывает проблемы с наличностью.
Двери также являются подвижными элементами кузова автомобиля, они выполняются съемными. Конструктивно дверь состоит из каркаса, который является опорой для обшивки. До последнего времени панель двери обычно подгонялась и приваривалась к каркасу точечной сваркой, потом стал распространяться иной способ - склеивание. Приклеивание обеспечивает наилучшую герметизацию в местах завальцовки, что в значительной степени снижает возможность образования коррозии.
При замене панели двери рекомендуется применять тот же способ установки, что и на заводе-изготовителе.
Другими деталями двери являются стекла, подъемник стекла, замок с дистанционным управлением, обивка, закрывающая внутреннюю поверхность двери в кабине.
Большинство дверей с незначительными повреждениями можно выправить. Однако на практике такая правка экономически не всегда выгодна, если деформирован, например, внутренний каркас двери. В этом случае поврежденную дверь заменяют новой и устанавливают на нее годные детали и узлы, снятые с поврежденной двери, за счет чего расходы владельца на ремонт несколько сокращаются.
Если внутренний каркас двери не поврежден, ремонт можно выполнять двумя способами: заменой поврежденной панели двери новой панелью или выправкой панели двери, если вмятина не вызвала значительного растяжения металла.
Для удобства выполнения рихтовочных работ дверь снимают. (Можно снять только оси шарниров и отсоединить ограничители двери). Затем дверь разбирают. Сначала снимают рукоятки стеклоподъемника и замка, фиксирующиеся на осях либо посредством стяжных колец и шплинтов, либо с помощью шпонок, доступ к которым затруднен, так как они закрываются декоративными накладками, которые, в свою очередь, прижимаются пружинами. Внутренняя обивка обычно крепится к двери с помощью разжимных прихватов, которые входят в отверстия внутренней полости двери. Чтобы снять обивку, нужно ввести лезвие отвертки (его предварительно покрывают тканью) между каркасом двери и обивкой вплотную к прихвату и нажать на него, как рычагом. Ткань предохраняет краску от непосредственного контакта с металлом отвертки, что может вызвать повреждение лакокрасочного покрытия кузова. Чтобы не разрушить соединение прихвата с обивкой двери, что иногда возможно из-за отсыревшей панели обивки, нельзя прикладывать к отвертке большое усилие.
Замену панели двери у некоторых моделей автомобилей можно выполнить без снятия стекол, стеклоподъёмника, а также других крепежных элементов. Вообще меняют панель двери только в том случае, если это предусмотрено изготовителем и если панель поставляется отдельной деталью.
Самый быстрый способ снятия панели двери заключается в выравнивании среза двери в местах завальцовки. Делается это следующим образом. Надо обрезать, если это необходимо, соединение сваркой в верхних точках; отсоединить полосу панели от каркаса двери, если она приварена точечной сваркой; выправить деформацию каркаса двери.
При установке панели на каркас двери предпочтение отдается склеиванию в случае, если это возможно выполнить или это рекомендовано изготовителем с целью предохранения от коррозии. Для склеивания выбирают рекомендованную клеевую мастику или похожую на нее.
При необходимости правки панели не всегда надо снимать стеклоподъемник и замок.
Правка панели двери - более тонкая работа, чем правка крыла. Глубина штамповки панели небольшая, а ее стороны жестко соединены с внутренним каркасом и имеют определенную форму и длину. Любое выстукивание молотком в результате растяжения металла создает выпуклость поверхности.
Но есть и удобства. Поверхность внутреннего каркаса, образующая перегородку кабины, имеет вырезы, в которые можно ввести инструмент и приложить к нему усилие, противоположное усилию, вызвавшему вмятину. Усилие на инструмент может быть создано посредством небольшого разжимного домкрата с ножным приводом или небольшого рычага. Усилие нужно прикладывать не к центру вмятины, а как можно ближе к точкам закрепления панели. Под действием усилия в основном восстанавливается форма панели двери, после чего остается лишь выровнять ее поверхность, на которой имеются складки в точках закрепления. Для их устранения панель нагревают в нескольких точках, затем охлаждают и производят выравнивание. Далее операцию повторяют до полного восстановления формы.
Если какая-либо часть внутреннего каркаса была отрезана для облегчения доступа к панели, то ее необходимо снова приварить на место.
Если центр вмятины панели имеет достаточно большую площадь, то в некоторых случаях ее можно выколотить как обычно изнутри с помощью кувалды, нанося удары около вершины вмятины. На панелях, имеющих резко выраженную кривизну, вмятина может быть выколочена с наружной стороны легкими ударами, наносимыми по периферии кратера вмятины. После выравнивания необходимо снова нанести на внутреннюю поверхность панели звукоизоляционное покрытие, затем установить принадлежности панели и обивку.
После обследования повреждений аварийный автомобиль может подвергаться одной из двух категорий ремонта:
если наружные повреждения съемных элементов не вызвали деформацию кузова и подрамника, то производится только малый ремонт обшивки кузова;
если сильные повреждения вызвали искажение размеров между точками крепления механических узлов, то требуется восстановление структуры кузова автомобиля или замена кузова (когда в результате повреждения кузов признан непригодным к ремонту или затраты на ремонт выше стоимости нового кузова).
Во всех случаях восстановление кузова должно обязательно сопровождаться контролем геометрии с применением шаблонов или посредством измерения размеров основания кузова. Но для ремонта наружных поверхностей требуется, скажем так, мелкий инструмент и незначительное количество оснастки, в то время как для восстановления кузова требуются различные сложные приспособления для правки, обеспечивающие качественное выполнение работ.
Большинство деталей, составляющих безрамный кузов, соединяются посредством точечной сварки
. На машиностроительных заводах точечная сварка осуществляется с помощью роботов, обеспечивающих шаг (расстояние между каждой точкой) сварки, определенный на стадии проектирования кузова. При ремонте рекомендуется придерживаться этого заданного шага сварных точек. Каждая точка легко различается по отпечатку электрода, оставленному на металле. Отпечаток представляет собой небольшую впадину глубиной несколько десятых долей миллиметра и диаметром, равным 4-6 мм в зависимости от толщины листового материала. Если отпечатки закрыты краской, ее необходимо счистить, чтобы вскрыть отпечатки. Отделять сварные детали можно тремя способами:
полным или частичным высверливанием точек сварки;
вырубкой точек сварки;
вырубкой листа как можно ближе к линии сварки, отрывом металла между точками сварки и последующей зачисткой.
Рассмотрим первый способ - сверление. Независимо от применяемого сверлильного инструмента необходимо накернить центры точек сварки, чтобы обеспечить центрирование сверла.
Сверлить можно специальными инструментами, работающими по типу фрез, применяемых при механической обработке. Фреза приводится в движение электродрелью и, вращаясь вокруг неподвижного центра, образует круговую выточку вокруг сварочной точки. Глубина фрезеровки выбирается предварительно равной толщине листа, что приводит к разделению сваренных элементов. На необработанном фрезой листе остается центральная часть сварной точки, которую можно срезать другой фрезой, вводимой в предварительно выполненную цилиндрическую выточку.
Чтобы удалить центр сварной точки сразу после вырезки цилиндрической канавки без смены инструмента, более удобно применять две электродрели. Можно также прорезать цилиндрическую канавку по всей сварочной точке и после разъединения сваренных деталей зачистить оставшийся в местах сварки металл. При этом форма листа, который не подвергался обработке ни сверлом, ни каким-либо другим инструментом, остается неизменной.
Можно сверлить спиральными сверлами, диаметр которых равен диаметру сварочного пятна. После высверливания всех точек сварки и разъединения деталей на опорной детали остается ряд сквозных отверстий. Эти отверстия можно закрыть припоем методом твердой пайки, а затем зачистить шлифовальным инструментом. Твердая пайка является более предпочтительной по сравнению с газовой сваркой, поскольку обеспечивает более низкую температуру нагрева и, как следствие, снижает коробление. Коробление устраняется рихтовкой.
Есть и такой способ - предварительное сверление отверстия малого диаметра, а затем зенковка. В центре сварочной точки сверлится небольшое отверстие диаметром 3 мм, не проходящее насквозь нижний лист. Это отверстие служит для направления режущей части сверла, диаметр которого принимается чуть больше диаметра сварочной точки. Режущая часть сверла затачивается под углом, близким к 180°, и оставляет на поверхности нижнего листа небольшую бобышку. В процессе зенковки надо следить, чтобы сверло не вошло слишком глубоко в металл и не просверлило насквозь нижний лист.
Вырубка сварочных точек осуществляется специальным зубилом, предназначенным для этой работы, вручную (ручное зубило) или с помощью пневматического инструмента. Зубило вводится между листами так, чтобы его прорезь охватывала вырубаемую точку сварки.
Рассмотрим вырубку листа, разъединение и последующую зачистку. Операция заключается в том, что вместо удаления поврежденной детали целиком ее удаляют частями. Сначала вырубают поврежденную деталь как можно ближе к линии расположения точек сварки. Вырубка может быть выполнена пневматическим инструментом, снабженным зубилом. Можно также выполнить эту операцию и обычным зубилом. Однако нельзя применять для этой цели кислородно-ацетиленовую горелку, так как она сильно нагревает металл (ухудшает все механические характеристики листового металла), вызывает загорание любых близких к очагу внутренних антикоррозионных покрытий и способствует развитию коррозии.
После вырубки остается лента металла, на которой приблизительно по центру располагаются точки сварки.
Другой способ заключается в применении ручной шлифовальной машинки, снабженной диском, выполняющим функцию режущего инструмента.
Есть способ вырезки с использованием аппаратов для дуговой плазменной резки
. Струя сжатого воздуха удаляет расплавленный металл и обеспечивает чистый рез шириной от 2 до 2,5 мм. Таким способом можно разъединить листы, соединенные точечной сваркой, однако при этом на обоих листах останутся отверстия.
После удаления детали, подлежащей замене, появляется доступ для правки детали. Необходимо выправить возможные деформации, отрихтовать места контакта, удалить все следы коррозии пескоструйным аппаратом или химическим способом. (Следует избегать удаления ржавчины режущим кругом, так как при этом уменьшается толщина листа, что вызывает снижение надежности соединения точечной сваркой). Затем надо тщательно вымыть обработанную часть детали и высушить.
Поверхность листов, соединяемых точечной сваркой, должна быть очень чистой, причем металл лицевой и оборотной сторон листов, где требуется выполнить точки сварки, должен быть зачищен.
Долгое время для предохранения металла от последующей коррозии
применяли сурик
, который накладывался на зону сварки сразу после сварки. В настоящее время рекомендуется на контактные поверхности наносить краску на основе цинковой пудры
и подсушивать ее в течение нескольких минут. В то же время имеются аэрозольные баллоны с цинковой краской, позволяющие гораздо быстрее выполнить эту работу и обеспечить более интенсивную сушку. Третьим решением является использование герметизирующих токопроводящих мастик
. Их наносят из краскопульта. Перед этим необходимо снять или удалить шабером любую другую краску, так как она выполняет роль изоляции. Ржавчина, сухая грязь затрудняют протекание электрического тока.
Новую деталь устанавливают на место и закрепляют с помощью зажимов или тисковых клещей. Проверяют размеры деталей, определяющих геометрию кузова и днища, и точность их установки на базовые поверхности. Проверяют зазоры и равномерность расположения прилагаемых листовых деталей. Выбирают соответствующий условиям выполняемой работы электрод. Рекомендуется брать наиболее короткий электрод, чтобы гарантировать достаточное прижатие соединяемых листов.
Для настройки реле времени установки для точечной сварки выполняют несколько сварочных точек на двух кусочках металла такой же толщины, тем самым определяя время сварки, а следовательно, и качество сварного соединения. Затем производят сварку, соблюдая первоначальный или рекомендуемый шаги сварки.
В случаях, когда нельзя отделить сваренные точечной сваркой детали обычным для этой цели инструментом, вырезают подлежащую замене часть детали как можно ближе к месту соединения. При частичной замене деталей, составляющих единое целое с кузовом, например, заднего крыла, являющегося неразъемной частью, вырезку осуществляют в недеформированной зоне с учетом рекомендаций изготовителя.
Часть детали, предназначенной для замены деформированного участка, вырезают из новой или выправленной детали с первоначальным припуском. Затем производят окончательную вырезку и подгонку путем измерения, если нельзя это сделать наложением, или накладывают предназначенную для замены часть детали на вырезанное место. Наложенную деталь закрепляют с помощью тисочных зажимов, затем обмечают чертилкой, снимают и обрезают (обрезать можно ручной ножовкой, пневматической или электрической пилой, "болгаркой"). При обрезке удаляют припуск. Если сварка предусматривается с отбортовкой, то для ее выполнения припуск оставляют.
Подгонку по месту можно также выполнить путем наложения и закрепления новой детали. Однако вырезка производится за один раз по разметке, выполненной на детали, наложенной внахлестку на ремонтируемое место. Это позволяет выполнить одновременно подгонку двух стыков, но не дает возможности выполнить отбортовку.
Сварщик производит сварку встык. Сварка в зоне вырезки может выполняться кислородно-ацетиленовой горелкой, а лучше сварочным аппаратом в среде защитного газа, который обеспечивает соединение сварочным швом или точечной сваркой с минимальным короблением и оголением места сварки. Скорость сварки при этом также более высокая, благодаря чему свариваемые листы не обгорают. Места сварки слегка выравнивают, а затем заглаживают оловом.
Если есть доступ к зоне сварки, применяют точечную сварку. При ремонте необходимо применить тот же способ сварки, что и при изготовлении на заводе, за исключением отдельных рекомендаций изготовителя. Перед сваркой необходимо зачистить следы от предыдущей точечной сварки.
Отбортовку обычно выполняют при частичной замене панелей. С этой целью с помощью специальных ручных или пневматических зажимов, обеспечивающих равномерный перепад высот поверхностей заплечиков и основной детали, на оставшейся детали кузова выполняют заплечики
. Затем новая часть детали устанавливается на заплечики с перекрытием на 10-15 мм. Сварка может выполняться наплавкой точек, если устанавливаемая деталь просверлена, либо сплошным швом, либо цепочным.
Для отделки сварочного соединения по отбортовке рекомендуется применять полиэфирную шпаклевку
вместо заглаживания оловом. Травление листа кислотой
способствует удержанию олова на его поверхности, однако вызывает коррозию в результате проникновения продуктов травления между отбортованными листами.
Кузов легкового автомобиля собирают из листовых, штампованных на прессе деталей. Штамповка создает в листовом металле усилия растяжения или сжатия, что приводит к относительному перемещению частиц металла. Другими словами, в металле возникают напряжения, удерживающие форму штампованной детали. Наружные штампованные детали кузова автомобиля обычно имеют выпуклую форму.
В результате удара в деталях кузова возникают новые напряжения. Местами выпуклая поверхность детали сжимается, выравнивается, затем становится вогнутой и, если удар очень сильный, металл вытягивается. Вокруг деформированной зоны создается граничный пояс, в этом месте металл подвергся наибольшей вытяжке, так как в момент сжатия он являлся своего рода шарниром, на который действовали усилия сжатия. Этот ограничительный пояс иногда образует резко выраженную кромку или складку и мешает восстановлению формы металла, так как является зоной возникновения максимальных внутренних напряжений.
Часто изменение напряжений в металле происходит не по всей панели, а лишь в зоне удара. Во многих случаях форма панели восстанавливается после разгрузки точек утяжки кромки, ограничивающей зону деформации. Перед выполнением работ в зоне утяжки металла шабером снимают краску и противошумную мастику, освобождают места утяжек, а затем начинают восстановление формы детали. Если вмятина обширная, но неглубокая, ее выправляют нанесением удара по вершине вмятины. Если вмятина более глубокая, то ее выправляют постепенно, начиная от края, при этом под выправляемую поверхность на границе вмятины подставляют наковаленку соответствующей формы. Если в деформированной зоне находятся более жесткие сечения (детали жесткости, подкладки, стойки), ремонтировать начинают в первую очередь эти детали, так как они обладают большим сопротивлением деформации и затрудняют восстановление формы листовых деталей. Восстановление формы включает в себя две основные операции: выколотку и выравнивание, или рихтовку.
Выколотка
- это операция, предназначенная для придания поврежденной части формы, близкой к ее первоначальному виду. Различие полученной формы с ее первоначальной устраняется выравниванием. Выколотка осуществляется приложением усилия, противоположного усилию, которое вызвало деформацию. Выколотку производят либо давлением
, либо молотком
, начиная с более жестких деталей от граничной кромки в направлении центра вмятины.
Выколотку можно начать и выдавливанием с помощью домкрата
или рычага
, следя за тем, чтобы создаваемое усилие не вызвало деформации в точках опоры. Операцию продолжают с помощью молотка
и ручной опорной наковаленки
.
Профиль наковаленок, применяемых для выколотки, выбирают похожим на профиль детали перед деформацией.
Ударные инструменты, применяемые при выколотке, не должны вызывать удлинение листа, нельзя применять ударные стальные инструменты, нанося удары по листу на наковаленке. Если позволяет рабочее пространство, желательно применять деревянные киянки
, которые обладают значительной опорной поверхностью и не оставляют следов на обработанной поверхности металла. Кроме того, выколотка киянками не вызывает никакого удлинения, так как дерево киянок недостаточно твердое, чтобы вызвать утончение металла. Выколотка киянкой, находящейся в хорошем состоянии, может даже обеспечить предварительное выравнивание высокого качества.
Широкое применение нашли стальные молотки
, в бойке которых находится резина. Этот инструмент более надежен и долговечен, чем киянки.
Когда после выколотки форма детали почти восстановлена, поверхность оказывается готовой под последующую рихтовку. Оценка качества восстановленной формы детали осуществляется сравнением с формой недеформированной детали.
Часто выколотку производят непосредственно на автомобиле, особенно в случае ремонта несъемной детали. Это работа в неудобных условиях. Если элемент съемный, его легче снять и выполнить работу на верстаке. Такими деталями являются двери, капоты и крылья некоторых автомобилей.
Особым рихтовочным инструментом являются рифленые кувалды
, рабочая поверхность которых напоминает поверхность напильника. Эти кувалды в меньшей степени вытягивают металл, так как профиль рифлений создает сжатие металла.
Несколько слов о ручном инструменте - самом ценном для мастера. Это поддержки, осадки, молотки
и т.д. Ручной инструмент обычно поставляется в наборе. Надо отметить, что содержимое набора - плод долгих трудов, поскольку приспособления, в него входящие, универсальны. Сделать универсальной кривизну рабочих поверхностей инструмента сложно. Это под силу только крупным фирмам, способным затратить на создание инструмента значительные средства, а случайные поделки хорошего мастера не удовлетворят. Сегодня за хороший комплект жестянщика надо уплатить от 600 у. е.
Рихтовка
- последняя операция обработки кузовных деталей. Так как операция является отделочной, ее необходимо выполнять тщательно, для чего часто требуется много времени.
Рихтовка заключается в устранении неровностей поверхности до такой степени, когда состояние ее становится почти таким же, как после штамповки. В процессе рихтовки возникает наклеп
, который вызывает упрочнение листа.
Рихтуют ударами молотка по листу, который опирают на наковальню
. Используемая для рихтовки наковальня должна обладать достаточной массой, чтобы поглощать удар, и иметь форму, схожую с формой рихтуемой части детали. Рабочая поверхность наковальни должна быть гладкой, чтобы не оставлять следов на поверхности листа.
При рихтовке применяются рихтовочные молотки
, называемые также гладилками
, и молотки-кувалды
. Молотки изготовляют из сталей, причем их бойки закаливают и полируют. Утончение листа, вызываемое обработкой молотком, происходит тем быстрее, чем сильнее наносимые удары. Так как объем металла остается постоянным, то его утончение сопровождается удлинением, которому препятствует металл необработанных молотком участков. В результате блокирования этой деформации происходит выпучивание поверхности листовой детали.
Лучший эффект достигается в случае рихтовки легкими частыми ударами с малой вытяжкой металла, чем при рихтовке сильными разрозненными ударами, оставляющими следы на поверхности и сильную вытяжку металла. При наличии на рихтуемой детали складки рихтовку начинают с выправления этой складки до окончательной формы, а затем рихтуют остальную часть детали.
Качество выполненной рихтовки оценивается визуально и ощупыванием поверхности ладонью руки. Визуально наиболее легко контролируются выпуклые или вогнутые поверхности путем просмотра их под углом или сбоку. Для контроля плоских поверхностей применяют линейки.
При ощупывании малейшая неровность ощущается ладонью руки. После рихтовки возможно образование двух видов дефектов поверхности:
на выпуклом участке небольшой листовой панели образуется впадина
, которую нельзя устранить выдавливанием;
на обширном участке листовой панели образуется пузырь
, который при нажатии на его выпуклую сторону попеременно перемещается то на одну, то на другую сторону листа.
При определении вида дефекта достаточно надавить на его выпуклую поверхность. Если участок листовой панели небольшой, то дефект не выжимается. Если участок листовой панели достаточно обширный, то выпуклая часть панели, называемая пузырем, перемещается и образует на другой стороне листа выпуклость, при этом возникает характерный шум (хлопок металла).
Как устранить такой дефект? Вначале необходимо определить по возможности границы пузыря и отметить мелом. Далее следует устранить удлинение металла.
При наличии на поверхности панели впадины достаточно произвести рихтовку в глубь двух небольших секторов с каждой стороны листа. При этом удары наносятся по возможности в центр впадины, а затем перемещаются к периферии с постепенным уменьшением силы удара.
При наличии на поверхности панели пузыря необходимо стянуть металл. Это можно выполнить только путем утолщения металла. Однако пластичность мягкой стали при комнатной температуре недостаточно высокая, в то же время металл, нагретый до достаточно высокой температуры (для мягкой стали это 800 °C), становится пластичным и легко деформируется. При этом нет необходимости нагревать весь пузырь, достаточно выбрать для этого несколько подходящих точек.
Более удобным источником нагрева является кислородно-ацетиленовая горелка. Операция заключается в устранении дефекта путем использования процессов расширения и усадки металла, возникающих при нагреве, и последующего охлаждения. Местные нагревы получили названия усадочных точек или усадочных нагревов. Механизм процесса заключается в следующем.
При нагреве точки металла узким пламенем кислородно-ацетиленовой горелки небольшой круг металла быстро разогревается докрасна. Но прежде чем металл станет красным, он начинает расширяться, и расширение может вызвать образование выпуклости. Как только металл нагреется докрасна, его пластичность резко возрастет. Под действием пружинящего эффекта окружающего не нагретого докрасна металла происходит усадка разогретой докрасна части металла. Так как расширению металла препятствует менее нагретый окружающий металл, то увеличение его объема происходит за счет утолщения. Как только металл разогреется докрасна, горелка отводится и начинается охлаждение: нагретый круг металла становится темно-красным, затем черным и продолжает далее охлаждаться.
При охлаждении металл сжимается, его объем уменьшается, но удерживается расположенным вокруг металлом, длина и ширина которого не изменялась. Необходимо, чтобы дополнительное утолщение, полученное при растяжении металла, было восстановлено после охлаждения. Но так как металл имеет температуру, не соответствующую максимальной пластичности, то, сжимаясь, он поглощает небольшую часть удлинения окружающего металла.
Усиление осаживания металла
осуществляется различными способами:
уменьшением скорости распространения теплоты путем создания кольца вокруг нагретой части металла из мокрой ветоши;
противодействием деформации путем нажатия на металл ручкой молотка или другим предметом около нагретой точки;
выстукиванием границ точки металла, нагретого докрасна, а затем и самой нагретой точки киянкой или рихтовочным молотком.
Наибольшее применение имеет последний способ.
Рассмотрим порядок выполнения технологических операций рихтовки различными способами.
При рихтовке нагреванием
и выстукиванием горелку быстро подводят к центру пузыря, прогревают его и горелку отводят, когда разогретое докрасна пятно достигнет диаметра, равного максимум 12 мм.
При нагреве необходимо следить, чтобы металл не начал плавиться. Если нагретое пятно будет большего диаметра, это вызовет гораздо большую усадку, чем надо. Если работа выполняется в одиночку, то горелку откладывают, под лист (почти под дефект) помещают наковаленку. Быстро выстукивают не покрасневший металл вокруг нагретой точки, а затем и нагретую точку, пока металл еще остается темно-красным.
Обработку предпочтительнее вести деревянной киянкой. При рихтовке молотком-гладилкой сила удара должна быть небольшой, чтобы не создать растяжения металла вместо усаживания.
Если пузырь небольшой, то достаточно провести обработку одной точки.
Работу можно считать завершенной только тогда, когда металл остынет до температуры окружающей среды. Для ускорения охлаждения применяют мокрую ветошь или пропитанную водой губку. Если необходимы дополнительные точечные нагревы, то их делают не более двух-трех между каждым охлаждением. Их располагают вокруг центральной точки.
После охлаждения нагретого листа проводят легкую рихтовку прогретого сектора, чтобы выровнять поверхность металла, которая имела до этого деформацию.
Расположение точек усадки зависит от формы пузыря. Если пузырь круглый, то точки располагаются по радиусу. Если пузырь длинный и узкий, то точки нагрева располагают узкими рядами.
Подчеркнем, рихтовка с применением точек усадки требует опыта, который приобретается со временем. Легче проводить такие работы на округлых деталях или сильно выпуклых, чем на почти плоских панелях или панелях с малой выпуклостью. Трудность заключается в восстановлении точной длины металла. Разгонять пузырь необходимо как можно осторожнее, так как рихтовка вызывает удлинение металла, которое должно обеспечить желаемую длину металла. Стоит только нанести несколько сильных ударов, как образуется новый пузырь. В то же время, если нанесено меньшее, чем необходимо, количество ударов, то неопытному может показаться, что металл вокруг пузыря слишком вытянут. Он будет пытаться устранить это точками усадки и выполнять их в большем количестве для достижения малоуловимого равновесия металла, чем опытный жестянщик.
Рассмотрим другой способ устранения пузыря - путем наложения влажного охлаждающего кольца
. Он осуществляется следующим образом. Смоченную в воде ветошь располагают вокруг нагреваемой точки, что затрудняет распространение теплоты и, как следствие, уменьшает деформацию, предшествующую нагреву металла докрасна. При этом металл получает большую усадку, чем без предварительного охлаждения, но меньшую по сравнению с применением выколотки.
Вместо ветоши можно использовать пасту. Паста выполняет такую же роль, что и влажное кольцо из ветоши, но действие оказывает более сильное.
При этом способе нагрев деформированной детали осуществляется пропусканием электрического тока большой силы и низкого напряжения. Вспомним, что точечная сварка легко нагревает докрасна металл, сжатый двумя электродами. Общий принцип действия всех промышленных аппаратов точечной сварки заключается в быстром местном нагреве металла, находящегося в контакте с угольным электродом, установленным в держателе. В зависимости от типа держателя и различной установки электродов сварка может осуществляться точками, прямыми строчками, кривыми строчками. Один провод подводит напряжение к держателю электрода, а второй соединяет лист с массой.
Для устранения пузыря этим способом проводят подготовительные работы. Сначала выправляют деформированную часть с помощью обычных инструментов. Если вмятины небольшие, можно обойтись без правки. С мест обработки удаляют краску (она является изолятором). Операция может выполняться как вручную шабером, так и шлифовальной машинкой. Зачищают также место соединения с массой.
В держатель устанавливают электрод, соответствующий выполняемой работе, если это предусмотрено конструкцией аппарата: электрод с плоским или выпуклым наконечником для выполнения точек усадки; электрод с острым наконечником для выполнения усадочных строчек. На вторичной обмотке регулируют напряжение.
В ремонтной практике применяют два основных типа аппаратов для нагрева зоны правки.
Аппарат со встроенной губкой
состоит из держателя электрода, самого электрода и силового провода, питающего держатель электрода. Провод соединяется с аппаратом дуговой сварки, обычно использующим электроды с покрытием, и подключается на место провода, питающего стандартный держатель электрода. Медный электрод установлен внутри держателя электрода и проходит через центральное отверстие кольцевой губки, установленной в корпусе из электроизоляционного материала. Отдельный провод соединяет обрабатываемый металл с массой.
Для тонких листов достаточна минимальная сила тока 40 А. При обработке более толстых листов или алюминия силу тока увеличивают. Губку смачивают в воде и устанавливают в корпусе. Роль губки - ограничивать зону нагрева и охлаждать. Электрод на короткое время вводится в контакт с металлом в зоне правки. Каждое контактирование электрода вызывает местный нагрев металла до красного цвета в результате сопротивления металла прохождению тока. Если аппарат не перемещают в стороны, то получаются точки нагрева. Если аппарат перемещают, получаются усадочные ряды. Нельзя долго держать электрод в контакте с листом, чтобы не прошить его насквозь.
Другой тип аппарата с вынесенной губкой. Он содержит электрический трансформатор с регулятором силы тока, силовой провод с держателем электрода и электродом, силовой кабель, соединяющий аппарат с источником электрического тока. Рабочее напряжение этого аппарата меньше и сравнимо с напряжением аппарата точечной сварки. Регулятор тока вторичной обмотки устанавливают в положение, соответствующее виду и толщине обрабатываемого металла. После каждого контакта электрода с листом нагретую зону протирают влажной губкой. В зависимости от природы деформации нагрев производят точками или рядами. Вначале охлаждают металл вокруг точек контакта, а затем их вершины.
В холодном состоянии удалить пузырь можно лишь в том случае, когда размеры пузыря небольшие и металл не сильно вытянут.д.ля этого ручную наковаленку заменяют мягкой поддержкой, выполненной, например, из твердого дерева, обработанного рашпилем по форме контура детали, или отлитой из свинца. Ударами рихтовочного молотка производят стяжку металла, опирающегося на поддержку, начинают от краев пузыря и движутся в направлении центра.
При рихтовке листа поддержка подвергается деформации, которая способствует равновесному распределению молекул металла. Результат зависит от степени вытяжки металла. Чтобы получить подходящий результат, необходимо, чтобы металл листа был достаточно пластичен, а пузырь имел небольшую выпуклость.
Случается, когда удары вызывают повреждения в труднодоступных местах кузова, а иногда в совершенно недоступных или когда для ремонта поврежденного участка требуется большая разборка. Чтобы избежать долгого и дорогостоящего ремонта с вырезкой и заменой деталей или чтобы не производить большой разборки ради устранения небольшой вмятины, можно выровнять вмятину другим способом. Наиболее старый способ, который можно применить для таких случаев, - пайка оловом. После очистки поверхности листа его лудят, а затем заделывают вмятину оловянным припоем. Припой опиливают (напильником с отогнутой ручкой), потом поверхность полируют.
Покрытие из припоя обладает достаточной твердостью и сцеплением. А недостатком этого процесса является необходимость нагрева - оловянный припой плавится при температуре, близкой к 250 °C.
Есть другой способ заделки вмятин, который заключается в применении шпатлевок на базе полиэфирных смол, накладываемых на тщательно зачищенную поверхность листа. Шпатлевки быстро твердеют и не усаживаются. Поверхность шпатлевок также опиливают и полируют. Стойкость накладываемых шпатлевок в большинстве случаев зависит от тщательности нанесения и сцепления (адгезии) первого слоя.
Стержневая вытяжка вмятин
Подвергшиеся деформации пустотелые детали кузова чаще всего заменяют. К таким деталям относятся пороги, стойки кузова, крылья сдвоенные и труднодоступные изнутри, траверса и некоторые другие. Но в зависимости от обстоятельств, в том числе материальных, в большинстве случаев устранение деформации оказывается возможным снаружи с помощью так называемых "гвоздей", привариваемых к вмятине. Наиболее часто применяются метод и набор инструментов, носящих название "гвоздодер
".
В чем его сущность?
Используется комплект инструментов, снабженный трансформатором, подобным трансформатору аппаратов точечной сварки. Питание осуществляется электрическим током напряжением 220/380 В. Аппарат приварки гвоздей похож на большой пистолет, на конце которого расположено медное сопло-зажим, в нем помещаются гвозди, а на краю установлено кольцо. Гвозди представляют собой стальные цилиндрические стержни диаметром от 2 до 3 мм в зависимости от типа. Конец стержня, образующий головку, приваривается к зачищенному участку деформированной детали кузова. Конструктивно инструмент правки представляет собой цилиндрический стержень, по которому скользит груз. На верхнем конце стержня имеется упор, а на нижнем конце установлен патрон для зажима гвоздей.
Сначала производят предварительную подготовку поверхности деформированной детали. Ее очищают от краски и других изоляционных продуктов, чтобы обнажить металл листа и обеспечить хороший контакт. Далее начинается правка.
В сопло пистолета устанавливается гвоздь, пистолет подключается к источнику питания. Устанавливают среднюю выдержку реле времени пистолета. Время выдержки определяет время сварки, т.е. время прохождения электрического тока.
Перед началом правки кузова надо провести несколько пробных сварок, чтобы определить лучший режим. Пробы проводятся на листе такой же толщины, что и лист детали.
Когда режим установлен, пистолет приставляют к деформированной зоне и начинают приварку от краев вмятины, если она обширная.
На пистолет нажимают так, чтобы его кольцо вошло в контакт с листом и обеспечило прохождение тока для сварки. После приварки гвоздя пистолет отводят.
Затем вводят маленький патрон "гвоздодера" на гвоздь и зажимают его, производят несколько вытяжек деформированного участка с помощью "гвоздодера", нанося удары грузом по упору.
Для завершения правки можно продолжить вытяжку вручную (за гвоздь), не ударяя грузом и производя одновременно выколотку по краям вмятины с помощью проковочного или гладильного молотка. Этот метод дает наилучшие результаты. После правки гвозди отваривают с помощью того же пистолета.
В наши дни все большую популярность приобретают так называемые "споты
". Это электрод, который временно приваривается к металлу для последующей вытяжки. Тот же "гвоздодер". Исполнений этого приспособления много. Можно сваривать с металлом электрод, можно приварить переходные элементы различной формы. Наконечник снабжен крючком или цанговым зажимом. Тянущее усилие создается рычагом или обратным молотком.
Кстати, споттером с угольным наконечником можно отжигать и осаживать выпуклости или "хлопуны", о которых рассказывалось выше. Основная ценность метода - возможность работать с лицевой стороны, нередко можно обойтись без разборки салона, что экономит время и средства.
Лонжерон: менять или ремонтировать
Лонжероны - это усилительные детали брызговиков, пола кузова и пола багажного отсека. Одновременно лонжероны играют роль амортизаторов объема передней части кузова, так как располагаются в зоне поглощения деформации.
Во время ремонта, требующего частичной замены лонжеронов, необходимо следить, чтобы их вырезка производилась в местах, указанных изготовителем. Так или иначе, эти места не должны располагаться в зонах, специально предназначенных для поглощения удара и смятия в результате его.
Перечислим способы придания амортизирующих свойств лонжеронам:
образование складок при штамповке, предусматривающее смятие лонжерона в гармошку при аварийном ударе;
придание лонжеронам S-образной формы;
выполнение специальных отверстий или сквозных прорезей;
применение штампованных профилей;
переменное сечение лонжеронов.
При частичной замене лонжерона особенностью процесса является то, что не требуется применения соединительной муфты. Нужна только дуговая сварка в среде защитного газа. Установка лонжерона производится следующим образом: обрезают лонжерон на 0,5 мм перед фартуком; после подгонки устанавливают новый лонжерон на шаблон.
Если эта операция выполняется на контрольно-измерительном стенде, то в качестве элемента жесткости применяют подвижную призму. Надо приварить новый лонжерон встык дуговой сваркой в среде защитного газа. Соединение лонжерона с брызговиком колеса осуществляется с помощью аппарата точечной сварки с удлиненными захватами для электродов.
При выполнении отделочных операций не надо зачищать сварочный шов лонжерона с фартуком, так как он покрывается слоем герметика. Надо нанести из краскопульта покрытие из жидкого воска на передние лонжероны и траверсу и покрыть нижнюю часть брызговиков звукоизоляционной мастикой.
Очень важно, чтобы любое вмешательство, связанное с выправкой или заменой (даже частичной) лонжерона, выполнялось на стенде с точной выверкой параметров.
Вырезают лонжерон ручной ножовкой или плазменным резаком.
Для облегчения подгонки новой части лонжерона вырез делается косым. Такой метод дает больше свободы при установке лонжерона. Разделение точек сварки осуществляется с помощью вырезных фрез, в результате просверленной оказывается только деталь, подлежащая замене.
После снятия лонжерона появляется возможность подготовки места соединения. Точки сварки удаляют с помощью ручной шлифовальной машинки. Ею удаляют также следы коррозии. Если есть доступ к обрабатываемой зоне, предпочтительнее удалять ржавчину с помощью пескоструйного аппарата.
Для обеспечения качественной точечной сварки новая часть лонжерона должна быть зачищена. Затем наносится антикоррозионное покрытие.
Далее новую деталь устанавливают на автомобиль, закрепляют тисочными зажимами к оставшейся на месте детали. Лонжерон приваривают точечной сваркой к брызговику или полу багажного отсека.
Установка для точечной сварки снабжается соответствующими кронштейнами, причем длину их выбирают наименьшей. Электроды должны быть тщательно заточены. Необходимо соблюдать шаг сварки, т.е. расстояние между каждой точкой. Разрез лонжерона сваривается встык непрерывным швом. Сварка должна быть сквозная, чтобы обеспечить необходимую механическую прочность соединения.
При ремонте лонжерона никогда нельзя упускать из вида, что он является усилительным элементом кузова и в значительной степени определяет его жесткость. Таким образом, при ремонте необходимо руководствоваться методом, описанным ранее, или методом, рекомендованным изготовителем автомобиля. Не рекомендуется усиливать лонжерон при частичной замене, главным образом, в передней и задней частях кузова, так как при этом увеличивается прочность зоны, предназначенной для смятия, т.е. для амортизации. Если амортизация этой зоны окажется недостаточной, то в случае возможного удара деформация кузова пройдет дальше, т.е. к кабине автомобиля, которая не должна деформироваться.
Решение о правке или замене лонжерона на поврежденной автомашине зависит в значительной степени от протяженности деформированной зоны, степени деформации, а также от квалификации ремонтника. При небольшой деформации лонжерона на большой длине даже при наличии мелкой складки не требуется замены лонжерона. С помощью домкрата или угольника можно восстановить первоначальную форму и положение лонжерона с сохранением его характеристик. С другой стороны, при значительной деформации лонжерон необходимо заменить, так как правка вызовет изменение структуры металла и прочности, что, в свою очередь, приведет к изменению характеристик самого кузова.
Как править среднюю стойку
Средняя стойка - деталь боковой части кузова и повреждается, как правило, одновременно с дверью. Деформация стойки влияет на состояние передней двери, расположение задней двери, оси которых установлены на средней стойке, а также вызывает деформацию крыши, поддерживаемой средней стойкой.
Средняя стойка состоит из двух основных частей: наружной штампованной части в форме балки и накладки, часто выполненной с отверстиями и привариваемой к отбортовке наружного профиля. Внизу стойка соединяется с порогом кузова, а верхняя часть стойки соединяется с верхом боковой части кузова. Способы соединения стойки с кузовом определяются изготовителем.
Применяются два вида ремонта: правка поврежденной стойки
и ее замена
.
Рассмотрим правку деформированной стойки. Ее осуществляют в следующей последовательности. Снимают двери и вынимают сиденья. Снимают со стойки декоративные накладки и ковер с пола кузова. Далее производят правку стойки с помощью домкрата, который упирают в две большие деревянные подкладки, расположенные у нижнего и верхнего основания стойки.
При рихтовке стойки наковаленку проводят через отверстия в накладке, а в случае необходимости прорезают накладку. После восстановления формы наружного профиля прорез для наковаленки заваривают и производят сборку разобранной части кузова.
При замене стойки, кроме разборки, указанной выше, необходимо снять обивку крыши, закрыть панель приборов и рулевое колесо тканью. Далее производят общую правку поврежденной стойки с помощью толкающего домкрата, а также, по возможности, правку порога так, чтобы поврежденные детали заняли свои первоначальные положения на боковой части кузова. Затем удаляют поврежденную стойку.
В зависимости от конструкции могут применяться следующие способы удаления стойки: вырезка; разделение точек сварки; комбинация этих двух способов
.
Обычно стойку срезают в верхней части на расстоянии нескольких сантиметров от конца (вне зоны сопряжения) или ниже радиуса сопряжения стойки с проемом двери. Накладку вырезают на несколько сантиметров ниже, посреди отверстия, если оно есть, чтобы сместить будущую сварку. Сварные точки сдвинутой части накладки высверливаются со стороны наружного профиля, чтобы не повредить остающуюся часть накладки.
Нижняя часть стойки выполняется в двух вариантах. Рассмотрим каждый в отдельности.
Если стойка выполнена как единое целое с порогом, то новая стойка заканчивается поперечной частью, представляющей собой отрезок порога кузова, посредством которого стойка соединяется с порогом. Поврежденную стойку удаляют "болгаркой" или высверливанием сварных точек. Размечают места разрезов с припуском под дальнейшую подгонку. Вырезают порог и разъединяют части, сваренные точечной сваркой. После удаления поврежденной стойки производят зачистку заусенцев, могущих остаться после вырезки, а также очищают поверхность металла от краски, ржавчины и др. Новую стойку зачищают, устанавливают на место и подгоняют.
Если стойка соединяется точечной сваркой либо с лонжероном, либо с порогом, либо одновременно с этими двумя деталями, для ее снятия удаляют сварные точки, применяя любые способы.
Как и в предыдущем случае, после удаления поврежденной стойки удаляют заусенцы и производят зачистку опорной поверхности металла. Очищают новую стойку, устанавливают на место и подгоняют.
Перед закреплением стойки по чертежу изготовителя проверяют размеры диагоналей. Затем закрепляют стойку предварительно, чтобы проверить зазоры дверей и их расположение. Предварительное крепление осуществляется с помощью ручных тисков, которые обеспечивают последовательное выставление дверей. Можно также закрепить стойку винтами-саморезами, что дает возможность одновременной установки и регулировки двух дверей за счет овальности отверстий.
После подгонки дверей их снимают и производят точечную сварку тех участков стойки с другими деталями, которые для этого предназначены. Разрезы, выполненные пилой, заваривают преимущественно сплошным швом кислородно-ацетиленовой горелкой в струе защитного газа. В местах, недоступных для точечной сварки, производят сварку глухими точками, затем заравнивают места сварки и ведут подготовку поверхностей.
Если стойка выполнена как единое целое с порогом, то ее нижнюю часть отрезают в поперечном направлении так же, как и ее верхнюю часть. Последующая сборка осуществляется сваркой.
Ремонт порогов
Обычно пороги привариваются к основанию кузова и образуют нижнюю часть кузова. У некоторых типов автомобилей пороги не устанавливаются с боковой стороны остова кузова, а выполняются съемными и крепятся к основанию кузова. Пороги размещаются с внешней и боковой сторон лонжеронов в зоне кабины, образуя защиту от различных выбросов и слабых ударов.
Рассмотрим сначала ремонт съемных порогов
. Крепление порогов часто осуществляется винтами-саморезами. Если порог имеет небольшое повреждение, вывинчивают винты крепления и снимают порог. Правку порога производят на верстаке с помощью обычного инструмента для правки и рихтовки.
Перед установкой отремонтированного порога необходимо покрыть внутренние поверхности антикоррозионной мастикой. Если порог имеет средние или значительные повреждения, дырки от коррозии, то ремонтировать его невыгодно, предпочтительнее заменить новым.
Приваренные пороги
. Если порог имеет незначительные повреждения, без резко выраженных складок, то его можно выправить вытяжкой снаружи. Для этого приваривают специально предназначенные для выправки "гвозди", а затем с помощью инерционного съемника или споттера производят последовательную вытяжку.
Если порог получил средние повреждения, то, учитывая большую трудоемкость снятия и установки порога, выгоднее ремонтировать поврежденный участок. После снятия дверей, сидений и покрытия пола, находящихся в зоне ремонта, ремонт может быть выполнен различными способами.
Например, вырезают сбоку порога прямоугольное окно, в которое можно ввести соответствующей формы наковаленку или другой инструмент, позволяющий осуществить вытяжку поврежденного участка, например, с помощью гидравлического приспособления. Когда форма участка порога восстановлена, вырезанное окно заваривают кусочком листа. Поскольку обратная сторона сварки является недоступной, нельзя осуществить общую выправку шва, поэтому внешний шов следует загладить оловянным припоем.
Или: вырезают отверстие на верхней части порога двумя поперечными резами, затем разъединяют точки сварки. Через эту вскрытую частично полость можно ввести наковаленку и выправить. После выправки поврежденной части вскрытое отверстие закрывают и заваривают.
Если поврежденная часть находится под дверью, ее вырезают и заменяют новой. Вырезают поврежденный участок за пределами поврежденной зоны, чтобы оставшаяся часть была неповрежденной. Из новой детали выкраивают соответствующую часть, подгоняют ее, устанавливают и приваривают.
Если порог получил серьезные повреждения, вырезают поврежденную часть "болгаркой" или с помощью пневматического зубила. Эти вырезы производятся около передней и задней дверей, а также около основания средней стойки.
Часто повреждается и сама стойка, поэтому ее заменяют одновременно с порогом. Вырезка лонжерона, а также средней стойки производится напротив крыши. После вырезки поврежденной части контролируют состояние лонжерона. Если надо выправить лонжерон, то проверяют состояние основания кузова, используя в случае необходимости соответствующий инструмент. Места установки новой части лонжерона зачищают, удаляя при этом частицы металла, оставшиеся после разделения сварочных точек. Далее выравнивают поверхности лонжерона. Новую часть лонжерона подгоняют по месту, устанавливают и предварительно закрепляют таким же образом, как это делалось со средней стойкой. Затем устанавливают новые или неповрежденные двери. После регулировки зазоров двери снимают. Производят точечную сварку деталей, которые были соединены точечной сваркой, а затем заканчивают соединение деталей с помощью кислородно-ацетиленовой горелки.
Как правило, крыша получает повреждения в результате бокового наезда на высокие препятствия, такие, как дерево, стена и т.п. В таком случае восстановление формы крыши очень трудоемко и, возможно, невыгодно. При нанесении (получении) слабых ударов выколотка деформированной поверхности с последующей рихтовкой может быть произведена.
Перед выполнением ремонтных работ необходимо снять сидения, разобрать обивку крыши, закрыть или снять рулевое колесо и панель приборов. При необходимости могут быть сняты одна или несколько дверей.
Выколотку листового металла
, открытого изнутри, производят по общей методике. Если вмятина большая, применяют толкающий домкрат. Он устанавливается на деревянную опору, передавая требуемое опорное усилие на пол кузова, последний подпирается домкратом, подставленным под днище кузова. Между головкой домкрата и крышей помещают фасонный клин или по возможности используют резиновую головку.
Как и при правке других деталей, производят разнообразные выдавливания вокруг вмятины
с целью постепенного выправления смятого металла. Одновременно происходит выправка верхней части боковой поверхности основания кузова с помощью клина, устанавливаемого между домкратом и внутренней поверхностью боковой стенки кузова.
Рихтовку крыши
необходимо производить легкими ударами точно так, как рихтовку дверей. Так как края крыши при рихтовке практически не деформируются, то возникающее удлинение листового металла создает выпучивание. В связи с тем, что поверхность крыши большая, может образоваться удлиненный пузырь. Следовательно, максимальный объем работы желательно выполнять деревянной киянкой, а рихтовочный молоток использовать лишь для тонкой отделочной рихтовки.
Рихтовку скругленных участков следует производить по направлениям, параллельным бортику крыши.
В некоторых случаях приходится заменять крышу. Если замена
осуществляется совместно с заменой ее продолжений, каковыми являются проем ветрового стекла и панели задней боковой стенки кузова, которые на некоторых моделях автомобилей выполняются как единое целое с крышей, то перед началом жестяных работ снимают двери, панель приборов, обивку крыши, сиденья, а также при необходимости - капот, крышку багажника и съемные крылья. На других моделях автомобилей задние боковые панели соединены с задними крыльями или являются их частью. После разделения точек сварки или разрезки пилой их закрепляют газовой сваркой.
Замена задних боковых панелей
производится редко и не представляет экономического интереса. Когда стойки проема ветрового стекла находятся в хорошем состоянии, разрезка их и соединение могут производиться на половине высоты. При этом передние крылья снимать необязательно.
К остову кузова крыша приваривается точечной сваркой. Чтобы произвести замену крыши, необходимо разъединить точечную сварку обычными способами. Если остов кузова деформирован, то вначале его выправляют. После удаления поврежденной крыши облегчается доступ к верхней части кузова. При наличии поврежденного места его выправляют, контролируя правильность формы установкой дверей и новой крыши. Если верхняя часть остова кузова сильно деформирована, то производят частичную замену деформированных зон новыми частями. Ограниченная замена с последующим соединением верхней части остова кузова с верхом панелей задней боковой стенки и со стойками ветрового стекла на половине их высоты намного уменьшает объем работ по разделению точечной сварки.
Разрезают стойки ветрового стекла на половине их высоты ножовкой, при этом необходимо следить, чтобы не разрезать остов кузова, если он не был деформирован.
Устанавливают новую крышу и ударами руки сверху подгоняют ее по месту. Крышу предварительно закрепляют и проверяют правильность формы рамки заднего и ветрового стекол. Проверка осуществляется либо установкой стекол, либо с помощью шаблонов, либо путем измерений, либо контроля щупами. Таким же образом производят установку дверей.
Установленные детали прихватывают в нескольких точках точечной сваркой и, убедившись, что геометрия осталась неизменной, производят окончательную сварку.
Разрез, выполненный на половине высоты стоек ветрового стекла, заваривается дуговой сваркой в среде защитного газа. Если крыша вырезалась по всем четырем углам, то предпочтительнее произвести твердую пайку швов, чтобы обеспечить наилучшую герметичность.
Несколько слов о пластмассовых крышах. Пластмассовые крыши крепятся специальными заклепками к остову металлического кузова, при этом места соединения покрываются герметиком. Снятие такой крыши заключается в высверливании заклепок и их удалении.
Если производится замена остова кузова и крыши
новыми деталями, то отверстия сверлят в местах, предусмотренных изготовителем. Затем детали разъединяют и покрывают места соединения герметиком. При установке соединяемых деталей совмещают отверстия с помощью оправок и вставляют заклепки.
Некоторые крыши из слоистого пластика завальцовываются в металл. Другие крыши крепятся изнутри винтами. Завальцованные панели являются съемными.
Технологический процесс замены узлов и деталей кузова более подробно рассмотрим на примере автомобилей ВАЗ.
Замена переднего крыла.
Передние крылья должны быть заменены при значительной деформации, разрывах, а также сквозной коррозии. Незначительные повреждения (вмятины, царапины и т.п.) правят непосредственно на автомобиле с обязательной последующей грунтовкой и окраской.
Замену переднего крыла необходимо выполнять в следующем порядке.
1. Снять передний бампер
, капот, антенну, переднюю дверь и осветительные приборы.
2. Срубить зубилом или срезать
механизированным инструментом соединения крыла
с панелью передка и кожухом фары, отступив от линии соединения на 2-3 мм; соединения крыла с передней стойкой боковины остова кузова - отступив на 2-3 мм от линии изгиба вертикального усилителя.
3. Высверлить металл
в точках контактной сварки соединения сточного желобка с брызговиком и отсоединить крыло вместе со сточным желобком от панели брызговика и рамы ветрового окна. Отогнув крыло, срубить его на горизонтальном участке в месте соединения с нижней частью боковой панели передка.
4. Удалить оставшиеся полоски металла
с помощью торцевых кусачек и тонкого зубила. Деформированные кромки панелей передка, брызговика и передней стойки по посадочным местам подрихтовать и зачистить шлифовальной машинкой.
5. Удалить грязь и ржавчину
из полости, закрываемой крылом, тщательно промыть водой, обдуть сжатым воздухом, обезжирить и на участки, зачищенные до металла, нанести грунт типа ГФ-073.
6. Прошить в новом крыле отверстия
диаметром 5 мм с шагом 40-50 мм по усилителю передней стойки, сточному желобку, по кромкам соединения крыла с кожухом фары и боковой панелью. Прошить отверстия в панели передка по кромке вертикальной отбортовки ниже кожуха фары.
7. Подогнать новое крыло
по месту посадки и быстро прихватить его зажимными клещами. При этом дверь и капот должны быть установлены на место, проверены равномерность зазоров по сопрягаемым деталям, а также допустимые размеры по выступающим и западающим частям лицевых поверхностей.
8. Прихватить
латунным припоем Л63 крыло в соединениях
: с рамой ветрового окна и верхней поперечиной передка - в трех точках; с панелью передка - в трех точках; с порогом - в двух точках; с усилителем передней стойки - в двух точках.
9. Приварить крыло
к сопрягаемым деталям передка кузова: к брызговику переднего лонжерона - по сточному желобку; к кожуху фары; к панели передка ниже кожуха фары, через отверстие в панели передка; к боковой панели остова кузова - по нижней горизонтальной части крыла; к передней стойке - по вертикальному усилителю.
Сварка - точечная, электродуговая, в защитном газе, по предварительно прошитым отверстиям. Допускается ацетилено-кислородная (газовая) сварка с применением в качестве присадочного материала проволоки Св-08 диаметром 1,5-3 мм, проволоки ЛКМЦ или латунного припоя Л63 диаметром 2-3 мм.
10. После сварки зачистить швы
шлифовальной машинкой заподлицо с основным материалом и загрунтовать. На отдельные места при необходимости нанести шпаклевку и зашлифовать поверхности.
Замена порогов
. Пороги заменяют при их значительной деформации или сквозных коррозионных разрушениях. Порядок выполнения работ следующий.
1. Двери, передние и задние крылья должны быть сняты. Порог срубить
. Накладку и соединитель при наличии сквозной коррозии заменить. В случаях аварийного повреждения эти детали должны быть выправлены.
2. Удалить полоски оставшегося металла
срубленной детали кусачками и зубилом, затем деформированные кромки накладки, соединителя и пола подрихтовать и зачистить шлифовальной машинкой.
3. Полости
, закрываемые порогом, и внутреннюю поверхность порога обработать цинкохроматным грунтом
ГФ-073.
4. По линиям сопряжения порога с накладкой (по всей длине верхней и нижней кромок) прошить отверстия
диаметром 5 мм с шагом 40-50 мм. Затем порог установить на место и закрепить быстрозажимными клещами.
Для контроля правильности сборки порога в проемы устанавливают двери и проверяют зазоры с сопрягаемыми деталями. Зазоры в сопряжении порога с дверями должны быть не более 5±2 мм. Допускается выдвижение дверей относительно лицевой неподвижной поверхности порога не более чем на 3 мм. Затем двери снимают.
5. Приварить порог
к сопрягаемым деталям: по стыкам с боковиной кузова спереди и сзади сплошным швом; по кромкам, прилегающим к накладке, - электрозаклепками через отверстия, прошитые в кромках порога; по месту сопряжения с центральной стойкой - сплошным швом.
6. Места сварки
порога с сопрягаемыми деталями независимо от вида сварного шва зачистить
заподлицо с основным металлом шлифовальной машинкой и загрунтовать.
Замена передка кузова
. Передок кузова заменяют в тех случаях, когда основные детали передка (панель передка с кожухом фар, передние крылья, силовые поперечины и особенно передние лонжероны с брызговиками) восстановить методами растяжки-правки невозможно. Порядок замены следующий.
1. Снять передний бампер
, капот, аккумуляторную батарею и осветительные приборы.
2. Снять двигатель с коробкой передач и передней подвеской,
а также навесные узлы, приборы и электропроводку, размещенные в моторном отсеке.
3. Срубить передние крылья
.
4. Срубить брызговики и передние лонжероны
от щитка передка и лонжеронов пола. Операцию выполняют острым зубилом по панели брызговиков на расстоянии 10-15 мм от щитка передка. Передние лонжероны отделяют от лонжеронов пола в местах их сопряжения по точкам контактной сварки.
5. Удалить оставшиеся полоски металла
кусачками и тонким острым зубилом. Деформированные кромки сопрягаемых деталей отрихтовать и зачистить шлифовальной машинкой.
6. Выставить кузов
на установку БС-123.000 по базовым точкам
, зафиксировать в специальных кронштейнах и закрепить выдвижными стойками за ребра жесткости порогов кузова с двух сторон.
7. Прошить отверстия
диаметром 5 мм в кромках брызговиков
по месту их сопряжения со щитком передка. Шаг 30-40 мм.
8. Подогнать новые лонжероны
с брызговиками по местам, сопрягаемым со щитком передка и лонжеронами пола. Закрепить лонжероны в кронштейнах крепления поперечины передней подвески и стабилизатора поперечной устойчивости. Прихватить газовой сваркой латунным припоем Л63 брызговики с лонжеронами к щитку передка и лонжеронам пола.
9. Прошить отверстия
диаметром 5 мм с шагом 30-40 мм в кромках нижней поперечины передка
.
10. Выставить нижнюю поперечину
передка по передним концам лонжеронов и приварить ее по сопрягаемым поверхностям в защитном газе.
11. Прошить отверстия в отбортовке щитков радиатора
, выставить их по месту и прихватить латунным припоем. К щиткам радиатора приварить верхнюю поперечину рамки радиатора.
12. Прошить отверстия
с шагом 30-40 мм в кромках панели передка
по местам сопряжения со щитками радиатора и по отбортовке в местах сопряжения с передними крыльями (ниже кожуха фары), выставить и прихватить ее латунным припоем.
13. Навесить крылья и капот
, выполнить предварительный контроль передка кузова по зазорам и плотности прилегания к сопрягаемым деталям. При соответствии требованиям детали передка кузова сварить окончательно.
Брызговики
к щитку передка приваривают точками по прошитым отверстиям в отбортовке:
а) передние лонжероны по отбортовке приваривают к щитку передка прерывистым швом длиной примерно 30 мм через каждые 40 мм; сварку в местах стыковки передних лонжеронов с лонжеронами пола выполняют сплошным швом;
б) щитки радиатора к нижней поперечине передка и к брызговику приваривают точками по прошитым отверстиям;
в) панель передка с кожухами фар и верхней поперечиной приваривают точками к щиткам радиатора через прошитые отверстия; нижнюю поперечину передка приваривают точками к панели передка по отверстиям, прошитым в ее кромках, а в верхней части сваривают по сопрягаемым местам с брызговиками передка.
Замена крыши
. Крышу заменяют в случае опрокидывания автомобиля или при значительной деформации крыши. Порядок выполнения работ следующий.
1. Снять ветровое и заднее стекла
, принадлежности и обивку крыши, накладки сточных желобков.
2. Выполнить разметку
левой и правой боковых панелей
и срубить крышу по разметке в соединениях с этими панелями.
3. Высверлить в крыше точки для контактной сварки
в соединениях: с панелью рамы ветрового окна; с поперечиной рамы заднего окна; со сточными желобками.
4. Отсоединить панель крыши от кузова
и удалить оставшиеся полоски металла от панели рамы ветрового окна, сточных желобков и поперечины рамы заднего окна.
5. Отрихтовать посадочные места
элементов кузова и зачистить их шлифовальной машинкой.
6. Обезжирить и установить на усилители крыши прокладки типа "Келлер"
размерами 200х60х2 мм, 9 шт.
7. Прошить по периметру кромок крыши отверстия
диаметром 5 мм с шагом 40-50 мм.
8. Подогнать по месту новую панель крыши
и прихватить ее газовой сваркой латунным припоем: к панели рамы ветрового окна по передним стойкам; к боковинам крыши в двух точках с двух сторон.
9. Проверить насадку панели крыши
по месту, проконтролировать размеры проемов переднего и заднего окон.
10. Приварить панель крыши
сплошным швом к боковым панелям и точечной сваркой к панели рамы ветрового окна, сточным желобкам и к поперечине рамы заднего окна (в верхней части).
Сварку выполняют полуавтоматом в защитном газе по предварительно прошитым отверстиям. Допускается газовая сварка с использованием в качестве присадочного материала латунной или стальной проволоки диаметром 2-3 мм.
11. Сварные швы
, соединяющие крышу с сопрягаемыми деталями, зачистить заподлицо
с основным металлом и загрунтовать цинкохроматным грунтом.
Замена заднего крыла
. Заднее крыло заменяют при значительной деформации, разрывах, а также в случаях сквозной коррозии. Небольшие вмятины, царапины устраняют методами правки и рихтовки. Порядок работ при замене крыла следующий.
1. Освободить багажник от запасного колеса
и инструмента, снять бампер, фонари, топливный бак, резиновый уплотнитель и коврик багажника.
2. Снять заднее крыло
тонким острым зубилом или каким-либо механизированным инструментом по соединениям: крыла с аркой заднего колеса по изгибу, отступив от кромки крыла на 12-15 мм; крыла с полом для запасного колеса (или топливного бака), отступив от кромки крыла на 2-3 мм; крыла с панелью задка кузова, отступив от линии на 2-3 мм; крыла с боковиной кузова по проему задней двери, отступив от кромки изгиба крыла на 2-3 мм; крыла с задней частью боковины крыши, отступив от кромки крыла на 15-20 мм.
3. Высверлить точки для контактной сварки
в соединениях крыла с поперечиной рамы заднего окна и задней боковой панелью, после чего отсоединить крыло от кузова.
4. Удалить оставшиеся полоски металла
торцевыми кусачками и острым зубилом. Деформированные кромки сопрягаемых деталей отрихтовать и зачистить шлифовальной машинкой.
5. Удалить грязь и ржавчину
из полости, закрываемой крылом над аркой заднего колеса, промыть, продуть сжатым воздухом и обезжирить. На участки, зачищенные до металла, нанести цинкохроматный грунт ГФ-073.
6. Подогнать новое крыло по месту посадки
и прихватить его ручной газовой сваркой латунным припоем Л63 к сопрягаемым деталям: к порогу кузова в двух точках; к боковой панели в двух точках; к поперечине рамы заднего окна и панели задка в трех точках.
7. Проверить посадку крыла в сопряжениях с деталями
задка кузова и приварить его точками по прошитым отверстиям: к панели задка; к поперечине рамы заднего окна; к наружной арке; к боковине по проему задней двери; к боковой панели; к полу для топливного бака. К полу для топливного бака крыло приваривают прерывистым швом длиной 10-15 мм через каждые 30 мм. Сварку выполняют полуавтоматом в защитном газе. Допускается ручная газовая сварка с применением в качестве присадочного материала сварочной проволоки: стальной диаметром 1,5-3 мм или латунной диаметром 2-3 мм.
Замена задка кузова
. Задок кузова заменяют в тех случаях, когда основные его детали (панель задка, пол багажника, пол для бензобака, пол для запасного колеса и задние лонжероны) восстановить методами растяжки-правки не удается. Порядок разборки следующий.
1. Снять крышку багажника
, инструментальные сумки, коврик багажника, задний бампер, осветительные приборы, электропроводку, запасное колесо и топливный бак.
2. Срубить задние крылья
; панель задка от усилителя панели, пола для топливного бака и пола для запасного колеса; пол для топливного бака от заднего лонжерона и внутренней арки заднего колеса; пол для запасного колеса от внутренней арки заднего колеса и заднего лонжерона; пол багажника от соединителя и задних лонжеронов; задние лонжероны от внутренних арок заднего колеса и соединителя.
3. Удалить полоски оставшегося металла
, отрихтовать деформированные кромки и зачистить их шлифовальной машинкой.
Порядок работ при сборке следующий.
1. Установить на место задние лонжероны
и прихватить газовой сваркой латунным припоем.
2. К низу пола багажника приварить центральный усилитель
, держатель с асбестовой прокладкой, кронштейн крепления глушителя (40-50 мм - шаг сварки в защитном газе).
3. Установить на место пол багажника
и прихватить латунным припоем.
4. К задним лонжеронам и аркам задних колес установить по месту пол для топливного бака
и пол для запасного колеса и прихватить латунным припоем.
5. Панель задка выставить по окнам кронштейнов
крепления заднего бампера, подвести к ней усилитель и прихватить латунным припоем.
6. Навесить задние крылья
, установить крышку багажника и произвести предварительный контроль сопрягаемых деталей.
7. Выполнить сварку
установленных деталей прерывистым швом (длина шва 10 мм, шаг 40-50 мм). Усилитель панели задка приварить к задней панели точечной сваркой, к задним лонжеронам - сплошным швом по длине отбортовки.
Сварку ведут в режиме: сила тока 50-90 А; напряжение 17-23 В. Проволока стальная омедненная Св-08ГС или Св-08Г2С, диаметр 0,8 мм. Сварка может быть выполнена полуавтоматами типов А-547У, А-825М, А-1230М, ПДГ-302, ПДГ-305 и др.
Возможна ручная газовая сварка с использованием в качестве присадочного материала стальной или латунной проволоки диаметром 2-3 мм.
Сварные швы на лицевых поверхностях кузовных деталей должны быть зачищены шлифовальной машинкой заподлицо с основным металлом.
Сварные швы на днище кузова автомобиля, внутри салона на полу кузова, в моторном отсеке и багажнике, т.е. расположенные не на лицевых поверхностях, должны быть зачищены в местах некачественных швов, а также по местам точечных выплесков сварного металла.
Все сварные швы независимо от их месторасположения должны быть обработаны цинкохроматным грунтом ГФ-073.
В целях надежной герметизации и защиты кузова от преждевременной коррозии на стыки и сварные швы при ремонте всего кузова, а также при замене его отдельных элементов должны быть нанесены уплотняющие мастики.
Съемными деталями кузова, которые чаще всего страдают при аварии, являются капот двигателя, крышка багажника, двери, бамперы
и крылья
. Если стоимость ремонта ниже стоимости замены поврежденной детали новой, то производят выколотку поврежденного участка. Если деформация съемных деталей кузова значительна, то предварительное восстановление формы должно выполняться посредством гидравлического или винтового домкрата, снабженного специальными приспособлениями, обеспечивающими выполнение данной операции.
Перед правкой необходимо снять съемные детали, которые могут быть повреждены при правке. Неподвижное закрепление домкрата производят на предусмотренных для каждого конкретного случая подставках или плите посредством цепей и зажимов.
После предварительной выправки с помощью домкрата производится рихтовка и выравнивание поверхности. Если при правке производился нагрев точек усадки, надо тщательно обработать поверхности, подвергшиеся нагреву, антикоррозионной мастикой.
Чтобы произвести правку кузова, жестянщику (кузовщику) приходится снимать детали, установленные на обшивку кузова, так как они либо находятся в зоне ремонта, либо в непосредственной близости от нее и могут быть повреждены. Кроме того, в обычной практике эти детали часто либо ремонтируют, либо меняют на новые, а до этого используют в качестве опор для растяжки поврежденных участков кузова.
Коротко остановимся на ремонте вспомогательных деталей.
Так, петли и замки
являются частью скобяных изделий кузова. Они устанавливаются на подвижные детали кузова - двери, капоты, багажники. Петли предназначены для шарнирного соединения съемных деталей одной стороной к кузову. Замки устанавливаются на стороне, противоположной шарнирному соединению, чтобы обеспечить открытие и закрытие дверей. Если замки находятся в положении "закрыто", их роль - обеспечить блокировку, предотвратить открытие дверей.
Замки и петли обычно устанавливают с возможностью регулировки, чтобы обеспечить наилучшее расположение деталей, на которые они установлены. В большинстве случаев ремонт этих деталей заключается в регулировке петель и замков для точного центрирования дверей. Если ремонт поврежденных деталей оказывается невыгодным, производят их замену. В этом отношении могут возникнуть некоторые проблемы, поскольку производство подобных деталей не стандартизировано, к каждой модели автомобиля выпускаются свои скобяные детали.
Дверные петли
изготовляют из мягкой стали в виде пластинок толщиной 3-4 мм. Каждая пластинка заканчивается трубчатой отбортовкой, обработанной так, чтобы в одной пластинке образовался паз, а в другой шип, посредством которого две пластинки соединяются между собой. Трубчатые участки пластинок образуют шарнирную ось, общую для петли.
В большинстве случаев оси петель выполняются из полых трубчатых разрезных штифтов или из сплошных цилиндрических прутков. Если петля съемная, то пластина петли, прикладываемая к передней или задней стойке, имеет несколько просверленных отверстий, которые предназначены для установки крепежных винтов. Вторая пластина обычно приваривается к внутреннему коробу двери.
Крепление съемных петель
осуществляется следующим образом. Во внутренней полости передней или задней стойки выполнена коробка из листового материала, в которой помещается пластинка с резьбовыми отверстиями. Диаметр отверстий, просверленных в листе стоек, несущих петли, больше диаметра, необходимого для прохода винтов. Зазор между отверстиями, а также между пластинкой с резьбовыми отверстиями и коробкой, в которую она установлена, обеспечивает возможность регулировки закрепленных деталей. Крепежные винты проходят через гладкое отверстие в крыле петли, затем через лист стойки и ввинчиваются в резьбовые отверстия внутренней планки.
Регулируют съемные петли так
. Ослабляют крепежные винты, ввинчивают винты и слегка закрепляют крыло петли. Закрывают дверь и с помощью деревянных клиньев центрируют дверь по высоте. Затем плавно открывают дверь и затягивают винты. Несколько раз открывают и закрывают дверь для контроля регулировки.
Если петли приварены к стойке, регулировка петель не производится, их заменяют. После снятия оси петли снимают дверь и с помощью кернера намечают центр каждой сварочной точки. С помощью дрели высверливают сварочные точки, затем снимают поврежденное крыло петли. На дверь устанавливают новую петлю, вводят крыло новой петли на место удаленной. Закрывают дверь. С помощью отогнутой чертилки намечают отверстия. Если так наметить отверстия не удается, слегка приоткрывают дверь и намечают отверстия в петле. Снимают дверь и вынимают ось петли. Производят разметку, сверление и нарезку резьбы на крыле петли. Вставляют петлю на место и закрепляют ее винтами. Устанавливают дверь, вставляют ось петли и проверяют центрирование двери. При необходимости отверстия в стойке разделывают под овал. Открывают дверь и выполняют крепление петли к стойке пайкой.
В некоторых моделях автомобилей встречаются специальные петли из тонкого листа. Речь идет не о петлях, сделанных обычным путем, а о непрерывном шарнирном соединении, изготовленном из тонкого листового профиля, соединенного точечной сваркой. Замена в таком случае заключается в разделении точечной сварки и приварке нового элемента на то же место. При этом перед окончательной сваркой необходимо обеспечить правильное расположение дверей. Петли такого типа установлены на капоте некоторых моделей "Ситроена".
Если дверные петли у многочисленных моделей автомобилей по своей конструкции в значительной степени похожи, то петли капота
представляют собой большое разнообразие форм даже для разных моделей одной и той же марки автомобиля. Главный признак этих петель - асимметрия шарниров. Один из шарниров более длинный и крепится под капотом чаще всего на некотором расстоянии от края. Причина создания именно такой конструкции в том, что капоты в большей части имеют большую выпуклость, чем двери, и им требуется больше свободного места в процессе поворота.
Так как капот открывается вверх, то вместе с петлями на него установлено устройство, предотвращающее возврат капота вниз под действием собственного веса. Профили, усиливающие панель капота, имеют небольшую высоту по сравнению с усилительными профилями внутреннего короба двери, поэтому петли капота крепятся иначе. Обычно петля капота устанавливается так, что одно крыло прямоугольной формы крепится к кузову, в то время как другое в форме крюка ("лебединая шея") устанавливается на внутреннюю поверхность капота.
Обычно регулировка капота
производится после снятия и последующей установки капота при ремонте автомобиля. Регулирование производится ослаблением винтов, крепящих петли к капоту. Принцип регулирования тот же, что и для петель съемных дверей. Продолговатые отверстия, через которые проходят винты, ввинчиваемые в пластинку с резьбовыми отверстиями, обеспечивают небольшое, но достаточное перемещение для центрирования. После центрирования капота крепежные винты затягивают окончательно. Регулировка капота должна производиться с помощью резиновых ограничителей, устанавливаемых в соответствующие места.
Дверные замки
устанавливают внутри дверного короба. Управление замком может осуществляться снаружи и изнутри автомобиля. Есть много разновидностей замков, их можно классифицировать по способу перемещения язычка: замки с прямолинейным перемещением язычка и замки с вращающимся язычком и храповиком.
Крепят замки винтами. Личинка замка устанавливается на среднюю или заднюю стойку лицевой поверхности к защелке при закрытой двери. Замок устанавливается в строго определенное место, которое нельзя изменить. Регулировка замка производится следующим образом: ослабляют винты крепления личинки, перемещают ее и снова затягивают крепежные винты (крепежные винты обычно имеют головку с крестовым шлицем). Винты входят в пластинку с резьбовыми отверстиями, которая может иметь небольшие перемещения при ослабленных винтах. Обычно для надежности личинки выполняются с двумя прорезями. Если одна прорезь не удерживает дверь, то вторая предотвращает самооткрывание двери на ходу автомобиля.
Личинка двери устанавливается в вертикальное положение, затем дверь плавно закрывают. Язычок замка входит в первую прорезь, о чем свидетельствует легкий щелчок защелки. Происходит сжатие резиновых уплотнений двери. Снова нажимают на дверь, чтобы язычок вошел во вторую прорезь личинки. Если язычок не входит во вторую прорезь, то открывают дверь, ослабляют винты крепления личинки, слегка перемещают личинку наружу и затягивают винты. Затем снова проверяют работоспособность двери. Если язычок прошел вторую прорезь, то при закрытии двери появляется в большей или меньшей степени громкий звук. Дверь открывают, слегка ослабляют винты крепления личинки, перемещают личинку внутрь, затягивают крепежные винты и снова проверяют работоспособность двери.
Дверь считается отрегулированной правильно, если не возникает громкого звука и не требуется прилагать большое усилие для закрытия замка. При регулировке замка надо помнить, что наружная панель двери должна находиться на одном уровне с другими деталями боковой поверхности кузова.
Блокировка закрытия капота и крышки багажника осуществляется автоматически. Разблокировка замка для открытия может осуществляться или только с внешней стороны автомобиля, или снаружи и изнутри. Управление замком изнутри автомобиля может осуществляться либо с помощью электрического кабеля, либо посредством системы рычагов и тяг с пружиной. Управление замком снаружи осуществляется непосредственно и может быть дополнено предохранительным запором.
Замок состоит из стопора, в выточку которого входит язычок замка, фиксируя таким образом капот или багажник. На автомобилях, передний капот которых открывается с переда назад, предохранительный стопор предназначен для предотвращения внезапного открывания капота при несвоевременном открытии основного фиксатора на ходу автомобиля. Пружины прижимают язычок замка к фиксатору. Положение этих деталей не регулируют, так как они занимают единственную позицию. Необходимо следить за их правильным центрированием, которое осуществляется при общем регулировании капота на петлях. Надо также периодически производить смазку осей, приводных тросов с дистанционным управлением, а также деталей, скользящих друг относительно друга. Эти детали легко снимаются - достаточно отвинтить винты или болты. Если детали повреждены или плохо работают, их заменяют.
В последние годы любительский автопарк нашей страны не только многократно вырос в количественном отношении, но и стал более разнообразным. На некоторых кузовах автомобилей типа "седан" или "лимузин" крыша выполнена не сплошной, а открывающейся
над передними сиденьями. С одной и другой стороны открывающейся части кузова выполнены рукоятки, обеспечивающие открытие и закрытие подвижной панели крыши, установленной на роликах. Перемещаясь в обратном направлении, панель осуществляет частичное или полное открытие крыши. Блокировочное устройство обеспечивает фиксацию подвижной панели в закрытом положении.
Этот механизм также не вечен. Чаще всего заедают ролики, что случается от попадания в механизм воды. Если заедание роликов незначительное, их слегка смазывают для облегчения вращения на осях. Если засорились водосливные отверстия, их прочищают.
Разнообразные шумы, стук устраняются путем замены изношенных гибких уплотнительных лент новыми. Шум воздуха обычно возникает из-за превышения подвижной части открывающейся крыши над основной крышей. Для устранения шума надо произвести регулировку открывающейся крыши в положении, когда она слегка отодвинута назад.
Следующая съемная часть кузова - сиденья
. Они предназначены для создания комфорта. В зависимости от типа автомобиля конструкция сидений может быть простой или более сложной и более комфортабельной с использованием материалов, применяемых для изготовления мебели.
Различают два основных вида сидений: сплошные (диванного типа) и раздельные. Передние сиденья обычно устанавливаются на направляющие или другую регулируемую систему перемещения, которая обеспечивает требуемое расположение сидений в зависимости от габаритов водителя или пассажира. Спинки сидений обычно выполняются регулируемыми по углу наклона. В большинстве случаев сиденья выполняются раздельными или сплошными с раздельными спинками. Задние сиденья чаще всего выполняются в виде диванчиков, исключение составляют автомобили с кузовом "универсал" и многоместные автомобили, у которых сиденья выполняются раскладными для увеличения объема перевозимых грузов.
Любое сиденье, независимо от его типа, состоит из металлического каркаса и набивки различной толщины и мягкости. Наружный видимый слой набивки представляет собой драпировку. Работы по набивке и драпировке сидений выполняются на предприятиях, производящих сиденья.
Каркас сиденья, конструкция которого изменяется в зависимости от типа автомобиля, обычно выполняется из жестких трубок. Каркас откидных спинок выполняется эластичным из спиральных пружин. В настоящее время пружины заменяют блоками из пенопласта различной плотности. Некоторые из применяемых для этой цели химических материалов обладают высокой стойкостью.
Если сиденье не нуждается в замене, то ремонту в основном подвергаются системы перемещения сидений и трубчатая арматура, в особенности это касается передних сидений. В случае загрязнения направляющих и помехи перемещению сидений необходимо прочистить направляющие. Если консольная часть направляющих деформирована, то при незначительной деформации их снимают и подвергают правке. Если направляющие сильно деформированы, их необходимо заменить новыми.
Трубки каркаса сидений иногда ломаются в местах, подвергаемых действию изгибающих усилий. Чтобы заварить трубки, сиденья снимают, частично или полностью снимают также драпировку. При частичной разборке сидений обивку защищают листовым металлом.
Автомобильные стекла производят двумя способами. Закаленное стекло получается в результате термической обработки листового стекла. При ударе стекло растрескивается на множество мелких осколков, из которых выпадают только те, которые находятся в зоне удара. На ветровых стеклах зона, расположенная перед водителем, подвергалась закалке с другим режимом, чтобы стекло не разлеталось на осколки одновременно с остальной частью ветрового стекла. Однако в настоящее время такой способ не применяется.
Пластинчатое стекло
получают путем установки между двумя листами стекла вставки из пластика. Собранные слои нагреваются в автоклаве, что обеспечивает хорошее склеивание их друг с другом. Ветровое стекло такого типа обладает несомненными преимуществами. Если по стеклу ударить с большой силой, оно остается прозрачным, как и до удара, а на месте удара появится звездочка. С таким стеклом можно ездить сколько угодно, оно защищает от непогоды и сохраняет свою прочность.
Со стеклами могут выполняться следующие ремонтные работы: снятие для выполнения ремонта и установка; замена разбитого стекла.
Из всех стекол автомобиля наиболее часто разбивается ветровое стекло. Ветровое стекло в автомобиле выполняется неподвижным. На старых машинах ветровые стекла выполнялись плоскими, а на некоторых моделях ветровые стекла устанавливались в поворотном приспособлении, что обеспечивало вентиляцию кабины.
Плоские ветровые стекла применяются и сегодня на автомобилях экономичного класса и в вездеходных автомобилях типа 4x4. На современных автомобилях ветровые стекла имеют одинарную или двойную кривизну, что не позволяет выполнять их поворотными. Кроме того, ветровые стекла, будучи установлены неподвижно, увеличивают прочность кузова после того, когда они плотно прижимаются и приклеиваются. Однако приклеивание стекол создает проблемы при их снятии для установки новых. Эта работа более трудоемкая, чем замена ветровых стекол, установленных на резиновые уплотнения.
Крепление ветрового стекла
может осуществляться установкой его в профильный паз резинового уплотнения замкнутого контура, форма которого соответствует форме проема ветрового стекла кузова. Вторым пазом уплотнительная резинка надевается на край проема ветрового стекла. В некоторых случаях для повышения герметичности применяют специальную герметизирующую мастику.
Второй способ крепления ветровых стекол, как говорилось, - приклеивание. Несмотря на сложности ремонта, этот способ получает все большее применение, так как позволяет повысить прочность структуры кузова. Так, повышение сопротивления изгибу при этом составляет около 35%, что является ценным вкладом в снижение массы кузова. Это позволяет уменьшить толщину листовой обшивки и количество усилительных элементов, а в конечном итоге достигаются те же характеристики прочности кузова или даже более высокие. Увеличение жесткости в общем составляет 12-15%.
Применяются различные способы приклеивания. В течение длительного времени предпочтение отдавали термоэлектрическому уплотнению. Но клеющаяся мастика на полиуретановой основе обладает более совершенными характеристиками, особенно это касается времени сушки.
Рассмотрим технологию замены стекол. Предварительно в местах возможного вылета осколков стекла внутреннюю и наружную поверхности кузова закрывают холстом. Снимают щетки, держатели щеток и другие принадлежности, установленные вблизи ветрового стекла.
Снимают ветровое стекло в следующем порядке.
1. Разбитое закаленное стекло
. Технически необходимо приклеить на стекло клейкую бумагу, подобную той, которую применяют при декоративной отделке, и ударить изнутри. При этом клейкая бумага удержит осколки стекла. Практически эту операцию выполняют более быстро, покрывая поверхность в кабине большим холстом, защемляя концы холста для его удержания с обеих сторон дверями. Нижняя часть холста закрывает край пола салона. Затем ударяют снаружи по стеклу, удары наносят вокруг места повреждения, чтобы осколки стекла падали на холст. Когда в пазу резинового уплотнения останется лишь узкая лента стекла, осколки вынимают из проема ветрового стекла. Потом вынимают наружу холст с осколками стекла. Снова расстилают холст и очищают обвод проема ветрового стекла. Убирают холст и пылесосом собирают осколки стекла, упавшие в кабину.
2. Разбитое слоистое стекло или неповрежденное ветровое стекло закаленное или слоистое
. Ветровое стекло поддерживают снаружи, чтобы оно не упало при выходе из рамки проема кузова. Надавливают на стекло по краям стекла изнутри наружу, начиная от верха, пока стекло не выйдет из рамки. После выемки стекла очищают обвод рамки стекла.
Устанавливают ветровое стекло так
. Берут новую уплотнительную резину, так как старая может пропускать воду. Надевают уплотнение на ветровое стекло так, чтобы оно заняло нужное положение. (По инструкции ветровое стекло устанавливается в проем кузова с наружной стороны кабины). Край уплотнения, охватывающий край рамки ветрового стекла, должен располагаться на внутренней поверхности кривизны ветрового стекла. В паз под эту кромку уплотнения вставляют шнурок, длина которого берется на 200-300 мм с каждого конца больше периметра, чтобы можно было тянуть с большой силой каждой рукой. Обычно диаметр шнурка выбирают равным 3-4 мм, однако для некоторых типов автомобилей необходимо применять шнурки большего диаметра. Перекрещивание концов шнурка осуществляется в середине нижней части ветрового стекла, что обеспечивает благоприятное действие веса стекла в направлении кузовщика в момент установки. Стекло поддерживают снаружи и вводят в проем кузова, а затем прижимают, чтобы оно плотно прилегало к рамке проема кузова. Концы шнура спадают внутрь кабины. Изнутри кабины один конец шнура натягивают под определенным углом, в то время как с наружной стороны стекло прижимается рукой. Шнурок, выходя из паза, приподнимает край уплотнительной резинки. Под действием прижимного усилия с наружной стороны и постепенного удаления шнурка край резинки отгибается по месту, одеваясь на кромку листа рамки проема ветрового стекла. Так постепенно край уплотнения одевается на весь обвод рамки.
Если в некоторых местах плотного прилегания уплотнительной резинки не получилось, необходимо снаружи произвести несколько нажатий вокруг всего стекла ладонью либо резиновой киянкой. Если изготовителем предусмотрено применение герметика, то его вводят в указанные места с помощью специального шприца.
На некоторых уплотнительных резинках предусматривается молдинг, который вставляется аналогичным способом.
При работе со слоистыми стеклами надо работать особенно осторожно.
Из всех стекол автомобиля в большинстве случаев разбиваются ветровые. Это объясняется тем, что они часто бьются камнями и гравием, вылетающими из-под колес едущих впереди встречных машин. Закаленное ветровое стекло под действием удара разбивается на куски, отлетающие с большой силой даже при невысокой скорости движения автомобиля. Они могут поранить лицо и глаза.
Технология производства слоистых стекол постоянно совершенствуется. В течение долгого времени специалисты по кузовам относились к этим стеклам с недоверием. Во-первых, слоистые стекла приводили к серьезным ранениям автомобилистов, не пристегнутых в момент аварии ремнями безопасности и вылетающих через ветровое стекло в результате удара. При этом голова пробивала стекло, режущие кромки которого впивались в лицо или шею. Во-вторых, эти стекла легко разбивались при установке. В настоящее время толщина промежуточного слоя выполняется несколько большей, что повышает прочность слоистого стекла.
Одним из последних технических решений является изготовление деформируемых слоистых стекол (при ударе стекло плотно облегает форму головы). В данном случае хрупкость стекла (хотя и является неизбежной) намного меньше.
Слоистые ветровые стекла (триплекс) устанавливаются так же, как и другие, однако необходимо соблюдать следующие меры предосторожности:
при транспортировке и переносе их следует устанавливать на ребро в таком положении, как и на автомобиле, то есть всегда вертикально. Это стекло нельзя деформировать как закаленное стекло, поэтому нельзя допускать деформации слоистого стекла под действием собственного веса, так как это вызывает его поломку.
При установке резинового уплотнения стекло кладут плашмя на покрывало и обеспечивают не менее двух линий опор, что создает распределение веса;
следует применять новый резиновый уплотнитель;
никогда не следует ударять по стеклу в процессе его установки. При установке стекла можно только прижимать его усилием руки под углом к поверхности стекла. Это дает возможность точно отцентрировать стекло перед установкой. Установка стекла облегчается смазыванием паза в резиновом уплотнителе, куда вставляется монтажный шнур.
Рассмотрим способы приклеивания стекла.
Термоэлектрическое уплотнение "Солбит"
специально предназначено для приклеивания ветровых стекол, задних стекол и других неподвижных стекол. Оно обладает хорошим сцеплением как со стеклом, так и с окрашенным металлом. Уплотнение выполнено в виде прессованной ленты, свернутой в спираль на пластмассовой пластине. В каждой упаковке длина ленты соответствует периметру каждого устанавливаемого стекла. Вначале лента располагается по краю стекла и обжимается по нему. Стекло устанавливают в проем кузова и центрируют. Затем производят вулканизацию ленты посредством небольшой электрической спирали, вмонтированной в ленте. При этом одновременно обеспечиваются закрепление и герметичность стекла.
Термоэлектрическое уплотнение "Солбит" изготовляется на базе неопрена. Электрический изолированный нагреватель в процессе изготовления устанавливается в центр ленты и заливается. Эта лента обладает достаточными клеющими свойствами и обеспечивает сцепление либо со стеклом, либо с окрашенным металлом (алюминий, стальной лист, коррозионно-стойкая сталь и т.д.), либо с различными пластическими материалами (полиэфирами), из которых изготовляют вспомогательные детали автомобиля и даже кузова. После установки закрепляемой детали в заданное положение концы ленты соединяются встык. Оголенные концы армированного в ленту электрического нагревателя выходят наружу и подсоединяются к электрическому низковольтному источнику соответствующего напряжения. Электрический ток, проходя по нагревателю, вызывает разогрев ленты, что приводит к значительному размягчению сырого неопрена, из которого изготовлена лента. В этот момент закрепляемую деталь крепко прижимают к месту установки, и лента, будучи очень пластичной, расплывается, закрывая неровности стекла, листового материала или пластмассы, из которых выполнена рамка проема кузова. Процедура приклеивания длится шесть минут, после чего прочность приклеивания становится достаточной для обеспечения герметичности уплотнения и закрепления ветрового стекла в нормальном рабочем положении.
Без вулканизации приклеивание осуществляется в течение двух или трех недель при нормальной температуре воздуха. Вулканизация ленты обеспечит оптимальную твердость и способность выдерживать температуру до -30 °C.
Рассмотрим технологию применения термоэлектрического уплотнения.
1. Сначала надо убедиться, что две соединяемые поверхности чистые и сухие.
2. На две поверхности наносят слой клеющего грунта.
3. В течение 30 секунд подогревают уплотнение "Солбит" от источника напряжением 6 В на один метр и силой тока 11 А, чтобы оно стало липким.
4. Укладывают уплотнение на одну или другую опорную поверхность.
5. Перекрещивают и разминают концы уплотнения для обеспечения герметичности.
6. Устанавливают стекло на уложенный в проеме кузова уплотнитель.
7. Снова подключают нагреватель к источнику тока того же напряжения.
8. По истечении одной минуты обжимают края стекла для обеспечения плотного контакта.
9. Выдерживают нагреватель под напряжением 5 минут или более (до 6 минут), затем отключают источник питания и обрезают выступающие концы.
10. Устанавливают молдинги, защитные накладки и другие детали, закрывающие уплотнение.
Если на автомобиле используются слоистые стекла (типа "триплекс"), то при снятии стекла уплотнение разрезают ножом. Если на автомобиле установлено закаленное ветровое стекло, закрепленное способом приклеивания, то может случиться, что под действием удара, вызывающего отделение кусочков ветрового стекла, само стекло может остаться на месте, так как оно удерживается прочнее в своей рамке, чем при закреплении в профильный резиновый уплотнитель.
Термоэлектрическое уплотнение "Солбит" выполняется достаточной длины в виде шнура диаметром 6,8-9,0 мм с оголенными концами нагревательных проводов. Уплотнение сохраняет свои свойства от одной до шести недель в зависимости от примененной композиции при температуре окружающей среды. Однако он может сохранять свои свойства в течение длительного времени в холодильнике при температуре ниже 00
С.
Есть и другие уплотнительные композиции, которые отличаются тем, что сохраняют свои свойства в течение шести месяцев, однако при использовании требуют более долгого прогрева.
В настоящее время наиболее распространенным является метод приклеивания ветровых и задних стекол с помощью прессованного полиуретанового уплотнения
. Большинство производителей автомобилей стремятся использовать этот тип уплотнения, так как он обладает более совершенными характеристиками как полимеризации, так и герметичности и долговечности.
Рассмотрим порядок снятия ветрового или заднего неповрежденного стекла.
Если зеркало заднего вида приклеено к ветровому стеклу, то слегка подогревают нижнюю часть основания. Обычно для отклеивания зеркала достаточно пламени зажигалки, которым подогревают стекло снаружи. Если зеркало заднего вида установлено на основание, то его снимают, сдвигая по направляющим основания. При наличии накладок стойки ветрового стекла их снимают. Вынимают наружный молдинг, стараясь не погнуть его.
При проведении этих работ нельзя применять инструмент с выступами, которые могут разбить стекло. Далее срезают приклеенное уплотнение стальной проволокой (струной от пианино). Эту операцию предпочтительно начинать с угла. Следует избегать пилообразных движений, так как это приводит к разрыву проволоки. Проволоку протягивают изнутри на всю длину, затем снаружи также на всю длину. Движения повторяют на всей длине периметра стекла. Снятие ветрового или заднего стекла производится двумя рабочими.
Далее начинается установка. Если уплотнение, оставшееся на рамке ветрового стекла, изготовлено на базе полиуретана, то достаточно изнутри автомобиля в месте наибольшего зазора между краем стекла и проема кузова, иголкой проткнуть отверстие, в которое ввести стальную проволоку длиной 500 мм. Один рабочий прокалывает уплотнительную мастику на расстоянии 300 мм от точки прохода проволоки, а другой тянет за ручку, закрепленную на другом конце проволоки, следуя тщательно кромке ветрового стекла. Эту операцию повторяют, прокалывая мастику через каждые 300 мм до полного срезания уплотнения. Далее резаком срезают и выравнивают ленту уплотнения, оставляя слой мастики на рамке 1-2 мм.
Если уплотнение изготовлено из другого материала, то его отделяют с помощью шпателя. Если при отделении уплотнения повреждается краска на рамке проема кузова, то необходимо нанести антикоррозионный грунт.
Чистой ветошью протирают паз рамки проема кузова, края ветрового стекла протирают ветошью, смоченной в растворителе, а после сушки покрывают зону клеющим грунтом для стекла с помощью тампона.
Устанавливают новое стекло и определяют места установки центровочных клиньев. Стекло снимают и затем на периферию внутренней стороны наносят специальный клеющий грунт для стекла, предварительно очистив обрабатываемую поверхность от жира растворителем.
Если уплотнение полностью отделено от металла, то на рамку ветрового стекла наносят клеющий грунт по металлу. Подсушивают нанесенный грунт в течение нескольких минут. С краскораспылителя, заряженного баллоном со специальной мастикой, выдавливают непрерывный шнур уплотнительной мастики на паз рамки ветрового стекла. На стекло прикрепляют две присоски. Устанавливают стекло на проем и располагают его на центровочные клинья. Просматривают края стекла, чтобы убедиться в его плотном прилегании на шнур из уплотнительной мастики. При наличии неплотностей в эти места выдавливают немного мастики. Как только начинается полимеризация, вынимают центровочные клинья, устанавливают молдинг.
По окончании установки стекла проверяют работу на герметичность, поливая стекло струей воды.
Все работы с задним стеклом следует выполнять по той же методике, что и с ветровым. На некоторых автомобилях, находящихся в эксплуатации, выполнены стекла нестандартного размера и формы. Уплотнительный резиновый профиль
выпускается прямым и продается на метры. Поэтому следует отрезать резиновый уплотнитель по длине периметра стекла. Края разреза точно стыкуют и располагают посреди нижней кромки стекла.
Некоторые уплотнители состоят из двух частей. Вторым элементом является стопорный профиль
, который с усилием вставляют в паз типа "ласточкин хвост". Этот профиль вставляется после того, когда стекло вместе с уплотнительным профилем установлены на кузов. Стопорный профиль прижимает с большим усилием резиновый уплотнитель к металлу рамки проема кузова, обеспечивая надежную герметичность.
Рассмотрим ремонтные работы дверных стекол. Стекла дверей обычно выполняются подвижными. Различают три типа дверных стекол:
поворотные стекла с вертикальной осью поворота (ветровики);
стекла поворотного типа с горизонтальной осью поворота, расположенной на половине высоты рамки двери. В верхней половине рамки установлено неподвижное стекло, к которому прилегает поворотное стекло;
стекла с вертикальным перемещением в направляющих. Этот тип стекол получил наибольшее распространение. Перемещение стекол осуществляется посредством стеклоподъемного механизма.
Работы по снятию и установке стекол двери выполняются в следующих случаях: для предохранения их от возможных ударов при правке двери и для замены разбитого стекла новым.
Поворотные стекла
устанавливаются в поворотной рамке. Ось поворота смонтирована на открывающейся рамке, которая, в свою очередь, крепится на дверь с помощью винта и гайки либо с помощью винтов-саморезов.
Чтобы снять поворотное стекло, вначале необходимо отсоединить поворотную рамку с осью от двери. Если нижняя часть рамки прикреплена к двери винтами с гайками, то гайки располагаются во внутренней полости двери, и для доступа к ним необходимо снять обивку двери. Если крепление осуществлено винтами-саморезами, то рамку можно снять без разборки двери. Чтобы увидеть эти винты, необходимо приподнять кромку резинового уплотнения.
Сборку ведут в следующей последовательности. Вначале устанавливают резиновое уплотнение, затем прикрепляют оси поворота или неподвижную рамку, несущую ось поворота, к двери. Устанавливают и проверяют работу стекла. Если стекло плохо отцентрировано, необходимо ослабить винты и изменить положение ветровика.
Поворотные стекла с горизонтальной осью поворота
открываются снизу вверх. Такие стекла могут разбиваться в результате резкого открывания или резкого захлопывания и в других случаях при движении. Замена таких стекол вместе с оправой производится так же, как и ветровиков.
Стекла с горизонтальным перемещением
. Подвижное стекло перемещается в направляющей и фиксируется в необходимом положении с помощью стопорного устройства. Для снятия стекла необходимо снять стопорное устройство и выдвинуть стекло в удобном направлении. При установке сначала вставляют стекло, затем устанавливают стопорное устройство. Если стекло заедает в направляющей, промывают направляющие и смазывают их парафином.
Стекла с вертикальным перемещением
. Стекло может перемещаться в направляющих и устанавливаться неподвижно между двумя конечными положениями. В верхнем положении стекло полностью закрывает проем. В нижнем положении стекло полностью убирается и размещается во внутренней полости двери. Направление стекла при его перемещении осуществляется с помощью направляющих, в которых скользят боковые кромки стекла. Направляющие выполняют из материала, имеющего низкий коэффициент трения или мягкий контакт со стеклом. Направляющие вставляются в стойки для стекол. Сами стойки устанавливаются в верхней части двери, если она образует рамку, и продолжаются во внутренней полости, где их крепят винтами. Нижняя кромка стекла вставляется в металлическую оправу. Между стеклом и пазом оправы вставлена резиновая прокладка, предотвращающая контакт стекла с металлом. Оправа стекла имеет удлиненные части, к которым подсоединяется стеклоподъемный механизм.
Чтобы снять стекло, производят разборку двери, снимают стеклоподъемный механизм. Если стекло не разбито, то перед снятием механизма стеклоподъемника его поднимают в самую верхнюю точку. Если стекло разбито, следует очистить нижнюю часть двери от осколков стекла. Потом снимают обтекательные накладки.
Снятие неповрежденного стекла, так же как и установка, могут осуществляться только через верхнюю часть двери.
Устанавливают стекло так. Надевают на стекло резиновый уплотнитель и вставляют его в металлическую оправу, соблюдая заданное положение, которое определяется размером между краем стекла и концом оправы. Затем вставляют стекло в сборе в верхнюю часть полости двери, располагая его перпендикулярно к нормальному положению. Затем стекло разворачивают, чтобы установить в рабочее положение и ввести в направляющую. Устанавливают обтекательные накладки и поднимают стекло в самую верхнюю точку. Соединяют оправу со стеклоподъемником и закрепляют. Затем производят сборку двери.
Ремонт стеклоподъемников
. Стеклоподъемники предназначены для перемещения стекол дверей в направляющих. Движение обеспечивается вращением рукоятки, установленной на внутренней поверхности двери. Рукоятка приводит в движение передачу. Передачи могут быть разными:
зубчатая передача с одним или двумя передающими рычагами;
передача с помощью блоков и троса с понижающим зубчатым редуктором;
цепная передача (для тяжелых стекол);
электрическая и гидравлическая передачи.
Ремонт механизма стеклоподъемника зависит от типа применяемой передачи.
Стеклоподъемник с зубчатой передачей и рычагами
: сначала производят разборку двери и проверку механизма. При отсутствии смазки возможно заедание передачи, тогда передачу смазывают и прокручивают стеклоподъемник. Если механизм сломан, его снимают и устанавливают новый. Во время замены механизма стекло должно находиться в верхнем положении. Фиксация стекла осуществляется несколькими штифтами.
Стеклоподъемник с блоками и тросом
: после разборки двери убеждаются, что все блоки вращаются, трос находится в хорошем состоянии и нормально натянут (с заданным прогибом). Регулировка натяжения троса осуществляется специально предназначенным для этой цели натяжным устройством. Потом графитовой смазкой покрывают желобки блоков, оси и трос.
При замене троса необходимо воспользоваться инструкцией завода-изготовителя, так как модели стеклоподъемников разные.
Кроме профильных резиновых уплотнений, предназначенных для герметизации ветровых и задних стекол, на автомобиле применяются и другие резиновые профильные уплотнения.
Они устанавливаются между подвижной деталью и остовом кузова. Если подвижная деталь автомобиля находится в закрытом положении, резиновое уплотнение сжимается и обеспечивает тем самым герметизацию. Кроме того, резиновые уплотнения устраняют стук металлических поверхностей, находящихся в контакте. Уплотнения приклеивают специальным клеем на обвод подвижной детали автомобиля или на неподвижную часть кузова напротив подвижной.
Со временем резиновые уплотнения разрушаются. Причины разрушения резиновых уплотнений следующие:
в результате старения резина теряет эластичность;
в летнее время уплотнения прилипают к нагретому металлу кузова;
в зимнее время уплотнения примерзают и отрываются при открывании подвижной детали.
Технология ремонта этих деталей проста. Поврежденное уплотнение отклеивают и соскабливают частички резины, оставшиеся на металле. Затем специально предназначенным для этой цели клеем смазывают поверхности металла и нового уплотнения. Дают выдержку, пока уплотнение размягчится под действием клея, и приклеивают уплотнение сначала одним концом, а затем равномерно укладывают, не допуская лишнего натяжения.
На многих отечественных легковых автомобилях ("Москвич", "Волга") уплотнение дверей осуществляется с помощью губчатых резиновых профилей, которые приклеивают на двери автомобилей и в проем клеем 78-БЦСП. Этот клей обеспечивает работоспособность клеевого соединения при температурах от 90 до -50 °C. Для надежного приклеивания используют клей, как правило, с вязкостью в стадии поставки 40-60 с (по ВЗ-4). Если вязкость выше, клей разбавляют смесью бензина с этилацетатом в соотношении 1: 2 по массе. Губчатый уплотнитель, предназначенный для приклеивания, обезжиривают бензином БР-1. Наносят клей и склеивают при 18-25 °C и относительной влажности не более 75%. Порядок такой: на склеиваемую поверхность губчатого уплотнителя кистью наносят равномерный слой клея и сушат его на воздухе 10-15 минут. (Допускается хранение уплотнителя с нанесенным клеем до 6-8 часов). На окрашенную поверхность металла кистью наносят первый равномерный слой клея и сушат его 3-5 минут, затем наносят второй слой клея, который сушат 0,5-1,5 минут. Уплотнитель плотно прижимают руками, а затем прикатывают его роликом.
Выдержав указанные режимы, можно обеспечить надежное приклеивание с высокими показателями на отрыв и отслаивание.
Для приклеивания уплотнителя можно использовать также клей 88-НП, но он обладает более низкой термостойкостью (до 60 °C).
Ремонт радиаторов и топливных баков
Для отвода теплоты от жидкости, которая циркулирует по радиатору, радиатор должен иметь большую поверхность теплоизлучения. Необходимый теплоотвод обеспечивается за счет ряда трубок, проходящих сквозь металлические пластины, повышающие способность к теплоизлучению. Трубки и пластинки, соединенные между собой, образуют корпус радиатора и обеспечивают хорошую проводимость теплоты. Активной частью радиатора является система трубок
.
При одинаковом первоначальном объеме плотность горячей воды меньше плотности холодной воды, горячая вода легче холодной за счет расширения при нагревании. Ряды трубок радиатора расположены вертикально, что способствует опусканию в радиаторе охлажденной воды из-за ее большей плотности. Для увеличения теплоотдачи необходимо приблизить центральные слои воды, циркулирующие в трубках, к их стенкам. С этой целью трубки выполняются сплюснутыми по сечению и имеют прямоугольное сечение со скругленными кромками. Трубки проходят через уже установленные пластинки и своими концами входят в бачки радиатора, где пропаиваются.
Бачки
представляют собой металлическую коробку в форме прямоугольного параллелепипеда с закругленными углами. У радиатора два бачка - верхний и нижний. Нижний с помощью патрубка соединяется с водяной рубашкой блока двигателя и сливным краном. Верхний бачок соединяется с насосом охлаждения, запорным краном для наполнения системы охлаждения и переливной трубкой.
Радиаторы изготовляют из меди, латуни, оцинкованной стали или алюминиевого сплава.
Причины выхода из строя радиатора бывают внешние и внутренние.
Одна из причин выхода из строя радиатора объясняется его расположением
. Радиаторы чаще всего устанавливаются в передней части автомобиля, где наиболее благоприятные условия для обдува охлаждающим воздухом. Но при повреждении передка автомобиля, даже не очень серьезном, радиатор оказывается заклиненным между двигателем и облицовкой радиатора, которая продавливается деталью, подвергшейся деформации в результате удара. При этом происходит сплющивание трубок (большее или меньшее) и радиатор деформируется.
Другая причина выхода из строя радиатора связана с температурным режимом его работы
. С течением времени охлаждающая жидкость испаряется, восстановление уровня производится много раз небольшими порциями. В добавляемой воде содержатся мельчайшие инородные частички. Размер внутренней полости сечения трубки находится в пределах 1-2 мм, трубки частично засоряются мелкими инородными частицами.
Даже если вода абсолютно чистая, в ней все равно содержатся растворимые соли, преимущественно известковые. Под действием теплоты эти соли выпадают в осадок и осаждаются на стенках трубок в зонах малых скоростей перемещения воды - так образуется накипь. Образование на стенках накипи приводит к полному закупориванию трубок. Частицы накипи могут отрываться от стенок и, в свою очередь, забивать трубки, как и инородные частицы.
Антифриз
способствует отрыву частиц накипи и частично выводит их из трубок радиатора, однако он не в состоянии полностью очистить трубчатую систему радиатора, и она засоряется, что из-за снижения интенсивности циркуляции воды приводит к перегреву двигателя.
Третья причина ремонта - растрескивание радиатора
. Под действием вибраций в радиаторе возникают мелкие трещины, преимущественно в месте сварки с недостаточным проваром. В результате возникают небольшие утечки, которые приводят к понижению уровня охлаждающей жидкости. Если утечка незначительная, ее не всегда можно заметить, так как нагретая вода быстро испаряется.
Рассмотрим ремонт радиаторов
. При аварии в результате удара часто происходит деформация только верхнего или нижнего бачка радиатора. Если деформация позволяет, бачки разъединяют распайкой, восстанавливают их форму и затем спаивают. Однако очень часто повреждается и трубчатая система, тогда непригодным к ремонту становится весь радиатор. Есть два варианта, из которых можно выбрать один:
заменить поврежденный радиатор новым;
заменить систему трубок новой, сохранив верхний и нижний бачки старого радиатора вместе с патрубками и элементами крепежа. Системы трубок поставляются специализированными предприятиями по ремонту автомобилей. Распайка верхнего и нижнего бачков радиатора
осуществляется путем прогрева на большой длине шва до расплавления олова. Затем бачки оттягивают и разъединяют.
Для проведения этой технологической операции обычно используют пламя кислородно-ацетиленовой горелки.
При необходимости верхний и нижний бачки подвергаются правке, рихтовке и травлению
. Затем бачки одевают на законцовочную пластину новой системы трубок сверху и снизу и припаивают оловом с помощью паяльника л (ибо пламени кислородно-ацетиленовой горелки). Горелка должна обеспечивать быстрый нагрев, что сокращает время работы. Однако горелка может вызвать перегрев небольшого участка, что приведет к возникновению на нем дефектов.
Ремонт, о котором рассказано, с экономической точки зрения менее дорогой, чем полная замена радиатора. В зависимости от модели автомобиля стоимость ремонта радиатора на 40-70% дешевле замены его новым.
Понятно, что засорение радиатора
случается на автомобилях, эксплуатируемых в течение длительного времени. В таких случаях радиаторы очищают. Очистку радиатора можно произвести двумя способами: химическим (без снятия радиатора) и механическим (со снятием радиатора).
Химическую очистку радиатора
нельзя производить любым травящим реактивом, поскольку среди них есть такие, которые взаимодействуют с металлом и разрушают его. В системе охлаждения двигателя применяются различные по своим свойствам металлы. Так, радиатор выполняется из латуни или оцинкованной стали, головка блока двигателя из алюминиевого сплава, а блок цилиндров из чугуна или алюминиевого сплава. При очистке реакция должна происходить между накипью и химическим реактивом без воздействия на металл. Промышленные реактивы для удаления накипи представляют собой химические вещества, применяемые для этой цели. Их добавляют в воду радиатора и включают двигатель. Время работы двигателя определяется инструкцией изготовителя реактива. После остановки двигателя из системы охлаждения спускают жидкость и тщательно ее промывают.
В качестве реактива для снятия накипи применяется каустическая сода
. Она применяется в том случае, если в системе охлаждения не содержится алюминиевых деталей или деталей из алюминиевых сплавов. Латунь и чугун не взаимодействуют с содой, однако алюминий и его сплавы реагируют тем интенсивнее, чем выше температура содового раствора в воде. Чтобы убедиться в этом, достаточно приготовить ванну с каустической содой, разогреть ее до 80 °C и бросить в нее кусочек алюминия. Непрерывное выделение пузырьков газа укажет на реакцию металла с каустической содой. При этом глубина травления алюминия зависит от времени его погружения в раствор соды. Следовательно, соду нельзя применять, если в системе охлаждения имеются детали из алюминия и его сплавов.
Раствор соляной кислоты
в системе охлаждения вызывает умеренное коррозирующее действие, при этом быстрого разрушения металлов, покрытых медью, и легких сплавов не наблюдается. Однако при высокой концентрации кислоты последние реагируют очень бурно. В данном случае время работы двигателя для промывки системы ограничивается пятнадцатью минутами, после чего система тщательно промывается.
Азотная кислота
является более предпочтительной, если в радиаторе не содержится никакого другого вещества для удаления накипи. Она не действует на алюминий и его сплавы. В то же время она вступает в реакцию с медью и латунью. Ход очистки можно контролировать визуально, наблюдая за состоянием видимой внутренней поверхности радиатора, частично сливая жидкость по мере необходимости. После полного удаления жидкости из системы производят обильную промывку при полностью открытых сливных отверстиях.
Во всех случаях надо иметь в виду, что химическое травление является эффективным лишь тогда, когда трубки радиатора закупорены не полностью и травящий раствор может циркулировать.
Применяется и механическая очистка радиатора
. При этом из системы охлаждения сливают жидкость и снимают радиатор. Для снятия радиатора выполняют следующие работы: снимают соединительные шланги и болты крепления верхнего и нижнего бачков к кузову. Далее работу выполняют на верстаке. Снимают переливную трубу и заливную пробку.
Для доступа к трубкам необходимо распаять по меньшей мере один из бачков. Чтобы удалить олово из места пайки, каждый шов, подвергаемый распайке, устанавливают так, чтобы олово стекало со шва в момент его плавления. В зависимости от удобства работы линия распайки может быть установлена вертикально или горизонтально, а открытый конец желобка направлен вниз. Расплавление припоя обычно производится пламенем горелки. В процессе распайки следует размягчить олово, чтобы произвести несколько растяжений и сдавливаний бачка радиатора, что вызывает разрушение оставшегося паяного шва.
При работе с горелкой надо следить за тем, чтобы не возникало перегрева, вызывающего деформацию и разрушение пайки около трубок. После снятия бачка законцовочная планка полностью освобождена.
Работа по механической очистке трубок заключается в том, что в каждую трубку вставляют стальной прут соответствующего сечения и длины и перемещают его возвратно-поступательно, чтобы он проходил по всей длине трубки и удалял внутренние отложения. При невозможности прочистить трубки с одной стороны отпаивают второй бачок, чтобы иметь возможность прочищать трубки и с другой стороны.
После очистки трубки промывают и протравливают кислотой для удаления оставшихся осадков, которые не удалось прочистить прутом. И снова промывают трубки.
Перед установкой бачков на место всю поверхность законцовочной пластинки вокруг трубок необходимо залудить для предотвращения возможных утечек, которые могут быть вызваны расшатыванием пайки в момент распайки и прочистки. Затем устанавливают на место каждый бачок и закрепляют точечной сваркой, после этого пропаивают с помощью паяльника либо пламени газовой горелки, снабженной соплом малой производительности.
По окончании работы трубки заглушают посредством пробок или герметичных заглушек. Заливают радиатор водой и производят испытание герметичности сварки. При проверке желательно приложить небольшое усилие на растяжение и сдавливание радиатора.
Для испытания не обязательно применять насос, достаточно расположить радиатор горизонтально и установить вертикально трубу, соединенную с переливным патрубком шлангом. Труба длиной 1 м создаст вполне достаточное давление для контроля. Испытание радиатора с помощью сжатого воздуха при опускании радиатора в воду может привести к повышению давления, если не установлен предохранительный клапан, что чревато, разрывом радиатора.
Есть и такой метод контроля. Он заключается в том, что из радиатора сливают воду и закупоривают патрубки пробками. Пробками могут служить наборы резиновых цилиндрических колец, которые сжимаются болтом через две металлические шайбы, установленные с двух сторон резинового блока. В результате сжатия блок шайб раздувается и создает герметичность. Переливная трубка радиатора соединяется гибким шлангом с источником сжатого воздуха, находящимся в мастерской. Радиатор погружается в бак с водой. При подаче в радиатор воздуха под небольшим давлением, в случае утечки пузырьки воздуха поднимаются вверх, указывая на негерметичность радиатора.
Часто приходится иметь дело с трещинами радиатора
. Ремонт в основном производят посредством пайки оловянным припоем. В большинстве случаев для выполнения пайки следует снимать радиатор. Перед работой необходимо отметить места утечек.
Есть тенденция применения радиаторов, состоящих из системы алюминиевых трубок и пластмассовых водяных бачков. Такие радиаторы ремонту не подлежат.
В большинстве случаев топливные баки состоят из двух деталей, получаемых вытяжкой и сваренных роликовой сваркой по отогнутым бортам. Металлом для топливных баков служит мягкий стальной лист, покрытый свинцом (либо луженый). В новых моделях автомобилей прослеживается тенденция использования композиционных материалов для изготовления баков. Применение композиционных материалов способствует снижению массы автомобилей, а также уменьшению стоимости топливных баков.
Причин повреждения топливных баков несколько. Так как бак устанавливается под автомобилем, его верхняя часть оказывается на уровне пола. На некоторых моделях автомобилей топливный бак установлен вертикально в багажном отсеке сбоку. Баки, находящиеся под автомобилем, могут повреждаться от ударов камней. Баки, установленные в багажном отсеке, повреждаются коррозией, возникающей от конденсации влаги.
Для ремонта стального топливного бака
сначала необходимо слить горючее, а затем снять бак. Если ремонт сводится к выправке вмятины и никаких утечек топлива не наблюдается, то операция заключается в подаче сжатого воздуха в бак через заправочную горловину или через отверстие, соединяющее бак с топливным насосом. Для этого необходимо выполнить следующее:
заглушить одно из двух отверстий в баке;
вставить в открытое отверстие бака конический резиновый наконечник, просверленный насквозь для обеспечения герметичности соединения бака с трубопроводом сжатого воздуха;
подать сжатый воздух в бак и произвести восстановление его размеров и формы.
В случае повреждения бака нельзя тотчас производить его сварку.
Внутри бака всегда остаются пары топлива (бензина или дизельного топлива), которые смешиваются с воздухом и образуют взрывчатую смесь. Пламя может вызвать взрыв содержащейся в баке смеси, что, в свою очередь, приведет к разрыву бака и ранению находящихся поблизости людей.
Чтобы вести паяльные работы
, необходимо промыть бак, затем наполнитьт его водой или инертным газом. Промывку можно произвести раствором моющего средства в горячей воде, при этом бак энергично встряхивают и затем выливают содержимое. Последующую промывку бака производят посредством полного его заполнения и сливания.
Если пайка бака производится оловянным припоем при помощи паяльника, паять можно без заполнения бака. Если при ремонте требуется нагрев бака пламенем, например, для выполнения горячей пайки, то предварительно необходимо наполнить бак водой, а затем установить его так, чтобы внутри, под местом пайки, оставался небольшой воздушный промежуток.
При проведении этой работы нельзя герметически закрывать бак, образующийся при пайке газ должен свободно выходить наружу или выдавливать воду из бака. Для этого предварительно подсоединяют гибкий шланг к заливной горловине, которая после переворота бака оказывается внизу. При этом для поддержания нужного уровня шланг изгибают.
Бензобаки можно ремонтировать жидкими полиэфирными смолами
. Этот способ ремонта обладает тем преимуществом, что устраняется возможность взрыва, присущая пайке с применением газовой горелки. Работа выполняется в следующей последовательности: в чистый сосуд наливают полиэфирную смолу и отвердитель (в пропорции в зависимости от марки), затем смолу и отвердитель тщательно перемешивают до получения однородной массы. Клей готов. Подготовленной смесью с помощью кисти покрывают ремонтируемое место бака накрест лежащими слоями. Потом следует подождать, пока произойдет полимеризация смолы, и тогда нанести второй и, возможно, третий слой.
Если пробоина в баке большая
, необходимо выполнить следующее:
покрыть края отверстия смолой, затем наложить на отверстие стеклоткань и покрыть ее смолой;
в том же порядке наложить еще 2-3 слоя стеклоткани, промазывая каждый слой смолой.
Отметим, что соединенные вместе слои стеклоткани и смолы обладают прочностными характеристиками, сравнимыми с характеристиками металла бензобака.
Во всех случаях ремонта перед установкой топливного бака необходимо убедиться в отсутствии в нем утечек.
Детали кузова из пластических материалов
Пластические материалы находят очень широкое применение в машиностроении. Кузова автомобилей из пластика производятся редко, но некоторые широко распространенные модели имеют наружные детали из пластика.
Если говорить о кузовах, полностью изготовленных из слоистых пластиков, они состоят из элементов, собранных между собой, так как форма кузова очень сложная, чтобы ее можно было сформовать целиком. Кузова из слоистого пластика не являются несущими, они устанавливаются посредством разъемного соединения на стальную раму, несущую механические узлы. Изготовление деталей осуществляется формовкой.
Чтобы изготовить деталь, нужна по меньшей мере одна форма, которая может быть охватываемой или охватывающей. Форма должна иметь уклон для извлечения из нее готового изделия. Качество поверхности формуемой детали будет тем выше, чем лучше отполирована форма.
При формовке выполняют следующие подготовительные работы. Внутреннюю поверхность формы покрывают веществом, способствующим выемке готовой детали из формы.
Исходя из сопротивления действующим нагрузкам и внешнего вида, выбирают соответствующую стеклоткань для армирования изготовляемой детали. Готовят шаблон из плотной бумаги, размечают и вырезают по шаблону стеклоткань.
Далее выбирают полиэфирную смолу соответствующего качества и характеристиками, необходимыми для последующей эксплуатации детали. В смолу вводят красители. Существует множество разновидностей смол, отличающихся различным химическим составом. Каждая из них соответствует определенному назначению. Смола, предназначенная для нанесения первого слоя на форму, получила название ледяного покрытия
. Стеклоткань применяется в виде плотного материала - войлока, состоящего из коротких нитей длиной приблизительно 50 мм, расположенных хаотически и связанных друг с другом тонким слоем смолы. Толщина стеклоткани находится в пределах 1-2 мм, однако чаще всего ее измеряют по массе 1 м2
. Наиболее часто встречаются значения 300, 450, 600, 900 г/м2
. Это ткани различного типа, отличающиеся способом изготовления, массой и природой стекловолокна. Наибольшее распространение получила "тафта", имеющая клеточную текстуру. Стекловойлоки обладают меньшей механической прочностью, чем ткани, однако они более удобны для изготовления сложных форм.
В серийном производстве применяют другой вид стекловолокна: резаные волокна, которые имеют длину волокон, аналогичную стекловойлоку или несколько меньшую. Их применяют для изготовления основы.
Формовать детали кузова можно различными способами, но в любом случае они должны обеспечивать следующее:
правильное размещение ткани в форме;
полную пропитку ткани полиэфирной смолой без малейшего пузырька воздуха;
достаточно высокую производительность, необходимую для серийного производства.
Для ознакомления с технологией производства рассмотрим формование на одной форме, или контактное формование. Это самый простой способ. При этой технологии уменьшается количество используемого материала, но требуется большее количество рабочей силы. Качество готовых деталей зависит от умения и от аккуратности исполнителей. Способ применим для изготовления одной детали, нескольких идентичных деталей или малой серии. Формы могут быть самыми различными, в том числе и очень больших размеров. Как уже говорилось, форма может быть охватываемой или охватывающей - в зависимости от желания получить хороший внешний вид внутренней или наружной поверхности детали.
Форма должна быть очень жесткой. Уклоны формы должны составлять не менее 3-5°. Если деталь, подвергаемая формовке, имеет обратный уклон, то форму выполняют из нескольких точно подогнанных частей.
Материал формы
зависит от типа производства, который она должна обеспечить. Так, например:
гипсовая форма удовлетворяет производству одной детали;
стальная форма обеспечивает ее максимальное использование при формовании нескольких тысяч деталей;
при изготовлении деталей мелкими сериями наиболее простым является изготовление модели, с которой затем снимают слепок формы. В этом случае форма получается из слоистого пластика (стекловолокно + полиэфирная смола). Усиление формы осуществляется посредством погружения в слоистый пластик профилированного картона или деревянных пластинок, что создает образование нервюр
. Такого типа форма обеспечит изготовление многих сотен деталей.
При подготовительной работе
обращается особое внимание на следующее. После вырезки полотен их помещают во влажное помещение и так, чтобы их можно было взять в порядке нанесения слоев. Среди различных по составу веществ, способствующих разделению изделия и формы, необходимо выбрать то, которое соответствует материалу формы. После сушки разделительного покрытия надо, по возможности, нанести первый закрывающий слой
специальной окрашенной смолы (в некоторых случаях с наполнителем), который скрывает волокна стеклоткани, делая их незаметными на поверхности детали. Толщина слоя должна быть в пределах 0,3-0,4 мм. Если слой очень толстый, то впоследствии возникнут трещины.
Если наличие видимых волокон стеклоткани на поверхности детали не имеет значения, тогда нет необходимости накладывать закрывающий слой. В этом случае можно сразу нанести достаточно толстый слой смолы.
Чтобы избежать подтеков на вертикальных стенках, в смолу добавляют наполнитель
. После нанесения первого слоя его высушивают до студнеобразного состояния перед наложением последующих слоев.
Студнеобразное состояние слоя определяют по легкому прилипанию при касании. В течение перерыва следует приготовить смолу, которая будет использоваться при формовке. Приготовление смолы осуществляют в два этапа: добавляют ускоритель полимеризации и смешивают его со всей предназначенной для использования смолой, а в случае необходимости подкрашивают.д.озирование и смешивание катализатора полимеризации является следующим этапом и производится по мере необходимости, т.е. в расчете на количество смолы, которая может быть использована в течение последующих 15 минут. Разделяют смолу, предназначенную на половину рабочего дня, на две равные порции. В одну емкость помещают полное количество ускорителя, в другую - полное количество катализатора. По мере необходимости готовят смесь равными порциями в третьей емкости. Такой способ позволяет избежать повторяющегося приготовления небольших количеств смолы и катализатора.
Дозировать смолу можно либо взвешиванием на весах, либо применением емкости, в которую помещается определенная масса смолы. Дозирование ускорителя и катализатора полимеризации производится с помощью мензурок очень маленькими дозами.
Как только покрывающий слой или первый слой смолы стал студенистым, накладывают первый слой стекловолокна. При этом можно применить легкий стекловойлок (300 г/м2
). При наложении первого слоя стекловолокна, как, впрочем, и при наложении последующих слоев, необходимо следить, чтобы стекловолокно ложилось в форму постепенно и ровно, особенно в местах закруглений, без образования воздушных карманов. (Карманы образуются в результате либо очень поспешного прижатия, либо неплотного сопряжения острого угла). Затем уложенное стекловолокно пропитывается. Для этого каждый рабочий снабжается банкой, содержащей количество смолы, рассчитанное на 12 мин применения, и инструментом для нанесения смолы. В качестве инструмента используют кисточки или валики. Если применяют кисточку, то лучше похлопывать концом кисти по поверхности стеклоткани, как это делается при крашении, чем растягивать слой.
После окончания пропитки не следует пытаться отделить стекловолокно, так как при этом волокна приподнимаются и вырываются. Затем, не дожидаясь загустения, укладывают слой стеклоткани. Для обеспечения высокой механической прочности можно укладывать поочередно слой стекловойлока и слой стеклоткани. Последним укладывают стекловойлок или отделочную стеклоткань (300 г/м2
).
При выполнении этой работы необходимо соблюдать следующие правила:
использовать только чистые полиэтиленовые или металлические банки;
полностью использовать смолу, содержащуюся в банке, перед заполнением ее новой порцией;
не поддающиеся устранению воздушные пузыри нужно убрать, надрезая их лезвием бритвы;
сразу же после применения промыть кисти, валики ацетоном или трихлорэтиленом. Промывку нужно производить до того, как произойдет полная полимеризация оставшейся и подлежащей удалению смолы;
чтобы избежать прямого контакта смолы с кожей, работать необходимо в резиновых перчатках;
работать можно только в вентилируемом помещении, так как пары полистирола вызывают раздражение глаз и слизистой оболочки;
нельзя тереть глаза, так как случайно попавшие на кожу стеклянные волокна проникают в нее и могут травмировать глаза;
помещение, в котором производится работа, должно быть защищено от холода, влажности и прямого солнечного света. Температура должна быть не ниже 20 °C;
нельзя курить и перемещать смолы перед пламенем, так как смолы являются огнеопасными;
выемку изделия следует производить через 12 часов. Это время можно сократить, если применить сушку в сушильной камере (температура не выше 60 °C) или нагрев инфракрасными лучами;
после выемки изделия необходимо обрезать и загладить края;
при желании окрасить деталь, ее зачищают шлифовальной шкуркой, а затем наносят полиуретановую краску;
если большое количество деталей подвергается сборке склеиванием, необходимо сделать шероховатыми контактные поверхности, промыть их ацетоном, а затем склеить либо специальным клеем, либо тесьмой, пропитанной полиэфирной смолой.
Описанная технология - это практически единственный способ, с помощью которого кузовщик может по заказу клиента изготовить из слоистого пластика какие-либо детали кузова.
Познакомимся также с формовкой деталей в мешке
. Работа выполняется так же, как описано выше, после чего на изделие в форме оказывают давление либо с помощью раздувающегося эластичного пузыря, помещенного в закрытую форму, либо посредством создания разрежения между гибкой мембраной и слоистым покрытием, нанесенным на форму. Полученные таким образом детали имеют наилучшее качество, так как обеспечивается более равномерная концентрация смолы. Этот способ применим для среднесерийного производства.
Чтобы обеспечить хороший внешний вид и высокое качество готового изделия, формовка во входящих друг в друга формах
может производиться либо со слабым сжатием, либо без него. Способ применим в среднесерийном производстве.
Формовка под давлением во входящих друг в друга формах может производиться укладкой стекловолокна, а затем отмеренного количества смолы на форму. Сжатие позволяет обеспечить равномерное распределение смолы в детали. Обычно формы подогревают, что дает возможность применить этот способ в крупносерийном производстве, а также при производстве с первоначальным изготовлением основы будущей детали.
Обрезанные стеклянные волокна за счет разрежения прижимаются к поверхности формы, выполненной из перфорированного листа. В этом состоянии волокна пропитывают смолой из краскопульта. Форму с нанесенной на нее основой детали помещают на несколько минут в камеру для сушки. Затем полуфабрикат отделяют от формы, помещают в окончательную форму, покрывают отмеренным количеством смолы и сжимают с одновременным подогревом весь комплект в течение нескольких минут.д.еталь готова. Этот способ применяют в серийном производстве кузовных деталей.
Ремонт кузова из слоистого пластика осуществляют только с наружной поверхности детали. Порядок таков. Если повреждение незначительное, поврежденную зону зашлифовывают, затем зачищенное место заполняют полиэфирной шпатлевкой. После затвердевания шпатлевку зашлифовывают, а затем красят.
Если поврежденная часть расколота со значительным количеством более или менее измельченных осколков, пилой вырезают поврежденную зону. По краям отверстия снимают фаски. Фаски должны быть очень пологими и шириной, равной как минимум трем толщинам. Ремонт можно производить как снаружи, так и изнутри детали. Фаску снимают с той стороны, откуда будет производиться ремонт. По форме ремонтируемого участка детали готовят металлический лист. Он предназначен для частичной замены исходной формы. Если ремонт производится снаружи, то лист помещают с внутренней поверхности детали. При проведении ремонта с внутренней стороны детали лист-форма должен быть расположен с наружной стороны, поверхность которой имеет лучшую отделку.
Фаску и ее края промывают ацетоном. Лист-форму покрывают разделительным веществом. Если ремонтируемая деталь по меньшей мере в одном направлении прямолинейная, то разделительное покрытие можно не наносить или помещать между листом и деталью лист полиэтилена или хлорвинила. Из стеклоткани вырезают кусочки для ремонта (заплаты) различного размера. Самый большой должен соответствовать внутренней форме поверхности фаски. Далее готовят смолу и выполняют работу так, как это описано в предыдущем разделе. Ремонт заканчивают шлифованием и покраской.
Если деталь сильно повреждена
, необходимо ее заменить целиком. Поврежденную деталь вырезают как можно ближе к соединительному шву. Вырезку, а также опиливание производят с помощью инструментов, применяемых для обработки легких сплавов. Контактные поверхности зачищают опиливанием (если сборка осуществлялась склеиванием с уплотнителем) или частичным высверливанием заклепок (соединение специальными заклепками). Поверхности, подвергаемые склеиванию, протирают ацетоном. Прикладывают новую деталь. Если деталь подходит, то производят сборку. Сборку осуществляют следующими способами.
Склеивание
: склеиваемые поверхности делают шероховатыми, а затем промывают ацетоном. Следует применять клей, указанный изготовителем автомобиля, с соблюдением указанных условий применения. Склеиваемые поверхности покрывают клеем, прижимают их друг к другу и удерживают, слегка прижимая, до затвердевания клеевого стыка.
Второй способ - клепка
. Новую деталь закрепляют на месте с помощью тисочных зажимов или струбцин, прокладывая между губками зажимов деревянные пластинки, чтобы не поломать пластик в местах зажима губками. Сверление отверстий под заклепки осуществляется либо встречным сверлением, если на опорной поверхности имеются отверстия, либо сквозным сверлением детали и опорной поверхности, если нет ни одного отверстия. Затем разделяют предварительно скрепленные детали. Очищают поверхности от стружки и пыли. Контактные поверхности покрывают герметизирующей мастикой, снова прикладывают и закрепляют детали, совмещая их установкой стержней в отверстия. Вставляют заклепки и расклепывают. При необходимости устанавливают накладку.
Несколько слов о работе с термопластичными материалами
. Эти пластики поставляются в виде полуфабрикатов: тонких листов, пластин, труб и прутков для сварки. Наиболее широкое применение среди них имеют:
полихлорвинил
, который из-за высокой химической стойкости применяется для изготовления устройств или деталей, работающих в коррозионной среде;
метилполиметакрилат
, который, будучи прозрачным, применяется в качестве задних стекол в некоторых моделях легковых автомобилей;
плексиглас
- также прозрачный материал, имеет такое же применение, что и метилполиметакрилат, а также используется для других застекленных частей кузовов, небольших фургонов, пассажирских автоприцепов.
Для разметки пластиков
применяют обычный карандаш или чернильный с тонким грифелем. Тонкие листы (толщиной до 1,5 мм) можно резать ножницами. Листы толщиной 2 мм и более разрезают пилами.
Для зачистки пластиков
используют станки с бесконечной абразивной лентой с крупным зерном. При зачистке необходимо быть осторожным, чтобы не вызвать нагрева пластических материалов.
Опиливают пластики
напильниками с насечкой в виде свиной кожи. Если такого напильника нет, можно применять рашпиль по дереву с тонкой насечкой.
Пластик гнут следующим образом
. Готовят деревянную форму со скругленными углами для создания опоры. Затем нагревают линию сгиба до температуры 120-130 °C. Нагревать можно пламенем горелки, находящейся на некотором удалении, или посредством струи нагретого воздуха, создаваемого сварочной горелкой. На предприятиях нагрев осуществляется инфракрасным излучением. Нагревают обе поверхности пластины. При достижении заданной температуры нагретая зона становится гибкой, как резина. Пластик вставляют в форму и удерживают до момента, когда температура при охлаждении достигнет 50-60 °C. Охлаждение можно ускорить путем протирки нагретого участка ветошью, смоченной в холодной воде. Если гибка выполнена не совсем так, как было задумано, то снова нагревают место изгиба, что приводит к выпрямлению пластины, затем опять производят гибку.
Нельзя перегревать место сгиба, так как это приводит к обугливанию пластика.
При необходимости объемной гибки операцию производят так же, как и предыдущую, нагревая более широкую зону и придавая ей форму цилиндра или конуса.
Сварка пластика
. Для этой операции нужен вентилятор-обогреватель, снабженный устройством нагрева посредством электричества или газа. Устройство нагрева нагревает змеевик, в котором прогоняется воздух регулируемого объема. Из сопла вентилятора выходит поток воздуха, нагретого до температуры около 300 °C.
Для стыковой сварки со свариваемых деталей снимают фаски под углом 60° независимо от толщины пластика. Затем устанавливают свариваемые части и придерживают их на гладкой опоре из твердого дерева. В качестве присадки используют пруток из того же материала, что и свариваемые детали. Запиливают конец прутка приблизительно под углом 30° и устанавливают его в место сопряжения фасок перпендикулярно к поверхности деталей. Подносят горелку и наклоняют сопло под углом приблизительно 45° так, чтобы выдуваемый горячий воздух вызывал одновременное размягчение деталей и сварочного прутка. Пруток прижимают сверху вниз. При достижении достаточного размягчения сварочный пруток под действием усилия сплющивается и соединяется с деталью. Горелке сообщают движение подачи с возвратом в направлении прутка для размягчения базы.
При сварке толстых листов горелку перемещают мелкими последовательными шагами (по способу дуговой сварки). По окончании сварки по краям сварочного шва образуются наплывы затвердевшей не обгоревшей пены.
Более производительные способы сварки применяются в серийном производстве.
Соединения на клею
. Детали, подлежащие соединению, должны быть точно подогнаны, обезжирены, иметь шероховатые поверхности контакта. Две склеиваемые поверхности покрывают тонким слоем клея, прижимают их друг к другу с небольшим усилием и удерживают до высыхания.
Обращаем внимание: необходимо применять именно тот клей, который предназначен для склеивания используемого пластика. Клей, который хорошо склеивает полихлорвинил, может не склеивать плексиглас или любой другой пластический материал.
Формообразование деталей из пластика осуществляется вытяжкой. Независимо от выбранного способа вытяжки необходимо, по меньшей мере, изготовить форму. Пластина, подвергающаяся вытяжке, нагревается до размягчения в печи либо инфракрасными лучами. Затем она кладется на форму. Формуют деталь следующими способами:
с помощью пуансона, как при вытяжке металла;
давлением воздуха - шайба прижимает пластину по контуру формы, а сжатый воздух прижимает размягченный лист пластика к стенкам формы;
посредством вакуума - лист крепится к форме, внутри которой создается разрежение. Размягченный лист втягивается и прижимается к стенкам формы.
Пластические материалы могут подвергаться сверлению и нарезке резьбы инструментами, применяемыми для обработки легких сплавов. Трубы можно сгибать, наполнив их сухим песком или вставляя внутрь валики. Быстро соединять трубы из пластика можно с помощью муфт, тройников, которые приклеивают к трубам.
Пластические материалы могут также применяться для выравнивания поверхности кузова, в частности, для этого используется пластмасса ТПФ-37.
Для получения покрытия на основе пластмассы ТПФ-37
необходима тщательная подготовка металлической поверхности - обезжиривание и зачистка для создания требуемой шероховатости и хорошего сцепления пластмассы с металлом. Поверхность готовят не ранее чем за 8 часов до нанесения пластмассы. Порошок пластмассы перед использованием подсушивают при температуре 70-75 °C в течение 2,5 часов, перемешивая через каждые 30 минут. Во время сушки толщина слоя порошка не должна превышать 50 мм. Высушенный материал хранят в герметичной таре, оберегая его от увлажнения.
Для нанесения пластмассы на поверхность кузова можно применять установки газопламенного напыления марок УПН-4 или УПН-6-63 со специальными горелками. В них подается очищенный от влаги и масла воздух под давлением 0,5-0,6 МПа и ацетилен под давлением 0,06-0,07 МПа.
Перед нанесением пластмассы поверхность металла нагревают пламенем горелки до появления золотисто-желтого цвета побежалости, соответствующего температуре 200-220 °C. Расстояние от головки горелки до поверхности должно быть в пределах 100-150 мм. При нагреве недопустимо образование окалины (синих цветов побежалости) на поверхности металла. Подачу порошка через распылительную горелку необходимо отрегулировать так, чтобы порошок от пламени горелки расплавлялся и изменял цвет от светло-серого до черного.
После прогрева металла полным пламенем наносят первый слой пластмассы толщиной не более 0,8 мм, последующие слои наносятся при меньшем пламени. Головка распылительной горелки должна располагаться по возможности перпендикулярно к поверхности металла и находиться от нее на расстоянии 100-300 мм. На тонкий слой пластмассы черного цвета накладывают основной слой. При этом не следует касаться пластмассы пламенем горелки. Пластмасса не должна перегреваться и вскипать, при появлении на поверхности вздутия его быстро снимают деревянной лопаточкой и производят повторное напыление.
Готовый слой пластмассы уплотняют металлическим катком и лопаточкой. Для предотвращения прилипания катка к пластмассе его смачивают водой. Затем пластмассу охлаждают до температуры окружающей среды. Охлажденную поверхность обрабатывают до получения поверхности необходимой формы фибровым диском с зерном № 40. Для труднодоступных мест применяют шабер. Могут применяться и специальные рихтовочные пилы. После рихтовки на поверхности пластмассы допускается незначительная пористость.
Современные термопластичные материалы позволяют изготовить кузовные детали для разных целей. Они применяются в серийном производстве принадлежностей и деталей кузова, могут применяться для ремонта кузовов при выполнении жестяных работ на автомобилях.
Химики разработали виды пластика для изготовления кузовов, обладающие высокой прочностью и не повреждаемые при сильных ударах. На некоторых из них нельзя даже сделать царапину. Однако их серийное производство и изготовление таких кузовов на заводах пока осложнено такими проблемами, как себестоимость, которая растет вместе с увеличением прочности, и горючесть пластиковых материалов.
Восстановление неметаллических деталей
Неметаллические материалы, используемые в кузовах, - это дерево
и другие материалы для декоративной отделки салонов кузовов
, а также обивочные материалы
.
Восстановленные деревянные детали должны быть без трещин, задиров и ступенчатости, торцы деталей - чистыми, без отслоений и сколов.
Поврежденные детали кузовов
, для изготовления которых применяют пластические массы, в процессе ремонта заменяют новыми, технология их изготовления проста и экономична. Детали, ремонт которых целесообразен и экономически оправдан, обычно восстанавливают склеиванием. Выбор клея для соединения пластмассовых материалов зависит от химической природы материала, условий работы клеевого соединения и технологии его нанесения.
Для изготовления деталей из пластических масс используют полиамид, органическое стекло, капрон
и др.
Технология склеивания
складывается из обычных операций подготовки поверхности, нанесения клея и выдержки клеевого состава под давлением. Детали, изготовленные из этрола, склеивают уксусной кислотой, которой промазывают склеиваемые поверхности, а затем соединяют их под небольшим давлением и выдерживают в течение 0,75-1 ч.
Для склеивания полиамидов
применяют растворы полиамидов в муравьиной кислоте или муравьиную кислоту. Детали из пластмассы на основе термореактивных смол склеивают клеем ВИАМ Б-3. Клей наносят на соединяемые поверхности и выдерживают их в открытом виде при комнатной температуре в течение 10-15 минут, затем детали собирают в прижимном приспособлении и выдерживают в нем 8-12 часов. Сегодня в продаже есть очень много самых разных клеев, высыхающих значительно быстрее.
Часто восстановлению подлежат детали, изготовленные из оргстекла
. При появлении трещины, в ее конце сверлят отверстия диаметром 3-4 мм для ограничения ее дальнейшего распространения; если появилась пробоина, ставят дополнительную ремонтную деталь.
Отверстия в органическом стекле сверлят обыкновенными инструментальными сверлами с углом при вершине 140°. Для склеивания деталей из органического стекла используют раствор, состоящий из 2-3% стружки оргстекла, перемешанной при температуре 20-25 °C в течение 25-30 минут в дихлорэтане. Раствор выдерживают в течение 2-3 суток до полного растворения стружки. Готовый клей может храниться в герметичной посуде в течение месяца.
Отделка органического стекла после ремонта состоит из шлифования абразивами для удаления глубоких царапин и шероховатостей в местах склеивания, полирования и промывки. При шлифовании необходимо захватывать значительную поверхность для предотвращения оптического искажения.
Полирование
применяется для зачистки поверхностей после шлифования и для удаления мелких рисок. Шлифование и полирование стекол выполняют на станках с вертикальной осью вращения круга при обильном смачивании обрабатываемой поверхности водой. При шлифовании на войлочную обивку круга наносят равномерный слой пасты, представляющей собой водный раствор порошка пемзы
. После шлифования со стекла смывают остатки шлифовальной пасты, на полировальный круг наносят водный раствор крокуса
и полируют стекло до получения необходимой прозрачности. По окончании полирования стекло обезжиривают и протирают сухой чистой ветошью.
Восстановление верхней обивки сидений
включает постановку вставок и новых частей вместо пришедших в негодное состояние; приклейку или пришивание оторванной части обивки; перелицовку загрязненной части обивки, не поддающейся очистке; устранение порезов и разрывов. При выполнении этих работ повторяют все операции, присущие процессу изготовления новой обивки, плюс дополнительные работы, связанные с разборкой обивки и очисткой ее деталей от концов ниток, пыли и загрязнений, а также подготовку участков, подлежащих ремонту.
Устранение порезов, разрывов
и постановку дополнительных ремонтных деталей
производят штуковочными стежками, которые малозаметны с лицевой стороны обивки, а также приклеиванием и вшиванием вставных и накладных вставок. Приклеивать вставки можно клеем типа БФ-6. После проглаживания утюгом, нагретым до 100-120 °C, через увлажненную ткань на приклеенную вставку не действуют ни температура, ни влага, ни химические растворители. Разрывы обивки, изготовленной из кожзаменителя или из поливинилхлоридной пленки, армированной или не армированной сеткой из синтетических волокон, устраняют подклейкой вставок полиамидным клеем ПЭФ-2/10. Склеивают при комнатной температуре с последующей выдержкой под прессом в течение 1-1,5 часов.
Для приклейки новой обивки к картону
применяют клей 88-НП. Материал для пошива новых деталей обивки раскраивают по разметке или шаблонам. Соединяемые детали обивки сшивают с определенным шагом строчки на заданном расстоянии от кромок одинарным или двойным швом с изнаночной стороны обивки.
Для увеличения прочности соединения верхней обивки подушки сидений применяют обточные швы с кантом
.
Обивка не должна иметь слабой затяжки, перекосов, морщин, складок и повреждений на лицевой стороне. Для сборки подушек и спинок сидений применяют пневматический стенд, позволяющий сжимать пружины подушек для обеспечения натяжения материала.
Обычно технологический процесс сборки кузовов состоит из сборки до окрашивания и общей сборки после окрашивания. Принципиально процесс общей сборки после окрашивания кузова при его ремонте ничем не отличается от сборки нового кузова, меняются лишь организационные формы сборки и соотношения трудоемкости отдельных видов работ.
Сборка кузова после капитального ремонта
должна производиться в той же последовательности и с той же тщательностью, что и сборка нового кузова. Характерная особенность сборки состоит в том, что здесь обнаруживаются все основные недостатки предыдущих технологических операций. Если они выполнены с отступлением от технических условий, то производят дополнительную обработку, подгонку и разного рода доделки, влияющие на трудоемкость и качество сборки.
При сборке кузовов особое внимание уделяют выбору инструментов и приспособлений
. Помимо универсальных инструментов и приспособлений, которые могут быть использованы на любой операции, соответствующей их назначению (гаечные ключи, отвертки и др.), широко применяют и специальные инструменты, предназначенные для выполнения одной вполне определенной операции. Применение специальных приспособлений или инструментов упрощает и облегчает процесс сборки.
Сборку любого кузова нельзя осуществлять в произвольной последовательности. Последовательность сборки
определяется прежде всего конструкцией собираемого узла, а также требуемым разделением сборочных работ. Для наглядности сборочные схемы принято изображать так, чтобы соответствующие узлы и детали были поставлены в порядке их введения в технологический процесс сборки.
В зависимости от качества ремонта, точности изготовления отдельных узлов и деталей кузова и количества пригоночных работ различают три основных вида сборки: по принципу полной взаимозаменяемости, по принципу индивидуальной пригонки и по принципу ограниченной взаимозаменяемости. Сборку по принципу полной взаимозаменяемости
применяют преимущественно в массовом и крупносерийном производстве. В мелкосерийном производстве, а тем более в единичном производстве принцип полной взаимозаменяемости экономически не оправдан, потому применяется лишь в отдельных случаях.
Сборка по принципу индивидуальной пригонки
, назначение которой - придать детали точные размеры или ту или иную геометрическую форму, осуществляется пригонкой соединяемых деталей друг к другу. Эта операция обычно очень сложная и трудоемкая, поэтому на современных предприятиях автосервиса сборка по принципу индивидуальной пригонки вытесняется более быстрой сборкой по принципу ограниченной взаимозаменяемости
.
Наиболее распространенными видами пригоночных работ при сборке кузова являются работы, связанные с постановкой деталей и узлов, снятых с кузова и подвергшихся ремонту или вновь изготовленных; это опиливание, сверление и развертывание отверстий по месту, нарезание резьбы, зачистка, гибка
. Механизация пригоночных работ при сборке осуществляется главным образом за счет применения универсальных и специализированных инструментов с электрическими и пневматическими приводами.
Сборка кузовов до окрашивания обычно связана со значительным объемом пригоночных работ и производится на участке ремонта кузова. На кузова легковых автомобилей до окрашивания устанавливают предварительно загрунтованные двери, передние и задние крылья, капот, облицовку радиатора, брызговики, крышку багажника
и другие детали, подлежащие окрашиванию вместе с кузовом.
Сборку кузова после окрашивания производят в последовательности, обратной разборке кузовов. Основные сборочные работы выполняют на окрашенном кузове, поэтому их следует проводить аккуратно.
Сборку легкового автомобиля начинают с постановки ограничителей открывания дверей
и укладки пучков электропроводки
в моторном отсеке, салоне кузова и багажном отделении. Далее на кузов устанавливают: омыватель ветрового стекла; валик привода акселератора
и замок капота с приводом; кронштейн педалей сцепления
и тормоза; термошумоизоляционные прокладки; обивку потолка; отопление
и вентиляцию кузова; ветровое
и заднее стекла; панель приборов; стеклоподъемники, замки
и обивку дверей; уплотнения
по проемам окон, дверей, моторного отсека и багажника; коврики пола
; передние и задние сиденья
.
Прокладка электропроводки. При сборке автомобилей ВАЗ передний пучок
проводов из салона пропускают через отверстие в переборке моторного отсека
, которое затем закрывают уплотнителем. Затем пучок укладывают в защитные трубы вдоль щитка передка
и с помощью отвертки и молотка закрепляют скобками. Правую ветвь закрепляют на брызговике
хомутом, левую вместе с трубкой омывателя стекла
- другим хомутом.
Отдельные провода
с соединительными колодками
или без них, каждый по своему месту, подводят для присоединения к следующим деталям: к стеклоочистителю
, к реле заряда аккумуляторной батареи
, к фарам
и подфарникам
, к генератору
, к подкапотной лампе
и датчику указателя давления масла
, к сигнализатору уровня жидкости
в бачке главного тормозного цилиндра
, к регулятору напряжения
.
В салоне кузова
провода пропускают через проем кронштейна вала рулевого управления
и закрепляют на поперечине панели приборов хомутами. С левой стороны на поперечине хомутом закрепляют провода, предназначенные для подключения заднего пучка проводов, соединение которых осуществляется через колодки. Выводы проводов предназначены для подключения: включателя стеклоочистителя, насоса стеклоомывателя, замка зажигания, розетки
для переносной лампы, прикуривателя, лампы освещения вещевого ящика, электродвигателя отопителя, комбинации приборов, центрального переключателя света, реле стеклоочистителя, реле поворотов
.
Задний пучок
проводов прокладывают по полу кузова с левой стороны и выводят по задней поперечине к правой центральной стойке, правой боковой панели передка
и в багажное отделение
. Пучок проводов фиксируют клейкой лентой. Провода "массы" левого и правого плафонов
прикрепляют к центральным стойкам самонарезающими винтами. Переднюю часть заднего пучка проводов закрепляют на левой боковой панели передка с помощью скоб и хомутов, среднюю и заднюю части - хомутами. Передний и задний пучки проводов между собой соединяются колодками.
В багажном отделении
задний пучок проводов прокладывают вдоль левого заднего лонжерона
и по нижней поперечине задка
, закрепив в пяти точках хомутами, выводят к задним фонарям
. В местах подвода к задним фонарям пучок проводов крепят скобами. На выходе в багажное отделение пучок проводов закрепляют с левой стороны в выштамповке скобой.
На провода фонаря освещения номерного знака и фонаря заднего хода
надевают уплотнитель, затем провода пропускают через отверстие в панели задка к потребителям, а в отверстие устанавливают уплотнитель. Провода лампы освещения багажника
и датчика уровня топлива
прокладывают на поперечине задней перегородки (
по усилителю правой арки заднего колеса) и закрепляют хомутами.
Омыватель ветрового стекла и его детали устанавливают на щитке передка
и панели рамы ветрового окна
. Ставят на место уплотнитель и через него пропускают трубку от бачка омывателя ветрового стекла к насосу
.
Затем прокладывают трубки к жиклерам стеклоомывателя
, закрепляя их на щитке передка скобами.
Всасывающий и нагнетающий концы трубок через тройник соединяют со штуцерами насоса
. Насос устанавливают на место и соединяют штекером с колодкой проводов
.
Валик привода акселератора, замок и привод замка капота устанавливают на щитке передка
с обязательной их регулировкой и смазыванием трущихся поверхностей смазкой ФИОЛ-1. Трос привода воздушной заслонки карбюратора
пропускают через уплотнитель и закрепляют его.
Кронштейн педалей сцепления и тормоза, главные цилиндры сцепления и тормоза устанавливают на щиток передка, предварительно смазанный по контуру проема невысыхающей мастикой 51-Г-7, затем соединяют провода с выключателем сигнала торможения и розеткой для переносной лампы.
Термошумоизоляционные прокладки изготовляют из пленочного поливинилхлоридного материала типа Р толщиной 0,1-0,4 мм. Они используются в качестве защитных пластин для передних и задних дверей.
Подушки, изготовленные из полистирола
, используются в одних случаях как термоизоляционные, в других - как выравнивающие или направляющие. Трехслойные обивки щитка передка и пола кузова
, изготовленные из битумного материала толщиной 2 мм и пористого материала марки 700, покрытого тонкой полиэтиленовой пленкой, служат в основном шумоизоляционными прокладками.
Работы по термошумоизоляции
проводят в следующем порядке. Клей ИПК-42 наносят кистью на изоляционную подушку правого переднего пола
, направляющие подушки среднего пола
и выравнивающие подушки. Затем каждую из них приклеивают по своему месту. Промазывают клеем ИПК-42 коробку воздухопритока
и закрепляют на ней обивки. Затем приклеивают и закрепляют скобами цельноформованную обивку щитка передка
и обивки боковины передка кузова
.
На передний пол укладывают правую и левую обивки переднего пола, обивку на кожух пола
и на средний пол. На полку задка укладывают войлочную прокладку, на пол под заднее сиденье - прокладку из пористого материала марки 700.
От проникновения пыли, грязи и влаги двери защищены пленочными пластинами ПВХ.
Обивку потолка
устанавливают по изоляционным прокладкам, предварительно приклеенным к внутренней поверхности потолка клеем 88-НП-35. Усилительные дуги
пропускают через обивку, а затем вставляют в гнезда верхних накладок боковин кузова
. Натяжку обивки потолка кузова начинают от проема заднего окна, укладывая края обивки на верхней части рамы боковых панелей крыши и закрепляя скобами. Число скоб, равномерно расположенных по периметру, должно быть не менее сорока. Но к верхним поперечинам ветрового и заднего окон
и в верхней части центральных стоек
обивку потолка приклеивают клеем ИПК-42.
Отопление и вентиляция кузова осуществляется через решетку забора наружного воздуха
, выштампованную на капоте, коробку воздухопритока
и крышку ее люка.
Система отопления и вентиляции состоит из радиатора
, который питается жидкостью из системы охлаждения двигателя, крана отопителя, рычагов управления, вентилятора
, установленного в кожухе на двух упругих опорах.
При установке отопителя
необходимо: провод "массы" от электродвигателя отопителя вставить под переднее левое крепление; провода красный и голубой с черной полосой переднего пучка соединить с электродвигателем отопителя
, прикрепить в четырех точках кожух радиатора
к кузову и соединить шлангами отопительный агрегат
с системой охлаждения двигателя
. Подтянуть стяжные хомуты шлангов, проверить отсутствие течи жидкости, закрепить рычаги и тросы управления краном отопителя
и крышкой люка воздухопритока
.
Остекление кузова
выполняют в следующей последовательности. Установка ветрового стекла
: пазы уплотнителя тщательно промывают бензином, уплотнитель надевают на стекло и в его профиль вводят окантовку. В паз, которым уплотнитель надевается на фланец проема окна, при помощи отвертки вставляют шнур. Стекло в сборе с уплотнителем устанавливают в проем кузова, и слесарь натягивает концы шнура изнутри кузова так, чтобы уплотнитель сел на место (при этом второй работник должен слегка надавливать на стекло снаружи).
Установка заднего стекла
ведется так же, как и установка ветрового стекла.
Последовательность установки панели приборов:
на поперечине передка по месту крепления нижней части панели устанавливают скобы;
панель ставят на место, провода потребителей выводят в проемы комбинации приборов и вещевого ящика;
через проемы в панели приборов верхнюю часть ее крепят в четырех точках к поперечине панели передка гайками;
присоединяют к лампе освещения вещевого ящика провод и с левой стороны корпуса устанавливают боковину;
устанавливают на место рычаги управления отопителем с кронштейном в сборе и дефлекторы с уплотнителями воздухопровода отопителя;
соединяют колодки комбинации приборов и устанавливают комбинацию приборов на место;
к трехклавишному переключателю присоединяют включатель стеклоочистителя, освещение приборов (желтый и белый провода), наружное освещение;
соединяют провода, надевают защитные резиновые трубки и устанавливают прикуриватель;
в гнездо панели приборов устанавливают пепельницу в сборе с корпусом.
Сборка передней двери начинается с установки верхнего ролика
на ось, предварительно смазанную "Литолом-24". Затем устанавливают верхнюю декоративную накладку обивки двери
и, не закрепляя ее, нижний ролик
. Закрепляют на место механизм стеклоподъемника
, на ролики надевают трос
и свободный конец троса временно прикрепляют к внутренней панели.
Затем последовательно устанавливают втулку кнопок блокировки, тягу выключения замка, наружную ручку с прокладками, резиновый буфер опускного стекла двери, замок двери, фиксатор замка, тягу замка, внутреннюю ручку двери, тягу и кнопку привода замка двери, опускное стекло с обоймой
. Во внутреннюю и наружную окантовки стекол устанавливают пластмассовые уплотнители, а на их концы - передние и задние облицовки.
После монтируют поворотное стекло
. Во внутреннюю часть рамы окна наносят клей типа 88-НП-35, приклеивают уплотнитель опускного стекла
и в него вводят стекло. С помощью натяжного ролика
натягивают трос стеклоподъемника
, закрепляют нижний ролик
, устанавливают на тpoc привода стеклоподъемника прижимную планку
и после регулировки трос окончательно зажимают. Трос и ролики стеклоподъемника смазывают "Литолом-24".
Ставят уплотнительную прокладку
на приводной валик стеклоподъемника
и прокладку под внутреннюю ручку
, после чего устанавливают обивку двери. Затем ставят розетку и ручку механизма стеклоподъемника
, зафиксировав ее пружиной. В последнюю очередь устанавливают облицовку с внутренней ручкой привода замка двери
и подлокотник
, затем проверяют качество работы механизма блокирования и замка двери.
Герметизация кузова обеспечивается применением различных уплотнителей, уплотнительных мастик, резиновых заглушек по технологическим отверстиям и тщательной подгонкой сопрягаемых деталей. При установке резиновых уплотнителей
не допускаются гофры и смятия металлического каркаса.
При установке уплотнителей проемов
дверей рекомендуется наносить под них клей 88-НП-35 от верхней кромки заднего крыла (по верху проемов дверей и по центральной стойке) до порогов дверей.
После установки дверей
по углам петель наносят уплотнительную мастику 51-Г-7. При замене или перестановке уплотнителей дверных проемов мастику 51-Г-7 наносят по верхним углам центральных стоек.
Коврики пола
в салоне кузова изготовляют из формованной резины, а в багажнике - из поливинилхлоридного материала толщиной 1,5 мм. После укладки и закрепления ковриков на своих местах, их дополнительно закрепляют в проемах дверей облицовками порогов.
<< предыдущий лист
следующий лист >>
Содержание 1 2 3 4 5 6 7 8 9 10 11 12 13 14 15 16 17 18 19 20 21 22 23 24 25 26 27 28 29 30 31 32
Главная > Каталог > ОБОРУДОВАНИЕ ДЛЯ КУЗОВНЫХ РАБОТ > Гидравлические системы для рихтовочных стендов
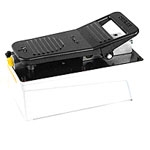
Shinn Fu А5701
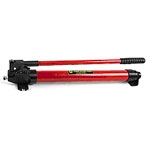
НРГ070-0,6СВ
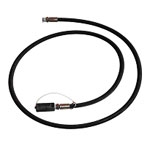
РВД6-70/2000/К3/8
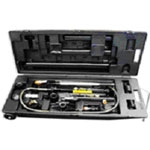
Shinn Fu AUTO BODY KIT
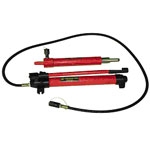
ЛВН Комплект гидрорастяжки
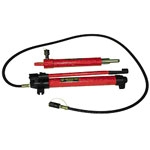
ЛВН Комплект гидростяжки
Стенд для ремонта аварийных кузавов Серия "СИВЕР DE"
Главная > Каталог > ОБОРУДОВАНИЕ ДЛЯ КУЗОВНЫХ РАБОТ > Стенд для ремонта аварийных кузавов Серия "СИВЕР de"

Сивер DЕ-105
Стенды для правки кузовов серии "СИВЕР"

Сивер DЕ-110
Стенды для правки кузовов серии "СИВЕР"

Сивер DЕ-205
Стенды для правки кузовов серии "СИВЕР"

Сивер DЕ-205/10
Стенды для правки кузовов серии "СИВЕР"

Сивер DЕ-210
Стенды для правки кузовов серии "СИВЕР"
Стенд для правки кузовов серии "СПК"
Главная > Каталог > ОБОРУДОВАНИЕ ДЛЯ КУЗОВНЫХ РАБОТ > Стенд для правки кузовов серии "СПК"
Рихтовочный стенд "СПК" предназначен для восстановления аварийных кузовов легковых автомобилей весом до 2000 кг. Оборудование имеет сертификат соответствия требованиям безопасности (РОСС RU. MT20. B 04941). Основа стенда - жесткая рама с зажимами для закрепления кузова автомобилей. Стенд комплектуется угловым силовым устройством с усилием растяжения до 10 т.
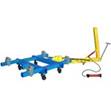
СПК-01С
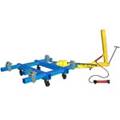
СПК-02С
Главная > Каталог > ОБОРУДОВАНИЕ ДЛЯ КУЗОВНЫХ РАБОТ > Аксессуары для рихтовочных стендов
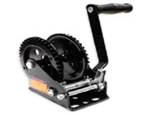
Shinn Fu 2119087
Главная > Каталог > ОБОРУДОВАНИЕ ДЛЯ КУЗОВНЫХ РАБОТ > Системы контроля геометрии кузова
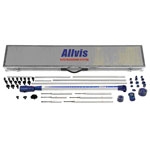
JNE AV310 Allvis
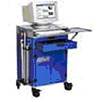
JNE AVS330

JNE UB200 Upperbody Laser
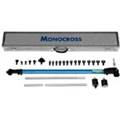
JNE MC4100 Monocross
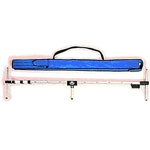
MB 170/N
Кузовной ремонт различной степени сложности автомобиля современных производителей выполняется на современном оборудовании. Все виды работ проводятся с соблюдением рекомендаций, определенных ведущими компаниями рынка.
В том случае, когда кузовной ремонт требует восстановления геометрии кузова, устранение дефектов происходит на базе стапелей. Использование стапелей ведущих компаний позволяет выполнять кузовной ремонт любых марок и моделей автомобилей отечественного и иностранного производства, в том числе рамных джипов и минивэнов. В случаях, когда детали кузова сделаны из алюминия при кузовном ремонте используется аргонная сварка. Подобная технология в ряде случаев позволяет сохранить дорогостоящую деталь от замены. При незначительных повреждениях лакокрасочного покрытия кузовной ремонт использует специальную технологию, при которой ремонту подвергается только место повреждения. В этом случае кузовной ремонт эффективен при царапинах, сколах, потертостях. Нередко такой ремонт кузова автомобиля сопровождается также ремонтом и покраской бамперов и пластиковых деталей.
|