Министерство образования Российской Федерации
Орловский государственный технический университет
Кафедра “Прикладная механика”
Пояснительная записка
к курсовому проекту
по дисциплине “Детали машин”
Привод ленточного конвейера
Студент: Блинчиков А.Е.
Группа: 31-АМ
Руководитель проекта: Савин Л.А.
Орел 2001
СОДЕРЖАНИЕ
Введение …………………………………………………………………….4
1. Кинематический расчет привода
1.1 Выбор электрического двигателя ………………………………………5
1.2 Определение передаточных отношений, силовых и энергетических параметров элементов привода…..…………..………………………….7
1.3 Результаты кинематических расчетов на ЭВМ……..………..…………9
1.4 Сравнительный анализ полученных результатов…………….……….11
2. Расчет и проектирование зубчатого редуктора.
2.1 Выбор материалов зубчатых колес и определение допускаемых напряжений………………………………………………..…………….……..12
2.2 Проектировочный расчет зубчатых передач ……….………….……...14
2.3 Проектировочный расчет валов………………………………………..16
2.4 Результаты расчетов напряжений, геометрических параметров с использованием автоматизированных систем расчета "Восход" и "АРМ"……………………………………………………………………….17
2.4 Эскизная компоновка редуктора………………………………….……27
2.5 Проверочный расчет зубчатых передач………………………………..31
2.6 Расчет (выбор) подшипников и уплотнений…………………………..33
2.7 Конструирование и проверочные расчеты валов на прочность, жесткость и колебания…………………………………………………...….35
2.8 Расчет и конструирование корпуса и крепежных деталей………...…..45
2.9 Тепловой расчет и смазка редуктора………………………………….....45
3. Расчет клиноременной передачи………………………………………………46
4. Подбор, проверка и эскизная компоновка муфты…………………………….48
5. Расчет и проектирование узла исполнительного механизма (барабана)……49
Список используемой литературы……………………………………...…..52
ВВЕДЕНИЕ
Цель курсового проекта заключается в проектировании привода цепного транспортера, который состоит из: электродвигателя, ременной передачи, муфты, 2-х ступенчатого соосного редуктора и приводного вала исполнительного органа. Электродвигатель, редуктор и опоры приводного вала барабана крепятся на общей раме. Привод работает в режиме переменной нагрузки. Учитывая предлагаемое применение привода и невысокую скорость движения ленты транспортера, элементы зубчатой передачи изготовлены не выше 9-ой степени точности. Подобные приводы используются в цехах при конвейерном производстве различных видов продукции.
По данным о работе данного привода выбрали электродвигатель 4А
112
МВ6УЗ
, который удовлетворяет предъявленным к приводу требованиям по мощности и частоте оборотов. Так как система работает при периодически изменяющейся нагрузке, то по рекомендации на входе привода была установлена ременная передача, соединяющая электродвигатель и редуктор. Она обеспечивает более плавную работу элементов привода. Предложенный и рассмотренный редуктор удовлетворяет требованиям к передаче мощности и сохранению определенного передаточного числа. С учетом окружных скоростей зубчатых колес заменяем прямозубую первую ступень на косозубую, так как первая будет работать за рекомендуемыми значениями округленных скоростей. Возникающая в результате замены осевая сила незначительна. В проекте выполнен кинематический расчет привода, проектно-проверочный расчет зубчатых передач, как по известным алгоритмам так и с использованием автоматизированных систем расчета “Восход” и “Кинематика”. Расчет на смазку редуктора показал, что естественного охлаждения для данного редуктора вполне достаточно. По выходным параметрам редуктора подходит зубчатая муфта, которая также удовлетворяет условию соосности валов и их радиального смещения. Опоры приводного вала размещаются на двутавровых балках, которые подходят по конструктивным особенностям. В целях экономии материала плиту делаем сварной из швеллеров. Рама привода крепится на бетоном фундаменте в крепление которого предусматривают её смещение для замены или ремонта. Крепежные детали, подшипники, шпонки выбирают согласно соответствующим ГОСТам.
1.Кинематический расчет привода
1.1
Выбор электрического двигателя
Определяем мощность на исполнительном органе по формуле:
P=F
.
V
,
(1.1)
где F= 4500 Н – окружное усилие на барабане;
V = 0.6 м/с – скорость цепи.
Данные значения подставляем в формулу (1.1):
Р=4500.0,6=2,7 (кВт)
Потребную мощность двигателя определяем по формуле:
, (1.2)
где hS
- суммарный КПД привода, вычисляемый по формуле:
, (1.3)
где - КПД муфты; - КПД редуктора;
- КПД пары подшипников;hрем
=0.95 - КПД ременной передачи.
Подставляем эти значения в формулу, получаем:

Тогда мощность двигателя равна:
(кВт)
Частоту вращения ведомого вала определяем по формуле:
, (1.4)
где D0
–диаметр барабана, равный D0=375 (мм)
Из формулы (1.4) находим:
.1(об/мин)
Оцениваем возможное передаточное отношение привода Uобщ
=Uр
.Uрем
. Задаем Uрем
=2,5 По таблице 14.2 (1) передаточное отношение редуктора Uр
= 10…25.Выбираем Uр
=12.
По графику рис.5.11(1) принимаем передаточное отношение быстроходной ступени равное Uб
=3.55. А передаточное отношение тихоходной ступени:Uт
=Uр
/Uб
=12/3.55=3.15 (1.5)
Тогда требуемая частота вращения вала электродвигателя определяется по формуле:
nдв
= nвых
.U = 31.30 = 930 (об/мин)
Определяем среднеквадратичную мощность двигателя используя график нагрузки:
, (1.6)
где Nn – значение мощностей в определенный момент цикла; t- время цикла.
.
По таблице 2 приложения 2(1) выбираем двигатель 4А112МВ6УЗ
, для которого
Nном
=4,0 кВт, nном
=960 (об/мин).
1.2 Определение передаточных отношений, силовых и энергетических параметров элементов привода
Фактическое передаточное отношение привода:
 (1.7)
Частота вращения двигателя:nдв
=960 (об/мин).
Частота вращения вала после ременной передачи:
n2
= n3
.Uр
=( 401(об/мин) (1.8)
Частоту вращения промежуточного вала определяем по формуле:
n2
`=n3
.U34
=31.1.3.15=97.9(об/мин) (1.9)
Частоту вращения вала после редуктора находим по формуле:
= (1.10)
Частота вращения вала после муфты:
n4
=n3
=nвых
=31.1 (об/мин).
Крутящий момент на валу электродвигателя находим по формуле:
, (1.11)
где N1
, n1
– соответственно мощность и частота оборотов вала электродвигателя
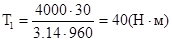
Крутящий момент на валу после ременной передачи находится по формуле:
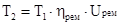 (1.12)
Крутящий момент на промежуточном валу редуктора находится по формуле:
Т'2
= Т2
.U2
.h1
=95 . 3,58 . 0,975 =332 (Н.м) (1.13)
Крутящий момент на валу после редуктора находим как:
= 95.0,9752
.31=2800 (Н.м) (1.14)
Крутящий момент на исполнительном органе находим по формуле:
 (1.15)
Угловая скорость соответственно для вала электродвигателя:
 (с-1
) (1.16)
Угловая скорость для входного вала редукторарассчитывается по формуле:
v2
=N2
/T2
=3960/95=42(с-1
) (1.17)
Угловая скорость для промежуточного вала редукторарассчитывается по формуле:
=3.14.97.9/30=10.25(с-1
) (1.18)
Вал после редуктора и вал исполнительного органа:
(1.19)
Определяем мощность на входном валу редуктора:
(1.20)
Мощность на промежуточном валу редуктора:
N2
`=N2
.hз
п
=3960.0.975=3860(Вт) (1.21)
Мощность на выходном валу редуктора:
= 3960 * 0.9752
= 3765 (Вт) (1.22)
Мощность на исполнительном органе определяем по формуле:
=3765. 0.99 =3727 (Вт) (1.17)
Найденные значения частот оборотов, крутящих моментов, угловых скоростей и мощностей на валах привода сносим в таблицу 1.2.1
Таблица 1.2.1
Кинематические,cиловые и энергические параметры элементов привода
№
|
Параметр
|
Обозн.
|
Разм.
|
Валы
|
1
|
2
|
3
|
4
|
5
|
1
|
Крутящий момент
|
Т
|
Н
×
м
|
40
|
95
|
332
|
2800
|
2772
|
2
|
Частота вращения
|
n
|
Об/мин
|
960
|
401
|
97,9
|
31,1
|
31,1
|
3
|
Угловая скорость
|
w
|
С-1
|
100,5
|
42
|
10,25
|
3,3
|
3,3
|
4
|
Мощность
|
N
|
Вт
|
4000
|
3960
|
3860
|
3765
|
3727
|
5
|
Передаточное
отношение
|
Ui
|
2.5
|
3.35
|
3.15
|
1.3. Результаты кинематических расчетов на ЭВМ
Кинематический расчет привода механизма в системе “Кинематик”
Расчет провел Blinchikov Alexey
Таблица исходных данных
Тип редуктора – 4. Цилиндрический двухступенчатый соосный.
Мощность на тихоходном валу конвейера Pt=2.70(кВт)
Частота вращения тихоходного вала конвейера nt=31.00(1/мин)
Наличие дополнительных передач на входе редуктора – Есть
Передаточное отношение дополнительной передачи на входе редуктора Uвх=3.00
КПД дополнительной передачи на входе редуктора Nвх=0.95
Наличие дополнительных передач на выходе редуктора - Нет
Число ступеней редуктора – 2
Передаточное отношение 1-й ступени U[1]=3.00
КПД 1-й ступени N[1]=0.96
Передаточное отношение 2-й ступени U[2]=3.00
КПД 2-й ступени N[2]=0.97
Таблица расчетных значений
Приблизительное общее передаточное отношение привода Usп=27.00
Общий КПД привода Ns=0.86
Приблизительная мощность двигателя Рдвп=3.15(кВт)
Приблизительная частота вращения вала электродвигателя ndп=837(об/мин)
Тип электродвигателя - 4А112МВ6У3
Мощность электродвигателя Рдв=4(кВт)
Частота вращения электродвигателя nдв=960(об/мин)
Отношение Тпуск/Тном=2.0
Отношение Тмах/Тном=2.5
Масса электродвигателя Мдв=56.0
Разбиение передаточного отношения редуктора по ступеням
Передаточное отношение быстроходной ступени редуктора Uб=3.55
Передаточное отношение тихоходной ступени редуктора Uт=3.15
Частота вращения быстроходного вала привода 960.00
Крутящий момент на быстроходном валу привода 39.79
Частота вращения быстроходного вала редуктора 401.60
Крутящий момент на быстроходном валу редуктора 96.10
Частота вращения 1-ого промежуточного вала редуктора 115.86
Крутящий момент на 1-ом промежуточном валу редуктора 331.73
Частота вращения тихоходного вала редуктора 30.00
Крутящий момент на тихоходном валу редуктора 2801.65
Кинематический расчет привода механизма в системе “Восход”
Расчет провел Blinchikov Alexey
*****************************************************************************
Исходные данные
*****************************************************************************
Цилиндрический горизонтальный соосный редуктор
Мощность тихоходного вала привода, кВт 2.70
Частота вращения тихоходного вала привода, с-1
31.0
Общее передаточное число привода 30.9
Передаточное число ременной передачи 2.50
*****************************************************************************
Результаты расчета
*****************************************************************************
Тип выбранного электродвигателя 4А112МВ6УЗ
Мощность выбранного электродвигателя, кВт 4.00
Частота вращения электродвигателя.с-1
960.00
Действительное передаточное число редуктора 12.06
Передаточное число быстроходной ступени 4.00
Передаточное число тихоходной ступени 3.15
Передаточное число ременной передачи 2.50
*****************************************************************************
Частота вращения быстроходного вала привода 960.00
Крутящий момент на быстроходном валу привода 39.87
Частота вращения быстроходного вала редуктора 400.86
Крутящий момент на быстроходном валу редуктора 95.50
Частота вращения 1-ого промежуточного вала редуктора 114.73
Крутящий момент на 1-ом промежуточном валу редуктора 332.42
Частота вращения тихоходного вала редуктора 30.30
Крутящий момент на тихоходном валу редуктора 2798.6
1.4. Сравнительный анализ полученных результатов
Таблица 1.4.1
Сравнительный анализ результатов
№
|
Параметр
|
Обозначение
|
ВАЛЫ
|
1 |
2 |
3 |
4 |
Расчет |
Расчет |
Расчет |
Расчет |
Ручной |
В системе
«Кинематик»
|
В системе
«Восход»
|
Ручной |
В системе
«Кинематик»
|
В системе
«Восход»
|
Ручной |
В системе
«Кинематик»
|
В системе
«Восход»
|
Ручной |
В системе
«Кинематик»
|
В системе
«Восход»
|
1
|
Крутящий момент, Н.м |
Т
|
40
|
39.79
|
39.87
|
95
|
96.1
|
95.5
|
332
|
331.73
|
332.42
|
2800
|
2801.7
|
2798.6
|
2
|
Частота вращения, об/мин |
n
|
960
|
401
|
401.6
|
400.86
|
115
|
115.9
|
114.73
|
31
|
30
|
30.3
|
3
|
Угловая скорость, 1/с |
v
|
100.5
|
42
|
12
|
3.3
|
4 |
Мощность, Вт |
N
|
4000
|
3960
|
3860
|
3765
|
5 |
Передаточное отношение |
U
|
2.5
|
3.58
|
3.55
|
4
|
3.58
|
3.55
|
4
|
3.35
|
3.15
|
3.15
|
Анализ: результаты расчета в системе «Восход» и «Кинематик» незначительно отличаются от ручного расчета. Отличия в результатах связаны с погрешностями вычислений и с применения эмпирических формул. Погрешность в расчетах составила меньше 4%.
2. Расчет и проектирование зубчатого редуктора
2.1 Выбор материалов зубчатых колес и определение допустимых напряжений
Так как к габариту и весу не предъявляются особые требования, то для колес и шестерен выбираем наиболее распространенную сталь 40Х. Термообработка: для колес обоих
ступеней и шестерни первой ступени назначаем улучшение, а зубья шестерни
тихоходной ступени закаляем токами высокой частоты.
Твердость колес обеих ступеней и шестерни первой ступени: 240НВ, а твердость зубьев
шестерни второй ступени 50HRC.
Допускаемые контактные напряжения по таблице 8.9 (2) для колес обеих ступеней и
шестерни первой ступени предел контактной выносливости:
(2.1)
Для шестерни второй ступени:
(2.2)
Коэффициент безопасности по таблице 8.9 (2) :
для первой ступени Sн = 1,1;
для второй ступени Sн = 1,2.
Число циклов напряжений для колеса второй ступени определяется по формуле:
(2.3)
где с = 1 – число зацеплений зуба за один оборот колеса;
- отношение соответствующего момента цикла к максимальному из моментов,
берем из графика нагрузки;
ti
– срок службы передачи, находим из формулы:
(2.4)
где Ч =Ксут
. 24 = 7 – количество часов работы в день;
Д – количество дней в году;
Р – количество лет работы передачи.
Подставляя получаем:
ti
= 7 * 182,5 * 5 =6387,5 (ч).
ni
=const = 31 (об/мин) – частота оборотов вала второй ступени;
Подставим значения в формулу (2.3):

По графику рис. 8.40 (2) базовое число циклов Nно
= 1.1 . 107
Находим коэффициент долговечности:
 > 1 (2.5)
Подставляя численные значения получим:
Принимаем Кне
= 1, т.к. Кне

Так как все другие колеса вращаются быстрее, то аналогичным расчетом и для них
NHE
>NHO
. При этом для всех колес передачи KHE
=1.
Допустимые контактные напряжения для второй ступени определяем по материалу колеса, как более слабому, по формуле:
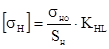 (2.6)
Для колеса первой ступени по той же формуле:
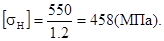
Для шестерни первой ступени допускаемое контактное напряжение такие же как и у ко
леса . Принимаем для первой ступени 
Допускаемые напряжения изгиба.
По таблице 8.9 для колес обоих ступеней и для шестерни первой ступени по формуле
находим предел выносливости зубьев:
(2.7)
Для шестерни второй тихоходной ступени .
Эквивалентное число циклов определяем по аналогичной формуле (2.3): NFE
= 4655995
Определяем коэффициент долговечности
(2.8)
Рекомендуется принимать NFO
= 4 . 106
для всех сталей.
Подставляя значения получаем:
< 1
По рекомендации выбираем KFL
=1.
В нашем случае нагрузка односторонняя, поэтому коэффициент, учитывающий влияние
двухстороннего приложения нагрузки KF
L
применяем равным 1.
По таблице 8.9 (2) принимаем коэффициент безопасности SF
= 1.75.
Находим допустимые напряжения изгиба по формуле:
(2.9)
Для колес обеих ступеней и для шестерни первой ступени подставляя значения в формулу(2.9) получим:
.
Для шестерни тихоходной ступени:
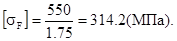
По таблице 8.9(2) находим предельные контактные напряжения:
для колес обоих ступеней и шестерни первой ступени:
;
для шестерни второй ступени:
.
Предельные напряжения изгиба для колес обеих ступеней и шестерни первой ступени:

Для шестерни второй ступени:
.
Значения допустимых предельных напряжений заносим в таблицу 2.1.1
Таблица 2.1.1
Допускаемые и предельные напряжения
Ступень |
Параметр |
Мпа |
Мпа |
МПа |
МПа |
1 |
500 |
247 |
1540 |
657 |
2 |
458 |
247 |
1540 |
657 |
2.2 Проектировочный расчет зубчатых передач
В начале рассматриваем вторую прямозубую пару как более нагруженную и в основном
определяющую габариты редуктора.
Из таблицы 8.4(2) для симметричного колеса, относительно межосевого расстояния
. Находим коэффициент ширины шестерни относительно диаметра по формуле:
, (2.10)
где U2
– передаточное отношение второй ступени, по рекомендации (рис. 8.38) принимаем
U2
' = 3.15, тогда:
.
Найденное значение согласно таблице 8.4(2). По графику рис.8.15(2)
находим коэффициент концентрации нагрузки .
Принимая, значения модуля упругости для материала колес Е1
=2,1*105
МПа и значения
модуля упругости для материала шестерен Е2
=7,1*105
Мпа, находим приведенный модуль упругости по формуле:
(2.11)
Находим предварительное межосевое расстояние по формуле:
(2.12)
где Т3
= 2800 (Н*м) - крутящий момент на выходном валу (таблица 1).
Подставляя значения формулу, получим :

Округляя по ряду Ra 40 до а2
=355 мм, находим предварительную ширину колеса по
формуле:
= 0,4*355 = 102(мм) (2.13)
По таблице 8.5 (2) принимаем и находим значение модуля по формуле:
 (2.14)
По таблице 8.1 (2) назначаем mn
= 2,5 (мм),
Определяем суммарное число зубьев:
 (2.15)
Число зубьев шестерни:
 (2.16)
Принимаем Z1
= 68 > Zmin
= 17.
Число зубьев колеса определяем по формуле:
= 284 – 68 = 216 (2.17)
Фактическое передаточное число:
 (2.18)
При этом для первой ступени
. (2.19)
Делительные диаметры шестерни и колеса:
d1
= Z1
mn
=62 . 2,5 = 155мм; (2.20)
d2
= Z2
mn
=222 . 2,5 = 555мм (2.21)
Рассчитываем первую косозубую ступень.
В виду соосности редуктора а1
= а2
= 355мм. Находим диаметры шестерни и колеса по следующим формулам:
 (2.22)
 (2.23)
Находим по формуле:
(2.24)
где Кнв
= 1 – коэффициент концентрации нагрузки.
Т'2
–крутящий момент на промежуточном валу
Подставляя значения в 2.24 получаем:

Находим ширину колеса по формуле
 (2.26)
При этом , что не превышает допустимых максимальных значений
(см. табл.8.4).
По таблице 8.5 (2) принимаем и находим модуль колеса по формуле:
 (2.27)
По таблице 8.1(2) и формуле 8.15(2) назначаем mn
= 1.5 мм.
Выполняя рекомендации ß8.7 (2) принимаем коэффициент осевого перекрытия 
и находим угол наклона зубьев по формуле
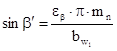 (2.28)
Отсюда в рекомендуемых пределах (см. § 8.7 (2)).
Находим число зубьев шестерни и колеса:
 (2.29)
 (2.29`)
Фактическое передаточное число первой ступени находим как
(2.30)
Фактическое передаточное отношение редуктора:
U = U1
* U2
= 3,35 * 3.58 = 11,99 (2.31)
Отклонение от заданного , где допустимое 
Уточняем значение по межосевому расстоянию:
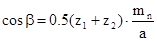 (2.32)
Отсюда 
2.3 Проектировочный расчет валов
Этот расчет сводится к определению диаметров валов привода исходя из полученных
значений крутящих моментов.
Расчет ведем по формуле:
, (2.33)
где Т- значения крутящих моментов
- допустимое касательное напряжение. Принимаем , тогда получим
следующие значения:
Вал двигателя:

Входной вал редуктора:

Промежуточный вал:

Выходной вал:

Приводной вал:
.
2.4.
Результаты
расчетов напряжений, геометрических параметров с использованием автоматизированных систем расчета «Восход» и «АРМ»
Расчет в системе «Восход»
Расчет зубчатых передач
2-я
ступень
И С Х О Д Н Ы Е Д А Н Н Ы Е
Цилиндрическая прямозубая передача с внешним эвольвентным зацеплением по ГОСТ 16532-70
Крутящий момент на колесе, Н*М 2800
Частота вращения колеса,1/мин 31.00
Требуемое передаточное число 3.15
Ресурс передачи, час 6358
Коэффициент кратности максимального момента 2.5
Твердость шестерни, HRC 50.0
Твердость колеса, HRC 24.0
Предел текучести материала шестерни, МПа 800
Предел текучести материала колеса, МПа 550
Коэффициент ширины колеса 0.250
Количество колес в зацеплении с шестерней 1
Количество колес в зацеплении с колесом 1
Расположение колеса относительно опор симметричное
Постоянная нагрузка, нереверсивная передача, закрытая передача.
Проектно-проверочный расчет.
Р Е З У Л Ь Т А Т Ы Р А С Ч Е Т А
ДОПУСКАЕМЫЕ НАПРЯЖЕНИЯ:
контактные 1392МПа изгибные для шестерни 441 МПа
изгибные для колеса 441 МПа
ДОПУСКАЕМЫЕ НАПРЯЖЕНИЯ ПРИ ПЕРЕГРУЗКЕ:
контактные 2320МПа изгибные для шестерни 1450МПа
изгибные для колеса 1450МПа
РАБОЧИЕ НАПРЯЖЕНИЯ:
контактные 1146МПа изгибные для шестерни 733 МПа
изгибные для колеса 761 МПа
РАБОЧИЕ НАПРЯЖЕНИЯ ПРИ ПЕРЕГРУЗКЕ:
максимальные контактные напряжения 1813МПа
максимальные изгибные напряжения шестерни 1833МПа
максимальные изгибные напряжения колеса 1901МПа
Г Е О М Е Т Р И Я П Е Р Е Д А Ч И
Модуль 2.5000мм
Число зубьев шестерни 68
Число зубьев колеса 216
Действительное передаточное число 3.35
Расчетная ширина колес 102.000мм
Делительный диаметр шестерни 155.000мм
Делительный диаметр колеса 555.00мм
Диаметр вершин зубьев шестерни 159.000мм
Диаметр впадин зубьев шестерни 150.000мм
Диаметр вершин зубьев колеса 559.00мм
Диаметр впадин зубьев колеса 550.00мм
Межосевое расстояние 355.00мм
Ширина зубчатого венца шестерни 104.000мм
Ширина зубчатого венца колеса 102.000мм
Расчетная степень точности 9
Расчет зубчатых передач
1-я
ступень
И С Х О Д Н Ы Е Д А Н Н Ы Е
Цилиндрическая косозубая передача с внешним эвольвентным зацеплением по ГОСТ 16632-70
Крутящий момент на колесе, Н*М 332.00
Частота вращения колеса,1/мин 115.00
Требуемое передаточное число 3.55
Ресурс передачи, час 6358
Коэффициент кратности максимального момента 2.5
Твердость шестерни, HRC 26.0
Твердость колеса, HRC 24.0
Предел текучести материала шестерни, МПа 560
Предел текучести материала колеса, МПа 550
Коэффициент ширины колеса 0.250
Количество колес в зацеплении с шестерней 1
Количество колес в зацеплении с колесом 1
Расположение колеса относительно опор несимметричное
Постоянная нагрузка, нереверсивная передача, закрытая передача.
Проектно-проверочный расчет.
Р Е З У Л Ь Т А Т Ы Р А С Ч Е Т А
ДОПУСКАЕМЫЕ НАПРЯЖЕНИЯ:
контактные 1125МПа изгибные для шестерни 454 МПа
изгибные для колеса 454 МПа
ДОПУСКАЕМЫЕ НАПРЯЖЕНИЯ ПРИ ПЕРЕГРУЗКЕ:
контактные 2320МПа изгибные для шестерни 1450МПа
изгибные для колеса 1450МПа
РАБОЧИЕ НАПРЯЖЕНИЯ:
контактные 986 МПа изгибные для шестерни 638 МПа
изгибные для колеса 665 МПа
РАБОЧИЕ НАПРЯЖЕНИЯ ПРИ ПЕРЕГРУЗКЕ:
максимальные контактные напряжения 1559МПа
максимальные изгибные напряжения шестерни 1594МПа
максимальные изгибные напряжения колеса 1662МПа
Г Е О М Е Т Р И Я П Е Р Е Д А Ч И
Модуль 1.500мм
Число зубьев шестерни 102
Число зубьев колеса 342
Действительное передаточное число 3.58
Угол наклона зуба 14.5град
Расчетная ширина колес 32.000мм
Делительный диаметр шестерни 163.000мм
Делительный диаметр колеса 547.000мм
Диаметр вершин зубьев шестерни 166.000мм
Диаметр впадин зубьев шестерни 160.000мм
Диаметр вершин зубьев колеса 550.000мм
Диаметр впадин зубьев колеса 544.000мм
Межосевое расстояние 355.00мм
Ширина зубчатого венца шестерни 34.000мм
Ширина зубчатого венца колеса 32.000мм
Расчетная степень точности 9
Расчет в системе «АРМ»
2.3 Эскизная компоновка редуктора
1) Проведем линии осей валов, изображаем контуры шестерни и колеса первой ступени.
В предыдущем пункте 2.4 рассчитан диаметр входного вала d1
=22.3 мм. В нашем случае
расчетное значение d1
меньше посадочного диаметра муфты равного 32мм. Поэтому
принимаем d1
=32мм. Принимаем диаметр вала под уплотнение d2
=35мм. При этом высота заплечика, равна 1,5 мм, больше фаски у отверстия ступицы муфты, равной 1 мм. По рекомендации принимаем диаметр вала под подшипник d3
=d2
=35мм.
В соответствии с рекомендациями выбираем третью схему опор. Учитывая, что от подшипников цилиндрических зубчатых колес не требуется повышенная жесткость, а осевыенагрузки относительно не велики, намечаем для обеих опор вала радиальные однорядныешарикоподшипники. Предварительно принимаем шарикоподшипники средней узкой серии №307: d =35мм, D=80мм, В=21мм.
По таблице 8.3(1) d4
=42мм. Сравнивая d4
c диаметром шестерни первой ступени
d=163мм и учитывая рекомендации, изготавливаем шестерни за одно целое с валом.
Находим наружный диаметр шестерни по формуле:
da
= d+2mn
= 163+2.1.5=166мм (2.34)
Диаметр окружности впадин зубьев находим по формуле
df
= d -2.5mn
= 163 – 2.5*1.5=159.25мм. (2.35)
2) Определяем длины участков входного вала.
Зазор между колесом и внутренней стенкой корпуса по таблице 10.4(1):
(2.36)
где - толщина стенки основания корпуса, находится по формуле:
 (2.37)
Принимаем , подставляя в (2.36)

Принимаем 
Рассчитываем размер гнезда подшипника
, (2.38)
где к1
– ширина фланца разъема корпуса, находится по формуле
(2.39)
где d'2
–диаметр стяжных болтов, находим по формуле:
(2.40)
где d'1
–диаметр фундаментных болтов, определяется по формуле:
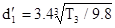 (2.41)
Принимаем болты М16, значение подставляем в формулу (2.40):

По ГОСТ 7808 – 76 принимаем болты М12, при этом:
,
L = 6,5 + 36 + 3 = 45,5 мм.
Принимаем накладные крышки гнезд подшипников. Толщина фланца крышки h1
=12мм. Толщина прокладок Между торцом муфты и крышкой подшипника оставляем зазор h = 8мм. Длина L2
шейки вала с номинальным диаметром d = 35мм, отодвигая подшипник от стенки на :
 (2.42)
Длину вала L1
с d = 32мм принимаем равной длине ступицы муфты:
= 138 – 80 – 3 = 55мм (2.43)
Длину участка d4
определяем из чертежа. Правый подшипник входного вала по условиям унификации принимаем таким же как и левый, и устанавливаем симметрично
относительно шестерни.
3) Конструируем выходной вал с опорами и колесом.
Ранее найден диаметр d7
= 67мм. По расчетам приведенным ниже, принята зубчатая
муфта d5
= 45мм. Учитывая фаску в отверстии муфты 1,5мм, принимаем диаметр вала
под уплотнение и подшипник d6
=65мм.
Правый и левый подшипники принимаем одинаковыми. Намечаем шарикоподшипники
средней узкой серии № 313: d = 65мм, D = 140мм, В = 33мм. По таблице 8.3 (1) d8
= 74мм.
Расстояние между подшипниками в средней опоре 3
=5мм и зависит от способа крепления подшипников на валах. Ширину буртика диаметром d8
принимаем . Длина шейки d7
определяется длиной l ступицы колеса. Учитывая рекомендации, назначаем l = b2
= 102мм, где b2
– ширина колеса. Причем отношение находится в рекомендуемых пределах. Центровка колеса на валу обеспечивается прессовой посадкой и прижимом ступицы к буртику вала при запрессовке.
Размер l проверяем по условию передачи крутящего момента.
Назначаем посадку и проверяем возможность передачи момента только за счет по
садки. По таблице 3.7 (4) минимальный натяг посадки = 31мкм.
Давление на поверхность посадки определяем по формуле:
(2.44)
где С1
=0.7;
;
u = 1.2(RZ1
– RZ2
) = 1.2(6+10) = 19мкм;
(2.45)
Тогда подставляя в 2.44:
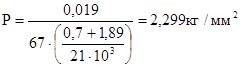
Крутящий момент, который может передать посадка,

Запас сцепления:
(2.46)
Усиливаем прессовое соединение шпонкой. По таблице 2.29(1) выбираем шпонку
b = 16мм, h = 10мм. Рабочая длина шпонки:
, (2.47)
где принято [sсм
] = 1500 кг/см2
с учетом прессовой посадки. Учитывая закругления
концов шпонки, получаем:
l = lp
+ b = 28.42 + 16 = 44.42мм (2.48)
По таблице 2.29(1) назначаем l = 45мм. Отмечаем, что длина ступицы достаточна для
размещения шпонки, так как b2
= 102мм.
Далее, по аналогии с входным валом определяем все недостающие размеры, учитывая,
что L = 45мм.
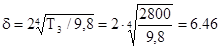
Принимаем d = 6.46 мм.
Δ ≥ 0,6d = 0,6 ∙ 6.46 = 3,88 мм
мм,
, 
h1
= 13мм, Δ1
= 1,5мм, h = 8мм, Δ2
= 4,5 мм
L2
= L + Δ1
+ Δ + h1
+ h = 45.5 + 3.6 + 1.5 + 13 + 8 = 71.6
L1
= L1м
– Lм
– 3 = 115 – 55 – 3 = 57 мм.
4) Рассчитываем промежуточный вал
Ранее был найден диаметр под колесо d10
= 33.7 мм, d9
= 22 мм. Намечаем шарикоподшипник
средней узкой серии № 305: d=25 мм, D=62 мм, В = 17 мм.
Принимаем d9
= 25 мм, d10
= 30 мм. Диаметр d11
принимаем равным диаметру вершин
второй ступени:
d11
= da
= dw
1
+ 2mn
= 155 + 2 ∙ 2.5 = 160 мм (2.49)
Так как размер L остаётся одинаковым, то размеры d,D, остаются теми же.
Длина размера посадки колеса d10
принимаемb2
= 17мм. Рассчитываем размер l по условию передачи крутящего момента аналогично выходному валу.
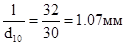
Назначаем посадку .
dр
= 0,012мм, С1
= 0,7, С2
= 2,19.
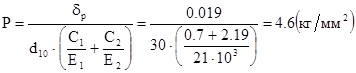
(кг/м2
)
Усиливаем шпонкой b = 12, h = 8

Назначаем l = lp
+ b = 15,4 + 12 = 27.4 мм, принимаем l = 28 мм
Длина ступицы l = 32мм, что достаточно для размещения шпонки.
Таблица 2.4.1
Геометрические размеры зубчатой передачи
Ступень |
Параметр |
mn
мм
|
Z1
|
Z2
|
d1
мм
|
d2
мм
|

мм
|
bw
мм
|

град
|
1 |
1.5 |
102 |
342 |
163 |
547 |
355 |
32 |
 |
2 |
2,5 |
68 |
216 |
155 |
555 |
355 |
102 |
 |
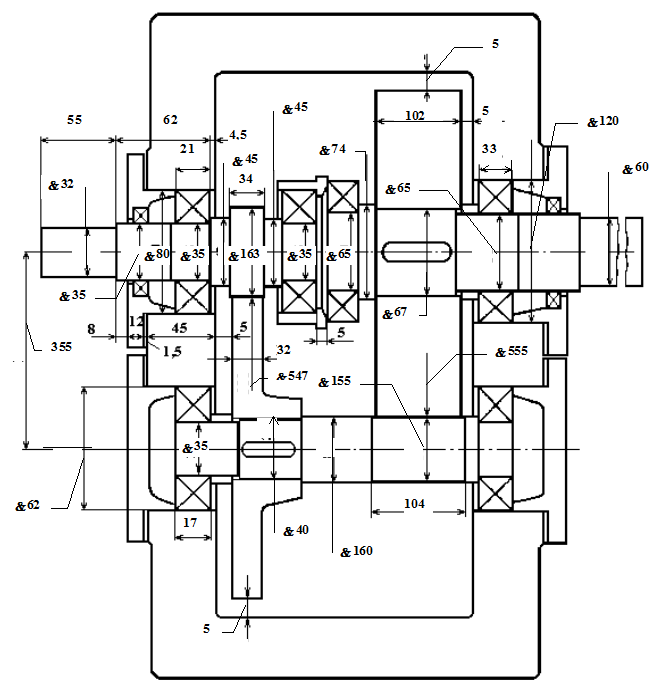
Рисунок 2.3.1. - Эскизная компоновка редуктора
2.5 Проверочный расчет зубчатых передач
Проверочный расчет на усталость по наименьшим напряжениям для второй ступени.
Находим окружную скорость по формуле:
 (2.34)
По таблице 8.2(2) назначаем 9-10 степень точности. По таблице 8.3(2) находим коэффициент динамической нагрузки . Ранее был найден . Находим коэффициент расчетной нагрузки:
= 1,09 . 1,04 = 1,133 (2.35)
Принимая , находим контактные напряжения по формуле:
=
(2.36)
Выполняем проверочный расчет по напряжениям изгиба.
По графику рис.8.20(2) при значении коэффициента смешения Х = 0 находим значение коэффициента формы зуба:
для шестерни - YF1
= 3.70
для колеса - YF2
= 3.75.
Находим отношение :
;
.
Расчет выполняем по тому колесу пары у которого отношение меньшее. В нашем
случае расчет ведется по колесу. Находим по графику рис.8.15(2) коэффициент концентрации нагрузки . По таблице 8.3(2) находим коэффициент динамической нагрузки . Тогда коэффициент расчетной нагрузки :
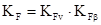 (2.37)
Находим окружную силу по формуле:
 (2.38)
Находим напряжения изгиба:
 (2.39)
Выполняем проверочный расчет на заданную нагрузку (допускаемые напряжения). Определяем максимальные контактные напряжения и напряжения изгиба:
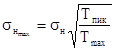 (2.40)
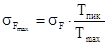 (2.41)
Выполняем проверочный расчет на усталость по контактным напряжениям для первой ступени. Определяем окружную скорость:
 (2.42)
По таблице 8.2(2) назначаем 8-ю степень точности. По таблице 8.3(2) находим коэффициент
динамической нагрузки Кнv
= 1,05, по рис. 8.15 . Находим коэффициент расчетной
нагрузки по формуле (2.34):

По таблице 8.7 находим дополнительный коэффициент . Находим коэффициент
торцевого перекрытия:
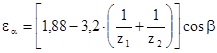 (2.43)
Находится в рекомендуемых пределах .
Находим коэффициент повышения прочности косозубых передач:
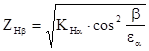 (2.44)
.При находим контактное напряжение по формуле:
=
(2.45)
Выполняем проверочный расчет по напряжениям изгиба.
Находим число зубьев эквивалентной прямозубой шестерни и колес:
(2.46)
(2.46`)
По графику рис. 8.20(2) при Х = 0 находим YF1
= 3.69, YF2
=3.74.Находим отношения [
Для шестерни: 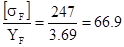
Для колеса: .
Расчет выполняем по наименьшему значению, т.е. по колесу.
По таблице 8.7 (2) коэффициент не равномерности нагрузки . Коэффициент учитывающий повышение изгибной прочности определяется по формуле:
(2.47)
Находим коэффициент повышения прочности:
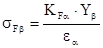 (2.48)
По графику рис. 8.15(2) , по таблице 8.3 КFV
= 1.11, тогда коэффициент расчетной
нагрузки определяем как:

Находим окружную силу по формуле (2.38):
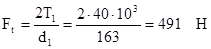
Находим напряжение изгиба по формуле:
 (2.49)
Заносим геометрические параметры зубчатой передачи в таблицу 2.4.1
2.6 Расчет (выбор) подшипников и уплотнений
Проверяем подшипники предварительно назначенные в пункте 2.3.
1) Подшипники выходного вала.
Были назначены радиальные, однорядные, шарикоподшипники средней узкой серии №313 с параметрами: динамическая грузоподъемность С = 72400Н, статическая С0
= 56700Н, L =20000ч, t < 100°C.
Находим реакции опор, для определения нагружения подшипника:
(2.50)
(2.51)
(2.52)
Знак ²-² означает, что реакция В2
направлена в противоположную сторону.
(2.53)
Для левой опоры:
(2.54)
Правая опора:
(2.55)
Правый подшипник нагружен больше, поэтому выполняем только его расчет.
Отношение , находим по таблице 16.5(2) значения коэффициентов радиальной и осевой нагрузок: x = 1, y = 0. По рекомендации к формуле 16.29(2) принимаем коэффициент безопасности, учитывающий характер нагрузки Кб
= 1.4, температурный коэффициентКt
=1, V коэффициент вращения, зависящий от того, какое кольцо вращается V = 1.
Находим постоянную радиальную нагрузку по формуле
 (2.56)
По таблице 8.10(2) для 3 режима нагружения находим коэффициент Кне
= 0,18. Находим эквивалентную долговечность по формуле:
 (2.57)
Находим ресурс работы:
(2.58)
По таблице 16.3(2) находим значение коэффициента надежности а1
= 1, обобщенный коэффициент совместного влияния качества металла и условий эксплуатации а2
= 0,8.
Динамическая грузоподъемность:
(2.59)
Условие С < Сг
выполняется, но паспортное значение С превышает потребное С0
на 30% < 60%, что допустимо.
Проверяем подшипник по статической грузоподъемности:
x0
= 0.6, y0
= 0.5, тогда
(2.60)
Условие Р0 [С0 соблюдается.
2) Подшипники входного вала.
Проверку проводим аналогично проверке выходного вала.
Используется подшипник №307. Параметры: С = 26200Н, С0
= 17900Н, L = 20000ч.
Реакции опор:




Для опоры А и В:
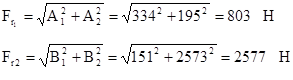
Правый подшипник нагружен больше.
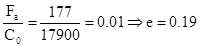
V = 1, тогда:
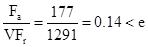
При этом: x = 1, y = 0, Kб
= 1,4, Kt
= 1, Kне
= 0,18.
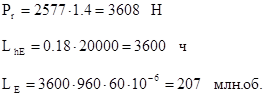
а1
= 1, а2
= 0,8

Разница составляет 12%, что допустимо.
Находим при статической нагрузке: хо
= 0,6, уо
= 0,5

Условие Р0 [С0 соблюдается.
3) Подшипники промежуточного вала
Используется подшипник №305. Параметры:С = 17600Н, С0
=11600Н, L=20000ч.
Реакции опор А и В:

Н

Для опор А и В:
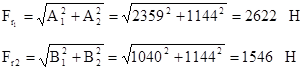
Левый подшипник нагружен больше.
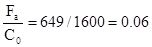
Принимаем x = 1, y = 0, Кб
= 1.4, Кt
= 1, Кне
= 0,18.
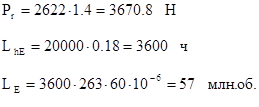
а1
= 1, а2
= 0,8

Разница составляет 57%, что допустимо
x0
= 0.6, y0
= 0.5
Условие Р0 [С0 соблюдается.
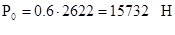
Значения расчета заносим в таблицу 2.6.1
Таблица 2.6.1
Паспортные и расчетные значения нагрузок подшипников
Подшипники |
Параметр |
Сг
, Н |
Сп
, Н |
С0
, Н |
Р0
, Н |
Входной вал
№307
|
26200 |
18089 |
17900 |
515 |
Промежуточный вал
№305
|
17600 |
7625,6 |
11600 |
956 |
Выходной вал
№313
|
72400 |
51844 |
56700 |
8493 |
2.7 Конструирование и проверочные расчеты валов на прочность, жесткость и колебания
1) Рассчитываем выходной вал.
Для выходного вала рассчитаны следующие величины: Т3
=2800Нм, n3
= 31 об/мин,
b2
= 102мм, sв
=850мПа, [t] = 18мПа, sт
= 550мПа.
Определяем силы в зацеплении.
Диаметр в месте посадки колеса d = 53мм. Допускаемая радиальная нагрузка при использовании редуктора для общего назначения:
 (2.61)
Определяем соответственно окружную, осевую и радиальную силы в зацеплении по формулам:
 (2.62)
 (2.63)
 (2.64)
Из компоновочной схемы находим размеры пролетов: а = 66 мм, b = 70 мм, с = 131 мм. Вычерчиваем расчетную схему вала (рис. 2.1) с соответствующими размерами и строим эпюру от приложенных сил.
Определяем моменты сил по формулам.
Момент от радиальной силы:
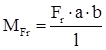 (2.65)
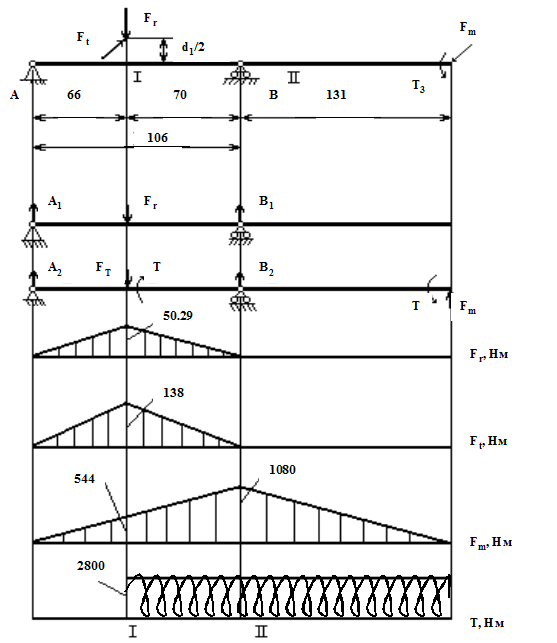
Рисунок 2.7.1.-Эпюра нагрузки выходного вала
Моменты от окружной силы:
 (2.66)
Моменты от силы муфты:
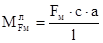 (2.67)
 (2.68)
Просчитываем два предполагаемых опасных сечения: 1-1 – ослабленное шпоночным пазом и сечение 2-2 – ослабленное галтелью.
Для 1-1 изгибающий момент:
 (2.69)
Для 2-2 изгибающий момент М »Fм
× с = 8242 × 0,131 =1080 Нм,
Крутящий момент Т3
= 2800 Нм.
Больше напряженно второе сечение.
Расчет на прочность.
Предел выносливости.
= 0,4 × 850 = 340 МПа (2.70)
= 0,2 × 850 = 170 МПА (2.71)
Амплитуды переменных составляющих циклов напряжений.
Напряжения изгиба:
 (2.72)
Напряжение кручения:
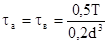 (2.73)
Коэффициенты, корректирующие влияние постоянной составляющей цикла напряжений на сопротивление усталости ys
= 0,15 и yt
= 0,1. Находим по таблице 15.1(2) эффективные коэффициенты концентрации напряжений при изгибе и кручении ks
= 1,62 и kt
= 1,3. По рис.15.5 (2) находим значения масштабного фактора kd
= 0.7 , по рис.15.6 (2) находим фактор шероховатости kF
= 1. Находим запас сопротивления усталости по изгибу и кручению, по следующим формулам:
(2.74)
(2.75)
При совместном действии напряжений кручения и изгиба запас сопротивления усталости определяют по формуле:
 (2.76)
.
Расчет на жесткость.
По условиям работы зубчатого зацепления опасным является прогиб вала под шестерней. Минимальный диаметр вала d = 45 мм.
Определяем момент инерции сечения по формуле:
 (2.77)
Прогиб в вертикальной плоскости от силы Fr
:
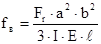 (2.78)
Прогиб в горизонтальной плоскости от силы Ft
и Fм
:
=
(2.79)
Суммарный прогиб:
 (2.80)
Допускаемый прогиб [f] » 0,01m = 0,01 × 2 = 0,02<0.00486 мм.
Необходимое условие работы вала - f[[f] выполняется.
Расчет на критические колебания
 (2.81)
Вал работает в до критической области.
2) Рассчитываем входной вал.
Расчет производим аналогично расчету выходного вала.
Параметры: Т2
= 95 Нм, n2
= 401 об/мин, d2
= 163 мм, b1
= 34 мм, sв
= 850 МПа, [t]=18МПа,sт
= 550МПа.
Определяем силы:

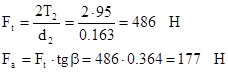

Размеры пролетов: а = 27мм, b = 32,5мм, с = 106,5мм, l = 59,5мм.
Определяем моменты сил (рис. 2.2):







Сечение 1-1.


Сечение 2-2.


Опасное сечение 2-2.
Расчет на прочность.




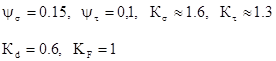
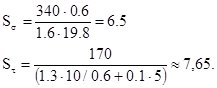

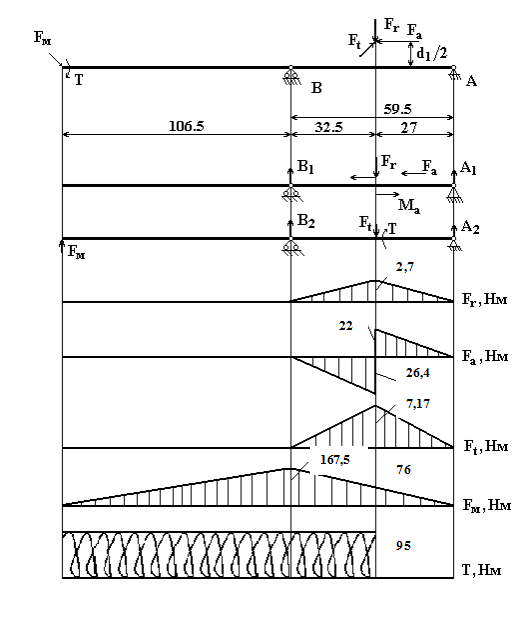
Рисунок 2.7.2.-Эпюра нагружения входного вала
Расчет на жесткость.
Е = 2,1 × 105
МПа, d = 32мм.
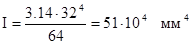
Прогиб в вертикальной плоскости:

Прогиб в горизонтальной плоскости:

Суммарный прогиб:

Допускаемый прогиб вала [f] = 0,015 мм.
Необходимое условие работы вала - f[[f] выполняется.
Расчет на критические колебания.

Вал работает в до критической области.
3) Рассчитываем промежуточный вал.
Параметры Т¢2
= 332 Нм, d =25 мм, d1
2
= 301 мм, d2
2
= 280 мм, sв
= 850 МПа, [t] = 18 МПа,
sт
= 550 МПа.
Силы определяем для двух сечений (рис. 2.3):
1-1:
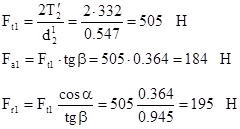
2-2:
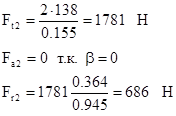
Размеры пролетов а = 35мм, b = 80мм, с = 55мм, l = 170мм.
Определяем моменты сил.
1-1:
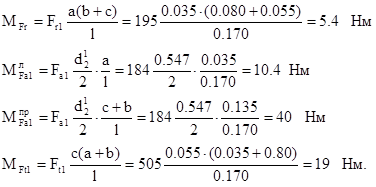
2-2:
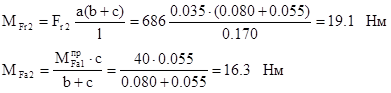

Суммарные моменты:
1-1:
,

2-2:


Опасным является сечение 1-1.
Расчет на прочность.
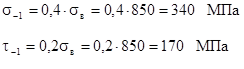
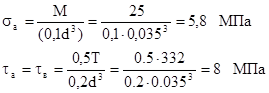

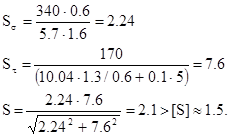
Расчет на жесткость.
Е = 2,1 × 105
МПа, d = 35мм.
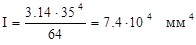


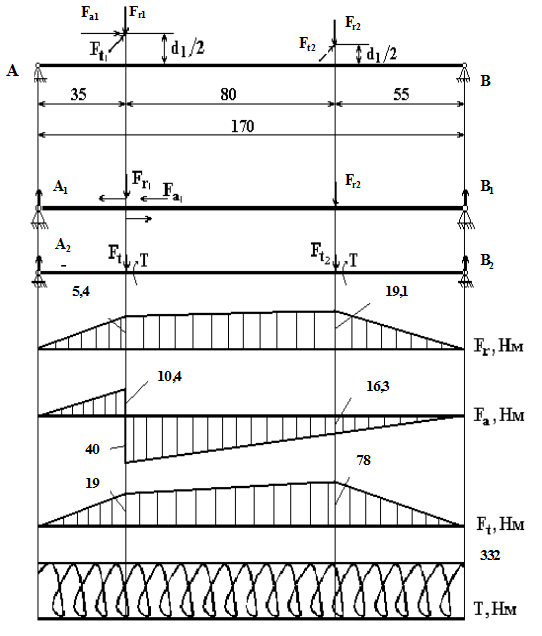
Рисунок 2.7.3.-Эпюра нагружения промежуточного вала

Допускаемый прогиб [f] = 0,02 мм.
Необходимое условие работы вала - f[[f] выполняется.
Расчет на критические колебания.

Значения прогибов, запасов сопротивления усталости и критических скоростей заносим в таблицу 2.6.1
Таблица 2.7.1
Значения запасов сопротивления усталости, прогибов и критических скоростей.
Вал |
Параметр |
S |
f, м |
n, об/мин |
Входной |
4,95 |
3×10-4
|
999950 |
Промежуточный |
2,1 |
1,24×10-12
|
2,4×1014
|
Выходной |
3 |
4,86×10-3
|
61728,4 |
2.8 Расчет и конструирование корпуса и крепежных деталей
Основные размеры редуктора рассчитаны в п.2.3. Рассчитываем дополнительные размеры корпуса по следующим формулам и зависимостям.
Высота ребра корпуса Н принимаем равной 5мм. Толщина стенки у основания ребер l = 5
мм, литейный уклон 2°.Диаметр стяжных болтов Принимаем d3
= 12мм. Расстояние между стяжными болтами принимаем по таблице 10.4 (1) l3
= 120мм.
Фланцы разъема корпуса:
Толщина: S = 1.5d3
= 1.5×12=18мм
S1
= 1.3d3
= 1.3×12 = 15.6мм
Принимаем S1
равным 16мм.
Ширина: k1
= 3d3
= 3×12 = 36мм
Фундаментные лапы:
Толщина:S2
= 1.5d3
= 1.5 × 12 = 18мм
Ширина: k2
= 3d3
= 3 × 12 = 36мм.
2.9 Тепловой расчет и смазка редуктора
По рекомендации главы 9(1) выбираем глубину погружения колеса второй ступени на две высоты зуба, но не менее 10мм: 2*2,25mn
= 2*2.25*2 = 9мм. (2.82)
Принимаем глубину 12мм с учетом ее уменьшения из-за разбрызгивания масла и прилипания его к стенкам корпуса и другим деталям.
Глубина погружения быстроходного колеса:
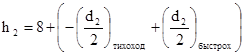 (2.83)
По значениям окружных скоростей колес (табл. 9.5(1)) находим соответствующую вязкость
масла: 180 сст. По таблице 9.1(1) выбираем по вязкости автотракторное масло АК-15
.
Проводим тепловой расчет.
Находим тепловую мощность
(2.84)
где Р1
= 3960 Вт – мощность на входном валу.
h = 0,9752
– КПД зубчатой передачи.

Через стенки корпуса редуктора тепло передается в окружающую среду, тем самым происходит естественное охлаждение. Количество теплоты, отданной в секунду или мощность теплоотдачи:
(2.85)
где k – коэффициент теплоотдачи, принимаем k = 18 Вт/м2
×°С,
А – площадь поверхности охлаждения:
(2.86)
где S1
= 0,920 × 0,250 = 0,23 м2
– площадь поверхности днища, которая учитывается, т.к. редуктор свободно обдувается воздухом.
S2
= 0,920 × 0,012 = 0,011 м2
- площадь боковой стороны редуктора соприкасаемая с маслом.
S3
= 0,250 × 0,012 = 0,003 м2
– площадь торцевой стороны редуктора соприкасаемая с маслом.
S4
= 0,005 × 0,3 × 2 = 0,003 м2
– площадь ребер охлаждения.
Подставляем значения в формулу (2.86):
А = 0,23+0,011+0,003+0,003 = 0,247 м2
t0
= 20°C – температура окружающего воздуха,
t1
= 90°C – внутренняя температура редуктора или температура масла.
Подставляем значения в формулу 2.85:

Необходимое условие выполнено.
Естественного охлаждения достаточно.
Удаление масла производится через сливную масленую пробку М24х1,5 ГОСТ 9833-73.
Контроль уровня масла производим с помощь трубчатого масло указателя Н = 210мм.
3. Расчет клиноременной передачи
По графику рис.12.23 (2) выбираем сечение ремня. Рекомендуют сечение Б. По графику рис.12.26 (2), учитывая рекомендацию 12.31(2), принимаем dр1
= 250 мм и находим Р0
=4.5 кВт. Рассчитываем геометрические параметры передачи: dр2
= dр1
.iрем
=250.2.5=625 мм, по ряду Ra40 принимаем dр2
=630 мм. По рекомендации 12.29(2) предварительно принимаем а9
= dр2
=630мм. По формуле:
l=2.a+0.5(d1
+d2
)+(d1
-d2
)2
(5.1)
находим: l=2.630+0.53.14(630+250)+(630-250)2
=2699 мм.
По таблице 12.2 принимаем l=2700 мм.
По формуле:
, (5.2)
где l - длинна ремня,l=2700 мм,
d1
и d2
- диаметры соответствующих шкивов, d1
=630 мм и d2
=250 мм,
а - межосевое расстояние,
уточняем:

По формуле:
a=1808-57(d2
-d1
)/a=1808-57(630-250)/627=1448 (5.3)
вычисляем угол обхвата ремня малого шкива. Значение находится в допускаемых пределах [см.рекомендации.12.29(2)]
По формуле:
Pp
=P0
.Ca
.Cl
.Ci
/Cp
,
(5.4)
где Сa
- коэффициент угла обхвата. Здесь Сa
=0.87[см. стр.272(2)],
Сl
- коэффициент длинны ремня, по рис.12.27(2) Сl
=1.05,
Ci
- коэффициент передаточного отношения, по рис.12.28(2) Ci
=1.135,
Cp
- коэффициент режима нагрузки, учитывая, что нагрузка с умеренными колебаниями, принимаем Cp
=1.2,
определяем мощность Рр
передаваемую одним ремнем:
Pp
=4,5.0.87.1.05.1.135/1.2=3.94 кВт
По формуле:
Z=P/Pp
.Cz
, (5.5)
где P -мощность на ведущем валу передачи,
Cz
- коэффициент числа ремней, Cz
=1, так как 1 ремень,
определяем число ремней. Z=4/3.94.1=1,условие z[6 выполняется.
По формуле:
F0
=0.85.P.CP
.Cl
!(Z.y.Ca
.Ci
)+Fy
, (5.6)
где Fy
=r.A.y2
- центробежная сила,
А - площадь сечения, А=138.10-6
м2
,
r=1250 кг/м3
,
y - скорость ремня при расчетной частоте вращения:
y=P.dp1
.n1
/60=3.14.0.25.960/60=12.56 м/с,
Fy
=1250.138.10-6
.12.5652.17 H,
находим предварительное натяжение ремня:
F0
=0.85.4.103
.1.2.1.05!(1.12.56.0.87.1.135)+2.17=348 H.
По формуле:
, (5.7)
сила, действующая на вал при b/2=(180-a)/2=(180-144)/2=18, в статическом состоянии передачи: Fr
=2.348.cos1885662.4 H, при n5960 мин-1
Fr
=662.4-2.Fr
.Z=662.4-2.2.7.1=656.64 H
В нашем случае влияние центробежных сил мало.
Ресурс наработки ремней находим по формуле:
T=Tcp
.k1
.k2
, (5.8)
где k1
- коэффициент режима нагрузки, k1
=1,
Тср
- ресурс наработки для эксплуатации при среднем режиме нагрузки, Тср
=2000ч.,
k2
- коэффициент климатических условий, k2
=1.
Т= Тср
=2000ч.
4. Подбор, проверка и эскизная компоновка муфты
Подбираем муфту для соединения вала редуктора с валом приводного конвейера. По техническим характеристикам требующим обеспечения муфтой передачи крутящего момента Т = 2800Н×м, частоты оборотов n = 31об/мин, перекос валов 0°30¢, радиальное смещение 0,18мм, выбираем зубчатую муфту М3 60 (рис.3.2) с параметрами:
Т = 2900Н×м;
с размерами: b = 20мм, z = 40, D1
= 150мм, h = 7.5мм.
Муфта компенсирует все виды несоосности валов. Допускаемые муфтой смещения валов определяют из условия, чтобы углы между осью обоймы и осью одного или другого вала были не больше 0°30¢.
Коэффициент динамической нагрузки к = 1,7.
Проводим расчет прочности зубьев по формуле:
 (3.2)
Принимаем [sсм
] = 12 ... 15МПа
Условие работоспособности выполняются.( [sсм
]/sсм
)
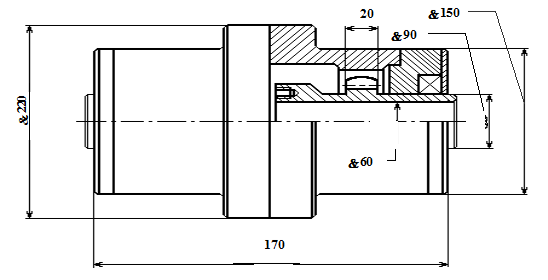
Рисунок 3.1.-Эскиз зубчатой муфты
5. Расчет и проектирование узла исполнительного механизма (барабана)
Определяем размеры вала.
Диаметр выходного конца муфты d = 60мм, поэтому в этом месте принимаем вал такого же диаметра. Диаметр в месте посадки подшипников и уплотнений d = 65мм. Диаметр вала в месте посадки звёздочки принимаем d = 70мм. Барабан располагается симметрично относительно опор. В качестве опор принимаем самоустанавливающиеся сферические
подшипники № 1209, которые на валу закрепляются в осевом направлении. По рекомендации главы Vlll §9 (1) выбираем неразъемный корпус подшипника СИМ 100.
Выполняем проверочный расчет вала
Параметры: T = 2772 H × м, n = 31об/мин, [t] = 18Мпа, sв
= 850Мпа,sт
= 550Мпа.
Определяем силы (для звездочки Fa
и Fv
малы).
Размеры пролетов из чертежа: , с = 140мм. 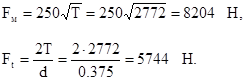
Определяем моменты сил (рис. 4.1)
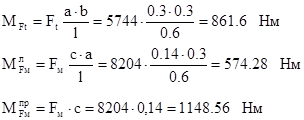
Сечение 1-1:


Сечение 2-2:

Опасное сечение 1-1.
Расчет на прочность.





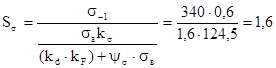
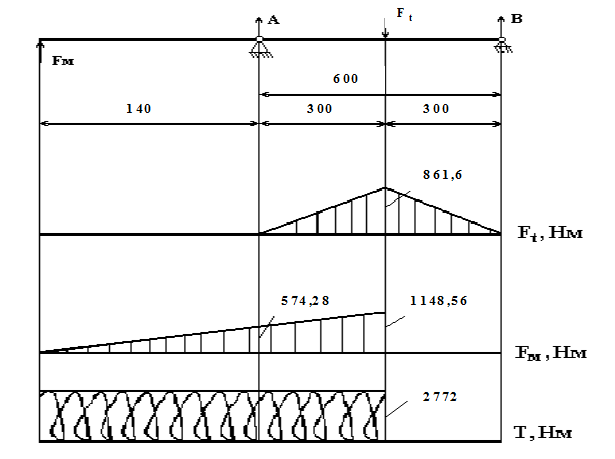
Рисунок 5.1.-Эпюра нагружения рабочего органа(барабана)
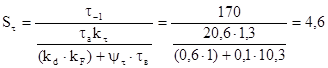

Полученные значения находятся в рекомендуемых пределах.
Расчет на жесткость.


Необходимое условие работы вала - f[[f] выполняется.
Расчет на критические колебания.

Вал работает в до критической области.
Выполняем проверочный расчет подшипников.
Расчет выполняется аналогично расчетам подшипников редуктора.
Параметры выбранных подшипников №1209:
Сг
= 17000 Н, С0
= 9770 Н, Ln
= 20000 ч.
Реакции опор (рис. 4.1):


Правый подшипник нагружен больше.
Находим: x = 1, y = 0, ks
= 1.4, kt
= 1,v = 1.



а1
= 1, а2
= 0,8

Назначаем шарикоподшипники радиальные сферические двухрядные средней узкой серии №1309:

Сг
> C на 45%, что допустимо.
x0
= 0.6, y0
= 0.5, тогда

Список используемой литературы.
1. Иванов М. Н. и Иванов В.Н.
Детали машин. Курсовое проектирование. Учеб. пособие для машиностроит. вузов. М.,
²Высш. школа², 1975 – 551с.
2. Иванов М. Н.
Детали машин: Учеб. для студентов высш. техн. учеб. заведений - 5-е изд., перераб.-М.:
Высш. шк., 1991. – 383с. ил.
3. Решетов Д. Н.
Детали машин: Атлас конструкций – М.: Машиностроение. – 1992. – 296с.
4. Анурьев В. И.
Справочник конструктора – машиностроителя. 3 т. М.: Машиностроение. - 1985
|